| Til bund | | Forside |
Miljøprojekt nr. 1103, 2006
Miljø- og sundhedsforhold for plastmaterialer
Indholdsfortegnelse
2 Forord
3 Sammenfatning
4 Summary
5 Læse - og brugsvejledning
6 Oversigtsfigur med links
7 Termoplastbranchens råvarer
8 UP-branchens råvarer
9 Polyurethanbranchens råvarer
10 Additiver
11 Compoundering
12 Blæsestøbning
13 Ekstrudering
14 Ekspandering af polystyren (EPS)
15 Kalandrering
16 Rotationsstøbning
17 Sprøjtestøbning
18 Termoformning
19 UP-branchen og dens processer
20 Polyurethanbranchens processer
21 Emissioner fra forarbejdning af termoplast
22 Emissioner ved forarbejdning af hærdeplast
23 Kemiske belastninger i arbejdsmiljøet
24 Energiforbrug ved forarbejdning af plast
25 Plast og affald
26 Brandegenskaber for udvalgte plasttyper
27 Migration
28 Miljø- og sundhedsvurderinger
29 Referencer
2 Forord
Miljøstyrelsen og Plastindustrien i Danmark har haft et fælles ønske om at få et overblik over den viden, der findes omkring miljø- og sundhedsforhold for plastmaterialer. En væsentlig baggrund for dette ønske har været at få et solidt grundlag for arbejdet med at etablere standardvilkår for miljøgodkendelser af danske plastforarbejdende virksomheder samt det fremadrettede arbejde omkring brug af kemiske stoffer og renere produkter.
Dette ønske har ført til tilblivelsen af denne rapport, der hovedsagelig er udarbejdet i 2005 og færdiggjort i første halvår af 2006. Anders Schmidt, FORCE Technology, har været hovedansvarlig for udarbejdelsen af rapporten. Allan Astrup Jensen, også FORCE Technology har været kvalitetskontrollør.
Til projektet har der været nedsat en følgegruppe bestående af:
Helle Petersen, Miljøstyrelsen
Anette Christiansen, Miljøstyrelsen
Lars Blom, Plastindustrien i Danmark
Kristina Elvebakken, Plastindustrien i Danmark
Lillian Petersen, Arbejdstilsynet
Heidi K. Stranddorf, Ballerup Kommune
Jacob Due Hansen, AMUSyd
Claus Jørgensen, Forbrugerrådet
En speciel tak skal rettes til Plastindustrien i Danmark (PD), der har været meget behjælpelig med at fremskaffe videnskilder og sørge for, at de blev opdateret, hvor det var relevant. PD har også sørget for, at dens medlemmer er blevet hørt gennem hele processen. Også en tak til følgegruppens øvrige medlemmer, der alle har medvirket til at gøre rapporten til et dokument, der forhåbentlig vil finde en bred anvendelse.
3 Sammenfatning
Se også:
Læsevejledning
Indholdsfortegnelse
Oversigtsfigur med links
Den nærværende rapport fra projektet ”Miljø- og sundhedsmæssige forhold for plastmaterialer” præsenterer information om et bredt spektrum af miljø- og sundhedsmæssige forhold, der knytter sig til forskellige aktiviteter i plastmaterialers livsforløb.
Selv om rapporten indeholder information om aktiviteter fra vugge til grav, er der ikke tale om en livscyklusvurdering af plastmaterialer. Det primære formål med projektet har været at etablere et videngrundlag for arbejdet med at etablere standardvilkår for miljøgodkendelse af danske plastforarbejdende virksomheder, og rapportens fokus er derfor først og fremmest de miljø- og sundhedsmæssige aspekter, som kan relateres til forhold på de danske plastvirksomheder og de valg, som virksomhederne træffer i deres daglige arbejde.
Der findes et meget stort antal forskellige plasttyper, og de fleste forarbejdes sandsynligvis og så i Danmark. I projektet er der blevet fokuseret på et begrænset udvalg af disse, nemlig dem, der udgør den altovervejende del af den plastråvare, der forarbejdes i Danmark. Der findes således i rapporten udførlige informationer om plasttyperne polyethylen (PE), polypropylen (PP), polystyren (PS), polyvinylchlorid (PVC), polyurethan (PUR) og umættet polyester (UP), mens der for plasttyper som polyamid (nylon, PA), polycarbonat (PC) og acrylonitril-butadien-styren (ABS) er en mindre mængde information, der primært omhandler forarbejdning og bortskaffelse af de pågældende plasttyper. Dertil kommer, at det for nogle af de vigtigste plasttyper er muligt at skelne mellem miljø- og sundhedsforhold for forskellige kvaliteter, og hvor dette har været muligt, er disse forskelle beskrevet i rapporten. Det skal bemærkes, at de tilgængelige informationer for de plasttyper, der er ”fravalgt”, vurderes at være meget begrænsede, specielt med hensyn til viden om udledninger til arbejdsmiljøet og det ydre miljø ved forarbejdning.
De informationer, der præsenteres i rapporten, er i altovervejende grad baseret på generel international viden og erfaringer. Processer, råvarer og additiver, som anvendes i den danske plastforarbejdende industri, svarer i al væsentlighed til dem, der anvendes i andre lande, og det er derfor nærliggende at udnytte den internationale viden til også at beskrive danske forhold.
Hvor der er fundet specifik dansk viden, er denne naturligvis blevet integreret i rapporten. Dette gælder først og fremmest formelle forhold, f.eks. omkring anvendelse af bestemte materialer i plastprodukter og vurderinger af arbejdsmiljøforhold, men også danske virksomheders erfaringer med hensyn til produktionstekniske forhold er medtaget i den udstrækning, sådanne erfaringer er stillet til rådighed for projektet.
Da rapportens overordnede formål er at præsentere en bred vifte af viden om vidt forskellige forhold, indeholder den ikke nogen konklusioner som sådan. Til gengæld er det muligt at finde veldokumenteret viden om følgende emner:
- Produktion af plastråvare, hvor der findes en kort beskrivelse af de grundlæggende egenskaber for de mest betydende råvarer, deres produktionsprocesser og hvilke udvekslinger, der sker med miljøet ved deres produktion.
- Additiver, hvor der gives en oversigt over de mest almindeligt forekommende typer af additiver og en kort beskrivelse af, hvilke additiver, som vides at være belastende for miljø og/eller sundhed. Additivområdet er dog meget komplekst, og rapporten giver derfor ikke et fyldestgørende teknisk eller miljømæssigt overblik.
- Forarbejdningsprocesser, hvor der gives en beskrivelse af de mest almindeligt forekommende processer i den danske plastindustri, f.eks. sprøjtestøbning, ekstrudering, termoformning, blæsestøbning (for termoplastindustrien), og håndoplæg, sprøjteoplæg, vikling, pultrudering, PUR-støbning osv. (for hærdeplastbranchen).
- Udledninger til arbejdsmiljø såvel som det ydre miljø ved forarbejdning af plast, hvor der gives kvantitative oplysninger om udledninger per kg forarbejdet plast og koncentrationer af de stoffer, som i de forskellige kilder er blevet anset for interessante.
- Plast som affald, hvor der gives en oversigt over forskellige behandlingsmetoder og hvordan de påvirker miljøet.
- Brandegenskaber, hvor der gives en beskrivelse af, hvilke stoffer, der dannes ved brand i plast, og hvor farlige de er.
- Migration, hvor der gives en oversigt over de væsentligste problemstillinger, der er knyttet til at stoffer i plastprodukter migrerer (vandrer, afdamper eller afsmittes) til omgivelserne.
- Miljø- og sundhedsvurderinger, hvor der beskrives en række værktøjer og videnkilder, der er operationelle i en konkret vurdering af bl.a. additiver og udledninger.
Som det fremgår af den ovenstående gennemgang af rapportens indhold er der for mange emner tale om, at de gennemgås på et forholdsvis overordnet niveau. Dette niveau er valgt på baggrund af projektets formål og målgruppe. For mange af de berørte emner er det muligt at gå væsentligt længere ned i detaljerne, og rapporten giver da også forslag til, hvor en sådan information kan findes.
4 Summary
The present report from the project ”Health and environmental aspects of plastic materials” presents information on a broad spectrum of issues that are related to different activities in the life cycle of plastics.
Although the report contains information on activities from cradle to grave it is not a life cycle assessment (LCA). The primary aim of the project has been to establish a knowledge base to be used in the development of standard conditions for environmental permits to Danish plastic processing companies. The focus of the report is therefore the health and environmental aspects that are related to the activities performed by Danish companies and the choices they make in their daily work.
There exist a large number of different plastics, and most of these are probably processed in Denmark. The project focuses on a limited range of these, namely those that are known to constitute the largest volume processed in Denmark. The report thus contains rather detailed information about polyethylene (PE), polypropylene (PP), polystyrene (PS), polyvinylchloride (PVC), polyurethane and unsaturated polyester (UP), while plastics like polyamide (nylon, PA), polycarbonate (PC) and acrylonitrile-butadiene-styrene (ABS) are described in less detail. Where possible and relevant the report also distinguishes between health and environmental properties of different qualities of the main plastics. It is remarked that the amount of available health and environmental information on the “deselected” plastics is very limited, especially with respect to emissions to the working environment and the natural environment during their processing.
The information in the report is predominantly based on international knowledge and experience. The raw materials, additives and processes used in Danish companies are essentially the same as in the rest of World and it was therefore an obvious choice to use the international knowledge to also describe Danish conditions.
Specific Danish knowledge has of course been integrated in the report, where available. This is primarily the case for more formal conditions, e.g. related to the use of certain materials and additives in plastic products, but also Danish knowledge and experiences related to actual processes have been integrated.
Since the primary aim of the report is to present knowledge about a broad spectrum of very different aspects, it does not contain any conclusions as such. It is, however, possible to find information well-documented facts about the following aspects:
- Production of plastic raw material, giving a short description of the basic properties of the most common plastics and their production processes as well as an overview of the exchanges with the environment from their production.
- Additives, giving an overview of the most common types of additivies together with a short description of specific additives that are known to have an impact on environment and/or human health. Additives are however a rather complex area and the report does not provide a full overview on neither technical nor environmental properties.
- Processes, giving a description of the most common processes used in Danish plastic processing companies, e.g. injection moulding, extrusion, thermoforming, blow moulding (all relating to companies processing thermoplastics) and hand lay-up, spray lay-up, pultrusion, PUR-moulding, etc. (relating to companies processing thermo-setting plastics).
- Emissions to the working environment as well as the natural environment, giving quantitative information on emissions per kg processed plastic and about the concentration of the chemical substances considered to be most interesting in the original investigations.
- Plastic waste, giving an overview of different ways of treatment and how this affects the environment.
- Fire properties, giving an overview of which chemical substances that are formed in a fire together with a description of relevant health properties.
- Migration, giving an overview of the most imminent problems related to migration of chemical substances from plastic products to the surroundings.
- Assessment of impacts on health and environment, describing a set of tools and knowledge sources considered to be operational in specific assessments of e.g. additives and emissions.
As indicated in the short overview above of the contents of the report, many subjects are dealt with on an overall level. This choice was deliberately made with a view to the purpose and target group for the project. Most of the subjects can be examined in significantly more detail, and the report therefore provides suggestions for how to find this information.
5 Læse – og brugsvejledning
Se også:
Indholdsfortegnelse
Oversigtsfigur
5.1 Introduktion
Projektet ”Miljø- og sundhedsmæssige forhold for plastmaterialer” afrapporteres primært som en form for elektronisk opslagsværk, hvor der linkes mellem relevante emner. Projektet afrapporteres også som en almindelig PDF-fil, som det er muligt at printe ud – eller at læse på skærmen.
Rapportens primære målgruppe er personer, der beskæftiger sig med plast, specielt plastforarbejdning, og miljø- og sundhedsforhold. Dette kan f.eks. være som miljøansvarlig på en plastforarbejdende virksomhed, som miljøansvarlig i en kommune eller som tilsynsførende på arbejdsmiljøområdet. Rapporten indeholder dog så bred en vifte af oplysninger, at den kan have interesse for mange andre som f.eks. miljøkonsulenter og undervisningsanstalter, for hvem det er ønskværdigt at kunne skabe et hurtigt og samlet overblik.
Rapporten – eller opslagsværket - er struktureret i ca. 25 selvstændige kapitler indenfor tre hovedområder, nemlig ”Råvarer”, ”Processer” og ”Egenskaber”. Denne struktur er valgt, fordi den giver mulighed for at linke fra et kapitel til relevant information i et andet kapitel. På denne måde undgås det at gentage den samme information i flere kapitler, og samtidig undgår læseren at skulle blade eller klikke sig frem mere end højst nødvendigt.
5.2 Hvad opslagsværket indeholder
Opslagsværket (og rapporten) indeholder som nævnt information om tre hovedområder, nemlig råvarer, processer og miljø- og sundhedsmæssige egenskaber. Denne overordnede inddeling findes ikke eksplicit i rapporten, men er afspejlet i rækkefølgen af de enkelte kapitler. Det er forsøgt at give kapitlerne overskrifter, der er så sigende som muligt, men det er naturligt nok en fordel at have en basal viden om plastbranchen.
Kapitlet ”Termoplastbranchens råvarer” indeholder således et afsnit om hvert af de fire mest betydende materialer (polyethylen (PE), polypropylen (PP), polystyren (PS og HIPS) og polyvinylchlorid (PVC). Afsnittene giver en kort beskrivelse af materialet samt værdier for de vigtigste udvekslinger med miljøet i aktiviteterne fra udvinding af råolie og naturgas til plastgranulat, der er klar til forarbejdning. Kapitlerne om UP- og PUR-branchens råvarer er lidt mere udførlige, fordi der er tale om en bredere vifte af råvarer.
Råvarekapitlerne suppleres med et kapitel om ”Additiver”, der er et integreret element i fremstilling af langt de fleste plastprodukter. Der findes i tusindvis af additiver, og kapitlet giver derfor en forholdsvis overordnet beskrivelse af additivers funktion og typiske indholdsstoffer.
På processiden findes der beskrivelser af de mest almindelige plastforarbejdningsprocesser som f.eks. sprøjtestøbning, ekstrudering og termoformning, og hvilke typer af produkter, som fremstilles med de enkelte processer. Processer og råvarer kan kombineres på mange forskellige måder, men rapportens struktur gør det muligt at finde oplysninger om både råvare, additiv, proces og miljø- og sundhedsforhold med ganske få museklik.
De miljø- og sundhedsmæssige egenskaber ved plastråvarer, plastforarbejdning og plastprodukter belyses fra forskellige vinkler. Fokus er på at beskrive hvilke stoffer, som mennesker og miljø bliver udsat for i forskellige situationer – og i hvor store mængder. Det er forsøgt at give så mange oplysninger som muligt, ikke alene om de ovennævnte råvarer, men også om andre plastmaterialer, der er almindeligt forekommende i den danske plastforarbejdende industri.
Oplysningerne er struktureret indenfor fire områder med hvert sit kapitel, ”Emissioner (til det ydre miljø) fra plastforarbejdning”, ”Kemiske belastninger i arbejdsmiljøet”, ”Brandegenskaber” og ”Migration”. Som nævnt er der tale om flere tusinde stoffer, der potentielt kan påvirke sundhed og miljø, og det har ikke været muligt indenfor projektets rammer at give en relevant vurdering af specifikke egenskaber for andet end et fåtal af stofferne. Til gengæld er der udarbejdet et værktøj, ”Miljø- og sundhedsvurderinger”, der sætter brugeren i stand til hurtigt at finde frem til relevante stofoplysninger på mange niveauer, fra deres klassificering til detaljerede toksikologiske profiler og databaser med testresultater.
5.3 Hvordan opslagsværket bruges
Det ideelle ville være, hvis man kunne nøjes med at skrive et enkelt eller få søgeord, hvorefter alle oplysninger knyttet til den pågældende søgeprofil kom frem. Men denne mulighed ville i praksis ofte give et meget omfattende resultat, og det er derfor valgt at give brugere mulighed for at stykke sit eget overblik sammen af de oplysninger, der ligger i de enkelte kapitler.
I indholdsfortegnelsen kan brugeren vælge sin indgang til oplysningerne. Nogle vil måske gerne vide ”alt” om polyethylen, og via kapitlet om ”Termoplastbranchens råvarer” er der kun et enkelt klik til de basale materialeoplysninger. Det er også muligt fra det første skærmbillede at klikke videre til oplysninger om, hvilke emissioner til det ydre miljø og til arbejdsmiljøet, der kan forventes ved forarbejdningsprocessen. Man kan også finde en beskrivelse af relevante forarbejdningsprocesser og oplysninger om råvarens brandegenskaber. Kort sagt er der altså adgang til alle relevante informationer fra det første skærmbillede i hvert kapitel.
Via indholdsfortegnelsen er det også muligt at gå direkte til et specifikt emne. Ved at vælge linket ”Emissioner fra forarbejdning af termoplast” kommer man f.eks. direkte til en oversigt over, hvilke udledninger, der er kendt fra laboratorieforsøg eller målinger på virksomheder i relation til en bred vifte af plasttyper og forarbejdningsprocesser. Med et enkelt klik kan man komme videre til det helt specifikke emne og finde de ønskede oplysninger.
Personer, der ønsker at få en vurdering af specifikke stofegenskaber, kan gå direkte ind i kapitlet ”Miljø- og sundhedsvurderinger”. Her findes der en række værktøjer, der med udgangspunkt i et stofnavn (eller bedre et CAS-nummer) giver oplysninger på forskellige niveauer som tilstedeværelse på udvalgte stoflister, klassificering, toksikologiske profiler, fysisk-kemiske data mm. I kapitlet findes der en kort beskrivelse af de enkelte værktøjer med hensyn til, hvordan de fungerer og hvad de kan, hvilket gør det nemt at vælge, hvilket link man ønsker at følge.
Det er også muligt at bruge oversigtsfiguren til at klikke sig vej til det ønskede emne. Oversigtsfiguren indeholder de vigtigste emner, der behandles i kapitler og enkeltafsnit, og ved at klikke på et emne, kommer man direkte til dette. Oversigtsfiguren giver også en indikation af hvilke emner, der er relateret til hinanden, og hvor der derfor findes links. I praksis findes der mange steder links på et væsentligt højere detaljeringsniveau, men dette er ikke muligt at vise på figuren.
Afslutningsvis skal det understreges, at det er forfatterens egne erfaringer, der ligger til grund for opbygningen af rapportens struktur. Andre ville måske have valgt en anden struktur, men det er håbet, at rapporten i sin nuværende form er så fleksibel, at den kan bruges intuitivt af langt de fleste personer med et basalt kendskab til plast og plastforarbejdning.
6 Oversigtsfigur med links
Klik her for at se figuren.
Figur 1. Oversigt over de vigtigste emner og overskrifter, og hvilke direkte links, der findes mellem dem.
7 Termoplastbranchens råvarer
Se også
Additiver
Compoundering
Ekstrudering
Ekspandering af EPS
Kalandrering
Sprøjtestøbning
Rotationsstøbning
Termoformning
Emissioner ved forarbejdning af termoplast
Kemiske belastninger i arbejdsmiljøet
Plast og affald
Miljø- og sundhedsvurderinger
Brandegenskaber for plast
Referencer
Indholdsfortegnelse
Oversigtsfigur
7.1 Introduktion
Den danske termoplastbranche forarbejder en bred vifte af råvarer. I de følgende afsnit gives der en kort introduktion til de fire vigtigste råvarer, nemlig polyethylen (PE), polypropylen (PP), polystyren (PS) og high-impact polystyren (HIPS) og polyvinylchlorid (PVC).
Introduktionen giver oplysninger de grundlæggende egenskaber for plasttyperne, deres femstillingsprocesser og molekylestruktur, og afsluttes med information om de udvekslinger med miljøet, som produktion af et kilo af plasttypen giver anledning til.
I andre kapitler af rapporten behandles også andre plasttyper. Dette er for eksempel tilfældet for ”Emissioner ved forarbejdning af termoplast”, hvor der findes oplysninger/data for omkring otte plasttyper, som også er almindeligt forekommende i dansk plastindustri, om end ikke i så store mængder som de fire plasttyper beskrevet nedenfor.
For alle plasttyperne gælder, at det i den tekniske litteratur er muligt at finde endog meget detaljeret information om produktionsmetoder, egenskaber m.v. Den interesserede læser vil uden nævneværdige problemer kunne finde ønsket information i f.eks. Ullmann’s og Kirk-Othmer, der begge er anerkendte opslagsværker for kemisk teknologi.
7.2 Polyethylen (PE)
7.2.1 Introduktion
PE - polyethylen - er en uklar, fleksibel og bøjelig plast med en glansløs voksagtig overflade. Materialet har gode elektriske isoleringsegenskaber og stor bestandighed over for vand og mange organiske opløsningsmidler og kemikalier. Polymeren er blandt de letteste plastmaterialer, og PE er ikke bestandig over for UV-lys.
PE-råvarer fremstilles alene i udlandet. PE fremstilles ved polymerisering af ethylen. I nedenstående figur er grundformlen for PE angivet.
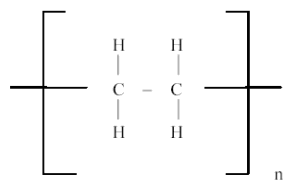
Figur 1. Grundformel for polyethylen
Processen kan foregå både ved højt og ved lavt tryk. Fremstilling ved højt tryk giver LDPE (Low Density PolyEthylene), som er en forgrenet og delkrystalinsk plast, hvorimod fremstilling ved lavt tryk giver HDPE (High Density PolyEthylene), som indeholder færre forgreninger og er mere krystallinsk end LDPE.
Ved at variere trykket og procesbetingelserne i øvrigt kan der fremstilles en lang række varianter af PE ud over de to nævnte. Specielt skal nævnes LLDPE (Linear Low Density PolyEthylene), som indeholder meget korte forgreninger i stort antal. Denne PE-type er af relativ ny dato og finder stadig større anvendelse. Endelig fremstilles PE i "Medium Density"-kvalitet (MDPE), som er en LDPE med middelhøj massefylde.
7.2.2 Udvekslinger med miljøet ved produktion af PE
Til fremstilling af PE medgår i gennemsnit 77 MJ/kg, idet der til fremstilling af LDPE, HDPE og LLDPE i gennemsnit medgår henholdsvis 78 MJ/kg, 77 MJ/kg og 74 MJ/kg. I energiforbruget er medregnet processer startende fra udvinding af olie/gas. De vigtigste forbrug af brændsler og udvekslinger med miljøet findes i Tabel 1.
|
Enhed |
LDPE |
HDPE |
LLDPE |
Energiforbrug |
|
|
|
|
Elektricitet |
MJ |
13,3 |
9,8 |
10,2 |
Olie/gas |
MJ |
35,1 |
37,6 |
34,2 |
Andet |
MJ |
29,3 |
29,2 |
29,6 |
Totalt |
|
77,8 |
76,6 |
74,0 |
|
|
|
|
|
Brændselforbrug (totalt) |
|
|
|
|
Råolie |
mg |
800.000 |
840.000 |
770.000 |
Gas/kondensat |
mg |
490.000 |
530.000 |
340.000 |
Kul |
mg |
130.000 |
110.000 |
110.000 |
Metallurgisk kul |
mg |
120 |
89 |
210 |
Brunkul |
mg |
360 |
61 |
240 |
Tørv |
mg |
1.900 |
1.500 |
170 |
Træ |
mg |
<1 |
<1 |
<1 |
|
|
|
|
|
Emissioner (luft) |
|
|
|
|
CO2 |
mg |
1.700.000 |
1.600.000 |
1.700.000 |
CO |
mg |
920 |
12.000 |
2.200 |
CH4 |
mg |
9200 |
9.000 |
7.400 |
SOx |
mg |
5.000 |
4.000 |
3.900 |
NOx |
mg |
3.400 |
2.900 |
2.800 |
Chlor |
mg |
<1 |
<1 |
<1 |
Kulbrinter (uspecificeret) |
mg |
2.700 |
3.400 |
1.800 |
Aromatiske kulbrinter (uspecificeret) |
mg |
33 |
80 |
23 |
Støv |
mg |
920 |
860 |
1.400 |
|
|
|
|
|
Emissioner (vand) |
|
|
|
|
COD |
mg |
200 |
200 |
300 |
BOD |
mg |
29 |
22 |
65 |
NO3- |
mg |
3 |
2 |
4 |
NH4+ |
mg |
3 |
3 |
2 |
Kulbrinter (uspecificeret) |
mg |
8 |
5 |
17 |
|
|
|
|
|
Affald |
|
|
|
|
Mineralsk affald |
mg |
1.500 |
270 |
1.000 |
Slagge og aske |
mg |
12.000 |
8.500 |
6.900 |
Blandet industriaffald |
mg |
-580 |
560 |
590 |
Regulerede kemikalier |
mg |
2.400 |
1.700 |
1.700 |
Inert kemikalieaffald |
mg |
900 |
650 |
300 |
Tabel 1. Udvekslinger med miljøet ved produktion af 1 kg PE (LDPE, HDPE og LLDPE). Udvalgt fra Boustead I. Eco-profiles of the European plastics industry. Polyolefins. A report for APME, Brussels, July 2003.
Af den anvendte energimængde resterer 43 MJ/kg som polymerens "brændværdi".
PE-råvaren indeholder sædvanligvis små mængder additiv og proceshjælpemiddel. En råvareproducent oplyser, at deres PE kan indeholde rester af chrom-, titan-, aluminium-, chlor-, og magnesiumforbindelser, som er katalysatorrester fra polymerisationsprocessen. Forbindelserne er til stede i følgende koncentrationer:
- Cr < 10 ppm
- Ti < 10 ppm
- Al < 200 ppm
- Cl < 20 ppm
- Mg < 10 ppm
Restmonomerindholdet i PE er under 10 ppm, typisk under 1 ppm. Fra producentens side er PE normalt tilsat forarbejdningsforbedrende additiver. De virker som smøremidler og består typisk af fedtsyresalte. Mest anvendt er calciumstearat, som tilsættes i andele på mindre end 0,2 pct. PE er normalt tilsat en standardstabilisator, som er baseret på højmolekylære, sterisk hindrede phenoler, og UV-stabilisatorer af HALS-typen (Hindered Amine Light Stabilisers) tilsættes ofte for at hindre nedbrydning.
7.3 Polypropylen (PP)
7.3.1 Introduktion
PP - polypropylen - er hvidlig og er den letteste volumenplast. Materialet har en høj stivhed og en god trækbrudstyrke. PP har i mange sammenhænge sammenlignelige egenskaber med PE og har således også gode elektriske isoleringsegenskaber og god bestandighed overfor vand, organiske opløsningsmidler, syrer og baser. PP er stivere og bevarer længere sin mekaniske egenskaber ved stigende temperatur end HDPE. PP oxideres let og tilsættes derfor antioxidanter i alle kommercielle kvaliteter.
PP-råvarer fremstilles alene i udlandet. PP fremstilles ved polymerisering af propylen. I nedenstående figur er grundformlen for PP angivet.
Figur 1. Grundformel for polypropylen (PP)
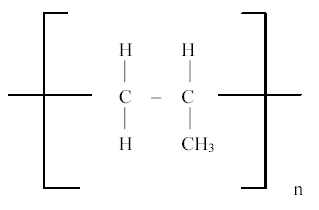
Processen kan give tre forskellige former for PP alt afhængigt af hvorledes CH3-grupperne er placeret i forhold til polymerkæden. De tre former er:
- Isotaktisk, hvilket vil sige, at alle CH3-grupperne er placeret på samme side af kæden.
- Syndiotaktisk, hvilket vil sige, at CH3-gruppernes placering i forhold til kæden alternerer.
- Ataktisk, hvilket vil sige, at grupperne er tilfældigt placeret.
Den førstnævnte (isotaktiske) form er den eneste, som har kommerciel betydning.
7.3.2 Udvekslinger med miljøet ved produktion af polypropylen
Til fremstilling af PP medgår omkring 73 MJ/kg. De vigtigste forbrug af brændsler og udvekslinger med miljøet findes i Tabel 2.
|
Enhed |
PP |
Energiforbrug |
|
|
Elektricitet |
MJ |
7,3 |
Olie/gas |
MJ |
42,5 |
Andet |
MJ |
23,0 |
Totalt |
MJ |
72,7 |
|
|
|
Brændselforbrug (totalt) |
|
|
Råolie |
mg |
950.000 |
Gas/kondensat |
mg |
360.000 |
Kul |
mg |
87.000 |
Metallurgisk kul |
mg |
83 |
Brunkul |
mg |
44 |
Tørv |
mg |
860 |
Træ |
mg |
<1 |
|
|
|
Emissioner (luft) |
|
|
CO2 |
mg |
1.700.000 |
CO |
mg |
5.800 |
SOx |
mg |
3.600 |
CH4 |
mg |
7.600 |
NOx |
mg |
2.800 |
Chlor |
mg |
<1 |
Kulbrinter (uspecificeret) |
mg |
2.700 |
Aromatiske kulbrinter (uspecificeret) |
mg |
33 |
Støv |
mg |
750 |
|
|
|
Emissioner (vand) |
|
|
COD |
mg |
250 |
BOD |
mg |
30 |
NO3- |
mg |
120 |
NH4+ |
mg |
3 |
Kulbrinter (uspecificeret) |
mg |
6 |
|
|
|
Affald |
|
|
Mineralsk affald |
mg |
260 |
Slagge og aske |
mg |
6.700 |
Blandet industriaffald |
mg |
850 |
Regulerede kemikalier |
mg |
1.400 |
Inert kemikalieaffald |
mg |
750 |
Tabel 2 Udvekslinger med miljøet ved produktion af 1 kg PP. Udvalgt fra Boustead I. Eco-profiles of the European plastics industry. Polyolefins. A report for APME, Brussels, July 2003.
Af den anvendte energimængde resterer 44,5 MJ/kg som polymerens "brændværdi".
En råvareproducent oplyser, at deres PP indeholder titan-, aluminium- og chlorforbindelser, som er katalysatorrester fra polymerisationsprocessen. Der anvendes ikke tungmetaller. Forbindelserne er til stede i følgende koncentrationer:
Ti < 100 ppm
Al < 200 ppm
Cl < 200 ppm
Chlorforbindelser er typisk til stede i koncentrationer på mindre end 50 ppm. Restmonomerindholdet i PP er under 10 ppm, typisk under 1 ppm.
Fra producentens side er PP normalt tilsat forarbejdningsforbedrende additiver. Disse virker som smøremidler og består typisk af fedtsyresalte. Hyppigst anvendt er calciumstearat, som tilsættes i andele på mindre end 0,2 pct.
PP er normalt tilsat en standardstabilisator (antioxidant), som er baseret på højmolekylære, sterisk hindrede phenoler eller phosphit/phosphonit-forbindelser, ligesom der ofte anvendes UV-stabilisatorer af HALS-typen (Hindered Amine Light Stabilisers).
7.4 Polystyren (PS)
7.4.1 Introduktion
Almindeligt ”General Purpose” polystyren (PS eller GPPS) er en klar plast med høj glans. Materialet er hårdt, stift og relativt skørt. Slagfast polystyren (High Impact PolyStyren, HIPS) er en copolymer med butadien, som forbedrer slagstyrken og sejheden. Expandable polystyen (EPS) svarer i al væsentlighed til GPPS, bortset fra at det er tilsat lavmolekylære kulbrinter (oftest pentan), der ved den efterfølgende forarbejdning fordamper og danner skum.
Figur 2. Grundformel for polystyren
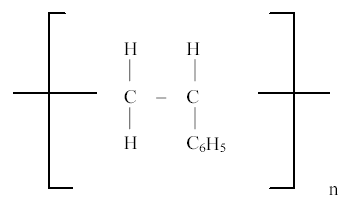
Slagfast polystyren (HIPS) fås ved copolymerisering af styren og butadien.
Figur 3. Grundformel for slagfast polystyren (HIPS)
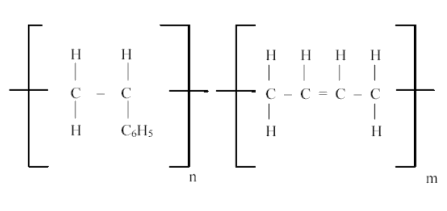
7.4.2 Udvekslinger med miljøet ved produktion af polystyren
PS-råvarer fremstilles alene i udlandet ved polymerisation af styren. Energiforbruget ligger mellem 84 og 92 MJ/kg. De vigtigste forbrug af brændsler og udvekslinger med miljøet findes i Tabel 3.
|
Enhed |
PS (general purpose) |
PS (High Impact) |
EPS (Ekspanderbar PS) |
Energiforbrug |
|
|
|
|
Elektricitet |
MJ |
3,6 |
4,7 |
3,4 |
Olie/gas |
MJ |
33,3 |
36,5 |
34,0 |
Andet |
MJ |
49,8 |
51,0 |
46,2 |
Totalt |
MJ |
86,7 |
92,2 |
83,6 |
|
|
|
|
|
Brændselforbrug (totalt) |
|
|
|
|
Råolie |
mg |
740.000 |
810.000 |
760.000 |
Gas/kondensat |
mg |
1.100.000 |
1.100.000 |
950.000 |
Kul |
mg |
58.000 |
95.000 |
88.000 |
Metallurgisk kul |
mg |
350 |
370 |
330 |
Brunkul |
mg |
8.300 |
8.100 |
22.000 |
Tørv |
mg |
13 |
18 |
620 |
Træ |
mg |
1 |
1 |
3 |
Biomasse |
mg |
1.400 |
1.500 |
1.200 |
Emissioner (luft) |
|
|
|
|
CO2 |
mg |
2.600.000 |
2.700.000 |
2.500.000 |
CO |
mg |
1.600 |
1.800 |
1.600 |
CH4 |
mg |
9.000 |
9.200 |
9.500 |
SOx |
mg |
9.500 |
11.000 |
9.700 |
NOx |
mg |
11.000 |
12.000 |
12.000 |
Chlor |
mg |
<1 |
<1 |
<1 |
Kulbrinter (uspecificeret) |
mg |
2.600 |
3.400 |
4.500 |
Aromatiske kulbrinter (uspecificeret) |
mg |
210 |
200 |
210 |
Støv |
mg |
1.500 |
1.800 |
1.800 |
|
|
|
|
|
Emissioner (vand) |
|
|
|
|
COD |
mg |
330 |
320 |
670 |
BOD |
mg |
46 |
35 |
140 |
NO3- |
mg |
3 |
3 |
4 |
NH4+ |
mg |
8 |
6 |
12 |
Kulbrinter (uspecificeret) |
mg |
94 |
100 |
97 |
|
|
|
|
|
Affald |
|
|
|
|
Mineralsk affald |
mg |
15.000 |
22.000 |
24.000 |
Slagge og aske |
mg |
3.000 |
4.000 |
3.900 |
Blandet industriaffald |
mg |
1.500 |
1.900 |
1.900 |
Regulerede kemikalier |
mg |
680 |
640 |
930 |
Inert kemikalieaffald |
mg |
2.300 |
2.100 |
8.000 |
Tabel 3. Udvekslinger med miljøet ved produktion af 1 kg polystyren. Udvalgt fra Boustead I. Eco-profiles of plastics and related intermediates. APME, Brussels, 1999.
Af den anvendte energimængde resterer ca. 42 MJ/kg som polymerens "brændværdi".
PS-råvarer indeholder spor (ppm-niveau) af katalysatorrester. Katalysatoren er typisk organiske peroxider. Herudover tilsættes små mængder fedtsyreestre og antioxidanter. Styrenmonomerindholdet er typisk mindre end 300 ppm. Ved fremstilling af polystyren anvendes der ikke tungmetaller.
7.5 Polyvinylchlorid (PVC)
7.5.1 Introduktion
PVC (polyvinylchlorid) er i sin rene form en stiv, transparent polymer, som udmærker sig ved god styrke og kemikalieresistens. PVC nedbrydes relativt hurtigt ved opvarmning og vil derfor altid være tilsat varmestabiliserende additiver.
PVC kan tilsættes op til over 50 pct. blødgører. Herved opnås en række fleksible plasttyper med et stort spektrum af anvendelsesmuligheder.
PVC-råvarer fremstilles udelukkende i udlandet. PVC fremstilles ved polymerisering af vinylchlorid. Der anvendes tre processer til produktion af PVC:
- Suspension, der giver ”almindelig” (general purpose) PVC til anvendelse i stive applikationer som rør, profiler og andre byggematerialer. Suspensions-PVC anvendes også til kabelisolering, folie og til sprøjtestøbte produkter
- Emulsion, der primært anvendes til coatnings-applikationer
- Bulk, der anvendes til specifikke typer af hårde plader og flasker
I nedenstående figur er grundformlen for PVC angivet.
Figur 4. Grundformel for polyvinylchlorid (PVC)
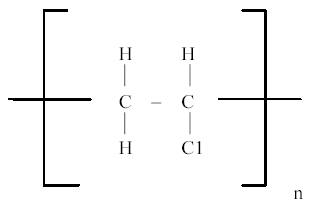
7.5.2 Udvekslinger med miljøet ved produktion af polyvinylchlorid
Til fremstilling af PVC medgår mellem 58 og 66 MJ/kg, afhængigt af hvilken produktionsproces, der anvendes. De vigtigste forbrug af brændsler og udvekslinger med miljøet findes i Tabel 4.
|
Enhed |
PVC (suspension) |
PVC (emulsion) |
PVC (bulk) |
Energiforbrug |
|
|
|
|
Elektricitet |
MJ |
14,1 |
16,0 |
17,6 |
Olie/gas |
MJ |
17,0 |
17,2 |
15,9 |
Andet |
MJ |
28,0 |
32,7 |
24,0 |
Totalt |
MJ |
59,1 |
65,9 |
57,5 |
|
|
|
|
|
Brændselforbrug (totalt) |
|
|
|
|
Råolie |
mg |
400.000 |
400.000 |
360.000 |
Gas/kondensat |
mg |
540.000 |
550.000 |
430.000 |
Kul |
mg |
170.000 |
350.000 |
97.000 |
Metallurgisk kul |
mg |
120 |
120 |
66 |
Brunkul |
mg |
51.000 |
140.000 |
36.000 |
Tørv |
mg |
860 |
860 |
190 |
Træ |
mg |
1.000 |
230 |
30 |
Biomasse |
mg |
8.600 |
8.000 |
16.000 |
|
|
|
|
|
Emissioner (luft) |
|
|
|
|
CO2 |
mg |
1.900.000 |
2.500.000 |
1.200.000 |
CO |
mg |
1.400 |
1.300 |
660 |
CH4 |
mg |
8.900 |
8.300 |
4.300 |
SOx |
mg |
9.600 |
11.000 |
5.700 |
NOx |
mg |
9.700 |
10.000 |
6.400 |
Chlor |
mg |
2 |
5 |
3 |
Kulbrinter (uspecificeret) |
mg |
2.300 |
2.400 |
1.400 |
Aromatiske kulbrinter (uspecificeret) |
mg |
6 |
6 |
6 |
Støv |
mg |
3.200 |
4.800 |
1.700 |
|
|
|
|
|
Emissioner (vand) |
|
|
|
|
COD |
mg |
1.500 |
1400 |
270 |
BOD |
mg |
340 |
98 |
41 |
NO3- |
mg |
6 |
1 |
1 |
NH4+ |
mg |
50 |
67 |
2 |
Kulbrinter (uspecificeret) |
mg |
25 |
26 |
25 |
|
|
|
|
|
Affald |
|
|
|
|
Mineralsk affald |
mg |
49.000 |
96.000 |
26.000 |
Slagge og aske |
mg |
13.000 |
33.000 |
16.000 |
Blandet industriaffald |
mg |
7.200 |
4.700 |
10.000 |
Regulerede kemikalier |
mg |
2.800 |
5.700 |
570 |
Inert kemikalieaffald |
mg |
4.000 |
9.500 |
900 |
Tabel 4. Udvekslinger med miljøet ved produktion af 1 kg PVC. Udvalgt fra Boustead I. Eco-profiles of the European plastics industry. Polyvinyl chloride. A report for APME and ECVM, Brussels, September 2002.
Af den anvendte energi resterer 18 MJ/kg som polymerens "brændværdi".
En råvareproducent oplyser, at deres rene PVC-råvare til sprøjtestøbning indeholder rester af polyvinylalkohol og emulgator (tensid) i koncentrationer op til 2 promille. Endvidere indeholder den rene råvare op til 1 promille rester af initiator (peroxid) samt op til 5 ppm restmonomer (vinylchlorid), typisk under 1 ppm. Endelig kan der forekomme op til 0,1 promille antioxidant.
Som varianter af PVC fremstilles også copolymerer mellem vinylchlorid og vinylacetat, ethylen eller propylen, som dog sjældent anvendes i Danmark.
8 UP-branchens råvarer
Se også:
UP-branchens processer
Additiver
Emissioner ved forarbejdning af hærdeplast
Kemiske belastninger i arbejdsmiljøet
Plast og affald
Miljø- og sundhedsvurderinger
Brandegenskaber for plast
Referencer
Indholdsfortegnelse
Oversigtsfigur
8.1 Introduktion
Dette kapitel er i al væsentlighed baseret på rapporten ”Renere teknologi i plastindustrien. Del B: Hærdende polyurethanplast” (Plastindustrien i Danmark, 2000c) og Jensen et al. (2005), suppleret med information fra den europæiske sammenslutning af plastproducenter, APME:
8.2 Matriksmaterialer
8.2.1 Umættet polyester indeholdende styren
Matriksmaterialet i GUP-produkter er fremstillet ved, at styren reagerer (tværbinder) med umættet polyester.
I den umættede polyester anvendes styren endvidere som opløsningsmiddel, der gør materialet flydende. Umættet polyester indeholder typisk 30 - 45 pct. styren.
Umættet polyester fremstilles hos (udenlandske) polyesterproducenter ved en kemisk reaktion mellem glykol, en mættet dibasisk, organisk syre og en umættet dibasisk syre (umættet = indeholder dobbeltbindinger).
Ved at vælge forskellige reagenser kan forskellige polyesterkvaliteter opnås.
Glykolen er typisk ethylenglykol eller propylenglykol. Sjældnere anvendt er neopentylglykol og bisphenol A.
Som mættet syre anvendes primært de tre isomere phthalsyrer (orto-, iso-, tere-). Som umættet syre anvendes typisk maleinsyre (som anhydrid) eller fumarsyre.
Polyesterens egenskaber kan endvidere ændres ved, at man ændrer reagensernes indbyrdes forhold, produktionsbetingelserne og ved tilsætning af additiver.
Under ”støbningen” vil en mindre del af styrenen afdampe. Afdampningsforholdet afhænger af processen samt af polyesteren. Ved at anvende LSE-polyester (Low Styrene Emission) kan afdampningen nedsættes. Den reducerede afdampning opnås ved at polyester/styrenblandingen er tilsat et overfladeaktivt additiv f.eks. paraffinvoks, som lægger sig på polyesterens overflade og forhindrer styrenen i at afdampe. Stort set al lamineringspolyester anvendt i Danmark er LSE-polyester. Det skal bemærkes, at styren af de fleste personer kan lugtes i forholdsvis lave koncentrationer. I Miljøstyrelsen liste over B-værdier angives lugtgrænsen således til 0,32 ppm, og det oplyses, at 10% af befolkningen med 85% sandsynlighed kan lugte stoffet i koncentrationer omkring 0,02 ppm (0,1 mg/m³), hvilket er væsentligt under stoffets B-værdi på 0,2 mg/m³.
Glykol og disyrer polymeriserer til polyester hos polyesterfabrikanterne ved en kondensationsproces. Restmonomerindholdet (udover styrenindholdet) i den umættede polyester er under 0,1 pct.
8.3 Gelcoat og topcoat
Produkternes farve fremkommer typisk ved, at det yderste lag fremstilles af pigmenteret umættet polyester, kaldet gelcoat eller topcoat. Gelcoaten påføres formen typisk i lag på 0,5 - 0,7 mm. Gelcoaten indeholder styren, hvoraf en del afdamper under påføringen.
8.4 Andre hærdeplaster
Den største mængde epoxyplast anvendes sandsynligvis i vindmølleindustrien, men plasttypen har en lang række andre anvendelsesområder, for eksempel til dele til biler og fly, brændstoftanke, gulve samt produkter indenfor farve/lak-industrien. Epoxyplast bruges enten i ren form eller forstærket med glas-, kul- eller aramidfibre.
Phenol-, melamin- og ureaplast anvendes til pressestøbte produkter, enten som enkeltmaterialer eller blandinger, hvori der også kan indgå formaldehyd. Fiberforstærkning anvendes i nogle produkter, f.eks. i visse elektriske artikler, mens der til produkter som toiletsæder og røreskåle, ikke anvendes fiberforstærkning. Materialerne anvendes også i laminater indenfor møbelindustrien.
Disse materialer er ikke yderligere beskrevet i nærværende rapport.
8.5 Hærder, accelerator og stabilisator
For at starte polymeriseringen tilsættes en hærder (initiator) lige før brug. Ved hærdning af umættet polyester anvendes normalt en organisk peroxidforbindelse.
Ved koldhærdning ønskes hastigheden af hærdeprocessen forøget. I så tilfælde bliver en accelerator tilsat råvaren. Acceleratoren er typisk coboltoctoat. I visse tilfælde anvendes en amin (anilinforbindelse).
Acceleratoren er normalt tilsat den umættede polyester. Ved fremstilling af produkter i kunstmarmor og polyesterbeton tilsættes acceleratoren hos producenten. Herudover tilsætter fabrikanterne kun undtagelsesvis accelerator.
Det skal nævnes, at umættet polyester kan hærdes med UV-lys. I så tilfælde anvendes en speciel accelerator.
Endelig er polyesteren tilsat en stabilisator, hvorved holdbarheden forøges. Ofte anvendes quinoner som stabilisatorer. Disse tilsættes stort set altid af råvareproducenten. Quinoner er tilsat polyesteren i koncentrationer op til et par hundrede ppm.
8.6 Tilsætningsstoffer
Umættet polyester til sprøjte- og håndoplæg er endvidere tilsat få procent tiksotropimidler (amorf kiselsyre, Kilde 1) og eventuelt pigmenter. Disse tilsættes typisk hos råvareproducenten. Herudover tilsættes i visse tilfælde fyldstoffer som kridt, grus og sten hos fabrikanten. Visse produkter indeholder op til 85 pct. grus og sten.
8.7 Glasfiber, kulfiber m.m.
Der anvendes glasfiber i form af måtter, roving, garn og væv samt huggede fibre. Udvalget af glas- og fiberkvaliteter er stort, og for hvert enkelt produkt overvejes nøje forstærkningens sammensætning, idet den er altafgørende for bl.a. styrken og stivheden af det færdige produkt.
Det skønnes, at der anvendes ca. 4.000 tons glasfiber pr. år i Danmark.
For at forbedre vedhæftningen mellem glasfiber og polyester behandles fiberoverfladen normalt kemisk med en silanforbindelse. (Kilde 2).
Denne proces foregår hos de udenlandske glasfiberproducenter og ikke hos danske polyesterforbrugere.
I visse tilfælde anvendes måtter belagt med termoplast (preform). Disse måtter kan i varm tilstand formes. Ved efterfølgende afkøling bevarer måtterne deres form og glasfiberen kan derefter påføres polyester.
Andre forstærkningsmaterialer som kulfibre og aramidfibre anvendes endvidere i Danmark i begrænset omfang. Det vurderes, at forbruget er under 1 pct. af det samlede fiberforbrug.
8.8 Brandhæmmere
Visse råvarer er brandhæmmet. Typisk anvendes antimontrioxid eller chlorerede paraffiner eventuelt i forbindelse med HET-syre (hexa-chlor-endomethylen-tetra-hydro-phthal-syre). Råvaren leveres som regel i brandhæmmet kvalitet. HET-syre reageres ind i den umættede polyester under fremstillingen og tilsættes således altid hos råvareproducenten. Visse producenter tilsætter selv antimontrioxid i form af pasta – ellere andre brandhæmmere.
8.9 Slipmidler
Formene påføres slipmidler, således at polyesteremnerne problemfrit kan afformes efter udhærdningen. To typer slipmiddel anvendes, nemlig hærdende slipmidler og voksbaserede slipmidler. De hærdende slipmidler består af en hærdende polymer, f.eks. en form for anti-graffiti lak eller teflon-lignende polymerer. Efter påføringen hærder polymeren til en tynd polymerfilm med den ønskede slipeffekt. Påføringen gentages efter ca. 30 afformninger. Hvad angår de voksbaserede slipmidler påføres disse oftere. Da voks ikke hærder, skal påføringen gentages med et par dages mellemrum. Slipmidlerne er typisk opløst i organiske ikke-chlorerede opløsningsmidler. Det totale forbrug af slipmidler i polyesterindustrien er relativt begrænset og udgør i Danmark godt 20 tons pr. år.
8.10 Rensemidler
Til afrensning af værktøjer, forme m.m. for polyester anvendes rensemidler.
8.10.1 Vandbaserede rensemidler
Vandbaserede rensemidler har fundet anvendelse indenfor visse områder til afrensning af uhærdet polyester. Nogle af disse midler skal anvendes ved temperaturer på 40 °C eller derover. Værktøjerne skal tørres omhyggeligt efter rensning, idet vand ødelægger polyesteren.
8.10.2 Acetone
I tilfælde hvor vandbaserede rensemidler ikke kan anvendes, bruges acetone, f.eks. ved rensning af værktøjer, som skal anvendes umiddelbart efter rensning eller ved afrensning af delvist hærdet polyester.
8.10.3 Methylenchlorid
I enkelte tilfælde hvor acetone ikke kan anvendes rengøres, med methylenchlorid, f.eks. hvor krav til rensemidlets opløsningsevne eller eksplosionsfare udelukker brug af acetone. Hvad angår renseevnen, anvendes methylenchlorid, specielt når der er behov for momentan rensning af maskindele samt i utilgængelige værktøjsdele så som gevind, små hulrum m.m., hvor hverken vandbaserede rensemidler eller acetone kan opløse delvist hærdet polyester.
8.10.4 Andre rensemidler
Der forhandles desuden forskellige rensemidler, som hverken indeholder vand eller letflygtige organiske opløsningsmidler.
Den aktive komponent er et N-substitueret cyklisk amid, der i ren tilstand i flere tilfælde fuldstændig kan erstatte methylenchlorid (og acetone). I fortynding vil opløsningen være et praktisk alternativ til acetone.
8.11 Sandwichkonstruktionsmaterialer
Sandwichkonstruktioner er en fællesbetegnelse for konstruktioner, der i proncippet er bygget op af to tynde skaller (stive og stærke men også tunge), der holdes adskilt af et relativt tykt lag af et let materiale med langt lavere styrke og stivhed.
Som skalmateriale anvendes typisk fiberforstærkede hærdeplastkompositter, især glasfiberforstærket polyester og epoxyplast forstærket med glad-, kul- eller aramidfibre.
Som kernemateriale anvendes især balsatræ og celleplast af PVC, polystyren, polyurethan, polymethaacrylamid og phenolplast. I konstruktioner, hvor vægten er afgørende, anvendes hyppigt såkaldte honeycombs som kerne. Honeycombs består af smalle og tynde strimler af papir, stof eller plast, som er imprægneret med en plastharpiks, eller af metal, f.eks. aluminium. De formes til en sekskantet bikubestruktur, hvor der kun er materiale, der hvor det behøves, nemlig på tværs af konstruktionen.
8.12 Lim
Kompositemner sammenlimes ofte. Der anvendes sædvanligvis 2-komponente klæbestoffer, typisk baseret på umættet polyester, eller MDI-hærdende (diphenyl-methan-di-isocyanat) polyurethan. I mindre omfang anvendes epoxy.
8.13 Udvekslinger med miljøet ved produktion af de vigtigste råvarer
Ingen af de mest almindeligt anvendte råvarer fremstilles i Danmark. Sammenslutningen af plastproducenter i Europa, APME, har udgivet en række rapporter om udvekslinger med miljøet ved produktion af en række basiskemikalier samt de vigtigste plasttyper. Blandt de basiskemikalier, der er blevet lavet såkaldte inventories for, er styren og methyl methacrylat, der er de vigtigste råvarer i UP-branchen. APME’s opgørelse er gengivet i Tabel 1 i forkortet form.
|
Enhed |
Styren |
Methyl methacrylat (MMA) |
Energiforbrug |
|
|
|
Elektricitet |
MJ |
1,98 |
12,85 |
Olie/gas |
MJ |
29,86 |
32,28 |
Andet |
MJ |
52,14 |
64,44 |
Totalt |
MJ |
83,98 |
109,57 |
|
|
|
|
Brændselforbrug (totalt) |
|
|
|
Råolie |
mg |
660.000 |
720.000 |
Gas/kondensat |
mg |
1.100.000 |
1.400.000 |
Kul |
mg |
57.000 |
220.000 |
Metallurgisk kul |
mg |
350 |
74 |
Brunkul |
mg |
5.800 |
65.000 |
Tørv |
mg |
3 |
29 |
Træ |
mg |
1 |
46 |
Biomasse |
Mg |
720 |
3.600 |
|
|
|
|
Emissioner (luft) |
|
|
|
CO2 |
mg |
2.400.000 |
5.400.000 |
CO |
mg |
1.600 |
5.700 |
CH4 |
mg |
7.900 |
23.000 |
SOx |
mg |
6.800 |
24.000 |
NOx |
mg |
9.200 |
24.000 |
Chlor |
mg |
< 1 |
< 1 |
Kulbrinter (uspecificeret) |
mg |
2.400 |
6.700 |
Aromatiske kulbrinter (uspecificeret) |
mg |
140 |
1 |
Støv |
mg |
1.100 |
4.900 |
|
|
|
|
Emissioner (vand) |
|
|
|
COD |
mg |
310 |
990 |
BOD |
mg |
21 |
230 |
NO3- |
mg |
3 |
2 |
NH4+ |
mg |
8 |
3.000 |
Kulbrinter (uspecificeret) |
mg |
76 |
57 |
|
|
|
|
Affald |
|
|
|
Mineralsk affald |
mg |
15.000 |
56.000 |
Slagge og aske |
mg |
1.900 |
15.000 |
Blandet industriaffald |
mg |
1.100 |
11.000 |
Regulerede kemikalier |
mg |
460 |
820 |
Inert kemikalieaffald |
mg |
1.100 |
4.800 |
Tabel 1. Udvekslinger med miljøet ved produktion af monomerer til umættet polyester. Udvalgt fra Boustead I. Eco-profiles of plastics and related intermediates. APME, Brussels, 1999.
