| Forside | | Indhold | | Forrige | | Næste |
Metoder til behandling af tungmetalholdigt affald - Fase 3
5 Belægningsdannelser i kedler og varmevekslere
5.1 Indledning
I projektet er der evalueret en række processer til behandling af tungmetalholdigt affald. Baseret på kendskabet til sammensætningen af disse affaldstyper vurderer vi, at der er en høj sandsynlighed for, at
der i sådanne anlæg kan opstå betydelige problemer med belægningsdannelse og med korrosion i hedeflader.
Enkelte koncepter er afprøvet i fuld skala gennem en kort årrække, dog typisk med relativt lave dampdata, og fra disse anlæg er det forsøgt at indhente relevante drifts- og vedligeholdelsesdata. Opgaven er
derfor, at vurdere problemernes karakter, størrelse samt mulige metoder til at håndtere disse problemer på basis af teoretiske overvejelser og de få praktiske erfaringer.
5.2 Teoretiske overvejelser af problemernes natur
Idet der kun findes få erfaringer med den relevante type anlæg, er det nærliggende at betragte problemstillingen ud fra de forhold som kendes fra andre affaldsfyrede anlæg og efterfølgende ekstrapolere på
basis af afvigelserne til de aktuelle koncepter. Sidstnævnte indbefatter primært de afvigende karakteristika af brændslerne og sekundært afvigelser i ovn- og kedeldesign.
Det er velkendt fra traditionelle affaldsfyrede anlæg med dampproduktion, at der ofte opstår betydelige problemer med korrosion og belægningsdannelse, som kræver store vedligeholdelsesomkostninger og
fører til forringet rådighed af anlæggene. I det følgende gives en beskrivelse af mekanismerne i disse problemer for traditionelle affaldsfyrede anlæg.
5.2.1 Korrosionsmekanismer
Undersøgelser udført på danske affaldsforbrændingsanlæg suppleret med litteraturoplysninger viser, at de væsentligst problemområder er nedbrydning af den ildfaste foring, korrosion af panelvæggene bag
den ildfaste foring, korrosion af ubeskyttede panelvægge efter afslutning af den ildfaste foring, korrosion af overhedere, belægningsdannelse på panelvægge i kedlens strålingstræk samt belægningsdannelse
på kedlens overhedere.
Nedbrydning af den ildfaste foring kan føre til følgende problemtyper:
- Hvis foringen forsvinder, øges varmeoverførslen og røggastemperaturen sænkes – dette kan vanskeliggøre overholdelse af miljøkrav – opretholdelse af en røggastemperatur på mindst 1100°C i 2
sekunder efter den sidste sekundærluftinddysning
- Hvis foringen slipper kontakt med panelvæggen, reduceres varmeoverførslen og røggastemperaturen stiger – dette kan føre til øgede korrosions- og belægningsproblemer i de efterfølgende områder af
kedel og overhedere
- Hvis foringen forsvinder øges korrosionen på de blotlagte kedelrør
- Salte kan gennemtrænge den ildfaste foring og føre til korrosion på de bagvedliggende kedelrør
Korrosion af kedelrør bag den ildfaste foring, ubeskyttede kedelrør efter afslutning af den ildfaste foring og overhedere har gentagne gange ført til rørsprængninger, uplanlagt udetid og store omkostninger til
udskiftninger.
Nedbrydningen af ildfaste foringer udgøres ofte af en kombination af forskellige mekanismer, og i mange tilfælde er det vanskeligt at afgøre, hvilke mekanismer har været de primære årsager til skaderne.
Væsentlige mekanismer i nedbrydningen af ildfaste foringer indbefatter:
- reaktion med slaggesmelte
- infiltration med slaggesmelte og nedrivning
- oxidation
- indtrængning af gasser
- kondensering af gasformige salte og medfølgende ekspansion
- reaktion mellem indtrængende gasser og foringskomponenter
- opløsning af foringens bindfase af gaskomponenter
- spændinger via ekspansion af faser og forskelle i termisk ekspansion mellem panelvæg og foring
- korrosion af stifter og beslag samt korrosion af panelvæg.
Korrosion af panelvægge bag ildfast foring har vist sig oftest at udgøres af saltsmeltekorrosion, hvor de primære korrosive smelter typisk udgøres af alkali- og tungmetalklorider, overvejende K-Zn-klorider.
