| Forside | | Indhold | | Forrige | | Næste |
Metoder til behandling af tungmetalholdigt affald - Fase 3
Bilag E
Logbog for besøg hos Igelstaverket, Söderenergi
1. Generelle oplysninger
1.1 Procestype
Fluid bed forbrænding – boblende bed.
1.2 Tilført affald
- Træaffald
- Nedrivningsaffald
- Creosot-imprægneret træ
- Plastaffald (ikke PVC) (forsøgsvis er kørt RDF m. 25% PVC)
- Papir
- Tørv
- Olie
1.3 Licenshaver og kontaktpersoner
Licenshaver
Foster Wheeler Energia Oy
Finland
Kontaktperson
Foster Wheeler Energia Oy
Att. Timo Anttikoski
Nuijamiestentie 3
FIN-0040 Helsinki
Finland
Tlf.: 358-10-39311
Fax: 358-10-393-6162
E-mail: timo.anttikoski@fwfin.fwc.com
1.4 Ejerforhold og kontaktpersoner for det besøgte anlæg
Tre kommuner nær Södertälje har dannet Söderenergi, der ejer Igelstaverket.
1.5 Beliggenhed for det besøgte anlæg
Igelsatverket
Nynäsvägen 43
S-152 07 Södertälje
Sverige
Kontaktperson: Driftsingeniør Sven Wallin.
1.6 Virksomhedens formål og idégrundlag
Fjernvarmeproduktion med minimal påvirkning af miljøet baseret på affaldsprodukter.
1.7 Kapacitet for det besøgte anlæg
Kedel 3:
Varme: |
max. 90 |
MWt |
Brændsel |
25-30 |
t/h |
Brændværdi: |
ca. 11 |
MJ/kg |
1.8 Byggeår og status for projektet
Iglestaverket blevet bygget i 1980 og producerer fjernvarme til de omliggende kommuner (40%) og Stockholm (60%). Værket har tre kedler, hvoraf kun kedel 3 er en fluid bed. Kedel 3 er oprindelige
bygget til kulfyring, men blev i 1994 ombygget af Alstom, så anlægget kunne forbrænde fugtig træflis. Kedlens oprindelige konvektionspart er bevaret.
2. Kortlægning og beskrivelse af anlægget
2.1 Procesdiagram
Kedel 3 er en boblende fluid bed bygget af Foster Wheeler i Finland.
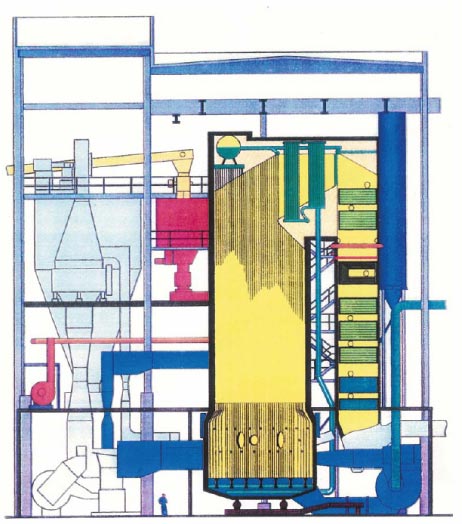
Figur 1. Skitse af Igelstaverkets fluid bed kedel (90 MWt) med hedelflader, etc.
De tre kedler har fælles røggasrensningssystem, som er vist i figur 2.
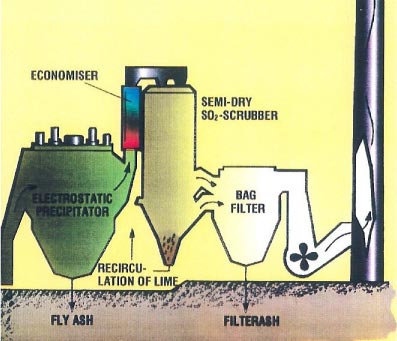
Figur 2. Røggasrensningssystem på Igelstaverket
Alle kedler har desuden separate SNCR NOx-rensningsanlæg i selve kedlen.
2.2 Affald
Kedlen fyres med
”Returlflis” (nedrivningstræ): |
86% |
Maskintørv: |
11% |
Fuelolie: |
3% |
men også papir og creosot-imprægneret træ indgår. Flere af affaldsstrømmene har et højt indhold af klor (Cl). Det er nødvendigt at fyre med tørv for at undgå korrosion.
Anlægget fyres ikke med skovflis.
Der er kørt forsøg med hollandske RDF-piller med max. 25% PVC.
