| Bottom | | Front page |
Environmental News No. 74 2004
Geographical, technological and temporal delimitations in LCA
The UMIP 2003 methodology
Contents
Preface to the series
Preface to the guideline
Summary
1. Introduction
2. Market-based system delimitation
3. Handling multi-functional systems
4. Forecasting procedures
Annex 1. Some important terms used in this document
Preface to the series
Life cycle thinking and life cycle assessment are key elements in an integrated product policy. There is a need for thorough and scientific wellfounded methods for life cycle assessment. Parallel to this, there is
a need for simple, easy-understandable methods, which reflect life cycle thinking. Which method to use must depend on the goal and scope in each case inclusive target group, publication strategy etc.
It is common for all life cycle assessments, that they have to give a solid and reliable result. A result, that is a good foundation for the decisions subsequently to be made.
During the last 10 years a number of projects concerning life cycle assessment and life cycle thinking has received financial support.
The main results of projects on life cycle assessments will from 2000 and in the next couple of years be published as a mini-series under the Danish EPA's series Environmental News (Miljønyt).
As the projects are being finalised they will supplement the results of the EDIP-project from 1996. The tools, experience, advice, help and guidance altogether form a good platform for most applications of
life cycle assessments.
Life cycle assessments is a field so comprehensive, that it is not likely to be possible to write one book, that will cover all situations and applications of life cycle assessments. The Danish EPA hopes, that the
LCA-publications together will present the knowledge available to companies, institutions, authorities and others, who wish to use the life cycle approach.
The Danish Environmental Protection Agency,
October 2000
Preface to the guideline
This guideline has been prepared within the Danish LCA methodology and consensus-creation project carried out during the period from autumn 1997 to 2003.
The guideline forms part of a series of guidelines dealing with key issues in LCA. These guidelines are planned to be published by the Danish Environmental Protection Agency during 2004. A primary
objective of the guidelines has been to provide advice and recommendations on key issues in LCA at a more detailed level than offered by general literature like the ISO standards, the EDIP reports, the
Nordic LCA project and SETAC publications. The guidelines must be regarded as an elaboration of and supplement to this general literature and not a substitution for this literature. The guidelines, however,
build on the line of LCA methodology known as the EDIP methodology. It is important to note that the guidelines were developed by a consensus process involving in reality all major research institutions
and consulting firms active in the field of LCA in Denmark. The advice given in the guidelines, thus, be said to represent what is generally accepted as best practice today in the field of LCA in Denmark. The
guidelines are supported by a number of technical reports, which present the scientific discussions and documentation for recommendations offered by the guidelines. These reports are also planned to be
published during 2004. The guidelines and the technical reports are presented in the overview figure below.
The development of the guidelines and the technical reports was initiated and supervised by the Danish EPA Ad Hoc Committee on LCA Methodology Issues in the period 1997-2001.
The research institutions and consulting firms active in the development and consensus process are:
COWI, Consulting Engineers and Planners (Project Management) Institute for Product Development, Technical University of Denmark FORCE Technology
The Danish Technological Institute
Carl Bro
The Danish Building Research Institute DHI - Water and Environment
Danish Toxicology Institute
Rambøll
ECONET
Danish Environmental Research Institute
This guideline has been written by Bo P. Weidema based on research performed by different research teams:
For chapter 2: Bo P. Weidema1, Anne-Merete Nielsen1, Klaus Hansen2, Henriette Øllgaard3, and Ebbe Holleris Petersen2
For chapter 3: Bo P. Weidema1, Nina Caspersen4,
Klaus Hansen2 and Claus Petersen5
For chapter 4: Bo P. Weidema1, Nina Caspersen4
Guidelines and technical reports prepared within the Danish LCA-methodology and consensusproject
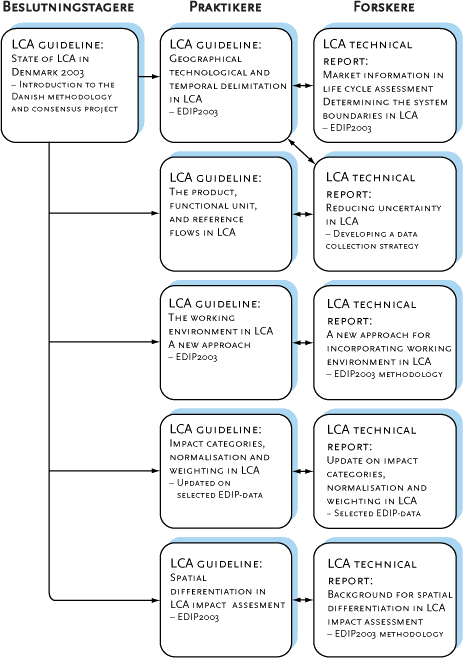
Summary
The subject of this guideline is the geographical, technological and temporal delimitation of the product systems included in life cycle assessments (LCAs).
The purpose of life cycle assessments is to assess the environmental impacts of a choice of one product instead of another (or the choice of a specific product instead of refraining from this product). A
specific choice of product may involve changes in processes and their environmental impacts throughout the life cycle of the products. For the assessment to give meaningful results, the affected processes
must be identified as precisely as possible, with respect to geography, time, and technology.
The guideline contains three complementary procedures, to be used in parallel or in iteration:
- A procedure for identifying the processes affected by a change in demand resulting from a choice between products.
- A procedure for identifying the processes affected when the choice involves multi-product systems that provide their products in different proportions. The procedure modifies the systems so that they
provide the same products in the same proportions. The procedure is illustrated with examples, including situations of material recycling and complex situations with several co-products from the same
process and where several of the involved processes in a system expansion have multiple products or applications.
- A procedure for identifying future processes. The procedure includes determination of the parts of the product systems that need to be forecasted, the necessary detail of forecasting, and the choice of the
relevant forecasting methods. Different forecasting methods and their relevance in different situations are described.
The aim of the three procedures is to reduce the arbitrariness in performing these crucial elements of a life cycle assessment. The procedures are equally relevant for detailed, quantitative life cycle
assessments and for qualitative and simplified studies, “screenings” and “matrix-LCAs”.
The three procedures all seek to identify the consequences of a choice between products, which implies a change in demand. Therefore, the procedures include the use of market information. Thereby, the
procedures provide a supplement to the traditional approach to system delimitation in life cycle assessment, which typically has been forced to disregard the actual market conditions and instead apply a
number of specific (implicit or explicit) assumptions.
1 Introduction
1.1 Perspective and purpose
The processes to include in a life cycle assessment (LCA) should as far as possible be the same as those that will actually be affected as a consequence of the decision that the specific life cycle assessment
is intended to support. This is the fundamental rule to apply in all methodological choices in a life cycle assessment. Thus, there is a close link between the purpose or application area of the life cycle
assessment and the methodological choices.
The purpose of life cycle assessments is to assess the environmental impacts of a choice of one product instead of another (or the choice of a specific product instead of refraining from this product). Such a
choice between products results in a substitution of products, and it is the environmental consequences of this potential product substitution that a life cycle assessment seeks to assess. This implies changes in
demand for the individual products, which may lead to changes in processes and their environmental impacts throughout the life cycle of the substituted products. To give meaningful results, the affected
processes must be identified as precisely as possible. Therefore, life cycle assessments rely heavily on market information, i.e. information on how the market affects the potential choices and how the markets will react to these choices.
The purpose of this guideline is to provide clear and unambiguous market-based procedures for identifying the affected processes and describe them with respect to geography, time, and technology. The
guideline contains three complementary procedures:
- A procedure for identifying the processes affected by a change in demand resulting from a potential product substitution (chapter 2)
- A procedure for identifying the processes affected by differences in the products provided by the substituting systems (chapter 3)
- A procedure for identifying future processes (chapter 4)
The aim of the three procedures is to minimise the arbitrariness in performing these crucial elements of a life cycle assessment.
1.2 Applications
The three procedures should be used in parallel or in iteration. For example, the processes to be identified by the procedures in chapters 2 and 3 (which are in themselves closely intertwined) may be affected
by the identification of future processes (the procedures of chapter 4).
The three procedures should be applied in the inventory analysis (see figure 1.1) in connection to the actual collection of data, and thereby contribute to a delimitation of the further data collection to those processes that are of importance to the result of the study.
Figure 1.1. The position of the issues of this guideline in the overall framework of a product life cycle assessment
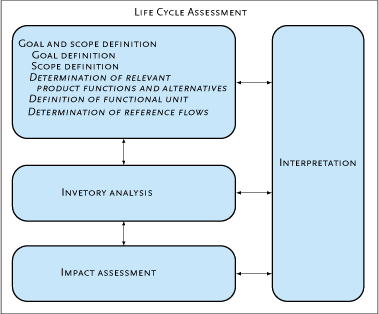
Thereby, the three procedures naturally comes after the subjects treated in the guideline “The product, functional unit and reference flows in LCA”, namely the determination of relevant product functions and
product alternatives, the definition of the functional unit, and the determination of the reference flows.
In a first iteration, starting with the reference flow of the product (for a composite product this is often identical to the parts list), a maximum of 2 hours should be used for a rough identification of the
processes to be included in the product systems – by applying the procedures in chapters 2 and 3 combined with readily available data and own order-of-magnitude estimates. Based on this, the procedures
in chapters 4 can be applied with equal coarseness. Such an initial application of the procedures will provide insight into the parts of the product systems that need to be determined with more precision in a
second iteration, and which parts of the procedures are most crucial to obtain this precision.
In general, applications of life cycle assessments differ in two dimensions:
- with regard to the time horizon of the study (short/medium or long term as determined by the period for which the conclusions of the life cycle assessment should be valid, plus the duration of the
consequences of the possible decision on the affected processes), and
- with regard to how specific the object of study is defined (a specific product for a specific market or a group of products aimed at several markets).
This gives four possible application areas, differing with respect to the product functions and product alternatives to be covered, see table 1.1.
Table 1.1 Main categories of application areas, illustrated by four examples
Coverage of solution space |
Specific solutions (relatively specific definition of the product to be studied) |
Broad coverage of solutions (broader definition of the object of study) |
Time horizon |
Short to medium term |
Typically: Enterprise internal studies aimed at supporting choice of suppliers or marketing claims |
Typically: Studies aimed at defining ecolabelling criteria for a product group |
The goal of such studies will be very narrowly defined in relation to the existing products of the enterprise |
Covering representative products in the relevant market segment |
Example: Marketing information on a specific chair |
Example: EU eco-labellingcriteria for computerworkstation chairs |
Long term |
Typically: for product development |
Typically: Studies aimed at supporting societal actionplans and legislation |
The goal of such studies is still linked to the specific interests of an enterprise, but due to the longer time horizon, it must cover a wider range of development alternatives |
Such studies cover not only representative products ina market, but also future changes in the market as well as the potential products in this market |
Example: Design for reuse of a specific chair |
Example: Strategic planning of office chair disposal in Denmark. |
While the general principles apply to all four application areas, some of the market-based procedures can be left out in applications where they are less relevant:
- Studies with a short to medium time horizon may not need the procedures for forecasting (chapter 4) and may more often involve changes within existing production capacity, and exclude changes with
respect to capital investment (section 2.2.1).
- Studies with a very specific definition of the product may more often involve specified suppliers, thus omitting the last 3 steps of the 5-step procedure in chapter 2.
Obviously, the longer the time horizon, the more uncertainty will be introduced in the determination of what processes will be affected by a specific product substitution.
The market-based procedures are equally relevant for detailed, quantitative life cycle assessments and for qualitative studies, “screenings” and “matrix-LCAs”.
1.3 The contribution of market-based procedures to improved system delimitation
In previous methodological guidelines for life cycle assessment, clear and unambiguous procedures have been missing for what assumptions shall be made as part of the system delimitation and thus what
processes shall be included in the product systems. This has also resulted in large differences in system delimitation in the life cycle assessments published up to now (see also the background report “Market
information in LCA”), where the environmental effects of the product systems are often either overestimated (when including processes that will not be affected in practice) or underestimated (when ignoring
processes that will actually be affected).
Compared to this, the market-based approach to system delimitation (presented in chapters 2 to 4) is more stringent, requiring specific procedures to be followed with respect to identification and
justification of the assumptions made regarding market conditions, so that the resulting system provides the best possible description of the consequences of the potential product substitution under study. This
can include issues such as market boundaries, production constraints, trends in market volumes, relative prices, and decision-making processes. By this inclusion of information on market conditions, the
procedures lead to a reduction in the possible errors related to system delimitation. Furthermore, the size of the product systems to investigate are reduced, since only those processes are included that will
actually be affected by the product substitution under study. Our experience shows that for more detailed life cycle assessments, which place a large demand on specific, high-quality data, the additional time
spent in collecting market data (see section 2.5) will quickly be outweighed by the timesaving in having fewer processes from which to collect detailed environmental data.
Lacking explicit procedures to determine the specific market conditions, it has been general practice to apply some default (implicit or explicit) assumptions on what processes are affected and thus to be
included in the product systems. Some typical assumptions have been:
- The processes that are affected are those in the current supply chains, in which case the product systems are constructed by linking the current suppliers and customers.