Samme korrosionsform forekommer typisk på ubeskyttede panelvægge i området umiddelbart efter afslutningen af den ildfaste foring og områder af ubeskyttet panelvæg, hvor strømningsforholdene betinger
en høj stoftransport til kedelvæggen.
Korrosion af overhedere er ofte præget af gasfase klorkorrosion og i mange tilfælde i kombination med smeltekorrosion, f.eks. af smelter i systemet KCl-FeCl2.
Ud over disse mekanismer kan forekomme korrosion forårsaget eller fremmet af lokalt reducerende forhold ved kedelvæggene. Lokalt forekommer også erosion i områder med uhensigtsmæssige
strømningsforhold. Mekanismerne i ovennævnte korrosionsformer er kort fortalt som nedenstående.
5.2.1.1 Cl-gas korrosion
Gasfase alkalimetal- og tungmetalklorider såsom KCl, NaCl, ZnCl2 og PbCl2 kondenserer på røroverfladerne og reagerer her med røggassens SO2 i dannelse af Cl-gas i høje koncentrationer ved
røroverfladen. Denne sulfateringsreaktion kan illustreres ved KCl: 2KCl+SO2+O2=K2SO4+Cl2. Denne Cl-gas reagerer med stålet efter: Fe+Cl2=FeCl2. Dette jernklorid er flygtigt ved korrosionsfronten
og føres som gas udad til oxidlaget, hvor det oxideres: 3FeCl2+2O2=Fe3O4+3Cl2. Den herved frigivne Cl-gas kan så atter reagere med stålet. Mekanismen kræver, at der kondenseres en af ovennævnte
metalklorider på rørene og at disse kan reagere med SO2 fra røggassen. Korrosionen vil formodentlig øges ved større Cl/S-forhold i brændslet, højere røggastemperatur og højere overfladetemperatur. Et
lavere Cl/S-forhold ville betyde, at sulfateringsreaktionen i højere grad foregår i røggassen, hvor frigivelse af Cl-gas er forholdsvis uskadelig. Denne type korrosion kan forekomme både på panelvægge og
overhedere.
5.2.1.2 Smeltekorrosion
Ved kondensation af ovennævnte metalklorider på ståloverfladen/oxidlaget kan der dannes forbindelser med smeltepunkter under de aktuelle overfladetemperaturer. Både vores egne få analyser og
litteraturdata tyder på, at det især er blanding af ZnCl2 og KCl, der giver problematiske smelter, men NaCl og PbCl2 kan også bidrage. Blanding af ZnCl2 og KCl kan have smeltepunkter ned til 230°C
afhængig af K/Zn-forholdet. Ved tilstedeværelse af sådanne smelter opløses stålet og/eller oxidlaget og det opløste jern genudfældes formodentlig som jernoxid uden over smelten. Mekanismen kræver at
forskellige metalklorider kondenserer på røroverfladen. I de fleste tilfælde vil det formodentlig være, at både ZnCl2 og KCl kondenserer og at ZnCl2 udgør mindst halvdelen af metalkloriderne.
Metaloverfladetemperaturen er af stor betydning, idet den bestemmer om kloriderne er smeltede. Denne type korrosion forekommer primært på panelvægge i området efter afslutning af ildfaste foringer.
5.2.1.3 Reducerende forhold/CO-korrosion
Lokalt lave iltkoncentrationer og høje CO-koncentrationer ved kedelvæggene kan fremme korrosion på forskellige måder, f.eks. ved at reducere stabiliteten af beskyttende jernoxider, fremme
sulfiddannelse, øge stabilitet af metalklorider og sænke smeltepunktet af belægninger. Denne korrosionsform kan specielt optræde ved dårlige forbrændingsforhold og dårlige opblandingsforhold i røggassen.
5.2.2 Belægningsdannelse
Mekanismer i belægningsdannelse har ikke været genstand for tilsvarende detaljerede undersøgelser som for korrosionens vedkommende. Undersøgelser af belægninger fra affaldsfyrede anlæg viser, at der i
ovnområdet sker en påbagning af smelteslagge på de ildfaste foringer og tykkelsen af smelteslaggen vil være afhængig af underlagets karakter og af slaggens viskositet og dermed af dets sammensætning.
