| Til bund | | Forside |
Miljøprojekt nr. 1067, 2006
Affaldsminimering i støberi- og maskinindustrien
Indholdsfortegnelse
Forord
Sammenfatning og konklusioner
Summary and conclusions
1 Baggrund
2 Projektforløb
3 Gennemførte indsatser
4 Medarbejderinvolvering i affaldsminimering
5 Udvikling i affaldsmængder i perioden
6 Konklusion på projektet
Bilag A
Forord
Følgende er en afrapportering af projekt "Affaldsminimering i støberi- og maskinindustrien". Projektet har været finansieret under Program for Renere Produkter m.v. 2001 –
Perspektivpuljen.
Projektet er gennemført af Vald. Birn A/S, der har været projektansvarlig over for Miljøstyrelsen. Vald. Birn A/S består bl.a. af Vald. Birn Jernstøberi A/S (VBJ) og Vald. Birn Maskinfabrik A/S (VBM).
Som underleverandør i forbindelse med medarbejderinddragelse og projektrapportering har Advisory i KPMG bistået Vald. Birn A/S.
Fra Vald. Birn A/S deltog følgende personer:
- Energi- og Miljøchef: Eddy Boe Nielsen, (VBJ) - Projektleder
- Teknisk Direktør: Ivan O. Bak (VBJ)
- Anlægs- og vedligeholdelseschef: Lars Hansen Biehl (VBJ)
- Projektingeniør: Allan Carstensen (VBJ)
- Direktør: Mogens Bach (VBM)
- Produktionschef: Christian Jørgensen (VBM)
- 40-50 medarbejdere fordelt på miljøgrupper i de to enheder Jernstøberiet og Maskinfabrikken
Fra KPMG deltog konsulenterne:
- Dorthe Nedermark (cand.techn.soc.)
- Lone Gjørret (cand.merc.jur.)
- I følgegruppen for projektet sad:
- Tonny Christensen, Miljøstyrelsen
- Kim Frese, Frese Metal & Stålstøberi A/S
- Ivan Bak, Vald. Birns Jernstøberi A/S
- Eddy Boe Nielsen, Vald. Birns Jernstøberi A/S
- Dorthe Nedermark, KPMG
Sammenfatning og konklusioner
Jernstøberi spinder guld på affaldet
Nordeuropas største kundestøberi Vald. Birn A/S har gennem de seneste fire år gjort en ekstra indsats for at nedbringe affaldsmængderne ved at afprøve nye teknikker til at genindvinde de ressourcer, som
ellers koster dyrt i indkøb og bortskaffelse. Samtidig har Vald. Birn A/S sammen med KPMG gennemført workshopforløb med det formål at bringe medarbejdernes ideer til affaldsminimering frem i lyset, og
her viste det sig, at der var guld at hente.
”
Baggrund og formål”
Projektet ”
Affaldsminimering i støberi- og maskinindustrien”
er finansieret af Perspektivpuljen under Program for renere produkter hos Miljøstyrelsen.
Støberibranchen er blandt dem der vejer tungt i affaldsstatistikkerne, og på Vald. Birn A/S bortskaffede man således ca. 22.000 ton affald i år 2000. Projektets formål har derfor været at undersøge
mulighederne for at minimere affaldsmængden fra udvalgte affaldsfraktioner inden for støberi- og maskinindustrien ved at genindvinde en større del af spildet fra produktionsprocesserne til eget brug samt
reducere den samlede spildmængde generelt.
Minimering af affaldsmængderne blev søgt opnået dels via udvikling og afprøvning af nye teknologier, dels via medarbejderinvolvering og træning i at se og fremkomme med forbedringsmuligheder.
”
Undersøgelse”
Der blev iværksat tre tekniske pilotforsøg samt et initiativ til medarbejderinvolvering. Det sidste havde til formål at uddanne- og holdningsbearbejde medarbejderne til at se affaldet som et tab for
virksomheden og fremkomme med deres ideer til at genindvinde affaldet i produktionsprocessen.
De tekniske pilotforsøg gik ud på at afprøve, om nedenstående ideer var realiserbare.
- Separation af det støbesand der opsamles i filtrene i sandtårnet, idet dette restprodukt har et højt indehold af kulstøv og lerpartikler, der ved udvinding fra det afsugede dødbrændte materiale på ny vil
kunne tilsættes støbesandet og derved reducere behovet for nyt kul og ler.
-
- Nedknuse de sandkerner, der kasseres pga. skader o.lign. og tilsætte det i mindre mængde som nyt kernesand.
- Forlænge levetiden væsentligt på kølesmøremidlerne ved at etablere et centralanlæg til behandling og vedligeholdelse og derved reducere behovet for nyt kølesmøremiddel.
”
Hovedkonklusioner”
Projektets hovedkonklusioner er følgende:
- Forsøg med at anvende trensosigte til at separere bentonit fra dødbrændt støbesand fungerede ikke optimalt, hvorfor der ikke vil blive arbejdet videre med denne teknologi.
- Forsøg med genindvinding af kernesand fra nedknusning af kasserede kernevrag har været en succes. Der er kørt forsøg med tilsætning af op til 7% genbrugskernesand i nysandet, uden at det
påvirker emnets styrke eller kvalitet. Der er ikke blevet testet for en øvre grænse for tilsætning af genbrugssand. Potentialet er, at alle usværtede kerner kan genbruges.
- Forsøg med centralanlæg til vedligeholdelse af kølesmøremidler har været en succes. Resultatet har været en forlængelse af kølesmøremidlernes levetid med en faktor fire. Dette svarer til 75% mindre
forbrug og mængde kølesmøremiddel til bortskaffelse. Samtidig er de nødvendige mandskabstimer til vedligeholdelse reduceret tilsvarende.
- Forsøg med medarbejderinvolvering i affaldsminimering har været en succes. Deltagerne har været engagerede, og deres ideer har været med til at flytte tallene i affaldsstatistikken. Således er f.eks.
C- og M-fraktionen tilsammen reduceret fra 49 til 25 kg/ton udtappet jern ved hjælp af medarbejdernes ideer til bl.a. sorteringsanlæg og fotodokumentation af sandtab på produktionslinjerne.
Ved at gennemføre de to pilotforsøg samt involvere medarbejderne og realisere deres ideer er opnået en reduktion af affaldsmængderne pr. ton udtappet jern på 14%, hvilket svaret til 36 kg/tons udtappet
jern. I forhold til mængden af udtappet jern i år 2004, giver dette en besparelse på 3.215 ton i affald i år 2004.
Med de bortskaffelses priser Vald. Birn havde i år 2004, svarer dette til en besparelse ca. 1,1 mio. kr. Her i er ikke medregnet værdien af den øgede genanvendelsesgrad, som er opnået i sammen periode
(fra 72% til 97%), hvilket har gjort bortskaffelsen endnu billigere for visse fraktioner.
Da den reducerede mængde spild erstatter tilsvarende nyindkøb af råvarer, udgør denne besparelse ca. 1,3 mio.kr.
I alt skønnes opnået en årlig besparelse på det faste affald på 2,5 mio.kr. årligt. Dertil kommer besparelserne fra implementering af det centrale KSM-anlæg i Maskinfabrikken, som forventes at udgøre 1
mio. kr. årligt, når anlægget er fuldt udbygget.
Betragtes indsatsen i forhold til reduktionen af kasseret mængde lerbundet formsand, er der for disse fraktioner opnået en reduktion på 15%. Overføres dette resultat til landsplan, hvor Støberiforeningen
anslår, at der årligt kasseres 60-70.000 ton lerbundet formsand fra støberibranchen, svarer det til en potentiel affaldsreduktion på 9-10.500 ton/år på landsplan.
