| Front page | | Contents | | Previous | | Next |
Detailed Review of Selected Non-Incineration and Incineration POPs Elimination Technologies for the CEE Region
6 Detailed review of selected POPs elimination technologies
6.1 Selection of POPs elimination technologies for detailed review
6.2 Review criteria
6.3 Destruction technologies
6.4 Gas phase chemical reduction (GPCR)
6.5 Base catalysed dechlorination (BCD)
6.6 Container based incineration system (CIS)
6.7 Cement kiln (CKI)
6.8 Cyclone reactor
6.9 Comparative evaluation of the 4 reviewed POPs elimination technology plants
6.10 Summary and discussion
Available POPs elimination technologies have been reviewed in detail based on the background information described in previous chapters. Material and listed perceptions (e.g. a future divided CEE Region, environmental and economic "climate" supporting future establishment of POPs elimination initiatives) have been assessed for 4 commercially, in the sense of free market availability, POP elimination technologies.
The review process has followed a number of steps, outlined in further details below, but in short it was selection of technologies and identification of appropriate and CEE Region selective evaluation criteria.
Of utmost importance for the detailed review was that all reviews have been performed on technologies in operational mode, although GPCR was reviewed in a down-scale test plant facility. However, the
facility was set in operational mode during the actual on-site review.
6.1 Selection of POPs elimination technologies for detailed review
Elimination of POPs differs from region to region. However, in the developing part of the world most elimination is based on various incineration techniques as an integrated part of the overall national
approach to treatment of hazardous and/or municipal waste. These facilities furthermore are the basic of a systematic commercial system of treatment capacities for imported waste originating from countries
in transition and/or without national treatment capacity. In e.g. Europe, the treatment capacities have increased, although the actual amount of treatable waste has reduced resulting in reduced treatment
prices, tempting certain countries to export e.g. hazardous waste instead of initiating precautionary measures for waste reduction and transformation from hazardous to non-hazardous waste.
In many parts of the world, and in particular in regions with economies in transition, like the CEE Region, former treatment habits are either non-competitive in economic sense with external commercial
treatment facilities or non existing due to society transformation and economic decline. Considering the CEE Region as a group of countries in economic transition, the countries are facing a situation where
national large scaled treatment facilities are almost unattainable due to mainly economic reasons, although recognising the enormous amount of hazardous substances potential for treatment. Alternatively,
national priorities must outline which hazardous substances possess the largest risks to environment, human and biota enabling competent authorities to prepare certified actions through e.g. National
Environmental Action Plans (NEAP). These could include investment into small-scale treatment capacities, allocation of funds for external treatment and/or various combined solutions allowing each country
to gain experiences supporting a long-term sustainable solution.
The key findings of Chapter 2 outlines the necessity of finding solutions for the CEE Region, which on one hand are realistic and originates in the region, but on the other hand have a long-term commitment to
the international trend aiming at reducing any impact from chemicals to the environment, human and biota in general. As base for this review study, the requirements defined in chapter 4 must, to the extent
possible, be compiled into any assessed solution.
Selection of POPs elimination technologies for review is a difficult process involving a number of selective parameters as highlighted in earlier chapters. The review of previous performed POPs elimination
reviews outline a number of alternatives to the existing elimination business mainly based on incineration technology. The project-frame leaves room for review of 4 technologies of which it has been decided
that two should have their origin within the existing market platform primarily based on incineration methodologies, while the remaining two consist of alternatives hereto.
The selection of present day available technologies in the CEE Region (e.g. cement kilns) and commercially economic viable technologies like semi-mobile incinerators and non-incineration alternatives
hereto, will allow key deciding resources within the national CEE administrations to have a better overview of advantages and/or disadvantages of a given technology. The review and comparison data will in
first place be compiled objectively without any interpretation of results in relation to national, regional and/or international requirements. This allows the technical experts to concentrate on performing a
consistent review as basic for the later discussion. The reviewed basic data have been presented to the advisory group members of the project involving both main NGO forums and the consultant
management experts.
A more detailed review of alternatives to incineration based technology reveal a situation where certain non-incineration alternatives are more commercial developed than others. Among the most recent
outlined list of “fully” commercialised alternative non-incineration technologies (reference to UNIDO paper “Available non-combustion POPs destruction technologies, October 2001”) are:
- Gas-Phased Chemical Reduction;
- Sodium Reduction Process;
- Base Catalysed Dechlorination; and
- Solvated Electron Process.
Additional, a number of 3-4 other alternatives are classified as “emerging technologies” and finally a few additional are classified as “demonstration technologies”. Finally, a number of CEE based alternative
merging technologies are screened including e.g. the Russian developed Cyclone technology.
Of the Russian facilities investigated so far, the cyclone plant appears to be technically and environmentally the most promising. They have minimised the problem with solid waste and made recycling of the
sodium chloride possible, and they have operating experience on dioxin treatment. Furthermore, they seem to have documented satisfactory results treating constituents similar to PCB. This will be further
evaluated in the ongoing NEFCO Fast Track project.
As basis for the final selection of two non-incineration technologies subject for review, the project has decided only to review technologies, which are characterised as “fully commercial available”.
Commercial available technologies mean that the technology has already been successfully operated in a full scale commercial (or other institutional) setting, and that vendor or vendors are available who can
provide not only the technology itself, but also can provide the know-how and support needed to successfully set up and operate the technology under circumstances such as those likely to be encountered in
the CEE Region.
Furthermore, the project has per default decided only to focuses on “inert” technologies, which are dedicated for the purpose of performing destruction of POPs chemicals. Only deviation is the including of
cement plants, which originally are set up as cement production units and where chemical destruction is a side activity utilising the high temperature production methodology. The selective process of only
involving dedicated POPs destruction technologies, beside cement kilns, furthermore supports the fact that many countries are looking for economic viable solutions, which partly could be based on a
co-financing model involving bilateral as well as regional funding mechanism. The project focuses on accessibility to primary affordable technologies supporting the philosophy of countries gaining their own
experiences when initiating the necessary planning process, implement public participation, secure necessary and skilled staff allocation, prepare and carry out educational programming and secure sufficient
infrastructure supplies.
The anticipated and partly confirmed magnitude of the problem (amount of obsolete pesticides and POPs) necessitates immediate actions related to the final elimination of these substances. Selection of
possible applicable elimination technologies must reflect both the critical conditions and possible impact from these partly uncontrolled stockpiles, but also be instrumented in an accessible form allowing
countries to proceed with elimination of hazardous substances on the one hand and instrument precautionary measures towards waste reduction with the other.
After consultation with the Advisory Group, the below two non-incineration technologies were selected for further review. The technologies were found as the optimum technologies complying with the CEE
Region's objectives for POPs elimination:
- Gas Phased Chemical Reduction (GPCR). The technology has been commercially used in e.g. Australia and USA for destruction of pesticides, chemical weapons etc; and
- Base Catalysed Dechlorination (BCD). The technology has for several years been commercially utilised for elimination of various POPs substances among others PCBs.
The final choice complies with recommendations put forward in the DANCEE report “Review on Obsolete Pesticides in Eastern and Central Europe”, May 2001, recommending the same non-incineration
technologies for further review in terms of their applicability for the CEE Region e.g. as BAT for POPs elimination.
Therefore the following non-incineration technologies have been chosen for detailed review in this project:
- Gas Phased Chemical Reduction Technology has in many studies and also in a recent UNIDO review showed promising results and commercial potential. The technology was reviewed in a
scaled-down version in Rockwood, Canada during June 2002;
- Base Catalysed Dechlorination, a fully commercialised technology available for potential review activities in Australia, USA, Mexico, Spain and New Zealand. After consultations with e.g. BCD Inc.
the project decided to carry out the review on the only operational BCD for organo-chlorinated pesticides in Sydney, Australia during April 2002.
In addition to the two selected non-incineration technologies, two incineration technologies have been selected. Pre-conditional for this selection, the consultant has put forward a number of statements, which
have been used during the selection procedure. These are:
- Optimal involvement of relevant experiences within incineration principles already present in the CEE Region;
- Technologies already available in the CEE Region are screened, and optimal efforts are initiated for inclusion of possible commercially developed POPs elimination facilities;
- The financial capacities of the CEE Region countries are limited and still under the influence of strong prioritisation;
- Many CEE countries are getting technical support through various bilateral, regional and/or international aid programmes on dedicated actions within chemical management. The programme policies
must comply with regional EU and/or international regulations for the environmentally sound elimination of hazardous substances;
- At present, certain indicators for recovery upon economic recession are in place, supporting the fact that the timing is considered appropriate to implement short-term solutions and start investment in
long-term commitments ensuring not only proper POPs elimination, but also support to a broader approach to improved national/regional hazardous waste management activities in general; and
- Finally, the inventoried obsolete pesticides and POPs in most CEE countries are found in stores of various scales, outfit and access conditions etc. including those that are lacking definite owners. This
strongly necessitate the involvement of State funds (either directly or through bilateral, regional and/or international grants) as one of the main financial mechanism supporting any further steps towards
improved chemical management in these countries.
Analysing the above characteristics of the region, the selection process must also consider the variety of national policies regarding hazardous waste management and willingness to comply with international
environmental instrumentation (protocols and conventions) in general, defining potential applicable POPs elimination technologies suitable for the CEE Region.
The DANCEE report “Review on Obsolete Pesticides in Eastern and Central Europe”, May 2001 recommended that the following incineration technologies to be subject for further review in terms of their
potential for the CEE Region, as e.g. BAT for POPs elimination:
- Dedicated Incineration (small-scale treatment methodology). The techno-logy was reviewed at Kommunekemi A/S in Denmark during March 2002 and can be seen in Latvia during summer 2003
operating in full scale;
- Cement kiln incineration (high level of availability in the CEE Region, mentioned as one of the options in many earlier documents). Reviewing activities could be performed on the Norwegian national
facility, although an alternative plant within the CEE Region (Poland) has been considered;
The selected non-incineration technologies follows in line with the result of recent preliminary assessment review of more than approx. 15 different available non-incineration technologies, performed within
the frame of the ongoing UNIDO POPs project. The selected incineration based technologies cover technologies, which at present, are seen as the most widespread in the CEE Region (cement kilns) and
most trustworthy incineration based alternative (dedicated incinerators) to the established “elimination infrastructure” within the region.
The detailed review of the 4 selected technologies was performed by a team of engineering and environmental experts from COWI A/S. The team managed to oversee all four selected technologies in on-site
operational mode, although GPCR and semi-mobile incineration facilities were in testing mode, due to lack of on-time fully operational full-scale units. In Table 6.1 time and contact persons from each of the
visited technologies are outlined.
Table 6.1.1 Contact persons and vendor information
POP elimination vendor |
Contact person and vendor information |
CIS (semi-mobile incinerator) - Visited 1 March 2002 |
Chemcontrol A/S
Lindholmvej 3
5800 Nyborg
Denmark
Contact person: Ole Møller
e-mail: olm@chemcontrol.com |
BCD - Visited 9-10 April 2002 |
The Enterra Pty Limited
12 Forrester Street
Kingsgrove NSW 2208
Sidney, Australia.
Contact person: Bala Kathiravelu (Principal process engineer).
e-mail: bala.k@compuserve.com |
GPCR (Eco-logic) - Visited 26-27June 2002 |
ELI Eco-Logic Inc.
143 Dennis Street
Rockwood ON
Canada N0B 2K0.
Contact person: Elisabeth Kümmling, M. Sc.
e-mail: kummlib@eco-logic-intl.com or
beth.kummling@ecologic.ca |
CKI (Cement kiln incineration) - Visited 27-28 August 2002 |
NORCEM AS.
Lilleakerveien 2B
P.O. Box 143 Lilleaker
N-0216 Oslo, Norway
Contact person: Per Brevik (Manager)
e-mail: per.brevik@NORCEM.no
NOAH (Norsk Avfallshandtering)
Tangenvejen 29
3950 Brevik, Norway
Contact person: Harald Gangmark (Operational Manager)
e-mail: herald.gangmark@noah.no |
6.1.1 Mobile versus stationary plants
It is often discussed if a plant shall be mobile or stationary as optimum POPs waste elimination technology. Stationary plants has several advantages in favour of mobile units, like
- Only one permit. Whenever a POPs elimination technology has to be moved, a new permit procedure must be carried out (maybe even a new EIA has to be made);
- Reduced transport risks. When transporting heavy destruction technology, it can easy happen that parts of the plant are destroyed (especially if there is brick built elements or painted surfaces etc.)
Furthermore, there are the normal risk when transporting heavy goods by road;
- Mobilisation costs reduced to zero. In some cases the displacement costs of a destruction plant equals up to 50% of the initial capital costs due to costs of braking down, cleaning up, transport and
establishment of new infrastructure support function (electricity, water, sewage systems etc.);
- Only one infrastructure set-up. Infrastructure at the destination is often costly, due to installation on the new site of concrete pavement, installation of supply lines (electricity, pressure air, water,
nitrogen, hydrogen, etc.) closed sewage system, erection of bunkers etc.;
- No repetition of the Not-In-My-Back-Yard (NIMBY) effect. Whenever a hazardous waste elimination facility has to be erected, public concerns are expressed. To avoid repetition of this normal
long lasting effect, a proper stationary placement is preferable;
- Continuation in staff. When a mobile plant is moved, the staff can not always follow due to family conditions, investment in residential actives (houses) etc. It is time consuming and costly to train
new operators. At a stationary plant you optimise the performance by increasing educated staff with little or no substitution. Furthermore, surrounding a potential POPs elimination facility, there could
be substantial need of pre-treatment facilities etc. which is crucial for the successful final elimination.
Nevertheless, mobile units are normally more economic accessible due to lower capital costs, they normally have lower capacity enabling countries to work with low-capacity units as a playground for
gaining experiences and finally mobile units could be regarded as more accepted by the public due to their “temporary outfit”.
We have examined the mobility of all the plants in this report, but we believe that even though a plant is declared mobile, it will have a tendency to become stationary.
6.2 Review criteria
Within the last 5-year period, a number of detailed POP elimination technology studies have been carried out primarily driven by US demand for destruction of stockpiled chemical weapons. In continuation
of the negotiation process leading forward to the Stockholm Convention, a number of dedicated studies focussing solely on POPs destruction opportunities and preparatory guidelines have been initiated
both through the UN-system as well as on bilateral basis. One of the key documents are the ongoing preparatory process under the Basel Secretariat (Technical Working Group) leading to a guideline on the
environmentally sound management of POPs as waste herein included demand for present and prospective future elimination of POP compounds. The technical guideline is expected to be present during
COP session under the Basel Convention during October 2004.
Furthermore, Article 6 in the Stockholm Convention outlines:
“Disposed of in such a way that the persistent organic pollutant content is destroyed or irreversibly transformed so that they do not exhibit the characteristics of persistent organic pollutants or
otherwise disposed of in an environmentally sound manner when destruction or irreversible transformation does not represent the environmentally preferable option or the persistent organic
pollutant content is low, taking into account international rules, standards, and guidelines, including those that may be developed pursuant to paragraph 2, and relevant global and regional
regimes governing the management of hazardous wastes;”
It is clear that the intent of the treaty is to "destroy" POP compounds in an economical favourable way and also at the same time avoid the formation and release of POPs. As such, those technologies which
can most effectively deal with the POPs wastes, and minimise or eliminate any further production of POPs wastes or formation or release should be rated highest.
In the overall assessment of the technologies, a rating system has been used where 5 is "Bad", 4 "Below average", 3 "Average", 2 "Above average" and 1 "Best".
6.2.1 Environment
Given a certain amount of substance to be treated, elimination technologies may differ from each other environmentally with respect to:
- Materials used for construction of the elimination plant (actual materials and quantities/lifetime of different parts) – the issue relates to the need for protection of scarce natural resources, but also to the
environmental impacts related to extracting and manufacturing such resources;
- Means of operation (materials as well as energy consumption) – the issue is related to natural resources as above and in particular energy resources. Attention should be paid to the fact that the energy
resource to be employed, in case extra energy for manufacturing processes is needed (either direct or as electricity) will typically be coal energy (at least in Europe), and that combustion of coal is an
important source for release of toxic substances like mercury and dioxins;
- Efficiency of the elimination process;
- Emissions (to air, water and soil – substances /quantities) – the issue relates to toxic substances as well as substances contributing to other environmental impacts like global warming, eutrofication etc;
- Residues (quantities, content of hazardous substances, acceptable options of disposal) – the issue relates to the mere issue of land filling capacity as well as the toxicity of the waste.
The environmental impacts related to the differences may include global warming, depletion of the stratospheric ozone layer, acidification, eutrofication, photochemical ozone creation, ecotoxicity, human
toxicity, different types of filling requirements, land use (may include area requirements as well as biodiversity etc. – not yet generally accepted as impact category) and consumption of natural resources and
materials (assessed for each resource/material).
The assessment tools are generally characterised as Life Cycle Assessment (LCA) tools, which typically is divided in tools for detailed calculations and tools for screening/hot spot assessments. The choice of
tool to be used normally depends on:
- Availability of data;
- Required reliability of the assessment; and
- Manpower to be invested.
In screening assessments, only the most important impact categories are included. Besides that, indicators may be used to simplify some categories. E.g. energy consumption may be used to represent global
warming, acidification and to some extent also categories like eutrofication, photochemical ozone creation and toxicity, which partly are influenced by energy production.
Considering that some of the elimination technologies are only available for review at pilot scale level, reliable data may not be available to an extent justifying a full detailed LCA, besides that a full and
detailed LCA may require more than one man month of work for each technology, it is proposed to adopt a screening/hot spot assessment. This screening/hot spot assessment has focused on the following
characteristics (a reference of 1 kg of POP substance treated is used in all cases):
- Materials consumption. Materials consumption generally relates to consumption of means of operation, while consumption related to plant construction typically is insignificant. However,
consumption of construction materials may also be important in those cases where large constructions with limited lifetime are used for elimination of small quantities of special chemicals. Attention
should be paid to recycling practices, scarcity as well as re-utilisation of the materials consumed. Data is organised as quantity of material consumed divided on the different materials. For materials
used for construction the consumption will be divided on the total amount of POP substance previously treated during the useful life of the plant. The criterion is in principle defined as: Less is better.
The criterion is used in a qualitative as well as a quantitative way depending on which data are easily available.
- Energy consumption. Energy consumption related to the energy consumption of the elimination process itself will normally be the dominating type of consumption, but could be taken to include also
the energy consumption for manufacturing of means of operation, while consumption related to construction and material consumption typically is insignificant. Energy consumption will be calculated as
consumption of primary energy resources to compensate for loss of conversion and transmission. The criterion is in principle defined as: Less is better. The criterion is used in a qualitative as well as a
quantitative way depending on which data are easily available.
- Chemicals. Chemicals cover the total quantity of chemicals being released by the process to air, water, soil and residues. The data should be organised as quantity of substance by route of release.
Focus is given to toxic substances. The criterion is in principle defined as: Less toxicity as well as less quantity is better. The criterion is used in a semi-qualitative way, a real quantitative assessment is
complicated and beyond the scope of this assignment;
- Other issues. Other issues focus on the amount and quality of residuals for disposal (less is better). The criterion is used in a qualitative as well as a quantitative way.
6.2.2 Technical
In order to make a detailed technical evaluation of selected POP elimination technologies, a number of different, and to large extent non-comparable criteria, must be assessed. These are as a minimum:
- Capacity of the technique. The technical capacity of the different techniques is important for many reasons. First of all, if the capacity is insufficient, the time for taking care of the job will be
unsatisfactory and even mean extended danger because POPs are standing untreated for a long time. There is example of techniques which treat 275 kg/day. In one year 100 tonnes might be treated.
Also the ability to treat halogenated waste may influence the capacity. If you have 2,000 tonnes of eligible POP waste for elimination, a 20-year period is needed for total elimination. Furthermore, the
technical capacity means something to the economy of the process. Too small a capacity might be to expensive; From this point of view e.g. the GPRC has a much bigger capacity for chlorine
containing waste such as PCB, where the GPCR capacity may be 3,000 tonnes per year; CIS 400-800 tonnes/year and the cement kiln 13-1,400 tonnes /year.
- Comprehensiveness of the technique. An important issue for a proper technique is the ability to treat broad versus narrow spectrum waste fractions, and what the physical constraint of the waste
is. The POPs wastes eligible for elimination are by experience stored in various forms of packaging material and sizes. Any needed additional pre-treatment possesses a risk for the occupational health
and increase of costs. All pre-treatment activities must be evaluated as part of the whole process with regard to environment, occupational health, economy, risk and complexity. Reviewing a
destruction technique must beside assessment of comprehensiveness to take POP-waste, also take into consideration that POPs-waste frequently are mixed with great variety of other kinds of
hazardous waste.
- Robustness and maintenance possibilities and expenses. The more technically refined and complicated the technology option is, the larger the risk of technical failure resulting in temporary
operational breakdown is assumed to be. Can the equipment be mended locally, or will spare parts and similar have to be purchased internationally? Does the elimination process require input
materials (chemical catalysts and similar), and if yes, are these input materials to be purchased abroad? There is also the question about currency exchange risks if spare parts or input materials can
only be purchased abroad. Most commercial technologies available on the market perform well during continuous operation, however most uncontrolled emission of e.g. dioxins occur during start-up
or closure operations, why all precautionary means must be focussing on parameters influencing chances for interruptive operations.
- Capacity building. Installation of whatever POP elimination technology of today encompasses a certain degree of high skilled engineering abilities. These must be available and applicable for
continuous operation and update. In many CEE countries and the region as such, skilled manpower is available, but there must be focus on intensive update and commitment.
- Supply lines. The need for production supplies e.g. electricity, chemicals, fuels, pressure air, light, water, nitrogen, hydrogen, sewage system, raw products must be estimated and their availability
evaluated. Furthermore, international demands for products quality must be critically evaluated avoiding negative impact on the operational routines and constancy.
- Generation. For every kind of technique, the first versions often suffer from first generation failures. Subsequently, alterations have been made to improve the technique. Therefore the length of
experience time, the amount of waste treated or the amount of test results must be evaluated to give an idea of the sturdiness of the technology. Furthermore, the solidity of the company must be
evaluated. Has the vendor the financial strength to ensure technical supply and support over the years etc.
- Residual products. Every present available technique produces residues of which some can be re-treated others being inert and available for direct deposit. This treatment must be looked upon as
part of the total process and evaluated together with the primary technique with regard to secondary release of POP's to environment, occupational health, economy, risk and complexity; For
comparison to the SC obligation see Article 6 in the Stockholm Convention outline as discussed above.
- Occupational health. Any kind of POPs elimination technology involves a number of potential and/or latent occupational health problems like e.g. noise, light, chemicals, air-pollution, heat, cold,
explosion risk etc. Track recording of failure reports from ongoing technologies shows that most operational interruption occurs due to mechanical and/or human failures. This just to underline the
importance of having assessed and evaluated all possible scenarios related to human safety.
- Operational risks. To operate this kind of technology in Europe, a risk analysis is mandatory. Therefore existing risk analyses of the technology must be evaluated, although recognizing that the
quantitative risk analyses is an inexact practice. Comparable analyses must to the extent be performed.
6.2.3 Economy
From an economic point of view, a given POP elimination technology option is not merely a matter of chemical processes and equipment. The long-term objective of the project is to make an impact in the
recipient countries in terms of actually eliminating POPs. To achieve this, a number of barriers and pitfalls will have to be closely observed, not only in terms of each technology's technical and environmental
performance, but also in terms of the institutional, organisational and financial constraints posed by each individual technology.
From the economist's point of view, the problem can therefore be formulated as follows:
- Identify a technology option, which is practically implementable and which enables sustained operations long enough to actually make an impact in accordance with the project's long-term objective.
The constraints to this problem are that the technology should be technically and environmentally satisfactory.
The project covers a wide array of countries and regions, which all have their specific characteristics relevant for dealing with the POPs problem. These characteristics include:
- fractions, compositions and amounts of POPs;
- existing facilities, know-how and culture for handling hazardous waste, including POPs;
- different regulatory set-ups;
- options of law enforcement;
- economical might and political prioritisation; and
- demographics.
The extent, to which the long-term objective can be met, very much depends on the actual circumstances in each country, or even in each region within the country. The present project does not consider
location specific solutions, which means that the criteria put forward must be generic to a certain extent.
Economic criteria
The list does not contain traditional criteria for the selective choice of an elimination technology. It is rather a list that highlights potential areas to be scrutinised and further considered when making the
technology evaluation.
Organisation
It is important to consider the organisational set-up to be promoted. Should the POP elimination process be run by some government agency, or should the government rather promote incentives (through
fees, charges, taxes etc.) in order to encourage private sector involvement? The answer to this question has a number of implications for the choice of technology: How should the operations be financed -
equipment transfer; subsidies to sustain operations and in case of the latter, who should be subsidised - POP owners or the organisation running the POP elimination process? The choice of technology may
depend very much on e.g. public budgets being available. If equipment is very expensive, the operational costs may be relatively less expensive, thus making operations more viable and attractive to private
sector involvement, if the capital investment is made e.g. by some foreign donor.
Transfer of know-how
Do future operators base the technology option on methods and equipment, which are either locally produced or at least well known? In case the option involves import of an entirely new and not locally
anchored technology to the country or region in question there will most likely be further obstacles to circumvent in order to actually achieve the long-term objective. How to ensure sustained operations also
after the foreign consultants have left the country? In other words, there should be good arguments for choosing e.g. western state-of-the-art technology, or at least the extra costs in terms of know-how
transfer and training local operational staff should be explicit.
Capacity
What is the capacity (not just technically, but in real life terms) of the technology option? Amounts of POPs to be treated by unit of time is important, but also what fractions (pesticides, PCB and similar) can
be eliminated under the constraint that it should be done technically and environmentally satisfactory. If the fractions change, how difficult/expensive is it then to alter the processes, e.g. change combustion
temperatures or change chemical compound in the catalysts applied in the process? Will one facility be dedicated to dealing with one specific fraction of POPs only, thus implying that several facilities are
needed in order to cope with the full range of POP related problems faced by the country or region? Information about fractions is important also because economical incentives related to safe disposal may
vary substantially from one fraction to the other (e.g. obsolete stockpiled pesticides versus PCB contained in electrical equipment still operational). Questions, which need answers for each technology option.
Robustness
The more technically refined and complicated the technology option is, the larger the risk of technical failure resulting in temporary operational breakdown is assumed to be. Can the equipment be mended
locally, or will spare parts and similar have to be purchased internationally? Does the elimination process require input materials (chemical catalysts and similar), and if yes, are these input materials to be
purchased abroad? There is also a question of currency exchange risks, if spare parts or input materials can only be purchased in the US or Canada for example. Again this kind of questions is important
because the long-term objective is to keep the operations running. Any technical breakdown will eventually put the ultimate objective at risk.
Logistics
There is an array of logistical questions to be raised concerning the practical handling of the POPs. Is the technology mobile or stationary? Will the facility come to the POPs or must the POPs be transported
to the facility site? What are the costs of transportation (including insurance, which is an important issue when dealing with hazardous waste)? What about means of storage of the POPs - if the chemicals
arrive at the facility in drums or containers, how then clean and handle these means of storage? See the discussion of mobile versus non-mobile in section 6.1.1. The conclusion is that the so called mobile
destruction plants of social reasons have a strong tendency to become stationary.
Process residues
What are the residues of the elimination processes offered by each technology option? How to dispose of the residues? Is it necessary to have specially controlled dumpsites near the facility or maybe
additional treatment facilities for lower classes of hazardous waste? What are the costs related to using these additional facilities?
Demand
This question is maybe one of the most critical areas at all, although the answer may not be within the scope of the present project, as context specific solutions are not considered. The long-term objective
will not be met if a steady and continuous supply of POPs to be eliminated cannot be secured (POP-elimination services are not in demand). The reasons are several, despite the fact that inventories and
other statistics indicate otherwise. Some POPs may be tied up in operational equipment, e.g. PCB in capacitors and transformers at steel mills or similar. This PCB will become available for elimination only
to the extent that the electrical equipment can be renewed thus keeping up production lines etc. In some regions and countries it may also be difficult to identify owners of e.g. obsolete pesticides, who are
willing to take responsibility (i.e. pay for a safe disposal). Some POP owners may also be reluctant to report correctly to environmental authorities, simply because they know that it will impose additional
costs to the enterprise or farm collective. Thus, the demand also very much involves the question about available fractions and treatment capacity. The demand will very much be dictated by the enactment
and enforcement of regulations on POPs and hazardous wastes. Also, as nations ratify SC, they must enact/regulate the legally binding provisions at a minimum. Waste treatment must always be law and
enforcement driven.
