| Til bund | | Forside |
Miljøprojekt nr. 1058, 2006
Effektivisering af distributions- og emballagesystemet til dagligvarer med fokus på udnyttelse af transportsystemet
Forord
Sammenfatning og konklusion
Summary in English
1 Projektets formål
2 Metode
3 Resultater og formidling
4 Projektets resultater
5 Detailhandelen
6 Leverandøren
7 Forventninger til dagligvaredistributionens fremtid
8 Retursystemer
9 Udvikling af værdikædemodel
10 Fremtidige udfordringer
11 Idékatalog
12 Bilag
Forord
Nærværende rapport og tilhørende bilagsmateriale tjener som afrapportering af projektet "Effektivisering af distributions- og emballagesystemet til dagligvarer med fokus på udnyttelse af transportsystemet".
Projektet er gennemført i samarbejde med en række forskellige aktører på det danske dagligvaremarked. Bredden af deltagerkredsen har sikret, at alle de diskuterende problemstillinger har fået en praktisk
tilgangsvinkel.
Det primære formål med projektet har været at opstille et idékatalog over de projekter, som det kan være værd for aktørerne i dagligvaremarkedet at arbejde videre med.
Projektet er igangsat på foranledning af Detailhandelspanelet og finansieret af midler fra program for Renere Produkter, der administreres af Miljøstyrelsen.
I projektet har der deltaget repræsentanter fra følgende virksomheder:
- Carlsberg Danmark A/S
- ContainerCentralen A/S
- Frode Laursen A/S
- Kraft Foods Danmark A/S
- Netto A/S
- SuperGros a/s
- LOGISYS A/S
Udover den faste deltagerkreds har Arla Foods amba medvirket i forbindelse med svenske retursystem.
LOGISYS A/S har varetaget projektledelsen og den praktiske gennemførelse af projektet.
I gennem projektforløbet har der været afholdt en række studiebesøg hos virksomheder i ind- og udland, som alle har velvilligt givet værdifuld viden og inspiration til projektet. Uden denne velvilje havde det
ikke været muligt at gennemføre projektet. Der skal lyde en samlet tak til alle, der har bidraget til projektets gennemførelse.
Sammenfatning og konklusion
De samlede distributionsprocesser af dagligvarer er omkostnings- og ressoucekrævende. Eftersom der er tale om relativt billigere varer kommer de samlede distributionsomkostninger til
at veje tungt i den samlende omkostningskalkulation. De parametere i distributionssystemet, der har afgørende indflydelse på omkostningsstrukturen er de anvendte emballagesystemer
og den måde hvorpå transportsystemer konstrueres og drives på. Den enkelte aktør i dagligvarekæden forsøger selvfølgeligt konstant at effektivisere sine egne processer, men det er
langt fra givet, at det, der er optimalt for den enkelte aktør, er opmitalt for den samlede varekæde. Kun ved at aktørene i varekæden samarbejder f.eks. omkring anvendelse en fælles
emballage- og transportsystemer kan der opnås væsentlige effektiviseringsgevinster fremover. Projektet har indgående beskæftiget sig med, hvorledes man samlet i dagligvarebranchen
kan opnå en højere grad af effektivitet.
Baggrund og formål
Udviklingen inden for lager- og distribution er i høj grad sket hos den enkelte aktør uden hensyntagen til de øvrige parter i forsyningskæden. Den enkelte part har optimeret sin del af distributions- og
emballagesystemet uden at tage nævneværdig hensyn til optimeringen af hele forsyningskæden. Dette har vanskeliggjort en effektiv udnyttelse af transport-systemerne og anvendelse af returbaserede systemer
og herunder udvikling af systemer, der sigter på at reducere miljøbelastningen.
På foranledning af Detailhandelspanelet og finansieret af midler fra program for Renere Produkter, der administreres af Miljøstyrelsen er der gennemført et projekt, der fokuserer på den fremtidige
distribution af dagligvarer.
Formålet med projektet har været at indsamle viden om anvendelse af effektive distributions- og emballagesystemer til dagligvarer med henblik på opstilling af et idékatalog. Der er blevet sat fokus på hele
forløbet fra fabrik til det punkt, hvor forbrugeren har adgang til produktet, samt hensyntagen til den emballage butik/forbruger modtager, hvilket vil bl.a. sige transportforløbet, transportemballager,
retursystemer og systemer til håndtering af dagligvarer. Indgangsvinklen har været den logistiske, praktiske og økonomiske vurdering med henblik på at sikre og udvikle et fortsat effektivt samarbejde i hele
forsyningskæden under hensyntagen til anvendelsen af ressourcer.
Det primære resultat fra projektet har været opstillingen af et idékatalog over projektidéer, som det kan være værd at arbejde videre med for at optimere distributionen af dagligvarer og reducere anvendelse
af transportemballage.
Undersøgelsen
Projektets deltagere har været en bred vifte af førende leverandører, detailhandel samt en 3. parts leverandør. Den samlede projektkreds har været Carlsberg A/S, Container Centralen A/S, Frode Laursen
A/S, Kraft Foods Danmark A/S, Netto A/S, SuperGros A/S og LOGISYS A/S, der også har varetaget projektlederrollen.
Projektet er gennemført som et samarbejdsprojekt hvor de deltagende virksomheder har deltaget aktivt i workshops og på studieture til England, Holland og Sverige.
I projektet er der blevet set nærmere på de forhold som må forventes at være gældende for der fremtidige dagligvaremarked.
Hovedkonklusioner
Projektet er nået frem til følgende konklusioner:
- På fremtidens dagligvaremarked vil butikskæderne i stor udstrækning sætte dagsordenen og leverandørerne skal efterleve deres krav
- Butikskæderne bliver i endnu større grad internationale
- For leverandørvirksomheder er det væsentligt at der på tværs af de forskellige dagligvarekæder kan opnås enighed om fælles systemer
- Det drejer sig bl.a. om følgende forhold:
- Større forståelse af sammenhængen i den samlede logistikkæde
- Etablering af fælles emballagesystemer
- Etablering af fælles standard for højden af pallelaster m.v.
- Fokusering på arbejdsmiljø
- Udvikling af hensigtsmæssige lastbærere
Projektresultater
Dagligvarelogistik i fremtiden
Der er fokuseret meget på samarbejdet mellem de forskellige aktører i dagligvarelogistikkæden, men samtidig er man også kommet til den erkendelse at konkurrencen mellem de forskellige afsætningskanaler
til stadighed bliver mere og mere intensiveret og at de enkelte afsætningskanaler fokuserer mere på komparativ effektivisering end den samlede effektivisering af hele dagligvaremarkedet.
I udlandet fokseres der meget på selve logistikken internt i butikkerne og ikke mindst i at butikker altid har en tilstrækkelig mængde friske varer. Dette indebærer, at der præcis føres den mængde varer frem
til butikken, som man forventer at sælge inden for den kommende periode og en periode kan godt være ned til 4-5 timer. De fleste dagligvarebutikker får som minimum 1 leverance fra distributionsterminaler
pr. dag og større butikker får op til 3 leverancer pr. dag alle dage året rundt. Denne snævre fokusering omkring butikkerne indebærer, at man ikke optimerer lastmængden ved transport i form af, at kasser
ikke er fyldt op med den mængde varer, der fysisk kan være i kasserne, men i stedet med den mængde varer, der kan sælges i den kommende periode.
Fremtidens dagligvaredistribution vil også i stigende omfang blive opbygget så den præcis passer til den butikstype, der skal leveres varer til. Her skelnes der mellem discountbutikker med et sortiment, der
måske kun består af 1.000 varenumre og fuld sortimentsbutikker, som har 10-20.000 varenumre. Når man som discountbutikskæder kun skal håndtere og distribuere et begrænset antal varenumre, har man
langt bedre muligheder for at automatisere mange processer for der i gennem at reducere omkostningerne.
Anvendelse af retursystemer
Rundt om i Europa anvendes der mange steder returtransportemballagesystemer. Det er miljø- og økonomiske hensyn, der er baggrunden for, at man benytter returtransportemballager. Nogle butikskæder
opererer med deres egne returkassesystemer, hvor leverandørerne bliver tvunget til at emballere netop i denne kædes returkasser. For leverandører indebærer dette, at samme vare skal emballeres i
forskellige kasser alt efter kunden. Andre steder findes der nationale kassesystemer eller systemer som bruges af flere butikskæder. Af nationale returtransportemballagesystemer kan især nævnes Svensk
Retursystem, som er et selskab, der ejes af den samlede svenske dagligvarehandel. Fordelen herved er at en leverandør så kun skal benytte én kassetype.
I stort set alle udenlandske returkassesystemer er selve driften, håndtering, vask og transport af tomme returkasser m.v. outsourcet til virksomheder, der har specialiseret sig i dette.
Men da de store internationale dagligvarekæder konkurrerer med hinanden på tværs af landegrænser vil nationale systemer, som oftest bliver "overrulet" af f.eks. de kædebaserede returemballagesystemer.
Denne erkendelse kan udtrykkes i gennem følgende konklusion:
- Flere afsætningskanaler øger kompleksiteten for leverandørerne og vanskeliggør anvendelsen af retursystemer
Idekatalog
Projektet påpeger en række områder, hvorved at distributionen af dagligvarer kan effektiviseres på udover returtransportemballager. Disse områder indgår også i det opstillede idékatalog.
Idékataloget indeholder følgende punkter:
- Skabe større forståelse for sammenhængen mellem logistikken hos leverandør og hos afsætningsleddet
- Etablere standard for højde af pallelaster
- I forlængelse af standarden for højde af pallelaster at vurdere mulighederne for anvendelse af dobbeltdækkere i transporten
- Vurdere mulighederne for at anvende ¼;- og ½-paller med hjul for at lette håndteringen i butikkerne
- Vurdere konsekvenserne ved indførsel af city-logistik
- Vurdere mulighederne for koordinering af udviklingen af nye enheder, der kunne sikre muligheden for at anvende automatiske anlæg i produktion og lager. Eksempelvis et fælles krav til bund og udformning
med henblik på fremførsel på conveyerbånd. Udformning af håndtag/løfteanordning der giver mulighed for anvendelse af automatisk udstyr til løft f.eks. i forbindelse med plukning og ekspedition
- Vurdere muligheder for automatisering af håndteringen af specielt kasser i relation til at forbedre arbejdsmiljø
- Udvikle ny ¼-"palle"-enhed, der tager højde for den internationale udvikling
- Revurdere om 1/1-pallen er den bedste grundflade for den fremtidige distribution alternativt hertil anvendelse af ½-paller
- Anvendelse af plastpaller til erstatning af træpaller
Det er åbent for enhver, at tage disse idéer op til en nærmere behandling.
Summary and conclusion
Distributing grocery products involves considerable costs and resources. Due to the fact that grocery products are relatively cheap, the distribution costs account for a large proportion of
total costs. It is mainly the transport packaging used and the transportation systems that determine the total costs of the distribution process. Actors in each link in the total supply chain
make constant efforts to improve their own sub-processes, but it is not certain that what is best for the individual part of the supply chain is also the best solution for the entire supply
chain. Only by co-operation between the links of the chain - e.g. on the use of common packaging and transportation systems - can important efficiency gains be achieved in the future.
This project examines thoroughly how overall efficiency improvements can be made in the total grocery supply chain.
Background and purpose
The development of warehousing and distribution processes has to a large extent taken place within each individual part of the supply chain, without any consideration about the other actors in the supply
chain. This has made it difficult to fully utilize the transportation systems and the returnable packaging systems and has hampered the development of systems that to a larger extent focus on environmental
aspects.
The Danish Environmental Protection Agency has launched and financed a project that focuses on the distribution of grocery products in the future.
The purpose of the project was to collect information regarding efficient distribution and packaging systems for grocery products, and to develop a catalogue of ideas. The project was focused on the entire
supply chain, from production to consumer access, and on the packaging that the retail shops and consumers receive, i.e. among other things the transportation process, transport packaging, returnable
packaging systems, and systems for the handling of groceries. The starting point was an assessment of logistical, practical and economic factors with the aim of securing and developing continued efficient
cooperation in the entire supply chain, taking into account the total use of resources.
The primary result achieved during the project was the development of a catalogue of project ideas that could be developed further in order to optimize the distribution of grocery and reduce the use of
transport packaging.
The survey
The participants were a wide range of leading suppliers, retailers and a third party logistics providers. The project participants were the companies: Carlsberg A/S, Container Centralen A/S, Frode Laursen
A/S, Kraft Foods Danmark A/S, Netto A/S, SuperGros A/S and LOGISYS A/S, who were also project leaders.
The project was carried out as a co-operation project, where the participants took active part in workshops and study tours to the UK, the Netherlands and Sweden.
During the project, focus was on the conditions that must be expected to prevail in the future grocery market place.
Main conclusions
The project reached the following conclusions:
- In the future, grocery market retailers will to a large extent set the agenda, and the suppliers will have to comply with their demands.
- The retailers will become even more international.
- It is crucial for the suppliers that the retail chains can agree on common solutions regarding the utilisation of packaging and transportation systems.
- The following topics are relevant:
- Greater understanding of the inter-dependence in the total supply chain
- Establishment of shared packaging systems
- Establishment of a common standard for load heights
- Focus on working environment aspects
- Development of appropriate unit loads
Project results
The logistics of groceries in the future
Great focus has been on co-operation between the different links in the grocery supply chain. However, the conclusion was drawn that the competition between the different sales channels will become
increasingly intensified and that each sales channel will focus more on comparative efficiencies rather than on the overall efficiency of the entire grocery market.
In the countries embraced by this study - excluding Denmark - great focus is on the internal shop logistics and not least on shops being able to always have adequate quantities of fresh products. This implies
that the quantity of goods delivered to the shop meets the demand for products expected to be sold within the coming period, often down to 4-5 hours. Most shops receive one delivery from the distribution
centre per day as a minimum, and bigger shops get as much as three deliveries per day all days of the year. This close focus on the shops implies that transportation is not optimized e.g. by ensuring that
boxes are fully loaded with products. Instead the boxes contain the quantity that can be sold in the coming period.
The future distribution of groceries will to an increased extent be developed in a way that fits exactly the type of shops it serves. A distinction must be made between discount shops with an assortment that
includes perhaps only around 1,000 products, and shops with a full grocery assortment of 10-20,000 different products. When a chain of discount shops has to handle and distribute only a limited number of
products, there are much better possibilities for automating processes with the purpose of reducing costs.