- The processes that are affected are specific potential suppliers/customers, e.g. it may be assumed that only processes with modern technology are affected, in which case the product systems are
constructed by linking these processes.
- A range of current or potential suppliers/customers may be affected, in which case the product systems are constructed by linking different possible processes in a number of scenarios, often a worst, best, and/or an average scenario, the latter being similar to:
- All actors on the markets are affected (and included) in proportion to their current or expected share in the supply, so that the product systems can be constructed as an average of the current or potential
suppliers/customers on the markets. The geographical and temporal delimitation of these markets have often been quite arbitrary, due to the disregard for market information.
Such default assumptions (and the corresponding assumptions regarding multi-product systems, see section 3.6) can be seen as specific cases of results you could also obtain from the market-based
procedures. However, it is unlikely that one of the above assumptions would in fact be generally valid throughout a product system.
Obviously, the market-based procedures can also be applied to different scenarios where the assumptions regarding the market conditions are varied, e.g. when you are in doubt about the actual market
conditions, or when the decision-maker is able to influence what markets are affected throughout the product life cycle, and what actors are affected on each of these markets. This may be the case e.g. in
studies by a market-leader or in studies aimed at societal action plans and legislation). Even in such cases, where the normal market mechanisms are overruled, the market-based procedures still provide a
good framework for explicitly documenting this dominating influence of the decision-maker.
The market-based procedures outlined in chapters 2 to 4 may be applied in two ways:
- as an alternative to the traditional default assumptions,
- as additional procedures to validate, adjust, and supplement a product system originally made with default assumptions.
There may be several arguments for using default assumptions first, and to use the market-based procedures as a supplement:
- The default assumptions may be used in a pedagogical introduction to life cycle studies, since at first sight it may appear simpler: All that is needed is knowledge on current or potential suppliers and
customers – other market relations may be disregarded, and data need only be collected from enterprises in one's own supply chain. As the life cycle is explored, and the understanding of the value chain
grows, a more differentiated view on market conditions may slowly be introduced. It should be noted that ignoring actual market conditions might lead to collection of data that later turn out to be irrelevant,
so unless data are readily available, it cannot be recommended to carry this approach through to a data collection strategy.
- The default assumptions may be useful in the early stages of a life cycle study, where there is a need simply to explore the life cycle, to increase the understanding of the value chain. This may be especially
relevant in a life cycle study performed for a decision-maker with a long time horizon and a strong influence on the actors and markets in the product chain. A study based on standard assumptions may pinpoint the
processes and relations most important to influence in a product system (known as “hot-spot-identification”). However, when this leads to suggesting a specific alternative measure or policy, the
consequences of the implementation of this alternative should anyway be assessed by the market-based procedures, to avoid the risk of sub-optimisation.
The market-based system delimitation can also be applied when the potential product substitution is unknown, as may be the case e.g. in life cycle assessments for hot-spot-identification, for setting priorities
that does not immediately involve a change, and for environmental labelling and environmental product declarations). It is not necessary to know the specific comparisons in which a product system may later
be used. The market-based procedures can be applied to delimit an isolated product system, occurring as the result of producing, using, and disposing one unit more or less of the product in question,
corresponding to the choice of the product as alternative to refraining from this product. This can be done independently for any product system. Later, when specific comparisons are required, these may be
obtained simply by subtracting the individual product systems.
2 Market-based system delimitation
2.1 Building product system models
To build a model of a product system, it is natural to start with the process in which the reference flow occurs (see the guideline “The product, functional unit and reference flows in LCA” for more
information on how to determine the reference flow). Each item in the reference flow is then linked to the next process both backwards and forwards in the life cycle. Backwards, the flow typically consists of
intermediate products, components, ancillary inputs, and raw materials. Forwards, the flow may also consist of final products, products for reuse or recycling, and waste to treatment. To make it simple, we
call all these flows “intermediate product flows”. Flows to the environment (environmental exchanges) are typically not included in the first description of a product system.
The purpose of the procedure presented in section 2.2 is to determine the process(es) that a specific intermediate product flow should be linked to, and which therefore should be included in the studied
product system. It is for these processes that data on environmental exchanges are later to be collected. The overall uncertainty of a life cycle assessment will often be determined by what processes are
included and excluded from the analysed product systems.
The procedure applies to each intermediate product flow between processes in the life cycle, but it may not be necessary to apply the entire procedure in detail for all intermediate products. The procedure is
primarily intended as a guideline for those instances where it is not immediately obvious which processes are to be linked. This may be the case when there are many possible suppliers with very different
production conditions or when one or more of the possible suppliers cannot immediately change production volume in response to a change in demand. In a first iteration, the procedure should only be
applied for such cases of constraints in production volumes (see section 2.2.4), or where there is an order-of-magnitude difference in expected environmental exchanges between different possible processes
(see also section 2.4 for a discussion of uncertainty of the procedure).
It should be noted that the suppliers that are identified by the procedure, and for which data on environmental exchanges are later to be collected, are not necessarily a part of the current supply chain.
The market information required for the procedure is typically available from marketing personnel dealing with each specific market. The collection of the necessary information has been found to be much
less demanding than the collection of data on the environmental exchanges of each process. When the necessary market information cannot be made available, the default assumptions and default data from
section 2.3 can be applied.
2.2 Procedure
Since the purpose of a life cycle assessment is to assess the possible environmental impacts of a potential product substitution, it is the processes affected by this product substitution that should be included in
the studied product systems. A product substitution (e.g. the choice of one chair design instead of another) will result in a change in demand for the intermediate products that enter into the process in which
the substitution occurs (e.g. the steel and plastic components that are used by the chair manufacturer), and likewise in the demand for the further intermediate products backwards in the life cycle (e.g. the
plastic raw materials). The procedure presented here identifies the processes that are expected to be affected by such a change in demand for a specific intermediate product.
A product substitution will also result in a change in supply of the intermediate products leaving the process in which the substitution occurs, and in supply of the further intermediate products forwards in the
life cycle (e.g. the distribution, retail sale, use and disposal of the chair). To make the description less abstract, the explanatory text in this section only covers the situation where an intermediate product is
followed backwards in the life cycle (identifying the effects of changes in demand). However, the 5 steps of the procedure, the decision tree in figure 2.1, as well as the general concepts in the explanatory
text, are also applicable when following an intermediate product flow forwards in the life cycle (identifying the effects of changes in supply).
By the procedure presented here, one or more suppliers will be identified as being affected by a change in demand. The identified suppliers will typically use a specific technology and/or be located within a
specific geographical region (since differences in market conditions and competitiveness typically depend on geographical and technological differences). The number of suppliers and the degree of detail of
describing their technologies, depends on:
- The difference between the suppliers in terms of environmental impacts. It may not always be necessary to distinguish between individual suppliers, when these use similar equipment and procedures.
- The scale and time horizon of the change. Large scale changes and changes over longer time spans may affect several separately identified suppliers or technologies, while for smaller and more temporary
changes one specific supplier or technology may be identified as the one affected. The implicit assumption of the presented procedure is that all other suppliers than the ones identified as most sensitive, will
not be affected by the changes in demand. If this assumption is regarded as too simple, all suppliers that are expected to change should be included in the product system. This can be done either as separate
scenarios or in the form of an average, weighted in proportion to the relative degree to which they are expected to be affected.
Figure 2.1 Decision tree outlining the 5-step procedure for identifying the processes affected by a change in demand for a specific intermediate product. Please se the text for detailed explanations
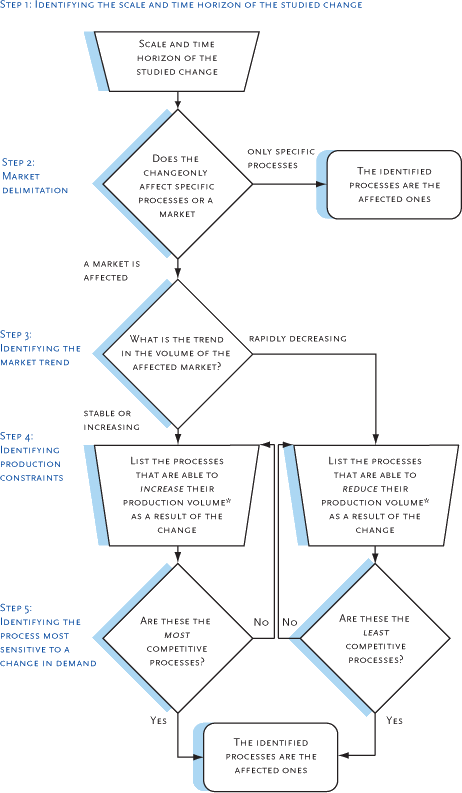
*) For long term changes, the volume relates to production capacity, while for short term changes it relates to output within the existing capacity, see also the text in section 2.2.1 and
2.2.3
2.2.1 Step 1: Identifying the scale and time horizon of the studied change
Before it can be determined what suppliers/technologies that may be affected by a change in demand for an intermediate product, it is necessary to know the scale and time horizon of the change.
Scale of change
If the object of study is a larger change (see Annex 1 for a definition), new suppliers, new markets, or even new products and technologies, may come into play, compared to a small change that only affects
the current suppliers. A small change does not affect the overall market trend, so that an increase in demand will affect the same suppliers as a decrease in demand, as determined by the overall market trend
(see also section 2.2.3). But for a large change that affects the overall market trend, it is necessary to take into account also the direction of the change (increase or decrease in volume), since it is typically
different suppliers that are affected by an increase or a decrease of the overall market.
Large changes are typically seen when introducing new technology or new regulation on a significant market, e.g. if all cars were to be made from polymers and carbon fibres in stead of steel, which among
other consequences would have the market for steel turning from increasing to decreasing. However, many small changes may accumulate to bring about a large change. Therefore, even in studies of small
changes it may sometimes be relevant to apply an additional scenario with the possible larger changes that could be the result of accumulated small changes. For example, even in a life cycle assessment
considering such a shift to polymers and carbon fibres for a single producer of cars, it may be relevant to investigate the possible consequences of other car producers following suit.
Time horizon
Most life cycle assessments study changes with a relatively long time horizon, but the life cycle methodology may also be used to study changes of a more intermediate character. The time horizon is important
for what suppliers may be affected, since:
- a change in the short term is restricted to the existing production capacity and thus does not affect capital investment (installation of new machinery or phasing out of old machinery), while a long-term
change is expected to affect capital investment.
- a change in the short term will typically affect the least competitive suppliers, while for long-term changes the affected suppliers depend on the overall market trend (see section 2.2.3).
In general, changes cannot be isolated to the short-term, since capital investment (i.e. long term changes) is typically a continuous process affected by the current and expected trends in the market volume,
resulting from the accumulation of a large amount of individual short-term purchase decisions.
This is obvious in markets with a short capital cycle (fast turnover of capital equipment, as e.g. in the electronics and polymer industries) and in free market situations (where market signals play a major role
when planning capacity adjustments), but it is also true for markets with a long capital cycle (as e.g. in the building and paper industries).
Thus, the isolated effects of short-term changes (i.e. effects within the existing production capacity) are only of interest in markets where no capital investment is planned (e.g. industries in decline), or where
the market situation has little influence on capacity adjustments (i.e. monopolised or highly regulated markets, which may also be characterised by surplus capacity).
Office chair example

Office chair example: This and the following steps in the procedure will be illustrated with examples taken from an LCA of an office chair. The LCA concerns the design for improved reuse of a
specific brand of office chairs.Thus, it is a case of a small change (since it concerns only one specific producer, not the entire market) with a long time horizon (since the new design can be
expected to affect future capital investment in the different processes in the life cycle).
An example of a change with a short time horizon could be an isolated decision to remove heavy metals from the polymers and surface coatings of the chair, which – all other things equal –
would not involve capital investment in the metal industry, since heavy metals are already being phased out.
2.2.2 Step 2: Market delimitation
Given the scale and time horizon of the studied change, the next step in the procedure is to determine the possible suppliers of the intermediate product.
Market ties
If only one specific supplier is possible, or a group of specified suppliers can be identified as the ones affected, the whole procedure may be cut short here. This is the case if:
- the decision-maker for the study is expecting to control or influence the production volume of a specified supplier or group of suppliers, or
- two or more companies are tied so closely together in a supply chain that the production volumes of the specific suppliers fluctuate with the demand of the specific customers.
Many examples can be found of the latter situation, especially:
- When products have a low price compared to their weight, so that transport costs prohibit all other than the local producers, as e.g. for the supply of straw for heat and power production, where only the
farmers closest to the power plant will supply the straw. Other examples of this can be found in the forestry sector and the building- and glass-industries.
- When two or more companies are tied together by tradition, or when a supplier has developed its product to meet specific demands of the customer.
- When the choice of supplier is not subject to normal market conditions.
If a specific supplier (or group of suppliers) is identified as the one affected, it may be useful to justify that the production volume of this process is actually able to change. For this purpose, step 4 in the
procedure (section 2.2.4) may be applied.