8.14 Råvarer til UP-produktion på europæisk niveau
IPPC’s udkast til referencedokument om Best Available Techniques in the Production of Polymers (IPPC, 2005) oplister de vigtigste råvarer til opfyldelse af forskellige funktioner ved produktion af umættet polyester. Terminologien afviger en smule fra de, der er anvendt i de foregående afsnit, og det understreges, at der ikke er konkret viden om, hvorvidt mange af stofferne i Tabel 2 rent faktisk anvendes i Danmark eller ej.
Stofnavn |
Funktionalitet |
CAS-nummer |
1,1,1-trimethylolpropan |
Glycol/alkohol |
77-99-6 |
2-ethylhexanol |
Glycol/alkohol |
104-76-7 |
Diethylenglycol |
Glycol/alkohol |
111-46-6 |
Dipropylenglycol |
Glycol/alkohol |
110-98-5 |
Monoethylenglycol |
Glycol/alkohol |
107-21-1 |
Isobutylalkohol |
Glycol/alkohol |
78-83-1 |
Propylenglycol |
Glycol/alkohol |
57-55-6 |
Neopentylglycol |
Glycol/alkohol |
126-30-7 |
Adipinsyre |
Anhydrid/di-syre |
124-01-9 |
Fumarsyre |
Anhydrid/di-syre |
110-17-8 |
HET-syre |
Anhydrid/di-syre |
115-28-6 |
Isophthalsyre |
Anhydrid/di-syre |
121-91-5 |
Maleinanhydrid |
Anhydrid/di-syre |
108-31-6 |
Phthalsyreanhydrid |
Anhydrid/di-syre |
85-44-9 |
Tetrahydrophthalsyreanhydrid |
Anhydrid/di-syre |
85-43-8 |
Tetrebromphthalsyreanhydrid |
Anhydrid/di-syre |
632-79-1 |
2,4’/4,4’ MDI |
Reaktant |
26447-40-5 |
Toluendiisocyanat |
Reaktant |
26471-62-5 |
Bisphenol epoxy novolac |
Reaktant |
1321-74-0/7525-62-4 |
Methacrylsyre |
Reaktant |
97-41-4 |
Dicyclopentadien |
Reaktant |
77-73-6 |
Divinylbenzen |
Reaktiv monomer |
1321-74-0 |
Alfa-methyl styren |
Reaktiv monomer |
98-83-9 |
Styren |
Reaktiv monomer |
100-42-5 |
Diallylphthalat |
Reaktiv monomer |
131-19-9 |
Methyl methacrylat |
Reaktiv monomer |
80-62-6 |
Dibutyltinoxid |
Katalysator |
818-08-6 |
N,N-dimetyl-p-toluidin |
Additiv/promoter |
99-97-8 |
N,N-diethylanilin |
Additiv/promoter |
91-66-7 |
Umættet polyester |
Råvare/mellemprodukt |
100-42-5 |
Epoxy resin |
Råvare/mellemprodukt |
25068-38-6 |
o-xylen |
Opløsningsmiddel |
95-47-6 |
Acetone |
Opløsningsmiddel |
67-64-1 |
Isododecan(2,2,4,6,6-pentamethylheptan) |
Opløsningsmiddel |
13475-82-6 |
Methanol |
Opløsningsmiddel |
67-56-1 |
p-benzoquinon |
Inhibitor |
106-51-4 |
2,6-di-tertbutyl-p-cresol |
Inhibitor |
128-37-0 |
Hydroquinon |
Inhibitor |
123-31-9 |
Mono-tertbutyl-hydroquinon |
Inhibitor |
1948-33-0/88-58-4 |
4-tertbutyl-pyrocatechol |
Inhibitor |
98-29-3 |
Trimethylhydroquinon |
Inhibitor |
700-13-00 |
Kaliumnitrat |
Additiv |
7757-79-1 |
Aeroail/fumed silica |
Additiv |
7631-86-9 |
Tabel 2. Råvarer til produktion af umættet polyester på europæisk plan. (Efter IPPC, 2005)
9 Polyurethanbranchens råvarer
Se også:
Polyurethanbranchens processer
Additiver
Emissioner ved forarbejdning af hærdeplast
Kemiske belastninger i arbejdsmiljøet
Plast og affald
Miljø- og sundhedsvurderinger
Brandegenskaber for plast
Referencer
Indholdsfortegnelse
Oversigtsfigur
9.1 Introduktion
Dette kapitel er i al væsentlighed baseret på rapporten ”Renere teknologi i plastindustrien. Del B: Hærdende polyurethanplast” (Plastindustrien i Danmark, 2000c) og Jensen et al. (2005), suppleret med oplysninger om udvekslinger med miljøet ved råvareproduktion, baseret på udgivelser fra den europæiske plastindustri, APME.
Råvaren ved fremstilling af polyurethan (PUR) består altid af isocyanat og en polyolblanding.
Isocyanater og polyolerne reagerer med hinanden ved dannelse af ure-thanbindinger, heraf navnet polyurethanplast. I nedenstående Figur 1 er strukturen for polyurethanbindinger angivet.
Figur 1. Struktur for polyurethanbindinger.
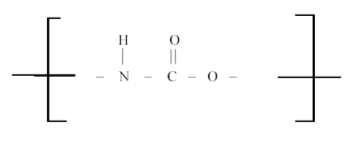
Polyolen leveres oftest som en del af et system, hvor der endvidere er tilsat additiver. "Polyolblandingen" skal således alene blandes med isocyanaten.
Enkelte virksomheder fremstiller deres egne polyolsystemer ved at blande de enkelte råvarer (polyoler, opskumningsmidler og additiver).
9.2 Polyoler
Kemisk er polyolen, som navnet angiver, kendetegnet ved at have to eller flere alkoholgrupper. De anvendte polyoler opdeles i to hovedgrupper nemlig polyethere og polyestere. Polyethere udgør mellem 80 og 90 pct. af polyolforbruget.
Polyolen er typisk iblandet katalysator, additiver m.m. og er typisk en del af et specielt "skræddersyet" system fremstillet til den enkelte PUR-producents specielle behov.
9.2.1 Polyetherpolyoler
Polyetherpolyoler til fleksibelt skum er typisk trifunktionelle forbindelser baseret på glycerin eller trimethylolpropan.
I nedenstående Figur 2 er en polyetherpolyol angivet.
Figur 2. Propylenoxid- og ethylenoxid-baserede polyetherpolyoler.
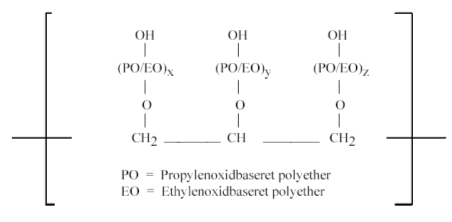
Alkoholgruppen (-OH) er den funktionelle gruppe, som kan reagere med isocyanat.
Polyetherpolyolernes molekylvægt kan varieres ved at variere alkoholgruppernes kædelængde (x,y,z). Til fleksibelt skum anvendes typisk polyethere med molekylvægt på 3.000 - 6.000 gram pr. mol. For hårdt skum er kæderne kortere, 500-2000 gram pr. mol, og antallet af funktionelle grupper ofte højere, typisk 3 - 5.
9.2.2 Polyesterpolyoler
De vigtigste polyesterpolyoler i PUR-sammenhæng fremstilles ud fra adipinsyre eller phthalsyreanhydrid, og alifatiske dioler med 2 - 6 C-atomer, diglykoler, glycerin eller trimethylopropan.
I Danmark er polyesterpolyoler typisk adipinsyrebaserede og anvendes fortrinsvis til fleksibelt skum.
Figur 3. Eksempel på en polyesterpolyol.
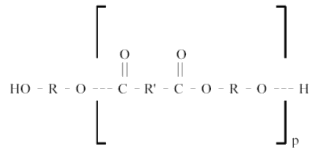
Ligeledes her er alkoholgruppen (-OH) den funktionelle gruppe, som kan reagere med isocyanat.
R kan være en hydrocarbon enten fra adipinsyre (alifatisk med 4 kulstofatomer), fra phthalsyreanhydrid (aromatisk med 6 kulstofatomer) eller hydrocarbon fra en alifatisk diol (med op til 4 kulstofatomer).
9.3 Isocyanater
Isocyanaten er den anden grundkomponent i PUR. Der findes mange forskellige isocyanatforbindelser. Ved fremstilling af PUR-produkter bruges altid isocyanater med minimum to funktionelle grupper. Disse kan reagere minimum 2 gange med polyolblandingens OH-grupper og danne polymerer.
I forbindelse med PUR anvendes altid isocyanater baseret på enten:
- MDI (diphenyl-methan-di-isocyanat) eller
- TDI (toluen-di-isocyanat)
I nedenstående Figur 4 er en isocyanatforbindelse angivet.
Figur 4. Eksempel på en isocyanatforbinelse
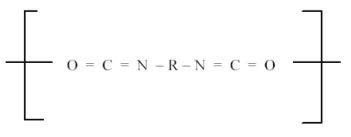
Isocyanater fremstilles ud fra reaktion mellem primære aminer og phosgen.
9.3.1 MDI
MDI anvendes typisk til fremstilling af isoleringsskum, fleksibelt formstøbt skum og integralskum. MDI findes i to forskellige former, nemlig monomer-MDI og polymer-MDI.
Monomer-MDI er "ren" ureageret monomer. Ved rumtemperatur er monomer-MDI et farveløst, krystallinsk stof. Monomer-MDI kan polymeriseres og danne polymer-MDI, som er en gulbrun væske. I praksis anvendes begge typer i plastbranchen.
I nedenstående Figur 5 er strukturformlen for MDI givet.
Figur 5. Strukturformel for monomer MDI.
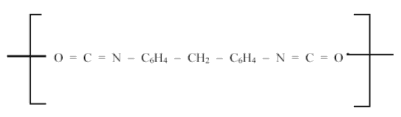
Polymer-MDI har typisk en gennemsnits-funktionalitet på 2,7 - 3 (monomer-MDI har funktionaliteten 2). Polymer-MDI's damptryk er stort set lig damptrykket for monomer-MDI. MDI's mættede damptryk ved 25°C er <0,00001 mbar.
9.3.2 TDI
TDI anvendes fortrinsvis i plastbranchen til fremstilling af blødt skum. Ved stuetemperatur er TDI en lavviskøs, glasklar væske.
I nedenstående figur 6 er strukturformlen for TDI angivet.
Figur 6. Strukturformel for TDI.
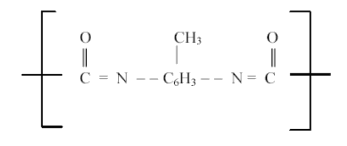
I forhold til MDI har TDI et relativt højt damptryk, hvilket medfører, at selv stænk og spild af små mængder kan give anledning til relativt høje TDI-koncentrationer i arbejdsmiljøet. Speciel opmærksomhed skal derfor rettes mod håndteringen heraf. TDI’s mættede damptryk ved 20°C er 0,02 mbar. I praksis anvendes en blanding af 2,4-TDI og 2,6-TDI i forholdet 80/20 – i sjældnere tilfælde også 65/35.
9.3.3 Præpolymerer
Isocyanater kan i visse specielle tilfælde være forpolymeriseret med polyol, hvorved der opnås en bedre kontrol over hærdeprocessen.
Dette anvendes kun i meget begrænset omfang og hovedsageligt til fleksibelt integralskum, hvor stor styrke er påkrævet. Præpolymeriserede isocyanater har en relativ høj viskositet, hvilket vanskeliggør anvendelsen i almindeligt produktionsudstyr.
9.4 Hjælpemidler og additiver
Der anvendes en bred vifte af hjælpemidler og additiver ved produktionen af PUR. I de følgende afsnit tegnes der et overordnet billede af, hvilke kombinationer af stofgrupper/funktioner, der typisk anvendes.
9.4.1 Katalysatorer
Til at katalysere dannelsen af urethanbindingen, samt for at begrænse dannelsen af uønskede sidereaktioner, anvendes basiske forbindelser som f.eks. tertiære aminer eller organiske metalforbindelser og tinforbindelser.
Katalysatorerne er typisk tilsat polyolen af systemproducenten i koncentrationer på i alt 0,5-3 pct. Enkelte producenter blander dog selv deres råvarer.
9.4.2 Tværbindere og kædeforlængere
Udover tilsætning af katalysatorer tilsættes typisk lavmolekylære, flerfunktionelle alifatiske eller aromatiske alkoholer eller aminer som kædeforlængere og cross-linkere (krydsbindere).
Stofferne deltager i polyol-isocyanat reaktionerne og får dermed en væsentlig indflydelse på polymerstrukturen og dermed på plastens mekaniske egenskaber.
Kædeforlængere er difunktionelle, tværbindere (cross-linkere) er tri- eller polyfunktionelle. Specielt anvendte kædeforlængere er 1,4-butandiol og diethyltoluendiamin. Som cross-linkere anvendes typisk glyceroler og di- samt triethanoldiaminer.
Kædeforlængere og cross-linkere er ligesom katalysatoren typisk tilsat polyolen af systemproducenten i koncentrationer på 2 - 5 pct.
9.4.3 Opskumningsmidler
Opskumningsmidler eller blæsemidler grupperes i to grupper nemlig fysiske opskumningsmidler og kemiske opskumningsmidler.
Fysiske opskumningsmidler. Reaktionen mellem isocyanat og polyol udvikler varme, hvorved de fysiske opskumningsmidler fordamper. Den dannede gas fastholdes i "lommer" i den hærdende PUR, hvorved cellestrukturen opstår.
Opskumningsmidlet tilsættes polyolråvaren. Tidligere har først CFC-gasser og siden HCFC-gasser været anvendt, men dette er ikke tilladt i dag på grund af deres uønskede egenskaber med hensyn til nedbrydning af ozonlaget og bidrag til klimaændringer. HFC- og FC-gasser anvendes stadig, men det vil som hovedregel ikke være tilladt at importere, sælge eller anvende HFC og andre industrielle drivhusgasser efter 1. januar 2006.
Som alternativ anvendes i dag kulbrinter som cyclopentan, isopentan og n-pentan til opskumning af PUR i fjernvarme- og køle/fryseskabsbranchen.
Kemiske opskumningsmidler. Kemiske opskumningsmidler virker ved at de som følge af en kemisk reaktion danner en gas, der jfr. de fysiske opskumningsmidler medvirker til cellestrukturdannelsen. I PUR-plast til fleksibelt skum og portpaneler anvendes vand, som reagerer med isocyanat og danner gassen CO2. Det er også muligt at anvende flydende CO2.
9.4.4 Cellestabilisatorer
For at stabilisere den dannede skum, indtil PUR-plasten er hærdet, tilsættes ofte en skumstabilisator. Denne er et overfladeaktivt stof f.eks. polysiloxan-polyether-copolymer eller analoge siliconeolier. Dette additiv styrer endvidere om cellestrukturen bliver åben eller lukket.
9.4.5 Brandhæmmere
Til visse anvendelser af PUR-plast er det nødvendigt at brandhæmme polymeren. Der kan anvendes fosfor-, halogen-, og kvælstofholdige forbindelser.
9.4.6 Andre additiver
Udover ovennævnte additiver tilsættes ofte organiske farvepigmenter og til visse typer fleksibelt skum endvidere blødgørende additiver. Disse virker ved at påvirke fordelingen af hårde og bløde segmenter i skummet.
Der kan tilsættes UV-stabilisatorer for at beskytte skummet mod sollys og hydrolysestabilisatorer (antioxidanter) for at modvirke hydrolyse af esterbindingerne. Disse stabilisatorer er tilsat af råpolyolfabrikanten.
Endelig kan PUR tilsættes "filler" i form af calciumcarbonat, formalet glas m.m.
9.4.7 Slipmiddel
Ved støbning af emner i PUR-plast påføres formen et slipmiddel, således at produktet slipper formen. Endvidere anvendes slipmidlet til at kontrollere glans m.m. på støbte emners overflade.
Slipmidlet er typisk et eller flere faste stoffer, der er opløst eller opslæmmet i et opløsningsmiddel.
9.5 Udvekslinger med miljøet ved produktion af råvarer
Sammenslutningen af plastproducenter i Europa, APME, har i deres rapporter blandt andet beskrevet udvekslingerne med miljøet ved produktion af de vigtigste råvarer til polyurethanproduktion, MDI, TDI og polyol. APME’s beregninger, der er dokumenteret i APME (1999), er gengivet i lettere bearbejdet/forkortet version i Tabel 1.
|
Enhed |
MDI |
TDI |
Polyol |
Energiforbrug |
|
|
|
|
Elektricitet |
MJ |
14,02 |
19,29 |
17,67 |
Olie/gas |
MJ |
21,61 |
23,43 |
34,28 |
Andet |
MJ |
59,35 |
66,65 |
41,30 |
Totalt |
MJ |
94,99 |
109,37 |
93,25 |
|
|
|
|
|
Brændselforbrug (totalt) |
|
|
|
|
Råolie |
mg |
500.000 |
550.000 |
780.000 |
Gas/kondensat |
mg |
1.100.000 |
1.200.000 |
720.000 |
Kul |
mg |
320.000 |
330.000 |
230.000 |
Metallurgisk kul |
mg |
18.000 |
21.000 |
550 |
Brunkul |
mg |
100.000 |
290.000 |
180.000 |
Tørv |
mg |
370 |
180 |
350 |
Træ |
mg |
810 |
390 |
1.000 |
Biomasse |
mg |
4.300 |
6.400 |
130.000 |
|
|
|
|
|
Emissioner (luft) |
|
|
|
|
CO2 |
mg |
3.400.000 |
5.000.000 |
3.100.000 |
CO |
mg |
2.800 |
3.400 |
1.800 |
CH4 |
mg |
18.000 |
23.000 |
12.000 |
SOx |
mg |
15.000 |
19.000 |
13.000 |
NOx |
mg |
15.000 |
21.000 |
14.000 |
Chlor |
mg |
1 |
<1 |
2 |
Kulbrinter (uspecificeret) |
mg |
4.000 |
4.400 |
2.600 |
Aromatiske kulbrinter (uspecificeret) |
mg |
73 |
130 |
7 |
Støv |
mg |
4.700 |
6.500 |
11.000 |
|
|
|
|
|
Emissioner (vand) |
|
|
|
|
COD |
mg |
5.300 |
1.200 |
3.400 |
BOD |
mg |
810 |
15 |
640 |
NO3- |
mg |
150 |
7.100 |
6.000 |
NH4+ |
mg |
200 |
840 |
9 |
Kulbrinter (uspecificeret) |
mg |
39 |
190 |
35 |
|
|
|
|
|
Affald |
|
|
|
|
Mineralsk affald |
mg |
84.000 |
120.000 |
220.000 |
Slagge og aske |
mg |
21.000 |
28.000 |
21.000 |
Blandet industriaffald |
mg |
11.000 |
6.900 |
31.000 |
Regulerede kemikalier |
mg |
4.700 |
11.000 |
40.000 |
Inert kemikalieaffald |
mg |
2.800 |
1.600 |
11.000 |
Tabel 1. Udvekslinger med miljøet ved produktion af 1 kg råvarer (MDI, TDI og polyol). Efter APME (1999).
10 Additiver
Se også:
Migration
Brandegenskaber for plast
Miljø- og sundhedsvurderinger
Referencer
Indholdsfortegnelse
Oversigtsfigur
10.1 Introduktion
Additiver er et centralt element i forarbejdningen af plast til færdige produkter. Nogle additiver tilsættes for at give en smidig forarbejdningsproces og nedsætte risikoen for produktion af emner, der ikke lever op til den ønskede kvalitet. Andre additiver tilsættes for at ændre ved de grundlæggende tekniske egenskaber for den anvendte polymer og derigennem skræddersy en materialekombination til at opfylde de tekniske krav, der stilles til det pågældende produkt.
Additiv-området er meget komplekst. Der findes bogstavelig talt tusindvis af additiver, der kan anvendes alene (i forskellige koncentrationer) eller i kombination med andre additiver. Det ligger udenfor denne rapports rammer at give en fyldig beskrivelse af additivernes funktion, ligesom det heller ikke er muligt at beskrive deres miljø- og sundhedsmæssige egenskaber. I de følgende afsnit gives der en kort introduktion til de forskellige typer af additiver, og der peges på få, udvalgte, additiver, som vides at være belastende for miljø og/eller sundhed. Det understreges, at det generelt tilrådes at foretage en konkret vurdering i hver enkelt case, for eksempel ved at bruge de værktøjer, der er beskrevet i kapitlet om miljø- og sundhedsvurderinger.
Der er i denne introduktion til additiver og deres funktion anvendt to hovedkilder, nemlig Jensen et al. (2005) og Miljùsamverkan (1998). Desuden gøres der opmærksom på, at der blandt andet i kapitlerne om både plastråvarer og forarbejdningsprocesser er oplistet en række additiver, som er eller har været anvendt af danske plastforarbejdende virksomheder. De enkelte kapitler supplerer således hinanden, men det pointeres at selv en total opsamling på alle additiver, der nævnes i denne rapport, kun vil give et begrænset billede af det fulde spektrum for additivanvendelse.
10.2 Stabilisatorer
10.2.1 Varmestabilisatorer
Ved forarbejdning af plastmaterialer er der en risiko for, at temperaturen bliver så høj, at molekylekæderne begynder at gå i stykker, hvilket nedsætter den tekniske kvalitet, f.eks. i form af reducerede styrkeegenskaber.
Den termiske nedbrydning er især udtalt ved forarbejdning af PVC, hvor der er risiko for nedbrydning ved temperaturer, der ligger væsentligt under den normale forarbejdningstemperatur. Der tilsættes derfor generelt varmestabilisatorer, der forsinker fraspaltning eller tilvækst af molekyler og som uskadeliggør nedbrydningsprodukterne.
Tungmetalforbindelser, især blybaserede, var i mange år den traditionelle løsning som varmestabilisator, men tungmetallernes uønskede miljø- og sundhedsegenskaber har medført en regulering, der betyder, at de for generelt ikke anvendes længere. I stedet anvendes organiske og uorganiske metalforbindelser, evt. sammen med organiske phosphitter og polyhydroxyforbindelser som sekundære stabilisatorer.
Miljùsamverkan (1998) peger på følgende varmestabilisatorer som de mest anvendte:
- Calcium/zink-forbindelser (også som substitution for bly)
- Barium/zinkforbindelser
- Organiske tinforbindelser (på listen over uønskede stoffer i Danmark, hvilket betyder at producenter/importører bør arbejde for at finde et alternativ.)
- Blyforbindelser (forbudt i Danmark)
- Barium/cadmiumforbindelser (anvendelse af cadmium er forbudt i Danmark)
Som co-stabilisatorer anvendes dipentaerytriol, pentaerytriol, sorbitol og epoxideret sojabønneolie. Der anvendes også hydrotalcitter, der er syntetisk fremstillet aluminium-magnesium hydroxycarbonat.
10.2.2 Antioxidanter
Antioxidanter tilsættes for at modvirke oxidativ nedbrydning af plasten under forarbejdning og/eller for at forlænge produktets levetid ved at forhindre nedbrydning under påvirkning af varme og lys ved produktets brug.
Ved en oxidativ nedbrydning dannes der frie radikaler, og nedbrydningen kan fortsætte ved en kæderaktion. Produkterne bliver misfarvede, og der kan eventuelt dannes revner.
Anvendelse af antioxidanter er meget udbredt ved stort alle typer af plastmaterialer og forarbejdningsprocesser, og der findes da også et meget stort udvalg af antioxidanter i handelen. Der kan skelnes mellem fire hovedtyper af antioxidanter:
- Phenoler. Monophenoler, bisphenoler, thiobisphenoler og polyphenoler udgør den største mængde af primære antioxidanter. I polyolefiner som PE og PP anvendes de typisk i mængder på 0,05-0,2%, mens der i styren-baserede plastmaterialer anvendes op til 2%
- Aminer. Amin-baserede antioxidanter anvendes især i syntetiske gummier i koncentrationer mellem 0,5 og 3%.
- Phosphitter. Phosphitter anvendes alene eller sammen med phenoler eller aminer. I polyolefiner anvendes 0,05 til 2%, i slagfast polystyren 0,05-1% (i visse tilfælde måske op til 2%) og i ABS op til 3%.
- Thioestere. Thioestere er vigtige for at forhindre molekylemasseændringer ved lang tids udsættelse for høje temperaturer. Dilaurylthiodiproprionat og distearylthiodiproprionat er almindeligt anvendt til polyolefiner i koncentrationer på 0,1-0,3%. I umættede polymerer kræves noget større koncentrationer.
Miljùsamverkan (1998) peger på følgende antioxidanter som de mest anvendte:
- Tetrakis (CAS-nr. 6683-19-8)
- BHT (butylhydroxytoluen, CaAS-nr. 128-37-0)
- Polyphenolphosphit (CAS-nr. 31570-04-4)
- Octadecyl (CAS-nr. 2082-79-3)
- Thiobisphenol (CAS-nr. 96-69-5)
- Tris(nonylphenol)phosphit (CAS-nr. 26523-78-4)
- Bisphenol A (CAS-nr.80-05-7) (en risikovurdering kan findes på http://ecb.jrc.it/esis/esis.php?PGM=ora)
- Benzophenon (CAS-nr. 1843-05-6)
Det skal bemærkes, at forbrugsmønstret sagtens kan være ændret i dag, for eksempel på grund af ny viden om stoffernes miljø- og sundhedsmæssige egenskaber. Dette gælder blandt andet bisphenol A, som er mistænkt for at have hormonforstyrrende effekter, og tris(nonylphenol)phosphit, der kan indeholde nonylphenol, der også er mistænkt for at være hormonforstyrrende.
10.2.3 UV-stabilisatorer
Ved stuetemperatur oxideres mange plastprodukter under indvirken af vejr og vind, specielt på grund af ultraviolet stråling fra solen. For at modvirke UV-strålingens nedbrydende effekt, der er mest udbredt for polyolefiner, anvendes forskellige typer af stoffer. Jensen et al. (2005) peger på phtahlater og kønrøg (carbon black), hvor sidstnævnte dog også har den egenskab, at alt materiale farves kulsort. Miljùsamverkan (1998) peger på følgende UV-stabilisatorer som de mest almindeligt anvendte:
- Hindrede aminer (HALS (Hindered Amine Light Stabilisers)
- Benzophenoner (først og fremmest i LDPE)
- Benzotriazoler
- Metalkomplekser med svovlforbindelser som for eksempel dialkyldithiocarbamat
10.3 Smøre- og glidemidler
Ved forarbejdning vil plastsmelten ofte være meget sejtflydende og have tilbøjelighed til at klæbe til værktøjets overflade. En forhøjelse af forarbejdningstemperaturen vil reducere problemet, men giver som beskrevet ovenfor et andet problem i form af øget termisk nedbrydning.
Der tilsættes derfor smøre. eller glidemidler, hvis hovedopgave er at forbedre flydeegenskaberne for den smeltede plast gennem at nedsætte adhæsionen mellem plastmateriale og forarbejdningsmaskine eller nedsætte den indre friktion i plastmaterialet. Smøremidlerne inddeles i fire grupper:
- Fedtsyrer som f.eks. stearin-, palmitin-, eruca- og myristinsyre. Stearinsyre anvendes eksempelvis i mængder på 0,1-0,2% ved kalandrering og ekstrudering af PVC.
- Amider og estere af fedtsyrer, f.eks. med glycerin. Klarheden af stiv PVC forbedres ved tilsætning af syntetiske estervokser, og amidvokser tjener som indre smøremiddel i ABS.
- Metalsalte af fedtsyrer, primært i form af aluminium-, calcium-, bly-, lithium-, magesium-, natrium- og zinkstearat. De virker som indre smøremiddel i koncentrationer på 0,05-3% ved forarbejdning af de fleste plasttyper, herunder PE, PP, PS, PVC, polyamider og celluloseplast.
- Langkædede hydrocarboner i form af mikrokrystallinske vokser, paraffiner, paraffinolier og montansyreester, eller naturlige vokser som carnubavoks og bívoks.
Det bemærkes, at valgte af smøremiddel som oftest er specifikt for en given kombination af plasttype og forarbejdningsmetode.
10.4 Farvestoffer og pigmenter
De fleste plastmaterialer er som udgangspunkt farveløse eller hvidlige, men der er stort set ubegrænsede muligheder for at indfarve plasten.
Man kan skelne mellem fire typer af farvestoffer:
- Opløselige farvestoffer, der generelt er aromatiske forbindelser, opløselige i almindelige opløsningsmidler. De anvendes f.eks. til at give strålende, transparent farvetoner i polystyren, og tilsættes i mængder fra 0,01-2,5%. Denne type farvestoffer har en lysægthed mellem 6 og 8, men er ikke særlig modstandsdygtige overfor kemikalier. De bør kun anvendes til amorfe materialer, hvorfra de ikke migrerer.
- Organiske pigmenter, der er uopløselige. Til gruppen hører blandt andet alizarinderivater, phthalocyanin, benzidin, kønrøg (carbon black) og metal-azoforbindelser, og de anvendes i koncentrationer på 0,001-2,5%.
- Uorganiske pigmenter, mest metaloxider og -salte er uopløselige og kemikaliebestandige. Zinksulfid, zinkoxid, jernoxid, cadmium-manganforbindelser, chrom- og molybdænforbindelser, ultramarin og titandioxid er vigtige eksempler. De uorganiske pigmenter kan anvendes til stort set alle polymertyper i koncentrationer på 0,01-10%.
- Specialfarvestoffer, hvor der f.eks. kan opnås metaleffekt med aluminium- og kobberpulver og perlemorseffekt med blycarbonat eller vismutoxichlorid.
Farvestoffer tilsættes primært som masterbatch, hvor et bestemt blandingsforhold med råplasten giver den ønskede farvenuance. Ved forarbejdning af blød PVC anvendes ofte pastaformige koncentrater, hvor farvestoffet er dispergeret i en blødgører. Indfarvningen kan også ske hos råvareproducenten, eller farven kan pålægges det færdige emne ved maling.
10.5 Brandhæmmere
Alle plastmaterialer er brandbare, men deres antændelighed er meget forskellig. På grund af øgede sikkerhedskrav indenfor områder som byggeri, transport og elektriske artikler tilsætter man brandhæmmere til den plast, der anvendes til disse typer af produkter. Man kan skelne mellem tre overordnede grupper af brandhæmmere:
- Organiske additiver, der blandes i polymeren. De vigtigste stoffer i denne gruppe er phosphorsyreestere (der udgør ca. 50% af det samlede forbrug af brandhæmmere) og chlorparaffiner.
- Uorganiske additiver som aluminiumsoxid, antimontrioxid, zinkborat og andre bor-, barium- og phosphorholdige kemikalier. De anvendes i koncentrationer fra 3-20%. EU har gennemført en risikovurdering af aluminiumsoxid, se http://ecb.jrc.it/esis/esis.php?PGM=ora.
- Reaktive brandhæmmere, som oftest chlor- eller bromholdige monomerer som vinylbromid, tetrachlorphthalsyreanhydrid, tetrabrombisphenol A og tetrachlorbisphenol A. Disse stoffer copolymeriseres sammen med basispolymeren, hvorved den brandhæmmende effekt så at sige indbygges i det færdige produkt.
Området er meget komplekst, og de nedenstående eksempler på brandhæmmende additiver kan ikke regnes som fyldestgørende.
10.5.1 Brandhæmning af polyethylen
De mest anvendte brandhæmmere er aluminium- og magnesiumhydoxid. Almindelig PE kan brandhæmmes med chloreret PE (CPE) med et chlorindhold på højst 43%. Der kan også anvendes halogenholdige paraffiner, eventuelt i kombination med antimontrioxid eller phosphor.
10.5.2 Brandhæmning af PVC
Indholdet af chlor i ren PVC gør polymeren selvslukkende. PVC er også selvslukkkende, hvis der er anvendt phosphorsyreester som blødgører, men hvis der er anvendt phthalater eller adipater som blødgører, kan det være nødvendigt at tilsætte 10% tricresylphosphat og eventuelt også antimontrioxid.
10.5.3 Brandhæmning af polystyren
Antimonforbindelser anvendes også til brandhæmning af polystyren, ligesom også chlorparaffiner ofte finder anvendelse. Blandinger af 20% chlorparaffin, 10% antimontrioxid og 3-10% phosphorsyreester giver erfaringsmæssigt gode resultater. Til ekspanderet polystyren har ammoniumphosphat, tetrabrommethan og tetrabromacetylen vist sig velegnet.
10.5.4 Brandhæmning af umættet polyester
Brandbarheden af umættet polyester reduceret ved anvendelse af reaktive monomerer som HET-syre (hexa-chloroendome-ethylen-tetrahydrophthalsyre), eller ved tilsætning af ikke-reaktive additiver som dichlorstyren og triallylphosphat. Også antimontrioxid og aluminiumtrihydrat anvendes.
10.5.5 Brandhæmning af polyurethanplast
Til polyurethan anvendes både reaktive brandhæmmere med indhold af phosphor og/eller halogener og ikke-reaktive typer, der typisk er lavmolekylære forbindelser med indhold af phosphor og/eller halogen.
10.5.6 Miljø- og sundhedsmæssige aspekter
Brand/flammehæmmere har igennem de sidste mange år været i nationale og supranationale myndigheders fokus. Specielt har de såkaldte bromerede flammehæmmere været genstand for mange undersøgelser på grund af deres potentielle virkninger på både menneskers sundhed og generelt i miljøet.
På Miljøstyrelsens hjemmeside (http://www.mst.dk/kemi/02150000.htm) findes information om hvordan stofferne påvirker miljøet og hvilke lovgivningsmæssige initiativer, der er eller vil blive taget. Plastindustrien i Danmark har fået udarbejdet en uafhængig vurdering af en række bromerede flammehæmmere (eventuel henvendelse gennem www.plast.dk).
I denne rapport skal der kun peges på, at i skrivende stund regnes grupperne PBB (polybromerede biphenyler) og PBDE (polybromerede diphenylethere) som de mest problematiske, og at penta- og octabromdiphenylether har været forbudt siden 15. august 2004 Det skal dog også bemærkes, at adskillige halogenerede flammehæmmere giver anledning til betænkelighed ved deres anvendelse eller bortskaffelse. Det samme er i øvrigt også tilfældet for mange af de andre brandhæmmende stoffer, der anvendes, og der bør derfor indgå miljømæssige overvejelser ved valget af brandhæmmer til et givet produkt.
10.6 Antistatiske midler
Ved forarbejdning af plast opstår der let en elektrostatisk opladning, statisk elektricitet, på de færdige emner. Dette tiltrækker støv, men mere problematisk er det, at den statiske elektricitet giver risiko for gnistdannelse og dermed også risiko for støveksplosioner eller antændelse af gasser og dampe.
For at undgå statisk elektricitet anvendes antistatika, enten direkte påført emnet (med kortvarig effekt) eller iblandet polymeren, hvorved der opnås en varig effekt. Der anvendes fire grundtyper af antistatika:
- Aminer
- Kvaternære ammoniumforbindelser
- Phosphorsyreestere
- Polyethylenglycolethere
Deres virkningsmåde er generelt, at de danner en molekylær vandhinde, som er elektrisk ledende.
Miljùsamverkan peger på følgende antistatika som de mest anvendte:
- Ethoylerede alkylaminer (til PE, PP og PS)
- Fedtsyreestere (til PE, PP, PVC og PS)
- Alkylsulfonater (til PVC og PS)
10.7 Blødgørere
Langt den største del (omkring 80%) af blødgørere anvendes i forbindelse med PVC, mens resten hovedsagelig bruges til celluloseplast. Der findes bogstaveligt talt hundredvis af forskellige blødgøringsmidler til forskellige formål, og disse kan opdeles i fire typiske stofgrupper:
- Estere
- Polymerer
- Chlorerede paraffiner
- Modificerede olieprodukter
Estere af phtalsyre (de såkaldte phthalater) har på samme måde som de bromerede flammehæmmere været i myndighedernes fokus gennem en årrække. Miljøstyrelsen udarbejdede allerede i 1999 en handlingsplan for at reducere og afvikle anvendelsen af phthalater i blød plast, og i 2003 udgav Styrelsen en status for phthalater, der blandt andet indeholder oversigter over forbrug af phthalater, forureninger, reguleringer og risikovurderinger i EU.
Flere af phthalaterne mistænkes for at have hormonforstyrrende effekter, men der er betydelige forskelle mellem de enkelte phthalater med hensyn til deres egenskaber og potens. Det står dog klart, at den mest anvendte phthalat, DEHP (di-2-ethyl-hexyl phthalat), generelt må regnes som uønsket i produkter på grund af stoffets hormonforstyrrende effekter, ligesom dibutylphthalat og butylbenzylphthalat regnes som problematiske. EU har gennemført en risikovurdering af en række phthalater, som kan ses på http://ecb.jrc.it/esis/esis.php?PGM=ora. Plastindustrien i Danmark har fået udarbejdet en stofprofil for nogle af de samme phthalater (eventuel henvendelse gennem www.plast.dk).
10.8 Opskumningsmidler
Ved at sætte opskumningsmidler til plastmaterialer skabes en cellestruktur i plasten. Dette er generelt materiale- og dermed omkostningsbesparende, men derudover opnås også ændrede materialeegenskaber, f.eks. i form af forbedrede lys- og varmeisolering og mere eller mindre stivhed efter ønske.
Når termoplast opskummes, vil hovedparten af cellerne være lukkede. Opskumningsmidlet vil altså til en vid grad forblive i produktet. I polyurethanskum er cellerne hovedsageligt åbne, hvilket betyder at opskumningsmidlet frigives fra produktet i løbet af produktionsprocessen.
Fysiske opskumningsmidler virker ved at fordampe fra væsketilstand eller ved ekspansion af en gas under tryk. Tidligere var CFC- og HCFC-gasser almindeligt anvendt, men det er ikke tilladt at anvende disse stoffer i dag, da de både bidrager til klimaeffekten og ozonlagsnedbrydning. I stedet anvendes pentan (f.eks. til ekspanderet polystyren (EPS)) og CO2/vand til opskumning af polyurethan. Det skal bemærkes, at der ved opskumning med pentan kan være en betydelig eksponering i arbejdsmiljøet, ligesom pentan, der udledes til det ydre miljø vil bidrage til fotokemisk ozondannelse. På længere sigt forventes inerte gasser som nitrogen, argon og neon at komme til at spille en væsentlig rolle.
Kemiske opskumningsmidler som azodicarbonamid, natriumbicarbonat og natriumborhydrid virker ved at danne gas i temperaturområdet for almindelig forarbejdning af det pågældende materiale.
10.9 Fyldstoffer
Indholdet af fyldstoffer i plast varierer fra ”ganske lidt” til op til 50%. Det kan i nogle tilfælde være svært at skelne mellem egentlige fyldstoffer og additiver med specifikke egenskaber. Det er dog klart at med billige fyldstoffer som træmel, stenmel, ler og kridt ønsker man først og fremmest at holde prisen lav på produkter, hvor der ikke er store krav til de tekniske egenskaber. Glas, specielt i form af lange fibre, giver øget slagsejhed i for eksempel umættet polyester, mens molybdænsulfid og grafit anvendes for at mindske friktionen og dermed også slitagen i bevægelige dele.
11 Compoundering
Se også:
Termoplastbranchens_råvarer
Emissioner ved forarbejdning af termoplast
Kemiske belastninger i arbejdsmiljøet
Referencer
Indholdsfortegnelse
Oversigtsfigur
11.1 Introduktion
Dette kapitel bygger i al væsentlighed på rapporten ”Renere teknologi i plastindustrien. Øvrige plastprocesser, råvarebehandling og færdiggørelsesteknikker” (Plastindustrien i Danmark, 2000b).
Der finder ikke kommerciel råvarefremstilling (polymerisering) af plastpolymerer sted i Danmark. Færdig polymer importeres derfor og ofte i form af granulat eller pulver, som er direkte klar til anvendelse i produktionen. Undtaget herfra er diverse hærdeplastmaterialer som bl.a. umættet polyester (UP), hvor blanding af råvarer og polymerisation finder sted i umiddelbar forbindelse med emneproduktionen.
Til stort set alle plastmaterialer er det nødvendigt at tilsætte andre stoffer (additiver og/eller fyldstoffer), for at tilføre plastmaterialet en bedre bestandighed. Stofferne kan bl.a. tilsættes for at forbedre plastmaterialets forarbejdningsegenskaber, hindre termisk nedbrydning, hindre nedbrydning af ultraviolet lys, hindre oxidering, hindre elektrostatisk opladning, reducere brændbarheden, give en ønsket farve eller få et stærkere materiale med forbedret træk- og brudstyrke.
Blandeprocessen af basispolymeren og additiver til et materiale, der er anvendelig til produktion af færdige emner kaldes compoundering. Inden for visse områder inkluderer compoundering fremstilling af granulat ved ekstrudering og pelletering, mens compounderingsprocessen for plastisoler (flydende) eller pasta ender ved dispersionsfremstillingen.
Compoundering har to vigtige funktioner, dels sikres en homogen fordeling af additiverne, som kan være tilsat i vidt forskellige mængder, og dels ændres plastmaterialets fysiske form ofte til en, som er mere velegnet procesmæssigt, eksempelvis fra pulver til granulat.
Hovedparten af de danske plastvirksomheder importerer ufarvet plastgranulat eller -pulver, der fra leverandørens side er tilsat de ønskede additiver bortset fra pigmenter. Ved produktion af farvede artikler tilsætter virksomheden selv pigmenterne og ofte i form af “masterbatch” d.v.s. en polymer, med en høj koncentration af pigment. Fordelene herved er, at virksomheden dels ikke er bundet af en standardfarve eller -nuance og dels ikke behøver at have så stor lagerkapacitet.
Når iblanding af masterbatch medregnes til compoundering, vurderes det, at mere end 90 pct. af plastbranchens virksomheder selv compounderer. Antallet af virksomheder, der også tilsætter andre additiver, vurderes ikke at udgøre mere end 10.
Tilsætning af masterbatch kan foretages umiddelbart i forbindelse med emneproduktionen, idet produktionsapparaturet, eksempelvis en ekstruder, kan være tilsluttet to doseringsenheder for råvarer.
Er produktionsapparaturet ikke tilsluttet en sådan enhed, eller ønskes der tilsat andre additiver end de fra leverandøren tilsatte, kan virksomheden ved compoundering selv fremstille den ønskede råvare.
11.2 Metoder
Compoundering eller blanding af plastråvarer kan finde sted ved forskellige metoder, alt efter om råvarerne alene er faste materialer, eller om der også indgår væsker. Endvidere kan det i visse tilfælde være nødvendigt at tilføre varme.
Et hyppigt problem ved tilsætning af additiver er, at additiverne ofte har en tendens til at agglomerere (klumpe sig sammen), hvilket forhindrer en ordentlig homogenisering og dermed forringer materialets egenskaber.
11.2.1 “Tør”-compoundering
Ved blanding af en lille mængde pulver eller granulat med en stor mængde af et andet pulver eksempelvis i forholdet 1:1000, kan det ofte være formålstjenligt først at blande additivet og en del af det øvrige materiale f.eks. i forholdet 1:10, hvorefter denne blanding tilsættes resten af materialet, eventuelt efter endnu et mellemtrin.
Der er udviklet et stort antal pulverblandere til simpel sammenrystning. Beholderen kan være udformet på flere måder, eksempelvis som en roterende tromle eller som en terningformet kasse, der roterer om en diagonal.
Nautablanderen er en speciel pulverblander. Den roterer ikke, men er i stedet forsynet med en snegl, der både drejer om sin egen akse via motoren for neden og rundt langs beholderens væg via den øverste motor.
Disse pulverblandere er baseret på batchvis/diskontinuerlig blanding. En kontinuerlig pulverblanding er imidlertid let gennemførlig, ved blot at føre de forskellige pulverstrømme ned i en transportsnegl, med en god blandevirkning (svarer til snekken i en ekstruder). Processen kompliceres dog ved, at den kontinuerlige dosering af de forskellige pulvere, kræver ret kostbare doseringsapparater.
11.2.2 “Våd”-compoundering
“Våd”-compoundering anvendes især til blødgøring (også kaldet plastificering) af PVC. Plastificeret PVC fremstilles ved compoundering af PVC-pulver med blødgøringsmidler og eventuelt stabilisatorer, fyldstoffer og andre additiver afhængigt af de ønskede egenskaber og den anvendte forarbejdningsproces.
Mængden af blødgøringsmidlet kan udgøre op til 50 pct. af compoundmængden. Hyppigst anvendes DEHP (di-(2-ethylhexyl)phthalat eller DINP (diisononylphthalat).
Ved høje blødgørerkoncentrationer (plastisol) anvendes ofte en intensiv blander, der er opdelt i to blandekar. I det første opvarmes massen på grund af hurtig omrøring og heraf følgende friktion samt eventuelt ved ekstern varmetilførsel. Når massen er tilstrækkelig homogen overføres den fra opvarmningskarret til det andet kar, hvori den afkøles under langsommere omrøring.
Jo lavere indhold af blødgøringsmiddel eller jo højere indhold af fyldstoffer, des højere bliver viskositeten. Der er derfor ofte tale om blanding af højviskøse væsker eller pasta, hvor det kan være nødvendigt med tilførsel af varme, for at mindske viskositeten og dermed lette blandingen. Varmetilførslen kan også have til formål at smelte visse additiver, så de kan diffundere ind i plastmatriksen.
Compoundens viskositet er ofte for høj til, at hurtige omrørearrange-menter er anvendelige. I stedet anvendes langsomme omrørere, der for at fremkalde tilstrækkelig blandeeffekt, ofte skal bestryge hele væskevolumet. Endvidere kan det være nødvendigt at anvende prelplader eller foretage andre foranstaltninger for at forhindre totalrotation.
I stedet for blanding ved omrøring, kan compoundmassen eventuelt æltes, f.eks. med en dobbeltskrueælter. I dobbeltskrueælteren sørger de to ælteorganer for en langsgående cirkulation i karret. Denne apparattype udføres i mange varianter. Hvis karret gøres langt og får et lille tværsnitsareal, kan æltningen fuldføres ved blot én passage gennem karret (svarer til snekkerne i en dobbelt-snekkeekstruder). Man får herved mulighed for at gøre æltningen kontinuerlig.
Ved vanskeligere æltningsopgaver, kan det være nødvendigt at behandle massen på to forskellige maskiner. Først på en ælter, som sørger for en grovere sammenblanding, dernæst på et valseværk, hvor de fremkaldte forskydningsspændinger kan medføre en intens gennemarbejdning af massen.
11.3 Granulering/pelletering
Kontinuerlig compoundering/blanding er ofte en ekstruderingsproces, hvor den blandede plastmasse ekstruderes ud i lange strenge, som overskæres til små granulater eller små pellets. Strengene kan eventuelt afkøles inden granuleringen/pelleteringen. Herved bliver snittene dog ikke så pæne, men får skarpe kanter og ofte revner.
Afkølingen af granulatet sker enten med vand eller luft. Det plastificerede materiale ekstruderes ud i strenge og afskæres samtidigt eventuelt under vand, hvori det afkøles. Flowet i vandet transporterer granulatet med, indtil vandet sies fra, og granulatet tørres inden det lagres.
11.4 Energiforbrug
Det største energiforbrug til en kold compoundering er til den mekaniske blanding/miksning. Ved en varm compoundering anvendes desuden en betydelig mængde energi til opvarmning og eventuelt plastificering af materialet.
11.5 Vandforbrug
Selve compounderingsprocessen giver ikke anledning til udledning af processpildevand, men i forbindelse med en granulering vil der kunne udledes en begrænset mængde spildevand. Procesvandet fra granuleringen bliver i høj grad recirkuleret efter frasining af granulatet.
12 Blæsestøbning
Se også:
Termoplastbranchens_råvarer
Emissioner ved forarbejdning af termoplast
Kemiske belastninger i arbejdsmiljøet
Miljø- og sundhedsvurderinger
Referencer
Indholdsfortegnelse
Oversigtsfigur
12.1 Blæsestøbningsbranchen og dens råvarer
Den følgende beskrivelse af blæsestøbningsbranchen og dens produkter er i al væsentlighed baseret på rapporten ”Renere teknologi i plastindustrien. Øvrige plastprocesser, råvarebehandling og færdiggørelsesteknikker” (Plastindustrien i Danmark, 2000b) og lærebogen ”Plastteknologi” (Jensen et al. (2005)).
De danske blæsestøbningsvirksomheder findes hovedsageligt indenfor emballagesektoren. Den vigtigste råvare er polyethylen (PE) med polyethylenterephthalat og polypropylen (PP) som andre betydende materialer. I de senere år er der sket en udvikling i råvareforbruget, specielt med hensyn til PEN (polyethylennaphthenat) til emballering af øl og legeringer af PET med LCP (Liquid Crystal Polymer).
12.1.1 Additiver
I forbindelse med blæsestøbning anvendes ofte antistatiske midler, antioxidanter samt slip-/glidemiddel eksempelvis af stearattype.
Der tilsættes masterbatch i en koncentration på 2-4 pct. Masterbatchen indeholder antistatiske midler og eventuelt farvestoffer eller pigmenter uden indhold af bly.
Der anvendes så vidt vides ikke brandhæmmere.
Til flerlagsprodukter af flere forskellige materialer kan det desuden være nødvendigt at anvende lim for at sammenholde de forskellige lag.
12.2 Processer til blæsestøbning
Ved blæsestøbning opblæses et råemne i en lukket form, hvorved plastmaterialet presses, eventuelt også strækkes, ud mod formvæggen, hvor den afkøles resulterende i, at artiklerne bliver hule.
Råemnet kan enten være rørformet fremstillet ved ekstrudering eller være en sprøjtestøbt præform.
Mens sprøjtestøbningen af præforme ofte ikke finder sted på samme lokalitet som opblæsningen, finder ekstruderingen af råemnet altid sted umiddelbart i forbindelse med opblæsningen.
Der er få danske virksomheder, som sprøjtestøber præforme og ikke med henblik på videresalg.
12.2.1 Ekstruderingsblæsestøbning
Ved ekstruderingsblæsestøbning ekstruderes først en slange af sejtflydende plast umiddelbart før blæsestøbningen. For at opnå en tilstrækkelig styrke i den ekstruderede slange anvendes ofte plastmaterialer med særligt høj grad af polymerisering. Herved bliver det færdige emnes mekaniske og kemiske egenskaber samtidigt bedre, end hvis emnet var fremstillet ved sprøjtestøbning af polymerer med lavere molvægt.
Når råemnet har nået en vis længde, omsluttes det af parterne fra et kølet formværktøj. Herved afskæres de dele af slangestykket, som ikke kan være i formværktøjet, samtidigt med at en blæsedorn indføres i slangen/råemnet. Luft under højt tryk indblæses derefter i råemnet, der presses ud til den kolde formvæg, hvorved plastmaterialet stivner, og emnet opnår den ønskede facon.
Formen holdes kold med kølevand gennem fine kanaler udboret så tæt på formoverfladen som muligt.
Emnet udtages, når det er tilstrækkeligt afkølet, hvorefter formen er parat til formgivning af næste emne. Den tid, det tager at ekstrudere råemnet, samt den tid, der går inden det færdige emne, er tilstrækkeligt afkølet, er de afgørende faktorer for, hvor hurtigt produktionen kan finde sted.
Skarpe hjørner og kanter samt store forskelle i emnets rumlige opbygning kan resultere i lokale områder med lave vægtykkelser og eventuelt huller. Ny teknologi åbner mulighed for, ved profilering af slangetværsnittet og/eller programmering af godstykkelsens forløb, at opfylde de ekstra godsbehov.
12.2.2 Sprøjteblæsestøbning/sprøjteblæsning
Ved sprøjteblæsestøbning anvendes et sprøjtestøbt råemne, en præform med lukket bund og perfekte detaljer i åbningen. Præformen er ikke nødvendigvis nyfremstillet.
Sprøjteblæsestøbning er udviklet for at udnytte de forbedrede egenskaber, som en del plastmaterialer kan vinde ved en biaksial orientering af materialet. Den biaksiale orientering kan opnås ved samtidig strækning af materialet i to retninger og udføres ved sprøjteblæsning ved temperaturer lige under materialets smeltepunkt.
Forbedringerne gælder trækstyrke, slagstyrke, glans og transparens samt at der opnås mindre permeabilitet, et forhold, som forklarer processens popularitet til fremstilling af PET-flasker til kulsyreholdige drikke.
Præformen opvarmes og indføres via en dorn i et formværktøj, hvori korpus oppustes (strækkes og trækkes) med trykluft indtil den ønskede facon opnås. Når emnet er tilstrækkeligt afkølet udtages det.
Såfremt det færdige emnes ydre diameter varierer, er det muligt at opnå en ensartet godstykkelse ved at anvende en præform med en tilsvarende varierende vægtykkelse, der korrigerer herfor.
Fordelene ved sprøjteblæsning i forhold til ekstruderingsblæsning er bl.a., at det færdige produkt fremtræder uden svejsesømme fra skærekanter, at gevindet har væsentligt bedre holdbarhed og styrke, at der ikke fremkommer affald ved hals- og bundsvejsninger, at materialefordelingen kan forbedres og at tolerancerne på emnevægt og –volumen kan reduceres.
