| Главная страница | | Низ |
Оценка поступлений ртути в окружающую среду с территории Российской Федерации
Сокращение выбросов ртути в атмосферу с территорий стран Арктики
Содержание
Предисловие
Аббревиатуры и акронимы
Резюме
1 Введение
2 Производство, импорт и экспорт ртути в России
3 Целевое использование ртути в России
4 Мобилизация ртути в качестве примеси
5 Оборот ртути при переработке отходов
6 Выводы
7 Источники информации и использованная литература
Приложение 1. Официальная статистика по поступлению ртути в окружающую среду
Приложение 2. Хранение ртутьсодержащих пестицидов
Приложение 3. Содержание ртути в углях основных угольных бассейнов России
Предисловие
Результаты реализации Программы арктического мониторинга и оценки (АМАП), включающей
и дополняющей целый ряд исследований в области охраны окружающей среды,
проводившихся в Арктике в течение нескольких десятилетий, свидетельствуют о том, что
население и окружающая среда этого региона в настоящее время подвергаются серьезному
риску, связанному с загрязнением ртутью и некоторыми другими токсичными веществами.
В рамках Совета стран Арктики восемь стран (Дания, Исландия, Канада, Норвегия, Россия,
США, Финляндия, Швеция) договорились о реализации мер по сокращению объемов
поступления в окружающую среду региона ряда основных загрязняющих веществ, включая
ртуть. Совет стран Арктики разработал План действий, включающий 6 проектов, касающихся
основных загрязняющих веществ. Дания является координатором проекта по ртути.
Основная цель данного проекта заключается в содействии мероприятиям по сокращению
выбросов ртути странами Арктики, частично путем разработки общей региональной структуры
плана действий или стратегии сокращения выбросов ртути, частично посредством оценки и
выбора одного или нескольких точечных источников в качестве объекта для реализации мер по
снижению загрязнения. Кроме того, результаты реализации проекта будут использованы для
усовершенствования исходных данных, необходимых для моделирования переноса ртути на
большие расстояния. Это предопределило необходимость составления подробного и полного
списка основных точечных источников выбросов ртути в атмосферу.
Настоящая оценка поступления ртути в окружающую среду с территории Российской
Федерации, выполненная в рамках общего проекта по сокращению выбросов ртути, будет
использована в качестве основополагающего отчетного документа для включения в общий
региональный пакет материалов по инвентаризации поступления ртути в окружающую среду.
Региональная инвентаризация выбросов ртути будет основана главным образом на
информации, представленной названными выше восемью странами Арктики.
Исследования были выполнены группой российских экспертов при координационной
поддержке COWI совместно с Министерством природных ресурсов РФ (МПР РФ). При
проведении инвентаризации, помимо официальных сведений, с целью получения более полной
картины перемещения ртути в техносфере России и поступления ее в окружающую среду с
территории страны использовались данные экспертных оценок, ответственность за степень
точности и достоверности которых несут авторы. В случае получения более точной
информации приводимые оценочные данные могут быть дополнены и(или) изменены.
Члены Наблюдательного Совета:
Микала Клинт (Дания) - председатель, Н. Б. Нефедьев (Российская Федерация), А.В. Печкуров
(Российская Федерация), О.Ю. Цитцер (Российская Федерация), Мэрлин Энгл (США), Дуглас
Стил (США), Стенли Дюрки (США), Грэйс Хоулэнд (Canada), Сьер Андерсен (Норвегия),
Бенте Слейр (Норвегия), Магнус Нистром (Финляндия), Матс Экенгер (Швеция), Джон Мунте
(Швеция), Халдор Торгейрсон (Исландия), Хенрик Сков (Дания), Гиннар Фунсэтер
(Секретариат ACAP), Ларс-Отто Рейрсен (Секретариат AMAP), Саймон Уилсон (Секретариат
AMAP), Гарислав Школенок (UNEP Chemicals), Хусамуддин Ахмадзай (NEFCO).
Координатор:
Датское Агентство по охране окружающей среды (DEPA), Микала Клинт.
Министерство природных ресурсов Российской Федерации (МПР РФ) (до апреля 2004 года):
Н.Б. Нефедьев (Управление организационно-методического обеспечения государственного экологического контроля),
А.В. Печкуров (Управление экологической безопасности),
Ю.Ю. Александровский (Управление международного сотрудничества в области охраны
окружающей среды).
Федеральная служба по экологическому технологическому и атомному надзору (после
апреля 2004 года):
А.В. Печкуров – Заместитель начальника Управления контроля и надзора в области охраны
окружающей среды – Начальник отдела по контролю и надзору за соблюдением требований
экологической безопасности при особых видах воздействия на окружающую среду
(государственного экологического контроля);
О.Ю. Цитцер – Главный специалист отдела по контролю и надзору за соблюдением требований
экологической безопасности при особых видах воздействия на окружающую среду
(государственного экологического контроля).
Консультанты:
COWI A/S (Дания), Карстен Лассен (руководитель проекта, редактор итогового отчет), Якоб
Мааг;
Московское представительство COWIconsult International Ltd., Т.В. Ефимова (заместитель
руководителя проекта, редактор итогового отчет), И.А. Чернакова.
Российские эксперты (авторы документов):
Ю.А. Трегер, Научно-исследовательский институт .Синтез. с КБ Минпромнауки РФ (ГУП
НИИ .СИНТЕЗ и КБ.);
Е.П. Янин, Институт геохимии и аналитической химии им. В.И. Вернадского РАН (ГЕОХИ
РАН);
Б.А. Ревич, Центр демографии и экологии человека Института народнохозяйственного
прогнозирования РАН;
Б.Е. Шенфильд, Уральский государственный научно-исследовательский институт
региональных экологических проблем МПР РФ (ФГУ УралНИИ .Экология.);
С.В. Дутчак, Метеорологический Синтезирующий Центр .Восток. (EMEП MСЦ-В);
Н.А. Озерова, Институт геологии рудных месторождений, петрологии, минералогии и
геохимии РАН (ИГЕМ РАН);
Т.Г. Лапердина, Институт геохимии и аналитической химии им В.И. Вернадского РАН
(ГЕОХИ РАН);
В.Л. Кубасов, Государственный научно-исследовательский институт цветных металлов
(Гинцветмет).
Российские технические эксперты:
Е.Ю. Быховская, В.И. Эбериль, А.З. Ощепкова, Ю.Г. Двоскин, М.И. Чубирко, Н.М. Пичужкина,
В.А. Синода, Л.Ф. Михайлова, В.А. Катаева, В.Л. Ковальский.
Международный эксперт:
Джон Мунте, Шведский институт экологических исследований IVL Ltd. в сотрудничестве с
ОАО «ВТИ» (Всероссийским теплотехническим научно-исследовательским институтом)
Рецензенты:
Марк Ричардсон (Канада), Леонард Серджес (Канада), Джозеф М. Пацина (Норвегия), Эдвард
M. Вейлер (США), Велу Сентил (США), Франк Анскомб (США); Александр МакБрайд,
(США); Дэвид Кирчгесснер, (США); Джон Кинсей, (США); Рассел Баллок, (США); Алексис
Кэйн, (США); Стефен Хоффман, (США); и Роберт Стивенс (США); Д-р Ричард Мейер (США);
Д-р Алан Колкер (США); Д-р Джон Де Янг (США): Уильям E. Брукс, (США); Д-р Ричард
Левин, (США); Д-р Томас Гунан, (США); Д-р Дэннис Костик, (США); Ричард Арц (США),
Марк Коэн (США), Джеймс Экман (США) и г-жа Мелисса Чен (США).
Финансовая поддержка:
Данное исследование проводилось при финансовой поддержке со стороны Дании, Канады,
США и Норвегии.
Благодарности:
Выражаем особую благодарность и искреннюю признательность российским организациям и
предприятиям, которые оказали поддержку в проведении исследований и инвентаризации
и/или предоставили необходимую информацию о применяемых технологиях и данные о
поступлении ртути в окружающую среду.
Аббревиатуры и акронимы
ПДСА/ACAP |
- План действий стран Арктики по предотвращению загрязнения Арктики; |
АМАП |
- Программа арктического мониторинга и оценки; |
OSPAR |
- Конвенция о защите морской среды северо-восточной части Атлантического океана; |
INTAS |
- Международная Ассоциация развития сотрудничества с учеными стран СНГ; |
РАН |
- Российская академия наук; |
ГОСТ |
- Государственный стандарт; |
Hg |
- химический знак ртути; |
ВХМ |
- винилхлоридный мономер; |
ПВХ |
- поливинилхлорид; |
ПДК |
- предельно допустимая концентрация; |
ПДД |
- предельно допустимая доза; |
РСО |
- ртуть содержащие отходы; |
ТБО |
- твердые бытовые отходы; |
ЭФ |
- электростатический фильтр; |
ОКОС |
- осадки очистных сооружений канализации; |
ГМК Норильский Никель |
- Горно-металлургический комбинат «Норильский Никель» |
СССР |
- Союз Советских Социалистических Республик; |
РФ |
- Российская Федерация |
Единицы измерения:
µg - 10-6 г;
ppm (parts per million) - внесистемная единица относительной величины (1 ppm = 1 мг/кг или 10-4%);
т - 1000 кг = метрическая тонна;
тонна(ы) - 1000 кг = метрическая тонна = т;
Резюме
Настоящая оценка была выполнена в рамках исследования Программы ПДСА/ACAP
“Сокращение выбросов ртути в атмосферу странами Арктики”. Оценка антропогенных
выбросов ртути с территории России была подготовлена с использованием официальных
статистических данных и экспертных оценок, основанных на количестве ртути, примененной
целенаправленно или мобилизованной (в качестве примеси) в различных секторах экономики.