The procedure can only be terminated here if the production volume of the specific suppliers is actually expected to change as a result of the studied product substitution, i.e. as a result of a change
in demand for the intermediate product. If the change in demand is transferred on to other suppliers of the intermediate product, the production volume of the specific supplier will not change. This may be
the case in spite of close relations between supplier and customer, even in spite of ownership relations or sole-supplier-status, i.e. it is not the closeness of the relation, which is important, but whether the
overall production volume of the supplier is actually expected to be affected.
An example of this is in-house electricity production. If the in-house production fluctuates with in-house demand and thereby does not affect the production volume of the general electricity market, then the
in-house production can be regarded as the affected electricity source for the in-house demand. However, if the in-house production takes place on normal market conditions, and the in-house production
does not fluctuate with in-house demand (even when the company is closed), then the electricity supply for the in-house demand must be regarded as coming from the general electricity market, and not from
the specific in-house production.
This also means that a life cycle assessment will only give credit for - and incentive to - a shift to specific products or suppliers with more environmentally friendly technologies, e.g. “green electricity”, when
this shift is actually expected to lead to an increase in the capacity of the “green” technology. If the shift only pretends to be an improvement, and no change is expected in the composition of the overall
output, no credit is given.
However, the effects of a shift may be delayed, so that the expected increase in the “green” technology will only appear after some time. An example of this may be the initial immature market for ecological
foods, where an increase in demand may not lead to an increase in production, because of the transaction costs of the initial small quantities or because of the time it takes to implement the new technology on
the farms. In such instances, a demand for “green” products should still be credited for its long-term influence on the production capacity of the “green” technology.
Also, the effects of a shift may be indirect, via the political signal that it sends. For example, a constraint on a specific “green” product may be overcome, e.g. by political intervention or because a private
company takes up the challenge, as a result of a consistent unsatisfied demand for this product. Likewise, a consumer boycott of a particular product may be followed up by political action or “voluntary”
changes in company behaviour that limits the production beyond the effects of the boycott itself.
Since such indirect effects may be controversial and difficult to predict, it may be preferable to include them in separate scenarios.
Market identification
In most situations, the intermediate product is demanded on a market with several potential suppliers. Therefore, the potential suppliers must be identified in terms of those who deliver:
- a product with the required obligatory product properties, described on the basis of the needs fulfilled by the product (very different products may serve the same need, thus being in competition on the
same market),
- within the geographical and temporal boundaries of the market affected by the specific demand.
The identification of the obligatory product properties and the geographical and temporal market boundaries is parallel to the first two steps described in the guideline “The product, functional unit, and
reference flows in LCA”. While the description in that guideline may be useful also for intermediate products, it should be noted that the procedure does not need to be elaborated in detail for every
intermediate product.
Office chair example

Office chair example: For most of the materials in the office chair (mainly steel and plastic materials), several suppliers are possible. These materials are traded on a competitive market
without specific ties between suppliers and customers. Therefore, a change in demand from the office chair manufacturer cannot be expected to only affect the current suppliers, but will rather
affect the entire market for these materials. This market can be identified as being European, since for steel and plastic materials, Europe constitutes a fairly closed market, as can be seen e.g.
from Eurostat production and trade statistics databases and publications (EUROPROMS; Panorama of European business; Intra- and extra-EU trade, and Iron and steel yearly statistics).
2.2.3 Step 3: Identifying the market trend
Within the identified market, not all suppliers will be equally affected by a change in demand. For short-term changes (see also section 2.2.1), the affected suppliers will typically be the least competitive
(often using older technology), since it is mostly these suppliers that have capacity available. For long-term changes, the affected suppliers depend on the overall market trend. In a market that decreases (at a
higher pace than what can be covered by the decrease from regular, planned phasing out of capital equipment) the affected suppliers will typically be the least competitive. If the market is generally increasing (or decreasing at a rate less than the
average replacement rate for the capital equipment), new capacity must be installed, typically involving a modern, competitive technology.
Therefore, it is important to identify the market trend (“Is the market increasing or decreasing?”) especially for long-term changes involving capacity adjustments.
It follows from the above distinction, that if the general market volume is decreasing at about the average replacement rate for the production equipment, the effect of a change may shift back and forth
between suppliers with very different technologies, which makes it necessary to make two separate scenarios. This may be relevant for a fairly large interval of trends in market volume, since the replacement
rate for production equipment is a relatively flexible parameter (planned decommissioning may be postponed for some time, e.g. by increasing maintenance).
Note that it is the overall market trend, which is of interest, and not the direction of the specific demand studied. This is because - as long as the overall trend in the market is not affected – it is the same
suppliers that will be affected by an increase in demand and a decrease in demand.
The trends in market volumes should preferably be determined using the same kind of information as that available to those deciding on capacity adjustments in the affected industry. This information is
typically a combination of statistical data showing the past and current development of the market and different forecasts and scenarios. If no information is available, it is safest to assume that the market is
increasing, since this is the most typical situation.
Office chair example

Office chair example: For most of the materials in the office chair the market trend is increasing.Trade statistics and forecasts are available from industry associations and consultants, for
steel e.g. the International Iron and Steel Institute (http://www.worldsteel.org/) and World Steel Dynamics (http://www.worldsteeldynamics.com/). Despite an increasing global trend, the
European production of steel is stagnating, however not below the replacement rate of the production equipment.This implies that the affected suppliers are to be found among the most
competitive steel makers in Europe, since it is here that new capacity is being installed.
The result of this step is that we can concentrate our search for the affected suppliers to one end of the market, either among the most competitive (for long-term changes in an increasing market) or among
the least competitive suppliers (for long term changes in a rapidly decreasing market and for short-term changes).
2.2.4 Step 4: Identifying production constraints
The possible suppliers (among the most or least competitive, depending on the conclusion of the previous step) may be subject to constraints that render them unable to react to a change in demand with a
change in production volume. Since their production volume (and environmental impacts) cannot be affected by the studied change in demand, such constrained suppliers should not be included in the
product system.
A supplier or an entire technology can be constrained in its ability to change its production volume in response to a change in demand, for one or more of the following reasons:
-
Political constraints, typically in the form of minimum or maximum quotas on the process (like the Danish minimum quotas on the use of biofuels for heat and electricity generation) or any of its exchanges,
e.g. product quotas (like the EU milk quotas) or emission quotas (like the Danish SO2 and NOX quotas for electricity generation, which limits the use of coal based technology).
- Constraints in the availability of raw materials, waste treatment capacity, or other production factors.
- If the change in demand is for a co-product, and the production volume of the co-producing process is determined by one or more of the other co-products. In general, this will be the case if the studied
product has a low value compared to the other co-products, so that the studied co-product cannot in itself provide an economic revenue that is adequate reason for changing the production volume (like
animal manure versus milk and meat, or rape seed cakes versus rape seed oil), or if the market trend for the studied co-product is low compared to the market trend for the other co-products. See section
3.2.2 for a precise procedure for identifying which co-products determine the production volume of a co-producing process.
In some cases, an entire market may be constrained, so that none of the suppliers will change their production volume in response to a change in demand. The change in demand will instead mean a change
in the supply of the intermediate product to that application area (or customer) of the product, which is most sensitive to a change in supply. Here, the change in supply will imply an equivalent change in
consumption.
Production constraints may change:
- over time,
- depending on location, and
- depending on the scale of change.
Thus, it is important to note the conditions for which the constraints are valid. Especially, when studying long-term changes (the typical situation for life cycle assessments, see section 2.2.1), it should be
avoided that a process is excluded from further considerations because of constraints that only apply in the short term (in day-to-day operations, many constraints apply, e.g. in raw material availability and production capacity, that are irrelevant when considering long-term changes).
In case of missing information on production constraints, it must be tentatively assumed that there are none. Unjustified exclusion of processes is thereby avoided. If a constrained process is thereby included,
this will normally be discovered in the next step in the procedure.
Office chair example

Office chair example: A change in demand for steel in the office chair cannot affect plants that use the electric arc furnace (EAF) technology, since this technology is constrained by the
availability of its main raw material (steel scrap).This leaves only the basic oxygen furnace (BOF) technology to be affected by a change in demand from the office chair manufacturer. Note
that we assume a small change with a long time horizon (see step 1), so that we expect the same reaction to an increase in demand as to a decrease in demand, and we look at changes in
production capacity.
2.2.5 Step 5: Identifying the suppliers/technologies most sensitive to a change in demand
Among the unconstrained suppliers/technologies, some will be more sensitive to a change in demand than others. For long-term changes in an increasing market, the most sensitive supplier/technology is
identical to the most competitive, while in a rapidly decreasing market and for short-term changes, the most sensitive supplier/technology is the least competitive (see section 2.2.3).
Competitiveness is typically determined by the production costs per unit. For capacity adjustments it is the expected production costs over long-term that matters. The distinction between constraints (section
2.2.4) and costs is not completely sharp, since some constraints may be translated into additional costs and some costs may be regarded as prohibitive and therefore in practice function as constraints.
However, if not taken too strictly, the distinction is useful for practical decision making. Also the definition of costs itself is not sharp, since concerns for flexibility (as a concern for future costs), environmental
costs and other externalities – whether monetarised or not - may enter the decision-making process. When predicting the actual decisions with regard to changes in capacity or capacity utilisation, it is
therefore necessary to include all those constraints and nonmonetarised costs which are relevant to the decision makers, but on the other hand not such which are not going to influence the actual decisions.
The kind of costs included may also vary depending on the interests of the decision makers, e.g. private investors may place less emphasis on environmental externalities than a public investor.
Thus, the most sensitive suppliers/technologies are determined from the production costs, while taking into account constraints and non-monetarised costs as perceived by those who decide about the change
in capacity (longterm) or capacity utilisation (short-term). The important point is to model as closely as possible the actual decision making context.
Data on production costs for individual plants, countries, or technologies are obtained from the industry in question, from industry consultants, or from research organisations, for steel e.g. World Steel
Dynamics. If data cannot be obtained, it may be assumed that modern technology is the most competitive and the oldest applied technology is the least competitive. With respect to geographical location, it
can be assumed that competitiveness is determined by the cost structure of the most important production factor (labour costs for labour intensive products, else energy and raw material costs). When
comparing labour costs, local differences in productivity and labour skills should be taken into account.
Office chair example

Office chair example:The source of the crude oil used for producing the plastic parts in the office chair will come from the most competitive oil sources (since the oil market is increasing).
According to the International Energy Agency (http://www.iea.org/),World Energy Outlook 1994, the most competitive sources (those with the lowest extraction costs) are the sources in the
Middle East and Venezuela, which are expected to increase their share in the global supply from 30% in 1991 to 45-57% in year 2010.
2.3 Default assumptions
For the initial phases of a life cycle study, and for parts of the life cycle that are less important, the procedure described in section 2.2 may be too elaborate and too demanding. Also, there may be situations
where it is not possible to obtain the necessary market information. In these situations, the defaults in table 2.1 may be applied. The detailed arguments for these defaults are given in LCA Report No. 1:
Market information in LCA.
Table 2.2 lists some typical processes, which may be assumed to be the ones affected by a change in demand for the listed products under the stated conditions. When used in a specific study, please check
whether the stated conditions apply. The conditions stated in table 2.2 are the expected conditions on the European market in the years 2000-2010, provided that the studied changes are small. Unless
otherwise stated, the defaults in table 2.1 apply. The main differences in assumptions between the products relate to differences in market trend (increasing to stable versus rapidly decreasing) and geographical market boundaries (local,
continental or global). For documentation and sources of these assumptions, please see the background report “Market information in LCA”.
It can be seen from table 2.2 that the specific affected suppliers/technologies are often very different from the corresponding average supplying the market. Thus, only in exceptional cases can average data
be used as proxy data, when market-based data are not available. This may e.g. be the case when the market in question is supplied exclusively by one main, slowly developing technology. In most other
situations, it is preferable to make one or more estimates of the affected process, based on the available data.
Table 2.1. Default assumptions on market conditions
Item: |
Default assumption: |
Scale of change |
Small |
Time horizon |
Long-term |
Market ties |
None |
Market segment |
Narrow, i.e. not assuming substitution between very different products |
Geographical market |
Products with a low value to weight ratio: Local market* Products with medium value to weight ratio: Continental market* Products with a high value to weight
ratio: Global market* |
Market trend |
Overall increasing production volume |
|
Production constraints Only for co-products with a low value relative to the remaining co-products from the same process |
Affected (most competitive) supplier/
technology |
Technology: Modern Geographical location (within the above defined geographical market): Depending on relative importance of labour costs and skills. |
* In that transport costs have been attributed large importance here. However, also other factors may be of significance, such as possible toll barriers, trade patterns, and geographical differences in overall
production volume.
If you have data for a market average, the market range may be estimated by coefficients of variance of:
- 10-30% for energy consumption,
- 10-20% for raw materials and regulated emissions that occur as a result of substances in fuels and raw materials,
- 60-150% for unregulated emissions that occur as a result of substances in fuels and raw materials. Substances that naturally vary significantly, e.g. cadmium, lead, mercury and other metals in coal and
crude oil, may in extreme cases give emissions that vary with a factor of 1000 or more.
