| Til bund | | Forside |
Miljøprojekt nr. 1055, 2006
Metoder til behandling af tungmetalholdigt affald - Fase 3
Indholdsfortegnelse
Forord
Sammenfatning og konklusioner
Summary and conclusions
1 Ajourføring af viden om behandlingsmetoder
2 Undersøgelse af teknologier
3 Sammenligning af behandlingsteknologier
4 Forslag til danske strategier
5 Belægningsdannelser i kedler og varmevekslere
6 Referencer
Bilag A Adresseliste for udvalgte virksomheder
Besøgsrapporter
Bilag B Borge Garveri (PyroArc) Termisk
Bilag C H.J. Hansen Miljøsystem Mekanisk
Bilag D Högdalenverket (Birka Energi) Termisk
Bilag E Igelstaverket (Söderenergi) Termisk
Bilag F Organic Power Termisk
Bilag G Procone Termisk
Bilag H R-plus Mekanisk
Bilag I S+S Mekanisk
Bilag J Salyp Mekanisk
Bilag K SSE Mekanisk
Bilag L SVZ, Schwartze Pumpe Mekanisk/termisk
Forord
Denne projektrapport markerer afslutningen på projektet "Metoder til behandling af tungmetalholdigt affald – Fase 3" og for hele projektet. I projektet er siden 1998 undersøgt det internationale teknologiske
stade for behandlingsteknologier til shredderaffald, imprægneret træaffald, læder- og garveriaffald, og galvanoaffald. Resultaterne af undersøgelsen er offentliggjort i rapporterne:
- Metoder til behandling af tungmetalholdigt affald - Fase 1: 1999
- Metoder til behandling af tungmetalholdigt affald - Fase 2A: 2000
Prioriteringsplan for besøg på virksomheder
- Metoder til behandling af tungmetalholdigt affald - Fase 2B: 2001
- Metoder til behandling af tungmetalholdigt affald - Fase 3: 2002
I denne sidste rapport sammenligner vi alle de tilgængelige teknologier, der er besøgt og undersøgt i detaljer i faserne 2b og 3. Vi foreslår desuden en strategi for behandlingen af shredderaffald, imprægneret
træaffald og læder- og garveriaffald i Danmark.
Udover det oprindelige formål, har projektet medvirket til at skabe et netværk mellem de mange danske og udenlandske aktører og potentielle investorer.
Alle projektets faser er udført af fagmedarbejdere hos dk-TEKNIK ENERGI & MILJØ, Teknologisk Institut, JO Consult, AB Torsburgen og H.J. Hansen Miljøsystem A/S, mens Tech-wise A/S og Elsam
A/S alene har deltaget i fase 3.
dk-TEKNIK ENERGI & MILJØ |
Jesper Cramer |
Teknologisk Institut |
Bjørn Malmgren-Hansen |
JO-Consult |
Jørgen Overgaard |
Tech-wise a/s |
Michael Skov Johansen |
Elsam A/S |
Ole Hede Larsen |
AB Torsburgen |
Åke Holmström |
H.J. Hansen Miljøsystem A/S |
Erling Møller Nielsen |
Samarbejdet frem mod denne rapport er blevet koordineret med en styregrupe, der ud over ovennævnte har haft følgende deltagere:
Miljøstyrelsen |
Tonny Christensen |
Arbejdstilsynet |
Annette Christiansen |
Elsam A/S |
Ivan Hundebøl |
Energi E2 A/S |
Erik Winther |
Genvindingsindustrien |
Klaus Müller |
Kommunekemi a/s |
Ole Kristensen |
Kommunernes Landsforening |
Niels Remtoft |
Miljøkontrollen i København |
Finn Rasmussen |
Plastindustrien i Danmark |
Lars Blom |
Renosam |
Henning Jørgensen |
Århus Kommunale Værker, Affaldskontoret |
Henning Ettrup |
Rapportens forfattere ønsker hermed at sige tak til Miljøstyrelsen for projektets finansiering og til styregruppens deltagere for deres medvirken. Vi ønsker også at takke de mange virksomheder verden over,
der har besvaret projektets henvendelser og bidraget med detaljerede informationer om deres anlæg og processer. Endelig retter vi en speciel tak til de virksomheder, som viste deres procesanlæg frem.
Januar 2003
Sammenfatning og konklusioner
Baggrund og formål
Projektet "Metoder til behandling af tungmetalholdigt affald" er igangsat af Miljøstyrelsen med baggrund i debatoplægget "Erhvervsaffald og udvalgte affaldsfraktioner" fra 1997. Debatoplægget fremhæver
udviklingen af alternative behandlingsmetoder som et nødvendigt indsatsområde, der skal gøre det muligt at udnytte affaldets energi- og råstofressourcer.
Målet med projektet er at give aktører i den danske affaldssektor en fuldt opdateret baggrundsviden om internationale erfaringer med behandlingsteknologier til de tungmetalholdige affaldsfraktioner
shredderaffald, CCA-imprægneret affaldstræ og læder- og garveriaffald. Den nye viden vil kunne danne baggrund for den danske strategi på området og dermed valget af de teknologier, der skal indføres
eller udvikles i Danmark.
Identifikation og undersøgelse af relevante teknologier
I projektet har vi identificeret, undersøgt og sammenlignet internationale anlæg eller teknologier, der kan behandle affald med høje koncentrationer af tungmetaller og foreslår strategier for, hvordan især tre
problematiske affaldsfraktioner (shredderaffald (SHR), CCA-imprægneret affaldstræ og læder- og garveriaffald) kan behandles i Danmark. Mulighederne for at behandle andre problematiske
affaldsstrømme med de samme teknologier er også blevet vurderet. Vi har desuden fokuseret på mulige løsninger af problemer med korrosion og belægningsdannelse i anlæg, der udnytter energien i affaldet.
Teknologierne er blevet vurderet ud fra følgende kriterier:
- Effektivitet i forhold til genanvendelse af metaller og andre stoffer
- Økonomi
- Miljøbelastning
- Arbejdsmiljø
- Driftssikkerhed
- Energiudnyttelse / -forbrug
- Mulighed for tilpasning til den danske affaldsstruktur
Projektet er gennemført i følgende faser 1, 2A, 2B og 3.
Fase 1
Opgaverne i projektets første fase, der sluttede i 1999, var:
- Afklaring af størrelsen og genanvendelsespotentialet for de affaldsfraktioner, der kunne komme på tale
- Vurdering af den forventede sammensætning af de relevante affaldsfraktioner
- Indhentning af information om internationale erfaringer med behandling af affaldsfraktioner med høje koncentrationer af tungmetaller.
- Evaluering af disse erfaringer.
- Udvælgelse af de mest lovende teknologier til dyberegående analyse.
Resultaterne af første fase, der er offentliggjort i rapporten: "Metoder til behandling af tungmetalholdigt affald - Fase 1" var, at de videre undersøgelser burde fokuseres på behandling af shredderaffald,
CCA-imprægneret affaldstræ og læder- og garveriaffald. Projektet identificerede og vurderede 11 relevante teknologier, som arbejdede med shredderaffald, mens vi ikke fandt fuldskala-erfaringer med
behandling af CCA-træ eller læder- og garveriaffald.
De mest lovende anlægsleverandører og behandlere til shredderaffald var på dette tidspunkt (1999):
Leverandør/behandler |
Proces |
CT Environment |
Mekanisk neddeling og separation i flere metalfraktioner og en brændbar fraktion, der forbrændes ved høj temperatur. Genanvendelse af
metaller |
EBARA / ABB |
Fluid-bed pyrolyse/forgasning med genanvendelse af metaller |
Mannesmann Demag Umwelttechnik GmbH |
Pyrolyse i roterovn |
NEXUS |
Batch-pyrolyse i kammerovn med separation af jern og ikke-jern-metaller fra koks |
PKA Umwelttechnik Gmbh & Co. KG |
Pyrolyse i roterovn, mekanisk/magnetisk separation af jern og ikke-jern-metaller, samt forglasning af mineraler |
Seiler |
Forgasning i roterovn, mekanisk/magnetisk separation af jern og ikke-jern-metaller, samt forglasning af mineraler |
Sekundärrohstoff Verwertungszentrum Schwartze Pumpe
GmbH |
Mekanisk/magnetisk separation af jern og ikke-jern-metaller, samt forgasning af organisk rest sammen med brunkul |
Takuma |
Pyrolyse i roterovn og mekanisk/magnetisk separation af jern og ikke-jern-metaller, samt forglasning af mineraler (Siemens KWU licens) |
Thermoselect |
Komprimering og højtemperaturpyrolyse/forgasning. Producerer syntesegas, mineralsk slagge og kobberholdig metallegering |
Von Roll |
Pyrolyse på rist med efterfølgende udvinding af jern-kobberlegering i smelteproces og zink-bly-koncentrat ved ekstraktion |
Tre processer blev identificeret som måske egnede til at behandle CCA-træ, idet ingen af disse tre processer genvinder eller stabiliserer tungmetaller, men udnytter kun energien.
Leverandør / behandler |
Proces |
Lurgi / Geertruidenberg |
Fluid-bed forgasningsanlæg |
Procone Gmbh / Espenhain |
Variant af medstrømsforgasser med produktion af kraft/varme via gasmotor |
British Lurgi / SVZ - Schwartze Pumpe GmbH
|
Forgasning af imprægneret træ sammen med brunkul i tryksat forgasser |
Fase 2A
Projektets næste fase (2A), som sluttede i år 2000, havde til formål at:
- kontakte alle virksomheder prioriteret under fase 1 med henblik på at:
- fastslå deres udviklingsmæssige status
- opdatere tekniske og økonomiske oplysninger fra fase 1
- indhente detaljerede oplysninger om nye processer
- beskrive og vurdere disse nye processer
- afklare muligheden for at overvære drift/forsøg med relevant affald i længere tid
- afklare behovet for korte besøg på relevante anlæg
- at udvælge de fem mest relevante virksomheder til et længerevarende besøg
- at udvælge 1-2 virksomheder til korte besøg
Resultatet af fase 2A var en prioriteringsplan med arbejdsplan og budget for besøg på disse processer/virksomheder (L: langt besøg, K: kort besøg):
Procesleverandør / behandler |
Erfaringer med |
L |
K |
Chartherm |
CCA-imprægneret affaldstræ |
|
X |
CT Environment |
SHR |
X |
|
EBARA / ABB |
SHR, plastaffald, MSW, RDF, slam, industriaffald |
X |
|
H.J. Hansen Miljøsystem A/S |
SHR |
|
X |
Lurgi Envirotherm GmbH |
Affaldstræ, celluloseaffald |
X |
|
Nexus |
SHR, læder, plastaffald, MSW, dæk |
|
X |
PKA Umwelttechnik GmbH & Co |
SHR, plastaffald, MSW, slam |
|
X |
Result Technologies |
Elektronik skrot / SHR |
|
X |
Salyp |
SHR |
|
X |
Takuma |
SHR |
X |
|
Von Roll AG |
MSW |
X |
|
Der er i hele projektets forløb sket en meget hurtig udvikling af teknologier, der kan behandle affald med højt indhold af tungmetaller. Der udvikles stadig nye metoder, mens andre har skiftet ejere, har
stoppet udviklingen eller er gået konkurs. Vi har derfor igennem alle projektets faser løbende holdt kontakt til udviklingsvirksomhederne og omprioriteret vores indsats mod de mest væsentlige teknologier.
Flere af de relevante anlæg/processer var desværre kun i drift med affald med andre men dog sammenlignelige typer affald.
Fase 2B
I fase 2B, der sluttede i 2001, gennemførte vi efter en løbende prioritering længere besøg hos:
Procesleverandør / behandler |
Affald |
CT Environment |
Shredderaffald og røggasrensningsprodukt fra MSW |
EBARA/Alstom Power |
Shredderaffald og slam |
von Roll AG |
Shredderaffald |
og korte besøg hos:
Procesleverandør / behandler |
Affald |
Mitsui |
Industri- og husholdningsaffald |
PKA |
Industriaffald med meget aluminium |
Takuma |
Shredderaffald |
Kawasaki Steel (Thermoselect) |
Industri- og husholdningsaffald |
Alle de besøgte anlæg er valgt med fokus på termisk behandling af shredderaffald. De syv relevante teknologier er nøje beskrevet i form af besøgsrapporter i: "Metoder til behandling af tungmetalholdigt
affald - Fase 2B". Rapporten indeholder desuden en beskrivelse af teknologien udviklet hos Citron AG og EPR-processen, som vi dog vurderer ikke er relevante til behandling af nogen af de tre
affaldsfraktioner.
Fase 3
Projektets fase 3, som beskrives i denne rapport, er en direkte forlængelse af fase 2B og indeholder en detaljeret undersøgelse af 11 teknologier. De studerede teknologier var dels de processer, som det
ikke var muligt at bearbejde i af økonomiske årsager i fase 2B - specielt mekaniske sorteringsprocesser til shredderaffald - og dels ny interessante processer til læder- og garveriaffald og CCA-imprægneret
affaldstræ.
Fase 3 indeholdt følgende delopgaver:
- Ajourføring af viden om behandlingsmetoder.
- Undersøgelse af teknologier.
- Sammenligning af behandlingsteknologier.
- Forslag til danske strategier.
- Mulige løsninger på problemer med korrosion og belægningsdannelse på hedeflader.
Under ajourføringen af viden fandt vi flere nye mekaniske separationsteknologier som R-plus, S+S og SSE samt tidligere kendte processer, som var kommet til et udviklingsniveau, der krævede en detaljeret
undersøgelse, fx Pyroarc-processen, Salyp og Procone.
I fase 3 har vi prioriteret, besøgt og vurderet følgende teknologier:
Procesleverandør / behandler |
Procestype |
Affald |
/ H.J.Hansen Miljøsystem A/S |
Neddeling og mekanisk separation |
Shredderaffald |
Foster Wheeler / Högdalenverket |
CFB forbrænding |
Affaldstræ, tørv, plastaffald, papir, pap |
Foster Wheeler / Igelstaverket |
FB forbrænding |
Affaldstræ, tørv, plastaffald, papir, pap |
Organic Power ASA |
Tværstrøms-/medstrøms-forgasning |
Sorteret industriaffald |
Procone |
Speciel medstrømsforgasser |
Rent affaldstræ |
PyroArc / Borge Garveri AS |
Skaktovnsforgasser med plasma-krakning af tjære |
Læder- og garveriaffald |
/ R-plus |
Mekanisk neddeling og sortering |
Shredderaffald |
S+S |
Maskiner til mekanisk separation |
Shredderaffald, metaller |
Salyp |
Mekanisk separation |
Shredderaffald |
British Lurgi / SVZ - Schwartze Pumpe |
Mekanisk separation og forgasning |
Industriaffald, MSW, SHR, jernbanesveller, mv. |
SSE |
Maskiner til mekanisk separation |
Shredderaffald, metaller, mineraler |
De 11 teknologier er nøje beskrevet i form af besøgsrapporter i bilag B-L.
Konklusioner
Ved dette projekts start i 1998 blev vi præsenteret for en hel række teknologier og virksomheder, der tilsyneladende var egnede til behandling af de prioriterede affaldsfraktioner. Nu ved projektets
afslutning næsten 5 år senere, må vi i 2003 konstatere, at der nu kun består en lille håndfuld af tilsyneladende levedygtige teknologier og virksomheder, der kan være interessante for danske investorer og
affaldsbehandlere.
Investering i en eller flere af disse teknologier må dog fortsat betragtes som risikofyldt, og den foreslåede danske strategi må derfor betragtes mere som en udviklingsstrategi end som en færdig og klarlagt vej
til behandling af de aktuelle danske affaldsfraktioner.
Sammenligning af behandlingsteknologier
Behandling af shredderaffald
Alle de undersøgte processer til shredderaffald udskiller frie metaller af affaldet og udnytter energien. Flere processer producerer udelukkende stabile produkter, der enten kan sælges, benyttes som vejfyld
eller byggematerialer eller deponeres på almindelige lossepladser.
De samlede behandlingsomkostninger varierer fra ca. 470 til 1.091 DKK/t SHR for et anlæg med en kapacitet på 50.000 t SHR/år.
Procesteknologierne til shredderaffald deler sig i to grupper:
- Mekanisk sortering efterfulgt af termisk proces (pyrolyse, forgasning, forbrænding, etc.)
- Termisk proces uden forbehandling
Mekanisk sortering efterfulgt af termisk proces
Mekanisk sortering
Metoderne hos H. J Hansen og R-plus opnår stort set de samme resultater. Begge processer fungerer så godt og fjerner så mange metaller fra shredderaffaldet, at dette er egnet til termisk behandling.
Suppleres metoderne med plastseparation (som fx Salyp) eller en simpel vægtfyldeseparering, vil der af den grove fraktion i begge processer kunne genvindes plast.
Udviklingen inden for mekanisk sortering er i rivende udvikling både hvad angår sensorsystemer og sorteringsmekanismer (Salyp, SSE, S+S, LLA, m.fl.)
Efterfølgende termiske processer
CT-Environment og von Roll har i større pilotforsøg vist, at deres teknologier kan behandle sorteret shredderaffald.
CT-Environment har i fuld skala vist, at deres smeltecyklon kan behandle shredderaffald samtidig med røggasrensningsprodukt fra affaldsforbrændingsanlæg. Processen fremstiller en metalsmelte og en
glasagtigt mineralsk slagge, hvis sammensætning sandsynligvis vil medføre, at slaggen kan overholde de danske krav i slaggekategori II. CT-Environment har ikke eftervist, at de selv behersker teknologi til
forbehandling. Schweiz har medio 2002 valgt CT-Environments teknologi til oparbejdning shredderaffald. Moderselskabet til CT-Environment, Babcock Borsig Power er i skrivende stund under
konkursbehandling. CT-Environment er netop blevet rekonstrueret med en ny ejerstab.
Von Roll behersker teknologier til termisk behandling af shredderaffald (bl.a. riste-pyrolyse). Von Rolls slaggebehandlingsovn giver en helt speciel mulighed for at kontrollere slaggesammensætningen, en
interessant mulighed som ikke er set praktiseret af andre. Von Roll tilbyder både ristepyrolyseprocessen og deres smelteteknologi på kommercielle vilkår til behandling af shredderaffald.
Sammenligning CT-Environment og Von Roll:
- von Rolls proces kræver etablering af en ekstra mekanisk forsorteringsproces, hvis den skal kunne udvinde metaller af høj kvalitet.
- von Rolls smelteteknologi vil kunne reducere oxider af kobber og jern til de frie metaller. Oxider af jern og kobber vil i CT-Environments teknologi indgå i slaggen.
- von Rolls behandlingspris anslår vi til 1.091 DKK/t SHR ved 45.000 t/år, mens CT-Environments pris er lavere, ca. 470 DKK/t SHR ved 100.000 t/år, idet CT's anlæg samtidigt behandler en
tilsvarende mængde røggasrensningsprodukt fra affaldsforbrændingsanlæg.
- Begge teknologier har i andre sammenhænge vist sig driftsikre, men langtidsdriftserfaringer med shredderaffald findes ikke.
- Begge teknologier vil kapacitetsmæssigt kunne tilpasses den danske affaldsstruktur og vil kunne behandle andre affaldstyper samtidigt, hvilket CT-Environment har demonstreret.
SVZ's, KSK's og PyroArcs skaktovnsprocesser og Kawasakis kombination af pyrolyse i en kanal og en skaktovn kan med visse begrænsninger behandle shredderaffald. Skaktovnsprocesserne kræver alle,
at shredderaffaldet tilføres som briketter, der er stabile over 1000 °C. SVZ og PyroArc mener at have løst dette problem, men egentlige driftserfaringer findes ikke. Kawasakis proces kræver supplerende
tilførsel af kul. Pyrolysekanalen og indfødningssystemet har problemer med shredderaffald.
Termisk processer uden forbehandling af shredderaffald
Ebara og Takuma er de to eneste dokumenterede velfungerende termiske og mekaniske processer, der behandler shredderaffald. Ebara og Takuma har 3 og 4 års driftserfaringer fra hvert sit kommercielle
anlæg og kan tilbyde anlæg internationalt med garantier.
Sammenligning Ebara og Takuma:
- Begge processer udvinder jern, kobber og aluminium i blandinger af affaldet og fremstiller et mineralsk granulat, som sandsynligvis vil kunne overholde de danske krav i slaggekategori II. Størsteparten
af Zn og Pb ender i røgrensningsproduktet, som deponeres.
- Behandlingsomkostningerne forventes for begge processer at ligge i størrelsesordnen 880 DKK/t SHR.
- Begge teknologier kan uden problemer tilpasses de danske krav til arbejdsmiljø og miljøpåvirkninger.
- Takuma har været i drift i ca. 4 år og har behandlet ca. 100.000 tons shredderaffald. EBARA har været i drift i snart 3 år og har behandlet over 120.000 tons shredderaffald.
- Ebaras og Takumas processer har samme energiudnyttelse af affaldet.
- Begge teknologier vil kunne tilpasses den danske affaldsstruktur. Kapacitetsmæssigt vil dette ikke give problemer, ligesom begge processer vil kunne behandle andre affaldstyper som
røggasrensningsprodukter samtidigt.
PKA har udviklet en proces, hvis energi-output er en brændbar gas. PKA har ikke fuldskalaerfaringer med shredderaffald, men har gennemført forsøg på et pilotanlæg. PKA er pt. under konkursbehandling.
Mitsuis proces er næsten identisk med Takumas, men Mitsui har koncentreret sig om husholdingsaffald.
Behandling af CCA-imprægneret affaldstræ
Der findes kun én kommerciel proces til behandling af imprægneret affaldstræ - et finsk genbrugssystem til imprægnerede stolper, sveller, mm., men det har ikke været muligt at få nogen form for detaljeret
information om de anvendte teknologier. Processen består af en patenteret forbrændingsproces efterfulgt af en kemisk oparbejdning af asken til nyt imprægneringsmiddel. Selve oparbejdningsprocessen kan
ikke umiddelbart overføres til Danmark, da CCA-imprægnering ikke er tilladt, og da typen af den termiske proces er ukendt.
Flere processer er under udvikling:
- Kommunekemi A/S har gennemført pilotforsøg med modtrømsforgasning og kemisk oparbejdning af asken og arbejder også med en proces baseret på lavtemperaturpyrolyse.
- Watech A/S arbejder med separationsprocesser, der kan fjerne tungmetaller i aske fra CCA-imprægneret træ, PVC, shredderaffald, mm.
- Udviklingsarbejde med PyroArc-processen indikerer, at denne og lignende skaktovnsprocesser sandsynligvis vil kunne behandle CCA-imprægneret affaldstræ sammen med jernholdigt materiale fx
oparbejdet shredderaffald. Processen vil da producere et hårdt bundet arsen-restprodukt og en slagge, som sandsynligvis vil kunne afsættes.
Behandling af læder- og garveriaffald
På Borges Garveri i Norge findes det eneste kommercielle anlæg, der behandler læder- og garveriaffald. Anlægget er baseret på Enviroarcs skaktovnsforgasser (Pyroarc) og producerer en
jern-krom-legering og smeltet slagge til genanvendelse. Anlægget har været i drift i ca. 1 år. Enviroarc har med succes af prøvet processen i pilotskala med shredderaffald og imprægneret affaldstræ.
Danske strategier
Strategi for behandling af shredderaffald
Vi forventer, at der i den nærmeste fremtid skal behandles ca. 100.000 t SHR/år i Danmark. Sammensætningen af affaldet vil stort set være som i 1996, men med en lidt lavere brændværdi (12 MJ/kg).
Procesteknologierne til shredderaffald deler sig i to grupper:
- Mekanisk sortering efterfulgt af termisk proces (pyrolyse, forgasning, forbrænding, etc.).
- Termisk proces uden forbehandling.
Der eksisterer i dag teknologier, som kan genvinde energien og nyttiggøre shredderaffaldet i en sådan grad, at EU-direktivet om udrangerede køretøjer kan opfyldes såvel i 2006 som i 2015.
De umiddelbart tilgængelige teknologier fra gruppe 2 er: EBARA og Takuma, der må betegnes som første generationsprocesser. Til gruppe 1 hører sandsynligvis CT-Environment i kombination med
mekaniske sorteringsprocesser som hos R-plus eller H. J. Hansen. CT-Environment endnu ikke er nået til første generation.
Ved fastlæggelsen af strategien for den fremtidige behandling af shredderaffald bør indgå overvejelser om:
- Medsmeltning af andet problematisk affald (fx røggasrensningsprodukt)
- Nye muligheder for udsortering med ny sensor- og computerteknologi
- Reduceret brændværdi pga. udsortering af plast
- Medforbrænding af trykimprægneret træ for at opnå tilstrækkelig brændværdi til smeltning af slaggen
- Behandling sammen med trykimprægneret træ i en kombineret proces hvor træet tilsættes i smelteprocessen for at opnå tilstrækkelig brændværdi til smeltning af slaggen (fx skaktforgassere som
Pyroarc)
Før der vælges teknologi, råder vi derfor til, at der gennemføres studier af:
- De økonomiske og miljømæssige muligheder for yderligere udsortering af plast.
- Relevansen af genvinding af tungmetaller enten i den mekaniske forsortering eller i en efterfølgende termisk proces.
- Andre muligheder for energiudnyttelse end kraft/varme-produktion.
- Mulighederne for opgradering af slaggen fra den termiske proces til højværdigt konstruktionsmateriale eller råmateriale.
- Miljømæssige og økonomiske aspekter ved medforbrænding af husholdnings- og industriaffald.
Strategi for behandling af CCA-imprægneret affaldstræ
Hovedindsatsen i behandlingen af CCA-imprægneret affaldstræ bør koncentreres om løsningen af problemerne med det meget giftige As, der skal stabiliseres, så det på den billigste måde kan deponeres
uden risiko for miljøet. En mulighed er at behandle affaldstræet sammen med en mindre mængde shredderaffald, som er oprenset for frie metaller eller læder- og garveriaffald med jern fra slam
behandlingsprocesser i en proces, der binder As i stabile jern- eller kobberforbindelser.
Brændværdien i affaldstræet skal udnyttes effektivt for at sikre en så stor CO2-fortrængning som muligt.
Genvindingen af Cu og Cr fra CCA-imprægneret affaldstræ må vurderes nøje i forhold til de behandlingsomkostninger, som er forbundet med oparbejdningen. I det omfang Cu og Cr ikke genvindes, bør de
under alle omstændigheder stabiliseres, så aske, slagge og andre restprodukter kan deponeres uden risiko for miljøet.
Detaljerne omkring det finske genbrugssystem, som producerer nyt imprægneringsmiddel, er ukendte. På grund af den manglende information om processen kan vi derfor ikke anbefale at overføre dette
system til Danmark.
Ved fastlæggelsen af strategien for den fremtidige behandling af imprægneret affaldstræ bør indgå overvejelser en kombineret proces, hvor shredderaffald eller garveriaffald behandles samtidigt med
trykimprægneret træ (fx muligvis Pyroarc).
Strategi for behandling af læder- og garveriaffald
Enviroarcs proces, som den er demonstreret hos Borge Garveri, vil kunne overføres til Danmark. Det danske potentiale for denne type affald er kun ca. 4.700 t affald/år, hvilket forventes at medføre
forholdsvis høje behandlingsomkostninger på 1.500-2.000 DKK/t affald. Tilføres andet affald vil behandlingsprisen kunne reduceres væsentligt.
I valget af strategi bør også indgå overvejelser om at behandle læderaffald sammen med aske fra neddelt imprægneret træ, som forgasses, forbrændes i fluid bed anlæg eller behandles i andre anlæg uden
smelteenhed. Krom og kobber vil sandsynligvis kunne udvindes af asken i en smelteovnsproces.
Belægningsdannelse og korrosion
Shredderaffaldets høje indhold af Cl, alkali og tungmetaller i forhold til normalt husholdnings- og industriaffald betyder, at der er en kraftigt forøget risiko for korrosions- og belægningsproblemer i kedler til
kraftvarmeproduktion.
Der er kun meget få driftserfaringer under de rette betingelser i de nødvendige 1-2 år, hvilket betyder, at disse problemer endnu ikke kan kvantificeres.
I rapporten angiver vi en række muligheder for at løse de meget sandsynlige problemer med nedbrydning af ildfaste foringer, korrosion af fordamperhedeflader under ildfaste foringer og efter afslutning af
ildfaste foringer samt korrosion af fordampere.
Vi vurderer, at korrosionsbeskyttelse af især fordamperhedeflader med Inconel oversvejsninger vil give en reduktion af vedligeholdelsesomkostninger og forbedret rådighed, som langt overstiger de ekstra
anlægsomkostninger.
Afslutning
Ved afslutningen af projektet må vi konstatere, at der stadig er et stykke vej endnu før de idriftværende anlæg kan betegnes som velafprøvede og robuste teknologier.
Ebara og Takuma kan betegnes som 1. generations anlæg, medens CT-Environment må betegnes som et 0. generations anlæg.
Dette betyder, at der kan forventes ukendte problemer ved længere tids drift, men til gengæld også, at der er uafprøvede muligheder for optimering af anlæggene, deres produkter og deres drift, hvilket på
sigt sandsynligvis vil medføre væsentlig lavere omkostninger pr. behandlet ton affald.
Der er stadig behov for at følge erfaringerne i de få anlæg, der kører kommercielt og de anlæg, der er under planlægning eller konstruktion. Flere interessante teknologier er på vej hos Enviroarc,
Kommunekemi, Watech, mfl.
Der er behov for at opstille krav til idealanlæg(gene), der skal behandle de prioriterede affaldsfraktioner.
Det bør overvejes, hvor danske virksomheder og udviklingsmiljøer kan være med i udviklingen/afprøvningen af nye teknologier.
Mange af processerne vil med få eller ingen tilpasninger vil kunne overføres til behandling af MSW.
Summary and conclusions
Background and objectives
The project ”Methods for Treatment of Waste Containing Heavy Metals” was started on the initiative of the Danish Environmental Protection Agency on the basis of the discussion paper “Industrial waste
and selected waste fractions” from 1997. The discussion paper points out the development in alternative methods for treating wastes as a necessary contribution that makes it possible to recover resources in
the form of energy and raw material.
The objective of the project is to give players in the Danish waste sector fully updated knowledge about international experience in technologies for treating shredder waste, impregnated waste wood, and
tannery and leather waste. This new knowledge will be used to form the background for a new Danish strategy for waste handling and the choice of technology to be introduced in or to be developed for
Denmark.
Identification and investigation of relevant technologies
The project has identified, investigated and compared international plants and technologies for treating wastes with high content of heavy metals. Based on these studies, the project proposes strategies for
treating and handling especially shredder waste, waste wood and tannery and leather waste in Denmark. An evaluation of the different technologies and their possibilities to treat other problematic waste
streams has also been made. Finally, focus has been on possible solutions for avoiding corrosion and deposits in plants for energy production.
The technologies have been evaluated on the basis of following criteria:
- The effectiveness of the technology to recover and reuse metals and other materials.
- Economy.
- Environmental impact.
- Working environment.
- Dependability.
- Energy yield.
- Possibilities to fit in the technology in the Danish waste structures.
The project includes the phases: 1, 2A, 2B and 3.
Phase 1
Phase 1 was finished in 1999, and the tasks in this part were:
- Estimation of the amount of the selected wastes, and estimation of the potential for reuse of metals and materials from the selected wastes.
- Estimation of expected present and future composition of relevant waste fractions.
- Gathering of information about international experience in treating waste fractions with high content of heavy metals.
- Evaluation of such experience.
- Selection of the most promising technologies for further investigation.
The results of the work in phase 1 are published in the report ”Methods for Treatment of Waste Containing Heavy Metals - Phase 1”. The main conclusions in this report were that further investigation should
focus on treatment of shredder waste, impregnated waste wood, and tannery and leather waste. During the project period, 11 relevant technologies for treating shredder waste were identified, while no
full-scale experiences for treating impregnated waste wood or tannery and leather waste were identified.
The most promising plant suppliers or plant operators for treating shredder waste (at that time, 1999) were:
Plant supplier / operator |
Process |
CT Environment |
Mechanical down-sizing and separation into fractions containing metals and a fraction containing a combustible fraction. This fraction is burned at high
temperature. Recycling of metals. |
EBARA / ABB |
Fluid-bed pyrolysis / gasification and recycling of metals. |
Mannesmann Demag Umwelttechnik GmbH |
Pyrolysis in rotary kiln. |
NEXUS |
Batch-pyrolysis in a furnace with separation of iron and non-iron metals from the coke. |
PKA Umwelttechnik Gmbh & Co. KG |
Pyrolysis in a rotary kiln, mechanical/magnetic separation of iron and non-iron metals and melting of minerals into a glassy slag. |
Seiler |
Pyrolysis in a rotary kiln, mechanical/magnetic separation of iron and non-iron metals and melting of minerals into a glassy slag. |
Sekundärrohstoff Verwertungszentrum Schwartze
Pumpe GmbH |
Mechanical/magnetic separation of iron and non-iron metals and gasification of organic fraction mixed with brown coal. |
Takuma |
Pyrolysis in a rotary kiln, mechanical/magnetic separation of iron and non-iron metals and melting of minerals into a glassy slag. (Siemens KWU
licence) |
Thermoselect |
Compression and high temperature gasification. Production of gas, glassy slag and an iron-cupper alloy. |
Von Roll |
Pyrolysis on a grid and melting. Production of a glassy slag and an iron-cupper alloy. |
Only three technologies were identified as being possibly qualified for treating impregnated waste wood. The reason why these technologies are only possibly qualified is that none of them recycle the metals
in the waste or stabilise the metals. Only the energy content is utilised.
Plant supplier / operator |
Process |
Lurgi / Geertruidenberg |
Fluid-bed gasifier |
Procone Gmbh / Espenhain |
Variation of gasifier combined with production of power and heat via gas engine. |
British Lurgi / SVZ - Schwartze Pumpe GmbH |
Gasification of impregnated wood mixed with brown coal in a pressurized gasifier. |
Phase 2A
The objectives of phase 2A of this project were:
- Contact to all companies with priority from phase 1, in order to:
=> determine the status for the development,
=> update technical and economic information from phase 1,
=> collect detailed information on new processes,
=> describe and evaluate these new processes,
=> make agreements for participating in trials at relevant plants,
=> make agreements for visiting relevant plants
- Select the five most interesting plants for a long visit, and
- Select one or two relevant plants for short visits.
The result of phase 2A was an action plan and a budget for visiting the following plants / companies: (L: long visit. S: short visit)
Plant supplier / operator |
Experiences concerning |
L |
S |
Chartherm |
CCA-impregnated waste wood |
|
X |
CT Environment |
Shredder waste, SHR |
X |
|
EBARA / ABB |
SHR, plastic waste, MSW, RDF, sludge, industrial waste |
X |
|
H.J. Hansen Miljøsystem A/S |
SHR |
|
X |
Lurgi Envirotherm GmbH |
Waste wood, cellulose waste |
X |
|
Nexus |
SHR, leader, plastic waste, MSW |
|
X |
PKA Umwelttechnik GmbH & Co |
SHR, plastic waste, MSW, sludge |
|
X |
Result Technologies |
Electronic scrap / SHR |
|
X |
Salyp |
SHR |
|
X |
Takuma |
SHR |
X |
|
Von Roll AG |
MSW |
X |
|
During the entire project period, a very rapid development of technologies for treating heavy-metal contaminated waste has occurred. New technologies have been developed, other technologies have been
taken over by new owners, and some have stopped further development or have gone bankrupt. In all the phases of the project, close contact has been established with all the interesting players, and
priorities have been currently changed, depending on the development within the most relevant technologies. However, some of the relevant technologies were in operation with other but still comparable
types of waste.
Phase 2B
Phase 2B was finished in 2001, and the long visits, which were reprioritised several times in this phase were:
Plant supplier / operator |
Waste |
CT Environment |
SHR and filter dust from incineration of MSW |
EBARA/Alstom Power |
SHR and sludge |
von Roll AG |
SHR |
And shor visits were paid to:
Plant supplier / operator |
Waste |
Mitsui |
Industrial waste and MSW |
PKA |
Industrial waste with high content of aluminium |
Takuma |
SHR |
Kawasaki Steel (Thermoselect) |
Industrial waste and MSW |
All the visits were planned with a view to focusing on thermal treatment of shredder waste. The visits relating to the seven relevant technologies are reported in the report: ”Methods for Treatment of Waste
Containing Heavy Metals – Phase 2B”. In addition, this report contains descriptions of technologies developed by Citron AG and EPR. It is concluded that these two technologies are not qualified for
treating shredder waste, impregnated waste wood, or tannery or leather waste.
Phase 3
Phase 3 of the project is described in the present report, which is a direct follow-up of the report for phase 2B. The present report contains descriptions of detailed studies of 11 technologies: partly
technologies that, for economic reasons, could not be investigated in phase 2B – especially mechanical separation technologies for shredder waste – and partly new interesting technologies for treating
impregnated waste wood and leather and tannery waste.
Phase 3 includes the following tasks:
- Update of know-how on technologies.
- Investigation of technologies.
- Comparison of the investigated technologies.
- Proposals for a Danish strategy.
- Investigations of possible solutions to avoid corrosion and deposits in boilers.
During task 1 in phase 3, several new mechanical separation technologies were found, for example R-plus, S+S, and SSE. In addition, some previously known technologies have developed further, to a level
that now makes them interesting for more detailed study. These are, for example, the Pyroarc process, Procone and Salyp.
In phase 3, the following priority and visits were made:
Plant supplier / Operator |
Type of Process |
Waste |
/ H.J.Hansen Miljøsystem A/S |
Mechanical down sizing and separation |
Shredder waste |
Foster Wheeler / Högdalenverket |
CFB combustion |
Waste wood, peat, plastic waste, paper, cardboard |
Foster Wheeler / Igelstaverket |
FB combustion |
Waste wood, peat, plastic waste, paper, cardboard |
Organic Power ASA |
“Cross-flow”-/co-current gasifier |
Upgraded industrial waste |
Procone |
Special co-current gasifier |
Clean waste wood |
PyroArc / Borge Garveri AS |
Shaft gasifier with plasma cracking of tar |
Leather and tannery waste |
/ R-plus |
Mechanical down sizing and separation |
Shredder waste |
S+S |
Machines for mechanical down sizing and separation |
Shredder waste, metals |
Salyp |
Mechanical separation |
Shredder waste |
British Lurgi / SVZ - Schwartze Pumpe |
Mechanical separation and gasification |
Industrial waste, MSW, SHR, sleepers, etc. |
SSE |
Machines for mechanical separation |
Shredder waste, metals, minerals |
The 11 technologies are described in more detail in the reports from visits shown in annexes B-L.
Conclusions
At the beginning of this project in 1998, a large number of technologies and companies were presented, which apparently were able to treat the prioritised fractions of waste. Now, at the end of this
investigation, almost five years later in 2003, it must be concluded that only a small handful of apparently surviving technologies and companies is interesting for Danish investors and operators of waste
treatment plants.
Investments in one or more of these technologies will still have to be regarded as risky, and the proposed Danish strategy should be regarded more as an strategy of development than as a complete and
clearly described way of treatment of the relevant Danish waste fractions.
Comparison of technologies for waste treatment
Treatment of shredder waste
All the processes investigated for shredder waste produce free metals of the waste and utilise the energy. A number of processes produce entirely stable products that can be sold, be used as road
construction or building materials - or be disposed of at an ordinary landfill.
The treatment costs vary from about DKK 470 to 1,091/t SHR for a plant with a capacity of 50,000 t SHR/year.
The process technologies for shredder waste falls in two groups:
- Mechanical separation succeeded by a thermal process (pyrolysis, gasification, combustion, etc.)
- Thermal process without pre-treatment
Mechanical separation succeeded by a thermal processMechanical separation
The methods used at H.J. Hansen and R-plus reach the same results. Both processes function well and separate so many metals from the shredder waste that the residue is suitable for thermal treatment.
If the methods are complemented with separation of plastic (i.e. Salyp) or a simple separation based on density, plastics could be produced from the coarse fraction.
The development of mechanical separation processes is very fast - both as regards sensor systems and sorting mechanisms (Salyp, SSE, S+S, LLA, etc.).
Succeeding thermal processes
CT-Environment and von Roll have, in large-scale pilot tests, shown that their technologies can process pre-treated shredder waste.
CT-Environment has shown, in full scale tests, that their melting cyclone can treat shredder waste and flue gas cleaning product from MSW incineration simultaneously. The process produces a metallic melt
and glassy mineral slag, with a composition that can possibly meet the Danish limit values for slag category II. CT-Environment has not demonstrated that they themselves master the technology of mechanical
pre-treatment. In the middle of 2002, the Swiss authorities chose the technology of CT-Environment for treatment of shredder waste. The parent company of CT-Environment, Babcock Borsig Power, is at
the moment under liquidation. Recently, CT-Environment was reconstructed with new owners.
Von Roll masters technologies for processing of shredder waste (including grate-pyrolysis). Von Rolls slag processing oven allows control of the composition of the slag - an interesting option that is not
offered by others. Von Roll offers both the grate-pyrolysis process and their melting technology at commercial conditions for processing of shredder waste.
Comparison of CT-Environment and Von Roll:
- The process of von Roll requires an extra mechanical pre-separation process, if metals of high quality have to be produced.
- The melting technology of von Rolls is able to reduce oxides of cupper and iron to free metals. In the CT-Environment process, oxides of iron and cupper end up in the slag.
- It is estimated that the treatment costs of a von Rolls plant is DKK 1,091/t SHR at 45,000 t/year, while CT-Environments costs are lower, approximately DKK 470/t SHR at 100,000 t/year, because
CT's plant simultaneously processes an equivalent amount of flue gas cleaning product from MSW incineration.
- Both technologies are working reliably when processing other materials, but long-term experience with shredder waste has not been found.
- The plant capacity of both technologies can be tailored to the structure of the Danish waste management system. Both technologies will also be able to process other waste fractions simultaneously, as
demonstrated by CT-Environment.
The SVZ, KSK and PyroArc shaft furnace process and the Kawasaki combination of pyrolysis in a duct and a shaft gasifier, can with certain constraints, process shredder waste. All shaft furnace processes
require that the shredder waste is feed as briquettes that are stable at temperatures above 1,000 °C. SVZ and PyroArc claim that they have solved this problem, but actual experience has not been found.
The process of Kawasaki requires additional supply of coal. The pyrolysis duct and the feeding system of the Kawasaki process have problems with shredder waste.
Thermal processes without pre-treatment of shredder waste
Ebara and Takuma are the only two documented well-functioning thermal and mechanical processes that are able to treat shredder waste. Both Ebara and Takuma have three and four years of production
experience from one commercial plant, and offer the plants with guarantees all over the world.
Comparison of Ebara and Takuma:
- Both processes produce iron, copper and aluminium in mixtures from the waste, and both processes produce a mineral granulate that can probably meet the Danish limit values for slag category II.
Most of the Zn and Pb end up in the flue gas-cleaning product, which has to be disposed of.
- The treatment costs of both processes are expected to be in the order of DKK 880/t SHR.
- Both technologies can, without any problems, meet the Danish requirements laid down for the working environment and for emissions.
- The Takuma plant has been in operation for four years and has processed approx. 100,000 tons shredder waste. The EBARA plant has been in operation for nearly three years and has treated more
than 120,000 tonnes shredder waste.
- The processes of Ebaras and Takumas have the same energy efficiency.
- Both technologies can be adapted to the structure of the Danish waste management system. The desired plant capacity is not at problem, and both processes will be able to process other types of
waste, like flue gas cleaning products, simultaneously.
PKA has developed a process, where the energy output is a combustible gas. PKA has no full-scale experience with shredder waste, but has performed pilot plant tests. The liquidation proceedings of PKA
are ongoing.
The process of Mitsui is almost identical to Takumas, but Mitsui has concentrated on the processing of MSW.
Processing of CCA-impregnated waste wood
Only one commercial process for treatment of CCA-impregnated waste wood was found: a Finish recycling system for impregnated poles, sleepers, etc. However, it has not been possible to get any kind of
detailed information about the technologies. The process consists of a patented combustion process succeeded by chemical processing of the ashes into a new impregnation liquid. The process cannot be
immediately transferred to Denmark, and the type of chemical process is unknown.
A number of processes are developed:
- Kommunekemi A/S has performed pilot plant tests with counter-current gasification succeeded by a chemical processing of the ash, and is also developing a process based on low temperature
pyrolysis.
- Watech A/S is working with separation processes that can extract the heavy metals in the ash from CCA-impregnated waste wood, PVC, shredder waste, etc.
- The development of the PyroArc process indicates that this and similar shaft gasifiers will probably be able to process CCA-impregnated waste wood together with iron-containing materials, like
pre-treated shredder waste. The process will then produce a strongly bound arsenic residue and a slag, which could probably be sold.
Treatment of leather- and tannery waste
Borge tannery, Norway, operates the only commercial plant treating leather-and tannery waste. The process is based on the shaft gasifier (Pyroarc) from the company Enviroarc, and the product is an
iron-chromium alloy and a melted slag for recycling. The plant has been in operation for approximately one year. Enviroarc has successfully tested the process in pilot scale with shredder waste and
impregnated waste wood.
Danish strategies
Strategy for treatment of shredder waste
It is expected that approximately 100,000 t SHR/year will have to be treated in Denmark in the near future. The composition of the waste will roughly be as in 1996, but with a slightly lower heating value
(12 MJ/kg).
The process technologies for shredder waste can be divided into two groups:
- Mechanical sorting followed by a thermal process (pyrolysis, gasification, combustion, etc.).
- Thermal process without pre-treatment.
Today's technologies recover energy and materials from shredder waste in amounts that are sufficient to meet the demands laid down in the EU Directive concerning end-of-life vehicles, in 2006 as well as
2015.
The now available technologies from group 2 are: EBARA and Takuma which are first-generation processes. A possible solution from group 1 is CT-Environment in combination with mechanical sorting
processes like R-plus or H.J. Hansen. However, the CT-Environment process is not yet established as a first-generation plant in operation.
In the preparation of a strategy for treatment of shredder waste in the future, the following subjects should be considered:
- Treatment of shredder waste in melting processes together with other problematic wastes (for instance residues from flue gas cleaning)
- New possibilities for sorting plastics, metals with new sensor and computer technologies
- Reduced heat value caused by recovery of plastics
- Treatment in a combined process with impregnated wood where the wood is added in the melting process in order to obtain sufficient heat value to melt the slag. (For instance in shaft gasifiers similar
to Pyroarc).
Before a technology is chosen, studies should be made of:
- The economic and environmental possibilities for further sorting and recovery of plastics.
- The relevance of recovering heavy metals either in mechanical pre-sorting or in the following thermal process.
- Alternative possibilities for other energy recovery than production of heat/power.
- Possibilities for upgrading the slag from the thermal process to construction material or raw material of higher value.
- Economic and environmental aspects of co-treatment with municipal solid waste and industrial waste.
Strategy for treatment of CCA-impregnated waste wood
The main effort in treatment of CCA- impregnated waste wood should be concentrated on solving problems with the toxic arsenic. Arsenic should be stabilized in the cheapest way where it can still be
deposited without risk for the surrounding environment. One possibility is to treat the waste wood together with a smaller amount of shredder waste where free metals has been removed, or leather and -
tannery waste with iron content from sludge treatment in a process which binds Arsenic in stable iron/copper compounds.
The heat value of the waste wood must be efficiently utilised to ensure the highest possible CO2-displacement.
The recovery of Copper and Chromium from CCA-impregnated waste wood must be prioritised in relation to the treatment costs associated with the recovery. To the extent that Copper and Chromium are
not recycled, they should in all circumstances be stabilized in such a way that slag and other residues do not present an environmental hazard.