The use of returnable packaging systems
In Europe a wide variety of returnable packaging systems are used. Normally, the background for using returnable transport packaging is consideration for environmental and economic aspects. Some
retailers run their own returnable packaging systems, and the suppliers are forced to packing products into the returnable distribution boxes provided by the retailer. For the suppliers, this implies that the
same product must be packed differently depending on the demands of the customers. In other countries, national returnable box systems are used by several retail chains. An example of such national
returnable transport packaging systems is the Swedish "Svensk Retursystem", a company that is owned by the entire Swedish retail trade. The advantage is that suppliers only have to use one type of
returnable boxes.
In most returnable box systems, handling, washing and transportation of empty returnable boxes have been outsourced to companies specializing in these areas.
However, as the big international retail chains are competing against each other across national borders, the national systems will often be "overruled" by e.g. the chain-based returnable packaging systems.
The implication of this fact can also be described as follows:
- More sales channels increase the complexity for the suppliers and make the use of returnable packaging systems more difficult
Catalogue of ideas
The project also highlights a number of topics, where the distribution of grocery products can be made more efficient in other areas than returnable transportation packaging. These topics are also included in
the idea catalogue developed.
The catalogue of ideas includes the following items:
- Create greater understanding of implications of logistics at both suppliers and retailers
- Establish standards for the height of pallet loads
- Associated to the height of pallet loads, assess the possibilities for utilizing double-deckers in transportation
- Assess the possibility of using ¼- and ½-pallets with wheels, to facilitate handling in shops
- Assess the consequences of implementing city logistics concepts
- Assess the possibility of coordinated development of new units, that e.g. facilitate the handling in automated warehousing and production systems
- Assess the possibilities of automating the handling of especially boxes – aiming at improving the working environment
- Develop a new ¼-pallet unit – taking the international development into consideration
- Re-assess whether the EUR pallet is the best size for the future distribution, alternatively examine the use of ½ pallets
- The use of plastic pallets to replace wooden pallets
These ideas are made open to anyone with an interest in these matters, for the purpose of further elaboration.
1 Projektets formål
1.1 Projektets formål
Formålet med projektet er at indsamle viden om anvendelse af effektive distributions- og emballagesystemer til dagligvarer med henblik på opstilling af et idékatalog. Der sættes fokus på hele forløbet fra
fabrik til det punkt hvor forbrugeren har adgang til produktet samt hensyntagen til den emballage butik/forbruger modtager, hvilket vil bl.a. sige transportforløbet, transportemballager, retursystemer og
systemer til håndtering af dagligvarer. Indgangsvinklen er den logistiske, praktiske og økonomiske vurdering med henblik på at sikre og udvikle et fortsat effektivt samarbejde i hele forsyningskæden under
hensyntagen til anvendelsen af ressourcer.
1.2 Projektets baggrund
Udviklingen inden for lager- og distribution er i høj grad sket hos den enkelte aktør uden hensyntagen til de øvrige parter i forsyningskæden. Den enkelte part har optimeret sin del af distributions- og
emballagesystemet uden at tage nævneværdig hensyn til optimeringen af hele forsyningskæden. Dette har vanskeliggjort en effektiv udnyttelse af transport-systemerne og anvendelse af returbaserede systemer
og herunder udvikling af systemer, der sigter på at reducere miljøbelastningen.
Dagligvarebranchen er på vej til at blive koncentreret på få aktører. Afsætningsleddet kan således forventes kun at komme til at bestå af 3-5 aktører dækkende det nordiske marked og der sker en
tilsvarende udvikling i det øvrige Europa. Det har bl.a. den konsekvens, at de enkelte aktører i afsætningsleddet får en størrelse, der medfører, at de vil udvikle egne systemer uden hensyntagen til de øvrige
aktører. Konkurrencen vil samtidig medføre, at den enkelte aktør i afsætningsleddet vil forsøge at integrere leverandøren med hensyn til bl.a. transportemballage, paller, ¼-paller og mærkning af enhederne i
form af stregkoder og anvendelsen af RFID (radiofrekvente tag, hvor information ligger i radiobølger f.eks. som alternativ til stregkoder). Beslutninger på disse områder vil oftest blive taget uden for
Danmarks grænser.
Der er derfor behov for at få afdækket udviklingen hos de væsentlige aktører i afsætnings-leddet i udlandet, da det forventes, at flere af disse aktører også vil agere på det danske og nordiske marked i
fremtiden. Hertil kommer, at deres krav overfor de større internationale leverandører vil medføre, at leverandørerne vil forsøge at tvinge f.eks. de danske og nordiske aktører i afsætningsleddet til også at
følge disse krav for herigennem at kunne sikre effektiviteten i logistikprocessen.
Der er bl.a. sat fokus på:
- En bedre udnyttelse af lastbilerne specielt på volumen – f.eks. i form af dobbeltdækker-lastbiler
- Anvendelse af retur-transportemballage mellem producent og butik
- Hensyntagen til reduktion af miljøbelastningen f.eks. gennem kørselsplanlægning
- Samdistribution med øvrige aktører
- Anvendelse af city-logistik
- Udvikling af nye lager- og distributionsformer
- Anvendelse af distributionssystemer der kan håndtere forskellige temperaturer
- Generel effektivitetsudnyttelse i transporten bl.a. gennem aflæsningstider m.v.
- Informationsudveksling i hele transportforløbet
1.3 Projektets målgruppe
Målgruppen for projektet er detailhandelen, dagligvareleverandører, transportører og emballageproducenter samt Miljøstyrelsen.
2 Metode
Projektet er gennemført som et samarbejdsprojekt, hvor de deltagende virksomheder har deltaget aktivt i workshops og besøg i England (Tesco, Marks & Spencer, Saintsbury, Linpac), Holland (Albert
Hein/Ahold, Blomsterdistribution, produktionsvirksomhed), Sverige (Svenske Retursystem, Arla Foods, butikker) og desuden er der besøgt butikker i Frankrig og Tyskland samt indsamlet materiale fra
LOGISYS's samarbejdspartnere i ELC Group.
På workshops er forskellige tanker og visioner blevet præsenteret og diskuteret i deltagekredsen.
Projektets arbejdstitel har været "Effektivisering af distributions- og emballagesystemet til dagligvarer med fokus på udnyttelse af transportsystemet".
Projektet afgrænses således til det segment, der internationalt betegnes som Fast Moving Consumer Goods (FMCG) og som på dansk kan oversættes til "Dagligvarebranchen".
2.1 Projektets aktiviteter
Projektet har fokuseret på varekæden gående fra dagligvareproducenter og indtil varerne står i butikken klar til salg til forbrugerne. Dette kan illustreres gennem følgende figur:
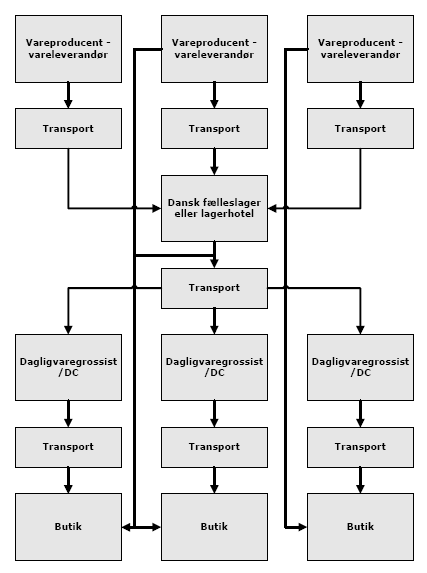
Principielt beskriver figuren situationen set fra en dagligvareleverandør. Mange danske dagligvareleverandører får i dag deres produkter fra flere forskellige vareproducenter, hvoraf nogle ofte er beliggende i
udlandet. Dette er også meget ofte tilfældet for indenlandske vareproducenter, som køber og markedsfører nogle handelsvarer fra andre producenter. Typisk vil produkterne fra de enkelte leverandører
komme til et samlet dansk lager, hvor der måske sker en ompakning, men i hvert tilfælde en konsolidering med de andre varer, når der skal ekspederes varer til kunderne, således at kunderne kun får én
leverance fra den aktuelle danske dagligvareleverandør. Mange af de produkter, som at dagligvaregrossisterne eller distributionscentralerne (DC), køber direkte fra udenlandske leverandører har som oftest
været forbi et nationalt lager.
Det overordnede mål med effektivisering er, at vareflowet gennem varekæden forløber med de færreste mulige omkostninger og den mindst mulige miljøbelastning. I de fleste sammenhænge vil der være en
direkte korrelation mellem økonomien og miljøbelastningen især, hvad angår transporten. Såfremt transporten kan effektiviseres, vil det indebære, at der samlet skal køres færre km og/eller at der skal bruges
et mindre samlet antal lastbiler til at gennemføre de nødvendige transportopgaver.
I projektet er der arbejdet med følgende faktorer:
- Anvendt emballage
- Anvendt transportemballage
- Anvendt lastbærer
- Anvendt lagerteknologi
- Anvendt informationsteknologi til identifikation
- Anvendt transportmiddel
- Udnyttelsesprocent af transportmiddel
- Transportafstande og tilhørende tidsforbrug
Som transportmiddel er der især fokuseret på lastbiltransport, men ved transport fra udenlandske fabrikker vil jernbane- og skibstransport også være en mulighed. Dette skal ikke mindst ses i lyset af de
forventede høje tyske vejtransportafgifter samt andre ændrede markedsvilkår for transporten. Eftersom mange dagligvarer har en begrænset holdbarhed, er det vigtigt at transporten sker hurtigt.
Et væsentligt kriterie vil være at skabe synlighed igennem varekæden, så alle aktører har information om, hvor i varekæden de aktuelle varer befinder sig og om hvor hurtigt det er muligt sikre en
genopfyldning. Dermed kan man reducere de varemængder, som ligger på lager og undgå at transportere flere varer frem gennem varekæden, end der rent faktisk er behov for.
De anvendte transportemballager og lastbærermedier i form af forskellige palletyper eller rullende transportmateriel har en afgørende indflydelse på, hvor effektivt at produkterne kan transporteres gennem
varekæden, derfor har disse indgået som væsentlige parametre.
Som transportemballager og lastbærere indgår såvel engangs- som returemballagesystemer. I de tilfælde hvor der benyttes returtransportemballage er returtagningen og organiseringen af denne tillige
beskrevet.
I projektet indgår distribution af tørvarer, kølevarer og dybfrost.
Anvendelse af detailemballager har projektet ikke fokuseret på.
Projektet har bl.a. beskæftiget sig med følgende effektivitetsparametre:
- Intelligente transport systemer; bl.a. udnyttelse af GPS-teknologi, styring af transporten ved hensyn til optimal rutevalg
- City-logistik; samling af alle transporter til centrale bykerne
- Samdistribution med andre varer udover city-logistik
- Stregkoder; identificering af varer, transporter m.v. især med henblik på at skabe bedre overskuelighed i varekæden, gøre identificering hurtigere samt reduktion af fejl
- RF-tags (radiofrekvente enheder); identificering af varer, transporter m.v. især med henblik på at skabe bedre overskuelighed i varekæden, gøre identificering hurtigere samt reduktion af fejl
- Rullende transportmateriel eller lastbærer; håndtering og lagring
- Anvendelse af lastbærere der kan fungere igennem hele varekæden
- Automatiske af- og pålæsningssystemer med henblik på mindre tidsanvendelse samt et bedre arbejdsmiljø
- Automatiske lagringssystemer; højlagre, automatisk udsortering og sampakning af varer
- Håndteringsgrej; nye palleløftere m.v.
- Antal kørte km
- Miljøbelastningerne pr. kørt km ved forskellige transportformer og kørsel på forskellige vejtyper
- Mængden af transportemballageaffald
- Mængde af varer der kan transporteres pr. tranportmiddelenhed
- Skabe en mindre mængde af ukurante varer bl.a. som følge forbedret holdbarhed
- Tidsforbrug til transport bl.a. gennem reducerede ventetider
- En standardisering af paller, således at lastbilerne er optimeret mht. til vægt og m3
Selve angrebsvinklen i projektet har været baseret på anvendelse af en lang række informationskilder. Her skal følgende nævnes:
- Gennemførte projekter i relation til ECR-konceptet. ECR – Efficient Consumer Response – er et koncept der har til formål at effektive samhandelen i dagligvarekæden.
- Anvendelse af de værktøjer til transportoptimering som bl.a. vil blive baseret på EU's white paper "European transport policy for 2010 – time to decide". Dette papir beskæftiger sig meget med intelligente
transportsystemer (ITS).
- Søgninger på internettet
- Henvendelse til forskellige aktuelle leverandører af udstyr og produkter
- Afholdelse af studieture
- Opstilling af scenarier for dagligvaredistribution
2.2 Projektets faglige indhold
Arbejdet med projektet er gennemført i følgende 5 hovedfaser:
Fase 1. Afholdelse af workshop
Workshops er afholdt for projektgruppen hvor alle idéer og konkret viden om alternative distributionsformer og tilhørende emballagesystemer er blevet fremlagt og diskuteret.
Fase 2. Opstilling af fremtidige scenarier for dagligvaredistribution
På basis at resultaterne fra workshoppen er der opstillet scenarier for alternative distributions- og emballagesystemer.
Fase 3. Informationssøgning af eksisterende distributions- og emballagesystemer
I denne fase er der gennemført en kortlægning af hvilke distributionsformer og transportemballage-systemer der anvendes i udlandet. Først er der sket en søgning gennem tilgængelige kilder, tidligere
rapporter, indlæg fra tidligere afholdte konferencer, søgning på internettet m.v. I forhold til de mest interessante distributions- og emballagesystemer har der været afholdt studierejser til inspektion af
systemernes drift og virke.
Fase 4. Overførelse af distributions- og emballagesystemer til det danske marked
I forhold til de beskrevne og reviderede scenarier for en effektiv dagligvaredistribution er der foretaget en vurdering af, hvilke der direkte kan overføres til det danske marked eller beskrivelse af hvilke
forudsætninger, der skal være opfyldt for at få succes på det danske marked. Det kan f.eks. være, at der skal opnås et fælles "fodslav" blandt en bredere kreds af interessenter herunder også blandt
konkurrerende virksomheder.
Der er udarbejdet en økonomimodel, der anskueliggør de omkostninger, der er forbundet med at transportere varerne gennem de beskrevne distributions- og emballagesystemer. Disse omkostninger
sammenholdes med de eksisterende omkostninger. Derudover kan modellen opgøre det samlede emballageforbrug.
Fase 5. Rapportering af projektet
På baggrund af den indsamlede viden er der udarbejdet et idékatalog over de alternative distributions- og emballagesystemer der umiddelbart vurderes at være mulige at implementere på det danske marked.
3 Resultater og formidling
Det indsamlede materiale er formidlet til projektets deltagende virksomheder og et summary herfra er gengivet i en PowerPoint præsentation samt i nærværende beskrivelse af hovedresultater og trends.
