| Front page | | Contents | | Previous
|
Waste Indicators
3 Assumptions for calculations
In this appendix, data bases and other specific assumptions for
the calculated examples of the waste fractions paper and cardboard, glass packaging (such
as deposit-return bottles) and aluminium are discussed. Furthermore, assumptions for the
LCA data that are new compared to EDIP/the EDIP PC tool database are established.
Paper, both in terms of consumption and recycling, is one of the materials contained in
waste that are best covered by statistics, and for which annual updates are made. Around
half of paper consumption is collected for recycling, and the remaining half is led to
incineration.
Waste statistics break down paper into the following types:
 | Newspapers and magazines |
 | Corrugated cardboard |
 | Other paper and cardboard |
 | Good quality paper |
Total consumption is broken down by a number of paper types. However, it is not always
possible to relate consumption directly to quantities collected, so as to state, for
example, how much newspaper is recycled and how much is incinerated.
To allow for an assessment of results of paper recycling it is also relevant to know
into what different paper types are recycled, as the principle for the statement of
environmental impacts from waste management is a statement of primary resources consumed
in recycling.
For example, recycling into paper such as writing paper of high quality will cause less
consumption of new, bleached paper of high quality (wood-free), whereas recycling into egg
boxes will substitute unbleached paper with large contents of wood. Since there are
significant differences in resource consumption and energy consumption associated with the
different paper types, loss of utility value of paper bulk depends on the extent of
exploitation of the properties of paper fibres upon recycling.
Even if it were possible to answer the above questions with supplementary statistical
surveys, it would still be difficult to provide data on manufacture of different paper
types and different recycling processes. The issue has been discussed often in life-cycle
analyses (such as /13/), but much of the data
material is confidential and cannot be used in reports available to the public.
So the only possibility left is to use average figures covering all paper types with
the uncertainty associated with such a solution. Paper quantities used in the calculation
are stated in Table 5.1 of the main report. In this table, all types of paper collected
for recycling have been aggregated.
Other paper waste has been calculated as the difference between used paper quantity and
recycled paper quantity. In principle, all paper that is not recycled is incinerated.
However, some tissue ends up in wastewater. In 1997, tissue accounted for around 6 % of
virgin paper /39/. Due to lack of more qualified
estimates, the calculation assumes a landfill share of 13% for paper that is not recycled.
This rate corresponds to the proportion of household waste that was landfilled in 1993. In
the calculation of potential for recycling paper, it has been assumed that the remaining
87 % can be collected potentially for recycling. In the above-mentioned source, the
realistic potential has been estimated at 80%.
In Chapter 1.4, actual energy recovery for the different materials upon
incineration in Denmark has been calculated. Where the figure is to represent an average
for the energy benefit from incineration of waste in Denmark, calculations are based on
the calorific value of materials that must be reduced by 30%. Materials calorific
value appears, for example, from /15/. If it is
assumed that cardboard accounts for one third of paper and cardboard collected for
incineration, this means that an energy recovery will be used amounting to 15 MJ - 30% =
10.5 MJ/kg corresponding to a credit of coal consumption of 420 g. Further, around 12% of
landfill requirement saved for coal waste in connection with extraction will be included.
Slag from coal combustion is recycled today at a rate of 100%.
3.1.3 Recycling processes
Upon recycling of paper and cardboard the same data basis has been used for the
recycling process as in the EDIP, using 1.15 kg paper for 1 kg recycled paper. This means
that if 1 kg waste paper is led to recycling, a recycling process for 0.87 kg finished
paper should be included, incl. residual waste.
Upon recycling of paper and cardboard, there is also a loss of utility value every time
paper fibres are led to recycling. For mixed paper types, the EDIP sets this loss at 20%.
This means that 20% virgin paper should be added to the system upon recycling, and that
this quantity of paper will become waste at some point. This is included in the indicator
as waste for landfilling.
3.1.4
Sensitivity assessment of indicator values for paper and cardboard
The most essential uncertainty in indicators for paper is the fact that the composition
of paper and cardboard for recycling and incineration cannot be stated. Some of the
extremes, for example, will be the landfill requirement for paper and cardboard with
filler materials. As filler materials can constitute up to 30%, landfilling after
incineration can vary from 0 to 300 g/kg paper incinerated. Energy consumption can vary to
a similar extent.