Brændselsanalyser fra d. 2002-04-18 viser store variationer i brændslets sammensætning. Se tabel 2.
2.3 Forbehandling
Alt brændsel neddeles til en størrelse på ca. 2 x 2 x 5 cm.
Brændselsstykker må højst være 5 x 5 x 30 cm store.
En overbåndsmagnet fjernet jern-metaller før indfyringen.
2.4 Proces(ser)
2.4.1 Fluid bed
Kedel 3 er en boblende fluid bed med følgende data:
Areal (kvadratisk) |
49 |
m² |
Bund |
Flad/vandret |
- |
Højden af fluidiseret lag |
1-2 |
m |
Fluidiseringsluft |
14 |
m³/s |
Sand |
48 |
t |
Indfødningspunkter |
4 |
- |
|
|
|
Tbed |
850 |
°C |
Luftoverskud |
3,5 - 5 |
% O2 |
Brændslet indfyres via fire skruefødere placeret over det fluidiserede lag.
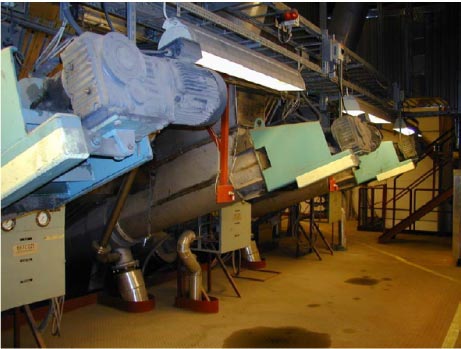
Figur 3. Tre af de fire skruefødere til igelstaverkets kedel 3.
Temperaturen i bedden reguleres ved hjælp af røggasrecirkulation og damptilførsel.
Aske og sand tages seks steder i bunden. Sandet sigtes og metaller fjernes inden de ca. 40 t sand recirkuleres pr. dag, og 5-6 t pr. dag nyt sand spædes til.
2.5 Røggasrensning
NOx reduceres ved indspøjtning af ammoniak (NH3) i fribordet på fluidbedden (SNCR-proces).
For at få en høj virkningsgrad gennem røggaskondensation opfugtes forbrændings- og fluidiseringsluften ved hjælp af røggassen i et system, der er vist i figur 4.
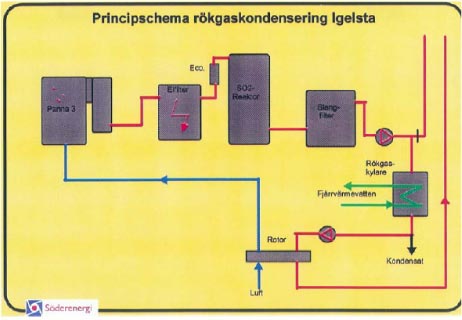
Figur 4. Principskitse for røggaskondensering og opfugtning af forbrændingsluft.
Røggastemperaturen efter de enkelte trin i røggasrensningen er:
El-filter: |
170 |
°C |
ECO: |
150 |
°C |
SO2-scrubber: |
115 |
°C |
Posefilter: |
100-110 |
°C |
Roterende luftbefugter: |
ca. 30 |
°C |
Skorstensrøret er af plast-materiale på grund af risiko for kondensation.
3. Observationer under besøget
3.1 Besøgets varighed
Den 2002-04-23 fra kl. 10:30 til kl. 15.
3.2 Tilførte materialer behandlet under besøget
Type (kvalitativ beskrivelse): |
Bygningsaffald: |
65% |
|
Tørv: |
10% |
|
RDF: |
25% |
Mængde i t/h: |
ca. 20 t/h |
|
Kapacitetsudnyttelse: |
66 % |
|
3.3 Driftsforhold
Driftstid: |
24 h/døgn |
Forventet produktionstid: |
7 måneder/år [1] |
Revisioner: |
2-3 pr. år |
3.4 Output under besøget
3.4.1 El/varme
Leveret varme: |
ca. 60 MW |
Virkningsgrad: |
108% |
Kedlen producerer damp ved 14 bar og 200°C. Dampen varmeveksles med fjernvarmevand.
Ved fuld last producerer kedel 3 90 MW, hvoraf ca. 20 MW kommer fra kondensation.
3.4.2 Restprodukter
Ved fuldlast med normal brændselssammensætning producerer anlægget følgende restprodukter:
Bundaske (mineraler, skrot): |
10 |
t/d |
Flyveaske (el-filter): |
0,45 |
t/d |
Restprodukt fra posefilter: |
36-48 |
t/d |
Kondensat: |
Opkoncentreres og recirkuleres |
|
Kondensatet indeholder ca. 200 mg NH4/l renses i Reverse Osmosis (RO)-anlæg. Rejectet (15%) indeholder over 1.000 mg NH4/l og recirkuleres via SNCR-systemet til kedlen.
