| Forside | | Indhold | | Forrige | | Næste |
Metoder til behandling af tungmetalholdigt affald - Fase 3
Bilag B
Logbog for besøg hos Borge garveri (Pyroarc processen)
1 Generelle oplysninger
1.1 Procestype
I Pyroarc-processen indgår forgasnings-, plasma- og forglasningsteknologi i et samlet koncept til behandling af al læder- og træaffald fra Borge Garveri.
Processen producerer en metallegering og et slaggeprodukt til genanvendelse, samt energi i form af kraft og varme til garveriet.
1.2 Tilført affald
Læderaffald i form af falsespåner, slam fra spildevandsanlæg, limlæder og træaffald
1.3 Licenshaver og kontaktpersoner
Licenshaver
Enviroarc Technologies AS er licenshaver.
Kontaktperson Steinar Lynum
Telefon: +47-24111252
Fax: +47-24111299
E-mail: steinar.lynum@enviroarc.com
1.4 Ejerforhold og kontaktpersoner for det besøgte anlæg
Anlægget er ejet af Borge Garveri AS og EnviroArc Technologies AS.
1.5 Beliggenhed for det besøgte anlæg
Pyroarc anlægget er beliggende ved
Borge Garveri AS
N5250 Lonevåg
Norge
Anlægget er vist på figur 1
Figur 1. Pyroarcanlægget ved Borge garveri.
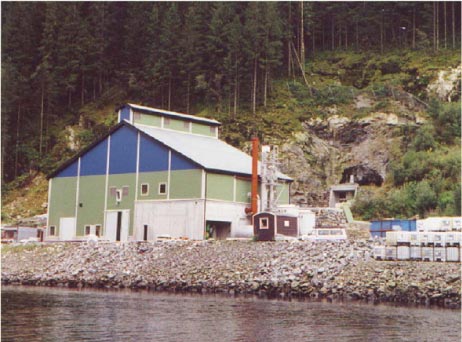
1.6 Virksomhedens formål og idégrundlag
Enviroarc sælger anlæg til behandling af alle typer affald herunder problemaffald og arbejder på at etablere Pyroarc-anlæg til behandling af imprægneret affaldstræ, shredderaffald og andre problematiske
affaldstyper.
Formålet med anlægget hos Borge Garveri er behandle læderaffaldet fra garveriet og producerer energi til garveriet, uden at der opstår restprodukter, som må deponeres. Anlægget producerer dels varme til
at tørre slam og dels til garveriets forbrug af varme i forbindelse med garvningsprocesserne.
1.7 Kapacitet for det besøgte anlæg
15.000 t affald (vådt)/år.
7.700 driftstimer pr. år
Kapaciteten af vådt affald er således ca. 2 t/time.
Forgasserens kapacitet af tørret affald, træflis mv. er ca. 0,7 t/time.
1.8 Byggeår og status for projektet
Pyroarcanlægget ved Borge garveri har været overtaget af garveriet siden januar 2002 og har pr. 1/10-2002 haft ca. 3.000 driftstimer. Driften har været baseret på 5 dages drift med 24 timer/døgn.
Gasmotoren benyttes ikke fuldt ud, da det i perioder med lidt affald er mest økonomisk at producere varmt vand til garveriet. Motoren har været i testet ved fuld kapacitet samt ved normal brug og kører
tilfredsstillende på den producerede gas.
Et pilotanlæg findes i Hofors.
Enviroarc arbejder med etablering af andre Pyroarcanlæg i Sverige, Italien, Tyskland, Polen, Malaysia og flere anlæg i Norge.
Enviroarc forventer at kunne bygge Pyroarcanlæg med kapaciteter op til 7 t/time (ca. 50.000 t/år).
2 Kortlægning og beskrivelse af anlægget
Et procesdiagram over anlægget er vist i Figur 2 og Figur 3.
2.1 Procesdiagram
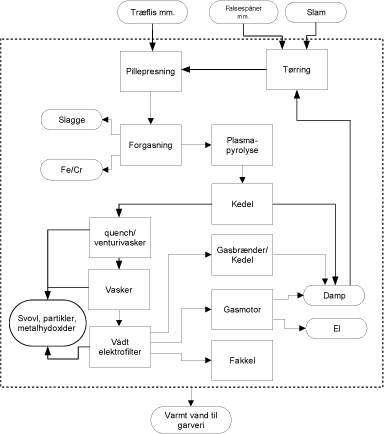
Figur 2 Procesdiagram for forgasningsanlægget
2.2 Affald
Affaldet som behandles stammer fra Borge garveri.