Ulemperne ved blæsestøbning hidrører dels fra de kostbare formværktøjer, dels fra at materialer til sprøjteblæsningen skal være forholdsvist lavpolymere, og derfor ikke er så kemisk bestandige som ekstruderingsblæsestøbematerialerne. Desuden er opbygningen af biaksiale barrierer en kompliceret proces.
12.2.3 Flerlagsblæsestøbning
Det er muligt ved blæsestøbning, nemmest ved ekstruderingsblæsestøbning, at anvende flere coaxiale plastlag, med hver deres tæthedsdata. Herved kan man kombinere forskellige materialeegenskaber og producere beholdere med specifikke barriereegenskaber.
Metoden åbner desuden mulighed for anvendelse af regenerat f.eks. i midterlag omgivet af virgint materiale, således at en migrering af eventuelle stoffer fra regeneratet hindres.
12.3 Kort beskrivelse af branchens produkter
Fællesnævneren for branchens produkter er, at de alle er hule. Produkternes godstykkelse er som regel lille i forhold til deres tværsnit. De fremstilles i mange forskellige former og størrelser.
Hovedparten af de blæsestøbte produkter er emballageprodukter som f.eks. flasker til opbevaring af alle mulige væsker, eksempelvis mineral- og sodavand. Til fremstilling af artikler, der er beregnet til emballering af fødevarer, må ikke anvendes andre stoffer end dem, der er anført i ”Bekendtgørelse om plastmaterialer og -genstande bestemt til at komme i berøring med levnedsmidler” (positivlisten). Desuden må migrationen af stoffer fra plastmaterialet over i levnedsmidlet ikke overskride fastsatte migrationsgrænser.
Af andre produkter kan nævnes emner som medicinbeholdere, benzintanke, legetøj f.eks. "gåbiler", vejpæle og tekniske artikler til f.eks. biler.
Størrelsesmæssigt varierer produkterne fra små emner som f.eks. medicinflasker til emner med et volumen på flere hundrede liter.
12.4 Energiforbrug
Der er ikke fundet oplysninger om typiske energiforbrug ved de forskellige blæsestøbningsprocesser.
Produktionens energiforbrug anvendes først og fremmest til fremstillingen af trykluft til opblæsningen samt til opvarmningen af plastmaterialet til forarbejdningstemperaturen.
Blæsestøbning er forbundet med et energitab via varmetab i forbindelse med opblæsning og afkøling af såvel maskiner som artikler.
En dansk virksomhed har reduceret energitabet kraftigt ved en betydelig investering i et stort varmegenindvindingsanlæg, således at virksomheden i dag udover egen rumopvarmning er i stand til at sælge varme til kommunen. Kølesystemet er baseret på, at al køling foregår med vand.
13 Ekstrudering
Se også:
Termoplastbranchens_råvarer
Emissioner ved forarbejdning af termoplast
Kemiske belastninger i arbejdsmiljøet
Miljø- og sundhedsvurderinger
Referencer
Indholdsfortegnelse
Oversigtsfigur
13.1 Introduktion
Den følgende beskrivelse af ekstruderingsbranchen og dens produkter er i al væsentlighed baseret på rapporten ”Renere teknologi i plastindustrien” (Plastindustrien i Danmark, 2000) og lærebogen ”Plastteknologi” Jensen et al. (2005). Det er ikke forsøgt at opdatere de to kilders oplysninger om råvareforbrug mv.
13.2 Kort om ekstruderingsbranchen
Ekstrudering er fællesbetegnelsen for en kontinuerlig proces, som anvendes til fremstilling af en lang række produkter, der kendes fra dagligdagen. Plastfolie (plastposer), rør, profiler, plader, kunstfibre, slanger og isolerede ledninger og kabler er alle eksempler på ekstruderede produkter.
Ekstruderingsbranchen er volumenmæssigt den største delbranche i Plastindustrien. Der anvendes en lang række råvarer, hvor polyethylen (PE), polypropylen (PP) og polyvinylchlorid (PVC) er de vægtmæssigt mest betydende, fulgt af polystyren (PS) og polyethylenterephthalat (PET) og i mindre omfang acrylonitril-butaidien-styren (ABS), polycarbonat (PC) og andre plasttyper.
Der anvendes en bred vifte af additiver ved ekstrudering. I de følgende afsnit nævnes en række additiver, der anvendes ved typiske produkter og processer, men listen er langt fra udtømmende.
13.3 Ekstruderingsprocessen
Et ekstruderingsanlæg består generelt af en eller flere ekstrudere samt noget følgeudstyr. Ekstruderen anvendes til at fremstille en sejtflydende, formbar plastmasse, som efterfølgende kan formes til f.eks. et af ovennævnte produkter, mens følgeudstyret er specielt fremstillet til det produkt, man ønsker at fremstille.
Ved fremstilling af de fleste af ovennævnte produkter kan coekstrudering komme på tale. Dette begreb dækker over anvendelsen af mere end 1 ekstruder til fødning af værktøjet. Herved er man i stand til at fremstille produkter sammensat af flere forskellige råvarer, hvilket giver mange interessante produktmuligheder.
Figur 1. Principskitse af ekstruder. (Kilde: PlastTeknologi-lærebogen udgivet af Erhvervsskolernes Forlag)
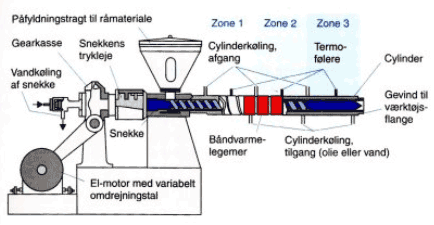
Råvaren, som oftest er i granulatform, fødes fra ekstruderens tragt til snekkens indtrækszone, hvorfra den føres fremad (som i en kødhakkemaskine) af den roterende snekke. Dels på grund af varmen fra den tempererede cylinder, men især på grund af friktionen mod cylinderen og den indre friktion i selve råvaren, opvarmes denne og bliver til en sejtflydende, formbar masse, lidt inden, den når enden af cylinderen. På grund af snekkens udformning opbygges der også et relativt højt tryk for enden af snekken, som skal bruges til at presse plastmassen igennem det værktøj, der spændes på enden af ekstruderen. Afhængigt af værktøjets udformning kan der herefter fremstilles (formes) en lang række forskellige produkter.
13.3.1 Folieekstrudering
Ved folieekstrudering er ekstruderen monteret med et folieværktøj, der kan lave en tyndvægget slange, som danner udgangspunkt for det færdige produkt. Normalt ekstruderes slangen i lodret, opadgående retning. Slangen føres op til aftræksvalserne, som klemmer slangen flad. Det er herefter muligt at blæse luft ind i slangen for at udvide den til den ønskede diameter, som er bestemmende for den færdige foliebredde, ligesom aftræksvalsernes hastighed kan indstilles, så man opnår den ønskede folietykkelse. Udvendig køles slangen (boblen) af med luft, og når aftræksvalserne er passeret, kan den fladlagte, orienterede plastslange spoles op. Denne kan så enten i processen eller senere skæres op i den ønskede bredde.
Figur 2. Principskitse af folieekstruder.. (Kilde: PlastTeknologi-lærebogen udgivet af Erhvervsskolernes Forlag)
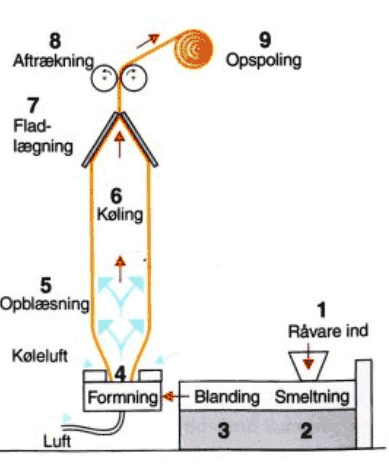
13.3.2 Ekstrudering af rør
Ved ekstrudering af rør fremstiller det værktøj, der monteres på enden af ekstruderen, et rør eller en slange med nogenlunde den dimension, man ønsker for det færdige produkt. Det kan dog varieres inden for visse grænser. Når den bløde slange forlader værktøjet, føres den ind i en kalibrering, som skal sørge for, at rørets eller slangens udvendige diameter bliver korrekt. Rørets/slangens overflade presses mod kalibreringen ved hjælp af vakuum eller trykluft. Under og efter kalibreringen afkøles plastmaterialet i et eller flere vandbade eller brusekamre. Fremføringen foregår mellem to larvefodslignende transportbånd, som holder en konstant aftrækshastighed, og til sidst sker der en afkortning eller opspoling af det færdige produkt.
Figur 3. Principskitse for en rørekstruder. (Kilde: PlastTeknologi-lærebogen udgivet af Erhvervsskolernes Forlag)
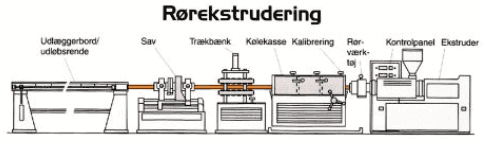
13.3.3 Profilekstrudering
Principielt er der ikke den store forskel på ekstrudering af rør/slanger og profiler. Ofte vil selve værktøjskonstruktionen dog være mere kompliceret. Profilværktøjet, som skal forme den bløde plastmasse til en profil, monteres for enden af ekstruderen. Umiddelbart efter dyseudløbet føres den varme profil ind i en vakuumkalibrering, som omslutter profilets udvendige overflade, for at holde de ønskede mål, mens profilet afkøles. Afkølingen foregår i et eller flere vandbade eller brusekamre. Fremføringen foregår mellem to larvefodslignende transportbånd, som holder en konstant aftrækshastighed. Afhængig af materialets stivhed og de ydre dimensioner sker der til sidst enten en afkortning eller opspoling af slutproduktet.
Figur 4. Priincipskitse af profilekstruder. (Kilde: PlastTeknologi-lærebogen udgivet af Erhvervsskolernes Forlag)
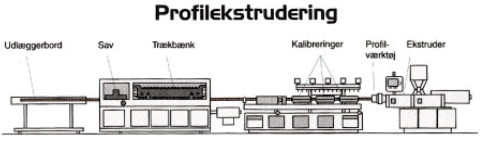
13.3.4 Plade- og planfolieekstrudering
Til plade- og planfolieekstrudering anvendes et fladdyseværktøj med en specielt udformet flydekanal, som former den bløde plastmasse til et bredt bånd. Straks efter, at båndet forlader dysen, føres det ind imellem et antal tempererede valser, som glatter og afkøler materialet. Herefter skæres kanterne af for at opnå den ønskede plade- eller foliebredde, og til sidst klippes pladerne til det ønskede længdemål eller rulles op i ”endeløse” baner.
13.3.5 Monofilamentekstrudering
Monofilamenter, som betyder enkelte tråde/fibre, fremstilles ved at spænde en dyse med et passende antal huller for enden af ekstruderen. Den varme plastmasse formes til et antal tråde, som føres lodret ned i en køletank med tempereret vand. Herefter føres trådene omkring et antal valser (ofte 7), som sørger for et konstant aftræk fra dysen. Herfra føres trådene gennem en luftovn eller et tempereret vandbad, som opvarmer trådene, og derefter omkring et antal valser (ofte 7), som kører ca. 8-10 gange hurtigere end de før omtalte. Herved strækkes trådene i længderetningen og øger derved trækstyrken betydeligt p.g.a. den langsgående orientering. Efter en yderligere opvarmning i en luftovn føres de strakte tråde omkring endnu et sæt valser, som kører lidt langsommere end ”strækvalserne”. Herved aflastes trådene, så de bliver mere fleksible, ligesom de vil krympe mindre ved en fornyet opvarmning under brug. Til sidst spoles monofilamenterne op på passende spoler og er herefter klar til brug.
Figur 5. Principskitse for en monofilamentekstruder. (Kilde: PlastTeknologi-lærebogen udgivet af Erhvervsskolernes Forlag)
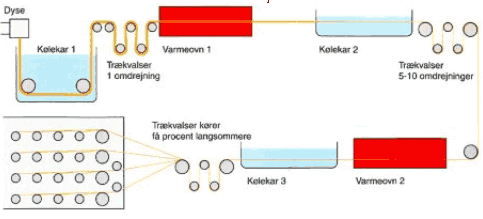
13.3.6 Kabelisolerings- og kapperørsekstrudering
Til dette formål monteres ekstruderen med et sidefødt rørværktøj, der kan forme et isolerende plastlag uden om det ledende materiale. Princippet kan også anvendes til plastbelægning af rør og lignende. Det forvarmede ledende materiale føres gennem dysens centrum og ekstruderen, som er placeret på den ene side af dysen, og føder denne med det isolerende plastmateriale, der lægger sig som et ”rør” uden om det materiale, der skal isoleres eller belægges. Herefter skal belægningen nedkøles i et kølebad, som kan være endog meget langt p.g.a kabelindustriens høje hastigheder. Hastigheden kontrolleres af en til formålet konstrueret ”trækbænk”, og det færdige produkt kan herefter afkortes på en indbygget sav eller opspoles, som det selvfølgelig sker for ledninger og kabler.
Figur 6. Principskitse af en ekstruder til kabelisolering. (Kilde: PlastTeknologi-lærebogen udgivet af Erhvervsskolernes Forlag)
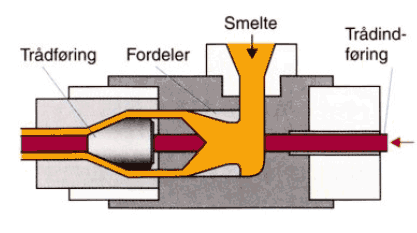
13.4 Ekstruderingsbranchens produkter og dens karakteristika
13.4.1 Rør
Produktionen i Danmark omfatter rør til ledning af vand, herunder trykrør (PE+PVC), afløbsrør (PE, PP og PVC), drænrør (PVC), gasrør (PE) og fjernvarmekapperør (PE).
13.4.1.1 Trykrør - PE
I Danmark findes 3 producenter af trykrør til vand. Rørene fremstilles i Danmark af MDPE og efter følgende standard: EN12201.
Rørproducenten tilsætter hverken pigmenter eller additiver selv. Der indkøbes færdigblandet råvare, såkaldt compound. Lyseblå rør er tilsat et blåt organisk pigment. Rørets blå farve er en kode for rør til drikkevand. Visse rør er endvidere farvet sorte ved tilsætning af pigmentet carbon black.
En leverandør oplyser, at den leverede polymer til PE-rør kan være tilsat UV-stabilisator, antioxidant og smøremiddel. UV-stabilisatoren er ofte sterisk hindrede aminer indeholdende ester- og/eller piperidingrupper. Antioxidanterne er typisk hydroxy-phenyl propionatbaserede og/eller fosfitbaserede. Smøremidlet er typisk calciumstearat, zink- eller natriumsalte eller blandinger heraf. Herudover er compounden ikke tilsat additiver.
13.4.1.2 Trykrør – PVC
I Danmark findes 2 producenter af PVC-trykrør. Trykrør af PVC fremstilles i Danmark blandt andet efter følgende standard: EN 1452.
Rørproducenten tilsætter selv additiver til råvaren. Som stabilisator anvendes Ca/Zn-forbindelser eller OBS (Organically Based Stabiliser), der angiveligt har et højere metalindhold end Ca/Zn-forbindelserne, på trods af navnet. Producenten tilsætter endvidere selv pigmenter. Det typiske pigment, som anvendes til PVC-trykrør til vand er enten et blåt organisk pigment eller carbon black. Endelig tilsættes der proceshjælpemidler, typisk i form af kridt. Herudover tilsættes PVC-polymeren til trykrør ikke yderligere additiver.
13.4.1.3 Afløbsrør - PE
I Danmark findes 1 producent af PE-afløbsrør. Rørene fremstilles i Danmark af HDPE og bl.a. efter standarden EN 13244. Rørene fremstilles på en måde, som adskiller sig radikalt fra den almindelige fremstillingsmetode til rør. Et bånd af HDPE ekstruderes og vikles omkring et roterende metalvæv. Samlingerne svejses sammen efterfølgende. Metoden anvendes til fremstilling af store rør (diameter > 1 m).
Der indkøbes såkaldt compound, og rørproducenten tilsætter hverken additiver eller pigmenter til råvaren.
PE-afløbsrør er sorte rør, og plastråvaren er tilsat pigmentet carbon black. Den leverede compound til afløbsrør er endvidere tilsat samme additiver (UV-stabilisator og antioxidant) som er tilfældet for blandt andet trykrør af PE. Herudover tilsættes compounden ikke additiver.
13.4.1.4 Faldrør og kloakrør af PP
Invendige faldrør og kloakrør fremstilles i Danmark efter standarderne EN 1451, henholdsvis EN 1852. De udgør cirka 10% af markedet. Der er ingen oplysninger om, hvordan plasten er modificeret eller farvet.
13.4.1.5 Afløbsrør – PVC
I Danmark findes 2 producenter af PVC afløbsrør. Afløbsrør af PVC fremstilles i Danmark efter følgende standard: EN 1401.
Rørproducenten tilsætter selv additiver til råvaren. Som stabilisator anvendes Ca/Zn-forbindelser eller OBS (Organically Based Stabiliser), der angiveligt har et højere metalindhold end Ca/Zn-forbindelserne, på trods af navnet. Producenten tilsætter endvidere selv pigmenter. Afløbsrør til indendørs brug er farvet grå med carbon black. Afløbsrør til udendørs brug er "lerfarvede". Der tilsættes fyldstoffer typisk i form af kridt. Herudover tilsættes PVC-polymere til afløbsrør ikke additiver.
13.4.1.6 Drænrør
I Danmark findes 2 producenter af drænrør. Drænrør af PVC fremstilles i Danmark efter følgende standard: DS 2077 del 1 og 2 + SBC 211.
Rørproducenten tilsætter selv additiver til råvaren. Som stabilisator anvendes Ca/Zn-forbindelser eller OBS (Organically Based Stabiliser), der angiveligt har et højere metalindhold end Ca/Zn-forbindelserne, på trods af navnet. Producenten tilsætter endvidere selv pigmenter. Drænrør er "lerfarvede". Herudover bliver PVC til drænrør tilsat slagmodificerende polymerer i koncentrationer på op til 5 pct. Polymererne kan bl.a. være af chloreret PE eller ABS. Der tilsættes fyldstoffer typisk i form af kridt. Herudover tilsættes PVC-polymerer til drænrør ikke additiver.
13.4.1.7 Gasrør
I Danmark findes 2 producenter af gasrør. Rørene fremstilles i Danmark af MDPE og efter følgende standard: EN 1555.
Rørproducenten tilsætter hverken additiver eller pigmenter til råvaren. Der indkøbes såkaldt compound.
Gasrør er farvet gule, idet gul er en farvekode, som signalerer en advarsel om fare for gasudslip. Det gule pigment er et organisk pigment. Indtil midten af 1980’erne siden var pigmentet cadmiumgult, men i dag fremstilles alle gasrør i Danmark med cadmiumfrie pigmenter. Visse gasrør kan endvidere også være farvet sorte med carbon black.
En leverandør oplyser, at den leverede polymer til PE-rør kan være tilsat UV-stabilisator, antioxidant og smøremiddel. UV-stabilisatoren er ofte sterisk hindrede aminer indeholdende ester og/eller piperidingrupper. Antioxidanterne er typisk hydroxy-phenyl-propionatbaserede og/eller fosfitbaserede. Smøremidlet er typisk calciumstearat, zink- eller natriumsalte eller blandinger heraf. Herudover er compounden ikke tilsat additiver.
13.4.1.8 Kapperør (til fjernvarmerør)
I Danmark findes 4 producenter af fjernvarmerør, som alle selv fremstiller kapper. Kapperør fremstilles af HDPE og efter standard EN 253. I denne standard er det bl.a. fastlagt, at kapperør max. må indeholde 15 pct. regenerat og at det skal være fra virksomhedens eget produktionsaffald. I standarden er vedhæftningen mellem kapperørets inderside og isole-ringsskummet endvidere fastlagt.
Rørproducenterne anvender enten færdig PE-compound eller tilsætter selv additiver og pigmenter i form af masterbatch til den leverede polymer. Både den færdigt compounderede og den masterbatchtilsatte polymer til kapperør indeholder carbon black (sort pigment + UV-stabilisator). En leverandør oplyser, at deres råvarer til kapperør herudover indeholder under 0,5 pct. varmestabilisator. Denne varmestabilisator er baseret på antioxidanter indeholdende hydroxy-phenyl-propionater. Herudover er compounden ikke tilsat yderligere additiver.
13.4.2 Slanger
Ekstruderede plastslanger anvendes fortrinsvis som haveslanger, industrislanger til transport af vand, væske og luft, levnedsmiddelslanger samt som medicinske slanger. Typisk er plastslanger fremstillet af blødgjort PVC. Ekstrudering af slanger adskiller sig i princippet ikke fra ekstrudering af rør. Den væsentligste forskel er, at slanger fremstilles i blødgjort PVC, og at ekstruderen til slangefremstilling typisk er enkeltsnekket.
PVC-slanger ekstruderes typisk ved en temperatur på 150-160 °C, og fremstillingen kræver totalt ca. 0,35 kWh pr. kg. råvare inkl. el til administration.
Slangerne er bl.a. kendetegnet ved lang levetid, god styrke og evne til at sikre et flow uden at kinke (knække sammen). Det skal nævnes, at der stilles særlige krav til fremstilling af medicinske slanger, bl.a. foregår produktionen af disse i specielle renrum.
13.4.2.1 PVC-slanger til industri, havebrug mm.
Industrislanger anvendes til transport af vand, væske og luft i industrien. En mindre mængde slanger anvendes i levnedsmiddelindustren. Endvidere anvendes PVC-slanger som haveslanger.
Slangerne består typisk af flere forskellige lag PVC, som coekstruderes omkring en armering af polyesterfibre. Der er to producenter af disse slanger i landet. Herudover findes en lille håndfuld producenter som fremstiller relativt små mængder specialslanger.
PVC-slangerne er blødgjort med ca. 30 pct. DEHP, dog er de levnedsmiddelslanger, som anvendes specielt til transport af mælk typisk blød-gjort med en polymer blødgører (adipinsyrebaseret polyester). Slanger fremstillet i Danmark stabiliseres altid med calcium-/zinkstabilisatorer. Både blødgøreren og stabilisatoren er tilsat den leverede råvare. Slangeproducenten tilsætter alene pigmenter til råvaren. Disse tilsættes i form af masterbatch. De typisk anvendte pigmenter er titanoxid, jernoxid, og carbon black. Herudover tilsættes endvidere en mindre del pigmenter alle af organisk karakter.
Udover blødgører og stabilisator indeholder PVC-råvaren et smøre-middel bestående af en amidvoks samt epoxyderet soyabønneolie (co-stabilisator). Herudover er den leverede compound ikke tilsat additiver.
Der anvendes ofte store dele PVC-regenerat som råvare ved fremstillingen af haveslanger. Regeneratet coekstruderes til de "indre lag" af slangerne.
13.4.2.2 Slanger til medicinsk brug
Produkterne i denne gruppe anvendes til hospitalsslanger, katetre, rør, sug etc. Der er 2 producenter af medicinske slanger i Danmark. Fremstilling af slangerne foregår i renrum. Materialekvalitetskravene til medicinske slanger er fastlagt i European Pharmacopeia VI, 1212.
Råvaren (compounden) til fremstilling af medicinske slanger er blødgjort med DEHP og stabiliseret med calcium/zink stabilisatorer samt med epoxyderet soyabønneolie (co-stabilisator). Herudover indeholder compounden et smøremiddel bestående af en amidvoks. Endelig kan compounden indeholde små mængder blå eller violet pigment. Begge pigmenter er af organisk karakter. Pigmentet tilsættes for at give slangen en neutralt udseende farve i modsætning til den lidt gullige nuance blødgøreren kan give.
Herudover er compounden til fremstilling af medicinske slanger ikke tilsat andre additiver.
13.4.3 Profiler
Ved ekstrudering fremstilles en stor og varieret gruppe af profiler i mange forskellige materialer, med vidt forskellige anvendelsesformål som f.eks. profiler til fremstilling af vinduesrammer (PVC), tagrender og nedløbsrør (PVC), tætningsrammer til køle- og fryseskabe (PVC samt blødgjort PVC). Profilekstrudering omfatter endvidere fremstilling af tagplader af PVC og PC, idet teknikken hertil er beslægtet med teknikken til fremstilling af profiler i almindelighed.
En restgruppe "andre" profiler, omfatter tusindvis af forskellige lister til vidt forskellige formål som f.eks. møbellister, plakatlister, gulvlister og "trælister", tekniske lister og kabelafdækningsbånd m.m. Disse profiler fremstilles fortrinsvis i PE, PVC, PS, ABS samt i termoplastiske elastomerer. Volumenmæssigt skønnes det, at denne rest-gruppe anvender få tusinde tons pr. år og at gruppens produkter fremstilles af ca. 10 producenter i Danmark.
13.4.3.1 PVC-profiler
Som det fremgår af ovennævnte tabel er størstedelen af profilerne fremstillet af PVC. Indenfor PVC-profilerne er vinduesprofilerne den type, som fremstilles i det største volumen.
Energiforbruget til fremstilling af PVC-profiler er typisk 0,5 kWh pr. kg PVC (totalt forbrug til ekstrudering, administration m.m.).
13.4.3.2 Vinduesprofiler
Vinduesprofiler fremstilles i Danmark af to producenter. Profilerne er omfattet af normen for vinduer "RAL 716/1 pkt. 1.2.2", der bl.a. angiver hvilke parametre og DIN-normer, som profilet skal overholde. Endvidere er vinduer, beregnet for det svenske marked, underkastet Verksnorm 3000. Begge normer foreskriver, at vinduet skal fremstilles i slagfast PVC, modificeret med CPE (chloreret polyethylen), EVA (ethylen-vinyl acetat) eller acrylat i mængder på 6-10%. Dansk Vindues Kontrol's (DVK) specifikationer for profilerne henviser til de to første normer. Endelig har British Standard i BS 7413 fastlagt normer for vinduesprofiler. Heraf fremgår bl.a. at et profil max. må indeholde 10 pct. regenerat fra eget produktionsaffald.
Vinduesprofiler fremstilles i hård PVC uden tilsætning af blødgører. En af producenterne compounderer selv råvaren. Profilerne ekstruderes typisk ved en temperatur på 180-205 °C.
PVC-vinduesprofiler har i mange år været stabiliseret med stabilisatorsystemer indeholdende bly eller cadmium. Dette er ikke tilladt længere i Danmark, men det vides ikke, hvilke stabilisatorer, der præcist har erstattet bly og cadmium. Endvidere tilsættes smøremidler til råvaren. Disse kan være paraffin-, voks-, stearat- eller oliederivatbaserede produkter. Stabilisator og smøremiddel udgør typisk et samlet system og tilsættes tilsammen i mængder varende til 3-5 pct. Typisk fremstilles profilerne i farverne hvid eller grå. Pigmenter anvendt hertil er titandioxid og kridt, eller carbon black. Endelig tilsættes 5-12 pct. kridt som fyldstof.
Mange PVC-profiler har farvet overflade. Disse farves ofte ved at co-ekstrudere et tyndt lag farvet PMMA (acryl) på overfladen af profilet. Endvidere farves profilerne ved pålægning af en farvet folie eller ved lakering.
13.4.3.3 Tagrender, nedløbsrør o.l.
Foruden tagrender og nedløbsrør omfatter produktgruppen profiler til afskærmning af bygningsdele mod vejrlig m.v. Produkterne fremstilles i Danmark af 2 producenter. Begge producenter compounderer deres egen råvare.
Tagrenderne og nedløbsrørene fremstilles i hård PVC uden tilsætning af blødgører. Profilerne ekstruderes typisk ved en temperatur på ca. 180 °C. Som for vinduesprofiler tilsættes der ikke længere bly eller cadmium ved produktion i Danmark, men hvilke stabilisatortyper, der har erstattet bly og cadmium vides ikke. Der tilsættes voks, stearat og oliederivater, som smøremiddel.
Stabilisator og smøremiddel udgør typisk et samlet system og tilsættes i mængder svarende til 3-5 pct. Normalt fremstilles profilerne i farverne hvid, grå, brun eller sort. Pigmenter anvendt hertil er titandioxid, carbon black og brunt organisk pigment. Typisk tilsættes endvidere 5-12 pct. kridt som fyldstof.
13.4.3.4 Rammer
PVC-rammer anvendes indenfor køle- og fryseskabsindustrien som tætningsrammer til døre, låger m.m.
I Danmark produceres disse af 2 producenter. Ingen af producenterne compounderer råvaren selv.
Rammerne består af et hårdt PVC-profil og et fleksibelt PVC-profil, som co-ekstruderes, udskæres og svejses sammen. Det fleksible profil fungerer som pakning, og svejsningen foregår ved varmsvejsning også kaldet stuksvejsning og spejlsvejsning.
Profilerne ekstruderes typisk ved en temperatur på 130-200°C. Det bløde profil er stabiliseret med calcium/zink.
Det fleksible profil er hovedsageligt blødgjort med DEHP. Blødgøreren tilsættes i forholdet 20-60 pct. alt afhængigt af profilets ønskede fleksibilitet.
Typisk fremstilles profilerne i farverne hvid, grå, brun eller sort. De anvendte pigmenter er titandioxid, kridt, carbon black og jernoxid. Udover pigment er råvaren tilsat mængder af paraffinolier på mindre end 1 pct., der virker som smøremiddel. Endelig er råvaren tilsat umættede fedtsyrer i mængder på under 1 pct., der virker som antioxidant.
13.4.4 Fladekstruderede plader og folie
Fladekstruderede plader og folier, fremstillet i Danmark, er fortrinsvis til videreforarbejdning (termoformning af emballager og tekniske artikler). Termoformningsprocessen er beskrevet i et selvstændigt afsnit. De mest udbredte materialer ved fladekstrudering er PS, PET, ABS, PP og PE.
I Danmark eksisterer 5 virksomheder, som fladekstruderer plader og folie, der fortrinsvis videreforarbejdes til emballage eller tekniske artikler ved termoformning.
Fremstillingen af plader og folie adskiller sig på visse områder fra fremstillingen af de hidtidigt omtalte produkter. Ved ekstrudering af plader og folier er der ikke monteret en kalibreringsdyse efter værktøjet, som ved de tidligere nævnte produkter. I stedet kalibreres og køles pladen eller folien ved at passere et sæt kølevalser, som er monteret umiddelbart efter værktøjet. En anden forskel er, at plader og folier ikke køles i vandbad.
De to sider i længderetningen af pladen eller folien er altid ujævn, hvorfor disse afskæres. Dette afskær hakkes og recirkuleres, hvis ikke folien er et laminat af flere forskellige polymertyper. Efter kølingen oprulles eller opskæres og stables ekstrudatet.
13.4.4.1 Plader og folie til emballage
Som angivet i Tabel 1 fremstilles plader til emballage fortrinsvis af PET og PS. Endvidere fremstilles der mindre mængder plader af PE, PP. Sundhedsstyrelsens bekendtgørelse om plastmaterialer og -genstande bestemt til at komme i berøring med levnedsmidler angiver en positivliste for råvarer, der er godkendt til at komme i kontakt med levnedsmidler og dermed bl.a. til levnedsmiddelemballage.
I Danmark er der 4 virksomheder, som fremstiller sådanne plader og folier.
PE- og PP-plader og folie til emballage
PE-plader fremstilles i HDPE. Over 95 pct. af pladerne anvendes til emballager til direkte kontakt med fødevarer. HDPE-plader og -folier ekstruderes ved en temperatur på 220-240 °C, mens temperaturen ved ekstrudering af PP-plader og folie normalt ligger i intervallet 230-250 °C.
Der anvendes både organiske og uorganiske pigmenter. De uorganiske pigmenter indeholder ikke tungmetaller. Tungmetaller i mængder på mindre end 0,015 pct. kan dog findes i de rene pigmenter. Fra råvareleverandørens side er polymeren normalt alene tilsat antioxidanter samt glidemiddel. Herudover er compounden ikke tilsat additiver.
PS-plader og –folie til emballage
PS-plasder og folie til emballage inkluderer også brugen af slagfast polystyren, HIPS. Plader og folie af slagfast PS fremstilles ofte med et tyndt toplag af ikke slagfast PS, PET eller mere sjældent med et toplag af PE. Toplaget coekstruderes samtidigt med selve folien. Ved laminering med PET coekstruderes et meget tyndt lag af ABS mellem toplag og selve folien. Mængdemæssigt udgør toplagene ca. 10 pct. af foliens masse, mellemlaget få procent.
Over 95 pct. af pladerne anvendes til emballager til direkte kontakt med fødevarer.
PS-plader og -folier ekstruderes ved en temperatur på 200-220 °C. Der anvendes både organiske og uorganiske pigmenter. De uorganiske pigmenter indeholder ikke tungmetaller. Tungmetaller i mængder på mindre end 0,015 pct. kan findes i de rene pigmenter. Fra råvareleverandørens side er polymeren normalt ikke tilsat andet. Under 1 pct. af folierne er dog tilsat antistatmiddel. Dette additiv består af et amorft syntetisk silikat. Polymeren tilsættes herudover kun pigmenter hos producenten.
13.4.4.2 Plader og folie til tekniske artikler
Fremstillingen af plader og folie til tekniske artikler adskiller sig i princippet ikke fra fremstillingen af plader og folie til emballage.
Pladerne fremstilles fortrinsvis af PS (inkl. HIPS) og ABS. En mindre mængde af pladerne fremstilles af PC og andre tekniske plasttyper. Disse andre plasttyper er ikke nøjere undersøgt.
Der var i 2000 to producenter af disse produkter i Danmark.
PS-plader og -folier ekstruderes typisk ved temperatur på 200-220°C.
Der anvendes både organiske og uorganiske pigmenter. De uorganiske pigmenter er ikke tungmetalbaserede. Tungmetaller i mængder på mindre end 0,015 pct. kan findes i de rene pigmenter.
Under 1 pct. af pladerne fremstilles af råvarer tilsat brandhæmmer. Denne brandhæmmer indeholder blandt andet bromerede forbindelser, men ikke polybromerede biphenyler. Råvaren indeholder i alt under 1 pct. brom. Brandhæmmeren indeholder endvidere antimontrioxid. Denne er tilsat i mængder svarende til over 0,1 pct. af den færdige compound.
Herudover er der normalt ikke tilsat additiver til PS plader og folie.
13.4.5 Mono- og multifilamenter
Filamenter eller plastfibre fremstilles ligeledes ved ekstrudering, med PP og PE som de altdominerende materialer i Danmark. Filamenter opdeles i to hovedområder, nemlig monofilamenter, der er enkeltfibre, samt multifilamenter, der betegner produkter bestående af bundter af meget fine enkeltfibre.
Monofilamenter anvendes typisk i væverier til fremstilling af bl.a. geotekstiler, afdækningsnet, armering samt til fletning af tovværk og fiskenet. Værktøjet, hvori monofilamenterne ekstruderes i hundredvis af fibre, som enkeltvis opspoles for videre forarbejdning. Multifilamenter anvendes hovedsageligt indenfor to områder, nemlig til hygiejneprodukter som bleer, bind og inkontinensprodukter og til tekstilindustrien til fremstilling af bl.a. geotekstiler, væksthustekstiler, tæpper samt møbel- og madrastekstiler.
Multifilamenterne fremstilles groft sagt på samme måde som monofilamenter, dog har multifilamenterne en finere diameter. Det videre forløb afviger dog, idet bundter med over 100.000 fibre opskæres i forskellige længder for derefter at blive pakket i baller med henblik på opbevaring inden videre forarbejdning.
Multifilamenterne til hygiejnemarkedet er typisk af en langt lettere kvalitet end multifilamenterne til tekstilindustrien.
Filamenter produceres i Danmark af i alt fire virksomheder, idet to virksomheder fremstiller monofilamenter og to virksomheder fremstiller multifilamenter.
Fremstillingen af monofilamenter adskiller sig fra fremstilling af de tidligere omtalte produkter. Filamenternes tykkelse beskrives ved at angive vægten af én 9 km lang fiber. Vægten af 9 km monofilament varierer fra små 200 g til godt 1500 g.
Efter værktøjet, som fremstiller 100-200 monofilamenter ad gangen, køles filamenterne ved at passere et vandbad.
Efter kølingen genopvarmes filamenterne delvist. I varm tilstand strækkes de i længderetningen. Herved orienteres molekylerne i hvert enkelt filament, hvilket øger filamentets styrke væsentligt.
Strækningen udføres ved, at filamenterne passerer en række ruller, hvor de sidste rullers omdrejningshastighed er større end de første rullers.
Efter endt strækning afkøles filamenterne endeligt, hvorefter de enkeltvis vikles på spoler med henblik på videre forarbejdning på bl.a. væverier.
Energiforbruget til fremstilling af monofilamenter incl. belysning, ventilation, tørring m.m. udgør ca. 1,25 kWh pr. kg. PP monofilamenter ekstruderes typisk ved temperatur på 250-270°C.
Monofilamenter fremstilles normalt i gennemfarvede kvaliteter.
Der anvendes både organiske og uorganiske pigmenter. De uorganiske pigmenter er ikke tungmetalbaserede.
25-50 pct. af filamenterne tilsættes UV-stabilisatorer af HALS-typen (hindrede aminer). Additivet tilsættes i form af masterbatch. UV-stabilisatoren tilsættes i omkring 0,5 pct.
Under 2 pct. af filamenterne fremstilles af råvarer tilsat brandhæmmer. Brandhæmmeren indeholder blandt andet bromerede forbindelser, men ikke polybromerede biphenyler. Råvaren indeholder i alt under 1 pct. brom. Brandhæmmeren indeholder endvidere antimontrioxid. Denne er tilsat i mængder svarende til over 0,1 pct. af den færdige compound.
Endvidere er råvaren leveret med indhold af smøremiddel og forarbejdnings- samt langtidsstabilisatorer. Smøremidlet er typisk calciumstearat og stabilisatorerne er antioxidanter. Herudover er råvaren ikke tilsat additiver.
13.4.5.1 PE monofilamenter
HDPE monofilamenter ekstruderes typisk ved temperatur på 240- 260°C.
Monofilamenter fremstilles normalt i gennemfarvede kvaliteter.
Der anvendes både organiske og uorganiske pigmenter. De uorganiske pigmenter er ikke tungmetalbaserede. (Kilde 29 og 30). Mellem 25 og 50 pct. af filamenterne tilsættes UV-stabilisator af HALS-typen. Additivet tilsættes i form af masterbatch. UV-stabilisatoren tilsættes i mængder omkring 0,5 pct.
En lille del af polymeren til monofilamenterne er tilsat glidemiddel. Glidemidlet er en modificeret polyolefin copolymer som tilsættes råvaren i form af masterbatch. Koncentrationen af det aktive stof i det færdige produkt overstiger ikke 500 ppm.
Under 2 pct. af filamenterne fremstilles af råvarer tilsat brandhæmmer. Denne brandhæmmer indeholder blandt andet bromerede forbindelser, men ikke polybromerede biphenyler. Råvaren indeholder i alt under 1 pct. brom. Brandhæmmeren indeholder endvidere antimontrioxid. Denne er tilsat i mængder svarende til over 0,1 pct. af den færdige compound.
Endvidere er råvaren leveret med indhold af smøremiddel og forarbejdnings- samt langtidsstabilisatorer. Smøremidlet er typisk calciumstearat og stabilisatorerne er antioxidanter.
Herudover er polymeren til PE-monofilamenter normalt ikke tilsat additiver.
13.4.5.2 Multifilamenter
Multifilamenter fremstilles næsten på samme måde som monofilamenter, men er som nævnt langt finere end monofilamenterne.
Multifilamenterne samles i bundter med flere hundrede tusinde enkelte fibre. Bundterne køles i vand, genopvarmes, strækkes, kruses, opskæres til stabelfibre i forskellige længder for endeligt at blive presset sammen til baller med henblik på videre forarbejdning til "non-woven" produkter.
I Danmark fremstilles multifilamenter hovedsageligt af PP.
Den enkelte fibers tykkelse angives blandt andet ved enheden Denier, som er vægten af 9 km fiber. Denne vægt varierer efter anvendelsen. Til non-woven produkter anvendes fra 15 gram og nedefter.
PP multifilamenter ekstruderes typisk ved en temperatur på 300°C. Energiforbruget til fremstilling af et kg PP multifilament er typisk 0,5 kWh.
Filamenter fremstilles typisk i hvid eller grå kvalitet, men farvede kvaliteter produceres også.
De normalt anvendte pigmenter er titanoxid, carbon black og jernoxid. Herudover anvendes mindre mængder organiske pigmenter. Der anvendes indfarvet polymer.
Råvaren er leveret med tilsætning af stabilisatorer. Der anvendes både phenol- og phosphitbaserede antioxidanter. De phenolbaserede er typisk hydroxyphenylpropionatestere og de phosphitbaserede er typisk hydroxybenzylphosphonater (butylphenoler).
Råvaren er endvidere leveret med et indhold af forarbejdningsforbedrende glidemiddel (calciumstearat).
Der tilsættes UV-stabilisatorer af HALS typen (Hindered Amine Light Stabilizers)til visse specielle multifilamenttyper. Disse specialtyper stabiliseres endvidere med hydroxybenzylforbindelser.
Herudover er polymeren normalt ikke tilsat additiver.
Efter ekstruderingen, men inden opskæringen, befugtes fibrene med spindeolie. Spindeolien forbedrer fibrenes forarbejdningsegenskaber idet den dels påvirker fibrenes overfladeegenskaber og dels reducerer evnen til elektrisk opladning. Denne olie er typisk rene polyglycolfedtsyreestre.
13.4.6 Elkabler
I Danmark fremstilles elkabler til spændingsområdet 0,005-400 kV, dvs. installationskabler, samt lav- og mellemspændingskabler.
Kort fortalt fremstilles kabler ved at ekstrudere op til flere lag plast omkring en eller flere elektriske ledere. Det inderste plastlag udgør et isoleringslag om den enkelte leder. Dernæst følger et fyldlag om et bundt isolerede ledere og yderst et robust beskyttende kappelag.
Materialevalget afhænger i særdeleshed af, hvilken spænding kablerne skal anvendes til, idet man til høj spænding fortrinsvis bruger PE samt tværbundet PE (= PEX), og til lavere spænding fortrinsvis anvender PVC. Herudover anvendes andre materialer (gummi, papir, asfalt, metal), som ikke beskrives i denne rapport.
I Danmark er der 1 stor og 2 mindre virksomheder, som fremstiller elkabler. Virksomhederne har produktion 5 steder i landet. Oplysningerne i denne rapport er baseret på oplysninger fra den ene store producent.
PVC anvendes fortrinsvis i lavspændingsområdet under 1.000 volt og PE fortrinsvis i højspændingsområdet over 1.000 volt.
PVC'en er blødgjort, og virksomheden compounderer selv sin råvare. Som noget specielt pelleterer producenten compounden efter compounderingen.
PE kvaliteterne er LDPE, MDPE og PEX (tværbundet PE).
Som tidligere nævnt fremstilles kabler ved at ekstrudere flere lag plast omkring en eller flere elektriske ledere af kobber eller aluminium.
Ekstruderingsværktøjet minder i princippet om et værktøj til rørfremstilling. I niplen, som danner rørets hulrum, bliver den elektriske leder trukket ind i kabelværktøjet og polymeren lægges som et rør omkring lederen.
Ekstruderingen foregår uden brug af kalibreringsdyse og ekstrudatet køles i vandbad.
Ved fremstilling af kabler med flere ledere (årer) ekstruderes først et isolerende lag omkring de enkelte ledere. Derefter bliver årerne opsamlet på store spoler. Inden det endelige kabel fremstilles, afspoles de ønskede årer og vikles sammen i et bundt.
Bundtet bliver herefter pålagt de forskellige plastlag. Viklingen danner hulrum mellem de enkelte årer, og for at opnå et pænt rundt kabel pålægges først et fyldlag med et såkaldt trykværktøj. Trykværktøjet presser den bløde compound ned i hulrummene mellem årerne.
I installationskabler er de forskellige plastlag adskilt af et fint lag talkum. Dette talkumlag sikrer bl.a., at lederen nemt kan afisoleres i forbindelse med installation, og påføres umiddelbart før et lag ekstruderes.
Lederen i højspændingskabler omgives af flere lag elektrisk halvledende og isolerende plast. De halvledende lag pålægges for at opnå en ensartethed i det elektriske felt omkring lederen.
Endelig skal det nævnes, at kabler til mellem- og højspændingsområdet ofte omvikles med kobberbånd, ledende papir, asfalt, bly eller kombinationer af disse. Brugen af disse materialer er ikke yderligere undersøgt i denne rapport.
Plasten bliver i visse tilfælde coekstruderet. Et eksempel herpå er ekstrudering af flerfarvede isoleringslag i installationskabler (gul/grøn = jordforbindelse) samt coekstrudering af ledende og isolerende lag i højspændingskabler.
Endelig skal det nævnes, at en linie ofte er monteret med flere ekstrudere, således at flere lag kan pålægges i umiddelbart forlængelse af hinanden. På figuren er der kun angivet brugen af en ekstruder.
Kabler indeholdende lag af PEX eller gummi skal efter ekstruderingen vulkaniseres. Vulkaniseringen foretages ved 300-400 °C og under forhøjet tryk. Trykket etableres i nitrogen atmosfære.
Ekstruderingstemperaturen for PVC, PE og EPDM er henholdsvis 180 °C, 220 °C og 80 °C. Energiforbruget til ekstrudering er ca. 0,25 kWh/kg for PE/PEX og ca. 0,15 kWh/kg for PVC (excl. køling, udsugning m.m.).
De anvendte pigmenter er alle, på nær mindre mængder titanoxid, af organisk karakter og anvendes i form af masterbatch.
PVC-råvaren er endvidere tilsat blødgører. Den anvendte blødgører er for 90 pct. vedkommende DEHP. De resterende 10 pct. er overvejende andre phthalatbaserede blødgørere. Chlorparaffiner anvendes ikke længere ved fremstilling af kabler i Danmark. Der anvendes i gennemsnit små 30 pct. blødgører pr. kg PVC-compound.
Som stabilisator anvendes hovedsageligt calcium-zink stabilisatorer. Det skal her nævnes, at den største danske producent er verdens første producent af blyfri PVC-kabler. En mindre mængde PVC til specialkabler og telekabler stabiliseres stadigvæk med blyholdige stabilisatorer.
Omkring 15 pct. af PVC-mængden bliver i dag brandhæmmet med antimontrioxid. Der tilsættes små 2 pct. antimontrioxid, som anvendes til visse specielle kabeltyper, primært til eksportmarkedet.
Blødgører, stabilisator og antimontrioxid tilsætter kabelproducenten selv til PVC-råvaren. Herudover tilsætter producenten 10-25 pct. kridt som fyldstof. Pigment tilsættes i form af masterbatch.
PE-råvarerne leveres som brugsklare compounds. Dog tilsætter producenten pigmenter i form af masterbatch.
Denne råvare er tilsat antioxidanter i mængder under 0,2 pct. Typen af antioxidant er fortrolig.
Under halvdelen af PE-råvaren er tilsat et organisk peroxid (dicumyl peroxid). Dette peroxids funktion er at initiere dannelsen af tværbindinger i PEX-laget. Der tilsættes omkring 1 pct. peroxid til polymeren.
14 Ekspandering af polystyren (EPS)
Se også:
Termoplastbranchens_råvarer
Emissioner ved forarbejdning af termoplast
Kemiske belastninger i arbejdsmiljøet
Miljø- og sundhedsvurderinger
Referencer
Indholdsfortegnelse
Oversigtsfigur
14.1 EPS-branchen og dens råvarer
Ekspanderet polystyren (EPS) er et celleprodukt, der af de fleste kendes under betegnelsen "flamingo". Produkter af ekspanderet polystyren anvendes inden for områderne emballage, isolering og tekniske artikler, og den danske produktion ligger tonnagemæssigt med hovedvægten på emballage- og isoleringsprodukter, mens tekniske artikler kun udgør en mindre del.
EPS-råvarer fremstilles i udlandet ud fra styren. Under fremstillingsprocessen polymeriseres styren til polystyren. Processen, som er en suspensionspolymerisation, foregår i vandigt miljø tilsat suspensionsmidler. Det færdige polymerisationsprodukt forefindes som små kugler (beads) svævende i den vandige fase. Ekspansionsmidlet (pentan) opløses i kuglerne efter, at polymerisationsprocessen er forløbet. De vigtigste nøgletal for miljøbelastningen ved produktion af råvaren ekspanderbar polystyren findes i afsnittet ”Produktion af polystyren (PS)”.
Når pentantilsætningen er tilendebragt sigtes kuglerne i forskellige størrelsesfraktioner. Kuglerne påføres en coatning, som modvirker, at kuglerne utidigt smelter sammen under de efterfølgende forarbejdningsprocesser hos EPS-producenterne. Sammen med coatningen kan evt. additiver tilsættes.
Den færdige EPS-råvare har form af små kugler, som for standardproduktets vedkommende består af ca. 94 pct. polystyren og ca. 6 pct. pentan. Kuglerne leveres i forskellige størrelsesintervaller inden for området 0,2-6 mm diameter.
14.2 Ekspandering af EPS
14.2.1 Produktionsproces for emballage og tekniske artikler
Produktionsprocessen består af forskumningsprocessen, mellemlagringsprocessen, støbeprocessen samt tørreprocessen.
Produktionen starter med en forskumning, hvor kuglerne opvarmes ved tilførsel af vanddamp. Varmetilførslen blødgør polystyren og fordamper ekspansionsmidlet, hvorved kuglerne opskummes. Herved øges kuglernes størrelse 15-30 gange i forhold til udgangsstørrelsen. Processen foregår kontinuerligt.
Efter forskumningen mellemlagres kuglerne i op til 2 døgn. Under mellemlagringen trykudligner atmosfærisk luft de opskummede kugler, hvorved der undgås opbygning af undertryk og dermed kollaps af kuglerne.
Efter forskumning og mellemlagring transporteres de forskummede kugler til en støbemaskine, der er forsynet med en form svarende til det ønskede produkt.
Den med vanddamp forvarmede form fyldes med kugler, og der tilføres varme ligeledes via vanddamp. Herved udvider kuglerne sig yderligere og svejses derved sammen. Formen afkøles med kølevand. Når produktet er afkølet, åbnes formen, og det færdige produkt kastes ud af formen ved hjælp af trykluft. Støbeprocessen varer ca. 1 1/2 minut.
DOR (2000a) giver følgende fordeling af pentanemissionen fra de forskellige procestrin:
Forskumning: 25 pct.
Mellemlagring 25 pct.
Udstøbning, tørring, emballering og lagring 20 pct.
Slutprodukt, 48 timers lagring 20 pct.
Slutprodukt, to måneders brug 10 pct.
Fordelingen kan dog variere med det producerede produkt, og pentanen frigives i vid udstrækning ved diffus emission. EPS-sektionen i Plastindustrien i Danmark er i skrivende stund i færd med at gennemføre en undersøgelse, der skal etablere et mere præcist billede af fordelingen fra de forskellige procestrin. De ovenstående tal skal derfor tolkes med forsigtighed.
14.2.2 Produktionsproces for isoleringsmateriale
EPS-isoleringsmateriale fremstilles efter samme princip som EPS-emballage, dog støbes isoleringsprodukter ikke direkte i den ønskede udformning, men i blokke, som efterfølgende opskæres.
Efter forskumning og mellemlagring fyldes kuglerne over i en stor blokstøbeform, hvor der tilføres vanddamp. Ved denne proces blødgøres kuglernes overflade, samtidig med at de presses sammen. Støbningen, som delvist foretages under vakuum, varer fra 3-6 min., hvorefter kuglerne hænger sammen og danner en blok.
Blokke støbes i forskellige størrelser med et rumfang fra 1,5-8 m³. Efter afkøling og tørring opskæres blokken til plader, der primært anvendes til isolering.
DOR (2000b) giver følgende fordeling af pentanemissionen fra de forskellige procestrin:
Forskumning: 25 pct.
Mellemlagring 25 pct.
Udstøbning, tørring, emballering og lagring 20 pct.
Slutprodukt, 48 timers lagring 20 pct.
Slutprodukt, to måneders brug 10 pct.
Fordelingen kan dog variere med det producerede produkt, og pentanen frigives i vid udstrækning ved diffus emission. EPS-sektionen i Plastindustrien i Danmark er i skrivende stund i færd med at gennemføre en undersøgelse, der skal etablere et mere præcist billede af fordelingen fra de forskellige procestrin. De ovenstående tal skal derfor tolkes med forsigtighed.
14.3 EPS-produkter og deres karakteristika
EPS er et termoplastisk materiale. Plasten er opbygget af lukkede celler, og denne celleopbygning giver EPS-produkter nogle helt specielle egenskaber med hensyn til vægt, isoleringsevne samt bestandighed mod fugtoptagelse.
Det skal nævnes, at XPS (ekstruderet polystyren) er et andet termoplastisk celleplastmateriale. Produktionsteknikken for produktion af XPS-produkter adskiller sig principielt fra produktionsteknikken for EPS-produkter. Produktion af XPS-produkter finder ikke sted i Danmark og beskrives ikke i denne rapport.
14.3.1 Emballageprodukter
EPS-emballage udmærker sig ved at have en meget lav egenvægt, yde god beskyttelse mod tryk og stød, være formstabil, være isolerende og ved ikke at optage vand eller fugt.
EPS-emballagers beskedne vægt skyldes, at EPS består af 98 pct. luft (celleplastens vægtfylde er typisk 15-25 kg/m³ og dette gør både emballagerne samt de færdigemballerede produkter håndterings- og brugervenlige.
EPS-emballagernes tryk- og stødabsorberende samt formstabile egenskaber udnyttes blandt andet ved emballager til tekniske artikler, for eksempel audio- og videoudstyr samt køle- og fryseskabe, hvor cellestrukturen forhindrer, at ødelæggende stød og bump under transporten forplanter sig til det emballerede produkt.