Desuden er der udarbejdet en artikel.
Endelig er der udviklet en økonomimodel, der giver mulighed for at kalkulere omkostningerne ved forskellige setup af retursystemer. Modellen er stillet til rådighed for projektets deltagere.
I løbet af efteråret 2005 vil der blive afholdt en konference, hvor hovedresultaterne fra projektet vil blive præsenteret sammen med en behandling af en række af de udpegede emner, som vil få væsentlig
betydning for den fremtidige udvikling af retursystemer.
Samlede er projektet dokumenteret på følgende vis:
- Sammenfattende rapport (nærværende)
- PowerPoint-præsentation, der nærmere beskriver strukturer, relationer m.v.
- Økonomi-model, der gør det muligt at beregne omkostninger ved at føre produkter frem gennem varekæden
- Referater fra samtlige møder og besøg
- Afholdelse af konference hvor projektets resultater nærmere præsenteres
I den sammenfattende rapport er referater og PowerPoint-præsentationer indlagt som bilag. En samlet planche-præsentation af hele projektet ses i Bilag F.
4 Projektets resultater
I de følgende 5 kapitler bliver projektets resultater nærmere beskrevet. I nærværende kapitel beskrives strukturen og sammenhængen i de efterfølgende kapitler.
I kapitel 5 bliver detailhandelssituationen eller snarere afsætningsleddet beskrevet. Med til detailhandelen hører også de bagvedliggende funktioner i form af en grossist- eller distributionscentralfunktion (DC).
At der startes med detailhandelen skyldes at, det som oftest er krav herfra, der er bestemmende for konstruktionen og udseendet af hele den resterende bagudrettede varekæde og ved returemballager også
den forudrettede varekæde.
Situationen og forudsætningerne for vareleverandørens eller producentens på de aktuelle områder bliver beskrevet i kapitel 6.
I kapitel 7 bliver der gjort et forsøg på at forudse, hvorledes den generelle udvikling i dagligvaredistributionen vil udvikle sig. Dette gøres ved at beskrive det udviklingsforløb branchen allerede har
gennemløbet og fra dette udgangspunkt at komme med et bud på fremtiden.
Anvendelse af returemballagesystemer er et centralt element, når der skal fokuseres på at reducere det samlede emballageforbrug. I kapitel 8 bliver forudsætninger og vilkår for etablering og drift af
returtransportemballagesystemer nærmere beskrevet.
Igennem de afholdte workshops blev behovet for udvikling af en model, hvori det er muligt at beregne de samlede omkostninger ved at føre et produkt igennem varekæden tydeliggjort. Derfor er der i regi af
projektet udviklet en sådan model. Baggrunden og indeholdet af modellen er beskrevet i kapitel 9.
De fremtidige udfordringer for dagligvaredistributionen bliver beskrevet i kapitel 10. I direkte forlængelse heraf bliver der i kapitel 11 opstillet et idékatalog over hvilke områder eller konkrete projekter, det
vil være formålstjeneligt at arbejde videre med. Der er ikke opsat nogle organisatoriske projektmæssige rammer for de punkter, der er listet i idékataloget. Det er således åbnet for enhver gruppe, branche
eller tilsvarende at tage de listede projektidéer op til en videre behandling.
Som tidligere nævnt der er til selve rapportet knyttet en række bilag, der nærmere dokumenterer det beskrevne i selve rapporten. I rapporten beskrives kun hovedresultater.
5 Detailhandelen
Dagligvarebranchen er på handelssiden karakteriseret ved at bestå af få og meget store aktører. I de enkelte nordiske lande er der typisk 2-3 væsentlige aktører i afsætningsleddet og som agerer som en
kapitalkæde med en meget central styring. Samtidig er de på vej til at etablere egentlige nordiske organisationer. En tilsvarende udvikling foregår på europæisk plan, hvorfor der må forventes på kort sigt kun
at være et yderst begrænset antal kæder og som vil sidde på en væsentlig markedsandel i hele Europa. Kapitalkæder med en discountprofil synes at have lettest ved at krydse landegrænserne og agere på de
forskellige markeder. Aldi og Lidl er gode eksempler på denne udvikling.
Scenariet for afsætningsleddet i Europa synes således at være en meget begrænset antal aktører – typisk med en discountprofil eller med et lavpriskoncept som vi kender det fra Bilka. Begge koncepter er
karakteriseret ved fokus på lave priser skabt gennem et stort volumen i indkøb og effektivitet i såvel butikkerne som i det bagvedliggende logistiksystem. For de store volumen produkter forventes det at
afsætningen gennem discountbutikker og lavprisvarehusene kommer over 50% og for visse produkter endda højere.
Det efterlader de traditionelle supermarkeder med et bredt sortiment og med en afsætning af de enkelte produkter, som er begrænset. I praksis er det umuligt for dem at konkurrere med discountbutikker og
lavprisvarehusene på pris selv for høj volumen produkterne, da omkostningerne for at drive butikkerne reelt vil være højere, ligesom det er svært for dem at opnå en tilfredsstillende effektivitet i den
bagvedliggende logistik, da de skal kunne håndtere et langt større antal produkter – måske 10-20.000 varenumre sammenlignet med discountbutikkers typiske 1.000 varenumre. Med henblik på at
differentiere sig forsøger nogle af supermarkederne sig med et meget bredt og specialiseret sortiment f.eks. inden for frugt og grønt, delikatesser etc.
Totalt set giver det et billede af et afsætningsled, som på en række områder vil agere meget forskelligt – discount-sektoren med få varenumre og et volumen, der gør det muligt for dem at opbygge deres eget
system inklusive det bagvedliggende logistiksystem. Konkurrencen mellem dem medfører også, at de opbygger logistiksystemet alene under hensyntagen til egen optimering og herigennem vil de stille krav om
produkt, emballage og transportmidler tilpasset deres system. Det er også karakteristisk, at de helt undlader at deltage i standardisering eller udvikling af fælles systemer.
Tilsvarende gør sig et lang stykke gældende for kæder med lavprisvarehuse (Carrefour, Metro og de engelske kæder) på logistikområdet, mens de dog på basale områder som f.eks. varenummerering og
udveksling af informationer deltager aktivt og på flere områder også har sat sig for bordenden, når der skal udvikles nye standarder f.eks. omkring RFID tags og oprettelse af datapools, som er fælles
databaser, hvor alle stamdata vedrørende leverandørens produkter findes. Herigennem skal stamdata om f.eks. indholdsmængder, dimensioner m.v. af produkter kun vedligeholdes ét sted, således at man er
temmelig sikker på de alle aktører i varekæden ligger inde med de samme korrekte informationer.
For supermarkederne og de mindre butikkers vedkommende er det svært – med et forholdsvist stor sortiment og lille salg per varenummer - at udvikle effektive logistiksystemer, ligesom det er svært for dem
at opnå enighed og derigennem få styrken til at efterspørge og udvikle effektive systemer til håndtering af de mange varenumre.
Udviklingen af effektive logistiksystemer er typisk sket hos den enkelte kæde eller leverandør. For leverandørens vedkommende er dette typisk sket inden for varegrupper med kort holdbarhedstid og hvor
leverandøren på grund af kort leveringstid har varetaget distributionen - herom mere senere. Kun i Sverige er det lykkes at skabe et fælles system initieret af detailhandel og leverandører i fællesskab
(Svenska Retursystem).
De forskellige retursystemer initieret af en enkelt kæde eller leverandør er typisk startet lokalt og udviklet i takt med virksomhedens udvikling. Et eksempel er Ahold i Holland som startede lokalt, men som
nu udbreder et retursystem til de nye markeder, hvor kæden etablerer sig som f.eks. på nye markeder i Østeuropa. I England har den enkelte kæde også udviklet sit eget system – her er dog valgt den
samme returkasse om end i forskellige farver. England adskiller sig på anden vis sig også fra resten af Europa, idet der her er meget stor fokus på effektiviteten i butikken samtidig med, at konkurrencen her i
stor grad fokuserer på friskhed. Det betyder at logistikken optimeres med udgangspunkt i at sikre varernes tilgængelighed i butikken uden at gå på kompromis med friskheden. Hellere føre 3 enheder frem til
butikken, hvis det er salget de næste timer end føre en hel kasse med 6 enheder frem til butikken selvom sidstnævnte ville være billigere set ud fra et logistisk synspunkt.
6 Leverandøren
I takt med den stigende konkurrence og fokus på prisen i afsætningsleddet har leverandøren været nødt til at mindske produktionsomkostningerne, hvilket typisk er sket gennem en centralisering af
produktionen og en reduktion i antallet af varianter. Specielt de store mærkevareleverandører har gennemført centralisering på deres volumen-produkter, hvilket har medført, at produkterne kan produceres
billigere og dermed kunnet tilfredsstille discount-sektoren og lavprisvarehusene, men til gengæld er det blevet svært at opfylde ønsker og krav om levering af varianter og tilpassede emballager.
For levering til det danske marked har det medført, at der må foretages en betydelig ompakning f.eks. til ¼-paller, som kan stilles direkte ind i butikken og butiksemballager med en deraf fordyrelse af
varerne. Med butiksemballager forstås emballager, som kan stilles direkte ind på hylden og f.eks. efter fjernelse af en side kan varerne stå eksponeringsklare. Afstanden i prisen mellem discountbutikker og
supermarkederne er dermed i praksis blevet endnu større og er med til at vanskeliggøre supermarkedernes konkurrence med discount-sektoren.
For de større producenter af specielt ferskvarer, brød, kød, charcuteri, øl og vand har disse traditionelt været direkte leverandører til butikkerne og har dermed været ansvarlig for logistikkæden og kunnet
udvikle effektive systemer. Specielt discount-kæderne har ønsket at sælge private labels og selv stå for distributionen. En private label eller handelmærke er et produkt, der fremstilles og markedsføres med
butikskædens navn – producentens navn fremgår ikke altid af emballagen. Dette har medført, at leverandørerne har været nødt til at tilpasse produkter og emballager m.v. til den enkelte discountkæde.
Det forhold, at de større producenter fremstiller sine produkter på forskellige fabrikker rundt om i Europa, indebærer, at det i mange tilfælde er nødvendigt at der foretages en national konsolidering af
varerne fra de forskellige fabrikker, således at der kan ske én samlet leverance til de danske kunder.
Den stigende koncentration og konkurrence mellem aktørerne i afsætningsleddet har medført, at leverandørerne tvinges til at levere private label eller i det mindste tilpasse produkt, emballage og
leveringsform til den enkelte aktør. Ud fra et salgs- og marketingsmæssigt synspunkt er det for leverandøren en fornuftig udvikling for derigennem at mindske den direkte mulighed for at lave
prissammenligninger. Men ud fra et omkostningsmæssigt synspunkt er det en meget stor udfordring, da der nu skal kunne håndteres en række forskellige logistiksystemer.
7 Forventninger til dagligvaredistributionens fremtid
Med først at beskrive det hidtidige udviklingsforløb for dagligvaredistributionens udvikling vil det blive forsøgt at skitsere en fremtidig udvikling.
Udviklingen kan opdeles i 3 faser – fortid, nutid og fremtid.
- I fortiden var der en balance mellem leverandør og afsætningsleddet, idet begge parter udgjorde mange aktører. I princippet kan vi tale om en mange – mange relation. For at udvikle effektive systemer
specielt i distributionen var det nødvendig at tale sammen og udvikle en fælles platform. Dimensionerne på pallen er vel et godt eksempel herpå. Desuden kunne en gruppe af leverandører finde sammen og
udvikle en fælles distributionsenhed. Eksempelvis returemballagen til mælk og til frugt og grønt. COOP i Danmark's udvikling af en intern distributionskasse er også et eksempel og som i øvrigt fortsat bruges.
For at styrke udviklingen blev enhederne desuden standardiseret – i første omgang nationalt og for eksempelvis pallen også internationalt.
Standardisering var en mulighed.
- I nutid er vi inde i en udvikling, hvor relationen nærmere må betegnes som mange leverandører – få afsætningskanaler. De få i afsætningsleddet sætter dagsordenen, som beskrevet i ovennævnte og tvinger
gennem deres indkøbsstyrke leverandørerne til at bruge deres dedikerede systemer med henblik på en optimering af egne systemer i konkurrence med konkurrenterne. For leverandørerne betyder det, at de
må opgive egne systemer og overgå til deres kunders systemer. I første omgang fastholdes egne systemer og tilpasningen sker typisk gennem en lokal ompakning evt. i et samarbejde med kunderne.
Alle venter og specielt leverandørerne afventer udviklingen.
- I fremtiden vil vi se, at relationerne fortsat vil være mellem mange (om end færre leverandører) – meget få aktører i afsætningsleddet. Leverandører og afsætningsleddet vil blive tættere og tættere integreret
og i praksis vil leverandørerne skulle udvikle produkter og tilhørende logistiksystemer i tæt overensstemmelse med den enkelte kunde. Enkelte leverandører er allerede nu gået så langt som etablering af
produktionsenheder, der alene producerer og leverer direkte til én enkelt kunde.
Få store i afsætningsleddet beslutter og udvikler egne systemer.
Strukturen for den forventede fremtidige dagligvaredistribution kan illustreres gennem følgende figur:
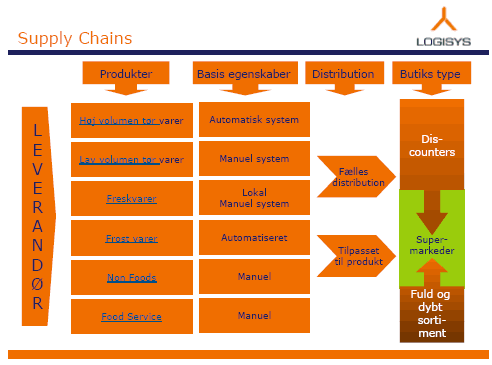
Figuren viser, at distributionsstrukturen tilpasser sig til produkttypen og afsætningskanalen. De forskellige karakteristika for de enkelte produkt- og butikstyper beskrives yderligere på plancher i bilag F.
Fremover vil der være tale om en blanding af automatiske og manuelle lager- og plukkesystemer. For høj volumen varer og rimelig standardiserende varer vil der i stor udstrækning blive benyttet automatiske
systemer, mens de øvrige vil blive håndteret gennem relative manuelle lager- og håndteringsprocesser.
8 Retursystemer
Miljøhensyn og ikke mindst økonomiske forhold har været med til at udvikle retursystemer. Særligt i England, Holland og Frankrig ses en udvikling af returbaserede systemer typisk omfattende
transportenheder (paller, rullecontainere) og plastkasser i forskellige udformninger. Udviklingen foregår hos den enkelte større aktør f.eks. Mark & Spencer, Tesco, Ahold m.fl. og er i mange tilfælde
outsourcet til en 3. parts leverandør. Denne påtager sig vedligeholdelse, vask og styring af systemet og evt. medvirken i formidlingen af systemets enheder til leverandørerne til den pågældende kæde/aktør.