Another source of uncertainty is the lack of published data on paper manufacture. In
this respect, it can be decisive for the result of the statement, whether for example
energy in the form of wood, hydropower or coal is used. Particularly the resource
indicator will depend strongly on this point.
One of the general and very important elements of the resource factor is how to
normalise and weight the different resources. In this project, factors of the EDIP project
have been used, supplemented with new values in the areas where data is not included in
the EDIP. In the preparation of the new values the same statement principles as in the
EDIP have been used. General experience shows that normalisation and weighting factors are
very significant for the result. However, no general estimate of the uncertainty
associated with the resource factors used has been made.
3.2.1 Quantities and statistics
Statistics for bottles and glass are very detailed and have been prepared annually
since 1989/1990. Most recent statistics derive from Waste Centre Denmark /18/, and give figures back to 1989.
Statistics cover bottles and glass packaging, but not crushed flat glass and glass
found in incandescent lamps. In addition, bottles from the Danish deposit-return scheme
are not included in the statement. Statistics on this consumption are available from other
sources than the ISAG, and it is possible to include this glass quantity in an overall
statement of consumption and recycling of glass, if so wished. The purpose of the trial,
however, has been to test the calculation method, and in this context it has not been
relevant to include additional information.
The EDIP project uses relatively old figures concerning the manufacture of virgin
glass that have been verified, however, in a can/bottle project from 1998 /24/ with figures from the glass manufacturer Holmegård
from 1992. Therefore, these figures have also been used for the indicator calculation. But
with data from the recently published LCA statement of Danish generated power and heat in
1997 it will be possible to update data for energy consumption for glass melting. This
also applies to remelting cullet. A 100% recovery of waste glass has been assumed, where
the EDIP uses a 1% loss. However, separated waste glass in the ISAG is stated separately
and is found in the present calculation as waste for landfilling. Waste separated for
recycling is thus recycled at a rate of 100%.
For washing of bottles, information from the can/bottle project has been used /24/. Here, only data for energy consumption analysed
between electricity and natural gas has been used, as well as information on the
proportion of bottles crushed in the process and becoming waste. 2.5% virgin glass has
been calculated for substitution of crushed bottles. However, cullet for landfilling has
not been included, as it is assumed that it is led directly to remelting.
The EDIP project uses a loss of utility value of 10% for each remelting of glass. The
loss of utility value is included in recycling of cullet for remelting, where 10% of
virgin glass is added to glass recycled as loss of utility value, and the same quantity is
included as loss upon landfilling. Just as the other losses of utility value used in the
EDIP, estimates are relatively rough, and subsequent assessments will most probably give
cause for a revision.
In the calculation of loss of virgin glass upon landfilling and incineration it is
assumed that half of the glass used is recycled cullet (where loss of utility value is
included in reprocessing) and the loss of utility value thus is only half of the 10%.
Thus, a loss of primary resources of 95% of virgin glass is included in landfilling and
incineration.
For incineration and landfilling 1 kg per 1 kg glass is landfilled (incl. 5% loss of
utility value). Incineration may allow for recycling of slag here 60% is included /40/. Finally, a minor amount of energy for heating glass
from ambient temperature to slag temperature has been included. However, this has not been
included here, as it accounts for a maximum of 0.2 MJ/kg, thereby disappearing in the
decimals.
Data used for manufacture, washing and remelting of glass is relatively well
verified in connection with a life-cycle survey for beverages packaging. However, the
picture may change, when the electricity data used is updated to the most recent figures
for the LCA project on electricity generation. For some parameters changes of 10-20 % may
arise compared to figures used.
In the ISAG, aluminium is included in other metals. The total metal fraction consists
primarily of iron and steel. A statement of quantities of aluminium disposed of and ways
of disposal must therefore be based on other data.
Imports and exports of scrap aluminium and production of secondary aluminium appear
from trade statistics from Statistics Denmark. For individual fractions of scrap
aluminium, however, aluminium only accounts for a minor part of scrap, and total
quantities led to recycling therefore can only be estimated on the basis of more detailed
knowledge of scrap composition. It is, however, estimated to be possible to get an
approximate figure for quantities led to recycling from statistics and data on composition
from the most recent mass-flow analysis for aluminium /1/.
Quantities led to incineration and landfilling cannot be estimated directly from
existing statistics and must therefore be based on more detailed, individual analyses. The
most recent mass-flow analysis for aluminium covers data for 1994. The mass-flow analysis
also covers non-metallic applications, and in the present analysis it has been necessary
to extract data concerning metallic applications.