Det rensede kondensat udledes til recipienten.
Bundasken sigtes og den fine fraktion (sand) recirkuleres til fluid bed'en.
Jern-metaller fjernes fra restfraktionen og afhændes som forbrændingsjern.
Alle andre faste restprodukter deponeres.
4. Kritiske delprocesser og driftsparametre
Under besøget blev følgende spørgsmål diskuteret:
- Er der forekomst af kondenserbare stoffer og forureninger i processernes forskellige trin; fx af tjære, sod, metaller, salte og oxider i pyrolyseovnens top, i gaskanaler eller i
efterforbrændingskamre?
Nej.
- Hvordan kontrolleres mængden af kondenserede stoffer, dvs. hvordan renses de kritiske procesafsnit for afsætninger?
Klor-indholdet i brændslet holdes så lavt som muligt.
Ca. 10% tørv med et svovlindhold på 0,2-0,3% indfyres for at binde klor.
- Forekommer der recirkulation af materiale i processen, så visse stoffer langsomt kan akkumuleres?
Sand, opkoncentreret ammoniumholdigt kondensat og filtreret røggas recirkuleres.
- Sandet, der udtages fra bunden af fluid bed'en sigtes og renses for metaller inden det recirkuleres, forventes ikke at medvirke til at akkumulere stoffer.
- Kondensatet fra SO2-scrubberen vil indeholde en del faste stoffer fx tungmetaller inkl. arsen. Efter opkoncentreringen i RO-anlægget vil remanensen stadig indeholde tungmetaller. Der er derfor risiko for
at recirkulationen af remanensen til kedlen via SNCR-anlægget kan medvirke til at akkumulere fx arsen i anlægget.
- Røggassen renses i scrubber, el-filter og posefilter før den recirkuleres og vil derfor ikke medvirke til akkumulere stoffer i anlægget.
- Hvilken kemisk stabilitet har restprodukter fra processen? Er de lagringsstabile mht. tungmetaller og dermed egnet til deponering (data for standardudvaskningstests), eller lækker der tungmetaller, og skal de betragtes som miljøfarligt affald?
Sven Wallin oplyste, at bundasken efter sigtning og fjernelse af magnetiske metaller i en overbåndsmagnet kun indeholder mineraler, der er uproblematiske.
Røggassrensningsproduktet indeholder tungmetaller og andre miljøskadelige stoffer vil i Danmark skulle på specialdeponi.
- Findes der dioxiner (eller andre halogenerede organiske stoffer) i restprodukter eller evt. mellemprodukter som skal oparbejdes andetsteds?
Dioxin i røggassen er målt én gang og lå da under 0,1 ng/Nm³.
- Korrosion og erosion
Der forekommer ikke korrosion af betydning i anlægget, men på grund af det høje indhold af partikler i røggassen, forekommer der en del erosion i kedlens konvektive træk.
5. Miljømæssige forhold
5.1 Emissioner til luften
Stof |
Målt (11% O2)
døgnmiddelværdi |
EU-krav
(11% O2, tør gas) |
|
mg/Nm³ |
mg/Nm³ |
SOx |
0,5 |
50 |
NOx |
< 25 |
200 |
HCl |
~0 |
10 |
CO |
45 |
50 |
Støv |
5 |
10 |
|
|
ng –TEQ/m³ |
ng- TEQ/m³ |
Dioxiner |
< 0,01 |
0,1 |
Tabel 1. Emissioner til luften fra Iglestaaverket.
Alle de målte emissioner overholder EU's krav. anlægget foretager ikke dioxin-målinger med faste mellemrum. Den viste måling er den eneste, der er foretaget på anlægget.
5.2 Spildevandsudledning
Spildevand fra scrubbere renses ved hjælp af RO-teknik til et ammoniumindhold på mindre end 5 mg/l og kan uden problemer udledes direkte til recipienten.
5.3 Støj
Normalt for forbrændingsanlæg.
5.4 Lugt
En svag lugt af forbrændt tørv vurderes ikke at skabe problemer i forhold til danske regler.
5.5 Affaldsproduktion
Intet – alle processer foregår i automatiske, lukkede systemer.
Se evt. afsnit 3.4.2 Restprodukter.
