| Forside | | Indhold | | Forrige | | Næste |
Membranfiltrering, erfaring og muligheder i dansk vandforsyning
Summary and conclusions
Membrane filtration has only been used in Denmark to a limited extent in connection with water supply, while
membrane technology internationally has had a wide spread in the extraction of drinking water.
The limited use of membrane plants in connection with water supply in Denmark seen so far has primarily been due
to the fact that Danish water supply traditionally has been based on unpolluted groundwater, which in order for the
drinking water demands to be kept only needs normal water treatment in the shape of aeration and filtration.
It is, though, difficult in several cases to maintain a drinking water supply that is based solely upon normal water
treatment.
The groundwater has in many places been contaminated with pesticides and nitrate as well as natural and extraction
based contaminants such as fluoride, arsenic and nickel. Without the application of extended water treatment such
as membrane filtration, parts of the groundwater resource are not fit as the basis for water supply.
In order to limit the extraction of water and the costs from the drain off of filter rinsing-water, several Danish
waterworks have established facilities to recover filter rinsing-water. Experience from Vandforsyningen I/S,
Birkerød Vandværk (Water Supply Partnership Birkerød Waterworks) has shown that membrane filtration can be
applied when recovering filter rinsing-water.
The purpose of this project is to describe how the membrane processes are used and what the possible
applications are for membrane filtration in connection with the water supply from ordinary Danish waterworks
based upon groundwater sources. Furthermore, different membrane principles and plant types are described, and
the membrane filtration is compared to alternative ways of cleaning the water.
The focus will be on the possibilities for membrane filtration for the following water types:
- Groundwater (in connection with normal water treatment)
- Recovery of filter rinsing-water
The application of membrane filtration is evaluated in comparison to the problem substances specified in Table 0.1,
which are to be found in Danish groundwater in greater or smaller amounts and to filter rinsing-water from normal
water treatment.
Substance group |
Substance |
Organic matter (native) |
Brown water (humus containing) |
Vaguely raised levels of NVOC |
Organic matter (non-native) |
Chlorinated solvents |
Pesticides (charged and uncharged) |
MTBE |
Inorganic salts |
Nitrate |
Fluoride |
Chloride |
Ammonium |
Hardness |
Inorganic tracers |
Nickel |
Arsenic |
Table 0.1 Overview of matters in groundwater of which the application of membrane filtration has shed light to.
Membrane filtration
The membrane filtration techniques are categorized according to the order of pore size in the membrane and
thereby the order of size of the substances which the membrane detains. According to descending size the following
four categories are:
- Microfiltration (MF)
- Ultrafiltration (UF)
- Nanofiltration (NF)
- Reversed osmosis (RO)
In Table 0.2 the sphere of each category is shown together with examples of the size of the substances.
Click to see Table 0.2 Illustration of the different membrane types' sphere.
The separation process in RO and NF is different from UF and MF by being diffusion controlled ,where as UF and
MF are controlled by a complete detention via filtration.
In RO and NF, where the detained matters typically are ions, the pressure gradient over the membrane as well as
the osmotic pressure are the controlling parameters of the flow through the membrane and thereby the production
of permeate (purified water). Furthermore, it is crucial for RO and NF that there are no deposits of firm substances
in the membrane (scaling), as this will result in a pressure loss over the membrane. The concentration and
dissolvability of the substances are therefore limited by the utilization degree that can be achieved in the membrane
plant.
By MF and UF the detained matters are often molecules and colloids, which are detained by the built-up of a cake
layer by the membrane surface (fouling). The controlling parameters in the process are therefore pore size, pressure
gradient as well as the extent and the capabilities of the built-up cake layer.
In order to lower the concentration of matter at the membrane surface, a flow is maintained along the membrane
(cross flow) in many membrane facilities, which has the effect that the concentration of residue is reduced, and the
scaling/fouling is thereby diminished.
Membrane plants and membranes
Membrane plants are modularly built, which makes it easy to scale and optimize the capacity as well as the degree
of utilization/exploitation, and the water quality of permeate and concentrate. Membrane plants are built up in
arrays, which are divided in a number of steps, of which each step consists of a number of membrane modules (see
Table 0.3). In this way the capacity and the degree of utilization is scaled and optimized according to need.