According to the mass-flow analysis the following quantities were treated in 1994:
 | 7,000-12,700 tonnes of metallic aluminium for waste incineration (average: 9,800
tonnes). |
 | 2,800-7,200 tonnes of metallic aluminium for landfilling (average: 5,000 tonnes). Of
this, 2,000-5,500 tonnes were disposed of through domestic waste and bulky waste, whereas
the remaining part consisted of production waste and shredder waste. |
 | 27,100-34,600 tonnes for recycling (average: 30,900 tonnes). |
Quantities of domestic waste and bulky waste led to incineration are estimated to have
increased at the expense of quantities led to landfilling in the period since 1994.
The element most relevant for use as a measurement for recycling will be the collection
of aluminium, whether the materials collected are reprocessed in Denmark or exported.
In connection with the mass-flow analysis, aluminium alloys have been converted into
pure Al on the basis of an average content of aluminium in the alloys. For calculation of
indicators, however, it will be most expedient to calculate the total weight of aluminium
alloys as aluminium, partly to simplify calculations, and partly to also incorporate alloy
elements in the calculation (that for reasons of simplicity are considered to correspond
to aluminium).
Quantities led to recycling can be calculated annually as follows, based on trade
statistics from Statistics Denmark:
Quantities collected = production of sec. Al in DK + exports of scrap Al ¸ imports of scrap Al. Contents of aluminium (incl. alloy elements)
in the different scrap fractions have been estimated on the basis of the mass-flow
analysis.
Table 3.1.
Metallic aluminium in Denmark in 1994 /1/
Code number |
Desig- nation |
Imports |
Exports |
Net |
|
|
Al% |
Tonnes/ year |
Tonnes Al/year |
Al% |
Tonnes/ year |
Tonnes Al/year |
Tonnes Al/year |
7602.00.11 |
Aluminium waste: Turnings, shavings,
chips, milling waste, sawdust and filings; waste of coloured, coated or bonded sheets and
foil |
100 |
6,941 |
6941 |
100 |
4,245 |
4245 |
-2696 |
7602.00.19 |
Other aluminium waste |
30 |
4,252 |
1275.6 |
90 |
5,919 |
5327.1 |
4051.5 |
7602.00.90 |
Aluminium scrap |
90 |
13,132 |
11818.8 |
90 |
21,048 |
18943.2 |
7124.4 |
7601.20.90 |
Production of secondary Al |
|
|
|
|
|
|
21,250 |
|
Total |
|
|
|
|
|
|
29,730 |
This method will often underestimate actual quantities, as aluminium included in mixed
scrap, which is entered in other code numbers, is not included.
Calculated in this way collected quantities can be estimated as follows for each year:
1991 30,752 tonnes
1994 29,730 tonnes
(the mass-flow analysis states an average of 30,900 tonnes Al)
1996 39,271 tonnes
1998 40,896 tonnes
3.3.2 LCA processes and data sources
Data for production of aluminium is found in environmental profiles for aluminium /16/. This data derives from the European aluminium
industry supplemented with the EDIP projects data for electricity consumption for
production of aluminium.
For recycling of aluminium the EDIP projects data has been used. However, a
conversion has been made, as the EDIP project assumes use of scrap aluminium with an
aluminium content of 93%. Together with loss upon oxidation of aluminium in the remelting
process of around 5-6% this means a total loss during collection and remelting of
aluminium of 13%.
As this statement uses pure aluminium it is assumed that it is only relevant to count
with a loss of around 5%, so 1 kg of scrap aluminium turns into 0.95 kg recycled
aluminium, which is assumed to be the case for Danish conditions according to the
mass-flow analysis for aluminium /1/.
Upon incineration of aluminium, 1.9 kg aluminium oxide will be generated for each kilo
of incinerated aluminium. Aluminium oxide will be bound in slag or filter dust. Therefore,
as a result of both incineration of aluminium and the loss occurring in remelting 1.9
times as much waste for landfilling as the lost aluminium has been used in the
calculation. Some slag is recycled, whereas filter dust is normally landfilled: around 60%
according to the ISAG for 1999 /40/.