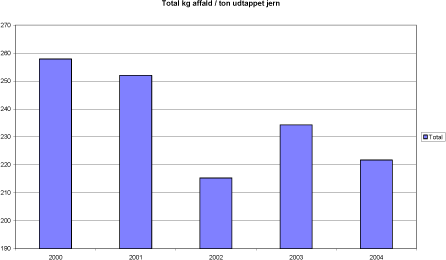
”Projektresultater”
Forsøgene med genindvinding af ler og kul fra filter i sandtårn viste, at den planlagte teknik med vibration over trensosigte ikke kunne honorere kravene til separering af partikler i den ønskede kornstørrelse.
De forsøg, der blev kørt, gav en genvinding på 40% af potentialet, men kørslerne viste for stor usikkerhed. Der arbejdes derfor fortsat med at finde andre tekniske løsninger.
Forsøget med nedknusning af kernevrag og tilsætning til nyt kernesand i små mængder viste sig at være en succes. 99% af de kernevrag der nedknuses kan tilsættes nysand, og der er kørt forsøg med op til
7% tilsætning til kernesand, uden at der har givet produktions- eller kvalitetsproblemer. Ved projektets afslutning genindvindes ca. 5 ton kernevrag om ugen svarende til ca. 200 ton årligt, og denne mængde
forventes at kunne øges.
Etableringen af et centralanlæg til behandling og vedligeholdelse af kølesmøremidlerne har vist sig at fungere rigtig godt. Ved projektets afslutning var der tilkoblet tre bearbejdningsmaskiner til anlægget, og
levetiden for kølesmøremidlerne er forlænget fra ca. 2 til 9 måneder. Dette giver en besparelse på indkøb og bortskaffelse af kølesmøremidler på ca. 75%. Samtidig er det blevet konstateret, at driften af
anlægget kræver tilsvarende færre mandskabstimer og færre maskinstop for rengøring og vedligehold.
Gennemførelse af workshopdage med det formål at uddanne- og holdningsbearbejde medarbejderne til at se affaldet som et tab for virksomheden og fange deres ideer til at reducere affaldsmængderne og
genindvinde spildet i produktionsprocessen, har været en succes.
Et synligt resultat, som fremgår af affaldsstatistikken, er udviklingen i mængden af sand på gulvet langs de 7 produktionslinjer. Sandet fjernes af rengøringsholdet vha. et centralstøvsugeranlæg. Efter at
rengøringsholdet har sat fokus på, hvor der bliver støvsuget mest og dokumenteret det med billeder, kan reparationsholdet prioritere indsatsen. Fra at skulle støvsuge 27 kg pr. ton udtappet jern op i 2000,
støvsuger holdet nu kun 19 kg pr. ton udtappet jern op.
”
Andre kilder”
: www.birn.dk www.kpmg.dk
Summary and conclusions
Iron foundry makes a fortune on waste
During the last four years, Vald. Birn A/S, the largest iron foundry in Northern Europe, has made an extraordinary effort to reduce the quantities of waste by testing new techniques for recovery of resources
that otherwise are expensive to purchase or dispose of. At the same time, Vald. Birn A/S has carried out a series of workshops together with KPMG with the purpose of highlighting the employees' own
ideas for waste reduction, and it has turned out that their ideas were worth a fortune.
"Background and purpose"
The project "Waste reduction within the foundry and machine industry" was financed by Perspektivpuljen through the Danish Environmental Protection Agency's programme for clean products.
The foundry industry outweighs many other industries in the waste statistics, and in year 2000, Vald. Birn A/S disposed of approx. 22,000 tonnes of waste. The purpose of the project was to analyse the
possibilities of waste reduction from selected waste fractions within the foundry and machine industry through recycling a large part of the waste from the production processes for internal use and by
reducing overall waste quantities in general.
Vald. Birn A/S took the initiative to achieve waste reductions partly through developing and testing new technologies, and partly through involving and training employees to identify and promote new
improvement ideas.
"Survey"
Three technical pilot projects were launched. A programme was also launched on involvement of employees through training and changing their attitudes so they regard waste as a loss for the company and
bring forward their own ideas to recycle the waste in the production process.
The purpose of the technical pilot projects was to test whether the following ideas could be feasible:
- Separation of foundry sand as this waste product holds a high content of coal dust and clay particles that can be added to the foundry sand again through recovery of the extracted, dead material, thus
reducing the requirement for new coal and clay.
- Demolition of sand cores that are scraped due to damage etc. and adding these as new core sand in small amounts.
- Significant extension of the life time of cooling lubricant through establishment of a central handling and maintenance unit, thus reducing the requirement for cooling lubricant.
The main conclusions of the project were:
- The tests with application of a Trenso separation table for segregation of bentonite from dead foundry sand does not work optimally, for which reason Vald. Birn A/S will not go on with this
technology.
- Tests with recovery of core sand from demolition of discharged core scrap have been a success. Tests have been carried out with addition of up to 7% of recycling core sand in new sand without
affecting the strength or quality of the mould. An upper limit for addition of recycle sand has not been tested. The potential is that all unsmoked cores can be recycled.
- Tests with a central unit for maintenance of cooling lubricant have proven a success. The result has been an extension of the life of the cooling lubricant by a factor of four, corresponding to a reduced
consumption and quantity of cooling lubricant for scrap of 75%. At the same time, the number of man-hours required for maintenance was reduced correspondingly.
- Tests with involvement of employees for waste reduction have been a success. The participants have been strongly committed, and their ideas have helped reduce the figures in the waste statistics. As
an example, the employees came up with an idea for a sorting unit and have documented the loss of sand at the production lines via photos resulting in that the C and M fraction together has been
reduced from 49 to 25 kg/tonne tapped iron.
By carrying out the pilot projects as well as involving the employees and their ideas, Vald. Birn A/S has achieved a reduction in waste per tonne tapped iron of 14% which corresponds to 36 kg/tonne
tapped iron. For the quantity of tapped iron in 2004, this results in a reduction of 3,215 tonne waste.
Based on Vald. Birn A/S' waste disposal prices in 2004, the above reduction in waste corresponds to a saving of DKK 1.1 million. The value of the increased recycling ratio achieved in the same period
(from 72% to 97%) has not been included, which makes the waste disposal significantly cheaper for certain fractions.
If we assume that the reduced quantity of waste replaces corresponding repurchase of raw materials, the saving amounts to DKK 1.3 million.
All in all, an estimated yearly saving of DKK 2.5 million is achieved on solid waste. In addition, there will be the savings from implementation of the central KSM unit in the machine shop, which is expected
to amount to DKK 1 million yearly, when the unit is fully developed.
If the effort is compared to the reduction in quantity of scrapped clay-bound moulding sand, a 15% reduction has been achieved for these fractions. If this result is extended to Denmark as a whole, where
Støberiforeningen (a Danish association of foundries) estimates that 60-70,000 tonnes clay-bound core sand are scrapped by the foundry industry, this corresponds to a possible waste reduction of
9-10,500
tonnes per year nationwide.
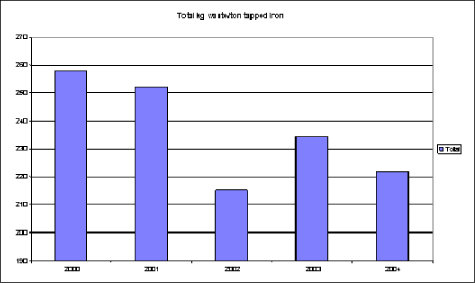
Project results
The tests of clay and coal recovery from filters in the sand towers show that the planned technique with vibration over a Trenso separation table cannot meet the requirements for separation of particles in the
requested grain size. The tests performed gave a 40% recovery of the potential, but the uncertainty in the test runs was too great. Vald. Birn A/S expects to find other technical solutions.
The test with demolition of core scrap and addition of new core sand in small quantities turned out to be a success. 99% of the core scrap demolished could be added as new sand, and tests were performed
where up to 7% addition of core sand did not cause production or quality problems. At the end of the project, approx. 5 tonnes of core scrap per week were recovered, corresponding to approx. 200
tonnes per year and Vald. Birn A/S anticipates being capable of increasing this quantity.