Den stillestående luft i den lukkede cellestruktur giver endvidere EPS-emballager fine isoleringsegenskaber. Den gode isoleringsevne udnyttes for eksempel ved transport af isafkølet fersk fisk i EPS-fiskekasser.
Materialets opbygning af lukkede celler bevirker endvidere, at vand og fugt kun i ringe grad kan trænge ind i cellerne. Denne egenskab udnyttes i forbindelse med emballering af blandt andet fødevarer, hvor materialet kan holde på kødsaft m.m.
Ofte udnyttes kombinationen af de tre ovennævnte egenskaber, f.eks. til emballage til grønsager. EPS-emballage sikrer grønsagerne mod stød og temperatursvingninger, og emballagen bliver ikke opløst af vand.
Det skal bemærker her, at der ikke må anvendes regenereret EPS til emballage, der kommer i kontakt med fødevarer.
14.3.2 Isoleringsprodukter
EPS-isoleringsprodukter udmærker sig først og fremmest ved den gode isoleringsevne, som skyldes dels det høje indhold af luft (ca. 98 pct.), dels den stillestående luft i materialets lukkede cellestruktur. EPS-isoleringsmaterialer kan leveres med forskellige varmeledningsevner tilpasset de enkelte anvendelsesformål. Lambda-værdien er typisk 0,039 W/mK (praktisk bestemt).
Endvidere er materialets formstabilitet en væsentlig egenskab. EPS-isoleringsplader kan bære mere end 2 tons/m². I kombination med den beskedne vægt (typisk 18 kg/m³) samt de mange bearbejdningsmuligheder er EPS et attraktivt byggemateriale til gulv-, væg- og tagisolering.
Herudover har EPS-materialet som nævnt den positive egenskab, at det kun i ubetydelig grad optager fugt. EPS-isoleringmaterialer bevarer derfor den gode isoleringsevne, samt sikrer et råd- og svampefrit byggeri.
I Danmark reguleres brugen af byggematerialer herunder isoleringsmaterialer af det gældende Byggereglement og Bygningsreglementet for småhuse. Isoleringsmaterialer skal som hovedregel være ubrændbare, men ikke ubrændbare isoleringsmaterialer (herunder EPS-isolering/celleplast) kan dog anvendes flere steder. Generelt kræves celleplast afdækket på overfladen med nærmere definerede ubrændbare materialer.
14.4 Energiforbrug ved ekspandering af EPS
Energiforbruget i EPS-virksomheder stammer i det væsentligste fra forbrug af olie/naturgas til produktion af vanddamp samt forbrug af el til ventilation, trykluft m.m.
Energiforbruget pr. vægtenhed EPS til produktion af emballage og tekniske artikler er større end energiforbruget til fremstilling af isolering på grund af et højere vanddamp- og elforbrug.
Der bruges en mindre og ikke nærmere undersøgt mængde energi til at tørre færdigstøbte emner for vanddampkondensat. Hertil bruges typisk spildvarme.
14.4.1 Dampforbrug
Vanddamp er en fortrinlig varmebærer og anvendes som nævnt for at tilføre forskumnings- og støbeprocessen energi. Der har gennem tiderne været gjort utallige forsøg med alternative procesenergiformer som for eksempel forvarmet luft og direkte elektrisk opvarmning, men ingen metoder har formået at udkonkurrere anvendelsen af vanddamp.
Vanddampforbruget til fremstilling af 1 kg EPS til emballage er som nævnt større end vanddampforbruget til fremstilling af 1 kg EPS-isolering.
Ved fremstilling af 1 kg EPS til emballager og tekniske artikler anvendes der i gennemsnit ca. 50 MJ (indfyret brændværdi) til vanddampproduktion. Energiforbruget varierer typisk mellem 35 MJ og 65 MJ, idet fremstillingen af celleplast med lav vægtfylde kræver mest vanddamp. Der anvendes mættet vanddamp med temperatur på små 100o C til forskumningen. Ved støbningen er vanddampens temperatur ca. 115o C. Ca. 95 pct. af vanddampforbruget anvendes til støbningen og kun ca. 5 pct. anvendes til forskumningen. Ved støbningen fordeles ca. 95 pct. af vanddampforbruget til foropvarmningen af formen, mens resten anvendes til selve støbningen.
For fremstilling af 1 kg EPS til blokke til isoleringsmaterialer anvendes der i gennemsnit ca. 10 MJ (indfyret brændværdi). Energiforbruget varierer typisk mellem 5 MJ og 15 MJ, idet fremstilling af EPS med lav vægtfylde kræver mest vanddamp.
Der anvendes vanddamp med samme tryk og temperatur som ved fremstilling af emballager. Ca. 50 pct. af vanddampforbruget anvendes til støbning og ca. 50 pct. anvendes til forskumning. Ved støbningen anvendes som nævnt stort set ingen energi til foropvarmning af formen.
Det større forbrug skyldes hovedsageligt, at støbeformen (ved fremstilling af emballager og tekniske artikler) afkøles efter hver støbecyklus. Følgelig skal formene opvarmes ved begyndelsen af hver ny støbecyklus, til hvilket der kræves vanddamp.
Vanddampforbruget ved fremstilling af blokke til isolering hænger som nævnt sammen med emnets vægtfylde, idet en lav vægtfylde kræver en lang opskumningstid og dermed mere vanddamp. Isolerings- og styrkekrav er dimensionerende for den ønskede vægtfylde af den producerede celleplast.
14.4.2 Elforbrug
Til fremstilling af EPS til emballage og tekniske artikler medgår der typisk 5-10 MJ pr. kg opskummet materiale i form af el. Elforbruget anvendes i det væsentligste til ventilation i produktionslokalerne, til produktion af trykluft samt til pumpning og køling af kølevand.
Elforbruget til fremstilling af isoleringsmateriale udgør typisk ca. 1,5 MJ/kg opskummet materialet. Elforbruget anvendes primært til ventilation. Ved fremstilling af isoleringsblokke anvendes der ikke trykluft eller kølevand, og elforbruget er følgelig lavere end ved emballageproduktion.
15 Kalandrering
Se også:
Termoplastbranchens_råvarer
Emissioner ved forarbejdning af termoplast
Kemiske belastninger i arbejdsmiljøet
Miljø- og sundhedsvurderinger
Referencer
Indholdsfortegnelse
Oversigtsfigur
15.1 Kort beskrivelse af branchen og dens råvarer
Dette kapitel bygger i al væsentlighed på rapporten ”Renere teknologi i plastindustrien. Øvrige plastprocesser, råvarebehandling og færdiggørelsesteknikker” (Plastindustrien i Danmark, 2000b).
I Danmark er der kun få virksomheder, der kalandrerer og fremstiller folier. Den vigtigste råvare er PVC-compound, mens andre plasttyper ikke anvendes i nævneværdigt omfang til kalandrering.
15.1.1 Additiver
Der anvendes DINP eller DEHP som PVC-blødgører og virksomheden compounderer selv sine råvarer.
Blødgørerindholdet udgør mellem 20 og 25 pct. af compoundmængden afhængigt af kundens behov.
I tilfælde af krav om brandhæmning anvendes der antimontrioxid samt/eller phosphatblødgørere som brandhæmmere afhængigt af kundens behov.
I forbindelse med kalandrering kan anvendes antistatiske midler samt slip- og/eller glidemiddel som stearinsyre eller calciumstearat. Herudover anvendes der altid varmestabilisatorer som f.eks. barium/zink og calcium/zink. Tidligere blev der i enkelte tilfælde, og i meget ringe grad, anvendt blyholdige pigmenter via masterbatch.
15.2 Kalandreringsprocessen
Ved kalandrering fremstilles folier ved, at blødgjort PVC-compound ekstruderes ud i en dejagtig pølse, som derefter indføres i et valseværk opbygget i sektioner med varmetromler, strækvalser, kølevalser, kontrol af folietykkelsen, skæresektion samt oprulning.
Spaltebredde mellem valserne aftager og temperaturen varierer gennem systemet, idet valserne eller tromlerne holdes varme ved brug af kogende vand under tryk. Der anvendes kogende vand og ikke olie af sikkerhedsmæssige årsager, idet en lækage såfremt der er tale om overophedet vand under tryk, “kun” vil resultere i undvigelse af kogende vanddamp på 100 °C, mens olien ville have en betydeligt højere temperatur.
Ved kalandreringen valses plastmassen ud i en folie med den ønskede tykkelse. Kanterne afskæres til opnåelse af den rigtige bredde. Under valsningen strækkes folierne både i ekstruderingsretningen og vinkelret herpå.
Materialet fra opstarten snittes sammen med de afskårne kanter og kan derefter føres direkte til ekstruderen, hvor det anvendes på lige fod med virgin PVC-plast.
Overfladen på det sidste valsepar er som regel graveret for at give folien en ønsket struktur.
15.3 Kort beskrivelse af branchens produkter
Der produceres folier i forskellige tykkelser fra 50 - 750 µm. Folierne bruges til diverse hospitalsartikler som f.eks. urinposer, til kontorartikler som f.eks. brevsamlere, til toilettasker mm.
15.4 Energiforbrug
Der er ikke fundet oplysninger om typisk energiforbrug ved kalandrering.
Energiforbruget til produktionen anvendes først og fremmest til plastificering af plastmaterialet og til opvarmning og rotation af valserne. Den valsede folie afkøles ved indirekte vandkøling, hvilket vil sige at folien valses gennem kølevalser, der via et lukket system indeholder kølevand på 20-21 °C.
16 Rotationsstøbning
Se også:
Termoplastbranchens_råvarer
Emissioner ved forarbejdning af termoplast
Kemiske belastninger i arbejdsmiljøet
Miljø- og sundhedsvurderinger
Referencer
Indholdsfortegnelse
Oversigtsfigur
16.1 Kort beskrivelse af branchen og dens råvarer
Dette kapitel bygger i al væsentlighed på rapporten ”Renere teknologi i plastindustrien. Øvrige plastprocesser, råvarebehandling og færdiggørelsesteknikker” (Plastindustrien i Danmark, 2000b).
Rotationsstøbning er forholdsvis ukompliceret, idet den ikke kræver et stort og indviklet produktionsudstyr. Til gengæld er processen meget løntung, da der er meget manuelt arbejde.
Maskinerne er umiddelbart lige så dyre som sprøjtestøbemaskiner, men til gengæld er formene billige. Rotationsstøbning egner sig derfor til produktion af små serier af store emner og til emner med kompliceret udformning.
Processen kan i princippet forarbejde alle termoplastiske materialer, og også hærdeplast. De langt hyppigst anvendte materialer er visse polyethylener, primært grovkornet LDPE-pulver, og PVC (PVC-pasta).
Årsagen til at PE anvendes i pulverform er, at plastmaterialet herved får den størst mulige overflade og dermed lettere sintrer (smelter), hvorved procestiden og dermed energiforbruget til processen reduceres. Pellets vil ikke kunne anvendes, da de ikke kan smelte tilstrækkeligt.
16.1.1 Additiver
Området additiver er meget komplekst, og er på grund af projektets rammer kun overfladisk bearbejdet. Grundlaget for systematisk at vurdere renere teknologimuligheder er således ikke tilbundsgående.
Der anvendes så vidt vides hverken brandhæmmere eller blyholdige pigmenter.
PVC-pastaen består af fint PVC-pulver opblandet i en flydende PVC-blødgører til en plastisol med høj viskositet.
Tidligere blev der i dansk produktion anvendt DEHP, men DEHP blev allerede for nogle år siden fuldstændigt substitueret til fordel for DINP.
I forbindelse med rotationsstøbning af PE-produkter anvendes der antioxidanter samt slip-/ glidemidler (0,2 pct. zinkstearat).
16.2 Processen
Rotationsstøbning anvendes ofte til produktion af hule, sømløse emner af enhver størrelse og form. Ved processen er det muligt at fremstille emner med mange og komplicerede detaljer i et stykke, næsten uden materialesamlinger og indre spændinger. Figur 1 viser et eksempel på et rotationsstøbt produkt.
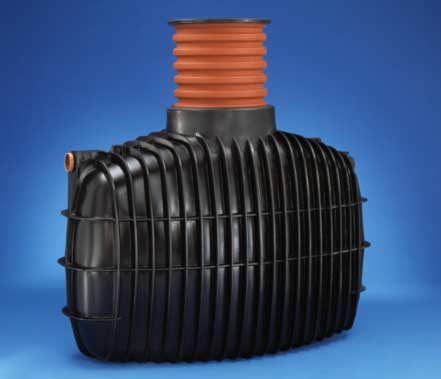
Figur 1. Eksempel på et rotationsstøbt produkt – en 3-kammertank (Wawin).
Emnerne fremstilles ved dosering af grovkornet plastpulver (PE) eller PVC-pasta (med et trykluftsdoseringsapparat) i en hul "støbeform", der består af to eller flere adskillelsesbare formdele. Formene lukkes, anbringes i en ovn og sættes til at rotere, oftest om to akser, hvorved plastmaterialet fordeles ensartet over den indre overflade.
Støbeforme fremstilles som støbte aluminiums forme, bearbejdede aluminiumsforme, elektrolytisk fremstillede kobberforme eller forme fremstillet af svejsede stålplader.
Når formen opvarmes vil der overføres varme til plastmaterialet, som løber ud til væggen. Når plastmaterialet bliver tilstrækkeligt opvarmet, begynder PVC-pastaen at gelere og PE-pulveret at smelte.
Alt efter formværktøjet og ovnens størrelse er det muligt at have faste rammer eller plader, hvorpå flere forme kan fastspændes, således at ovnen kan udnyttes bedst muligt.
Ovntemperaturen er på 190-220 °C for PVC og 220-300 °C for PE. Opholdstiden i ovnen er fra 8 til 30 min. og er bl.a. afhængig af ovntemperaturen, plastmaterialet, formens vægtykkelse og varmeledningsevne samt emnets størrelse og godstykkelse.
Plastmaterialet må ikke udsættes for høj temperatur i for lang tid, idet materialet herved nedbrydes termisk. Den optimale arbejdstemperatur og procestid er derfor specifik for hver enkelt form og produktserie.
Efter afkøling af form og emne kan emnet frigøres, udtages og processen gentages. For bedst at kunne udnytte energiforbruget til ovnopvarmningen anvendes der typisk tre hold forme pr. ovn, således at der hele tiden er et hold i ovnen, et hold, der afkøler og et, som afformes og genfyldes.
Afkølingsmetoden afhænger af det anvendte plastmateriale, idet et emne i blødgjort PVC kan tåle en brat afkøling med neddypning i vand umiddelbart efter udtagelsen fra ovnen. Et emne i PE kræver derimod en væsentlig langsommere nedkøling for ikke at krympe og herved ødelægge/eller forringe plastmaterialets krystallinitet. Emner i PE afkøles derfor enten først vha. vanddyser og derefter i luft eller ved både vanddyser og luftkøling samtidigt alt afhængigt af hvilken form, som anvendes.
Inden formene åbnes, fjernes vandet fra formenes ydersider, hvilket eventuelt gentages på formens inderside lige inden formene genfyldes. Til visse produkter er det vigtigt, at der ikke kommer vand i formen, da vandet under rotationen vil ødelægge emnet.
For at lette afformningen kan formene desuden coates f.eks. med silikone på den indvendige overflade.
16.3 Kort beskrivelse af branchens produkter
Som eksempler på produkter, der fremstilles ved rotationsstøbning, kan nævnes dukkedele, sparebøsser, fendere, kar, gødningsbeholdere, store tanke, store rørsamlinger, paller, brønde, kasser og beholdere.
16.4 Energiforbrug
En dansk producent angiver energiforbruget ved rotationsstøbning til 9,1 MJ/kg.
Det største energiforbrug i forbindelse med rotationsstøbning går til opvarmning af ovnene og dermed til at plastificere plastmaterialet.
I en forholdsvis “gammel” produktionslinie, roterer én form ad gangen henover en gasflamme. Denne opvarmningsform sætter begrænsninger for produktionsstørrelsen , da der kun kan anvendes en form ad gangen. Samtidig er produktionstiden relativt lang pga. den ujævne opvarmning, der er dog ikke risiko for termisk nedbrydning.
En typisk nutidig ovn består af et ovnkammer, hvor formene føres igennem. I forbindelse med produktionsplanlægningen bør der indgå overvejelser om, hvorledes ovnkapaciteten bedst muligt udnyttes, således at energiforbruget per produkt minimeres.
For produkterne i blød PVC kan der opstå en begrænsning i antallet af forme, da emnerne afformes mens de stadig er tilstrækkeligt varme og bløde til at kunne suges tomme for luft, og emnet udtages gennem et relativt “lille” hul i forhold til emnets egen diameter. Afformningen skal altså finde sted, inden emnerne afkøles for meget og dermed bliver for stive.
Processen afgiver en betydelig mængde varme til omgivelserne, som det p.t. ikke er muligt at genvinde, men højst begrænse. Det er måske muligt i enkelte tilfælde stadig at reducere varmeforbruget ved at forøge isoleringen omkring ovnen.
17 Sprøjtestøbning
Se også:
Termoplastbranchens_råvarer
Emissioner ved forarbejdning af termoplast
Kemiske belastninger i arbejdsmiljøet
Miljø- og sundhedsvurderinger
Referencer
Indholdsfortegnelse
Oversigtsfigur
17.1 Kort om sprøjtestøbningsbranchen og dens råvarer
Den følgende beskrivelse af sprøjtestøbningsbranchen og dens produkter er i al væsentlighed baseret på rapporten ”Renere teknologi i plastindustrien” (Plastindustrien i Danmark, 2000) og lærebogen ”Plastteknologi” (Jensen et al. (2005)). Det er ikke forsøgt at opdatere de to kilders oplysninger om råvareforbrug mv.
Sprøjtestøbning er den mest udbredte plastforarbejdningsproces i Danmark. Virksomhedernes størrelse er særdeles varieret. Variationen spænder over virksomheder med blot én maskine op til formentlig verdens største sprøjtestøbevirksomhed. Typisk ses, at danske virksomheder har 10-20 sprøjtestøbemaskiner.
Størstedelen af producenterne arbejder som underleverandører, og kun et mindre antal producenter fremstiller og markedsfører egne produkter. Konsekvensen heraf er, at producenten kun i en vis udstrækning har indflydelse på design og materialevalg.
Polypropylen (PP) og polyethylen (PE) er de mængdemæssigt mest betydende råvarer, men der foretages sprøjtestøbning af stort set alle plastråvarer, der egner sig hertil. Den anvendte råvare købes typisk færdig og klar til brug, dog tilsætter producenten ofte selv pigmenter i form af masterbatch.
17.2 Sprøjtestøbningsprocessen
I sprøjtestøbeprocessen føres plastgranulat ned i en cylinder med en roterende snekke. Ved en kombination af mekanisk arbejde fra den roterende snekke og varme fra elektriske varmelegemer, der omslutter cylinderen, plastificeres (blødgøres) materialet. Under plastificeringen transporteres materialet frem foran snekken, der samtidig bevæger sig bagud i cylinderen for at give plads til det smeltede materiale. Derefter fungerer snekken som et stempel, der skydes frem i cylinderen og presser det smeltede plastmateriale ind i et formværktøj. Materialet afkøles herefter til en temperatur, hvor det er formstabilt (afhængigt af typen), hvorefter formen åbnes, og det støbte emne stødes ud.
Hele processen varer fra nogle få sekunder til flere minutter, afhængigt af plasttypen og emnets godstykkelse. Emnerne kan veje fra under et gram og op til adskillige kilogram.
Sprøjtestøbemaskiners størrelse angives normalt efter deres lukkekraft og varierer typisk fra 250 kN (25 tons) til mere end 10.000 kN (1.000 tons). Hovedparten af de maskiner, der er på det danske marked er mellem 500 og 1.000 kN (50 og 100 tons).
Maskinernes tekniske opbygning er som regel baseret på et hydraulisk system, der via en elektromotor og en pumpe omdanner den tilførte elektriske energi til hydraulisk energi. Hydraulikolien føres via rør, slanger og div. ventiler til hydrauliske cylindre og motorer, hvorigennem sprøjtestøbeprocessen får tilført energien. Som alternativ til den hydrauliske opbygning er visse maskinfabrikanter begyndt at lancere sprøjtestøbemaskiner, hvis opbygning enten helt eller delvist bygger på et elektrisk styret system.
For at sprøjtestøbeprocessen i praksis skal fungere kan det være nødvendigt med flere hjælpeforanstaltninger. Til køling af maskinens hydrauliksystem, formværktøjet m.m. anvendes et system, der via kølevand bortleder størstedelen af den tilførte energi. Kølesystemerne er for hovedpartens vedkommende (>90 pct.) opbygget omkring en konventionel kølekompressor, der i mindre udstrækning kan være suppleret med anlæg for naturlig køling. De resterende anlæg er baseret på køling gennem åbne køletårne.
Køleanlæggenes primære opgave er at køle det opvarmede returvand fra maskinerne og recirkulere det ved konstant fremløbstemperatur, typisk mellem 8 og 15 °C. For at kunne styre formværktøjets temperatur under sprøjtestøbeprocessen er det vigtigt, at man kan regulere temperaturen af kølemediet. Det gøres ved anvendelse af et tempereringsaggregat, der placeres ved siden af sprøjtestøbemaskinen.
Tempereringsaggregatet har endvidere til formål at sikre opvarmningen af formværktøjet til den ønskede drifttemperatur før brug. Det er ofte opbygget som en enhed, der via en vandtank forsyner formværktøjet med vand. Vandet varmeveksler enten med det centrale kølevandssystem eller med elvarmelegemer alt afhængigt af, om vandet skal køles eller opvarmes.
Trykluft anvendes oftest som hjælpeværktøj til afformning af emner, enten ved direkte at blæse emnerne ud af formværktøjet eller indirekte ved at styre en robot, der udøver samme funktion. Trykluftanlæggene er som oftest opbygget omkring en hovedkompressor, hvis drifttryk typisk ligger mellem 7 og 8 bar.
Endelig skal materialetørring nævnes, idet dette er en proces, der ofte anvendes forud for sprøjtestøbeprocessen. Dette skyldes, at langt de fleste materialer i større eller mindre grad er hygroskopiske (vandsugende), og indeholder fugt. Dette er uønsket i en sprøjtestøbeproces.
Der anvendes to forskellige tørremetoder, varmluft- og tørluftmetoden. Ved begge metoder anvendes tørring med opvarmet luft, der blæses gennem materialet. Ved tørluftmetoden affugtes og recirkuleres luften, hvilket ikke er tilfældet ved varmluftmetoden.
17.3 Sprøjtestøbningsbranchens produkter og deres karakteristika
Sprøjtestøbning er en proces, der giver stor formgivningsfrihed, og som anvendes til formning af såvel enkle som meget komplicerede emner. Værktøjerne, hvori emnerne formes, er ofte dyre, og processen egner sig derfor fortrinsvis til fremstilling af store serier.
Med udgangspunkt i de anvendte materialer er det valgt at gruppere produkterne inden for emballage, legetøj, farmaceutiske artikler, tekniske artikler og husholdningsartikler. Denne produktopdeling er foretaget alene med henblik på denne gennemgang og anvendes herudover ikke i praksis. Grupperingen lider af den mangel, at mange produkters tilhørsforhold ikke entydigt vil kunne bestemmes.
17.3.1 Emballage
Det vurderes, at 30-40 pct. af råvareforbruget anvendes til fremstilling af sprøjtestøbt emballage (spande, bøtter, bægre og lign.). Halvdelen anvendes til fødevareemballage. For begge emballagetyper gælder typisk, at råvaren er godkendt til at komme i kontakt med fødevarer, hvilket miljømæssigt har den konsekvens, at bl.a. brugen af tungmetalbaserede pigmenter og brandhæmmere er udelukket.
17.3.2 Legetøj
10-20 pct. af plastforbruget til sprøjtestøbning anvendes til fremstilling af legetøj. Legetøj skal overholde EU's Legetøjsdirektiv, hvilket udelukker brugen af tungmetalbaserede additiver og brandhæmmere.
17.3.3 Farmaceutiske artikler
10-20 pct. af plastforbruget til sprøjtestøbning anvendes i den medicinske sektor og omfatter bl.a. fremstilling af engangssprøjter, tragte til katetre og diverse laboratorieudstyr. Brug af tungmetalbaserede pigmenter og brandhæmmere er ligeledes udelukket i denne sektor.
17.3.4 Tekniske artikler m.m.
Det vurderes, at 10-20 pct. af plastforbruget anvendes til tekniske artikler. Det skønnes, at ca. halvdelen af plastvolumenet er materiale godkendt til at komme i kontakt med fødevarer evt. alene tilsat glasfyld og/eller pigmenter. Hvad angår den sidste halvdel af volumenet er denne delt op på en lang række tekniske termoplasttyper, termoplastiske elastomerer og blandinger heraf (blends).
En nøjere gennemgang af denne produktgruppes brug af materialer er udeladt. Begrundelsen herfor er, at gruppen dækker over en lang række vidt forskellige produkter fremstillet af mange forskellige polymertyper, hvor en række forskellige additiver er tilsat. En systematisk gennemgang af denne restgruppe ville tage uforholdsmæssigt lang tid, og er derfor fravalgt.
17.3.5 Husholdningsprodukter
Udover ovennævnte grupper, skal nævnes produkter til husholdningsområdet. Dette område dækker over et stort og meget varieret sortiment, heriblandt blomsterpotter, engangsservice, husholdningsartikler etc. Området har en materialemæssig fællesnævner, idet produkterne hovedsageligt fremstilles i de typiske volumenplastmaterialer (PE, PP og PS). Produkterne fremstilles sjældent i kvaliteter, der ikke er godkendt til at komme i kontakt med fødevarer og vil normalt ikke indeholde specielle additiver ud over pigmenter og/eller fyldstoffer. Det vurderes, at 10-20 pct. af det danske sprøjtestøbevolumen anvendes inden for dette område.
17.4 Energiforbrug ved sprøjtestøbning
Energiforbruget til sprøjtestøbeprocessen angives i flere kilder til 1-2 kWh pr. kg produceret emne. Nyere grønne regnskaber og Miljørapporter fra danske plastproducerende virksomheder tyder dog på, at forbruget er noget lavere, måske kun halvt så stort. Det er dog klart, at energiforbruget varierer fra produkt til produkt, specielt som funktion af emnestørrelse og plasttype/forarbejdningstemperatur, og det er ikke muligt at give præcise nøgletal.
Energiforbruget til sprøjtestøbning vedrører først og fremmest el til hydraulikmotorer og varmebånd, trykluft, materialetørring og køling. Disse forhold er nærmere undersøgt i “Brancheenergianalyse i Plastindustrien’95”, og med hensyn til spareforanstaltninger henvises til denne analyses konklusioner. Det anføres dog her, at analysen anbefaler sprøjtestøbevirksomhederne at kigge på følgende tre indsatsområder:
- Procesudstyr, herunder procesvarme og tomgangsforbrug.
- Procesrelaterede hjælpeudstyr, herunder køling, trykluft og genvin-ding.
- Perifert udstyr, herunder rum- og vandopvarmning (el og brændsel), rumventilation og belysning.
Analysen fremhæver udover en lang række generelle besparelsesemner følgende branchespecifikke besparelsesemner:
- Omdrejningsregulering af kølevandspumper samt etablering af naturlig køling
- Isolering af varmelegemer samt reduktion af standby-forbrug
18 Termoformning
Se også:
Termoplastbranchens_råvarer
Emissioner ved forarbejdning af termoplast
Kemiske belastninger i arbejdsmiljøet
Miljø- og sundhedsvurderinger
Referencer
Indholdsfortegnelse
Oversigtsfigur
18.1 Kort om termoformningsbranchen og dens råvarer
Den følgende beskrivelse af termoformningsbranchen og dens produkter er i al væsentlighed baseret på rapporten ”Renere teknologi i plastindustrien” (Plastindustrien i Danmark, 2000) og lærebogen ”Plastteknologi” (Jensen et al. (2005)).
Termoformningsbranchen i Danmark kan opdeles i tre kategorier, nemlig få store emballageproducenter eventuelt med egen foliefremstilling (ekstrudering), få store fødevareproducenter med egen termoformlinie og endelig en blanding af store og mindre virksomheder, som fremstiller en lang række forskellige termoformede tekniske artikler, displays, legetøj m.m.
Variationen spænder over virksomheder med få maskiner op til virksomheder med 20 maskiner.
Volumenmæssigt ligger hovedvægten af forbruget på polystyren (PS) og polyethylenterephthalat (PET) Størstedelen skønnes anvendt til produktion af emballage, mens tekniske artikler og legetøj udgør en mindre del, sammen med displays.
Udover de nævnte polymertyper anvendes mindre mængder PC (polycarbonat), PMMA (polymethylmethacrylat eller acryl), POM (polyoxymethylen) PA (polyamid) og PVC (polyvinylchlorid). Forbruget af disse polymerer er i denne sammenhæng beskedent. Endelig anvendes der ved fremstilling af emballage i visse tilfælde folielaminater bestående af flere forskellige lag af de nævnte polymertyper.
18.1.1 Additiver
Under selve termoformprocessen anvendes ingen additiver. Den færdige folie indeholder typisk additiver, der er tilsat i forbindelse med ekstruderingen af folien. Plastindustrien i Danmark vurderede i 2000, at omkring 15 pct. af forbruget af plader til tekniske artikler er tilsat brandhæmmende additiv.
18.2 Termoformningsprocessen
Alle termoformede emner fremstilles ud fra det samme grundprincip, nemlig at en tynd plade eller folie af termoplastisk materiale opvarmes til materialets blødgøringstemperatur, hvorefter pladen eller folien formes i et værktøj til den ønskede form. Værktøjet er perforeret, og pladen eller folien suges tæt ind til formen med vakuum. Termoformprocessen benævnes derfor ofte også vakuumformning.
Folien eller pladerne kan tilføres termoformanlæggene på to principielt forskellige måder, idet emballage fremstilles ud fra folie i ruller, hvorimod tekniske artikler, legetøj og displays fremstilles ud fra plader (tykkere folie opskåret i ark).
18.2.1 Produktion af emballage
Forud for selve formningen skal plastmaterialet blødgøres. Dette sker ved at opvarme materialet til dets blødgøringstemperatur. Normalt foretages opvarmningen med strålevarme. Varmen frigives typisk fra keramiske elementer, som opvarmes elektrisk. Termoformanlæg indeholdt i pakkeanlæg hos fødevareproducenter anvender dog typisk kontaktvarme. Her presses en varmeplade, som holder plastens blødgøringstemperatur, direkte ind på folien, hvorved kontaktvarmen overføres.
Når folien har nået blødgøringstemperaturen skal den formes. Den blødgjorde folie suges som nævnt ned i en form. Formen er vandkølet, og plastmaterialet størkner efter nogle få sekunder. I visse maskiner "forblæses" folien, og i nogle processer anvendes endvidere overtryk til at presse folien ned i værktøjet.
Når materialet er størknet, skal emballagen udstanses af folien. Dette kan enten ske, mens emballagen stadigvæk findes i formen, eller efterfølgende i en særligt udstansningsmekanisme. Det overskydende materiale, også kaldet stansegitteret, opsamles med henblik på materialegenvinding. Efter udstansningen stables emballagen og er klar til transporten ud til kunden.
18.2.2 Produktion af tekniske artikler, legetøj, displays m.m.
Ovennævnte emner fremstilles i princippet som under Emballage, dog med den undtagelse, at plastmaterialet leveres som ark (plader) og ikke i folieruller. Årsagen hertil er kravet om væsentligt kraftigere godstykkelser end gældende for emballager.
Pladerne kan følgelig ikke oprulles som folien, hvorfor fremstillingsprocessen derfor ikke kan gøres kontinuerlig som ved emballageproduktionen.
Ved termoformning af ark opvarmes plasten altid med strålevarme og udstansningen foregår altid efter afformningen. Da disse emners gods-tykkelse er større end emballagens og derfor optager større energimængder, foretages supplerende køling i form af trykluft kombineret med vanddyser.
Udstansningen og eventuel fræsning og boring foregår både manuelt, halvautomatisk og under anvendelse af CNC-styrede robotter.
18.3 Termoformningsbranchens produkter og deres karakteristika
18.3.1 Emballage
Termoformet emballage, fortrinsvis bægre og bakker i store styktal til fødevarer, fremstilles enten hos emballageproducenten eller hos fødevareproducenten.
Førstnævnte emballagetype bliver efter fremstillingen stablet og fragtet til kunden, hvor emballagen automatisk fyldes med for eksempel pålæg, salater og færdigretter, hvorefter bægret eller bakken lukkes og forsegles.
Bakker til pakning af kød, grønt og lignende til manuel eller automatisk pakning i detailhandelen fremstilles ligeledes ved termoformning.
Som nævnt termoformer visse fødevareproducenter deres egen emballage. I disse anlæg termoformes, påfyldes, forsegles og udstanses emballagen i én proceslinie.
18.3.2 Tekniske artikler og legetøj
Rækken af tekniske artikler fremstillet ved termoformning er lang og mangeartet. Maskin- og lampekabinetter, køle- og fryseskabe samt autotilbehør i mindre serier er eksempler på termoformede emner.
Emnernes størrelse varierer. Visse produkter, som f.eks. ladforinger til varevogne eller skibokse til tagbagagebærere måler over 2 meter i længden.
18.3.3 Displays m.m.
Endelig fremstilles salgsdisplays og skilte ofte ved termoformning. Denne fremstillingsform er kendetegnet ved, at serierne typisk er mindre, og at produkterne ofte efterfølgende dekoreres.
18.4 Energiforbrug
Energiforbruget til termoformning anvendes først og fremmest til strålevarme til opvarmning af plasten til blødgøringstemperaturen.
Et fuldt elektrisk termoformanlæg, hvori alle mekaniske dele bevæges ved hjælp af el-motorer, forbruger eksempelvis ved fremstilling af drikkebægre små 0,2 kWh pr. kg materiale indført (inkl. stansegitter). I et sådant anlæg udgør trykluftforbruget til formningen omkring 1 pct. af energiforbruget.
I tilsvarende anlæg, hvor de mekaniske dele drives ved hjælp af trykluft, udgør forbruget til trykluft ca. 10 pct. af maskinens energiforbrug.
19 UP-branchen og dens processer
Se også:
UP-branchens råvarer
Additiver
Emissioner ved forarbejdning af hærdeplast
Kemiske belastninger i arbejdsmiljøet
Miljø- og sundhedsvurderinger
Brandegenskaber for plast
Referencer
Indholdsfortegnelse
Oversigtsfigur
19.1 Introduktion
Dette kapitel er i al væsentlighed baseret på rapporten ”Renere teknologi i plastindustrien. Del B: Hærdende polyurethanplast” (Plastindustrien i Danmark, 2000c) og Jensen et al. (2005).
Fremstilling og blanding af råvarer og hjælpestoffer er kort beskrevet i kapitlet ”UP-branchens råvarer”.
19.2 Kort beskrivelse af UP-Branchen
Kompositbranchen i Danmark forarbejder primært glasfiberforstærket umættet polyester (GUP) og fremstiller hovedsageligt produkter som vindmøllevinger, fly- og off-shorekonstruktioner, togkonstruktioner, lagertanke, kølecontainere, kunstmarmor, polyesterbeton, både, overfladebehandling af stål og beton og mange teknisk avancerede komponenter.
19.3 UP-branchens processer
Ca. 55 pct. af den umættede polyestermængde anvendes til åbne processer. De resterende ca. 45 pct. anvendes til lukkede processer, og udviklingen går mod en vækst heraf.
Emnet påføres ofte en topcoat for at beskytte laminatet fra bagsiden. Tilsvarende beskytter gelcoaten laminatet fra formsiden.
Efter hærdningen afformes emnet, og overskydende polyester og glasfiber fra emnets kant skæres og slibes væk.
19.3.1 Håndoplæg
Håndoplæg er den traditionelle metode til at fremstille emner i GUP. Ved håndoplæg opbygges emnet i eller på en åben form. Først påføres et slipmiddel, som bevirker, at det færdige emne nemt kan afformes efter hærdningen. Slipmidlet påføres manuelt eller sprøjtes på formen.
Hvis emnets overflade skal være farvet, påsprøjtes eller håndlægges et lag indfarvet gelcoat. Herefter påføres det første lag polyester, glasfibermåtter eller -væv oplægges i den endnu flydende polyester, og med ruller presses luft ud af glasset. Herefter påføres mere polyester, og yderligere glasfiber oplægges, indtil den ønskede godstykkelse er opnået.
Polyesteren kan påføres med malerrulle eller med pensel. Specielle påføringsruller tilsluttet automatisk doseringsanlæg er meget anvendt.
19.3.2 Sprøjteoplæg
Ved sprøjteoplæg er arbejdsgangen beslægtet med arbejdsgangen ved håndoplæg, blot med den forskel, at polyester og glas påføres samtidigt med sprøjtepistol og tilhørende huggeværk. Glasfibrene påføres sammen med polyesteren, ved at fibre kontinuerligt tilføres sprøjtepistolen, hvor de klippes i småstykker på 20 -40 mm og ”blæses” op på emnet.
19.3.3 Kontinuerlig imprægnering
Store plader fremstilles, ved at man lader et bord belagt med bærevæv bevæge sig langsomt forbi en dyse, hvorigennem polyester tilsættes. Samtidig tilsættes huggede fibre. Efter at en tilpas godstykkelse er opnået, rulles luften ud, og laminatet hærdes og afformes med henblik på videre forarbejdning og anvendelse f.eks. i sandwichkonstruktioner.
19.3.4 Vikling
Ved fremstilling af store rørsvøb til tanke og lignende vikles glasfiberen omkring en stor, roterende metaldorn. Under viklingen påføres polyester og eventuelt huggede fibre, samtidig med at luft "rulles" ud manuelt. Når en passende godstykkelse er opnået, hærdes den umættede polyester, og svøbet trækkes af dornen.
19.3.5 Presning
Presning foretages på to forskellige måder, nemlig ved kold-/vådpresning og ved varmpresning.
19.3.5.1 Kold eller vådpresning
Ved kold-/vådpresning fores en form med glasfibermåtter, og en afmålt mængde (flydende) polyester/initiatorblanding hældes i formen. Herefter presses et stempel ned i formen, hvorved polyesteren presses ud og fordeler sig i glasfiberen. Pressetrykket er typisk ikke over 1 kp/cm² (98 kPa). Polyesteren hærder i formen i lukket tilstand, hvorefter emnet kan tages ud til videre bearbejdning.
I visse processer opvarmes formen, hvorved hærdehastigheden forøges. Formtemperaturen kan varieres fra 30 - 130°C. (Kilde 7).
19.3.5.2 Varmpresning
Ved varmpresning sker hærdningen ved højere temperaturer, hvilket bl.a. er hurtigere, men der kræves nogle stærkere - og dyrere -forme, som normalt er lavet af stål. Varmpresning anvendes derfor typisk i forbindelse med fremstilling af større serier.
Formtemperaturen er typisk 90 - 150°C, og pressetrykket er typisk 20 kp/cm² (1,96 MPa). (Kilde 6).
Varmpresning omfatter tre varianter af metoden, nemlig preform, SMC (Sheet Moulding Compound eller prepreg) og BMC (Bulk Moulding Compound eller premix).
SMC-råvarer består af glasfiberlag og umættet polyester leveret i en forseglet ”klar til brug”-pakning. Et passende stykke SMC frigøres fra forseglingen og lægges i formen, hvorefter presning og hærdning foretages.
BMC-råvarer er en dejagtig blanding af umættet polyester og glasfiber samt fyldstoffer. En "dejbolle" lægges i formen, hvorefter presningen og hærdningen foretages.
19.3.6 Profiltrækning/pultrudering
Fremstilling af profiler foregår, ved at man trækker glasfibre i form af uendeligt lange rovings og væv igennem et stålværktøj, hvor man indledningsvis styrer fibrene på plads. Derefter imprægneres fibrene i et imprægneringskammer, og i den sidste del af værktøjet, som er opvarmet, udhærdes og kalibreres profilerne. Profiltrækning, som den anvendes her i landet, er en lukket proces.
Efter formningen afskæres profilerne i passende længder.
19.3.7 Kloakrenovering
Renovering af utætte kloaksystemer foregår bl.a. ved at man trækker en "strømpe" af glasfiber- eller polyestervæv befugtet med umættet polyester igennem den utætte kloakstrækning. "Strømpen", som forer det utætte kloakrør indvendigt, hærdes på stedet med UV-lys eller varmt vand.
19.3.8 Polyesterbeton og kunstmarmor
Polyesterbeton og kunstmarmor fremstilles af umættet polyester iblandet hærder og accelerator samt pigment og mere eller mindre finkornet fyldstof. Af blandingen støbes en lang række forskellige produkter så som håndvaske og facadebeklædninger.
Blandingen foretages automatisk på blandeanlæg, hvor de forskellige råvarer blandes i en blandesnegl. Blandesneglen renses med methylenchlorid. Der er i dag ikke kendskab til alternative rensemidler.
19.3.9 Injektionsstøbning
Ved injektionsstøbning pumpes polyesteren ind i en lukket form. Forud for injektion beklædes den ene formhalvdel med glasfiber, hvorefter formen lukkes, og indsprøjtningen foretages.
19.3.10 Vakuumstøbning
Ved vakuumstøbning suges den umættede polyester ind mellem to formskaller, ved at sætte hulrummet mellem formskallerne under vakuum. Forud for samling af formskallerne er den ene skal blevet beklædt med slipmiddel, gelcoat og glasfiber.
19.3.11 Andre metoder
I tidens løb er forskellige kombinationer af de ovenfor omtalte produktionsmetoder blevet udviklet. Et eksempel er kombineret injektionsvakuumstøbning, som er en lukket støbeproces, hvor den umættede polyester sprøjtes ind i formen, samtidig med at formen sættes under vakuum. En anden metode er vakuumfolieteknikken, som er beslægtet med vakuumstøbningen, men hvor den ene støbeskal er erstattet med en fleksibel folie. Fælles for disse støbemetoder er, at de er lukkede, hvorved styrenafdampningen reduceres.
19.4 Kort beskrivelse af UP-branchens produkter
Som nævnt fremstilles en lang række vidt forskellige produkter i fiberforstærket polyester. Nyttige materialeegenskaber, som specielt skal fremhæves, er stor styrke og stivhed, lav vægt, korrosionsbestandighed, reduceret vedligeholdelsesbehov og gode elektriske og termiske isoleringsegenskaber.
Materialets gode styrke/vægtforhold udnyttes bl.a. i transportsektoren, hvor anvendelsen medvirker til at reducerer energiforbruget.
Materialets vejr- og korrosionsbestandighed gør, at emner normalt hverken skal males eller vedligeholdes.
Vindmøllevinger, lagertanke, kølecontainere og både er eksempler på produkter af kompositmateriale, hvor samspillet mellem materialets lange levetid, styrke og vedligeholdelsesfri overflade med fordel udnyttes.
Endelig skal det nævnes, at produktionsserierne ofte er relativt små.
20 Polyurethanbranchens processer
Se også:
Polyurethanbranchens råvarer
Additiver
Emissioner ved forarbejdning af hærdeplast
Kemiske belastninger i arbejdsmiljøet
Miljø- og sundhedsvurderinger
Brandegenskaber for plast
Referencer
Indholdsfortegnelse
Oversigtsfigur
20.1 Introduktion
Dette kapitel er i al væsentlighed baseret på rapporten ”Renere teknologi i plastindustrien. Del B: Hærdende polyurethanplast” (Plastindustrien i Danmark, 2000c) og Jensen et al. (2005). Kapitlet fokuserer på støbning og opskumning af hærdende polyurethanplast (PUR). Sprøjtestøbning af termoplastisk polyurethan (TPU) er procesmæssigt behandlet i kapitlet om sprøjtestøbning, men de basale informationer om branchens råvarer findes i dette kapitel.
Fremstilling og blanding af råvarer og hjælpestoffer er kort beskrevet i kapitlet ”Polyurethanbranchens råvarer”.
20.2 Kort beskrivelse af polyurethanbranchen
Der anvendtes i Danmark ca. 43.000 tons PUR i 2003 til støbning og opskumning.
Branchens produktion foretages af 25-50 virksomheder hvoraf de 10 største virksomheder fremstiller over 3/4 af Danmarks PUR-produktion. Branchens produktion kan opdeles i følgende områder:
- Fleksibelt skum, som udgør ca. 52% af branchens produktion
- Isolering af fjernvarmerør, ca. 15%
- Kabinetter til husholdningsapparater, ca. 15%
- Paneler og beholdere, ca. 10%
- Forskellige støbte produkter og elastomerer, ca. 8%
PUR er som nævnt en hærdeplast, og PUR-virksomhederne adskiller sig generelt fra virksomheder som forarbejder termoplast.
På hærdeplastvirksomheder foregår plastforarbejdningen ved hjælp af en hærdning eller en polymerisation, i modsætning til termoplastvirksomhederne, hvor plasten smeltes/størkner.
20.3 Polyurethanbranchens processer
20.3.1 Støbemaskiner
Polyurethanskum fremstilles i polyurethanstøbemaskiner. Man skelner mellem to maskintyper nemlig højtryksmaskiner og lavtryksmaskiner. Maskinerne er af varierende konstruktion med kapacitet fra få gram til ca. 350 kg/min.
PUR-maskinens blandehoved er en central maskindel ved fremstilling af PUR-plast. I blandehovedet blandes polyolen med isocyanaten og eventuelle additiver. Doseringen og blandingen foregår automatisk umiddelbart inden blandingen skal bruges.
I højtryksmaskinen blandes komponenterne ved dosering gennem dyser ind i blandehovedets blandekammer under højt tryk, hvorved komponenterne atomiseres og blandes.
Højtryksmaskiner opererer med tryk på 100 - 200 bar. Maskinen udmærker sig blandt andet ved en effektiv miksning samt ved at blandehovedet renses mekanisk mellem hvert skud. I 2000 blev det skønnet, at der fandtes 100-150 højtryksmaskiner i Danmark, men tallet er sikkert højere i dag.
Mindre maskiner til blanding af højviskøse komponenter samt råvarer indeholdende filler er dog ofte lavtryksmaskiner.
I lavtryksmaskiner blandes komponenterne i stedet i blandehovedets blandekammer ved mekanisk sammenpiskning. Blandingen i denne type maskiner foregår under lavt tryk på 3-10 bar. I modsætning til højtryksmaskinen er lavtryksmaskinen ikke selvrensende og blandekammeret renses efter brug med vandige eller organiske rensemidler. I 2000 blev det skønnet, at der fandtes ca. 35 - 50 lavtryksmaskiner i Danmark, men tallet er sikkert højere i dag.
Specielt inden for blokstøbning findes både lavtryksmaskiner, hvor råvaren doseres under højtryk (>80 bar) samt maskiner, hvor råvaren doseres under lavtryk (<10 bar). I begge anlægstyper udføres en mekanisk sammenpiskning af råvarerne. Det skal for helhedens skyld nævnes, at disse maskintyper også benævnes højtryksmaskiner henholdsvis lavtryksmaskiner.
20.3.2 Fremstilling af hårdt PUR-skum
Ved at anvende en polyol, som er lavmolekylær, og som har tre eller flere reaktive centre, kan man under polymeriseringen danne en stærkt forgrenet og tætmasket bindingsstruktur, som giver en stiv polymer. Til fremstilling af hårdt skum anvendes i Europa udelukkende polymer MDI.
Hårdt skum anvendes først og fremmest til isoleringsformål i fjernvarmerør og køle/fryseskabe, men ligeledes i sandwichkonstruktioner til isoleringspaneler.
Densiteten af isoleringsskummet er typisk 30-60 kg/m³ i fjernvarmerør dog 80 - 100 kg/m³.
Ved produktion af ovennævnte produkter indgår skummet som bærende element i konstruktionen, idet de sammenblandede råvarer injiceres i hulrummet og udfylder dette.
Injiceringsprocessen kan foregå både hel- og halvautomatisk. Ved halvautomatisk produktion fører operatøren blandehovedet hen til hulrummet, hvor det aktiveres. Råvarerne pumpes fra råvaretanke via rørsystemer frem til produktionen, hvor blandehovedet er tilsluttet med slanger. Under hærdningen udvikles varme og temperaturen er typisk omkring 150°C i kernematerialets midte. Afformningen tager omkring 5 - 45 minutter. Den endelige udhærdning tager 15 - 20 timer.
Som opskumningsmiddel anvendes primært cyklopentan, ispopentan og n-pentan. Cellegassen er isolerende, og da hårdt isoleringskum bør indeholde minimum 90 pct. lukkede celler opnås normalt en god isoleringsevne.
Til at katalysere dannelsen af urethanbindingen, samt for at begrænse dannelsen af uønskede sidereaktioner, anvendes basiske forbindelser som f.eks. tertiære aminer eller organiske metalforbindelser og tinforbindelser.
Katalysatorerne er typisk tilsat polyolen af systemproducenten i koncentrationer på typisk 0,5-3 pct. Enkelte producenter blander dog selv deres råvarer.
20.3.3 Fremstilling af fleksibelt PUR-skum
Ved fremstilling af fleksibelt PUR-skum anvendes overvejende en blanding af langkædede trioler som polyol. Polymerisering danner, ligesom under dannelsen af hård PUR, et netværk af bindinger. I modsætning til hårdt PUR er tværbindingerne i blødt PUR imidlertid nærmest inhomogent fordelt, idet urethanbindingerne er samlet i celler omgivet af en fase af polyolkæder. Da polyolkæderne er "elastiske" giver de skummet en fleksibel natur.
Skummet anvendes først og fremmest til møbler, madrasser m.m. Densiteten af skummet er typisk 18 - 50 kg/m³.
Fleksibelt skum fremstilles på to forskellige måder nemlig ved slabstock (blokstøbning) eller ved formstøbning.
20.3.3.1 Slabstock
I "Slabstock"-processen fremstilles skummet i endeløse blokke med tværsnit på op til 1,5 x 2,5 meter, som efterfølgende skæres op i længder på op til 65 meter.
Under opskumningen føres råvarerne fra råvaretankene via rørsystemer til et lavtryksblandehoved. Råvaren doseres til blandehovedet under både højtryk og lavtryk alt afhængigt af anlægstypen.
Blokkene opskummes i en lang kanal, der har blokkens dimensioner og som er foret med papir. Bunden af slisken er udformet som et transportbånd. Under opskumningen doseres råvaren på papiret i kanalens ene ende, mens transportbåndet langsomt trækker papir og udstøbt PUR væk. Under transporten begynder hærdningen og PUR-plasten hæver. Når den ønskede bloklængde er opnået, afskæres blokken og fragtes til mellemlager for færdighærdning.
Den initielle hærdning foregår med kernetemperaturer omkring 150 -
170°C. Efterhærdningen varer typisk et døgn, hvorunder temperaturen stadig falder. Efter hærdningen kan blokken opskæres til madrasser, hynder, møbelpolster m.m.
Til blokskum har der traditionelt været anvendt TDI, idet denne giver de lette og stærke kvaliteter. I dag anvendes dog også modificeret MDI.
Som tidligere nævnt er det nødvendigt at rense lavtryksmaskinernes blandehoveder med vandige eller organiske opløsningsmidler. Ved blokstøbning renses blandehovederne dog med polyol.
Blødt skum kan bestå af både lukkede og åbne celler alt afhængigt af anvendelsesformålet. Som opskumningsmiddel anvendes vandbaserede systemer. En mindre del af det bløde skum fremstilles i brandhæmmede kvaliteter.
Blokskum farves ofte en anelse, således at kunden kan skelne blokke af forskellige typer fra hinanden. Til dette formål anvendes organiske pigmenter.
20.3.3.2 Formstøbning
Fleksibelt skum kan endvidere fremstilles som formstøbt skum. Denne produktionsproces anvendes typisk til fremstilling af møbelpolster og lignende. Til forskel fra fremstilling af blokke støbes emnerne i en form i den facon, som de endelige produkter ønskes i.
Der anvendes normalt højtryksmaskiner til at blande komponenterne med. Der anvendes hovedsageligt MDI, men blandinger af MDI og TDI anvendes også. Opskumningen foregår som hovedregel ved hjælp af vand, som danner CO2.
Forud for støbningen påføres formen et slipmiddel, enten organiske opløsningsmidler med lavt flammepunkt eller vand. Vand kan ikke altid anvendes, da tilstedeværelsen af vand ødelægger PUR-processen. Vælges organiske opløsningsmidler skal fabrikkerne være sikret mod eksplosionsfaren.
Hærdningen foregår i en tempereret form med temperatur på omkring 30 - 60°C. Afformningstiden er normalt 10 - 30 minutter.
Produktion gennemføres på både halv- og helautomatisk vis. Hvor der indgår TDI-isocyanat anvendes så vidt muligt robotter.
20.3.4 Integralskum
20.3.4.1 Hårdt integralskum
Hårdt integralskum fremstilles tilnærmelsesvis på samme måde som formstøbt fleksibelt skum. Produkterne er opbygget af en cellulær kerne med en massiv og porefri overflade. Konstruktionen gør produkterne lette og modstandsdygtige mod fysisk og kemisk påvirkning. Kabinetter, valser til fremkaldermaskiner, tekniske artikler, vinduesprofiler m.m. er produkter, som fremstilles i hårdt integralskum.
Til fremstilling af integralskum anvendes både højtryks- og lavtryksblandemaskiner. Der anvendes udelukkende MDI.
Forud for støbningen påføres formen slipmiddel. Hærdningen foregår i en varm form med temperatur omkring 40 - 60 °C. Afformningstiden er 3 - 15 min., afhængig af godstykkelsen.
Der anvendes de samme katalysatorer, som ved fremstilling af hårdt skum.
Opskumningen foregår ved hjælp af vand, som danner CO2, og densiteten af skummet varierer fra 40 - 600 kg/m³. Ved de lave skumdensiteter anvendes desuden et fysisk opskumningsmiddel. Opskumningsmidlet kondenserer på formens overflade, hvorved den højere densitet i randzonen opnås.