По каждой области деятельности прослежен путь ртути от производства/добычи до
выбросов/сбросов или размещения отходов. В ходе исследования возможное использование
ртути в оборонной промышленности не рассматривалось.
Целевое использование ртути в России
По оценкам экспертов, общее количество целенаправленно использованной ртути в
России в 2001/2002 г.г. составило 151-160 т/год (табл. 1). Сведения, представленные в таблице,
являются сугубо оценочными, поэтому в целях получения более детальной информации о
степени неопределенности, следует обратиться к Главе 6 настоящего отчета.
Общее потребление ртути в стране за последнее десятилетие существенно снизилось
(рис. 1). Согласно имеющимся сведениям, общее целевое использование ртути в 1985 г. и 1993
г. составило примерно 1300 и 500 т/год соответственно. Таким образом, тенденции
потребления ртути в России развиваются параллельно с общемировыми тенденциями. По
данным Департамента финансов Министерства экономического развития и торговли РФ, общая
потенциальная потребность российских предприятий в ртути в 1999-2001 г.г. составляла 280-
300 т/год. Несоответствие этих данных и результатов настоящего исследования может быть
частично вызвано неполной загруженностью проектных мощностей предприятий, снижением
потребления ртути и разницей в объемах использования ее по годам, и, возможно, отчасти тем
фактом, что в данном исследовании рассматривалось потребление ртути только в гражданских
секторах экономики.
Основной областью целевого применения ртути является хлорно-щелочное
производство, в котором ртуть используется в качестве электрода. В 2002 г. на эти цели было
использовано около 103 т, причем этот показатель изменяется каждый год. Вся ртуть,
использованная в хлорно-щелочном производстве, в конечном счете, поступает или в
окружающую среду или на свалки/полигоны отходов. Непосредственные выбросы металла в
атмосферу предприятиями данной отрасли оцениваются в 1,2 т/год. Однако неучтенные потери
ртути в хлорно-щелочном производстве составляют более 50 т/год, из которых определенная
часть концентрируется в грунтах промышленных площадок предприятий, а некоторое ее
количество, очевидно, поступает в атмосферу. Содержащие ртуть твердые отходы
размещаются в основном на полигонах и в шламохранилищах. В настоящий момент в хлорно-
щелочном производстве применяется повторное использование ртути (в небольших объемах).
Поскольку российские предприятия по производству хлора и каустика используют различные
технологии, то удельные потери ртути на конкретных заводах существенно различаются.
Оценка показывает наличие значительного потенциала по сокращению выбросов ртути даже
только за счет совершенствования практики управления, хотя и это потребует определенных
трудозатрат и расходов.
В химической промышленности ртуть, помимо хлорно-щелочного производства,
используется также в качестве катализатора на заводах по получению винилхлоридных
мономеров для ПВХ. Образующиеся здесь ртутьсодержащие отходы в значительной степени
утилизируются с получением вторичной ртути.
Современное потребление ртути в химической промышленности по сравнению с уровнем
1985 г, равного примерно 900 т, существенно сократилось. Основная часть ртути, используемой
в этом секторе, размещается на полигонах отходов или поступает в грунты на
территории/вокруг производственных объектов. Общее количество ртути, размещенной в
составе отходов на полигонах (действующих или закрытых) предприятиями химической
промышленности, согласно оценкам, составляет более 3000 т. Масштабы потребления ртути в
данном секторе в прошлые годы свидетельствуют о том, что фактическое количество металла,
депонированного на полигонах и в грунтах промплощадок, может быть гораздо больше
расчетного.
Использование ртути для производства электротехнических приборов и измерительного
оборудования также заметно сократилось за последнее десятилетие. В 1989 г. в этом секторе
было использовано примерно 240 т ртути; в 2001 г. – около 30-40 т. Основная доля ртути
применяется для производства ртутных термометров и ртутных источников освещения
(ртутных ламп). На эти цели в 2001 г. было использовано 26 т и 7,5 т ртути соответственно. В
ежегодно поставляемых на внутренний рынок страны ртутных термометрах содержится около
10 т ртути. Практически все использованные ртутные термометры поступают на
полигоны/свалки ТБО, являясь вместе с другими приборами основными источниками
попадания ртути в отходы, и, следовательно, основным источником атмосферных выбросов
ртути от мусоросжигательных установок. Определенное количество ртутных ламп
перерабатывается с целью извлечения ртути или временно складируется для возможной
последующей переработки. Общее количество ртути, полученной в результате утилизации
источников освещения в 2001 г., составило менее 10% от ее количества, содержащегося в
ртутных лампах, размещенных на полигонах отходов. Непосредственные выбросы ртути в
атмосферу при производстве ртутьсодержащих изделий довольно незначительны, например, по
сравнению с выбросами с установок по сжиганию угля или предприятий цветной металлургии.
Таблица 1. Обобщенные данные по потреблению/мобилизации ртути, ее выбросам в атмосферу
и размещению в составе отходов на полигонах/свалках, 2001/2002, т/год *
Отрасль/область деятельности |
Потребление /мобили- зация ртути |
Выбросы ртути в атмосферу |
Ртуть в отходах, размещаемых на полигонах/свалках |
Целевое использование ртути |
Хлорно-щелочное производство |
103 |
1,2** |
39 |
Производство ВХМ |
7,5 |
0,02 |
0,0 |
Добыча золота с применением метода амальгамации |
5,5 |
3,1 |
1,1 |
Производство термометров |
26 |
0,009 |
0,1 |
Производство источников освещения |
7,5 |
0,15 |
0,001 |
Другие области целенаправленного использования |
5,8 (+ ?) |
0,06 (+ ?) |
2,4 (+ ?) |
Всего |
155 |
4,5 |
43 |
Мобилизация ртути в качестве примеси |
Уголь - электроэнергетика |
10 |
8,0 |
2,0 |
Уголь - другое применение (включая отходы добычи) |
12 |
6,3 |
3,6 |
Нефтепереработка и использование нефтепродуктов |
33 |
3,4 (+ ?) |
? |
Газ, горючие сланцы и биотоплива |
8,0 |
1,0 |
? |
Производство цинка и свинца |
31 |
1,9 |
8,5 |
Производство никеля и меди |
28 |
5,3 |
6,6 |
Производство других металлов |
7,8 |
2,6 |
4,2 |
Производство цемента и извести |
2,0 |
1,6 |
0,4 |
Всего |
132 |
30 |
22 |
Переработка отходов |
Сжигание отходов |
|
3,5 |
|
Размещение на полигонах/свалках |
|
|
24 |
Осадок сточных вод |
|
<0,1 |
5,7 |
Всего |
|
4 |
30 |
Общий итог |
287 |
38 |
95 |
* Приведены наилучшие оценки; знак.(+ ?). обозначает, что показатель отражает только оцененную
деятельность, т. е. данные по некоторым областям деятельности, которые не были проанализированы,
могут существенно повлиять на итоговый результат.
** Прямая эмиссия в ходе хлорно-щелочного производства. В атмосферу может также поступать
определенная часть ртути из ее так называемых .неучтенных потерь., общий объем которых в 2002 г.
оценивается в 56 т.
Потребление ртути для изготовления зубных амальгамных пломб сократилось за
последнее десятилетие с 6 т до 0,8 т в 2001 г. По причине замены ртутных амальгамных пломб
на другие виды пломб, в России на эти цели используется гораздо меньше ртути, нежели в
других странах. Количество ртути, поступившей в отходы и канализационные сооружения в
составе амальгамных пломб, отражает объемы ее потребления десять лет назад и, согласно
оценкам, может достигать 6 т/год. Амальгамы, поступающие в канализационные сети,, могут
являются одним из значимых источников попадания ртути в городскую канализацию.
Применение ртути для добычи золота с использованием способа амальгамации в России
было запрещено более 10 лет назад. Тем не менее, по имеющимся данным, на некоторых
отдаленных территориях страны данный метод все еще может (нелегально) применяться.
Кроме того, в настоящее время активно практикуется извлечение золота с из отходов
золотодобычи и техногенных россыпей, отрабатывавшихся ранее с применением
амальгамации. При переработке такого сырья существенная часть ртути, содержащейся в нем,
поступает в атмосферу. Согласно ориентировочным оценкам, эмиссия ртути в окружающую
среду при осуществлении данного вида деятельности может составлять 1,5-6,5 т. Известно, что
за всю историю золотодобычи в России было использовано более 6000 т ртути, поэтому
количество ее, потенциально способное поступить окружающую среду при извлечении золота
из техногенного сырья, может быть очень значительным.
В настоящее время промышленное производство ртутьсодержащих пестицидов и
биоцидов в России отсутствует, а их применение запрещено. Тем не менее, согласно оценкам
Минздрава РФ, в 2001 г. в практических целях было использовано 20-40 т таких пестицидов
(содержащих около 0,6 т ртути). Очевидно, что используются их старые запасы.
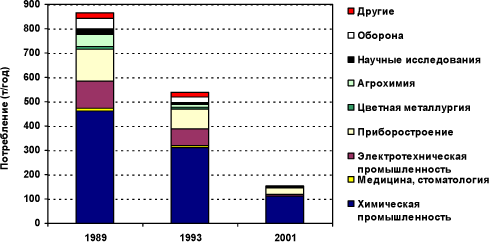
Рис. 1.Потребление ртути в Российской Федерации, 1989-2001 г.г.
Производство и рециклинг ртути
В настоящее время в России производство первичной ртути отсутствует (оно прекращено
в 1995 г.). В 2001 г. за границу на утилизацию были вывезены отходы (шламы) производства
цинка, содержащие около 5 т ртути. При переработке ртутьсодержащих отходов, в том числе
образовавшихся при производстве винихлорида, в 2001 г. получено около 30 т вторичной
ртути.