Gennem de tomme træk sker der en stigende kondensation af salte på hedefladerne. Typisk vil initiallagene i belægningerne bestå af næsten rene salte af alkali- og tungmetalklorider og –sulfater og disse salte
optræder desuden også i de øvrige dele af belægningerne. Længere omme i de tomme træk og i overhederområdet observeres en tiltagende sulfatering af belægningerne, og der synes at være en tendens til,
at kedler med væsentlige belægningsproblemer også er karakteriserede ved forøgede indhold af sulfat i belægningerne. Dette peger på sulfatsintring som en betydende mekanisme i belægningsdannelsen.
5.3 Affaldssammensætningens indflydelse på korrosion og belægningsdannelse
5.3.1 Shredderaffald
I forhold til “normalt affald“ kendt fra de andre affaldsforbrændingsanlæg (ca. 85% husholdningsaffald og 15% industriaffald), vil shredderaffald have en række afvigende karakteristika. De væsentligste
karakteristika i denne sammenhæng er brændværdi og indholdet af en rækkegrundstoffer. I nedenstående skema er vist disse parametre for normalt affald og for shredder affald. Værdierne for shredder
affald er indhøstet i nærværende projekt. Sparsomme oplysninger om massebalancer for EBARA processen peger på, at den overvejende mængde af klor, svovl, alkali, zink og bly går videre til
forbrændingsprocessen. Værdierne vil dog være afhængige af den aktuelle forbehandlingsproces. Værdierne for normalt affald er indhentet for de ikke flygtige komponenters vedkommende fra
massebalancemålinger på Sønderborg KVV, og Cl og S værdierne er baseret på emissionsmålinger og spildevandsmålinger fra Odense Kraftvarmeværk. Normalt affald dækker her en blanding af normalt
affald og industriaffald som er det normale brændselsblanding på danske affaldsforbrændingsanlæg. Værdierne er kun retningsgivende, idet der vil forekomme meget betydende variationer i
sammensætningerne.
Tabel 9. Sammensætning af forskellige typer affald
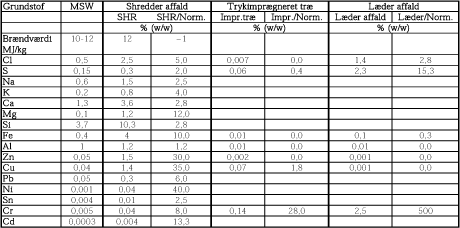
Det fremgår heraf, at shredderaffald har samme eller lidt højere brændværdi end normalt affald. Desuden ses en meget betydelig afvigelse i sammensætning, idet shredder affald har betydeligt større indhold
af Cl, alkali og tungmetaller men kun lidt højere indhold af S end normalt affald.
En lidt højere brændværdi kan, afhængigt af hvorledes forbrændingen styres, føre til højere forbrændingstemperaturer, hvilket kan føre til en større frigivelse af metalklorider såsom alkali- og
tungmetalklorider.
Det højere kloridindhold i shredderaffald er meget væsentligt, idet det kan føre til en væsentlig større frigivelse af metalklorider i forbrændingen, og kombineret med et øget indhold af alkali og tungmetaller
kan der forventes en massiv forøgelse af indholdet af gasfase alkali- og tungmetalklorider i forhold til forbrænding af normalt affald. Hvorvidt dette vil ske, vil dog også være afhængig af, hvorledes
reaktanterne (pyrolysegas, forgasningsgas, koksrest) blandes. Det er vanskeligt at forudse præcist, hvorledes reaktionerne vil forløbe.
Der er således høj sandsynlighed for en markant forøgelse af indhold af gasfase metalklorider umiddelbart efter forbrændingen i forhold til traditionelle affaldsfyrede anlæg. Denne forøgelse af gasfase
alkaliklorider og tungmetalklorider medfører et øget potentiale for korrosion og belægningsdannelse i de efterfølgende kedeldele. Hvorvidt problemerne vil være af overvejende korrosions- eller
belægningsmæssig karakter afhænger i meget høj grad af, om disse gasfase metalklorider sulfateres i røggassen og afsættes som metalsulfater eller om de primært afsættes som metalklorider og efterfølgende
sulfaterer i belægningerne.