Energy recovery upon incineration of aluminium has been set at a calorific value of
around 31 MJ per kg reduced by 30%, which gives a credit of 21.7 MJ/kg converted into a
credit of 879 g coal per kg aluminium and around 12% saved landfilling of coal waste in
connection with extraction. Coal slag is recycled 100% today /23/.
In the EDIP it is assumed that aluminium led to incineration plants typically is of a
thickness that allows for burning. Other surveys show that, for example, foil sleeves
normally do not burn, but are found unburned in the slag. Figure 5.3 in the main report
shows that the effect of changing the percentage burned to 50%, for example, will be
marginal. However this assumption should be reassessed in connection with an indicator
calculation for the entire waste management field. Aluminium of a larger thickness that
cannot burn 100% is assumed to be collected and remelted.
Aluminium is recycled as aluminium, and in the revised EDIP project no loss of utility
value has been included for aluminium. Therefore, no loss of utility value has been
included for primary aluminium when it is disposed of by landfilling or incineration.
3.3.3 Data quality and sensitivity
There is a significant difference in the resource evaluation, depending on whether
aluminium is recycled or landfilled. Therefore, good LCA data for production and recycling
of aluminium is decisive. Especially the electricity scenarios used are important, and the
EDIP data dates from 1992. Most recent electricity data for Danish electricity generation
has changed by 10-20% in some areas, and an update of the data basis for the electricity
scenario used will change aluminium indicators correspondingly. However, in general
aluminium data used is estimated to be of good quality, and it is based on Danish
conditions.
Normalisation and weighting factors for a number of raw materials have been estimated
in the EDIP project and are covered by the database. For many raw materials no
normalisation and weighting factors are available in the EDIP database. To be able to
include these raw materials factors have been estimated here according to methods that are
comparable with the methods of calculation of normalisation and weighting factors in the
EDIP. Factors calculated appear from the following table.
Table 3.2.
Supplementing normalisation and weighting references
|
Weighting factor
1/year |
Normalisation reference
kg/pers./year |
Limestone 1) |
0.002 |
598 |
Uranium ore 2) |
0.015 |
0.007 |
Sulphur 3) |
0.036 |
9.6 |
Quartz sand 4) |
0.005 |
36 |
Gravel and sand 5) |
0.005 |
5.6 (m3/pers./year) |
|
|
1) |
In the EDIP database there are no normalisation and
weighting factors for lime. There is no statement of global consumption of lime, and a
large part of the consumption of limestone in statements from the US Geological Survey has
been entered under stone. The normalisation factor for lime therefore will be based on the
local (national) consumption of lime. Total extraction of lime and chalk in Denmark in
1990 amounted to 2,924,000 m3 /29/.
Consumption of lime with finished goods for 1995 has been stated at 3,052,000 tonnes /6/. With offset in this statement, consumption of lime
can be calculated at 598 kg/person. A large part is used in the form of cement. No
statement is available of global or regional reserves of lime, but resources are very
large, so the weighting factor has been set roughly at 0.002 corresponding to a
supply perspective of 500 years (see also statements in /6/). |
2) |
In the EDIP database there are no normalisation and
weighting factors for uranium. Factors have therefore been fixed here on the basis of a
stated consumption (mining) of 34,583 tonnes in 1992 and stated reserves of 2,255,000
tonnes /26/. |
3) |
Global extraction of sulphur in 1994 has been stated by
the USGS at 51 million tonnes /36/. Global reserves
have been stated at 1,400 million tonnes, corresponding to a supply perspective of around
27 years. Global resources have been stated at 5 billion tonnes, but there are very large
alternative resources, for example at least 500 billion tonnes in coal, oil etc. and very
large resources in gypsum and anhydrite. |
4) |
Extraction of quartz sand in 1990 amounted to 186,000
tonnes. It was mainly used as foundry sand, sand blasting and concrete sand. No total
statement of Danish resources of quartz sand is available. According to statements from
the USGS (1999) global resources of quartz sand are very large, and from a resource point
of view it is mainly a question of increased transportation of raw materials. To get a
measurement that can be used to indicate whether consumption of quartz sand is of
significant resource-related impact, the supply perspective is estimated at roughly 200
years. |
5) |
In the EDIP database there are no normalisation and
weighting factors for sand and gravel. In Danish life-cycle analyses under the EDIP method
the use of these raw materials has been disregarded. Total Danish consumption of gravel
and sand in 1990 amounted to 22.4 million m3 from land and 6.2 million m3
from the seabed /29/, corresponding to a total
average per person of around 5.6 m3. At present no statement of
total Danish raw material resources on land is available /21/.