5.6 Samlet dioxinemission
Der er kun foretaget en enkelt måling af dioxin-indholdet i røggassen, men ingen i restprodukterne.
6. Arbejdsmiljømæssige forhold
6.1 Støvbelastning
Al transport af brændsel, mellemprodukter, produkter og restprodukter sker i lukkede systemer.
Vi bemærkede dog, at der var en del støv i brændselslagrene, hvilket må skyldes utætheder og overtryk i de lukkede transportsystemer.
Hvis et lignende anlæg skal behandle imprægneret affaldstræ, skal anlægget derfor udstyres med meget effektive støv-begrænsende foranstaltninger, så driftspersonale kan undgå kontakt med både støv fra
neddeling og transport af brændsel og med restprodukter.
6.2 Internt støjniveau
Det interne støj-niveau var lavt og vil med stor sandsynlighed kunne overholde danske krav.
6.3 Tungmetalbelastning
Besøget var for kort til at vi kunne foretage en egentlig analyse. Tungmetaller er normalt bundet i støv og bortset fra forholdene på brændselslageret lå der ikke støv andre steder på værket.
Da brændslet indeholder en del metaller, vil flyveasken fra el-filteret vil sandsynligvis indeholde en del tungmetaller fx Pb, Zn og Cd. Driftspersonalet bør derfor have støvmasker og handsker på, når de
arbejder med håndtering af støvende restprodukter.
6.4 Dioxinbelastning
Ukendt. Der vil formentlig findes dioxiner i flyveaske fra el-filteret og i røggasrensningsproduktet.
6.5 Andet - fx lugtgener, vilkår i forbindelse med reparationsarbejde mv.
Besøget var for kort til, at vi kunne foretage en detaljeret vurdering.
7. Beskrivelse af input
Anlæggets hovedbrændsel (normalt ca. 85%) er ”retur-flis”, som er nedrivningsaffald mm. På billederne i figur 5 og figur 6 kan man se, at brændslet indeholder båder metaller, spånplader, malet træ og plastrester.
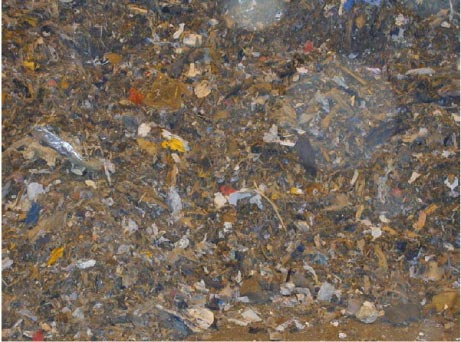
Figur 5. Fluid bed kedlens hovedbrændsel (ca. 85%), ”Returflis”, som er neddelt nedrivningsaffald mmm.
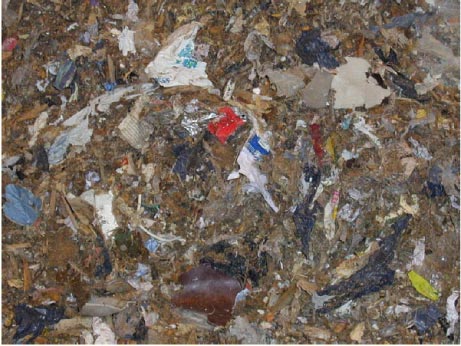
Figur 6. Nærbillede af ”Retur-flis”, som indeholder store mængder papir, spånplader, malet træ, metaller og plast (efter sigende uden PVC).
Affaldet passerer en overbåndsmagnet for at fjerne de magnetiske metaller. Herefter indeholder brændslet kun ca. 0,3 % frie metaller.
En analyse af brændselssammensætningen fra marts 2002 viser, at der er store variationer i sammensætningen.
Klik her for at se Tabel 2
Tabel 2. Brændselsanalyse fra igelstaverkets kedel 3 marts 2002.
Brændværdien af brændslet er temmelig konstant – i gennemsnit ca. 11 MJ/kg.
Svovlindholdet er lavt i returflis ca. 0,06 % (w/w) TS, men ca. 5 gange højere i maskintørv – typisk 0,3 %.
Tungmetalindholdet i returflis er ikke ubetydeligt, specielt Pb og Zn findes koncentrationer på:
Pb: 0,021 % (w/w)
Zn: 0,195 % (w/w)
De høje indhold af Cu og Mn stammer fra bark eller tørv, der også bidrager med et højt indhold af kvælstof.
8. Beskrivelse af output
8.1 Kraft/varme
Fluid bed kedlen har en termisk virkningsgrad på 89% og med bidraget fra røggaskondensationen bliver den samlede termiske virkningsgrad ca. 108%.