I tilfælde af en langsom sulfateringsrate, vil der i høj grad ske afsætning af metalklorider, hvilket vil fremme saltsmeltekorrosion og gasfase klorkorrosion. En højere sulfateringsrate vil derimod øge
belægningsproblemerne idet sulfaterne fører til øget sintring af belægningerne således at disse kun vanskeligt fjernes under drift. I tilfælde af en næsten komplet sulfatering af metalkloriderne i røggassen vil
korrosionsbelastningen reduceres betydeligt.
Som det fremgår af ovenstående tabel, er Cl-indhold øget væsentlig mere end S-indholdet i forhold til normal affald, hvilket giver et højere Cl/S-forhold. Dette peger i retning af, at det især er korrosionen,
som vil forøges. En anden væsentlig faktor er dog en øget tilstedeværelse af en række metaller som formodes at have en katalytisk virkning på oxidationen af SO2 til SO3 og dette vil trække den anden vej,
mod en hurtigere sulfatering og tendens til mere belægningsdannelse.
En yderligere væsentlig faktor er indholdet af Zn, Pb og alkali. Indholdet af disse grundstoffer er alle højere i shredder affald end i normalt affald, men indholdet er markant større for Zn og Pb end for alkali.
Flyveaskeanalyser fra nogle affaldsforbrændingsanlæg tyder på, at en stor del af brændslets alkaliindhold fordamper som klorider under forbrændingen, hvorimod det kun er en lille del af brændslets Zn- og
Pb-indhold, der fordamper som klorider. Dette peger på, at der vil være rigeligt alkali til dannelse af gasfase alkaliklorider i røggassen, og samtidig vil det højere indhold af Zn og Pb i affaldet formodentlig
føre til større dannelse af Zn- og Pb-klorider, der sammen med alkalikloriderne kan kondensere på røroverfladerne. Dette peger i retning af, at der med shredderaffald vil forekomme en større kondensering
af klorider på røroverfladerne, og at de kondenserede klorider vil have et højere Zn/alkali-forhold. Dette betyder igen, at der bliver større risiko for dannelse af korrosive smelter.
For koncepter, hvor dele af flyveasken recirkuleres, forventes dette at føre til en endnu mere aggressiv atmosfære, som vil forstærke korrosions- og belægningsproblemerne, idet indholdet af metalklorider
forventes at øges.
Hvorvidt der med det pågældende affald optræder mere eller mindre CO-korrosion afhænger mest af neddelingsgraden af affaldet samt design af ovnen.
Sammenfattende peger en kvalitativ vurdering i retning af, at både korrosion og belægningsdannelse vil øges ved forbrænding af shredderaffald i forhold til normalt affald. Størrelsen af stigningen i korrosion
og belægningsdannelse kan ikke forudses præcist, men vurderes at være af betydelig størrelsesorden på basis af shredderaffaldets sammensætning. En bestemmelse heraf bero på erfaringer fra og forsøg på
pilot- eller fuldskala anlæg med det relevante brændsel
5.3.2 Imprægneret affaldstræ
Trykimprægneret træ har meget lavere indhold af Cl, alkali, Zn og Pb samt et lavere Cl/S-forhold end både normalt affald og shredder affald, hvilket tyder på at der ikke vil forekomme betydende problemer
med korrosion og belægningsdannelse ved traditionelle dampdata.
5.3.3 Læder- og garveriaffald
Læderaffald har et Cl-indhold, der ligger mellem normalt affald og shredderaffald. Samtidig er S-indholdet højt, således at Cl/S-forholdet er væsentligt lavere end for normalt affald og shredder affald.
Endeligt er indholdet af alkali, Zn og Pb lavt i læderaffald. Disse forhold betyder ligeledes, at potentialet for korrosions- og belægningsproblemer er forholdsvis lavt.