The details concerning the Finnish recycling system, producing new substances for impregnation of wood, are not known. Due to the lack of information on the process, transfer of the system to Denmark
cannot be recommended.
In the preparation of a strategy for treatment of impregnated waste wood in the future, a combined process should be considered, in which impregnated waste wood is treated with shredder waste where
free metals have been removed or with tannery waste (for instance in a shaft gasifier such as Pyroarc).
Strategy for treatment of leather- and tannery waste
The process of Enviroarc, as demonstrated at Borge Tannery, can be utilised in Denmark. The Danish potential for this type of waste is only approximately 4,700 t waste/year, which is expected to lead to
rather high treatment costs approx. DKK 1,500-2,000/t waste. If other waste is added, the treatment costs can be reduced.
In the choice of strategy another possibility for treatment of leather waste should be considered in which the waste is treated together with downsized impregnated wood waste in gasification plants, fluid bed
combustion plants or other plants without melting units - followed by recovery of chromium and copper from the residues.
Formation of Scaling and corrosion
The large content of chlorine, alkali and heavy metals in shredder waste in comparison with the content in normal municipal solid waste and industrial waste, presents a drastically increased risk of corrosion -
or scaling problems in boilers for production of heat and power.
Only scarce experience of operation exists under the right conditions and in the one or two years required. Therefore, the above-mentioned problems cannot be quantified yet.
The report presents a number of possibilities for solving the most likely problems with break-down of fireproof lining, corrosion of evaporator heating surfaces either under the fireproof lining or in areas
without fireproof lining and corrosion of evaporator tubes.
It is assessed that corrosion protection of especially evaporator heating surfaces can be obtained by welding on to the surfaces a layer of Inconel steel, which reduces the costs of maintenance and increases
the service intervals, with savings that by far exceed the extra costs for the protective layers.
Final conclusion
At the closing of the project further operational experience with the plants in operation is still required before they can be considered as thoroughly tested and sturdy technologies.
The Ebara and Takuma processes may be characterized as first-generation plants, while the CT-environment process must be characterized as a 0. generation plant.
This means that unknown problems can be expected after longer periods of operation, but also a large potential for optimisation. Better plant design, operation and product qualities will probably lead to
significantly lower treatment costs pr. treated tonne of waste.
There is still a need for following the experience of the commercial plants and the plants under planning or construction. Several interesting technologies are being developed at Enviroarc, Kommunekemi,
Watech and other companies.
There is a need to draw up requirements for ideal plants, which are to treat the prioritised waste fractions.
It should be considered where Danish companies and development environments could participate in the development and test of new technologies
Many of the processes will, with few or no adaptations, be able to treat normal municipal solid waste and industrial waste.
1 Ajourføring af viden om behandlingsmetoder
Dette kapitel indeholder en opsummering af status for alle relevante teknologier, som vi har undersøgt i fase 2b og 3.
Den teknologiske udvikling inden for processer, der behandler tungmetalholdigt affald, sker i øjeblikket meget hurtigt. For at sikre at alle relevante teknologier blev undersøgt, har vi i begyndelsen af projektet
afsøgt danske og internationale databaser, videncentre, nyhedsbreve, etc. inden for affaldssektoren for nyheder. Status for alle de teknologier, som blev undersøgt i fase 2b, har vi desuden ajourført. Status
pr. 2002-02-20 var udgangspunktet for prioriteringen og udvælgelse af de virksomheder, som skulle besøges og beskrives i detaljer. Helt frem til projektets allersidste tid er nye teknologier kommet frem og
andre stoppet, hvilket har medført en løbende evaluering og prioritering af alle teknologier.
Status pr. 2002-11-01 for de mange teknologier er vist i tabel 1.
Tabel 1. Status pr. 2002-11-01 for alle undersøgte teknologier. Besøgte anlæg vist med fed.
Procesnavn |
Procestype |
Affald |
Status og kort konklusion |
Chartherm |
Lavtemperaturpyrolyse |
Imprægneret træaffald |
Pilotanlæg bygget. Forsøgsresultater ikke offentliggjort. Chartherm er gået konkurs. Kommunekemi
har bygget et forsøgsanlæg, der skal prøve at gentage Chartherms proces, der skulle give en aske,
hvorfra metaller og As skulle kunne udskilles mekanisk. Se Kommunekemi. |
Citron |
Termisk, kemisk |
Tungmetalholdigt affald |
Velegnet til affald som batterier, hydroxidslam, etc. For dyr til shredderaffald. Processen er
beskrevet nøjere i rapporten fra fase 2b. |
CT Environment |
Mekanisk neddeling, sortering og
smeltecyklon |
shredderaffald og
røggasrensningsprodukt |
Velegnet til shredderaffald og røggasrensningsprodukt. Fuldskalaforsøg gennemført dog
uden mekanisk oparbejdning. CT Environment er rekonstrueret med en ny ejerkreds efter
Babcock Borsig-koncernens konkurs. CT-Env. har ordre på det første anlæg i Schweiz til
behandling af shredderaffald. |
EBARA |
FB pyrolyse / forgasning |
Shredderaffald |
Kommercielt anlæg i Japan idriftsat 2000. Modificering af kedel og introduktion af et nyt
højeffektivt rensesystem er påbegyndt i 2001. Siden februar 2002 har det ikke været
nødvendigt at rense den kedel, der er færdigombygget manuelt. Det ser derfor ud til, at de
væsentligste problemer er løst i et anlæg, der nu kan betegnes som et 2. generations
anlæg. Indtil november 2002 er behandlet 145.000 t shredder affald og 25.000 t slam med
sammenlagt 17.000 driftstimer . Det meste af tiden er driften sket på en linie, mens den
anden er blevet modificeret. Fra december 2002 skulle begge linier være i drift efter
ombygning til det nye kedeldesign.
EBARA kan give kommercielle garantier. Meget relevant for det danske affaldssystem. |
Energos |
Forbrænding |
Delfraktion af SHR |
I et forsøg med shredderaffald fra STENA har man forbrændt de ca. 40 % af shredderaffaldet med
stykstørrelse over 10 mm. Har haft mange af de forventede problemer med processen, og har siden
overvejet, hvad man skal gøre med den metalrige slagge.
Bedømmes til ikke at være relevant til behandling af SHR. |
EPR |
Mekanisk neddeling og separering af
metaller, etc. |
Elektronikskrottet |
Ikke relevant. Processen er beskrevet nøjere i rapporten fra fase 2b. |
Finsk recycle system |
Termisk + kemisk oparbejdning |
Imprægneret træ, stolper |
Patenteret termisk proces og kemisk oparbejdning af metaller i aske til ny imprægneringsmiddel.
Ikke muligt at fremskaffe nogen yderligere information om processerne. Kemisk proces ikke relevant
efter danske forhold, da CCA-imprægnering er forbudt i DK. Systemet kan ikke vurderes pga.
manglende information. |
FLS miljø A/S |
Ristepyrolyse |
Dæk |
Velfungerende proces demonstreret i fuld skala. Ikke velegnet til shredderaffald, impr. træaffald eller
læderaffald. |
Foster Wheeler |
FB/CFB forbrænding |
Affaldstræ, tørv,
plastaffald, papir, pap |
Velfungerende fluid bed forbrændingsanlæg i bl.a. Sverige. Velegnet og relativ billig proces
til udnyttelse af energien i imprægneret affaldstræ. Da processen ikke stabiliserer
restprodukterne eller udskillelse af metaller mm. fra aske kan processen ikke anbefales
uden efterfølgende oparbejdningsprocesser. |
H.J. Hansen Miljøsystem
A/S |
Neddeling og mekanisk separation |
Shredderaffald |
Velfungerende mekanisk anlæg med traditionelle processer i kombination med den nyeste
separationsteknologi. Kan håndtere H.J.Hansens shredderaffald. Termisk proces til
restfraktion under overvejelse. Meget relevant. |
Kommunekemi A/S |
Lavtemperaturpyrolyse |
Imprægneret affaldstræ |
Pilotanlæg opbygget. Forsøg ultimo 2002. Relevant proces med mulighed for let udskillelse af Cu, Cr
og As. |
Kommunekemi A/S |
Modstrømsforgasning |
Imprægneret affaldstræ |
Pilotforsøg gennemført med succes. Lab.skalaforsøg med kemisk oparbejdning af aske succesfulde.
Fuldskalanlæg planlagt. Relevant proces. |
KSK |
Skaktovnsforgasser |
Shredderaffald |
Kan vise sig at være en relevant proces for behandling af mekanisk sorteret shredderaffald. Har dog
indtil videre ingen erfaring med højere indsats af shredderaffald end ca. 15% pga. problemer med
brikettering af shredderaffaldet. Andre lignende skaktovnsprocesser er blevet besøgt (se
Pyroarc/Borge og SVZ). |
LLA Instruments GmbH |
Plastseparation (NIR) |
Plastkomponenter biler |
Anlæg findes I Zwickau, Tyskland (LLA samarbejde med DaimlerChrysler, Ford, BMW) til
separation af manuelt adskilt plast fra biler. Plasten neddeles til 30 mm, PUR-skum og partikler
fjernes med vindsigtning. Plast separeres i plasttyper efter polymertype med NIR identifikation og
separation med luftdyser. Relevant ved fjernelse af større plastdele fra biler. |
Lurgi Envirotherm GmbH |
CFB-forgasning |
Affaldstræ, creosotimpr. træ |
Fuldskalanlæg i Holland med store driftsproblemer med en gaskøler, der er for lille og ikke kan
håndtere tjære og støv. Det er besluttet at re-designe store dele af gasrensningssystemet. Ikke
afprøvet med CCA-imp. Ikke velegnet i det nye design. |
Mannesmann Demag |
- |
- |
Mannesmann Demag er i 1999 opsplittet i to selskaber: Mannesmann Demag Kraus-Marffei AG og
SMS Demag AG. Ingen af disse selskaber beskæftiger sig med bortskaffelse / nyttiggørelse af affald. |
Mitsui, Yame Seibu Clean
Centre |
Siemens KWU proces.
Pyrolyse i roterovn. |
MSW |
Det besøgte anlæg behandlede kun MSW, men Mitsui har i pilotanlæg kørt forsøg med
shredderaffald, og det vurderes at være sandsynligt, at Mitsui vil tilbyde anlæg til
shredderaffald. |
MVF |
Skaktovnsforgasser |
Shredderaffald |
MVF er gået konkurs. Procesudvikling stoppet. Ikke relevant. |
NEXUS |
Pyrolyseproces i kammer |
Shredderaffald |
Nexus er gået konkurs. Procesudvikling stoppet. Ikke relevant. |
NOMI (DK) |
Mekanisk sortering |
Industriaffald |
Benytter kun magnetisk separation af jern-metaller og massefyldeseparation til separation af
ikke-jern metaller (rystebord). Ikke designet til shredderaffald, men de indgående
separationsteknologier (massefyldeseparation) er relevante til behandling af shredderaffald (se
R-plus). |
Organic Power ASA |
Tværstrøms / medstrøms-forgasning |
Sorteret industriaffald |
Meget billig termisk proces. Processen er ikke velegnet til tungmetalholdigt affald pga.
ujævne procesbetingelser.
Organic Power er erklæret konkurs. Ikke relevant. |
PKA |
Pyrolyse i roterovn |
Industriaffald og Al-affald |
Muligvis relevant til shredderaffald. Det er sandsynligt, at processen kræver et
energitilskud i form af kul eller koks for at have energi nok til at smelte shredderaffaldets
mineralske del.
PKA er under konkursbehandling. |
Procone |
Speciel medstrømsforgasser |
Rent affaldstræ |
Industrielt anlæg i drift. Vurderes til at kunne behandle imprægneret affaldstræ - er dog
ikke afprøvet. Ikke erfaringer med metaludvinding. Fuldskalaanlæg i Siebelehn
oversvømmet og elektronik ødelagt. Der arbejdes på retablering. Mindre pilotanlæg haves
og anlæg til forgasning af slam er under test i pilotskala |
PyroArc |
Skaktovnsforgasser med
plasma-krakning af tjære |
Læder- og garveriaffald |
Industrielt anlæg hos Borge Garveri er under indkøring. Producerer Cr-legering og
mineralsk fraktion. Anlægget har kapacitet som hele den tilsvarende danske affaldsstrøm.
Meget relevant til dansk læder- og garveriaffald og imprægneret affaldstræ. Drift med
gasmotor indkoblet forløber tilfredsstillende senest ved en uges test i uge 44/2002.
Endvidere er gennemført pilotforsøg med imprægneret affaldstræ og shredderaffald. |
Result Technologies |
Mekanisk neddeling og sortering |
Elektronikskrot |
Velfungerende proces til elektronikskrot. For dyr til shredderaffald. |
R-plus |
Mekanisk neddelings og sortering |
shredderaffald |
Videreudvikling af LSD/ARGE AltAuto proces. Benytter traditionelle metoder (forskellige
fra de nye teknikker, som markedsføres af S+S el. SSE). Velfungerende proces. Driftsklar
- men stoppet pga. lave deponiomkostninger. Meget relevant for Danmark. |
S+S |
Maskine til mekanisk separation |
Shredderaffald, metaller |
Velfungerende fleksible maskiner til mekanisk separation af metaller. Har leveret mere
end 140 metalseparationsanlæg til meget forskellige affaldsstrømme. Meget relevante til
udsortering af metaller fra shredderaffald. |
Salyp |
Mekanisk separation |
Shredderaffald |
Demonstrationsanlæg med plastseparation. Delprocesser til genvinding af skumplast og
termoplast. Restfraktionen efter udsortering af plast er problematisk og vanskelig at
nyttiggøre. |
Schwartze Pumpe SVZ |
Mekanisk separation og
smelteforgasning |
Industriaffald, MSW.
SHR, jernbanesveller mv. |
Fuldskalaanlæg, der sorterer industriaffald, plast og MSW til fremstilling af
brændselspiller til SVZ's forgasserer. Fremstilling af brændselspiller af SHR er
problematisk. SVZ's nye smelteforgasser en mulig proces til behandling af sorteret,
briketteret shredderaffald. Indtil videre kun erfaring med tilførsel af op til 15%
shredderaffald af den indfyrede affaldsmængde. |
Seiler
Hochtemperatur-Trennanlagen
AG |
Mekanisk separation og Smelteproces |
Shredderaffald |
Procesudvikling stoppet pga. konkurs. |
SSE |
Maskine til mekanisk separation |
Shredderaffald, metaller,
mineraler |
Velfungerende fleksible maskiner til mekanisk separation. Afprøvet og idriftsat i fuldskala
hos på shredderaffald. Meget relevante til udsortering af alle typer frie metaller, mineraler
etc. fra shredderaffald. |
STENA |
Mekanisk s separation med
efterfølgende eddy current |
Shredderaffald |
Målsætningen har været at opdele shredderaffaldet i to fraktioner: 1) Et brændsel med meget lavt
indhold af mineraler og metaller og høj brændværdi. 2) En deponerbar fraktion med forholdsvis lavt
metalindhold.
Så vidt vi er orienterede har STENA nu ændret målsætning og påtænker, at udvikle en termisk
proces, der gør den smeltede slagge genanvendelig. |
Takuma |
Siemens KWU proces. Pyrolyse i roterovn. |
Shredderaffald |
Fuldskalanlæg i drift i Japan siden april 1998. Anlægget var allerede i 2000 i drift 6700
timer ud af de planlagte 7300 årlige driftstimer. Takumas teknologi er yderst relevant til
behandling af dansk shredderaffald. Det har ikke været muligt at få oplysninger om
driftsforhold som korrosion mm. |
Thermoselect S.A. /
Kawasaki Steel |
Komprimering og
højtemperaturpyrolyse / forgasning |
Industriaffald |
Anlæg i Japan har været i kommerciel drift siden 2000. Shredderaffald har været forsøgt
behandlet, men kræver ekstra indsats af kul for at have tilstrækkelig energi til smeltning
af shredderaffaldets mineralske del. |
TPS |
- |
- |
TPS har ingen teknologi til behandling af shredderaffald eller affaldstræ. |
Von Roll AG |
Pyrolyse på rist + smelteproces |
Shredderaffald |
Fuldskalaforsøg gennemført med succes. von Roll har ikke leveret kommercielle anlæg.
Von Roll teknologien i sin nuværende udformning er en kompliceret teknologi, som kræver
videre udvikling, inden den kan anbefales til danske forhold. Von Roll har dog vist, at de
behersker de(n) nødvendige teknologi(er) til oparbejdning af sorteret shredderaffald.
Processerne tilbydes kommercielt. |
2 Undersøgelse af teknologier
Afsnit 2.1 omtaler kort de 11 besøgte anlæg, mens de udførlige rapporter fra besøgene på fuldskalaanlæg er i appendiks B til L.
Processerne er blevet vurderet på deres:
- Effektivitet i forhold til genanvendelse af metaller og andre stoffer
- Økonomi
- Miljøbelastning
- Arbejdsmiljø
- Driftssikkerhed
- Energiudnyttelse / -forbrug
- Mulighed for tilpasning til den danske affaldsstruktur
2.1 fuldskala-anlæg besøgt i fase 3
2.1.1 Shredderaffald
- H.J. Hansen Miljøsystem
- Organic Power
- R-plus
- S+S - Search and Separate
- Salyp
- SVZ - Schwartze Pumpe
- SSE - Separation Systems Engineering Gmbh
2.1.2 Imprægneret affaldstræ (CCA, CCP, CKB, etc.)
- Högdalenverket (Birka Energi)
- Igelstaverket (Söderenergi)
- Organic Power ASA
- Procone
- SVZ - Schwartze Pumpe
2.1.3 Læder- og garveriaffald
2.2 Oversigt over alle besøgte anlæg (fase 2b + 3)
I tabel 2 er en alfabetisk ordnet liste med alle de anlæg, som projektets deltagere har besøgt i fase 2b og 3. Flere af de virksomheder, der er nævnt i tabel 1, er blevet besøgt i forbindelse med andre
projekter fx Kommunekemi, NOMI, Result Technology.
Tabel 2. Oversigt over alle anlæg som er besøgt i projektet.
Procesnavn |
Procestype |
Affald |
Besøgt i fase |
CT Environment |
Mekanisk neddeling, sortering og smeltecyklon |
shredderaffald og røggasrensningsprodukt |
2b |
EBARA |
FB pyrolyse / forgasning |
Shredderaffald |
2b |
H.J. Hansen Miljøsystem A/S |
Neddeling og mekanisk separation |
Shredderaffald |
3 |
Högdalenverket
(Foster Wheeler) |
CFB forbrænding |
Affaldstræ, tørv, plastaffald, papir, pap |
3 |
Igelstaverket
(Foster Wheeler) |
FB forbrænding |
Affaldstræ, tørv, plastaffald, papir, pap |
3 |
Mitsui, Yame Seibu Clean Centre |
Siemens KWU proces. Pyrolyse i roterovn. |
MSW |
2b |
Organic Power ASA |
Tværstrøms/medstrøms-forgasning |
Sorteret industriaffald |
3 |
PKA |
Pyrolyse i roterovn |
Industriaffald og Al-affald |
2b |
Procone |
Speciel medstrømsforgasser |
Rent affaldstræ |
3 |
PyroArc |
Skaktovnsforgasser med plasma-krakning af tjære |
Læder- og garveriaffald |
3 |
R-plus |
Mekanisk neddeling og sortering |
Shredderaffald |
3 |
S+S |
Maskine til mekanisk separation |
Shredderaffald, metaller |
3 |
Salyp |
Mekanisk separation |
Shredderaffald |
3 |
Schwartze Pumpe |
Mekanisk separation og
forgasning |
Industriaffald, MSW. SHR, jernbanesveller mv. |
3 |
SSE |
Maskine til mekanisk separation |
Shredderaffald, metaller, mineraler |
3 |
Takuma |
Siemens KWU proces.
Pyrolyse i roterovn. |
Shredderaffald |
2b |
Thermoselect S.A. / Kawasaki Steel |
Komprimering og højtemperaturpyrolyse/forgasning |
Industriaffald |
2b |
Von Roll AG |
Pyrolyse på rist + smelteproces |
Shredderaffald |
2b |
3 Sammenligning af behandlingsteknologier
I afsnit 2 omtales kort de anlæg, som projektet har besøgt i denne fase 3 af projektet, mens udførlige rapporter fra besøgene på 11 fuldskalaanlæg findes i appendiks B - L.
I de følgende afsnit vil de bedste teknologier blive vurderet og sammenlignet i forhold til disse kriterier:
- Effektivitet i forhold til genanvendelse af metaller og andre stoffer
- Økonomi
- Miljøbelastning
- Arbejdsmiljø
- Driftssikkerhed
- Energiudnyttelse / -forbrug
- Mulighed for tilpasning til den danske affaldsstruktur
Da stort set alle de kendte processer er udviklet med henblik på at behandle shredderaffald, vil hovedvægten i bedømmelsen tage udgangspunkt i denne affaldstype og deres muligheder for at behandle andre
affaldstyper.
Processer til behandling af imprægneret affaldstræ og læder- og garveriaffald sammenlignes sidst i afsnittene 3.2 og 3.3.
3.1 Behandlingsteknologier egnede til shredderaffald
Tabel 3 viser de bedste teknologier til behandling af shredderaffald og deres udviklingsstade. Processerne er karakteriseret ud fra deres krav til forbehandling, procestemperatur og mulighed for
slaggeraffinering.
Tabel 3. Teknologier til behandling af shredderaffald og deres udviklingsstade
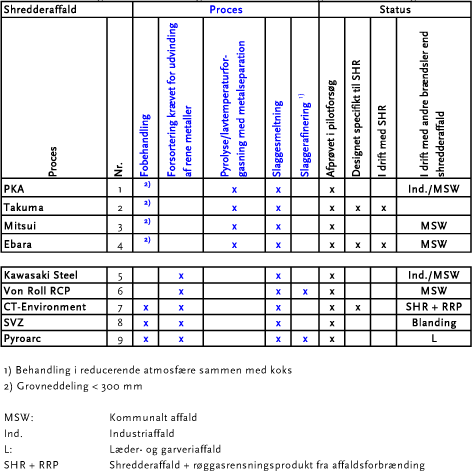
Tabel 4 angiver, hvilke produkter og restprodukter processerne er i stand til at producere. De enkelte processer vurderes også på deres evne til at producere kraftvarme og dioxindannelse.
Tabel 4. Produkter og restprodukter fra processer til behandling af shredderaffald
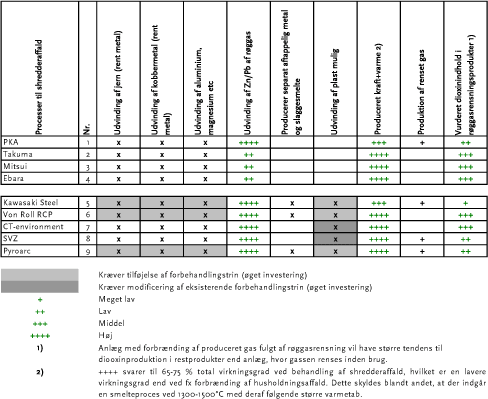
Behandlingsteknologierne, der er egnede for behandling af shredderaffald kan opdeles i følgende kategorier:
- Behandlingsmetoder, der er kombinationer af en indledende mekanisk sortering og en efterfølgende termisk behandling. Se afsnit 3.1.1.1 og 3.1.1.2.
- Behandlingsmetoder, der er egnede til behandling af shredderaffald uden forbehandling. Se afsnit 3.1.2.
Der vil i det følgende blive lavet en sammenligning mellem de tilgængelige teknologier inden for disse kategorier. For en mere detaljeret beskrivelse af de omtalte processer henvises til logbøgerne.
3.1.1 Mekanisk sortering og efterfølgende termisk behandling
3.1.1.1 Mekanisk sortering

Metoderne, som praktiseres hos H. J Hansen og hos R+, opnår stort set de samme resultater. Suppleres metoderne med plastseparation (fx Salyp) eller en simpel vægtfyldeseparering for genvinding af plast,
vil der af den grove fraktion i begge processer kunne genvindes plast.
Begge mekaniske sorteringsprocesser er økonomisk fordelagtige, de har begge høj driftsikkerhed, danske miljøkrav og krav til arbejdsmiljø vil kunne indfris uden problemer, og teknologierne lader sig
indpasse i den danske affaldsstruktur.
Begge processer er i stand til med et moderat energiforbrug at genvinde næsten alle ubundne metaller af shredderaffaldet, men de oxiderede metaller genvindes ikke ad denne vej.
Kombinationen med Salyp eller en anden simplere proces, der kan genvinde plast (ikke beskrevet i denne undersøgelse) kan være økonomisk fordelagtig i den udstrækning, der kan findes aftagere af den
genvundne plast.
Konklusionen af denne sammenligning er, at der findes processer til mekanisk sortering, der fungerer så godt og fjerner så mange metaller fra shredderaffaldet, at dette er egnet til termisk behandling i en af
de nævnte processer i afsnit 3.1.1.2.
De nævnte teknologier er kommercielt tilgængelige.
Der forgår en meget hurtig udvikling inden for mekanisk sortering baseret på identifikation af metal eller plastemner med sensor-systemer og sorteringsmekanismer med luftdyser (fx ved SSE, S+S, LLA
instruments og en række andre virksomheder). Der udvikles løbende udstyr, som kan separere stadig mindre partikler og således konkurrere med traditionelle separationsmetoder som fx
massefyldeseparation.
3.1.1.2 Efterfølgende termiske processer

CT-Environment har i et større pilotforsøg vist, at den anbefalede teknologi er en mulighed for termisk behandling af shredderaffald med samtidig nyttiggørelse af røggasrensningsprodukt fra
affaldsforbrændingsanlæg. Teknologien er medio 2002 valgt af Schweiz, som den teknologi man her vil bruge til oparbejdning shredderaffald. CT-Environment tilbyder såvel forbehandling af shredderaffaldet
som den termiske behandling. CT-Environment har dog ikke været i stand til over for os at demonstrere, at de behersker en teknologi til forbehandling af shredderaffaldet med genvinding af metallerne. Det
vil derfor være fornuftigt at kombinere den termiske del af processen med en mekanisk sortering, som den praktiseres hos H. J. Hansen eller måske R+. Den valgte teknologi til sortering skal dog suppleres
med en ekstra neddelingsproces, idet den termiske proces kræver findelt materiale med en partikelstørrelse helst ikke over 4 mm.
Den termiske proces, smeltecyklonen, er en robust og driftsikker smeltereaktor, der er i kommerciel drift til en lang række forskellige materialer. Bl.a. har den været anvendt til oparbejdning af zink fra støv
fra røggasrensning i elektrostålværker.
Det første kommercielle anlæg til behandling af shredderaffald forventes sat i drift i Schweiz i 2005.
Moderselskabet til CT-Environment, Babcock Borsig Power er i skrivende stund under konkursbehandling. CT-Environment er netop blevet rekonstrueret med en ny ejerstab.
Von Roll har i et længere forsøg i et demonstrationsanlæg i Bremerhaven oprindeligt bygget til behandling af husholdningsaffald vist, at de behersker teknologier til termisk behandling af shredderaffald. Von
Roll teknologiens slaggebehandlingsovn giver en helt speciel mulighed for at kontrollere og styre slaggesammensætningen, en mulighed som ikke er set praktiseret af andre, og som er en interessant option.
Det besøgte anlæg var oprindeligt bygget til behandling af husholdningsaffald, og da von Roll senere har indset, at konceptet er for dyrt til behandling af husholdningsaffald, er anlægget senere ombygget.
Von Rolls tilbyder både ristepyrolyseprocessen og deres smelteteknologi på kommercielle vilkår til behandling af shredderaffald.
Sammenligning CT-Environment og Von Roll:
- Effektivitet i forhold til genanvendelse af metaller og andre stoffer.
Genanvendelsen af metaller er først og fremmest afhængig af den mekaniske sortering, men da Von Roll teknologien i kraft af ovnen til slaggebehandling kan køres som en stærk reducerende proces,
vil også oxider af kobber og jern udfældes i en metalfase, som kan genvindes. Disse oxider vil i CT-Environment teknologien indgå i slaggen.
- Økonomi
Se herom senere (afsnit 3.1.3).
- Miljøbelastning
Begge teknologier kan uden problemer tilpasses de danske krav til arbejdsmiljø og miljø.
- Driftssikkerhed
Smeltecyklonen i CT-Environments teknologi er i andre sammenhænge en i driftssikker enhed. Von Roll teknologien i den undersøgte form er kompliceret, og vi formoder derfor ret sårbar. Der er dog
ingen grund til at tro, at selve pyrolyseenheden og smelteovnen skulle være mere sårbare end andre tilsvarende anlæg.
- Energiudnyttelse/forbrug
I princippet er teknologierne sammenlignelige, men da CT-Environment baserer sin teknologi på at smelte andre affaldstyper uden brændværdi, vil energiproduktionen være lavere, idet en del af
energien bruges hertil.
- Mulighed for tilpasning til den danske affaldsstruktur
Begge teknologier vil kapacitetsmæssigt kunne tilpasses den danske affaldsstruktur og vil kunne behandle andre affaldstyper samtidigt, hvilket CT-Environment har demonstreret. Von Roll har
praktiseret oparbejdning af husholdningsaffald gennem længere tid på anlægget.
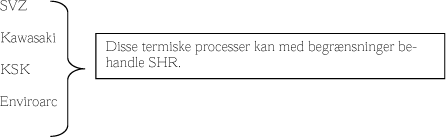
De nævnte teknologier er alle baseret på skaktovnsprocesser. Dog er Kawasaki en kombination af pyrolyse i en kanal og skaktovnsprincippet. Processerne udmærker sig ved at kunne køres stærkt
reducerende og dermed omsætte metaloxiderne i shredderaffaldet til en metalfase, hvilket vil medføre et mindre metalindhold i slaggen i forhold til mindre reducerende processer.
Processerne udmærker sig alle desuden ved, at det termiske output er en brændbar gas, der kan anvendes til drift af forbrændingsmotorer eller som procesgas i industrien.
Begrænsningerne i behandling af shredderaffald ligger for SVZ, KSK og Enviroarcs vedkommende i, at skaktovne kræver tilførsel af briketter, der er stabile ved temperaturer over 1000 °C. Shredderaffald
er svært at brikettere, hvorfor tilførslen af dette affald er begrænset til ca. 15% af den indfyrede affaldsmængde. Dog har SVZ med ekstruderet shredderaffald forsøgt sig med større andel af shredderaffald,
men ekstruderingen er dyr. SVZ oplyser, at deres omkostninger til ekstrudering er 600 DKK/t. Enviroarc hævder dog at være i stand til at indføde 100% shredderaffald i briketteret form og åbenbart til
væsentlig lavere omkostninger. (Jvf. de økonomiske sammenligninger 3.1.3).
Kawasaki har kørt forsøg med shredderaffald. Dette krævede tilførsel af supplerende kul. Desuden gav pyrolysekanalen og indfødningssystemet visse problemer.
3.1.2 Behandlingsmetoder til af shredderaffald uden forbehandling
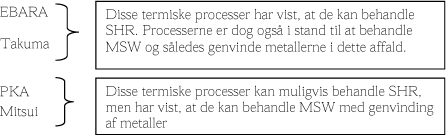
De fire er nævnte processer er alle opbygget med en pyrolyse- eller forgasningsdel, et system til metalseparation og en smelteovn.
Takuma og Mitsui er i princippet den samme proces, idet idegrundlaget for begge er en licens fra Siemens-KWUprocessen. Takuma har videreudviklet denne proces for shredderaffald, og Mitsui har
primært koncentreret sig om husholdningsaffald.
PKA har udviklet en proces, hvor det termiske output er en brændbar gas. PKA har dog ikke i det besøgte anlæg forsøgt sig med shredderaffald, men har dog gennemført forsøg på et pilotanlæg. PKA er
pt. under konkursbehandling.
EBARA-processen adskiller sig fra de andre processer i det første termiske trin, som er en lavtemperatur fluid bed-forgasser, medens de tre andre processer betjener sig af roterovne til pyrolyseprocessen.
Fluid bed-forgasseren i EBARA-processen har flere gode egenskaber sammenlignet med roterovne. Disse er følgende:
- Robust proces med høj kapacitet pr. volumenenhed.
- God proceskontrol for temperatur og tryk.
- Pyrolysetemperaturen er let at styre gennem f.eks. mængden af tilført luft eller recirkuleret produktgas. Pyrolysetemperaturen kan desuden styres ved at ændre slam-andelen i det tilførte brændsel.
- Forgasseren har ingen bevægelige dele og i sammenligning med roterovne ingen væsentlige tætningsproblemer i forbindelse med indfødning og udtagning, som ville kunne give mulighed for udsivning af
gas.
- Det ekstra behandlingstrin til adskillelse af koks og metaller som ved anvendelse af roterovne undgås.
- Partikler > 0,3 mm udskilles sammen med metaller gennem bundasken, hvorved metaller ned til 0,3 mm i princippet kan genvindes. Det kan dog typisk ikke betale sig at separere metaller under 2..5
mm, hvorfor denne fraktion sendes retur til forgasseren for til sidst at ende i smelteprocessen.
Sammenligning EBARA og Takuma:
- Effektivitet i forhold til genanvendelse af metaller og andre stoffer.
Genanvendelsesgraden af metaller og andre stoffer må anses for at være nogenlunde ens for de to processer. Takuma har dog udviklet et system til at fraseparere sammenfiltrede kobberledningsnet fra
biler, som herefter kan afsættes som en nogenlunde ren fraktion af kobber. Genvinding af kobbertråde fra ledninger vil i Ebara-processen kræve oparbejdning af den restfraktion, som opstår af
keramik og metal >2.. 5mm, hvorfra jern og større stykker aluminium og kobber er fjernet. Denne oparbejdning udføres delvist af shredderoperatøren. Takuma-processen producerer også en fraktion
af ikke-jernmetaller, som skal oparbejdes andetsteds for at separere indholdet af mindre stumper kobber, aluminium etc. Endvidere mistes metaller under soldstørrelsen (7 mm) i Takuma-processen,
da denne nedmales og sendes over i smelteprocessen på samme vis som i Ebara-processen.
- Økonomi.
Se herom senere (afsnit 3.1.3).
- Miljøbelastning.
Begge teknologier kan uden problemer tilpasses de danske krav til arbejdsmiljø og miljø.
- Driftssikkerhed.
Takuma har været i drift i ca. 4 år og har behandlet ca. 100.000 tons shredderaffald. EBARA har været i drift i snart 3 år og har behandlet over 120.000 tons shredderaffald. Disse anlæg er klart de to anlæg i hele verden, der har vist længst stabil drift.
- Energiudnyttelse/forbrug.
I princippet er teknologierne sammenlignelige og energiudnyttelsen afviger ikke for de to processer.
- Mulighed for tilpasning til den danske affaldsstruktur.
Begge teknologier vil kunne tilpasses den danske affaldsstruktur. Kapacitetsmæssigt vil dette ikke give problemer, idet begge processer er fleksible i deres opbygning, ligesom begge processer vil kunne behandle andre affaldstyper samtidigt.
For alle de her nævnte termiske processer er hovedproduktet ud over energiproduktion i form af varme eller syntesegas en glasagtig slagge, der i alle økonomiske beregninger er ansat til en meget lav værdi,
idet vi har antaget, at den kan afsættes til vejbygningsmateriale, opfyldning eller lignende.
Det er dog sandsynligt, at slaggen ved en mindre, supplerende metallurgisk behandling vil kunne omdannes til et mere værdifuldt materiale med andre anvendelsesmuligheder. Eksempelvis kan det nævnes, at
Sverige i flere århundrede har benyttet slaggen fra højovne til fremstilling af mursten. Sådanne og lignende overvejelser bør gøres inden endelig valg af teknologi.
I denne forbindelse kan der være fordele ved at benytte processer, der kan køres reducerende, idet man her har større muligheder for dirigere metallerne derhen, hvor det vil være formålstjenlig at have dem.
(Jvf. Tabel 5).
Tabel 5. Termiske processer opdelt efter oxidationsgraden i smelteprocessen
Procestype |
Stærkt reducerende |
Svagt reducerende |
Neutralt |
Svagt oxiderende |
Betydning |
FeO=>Fe + O
CuO=>Cu + O
PbO=>Pb + O
ZnO=>Zn + O |
PbO=>Pb + O
ZnO=>Zn + O |
--------- |
PbO<=Pb + O
ZnO<=Zn + O |
Processer |
SVZ
Kawasaki
KSK
Pyroarc
PKA
Von Roll |
CT-Environm.
Von Roll |
|
Von Roll 1)
EBARA
Takuma
Mitsui |
1) Von Roll uden HSR-slaggebehandlingsanlæg. Se logbog fra besøget, fase 2b).
3.1.3 Omkostninger for teknologier til behandling af shredderaffald
I dette afsnit sammenlignes økonomien i de syv bedste processer.
De fælles forudsætninger for de økonomiske beregninger er:
Investering i bygninger, grunde, etc. |
Inkl. kapitalomk. |
til bygn. |
Forsikringer etc. |
medregnes ikke |
|
Afskrivning af fabriksanlæg |
7% p.a., |
15 år |
Afskrivning af maskiner (sorteringsudst.) |
7% p.a., |
7 år |
Gennemsnitlig løn |
300.000 |
DKK/år |
El-køb |
390 |
DKK/MWh |
El-salg |
350 |
DKK/MWh |
Varmesalg |
150 |
DKK/MWh |
Deponiomkostninger for farligt affald 1) |
675 |
DKK/t |
Deponiomkostninger for ask og slagge 1) |
0 |
DKK/t |
Salg af kobber (Cu) 2) |
7.000 |
DKK/t |
Salg af aluminium (Al) |
4.000 |
DKK/t |
Salg af metalblanding fx Cu/Al |
2.000 |
DKK/t |
Salg af jern (Fe) |
500 |
DKK/t |
Brændværdi af shredderaffald 3) |
13,3 |
GJ/t |
1) Inklusiv statsafgift, eksklusiv moms.
2) Pris for legeringer proportional med Cu-koncentrationen.
3) Ca. 10% vand, ca. 48% aske.
Sekundære udgifter til fx brændsel, O2 og andre hjælpestoffer, som er specifikke for de enkelte teknologier, er vist i besøgsrapporter fra de pågældende virksomheder/processer.
Priser ved køb og salg af el og salg af varme er fastlagt som gennemsnittet for danske affaldsforbrændingsanlæg.
Omkostninger til deponering er ansat ud fra oplysninger fra et bredt udsnit af private og kommunale priser.
Priser ved salg af metallerne Cu, Al og Fe er fastsat ud fra praktisk opnåelige verdensmarkedspriser for skrot-metaller.
Bemandingen på alle anlæg er skønnet den samme - nemlig 25 mand svarende til 5 mand per skift ved femholdsskift uanset om kapaciteten er 27.000 eller 100.000 t/år, idet den nødvendige bemanding ikke
forventes at variere væsentligt med mindre ændringer i kapaciteten af anlæggene. Den nødvendige bemanding vil være afhængig af de lokale forhold herunder eventuel udnyttelse af eksisterende personale,
som betjener andet udstyr.
Det skal bemærkes, at der regnes med en forrentning over 15 år. En forrentning over fx 8 år vil således forøge kapitaludgiften og dermed behandlingsomkostningerne for et anlæg med en investering på 300
mio. DKK med ca. 350 DKK/t.
Der regnes endvidere ikke med et eventuelt overskud til anlægsoperatøren.
For alle anlæg regnes med de driftsudgifter, som er opgivet af leverandørerne i logbøgerne. Driftsudgifterne er dog opgivet med forskellig bemanding, hvorfor der her er korrigeret til den samme bemanding
på 25 personer.
I logbøgerne har de enkelte leverandører opgivet forskellige indtægter for salg af metaller og kraft/varme, da en del af økonomiberegningerne omfatter udenlandsk affald eller affald af anden type. Det er
derfor her forsøgt at skønne realistiske virkningsgrader og salgspriser for de genvundne metaller for at gøre en sammenligning mulig. Skønnene er forbundet med en vis usikkerhed.
Tabel 6. Sammenligning af økonomien for de bedste behandlingsteknologier.
Anlæg |
SHR Kapacitet |
Kapital-omkostning |
Driftsudgifter totalt |
Indtægt metal/andre produkter |
indtægt el + varme |
Behandlings-omkostning ² |
|
t/år |
DKK/t SHR |
Ebara ¹ |
50.000 |
905 |
565 |
80 |
509 |
881 |
Takuma/Mitsui ¹ |
27.000 |
871 |
588 |
80 |
509 |
870 |
von Roll ¹ |
45.000 |
873 |
727 |
0 |
509 |
1.091 |
CT-Environment ¹ |
100.000 |
478 |
581 |
80 |
509 |
470 |
Thermoselect |
50.000 |
543 |
408 |
0 |
394 |
587 |
SVZ |
100.000 |
|
|
|
|
975 |
Pyroarc ¹ |
50.000 |
538 |
387 |
|
441 |
484 |
1 Kapitalomkostninger er inkl. bygninger.
2 De beregnede behandlingsomkostninger er baseret på en række forudsætninger, som medfører en vis usikkerhed og må betragtes som vejledende.
Omkostningerne i tabel 6 er opgivet som uforpligtende oplysninger af leverandørerne.
Forudsætningerne for de enkelte anlæg er
Ebara
Fra logbogen fra besøget hos Ebara benyttes følgende data om energiproduktion: Dampdata: 400 C, 38 bar, netto el-produktion: 14%, netto total virkningsgrad: 74%. Total virkningsgraden er sat
konservativt til 70%. Der er regnet med genvinding af 2% jernmetal fra shredderaffaldet og 3,5% kobber/aluminium med salgspris 2 DKK/t.
Takuma/Mitsui
Udfra oplysninger i logbøgerne og leverandøroplysninger vurderer vi, at et anlæg kan leveres med nogenlunde samme dampdata som Ebaras og dermed nogenlunde samme netto el virkningsgrad (14%) og
nogenlunde samme totale virkningsgrad (70%).
Der er regnet med genvinding af 2% jernmetal fra shredderaffaldet og 3,5% kobber/aluminium med salgspris 2 DKK/t.
Von Roll
Det forudsættes, at kapaciteten på smelteenheden, som indgår i von Rolls RCP proces, øges med 50%, så den svarer til kapaciteten af den foranliggende proces.
Udfra logbogen og leverandøroplysninger vurderer vi, at et anlæg kan leveres med nogenlunde samme dampdata som Ebaras og dermed nogenlunde samme netto el-virkningsgrad (14%) og samme totale
virkningsgrad (70%).
Den producerede jernkobberlegering antages at kunne afsættes til 0 DKK/t inkl. transport.
CT-Environment
Økonomiberegningerne er baseret på et anlæg med den dobbelte kapacitet af Ebaras svarende til 100.000 t shredderaffald/år. Vi vurderer, at et anlæg kan leveres med nogenlunde samme dampdata som
Ebaras og dermed nogenlunde samme netto el-virkningsgrad (14%) og samme totale virkningsgrad (70%). Anlægget er designet til samtidigt at kunne behandle 90.000 t røggasrensningsprodukt/år. Der er
regnet med genvinding af 2% jernmetal fra shredderaffaldet og 3,5% kobber/aluminium med salgspris 2 DKK/t, hvilket forudsætter etablering af en forbehandlingsproces, som er i stand til at udskille de frie
metaller.
Thermoselect
Kapitalomkostninger og driftsomkostninger er behæftet med en del usikkerhed.
Udfra data i logbogen og leverandøroplysninger vurderer vi, at et anlæg kan leveres med nogenlunde med nogenlunde samme netto el-virkningsgrad som Ebaras (14%). Til gengæld forventes en lavere total
energieffektivitet på ca. 50%, idet der i Thermoselect-processen indgår bratkøling af den 1200 C varme gas til under 80C, så der ikke kan produceres så store mængder fjernvarme. I princippet vil varmen
dog kunne udnyttes til andre "lavtemperatur" formål fx garverier og industrier med stort forbrug af varmt vand.
Den producerede jernkobberlegering antages at kunne afsættes til 0 DKK/t inkl. transport.
SVZ
SVZ opgiver en ”gatefee” ved behandling hos SVZ. De økonomiske forhold hos SVZ er meget sammensatte. Det er dog tvivlsomt om denne "gatefee" afspejler de reelle behandlingsomkostninger.
Pyroarc
Behandlingsomkostningerne er baseret på et estimat for behandling af shredderaffald med fugtindhold mindre end 10%. Beregningen omfatter et komplet turn-key-anlæg inklusive anlæg til fremstilling af
briketter. Der forventes en netto el-virkningsgrad for Pyroarc-processen på ca. 5% hvilket er lavere end for de anlæg, som ikke er skaktovnsbaserede. Anlæggets el-produktion er relativ lav, fordi
fremstillingen af brændselspiller og selve plasmageneratoren bruger megen energi. Den totale virkningsgrad forventes at kunne nå nogenlunde samme niveau som de ikke skaktovnsbaserede anlæg (65-75%),
hvorfor den totale virkningsgrad er sat til 70%.
Hvis man antager, at Pyroarc processen kombineres med en mekanisk forbehandling af shredderaffaldet med fraseparering af større stykker metaller (over ca. 6 mm) inden restaffaldet tilføres Pyroarc
processen, vil den mekaniske behandling medføre en merudgift i de samlede kapitaludgifter og driftsomkostninger. Vi vurderer, at indtægterne fra salg af metaller fra den mekaniske proces overstiger
udgifterne, så de samlede behandlingsomkostninger for en mekanisk proces kombineret med Pyroarc-processen eller lignende skaktovne ikke øges.
Diskussion
Kapitalomkostningerne og dermed investeringen per ton varierer fra 478 DKK/t til 905 DKK/t for de viste anlæg. En del af de viste anlæg har en kapacitet på ca. 50.000 t/år, men for nogle anlæg er
kapaciteten to gange større eller 2 gange mindre, hvorfor man skal være forsigtig med sammenligninger, da kapitalomkostningerne vil varierer på forskellig vis med kapaciteten. Kapitalomkostningerne er den
største udgiftspost for anlæggene og har derfor afgørende betydning for behandlingsprisen.
Det ses, at behandlingsomkostningerne inkl. bygninger ligger fra ca. 470 til 1.091 DKK/t.
Herfra skal trækkes sparede deponeringsudgifter i størrelsesordenen 675 DKK/t inkl. affaldsafgift. Nogle af processerne ser således ud til at kunne opnå et lille overskud, hvis der benyttes en
afskrivningsperiode på 15 år.
Det ses, at salg af kraft/varme udgør den største indtægt. Energien kan alternativt benyttes til smeltning af røggasrenseprodukter, såfremt processerne er designet til dette. CT-Environment tilbyder en proces
med samtidig smeltning af røggasrensningsprodukter, og vi forventer, at en del andre processer til en vis grad også vil kunne gøre dette. Således recirkulerer fx Ebara, Takuma og Enviroarc deres egne
røggasrensningsprodukter i processerne, hvorved en del af røggasrensningsprodukterne smeltes til en slagge. Det skal dog bemærkes, at Ebaras og Takumas anlæg er udlagt til at producere varme af al
energien i affaldet, hvilket medfører dyrere kedelanlæg, end hvis man vælger at udnytte energien til smeltning af røggasrensningsaffald og kun producerer damp af den lille rest overskudsvarme.
Indtægter fra salg af metaller kan variere meget afhængigt af om det lykkes at udvinde rene metaller, blandinger eller legeringer.
3.2 Behandlingsteknologier til CCA-imprægneret affaldstræ
Imprægnering af træ med Cr, Cu og As benyttes stort set kun i de nordiske lande og i USA, hvilket betyder, at potentialet for virksomheder, der udvikler affaldsbehandlingsteknologi, er begrænset. Vores
undersøgelse af internationale teknologier, der genvinder metallerne af imprægneret affaldstræ, har da også vist, at der stort set kun foregår udviklingsarbejder i Danmark, Norge, Sverige og Finland.