Analytical costs
Experience shows that analytical costs can contribute significantly to the overall operational costs in the range of 20-50%, highly depending on regional/
national authorities demand and development stage of the technology. For merging technologies like e.g. the BCD in Australia, on-site responsible authorities traditionally set forward high demands for
chemical analytical documentation related to air emissions, residues and effluent process water. In certain cases even restricted demands are set forward to environmental monitoring in vicinity areas. In a free
market environment, such costs are normally regarded as development costs provided for by the vendor. However, in order to re-capture development costs, these will likely increase the capital investment
costs of such technologies. The performed review has aimed to give objective information, also on the analytical costs. For comparative reasons, the analytical costs are regarded as equal for all the
scheduled and reviewed technologies.
6.3 Destruction technologies
In the last 30 years increasing problems with hazardous waste have been recognised in most countries worldwide. Hazardous waste is the most toxic part of the general waste problem. Often even small
amounts of hazardous waste can be more harmful than big amounts of normal organic household waste. As all POPs are hazardous waste, they are also covered in this description.
Hazardous waste stems normally from industry, producing all kinds of normal very useful products. Everybody is today surrounded by products, which in the production phase have resulted in hazardous
waste. From the cloth, spectacles, jewellery we use to the floor, wall, ceiling, kitchen elements, water tap, zinc, light bulbs, lamps, windows, pots and pans etc. in our homes. From the bicycles, cars, busses,
trains, aeroplanes to the roads, rails for our transport, to our working places. Everywhere you turn there are valuable products, which in the production phase is likely to produce hazardous waste.
This project review has tried to focus on the scenarios of available POP elimination technologies possessing the least secondary problems. POP waste must be treated to the highest degree possible
according to the requirements and intents of the Stockholm Convention.
In the following Section, please find a detailed environmental, technical and economical review of the 4 selected POP elimination technologies. Furthermore, in Section 6.8, a brief description and assessment
is made for one of the most promising technologies developed within the CEE Region (Russia), the Cyclone Reactor.
6.4 Gas phase chemical reduction (GPCR)
6.4.1 Introduction
Gas phase chemical reduction (GPCR) developed in Canada by Eco-Logic has been heralded as an alternative to incineration. The process involves the gas-phase chemical reduction of organic compounds
using hydrogen at temperatures of approx. 850°C and ambient pressure. The organic compounds are reduced by hydrogen to give methane, other light hydrocarbons, and hydrochloric acid gas (chlorinated
waste streams). The hydrochloric acid is neutralised by addition of caustic soda during initial cooling of the process gas. Dioxins and furans are not formed due to the reducing conditions prevalent in the
reactor.
The process needs tight control to ensure the hydrogen gas and flammable product gases do not form explosive mixtures with air. Destruction efficiencies are high and the system can theoretically operate
without an external source of hydrogen, although this does not occur in practise due to the increase in complexity. The process is non-discriminatory, decomposing all organic compounds. With the addition
of thermal desorption front-end systems, the process can treat contaminated soil and electrical equipment, and can also evaporate volatile pesticides directly from drums.
Many demonstration tests have been performed using the GPCR process and Eco-Logic has designed, built and delivered portable demonstration plants to both American and Japanese clients. Eco-Logic
has operated two full-scale plants, one in North America and one in Australia. From 1995 to 2000, Eco-Logic treated in the excess of 2,000 tonnes of waste at the full-scale plant in Australia with 1,500
tonnes being treated in the last two and a half years of operation alone. During those last two years, Eco-Logic installed a bigger, new Thermal Reduction Batch Processor (TRBP) for the solid waste
treatment that had greater capacity, greater reliability, and decreased cycle time. The plant could then operate with two TRBPs and concurrently treat liquid PCB waste resulting in improved process
performance.
6.4.2 Description of the technology
The GPCR process is a closed process. The treated solids are analysed before release, the treated flue gas is collected in tanks and analysed before release (by gas chromatographic techniques). The treated
scrubber water is collected and analysed before release. The process is based on gas-phase reaction of hydrogen with organic compounds. At 850°C or higher, hydrogen combines with organic compounds
in a reaction known as reduction to form smaller, lighter hydrocarbons, primarily methane. For chlorinated organic compounds, such as PCBs, the reduction products include methane and hydrogen chloride.
This reaction is enhanced by the presence of water, which acts as a reducing agent and a hydrogen source.
The process is non-discriminatory; that is organic compounds such as PCBs, PAHs, Chlorophenols, Dioxins, Chlorobenzenes, pesticides, herbicides and insecticides, chemical warfare agents are
quantitatively converted to methane. The overall outline of the reaction mechanism is shown in Figure 6.4.1. below:
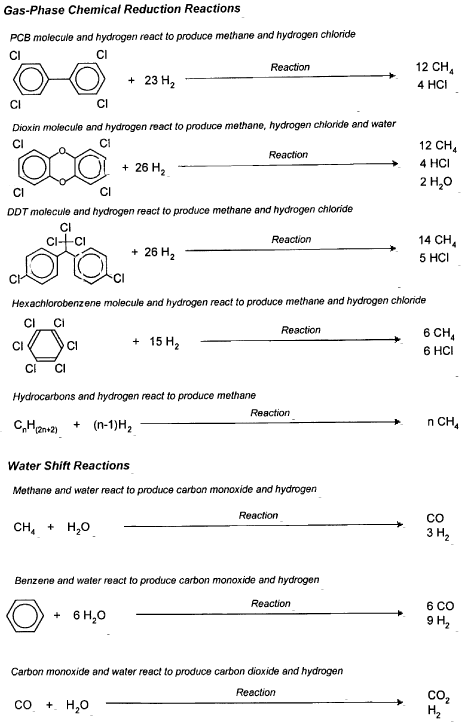
Figure 6.4.1 GPCR reaction scheme.
Hydrogenation
Hydrogen can be used to break down organic contaminants into methane. This reaction can take place in a sealed system which operates at essential ambient pressure in an oxygen free environment.
Hydrogen can be explosive only when combined with oxygen or air, and exposed to sparks. If enough measures to ensure tightness of the system, several plants have been developed to use hydrogenation
as an industrial process.
Hydrogen has been used in large quantities in the petroleum refining, chemical, petrochemical and synthetic fuel industries for decades. Therefore, the use of hydrogen in industry is fairly routine. The electrical
utility industry has also successfully used hydrogen gas for more than forty years, for such operations as cooling rotor and stator coils in large turbine generators. Hydrogen is an accepted fuel in the
aerospace industry, and has been safely handed for years in large quantities.
Although hydrogen has been used in industrial processes for decades, it is relative unknown to the public. However, there are strict guidelines for the safe handling and use of hydrogen from the authorities.
Disadvantage
Beside the need for very tight supervision and tight sealing of the hydrogenation process, this process also suffers from the fact that it is a batch process and not a continuous process. This can be partly
overcome by erecting several parallel processes, but that might influence the cost per kg treated waste.
Advantage
The Gas Phase Chemical Reduction Process (GPCR) uses hydrogen to break down organic contaminants to methane which then is burned in a conventional process. Toxic material comprising up to 100%
pure chlorinated hydrocarbons can be destroyed, which is an advantage of this process compared to incineration that can only treat material containing from 2% to 10% of chlorine.
Furthermore, the hydrogenation process has a very low side production of dioxins and other harmful compounds in comparison to e.g. the incineration process.
6.4.3 Description of the plant
The GPCR process is comprised of a central reactor for the actual destruction of organic waste, with an attached multi-stage scrubbing system to remove inorganic contaminants and light hydrocarbons from
the reacted gas stream. Depending on the waste type, various waste preparation and feed mechanisms are used to introduce the contaminants to the reactor.
All of the equipment comprising the GPCR process is broken down into Major Equipment Groups (MEG). Each MEG has an associated equipment list with specifications and a Piping and Instrumentation
Diagram (P&ID). The MEGs and their descriptions are presented in Table 6.4.1.
Table 6.4.1 Summary of the GPCR process control MEGs
MEG (Major Equipment Group) |
Description |
Purpose |
03 |
Pre-heater |
Gas heater, mixer and their associated
burners |
The pre-heater MEG includes all the equipment required to heat any combination of the gas inputs from the hydrogen and
steam supply, the off-gases from the TRBP and liquid waste, and the product gas from the MEG 17 hold/test/release
vessels. The pre-heater supplies the reactor (MEG 05) and the thermal reduction batch processors (MEG 16) with
preheated hydrogen and superheated steam. Three (3) direct fired heat exchangers preheat the hydrogen, steam and
waste gases. |
04 |
Compressor |
Compressors, heat exchangers and
temperature controllers |
The compressor MEG includes all equipment required to efficiently remove product gas from the process while
maintaining system pressure. The product gas is compressed so that it can be held and tested to verify destruction prior to
release as a fuel. |
05 |
Reactor |
Reactor and its temperature/heating
controls |
The Reactor MEG includes all equipment required to efficiently heat and chemically-reduce the organic contaminants from
the various input waste streams. |
06 |
Scrubber |
Scrubber and associated pumps and heat
exchangers |
The Scrubber MEG includes all equipment required to efficiently remove heat, particulate, and acid gases from the
Product Gas stream from the Reactor (MEG 05). |
07 |
Process water
treatment |
Decant tanks, filters, and clean water
storage tanks |
The Water Treatment MEG includes all equipment required to efficiently cool, filter, and neutralize the water from the
scrubber system. |
10 |
Nitrogen supply |
Cryogenic storage tanks evaporator and
associated control valves |
This system introduces nitrogen to the system components when such an environment is required. I.e. purging and cooling. |
11 |
Hydrogen supply |
Hydrogen storage tanks and associated
control valves |
This system introduces hydrogen to system components when such an environment is required. Hydrogen is used as a
carrier gas and is essential for chemical reduction. |
12 |
Process gas
monitoring |
Gas analyzers, filters and pumps |
The process gas monitoring MEG includes all equipment required to direct process gases through analysers from various
locations. Both conditioned and non-conditioned gas streams are analysed for bulk gas components, agent, and trace
organic compounds. |
13 |
Boiler |
Boiler and ancillary equipment |
This boiler system provides steam to the system. Steam is used for heating, cleaning and for water addition to the
reduction reactions in the process. |
16 |
Thermal reduction
batch processor
(TRBP) |
TRBP and associated temperature/heating
controls |
The TRBP MEG includes all the equipment required to efficiently heat and volatilise the organic contaminants from the
surfaces of bulk solid materials as well as vaporize organic matrices such as cellulose (wood pallets) and plastics. |
17 |
Product gas storage |
Product gas storage tank |
The Product Gas Storage MEG includes all the equipment required to hold test and release product gas received from the
Compressor MEG. The Product Gas MEG has the ability to recycle product gas to the TRBPs and Pre-heater MEGs.
MEG 17 also supplies product gas for fuel gas to the Product Gas Burner and Pre-heater Burner. |
18 |
Cooling water |
Cooling water towers and surge tank |
This system provides water for use in the clean/cold side of system heat exchangers. |
19 & 20 |
Instrument air (19)
and plant air (20) |
Compressors, air and plant accumulators
and instrument air piping, plant air piping |
This system supplies instrument air and plant air to meet the requirements of the R1 plant. |
21 |
Fuel Supply |
Tanks and regulators |
This system supplies fuel to meet the requirements of all the burners. LPG/Natural Gas is the fuel used. |
22 |
Blower |
Various blowers, silencer/knockout,
expansion bellows |
This system controls the flow of product gas throughout the system. |
23 |
Product gas burner |
Product gas burner, combustion air fan
and stack |
This system burns the excess product gas generated by the destruction process. It is also designed to mix various
combustion exhaust gases prior to exhausting to the atmosphere. |
25 |
Carbon dioxide
supply |
Tank and evaporator |
This system supplies carbon dioxide, which is used as an inert purge gas. |
26 |
Water supply |
Piping and backflow preventer |
This system provides the necessary water to plant equipment, employee requirements and emergency systems. |
27 |
Caustic supply |
Tanks, pumps and piping |
This system provides the necessary caustic to the scrubber (06) for pH control of the acids formed in the reduction of
wastes. |
28 |
Solid waste
pre-processing |
Pre-processing unit |
This system is a workstation that provides a unit to punch holes in the solid waste equipment to allow the PCB oil to drain
out. |
29 |
Liquid waste
pre-processing |
Tanks associated piping and
interconnecting piping |
The liquid waste pre-processing MEG includes all equipment required to separate, filter, store, and deliver liquid waste to
MEG 03. |
31 |
Electrical distribution |
Electrical substation, main power panel,
reformer panel, boiler panel, stripper box
panel, reactor and cooling tower MCC |
This system provides the details of the electrical distribution system for the plant. Specifically this system provides the
required electrical power to various electrical drives, heaters and other requirements such as control panels, lighting and
process control system. |
32 |
Process Control |
I/Os (digital and analogue), control
modules and computers |
This system provides a robust control system that allows complete control and monitoring of plant operational parameters. |
In Figure 6.4.2 please find a process diagram showing the overall process components and their treatment potential (liquids, soil, sediments, bulk etc.) and the process material streams.
Click here to see Figure 6.4.2
Figure 6.4.2 Process diagram
Click here to see Figure 6.4.3
Figure 6.4.3 The process diagram divided into MEG's
6.4.4 Description of the operation
A detailed description of waste preparation and feeding actions needed is outlined in the following.
Bulk solid material
Large bulk solids such as drums, electrical equipment, and process wastes are treated in the Thermal Reduction Batch Processor (TRBP). The TRBP consists of an oven-type chamber where organic
contaminants, oil, and any solvents contained in the bulk material are volatilised. The organic vapours are then swept into the reactor by the hydrogen-rich hot re-circulation gas for complete reduction. Batch
quantities of soil can also be treated in the TRBP; batch processing meaning that following waste treatment, the TRBP is cooled and the hydrogen purged with nitrogen before the treated residues can be
removed and a new batch of waste loaded into the TRBP.
When treating transformers, the PCB oil is drained before the transformer is loaded into the TRBP. The organic contaminants in the waste are thermally desorbed and swept into the reactor by the
hydrogen-rich, hot recirculation gas.
During full-scale operations in Australia, the TRBP treated 15 tonnes of waste in open drums. The drums are then sparged with hot hydrogen. Wipe tests following GPCR verified the drums to be free of
organic contamination allowing the drums to be disposed of off-site. Contaminated electrical equipment processed in the TRBP constitutes a relatively small organic load to the GPCR reactor. High-strength
organic wastes such as Askarel can be processed simultaneously.
The TRBP is also suitable for processing high-strength organic wastes such as obsolete pesticides, which are sufficiently volatile to evaporate directly from drums. One advantage of this approach is reduced
waste handling, which minimises fugitive emissions at the site.
Watery wastes and high-strength oily wastes
Experience has shown that fewer undesirable by products are formed when wastes are pre-heated and well mixed. Watery wastes and high-strength oily wastes are injected into a pre-heater that vaporises
the liquids in an indirectly fired heat exchanger. The gases are mixed with hydrogen and steam to a temperature of 600°C prior to introduction to the reactor. Another method of preheating liquid wastes is
spraying them into the TRBP, which also volatilises the contaminants. This has been used very effectively at Eco-Logic's plant in Australia.
Soil and sediments
A front-end device developed by Torftech Inc. (the TORBED Reactor System) is used to separate contaminants from soil or sediment. The TORBED system heats the soil to 600°C, which desorbs the
organic contaminants; these contaminants are then conveyed on a continuous basis to the reactor for complete destruction of the compounds. Treated material exits the TORBED system as a clean, dry,
silica-rich material.
Waste treatment
Breakdown of organic contaminants into re-useable or disposable products occurs in the GPCR reactor vessel. The gas mixture from the TRBP enters the reactor, is heated with internal electric heating
elements, and then exits through a central vortex tube. By the time it reaches the bottom of the reactor (prior to exiting through the tube), the gas mixture has reached a temperature of approx. 850°C. The
optimal process reactions take place from the bottom of the vortex tube onwards, and take less than one second to complete. Gas leaving the reactor is scrubbed to remove acids, water, heat, fine
particulates, aromatic compounds and carbon dioxide. The cooled and scrubbed product gas is a mixture of hydrogen, methane, carbon monoxide and other light hydrocarbons.
Some of the gas is reheated and re-circulated back into the pre-heater or through the TRBP as sweep gas. Excess product gas is removed from the system, compressed and stored. The stored product gas
is continually analysed and subsequently used as fuel to heat the TRBP, pre-heater, or burned in an auxiliary (excess) gas burner.
Output recovery
System outputs include clean water, treated solids and product gas. Outputs are stored and analysed prior to off-site disposal or reuse. Please find below a detailed description of output recovery detected
for the technology.
Water
The scrubber system after the GPCR reactor uses water and NaOH to scrub out acids from the gas. It is important that the scrubber system is effective because HCl in the product gas may cause creation of
dioxins when product gas is used as fuel. Water can only be used to wash out small concentrations of H2S, if a GPCR plant is expected to treat large amounts of sulphur-containing waste. It can be
equipped with a specialized H2S scrubbing system. All water generated from site activities undergoes activated carbon filter treatment. The treated water is stored and chemically tested for waste-specific
contaminants. After confirmation that the water is free of contaminants, it is either discharged to a sewer or reused in the system;
Treated bulk solids
Solids remaining in the TRBP following waste treatment are normally free of any hazardous compounds and consist of inorganic compounds, heavy metals or elemental carbon. All material in the TRBP is
subjected to chemical testing to verify adequate removal of the contaminants. Following confirmation of complete decontamination, the material can be shipped off-site for recycling;
- Treated granular solids. Granular solids generated during operations include treated soil and scrubber particulate. The treated soil is an inert silica-rich, organic-free material that can be replaced
on-site, or transported off-site for a variety of uses. Scrubber particulate is reprocessed in the TRBP to eliminate hydrocarbon contamination;
- Product gas. Product gas is generated from the breakdown products of the GPCR reactions. Following scrubbing, the product gas, composed primarily of hydrogen and methane, is compressed and chemically tested prior to its use as fuel for various system components. The product gas contains about 60% hydrogen, 20% methane, 10% CO, 10% CO2, 3-6% moisture (water) and 20-60 mg/m³ of benzene, and the product gas contains about 12,000 BTU/m³ corresponding to 13 MJ/m³, and is roughly similar to coal gas. The product gas can be recycled until the hydrogen concentration reaches a minimum of 60% in the reactor.
The product gases are continuously monitored using a micro-gas chromatograph to detect possible organic pollutants. Before the product gas is sent to the product gas burner, it is analysed to ensure it is
free of organic contaminants. This allows for continuous monitoring of product gas (both immediately after processing and in the compressed storage) for specific compounds indicative of incomplete
destruction of waste. Product gas outside normal operating maximums is re-routed to the pre-heater for re-processing. Data are stored historically in the process control computer for future analysis and
review.
Limitation to the process
If the waste contains compounds like Hg, S, As, or Pb, this could create problems. In the reaction chamber these compounds give rise to AsH3 and H2S, which are both very poisonous, and the heavy
metals Hg and Pb may evaporate and end up in either the scrubber water or the product gas. Nevertheless, the AsH3 and the H2S can be caught in the scrubber water and Eco-logic has also experienced
that they may take care of the heavy metals separately by evaporating them before the rest of the waste, but they try to avoid the problems by avoiding these substances in the waste. A disadvantage of the
process is that the TRBP front-end device is a batch process, where it is necessary to cool down and empty the TRBP and fill it again. However, liquids and gases can be treated on a continuous basis. It is
therefore an advantage to have two TRBPs in combination with liquid input to the reaction chamber, to optimise the operation.
6.4.5 Plant capacity
The throughput capacity of the GPCR process is dictated by the number of TRBP units installed. However, it seem as all capacities have a cost interval close to 1,000 USD/ton of pure chemical treated (e.g.
PCB/chlorbenzene mixture with 50% chlorine). If the hazardous chemical fraction of the waste is less, the treatment price per ton will be lower (e.g. if a pesticide is formulated with a lot of talcum (e.g. up to
99%) then the treatment of the active substance will be quicker).
On the head-office location in Toronto, Eco-Logic has in Canada a demonstration facility with a capacity of 5-50 tonnes/year. Furthermore, capacity is established in Japan with a mobile facility of 850
tons/year. Formerly, Eco-Logic operated a full scale facility at 1,800 tons/year in Australia and St. Catharines in Canada.
For the purpose of making possible up-scaling of the technology in order to increase its availability to the CEE market platform with extensive amounts of POP/OP waste, the following additional must be
compiled:
- Treatment of e.g. 3,000 tonnes annually: 1 reactor, 2 TRBP and hydrogen plant (from natural gas) are needed;
- Treatment of e.g. 10,000 tonnes annually: 3 reactors, 6 TRBP and hydrogen plant (from natural gas) are needed.
6.4.6 Practical experience
Eco-Logic has considerable practical experience with the GPCR system. The GPCR process was demonstrated in public for the first time in 1991 treating harbour sediment containing coal tar at
concentrations up to 300 g/kg. The concentration of PCBs in the air emissions, liquid effluent and processed solids following GPCR treatment were all below the detection limits resulting in a documented
PCB Destruction and Removal Efficiency (DRE) of at least 99.9999%.
Over the past 10 years, Eco-Logic has successfully completed a variety of demonstration projects, including the US-EPA SITE demonstration in 1992 and numerous testing programs for the US Army
under their chemical demilitarisation program.
The majority of waste treatment activities using GPCR have occurred at Eco-Logic's full-scale commercial plant in Kwinana, Western Australia, which began commissioning operations in 1995 and achieved
commercial throughputs by 1998. The plant operated through 2000, and treated in excess of 2,000 tonnes of waste including PCBs, pesticides and other POPs, with most – up to 1,500 tonnes –treated in
the final 2.5 years. Another large-scale operation was conducted at General Motors of Canada Limited (GMCL) in St. Catharines, Ontario. This demonstration project, which began in February 1996 and
concluded in September 1997, destructed approx. 1,000 tonnes of PCB-contaminated electrical equipment (transformers, capacitors, ballasts), concrete, oil, soil and miscellaneous other solids and liquids.
Recently (2000), the plant participated in the US Assembled Chemical Weapons Assessment (ACWA) program under contract to the US Army, with success. This testing included a thorough risk analysis
which addressed important design changes in the full-scale plant designed for the Army.
To date, more than 3,000 tonnes of contaminated waste, including PCBs, dioxin, HCB and chemical warfare agents, have been treated using the GPCR technology, and more than 30,000 commercial
operating hours have been recorded.
Demonstration plants continue to operate in North America and Japan.
6.4.7 Maintenance and services requirements
The GPCR process, as mentioned previously, is a closed loop process. Nearly all the processing has been made automatically regulated via an SRM (Steering, Regulating and Monitoring) computer. Most
of the streams are fitted with actuator valves, pressure meters, thermometers, and at selected places there are hydrogen measurements.
One of the biggest challenges is to keep the system airtight. For that reason special packing and seals are used. These packing and seals are of Teflon, Viton and synthetic rubber - EPDM (Ethylene
Propylene Diene Monomer), which are available off-the-shelf. The GPCR reactor is Hastelloy stainless steel, which is available all over the world. The problem of the availability of packing, seals and
actuators may be solved by having the necessary stocks of maintenance material.
Hydrogen, nitrogen, and activated carbon are easily attainable, which means maintenance issues may be easily overcome. The following supply lines and raw materials are required for plant operations.
Supply lines
The following infrastructure support is needed for a full operational mode:
- Electricity, 1,500 kW installed load with maximum load of 1,125 kW supply;
- Water supply (for plant water, decontamination, sanitation, etc.);
- Nitrogen supply;
- Hydrogen supply with a maximum of 600 m³/hour. A hydrogen generation plant is included in the cost estimates for a plant facility; and
- Compressed air.
Raw materials
The following raw materials are needed in the process:
- Activated carbon;
- Sodium hydroxide; and
- Natural gas.
6.4.8 Occupational health and safety
The most important occupational health problems occur in connection with the handling and loading of the waste before treatment. This concern is mitigated by handling waste in drums, and if necessary to
work with appropriate personal protective equipment (PPE).
Any hydrogen that may leak into the working area is detected by hydrogen detectors placed in central places. The working area is ventilated and all electricity is ex-proved to secure against electricity
induced ignition. Therefore, explosion risk due to hydrogen seems to be eliminated.
Noise may be a problem when the compressor for the product gas is running. Because of the continuously heating of both the TRBP and the reaction chamber, devices must be well insulated to prevent the
working area from getting too hot.
6.4.9 Operational risks
In 1998, Richard W. Prugh from Process Safety Engineering, Inc. conducted an independent review of the safety of the GPCR technology, specifically to examine the use and handling of hydrogen in the
process. He identified potential hazards associated with the use of hydrogen in the GPCR process at that time and made 19 recommendations to improve the plant. Since then, design changes to the GPCR
process have been implemented based on Mr. Prugh's process design recommendations, although his design recommendations were primarily related to the use of GPCR as part of a Total Solution for
chemical weapons treatment.
In 2001, as part of the work conducted for the US Army for the Assembled Chemical Weapons Assessment (ACWA) program, the GPCR technology underwent a preliminary hazards analysis, which is
reported in the following publication "Engineering Design Package Volume VII, Preliminary Hazards Analysis, 14 December 2001" prepared for the Assembled Chemical Weapons Assessment Program,
US Army.
From the independent review and the preliminary hazards analysis, it may be concluded that Eco-Logic's GPCR technology operates to strict risk reduction criteria and is intrinsically safe.
6.4.10 Plant mobilisation/demobilisation
For a 3,000 tonnes/year plant it takes 2-3 months to dismantle - move and re-erect the system somewhere else. The cost of re-locating a plant facility is in the range of 15-25% of the initial capital costs with
additional costs required for sampling, analysis, and transportation. It is estimated that the 3,000 tonnes plant facility could be moved for a maximum of 3 to 4 Mill USD incl. decommissioning, transport,
crane assistance, re-installation and re-commissioning.
6.4.11 Capacity building
Eco-Logic has twice proved that they can transfer the know-how of running the plant to a new company. An objective of the ACWA demonstration testing program for the US Army was to demonstrate
that government operators could be trained to operate the GPCR technology. This objective was successfully completed since Tennessee Valley Authority personnel operated the GPCR process after
receiving training from Eco-Logic on technology operation.
Also Eco-Logic's Japanese partners were trained with success. The training is made easier because there are only a few critical process parameters that have to be followed (such as temperature, hydrogen
concentration, and the amount of water vapour, etc.).
6.4.12 Environmental impact of the technology
The assessment of the environmental impacts is based on the criteria presented in Section 6.2.
Materials consumption
The total mass of a full-scale plant facility including fundament is estimated by Eco-Logic to around 1,100 tonnes. The main construction parts are construction steel (approx. 400 tonnes), concrete for
fundament etc. (approx. 380 tonnes) and specialty alloys/equipment (approx. 265 tonnes).
The annual amount of waste treated in a "normal one reactor facility" is assumed to be in the range of 1,000-1,800 tonnes although depending on the waste type. Assuming an overall life of around 10 years
of the plant constructions, the consumption of construction materials will be in the range of 0.06-0.11 kg pr. kg of waste treated. Assuming an overall recycling rate of approx. 90%, which should be
considered realistic in most countries, the consumption of construction materials is reduced to ≤ 0.01 kg material pr. kg of waste treated. Compared to the consumption of means of operation indicated
below the consumption of construction materials should be regarded as insignificant. It should, however, be noted that no information regarding material composition of special alloys/equipment has been
available. Thus, it is not known whether these alloys and equipment contain very scarce and valuable materials.