Setting up a central unit for handling and maintenance of cooling lubricants has turned out to work very satisfactorily. At the end of the project, three salvaging machines were linked to the unit and the life
time of the cooling lubricants had been extended from approx. two to nine months, leading to an approx. 75% saving on purchase and disposal of cooling lubricants. At the same time, it was stated that the
operation of the unit required fewer man-hours and machine stops for cleaning and maintenance.
The workshops for training and working with change of employee attitudes so that they regard waste as a loss for Vald. Birn A/S were very successful. Listening to the employees' ideas in respect of waste
reduction and recovery of waste in the production process yielded great results.
A visible result is the development in the quantity of sand on the floor along the seven production lines. The sand is removed by the cleaning team by means of a central aspirator unit. After the cleaning team
had focused on where the aspirator was used the most, they documented it via photos and the repair team is now capable of setting priority for work during the weekend. From having to vacuum 27 kg per
tonne tapped iron in 2000, the team now only vacuums 19 kg per tonne tapped iron.
"Other sources": www.birn.dk www.kpmg.dk
1 Baggrund
1.1 Baggrund
Vald. Birn koncernen består blandt andet af Vald. Birns Jernstøberi A/S og Vald. Birns Maskinfabrik A/S. Jernstøberiet er Nordeuropas største kundestøberi og har en årskapacitet på 65.000 ton
støbejern, mens maskinfabrikken er en af Europas førende producenter af transmissionselementer. Udover transmissionselementer har maskinfabrikken også en bearbejdningsafdeling, hvor støbegods til
bilindustrien bearbejdes, samt en værktøjsafdeling hvor der fremstilles værktøj manuelt.
Virksomhederne er beliggende på samme matrikel og har tilsammen ca. 720 medarbejdere.
Virksomhederne er certificeret efter QS 9000,
ISO 9002, ISO 14001, OHSAS 18001 og DS 2403. For begge virksomheder gælder, at der til stadighed fokuseres på anvendelse af nyeste teknologi bl.a.
med det formål at kunne udnytte ressourcerne optimalt.
Virksomheden ønsker i tråd med miljøpolitikken at få sat yderligere fokus på affaldsfrembringelse og om muligt finde nye teknologier eller metoder til at genanvende en del af de spildprodukter, der
fremkommer som konsekvens af produktionen.
Vald. Birn Jernstøberi A/S repræsenterer en branche, hvor det anslås, at der årligt kasseres 60-70.000 ton lerbundet formsand.
Vald. Birns Jernstøberi A/S havde i år 2000 omkring 22.000 ton overskudsmateriale.
Vald. Birns Maskinfabrik A/S havde et væsentligt affaldsprodukt i år 2000 nemlig kølesmøremidler, som udgjorde ca. 480.000 liter
Vald. Birn A/S ønskede derfor specifikt at sætte fokus på minimeringsmulighederne for:
- Støbesand, idet dette restprodukt har et højt indehold af kulstøv og lerpartikler, der ved udvinding på ny vil kunne tilsættes sandet og derved reducere behovet for nyt kul og ler.
- Kernevrag, der ved nedknusning vil kunne tilsættes i mindre mængde som nyt kernesand.
- Kølesmøremidler, der i dag er vanskelige at vedligeholde i de separate kølesmøreanlæg på de enkelte maskiner, men som ved samling på et anlæg vil give mulighed for øget behandling og
regenerering, og dermed forlænge levetiden og reducere behovet for nyt kølesmøremiddel.
Derudover ønskede Vald. Birn at gøre en generel indsats for at reducere spildmængderne ved at motivere medarbejderne til at sætte fokus på håndteringen af råvarer og hjælpestoffer og mulighederne for
spildminimering.
1.2 Formål
Projektets formål var således at minimere affaldsmængden i udvalgte affaldsfraktioner inden for støberi- og maskinindustrien ved at reducere spildmængden generelt og genbruge en større del af det spild, der
kom fra produktionsprocesserne, og som blev bortskaffet som affald.
En øget affaldsminimering skulle opnås dels via udvikling og afprøvning af nye teknologier, dels via medarbejderinddragelse og forståelse for, at affald er en spildt ressource.
Potentialet for at øge genanvendelsen i virksomhederne er forsøgt opgjort både mængdemæssigt og økonomisk, og resultatet heraf anvendt til at belyse hvilke affaldsminimeringsperspektiver, der kan være
ved at udbrede de foreslåede teknologier i den øvrige del af støberibranchen.
1.3 Målgruppe
Målgruppen for projektet er støberier og maskinfabrikker samt tilhørende brancheorganisationer.
2 Projektforløb
2.1 Aktiviteter
Projektet har været opdelt i nedenstående 6 faser:
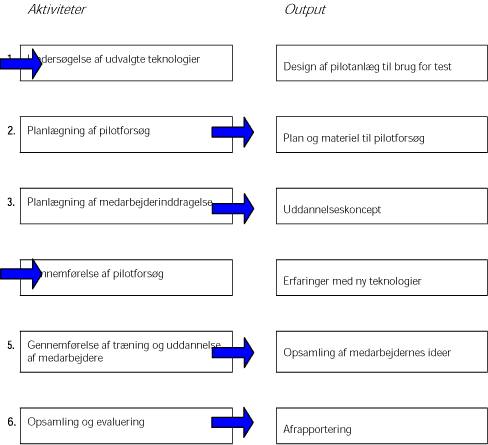
3 Gennemførte indsatser
3.1 Reduktion af spildproduktet støbesand fra filtre
3.1.1 Reduktion af støbesand til deponi, ved genanvendelse af filterstøv
Det var formålet at separere støberisandet, som består af filterstøv fra sandtårnsfilteret og genanvende det. Filterstøvet indeholder store mængder bentonit, hvilket er en af ingredienserne i blandingen af
støbesand. Resten af denne fraktion består af mere eller mindre dødbrændte sandpartikler, som ikke ønskes tilbage i støbesandet.
Til at separere filterstøvet blev forsøgt anvendt en Trenso sigte. Trenso sigten består af en perforeret vibrationsrende. Der sættes luft under renden, hvorved de lette dele af fraktionen bliver luftbårne. De
tunge dele af fraktionen bliver på renden og kommer ud i den ene ende, og de luftbårne kommer ud i den anden ende.
Ved at regulere luftstrømmen kan man bestemme, hvor skillelinjen mellem tung og let fraktion skal gå.
Efter sorteringen var ideen at tilsætte den lette fraktion, ved hjælp af et pneumatisk skydeanlæg, direkte ind i sandblanderen (speedmullor), hvor det erstatter nyindkøbt bentonit og kul.
Potentialet skønnedes at være 40% af det filterstøv, der blev deponeret i 2001. Det indebærer et økonomisk besparelsespotentiale til nyindkøb og bortskaffelse på ½
mio.kr pr. år.
Udlæg til pilotanlæg til genbrug af filterstøv ved separering |
|
Budget |
Realiseret |
Trenso sigte |
200.000 kr. |
0 kr. |
Indløbssystem |
50.000 kr. |
0 kr. |
Sug på sigte |
150.000 kr. |
0 kr. |
Skydesystem |
150.000 kr. |
0 kr. |
Installation |
200.000 kr. |
0 kr. |
I alt |
750.000 kr. |
0 kr. |
3.1.2 Erfaringer med genanvendelse af filterstøv
For at vurdere sigtens potentiale blev der sendt en sandprøve ned til Trenso for at foretage en prøvesortering på et lille pilotanlæg.
Prøverne viste, at det var vanskeligt for sigten at sortere sandet i de meget fine fraktioner, som var nødvendigt. Hos virksomheden Nomi, hvor udstyret anvendes, sorteres fraktioner mellem 1- 10 gram,
mens behovet hos Vald. Birn A/S er en sortering i området omkring 0,25 g. Det blev således konklusionen, at udstyret ikke kunne håndtere sorteringskravet, idet den mindste ændring af paramenterne f.eks.
tilgangsluften medførte at sorteringen blev skæv. At køre med en sådan sigte vil kræve for mange ressourcer, da sigten til stadighed vil skulle kalibreres. Endvidere var indkøbsprisen på sigten (ca. 1 mio.kr.