Der findes ingen fuldskala teknologier, der behandler CCA-imprægneret affaldstræ med oparbejdning af metallerne. Der eksisterer dog et system til genanvendelse af CCA-imprægnerede stolper, sveller,
mm. i Finland; men det har ikke været muligt at få tilstrækkelig detaljeret information om de forskellige termiske og kemiske processer til, at vi har kunnet vurdere, om systemet er egnet til danske forhold.
Det finske system oparbejder Cu, Cr og As i affaldstræet til nyt imprægneringsmiddel.
Kommunekemi har gennemført vellykkede forsøg i pilotskala med modstrømsforgasning af imprægneret affaldstræ og optimeret en kemisk proces til oparbejdning af asken fra forgasseren. Kommunekemi
planlægger at bygge et behandlingsanlæg, men de forventede behandlingsomkostninger er ikke kendte. En kemisk oparbejdning af asken forventes dog at være en forholdsvis dyr proces, hvor mængden af
aske og eventuelle rester af jord og anden forurening af træet kan øge behandlingsomkostningerne betragteligt.
Kommunekemi har desuden opbygget et pilotanlæg til pyrolyse af forskellige affaldstyper og planlægger at afprøve Chartherms koncept med lavtemperaturpyrolyse af imprægneret affaldstræ (se tabel 1).
Målet er at bringe Cr, Cu og As på en form, der gør det muligt at adskille de metalholdige partikler fra kokspartikler med mekaniske separationsprocesser. KK planlægger at gennemføre forsøgene tidligt i
2003.
Enviroarc har for afprøvet deres skaktovns-proces (Pyroarc) med imprægneret affaldstræ i pilot-skala. Ved behandling af CCA-imprægneret træ forventer Enviroarc, at hovedparten arsen-indholdet i træet
findes i procesgassen, hvorfra det kan udsepareres i et slamprodukt via en renseproces. Ved tilbageføring af slammet til forgasseren og tilsætning af jernholdigt materiale bør der ifølge Enviroarc kunne
produceres en jern-arsen-holdig smelte, hvor arsen er hårdt bundet. Kobber og krom vil fordele sig på forskellig vis mellem den smeltede slagge og metalsmelter. Der er ikke fremlagt tilstrækkelige
forsøgsdata til at kunne dokumentere fremgangsmåden nærmere.
Udover evt. udvundne metalfraktioner vil mineraler og oxiderede metaller findes i en tæt glasagtig slagge, som sandsynligvis vil kunne overholde kravene til genanvendelse i den danske
restproduktbekendtgørelse for kategori III og muligvis også kategori II. Dette bør dog undersøges nærmere.
Processen er ikke afprøvet i fuld skala, men leverandøren har udført et overslag på behandlingsomkostningerne for trykimprægneret affaldstræ er 400-500 DKK/t for et anlæg med en kapacitet på 50.000
t/år (se logbogen for Pyroarcanlægget ved Borge garveri). Andre skaktovnsprocesser fra fx KSK og British Lurgi (SVZ) forventer vi i grove træk vil kunne gennemføre nogenlunde samme behandling af
imprægneret træ som Pyroarc-processen. Med de foreliggende oplysninger er der mulighed for at skaktovnsprocesserne kan udvikles til en forholdsvis billig total løsning, men formentlig ikke med så høj en
genanvendelsesgrad af metaller som ved en kemisk oparbejdning af restprodukterne.
Også danske virksomheder er begyndt at udvikle processer, der kan ekstrahere tungmetallerne fra aske og koks fra imprægneret affaldstræ. Watech A/S arbejder med separationsprocesser, der kan fjerne
tungmetaller i aske fra CCA-imprægneret træ, PVC, shredderaffald, mm. Teknologien er meget lovende og relativt billig og er demonstreret i industriel skala med PVC.
Hvis udgangspunktet for vurderingen af processerne er, at energien i affaldstræet skal udnyttes bedst muligt, mens metallerne i aske/slagge/restprodukter skal oparbejdes i en efterfølgende proces, findes flere
termiske processer fra pyrolyse, over forgasning til forbrænding. Fælles for alle processerne er, at As vil ende i alle udgående strømme: Støv, røggasrensningsprodukt, tjære, aske/slagge, metallegeringer, etc.
Det vil derfor være nødvendigt, at alle de termiske processer efterfølges af flere rensningsprocesser, der kan fjerne og fiksere As til deponering.
Foster Wheelers boblende eller cirkulerende fluid bed forbrændings- eller forgasningsprocesser vil sandsynligvis også være velegnede til imprægneret affaldstræ. De to svenske værker på hver 90 MW
(Iglestaverket og Högdalenverket) brænder nedrivningsaffald uden problemer. Begge processer vil skulle efterfølges af restproduktoprensnings- og slaggestabiliseringsprocesser.
3.3 Behandlingsteknologier til læder- og garveriaffald
Der er kun fundet og besøgt en proces, som behandler læderaffald (Pyroarc).
Pyroarc-processen er udviklet til decentral placering ved et garveri og løser som sådan alle garveriets affaldsproblemer, idet alle affaldsstrømme kan behandles, uden at der forekommer affald, som må
deponeres. I bilag B findes en nøjere beskrivelse af Pyroarc-processen.
Processen er opbygget omkring en skaktovn, som producerer en jern-krom metallegering og en smeltet slagge til genanvendelse.
Processen er forholdsvis dyr i den lille kapacitet på 5.000 t/år læderaffald på tørstof basis, som haves fra garveriet men formodentlig ikke væsentligt mere end tilsvarende løsninger, hvor der produceres en
smeltet slagge og en metallegering, der uden yderligere oparbejdning kan afsættes til genanvendelse.
Andre skaktovnsprocesser eller reducerende smelteprocesser forventes at ville kunne være en mulig løsning til behandling af læderaffald uden restprodukter til deponi fx:
- KSK
- Thermoselect
- SVZ
- Von Roll
4 Forslag til danske strategier
4.1 Strategi for shredderaffald
Strategien for oparbejdning af shredderaffald i Danmark bør tage udgangspunkt i følgende:
- EU-direktivet om udrangerede køretøjer og dets indflydelse på mængde og sammensætning af affaldet.
- Den fremtidige sammensætning af shredderaffaldet.
- De fremtidige mængder af shredderaffald.
Desuden bør strategien være afpasset i overensstemmelse med den bedste tilgængelige teknologi på området.
EU-direktivet om udrangerede køretøjer forlanger, at der i 2006 nyttiggøres min. 85% af de udrangerede køretøjers vægt inkl. max. 5% energigenvinding. I 2015 er disse krav ændret til min. 95%
nyttiggørelse inkl. max. 10% energigenvinding.
Da samtidig bilernes sammensætning, som det fremgår af tabel 7, har ændret sig væsentlig gennem de seneste 30 år, står man over for væsentlige udfordringer.
Tabel 7. Udviklingen i sammensætningen af biler.
Bilers sammensætning 1) |
1980 |
1990 |
2000 |
|
% |
kg |
% |
kg |
% |
kg |
Stålskrot |
69 |
702 |
65,5 |
661 |
58 |
574 |
NE-metal |
4,5 |
45 |
5,2 |
45 |
6,0 |
59 |
Gummi |
5,2 |
53 |
5,0 |
51 |
5,0 |
50 |
Plast |
4,5 |
45 |
9,0 |
91 |
16,0 |
158 |
Glas |
3,9 |
40 |
4,0 |
40 |
4,0 |
40 |
Andet |
12,8 |
130 |
11,3 |
114 |
11,0 |
109 |
Total |
|
1.015 |
|
1.010 |
|
990 |
Heraf ikke metal |
26 |
268 |
29 |
296 |
36 |
357 |
1. Ref. 5: Technologien und Wirttschaftlichkeit von Recycling und Entsorgung von Altautos. Alekxander Stückeli, maj 2000.
En markant ændring har været indholdet af plast, der har været konstant stigende fra ca. 4,5% i 1980 til 16% i år 2000, primært på bekostning af jern og metal. Plastindholdet forventes at stagnere omkring
de 16% i de kommende år. Samtidig og især gennem 1990'erne har miljøbehandling af biler før shredning i Danmark medført, at flere og flere dele afmonteres. Det drejer sig om batterier, dæk og væsker.
Fremover skal også glas og visse plastmaterialer enten afmonteres før shredning eller, hvis dette er muligt, genvindes som glas og plast efter shredning.
Forudsætter man, at alt glas afmonteres, hvilket i realiteten jo kun vil ske i ikke havarerede biler, fjernes 40 kg glas fra hver bil. Hvis også 30 kg plast i form af diverse kofangere fjernes før shredning vil disse
tiltag under danske forhold, hvor biler udgør ca. 25% af formaterialet til shredderen, pr. 1000 kg shredderaffald medføre en reduktion på 8 kg glas og 7,5 kg plast. Denne ændring anses for at have minimal
betydning for sammensætning og brændværdi for shredderaffaldet, og dermed for valg af fremtidig oparbejdningsmetode for shredderaffald.
Den største betydning for shredderaffaldets fremtidige sammensætning vil være valget mellem en mekanisk forbehandling inden termisk oparbejdning eller ingen yderligere forbehandling.
I efterfølgende tabel 8 angiver kolonne 3 en sandsynlig sammensætning af shredderaffald, der ikke har gennemgået en yderligere raffinering og kolonne 4 angiver en sandsynlig sammensætning af
shredderaffald, der har gennemgået en økonomisk overkommelig raffinering. (Resultatet er fremkommet som et kvalificeret gæt på grundlag af de erfaringer, vi har samlet under vore observationer og især fra
én lang række analyser gennemført på shredderaffaldet hos STENA).
Raffineringen kan evt. bestå af følgende trin:
- Neddeling.
- Sigtning.
- Vægtfyldeseparation og/eller separation af metaller ved computer scanning og afblæsning af metaller. Jvf. de beskrevne metoder fra R+ og H.J. Hansen.
Tabel 8. Sammensætning af shredderaffald i danmark.
Analyse |
DK
1996 |
DK 2002 =>
Uden raffinering |
DK 2002 =>
Raffineret *****) |
Fe |
13,2 % |
12% *) |
4% *) |
Al |
2,5% |
2,2% **) |
1,2% **) |
Zn |
1,9% |
1,9% |
1,5% |
Cu |
1,2% |
2% ***) |
1,4% ***) |
Pb |
0,35% |
0,3% |
0,3% |
Ni |
0,04% |
0,04% |
0,04% |
Sn |
0,01% |
0,01% |
0,01% |
Cr |
0,04% |
0,04% |
0,04% |
Cd |
0,004% |
0,004% |
0,004% |
Metal |
19,2% |
18,5% ****) |
8,5% ****) |
Cl |
2,0% |
2,5% |
2,5% |
Vand |
Ca. 10% |
Ca. 10% |
Ca. 10% |
Aske i alt |
48,6% |
Ca. 48% |
Ca. 38% |
Brændværdi |
13,9 MJ/kg |
Ca. 12 MJ/kg |
Ca. 13 MJ/kg |
*) Ca. 3% foreligger som oxider.
**) Ca. 1% foreligger som oxider.
***) Ca. 1% foreligger som oxider.
****) Ca. 5% foreligger som oxider.
*****) Med den nuværende teknologi. Sammensætningen vil ændre sig med udviklingen af nye teknologier.
Mængdemæssigt reduceres den samlede mængde shredderaffald naturligvis med de metaller, glas og plast, der fjernes fra affaldet. Reduktionen vil altså være knap 12% i forhold til den mængde, der ville
være tale om, hvis shredderaffaldet ikke blev behandlet. Der vil således i den nærmeste fremtid være behov for at behandle op mod 100.000 tons shredderaffald pr. år i Danmark.
Grundstoffer som bly, zink og klor, som er problematiske for den efterfølgende termiske behandling, fjernes imidlertid ikke ved denne mekaniske oparbejdning. Disse stoffer vil også fremover - endda i
relativt forøgede mængder - være tilstede i shredderaffaldet.
Der eksisterer i dag teknologier, som kan genvinde energien og nyttiggøre shredderaffaldet i en sådan grad, at EU-direktivet om udrangerede køretøjer kan opfyldes såvel i 2006 som i 2015.
De umiddelbart tilgængelige teknologier er EBARA, Takuma og sandsynligvis også CT-Environment i kombination med R+ eller H. J. Hansen. Om disse teknologier kan siges, at EBARA og Takuma endnu
er første generations processer med de problemer, dette naturligt medfører. CT-Environment er endnu ikke nået til første generation.
Det bør dog nævnes, at også teknologierne udviklet af von Roll, Thermoselect, PKA og skaktovne som SVZ, Pyroarc eller sammenlignelige processer ved videreudvikling og i kombination med mekaniske
sorteringsprocesser er interessante.
Ved fastlæggelse af strategien for fremtidig behandling af shredderaffald bør følgende spørgsmål overvejes:
- Medsmeltning af problematisk affald for udnyttelse af brændværdien i shredderaffaldet.
- Med moderne computerteknologi er der store muligheder for yderligere udvikling af scanningsteknologien, hvilket kan medføre udsortering og genvinding af stoffer, som ikke i dag kan genvindes.
- Hvis dette eller andre tiltag muliggør en væsentlig øgning i plastgenvindingen, kan dette på sigt medføre et så stort fald i brændværdi for shredderaffaldet, at energiindholdet bliver for lavt til at smelte
slaggen uden tilsats af anden energi.
- Eventuel medforbrænding / smeltning af trykimprægneret træ for at opnå tilstrækkelig brændværdi til smeltning af slaggen. Dette bør da ske i reducerende proces, der bedst sikrer en genanvendelig
slagge og størst mulig metalfase.
- Med de nyeste udmeldinger, som netop er modtaget fra Enviroarc, bør mulighederne i Pyroarc-processen studeres nærmere, såvel hvad angår behandling af shredderaffald som måske en kombineret
proces, hvor shredderaffald og trykimprægneret træ behandles samtidig.
Før der vælges teknologi, råder vi derfor til, at der gennemføres studier af:
- De økonomiske og miljømæssige muligheder for yderligere udsortering og genvinding af plast efter en mekanisk forsortering.
- Undersøge relevansen af genvinding af tungmetaller enten i den mekaniske forsortering eller i en efterfølgende termisk proces.
- Vurdere om el- og varmeproduktion fra den termiske proces er den optimale energiudnyttelse af shredderaffaldets brændværdi.
- Studere mulighederne for opgradering af slaggen fra den termiske proces til højværdigt konstruktionsmateriale eller råmateriale.
- Gennemføre kalkuler, der belyser de miljømæssige og økonomiske aspekter ved medforbrænding af husholdnings- og industriaffald, som også indeholder mange metaller eller evt. imprægneret træ for
binding af asen i en metalfase. Flere processer tilbydes til behandling af husholdnings- og industriaffald og er etableret med dette formål i bl.a. Japan.
Disse studier vil kunne finde frem til en til en definition af ideal anlægget til behandling af shredderaffald.
Under alle omstændigheder er de senest tilkomne informationer fra Enviroarc så interessante, at disse bør undersøges nærmere.
4.2 Strategi for imprægneret træaffald
4.2.1 Økonomiske betragtninger
Hovedproblemet med CCA-imprægneret affaldstræ er det meget giftige arsen (As). Foruden As indeholder træet de to tungmetaller kobber (Cu) og krom (Cr), der har en vis handelsværdi som frie metaller.
Endelig har spildtræ en meget stor brændværdi.
Potentialet for den danske produktion af imprægneret affaldstræ har vi i projektets første fase skønnet til ca. 18.500 t i 1997 og ca. 90.000 t i 2020 svarende til ca. 10 t Cu + 22 t Cr i 1997 og ca. 70 t Cu
+ 140 t Cr i 2020 (se ref. 1).
Salgsprisen af tungmetallerne og den frigjorte energi ved forbrænding i det imprægnerede affaldstræ udgør den samlede værdi af affaldet.
Idet vi benytter de samme salgspriser for Cu og Cr som for Cu i de økonomiske beregninger i afsnit 3.1.3 (4.000 DKK/t), bliver salgsværdien for metallerne i 1997 128.000 DKK og 840.000 DKK i
2020.
Til sammenligning udgør den skønnede samlede brændværdi i 1997 0,283 PJ/år og forventes at blive1,37 PJ/år i 2020. Set i forhold til det samlede forbrug af skovflis på alle danske varme- og
kraftvarmeværker i 2001 på 3,53 PJ, repræsenterer potentialet i CCA-imprægneret affaldstræ altså ikke mindre end ca. 10%.
Med en termisk virkningsgrad på 85% og en salgspris på 150 DKK/MWh, vil denne varme kunne indbringe ca. 10 mio. DKK i 1997 og ca. 49 mio. DKK i 2020. Hvis behandlingsanlæggene producerer
elektricitet, vil den samlede energi-salgspris være ca. 5-10% højere.
Brændværdien udgør altså mere end 98% af affaldstræets værdi.
Kobber ”tabes” mange steder i det danske ”Cu-kredsløb” fx i slagge fra affaldsforbrændingsanlæg og i skrot, der genbruges til stålproduktion.
I Danmark forbrændes ca. 3 mio. t affald/år i affaldsforbrændingsanlæg. Hvis man antager et gennemsnitligt askeindhold på ca. 20% med en Cu-koncentration på ca. 0,5%, betyder det, at der årligt
deponeres ca. 3.000 t Cu i affaldsslagge fra danske affaldsforbrændingsanlæg.
Den danske ”produktion” af jernskrot er på ca. 1 mio. t/år. Hvis vi antager et gennemsnitligt Cu-indhold på 0,25%, svarer det til, at ca. 2.500 t Cu/år forsvinder fra ”Cu-kredsløbet”.
Disse to restprodukter står altså for et samlet årligt Cu-tab på mindst 5.500 t.
Cu-mængden i imprægneret affaldstræ udgør altså ca. 0,2% (1997) af det samlede ”tab” af Cu i disse tre affaldsstrømme (slagge fra affaldsforbrænding, jernskrot og imprægneret affaldstræ).
4.2.1.1 Konklusion
Hovedindsatsen i behandlingen af CCA-imprægneret affaldstræ bør derfor koncentreres om løsningen af problemerne med det meget giftige As, der skal stabiliseres / bindes, så det på den billigste måde kan
deponeres uden risiko for miljøet. En mulighed er at behandle affaldstræet sammen med en mindre mængde shredderaffald eller læder- og garveriaffald i en proces, der binder As i stabile jern- eller
kobberforbindelser.
Brændværdien i affaldstræet skal udnyttes effektivt for at sikre en så stor CO2-fortrængning som muligt.
Genvindingen af Cu og Cr fra CCA-imprægneret affaldstræ må prioriteres i forhold til de behandlingsomkostninger, som er forbundet med oparbejdningen. I det omfang Cu og Cr ikke genvindes bør de
under alle omstændigheder stabiliseres, så aske, slagge og andre restprodukter kan deponeres uden risiko for miljøet.
Vi forventer, at det er væsentligt mere økonomisk fordelagtigt at udvinde en del af rest kobberindholdet fra affaldsslagge og skrot end at genvinde kobber fra imprægneret træ. En sådan udvinding kan fx
foregår med mekanisk separationsudstyr baseret på sensorbaserede metalseparatorer (fx S+S, SSE).
4.2.2 Strategi med genvinding af metaller
Ud over det ”lukkede” finske system, som oparbejder metallerne i CCA-imprægnerede stolper til nyt imprægneringsmiddel, har vi ikke kunnet finde erfaringer fra fuldskala-anlæg, der genvinder metaller og
energi fra imprægneret affaldstræ.
Kommunekemi og Teknologisk Institut har i pilotanlæg vist, at en modstrømsforgasser kan forgasse imprægneret affaldstræ. Der findes kun erfaringer i laboratorie-skala med en kemisk oparbejdning af
metallerne. Nye lovende og billige processer er under udvikling hos Watech A/S.
Pilot-forsøg med Pyroarc-processen og oplysninger fra Enviroarc viser en interessant mulighed for at udnytte processen til effektivt at binde arsen til jern. Enviroarc forventer, at Pyroarc-processen
herudover vil kunne producere en lagringsstabil slagge med indhold af mineraler og oxiderede metaller samt en metal-legering, som eventuel vil kunne afsættes. Processen er ikke afprøvet i fuld skala. Da
Pyroarc-processen også kan behandle læder- og garveriaffald og sandsynligvis også shredderaffald, bør denne proces følges nøjere.
Genvindingen af energien i træet er meget vigtig, da den udgør over 98% af affaldets værdi. Da salgsværdien af metallerne er relativ lille, skal den efterfølgende oparbejdningsproces være så billig som
overhovedet mulig. I modsætning til metallerne Cu og Cr har As negativ værdi og bør derfor bringes på en form, så omkostningerne til deponering bliver mindst muligt.
Set i forhold Cu- og Cr-indholdet i tre danske affaldsstrømme (slagge fra affaldsforbrænding, jernskrot og imprægneret affaldstræ) udgør disse metaller en meget lille andel (ca. 0,2%).
4.2.3 Strategi uden genvinding af metaller
Energien i det imprægnerede affaldstræ kan nyttiggøres i mange af de undersøgte termiske processer, men man vil kunne opnå endnu større fordele, hvis affaldstræet behandles sammen med en mindre
mængde jern- eller kobber-holdigt affald som oparbejdet shredderaffald eller læder- og garveriaffald. (Med oparbejdet shredderaffald menes shredderaffald, hvor alle større stykker metal (over 3-5 mm) er
fjernet med mekaniske separationsmetoder; men hvor affaldet stadig indeholder oxider og mindre stykker af metallerne). Under de rette termiske forhold danner As meget stabile kemiske forbindelser med
både jern og kobber.
Ebaras og Takumas processer vil ikke være velegnede, da As-forbindelser vil kunne forurene overfladen af de frie metaller. De efterfølgende smelteprocesser sker ikke under reducerende forhold og vil
derfor ikke kunne danne de frie metaller, der er nødvendige for at binde As.
Vi vurderer, at de reducerende termiske processer hos SVZ, Pyroarc, KSK, Kawasaki og PKA sandsynligvis alle vil kunne behandle en blanding af 15% oparbejdet shredderaffald og 85% imprægneret
affaldstræ. Jern- og kobber-indholdet i affaldet vil kunne udnyttes til at binde arsen i meget stabile jern- eller kobber-forbindelser. Da energien i træet og de reducerende forhold vil kunne udreducere flere
frie metaller, end der er nødvendigt for at binde As, forventes processerne desuden at producere Cu/Cr/Fe-legeringer, der muligvis vil kunne afsættes. En del af metallerne vil afhængigt af driftsbetingelserne
kunne findes i oxideret form i et slaggeproduktet. Afhængigt af mængden af tilsat svovl vil processerne desuden kunne produceres sulfidsmelter af krom og kobber.
4.3 Strategi for læder- og garveriaffald
Mængden af læderaffald i Danmark udgør ca. 4.300 t i produkter og 400 t fra garveriindustri og forarbejdning (estimat fra projektets fase 1). Indholdet af Cr er anslået til 92 t, hvilket er i samme
størrelsesorden som det forventede indhold i trykimprægneret træ år 2020 (125 t Cr) fra 80.000 t trykimprægneret træ.
Der er flere muligheder for at behandle læderaffald med udvinding af metaller.
- Behandling i separat anlæg
Behandlingen kan ske i et Pyroarc-anlæg eller et andet skaktovnsanlæg, som separerer i slagge og metalsmelte. Ved behandling sammen med en tilstrækkelig mængde jernholdigt affald fx jernoxidaffald eller
jernpartikler samt koks, træflis eller andet reduktionsmiddel vil anlægget kunne producere en jernkromlegering, som kan afsættes til stålværker. Behandling af kun den danske affaldsfraktion af læder
forventes at medføre en forholdsvis høj behandlingsomkostning på ca. 1.500-2.000 DKK/t affald. Hvis der tilsættes andet affald sammen med læderaffaldet, som ikke ødelægger jernkromlegeringens
egenskaber, vil der kunne bygges et anlæg med større kapacitet og lavere driftsomkostninger. Hvis der tilsættes andet affald, skal specielt kobberindholdet være meget begrænset for ikke at ødelægge den producerede metallegerings kvalitet.
- Behandling af læderaffald sammen med neddelt imprægneret træ, som forgasses eller forbrændes i fluid bed anlæg og efterfølgende oparbejdes med udvinding af krom og kobber.
Da læderaffaldet udgør en mindre mængde end den forventede mængde imprægneret affaldstræ, vil læderaffaldet efter neddeling med fordel kunne blandes med nedfliset imprægneret affaldstræ og
forgasses/forbrændes. Læderaffaldet forventes pga. det høje indhold af krom at øge kromkoncentrationen i slaggen/flyveasken. Hvis den termiske proces er efterfulgt af en kemisk baseret proces til
genvinding af krom og kobber fra slagge og /eller flyveaske, formoder vi, at den højere kromkoncentration i slagge/flyveaske fra læderaffaldet vil forbedre behandlingsøkonomien. Under de rette forhold vil
svovl, der findes i høje koncentrationer i garveriaffald, kunne binde As samtidig med, at Cu og Cr samles i en sulfidsmelte.
5 Belægningsdannelser i kedler og varmevekslere
5.1 Indledning
I projektet er der evalueret en række processer til behandling af tungmetalholdigt affald. Baseret på kendskabet til sammensætningen af disse affaldstyper vurderer vi, at der er en høj sandsynlighed for, at
der i sådanne anlæg kan opstå betydelige problemer med belægningsdannelse og med korrosion i hedeflader.
Enkelte koncepter er afprøvet i fuld skala gennem en kort årrække, dog typisk med relativt lave dampdata, og fra disse anlæg er det forsøgt at indhente relevante drifts- og vedligeholdelsesdata. Opgaven er
derfor, at vurdere problemernes karakter, størrelse samt mulige metoder til at håndtere disse problemer på basis af teoretiske overvejelser og de få praktiske erfaringer.
5.2 Teoretiske overvejelser af problemernes natur
Idet der kun findes få erfaringer med den relevante type anlæg, er det nærliggende at betragte problemstillingen ud fra de forhold som kendes fra andre affaldsfyrede anlæg og efterfølgende ekstrapolere på
basis af afvigelserne til de aktuelle koncepter. Sidstnævnte indbefatter primært de afvigende karakteristika af brændslerne og sekundært afvigelser i ovn- og kedeldesign.
Det er velkendt fra traditionelle affaldsfyrede anlæg med dampproduktion, at der ofte opstår betydelige problemer med korrosion og belægningsdannelse, som kræver store vedligeholdelsesomkostninger og
fører til forringet rådighed af anlæggene. I det følgende gives en beskrivelse af mekanismerne i disse problemer for traditionelle affaldsfyrede anlæg.
5.2.1 Korrosionsmekanismer
Undersøgelser udført på danske affaldsforbrændingsanlæg suppleret med litteraturoplysninger viser, at de væsentligst problemområder er nedbrydning af den ildfaste foring, korrosion af panelvæggene bag
den ildfaste foring, korrosion af ubeskyttede panelvægge efter afslutning af den ildfaste foring, korrosion af overhedere, belægningsdannelse på panelvægge i kedlens strålingstræk samt belægningsdannelse
på kedlens overhedere.
Nedbrydning af den ildfaste foring kan føre til følgende problemtyper:
- Hvis foringen forsvinder, øges varmeoverførslen og røggastemperaturen sænkes – dette kan vanskeliggøre overholdelse af miljøkrav – opretholdelse af en røggastemperatur på mindst 1100°C i 2
sekunder efter den sidste sekundærluftinddysning
- Hvis foringen slipper kontakt med panelvæggen, reduceres varmeoverførslen og røggastemperaturen stiger – dette kan føre til øgede korrosions- og belægningsproblemer i de efterfølgende områder af
kedel og overhedere
- Hvis foringen forsvinder øges korrosionen på de blotlagte kedelrør
- Salte kan gennemtrænge den ildfaste foring og føre til korrosion på de bagvedliggende kedelrør
Korrosion af kedelrør bag den ildfaste foring, ubeskyttede kedelrør efter afslutning af den ildfaste foring og overhedere har gentagne gange ført til rørsprængninger, uplanlagt udetid og store omkostninger til
udskiftninger.
Nedbrydningen af ildfaste foringer udgøres ofte af en kombination af forskellige mekanismer, og i mange tilfælde er det vanskeligt at afgøre, hvilke mekanismer har været de primære årsager til skaderne.
Væsentlige mekanismer i nedbrydningen af ildfaste foringer indbefatter:
- reaktion med slaggesmelte
- infiltration med slaggesmelte og nedrivning
- oxidation
- indtrængning af gasser
- kondensering af gasformige salte og medfølgende ekspansion
- reaktion mellem indtrængende gasser og foringskomponenter
- opløsning af foringens bindfase af gaskomponenter
- spændinger via ekspansion af faser og forskelle i termisk ekspansion mellem panelvæg og foring
- korrosion af stifter og beslag samt korrosion af panelvæg.
Korrosion af panelvægge bag ildfast foring har vist sig oftest at udgøres af saltsmeltekorrosion, hvor de primære korrosive smelter typisk udgøres af alkali- og tungmetalklorider, overvejende K-Zn-klorider.
Samme korrosionsform forekommer typisk på ubeskyttede panelvægge i området umiddelbart efter afslutningen af den ildfaste foring og områder af ubeskyttet panelvæg, hvor strømningsforholdene betinger
en høj stoftransport til kedelvæggen.
Korrosion af overhedere er ofte præget af gasfase klorkorrosion og i mange tilfælde i kombination med smeltekorrosion, f.eks. af smelter i systemet KCl-FeCl2.
Ud over disse mekanismer kan forekomme korrosion forårsaget eller fremmet af lokalt reducerende forhold ved kedelvæggene. Lokalt forekommer også erosion i områder med uhensigtsmæssige
strømningsforhold. Mekanismerne i ovennævnte korrosionsformer er kort fortalt som nedenstående.
5.2.1.1 Cl-gas korrosion
Gasfase alkalimetal- og tungmetalklorider såsom KCl, NaCl, ZnCl2 og PbCl2 kondenserer på røroverfladerne og reagerer her med røggassens SO2 i dannelse af Cl-gas i høje koncentrationer ved
røroverfladen. Denne sulfateringsreaktion kan illustreres ved KCl: 2KCl+SO2+O2=K2SO4+Cl2. Denne Cl-gas reagerer med stålet efter: Fe+Cl2=FeCl2. Dette jernklorid er flygtigt ved korrosionsfronten
og føres som gas udad til oxidlaget, hvor det oxideres: 3FeCl2+2O2=Fe3O4+3Cl2. Den herved frigivne Cl-gas kan så atter reagere med stålet. Mekanismen kræver, at der kondenseres en af ovennævnte
metalklorider på rørene og at disse kan reagere med SO2 fra røggassen. Korrosionen vil formodentlig øges ved større Cl/S-forhold i brændslet, højere røggastemperatur og højere overfladetemperatur. Et
lavere Cl/S-forhold ville betyde, at sulfateringsreaktionen i højere grad foregår i røggassen, hvor frigivelse af Cl-gas er forholdsvis uskadelig. Denne type korrosion kan forekomme både på panelvægge og
overhedere.
5.2.1.2 Smeltekorrosion
Ved kondensation af ovennævnte metalklorider på ståloverfladen/oxidlaget kan der dannes forbindelser med smeltepunkter under de aktuelle overfladetemperaturer. Både vores egne få analyser og
litteraturdata tyder på, at det især er blanding af ZnCl2 og KCl, der giver problematiske smelter, men NaCl og PbCl2 kan også bidrage. Blanding af ZnCl2 og KCl kan have smeltepunkter ned til 230°C
afhængig af K/Zn-forholdet. Ved tilstedeværelse af sådanne smelter opløses stålet og/eller oxidlaget og det opløste jern genudfældes formodentlig som jernoxid uden over smelten. Mekanismen kræver at
forskellige metalklorider kondenserer på røroverfladen. I de fleste tilfælde vil det formodentlig være, at både ZnCl2 og KCl kondenserer og at ZnCl2 udgør mindst halvdelen af metalkloriderne.
Metaloverfladetemperaturen er af stor betydning, idet den bestemmer om kloriderne er smeltede. Denne type korrosion forekommer primært på panelvægge i området efter afslutning af ildfaste foringer.
5.2.1.3 Reducerende forhold/CO-korrosion
Lokalt lave iltkoncentrationer og høje CO-koncentrationer ved kedelvæggene kan fremme korrosion på forskellige måder, f.eks. ved at reducere stabiliteten af beskyttende jernoxider, fremme
sulfiddannelse, øge stabilitet af metalklorider og sænke smeltepunktet af belægninger. Denne korrosionsform kan specielt optræde ved dårlige forbrændingsforhold og dårlige opblandingsforhold i røggassen.
5.2.2 Belægningsdannelse
Mekanismer i belægningsdannelse har ikke været genstand for tilsvarende detaljerede undersøgelser som for korrosionens vedkommende. Undersøgelser af belægninger fra affaldsfyrede anlæg viser, at der i
ovnområdet sker en påbagning af smelteslagge på de ildfaste foringer og tykkelsen af smelteslaggen vil være afhængig af underlagets karakter og af slaggens viskositet og dermed af dets sammensætning.
Gennem de tomme træk sker der en stigende kondensation af salte på hedefladerne. Typisk vil initiallagene i belægningerne bestå af næsten rene salte af alkali- og tungmetalklorider og –sulfater og disse salte
optræder desuden også i de øvrige dele af belægningerne. Længere omme i de tomme træk og i overhederområdet observeres en tiltagende sulfatering af belægningerne, og der synes at være en tendens til,
at kedler med væsentlige belægningsproblemer også er karakteriserede ved forøgede indhold af sulfat i belægningerne. Dette peger på sulfatsintring som en betydende mekanisme i belægningsdannelsen.
5.3 Affaldssammensætningens indflydelse på korrosion og belægningsdannelse
5.3.1 Shredderaffald
I forhold til “normalt affald“ kendt fra de andre affaldsforbrændingsanlæg (ca. 85% husholdningsaffald og 15% industriaffald), vil shredderaffald have en række afvigende karakteristika. De væsentligste
karakteristika i denne sammenhæng er brændværdi og indholdet af en rækkegrundstoffer. I nedenstående skema er vist disse parametre for normalt affald og for shredder affald. Værdierne for shredder
affald er indhøstet i nærværende projekt. Sparsomme oplysninger om massebalancer for EBARA processen peger på, at den overvejende mængde af klor, svovl, alkali, zink og bly går videre til
forbrændingsprocessen. Værdierne vil dog være afhængige af den aktuelle forbehandlingsproces. Værdierne for normalt affald er indhentet for de ikke flygtige komponenters vedkommende fra
massebalancemålinger på Sønderborg KVV, og Cl og S værdierne er baseret på emissionsmålinger og spildevandsmålinger fra Odense Kraftvarmeværk. Normalt affald dækker her en blanding af normalt
affald og industriaffald som er det normale brændselsblanding på danske affaldsforbrændingsanlæg. Værdierne er kun retningsgivende, idet der vil forekomme meget betydende variationer i
sammensætningerne.
Tabel 9. Sammensætning af forskellige typer affald
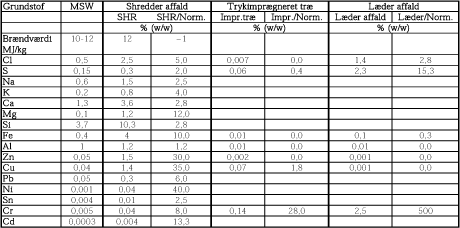
Det fremgår heraf, at shredderaffald har samme eller lidt højere brændværdi end normalt affald. Desuden ses en meget betydelig afvigelse i sammensætning, idet shredder affald har betydeligt større indhold
af Cl, alkali og tungmetaller men kun lidt højere indhold af S end normalt affald.
En lidt højere brændværdi kan, afhængigt af hvorledes forbrændingen styres, føre til højere forbrændingstemperaturer, hvilket kan føre til en større frigivelse af metalklorider såsom alkali- og
tungmetalklorider.
Det højere kloridindhold i shredderaffald er meget væsentligt, idet det kan føre til en væsentlig større frigivelse af metalklorider i forbrændingen, og kombineret med et øget indhold af alkali og tungmetaller
kan der forventes en massiv forøgelse af indholdet af gasfase alkali- og tungmetalklorider i forhold til forbrænding af normalt affald. Hvorvidt dette vil ske, vil dog også være afhængig af, hvorledes
reaktanterne (pyrolysegas, forgasningsgas, koksrest) blandes. Det er vanskeligt at forudse præcist, hvorledes reaktionerne vil forløbe.
Der er således høj sandsynlighed for en markant forøgelse af indhold af gasfase metalklorider umiddelbart efter forbrændingen i forhold til traditionelle affaldsfyrede anlæg. Denne forøgelse af gasfase
alkaliklorider og tungmetalklorider medfører et øget potentiale for korrosion og belægningsdannelse i de efterfølgende kedeldele. Hvorvidt problemerne vil være af overvejende korrosions- eller
belægningsmæssig karakter afhænger i meget høj grad af, om disse gasfase metalklorider sulfateres i røggassen og afsættes som metalsulfater eller om de primært afsættes som metalklorider og efterfølgende
sulfaterer i belægningerne.
I tilfælde af en langsom sulfateringsrate, vil der i høj grad ske afsætning af metalklorider, hvilket vil fremme saltsmeltekorrosion og gasfase klorkorrosion. En højere sulfateringsrate vil derimod øge
belægningsproblemerne idet sulfaterne fører til øget sintring af belægningerne således at disse kun vanskeligt fjernes under drift. I tilfælde af en næsten komplet sulfatering af metalkloriderne i røggassen vil
korrosionsbelastningen reduceres betydeligt.
Som det fremgår af ovenstående tabel, er Cl-indhold øget væsentlig mere end S-indholdet i forhold til normal affald, hvilket giver et højere Cl/S-forhold. Dette peger i retning af, at det især er korrosionen,
som vil forøges. En anden væsentlig faktor er dog en øget tilstedeværelse af en række metaller som formodes at have en katalytisk virkning på oxidationen af SO2 til SO3 og dette vil trække den anden vej,
mod en hurtigere sulfatering og tendens til mere belægningsdannelse.
En yderligere væsentlig faktor er indholdet af Zn, Pb og alkali. Indholdet af disse grundstoffer er alle højere i shredder affald end i normalt affald, men indholdet er markant større for Zn og Pb end for alkali.
Flyveaskeanalyser fra nogle affaldsforbrændingsanlæg tyder på, at en stor del af brændslets alkaliindhold fordamper som klorider under forbrændingen, hvorimod det kun er en lille del af brændslets Zn- og
Pb-indhold, der fordamper som klorider. Dette peger på, at der vil være rigeligt alkali til dannelse af gasfase alkaliklorider i røggassen, og samtidig vil det højere indhold af Zn og Pb i affaldet formodentlig
føre til større dannelse af Zn- og Pb-klorider, der sammen med alkalikloriderne kan kondensere på røroverfladerne. Dette peger i retning af, at der med shredderaffald vil forekomme en større kondensering
af klorider på røroverfladerne, og at de kondenserede klorider vil have et højere Zn/alkali-forhold. Dette betyder igen, at der bliver større risiko for dannelse af korrosive smelter.
For koncepter, hvor dele af flyveasken recirkuleres, forventes dette at føre til en endnu mere aggressiv atmosfære, som vil forstærke korrosions- og belægningsproblemerne, idet indholdet af metalklorider
forventes at øges.
Hvorvidt der med det pågældende affald optræder mere eller mindre CO-korrosion afhænger mest af neddelingsgraden af affaldet samt design af ovnen.
Sammenfattende peger en kvalitativ vurdering i retning af, at både korrosion og belægningsdannelse vil øges ved forbrænding af shredderaffald i forhold til normalt affald. Størrelsen af stigningen i korrosion
og belægningsdannelse kan ikke forudses præcist, men vurderes at være af betydelig størrelsesorden på basis af shredderaffaldets sammensætning. En bestemmelse heraf bero på erfaringer fra og forsøg på
pilot- eller fuldskala anlæg med det relevante brændsel
5.3.2 Imprægneret affaldstræ
Trykimprægneret træ har meget lavere indhold af Cl, alkali, Zn og Pb samt et lavere Cl/S-forhold end både normalt affald og shredder affald, hvilket tyder på at der ikke vil forekomme betydende problemer
med korrosion og belægningsdannelse ved traditionelle dampdata.
5.3.3 Læder- og garveriaffald
Læderaffald har et Cl-indhold, der ligger mellem normalt affald og shredderaffald. Samtidig er S-indholdet højt, således at Cl/S-forholdet er væsentligt lavere end for normalt affald og shredder affald.
Endeligt er indholdet af alkali, Zn og Pb lavt i læderaffald. Disse forhold betyder ligeledes, at potentialet for korrosions- og belægningsproblemer er forholdsvis lavt.
5.4 Praktiske erfaringer
En gennemgang af besøgsrapporterne suppleret med nye informationer om driften af anlæggene viser, at for de undersøgte koncepter er den termiske proces ved forbrænding af produkter efter
forgasning/pyrolyse enten ikke demonstreret, demonstreret uden kraftvarmeproduktion, demonstreret med kedler med lave dampdata, demonstreret med mindre aggressivt affald eller kun med kontinuert
driftstid under et år. Eksempelvis er Mitsuis proces demonstreret, men kun med husholdningsaffald i fuld skala, og shredder affald i pilot skala; Takumas proces er demonstreret over flere år, men ved
moderate dampdata (270°C/ 48 bar) og frigivne oplysninger er yderst sparsomme; EBARAs proces er demonstreret med shredderaffald med rimelige dampdata (400°C/ 38 bar). Siden besøget er kedlen
blevet modificeret og et nyt rensesystem er påbygget. Der er herefter kun ca. 8 måneders drift med fire nedlukninger som ikke skyldes belægninger.
Der er således kun få beskrivelser af problemer af ovennævnte karakterer - de beskrevne problemer er primært belægningsproblemer, og der er typisk ikke beskrevet problemer med korrosion og levetid af
ildfaste foringer. En væsentlig grund til sidstnævnte er formodentlig, at belægningsproblemer vil vise sig efter relativ kort driftstid, hvorimod problemer med korrosion og nedbrydning af ildfaste foringer ofte
først vil vise sig tydeligt efter længere driftstid.
Undersøgelserne har vist, at der er løbende bestræbelser på at opsamle driftserfaringer fra processerne, men dels tager det nogen tid inden, der kan indhøstes kvantitative data for korrosion, nedbrydning af
ildfaste foringer og belægningsdannelse, og dels er det ofte svært at få driftserfaringer fra producenterne, idet dette betragtes som kerneviden. For en nærmere vurdering af omfanget af disse problemer er det
stadig yderst vigtigt at følge driftserfaringerne på de pågældende anlæg løbende.
5.5 Løsningsmuligheder
For at modvirke problemerne med belægningsdannelse og korrosion, bør man se på både primære tiltag som sigter mod at ændre røggasatmosfærens karakteristika og sekundære tiltag som sigter mod at
mildne effekten af røggasatmosfærens påvirkninger af kedlen.
5.5.1 Primære tiltag
De tiltag, som kan anbefales for minimering af korrosion, er de samme som gælder for kedler, der forbrænder normalt affald. Blot er tiltagene endnu vigtigere på grund af det mere korrosive brændsel.
Der findes i dag ingen entydige og afprøvede løsninger på korrosionsproblemerne. Der findes en række muligheder, som formodentlig kan reducere problemerne, men disse bliver først endeligt afklarede
gennem yderligere undersøgelser. Derfor må der gives en anbefaling, som skal baseres på det nuværende grundlag men i erkendelse af, at det er mangelfuldt.
Sænkning af tryk på vand/dampsiden vil være et af de mest effektive midler til at reducere korrosion af panelvægge, idet dette reducerer overfladetemperaturen. Ligeledes kan en lavere damptemperatur
reducere korrosion af overhederne, men til dette er det mindst lige så vigtigt at reducere røggastemperaturen før overhederne. Det vurderes, at korrosionsproblemerne kan elimineres ved at begrænse
dampdata til maksimalt 30 bar og 350 C eller ved at anvende en fjernvarmekedel.
Minimering af korrosion kræver, at der er så gode forbrændingsbetingelser som muligt for mindske dannelsen af korrosive stoffer, og at kedelvæggene beskyttes mod de korrosive komponenter, som
alligevel vil dannes i større eller mindre omfang. Sikring af gode forbrændingsbetingelser stiller en række krav til design af forbrændingsområdet og til driften af anlægget. På nuværende tidspunkt er der ikke
noget samlet overblik over, hvorledes de enkelte forbrændingsparametre indstilles optimalt, så det er derfor vigtigst at sikre så gode reguleringsmuligheder som muligt især for parametre som luftfordelinger.
Ligeledes bør ovn og kedel være udrustet med registreringsmuligheder for røggastemperaturer, målesteder for CO-målinger og målesteder for spektroskopimålinger af gasfase metalklorider.
5.5.2 Sekundære tiltag
For ovn og efterforbrændingszonen skal rørvæggene have påført en ildfast foring for opretholdelse af en tilstrækkelig røggastemperatur (>1100 C i minimum 2 sekunder) og som også beskytter den
bagvedliggende rørvæg mod korrosion. For valg af foringsmateriale og påføringsmetode kan man i nogen grad hælde sig til erfaringerne fra tidligere anlæg. Der kan ikke gives endelige anbefalinger om
anvendelse af kakler versus støbemasser. Fuldskalaforsøg peger på, at der kan være muligheder i anvendelse af kakler med spærreluft (hinterlüftet) til yderligere at sikre mod indtrængning af korrosive
komponenter.
Det sværeste område i korrosionsmæssig henseende er rørvæggen efter afslutning af den ildfaste foring. På basis af de hidtidige iagttagelser må det forventes, at der kan forekomme en kraftig
korrosionsbelastning i dette område. Korrosionsbelastningen vil være kraftigst umiddelbart efter afslutningen af den ildfaste foring, men kraftig korrosionsbelastning kan forekomme over et større område
herefter. På anlæg, hvor man har søgt at løse et korrosionsproblem dette sted ved at føre den ildfaste foring længere om i trækkene er det oftest konstateret, at korrosionsproblemet blot følger med.
Endvidere kan dette give anledning til en forøgelse af røggastemperaturen ved indgang til overhederne og dermed øge korrosionsbelastningen dette sted.
Det er derfor meget sandsynligt at foring af en større del af rørvæggene i 1. og 2. træk ikke vil løse korrosionsproblemet.
5.5.2.1 Materialevalg
På nuværende tidspunkt synes den eneste løsning på korrosionsproblemet at være påføring af et metallisk lag af korrosionsbeskyttende materiale på rør og finner. På baggrund af de hidtidige erfaringer,
primært i udlandet, bør der vælges et Alloy 625 materiale, altså Ni-baseret med høj Cr-indhold og lavt Fe-indhold. Der kan vælges forskellige påføringsmetoder: påsvejst, påsprøjtet eller co-ekstruderet.
Disse 3 metoder har indbyrdes en række fordele og ulemper som skal afvejes mod hinanden.
De fleste erfaringer er baseret på påsvejst Inconel 625 og der foreligger overvejende positive erfaringer i tilfælde, hvor der er påsvejst på frisk panelvæg. Påsvejsningen har fordel af en god tykkelse (2-3
mm) og formodentlig god kvalitet med hensyn til vedhæftning, porøsitet og permeabilitet. Ulempen i forhold til de to andre er opblandingen med rørmaterialet der giver et væsentlig højere Fe-indhold og
dermed muligvis reduceret korrosionsbestandighed. Dette kan minimeres ved optimering af svejseproceduren og anvendelse af stort overlap mellem svejsestrengene.