Affaldet fra garveriet består af
- falsespåner som opstår ved tykkelsesjusteringen af læderet
- afskær fra læderproduktionen
- slam fra garveriets spildevandsrensning, som indeholder jern fra fældningsprocessen. Der behandles endvidere slam fra en tidligere aluminiumsbaseret fældningsproces.
- håraffald
- limlæder som er fedt fjernet fra de modtagne huder
- træaffald fra engangspaller mv.
Mængdemæssigt er slammet langt den største affaldsfraktion.
Garveriet behandler pt. alle affaldsfraktioner bortset fra den lille fraktion af afskær, da Borge endnu ikke er anskaffet en passende neddeler.
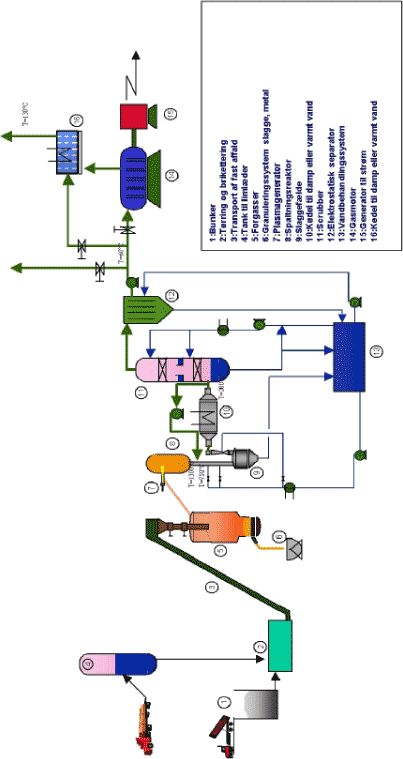
Figur 3. Opbygning af Borges Pyroarc-anlæg.
2.3 Forbehandling
Falsespåner og håraffald blandes med det afvandede slam, som opbevares i bigbags. Blandingen tilføres anlæggets lagerbunker, som er opdelt i sektioner til de forskellige typer affald.
Herfra tilføres blandingen tørreanlægget sammen med indpumpet limlæder. Tørreren er en "multicoil" modstrømstørrer, som opvarmes med damp fra Pyroarc-anlægget.
Affaldet tørres ned til < 5% fugtindhold, hvorefter blandingen føres til et pillepresningsanlæg med ringmatrice. Pillepressen producerer brændselspiller med en diameter på 50 mm. De færdigproducerede
piller føres til en lagerbunker.
2.4 Forgasning
Brændselspillerne tilføres en modstrøms skaktovnsforgasser sammen med koks og træflis fra nedfliset affald. Affaldet forgasses ved 1500°C sammen med tilsatte siliciumholdige sten med brug af forvarmet
luft. Herved produceres en flydende slagge og en jern/krom-metallegering. Da forgasseren arbejder efter modstrømsprincippet, indeholder produktgassen en del tjærestoffer og ledes derfor forbi en
plasmagenerator. Produktgassen fra forgasseren blandes i et reaktionskammer med en plasmagas med en temperatur på op til 5000°C og opnår derved temperaturer på over 1200°C i ca. 0,5 sekunder (se
figur 4). Herved nedbrydes alle organiske stoffer til simple molekyler, så der dannes en syntesegas af brint, kulmonooxid, kuldioxid, vanddamp og kvælstof.
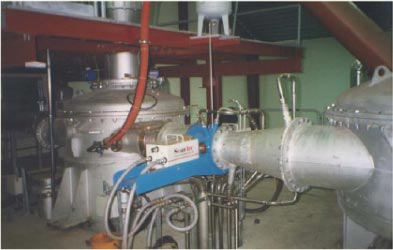
Figur 4. Top af forgasser med plasmagenerator (blå).
2.5 Energiproduktion og røggasrensning
Syntesegassens temperatur sænkes fra ca.1200°C til ca. 650°C ved recirkulering af produktgas. Herefter produceres damp i en kedel med en syntesegastemperatur efter kedlen på ca. 200°C.
Kedlen renses ved gennemblæsning af produktgas.
Rensningen af syntesegassen sker i en venturiskrubber, hvor gassen bratkøles ved indsprøjtning af vand. Herved fjernes salte og partikler. Efterfølgende passerer gassen en cyklon, hvorefter gassen renses i
et vasketårn, hvor der tilsættes base. Herved fjernes tilstrækkeligt svovlbrinte til at kunne overholde krav for udledning af SO2 efter forbrænding. Til sidst følger et vådt elektrofilter.
Herefter kan gassen enten ledes til en gasfyret dampkedel eller til gasmotor med generator til produktion af kraft og varme. Den maksimale el-produktion er omkring 580 kW. Herudover findes en
sikkerhedsfakkel.