The main means of operation and consumption related to the selected waste types are listed in Table 6.4.2. Among the minor ancillary materials consumed but not listed in Table 6.4.2 may be mentioned
activated carbon used for cleaning of air and water emissions. The mass of carbon used corresponds to around 6-7% of the waste treated (measured as dry matter on a mass basis). The carbon is after use
treated and destructed in the plant parallel to other waste.
Table 6.4.2 Consumption of important means of operation
Means of operation |
Unit |
Waste Types (*1) |
Pesticide Mix |
DDT |
PCBs (oil) |
Natural gas |
kg gas/kg waste |
0.45 |
0.26 |
0.29 |
Electricity |
kWh/kg waste |
2.6 |
1.5 |
1.7 |
Sodium hydroxide (* 2) |
kg NaOH/kg waste |
0.175 |
0.56 |
0.54 |
*1: Waste types are characterised as follows:
Pesticide mix contains 10% chlorine, 2.5% sulphur, 86% carbon and 1% hydrogen.
DDT contains 50% chlorine, 0% sulphur, 47.4% carbon and 2.6% hydrogen.
PCBs contain 49% chlorine, 0% sulphur, 49% carbon and 2% hydrogen - in practical tests a mixture of PCBs and chlorobenzenes with 48-54 % PCBs and 26-33% chlorobenzenes
*2: Figures stated as 100% NaOH
Of the means of operation listed in Table 6.4.2, electricity is a energy source and will be considered only as such while natural gas is a non-renewable resource used as energy source, and therefore will be
considered in terms of material consumption as well as energy consumption. Finally, sodium hydroxide should be regarded as a renewable resource as well as a source of energy consumption as energy is
being used for extraction, preparation and refining.
The material consumption for the GPCR-process related to the selected waste types may thus be presented as in Table 6.4.3.
Table 6.4.3 Material consumption related to the GPCR process
Material consumption |
Unit |
Waste types (*1) |
Pesticide Mix |
DDT |
PCBs (oil) |
Construction materials |
kg/kg waste |
≤ 0.01 |
≤ 0.01 |
≤ 0.01 |
Means of operation - non-renewable |
kg/kg waste |
0.45 |
0.26 |
0.29 |
Means of operation - renewable |
kg/kg waste |
0.18 |
0.56 |
0.54 |
*1: Waste types are characterised as follows:
Pesticide mix: contains 10% chlorine, 2.5% sulphur, 86% carbon and 1% hydrogen.
DDT: contains 50% chlorine, 0% sulphur, 47.4% carbon and 2.6% hydrogen.
PCBs: contains 49% chlorine, 0% sulphur, 49% carbon and 2% hydrogen - in practical tests a mixture of PCBs and chlorobenzenes with 48-54% PCBs and 26-33% chlorobenzenes.
Energy consumption
The energy consumption related to consumption of electricity, energy materials and significant means of operation is calculated in Table 6.4.4
Table 6.4.4 Energy consumption related to the GPCR-process
Material |
Unit |
Waste types |
Pesticidemix |
DDT |
PCBs (oil) |
Natural gas (*1) |
MJ/kg waste |
22 |
12 |
14 |
Electricity (*2) |
MJ/kg waste |
9.4 |
5.4 |
6.2 |
Sodium hydroxide (*3) |
MJ/kg waste |
3.9 |
12 |
12 |
Total |
MJ/kg waste |
35 |
29 |
32 |
*1: The energy consumption related to consumption of natural gas is based on a figure of 48 MJ/kg gas, of which 45 MJ is the energy content and 3 MJ is the energy used for extraction and refining of gas.
*2: 1 kWh = 3.63 MJ. The choice is made not to compensate for loss of energy due to conversion and transport as the actual loss depends on the primary energy source combined with local conditions. Often energy efficiency related to electricity may be down to around 35% in case the primary energy source is coal used on central power plants without utilisation of heat.
*3: The energy used for extraction, preparation and refining is assumed to come up to around 22 MJ/kg.
Chemicals, emissions, residues and elimination efficiency
According to information received from Eco-Logic, the emissions and residues related to the selected waste types can be stated as in Table 6.4.5.
Table 6.4.5 Generation of emissions and residues
Emissions and residues |
Unit |
Waste types (*1) |
|
|
Pesticidemix |
DDT |
PCBs |
Emission to air (*2) |
Nm³/kg waste |
201 |
58 |
66 |
Wastewater |
Lit. /kg waste |
2.5 |
2.8 |
2.9 |
Slag/clinker |
kg/kg waste |
0.01 |
0.01 |
0 |
*1: Waste types are characterised as follows:
Pesticide mix: contains 10% chlorine, 2.5% sulphur, 86% carbon and 1% hydrogen.
DDT: contains 50% chlorine, 0% sulphur, 47.4% carbon and 2.6% hydrogen.
PCBs: contain 49% chlorine, 0% sulphur, 49% carbon and 2% hydrogen - in practical tests a mixture of PCBs and chlorobenzenes with 48-54 % PCBs and 26-33% chlorobenzenes.
2*: Emission to air of clean flue gas stated by Eco-Logic as 450 Nm³/min for pesticide mix, 230 Nm³/min for DDT and 230 Nm³/min for PCBs. Total air flow per kg waste has been calculated by assuming 7,450 annual working hour and annually treated waste quantities of 1,000 tonnes of pesticide mix, 1,760 tonnes of DDT and 1,560 tonnes of PCBs.
The available data on the content of POPs and similar substances including decomposition substances in emissions and residuals from the GPCR-process have been summarised in Table 6.4.6. It is noted that measurements addressing the substances treated or organic chlorine in general have been available only with respect to PCBs and only with respect to air emissions. Thus, it is only possible to partly assess the elimination efficiency of the GPCR-technology.
Table 6.4.6 Content of substances in emissions and residues by treatment of PCBs by the GPCR process
Substance |
Concentration registered |
Criteria |
Air emission µg/Nm³ |
Wastewater µg/lit |
Slag/Clinker mg/kg (*2) |
Total hydrocarbons (*1) |
0.3-7.5 × 10³ |
? |
0? |
Air emission: < 10 mg/Nm³ |
Total chlorobenzenes |
≤ 2.1 |
NDA |
0? |
|
Total polychlorinated biphenyls |
≤ 0.41 |
NDA |
0? |
|
Other chlorinated organic substances (*3) |
≤820 |
NDA |
0? |
|
Dioxins/furans (as I-TEQ) |
≤2 × 10-5 |
≤6.3 × 10-6 |
0? |
Air emission: < 0.1 ng/Nm³ |
NDA: No data available.
*1: Registered concentrations of 0.4-2.3 ppm. Concentrations are transformed into µg/Nm³ by assuming 760 mbar, 20°C and that THC in this case is composed of methane or benzene only;
*2: Claimed to pure carbon with no residues of the substances treated;
*3: Mainly chloromethane with small quantities of substances like chloroform, dichloromethane, dichlorodifluoromethane, trichloroethane and trichlorofluoromethane.
Using the amount of organic chlorine and the amount of relevant substances as measurement units, DRE (destruction and removal efficiency) can be estimated as shown in Table 6.4.7. However, due to lack
of data it is not possible to assess DE (destruction efficiency). The concepts of DE and DRE are defined and discussed in Section 6.6.2.
Table 6.4.7 Assessment of DE and DRE for the GPCR-process
Item |
Waste type (*1) |
Pesticidemix |
DDT |
PCBs (oil) |
Content of organic chlorine in 1 kg untreated waste |
100 mg |
500 mg |
? |
Content of chlorobenzenes in 1 kg untreated PCB waste |
- |
- |
300 g |
Content of PCBs in 1 kg untreated PCB waste |
- |
- |
500 g |
Air emission of organic chlorine from treatment of 1 kg PCB waste (*2) |
? |
? |
≤30 mg |
Air emission of chlorobenzenes from treatment of 1 kg PCB waste (*2) |
- |
- |
≤0.11 mg |
Air emission of PCBs from treatment of 1 kg PCB waste (*2) |
- |
- |
≤0.027 mg |
Wastewater from 1 kg waste (*3) |
? |
? |
? |
Slag from 1 kg waste |
? |
? |
0? |
DE |
? |
? |
? |
DRE related to organic chlorine |
? |
? |
? |
DRE related to chlorobenzenes |
? |
? |
≥ 99.9997 |
DRE related to PCBs |
? |
? |
≥ 99.9998 |
*1: Waste types are characterised as follows:
Pesticide mix: contains 10% chlorine, 2.5% sulphur, 86% carbon and 1% hydrogen;
DDT: contains 50% chlorine, 0% sulphur, 47.4% carbon and 2.6% hydrogen;
PCBs: contain 49% chlorine, 0% sulphur, 49% carbon and 2% hydrogen - in practical tests a mixture of PCBs and chlorobenzenes with 48-54 % PCBs and 26-33% chlorobenzenes.
*2: All calculations of air emissions are based on air flow stated in Table 6.4.9 and substance concentrations stated in Table 6.4.10. Chloromethane is assumed to contain approx. 69% chlorine.
Other issues
The amounts of residuals for disposal are outlined in Table 6.4.7 under "slag/clinker" and "wastewater". The amount of solid waste - the slag/clinker - should be regarded as extremely low. Assuming that the
slag/clinker consist of pure carbon with no traces of POPs and other hazardous substances, the slag/clinker can be disposed of with few - if any - restrictions. The amount of wastewater is on the other hand
relatively high.
6.4.13 Economy
Based on information from Eco-Logic, the following general pricing can be outlined for the establishment of annually POP elimination treatment capacity of 3,000 and 10,000 tonnes, respectively.
Annual treatment capacity - 3,000 tonnes
One reactor, two TRBP and a hydrogen plant (from natural gas) is needed at an estimated cost of 15 million USD. Subdividing of the capital costs on interest and repayment, operation and labour costs are
outlined below based on the elimination of an annual anticipated amount of 3,000 tonnes of POPs waste:
Interest and repayment |
600-700 USD/t |
Operating costs |
350-450 USD/t |
Labour costs (salary for 22) |
250-350 USD/t |
Total |
1,200-1,500 USD/t |
Annual treatment capacity - 10,000 tonnes
Three reactors, six TRBP and a hydrogen plant (from natural gas) are needed at an estimated cost of 30 million USD. Subdividing of the capital costs on interest and repayment, operation and labour costs
are outlined below based on the elimination of an annual anticipated amount of 10,000 tonnes of POPs waste:
Interest and repayment |
350-450 USD/t |
Operating costs |
350-450 USD/t |
Labour costs (salary for 40) |
150-200 USD/t |
Total |
850-1,100 USD/t |
The cost estimates largely includes license, design, hydrogen production and overhead. Labour costs are of course country dependent. By experience from increasing international demands for technology
control and assessment, analytical costs can comprise up to 50% of the project costs for demonstration facilities.
6.4.14 Evaluation of the GPCR technology
Technical evaluation
The technical evaluation is beside the topics mentioned above also based on supplementary information extracted from the "Assembled Chemical Weapons Assessment Program, Supplemental Report to
Congress, June 2001" report.
GPCR has historical, full-scale commercial experience. There are still believed to exist some technical risks associated with scale-up of batch processing with assembled chemical weapon feed streams and
generation of carbonaceous material in GPCR, although the vendor claims that these has been overcome within e.g. the ACWA program.
The primary destruction process for the chemical agent operates at low temperature and ambient pressure. The GPCR process utilizes four major hazardous process chemicals: sodium hydroxide, hydrogen,
kerosene and natural gas. Some of these materials are used in large quantities, and all pose some routine exposure risk to workers during feed preparation and maintenance of process equipment. However,
all process materials for the GPCR process have moderate to low toxicity and persistency, are commonly used in industry, and can be handled in accordance with well-established industrial safety practices.
Analysis
Containment of phosphorous elements in the waste fraction will lead to product gases containing phosphine at a level of 0.01-0.06%. Further reduction of the phosphine level would require modification of
the scrubber system. The scrubber removes HF. Benzene was also detected at 0.02-0.07% in GPCR product gas possibly as a contaminant. However, levels in stack gases could not be determined
because samples could not be sent to off-site laboratories. GPCR product gases from sulphur containing waste contained hydrogen sulphide at 1.9% and benzene at 0.2%. Levels in stack gases again could
not be determined because samples could not be analysed at off-site laboratories.
Wood spiked with PCP was treated in the GPCR with no detectable PCP (at levels as low as 1,300 µg/m³) in the product gas. GPCR has previously been permitted under "Toxic Substance Control Act"
for PCB destruction, with tests showing >99.9999% DE.
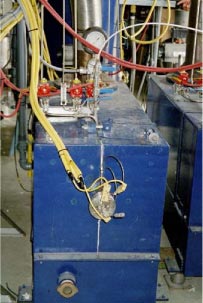
Figure 6.4.4 The Thermal Reduction Batch Processor, Canada June 2002
Scrubber
The scrubbing systems for GPCR off gas are of a common, commercial design. However, the materials of construction for the GPCR off gas scrubber system need to be addressed. Eco-Logic states that
now appropriate materials of construction have been selected based on 2001 and 2002 engineering studies.
Maturity
The maturity of the industrial GPCR provides a certain degree of confidence that the system can be operated as a stable treatment unit. However, some controllable instability observed during demonstration
of GPCR is of concern for larger scale utilization. Specifically, gas evolution resulting from ramping up the temperature too quickly is of concern. Due to the batch nature of GPCR, the system could become
unstable if heat ramp-up to the TRBP is sudden and gas evolves at a faster rate than can be controlled downstream. While the system has a control system for automatic shutdown, the large mass of material
with a high heat capacity present in the TRBP could continue to create an upset that can only be controlled with a proper high-pressure abatement strategy.
Individual feeds require individual control strategies for heat input to the TRBP, and additional data for each feed is required to develop these strategies. In addition, the passage of excess energetic (e.g.,
un-dissolved burster material) to the TRBP is still of some risk because the operational safety margins for expected feeds are not known.
There are known or standard preventive and routine maintenance requirements for the commercial GPCR. Requirements for cleaning carbonaceous residues and other solids out of TRBPs, GPCR reactors,
and downstream gas polishing units could be extensive.
Eco-Logic states that the above comments are irrelevant to conventional hazardous waste – they have proven that the problems identified can be easily
handled, or do not occur. We agree with Eco-Logic in their comments, they have already proved at several occasions that they can operate in a stable way.
Monitoring
The effectiveness of the monitoring and control approach was also validated in demonstration testing for GPCR. The GPCR process control software is identical to that already used in an existing large-scale
Eco-Logic commercial unit and is proposed for use at full-scale. The technology provider states that a full-scale system would not be significantly more complex than the demonstration unit - as demonstrated
by commercial operations in Western Australia.
During an automatic shutdown of GPCR, the shutdown procedures for GPCR were implemented properly, indicating that the control system had performed adequately. The computer control system and its
programmed alarms and interlocks were adequate to allow for safe and controlled shutdowns each time they occurred as intended.
However, control of the heat input to the TRBP (the primary control of GPCR) is manual, putting a large responsibility on the operator. There is a potential in GPCR for the slow, controlled rate of heating to
exceed the level at which gas evolution is effectively controlled. Pressure spikes in the TRBP occurred during several validation runs, but they were handled by the control system.
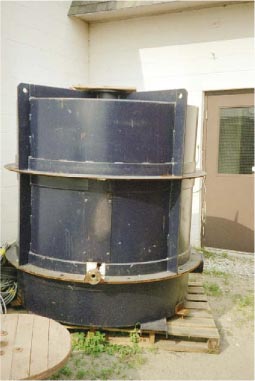
Figure 6.4.5 A 1m³-version of the TRBP, Canada, June 2002
Nonetheless, the amount of gas evolution may be of concern at full-scale. In demonstration and at full-scale, high gas evolution is controlled by operating two compressors at all times with a third used as a
backup. As a minimum, the nature of GPCR requires “trial and error” treatment methods with multiple runs of every type of feed proposed for full-scale. This is required in order to gain experience with how
fast the heat transfer to the TRBP can be ramped up.
Completeness of effluent characterization
Sufficient characterization of the effluent process streams was achieved with the exception of the effluent gas stream associated with GPCR agent operations. Currently, there is no reliable sampling and
analysis approach for the effective measurement of chemical agents in the GPCR process effluent gas stream. In addition, most of the gas samples from the product gas burner and some of the product gas
samples were not collected during some of the runs due to a change in test facility policy. This led to an incomplete characterization and the inability to validate the gas stream mass balance for GPCR with
certain compounds (from "Assembled Chemical Weapons Assessment Program, Supplemental Report to Congress, June 2001").
Two concerns exist relating to the GPCR system, chemical agent monitoring in the GPCR product gas stream and control of energetic levels in the feed, which can be resolved through improved design and
additional development.
GPCR utilize process materials that are commonly used in industry, and can be handled in accordance with well-established industrial safety practices. GPCR is a remote operation, which generally protect
workers from chemical and physical hazards. However, there are still inherent risks associated with a high volume of hazardous chemicals used in the process, and the use of high temperature hydrogen in the
GPCR process.
GPCR operates at high temperatures (above 815°C), and utilizes hydrogen (a potentially explosive or flammable gas) in the process. However, the safeguards, monitoring, and controls that minimize worker
impact in the event of a facility accident are similarly beneficial with respect to public impact. These provisions mitigate the risk of an accidental release of agent or process chemicals that could otherwise
disperse to the public. Even if an accident occurred during operations, public impact is minimized or eliminated since several layers of system and facility secondary containment should sufficiently contain the
effects and prevent public exposure.
All waste streams generated during demonstration were characterized with the exception of GPCR gas effluents during agent operations. Proposed full-scale disposal options were specified for all waste
streams. There are no external liquid effluents. The only solid products from the total solution include solid residue from GPCR. Solid residue from GPCR collected during the demonstration passed the
TCLP (toxicity characteristic leaching procedure) requirements. The gaseous emissions from GPCR will undergo "hold, test and release" prior to use as a fuel.
All primary destruction processes and their associated intermediate waste streams are held tested and reworked (if necessary) before release. GPCR product gas (containing hydrogen, methane, CO2, CO
and acid gases) is scrubbed with caustic and then held for agent testing. Once cleared, the product gas is burned in a boiler or other energy recovery device and the combustion products are then passed
through a catalytic converter.
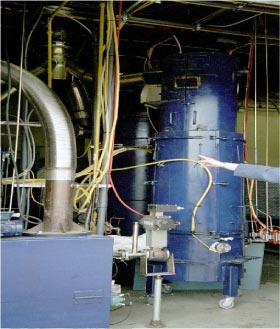
Figure 6.4.6 The GPCR reactor in Canada, June 2002
The gas product from GPCR is in principle a hazardous waste, but may be burned in the process if it meets certain requirements (the boiler or industrial furnace (BIF) exemption). Based on demonstration
results, it appears that the GPCR product gas exceeds the minimum required heating value of 5,000 BTU/lb, which is used as a key test to determine the applicability of the BIF exemption.
In summary, there are no liquid effluents, and the gaseous and solid effluents from demonstration appear to present a low hazard. GPCR gaseous effluents are held, tested, and reworked (if necessary) prior
to release. However, the overall impact on human health and the environment could not be fully ascertained due to the lack of validation for the method for detection of agent in GPCR gas effluents.
GPCR has a history of successful permitting for PCB destruction in the US. The permitting strategy includes discussion of options for effluents to air (GPCR gases to boiler, and other air effluents through
plant filters (burning and/or active carbon filter) with no expected permitting issues), no discharges to water are proposed, and all solid wastes are treated and decontaminated completely of agent and may
be released for general use or sold to the public.
Environmental evaluation
Material consumption
Material efficiency is outlined in Table 6.4.8 and is found to be above average for this technology.
Table 6.4.8 Comparative assessment of material consumption
Material consumption |
Unit |
Gas Phase Chemical Reduction (GPCR) |
Construction materials (*1) |
kg/kg waste |
≤0.01 |
Means of operation excl. energy - non-renewable |
kg/kg waste |
- |
Means of operation excl. energy - renewable (*2) |
kg/kg waste |
0.18-0.56 |
Overall assessment |
|
2 |
-: Insignificant
*1: All materials are weighted equally and no consideration has been paid to scarcity and whether the material is renewable.
*2: Addresses in reality the consumption of NaOH only.
Energy consumption
Energy consumption, as outlined in Table 6.4.9, is rated as middle in comparison to the other reviewed elimination technologies.
Table 6.4.9 Comparative assessment of energy consumption
Energy consumption |
Unit |
Gas Phase Chemical Reduction (GPCR) |
Energy consumption |
MJ/kg waste |
29 - 35 |
Overall assessment |
|
3 |
Chemicals, emissions and elimination efficiency
It should be noted that the DE and DRE values quoted represents specific highly chlorinated substances as PCBs. However, such DE and DRE values do not address the issue of, whether more toxic
decomposition products of the treated substances are created during the process. It is emphasized that no indication of such reactions exist, and the issue is raised mainly to bring attention to whether it would
be possible to supplement the very specific parameters of PCBs by more broad parameters covering also relevant decomposition products.
Considering, furthermore, the very low level of dioxin emission to all media and residues from the GPCR-process it seems appropriate to rate this process as good and clearly above middle as outlined in
Table 6.4.10 below.
Table 6.4.10 Assessment of emissions and elimination efficiency
Elimination efficiency |
Unit |
Gas Phase Chemical Reduction (GPCR) |
Destruction efficiency |
% |
? |
Destruction and removal efficiency |
% |
99.98-=99.996 |
Dioxin emission to air |
ng I-TEQ/ kg waste |
1.1 |
Dioxin emission - all media and residues |
ng I-TEQ/ kg waste |
1.1 |
Overall assessment |
|
1 |
?: No data available
Other issues
The GPCR-process does not generate any hazardous waste that requires further treatment or special disposal. The amount of solid waste is very low, while the amount of wastewater hardly can be regarded
as a problem, considering it is cleaned by an activated carbon filter. For these reasons, the GPCR process is ranked high as outlined in Table 6.4.11.
Table 6.4.11 Residues
Residues |
Unit |
Gas Phase Chemical Reduction (GPCR) |
Waste for further treatment/disposal - hazardous waste |
kg/kg waste |
- |
Waste for further treatment/disposal -solid waste |
kg/kg waste |
0.01 |
Waste for further treatment/disposal -wastewater |
lit/kg waste |
2.5-2.9 |
Overall assessment |
|
2 |
-: Insignificant
6.5 Base catalysed dechlorination (BCD)
6.5.1 Introduction
In April 2002, the review expert team visited the ongoing Base Catalysed Dechlorination (BCD) process plant used on the Olympic Coordination Authority site at Homebush Bay, New South Wales,
Australia for degradation and final elimination of organic chlorine compounds.
The original plant design was based on a pipe flow reactor concept. Problems encountered during the commissioning phase and subsequent plant modifications resulted in the conversion of this pipe flow
reactor into a batch plant utilising an agitated, externally heated reaction vessel, with caustic shearing and oil pre-heating systems.
This description specifically covers the BCD plant in its current agitated vessel configuration.
The Sydney Olympic Site
The Enterra BCD process was licensed by the New South Wales (NSW) Environmental Protection Authority (EPA), to treat Scheduled Chemical Waste (SCW) and dioxin/furan impacted soils and wastes,
at the Sydney Olympic site.
During the general remediation earthworks on the Olympic site, any materials suspected to be contaminated with SCW and/or dioxin/furan, were segregated out for separate treatment. This segregation
resulted in approx. 450 tonnes of soil contaminated with SCW and dioxin/furans. In addition about 10 tonnes of pure SCW concentrate required treatment.
Under the NSW Environmentally Hazardous Chemicals Act (1985), an SCW is defined as any chemical listed under Schedule 1 of the regulations appended to the act. These compounds are mainly
persistent chlorinated organic pesticides including Chlorobenzenes (CBs) and Chlorophenols (CPs). In the case of the Sydney Olympic project, the SCW compounds of concern were determined to be as
follows:
- 1,2,4-trichlorobenzene;
- 1,2,4,5-tetrachlorobenzene;
- pentachlorobenzene;
- hexachlorobenzene;
- 2,3,4,6-tetrachlorophenol;
- pentachlorophenol;
- hexachlorophenol;
- DDT;
- DDE;
- DDD; and
- α-chlordane.
Other compounds of concern that required treatment included 2,4,5-trichlorophenol, 2,4,6-trichlorophenol, 1,2-dichlorobenzene, 1,4-dichlorobenzene, 1,2,3,4-tetrachlorobenzene and
2,3,4,5-tetrachlorophenol.
Enterra used an Indirect Thermal Desorption (ITD) plant to remove the contaminants from the soil, generating approx. 13 tonnes of highly concentrated condensate sludge. In addition to this, a small amount
of miscellaneous waste containing SCW and variable amounts of soil and other solid materials, including 2 tonnes of spent activated carbon, was pre-processed using a ball mill and subsequently treated
directly in the BCD reactor.
The initial aggregate concentration of CPs and CBs in the contaminated soil was about 20,000 mg/kg (ppm). After thermal desorption the aggregate CB and CP content was reduced to less than 1 mg/kg
(ppm). Dioxin/furans were not detected in the treated soil, which was disposed of to a licensed landfill.
The 10 tonnes of concentrated CBs and CPs and 13 tonnes of sludge condensate generated from the ITD process were then processed in the batch BCD reactor. For all batches processed, the reactor
output was less than 1 mg/kg (ppm) SCW and less than 10 µg/kg (ppb) dioxin. As it can be seen, this data shows that the destruction efficiency for Schedule Chemical Wastes is typically around 99.9999%.
The Enterra plant was licensed to run under a licence strictly controlled and monitored by the NSW EPA. The EPA licence regulated issues such as off-gas discharge, with regular periodic monitoring,
validation of treated waste, discharge water quality, noise monitoring, dust/air quality monitoring and all other environmental considerations
6.5.2 Description of the technology
Chlorinated organic compounds can be detoxified by reaction with sodium or potassium hydroxide in an oil carrier liquid at temperatures between 300°C and 350°C. In the presence of an organic
accelerator, which is a source for free radicals in the system, the de-chlorination reaction proceeds to a very high level of completion, within a few hours, leaving a residue that is a suspension of carbon,
sodium chloride and unspent sodium hydroxide in the carrier oil. This reaction product usually requires no further treatment.
This process has been patented worldwide by the BCD Group in the USA. Enterra Pty Ltd is a licensee of the BCD Group. Enterra Pty Ltd and the BCD Group are jointly promoting this technology as the
BCD process.
The BCD process has been successfully applied for the destruction of scheduled organo-chlorine wastes including the following:
- PCBs (Polychlorinated biphenyls);
- HCB (Hexachlorbenzene);
- PCP (Pentachlorphenol);
- Lindane;
- DDT;
- Dioxin;
- Hexane chlorides;
- Chlorinated pesticides; and
- Phosphor pesticides.
The BCD process has the advantage of being able to treat compounds with up to 50% of chlorine (typical concentrations are usually 25-30% chlorine).
The reaction
The products of the BCD reaction are carbon, sodium chloride (common salt), potassium chloride (where potassium hydroxide is used) and unspent sodium hydroxide (caustic soda) suspended in the oil
carrier liquid.
The raw materials used for the Sydney Olympic project are sodium hydroxide, accelerator (a vegetable oil, fatty acid or alcohol) carrier oil and the organo-chlorine compound (i.e. waste), which can be in
solid form or often in solution or a slurry in the carrier oil. The reaction process is conducted on-site in a 3 m³ carbon steel, externally electrically heated vessel equipped with appropriate condensing and
vapours treatment systems. The reactor is pressurised and all oxygen is excluded by the introduction of nitrogen gas utilised as a safety blanket.
Reaction mechanism
The chemical reaction that was thought to occur is broadly represented in the following equation. It can be interpreted as a hydro-dechlorination reaction where the chlorine atoms on the aromatic nucleus are
replaced by hydrogen atoms. Detailed chemical reaction mechanism can be seen in below.

Where:
R-(Cl)X : organo-chlorine compound;
R1 : hydrogen donor (oil);
R - H : hydrogenated organo-chlorine compound, and
R11 : dehydrogenated donor.
Whilst the above reaction does occur to some extent, particularly when low concentrations of organo-chlorine compounds are treated, the main product that is observed is carbon. This cannot be explained
by the simple hydro-dechlorination reaction mechanism shown above.