Der findes væsentlig færre erfaringer med påsprøjtet Inconel 625 og erfaringsmaterialet i primært mindre indbygningsforsøg med overhederrør. Påsprøjtningen er tyndere (0,5-0,7 mm) end påsvejsning, men
til gengæld ændres sammensætningen ikke i forhold til Inconel 625. I flere tilfælde har forsøg med påsprøjtede coatings udvist problemer med revnedannelse som har ført til accelereret korrosion og
afskalning af coatings. Der pågår en del udviklingsarbejde med coatings og der kan måske fremkomme væsentligt forbedrede produkter.
Den tredje mulighed er co-ekstruderede rør. På indeværende tidspunkt markedsføres kun hele rør som co-ekstruderede rør med yderlag som kan være mere eller mindre svarende til Inconel 625 og sort
stål inderst. I tilfælde af, at der skal produceres panelvægge kan der anvendes en Inconel 625 finne. Der er relativt få indbygningsforsøg, men resultaterne er overvejende positive, dog er der også konstateret
korrosionsskader på sådanne rør.
Prismæssigt er påsprøjtning det billigste med ca. 8-10.000 DKK/m². Påsvejsning er lidt dyrere med ca. 15-20.000 DKK/m². For co-ekstruderede rør er prisen formodentlig 25.000-30.000 DKK/m².
Disse priser skal dog tages med forbehold. Umiddelbart vil anvendelse af påsvejst Inconel 625 kunne anbefales, idet der foreligger flest erfaringer med denne løsning. De forøgede anlægsomkostninger
forårsaget af Inconel oversvejsning vil efter al sandsynlighed blive rigeligt modsvaret af reducerede vedligeholdelsesomkostninger.
Anvendelse af varmeveksling baseret på keramiske rør med luftkøling er måske en mulighed, men der er uløste problemer med materialer og slaggedannelse.
5.5.2.2 Kedelkonfiguration
For opnåelse af en rimelig levetid af overhederne er det især vigtigt, at reducere røggastemperaturen før overhederne og så vidt muligt placere slutoverhederen medstrøms. Der bør opretholdes en
røggastemperatur før overhederne på mindre end 650°C, også ved snavset kedel, og jo lavere røggastemperatur, jo lavere bliver korrosionsraten. Muligvis bør der vælges en lavere temperaturgrænse end
de 650°C ved højere indhold af Zn- og Pb-klorider; dette vil måske kunne afklares ved at finde damptryksdata for disse klorider i litteraturen. Der kan med fordel indsættes en fordamperhedeflade lige før
overhederne, hvilket både vil reducere røggastemperaturen og give en bedre opblanding af røggassen før overhederne. Det bør også overvejes at indsætte renseanordninger i de tomme træk, i form af
sodblæsere eller ultralydrensning. Det er tænkeligt at problemaffaldet vil føre til forøget belægningsdannelse og tykke belægninger kan føre til øget korrosion på panelvægge og overhedere, sidstnævnte især
på grund af øget røggastemperatur.
Nedkøling af røggassen fra 1100 C i efterforbrændingsområdet til under 650 C før overhederne stiller krav til større hedeflade i dette område end i traditionelle affaldskedler.
Mulighed for at reducere indholdet af gasfase metalklorider gennem tilsætning af additiver såsom svovl eller aluminosilikater bør også overvejes. Der er udført forsøg på et traditionelt affaldsfyret anlæg som
peger på, at der er muligheder for at reducere både belægningsdannelse og korrosion ved denne fremgangsmåde. Dette kræver dog yderligere forsøg for en nærmere afklaring af muligheder og økonomi.
Det er dog overvejende sandsynligt, at der også skal foretages yderligere tiltag for at reducere belægningsproblemer i ovn, tomme træk og i overhederne. I ovnen kan det foreslås at anvende Inconel
oversvejste rør på siderne ved risten, idet dette vil modvirke opbygning af slaggepåbagninger.
5.5.2.3 Kedelrensning
I de tomme træk kan det blive nødvendigt at installere anordninger til fjernelse af belægninger. Dette kan være dampsodblæsere, vandsodblæsere, tankspulere, styrede vandlanser, akustiske
renseanordninger og eksplosiver. Der er gode erfaringer på nogle danske anlæg med renseanordninger baseret på traditionelle tankspulere.
I overhederområdet anbefales anvendelse af bankeværker for at reducere opbygningen af belægninger. Det er svært på forhånd at vurdere, om dette vil være tilstrækkeligt og det kan være nødvendigt med
yderligere rensninger, såsom flere rensestop om året eller online rensninger med eksplosiver. Det sidstnævnte kræver dog også, at anlægget er udlagt med gode muligheder for fjernelse af store
belægningsmængder på kort tid.
5.6 Konklusion
Shredderaffaldets karakteristika - specielt det højere indhold af Cl, alkali og tungmetaller i forhold til normalt husholdnings- og industriaffald - betyder, at der er en kraftigt forøget risiko for korrosions- og
belægningsproblemer i kedler til kraftvarmeproduktion.
Der er kun meget få driftserfaringer under de rette betingelser, hvilket betyder, at disse problemer endnu ikke kan kvantificeres. Demonstration af fuldskala drift under de rette betingelser i en driftsperiode på
1-2 år er nødvendig for at kunne kvantificere problemerne med rimelig sikkerhed.
Der er angivet en række muligheder for at løse de meget sandsynlige problemer med nedbrydning af ildfaste foringer, korrosion af fordamperhedeflader under ildfaste foringer og efter afslutning af ildfaste
foringer samt korrosion af fordampere.
Korrosionsbeskyttelse især af fordamperhedeflader med Inconel oversvejsninger vurderes at give en reduktion af vedligeholdelsesomkostninger og forbedret rådighed, som langt overstiger de ekstra
anlægsomkostninger.
6 Referencer
Ref. 1: Malmgren-Hansen, Bjørn; Overgaard, Jørgen; Cramer, Jesper; Metoder til Behandling af Tungmetalholdigt Affald. Fase 2B; Miljøstyrelsen; 2001.
Ref. 2: Malmgren-Hansen, Bjørn; Overgaard, Jørgen; Cramer, Jesper; Metoder til Behandling af Tungmetalholdigt Affald. Fase 1; Miljøstyrelsen; 1999.
Ref. 3: Terkildsen, L; Forbrænding af forurenet spildtræ, fase 1: Litteraturrapport; December 1994; ISBN nr.: 87-7782-054-1.
Ref. 4: Terkildsen, L; Forbrænding af forurenet spildtræ, Undersøgelse af miljøbelastende stoffer i udgående strømme fra et affaldsforbrændingsanlæg med og uden tilsætning af forurenet spildtræ til affaldet;
December 1994; ISBN nr.: 87-7782-054-1.
Ref. 5: Technologien und Wirttschaftlichkeit von Recycling und Entsorgung von Altautos. Alekxander Stückeli, maj 2000.
Bilag A
Adresseliste for udvalgte virksomheder
Virksomhed |
Adresse |
Postnr. og by |
Land |
Borge Garveri AS
Att. Johannes Borge |
|
N-5250 Lonevåg |
Norge |
CT Environment
Att. Martin Schaub |
Neuwiesensstrasse 15 |
CH-8401 Winterthur |
Schweiz |
EBARA
Att. Dr. Adrian Selinger |
Thurgauerstrasse 40 |
CH-8050 Zurich |
Schweiz |
Enviroarc Technologies AS
Att. Steinar Lynum |
Karenslyst Allé 11, 3. etage
POB 673 |
N-0214 Oslo |
Norge |
Foster Wheeler Energia Oy
Att. Timo Anttikoski |
Nuijamiestentie 3 |
FIN-0040 Helsinki |
Finland |
H.J.Hansen Recycling Industry Ltd
Att. Erling Møller Nielsen |
Havnegade 110 |
DK-5100 Odense C |
Danmark |
Högdalenverket / Birka Värme AB
Birka service / Göran Eidensten |
Kvicksundsvägen 16 |
S-124 59 Bandhagen |
Sverige |
Igelstaverket
Att. Sven Wallin |
Nynäsvägen 43 |
S-152 07 Södertälje |
Sverige |
Kawasaki Steel
Att. General Manager Noburu Yasukawa |
Chiba |
|
Japan |
MEFOS
Att. Lars-Gunnar Johansson |
Box 812 |
SE-971 25 Luleå |
Sverige |
Mitsui, Yame Seibu Clean Centre
Att. General Manager Satoshi Ito |
2088-6 Oaza Maezu |
Chikugo-City
Fukuoka pref. |
Japan |
Organic Power ASA
Att. Hans Bjerkvig |
Klingenberggaten 7 a |
N-0110 Oslo |
Norge |
PKA Umwelttechnik GmbH & Co. KG |
Heinrich-Rieger-Str. 5 |
D-73430 Aalen |
Tyskland |
PPS Pipeline Systems Gmbh |
Steyermühle 1-3 |
D-09634 Siebenlehn |
Tyskland |
Procone Vergasungssysteme Gmbh Geschäftsstelle Schweitz |
Allmendstrasse 398 |
CH-4617 Gunzgen |
Schweiz |
R-plus Recycling GmbH |
Heilbronner Strasse 13 |
D-75031 Eppingen |
Tyskland |
S+S Metallsuchgeräte und Recyclingtechnik Gmbh |
Regener Straße 130 |
D-94513 Schönberg |
Tyskland |
Salyp nv
Att. Ivan Vanherpe |
Oostkaai 62 |
B-8900 Ypres |
Belgien |
SSE - Separation Systems Engineering GmbH
Att. Eric van Looy, Managing Director |
Rosengarten 10 |
D-22 880 Wedel |
Tyskland |
SVZ
Skundärrohstoff-Verwertungszentrum Schwarze Pumpe GmbH
Att. Hartmut Huck / Jörg Buchholz |
Suedstrasse |
D-02979 Spreetal OT Spreewitz |
Tyskland |
Takuma Co. Ltd.
Att. Daisuke Ayukawa Manager environmental eng. dept II |
2-33 Kinrakuji-cho 2-chome, Amagasaki |
Hyogo 660-0806 |
Japan |
Thermoselect S.A. |
Piazza Pedrazzini 11 |
CH-6600 Locarno |
Schweiz |
Voest-Alpine Industrieanlagenbau GmbH & Co
Att. Fried Sauert |
Postfach 4 |
A-4031 Linz |
Østrig |
Von Roll Environmental Technology Ltd.
Att. Bruno Andreoli |
Hardturmstrasse 133
P.O. Boks 760 |
CH-8037 Zurich |
Schweiz |
Bilag B
Logbog for besøg hos Borge garveri (Pyroarc processen)
1 Generelle oplysninger
1.1 Procestype
I Pyroarc-processen indgår forgasnings-, plasma- og forglasningsteknologi i et samlet koncept til behandling af al læder- og træaffald fra Borge Garveri.
Processen producerer en metallegering og et slaggeprodukt til genanvendelse, samt energi i form af kraft og varme til garveriet.
1.2 Tilført affald
Læderaffald i form af falsespåner, slam fra spildevandsanlæg, limlæder og træaffald
1.3 Licenshaver og kontaktpersoner
Licenshaver
Enviroarc Technologies AS er licenshaver.
Kontaktperson Steinar Lynum
Telefon: +47-24111252
Fax: +47-24111299
E-mail: steinar.lynum@enviroarc.com
1.4 Ejerforhold og kontaktpersoner for det besøgte anlæg
Anlægget er ejet af Borge Garveri AS og EnviroArc Technologies AS.
1.5 Beliggenhed for det besøgte anlæg
Pyroarc anlægget er beliggende ved
Borge Garveri AS
N5250 Lonevåg
Norge
Anlægget er vist på figur 1
Figur 1. Pyroarcanlægget ved Borge garveri.
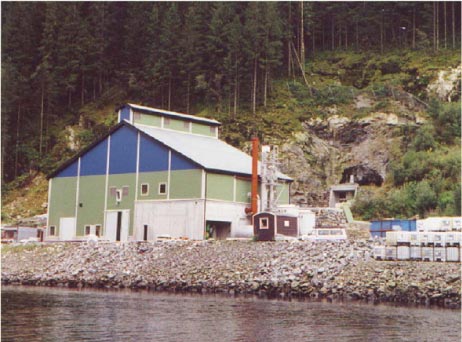
1.6 Virksomhedens formål og idégrundlag
Enviroarc sælger anlæg til behandling af alle typer affald herunder problemaffald og arbejder på at etablere Pyroarc-anlæg til behandling af imprægneret affaldstræ, shredderaffald og andre problematiske
affaldstyper.
Formålet med anlægget hos Borge Garveri er behandle læderaffaldet fra garveriet og producerer energi til garveriet, uden at der opstår restprodukter, som må deponeres. Anlægget producerer dels varme til
at tørre slam og dels til garveriets forbrug af varme i forbindelse med garvningsprocesserne.
1.7 Kapacitet for det besøgte anlæg
15.000 t affald (vådt)/år.
7.700 driftstimer pr. år
Kapaciteten af vådt affald er således ca. 2 t/time.
Forgasserens kapacitet af tørret affald, træflis mv. er ca. 0,7 t/time.
1.8 Byggeår og status for projektet
Pyroarcanlægget ved Borge garveri har været overtaget af garveriet siden januar 2002 og har pr. 1/10-2002 haft ca. 3.000 driftstimer. Driften har været baseret på 5 dages drift med 24 timer/døgn.
Gasmotoren benyttes ikke fuldt ud, da det i perioder med lidt affald er mest økonomisk at producere varmt vand til garveriet. Motoren har været i testet ved fuld kapacitet samt ved normal brug og kører
tilfredsstillende på den producerede gas.
Et pilotanlæg findes i Hofors.
Enviroarc arbejder med etablering af andre Pyroarcanlæg i Sverige, Italien, Tyskland, Polen, Malaysia og flere anlæg i Norge.
Enviroarc forventer at kunne bygge Pyroarcanlæg med kapaciteter op til 7 t/time (ca. 50.000 t/år).
2 Kortlægning og beskrivelse af anlægget
Et procesdiagram over anlægget er vist i Figur 2 og Figur 3.
2.1 Procesdiagram
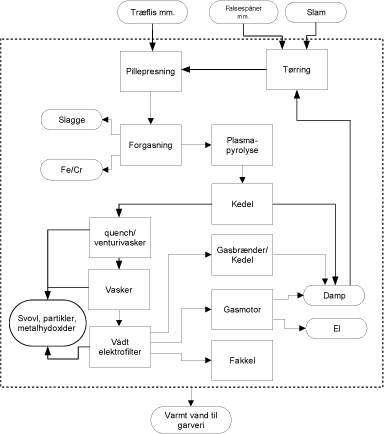
Figur 2 Procesdiagram for forgasningsanlægget
2.2 Affald
Affaldet som behandles stammer fra Borge garveri.
Affaldet fra garveriet består af
- falsespåner som opstår ved tykkelsesjusteringen af læderet
- afskær fra læderproduktionen
- slam fra garveriets spildevandsrensning, som indeholder jern fra fældningsprocessen. Der behandles endvidere slam fra en tidligere aluminiumsbaseret fældningsproces.
- håraffald
- limlæder som er fedt fjernet fra de modtagne huder
- træaffald fra engangspaller mv.
Mængdemæssigt er slammet langt den største affaldsfraktion.
Garveriet behandler pt. alle affaldsfraktioner bortset fra den lille fraktion af afskær, da Borge endnu ikke er anskaffet en passende neddeler.
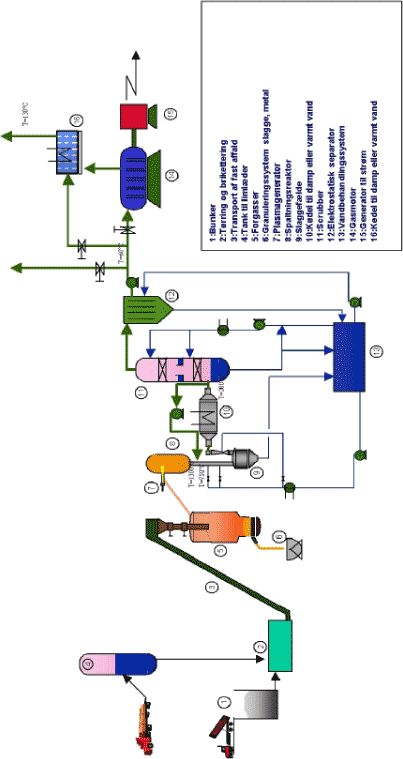
Figur 3. Opbygning af Borges Pyroarc-anlæg.
2.3 Forbehandling
Falsespåner og håraffald blandes med det afvandede slam, som opbevares i bigbags. Blandingen tilføres anlæggets lagerbunker, som er opdelt i sektioner til de forskellige typer affald.
Herfra tilføres blandingen tørreanlægget sammen med indpumpet limlæder. Tørreren er en "multicoil" modstrømstørrer, som opvarmes med damp fra Pyroarc-anlægget.
Affaldet tørres ned til < 5% fugtindhold, hvorefter blandingen føres til et pillepresningsanlæg med ringmatrice. Pillepressen producerer brændselspiller med en diameter på 50 mm. De færdigproducerede
piller føres til en lagerbunker.
2.4 Forgasning
Brændselspillerne tilføres en modstrøms skaktovnsforgasser sammen med koks og træflis fra nedfliset affald. Affaldet forgasses ved 1500°C sammen med tilsatte siliciumholdige sten med brug af forvarmet
luft. Herved produceres en flydende slagge og en jern/krom-metallegering. Da forgasseren arbejder efter modstrømsprincippet, indeholder produktgassen en del tjærestoffer og ledes derfor forbi en
plasmagenerator. Produktgassen fra forgasseren blandes i et reaktionskammer med en plasmagas med en temperatur på op til 5000°C og opnår derved temperaturer på over 1200°C i ca. 0,5 sekunder (se
figur 4). Herved nedbrydes alle organiske stoffer til simple molekyler, så der dannes en syntesegas af brint, kulmonooxid, kuldioxid, vanddamp og kvælstof.
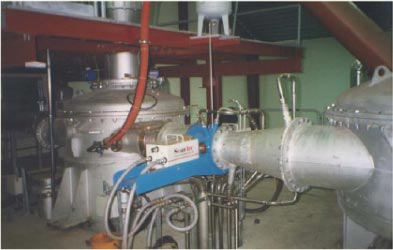
Figur 4. Top af forgasser med plasmagenerator (blå).
2.5 Energiproduktion og røggasrensning
Syntesegassens temperatur sænkes fra ca.1200°C til ca. 650°C ved recirkulering af produktgas. Herefter produceres damp i en kedel med en syntesegastemperatur efter kedlen på ca. 200°C.
Kedlen renses ved gennemblæsning af produktgas.
Rensningen af syntesegassen sker i en venturiskrubber, hvor gassen bratkøles ved indsprøjtning af vand. Herved fjernes salte og partikler. Efterfølgende passerer gassen en cyklon, hvorefter gassen renses i
et vasketårn, hvor der tilsættes base. Herved fjernes tilstrækkeligt svovlbrinte til at kunne overholde krav for udledning af SO2 efter forbrænding. Til sidst følger et vådt elektrofilter.
Herefter kan gassen enten ledes til en gasfyret dampkedel eller til gasmotor med generator til produktion af kraft og varme. Den maksimale el-produktion er omkring 580 kW. Herudover findes en
sikkerhedsfakkel.
Da garveriet bruger store mængder vand ved lave temperaturer, kan der opnås en høj energiudnyttelsesgrad, idet restvarme i kondenserede dampstrømme og anden overskudsvarme ved lav temperatur kan
udnyttes til forvarmning af vand til garveriet.
3 Observationer under besøget
3.1 Besøgets varighed
Den 18/9 2002 fra kl. 11:30 til kl. 15. (Uge 38).
3.2 Indsatsmaterialer behandlet under besøget
Type:
Mængde i t/h: 0 t/h
Kapacitetsudnyttelse: 0 %
Anlægget var stoppet på grund af en mindre reparation under besøget.
3.3 Driftsforhold
Driftstid: 24 timer/døgn, 5 dage per uge hvis der findes tilstrækkeligt affald.
Revisioner: 1 pr. år.
Idet der pt. ikke er nok affald på garveriet, samt eksternt affald til 7 dages drift køres 24 timer/døgn i 5 dages perioder, mens anlægget lukkes ned i weekenderne. Dette er ikke optimalt udfra et
driftssynspunkt, da op og nedlukninger reducerer levetiden af udmuringer, men er stadig den bedste økonomiske løsning, indtil der skaffes mere affald.
Driftsresultater for uge 36.
Driftstid: 113 timer
Tilført brændsel til forgasser:
- Læderaffaldsbriketter 39,5 t
- Koks: 3,5 t
Mængden svarer til 0,38 t/time eller ca. 50% af forgasserens kapacitet.
Briketteproduktion:
- Behandlet slam, limlæder håraffald og falsespåner: 90 t
Dette svarer til 0,8 t vådt affald/time eller ca. 45% af brikettepressens kapacitet.
Der produceres kun el, når der er tilstrækkeligt med affald til, at dette er lønsomt. Så længe der ikke er mere affald end, at energien herfra kan udnyttes til tørring af slam og levering af varme til garveriet, kan
det ikke betale sig at producere strøm til nettet. Gasmotoren kan operere ned til 50% af nominel kapacitet dvs. ca. 290 kW.
3.4 Output under besøget
3.4.1 Restprodukt
Ingen produktion under besøg
3.4.2 El/varme
Ingen produktion under besøg
Anlægget producerede i uge 36:
Slagge: |
1.780 |
kg |
Metallegering: |
200 |
kg |
Damp: |
79.180 |
kWh |
4 Kritiske delprocesser og driftsparametre
Under besøget blev følgende spørgsmål diskuteret:
- Er der forekomst af kondenserbare stoffer og forureninger i processernes forskellige trin; fx af tjære, sod, metaller, salte og oxider i pyrolyseovnens top, i gaskanaler eller i
efterforbrændingskamre?
Der er ikke registreret problemer med tjære fra forgasningsskakten til plasmageneratoren.
Efter ombygning af spaltningsreaktoren har der ikke været problemer med afsætning eller kondensering af stoffer på procesenhederne nedstrøms i spaltningsreaktoren.
- Hvordan kontrolleres mængden af kondenserede stoffer, dvs. hvordan renses de kritiske procesafsnit for afsætninger?
Gassen fra spaltningsreaktoren, som har en temperatur på 1200-1300°C, bratkøles med recirkuleret gas til 650°C for at kondensere salte og derved undgå at klæbrige partikler sætter sig på
overflader nedstrøms i anlægget.
Kedlen holdes ren med et "big blaster" system, som i faste sekvenser skyder kedlen ren med komprimeret produktgas.
- Hvilken kemisk stabilitet har restprodukter fra processen? Er de lagringsstabile mht. tungmetaller og dermed egnet til deponering (data for standardudvaskningstests), eller
lækker der tungmetaller, og skal de betragtes som miljøfarligt affald?
Udvaskningsdata viser at slaggen tilfredsstiller danske krav til udvaskning for kategori II (se tabel 7).
- Findes der dioxiner (eller andre halogenerede organiske stoffer) i restprodukter eller evt. mellemprodukter som skal oparbejdes andetsteds?
Affaldet omdannes til renset brændbar gas, slagge og metal.
Fra gasrensningen opstår spildevandsslam, som behandles på vandrensningsanlægget ved Borge garveri. Fra vandrensningsanlægget ledes produceret fældningsslam retur til Pyroarc processen. Der er
ikke påvist dioxiner eller halogenerede hydrokarboner i fældningsslammet fra spildevandsanlægget.
Røggas fra anlægget indeholder væsentligt mindre end 0,1 ng/Nm³ dioxin.
Slagge og metal bør grundet den høje behandlingstemperatur og et lavt kulstofindhold ikke indeholde dioxin. Der er ikke målt for dioxin i slagge eller metaller, men resultater for andre smelteprocesser
viser en meget lav koncentration (se besøgsrapport for Thermoselectprocessen ved Kawasaki steel, fase 2B).
5 Miljømæssige forhold
5.1 Emissioner til luften
Tabel 1. Emissioner til luften.
|
Målt/garanti (11% O2) |
EU-krav (11% O2, tør gas) |
|
mg/Nm³ |
mg/Nm³ |
SOx |
30 |
50 (24 h) |
NOx |
80 * |
200 (24 h) |
HCl |
<0,2 |
10 (24 h) |
CO |
50 (tilladelse på 3000) * |
50 (24 h) |
Støv |
1,7 (30 min) |
30 (30 min) |
TOC |
<0,02 |
10 (24 h) |
Sb+As+Pb+Cr+Co+Cu+Mn+Ni+V |
0,0075 |
0,5 |
Cd+Tl |
0,000037 |
0,05 |
|
|
ng –TEQ/m³ |
ng- TEQ/m³ |
Dioxiner |
0,05 |
0,1 |
* Måling udført under operation af gasmotor
5.2 spildevandsudledning
Slammet fra gasrensningen behandles i garveriets spildevandsrensningsanlæg, før det sendes tilbage til Pyroarcanlægget sammen med andet slam fra garveriet.
5.3 Støj
Støjniveauet kunne ikke vurderes under besøget, men forventes at være af samme størrelse som for andre termiske anlæg.
5.4 Lugt
Da anlægget var ude af drift under besøget, kunne vi ikke vurdere evt. lugtproblemer. Der må dog altid forventes en hvis afgivelse af lugt fra garveri-rester. Forgasningsanlægget kan ikke afgive lugt da
kravene til tæthed er langt større end ved et forbrændingsanlæg.
5.5 Affaldsproduktion
Slam fra glasrensning behandles på garveriets spildevandsrenseanlæg før det recirkuleres tilbage i Pyroarcanlægget sammen med andet slam fra garveriet.
5.6 Samlet dioxinemission
Dioxinindholdet i metaller og slagge kendes ikke.
Der bør dog ikke kunne forekomme dioxiner i nogle af fraktionerne dels grundet den høje temperatur, som smelter og metallegeringer har været udsat for, dels på grund af den reducerende atmosfære, som
røggasrensningsprodukterne udvindes ved.
Dioxinindholdet i røggasrenseprodukter måles to gange årligt
6 Arbejdsmiljømæssige forhold
6.1 Støvbelastning
Besøget var for kort til at bedømme støvbelastningen. Når anlægget er i drift , kan der kun forekomme støv ved brændselsproduktion. Under reparationer, hvor anlægget åbnes, må der tages samme
forholdsregler som ved reparationer af andre termiske anlæg med anvendelse af passende beskyttelsesudstyr. Der er installeret et centralt afsugningssystem, som fjerner støv fra eventuelle udslip ved
reparationer o. lign. Opsamlet støv tilføres briketteringsanlægget og efterfølgende forgasningsanlægget.
6.2 Internt støjniveau
Kunne ikke bedømmes.
6.3 Tungmetalbelastning
Her gælder samme forholdsregler ved reparationer, som er nævnt i afsnit 6.1.
6.4 Dioxinbelastning
Vi vurderer, at der ikke emitteres dioxiner fra anlægget.
6.5 Andet; fx lugtgener, vilkår i forbindelse med reparationsarbejde mv.
Garveriaffald afgiver en vis lugt, indtil der er fremstillet brændselspiller.
7 Beskrivelse af input
Mængden af affald til garveriet er i dag mindre end forudsat i designet af anlægget. Mængden og sammensætningen kan variere, men som udgangspunkt for designet af anlægget blev benyttet
sammensætningen angivet i tabel 2.
Tabel 2. Designdata for tilførte mængder affald
Type |
Tørstofindhold
(vægt %) |
Brændværdi
(MJ/kg tør) |
Affald
(kg/h) |
Slam (Borge Garveri ¹) |
30 |
16 |
394 |
Slam (Lager ²) |
30 |
16 |
1.221 |
Limlæder |
15 |
25 |
197 |
Håraffald |
40 |
29 |
46 |
Rotosil |
40 |
29 |
16 |
Spalt |
40 |
21 |
3 |
Klippefiller |
85 |
21 |
2 |
Falsespåner |
50 |
21 |
25 |
Andet usorteret |
70 |
14 |
14 |
Plast |
98 |
26 |
3 |
Træaffald |
50 |
19 |
10 |
SUM |
|
|
1.931 |
1 Jernholdigt slam
2 Aluminiumholdigt slam. Kan kun indfyres i begrænset mængde sammen med jernholdigt slam af hensyn til slaggens smeltepunkt
Brændselspillerne er vist på figur 5.
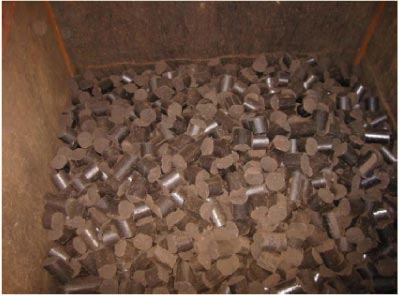
Figur 5. brændselspillerne til Borges Pyroarc-anlæg er ca. 50 mm i diameter.
Ved behandling af alternative brændsler som træflis mm. bør affaldet have en brændværdi på mindst 10-12 MJ/kg og højst 35-40% fugtindhold.
8 Beskrivelse af output
Borge har oplyst denne typiske masse- og energibalance (se tabel 4).
8.1 Kraft/varme
Der produceres el af den rensede produktgas i en gasmotor/generator til dækning af anlæggets energiforbrug. Der kan maximalt produceres 580 kW med den eksisterende motor. Det vil dog være muligt at
producere 650 kW el med en større motor.
Anlæggets el-forbrug er 540kW, så der opnås et lille overskud. De 73 kW stammer fra el-forvarmning af luft, som vil kunne klares med damp, hvorved det teoretisk vil være muligt at opnå et overskud på
183kW med anden motor.
Anlægget producerer også damp og varme, som benyttes i garveriet og til tørring af slam til brændselspiller.
I tabel 3 er vist et energiregnskab for det termiske anlæg henholdsvis uden og med energiforbrug til tørring af slam
Tabel 3. Energibalance for termisk anlæg.
|
Med slamtørring |
Uden slamtørring |
Brændselspiller |
670 kg/h |
670 kg/h |
Energiindhold |
14.8 MJ/kg |
14.8 MJ/kg |
Koks |
30 kg/h |
30 kg/h |
Energiindhold |
28.5 MJ/h |
28.5 MJ/h |
Virkningsgrad gasmotor |
35 % |
35 % |
Maksimal el-produktion |
580 KW |
580 KW |
|
|
|
Energi input |
kW |
kW |
Brændselspiller |
2.754 |
2754 |
Koks |
238 |
238 |
Forvarmet luft (el) |
73 |
73 |
Plasmagenerator (el) |
267 |
267 |
Diverse motorer |
200 |
200 |
Dampforbrug tørring |
1.086 |
0 |
Sum |
4.619 |
3.533 |
|
|
|
Energi output |
|
|
Forbrændingsvarme |
1.913 |
1.913 |
Følbar varme |
1.128 |
1.128 |
Slagge og metal |
86 |
86 |
Varmetab forgasser |
70 |
70 |
Varmetab reaktor |
100 |
100 |
Varmetab Plasmagenerator |
38 |
38 |
Diverse tab |
198 |
198 |
Varmetab tørring |
435 |
0 |
Genvunden energi tørring |
652 |
0 |
Sum |
4.619 |
3.533 |
Produceret energi og tab |
|
|
Produceret el |
580 |
580 |
Produceret damp + varmt vand |
2.945 |
2.345 |
Internt forbrug og tab |
1.094 |
608 |
Sum |
4.619 |
3.533 |
I tabel 4 er vist en samlet masse og energibalance ekskl. energiforbrug til slamtørring.
Tabel 4. Masse- og energibalance for Pyroarc-anlæg ved fuld kapacitet (ekskl. slamtørring)
Proces |
Pyroarc |
Affald |
Tørt affald |
Massebalance |
Input |
Output |
|
kg/h |
GJ/t |
kg/h |
GJ |
Brændselspiller |
670 |
14,80 |
|
Koks |
30 |
28,5 |
|
|
|
Slagge |
|
136 |
|
Jernkromlegering |
24 |
|
Svovl |
0 |
|
metalhydroxider |
0 |
|
røggasrenseprodukt |
0 |
|
Brændsel konverteret til produktgas |
540 |
|
Sum brændsel |
700 |
15,39 |
|
|
Total Sum |
700 |
|
700 |
|
Energibalance |
Input |
Output |
|
GJ |
MW |
GJ |
MW |
Input energi brændsel |
10,77 |
2,99 |
|
|
|
|
|
|
|
Forbrug el plasmapyrolyse |
0,96 |
0,27 |
|
|
Forbrug el motorer mv. forgasser |
0,72 |
0,20 |
|
|
Forbrug el forvarmet luft |
0,26 |
0,07 |
|
|
Sum el forbrug |
1,94 |
0,54 |
|
|
|
|
|
|
|
Brutto Produceret el |
|
|
2,02 |
0,58 |
Netto Produceret damp + varme |
|
|
8,51 |
2,36 |
|
|
|
|
|
Netto Produceret el |
|
|
|
0,04 |
Netto totalt produceret el + varme |
|
|
|
2,38 |
|
|
|
|
|
Netto total virkningsgrad |
|
|
|
80 |
Den forholdsvis høje virkningsgrad skyldes, at varmt vand med lav temperatur kan afsættes til garveriet.
I ovenstående er ikke inkluderet nettoenergiforbruget til slamtørring. Fra processen til slamtørring genvindes 60% af den forbrugte energi.
8.2 Metaller og slaggegranulat
Anlægget producerer en jern/krom-legering med en sammensætning som vist i tabel 5. Legeringen afsættes til stålværk med en positiv afregningspris.
Tabel 5. Metalanalyse.
Grundstof |
Vægt % |
C |
1,9 |
Si |
2 |
Fe |
88 |
P |
4 |
S. |
1,2 |
Cr |
3 |
Slaggens sammensætning er vist i tabel 6. Slaggen tappes pt. i store portioner. Et alternativ er at bratkøle slaggen med vand for at producere 2-5 mm store slaggekorn. Generelt genvindes metaller, som er
ædlere end jern med metalfraktionen, mens andre metaller indgår i oxideret form i slaggen.
Tabel 6. Slaggeanalyse
Indhold |
Vægt % |
Na20 |
2,7 |
MgO |
5,5 |
K2O |
0,40 |
CaO |
23,5 |
TiO2 |
1,1 |
V205 |
0,03 |
Cr203 |
3,2 |
MnO |
0,26 |
FeO |
7,6 |
NiO |
0 |
CuO |
0,01 |
ZnO |
0,01 |
Al2O3 |
21,4 |
SiO2 |
32,8 |
P2O5 |
0,25 |
PbO |
0 |
C |
0,06 |
S |
3,3 |
På figur 6 er vist et stykke af metallegeringen og et stykke af slaggen.
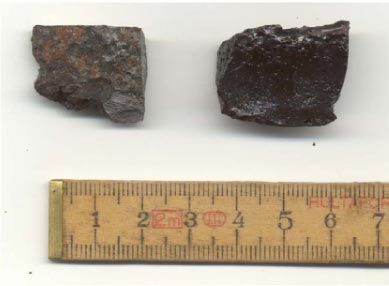
Figur 6. metallegering (til venstre) og slagge (til højre).
Slaggen har udvaskningsdata som vist i tabel 7.
Tabel 7. Udvaskningsdata for slagge fra Borges Pyroarc-anlæg.
Stof |
Målt * |
Dansk slagge-
Kategori II |
Dansk slagge-
kategori III |
|
µg/l |
µg/l |
µg/l |
As |
<1,0 |
0 – 8 |
8 - 50 |
Ba |
48,6 |
0 - 300 |
300- 4000 |
Pb |
0,63 |
0 – 10 |
10 - 100 |
Cd |
0,077 |
0 – 2 |
2 - 40 |
Cr (total) |
0,81 |
0 – 10 |
10 - 500 |
Cu |
6,2 |
0-45 |
45-2000 |
Hg |
- |
0 – 0,1 |
0,1- 1 |
Mn |
53,7 |
0- 150 |
150- 1000 |
Ni |
8,8 |
0 - 10 |
10- 70 |
Zn |
14,6 |
0- 100 |
100 - 1500 |
Sb |
0,23 |
Ingen krav i DK |
Ingen krav i DK |
*Slaggen overholder som det ses de danske krav for udvaskning i kategori II
8.3 Restprodukter
Slam fra gasrensningsanlægget behandles i garveriets vandrensningsanlæg før det recirkuleres til Pyroarc-processen sammen med andet slam fra garveriet.
9 Økonomi
9.1 Nødvendige investeringer til etablering af anlægget
I det følgende er foretaget en beregning af behandlingsomkostningerne baseret på økonomidata for anlægget ved anvendelse til behandling af læderaffald med produktion af brændselspiller udfra slam, som
tørres med damp fra anlægget.
Anlægsstørrelse: |
15.000 t vådt affald/år |
Rente: |
7% p.a. |
Tilbagebetalingstid: |
15 år |
Investeringssum inkl. bygninger: |
50 mio. DKK. |
9.2 Salgspriser for produkter
Salg af elektricitet: |
0,35 DKK/kWh |
Salg af varme: |
0,15 DKK/kWh |
Salg af metallegering samt udgift til transport: |
0,00 DKK/kg |
Salg af slagge: |
0,00 DKK/kg |
Der regnes med en netto overskudsproduktion af damp/varme på 2,36 MW svarende til 1.100 kWh/t tilført vådt affald (~ 2,1 t vådt affald/time). Salgsprisen for damp/varme afregnes til 15 øre/kWh, selv
om dampindholdet kan afsættes til en højere pris.
9.3 Udgifter til deponering og løn
Gennemsnitlig løn til personale: |
300.000 DKK/person |
9.4 Driftsudgifter
Energi: |
0 DKK da der produceres overskud af strøm og varme |
Personale: |
16 (basis: 24 h, 320 dage) |
Kemikalieforbrug: |
914.700 DKK/år |
Vandforbrug/gasbehandling |
200.400 DKK/år |
Vedligehold og reparation: |
1.090.655 DKK/år |
Div. forsikringer mv.: |
Ikke medtaget |
Administration og overhead: |
Ikke inkluderet |
9.5 Behandlingsomkostninger
Beregningen af behandlingsomkostninger er et estimat, som skal vise niveauet for behandlingsomkostningerne. Den endelige behandlingspris vil være afhængig af anlægsplacering, faciliteter til stede, valgte
bygningsstandarder osv. samt størrelsen af den rabat, der ved forhandling kan opnås på købsprisen for anlægget.
Beregningen viser følgende udgifter
Kapitaludgifter: |
366 DKK/t |
Driftsudgifter: |
467 DKK/t |
Indtægter: |
165 DKK/t |
Behandlingsprisen estimeres således til ca. 670 DKK/t vådt affald inkl. bygninger for et turn-key-anlæg ved en tilsvarende placering i Danmark.
Der regnes ikke med sparede udgifter til deponering af læderaffaldet. Anlægget giver ved placeringen ved Borge overskud, når disse udgifter fratrækkes.
Det skal bemærkes at prisen er pr. ton vådt affald. Hvis der regnes pr. ton tørret affald tilført forgasningsanlægget, er behandlingsprisen omkring 2.000 DKK/t. Hvis der behandles affald, som ikke skal
tørres (fx træflis), er behandlingsprisen i størrelsesordenen 1.200-1.400 DKK/ton for så lille et anlæg.
9.5.1 Anvendelse af PyroArc processen til shredderaffald og imprægneret træ
Enviroarc har efter besøget leveret et overslag over økonomien i Pyroarc- anlæg, der behandler trykimprægneret træ og shredderaffald.
Pyroarc processen har været afprøvet med briketteret shredderaffald og imprægneret træ i forsøgsanlægget i Hofors.
Enviroarc har foretaget en økonomiberegning for turn-key anlæg til henholdsvis shredderaffald og imprægneret affaldstræ baseret på følgende forudsætninger:
Anlægsstørrelse: 50.000 ton/år (ca. 7 t /h)
Der regnes med 15 års afskrivning og 7% rente.
Anlæggene omfatter gasmotorer til produktion af elektricitet og varme og en kedel, der producerer damp af den varme produktgas. Der regnes med levering af fjernvarme ved ca. 120°C. De producerede
mængder energi er konservativt sat, og der vil kunne opnås en højere virkningsgrad, hvis der er mulighed for at afsætte energi med lavere temperatur fx til forvarmning af fjernvarmevand.
Anlægget til shredderaffald omfatter brikettering af brændselspiller, men ikke tørring til < 10% fugtindhold, som kræves for at kunne presse stabile briketter.
For shredderaffald er regnet med en nedre brændværdi på 13 MJ/kg og et askeindhold på 40-50% inkl. metaller. Der produceres en jern/kobber-baseret legering og en slagge med forventede gode
udvaskningsresultater.
For CCA imprægneret træ er regnet med en nedre brændværdi på 15,4 MJ/kg, 1-2% askeindhold inkl. metaller og 25% fugtindhold.
Enviroarc forventer, at 50-80% af arsenindholdet i træet ender i procesgassen, hvorfra det kan udsepareres i et slamprodukt via en renseproces. Ved tilbage-føring af slammet til forgasseren og tilsætning af
jernholdigt materiale, bør der ifølge Enviroarc kunne produceres en jern-arsenholdig smelte, hvor arsen er hårdt bundet. Kobber og krom vil fordele sig på forskellig vis mellem den smeltede slagge og
metalsmelter. Der er ikke fremlagt tilstrækkelige forsøgsda-ta til at kunne dokumentere fremgangsmåden nærmere.
Der er regnet med en lønomkostning på 300.000 DKK/år i gennemsnit for 23 mand + 600.000 DDK/år til en anlægsejer.
Tabel 8. Behandlingsomkostninger ved behandling af shredderaffald og CCA-imprægneret træ
Brændsel |
Shredderaffald |
CCA-imprægneret træ |
Investering inkl. bygninger ¹ |
245 mio. kr. |
236 mio. kr. |
Salg af elektricitet |
1,5 MW |
3,9 MW |
Salg af fjernvarme |
11,2 MW |
13,7 MW |
Kapitaludgifter |
538 DKK/t |
518 DKK/t |
Driftsudgifter |
387 DKK/t |
382 DKK/t |
Indtægter |
315 DKK/t |
489 DKK/t |
Behandlingsomkostning |
610 DKK/t |
411 DKK/t |
1 Omfatter udgifter til bygninger og anlægsarbejde på 36 mio. DKK.
De beregnede behandlingsomkostninger er ekskl. sparede deponeringsomkostninger og skal kun betragtes som et vejledende niveau.
10 Konklusioner og anbefalinger
10.1 Egnethed for den danske affaldsstruktur
Anlægget bedømmes anvendeligt til behandling af danske affaldsfraktioner, som indeholder metaller og mineraler med tungmetalindhold. Udover læderaffald vil et sådant anlæg kunne tænkes benyttet til
smeltning af mineralfraktioner fra shredderaffald, hvis større metaldele er fjernet, eller til behandling af imprægneret affaldstræ. Det nuværende forbrug af koks vil kunne erstattes af træflis fra fx
creosot-imprægneret træ eller andet træ. Vi forventer, at Pyroarcanlæg kan forgasse imprægneret træ uden problemer. Anlægget ved Borge garveri startes således altid op på træflis, som er et velfungerende
brændsel.
Enviroarc har udført forsøg med briketteret shredderaffald og CCA-imprægneret træ på forsøgsanlægget i Hofors og mener udfra de samlede erfaringer, at de vil kunne håndtere affaldstyperne med Pyroarc
processen.
Enviroarc har imidlertid ingen langtidserfaring med behandling af shredderaffald og CCA-imprægneret træ.
10.2 Omkostningsstruktur
Behandlingsomkostningerne for læderaffald er omkring 700 DKK/t tilført vådt affald. Det tilførte våde affald læderaffald omfatter slam og udgør 15.000 t/år mens det tørrede affald til forgasseren udgør ca.
5.000 t/år.
Behandlingsomkostninger for et anlæg til shredderaffald på 50.000 t/år er anslået til ca. 600-650 DKK/t mens behandlingsomkostningerne for et anlæg til imprægneret træ med en kapacitet på 50.000 t/år er
anslået til 400-450 DKK/t ekskl. sparede deponeringsomkostninger.
10.3 Affaldets udnyttelsesgrad
Anlægget genvinder metaller ved smeltning. Hvis der tilsættes affald, som hovedsageligt er baseret på kobber og jern som fx rester af shredderaffald, vil anlægget kunne producere en jern/kobber-legering.
Hvis der behandles læderaffald inkl. jernholdigt slam, kan anlægget producere en jern/krom legering.
Ved behandling af CCA-imprægneret træ forventer Enviroarc, at hovedparten arsenindholdet i træet genfindes i procesgassen, hvorfra det kan udsepareres i et slamprodukt via en renseproces. Ved
tilbageføring af slammet til forgasseren og tilsætning af jernholdigt materiale, bør anlægget ifølge Enviroarc kunne producere en jern-arsen-holdig smelte, hvor arsen er hårdt bundet. Der er ikke fremlagt
tilstrækkelige forsøgsdata til at kunne dokumentere frem-gangsmåden nærmere.
Udover udvundne metalfraktioner vil mineraler og oxiderede metaller findes i en tæt glasagtig slagge, som forventes at overholde kravene til genanvendelse i den danske restproduktbekendtgørelse for
kategori III og muligvis også kate-gori II. Dette bør dog undersøges nærmere.
Slagge, der overholder udvaskningskravene, vil kunne anvendes til vejfyld eller indgå i byggematerialer.
Metaller som aluminium vil mistes sammen med slaggen
10.4 Miljømæssige problemstillinger
Emissioner fra anlægget overholder de europæiske krav. Anlægget producerer ingen restprodukter til deponering ved behandling af læderaffald.
10.5 Muligheder for knowhow-formidling
Knowhow-formidling kan ske via Enviroarc.
Bilag C
Logbog for besøg hos H.J.Hansen
1. Generelle oplysninger
1.1 Procestype
Mekanisk sorteringsanlæg for shredderaffald
1.2 Tilført affald
Shredderaffald direkte fra shredderen.
1.3 Licenshaver og kontaktpersoner
Anlæggets opbygning og sammensætning af udstyr er udviklet af og hos H.J. Hansen i Odense. Knowhow er tilstede hos H.J. Hansen, der dog ikke er licenshavere.
Kontaktperson er Produktionsdirektør, Erling Møller Nielsen
Tlf.: +45 63109100
Fax: +45 63109101
E-mail: emn@hjhansen.dk
1.4 Ejerforhold og kontaktpersoner for det besøgte anlæg
Anlægget ejes af H.J.Hansen og kontaktpersonen er Erling Møller Nielsen.
1.5 Beliggenhed for det besøgte anlæg
Anlægget er beliggende hos:
H.J.Hansen
Recycling Industry Ltd
Havnegade 110
Dk 5100 Odense C
1.6 Virksomhedens formål og idégrundlag
Det er anlæggets formål ved sortering at genvinde de fri metaller af jern, kobber og aluminium samt legeringer af disse metaller.
1.7 Kapacitet for det besøgte anlæg
Kapaciteten for anlægget er udlagt således, at det kan behandle alt affald fra shredderen og synke/flyde-separationsanlægget hos H. J. Hansen. Anlægget kan behandle op til 30 tons pr. time i
spidsbelastningssituationer.
1.8 Byggeår og status for projektet
H. J. Hansen har siden starten af 1990érne udført en række forsøg med nyttiggørelse af shredderaffald. I de første år blev der udført forsøg med forbrænding af visse fraktioner af shredderaffald, evt. skulle
dette ske i samforbrænding med husholdningsaffald. Alle forbrændingsforsøg gav problemer med belægninger i kedler.
