| Forside | | Indhold | | Forrige | | Næste |
Termisk assisteret oprensning af høfdedepotet, Høfde 42, Harboøre Tange
Bilag D
Health and safety Plan, Rocky Mountain Arsenal
1. General
This task-specific health and safety plan (HASP) provides safety-related information and requirements specific to the task and work location(s) described. General requirements contained in the PMC HASP for Rocky Mountain Arsenal (RMA) along with this task-specific HASP will be implemented except where noted. Significant changes to this HASP shall be documented and approved using a field change request or re-submittal of a revised task-specific HASP.
Project Name: |
Hex Pit Soil Remediation |
Subcontract Submittal Number: 036430 |
Task Name: |
In-Situ Thermal Destruction |
Revision No.: 01
Date: 10/3/01 |
Performing Organization(s): |
TerraTherm, Inc.
Envirocon (Site preparation, general labor, operation)
Montgomery Phillips (Surveyor)
American Drilling Services (Driller)
Oilind (Supplied Air)
ENSR International (Safety)
International Electric Service (Electrician)
Propane Vendor (to be determined)
EPA SITE (& their stack testing subcontractor) |
Duration of Field Activities: |
October 2001 through July 2002 |
2. scope of work
Breakdown and description of work activities: |
Site mobilization: move equipment and trailers to site; set up fence, decon. area, and supplied-air trailer; site support area surface preparation.
Close existing subsurface utilities: excavate and plug;
Install wells: heater wells, vacuum wells, and monitoring points – combination of auger drilling & direct push;
Connect piping and electrical wiring;
Shake-down and Operation of In-situ Thermal Destruction System: operate heaters, vacuum and emission control systems;
System Monitoring: collect appropriate measurements (flow, temp., pressure, voltage, amperage, etc. and air samples for quality assurance and worker protection;
Decontamination: thoroughly clean and decon all equipment leaving the site; dispose of other equipment;
Demobilization: remove equipment and facilities from the site. |
3. location
Identify work locations at RMA: |
Hex Pit Site in South Plants area |
4. personnel
Assigned Responsibility |
Name and Organization: |
Phone Number: |
Task Site Supervisor |
Keith Bowden – TerraTherm, Inc. |
(832) 439-4110 (cell) |
Task Health and Safety Supervisor |
Joe Sanders, CIH – ENSR |
(970) 493-8878 |
5. work plan
A work plan has been developed, reviewed, and accepted for use at RMA for the work described.
Work plan title and date: |
Reviewed and accepted by: |
Hex Pit Final (100%) Design Package, March 2001 |
Subcontractor Project Manager:
Ralph Baker – TerraTherm, Inc. |
PMC Project Manager:
Ron Versaw - FWENC |
6. task hazard(s) summary
The potential health and safety hazards of this task are summarized below. The potential for encountering these hazards is ranked (high, medium, or low) based on the work to be performed and the hazard control measures to be used.
Summary |
Hazard potential |
Description of potential hazards |
___ Safety
Slips, trips and falls, strains and sprains, heavy equipment, traffic, excavations, power and hand tools, materials handling, hot work, electrical safety. |
Medium |
Narrow and uneven walking and working surfaces
Strains and sprains from lifting equipment / material
Heavy equipment: drill rig, backhoe, bobcat, dozer, etc.
Excavation cave-ins; hand tool trauma.
Falls (if equipment climbed)
Electrical shock from high voltage |
___ Utilities
Closing of exist. buried utilities; installation of new aboveground and underground utilities. |
Medium |
Excavation hazards in closing buried utilities (water / sewer);
Potential electric shock during installation of distribution panels and system wiring.