Flere af systemleverandørerne har mulighed for at tilbyde deres forskellige enheder også til konkurrerende parter hos såvel detailhandelen som hos leverandørerne. Eksempelvis er CHEP og IFCO
eksempler på at deres enheder bruges af flere konkurrerende aktører. Der synes dog ikke at være udsigt til at opnå et fælles system for Europa, idet afsætningsleddet ser anvendelsen af retursystemer som
en del af deres evne til at skabe et effektivt logistiksystem og gøre det bedre end deres konkurrenter. Disse fælles systemer har dog haft vanskeligheder på det seneste med at konkurrere med kæde- og
landespecifikke systemer.
Desuden er udviklingen præget af, at når der er foretaget en investering og igangsat et system, er det yderst vanskelig at ændre på systemet og dets komponenter, idet der hurtig bindes store investeringer i
udstyr til håndtering og lagring af de pågældende enheder.
Det svenske retursystem (SRS) adskiller sig væsentlig fra de andre udbydere ved at være etableret og ejet af den svenske detailhandel og leverandører i fællesskab. Hvor de øvrige systemer er relateret til en
eller flere aktører, er SRS et nationalt system. Dette giver en række fordele for de nationalt baserede leverandører, idet de kan anvende de samme enheder til alle kunder. For de multinationale kunder med
produktion centralt eller uden for Sverige indebærer det, at de får de samme udfordringer, som når de øvrige systemer skal håndteres. Når detailhandelen i Sverige internationaliseres udestår spørgsmålet om
det svenske SRS system fortsat vil blive anvendt nationalt, eller vil en international kæde tvinge leverandørerne til at anvende det af dem valgt system. Lidl har eksempelvis valgt at stå uden for SRS, idet de
alene arbejder med deres egne systemer.
For leverandørerne er anvendelsen af retursystemer en stor udfordring – ikke blot skal de fleste formentlig kunne håndtere forskellige systemer for at opfylde kundekravene. Det må også erkendes, at flere
systemer er udviklet over tid og i sin udvikling har haft fokus på anvendelsen i forbindelse med håndtering og evt. eksponering i butikkerne, mens der ikke er taget hensyn til den bagvedliggende logistik og
her særlig pakkeprocessen der er vanskelig at automatisere.
9 Udvikling af værdikædemodel
I regi af projektet er der blevet udviklet en værdikædemodel, hvori det er muligt at beregne omkostningerne ved at føre et produkt i gennem en defineret varekæde. Formålet med modellen er at
anskueliggøre, hvor i varekæden at de største omkostninger til den samlede distribution ligger og i forlængelse heraf at illustrere hvad de økonomiske konsekvenser for alle aktørerne i varekæden vil være
ved at ændre på nogle af parametrene. De væsentligste parametre i modellen er de anvendte transportemballager og lastbærer. For transportemballagernes vedkommende er der følgende muligheder:
- En traditionel bølgepapkasse
- Display-pakning, hvor der ikke anvendes nogen egentlig transportemballage
- Retur-transportemballager – typisk i form af en plastkasse
For lastbærerene er der følgende muligheder i modellen:
- EUR-palle
- ½-palle
- ¼-palle
- Rullebur
- Dolly – principielt en palle med hjul under, fremstillet af stål eller plast
Derudover kan modellen håndtere flere forskellige distributionsveje. I modellen er der indlagt en lang række stamdata som f.eks. løn-omkostninger pr. time, transportpriser og ikke mindst et tidsforbrug til at
foretage de mange operationer/håndteringer, der typisk foregår i en varekæde. Tidsforbruget hertil baserer sig i stor udstrækning på konkrete tidsstudier foretaget i et tidligere projekt.
De samlede varekædeomkostninger beregnes i 33 forskellige moduler, der hver repræsenterer en del-proces i varekæden.
Selve beregningen i værdikædemodellen starter i det øjeblik, at et produkt er blevet emballeret i den emballage, som den endelige forbruger køber produktet i. Selve salgsemballagen tages således for givet i
modellen. Udgiften til transportemballagen indgår i kalkulationen og vil ofte være den største enkelte omkostning i et varekædescenarie.
Opgørelsesenheden i modellen er 1 forbrugerenhed.
Rent teknisk er modellen udviklet i Excel, hvorved det er forholdsvis let at foretage ændringer i modellen og de tilhørende parametreværdier.
I modellen bliver det samlede transportemballageforbrug også opgjort, gennem at det for hvert scenarie bliver opgjort hvor mange transportemballager, der skal anvendes til at emballere varemængden. Dette
antal ganges så op med nogle standardværdier for vægten af transportemballager.
Det er væsentligt at påpege, at resultaterne fra modellen helt afhænger af de værdier og øvrige egenskaber der indlægges i de konkrete beregningscases. De områder, der har størst betydning for den
samlede økonomi, er følgende:
- Udgiften til transportemballage
- Udnyttelsesprocenter af transportemballager og lastbærere
- Håndteringen af varer i butikken
I bilag G findes en nærmere præsentation af modellen samt resultatet af en case-beregning.
10 Fremtidige udfordringer
Der er ikke tvivl om, at de store aktører i afsætningsleddet vil fortsætte udviklingen omkring effektivisering af logistikkæden fra leverandør og frem til, at varen går ud af butikkerne. Specielt i England, men
også i Tyskland, Holland og Frankrig har vi set en tæt integration af leverandør og den enkelte aktør og hvor kæden har sat rammerne for samarbejdet og herunder også fastlagt, hvorledes varen skal
emballeres og leveres. Det er også typisk, at anvendelsen af retursystemer til erstatning af kolli er under hastig udvikling. Dette sker primært med begrundelsen om at være effektiv og hygiejnisk i butikkerne,
hvor de undgår at skulle fjerne pap og plast-emballage. Anvendelsen af retursystemer giver desuden mulighed for en hurtigere opfyldning af hylderne og det på en måde, som tilgodeser forbrugerne i
butikkerne.
For leverandørens vedkommende er udfordringen at kunne levere i det af kæden fastsatte logistiksystem indeholdende returkasser, paller og mærkning af enhederne – evt. påførsel af RFID tags. Der er
heller ingen tvivl om, at de enkelte kæder vælger forskellige systemer, så det for leverandøren bliver et spørgsmål om at kunne håndtere de forskellige kunders systemer på en effektiv måde.
Hertil kommer selvfølgelig en række krav om hurtig levering og levering i mængder tilpasset den enkelte kæde og dens butikker. Her kommer kravet om reaktionsevne i forhold til ordretidspunktet til at blive
en væsentlig parameter. For ferske produkter har flere kæder allerede 4 timer som reaktionstid fra ordre til levering og det må forventes også at komme til at gælde for andre produktområder med kort
holdbarhedstid.
Specielt i England er stor fokus på de sidste 50 meter før hylden i butikkerne – fra varemodtagelse frem til eksponeringspladsen. Konkurrencesituationen i England har vænnet forbrugeren til friske produkter
og høj service med hensyn til tilgængelighed af produkterne, hvorfor "available on shelf" (tilstedeværelsen på butikshylden) tillægges meget stor betydning og kommer forud for effektiviteten af logistikkæden
fra leverandør og frem til butikken. Dette indebærer bl.a., at der ikke altid køres med med fyldte biler til butikkerne.
I denne sammenhæng kan der så stilles spørgsmålet om hvem kommer til at sætte dagsordenen for standardisering. Med hensyn til udvikling af retursystemer forventes det fortsat at ske hos de store i
afsætningsleddet og i samarbejde med 3. parts leverandører. Logistik og anvendelse af retursystemer forventes i et stadig stigende omfang at indgå i kædernes strategiske overvejelser og anvendt til at sikre
den størst mulige effektivitet i egne systemer.
For leverandørernes vedkommende vil det blive stadig vanskeligere at opretholde egne retursystemer, idet den direkte adgang til butikkerne ikke kan opnås. Der må imødeses et stigende krav om at kunne
håndtere forskellige systemer alternativt opbygge produktionsenhederne i en stadig tættere integration med de største kunder. Endelig skal der tages højde for brancheglidningen og forskellig udvikling i
forskellige segmenter f.eks. vil catering området fortsat adskille sig fra den traditionelle dagligvarehandel. Men også på dette område sker der en centralisering og en højere grad af professionalisering.
11 Idékatalog
I fortsættelse af projektet har projektets deltagere opstillet et idékatalog over opgaver, der bør prioriteres med henblik på at sikre effektivitet og udvikling af retursystemer i dagligvarebranchen. Idéerne er
ikke prioriteret.
- Skabe større forståelse for sammenhængen mellem logistikken hos leverandør og hos afsætningsleddet
- Etablere standard for højde af pallelaster
- I forlængelse af standarden for højde af pallelaster at vurdere mulighederne for anvendelse af dobbeltdækkere i transporten
- Vurdere mulighederne for at anvende ¼- og ½-paller med hjul for at lette håndteringen i butikkerne
- Vurdere konsekvenserne ved indførsel af city-logistik
- Vurdere mulighederne for koordinering af udviklingen af nye enheder, der kunne sikre muligheden for at anvende automatiske anlæg i produktion og lager. Eksempelvis et fælles krav til bund og udformning
med henblik på fremførsel på conveyerbånd. Udformning af håndtag/løfteanordning der giver mulighed for anvendelse af automatisk udstyr til løft f.eks. i forbindelse med plukning og ekspedition
- Vurdere muligheder for automatisering af håndteringen af specielt kasser i relation til at forbedre arbejdsmiljø
- Udvikle ny ¼-"palle"-enhed, der tager højde for den internationale udvikling
- Revurdere om 1/1-pallen er den bedste grundflade for den fremtidige distribution alternativt hertil anvendelse af ½-paller
- Anvendelse af plastpaller til erstatning af træpaller
Det er åbent for alle at arbejde videre med disse projektidéer.
12 Bilag
I gennem projektet er der udarbejdet en række materialer, som dokumenterer projektets gennemførelse. Disse bilag har også i stor udstrækning fungeret som arbejdsgrundlag for projektgruppen.
Følgende bilag findes og er indarbejdet i rapporten:
A. Noter fra workshop 1 afholdt d. 4. marts 2004
B. Noter fra workshop 2 afholdt d. 24. november 2004
C. Besøgsrapport fra Englandstur
D. Besøgsrapport fra Arla Foods, Götene
E. Besøgsrapport fra Ahold/Albert Hein, Holland
F. PowerPoint præsentation af projektetresultater
G. PowerPoint præsentation af værdikæde-model inkl. case
Bilag A
Workshop afholdt d. 4. marts 2004
Stikord fra workshop
Anvendelse af paller
Ved leverandørernes pakning skal der skelnes mellem, om den sker direkte på pakkelinien, eller om der er tale om en efterfølgende - ofte ekstern og manuel - pakning.
Der er en barriere for at få udenlandske leverandører til at pakke på 1/4-paller.
Brug af dobbeltdækkere til 1/4-paller kræver hele dæk og ikke bjælker.
Halvdelen af varerne på 1/4-paller bliver efterfølgende manuelt håndteret, fordi varemængden ikke længere er i tag-højde. Restmængden placeres især ved kampagner oven på nye 1/4-paller. En 1/4-palle,
der er plukket i, er en dårlig logistisk enhed at transportere rundt. Der er mange dårlige 1/4-paller bl.a. med falsk bund. Ofte er der tale om et dobbelt emballageforbrug, da produkterne først pakkes i karton
og derefter pakkes på 1/4-paller, hvorefter karton bliver kasseret.
1/4-paller håndteres alle steder manuelt - intet automatisk udstyr i form af kædetræk, rullebaner m.v.
CHEP's 1/4-palle kan ikke bruges p.g.a. benenes placering; kan ikke fungere sammen med de øvrige 1/4-paller.
CHEP-paller begynder at dukke op. Kraft International bruger CHEP-paller. Carlsberg har egne 1/4-paller konstrueret direkte til flasker. Netto får ingen udenlandske 1/4-paller og bruger ej heller
1/4-paller - enkelte "slipper" dog igennem. Ellers bruger Netto 1/2-paller.
Det forventes at CHEP-paller kommer til landet. Kædesystemer til intern transport af den sorte 1/4-palle fungerer dårligt.
Som multinational virksomhed giver CHEP-1/4-pallen problemer, fordi den danske handel ikke accepterer den. Dette indebærer, at en ompakning er nødvendig.
Unilever i Helsingborg skal bruge CHEP til Tyskland og EUR-paller til Sverige og skal derfor have 2 pallesystemer til de samme varer.
I Norden ser man en stigende anvendelse af 1/2-paller.
I Sverige har ICA et lukket pallesystem. Man kan ikke opnå en effektivisering af 1/4-pallehåndteringen med 4 forskellige systemer. I Italien bruges CHEP 1/4-paller.
Det er kun Coop, der sætter 4 1/4-paller på en EUR-paller - alle andre håndterer 1/4-paller på gulvet.
Behovet for ompalletering i butik afhænger af butikkens størrelse - nogle 1/4-paller tømmes flere gange om dagen.
I Finland sættes 1/4- og 1/2-paller neden under hylden. Så sættes specialiteter på hylden oven over. Dette vurderes at give en bedre udnyttelse af butikken. Tesco bruger en tilsvarende model.
Problemet med den sorte og brune 1/4-palle på det danske marked er løst.
Der findes ikke standarder for 1/4-paller, men det er ikke nogen begrænsning, da det er frivilligt, om man vil følge en standard eller ej.
Omkostning frem til butik contra omkostninger i butikken. Transporten er billigere end butikshåndteringen. Der er behov for en værdikædeberegning - økonomisk vurdering.
Nogle vil gerne gå over til plastpaller. I USA må der ikke anvendes træpaller til fødevaredistribution - EU arbejder med sagen. Det er hygiejnekrav, der spiller ind her. Plastpaller kan prismæssigt matche
træpaller. Rosti undersøger mulighederne for at fremstille plastpaller. Måske må man fremover ikke køre varer ind i butikken på træpaller. Plastpaller har en længere levetid og er derfor billigere i drift.
Plastpaller kan cirkulere 6-8 gange mere end træpaller. En træpalle cirkulerer 8 - 10 gange. Rosti kalkulerer med en pris på 150 kr. En plastpalle skal kunne klare 1 tons. Plastpaller kan rengøres.
Aldi og Lidl håndterer kun 1/1-paller.