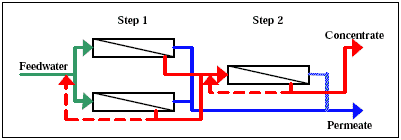
Table 0.3: An example of the construction of a membrane plant. The plant is described as a 2-1 array plant.
In the running of the membrane plant periodic back washes/chemical rinses of the membranes are normally made.
Often these periodic rinses of the membrane are supplemented with some extraordinary rinses with stronger
chemicals than those used in the daily run.
Membranes are made from many different materials such as cellulose acetate, polyamide or poly-sulphone. The
materials are modified in different ways, so that they separate themselves by having specific qualities in proportion
to porosity, size of the pores and resistance to different substances and liquid mediums.
The geometric shapes of the membranes are of the outmost importance to how the hydraulic conditions are inside
the membrane. These hydraulic conditions are a crucial factor for the membrane's capabilities to avoid the build up
of fouling. Furthermore the geometry is also important for the membrane plants' physical shape and how easy the
membranes are to rinse.
The four dominant geometric shapes in water treatment are:
- Spiral wound membranes
- Tubular membranes
- Hollow fibres
- Plate and frame membranes
The geometric shapes of the membranes provide different hydraulic conditions, and combined with the choice of
membrane material the membranes get their specific qualities. Table 0.2 lists a number of general conditions of the
specific geometric shapes.
Design |
Parameter |
Spiral wound |
Hollow fibres |
Tubular |
Plate and frame |
Price |
Low |
Low |
High |
High |
Area/volume |
High |
UF – High
RO – very high
|
Low |
Moderate |
Pressure gradient |
High |
UF – Low
RO – High
|
UF – Low
RO – medium
|
High |
Ability to avoid fouling |
Medium |
UF – Good
RO - bad
|
Very good |
Medium |
Opportunity for cleaning |
Good |
UF - very good
RO – bad
|
Very good |
Good |
Table 0.2 shows an overview of the general characteristics of the four
membrane configurations.
The typical price of a total membrane plant is 50.000 – 100.000 DKK pr. m3/h. For small plants the price might
be higher. When talking about membranes placed below the water surface, up to 50% of the cost price is related to
the membrane plant itself, while the price for other membrane plants is only 20-30 % of the construction price,
which is affiliated with the membrane plant itself.
Operational and environmental aspects of membrane filtration
In connection with membrane filtration a certain amount of chemical use is normally required. The chemical use may
in principle occur in three parts of the process:
- Pre-treatment of feed water
- After-treatment of permeate
- Cleaning/rinsing of membranes
In order to avoid damage of the membrane, membrane fouling, and the deposit of foreign matter in the membrane it
is often necessary to undertake a pre-treatment of the feed water, which might in some cases include the use of
chemicals.
In the case of MF and UF coagulating or flocculating agents such as poly-aluminium-chloride, ferric chloride, iron
sulphate and polymer are often used, which ensures that the degree of recovery is satisfying.
In the case of NF and RO, which are diffusion controlled, pre-treatment is typically undertaken in order to avoid
deposits in the membrane. This is normally done by adding acids/basifiers or different kinds of antiscaling agents
such as hexa-meta-phosphate. Addition of chemicals depends on which substances are limiting the process in
connection with concentration and dissolvability. The chemicals are used to bind ions in coordination and, thus,
lower the risk of precipitation. Normally an effective removal of particular substances is undertaken before the NF
and RO membrane filtration.
The after-treatment of the permeate is especially relevant in connection with RO and NF filtration, as these
processes often influence the pH and greatly reduce hardness and alkalinity. An after-treatment is therefore often
necessary to obtain the wanted qualities in terms of taste and corrosion. Addition of different calcium products in
order to stabilize the water in consideration of the pH and alkalinity is therefore necessary. Furthermore, it might be
necessary to add different salts in order to obtain the wanted taste. After-treatment might in several cases be
avoided by mixing in water from other boreholes or establishing a bypass in connection with the membrane plant.
Cleaning of membranes is often undertaken with acidic/basic solutions to dissolve the residue which in the process
will get stuck in the membrane. To disinfect, chlorination is often used.
The energy consumption in membrane filtration might vary considerably from plant to plant, depending on the pore
size in the membrane, the concentration of foreign substances, the pre-treatment as well as the pressure gradient.