5.4 Praktiske erfaringer
En gennemgang af besøgsrapporterne suppleret med nye informationer om driften af anlæggene viser, at for de undersøgte koncepter er den termiske proces ved forbrænding af produkter efter
forgasning/pyrolyse enten ikke demonstreret, demonstreret uden kraftvarmeproduktion, demonstreret med kedler med lave dampdata, demonstreret med mindre aggressivt affald eller kun med kontinuert
driftstid under et år. Eksempelvis er Mitsuis proces demonstreret, men kun med husholdningsaffald i fuld skala, og shredder affald i pilot skala; Takumas proces er demonstreret over flere år, men ved
moderate dampdata (270°C/ 48 bar) og frigivne oplysninger er yderst sparsomme; EBARAs proces er demonstreret med shredderaffald med rimelige dampdata (400°C/ 38 bar). Siden besøget er kedlen
blevet modificeret og et nyt rensesystem er påbygget. Der er herefter kun ca. 8 måneders drift med fire nedlukninger som ikke skyldes belægninger.
Der er således kun få beskrivelser af problemer af ovennævnte karakterer - de beskrevne problemer er primært belægningsproblemer, og der er typisk ikke beskrevet problemer med korrosion og levetid af
ildfaste foringer. En væsentlig grund til sidstnævnte er formodentlig, at belægningsproblemer vil vise sig efter relativ kort driftstid, hvorimod problemer med korrosion og nedbrydning af ildfaste foringer ofte
først vil vise sig tydeligt efter længere driftstid.
Undersøgelserne har vist, at der er løbende bestræbelser på at opsamle driftserfaringer fra processerne, men dels tager det nogen tid inden, der kan indhøstes kvantitative data for korrosion, nedbrydning af
ildfaste foringer og belægningsdannelse, og dels er det ofte svært at få driftserfaringer fra producenterne, idet dette betragtes som kerneviden. For en nærmere vurdering af omfanget af disse problemer er det
stadig yderst vigtigt at følge driftserfaringerne på de pågældende anlæg løbende.
5.5 Løsningsmuligheder
For at modvirke problemerne med belægningsdannelse og korrosion, bør man se på både primære tiltag som sigter mod at ændre røggasatmosfærens karakteristika og sekundære tiltag som sigter mod at
mildne effekten af røggasatmosfærens påvirkninger af kedlen.
5.5.1 Primære tiltag
De tiltag, som kan anbefales for minimering af korrosion, er de samme som gælder for kedler, der forbrænder normalt affald. Blot er tiltagene endnu vigtigere på grund af det mere korrosive brændsel.
Der findes i dag ingen entydige og afprøvede løsninger på korrosionsproblemerne. Der findes en række muligheder, som formodentlig kan reducere problemerne, men disse bliver først endeligt afklarede
gennem yderligere undersøgelser. Derfor må der gives en anbefaling, som skal baseres på det nuværende grundlag men i erkendelse af, at det er mangelfuldt.
Sænkning af tryk på vand/dampsiden vil være et af de mest effektive midler til at reducere korrosion af panelvægge, idet dette reducerer overfladetemperaturen. Ligeledes kan en lavere damptemperatur
reducere korrosion af overhederne, men til dette er det mindst lige så vigtigt at reducere røggastemperaturen før overhederne. Det vurderes, at korrosionsproblemerne kan elimineres ved at begrænse
dampdata til maksimalt 30 bar og 350 C eller ved at anvende en fjernvarmekedel.
Minimering af korrosion kræver, at der er så gode forbrændingsbetingelser som muligt for mindske dannelsen af korrosive stoffer, og at kedelvæggene beskyttes mod de korrosive komponenter, som
alligevel vil dannes i større eller mindre omfang. Sikring af gode forbrændingsbetingelser stiller en række krav til design af forbrændingsområdet og til driften af anlægget. På nuværende tidspunkt er der ikke
noget samlet overblik over, hvorledes de enkelte forbrændingsparametre indstilles optimalt, så det er derfor vigtigst at sikre så gode reguleringsmuligheder som muligt især for parametre som luftfordelinger.
Ligeledes bør ovn og kedel være udrustet med registreringsmuligheder for røggastemperaturer, målesteder for CO-målinger og målesteder for spektroskopimålinger af gasfase metalklorider.
5.5.2 Sekundære tiltag
For ovn og efterforbrændingszonen skal rørvæggene have påført en ildfast foring for opretholdelse af en tilstrækkelig røggastemperatur (>1100 C i minimum 2 sekunder) og som også beskytter den
bagvedliggende rørvæg mod korrosion. For valg af foringsmateriale og påføringsmetode kan man i nogen grad hælde sig til erfaringerne fra tidligere anlæg. Der kan ikke gives endelige anbefalinger om
anvendelse af kakler versus støbemasser. Fuldskalaforsøg peger på, at der kan være muligheder i anvendelse af kakler med spærreluft (hinterlüftet) til yderligere at sikre mod indtrængning af korrosive
komponenter.