- Larger variation (factor 5-10) should be applied for emissions that are created during the production process, and which vary significantly depending on the physical conditions during production, and
emissions that occur from the use of specific chemicals during the production process.
When the range is known or has been estimated, the affected process can then be assumed to be at one of the ends of this range, depending on realistic assumptions with respect to the items listed in table 2.1. It is thereby assumed that all the above exchanges co-vary, so that large energy consumption is linked to large raw material consumptions and large
exchanges to the environment.
When relevant, several alternative scenarios should be included to reflect the limits of knowledge.
Table 2.2 Default list of processes affected by a change in demand for selected products, under the expected conditions for the European market in the years 2000-2010 and when the studied changes are small
NACE-code |
Product |
Geography |
Market trend |
Other differences in assumptions compared to table 2.1 |
Affected supplier/technology |
01.1 |
Crops in general |
EU I |
Increase |
Limits on fertiliser per ha in some areas |
Current suppliers, increasing yield per ha by additional fertiliser. When not possible, or for larger changes, barley will be displaced. |
01.1 |
Fodder protein |
Global |
Increase |
None |
Soy bean (Brazil) |
02.01 |
Wood for pulp |
Local |
Increase |
None |
Local |
11.1 |
Crude oil |
Global |
Increase |
None |
Heavy crude from Venezuela or Middle East |
13.2 |
Aluminium |
Global |
Increase |
None |
Hall-Heroult. Point feeders. Separate electricity market. |
13.2 |
Copper |
Global |
Increase |
None |
Modern, raw material flexible: Solvent-
extraction-electrowinning |
13.2 |
Cadmium, Mercury, Lead |
Global |
Decrease |
None |
Recycled material (reducing the material going to waste deposits) |
15.4 |
Vegetable fat |
Global |
Increase |
No |
Specific fatty acid composition requested EU rape oil |
20 |
Wood and products of wood |
Depending on product requirement |
Increase |
None |
Modern, often local: Drying plants with heat pumps and variable speed |
21.2 |
Pulp, paper, board |
Local to regional |
Increase |
None |
Local to regional, modern |
23.2 |
Propylene |
EU |
Increase |
None |
Fluid catalytic cracking off-gas cleaning |
23.2 |
Ethylene |
EU |
Stable to increase |
None |
Steam cracking of LPG or gas oil |
24.13 |
Chlorine |
Europe |
Decrease |
None |
Old technology (mercury process) |
24.15 |
Ammonia |
Europe |
Decrease |
Surplus capacity in Eastern Europe |
Older natural-gas based technology (Eastern Europe or Greece) |
25.1 |
Rubber |
Global |
Increase |
None |
Synthetic rubber from modern plants |
26.4 |
Bricks |
Local |
Decrease |
None |
Oldest local tunnel kiln |
26.5 |
Cement clinker |
Local |
Decrease |
Technology is raw material dependent |
Wet process in Denmark. Dry process in general. |
26.5 |
Cement |
Local |
Decrease |
Fly ash cements etc. constrained by raw material availability |
Portland. Older, local plants. |
27.1 |
Steel |
Europe |
Increase |
Electric Arc Furnace technology constrained by scrap availability |
Modern Basic Oxygen Furnace technology |
40.1 |
Grid electricity |
Central Europe |
Increase |
Nuclear, hydro and lignite based power politically constrained |
Coal-based technology |
40.1 |
Grid electricity |
North Europe |
Increase |
As above + emission limits for SO2, NOx (and CO2). Surplus coal based capacity. |
Coal-based technology within existing capacity likely to cover demand for next 10 years. Else: natural gas-based technology. |
40.1 |
Grid electricity |
Greece |
Increase |
Nuclear and hydro power politically constrained |
Lignite-based technology |
2.4 Uncertainties in identifying the correct processes to include
The procedures for identifying the correct processes to include in the studied product systems, as described in section 2.2, rely on market data,
in which the following uncertainties are of importance:
- Uncertainty re. the scale of change that may influence the boundary conditions of the market.
- Uncertainty re. what intermediate products will substitute each other in different market segments and geographical markets.
- Uncertainty re. the temporal and geographical boundaries of the actual market of an intermediate product.
- Uncertainty re. what technologies and processes are constrained in their ability to change their volume in response to a change in demand.
- Uncertainty re. market trends.
- Uncertainty re. the parameters that influence decisions on capacity adjustment, e.g. prices of different technologies and the effect of information on buying behaviour and investment decisions.
These uncertainties will often be dominating the overall uncertainty of a life cycle assessment, since they may affect which processes are included and excluded from the analysed product systems. The
importance increases in proportion to the possible variation in the technologies and processes that may be substituted, i.e.:
- Variation in the relevant technologies and processes between different possible markets.
- Variation in the relevant technologies and processes within the same market, especially the variation between the least and the most competitive technology/process.
This means that the higher the variation in possible outcomes, the higher is the demand on the quality of the market data.
A reduction of the uncertainty can only be obtained through a better understanding of the different intermediate products in the life cycle and the markets on which they are traded. Thereby, the individual
processes to be included in the product system can be determined with more precision. Use of quality assurance and critical review as part of the life cycle assessment can contribute to the reduction of
uncertainties.
The above considerations are also valid for the standard assumptions in traditional system delimitation (see section 1.3), but since this does not include market information it will be difficult to estimate the real
uncertainties as a result of the system delimitation. The uncertainty on a traditionally delimited system will therefore typically be calculated from the uncertainties on the average data for the included processes.
Since this uncertainty is an expression of a real variation, it cannot be reduced through additional data collection.
When relevant, several alternative scenarios should be included to reflect the limits of knowledge.
The mentioned major sources of uncertainty also apply to the handling of multi-functional systems, following the procedure described in chapter 3.
The issue of uncertainty is dealt with in more detail in the technical report “Reducing uncertainty in LCI.”
3 Handling multi-functional systems
3.1 Solving the co-product allocation problem: From multiple to single functions
Few (if any) products are produced, consumed and disposed of in isolation. Thus, most (if not all) product systems will provide more than one product (material goods or services), either as a part of the
functional unit (see “LCA Guideline no. 2: Determining the object of study, the functional unit, and the reference flow”) or as co-products from one or more of the processes in the life cycle.
To study the environmental impacts of an isolated product substitution, it is therefore necessary to isolate the processes that are affected by the specific substitution, from those processes that are physically
linked to the product systems, but which are nevertheless not affected by the substitution. For those processes that are affected, it is furthermore necessary to determine the extent to which they are affected:
Will it imply a change in the volume of the affected process or only in some specific exchanges? Will a change in volume depend solely on the studied substitution or should the change in volume be shared
with other product systems?
The last question is what is usually referred to as “the (co-product) allocation problem”. Co-product allocation is the partitioning and distribution of the exchanges of a process with multiple co-products over
these co-products. It has been one of the most controversial issues in the development of the methodology for life cycle assessment, as it may significantly influence or even determine the result of the
assessments. In general, the co-product allocation problem can be avoided through the procedure presented in section 3.2. This procedure is in line with the recommendations of ISO 14041 and includes the
traditional allocation procedure (which simply distributes the exchanges of a co-producing process over the co-products according to some allocation factor) as a special case (see section 3.6).
3.2 Procedure
An initial distinction can be made between joint production, where the relative output volume of the co-products is fixed (e.g. chemical processes where outputs are determined by stochiometry), and
combined production with independently variable output volumes (e.g. when different products share the same service). For combined production, allocation can be avoided simply by modelling directly the
consequences of a change in the output of the co-product of interest (that which is used in the product system under study) without change in the output of the other co-products. This situation is dealt with in
step 1 of the procedure (section 3.2.1). The remaining part of the procedure (steps 2 to 4) deals with the situation of joint production where allocation can only be avoided through system expansion.
System expansion is illustrated in figure 3.1, showing a co-producing process with one determining co-product (product A), i.e. a co-product that determines the production volume of that process. In figure
3.1, also just one dependent co-product is shown, but in practice there may be any number of co-products.
Figure 3.1 Model for describing system expansion and delimitation for joint production, valid both when product A and product B is the product used in the life cycle study

Performing a system expansion in relation to joint production is to answer the question: How will the production volume and exchanges of the processes in figure 1 be affected by a change in demand
for the co-product that is used in the life cycle study?
This question is equally relevant when the co-product used in the life cycle study is the determining product for the co-producing process (A) and when it is the product in which the dependent co-product is
utilised (B).
A complete identification of changes in production volume as a function of change in demand would require an economic model for all the involved processes and product flows. The procedure presented
here involves the simplifying assumption that a change in demand for a dependent co-product does not affect the production volume of the co-producing process[6].
The three rules in Box 3 provides the answer of the simplified procedure to the above question.
Box 3: Rules for system expansion and delimitation for joint production
-
The co-producing process shall be ascribed fully (100%) to the determining co-product for this process (product A).
-
Under the condition that the dependent co-products are fully utilised, i.e. that they do not partly go to waste treatment, product A shall be credited for the processes that are displaced by the dependent co-products. The intermediate treatment shall be ascribed to product A. If there are differences between a dependent co-product and the product it displaces, and if these differences cause any changes in the further life cycles in which the dependent co-product is used, these changes shall likewise be ascribed to product A.
- When a dependent co-product is not utilised fully (i.e. when part of it must be regarded as a waste), the intermediate treatment shall be ascribed to the product in which the dependent co-product is used (product) B, while product B is credited for the avoided waste treatment of the dependent co-product.
It should be noted that system expansion implies that data are to be collected for processes that are not necessarily part of the current supply chain.
The amounts to be ascribed from the different processes depend on the amount of co-product used in the specific product system under study. For example, a unit output of product A shall be ascribed the
exchanges from process A relating to the production of this unit, and for the situation when the dependent co-product is not utilized fully, product A shall furthermore be ascribed the waste treatment of that
amount of the dependent co-product, which is co-produced with that one unit of product A. In the same situation, a unit output of product B shall be ascribed the intermediate treatment of this unit, while
being credited for the displaced waste treatment of this unit.
The rationales behind the three rules in Box 3 are:
Rule no. 1 follows logically from product A per definition being the co-product, which causes the changes in production volume of the co-producing process.
Rule no. 2 follows – under the stated condition – from the fact that both the volume of intermediate treatment and the amount of product which can be replaced, is determined by the amount of dependent
co-product available, which again is determined by the change in production volume in the co-producing process, which is finally determined by the change in demand for product A. It follows from this rule
that product B is ascribed neither any part of the co-producing system, nor any part of the intermediate treatment. When studying a change in demand for product B, this product shall be ascribed the change
at the supplier most sensitive to a change in demand (identified by the procedure described in chapter 2), i.e. the same process, which is displaced by a change in demand for product A (but see also rule no. 3). If the condition stated in rule no. 2 (that the co-product is fully utilised in other processes) is not fulfilled, rule no. 3 applies.
Rule no. 3 applies to the situation where a dependent co-product is not utilised fully. In this situation, the volume of the intermediate treatment (and the displacement of waste treatment) is determined by how
much is utilised in the receiving system, and not by how much is produced in the co-producing process. Another way of saying this is that in this situation, process I (the intermediate treatment) is that supplier
to process B, which is most sensitive to a change in demand for product B.
3.2.1 Step 1: Treating combined production: co-products with independently variable outputs
If the output volume of the co-products can be independently varied (combined production), it is possible to describe directly the consequences of a change in the output of the co-product of interest without
change in the output of the other co-products.
Some co-products may be separated completely, so that each co-product can be produced alone, allowing separate description of this pure production. However, the combined production of these
co-products is typically done to take advantage of some benefit of co-production, e.g. joint use of capital equipment, reduction in energy or raw material consumption, or reduction in waste generation. Since
a description of the separate pure production does not encompass these advantages, it will not provide a correct reflection of the actual conditions.
Rather, what should be included in the product system is a description of the consequences of the studied change in relative outputs, i.e. the changes in process exchanges as a result of a change in the output
of the co-product of interest while the output of the other co-products is kept constant. In this way, the benefits of the combined production are inherent to the description and will be reflected in the
outcome.
In general, a physical parameter can be identified, which - in a given situation – is the limiting parameter for the co-production. It is the contribution of the co-product of interest to this parameter, which
determines the consequences of the studied change.
Example 1: Combined surface treatment
Surface treatment is often performed on different objects in combination (e.g. legs for chairs in combination with legs for tables), to limit the loss of surface agent (e.g. paint) and to save machine time. Although the different legs might be treated individually to obtain a measure of the environmental exchanges for each treated product, it would be more correct to model the changes in process exchanges when changing the amount of chair-legs while keeping the output of table-legs constant and vice versa. In this case, a physical parameter can be identified, which determines the change in exchanges: additional surface area treated (treated surface area of the leg plus border area). The size of the border area will depend on the extent to which the additional chair-legs will utilize an area that is already border area, or whether the existing border area is already utilized fully so that the additional chair-legs anyway need to be treated separately.