The energy consumption mainly relates to the pressure gradient over the membrane, which is generally ascending
when the pore size is descending. Typically, the following energy consumption pr. m3 produced water is found:
- UF 0.2 – 1.0 kWh
- NF 0.7 – 1.5 kWh
- RO 1.5 – 3 kWh ( though 6 – 10 kWh/m3 when desalinating seawater)
In general the degree of utilization correlates with the size of the pores in and the pressure gradient over the
membrane, so that the degree of utilization-correlation within the four membrane techniques is as specified in Table
0.3, where some adequate intervals are given.
|
RO |
NF |
UF |
MF |
Utilization degree |
70-75 % |
80-90 % |
80-90 % |
98 % |
Table 0.3: typical degrees of utilization in the different membrane filtration methods.
The degree of utilization varies depending on plant design and other matters, such as treatment and managing of the
concentrate.
Often the only way of disposing of the concentrate is by discharge to the waste water system. In the case of
discharge expenses of for example 15 DKK/m3, the costs will be dominant and often amount to up to 50% of the
costs relating to membrane filtration. It is therefore crucial that the concentrate can be handled in a different way;
for example by injecting into the ground water reservoir, infiltration, or by discharge to recipient. The possibilities of
an alternative handling of the concentrate depend on local conditions and the concentrate's content of substances
that are unwanted in the environment.
Even though membrane filtration is a fully automatic process, the process must be supervised manually to ensure
careful monitoring of the running of the plant. 5-10 man-hours per Week must be expected, depending on the size
of the plant. Many waterworks will have to enter a contract with specialized firms about service and renewal of
membranes.
Danish and foreign experience
The empirical knowledge concerning the use of membrane filtration plants in Danish water supply is sparse. To this
day we only have two running plants: at Birkerød Waterworks (used to recover filter rinsing-water) and at Enø
Strand Waterworks AMBA (desalination of chloride-containing groundwater). The membrane technique has
furthermore been tested in pilot projects at a few waterworks.
The membrane plant at Enø Strand waterworks is a RO plant established in order to remove 400-500 mg/l
chloride from the ground water. The plant has a capacity of 0.6 –0.8 m3/h, is fully automatic and is running
continuously. The coefficient of utilization is 55-65%. No pre-treatment other than the normal water treatment is
undertaken. The waterworks has deliberately chosen to accept a low degree of utilization to avoid the use of
chemicals for softening and antiscaling.
The cost of construction for the membrane plant amounted to approximately 200.000 DKK in the beginning of the
90's, which equals construction costs of about 275.000 per m3/h.A detailed statement of the expenses relating to
the construction costs concerning the membrane plant is not available, but the primary operational costs include the
use of electricity and service. The electricity consumption is estimated at approximately 2kWh/m3 produced water.
The membrane plant at Birkerød Waterworks is a UF plant, which is established to recover filter rinsing water. The
plant, which has a capacity of 5m3/h and a utilization degree of 75-80%, cleans rinsing-water with a concentration
of iron of about 50 mg/l. The plant is fully automatic, and permeate is returned to the oxidation stairs.
The costs of construction for the membrane plant amounted to 550.000 DKK, i.e. 100.000 DKK for an extension
and 450.000 DKK for the membrane plant itself, which equals a cost of construction of about 110.000DKK per
m3/h. The expenses of running the plant, which include the use of electricity, chemicals, renewal of membranes and
outside assistance, amount to approximately 40.500 DKK/ per year (about 4 DKK/m3 treated water). The
membrane plant at Birkerød Waterworks has a payback time of 4-5 years.
Experiences from pilot plants at Fjand Waterworks, Kisserup Waterworks, and Skagen Waterworks show that
organic matter can be effectively removed from groundwater containing humus. The process requires thorough
pre-treatment to remove particular matter. In the membrane process residue of iron and calcareous water types
reduces the harshness. Chemicals have not been used, except those that are used for cleaning the membranes.
In Greenland the membrane technique has been used for the water supply in a number of villages. Experience
gained in Greenland cannot be directly translated to Danish conditions, as the experiences from Greenland are
based upon desalination of seawater, which is not relevant in Denmark. Furthermore, the plants are small compared
to the typical Danish water supply plants, and in several areas the conditions for establishing and operating a
membrane plant in Greenlandic villages are quite different from Danish conditions.