Potential fire and explosion during installation/operation of fuel lines. |
___ Chemical
(All chemical hazards are identified in the PMC HASP, Section 5) |
Medium |
Hexachlorocyclopentadiene
Hexachlorobenzene
Aldrin
Chlordane
Dieldrin
Endrin |
___ Physical
Heat, cold, burns, noise |
Medium |
Heat stress from impervious PPE and hot equipment;
Cold stress during Winter;
Burns from hot equipment
Noise from drill rig or equipment |
___ Biological
Plants, animals, insects, spiders |
Low |
Animals: prairie dogs, deer, snakes, etc. (disease vectors)
Insects/spiders: unlikely, but could be on site (bites, disease)
Plants: nettles may be present (skin irritation) |
___ Chemical Warfare Material |
Low |
Not expected, but possible |
___ Ordnance |
Low |
Not expected, but possible. |
7. Hazard Control Measures
Safe work practices and control measures to be used for performing this task are identified in several documents. Site-wide hazards and control measures are described in the PMC HASP. Site-wide safety practices are specified in the Project Rules Handbook for the RMA PMC, Volume I and Volume II. TerraTherm and ENSR Health and Safety Procedures are listed in Section 8, below.
Task-specific hazard control measures are specified in the Activity Hazard Analysis (AHA). The AHA has been developed for the following activities and are included as Attachment _A__.
Activities with an AHA: |
Site Mobilization/Demobilization |
Pipe Connection |
Existing Utility Closure (Excavation) |
Electrical Installation |
Well / Monitoring Point installation / removal |
ISTD Shakedown and System Operation |
Heavy Equipment Operation & Material Handling (Backhoe, Bobcat & Forklift) |
Personal and Equipment Decontamination |
Surface Cover Installation |
|
8. Written safety procedures and programs
Work at the Hex Pit will be performed in accordance with TerraTherm’s Corporate Health & Safety Policy (submitted with our proposal). Since Joe Sanders, CIH of ENSR will be acting as Site Safety Officer, TerraTherm has decided to adopt the following sections of existing ENSR safety procedures and programs for this project. Copies of applicable procedures and programs are included as Attachment __B__.
Reference Procedure or Program |
Applicable Section(s) |
ENSR H&S SOP 5.1, Hazard Communication |
All |
ENSR H&S SOP 8.1, Respiratory Protection |
All |
ENSR H&S SOP 10.2, Noise |
All |
ENSR H&S SOP 10.3, Cold Stress |
All |
ENSR H&S SOP 10.4, Hot Environments |
All |
ENSR H&S SOP 11.5, Environmental Drilling |
All |
ENSR H&S SOP 11.7, Fall Protection |
All |
ENSR H&S SOP 11.1, Excavation |
All |
ENSR H&S SOP 11.8, Lockout-Tagout |
All |
9. Permits
The following permits are required for work. Applicable completed permits and/or permit forms are included as Attachment __C__
Permit |
Notes and comments (reference activities, procedures, and coordination with appropriate organizations): |
___ Hot Work |
Required only if ignition sources are to be used in potentially explosive atmospheres (not expected). |
_Ö__ Excavation |
TerraTherm will apply for a permit to conduct intrusive work activities for specific tasks at the Hex Pit site. |
___ Confined Space |
Not expected. |
_Ö_ Lockout/Tagout |
TerraTherm will apply for a LO/TO permit, if necessary. |
10. Personal Protective Equipment
The following personal protective equipment (PPE) will be used for the identified activities.