The exact mechanism for (what is) a carbonisation reaction is not yet clear. It is likely from the evidence currently available that the organo-chlorine compound is attacked by free radicals formed by a
reaction between the sodium hydroxide and the accelerator. The concentration of these free radicals builds quickly in the initial phase of the process - stabilized it seems by the carbon particles formed.
Intermediate products that arise from the sequential dechlorination of an aromatic nucleus are not observed to any significant degree. Thus, for hexachlorobenzene, which contains six chlorine atoms,
pentachloro, tetrachloro or other lower chloro substituted benzenes are not detected - the main reaction product is carbon. This observation seems to persist regardless of the nature of the original
organo-chlorine compound.
Clearly, ring opening reactions are occurring during the dechlorination of the organochlorine compounds but there is no agreed mechanism as to exactly how this occurs. Chlorine atoms that are stripped from
the original compound are rapidly mineralised as sodium chloride in the reaction medium. This is insoluble in the carrier oil and remains suspended in the mixture.
Limitation to the process
Any reaction, which consumes caustic in preference to bonding with free chlorine, decreases the efficiency of the treatment process. If reactants such as these can be identified in the feed, additional caustic
can be added to compensate. Acidic feed materials generally consume caustic and additional caustic is required to be added to compensate for the neutralisation effect that would normally use the caustic fed
with the batch.
Formulations which contain aluminium or zinc in large quantities can also react with caustic to form a gel and slow down the reaction. Sulphur containing feed will create sulphuric acid and oxides of sulphur in
addition to reacting with caustic to produce hydrogen sulphide and give rise to corrosion problems at elevated temperatures.
Simple process flow diagram
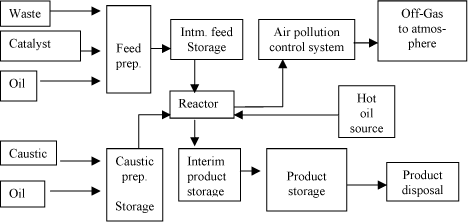
Figure 6.5.1 Simplified flow diagram of the plant
The process can be sub-divided in six unit operations:
- Waste or feed preparation;
- Caustic preparation;
- Hot oil pre-heating and transfer;
- Caustic and waste injection;
- Reaction, sampling and testing; and
- Treated product transfer.
Disadvantage
Beside the fact that this process can only treat (directly) fluids, the process also suffers from being a batch process and not a continuous process. This can be partly overcome by erecting several parallel
processes, but that might influence the cost per kg treated waste. Furthermore, the process demands the heating up and successive cooling down of bearing oil for the process to run, which is demanding
much energy. Finally, the process produces a rest product that needs conventional incineration, and because of the high load of chloride herein there is an intrinsic risk of dioxin production from this.
Advantage
Toxic material comprising up to 100% pure chlorinated hydrocarbons can be destroyed in 30 to 90 minutes. This is one of the big advantages of the BCD- technology compared to incineration technology
that can only treat material containing from 2 to 10% chlorine. Furthermore, the gas production from the process is low and seems to be very low in dioxin emission.
6.5.3 Description of the plant
The main processing plant and control room are constructed within two standard 40 foot ISO container framework. These ISO container frameworks have been issued with CFC plates for all modes of
transportation. Various support facilities required for the operation of the plant are located adjacent to the processing plant. One container framework is assembled on top of the second container
framework.
The bottom container framework contains the following process plant: control room, pre oil heating tank, oil circulation pump, in line heaters and piping, waste feed tank, caustic shearing tank, condensate
tanks, refrigeration system associated with APC system, associated process piping and bound floor area.
The top container framework contains the following process plant: waste loading system, waste preparation system, caustic loading chute, reactor, air pollution control system and emission monitoring
system.
Various piping spool pieces and junction boxes are provided between the container framework, to enable connection or disconnection of the two-container framework.
The various support facilities are located adjacent to the plant and these include the following: waste storage container(s), caustic and catalyst storage container, bulk carrier oil storage tank, intermediate
carrier oil storage tank, electrical generator, emergency electrical generator, nitrogen supply system, air cooled radiator system, sludge drying facility, intermediate product storage tank and bulk product
storage tanks.
All storage facilities are provided with containment bounding arrangement. This bounding arrangement ranges from clay lined bunds, metal tray bunds and individual containment tanks, depending upon the
size, location and material required to be contained.
6.5.4 Description of the operation
The following is a typical reaction batch procedure that also describes the process flows involved in the destruction of organo-chlorine compounds in the plant.
Feed preparation
Approx. 50 to 100 kg of pure waste and an equal quantity of carrier oil are mixed and heated to 60°C in the feed preparation vessel. The required amount of catalyst is also added at this stage of the
process. (If the feed is already in the liquid phase at ambient temperatures, this feed preparation stage is not necessary, as the waste can be injected directly into the reactor.)
The waste feed mixture is then transferred into the intermediate feed storage tank and sampled for analysis to enable the preparation of a batch sheet. The waste feed mixture is maintained at 60°C in the feed
storage tank while awaiting laboratory analysis and charging of the reactor with oil and caustic.
If the plant has been shut down or returned to service after maintenance, the reactor will be empty and at ambient temperature. Pending on availability of hot oil supply, the oil for the next batch may be
heated in the reactor itself or supplied from hot oil supply tank.
If the reactor is to be used to heat up the oil for the batch, the required quantity of oil is transferred from clean oil storage tank. The reactor is then purged with a nitrogen blanket, the agitator is started and
the band heaters are turned on to heat the oil to the required reaction temperature. The time taken to heat the oil from ambient to 350°C is approximately 4 to 5 hours.
Caustic preparation
Oil and caustic are added to the caustic-mixing vessel where they are stirred using a high speed shear mixer. Oil/caustic slurry is made in such a quantity to allow it to be made available to the reactor at all
times during the reaction stage.
Oil pre-heating
A separate oil pre-heating system is used to heat the carrier oil for each batch. Hot oil at 325°C can also be made available to the reactor vessel at all times during the reaction stage in a similar manner to the
oil/caustic slurry.
Charging of the reactor
When the reactor is ready to receive hot oil, approximately 800 litres of hot carrier oil is pumped from the oil pre heat tank to the reactor. The reactor is then heated to 345°C with the aid of external band
heaters on the reactor vessel. The required amount of oil/caustic slurry as per batch calculation sheet is then injected into the reactor.
Caustic is injected in stages due to heat loss in the reactor by addition of the oil/caustic slurry which is at 60°C. After each injection stage, the temperature is allowed to rise to reaction temperature, before
more oil/caustic is injected. The bulk of the heat loss is due to the heat of dissolution for caustic from the solid to liquid phase. The reaction mixture is maintained above 330°C at all times when adding
oil/caustic slurry.
The mixture is agitated and heated and maintained above 330°C after addition of all the required caustic for the batch. The waste is then injected at a controlled rate into the hot oil and caustic mixture. At all
times, the reaction is conducted in an oxygen free environment under a nitrogen gas blanket.
Rather than using preheating of the oil, the carrier oil may also be heated in the reactor if necessary, however batch cycle time will be increased. In the initial heat up cycle, moisture and low boiling volatiles
are driven off and pass into a condensing system. The treatment of these gases is discussed in more detail below.
At a temperature of about 325°C, roughly corresponding to the melting point of the sodium hydroxide the chemical reaction commences with a rapid attack of the organo-chlorine compounds by free
radicals resulting in the formation of a chlorine free carbonaceous product, sodium chloride and water. The onset of the reaction is observed by a rise in the temperature of the venting gas stream from the
reactor, due to the release of water which is steam at 325°C.
In practice there is also an observed rise in temperature of a few degrees in the reaction medium when the reaction starts. This can be controlled by the rate of additional organo-chlorine compounds to the
reactor.
The concentration of the organo-chlorine compounds falls rapidly and within 0.5 to 1.5 hours at the reaction temperature, the SCW concentration has been reduced to below 1 ppm (the level below which
the fluid is regarded as “non scheduled” waste).
Waste treatment in the reactor
Prior to the injection of waste into the reactor, the on site laboratory is notified. This is done to enable laboratory personnel to set up and commence emission monitoring during the treatment cycle, as per
EPA licence requirements. Emission monitoring is performed by the use of sorbent tubes, connected to samp-ling points between carbon filters in the off-gas stream.
Waste injection can commence once emission monitoring is in progress. Emission monitoring during waste injection continues for at least three hours, even though the waste injection time is approximately 1.5
hours.
As de-chlorination reactions are highly exothermic, the waste is injected into the reactor at a controlled rate ranging from 5 - 15 litres per minute depending on concentration of the waste. During each stage
of the injection, temperature is monitored closely, so that when waste is injected, an increase in temperature is noted. Injection stops when the temperature reaches an upper allowed limit and no further
waste is injected until the temperature drops to the reaction temperature again.
The chemical reaction commences with the thermal decomposition of the organo-chlorine compounds with rapid attack of free radicals resulting in the formation of carbon, sodium chloride and water. The
production of water increases the reactor pressure, as the water is converted to steam.
The rate of reaction is observed by a rise in the temperature of venting gas stream, as the reactor vents to maintain the set operational pressure of 125 kPa.
The waste is injected at a controlled rate in maintaining the gas stream temperature 50°C to 80°C below the liquid reactor temperature. Each injection of waste is followed by injection of clean oil to flush the
injection line to prevent any blockage that may arise due to solidification and/or settling of feed in the injection line.
Sampling and testing
When all the waste or feed for the batch has been injected, the laboratory is notified in preparation for analysis of a treated sample. The reactor is held at 330°C for one hour and a sample is taken after this
period. The sample is cooled and sent to the laboratory to be analysed for SCW.
If the analysis of the first sample detects SCW above the onsite screening criteria of 0.5 ppm, additional caustic may be injected into the reactor pending level of SCW. A second sample will then be taken
for on site analysis. The reactor is maintained at 330°C during the sampling and testing period by turning the band heaters on and off.
When the batch sample has a SCW concentration less than or equal to 0.5 ppm using the on-site laboratory, the batch is regarded as having been completed and is now ready to be discharged from the
reactor.
Reactor product discharge
When the batch cycle has been completed, the batch is ready to be discharged into the dump tank. In preparation for the discharge of reactor into the dump tank, the following operations and checks are
carried out.
- heat tracing on-line connecting the reactor to the dump line is switched on so that the temperature at the line is 330°C;
- the reactor vent valve is closed and the reactor is pressurised to 200 kPa using nitrogen gas;
- the pressure in tank dump tank is lowered to 25 kPa by venting via the filter of the plant; and
- oxygen level of the tank is checked to ensure that it is below 3%.
When the above-mentioned operations and checks have been completed, the nitrogen supply valve to the reactor is opened followed by the reactor drain valve. When the pressures of these two tanks have
equalised, the dump operations are deemed to be complete and the reactor drain valve is closed. Clean oil is used to flush the dump transfer line and the oil ends up in the dump tank. The dump tank is
provided with an external water spray system, to cool the tank and these are turned on after the dumping operation is complete.
Intermediate product storage
When the dump tank is full, the contents of the dump tank are pumped out to the intermediate product storage tanks. Prior to pumping out of the dump tank, the dump tank needs to be depressurised and
cooled down below 60°C.
Treatment of vapors and gases
During the reaction, water is liberated and some small fraction of the carrier oil is also volatilised. In addition, there may in some circumstances be carry over of organo-chlorine compounds. The latter are
collected and are returned to the reaction vessel to prevent any collection of organo-chlorine compounds in the plant at the end of the run.
Non condensable gases, mainly nitrogen and methane are released to the atmosphere after passing through a carbon absorption system. Discharge of these gases is monitored through the analysis of a
Poly-Urethane-Foam (PUF) cartridge, which is analysed for SCW and dioxin/furan at a frequency determined by the NSW EPA.
Disposal of the products
At the conclusion of the reaction the heaters are turned off and the reactor pressurised. The hot reaction mixture is dumped into a dump tank and allowed to cool in the dump tank under the nitrogen gas
blanket. After several batches, when the dump tank is full and the temperature below 80°C, the contents of the dump tank are transferred into the product storage tank.
The product of reaction is a suspension of carbon, sodium chloride and unspent sodium hydroxide in carrier oil. This material is a non-scheduled waste.
The residual product is then removed from site and utilised by a licensed oil-recycling company. On the Sydney Olympic Project, the product oil has been sprayed on coal stockpiles, prior to being sent
through the coke oven at a nearby steelworks. Activated carbon is treated in the BCD plant. This treatment equals 2-3 bathes per year.
6.5.5 Plant capacity
The plant has a capacity to handle 100 kg of pure SCW containing 25% to 30% chlorine per batch. Batch cycle time is approx. 12 hours. Plant availability is estimated to be about 90-95% and approx.
5-10% downtime. The plant is operated in two12-hour shifts operating 7 days a week, for about 7,200 hours. The plant has a 10 year life cycle with a potential of 600 batches per year corresponding to a
total of 60 tonnes a year.
6.5.6 Practical experience
The BCD concept has been used in several places for soil cleaning purposes, and has references from many places in the world. For the destruction of concentrated/pure chemicals, however, the only known
reference is the BCD plant on the Olympic Site in Sydney Australia.
6.5.7 Maintenance and services requirements
The components used in the plant were normally a readily available "off the shelf” from most engineering type suppliers. The compact construction of the plant, however, makes repairs difficult. Beside the
danger of very hot caustic, there is no problem with dangerous chemicals. However, when the chemicals are heated to 400°C there is danger of gas explosions under wrong conditions.
The reactor product ends up in a big horizontal tank with a small manhole in the end. When the reactor product becomes cold, it is difficult to get out of the tank and creates bad working conditions. Because
the entrance to the reactor is a small 1/2" tube, it makes it difficult to load solid materials. In order to be able to suspend the solids in liquid, the solids are crushed in an open ball mill, causing bad working
conditions.
The following services and raw materials are required for the operations of the plant.
Supply lines
The following infrastructure support is needed to obtain full operation:
- Electricity, 250 kW installed load with maximum load of 350 kVA supply;
- Emergency power to keep reactor stirrer and instrumentation operational during power failure;
- Water hose on tap. Zero usage on plant except for eyewash and safety shower supply;
- Compressed air; and
- Nitrogen supply for blanketing reactor. Use liquid nitrogen on hire.
Raw materials
The following raw materials are deemed necessary to obtainment full operation, Carrier oil, Catalyst and Caustic.
6.5.8 Occupational health and safety
All waste to be processed was stored in open top 200 litre drums with lids. The waste was heated with the aid of a band drum heater to melt the waste. The melting of the waste was carried out in the feed
preparation enclosure of the plant, which is vented to two activated carbon canisters.
The melted waste was then loaded into the feed preparation vessel containing the carrier oil. Operators wore appropriate personnel protection equipment (PPE) during the loading operations to prevent
exposure to vapour and dust from the waste.
Also the loading of caustic into the caustic shear tank is carried out in the feed preparation enclosure. Operators wore PPE during the caustic loading operations to prevent exposure to caustic dust. Some
waste required size reduction to enable both material handling and treatment. This was carried out in a small ball mill.
6.5.9 Operational risks
After a fire at the BCD-plant (not the Enterra BCD Plant) in Australia, a full HAZOP risk analysis has been carried out on the BCD plant. The fire was generated because a product tank receiving 400°C
hot product oil lost its nitrogen blanketing and the auto ignition temperature of the hot oil was exceeded. However, based on the risk analysis, the BCD plant must generally be considered to be a low risk
technology.
6.5.10 Plant mobilisation/demobilisation
According to information received from the vendor the cost of plant mobilisation in case of re-location from one site to another is approx. US$ 50,000 (corresponding to about 5% of the capital cost) and
takes approx. 2 to 3 months, including all site preparation work. The announced costs seem doubtfully low compared with general experience from other "mobile" installations.
6.5.11 Capacity building
As the BCD technology has been implemented in various versions globally, it is proved that concept holder can transfer the know how of running the plant to a new company. However, the pipe flow reactor
concept is not suited to the BCD process as the solid loading contributed many process problems. These problems were overcome by conversion of the pipe flow reactor design to a stirred batch reactor
design.
6.5.12 Environmental impact of the technology
The assessment of the environmental impacts is based on the criteria presented in Section 6.2.
Materials consumption
The total mass of a full scale BCD facility including fundament is estimated to 40-50 tonnes. The main construction parts are:
- Construction steel (approx. 23-32 tonnes);
- Concrete for foundations, etc. (approx. 15 tonnes); and
- The remainder consists of materials and items like electrical engines and cables, stainless steel, aluminium, rock wool and PVC.
The amount of waste treated in the plant will be around 60-180 tonnes per year depending on the waste type. Assuming an overall life of around 10 years of plant constructions the consumption of
construction materials is in the range of 0.02-0.08 kg pr. kg of waste treated. Assuming an overall recycling rate of approx. 90%, which should be considered realistic in most countries, the consumption of
construction materials is reduced to less than 0.01 kg material pr. kg of waste treated. Compared to the consumption of means of operation indicated below, the consumption of construction materials should
be regarded as insignificant.
The main means of operation and consumption related to selected waste types are listed in Table 6.5.2. Among the minor ancillary materials consumed, but not listed in Table 6.5.2, are nitrogen used in the
process and activated carbon used for cleaning of air emissions. After use, the carbon is treated in the plant parallel to other waste.
Table 6.5.2 Consumption of important means of operation
Means of operation |
Unit |
Waste types (*1) |
Mixed organo-chlorines |
Sludge contaminated by organo-chlorines |
Electricity |
kWh/kg waste |
156 |
52 |
Sodium hydroxide (*2) |
kg NaOH/kg waste |
2 |
1.3 |
Carrier oil |
kg oil/kg waste |
12-13 |
4-4.3 |
Catalyst (wax) |
kg wax/kg waste |
0.2 |
0.07 |
*1: Waste types are characterised as follows:
Mixed organo-chlorines: contains 25% chlorine and <1% sulphur.
Sludge: contaminated by organo-chlorines contains 1-2% chlorine, very low amounts of sulphur and dioxins may be present.
*2: Figures stated as 100% NaOH.
Of the means of operation listed in Table 6.5.2 electricity is an energy source and will be considered only as such. The carrier oil and the catalyst are assumed to be based on mineral oil and therefore must
be classified as non-renewable resources. Besides, they add to the energy consumption as energy is being used for extraction and refining. Finally, both materials contain energy. Sodium hydroxide should be
regarded as a renewable resource as well as a source of energy consumption as energy is being used for extraction, preparation and refining.
The material consumption for the BCD-process related to the selected waste types is presented in Table 6.5.3.
Table 6.5.3 Material consumption related to the BCD-process
Material consumption |
Unit |
Waste types (*1) |
Mixed organo-chlorines |
Sludge contaminated by organo-chlorines |
Construction materials |
kg/kg waste |
<0.01 |
<0.01 |
Means of operation - non-renewable |
kg/kg waste |
12-13 |
4-4.4 |
Means of operation - renewable |
kg/kg waste |
2 |
1.3 |
*1: Waste types are characterised as follows:
Mixed organo-chlorines: contains 25% chlorine and <1% sulphur.
Sludge: contaminated by organo-chlorines contains 1-2% chlorine, very low amounts of sulphur and dioxins may be present. Pesticide mix contains 10% chlorine, 2.5% sulphur, 86% carbon and 1%
hydrogen.
Energy consumption
The energy consumption related to consumption of electricity, energy materials and significant means of operation is calculated in Table 6.5.4.
Table 6.5.4 Energy consumption related to the BCD-process
Material |
Unit |
Waste types |
Mixed organo-chlorines |
Sludge contaminated by organo-chlorines |
Electricity (*1) |
MJ/kg waste |
565 |
190 |
Sodium hydroxide (*2) |
MJ/kg waste |
44 |
29 |
Carrier oil (*3) |
MJ/kg waste |
550-600 |
185-200 |
Catalyst (*4) |
MJ/kg waste |
14 |
5 |
Total |
MJ/kg waste |
1,170-1220 |
410-425 |
*1: 1 kWh = 3.63 MJ. The choice is made not to compensate for loss of energy due to conversion and transport as the actually loss depends on the primary energy source combined with local conditions.
Often energy efficiency related to electricity may be down to around 35% in case the primary energy source is coal used on central power plants without utilisation of heat.
*2: The energy used for extraction, preparation and refining is assumed to come up to around 22 MJ/kg.
*3: The energy consumption related to consumption of oil is based on a figure of 46 MJ/kg oil of which 42 MJ is the energy content and 4 MJ is the energy used for extraction and refining of oil.
*4: The energy consumption related to consumption of wax is based on a figure of 69 MJ/kg wax of which 43 MJ is the energy content and 26 MJ is the energy used for manufacturing processes.
It should be noted that the carrier oil will be present in the residual product from the process. To the extent the heat value of the carrier oil in the residual product could be utilised, e.g. combustion under
circumstances allowing heat recovery from the combustion process, it would be fair to deduct the anticipated heat energy recovered from the energy consumption calculated in Table 6.5.3.
In rounded figures this would a mean reduced energy consumption of approx. 400 MJ/kg mixed organo-chlorine waste. Whether a heat recovery activity may be established or not depends on local
conditions and cannot be guarantied. Such a heat recovery activity is therefore not reflected in the figures stated in Table 6.5.4.
Chemicals, emissions, residues and elimination efficiency
According to Enterra, the emissions and residues related to the selected waste types can be stated as in Table 6.5.5.
Table 6.5.5 Generation of emissions and residues from the BCD-process
Emissions and residues |
Unit |
Waste types (*1) |
Mixed organo-chlorines |
Sludge contaminated by organo-chlorines |
Emission to air |
Nm³/kg waste |
0.2 |
0.07 |
Wastewater (condensed steam) |
Lit. /kg waste |
0.3-0.4 |
0.1-0.13 |
Residual product |
Lit./kg waste |
18 |
6 |
*1: Waste types are characterised as follows:
Mixed organo-chlorines: contains 25% chlorine and <1% sulphur.
Sludge: contaminated by organo-chlorines contains 1-2% chlorine, very low amounts of sulphur and dioxins may be present.
Concerning the emissions of substances and the content in residuals from the process, the figures in Table 6.5.6, which relates to batch no 96 processed on 26 November 2001 and wastewater sample of 23
November 2001, are anticipated to be representative for both waste types listed.
Table 6.5.6 Content of substances in emissions and residues from the BCD-process
Substance |
Concentration registered |
Criteria |
Air emission (*1) µg/Nm³ |
Wastewaterµg/lit |
Residual product mg/kg |
1,2,4 Trichlorobenzene |
< 0.15 |
0.1 |
0.26 |
The criteria on air emissions for each substance are 1 ppm, which is assumed to correspond to 7.6 - 12 mg/Nm³ depending on the substance in question.
In the residual product the aggregated content of organo-chlorines must be below 1 mg/kg and dioxins/furans below 0.01 mg/kg I-TEQ. |
1,2,4,5 Tetrachlorobenzene |
0.46 |
<0.02 |
0.22 |
|
Pentachlorobenzene |
0.42 |
<0.02 |
0.14 |
|
Hexachlorobenzene |
< 0.24 |
5.6 |
<0.03 |
|
2,3,4,6 Tetrachlorophenol |
< 1.9 |
<0.8 |
<0.03 |
|
Pentachlorophenol |
< 2.2 |
<0.5 |
<0.03 |
|
Dioxins/furans (as pg I-TEQ) (*2) |
- |
- |
4.01 x 10-4 |
|
-: No data available
*1: Emission figures are transformed from original data in ppm assuming 760 mbar and 20°C .
*2: No exact measurements of emission to air are available. The emission is cleaned by a carbon absorption unit, and the air is afterwards passed through a PUF cartridge. The content of dioxin in this cartridge is used as indicator of whether further investigations of dioxin emission are required. The trigger level for such investigations has so far not been exceeded and it must be assumed fair to accept that the actual emission is very low and most likely at a level not calling for concern.
Using the amount of organic chlorine as the measurement unit, DE ("destruction efficiency" and DRE (destruction and removal efficiency) may be estimated as shown in Table 6.5.7.
Table 6.5.7 Assessment of DE and DRE related to the BCD-process
|
Waste type |
Content of organic chlorine in: |
Mixed organo-chlorines |
Sludge contaminated by organo-chlorines |
1 kg untreated waste |
0.250 kg |
0.01-0.02 kg |
Residual product from 1 kg waste (*1) |
8 mg |
3 mg |
Air emission from 1 kg waste (* 2) |
0.0007mg |
0.0003 mg |
Wastewater from 1 kg waste (* 3) |
0.002 mg |
0.001 mg |
DE |
99.997 % |
99.97-99.985 % |
DRE |
> 99.9999… |
> 99.9999… |
*1: A mass weight of 0.9 kg/l of the residual product and a total content of 0.5 mg organic chlorine pr. kg residual product is assumed;
*2: The air emission is assumed to contain approx. 3.5 µg/Nm³ of organic chlorine;
*3: A total content of approx. 5 g organic chlorine/lit is assumed.
It should be noted that the calculation of DE and DRE is based on concentrations of a few specific substances in emissions and residues and not on broad parameters like organic chlorine or total organic
carbon. It must be considered likely that other organic chlorinated substances will be present in emissions and residues. Therefore the values calculated for DE and DRE are most likely too optimistic.
Other issues
The amounts of residuals for disposal are stated in table 6.5.6 in the rows "residual product" and "wastewater". The residual product is not schedule waste, but must be characterised as liquid hazardous
waste, as it contains carrier oil, NaOH and NaCl (15-20% weight based).
The amount of residual product must be considered rather high. Furthermore, resource recovery of the residual product requires a facility specialised in liquid hazardous waste. If the residual product should
be disposed of under inappropriate circumstances, like e.g. uncontrolled burning, significant formation of dioxins and other organo-chlorines may take place. This situation is not reflected in the values for DE
and DRE calculated above.
6.5.13 Economy
Plant and operational cost
Process plant built to Australian Standard, with a PLC control system will cost approx. 0.8-1.3 Mill USD. The plant operational cost will depend on the specific project hereunder the site location and the
requirements specific to the project and the cost detailed below are an indicative cost.
Soil cleaning costs
The costs of Indirect Thermal Desorption (ITD) range from 3.3-6.6 USD per kg depending on the contamination matrix and quantity of material to be treated. The condensate/sludge produced from the ITD
process would then be processed through the BCD plant.
BCD License
In addition to an EPA license, a BCD process license is required for the operation of the plant:
- The BCD Sub Licence will include Technical Data Package containing Standard Operating Instructions and other relevant technical data required for the operations of the plant and technical
assistance training and operations of the plant;
- The price of the Licence is set by BCD Group in the US for each individual Licence and varies according to the details of the Licence issued. The Royalty payable is based on a sliding scale of 2%,
3% or 4% on the gross margin value of only the BCD Technology component of each individual project.
Main plant operational elements
The main plant operational costs elements are listed below:
- 2,500 l of carrier oil per batch;
- 200-250 kg of NaOH per batch;
- Electrical heating required to heat oil and caustic to 350°C;
- Activated carbon use in the air pollution control system;
- Supervision / Operational / Laboratory labour cost;
- On site laboratory screening analytical cost; and
- Cost of external laboratory analysis for validation.
The costs of processing in the BCD plant range from 11-15.6 USD per kg although excluding costs of analysis by external laboratory. The costs cover one reactor treating one batch per day. The analysis
costs vary depending on licence requirements by local/regional and national environmental authorities.
Analytical costs
The analytical costs vary depending on the level of testing required as per EPA Licence requirements for the project. For the OCA Project, the EPA Licence stipulated the following testing requirement for
each batch:
- Feed sample;
- Air monitoring samples between the carbon filters;
- Final reaction product;
- Air emission to the atmosphere;
- Final treated water samples; and
- Dioxin analysis was required for each batch treated.
As plant operations required a quick turn around time, Enterra in conjunction with Cape Technologies developed and used an immunoassay test for dioxin. These were carried out in the on-site laboratory.
The cost of this test is 300 and 165 USD for a 6 and 24 hours turn around time respectively. However, a validation dioxin analysis by an external laboratory was still required in this project. Initially, this was
required for each batch and subsequently one for every 6 batches, at a cost of 880 USD per sample.