Example 2: Combined transport I
When the same vehicle transports several items, e.g. both plastic chairs and wooden chairs, the effect of adding another item to be transported depends on what physical parameter is limiting the transport capacity. When there are more of the heavy wooden chairs, the transport capacity is limited by weight, which means that the truck volume is not utilised fully. In this situation, adding an extra chair will increase the exchanges from the transport process in proportion to the weight of the extra chair. Heavy ooden chairs demand more trucks than light plastic chairs, even when the chairs have the same volume. However, when there are more of the plastic chairs, it may be the space limit that is reached first, so that the vehicles cannot be loaded at full weight capacity. In this situation, the exchanges from the transport will change in proportion to the volume of the two kinds of chairs. For trucks, the weight capacity is typically utilised fully at a density of 250-300 kg/m3. If the density is lower than this limit, the transport capacity is limited by volume.
3.2.2 Step 2: Identifying a product as determining for the volume of the co-producing process
Identifying a joint product (a product from joint production) as a determining co-product is the same as
showing that the co-producing process will be affected by a specific change in demand for this product. When the co-producing process is identified as the affected process by using the procedure in chapter
2, we have in fact at the same time identified the co-product under study as being a determining co-product.
For a co-product, the crucial point in the procedure in chapter 2 is the identification of the other co-products as production constraints (third bullet of step 4 in section 2.2.4.). The production volume of the
co-producing process is constrained by the demand for the determining joint product(s). Independently variable (combined) co-products cannot provide a constraint and may be simultaneously determining
(as described in the previous step).
To be a determining co-product, a joint product (or a combination of joint products in which the co-product takes part) shall:
-
provide an economic revenue that is in itself adequate reason for changing the production volume
and
- have a larger market trend (change in overall demand) than any other joint product or combination of joint products that fulfil the first condition (taking into account the relative outputs of the co-products).
The reason for this is that the joint product (or combination) with the largest market trend provides a constraint on the ability of the other joint products to influence the production volume of the co-producing
process. Note that within a combination of joint products, the co-product with the smallest market trend is determining the ability of the combination to influence the production volume.
See also Box 4 for an illustration of this.
It follows from the above condition that if more than one joint product or combination of joint products fulfil the condition to provide an adequate economic revenue to change the production volume, only
that co-product or combination which has the relatively largest change in overall demand (market trend) is actually determining. Thus, at any one given moment, typically only one of the joint products
determines the production volume. A notable exception is when no relevant alternative production routes exist for the joint products and their prices therefore must be adjusted to ensure that all the joint
products have the same market trend, since only then the market will be cleared (see example 6). In this situation, a change in demand for one of the joint products will influence the production volume of the
joint production in proportion to its share in the gross margin of the joint production. This is equivalent to the result of an economic co-product allocation. However, the resulting change in output of the other
joint products influences their further downstream lifecycles, including their consumption and disposal phases, and thus requires the inclusion of the processes affected. This latter aspect of system expansion
is ignored in a pure economic allocation of the joint production.
Box 4: Illustration of the constraints between joint products
Assume a process with the 4 joint products A, B, C and D, with the following relative market trends and economic revenues:
Co-product |
Marginal economic revenue |
Relative market trend |
A |
10 |
small |
B |
6 |
medium |
C |
5 |
large |
D |
1 |
large |
Note that the stated market trends and economic revenues are relative to the normalised output volumes of the co-producing process, i.e. differences in the actual physical quantities have already been eliminated.
At a marginal production cost for the co-producing process of 9, only one co-product (A) can provide an adequate economic revenue to change the production volume alone. Product C cannot alone influence the production volume, in spite of the large market trend for this product. However, the combination B and C also fulfil the condition (of providing an adequate economic revenue). The possible influence on the production volume from this combination is determined by the smallest of the trends in the combination, which is the medium trend of product B. Since this is still larger than the trend of product A, product B becomes the co-product that determines the production volume.
Example 3: Joint production of food products and animal fodder I
Many of the less valuable co-products of the food industry are used as animal fodder, and typically there is no alternative way to produce the food product in question. For example, wheat bread can only be produced from wheat, which is milled to flour, while the other fractions (germ, bran, and husk) are used for animal fodder (with the exception of a very small part that is used in speciality products for human consumption). In this case, there is little doubt that the flour is the only co-product that can provide adequate economic revenue to change the production volume of the milling process (and the wheat production), and that the flour is therefore the determining co-product.
Example 4: Joint production of zinc and heavy metals I
Approximately 90% of all primary cadmium are a co-product of zinc extraction. In addition, lead and sulphur are produced as co-products of zinc extraction. The demand for zinc is increasing moderately, while the demand for the heavy metals cadmium and lead is stagnating mainly due to environmental regulations. The supply of cadmium from compulsory take-back and recycling of cadmium-containing products means that some primary cadmium is currently deposited. The same situation can be expected in the future for the other heavy metals. Sulphur is increasingly produced from desulphurisation of flue gases from refineries, power plants etc. In Europe, there is no longer demand for primary production of sulphur. Thus, it should be clear that only changes in demand for zinc can be determining the size of the primary extraction.
Example 5: Joint production of chlorine and sodium hydroxide I
The joint production of chlorine and sodium hydroxide is one of the classical examples of allocation problems. The chlor-alkali process yields three co-products:
2 NaCl + 2 H2O ⇔ 2 NaOH + Cl2 + H2
Hydrogen is produced in relatively small quantities (27 g for every kg of chlorine) providing approximately 3% of the world market for hydrogen. The main production route is steam reforming of natural gas and this will probably also be the most competitive process to cover a change in demand for hydrogen. Thus, hydrogen cannot be the determining co-product.
In practice, the chloralkali process is the exclusive production route for chlorine, which cannot be easily stored and is typically sold locally. Sodium hydroxide is a more flexible product that can be stored and transported over long distances. Sodium hydroxide can be substituted by soda ash directly or by sodium hydroxide produced by caustification of soda ash, thus providing both a floor and a ceiling on the price of this co-product. Chlorine and sodium hydroxide are produced in approximately equal quantities by the chloralkali process and their share in the total income for the process is approximately the same. However, during the last 10 years there has only been one short period in 1990/1991 where the price of sodium hydroxide was so high that it could by itself provide adequate revenue to change the production volume.
Based on this analysis of the market situation, it is concluded that long-term decisions on capacity adjustments are based on the existence of local, stable demands for chlorine, making chlorine the determining co-product for the chloralkali process when applied in LCAs with a long time horizon.
Example 6: Pork production
In the abattoir, the slaughtered pig is separated into a large number of co-products. Independent variation among co-products is limited, although some flexibility exists, notably in the share of minced meat. All co-products must therefore be regarded as joint, and with some minor exceptions no alternative production routes exist. Thus, the pork market is governed solely by the output from the abattoirs and all prices are continuously adjusted so that all products are sold. Market trends are therefore aligned so that all joint products are simultaneously determining for the production volume. A change in demand for one specific part of the pig, e.g. tenderloin, will therefore influence the volume of production in proportion to the gross margin obtained for this part, relative to the average gross margin, equivalent to the result of an economic allocation. Since there are no alternative production routes, this change in production volume in turn affects the output, pricing and consequent consumption of all other parts of the pig.
The illustration in Box 4 also shows that:
- the determining co-product is not necessarily the co-product, which yields the largest economic value to the process (although this will often be the case),
- the determining co-product is not necessarily the co-product, which is having the largest increase (or decrease) in demand.
If adequate data are not available to allow one of the joint products to be identified as determining, several scenarios should be used to reflect the limited knowledge. A scenario may be made for each
product that may possibly be determining. The scenarios may be presented separately or as a combination of the relevant scenarios weighted in proportion to their expected probability or in proportion to the
relative expected influence of the joint products on the production volume of the co-producing process[7].
3.2.3 Step 3: Identifying the co-product that determines the volume of intermediate processes
The intermediate processes are those processes that take place between the split-off point where a dependent co-product leaves the processing route of the determining co-product and the point of
displacement where the dependent co-product can displace another product. While it is always relevant to determine the split-off point, it is only relevant to determine a point of displacement when the
dependent co-product is utilised fully in other processes and actually displaces other products there (i.e. when rule no. 2 of Box 3 applies).
The determining co-product for the intermediate processes is identified by investigating whether the condition of rule no. 2 is fulfilled or not, i.e. whether the dependent co-product is utilised fully in other
processes.
If the condition is fulfilled, the volume of intermediate treatment (and the amount of product being displaced) depends on the product volume of dependent co-product. Since the co-products cannot be
independently varied, this volume is fixed by the determining product of the co-producing process (product A in figure 3.1). A change in demand for the dependent co-product will not lead to any change in
the intermediate treatment (exactly because it is not determining, i.e. it cannot affect the volume of the co-producing process). Thus, the intermediate treatment and the co-producing process have the same
determining product, and (as stated by rule no. 2 of Box 3) the intermediate process shall be fully ascribed to this product (A).
Example 7: Joint production of chlorine and sodium hydroxide II
When chlorine is the determining co-product, chlorine is ascribed the full chlor-alkali process, the intermediate processes (concentration, transport, and storage of the sodium hydroxide), but is credited for the avoided production, transport and storage of sodium hydroxide from caustification of soda ash (see example 14 in section 3.5.3 for further treatment of this avoided process).
Example 8: Co-generation of electricity and heat I
Electricity is often co-generated with heat, since the overall efficiency of combustion is much higher when the heat can also be utilised. When the heat is fully utilised, a change in the production of electricity will affect the distributed amount of co-generated heat and will affect the alternative heat source. Thus, in this situation the electricity shall be ascribed the additional energy requirement for distribution and credited for the alternative heat supply which is displaced. A change in demand for heat cannot be covered by co-generated heat (since this is already utilized fully) and will therefore affect the alternative heat source.
Since in this situation, where the dependent co-product is fully utilised, it is product A that determines the amount of product being displaced, product A shall also be ascribed other possible changes resulting
from this displacement. This applies to the changes in the alternative raw material supply, as in the examples above, where product A is ascribed (credited for) the changes in the displaced process D (still
referring to figure 3.1), but also to such changes in the further life cycle of the dependent co-product (process B in figure 3.1) that are a consequence of differences between the dependent co-products and
the products they displace.
Example 9: Consequences of quality differences when using co-products
Compared to the displaced product, the co-product may be of a different (typically lower) quality than the displaced product. This is often of no importance to the user (else the substitution would not have been accepted) but sometimes it may lead to an additional need for maintenance or other supplementary activities. These additional activities shall be ascribed to product A.
Example 10: Contaminated co-product
Compared to the displaced raw material, the co-product may contain a contamination, e.g. of heavy metals, which gives it a different performance during the final waste treatment of product B. The difference in waste treatment and/or in environmental exchanges form the waste treatment shall be ascribed to product A.
If the condition of full utilisation is not fulfilled, it means that part of the dependent co-product is treated as a waste. In this situation, the volume of the intermediate treatment (and the displacement of waste
treatment) is determined by how much is utilised in the receiving system, and not by how much is produced in the co-producing process. Thus, product B is the determining product for the intermediate process and shall
be ascribed these (while being credited for the avoided waste treatment), as stated by rule no. 3 of Box 3.
Example 11: Co-generation of electricity and heat II
When the market for co-generated heat is saturated and the heat is still not fully utilized, a change in the production of electricity will just produce more surplus heat, but not affect the distributed amount of co-generated heat. A change in demand for heat in this situation will not affect the amount of heat generated, but will influence the amount distributed.
Thus, the energy requirement for heat distribution shall be ascribed to the heat, while the electricity is ascribed the co-generation, but is given no credit for displacement (since there is none).
As illustrated by the examples 8 and 11, whether a co-product is utilised fully and whether it displaces other products, depend on market conditions that may change:
- over time,
- depending on location, and
- depending on the scale of change.
Thus, it is important always to note the conditions under which the determinant for the intermediate processes has been identified.
If the investigated change is of such a size that it in itself changes the conditions for the system expansion, i.e. changes which product is determining or whether the dependent co-product is utilised fully, the
system expansion shall be calculated on the basis of the resulting conditions after the change.
The information needed to determine whether a dependent co-product is fully utilised are obtained from market and waste statistics and market studies, often available in-house in the involved industries. If it
is uncertain whether this condition is fulfilled, it may be necessary to apply different scenarios to reflect the limited knowledge.
3.2.4 Step 4: Identifying displaced processes
System expansion typically involves displaced or avoided processes, either avoided raw material supply (process D in figure 3.1) or avoided waste treatment (process W in figure 3.1). Thus, the final step of
the system expansion is to identify the displaced processes more precisely. This is done by applying the procedure in chapter 2 to the market situation of the displaced processes.
3.2.5 The procedure as a flow-chart
Figure 3.2 presents an overview of the procedure in the form of a flow-chart.