Til rensning af lavtryksmaskiner bruges i dag typisk rent postevand eventuelt tilsat et par procent sprit. Hvis cyklustiden er for kort til, at vandet kan fordampe fuldstændigt, anvendes dichlormethan.
Tekniske artikler fremstillet i hårdt integralskum er typisk brandhæmmede. Den anvendte brandhæmmer er som regel et halogenfrit phosphorsyrederivat. Endvidere anvendes organiske pigmenter.
20.3.4.2 Fleksibelt integralskum
Fleksibelt integralskum fremstilles tilnærmelsesvis på samme måde som hårdt integralskum.
Produkterne er, ligesom de hårde integralskumsprodukter, opbygget af en cellulær kerne omgivet af en porefri overflade. Konstruktionen gør produkterne lette, modstandsdygtige og fleksible. Skosåler og polstring til kontormøbler er eksempler på produkter, der fremstilles i blødt integralskum.
Der anvendes både højtryks- og lavtryksmaskiner til fremstilling af fleksibelt integralskum. Der anvendes MDI. Opskumningen foregår dels ved hjælp af vand, som danner CO2, dels ved hjælp af fysiske opskumningsmidler som pentan. Densiteten af skummet varierer mellem 100 og 400 kg/m³. Hærdningen foregår i en form, hvis temperatur typisk er 30 - 40 °C. Formtiden er få minutter.
Fleksibelt integralskum brandhæmmes normalt ikke. Undtaget herfra er armlæn til sæder i fly og biler, der næsten altid brandhæmmes. Det blev i Plastindustrien (2000c) skønnet, at i alt 300 tons brandhæmmes om året. Brandhæmmeren, som blev anvendt i koncentrationer omkring 5%, var typisk en chloralkylphosphatester med ca. 10 pct. halogen.
Som pigment anvendes fortrinsvis carbon black.
20.3.5 Massiv PUR
Et mindre anvendelsesområde er, som nævnt, fremstilling af massive emner samt brug af PUR-støbemasse.
Massive emner fremstilles stort set af samme type råvare som integralskumsprodukter. Råvaren til massive produkter indeholder dog ingen opskummende komponenter.
Hårde massive emner er typisk tekniske artikler, hvor der stilles store krav til det færdige emnes fysiske og kemiske robusthed. Kemikalie-kar, kabinetter, pumpehjul m.m. er produkter i massiv hård PUR. Til sådanne produkter anvendes udelukkende MDI.
Et helt specielt anvendelsesområde er fremstilling af massive elastiske emner. Hærdningen foregår typisk i en varm form, som er omkring 100°C. Efter formningen efterhærder emnerne typisk et døgns tid i ovn. Der anvendes hovedsageligt TDI p.g.a. krav om stor rivstyrke.
20.4 Beskrivelse af branchens produkter
Branchens produktion kan kort beskrives ud fra en opdeling af materialet i hårdt skum, blødt skum og integralskum samt støbemasser m.m.
For alle typer gælder, at råvaren er flydende og består af to eller flere komponenter, som blandes og gennemgår en hærdning for at danne det endelige produkt. Udgangsprodukterne er altid isocyanater og polyoler.
20.4.1 Hårdt skum
Ved at anvende en speciel type polyolråvare opnås hårdt PUR-skum. Polyoltyperne er nærmere beskrevet i kapitler om ”Polyurethanbranchens råvarer”.
Hårdt PUR-skum anvendes hovedsageligt til isoleringsformål i fjernvarmerør, køle/fryseskabe, isoleringspaneler og varmtvandsbeholdere. Skummets isolerende egenskaber opstår ved dannelsen af et stort antal lukkede celler. Disse celler fremkommer ved brug af et opskumnings-middel, som fordamper under fremstillingsprocessen og indkapsles som gasblærer i plastmatriksen og/eller som et reaktionsprodukt (CO2) mellem isocyanat og vand.
Hårdt PUR-skum er et stabilt og stærkt materiale, og skummet kan indgå som en bærende del af flerlagskonstruktioner, idet skummet stabiliserer opbygningen ved at udfylde og afstive mellemrummet mellem to skaller.
20.4.2 Fleksibelt skum
Ved at justere polyol-råvarevalget kan man opnå, at den færdighærdede PUR-plast besidder fleksible egenskaber. Fleksibelt skum bruges i vid udstrækning til møbelpolstring og skummadrasser samt til vaskesvampe og engangsklude.
I Danmark fremstilles to forskellige typer fleksibelt skum, nemlig blokskum (slab-stock) og formskum.
20.4.3 Integralskum m.m.
Ved at variere recepturen og procesbetingelserne kan man opnå, at PUR-polymeren opskummer partielt, således at emnet dannes med en porefri overflade. Skum fremstillet på denne måde kaldes integralskum. Integralskum laves både fleksibelt og hårdt. Opskumningsgraden og dermed densiteten af skummet kan styres ved råvarevalget og procesparametrene.
Hårdt integralskum anvendes typisk til fremstilling af kabinetter i mindre serier. Herudover fremstilles vinduesprofiler samt valser til fremkalder- og reproanlæg i integralskum. Integralskumsstrukturen giver produkterne en høj styrke og lav vægt samtidig med, at den massive PUR's gode materialemæssige egenskaber bevares.
Fleksibelt integralskum anvendes først og fremmest til skosåler og møbelpolster. Her udnyttes luftlommernes fjedrende og vægtreducerende virkning i kombination med den massive overflades styrke overfor kemisk og fysisk påvirkning.
20.4.4 Massivt PUR
Massivt fleksibelt PUR anvendes til fremstilling af tekniske artikler, som udsættes for særlige kemiske eller fysiske påvirkninger. Et eksempel herpå er truckhjul.
Produktion af hårdt massivt PUR er mængdemæssigt mindre. Materialet bruges fortrinsvis til støbning af mindre serier tekniske artikler, hvor slidstyrke, termisk stabilitet og kemikalieresistens er blandt de ønskelige kvaliteter. Massivt polyurethan anvendes endvidere som tekniske støbemasser.
20.5 Energiforbrug
Energiforbruget til fremstilling af PUR består af forbrug af el til intern transport og blanding af råvarer, ventilation og eventuel formopvarmning.
Store forskelle i branchens produktionsmetoder og produkter vanskeliggør udarbejdelse af simple brancheenerginøgletal.
For at illustrere variationen af energiforbruget pr. kg produceret skum angives herunder strømforbruget fra to producenter med et specielt el-forbrug til henholdsvis formopvarmning og ventilation. Det skal nævnes, at materialeflowet gennem den sidstnævnte virksomhed er mange gange større end materialeflowet gennem den først nævnte.
En virksomhed, der støber tekniske artikler i stift integralskum i elopvarmede forme, angiver at virksomhedens totale el-forbrug er på 2½ kWh/kg produceret PUR-plast.
En anden virksomhed, der fremstiller blokskum, og som derfor har et stort ventilationsbehov, angiver virksomhedens totale el-forbrug til 0,33 kWh/kg produceret PUR-skum.
Det vurderes, at energiforbruget fra de øvrige produktionsmetoder ikke overstiger intervallet afgrænset af ovennævnte virksomheders forbrug.
21 Emissioner fra forarbejdning af termoplast
Se også:
Arbejdsmiljø ved forarbejdning af plast
Miljø- og sundhedsvurderinger
Referencer
Indholdsfortegnelse
Oversigtsfigur
21.1 Processers og målingers karakteristika
21.1.1 Virksomhedsmålinger/Laboratorieforsøg
Udledningerne ved plastforarbejdning vurderes på baggrund af tre forskellige typer af analyser.
Laboratorieforsøg har igennem årene været anvendt til specielt kvalitativ analyse af, hvilke nedbrydningsprodukter, der dannes ved opvarmning af plasttyper. Laboratorieforsøg adskiller sig fra ”det virkelige liv” på mange måder, idet det som oftest er tale om meget små mængder plast, der opvarmes, samtidigt med at temperatur, opholdstid og luftforhold ikke svarer til dem, der er normale ved plastforarbejdning.
Det, at det er små mængder plast, der opvarmes, gør at emissionerne per opvarmet enhed vil være større end ved almindelige forarbejdningsprocesser. Nedbrydningen af plast sker på overfladen af emnerne, og her vil små pellets, som ofte anvendes i laboratorieforsøg, nedbrydes relativt hurtigere end større emner. Samtidigt er der i visse laboratorieforsøg tale om væsentlige overskridelser af den anbefalede procestemperatur, hvilket også medfører en hurtigere nedbrydning. Endelig vil en lang opvarmningstid betyde, at den samlede nedbrydning øges.
Fra danske virksomheder foreligger der en række analyser af varierende kvalitet og udsigelseskraft. Ofte er analyserne gennemført for at få be- eller afkræftet, om en given proces giver anledning til udledning af et eller få bestemte stoffer i mængder, der overstiger koncentrationer og massestrømsgrænser i Miljøstyrelsens Luftvejledning. Et andet formål kan være at forsøge at identificere hvilke stoffer, der kan være årsag til lugtgener, hvilket kræver en bredere analyse.
Fra udlandet, specielt USA, foreligger der en række undersøgelser, der med udgangspunkt i forudgående laboratorieforsøg kvantificerer udledningerne af en række stoffer, der formodes at blive dannet om som ofte også har uønskede virkninger på mennesker og miljø. Undersøgelserne er gennemført under forhold, der langt hen ad vejen svarer til normale procesforhold (samme forarbejdningsudstyr, realistiske forhold med hensyn til temperatur og opholdstid, prøvetagning på relevante punkter, etc.). Disse undersøgelser er af forholdsvis ny dato, og må som udgangspunkt regnes for at give det mest præcise billede af udledninger ved normale procesforhold. Det skal dog bemærkes, at de fleste undersøgelser kun ser på ekstrudering af plast, og resultaterne er derfor ikke nødvendigvis repræsentative for andre forarbejdningsmetoder som f.eks. sprøjtestøbning. Da ekstrudering karakteriseres som en ”halvåben” proces i modsætning til sprøjtestøbning, der er karakteriseret som ”lukket” (se nedenfor), må det dog antages, at resultaterne ikke stiller plasttyperne i et urealistisk positivt lys.
På trods af den begrænsede værdi af specielt laboratorieforsøg er de alligevel refereret i denne rapport, idet de kan nuancere det kvalitative billede af nedbrydningsprodukter ved forarbejdning. Det anbefales dog at lægge størst vægt på de amerikanske undersøgelser, hvis der er behov for en detaljeret vurdering på en virksomhed.
Det skal understreges, at kombinationen af rigtig procestemperatur og opholdstid i f.eks. et sprøjtestøbningsværktøj er afgørende for det færdige produkts kvalitet. For høj temperatur eller for lang opholdstid giver blandt andet misfarvning af emnerne, hvilket er tegn på uønsket nedbrydning. Virksomheder, der ikke i tilstrækkelig grad har styr på disse parametre, risikerer dermed at levere produkter af dårlig kvalitet og samtidig give anledning til unødvendigt høje udledninger – uden at udledningerne nødvendigvis er højere end kravene i lovgivningen.
21.1.2 Lukkede processer
Lukkede processer som f.eks. sprøjtestøbning foregår i lukkede, kølede forme og giver normalt ikke anledning til særlige foranstaltninger til emissionsbegrænsning til det eksterne miljø. Varme maskindele kan ved unormal drift og ved maskinrensning medvirke til termisk nedbrydning af polymeren med potentiel mulighed for afdampning af stoffer, som er klassificeret som irriterende og kræftfremkaldende. Sprøjtestøbemaskiner bør derfor normalt være udstyret med effektiv punktudsugning.
Hvilke nedbrydningsprodukter, der dannes, er først og fremmest afhængig af plasttype, forarbejdningstemperatur og tilstedeværelse af ilt. Det er således af betydning, om nedbrydningen sker inde i værktøjet eller i forbindelse med, at varm plast for eksempel drypper ned på varme maskindele.
Der er foretaget relativt få målinger, der kvalitativt og eventuelt også kvantitativt beskriver nedbrydningsprodukter fra lukkede processer. Målinger kan gennemføres som arbejdsmiljømålinger, f.eks. med personbåret udstyr til målinger af stoffer i åndedrætszonen, som miljømålinger, hvor der måles i afkastet fra en virksomhed, eller som laboratorieforsøg, hvor mere eller mindre realistiske procesbetingelser er anvendt.
Laboratorieforsøg kan give en indikation af, hvor store mængder af luftforureninger, der fremkommer ved termisk nedbrydning af plast. Forsøgsomstændighederne varierer imidlertid betragteligt, alt efter hvilke formål de enkelte forsøg har, og det er derfor vigtigt at have disse in mente, når resultaterne vurderes. Som væsentlige afvigelser fra daglig praksis i en given produktion skal fremhæves, at temperaturen i forsøgene ofte er højere end den anbefalede procestemperatur, samt at nogle forsøg gennemførtes i en kvælstofatmosfære, der modvirker dannelse af oxidationsprodukter, men som er tænkt at simulere forholdene i et forarbejdningsværktøj.
For de plasttyper, der er medtaget i denne rapport, er viden om emissioner ved forskellige forarbejdningsprocesser og procesbetingelser forsøgt summeret for hvert enkelt materiale. Det bemærkes, at der ikke som udgangspunkt nødvendigvis er forskel på, hvilke stoffer der afgives ved forskellige processer, men at det som nævnt er forarbejdningstemperatur og tilstedeværelse af ilt, der betinger, hvilke stoffer, der dannes, og i hvor store mængder.
21.1.3 Halvåbne processer
Ekstrudering og termoformning er eksempler på processer, der kan kaldes halvåbne. Baggrunden for denne karakterisering er, at den forarbejdede, men stadig varme plastmasse kontinuerligt ledes ud i arbejdslokalet, hvor den kan afgive de nedbrydningsprodukter, der eventuelt er dannet under opvarmningen. Det skal bemærkes, at både lukkede og halvåbne processer finder sted under nøje temperaturkontrol for at hindre nedbrydning af plastmaterialet og sikre en høj og ensartet kvalitet af de produkter, der fremstilles.
21.1.4 Åbne processer
Åbne processer finder stort set ikke anvendelse ved forarbejdning af termoplast. Svejsning af folie er dog et eksempel på en proces, som kan karakteriseres som åben, men denne type proces er ikke almindeligt forekommende på plastforarbejdende virksomheder. Den finder snarere sted i andre typer af industrier, f.eks. i form af varmetrådssvejsning af emballage til fødevarer, tekstiler m.v.
Dette understreges af, at en af de hyppigst rapporterede gener/sygdomme i relation til plastforarbejdning er den såkaldte ”Meat wrappers asthma”, der oftest er observeret hos ansatte i levnedsmiddelindustrien, der anvendte en varmetråd til at skære phthalat-blødgjort PVC-folie over. Ved denne proces kan små stykker plast blive siddende på den varme tråd, hvorved de nedbrydes til blandt andet phthalsyreanhydrid og hydrogenchlorid, der er kendt for henholdsvis at kunne inducere asthma og være stærkt irriterende for luftvejene.
De ”åbne” processer er derfor sammenlignelige med de forhold, der ses ved ”unormal” drift i en plastforarbejdningsvirksomhed, f.eks. ved værktøjsskift, hvor den resterende plastmasse presses ud af maskinen, med risiko for at lande på varme maskindele og dermed også med risiko for at blive nedbrudt.
21.2 Nedbrydningsprodukter ved forarbejdning af polyethylen (PE)
Der findes en række undersøgelser og målinger der kan belyse, hvilke emissioner og i hvor store mængder, der kan findes ved forarbejdning af polyethylen.
Målinger i arbejdslokalet, der rapporterer værdier i enheden ppm eller mg/m³ er velegnede som led i en vurdering af arbejdsmiljøforhold, mens målinger, der rapporteres i enheden mg/kg (forarbejdet plast) er egnede som led i en vurdering af belastningen af miljø og sundhed i virksomhedens omgivelser – og dermed også som element i at udarbejde vilkår for en miljøgodkendelse. Enheden mg/kg forarbejdet plast kan for eksempel beregnes ud fra viden om koncentrationen i afkastet, luftskiftet (antal Nm³/time) og forarbejdet mængde plast.
21.2.1 Virksomhedsmålinger
21.2.1.1 Fremstilling af monofilamenter af HDPE
En dansk virksomhed fik i 1991 målt følgende emissioner ved produktion af monofilamenter af HDPE (forbrug 480 kg/h). De med (<) angivne stoffer har ikke kunne detekteres, og den angivne værdi er alene et udtryk for detektionsgrænsen ved den pågældende måling.
Stof |
Emitteret luftmængde
/emission |
Stofkoncentration |
Målemetode |
|
3170 Nm3/h |
|
|
Myresyre |
< 7 mg/kg |
< 1 mg/Nm3 |
Kemosorbtionsrør m. chromosorb P NAW coated m. Na2CO3/desorbtion m. vand/methylering/gaskromatografi(head-spaceteknik |
Eddikesyre |
< 10 mg/kg |
< 1,5 mg/Nm3 |
Som for myresyre |
Aldehyder |
< 1 mg/kg |
< 0,17 mg/Nm3 |
Kemosorbtionsrør m. silicagel coated m. 2,4-dinitro-phenyl-hydrazin/desorption m. vand+ethanol/højtryksvæskekromatografi |
Aerosoler |
4,8 mg/kg |
0,73 mg/Nm3 |
Opsamling på planfilter/differensvejning |
Tabel 1. Emissioner ved ekstrudering af monofilamenter af HDPE (480 kg/time).
Aerosol er således det eneste ”stof”, der var til stede over detektionsgrænsen. Udledningen af aerosol kan beregnes til ca. 2300 mg/time, hvilket er mindst en faktor 2 lavere end den laveste grænse for massestrøm i Luftvejledningen. Ifølge Jensen, Schmidt & Wolkoff (1989) kan der være bundet diverse nedbrydningsprodukter til aerosolen, og der er dermed risiko for eksponering for sådanne stoffer, selvom de ikke har kunnet detekteres. Det er dog tvivlsomt, om der i dette tilfælde er tale om en signifikant eksponering, taget i betragtning at målestrategien har været at finde netop de stoffer, der regnes for at være mest belastende.
21.2.1.2 Blæsestøbning af polyethylen
Forrest et al. (1995) undersøgte emissioner fra blæsestøbning af polyethylen på en amerikansk virksomhed, der karakteriseres som ”meget ren”. Forfatterne bemærker, at blæsestøbning notorisk kun danner meget lidt dampe, og at det derfor ikke er overraskende, at der kun findes simple kulbrinter og toluen i meget små koncentrationer (højeste værdi er 0,03 mg/m³).
21.2.1.3 Rotationsstøbning af tværbundet polyethylen (PEX)
En dansk virksomhed fik i 1998 foretaget en analyse og vurdering af emissionerne ved rotationsstøbning af tværbundet polyethylen. Analysen er foretaget ved i en testovn at simulere produktionsprocessen med hensyn til opholdstid og temperatur, om end temperaturforholdene ikke er helt de samme, fordi prøvekolben ikke roteres. Analysen er også foretaget på en mindre prøve, end de der normalt støbes i processen. Analysen kan derfor ikke karakteriseres som en reel virksomhedsmåling, men snarere som et laboratorieforsøg med temperatur- og opholdstid, der svarer nogenlunde til den grundlæggende proces.
PEX-pulver blev anbragt i en kolbe og opvarmet i en ovn til ca. 180°C i 35 minutter, hvorefter en prøve blev udtaget og analyseret ved GC-MS (gaschromatografi kombineret med massespektroskopisk detektion). Analyseresultaterne blev efterfølgende opskaleret til fuldskalaforhold og koncentration og massestrøm i afkastet beregnet.
Analysen viste tilstedeværelse af 27 forskellige stoffer, hvoraf fire ikke kunne identificeres. Tabellen viser de beregnede middelværdier for koncentration og massestrøm ved en luftstrøm på ca. 9200 Nm³/h for de otte stoffer, der blev fundet i de største koncentrationer. Beregningen er foretaget for et emne på ca. 35 kg.
Stofnavn |
Koncentration
i afkast (mg/Nm³) |
Massestrøm
(mg/h) |
Emission
(mg/kg) |
Uidentificeret (muligvis cyclisk alkohol eller ether) |
348 |
3.203 |
76 |
Uidentificeret (muligvis cyclisk alkohol eller ether) |
103 |
945 |
23 |
Acetone |
76 |
704 |
17 |
Uidentificeret (sandsynligvis umættet dialkohol) |
49 |
454 |
11 |
Tert-butylalkohol |
36 |
334 |
8,0 |
Formaldehyd |
23 |
210 |
5,0 |
Methanol |
16 |
149 |
3,6 |
Kulbrinter (ligekædede C10-C18 kædelængde) |
13,2 |
122 |
2,9 |
Triallylcyanurat |
13,2 |
122 |
2,9 |
Total |
702 |
6.455 |
154 |
Tabel 2. Emissioner ved rotationsstøbning af tværbundet polyethylen.
I vurderingen af målingerne, som er lavet af dk-TEKNIK, konkluderes det, at kravene i Miljøstyrelsens Vejledning nr. 6 1990 om laveste emissionsgrænse på 5.000 mg/m³ og massestrømsgrænse på 100.000 mg/h er overholdt med en meget stor margin. Formaldehyd, som formodentlig er det eneste af de nævnte stoffer, der tilhører hovedgruppe 1 i Vejledningen, har en emissionsgrænse på 1.000-5.000 mg/m³ og en massestrømsgrænse på 25.000 mg/h. Begge disse grænser er overholdt med meget stor margin. De øvrige stoffer ligger alle under Vejledningens laveste grænse for massestrøm på 500 mg/h og emissionsgrænse på 100 mg/m³.
21.2.1.4 Ekstrudering af polyethylen
Barlow et al. (1996) undersøgte emissionerne ved forarbejdning af forskellige polyethylenkvaliteter ved typiske procesbetingelser for ekstruderings-coating (hvor den ekstruderede film bruges til at coate et fladt substrat som pap eller metalfolie), filmblæsning og blæsestøbning. Den samme ekstruder med en 1,5” enkeltskrue blev anvendt til alle forsøg, mens variable som resintype, temperatur og opholdstid blev justeret til at simulere typiske procesbetingelser.
De tre polyethylenkvaliteter, der blev undersøgt, var:
- LDPE til ekstruderingscoating (uden additiver)
- LLDPE til filmblæsning (antioxidant/stabilisator: 1775 ppm; proceshjælpestoffer: 580 ppm; antiblokmiddel: 4750 ppm)
- HDPE til blæsestøbning (antioxidant/stabilisator: 350 ppm; proceshjælpestoffer: 200 ppm)
Resintype |
LDPE |
LLDPE |
HDPE |
Proces |
Ekstruderingscoating |
Filmblæsning |
Blæsestøbning |
Temperatur (°C) |
260 |
316 |
179 |
202 |
232 |
260 |
193 |
221 |
Partikler (µg/g) |
30,9 |
242,2 |
2,4 |
21,7 |
24,7 |
59,9 |
19,6 |
26,6 |
VOC |
|
|
|
|
|
|
|
|
Kulbrinter (C4-C16) |
17,0 |
76,6 |
13,9 |
15,3 |
15,4 |
21,3 |
25,0 |
38,5 |
Ethan |
0,09 |
1,21 |
0,02 |
0,03 |
0,03 |
0,04 |
0,02 |
0,02 |
Ethylen |
0,05 |
1,58 |
0,01 |
0,03 |
0,01 |
0,02 |
0,02 |
0,01 |
Propylen |
0,02 |
0,38 |
<0,01 |
0,01 |
<0,01 |
<0,01 |
0,01 |
<0,01 |
Aldehyder |
|
|
|
|
|
|
|
|
Formaldehyd |
0,10 |
8,11 |
0,09 |
0,04 |
0,14 |
0,20 |
0,06 |
0,06 |
Acrolein |
<0,01 |
0,07 |
<0,02 |
<0,02 |
0,02 |
0,05 |
<0,02 |
0,02 |
Acetaldehyd |
0,12 |
4,43 |
0,03 |
0,03 |
0,09 |
0,16 |
0,04 |
0,05 |
Propionaldehyd |
0,07 |
3,26 |
<0,02 |
<0,02 |
0,02 |
0,05 |
<0,02 |
0,02 |
Ketoner |
|
|
|
|
|
|
|
|
Acetone |
0,02 |
0,04 |
0,08 |
0,07 |
0,08 |
0,08 |
0,02 |
0,03 |
Methyl ethyl keton |
0,10 |
5,25 |
<0,02 |
<0,02 |
0,02 |
0,04 |
0,05 |
0,02 |
Organiske syrer |
|
|
|
|
|
|
|
|
Myresyre |
0,34 |
12,3 |
<0,17 |
<0,17 |
<0,17 |
<0,17 |
<0,17 |
<0,17 |
Eddikesyre |
<0,17 |
2,00 |
<0,17 |
<0,17 |
<0,17 |
<0,17 |
<0,17 |
<0,17 |
Acrylsyre |
<0,02 |
<0,02 |
<0,02 |
<0,02 |
<0,02 |
<0,02 |
<0,02 |
<0,02 |
Tabel 3. Emissioner ved forarbejdning af polyethylen ved normale procesbetingelser for de pågældende kvaliteter/processer. Alle emissioner er givet i enheden µg/g, der svarer til mg/kg eller g/ton. (Efter Barlow et al., 1996).
Barlow et al. (1996) peger i deres analyse af resultaterne på, at forarbejdning af LDPE ved en høj temperatur (316°C) giver anledning til væsentligt højere emissioner end ved lave temperaturer. Specielt peger de på formaldehyd og andre aldehyder, der emitteres i mængder over 1 mg/kg, mens der ved en lav forarbejdningstemperatur ikke ses værdier over 1 mg/kg, undtagen for samleparameteren kulbrinter.
De samlede udledninger af VOC ligger mellem 8 og 157 mg/kg, mens partikler (eller rettere ikke-flygtige forbindelser) blev fundet i mængder op til 242 mg/kg.
Endelig skal det bemærkes, at Barlow et al. (1996) i deres arbejde også har udviklet algoritmer, der forudsiger emissionsniveauer som funktion af forarbejdningstemperatur. Det har ligget udenfor dette projekts rammer at bearbejde disse algoritmer til SI-enheder.
Værdierne i Tabel 3 kan bruges til at give et skøn over udledningerne (massestrømmen) fra en given virksomhed. I princippet er det eneste, der behøves, oplysninger om hvor stor en mængde, der forarbejdes indenfor en givet tidsenhed. Den simple formel kan opstilles på følgende måde:
Massestrøm = Emission af stof * forarbejdet mængde/tid
For en virksomhed, der dagligt forarbejder 5 ton LLDPE med typiske additiver over en 7-timers periode, kan massestrømmen for acetaldehyd beregnes til at ligge mellem:
Nedre værdi: 0,03 µg/g * 5.000.000 g/7 timer, svarende til ca. 0,02 g/time
Øvre værdi: 0,16 µg/g * 5.000.000 g/7 timer, svarende til ca. 0,14 g/time
Sammenholdt med grænseværdien i Miljøstyrelsens Luftvejledning er de beregnede værdier forholdsvis uproblematiske, idet massestrømsgrænsen for acetaldehyd er 25 g/time. Udledningen af de øvrige stoffer, både enkeltvis og samlet, skønnes også at ligge under massestrømsgrænserne med en forholdsvis bred margin.
21.2.2 Laboratorieforsøg
Frostling et al. (1982) undersøgte nedbrydningsprodukter ved opvarmning af polyethylen til fire temperaturer, der ligger omkring eller lidt over den temperatur, der generelt anvendes ved PE-forarbejdning. Opvarmningstiden i forsøgene var fire minutter, hvilket er signifikant længere end den normale forarbejdningstid. Værdierne, der i den nedenstående tabel er angivet i mg/kg plast, er derfor med stor sandsynlighed væsentligt højere end de værdier, der vil kunne måles under normale procesbetingelser.
|
|
Forarbejdningstemperatur |
|
|
264°C |
274°C |
280°C |
289°C |
Stof |
|
|
|
|
|
Aldehyder |
|
|
|
|
|
Formaldehyd |
mg/kg |
900 |
1320 |
1780 |
2380 |
Acetaldehyd |
mg/kg |
1370 |
1770 |
1950 |
2400 |
Propanal |
mg/kg |
270 |
|
370 |
440 |
Acrolein |
mg/kg |
230 |
|
280 |
440 |
Butanal |
mg/kg |
|
|
700 |
|
Pentanal |
mg/kg |
|
|
540 |
|
|
|
|
|
|
|
Ketoner |
|
|
|
|
|
Acetone |
mg/kg |
|
|
250 |
|
Methylethylketon |
mg/kg |
|
|
320 |
|
Mehylvinylketon |
mg/kg |
|
|
30 |
|
Methylpropylketon |
mg/kg |
|
|
290 |
|
|
|
|
|
|
|
Syrer |
|
|
|
|
|
Myresyre |
mg/kg |
2440 |
2980 |
3450 |
4120 |
Eddikesyre |
mg/kg |
870 |
1200 |
1400 |
1760 |
Propionsyre |
mg/kg |
|
660 |
700 |
780 |
Akrylsyre |
mg/kg |
|
120 |
180 |
340 |
Smørsyre |
mg/kg |
85 |
205 |
230 |
300 |
|
|
|
|
|
|
Lactoner |
|
|
|
|
|
Butyrolacton |
mg/kg |
|
|
290 |
|
Tabel 4. Emissioner ved opvarmning af PE-plast under laboratorieforhold
Frostling et al. bemærker, at det er primært myresyre, eddikesyre, acetaldehyd og formaldehyd, der dannes i større mængder, mens de mest toksiske stoffer som acrolein, methylvinylketon og acrylsyre dannes i relativt små mængder. Det skal dog hertil bemærkes, at både formaldehyd og acetaldehyd af Arbejdstilsynet regnes for at være kræftfremkaldende.
21.2.3 Opsummering – polyethylen
Frostling et al. (1982) har i deres laboratorieundersøgelse af emissioner fra PE fundet meget højere værdier i modsætning af resten af det tilgængelige datamateriale. De svenske tal er fra 200-1000 gange højere and andet tilgængeligt materiale. Det virker ikke sandsynligt, at der er tale om en faktor 1000 fejl, da tallene er citeret 2 steder, men samtidig har originalmaterialet har ikke været muligt at fremskaffe. Svenskerne fremhæver selv, at opholdstiden er væsentlig længere end normal opholdstid i produktion, hvilket medfører en overestimering af emissionen. Samtidig er ilt tilstede i hele forsøgsperioden, hvor ilt kun er til stede ved nedkøling under normal produktion.
Undersøgelsen af PEX i headspace er også et laboratorieforsøg med endnu længere opholdstid og lavere temperatur. Denne undersøgelse giver langt fra anledning til emissioner i samme størrelsesorden som i den svenske undersøgelse.
Den amerikanske undersøgelse (Barlow et al. (1996)) er baseret på virkelighedstro produktion og virker grundig i forsøgsplanlægning, valg af målemetoder mv. De fundne størrelsesordener understøttes af det resterende materiale (bortset fra den svenske undersøgelse).
I denne rapports anbefalinger vælges det at se bort fra resultaterne i den svenske undersøgelse, da meget tyder på at resultaterne er urealistisk høje, enten fordi formålet med undersøgelsen har været at kvalificere og udvikle målemetoder snarere end at kvantificere, eller simpelthen fordi opholdstiden, tilstedeværelsen af ilt eller temperaturen ikke svarer til ”normale” procesforhold. Det anbefales derfor, at resultaterne fra Barlow et al. (1996) benyttes ved vurdering af danske PE-forarbejdende virksomheders miljøforhold.
21.3 Nedbrydningsprodukter ved forarbejdning af polypropylen (PP)
De vigtigste variable ved forarbejdning af polypropylen er (Adams et al. (1999):
- Ekstruder størrelse og type
- Smeltetemperatur og –rate
- Forholdet mellem overflade og volumen for det ekstrudat, der udsættes for luft
- Afkølingsrate for ekstrudatet
- Skæreeffekten fra ekstruderskruen
- Resintype og –alder
- Additivtyper og -mængder
De mange variable gør det vanskeligt at præcist forudsige udledningerne fra en given proces, men ved at udvælge typiske procesvariable kan det lade sig gøre at få et overblik over sandsynlige niveauer ved de mest almindelige forarbejdningsprocesser. Dette er blandt andet gjort i en række nyere amerikanske undersøgelser, der citeres i de følgende afsnit.
Overordnet skal det bemærkes, at de amerikanske undersøgelser viser et niveau af emissioner, der er en til to størrelsesordener lavere end de værdier, som den amerikanske miljøstyrelse, EPA, tidligere har rapporteret. Det har ikke været muligt at finde en forklaring på disse forskelle, men det vurderes, at de nye amerikanske undersøgelser er tilrettelagt på en måde, der skulle give et konsistent og pålideligt billede af plastforarbejdning. For en god ordens skyld inddrages også viden fra andre litteraturkilder, ligesom der i de enkelte afsnit suppleres med resultaterne af målinger på danske virksomheder i den udstrækning sådanne oplysninger har været tilgængelige.
21.3.1 Ekstrudering af polypropylen
Adams et al. (1999) undersøgte emissionerne ved ekstrudering af fem forskellige PP-kvaliteter:
- Controlled rheology homopolymer (antioxidant: 1700 ppm; proceshjælpestoffer: 1000 ppm)
- Controlled rheology homopolymer med antistatikum (antioxidant: 1700 ppm; antistatikum: 3400 ppm; proceshjælpemiddel: 2500 ppm)
- Reactor grade homopolymer (antioxidant: 1700 ppm; proceshjælpestoffer: 900 ppm)
- Reactor impact copolymer med 15-20 vægtprocent ethylen-propylen gummi (antioxidant: 2500 ppm; proceshjælpestoffer: 1500 ppm)
- Random copolymer med 3-6 vægtprocent ethylen (antioxidant: 2000 ppm; proceshjælpestoffer: 2200 ppm; slipmiddel/antiblokmiddel: 3000 ppm)
Nogle af kvaliteterne blev undersøgt ved forskellige temperaturer (204-318°C), der alle ligger indenfor den normale forarbejdningstemperatur for PP. Resultaterne fra målingerne er gengivet i Tabel 5. For en nærmere beskrivelse af prøvetagning og analysemetoder henvises til originalartiklen.
Klik her for at se tabellen.
Tabel 5. Emissioner ved forarbejdning af forskellige PP-kvaliteter i det normale temperaturinterval. Alle emissioner er givet i enheden µg/g, der svarer til mg/kg eller g/ton. (efter Adams et al., 1999)
Adams et al.(1999) peger i deres analyse af resultaterne på, at at ”controlled rheology homopolymer” forårsager de største udledninger af partikler og VOC. De peger også på, at en øgning af forarbejdningstemperaturen fra 204 til 318 °C medfører en signifikant forøgelse af udledninger, men påpeger, at værdier ikke kan bruges til at ekstrapolere til de højere temperaturer, som man f.eks. bruger ved ”melt spinning” af polypropylen.
Værdierne i skemaet kan bruges til at give et skøn over udledningerne (massestrømmen) fra en given virksomhed. I princippet er det eneste, der behøves, oplysninger om hvor stor en mængde, der forarbejdes indenfor en givet tidsenhed. Den simple formel kan opstilles på følgende måde:
Massestrøm = Emission af stof * forarbejdet mængde/tid
For en virksomhed, der dagligt forarbejder 5 ton almindeligt PP (f.eks. reactor grade homopolymer) over en 7-timers periode, kan massestrømmen for formaldehyd beregnes til at ligge mellem:
Nedre værdi: 0,17 µg/g * 5.000.000 g/7 timer, svarende til ca. 0,12 g/time
Øvre værdi: 7,05 µg/g * 5.000.000 g/7 timer, svarende til ca. 5 g/time
Sammenholdt med grænseværdien i Miljøstyrelsens Luftvejledning er de beregnede værdier forholdsvis uproblematiske, idet massestrømsgrænsen for formaldehyd er 25 g/time.
21.4 Nedbrydningsprodukter ved forarbejdning af polyvinylchlorid (PVC)
21.4.1 Ekstrudering af PVC
Ernes and Griffin (1996) undersøgte emissionerne ved ekstrudering af PVC under betingelser, der svarer til faktisk produktion med hensyn til blandt andet forarbejdningstemperatur, compunder- og ekstruderstørrelse, forarbejdet mængde per tidsenhed. Den PVC, der blev ekstruderet, var stabiliseret med calciumstearat, og derudover var den tilsat voks, carbonat og titandioxid.
Først gennemførte de en screening i form af en kvalitativ analyse af, hvilke stoffer, der blev afgivet. Screening var en headspace analyse af en prøve, der blev opvarmet ved konstant temperatur (190°C) i 20 minutter. Til at simulere ekstrudering af rør blev der først anvendt en compunder, hvor plasten i to tempi blev blandet ved temperaturer på 74, henholdsvis 115°C. Derefter blev compounden overført til et mellemlager, og sluttelig blev den ekstruderet i en proces over 10 minutter ved en temperatur på 190°C.
Analyserne blev både i screeningen og fuld-skalaforsøget fokuseret på måling af VOC samt en screening for farlige stoffer, som de er defineret af den amerikanske miljøstyrelse (HAP-listen (Hazardous Air Pollutants). Resultaterne viser, at der kun blev identificeret få stoffer, hvoraf ingen var på HAP-listen (Tabel 6).
Stof |
Forsøg 1 |
Forsøg 2 |
Forsøg 3 |
Gennemsnit |
Acetone |
0,03 |
0,03 |
0,04 |
0,03 |
Thiirane |
0,63 |
0,59 |
0,63 |
0,62 |
2-ethylhexanal |
0,28 |
0,26 |
0,23 |
0,26 |
2-ethylhexanol |
1,58 |
1,35 |
1,23 |
1,39 |
Kulbrinter (primært C10-C11) |
25,7 |
24,0 |
22,2 |
23,7 |
VOC (total) |
28,3 |
26,3 |
24,1 |
26,0 |
TOC (Total Organic Carbon) |
|
|
|
54,1 |
Tabel 6. Udledninger ved ekstrudering af PVC. Alle værdier i mg/kg forarbejdet plast.
Ernes og Griffin (1996) konkluderer på baggrund af de ovenstående resultater, at tidligere værdier for emissioner har været overestimeret med en faktor 1000, men gør ikke noget forsøg på at forklare dette. De konkluderer også, at det ikke var muligt at detektere farlige stoffer, således som de er defineret i den amerikanske Clean Air Act, herunder benzen, toluen og vinylchlorid.
Det skal bemærkes, at Ernes og Griffins målinger kun identificerer et beskedent antal stoffer, sammenlignet med blandt andet de arbejdsmiljømålinger, der er citeret andetsteds. Det er desværre ikke muligt at få det fulde overblik over det gennemførte måleprogram.
21.4.2 Virksomhedsmålinger
21.4.2.1 Ekstrudering af PVC-slanger
En dansk virksomhed, der ekstruderer PVC-slanger, har i 1989 fået målt emissionen i afkastet fra PVC-ekstrudere (Tabel 7). De med (<) angivne stoffer har ikke kunne detekteres, og den angivne værdi er alene et udtryk for detektionsgrænsen ved den pågældende måling. Under målingerne blev der brugt 175 kg PVC i timen.
I RT-rapporten om termoplast (Plastindustrien i Danmark (2000) nævnes det, at afdampningen ved ekstrudering af blød PVC normalt udgør 0,02-0,007 pct. af blødgørerindholdet. Det har ikke været muligt at verificere dette typetal.
På grund af ensartede procesforhold må det formodes at emissionsforholdene for andre producenter af slanger eller producenter af blødgjorde profiler ikke adskiller sig væsentligt fra ovennævnte forhold.
Stof |
Emitteret luftmængde
/emission (mg/kg) |
Stofkoncentration
(mg/Nm³) |
Målemetode |
|
1040 Nm3/h, tør |
|
|
Formaldehyd |
0,24 |
0,04 |
Kemosorbtionsrør m. silicagel coated m. 2,4-dinitro-phenylhydrazin/desorbtion m. ethanol+vand/højtryksvæskekromatografi m. UV detektion |
Acetaldehyd |
<0,48 |
<0,08 |
Samme som for formaldehyd |
Acrolein |
<0,12 |
<0,02 |
Samme som for formaldehyd |
Phthalater |
<2,4 |
<0,4 |
XAD 2-rør/desorberet m. ethanol/gaskromatografi |
Benzen |
<3,0 |
<0,5 |
Adsorbtionsrør m. kul+silicagel/gaskromatografi |
Phthalsyreanhydrid |
<0,059 |
< 0,01 |
Hydrolyse af støv m. ammoniakvand/højtrykvæskekromatografi |
Hydrogenchlorid |
<7,7 |
<1,3 |
Vaskeflaske m. destilleret vand/ionkromatografi |
Bly |
<0,012 |
< 0,002 |
Syreekstration af støv/atomabsorbtionsspektrofotometrisk analyse |
Zink |
<0,030 |
< 0,005 |
Syreekstration af støv/atomabsorbtionsspektrofotometrisk analyse |
Barium |
<0,0059 |
< 0,001 |
Syreekstration af støv/atomabsorbtionsspektrofotometrisk analyse |
Cadmium |
<0,0059 |
< 0,001 |
Syreekstration af støv/atomabsorbtionsspektrofotometrisk analyse |
Total støv |
10 |
1,7 |
Isokinetisk måling/planfiltre/elektronisk mikrovægt |
Tabel 7. Emissioner ved ekstrudering af PVC-slanger (175 kg/time)
Det er således kun formaldehyd og total støv, der er målt i koncentrationer over detektionsgrænsen.
21.4.2.2 DEHP ved ekstrudering af PVC-slanger
En dansk virksomhed, der ekstruderer PVC-slanger i blød PVC, har i 1999 fået målt emissionen af DEHP i afkastene fra PVC-ekstrudere. Der er ikke præcise angivelser af produceret mængde. Den samlede emission er vurderet på baggrund af målinger i udvalgte afkast samt opskalering til totalt for fabrikken. Til gengæld er alle værdier over detektionsgrænsen.
Proces |
Stof |
Emitteret luftmængde
/emission (mg/h) |
Stofkoncentration
(mg/Nm³) |
Målemetode |
Ekstrudering af PVC-slanger (mængde ukendt , 16 maskiner i drift) |
|
30.200 Nm3/h |
|
|
|
DEHP |
3880 mg/h |
0,13 |
isokinetisk udsugning, filter og XAD-2/desorberet m. dichlormethan/GC/MS |
Tabel 8. Emissioner ved ekstrudering af PVC-slanger
På grund af manglende information om produceret mængde er det ikke muligt at estimere emissionen i mg/kg forarbejdet plast. Da en total massestrøm for virksomheden kan beregnes og sammenlignes med massestrømsgrænsen vurderes resultaterne relevante. Massestrømsgrænsen for DEHP er i Luftvejledningen fastsat til 25.000 mg/h. Virksomheden udleder også DEHP fra andre produktionstyper (sprøjtestøbning og svejsning) og den samlede DEHP emission fra virksomheden er bestemt til 4.800 mg/h, svarende til ca. 20 % af massestrømsgrænsen. Immissionskoncentrationsbidraget for DEHP er uden for virksomhedens skel ca. 30 % af B-værdien.
21.5 Nedbrydningsprodukter ved forarbejdning af polystyren (PS)
21.5.1 Virksomhedsmålinger
Der er ikke fundet virksomhedsmålinger vedrørende forarbejdning af polystyren, hverken fra Danmark eller udlandet.
21.5.2 Laboratorieforsøg
Forarbejdningstemperaturen for polystyren ligger normalt i intervallet fra 150-300°C, men ved for eksempel varmetrådsskæring kan temperaturen være væsentligt højere, hvilket medfører en øget nedbrydning af polymeren.
Frostling et al. (1982) undersøgte nedbrydningsprodukter ved opvarmning af polystyren til temperaturer, der ligger omkring eller lidt over den temperatur, der generelt anvendes ved PS-forarbejdning. Forsøgene gennemførtes i både kvælstof-atmosfære og atmosfærisk luft. Resultaterne er summeret i nedenstående tabel, men det skal bemærkes, at kilden ikke indeholder oplysninger om, hvor længe plasten var udsat for den pågældende temperatur:
Plasttype |
Temperatur (°C) |
Styren (mg/kg) |
BHT (mg/kg) |
Benzaldehyd
(mg/kg) |
Benzoesyre (mg/kg) |
Acetophenon (mg/kg) |
PS |
255 i kvælstof |
320 |
|
|
|
|
PS |
260 i kvælstof |
520 |
|
|
|
|
PS |
250 i luft |
740 |
|
2300 |
570 |
380 |
PS |
240 i luft |
520 |
|
800 |
300 |
180 |
HIPS |
260 i kvælstof |
290 |
90 |
|
|
|
HIPS |
240 i kvælstof |
390 |
440 |
|
|
|
HIPS |
250 i luft |
280 |
70 |
300 |
160 |
|
HIPS |
224 i luft |
310 |
290 |
130 |
|
|
Tabel 9. Nedbrydningsprodukter ved forarbejdning af PS og HIPS.
I et andet forsøg måltes nedbrydningen af PS som funktion af tid ved opvarmning til mellem 200-260°C. Der blev målt et vægttab på omkring 500-1000 mg/kg efter et minut, og efter 10 minutters ophold i kvælstofatmosfæren var vægttabet mellem 1.500 mg/kg og 11.000 mg/kg.
I Miljøstyrelsens Luftvejledning findes styren i Hovedgruppe 2, Klasse II med en massestrømsgrænse på 2000 g/time og en B-værdi på 0,2 mg/m³. Med en emission af styren på 740 mg/kg (største værdi fra Tabel 9) betyder det, at en virksomhed kan forarbejde omkring 2700 kg polystyren i timen, før massestrømsgrænsen for dette stof overskrides.
Acetophenon er også placeret i Hovedgruppe 2 i Luftvejledningen, men i Klasse 1, hvor massestrømsgrænsen er 100 g/time. Med emissionsværdien for acetophenon fra Tabel 9 på 380 mg/kg betyder det, at der kun kan forarbejdes omkring 260 kg polystyren i timen, før massestrømsgrænsen overskrides. Derudover kan det tænkes, at de emitterede stoffer har same effekter og virkemåde, hvilket betyder at der skal tages udgangspunkt i en samlet B-værdi, og dermed at massestrømsgrænsen sandsynligvis reduceres. Der er ikke foretaget en beregning med disse (tænkte) forudsætninger.
21.5.3 Diskussion
Værdierne for emissioner i den svenske undersøgelse af PS er af samme størrelsesorden som i den tilsvarende svenske laboratorieundersøgelse af PE. For PS’ vedkommende har det ikke været muligt at krydsreferere med andre kilder med hensyn til emissioner per kilo forarbejdet materiale.
Den umiddelbare konklusion er derfor, at de værdier, der citeres for forarbejdning af PS og HIPS er urealistisk høje. Denne konklusion understøttes af, at de svenske forskere ved arbejdspladsmålinger har målt værdier for styren i åndedrætszonen, der er 25 gange højere end ved tilsvarende amerikanske undersøgelser. Et andet element, der understøtter formodningen om ”for høje værdier” i den svenske undersøgelse er, at en så udtalt nedbrydning af materialet må have en markant indflydelse på de færdige produkters kvalitet – og dermed ikke være repræsentativ for generelle produktionsforhold.
21.6 Emissioner ved ekspandering af polystyren (EPS)
Ekspandering af EPS adskiller sig væsentligt fra andre kombinationer af forarbejdningsproces og materiale med hensyn til, hvilke udledninger, der forekommer.
Råvaren indeholder nemlig ca. 6% pentan, som for størstedelens vedkommende (70-75%) bliver udledt i forskellige trin af produktionsprocessen, mens den resterende mængde diffunderer fra produktet til omgivelserne under produktets brug. Der bliver med andre ord udledt ca. 60 g pentan per kg produceret EPS, hvoraf omkring 45 gram bliver udledt fra virksomhedens afkast.
Mængden af afkastluft fra virksomhederne ligger i intervallet 10 -50.000 m³ pr. time og det gennemsnitlige pentanindhold er typisk nogle hundrede mg/m³. For større virksomheder kan pentankoncentrationen således periodevis overstige 300 mg/m³.
Både volumenstrømmen og pentankoncentrationen er stærkt afhængig både af virksomhedsstørrelsen og det enkelte anlæg. På hver enkelt virksomhed varierer pentanemissionen, først og fremmest afhængigt af pentanindholdet i råvaren og det aktuelle produktionsniveau, og af om der forskummes.
Fordelingen af pentanemissionen fra de forskellige procestrin er som følger (DOR, 2000b):
Forskumning: 25 pct.
Mellemlagring 25 pct.
Udstøbning, tørring, emballering og lagring 20 pct.
Slutprodukt, 48 timers lagring 20 pct.
Slutprodukt, to måneders brug 10 pct.
Udover pentan emitteres der også en mindre mængde styren, som hovedregel under 0,10 pct. (w/w) af den forarbejdede mængde. Den emitterede styren er primært ureageret monomer i råvaren, mens afgivelse på grund af opvarmning og termisk nedbrydning vurderes som værende ubetydelig på grund af den lave forarbejdningstemperatur.
21.7 Nedbrydningsprodukter ved forarbejdning af polycarbonat (PC)
Rhodes et al. (2002) undersøgte nedbrydningsprodukterne ved forarbejdning af otte forskellige kommercielle kvaliteter af polycarbonat, beregnet til formål som blandt andet fødevareemballage og compact discs (CD’ere) og til markedet for UV- stabiliserede, flammehæmmede og slagfaste produkter. Endvidere blev en blanding af PC/ABS undersøgt. Det vurderes, at der er tale om et repræsentativt udvalg af råvarer, og det skal bemærkes, at der er forholdsvis store forskelle i udledninger mellem de forskellige kvaliteter.
Analyserne fokuserede på udvalgte nedbrydningsprodukter ved ekstrudering under normale procesforhold (8 flygtige forbindelser, fire halvflygtige forbindelser samt partikler). De flygtige forbindelser blev opsamlet i SUMMA 6-L beholdere og analyseret med et GC system med parallel flammeioniseringsdetektor og massespektroskopi. De halvflygtige forbindelser blev opsamlet på XAD-2 adsorberrør og analyseret med GC/MS. Partikler blev målt med gravimetri.
Tabel 10. Nedbrydningsprodukter ved forarbejdning af forskellige kommercielle PC- og PC/ABS-kvaliteter. Alle værdier er i g/ton, svarende til mg/kg.
Klik her for at se tabellen.
Resultaterne viser, at udledningerne ved forarbejdning af polycarbonat varierer en del, alt efter hvilken kvalitet, der er tale om. Det må antages, at det er diverse additiver, der er den primære årsag til forskellene.
Værdierne i skemaet kan bruges til at give et skøn over udledningerne (massestrømmen) fra en given virksomhed. I princippet er det eneste, der behøves, oplysninger om hvor stor en mængde, der forarbejdes indenfor en givet tidsenhed. Den simple formel kan opstilles på følgende måde:
Massestrøm = Emission af stof * forarbejdet mængde/tid
For en virksomhed, der dagligt forarbejder 1000 kg slagfast PC over en syv-timers arbejdsdag, kan massestrømmen for diphenylcarbonat f.eks beregnes til (6.36 g/ton * 1 ton)/ 7 timer = 0,9 g/time. Der findes ikke en B-værdi eller en massestrømsgrænse for diphenylcarbonat, men massestrømmen ligger under den værdi på 25 g/time, der er gældende for stoffer i Luftvejledningens Hovedgruppe 1, Klasse II-stoffer.
21.8 Nedbrydningsprodukter ved forarbejdning af ethylen-vinylacetat og ethylen-methylacrylat copolymer (EVA og EMA)
Barlow et al. (1997) undersøgte nedbrydningsprodukterne ved forarbejdning af ethylen-vinylacetat copolymer (EVA) og ethylen-methacrylat copolymer (EMA).
Undersøgelsen omfattede ekstrudering af tre blandinger af EVA-copolymere med henholdsvis 9, 18 og 28% vinylacetat (VA) og to blandinger af EMA-copolymere, hver med 20% methylacrylat (MA). Som kontrol blev to blandinger af LDPE analyseret. Der var i alle tilfælde tale om blandinger af kommercielle produkter, med tilsætning af additiver som beskrevet i Tabel 11.
Tabel 11. Additivindhold og forarbejdningstemperatur for de undersøgte plasttyper.
Plasttype |
Slipmiddel |
Anti-blok |
Antioxidant |
Forarbejdnings-temperatur (max) |
Typisk anvendelse |
EVA (9% VA) |
300 ppm |
1500 ppm |
150 ppm |
224°C |
Film, laminering, hot-melt |
EVA (18% VA) |
0 ppm |
0 ppm |
138 ppm |
171°C |
Film, laminering, hot-melt |
EVA (27% VA) |
0 ppm |
0 ppm |
263 ppm |
171°C |
Film, laminering, hot-melt |
EMA (20% MA) |
0 ppm |
0 ppm |
250 ppm |
177°C |
Filmblæsning, ekstruderings-coatning |
EMA (20% MA) |
0 ppm |
0 ppm |
250 ppm |
296°C |
Filmblæsning, ekstruderings-coatning |
LDPE |
156 ppm |
300 ppm |
340 ppm |
171°C |
|
Der blev analyseret for 14 stoffer, der var udvalgt på grund af deres potentielle farlighed eller fordi de var forventet som nedbrydningsprodukt. Organisk syrer blev opsamlet på KOH-imprægneret filter, aldehyder og ketoner på DNPH-rør, VOC i SUMMA-beholdere og partikler på glasfiberfiltre. Analysemetoderne var ion-exclusion chromatografi (organiske syrer), HPLC (aldehyder og ketoner), GC/MS og GC/FID (VOC) og gravimetri (partikler).
Resultaterne er sammenfattet i Tabel 12.
Tabel 12. Nedbrydningsprodukter ved forarbejdning af EVA og EMA samt LDPE. Alle værdier er i mg/kg, svarende til g/ton.