In addition, plant emission, mainly consisting of non-condensable gasses, mostly nitrogen from the purging process and methane from the cracking process of the oil, was also monitored and tested for SCW
and dioxin. The emission criterion is less than 0.01 mg/kg or 10 µg/kg ITEQ.
As the processing was carried out on a "temporary” site, the underlying soil required validation analysis after the plant and all equipment has been removed. The frequency of soil analysis was determined by
the NSW EPA.
Total costs
The total costs (Table 6.5.8) for treatment of chemical substances leaving out the pre-treatment of polluted soil can be summarised as follows:
Table 6.5.8 Total costs (USD)
Item |
Costs (USD) |
Plant capital costs |
0.8 to 1.3 Mill. |
Interest and repayment |
included in treatment costs |
Treatment costs (incl. raw materials, license and overhead) |
5,5- 22/kg (mean 13.8/kg) |
Treatment costs of residual products |
included in treatment costs |
Labour costs (8 persons) |
included in treatment costs |
Analytical costs |
12/kg |
Total costs* |
25.8/kg |
*: Including only the mentioned parameters. It is anticipated that the cost of final treatment of residual product is of minor importance. As can be seen, the demand to perform the expensive dioxin analysis
has been intensive. They count for about 43% of the total expenses. It may be anticipated that the analytical cost for the different technologies investigated in this report should more or less be the same.
Therefore seen from that point the total treatment costs would normally be much lower.
6.5.14 Evaluation of the BCD technology
The evaluation is solely based on the performed site visit at the Olympic Stadium Homebush, Australia in April 2002 and is not based on either thorough testing or huge inside information as for some of the
other plants.
Technical Evaluation
The plant is placed on non paved area, creating the risk of polluting the ground due to spills. All the facilities are placed in containers (laboratory, maintenance, water cleaning, offices etc.) next to the plant,
see Figure 6.5.2.
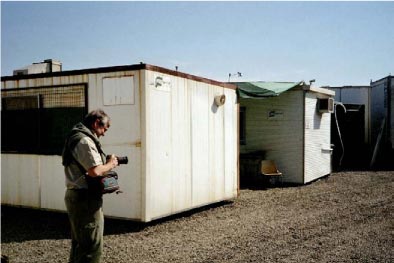
Figure 6.5.2 Facilities in containers
The plant itself was planned as an escalation of a smaller pilot plant. From the beginning everything was designed to be able to fit into a mobile unit. As the construction phase went on, more and more things
had to be built in the plant, and because it was designed to be mobile, everything is placed in a very small place, resulting in a very compact plant.
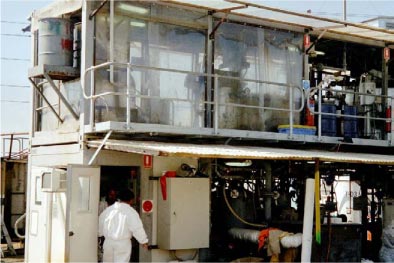
Figure 6.5.3 BCD plant April 2002, control room
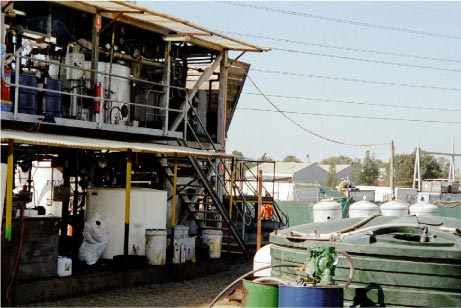
Figure 6.5.4 BCD plant April 2002. Reaction tank and holding tank
Maturity
The maturity of the plant is not yet complete. The plant can only treat liquid organics (containing high amount of halogen) or waxy material that can be melted into liquid form. The drums are emptied via an
elevator. The emptied drums are washed manually, making it necessary to use personal protection equipment. The wash water is treated as well.
Smaller solids can be crushed in a ball mill before suspended into liquid and treated. The ball mill is open and also making it necessary to use personal protection equipment. The cycle time is very long,
mainly due to analytical procedures.
The responsible persons working with the development of the plant in Australia have done a large amount of work and improved the process. Now, in contrast to the original process, the reaction is running
to an end leaving no halogenated compounds in the reaction mixture.
The residual product from the reaction mixture ends up in a large horizontal tank with a small manhole in the end. When the residual product becomes cool it is difficult to get out of the tank which impacts the
general working conditions significantly.
Capacity
The rather low capacity is a problem taking into account the relatively high production costs. Many things could however lower the production costs, and reducing analytical costs which count for more than
40% of the total costs. Despite this, it still needs to be proved before the process can be really compatible.
Mobility
The plant is a mobile structure, but the consultant is very critical to the announced re-location costs, which should only count for 10% of the initial capital costs. The pricing for re-location is assessed to be
higher and follows in line with e.g. GPCR and Semi mobile incineration units (up to 40-50% of investment capital costs).
Workers' health and safety
Workers' health and safety conditions are assessed as generally acceptable at the BCD plant, although the workers' safety on small, narrowed industrial complex structures should always be in focus.
Environmental evaluation
Material consumption
The BCD system has an outstanding high consumption of mineral oil used in the operation placing this solution un-disputably as the worst in this regard (see Table 6.5.10).
Table 6.5.9 Comparative assessment of material consumption
Material consumption |
Unit |
Base Catalysed Dechlorinated (BCD) |
Construction materials (*1) |
kg/kg waste |
<0.01 |
Means of operation excl. energy - non-renewable |
kg/kg waste |
4-13 |
Means of operation excl. energy - renewable (* 2) |
kg/kg waste |
1-2 |
Overall assessment |
|
5 |
*1: All materials are weighted equally and no consideration has been paid to scarcity and whether the material is renewable;
*2: Addresses in reality only the consumption of NaOH;
Energy consumption
The BCD system is indisputably ranked low due to outstanding high energy requirements coming from consumption of electricity as well as the carrier oil (Table 6.5.10).
Table 6.5.10 Comparative assessment of energy consumption
Energy consumption |
Unit |
Base Catalysed Dechlorination (BCD) |
Energy consumption |
MJ/kg waste |
400-1,200 |
Overall assessment |
|
5 |
The great variation depends on whether support fuel is needed or not. As an average the need for support fuel should be anticipated to be in the low end of the interval.
Chemicals, emissions and elimination efficiency
The BCD-process is rated above middle primarily due to the values for DE and DRE. The process suffers from a high content of dioxin in the residual product, and no data on emission of dioxin to air is
available although the actual emission must be assumed low. However, there is no reason for assuming the CIS and the CKI processes to perform better than BCD on the issue of dioxin as all experience
with incineration based systems points at quantities of dioxin in fly ash and other flue gas cleaning residues (Table 6.5.11).
Table 6.5.11 Emissions and elimination efficiency
Elimination efficiency |
Unit |
Base Catalysed Dechlorination (BCD) |
Destruction efficiency |
% |
99.97-99.997 |
Destruction and removal efficiency |
% |
> 99.9999 |
Dioxin emission to air |
ng I-TEQ/ kg waste |
Low (*1) |
Dioxin emission - all media and residues |
ng I-TEQ/ kg waste |
2,200-6,600 (*2) |
Overall assessment |
|
2 |
?: No data available
*1: No exact measurement of emission to air is available. The emission is cleaned by a carbon absorption unit, and the air is then passed through a PUF cartridge. The content of dioxin in this cartridge is used as indicator of whether further investigations of dioxin emission are required. The trigger level for such investigations has so far not been exceeded and it must be assumed fair to accept that the actual emission is very low and most likely not subject to concern.
*2: The figure stated covers the residual product only. A mass weight of 0.9 kg/lit. of the residual product is assumed; The figure is calculated as 6-18 kg residual product/kg waste times 0.9 kg/lit. times 4.01 x 10-4 mg I-TEQ/kg (reference is made to Table 6.5.5 - 6.5.6).
Other issues
The BCD process presents a special set of problems, as it generates a relatively high quantity of residual product composed of carrier oil together with remains of NaOH and a significant content of chlorine
from the decomposed substances. Uncontrolled burning of this product could lead to significant dioxin formation and appropriate disposal must include treatment on a facility specialised in treatment of liquid
chemical waste. For this reason, the BCD process is ranked low (Table 6.5.12).
Table 6.5.12 Other environmental issues
Residues |
Unit |
Base Catalysed Decomposition (BCD) |
Waste for further treatment/disposal - hazardous waste |
kg/kg waste |
5.4-16 |
Waste for further treatment/disposal -solid waste |
kg/kg waste |
- |
Waste for further treatment/disposal -wastewater |
lit/kg waste |
0.1-0.4 |
Overall assessment |
|
4 |
-: Insignificant
6.5.15 Comments from BCD. CZ
In the Czech Republic, the company BCD.CZ is in the process of treating a pesticide polluted site (the "Spolana site area"). As the BCD technology occurs in various outfits based on obtainment of licences,
the authors of this report have agreed to include extra information received from the CEE based BCD experience in the Czech Republic. As the technology actually is being used, we believe it is fair to
include the comments which are shown in the following:
"COWI has requested an understandable detailed cost breakdown, including plant and financing costs related only to the treatment of pure chemicals such as pesticides, production wastes,
PCB's in their pure form etc and not to the clean up of contaminated sites.
The companies which have or have had BCD licenses are not companies whose prime function is to sell chemical plant and technology packages to third party operators, but are operating
companies themselves who offer primarily a package solution to particular problems.
This involves erecting a plant to treat the wastes, at their own cost, with or without external engineering support, and operating the plant themselves to treat pollutants. The cost of the
equipment is to a certain degree proprietary commercial data. This does NOT mean that we, BCD.CZ are unwilling to supply plant and technology. We would be prepared to consider all
options within the geographical limits of our licence, but would generally prefer either to do the job as a contract, or to enter into a teaming arrangement with local entities. Everything is
possible, but to date the sale of plant and technology to third parties is not included in the licensing agreements with the BCD Group. The plant described below, which treats concentrates and
where needed 150 t/month pure chemicals, is built to EU safety and environmental standards, costs us US $ 4 mio.
With the exception of the particular operation in the Basque country, the operations of BCD Technologies in Brisbane and the operation of S.D Meyers de Mexico, all other projects have been
site remediations which included the treatment of pesticide residues which were on the particular sites as well as the treatment of contaminated soil and other matrices.
Our remediation project in the Czech Republic is primarily the remediation of a complex contaminated site, included in the complete package is the decontamination and demolition of
complicated buildings, the treatment of the building rubble and large quantities of surrounding soil as well as the treatment of pure chemicals, chemical waste and production residues. This last
group we expect to total roughly 300 tonnes. Contaminant concentrates from treating the bulk streams in the desorber are expected to be about 3,000 tonnes, excluding aqueous condensate.
However, we have extracted the cost data related to the treatment of pure chemicals and present this data. The sales price for treating highly chlorinated organic chemicals (55/65% Cl) ranges
from;
US $ 2,150 to US $ 2,500 per tonne of pure chemical
The price range reflects the differences in any costs for disposal of reaction residue. The basis for this cost is:
A plant with 2 lines and a combined capacity of 150 t/month pure chemicals.
Recycling of carrier oil and treatment or partial treatment of reaction residue, depreciation of the plant and all installation investment over 5 years, royalties and management (1 PM and 1
accountant), raw materials and utilities, labour (4 shift system with 1 supervisor and 2 operators/shift), OHSA, disposal costs, emission control, analysis, QC/QA, repair and maintenance.
Residue treatment and disposal:
The BCD process requires a relatively large quantity of reaction carrier oil. Pure chemicals such as pure PCB's are added to this oil in the reactor. The limiting quantity, please note quantity
not concentration, of initial PCB waste is limited only by the solids content of the mix. In the case of pure chemicals, this is NaCl, residual NaOH and any carbon from breakdown of the parent
molecule. We limit the solids content to 30% in order to have efficient stirring in the reactor.
The approach taken by some operators is to use cheap fuel oil and to export the mix after the reaction completion has been verified as fuel oil e.g. in a cement kiln. This is particularly
attractive if the medium being treated is transformer oil contaminated with residual PCB's.
Our approach is different. We use refined, sulphur free oil, such as a lube oil cut, and treat the reaction products. The carrier oil is recovered with efficiency over 80% and recycled to the
reactor to be re-used. The salt and residual caustic are removed in a hot water wash, similar to de-salting operations in petroleum refining. In the case of our present job, the strong alkali
solution will be used locally to neutralise acidic wastewater from other plants. Whatever process you use, somewhere you have to dispose of the salt.
The solid residue remaining from pure chemicals is carbonaceous and slurried with oil that leaves as fuel, in our case to a controlled incinerator, who charges for the privilege. For this project,
solid residue will be almost completely mineral; sand, clay etc. This we recycle to the thermal desorber to remove residual oil, which returns to the BCD reactor with the pollutant concentrate.
Comments by COWI:
Based on the new information, we recognise that costs have been considerably lowered from 27 USD/kg to 2.1-2.5 USD/kg, however still exceeding anticipated treatment costs of e.g. GPCR and the CIS
technologies. The treatment of the residual product corresponds to observations from the Australia plant site.
6.6 Container based incineration system (CIS)
6.6.1 Introduction
The container-based incineration system is designed for the incineration of solid, pasteous and liquid hazardous waste such as waste oil, organic solvents, paint sludge, laquers, plastic, synthetic material,
rubber halogenated waste, pesticides, PCB, hospital waste and infectious waste (optional). The CIS is a small (mobile) rotary kiln and is just now being tested in Latvia and we look forward to hear about
the future experiences of its performance.
The capacity of the plant is 2,000-4,000 ton pr. year, depending on the bulk density and the heat value of the waste. The CIS cannot incinerate pure PCB, as the chlorine content in the waste must not
exceed 10 %, subsequently only allowing a treatment capacity of 400-800 tonnes/year of e.g. PCB containing 50 % (w/w) of chlorine. However, in the mean time it can destroy other non halogenated
hazardous waste. The incinerator is a turnkey installation consisting of two standard 40 ft. and one 20 ft. containers thus simplifying transportation and installation on site. The unit is complete with feeding
system, rotary kiln, secondary combustion chamber, flue gas cooling system, flue gas cleaning, electrical wiring, control system, etc.
The operating temperature of the rotary kiln is 1,100°C and the subsequent secondary combustion chamber ensures destruction of the organic components at a residence time of 2 seconds at 1,100°C. The
flue gas cooling system consists of a quench in which the flue gas is cooled by evaporation of water before it enters a heat recovery boiler. The boiler produces hot water, which can be utilised in several
ways, for example for district heating.
The flue gas cleaning system is equipped with bag filter, quench and wet scrubber, which according to vendor information ensure fulfilment of the emission requirements specified in e.g. the EU Directive
94/67/EC on incineration of waste.
The market platform for semi-mobile incineration units is relatively large, why it has been decided to include the one produced by Chemcontrol A/S and Soil Recovery A/S from Denmark. These companies
have operational experiences from similar installations from Denmark and Malaysia. Furthermore, a cooperative agreement between the Latvia responsible authorities and the Danish vendor establishing a
similar plant facility in Latvia has keen interest for this review project focussing on the CEE Region.
6.6.2 Description of the technology
Chemcontrol A/S and Soil Recovery A/S have designed and constructed a mobile Container-based Incineration System (CIS), for high temperature incineration of toxic and hazardous wastes, hospital
waste and other industrial wastes, designed on a modular basis to facilitate shipping and erection. Each module is completed with all pipe-works and electrical installations and during pre-assembly all
connections between modules are made and the entire plant is "hot-dry" tested before deliverance meaning that all basic functions have been tested. Oil has been burned in the kiln reaching normal operation
temperature.
The CIS has a rotary kiln incineration system with a flue gas cleaning system, and works at an operating temperature of 1,100°C to 1,200°C in is a fully automatic and computer controlled operation.
The CIS is designed for incineration of all kinds of organic hazardous wastes ranging from general industrial waste over hospital waste to highly halogenated chemical waste. It can process waste that is solid,
liquid and pasteous including:
- Solvents (e.g. gasoline, turpentine, thinner, toluene, alcohol, or acetone);
- Halogenated and sulphur containing solvents (e.g. trichlorethylene, freon, carbon disulphide, mercaptans, PCB, etc);
- Mineral oils (e.g. lubricating oil, gas oil, or diesel oil, possibly mixed with water, soil, or gravel etc.);
- Organic pesticides, (e.g. Aldrin, Chlordane, Dieldrine, DDT, Endrin, Heptachlor, Hexachlorbenzene, Mirex, Toxaphene, POPs, empty pesticide containers etc.);
- Special waste ( e.g. medicines, isocyanates); and
- Others (e.g. bitumen, amines, acetic acid, latex, glue, phenols synthetic oils, organic acids, paint).
Incineration
Incineration is a high-temperature thermal oxidation process in which organic molecules are decomposed into gases and non-combustible solids. The solids consist of ash and slag and are disposed of by land
filling. Stack gases are largely water vapour and carbon dioxide, but include acid gases, toxic gases like dioxins, and toxic ash and metal oxide particles. To control pollution, incinerators should be equipped
with gas cleaning equipment, such as a scrubber, electrostatic filters and activated carbon filters.
The rotary kiln system has proven especially good for hazardous waste because a rotary kiln can handle solids, solvents and gases at the same time. For municipal waste, normally all solid waste, a roasting
furnace is the normal device.
The functional basis for all kilns is the same and can be characterised with the 3 T's (Temperature, Time, and Turbulence).
Temperature
Through the years a lot of time and resources have been spent on optimisation of the operation temperature in the different furnace designs. Normally the kiln for incineration of hazardous waste is not that
long about 10-12 m and with a diameter of 3.5-5 m and the temperature in the kiln is normally kept at 1,100-1,300°C. However, the demands of the authorities are not pointed at the temperature in the kiln
but in the secondary incineration chamber (the last place the gasses are destroyed). By incineration of halogenated compounds the authorities demands a temperature of minimum 1,100°C.
Time
The retention time for the gasses in the incinerator is very important for the quality of the incineration. Normally a retention time for the flue gasses in the secondary incineration chamber must be minimum 2
seconds at 1,150°C and can be lower by higher temperatures.
Turbulence
The above mentioned demands are not good enough if not all the gasses are exposed to these conditions. To secure this there is a demand that the turbulence shall correct in the secondary incineration
chamber. A Reynolds number of > 65,000 is looked upon as a suitable measure for the turbulence.
Hazardous waste incineration
Hazardous waste incinerators have a main chamber for burning wastes and a secondary incineration chamber to achieve maximum destruction of hazardous organic by-products. Air and natural gas are burnt
to keep the combustion gases at the appropriate temperature (1,150°C) for at least two seconds (residence time). Off gases are cooled to approx. 20°C before entering the gas cleaning processes.
Properly managed incineration can, in principle, destroy pesticide waste with a Destruction and Removal Efficiency (DRE) of 99.99 percent or higher. Some incinerators even claim DRE values of up to 99.99995 percent. However, the DRE is defined as DRE = Mi-Ms/Mi x 100, where Mi is the mass of a chemical fed into the destruction system during a known period of time and Ms is the mass of the chemical released in stack gases during the same period of time. The releases of chemicals via fly ash, bottom ash and scrubber water is not reported this way.
A better measurement of destruction is the "Destruction Efficiency (DE)" which is defined as DE=Mi-Mo/Mi x 100, where Mi is the mass of a chemical fed into the destruction system during a known period of time and Mo is the mass of that same chemical released in stack gases, fly ash, scrubber water, bottom ash and any other incinerator residue.
This principle shall also cover when reporting on the generation of products of incomplete combustion (PIC). The most famous PICs are dioxins and furans and when the emission of PICs are reported is must also cover the mass of PICs that is released in stack gases, fly ash, scrubber water, bottom ash and any other incinerator residue.
Disadvantages
Effective incineration is complex and depends on many factors, such as: equipment and process design, process control and maintenance of the correct residence time, temperature and turbulence, type of products incinerated, and capacity and effectiveness of air pollution control devices.
Public perception of incineration is becoming increasingly negative due to real and perceived threats posed by incineration to the environment and public health. The main concerns are the formation of
polychlorinated dibenzodioxins and polychlorinated dibenzofurans (often referred to simply as dioxins) when chlorinated waste is incinerated. Also the releases of heavy metals and dust are of concern.
Dioxins, which are extremely toxic and persistent in the environment, are formed as the result of a reaction during the cooling of the stack gases. The formation of dioxins has been minimised in modern
incinerators either by cooling down in boilers taking out the heat of the flue gas or by quenching off gases quickly to below 250°C and the release of dioxins, heavy metals and dust are carefully controlled by
passing off gases through intensive flue gas cleaning processes.
Reports of many different kinds of releases from incineration plants are in modern flue gas cleaning systems collected either in the dust filters, in the scrubber systems or in the activated carbon filters.
Activated carbon filters will collect all kind of organic products, and as the activated carbon is incinerated after use, these compounds are collected and destroyed.
A disadvantage though is the poor control of the residual products placed as hazardous waste on landfill, which may contain high levels of POPs and other toxic chemicals.
High temperature incinerators are complex pieces of equipment, which require highly skilled personnel and constant monitoring to maintain stable operating conditions.
The requirements to stable operating conditions are uniform for all reviewed technologies, but are of further importance for open-processes than for closed processes. Many studies have revealed that
uncontrolled release of e.g. dioxins from incineration process can be controlled although increased risks for emissions are recognised during start-up and close-down of operation.
Advantages
The process of incineration has shown to be a very useful way of transforming a big amount of dangerous waste types into reduced amount of environmental less problematic compounds to be placed in
landfills. However as noted above, the lack of control of the content of dioxins and other POP's, particularly in the residues, is still problematic.
Incineration of organic chemical waste has the following advantages:
- Reduction of volume of waste from 100% to about 12-13% of slag and
6-7% of fly ash and material from flue gas cleaning;
- Detoxification of many different toxic compounds at the same time especially carcinogens, pathologic materials and all kind of toxic chemicals;
- Reduction of the impact on the environment, e.g. if the alternative is direct land filling where organic and soluble inorganic compounds easy leaks out into the environment; and
- Energy recovery, especially when big amounts of waste are available in a continuous stream from the waste producers.
Finally, the incineration processes at a single process destroys all organic compounds and change their dangerous chemistry radically to something less dangerous. These advantages, in combination with
extensive use for municipal waste treatment and combined energy utilisation (distinct heating and electricity utilization) are the background for the very general use of incineration and have made the basis for
the development of many different incineration systems.
6.6.3 Description of the plant
Feeding system (1)
The solid waste feeding system of the CIS consist of a hopper with a screw conveyor. The CIS may be supplied with a shredder system leading the shredded waste into the hopper. The hazardous waste is
placed into the hopper and then screwed into the rotary kiln.
Liquid wastes are pumped into the kiln through lance, and the continuous correct dosing of the waste is secured via the CRS-system (Control, Regulating and Supervision system).
Rotary Kiln (2)
The rotary kiln has a thermal capacity of 7.26 GJ/hour, and is designed to incinerate 300 kg waste per hour, with an average heating value of 24.2 MJ/kg. The design ensure a residence time of 100 minutes
in the kiln of the waste, sufficient to ensure complete burn out of the waste.
Slag bath
The slag handling system consist of a water filled bath and a heavy conveyor system, elevating and draining the residues before discharging into a transport container.
Temperature and oxygen concentration in the kiln is controlled currently by a Programmable Logic Controller (PLC) ensuring a fully automatic operation.
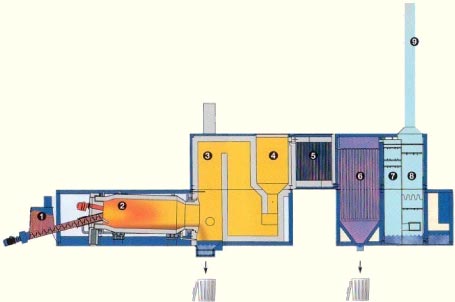
Figure 6.6.1 Flow diagram of CIS
The secondary combustion chamber (3)
The secondary combustion chamber ensures a complete destruction of organic rest products in the flue gas by incineration at 1,100-1,200°C for 2 seconds.
Quench (4)
The secondary combustion chamber is succeeded by the primary quench where the flue gas is cooled with water, reducing the temperature from 1,100/1,200°C to 600°C. This temperature drop has made it
possible to introduce a heat recovery boiler section.
Heat recovery boiler (5)
In the heat recovery boiler the hot flue gas is cooled from 600°C to 180°C. The boiler delivers hot water at a temperature of 130°C. The hot water can be utilised in several ways, for example for the
production of district heating.
Bag filter (6)
The bag filter secure that EU requirements to dust removal are met. It is important to keep the right temperature (below 260°C) of flue gas entering the filters to avoid destruction of filters.
Secondary quench (7)
The secondary quench is a vertical column unit with water cooling of the flue gas from 180°C to about 75°C and removal of HCl from the flue gas.
Wet scrubber (8)
The wet scrubber is a vertical column unit with packing and where solution of sodium hydroxide is removing the SO2 in the flue gas.
Stack
The stack is 15 m high and made of 4 mm steel lined with a polymer.
6.6.4 Description of the operation
Comprehensiveness
The CIS system will incinerate solid, pasteous and liquid hazardous waste such as waste oil, organic solvent, paint sludge, lacquers, plastic, synthetic material rubber, halogenated waste, pesticides, PCB,
hospital waste and infectious waste. The waste needs in some occasion to be pre-treated until the waste can pass the circular opening of 400 mm in diameter. That means that the installation of a shredder
system for the pre-treatment of the hazardous waste must be taken into consideration. A proper shredder system may be rather expensive.
Robustness
The CIS system is guarantied to operate 7,000 hours per year. The system has already documented its operational guarantees in Malaysia, where it has been running for a year. It takes one to two years to
learn how to run the system properly. The components are delivered by the vendor, and about 80-90% are standard components.
The CIS system is delivered with a 2 year guarantee. A longer guarantee may be negotiated. In the system launched for e.g. Latvia, a 1-year commissioning and 2 years of guarantee related to the equipment
has been agreed.
Residual products
The CIS system produces:
- Ash/slag;
- Fly ash (basic);
- Scrubber sludge (basic);
- Fly ash (boiler - acidic);
- Quench sludge (acidic);
- Wastewater (to be neutralised, precipitated, flocculated and filtrated); and
- Air emission.
A landfill is needed to deposit these rest products. There exists analysis for dioxin of flue gas and wastewater, but the CIS has never been tested for dioxin etc. in the other rest products (slag, fly ash,
sludge).
6.6.5 Plant capacity
The capacity of the plant is 2,000-4,000 ton pr. year, depending on the bulk density and the heat value of the waste. Furthermore, the waste can contain up to 2.5 % Sulphur (S) and 10 % halogen (mostly
chlorine (Cl), which makes this technology more "narrow-minded" versus treatment of high content of POPs.
6.6.6 Practical experience
In 1999, the CIS was started up in Austria at the Austrian hazardous waste treatment plant near Vienna. The CIS are used for treatment of mercury containing batteries in Austria. The organic content of the
batteries are burnt in the CIS, after which the flue gas is treated to remove the mercury content.
In 2000, Chemcontrol sold two CIS-plants to Kualiti Alam (concession national treatment facility for hazardous waste in Malaysia) in Malaysia for treatment of hazardous waste.
Furthermore, in 2001 a CIS-test plant facility was erected at the mother company Kommunekemi A/S. In 2002, Soil Recovery A/S, another Kommunekemi subsidiary, who has taken over the business with
the CIS, entered a final agreement with the Latvian Ministry of Environment setting up a plant facility during 2003/2003 with anticipated start operations in 2nd half 2004. The plant facility is co-financed by
the Danish EPA and the Latvian authorities. Furthermore, the Danish EPA through its DANCEE programme has released funds for a technical assistance framework supporting the Latvian authorities
complying with any national, regional and international regulation and implementation of necessary public information activities.
6.6.7 Maintenance and service requirements
To operate the CIS incineration facility, the following support staff is necessary; blacksmiths, electricians, machine operators, laboratory personnel (internal, external), landfill operators and water cleaning
operators.