Da garveriet bruger store mængder vand ved lave temperaturer, kan der opnås en høj energiudnyttelsesgrad, idet restvarme i kondenserede dampstrømme og anden overskudsvarme ved lav temperatur kan
udnyttes til forvarmning af vand til garveriet.
3 Observationer under besøget
3.1 Besøgets varighed
Den 18/9 2002 fra kl. 11:30 til kl. 15. (Uge 38).
3.2 Indsatsmaterialer behandlet under besøget
Type:
Mængde i t/h: 0 t/h
Kapacitetsudnyttelse: 0 %
Anlægget var stoppet på grund af en mindre reparation under besøget.
3.3 Driftsforhold
Driftstid: 24 timer/døgn, 5 dage per uge hvis der findes tilstrækkeligt affald.
Revisioner: 1 pr. år.
Idet der pt. ikke er nok affald på garveriet, samt eksternt affald til 7 dages drift køres 24 timer/døgn i 5 dages perioder, mens anlægget lukkes ned i weekenderne. Dette er ikke optimalt udfra et
driftssynspunkt, da op og nedlukninger reducerer levetiden af udmuringer, men er stadig den bedste økonomiske løsning, indtil der skaffes mere affald.
Driftsresultater for uge 36.
Driftstid: 113 timer
Tilført brændsel til forgasser:
- Læderaffaldsbriketter 39,5 t
- Koks: 3,5 t
Mængden svarer til 0,38 t/time eller ca. 50% af forgasserens kapacitet.
Briketteproduktion:
- Behandlet slam, limlæder håraffald og falsespåner: 90 t
Dette svarer til 0,8 t vådt affald/time eller ca. 45% af brikettepressens kapacitet.
Der produceres kun el, når der er tilstrækkeligt med affald til, at dette er lønsomt. Så længe der ikke er mere affald end, at energien herfra kan udnyttes til tørring af slam og levering af varme til garveriet, kan
det ikke betale sig at producere strøm til nettet. Gasmotoren kan operere ned til 50% af nominel kapacitet dvs. ca. 290 kW.
3.4 Output under besøget
3.4.1 Restprodukt
Ingen produktion under besøg
3.4.2 El/varme
Ingen produktion under besøg
Anlægget producerede i uge 36:
Slagge: |
1.780 |
kg |
Metallegering: |
200 |
kg |
Damp: |
79.180 |
kWh |
4 Kritiske delprocesser og driftsparametre
Under besøget blev følgende spørgsmål diskuteret:
- Er der forekomst af kondenserbare stoffer og forureninger i processernes forskellige trin; fx af tjære, sod, metaller, salte og oxider i pyrolyseovnens top, i gaskanaler eller i
efterforbrændingskamre?
Der er ikke registreret problemer med tjære fra forgasningsskakten til plasmageneratoren.
Efter ombygning af spaltningsreaktoren har der ikke været problemer med afsætning eller kondensering af stoffer på procesenhederne nedstrøms i spaltningsreaktoren.
- Hvordan kontrolleres mængden af kondenserede stoffer, dvs. hvordan renses de kritiske procesafsnit for afsætninger?
Gassen fra spaltningsreaktoren, som har en temperatur på 1200-1300°C, bratkøles med recirkuleret gas til 650°C for at kondensere salte og derved undgå at klæbrige partikler sætter sig på
overflader nedstrøms i anlægget.
Kedlen holdes ren med et "big blaster" system, som i faste sekvenser skyder kedlen ren med komprimeret produktgas.
- Hvilken kemisk stabilitet har restprodukter fra processen? Er de lagringsstabile mht. tungmetaller og dermed egnet til deponering (data for standardudvaskningstests), eller
lækker der tungmetaller, og skal de betragtes som miljøfarligt affald?
Udvaskningsdata viser at slaggen tilfredsstiller danske krav til udvaskning for kategori II (se tabel 7).
- Findes der dioxiner (eller andre halogenerede organiske stoffer) i restprodukter eller evt. mellemprodukter som skal oparbejdes andetsteds?
Affaldet omdannes til renset brændbar gas, slagge og metal.
Fra gasrensningen opstår spildevandsslam, som behandles på vandrensningsanlægget ved Borge garveri. Fra vandrensningsanlægget ledes produceret fældningsslam retur til Pyroarc processen. Der er
ikke påvist dioxiner eller halogenerede hydrokarboner i fældningsslammet fra spildevandsanlægget.
Røggas fra anlægget indeholder væsentligt mindre end 0,1 ng/Nm³ dioxin.