Мобилизация ртути в качестве примеси
Поскольку целенаправленное использование ртути снижается, то мобилизация этого
металла, присутствующего в качестве естественной примеси в
используемых/перерабатываемых сырье и материалах, с каждым годом составляет все
большую и большую долю в его общем антропогенном потоке. Общее количество ртути,
мобилизованной в качестве примеси в России в 2001 г., оценивается примерно в 138 т
(интервальная оценка 66-198 т), причем основная ее масса связана с углем, нефтью и рудами
(концентратами) цветных металлов (см. табл. 1).
Значительная часть ртути, содержащейся в сжигаемом топливе, поступает в атмосферу.
Общий объем выбросов ртути в атмосферу при сжигании угля в 2002 году был равен примерно
14,3 т (8+6,3, см. Таблицу 1), что составляет около 37 % общих учтенных атмосферных
выбросов ртути в России. В то же время по данным за 2001 год, общее содержание ртути в
использованном угле составило 15,4 тонн, из которых 13,2 тонны составили атмосферные
выбросы, а в отходы ушло примерно 2,2 тонны.
На основе небольшого числа имеющихся анализов содержания ртути в российской сырой
нефти, был сделан вывод, что при ее переработке может мобилизоваться примерно 33 т ртути.
В глобальном масштабе содержания ртути в нефти и газе существенно варьируются в
зависимости от региона. Имеющиеся данные говорят о том, что содержание ртути в сырой
нефти и газе, добываемых в России, может быть относительно высоким. Но, к сожалению, эти
данные слишком скудны для того, чтобы иметь возможность сделать более точные заключения.
На основе нескольких измерений содержания ртути в нефтепродуктах можно сделать вывод,
что общий объем ее атмосферных выбросов при использовании (сжигании) нефтепродуктов
составляет примерно 3,4 т. В России, как и во многих других странах, имеется очень мало
сведений о том, что происходить с ртутью в процессе первичной переработки и перегонки
нефти. Существующие данные указывают на то, что эти процессы могут вносить заметный
вклад в ртутное загрязнение воздуха и водных объектов, но нехватка необходимых сведений не
позволяет сделать даже исходные приблизительные подсчеты. Установлено, что при
переработке природного газа существенное количество ртути поступает в конденсат и серу,
поэтому ее содержание в экспортируемом и поставляемом внутренним потребителям товарном
газе незначительно.
Согласно оценкам, в России около 31-92 т ртути мобилизуется при добыче и переработке
руд цветных металлов. В данном случае ртуть поступает либо непосредственно в окружающую
среду, либо размещается в отвалах, шламохранилищах и на полигонах в составе различных
отходов и промпродуктов. Общий объем выбросов ртути в атмосферу предприятиями цветной
металлургии оценивается примерно в 8,2 т, что составляет около 22 % от объема общих
учтенных атмосферных выбросов. Эти оценки являются очень неопределенными, для их
уточнения требуется проведение измерений выбросов ртути с плавильных установок.
Выбросы ртути в атмосферу
По официальным данным, общий объем выбросов ртути российскими предприятиями,
обязанными отчитываться о ее эмиссии , составил 2,9 т. Эти данные, однако, не учитывают
поступление значительного количества ртути с площадных источников, а также в результате
процессов, в которых используется/перерабатывается сырье, содержащее ртуть в качестве
естественной примеси. Общий объем выбросов ртути в атмосферу, определенный в ходе
настоящего исследования, составил для территории России 39 т, из которых 77% приходятся на
процессы, при которых ртуть мобилизуется в качестве примеси. Производственные процессы,
где ртуть используется целенаправленно, дают лишь 3% от общего объема ее выбросов в
атмосферу.
Выбросы ртути в атмосферу оценивались экспертами на основе информации о содержании
ртути в топливе и сырье, также данных об использовании и образовании ртути в различных
технологических процессах. Результаты оценок поступления ртути в атмосферу имеют
высокую степень неопределенности, поэтому существует острая необходимость проведения
дальнейших измерений фактических выбросов с целью снижения уровня неопределенности и
получения более надежной основы для разработки мер по сокращению поступления ртути в
окружающую среду.
Основными источниками атмосферных выбросов ртути являются установки по сжиганию
угля и нефтепродуктов, а также предприятия цветной металлургии. Из-за отсутствия
необходимых данных невозможно было дать количественную оценку выбросов ртути с
нефтеперерабатывающих предприятий и ее неорганизованных выбросов с хлорно-щелочных
производств. Таким образом, эти источники эмиссии ртути в инвентаризации не учитывались.
Ртуть в сточных водах и ее поступление в водные объекты
В отличие от атмосферных выбросов непосредственные сбросы в водные объекты
являются несущественными источниками проникновения ртути в окружающую среду из
техносферы. По официальным статистическим данным, общее количество ртути в стоках,
сбрасываемых промышленными предприятиями России в водные объекты, составляет 0,16 т,
причем основными источниками ее поставки являются хлорно-щелочные заводы.
Расчеты, основанные на данных по содержанию ртути в осадках муниципальных сточных
вод, показывают, что на очистные канализационные сооружения российских городов ежегодно
может поступать 3,4-11,9 ртути. В ходе очистки стоков бóльшая часть ее концентрируется в
осадках сточных вод, которые в основном размещаются на иловых картах и полях фильтрации.
Наряду с поступлением в составе промышленных стоков, непосредственно сбрасываемых в
водные объекты, ртуть также может содержаться в промышленных сточных водах,
поступающих в муниципальные канализационные системы. Основными источниками ртути в
муниципальные сточные воды являются, очевидно, стоматологические лечебные учреждения,
разбитые ртутные термометры и сломанные электротехнические приборы (переключатели и т.
д.). Ртуть поступает в водные объекты также в составе поверхностного (дождевого и талого)
стока. Существенная часть ртутьсодержащих приборов, произведенных 10 лет назад, судя по
всему, все еще находиться в пользовании, и по мере того, как они будут приходить в
негодность, определенное количество содержащейся в них ртути может попасть в
канализационную систему.
Оценка количества ртути, присутствующей в технической воде, используемой при
добыче нефти и газа, не проводилась, но, вероятно, это может быть существенным источником
сброса ртути в водные объекты.
Прямое поступление ртути в грунты
Основным источником непосредственного поступления ртути в грунты (за исключением
мусорных свалок и полигонов отходов) является хлорно-щелочное производство.
Предполагается, что неучтенные потери ртути, поступившие в грунты на территории и за
пределами предприятий данного сектора, составляют 50 т/год.
В 2001 г. до 0,6 т ртути было использовано в составе пестицидов (главным образом,
гранозана). Применение ртутьсодержащих пестицидов в Российской Федерации запрещено,
поэтому в настоящее время они в стране не производятся. В целом в различных регионах
России в составе устаревших пестицидов хранится до 20 т ртути.
Масштабы применения осадков городских сточных вод в качестве агромелиорантов в
России невелики (первые проценты от ежегодно образующейся общей их массы). При этом, как
правило, уровни содержания в них ртути гораздо ниже ее ПДК в осадках, предназначенных для
использования в сельском хозяйстве. Количество ртути, поступающей с ними на
сельскохозяйственные угодья, составляет менее 1 т в год.
Размещение ртути на свалках/полигонах в составе отходов и ее эмиссия при их
сжигании
Каждый год около 95 т ртути размещается в составе различных отходов на полигонах и
свалках. Определенная часть этой ртути может впоследствии поступить в атмосферу, грунты,
поверхностные и грунтовые воды. Как показано в Таблице 1, количество мобилизованной
ртути превышает общее поступление ртути в атмосферу и отходы производства на 80 тонн. Эта
разница отражает ситуацию, при которой фактическое количество мобилизованной ртути
неизвестно, и что фактические объемы ртути в конечных отходах могут быть существенно
выше.
Основным источником поступления ртути на полигоны при ее целевом использовании в
промышленности являются отходы хлорно-щелочного производства. Применение
золотодобывающими предприятиями амальгамации для извлечения золота может приводить к
ежегодному поступлению 0,3-0,8 т ртути в отвалы и хвосты, что по грубой оценке составляет
примерно 10 % от общих затрат ртути на обогащение золота (3,5 т/год).
Большая часть ртутьсодержащих продуктов размещается на полигонах/свалках или
сжигается. По крайней мере, 24 т ртути, содержащейся в изделиях, утилизируется в составе
твердых отходов. Основные изделия и приборы, содержащие ртуть, - это термометры,
источники освещения, переключатели, батарейки, зубные амальгамные пломбы. Количество
ртути в отходах, образующихся в настоящее время, в определенной степени отражает ее
потребление несколько лет назад, когда оно было гораздо выше, нежели сейчас. Около 2-3%
ТБО сжигается, что обеспечивает ежегодный выброс в атмосферу примерно 3,5 т ртути.
Перспективы дальнейшей оценки поступления ртути в окружающую среду
В целом существуют достаточно определенные данные о целевом потреблении ртути,
поскольку удалось получить конкретную информацию от большей части российских
предприятий, использующих ее в своих технологических процессах. В разделе .Другие области
применения. настоящего документа дано лишь качественное описание некоторых областей
применения ртути в России; более точная оценка может быть сделана при условии наличия
дополнительной конкретной информации.
Общее количество мобилизованной в различных областях хозяйственной деятельности
ртути в виде примеси может быть оценено с большой долей неопределенности. Если учитывать
неопределенность, связанную с поступлением ртути в окружающую среду при
переработке/сжигании различных материалов и сырья, то она достаточно велика для оценок ее
атмосферных выбросов – Следует отметить, что такая ситуация типична для большинства стран
мира.