Activity |
Head/Face |
Foot |
Hands |
Respiratory |
Clothing |
Mobilization/
Demobilization |
Hard hat & safety glasses1 |
Safety boots/ impervious or
Covered |
Work Gloves
over
Impervious
Gloves² |
None³ |
Cotton coveralls (TyvekÒ)² |
Close Existing Utility |
Hard hat & Safety glasses |
Safety boots/ impervious or covered |
Work Gloves over Impervious Gloves² |
Supplied Air (SA) |
Cotton coveralls TyvekÒ SaranexÒ as necessary² |
Well Installation |
Hard hat
Safety glasses1 |
Safety boots/
Impervious or
Covered |
Work Gloves
over Impervious gloves |
None³ for pushing/driving;SA for augering activities |
Cotton coveralls & SaranexÒ |
Connect Piping / Electrical Wiring |
Hard hat
Safety glasses1 |
Safety boots/ impervious or covered |
Work Gloves as necessary (Impervious Gloves)² |
None³ |
Cotton coveralls (TyvekÒ)² |
Shake-down System / Operate In-situ System |
Hard hat & Safety glasses As necessary1 |
Safety boots/
Impervious or
Covered |
As necessary1,2 |
As necessary1,2,3 |
Cotton coveralls TyvekÒ², SaranexÒ as necessary1,2,3 |
System Monitoring |
Hard hat & Safety glasses As necessary1,2,3 |
Safety boots/
Impervious or
covered |
Impervious
Gloves |
None³ (APR or SA if needed during chemical sampling) |
Cotton coveralls TyvekÒ SaranexÒ as necessary² |
Personal / Equipment Decontamination |
Hard hat & Safety glasses As necessary1,2,3 |
Safety boots/
Impervious or
covered |
Impervious gloves |
APR³ |
Cotton coveralls TyvekÒ SaranexÒ as necessary² |
Heavy Equipment Operation |
Hard hat & Safety glasses As necessary1,2,3 |
Safety boots/ Impervious or covered |
Work gloves over impervious gloves² |
None (SA in EZ during intrusive activities)³ |
TyvekÒ outside the EZ; SaranexÒ in the EZ during intrusive activities |
1. Unless inside trailer
2. SaranexÒ/TyvekÒ and impervious gloves if contaminant contact is likely
3. Air Purifying Respirator (APR) or Supplied Air (SA) if air monitoring indicates potential exposure.
The following competent person certifies that a hazard assessment for the identified activities has been performed and the selection of personal protective equipment is based on best available information.
Printed name |
Signature |
Date |
Joseph E. Sanders, MS, CIH
Regional H&S Manager
ENSR International |
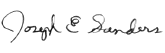 |
9/4/01 |
11. Site Monitoring
Task-specific monitoring requirements are identified below.
Direct Reading Exposure Monitoring (to monitor potential worker exposure)
Activity(s) |
Instrument |
Action Level(s) |
Actions |
Organic Vapors |
Rae Systems “MiniRae” or Photovac “MicroTip” |
1 unit for 15 minutes |
Respirators or cessation |
Total Dust |
MiniRam |
0.3 mg/m³ for 15 min |
Respirators/work cessation |
Noise |
Type I Noise Meter |
85 dBA |
Hearing Protection |
Temperature Extremes |
Psychrometer |
79 WBGT |
Work/Rest Regimen, per ACGIH |
Comments or special instructions: |
Integrated Personal Air Monitoring (full-shift worker exposure sampling and/or analysis)
Activity(s) |
Contaminant |
Method |
Frequency |
Facility Installation |
Hexachlorocyclo-
pentadiene |
NIOSH 2518 |
2 samples (1 during utility closure & 1 during drilling) |
|
Pesticides (aldrin,
dieldrin, endrin, etc.) |
NIOSH 5510 |
2 samples (1 during utility closure & 1 during drilling) |
|
Metals (As, Cd, Hg) |
NIOSH 7300 (As,Cd)
NIOSH 6009 (Hg) |
2 samples (1 during utility closure & 1 during drilling) |
|
Total Silica |
NIOSH 7500 |
2 samples (1 during utility closure & 1 during drilling) |
|
Respirable Silica |
NIOSH 0600 |
2 samples (1 during utility closure & 1 during drilling) |
ISTD Operation |
Hexachlorocyclo-
pentadiene |
NIOSH 2518 |
1 day |
|
Pesticides (aldrin,
dieldrin, endrin, etc.) |
NIOSH 5510 |
1 day |
|
Metals (As, Cd, Hg) |
NIOSH 7300 (As, Cd)
NIOSH 6009 (Hg) |
1 day |
|
Total Silica |
NIOSH 7500 |
1 day |
|
Respirable Silica |
NIOSH 0600 |
1 day |
Comments or special instructions: |
Perimeter or Work Area Monitoring (ambient work area or fence line monitoring)
Activity(s)/Location |
Contaminant(s) |
Method |
Frequency |
Facility Installation |
Hexachlorocyclo-
pentadiene |
NIOSH 2518 |
As necessary, if work zone monitoring indicates need |
ISTD Operations |
Pesticides (aldrin, dieldrin, endrin) |
NIOSH 5510 |
As necessary, if work zone monitoring indicates need |
Comments or special instructions: Perimeter monitoring only if indicated by other air monitoring. |
12. Site Control
The PMC HASP, Central Remediation Area Access Control Procedure, and RVO Access Control Procedure govern general site access and control for workers and equipment. Task-specific site control measures are specified below.