Plasttype |
LDPE |
LDPE |
EVA (18% VA) |
EVA (28% VA) |
EVA 9% VA |
EMA (20% MA) |
EMA (20% MA) |
Forarbejdnings temperatur |
171°C |
171°C |
171°C |
171°C |
224°C |
171°C |
296°C |
Partikler (mg/kg) |
<1 |
1,5 |
<1 |
<1 |
<1 |
4,1 |
61,5 |
VOC (total minus methan) (mg/kg) |
106,7 |
106,9 |
128,2 |
123,4 |
99,7 |
45,7 |
117,2 |
Tunge hydrocarboner (mg/kg) |
86,0 |
83,0 |
108,3 |
109,9 |
86,4 |
44,2 |
90,0 |
Ethan (mg/kg) |
0,02 |
0,02 |
0,01 |
0,01 |
0,03 |
0,02 |
0,49 |
Ethylen (mg/kg) |
0,01 |
0,01 |
0,01 |
0,01 |
0,02 |
0,02 |
0,36 |
Propylen (mg/kg) |
0,01 |
0,01 |
0,01 |
0,01 |
0,01 |
0,01 |
0,14 |
Vinylacetat (mg/kg) |
<0,01 |
<0,01 |
<0,01 |
6,22 |
<0,01 |
<0,01 |
<0,01 |
Methylacrylat (mg/kg) |
<0,01 |
<0,01 |
<0,01 |
<0,01 |
<0,01 |
<0,01 |
<0,01 |
Formaldehyd (mg/kg) |
0,42 |
0,28 |
0,08 |
0,08 |
0,13 |
0,09 |
1,07 |
Propionaldehyd (mg/kg) |
0,02 |
0,01 |
0,01 |
0,01 |
0,02 |
<0,01 |
0,31 |
Butyraldehyd (mg/kg) |
0,02 |
0,02 |
0,01 |
0,01 |
0,04 |
0,02 |
0,49 |
Benzaldehyd (mg/kg) |
0,02 |
0,02 |
0,03 |
0,025 |
0,05 |
0,03 |
0,23 |
Acetone (mg/kg) |
0,15 |
0,13 |
0,10 |
0,10 |
0,13 |
0,10 |
0,34 |
Methyl ethyl keton (mg/kg) |
<0,01 |
<0,01 |
<0,01 |
<0,01 |
<0,01 |
<0,01 |
<0,01 |
Myresyre (mg/kg) |
0,27 |
0,22 |
3,85 |
3,11 |
6,05 |
4,40 |
4,66 |
Acrylsyre (mg/kg) |
<0,02 |
<0,02 |
<0,02 |
<0,02 |
<0,02 |
<0,02 |
<0,02 |
Forfatterne konkluderer, at der udledes mere VOC end iltholdige forbindelser (oxygenater) som f.eks. ketoner. Ikke overraskende giver højere forarbejdningstemperaturer anledning til større emissioner, men selv ved de højeste testtemperaturer er der ikke nogen VOC-udledning af enkeltstoffer, der overstiger 5 ppm.
Værdierne i skemaet kan bruges til at give et skøn over udledningerne (massestrømmen) fra en given virksomhed. I princippet er det eneste, der behøves, oplysninger om hvor stor en mængde, der forarbejdes indenfor en givet tidsenhed. Den simple formel kan opstilles på følgende måde:
Massestrøm = Emission af stof * forarbejdet mængde/tid
For en virksomhed, der dagligt forarbejder 1,4 ton EVA (18%VA) over en 7-timers periode, kan massestrømmen for vinylacetat beregnes til (6,22 g/ton * 1,4 ton)/ 7 timer = 1,2 g/time. Denne værdi er signifikant lavere end massestrømsgrænsen for vinylacetat, der i Luftvejledningen er fastsat til 2000 g per time for Hovedgruppe 2, Klasse II-stoffer.
21.9 Nedbrydningsprodukter ved forarbejdning af polyamid (PA6 og PA66)
Kriek et al. (2001) undersøgte nedbrydningsprodukterne ved forarbejdning (ekstrudering) af forskellige kvaliteter af polyamid (nylon (PA6 og PA6.6). I alt blev nedbrydningsprodukterne ved ekstrudering af syv kommercielle nylontyper med forskellige additiver tilsat analyseret (se Tabel 13).
Tabel 13. Additiver i de undersøgte polyamidkvaliteter og forarbejdningstemperatur.
Plasttype |
Additiv |
Temperatur (max) |
|
Almindelig PA6.6 |
Proceshjælpemiddel
Slipmiddel
Smøremiddel |
288°C |
|
Almindelig PA6 |
Slipmiddel |
271°C |
|
Copolymer PA6/PA6.6 |
Proceshjælpemiddel
Smøremiddel |
246°C |
|
EPDM-modificeret PA6.6 |
”Sej-gører” (toughener)
Smøremiddel |
288°C |
EPDM er en gummitype (ethylen-propylen dimer) |
Sejgjort PA6 |
”Sej-gører” (toughener)
Smøremiddel |
288°C |
Forstærkning ikke nærmere beskrevet |
PA6 eller PA6 flammehæmmet |
Melamin-baseret flammehæmmer
Proceshjælpemiddel
Slipmiddel
Smøremiddel
Farvestof |
246°C |
|
PA6.6/PA6 flammehæmmet |
Dechlorane plus flammehæmmer
Slipmiddel
Smøremiddel
Farvestof |
249°C |
Ikke yderligere oplysninger om flammehæmmer, men højt indhold af chlor |
Der blev analyseret for ni udvalgte stoffer/stofgrupper. For en beskrivelse af opsamlings- og analysemetoder henvises til originalarbejdet. Stofferne blev udvalgt, fordi de enten er restmonomerer, er på den amerikanske liste over farlige luftforureninger eller er forventede nedbrydningsprodukter ved forarbejdning af polyamid. Analyseresultaterne er sammenfattet i Tabel 14, idet den største værdi af to prøver er angivet.
Tabel 14. Nedbrydningsprodukter ved forarbejdning af kommercielle polyamid-kvaliteter. Alle værdier er i g/ton, svarende til mg/kg.
Klik her for at se tabellen.
Forfatterne konkluderer, at total VOC og partikler er de største emissioner fra forarbejdning af typiske polyamider, men de peger også på caprolactam som en vigtig udledning ved forarbejdning af PA6 og copolymerer.
Værdierne i skemaet kan bruges til at give et skøn over udledningerne (massestrømmen) fra en given virksomhed. I princippet er det eneste, der behøves, oplysninger om hvor stor en mængde, der forarbejdes indenfor en givet tidsenhed. Den simple formel kan opstilles på følgende måde:
Massestrøm = Emission af stof * forarbejdet mængde/tid
For en virksomhed, der dagligt forarbejder 1,4 ton PA6/PA6.6 copolymer over en 7-timers periode, kan massestrømmen for caprolactam beregnes til (25,6 g/ton * 1,4 ton)/ 7 timer = 5,12 g/time. Denne værdi er signifikant lavere end massestrømsgrænsen for caprolactam, der i Luftvejledningen er fastsat til 100 g per time for Hovedgruppe 2, Klasse 1-stoffer.
Man skal dog være opmærksom på, at udledningen af caprolactam ved ekstrudering af en PA-kvalitet, der er flammehæmmet med Dechlorane Plus, er estimeret til at være seks gange større end ved forarbejdning af den ”almindelige” co-polymer. Der er ikke i originalartiklen givet nogen forklaring på, hvordan dette estimat er fremkommet, men resultatet indikerer, at der i specielle tilfælde kan blive tale om værdier, der ligger i nærheden af den øvre grænse for massestrøm.
21.10 Nedbrydningsprodukter ved forarbejdning af ABS-plast
Contos et al. (1995) undersøgte nedbrydningsprodukterne ved ekstrudering af fire ABS-kvaliteter, der repræsenter typiske råvarer til almindelige sprøjtestøbte produkter, bilindustrien, rør og køleskabe/frysere. Hver kvalitet blev blandet af råvarer fra tre forskellige leverandører. Det er ikke oplyst, om de undersøgte plasttyper var tilsat additiver, eller om der blev anvendt proceshjælpemidler. Forarbejdningstemperaturen var i alle tilfælde 232°C.
Analyserne var fokuseret på at kvantificere ni forskellige stoffer, der var udvalgt på baggrund af indledende laboratorieforsøg. Resultaterne af analyserne er sammenfattet i Tabel 15.
Tabel 15. Nedbrydningsprodukter ved forarbejdning af forskellige ABS-kvaliteter. Alle værdier er i mg/kg, svarende til g/ton.
Anvendelse |
Bilindustri |
Sprøjtestøbning generelt |
Rør |
Køleskabe og frysere |
1,3-butadien |
0,93 |
ND |
1,99 |
ND |
Acrylonitril |
5,74 |
7,79 |
9,75 |
10,4 |
4-vinyl-1-cyclohexen |
0,50 |
1,61 |
13,4 |
2,76 |
Ethylbenzen |
27,6 |
8,02 |
69,20 |
13,9 |
Styren |
130 |
126 |
402 |
156 |
Isopropylbenzen |
3,29 |
2,68 |
22,2 |
2,55 |
n-Propylbenzen |
2,37 |
1,65 |
1,06 |
1,70 |
Methylstyren |
1,29 |
13,43 |
62,41 |
4,16 |
Acetophenon |
2,78 |
9,29 |
72,1 |
4,25 |
Total VOC (GC/FID) |
190 |
185 |
653 |
231 |
Værdierne i skemaet kan bruges til at give et skøn over udledningerne (massestrømmen) fra en given virksomhed. I princippet er det eneste, der behøves, oplysninger om hvor stor en mængde, der forarbejdes indenfor en givet tidsenhed. Den simple formel kan opstilles på følgende måde:
Massestrøm = Emission af stof * forarbejdet mængde/tid
For en virksomhed, der dagligt (arbejdsdag 7 timer) forarbejder 1 ton ”almindelig” ABS ved sprøjtestøbning, kan udledningen af acrylonitril beregnes til (7,79*1)/7 = 1,1 g/time. Denne værdi er signifikant lavere end massestrømsgrænsen for acrylonitril, der i Luftvejledningen er fastsat til 25 g per time for Hovedgruppe 1, Klasse II-stoffer. Med de samme forudsætninger kan udledningen af styren beregnes til (126*1)/7 = 18 g/time, hvor massestrømsgrænsen i Luftvejledninger er 2000 g/time for styren, der er et Hovedgruppe 2, Klasse II-stof. Der er således for begge stoffer en bred margin i forhold til Luftvejledningens krav, under de givne forudsætninger.
22 Emissioner ved forarbejdning af hærdeplast
Se også:
Arbejdsmiljø ved forarbejdning af plast
Miljø- og sundhedsvurderinger
Referencer
Indholdsfortegnelse
Oversigtsfigur
22.1 Emissioner ved forarbejdning/produktion af polyurethan
22.1.1 Laboratorieforsøg
Der er ikke fundet litteraturkilder, der giver en kvantitativ eller kvalitativ vurdering af emissionerne ved polyurethanstøbning, målt ved forsøg i laboratoriet.
22.1.2 Fremstilling af MDI-baseret isoleringsskum
En producent af isolerede porte og døre har fået foretaget målinger af isocyanatemissionen i 1990. Under normal produktion blev der foretaget tre målinger i luftafkastet. Alle tre målinger viste, at isocyanat-koncentrationen var under 0,005 mg/m³ (detektionsgrænsen). Der emitteres 4.500 m³ tør luft/h. Isocyanaterne blev opsamlet i en vaskeflaske med nitroreagens i toluen. Mængden af isocyanat blev bestemt ved højtryksvæskekromatografisk analyse.
22.1.3 Fremstilling af fleksibelt skum
Hos en producent af blokskum blev der i foråret 1994 udført tre målinger i luftafkastet ved fremstilling af forskellige typer skum. Der blev målt på TDI i luftafkast stammende fra udsugning fra råvaredoseringen, fra udsugning over slisk (efter kulfilter) samt fra rumudsugning fra hærdehallen. Resultaterne var følgende:
Tabel 1. Udledninger ved fremstilling af fleksibelt skum. Tre målinger fra samme virksomhed. (”Vol.” i tabellen er luftstrøm i afkastet).
|
|
Proces |
Nøgletal for TDI-udledning |
|
TDI-Forbrug |
Dosering |
Slisk |
Opskæring |
TDI-Konc. |
Vol. |
TDI-Konc. |
Vol. |
TDI-Konc. |
Vol. |
Samlet udledning |
Udledning pr. enhed |
Enhed |
Kg/time |
mg/m³ |
m³/s |
mg/m³ |
m³/s |
mg/m³ |
m³/s |
mg/time |
mg/kg |
Måling 1 |
3800 |
0,07 |
0,57 |
0,005 |
4,8 |
0,047 |
1,6 |
501 |
0,13 |
Måling 2 |
4800 |
0,13 |
0,57 |
0,0054 |
4,7 |
0,09 |
1,7 |
909 |
0,19 |
Måling 3 |
4800 |
0,23 |
0,57 |
0,0037 |
4,7 |
0,09 |
1,7 |
1085 |
0,23 |
Ovennævnte målinger er udført ved at suge en delluftmængde igennem to seriekoblede vaskeflasker indeholdende ethanol. Flaskernes indhold er analyseret for TDI ved HPLC.
22.1.4 Fremstilling af integralskum
En dansk producent af stift integralskum har i 1988 fået målt emissionen af MDI i luftafkastet. Resultaterne fra målingerne (3 i alt) var alle under detektionsgrænsen på 0,001 mg/m³. Isocyanaterne blev opsamlet i en vaskeflaske indeholdende "nitroreagens" i toluen. Art og mængde af de opsamlede monomerer mono-, di-, og tri-isocyanater blev bestemt ved højtryksvæskekromatografisk analyse.
22.1.5 Fremstilling af formstøbt skum
Hos en dansk producent af fleksibelt formstøbt skum er der foretaget målinger af luftafkastet til det eksterne miljø for triethyldiamin. Målingerne blev udført i 1992 og ved normal produktion. Der blev målt i ca. 1 time i alle 5 afkast.
Triethyldiamin
Afkast 1 < 0,6 mg/m³
Luftmængde 3600 Nm³/h,tør
Afkast 2 < 0,8 mg/m³
Luftmængde 15800 Nm³/h,tør
Afkast 3 < 0,8 mg/m³
Luftmængde 11700 Nm³/h,tør
Afkast 4 < 0,7 mg/m³
Luftmængde 5400 Nm³/h,tør
Afkast 5 < 1,6 mg/m³
Luftmængde 3300 Nm³/h,tør
Alle målingerne var under detektionsgrænsen. Prøverne blev opsamlet på aminrør indeholdende svovlsyrecoated silicagel. Efter desorption med vand blev triethyldiamin bestemt med gaskromatograf.
I 1990 blev der målt MDI og TDI i 8 luftafkast. Alle målingerne viste isocyanatkoncentrationer under detektionsgrænsen, som var på 0,01 mg isocyanat/Nm³. Virksomhedens samlede emission af TDI eller MDI var for hvert enkelt stof under 0,43 g/h. Isocyanaterne er opsamlet i vaskeflasker indeholdende nitroreagens i toluen og bestemt ved højtryksvæskekromtografi.
22.1.6 Opsummering – PUR- forarbejdning
De fundne emissioner af TDI og MDI ligger ofte under detektionsgrænsen, og i de tilfælde, hvor der rent faktisk er konstateret et indhold, ligger den samlede udledning væsentligt under massestrømsgrænsen i luftvejledningen (100 g/time) for Hovedgruppe 2, Klasse I stoffer, som isocyanaterne tilhører.
22.2 Emissioner ved forarbejdning af umættet polyester
Styren er den dominerende faktor ved forarbejdning af umættet polyester, både fordi en stor del af styrenen fordamper ved processen og fordi stoffet har kendte og uønskede virkninger på mennesker og miljø.
Med de meget forskelligartede procesforhold ved forarbejdning af umættet polyester vil der være relativt store variationer i, hvor meget styren der fordamper, og der kan derfor ikke peges på en enkelt eller simpel model til beregning af styrenemissioner for branchen som helhed.
I USA har man ved en vurdering af de hidtil anvendte modeller til beregning af styrenemission fundet, at de med stor sandsynlighed underestimerede udledningernes størrelse. Den amerikanske miljøstyrelse, EPA, og den amerikanske sammenslutning af producenter af plastkompositter, CFA (Composites Fabricators Association) har samarbejdet om at lave en revideret model til brug ved udarbejdelse af miljøgodkendelser, men er ikke enige om det nødvendige detaljeringsniveau. De har derfor udarbejdet forskellige forslag til modeller, som beskrives kort i de følgende afsnit.
Det skal understreges, at den danske UP-industri på mange områder er vidt forskellig fra den amerikanske med hensyn til både, hvordan den enkelte proces er tilrettelagt og sammensætningen af industriens proces- og produktporteføjle. De amerikanske modeller giver derfor ikke resultater, der er repræsentative for emissionerne fra danske virksomheder, men selve udviklingen af modellen og dens elementer kan dog være af interesse.
22.2.1 Amerikanske modeller
22.2.1.1 EPA’s model
EPA-modellen, der er dokumenteret i Nunez et al. (1999), kan beregne emissioner ved følgende processer:
- Håndoplæg
- Presning
- Sprøjteoplæg
- Gel coating
- Kontinuerlig imprægnering/pultrudering)
Modellen kræver viden om følgende faktorer for at kunne gennemføre beregningerne:
- Styrenindhold (”Neat styrene content”) før eventuelle fillers tilsættes
- Brug (”ja/nej”) af tilsætningsstoffer, der undertrykker fordampningen af styren (typisk voks-baserede)
- Afstand fra spraypistol til formen (målt i tommer)
- Andel af materiale, der lander uden for formen (tørstofindhold)
- Emnetykkelse (målt i tusindedele af tommer)
- Cup gel tid (målt i minutter)
- Påføringsrate (målt i pund/minut (lb/min))
- Lufttemperatur (målt i °F)
- Lufthastighed over formen (målt i fod/minut (ft/min))
EPA anbefaler brug af ”deres” model til beregning af emissionernes størrelse og har til dette formål udarbejdet en PC-baseret model med tilhørende brugervejledning. Modellen kan downloades uden beregning fra http://www.epa.gov/ttn/chief/efdocs/, men det bemærkes igen, at dens resultater ikke er relevante i en vurdering af danske forhold.
Producentforeningen CFA anfører i deres kritik af modellen, at den indeholder datakrav, der er uden praktisk betydning for emissionerne, eller som ikke kan måles eller estimeres på en troværdig måde. Det anerkendes dog, at modellen er god i forbindelse med forskningsarbejde, hvor den nødvendige viden om de enkelte parametre typisk vil være til stede.
22.2.1.2 CFA’s model
Parallelt med udviklingen af EPA’s model har den amerikanske kompositindustri udviklet sin egen model (eller rettere to modeller), der er mindre krævende med hensyn til inputdata (Haberlein (1999 a,b)). Den mest avancerede model fra CFA kræver oplysninger om styrenindhold, laminattykkelse, geltid, appliceringshastighed og luftflow omkring formen. Den simple model fra CFA kræver kun oplysning om styrenindholdet.
Begge modeller giver mulighed for beregning af emissionerne ved de følgende processer, men det understreges, at heller ikke disse modeller giver resultater, der er repræsentative for danske forhold.
- Håndoplægning
- Sprøjteoplægning
- Gelcoating
- Vikling (Filament winding)
Modellerne indeholder også muligheden for at inkludere en reduktionsfaktor for såkaldt kontrolleret sprøjteoplæg, tildækket hærdning
og for anvendelse af hæmmet resin. Endelig indeholder modellen også mulighed for at beregne emissionen af methylmethacrylat, der ofte er en komponent i polyesterblandingen.
22.2.1.3 Danske erfaringer
Miljøstyrelsen er i skrivende stund ved at udarbejde standardvilkår for miljøgodkendelse af virksomheder, der fremstiller produkter af umættet polyester. Som et element i dette arbejde har de amerikanske modeller været præsenteret for en række relevante danske virksomheder, og de danske virksomheders indtryk er, at de amerikanske modeller giver alt for høje emissionsværdier. De præcise årsager til disse forskelle er ved at blive kortlagt, og det kan forventes at de branchebilag, der udarbejdes som et led i fastsættelse af standardvilkårene, vil inkludere denne diskussion. Der henvises derfor til Miljøstyrelsens hjemmeside (www.mst.dk), hvor både standardvilkår og branchebilag vil blive offentliggjort.
23 Kemiske belastninger i arbejdsmiljøet
Se også:
Emissioner ved forarbejdning af termoplast
Emissioner ved forarbejdning af hærdeplast
Miljø- og sundhedsvurderinger
Referencer
Indholdsfortegnelse
Oversigtsfigur
23.1 Introduktion
De følgende afsnit giver et bredt overblik over, hvilke stoffer der dannes ved forarbejdning af forskellige plasttyper under forskellige betingelser. Overblikket er primært opstillet på baggrund af oversigtsartikler, der har gennemgået den eksisterende litteratur på området.
Som udgangspunkt skelnes der i overblikket ikke mellem arbejdspladsmålinger og forsøg i laboratoriet under mere eller mindre proceslignende forhold. Med det store antal mulige kombinationer af plasttype, additiver og forarbejdningsprocesser er det ikke realistisk at dække bare en lille del, så der vil ofte være behov for at tage individuel stilling til et konkret problem på arbejdspladsen.
Det skal dog fremhæves, at irritation af øjne, næse og luftveje er det mest udbredte arbejdsmiljøproblem ved forarbejdning af plast, idet dette problem er observeret og rapporteret ved forarbejdning af mange forskellige plasttyper. Sensibilisering af luftvejene må regnes for det alvorligste problem, idet en erhvervsinduceret asthma ofte vil være en sygdom, der følger en person resten af livet.
Hærdeplasttyperne (her umættet polyester og polyurethan) må regnes for de mest kritiske i arbejdsmiljømæssig henseende, idet det er på dette område, der historisk set er blevet rapporteret om de fleste alvorlige gener. Årsagen er med stor sandsynlighed, at hærdeplasterne er blevet forarbejdet ved åbne processer, hvor der er eller har været stor risiko for høj eksponering for f.eks. udgangsstoffer som styren og isocyanater.
Ved både arbejdsplads- og laboratoriemålinger er der endvidere funder stoffer, der er på Arbejdstilsynets liste over stoffer, der mistænkes for at være kræftfremkaldende. Der er så vidt vides dog ikke undersøgelser, der peger på en forøget kræftrisiko ved plastforarbejdning, og i langt de fleste tilfælde vil eksponeringen af de ansatte ligge langt under grænseværdien for de pågældende stoffer. Man skal dog være opmærksom på, at der for visse stoffer er specielle regler for, hvordan de skal håndteres i arbejdsmiljøet. Det skal også bemærkes, at grænseværdier kun er vejledende ved en vurdering af, om sundhedsfarlige forhold eksisterer, og at koncentrationen af alle luftforureninger derfor generelt bør holdes så langt under grænseværdien som muligt.
Overordnet set tegner der sig et billede af en række processer, hvor der er mulighed for eksponering for en bred vifte af kemiske stoffer i lave koncentrationer. Dette kan erfaringsmæssigt give anledning til (mindre) problemer, f.eks. i form af luftvejsirritation, specielt hvis der ikke er etableret tilstrækkelig ventilation. Hvis den anbefalede forarbejdningstemperatur overskrides kan der forventes en lidt højere koncentration af nedbrydningsprodukter. Da produktkvaliteten samtidig forringes, ofte ud over det acceptable, er der således både arbejdshygiejnisk og økonomisk motivation for en tæt styring af processen. Ved ”purging” af plast ved afslutning af en serie kan der teoretisk forventes en kortvarig øgning af koncentrationen i arbejdsområdet, men de undersøgelser, der citeres i de følgende afsnit, viser ikke et entydigt billede.
23.2 Kemisk arbejdsmiljø ved forarbejdning af polyethylen (PE)
23.2.1 Litteraturreviews
Den normale forarbejdningstemperatur for PE angives af Jensen, Schmidt og Wolkoff (1989) til at ligge mellem 140-240 °C, men kan ved coatningsprocesser være op til 330 °C.
Patel & Xanthos (1995) giver et overblik fra forskellige kilder over, hvilke stoffer, der er fundet ved forarbejdning af forskellige kvaliteter af PE under forskellige procesbetingelser. Overblikket gengives i lettere revideret form i Tabel 1 sammen med Jensen, Schmidt & Wolkoff’s vurdering af, hvilke stoffer der må anses for at være toksikologisk relevante, d.v.s. at udgøre den største potentielle belastning i arbejdsmiljøet.
Det skal bemærkes, at både Patel & Xanthos og Jensen, Schmidt & Wolkoff ikke har gennemført egne undersøgelser, men alene baserer sig på en gennemgang af litteraturkilder. Der kan altså være forskelle i målemetoder, målestrategi og vurderinger mellem de enkelte undersøgelser, der refereres, men tilsammen må de anses for at give et bredt overblik over forarbejdning af PE.
Plasttype |
LDPE |
LDPE |
LDPE |
PE |
HDPE
170-320 °C |
Toksi-
kologisk relevante stoffer (Plastbase, 1989) |
Betingelser, bemærkninger |
Ustabiliseret, thermoxidation i luft ved 264-289 °C i 4 minutter |
113-mm ekstruder
220-280 °C |
Ekstruder coater
295-300 °C |
2 % dicumylperoxid; lukket ampul i N2-atmosfære og 140 °C |
|
|
Stof |
|
|
|
|
|
|
Acetaldehyd |
X |
|
|
|
|
X |
Formaldehyd |
X |
0,7-1,1 ppm |
|
|
0,2-0,5 ppm |
X |
Propanal |
X |
|
|
|
|
|
Acrolein |
X |
0,02-0,1 ppm |
|
|
0,2-1,9 ppm |
X |
Crotonaldehyd |
|
|
|
|
|
X |
Butanal |
X |
|
|
|
|
|
Pentanal |
X |
|
|
|
|
|
Acetone |
X |
|
|
|
|
|
2-Butanon |
X |
|
|
|
|
|
2-Pentanon |
X |
|
|
|
|
|
Isovalerinsyre |
X |
|
|
|
|
|
Hydroxyvalerinsyre |
X |
|
|
|
|
|
Crotonsyre |
X |
|
|
|
|
|
Caproinsyre |
X |
|
|
|
|
|
Myresyre |
X |
|
|
|
|
X |
Eddikesyre |
X |
|
|
|
|
X |
Propionsyre |
X |
|
|
|
|
|
Acrylsyre |
X |
|
|
|
|
|
Butyrsyre |
X |
|
|
|
|
|
Cyclopropan |
X |
|
|
|
|
|
Furan |
X |
|
|
|
|
|
Tetrahydrofuran |
X |
|
|
|
|
|
Isobutyraldehyd |
X |
|
|
|
|
|
Methyl vinyl keton |
X |
|
|
|
|
X |
Valerolacton |
X |
|
|
|
|
|
Butyrolacton |
X |
|
|
|
|
|
Vand |
X |
|
|
|
|
|
Alkoxyradikaler |
|
|
|
|
|
X |
Carbonmonoxid |
|
30-70 ppm |
0,0-1,0 ppm |
|
20-100 ppm |
|
Methan |
|
|
|
X |
|
|
a a,a-Dimethyl-
benzylalkohol |
|
|
|
X |
|
|
Tabel 1. Emissioner ved forarbejdning af forskellige kvaliteter af PE under varierende procesbetingelser. (Efter Patel & Xanthos (1995) og Jensen, Schmidt & Wolkoff (1989)).
Som det fremgår af Tabel 1 dannes der ved termooxidation i fire minutter af ustabiliseret LDPE en lang række forskellige stoffer, der repræsenterer kulbrinter, alkoholer, aldehyder, ketoner, syrer, cykliske estere og estere. Der dannes også kulilte, methan mm., men Patel & Xanthos konkluderer, at niveauet uden besvær kan holdes under gældende grænseværdier med et tilstrækkeligt udsug.
23.2.2 Arbejdspladsmålinger
Frostling et al. (1982) har gennemført arbejdspladsmålinger under normale forarbejdningsbetingelser, med temperaturer mellem 140 og 250 °C. Resultaterne af disse målinger er sammenfattet i nedenstående tabel:
Stof |
Grænseværdi (mg/m³)1 |
Koncentration (mg/m³) |
Spredning |
Højeste værdi |
Total aldehyd |
|
2,20 |
0,62 |
18,1 |
Formaldehyd |
0,4 |
0,10 |
0,02 |
0,2 |
Acetaldehyd |
45 |
0,16 |
0,05 |
0,4 |
Acrolein |
0,13 |
<0,02 |
- |
- |
Acetone |
600 |
0,78 |
0,12 |
- |
Total syrer |
|
15,4 |
1,41 |
46,7 |
Myresyre |
9 |
0,83 |
0,13 |
2,1 |
Eddikesyre |
25 |
0,86 |
0,39 |
4,9 |
Aerosol |
21 |
1,2-3,5 |
- |
- |
Tabel 2. Resultater fra arbejdspladsmålinger ved forarbejdning af polyethylen (flere processer).
1. Grænseværdien er for paraffinrøg (Arbejdstilsynet, 2002)
De rapporterede målinger giver en indikation af, hvor store mængder af de udvalgte stoffer, man udsættes for. Det skal dog bemærkes, at der som beskrevet dannes en længere række stoffer, som der ikke findes måleværdier for.
En dansk virksomhed fik målt koncentrationen af aerosol (plastrøg) ved ekstrudering af polyethylen med 1-buten som copolymer. Målingen blev gennemført af Borealis, en fremtrædende leverandør, med det formål at teste en ny metode til aerosolmåling med direkte visende udstyr. I rapporten anføres det, at udstyret er kalibreret mod anerkendte målemetoder, men præcisionen er ikke angivet.
Der blev foretaget målinger (stationære) ved to maskiner. Ved den ene, hvor forbruget var 73 kg polymer per time, var koncentrationen 0,124 mg/m³, og ved den anden, hvor forbruget var 23 kg/time, var gennemsnitskoncentrationen 0,056 mg/m³. Målingerne viste endvidere, at 80 % af aerosolerne havde en partikelstørrelse på 0,5-5m. I begge tilfælde er der tale om koncentrationer, der er væsentligt lavere end de, der blev fundet af Frostling (1982), men der gøres ikke noget forsøg på at finde en eventuel årsag.
Forrest et al. (1995) undersøgte emissionerne ved filmblæsning af en blanding af LDPE og LLDPE. De anvendte to forskellige opsamlingsmetoder og målte tre steder: ved maskinen, ved operatøren og i baggrunden (4-6 m fra maskinen). Resultaterne af målingerne ses i Tabel 3.
|
Koncentration (mg/m³) |
Stof |
Maskine |
Operatør |
Baggrund |
Hexan |
<0,1 |
Nd |
0,14 |
Kulbrinte (C6) |
<0,1 |
0,15 |
<0,1 |
Xylen isomere |
<0,1 |
0,12 |
0,12 |
a-Methylstyren |
0,89 |
1,16 |
1,11 |
Benzen, trimethyl isomer |
0,16 |
0,13 |
0,13 |
Kulbrinter (C10-C12) |
3,93 |
2,16 |
3,14 |
Benzen, trimethyl isomer |
0,31 |
<0,1 |
<0,1 |
Benzen, ethyl, dimethyl isomer |
<0,1 |
0,12 |
<0,1 |
Alifatisk aldehyd (C10) |
0,32 |
0,34 |
0,30 |
Benzen, dimethyl, pentyl isomer |
0,12 |
<0,1 |
Nd |
Alifatiske aldehyder (C11) |
0,69 |
0,39 |
Nd |
Kulbrinte (C11-C13) |
0,50 |
0,23 |
1,61 |
Alifatisk aldehyder (C12) |
0,12 |
Nd |
Nd |
Kulbrinte (C12-C14) |
0,10 |
0,10 |
0,90 |
Tabel 3. Emissioner ved filmblæsning af en blanding af LDPE og LLDPE.
I en supplerende undersøgelse under laboratorieforhold fandt Forrest et al. (1995) kun meget små emissioner ved filmblæsning af ren LDPE. Opsamlingen skete på Tenax, og analyserne viste maksimumkoncentrationer på 0,11 mg/m³ for toluen og 0,02 mg/m³ for kulbrinte (C9-C11), mens de øvrige analyser lå på eller under 0,01 mg/m³ eller under detektionsgrænsen.
23.2.3 Opsummering for polyethylen
Jensen, Schmidt og Wolkoff (1989) konkluderer at ved overophedning eller langsom opvarmning under luftens adgang dannes der slimhinde- og luftvejsirriterende oxidationsprodukter (aldehyder, ketoner og peroxider), mens der ved normale procesbetingelser hovedsagelig kun dannes oligomerrester, til dels i form af aerosol.
Denne vurdering understøttes af andre undersøgelser, der er citeret i de ovenstående afsnit. Aerosoldannelse regnes også her for den potentielt største belastning, med risiko for at overskride grænseværdien for paraffinrøg under normale procesforhold. Ifølge Arbejdsministeriets bekendtgørelse nr. 96 af 13. februar 2001 om faste arbejdssteders indretning, § 35 om procesventilation, skal der etableres mekanisk udsugning, der så vidt muligt fjerner denne type af forurening på det sted, hvor den udvikles.
23.3 Kemisk arbejdsmiljø ved forarbejdning af polypropylen (PP)
Den normale forarbejdningstemperatur for PP er op til 310 °C. Ren PP termooxiderer nemmere end PE, men tilsætning af antioxidanter hæmmer termooxidationen effektivt (Jensen, Schmidt & Wolkoff, 1989).
23.3.1 Litteraturreviews
Jensen, Schmidt & Wolkoff (1989) giver i Plastbase et overblik over hvilke stoffer, der er fundet ved laboratorieforsøg og ved industrielle processer. Det gengives i lettere revideret form i Tabel 4 sammen med deres vurdering af, hvilke emissioner, der må regnes for at være mest relevante fra et toksikologisk synspunkt. Patel & Xanthos (1995) giver også et overblik over, hvilke stoffer, der dannes ved termoxidation af PP. De medtager imidlertid ikke helt så mange stoffer som Jensen, Schmidt & Wolkoff, og det er derfor valgt at tage udgangspunkt i Plastbase, og supplere med Patel & Xanthos informationer om niveauer ved filmekstrudering.
Betingelser – bemærkninger |
Ustabiliseret PP, termoxidation i rør ved 220-280 °C i to minutter |
Ekstrudering af film ved 220 °C |
Toksikologisk relevante stoffer |
Ethylen |
X |
|
|
Ethan |
X |
|
|
Isopropan |
X |
|
|
Isobutan |
X |
|
|
Isobutylen |
X |
|
|
Pentadiene |
X |
|
|
2-Methyl-1-penten |
X |
|
|
Xylen |
X |
|
|
Methanol |
X |
|
|
Ethanol |
X |
|
|
2-Methyl-2-propen-1-ol |
X |
|
|
2-Methylfuran |
X |
|
|
2,5-Dimethylfuran |
X |
|
|
Formaldehyd |
X |
0,2 ppm |
|
Acetaldehyd |
X |
|
X |
Propanal |
X |
|
|
Acrolein |
X |
<0,01 ppm |
X |
2-Methylpropanal |
X |
|
|
Butanal |
X |
|
|
Methacrolein |
X |
|
X |
2-Vinylcrotonaldehyd |
X |
|
|
Acetone |
X |
|
|
1-Hydroxy-2-propanon |
X |
|
|
Methylethylketon |
X |
|
|
Methylcyclopropanon |
X |
|
|
Methylvinylketon |
X |
|
|
2,3-Butandion |
X |
|
|
2-Pentanon |
X |
|
|
2,4-Pentandion |
X |
|
|
3-Penten-2-on |
X |
|
|
3-Methyl-3-buten-2-on |
X |
|
|
3,4-epoxy-2-pentanon |
X |
|
|
4-Methyl-2-pentanon |
X |
|
|
3,4-Epoxy-3-ethyl-2-butanon |
X |
|
|
4-Methyl-2-heptanon |
X |
|
|
Myresyre |
X |
|
X |
Eddikesyre |
X |
|
|
Propionsyre |
X |
|
|
Methylformiat |
X |
|
|
Carbonmonoxid |
X |
30 ppm |
|
Aerosol |
|
|
X |
Tabel 4. Emissioner ved forarbejdning af PP under varierende procesbetingelser. (Efter Patel & Xanthos (1995) og Jensen, Schmidt & Wolkoff (1989).
Det skal bemærkes, at Jensen, Schmidt & Wolkoff peger på aerosoldannelse som den alvorligste luftforurening under normale procesbetingelser, men at der ved høj forarbejdningstemperatur er risiko for termooxidation fra udsatte overflader. Ved termooxidation findes formaldehyd, acetaldehyd, eddikesyre, acetone og a-methylacrolein i de højeste koncentrationer.
23.3.2 Arbejdspladsmålinger
Follett et al. (1995) undersøgte emissioner ved ekstrudering af PP-tape på en amerikansk virksomhed. Der var en tydelig træk under målingerne, der derfor blev gennemført på både vind- og læsiden, med tydelige forskelle til følge.
Rapporten identificerer kun få udledninger entydigt:
- Xylen isomere: 0,22-1,65 mg/m³
- a-Methylstyren: maksimumværdi: 0,16 mg/m³
23.3.3 Opsummering for polypropylen
Polypropylen er ikke så velundersøgt et materiale som polyethylen. Med tanke på, at de to polymerer er forholdsvis ens i deres opbygning er det dog oplagt, at arbejdsmiljøbelastningen er af samme karakter, d.v.s. at aerosoldannelse må regnes for at udgøre den største belastning i arbejdsmiljøet, specielt fordi indholdet af nedbrydningsprodukter i aerosolen kan give anledning til luftvejsirritation. Ifølge Arbejdsministeriets bekendtgørelse nr. 96 af 13. februar 2001 om faste arbejdssteders indretning, § 35 om procesventilation, skal der etableres mekanisk udsugning, der så vidt muligt fjerner denne type af forurening på det sted, hvor den udvikles.
23.4 Kemisk arbejdsmiljø ved forarbejdning af polyvinylchlorid (PVC)
Den normale forarbejdningstemperatur for PVC ligger mellem 145-210 °C.
23.4.1 Litteraturreviews
Jensen, Schmidt og Wolkoff peger i Plastbase (1989) på følgende udledninger fra PVC-forarbejdning som værende toksikologisk relevante:
Stof |
Kommentar |
Hydrogenchlorid |
|
Benzen |
|
Acetaldehyd |
|
Acrolein |
|
Formaldehyd |
|
Benzal chloride |
|
Benzyl chloride |
|
Phenol |
|
Vinylchlorid |
Monomer |
Aerosol |
|
Alkoxyradikaler |
|
Blystearat |
Stabilisator |
Phthalsyre anhydrid |
Nedbrydningsprodukt fra blødgører |
Di-(2-ethylhexyl)phthalat |
Blødgører |
Dibutylphthalat |
Blødgører |
Diethylphthalat |
Blødgører |
Dioctylphthalat |
Blødgører |
Azodicarbonamid |
Opskumningsmiddel |
Tabel 5. Toksikologisk relevante stoffer ved forarbejdning af PVC (Efter Jensen, Schmidt & Wolkoff, 1989)
Jensen, Schmidt & Wolkoff (1989) peger på, at nedbrydning af PVC ved normale procestemperaturer kun medfører dannelse af meget små mængder flygtige forbindelser. Additiver, især blødgørere, kan medføre at der dannes en kompleks, respirabel aerosol, som kan indeholde aldehyder, ketoner, anhydrider, m.v, der giver anledning til luftvejsirritation og evt. til en mild form for asthma, den såkaldte ”meat wrappers’ asthma”.
Patel & Xanthos (1995) giver et overblik fra forskellige kilder over, hvor store mængder af tre vigtige stoffer, der er fundet ved forarbejdning af PVC (blødgjort/ikke-blødgjort) ved forskellige processer. Overblikket gengives i lettere revideret form i Tabel 6.
Proces |
Temperatur ( °C) |
Blødgører ( %) |
Hydrogen-chlorid
(mg/m³) |
Dioctyl-phthalat
(mg/m³) |
Phthalsyre-anhydrid
(mg/m³) |
Ekstrudering |
150-200 |
2,4 |
0,15±0,06 |
0,05±0,03 |
Ikke målt |
Esktrudering |
150-195 |
Ukendt |
0,09-±,010 |
0,3±0,2 |
0,3±0,5 |
Kalandrering |
130-200 |
6,5-15 |
0,15±0,03 |
0,5±0,5 |
0,2±0,1 |
”Hot embossing” |
180 |
Ukendt |
0,03±0,02 |
0,05±0,02 |
Ikke målt |
Sprøjtestøbning |
180-190 |
Ukendt |
0,05±0,00 |
0,02±0,01 |
<0,02 |
Svejsning |
400 (ved lampen) |
Ukendt |
0,3±0,02 |
0,3±0,05 |
5,0±2,0 |
Compoundering |
120 |
20 |
Ikke målt |
0,02±0,01 |
Ikke målt |
Termoformning |
120-130 |
Ukendt |
Ikke målt |
0,02±0,02 |
0,1±0,05 |
Højfrekvenssvejsning |
Ukendt |
Ukendt |
<0,03 |
±0,02 |
Ikke målt |
”Spread coating” |
160-205 |
35 (DINP) |
Ikke målt |
Ikke malt (DINP) |
1,2±0,2 |
Blæsestøbning |
150-190 |
Ingen |
0,05±0,02 |
Ingen blødgører |
Ingen blødgører |
Kompressions støbning |
150 |
Ingen |
0,04±0,01 |
Ingen blødgører |
Ingen blødgører |
Tabel 6. Emissioner af hydrogenchlorid, dioctylphthalat og phthalsyreanhydrid ved forarbejdning af PVC ved forskellige processer (Efter Patel & Xanthos, 1995).
23.4.2 Arbejdspladsmålinger
Forrest et al. (1995) undersøgte emissionerne ved sprøjtestøbning og ekstrudering af kabler af PVC. Den PVC, der blev sprøjtestøbt, var ikke blødgjort, mens PVC’en til kabler var blødgjort, uden beskrivelse af hvilken blødgører, der blev anvendt. Resultatet af analysen af sprøjtestøbning med PVC fremgår af nedenstående tabel. Der er foretaget målinger tre forskellige steder (operatørbåren, ved maskinen og i baggrunden (4-6 meter fra maskinen), samt målinger af koncentrationen ved maskinen og i baggrunden, når restmateriale blev purged fra maskinen.
Stof |
Koncentration (mg/m³) |
|
Operatør |
Maskine |
Baggrund |
Maskine (v. purging) |
Baagrund (v. purging) |
Dichlormethan |
Nd |
<0,1 |
<0,1 |
1,72 |
1,13 |
Ethylacetat |
Nd |
0,60 |
0,84 |
0,68 |
0,64 |
Trichlorethen |
<0,1 |
0,13 |
0,12 |
<0,1 |
<0,1 |
Kulbrinte (C6-C8) |
<0,1 |
<0,1 |
0,10 |
0,12 |
1,17 |
Toluen |
<0,1 |
<0,1 |
<0,1 |
0,24 |
0,16 |
Chlorbenzen |
0,43 |
0,42 |
0,55 |
0,24 |
0,11 |
Xylen isomere |
<0,1 |
<0,1 |
0,1 |
0,60 |
1,26 |
Cykliske alkener (C10H6) |
<0,1 |
0,15 |
0,14 |
0,12 |
0,10 |
a-Methylstyren |
Nd |
Nd |
Nd |
3,44 |
2,30 |
Benzen, alkyl derivat |
Nd |
Nd |
Nd |
Nd |
0,15 |
Kulbrinte (C10-C12) |
0,85 |
0,80 |
1,03 |
1,65 |
2,44 |
Benzen, methyl, propyl isomer |
Nd |
Nd |
Nd |
Nd |
0,51 |
Kulbrinte (C11-C13) |
<0,1 |
0,31 |
0,17 |
0,16 |
0,14 |
Tabel 7. Emissioner ved sprøjtestøbning af PVC ved 180 °C. (Adsorbent: Tenax).
Ved ekstrudering af kabler af blødgjort PVC blev følgende emissioner målt:
|
Koncentration (mg/m³) |
Stof |
Maskine/ operatør
Tenax |
Maskine/ operatør
Tenax |
Maskine/ operatør
Poropak |
Maskine/ operatør
v. purging
Tenax |
Baggrund (Tenax 1) |
Baggrund (Tenax 1) |
1,1,1-trichlorethan |
0,02 |
0,01 |
0,03 |
0,01 |
0,01 |
0,03 |
Toluen |
0,18 |
0,01 |
0,01 |
0,10 |
0,04 |
0,01 |
Xylen isomere |
0,03 |
0,01 |
0,04 |
0,02 |
0,02 |
0,04 |
Kulbrinte (C8-C10) |
0,57 |
0,03 |
0,22 |
0,31 |
0,21 |
0,22 |
Benzen, trimethyl isomere |
0,05 |
0,01 |
0,05 |
0,05 |
0,05 |
0,05 |
Benzen, ethyl, dimethyl isomer |
0,01 |
<0,01 |
<0,01 |
<0,01 |
<0,01 |
<0,01 |
Kulbrinte (C9-C11) |
0,43 |
0,17 |
0,64 |
0,28 |
0,44 |
0,64 |
Kulbrinte (C10-C12) |
0,09 |
0,04 |
0,03 |
0,05 |
0,07 |
0,03 |
Kulbrinte (C11-C11) |
<0,01 |
<0,01 |
0,07 |
0,04 |
<0,01 |
0,07 |
Tabel 8. Emissioner ved ekstrudering af PVC-kabler (blødgjort PVC) v. 140 °C og 180 °C (ved purging).
Forrest et al. (1995) peger i deres analyse af resultaterne på, at baggrundsniveauet ved purging af restmateriale var højere for nogle stoffers vedkommende, sammenlignet med niveauet tæt på processen under normale procesbetingelser. De monomerlignende stoffer, der blev fundet, mener forfatterne ikke stammer fra den undersøgte proces, men derimod fra additiver, der blev anvendt i anden forarbejdning af PVC tæt på, hvor målingerne fandt sted.
Det skal bemærkes, at de ovenstående tabeller ikke giver det fulde billede af, hvilke stoffer, der kan dannes ved forarbejdning af PVC. Specielt vil der ved tilsætning af additiver være mulighed for dannelse af nedbrydningsprodukter fra disse, ligesom det også kan være muligt at identificere de rene additiver ved en fokuseret analysestrategi. Tabellerne giver således en første indikation af, hvilke stoffer, der kan være problematiske, men man skal være opmærksom på, at der kan være kvalitative forskelle mellem emissioner fra forskellige processer, ligesom der med stor sandsynlighed også kan være kvantitative forskelle i emissionernes størrelse, afhængigt af procesbetingelserne.
23.4.3 Opsummering for PVC
De undersøgelser, der er præsenteret for PVC, giver et inhomogent billede af, hvilke stoffer, der eventuelt bidrager til en belastning i arbejdsmiljøet. Jensen, Schmidt og Wolkoff (1989) konkluderer, at der kun dannes meget små mængder af flygtige forbindelser, langt under grænseværdien, mens anvendte additiver, især blødgørere, kan medføre at der dannes en kompleks, respirabel aerosol, som kan give anledning til luftvejsirritation. Generne bliver mere udbredte ved forhøjede procestemperaturer.
Patel og Xanthos (1995) bekræfter dette billede, om end der kun er få stoffer medtaget i deres oversigt. Forrest et al. (1995) konkluderer på samme måde som Jensen, Schmidt og Wolkoff, at det er additiver, der er årsag til dannelsen af flygtige forbindelser.
Det er på denne baggrund vanskeligt at drage faste konklusioner ud over at forarbejdning af ”ren” PVC under normale procesbetingelser generelt ikke giver anledning til emissioner, der overstiger grænseværdien for de pågældende stoffer. Da der sædvanligvis anvendes en lang række additiver i PVC, har denne konklusion kun begrænset værdi. Det skal også bemærkes, at grænseværdier kun er vejledende ved en vurdering af, om sundhedsfarlige forhold eksisterer, og at koncentrationen af alle luftforureninger derfor generelt bør holdes så langt under grænseværdien som muligt.
23.5 Kemisk arbejdsmiljø ved forarbejdning af polystyren (PS og HIPS)
Den normale forarbejdningstemperatur for PS og HIPS ligger i et bredt interval, mellem 150 og 300 °C.
23.5.1 Litteraturreviews
Jensen, Schmidt og Wolkoff peger i Plastbase (1989) på følgende udledninger fra PS og HIPS-forarbejdning som værende toksikologisk relevante:
Plasttype
Stof |
PS |
HIPS |
Styren (+ dimer 0g trimer) |
X |
X |
2-Phenylpropenal |
X |
|
Aerosol |
X |
X |
Alkoxyradikaler |
X |
|
Styrenoxid |
X |
|
Tabel 9. Toksikologisk relevante stoffer ved forarbejdning af PS og HIPS. (Efter Jensen, Schmidt og Wolkoff, 1989).
Patel & Xanthos (1995) giver et overblik over forskellige undersøgelser af emissioner ved forarbejdning af PS. Overblikket gengives i lettere revideret form i Tabel 10.
Betingelser – bemærkninger |
TG ved 260 °C |
Blanding, støbning |
Sprøjtestøbning 200-300 °C i 0,5-5 min. |
Food grade PS 200-280 °C |
Ekstrudering; PS m. 0,18 % styren |
Stof |
|
|
|
|
|
Benzen |
< 1 ppm |
|
|
X |
0,32 ppm |
Styren |
< 50 ppm |
X |
X |
X |
4.27 ppm |
Carbonmonoxid |
|
X |
X |
|
|
Toluen |
|
|
|
X |
0,11 ppm |
Ethylbenzen |
|
|
|
X |
2,66 ppm |
Isopropylbenzen |
|
|
|
X |
|
Phenylacetate |
|
|
|
X |
|
aa-Methylstyren |
|
|
|
X |
|
Benzaldehyd |
|
|
|
X |
|
Hydrogensulfid |
|
|
|
(> 250 °C) |
|
Svovldioxid |
|
|
|
(> 250 °C) |
|
Xylener |
|
|
|
|
0,42 ppm |
Ikke-aromatiske kulbrinter (C4-C8)
(formodentlig fra additiv) |
|
|
|
|
0,67 ppm |
Kulbrinter (C9+, formodentlig fra additiv) |
|
|
|
|
8,86 ppm |
Tabel 10. Emissioner ved forarbejdning af PS under forskellige forhold. (Efter Patel & Xanthos, 1995).
Foruden de stoffer, der nævnes i Tabel 10, er der påvist en lang række kulbrinte-specier, hvoraf mange er aromatiske. En mere komplet oversigt kan således findes i Jensen, Schmidt & Wolkoff (1989). I praksis er det dog styren (+ dimer og trimer), der er den dominerende emission, men også emission af styrenoxid, der ligesom styren er på Arbejdstilsynets liste over stoffer, der anses for at være kræftfremkaldende, reaktive alkoxyradikaler og aerosol kan være problematisk i den givne proces.
23.5.2 Arbejdspladsmålinger
Frostling et al. (1982) undersøgte koncentrationen af udvalgte stoffer ved almindelig forarbejdning af PS og HIPS. Målingerne blev gennemført under normale procesbetingelser. Der blev målt lave koncentrationer af styren, 0,17 ppm (0,73 mg/m³), og det totale indhold af oxiderede luftforureninger var i samme størrelsesorden som ved forarbejdning af polyethylen (se afsnit 1.2). Der blev endvidere fundet aerosol-lignende nedbrydningsprodukter i koncentrationer på 37 ± 13 mg/m³ (ved væskeabsorption) og 0,9 ± 0,5 mg/m³ (ved gravimetriske analyser). En GC/MS-analyse viste, at de pågældende forureninger var isomerer af styren-oligomere (dimer, trimer og tetramer), eventuelt med indhold af carbonyl-grupper. Endelig blev der fundet frie radikaler i størrelsesordenen 0,06 ppm.
Nitten amerikanske plastforarbejdende virksomheder gennemførte i 1993 en række analyser af emissioner ved forarbejdning af forskellige plastmaterialer (Forrest et al. 1995). Analyserne blev foretaget ved normal drift af forskellige processer, samt i visse tilfælde også ved purging, hvor varmt, resterende plastmateriale pumpes ud på gulvet, f.eks. når en serie afsluttes og der skal skiftes værktøj. Ved purging kan restmaterialet ende på varme maskindele, hvor det bliver nedbrudt (oxideret) under betingelser, der er væsentligt forskellige fra den normale forarbejdningsproces.
Målingerne blev primært foretaget for at belyse arbejdsmiljømæssige eksponeringer, og der blev derfor opstillet en målestrategi, hvor op til fire målinger blev foretaget:
- Statiske baggrundsmålinger, hvor prøvetagningen skete 4-6 meter fra processen og ca. 1,5 m over jorden
- Operatørmålinger, hvor maskinoperatøren bar opsamlingsrør (Tenax, Poropak eller Chromosorb)
- Procesmålinger, hvor prøvetagningen skete 0,5-3 meter fra maskinen
- ”Purge”-målinger (uden præcis beskrivelse af placering af prøverør)
”Purge”-målinger kan betragtes som worst-case eksponeringer, der typisk vil være begrænset til korte perioder i løbet af en arbejdsdag, mens operatør- og procesmålinger kan betragtes som repræsentative for eksponering i det daglige arbejde.
Forfatterne peger på, at resultaterne kan anvendes i en vurdering af, hvordan den fysiske placering af en proces i et arbejdslokale kan påvirke arbejdsmiljøbelastningen.