Experience from the Netherlands were gathered by contacting and visiting the KIWA, which were very helpful in
evaluating especially the economic and environmental consequences in implementing membrane filtration. In the
Netherlands experience was gained with building big modern membrane plants and implementing membrane
filtration at small, older waterworks in peripheral regions. The waterworks treat water with raised concentrations of
natural matter and xenobiotic organic matter, salts and metals, and the experiences from the Netherlands are
therefore relevant to Danish water supply.
In the Netherlands much work has been done to optimize the environmental performance of the plants. Amongst
other things they work with a concept where the utilization degree for the NF/RO membrane plants is kept at
approximately 50% to avoid the use of chemicals for antiscaling, and subsequent reinfiltration of the concentrate to
the ground water reservoir. The energy consumption in this concept is considerably reduced, as the pressure
gradient over the membrane can be lowered considerably. When using this method a considerably reduced energy
and chemical consumption is achieved, and no discharge occurs.
On the basis of the Dutch experiences KIWA evaluates that membrane filtration generally requires professional
personnel, and the costs of producing drinking water by introducing membrane filtration lies in the interval 2.2 – 4.8
DKK/m3 (depending on the size and capacity of the plant). To this must be added possible expenses concerning
normal water treatment.
Capacity |
NF |
RO |
75,000 m3/year |
4.5 DKK | 4.8 DKK |
400,000 m3/year |
3.0 - 3.7 DKK | 4.1 DKK |
1,000,000 m3/year |
2.2 - 3.0 DKK | 3.3 DKK |
Table 0.4 The production price of 1 m3 produced in a membrane plant. Dutch experiences.
The rinsing of problem substances by membrane filtration
In evaluating whether membrane filtration is relevant for the rinsing of each single substance, operating costs have
been calculated, based upon a number of presupposed conditions and on volumes of water of 10m3/h, 50m3/h and
130m3/h. These capacities equal the typical treatment capacity of Danish water supply plants pumping out 75,000
m3/per year, 400,000 m3/per year and 1,000,000 m3/year.
Table 0.5 gives an overview of the estimated operation costs when using membrane filtration in connection with the
stated problem substances. It should be noted that the cost price includes capitalisation of the production costs
over 20 years as well as operational expenses. Furthermore, it must be noted that the calculation presupposes
discharge of concentrate to the public sewage discharge system, and that the costs of this might be more than 50%
of the total production costs.
Problem substance |
Membrane technique |
Feed water concentration |
Demands for degree of purification (%) |
Bypass
(%)
|
Degree of utillization
(%)
|
Production price
(DKK./m³)
|
Brown water |
UF/NF |
100 mg C/l |
97 |
0 |
80 |
5.8 – 7.1 |
Slightly raised NVOC |
UF/NF |
10 mg C/l |
90 |
0 |
90 |
4.1 – 5.4 |
Chlorinated solvents |
NF/RO |
10 µg/l |
95 |
0 |
80 |
6.4 – 7.9 |
Pesticides |
NF/RO |
1 µg/l |
95 |
0 |
80 |
6.4 – 7.9 |
MTBE |
NF/RO |
10 µg/l |
80 |
0 |
80 |
6.4 – 7.9 |
Nitrate |
NF/RO |
100 mg/l |
60 |
40 |
80 |
4.3 – 4.8 |
Chloride |
RO |
1.000 mg/l |
80 |
20 |
75 |
6.6 – 7.3 |
Fluoride |
RO |
5 mg/l |
75 |
25 |
75 |
6.2 – 6.9 |
Ammonium |
RO |
2,5 mg/l |
99 |
0 |
75 |
8.3 – 9.1 |
Hardness |
NF |
40 dH |
50 |
50 |
65 |
4.5 – 5.0 |
Nickel |
NF/RO |
25 µg/l |
40 |
60 |
80 |
2.8 – 3.3 |
Arsenic |
NF/RO |
15 µg/l |
80 |
20 |
80 |
5.6 – 6.3 |
Filter rinsing-water |
MF/UF |
- |
- |
0 |
80 |
6.9 – 21.1 |
Table 7.5: Overview of purification with membrane filtration
The cost of production in Table 0.5 is stated as an interval specifying plants with a treatment capacity of 10-130
m3/h under the explained circumstances (when talking about filter rinsing water the figures are 1.3 and 5 m3/h). The
cost of production decreases with increasing plant capacity.
Comparison between membrane filtration and alternative rinsing technologies
For the various water types and substance groups a brief comparison is made between membrane filtration and
alternative rinsing technologies. The purpose is to evaluate whether membrane filtration in comparison to alternative
technologies presents a possible application potential in Danish water supply.