Slagge og metal bør grundet den høje behandlingstemperatur og et lavt kulstofindhold ikke indeholde dioxin. Der er ikke målt for dioxin i slagge eller metaller, men resultater for andre smelteprocesser
viser en meget lav koncentration (se besøgsrapport for Thermoselectprocessen ved Kawasaki steel, fase 2B).
5 Miljømæssige forhold
5.1 Emissioner til luften
Tabel 1. Emissioner til luften.
|
Målt/garanti (11% O2) |
EU-krav (11% O2, tør gas) |
|
mg/Nm³ |
mg/Nm³ |
SOx |
30 |
50 (24 h) |
NOx |
80 * |
200 (24 h) |
HCl |
<0,2 |
10 (24 h) |
CO |
50 (tilladelse på 3000) * |
50 (24 h) |
Støv |
1,7 (30 min) |
30 (30 min) |
TOC |
<0,02 |
10 (24 h) |
Sb+As+Pb+Cr+Co+Cu+Mn+Ni+V |
0,0075 |
0,5 |
Cd+Tl |
0,000037 |
0,05 |
|
|
ng –TEQ/m³ |
ng- TEQ/m³ |
Dioxiner |
0,05 |
0,1 |
* Måling udført under operation af gasmotor
5.2 spildevandsudledning
Slammet fra gasrensningen behandles i garveriets spildevandsrensningsanlæg, før det sendes tilbage til Pyroarcanlægget sammen med andet slam fra garveriet.
5.3 Støj
Støjniveauet kunne ikke vurderes under besøget, men forventes at være af samme størrelse som for andre termiske anlæg.
5.4 Lugt
Da anlægget var ude af drift under besøget, kunne vi ikke vurdere evt. lugtproblemer. Der må dog altid forventes en hvis afgivelse af lugt fra garveri-rester. Forgasningsanlægget kan ikke afgive lugt da
kravene til tæthed er langt større end ved et forbrændingsanlæg.
5.5 Affaldsproduktion
Slam fra glasrensning behandles på garveriets spildevandsrenseanlæg før det recirkuleres tilbage i Pyroarcanlægget sammen med andet slam fra garveriet.
5.6 Samlet dioxinemission
Dioxinindholdet i metaller og slagge kendes ikke.
Der bør dog ikke kunne forekomme dioxiner i nogle af fraktionerne dels grundet den høje temperatur, som smelter og metallegeringer har været udsat for, dels på grund af den reducerende atmosfære, som
røggasrensningsprodukterne udvindes ved.
Dioxinindholdet i røggasrenseprodukter måles to gange årligt
6 Arbejdsmiljømæssige forhold
6.1 Støvbelastning
Besøget var for kort til at bedømme støvbelastningen. Når anlægget er i drift , kan der kun forekomme støv ved brændselsproduktion. Under reparationer, hvor anlægget åbnes, må der tages samme
forholdsregler som ved reparationer af andre termiske anlæg med anvendelse af passende beskyttelsesudstyr. Der er installeret et centralt afsugningssystem, som fjerner støv fra eventuelle udslip ved
reparationer o. lign. Opsamlet støv tilføres briketteringsanlægget og efterfølgende forgasningsanlægget.
6.2 Internt støjniveau
Kunne ikke bedømmes.
6.3 Tungmetalbelastning
Her gælder samme forholdsregler ved reparationer, som er nævnt i afsnit 6.1.
6.4 Dioxinbelastning
Vi vurderer, at der ikke emitteres dioxiner fra anlægget.
6.5 Andet; fx lugtgener, vilkår i forbindelse med reparationsarbejde mv.
Garveriaffald afgiver en vis lugt, indtil der er fremstillet brændselspiller.
7 Beskrivelse af input
Mængden af affald til garveriet er i dag mindre end forudsat i designet af anlægget. Mængden og sammensætningen kan variere, men som udgangspunkt for designet af anlægget blev benyttet
sammensætningen angivet i tabel 2.
Tabel 2. Designdata for tilførte mængder affald
Type |
Tørstofindhold
(vægt %) |
Brændværdi
(MJ/kg tør) |
Affald
(kg/h) |
Slam (Borge Garveri ¹) |
30 |
16 |
394 |
Slam (Lager ²) |
30 |
16 |
1.221 |
Limlæder |
15 |
25 |
197 |
Håraffald |
40 |
29 |
46 |
Rotosil |
40 |
29 |
16 |
Spalt |
40 |
21 |
3 |
Klippefiller |
85 |
21 |
2 |
Falsespåner |
50 |
21 |
25 |
Andet usorteret |
70 |
14 |
14 |
Plast |
98 |
26 |
3 |
Træaffald |
50 |
19 |
10 |
SUM |
|
|
1.931 |
1 Jernholdigt slam
2 Aluminiumholdigt slam. Kan kun indfyres i begrænset mængde sammen med jernholdigt slam af hensyn til slaggens smeltepunkt
Brændselspillerne er vist på figur 5.