Furthermore, to obtain full operation of the facility, the following infrastructure is considered necessary:
- Electricity (120 kW);
- Water (2" feeding line, 5-10 m³/h);
- Diesel;
- Pressure air;
- Sewage system;
- Fire extinguishing system;
- Sodium hydroxide; and
- Activated carbon.
Maintenance is somewhat hindered by the very compact construction of the plant. Because of the small construction many features are on one hand placed at the outside easy to go to, but on the other hand
there are important features difficult to reach. However, the fact that the plant has been running already for several years in Malaysia, and 2-3 years in Austria, tells that maintenance is manageable even
though there has been several problems as described later.
6.6.8 Occupational health and safety
The most obvious occupational health problem that could be detected at the visit is situated around the hopper. The feeding is done by help of truck emptying drums down into the hopper. If there are any
dusty powders, dust will appear in the working area. Apart from this, the hopper is supplied with a hood and a ventilation system that transfers any vapours into the incineration zone.
Also by emptying drums with liquids into the hopper, splashes can be expected, polluting the working area and the nearby instruments.
The emptying of drums into the hopper is surely a weakness of the CIS system.
6.6.9 Operational risks
An emergency stack is connected to the secondary combustion chamber, to be used if the temperature in the combustion chamber and the filter bags gets out of range.
There are 3 levels of interlocking to control the system:
- The first level always stops feeding of waste;
- Second level secure the plant component; and
- The third level is used in case of emergency including opening of the emergency stack.
This emergency stack has been used rather often in the trial run, because it can be difficult to control the calories in the waste introduced into the rotary kiln. If the temperature becomes too high, it is
necessary to stop the feeding of waste, close the duct to the filters, or open the emergency stack, which will cause that un-cleaned flue gas reaches the atmosphere. Furthermore, the CIS-system has had the
problem that by feeding high loads of zinc compounds there have been high emissions of zinc.
6.6.10 Plant mobilisation/demobilisation
The CIS system is semi-mobile of nature. It will take 2-3 months to dismantle - move and re-locate the system. The relocation costs will estimate 20% of the initial capital costs corresponding to about
500,000 USD incl. decommissioning, transport, crane assistance, re-installation and re-commissioning. However, new installation of supply lines, planning approval etc. will mean further costs, why a general
perception is that a relocation to obtain full operational mode will require additional costs equivalent to approx. 50% of the capital investment costs. A new system capable of treating about 2,500
tonnes/year cost approx. 3 million USD. The time from signing off contract to start-up operation of the CIS-system, a 1- year period must be anticipated.
6.6.11 Capacity building
In co-operation with Chemcontrol, Soil Recovery may submit key personnel for a period in order to assist in the day-to-day operation and handling of the incoming waste. There may be training of key staff,
especially transport crew, laboratory staff, sampling personnel and plant operators. The needed capacities are available within the vendor organisation. However, the amount of these services will be
designed for each contract.
6.6.12 Environmental impact of the technology
The assessment of the environmental impacts is based on the criteria presented in Section 6.2.
Materials consumption
According to information received the total mass of the plant including fundament comes up to around 270 tonnes. The main construction parts are:
- Construction steel (approx. 60 tonnes);
- Concrete for fundament etc. (approx. 170 tonnes); and
- Fire resistant bricks inside the oven (approx. 30 tonnes).
The remainder consists of materials and items like electrical engines and cables, stainless steel and fibre glass.
The amount of waste treated in the plant will be around 2,100 tonnes per year. Assuming an overall life of around 10 years of plant constructions, the consumption of construction materials will be around
0.013 kg pr. kg of waste treated. Assuming an overall recycling rate of approx. 90%, which should be considered realistic in most countries, the consumption of construction materials is reduced to <0.002
kg material pr. kg waste treated. Compared to the consumption of means of operation indicated below the consumption of construction materials should be regarded as insignificant.
The main means of operation and consumption related to selected waste types are listed in Table 6.6.1 and 6.6.2. Among the minor ancillary materials consumed but not listed in Table 6.6.2 may be
mentioned activated carbon used for cleaning of air emissions and TMT used for precipitation of heavy metals in the wastewater. After use, the carbon is treated in the plant parallel to other waste.
Table 6.6.1 Consumption of important means of operation related to the CIS-process
Means of operation |
Unit |
Waste types (*1) |
Pesticide waste |
Mixed chemical waste |
Electricity |
kWh/kg waste |
0.27 |
0.27 |
Diesel oil as support fuel |
kg oil/kg waste |
0-0.83 |
0-0.83 |
Sodium hydroxide for air scrubber (*2) |
kg NaOH/kg waste |
0.09 |
0.01 |
Sodium hydroxide for wastewater treatment (*2) |
kg NaOH/kg waste |
0.09 |
0.01-0.02 |
*1: Waste types are characterised as follows:
Pesticide waste contains 10% chlorine and 2.5% sulphur and has a heat value of 12.3 MJ/kg.
Mixed chemical waste contains 0.3% chlorine and 0.3% sulphur and has a heat value of 24.2 MJ/kg;
*2: Figures stated as 100% NaOH.
Of the means of operation listed in Table 6.6.1, electricity is an energy source and will be considered only as such. The diesel oil is a non-renewable resource besides that it adds to the energy consumption,
as energy is being used for extraction and refining besides that diesel oil contains energy. Finally, sodium hydroxide should be regarded as a renewable resource as well as a source of energy consumption as
energy is being used for extraction, preparation and refining. The material consumption for the CIS-process related to the selected waste types is presented in Table 6.6.2.
Table 6.6.2 Material consumption related to the CIS-process
Material consumption |
Unit |
Waste types (*1) |
MIxed organo-chlorines |
Sludge contaminated by organo-chlorines |
Construction materials |
kg/kg waste |
<0.002 |
<0.002 |
Means of operation - non-renewable |
kg/kg waste |
0-0.83 |
0-0.83 |
Means of operation - renewable |
kg/kg waste |
0.018 |
0.02-0.03 |
*1: Waste types are characterised as follows:
Pesticide waste contains 10% chlorine and 2.5% sulphur and has a heat value of 12.3 MJ/kg.
Mixed chemical waste contains 0.3% chlorine and 0.3% sulphur and has a heat value of 24.2 MJ/kg
Energy consumption
The energy consumption related to consumption of electricity, energy materials and significant means of operation is calculated in table 6.6.3. The overall energy consumption depends significantly on the
need for support fuel. The interval stated indicates the variation observed. Based on information received from Chemcontrol it is should be deemed fair to accept that on average, the consumption will be in
the lower end of the interval stated.
The CIS-process being an incineration process typically develops excess heat that may be recovered and used for district heating and other purposes. Whether a heat recovery activity may be established or
not depends on local conditions. In general, the heat output is 1 MW/hour corresponding to approx. 12 MJ/kg waste and can give rise to an income in case the heat can be utilised. As heat utilisation cannot
be guarantied, the choice is made not directly to reflect such a heat recovery activity in the figures stated in Table 6.6.3.
Table 6.6.3 Energy consumption of the CIS-process
Material |
Unit |
Waste types |
Pesticide waste |
Mixed chemical waste |
Diesel oil (*1) |
MJ/kg waste |
0-38 |
0-38 |
Electricity (*2) |
MJ/kg waste |
1 |
1 |
Sodium hydroxide (*3) |
MJ/kg waste |
4 |
0.4-0.7 |
Total |
MJ/kg waste |
5-43 |
1.4-40 |
*1: The energy consumption related to consumption of diesel oil is based on a figure of 46 MJ/kg gas, of which 42 MJ is the energy content and 4 MJ is the energy used for extraction and refining of gas;
*2: 1 kWh = 3.63 MJ. The choice is made not to compensate for loss of energy due to conversion and transport as the actual loss depends on the primary energy source combined with local conditions.
Often energy efficiency related to electricity may be down to around 35% in case the primary energy source is coal used on central power plants without utilisation of heat;
*3: The energy used for extraction, preparation and refining is assumed to come up to around 22 MJ/kg.
Chemicals, emissions, residues and elimination efficiency
According to Chemcontrol the emissions and residues related to the selected waste types can be stated as in Table 6.6.4.
Table 6.6.4 Generation of emissions and residues from the CIS-process
Emissions and residues |
Unit (*1) |
Waste types (*2) |
Pesticide waste |
Mixed chemical waste |
Emission to air |
Nm³/kg waste |
12 |
16 |
Wastewater (from scrubber) |
Lit. /kg waste |
0.6 |
0.07 |
Slag |
kg DM/kg waste |
0.37 |
0.13-0.8 |
Quench |
kg DM/kg waste |
1.6 |
0.05-1 |
Fly-ash bag-house filter |
kg DM/kg waste |
0.09 |
0.02-0.18 |
*1: DM = dry matter
*2: Waste types are characterised as follows:
Pesticide waste contains 10% chlorine and 2.5% sulphur and has a heat value of 12.3 MJ/kg.
Mixed chemical waste contains 0.3% chlorine and 0.3% sulphur and has a heat value of 24.2 MJ/kg.
Concerning the constituents in emissions and residuals from the process, the figures in Table 6.6.5 and Table 6.6.6, which relates to measurements during spring 2002 (reference to Mr. Lennart Scherman,
Chemcontrol, October 2002) are anticipated to be representative for both waste types indicated.
Table 6.6.5 Content of substances in emissions and residues - registered concentrations for pesticide waste
Substance |
Concentration registered |
Criteria |
Air emission
µg/Nm³ |
Waste-water
µg/lit |
Slag
mg/kg |
Quench
mg/kg |
Flyash
mg/kg |
Total organic carbon |
< 1 |
? |
? |
? |
? |
Air emission: < 10 mg/Nm³Slag: < 2% DM |
Dioxins/furans (as I-TEQ) |
6 x 10-5 |
? |
? |
? |
? |
Air emission: < 0.1 ng/Nm³ |
?: No data available.
Table 6.6.6 Content of substances in emissions and residues - registered concentrations for mixed chemical waste
Substance |
Concentration registered |
Criteria |
Air emission
µg/Nm³ |
Waste-water
µg/lit |
Slag
mg/kg |
Quench
mg/kg |
Flyash
mg/kg |
Total organic carbon |
< 1 |
? |
? |
? |
? |
Air emission: < 10 mg/Nm³Slag: < 2% DM |
Dioxins/furans (as I-TEQ) |
8 x 10-5 |
? |
? |
? |
? |
Air emission: < 0.1 ng/Nm³ |
?: No data available.
Using the amount of organic carbon as the measurement unit, DRE (destruction and removal efficiency) may be estimated as stated in Table 6.6.7. The data available does not allow estimation of DE
(destruction efficiency).
It should be noted that the general criteria on the content of TOC in the slag allows up to 2% carbon to be present, which reflects a DE value for organic carbon of 97-98%.
Table 6.6.7 Assessment of DRE
Items |
Waste type |
Content of organic carbon in: |
Pesticide waste |
Mixed chemical waste |
1 kg untreated waste (*1) |
0.3-0.5 kg |
~ 0.6 kg |
Air emission from 1 kg waste (*2) |
<12 mg |
< 16 mg |
Wastewater from 1 kg waste |
? |
? |
Slag from 1 kg waste |
? |
? |
Quench output from 1 kg waste |
? |
? |
Fly ash from 1 kg waste |
? |
? |
DRE |
> 99.996 % |
> 99.997% |
?: No data available
*1: Content of carbon is estimated partly based on heat value (reference to Mr. Lennart Scherman, Chemcontrol, October 2002).
*2: Calculated based on figures in Table 6.6.5 - 6.6.6.
It is noted that no data on the content of dioxin in the fly-ash is available. For incineration plants, this figure is often high and must be assumed to be high unless the opposite is documented by measurements.
Attention must also be paid to the fact that incineration of hazardous waste in a small unit like CIS is a process depending strongly on the heat value of the waste and therefore occasionally/potentially difficult
to control. In serious cases it may be necessary to close down the process and allow flue gas to be released to the environment without being subject to flue gas cleaning. Such incidents, which are difficult to
quantify, are not reflected in the figures stated above, but should not be overlooked.
Other issues
The amount of residuals for disposal are stated in Table 6.6.6 in the rows "slag", "quench", "fly ash" and "wastewater". As stated above fly ash must be assumed to contain high concentrations of dioxin and
will likely have to be disposed of as hazardous waste for land filling. Also the slag and the quench are residues requiring landfill capacity.
6.6.13 Economy
For the treatment of about 3,000 ton/year is needed one CIS plant including boiler and flue gas cleaning, at the costs of 2.6-3 mill. USD. Operational costs are highlighted in Table 6.6.8 below.
Table 6.6.8 Break down of CIS costs per kg hazardous waste
Item |
Costs (USD) |
Comments |
Plant capital costs |
2.6 - 3 mill. |
One basic CIS model |
Interest and repayment |
0.02 USD/kg |
|
Treatment costs (incl. raw materials, license and overhead) |
0.3 USD/kg |
Average for liquid and solid waste |
Treatment costs of residual products |
0.02 USD/kg |
|
Labour costs (3 persons) |
0.35 USD/kg |
2 operators and 1 operation manager |
Analytical costs |
0.3 USD/kg |
Average 2 analysis per hour |
Total costs |
1.00 USD/kg |
All prices based on Danish price level. |
The estimated prices include license, design, and overhead. Labour costs are of course country dependent. As has been seen from other technologies, the analytical costs are high and can comprise up to
30-40% of the project costs. The analytical costs also include 4 independent analyses per year by the authorities of dioxin, dust and other required parameters of air and water emissions.
Furthermore, the hopper system of the CIS requires that the waste is fed in small pieces and as an adequate mixture of solid and liquefied waste. Fluids can not be fed in this way, and paint containers will be
too big and must be shredded first.
Costs of shredder system have not been included. In addition to the plant capital cost, pre-treatment and storage facility is needed for liquid, solid and pasty waste. The plant capital cost for such equipment
such as shredder tanks mixer and pumps is in the range of USD 150,000 to 1,500,000, meaning that the total costs of the plant may reach 4-4.5 mill. USD and more or less double the amount paid for
interest and repayment.
6.6.14 Evaluation of the CIS technology
Technical evaluation
The Container-based Incineration System (CIS) is made as scale 1:10 copy of the big rotary kiln incinerators at Kommunekemi, the central hazardous waste incineration facility in Denmark. The CIS has
been operating in Austria and in Malaysia for more than 3 years now, and had many early problems in the commissioning period.
There have been problems with sufficient oxygen content (maybe too much waste fed in) some of the stuffing boxes were un-tight, rotary kiln lining, etc. Some of the more specific problems encountered are
looked upon beneath. However according to the company, these problems have been corrected and improved in the recent edition of the CIS.
The hopper system
The Hopper consists of a container of about 1 m³ in volume equipped with 2 screws pressing the waste down into a screw conveyer. The screw conveyor is leading to the incinerator. The waste in the
screw conveyor must constantly make a plug to avoid air coming in this way
This system demands that the waste is fed in small pieces and as an adequate mixture of solid and liquefied waste. Fluids cannot be fed this way.
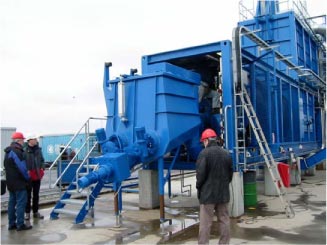
Figure 6.6.2 The hopper of the CIS, Denmark, May 2002
The screw conveyor has been improved to avoid the waste to stick to it. When the screw conveyor is not totally tight, then gas from the incinerator can be pressed out backwards and make the content in
the hopper create vapours. However, the incinerator is only allowed to be operational if the screw conveyor is covered of waste.
The control box and main switches on the outside of the incinerator are placed near the hopper and easily risk getting dirty when emptying drums into the hopper.
Incinerator Kiln
There have been problems in controlling the inlet temperature in the rotary kiln, resulting in build up of slag inside the kiln. Furthermore, there have been problems in controlling the temperature between the
boiler and the filter. If the temperature is too high when the flue gas enters the filter bag section, the expensive filter bags melt/ignite and start to burn. Both problems seem to have been solved in the new
generation of CIS.
Quench
The regulation of the quench has given some problems. Especially in closing down periods ("interlock mode") when opening of emergency stack then water continued to be pumped into the plant, causing
dust clogging like stones on the damper. This created the problem that they could not close in the boiler and the heat continued into the bag house filters and they melted. Furthermore, also the boiler tubes
were choking.
Bag house filter
There have been problems with high humidity in the bag house filter resulting in clogging of the active carbon and dust, giving rise in the emissions.
Special waste
There have been some problems with certain types of waste containing volatile heavy metals (e.g. zinc) The amount of volatile metals in the waste must be kept low in order for the scrubber system to clean
the flue gas.
Maturity
There have been many early start failures to the CIS, but these failures is anticipated to result in an optimised and more mature design of the newly build CIS standing at Kommunekemi. Again this has to be
proven by the performance of the CIS in e.g. Latvia during operations in 2004/2005.
Versatility/robustness
The advantage of the CIS system is the 1:1 scale set-up test field at Kommunekemi enabling full scale testing of any waste types. Furthermore, the mother company has extensive in-house capacity and
capabilities incinerating hazardous waste and sufficient financial strength enabling the facility to work on the commercial market ensuring full in-line supervision and maintenance support.
Capacity
The CIS as it stands has a capacity of 2,000-4,000 tonnes a year (corresponding to 400-800 tonnes/year of POPs containing 50% chlorine) depending on the type of waste. However, as the CIS is just a
rotary kiln incinerator, it can be delivered in any size wanted, depending of the price although the present outfit and installations complies with a 2,000-4,000 tonnes annual capacity.
Mobility
The CIS is as semi-mobile as the other plants mentioned in this report (except CKI).
Worker's health and safety
Worker's health and safety is high around the CIS, where the workers seldom are in contact with the waste, as it could be seen at our inspection of the plant. However by the emptying of the drums with
waste the hopper (or the shredder) has to be opened with possibility for exposure of vapours to local atmosphere. Furthermore a problem exists around the emptied drums that are still polluted with residues
of hazardous waste, if a shredder is not used.
Environmental evaluation
Material consumption
The CIS solution allows a high flow of waste materials through the system. Thereby the CIS system obtain a higher material efficiency and deserves to be rated above average in this regard (Table 6.6.9).
Table 6.6.9 Material consumption of the CIS system
Material consumption |
Unit |
Container-based Incineration System (CIS) |
Construction materials (*1) |
kg/kg waste |
<0.002 |
Means of operation excl. energy - non-renewable |
kg/kg waste |
- |
Means of operation excl. energy - renewable (*2) |
kg/kg waste |
0.01-0.1 |
Overall assessment |
|
2 |
-: Insignificant
*1: All materials are weighted equally and no consideration has been paid to scarcity and whether the material is renewable;
*2: Addresses in reality only the consumption of NaOH.
Energy consumption
The DRE value for CIS is based on a balance for total organic carbon. The low DRE value for organic carbon and low dioxin emission to air should be recognised. However, as stated above the dioxin
content in flue gas residues should be expected to be high and the overall destruction efficiency remains to be proven considering that up to 2% carbon is allowed in the slag (Table 6.6.10).
Table 6.6.10 Energy consumption of the CIS system
Energy consumption |
Unit |
Container-based Incineration System (CIS) |
Energy consumption (*1) |
MJ/kg waste |
1-43 |
Overall assessment |
|
2 |
*1: The large variation depends on whether support fuel is needed or not. As an average, the need for support fuel should be anticipated to be in the low end of the interval.
Destruction efficiency
Attention must also be paid to the fact that incineration of hazardous waste in a small unit like CIS is a process depending strongly on the heat value of the waste and therefore occasionally/potentially difficult
to control. In serious cases it may be necessary to close down the process and allow flue gas to be released to the environment without being subject to flue gas cleaning. Such incidents, which are difficult to
quantify, are not reflected in Table 6.6.11 below, but should not be overlooked.
Table 6.6.11 Emissions and elimination efficiency
Elimination efficiency |
Unit |
Container-based Incineration System (CIS) |
Destruction efficiency |
% |
? |
Destruction and removal efficiency |
% |
>99.996 |
Dioxin emission to air |
ng I-TEQ/ kg waste |
≤1.3 |
Dioxin emission - all media and residues |
ng I-TEQ/ kg waste |
? |
Overall assessment |
|
4 |
?: No data available
-: Insignificant
Other issues
Regarding the CIS process, the fly ash, the slag and the quench residues will likely have to be disposed of as hazardous waste to a special landfill due to the content of dioxin, other POP's as well as other
pollutants indicating that there is a need for landfill capacity. Table 6.6.12 outlines other issues.
Table 6.6.12 Other environmental issues
Residues |
Unit |
Container-based Incineration System(CIS) |
Waste for further treatment/disposal - hazardous waste |
kg/kg waste |
0.02-0.18 |
Waste for further treatment/disposal -solid waste |
kg/kg waste |
0.2-2 |
Waste for further treatment/disposal -wastewater |
lit/kg waste |
0.07-0.6 |
Overall assessment |
|
4 |
6.7 Cement kiln (CKI)
6.7.1 Introduction
A cement kiln is a kiln that slowly rotates to expose limestone, sand and clay evenly to very high temperatures (1,400-2,000oC) to make cement clinker. Organic waste can be injected into the kiln with the
fuel or directly into the flame. The high temperature and long residence time (6-10 seconds) effectively oxidise the organic waste. Acid gases resulting from organo-chlorine chemicals are supposed to be
mostly neutralised by the alkaline cement eliminating the need for a caustic scrubber. Only modern cement kilns with bag house filters and bypass systems can be used for pesticide incineration. Special
modifications and parts are needed for injecting pesticides into the kiln, which can be costly.
6.7.2 Description of the technology
Burning of hazardous industrial wastes in cement kilns are being used for the disposal of hazardous wastes in France and Norway and a number of other European countries.
The principal processes employed in making cement clinker can be broadly classified as either "wet" or "dry" depending on the method used to prepare the kiln feed.
In the wet process the feed material is slurried and fed directly into the kiln. In the dry process the kiln exhaust gases are used to dry the raw meal (a mixture of limestone and other raw materials) while it is
being milled.
A cement kiln typically comprises a long cylinder of 50 to 150 metres, inclined slightly from the horizontal (3% to 4% gradient) which is rotated at about 1 to 6 revolutions per minute. The solid material
passes down the kiln as a result of rolling and slipping as the kiln rotates. The material flows counter current to the combustion gases and fuel is fired at the lower (front) end of the kiln. Gases discharged
from the kiln are normally cleaned of particulate matter by passing them through an electrostatic precipitator. Dust collected in the precipitator can be returned to the process.
Kiln fuel firing systems are designed to minimise energy consumption and to provide appropriate flame shape for clinkering the raw materials.
Operating conditions within the kiln are maintained and controlled by monitoring numerous plant operating parameters throughout the system. These include feed material composition, gas temperatures and
gas flow rates. These parameters are used for control of feed flow rates into the unit (for raw meal and fuel) and for controlling discharge gas flows from the unit.
The clinker manufacturing process starts by producing a fine powder containing strictly controlled proportions of:
- limestone - to provide calcium carbonate, and
- clay - to provide silica, alumina and iron oxides.
When the powder is homogenised and heated to 1,450°C in the kiln, the lime molecules combine with all the silica, alumina and iron oxide molecules to form clinker. The raw materials are transformed into
clinker in several stages:
- up to 550°C the mixture is dried and the clay dehydrates;
- from 550°C to 900°C pre-heating and decarbonisation takes place (calcining);
- from 900°C to 1,300°C the di-calcium silicates, aluminates and ferro-aluminates are formed; and
- from 1,300°C to 1,450°C the formation of tri-calcium silicate takes place.
The material can only form at this temperature and consequently the material must reach this temperature to make clinker.
After reaching this temperature, the clinker is rapidly cooled. The clinker is finely grounded, 3% to 5% gypsum is added to control the setting rate and other additives (slag, fly-ash, limestone filler, etc.) may
be introduced to form the final product.
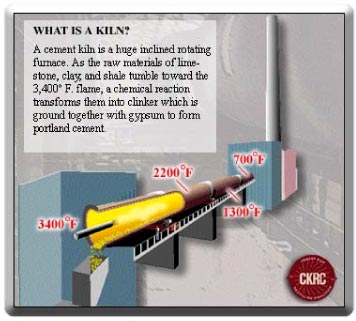
Figure 6.7.1 Schematic diagram of a typical cement kiln
At the very high temperature of the cement kiln, and with the long residence times available, high destruction efficiency is possible for scheduled wastes including POP's.
The highly alkaline conditions in a cement kiln are supposed to be ideal for decomposing chlorinated organic wastes. Chlorinated liquids, chlorine and sulphur are neutralised in the form of chlorides and
sulphates, however measurements shows that there is still some HCl-emission from a cement kiln burning halogenated waste.
The quantities of the inorganic and mineral elements added in treating scheduled wastes are usually limited (and in general will be a small proportion of the large feed requirements of a commercial kiln), and
should not adversely affect the quality of the clinker product. No liquid or solid residues requiring disposal are generated as all residues are bound within the product.
In some dry and some wet cement kiln processes there is a slight concentration of heavy metal in the by-pass dust waste produced when inorganic materials are included in the scheduled waste being treated.
Dust waste can be utilised as fertiliser, for liming or is dumped.
Incineration
The treatment process in a cement kiln is principle the same as in a dedicated incineration plant. The big difference lies in the pre-treatment part and in the flue gas cleaning part.
Pre-treatment
The specialist at cement kiln knows how to make cement and not how to treat hazardous waste. Hazardous waste always needs a lot of pre-treatment before it can be treated in a destruction plant. This
pre-treatment demands knowledge and skills not normally present in a cement kiln. Also it is important that the management at a cement kiln acknowledge this fact and build up a special team for hazardous
waste pre-treatment.
Flue gas cleaning
Flue gas cleaning in a cement kiln destroying hazardous waste is less demanding than in a dedicated hazardous waste incineration plant because the cement process performed in a caustic environment
neutralise all acidic gasses produced by the incineration of halogen and sulphur containing compounds. Also heavy metals may be precipitated as hydroxides in the cement.
However, dust emission is a big problem for many cement kilns, and as long this has not been taken under control, hazardous waste treatment in such a plant is regarded as "not immediate recommended". If
any dioxins are being produced in the cooling process, it may be released hanging on the dust. Furthermore, if heavy metals are being treated they may also be found in the dust. Even HCl has been seen
leaving the cement kiln via the flue gases, so emissions must be under control before treating hazardous waste in a cement kiln.
Wastewater and rest products
One of the big advantages of destruction in cement kilns is that there is not produced any polluted wastewater or other polluted residue products beside dust in stock emission.
6.7.3 Description of the plant
The treatment of hazardous waste in Norway is in fact divided between two plants i.e. NOAH who does all the pre-treatment and NORCEM the cement factory who destructs the pre-treated hazardous
waste. NOAH has two plants; a pre-treatment plant for organic hazardous waste in Brevik neighbour to the NORCEM and a treatment plant for inorganic hazardous waste on the island Langoya. There is
an agreement between NOAH and NORCEM regulating the economic relationship.
In Brevik, NOAH has a modern high tech hazardous waste pre-treatment plant. The plant consist of an administration building, a laboratory, a storage house for received drums, a shredder system for the
drums containing organic liquids and solids, a filtering system for the removal of metal from the solids, a mixing system for solid waste with wood chips, a holding tank for the solid waste mixed with solid and
a tank yard for solvents. Please refer to Figure 6.7.2.
All emissions are monitored and controlled. The whole area is paved with a local closed sewage system. An automatic fire extinguishing system has been erected, and they have their own fire brigade. In case
of fire there is a holding system for the water used to extinguish the fire.
At NORCEM the plant consists of an area for reception of bulk hazardous waste, a system of hydraulic pressures, screw and envelop conveyors, holding tanks for reception of solvents, system of lances for
the introduction of the hazardous waste into the cement kiln, an electro filter to filter dust from the flue gas and a bag house filter to improve the dust filtering.
6.7.4 Description of operation
NOAH
NOAH receives waste in drums, in tankers and in bulk. The drums are placed in a storage house after leaving the quarantine area. The bulk liquid is placed in nitrogen covered tanks (100 m³) and the bulk
solid is placed in a bunker and mixed with other bulk solid and wooden chips.