Проведенная оценка показывает, что нефтепереработка и использование нефтепродуктов
могут быть основным источником выбросов ртути в атмосферу в Российской Федерации, но
следует учесть, что эта оценка была основана на достаточно скудных данных. Для получения
более точных показателей необходимо продолжить исследования по изучению распределения
ртути в сырой и товарной нефти и поведения ртути при нефтепереработке.
Еще одним существенным источником атмосферного ртутного загрязнения, судя по
всему, являются заводы по первичной выплавке цветных металлов. Для обеспечения точности
и полноты оценок требуется получить более точную информацию о фактическом содержании
ртути в рудах и концентратах, используемых на конкретных предприятиях, а также данные
фактических измерений ртутных выбросов.
Согласно выполненным оценкам, весьма существенный в загрязнения атмосферы ртутью
может вносить добыча золота из отходов и техногенных россыпей, отрабатывавшихся ранее с
использованием метода амальгамации. Однако для более корректной количественной оценки
эмиссии ртути за счет этого вида деятельности необходимо проведение детальных
исследований.
1 Введение
1.1 Предыдущие исследования по проблеме ртутного загрязнения окружающей среды
1.2 Регулирование поступления ртути в окружающую среду
1.3 Методология оценки
1.4 Химия ртути
1.5 Круговорот соединений ртути в природе – концептуальная модель
1.1 Предыдущие исследования по проблеме ртутного загрязнения
окружающей среды
В 1998 г. Комитет по экологии Государственной Думы Российской Федерации и
Правительство Российской Федерации поручили Государственному комитету по охране
окружающей среды Российской Федерации (Госкомэкологии РФ) подготовить
Государственный Доклад .О ртутном загрязнении окружающей среды в Российской Федерации
и его воздействии на здоровье населения.. К сожалению, это поручение не было выполнено.
Тем не менее Научно-исследовательский центр по проблемам управления ресурсосбережением
и отходами (НИЦПУРО) при Минэкономики России и Госкомэкологии России в 1999 г. при
участии специалистов других организаций подготовил отчет по теме .Анализ ртутного
загрязнения окружающей среды в Российской Федерации. [198], основной задачей которого
являлись определение источников ртутного загрязнения территории страны и разработка
рекомендаций для подготовки соответствующей Государственной программы по его изучению
и снижению.
В указанном отчете основными источниками ртутного загрязнения в России признаны
отходы производства и потребления. Отмечено также, что из-за недостаточного
государственного контроля за потреблением и применением ртути и ртутьсодержащих
соединений невозможно было полномасштабно и с точностью оценить объемы техногенного
поступления ртути в окружающую среду от каждого источника.
Кроме того, были определены отличительные черты и специфические условия России,
которые должны быть приняты во внимание при разработке Государственной программы по
изучению и снижению ртутного загрязнения окружающей среды, а именно:
- практически полное отсутствие крупных собственно ртутных месторождений в РФ
и тенденции увеличения количества попутной ртути, поступающей в составе
пиритных, цинковых и медных концентратов;
- разбросанность и удаленность многих потребителей ртути от ее производителей;
- отсутствие постоянного контроля за потреблением и повторным использованием
ртути;
- отсутствие на внутреннем рынке высокоэффективных сорбентов для улавливания
ртути из газообразных и жидких выбросов/сбросов;
- отсутствие стандартной возвратной тары для сбора, транспортировки и хранения
ртутьсодержащих отходов;
- отсутствие технологий по переработке многих видов ртутьсодержащих отходов;
- нехватка существующих в стране производственных мощностей для переработки
ртутьсодержащих отходов с применением имеющихся технологий.
Была также в определенной степени систематизирована нормативно-правовая база,
разработанная в 1970-1980-е г.г. и регулирующая вопросы, связанные с ртутным загрязнением.
Установлено, что существующие нормативные документы, как правило, затрагивают только
общие вопросы ртутного загрязнения и обращения с ртутью и ртутьсодержащими отходами и
не включают конкретные требования.
По мнению авторов указанного отчета, одной из основных причин ртутного загрязнения
в России является отсутствие в стране системы обращения с ртутьсодержащими отходами,
обеспечивающей их сбор, хранение, транспортировка и обезвреживание. Сбор, хранение и
транспортировка ртутьсодержащих отходов признаны наиболее сложной проблемой в области
их утилизации и обезвреживания. Отсутствие согласованных документов и наличие
противоречивых требований, предъявляемых различными ведомствами и местными органами
власти, не позволяют осуществлять эффективный сбор и доставку ртутьсодержащих отходов к
месту переработки/размещения. Авторы отчета пришли к выводу, что решение проблемы
Программы .Отходы., для реализации которой в части управления ртутьсодержащими
отходами рекомендованы следующие мероприятия:
- разработка прогноза потребления ртути до 2010 г. и определение сырьевой базы
вторичной ртути;
- разработка и реализация системы контроля за потреблением и повторным
использованием ртути;
- Разработка нормативной базы, регулирующей потребление и повторное использование
ртути (или объем общих потерь ее);
- Проведение государственной инвентаризации и паспортизации ртутьсодержащих
отходов на всех предприятиях, потребляющих ртуть и перерабатывающих ртутьсодержащие
отходы;
- Разработка и производство возвратной тары для сбора, хранения и транспортировки
ртутьсодержащих отходов;
- Разработка новых технологий переработки отдельных видов ртутьсодержащих отходов.
1.2 Регулирование поступления ртути в окружающую среду
Содержание ртути в различных объектах окружающей среды регулируется
установлением уровней предельно допустимых концентраций (ПДК), которые включены в
нормативно-методические документы, утвержденные исполнительными органами власти
Российской Федерации и/или бывшего СССР (табл. 1,1-1,6).
Таблица 1.1 Перечень основных нормативно-методических документов по защите окружающей
среды и населения от потенциально опасных загрязнений, в том числе ртути и ее
соединений
Наименование документа |
Утверждено |
1. Охрана поверхностных вод |
Гигиенические нормативы ГН 2.1.5.689-98. Предельно допустимые
концентрации (ПДК) химических веществ в воде водных объектов
хозяйственно-питьевого и культурно-бытового водопользования. |
Минздрав РФ, 04.3.98,
№ 9. |
Санитарные правила и нормы охраны поверхностных вод от загрязнения. |
Минздрав СССР,
09.7.88 г., № 4630-88 |
Методические указания по санитарной очистке водоемов при добыче и
обогащении руд цветных металлов. |
Минздрав СССР,
№ 20-38-79 |
Методические указания по определению содержания растворенных форм
ртути в жидких средах (природных, сточных водах, объектах
водопользования, питьевой воде, растворах). |
Минздрав РФ, 16.2.94 г.,
№ 4.1.006 |
2. Защита атмосферного воздуха |
Охрана природы. Атмосфера. Правила установления допустимых выбросов
вредных веществ промышленными предприятиями. |
ГОСТ 17.2.3.02-78 |
Временные инструктивно-методические указания по оценке степени
загрязнения атмосферного воздуха. |
Минздрав СССР,
23.2.76 г. |
Методические рекомендации по гигиенической оценке загрязнения
атмосферного воздуха в районах размещения предприятий по производству
и применению ртути. |
Минздрав СССР,
13.7.89 г., № 5050-89 |
Методические рекомендации по определению разовой нагрузки на человека
химических веществ, поступающих с атмосферным воздухом, водой и
пищевыми продуктами. |
Минздрав СССР,
№ 2983-84 |
Методические указания по определению содержания паров ртути в воздухе
рабочей зоны и атмосферном воздухе населенных пунктов методом атомно-
абсорбционной спектрометрии. |
Минздрав РФ, 16.2.94 г.,
№ 4.1.005 |
3. Охрана почв, бытовые и промышленные отходы |
Охрана природы. Почва. Номенклатура показателей санитарного состояния. |
ГОСТ 17.4.2.01-81 |
Охрана природы. Почва. Классификация химических веществ для контроля
загрязнения. |
ГОСТ 17.4. 1.02-83 |
Лом и отходы цветных металлов и сплавов. Общие технические условия. |
ГОСТ 1639-78 |
Предельное содержание токсичных соединений в промышленных отходах,
обуславливающих отнесение этих отходов к категории по токсичности. |
Минздрав СССР, 12.2.84 г.,
№ 3170-84 |
Санитарные правила СП 3183-84. Порядок накопления, транспортировки,
обезвреживания и захоронения токсичных промышленных отходов. |
Минздрав СССР, 29.2.84 г.
№ 3183-84 |
Предельное количество накопления токсичных промышленных отходов на
территории предприятия (организации). |
Минздрав СССР,
01.2.85 г., №3209-85 |
Предельное количество токсичных промышленных отходов, допускаемых
для складирования в накопителях (полигонах) твердых бытовых отходов. |
Минздрав СССР,
30.5.85 г., №3897-85 |
Предельное содержание токсичных соединений в промышленных отходах
накопителях, расположенных на территории предприятия (организации). |
Минздрав СССР,
19.1.85\г., №4015 |
Методические указания для органов и учреждений санитарно-
эпидемиологической службы по контролю за реализацией мероприятий,
направленных на санитарную охрану окружающей среды от загрязнения
твердыни и жидкими токсичными отходами производства. |
Минздрав СССР,
12.7.85 г., № 3912-85 |
Ресурсосбережение. Обращение с отходами. Методика определения ртути в
ртутьсодержащих отходах. Общие требования. |
ГОСТ Р 51768-2001 |
Ресурсосбережение. Обращение с отходами. Паспорт опасности отходов.