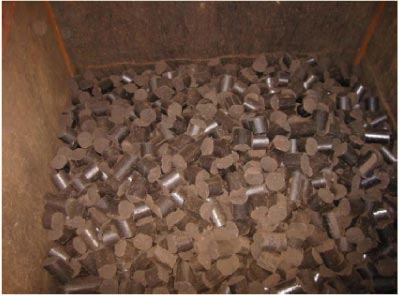
Figur 5. brændselspillerne til Borges Pyroarc-anlæg er ca. 50 mm i diameter.
Ved behandling af alternative brændsler som træflis mm. bør affaldet have en brændværdi på mindst 10-12 MJ/kg og højst 35-40% fugtindhold.
8 Beskrivelse af output
Borge har oplyst denne typiske masse- og energibalance (se tabel 4).
8.1 Kraft/varme
Der produceres el af den rensede produktgas i en gasmotor/generator til dækning af anlæggets energiforbrug. Der kan maximalt produceres 580 kW med den eksisterende motor. Det vil dog være muligt at
producere 650 kW el med en større motor.
Anlæggets el-forbrug er 540kW, så der opnås et lille overskud. De 73 kW stammer fra el-forvarmning af luft, som vil kunne klares med damp, hvorved det teoretisk vil være muligt at opnå et overskud på
183kW med anden motor.
Anlægget producerer også damp og varme, som benyttes i garveriet og til tørring af slam til brændselspiller.
I tabel 3 er vist et energiregnskab for det termiske anlæg henholdsvis uden og med energiforbrug til tørring af slam
Tabel 3. Energibalance for termisk anlæg.
|
Med slamtørring |
Uden slamtørring |
Brændselspiller |
670 kg/h |
670 kg/h |
Energiindhold |
14.8 MJ/kg |
14.8 MJ/kg |
Koks |
30 kg/h |
30 kg/h |
Energiindhold |
28.5 MJ/h |
28.5 MJ/h |
Virkningsgrad gasmotor |
35 % |
35 % |
Maksimal el-produktion |
580 KW |
580 KW |
|
|
|
Energi input |
kW |
kW |
Brændselspiller |
2.754 |
2754 |
Koks |
238 |
238 |
Forvarmet luft (el) |
73 |
73 |
Plasmagenerator (el) |
267 |
267 |
Diverse motorer |
200 |
200 |
Dampforbrug tørring |
1.086 |
0 |
Sum |
4.619 |
3.533 |
|
|
|
Energi output |
|
|
Forbrændingsvarme |
1.913 |
1.913 |
Følbar varme |
1.128 |
1.128 |
Slagge og metal |
86 |
86 |
Varmetab forgasser |
70 |
70 |
Varmetab reaktor |
100 |
100 |
Varmetab Plasmagenerator |
38 |
38 |
Diverse tab |
198 |
198 |
Varmetab tørring |
435 |
0 |
Genvunden energi tørring |
652 |
0 |
Sum |
4.619 |
3.533 |
Produceret energi og tab |
|
|
Produceret el |
580 |
580 |
Produceret damp + varmt vand |
2.945 |
2.345 |
Internt forbrug og tab |
1.094 |
608 |
Sum |
4.619 |
3.533 |
I tabel 4 er vist en samlet masse og energibalance ekskl. energiforbrug til slamtørring.
Tabel 4. Masse- og energibalance for Pyroarc-anlæg ved fuld kapacitet (ekskl. slamtørring)
Proces |
Pyroarc |
Affald |
Tørt affald |
Massebalance |
Input |
Output |
|
kg/h |
GJ/t |
kg/h |
GJ |
Brændselspiller |
670 |
14,80 |
|
Koks |
30 |
28,5 |
|
|
|
Slagge |
|
136 |
|
Jernkromlegering |
24 |
|
Svovl |
0 |
|
metalhydroxider |
0 |
|
røggasrenseprodukt |
0 |
|
Brændsel konverteret til produktgas |
540 |
|
Sum brændsel |
700 |
15,39 |
|
|
Total Sum |
700 |
|
700 |
|
Energibalance |
Input |
Output |
|
GJ |
MW |
GJ |
MW |
Input energi brændsel |
10,77 |
2,99 |
|
|
|
|
|
|
|
Forbrug el plasmapyrolyse |
0,96 |
0,27 |
|
|
Forbrug el motorer mv. forgasser |
0,72 |
0,20 |
|
|
Forbrug el forvarmet luft |
0,26 |
0,07 |
|
|
Sum el forbrug |
1,94 |
0,54 |
|
|
|
|
|
|
|
Brutto Produceret el |
|
|
2,02 |
0,58 |
Netto Produceret damp + varme |
|
|
8,51 |
2,36 |
|
|
|
|
|
Netto Produceret el |
|
|
|
0,04 |
Netto totalt produceret el + varme |
|
|
|
2,38 |
|
|
|
|
|
Netto total virkningsgrad |
|
|
|
80 |
Den forholdsvis høje virkningsgrad skyldes, at varmt vand med lav temperatur kan afsættes til garveriet.