An overview is given in Table 0.6, which shows the alternative ways of rinsing the water used in the comparison
and the extent to which the membrane filtration is evaluated as performing a relevant treatment technique compared
to the alternative rinsing technologies.
Problem substances |
Membrane filtration |
Alternative way of purification |
Very suited |
Suited |
Possibly suited |
Not suited |
Brown water |
X |
|
|
|
Chemical precipitation |
Slightly raised NVOC |
|
X |
|
|
Chemical precipitation |
Chlorinated solvents |
|
|
|
X |
Blow off
Adsorption on active carbon
|
Pesticides (Charged and uncharged) |
|
|
|
X |
Adsorption on active carbon |
MTBE |
|
|
X |
|
Stripping and breakdown on waterworks filters |
Nitrate |
|
X |
|
|
Ion exchange
Biological denitrification
|
Fluoride |
X |
|
|
|
Ion exchange |
Chloride |
X |
|
|
|
Ion exchange
(Demineralization)
|
Ammonium |
|
|
|
X |
Biological filter |
Hardness |
|
X |
|
|
Ion exchange (softening) |
Nickel |
|
|
X |
|
Chemical adsorption |
Arsenic |
|
|
X |
|
Normal water treatment |
Filter-rinsing-water |
|
X |
|
|
Precipitation, filtration on sandfilter and UV- disinfection. |
Table 0.6: Overview of the use of membrane filtration compared to alternative purification technologies.
The conclusion of the report regarding the usability potential of membrane filtration in Danish water supply shows
that in several cases the use of membranes to rinse groundwater to make it suitable for drinking water purposes
presents a number of advantages.
From a technological and economic point of view it is concluded that membranes can be used to rinse ground
water with raised levels of organic matter (brown water) found naturally in the ground water of especially coastal
areas and on certain islands in Denmark presents a number of advantages. In these areas alternative water types of
a better quality are limited, which means that local supply can be maintained by means of membrane filtration.
Operationally this solution is seen as unproblematic. The method can therefore be recommended if there are areas
with brown water and no alternative resources.
The same way of presenting the problem and conclusion can be made for the elements chloride and fluoride, where
membrane filtration is the best solution. In these situations, where alternative resources of a better quality do not
exist, it is recommended to apply membrane technology to produce drinking water. This situation might be relevant
on islands and in coastal areas where a local supply plant should be maintained.
Furthermore, membrane filtration is a favourable way of purifying filter rinsing-water that should be recovered.
Experience gas been gained by a plant in Denmark, and the conclusion from this plant shows that it is technically
and economically favourable. The recovery of rinsing water is current in areas with limited resources, either for
natural causes or because the ground water is contaminated. These positive experiences should give food for
thought at other water supplies faced with in similar conditions.
When rinsing ground water into drinking water, by removing the other mentioned substances, membrane technology
is not competitive enough to compete on operational costs. Especially the discharge of concentrate affects the
operational expenses, and if it is possible locally to discharge concentrate at less cost than discharge to sewage
disposal plants, operational expenses will be reduced, and membrane filtration will, thus, be more competitive.
The potential for using membranes to purify drinking water will, however, be larger if it is decided at a larger scale
to use contaminated groundwater of a quality that, today, is normally not wanted for water supply purposes. For
the purpose of rinsing out xenobiotic substances or contamination resulting to recovery, the use of membranes will
still be more expensive than other purifying methods, but often several problem substances occur at the same time,
that will require each their purifying technology. Membrane recovery will be able to treat several components in the
same process. This kind of problem is for example relevant in large parts of Zealand, where raised levels of nickel
occur concurrently with contamination from pesticides. Such water types can be purified with membrane filter at a
competitive cost.
From experience we know that the use of chemicals in connection with membrane filtration is not a problem in
relation to the working environment. The waterworks can either upgrade a few workers' knowledge of how to
handle chemicals, or make a contract with external consultants about the discharge of this function.
Membrane filtration is evaluated to be an operationally simple, robust, and as far as water quality is concerned, a
safe way of treatment, which without any big problems can be implemented in all sizes of waterworks and water
supply systems in Denmark. This is clearly supported by foreign experiences.
| Forside | | Indhold | | Forrige | | Næste | | Top |
Version 1.0 December 2003, © Miljøstyrelsen.
|