Siden 1998 har man koncentreret sig om ved mekanisk sortering at genvinde shredderaffaldets frie metaller.
Et raffineringsanlæg er siden blevet opbygget, og dette anlæg er fortsat at betragte som en prototype under udvikling og udbygning.
Anlægget påtænkes nu udbygget således, at også glas og plast kan udsorteres af shredderaffaldet til genbrug.
2. Kortlægning og beskrivelse af anlægget
2.1 Procesdiagram
H.J.Hansen ønsker af hensyn til konkurrencen på markedet ikke at give detaljerede oplysninger om anlæggets opbygning. En principskitse er dog vist i figur 1.
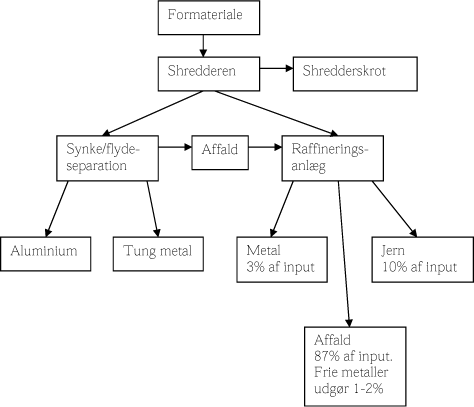
Figur 1. Principdiagram
2.2 Affald
Anlægget behandler hovedsageligt shredderaffald direkte fra shredderen. Desuden behandles affaldet fra synke/flyde-separationsanlægget.
2.3 Forbehandling
Ingen forbehandling af shredderaffaldet er muligt i den konstellation, man har valgt og er heller ikke nødvendigt.
2.4 Proces(ser)
Raffineringsanlæggets processer består af mekaniske neddelingsprocesser og sigtningsprocesser. Desuden anvendes moderne sensor- og sorteringsteknologi. Disse processer vil på grund af H.J.Hansens
ønsker om hemmeligholdelse ikke blive omtalt nærmere.
3. Observationer under besøget
3.1 Besøgets varighed
Den 2002-08-14 fra kl. 10:00 til kl. ca.15:00.
3.2 Tilførte materialer behandlet under besøget
Shredderaffald.
3.3 Driftsforhold
Driftstid efter behov således, at alt shredderaffald behandles
3.4 Output under besøget
Processens output er jern og ikke-jern-metaller samt restprodukt, som ind til videre deponeres i specialdepot.
4. Kritiske delprocesser og driftsparametre
Der må på grund af shredderaffaldets sammensætning og indhold af især glas og metaller forventes en vis slidtage på neddelingsaggregater, men egentlig kritiske delprocesser kan man ikke tale om.
5. Miljømæssige forhold
5.1 Emissioner til luften
Anlægget er i dag placeret i et telt, men vil i sin endelige udformning blive placeret i en lukket hal med ventilation og filtrering af luften. Der vil derfor ikke forekomme nogen emissioner til luften af miljømæssig
betydning.
5.2 Spildevandsudledning
Der er ingen spildevand fra processen.
5.3 Støj
Det vurderes, at der ikke vil være nogen problemer med overholdelse af støjkrav.
5.4 Lugt
Der er ingen lugtgener fra anlægget.
5.5 Affaldsproduktion
Restproduktet er shredderaffald, der stort set er befriet for frie metaller.
6. Arbejdsmiljømæssige forhold
6.1 Støvbelastning
Alle støvende delprocesser (neddeling, sigtning sortering mv.) foregår i lukkede systemer med afsugning.
6.2 Internt støjniveau
Det interne støj-niveau var lavt og vil med stor sandsynlighed overholde de danske krav. Driftspersonalet har normalt ingen arbejdsopgaver i nærheden af de mest støjende delprocesser. Når eller hvis
inspektion er nødvendigt, må høreværn anbefales.
6.3 Tungmetalbelastning
Under normale driftsforhold skønnes det ikke at være nødvendigt at foranstalte særlig beskyttelse af driftspersonalet mod tungmetalbelastning, dels på grund af et lavt støvniveau og dels på grund af, at der
ikke er faste arbejdspladser i nærheden af de mest støvende delprocesser.
Under reparations- og rengøringsarbejde vil det nok være fornuftigt at kræve åndedrætsværn. Vi har dog ikke under det korte besøg kunnet danne os en mening om disse forhold
7. Beskrivelse af input og output
Input til processen er shredderaffald fra shredderanlægget og synke/flyde-separationsanlægget hos H. J. Hansen.
Analysen af inputtet antages at være som beskrevet tabel 1, som er identisk med tabel 1 i dette projekts fase 1.
Tabel 1. Sammensætning af shredderaffald
Komponent |
DK
1996 |
Fe |
13,2 % |
Al |
2,5% |
Zn |
1,9% |
Cu |
1,2% |
Pb |
0,35% |
Ni |
0,04% |
Sn |
0,01% |
Cr |
0,04% |
Cd |
0,004% |
Metal |
19,2% |
Cl |
2,0% |
Vand |
Ca. 10% |
Brændværdi |
13,9 MJ/kg |
Af de 19,2% metaller i dette affald anslås ca. 5% at foreligge som oxider og ca.14,2% foreligger som frie metaller.
Outputtet efter raffineringsanlægget indeholder 1 – 2 % frie metaller. Senest opnåede resultater har vist, at frie metaller udgør 1,08%
7.1 Metaller
De udsorterede metaller kan sælges til genbrug.
8. Økonomi
8.1 Nødvendige investeringer til etablering af anlægget
Udgifterne til etablering af anlægget er ikke oplyst til os og er svære at estimere.
8.2 Omkostningsstruktur
Nedenstående forudsætninger og data er vort bedste skøn, idet H. J. Hansen ikke har ønsket at give os oplysninger om disse forhold.
Anlægsstørrelse: |
> 20 tons SHR/h |
>100.000 t/år |
Investeringer: |
Ca. 20.000.000 DKK. |
|
Rentefod: |
7% p.a. |
|
Afskrivningstid: |
7 år. |
|
Driftsomkostninger
Løn til personale: |
300.000 DKK/år. |
6 personer |
Elektricitet: |
390 DKK/MWh |
700 MWh/år. |
Vedligehold: |
ca. 5% af investering |
|
Skønnede behandlingsomkostninger
De endelige behandlingsomkostninger vil være særdeles afhængige af den pris, man kan få for de genvundne metaller, som ikke er medtaget i denne beregning, men de direkte behandlingsomkostninger inkl.
kapitalomkostninger er med de nævnte forudsætninger ca. 72 DKK/t shredderaffald. Heri er ikke medtaget de sparede omkostninger til deponering af restaffaldet, ligesom salgspriser for de genvundne
metaller ikke er medtaget.
9. Konklusioner og anbefalinger
9.1 Egnethed for den danske affaldsstruktur
H. J. Hansens koncept anvendes på den danske affaldsstruktur og må naturligvis anses for at være særdeles velegnet hertil. Det skal dog bemærkes, at anlægget er under fortsat udvikling. Man forventer
således, at en del glas og en dels plast fremover vil kunne genvindes fra raffineringsanlægget.
Den fremtidige udvikling vil bl.a. omfatte rysteborde til yderligere metalgen-vinding.
9.2 Affaldets udnyttelsesgrad
Anlægget er i fuld kommerciel drift og genvinder stort set alle frie metaller fra shredderaffaldet. Dette gør, at restaffaldet vil være velegnet som indsatsmateriale i alle tilgængelige termiske teknologier, der er
egnet til behandling af shredderaffald.
9.3 Miljømæssige problemstillinger
Ingen væsentlige.
9.4 Muligheder for know-how-formidling
H. J. Hansen Recycling Industry Ltd.
Att.: Produktionsdirektør Erling Møller Nielsen
Havnegade 110
5100 Odense C
Telefon: 63 10 91 00
E-mail: genvinding@hjhansen.dk
Bilag D
Logbog for besøg hos Högdalenverket
1 Generelle oplysninger
1.1 Procestype
Forbrænding i cirkulerende fluid bed med produktion af damp til kraft/varme produktion
1.2 Tilført affald
Det tilførte affald består af en blandet neddelt affaldsfraktion fra husholdninger og virksomheder med et stort indhold af neddelt bygningsaffald.
1.3 Licenshaver og kontaktpersoner
Licenshaver
Foster Wheeler Energia Oy
Finland
Kontaktperson
Foster Wheeler Energia Oy
Att. Timo Anttikoski
Nuijamiestentie 3
FIN-0040 Helsinki
Finland
Telefon: 358-10-39311
Fax: 358-10-393-6162
E-mail: timo.anttikoski@fwfin.fwc.com
1.4 Ejerforhold og kontaktpersoner for det besøgte anlæg
Birka service
Göran Eidensten
Telefon: +46 -8-619-47-00
1.5 Beliggenhed for det besøgte anlæg
Högdalenverket
Kvicksundsvägen 16
Högdalen
1.6 Virksomhedens formål og idégrundlag
Virksomheden producerer kraftvarme til Stockholm
1.7 Kapacitet for det besøgte anlæg
Linie 6 har en kapacitet på 91,2 MWh svarende til ca. 25 ton neddelt bygningsaffald per time eller 200.000 t/år ved 8000 driftstimer
1.8 Byggeår og status for projektet
Anlægget har været i kommerciel drift siden starten af 2000, men der foregår stadig en optimering med henblik på at mindske driftsstop. Anlægget har per 1. august 2002 haft mere end 15.000 driftstimer.
2 Kortlægning og beskrivelse af anlægget
2.1 Procesdiagram
Under besøget blev anlægget kortlagt som vist i Figur 1:
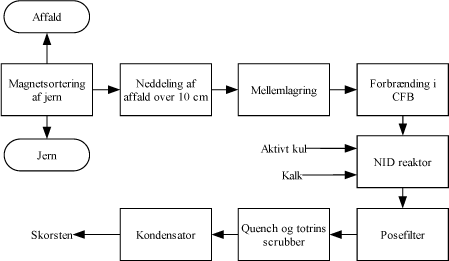
Figur 1. Procesdiagram for Högdalenverket.
2.2 Affald
Det tilførte affald består af en blandet neddelt affaldsfraktion fra husholdninger og virksomheder. Affaldet stammer fra savværker, emballageproduktion, papir og pap rester, træholdigt byggeaffald, træaffald,
kildesorteret træ og papiraffald, centralt sorteret træ og papiraffald
Det træholdige byggeaffald kaldes også ”Returbrändsel” og er en blanding af papir, træ, plast, gummi, tekstil, metaller mm.
Affaldet modtages fortrinsvis neddelt til under 10 cm. En mindre del neddeles af værket selv.
Sammensætningen af ”Returbrändsel” varierer men overholder data i tabel 1.
Tabel 1. ”returbrändsel”.
Materiale |
% (w/w) |
Papir |
< 90 |
Træ |
20 - 90 |
Plast |
< 20 |
Gummi |
< 5 |
Tekstil |
< 5 |
Øvrigt brændbart |
< 5 |
Metaller |
< 5 |
Øvrigt ubrændbart |
< 10 |
Aluminium |
< 0,25 |
2.3 Forbehandling
Affald med indhold af jern magnetsorteres hvorefter affaldet passerer et sold hvor det der er over 10 cm føres retur til neddeling. Større træaffald som paller etc. neddeles ligeledes til < 10 cm. Affaldet føres
til 2 stk. 4000 m³ lagerbunkere. Brændsel føres herfra til en yderligere magnetseparator (overbåndsmagnet) til 3 mellemsiloer.
2.4 Cirkulerende fluid-bed
Affaldet tilføres fra mellemsiloer til den cirkulerende fluidbred via tre parallelle indfødningssystemer. På transportørbåndet er placeret et justerbart overløb der fyldes op hvorefter der indfødes et ønsket
volumen pr. tid ved at variere båndhastigheden.
Fluid-breddens bundareal er 3*8 m. I bunden er placeret dyser som blæser luft mod midten af fluid-bedden. Dysernes placering falder ind mod midten hvor de tre askeudtag findes. Der er problemer med
slid og korrosion af dyserne. I fluid-bedden cirkulerer 40 tons sand med en diameter på 0,78 mm. Fluid-bedden forbrænder ved 850°C med ca. 5% ilt i den producerede røggas og sandet recirkuleres via
cyklonkammeret i toppen (se Figur 2). Der benyttes recirkuleret røggas fra efter sugetræksblæser som til temperaturstyringen.
I cyklonkammeret doseres ammoniak til reduktion af NOx. I bunden af cyklonkammeret passerer røggassen den 3.die overheder i en lille boblende fluid-bed. Røggassen ledes efter passage af 2.overheder,
1.overheder og økonomiser til røggasrensningsanlægget. Ved 2.overheder renses for belægninger med hamre mens der ved 1.overheder benyttes damprensning.
Der produceres damp ved 59 bar, 480°C fra 3. overheder.
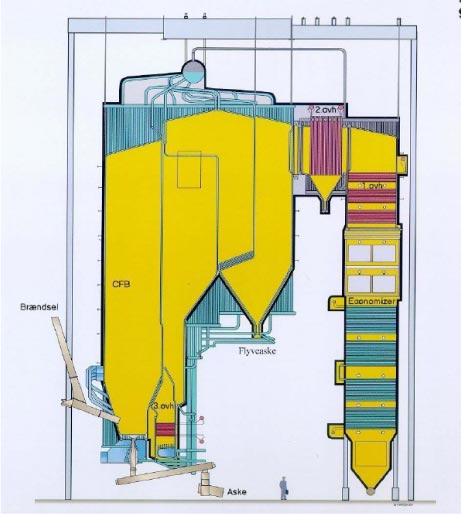
Figur 2. CFB anlægget på Högdalenverket.
2.5 Røggasrensning
Røggassen renses først ved dosering af kalk og aktivt kulstof i en NID reaktor med efterfølgende fjernelse af røggasrenseproduktet i posefilter ved 140°C. Røggassen bratkøles herefter til 60°C og vaske i
en vådvasker med surt trin og neutralt trin. Efter et dråbefang kondenseres vandet ud af røggassen til ca. 40°C hvorefter røggassen genopvarmes til 60°C og ledes til skorsten.
Vandet fra kondenseringen renses ved tilsætning af natriumsulfat og fældning i to trin, behandling i sandfilter og ved behandling med brintperoxid.
2.6 Energiproduktion
Der var under besøget ved at blive idriftsat en turbine/generator som producerer strøm fra fluid-beddens 59 bar damp på primærkredsen, samt udnytter dampen på 36 bar fra de eksisterende ristebaserede
linier i sekundærkredsen. Når der ikke produceres strøm produceres fjernvarme af al energien til Stockholms fjernvarmenet.
3 Observationer under besøget
3.1 Besøgets varighed
Den 24/4 2002 fra kl. 10:00 til kl. 14:30.
3.2 Indsatsmaterialer behandlet under besøget
Type: Normal blanding hvoraf en stor del er neddelt
træholdigt byggeaffald ”returbrändsel”.
Mængde i t/h: 25 t/h eller 3.000 m³/døgn
Kapacitetsudnyttelse: 100 %
3.3 Driftsforhold
Driftstid: 24 h/døgn
Forventet produktionstid: 8.000 h/år
Revisioner: Planlagt til 4 uger+ 1 lille inspektionsstop af
3 dage pr. år
For nuværende kræves et stop hver 6. uge men
dette er under forbedring.
3.4 Output under besøget
Metaller og restprodukter fra anlægget blev kort besigtiget. Besøget var for kort til at kunne give en
beskrivelse af produktionsmængderne men typiske mængder er vist i tabel 2.
Tabel 2. Restprodukter fra CFB anlægget
Fraktion |
Mængde |
Behandling |
Bundaske |
Alle partikler > 1-2 mm |
Deponeres |
Flyveaske |
12 ton/dag |
En del deponeres og en del recirkuleres til CFB |
Røggasrenseprodukt fra posefilter |
12 ton/dag |
Stabiliseres og deponeres derefter |
Restprodukt fra skrubber surt trin |
|
Behandles i eksisterende risteforbrændingsanlæg |
Restprodukt fra skrubber neutralt trin |
|
Anvendes til opløsning af kalk i NID reaktor |
Renset vand fra kondensering |
|
Til afløb |
Metaller |
Ca. 15 m³/døgn med ca. 50% (v/v) plast mm. |
Genvindingsindustri |
El/varme
Den termiske virkningsgrad er opgivet til 91% ved brændsel med en nedre brændværdi på 13 MJ/kg, men kendes normalt ikke grundet manglende kendskab til brændværdien i affaldet.
El virkningsgraden med den nye turbine/generator er endnu ikke kendt.
4 Kritiske delprocesser og driftsparametre
Under besøget blev følgende spørgsmål diskuteret:
- Er der forekomst af kondenserbare stoffer og forureninger i processernes forskellige trin; fx af tjære, sod, metaller, salte og oxider i pyrolyseovnens top, i gaskanaler eller i
efterforbrændingskamre?
Der er problemer med afsætninger på panelvægge inden anden overheder. Der arbejdes med påbygning af rensningssystemer til dette. I de tre overhedere og økonomiseren er der ingen problemer.
Der forekommer korrosion og slid af dyser i Fluid-bedden.
Indfødningssluserne blokeres af og til af metaller ikke magnetiske metaller som rustfrit stål og aluminium
- Hvordan kontrolleres mængden af kondenserede stoffer, dvs. hvordan renses de kritiske procesafsnit for afsætninger?
I økonomiseren er rensning ikke nødvendig. 1. overheder renses med damp, anden overheder renses med hamre og for tredie overheder er rensning ikke nødvendig.
- Hvilken kemisk stabilitet har restprodukter fra processen? Er de lagringsstabile mht. tungmetaller og dermed egnet til deponering (data for standardudvaskningstests), eller
lækker der tungmetaller, og skal de betragtes som miljøfarligt affald?
Data haves ikke.
- Findes der dioxiner (eller andre halogenerede organiske stoffer) i restprodukter eller evt. mellemprodukter som skal oparbejdes andetsteds?
Bundasken er næsten 100% udbrændt og forventes at have et lavt dioxinindhold.
Flyveaske og røggasrenseproduktet fra posefiltret vil formentlig indeholde en vis mængde dioxiner.
5 Miljømæssige forhold
5.1 Emissioner til luften
Tabel 3. Emissioner til luft.
Stof |
Målt/garanti (11% O2) |
EU-krav (11% O2 ,tør gas) |
|
mg/Nm³ |
mg/Nm³ |
SOx |
Virkede ikke under besøg |
50 |
NOx |
45 |
200 |
HCl |
Virkede ikke under besøg |
10 |
CO |
Virkede ikke under besøg |
50 |
Støv |
0,5 |
10 |
|
|
|
|
ng –TEQ/m³ |
ng- TEQ/m³ |
Dioxiner |
Måles ikke |
0,1 |
5.2 Spildevandsudledning
Der udledes renset spildevand til afløb. Rensningen er ikke optimal og der har været problemer med overholdelse af emissionstilladelser. Dette har dog intet med fluid-bed teknologien at gøre men er blot
udslag af et lidt forkert design af rensningsanlægget.
5.3 Støj
Støjniveauet er normalt for denne type anlæg.
5.4 Lugt
Der er ikke observeret lugtproblemer
5.5 Affaldsproduktion
De væsentligste affaldsprodukter er røggasrenseproduktet fra posefiltret samt flyveasken som formodes at indeholde hovedparten af dioxiner
5.6 Samlet dioxinemission
Kendes ikke
6 Arbejdsmiljømæssige forhold
6.1 Støvbelastning
Der konstateredes en del støv på anlægget pga. manglende rengøring herunder i brændselslagre, hvor neddeling og transport af brændsler foregår uden udsugning. Generelt foregår al brændselstransport i
lukkede rør, men nogle steder forekommer utætheder.
Hvis et lignende anlæg skal behandle imprægneret affaldstræ, skal anlægget derfor udstyres med meget effektive støv-begrænsende foranstaltninger herunder afskærmning, afsugning mv., så driftspersonale
kan undgå kontakt med både støv fra neddeling og transport af brændsel og med restprodukter.
6.2 Internt støjniveau
Støjniveauet vurderes som normalt for denne type anlæg. Turbine findes i separat rum hvor der kræves høreværn.
6.3 Tungmetalbelastning
Støvet fra brændslet kan medføre eksponering for metaller men også andre skadelige stoffer fra neddeling af byggematerialer. Dette kan dog løses med et bedre brændselstransportsystem og er et problem
som ikke vedrører kerneteknologien –den cirkulerende fluid bed.
6.4 Dioxinbelastning
Dioxiner forventes kun at forekommer i restprodukter fra posefiltre, samt flyveaske der håndteres i lukkede systemer og således ikke udgør en risiko.
6.5 Andet; fx lugtgener, vilkår i forbindelse med reparationsarbejde mv.
Forventes at være sammenligneligt med tilsvarende arbejde ved traditionelle forbrændingsanlæg
7 Beskrivelse af input
Det typiske brændsel er neddelt byggeaffald af sammensætning som i Tabel 2.1.
Det neddelte bygningsaffald er vist på Figur 3 og Figur 4.
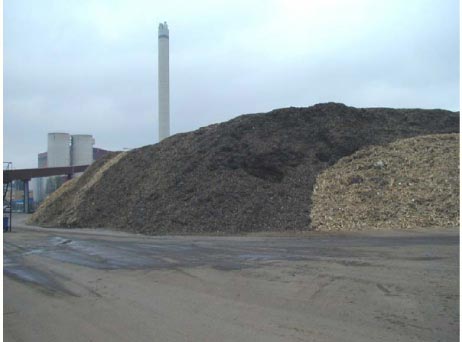
Figur 3 Neddelt bygningsaffald som tilføres CFB anlægget (lagerkapacitet)
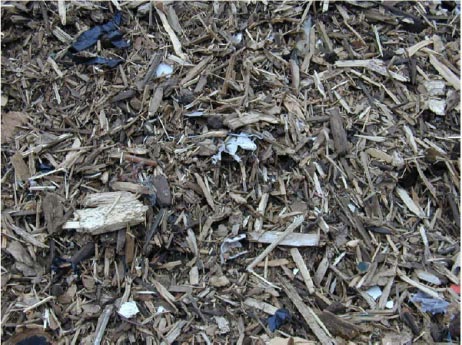
Figur 4. Neddelt bygningsaffald som tilføres CFB anlægget (detaljer).
Der behandles endvidere forsøgsvis en række andre brændsler. På Figur 5 er således vist blandet plastaffald fra det tyske DSD-system som er presset til piller.
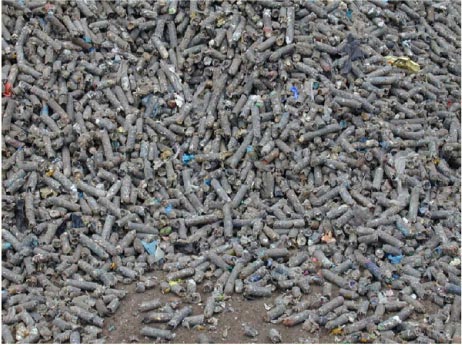
Figur 5 plastpiller fra DSD-systemet i Tyskland
Fluid-bedden må tilføres 10 t frisk sand pr. døgn
8 Beskrivelse af output
Besøget var for kort til en detaljeret beskrivelse af outputs.
8.1 Kraft/varme
Der produceres damp ved 59 bar, 480°C som leverer varme til fjernvarmenettet i Stockholm. Prøvedrift er påbegyndt af turbine/generator til el-produktion.
8.2 Metaller
Metaller fra magnetsortering af det tilførte brændsel er vist på Figur 6
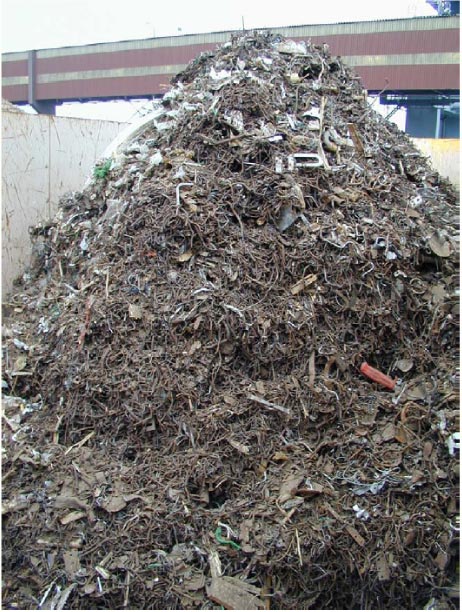
Figur 6 Metaller
8.3 Restprodukter
Bundasken er vist på Figur 7.
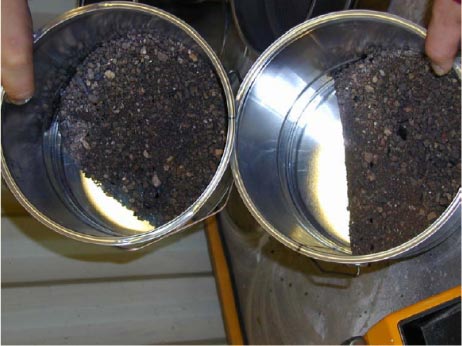
Figur 7. Bundaske fra Högdalenverket.
Der forventes et meget lavt kulstofindhold i bundasken grundet den gode udbrænding, men data haves ikke.
Flyveasken er vist på Figur 8.
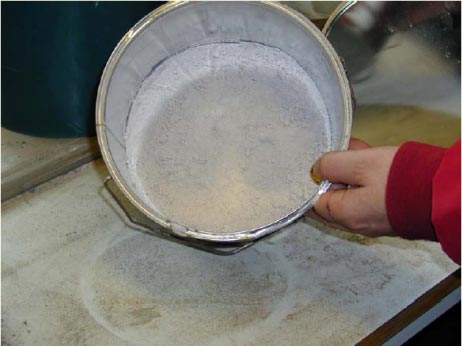
Figur 8. Flyveaske fra Högdalenverket.
9 Økonomi
9.1 Nødvendige investeringer til etablering af anlægget
Det har ikke været muligt at indhente detaljerede oplysninger om økonomien.
Investeringen er dog opgivet til 600 mio. SEK for et komplet anlæg uden turbine/generator
Dette svarer til ca. 470 mio. DKK Investeringen vurderes som væsentligt mindre end for tilsvarende ristebaserede anlæg med samme kapacitet.
Hvis et tilsvarende anlæg skal behandle CCA-imprægneret affaldstræ, vil investeringen anlægget skulle omfatte udstyr, der sikrer mod støvemission og kontakt med restprodukterne.
9.2 Driftsudgifter
Udgifter til drift og vedligehold forventes at være lidt højere end ved ristebaserede anlæg bl.a. grundet et sandforbrug på 10 t/døgn, samt ekstra mandskab til løsning af nuværende problemer med stop i
brændselstransportsystemet.
Udgift til sand udgør 1.000 DKK/t + deponeringsudgifter anslået 500 DKK/t.
Da der indfødes 600 t affald per dag svarer dette til 25 DKK/t tilført affald, så denne udgift er begrænset.
10 Konklusioner og anbefalinger
10.1 Egnethed for den danske affaldsstruktur
Anlægget er designet til brændsel med en høj brændværdi som fx træflis. Hvis store mængder af sådant affald ønskes behandlet er denne type anlæg en mulig løsning med en høj virkningsgrad. Man kunne fx
tænke sig en sådan løsning til behandling af imprægneret træ hvor restprodukterne fra affaldet opsamles og evt. viderebehandles med henblik på udvinding af metaller eller stabilisering af miljøfarlige stoffer
som arsen. Det vides dog ikke om røggasrensningsanlægget er tilstrækkeligt til at kunne håndtere arsen.
Hvis et tilsvarende anlæg skal behandle CCA-imprægneret affaldstræ, vil den store mængde nedslidte sand være forurenet med As, som derfor skal behandles som specialaffald i forbindelse med
deponering. Det høje sandforbrug er en ulempe ved processen.
10.2 Omkostningsstruktur
Der findes ikke tilstrækkelige data til en total økonomisk analyse men kapitalomkostningerne, der typisk udgør omkring 60-70% af omkostningerne til store anlæg, er noget lavere for dette fluid-bed-anlæg
end for ristebaserede forbrændingsanlæg. Det skal her bemærkes, at anlægget i modsætning til ristebaserede anlæg kræver en neddeling af det tilførte affald, og at det nuværende forbehandlingssystem ikke
er egnet til fugtige materialer som organisk affald eller CCA-imprægneret affaldstræ.
Et fluid bed anlæg, der skal behandle imprægneret affaldstræ, vil kræve en investering i et passende neddelingsudstyr, der sikrer mod emission af tungmetalholdigt støv.
10.3 Affaldets udnyttelsesgrad
Anlægget har en høj termisk virkningsgrad. Jernbaserede metaller fjernes fra det neddelte affald inden indfødning og genvindes i en god kvalitet. Det vurderes muligt også at fjerne eventuelle
ikke-jernbaserede metaller som aluminium og kobber.
10.4 Miljømæssige problemstillinger
Anlægget opnår en højere udbrænding af bundasken end den tilsvarende slagge fra ristefyrede anlæg hvilket kan have betydning for udvaskning af skadelige stoffer. Imidlertid deponeres bundasken ligesom
alle andre restprodukter deponeres. Det vides ikke om bundasken vil kunne genanvendes eller evt. oparbejdes så den kan genanvendes.
10.5 Muligheder for knowhow-formidling
Knowhow-formidling kan ske ved henvendelse til Foster-wheeler.
Bilag E
Logbog for besøg hos Igelstaverket, Söderenergi
1. Generelle oplysninger
1.1 Procestype
Fluid bed forbrænding – boblende bed.
1.2 Tilført affald
- Træaffald
- Nedrivningsaffald
- Creosot-imprægneret træ
- Plastaffald (ikke PVC) (forsøgsvis er kørt RDF m. 25% PVC)
- Papir
- Tørv
- Olie
1.3 Licenshaver og kontaktpersoner
Licenshaver
Foster Wheeler Energia Oy
Finland
Kontaktperson
Foster Wheeler Energia Oy
Att. Timo Anttikoski
Nuijamiestentie 3
FIN-0040 Helsinki
Finland
Tlf.: 358-10-39311
Fax: 358-10-393-6162
E-mail: timo.anttikoski@fwfin.fwc.com
1.4 Ejerforhold og kontaktpersoner for det besøgte anlæg
Tre kommuner nær Södertälje har dannet Söderenergi, der ejer Igelstaverket.
1.5 Beliggenhed for det besøgte anlæg
Igelsatverket
Nynäsvägen 43
S-152 07 Södertälje
Sverige
Kontaktperson: Driftsingeniør Sven Wallin.
1.6 Virksomhedens formål og idégrundlag
Fjernvarmeproduktion med minimal påvirkning af miljøet baseret på affaldsprodukter.
1.7 Kapacitet for det besøgte anlæg
Kedel 3:
Varme: |
max. 90 |
MWt |
Brændsel |
25-30 |
t/h |
Brændværdi: |
ca. 11 |
MJ/kg |
1.8 Byggeår og status for projektet
Iglestaverket blevet bygget i 1980 og producerer fjernvarme til de omliggende kommuner (40%) og Stockholm (60%). Værket har tre kedler, hvoraf kun kedel 3 er en fluid bed. Kedel 3 er oprindelige
bygget til kulfyring, men blev i 1994 ombygget af Alstom, så anlægget kunne forbrænde fugtig træflis. Kedlens oprindelige konvektionspart er bevaret.
2. Kortlægning og beskrivelse af anlægget
2.1 Procesdiagram
Kedel 3 er en boblende fluid bed bygget af Foster Wheeler i Finland.
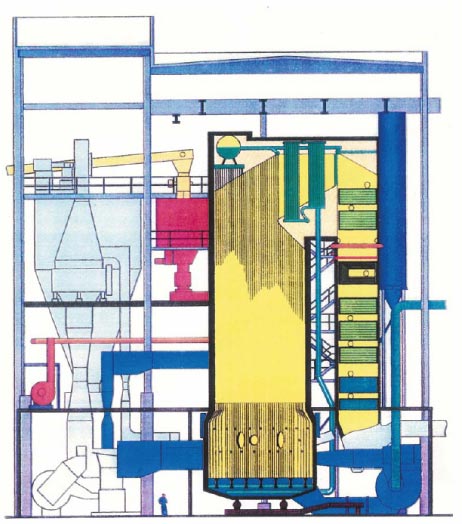
Figur 1. Skitse af Igelstaverkets fluid bed kedel (90 MWt) med hedelflader, etc.
De tre kedler har fælles røggasrensningssystem, som er vist i figur 2.
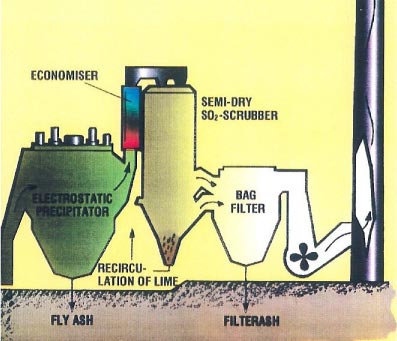
Figur 2. Røggasrensningssystem på Igelstaverket
Alle kedler har desuden separate SNCR NOx-rensningsanlæg i selve kedlen.
2.2 Affald
Kedlen fyres med
”Returlflis” (nedrivningstræ): |
86% |
Maskintørv: |
11% |
Fuelolie: |
3% |
men også papir og creosot-imprægneret træ indgår. Flere af affaldsstrømmene har et højt indhold af klor (Cl). Det er nødvendigt at fyre med tørv for at undgå korrosion.
Anlægget fyres ikke med skovflis.
Der er kørt forsøg med hollandske RDF-piller med max. 25% PVC.
Brændselsanalyser fra d. 2002-04-18 viser store variationer i brændslets sammensætning. Se tabel 2.
2.3 Forbehandling
Alt brændsel neddeles til en størrelse på ca. 2 x 2 x 5 cm.
Brændselsstykker må højst være 5 x 5 x 30 cm store.
En overbåndsmagnet fjernet jern-metaller før indfyringen.
2.4 Proces(ser)
2.4.1 Fluid bed
Kedel 3 er en boblende fluid bed med følgende data:
Areal (kvadratisk) |
49 |
m² |
Bund |
Flad/vandret |
- |
Højden af fluidiseret lag |
1-2 |
m |
Fluidiseringsluft |
14 |
m³/s |
Sand |
48 |
t |
Indfødningspunkter |
4 |
- |
|
|
|
Tbed |
850 |
°C |
Luftoverskud |
3,5 - 5 |
% O2 |
Brændslet indfyres via fire skruefødere placeret over det fluidiserede lag.
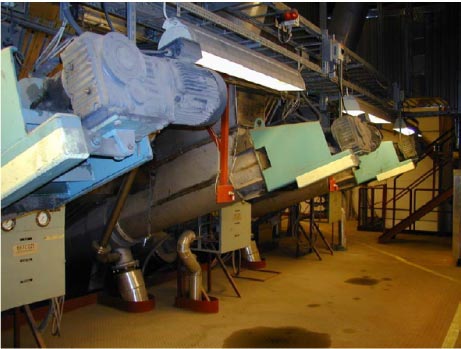
Figur 3. Tre af de fire skruefødere til igelstaverkets kedel 3.
Temperaturen i bedden reguleres ved hjælp af røggasrecirkulation og damptilførsel.
Aske og sand tages seks steder i bunden. Sandet sigtes og metaller fjernes inden de ca. 40 t sand recirkuleres pr. dag, og 5-6 t pr. dag nyt sand spædes til.
2.5 Røggasrensning
NOx reduceres ved indspøjtning af ammoniak (NH3) i fribordet på fluidbedden (SNCR-proces).
For at få en høj virkningsgrad gennem røggaskondensation opfugtes forbrændings- og fluidiseringsluften ved hjælp af røggassen i et system, der er vist i figur 4.
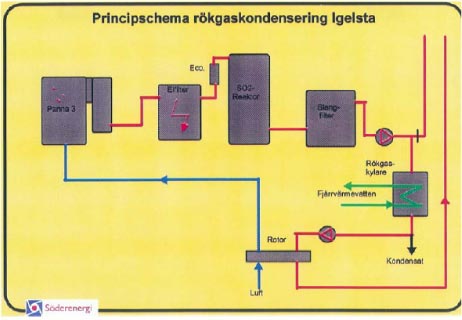
Figur 4. Principskitse for røggaskondensering og opfugtning af forbrændingsluft.
Røggastemperaturen efter de enkelte trin i røggasrensningen er:
El-filter: |
170 |
°C |
ECO: |
150 |
°C |
SO2-scrubber: |
115 |
°C |
Posefilter: |
100-110 |
°C |
Roterende luftbefugter: |
ca. 30 |
°C |
Skorstensrøret er af plast-materiale på grund af risiko for kondensation.
3. Observationer under besøget
3.1 Besøgets varighed
Den 2002-04-23 fra kl. 10:30 til kl. 15.
3.2 Tilførte materialer behandlet under besøget
Type (kvalitativ beskrivelse): |
Bygningsaffald: |
65% |
|
Tørv: |
10% |
|
RDF: |
25% |
Mængde i t/h: |
ca. 20 t/h |
|
Kapacitetsudnyttelse: |
66 % |
|
3.3 Driftsforhold
Driftstid: |
24 h/døgn |
Forventet produktionstid: |
7 måneder/år [1] |
Revisioner: |
2-3 pr. år |
3.4 Output under besøget
3.4.1 El/varme
Leveret varme: |
ca. 60 MW |
Virkningsgrad: |
108% |
Kedlen producerer damp ved 14 bar og 200°C. Dampen varmeveksles med fjernvarmevand.
Ved fuld last producerer kedel 3 90 MW, hvoraf ca. 20 MW kommer fra kondensation.
3.4.2 Restprodukter
Ved fuldlast med normal brændselssammensætning producerer anlægget følgende restprodukter:
Bundaske (mineraler, skrot): |
10 |
t/d |
Flyveaske (el-filter): |
0,45 |
t/d |
Restprodukt fra posefilter: |
36-48 |
t/d |
Kondensat: |
Opkoncentreres og recirkuleres |
|
Kondensatet indeholder ca. 200 mg NH4/l renses i Reverse Osmosis (RO)-anlæg. Rejectet (15%) indeholder over 1.000 mg NH4/l og recirkuleres via SNCR-systemet til kedlen.
Det rensede kondensat udledes til recipienten.
Bundasken sigtes og den fine fraktion (sand) recirkuleres til fluid bed'en.
Jern-metaller fjernes fra restfraktionen og afhændes som forbrændingsjern.
Alle andre faste restprodukter deponeres.
4. Kritiske delprocesser og driftsparametre
Under besøget blev følgende spørgsmål diskuteret:
- Er der forekomst af kondenserbare stoffer og forureninger i processernes forskellige trin; fx af tjære, sod, metaller, salte og oxider i pyrolyseovnens top, i gaskanaler eller i
efterforbrændingskamre?
Nej.
- Hvordan kontrolleres mængden af kondenserede stoffer, dvs. hvordan renses de kritiske procesafsnit for afsætninger?
Klor-indholdet i brændslet holdes så lavt som muligt.
Ca. 10% tørv med et svovlindhold på 0,2-0,3% indfyres for at binde klor.
- Forekommer der recirkulation af materiale i processen, så visse stoffer langsomt kan akkumuleres?
Sand, opkoncentreret ammoniumholdigt kondensat og filtreret røggas recirkuleres.
- Sandet, der udtages fra bunden af fluid bed'en sigtes og renses for metaller inden det recirkuleres, forventes ikke at medvirke til at akkumulere stoffer.
- Kondensatet fra SO2-scrubberen vil indeholde en del faste stoffer fx tungmetaller inkl. arsen. Efter opkoncentreringen i RO-anlægget vil remanensen stadig indeholde tungmetaller. Der er derfor risiko for
at recirkulationen af remanensen til kedlen via SNCR-anlægget kan medvirke til at akkumulere fx arsen i anlægget.
- Røggassen renses i scrubber, el-filter og posefilter før den recirkuleres og vil derfor ikke medvirke til akkumulere stoffer i anlægget.
- Hvilken kemisk stabilitet har restprodukter fra processen? Er de lagringsstabile mht. tungmetaller og dermed egnet til deponering (data for standardudvaskningstests), eller lækker der tungmetaller, og skal de betragtes som miljøfarligt affald?
Sven Wallin oplyste, at bundasken efter sigtning og fjernelse af magnetiske metaller i en overbåndsmagnet kun indeholder mineraler, der er uproblematiske.
Røggassrensningsproduktet indeholder tungmetaller og andre miljøskadelige stoffer vil i Danmark skulle på specialdeponi.
- Findes der dioxiner (eller andre halogenerede organiske stoffer) i restprodukter eller evt. mellemprodukter som skal oparbejdes andetsteds?
Dioxin i røggassen er målt én gang og lå da under 0,1 ng/Nm³.
- Korrosion og erosion
Der forekommer ikke korrosion af betydning i anlægget, men på grund af det høje indhold af partikler i røggassen, forekommer der en del erosion i kedlens konvektive træk.
5. Miljømæssige forhold
5.1 Emissioner til luften
Stof |
Målt (11% O2)
døgnmiddelværdi |
EU-krav
(11% O2, tør gas) |
|
mg/Nm³ |
mg/Nm³ |
SOx |
0,5 |
50 |
NOx |
< 25 |
200 |
HCl |
~0 |
10 |
CO |
45 |
50 |
Støv |
5 |
10 |
|
|
ng –TEQ/m³ |
ng- TEQ/m³ |
Dioxiner |
< 0,01 |
0,1 |
Tabel 1. Emissioner til luften fra Iglestaaverket.
Alle de målte emissioner overholder EU's krav. anlægget foretager ikke dioxin-målinger med faste mellemrum. Den viste måling er den eneste, der er foretaget på anlægget.
5.2 Spildevandsudledning
Spildevand fra scrubbere renses ved hjælp af RO-teknik til et ammoniumindhold på mindre end 5 mg/l og kan uden problemer udledes direkte til recipienten.
5.3 Støj
Normalt for forbrændingsanlæg.
5.4 Lugt
En svag lugt af forbrændt tørv vurderes ikke at skabe problemer i forhold til danske regler.
5.5 Affaldsproduktion
Intet – alle processer foregår i automatiske, lukkede systemer.
Se evt. afsnit 3.4.2 Restprodukter.
5.6 Samlet dioxinemission
Der er kun foretaget en enkelt måling af dioxin-indholdet i røggassen, men ingen i restprodukterne.
6. Arbejdsmiljømæssige forhold
6.1 Støvbelastning
Al transport af brændsel, mellemprodukter, produkter og restprodukter sker i lukkede systemer.
Vi bemærkede dog, at der var en del støv i brændselslagrene, hvilket må skyldes utætheder og overtryk i de lukkede transportsystemer.
Hvis et lignende anlæg skal behandle imprægneret affaldstræ, skal anlægget derfor udstyres med meget effektive støv-begrænsende foranstaltninger, så driftspersonale kan undgå kontakt med både støv fra
neddeling og transport af brændsel og med restprodukter.
6.2 Internt støjniveau
Det interne støj-niveau var lavt og vil med stor sandsynlighed kunne overholde danske krav.
6.3 Tungmetalbelastning
Besøget var for kort til at vi kunne foretage en egentlig analyse. Tungmetaller er normalt bundet i støv og bortset fra forholdene på brændselslageret lå der ikke støv andre steder på værket.
Da brændslet indeholder en del metaller, vil flyveasken fra el-filteret vil sandsynligvis indeholde en del tungmetaller fx Pb, Zn og Cd. Driftspersonalet bør derfor have støvmasker og handsker på, når de
arbejder med håndtering af støvende restprodukter.
6.4 Dioxinbelastning
Ukendt. Der vil formentlig findes dioxiner i flyveaske fra el-filteret og i røggasrensningsproduktet.
6.5 Andet - fx lugtgener, vilkår i forbindelse med reparationsarbejde mv.
Besøget var for kort til, at vi kunne foretage en detaljeret vurdering.
7. Beskrivelse af input
Anlæggets hovedbrændsel (normalt ca. 85%) er ”retur-flis”, som er nedrivningsaffald mm. På billederne i figur 5 og figur 6 kan man se, at brændslet indeholder båder metaller, spånplader, malet træ og plastrester.
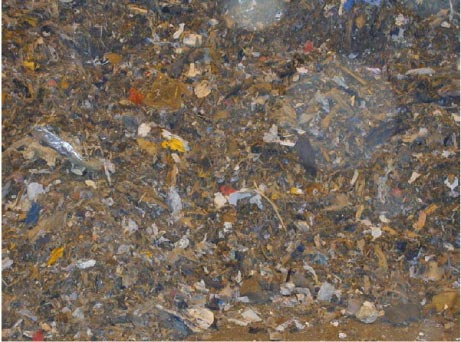
Figur 5. Fluid bed kedlens hovedbrændsel (ca. 85%), ”Returflis”, som er neddelt nedrivningsaffald mmm.
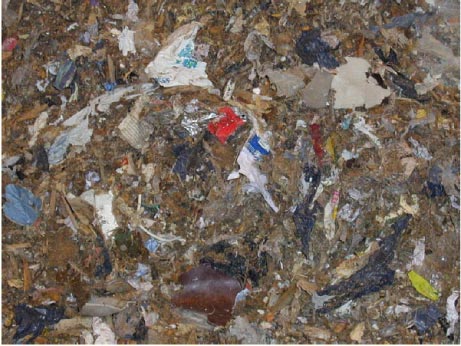
Figur 6. Nærbillede af ”Retur-flis”, som indeholder store mængder papir, spånplader, malet træ, metaller og plast (efter sigende uden PVC).
Affaldet passerer en overbåndsmagnet for at fjerne de magnetiske metaller. Herefter indeholder brændslet kun ca. 0,3 % frie metaller.
En analyse af brændselssammensætningen fra marts 2002 viser, at der er store variationer i sammensætningen.
Klik her for at se Tabel 2
Tabel 2. Brændselsanalyse fra igelstaverkets kedel 3 marts 2002.
Brændværdien af brændslet er temmelig konstant – i gennemsnit ca. 11 MJ/kg.
Svovlindholdet er lavt i returflis ca. 0,06 % (w/w) TS, men ca. 5 gange højere i maskintørv – typisk 0,3 %.
Tungmetalindholdet i returflis er ikke ubetydeligt, specielt Pb og Zn findes koncentrationer på:
Pb: 0,021 % (w/w)
Zn: 0,195 % (w/w)
De høje indhold af Cu og Mn stammer fra bark eller tørv, der også bidrager med et højt indhold af kvælstof.
8. Beskrivelse af output
8.1 Kraft/varme
Fluid bed kedlen har en termisk virkningsgrad på 89% og med bidraget fra røggaskondensationen bliver den samlede termiske virkningsgrad ca. 108%.
Værket levere udelukkende fjernvarme til Södertälje og Stockholm.
Prisen for fjernvarme 0,13 SEK/kWh svarende til ca. 0,11 DKK/kWh.
8.2 Metaller
Magnetiske metaller fjernes fra bundasken fra FB-kedlen. Anlægget producerer ca. 2 t/d forbrændingsjern, der afhentes af en skrothandler.
8.3 Granulat/restprodukt
Anlægget produceret ca. 8 t/d mineralsk restprodukt, der hovedsagelig består af silicium og calcium oxider. Glødetabet er relativt højt ca. 10%. Der foreligger ingen analyse af tungmetalindholdet i
restproduktet.