I ovenstående er ikke inkluderet nettoenergiforbruget til slamtørring. Fra processen til slamtørring genvindes 60% af den forbrugte energi.
8.2 Metaller og slaggegranulat
Anlægget producerer en jern/krom-legering med en sammensætning som vist i tabel 5. Legeringen afsættes til stålværk med en positiv afregningspris.
Tabel 5. Metalanalyse.
Grundstof |
Vægt % |
C |
1,9 |
Si |
2 |
Fe |
88 |
P |
4 |
S. |
1,2 |
Cr |
3 |
Slaggens sammensætning er vist i tabel 6. Slaggen tappes pt. i store portioner. Et alternativ er at bratkøle slaggen med vand for at producere 2-5 mm store slaggekorn. Generelt genvindes metaller, som er
ædlere end jern med metalfraktionen, mens andre metaller indgår i oxideret form i slaggen.
Tabel 6. Slaggeanalyse
Indhold |
Vægt % |
Na20 |
2,7 |
MgO |
5,5 |
K2O |
0,40 |
CaO |
23,5 |
TiO2 |
1,1 |
V205 |
0,03 |
Cr203 |
3,2 |
MnO |
0,26 |
FeO |
7,6 |
NiO |
0 |
CuO |
0,01 |
ZnO |
0,01 |
Al2O3 |
21,4 |
SiO2 |
32,8 |
P2O5 |
0,25 |
PbO |
0 |
C |
0,06 |
S |
3,3 |
På figur 6 er vist et stykke af metallegeringen og et stykke af slaggen.
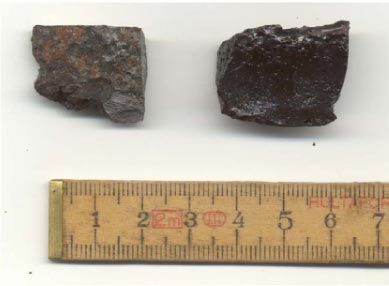
Figur 6. metallegering (til venstre) og slagge (til højre).
Slaggen har udvaskningsdata som vist i tabel 7.
Tabel 7. Udvaskningsdata for slagge fra Borges Pyroarc-anlæg.
Stof |
Målt * |
Dansk slagge-
Kategori II |
Dansk slagge-
kategori III |
|
µg/l |
µg/l |
µg/l |
As |
<1,0 |
0 – 8 |
8 - 50 |
Ba |
48,6 |
0 - 300 |
300- 4000 |
Pb |
0,63 |
0 – 10 |
10 - 100 |
Cd |
0,077 |
0 – 2 |
2 - 40 |
Cr (total) |
0,81 |
0 – 10 |
10 - 500 |
Cu |
6,2 |
0-45 |
45-2000 |
Hg |
- |
0 – 0,1 |
0,1- 1 |
Mn |
53,7 |
0- 150 |
150- 1000 |
Ni |
8,8 |
0 - 10 |
10- 70 |
Zn |
14,6 |
0- 100 |
100 - 1500 |
Sb |
0,23 |
Ingen krav i DK |
Ingen krav i DK |
*Slaggen overholder som det ses de danske krav for udvaskning i kategori II
8.3 Restprodukter
Slam fra gasrensningsanlægget behandles i garveriets vandrensningsanlæg før det recirkuleres til Pyroarc-processen sammen med andet slam fra garveriet.
9 Økonomi
9.1 Nødvendige investeringer til etablering af anlægget
I det følgende er foretaget en beregning af behandlingsomkostningerne baseret på økonomidata for anlægget ved anvendelse til behandling af læderaffald med produktion af brændselspiller udfra slam, som
tørres med damp fra anlægget.