Основные требования. |
ГОСТ 30774-2001. |
Ресурсосбережение. Обращение с отходами. Документирование и
регулирование деятельности по обращению с отходами. Основные
положения. |
ГОСТ Р 51769-2001. |
Ресурсосбережение. Обращение с отходами. Классификация,
идентификация и кодирование отходов. Основные положения. |
ГОСТ 30775-2001. |
4. Защита рабочей зоны |
Межотраслевые правила по охране труда при производстве и применении
ртути. ПОТ РМ-009-99 (введены в действие с 1 февраля 2000 г.). |
Минтруда РФ, 14.9.99 г.,
№ 37 |
Ртуть. Технические условия. |
ГОСТ 4658-73 |
ССБТ. Работы со ртутью. Требования безопасности. |
ГОСТ 12.3.031-83 |
СП 4607-88. Санитарные правила при работе со ртутью, ее соединениями и
приборами с ртутным заполнением. |
Минздрав СССР, 04.4.88
г., №4607-88 |
Санитарные правила по проектированию, оборудованию, эксплуатации и
содержанию предприятий, производящих ртуть. |
Минздрав СССР 27.2.79 г.,
№2116-70 |
Гигиенические нормативы ГН 2.2.5.686-98. Предельно допустимые
концентрации (ПДК) вредных веществ в воздухе рабочей зоны. |
Минздрав РФ, 04.2.98 г., №
4 |
Санитарные правила для предприятий цветной металлургии. |
Минздрав СССР,
24.2.82 г., № 2528-82 |
Инструкция по очистке спецодежды, загрязненной металлической ртутью
или ее соединениями. |
Минздрав СССР, 20.7.76 г.,
№ 1442-76 |
5. Защита продуктов питания |
Медико-биологические требования и санитарные нормы качества
продовольственного сырья и пищевых продуктов. |
Минздрав СССР,
01.8.89 г. |
Временные гигиенические нормативы содержания токсичных элементов
(тяжелых металлов) в зерновых продуктах, предназначенных для детского
питания. |
Минздрав СССР,
№ 3091-84 |
Предельно-допустимые концентрации тяжелых металлов и мышьяка в
производственном сырье и пищевых продуктах. |
Минздрав СССР,
№ 4089-86 |
Санитарные правила и нормы. СанПиН 2.1.4.559-96. Питьевая вода.
Гигиенические требования к качеству воды централизованных систем
питьевого водоснабжения. Контроль качества. |
Минздрав РФ, 24.0.96,
№ 26 |
6. Оценка загрязнения и демеркуризационные мероприятия |
Территориальный газо-ртутный мониторинг непроизводственных объектов.
Методические рекомендации. |
Минздрав РФ,
№ 2001/159. |
Методические рекомендации по контролю за организацией текущей и
заключительной демеркуризации и оценке ее эффективности. |
Минздрав СССР, 31.2.87г.
№4545-87 |
Методические рекомендации по организации и проведению демеркуризации. МЧС России, 1998
Информационно-методическое письмо о гигиенических мероприятиях и
оценке риска для здоровья населения в очагах загрязнения ртутью жилых и
общественных зданий. |
Минздрав РСФСР,
05.2.90 г., № 23-01-2/101 |
Гигиеническая оценка качества почвы населенных мест. Методические
указания. |
Минздрав РФ, 07.2.99 г., №
2.1.7.730-99
|
Таблица 1.2 ПДК ртути и ее соединений в атмосферном воздухе населенных мест [62]
Вещество * |
ПДК, мг/м³ |
Максимальная разовая |
Среднесуточная |
Ртуть металлическая |
- |
0,0003 |
Диэтилртуть ** |
0,0003 |
- |
Ртути** |
- |
0,0003 |
(II) динитрат |
- |
0,0003 |
(I) нитрат |
- |
0,0003 |
(II) амидохлорид |
- |
0,0003 |
(II) йодид |
- |
0,0003 |
(II) оксид |
- |
0,0003 |
(II) ацетат |
- |
0,0003 |
(I) хлорид |
- |
0,0003 |
(II) дихлорид |
- |
0,0003 |
* Все нормируемые вещества относятся к 1-му классу опасности.
** ПДК для соединений ртути даны в пересчете на ртуть.
Таблица 1.3 ПДК ртути и ее соединений в воздухе рабочей зоны [63, 245]
Вещество * |
ПДК, мг/м³ |
Преимущественное агрегатное состояние в условиях производства |
Максималь ная |
Среднесмен ная |
Ртуть металлическая |
0,01 |
0,005 |
Пары |
Диэтилртуть |
- |
0,005 |
Пары |
Ртути, неорганические соединения ** |
0,2 |
0,05 |
Аэрозоль |
Этилмеркурфосфат ** |
- |
0,005 |
Смесь паров и аэрозоля |
Этилмеркурхлорид ** |
- |
0,005 |
Смесь паров и аэрозоля |
* Все нормируемые вещества относятся к 1-му классу опасности.
** ПДК для соединений ртути даны в пересчете на ртуть (при воздействии неорганических
соединений требуется специальная защита кожи и глаз).
Таблица 1.4 ПДК ртути и ее соединений в воде водных объектов хозяйственно-питьевого и
культурно-бытового водопользования [64]
Вещество * |
ПДК, мг/л ** |
Диэтилртуть |
0,0001 |
Ртуть (для неорганических соединений с учетом валового содержания всех форм) |
0,0005 |
Этилмеркурхлорид |
0,0001 |
* Все нормируемые вещества относятся к 1-му классу опасности.
** Поступление неорганической ртути (Hg2+) и сулемы в водные объекты, используемые для
рыбохозяйственных целей, недопустимо.
Таблица 1.5 Допустимые остаточные количества (ДОК) содержания ртути в продуктах питания
[245]
Вид продуктов |
ДОК, мг/кг |
Рыбные |
0,5 |
Мясные |
0,03 |
Молочные |
0,005 |
Овощи |
0,02 |
Хлеб и зерновые |
0,01 |
Фрукты |
0,01 |
Соки |
0,05 |
Таблица 1.6 ПДК валовой концентрации ртути и допустимые уровни ее содержания по
показателям вредности в почве [60]
ПДК, мг/кг |
Показатели вредности и значения их лимитирующих концентраций, мг/кг * |
Транслока- ционный |
Миграционный |
Общесани- тарный |
водный |
воздушный |
2,1 |
2,1 |
33,3 |
2,5 |
5 |
** Транслокационный показатель вредности характеризует возможность перехода ртути в
сельскохозяйственные растения и накапливаться там в концентрациях, превышающих установленную
для них ПДК. Миграционный водный показатель вредности характеризует способность перехода ртути
из почвы в грунтовые и поверхностные воды и концентрироваться в них в количествах, превышающих
установленную для воды ПДК. Миграционный воздушный показатель вредности характеризует
возможность перехода ртути из почвы в атмосферный воздух с достижением концентраций,
превышающих уровень ПДК, установленный для атмосферы. Общесанитарный показатель вредности
характеризует влияние ртути на самоочищающую способность и биологическую активность почвы.
Российским законодательством определено, что тот показатель вредности, который имеет наименьшую
пороговую величину, избирается как лимитирующий показатель вредности и принимается за ПДК
данного химического элемента (вещества) в почве. В случае с ртутью – это транслокационный
показатель, равный 2,1 мг/кг.
Правила сбора, хранения, упаковки, транспортирования и приема ртутьсодержащих
отходов в свое время были определены в Инструкции Министерства цветной металлургии
СССР, утвержденной 27.0.1966 г., многие положения которой к настоящему времени устарели.
Сейчас в регионах Российской Федерации, где имеются предприятия по сбору и переработке
ртутьсодержащих отходов потребления (главным образом, люминесцентных ламп),
разработаны региональные правила обращения с указанными видами отходов.
1.3 Методология оценки
Настоящая оценка поступления ртути в окружающую среду с территории России была
выполнена с применением так называемого метода жизненного цикла. По каждой области
целевого применения ртути и по каждому виду хозяйственной деятельности, в результате
которой происходит мобилизация ртути, содержащейся в качестве естественной примеси в
используемых материалах или сырье, оценивалась ее судьба (жизненный цикл), начиная от
приобретения/добычи и заканчивая эмиссией в окружающую среду или поступлением в
отходы.
Методология данного подхода основана на принципе масс-баланса: вся ртуть,
поступившая в обращение (в техносферу), рано или поздно в конечном итоге поступает в
окружающую среду в составе отходов, выбросов, стоков. Для каждой области целевого
использования ртути осуществлялся анализ ее поведения и распределения в производственных
процессах и содержания в продукции, который базировался на информации, предоставленной
конкретными предприятиями или, если такая информация была недоступна, на результатах
предыдущих исследований. Оценка объемов эмиссии ртути в окружающую среду выполнялась
на основе данных, полученных непосредственно от предприятий, с использованием
официальной статистической информации Госкомстата РФ по поступлению ртути в атмосферу,
водные объекты и отходы (см. Приложение 1). В ходе выполнения работ экспертами были
посещены российские предприятия, являющиеся основными потребителями ртути.
По областям хозяйственной деятельности, где ртуть поступает в технологические
процессы в качестве естественной примеси в перерабатываемых/используемых сырье и
материалах, расчет общего количества мобилизованного металла производился путем
умножения его концентрации в материалах или сырье (например, в угле) на массу (объем)
этого сырья.
В целом это может быть выражено следующим образом:

где общее масса мобилизованной ртути (.мобилизация.) рассчитывается путем сложения
количества ртути во всех использованных сырьевых материалах. Количество ртути,
содержащееся в каждом сырьевом продукте, рассчитывается путем умножения массы (объема)
потребляемого сырья (.потреблениеx.) на концентрацию ртути в сырье (.концентрацияx.).