Værket levere udelukkende fjernvarme til Södertälje og Stockholm.
Prisen for fjernvarme 0,13 SEK/kWh svarende til ca. 0,11 DKK/kWh.
8.2 Metaller
Magnetiske metaller fjernes fra bundasken fra FB-kedlen. Anlægget producerer ca. 2 t/d forbrændingsjern, der afhentes af en skrothandler.
8.3 Granulat/restprodukt
Anlægget produceret ca. 8 t/d mineralsk restprodukt, der hovedsagelig består af silicium og calcium oxider. Glødetabet er relativt højt ca. 10%. Der foreligger ingen analyse af tungmetalindholdet i
restproduktet.
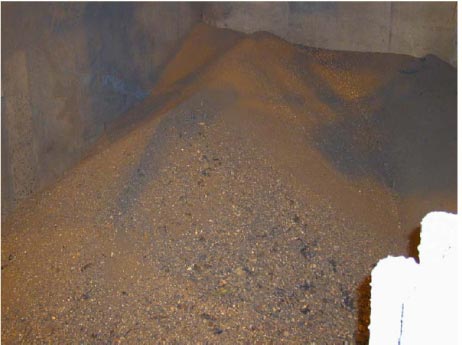
Figur 7. Restprodukt fra el-filter efter sigtning og fjernelse af jern-metaller.
Udvaskningsegenskaberne af restproduktet er ikke kendt.
Restproduktet deponeres.
9. Økonomi
9.1 Nødvendige investeringer til etablering af anlægget
Kedel 3 er som tidligere nævnt ombygget fra kulfyring til fluid bed forbrænding af træaffald. Det er derfor ikke relevant at benytte de økonomiske tal fra dette anlæg til en bedømmelse af
behandlingsomkostningerne.
Hvis et tilsvarende anlæg skal behandle CCA-imprægneret affaldstræ, vil investeringen anlægget skulle omfatte udstyr, der sikrer mod støvemission og kontakt med restprodukterne.
10. Konklusioner og anbefalinger
10.1 Egnethed for den danske affaldsstruktur
Fluid bed anlægget fungerer uden problemer med et affaldsbrændsel, der indeholder ret høje koncentrationer af tungmetaller og klorider, som også findes i CCA-imprægneret affaldstræ.
Vi forventer, at alle tungmetaller (imprægneringssalte og andre tilførte metaller) ender i flyveasken fra el-filteret eller i restproduktet fra røggasreningsprocessen opsamlet i posefiltret. Arsen vil sandsynligvis
findes på partikulær form, og en eventuel rest vil blive fanget i SO2-scrubberen og RO-remanensen.
Flyveasken vil eventuel kunne oparbejdes, men der foreligger ingen analyser af indholdet restproduktet.
Der bør dog sikres, at remanensen fra RO-anlægget renses for tungmetaller, inden den recirkuleres til kedlen via SNCR-anlægget.
Hvis et lignende anlæg skal behandle CCA-imprægneret affaldstræ vil det efter danske forhold være nødvendigt at stabilisere restprodukter, der indeholder As, Cu og Cr, eller hvis det er muligt at oparbejde
Cu og Cr til frie metaller.
10.2 Omkostningsstruktur
Omkostningsstrukturen for anlægget er ikke kendt.
Hvis et tilsvarende anlæg skal behandle CCA-imprægneret affaldstræ, vil investeringen anlægget skulle omfatte udstyr, der sikrer mod støvemission og kontakt med restprodukterne.
10.3 Affaldets udnyttelsesgrad
Anlægget er i fuld kommerciel drift, men benyttes som spidslastcentral og er derfor kun i drift ca. 7 mdr. om året.
10.4 Miljømæssige problemstillinger
Hvis et tilsvarende anlæg skal behandle CCA-imprægneret affaldstræ, vil det nedslidte sand være forurenet med As, som derfor skal behandles som specialaffald i forbindelse med deponering.
10.5 Muligheder for know-how-formidling
Foster Wheeler Energia Oy
Att. Timo Anttikoski
Nuijamiestentie 3
FIN-0040 Helsinki
Finland
Tlf.: 358-10-39311
Fax: 358-10-393-6162
E-mail: timo.anttikoski@fwfin.fwc.com
Fodnoter
[1] Igelstaverket er en spidslastenhed. Værket forventes at kunne køre 8.000 h/år ved normal drift.
| Forside | | Indhold | | Forrige | | Næste | | Top |
Version 1.0 Februar 2006, © Miljøstyrelsen.
|