Statements of raw material resources are carried out at the regional level. The Danish
Forest and Nature Agency assesses that in a few years a total statement and assessment of
raw material resources will be made. Resources of sand, stone and gravel in the seabed
were stated in 1998 at around 4,500 million m3, corresponding to around 725
times the present annual extraction from the seabed of 6.2 million m3 or 150
times the total annual extraction of sand and gravel /17/.
However, there are large variations in the composition of resources, and gravel and pebble
gravel/stone are stated to be a limited resource.
For the other raw materials the supply perspective is calculated in the EDIP (and
used for the weighting) on the basis of global "reserves" and not total
estimated global resources. Reserves will typically be around 10-20% of estimated total
resources. Resource statements for the Danish marine area cover both "probable
resources" and "speculative resources" and cover thus a considerably larger
part of resources than the quantity referred to as "reserves".
However, for sand and gravel there do generally not seem to be supply problems at
present, and to get a measurement that can be used to indicate whether consumption of sand
and gravel is of significant resource-related impact, the supply perspective is estimated
roughly at 200 years. |
Energy consumption in Denmark in 1995-1999 amounted to a total of 840 PJ (corrected
for climate and for fluctuations due to exports of energy). As for waste, an average has
been chosen for recent years, even if values have only fluctuated little over the years.
This gives a consumption of 160 GJ per person in Denmark, which corresponds to the
calorific value of around 3800 litres of oil /9/. The
normalisation factor is 0.00625.
It is estimated that direct comparison across the three indicators is not relevant, and
therefore it has been decided not to use a weighting factor for energy.
In the normalisation of waste quantities in the EDIP, waste output is normalised in
relation to waste generated, analysed into four types: radioactive waste, hazardous waste,
bulk waste, and ash and slag. Radioactive waste is normalised in relation to the average
for Europe, whereas the other three are normalised in relation to waste generation per
capita in Denmark in 1992.
In the waste indicator project it has been decided instead to normalise in relation to
waste quantities landfilled. This choice has been made based on the consideration that
waste led to landfilling constitutes the actual waste problem. Waste incinerated is
converted into other types of pollution and slag for landfilling.
In setting up normalisation values, an average of waste landfilled in the period 1995 -
1998 has been used, which is quantities landfilled in the last four years. The average for
the period has been chosen, as there are large fluctuations over the years, and the four
annual values are close to the average, of 2,116,000 tonnes. Population in Denmark in the
same period was around 5.25 million /40/. This gives
a normalisation value for waste landfilled of 403 kg per person-equivalent.
It is estimated that direct comparison across the three indicators is not relevant, and
therefore it has been decided not to use a weighting factor for landfill requirement.
In setting up the three LCA indicators for resources,
energy and landfilling upon landfilling of waste paper account is taken of the fact that a
corresponding amount of virgin paper must be manufactured, and that waste paper is
landfilled 100%.
Paper to be manufactured to substitute paper disposed of is based on a mix of 50%
primary paper and cardboard and 50% recycled paper. The proportion of paper for recycling
has been set relatively high, but considering that half of total consumption of paper and
cardboard for recycling has been separated, it is not unreasonable to assume that the
qualities remaining are the poorest ones.
For the share of recycled paper, the resource loss should only be calculated with the
utility value of the recycled fibres, i.e. 80% according to the EDIP, as the paper in
question is mixed. This means that for paper landfilled or incinerated, a resource loss of
primary paper is included of 50% + 0.8 times 50%, i.e. 90% resource loss.
Data for paper manufacture for primary paper is an average for different types of
primary paper processes that the Institute for Product Development has supplied in
connection with the project on the environmental impact of the family. The average has
been weighted in relation to the Danish consumption in 1998 /39/ to the extent that is has been possible to find data
for manufacture of the different paper types.
Upon landfilling only the actual landfilling has been included and
transportation of paper as well as establishment, operation and maintenance of the
landfill site are disregarded.
In the statistics on energy-generating plants /33/ for 1999, 29,105 TJ gross energy from waste for
incineration is entered in 1999. According to waste statistics for 1999, around 2,700
tonnes of waste was led to incineration (for example incineration of sludge).
This gives a calorific value of 10.8 MJ per kilo waste. Incineration of different
plastic types gives more energy, whereas non-burnable material and wet organic waste
reduces the average.