Расчет поступления ртути в различные компоненты окружающей среды в результате
производственных процессов (например, при сжигании угля) производится путем умножения
общего количества мобилизованной ртути (.мобилизация.) на коэффициент удельного
специфического распределения ртути (.распределение.):
Выбросвоздух = Мобилизация * Распределениевоздух,
где Распределениевоздух – это коэффициент распределения, выражающий долю всей
мобилизованной ртути, попадающей в атмосферу в результате производственного процесса.
Коэффициенты распределения определяются либо на основе специальных исследований
производственных процессов в Российской Федерации, либо на основе коэффициентов
распределения, полученных для других стран, применяющих схожие технологии.
Практически все данные, использованные для оценки, имеют ту или иную степень
неопределенности. Насколько это возможно, все величины были представлены как .наилучшая
оценка. и с указанием конкретной степени неопределенности. В большинстве случаев
неопределенность невозможно оценить с использованием стандартных статистических
методов; эта оценка скорее может быть основана на экспертных суждениях. Диапазоны,
используемые при оценке, должны отражать диапазоны, в рамках которых эксперты оценивают
точность/правильность значения с вероятностью в 90%. Это означает, что для 10% оценок
истинное значение может выходить за рамки указанного диапазона. Распределение
вероятностей необязательно является симметричным распределением вокруг среднего
значения. Например очень неопределенные оценки скорее должны предполагать
логнормальное распределение (вероятность, того, что истинное значение в два раза превышает
.наилучшую оценку. равна вероятности того, что она составляет половину .наилучшей
оценки.). Возможное потребление ртути в оборонной промышленности в данном исследовании
не рассматривалось.
Главной целью настоящей оценки являлось изучение поведения ртути в техносфере (рис.
1.1). Особенности концентрирования и распределения ртути в различных компонентах
окружающей среды, а также ее воздействие на здоровье населения и природные экосистемы
кратко описаны в некоторых главах, но в целом в отчете эти вопросы не рассматриваются.
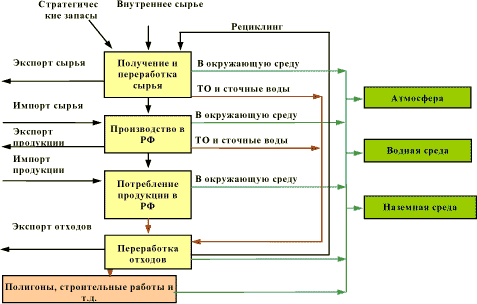
Рисунок 1.1.Схематическое изображение перемещения ртути в техносфере
1.4 Химия ртути
Ртуть и некоторые ее соединения используются человеком с древнейших времен. Первое
письменное упоминание о ртути принадлежит Аристотелю и относится примерно к 350 г. до н.
э. О ртути писал также его ученик, основатель минералогии Тиртамос из Эреза, прозванный
Феофрастом (т. е. божественным оратором). Химический знак ртути “Hg” образован от ее
латинского названия “hydrargyrum.. Считается, что латинское название ртути “hydrargyrum”
(от греческих слов “hydor” - вода и “árgyros” – серебро, т. е. “жидкое серебро”, или “серебряная
вода”) впервые встречается у Плиния Старшего (I в. н. э.). Некоторые историки автором этого
термина называют жившего в I в. н. э. древнегреческого врача Диоскорида.
Алхимики назвали ртуть “mercurius” в честь римского бога торговли, прибыли и
обогащения, охранителя дорог, путешественников и мореплавателей, покровителя искусств и
ремесел, знатока тайн магии и астрологии, проводника душ в мире мертвых Меркурия,
отождествлявшегося с греческим Гермесом. Происхождение русского названия .ртуть. не
установлено. Приоритет утверждения ртути самостоятельным металлом принадлежит
знаменитому Агриколе. Твердая ртуть впервые получена в 1759 г. в Петербурге М.П. Брауном
и М.В. Ломоносовым, которым удалось заморозить ее в смеси снега с концентрированной
азотной кислотой.
Представленная далее информация главным образом взята из Справочника .The Global
Mercury Assessment., подготовленного UNEP Chemicals (UNEP 2002), из “Химической
энциклопедии” [304], Справочника “Свойства элементов” [257] и “Геологического справочника
по ртути” [296].
Ртуть – химический элемент II группы периодической системы Менделеева; атомный
номер 80, относительная атомная масса 200,59. Известно 7 стабильных и более 20
радиоактивных изотопов ртути. Ртуть в обычных условиях представляет собой тяжелый
жидкий металл. В специальной литературе такую ртуть называют “элементарной” или
“металлической” (Hg(0) или Hg0). Ртуть относительно редко встречается в природе в жидком
(металлическом) состоянии, чаще ее можно найти в составе органических и неорганических
соединений , в которых она может быть как одновалентной, так и – чаще всего - двухвалентной
- Hg(I) и Hg(II) (или Hg2+) соответственно. Под воздействием некоторых микроорганизмов и
естественных (гипергенных) процессов ртуть в природе может изменять форму своего
нахождения. Элементарная ртуть, содержащаяся в виде паров в атмосфере, может
трансформироваться в неорганические ртутные соединения, обеспечивая тем самым
значительную возможность для осаждения поступающей в воздух “техногенной” ртути.
В природе ртуть – весьма редкий элемент; ее среднее содержание в земной коре и
основных типах горных пород, по разным оценкам, колеблется в пределах 3.9 * 10-6 % (по
массе). Масса ртути, сосредоточенная в поверхностном слое земной коры мощностью в 1 км
оценивается в 100000000000 т (сто миллиардов тонн), их которых в ее собственных
месторождениях находится только 0,02%. Оставшаяся часть ртути существует в состоянии
крайнего рассеяния, по преимуществу в горных породах. Именно эта рассеянная ртуть создает
природный геохимический фон, на который накладывается ртутное загрязнение,
обусловленное деятельностью человека.
К настоящему времени в природе обнаружено более 80 ртутных и несколько десятком
ртутьсодержащих минералов. Основным рудным минералом, определяющим промышленную
значимость собственно ртутных месторождений, является киноварь (сульфид ртути, HgS).
Самородная (металлическая) ртуть, метациннабарит, ливингстонит и ртутьсодержащие
блеклые руды имеют резко подчиненное значение и добываются попутно с киноварью. Всего в
мире зафиксировано около 5000 ртутных месторождений, рудных участков и рудопроявлений,
получивших самостоятельные наименования, из них в разные годы разрабатывались около 500.
В последние годы установлено, что ртуть образует заметные концентрации не только в
собственных ее месторождениях, но и в рудных месторождениях нертутного состава:
колчеданных, полиметаллических, медных, золоторудных и других, а также в газовых и
газонефтяных месторождениях.
В промышленности для получения металлической ртути используют главным образом
два варианта технологии ее извлечения из руд: окислительно-дистилляционный обжиг (в
основном киноварных руд) при температуре выше 540°С с выделением ртути из газовой фазы и
(реже) комбинированный способ, включающий предварительное обогащение руд и затем
пирометаллургическую переработку полученных концентратов.
Элементарная ртуть – это блестящий серебристо-белый металл, имеющий жидкое
состояние при комнатной температуре; он традиционно используется для изготовления
термометров и некоторых типов электрических переключателей. Удельный вес металлической
ртути при 20оС составляет 13,54616 г/см³; температура плавления равна –38,89°С, кипения
+357,25°С. При замерзании (при –38,89°С) ртуть становится твердой и легко поддается ковке.
Обладая высоким потенциалом ионизации, высоким положительным окислительным
потенциалом, ртуть является относительно стойким в химическом отношении элементов. Это
обусловливает ее способность восстанавливаться до металла из различных соединений и
объясняет случаи ее нахождения в природе в самородном состоянии.
Даже в обычных условиях элементарная ртуть обладает повышенным давлением
насыщенных паров и испаряется с довольно высокой скоростью, которая с ростом температуры
увеличивается. Это приводит к созданию опасной для живых организмов ртутной атмосферы.
При действии на ртутные пары вольтовой дуги, электрической искры и рентгеновских лучей
наблюдаются явления люминесценции, флюоресценции и фосфоресценции. В вакуумной
трубке между ртутными электродами при электрических разрядах получается свечение, богатое
ультрафиолетовыми лучами, что используется в технике при конструировании ртутных ламп.
Еще одно свойство элементарной ртути связано с тем, что при растворении в ней металлов
образуются амальгамы – металлические системы, одним из компонентов которых является
ртуть. Они не отличаются от обычных сплавов, хотя при избытке ртути представляют собой
полужидкие смеси. Амальгамированию подвергаются только металлы, смачиваемые ртутью.
Соединения, получающиеся в результате амальгамирования, легко разлагаются ниже
извлечении золота и серебра из руд.
Из неорганических ртутных соединений наибольшее практическое значение имеют
сульфид ртути (HgS), оксиды ртути (HgO и Hg2O), иодная ртуть (HgI), хлористая ртуть, или
каломель (Hg2Cl2), хлорная ртути, или сулема (HgCl2). Эти соединения также называют солями
ртути.
Сульфид ртути HgS – самое распространенное в природе соединение ртути, которое
известно в 3-х модификациях: красная (идентичная минералу киноварь), черная (черный
сульфид ртути, или метациннабарит) и .-киноварь (в природных условиях не обнаружена).
Иодная ртуть существует в 2-х модификациях – красной и желтой.
Каломель представляет собой бесцветные тетраэдрические кристаллы, постепенно
темнеющие вследствие распада под действием света на сулему и ртуть. Сулема имеет вид
бесцветных кристаллов ромбической формы.