Nogle virksomheder i mejeri-branchen accepterer kun stålpaller. De koster også 150 kr. pr. palle. Stålpaller kan klare større mængder vægtmæssigt.
Kolliemballage
Kolliemballagen fra industrien bliver dårligere. Kolliemballagen skal være sorteringsvenlig, have styrke og ingen løse låg.
Kolliemballagen skal være let at åbne uden brug af kniv. Anvendelsen af knive giver mange skæreskader på såvel medarbejdere som produkter. Af hensyn til ergonomi skal kolliemballager have bæregreb
og må maksimalt veje 12 kg.
En medarbejder må maksimalt løfte 3 tons pr. dag.
Emballagerne er ikke modultilpasset. Ved opbygning af en butikspalle skal kolli vendes og drejes.
Arbejdstilsynet kommer med krav til skub og træk. Maksimalt må der anvendes en trækkraft på 25 kg til at trække i gang. Hvor stor en kraft skal der til, for at trække rullede materiel i gang er en aktuel
problemstilling. Dette er bl.a. aktuelt ved løftevogne - så må man bruge hårdere hjul, som har en mindre friktion, men til gengæld støjer de mere.
I Europa sælges varer hurtigere derfor større enheder. For Danmarks vedkommende er der holdbarhedsproblematikken for varerne, der spiller ind. I DK har man flere forskellige butikskoncepter og
-størrelser. Dette kunne indebære, at der skulle være forskellige salgsenheder afhængig af butiksstørrelsen.
De butiksplukkede paller skal opfylde samme krav, som de paller der kommer ind på lageret. Nogle af de plukkede paller skal ind på lageret igen indtil transport til butik.
Robotplukning er nok ikke den rigtige løsning i dag.
Årsagen til investeringen i automatiske anlæg er begrundet i arbejdsmiljøhensyn og omkostningseffektivitet. Arbejdsmiljøhensyn vedrører også de eksisterende distributionsbiler, hvor mindre ordrer på under
25 kasser plukkes direkte på bilen - ordrer til butikker og HORECA.
Distribution
Håndtering hos kunderne udgør et problem. Bryggeriforeningen har samlet lavet et sæt krav til modtagerforhold - alternativt må kunder selv bære kasser ind.
City-logistik er et problem - i det centrale Kolding er der en 6 tons grænse for lastbiler. I Paris og Amsterdam findes samlastecentraler. Anvendelse af "Peters budcentral" er ikke løsning på city-logistik for
Carlsberg, da vedkommende ikke kan yde nogen form for service.
Ved cross-docking er det afgørende; hvem og hvor at selve plukkeprocessen til butikken foregår. Ved cross-docking forstås at leverandøren plukker og pakker præcis den mængde varer som de butikker,
der er tilknyttet til en distributionscentral, har bestilt. Det vil sige, at varen ikke er en lagervare hos DC. Ved butiks-cross-docking pakker leverandøren en lastbærer-enhed til hver butik. Derved skal
varernes ikke plukkes på DC-lageret, men hele den færdige lastbærer kan blot transporteres ud til den bil, der sørger for transporten til den aktuelle butik.
Kunderne vil have differentierede løsninger for at profilere sig. Det er svært at harmonisere varer. "Vil have andre varer og leveret på en anden måde". Forskellige løsninger til forskellige kunder og samtidig
cost effektiv. Hvis man vil have et volumensalg skal der arbejdes display, tilbudsavisannoncer og/eller prisreduktion. Hvis man vil have noget kundespecifikt, skal der ske en postponement af slutmontage -
f.eks. oppakke til 1/4-paller så sent og så tæt på kunden som muligt. "Adding value".
For nogle internationale produkter er der sket en nordificering af emballagen således, at de kan distribueres direkte fra et fælles lager, men når der kræves 1/4-paller giver det en dårlig transportøkonomi.
Derfor bør opbygning heraf ske lokalt.
I Danmark kræver kunder, at SSCC-stregkoden står separat, derfor er det vanskeligere et ændre produktet sent. "Cost to serve" er et fokusområde.
Et enkelt led i varekæden kan ikke løse problemet alene. Nøgleord: Dynamisk, fleksibel og billigt. Der hvor pengene genereres bestemmer.
De små varenumre kan kræve en anden produktion end de 600 største varenumre i dansk dagligvarehandel.
Out-of-stock er lig med tabt salg; den ligger nok på 8-12%, men kan aldrig måles. Varerne er måske ikke fyldt op, ligger på baglager. On-shelf-avaibility - det er det der skal måles på.
Transportenheden skal gerne defineres på nordisk plan samt en standardisering af pallehøjden, men højden på paller kan ikke blive ens. Der skal være 750 kg pr. palle for at udnytte vægtgrænserne effektivt.
I Sverige har man en vægtgrænse på 60 tons for lastbiler mod 48 tons i Danmark. I Sverige har bilerne også 2 aksler mere.
Dobbeltdækkere kan anvendes, hvis varerne kan stå dobbelt - det gælder f.eks. chips og papirvarer. Der kan kun medtages 1/1-paller, hvis man har stænger i lastrummet. Der sker kun en indlæsning bagfra,
da man ikke vil have et beskidt lager (ved læsning og losning fra siden på lastbilen kan man ikke køre til porte, men må i stedet foretage læsning og losning udendørs).
Dobbeltdækkere er ikke løst.
Chaufførløn udgør 35-40% af lastbilens samlede omkostninger. Denne andel falder, når Østeuropa bliver mere integreret i det "gamle" EU-område. Logistikadministration vil blive out-sourcet til Indien.
Emballage bliver ens rigtigt - den rette differentiering af emballagens kvalitet. Kravet om friske varer giver dårligere effektivitet i transporten.
Distributionsomkostningerne udgør en beskeden del af de samlede omkostninger - omkring 1%.
Derimod er tilgængelighed, holdbarhed og sporbarhed afgørende.
Natdistribution i byerne kan ikke tillades, men store distributionsmængder til lagre m.v. vil i øget omfang blive leveret om natten.
Man skal starte fra kundens (butikkens/forbrugernes) synspunkt.
Sporbarhed giver meget bedre data, som også giver fordele andre steder.
Returlogistik er generelt et lavinteresseområde. Der er få varer der benytter sig af returlogistiksystemer.
I Holland anvender Albert Hein mange standardplastkasser, som kan fungere i automatiske systemer, men man opnår ikke fuld udnyttelse af kasser. Man mangler et samlet billede af omkostningsstrukturen i
logistikkæden.
Der skal fokuseres på butiksomkostningerne - produktion og transport er billig.
RFID-brikker kan i dag fås for 2 kr. pr. styk. WalMart og Albert Hein er enige om standard for radiofrekvens. Dermed kan varer, emballage parres sammen med leverancen og varenr. - det er let at
foretage optælling.
Metro og Spar i Tyskland benytter 1/4-paller på hjul. Der bør laves en test af værdien af datafangt ved hjælp af RFID.
Opsummering
Videre arbejdstemaer:
- Værdikædemodel ; Case
- Butiksstruktur - afsætningskanaler
- Standardvarer - postponement af produkter / ompakning
- De 500 største varenr. contra den samlede mængde på 10.000 varenr.
- Anvendelse af RFID indlægges under værdikædebetragtning
Begrænsninger: Forhold der kommer ude fra, som man ikke har styr på:
- Arbejdstilsyn krav
- Automatisering
- City-logistik
- Mega-vogntog
Betragtningsområdet er Norden.
Fokuspunkter:
- Cross-docking
- City-logistik
- Total varekædeøkonomi - generel og cases
- Differentierede afsætningskanaler
- Store produktionsserier contra fleksibilitet
- Returemballager - lastbærer og kolli
- Standarder
- Hjul på lastbærere og kolli
- RFID-tags
- Standardhøjde
- Udgangspunkt; butik og forbruger
- Traceability
- Fremtidens 1/4-palle
- Butiksstruktur - discount - indretning
- Hvem beslutter udviklingen; butik, kæde, logistik
- 1/4-palle værdikæde beregning
- Arbejdstilsyn - løft, skub og træk
- Lagerautomatisering; emballager, kolli
- Transportmidlet; størrelse og udformning
- Out-of-shelf
Bilag B
Workshop afholdt d. 24. november 2004
Trends i Europa
Der blev rapporteret fra studierejse og ECR-konference. Overalt i Europa konkurreres der på alle områder – herunder også logistikken. Alle de store kæder laver deres egne systemer.
I UK fokuseres der meget meget de sidste meter ind i butikken. On-shelf har størst betydning, når sortimentet er snævert – out-of-stock har en selvaccelererende effekt, når først et varenummer mangler.
Dette afhænger også af varernes omsætningshastighed og ikke mindst antallet af leverancer pr. uge til butikken. Mange butikker i Europa får flere leverancer pr. dag fra grossisten eller DC.
Generelt er leverandørerne dårlige til at foretage nødleverancer.
Det kunne være interessant at lave et projekt hvor der pakkes direkte i de kasser, som Dansk Supermarked, Holme anvender i deres mini load-lager. Til sådanne automatiske anlæg vil der fortsat blive
anvendt individuelle kassesystemer. Det eneste lastbærer-medie, der er nogenlunde fælles er pallen. Generelt er standardiseringen for dårlig – de opstillede standarder har ikke en tilstrækkelig udbredelse.
I Holland er det et problem at skaffe personale. Den gennemsnitlige afsættelsesperiode på Albert Hein's lager er 6 uger.
Én virksomhed bør hente alt tom emballage gods fra butikken og så efterfølgende foretage sortering og transport til de rette ejermænd. Sorteringsomkostningerne er store og det gælder om at have fuld
udnyttelse af returlogistikken.
Såfremt pakning i de "rigtige" returkasser skal ske allerede hos producenten, skal man kende kunden på pakningstidspunktet – det gør man ikke altid – det afhænger af samhandelsformen; kontraktkøb eller
auktionskøb. Hvis den endelige kunde ikke kendes ved pakningstidspunktet må der nødvendigvis pakkes i standardkasser og efterfølgende foretages en ompakning.
Pallehøjden er efterhånden ved at være standardiseret omkring 1,20 – 1,24 m. Men den burde komme op i ca. 1,30 m for at få fuld udnyttelse af transportmidler. Mange varer er selvbærende, således at 2
paller godt kan stå direkte over på hinanden. Men det giver problemer med flere håndteringer. Længden på distributionsture bliver også længere.
Alle Netto's lagerlokationer er 2 meter høje. Ved at arbejde med differentierende lagerreolhøjder mister man meget i fleksibilitet.
Hos SuperGros er de 1.000 største varenumre et mix af kollivarer og ¼-paller. Derfor burde man i stedet automatisere håndteringen af de 1.000 næste varenumre i størrelsesordenen.
Eventuelt bør man gå op på ½-palle-niveau i stedet for.
SuperGros går væk fra bure.
Der findes ingen automatisk håndtering af 1/4-paller. Man har generelt 5-6 gange flere skader på ¼-paller end på kollivarer. Der skyldes også at ¼-paller ofte anvendes bredt til sårbare varer som f.eks.
flasker.
Der bør findes et system der automatisk kan stakke op i 2 pallehøjder og tilsvarende ned igen.
Set ud fra ergonomiske krav er 1,80 meter måske allerede i dag for højt. Ved de-plukning i butik er for høje paller et problem.
Høj volumenvarer skal måske ikke i retursystemer.
Der bør regnes med flere leveringsmodeller:
- Cross docking (levering i præcist det antal der svarer til afsætningen – terminal-leverance)
- Traditionel pluk
- Direkte distribution
Brød og mælk vil arbejde med et friskhedskoncept; derfor er der ikke tid til at disse produkter skal over et lager.
Inden for frugt og grønt-branchen er der endnu ikke sket en konsolidering – hele sortimentet kan ikke købes fra én leverandør.
For frostvarer skal lager og distribution ses som ét hele. Her bliver kravet til kvalitet i form af temperaturen stadigvæk meget centralt og der vil blive foretaget flere kontroller. Bl.a. vil leverandører forsyne
emballager med farveindikatorer, der angiver, om produktet har været opbevaret ved en for høj temperatur. Temperaturen i frostdistribution stiger som følge af at døre åbnes og lukkes.
Ved food-service (catering) er aflæsseforholdene ofte meget dårlige. Man skal have alle 3 temperaturzoner med på bilen.
Tømning af containere er et arbejdsmiljøproblem.
Værdikædemodel
Den viste økonomimodel suppleres med et terminal (cross docking) modul samt køle- og frostdistribution. Køle og frostdistribution skal ses som forskellige distributioner.
Bilag C
Besøgsrapport fra Englandstur
1.1 Besøg hos Intelledent Ltd, Jim Hopwood, Managing Director
Virksomheden er ejet af LinPac og fungerer som system-integrator. Køber OEM blokke og bygger dem sammen med interface til forskellige systemer. Har lavet integration til alle systemer. Arbejder såvel
med stregkoder som RF-tags. "Re-bygger" tags fra forskellige leverandører.
Op til 100 forskellige tags kan blive læst på samme tid. Prisen pr. tag ligger på omkring 50 pence afhængig af antal og "package" af tags (fysisk/tekniske egenskaber).
Der er forskel på performance af de forskellige brugbare frekvenser.
UHF er den "rette" teknologi, men der er problemer med forskellige frekvensområder – og i Europa er kanalbåndet smalt.
Marks & Spencer er den største kunde. I dag har de både RF-tags og stregkoder på kasser. Har udviklet en læser, der kan læse på begge frekvensområder. En leverandør har lavet en læsere der kan klare
begge, men der er reelt blot tale om, at 2 læsere sættes sammen til én enhed. Håndholdte læsere har ikke tilstrækkelig batterikapacitet til at fungere på distributionscentre. Bruger mange kræfter på at lave
systemer til industrielle miljøer.
Typisk bliver RF-tags på kasser limet på ved hjælp af hot melt i stedet for at støbe dem ind – derved kan de udskiftes, hvis teknologien ændrer sig.
Tags og stregkoder vil køre parallelt i et stykke tid.
Alle tags bliver testet inden påsætning. Man skal teste der, hvor tag'en bliver placeret; skal beskyttes mod fysiske påvirkninger – f.eks. placeres mellem ribber på kasser. Man skal også se på, hvorledes
enheder bliver stakket.
Marks & Spencer – case
Ca. 200 frugt og grønt leverandører leverer i kasser med RF-tags. Systemet bruges primært til kontrol af shelf life. M&S leverer kasserne til leverandørerne. Leverandørerne er tvunget til at skrive ned i
RF-tags efter M&S's egen informationsstruktur.
Til små leverandører er der udviklet en håndholdt løsning til at skrive i tags. For lidt større leverandører findes en løsning med rullebaner. Men generelt virker systemet med at overføre information til tags
meget simpelt.