Some heat from waste is cooled off in cooling towers during summer this means
that energy is not recovered fully for district heating, and some heat is utilised
internally for the operation of the waste treatment plant, for example for drying waste.
According to the statistics on energy-generating plants, waste incineration plants supply
a total of 20,825 TJ heat and 5,150 TJ power. For the generation of this energy, waste is
used with a calorific value of 29,105 TJ and auxiliary fuel of a total of 4,934 TJ. This
gives a total efficiency in waste incineration of 76%, and the result is 8.2 MJ/kg waste
delivered to the district heating network.
However, the above only applies to a consideration of
waste treatment in a closed system. If the system is extended to cover the entire power
and heat supply of Denmark, it will also be necessary to try to include resulting changes
to the remaining system from waste incineration. Based on the statistics on
energy-generating plants it has been sought to identify district heating systems where
heat from waste is recovered.
The statistics on energy-generating plants for 1999 contain information on fuel
consumption analysed by types and generation of power and heat for each individual plant.
Statistics also contain information on affiliation of the plants to the district heating
network.
An analysis of recovery of energy from waste shows that around 67% of waste is
incinerated in plants co-generating power and heat. The efficiency for power fluctuates
between 15 and 25% of energy fired. In this case waste will substitute other power and
heat generation, typically using fossil fuels such as coal, natural gas, and oil. Waste
incineration substitutes the base load of power plants and thus typically substitutes
coal-fired power and heat plants.
33% of waste is incinerated in waste incineration plants that supply heat to district
heating networks only. A small number of these networks is not affiliated to other power
and heat generating plants, and the heat generated from waste for these networks (about 7
%) substitutes other fuel types 100%, typically natural gas or oil, as the plants in
question are small.
The remaining 26% of total energy from waste is delivered to district heating networks
to which power generating plants are also affiliated. This 26% includes the incineration
plant of Vestforbrænding (in the western part of Copenhagen), as heat from incineration
in this plant limits the possibilities of exploiting more waste heat from the many other
power and heat plants in the area.
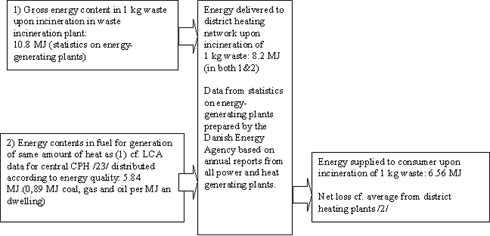
Figure 3.1.
Energy substitution from waste incineration
The figure shows the result of incinerating 1 kg of waste (1) and what is saved from
co-generating heat and power (2), cf. energy generation figures from the most recent LCA
review of power and heat generation in Denmark /23/.
In a system only covering waste incineration, most heat
from waste incineration is recovered for energy generation either for power and
heat or only heat generation. But if the system is extended to cover the entire power and
heat generation, around 26% of heat from waste will substitute recovery of waste heat from
cogeneration, so that it leads to lower rate of exploitation at the central power and heat
plants.
This means that energy recovery of waste, on average 8.2 MJ/kg waste, must be reduced
to 5.84 MJ to compensate for the 26% of waste that competes directly with combined power
and heat generation. It costs 5.84 MJ to generate district heating in connection with
power and heating plants /23/. This means that the
average energy recovery of 8.2 MJ upon incineration of 1 kg waste in Denmark is reduced to
an average of 7.6 MJ. This means that around 70% of the calorific value of waste is
recovered in the present system. Other surveys reach a figure of around 75%, but they do
not include a "system loss" for increased wastage from power and heat plants.
This figure is only slightly lower than a calculation carried out by the Danish Energy
Authority on the basis of the statistics on energy-generating plants for 1998, which has
been used in an LCA of packaging. The Danish Energy Authority assumes an average recovery
of 75% of energy generated, but does not take the above "extended system loss"
into account.
Below, the actual energy recovery for the different materials is calculated based on
materials calorific value that must be reduced by 30%, when the figure is to
represent an average for energy benefits from incineration of waste in Denmark. Calorific
values of materials appear, for example, from /15/.
If it is assumed that cardboard accounts for one third of total quantities of paper and
cardboard for incineration it means that an energy recovery must be included of 15 MJ -
30% = 10.5 MJ/kg, corresponding to a credit of coal consumption of 420 g. Furthermore,
around 12% of landfilling of coal waste saved in connection with extraction is included.