+ montage) væsentlig højere end forventet.
Grundet ovennævnte faktorer blev projektet forkastet allerede i undersøgelsesfasen.
3.2 Reduktion af spildproduktet kerner
3.2.1 Design af pilotforsøg med kerner
I produktionen af støbegods bruges der sandkerner til at lave hulrum, f.eks. hulrummet i en pumpe. I denne produktionsproces fremkommer der et vist spild af kerner og kernesand, som ikke genanvendes.
Ved at knuse en lille mængde kerner manuelt blev der foretaget et forsøg, hvor der blev tilsat 5% knust kernesand. Dette forsøg faldt positivt ud, da det ikke påvirkede kernernes styrke væsentligt.
Til at omdanne kernerne til et anvendeligt produkt bruges en vibrationssigte, der anvendes til et tilsvarende formål, nemlig at knuse de kernestumper, der sorteres fra sigten i sandanlægget.
En vibrationssigte fungerer ved, at kernerne hældes i en tragt og ned i et perforeret kar med 4 mm huller, hvor det nedknuses. Efter knusningen vibreres sandet over en sol med en hulstørrelse på 1,2 mm.
Herved opnås ca. 1% restprodukt og 99% af udgangsmaterialet, der forventes at kunne genanvendes.
Potentialet skønnedes at være 50% af kernevragene og afhærdet kernesand, der blev deponeret i 2000. Dette giver et økonomisk besparelsespotentiale til nyindkøb og bortskaffelse på 150.000 kr. pr. år.
Omkostninger ved pilotanlæg til genbrug af kerner:
Kerneknuser |
Budget |
Realiseret |
FAT kerneknuser |
200.000 kr. |
136.601 kr. |
Installation |
80.000 kr. |
78.019 kr. |
Indløbstragt + udløbstragt + containere |
80.000 kr. |
161.593 kr. |
Installation el |
80.000 kr. |
67.501 kr. |
I alt |
440.000 kr. |
443.714 kr. |
|
Buffersilo |
|
Buffersilo + smede installation |
|
295.373 kr. |
Installation el |
|
83.866 kr. |
I alt |
|
379.239 kr. |
|
|
|
Totalt |
|
822.953 kr. |
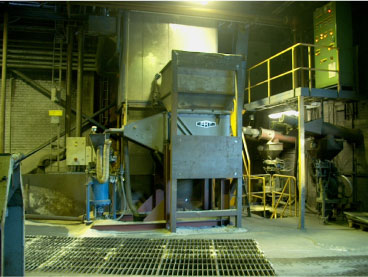
Kerneknuser og buffersilo
3.2.2 Erfaringer med reduktion af spildproduktet kerner
Det har vist sig, at pilotanlægget, som det oprindeligt var konstrueret, ikke kunne håndtere de mængder knust kernesand, som det var tiltænkt. Dette skyldtes, at forbruget af knust kernesand kan variere
meget, alt efter hvilken model der produceres. Dette gør, at når der produceres en model med et stort sandforbrug, kan der ikke tilsættes de planlagte 5%, da der ikke er den mængde knust kernesand til
rådighed. Endvidere viste det sig at være nødvendigt at køre nogle af kernevragene ”
den gamle vej”
i containere, da der ikke var kapacitet til at opbevare de mange knuste kerner.
Til løsning af dette problem blev der bygget en buffersilo til opbevaring af knust kernesand.
Siloen har en kapacitet på 25 m³
og er forsynet med en pneutisk skyder til videretransport af det knuste kernesand.
Konklusion på pilotforsøg
Pilotforsøget er forløbet uden problemer. Det viste sig at der ikke var styrkeproblemer ved at tilsætte knuste kerner ved produktion af nye kerner. Andelen af tilsat knust kernesand i nysandet udgør ved
forsøgsperiodens udløb 7%, hvilket svarer til en genindvinding af 5,2 ton om ugen eller ca. 200 ton om året. Dette svarer til en årlig besparelse til nyindkøb og bortskaffelse på 92 t.kr. årligt. Det er målet at
fortsætte med at øge genvindingsgraden.
3.3 Reduktion af spildproduktet kølesmøremidler
3.3.1 Design af pilotforsøg med kølesmøremidler
Vandbaserede kølesmøremidler fremstilles ved fortynding af et koncentrat med ledningsvand. De vandbaserede kølesmøremidler har gennem de seneste 10 år undergået en udvikling i retning af at indeholde
færre stoffer, der skønnes at give helbredsmæssige problemer. Dette har imidlertid medført, at kølesmøremidlerne er blevet meget sårbare overfor uønskede bestanddele, såsom metalspåner, lækolie,
mikroorganismer m.v.
Produkternes sårbarhed overfor ovennævnte nedsætter kølesmøremidlets levetid dramatisk og hermed efterfølgende behov for udskiftning af kølesmøremidlet og rengøring af maskinen.
Hver maskine har i princippet sit eget kølesmøremiddelanlæg med filter, pumper osv. Disse decentrale anlæg er ikke i stand til at vedligeholde kølesmøremidlet, hvilket betyder, at kølesmøremidlet i
gennemsnit kun har en levetid på 8 uger.
Ved at indføre et centralt anlæg bliver det muligt at foretage en mere omfattende og effektiv vedligeholdelse af kølesmøremidlet, således at levetiden kan forlænges. Behandlingen skal bestå i separation af
spåner, filtrering, fjernelse af lækolie, opsplitning samt eventuelt varmebehandling, køling og automatisk efterfyldning og dosering.
Vedligeholdelsen havde ikke kun til formål at holde kølesmøremidlet i en funktionsduelig tilstand, men også at forlænge levetiden til det maksimale. Forhåbningen var at forlænge levetiden fra 2 måneder til en
levetid på 8 til 12 måneder.
Besparelsespotentialet for hele fabrikken kan beregnes ud fra følgende: Totalt indkøbes der ca. 50 ton KSM årligt til en værdi af ca. 1.350 t.kr. Samme mængde bortskaffes til et gebyr på ca. 23 t.kr./årligt.
Forlænges levetiden til 8 måneder opnås der således en besparelse på 75% på henholdsvis indkøb og bortskaffelsen svarende til ca. 1 mio. kr. årligt samt en reduktion i mandskabstimer til rengøring og
vedligeholdelse af KSM-anlæg, ligeledes på 75% af de nuværende driftsomkostninger.
Udlæg til centralrensning af KSM |
|
Budget |
Realiseret |
Opsamlingstank til kølesmøremidlet |
350.000 kr. |
|
Opsamlingssystem |
108.000 kr. |
ikke specificeret |
Opsamling af procesdata |
100.000 kr. |
|
Pumpestationer og spånknuser |
75.000 kr. |
|
Installation af rørledninger |
45.000 kr. |
|
I alt |
678.000 kr. |
1.398.030 |
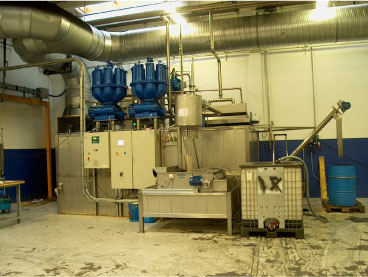
KSM-anlæg
3.3.2 Erfaringer med centralrensning af kølesmøremidler
Forsøg med centralanlæg til rensning og justering af kølesmøremidler, er blevet etableret og fungerer i dag på 3 bearbejdningsmaskiner.
Konklusion på pilotforsøg
Målet om forlængelse af levetiden på kølesmøremidlet fra 2 måneder til 8-12 måneder er lykkedes. Levetiden er i dag på ca. 9 måneder, men der arbejdes fortsat mod en levetid på 12 måneder.