Site Control for General Work Area(s)
Location |
Site Control Procedure (discuss important elements such as signs, barricades, fencing, briefings, sign-in/out logs, etc.) |
Hex Pit area |
Orange safety fencing will be erected around the entire site. Additional orange safety fence will separate the Hex Pit exclusion zone from the remainder of the work site. Warning signs will be posted. Access to the Support & Exclusion Zones will be controlled via TerraTherm administrative procedures. Only RMA, PMC, TerraTherm, TerraTherm subcontractors, ENSR, agency personnel (and their subcontractors) will be allowed in the Hex Pit area during work. Sign-in will be required. |
Site Control for Potentially Contaminated Area(s)
Location |
Site Control Procedure (discuss important elements such as signs, barricades, briefings, qualifications, required supplies and equipment, sign-in/out logs, etc.) |
Support Zone |
Access to the Support Zone and areas around the EZ will be controlled administratively. The Exclusion Zone will be demarcated with high visibility yellow rope and/or orange safety fence and signs. |
Contamination Reduction Zone |
The Contamination Reduction Zone (Decon Area) will serve as the only entrance to and egress from the Exclusion Zone. Access will be controlled with high visibility yellow rope and/or orange safety fence. |
Exclusion Zone |
The Exclusion Zone will be demarcated with orange safety fence and signs. Personnel entry and egress will be via the Contamination Reduction Zone (Decon Area) only. |
13. Decontamination
Required decontamination procedures are described below.
Type of decontamination |
Identify activity(s) requiring decontamination, and describe decontamination steps, location, required equipment, and collection and disposal of potentially contaminated liquids and solids. |
Personnel decontamination |
Work inside the Exclusion Zone during invasive activities (e.g., drilling & utility closure) will require personnel decontamination. Hex Pit personnel will pass through the Contamination Reduction Zone in leaving the Exclusion Zone after invasive activities. Boots will be washed, and contaminated disposable PPE will be removed and placed in a container for disposal as IDW. Decon wash water will be containerized and disposed in accordance with Spec. 01560 and the project-specific ECMMP. Site personnel will shower at the South Plants shower facility prior to leaving the site. |
Equipment decontamination |
Equipment used in the Exclusion Zone during invasive activities will be decontaminated or disposed of prior to removal from the site. Vehicles will proceed to the South Plants decon facility prior to leaving South Plant. Heavy equipment will be decontaminated in the vehicle decontamination facility prior to leaving South Plants. Sampling equipment will be decontaminated in the exclusion zone using detergent and rinse water. All decon waste will be contained and disposed of according to Spec. 01420 and 01560, and the project-specific CCP and ECMMP. |
Other:______________ |
Contaminated materials (disposable PPE, etc.) will be drummed and disposed of in accordance with RMA procedures. IDW soils will be placed on the Hex Pit for in-situ decontamination or transported to an on-post disposal facility. |
14. Communications
Primary and back-up means of communications for field crews have been established as described below.