Har en "læservæg", hvor hele stablen af RF-påførte returkasser læses på én gang.
For tøj er der i dag generelt en stor forskel på den systemmæssige lagerbeholdning og den faktiske lagerbeholdning. Har derfor udviklet et RF-system hertil. Der sker i dag en RF-mærkning af herre
jakkesæt. Ved hjælp af en mobil RF-læserenhed læses alle tags en gang om dagen og mankoer i størrelser og typer, farver genbestilles straks til levering fra lageret. Det primære formål er at undgå tabt salg.
Resultatet er et øget salg. Tagen fungerer som en engangstag, men kan genbruges, men det er rart at tagen er på tøjet, såfremt kunden returnerer det igen. Mobillæseren sidder på en slags rullevogn.
Har et testcenter hvor radiokommunikation for RF-tags kan testes. Bl.a. undersøges hvilke enheder der fanges, undersøgelse af anternernes reaktionstider m.v.
Ved biblioteker kan RF-tags have en sikkerhedsalarm der de-aktiveres ved check out.
1.2 Besøg hos LINPAC Materials Handling, Rodney Cooper, International Retail Director og Carsten Skouboe, Sales
Manager, Denmark
Svensk Retursystem er den største kunde; de har kasser i forskellige størrelser.
Generelt fokuserer LINPAC på udnyttelse og effektivitetet. Berettigelsen for genbrugstransportemballager er, at kunderne skal spare penge totalt set. Hvis ikke det er tilfældet, skal man bruge
engangsemballage.
Man skal "tilbyde" besparelser for at kunne sælge returkassesystemer.
Fokuseringen er, hvordan kan LINPAC konstruere et system, der kan trække omkostninger ud af kundernes systemer samt fokusere på eksponering.
Food-virksomheder vil helst kun have en operator til kassehåndtering. Non-food vil helst selv købe kasser.
I Frankrig sker der en automatisk håndtering af kasser. I øvrigt er automatiseringsgraden højere i andre lande end England p.g.a. mindre lønomkostninger.
For tøj fra fjernøsten sker der en ompakning til plastkasser med splitlåg. Carrefour bruger labels, men der er plads til RF-tags på deres kasser.
Producerer Home Delivery kasser til nethandel.
Brød går stadigvæk direkte til butikker fra brødfabrikker. Derfor benytter de stadigvæk deres egne kasser.
Dry goods (tørvarer/kolonialvarer) ligger stadigvæk i bølgepapkasser.
Frugt og grønt-sektoren er de store brugere af returkasser. IFCO (fælles europæisk returkassesystem) har kun en meget lille andel hos Waitrose, ellers findes de ikke i England.
Der findes intet systematisk system til food service (catering), men der sker noget i Spanien på dette område.
Der transporteres LINPAC-kasser til Spanien til påfyldning der; det gøres fordi man kan udnytte en tom returtransport.
Kasserne er gererelt fremstillet i PP og der er ingen rengøringsproblemer ej heller ved bøjlerne. Rundt om i Europa bruger man mere foldekasser. Foldekasser har ikke nesting – så derfor optager de mindre
plads efter tømning og returtransport.
Nye rullebure laves i plast, fordi de giver mindre støj – især et problem ved natleverance til butikker.
Kasserne bruges som eksponeringskasser.
Discountbutikker anvender ikke returkasser i stor stil. Men da de arbejder i lukkede kredsløb, så er der et potentiale og kasserne kan give en god eksponering.
Dolly'er bruges i UK. En dolly er en ramme med hjul, hvorpå varer kan placeres. Dolly'er har den fordel, at man ikke skal bruge en løftevogn til at transportere dem rundt, men blot kan skubbe eller trække
dem rundt. I resten af Europa er pallen fortsat den foretrukne lastbærer. Paller kræver mere plads i butik for, at kunne blive placeret korrekt.
Knive er farlige og giver mange skader såvel på medarbejdere som på produkter – et argument for returkasser. Ved bølgepapkasser er arbejdet med at fjerne dem også større, da de ofte skal skæres op for
at kunne transporteres. Fjernelse af emballage er en omkostningstung funktion.
Alle de store kæder i UK benytter 3. parts logistik-firmaer til butiksdistribution. F.eks. kører Hays for Sainsbury's.
Det er forskelligt hvem, der ejer returkasser. Men der en generelt tale om kædespecifikke kasser. Der findes intet åbnet system i UK, som f.eks. Svensk Retursystem, der for øvrigt har 5 mio. kasser.
Leverandørerne betaler en brugerafgift pr. kassetrip. Trip-prisen ligger i øjeblikket på ca. 20 pence. Denne pris skal være mindre end den tilsvarende pris for anskaffelse af en ny bølgepapkasse. De 20
pence svarer til ca. 2 kr. – en bølgepapkasse koster mellem 3 - 5 kr. afhængig af størrelse, kvalitet og tryk.
1.3 Butiksbesøg hos Marks & Spencer
Kæden har et stort sortiment i færdigmad og tilberedte ingredienser – på bekostning af standard fødevarer. Desuden er der stor fokus på tøj. Sælger næsten udelukkende private label produkter.
Mange leverandører har hele fabrikker, der udelukkende producerer til Marks & Spencer.
Bruger mange returplastkasser af bøjlemodellen. Til nogle produktgrupper er kasserne påført en RF-tag, der er hot meltet på. Der bruges meget dolly'er. 2 dolly'er kan låses sammen, således at de kan
transporteres samlet. Ved brug af dolly'er skal der ikke benyttes løftegrej – der kræves også et mindre pladsareal i butikken for at få en dolly på plads sammenlignet med en ¼-palle.
På et depot bruger Marks & Spencer RF-tags.
Returkasser – f.eks. til frugt og grønt – pakkes hos leverandører. Til nogle produkter bruger leverandørerne en pose i kassemål, som lægges i kassen som et slags for inden produkterne anbringes i kassen.
Varerne modtages i bagbutikken, hvorfra de køres direkte ind i butikken. Tom emballage i form af returkasser køres direkte ud i en tom trailer, der altid står der (for at spare plads, da bagbutikken er meget
snæver).
Varer bestilles automatisk på basis af salgsmængder og lagerbeholdninger. Alle produkter leveres hver dag og der kommer 3 leveringer pr. dag. Et nathold sørger for vareopfyldning. Varerne checkes ikke
ved ankomsten. Kalkulerer med et samlet svind på 10%.
I hver returkasse findes der kun et varenummer og dette indebærer i nogle tilfælde, at kasseudnyttelsen er meget dårlig. Gennem bøjlen opnås en fleksibilitet i kassehøjden og dermed udnyttelsesprocenten.
Alle varer pakkes hos leverandører, som leverer varerne til Marks & Spencer's depoter. For lån af kasser er der en trip-afgift på 20 pence.
Nogle kasser sendes til leverandører i Spanien.
1.4 Butiksbesøg hos Tesco
Butikskonceptet er "full and fresh" og der er mange varer i butikken.
Tesco bruger en anden og mere simpel type kasse, som også er noget ældre og bruger også dolly'er. Disse findes også i ½-pallemodul. Der er tale om samme kassetype som hos Marks & Spencer, men
kasserne har en anden farve. Ved hjælp af bøjleplaceringen kan hver kasse have 2 forskellige højder.
Til tørvarer anvendes stålbure. Til non-food anvendes blå returkasser. Til øl og vand anvendes ½-paller på hjul – der er tale om tunge paller, der med produkt vejer ca. 400 kg. Til drikkevarer benyttes der
også her bakker i pallemål til placering af de enkelte flasker.
Det er kun til frugt og grønt at der anvendes displaykasser. Alt leveres i dobbelt dolly-format. Farven på bøjlen angiver højden af kasserne. Nesting problemet blev diskuteret. Der benyttes pallecontainer til
kartofler – siden kan lukkes ned, så der sikres en tilgængelighed til produktet. Bruges også til æg.
Tesco har en servicevogn med PC-terminal, hvorfra der plukkes til home shopping. En butiksmedarbejder plukker direkte fra butikken. På vognen er der omkring 6 returkasser (plukker vel så samlet til 6
ordrer af gangen).
Returkasser mærkes med en stregkodelabel i EAN 128 format, som indeholder EAN-varenummer og sidste salgsdato. Det er leverandøren, der sætter denne label på.
1.5 Butiksbesøg hos Sainsbury's
Sainsbury's bruger sorte returkasser og nedklappelige pallecontainere. Returkasser og bølgepapkasser pakkes sammen på rullebure. Sainsbury's er ved at installere automatiske anlæg på distributionscentre,
men der er såvel tekniske som økonomisk problemer. De tekniske problemer skyldes bl.a. returkassernes alder.
1.6 Butiksbesøg hos Asda
Asda er ejet af Wal-Mart og butikkerne ligner meget Wal-Mart-butikker. Den besøgte butik fungerer som testbutik. Der anvendes 2 forskellige returkassesystemer, 1 til non-food og 1 til normale ferskvarer.
Ferskvarekasserne er brune, således at de i nogen udstrækning ligner bølgepapkasser. Til økologiske varer anvendes grønne kasser.
Ved distribution af pallecontainere kan der sættes løse kolli oven på.
Brød ankommer i containere til butikken, men disse tømmes og der anvendes almindeligt display af enkelte brød på hylden.
1.7 Besøg hos logistikfirma Christian Salvesen
Christian Salvesen er et logistikfirma med norske rødder – oprindeligt et hvalfanger-firma. Men har i dag ingen relationer til Norge.
Det besøgte anlæg beskæftiger sig med reverse logistics (returlogistik). De modtager dolly'er med returkasser fra butikker samt bølgepap og anden emballage. Kasserne vaskes og stilles på paller og
wrappes med en enkelt omvikling samt mærkes.
Leverandørvirksomheder bestiller så kasser til genopfyldning. Man håndterer 200 mio. returkasser for Tesco. Christian Salvesen har 11 af sådanne anlæg i UK.
Til anlægget ankommer der ca. 200 biler pr. dag. Der er en høj biludnyttelse. Efter tømning kører lastbilerne over til den nærliggende Tesco ferskvareterminal og får fyldt bilerne med varer, der transporteres
til butikker, hvorefter tomme returemballager tages med retur til Christian Salvesen.
Selve vaskningen af kasserne sker i en kassevasker, men depalleteringen fra dolly'er og placering på paller sker manuelt. I resten af Europa er mange af disse funktioner automatiseret, men
lønomkostningerne er generelt lave i UK.
Butikker skal generelt ren-sortere kassetyper, men denne sortering er af varierende kvalitet, men man "straffer" sjældent butikker, men opfordrer dem til at ren-sortere bl.a. ved hjælp af informationstavler.
Dårlige kasser eller kasser der skal repareres frasorteres.
Der håndteres 11 forskellige typer kasser, hvoraf de 10 er til food-produkter.
Puljen af kasser styres i et samarbejde mellem: emballageleverandør, grossist og kassevaskeri.
Tesco betaler for dolly håndtering. Dolly'er vaskes ikke hver gang.
Kasserne har ca. 20 - 21 trip pr. år – afhængig af kassetypen og til hvilke varegrupper at den anvendes, som igen bestemmes af varens omsætningshastighed.
Non-food-kasser cirkulerer ca. 10 gange pr. år. Kasserne kan holde i 10 år. Herefter granuleres kasserne og der produceres nye kasser.
Der er forskellige finansieringsmodeller for investering i returkasser. Mange arbejder med en pant plus trip-fee model.
Christian Salvesen modtager også plastfolie og bølgepap retur fra butikkerne. Dette balles op og sælges til recycling virksomheder.
Et andet af Christian Salvesen's produkter er at håndtere returvarer fra butikker og gøre dem salgsklare igen.
1.8 Besøg hos ferskvaredepot for Tesco
Depotet er det største af Tesco's i UK. Anlægget er stort; der er mange haller. Alle haller er temperaturreguleret – enten til køl- eller frost-temperaturer. Anlægget er bemandet døgnet rundt hele året. Her
håndteres alle ferskvarer med undtagelse af brød.
Der arbejdes efter cross docking princippet – forstået på den måde at der er kunder/butikker, der har bestilt alle de varer, der ankommer til anlægget. Der er således principielt ingen lagervarer.
Fra det centrale butiksvarebestillingssystem opgøres behovet fra varer. Derfra sendes en bestillingsordre til den aktuelle leverandør på præcis den mængde varer pr. varenummer, som samtlige butikker skal
have. Leverandøren har så en forholdsvis kort tid til at levere den bestilte varemængde til depotet. Leverandøren sørger selv for ind-transport. Ved ankomst til depotet registreres varemodtagelsen og der
udskrives labels til hver eneste kolli. Kolli kan i denne sammenhæng være både returkasser og bølgepapkasser. På denne label står hvilken butik, der skal have varerne i kollien. En medarbejder får en
strimmel med labels, der svarer til antallet af modtagne kolli pr. varenummer. Medarbejderen tager dolly'en, pallen eller rulleburet og kører ned gennem lageret. På lageret har hver butik en fast lokation i hver
hal, hvor deres varer står. På basis af labels plukkes kolli fra leverandør-lastbæreren og placeres på butikslastbæreren, som enten er en dolly eller et rullebur. Rullebure anvendes primært hvis der skal ske en
sampakning mellem returkasser og bølgepapkasser. Labelen placeres på den plukkede kolli. Når kollien af ét varenummer er placeret ud til butik fortsættes der med det næste varenummer.
I de fleste kølehaller er der ingen pallereoler, selvom der er højt til løftet. På frostlageret er der pallereoler.
Til bananer har man udviklet en speciel vogn, som fjerner håndtering af tunge banankasser i butikkerne. Vognen, som også er på hjul, fungerer tillige som display-medie i butikker.
Bilerne kører rundt om bygningen og læsser varer på fra de forskellige haller. Bilerne kan køre med både frost- og kølevarer på samme tur. Temperaturzonerne er adskilt med en væg. Generelt har hver bil
kun varer med til én butik pr. tur.
Bilag D
Besøgsrapport fra Arla Foods, Götene
Formålet med besøget var at se, hvorledes en dagligvareleverandør pakker produkter i returemballager samt at få en præsentation af Svensk Retursystem (SRS).
Arla Foods anlæg i Götene fremstiller ost og smør samt modtager oste fra andre svenske Arla Foods mejerier til modning, opskæring og pakning. Ostene bliver distribueret herfra til kunder.