Forlængelsen af levetiden har givet en reduktion på 75% i indkøbs- og bortskaffelsesomkostningerne for KSM samt en reduktion, ligeledes på ca. 75% i mandskabstimer, til rengøring og vedligehold af det
decentrale KSM-anlæg. Der vil i løbet af efteråret 2005 blive koblet yderligere bearbejdningsmaskiner op på centralanlægget.
4 Medarbejderinvolvering i affaldsminimering
4.1 Design af informationsforløb for medarbejderinvolvering
Formålet var at strukturere et tilpasset informations- og uddannelsesforløb, der involverede medarbejderne og skabte fokus og engagement omkring affaldsminimering i virksomheden.
Som målgruppe for informations- og uddannelsesforløbet var de medarbejdere, der har størst kontakt med affaldet i kraft af deres jobfunktioner.
Selve informations- og uddannelsesforløbet blev baseret på Miljøstyrelsens Affaldskortlægningsmodel.
Første element i informations- og uddannelsesforløbet var at opstille nogle rammer for, hvad der er virksomhedens væsentligste miljøforhold, og hvilken rolle og betydning det har, at medarbejderne tager del
i og ansvar for virksomhedens miljøarbejde.
Efterfølgende blev deltagerne introduceret til Miljøstyrelsens Affaldskortlægningsmodel for gennem anvendelse af modellen at blive trænet i at kortlægge og analysere, hvor i deres arbejdsområde spildet
opstod.
På baggrund af de fremkomne forbedringsforslag vurderede de miljøansvarlige på Vald. Birn A/S hvilke initiativer, der skulle i værksættes.
4.2 Erfaringer med medarbejderinvolvering i affaldsminimering
Informations- og uddannelsesforløbet blev struktureret forskelligt på de to enheder Jernstøberiet og Maskinfabrikken.
På sidstnævnte blev, som planlagt, afholdt et action-leaningforløb, hvor deltagerne mødtes ad to omgange i forlængelse af arbejdsdagen. Første gang for at blive introduceret til kortlægnings- og
analysemetoden, anden gang for at drøfte resultaterne af kortlægningen og analysen og lægge planer for gennemførelse af forbedringsforslagene.
Oplevelsen var, at det var vanskeligt at være motiveret efter en arbejdsdag, samt at der allerede var taget hånd om Maskinfabrikkens væsentligste affaldsprodukter d.v.s., spåner og KSM, hvorfor ideerne til
affaldsminimering var sparsomme.
Resultaterne af forløbet gav dog følgende ideer, primært til affaldsminimering af brændbart affald:
Vald. Birn Maskinfabrik - Ændringsforslag
- Erstatte foliewrap på filterpaller med pallebånd ved at stille krav til leverandører
- Modtage reservedele i kuverter frem for papkasser, når det er muligt
- Udarbejde retningslinjer for tømning af dunke og bøtter
- Nyt system for jobkort, så der ikke skal printes 6-8 stk. pr. ordre
- Satse på designemballage, som passer til produktet, og som kommer retur fra kunden
- Ny mærkning af papirkasser ved printere (i dag står der ”
alt brændbart”
i stedet for papir)
- Undersøge om masonitplader kan gå som træaffald
- Frasortere flamingo til brug for egne forsendelser
- "Kontrol" med udlevering af handsker
- Kapsler sorteres til metal
- Generelt bedre instruktion til nyansatte og afløsere omkring affaldssortering
- Bedre introduktion fra miljøchef til arbejdsledere/værkfører om affaldsplan
- Kommunikation mellem dag- og aftenhold (2x5 min. overlap en gang om ugen)
- Krav til leverandør om at tage spild af pulvermaling retur ligesom andre leverandører tilbyder
- Præmiering af gode ideer og/eller optimal sortering, der er omkostningsbesparende.
Da der ikke umiddelbart var de store problematikker eller potentialer i de foreslåede forbedringsforslag, blev det besluttet at gennemføre de realiserbare forslag og fokusere på at få kortlagt de resterende
affaldsfraktioner i Maskinfabrikken/malerafdelingen.
Vald. Birn Jernstøberi –
Kortlægning og ændringsforslag
På Jernstøberiet blev forløbet grebet anderledes an, da man her havde gode erfaringer med at tage væk fra virksomheden en hel dag. Således blev der i hhv. år 2002 og 2004 afholdt en workshopdag på
Pinenhus i Glyngøre for 20-25 deltagere.
Workshopdagene startede med en status over udvikling i affaldsmængder og økonomien i Jernstøberiet. Efterfølgende blev deltagerne introduceret til affaldskortlægningsmodellen og besluttede ud fra
kriterierne mængde og økonomi, hvilke fraktioner de ville arbejde videre med. Deltagerne delte sig i grupper efter interesse og udarbejdede nedenstående analyse og forbedringsforslag til de fire fraktioner:
”
Ikke brændbart”
, ”
Slagger fra smelteovn”
, ”
Kernerester”
og ”
Filterstøv fra sandtårn”
. De to sidste fraktioner var de samme, som der blev arbejdet med tekniske løsninger i forhold til. På anden
workshopdag blev der desuden arbejdet med temaet ”
Kommunikation om affald”
.
Oplevelsen på de to workshopdage var, at deltagerne var motiverede og engagerede i opgaven og fremkom med ideer til flere års indsats for affaldsminimering på Jernstøberiet.
4.2.1 C – fraktion, ikke brandbart affald
4.2.1.1 Kortlægning:
Affaldsprodukt |
Hvor og hvordan opstår det? |
Sand |
Rengøring i støberi/maskinspild/forkert fyldt
vippekasse |
Sværteslam |
Bundfald i sværte i kernemageriet |
Kernerester |
Støberiet |
Jern |
Støbesprøjt |
Opfej |
Fra opfej i støberiet |
Der blev i år 2000 bortskaffet ca. 1.900 ton til deponi, hvilket udgjorde en omkostning på ca. 1,12 mio.kr.
4.2.1.2 Forbedringsforslag:
C –
fraktionen kan ikke helt undgås, men kan måske reduceres ved:
Ideer 2002 |
Status november 2004 |
1) Sortere C-fraktionen, så mere kan genbruges (jern, sand, kerner og
andet). For at kunne sortere, kræves: bord –
magneter –
sigte
I gruppen mener man, at de forskellige typer affald i C-fraktionen fordeler sig således:
Omkostninger ved bortskaffelse til deponi 610 kr./t og til genbrug 150 kr./ton
80% |
sand 610-150 kr./t |
= |
460 kr./t |
10% |
jern 610kr./t + indkøbspris |
= |
610 kr./t |
5% |
kerner 610-150kr./t |
= |
460 kr./t |
5% |
andet 0kr. |
= |
0 kr./t |
Besparelse ved f.eks. 1.000 t/år
Sand |
800t x 460kr./t |
= |
368.000 kr. |
|
|
Jern |
100t x 610kr./t |
= |
61.000 kr. |
+ |
indkøbspris |
Kerner |
50t x 460kr./t |
= |
23.000 kr. |
|
|
I alt |
|
|
452.000 kr. |
+ |
indkøbspris/jern |
Forventet tilbagebetaling 2 –
3 år |
|
Der er bygget et sorteringsanlæg til sigtning af C-fraktionen (ikke brændbart affald til deponi), som i 2000 udgjorde 1.900 ton. Sorteringsanlægget består af en elevator, der hejser
C-containerne op i et tårn, og tømmer dem over et ristesystem og videre over en sigte. |
2) Bedre information omkring sortering |
|
Er en løbende proces |
3) Plancher/billeder på container |
|
Er gennemført |
4) Hælde boller der går i stykker og opfej i udslager, så det bliver genanvendt samtidig med at jern tages fra.