3.3 Waste or co-product?
In the procedure presented here, the distinction between wastes and co-products is not important. If in doubt whether an output is a waste or a co-product, the output can be regarded as a dependent
co-product and passed through the procedure. It will then either fall under rule no. 2 (if the output is utilised fully, but does not displace any other products, it is a waste, and product A is ascribed all
processes in the waste treatment) or rule no. 3 (for “near-to-wastes” that are not fully utilised). Even when an output is without economic value to the process that produces it, the “waste treatment” for the
utilised part is in fact a recycling (process I in figure 3.1), and rule no. 2 or 3 should therefore be applied in order to model correctly the consequences of this “waste treatment.”
Figure 3.2. Decision tree showing the 4-step procedure for handling multifunctional processes. For definition of determining co-products, see the text (especially section 3.2.2). For explanation of the rules and process
lettering, see the text, Box 3 and Figure 3.1 in this section
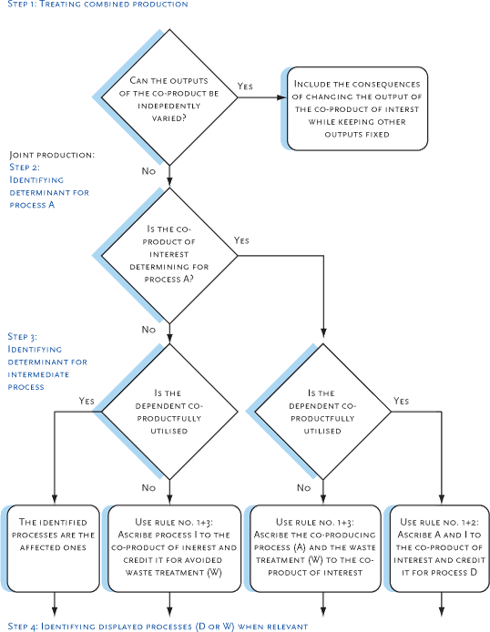
3.4 Recycling
Recycling is often mentioned as presenting distinct allocation problems needing a separate treatment. However, the procedure in section 3.2 is equally applicable to recycling as to any other situation where
the same processes are shared by several products. In figure 3.3 the recycling situation is presented, re-using the layout and lettering of figure 3.1.
In this situation, it is no problem to identify the determining product for the primary life cycle. This is obviously the product of this life cycle (product A), not the scrap.
The central issue is what determines the recycling rate and thus the degree to which the scrap is utilised in the secondary life cycle.
Figure 3.3 Model for describing system expansion and delimitation in relation to recycling
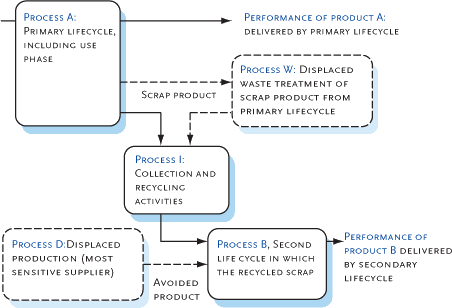
In an increasing market for the scrap product, as is currently the case e.g. for most metals, all scrap collected will be used. In this situation, a change in the volume of the primary life cycle will lead to a
change in the amount of scrap available for collection, and a consequent change in the amount collected (provided the collection percentage is constant), which finally will result in a change in the amount of
scrap utilised in secondary life cycles, and thus in the displacement of “virgin” production (i.e following rule no. 2 of Box 3). A change in the volume of the secondary life cycle will have no direct influence on
the amount of scrap utilised, since all the scrap collected is already utilised fully. Thus, the change in the volume of the secondary life cycle must be covered by a change in “virgin” production (i.e. still
following rule no. 2). Thus, in an increasing market, all changes in all life cycles affect the amount of “virgin” material extraction, and only the production that ensures an increase in the collection (by providing more material for recycling, or by specifically increasing recycling capacity, either technically, by economic support, or by stimulating political intervention) will be credited for the resulting increase in recycling (displacement of “virgin” extraction and decrease in waste handling).
It should be noted that an increase in recycling can be an indirect or delayed consequence of the signal that is sent by a change in demand for scrap, e.g. via political intervention or private investment in
capacity increases, as also described in section 2.2.2. Of course, such indirect effects are only possible when significant quantities of scrap are available for collection, in addition to the amount already
collected. Since such indirect effects can be controversial and difficult to predict, it may be preferable to include them in separate scenarios.
In a decreasing market, some of the available material is being deposited, since there is not an adequate demand. A change in volume of the primary life cycle will only lead to a change in the amount of
material to be deposited, while a change in the volume of the secondary life cycle will lead to a change in the amount being recycled, and thus indirectly also to a change in the amount being deposited (i.e.
following rule no. 3 of Box 3). This is the situation for cadmium and some other materials that are being phased out because of their severe environmental impacts (this example does not imply a
recommendation to increase the use or reuse of these substances). Thus, in a decreasing market without “virgin” inflow, all life cycles that utilize scrap products will be credited for the resulting increase in
recycling (decrease in waste handling), and no life cycle will be credited for supplying additional material to recycling (since this would just mean that an equivalent amount would require waste treatment
elsewhere).
In this way, the procedure provides incentive for using scrap when the market for the material in question is decreasing, and for supplying scrap when the market is increasing, which is exactly what is
needed to increase recycling in these two respective situations. When the recycling rate is below its environmental optimum, the procedure furthermore gives credit for specific actions that increase recycling
capacity.
It may be argued that the studied changes in either the primary or secondary life cycle may also have a secondary effect on the market prices, and that this would equally affect the price of the primary
product and of the collected scrap. However, the “virgin” production and the collection do not react to a price change with the same change in volume. At the high collection rates that exist in a free market
situation, the resulting volume change in collection is likely to be much less (probably often negligible) compared to the change in “virgin” production. This would support the above conclusion of applying rule
no. 2 in the situation of increasing markets. Also in the case of a moderately decreasing market, where the supply from “virgin” production still plays a role, the difference in reaction to a price change would imply that the “virgin” production is affected most. However, in a
rapidly decreasing market, the scrap can cover the entire demand and virgin supply would not be relevant. In this situation, a small change in volume of the secondary life cycle would only be able to affect
the scrap collection, which is in line with our above conclusion of applying rule no. 3 in case of decreasing markets.
3.4.1 Downcycling
In some situations, the recycled material cannot displace “virgin” material, either
- because its technical properties have been reduced (e.g. paper fibres that become shorter for each recycling, so that after approximately 6 cycles they are so short that they must be discarded), or
- because it has been contaminated (e.g. silicon alloys of aluminium cannot be recycled with the ordinary aluminium scrap).
In these cases, several distinct markets may exist for different qualities of recycled material, and the displacements that will occur will be determined by the supply and demand on these markets, see figure
3.4, which shows three markets for recycled material (scrap qualities 1, 2 and 3) besides the market for “virgin” material. If a demand for a specific scrap quality is not satisfied completely, scrap of higher
quality or virgin material may be used (dotted lines connecting processes I and D in figure 3.4), while scrap of lower quality cannot be used. When upstream processes deliver more scrap than the capacity of
its downstream markets, some of the scrap will not be used.
Thus:
- A change in demand for a specific scrap quality will affect the next upstream, unused supply and will displace waste there. If all upstream supplies are used fully, it will affect “virgin” production.
- A change in supply of a specific scrap quality will affect the next downstream, unsatisfied demand. If no downstream markets have unsatisfied demands, the scrap produced will not be used, thus affecting
the immediate waste treatment.
A change in demand for a specific product, produced with scrap material, will cause both of the above. For example, a change in demand for product B in figure 3.4 will lead both to a change in demand for
scrap quality 1 and a change in the supply of scrap quality 2.
Figure 3.4 System expansion and delimitation in relation to downcycling
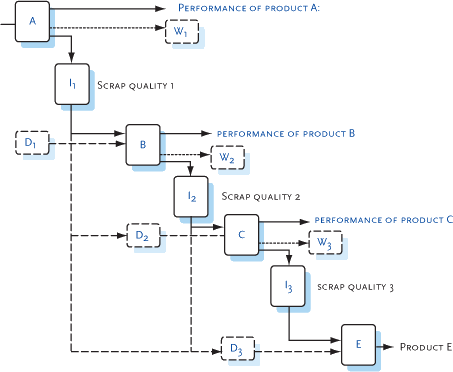
Example 12: Paper recycling I
In recycling of newsprint, we have at least three pools of recycled material with distinct qualities:
- the recycled newsprint pool, which can be used in production of tissue paper, cardboard, moulded paper and a lot of other paper products (and typically 20% in newsprint itself),
- the cardboard pool, which can be used e.g. for corrugated board production (product C),
- the corrugated board pool, which is a nearly closed loop with a recycling of approx. 75% (i.e. in this case product E and product C is identical).
The volume of the “recycled newsprint pool” is determined by the supply to this pool, since the demand for recycled newsprint is currently larger than the supply in most markets, due to the many possible applications. Due to the high recycling rate in the corrugated board loop, the demand for recycled cardboard is easily saturated, which means that the demand for corrugated board may typically determine the volume of recycling in this pool.
In this market situation, “virgin” paper will be affected both by a change in supply of recycled newsprint (by displacement) and by a change in demand for recycled newsprint (because “virgin” is the next upstream unused supply). The recycling process itself (I1) shall be ascribed to the newsprint (product A). An increased supply of or demand for recycled cardboard will affect the alternative waste treatment of this cardboard (W2) and the recycling process (I2) shall be ascribed to the user of the recycled cardboard (typically the corrugated board production).
In the case of contamination of virgin material, it should be noted that it is not only the current market situation that must be considered, but rather a very long-term market situation. As long as the current
demand for scrap qualities is larger than the supply, all the contaminated scrap will be used and will displace “virgin” material. The contamination will be diluted due to the constant inflow of virgin material.
However, at some stage in the future the scrap markets may become saturated, so that the contamination becomes a limitation for the recycling. The current contamination may thus lead to a future need for
waste treatment of the contaminated material, or at least to a different displacement than on the current market. It is this future market situation that should be used to determine what processes to include in
the system expansion, since the immediate displacement of “virgin” material is only a temporary postponement of the necessary supply of “virgin” material in the future situation, when the contaminated
material can no longer be used. The need to take into account these future effects is included in the third sentence of rule no. 2 of Box 3: “If there are differences between a dependent co-product and the
product it displaces, and if these differences cause any changes in the further life cycles in which the co-product is used, these changes shall likewise be ascribed to product A.”
Example 13: Copper-contamination of steel
The current demand for steel allows copper-contaminated fractions to be incorporated in hot-rolled steel (contamination limit approximately 0.28%). However, in the (not-so-far-away) future, a further supply of copper-contaminated fractions may no longer find a market. These fractions will then be deposited instead of being recycled. Thus, a current copper-contamination of steel can be predicted to incur a future deposition of the contaminated steel. This implies that although the contaminated steel is currently recycled and not deposited, the life cycle causing the contamination should not be credited for the recycling of this steel, but instead be burdened with its (future) deposition.
For materials where the technical properties are reduced on recycling, each additional life cycle will imply a change in the quality of the material in the recycling pools, influencing the requirements for supplies
of “virgin” material to the pools. The need for new material may be caused e.g. by degradation of fibres or polymers, as can be seen with paper or plastics. Thereby, the change in material quality may also
be expressed as a change in the ability of the material to displace “virgin” material. A life cycle that delivers as much material to recycling as it receives will cause a change in material quality equivalent to the
amount of “virgin” material supply that is needed to compensate for the reduction in technical properties (see also example 14). When less material is sent to recycling than what is received (i.e. when material
is sent to waste treatment), the change in requirements for supplies of “virgin” material to the recycling pool (the change in displacement ability) will depend on the actual quality of the material that is thereby
leaving the recycling systems. The quality (the ability to displace “virgin” material) can be estimated specifically by the physical properties or be calculated theoretically from the average recycling rate in the specific
recycling pool, since the material quality will be reverse proportional to the recycling rate (with a low recycling rate the supplies of “virgin” material will be relatively large, which gives a relatively high material
quality in the recycling pool – and opposite with a high recycling rate, see also example 14).
3.4.2 Relation to the EDIP'97-procedure
The EDIP'97-method[8] applies a factor, called the grade loss, to express the loss of grade or material quality on recycling. This grade loss is used as an allocation factor, in that every life cycle using the material is burdened with this fraction of the primary material production. The grade loss is calculated as the percentage of virgin material that must be introduced on recycling. Therefore, in terms of system expansion, the grade loss is equivalent to the difference between the amount used in a lifecycle and the amount displaced by the recycling from this life cycle, expressed in percentage of the amount used, i.e. the change in displacement ability as explained in the previous section. Thus, given the same information on displacement, the EDIP’97-procedure will lead to the same result as the procedure presented here. Note, however, that he EDIP'97-method does not take into account the situation where the recycling pools are not utilised fully, which implies e.g. that in EDIP'97 the recycling process is always ascribed to the preceding life cycle.