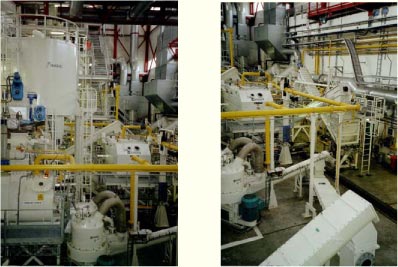
Figure 6.7.2 The shredder and waste sorting plant, Norway, August 2002
The solid waste in drums are shredded and mixed with bulk waste and then mixed with wood chips to dry up the waste. All iron in the process is removed by sieving the dried waste before the deliverance to
NORCEM. Iron would be a problem in the cement production. The sieving of the waste sucked into wood chips is obviously not a problem as could have been expected. We have not been informed how
the iron residues are cleaned afterwards.
Hazardous fluid waste received in drums is shredded in a closed system and the metal is removed before the waste is send to a holding tank and from there to the tank yard.
NOAH has 5-10 chemical experts or waste evaluators that are responsible for the reception and the evaluation and proper treatment of the waste. The ground staff at the plant does not have any special
education, but they can ask for assistance from the waste evaluators in special situations.
A thorough risk analysis has been made of the company, and most sensitive areas are covered by nitrogen, and mounted with gas measurement instruments.
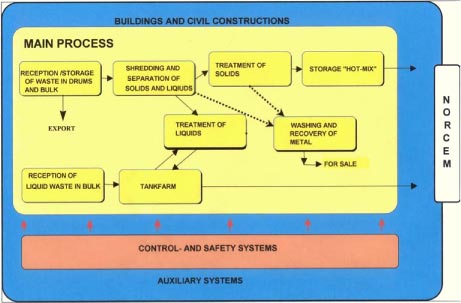
Figure 6.7.3 Process diagram for the NOAH pre-treatment
The working environment is found to be good due to the fact that all chemical processes take place in a closed environment. There is no smell of chemicals at the plant. For a more detailed process diagram,
please refer to Figure 6.7.3.
NORCEM
NORCEM treats 1.6 million tonnes limestone per year during app. 6,800 hours of operation. As fuel they use about 17 tonnes of fuel per hour (or 65% coal and 35% alternative fuels). The main fractions
are 6-10 tonnes coal, 3-5 tonnes animal meal, 3-5 tonnes per hour of residue derived fuel (municipal waste), and 3-5 tonnes hazardous waste).
NORCEM had an electro filter before the agreement with NOAH was assigned. As part of the agreement, NORCEM installed a bag house filter after the electro filter. The bag house filter covers around
1/3 of the air emission (200,000 m³/hour, whereas the remaining 100,000 m³/h is still only covered by an electro filter.
A reception facility to the solid hazardous waste and a tank facility to the fluid hazardous waste were also erected. The capacity is about 500 m³ for the solid waste and 260 m³ for fluid waste.
The bunker for solid hazardous waste is one of 3 equal bunkers (Figure 6.7.4) where the two others are used for bone flour and residue derived fuel (municipal waste). Underneath the bunkers is a huge
hydraulic station, constructed so it possible to press the waste into a screw conveyor that is feeding an envelop conveyor belt feeding the cement kiln.
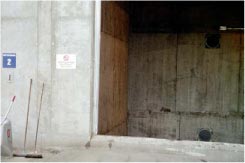
Figure 6.7.4 Hazardous waste bunker, NORCEM, Norway, August 2002
The transport to NORCEM of solid waste mixed with wood chips and al iron removed is done in open containers on a truck (500 m) and tipped into the ventilated bunker. For safety reasons, the tanks for
the fluid waste were placed inside a mountain. NOAH pumps the solvents 400 m up to the tanks in the mountain. From there NORCEM pumps the solvents 400 m down.
The introduction of coal, meat, animal meal, and waste oil is done through a special lance into the cement kiln. The cement kiln (dry process) is 80 m long and is regulated for the control room. The solid
waste is used in the calcinations end (1,000-1,100°C) of the cement kiln, whereas the fluid waste is used in the hot end (>2,000°C). The solid waste will be led through the kiln and be treated at high
temperatures too.
This cement process does not produce any scrubber water and no slag. The process has unplanned stops, but as soon as this is detected, the use of hazardous waste is aborted, and because it takes several
hours before the temperature is going down in the incinerator, the left-behind waste is burned before total stop for repair.
One of the steering parameters is the chlorine content. According to the agreement NORCEM can feed up to 100 kg of chlorine per hour. Too much HCl in the flue gas will give production problems. As the
amount of waste used per hour corresponds to about 5 tonnes, 100 kg corresponds to a Cl-content of about 2%, or at 6,500 hours to 1,300 tonnes/year of POPs containing 50% chlorine.
In the solid waste, the Cl is mixed down to 1% and S to about 3%. The amount of S from the solid hazardous waste is calculated in kilo, corresponding to amount in tonnes from the limestone and is
therefore not seen as a problem.
Limitations
The biggest problem for the cement kiln arises from the factor that it does not have a scrubber system. Therefore there is a rather large emission of SO2 (1,734 kg/24 hours ~ 240 mg/m³) and mercury (39
kg/year ~20 µg/m³). Surprisingly there also is an emission of HCl although small and below the EU limits (42 kg/24 hours ~ 6 mg/m³). The SO2 comes from the limestone (S) and the Hg mostly comes from
the coal and the limestone. The emission of dust is about 211 kg/24 hours ~ 30 mg/m³. The emission of dioxins from NORCEM is 0.199 g/year ~ 0.1 ng/m³. The emission of dust and dioxin is within
existing EU-limits.
6.7.5 Plant capacity
The heat value of the mixed solid waste and the fluid waste is around 13-17 MJ/kg. About 2.5 tonnes per hour of hazardous waste is used in 6,500 operational hours corresponding to 16-17,000 ton/year at
NORCEM.
NOAH estimates an annual treatment capacity of 30,700 tonnes of waste based on two shifts. At present, they treat approx. 16-17,000 ton in 2,400 hours of operation. There are 28-29 full time employees
at NOAH and two at NORCEM.
NOAH does not receive pesticides and PCB but they can treat it. They can however not empty a PCB container. All other types of container are treatable in their shredder system. In terms of POPs
treatment, this is of course a serious limitation. However, a shredder system able to shred PCB capacitors may be installed for a combined solution if necessary.
6.7.6 Practical experience
The 3 years of practical experience from NOAH/NORCEM has not been copied yet in other parts of the world. However, in France, Holland, Belgium, United Kingdom and USA, the fuel concepts are
developed where hazardous companies blend certain kinds of solvents and sell this to the cement kilns as replacement for coal firing. But this total concept for both solvents and solids developed in Norway
is not seen anywhere else as far it is known.
6.7.7 Maintenance and service requirements
The cement process has a run time of about 80-85%, including 4 yearly times of planned maintenance. The pre-treatment plant at NOAH has a crew that constant takes care of maintenance. A lot of
procedures have to be followed when maintaining a hazardous waste plant and the mechanics that has to perform the maintenance must be able to read, understand and follow written instructions.
To operate the facility, the following staff support is considered necessary:
- Blacksmiths;
- Electricians;
- Machine operators;
- Laboratory personnel (internal, external); and
- Water cleaning operators.
Furthermore, the pre-treatment plant has service lines of electricity, water, pressure air, nitrogen, sewerage system, fire extinguishing system, sodium hydroxide and activated carbon.
6.7.8 Occupational health and safety
The working environment is assessed as close to optimal, due to the fact that almost all chemical processes are made in closed environments. Chemicals can not to be smelled at the plant. The driving with
the solid waste sucked into wood chips do not pose any problem the distance being only 300 m and the receiving bunkers are closed and well ventilated.
6.7.9 Operational risks
A thorough risk analysis has been made of NOAH, and the most sensitive areas are covered by nitrogen, and mounted with gas measurement instruments.
6.7.10 Plant mobilisation/demobilisation
Mobilisation, demobilisation is not possible with this technology which is a combined technology.
6.7.11 Capacity building
NORCEM/NOAH has no plans for commercial utilisation of the technology and technique.
6.7.12 Environmental impact of the technology
The assessment of the environmental impacts is based on the previous used criteria.
Materials consumption
As the main activity of NORCEM is manufacturing of cement, consumption of materials related to destruction of POPs is anticipated to include only those extra facilities deemed necessary to undertake the
destruction activities. The extra facilities comprised a bag filter with its own bag house and reception/storage facilities for solid and liquid hazardous waste located partly at NORCEM and partly at NOAH.
The total mass of these facilities, including fundament, is estimated to around 15,000 tonnes. The main construction parts are:
- Construction steel (approx. 500 tonnes);
- Concrete for fundament etc. (approx. 12,000 tonnes); and
- Asphalt (approx. 2,500 tonnes).
The amount of waste treated in the plant is around 16,500 tonnes per year. Assuming an overall life of around 10 years of plant constructions, the consumption of construction materials will be in the range of
0.09 kg pr. kg of waste treated. In technical terms, most of the construction will have an effective life of 20 years or more. The real life will depend heavily on the conditions for cement manufacturing
operation.
Assuming an overall recycling rate of approx. 90%, which should be considered realistic in most countries, the consumption of construction materials is reduced to <0.01 kg material pr. kg waste treated.
Thus consumption of construction materials should be regarded as insignificant.
The means of operation includes:
- Wood chips for absorption of the liquid waste; and
- Extra diesel oil and electricity for various processes including mixing of wood chips with liquid waste, operation of bag filter and transport operations.
It has, however, not been possible to quantify the consumption of these means of operation. The waste treated is characterised as mixed chemical waste containing around 1% chlorine and various
concentrations of sulphur having a heat value of 13-17 MJ/kg.
Energy consumption
Alternative fuels correspond to 30-35 % of the thermal energy at NORCEMs plant in Brevik. Hazardous waste represents approx. 10% of the total energy. The substitution rate was 10-12% until 1999.
The new equipment has resulted in a considerable increase. In 2001, a total of 65,000 tonnes of waste derived fuels were used.
The heating value is in average 60% of the heating value of coal. The Cement Kiln Incineration may be rated above average or even best on the energy issue. This is due to the effective utilisation of the heat
value of the waste directly as process energy. Besides that, other operations at the cement plant may hardly be influenced by the burning of mixed chemical waste.
Chemicals, emissions, residues and elimination efficiency
Emissions and residues from the operation is limited to air emission only as the fly ash is integrated in the cement produced and the factory has no emission of process wastewater.
The total emission of dioxin to air in 2001 is stated at 0.199 g/year approximately corresponding to 0.1 ng/Nm³ (reference to NORCEM information on measurements by the authorities, August 2002).
Assuming this figure to equal I-TEQ, the emission corresponds to approx. 12 ng I-TEQ/kg waste. As part of this emission is caused by ordinary cement manufacturing, the correct figure is <12 ng I-TEQ/kg
waste.
No other data relevant for assessing the content of organic substances in the emission to air and fly ash is available. It should be noted, that unless otherwise documented, it must be assumed that the fly ash
from the process may contain significant quantities of dioxin. As the relevant data are not available, it is not possible to assess neither DRE (destruction and removal efficiency) nor DE (destruction efficiency)
of the process.
Other issues
As the Cement Kiln Incineration process eliminates waste products by integrating these into the final product - the cement - this process may be ranked highest. However, as discussed above it is debatable
whether this way of disposing of fly ash etc. should be considered acceptable. Based on the information we know, the CKI is ranked middle on this matter.
6.7.13 Economy
NORCEM had an electro filter before the idea of using hazardous waste came up. When they started to use hazardous waste they installed a bag house filter after the electro filter. NORCEM invested 140
million NOK (app. 24 million USD) for the above mentioned facilities, whereas NOAH invested about 400 million NOK (app. 68 million USD) for the building of the total new pre-treatment plant. Table
6.7.1 outlines main economic parameters.
The price of the waste treatment can be seen in the pricelist, but for chlorinated waste it is typical about 5-6,000 NOK (app. 950 USD) per ton. On the other hand, the treatment of PCB cost 35,000 NOK
(6,000 USD) per ton and for pesticides, official prices are 15,000 NOK (2,500 USD) per ton.
Table 6.7.1 Main costs
Item |
Costs (USD) |
Plant capital cost |
92* mill. |
Interest and repayment |
Commercial price by direct contracting |
Treatment costs (incl. raw materials, license and overhead) |
2.5/kg (pesticides) 1/kg(Chlorinated substances) 6/kg (PCB) |
Treatment costs of residual products |
included |
Labour costs |
included |
Analysis costs |
included |
Total costs |
1-6,000/ton depending on type of chemical |
* Comprises 24 million USD investments in the cement kiln and 68 million USD for the hazardous waste treatment plant. Both investments are necessary for the correct treatment, but the idea is that many
kinds of hazardous waste carry the economic burden, not only POPs.
6.7.14 Evaluation of the CKI technology
Technical evaluation
The most appropriate waste for disposal in cement kilns are those which provide additional energy value as a substitute fuel or material value as a substitute for portions of the raw material feed (e.g. calcium,
silica, sulphur, aluminium or iron). Liquid wastes or low ash wastes are relatively easy to burn in a cement kiln. The material is fed in dry or in slurry form (especially for the 'wet' process), or as a fuel
supplement into the burning zone of the kiln. In this zone, the temperature of 1,450°C is able to perform high destruction efficiency as the gas passes through the kiln. No liquid or solid residues requiring
disposal are generated since all residues are bound within the product.
For the typical counter current process configuration, polluted-soils and solid waste cannot be fed into the firing end of the kiln, since they would discharge in the clinker without adequate treatment; besides,
they cannot be fed into the cool end of the kiln, as the waste would volatilise and would not be adequately destroyed. When operated properly, destruction of chlorinated compounds in cement kilns can be
>99.00% complete with no adverse effect on the quality of the exhaust gas. Anyway, it can be seen that NORCEM as even a very modern cement plant has an emission of 42 kg of HCl per 24 hours. And
if the POPs are containing sulphur then the emission of SO2, is already over the allowed limits.
However, the contribution of waste materials to the exhaust gases are relatively low given that the waste are only used as a minor supplement to the main energy or raw material stream. Furthermore, is
important that the cement kiln has modern dust emission reducing equipment. Many pollutants will have a tendency to stick to the dust.
NORCEM has a flue gas emission of 300,000 m³/hour and emits 8.8 kg dust per hour (~30 mg/m³) giving rise to 0.1 ng/m³ dioxin (on the limit according to EU-directive). Cement kilns are allowed to have
a dust emission of 30 mg/Nm³ according to the EU-directive. As can be seen, a reduction of the dust emission would most possibly also cause a fall in the dioxin emission. For comparison, the dust emission
from a hazardous waste is around 2-3 mg/m³ and must not exceed 10 mg/m³ according to the EU-directive.
As it can be seen, the Norvegian solution with a company as NOAH conducting a lot of special pre-treatment makes the use of the cement kiln solution possible. The energy from the hazardous waste is
used in the cement produc-tion. However, it must be remembered that liquid hazardous waste traditionally consists of polluted water, with a water content up to 90%. This kind of waste must also be
treated, and that is not very wanted by the cement kilns. In Norway they come around the problem by sucking this kind of waste into wood chips, making the waste still burnable. Furthermore, the
incomming waste to NOAH in general has a low water content. Water containing waste is treated elsewhere.
Many of the older types of cement kilns, which are seen all over the CEE Region, are not assessed as suitable for international compliant hazardous waste treatment. Only a few of the cement kilns in
developing countries meet the technical requirements that, in principle, makes them egliable for incineration of certain groups of hazardous waste including POPs. Expert advice is needed to assess whether
kilns can be used and special equipment is required to inject the hazardous waste into the kiln, or if extra filters are needed, not mentioning scrubber systems etc. Such equipment is expensive and should only
be installed and used under expert supervision.
Furthermore, an important feature that has been complied with in Norway, but has a tendency not always to be considered, is to concentrate the work with the hazardous waste on specialists. People
working in a cement plant are specialists in making cement, nobody is better than them to do that. However, they are not experts in how to treat hazardous waste. Consequently, the pre-treatment of
hazardous waste shall be put in specialist hands in special designed surroundings as in NOAH in Norway.
The erection of a plant facility, like the one at NOAH in Norway is expensive and estimated costs exceeds 90 million USD. The updating of the cement kiln with a bag house filter and miscellaneous
additionals costed 20 million USD. Such systems must be regarded as non-applicable to the CEE Region due to total lack of affordability.
Finally, the global cement industry these years is under stress for constant consolidation, which make today's ownership and eventual related investment projects (pre-treatment, etc.) vulnerable for structural
change in the ownership set-up.
Environmental evaluation
Material consumption
The cement kiln incineration solution has been difficult to rank low despite the lack of precise data and should be expected to perform rather good on this issue. The fact that the main energy source is coal
which is not renewable and is a major green house gas source is not considered in this report (Table 6.7.2).
Table 6.7.2 Comparative assessment of material consumption
Material consumption |
Unit |
Cement Kiln Incineration (CKI) |
Construction materials (*1) |
kg/kg waste |
<0.01 |
Means of operation excl. energy - non-renewable |
kg/kg waste |
- |
Means of operation excl. energy - renewable |
kg/kg waste |
- |
Overall assessment |
|
1 |
-: Insignificant
*1: All materials are weighted equally and no consideration has been paid to scarcity and whether the material is renewable.
Energy consumption
The Cement Kiln Incineration turns out to be a good energy solution, which is due to the utilisation of the heat value directly in the process. Furthermore, other operations at the cement plant may hardly be
influenced by the burning of mixed chemical waste (Table 6.7.3).
Table 6.7.3 Comparative assessment of energy consumption
Energy consumption |
Unit |
Cement Kiln Incineration (CKI) |
Energy consumption |
MJ/kg waste |
- |
Overall assessment |
|
1 |
-: Insignificant
Chemicals, emissions, residues and elimination efficiency
Considering these issues the Cement Kiln Incineration is rated "below average", or more or less equal to the CIS-system. This rating is among others due to lack of data of how much dioxin is created in the
cooling of the fly ash. Unless otherwise documented, it must be assumed that the fly ash from the process may contain quantities of dioxin. Furthermore, it is not clear how the control is carried out of the
emission by-passing the bag house filter systems.
It is also noted that it is rather difficult to document the environmental performance of CKI as substances and decomposition products originating from hazardous waste is strongly diluted by emissions and
residues originating from raw materials for cement manufacturing.
Special attention must be paid to the procedure of integrating fly ash and other flue gas cleaning residues in the final product - the cement. It is noted that many countries (e.g. Denmark) as a general policy
does not accept the strategy of dilution as a way of solving the problem of disposal of residual products containing hazardous substances.
Furthermore, an amount of 30-35% alternative fuel gives rise to an emission of 0.1 ng/Nm³ of dioxin or <12 ng I-TEQ/kg waste (Table 6.7.4). This is a high level compared to dedicated hazardous waste
destruction plants. Reference is made to the GPCR-plant with an emission of 1.1 ng I-TEQ/kg waste and the CIS-plant with an emission of 1.3 ng I-TEQ/kg waste.
Table 6.7.4 Emissions and elimination efficiency
Elimination efficiency |
Unit |
Cement Kiln Incineration (CKI) |
Destruction efficiency |
% |
? |
Destruction and removal efficiency |
% |
? |
Dioxin emission to air |
ng I-TEQ/ kg waste |
<12 |
Dioxin emission - all media and residues |
ng I-TEQ/ kg waste |
? |
Overall assessment |
|
4 |
?: No data are available:
The figure stated covers the residual product only. A mass weight of 0.9 kg/litre of the residual product is assumed.
Other issues
As the Cement Kiln Incineration process eliminates waste products by integrating these into the final product - the cement - this process may be ranked highest. However, as discussed above it is debatable
whether this way of disposing of fly ash etc. should be considered acceptable. Based on the information we know, the CKI is ranked average on this matter (Table 6.7.5).
Table 6.7.5 Other environmental issues
Residues |
Unit |
Cement Kiln Incineration (CKI) |
Waste for further treatment/disposal - hazardous waste |
kg/kg waste |
0? |
Waste for further treatment/disposal -solid waste |
kg/kg waste |
0? |
Waste for further treatment/disposal -wastewater |
lit/kg waste |
0? |
Overall assessment |
|
3 |
6.8 Cyclone reactor
The main information outlined about the Russian developed cyclone reactor is extracted from the NEFCO PCB Fast Track Project - Feasibility report, February 2002.
6.8.1 Introduction
The company JSC Tekhenergokhimprom, a privatised company of some 20 employees, with the department for concepts and design located in Moscow, Russia and with test facilities in Orekhovo-Zuevo
has developed the basic technology. Their basic business is waste treatment, and hereunder the incineration of hazardous waste. They are not themselves interested in transformer handling and cleaning, but
they are interested in PCB destruction and are completely open to the possibility of co-operating with a transformer cleaning company.
The testing centre in Orekhovo-Zuevo for treatment of highly toxic waste was established in 1973. It started with destruction of different types of chemical waste. Already then, the technology was one of the
controlled incineration with high-temperature neutralisation of the acids in gas/solid phase reactions. Similar facilities have for a long time been used to clean wastes from the pesticide industry.
Formerly, Tekhenergokhimprom was a state owned company which in 1980 was nominated as the key institute for the incineration and neutralisation of solid and liquid chemical wastes as well as sludge in
the RF.
6.8.2 Description of the technology
The description is based on 4 pilot test lines for incineration of toxic waste containing organic chemicals in which chlorine, phosphorous or sulphur is a constituent. Being a test facility, the various lines are
manually operated. The assessed test line includes:
- A pilot test line for the incineration of up 40-400 kg/h of liquid toxic waste (in organic or in aqueous phases). The line has a vertical combustion chamber. Due to the common bag filter, the capacity is
limited to 100 kg/h when burning aqueous waste;
- A pilot line for incineration of 100 kg/h of solid waste with a shredder for particle size reduction followed by fluidised bed incineration;
- A pilot line for incineration of 150 kg/h of sludge or paste-like wastes (with a screw feeder); and
- A small pilot line with horizontal incineration chamber for 10 kg/h of liquid wastes.
The tests have been public approved by two organisations, the first one approving the technical description of the facility, and the second issuing an operating permit granted by the Moscow Health
Authorities and is valid for a 3-year period (2000-2003). This permit comprises the incineration of all toxic organic substances (Russian class 1-4) covering PCB.
In the beginning of the 90s it became necessary for the organisation to reorient the work from mostly research towards commercial incineration of toxic wastes from the Moscow region. Among other, also
non-PCB containing transformer liquids are being incinerated here. For this, the liquid from an old transformer at a potential client is sampled and analysed for chlorine content. And if not found, the
transformer is then transported to the site and emptied. In case chlorine is found, they refuse to handle the oil from that transformer.
Actual projects
This drive for commercialisation has led to the following projects of interest for development of a future platform for POPs elimination technologies based on existing CEE market platform:
- A 100 kg/h test facility for organic toxic waste, solid as well as liquid, was established in South Korea in 1995. This facility was used to demonstrate the technology and served as a basis for deciding
to go ahead with the next;
- A 1.3 t/h full-scale facility for incineration of liquid organic waste was established in 1998 (erected in three months, and using the cyclone reactor type described below) also in South Korea with
requirements for combustion temperature exceeding 1200°C. The Korean operating permit for this facility was granted 25 September 2000 for any type of liquid waste (also PCB). Before PCB can
be incinerated, however, some tests must be carried out. In this unit, a combustion air pre heater heats the air to 3-400°C. The heat recovery system is part of the quench design. This unit is fully
automated and has been designed for continuous operation, however, still requiring some 2-3 operators (examples of duties: tank operations, removal of salt from bag filters, changing of nozzles etc.);
- Khimprom in the city Ufa, Russia, where a unit has been established a few years ago for the destruction of pesticides; and
- The Korean waste handling company having purchased the above units has sold one unit to Japan for handling of 5 t/d of PCB and 4 t/d of PCB-polluted organic washing liquids from transformers,
using 35 t/d of soda-containing wastewater for neutralisation. By July 2001, the work was in progress for delivery of design documents as well as a cyclone unit later in 2001.
6.8.3 Description of cyclone process
The heart of the Cyclone Process is the incineration chamber. The one from the test installation in Orekhovo-Zuevo is shown in Figure 6.8.1.
As illustrated, the name Cyclone Reactor comes from the swirl movement of the combustion gases – this same movement that ensures a high degree of turbulence and thus efficient mixing.
Figure 6.8.1 Brick lined top of cyclone reactor in Orekhovo-Zuevo
The cyclone reactor is a vertically mounted cyclone type incinerator in which the combustion air and the fuel enter with a velocity around 100 m/s thus ensuring intimate mixing and high turbulence. The
retention time here is around 0.3 seconds and the temperature 1,600-1,700°C (lining with chromium magnesite or Al2O3).
The caustic solution is then added through nozzles and the temperature drops to between 1,250 and 1,400°C, and in the subsequent brick-lined afterburner is ensured another 1.7 seconds of retention time.
The main principles (process diagram) of the entire installation are shown below.
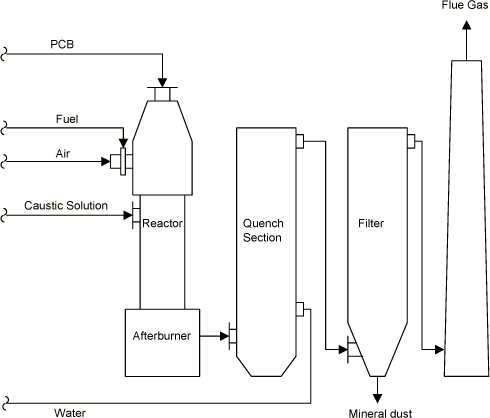
Figure 6.8.2 Process flow diagram for the cyclone process
The cyclone reactor technology contains a high-temperature gas/solid phase reaction. This takes place between the caustic (dissolved Na2CO3 or NaOH or Ca(OH)2) and the acid gases formed by the
incineration of S-, P- or Cl-containing organic substances.
In all cases, the reaction products come out as a powder of salts, retained in bag filters as opposed to the other processes where more or less polluted brine is the waste product. Because it is introduced into
the hot combustion zone, liquid spent caustic solutions may be used as a cheap source of sodium hydroxide. If not available, a solution is prepared from purchased chemicals.
The primary reaction is the gas phase reaction (simplified) where practically all hydrochloric acid reacts with the caustic:
NaOH + HCl → NaCl + H2O
The remaining caustic reacts with carbon dioxide:
2NaOH + CO2 → Na2CO3 + H2O
This core of the method was patented in Russia, but the patent was not maintained and is thus no longer valid, and the system has been copied in Germany and in Scotland.
With certain chemicals, the salts are actually melting and collecting on the surface of the incineration chamber, and subsequently flow out from the bottom. But in the case of PCB, it is to be expected that
NaCl powder will travel through the system to be collected in the bag filter.
The exact temperatures and injection points depend on the product to be incinerated. In the case of PCB, the design would be with the support fuel in the top of the combustion cyclone and the PCB
intimately pre-mixed with the caustic solution a little further down. The need for support fuel depends on the material to be incinerated.
In the combustion process it is important to have a surplus of steam to avoid any tendency for soot formation from incinerating of the cyclic organic components (the shift reaction will ensure the formation of
CO instead). Steam is present from the natural gas incinerated as well as from the subsequent injection of NaOH solution. With certain cyclic organic chemicals it is necessary to add more in the form of
water; but this is not required for the combustion of PCB.
Downstream of the afterburner, the hot gases enter a quench tower, where the temperature is taken down to approx. 200°C (possible range 160-220°C) the exact level being determined by the bag filter
operation. At these temperatures the salts solidify from the gas phase, forming a fine powder.
High temperature fibres are then used in the bag filter, thus allowing the flue gas to stay well clear of lower temperatures where the salts would become sticky due to the high humidity in the flue gas.
During earlier tests, the company Taifun made 3-5 analyses for dioxins in this powder, but even traces could not be detected, and further analyses were therefore abandoned. In the flue gas, many
measurements of dioxins have been made, and these results have shown values below 0.1 ng/Nm³.