Der skal måske ændres på en dør, så det bliver muligt at tømme vippekasser i udslager. |
|
Er forsøgt, kunne ikke lade sig gøre |
5) Stop ved klatter på fremføringsskinner |
|
Er en løbende proces |
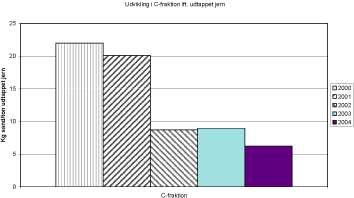
4.2.1.3 Udvikling i C-fraktionen i perioden
Udviklingen i C-fraktionen i perioden år 2000 til 2004 viser et drastisk fald. I år 2004 deponeres der således kun 6 kg C-affald pr. ton udtappet jern mod 22 kg i år 2000. En ændring på ca. 72%. Hvilket
bl.a. skyldes, at der er blevet etableret sortering af C-fraktionen.
Betragtes den totale mængde C-affald før sortering i år 2004, er den faktiske mængde reduceret med 200 ton (selvom udtapningen af jern var øget med 4,5%), og ved sortering blev indvundet ca. 400 ton
jern til genanvendelse internt, og ca. 700 ton sand til genanvendelse eksternt, mens resten ca. 550 ton fortsat kom på deponi. Deponeringsomkostningen udgjorde i år 2004 ca. 325.000 kr., hvilket er en
besparelse på ca. 816.000 kr. og en reducerede mængde affald til deponi på 1.300. Der til kommer værdien af det genindvundne jern.
Fremtidige indsatser i forhold til C-fraktionen, ikke brændbart
Ideer 2004 |
- Bedre information omkring sortering
- Involvering/information ved ændringer
- Mindre håndtering af containere i forbindelse med sorteringsanlægget
- Anlægget er for følsomt (elevator + microswitch ved dør)
- Betjeningspult på anlægget er ikke optimal, der mangler display
- Mere sand ind over anlægget, så det hele sorteres
- Bedre indretning af pladsen med sorteringsanlægget
- Bedre opsamling i container
- Forsortering for at fjerne de ”
store”
ting evt. ved dobbelt forskudt rist
- Sigteanlægget udbygges.
|
4.2.2 K – fraktion, slagger fra smelteovnene
4.2.2.1 Kortlægning:
Affaldsprodukt |
Hvor og hvordan opstår det? |
Slagge |
Hvor der smeltes. Jern iltes. |
Der blev i år 2000 bortskaffet ca. 1.000 ton slagge til en bortskaffelsespris på ca. 150.000 kr. Denne omkostning kan reduceres, hvis slaggen kan undgås eller afsættes til genanvendelse.
4.2.2.2 Forbedringsforslag
Slagge kan ikke helt undgås, men kan måske reduceres ved:
Ideer 2002 |
Status november
2004 |
1) Rensning af omgangsjern |
|
Der er opsat knuser til knusning af indløb |
2) Indkøb af bedre og renere skrot |
|
Skrothandlerne skal levere skrot, der er så rent, at vi umiddelbart kan bruge det.
Skrot kontrolleres ved indvejning. |
3) Undersøge om slaggen kunne genanvendes som råvare for en anden virksomhed f.eks. sten i ovne ved glasuldfremstilling, fyld i asfalt, erstatning for stabilgrus på skovvej, markvej
eller rastepladser, erstatning for byggematerialer. |
|
Slaggen knuses og afsættet til vejprojekter. |
4) Knusning og rensning af slagge for jern inden afsætning.
Ved knusning af slaggen bliver jernet frigjort og kan anvendes igen, samtidig reduceres den samlede mængde slagge. Gruppen regner med at kunne frigøre ca. 100 ton jern om året.
For at kunne frigøre jern fra slagge kræves en maskine, der kan knuse slagger, f.eks. en valse og en magnet som kan skille jernet fra slaggen.
Man vil kunne spare et mellemled samtidig med, at man får op til 100 ton jern pr. år ”
gratis”
. Slaggen bliver ren og kan sælges eller anvendes direkte, da man selv bestemmer, hvor grov
slaggen er.
Der spares også transporttid. |
|
Der er for stor del af restslagge i jernet til at vi kan anvende det igen.
Andelen af jern i slaggen er blevet væsentlig mindre. |
4.2.2.3 Udvikling i K-fraktionen i perioden
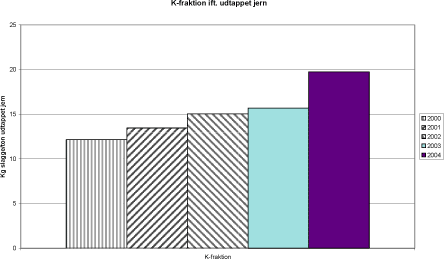
Slaggen bortskaffes nu til genanvendelse i stedet for deponi, hvilket giver en reduceret bortskaffelsespris. Mængden af slagge afhænger at renheden af råvaren, og det er vanskeligt at få råvarerne så rene som
ønskeligt.
4.2.2.4 Fremtidige indsatser i forhold til K-fraktionen, Slagger
Der er ikke arbejdet med yderligere indsatser i forhold til K-fraktionen.
4.2.3 N – fraktion, kernerester
4.2.3.1 Kortlægning:
Affaldsprodukt |
Hvor og hvordan opstår det? |
Coldbox kerner |
Itu |
Blandet sand |
Ved tømning af maskiner/dårlig blanding |
Dårlige kerner |
Amin tilsætning/kernekasse/ håndtering/transport |
Besparelsespotentialet på bortskaffelsesomkostningerne er samlet set 500 t.kr./år, hvis man kunne genindvinde kernesandet til egen produktion.
4.2.3.2 Forbedringsforslag
N –
fraktionen kan ikke helt undgås, men kan måske reduceres ved:
Ideer 2002 |
Status november 2004 |
1) Ændre konstruktion af indskydning i kernekasserne |
|
Der arbejdes med ændring af indskydning på de kernekasser, hvor det kan betale sig. |
2) Anvende alle kerner |
|
Nyt edb-system fortæller, hvor mange kerner der skal være på stativerne, så kernerne ikke går itu under transport. |
3) Håndteringen af de færdige kerner |
|
Mikrobølgeovn og Disa 4 har bevirket, at kernerne håndteres og flyttes mindre. |
4) Bedre sortering |
|
Med de nye vippekasser og udlevering af folder til nye medarbejdere kan det ikke gøres bedre |
5) Afpasse sandmængden ved kernekasseskift og arbejdstids ophør |
|
Er blevet bedre men er stadig et problem. Der arbejdes videre på løsning af problemet. |
6) Mængden af N –
fraktionen der genanvendes kan måske øges. |
|
Tilsætningsgraden af knuste kerner til kernesand skal øges, hvis alle knuste kerner skal kunne genanvendes, alternativt kan kernesandet måske tilsættes formsandet. |
7) Ændret adfærd |
|
Der er sket en ændring af adfærden i kernemageriet til det bedre. |
8) Planlægning af små ordrer |
|
Ingen indsats
da dette bliver behandlet i det nye edb-system. |
4.2.3.3 Udvikling i N-fraktionen i perioden
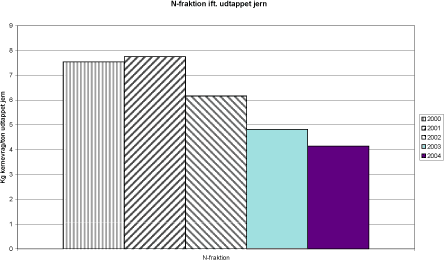
Den opnåede besparelse på N-fraktionen i forhold til år 2000 er 380.000 kr., når den ændrede bortskaffelsesform, reduceret mængde og værdien af det genvundne kernesand medregnes.
4.2.3.4 Fremtidige indsatser i forhold til N –
fraktion, kernerester
Ideer 2004 |
9) Forebygge fejl i kernemageri:
- Ved bearbejdning og sværtning.
- Undgå gamle (dårlige) vaner.
- Ved produktion af kerner.
|
10) Cronitkerner - anvendes til skalsand, hvis de ikke er hærdet. |
11) Genanvende sand fra sværtede kerner (alle kerner).