При продолжительном нагреве до температур, близких к температуре кипения,
элементарная ртуть соединяется с кислородом воздуха, образуя красный оксид (II) ртути HgO,
в котором степень окисления ртути равны +2. Желтый оксид ртути HgO получается при
добавлении щелочей к водному раствору соли Hg(II). Существует оксид ртути черного цвета
(Hg2O), нестойкое соединение, степень окисления ртути в котором равна +1. Во всех
соединениях ртути (I) ее атомы связаны между собой, образую двухвалентные группы –Hg2–
или –Hg–Hg–. Подобная связь сохраняется и в растворах солей ртути (I).
Из других неорганических соединений известны гремучая ртуть Hg(ONC)2, нитрат ртути
Hg(NO3)2, сульфат ртути HgSO4, сульфит ртути HgSO3 и др. При воздействии на соли ртути
аммиака образуются многочисленные комплексные соединения.
Некоторые соли ртути (например HgCl2) являются достаточно летучими для того, чтобы
содержаться в атмосферном газе. Однако водорастворимость и химическая реактивность этих
неорганических (ионных) ртутных газов способствует гораздо более быстрому осаждению их
из атмосферы, чем в случае с металлической ртутью. Это существенно сокращает срок
пребывания в атмосфере этих ионных (например, двухвалентных) ртутных газов по сравнению
с парами металлической ртути.
Существует большое количество ртутьсодержащих органических соединений, в которых
атомы металла связаны с атомами углерода. Химическая связь углерода и ртути очень
устойчива. Она не разрушается водой, ни слабыми кислотами, ни основаниями.
Известны два основных типа ртутьсодержащих органических соединений: R–Hg–R‘ и R–HgX, где R и R‘ - органические радикалы, Х – кислотный остаток. Первая группа включает
неполярные соединения, почти нерастворимые в воде и очень летучие. Вторая группа включает
соединения ртути, характеризующиеся хорошей водной и липидной растворимостью и высокой
устойчивостью в водной среде, например, ион метилртути (СН3–Hg+). Наиболее известны такие
ртутьорганические соединения, как диметилртуть, фенилртуть, этилртуть и метилртуть, причем
до настоящего времени наиболее распространенным из них является метилртуть. С позиций
опасности для живых организмов наиболее токсичными из органических соединений ртути
являются алкилртутные соединения с короткой цепью, в которых ртуть присоединяется к атому
углерода из метиловой, этиловой и прониловой группы (прежде всего, метилртуть).
Так же как и неорганические ртутные соединения метилртуть и фенилртуть существуют
в виде .солей. (например, хлорид метилртуть или фенилртутьацетат). В чистом виде
метилртуть и фенилртуть в большинстве случаев являются белыми кристаллическими
твердыми веществами; диметилртуть представляет собой бесцветную жидкость.
Метилртуть может образовываться в природе (особенно в водоемах) в результате
метаболизма микробов (биотические процессы) и в результате химических процессов, в
которых не участвуют живые организмы (абиотические процессы). Основными продуктами
природного метилирования ртути являются моно- и диметилртуть. Если образуется
диметилртуть, то благодаря своей низкой растворимости в воде и высокой летучести она легко
испаряется в атмосферу, где подвергается разложению до элементарной ртути под
воздействием ультрафиолета солнечной радиации. Если же образуется монометилртуть (ее
чаще и называют метилртутью), то она способна активно и быстро накапливаться в живых
организмах до токсичных уровней. Считается, что образование метилртути в природе
происходит главным образом благодаря биотическим процессам. Основные прямые
антропогенные источники метилртути на настоящий момент не известны, хотя существуют
определенные исторические сведения на этот счет. Тем не менее антропогенное загрязнение
косвенно способствует росту уровня содержания этого соединения в природе из-за
возможности ее образования из других поступающих в окружающую среду соединений ртути.
Примером непосредственного сброса органических соединений ртути в окружающую
среду является известный случай в Минамате, который произошел в 1950-х годах, когда с
промышленной установки по производству ацетальдегида осуществлялся сброс
ртутьорганических соединений в морскую бухту, что привело к накоплению метилртути в
морепродуктах и к массовому отравлению и гибели японских рыбаков, употреблявших их в
пищу. Не менее известен и случаи массового отравления и гибели людей в Ираке, когда мука,
полученная из семян, обработанных смесью, содержащей органическую ртуть, была
использована для выпечки хлеба.
Недавние исследования показали, что метилртуть может поступать в окружающую среду
непосредственно с полигонов бытовых отходов и с канализационных очистных сооружений, но
пока неизвестно насколько существенный вклад в общее ртутное загрязнение вносят эти
источники.
Будучи химическим элементом, ртуть не может распадаться или разлагаться,
превращаясь в безопасные вещества. Она может изменять состояние и формы нахождения в
процессе своего жизненного цикла, но ее простейшая форма – элементарная ртуть - сама по
себе представляет опасность для здоровья человека и окружающей среды. Как только
происходит высвобождение ртути при переработке руд, сжигании ископаемых топлив или в
результате ее дегазации из земной коры в биосферу, она может быть очень мобильной,
циркулируя между поверхностью земли и атмосферой. Почвенный покров, водные объекты и
донные отложения являются своеобразными первичными приемниками, временно
депонирующими ртуть.
1.5 Круговорот соединений ртути в природе – концептуальная модель
Концептуальные модели, как правило, содержат письменное и графическое описание ситуации
на основе имеющихся знаний о:
- физических, биологических и химических свойствах вещества или химического соединения,
важных с точки зрения оценки активности этого вещества и путей его перемещения в
окружающей среде, а также вида и степени воздействия;
- причинных связей, с определенной степенью детализации, источников, путей переноса,
стрессоров, и рецепторов человека и живой природы.
Подобные модели предоставляют необходимую информацию об основных объектах
мониторинга (напр. источниках, средах и рецепторах), а также необходимости проведения
временного или пространственного мониторинга какого-либо химического соединения. Кроме
того, можно получить информацию о взаимосвязи между различными средами, что позволит
представить полную мультимедийную картину поведения вещества в окружающей среде.
Концептуальная модель циркуляции ртути в окружающей среде представлена на Рис 1,1. Как
видно из данного рисунка, выбросы ртути в атмосферу происходят из естественных и
антропогенных источников, и ртуть может циркулировать в глобальном масштабе, постоянно
перемещаясь из одной среды в другую, посредством сложных схем переноса и трансформации
и, в конечном итоге, оказывает воздействие на человека и живую природу.
Одним из основных путей поступления ртути в окружающую среду являются выбросы в
атмосферу. Во многих странах, крупнейшими источниками атмосферных выбросов ртути
являются угольные электростанции, промышленные котельные и различные виды установок
ртути в атмосферу, например вулканы. Ртуть может поступать в окружающую среду и другими
путями, например, со стоками промышленных предприятий, сбрасываемыми в водные
объекты. Несмотря на то, что сбросы ртути в водную среду в большинстве стран считаются
незначительными, по сравнению с атмосферными выбросами, они могут иметь существенное
локальное воздействие. Например, сбросы ртути в поверхностные водные объекты с
заброшенных золоторудных и ртутных месторождений часто является причиной содержания
метилртути в рыбе.
Рисунок 1.2 Круговорот соединений ртути . концептуальная модель
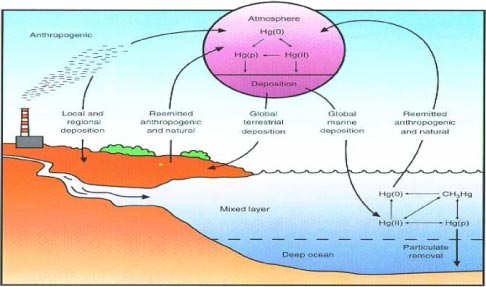
2 Производство, импорт и экспорт ртути в России
2.1 Производство ртути в Российской Федерации
2.1.1 Исторический обзор
2.1.2 Добыча и производство первичной ртути в СССР и России
2.1.3 Производство вторичной ртути
2.2 Экспорт и импорт ртути
2.3 Внутренний рынок ртути в России
2.1 Производство ртути в Российской Федерации
2.1.1 Исторический обзор
Первые сведения об организации ртутного производства в России относятся к 1725 г.,
согласно которым купец Петр Анисимов завел ртутную фабрику, причем источники сырья он
держал в секрете [140]. Промышленная добыча ртутной руды (киновари) в России впервые
началась в 1759 г. на Ильдиканском месторождении в Забайкалье и в незначительных объемах
периодически продолжалась до 1853 г. [131]. Здесь же была получена первая российская
металлическая ртуть. В конце XIX - начале ХХ вв. киноварь в небольших количествах
добывалась из аллювиальных россыпей в Амурской области. Примерно в это же время
осуществлялась отработка отдельных участков ртутных месторождений Бирксуйского рудного
поля (Южная Фергана) и месторождения Хпек (Южный Дагестан).
В 1879 г. было открыто Никитовское ртутное месторождение (Украина), эксплуатация
которого (одновременно с выплавкой металла) началась в 1887 г. [13]. В 1887-1908 г.г. годовое
производство ртути на Никитовском руднике варьировалось в пределах 47,3-615,9 т). Расчеты,
основанные на данных [13, 24, 45, 247], показывают, что с 1887 по 1917 г. здесь было получено
6762 т металлической ртути, существенная часть которой шла на экспорт (с 1889 г. по 1907 г. за
границу было вывезено более 5145 т ртути). В начале ХХ в. Россия также импортировала
киноварь и ртуть. Например, в 1913 г. в страну было ввезено 56 т киновари и 168 т ртути, в
1914 г. - 41 т киновари и 129 т ртути [45].