Experience with difficult chemicals
In 1992, when producing a pesticide similar to Agent Orange (with high concentrations of dioxins and furans) the Khimprom factory realised they had problems with waste incineration as temperatures of
2,000 or even 3,000°C would be required. It was because of this JSC tested the product and obtained the results now published in the article in “Ekip” from February 2000. In this article is clearly
demonstrated the influence of incineration temperature on dioxin emissions when incinerating a dioxin.
Much research work is behind the curve presented in this article. So, if the incineration process may be controlled well enough, then traditional incineration is a fine way to dispose of such toxic chlorinated
organic components. It is this work, on the incineration of components very similar to PCB that gives reason to believe, that the test will prove PCB incineration to be very efficient and satisfactory in a CEE
developed context.
6.8.4 Description of operation
One of the potentially important features of the process is the lining with insulating bricks. In Korea, fine quality bricks made of 95% pure corundum exists which makes them very resistant to heating and
cooling. In Russia, only an 85% quality is available. The practice in Korea to start up and shut down the unit every day should therefore not be attempted with a Russian-made installation. Here, continuous
operation should be foreseen as much as possible. A PCB collection tank should hold at least a week's consumption before the unit is started up. Hereafter the unit should be operated continuously until the
tanks is empty. Such mode of operation requires 5 shifts with 2-3 operators in each shift.
The cyclone reactor facility is not very complicated to operate. The four important parameters to master and control are:
- Retention time: should be two seconds above 1,200°C (experience based on incinerating dioxin-containing waste), and this is ensured in the brick-lined canal after the burner;
- Operating temperatures in chamber and afterburner;
- Amount of excess oxygen in the flue gas; and
- Turbulence in combustion chamber for homogenous mixing.
As a supplement to the above, the CO level is monitored closely, mainly because combustion of CO is slower than that of dioxins. Experience has shown that if CO is below 5 mg/m³, the dioxin level is
below 0.1 ng/m³. For this reason there shall be at least approx. 3% oxygen in the flue gas (excess air in the combustion).
Furthermore, it has been experienced that dioxin levels rise (a fivefold number has been measured, or 0.5 ng/m³) during start-up and shutdown of the unit. For this reason, waste should only be injected,
once the unit is heated up and operating.
In Korea, among many other types of hazardous waste, three types of chlorinated chemicals (methylene chloride/chloroform, carbon tetrachloride, and chlorobenzene) have been incinerated in the cyclone
reactor without any traces of dioxins measured in the flue gas.
6.8.5 Evaluation of the cyclone reactor plant
In general, the process is well proven and mature, but not for the specific application of PCB destruction. Like any other elimination technologies, the cyclone reactor has positive and negative effects.
Advantages
The main advantages are:
- Clean waste powder is claimed (has to be tested), consisting almost entirely of NaCl and Na2CO3 salts. This may either be recycled to chemical industry (for NaOH and Cl2 production), or
ultimately placed on a controlled dumpsite; and
- Any kind of spent caustic with organic pollution may be used for the neutralisation since this is injected directly into the flame and any such pollutants are undergoing the same efficient combustion as
the PCB.
Disadvantages
The main disadvantages are:
- Start-up and shutdown is slow due to the necessary protection of the brick lining; and
- This technology can only treat dissolved POPs, such as fluid PCB, but no solids.
Technical evaluation
The patented system for injection of caustic solution directly into the hot reaction chamber results in the direct formation of gaseous NaCl, thus removing Cl from the reactants. For this reason, the formation
of dioxins is claimed much less likely than in traditional incineration and it is also believed that the binding of Cl also contributes to the complete destruction of PCB.
Downstream of the hot zone, all equipment may be made of plain carbon steel.
Maturity of technology
The technology has been proven on other toxic organic substances such as pesticides and on organic chemicals with relatively high levels of dioxins, but not specifically on PCB. The system has been in
operation for the last 30-40 years with different chemicals; the older systems were designed for much lower combustion temperatures though, because at that time problems with dioxins were not designed
for.
Incineration is the best known of all technologies. The traditional criterion for PCB incineration with minimum 1,100°C and min. 2 seconds retention time is complied with. Together with practical experience
with incineration of other halogenated components – additional research is carried out at present. Tentative results show that operating improvements are obtainable by the Cyclone Reactor with caustic
injection in the hot zone.
Any of the following caustic liquids may be used – also those that might be polluted with organic matter: NaOH, Na2CO3, KOH, K2CO3 (the two carbonates are the least expensive, and therefore
normally chosen, when fresh chemicals are to be purchased).
Versatility/robustness
The process is claimed capable of coping with any concentration of PCB in the liquid waste to be incinerated and it can handle many types of halogenated organic compounds.
Capacity
The capacity of the Cyclone Reactor can be tailor-made for a range of 40 kg/h to around 16 tonnes per hour. It can therefore easily be designed to accommodate the desired capacity under the ongoing
NEFCO-PCB Fast Track Project.
Utility requirements have – on a preliminary basis been determined to:
- Electric power: minimal, for pumps only;
- Natural gas: 1,700 kg/ton PCB (could be kerosene instead);
- Sodium hydroxide: 740 kg/ton PCB;
- Cooling/quenching water. 27 ton/ton PCB, and
- Some nitrogen is required for purging during start-up and shutdowns.
More accurate estimates will be available after specific tests related to actual waste.
Mobility of facility
If designed with kerosene as main fuel, the facility is not bound by anything but requirements to water and a modest power supply. This process therefore has the biggest potential for being designed as a
mobile facility. It may fit into a few containers. However, the necessary brick lining is fragile if transported on bumpy roads, thus limiting the practicality of a mobile unit.
Workers health and safety
Occupational health levels are to be determined and optimized during the operation of the plant in the NEFCO funded PCB Fast Track project. This shall include waste handling, pre-treatment, start-up,
operation and close down of plant.
Environmental evaluation
Airborne emissions
Small amounts of CO and NOx can be found in the flue gas. Some salt dust will - depending on the quality of the bag filter – pass through the filter and emitted with the flue gas. Tests shall decide if the plant
can meet the emission requirements e.g. set forward by the EU-directive on incineration of waste.
Noise
Low, a draft fan is part of the installation and does make itself heard.
Waterborne emissions
None, only cooling water is used.
Waste generation
A dry powder/ash consisting mainly of NaCl and of a little NaHCO3 is produced. It remains to be proven as a result of a test, but it is expected that there will be very little and possibly no traces of dioxins
in the ash. Perhaps there will not even be traces of PCB.
It is therefore expected that these ashes may be disposed of in a properly conceived waste dumpsite. This however, still has to be proven.
Energy conservation
Some heat recovery will be built into the quench section, serving to preheat the air used in the incineration to 300-350°C. The requirement to sudden cooling of the flue gases in order to avoid the formation of
dioxins puts a limit to, how much heat recovery is possible with such an incineration process for e.g. PCB destruction.
Compliance with emission norms
It is expected, however at the present stage not sufficient documented, that applicable norms for e.g. dioxins will comply.
Prohibitive features
Of the CEE facilities investigated so far, the cyclone technology appears to be technically and environmentally the most promising. The problem with solid waste has been tried minimised, and there is real
operating experience on dioxin incineration with one unit. Further tests will show if the facility cope with the environmental demands according to the EU-directive.
6.9 Comparative evaluation of the 4 reviewed POPs elimination technology plants
6.9.1 Environmental evaluation
The environmental comparative assessment of the 4 reviewed elimination technologies presented in the previous chapters (the cyclone incinerator excluded) focuses on the following issues:
- Consumption of materials;
- Energy consumption;
- Chemicals, emissions, residues and elimination efficiency; and
- Other issues.
Consumptions of materials
The key figures concerning consumption of materials are summarised in Table 6.9.1. The main focus is given to consumption of means of operation as the comparative assessment with respect to construction
materials should be regarded as a rough and partly incomplete assessment that does not consider issues like material scarcity and renewability.
Still, the comparison regarding construction materials is interesting indicating a trend consistent with the figure shown by consumption of means of operation, namely that the CIS solution allows for a higher
flow of waste materials through the system than the chemical decomposition systems. The CIS system thus obtains a higher material efficiency and deserves to be rated best in this regard.
The GPCR technology equals the CIS technology on the comparison of material consumption. The BCD system on the other hand stands out as having an out standing high consumption of mineral oil used in
the operation placing this solution un-disputably as the worst in this regard. The CKI solution has to be ranked low due to the lack of precise data.
Table 6.9.1 Comparative assessment of material consumption
Material consumption |
Unit |
Gas-Phased Chemical Reduction
(GPCR) |
Base Catalysed Dechlorinaion
(BCD) |
Container-based Incineration System
(CIS) |
Cement Kiln Incineration
(CKI) |
Construction materials (*1) |
kg/kg waste |
≤0.01 |
<0.01 |
<0.002 |
<0.01 |
Means of operation excl. energy - non-renewable |
kg/kg waste |
- |
4-13 |
- |
- |
Means of operation excl. energy - renewable (*2) |
kg/kg waste |
0.18-0.56 |
1-2 |
0.01-0.1 |
- |
Overall assessment |
|
2 |
5 |
2 |
1 |
-: Insignificant
*1: All materials are weighted equally and no consideration has been paid to scarcity and whether the material is renewable;
*2: Addresses in reality only the consumption of NaOH.
Energy consumption
Concerning energy consumption the key figures are summarised in Table 6.9.2. The picture shown resembles the picture of material consumption, which is hardly surprising as the consumption of means of
operation also strongly influences the energy consumption. However, a significant difference is that the Cement Kiln Incineration could turn out to be the best solution, which is due to the utilisation of the heat
value. Besides that, other operations at the cement plant may hardly be influenced by the burning of mixed chemical waste. Unfortunately, any solid conclusions in this regard are prevented by the lack of
precise data.
Comparing the CIS system with the GPCR system, CIS is assessed slightly better as the energy consumption in most cases should be expected to be lower than for the GPCR system. Generally, the better
the heat value of the waste, the better performance of CIS compared to GPCR and vice versa.
Again the BCD system is indisputably ranked lowest due to outstanding high energy requirements coming from consumption of electricity as well as the carrier oil.
Table 6.9.2 Comparative assessment of energy consumption
Energy consumption |
Unit |
Gas-Phased Chemical Reduction
(GPCR) |
Base Catalysed Dechlorination
(BCD) |
Container-based Incineration System
(CIS) |
Cement Kiln Incineration
(CKI) |
Energy consumption (*1) |
MJ/kg waste |
29 - 35 |
400-1200 |
1-43 |
- |
Overall assessment |
|
3 |
5 |
2 |
1 |
-: Insignificant
*1: The great variation depends on whether support fuel is needed or not. As an average, the need for support fuel should be anticipated to be in the low end of the interval.
As cement kiln incineration could turn out to be the best solution, the choice has been made not to use the rating of "best" for other systems.
Chemicals, emissions, residues and elimination efficiency
The knowledge available concerning emissions and elimination efficiency is presented in Table 6.9.3. Unfortunately, the available data are in several ways inadequate, but seems anyhow to present a
trustworthy picture. The DRE figures for the GPCR process are slightly better than the DRE figures for the BCD and the CIS processes. It should be noted that the DRE values quoted for the GPCR and the
BCD processes represent specific highly chlorinated substances, while the DRE value for CIS is based on a balance for total organic carbon. Considering the very low level of dioxin emission to all media
and residues from the GPCR process it also seems appropriate to rate this process as the "best".
The BCD process is rated second primarily based on the values for DE and DRE. The process suffers from a high content of chloride in the residual product, and no data on emission of dioxin to air is
available from the destruction (by incineration) of the residual product. It is however recognised that all experience with incineration based systems points at quantities of dioxin in fly ash and other flue gas
cleaning residues. Thus, there is no reason for assuming the CIS and the CKI processes to perform better than BCD on the issue of dioxin.
The CIS is rated low. The DRE value for organic carbon and low dioxin emission to air should although be recognised. However, as stated above, the dioxin content in flue gas residues should be expected
to be high and the overall destruction efficiency remains to be proven considering that up to 2% carbon is allowed in the slag.
Attention must also be paid to the fact that incineration of hazardous waste in a small unit like CIS is a process depending strongly on the heat value of the waste and therefore occasionally/potentially difficult
to control. In serious cases it may be necessary to close down the process and allow flue gas to be released to the environment without being subject to flue gas cleaning. Such incidents, which are difficult to
quantify, are tried reflected in the figures below, and should not be overlooked.
The Cement Kiln Incineration is also rated low due to lack of data. It is noted that it is rather difficult to document the environmental performance of CKI as substances and decomposition products
originating from hazardous waste destruction are diluted in emissions and residues originating from raw materials from the cement manufacturing.
In this case, special attention must be paid to the procedure of integrating fly ash and other flue gas cleaning residues in the final product - the cement. Until better knowledge has been developed, it must be
assumed that this procedure in reality is a way of "hiding" dioxin in cement and spread it into the society and the environment as a consumer product.
Table 6.9.3 Comparative assessment of emissions and elimination efficiency
Elimination efficiency |
Unit |
Gas-Phased Chemical Reduction
(GPCR) |
Base Catalysed Dechlorination
(BCD) |
Container-based Incineration System
(CIS) |
Cement Kiln Incineration
(CKI) |
Destruction efficiency (DE) |
% |
? |
99.97-99.997 |
? |
? |
Destruction and removal efficiency
(DRE) |
% |
99.98-≥99.996 |
> 99.9999 |
>99.996 |
? |
Dioxin emission to air |
ng I-TEQ/ kg waste |
1.1 |
? |
≤1.3 |
<12 |
Dioxin emission - all media and residues (*1) |
ng I-TEQ/ kg waste |
1.1 |
2200-66001) |
? |
? |
Overall assessment |
|
1 |
2 |
4 |
4 |
?: No data available
*1: The figure stated covers the residual product only. A mass weight of 0.9 kg/lit. of the residual product is assumed.
Other issues
Other environmental issues focus on the amount of waste generated by the processes and the hazards related to this waste. No other issues are deemed relevant to consider.
As the Cement Kiln Incineration process eliminates waste products by integrating these into the final product - the cement - this process may be ranked highest. However, as discussed above it is debatable
whether this way of disposing of fly ash etc should be considered acceptable.
The GPCR process distinguishes itself from the BCB and CIS processes by not generating any hazardous waste that requires further treatment or special disposal. The amount of solid waste is very low,
while the amount of wastewater hardly can be regarded as a problem, considering that is cleaned by an activated carbon filter. For these reasons, the GPCR process is ranked "highest" of the remaining
processes.
Regarding the CIS process, the fly ash, the slag and the quench residues are likely to be disposed of as hazardous waste to a special landfill due to the content of dioxin as well as other pollutants indicating
that there is a need for landfill capacity. Thus the CIS process is ranked below the GPCR process.
The BCD process presents its own special set of problems, as it generates a relatively high quantity of residual product, which is composed of carrier oil together with remains of NaOH and a significant
content of chlorine from the decomposed substances. Uncontrolled burning of this product could lead to significant dioxin formation and appropriate disposal must include treatment on a facility specialised in
treatment of liquid chemical waste. For this reason, the BCD process is also ranked below the GPCR-process (Table 6.9.4).
Table 6.9.4 Other environmental issues
Residues |
Unit |
Gas-Phased Chemical Reduction
(GPCR) |
Base Catalysed Decomposition
(BCD) |
Container-based Incineration System
(CIS) |
Cement Kiln Incineration
(CKI) |
Waste for further treatment/disposal - hazardous waste |
kg/kg waste |
- |
5.4-16 |
0.02-0.18 |
0? |
Waste for further treatment/disposal - solid waste |
kg/kg waste |
0.01 |
- |
0.2-2 |
0? |
Waste for further treatment/disposal - wastewater |
lit/kg waste |
2.5-2.9 |
0.1-0.4 |
0.07-0.6 |
0? |
Overall assessment |
|
2 |
4 |
4 |
3 |
0?: No data are available, but could be 0.
-: Insignificant
6.9.2 Technical evaluation
Capacity
The best capacity for highly chlorinated waste is the GPCR technology as shown in Table 6.9.5.
Table 6.9.5 Capacity
|
Unit |
Gas-Phased Chemical Reduction
(GPCR) |
Base Catalysed Dechlorination
(BCD) |
Container-based Incineration System
(CIS) |
Cement Kiln Incineration
(CKI) |
Capacity (50% Cl) |
Ton/year |
2,000 |
60 |
400-800 |
1,300 |
Overall assessment |
|
1 |
5 |
2 |
2 |
Comprehensiveness
The CIS and the CKI have the advantage to be continued operations, whereas the GCPR is continuous only with fluid waste, and both the BCD and the GCPR are batch operated with solids.
All the plants can treat most types of containers and most types of wastes, although they all have their special compounds they have to avoid or minimise. Table 6.9.6 outlines the performed assessment.
Table 6.9.6 Comprehensiveness
|
Gas-Phased Chemical Reduction
(GPCR) |
Base Catalysed Dechlori-nation
(BCD) |
Container-based Incineration System
(CIS) |
Cement Kiln Incineration
(CKI) |
Types of waste |
solid & fluid |
fluid |
solid & fluid |
solid & fluid |
Type of operation |
batch (solid) |
batch |
continuous |
continuous |
Overall assessment |
3 |
4 |
2 |
2 |
Maintenance
Information about maintenance expenses has been few, but it is anticipated that the plant with the most moving parts are most expensive and that the heavy
system of the CKI results in low maintenance. Table 6.9.7 shows the assessment of maintenance.
Table 6.9.7 Maintenance
|
Gas-Phased Chemical Reduction
(GPCR) |
Base Catalysed Dechlo-rinated
(BCD) |
Container-based Incineration System
(CIS) |
Cement Kiln Incineration
(CKI) |
Maintenance |
few moving parts |
few moving parts |
moving parts |
heavy |
Overall assessment |
2 |
2 |
3 |
2 |
Transfer of know-how
The companies behind the GPCR and the CIS have already developed programmes for transfer of know-how, which is not the case in the same extent for the BCD and CKI technologies. The technology
transfer for CKI is not practised at all, whereas the BCD company was open for development of this.
Table 6.9.8 highlights the assessment of transfer of know-how abilities, which for a CEE context is of major importance, due to a relatively weak, highly complex industrial sector.
Table 6.9.8 Transfer of know-how
|
Gas-Phased Chemical Reduction
(GPCR) |
Base Catalysed Dechlorination
(BCD) |
Container-based Incineration System
(CIS) |
Cement Kiln Incineration
(CKI) |
Transfer of know-how |
Existing programme |
Willing to develop aprogramme |
Existing programme |
No programme |
Overall assessment |
1 |
2 |
1 |
3 |
Special supply lines
The supply lines are more or less the same. The GPCR though has a need for hydrogen supply, which requires high attention. Table 6.9.9 outlines the assessment.
Table 6.9.9 Special supply lines
|
Gas-Phased Chemical Reduction
(GPCR) |
Base Catalysed Dechlorination
(BCD) |
Container-based Incineration System
(CIS) |
Cement Kiln Incineration
(CKI) |
Special supply lines |
Hydrogen, nitrogen, natural gas |
Nitrogen, |
Nitrogen, natural gas |
Long pipe for transport of waste |
Overall assessment |
3 |
2 |
2 |
2 |
Residual products
The GPCR has very good control with all residual products, whereas both BCD and CIS have no data on the final residual product. The CKI has no residual products, and in this scheme that would
normally be rated high, but as the residual products are ending in the cement and we have no data for this, the CKI is rated as if we have no data. Table 6.9.10 outlines the assessment of residues
environmental impact.
Table 6.9.10 Residual products under control
|
Gas-Phased Chemical Reduction
(GPCR) |
Base Catalysed Dechlorination
(BCD) |
Container-based Incineration System
(CIS) |
Cement Kiln Incineration
(CKI) |
Rest products |
Small amounts, controlled |
Lack of data for residual products |
Lack of data for residual products |
No residual products |
Overall assessment |
2 |
4 |
4 |
4 |
Occupational health
The protection of workers was looked upon during visit at the various plants. The CKI has a problem with cement dust, but seen from a POP waste angle, the working surroundings were well planned and
clean, and the same was seen at the GPCR and at the CIS plant. At BCD people had to wear protection suits and masks, which seemed necessary at that plant. This may be improved. Table 6.9.11 outlines
the assessment.
Table 6.9.11 Occupational health
|
Gas-Phased Chemical Reduction(GPCR)
|
Base Catalysed Dechlori-nation(BCD)
|
Container-based Incineration System
(CIS) |
Cement Kiln Incineration
(CKI) |
Occupational health |
Found OK by inspection |
Found less OK by inspection |
Found OK by inspection |
Found OK by inspection |
Overall assessment |
2 |
4 |
2 |
2 |
Operational risk
Risk analysis performed for all plants, however this does not mean that there is no risk so all plants are rated about middle in Table 6.9.12.
Table 6.9.12 Operational risk
|
Gas-Phased Chemical Reduction
(GPCR) |
Base Catalysed Dechlori-nation
(BCD) |
Container-based Incineration System
(CIS) |
Cement Kiln Incineration
(CKI) |
Occupational risk |
Risk analysis |
Risk analysis |
Risk analysis |
Risk analysis |
Overall assessment |
2 |
2 |
2 |
2 |
Mobility
The mobility of each of the 4 review technologies is relatively. The immediate costs related to relocation normally equal 40-50% of the capital investment costs. However, the BCD was reviewed most
mobile, while the CKI technology is strictly stationary. Table 6.9.13 outlines the assessment performed on mobility.
Table 6.9.13 Mobility
|
Gas-Phased Chemical Reduction
(GPCR) |
Base Catalysed Dechlorination
(BCD) |
Container-based Incineration System
(CIS) |
Cement Kiln Incineration
(CKI) |
Mobility |
Semi mobile |
Rather mobile |
Semi mobile |
Not mobile |
Overall assessment |
3 |
2 |
3 |
5 |
6.10 Summary and discussion
In Table 6.10.1 please find the overall rating scheme as a conclusive result of the performed detailed review based on 21 selected review criteria covering technical, environmental and economic issues.
Table 6.10.1 Overall rating of the review of selected POP elimination technologies
Parameters |
GPCR |
BCD |
CIS |
Cement Kiln |
1. Materials consumption |
2 |
5 |
2 |
1 |
2. Energy consumption |
3 |
5 |
2 |
1 |
3. Emission |
1 |
2 |
4 |
4 |
4. Others |
2 |
4 |
4 |
3 |
5. Overall environmental evaluation - mean |
8/4=2 |
16/4=4 |
12/4=3,0 |
8/4=2.2 |
Environmental evaluation |
2 |
4 |
3 |
2 .2 |
6. Treatment costs |
1 |
5 |
1 |
1 |
7. Analytical costs |
1 |
5 |
1 |
1 |
8. Capital investment costs |
4 |
1 |
1 |
5 |
9. Marginal costs of investment |
2 |
5 |
1 |
1 |
10. Cost of relocation (not part of "mean" below) |
(3) |
(2) |
(3) |
(5) |
11. Overall economic evaluation - mean |
8/4=2 |
16/4=4 |
4/4=1 |
8/4=2 |
Economic evaluation |
2 |
4 |
1 |
2 |
12. Capacity |
1 |
5 |
2 |
2 |
13. Comprehensiveness |
3 |
4 |
2 |
2 |
14. Maintenance (Robustness) |
2 |
2 |
3 |
2 |
15. Transfer of Know-How |
1 |
2 |
1 |
3 |
16. Special supply lines |
3 |
2 |
2 |
2 |
17. Rest products under control |
2 |
4 |
4 |
4 |
18. Occupational health |
3 |
4 |
2 |
2 |
19. Operational risks |
2 |
2 |
2 |
2 |
20. Mobility |
(3) |
(2) |
(3) |
(5) |
21. Overall technical evaluation - mean |
17/8=2.1 |
25/8=3.1 |
18/8=2.3 |
19/8=2,4 |
Technical evaluation |
2.1 |
3.1 |
2.3 |
2.4 |
Total mean (5+11+21/3) |
6.1/3: 2.0 |
11.1/3: 3.7 |
6,3/3: 2,1 |
6.6/3: 2.2 |
6.10.1 Critical assumption
It has to be emphasised that Table 6.10.1 is entirely subjective and the scheme should only be read together with the total text of this chapter. However, the scoring and the weighing of scores are based on
our best estimate. Furthermore, who can decide what is most important: technology, environment or economy? What about the missing issues? In fact it can be proven mathematically that this way of
comparing things is not possible. Nevertheless, the scheme hopefully makes it easier for relevant CEE key resources to discuss and overview the extensive amount of relevant information in a single glance
with the risks of oversimplifying the complexity of the technology related review.
Evaluation
During 2002, the consultant's expert team visited plants in Australia, Canada, Norway and Denmark, made detailed interviews, asked critical questions, performed literature review and customers
re-evaluation of the technologies to the extent possible. The detailed description of the technical, environmental and economic elements of each technology is our conception of the technologies based on our
visit and of our reading of technical material. Finally, prior to publishing, the participating vendors have reviewed the early drafted material for major corrections of errors and any mishaps.
We have evaluated the technologies against each other. The cyclone reactor though, has not been visited and examined by the present authors, but we rely on information received from other COWI
employers working closely with this technology. However, due to lack of exact knowledge on key areas of economy and environmental performance, it has been decided not to give any evaluation of that
plant.
As outlined in Table 6.10.1, the technical, environmental and economic criteria were reviewed in detail.
Technical performance
When reviewing the technical performance it was revealed that the GPCR, the CIS and CKI are rated above average.
Generally, the 3 technologies are equal in technical performance. The BCD plant on the contrary came out below average in the technical evaluation, mostly due to low capacity, weak performance of
comprehensiveness, and weaker occupational health control.
Environmental performance
In the environmental performance, the report finds the performance of the GPCR the best, whereas the CIS and the CKI are still rated above average, but not as good as the GPCR, mainly due to lack of
knowledge about emissions in residual products. Again, the BCD plant was evaluated below average on all points beside on emission where it was fine and above average.
Economic performance
In the economic performance, the report outlines the performance of the CIS plant as the best on all points. The GPCR and the CKI is still above average, but not as good as the CIS (even if you take into
account that the CIS can not treat as much halogen containing materials per hour as the GPCR), mainly due to the capital investment costs. Again, the BCD plant is evaluated to below average on all points
beside capital investment costs.
Evaluation summary
Looking on the overall evaluating process, a group of 3 technologies seems to perform (technical, environmental and economical) better than the BCD technology. These are GPCR, CIS and CKI that are
evaluated above average in mean. On the other hand, the BCD plant is evaluated to below average and not as mature and versatile as the other plants.
The three plants in the first group are more or less equal in the environmental and the technical evaluation, but are diverting in the economical part. The capital investment costs are higher for the GCPR than
for the comparable CIS. The cement kiln is in that respect in a class by itself. On the other hand, if one uses an existing up-to date cement kiln, then the treatment costs per tonne are comparable.
The general conclusion of the performed detailed review outlines that based on global market survey and filtration of incoming information on a number of merging technologies, two technologies seems to
have the potential as optional POPs waste eliminators in the CEE Region, the GPCR and CIS technologies.
This is further underlined by the fact that the CIS technology has scheduled operational activities ongoing in Latvia (Latvia is also in the recent DG-Environment report on Obsolete Pesticides Status in the
candidate countries grouped in category 1 - countries which are far advanced in their efforts solving the obsolete pesticides problems).
In parallel, the GPCR technology is in progress of scheduled activities in the Slovak Republic via a basket funded project (Slovak government, private industry, GEF funds, etc.). Both technologies wish to
utilise these market platform options as demonstration objects for further exploitation. As described earlier in the report, the market in the CEE Region is not at present open for commercially operated POPs
waste elimination technologies. However, through these two "ice-breaking" initiatives, a new era within OP/POPs elimination is hopefully initiated leading to more broad solutions on hazardous waste in
general in a specific CEE context complying with not only national priorities, but also with international binding environment protocols and conventions related to POPs and related chemicals.
| Front page | | Contents | | Previous | | Next | | Top |
Version 1.0 March 2005, © Danish Environmental Protection Agency
|