| Forside | | Indhold | | Forrige | | Næste |
Metalafgivelse til drikkevand, DEL 2
Appendix B
1. TEST METHOD
Danish Test rig, Metal release to drinking water
Design of test rig
24 test-items are installed in the test rig in a plastic pipe system with plastic stop valves and tap valves. The structural design of
the testing allows simulated use of water and sampling of stagnated water from each test-item separately. ABS-plast jointed by
gluing is used for pipes, fittings, air escape valves, stop valves and tap valves in the test rig.
The water pressure is controlled at 3 BAR by a regulation valve at the inlet. There is simulated use of water. A timer for
systematic water outlet controls the flow regime. Test rigs are placed at the waterworks, where the alternations of the water
composition are limited and the room temperature is stable and low. The water temperature at the inlet is a little lower, 10 -
12°C throughout the year.
The pipe arrangement in the test rig is shown in the figure below.
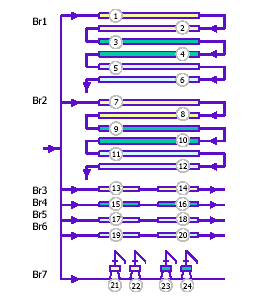
Figure of test rig
Schematic sketch of the Danish test rig. The test-items nos. are illustrated.
Arrangement of metallic test pieces (pipes, fittings and valves)
All pieces are tested in duplicate. Test pieces made of the same group of materials are placed in series in the test rig. Test
pieces of various groups of material are placed in parallel. Thus the test rig contains 7 parallel branches.
Example 1
In the first test-run May 1999 - May 2000 the test samples were distributed as follows (from top):
Branch 1: 2 x 3 stainless steel pipes, pieces 1 - 6
Branch 2: 2 x 3 galvanised steel pipes, pieces 7 - 12
Branch 3: 2 joined items of brass valve bodies, pieces 13 - 14
Branch 4: 2 brass manifolds, pieces 15 - 16
Branch 5: 2 joined items of DZR brass valve bodies, pieces 17-18
Branch 6: 2 joined items made of chromium plated brass ball valves, pieces 19-20*
Branch 7: 2 x 2 mixer taps of chromium plated brass, pieces 21-24**
* The valves are tested in full open position
** The mixer taps have got open valves in the daily service condition. This means that water is streaming out in an open drip
tray when the timer activates the automatic stop valve for the test rig. When the water is stagnant in the daily flow regime, the
spout in the mixer taps will be full of water, if there is no space of air in the spouts. The water sampling for analysis is done
backwards from the tap valve placed on the pipe below the mixer taps.
Procedure
In the first test run, May 1999 - May 2001, the four test-rigs were placed at 4 different waterworks with a variety in water
composition. The exposed test pieces were identical at the four sites.
In the second test run, March 2002 – March 2003, the test rigs were again placed at 4 water works, but one rig was moved to
another water work.
In the second test run only 2 x 4 test pieces were identical in the 4 water works. 2 x 6 test pieces were a continuation of pieces
from the first test run. They were exposed in a prolonged period of approximately 4 years. Some test pieces were tested in one
water work only.
Service conditions for test rigs
For simulating daily use of water, a flow regime of two times 15 minutes in 24 hours is chosen. The rest of the time the water is
stagnant. The flush of the system is made at 8 a.m. and at 4 p.m. The average use of water on a test rig is approximately 1400 l
per day. The water is distributed in the 7 branches in the test rig. Each branch varies internally in geometry and length and
therefore the pressure-loss, water amount and velocity vary. The average amount of water flowing in a branch is 200 litres per
day and in many items the velocity is around 0.6 m/s. While the condition stagnation time/flow time is constantly
23½hour/½hour, the amount of water passing is variable and the velocity is not exactly the same in all items. Yet, every
exposure represents a situation in a practical system, where the variations are numerous. But the structural design determines a
test, where the precise exposure of an item is not completely comparable to another item in the test-rig.
Sampling of stagnation water
12 hours stagnation test
12 hours stagnation tests were sampled 9 times over the one-year exposure period in first test run and 8 times in the second test
run. The measurements were most frequent in the first months, when the changes in metal release were extensive.
Before sampling the motor valve was switched to manual mode. Then the test rig was flushed with water for 10 minutes and
water samples for blind metal analysis and water samples for the water parameter analyses pH, HCO3-, Cl- and conductivity
were taken.
Then the other valves were closed, the water pressure was closed and all stop valves among the test pieces were closed. 12
hours later the test-pieces were successively emptied for water. The water was sampled in rinsed and pre-marked plastic
bottles. The first 50 ml of water from the plastic taps was thrown away. For branches 1 and 2, the sampling was made with
start from the top of the test rig after the air escape valve had been opened.
Short period stagnation measurements (run time curves)
After one year in operation, all waterworks in the first run made series of short period stagnation measurements at ½h, 2hrs, 4
hrs, 8 hrs and 12 hrs. The tests were made in the same way as the 12 hours stagnation sampling only the period of stagnation
was shortened.
The test rig is not designed for ½h stagnation sampling. The stagnation time has not been exact for the ½h samples, thus these
samples are much more subjected to inaccuracy than are the other measurements.
Chemical analyses
The metal analyses of the water samples were made at an accredited laboratory by atomic absorption to the detection limits:
0,01 μg/l for Cd
0,1 μg/l for As, Pb, Su, Cr, Ni and Mo
0,2 μg/l for Sb
50 μg/l for Cu
100 μg/l for Zn
| Forside | | Indhold | | Forrige | | Næste | | Top |
Version 1.0 December 2004, © Miljøstyrelsen.
|