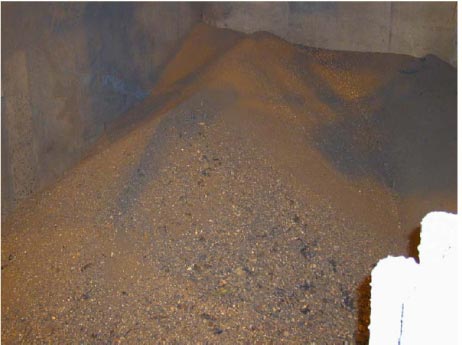
Figur 7. Restprodukt fra el-filter efter sigtning og fjernelse af jern-metaller.
Udvaskningsegenskaberne af restproduktet er ikke kendt.
Restproduktet deponeres.
9. Økonomi
9.1 Nødvendige investeringer til etablering af anlægget
Kedel 3 er som tidligere nævnt ombygget fra kulfyring til fluid bed forbrænding af træaffald. Det er derfor ikke relevant at benytte de økonomiske tal fra dette anlæg til en bedømmelse af
behandlingsomkostningerne.
Hvis et tilsvarende anlæg skal behandle CCA-imprægneret affaldstræ, vil investeringen anlægget skulle omfatte udstyr, der sikrer mod støvemission og kontakt med restprodukterne.
10. Konklusioner og anbefalinger
10.1 Egnethed for den danske affaldsstruktur
Fluid bed anlægget fungerer uden problemer med et affaldsbrændsel, der indeholder ret høje koncentrationer af tungmetaller og klorider, som også findes i CCA-imprægneret affaldstræ.
Vi forventer, at alle tungmetaller (imprægneringssalte og andre tilførte metaller) ender i flyveasken fra el-filteret eller i restproduktet fra røggasreningsprocessen opsamlet i posefiltret. Arsen vil sandsynligvis
findes på partikulær form, og en eventuel rest vil blive fanget i SO2-scrubberen og RO-remanensen.
Flyveasken vil eventuel kunne oparbejdes, men der foreligger ingen analyser af indholdet restproduktet.
Der bør dog sikres, at remanensen fra RO-anlægget renses for tungmetaller, inden den recirkuleres til kedlen via SNCR-anlægget.
Hvis et lignende anlæg skal behandle CCA-imprægneret affaldstræ vil det efter danske forhold være nødvendigt at stabilisere restprodukter, der indeholder As, Cu og Cr, eller hvis det er muligt at oparbejde
Cu og Cr til frie metaller.
10.2 Omkostningsstruktur
Omkostningsstrukturen for anlægget er ikke kendt.
Hvis et tilsvarende anlæg skal behandle CCA-imprægneret affaldstræ, vil investeringen anlægget skulle omfatte udstyr, der sikrer mod støvemission og kontakt med restprodukterne.
10.3 Affaldets udnyttelsesgrad
Anlægget er i fuld kommerciel drift, men benyttes som spidslastcentral og er derfor kun i drift ca. 7 mdr. om året.
10.4 Miljømæssige problemstillinger
Hvis et tilsvarende anlæg skal behandle CCA-imprægneret affaldstræ, vil det nedslidte sand være forurenet med As, som derfor skal behandles som specialaffald i forbindelse med deponering.
10.5 Muligheder for know-how-formidling
Foster Wheeler Energia Oy
Att. Timo Anttikoski
Nuijamiestentie 3
FIN-0040 Helsinki
Finland
Tlf.: 358-10-39311
Fax: 358-10-393-6162
E-mail: timo.anttikoski@fwfin.fwc.com
Fodnoter
[1] Igelstaverket er en spidslastenhed. Værket forventes at kunne køre 8.000 h/år ved normal drift.
Bilag F
Logbog for besøg hos Organic Power ASA
1. Generelle oplysninger
1.1 Procestype
Forgasning, ”tværstrøm” / medstrøm.
1.2 Tilført affald
- Industriaffald - papir, plast og pap i baller (Norge).
- Husholdningsaffald med 50% organisk materiale (Sydkorea).
- Forsøgsvis creosot-imprægneret affaldstræ
1.3 Licenshaver og kontaktpersoner
Licenshaver
Organic Power ASA
Klingenberggaten 7 a
Pb 1237 Vika
N 0110 Oslo
Norge
Kontaktperson:
Hans Bjerkvig
Telefon: +47 23 11 59 00
Fax: +47 23 11 59 01
E-mail: hans.bjerkvig@organicpower.com
Internet: www.organicpower.com
1.4 Ejerforhold og kontaktpersoner for det besøgte anlæg
Anlægget på 4 MWth er ejet af Lier Fjernvarme.
Lier Fjernvarme er ejet af Birka Energi and Lier Elektrisitetsverk.
Varmeværket forsyner Osmund Espedal Handelsgartneri med varme.
1.5 Beliggenhed for det besøgte anlæg
Lier Fjernvarme
Drammen
Norge
1.6 Virksomhedens formål og idégrundlag
Organic Power ASA udvikler og markedsfører mindre, modulære og kosteffektive forgasningsanlæg til konvertering af sorteret affald og biomasse til energi. Anlæggene kan køre med et bredt spektrum af
brændsler.
Organic Powers standard modul, SK1000, har en kapacitet på ca. 2 MW.
1.7 Kapacitet for det besøgte anlæg
Lier Fjernvarme består af 2 linier på hver 2 MWth.
1.8 Byggeår og status for projektet
Organic Power har leveret tre anlæg på kommercielle vilkår:
Tabel 1. Anlæg leveret af Organic Power.
Lokalitet |
Status |
Effekt |
Brændværdi |
Boseong City, Sydkorea |
Idriftsat juni 2001 |
1 x 2 MW |
5–6 MJ/kg |
Lier, Norge |
Idriftsat september 2002 |
2 x 2 MW |
ca. 10 MJ/kg |
Elverum, Norge |
Idriftsættes september 2002 |
2 x 2 MW |
ca. 10 MJ/kg |
Alle Organic Powers anlæg i Norge ombygges i øjeblikket, så affaldet neddeles umiddelbart før, det indfyres i forgasseren.
Organic Power har ordre på flere anlæg:
Nakskov, Danmark: |
6 x 2 MW |
Gyeryong City – South Korea: |
1 x 2 MW |
Haenam City, South Korea: |
1 x 2 MW |
NTE - Sundnes Varmesentral, Norge: |
1 x 2 MW |
Organic Powers udviklingsplaner omfatter test med flere nye affaldstyper:
- CCA-imprægneret affaldstræ
- shredderaffald blendet med andet affald
- industrislam
I øjeblikket kan SK1000-modulet operere fra 0,5 – 2,4 MWth, men OP forventer, at kunne nå betydeligt højere, når kammerets design og processtyringen optimeres.
Nakskov Kommune har opsagt sin kontrakt med Organic Power om byggeri af et forgasningsanlæg. Nakskov har varslet en erstatningssag med det resultat, at Organic Power har
erklæret sig konkurs d. 2002-10-30.
2. Kortlægning og beskrivelse af anlægget
2.1 Procesdiagram
Organic Powers proces består af et forgasningskammer, der er beskrevet nøjere i afsnit 2.4, et kort sekundærkammer og en varm cyklon, hvor syntesegassen forbrænder inden den ledes til en kedel og et
røggasrensningssystem. En del af røggassen recirkuleres efter posefilteret til forgasningskammeret.
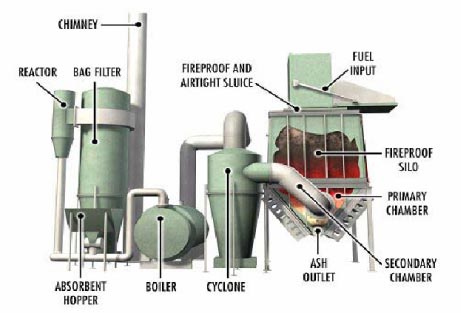
2.2 Affald
- Sorteret husholdningsaffald
- Industriaffald - plast, pap, papir, mm.
Anlæggenes modtagefaciliteter er typisk beregnet til brændsel, der er presset til baller og pakket i PVC-fri plastfolie (se figur 7).
Processen kan behandle meget uhomogent affald.
2.3 Forbehandling
Anlæggene i Norge er oprindeligt designet til, at affaldet indfyres i hele baller, men problemer med ustabile driftsforhold har betydet, at alle tre anlæg nu udbygges med en opriver umiddelbart over
indfødningstragten (figur 1).
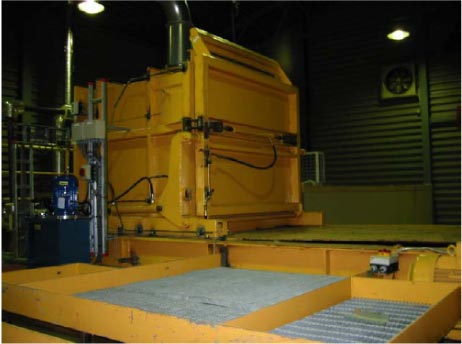
Figur 1. Lier Fjernvarme: Indfødningssluse oven på forgasningskammer.
2.4 Proces(ser)
Organic Powers forgasningsproces er oprindelig udviklet i 1970'erne på en norsk landbrugshøjskole med henblik på at forgasse blandet landsbrugsaffald. Processen sker i et kammer som vist i figur 2:
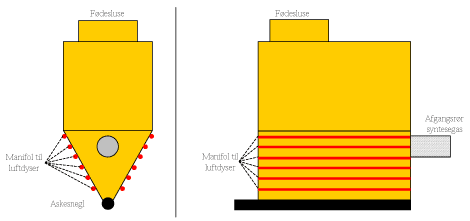
Figur 2. Skitse af Organic Powers forgasningskammer set i to lodrette snit.
Figur 3 viser den virkelige udformning af manifolerne til luftdyserne i bunden af forgasningskammeret.
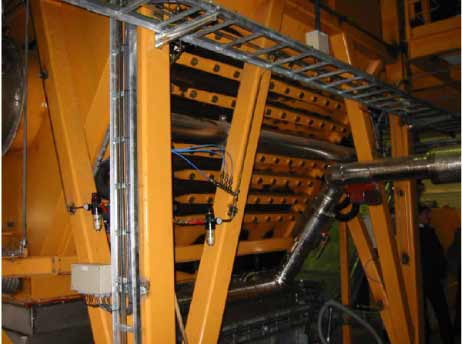
Figur 3. Manifold til luftdyser i bunden af forgasningskammeret.
Forløbet af den termiske omsætning i forgasseren er vist i figur 4.
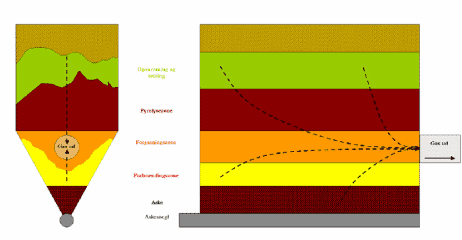
Figur 4. Termiske processer i Organic Powers ”tværstrøms-forgasser. De stiplede linier angiver formodede interne gasstrømme.
Processen styres med lufttilsætningen i den koniske del af kammeret, så temperaturen i starten af afgangskanalen holdes konstant. Da der ikke nogen styring af lufttilsætningen på langs af kammeret, vil
driftsbetingelserne variere i fra den ene til den anden ende. Temperaturen når op på ca. 800°C i forbrændingszonen.
Det er centralt for processen, at alle gasser trækkes gennem forgasningszonen med den understøkiometriske forhold, før de forlader kammeret.
På grund af den usymmetriske opbygning og det specielle strømningsmønster i forgasseren, vil affaldet blive udsat for meget forskellige opholdstider og temperaturforløb.
Bundasken tages ud med sneglen i bunden af kammeret. Sneglen kan transportere metal- og stenstykker 20 cm i længden og en diameter på ca. 5 cm.
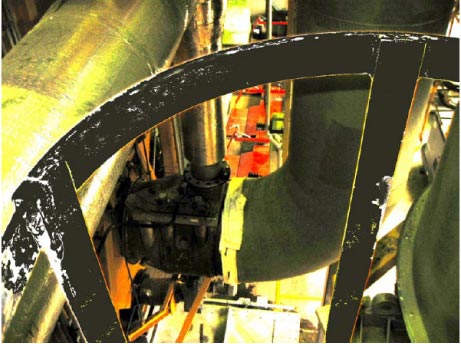
Figur 5. Afgangsrør for syntesegassen og tilsætningen af sekundærluft (lodret rør).
Umiddelbart efter gasserne har forladt kammeret tilsættes sekundærluft (se figur 5), hvorefter udbrændingen sker i et kort sekundærkammer og i en varm cyklon. De varme gasser fortsætter herefter til
kedlen, der i Lier er en opretstående dampkedel med kuglerensning, for til sidst at gå videre til røggasrensningssystemet, som vist på figur 6.
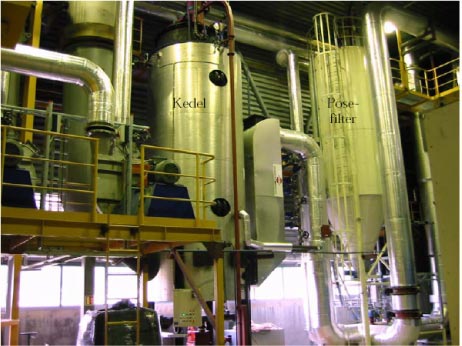
Figur 6. Lier Fjernvarme: Opretstående kedel med kuglerens og posefilter.
2.5 Røggasrensning
Efter kedlen indblæses en blanding af hydratkalk og aktivt kul i røggassen. Hydratkalken reagerer med sure gasser (HCl, HF, SO2, SO3, ...) i røggasserne, mens aktivt kul absorberer organiske stoffer, fx
evt. rester af dioxiner. Røgrensningsprodukterne opsamles i det efterfølgende posefilter.
3. Observationer under besøget
3.1 Besøgets varighed
Den 2002-09-19 fra kl. 13:30 til kl. ca. 15.
3.2 Tilførte materialer behandlet under besøget
Forgasningsanlægget i Lier er designet til sorteret husholdningsaffald.
3.3 Driftsforhold
Anlægget var under indkøring og ude afdrift under besøget, fordi der skulle installeres en neddeler til affaldet før den eksisterende indfødningssluse.
OP's ældste anlæg i Boseong City, Sydkorea
3.4 Output under besøget
Intet.
4. ritiske delprocesser og driftsparametre
Under besøget blev følgende spørgsmål diskuteret:
- Er der forekomst af kondenserbare stoffer og forureninger i processernes forskellige trin; fx af tjære, sod, metaller, salte og oxider i pyrolyseovnens top, i gaskanaler eller i
efterforbrændingskamre?
I OP's forgasningsproces ledes alle gasser gennem den reducerende forgasningszone inden de forlader anlægget. Tjæreindholdet i syntesegassen er derfor meget lavt.
- Hvordan kontrolleres mængden af kondenserede stoffer, dvs. hvordan renses de kritiske procesafsnit for afsætninger?
Eventuelle belægninger på dyserne i den nederste del af procesanlægget vil kunne fjernes, idet dyserne kan trækkes ud og renses under drift.
- Forekommer der recirkulation af materiale i processen, så visse stoffer langsomt kan akkumuleres?
Da røggassen recirkuleres efter rensning i posefilteret vil indholdet af faste stoffer vil være meget og ikke give problemer med akkumuleringer i anlægget.
- Hvilken kemisk stabilitet har restprodukter fra processen? Er de lagringsstabile mht. tungmetaller og dermed egnet til deponering (data for standardudvaskningstests), eller lækker der tungmetaller, og skal de betragtes som miljøfarligt affald?
Røggasrensningsprodukt skal deponeres.
- Findes der dioxiner (eller andre halogenerede organiske stoffer) i restprodukter eller evt. mellemprodukter som skal oparbejdes andetsteds?
Dioxiner og andre halogenerede organiske stoffer fjernes effektivt med aktivt kul, der indblæses i røggassen efter kedlen. Posefilteret opsamler røgrensningsproduktet.
5. Miljømæssige forhold
5.1 Emissioner til luften
Målinger af emissioner til luften målt på OP's anlæg i Boseong City, Sydkorea er vist i tabel 2.
Tabel 2. Emissioner til luften fra Organic Powers anlæg i Boseong City, Sydkorea
Stof |
Målt/garanti (11% O2) |
EU-krav (11% O2, tør gas) |
|
mg/Nm³ |
mg/Nm³ |
SOx |
8 |
50 |
NOx |
107 |
200 |
HCl |
13 [1] |
10 |
CO |
18 |
50 |
Støv |
8 |
10 |
|
|
|
|
ng –TEQ/m³ |
ng- TEQ/m³ |
Dioxiner |
0,067 |
0,1 |
5.2 Spildevandsudledning
Der er intet spildevand fra processen.
5.3 Støj
Emissionen til omgivelserne vil være mindre end 45 dB.
5.4 Lugt
Vi forventer ingen lugtproblemer fra luftafkastet fra OP's anlæg.
Anlæggene opfylder - på nær HCl - EU-direktivets krav til affaldsforbrændingsanlæg (bl.a. opholdstid 2 s /850°C), hvilket også sikrer mod lugtemissioner. En bedre rensning i fx en skrubber forventes at
kunne bringe emissionen under EU's grænseværdi.
Røggassen renses i øvrigt med bl.a. aktivt kul, der også ville kunne fjerne lugt.
5.5 Affaldsproduktion
Asken fra forgasningsprocessen indeholder ca. 2-3 % uforbrændt, hvilket er i overensstemmelse med EU's direktiv. Det er ikke muligt at forudsige, hvilken slagge kategori asken vil ligge, da
udvaskningsegenskaberne ikke er målt.
Røggasrensningsproduktet ville i Danmark pga. indholdet af tungmetaller etc. skulle deponeres på specialdeponi.
5.6 Samlet dioxinemission
Den samlede dioxinemission fra anlægget er ikke kendt, da der ikke er målt dioxiner i restprodukterne
6. Arbejdsmiljømæssige forhold
6.1 Støvbelastning
Al transport af støvende materiale sker i lukkede systemer.
Det er vigtigt, at den fremtidige neddeling af affaldet sker i et lukke system med afsugning af støv.
6.2 Internt støjniveau
Som på andre affaldsforbrændingsanlæg - dog er ventilatorerne på anlægget i Lier, der recirkulerer røggassen til forgasningskammeret placeret i selve ovnhallen.
6.3 Tungmetalbelastning
Ingen - aske og røggasrensningsprodukt transporteres i lukkede systemer.
6.4 Dioxinbelastning
Ingen - røggasrensningsproduktet transporteres i lukkede systemer.
6.5 Andet - fx lugtgener, vilkår i forbindelse med reparationsarbejde mv.
7. Beskrivelse af input
Organic Powers anlæg behandler:
- Sorteret husholdningsaffald
- Industriaffald - plast, pap, papir, mm.
Anlæggenes modtagefaciliteter er typisk beregnet til brændsel, der er presset til baller og pakket i PVC-fri plastfolie (se figur 7).
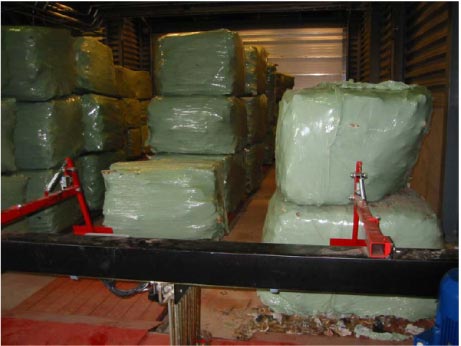
Figur 7. Lier Fjernvarmes modtagefacilitet for baller af industriaffald.
Organic Powers krav til affaldet er:
- Højst 5% (w/w) ubrændbart.
- Nedre brændværdi: 10-18 MJ/kg.
- Kvælstofindhold: < 1% (w/w)
- Klorindhold: < 1% (w/w)
- Partikelstørrelse:
- Organisk materiale: 7 x 10 x 20 cm.
- Ikke-brændbart: Ø5 x 20 cm.
8. Beskrivelse af output
8.1 Kraft/varme
Varmeværket i Lier forsyner Osmund Espedal Handelsgartneri med varme.
Virkningsgraden er ca. 85%.
Fjernvarmeprisen er 130 NOK/MWh svt. 130 DKK/MWh.
8.2 Metaller
Anlægget producerer ingen metaller.
8.3 Granulat/restprodukt
Bundaske og røggasrensningsproduktet skal deponeres.
Bundasken indeholder 2-3% uforbrændt materiale.
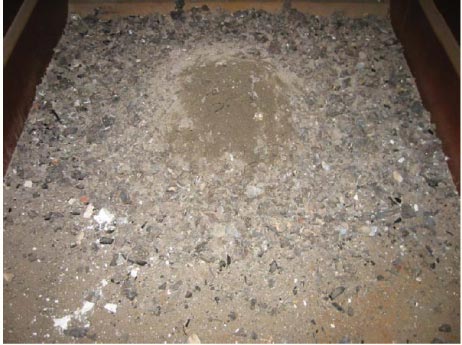
Figur 8. Bundaske fra forgasningsanlægget hos Lier Fjernvarme.
Udvaskningsegenskaberne er ikke undersøgt.
9. Økonomi
9.1 Nødvendige investeringer til etablering af anlægget
Organic Power skal levere et anlæg til Nakskov Kommune bestående af 6 linier á 2 MW. Prisen er 84 mio. DKK.
9.2 Omkostningsstruktur
Nedenstående forudsætninger og data er anvendt i forbindelse med et skøn over behandlingsprisen. Alle data er opgivet af Organic Power med undtagelse af rentefod samt priser på el og varme, der er
tilpasset danske forhold.
Anlægsstørrelse: |
36.000 |
t industriaffald/år |
|
Investering ekskl. bygninger: |
84.000.000 |
DKK |
Rentefod: |
7 |
% p.a. |
Tilbagebetalingstid: |
15 |
år |
Udgifter til deponering
Bundaske: |
0 |
DKK/t |
Røggasrensningsprodukt: |
675 |
DKK/t |
Driftsudgifter
Gennemsnitlig løn til personale: |
300.000 |
DKK/person |
6 |
personer |
Elektricitet: |
390 |
DKK/MWh |
1.000 |
MWh/år |
Andre driftsudgifter |
5.040.000 |
DKK/år |
|
|
Vedligehold og reparation:
Normalt maskineri |
2 |
% af investering |
Salgspriser for produkter
Udgifter til forsikringer er ikke inkluderet.
Skønnede behandlingsomkostninger
Kapitalomkostninger |
256 |
DKK/t |
Driftsomkostninger |
261 |
DKK/t |
Indtægter |
300 |
DKK/t |
Den endelige behandlingspris vil være afhængig af anlægsplacering, faciliteter til stede, valgte bygningsstandarder osv. og den endelige pris, som vil kunne opnås for anlægget efter forhandlinger.
Behandlingsprisen skønnes at blive 217 DKK/t industriaffald for et turn-key anlæg.
Behandlingsomkostningerne for anlæg med en lavere kapacitet på f.eks. 12.000 t industriaffald/år vil blive noget højere.
10. Konklusioner og anbefalinger
10.1 Egnethed for den danske affaldsstruktur
Organic Powers proces er en meget billig og robust forgasningsproces, der har vist sin berettigelse til husholdningsaffald og industriaffald uden indhold af frie metaller. På grund af den usymmetriske
opbygning af forgasningskammeret og det specielle strømningsmønster i forgasseren, vil affaldet blive udsat for meget forskellige opholdstider og temperaturforløb. Den specielle forgasningsproces
producerer meget lidt tjære.
Virksomheden har ikke erfaringer med oparbejdning af metaller eller andre restprodukter.
Processen vil sandsynligvis være egnet til termisk behandling af CCA-imprægneret affaldstræ, men Organic Power har ikke udført forsøg med denne form for affald.
Processen kan ikke anbefales til behandling af shredderaffald eller andet affald med et væsentlig indhold af frie metaller og tungmetalforbindelser med mindre de frie metaller fjernes fra affaldet før
forgasningen eller fra asken. På grund af tungmetalindholdet i shredderaffald vil asken fra OP's proces under alle omstændigheder forglasses i en termisk proces for at sikre tilstrækkelig gode
udvaskningsegenskaber.
10.2 Affaldets udnyttelsesgrad
Den termiske virkningsgrad er ca. 84%, men evt. metaller eller andre stoffer i affaldet udnyttes ikke.
10.3 Miljømæssige problemstillinger
Organic Powers anlæg overholder alle krav i EU's direktiv for affaldsforbrænding.
10.4 Muligheder for know-how-formidling
Organic Power ASA
Klingenberggaten 7 a
Pb 1237 Vika
N 0110 Oslo
Norge
Kontaktperson:
Hans Bjerkvig
Telefon: +47 23 11 59 00
Fax: +47 23 11 59 01
E-mail: hans.bjerkvig@organicpower.com
Internet: www.organicpower.com
Fodnoter
[1] Overholder Koreanske krav.
Bilag G
Logbog for besøg hos Procone
1 Generelle oplysninger
1.1 Procestype
Forgasning af affaldstræ
1.2 Tilført affald
Affaldstræ
1.3 Licenshaver og kontaktpersoner
Licenshaver
Procone Vergasungssysteme Gmbh
Geschäftsstelle Schweitz
Allmendstrasse 398
CH-4617 Gunzgen
Schweitz
Kontaktperson
Adrian Fürst
Telefon: +41-62-216-80-80
Fax:
E-mail: procone@swissonline.ch
1.4 Ejerforhold og kontaktpersoner for det besøgte anlæg
PPS Pipeline Systems Gmbh.
1.5 Beliggenhed for det besøgte anlæg
PPS Pipeline Systems Gmbh
Steyermühle 1-3
09634 Siebenlehn
Tyskland
Anlægget er vist på figur 1
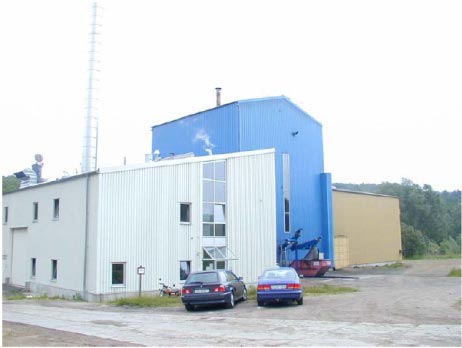
Figur 1. Forgasningsanlægget ved Siebenlehn.
1.6 Virksomhedens formål og idégrundlag
At producere kraft/varme af affaldstræ.
1.7 Kapacitet for det besøgte anlæg
2,5 t/time
8.000 driftstimer per år
1.8 Byggeår og status for projektet
Anlægget er sat i drift i løbet af år 2000, og forgasseren har pr. 6/6-2002 haft 8.300 driftstimer.
Gasturbinen har dog først været i drift siden december 2001.
Anlægget er pt. lukket, da det blev oversvømmet, da Elben stod over sine bredder. Endvidere er Babcock-Borsig og dermed PPS ved at blive rekonstrueret efter konkurs, hvorfor anlægget forsøges solgt til
anden side
Et andet anlæg findes i Espenhain, hvor man har prøvet slam, shredderaffald mm.
På anlægget blev gennemført en 3 måneders prøvetid med en gasmotor i år 2000 med 75% oppetid.
Med produktion af 450 kW el og 600 kWh varme. Motoren overholdt ikke 17. BlmschV.
I Schweiz er et pilotanlæg til slam med 50-60% aske under afprøvning. Anlægget har et forbedret efter-forgasningskammer, hvor restkoks i asken kan oxidere fuldstændigt. Test pågår i 2003, hvorefter det
afgøres, om et fuldskalaanlæg skal bygges (6.000 t/år)
2 Kortlægning og beskrivelse af anlægget
2.1 Procesdiagram
Et procesdiagram over anlægget er vist i figur 2:
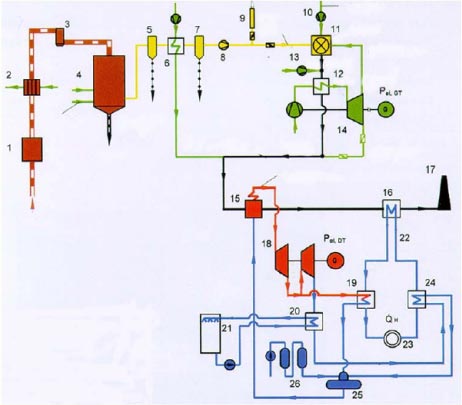
Figur 2. Procesdiagram for Procone forgasningsanlægget.
Symboler:
1: Brændsels bunker
2: Tørring (benyttes ikke)
3: Mellem lager og brændselsindfødning
4: Forgasser
5: Cyclon (benyttes ikke)
6: Gas køler
7: Fin filter (benyttes ikke)
8: Blæser
9: Sikkerhedsfakkel til opstart og nedlukning
10: Kold luft blæser 1
11: Forbrændingskammer
12: Højtemperaturvarmeveksler
13: Kold luft blæser 2
14: Gasturbine
15: Dampkedel til produktion af damp fra spildvarme
16: Røggasvarmeveksler
17: Skorsten
18: Kondensationsdampturbine
19: Varmeveksler
20: Kondensator
21: Køletårn
22: Lokalt varmesystem
23: Fjernvarme
24: Condensat økonomiser
25: Fødevandstank
26: Fødevandskonditionering
2.2 Affald
Det modtagne affald består af affaldstræ (”altholz” eller ”restholz”) i henhold til de tyske klasser 1 eller 2.
- Klasse 1 er ubehandlet affaldstræ
- Klasse 2 er malet, lakeret eller limet træ uden brug af halogenholdige midler samt uden imprægneringsmidler.
2.3 Forbehandling
Det modtagne træ leveres som flis renset for sten og metal til en 1.000 m³ lagerbunker (figur 2, (1)). Træet er neddelt til mellem 2og 16 cm og har et fugtindhold mindre end 30%. Forgasseren kan dog
behandle træ med op til 45% fugt.
2.4 Forgasning
Flisen tilføres fra lagerbunkeren til en lagersilo (800 m³), hvorfra den tilføres forgasseren via en sluse i toppen af forgasseren (se figur 3). Forgasseren er en medstrømsforgasser, hvor røggassen passerer ud
samme vej som asken fra brændslet. Brændslet passerer ned gennem en kegleformet skakt, hvor der først sker en tørring, dernæst en pyrolyse og forgasnings fulgt af en oxidationszone i midten af
forgasseren. Keglen opbygges af slagge under drift grundet den nedenfor værende kegleformede slaggeudmader. I pyrolysezonen dannes brændbare gasser som brint og kulmonooxid, samt tjære. I
forgasningszonen dannes yderligere gas fra koks og tjære og i oxidationszonen nedbrydes rester af højere kulbrinter lige som lidt af de dannede gasser forbrændes indtil ilten er opbrugt. I oxidationszonen
opstår temperaturer på op mod 2000°C hvorved der dannes en smeltet slagge. Efter oxidationszonen udvider forgasningskammeret sig ned mod askeudmader, der er udformet som en roterende keglestub,
og som kan justeres i højden og i rotationshastighed. Den kegleformede slaggeudmader kan hæves og sænkes ca. 40 cm, men justeres kun ca. 1 cm under drift. I forgasningskammeret er der en reducerende
atmosfære, så der ikke sker yderligere omsætning af gassen og gas, og at slaggegranulatet afkøles til under 500°C. Asken passerer herefter en partiel oxidationsreaktor for at få oxideret rester af kulstof.
Denne reaktor er for lille til at kunne forgasse al restkulstof på dette anlæg. Et pilotanlæg til forgasning af slam i Schweiz har monteret et efter-forgasningskammer (en lille modstrømsforgasser) med en korrekt
dimensionering, hvorved restkulstof i asken undgås.
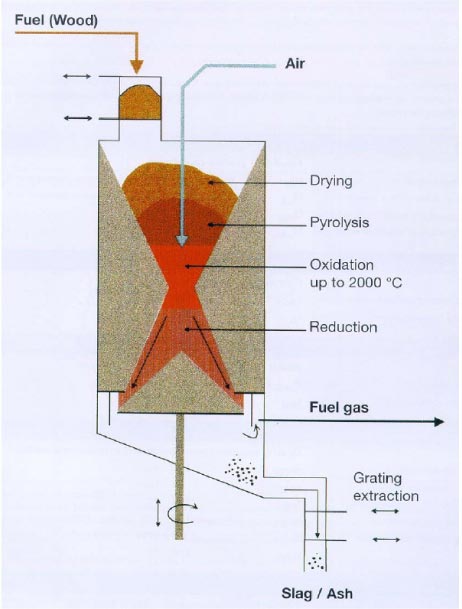
Figur 3. Principskitse af Procones medstrømsforgasser.
2.5 Energiproduktion og røggasrensning
Energien fra i den brændbare forgasningsgas udnyttes til produktion af kraft/varme i Combined Cycle kraft/varme-anlæg. Fra afgangen af forgasseren passerer gassen en røggaskøler (figur 2, (6)), der
producerer damp ved 400°C. Gassen forbrændes dernæst ved 1080°C og passerer en varmeveksler (figur 1, (12)), der sænker temperaturen af den forbrændte gas til 450°C og producerer varmluft på
850°C. Den varme luft ledes dernæst til en varmluftturbine, som producerer el. Afgangsluften på 450°C ledes dels retur til brændkammer, dels videre sammen med den forbrændte gas. Ved at benytte den
varme luft til forbrændingen kan opnås en høj forbrændingstemperatur. Røggassen fra afgangen af varmeveksleren, luften fra gaskøleren (figur 1, (6)) og varmluften fra afgangen af varmluftturbinen ledes til en
dampkedel (figur 1, (15)), hvor der produceres damp af den ca. 400-450°C varme røggas som udnyttes til produktion af el i en dampturbine (figur 1, (18)). Restvarmen fra røggassen udnyttes til produktion
af fjernvarme via en varmeveksler (figur 1, (16) ), ligesom der produceres fjernvarme af den kondenserede damp fra turbinen. Da der kun forgasses træflis i klasse I og II, har det ikke været nødvendigt med
røggasrensning for at kunne overholde kravene i TA-luft.
3 Observationer under besøget
3.1 Besøgets varighed
Den 6/6 2002 fra kl. 9:30 til kl. 13.
3.2 Indsatsmaterialer behandlet under besøget
Type:
Mængde i t/h: 0 t/h
Kapacitetsudnyttelse: 0 %
Anlægget var under opstart efter driftsstop
3.3 Driftsforhold
Driftstid: 24 timer/døgn
Forventet produktionstid: 8.000 h/år
Revisioner: 6-7 pr. år
Anlægget kører i perioden op til besøget op til 6 uger. Der regnes med, at man vil kunne opnå 8 ugers driftsperioder, hvorefter der må udføres 1-2 dages rensning mm. I alt forventes at kunne opnås 8.000
driftstimer pr. år.
Ved besøget var den totale driftstid for forgasseren 8.300 timer.
3.4 Output under besøget
3.4.1 Restprodukt
Da anlægget var under opstart blev der ikke produceret restprodukter, men slaggen fra tidligere produktion blev besigtiget.
3.4.2 El/varme
Der blev ikke produceret varme, da anlægget var under opstart.
4 Kritiske delprocesser og driftsparametre
Under besøget blev følgende spørgsmål diskuteret:
- Er der forekomst af kondenserbare stoffer og forureninger i processernes forskellige trin; fx af tjære, sod, metaller, salte og oxider i pyrolyseovnens top, i gaskanaler eller i
efterforbrændingskamre?
Anlægget producerer meget fint kulstøv, som ved normal drift ikke kommer ud af anlægget. Dog vil der kunne afgives kulstøv ved reparationer og planlagte start/stop, hvilket har givet problemer med kortslutninger i el-tavler og afsætning i sugetræksblæsere.
- Hvordan kontrolleres mængden af kondenserede stoffer, dvs. hvordan renses de kritiske procesafsnit for afsætninger?
Anlægget renses for kulstøv ca. hver anden måned.
- Hvilken kemisk stabilitet har restprodukter fra processen? Er de lagringsstabile mht. tungmetaller og dermed egnet til deponering (data for standardudvaskningstests), eller lækker der tungmetaller, og skal de betragtes som miljøfarligt affald?
Asken overholder tyske krav til deponering af slagge fra denne type anlæg.
- Findes der dioxiner (eller andre halogenerede organiske stoffer) i restprodukter eller evt. mellemprodukter som skal oparbejdes andetsteds?
Dioxinindholdet i restprodukterne er ikke blevet målt.
5 Miljømæssige forhold
5.1 Emissioner til luften
Tabel 5.1. Emissioner til luften.
Stof |
Målt/garanti (11% O2) |
EU-krav (11% O2, tør gas) |
|
mg/Nm³ |
mg/Nm³ |
SOx |
|
50 |
NOx |
overholder TA luft |
200 |
HCl |
|
10 |
CO |
overholder TA luft |
50 |
Støv |
|
10 |
|
|
ng –TEQ/m³ |
ng- TEQ/m³ |
Dioxiner |
|
0,1 |
5.2 Spildevandsudledning
Spildevand med svagt forøget saltindhold ledes til det nærmeste spildevandsrensningsanlæg.
5.3 Støj
Støjniveauet kunne ikke bedømmes grundet anlægsstop. Vi vurderer, at niveauet er af samme størrelse som andre termiske anlæg og overholder tyske regler i TA Lärm.
5.4 Lugt
Kunne ikke vurderes grundet anlægsstop, men der forventes ingen lugtproblemer med denne type anlæg, da det er et krav, at forgasningsanlæg skal være meget tætte for at undgå udslip af
forgasningsgassen.
5.5 Affaldsproduktion
Der produceres slagge med et ret stort restindhold af kulstof hvilket kan være problematisk i forbindelse med genanvendelse af slaggen. Kulstof indholdet vil dog mindskes i en nyere version af anlægget med
en partiel efter-oxidation.
5.6 Samlet dioxinemission
Der er ikke målt for dioxinemission, men der forventes ingen dioxiner i forgasningsgassen grundet den reducerende atmosfære. Ved forbrænding af gassen i forbrændingskammeret forventes ikke dannet
dioxiner grundet den høje temperatur, men der kan i princippet dannes dioxiner under afkølingen af gassen afhængigt af designet af forbrændingsprocessen. Evt. dannede dioxiner vil kunne fjernes med aktivt
kul som på moderne forbrændingsanlæg.
6 Arbejdsmiljømæssige forhold
6.1 Støvbelastning
Ved åbning af anlægget for inspektion og reparation kan forekomme eksponering for en del fint kulstøv. Der bør derfor benyttes passende beskyttelsesudstyr ved åbning af anlægget.
6.2 Internt støjniveau
Dette kunne ikke bedømmes.
6.3 Tungmetalbelastning
Da der ikke behandles træ belastet med tungmetaller, vil der ikke være nogen eksponering for disse ved åbning og inspektion af anlægget.
6.4 Dioxinbelastning
Denne kendes ikke.
6.5 Andet; fx lugtgener, vilkår i forbindelse med reparationsarbejde mv.
Ingen særlige gener.
7 Beskrivelse af input
Besøget var for kort til at beskrive input i detaljer. Input er træflis..
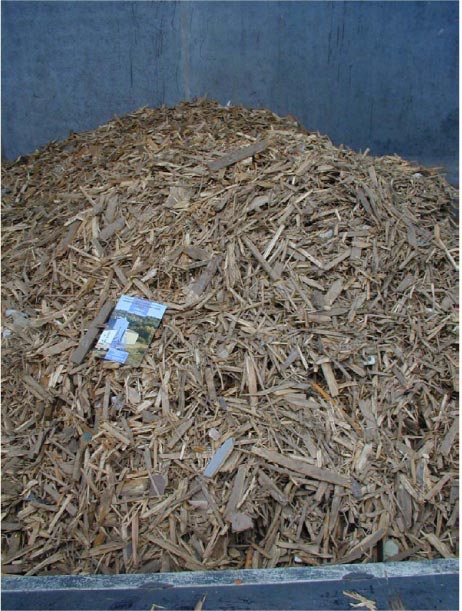
Figur 4. brændselsflis til procones anlæg.
8 Beskrivelse af output
Besøget var for kort til at kunne beskrive output i detaljer
8.1 Kraft/varme
Procones anlæg producerer kraft/varme. I tabel 8.1 er vist en masse og energibalance for anlægget.
Tabel 8.1. Masse og energibalance for (vinter-drift).
Anlæg |
Procone forgasser, Siebenlehn |
Affald |
Træflis |
Flow |
Input |
Output |
|
kg |
GJ/ton |
kg |
GJ |
Affald |
1.000 |
13,60 |
|
|
|
Slagge |
20 |
|
|
|
|
Materiale konverteret til gas |
980 |
|
Sum Brændsel |
1.000 |
13,60 |
|
|
Total Sum |
1.000 |
|
1.000 |
|
|
Energibalance (1 ton affald) |
|
Effektivitet % |
GJ |
MW |
GJ |
Tilført energi |
|
13,60 |
3,78 |
|
Energi i forgasningsgas |
90 |
12,24 |
3,40 |
|
Netto produceret varme |
|
|
1,80 |
6.48 |
Produceret elektricitet |
|
|
0,80 |
2.88 |
Elforbrug |
|
|
0,10 |
0.37 |
Netto produceret elektricitet |
|
|
0,70 |
2.51 |
|
|
|
|
|
Net. elektrisk virkningsgrad % |
|
|
|
18.4 |
Total virkningsgrad % |
|
|
|
66.1 |
Netto el-produktion kWh/t affald |
696 |
Data i tabel 8.1 er baseret på følgende opgivne data for energieffektivitet af forgasseren:
Tilført træflis |
:2,5 t/h |
Vandindhold |
:25% |
Nedre brændværdi våd |
:13,6 MJ/kg |
Produceret el fra gasturbine |
:1,3 MW |
Produceret el med dampturbine (sommer-drift) |
:1,0 MW |
Produceret el med dampturbine (vinter-drift) |
:0,7 MW |
Eget forbrug af strøm (0,2-0,32 MW) |
:0,26 MW |
Procone har oplyst en beregnet samlet virkningsgrad udfra energiindholdet i forgasningsgassen (8,5 MW) på 73% ved sommer-drift og 39% ved vinter-drift.
Hvis virkningsgraden baseret på energiindholdet i gassen omregnes til en virkningsgrad baseret på nedre brændværdi i træflisen (13,6 MJ/kg eller 9,44 MW), fås virkningsgrader som angivet i tabel 8.2.
Tabel 8.2 Virkningsgrader for anlægget i Siebenlehn
|
Sommer-drift % |
Vinter-drift % |
Netto elektrisk virkningsgrad |
21,6 |
18,4 |
Netto total virkningsgrad |
35,4 |
66 |
Varmen sælges til et nærtliggende garveri.
8.2 Metaller
Der udsorteres ingen metaller fra brændslet på anlægget. Hvis det er nødvendigt at frasortere metal, sker det hos leverandørerne af træflisen.
8.3 Granulat/restprodukt
Der produceres en slagge som består af smeltede mineraler opblandet med medrevet kulstof (ca. 13-16%). Slaggen er vist på figur 5.
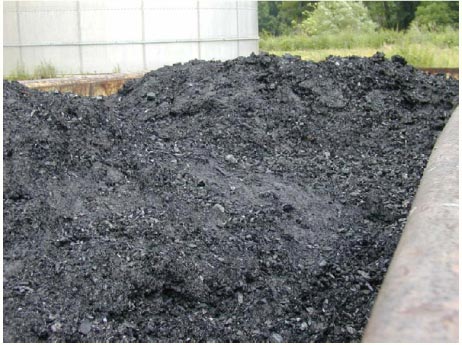
Figur 5. Slagge fra Procones forgasningsanlæg.
Det åbenlyse høje kulstofindhold skyldes den underdimensionerede sekundær forgasningsreaktor til forgasning af restkulstofindholdet i slaggen. I Schweiz er opstillet et pilotanlæg til behandling af slam med
en korrekt dimensioneret sekundær forgasningsreaktor. Med dette anlæg opnås et restindhold af kulstof i slaggen på mindre end 0,1%.
Tabel 8.3 Udvaskningsegenskaber for slaggen fra Procones anlæg.
Stof |
Målt |
Dansk slagge-
Kategori II |
Dansk slagge-
kategori III |
|
µg/l |
µg/l |
µg/l |
Hg total |
|
0 – 0,1 |
0,1 – 1 |
Pb |
|
0 – 10 |
10 – 500 |
Cd |
|
0 – 2 |
2 – 40 |
Cr (VI) |
|
0 – 10 (Cr total) |
10 - 500 (Cr total) |
As |
|
0 – 8 |
8 – 50 |
Se |
|
|
|
Slaggen overholder tyske krav for slagge til deponering; men vi har ikke kunnet fremskaffe eksakte måleværdier.
9 Økonomi
9.1 Nødvendige investeringer til etablering af anlægget
Der haves ikke data for økonomien i anlægget ved Siebenlehn, men i stedet er vist et estimat for et anlæg med brændselslager, forgasser, gasbehandlingsanlæg, 2 gasmotoragregater med produktion af strøm
og produktion af fjernvarme ud fra motorvarme (Frem: 90°C, retur: 70°C).
Estimatet er udregnet for danske forhold og gælder kun for brug af ren træflis. Hvis trykimprægneret træ skal forgasses, forventer vi, at røggasrensningen skal modificeres ligesom bemanding mm. formentlig
skal forøges til konstant bemanding.
Anlægsstørrelse: |
9.600 t/år |
Brændsel: |
træflis 14,4MJ/kg nedre bv. våd |
Driftstimer |
8000 timer |
Rente: |
7% p.a. |
Tilbagebetalingstid: |
15 år |
Investeringssum inkl. bygninger: |
23,5 mio. DKK. |
9.2 Salgspriser for produkter
Salg af elektricitet: |
0,35 DKK/kWh |
Salg af varme: |
0,15 DKK/kWh |
Salg af slagge: |
0,00 DKK/kg |
I beregningseksemplet producerer anlægget:
- Netto leveret til net 8.800 MWh el/år.
- Fjernvarme 14.400 MWh/år med 90/70°C.
- Anden varme 3.600 MWh/år med 60/40°C.
Med de angivne data opnås en netto el-virkningsgrad på 23% og en total netto virkningsgrad på 70%.
9.3 Udgifter til Bortskaffelse og løn
Deponeringsudgifter: |
Ingen |
Rensning af spildevand (kondensat): |
25 DKK/t |
Gennemsnitlig løn til personale: |
300.000 DKK/person |
9.4 Driftsudgifter
Energi: |
0 DKK da der produceres overskud af strøm og varme |
Personale: |
Anlægget kan formentlig bygges til at drives af 4 personer (2*2 pers)+anlægsopkald om natten og i weekend.
Men ved farligt affald kræves fuld bemanding svarende til 10-14 pers. Der er antaget 12 personer. |
Kemikalieforbrug: |
Negligeabelt ved træflis. Hvis der forgasses trykimprægneret træ, vil formentlig skulle doseres kalk o. lign. |
Mængder til deponering: |
|
Det antages at slaggen grundet smeltning kan genanvendes. Der haves ikke data til at kunne vurdere udvaskningsegenskaberne.
Røggasrensningsprodukt |
(Kondensat: 52 l/ton) |
Vedligehold og reparation: |
(3%) af investering. |
Div. forsikringer mv.: |
Ikke inkluderet. |
Administration og overhead: |
Ikke inkluderet. |
9.5 Behandlingsomkostninger
Beregningen af behandlingsomkostninger er kun foreløbige skøn, som skal vise niveauet for behandlingsomkostningerne. Den endelige behandlingspris vil være afhængig af anlægsplacering, faciliteter til stede,
valgte bygningsstandarder osv. samt størrelsen af den rabat der ved forhandling kan opnås på købsprisen for anlægget.
Beregningen viser følgende udgifter.