- Evt. også i formsand (måske sigtet).
- Evt. højere andel i nye kerner.
|
Målet er, at alle kerner genanvendes!
4.2.4 B – fraktion, overskudssand fra filter i sandtårn
4.2.4.1 Kortlægning
Affaldsprodukt |
Hvor og hvordan opstår det? |
Filterstøv (40% bentonit
og kul samt 60%
dødbrændt sand) |
Afsugning i sandtårn |
Overskudssandet fra filterne indeholder ca. 40% bentonit og kul, og har derfor en nyværdi på ca. 2.000 t.kr./år.
4.2.4.2 Forbedringsforslag
Filterstøv kan ikke helt undgås, men kan måske reduceres ved:
Ideer 2002 |
Status november 2004 |
1) Der skal udarbejdes et vægtstyret doseringssystem samt en silo. Gruppen mener, man skal starte forsigtigt med at tilbageføre en passende støvmængde. Ca. halvdelen af det ”rigtige” støv er aktive bestanddele, der gør det muligt at spare nye materialer samt at op- og nedjustere så meget. |
|
Undersøgelse er i gang |
2) Udvinding af aktive bestanddele af støv kan være et væsentligt supplement af tilsætningen af nye materialer. |
|
Undersøgelse er i gang |
3) Større lagerkapacitet til formsand |
|
Der har ikke manglet lagerkapacitet til sand de sidste 2 år. |
4) Silo til støvsugersand |
|
Siloen til støvsugersand er opsat. |
4.2.4.3 Udvikling i B-fraktionen i perioden
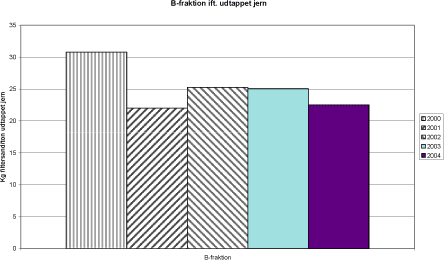
Variationen i B-fraktion er afhængig af belastningen af sandet, primært størrelsen af emnerne der støbes, således giver store emner en stor belastning af sandet og resulterer i en større mængde dødbrændt
sand, der suges op i filtrene i sandtårnet.
4.2.4.4 Fremtidige indsatser i forhold til B-fraktionen, overskudssand fra filter i sandtårn
Ideer 2004 |
- Yderligere forsøg med adskillelse af bentonit og ”
dødbrændt”
sand f.eks. separation ved luftstrøm
- Forsøg med tilsætning af filterstøv inklusive dødbrændt sand i forskellige blandingsforhold
- Støv –
kernesand = slemstof.
- Tilsætte kerner
|
4.2.5 Nyt indsatsområde er ”Kommunikation”
Ideer 2004 |
- Mere oplysning til alle hold.
- Oplysning om omkostninger ved affald.
- Evt. 1 times kursus i affaldsminimering til samtlige ansatte.
- K. B. Larsen kunne evt. orientere om affaldsminimering/sortering på Kvalitet/Miljø/Sikkerhedskurset.
- Tilbagemelding vedr. resultater enten personligt (møder) eller skriftligt (brev eller i medarbejderbladet) om mængder/økonomi og tendenser i udviklingen.
- Ved nye projekter skal der tænkes på affaldsmængder.
|
4.2.6 Øvrige tiltag i perioden
Spånpresse
De jernspåner, som produceres i forbindelse med bearbejdning af emner på Maskinfabrikken, presses nu sammen med spåner udefra. Jernbriketterne kan nu anvendes direkte i smeltediglen og udvikler
væsentlig mindre røg end de løse spåner, da kølesmøremidlerne er presset ud. (se bilag A)
Foto og registrering af spild langs støbelinjerne
Et forslag fra støberiets reparations- og vedligeholdelsesmester har på to år bragt spildet af sand fra transportbåndene fra 75 tons til 14 tons om ugen. Metoden er et weekendhold, som reparerer utætheder
på båndene, der hvor støberiets støvsugerhold bruger længst tid på at rydde op. En opgave der ikke før var ressourcer til at nå i løbet af ugen.
Udover at registrere ved hvilket af de 7 bånd, der bliver støvsuget mest, bliver der også taget billeder af de steder, hvor der er spild eller andre afvigelser. Billederne taler for sig selv og fungerer dermed som
en slags fejlrapport, der eksempelvis indikerer, hvor weekendholdet skal tage fat. Fotografen er en af de ansatte på virksomheden, og billederne er bare en del af hans virke som krumtap i arbejdet, som han
fremlægger på det ugentlige produktionsmøde.
5 Udvikling i affaldsmængder i perioden
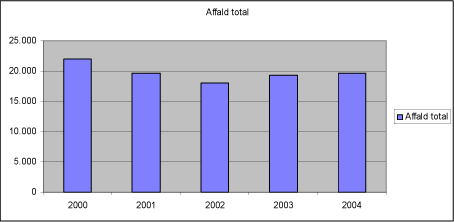
Affaldsfraktioner i totale mængder (ton)
Fraktion |
2000 |
2001 |
2002 |
2003 |
2004 |
Diff. |
A Container |
3.671 |
3.034 |
3.312 |
2.357 |
3.678 |
7 |
B Container |
2.617 |
1.712 |
2.114 |
2.065 |
2.001 |
-616 |
C Container |
1.868 |
1.564 |
727 |
738 |
553 |
-1.315 |
D Container |
8.909 |
8.084 |
7.316 |
10.307 |
8.804 |
-105 |
H Container |
856 |
855 |
915 |
679 |
883 |
27 |
K Container |
1.034 |
1.047 |
1.258 |
1.293 |
1.753 |
720 |
M Container |
2.326 |
2.703 |
1.856 |
1.469 |
1.649 |
-677 |
N Container |
641 |
603 |
516 |
397 |
368 |
-273 |
Total |
21.922 |
19.602 |
18.014 |
19.305 |
19.689 |
-2.233 |
Som det fremgår af såvel tabellen som figuren, har der generelt været en positiv udvikling i den samlede mængde affald fra år 2000, hvor Vald. Birn havde en samlet affaldsmængde på omkring 22.000 ton til
19.700 ton i 2004. Det er et fald på omkring 10%. Udviklingen har dog ikke været jævnt faldende, men derimod faldende indtil 2002, hvorefter den er steget igen. Dette skyldes blandt andet udviklingen i
mængden af udtappet jern.
Tages der hensyn til den samlede mængde udtappet jern, ser billedet således ud:
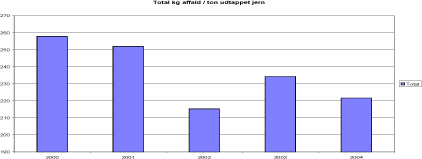
Ser man på udviklingen i den totale affaldsmængde pr. ton udtappet jern, er der samlet set sket en reduktion på 36 kg/ton udtappet jern i perioden fra 2000 til 2004. Det svarer til et fald på 15% i den
samlede mænge affald pr. ton udtappet jern, men også her svinger udviklingen fra år til år.
Ses der på udviklingen i mængden af affald i forhold til udtappet jern fordelt på de væsentligste affaldsfraktioner (fraktioner der udgør mere end 5%), varierer udviklingen betydeligt fra fraktion til fraktion.