23.5.2.1 Foliekstrudering – HIPS
|
Koncentration (mg/m³) |
HIPS Folieekstrudering v. 193 °C |
Statisk baggrundsmåling |
Operatør |
Statisk procesmåling (1) |
Statisk procesmåling (2) |
Acrylonitril |
Nd |
Nd |
nd |
0,01 |
Methyl propenoinsyre, methyl ester |
Nd |
0,01 |
<0,01 |
0,07 |
Toluen |
<0,01 |
0,01 |
<0,01 |
0,07 |
Ethenyl cyclohexen |
<0,01 |
0,01 |
<0,01 |
0,05 |
Xylen isomere |
<0,01 |
0,03 |
0,01 |
0,38 |
Styren |
0,03 |
0,13 |
0,05 |
1,48 |
Kulbrinte (C8-C10) |
<0,01 |
0,01 |
0,01 |
0,02 |
Benzen, propyl isomere |
<0,01 |
0,01 |
<0,01 |
0,13 |
a-Methylstyrene |
<0,01 |
0,01 |
<0,01 |
0,10 |
Ethenyldimethylcyclohexen |
<0,01 |
0,20 |
<0,01 |
<0,01 |
Acetophenon |
<0,01 |
<0,01 |
<0,01 |
0,02 |
Propenylbenzen, isomere |
<0,01 |
0,02 |
<0,01 |
0,02 |
Kulbrinte (C10-C12) |
<0,01 |
0,02 |
<0,01 |
0,01 |
Tabel 11. Emissioner ved ekstrudering af HIPS-folie (Forrest et al., 1995).
Forskellen mellem de to statiske procesmålinger er ifølge forfatterne relateret til monitorens placering, idet måling (2), der giver de højeste værdier, fandt sted mellem maskinen og en tilstødende væg, mens måling (1) fandt sted i et åbent område i samme afstand fra maskinen som måling (2).
23.5.2.2 Sprøjtestøbning – HIPS
Målingerne ved sprøjtestøbning af HIPS blev foretaget med to adsorbenter, Tenax og Chromosorb. Tenax-målingerne gav generelt de højeste værdier, og det er disse, der er angivet i nedenstående tabel.
|
Koncentration (mg/m³) |
HIPS Sprøjtestøbning v. 225 °C |
Statisk baggrundsmåling |
Statisk procesmåling |
Operatør |
Purging |
Dichlormethan |
0,36 |
0,36 |
0,36 |
0,27 |
Toluen |
0,28 |
0,31 |
0,25 |
0,32 |
Alkohol (C5) |
0,30 |
0,33 |
0,22 |
0,46 |
Kulbrinte (C7) |
<0,1 |
0,13 |
<0,1 |
<0,1 |
Xylen isomere |
0,66 |
1,60 |
0,49 |
0,40 |
Kulbrinte (C9) |
0,12 |
<0,1 |
<0,1 |
<0,1 |
Benzen, propyl isomer |
0,38 |
<0,1 |
<0,1 |
Nd |
Benzen, ethyl, methyl isomer |
0,18 |
0,21 |
<0,1 |
<0,1 |
Benzen ethyl, methyl isomer |
0,10 |
0,12 |
<0,1 |
Nd |
Benzen, trimethyl isomer |
0,28 |
0,31 |
0,13 |
0,12 |
Benzen, dichlor isomer |
0,46 |
0,65 |
0,78 |
0,50 |
Benzen, trimethyl isomer |
0,25 |
<0,1 |
<0,1 |
Nd |
Kulbrinte (C10) |
0,25 |
0,42 |
0,21 |
0,17 |
Kulbrinte (C11) |
0,47 |
0,66 |
0,33 |
0,21 |
Kulbrinte (C12) |
0,38 |
0,62 |
0,21 |
0,12 |
Kulbrinte (C13) |
0,15 |
0,15 |
<0,1 |
<0,1 |
Tabel 12. Emissioner ved strøjtestøbning af HIPS (Forrest et al., 1995).
Det er interessant at notere, at niveauet ved baggrundsmålingerne (kolonne 1) i mange tilfælde er højere end ved ”purge”-målinger. Der er ikke givet en forklaring på dette i originalarbejdet.
23.5.3 Opsummering – PS og HIPS
De citerede undersøgelser bekræfter langt hen ad vejen den konklusion, som er givet af Jensen, Schmidt og Wolkoff (1989), nemlig at styren er det dominerende nedbrydningsprodukt ved forarbejdning af polystyren (PS) og high impact polystyren (HIPS). Aerosoldannelse kan medføre, at emissionerne når dybere ned i luftvejene, hvilket gør også andre stoffer interessante i en samlet arbejdsmiljøvurdering.
Ud fra de foreliggende data er der ikke noget, der tyder på at grænseværdien for styren i arbejdsmiljøet på 25 ppm eller 105 mg/m³ vil blive overskredet under normale procesbetingelser. Det er ikke muligt at lave den samme konklusion for de andre stoffer, der kan dannes ved forarbejdning af PS og HIPS. Det skal bemærkes, at grænseværdier kun er vejledende ved en vurdering af, om sundhedsfarlige forhold eksisterer, og at koncentrationen af alle luftforureninger derfor generelt bør holdes så langt under grænseværdien som muligt.
23.6 Kemisk arbejdsmiljø ved forarbejdning/fremstilling af umættet polyester
23.6.1 Litteraturreviews
Jensen, Schmidt og Wolkoff (1989) giver i Plastbase en oversigt over de, stoffer, som litteraturkilder angiver er blevet identificeret ved forarbejdning af umættet polyester:
- Styren
- a-Methylstyren
- Benzaldehyd
- Acetophenon
- Aerosol (styrenholdig)
- Glasfibre
- Plaststøv
- Triethylphosphat
- Styrenoxid
Jensen, Schmidt og Wolkoff (1989) citerer en række undersøgelser, der kæder forarbejdning (først og fremmest håndoplægning) af umættet polyester sammen med sygdomme som asthma, bronchitis, lungefunktionsnedsættelse og luftvejsirritation sammen.
Disse undersøgelser er af forholdsvis ældre dato, og sammenhængen er ikke nødvendigvis gældende for dagens danske forhold. Der er ikke foretaget en ny litteratursøgning på området, men det vurderes at manuelle forarbejdningsprocesser som håndoplægning og mekanisk bearbejdning kræver stor omhu ved procestilrettelæggelsen for at undgå eksponering over grænseværdien. Det skal bemærkes, at grænseværdier kun er vejledende ved en vurdering af, om sundhedsfarlige forhold eksisterer, og at koncentrationen af alle luftforureninger derfor generelt bør holdes så langt under grænseværdien som muligt.
23.7 Kemisk arbejdsmiljø ved forarbejdning/fremstilling af polyurethan (PUR)
Som beskrevet i kapitlet om ”Polyurethanbranchens råvarer”, er produktion af polyurethan-produkter ikke en veldefineret proces, men snarere en vifte af muligheder for at kombinere råvarer (primært isocyanater og polyoler) og åbne/lukkede værktøjer med henblik på at opnå den ønskede form og de ønskede tekniske egenskaber for det færdige produkt.
I praksis betyder dette, at mange virksomheder indenfor polyurethanbranchen skal håndtere en ny problemstilling med hensyn til arbejdsmiljø, hver gang en ny produktion startes. Mange af processerne indebærer manuel håndtering af doseringsudstyr og råvarer, hvilket giver en relativ høj risiko for eksponering i arbejdssituationen.
Fremstilling af PUR og bearbejdning af ikke-udhærdede polyurethaner er omfattet af Arbejdstilsynets specielle regler, idet det generelt er forbundet med store sundhedsmæssige risici. Eksponering for monomer isocyanat kan, selv i lave koncentrationer, medføre sensibilisering og en alvorlig asthma. 2,4- og 2,6-toluendiisocyanat er desuden på Arbejdstilsynets liste over stoffer, der anses for at være kræftfremkaldende.
Arbejdsmiljø-generne er primært knyttet til fri isocyanater, der er kraftige irritanter og alleregener. Historisk set har toluendiisocyanat (TDI) været årsag til mange af problemerne, men også mindre flygtige isocyanater som diphenylmethandiisocyanat (MDI) er kendte irritanter og allergener. Hvis det er muligt, bør man dog altid vælge de mindst flygtige udgangsstoffer. Tertiære aminer, der anvendes som katalysatorer, er ofte også stoffer, der er problematiske i arbejdsmiljøet.
Termisk forarbejdning af PUR adskiller sig fra opskumning ved at finde sted ved f.eks. sprøjtestøbning, hvor eksponeringsniveauet er væsentligt mindre. Der er ikke fundet oplysninger om emissioner og/eller koncentrationer af stoffer, men det må anses for sandsynligt, at der vil kunne findes lave koncentrationer af udgangsstofferne ved en eventuel måling.
23.7.1 Litteraturreviews
Jensen, Schmidt & Wolkoff peger i Plastbase (1989) på følgende stoffer, der er toksikologisk relevante ved forarbejdning af PUR:
- Acetaldehyd
- Formaldehyd
- 1,6-Hexamethylendiamin
- Diphenylmethandiamin
- Methyl-aniliner
- p-Toluidin
- 1,4-Tetramethylendiisocyanat
- 1,5-Naphthylendiisocyanat
- 1,6-Hexamethylenaminoisicyanat
- 1,6-Hexamethylendiisocyanat
- 2,4-Toluendiisocyanat
- 2,6-Diisopropylphenylisocyanat
- 2,6-Toluenaminoisocyanat
- 2,6-Toluendiisocyanat
- p-Toluenisocyanat
- Diphenylmethandiisocyanat
Listen kan ikke anses for at være fuldstændig, idet PUR er en fællesnævner for de mange materialer, der kan fremstilles ud fra det samme kemiske grundprincip. Arbejdsmiljøbelastningen bør derfor vurderes i hvert enkelt tilfælde, idet der både tages hensyn til udgangsstoffernes og additivernes giftighed og procesbetingelserne.
23.7.2 Nordiske undersøgelser
I Tabel 1 opsummeres resultaterne af en svensk undersøgelse af eksponeringsforholdene i 13 svenske virksomheder, der fremstiller forskellige polyurethanprodukter (Littorin et al., 2003). Eksponeringen er bestemt ved hjælp af personbårne målinger.
Tabel 1. Eksponeringsniveauer ved forskellige forarbejdningsprocesser og for forskellige råvarer i polyurethanindustrien i Sverige
|
Proces el. produkt |
Råvare |
Antal personer |
TDI (mg/m³) |
NDI (mg/m³) |
MDI (mg/m³) |
FI (mg/m³) |
|
|
|
|
Median |
Range |
Median |
Range |
Median |
Range |
Median |
Range |
A |
Laminering |
TDI |
5 |
0,3 |
0,2-0,7 |
|
|
|
|
|
|
B |
Forbruger-produkter |
TDI, MDI |
3 |
0,1 |
0,1-0,4 |
|
|
0,4 |
0,1-0,6 |
|
|
C |
Opskumning |
TDI |
6 |
4,5 |
0,6-22 |
|
|
|
|
|
|
D |
Støbning |
TDI (MDI) |
9 |
2,7 |
0,4-5,1 |
|
|
|
|
|
|
E |
Støbning |
TDI |
7 |
4,6 |
1,6-9,5 |
|
|
|
|
|
|
F |
Støbning |
TDI (MDI) |
19 |
1,2 |
0,8-2,2 |
|
|
|
|
|
|
G |
Støbning |
NDI |
12 |
|
|
3,4 |
1,5-15 |
|
|
|
|
H |
Støbning |
TDI |
6 |
5,4 |
2,8-8,2 |
|
|
|
|
|
|
I |
Støbning |
TDI, MDI, IPDI |
24 |
3,6 |
1,5-15 |
|
|
|
|
|
|
J |
Støbning |
NDI, MDI |
5 |
|
|
0,15 |
<0,1-8,3 |
3,5 |
<0,1-7,3 |
|
|
K |
Flamme-
laminering |
TDI (PI) |
8 |
11 |
3,7-26 |
|
|
|
|
|
|
L |
Opskumning |
TDI |
4 |
30 |
22-38 |
|
|
|
|
|
|
M |
Flamme-
laminering |
TDI (FI) |
3 |
5,2 |
5,0-9,8 |
|
|
|
|
0,3 |
0,1-0,4 |
TDI = Toluendiisocyanat (2,4- og 2,6-)
MDI = Diphenylmethan-4,4’- diisocyanat
NDI = Naphthylendiisocyanat
IPDI = Isophorondiisocyanat
FI = Phenyl isocyanat
Overordnet konkluderes det i undersøgelsen, at eksponeringen er under – i de fleste tilfælde klart under – de gældende grænseværdier for de pågældende isocyanater:
TDI: 35 mg/m³
MDI: 50 mg/m³
NDI: 40 mg/m³
IPDI: 45 mg/m³
FI: 20 mg/m³ (Sverige)
15 af 111 middelværdier over en arbejdsdag lå over 10 mg/m³; ved fire af disse 15 tilfælde blev der båret personlige værnemidler i noget af tiden.
Den virksomhed (”L” i tabellen), som havde de højeste målte medianværdier, var en af de virksomheder, hvor der blev anvendt personlige værnemidler. En anden virksomhed (”C”) med en tilsvarende produktion havde en betydelig lavere medianværdi. Forskellen skyldes sandsynligvis utilstrækkelig ventilation på virksomhed L, idet også prøver taget udenfor området med den højeste eksponering viste betydeligt højere værdier end på virksomhed C. Forfatterne understreger, at lokale forhold spiller en stor rolle, herunder blandt andet at man på forskellige skift laver forskellige produkter, og at aktivitetsniveauet er meget varierende.
En norsk undersøgelse (Rønning et al. 2002) når frem til følgende konklusioner vedrørende eksponeringsforhold ved produktion af polyurethanprodukter:
Tabel 2. Hovedkonklusioner fra en norsk undersøgelse af PUR-industrien i Norge.
Virksomhed/proces |
Råvare |
Hovedresultat |
Injektion, stift skum i paneler |
MDI |
Den, der sprøjter MDI ind i formen, risikerer eksponering over grænseværdien i kort tid (1-2 minutter). Beregnet som middelværdi over 8 timer vil eksponeringsniveauet være væsentligt lavere end grænseværdien.
Personer i randzonen risikerer en vis eksponering for isocyanater, men niveauet vil være lavt med tanke på både korttidseksponering og middelværdi over 8 timer.
Personer med lagerarbejde i nærheden af nyfremstillede plader var ikke eksponeret for isocyanater eller aminer. |
Stift skum i blokke |
MDI |
Meget lille risiko for eksponering for MDI ved normale driftsforhold. Gælder både operatører og personer i randzonen. |
Isoleringsblokke – stift skum |
MDI |
Meget lille risiko for eksponering for MDI ved normale driftsforhold. Gælder både operatører og personer i randzonen. |
Produktion af blødt, armeret skum |
TDI |
Operatøren eksponeres for høje koncentrationer under selve arbejdsprocessen.
Personer i randzonen risikerer en vis eksponering for isocyanater, men niveauet er lavt. |
Blokstøbning – blødt skum |
TDI |
Både operatører og andre personer i arbejdslokalet risikerer eksponering over grænseværdi. |
Flammelaminering – blødt skum |
TDI |
Der er ikke påvist eksponering for TDI hverken ved personbårne eller stationære målinger. |
Formstøbning – blødt skum |
TDI |
Personer, der udfører opgaver der er knyttet direkte til arbejdsprocessen, risikerer en vis eksponering, men niveauet er væsentligt lavere end grænseværdien. Også andre personer, der opholder sig i arbejdslokalet risikerer en eksponering, om end niveauet er lavt. |
Rapporten giver ikke oplysninger om faktiske eksponeringsniveauer, men forfatterne konstaterer på linie med Littorin et al, 2003, at lokale forhold spiller en væsentlig rolle for eksponeringen. Rønning et al. peger i denne forbindelse på arbejdslokalets størrelse, installeret punktudsugning, dimensionering og effektivitet af generel ventilation og åbne døre og porte som nogle af de vigtige variable.
23.7.3 Danske virksomhedsmålinger
En dansk virksomhed fik i 1986 foretaget målinger af MDI ved personbårne og stationære målinger. Målingerne viste koncentrationer af MDI mellem 0,0002 og 0,002 mg/m³, altså væsentligt under grænseværdien på 0,05 mg/m³. Ved tidligere tilfælde havde en enkelt måling ligget over grænseværdien (0,086 mg/m³), men Bedrift-Sundhedscenter Fyn konkluderer i deres rapport, at dette må betragtes som et enkeltstående tilfælde. Målinger for triethylamin og triethylendiamin lå alle under 0,001 mg/m³.
24 Energiforbrug ved forarbejdning af plast
Se også
Compoundering
Ekstrudering
Ekspandering af EPS
Kalandrering
Sprøjtestøbning
Rotationsstøbning
Termoformning
Referencer
Indholdsfortegnelse
Oversigtsfigur
24.1 Introduktion
Energiforbruget ved forarbejdning af plast varierer betydeligt som funktion af en række faktorer, der til dels er indbyrdes afhængige:
- Proces
- Plasttype
- Forarbejdningstemperatur
- Emnestørrelse
- Overhead (energi til belysning, ventilation m.v.)
I den nedenstående Tabel 1 er der givet en række eksempler på energiforbrug i forskellige situationer. Eksemplerne stammer fra forskellige kilder, men det skal bemærkes at kilderne ”Plastindustriens RT-rapporter” og ”Grønt regnskab” giver danske eksempler, mens ”UMIP” er en database, der for plastforarbejdningsprocesser indeholder data, publiceret af den europæiske plastindustri (APME). UMIP-databsen er i dag integreret i PC-programmet GaBi 4, der markedsføres af LCA Center (www.lcacenter.dk).
Energiforbrugene i UMIP-databasen er regnet tilbage til primær energi, d.v.s. at der er taget højde for det energitab, der sker ved konvertering fra brændsler til elektricitet. Dette betyder, at UMIP-tallene automatisk bliver væsentligt højere end de andre tal, der afspejler aflæsninger på el-målere eller afregninger med el-leverandører. Talsættene kan derfor ikke sammenlignes uden kendskab til energieffektiviteten ved produktion af elektricitet i Danmark og de lande, hvor UMIP’s (APME) data stammer fra.
Tabel 1. Rapporterede energiforbrug ved forarbejdning af plast.
Proces |
Materiale/produkt |
Energiforbrug/kg |
Kommentarer |
Kilde |
Ekstrudering |
PVC-profiler |
0,5 kWh |
Incl. Overhead |
Plastindustrines RT-rapporter |
Ekstrudering |
PP-monofilamenter |
0,5 kWh |
Excl. overhead |
Plastindustrines RT-rapporter |
Ekstrudering |
PP-monofilamenter |
1,25 kWh |
Incl. Overhead |
Plastindustrines RT-rapporter |
Ekstrudering |
PE/PEX –kabler |
0,25 kWh |
Excl. Overhead |
Plastindustrines RT-rapporter |
Esktrudering |
PVC/kabler |
0,15 kWh |
Excl. overhead |
Plastindustrines RT-rapporter |
Produktion af stift integralskum |
PUR |
2,5 kWh |
Incl. Overhead |
Plastindustrines RT-rapporter |
Blokskumning |
PUR |
0,33 kWh |
Incl. Overhead |
Plastindustrines RT-rapporter |
Termoformning |
PS |
0,2 kWh |
Excl. Overhead |
Plastindustrines RT-rapporter |
Blandet |
Blandet |
2 kWh |
Primært ekstrudering og sprøjtestøbning af PC og PP |
Grønt regnskab |
Blandet |
Blandet |
1,6 kWh |
Primært blæsestøbning og sprøjtestøbning af PE (og PET) |
Grønt regnskab |
Sprøjtestøbning |
PET |
3,8 kWh |
Incl. Overhead |
Grønt regnskab |
Vacuuminjektion |
Epoxy |
0,6 kWh |
Incl. Overhead |
Grønt regnskab |
Ekspandering |
PS (emballage, tekniske artikler) |
1,5-3 kWh el
35-65 MJ damp |
Afhængig af densitet |
Plastindustriens RT-rapporter |
Ekspandering |
PS (isolering) |
0,4 kWh
5-15 MJ damp |
Afhængig af densitet |
Plastindustriens RT-rapporter |
Rotationsstøbning |
PVC |
2,5 kWh |
Store emner |
Oplysninger fra dansk producent |
Sprøjtestøbning |
ABS |
3,65 kWh |
Emnestørrelse 10-100 gram |
UMIP |
Sprøjtestøbning |
ABS |
1,39 kWh |
Emnestørrelse >100 gram |
UMIP |
Sprøjtestøbning |
PET |
6,33 kWh |
Emnestørrelse < 10 gram |
UMIP |
Sprøjtestøbning |
PE og PP |
0,39 kWh |
Emnestørrelse < 10 gram |
UMIP |
Sprøjtestøbning |
PA |
1,67 kWh |
Emnestørrelse 10-100 gram |
UMIP |
25 Plast og affald
Se også:
Referencer
Indholdsfortegnelse
Oversigtsfigur
25.1 Introduktion
Med et stigende forbrug af plastprodukter og produkter, hvor plast indgår som en vigtig bestanddel (f.eks. i elektronikprodukter) er det naturligt, at der også er sket en væsentlig stigning i mængden af plast, der ender som affald.
Det er vanskeligt at give en entydig anvisning på, hvordan dette affald behandles bedst muligt ud fra en miljømæssig vurdering. I det følgende belyses nogle vigtige aspekter ud fra affaldshierarkiet: Genbrug, materialegenvinding, energigenvinding og deponering.
Det er vigtigt at være opmærksom på, at når der skal vælges affaldsløsninger, skal affaldshierarkiet ikke følges slavisk, men kan fraviges, hvis det er miljømæssigt og økonomisk velbegrundet.
25.2 Genbrug
Når et produkt genbruges, spares der generelt en væsentlig mængde ressourcer. Det mest kendte eksempel er nok (plast)flasker, der kan genpåfyldes et vist antal gange, inden deres kvalitet er så dårlig, at de må sendes til materialegenvinding. Vask af flaskerne koster en indsats af vand, energi og kemikalier, men i det samlede billede er disse omkostninger små i forhold til, hvad produktion af flasker ud fra nyt (virgint) materiale koster i miljøbelastninger (Ekvall et al. 1998).
Genbrug kræver veletablerede indsamlingssystemer, der kan håndtere en mindre vifte af produkter. Indsamlingssystemerne er ofte bundet tæt sammen med en pantordning, der sikrer en økonomisk forsvarlig løsning.
I Danmark – og de fleste andre steder i verden – er det hovedsagelig flasker af PET (polyethylenterephthalat), der indgår i returordninger. Der er dog ikke i princippet praktiske hindringer for at anvende andre materialer, så længe de overholder kravene til emballering af det pågældende produkt.
25.3 Genanvendelse
Genanvendelse er i relation til plast stort set synonymt med materialegenvinding. Ved materialegenvinding af plast spares der også en væsentlig mængde ressourcer, om end det som minimum er nødvendigt at regranulere plastmaterialet, inden det er egnet til at blive forarbejdet på ny.
I Figur 1 er materialestrømmene ved materialegenvinding og energigenvinding (forbrænding) skitseret.
Langt de fleste plastforarbejdende virksomheder genanvender produktionsspild og fejlproduktion internt. Dette gøres ved at kværne indløb, kasserede produkter mm. i en mekanisk kværn, hvorved der fremkommer granulat af samme størrelse som nyt granulat. Erfaringsmæssigt kan mange produkter fremstilles med 10% regenerat uden praktiske eller kvalitetsmæssige problemer, og anvendelse af regranulat er derfor en god ide både ud fra miljømæssige og økonomiske årsager. Man skal dog også være opmærksom på, at nogle produktstandarder ikke tillader, at der anvendes regranulat.
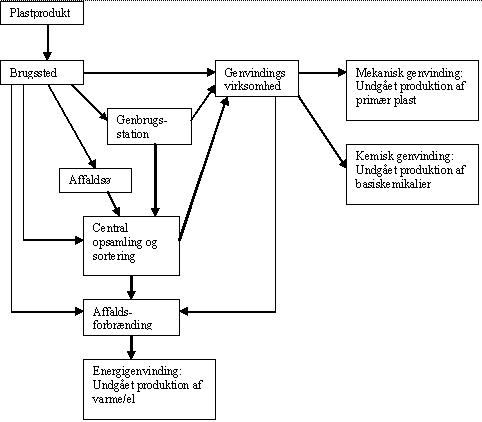
Figur 1. Materialestrømme ved bortskaffelse af plast
Plast, der har været gennem en brugsfase, adskiller sig på mange måder fra internt produktionsspild i virksomhederne. For det første kræver det ofte specialviden for at kunne identificere, hvilken eller hvilke plasttyper, produktet er fremstillet af. Dernæst er produkterne ofte forurenet på en eller anden måde, f.eks. med madrester eller lak, eller det er sat sammen med andre materialetyper som f.eks. metaller. Endelig er langt den største del af plastaffaldet fra husholdningerne blandet sammen (både med anden plast og andre fraktioner), hvilket i praksis gør materialegenvinding umuligt.
Den første forudsætning for at kunne genvinde plastmaterialet er derfor, at der sker en sortering allerede ved kilden, og at de udsorterede materialer kan holdes separeret indtil de er oparbejdet. Dette er ofte en logistisk udfordring, idet det for eksempel kan være svært for personer i en husholdning at vurdere, om et emballageprodukt er fremstillet af PVC, PP, PE eller måske en helt anden plasttype. For andre produkttyper er det væsentligt nemmere at etablere systemer, der håndterer de logistiske problemer. Et godt eksempel er plastfolie, der anvendes til overdækning af landbrugsjord. Denne folietype er fremstillet af polyethylen, og der anvendes meget af den, hvilket er med til at sikre at ordningen har tilstrækkeligt økonomisk potentiale til at være bæredygtig.
Danmark skal opfylde Emballagedirektivets krav om genanvendelse af mindst 22,5 % plastemballage senest 31. december 2008, og for at nå dette mål skal der større fokus på udsortering af plastemballage fra erhverv og husholdninger. Fra 1. august 2006 skal kommunerne anvise genanvendeligt plastemballageaffald fra virksomheder til genanvendelse samt etablere indsamlingsordninger for genanvendeligt plastemballageaffald i form af plastflasker og -dunke fra husholdningerne.
En anden forudsætning for et bæredygtigt genanvendelsessystem er, at der er afsætningsmuligheder for både indsamlet og genvundet plast. Med den stærke økonomiske vækst i Kina og andre asiatiske lande er der samtidigt opstået et stort marked for sekundære materialer, herunder plast, og dette marked aftager en stor del af den plast, der indsamles i Danmark og andre EU-lande. Den største del af det danske plastaffald opkøbes af tyske mellemhandlere, der formodes at videreeksportere plasten, men en stor del sælges også direkte til virksomheder eller agenter i Hong Kong og Kina. Det er i praksis svært at følge materialestrømmen præcist, fordi aktørerne ønsker at beskytte sig selv og de kontakter, man måtte have i Fjernøsten (Tønning og Ottosen, 2005).
Tønning og Ottosen (2005) angiver, at det fremgår af en række artikler fundet på Internettet, at oparbejdning af plastaffald i Kina sker på virksomheder der spænder lige fra små familievirksomheder med manuel oparbejdningsteknik og dårligt ydre miljø og arbejdsmiljø til forholdsvis store fabrikker med moderne oparbejdningsteknik og bedre ydre miljø og arbejdsmiljø.
I Danmark er der en række (omkring 25) virksomheder, der beskæftiger sig med indsamling og/eller oparbejdning af plast. Som nævnt er det kun en mindre del af den indsamlede plast, der rent faktisk oparbejdes i Danmark, men i stedet eksporteres til Kina og Hong Kong, eventuelt via et mellemlager.. Til gengæld importeres der også indsamlet plast til Danmark. Denne bliver enten oparbejdet i Danmark, typisk de reneste fraktioner, eller reeksporteret til udlandet, primært Asien. De plasttyper, der håndteres af danske aktører er først og fremmest PE og PP, men der sker formodentlig også en mindre genanvendelse af opskummet PS.
I de efterfølgende afsnit beskrives typiske forløb omkring oparbejdning og anvendelse af sekundær plast for de mest almindelige termoplaster:
25.3.1 Polyethylen
Polyethylen kan oparbejdes både ved en mekanisk proces og ved en termisk proces. I den mekaniske proces shreddes og granuleres plastaffaldet, hvorefter det f.eks. kan bruges i mængder på 10% som tilsætning til primært materiale. Denne mulighed udnyttes først og fremmest ved intern genanvendelse på plastforarbejdende virksomheder, men kan også anvendes ved ekstern genanvendelse af ensartede materialefraktioner til f.eks. affaldssække. Ved en termisk proces gennemgår affaldet en serie trin, typisk mekanisk neddeling, vask, synke/flyde-separation og tørring, hvorefter det smeltes i en ekstruder og granuleres. Det herved fremkomne granulat kan anvendes til f.eks. blæsestøbning af flasker. TÜV Rheinland (1999) peger på, at det sekundære granulat kun behøver at blive blandet med små mængder virgin plast, når det drejer sig om flasker til gødning, mens det ved blæsestøbning af flasker til detergenter kun kan bruges som et mellemlag på grund af lav kvalitet.
25.3.2 Polypropylen
Polypropylen kan oparbejdes på samme måde som PE. Det er også muligt at blande PE og PP affald. Ved fremstilling af plastpæle neddeles den blandede plast og renses for urenheder i form af snavs og andre materialer i form af emballage og metaller. Det neddelte materiale kan ekstruderes med tilsætning af en farvebatch og efterfølgende støbes til plastpæle (TÜV Rheinland, 1999). Det bemærkes, at den genanvendte plast i sådanne tilfælde ikke erstatter primær plast, men træ eller beton, der typisk vil være det almindelige materialevalg til disse typer af produkter.
25.3.3 Ekspanderet polystyren og polystyren
Ekspanderet polystyren (EPS) kan genanvendes ved at blive neddelt og anvendt som løsfyld eller som tilsætning til virgin plast ved støbning af ny emballage eller forbrugerprodukter som videokassetter og potteplanter. Neddelt EPS kan også blandes med cement og bruges ved støbning af swimming pools og flade tage (EPS Recycling International (http://www.epsrecycling.org/pages/recycle4.html).
Polystyren (PS) kan principielt oparbejdes ved en termisk proces på samme måde som PE og PP. Anvendelsesområderne for sekundært granulat er de samme som for ekspanderet polystyren.
25.3.4 Polyethylenterephthalat
Polyethylenterephthalat (PET) oparbejdes på stort set samme måde som PE og PP. Hvis PET-affaldet stammer fra emballage (flasker) vil det ofte være nødvendigt at fjerne etiketter ved hjælp af en ekstra vaskeproces, hvor limen opløses ved hjælp af damp. PET’en adskilles fra andre plastmaterialer (f.eks. PE eller PP i kapsler) ved flydeseparation, hvorefter det tørres og neddeles. Det neddelte materiale kan eventuelt oparbejdes/homogeniseres ved tilsætning af en masterbatch i en ekstruderingsproces, hvorefter det kan anvendes til f.eks. fleece-fibre, rygsække, sko, tæpper eller emballageprodukter.
25.3.5 Polyvinylchlorid
Polyvinylchlorid (PVC) materialegenvindes kun i beskedent omfang. Årsagen til dette er, at PVC-baserede produkter generelt indeholder additiver, der enten vanskeliggør oparbejdningen (typisk for blød PVC), eller er af en sådan karakter, at man ikke ønsker dem spredt i miljøet (f.eks. tungmetal-stabiliserede PVC-produkter af ældre dato).
I stedet er det i princippet muligt at gennemføre en kemisk genanvendelse, en såkaldt de-polymerisering, hvorved der fremkommer nogle råvarer (primært olie og salt), der langt hen ad vejen svarer til dem, der blev anvendt ved produktionen af den primære plast, eller som kan substituere disse råvarer i forskellige anvendelser. Den faste behandlingsrest efter den kemiske proces kan anvendes til at producere et middel til sandblæsning. I Danmark har virksomheden RGS90 i Stigsnæs opbygget et demonstrationsanlæg, men ikke alle funktionstests har været succesfyldte. I skrivende stund er det derfor RGS 90 vurdering, at kommerciel udnyttelse af teknologien er præmatur med hensyn til både de teknologiske løsninger og de høje behandlingsomkostninger.
I Tyskland anvendes kommercielt en lidt anden proces på ”Schwarze Pumpe”-anlægget. Her er slutproduktet først og fremmest syntesegas, der anvendes til produktion af methanol og elektricitet, og gips. Hvad der sker med chlorindholdet i PVC’en har det ikke været muligt at belyse (Tukker et al, 1999).
25.3.6 Hærdeplaster
Hærdeplaster som PUR og umættet polyester kan ikke materialegenvindes. Deres energiindhold kan imidlertid udnyttes, se nedenfor. Det skal bemærkes, at produkter, der indeholder bromerede flammehæmmere, ikke anses for at være forbrændingsegnede og derfor skal deponeres. Det skal også bemærkes, at glasfibre fra produkter af umættet polyester vil ende i slaggen fra forbrændingsanlæg.
25.4 Forbrænding af plastaffald
En meget stor del af vores plastaffald ender i forbrændingsanlæg, hvor plastens energiindhold udnyttes til produktion af elektricitet og varme. De enkelte plastmaterialers forskellige molekylestruktur betyder, at der også er forskelle i, hvor stort et energiindhold, der er i plasten, og hvilke emissioner, der kommer ved forbrændingsprocessen.
Nedenfor præsenteres molekyleformel og beregnede brændværdier for de mest almindelige plasttyper (Frees et al., 2004):
Figur 2. Brændværdier for de mest almindelige plasttyper
Plasttype |
Brændværdi |
Polypropylen, PP (C3H6) |
43,3 MJ/kg. |
Polystyren, PS (C8H8) |
39,4 MJ/kg. |
Polyethylen, PE (C2H4) |
43,3 MJ/kg. |
Polyvinychlorid, PVC (C2H3Cl) |
17,93 MJ/kg. |
Polycarbonat, PC (C16H14O3) |
29,5 MJ/kg. |
Polyethylenterephthalat, PET (C10H8O4) |
22,1 MJ/kg. |
Polyamid, PA (C6H11N1O1) |
30,6 MJ/kg |
Polyurethan, PUR (C3H8N1O1) |
22,9 MJ/kg. |
Styren-acrylonitril, SAN (C27H27N1) |
38,1 MJ/kg. |
Acryonitril-butadien-styren, ABS (C15H17N1) |
37,7 MJ/kg. |
Det skal bemærkes, at det er et generelt ønske at holde PVC ude af forbrændingsanlæg. Ganske vist har materialet en brændværdi, der kan udnyttes, men chlorindholdet medfører, at røggassen skal renses. Dette skaber betydelige mængder restprodukt (0,4-1,7 kg/kg, afhængigt af rensningsproces (Frees et al, 2004)), som skal deponeres på specialdeponi.
25.5 Deponering
Forbrændingsegnet affald, herunder de fleste plasttyper, må ikke deponeres i Danmark. I stedet skal det genanvendes eller dets energiindhold udnyttes, som beskrevet ovenfor.
Som nævnt er det et generelt ønske at holde PVC og andre halogenholdige plasttyper ude af forbrændingsanlæggene. I praksis betyder det, at en del af de pågældende plasttyper deponeres på specialdeponi. Langtidseffekten af deponering kendes ikke, men selve plastmaterialet giver ikke anledning til større betænkelighed, udover at et af de langsigtede nedbrydningsprodukter med stor sandsynlighed vil være methan, der bidrager til drivhuseffekten.
Derimod anses en del af de anvendte additiver (f.eks. tungmetaller, blødgørere og bromerede flammehæmmere) som betænkelige, hvis de udvaskes til grundvandet eller det marine miljø. Nyere undersøgelser (f.eks. Hansen et al. (2004)) viser dog, at udvaskningen af f.eks. tungmetaller fra velindrettede deponier for restprodukter er meget lille (størrelsesorden mikrogram/kg) i de første hundrede år af deponiets levetid. Selvom der kun er set en meget ringe nedbrydning af de mest almindelige plasttyper efter 25 år i et deponi, er det svært at forestille sig, at de vil forblive uændrede til evig tid. Der er altså en risiko for, at additiverne på et tidspunkt vil blive frigivet til vandmiljøet eller jorden.
26 Brandegenskaber for udvalgte plasttyper
Se også:
Emissioner ved forarbejdning af termoplast
Emissioner ved forarbejdning af hærdeplast
Kemiske belastninger i arbejdsmiljøet
Miljø- og sundhedsvurderinger
Referencer
Indholdsfortegnelse
Oversigtsfigur
26.1 Introduktion
Dette kapitel om brandegenskaber er i al væsentlighed baseret på Hilado (1998). Hvor andre kilder er anvendt, er dette nævnt. Kapitlets fokus er på, hvilke stoffer, der dannes når en given plasttype brænder, og deres sundhedsmæssige egenskaber.
Som udgangspunkt er det den grundlæggende kemiske sammensætning af en polymer, der er bestemmende for, hvilke stoffer, der dannes, når den nedbrydes med eller uden tilstedeværelse af ilt. Temperaturen – og hastigheden af temperaturændringer - spiller også en rolle, men vil ikke blive diskuteret nærmere her.
26.2 Væsentligste nedbrydningsprodukter ved brand i plast
Den følgende tabel giver et overblik over de almindeligst forekommende gasformige nedbrydningsprodukter ved brand i plast, der er bygget omkring forskellige grundstoffer:
Grundstof |
Eksempel på plasttype |
Nedbrydningsprodukter |
Carbon (C) |
Alle plasttyper indeholder kulstof |
Carbon dioxid (CO2)
Carbon monoxid (CO) |
Hydrogen (H) |
Alle plasttyper indeholder brint |
Vanddamp (H2O) |
Chlor (Cl) |
PVC, PVDC, chloreret PE |
Hydrogenchlorid (HCl)
Phosgen (COCl2)
(Dioxin) |
Svovl (S) |
PPS, PSU, visse gummityper |
Svovldioxid (SO2)
Hydrogensulfid (H2S) |
Nitrogen (N) |
PA6, PA6.6, PUR |
Ammoniak (NH3)
Nitrogenoxider (NO, NO2) |
Fluor |
PTFE, FEP |
Hydrogenfluorid (HF) |
Tabel 1. Almindeligt forekommende nedbrydningsprodukter ved brand i plast.
Foruden de stoffer, der er nævnt i Tabel 1, dannes der en lang række andre stoffer, om end i mindre mængder. En indikation af, hvilke stoffer, der er tale om, kan fås ved at kigge på nedbrydningsprodukterne ved forarbejdning af plast (se kapitlerne om emissioner/arbejdsmiljø ved forarbejdning af termo- og hærdeplast).
26.3 Nedbrydningsprodukternes effekter på mennesker
Nedbrydningsprodukternes effekter på mennesker er velkendte. I de følgende tabeller opsummeres kort sammenhængen mellem koncentrationen af et stof og de symptomer og effekter, det har på mennesker.
26.3.1 Carbondioxid
Koncentration |
Symptom |
250-300 ppm |
Normal koncentration i atmosfærisk luft |
900-1500 ppm |
Ingen effekt |
18.000 ppm |
Åndedrættet øges med 50% |
25.000 ppm |
Åndedrættet øges med 100% |
30.000 ppm |
Svag narkotisk virkning. Øgning af puls og blodtryk, manglende skarphed i hørelsen |
50.000 ppm |
Forgiftningssymptomer efter 30 minutter. Hovedpine, svimmelhed. |
80.000 ppm |
Svimmelhed, sløvhed, bevistløshed |
120.000 ppm |
Øjeblikkelig bevidstløshed. Døden indtræffer i løbet af minutter. |
200.000 ppm |
Øjeblikkelig bevidstløshed, død ved kvælning |
Tabel 2. Symptomer og effekter ved udsættelse for carbondioxid.
26.3.2 Carbonmonoxid (kulilte)
Koncentration (ppm) |
Symptom |
100 |
Ingen symptomer, heller ved længerevarende udsættelse |
200 |
Hovedpine efter 2-3 timer, kollaps efter 4-5 timer |
300 |
Hovedpine efter 1,5 time, udtalt forgiftning efter 2-3 timer, Kollaps efter 3 timer |
400 |
Udtalt forgiftning, frontal hovedpine og kvalme efter 1-2 timer, kollaps efter 2 timer, døden indtræffer efter 3-4 timer |
500 |
Hallucinationer efter 30-120 minutter |
800 |
Kollaps efter 1 time, døden indtræffer efter 2 timer |
1500 |
Døden indtræffer efter 1 time |
3000 |
Døden indtræffer efter 30 minutter |
>8000 |
Øjeblikkelig kvælningsdød |
Tabel 3. Symptomer og effekter ved udsættelse for carbonmonoxid.
26.3.3 Hydrogenchlorid
Koncentration (ppm) |
Symptom |
1-5 |
Lugtgrænse |
5-10 |
Mild irritation af slimhinder |
35 |
Irritation af halsen ved kort eksponering |
50-100 |
Knap udholdeligt |
1000 |
Risiko for lungeødemer efter kort tids eksponering |
Tabel 4. Symptomer og effekter ved udsættelse for hydrogenchlorid.
26.3.4 Svovldioxid
Koncentration (ppm) |
Symptom |
3-5 |
Lugtgrænse |
8-12 |
Let irritation af øjne og hals, øget luftvejsmodstand |
20 |
Hoste og øjenirritation |
30 |
Øjeblikkelig og stærk irritation, vedblivende ubehageligt |
100-250 |
Livstruende |
600-800 |
Døden indtræffer i løbet af få minutter |
Tabel 5. Symptomer og effekter ved udsættelse for svovldioxid.
26.3.5 Hydrogensulfid
Koncentration (ppm) |
Symptom |
20-30 |
Øjenbetændelse |
50 |
Øget lysfølsomhed, tåredannelse |
50-500 |
Irritation af luftvejene |
200-400 |
Lette forgiftningssymptomer efter flere timers udsættelse |
250-600 |
Lungeødemer og lungebetændelse efter længere tids udsættelse |
1000 |
Akut forgiftning |
>2000 |
Akut, dødelig forgiftning |
Tabel 6. Symptomer og effekter ved udsættelse for hydrogensulfid.
26.3.6 Ammoniak
Koncentration (ppm) |
Symptom |
1-50 |
Genkendelig lugt |
100 |
Let irritation af næse, hals og øjne |
200 |
Irritation af slimhinderne |
500-1000 |
Stærk irritation af de øvre luftveje |
>1000 |
Dødelig |
Tabel 7. Symptomer og effekter ved udsættelse for ammoniak.
26.3.7 Hydrogencyanid
Koncentration (ppm) |
Symptom |
0,5-5,1 |
Lugtgrænse |
18-36 |
Lette symptomer, hovedpine efter flere timers udsættelse |
45-54 |
Kan udholdes 0,5-1 time uden besvær |
100 |
Dødelig i løbet af en time |
135 |
Dødelig efter 30 minutter |
181 |
Dødelig efter 10 minutter |
280 |
Øjeblikkelig dødelig |
Tabel 8. Symptomer og effekter ved udsættelse for hydrogencyanid.
26.3.8 Hydrogenfluorid
Koncentration (ppm) |
Symptom |
3-5 |
Irritation af næse og øjne efter en uges udsættelse, rødme af huden |
32 |
Irritation af øjne og næse |
60 |
Hudkløen, irritation af luftvejene efter 1 minuts udsættelse |
120 |
Irritation af luftvejene kan lige udholdes i 1 minut |
50-100 |
Livstruende efter få minutters udsættelse |
Tabel 9. Symptomer og effekter ved udsættelse for hydrogenfluorid.
26.3.9 Dioxin
Dannelse af dioxin er et potentielt problem ved brand i chlorholdig plast. Schleicher og Jensen (2004) har i en rapport til Miljøstyrelsen analyseret effekterne af en række ukontrollerede brande, hvor man ved eller har mistanke om, at større mængder PVC er brændt.
Ved to brande i plastforarbejdende virksomheder blev der efterfølgende fundet dioxin i omgivelserne i koncentrationer, der ikke overstiger Miljøstyrelsens grænseværdi for dioxin i jord. Det samme var tilfældet ved analysen af en lossepladsbrand.
Schleicher og Jensen (2004) vurderer, at selvom der i særlige tilfælde kan være meget høje koncentrationer af dioxin i røgen fra en brand, vil det være umuligt direkte at indånde så store mængder røg, som der skal til for at give akutte virkninger af dioxiner, uden først at pådrage sig svære skader forårsaget af andre stoffer i røgen.
Indånding af fortyndet røg og luft fra røgfanens influensområde vil medføre indtagelse af en forøget mængde dioxin, men mængden vil alligevel være lille i forhold til den normale daglige indtagelse af dioxin via føden.
Det anses derfor kun at være relevant at vurdere langtidsvirkningen af eventuelle udledte dioxiner og andre miljøskadelige stoffer, som f.eks. bromerede dioxiner, PCB, PAH og tungmetaller fra brande.
Schleicher og Jensen (2004) nævner også, at det fra udlandet vides, at både legal og illegal afbrænding af kabelskrot kan være en meget væsentlig kilde til dioxinforurening. Herhjemme har vi ingen legal afbrænding af kabelskrot. En mindre, ikke publiceret, undersøgelse af jord fra en illegal afbrænding af kabelskrot viste et indhold af hepta- og octa- PCDD+F congenere på 25.700 ng/kg tør jord, hvilket var 50 gange baggrundsniveauet1. Undersøgelsen viser tydeligt, at der alene på grund af indholdet af kabler i en bygningsbrand kan dannes dioxiner.
26.4 Røgens giftighed
Neviaser og Gann (2004) har lavet et review af den eksisterende litteratur om giftigheden af brandrøg under forskellige betingelser. De deler brandbetingelserne op i følgende hovedgrupper:
- Oxidativ pyrolyse, hvor materialerne ophedes uden selv at bryde i flammer
- Velventileret forbrænding med flammedannelse
- Forbrænding med begrænset ventilation
- Ulmende ild
Til at vurdere toksiciteten af røgen anvender de LC50-værdier, der angiver hvor stor en koncentration af røgen, der medfører at 50 % af de eksponerede dyr omkommer. Da de sammenstiller data fra mange forsøgsserier, har de også beregnet et konfidensinterval, der blandt andet tager usikkerheden som følge af forskellige eksponeringstider i betragtning.
Neviaser og Gann’s beregninger er sammenfattet i Tabel 10.
Materiale |
Vel-ventileret forbrænding |
Forbrænding med begrænset ventilation |
Oxidativ pyrolyse |
Polyethylen |
36,8 (30,1-43,0) |
|
5,8 (3,5-8,9) |
Polystyrenskum |
35,6 (33,4-37,9) |
|
43,5 (41,1-45,6) |
PVC |
20,0 (16,8-23,2) |
|
16,1 (13,2-19,3) |
PVC (blødgjort) |
26,2 (20,1-33,2) |
16,0 (13,7-17,5) |
22,9 (11,8-34,4) |
PUR (stift) |
13,0 (11,6-14,5) |
14,0 (13,4-14,5) |
29,5 (25,2-33,9) |
PUR (fleksibel) |
35,4 (31,8-38,9) |
20,4 (16,0-24,9) |
29,9 (26,5-33,0) |
Tabel 10. Estimerede LC50-værdier (g/m³) med tilhørende konfidensintervaller, Efter Nevasier og Gann (2004).
26.5 Andre brandegenskaber
Foruden de giftige gasser er der en række andre faktorer, der spiller ind ved en vurdering af, hvor farlig en brand er for mennesker. Hilado (1998) peger på følgende:
- Nedsat iltkoncentration. Forbrændingsprocessen bruger ilt, og samtidig kan anstrengelse og ophidselse medføre et øget behov for ilt hos mennesker, der oplever en brand. Resultatet er i visse tilfælde kvælning – et iltindhold på 10 % regnes for minimumsgrænsen for overlevelse.
- Flammer. Mennesker får brandsår, hvis hudtemperaturen er over 66 °C i et sekund. Meget høje flammetemperaturer eller strålevarme kan være øjeblikkelig dødelig.
- Varme. Varme påvirker ikke bare mennesker, der er direkte udsat for brand, men eventuelt også mennesker, der opholder sig i nærheden. Varm luft kan medføre brandsår, dehydrering og eventuelt ødemer, der blokerer luftvejene.
- Røg. Den største risiko ved røgudvikling er, at den hindrer beboeres flugt og samtidigt forhindrer brandfolk i at trænge ind i en brændende bygning og slukke ilden. Røg medvirker også til at skabe panik på grund af dens synsnedsættende og irritative effekter.
- Nedsættelse af strukturers styrke. Brand og varme kan nedsætte styrken af bygningsstrukturen (gulve, vægge, lofter), hvilket bevirker sammenstyrtninger.
Det ligger udenfor denne rapports rammer at give en nærmere vurdering af, hvordan de enkelte plasttyper opfører sig under en brand. Det er dog muligt at give et overblik over nogle af de (risiko)faktorer, man analyser ved de enkelte materialer
Plasttype
Faktor |
PE |
PP |
PVC |
PS |
UP |
PUR |
Nedbrydningstemperatur (°C) |
335-450 |
328-410 |
200-300 |
285-440 |
- |
- |
Selvantændelsestemperatur (flammeeksponering)(°C) |
341-357 |
- |
391 |
345-360 |
346-399 |
310 |
Selvantændelsestemperatur (varmeeksponering)(°C) |
349 |
570 |
454 |
488-496 |
483-488 |
416 |
Oxygen Index (%) |
17,3-30,2 |
17,0-29,2 |
20,6-80,7 |
17,0-23,5 |
20-60 |
- |
”Tid til døden indtræffer” i minutter (v. Dome Chamber Toxicity Test) |
17,3±3,7 |
20,9±0,8 |
16,6±0,3 |
23,1±4,3 |
- |
15,5±4,1 |
LC50 (mg/l)(v. Dome Chamber Toxicity Test) |
11,8-14,9 |
- |
- |
- |
- |
13,2-16,6 |
Minimum antændelsestemperatur for støvlag (°C) |
380 |
- |
290-400 |
470-500 |
- |
390-400 |
Minimum antændelsestemperatur for støvskyer (°C) |
410-450 |
420-460 |
660-730 |
490-500 |
- |
510-550 |
Minimum koncentration for støveksplosioner (g/m³) |
20-25 |
20-55 |
>200 |
15-25 |
- |
25-30 |
Tabel 11. Faktorer, der kan være vigtige i en vurdering af materialers brandegenskaber.
Det skal bemærkes, at Tabel 11 er en simplificering og sammenstilling af en lang række tabeller i Hilado (1998). Som for produktion, forarbejdning, brug og bortskaffelse er der store variationer mellem de enkelte egenskaber alt efter mængde og type af de additiver, der er tilsat. Værdierne i tabellen afspejler den spredning, som Hilado (1998) har fundet ved forskellige forsøg, men det ligger udenfor rapportens rammer at give mere præcise oplysninger om, hvilke modifikationer, der er foretaget på de materialeprøver, der ligger til grund for analyserne. Det ligger også udenfor rapportens rammer at beskrive de (standard)betingelser og –procedurer, der anvendes ved de enkelte tests, men deres betydning beskrives kort i de følgende afsnit.
26.5.1 Nedbrydningstemperatur
Nedbrydningstemperaturen er vigtig i en vurdering af, om en de bærende egenskaber kan være ændret. Det skal bemærkes, at plasttyperne ved de givne temperaturer er flydende, idet temperaturerne er over den normale forarbejdningstemperatur.
26.5.2 Selvantændelsestemperatur
Selvantændelsestemperaturen, både hvis materialet er udsat for direkte flammer eller hvis det alene er udsat for varme, er et udtryk for, hvor let et materiale bliver antændt.
26.5.3 Oxygen Index
Oxygen Index angiver, hvor stor en koncentration af ilt, der skal være til stede for at et materiale vedbliver at brænde under veldefinerede testbetingelser.
26.5.4 ”Tid til døden indtræffer”
”Tid til døden indtræffer” er et mål for, hvor giftige, der gasser, der dannes ved en brand i et materiale, er. Som for de andre parametre i tabellen findes værdierne under standardiserede testbetingelser, og de er derfor mest egnede til at vurdere forskellige materialer i forhold til hinanden.
26.5.5 LC50
LD50 er et andet mål for forbrændingsprodukternes giftighed. Det angiver, hvor høj en koncentration af røgen fra en standardiseret forbrændingsproces, der skal til for at halvdelen af en gruppe forsøgsdyr omkommer. En sammenligning mellem Tabel 10 og Tabel 11 viser, at der er signifikante forskelle mellem de to kilder, der citeres. Der er ikke gjort forsøg på at finde eller forklare disse forskelle.
26.5.6 Minimum antændelsestemperatur for støvlag og støvskyer
Den mindste antændelsestemperatur for støvlag og støvskyer giver en indikation af risikoen for støveksplosioner. Med i dette billede hører også ”støvkoncentrationer”, der er et udtryk for hvor stor en koncentration af materialet, der skal til før det udgør en risiko.
27 Migration
Se også:
Miljø- og sundhedsvurderinger
Referencer
Indholdsfortegnelse
Oversigtsfigur
27.1 Introduktion
Stoffer, der anvendes ved plastproduktion, kan vandre (migrere) fra plastproduktet til omgivelserne. En anden form for migration er afsmitning, hvor stoffer/molekyler slider eller rives af plastoverfladen og ender i det omgivende medie. De migrerende bestanddele er lavmolekylære komponenter, såsom additiver, restmonomerer og biprodukter fra fremstillingen af plastemballagen eller plastproduktet.
Hvis omgivelserne er fødevarer eller drikkevand, betyder dette at mennesker indtager stofferne gennem mave-tarmkanalen og dermed udsætter sig for en mulig sundhedseffekt. Hvis migration sker til overflader i hjemmet, ender migrationsprodukterne i husstøv og giver dermed mulighed for påvirkning via luftvejene.