Anlægsstørrelse: |
15.000 t vådt affald/år |
Rente: |
7% p.a. |
Tilbagebetalingstid: |
15 år |
Investeringssum inkl. bygninger: |
50 mio. DKK. |
9.2 Salgspriser for produkter
Salg af elektricitet: |
0,35 DKK/kWh |
Salg af varme: |
0,15 DKK/kWh |
Salg af metallegering samt udgift til transport: |
0,00 DKK/kg |
Salg af slagge: |
0,00 DKK/kg |
Der regnes med en netto overskudsproduktion af damp/varme på 2,36 MW svarende til 1.100 kWh/t tilført vådt affald (~ 2,1 t vådt affald/time). Salgsprisen for damp/varme afregnes til 15 øre/kWh, selv
om dampindholdet kan afsættes til en højere pris.
9.3 Udgifter til deponering og løn
Gennemsnitlig løn til personale: |
300.000 DKK/person |
9.4 Driftsudgifter
Energi: |
0 DKK da der produceres overskud af strøm og varme |
Personale: |
16 (basis: 24 h, 320 dage) |
Kemikalieforbrug: |
914.700 DKK/år |
Vandforbrug/gasbehandling |
200.400 DKK/år |
Vedligehold og reparation: |
1.090.655 DKK/år |
Div. forsikringer mv.: |
Ikke medtaget |
Administration og overhead: |
Ikke inkluderet |
9.5 Behandlingsomkostninger
Beregningen af behandlingsomkostninger er et estimat, som skal vise niveauet for behandlingsomkostningerne. Den endelige behandlingspris vil være afhængig af anlægsplacering, faciliteter til stede, valgte
bygningsstandarder osv. samt størrelsen af den rabat, der ved forhandling kan opnås på købsprisen for anlægget.
Beregningen viser følgende udgifter
Kapitaludgifter: |
366 DKK/t |
Driftsudgifter: |
467 DKK/t |
Indtægter: |
165 DKK/t |
Behandlingsprisen estimeres således til ca. 670 DKK/t vådt affald inkl. bygninger for et turn-key-anlæg ved en tilsvarende placering i Danmark.
Der regnes ikke med sparede udgifter til deponering af læderaffaldet. Anlægget giver ved placeringen ved Borge overskud, når disse udgifter fratrækkes.
Det skal bemærkes at prisen er pr. ton vådt affald. Hvis der regnes pr. ton tørret affald tilført forgasningsanlægget, er behandlingsprisen omkring 2.000 DKK/t. Hvis der behandles affald, som ikke skal
tørres (fx træflis), er behandlingsprisen i størrelsesordenen 1.200-1.400 DKK/ton for så lille et anlæg.
9.5.1 Anvendelse af PyroArc processen til shredderaffald og imprægneret træ
Enviroarc har efter besøget leveret et overslag over økonomien i Pyroarc- anlæg, der behandler trykimprægneret træ og shredderaffald.
Pyroarc processen har været afprøvet med briketteret shredderaffald og imprægneret træ i forsøgsanlægget i Hofors.
Enviroarc har foretaget en økonomiberegning for turn-key anlæg til henholdsvis shredderaffald og imprægneret affaldstræ baseret på følgende forudsætninger:
Anlægsstørrelse: 50.000 ton/år (ca. 7 t /h)
Der regnes med 15 års afskrivning og 7% rente.
Anlæggene omfatter gasmotorer til produktion af elektricitet og varme og en kedel, der producerer damp af den varme produktgas. Der regnes med levering af fjernvarme ved ca. 120°C. De producerede
mængder energi er konservativt sat, og der vil kunne opnås en højere virkningsgrad, hvis der er mulighed for at afsætte energi med lavere temperatur fx til forvarmning af fjernvarmevand.
Anlægget til shredderaffald omfatter brikettering af brændselspiller, men ikke tørring til < 10% fugtindhold, som kræves for at kunne presse stabile briketter.
For shredderaffald er regnet med en nedre brændværdi på 13 MJ/kg og et askeindhold på 40-50% inkl. metaller. Der produceres en jern/kobber-baseret legering og en slagge med forventede gode
udvaskningsresultater.
For CCA imprægneret træ er regnet med en nedre brændværdi på 15,4 MJ/kg, 1-2% askeindhold inkl. metaller og 25% fugtindhold.
Enviroarc forventer, at 50-80% af arsenindholdet i træet ender i procesgassen, hvorfra det kan udsepareres i et slamprodukt via en renseproces. Ved tilbage-føring af slammet til forgasseren og tilsætning af
jernholdigt materiale, bør der ifølge Enviroarc kunne produceres en jern-arsenholdig smelte, hvor arsen er hårdt bundet. Kobber og krom vil fordele sig på forskellig vis mellem den smeltede slagge og
metalsmelter. Der er ikke fremlagt tilstrækkelige forsøgsda-ta til at kunne dokumentere fremgangsmåden nærmere.