Type of communication |
Primary means |
Back-up means |
Communications with Fire and Emergency Services |
Radio (RMA Ch.1) |
Cell Phone |
Communications with home base |
Radio |
Cell Phone |
Communications among field crew members |
Voice |
Hand Signal |
15. Medical Surveillance and Qualification
The following medical surveillance is required for on-site personnel working in the field. Medical surveillance qualification records and a medical data sheet will be kept on-site at RMA.
Required medical surveillance: |
Task-specific medical testing: |
√ Hazardous Waste
√ Respirator Use
√ Hearing Conservation
Other: |
RBC Cholinesterase (baseline) testing for all field personnel entering the South Plants Work Area. |
Location of qualification records and data sheets: |
Exempted on-site personnel: |
TERRATHERM Operations Trailer |
Personnel not entering the South Plants work area. |
16. Training
The following training is required for on-site personnel working in the field. Copies of training certificates and training records will be kept on-site at RMA.
Required worker training: |
Task-specific training requirements: |
__√_ 40-hour General Site Worker
__√_ 8-hour Supervisor (Site Mgr. As a minimum)
__√_ 3-day On-the-job
__√_ 8-hour Refresher
__√_ Site-Specific Briefing (Task-Specific)
__√_ PMC Orientation
__√_ CRA Access Control
Other: |
__√__ Hazard communication
__√__ Task-specific briefing
__√__ Hearing conservation
__√__ South Plants Training
__√__ ECMMP (decontamination waste management )
Other: |
Location of training records:
TERRATHERM Operations Trailer |
Exempted on-site personnel:
Personnel not entering the South Plants work area.
(Electricians will be exempted from respirator certification since they will be evacuated from the area if air monitoring indicates respiratory protection is required) |
17. Hazardous Chemicals
Hazardous chemicals (as defined in 29 CFR 1910.1200) to be brought or used on-site are identified below. This chemical inventory will be maintained up to date by the HSS, and Material Safety Data Sheet (MSDS) shall be maintained at the task or project support facilities and made available for review by site workers the PMC or RVO.
Chemical Name |
Amount |
Location |
Purpose |
Alconox |
5 lb. |
Decon. Station |
Decontamination |
Isobutylene |
2.2 CF |
Office trailer |
Calibration |
Miscellaneous CEM calibration gases |
Cylinder bottles |
Operation trailer |
Calibration |
Propane |
(3) 1,000 gal tanks |
Support Area |
Supplemental fuel for oxidizer |
Diesel fuel |
1,000 gal tank (typ. only 200 gal) |
Support Area |
Fuel for emergency generator |
|
|
|
|
|
|
|
|
|
|
|
|
18. Required Facilities and Equipment
The following facilities and equipment are required for safe completion of work.
Facility |
Type: |
Location: |
__√_ Worker Showers/Lockers |
Envirocon |
7th and D Street |
__√_ Restrooms |
Portable |
Support Area & Operations Trailer |
_√_ Supplementary Illumination |
Portable |
As necessary |
__√_ Emergency eyewash |
Portable |
Support Area & Operations Trailer |
__√_ First Aid Supplies |
10-person |
Support Area & Operations Trailer |
__√_ Fire Extinguishers |
10 BC |
Support Area & Operations Trailer |
_√__ Hazardous Materials Storage |
Decontamination solvents will be stored in safety cans |
Operations Trailer |
_√_ Spill Containment /Clean-up |
Spill response kit/absorbents on site |
Support Area |
___ Other:____________________ |
|
|
19. Emergency Action and response
Personnel responsible for coordinating emergency situations during site activity are identified below. A site map showing assembly points and directions to the authorized medical facility is attached. Documented rehearsal and critique of this plan is required at least once during the task, or more often as necessary.