Det sværeste område i korrosionsmæssig henseende er rørvæggen efter afslutning af den ildfaste foring. På basis af de hidtidige iagttagelser må det forventes, at der kan forekomme en kraftig
korrosionsbelastning i dette område. Korrosionsbelastningen vil være kraftigst umiddelbart efter afslutningen af den ildfaste foring, men kraftig korrosionsbelastning kan forekomme over et større område
herefter. På anlæg, hvor man har søgt at løse et korrosionsproblem dette sted ved at føre den ildfaste foring længere om i trækkene er det oftest konstateret, at korrosionsproblemet blot følger med.
Endvidere kan dette give anledning til en forøgelse af røggastemperaturen ved indgang til overhederne og dermed øge korrosionsbelastningen dette sted.
Det er derfor meget sandsynligt at foring af en større del af rørvæggene i 1. og 2. træk ikke vil løse korrosionsproblemet.
5.5.2.1 Materialevalg
På nuværende tidspunkt synes den eneste løsning på korrosionsproblemet at være påføring af et metallisk lag af korrosionsbeskyttende materiale på rør og finner. På baggrund af de hidtidige erfaringer,
primært i udlandet, bør der vælges et Alloy 625 materiale, altså Ni-baseret med høj Cr-indhold og lavt Fe-indhold. Der kan vælges forskellige påføringsmetoder: påsvejst, påsprøjtet eller co-ekstruderet.
Disse 3 metoder har indbyrdes en række fordele og ulemper som skal afvejes mod hinanden.
De fleste erfaringer er baseret på påsvejst Inconel 625 og der foreligger overvejende positive erfaringer i tilfælde, hvor der er påsvejst på frisk panelvæg. Påsvejsningen har fordel af en god tykkelse (2-3
mm) og formodentlig god kvalitet med hensyn til vedhæftning, porøsitet og permeabilitet. Ulempen i forhold til de to andre er opblandingen med rørmaterialet der giver et væsentlig højere Fe-indhold og
dermed muligvis reduceret korrosionsbestandighed. Dette kan minimeres ved optimering af svejseproceduren og anvendelse af stort overlap mellem svejsestrengene.
Der findes væsentlig færre erfaringer med påsprøjtet Inconel 625 og erfaringsmaterialet i primært mindre indbygningsforsøg med overhederrør. Påsprøjtningen er tyndere (0,5-0,7 mm) end påsvejsning, men
til gengæld ændres sammensætningen ikke i forhold til Inconel 625. I flere tilfælde har forsøg med påsprøjtede coatings udvist problemer med revnedannelse som har ført til accelereret korrosion og
afskalning af coatings. Der pågår en del udviklingsarbejde med coatings og der kan måske fremkomme væsentligt forbedrede produkter.
Den tredje mulighed er co-ekstruderede rør. På indeværende tidspunkt markedsføres kun hele rør som co-ekstruderede rør med yderlag som kan være mere eller mindre svarende til Inconel 625 og sort
stål inderst. I tilfælde af, at der skal produceres panelvægge kan der anvendes en Inconel 625 finne. Der er relativt få indbygningsforsøg, men resultaterne er overvejende positive, dog er der også konstateret
korrosionsskader på sådanne rør.
Prismæssigt er påsprøjtning det billigste med ca. 8-10.000 DKK/m². Påsvejsning er lidt dyrere med ca. 15-20.000 DKK/m². For co-ekstruderede rør er prisen formodentlig 25.000-30.000 DKK/m².
Disse priser skal dog tages med forbehold. Umiddelbart vil anvendelse af påsvejst Inconel 625 kunne anbefales, idet der foreligger flest erfaringer med denne løsning. De forøgede anlægsomkostninger
forårsaget af Inconel oversvejsning vil efter al sandsynlighed blive rigeligt modsvaret af reducerede vedligeholdelsesomkostninger.