Example 14: Paper recycling II
If it is assumed that paper fibres can only be used on average 6 times since the fibres become shorter and eventually must be discarded, each life cycle will imply an average loss of 17% of the “virgin” material. In EDIP'97-terminology this is expressed by a grade loss for paper of 0.17 per use, which means that a life cycle that receives 1 ton of recycled paper and after use sends 1 ton to recycling should be ascribed 17% of the exchanges from the primary production of 1 ton of paper and 17% of the exchanges from disposal of 1 ton of discarded fibres. In the terminology of system expansion, the life cycle that receives 1 ton of recycled paper (under the condition of full utilisation of the specific recycling pool and that “virgin” paper is displaced in the proportion 1 to 1) shall be ascribed a consumption of 1 ton of “virgin” paper, and – when 1 ton is sent to recycling after use – be ascribed the waste treatment from this (the scrapping of 170 kg discarded fibres) and be credited for the displacement ability of this after one life cycle (830 kg primary production; again under the condition of full utilisation of the recycling pool). The result is that this life cycle is ascribed 170 kg primary production and 170 kg waste treatment, exactly equivalent to the 17% of the used amount of 1 ton prescribed by the EDIP'97-method. When less material is sent to recycling than what is received, or when the receiving market is saturated, less “virgin” material is displaced, depending on the material quality in the lost material, for example the displacement ability of recycled newsprint in 1995 could be estimated to be 50% (based on a realised recycling rate of 65%) and for corrugated board with a recycling rate of 75% the displacement ability will be approximately 32% (meaning that for each time 1 ton of corrugated board is sent to waste treatment, the requirement for “virgin” material in the recycling pool is increased with 320 kg). The displacement ability is directly corresponding to the concept of “residual material grade of scrap” in the EDIP'97-method.
3.5 Complex situations
The situation described by figure 3.1 (and 3.3) is a simplification, in that there is only one determining and one dependent co-product shown (i.e. only two products coming out of process A) and none of the
other processes have co-products. Therefore, this section deals with the more complex situations:
- where process A has more than two co-products,
- where the intermediate process has multiple products or the dependent co-products have other applications than in process B, and
- where the displaced process has multiple products.
3.5.1 More than two co-products
Most of the examples in the previous sections actually involve more than two co-products. It seems to be rather the rule than the exception that processes with more than one product also have more than
two co-products. This, however, poses no problem for the procedure in section 3.2. Each co-product can be treated separately:
- when studying a change in output of a determining co-product, and there are more than one dependent co-product, the consequences for each of the dependent co-products can be analysed in isolation,
one at a time,
- when studying a change in output of a determining co-product, and there are more than one determining co-product, the changes in the co-producing process can be analysed in isolation, separately from
the analysis of any dependent co-products,
- when studying a change in output of a dependent co-product, the only thing to be investigated is whether the dependent co-product is utilised fully or not, which can be done without concern for any of the
other co-products.
3.5.2 Intermediate processes that have multiple products
After the split-off point (see section 3.2.3) and before displacing other products, a dependent co-product may be split up in two or more fractions, each following its own route. Each fraction may be fully
utilised in other processes (rule no. 2, see Box 3) or only partly (rule no. 3). Each fraction can be treated separately, although fractions that follow the same rule may be treated together for convenience
(listing the affected products and processes together).
Example 15: Recycling of demolition waste
Mixed demolition waste may be processed separating a large number of fractions. The concrete alone may be separated into fractions that substitute sand, gravel and crushed stone, respectively. Depending on the local demand (these materials are not valuable enough to justify transport over longer distances) the fractions may be fully or partially utilised. When larger quantities are available, crushing of demolition waste will be economically preferable to “virgin” extraction, and full utilisation will therefore often be possible. For those fractions that are expected to be fully utilised, the primary building may be credited for the displaced primary production, while the fractions that are not expected to be fully utilised, are calculated with full waste handling and no displacement. A building that utilises recycled materials is ascribed the additional efforts in demolition, crushing and separation, and the displaced waste treatment for the fractions that are not fully utilised, while the fractions that are fully utilised is calculated as primary materials.
Even when the co-product is not composed of separable fractions, it may have many different applications. The process which is affected (i.e. process B in figure 3.1) is the application most sensitive to a
change in supply (as identified by the procedure in chapter 2).
3.5.3 Displaced processes that have multiple products
When a displaced process does not only yield the displaced product, but also other co-products, see figure 3.5, these co-products are also displaced and the demand that they fulfilled must now be met in
another way. Thus, the procedure must be repeated for these co-products, but with a negative sign.
If this leads again to another process with multiple products, as illustrated by process E in figure 3.5, one might fear that this system expansion would continue without end. However, the number of possible
processes involved in the system expansion is limited by the very procedure, since:
- the number of markets affected by each displaced process is limited, and the displaced process is only that specific supplier to each market, which is most sensitive to a change,
- the three rules for system expansion (Box 3) provides clear cut-offs between the different product systems involved (either a process is included or excluded from the studied system),
- for each time the system expansion is iterated, both the economic value and the volume of the displaced processes tend to decrease, because in each iteration the avoided product is the determining
co-product of the displaced process and therefore typically of higher value (and often also larger in quantity) than the dependent co-products which go on to the next iteration. The system expansion can
therefore be terminated when the amount of product that goes on to the next iteration is below the uncertainty on the initial amount of co-product.
Example 16: Joint production of chlorine and sodium hydroxide III
In Europe, the displaced production route for sodium hydroxide (see also examples 5 and 7) is assumed to be the combination of the Solvay process: 2 NaCl + CaCO3 ⇔ Na2CO3 + CaCl2 and the lime-soda process (caustification): Na2CO3 + Ca(OH)2 ⇔ 2 NaOH + CaCO3 with recycling of the calcium carbonate, giving net process: 2 NaCl + Ca(OH)2 ⇔ 2 NaOH + CaCl2. Thus, this displaced production route has a co-product, calcium chloride, which can be used for de-icing and dust control because of its hygroscopic properties. However, it is not a very valuable product and part of it is deposited. Thus, following rule no. 3 (see Box 3), the displacement of the alternative production route for sodium hydroxide will lead to a reduction in calcium chloride deposition. In summary, chlorine will be ascribed the displacement of the alternative production route for sodium hydroxide and credited for the reduced calcium chloride deposition. Using the nomenclature of figure 3.5, the cut-off is after process D and W2, since there is no displacement of alternative supplies to process C (de-icing and dust control with calcium chloride) as long as there are adequate unused supplies in W2. Therefore, proces G is not affected by the changes in the chlor-alkali system and can be excluded from the analysis.
Figure 3.5 System expansion and delimitation when the displaced process has multiple outputs
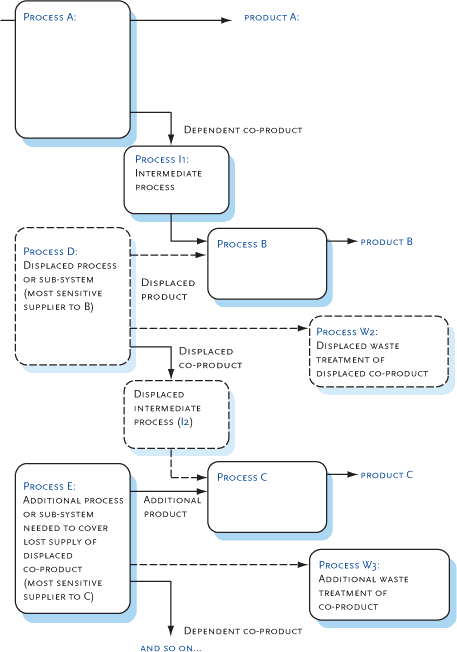
Example 17: Ethylene and propylene
The main production route for ethylene is steam-cracking, which yields ethylene in a relatively high proportion. For each raw material (ethane, LPG, naphta, or gasoil), the relative outputs of ethylene and the by-product propylene is fixed. The raw material that will be affected by a change in demand for ethylene depends on the current the raw material market. In Europe, we may consider a current situation in which LPG is the affected raw material (see table 2). In this case, the additional output of 1 kg ethylene will yield 0.42 kg propylene, which will displace an alternative production route yielding a larger proportion of propylene. This secondary route uses the off-gases from fluid catalytic cracking (FCC) yielding 0.3 kg ethylene per 0.42 kg propylene.
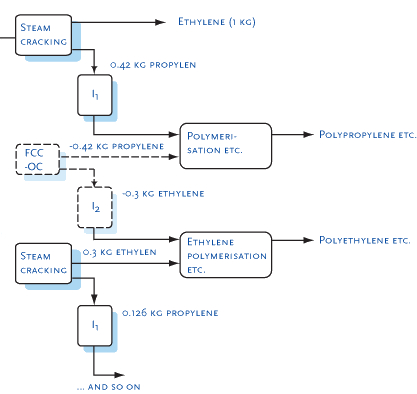
By iteration, it can be calculated that 1 kg of additional ethylene output requires the following system expansion: a reduction in volume of fluid catalytic cracking off-gas cleaning (FCC-OC) corresponding to an output of 0.3 + 0.32 +0.33 + …. = 0.43 kg ethylene, and an increase in steam cracking corresponding to an output of 1 + 0.3 + 0.32 +0.33 + …. = 1.43 kg ethylene.
The same calculations can be made for changes in the demand for propylene, in which case process A would be the FCC-OC route. In practice, the two process routes have a number of other by-products, which would also have to be accounted for. The use of linear regression models of the refinery industry facilitates such calculations.
3.6 Traditional co-product allocation as a special case of the presented procedure
In traditional co-product allocation, the exchanges of the co-producing process is partitioned and distributed over several of the co-products, and there is no inclusion of intermediate and displaced
processes. Thus, traditional co-product allocation may be regarded as a special case of the procedure in section 3.2, occurring when:
- several co-products are determining the volume of the co-producing process in different periods within the time horizon of the study, so that the exchanges of the co-producing process can be allocated
over the co-products in relation to the relative lengths of these periods[9], and
- the co-products can be stored (without additional environmental impact) during the periods that they are not determining, so that no additional intermediate treatment and no displacement occurs.
3.7 Relation to the procedure of ISO 14041
Applying the procedure in section 3.2 will lead to the same results as if applying the stepwise procedure of ISO 14041:
- Step 1 in the ISO procedure requires that system expansion shall be performed wherever possible. As shown above, system expansion is always possible for cases of joint production, by following steps 2
to 4 of the procedure in section 3.2.
- Step 2 in the ISO procedure requires that when ISO step 1 cannot be applied, allocation should be done according to physical relationships (causalities). This is equivalent to step 1 of the procedure in
section 3.2, and is relevant for cases of combined production.
- Step 3 in the ISO procedure (allocation according to other relationships) does not come into play, since all possible cases can be covered by either step 1 or 2.
In the procedure in section 3.2, step 1 deals with combined production (ISO step 2), while steps 2 to 4 deals with system expansion (ISO step 1), since it appears more logical to deal first with the simple
case, where the outputs of the other co-products can be kept constant without system expansion, before dealing with the more complicated cases, where the outputs of the other co-products can only be
kept constant by applying system expansion. However, in practice the order does not matter: If applying system expansion to a case of combined production, the same result will be obtained as when
applying the more simple procedure of step 1 (in section 3.2).
Besides the three-step procedure, the ISO 14041 (section 6.5.2) states an allocation principle, which has popularly become known as “the 100% rule”:
“The sum of the allocated inputs and outputs of a unit process shall equal the unallocated inputs and outputs of the unit process”, i.e. there should not be any exchanges that are allocated twice or not
allocated at all. Although, according to the ISO text, this principle applies only to allocation and not to avoiding allocation, it is worth noting that the procedure in section 3.2 adheres to this principle: The
three rules in Box 3 ensures that all processes are fully ascribed to (allocated to) either one or the other co-product.
4 Forecasting procedures
4.1 Introduction
The previous chapters included considerations on the time horizon of the studied change, and it was made clear that the processes to include in the studied product systems may change over time, depending
on the future market situation. However, no recommendations were given for the actual forecasting procedures to be applied. This is the topic of this chapter.
4.2 Determining the parts of the product systems for which forecasting is relevant
It may not be equally important to forecast all parts of a product system. There may even be entire life cycle assessments where forecasting is not necessary. The factors that need to be considered are:
- The general speed of development of the relevant markets, technologies and exchanges
- Expectations about radical or untypical developments
- The time horizon of the study relative to the expected development
- The position of the specific process in the life cycle of the product
Speed of development
Markets generally develop more slowly as they mature. With time, the product becomes more well-defined (the obligatory product properties tending to become more encompassing), and the market
boundaries and production constraints less volatile (tending to be determined more by natural geography, such as climate and natural transport barriers, than by administrative differences). Likewise, the
production costs and technologies develop more slowly as the ultimate physical constraints of each material, process or technology is approached. There has been several attempts at classifying different
industrial sectors according to their speed of development, but none of them are fully satisfactory. For a given technology, the size of most process exchanges will decrease over time, following the general
efficiency development in the corresponding technology, but for exchanges that are in focus because of their economic value or their known environmental impacts, the speed of development may be above
average (example: the phasing out of CFC's).