1.1 Præsentation af Svensk Retursystem (SRS)
Selskabet ejer også datterselskabet AB Palletten, som udlejer plast-paller i EUR-pallemål. Selskabet blev etableret i 1990, hvor der blev lavet en ny palle til bryggeri-industrien og Systembolaget. Fra den
samlede handel og leverandørkreds kom et ønske om, at der skulle etableres ét fælles returkassesystem. Handelen ønskede én kasse til samtlige produktgrupper. I starten af 90erne blev der gennemført
forskellige undersøgelser herom og i 1996 blev Svensk Retursystem etableret. Det var et væsentligt krav, at systemet var gennemprøvet inden det blev sat i drift. Selskabet er ligeligt ejet af handelen og
leverandørkredsen. Sidstnævne er repræsenteret gennem DLF. Handelens ejerdel er direkte fordelt mellem de 3 store dagligvaregrossister med en ejerandel, der afspejler deres markedsandel. Formanden
for bestyrelsen er en neutral person uden relationer til branchen i øvrigt.
Udgangspunktet for systemet har været; omkostningsreduktioner, miljø, standardisering, retursystem og pant. Man har en målsætning om, at Norden er arbejdsområdet. Den operative drift blev startet i
1999.
Der er nedsat tekniske grupper, som beslutter hvilke kasse- og palletyper, som systemet skal tilbyde. Der er en teknisk gruppe pr. varegruppe. De tekniske grupper tager også stilling til farvevalg for kasser
og paller. Der er tekniske grupper for følgende produkter: Frugt og grønt, kød og viktualie, ost og mejeri samt kolonial og dybfrost. Den sidste grupper beskæftigerer sig hovedsageligt med paller.
SRS arbejder løbende på at overbevise flere leverandører om at bruge returkasser. Man kikker efter at finde hensigtsmæssige produkter. Der findes projekter, hvor returkasserne kan bruges til
kolonialprodukter, men de bruges ikke i dag i praksis.
Det første vaskeanlæg blev etableret i Helsingborg, hvilket skyldes at de fleste frugt og grøntavlere er lokaliseret i Sydsverige. Herefter er der etableret vaskeanlæg i Örebro og Västerås. Paller vaskes i
Helsingborg og Örebro. Alle vaskeanlæg er fuldautomatiske. I dag er der i alt 5 vaskeanlæg (linier) i drift. Man benytter kanalvask, hvor hele kassen kommer ned i vand. En anden mulig metode er
højtryksspuling. De vaskede kasser stables i 4 søjler på paller i en højde på 1,2 meter.
Paller spules i vaskeanlæg. Der anbringes 8 paller i højden, så pallen bliver 1,25 m i højden og 2 paller stables oven på hinanden. Der skal 4 personer til at passe ét vaskeanlæg pr. skift. Der køres i 5 skift.
Der er ansat 60 personer i hele SRS, heraf 9 personer på kontoret i Stockholm. IT og logistik er out-sourcet. Det er DHL, der sørger for transport. Ordre- og planlægningsprocessen er også out-sourcet –
omkring 8-9 personer varetager disse opgaver. At drift af vaskeanlæg ikke er out-sourcet skyldes, at der ikke findes nogen operatør, der på daværende tidspunkt var i stand til at foretage denne opgave i
henhold til de stillede kvalitetskrav især med hensyn til hygiejne.
Afgiftsstrukturen er ens for alle. De enkelte virksomheder må selv opstille de økonomiske kalkulationer. Men generelt er retursystemet kost-effektivt i forhold til engangsemballager på grundlag af følgende
forhold:
- Lavere indkøbspriser til emballage (afgift på returkasser contra køb af bølgepapkasser)
- SRS er et non-profit-selskab
- Mindre kassation af produkter, fordi returkasser giver en bedre beskyttelse – dette gælder især for frugt og grønt
- Effektiv håndtering i alle led i varekæden
- Miljø
- Bedre arbejdsmiljø
- Forenklet håndtering
- Ofte bruges kasser til eksponering i butik
Dette giver samlet set store besparelser i varekæden. Der er gennemført et EU-projekt under Life-programmet til dokumentation herfor. I dette projekt blev der peget på, at der ville være store fordele, hvis
der blev indført ét samlet system for hele Europa. Men det er ikke EU's opgave at drive et sådant fælles retursystem i gang.
Fordelen ved det svenske system er, at man har ét fælles system på tværs af kæder i modsætning til i UK, hvor alle kæder har deres egne systemer.
De tomme kasser hentes hos grossisternes terminaler. Det er grossisternes biler, der tager kasser med retur fra butikkerne. De enkelte grossistterminaler er ikke tilknyttet et fast vaskeanlæg. Der afhentes
dagligt returkasser fra grossist-terminalerne. Alle kasser vaskes ved returnering. De vaskes alle efter den maksimale hygiejne-standard, som er i forhold til kød-standarden. Grossisterne bruger også
returkasserne til at plukke visse non-food-varer, men kasserne returneres altid efter hvert brug.
Generelt bliver kassestørrelserne mindre, fordi indholdsmængden skal tilpasses butikkernes afsætning. Tidligere havde man ikke mange forskellige kassevarianter i systemet.
Der er 5 mio. kasser, 2 mio. ½-paller og 300.000 hel-paller i cirkulation. Alle ½-paller vaskes ved hver cirkulation, mens kun 20% af hel-pallerne vaskes, men det forhold diskuteres løbende. Beholdningen
af returkasser cirkulerer i alt 63 mio. gange pr. år. Cirkulationstiden pr. kasse er i gennemsnit 1 måned, men længden af perioden afhænger af, om butikkerne anvender kasserne til eksponering eller ej.
Pallerne cirkulerer 4 gange pr. år.
Det koster 18 kr. pr. ½-palle i lejeafgift. Det har dog været nødvendigt at differentiere omkostningen efter afsætningens størrelse. De store virksomheder slipper billigere end de små. Dette gælder dog
foreløbigt kun for paller. Der er ingen geografisk differentiering i afgiftens størrelse.
Der er valgt bøjlekasser i stedet for foldekasser, idet foldekasser ikke er egnet til formålet. Kasserne har samme grundmodul som de engelske kasser og samme indre mål. Kasserne har en høj
komprimeringsfaktor. I høj tilstand kan der være 6 kasser i højden. I tom tilstand kan der være 20 kasser. Kasserne er ikke følsomme for fugt. Der er 5 kassemoduller. Bøjlekasserne kan indstilles i 2 højder
110 eller 140 mm, eller 50 eller 80 mm ved små kasser. Disse kasser kaldes dual-kasser. Det er markedet, der afgør hvilke kasser der udbydes. Man kikker løbende på fyldningsgraden. De lave kasser
bruges meget til detailpakket kød. Den grå farve er valgt, fordi den er meget neutral. Ved vask er temperatur og ph-værdi vigtige parametre. Hvis vandet er for varmt, brænder kød-rester fast.
Frugt og grønt er den største varegruppe. 40% er svensk avlet og 80% heraf pakkes i returkasser. Hos avlerne plukkes der direkte i returkasserne. Tomme kasser køres også til Spanien for pakning.
Derimod går udbredelsen til større industri-producenter med automatiske pakke-anlæg m.v. noget mere trægt. Indtil videre har det været svært at påvise driftsmæssige gevinster, men det afhænger også af,
hvilke afskrivningsperioder virksomhederne indregner.
Tomme kasser transporteres også til kød-producenter i Danmark og Irland. I denne sammenhæng skal man også huske på, at engangsemballager skal transporteres. Der er lavet livs-cyklus-analyser, der
beskriver forholdet.
Bananer kommer ikke i returkasser. Der sker ingen ompakning af produkter, der er pakket i engangsemballager. Ompakning sker kun for produkter, der kommer hjem i bulk. Det er de tekniske
produktgrupper, der beslutter hvilke produktgrupper, der skal i returkasser. Eventuelt kan komsumentpakningen omdimensioneres således at de passer bedre til returkasserne, så kan de også detailmærkes
til forbrugerne.
Pallerne er forsynet med en RFID-tag, som ligger i palleklodsen. Tagen bruges til sortering på anlæg, men der er endnu ikke nogle kunder, der bruger den. Der er tale om 4-vejs paller.
Alle emballager pålægges pant, som føres igennem varekæden. SRS bestiller kasser hjem fra grossisterne og arrangerer transporten. Udtransport af fyldte kasser kan være mere ineffektiv end
engangsemballager, men det er meget produktafhængig. Ved hver anlæg findes et sikkerhedslager af tomme kasser.
SRS har også etableret en transporttgruppe, hvor der også deltager folk fra grossisterne.
Lejeafgiften pr. kasse er 2,00 - 3,50 SEK pr. gang. Panten er på 40 kr. Afgiften for paller er 18 SEK og panten er 200 SEK. For helpalller er der i stedet for en døgnafgift. Afgifterne dækker transport,
brug og vask. Al registrering og bestilling sker gennem en web-side.
De fyldte paller stables i 1,25 meter i højden – drikkevarer dog 1,8 m.
1.2 Rundvisning på Arla Foods anlæg
Hos Arla Foods, Götene fremstilles smørprodukter og visse osteprodukter desuden modnes oste fra andre mejerier. Desuden fungerer anlægget som pakkeanlæg for andre af Arla Foods's
osteproduktionsstedser i Sverige. Det vil sige, at på de andre ostemejerier fremstilles oste, som så transporteres til Götene, hvor de færdigmodnes og detailpakkes. Det skal næves, at Arla Foods i Sverige
ikke har samme markedsandel i Sverige som i Danmark. Det skal også nævnes at eksporten fra Arla Foods, Sverige er væsentlig mindre end fra Danmark.
I lageret er der plads til 26.000 paller og lageret har 3 temperaturzoner. Dagligt går der 600 paller ud og ind af lageret svarende til 30-40 lastbiler pr. dag.
Arla Foods har investeret 33 mio. SEK i det automatiske anlæg. Selve pakningen i kasser sker manuelt, idet investeringen i automatik er for stor. Problemet heri forårsages primært af, at returkasserne er
koniske. For det fulde sortiment er merkostningen pr. kg på 0,55 SEK. Anlægget afskrives over en periode på 6-8 år.
Arla Foods har gennemført en holdningsundersøgelse til returkasser blandt kunderne og de er generelt positive overfor anvendelsen af returkasser. Returkasser til produkterne indføres succesivt, men der
føres ingen dobbelt varenumre med undtagelse af 8 produkter til catering og Lidl, som ikke vil have returkasser. En stor del af Arla's sortiment emballeres stadigvæk i engangsemballage.
Der pakkes 2.400 kasser i timen svarende til 80 paller pr. time.
Returkasserne fylder 15-18% mere volumenmæssigt, men eftersom Arla Foods kan
dobbeltstable i bomtrailere, kan man alligevel udfylde bilens max last - præcis som når der anvendes engangsemballager. Dobbeltstabling i bomtrailere er en forudsætning i begge tilfælde, for at nå max.
vægten.
At køre med returkasser på det automatiske anlæg kræver meget overvågning, idet man skal undgå kasser, der er gået i stykker. Ved produkt-etikettering kræves der bedre etiketter, idet pappet tidligere
kunne opsuge den overskuende væde.
Hvis man manuelt skal adskille kasser fra hinanden, skal alt klister fra etiketter væk. SRS anbefaler særlige lim- og etikettyper. Etiketter skal altså placeres på en nobret overflade. På kasserne ses der
generelt mange etiketrester.
I anlægget skal returkasserne styres væsentligt mere end engangsemballager – f.eks. i forhold til ting der stikker ud fra kassen. Der er 3 minutters buffer i systemet, inden hele linien stopper. Der er flere stop
på linierne med returkasser end på linierne med engangskartonemballage. Antallet af interne transporter stiger som følge af, at der kan være en mindre varemængde på én palle med returkasser end med
engangsemballage.
Arla Foods har testet tags, men har forkastet at bruge dem p.g.a. problemer med metal og væde.
Derefter var Arla Foods vært for en interessant rundtur på anlægget. Flowet i pakkeprocessen er som følger:
- De rengjorte returkasser ankommer fra et af Svensk Retursystems vaskeanlæg
- Returkasserne de-palleteres automatisk
- Parallelt skæres oste i portioner, pakkes i detailemballage, vejes og prismærkes om nødvendigt
- Returkasser kører til en pakkestation på rullebaner eller båndtransportører
- Ostene transporteres på tilsvarende vis frem til det aktuelle pakkebord
- Ostene pakkes manuelt i returkasser i henhold til specifikation med hensyn til antal styk
- Returkasserne vejes og påføres en stregkodemærkning i henhold til EAN 128-standarden
- Returkasserne kører på en fælles rullebane for de forskellige pakkestationer frem til en station, som løfter bøjlerne på kasserne op, så at kasserne kan stables oven på hinanden, således at de ovenstående
kasser hviler på bøjlerne og ikke på de underliggende produkter
- Returkasser sorteres efter produkttype og kører ud på forskellige rullebaner, således at der på en rullebane kun findes én produkttype
- En robot palleterer returkasser på hver sin produkttypemæssige palle. En robot palleterer op til 8 forskellige produkter af gangen
- Den færdig palleterede palle køres på rullebane til en mærkningsstation, hvor pallen mærkes med en palleetiket i henhold til EAN 128-standarden
- Pallerne transporteres ind på det automatiske højlager
- Når der kommer kundeordrer plukkes paller og kasser fra højlageret og ekspederes til kunderne
Pakning i engangsemballage sker for størstedelens vedkommende automatisk, men pakkemaskinerne kan ikke bruges til returkasserne. For Arla Foods er det dyrere at pakke produkter i returkasser end i
engangsemballager.
1.3 Europæiske returemballagesystemer
Carsten Skoubo, Linpac gennemgik hvilke returkassesystemer der anvendes rundt om i de europæiske lande. Ved returnering af kasser kan en kasse reduceres ned til 15%. Stabelbarekasser vinder mere og
mere frem. Der er mere håndtering ved foldekasser.
I UK er de glade for at have hjul på transportenheder ind i butikken. CHEP er ude af returkassemarkedet i UK og Irland. Men CHEP er igen begyndt at gå ind på returkassemarkedet efter en krise. Hays
og Christian Salvesen har overtaget markedet. Logtec, som ejes af Linpac er en mindre spiller.
De engelske systemer er kædestyret og kasserne ejes af kæderne, men en operatør driver systemet og det kører helt lukket. Som producent er man tilknyttet én detailhandelskæde.
CHEP, IFCO og Europool har faste priser over landegrænser. Generelt er priserne høje for leje (5,10 kr.). Fylderen af kassen giver operatøren besked om, hvem der har modtaget kassen. Kasser skal
rotere 10-12 gange pr. år og operatøren skal have styr på, hvor kasserne befinder sig. Der opereres ikke med pant.
Når kæderne ekspanderer til andre lande, "bærer" de deres egne systemer med. Dette giver en modsætning mellem kædebaserede systemer og eventuelle nationale systemer.