Kapitaludgifter: |
269 DKK/t |
Driftsudgifter: |
464 DKK/t |
Indtægter: |
583 DKK/t |
Behandlingsprisen skønnedes således at blive 149 DKK/t inkl. bygninger for et turn-key-anlæg.
Hvis anlægget ligger op ad andet anlæg og kan drives via et fælles operatørrum kan bemandingen sænkes væsentligt. En bemanding på 6 personer sænker således driftsudgifterne til 276 DKK/t, hvorved
processen giver overskud.
10 Konklusioner og anbefalinger
10.1 Egnethed for den danske affaldsstruktur
Procones forgasser vurderes at kunne behandle imprægneret træ. Det forventes dog, at der skal etableres en bedre røggasrensning for at kunne overholde krav til emission af arsen og tungmetaller. Arsen
forventes at ende i henholdsvis i røggasrenseprodukt og slagge. Fordelingen kendes ikke, da der ikke er lavet forsøg med dette. Resultater af forsøg med modstrømsforgasning af CCA-imprægneret træ
viser at en væsentlig del af arsen-indholdet i brændslet (ca. 70-80%) ender i røggasrenseprodukterne. I Procones forgasser ledes pyrolysegasserne ud sammen med slaggen, men passerer dernæst en
sekundærforgasser, som kan betragtes som en modstrømsforgasser. Evt. udkondenserede arsen-partikler formodes at genfordampe i sekundærforgasseren, så det er muligt, at fordelingen mellem
forgasningsgas og slagge vil være af samme størrelsesorden som for en modstrømsforgasser.
Kobber og krom formodes primært at fanges i slaggen.
Hvis metaller ønskes oparbejdet, skal dette således udføres ved en efterfølgende behandling af slaggen. Her skal det bemærkes, at metaller i slaggen grundet smeltningen formodes at være bundet hårdere
end i slagge, som ikke har været smeltet. Herved formodes evt. oparbejdning ved opløsning med kemikalier og genudfældning af metaller at være lidt vanskeligere end fra slagge, som ikke har været smeltet.
10.2 Omkostningsstruktur
Behandlingsomkostningerne for et anlæg med en kapacitet på 9.600 t/år med en bemanding på 12 personer er i størrelsesordenen 150 DKK/t. Her skal bemærkes, at røggasrensningen kun er udlagt til
træflis, ligesom der ikke indgår nogen udvinding af metaller fra slaggen. Anlæggets økonomi er selvfølgelig afhængig af antallet af ansatte. Der er regnet med 24 timers drift med en minimumsbemanding på 2
mand per skift i 5 skift, samt 2 andre ansatte, hvilket primært er af sikkerhedshensyn. Dette vil også være tilstrækkeligt ved et anlæg med den dobbelte kapacitet (2,5 t/time) hvilket forbedrer økonomien
væsentligt. En grov opskalering giver således en behandlingsudgift på –150 DKK/t. Der er ikke medregnet sparede deponeringsudgifter til det trykimprægnerede træ.
10.3 Affaldets udnyttelsesgrad
Anlægget forventes at kunne opnå 8.000 driftstimer pr år.
10.4 Miljømæssige problemstillinger
Procones eksisterende anlæg vurderes pt. ikke at være udstyret med tilstrækkelig røggasrensning til at kunne behandle trykimprægneret træ, idet anlæggene er udlagt til behandling af tysk klasse I og II træ.
En sådan nødvendig røggasrensning vurderes dog at kunne etableres med standardkomponenter for en merpris. Arsen fra brændslet vil fordele sig mellem slagge og røggasrenseprodukter.
Røggasrenseprodukter vil skulle specialbehandles grundet et formodet arsen-indhold, mens slagge afhængigt af udvaskningsdata enten skal deponeres, vil kunne oparbejdes med metaludvinding eller evt. kan
genanvendes som fyldmateriale.
Hvis et lignende anlæg etableres til behandling af imprægneret træ må indføres en række forholdsregler herunder afskærmning, afsugning mv. for at undgå kontakt med støv eller restprodukter.
10.5 Muligheder for knowhow-formidling
Knowhow-formidling kan ske via Procone.
Bilag H
Logbog for besøg hos R-plus
1. Generelle oplysninger
1.1 Procestype
Mekanisk / magnetisk / elektrisk affaldssortering.
1.2 Tilført affald
Friskt shredderaffald.
1.3 Licenshaver og kontaktpersoner
Licenshaver
R-plus Recycling GmbH
Heilbronner Strasse 13
D-75031 Eppingen
Tyskland
Kontaktperson
Rolf Hengerer, Dr. Ing., Geschäftsführer
Telefon: +49 72 626 12 12
Fax: +49 72 626 12 19
E-mail: rolf.hengerer@r-plus.de
www: http://www.r-plus.de
1.4 Ejerforhold og kontaktpersoner for det besøgte anlæg
R-plus ejes af U-plus Umweltservice AG, der er holdingselskab for en gruppe af selvstændigt styrede virksomheder inden for affaldsindustrien. U-plus-gruppen ejes 100% af EnBW Energie
Baden-Württemberg AG, der er et tysk energi- og affaldsselskab med ca. 1.800 ansatte.
R-plus har 140 medarbejdere og havde i 2001 en omsætning på 23 mio. EUR.
Kontaktperson
Rolf Hengerer, Dr. Ing., Geschäftsführer
Telefon: +49 72 626 12 12
Fax: +49 72 626 12 19
E-mail: rolf.hengerer@r-plus.de
1.5 Beliggenhed for det besøgte anlæg
R-plus Recycling GmbH
Heilbronner Strasse 13
D-75031 Eppingen
Tyskland
1.6 Virksomhedens formål og idégrundlag
Genanvendelse af metaller og elektronik.
R-plus har ændret og videreudviklet LSD's anlæg til mekanisk sortering af shredderaffald fra behandling af biler.
Anlægget, der behandler shredderaffald, er fuldt driftsklart, men er ikke i drift.
De meget lave deponeringsomkostninger på mindre end 51 EUR/t i Tyskland gør anlægget urentabelt.
Anlægget vil sandsynligvis blive aktiveret, når TA i 2005 forbyder deponering af brændbart affald.
Et EU-direktiv forbyder deponering af brændbart affald fra 2006.
1.7 Kapacitet for det besøgte anlæg
12.000 t shredderaffald/y svarende til 4 t shredderaffald/h, 2 skift, 3.200 h/y.
1.8 Byggeår og status for projektet
Anlægget blev første gang afprøvet i 1999 men kunne ikke overholde de specificerede krav til kapacitet og renhed af produkterne. Anlægget er siden blevet kraftigt ombygget med:
- nye møller fra nye leverandører: MEVA og Eldan Scandinavian Recycling A/S (DK)
- nye sorteringsmaskiner bl.a. hvirvelstrømsseparatorer (eddy current)
- ny hovedsigte
- tilførsel af shredderaffald direkte fra shredderen, så tørring undgås.
- udtag af rene delstrømme tidligt i processen, så kun blandede delstrømme sorteres.
Hele processen er afprøvet, og dens kapacitet og effektivitet dokumenteret.
2. Kortlægning og beskrivelse af anlægget
2.1 Procesdiagram
R-plus's proces er en videreudvikling af LSD/ARGE AltAutos proces, der ikke kunne overholde de lovede krav til kapacitet mm. R-plus har forbedret processen med nye granulatorer (neddelere) og ved at
tage produktstrømme ud så tidligt i processen som muligt, så de efterfølgende delprocesser ikke belastes.
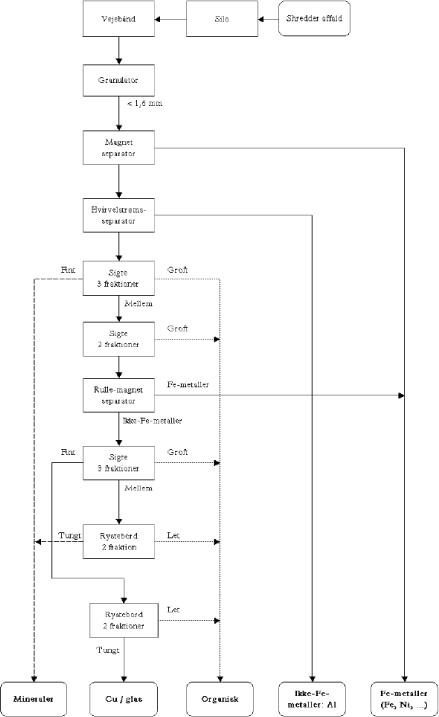
Figur 1. Procesdiagram for R-plus's mekaniske sorteringsanlæg.
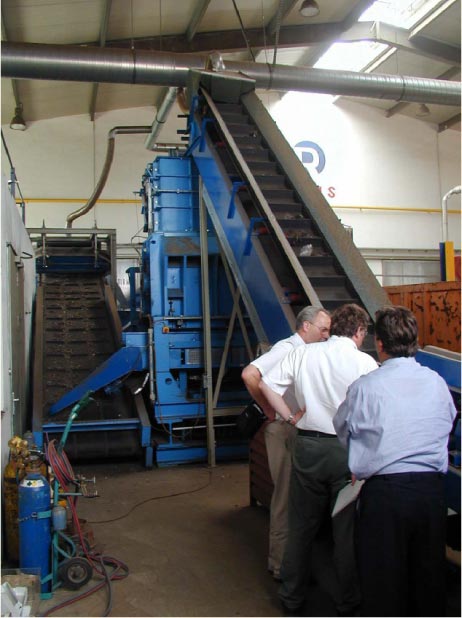
Figur 2. Granulator (mølle) med tilførsel af friskt shredderaffald (th.)og udgående strøm (tv.).
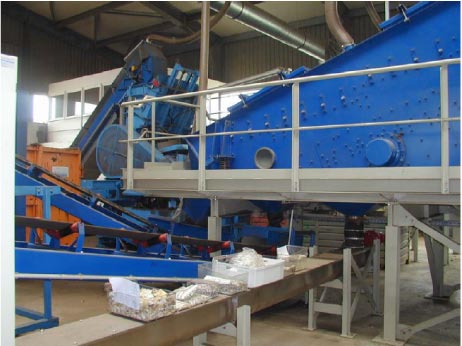
Figur 3. Sigte med transportører til tre fraktioner (R-plus).
2.2 Affald
Anlægget vil kunne behandle shredderaffald direkte (uden tørring) fra shreddere på R-plus egne skrotningsanlæg.
2.3 Forbehandling
Shredderaffaldet føres uden forbehandling direkte fra shredderen til anlægget.
2.4 Proces(ser)
Anlægget indeholder kun mekaniske processer.
3. Observationer under besøget
3.1 Besøgets varighed
Den 2002-06-04 fra kl. 9:30 til kl. 14.
3.2 Tilførte materialer behandlet under besøget
Type (kvalitativ beskrivelse): shredderaffald
Mængde i t/h: 4 t/h
Kapacitetsudnyttelse: 100 %
3.3 Driftsforhold
Driftstid: Ca. 1 time
Anlægget blev udelukkende startet for at demonstrere
processen under besøget.
Forventet produktionstid: 8.000 h/år
3.4 Output under besøget
Der er altid store variationer i sammensætningen af shredderaffald. Den gennemsnitlige sammensætning af affaldet til R-plus's sorteringsanlæg giver følgende fraktioner:
Produktstrøm |
Anvendelse |
Organisk materiale |
Den organiske fraktion, der har høj brændværdi, er svær at afsætte til fx stålværker pga. det høje indhold af natrium (Na). |
Fe-metaller |
Sælges til genanvendelse. |
Al |
Sælges til genanvendelse. |
Cu + glas |
Sælges til genanvendelse. |
Mineraler |
Deponeres i gamle saltminer
Benyttes til vejfyld
Anvendes som sand i fluid bed anlæg |
Ferro-magnetiske småpartikler |
Deponi |
Støv mm. |
Deponi |
4. Kritiske delprocesser og driftsparametre
I mekaniske processer som R-plus's er der et stort slid på specielt neddelingsudstyr som granulatorer etc., hvilket medfører relativt høje omkostninger til vedligeholdelse på ca. 10% af investeringen om året
(se også afsnit 9.2 Udgiftsstruktur).
5. Miljømæssige forhold
5.1 Emissioner til luften
R-plus' anlæg er placeret i en lukket hal med ventilation og filtrering af luften.
Der forekommer ingen emissioner til luften af miljømæssig betydning.
5.2 Spildevandsudledning
Der er intet spildevand fra processen.
5.3 Støj
Anlægget er placeret i en lukket hal og overholder tyske krav til støjemission.
5.4 Lugt
Der er ingen lugtgener fra anlægget.
6. Arbejdsmiljømæssige forhold
6.1 Støvbelastning
Alle støvende processer (neddeling, sigtning, etc.) sker i lukkede delprocesser med afsugning.
Der var meget lidt støv i hallen, og hele procesanlægget virkede rent.
6.2 Internt støjniveau
Sigter og granulatorer gav et vist støjniveau. Det vil sandsynligvis være nødvendigt, at driftspersonale bærer høreværn.
6.3 Tungmetalbelastning
Da der er ingen støvbelastning er i produktionshallen, er der ingen risiko for tungmetalbeslastning af driftspersonalet.
6.4 Andet - fx lugtgener, vilkår i forbindelse med reparationsarbejde mv.
Af hensyn til tungmetaller og bakteriologisk vækst den organiske del af shredderaffaldet må driftspersonalet bære handsker og støvmaske under reparationsarbejde.
7. Beskrivelse af input
Shredderaffaldet fra R-plus' shredderanlæg indeholder relativt lidt jern og metaller i forhold til dansk shredderaffald, hvilket er almindeligt i Tyskland. Årsagen er sandsynligvis, at tyske shredderoperatører
ofte arbejder med en relativ lille luftstrøm gennem shredderen, så en større del af metallerne ender i den tunge fraktion, mens shredderaffaldet kun indeholder lettere og finere partikler. Vi har ikke studeret
shredderskrottet nærmere; men vi forventer, at shredderskrottets renhed ikke er så høj, som det ville være med en kraftigere afsugning.
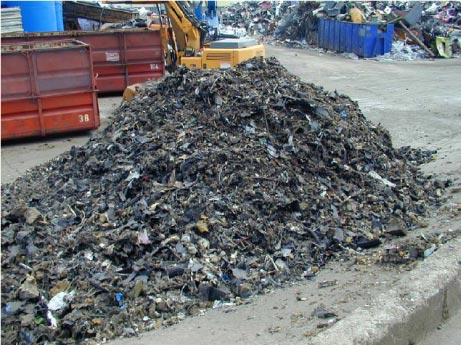
Figur 4. Shredderaffald hos R-plus.
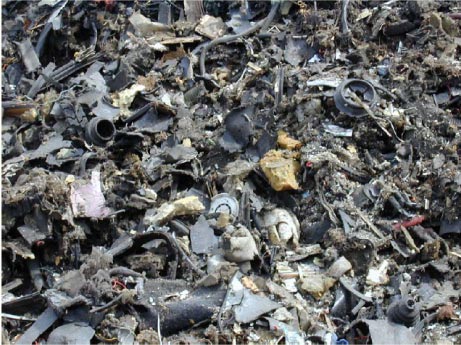
Figur 5. Nærbillede af shredderaffald hos R-plus.
7.1 Kvantitativ beskrivelse. Mængde og analyser.
Tabel 1. Sammensætning af shredderaffald fra R-plus' anlæg
Fraktion |
% (w/w) |
Organisk |
52 |
Fe-metaller |
1 |
Al |
1 |
Cu + glas |
1 |
Mineraler |
23 |
Ferro-magnetiske småpartikler |
9 |
Støv mm. |
6 |
Sum |
93 |
8. Beskrivelse af output
8.1 Metaller
R-plus' mekaniske sorteringsanlæg vil kunne producere følgende metalfraktioner:
- Fe-metaller (Fe, Ni, ..)
- Grov fraktion (afsættes i genvindingsindustrien)
- Fin fraktion (deponi)
- Ikke-Fe-metaller (Al, ..)(afsættes i genvindingsindustrien)
- Cu/glas
Figurerne nedenfor viser fotos af disse fraktioner og/eller mellem fraktioner.
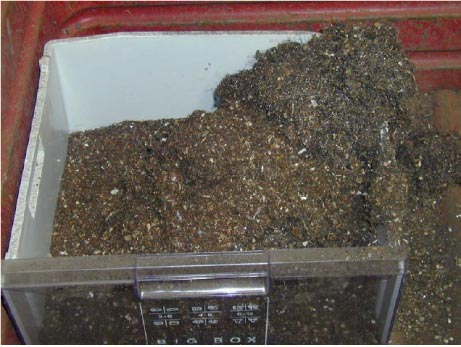
Figur 6. grov fraktion af Fe-metaller fra R-plus' sorteringsanlæg
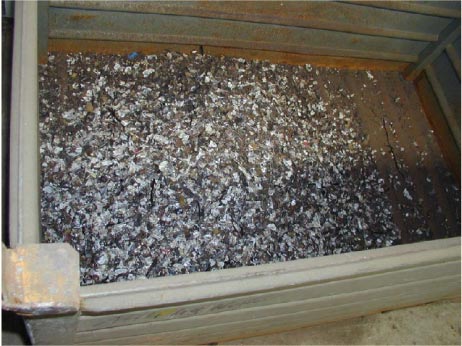
Figur 7. Ikke-Fe-metaller - grov fraktion (hovedsageligt Al).
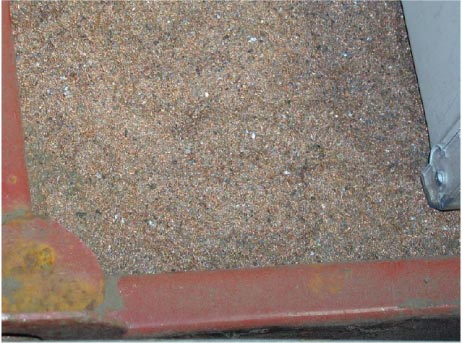
Figur 8. Ikke-Fe-metaller - fin fraktion (hovedsageligt Cu og glas).
R-plus forventer at kunne sælge blandingen af kobber og glas, der dog relativt let vil kunne separeres i to rene fraktioner i et efterfølgende procestrin fx ved sortering efter farve eller vægtfylde.
R-plus har ikke kunnet oplyse renheden af metalproduktstrømmene, men de salgbare afsættes uden yderligere oprensning.
8.2 Granulat/restprodukt
Anlægget producerer desuden to restprodukter:
- Organisk materiale ("fluff")
- Mineralsk fraktion
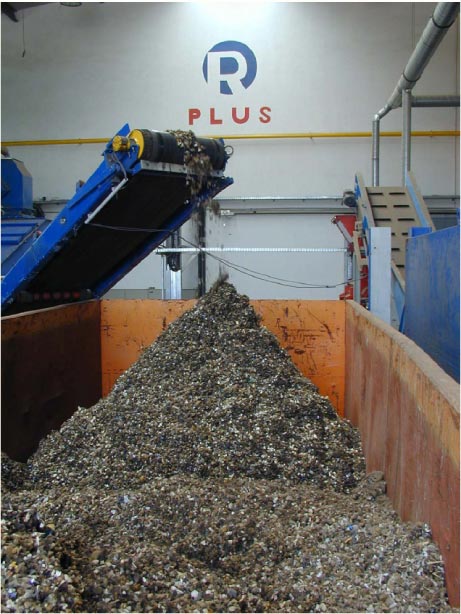
Figur 9. Organisk fraktion (”fluff”) fra R-plus' sorteringsanlæg.
R-plus forventer at kunne afsætte den organiske restfraktion som brændsel til flere aftagere:
- Schwartze Pumpe (SVZ)
- Højovne
- Cementindustrier
- Alternative forgasnings- og pyrolyseanlæg
- udvalgte kraftværker
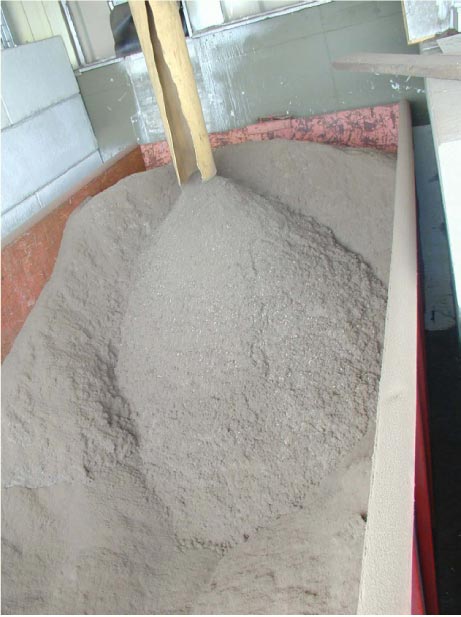
Figur 10. Mineralsk restprodukt fra R-plus' sorteringsanlæg.
Vi vurderer, at det organiske restprodukt sandsynligvis vil kunne afsættes til Schwartze Pumpe, cementindustrien eller alternative forgasnings- og pyrolyseanlæg, mens hverken højovne eller udvalgte danske
kraftværker vil modtage den organiske restfraktion som brændsel på grund af dens indhold af tungmetaller.
R-plus regner med, at den mineralske fraktion i Tyskland vil kunne
- deponeres i gamle saltminer
- benyttes til vejfyld
- anvendes som sand i fluid bed anlæg
Udgifterne til deponi i gamle saltminer vil udelukkende være transportomkostningerne.
På grund af den meget brede partikelstørrelsesfordeling vurderer vi dog, at den mineralske fraktion ikke vil kunne anvendes fluid bed anlæg. Indholdet af tungmetaller i denne fraktion gør den også uegnet til
vejfyld, fordi tungmetallerne ikke er immobiliseret ved en smeltning/glasifisering.
8.2.1 Udvaskningsegenskaber
Der foreligger ingen analyser af udvaskningsegenskaberne for den mineralske fase, der sandsynligvis skal vitrificeres, før den vil kunne opnå de udvaskningsegenskaber, der er nødvendige for at den kan
anvendes til vej- eller bygge materialer.
8.3 Massebalance
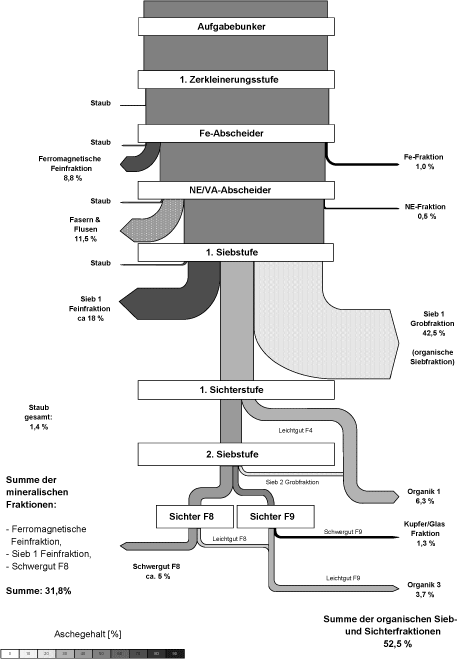
Figur 11: Massebalance for R-plus' mekaniske sorteringsanlæg til shredderaffald .
9. Økonomi
9.1 Nødvendige investeringer til etablering af anlægget
Udgifterne til etablering af anlægget er svære at fastlægge, da det oprindeligt ikke levede op til de kontraktmæssige krav. Siden er anlægget er blevet ombygget for et betydeligt beløb.
9.2 Udgiftsstruktur
Nedenstående forudsætninger og data er anvendt i forbindelse med et skøn over behandlingsprisen. Alle data er opgivet af R-plus med undtagelse af rentefod, lønninger samt priser på el og varme, der er
tilpasset danske forhold.
Udgiftsstrukturen for et nyt anlæg til 32.000 t SHR/y svarende til 8.000 h/y ser således ud:
Anlægsstørrelse: |
32.000 |
t SHR/år |
Investering ekskl. bygninger: |
9.500.000 |
DKK |
Rentefod: |
7 |
% p.a. |
Tilbagebetalingstid: |
7 |
år |
Driftsudgifter
Gennemsnitlig løn til personale [1]: |
300.000 |
DKK/person |
5 |
personer |
Andre driftsudgifter: |
570.000 |
DKK/år |
|
|
Elektricitet: |
390 |
DKK/MWh |
1.000 |
MWh/år |
Vedligehold og reparation:
Normalt maskineri |
9,6 |
% af investering |
Udgifter til forsikringer er ikke inkluderet.
Skønnede behandlingsomkostninger
En økonomiberegning giver følgende resultat:
Kapitaludgifter: |
55 |
DKK/t |
Driftsudgifter: |
110 |
DKK/t |
Den endelige behandlingspris vil være afhængig af anlægsplacering, faciliteter til stede, valgte bygningsstandarder osv. og den endelige pris, som vil kunne opnås for anlægget efter forhandlinger.
Behandlingsprisen skønnes at blive 165 DKK/t shredderaffald for et turn-key anlæg.
Behandlingsomkostningerne for anlæg med en højere kapacitet på f.eks. 90.000 t SHR/år vil blive noget lavere.
10. Konklusioner og anbefalinger
10.1 Egnethed for den danske affaldsstruktur
R-plus' koncept er særdeles velegnet til den danske affaldsstruktur, idet det øger kvaliteten i behandlingen af shredderaffald, så kun den mineralske fraktion ikke umiddelbart kan genanvendes. Kapaciteterne
af anlæggets delprocesser skal dog tilpasses sammensætningen af dansk shredderaffald.
For at passe til den danske forhold bør det mineralske restprodukt smeltes for at binde tungmetaller. Dette kan evt. gøres ved at blande den mineralske og den organiske fraktion og smelte asken i en
passende termisk proces.
Problemet med genanvendelse af ferromagnetiske småpartikler er ikke løst.
10.2 Udgiftsstruktur
Den forventede behandlingspris på R-plus anlæg er 165 DKK/t for et anlæg med en kapacitet på 32.000 t shredderaffald/y.
10.3 Affaldets udnyttelsesgrad
På trods af det lave metalindhold i udgangsmaterialet er anlægget i stand til at genvinde stort set alle frie metaller på en form, så de kan afsættes til en positiv pris. R-plus har flere muligheder for at afsætte den
organiske rest, så energien udnyttes. Den mineralske rest vil enten kunne deponeres i gamle saltminer, benyttes til vejfyld eller anvendes som sand i fluid bed anlæg.
10.4 Miljømæssige problemstillinger
Ingen specielle. Af hensyn til arbejdsmiljøet bør anlægget være forsynet med lukkede transportsystemer med afsugning ligesom støjende udstyr bør afskærmes.
10.5 Muligheder for know-how-formidling
R-plus Recycling GmbH
Heilbronner Strasse 13
D-75031 Eppingen
Tyskland
Fodnoter
[1] Forudsætning: Personale på shredderanlægget servicerer delvist sorteringsanlægget, så der kun er behov for 5 personer, der arbejder i treskift.
Bilag I
Logbog for besøg hos S+S
1 Generelle oplysninger
1.1 Procestype
Detektering og fraseparering af metaller fra affaldsstrømme
1.2 Tilført affald
Tung fraktion fra shredderanlæg
1.3 Licenshaver og kontaktpersoner
Licenshaver
S+S Metallsuchgeräte und Recyclingtechnik Gmbh
Regener Straße 130
D-94513 Schönberg
Kontaktperson
Werner Neumüller
Telefon: +49-8554-308-0
Fax:
E-mail: info@ss-gmbh.de
1.4 Ejerforhold og kontaktpersoner for det besøgte anlæg
RGW Recycling und Rückgewinnungs Gmbh
1.5 Beliggenhed for det besøgte anlæg
RGW Recycling und Rückgewinnungs Gmbh
Siemensstraße 44
D-84109 Wörth
1.6 Virksomhedens formål og idégrundlag
At udvinde metaller fra skrot til genanvendelse
1.7 Kapacitet for det besøgte anlæg
2,5 t/time
1.8 Byggeår og status for projektet
S+S startede for over15 år siden. Firmaet producerer udover metalseparatorer udstyr til farvesortering af fx glasskår. S+S har 75% af markedet for sortering af glasskår i Tyskland.
Der er leveret mere end 140 metalseparationsenheder worldwide til behandling af træflis, container glasskår, fladglas, CRT-glas, elektronikaffald, plastgranulat/affald af en række typer og shredderaffald (6
installationer).
2 Kortlægning og beskrivelse af anlægget
2.1 Proces
Under besøget blev shredderanlægget besøgt ved RGW se figur 1.
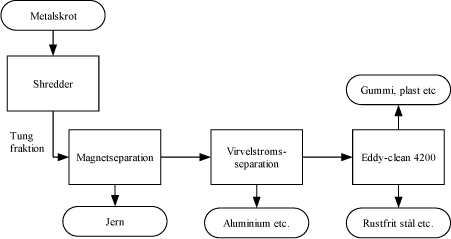
Figur 1 Procesdiagram for RGW
2.2 Affald
Affaldet som tilføres shredderanlægget er forskelligt metalskrot af mindre dimensioner end biler.
2.3 Forbehandling
Den tunge fraktion fra shredderen tilføres en overbåndsmagnet som fjerner jern. Herefter fjernes ikke jernmetaller (typisk aluminium) med hvirvelstrømsseparation.
2.4 Separation med S+S udstyr
Affaldet fra hvirvelstrømsseparationen tilføres S+S separationsudstyret.
Udstyret består af en Eddy-Clean 4200 metalseparator med 1024 mm båndbredde. Et diagram er vist på figur 2
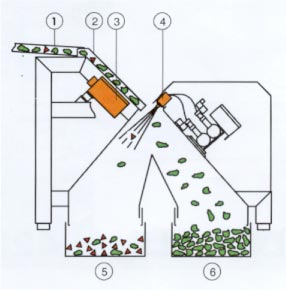
Figur 2 1:transportbånd, 2:Føde transportbånd, 3:detektionsenhed, 4:Dyser, 5:Metaller, 6:Metalfri rest
Princippet virker ved at affald doseres til et hurtigløbende transportbånd (1) så alle partikler ligger i et enkelt lag. Over fødetransportbåndet (2) sidder en detektorenhed med en række detektorer (3). Når en
metalpartikel passerer en detektor opstår en strøm hvorefter en computer registrerer partiklens position og hastighed. Senere passeres et arrangement med dyser (4) og her aktiveres den dyse som er udfor
metalpartiklen. Metalpartiklen blæses dernæst væk med trykluft fra de andre partikler og ender i en separat opsamlingsbeholder (5).
Detektorenheden består af to rækker forskudte detektorer. I den mest følsomme version er der 32 mm mellem detektorelementerne i en række. Da de to rækker er forskudte vil en passerende metalpartikel
give signal af forskellig størrelse fra de to elementer i de to rækker hvorved den nøjagtige position og hastighed kan bestemmes med en meget større nøjagtighed end de 32 mm der er mellem detektorerne i
hver række. Således kan detekteres jernbaseret materiale ned til 2 mm og aluminium ned til 3 mm partikelstørrelse. Dyserne er placeret med ca. 16 mm afstand, idet der er 64 stk. for en 1024 mm
båndbredde. Da hver dyse består af en række små huller vil man altid kunne fjerne alle detekterede metalpartikler som er større end følsomheden (2-3 mm), men hvis der samtidig forekommer ikke ledende
materiale (plast etc.) over det dyseelement på 16 mm der aktiveres vil det ikke ledende materiale bliver fjernet sammen med metallet. Således opnås altid et meget højt metaludbytte og renhedsgrad af
restfraktionen, men renhedsgraden af metalfraktionen kan godt være lavere idet noget ikke-ledende materiale kan blive revet med. Dette kan i øvrigt også forekomme med et større antal dyser hvis affaldet
ikke er ordentligt neddelt eller plast, fibre mm hænger sammen med metalpartikler, stumper af filtrede ledninger etc.
Den maksimale partikelstørrelse som kan tilføres udstyret er 100 mm. En anden model MAG 4200 har en større følsomhed på ned til 0,6 mm partikler da dyserne er placeret i flere lag.
Til farvesortering af fx glas eller metaller efter farve kan leveres modellen "Spectrum" som i stedet for metaldetektor har et CCD farvekamera. Partikler >5 mm kan separeres efter valgte farver. Op til 16
maskiner kan fjernstyres via computer.
Der kan levere kombinerede systemer med flere detektorer. Fx er leveret et system med en metaldetektor og transparensdetektor til glasseparation
S+S udvikler og producerer selv dyser og detektorer.
3 Observationer under besøget
3.1 Besøgets varighed
Den 5/6 2002 fra kl. 14:00 til kl. 17:30.
3.2 Indsatsmaterialer behandlet under besøget
Type:
Mængde i t/h: ca.8 t/h *
Kapacitetsudnyttelse: 300 %
* EddyClean 4200 udstyret blev ikke udnyttet efter forskrifterne da der tilførtes for meget affald så dette ikke lå i et enkelt lag men derimod i et meget tykt lag og endda med en delvis blokering i den ene
side. Herudover var nogle stykker større end udstyrets anbefalede grænse på 100 mm (nogle op til 300 mm). Derfor blev en del organisk materiale medrevet men udstyret var stadig i stand til at fjerne
hovedparten af metalstykkerne af rustfrit stål. Udstyret måtte også stoppes og startes af og til. Årsagen til denne driftsmåde var at der var ansat personale til at finsortere fraktionen med rustfrit stål og
personalet kunne følge med til den meget forhøjede kapacitet. Umiddelbart må det betragtes som en mere optimal løsning at neddele metalskrottet til under den angivne grænse på 100 mm og dernæst
dosere i et enkelt lag. Herved bør kunne opnås en så høj renhedsgrad af det frasorterede rustfrie stål at efter-sortering ikke er nødvendig, men det har man altså ikke valgt ved genvindingsvirksomheden.
3.3 Driftsforhold
Driftstid: |
ca. 8-12 timer/døgn ved det besøgte anlæg men med mange start og stop |
Anbefalet driftstid for apparatur |
24 timer/døgn |
Forventet produktionstid: |
8000 timer/år |
Revisioner: |
1 pr. år samt evt. kortvarig rengøring |
Det skal bemærkes at dyser/ventiler kan klare 4-5 millioner pulser inden udskiftning
3.4 Output under besøget
Der produceredes samlet ca. 8 t/time af en blanding af rustfrit stål og ikke metallisk medrevet materiale som blev frasorteret manuelt, samt en restfraktion uden rustfrit stål.
3.4.1 Restprodukt
Restproduktet bestod af en blanding af gummi, fibre , andet ikke metallisk og mindre metalstykker som kobbertråde etc.
4 Kritiske delprocesser og driftsparametre
Under besøget blev følgende spørgsmål diskuteret:
- Er der forekomst af kondenserbare stoffer og forureninger i processernes forskellige trin; fx af tjære, sod, metaller, salte og oxider i pyrolyseovnens top, i gaskanaler eller i
efterforbrændingskamre?
Støv kan samle sig i udstyret hvis det ikke holdes i kontinuerlig drift, men det er ikke særligt følsomt.
- Hvordan kontrolleres mængden af kondenserede stoffer, dvs. hvordan renses de kritiske procesafsnit for afsætninger?
Støv er normalt ikke et problem. Det kan dog være påkrævet med simpel rengøring for støv hvis anlægget ikke holdes i kontinuerlig drift.
- Hvilken kemisk stabilitet har restprodukter fra processen? Er de lagringsstabile mht. tungmetaller og dermed egnet til deponering (data for standardudvaskningstests), eller lækker der tungmetaller, og skal de betragtes som miljøfarligt affald?
Ikke relevant for processen
- Findes der dioxiner (eller andre halogenerede organiske stoffer) i restprodukter eller evt. mellemprodukter som skal oparbejdes andetsteds?
Processen medfører ingen fysisk eller kemisk ændring af det behandlede materiale, ligesom der ikke udvikles varme hvorfor der ikke kan produceres dioxin
5 Miljømæssige forhold
5.1 Emissioner til luften
Der kan forekomme støvemissioner fra processen grundet jetpulserne der blæser metallerne væk. Støvemissionen kan nemt kontrolleres ved korrekt afskærmning og afsugning
5.2 Spildevandsudledning
Ingen
5.3 Støj
Støjniveauet kan være højt når der skydes jetpulser, hvorfor der bør afskærmes og bæres høreværn ved arbejde omkring udstyret.
5.4 Lugt
Der forekommer ingen lugt som følge af udstyret
5.5 Affaldsproduktion
Udstyret separerer en affaldsfraktion i en metalholdig fraktion og en ikke metalholdig fraktion. Afhængigt af de separerede fraktioners sammensætning og værdi vil de kunne sælges (fx metalfraktionen) eller
må viderebehandles fx ved yderligere oparbejdning for restmetaller af lille partikelstørrelse , plastmaterialer mv. eller alternativt behandles i et termisk anlæg eller deponeres.
5.6 Samlet dioxinemission
Der produceres ingen dioxin
6 Arbejdsmiljømæssige forhold
6.1 Støvbelastning
Der kan afgives støv fra affaldet hvis udstyret ikke er tilstrækkeligt afskærmet eller forsynet med tilstrækkelig afsugning. Forholdsreglerne er af samme type som for andre mekaniske processer i et
shredderanlæg
6.2 Internt støjniveau
Høreværn er påkrævet
6.3 Tungmetalbelastning
Ved ukorrekt afskærmning vil der kunne afgives tungmetalholdigt støv
6.4 Dioxinbelastning
Anlægget producerer ikke dioxin
6.5 Andet; fx lugtgener, vilkår i forbindelse med reparationsarbejde mv.
Der er ingen lugtgener i forbindelse med udstyret anden end den lugt der kan komme fra affaldet.
7 Beskrivelse af input
Besøget var for kort til at beskrive input i detaljer. Det tilførte affald er den tunge fraktion fra shredderanlægget.
Anlægget bruger ca. 0,5 kWh el og herudover ca. 1m³ trykluft/min, 6bar. Trykluften skal være renset for at undgå tilstopning af dyser.
8 Beskrivelse af output
Besøget var for kort til en detaljeret beskrivelse af output.
Anlægget separerer det tilførte affald i en fraktion med alle metalstykker med partikelstørrelse over anlæggets separationsgrænse og i en fraktion uden metalstykker.
8.1 Metaller
Metalfraktionen bestod primært af rustfri stål emner af størrelse mindre end 300 mm
8.2 Granulat/restprodukt
Restfraktionen bestod af gummi, plast fibre mm.
9 Økonomi
9.1 Nødvendige investeringer til etablering af anlægget
Nedenstående beregning er for anvendelse i Danmark.
Investeringen i en Eddyclean 4200 til metalseparation med 1024 mm båndbredde udgør ca. 75.000 Euro svarende til ca. 560.000 DKK.
Prisen for en Mag 4200 til separation efter farve er ca. 86000 Euro svarende til 645.000 DKK.
Dertil skal lægges en vibrationsføder som er en mindre udgift.
Nedenstående data er anvendt i beregningen af en skønnet behandlingspris.
Bemanding: |
1 person. |
Strømforbrug: |
312 MWh/år. |
Vedligehold og reparation: |
72.500 DKK/år. |
9.2 Indtægter
Her vil indtægten variere med affaldets sammensætning
Hvis der fx produceres en 1,5% metal med en værdi på 3 DKK/kg (fx aluminium) af den tilførte mængde fås en indtægt på 45 DKK/t
Hvis man opkoncentrerer det tilførte shredderaffald inden tilførsel til udstyret så metalkoncentration er væsentligt højere fx ved at frasigte fine fraktioner og fjerne det magnetiske materiale vil indtægten/t blive
langt højere
9.3 Behandlingsomkostninger
Der er kun udført en beregning af kapitaludgifter og driftsomkostninger
Beregningen viste følgende udgifter.
Kapitaludgifter: |
6 DKK/t |
Driftsudgifter: |
27 DKK/t |
Indtægter: varierer med affald
Hvis der produceres 1,5% metal med en værdi på 3 DKK/kg (fx aluminium) svarende til en indtægt på 45 DKK/t fås et overskud på 13 DKK/t tilført affald. (behandlingspris = -13 DKK/t)
Det skal bemærkes at denne type separationsudstyr vil kunne erstatte andet udstyr og arbejdsgange i genvindingsindustrien hvorved opnås et endnu større overskud.
10 Konklusioner og anbefalinger
10.1 Egnethed for den danske affaldsstruktur
Udstyret er velegnet som del af oparbejdningsprocesser hvor metaller ønskes fjernet fra affaldsstrømme
10.2 Omkostningsstruktur
Behandlingsomkostningerne varierer med affaldets sammensætninger. Da kapitalomkostninger og driftsomkostninger er lave (32 DKK/t) kan opnås overskud ved behandling af mange metalholdige
affaldsfraktioner herunder shredderaffald.
10.3 Affaldets udnyttelsesgrad
Anlægget kan køre i døgndrift med 2-3 årlige serviceeftersyn og korte stop til eventuel rengøring.
10.4 Miljømæssige problemstillinger
Der er ingen miljømæssige problemer med processen ved korrekt afskærmning mht. støj og støvemission.
10.5 Muligheder for knowhow-formidling
Knowhow-formidling kan ske via S+S.
Bilag J
Logbog for besøg hos Salyp i Ypres, Belgien
1. Generelle oplysninger
1.1 Procestype
Anlægget er et demonstrationsanlæg til genvinding af plast og plastskum fra forskellige blandede plastaffaldsstrømme og fra shredderaffald.
1.2 Tilført affald
1.3 Licenshaver og kontaktpersoner
Licenshaver
Salyp nv.
Kontaktperson
Salyp nv
Oostkaai 62
8900 Ypres
Belgien
Tlf.: +32 57228044
Fax: +32 57228049
E-mail: info@salyp.com
Hjemmeside: www.salyp.com
1.4 Ejerforhold og kontaktpersoner for det besøgte anlæg
Anlægget ejes af Salyp.
Kontaktpersoner:
Ivan Vanherpe
Wilfried Mortier
1.5 Beliggenhed for det besøgte anlæg
Oostkaai 62
8900 Ypres
Belgien
1.6 Virksomhedens formål og idégrundlag
Anlægget er opbygget som et demonstrationsanlæg, med det formål at vise potentielle kunder, at genvinding af visse plasttyper er muligt og rentabelt. Til det formål benyttes anlægget med henblik på at sælge
knowhow og udstyr.
1.7 Kapacitet for det besøgte anlæg
Anlæggets kapacitet er 5 – 8 t/h afhængig af inputtets egenskaber.
1.8 Byggeår og status for projektet
Demonstrationsanlægget, ”The Salyp ELV Centre” er færdigbygget i 2002, men udviklingen i forbindelse med genvinding af plast, skumplast og oxider har stået på siden 1997. Demonstrationsanlægget er
opbygget således, at forskellige ønsker fra interessenter kan afprøves. Anlægget er således udlagt til behandling af blandet plastaffald, madrasser, elektronikaffald og shredderaffald.
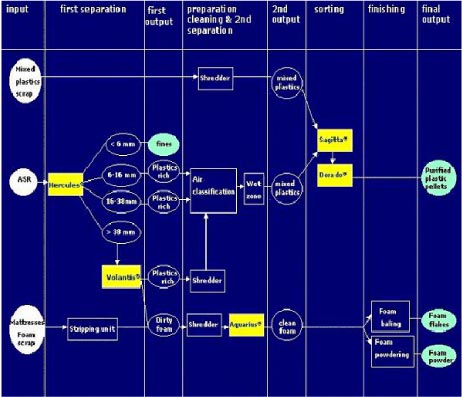
Figur 1. Oversigtsdiagram for demonstrationsanlægget.
I det følgende vil kun proceskæden til behandling af shredderaffald blive beskrevet.
2. Kortlægning og beskrivelse af anlægget
2.1 Procesdiagram
Den af Salyp anbefalede og foreslåede samt i det følgende gennemgåede proceskæde til behandling af shredderaffald er vist på figur 2.
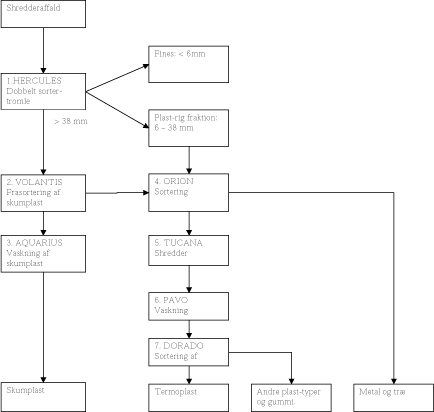
Figur 2. Procesdiagram til behandling af shredderaffald.
De enkelte delprocesser vil blive nærmere gennemgået i det følgende, hvor også de af Salyp anslåede mængder for shredderaffald fra bilskrotning vil blive anført.
2.2 Affald
Den på figur 2 viste procesrækkefølge er specielt designet til behandling af shredderaffald, som det måtte falde hos shredderoperatøren. Erfaringerne er hos Salyp dog størst i behandling af shredderaffald fra
shredning af biler.
2.3 Forbehandling
Ingen forbehandling er normalt nødvendigt. Shredderaffaldet kan behandles, som det måtte foreligge hos shredderoperatøren i stykstørrelse op til 200 mm.
2.4 Proces(ser)
2.4.1 HERCULES
HERCULES er bygget som to tromler oven på hinanden for at spare plads. Tromlerne roterer og er stillet i en vinkel på nogle grader med horisonten for at materialet kan bevæge sig gennem tromlerne under
rotationen. Den øverste tromle har en regulerbar sigte, medens den neste har en fast sigte med 6,35 mm diameter. Hele konstruktionen kan indkapsles for at forhindre støv i at trænge ud i lokalet.
Transportbånd er forudset til at tilføre materiale og fjerne materialestrømmene efter sortering.
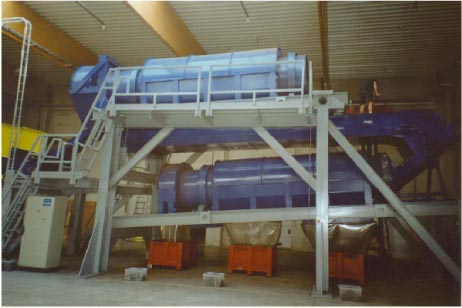
Figur 3. HERCULES
Input: |
Shredderaffald < 200 mm. |
Output: |
Fire strømme: |
1. < 6mm: |
Ingen behandlingsmetode |
2. 6 – 16 mm: |
=> Orion |
3. 16 – 38 mm: |
=> Orion |
4. > 38 mm: |
=> Volantis |
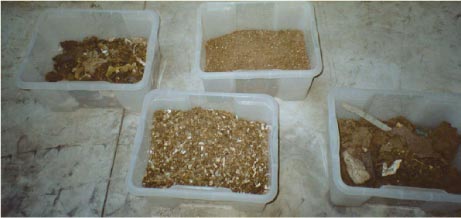
Figur 4. Output fra HERCULES.
Af de fire outputs går output 4 videre til VOLANTIS, outputs 2 og 3 går til ORION, og output 1, fines < 6 mm har man på nuværende ingen metode til
genvinding.
2.4.2 VOLANTIS
VOLANTIS modtager den grove fraktion, partikler > 38 mm fra HERCULES. I denne fraktion findes næsten alt skumplast, der ved en særlig teknik frasorteres i VOLANTIS.
Den særlige teknik består i, at inputmaterialet accelereres på et transportbånd, hvor der ved enden findes en rulle, der komprimerer materialet. Især Plastskummet komprimeres her, og derved får skummet
en ekstra acceleration i forhold til andre svært komprimerbare materiale. Inputmaterialet deles derved i to fraktioner: En fraktion kun bestående af skumplast og en fraktion bestående af andre plasttyper og
gummi mv.