Der er regnet med en lønomkostning på 300.000 DKK/år i gennemsnit for 23 mand + 600.000 DDK/år til en anlægsejer.
Tabel 8. Behandlingsomkostninger ved behandling af shredderaffald og CCA-imprægneret træ
Brændsel |
Shredderaffald |
CCA-imprægneret træ |
Investering inkl. bygninger ¹ |
245 mio. kr. |
236 mio. kr. |
Salg af elektricitet |
1,5 MW |
3,9 MW |
Salg af fjernvarme |
11,2 MW |
13,7 MW |
Kapitaludgifter |
538 DKK/t |
518 DKK/t |
Driftsudgifter |
387 DKK/t |
382 DKK/t |
Indtægter |
315 DKK/t |
489 DKK/t |
Behandlingsomkostning |
610 DKK/t |
411 DKK/t |
1 Omfatter udgifter til bygninger og anlægsarbejde på 36 mio. DKK.
De beregnede behandlingsomkostninger er ekskl. sparede deponeringsomkostninger og skal kun betragtes som et vejledende niveau.
10 Konklusioner og anbefalinger
10.1 Egnethed for den danske affaldsstruktur
Anlægget bedømmes anvendeligt til behandling af danske affaldsfraktioner, som indeholder metaller og mineraler med tungmetalindhold. Udover læderaffald vil et sådant anlæg kunne tænkes benyttet til
smeltning af mineralfraktioner fra shredderaffald, hvis større metaldele er fjernet, eller til behandling af imprægneret affaldstræ. Det nuværende forbrug af koks vil kunne erstattes af træflis fra fx
creosot-imprægneret træ eller andet træ. Vi forventer, at Pyroarcanlæg kan forgasse imprægneret træ uden problemer. Anlægget ved Borge garveri startes således altid op på træflis, som er et velfungerende
brændsel.
Enviroarc har udført forsøg med briketteret shredderaffald og CCA-imprægneret træ på forsøgsanlægget i Hofors og mener udfra de samlede erfaringer, at de vil kunne håndtere affaldstyperne med Pyroarc
processen.
Enviroarc har imidlertid ingen langtidserfaring med behandling af shredderaffald og CCA-imprægneret træ.
10.2 Omkostningsstruktur
Behandlingsomkostningerne for læderaffald er omkring 700 DKK/t tilført vådt affald. Det tilførte våde affald læderaffald omfatter slam og udgør 15.000 t/år mens det tørrede affald til forgasseren udgør ca.
5.000 t/år.
Behandlingsomkostninger for et anlæg til shredderaffald på 50.000 t/år er anslået til ca. 600-650 DKK/t mens behandlingsomkostningerne for et anlæg til imprægneret træ med en kapacitet på 50.000 t/år er
anslået til 400-450 DKK/t ekskl. sparede deponeringsomkostninger.
10.3 Affaldets udnyttelsesgrad
Anlægget genvinder metaller ved smeltning. Hvis der tilsættes affald, som hovedsageligt er baseret på kobber og jern som fx rester af shredderaffald, vil anlægget kunne producere en jern/kobber-legering.
Hvis der behandles læderaffald inkl. jernholdigt slam, kan anlægget producere en jern/krom legering.
Ved behandling af CCA-imprægneret træ forventer Enviroarc, at hovedparten arsenindholdet i træet genfindes i procesgassen, hvorfra det kan udsepareres i et slamprodukt via en renseproces. Ved
tilbageføring af slammet til forgasseren og tilsætning af jernholdigt materiale, bør anlægget ifølge Enviroarc kunne producere en jern-arsen-holdig smelte, hvor arsen er hårdt bundet. Der er ikke fremlagt
tilstrækkelige forsøgsdata til at kunne dokumentere frem-gangsmåden nærmere.
Udover udvundne metalfraktioner vil mineraler og oxiderede metaller findes i en tæt glasagtig slagge, som forventes at overholde kravene til genanvendelse i den danske restproduktbekendtgørelse for
kategori III og muligvis også kate-gori II. Dette bør dog undersøges nærmere.
Slagge, der overholder udvaskningskravene, vil kunne anvendes til vejfyld eller indgå i byggematerialer.
Metaller som aluminium vil mistes sammen med slaggen
10.4 Miljømæssige problemstillinger
Emissioner fra anlægget overholder de europæiske krav. Anlægget producerer ingen restprodukter til deponering ved behandling af læderaffald.
10.5 Muligheder for knowhow-formidling
Knowhow-formidling kan ske via Enviroarc.
| Forside | | Indhold | | Forrige | | Næste | | Top |
Version 1.0 Februar 2006, © Miljøstyrelsen.
|