Derudover findes der mange kæde-lukkede systemer, som drives af transportører eller detailhandelen selv.
1.4 Diskussionen om fremtiden for returemballager
Hvilke systemer der vil klare sig er et spørgsmål om markedsniveau for anvendelse af returemballager. Her spiller eksisterende systemer en central rolle, idet der er bundet mange penge heri. Visse systemer
skal eventuelt købes ud.
Ejerstrukturen bag kasserne er måske afgørende.
Det er et åbent spørgsmål, om dansk dagligvarehandel kan blive enige om ét system.
SRS vil udvide deres område til også at omfatte cateringmarkedet og vil satse på at få større importvolumener over i returkasser.
COOP's nordiske etablering kan også få en central rolle. ICA har allerede fælles indkøb for Norge og Sverige. Der er dannet en norsk pallepool og SRS samarbejder med dem gennem norsk DLF. Men
SRS vil ikke direkte etablere sig i Norge. Dagligvarehandelen i Norge har besluttet sig for at overgå til plastpallen. Norge laver også deres egen prisstruktur. De generelle priser vil falde. Visse danske
eksportører benytter i dag den svenske ½-palle til eksport til Sverige. Generelt er det DagSam's politik ikke at gøre noget på dette område – dette skal især ses i sammenhæng med omfanget af
multinationale leverandører, hvor der fra ét produktionssted skal leveres til mange markeder. Men måske kommer der et fælles system i Danmark, men priserne skal ned, idet det er økonomien, der er
afgørende.
De økonomiske kalkulationer vanskeliggøres af investeringer i udstyr og hvorledes disse udgifter indregnes. Man må forvente at detailhandelen laver individuelle analyser. Forudsætningerne for de enkelte
leverandører er meget forskellige.
Bilag E
Besøgsrapport fra besøg hos Albert Hein/Ahold
DC - distributionslager beliggende i udkanten af Amsterdam, Zaandam
Der fokuseres på City-logistik i Holland – har deltaget i et projekt med en "Stadsbox", som ligner en luftfragtcontainer og containeren leveres direkte til butikken.
Lageret er opdelt i 3 sektioner:
- Ferskvarer
- Tørvarer
- Tom gods; inkl. drikkevareemballage
Der er automatisk ordreafgivelse fra butik og videre bagud til leverandører.
Der er en stor størrelsesmæssig forskel i butikkerne i Albert Hein – de er organiseret i kæder; gående fra Albert Heijn til XL. Omsætningen pr m2 er høj, fordi der er så lidt plads i byerne. Der bor 8 mio.
indbyggere inden for et meget lille område. Derfor er lagermængderne små, mens der i stedet er hyppige leverancer. Der distribueres 100% på hjul. Palleenhederne bliver mindre og mindre.
"Det er logistik- og informationssystemer, der sørger for at tingene sker".
Man kikker hele tiden efter automatik, der kan effektivisere håndteringen, men p.g.a. de forskellige dimensioner, der er på tørvarer, er det vanskeligt. Det er lettere på ferskvarer, hvor det meste pakkes i
standardkasser.
Vil gerne kunne automatisere hele plukkeprocesen. Karruselplukning, hvor varerne kommer til plukkeren, kan komme på tale.
"Find kunderne på alle tidspunkter, transporter til store butikker, der ligger ved store veje"
Til små butikker foretages der gruppeplukning.
"Gør logistik og transportsystemer simple". Simplificer logistikflow – ikke mange forskellige flows.
Butikkerne har faste varemodtagelsestidspunkter.
Fra leverandører er der 18 timers lead time. Med undtagelse af brød og aviser er der ingen direkte butiksleverancer. Kampagnevarer kører også igennem lageret – det er stop ved butikker, der koster. Alle
produkter kan leveres hver dag til butikker. Store butikker får op til 3 leverancer pr. dag. Alle modtagne produkter anbringes direkte på hylden, da butikkerne ikke har noget baglager.
Antallet af ordrelinier stiger, mens mængden pr. ordrelinie falder.
Slow movers leveres fra et særskilt lager. Levering sker som cross docking gennem det tilknyttede DC-lager. På slow movers lageret er der 9.000 tørvare-artikler og 700 ferskvare-artikler. På dette lager
anvendes karruselplukning.
Der er 2.000 varenumre af tørvarer på det regionale DC lager og 1.800 ferskvare-artikler (frugt og grønt, kød, mejeri og frost) og så cross docking fra slow movers lageret.
Alle butikker ligger inden for en køreafstand på 1 time. Hver butik får varer fra 2 biler – en med tørvarer og 1 med varer, der kræver temperatur-regulering. I Danmark har man altid arbejdet med en
længere afstand.
Ahold ejer ikke selv lastbiler.
Hver mand på lageret kan klare 125 pluk pr. time.
Lead time overfor leverandører er 4-48 timer og overfor butikker 8-18 timer.
"Cost leadership demands standardization". Standardisering af hele processer således at de kan automatiseres. Man har et fælles Hollandsk kassesystem, men der er en konflikt over til nationale systemer,
når Albert Hein etablerer sig i udlandet. Selv når Albert Hein har solgt kæder, er Albert Heins logistiksystem bevaret – dette er f.eks. sket i Sydamerika.
Bruger faste kasser, der ikke kan reduceres.
Til leverandører – vær fleksible. Albert Hein har forskellige kassestørrelser til forskellige butiksstørrelser.
Man har samme udsalgspriser i alle Albert Heins butikker med undtagelse af visse butikker i det centrale Amsterdam.
Logistik fokuserer på "performance and cost".
Leverandører får aggregerede mængde forecast.
Håndteringsomkostningen er på 0,68 € pr. kolli – svarende til 5,10 DKK.
Bilag F
Generel præsentation af projektet
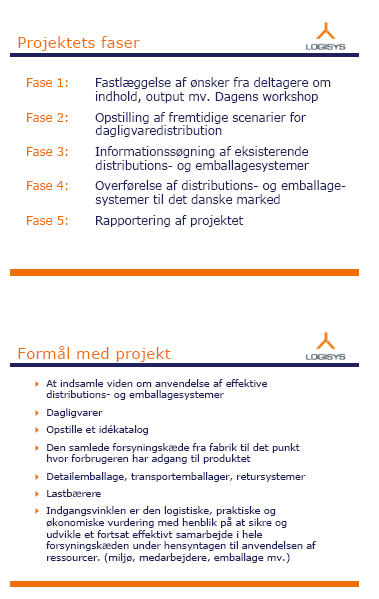
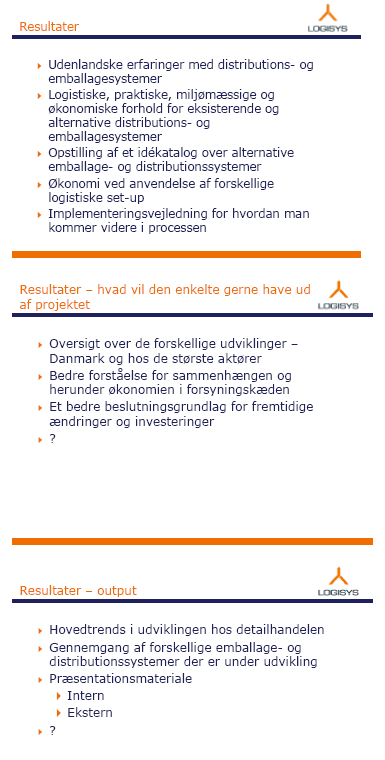

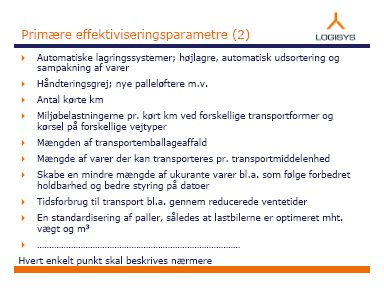
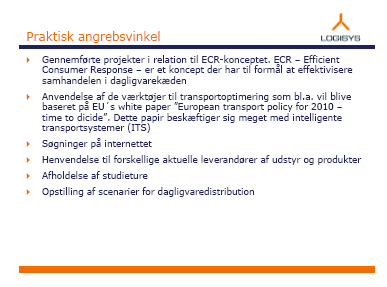
Klik her for at se figuren.
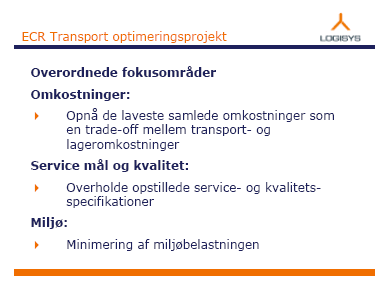
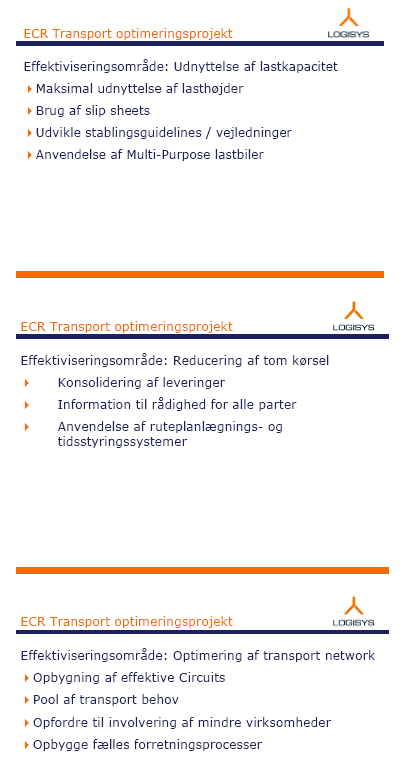
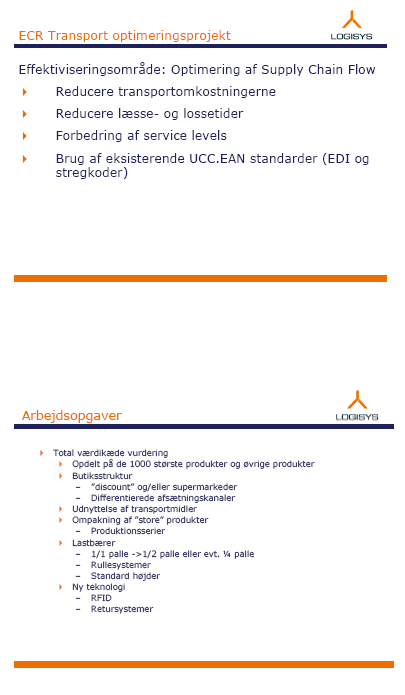
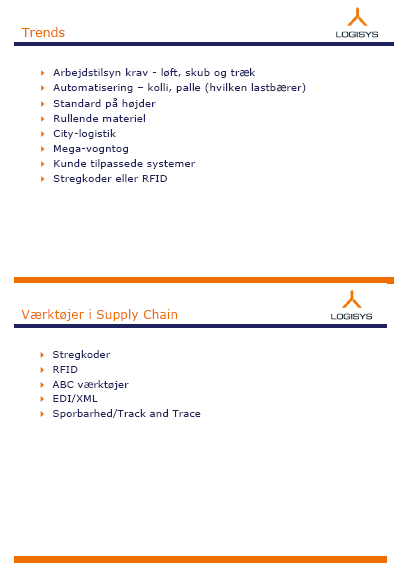
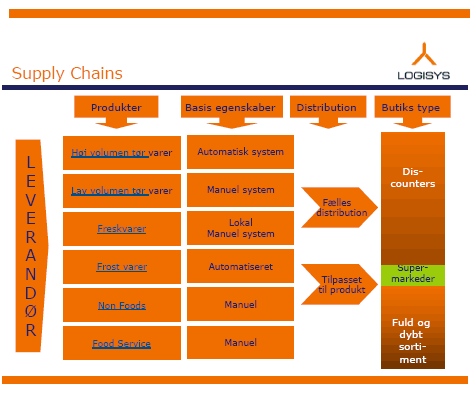

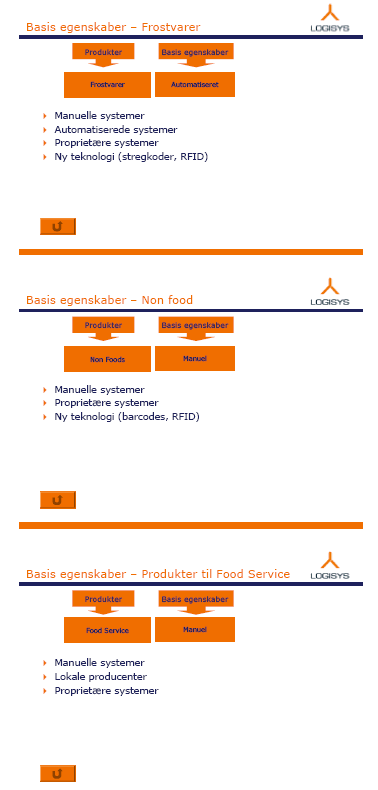
Bilag G
Beskrivelse af værdikædemodel
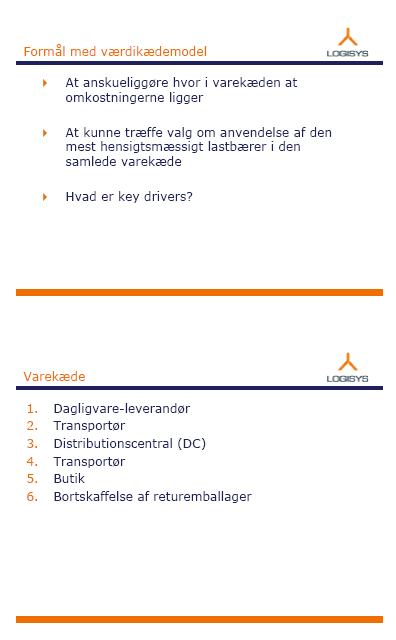
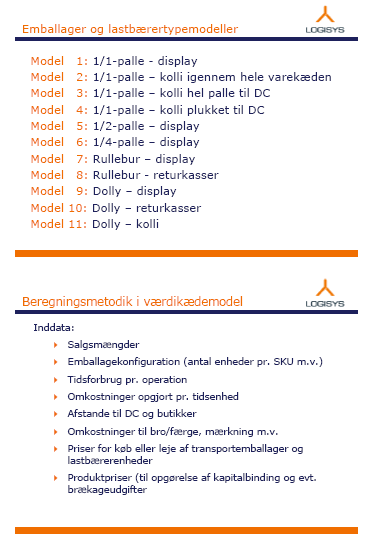
Klik her for at se figuren.
| Til Top | | Forside |
Version 1.0 Januar 2006 • © Miljøstyrelsen.
|