Today, slag from coal combustion is recycled 100%.
If the use of slag for construction purposes is to be included in the calculation of
the indicator for resources, it is necessary to clarify which raw materials are actually
substituted through the use of slag, and to set up normalisation and weighting factors for
these raw materials.
In 1998, 80% of 551,000 tonnes of slag generated was used for construction purposes.
The use of slag depends on requirements for the structure in which it is used. On bicycle
paths and parking grounds, slag can be used as sub-base, thus substituting stable gravel.
For roads, slag is normally not used as sub-base, but as pitching and friction filler.
Materials substituted in this case will typically be sand or soil.
In the new Statutory Order on residues and soil for building and construction purposes,
limits to the use of slag have been set up, depending on the contents of problematic
substances in slag /34/. After 1 January 2001 slag in
the most contaminated category 3, (where most slag is expected to belong), can only be
used for roads with tight paving and discharge of surface water, paths and conduits with
solid paving as well as foundations and floors below buildings (where soil must not cause
indoor climate problems).
If the resource-related benefit from using slag is to be included in the calculated
indicators, it will be necessary to set up normalisation and weighting factors for the
materials substituted by slag. Without these, in the calculation of indicators for
resources it would be of no importance whether or not slag is recycled. In the calculation
of the indicator for landfill requirement it will always be important whether slag is
recycled or landfilled.
In statistics on raw material extraction in Denmark, sand, gravel and stone are listed
together, and with data available on resources of the different fractions within this
group it will not be expedient to make a further division. Total Danish extraction of
gravel and sand in 1990 amounted to 22.4 million m3 from land and 6.2 million m3
from the seabed /29/, corresponding to a total
average per person of around 5.6 m3. If an average density of 2 tonnes/m3
is used, this corresponds to 11.2 tonnes.
At present no statement of total Danish raw material resources on land is available /21/. Statements of raw material resources are carried
out at regional level. The Danish Forest and Nature Agency assesses that in a few years a
total statement and assessment of raw material resources will be made.
Resources of sand, stone and gravel in the seabed was stated in 1998 at around 4,500
million m3, corresponding to around 725 times the present annual extraction
from the seabed of 6.2 million m3 or 150 times the total annual extraction of
sand and gravel /17/. However, there are large
variations in the composition of resources, and gravel and pebble gravel/stone are stated
to be a limited resource.
For the other raw materials the supply perspective is calculated in the EDIP (and used for
the weighting) on the basis of global "reserves" and not total estimated global
resources. Reserves will typically be around 10-20% of estimated total resources. Resource
statements for the Danish marine area cover both "probable resources" and
"speculative resources" and thus cover a considerably larger part of resources
than the amount referred to as "reserves".
As mentioned, no total statement of resources on land is available, but for sand and
gravel there do not generally seem to be supply problems at present, and to get a
measurement that can be used to indicate whether consumption of sand and gravel is of
significant resource-related impact, the supply perspective is estimated roughly at 200
years.
To survey the resource-related impact of recycling slag, a brief calculation is made
below for recycling of 500,000 tonnes of slag.
The following assumptions have been made:
 | The 500,000 tonnes of slag substitutes 500,000 tonnes of sand and gravel |
 | Transportation of slag for use in construction corresponds to transportation of slag for
landfilling |
 | The normalisation factor for sand and gravel is 11.2 tonnes/person/year |
 | The weighting factor for sand and gravel is 0.005 (corresponding to a supply perspective
of 200 years) |
With these assumptions, resource-related savings from recycling of 500,000 tonnes of
slag excluding extraction and transportation of sand and gravel amount to
223 PR.
In comparison, total resource consumption associated with disposal of aluminium and
manufacture of substitute materials is calculated at 23,000 PR. Thus, with the above
calculation, resource-related savings from recycling of slag are modest. Uncertainties in
relation to supply perspective thus do not have a significant impact on global results.
In the calculations, recycling of slag has been included, as it has a significant
impact on the landfill indicator. Resource savings from recycling slag for substitution of
sand and gravel, by contrast, have not been included as, cf. the above, it has no
significant impact in relation to other resource consumption. Thus, slag is primarily
recycled to reduce landfill requirements and not because it solves a significant
resource problem.
| Front page | | Contents | | Previous
| | Top | |