Responsibility |
Name |
Phone Number(s) |
Task Emergency Coordinator |
Joseph E. Sanders (or on-site H&S representative) |
970-481-7851 (cellular) |
Alternate Emergency Coordinator |
Keith Bowden – TerraTherm, Inc. |
(832) 439-4110 |
Type/Frequency of Rehearsal |
One pre-job review; monthly reviews during project. |
If an emergency situation develops which requires evacuation of the work area, the following steps shall be implemented.
Evacuation Step |
Methods and comments: |
Notify affected workers |
Voice/radio. |
Evacuate to safe location |
First refuge: graveled staging area. Second refuge: Corner of ingress road & 7th Avenue or Fire and Emergency Services (FES) if so directed by SSO |
Assemble and account for workers |
On-site H&S officer will account for all personnel. |
Notify Fire and Emergency Services |
On-site H&S officer will notify FES and will contact FES for transfer of personnel to medical facility, if necessary. |
Complete incident report |
On-site H&S officer will complete the report. |
Potential emergency situations and response actions are identified below.
In case of: |
Response actions: |
Injury or illness |
Administer first aid as necessary; decon or double TyvekÒ; Notify FES for transport to hospital; |
Chemical exposure |
Remove from exposure; administer first aid if necessary; decontaminate the victim or double TyvekÒ, and notify FES for transport to hospital if necessary. Follow-up medical exam. |
Fire or explosion |
Notify FES; evacuate personnel if necessary; attempt extinguishment IF TRAINED TO DO SO. |
Material Spill or Release |
Remove/evacuate personnel; control if possible; barricade spills; contact FES and notify PMC spill coordinator/Environmental Compliance Group. |
Adverse weather |
Remove personnel from the Exclusion Zone; decontaminate; communicate with PMC and the FES; evacuate if necessary. |
Underground Utility Line Closure |
Complete PMC Line Breaking Checklist (Figure 16.5 of PMC HASP) prior to start of work. Follow procedures outlined in CCP and ECMMP to control/contain residual liquids during breaching & plugging of existing underground utility lines. In the event of an uncontrolled release or chemical exposure, follow emergency procedures outlined above. |
20. Approvals
This task-specific HASP has been reviewed and accepted for work at RMA.
Title/Organization |
Printed name: |
Signature: |
Date: |
Task Site Supervisor |
Keith Bowden |
|
|
Task Health and Safety Supervisor |
Joseph E. Sanders |
|
|
PMC Project Manager |
Ron Versaw |
|
|
PMC Health and Safety Manager |
Andy Strickland |
|
|
21. attachments
Applicable attachments to the task-specific health and safety plan are identified below.
Attachment Number: |
Title: |
A
B
C
D |
Activity Hazard Analysis
Safe Work Practices or Procedures
· Hazard communication program
· Respiratory protection program,
· Lockout/tagout program,
· Excavation safety procedures
· Fall protection program
· Environmental Drilling
· Heat & cold stress prevention
· Noise (Hearing Conservation)
Material Safety Data Sheets
Site Access Map (showing support facilities, route to designated medical facility and location of Fire/EMS station) – Refer to Design Drawing C-104 (Site Access Plan)
Hex Pit Site Map (showing site layout, rally points and exclusion zone) – Refer to Design Drawing C-106 – (General Site Plan) |
ATTACHMENT A
ACTIVITY HAZARD ANALYSIS
ATTACHMENT B
SAFE WORK PRACTICES & PROCEDURES
Includes the following:
- Hazard Communication Program (SOP 5.1)
- Respiratory Protection Program (SOP 8.1),
- Noise (Hearing Conservation) (SOP 10.2)
- Heat & Cold Stress Prevention (SOP 10.3 & 10.4)
- Excavation Safety Procedures (SOP 11.1)
- Environmental Drilling (SOP 11.5)
- Fall Protection Program (SOP 11.7)
- Lockout/Tagout Program (SOP 11.8)
| Forside | | Indhold | | Forrige | | Næste | | Top |
Version 1.0 Oktober 2007, © Miljøstyrelsen.
|