Den mulige påvirkning af sundheden har betydet, at myndighederne i mange år har haft fokus på problemstillingen, og området er langt hen ad vejen velreguleret i forhold til danske virksomheder. De følgende afsnit giver et hurtigt overblik over de væsentligste problemstillinger, men det ligger udenfor rapportens rammer at give et detaljeret indblik i den viden og de vurderinger, der ligger bag ved diverse lovgivningsinitiativer.
27.2 Migration fra plast til fødevarer
En stor del af de stoffer, der anvendes i produktionen af emballage, er endnu ikke vurderet af toksikologer. Men virksomheder, der producerer, importerer og/eller bruger emballagen, har ansvar for at lave en vurdering, før emballagen eller køkkengrejet sælges og anvendes.
I Danmark er der generelle regler for alle de materialer, genstande og stoffer, der er beregnet til at komme i kontakt med mad, og der er grænseværdier for en række stoffers afgivelse til maden. Reglerne omfatter forordning 1935/2004/EU samt bekendtgørelse nr. 80 af 27. januar 2005. Desuden findes cirkulære om kontrol af de specifikke regler. Man skal sikre sig, at både bestemmelserne i forordningen og i bekendtgørelserne er overholdt. Det skal dog bemærkes, at forordningens artikel 17 om sporbarhed først træder i kraft 27. oktober 2006. Bekendtgørelserne og cirkulæret findes kun på dansk, men da størstedelen af bestemmelserne er implementering af EU-direktiver kan disse findes på de officielle EU-sprog, ligesom rammeforordningen findes på de officielle EU-sprog.
Desuden findes der en vejledning til området (”Vejledning om genstande og materialer bestemt til at komme i kontakt med fødevarer” (VEJ 12114 af 2001), hvor der bl.a. er råd til den, der er ansvarlig for materialet eller genstanden dvs. producenter af materialer og genstande samt fødevarer samt importører. I Fødevaredirektoratets folder "Om-emballage m.v." er en kort introduktion til området, der også omfatter en tjek-liste til virksomhedernes egenkontrol.
Plastbestemmelserne er blevet til på grundlag af EU s plastdirektiv (2002/72/EC) med senere ændring. Der er her fastsat regler bl.a. for total migration og specifik migration samt en udtømmende positivliste over, hvilke monomere og andre udgangsstoffer der må benyttes til fremstilling af plastmaterialer og -genstande bestemt til at komme i berøring med fødevarer. For en del af stofferne eller for stofgrupper på denne liste er der grænser for specifik migration. Den udtømmende liste over monomere og andre udgangsstoffer, der må anvendes, findes i bekendtgørelsens bilag 2.
Plastbestemmelserne indeholder specielle regler for plastvarer, hvori polyvinylchlorid (PVC) indgår. Monomerindholdet af vinylchlorid (VCM) er reguleret dels som indhold i plasten, dels i indhold i fødevarerne.
Plastdirektivet revideres fortsat i disse år. I 1995 blev direktivet udbygget med en liste over nogle af de additiver (tilsætningsstoffer), der må benyttes til fremstilling af plastmaterialer og -genstande. Denne liste findes i bekendtgørelsens bilag 3 og er en ikke udtømmende liste. Listen over additiver udbygges således, at den efter planen bliver en udtømmende positivliste over tilladte additiver til plast i løbet af nogle år.
27.3 Migration fra plastrør til drikkevand
Det efterfølgende afsnit bygger i al væsentlighed på en rapport udarbejdet for Vandpanelet i 2004.
Omkring 1960 begyndte man i de danske vandforsyninger at anvende rør af plastmateriale til forsyningsledninger. Der er med få undtagelser tale om rør af PVC eller PE. I 1980’erne blev der introduceret plastrør til installationer inde i bygninger - her anvendes PEX-rør.
Alle produkter, der er beregnet til drikkevandsinstallationer i ejendomme, skal være godkendte for at måtte installeres. I Danmark eksisterer to godkendelsesordninger for plastrør, som anvendes til drikkevandsformål. VA-godkendelsesordningen omfatter alle ikke-standardiserede plastrør, der anvendes i drikkevandsinstallationer i ejendomme. Denne ordning tager sit afsæt i bygningslovgivningen og omfatter f.eks. PEX-rør. DS-mærkning er en certificeringsordning, som de enkelte fabrikanter selv kan vælge at lade deres produkter underlægge. Der findes DS-mærkning for rør af typerne PE og PVC. I de danske normer DS 441 og DS 442 for henholdsvis almene og ikke-almene vandforsyningsanlæg er det anført, at de anvendte rørmaterialer m.v. skal være i overensstemmelse med gældende normer og standarder. Det betyder, at de plastrør, som vandforsyningerne anvender i anlæg til produktion og distribution af drikkevand bør være DS-mærkede.
Dansk Standard står for udformningen af de krav, som skal gælde for at et produkt kan opnå DS-mærkning, og Dansk Standard er tillige den instans, der skal sikre at kravene i mærkningsordningen overholdes. I ordningen er der endvidere krav om, at rørene skal være accepteret uden anmærkning af Miljøstyrelsen. Retningslinerne for Miljøstyrelsens sagsbehandling er formuleret i en intern vejledning. Godkendelsesproceduren omfatter blandt andet en vurdering af, om det er sandsynligt, at der kan afgives stoffer, som er sundhedsmæssigt uønskede i forbindelse med drikkevand. Hvis dette er tilfældet undersøges, om afgivelse af stofferne vil kunne ske i et omfang, der kan være sundhedsmæssigt problematisk. Dette sker f.eks. på baggrund af grænseværdier og i hvilke mængder, de indgår i rørmaterialet.
I efteråret 2002 kom der fokus, inklusive en del omtale i dagspressen, på forskningsresultater, der pegede på, at der kunne afgives uønskede stoffer til drikkevand fra de plastrør, der anvendes til vandforsyningsformål. Efterfølgende blev der nedsat en arbejdsgruppe, der havde til formål at identificere potentielle organiske stoffer, der vil kunne afgives fra de plastrør, der indtil i dag har været anvendt til distribution af drikkevand i Danmark, om som vil være relevant at medtage i en konkret analyse af drikkevand, der distribueres gennem plastledninger.
27.3.1 Additiver i plastrør
I Tabel 1 findes en oversigt over de additiver, som arbejdsgruppen fandt var blevet anvendt i forbindelse med produktion af PE og PEX rør i Danmark.
Tabel 1. Additiver, som vides at have været anvendt ved produktion af PE og PEX rør i Danmark (Efter Vandpanelet, 2004).
Funktion og rørtype |
Kemisk navn |
CAS nr. |
Anvendte
mængder, % |
Stabilisator
PE og PEX |
Tetrakis[methylen(3,5-di-tert-butyl-4-hydroxy)hydrocinnamat)]methan |
6683-19-8 |
0,15 – 0,2 |
Stabilisator
PE og PEX |
Octadecyl 3-(3,5-di-tert-butyl-4-hydroxyphenyl)propionat |
2082-79-3 |
< 0,1 |
Stabilisator
PE og PEX |
1,3,5-Trimethyl-2,4,6-tris(3,5-di-tert-butyl-4-hydroxybenzyl)benzen |
1709-70-2 |
0,5 |
Stabilisator
PE og PEX |
2,2'-Oxamidobis(ethyl-3-(3,5-di-tert-butyl-4-hydroxyphenyl)propionat) |
70331-94-1 |
0,2 |
Stabilisator
PE |
Tris(2,4-di-tert-butylphenyl)phosphit |
31570-04-4 |
0,1 – 0,2 |
Stabilisator
PE |
Dimethylsuccinat-1-(2-hydroxyethyl)-4-hydroxy-2,2,6,6-tetramethylpiperidin copolymer |
65447-77-0 |
0,2 – 0,3 |
Stabilisator
PE |
1-Propen, 1,1,2,3,3,3-hexafluor-, polymer med 1,1-difluorethen |
9011-17-0 |
0,01 |
Stabilisator
PE |
Ethylen-vinylacetat copolymer |
|
0,5 |
Stabilisator
PE |
Fluor elastomer / polyethylen blanding |
0/9002-88-7 |
0,01 |
Stabilisator
PE |
Phthalocyaninato(2-)-n(29),n(30),n(31),n(32)] |
14832-14-5 |
0,0138 |
Stabilisator
PE |
2-Hydroxy-4-n-octoxy-benzophenon |
1843-05-6 |
max 0.25 |
Stabilisator
PE |
2-(2'- Hydroxy –3,-tert-butyl-5'-methylphenyl)-5-chlorbenzotriazol |
3896-11-5 |
|
Stabilisator
PE |
Poly[oxiran-co-(1,2-epoxypropan)] |
06-11-9003 |
0,0007 |
Stabilisator
PE |
Polydimethylsiloxan |
9016-00-6 |
0,0013 |
Stabilisator
PE |
Polytetrafluorethylen |
9002-84-0 |
max 0.01 |
Stabilisator
PEX |
Pentaerythritol tris ester med 3-(3,5-di-tert.butyl-4-hydroxyphenyl) propionsyre |
84633-54-5 |
0,001 |
Stabilisator
PEX |
tert-Butylperoxid |
110-05-4 |
|
Stabilisator
PEX |
Trimethylpropantrimethacrylat |
3290-92-4 |
|
|
|
|
|
Hjælpestof PE |
Calciumstearat |
1592-23-0 |
0,1 – 0,2 |
Hjælpestof PE |
Zinkstearat |
557-05-1 |
max 0,1 |
Hjælpestof PE |
Silicumdioxid, amorf |
112945-52-5 |
op til 25 |
Hjælpestof PE |
Titaniumdioxid |
13463-67-7 |
< 0,5 |
Hjælpestof PE |
Aluminumoxid |
1344-28-1 |
0,0044 |
Hjælpestof PE og PEX |
Vinylacetat |
108-05-4 |
0,5 |
Hjælpestof PE |
Calciumsalte af fedtsyrer C16-C18 |
85251-71-4 |
max 0,15 |
Hjælpestof PE |
Polyethylenglycol |
25322-68-3 |
0,025 |
Hjælpestof PE |
Hydrocarboner (C6-C7) |
|
|
|
|
|
|
Farvestof PE |
Carbon Black |
1333-86-4 |
Op til 2,5 |
Farvestof PE |
Kobberphthalocyanin |
147-14-8 |
Op til 2,5 |
Farvestof PE |
Ultramarine Blue |
57455-37-5 |
max 0,5 |
27.3.2 Migrationsprodukter
Det er imidlertid ikke additivstofferne i sig selv, der identificeres ved undersøgelser af vandet, men i langt højere grad deres nedbrydningsprodukter. Vandpanelet (2004) giver på baggrund af informationen i en række videnskabelige undersøgelser følgende bud på, hvilke stoffer, der kan være relevante at inddrage i en vurdering, fordi deres forekomst er kendt:
Tabel 2. Nedbrydningsprodukter fra PE og PEX rør (Efter Vandpanelet, 2004)
Stof |
Rørtype |
4-ethyl phenol |
PE |
4-tert-butyl phenol |
PE |
2,6-Di-(tert-butyl)-p-benzoquinon |
PE |
2,4- Di -tert-butylphenol |
PE |
3,5- Di -tert-butyl-4-hydroxystyren |
PE |
3,5-d Di -tert-butyl-4-hydroxybenzaldehyd |
PE og PEX |
3,5- Di -tert-butyl-4-hydroxyacetophenon |
PE og PEX |
Cyclohexa-1,4-dien, 1,5-bis (tert butyl), 6-on,-4-(2-carboxy-ethyldien) |
PE og PEX |
3-(3,5-Di-tert-buyl-4-hydroxyphenyl)methylpropanoat |
PE |
3-(3,5-Di-tert-buyl-4-hydroxyphenyl)methylpropanonsyre |
PE |
Methyl-tert-butylether |
PEX |
Tert-Butylalkohol |
PEX |
4-Butoxyphenol |
PEX |
5-Methyl-2-hexanon |
PEX |
Mesityloxid |
PEX |
tert-Butyl isobutylether |
PEX |
27.3.3 Arbejdsgruppens konklusioner
Det ligger udenfor denne rapports rammer at gå ind i en diskussion af betydningen af, at disse stoffer afgives til drikkevandet. Arbejdsgruppen bag rapporten nåede frem til blandt andet følgende konklusioner:
- En egentlig kortlægning af de tilsætningsstoffer der indgår i fremstillingen af de PE-rør, der ligger i jorden i dag, er ikke mulig. For det første er recepturen til de anvendte plastmaterialer firmahemmeligheder, for det andet har sammensætningen ændret sig over tid, og for det tredje findes der kun få tilstrækkelig detaljerede registreringer af hvilke fabrikater, der har været anvendt. Der findes en fortegnelse over de mest anvendte antioxidanter.
- Ud fra den foreliggende viden vil der kun ske en meget begrænset afsmitning fra forsyningsrør af PVC. Den foreliggende information peger på, at der vil kunne forekomme afsmitning af dibutyltin.
- De foreliggende laboratorieundersøgelser af afsmitningen fra PE-rør peger på, at der er en målbar afsmitning af nedbrydningsprodukter fra de anvendte antioxidanter. Undersøgelserne peger samtidig på, at der er en betydelig variation i såvel hvilke stoffer, der afgives, som mængderne de afgives i, selv inden for samme type rør. Ud fra de foreliggende undersøgelser kan det ikke afvises, at denne afsmitning vil kunne foregå over hele rørenes levetid. Ud fra litteraturen kan der identificeres 11 specifikke stoffer, der potentielt kan give afsmitning fra PE rør.
- Selvom de anvendte antioxidanter måtte være godkendte til anvendelse i emballager til fødevarer, omfatter den sundhedsmæssige vurdering i denne forbindelse ofte ikke de mulige nedbrydningsprodukter af stofferne.
- Der foreligger kun få undersøgelser, som vurderer de sundhedsmæssige konsekvenser af de miljøfremmede stoffer, der kan frigives til drikkevand. Der foreligger kun toksikologisk vurdering af ét af de 11 nedbrydningsprodukter, som er påvist i testen af PE rørene. Denne vurdering peger på, at en grænseværdi for drikkevand vil komme til at ligge i størrelsesordenen 20 µg/l. Ud fra analog betragtning vurderer Miljøstyrelsen, at der vil gælde en tilsvarende grænseværdi for de øvrige påviste nedbrydningsprodukter. De påviste koncentrationer af nedbrydningsprodukter i eluatet i laboratorieforsøgene ligger for ét enkelt rør væsentligt over denne værdi, hvorfor det kan være relevant at klarlægge koncentrationen af nedbrydningsprodukter i det eksisterende ledningsnet.
- Den nuværende DS-certificering af PE-rør tager ikke højde for frigivelse af de specifikke nedbrydningsprodukter, da den anvendte metode til analyse af phenoler (DS281) ikke medtager alle disse stoffer.
- Såfremt man ved fremtidige godkendelser af PE og PVC rør ønsker en godkendelsesordning som medtager nedbrydningsprodukterne, vil det være nødvendigt at indføre specifikke analyser, som kan påvise de omtalte nedbrydningsprodukter.
27.3.4 Feltundersøgelse af vandrør
Som opfølgning på Vandpanelets rapport er der gennemført en feltundersøgelse af afsmitningen fra de plastrør, der gennem årene har været anvendt til at opbygge det ledningsnet, som leverer drikkevand til de danske forbrugere (Nielsen et al. (2005).
Der blev udtaget prøver på 10 strækninger, 7 med PE-ledninger (1-3 år gamle) og 3 med PVC-ledninger (ca. 15 år gamle). I de syv feltprøver fra PE-rør blev der kun påvist nedbrydningsprodukter på de to strækninger og kun i de første to prøver. Der blev påvist henholdsvis et og tre stoffer på de to strækninger, og den højeste samlede koncentration var 3 mg/l.
Til sammenligning blev nye PE-rør testet. Her blev der påvist 6 af de ti nedbrydningsprodukter fra PE-rør, der er nævnt i afsnit 1.3.2, i koncentrationer mellem 0,05 og 1,5 µg/l.
Undersøgelsen af PE-rør viser, at de undersøgte rør overholder de krav, der er stillet i den nuværende DS-ordning for plastrør til drikkevandsforsyning. Der er meget begrænset viden om den toksiske effekt af de målte nedbrydningsprodukter, men en vurdering af et af nedbrydningsprodukterne indikerer, at en grænseværdi, baseret på en sundhedsmæssig vurdering, bør ligge i størrelsesordenen 20 µg/l, altså noget højere end de målte værdier.
I rapporten er afsmitningen beregnet for andre rørdimensioner og opholdstider. Beregninger baseret på de højest samlede afsmitning målt i laboratorietest indikerer, at afsmitningen af nedbrydningsprodukter ikke vil udgøre noget sundhedsmæssigt problem under normale omstændigheder.
Laboratorieundersøgelsen af PVC-rør viste ikke afsmitning af organiske stoffer, men undersøgelser af gamle rør, der er opgravet, viste afsmitning af bly fra alle tre rørstykker i koncentrationer op til 0,82 µg/l. Grænseværdier for bly er 5 µg/l ved indgang til ejendommen, og det skal bemærkes, at det siden 2001 ikke har været tilladt at tilsætte bly i PVC-rør til drikkevand.
Feltundersøgelser af PVC-rør viste heller ingen afsmitning af organiske stoffer eller bly. På en af de tre strækninger, der blev undersøgt, blev der påvist afsmitning af organotinforbindelser i koncentrationer op til 0,031 µg/l. Der findes ikke i dag grænseværdier for dette stof.
27.4 Afdampning
De følgende afsnit er i overvejende grad baseret på et udkast til en rapport til Miljøstyrelsen (Jensen og Knudsen (under udgivelse)).
Mange af de forbrugerprodukter, vi omgiver os med, er fremstillet af plast eller indeholder plastkomponenter. De stoffer, som produkterne er baseret på (monomerer og additiver), kan i visse tilfælde afgives fra produkterne som følge af slid, varme eller påvirkning af lys, og de udgør dermed også en potentiel kilde til påvirkning af menneskers sundhed.
Overordnet er det meget vanskeligt at relatere forureninger i indeklimaet til specifikke produkter. Et stof som f.eks. formaldehyd kan stamme fra flere forskellige kilder, idet det har en række anvendelser blandt andet i byggematerialer, hvorfra det kan frigives med varierende hastighed, ligesom det kan dannes som følge af mange af vores daglige aktiviteter som tobaksrygning, madlavning mm.
Miljøstyrelsen har i en række forbrugerprodukt-undersøgelser kortlagt indhold af stoffer i indeklimarelevante produkter og, for nogle af produkternes vedkommende, også foretaget målinger af, hvilke stoffer, der afgives, og i hvor store mængder.
27.4.1 Afgivelse af phthalater
Enkelte af de undersøgte produkter kan karakteriseres som deciderede plastprodukter. Det drejer sig f.eks. om badeforhæng, tasker, handsker, vinylgulve, tæppefliser og vinyltapeter, hvor alle de undersøgte produkter var fremstillet af blødgjort PVC. Der blev fundet mindst én type af phthalater i samtlige prøver. Mest forekommende var DEHP i 10 ud af 12 varer fulgt af DINP/DIDP i halvdelen af varerne, DBP i en tredjedel og BBP i to produkter. Det var endvidere kendetegnende for prøverne, at phthalater var til stede i stor mængde varierende fra 2,5% til 63%.
Der blev påvist et væsentligt indhold af organiske tinforbindelser i 5 ud af 12 prøver. Summen af de organiske tinforbindelser var op til 0,03%. Dibutyltin optrådte typisk i størst koncentration. Tributyltin fandtes kun i 2 prøver. Produkterne blev dog ikke undersøgt for afgivelse af de pågældende stoffer.
Jensen og Knudsen (under udgivelse) indeholder en sammenfatning af en række undersøgelser, hvor mængden af blødgørere i husstøv er blevet undersøgt i forskellige lande. Tabel 2 giver et summarisk overblik over undersøgelsernes resultater:
Tabel 3. Resultater af målinger af blødgørere i husstøv. (Efter Jensen og Knudsen (under udgivelse)).
|
Husstøv I Tyskland (mg/kg) |
Husstøv fra svenske hjem med PVC-gulve (mg/kg) |
Husstøv fra norske hjem(mg/kg) |
|
< 2mm |
< 63mm |
|
|
|
|
Median |
Max |
Median |
Max |
Gennemsnit |
Gennemsnit |
Max |
Dimethylphthalat (DMP) |
0,27 |
580 |
0,57 |
1300 |
|
|
|
Diethylphthalat (DEP) |
2,8 |
730 |
4,8 |
1200 |
31 |
10 |
110 |
Benzylbutylphthalat (BBP) |
5,8 |
340 |
13 |
460 |
319 |
110 |
440 |
Dibutylphthalat (DBP) |
21 |
880 |
29 |
740 |
226 |
100 |
1030 |
Diisobutylphthalat (DIBP) |
17 |
350 |
33 |
310 |
97 |
10 |
300 |
Di(2-ethylhexyl)phthalat (DEHP) |
240 |
3800 |
480 |
5100 |
310 |
640 |
610 |
Diisoheptylphthalat (DIHP) |
3,5 |
400 |
18 |
530 |
|
|
|
Diisononylphthalat (DINP) |
28 |
920 |
80 |
1400 |
639 |
|
|
Diisodecylphthalat (DIDP) |
15 |
1100 |
60 |
2600 |
|
|
|
Di(2-ethylhexyl)adipat (DEHA) |
0,4 |
270 |
0,4 |
14 |
|
|
|
Tungere phthalater |
|
|
|
|
|
100 |
1380 |
Total phthalater |
|
|
|
|
|
960 |
2920 |
I den svenske undersøgelse blev der konstateret en sammenhæng mellem astma/allergi hos børn og forekomst af phthalater i husstøv fra PVC-gulve. En opfølgende undersøgelse af de 6 phthalater i støv fra børneværelser i 390 hjem i Sverige viste, at PVC gulve ikke er hele forklaringen. PVC tapeter har også stort bidrag. Herudover var der i undersøgelsen højere phthalatkoncentration i:
- Flerfamiliehuse
- Huse med betonfundament men uden kælder
- Huse fra før 1960 med PVC gulve
- Huse med højere luftskifte
- Huse med vandskade.
Jensen og Knudsen (under udgivelse) citerer også en amerikansk undersøgelse (Uhde et al, 2001), hvor afgivelsen af phthalater fra PVC vægtapet med et indhold på 30% blødgører blev målt i testkammerforsøg over 14 dage. Koncentrationen af blødgører i luften i kammeret holdt sig nogenlunde konstant over det meste af perioden. Kondensering på kold metalplade blev også målt (se tabellen nedenfor).
Tabel 4. Phthalatkoncentrationer i testkammer og ved kondensering
Phthalat |
Max. kammer konc.. (µg/m³) |
Kondensat på metalplade (µg) |
Tolerabel daglig indtagelse
(µg/kg lgv./d) |
Dibutylphthalat (DBP) |
5,1 |
1,3 |
66 |
Dipropylphthalat (DPP) |
2,1 |
18 |
|
Di(2-ethylhexyl)phthalat (DEHP) |
0,9 |
60 |
37 |
Diisobutylphthalat (DIBP) |
0,5 |
0,8 |
|
Clausen et al. (2004) undersøgte afgivelsen af DEHP fra PVC-gulvbelægning i to forskellige testkammerundersøgelser, der varede op til 472 dage. Koncentrationen af DEHP steg langsomt i løbet af de første 150 dage og nåede et såkaldt quasi-statisk ligevægt på omkring 1mg/m³.
27.4.2 Afgivelse af bromerede flammehæmmere
Dette afsnit er ligesom afsnittet om phthalater i altovervejende grad baseret på Jensen og Knudsen (under udgivelse).
27.4.2.1 Afgivelse fra polyurethan skumplast
Indholdet i og afgivelsen af bromerede flammehæmmere (21 congenere - dog ikke BDE 209) fra blød polyurethan-skum benyttet i kontorstole, bilsæder og møbler er ganske betydelig i laboratorieforsøg (Wilford et al. (2003)). I gennemsnit blev der fra forsøgskammeret afgivet 500 ng PBDE/m³ per gram skumplast. Afgivelsen af flammehæmmer fra en kontorstol kan være flere hundrede mikrogram per dag. Med alderen af skummet frigøres mere støv. De lavere PBDE afgives hurtigst. Indholdet af PBDE var op til 5,5% i PUR-skum.
27.4.2.2 PBDE i elektronik og husstøv
På samme måde som for blødgørere er der foretaget en række målinger af indholdet af bromerede flammehæmmere i husstøv. Jensen og Knudsen (under udgivelse) opsummerer resultaterne fra de enkelte undersøgelser, og denne opsummering er sammenfattet i Tabel 3.
Som det fremgår af tabellen, er der meget stor variation i de fundne koncentrationer, specielt er der forskel mellem de koncentrationer, der er fundet i Tyskland og USA. Det skal bemærkes, at det høje indhold af BDE 209 i den ene tyske undersøgelse er fundet i støv fra en polyurethan-madras. Jensen og Knudsen (under udarbejdelse) bemærker omkring undersøgelsen af støv fra Washington, DC, at der var ingen sammenhæng med alder af huset, gulvmaterialer eller antal TV-apparater og PC’er. Dog blev fraktionen af BDE 209 mindre med øget areal af måleområde.
Tabel 5. Koncentrationsintervaller for bromerede flammehæmmere i husstøv opsamlet med støvsuger. Resultater fra fire undersøgelser. Sammenfattet fra Jensen og Knudsen (under udarbejdelse).
|
Koncentrationsinterval i støv (ng/g) |
Stof |
Støvsugerstøv
Tyskland |
Støvsugerstøv USA |
Støvsugerstøv Tyskland |
Støvsugerstøv Washington DC, USA |
Støvsugerstøv Dallas, USA |
BDE 28 |
|
|
0,2-4,4 |
|
|
BDE 47 |
<14-22 |
230-3.000 |
3,3-1.910 |
103-7.610 |
49-10.538 |
BDE 49 |
|
|
0,5-282 |
|
|
BDE 85 |
|
|
0,1-75 |
|
|
BDE 99 |
<4-38 |
69-3.700 |
2,6-2.850 |
162-13.800 |
79-18.841 |
BDE 100 |
<6-7 |
15-660 |
0,5-314 |
25-2.090 |
13-2.605 |
BDE 153 |
<6-22 |
5-650 |
0,4-420 |
11-1.510 |
7-1.100 |
BDE 154 |
<6 |
<7-260 |
0,3-210 |
12-1.250 |
6-1.100 |
BDE 183 |
<5-121 |
<8-4.000 |
0,9-464 |
|
|
BDE 209 |
<5-410 |
120-21.000 |
18,6-19.100 |
162-8.750 |
536-65.770 |
27.4.2.3 PBDE i indeluft kontra udeluft
Koncentrationen af bromerede flammehæmmere (PBDE 47, 99, 100, 153 og 154) var mere end 20 gange højere i indeluften end i udeluften i England (Harrad et al. (2004)). I 6 udendørsprøver var koncentrationsintervallet 10-33 pg PBDE/m³ (median 18 pg PBDE/m³) og for 17 indendørs prøver 60-15.509 pg PBDE/m³ (median 762 pg PBDE/m³). Median koncentrationen indendørs var højere i kontormiljøer (1082 pg PBDE/m³) end i boliger (128 pg PBDE/m³).
Der var desuden en direkte sammenhæng mellem luftkoncentrationen indendørs og antallet af elektriske apparater og antallet af polstrede møbler i hjemmet.
I Ottawa, Canada, var koncentrationen af bromerede flammehæmmere (PBDE 17, 28, 47, (66), (71), (85), 99, 100, (153) og (154)) 50 gange højere i indeluften (10 congenere bestemt) end i udeluften (5 congenere bestemt) med anvendelse af passiv prøveopsamling (Wilford et al. (2004)). Koncentrationsintervaller var henholdsvis <2-4,4 pg PBDE/m³ (median 2,6 pg PBDE/m³) for luft syv steder udendørs, og 2-3600 pg PBDE/m³ (100 pg PBDE/m³) for indendørs luft i de 74 tilfældigt valgte hjem.
I Toronto, Canada, var koncentrationerne af PBDE i udeluft (2 prøver) henholdsvis 39-48 pg/m³ og 76-2088 pg/m³ (4 boliger) (Wilford et al. (2004)). Der blev analyseret for 9 PBDE congenere, dog eksklusive BDE 209.
27.4.3 Afgivelse af toluendiisocyanat
Forskellige husholdningsprodukter (tæppeunderlag, møbelpuder, skumplader, lak og fugemasser/tætningsmidler) og materialer af polyurethan er undersøgt i forsøgskammer for afgivelse af toluendiisocyanat (TDI) (Kelly et al, 2004). Ved stuetemperatur var emissionen fra nogle kommercielt tilgængelige fugemasseprodukter omkring 300 mg TDI/m² per time. Inden emissionen ophørte efter ½ time ved 21°C og 1 time ved 27°C var der afgivet 35-179 µg TDI fra de undersøgte produkter.
27.4.4 Afgivelse fra personlige computere
En undersøgelse af computeres påvirkning af et kontormiljø viste at luftkvaliteten blev forringet (Bako-Biro et al. (2004). Emissionen fra computerne blev analyseret og emissionshastigheden bestemt. Derefter blev luftkoncentrationer modelleret. Forekomsten af 2-ethylhexanol stammer formentlig fra nedbrydning af blødgørere.
Tabel 6. Emission fra personlige computere.
Stof |
Emissionshastighed
per PC (µg/time) |
Modelleret koncentration (µg/m³) |
Phenol |
63 |
1,7 |
Sum af C6-C10 aromater |
46 |
1,3 |
Sum af aromater med højt kogepunkt (toluen-eq.) |
58 |
1,6 |
Sum af isomere bicycliske aromater (toluen-eq.) |
41 |
1,1 |
Toluen |
47 |
1,3 |
Styren |
7,6 |
0,2 |
Xylener |
10 |
0,3 |
Formaldehyd |
5,2 |
0,1 |
2-Ethylhexanol |
20 |
0,5 |
Forgrenede mono-umættede C12 |
22 |
0,6 |
Decan |
12 |
0,3 |
Undecan |
7,6 |
0,2 |
Sum af andre SVOC’er (octan-eq.) |
9,4 |
0,3 |
Sum af andre VOC’er |
120 |
3,3 |
TVOC’er |
469 |
13 |
28 Miljø- og sundhedsvurderinger
Se også:
Brandegenskaber for plast
Referencer
Indholdsfortegnelse
Oversigtsfigur
28.1 Introduktion til miljø- og sundhedsvurderinger
Der forekommer mange stoffer i livsforløbet af plastmaterialer. Produktion af råvarer sker ved mere eller mindre komplicerede synteseprocesser, hvor der ofte anvendes katalysatorer, ligesom der kan være en lang række mellemprodukter. Ved forarbejdningen tilsættes der en bred vifte af additiver med forskellige formål, og i forarbejdningsprocessen dannes der forskellige nedbrydningsprodukter alt efter hvilken kombination af materiale, additiv(er) og proces, der er tale om. I brugsfasen kan nogle af udgangsstofferne (monomerer) og additiver afdampe, migrere eller smitte af på hud og slimhinder, og ved en eventuel affaldsforbrænding nedbrydes plasten med afgivelse af forbindelser, der er relateret til indholdet af grundstoffer.
Det er ikke realistisk at give et bare nogenlunde operationelt billede af de mange stoffers mulige effekter på mennesker og miljø indenfor denne rapports rammer. I stedet er det valgt at pege eksplicit på de stoffer, hvor man med stor sikkerhed ved, at de har problematiske egenskaber, og henvise til videnkilder, hvor man kan finde uddybende information. Her er det i første række Miljøstyrelsens vurderinger, der anvendes, f.eks. i form af specifikke hjemmesider om ”hormonforstyrrende stoffer” og ”PVC og phthalater”.
Til vurdering af de potentielle virkninger af stoffer, der ikke har været så meget i fokus for myndighedsinitiativer, kan man tage udgangspunkt i deres tilstedeværelse på diverse lister. Dette giver en hurtig indikation af, om et givet stof er problematisk, men giver sjældent en uddybende forklaring på, hvorfor dette er tilfældet.
En sådan forklaring kan man få, hvis man anvender kriteriedokumenter, primært på engelsk, der netop er lavet med henblik på at give en fyldestgørende baggrundsviden om stoffernes miljø- og sundhedsmæssige egenskaber. Derudover findes der internationalt accepterede sammenfatninger af stofvurderinger i form af datablade, der kort og præcist beskriver stoffernes potentielle effekter, giver anvisning på deres håndtering og ofte forslag til en grænseværdi i arbejdsmiljøet. Det skal bemærkes, at selvom der generelt er international enighed om, hvordan et stofs egenskaber skal vurderes, er der også eksempler på vurderinger, hvor enkeltlandes (f.eks. Danmark) holdning afviger fra den, der er afspejlet i dokumentet. I sådanne tilfælde er det naturligvis den danske holdning og vurdering, der som udgangspunkt skal lægges til grund.
28.2 Kemiguiden
Kemiguiden (www.kemiguiden.dk) giver et nemt og hurtigt overblik over hvilke lister, et givet stof findes på. Den samme information kan findes i henholdsvis Miljøstyrelsens og Arbejdstilsynets publikationer og på deres hjemmeside, men dette kræver enkeltvis søgning i de enkelte lister. Kemiguiden omfatterfølgende lister over stoffer, der anses for at være mere eller mindre problematiske i en given sammenhæng.
28.2.1 Listen over farlige stoffer (LOFS)
Listen over farlige stoffer indeholder 7.000 opslag til kemiske stoffer og stof-grupper, som er vurderet og klassificeret efter EU's fælles regler for klassificering og mærkning. Listen er senest opdateret den 3. juni 2002.
Entydig definerede stoffer på listen er angivet med CAS-nummer. Der er ca. 3.000 forskellige CAS-numre på listen, og således langt flere opslag end CAS-numre. Det skyldes blandt andet at stofgrupper som eksempelvis blyalkyler og blyforbindelser ikke er angivet med CAS-nummer.
På Miljøstyrelsens hjemmeside, http://www.mst.dk/kemi/02010100.htm, er der adgang til selve bekendtgørelsen samt mulighed for at søge i listen. Som søgekriterium kan man anvende CAS nummer, Index nummer, EF nummer og stofnavn.
Ved undersøgelse af, om et givet stof står på listen, er det vigtigt at vide, at især nye stoffer i EU kan være klassificeret og optaget på EU's liste over farlige stoffer uden at have fået tildelt et CAS-nummer. Der er således ca. 130 stoffer på den nuværende liste uden CAS-nummer.
28.2.2 Effektlisten
Effektlisten danner udgangspunkt for Listen over uønskede stoffer. Effektlisten består af ca. 6400 stoffer, som er udvalgt efter af Miljøstyrelsen fastsatte kriterier. Stofferne er udtrukket fra Listen over farlige stoffer (2002), EU's liste over stoffer med dokumentation for hormonforstyrrende effekter, som er prioriteret til yderligere testning, højtonnage stoffer som man i EU har mistanke om har PBT (persistente, bioakkumulerende og toksiske) og vPvB (meget persistente meget bioakkumulerende) egenskaber, og Miljøstyrelsens Vejledende liste til selvklassificering af farlige stoffer. Listen – og baggrunden for udvælgelse af stofferne på listen, kan findes på http://www.mst.dk/effektliste/.
28.2.3 Listen over uønskede stoffer (LOUS)
LOUS er en bearbejdet signalliste over kemiske stoffer. Udgangspunktet er LOUS 2004, der er udgivet af Miljøstyrelsen og indeholder 68 enkeltstoffer og stofgrupper. Publikationen kan findes på Miljøstyrelsens hjemmeside, http://www.mst.dk/udgiv/publikationer/2004/87-7614-312-0/html.
Kemiguidens bearbejdede LOUS indeholder enkeltstofferne fra Miljøstyrelsens LOUS og ca. 500 forslag til enkeltstoffer, der tilhører de forskellige stofgrupper på Miljøstyrelsens liste.
28.2.4 Miljøstyrelsens vejledende liste til selvklassificering af farlige stoffer
Miljøstyrelsen har udarbejdet en vejledende liste til selvklassificering af farlige stoffer. Listen, der kan findes på Miljøstyrelsens hjemmeside (http://www.mst.dk/kemi/02040300.htm), indeholder vejledende klassificeringer for 20.624 stoffer. Klassificeringerne er baseret på computerberegninger med brug af såkaldte QSAR-modeller (Quantitative Structure-Activity Relationship). Selvom det er computerbaserede vurderinger er værktøjet anbefalelsesværdigt, fordi det er en nem vej til information om rigtig mange stoffer. Miljøstyrelsen anser i øvrigt QSAR-vurderingerne som meget troværdige, fordi de med dagens viden og teknologi kan baseres på komplekse, men veldokumenterede sammenhænge mellem kemiske stoffers struktur og deres effekter. Listen er endvidere et godt værktøj, fordi den også giver forslag til klassificering af miljømæssige egenskaber.
Det kan middelbart virke svært at søge i listen, men en god måde er at bruge ”CTRL+F”, hvorved man kan skrive en søgestreng i form af for eksempel CAS-nummeret på et givet stof).
28.2.5 Arbejdstilsynets grænseværdiliste
Listen er offentliggjort som bilag i At-vejledning C.0.1, oktober 2000 (http://www.at.dk/graphics/at/pdf/at-vejledninger/gv-liste-april-2005.pdf). Listen indeholder Arbejdstilsynets administrative normer for luftforureningen i form af grænseværdier (GV) for en række stoffer og materialer, hvor der foreligger dokumentation for, at de er sundhedsfarlige. Grænseværdien udtrykker værdien for stoffets gennemsnitskoncentration i løbet af en ottetimers arbejdsdag, men omfatter herudover også korttidsværdier og loftværdier.
28.2.6 Arbejdstilsynets kræftliste
Listen er offentliggjort som bilag 3.6 i At-vejledning C.0.1, oktober 2000 (http://www.at.dk/graphics/at/pdf/at-vejledninger/gv-liste-april-2005.pdf). Stofferne på listen opfylder de kriterier, som er beskrevet i Arbejdsmiljøinstituttets rapport nr. 7/1981 om kræft og kemiske stoffer, og bygger i øvrigt på lister over stoffer, der er offentliggjort af WHO's kræftforskningsinstitut IARC (International Agency for Research on Cancer) samt vurderinger foretaget af EU.
Stoffer, der anses for at være kræftfremkaldende er desuden markeret med et K i kolonnen "Anmærkninger" i grænseværdilisten.
28.2.7 Arbejdstilsynets liste over organiske opløsningsmidler
Listen er offentliggjort som bilag i At-vejledning C.0.1, oktober 2000 (http://www.at.dk/graphics/at/pdf/at-vejledninger/gv-liste-april-2005.pdf) og indeholder de stoffer, som Arbejdstilsynet anser for at være organiske opløsningsmidler.
Sikkerhedsdatablade for produkter, der indeholder 0,5% eller mere af opløsningsmidler, som optræder på listen, skal forsynes med information om indholdet og navnet på opløsningsmidlerne, hvis de indgår med mere end 1%.
28.2.8 921-listen
Denne liste er bilag 2 til Miljøstyrelsens bekendtgørelse nr. 921 fra 1996 om kvalitetskrav for vandområder og krav til udledning af visse farlige stoffer til vandløb, søer eller havet. Listen repræsenterer således stoffer der må forventes at blive stillet særlige krav til bl.a. i forbindelse med ansøgninger om spildevandstilladelser og miljøgodkendelser.
Det skal bemærkes, at listen i sin form i Kemiguiden kun består af CAS-numre, hvilket vanskeliggør søgning og vurdering. Den originale bekendtgørelse med forudsætninger og kvalitetskrav kan findes på http://www.retsinfo.dk/_GETDOCM_/ACCN/B19960092105-REGL.
28.2.9 OSPAR-listen (List of Substances of Possible Concern)
OSPAR kommissionen arbejder med at beskytte havmiljøet og har i den forbindelse udarbejdet denne liste med stoffer, der giver anledning til bekymring. Indsatsen med at begrænse anvendelsen og dermed udledninger bliver løbende prioriteret, og nye stoffer bliver løbende optaget på listen. Listen, der kan downloades fra http://www.ospar.org/, er således dynamisk og bliver løbende opdateret
28.3 Sikkerhedsdatablade (MSDS)
Alle producenter skal udarbejde sikkerhedsdatablade (engelsk: Material Safety Data Sheets (MSDS)) for deres kemiske stoffer og præparater. Databladene er bygget op omkring en fast skabelon, der blandt andet omfatter sammensætning af produktet, fareidentifikation, førstehjælpsforanstaltninger, brandbekæmpelse, forholdsregler ved udslip og uheld, sundhedsfarlige egenskaber, miljøoplysninger, reaktivitet og nedbrydningsprodukter, m.v.
Sikkerhedsdatabladene, der skal findes på arbejdspladsen, kan dermed være kilde til de mest basale miljø- og sundhedsoplysninger, men kan også give input i form af stofnavne og CAS-numre, der kan bruges i en udvidet informationssøgning. Det er også værd at notere sig, at sikkerhedsdatabladene indeholder oplysninger om mængder, således at man forholdsvis enkelt kan beregne, hvor store udslip der i værste fald kan være tale om.
28.4 International Chemical Safety Cards
International Chemical Safety Cards udarbejdes af WHO, IPCS (International Programme for Chemical Safety) og ILO (International Labour Organisation). Der findes datablade for en lang række kemiske stoffer, der hver især indeholder information om eller vurdering af følgende aspekter:
- Synonymer
- Faretyper (brand og eksplosion)
- Eksponering (inhalation, hudkontakt, øjne, indtagelse)
- Håndtering af spild
- Opbevaring
- Emballering, mærkning og klassificering
- Effekter på mennesker (eksponeringsveje, risiko ved inhalation, effekter af korttids- og langtids/gentagen ekspoering)
- Grænseværdier i arbejdsmiljøet (for flere lande/regioner)
- Fysisk-kemiske data
- Miljømæssige effekter
Databladene, der findes på en række sprog (dog ikke dansk), kan downloades fra adressen www.ilo.org/public/english/protection/ safework/cis/products/icsc/dtasht/index.htm
For at finde det ”rigtige” dokument skal man anvende et af de registrerede synonymer eller stoffets CAS-nummer. Fra det ovennævnte link er det dog også muligt at komme til en alfabetisk oversigt over, hvilke stoffer der findes datablade for.
28.5 IRIS (Integrated Risk Information System)
IRIS er en database med information om, hvilke sundhedseffekter, der kan forekomme som følge af udsættelse for kemiske stoffer i miljøet. IRIS er udviklet (og vedligeholdes) af den amerikanske miljøstyrelse, EPA. Den findes i elektronisk version på http://www.epa.gov/iris/, men kun i en engelsksproget udgave.
Databasen henvender sig til personer uden specielt toksikologisk uddannelse, men kræver dog sundhedsfaglig viden på en række områder. Den kan på denne baggrund ikke anbefales som simpelt opslagværk til alle, men mere som en mulighed for at finde information, der understøtter vurderingen i de mere strømlinede værktøjer som de ovennævnte lister.
IRIS indeholder vurderinger af mere end 500 kemiske stoffer, herunder både udgangsmonomerer for plastproduktion og nogle af de nedbrydningsprodukter, der typisk forekommer ved plastforarbejdning. Nogle af de kemiske stoffer, der indgår i plastadditiver, er også med i IRIS. Den umiddelbare indgang til databasen er via den alfabetiske oversigt over de stoffer, der er med i databasen.
28.6 Vurderinger fra ATSDR (Agency for Toxic Substances and Disease Registry)
ATSDR (Agency for Toxic Substances and Disease Registry) udarbejder på mandat af den amerikanske kongres toksikologiske profiler for kemiske stoffer. Indtil nu er der udarbejdet ca. 275 profiler, der giver et meget detaljeret billede af de kemiske stoffers potentiale for at forårsage uønskede virkninger på mennesker.
Vurderingerne er tilgængelige via internettet (www.atsdr.cdc.gov/toxprofiles/), og det er meget enkelt at finde frem til, om et stof er blevet vurderet af ATSDR. Den umiddelbare indgang til databasen er via den alfabetiske oversigt over de stoffer, der er med i databasen. I relation til miljø- og sundhedsvurderinger af kemiske stoffer, der forekommer i forbindelse med plastforarbejdning, er ATSDR-dokumenternes styrke, at de i en sammenfatning fortæller i et ligefremt sprog (engelsk), hvilke effekter et givet stof kan forårsage, og ved hvilke koncentrationer. Niveauet for denne information skønnes at være relevant i en dialog mellem myndigheder og virksomheder, men databladene kan også bruges som udgangspunkt for information til mennesker, der af en eller anden grund har behov for at vide mere end hvad der for eksempel kan udledes fra diverse stoflister.
28.7 EPA’s Ecotox database
Den amerikanske miljøstyrelse EPA har samlet information om de økotoksikologiske egenskaber ved kemiske stoffer i en database, ECOTOX (http://www.epa.gov/ecotox/). Databasen, der primært er baseret på originale videnskabelige artikler og arbejder, giver oplysninger om giftigheden af stoffer overfor både vand- og jordlevende organismer samt planter.
Indgangsnøglen til databasen er enten et kemisk stofnavn eller et CAS-nummer, og oplysningerne i databasen genererer en rapport, der efterfølgende kan skrives ud. Rapporten indeholder en opsummering af den artikel, der ligger til grund, samt EPA’s ”oversættelse” af de vigtigste fund i form af end-point-værdier, f.eks. for EC50, LC50 og LD50.
EPA understreger, at det er tilrådeligt at konsultere originalarbejdet, for at være sikker på at få placeret et resultat i den rigtige sammenhæng. For et givet stof giver det simple output fra databasen dog en god indikation af stoffets virkning på økosystemer.
28.8 PubChem-databasen
PubChem-databasen indeholder blandt meget andet synonymer, fysisk-kemiske egenskaber og strukturformler, men giver desuden en lang række links til informationskilder om andre egenskaber.
Databasen, der findes på http://pubchem.ncbi.nlm.nih.gov/, er etableret af det amerikanske National Center for Biotechnology Information (NCBI). Den er primært baseret på videnskabelige originalartikler, men giver for nogle stoffer også en kort opsummering fra anerkendte lærebøger.
29 Referencer
Se også:
Indholdsfortegnelse
Oversigtsfigur
Adams K, Bankston J, Barlow A et al. (1999). Development of emissions factors for polypropylene processing. J. Air & Waste Manage. Assoc. 49:49-56
Arbejdstilsynet (2002). At-Vejledning. Stoffer og materialer C.o.1. Grænseværdier for stoffer og materialer.
Bako-Biro Z et al. (2004). Effects of pollution from personal computers on perceived air quality, SBS symptoms and productivity in offices. Indoor Air 14:178-187
Barlow A, Contos DA, Holdren MW et al. (1996). Development of emission factors for polyethylene processing. J. Air & Waste Manage. Assoc. 46:569-580
Barlow A, Moss P, Parker E et al. (1997). Development of emission factors for ethylene-vinylacetate and ethylene-methyl acrylate copolymer processing. J.Air & Waste Manage. Assoc 47:1111-1118.
Boustead I (1999). Eco-profiles of plastics and related intermediates. Published by APME, Brussels, 1999.
Boustead I (2002). Eco-profiles of the European plastics industry. Polyvinyl chloride. A report for APME and ECVM, Brussels, September 2002.
Boustead I (2003). Eco-profiles of the European plastics industry. Polyolefins. A report for APME, Brussels, July 2003.
Clausen PA, Hansen V, Gunnarsen L, Afshari A, Wolkoff P (2004). Emission of di-2-ethylhexyl phthalate from PVC flooring into air and uptake in dust: emission and sorption experiments in FLEC and CLIMPAQ. Environ Sci Tenchnol 38(9): 2531-2537.
Contos DA, Holdren MW, Smith DL et al. (1995). Sampling and analysis of volatile organic compounds evolved during thermal processing of acrylonitrile butadiene styrene composite resins. J. Air & Waste Manage. Assoc. 45: 686-694.
DOR (2000a). Miljøvurdering af EPS-fiskekasse. Plastindustrien i Danmark. Sektionen for EPS-producenter.
DOR (2000b). Miljøvurdering af EPS-isoleringsplade. Plastindustrien i Danmark. Sektionen for EPS-producenter.
Ekvall T, Person L, Ryberg A et al. (1998). Life cycle assessment of packaging systems for beer and soft drinks. Environmental Project No. 399, 1998. Miljøstyrelsen.
Ernes DA, Griffin JP (1996). Process emissions for vinyl pipe industry. Journal of Vinyl and Additive Technology 2(3): 180-183.
Forrest, Jolly, Holding and Richards (1995). Emissions from Processing Thermoplastics. A study of the emissions present in the workplace. Rapra Technology Ltd.
Frostling H, Hoff A, Jacobsson S, Pfäffli P & Zitting A (1982). Termiska sùnderfallsprodukter från plaster. 1 Polyeten och styreninnehållande plaster. SAF Svenska Arbetsgivarefùreningen.
Haberlein RA (1999 a). Technical discussion of the Unified Emissions Factors for open molding of composites. http://www.acmanet.org/ga/ueftext.pdf
Haberlein RA (1999b). Annotated CFA emissions models for the reinforced plastics industries. http://www.acmanet.org/ga/cfamodelreport.pdf
Harrad S et al. (2004). Preliminary assessment of U.K. human dietary and inhalation exposure to polybrominated diphenyl ethers. ES&T 38:2345-2350.
Hilado CJ (1998). Flammability handbook for plastics. Fifth Edition. Technomic Publishing Co. Inc. Lancaster.
IPPC (2005). Integrated Pollution and Prevention Control. Draft refrence documenton Best Available Techniques in the Production of Polymers. Draft April 2005. IPPC, Sevilla.
Jensen AA, Knudsen HN (under udgivelse). Samlet sundhedsmæssig vurdering af kemiske stoffer i indeklimaet fra udvalgte forbrugerprodukter. Kortlægning af kemiske stoffer i forbrugerprodukter Nr. XX, Miljøstyrelsen. (Udkast 21/11-05)
Jensen B, Johansen J, Karbæk K et al. (2005). Plastteknologi. Erhvervsskolernes Forlag. ISBN: 87-7881-550-9.
Jensen B, Schmidt A, Wolkoff P (1989). Plastbase. En database over luftforureninger i plastindustrien og deres sundhedsmæssige virksninger. Arbejdsmiljøfondet.
Kelly TJ et al. (1999). Testing of household products and materials for emission of toluene diisocyanate. Indoor Air 9:117-124.
Kriek G, Lazear N, Rhodes V et al. (2001). Development of emission factors for polyamide processing. J. Air & Waste Manage. Assoc. 51:1001-1008.
Littorin M, Hagmar L, Mikocky Z et al. (2003). Isocyanater – Medicinska risker, biologiske mekanismer samt medicinsk og socia prognos (AFA/AMF/AGSs projekt 474. Slutrapport 2003-03-05. Yrkes- och miljùmedicin, Universitetssjukhuset, Lund, Sverige.
Neviaser J, Gann RG (2004). Evaluation of toxic potency values for smoke from products and materials. Fire Technology 40:177-199.
Nunez CM, Ramsey GH, Bahner MA, Clayton CA (1999). An empirical model to predict styrene from fiber-reinforced plastics fabrication processes. J. Air Waste Manage. Assoc. 49(10): 1168-1178.
Plastindustrien i Danmark (2000). Renere teknologi i plastindustrien. Sprøjtestøbning, ekstrudering, folieblæsning, termoformning og ekspandering af polystyren. Kan downloades fra Plastindustriens hjemmeside (http://www.plastic.dk/billeder/Publikationer/TERMO-juli2000.pdf).
Plastindustrien i Danmark (2000b). Renere teknologi i plastindustrien. Øvrige plastprocesser, råvarebehandling og færdiggørelsesteknikker. Kan downloades fra Plastindustriens hjemmeside (http://www.plastic.dk/billeder/Publikationer/Andet-juli2000.pdf).
Plastindustrien i Danmark (2000C). Renere teknologi i plastindustrien. Del B: Hærdende polyurethanplast. Kan downloades fra Plastindustriens hjemmeside (http://www.plastic.dk/billeder/Publikationer/HÆRDEjuli2000.pdf).
Rønning A, Brekke O, Vold M, et al. (2002). Sikker produksjon og bruk af polyurethanskum – en vurdering av arbeidsmiljø og ytre miljø. Stiftelsen Østfoldsforskning. STØ rapport OR 02.02. (http://www.pif.no/pur/media/hovedrapport_PUR_12-3-2002.pdf)
Rhodes VL, Kriek G, Lazear N et al. (2002). Development of emission factors for polycarbonate processing. J. Air & Waste Manage. Asscc. 52:781-788.
Schleischer O, Jensen AA (2004). Håndbog om vurdering af spredning af dioxin og andre miljøskadelige stoffer fra ukontrollerede brande. Miljøprojekt nr. 918, 2004. Miljøstyrelsen.
Tønning K, Ottosen LM (2005). Genanvendelse af dansk plast-, pap- og papiraffald i udlandet. Miljøprojekt Nr. 959, 2005. Miljøstyrelsen.
Vandpanelet (2004). Afsmitning til drikkevand fra plastrør anvendt til vandforsyningsformål. Identifikation af potentielle stoffer. Rapport udarbejdet for Vandpanelet. September 2004.
Wilford BH et al. (2003). Polyurethane foam as a source of PBDEs to the environment. Organohalogen Compounds 2003;61:219-223.
Wilford BH et al. (2004). Passive sampling survey of polybrominated diphenyl ether flame retardants in indoor and outdoor air in Ottawa, Canada: Implication for source and exposure. ES&T 38:5312-5318.
Uhde E et al. (2001). Phthalic esters in the indoor environment – test chamber studies on PVC-coated wallcoverings. Indoor Air 11:150-155.
| Til Top | | Forside |
Version 1.0 Juli 2006 • © Miljøstyrelsen.
|