Anvendelse af varmeveksling baseret på keramiske rør med luftkøling er måske en mulighed, men der er uløste problemer med materialer og slaggedannelse.
5.5.2.2 Kedelkonfiguration
For opnåelse af en rimelig levetid af overhederne er det især vigtigt, at reducere røggastemperaturen før overhederne og så vidt muligt placere slutoverhederen medstrøms. Der bør opretholdes en
røggastemperatur før overhederne på mindre end 650°C, også ved snavset kedel, og jo lavere røggastemperatur, jo lavere bliver korrosionsraten. Muligvis bør der vælges en lavere temperaturgrænse end
de 650°C ved højere indhold af Zn- og Pb-klorider; dette vil måske kunne afklares ved at finde damptryksdata for disse klorider i litteraturen. Der kan med fordel indsættes en fordamperhedeflade lige før
overhederne, hvilket både vil reducere røggastemperaturen og give en bedre opblanding af røggassen før overhederne. Det bør også overvejes at indsætte renseanordninger i de tomme træk, i form af
sodblæsere eller ultralydrensning. Det er tænkeligt at problemaffaldet vil føre til forøget belægningsdannelse og tykke belægninger kan føre til øget korrosion på panelvægge og overhedere, sidstnævnte især
på grund af øget røggastemperatur.
Nedkøling af røggassen fra 1100 C i efterforbrændingsområdet til under 650 C før overhederne stiller krav til større hedeflade i dette område end i traditionelle affaldskedler.
Mulighed for at reducere indholdet af gasfase metalklorider gennem tilsætning af additiver såsom svovl eller aluminosilikater bør også overvejes. Der er udført forsøg på et traditionelt affaldsfyret anlæg som
peger på, at der er muligheder for at reducere både belægningsdannelse og korrosion ved denne fremgangsmåde. Dette kræver dog yderligere forsøg for en nærmere afklaring af muligheder og økonomi.
Det er dog overvejende sandsynligt, at der også skal foretages yderligere tiltag for at reducere belægningsproblemer i ovn, tomme træk og i overhederne. I ovnen kan det foreslås at anvende Inconel
oversvejste rør på siderne ved risten, idet dette vil modvirke opbygning af slaggepåbagninger.
5.5.2.3 Kedelrensning
I de tomme træk kan det blive nødvendigt at installere anordninger til fjernelse af belægninger. Dette kan være dampsodblæsere, vandsodblæsere, tankspulere, styrede vandlanser, akustiske
renseanordninger og eksplosiver. Der er gode erfaringer på nogle danske anlæg med renseanordninger baseret på traditionelle tankspulere.
I overhederområdet anbefales anvendelse af bankeværker for at reducere opbygningen af belægninger. Det er svært på forhånd at vurdere, om dette vil være tilstrækkeligt og det kan være nødvendigt med
yderligere rensninger, såsom flere rensestop om året eller online rensninger med eksplosiver. Det sidstnævnte kræver dog også, at anlægget er udlagt med gode muligheder for fjernelse af store
belægningsmængder på kort tid.
5.6 Konklusion
Shredderaffaldets karakteristika - specielt det højere indhold af Cl, alkali og tungmetaller i forhold til normalt husholdnings- og industriaffald - betyder, at der er en kraftigt forøget risiko for korrosions- og
belægningsproblemer i kedler til kraftvarmeproduktion.
Der er kun meget få driftserfaringer under de rette betingelser, hvilket betyder, at disse problemer endnu ikke kan kvantificeres. Demonstration af fuldskala drift under de rette betingelser i en driftsperiode på
1-2 år er nødvendig for at kunne kvantificere problemerne med rimelig sikkerhed.
Der er angivet en række muligheder for at løse de meget sandsynlige problemer med nedbrydning af ildfaste foringer, korrosion af fordamperhedeflader under ildfaste foringer og efter afslutning af ildfaste
foringer samt korrosion af fordampere.
Korrosionsbeskyttelse især af fordamperhedeflader med Inconel oversvejsninger vurderes at give en reduktion af vedligeholdelsesomkostninger og forbedret rådighed, som langt overstiger de ekstra
anlægsomkostninger.
| Forside | | Indhold | | Forrige | | Næste | | Top |
Version 1.0 Februar 2006, © Miljøstyrelsen.
|