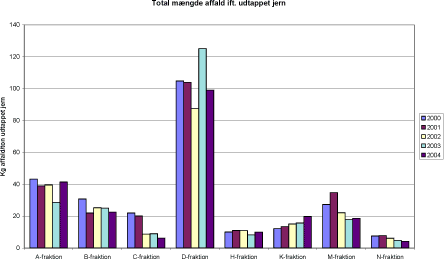
Affaldsfraktioner i kg/ton udtappet jern
Fraktion |
2000 |
2001 |
2002 |
2003 |
2004 |
Diff. |
A Container |
43 |
39 |
40 |
29 |
41 |
-2 |
B Container |
31 |
22 |
25 |
25 |
23 |
-8 |
C Container |
22 |
20 |
9 |
9 |
6 |
-16 |
D Container |
105 |
104 |
87 |
125 |
99 |
-6 |
H Container |
10 |
11 |
11 |
8 |
10 |
-0 |
K Container |
12 |
13 |
15 |
16 |
20 |
8 |
M Container |
27 |
35 |
22 |
18 |
19 |
-9 |
N Container |
8 |
8 |
6 |
5 |
4 |
-3 |
Total |
258 |
252 |
215 |
234 |
222 |
-36 |
Ser man på udviklingen i de fraktioner, der udgør tab af lerbundet formsand, har denne været særdeles positiv. Mængden af kasseret kilo overskudssand pr. ton udtappet jern er således faldet fra 226 kg til
192 kg, hvilket svarer til en reduktion på 15%.
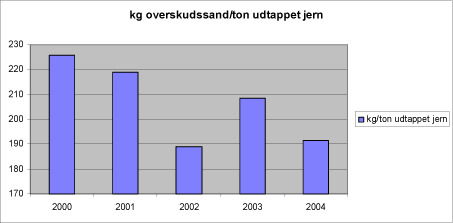
Udviklingen i den samlede genanvendelsesprocent fra 2000 til 2004 er meget positiv, idet en stor del af den mængde affald, der tidligere gik til deponi, nu genanvendes. Fra 2000, hvor 72% blev genanvendt,
til 2004 hvor 97% af den samlede affaldsmængde genanvendes.
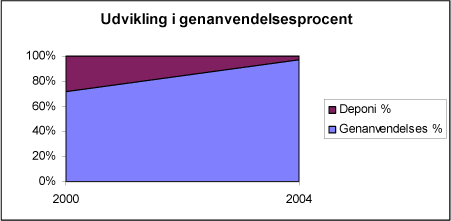
6 Konklusion på projektet
På grundlag af arbejdet med de tre pilotforsøg kan det konkluderes, at der er basis for at arbejde videre med to af tre testede teknologier.
I det sidste pilotforsøg, som omhandlede separation af bentonit og kul fra filterstøv, er der fortsat et økonomisk potentiale på ca. 2 mio. kr. årligt, men de afprøvede teknologier har ikke kunnet klare
opgaven på en driftssikker måde. Et alternativ kan være, som foreslået af medarbejderne, at køre forsøg med at tilsætte mindre mængder af filterstøvet usepareret, således at både bentonit og kul (40%) og
dødbrændt sand (60%) tilsættes forsøgsvis. En anden mulighed kunne være at forsøge en andet separationsteknologi som f.eks. separation ved brug af vindcyclon.
De to øvrige pilotforsøg fungerede som planlagt. Undervejs viste det sig, at der var behov for en øget opbevaringskapacitet for nedknuste kernevrag, således at det var muligt at køre en jævn produktion
med tilsætning af samme mængde genbrugskernesand gennem en hel produktionsordre. Den nødvendige bufferkapacitet til nedknust kernevrag blev etableret under forsøgsperioden, men det kunne ved
projektets afslutning konstateres, at der også er et behov for yderligere opbevaringskapacitet til kernevrag, idet en del vrag fortsat køres til deponi, fordi der ikke er kapacitet på nedknusningsanlægget.
Andelen af tilsat genbrugskernesand til nysandet udgør ved forsøgsperiodens udløb 7%, hvilket svarer til 5,2 ton om ugen eller ca. 200 ton om året. Dette giver en besparelse til nyindkøb og bortskaffelse på
82 t.kr. årligt. De 200 ton udgør ca. 33% af N-fraktionen, så det er målet at fortsætte med at øge genvindingsgraden, blandt andet ved at se på mulighederne for også at genbruge sværtede kerner.
Centralrenseanlægget til kølesmøremidler fungerede ved projektets afslutning med tre bearbejdningsmaskiner tilkoblet. Pilotforsøget har vist, at der kan opnås en besparelse på 75% af omkostningerne til
indkøb og bortskaffelse af kølesmøremidler samt på mandskabstimer til rengøring og vedligeholdelse. Dette er ensbetydende med en potentiel besparelse på ca. 1 mio.kr. årligt svarende til et reduceret
indkøb af KSM på 37,5 m³
årligt, hvis systemet udbygges til at dække alle bearbejdningsmaskiner. Maskinfabrikken har derfor planer om at koble flere bearbejdningsmaskiner på centralanlægget, startende
i efteråret 2005.
Resultatet af forløbet med involvering og kvalificering af medarbejderne har været en succes for Jernstøberiet, hvor de intensive workshopdage har givet et stort udbytte med hensyn til ideer til
affaldsminimering. Udbyttet af det opdelte forløb på Maskinfabrikken var mere sparsomt. Dette kan enten skyldes formen på forløbet eller at der er væsentligt mindre affaldspotentiale at tage fat på i
Maskinfabrikken eller en blanding af begge dele.
Det er den umiddelbare subjektive vurdering, at der er kommet øget fokus på spild i virksomheden. Der orienteres mere om affaldssortering og udviklingen i affaldsmængderne, og der er opnået bedre
sortering af affaldet og skabt større bevidsthed om ikke at ”
tabe”
ressourcerne på gulvet. Indsatser såsom at bygge et sorteringsanlæg til C-fraktionen, som medarbejderne foreslog på første workshop og
lade rengøringen bruge fotodokumentation til at illustrere, hvor der spildes ressourcer ved støbelinjerne, er med til at skabe synlighed i forhold til affaldsindsatsen.
Ved at gennemføre de to pilotforsøg samt involvere medarbejderne og realisere deres ideer er der opnået en reduktion af affaldsmængderne pr. ton udtappet jern på 14%.
I nedenstående tabel ses differencen i nøgletallet kg affald pr. ton udtappet jern totalt for alle fraktionerne. Samlet set er det sket en reduktion på 36 kg pr. ton udtappet jern i perioden fra år 2000 til år 2004.
Sammenholdes denne reduktion med den faktiske mængde udtappet jern i 2004, er der opnået en affaldsreduktion på 3.222 ton affald.
Nøgletal |
Difference i kg/ton
udtappet jern (2000
ift. 2004) |
reduceret ton
affald i forhold til
udtappet jern 2004 |
Reduceret
bortskaffelses-
omkostninger tkr. |
Reduceret
omkostning til ny
indkøb tkr. |
Total |
36 |
3.222 |
1.091 |
1.313 |
Med de bortskaffelsespriser Vald. Birn havde i år 2004, svarer dette til en besparelse ca. 1,1 mio. kr. Her i er ikke medregnet værdien af den øgede genanvendelsesgrad som er opnået i sammen periode
(fra 72% til 97%), hvilket har gjort bortskaffelsen væsentlig billigere for visse fraktioner.
Da den reducerede mængde spild erstatter tilsvarende nyindkøb af råvarer, udgør denne besparelse ca. 1,3 mio.kr.
I alt skønner Vald. Birns miljøchef, at den opnåede årlige besparelse på det faste affald beløber sig til 2,5 mio. kr. årligt. Dertil kommer besparelserne fra implementering af det centrale KSM-anlæg i
Maskinfabrikken, som forventes at udgøre 1 mio.kr. årligt, når anlægget er fuldt udbygget.
Vurderes indsatsen alene på reduktion af virksomhedens kasserede mængde lerbundet formsand, er der for disse fraktioner opnået en reduktion på 15%. Overføres det på landsplan, hvor Støberiforeningen
anslår, at der årligt kasseres 60-70.000 ton lerbundet formsand fra støberibranchen, vil det svare til en potentiel affaldsreduktion på 9-10.500 ton/år på landsplan.
Bilag A
Klik her for at læse Bilag A
| Til Top | | Forside |
Version 1.0 Februar 2006
• © Miljøstyrelsen.
|