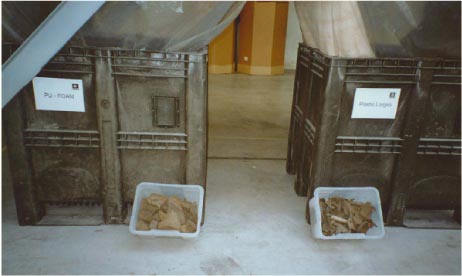
Figur 5. Output fra VOLANTIS.
Skumplasten ledes videre til AQUARIUS, og den anden fraktion ledes videre til ORION.
2.4.3 AQUARIUS
AQUARIUS modtager fra VOLANTIS det sorterede skumplast, der endnu er snavset, og derfor ikke kan genbruges uden rensning eller vaskning. AQUARIUS er en vaskemaskine, der ved flere efter
hinanden følgende sammentrykninger og udvidelser af materialet i en blanding af vand og sæbe renvasker plastskummet. Efterfølgende tørres materialet, der derefter kan afsættes og genbruges.
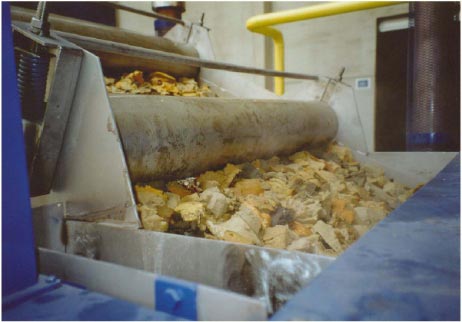
Figur 6. Output fra AQUARIUS.
2.4.4 ORION
ORION modtager fraktionerne 2 og 3 fra HERCULES og den plastrige fraktion fra VOLANTIS. Træ og metal frasortes disse inputs og resten, som er rig på plast, ledes videre til TUCANA.
ORION er leveret af SSE, som har et samarbejde med Salyp om markedsføring af denne proces. Teknikken vil ikke her blive nærmere beskrevet, men der henvises til logbogen fra besøg hos SSE.
2.4.5 TUCANA
TUCANA er en shredder, der er specielt bygget til at neddele et materiale, der er rigt på plast til en størrelse på 25 – 35 mm.
Outputtet ledes til PAVO.
2.4.6 PAVO
PAVO er en vaskemaskine, der renser den snavsede plast. Dette sker i en tromle på ca. 1 m diameter og en længde på ca. 2,5 m. Heri udsættes det let forurenede plast for en højtryksspuling, som er
sammenlignelig med processen i et bilvaskeanlæg
2.4.7 DORADO
I DORADO føres materialet frem via et transportbånd til et panel af infrarøde lamper, hvor materialet opvarmes til temperaturer mellem 90 og 140°C afhængigt af hvilke plasttyper, man ønsker at udsortere.
Termoplast blødgøres ved disse temperaturer, og ved passage af et efterfølgende sæt af ruller med små riller trykkes de ønskede plasttyper fast i disse ruller og frasorteres.
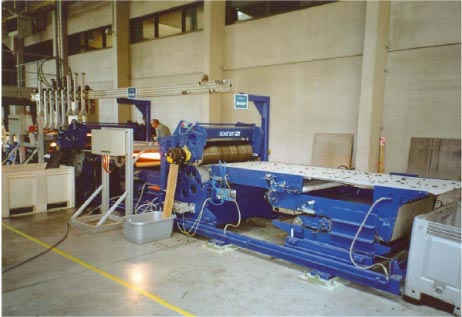
Figur 7. DORADO.
3. Observationer under besøget
3.1 Besøgets varighed
Den 2002-07-27 fra kl. 09:00 til kl. ca. 15.
3.2 Tilførte materialer behandlet under besøget
Anlægget blev demonstreret for os under besøget med indsats af Italiensk shredderaffald i HERCULES. Shredderaffaldet lignede shredderaffald, som det også forefindes i Danmark.
Til demonstration af genvinding af termoplast i ORION – DORADO havde man dog fundet et andet udgangsmateriale, som ikke var nærmere defineret, men som sandsynligvis stammede fra elektronikskrot.
3.3 Driftsforhold
Anlægget er et demonstrationsanlæg, der kun er i drift i forbindelse med forsøg for potentielle kunder. Anlægget blev startet i forbindelse med vort besøg for at vise os dets formåen.
3.4 Output under besøget
Følgende output fra de forskellige procestrin kunne iagttages:
Output fra HERCULES:

Output fra AQUARIUS
- Renset skumplast til genbrug.
Output fra ORION

Output fra DORADO
- Termoplast til genbrug.
- Andre plasttyper og gummi.
3.5 Restprodukter
Især fra AQUARIUS og i mindre grad fra PAVO vil der fremkomme et restprodukt bestående af spildevandsslams med et indhold af tungmetaller.
4. Kritiske delprocesser og driftsparametre
Under besøget og drøftelserne med Salyp blev der ikke identificeret egentlige kritiske delprocesser og driftsparametre.
5. Miljømæssige forhold
5.1 Emissioner til luften
Delprocesser med emissioner til luften er:
- HERCULES i indkapslet udgave med etableret afsugning vil der være et mindre afkast til luften, der dog ved fornuftig filtrering ikke vil indebære nogen miljømæssig belastning af betydning for
omgivelserne.
- AQUARIUS har en emission til luften, primært af damp fra tørringsprocessen.
- DORADO kan evt. forsynes med et filter til fjernelse af lugt, der kan fremkomme under den infrarøde opvarmning af materialet.
Der vurderes ikke at være nogen problemer med overholdelse af danske miljøkrav.
5.2 Spildevandsudledning
Spildevandsudledning findes fra delprocesserne:
- AQUARIUS, hvor skumplasten vaskes. Dette spildevand må formodes at indeholde tungmetaller. Vandforbruget er ca. 110 kg pr. time.
- PAVO, hvor termoplasten vaskes før sortering. Belastningen af tungmetaller forventes her ikke særlig høj, men vandet skal behandles i et rensningsanlæg. Vandforbrug ca. 110 kg pr. time.
Mængden af det udledte spildevand vil være op mod 220 kg pr. time. Desuden vil der fremkomme en mængde tungmetalholdigt slam. Denne mængde kan ikke på det grundlag, vi kender, kvantificeres.
5.3 Støj
Støj forventes ikke at give nogen belastning, der har nogen miljømæssig betydning.
5.4 Lugt
Der var ikke i bygningen, hvor anlægget var placeret eller uden for nogen lugt, der kunde identificeres med anlægget at spore. Dette selv om DORADO ikke var udstyret med filter til lugtfjernelse.
5.5 Affaldsproduktion
Affald fra processen er primært spildevandsslam, som dog ikke kan kvantificeres på grundlag af de oplysninger, vi er i besiddelse af.
6. Arbejdsmiljømæssige forhold
6.1 Støvbelastning
Der var ikke nogen støvbelastning af betydning i hallen. Dette selv om HERCULES ikke var indkapslet og forsynet med afsugning, som det forventes at ville være tilfældet i et egentligt produktionsanlæg.
6.2 Internt støjniveau
Det interne støj-niveau var lavt og vil med stor sandsynlighed kunne overholde danske krav.
6.3 Tungmetalbelastning
Demonstrationsanlægget var meget rent. Der var ingen støv på gulvet, hvorfor det ikke forventes at et produktionsanlæg vil give problemer med støvbelastning og deraf følgende belastning med tungmetaller.
6.4 Andet - fx lugtgener, vilkår i forbindelse med reparationsarbejde mv.
Besøget var for kort til, at vi kunne foretage en detaljeret vurdering. Der var dog ingen mærkbare lugtgener under demonstrationen, men reparationsarbejde bør nok foretages med åndedrætsværn og evt.
beskyttelsesdragt.
7. Beskrivelse af input
Billedet i figur 1 viser det indsatsmateriale, der blev benyttet under demonstration af anlægget under vort besøg.
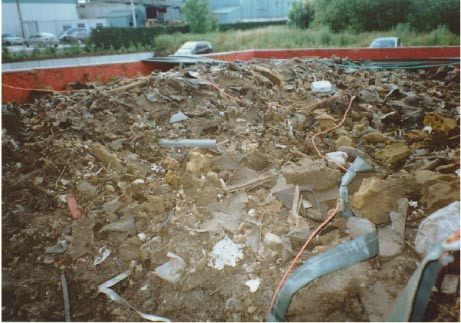
Figur 8. Indsatsmaterialet. Shredderaffald fra Italien
Materialets sammensætning kunne ikke oplyses, men man mente, at det var fremkommet udelukkende fra shredning af biler, som er det normale for de fleste shredderanlæg.
8. Beskrivelse af output
8.1 Generelt
Som det fremgår af Figur 2. Procesdiagram til behandling af shredderaffald. er der følgende outputs fra processen:
- Fra HERCULES: Fines < 6 mm.
- Fra AQUARIUS: Skumplast.
- Fra ORION: Metal og træ
- Fra DORADO: Termoplast samt andre plasttyper og gummi.
Besøgets varighed gav ingen muligheder for at analysere eller vurdere disse outputstrømme nærmere, hvorfor den følgende kvantificering udelukkende er baseret på oplysninger modtaget af Salyp under
besøget. Der kan således ikke på grundlag af de følgende oplysninger opstilles nogen generel massebalance for shredderaffald. Massebalancen for dansk shredderaffald vil sikkert afvige en del på grund af
shredderformaterialets noget anderledes sammensætning i Danmark.
8.2 Fines
Fines < 6 mm, som er output fra HERCULES, udgør ca. 50 % af shredderaffaldet. Fines består af ca. 50 % magnetisk materiale og ca. 50 % umagnetisk materiale.
Salyp erkender, at denne del endnu er problematisk at afsætte, men har formodninger om, at den magnetiske del kan afsættes til stålindustrien til genvinding af jern. Især hvis materialet briketteres, er der
muligheder for afsætning.
8.3 Skumplast
Skumplast, som er output fra AQUARIUS udgør vægtmæssigt ca. 4 % af shredderaffaldet. Den genvundne skumplast har en kvalitet, så den problemløst kan afsættes til genbrug.
Volumenmæssigt udgør dette output naturligvis en anselig andel.
8.4 Metal og træ
Metal og træ samt diverse er output fra ORION. Der er ikke givet nogen nærmere beskrivelse af dette output og dets evt. værdi og genvindingsmuligheder.
8.5 Termoplast og andre plasttyper samt gummi
Termoplast er outputtet fra DORADO. Restmaterialet efter frasortering af termoplast er primært andre plasttyper og gummi. Sammen med skumplast udgør disse outputs efter Salyps oplysninger op til 35%
af shredderaffaldet.
9. Økonomi
9.1 Nødvendige investeringer til etablering af anlægget
Udgifterne til etablering af anlægget består dels i de i figur 2 skitserede delprocesser, dels i bygninger og dels i de nødvendige forsyningsanlæg og spildevandsanlæg.
Salyp har udarbejdet et tilbud på leverance og opstilling af delprocesserne beskrevet i figur 1. Dette tilbud lyder på 15.502.500 DKK.
Hertil kommer nødvendige bygninger, nødvendige forsyninger af el, vand mv.
Spildevandrensning er ikke inkluderet i ovennævnte investeringer.
9.2 Udgiftsstruktur
Nedenstående data og forudsætninger er anvendt i beregning af omkostningerne til behandling af shredderaffald i Salyp-processen.
Anlægsstørrelse: |
35.000 t SHR/år |
Driftstid: |
7.000 h/år. |
Investering ekskl. bygninger: |
15.502.500 DKK |
Rentefod: |
7 % p.a. |
Afskrivningsperiode: |
7 år. |
Driftsomkostninger
Gennemsnitlig løn til personale: |
300.000 DKK/år. |
20 mand. |
Elektricitet: |
390 DKK/MWh. |
2.345 MWh/år. |
Vedligehold og reparation: |
9 % af investering pr. år. |
Beregnede udgifter
Under ovennævnte forudsætninger bliver de samlede behandlingsomkostninger pr. ton shredderaffald 320 DKK.
Der er heri ikke medregnet indtægter ved salg af genvundet materiale, ligesom besparelser ved mindre mængder materialer til deponering ikke er medregnet.
Hvis det tilførte affald indeholder 35% plast, som kan sælges for blot 1 DKK/t, vil ”break even” være nået. På grund af det lave indhold af Fe og Al i affaldet vil salget af metaller kun bidrage meget lidt til
den samlede økonomi.
10. Konklusioner og anbefalinger
10.1 Egnethed for den danske affaldsstruktur
Hvis processer af denne type skal behandle alt shredderaffald i Danmark, kræver dette, at der bygges 2 - 3 anlæg.
10.2 Affaldets udnyttelsesgrad
Salypprocessen kan efter udsagn fra Salyp genvinde ca. 35 % af shredderaffaldet i form af forskellige plasttyper.
Til gengæld står man tilbage med 65 % af shredderaffaldet, hvoraf fines udgør ca. 50 % af shredderaffaldet. Denne tilbageværende restdel vil have en meget lav brændværdi, der betyder, at der må tilføres
energi, hvis denne restdel skal behandles termisk i en smelteproces. Det er vores vurdering, at det vil være svært at finde genanvendelsesmuligheder for denne restdel.
10.3 Økonomien
Processens økonomiske muligheder kan belyses ud fra følgende eksempel:
- Ved genvinding af 350 kg plast pr. tons shredderaffald sparres ca. 236 kr. i deponeringsomkostninger pr. tons shredderaffald.
- Genvindingsomkostningerne er beregnet til 320 kr. tons shredderaffald.
Det kan herefter konkluderes, at hvis man kan opnå en pris på 0,24 kr. pr. kg genvundet plast, er break even opnået. I denne udregning er investeringerne i bygninger og spildevandrensningssystemer ikke
medtaget.
For rimeligt rent genbrugsplast vil der sandsynligvis kunne opnås væsentlig højere priser.
Det skal dog hertil bemærkes, at Salyp ikke over for os har demonstreret, at deres proces kan genvinde plast i de nævnte mængder fra shredderaffald.
10.4 Miljømæssige problemstillinger
Processen hos Salyp medfører ikke direkte væsentlige miljøproblemer, men indirekte kan man være bekymret for, om processen efterlader en restdel, der fortsat skal deponeres.
10.5 Muligheder for know-how-formidling
Salyp nv
Oostkaai 62
8900 Ypres
Belgien
Tlf.: +32 57228044
Fax: + 32 57228049
E-mail: info@salyp.com
Bilag K
Logbog for besøg hos Separation Systems Engineering GmbH (SSE)
1. Generelle oplysninger
1.1 Procestype
Maskiner til mekanisk sortering af partikulært affald.
1.2 Tilført affald
SSE's maskiner kan sortere fx. glas, mineraler, metaller, plastik, fødevarer.
1.3 Licenshaver og kontaktpersoner
Licenshaver
Separation Systems Engineering GmbH (SSE)
Rosengarten 10
D-22 880 Wedel
Tyskland
Kontaktperson
Eric van Looy, Managing Director
Telefon: +49 4103 80 89 870
Fax: +49 4103 80 89 877
E-mail: info@metall-sse.de
1.4 Ejerforhold
SSE er en del af CommoDas koncernen:
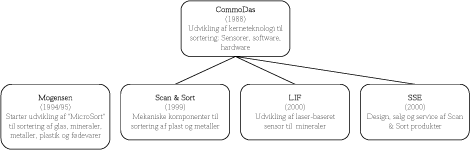
der udvikler og leverer avanceret sorteringsudstyr.
1.5 Beliggenhed for det besøgte anlæg
Vi besøgte SSE's og Scan & Sorts administration, teststation og produktionsfaciliteter i Wedel, Tyskland.
1.6 Virksomhedens formål og idégrundlag
SSE designer, sælger og yder service af Scan & Sort maskiner.
Til metalsortering benytter SSE en kombination af metaldetektorer og farve-scannere til identifikation.
CommoDas gruppen har i alt 60 ansatte og forsker i sensorer, elektronik og software til sortering af alle typer affald og produktstrømme. SSE markedsfører færdige, kundetilpassede løsninger.
1.7 Referencer
SSE har solgt 26 sorteringslinier i Europa (GB, NL, D, DK, FI, E, FR, N) til sortering af
- shredderaffald
- rustfrit stål fra andre metaller
- tungmetaller 20-100 mm
- tungmetaller 4-20 mm
- tungmetaller 0-30 mm
- metaller fra affald
- metaller fra affald/sten
1.8 Byggeår og status for projektet
Anlæggene er leveret og idriftsat siden 2000-09.
2. Kortlægning og beskrivelse af anlægget
2.1 Maskiner
SSE leverer følgende sorteringsmaskiner:
§ ”MagnoSense” sorterer metaller fra ikke-metaller.
§ ”SpectraSense” er et intelligent system, der kan sortere efter kriterier som: form, størrelse, lysreflektion og efter sand farve. SpectraSense kan sortere partikler ned til 1 mm.
§ ”CombiSense” arbejder både metaldetektorer og farvekameraer og kan fx sortere metal/ikke-metal, kobber, messing, rustfrit stål, bly, aluminium, zink og magnesium.
§ ”Finder” er en mere kompakt og billig løsning til sortering af alle metaller fra fx slagge fra affaldsforbrænding.
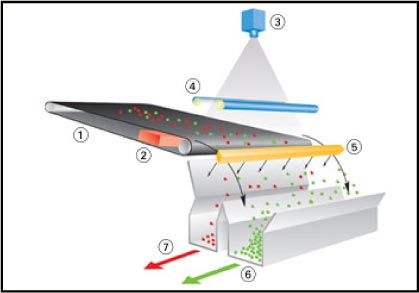
Figur 1. Princip-skitse af SSE's Metal ”X” MagnoSense, SpectraSense og CombiSense.
- Fødebånd
- Metalsensorer
- Farvekamera (scanner)
- Belysning
- Luftdyser m. magnetventiler
- Hovedstrøm
- Frasorteret materiale
MagnoSense og Finder har udelukkende metaldetektorer, SpectraSense kun kameraer og CombiSense begge typer sensorer.
Metalsensorerne har i de nuværende modeller en indbyrdes afstand på 3,2 mm, som forventes at blive 1,5 mm i fremtidige applikationer. Den kortere afstand vil betyde, at endnu mindre partikler vil kunne
detekteres og sorteres. Den største udfordring ligger i følge SSE i den efterfølgende separation af partikler.
Dyserne, der er udviklet af CommoDas er state-of-the-art, fungerer efter samme princip som dyserne i ”boble jet” printere og er meget driftssikre. Den forventede levetid er ét år.
Affaldet transporteres til sorteringsmaskinen ved hjælp af rysterender og til sidst et transportbånd med en hastighed på 3 m/s.
I alle maskiner indgår en computer med meget hurtig software, der beregner den forventede placering af hvert emne, der skal frasorteres. Ud fra størrelsen af emnet beregnes, hvornår og hvor længe en given
luftdyse skal åbnes.
Flere sorteringsmaskiner kan styres af én computer. For eksempel Metal ”X” Finder og MagnoSense udstyres med en ”post picker”, der sorterer metaller efter fx. farve.
CommoDas-gruppen introducerer snart en videreudviklingen ”MultiSense” af CombiSense. MulitSense kan arbejder med flere sensorer samtidigt og er forberedt for en hvilken som helst type sensor.
Desuden udvikles i øjeblikket maskiner til frasortering af metaller fra husholdningsaffald før forbrænding.
2.1.1 Kapacitet
Kapaciteten af Metal ”X” 600 og 1200 afhænger af affaldets størrelsesfordeling og vægtfylde.
Renheden af de frasorterede strømme er 93-98 %
Tabel 1. Kapacitet af Metal “X” 1200 ved sortering af metaller fra blandet affald.
Størrelse [mm] |
Metal ”X” 1200
Kapacitet [t/h] |
0 – 10 |
1 – 1,5 |
10 – 50 |
5 – 8 |
50 - 100 |
10 |
Tabel 2. Kapacitet af Metal ”X” 600 ved sortering af gråt metal fra blandet metal.
Størrelse [mm] |
Metal ”X” 1200
Kapacitet [t/h] |
2 – 5 |
< 3 |
10 – 50 |
3 – 5 |
50 - 100 |
< 8 |
2.2 Affald
SSE har leveret sorteringsudstyr til
- shredderaffald
- rustfrit stål fra andre metaller
- tungmetaller
- metaller fra affald
- metaller fra affald/sten
2.3 Forbehandling
Affaldet skal være partikulært og fritflydende. Den bedste sortering fås, når partikelstørrelsesfordelingen er snæver.
3. Observationer under besøget
3.1 Besøgets varighed
Den 2002-06-03 fra kl. 12 til kl. 16.
3.2 Tilførte materialer behandlet under besøget
SSE's Metal ”X”, CombiSense 1200 blev demonstreret på tre affaldsstrømme:
- Shredderaffald – sigtet fraktion > ca. 10 mm
- Blanding af messing/kobber-skrot og gråt metal - ca. 2-20 cm
- Blanding af messing- og kobber-skrot - ca. 2-20 cm
Et mindre forsøgsanlæg (Metal ”X” SpectraSense) sorterede:
- Blanding af kobber og aluminium – ca. 2-3 mm
3.3 Driftsforhold
3.3.1 SSE's Metal ”X”, CombiSense
Driftstid: Demonstrationen var kortvarig (få minutter).
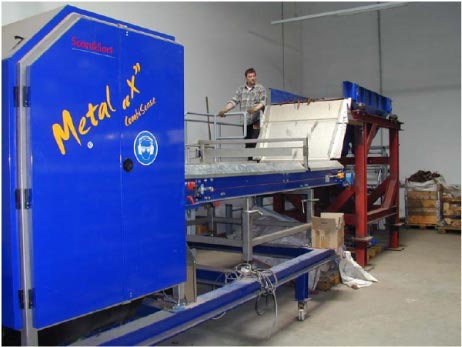
Figur 2. SSE's demonstrationsanlæg: Metal ”X” CombiSense.
Indfødningen sker manuelt øverst til højre på rysterenden.
3.3.2 Pilotanlæg, Metal ”X” SpectraSense
Driftstid: Anlægget blev før, under og efter besøget benyttet til optimering af driftsparametre til sortering af en Al/Cu-blanding (2-3 mm).
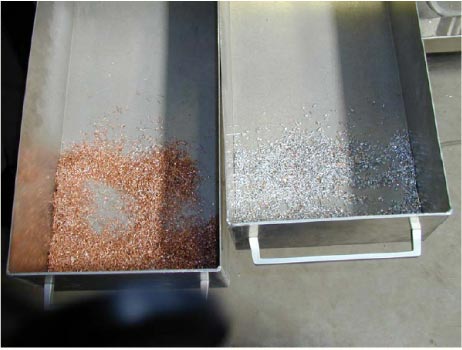
Figur 3. Udsorterede produkter (Cu og Al) fra Metal ”X” SpectraSense.
Tilfældig test-kørsel.
4. Kritiske delprocesser og driftsparametre
SSE's teknologi er meget robust og har vist sig at fungere under realistiske betingelser fx hos H.J. Hansen Miljøsystem i Odense.
Det er vigtigt, at affaldet er fritflydende og de enkelte partikler er adskilt fra hinanden, før det møder de første sensorer. Anlæggene er derfor udstyret med lodret pegende dyser umiddelbart før
metalsensorerne.
På grund af luften fra de dyser, der blæser på de partikler, der skal frasorteres, er der risiko for støv inde i selve sorteringsmaskinen. Støvet kan sætte sig på kameraer og andet følsomt udstyr. Det er derfor
vigtigt, at luften suges væk på en hensigtsmæssig måde i sorteringsmaskinen. SSE arbejdede på at løse dette relativt enkle problem.
Den højeste renhedsgrad af produktstrømmene fås, hvis partikelstørrelsesfordelingen er snæver, men maskinerne kan sagtens sortere affald med forskellig størrelse.
5. Miljømæssige forhold
5.1 Emissioner til luften
Da sorteringsmaskinerne vil blive udstyret med passende udsugning i de centrale dele, vil støvemissionen være fuldt acceptabel.
5.2 Spildevandsudledning
Ingen.
5.3 Støj
Placeres sorteringsanlæggene i lukkede bygninger vil anlæggene kunne overholde danske krav til støj-emission.
5.4 Lugt
Der forventes ikke problemer med at overholde grænser for lugt-emissionen, hvis støv fra anlægget suges bort og fanges i et filter, før luften udsendes.
6. Arbejdsmiljømæssige forhold
6.1 Støvbelastning
Det er vigtigt, at sorteringsanlæggene er udstyret med en effektiv punktudsugning, hvor produktstrømmene forlader maskinen. Transportsystemer bør være i lukkede anlæg med udsugning for at forhindre
støv i arbejdsområdet.
6.2 Internt støjniveau
Støj fra vibrationstransportører og luftdyser gør det nødvendigt, at driftspersonale bærer høreværn.
6.3 Tungmetalbelastning
Med den korrekte udsugning og ventilation forventes støv- og dermed tungmetalbelastningen ikke at være et problem.
6.4 Andet - fx lugtgener, vilkår i forbindelse med reparationsarbejde mv.
På grund af aflejringer af støv bør driftspersonale bære handsker og støvmaske under reparationsarbejder.
7. Beskrivelse af input/output
7.1 Demonstration af Metal ”X”, CombiSense 1200
Input under demonstrationskørslen var:
- Shredderaffald – sigtet fraktion > ca. 10 mm
- Blanding af messing/kobber-skrot og gråt metal - ca. 2-20 cm
- Blanding af messing- og kobber-skrot - ca. 2-20 cm. Denne fraktion var resultatet af en sortering af input 2.
7.1.1 Demonstration 1: Sortering af shredderaffald
Input og de to output-strømme fra første demonstration er vist på de følgende fotos.
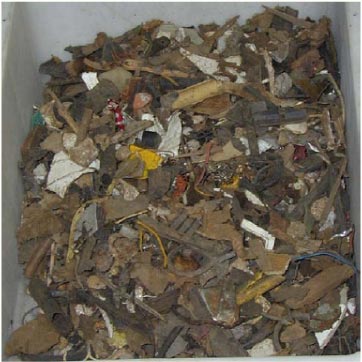
Figur 4. Input til demonstration 1: Shredderaffald – sigtet fraktion > ca. 10 mm.
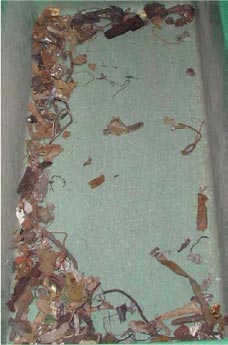
Figur 5. Output 1, demonstration 1: Metaller
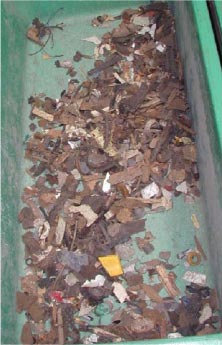
Figur 6. Output 2, Demonstration 1: ikke metaller
Fraktionen med metaller indeholder en del ikke-metaller, idet metalsensorerne også detekterer affaldsstykker, hvor kun en mindre del er metal (fx en tøjrem med metalspænde).
7.1.2 Demonstration 2: Sortering af blanding af messing/kobber-skrot og gråt metal - ca. 2-20 cm
Input og de to output-strømme fra anden demonstration er vist på de følgende fotos.
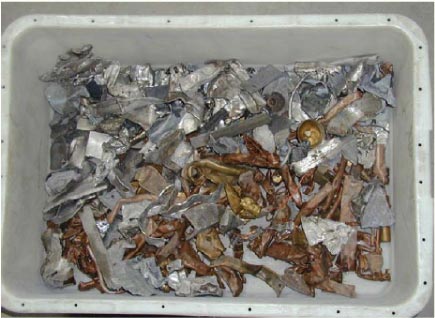
Figur 5. Demonstration 2: Input: Blanding af messing/kobber-skrot og gråt metal - ca. 2-20 cm.
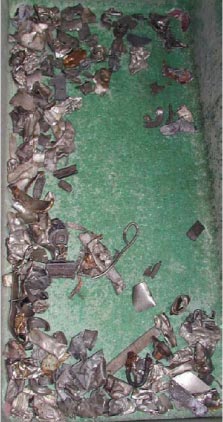
Figur 6. Output 1, demonstration 2: gråt
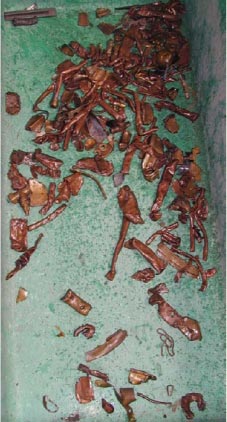
Figur 7. Output 2, demonstration 2: Metal Kobber og messing
De to produktfraktioner er begge meget rene.
7.1.3 Sortering af output strøm 2 fra demonstration 2
Blandingen af messing- og kobber fra demonstration 2 sorteres efter farve.
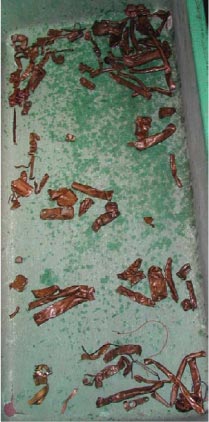
Figur 10. Messing-fraktion
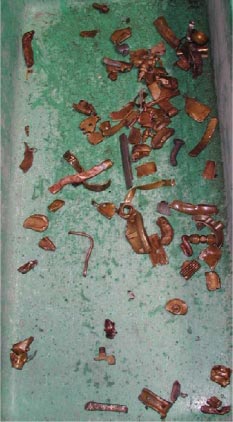
Figur 11. Kobber-fraktion
Selv efter en nøje visuel inspektion er det meget svært at afgøre, om de anløbne metalstykker består af kobber eller messing. SSE har med kontrolleret, at sorteringen er korrekt, og at de to fraktioner har en
meget høj renhed.
8. Økonomi
8.1 Nødvendige investeringer til etablering af anlægget
SSE angiver følgende priser for deres sorteringsmaskiner:
Tabel 3. Prisliste for SSE's sorteringsmaskiner
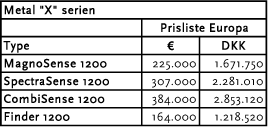
Alle priser er eksklusiv moms, transport og idriftsætning.
8.2 Udgiftsstruktur
Nedenstående forudsætninger og data er anvendt i forbindelse med et skøn over behandlingsprisen. Alle data er opgivet af SSE med undtagelse af rentefod samt priser på el og varme, der er tilpasset danske
forhold.
Anlægstyper: |
|
MagnoSense 1200 |
Anlægsstørrelse: |
24.000 |
t tilført affald/år |
|
|
|
Investering inkl. bygninger: |
1.671.750 |
DKK |
Rentefod: |
7 |
% p.a. |
Tilbagebetalingstid: |
7 |
år |
Driftsudgifter
Gennemsnitlig løn til personale [1]: |
300.000 |
DKK/person |
1 |
person |
Elektricitet: |
390 |
DKK/MWh |
632 |
MWh/år |
Vedligehold og reparation:
Reservedele |
4,7 |
% af investering |
Maskineri med udsatte sliddele |
3,3 |
% af investering |
De ukendte indtægter ved salg af metaller etc. er ikke medtaget ligesom besparelser i bemanding ikke er inkluderet.
Udgifter til forsikringer er ikke inkluderet.
Skønnede behandlingsomkostninger
Den endelige behandlingspris vil være afhængig af anlægsplacering, faciliteter til stede, valgte bygningsstandarder osv. og den endelige pris, som vil kunne opnås for anlægget efter forhandlinger.
Behandlingsprisen skønnes at blive 42 DKK/t tilført affald.
9. Konklusioner og anbefalinger
9.1 Egnethed for den danske affaldsstruktur
SSE's sorteringsmaskiner er meget fleksible og vil kunne benyttes sammen med eller i stedet for traditionelle metoder til sortering af fx
- shredderaffald
- metaller fx stålemballage og hvidblik i slagge fra affaldsforbrændingsanlæg
- industriaffald
Den samme maskine vil i løbet af meget kort tid (minutter) kunne skifte ”program” og dermed sortere vidt forskellige affaldstyper og produktstrømme fra tidligere sorteringer.
SSE har med succes langtidsafprøvet Metal ”X” MagnoSense på shredderaffald.
SSE / CommoDas arbejder på et system til sortering af metaller fra husholdningsaffald før forbrændingen.
9.2 Affaldets udnyttelsesgrad
Renheden af produktstrømmene fra SSE's maskiner afhænger af vægtfylde, størrelsesfordeling og andelen af den fraktion, der skal udsorteres. Typisk ligger renheden mellem 93 og 98% ved én sortering.
9.3 Miljømæssige problemstillinger
Der er ingen miljømæssige problemer med processen ved korrekt afskærmning mht. støv- og støvemission.
9.4 Muligheder for know-how-formidling
Separation Systems Engineering GmbH (SSE)
Rosengarten 10
D-22 880 Wedel
Tyskland
Kontaktperson
Eric van Looy, Managing Director
Telefon: +49 4103 80 89 870
Fax: +49 4103 80 89 877
E-mail: info@metall-sse.de
Fodnoter
[1] Personale fra selve shredderanlægget antages også at kunne servicere sorteringsanlægget.
Bilag L
Logbog for besøg hos SVZ, Sekundärrohstoff VerwertungsZentrum Schwarze Pumpe
1. Generelle oplysninger
1.1 Procestype
SVZ råder over tre forskellige typer tryksatte modstrømsforgasser. Disse er:
- 7 stk. fixed-bed-modstrømsforgassere med en kapacitet hver på 15 t/h. Disse arbejder med fast affald ved temperaturer op til 1300°C.
- 2 stk. flugstrom-forgasser med en kapacitet hver på 45.000 m³ rågas /h. Disse arbejder med flydende affald. Forgasseren arbejder ved temperaturer op til 1800 0C.
- 1 stk. slaggebadsforgasser til behandling af forberedt, pelleteret fast affald med en kapacitet på ca. 30 t/h. Denne forgasser arbejder ved temperaturer på ca. 1600 0C.
Alle tre forgassertyper arbejder under tryk på ca. 25 bar.
1.2 Tilført affald
SVZ oparbejder en række affaldsfraktioner. De vigtigste er:
- Spildevandsslam.
- Plastaffald.
- Husholdningsaffald.
- Forurenet træ, f.eks. jernbanesveller.
- Industriaffald, herunder shredderaffald
- Tjæreslam mv.
1.3 Licenshaver og kontaktpersoner
SVZ er et affaldsbehandlings selskab, der lever af at behandle og oparbejde forskellige affaldsfraktioner. Knowhow formidling kan derfor ikke ske gennem SVZ, men ønsker man at investere i lignende
anlæg, kan formidling sikkert ske gennem deres leverandører.
1.4 Ejerforhold og kontaktpersoner for det besøgte anlæg
SVZ er siden delprivatiseringen i 1995 af Berlinwasser Holding AG en 100 % ejet datterselskab af dette selskab.
Kontakt til selskabet kan ske gennem
Hartmut Huck eller Jörg Buchholz
Telefon: +49 3564 6-93770
E-mail: buchholzj@svz-gmbh.de eller huckh@svz-gmbh.de
1.5 Beliggenhed for det besøgte anlæg
Skundärrohstoff-Verwertungszentrum Schwarze Pumpe GmbH
Suedstrasse
D-02979 Spreetal OT Spreewitz
Tyskland
1.6 Særlige interessante anlæg hos SVZ Schwarze Pumpe
SVZ har siden januar 2002 har haft den nye BGL forgasser (British Gas/LURGI) i drift. Garantitesten på 30 tons pr. time med 75% affald som indsats er vel overstået. Der er tale om en smelteforgasser, der
arbejder ved ca. 1600°C. Denne forgasser vil være velegnet til forgasning også af shredderaffald. Forsøg med shredderaffald har indtil da været udført på fixed-bed forgasseren hos SVZ nu gennem 7 år.
Denne forgasser arbejder ved temperaturer på 800 – 1300°C.
De væsentligste krav til shredderaffaldet, for at det kan behandles i forgasseren, drejer sig om krav til:
- Stykstørrelsen
- Vægtfylden
- Mekanisk styrke
- Varme stabilitet.
Shredderaffald indsættes i følgende form:
- Som leveret fra shreddderen
- Kompakteret ved hjælp af eksterne ekstrudere
- Pelletiseret på SVZ’s affaldsbehandlings anlæg.
Den fine andel af shredderaffaldet udgør det største problem i forgasseren. SVZ har derfor arbejdet på at udvikle et behandlingssystem, hvor shredderaffald pelleteres sammen med husholdningsaffald.
Mængden af shredderaffald har været begrænset til maks. 15% af den samlede tilførte affaldsmængde.
Hovedopgaven for SVZ for at kunne være konkurrencedygtig ved oparbejdning af shredderaffald er at finde metoder til at reducere mængden af fine partikler i affaldet. SVZ efterlyser samarbejdspartnere
på dette område.
I det følgende vil primært smelteforgasseren og anlægget til materialeforberedelse blive behandlet.
2. Kortlægning og beskrivelse af anlægget
2.1 Processen
Kernen i processen er smelteforgasseren vist på figur 1. Som fødning anvendes forberedt, pelleteret affald, der blandes med koks og brunkul. Indsatsen sker gennem en dobbelt sluse, der sikrer
opretholdelse af driftstrykket på ca. 25 bar.
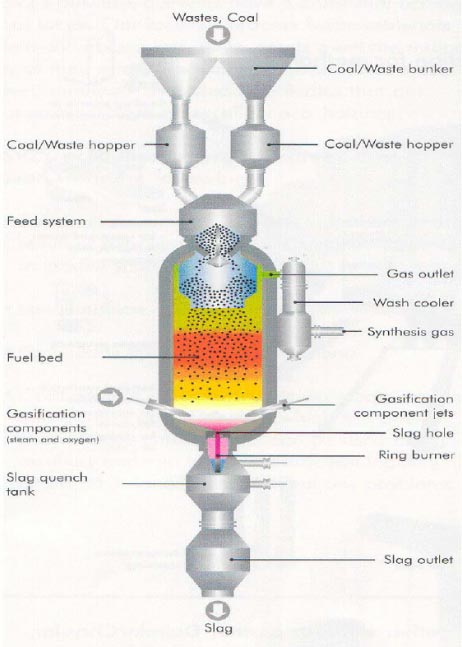
Figur 1. Principdiagram for slaggebadsforgasseren hos SVZ.
Til angivelse af forgasserens størrelse kan anføres følgende:
- Indsats: 27 – 30 tons/time.
- Indre diameter i forgasseren: 3,6 m.
- Gasmængde: 35.000 Nm³/time.
- Iltforbrug: 6.000 Nm³/ time.
- Dampforbrug: 6 – 9 tons/time.
Som forgasningsmiddel anvendes damp og ilt, og forgasningen finder sted ved ca. 1600 0C.
Slaggen udtages i flydende form og granuleres ved chokkøling i vand. Slaggemængden i denne forgasser kan udgøre 30 – 40 % af indfødningen, hvilket er ca. en fordobling i forhold til de ældre forgassere.
Dette forhold gør smelteforgasseren egnet til behandling af shredderaffald uden at begrænse indfødningen på grund af dette affalds høje slaggeindhold.
2.2 Oparbejdning af affaldet
Før det faste affald føres til forgasserne undergår en del af det en oparbejdning, som gør det egnet til indfødning i modstrømsforgassere, som kræver, at affaldet er stykformet eller briketteret, og at det er
varmebestandig og kan modstå høje temperaturer i længere tid uden at nedbrydes.
Husholdningsaffald, affald af plast, shredderaffald og visse andre fraktioner sendes derfor gennem oparbejdningsanlægget, som med en kapacitet på ca. 500 tons pr. dag briketterer dette affald.
Oparbejdningsanlægget består af følgende delprocesser:
- Forbehandling.
I forbehandlingsenheden anvendes shreddere til neddeling af affaldet. Desuden anvendes magnetseparation og eddy current til udsortering af henholdsvis jern og ikke-jern-metaller af affaldet.
- Tørring.
Næste trin forbehandlingen er tørring af affaldet. Dette sker af hensyn til kapaciteten i to linier.
- Sigtning.
Efter tørringen sigtes materialet for adskillelse af tunge (mineralske) og lette (organiske) fraktioner. De tunge fraktioner udsorteres og deponeres, medens de lette fraktioner sendes videre i
oparbejdningsprocessen.
- Pelletering.
Her pelleteres affaldet og nedkøles derefter.
3. Observationer under besøget
3.1 Besøgets varighed
Den 2002-06-07 fra kl. 10:00 til kl. 12.30.
Smelteforgasseren blev fremvist under besøget, men desværre var den ikke i drift, men under reparation.
Desuden blev pelleteringsanlægget for pelletering af affald fremvist.
4. Kritiske delprocesser og driftsparametre
Der var under besøget ikke tid til at gå i detaljer omkring kritiske delprocesser og driftsparametre, men et væsentligt generelt problem for skaktovne og modstrømsforgassere blev dog diskuteret.
Dette problem er indfødningsmaterialets varmebestandighed. Processer af denne art kræver en stor del af indsatsmaterialet som grovkornet, briketlignende materiale. Bliver finandelen for høj, hæmmes
luftgennemgangen gennem skakten og processen går i stå eller må stoppes på grund af ukontrollerbare gasstrømninger gennem skakten.
Shredderaffald har en stor finandel og derfor problematisk i denne proces, med mindre shredderaffaldet briketteres, hvilket kan ske ved ekstrudering. Ekstrudering er imidlertid en meget dyr løsning, der efter
udsagn fra SVZ koster op mod 500 kr. pr ton shredderaffald, hvilket vil være en meget omkostningsforøgende del.
Indtil videre har SVZ valgt at begrænse indsatsen af shredderaffald til maks. 15%, men efterlyser samarbejde om udvikling af bedre og billigere metoder.
5. Miljømæssige forhold
Besøgets varighed var for kort til at gå i detaljer omkring de miljømæssige forhold.
Der er siden 1995 investeret mere end 250 millioner EURO i modernisering af anlæggene og hele virksomhedens område. Anlæggene fremstod vel vedligeholdte, og renlighed og ryddelighed prægede hele
området.
Der er ingen grund til at betvivle at SVZ i dag overholder alle tyske krav til emissioner til luft og vand.
6. Arbejdsmiljømæssige forhold
Besøget var af for kort varighed til at vurdere de arbejdsmiljømæssige forhold, men ud fra de observationer, der dog blev gjort, kan man konkludere, at anlægget burde kunne overholde de danske krav til
støv, støj og tungmetalbelastning. Forgasserne arbejder jo alle under tryk og må bl.a. af den grund være absolut tætte. Der er derfor ingen udslip af støv og gasser i driftssituationen. I forbindelse med visse
reparationer på anlæggene må man antage , at det vil være nødvendigt at anvende åndedrætsværn og måske beskyttelsesdragter.
7. Beskrivelse af input
7.1 Input
SVZ oparbejder en lang række affaldsfraktioner. Der er oprettet interne kataloger til beskrivelse af såvel flydende affald som fast affald med angivelse af behandlingsmetode.
De vigtigste er affaldstyper er følgende:
- Spildevandsslam.
- Plastaffald.
- Husholdningsaffald.
- Forurenet træ, f.eks. jernbanesveller.
- Industriaffald, herunder shredderaffald
- Tjæreslam mv.
Den normale brændselsblanding består af:
Pelleteret affald: |
850 kg |
Stenkul: |
110 kg |
Brunkul: |
40 kg |
Indsats blanding: |
1000 kg |
Figur 2 viser pelleteret affald, som det oparbejdes på SVZ’s pelleteringsanlæg.
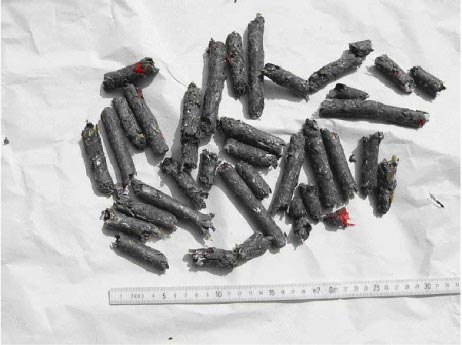
Figur 2. Pelleteret affald til indsats i slaggebadsforgasseren.
Shredderaffald modtages til oparbejdning i følgende tre former:
- Som ekstruderet materiale i størrelser fra 30 mm op til 80 mm, dog med en overstørrelse op til 120 mm, hvis denne udgør mindre end 5%. Vandindhold < 20%.
- Løst shredderaffald fra 10 mm op til 300 mm. 10% tillades at være < 10 mm, ligesom 10% tillades at være op til 500 mm. Dette materiale pelleteres før indsats. Vandindhold < 40%.
- Løst shredderaffald 4 – 80 mm til direkte indfødning i forgasseren. Også her tillades en overstørrelse op til 120 mm, hvis den udgør mindre end 5% og en understørrelse mindre end 4 mm, hvis den
udgør mindre end 10%. Vandindhold < 40%.
En del af shredderaffaldet der tilføres under forsøg har været ekstruderet. Ekstruderet shredderaffald er velegnet til behandling i forgasseren, men ekstrudering er en dyr proces. SVZ oplyste, at
omkostningerne til ekstrudering er ca. 500 kr. pr. tons shredderaffald.
8. Beskrivelse af output
8.1 Kraft/varme
Der produceres samlet i de i driftsværende forgassere 240 t damp pr. time. Dampdata er ikke oplyst for os.
Dampen anvendes delvis til drift af dampturbiner og delvis til pyrolyse i forgasseren. Syntesegassen anvendes delvis til drift af gasturbiner og delvis til fremstilling af metanol. Der er således installeret en
elektrisk effekt på 30MW.
Desuden er der installeret en elektrisk effekt på 44,5 MW i form af gasturbiner.
8.2 Produkter
Hovedproduktet hos SVZ er metanol, CH3OH, der fremstilles ud fra den rensede syntesegas. SVZ fremstiller ca. 100.000 tons metanol pr. år.
8.3 Granulat/restprodukt
Slaggen har SVZ indtil nu opfattet som affald, der skulle deponeres. Dette er sket i egne deponier. Med smelteforgasserens opstart har man imidlertid indset, at slaggen bør kunne anvendes som
konstruktionsmateriale.
9. Økonomi
9.1 Omkostningsstruktur
Omkostningsstrukturen hos SVZ er ikke kendt af os og vil ikke blive beregnet, men på forespørgsel oplyste SVZ, at den pris de ville forlange for oparbejdning af 100.000 tons shredderaffald pr. år ville
være ca. 130 EURO, svarende til 967 DKK/t.
10. Konklusioner og anbefalinger
10.1 Egnethed for den danske affaldsstruktur
SVZ har mange års erfaring i behandling af forurenet affaldstræ. SVZ har dog ingen erfaring i eller teknologi til genvinding af metallerne i trykimprægneret træ.
Hvad angår shredderaffald, har SVZ gennem flere år kørt forsøg med oparbejdning af shredderaffald, der efter de indhøstede erfaringer er velegnet til metanolproduktionen.
Med mekanisk sorteret shredderaffald, som det i dag foreligger hos bl.a. H. J. Hansen og R-plus, må den nu i driftsværende slaggebadsforgasser anses som egnet til oparbejdning af denne type affald.
Forudsætningen herfor er dog, at der kan fremstilles stabile briketter til rimelig pris. I modsat fald må indsatsen af shredderaffald begrænses til måske kun 15%.
10.2 Miljømæssige problemstillinger
SVZ opfylder i dag sikkert alle miljøkrav i Tyskland, og kan ikke af miljømæssige grunde lades ude af betragtning i forbindelse med oparbejdning af affald.
10.3 Yderligere oplysninger
Tlf.: +49 35646-92041
E-mail: huckh@svz-gmbh.de
| Til Top | | Forside |
Version 1.0 Februar 2006 • © Miljøstyrelsen.
|