Radical or untypical developments
The general considerations in the preceding paragraph may be overruled by specific knowledge in specific situations. Even traditional sectors may be subject to sudden, radical changes determined by larger
shifts in other sectors or in general technological developments or socio-economic conditions. For example, over the last decade development in the vehicle sector has been speeded up by pre-announced
regulation on emissions. Another example is the introduction of genetic engineering, which may cause sudden, radical changes to the otherwise technologically mature food sector.
Time horizon of study
The general need for forecasting depends on the relation between the time horizon of the study and the general speed of development, taking into account also any untypical developments. The time horizon
of the study is determined by the period for which the conclusions of the life cycle assessment should be valid plus the life time of the affected capital investments. This period is typically considerably longer
than the lifetime of the product. The period for which the conclusions should be valid is related to the application area of the study (cf. table 1.1). Forecasting is typically relevant if the time horizon of the
study is longer than 5 years. In addition, forecasting is relevant in sectors with rapid development or if radical or untypical developments can be expected.
Position in the life cycle
Even when the time horizon of the study is longer than 5 years, not all processes in the life cycle may be affected so far into the future that forecasting becomes relevant (see figure 4.1 for an illustration of this
situation).
Figure 4.1 The environmental impacts (arbitrary values) of an electricity-consuming product as a function of the lifetime, showing the parts of the life cycle for which forecasting is relevant
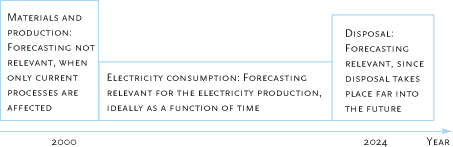
4.3 Determining the necessary detail of forecasting
As any other aspect of life cycle assessment, forecasting may be made in more or less detail. Covering the most important processes in the studied life
cycles, a forecast may include (in order of increasing detail):
- the general direction of the development, in terms of technology and exchanges,
- the relative speed of development of the relevant processes,
- the situation at specific points in time, corresponding to the time horizon of the study,
- the specific technology and its exchanges at such specific points in time.
If the general direction of development confirms or enhances the current situation, this qualitative information may be adequate as an addition to a life cycle study based on current or historical data. For
example, to conclude that an alternative energy source that is currently competitive versus fossil fuels will continue to be competitive, it is adequate to have the general knowledge that costs of fossil fuel
resources will be slowly increasing on the long term (as reserves are depleted) and that costs of the alternative energy source will continue to fall (following an ordinary learning curve).
The relative speed of development of different processes must be taken into account if the direction of development does not in itself provide a clear indication, and if the speed of development is not uniform
for all the involved processes. This information, which is still qualitative, may sometimes be adequate basis for a conclusion. For example, when the price of all fossil fuels are expected to increase in the long
run, it is necessary to know the relative speed of price developments for coal, oil, and natural gas, in order to determine which fossil fuel will be the most competitive in the future.
Combining knowledge on the direction and speed of development with more quantitative information allows forecasts of the market situation and the technologies involved at specific points in time. For
example, information on the current costs of coal and wind power and the actual speed of cost developments for these two technologies (e.g. expressed in average percentage change in raw material costs
and efficiency per year and/or as a coefficient of a learning curve) will allow to forecast whether wind power or coal power is the most competitive at a specific point in time.
If necessary, the relevant technologies may then be further quantified, also in terms of exchanges, by combining specific technical information with general forecasts on technical efficiency and emission
control.
4.4 Choosing the relevant forecasting method
Several methods can be used for forecasting. For our purpose, the methods can be classified under six headings:
- Extrapolation, which is based on extending historical and current trends into the future. This may be adequate for short-to-medium term forecasts of specific processes, when no radical or untypical
developments are expected.
- Modelling, which seeks to identify the determining mechanisms and to model how the combined effects of several mechanisms will influence the future.
- Participatory methods, which seek the insight and opinions of experts and stakeholders.
- Exploratory methods, which seek to structure all possible futures by combining analytic techniques, that give an exhaustive qualitative description of the field, with imaginative techniques aimed at filling all
gaps in the analytical structure. In this way, possibilities rather than probabilities are considered. This may be useful in product development, for those processes upon which the decision-maker has a large
potential influence.
- Normative (or goal-oriented) methods, which begin with stating the desired future and then move backwards in time to identify the necessary steps for reaching this goal. Besides this particularity, any of the above mentioned methods may be applied also in normative forecasting. Like exploratory methods, normative forecasting may be useful in
product development, for those processes upon which the decision-maker has a large potential influence.
- Scenario methods, which combine aspects of the other methods, especially participatory, modelling and exploratory methods. For long-term forecasts in complex situations where many interdependent
forces are at play, it is unlikely that a specific forecast can be identified as the single “most likely” description of the future. Instead, scenario methods aim at presenting a broad range of plausible outcomes
(scenarios), which can serve as a basis for robust conclusions that are viable over the wide range of possible futures.
The forecasting method to apply in a specific situation depends on the time horizon of the forecast and the predictability and complexity of the item to be forecast (see table 4.1). The choice of method does
not depend on the required detail.
Table 4.1 Relevance of forecasting methods depending on time horizon and complexity
|
Forecasts for specific processes, when no radical or untypical developments are expected, or where such developments are under the control of the decision maker |
Forecasts for less predictable processes and more complex systems |
Long term (5-25 years) |
Modelling, exploratory and normative methods |
Scenario methods |
Short-medium term (1-5 years) |
Extrapolation methods |
Modelling and participatory methods |
The divisions in table 4.1 should be seen as guiding only. In practice, the distinction between the different situations and relevant methods is not sharp, and more than one method may be relevant in a specific
situation. Often, different methods can be combined to give a more reliable forecast.
Only extrapolation is treated in more detail in this guideline (see section 4.5), since it is the simplest form of forecasting, and therefore may be relevant to perform as an integrated part of a life cycle
assessment. The other forecasting methods are expected to be applied primarily for other purposes than life cycle assessments, while their results may afterwards be used in a life cycle assessment. These
methods are described in more detail in the complementary Technical Report: “Market information in life cycle assessments.”
It should be noted that in life cycle studies with a long time horizon, the dominating uncertainty will be from forecasting, especially with regard to the determination of market constraints and market trends, but
also technology development.
4.5 Forecasting by extrapolation
Extrapolation is the simple (linear or non-linear) prolongation into the future of historical relations (see figure 4.3 for an example).
While all time series of data may be extrapolated, it is not all data that it is meaningful to extrapolate. To improve the reliability:
- The extrapolation should preferably be based on the determining factor for the expected development and the trend of this factor.
- Data for an extrapolation should at least go five years back, preferably 10 years. However, when radical changes have taken place, which have altered or radically influenced the determining factors, it
does not make sense to include data from before such changes.
- Any constraints on the extrapolation should be taken into account (e.g. physical or political boundaries for the development of the extrapolated factor). When approaching a constraint, the extrapolation will
no longer be a good approximation.
Some general conclusions from empirical observations may be applied:
- The introduction of a new technology tends to follow an S-curve, so that the initial penetration is slow but with a logarithmic increase, followed by a linear growth again followed by a logarithmic decrease in
cumulative penetration until the market is saturated.
- Production costs tend to decrease with cumulative production capacity, following a so-called learning curve, a logarithmic curve typically described by a learning factor, which is the cost reduction
achievable by doubling the cumulative production. The learning factor, which tends to be fairly stable for each specific technology (see figure 4.2), is typically between 0.9 and 0.75, meaning a cost reduction
of 10-25% when doubling cumulative production. More innovative technologies tend to have the lowest learning factors (largest cost reductions) compared to more established technologies (cf. also figure
4.2), which also implies that the learning factor does change when seen over very long time horizons. The learning curves for cost reductions mainly reflect savings in manpower, but physical efficiency
improvements also play a role. Conservative learning factors (i.e. 0.85 - 0.95) may therefore be used as proxies for the physical flows in a life cycle study when the physical efficiency improvements in these
flows are not known from other sources.
Figure 4.2 Learning curves for selected energy technologies. From M. Pehnt: Life Cycle Assessment of Fuel Cells in the Energy and Transportation Sector. Dissertation to be published in summer 2001, Institute for Technical Thermodynamics, German Aerospace Center, Stuttgart
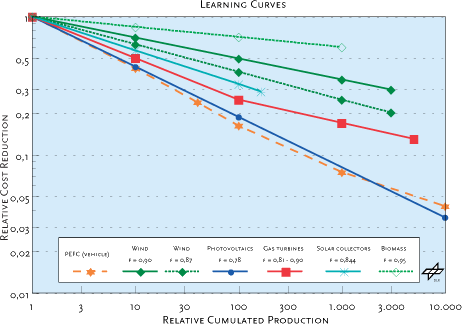
Sources of time series may be:
- Technical literature and technical experts re. the process in question.
- Statistics of industrial associations.
- General statistical publications.
Figure 4.3 shows a simple linear extrapolation of a time series of aluminium recycling rates. The recycling rates are extrapolated by dividing the secondary production of a metal with the primary production.
Since recycling rates are influenced by many different conditions, both technical and political, this may be an example of an area where simple extrapolations may not be valid beyond a few years.
Figure 4.3 Simple linear extrapolation of the recycling rate of aluminium
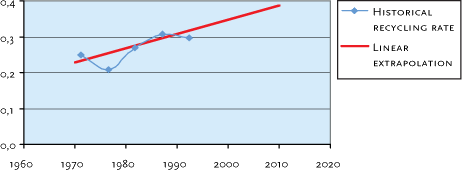
As shown by example 18 an extrapolation is not necessarily quantitative, but can be e.g. a text description of the consequences of extending the prevailing trends into the future.
Example 18: Qualitative extrapolation re. the European electricity market
Current trends of harmonisation and liberalisation of the market will continue. The transmission capacity will continue to be expanded according to the market demand. The result is that current boundaries between electricity markets in Europe will cease to exist, so that geographically there will be only one single European market. The current situation, in which the building of nuclear and hydro power plants in Europe is politically constrained, will continue to prevail. Emission quotas will continue to be in effect or even tightened. The system delimitation can therefore be based on these conditions.
Limitations of extrapolation in forecasting
Since extrapolation is based on historical data alone, and does not include combined effects of several developments, it can only be used for medium or short-term forecasts for smaller, specific areas, where
no radical or untypical developments are expected.
In spite of its limitations, an extrapolation is a better forecast than an assumption of status-quo. Thus, even when there is no time or resources to involve technical experts, it may be justified that a non-expert
makes a simple extrapolation as a first approximation.
Annex 1 Some important terms used in this document
A product substitution is a replacement of one product or group of products with another product or group of products. A product substitution can be defined as small, marginal or large according to the
following definitions:
A product substitution is defined as small or marginal when it does not affect the determining parameters of the overall market situation, i.e. the direction of the trend in market volume and the constraints on
and production costs of the involved products and technologies. The consequences of the substitution can thus be assumed linearly related to the size of the substitution.
A product substitution is defined as large when it affects the determining parameters for the overall market situation, i.e. the direction of the trend in market volume and the constraints on and production
costs of the involved products and technologies.
A functional unit is a quantified description of the performance of the product systems, for use as a reference unit.
A reference flow is a quantified amount of product(s), including product parts, necessary for a specific product system to deliver the performance described by the functional unit.
A co-product is a product from a unit process that has two or more products.
A system expansion is the modification of the system boundaries to include all processes, which are significantly affected by the studied substitution.
The environment is the surroundings in which an organisation operates.
An environmental impact is any change to the environment, whether adverse or beneficial, resulting from an organisation's activities or products.
Environmental exchanges are environmental inputs to a product system (resources), environmental outputs from a product system (emissions to air, water and soil) as well as environmental relations of a
product system which are not directly connected to its inputs and outputs (e.g. land use, physical impacts, non-chemical aspects of occupational health, welfare of workers and domestic animals).
Foot notes
1 2.-0 LCA consultants, Amagertorv 3, 2., 1160 København K.
2 Danish Building Research Institute, Dr. Neergaardsvej 15, 2970 Hørsholm, Denmark
3 Technological Institute, Gregersensvej, 2630 Taastrup, Denmark
4 Institute for Product Development, Building 424, 2800 Lyngby, Denmark
5 Eco-net, Klampenborgvej 239, 2800 Lyngby, Denmark
6 When this assumption is regarded as too simplified (especially as it may change over time, depending on location, and depending on the scale of change), i.e. when more than one joint product is found to be determining within the studied scale or geographical or temporal horizon, a scenario may be calculated for each joint product that may be determining. See also footnote 7.
7 Aggregating scenarios with different determining co-products is parallel to an allocation of the co-producing process, where the allocation factor is the expected probability that a co-product is determining (or the relative expected influence of the co-product). Some economic allocation factors can be justified as representing such relative expected influence. See also section 3.6.
8 Wenzel H, Hauschild M, Alting L.: Environmental assessment of products. Vol. I: Methodology, tools, techniques and case studies in product development. London: Chapman & Hall, 1997.
9 This may also be expressed in terms of relative influence of the co-products on the production volume of the co-producing process, which may be represented by certain economic allocation factors.
| Top | | Front page |
Version 1.0 December 2005, © Danish Environmental Protection Agency
|