В 1900-1908 г.г. потребление металлической ртути в России колебалось в пределах 49-
118 т/год [45]. В это время ртуть применялась в медицине и фармацевтике, при изготовлении
зеркал и красок, при производстве термометров, барометров, манометров и других приборов,
использовалась для натирания подушек электрических машин, извлечения золота и серебра
амальгамным способом, золочения меди и бронзы, очистки войлока (фетра), в золотошвейном
деле и лабораторной практике.
2.1.2 Добыча и производство первичной ртути в СССР и России
До распада СССР потребности российских промышленных предприятий в металлической
ртути удовлетворялись главным образом за счет поставок ее из Украины (Никитовка) и
Киргизии (Хайдаркан) (табл. 2.1). Доля ртути, ежегодно производимой в пределах России,
обычно не превышала 3-5% общего ее производства в Советском Союзе (табл. 2.2). Всего в
пределах бывшего СССР было выплавлено порядка 77 тыс. т. ртути, из которых около 7,3 тыс.
т - непосредственно на российских предприятиях[1].
В настоящее время в России Государственным балансом запасов полезных ископаемых
учтено 24 месторождения ртути, характеризующихся в основном рудами низкого качества
(табл. 2.3). Большинство месторождений относится к собственно ртутным (киноварным) с
запасами, как правило, не более 2 тыс. т металла. Только четыре месторождения являются
сравнительно крупными - Тамватнейское (14 тыс. т), Западнопалянское (10,1 тыс. т), Чаган-
Узунское (14 тыс. т), “Звездочка” (3 тыс. т) [169].
Таблица 2.1 Основные центры бывшего СССР по производству первичной ртути * [16, 41, 105,
164-169, 184, 240, 241, 295, 322, 329]
Предприятие, месторождение |
Период эксплуатации |
Масса полученной ртути |
Примечание |
Украина |
Никитовский ртутный комбинат, месторождения Никитовского рудного поля (главным образом, Никитовское месторождение) |
1887-1995 г.г. |
Более 35000 т |
С 1996 г. добыча руд и производство первичной ртути прекращены; есть сведения, что во 2-й половине 1990-х г.г. здесь производилась вторичная ртуть из отходов, а также ртуть из ранее добытых руд (по 20-50 т/год) |
Месторождение Боркут, Закарпатская область |
Середина 1960-х - начало 1980-х г.г. |
Около 500 т |
Разработка месторождения осуществлялась подземным способом |
Кыргызстан |
Хайдарканский горно-металлургический комбинат, Хайдарканское, Новое, Чаувайское, Чонкойское месторождения |
С 1942 г. по настоящее время |
Более 32000 т |
В 1995-2000 г.г. производство первичной ртути составляло 380-620 т/год |
Таджикистан |
Концентрат, получаемый на обогатительной фабрике Анзобского комбината (Джижикрутское сурьмяное месторождение), перерабатывался в Хайдаркане |
Конец 1960-х - 1980-е г.г. |
Около 1000 т |
В 1993-2000 г.г. из концентрата, поступавшего на Хайдаркан, получали до 9-80 т ртути в год |
Азербайджан |
Месторождения Шорбулак и Агятаг (Нагорный Карабах) |
1970-е г.г. |
Около 150 т |
Месторождения практически полностью отработаны |
Казахстан |
Свинцово-цинковый комбинат, г. Усть-Каменогорск (Казахстан), попутная ртуть |
1970-80-е г.г. |
Около 130 т (в среднем 4-6 т/год) |
В 1996-2000 г.г. производство попутной ртути составляло 10-20 т/год ** |
Россия *** |
ГУП “Акташское горно-металлургическое предприятие”, Алтайский край, Акташское месторождение. |
1941-1990 г.г. |
Около 5 тыс. т (при годовом объеме от 30 до 130 т) |
В 1990-х г.г. периодически осуществлялась выплавка вторичной ртути из отработавших ячеек электролизеров хлорно-щелочных заводов, отходов
производства оксидов ртути и пр.). |
ЗАО “Кубаньцветмет” (бывший “Краснодарский рудник”), Сахалинское месторождение, Краснодарский край |
С 1970-х г.г. до 1994 г. |
Более 500 т |
По экономическим причинам в 1990 г. подземная часть месторождения законсервирована, а в 1993 г. были прекращены работы на карьере; сейчас осуществляется выпуск вторичной ртути |
Месторождение Терлигхайское, Тыва |
1970-1972 г.г. |
40 т |
Рудник законсервирован |
Месторождение Пламенное, Чукотка |
1970-е г.г. |
Около 150 т |
Месторождение отработано |
* В металлургии и экономике ртути обычно принято различать первичную ртуть (получают из
ртутных руд), попутную ртуть (получают попутно при переработке руд других металлов, в которых
ртуть содержится в виде нежелательной примеси) и вторичную ртуть (получают из отходов).
** Данная оценка, приводимая в различных источниках, явно завышена.
*** В Сибири (Алтай, Кузнецкий Алатау, Забайкалье, Хабаровский край) в разное время
старателями и мелкими разведочно-эксплуатационными предприятиями отрабатывались небольшие
ртутные месторождения (Сухонькое, Белоосиповское, Чуйское, Ланское и др.); общая масса полученной
на этих объектах металлической ртути составляет порядка 150 т.
Источники: Багатаев, 1998 год, Бутов и соавторы, 1997; Справочник, 2002 год; Мировые минеральные ресурсы на
начало 1994 года, 1995 год; Мировые минеральные ресурсы на начало 1997 года, 1998 год; Мировые
минеральные ресурсы на начало 1998 года, 1999; Мировые минеральные ресурсы на начало 1999 года, 2000 год;
Мировые минеральные ресурсы на 1.1.2000 год, 2001, 2002; Оболенский и соавторы, 1995 год, Ртуть в
окружающей среду Сибири, 1995; Федорчук, 1983; Ягольницер и соавторы, 1995;
http://www.rambler.ru/db/news/msg.html])
Таблица 2.2 Структура добычи и производства ртути в СНГ, 1991 г. [234]
Страна |
В процентах от общего количества |
Добыча |
Производство |
Киргизия/td>
| 57/td>
| 60 |
Украина/td>
| 31/td>
| 37 |
Таджикистан/td>
| 5/td>
| - |
Казахстан/td>
| 4/td>
| 0,5 |
Россия/td>
| 3/td>
| 2,5 |
Таблица 2.3 Региональная структура балансовых запасов ртути в России [41]
Субъект Федерации |
Месторождение |
Геолого-промыш-ленный тип |
Доля в запасах (В+С1+С2), % * |
Содержание Hg в руде, % ** |
Собственно ртутные месторождения |
Алтайский край |
Сухонькое |
Карбонатный |
0,6 |
0,24 |
Камчатская область |
Ляпганайское |
Опалитовый |
3,5 |
0,63 |
Алюторское |
Опалитовый |
1,7 |
1,05 |
Чемпуринское |
Опалитовый |
0,7 |
1,07 |
Кемеровская область |
Куприяновское |
Кварц-диккитовый |
0,2 |
0,32 |
Красноярский край |
Белокаменное |
Кварц-диккитовый |
2,3 |
0,47 |
Салинское |
Кварц-диккитовый |
2,4 |
0,42 |
Дальнее |
Кварц-диккитовый |
1,8 |
0,31 |
Каскадное |
Кварц-диккитовый |
0,1 |
0,14 |
Республика Алтай |
Чаган-Узунское |
Лиственитовый |
7,0 |
0,42 |
Черемшанское |
Карбонатный |
0,1 |
0,50 |
Республика Саха (Якутия) |
Звездочка |
Кварц-диккитовый |
6,2 |
1,59 |
Гал-Хая |
Кварц-диккитовый |
1,1 |
0,60 |
Северное |
Кварц-диккитовый |
0,4 |
1,09 |
Среднее |
Кварц-диккитовый |
0,3 |
3,40 |
Балгикакчан |
Кварц-диккитовый |
0,1 |
1,63 |
Республика Тыва |
Терлигхайское |
Полиаргиллитовый |
5,1 |
0,22 |
Республика Сев. Осетия - Алания |
Тибское |
Кварц-диккитовый |
1,6 |
0,25 |
Хабаровский край |
Ланское |
Полиаргиллитовый |
1,2 |
0,52 |
Чукотский автономный округ |
Тамватнейское |
Лиственитовый |
33,1 |
0,70 |
Западнопалянское |
Кварц-диккитовый |
24,0 |
0,53 |
Ртутьсодержащие месторождения (попутная ртуть) |
Республика Башкортостан |
Подольское |
Медно-колчеданный |
4,6 |
0,0025 |
Челябинская область |
Талганское |
Медно-колчеданный |
0,6 |
0,0059 |
Свердловская область |
Сафьяновское |
Медно-колчеданный |
0,2 |
0,0014 |
* Выявленные запасы ртути в России на начало 2001 г. оценивались в 45,3 тыс. т, из которых 15,6
тыс. т - запасы промышленных категорий.
** Среднее содержание ртути в рудах составляет 0,453%.
Ртуть образует заметные концентрации в рудах медно-колчеданных, полиметаллических,
золотосеребряных и других типов рудных месторождений [33, 188, 229, 295, 296]. Так, в
повышенных количествах (до 88-800 мг/кг) ртуть присутствует в медно-колчеданных
месторождениях Южного Урала (Учалинское, Узельгинское, Сибайское, Бурибайское, Бакр-
Тау, Юбилейное, Гайское и др.). В рудах месторождений золотосеребряной формации Северо-
востока России отмечены концентрации ртути, достигающие в среднем 8-75 мг/кг
(максимально до 150-700 мг/кг) [254].
При существующих в России технологических схемах переработки, например, медно-
колчеданных руд попутная ртуть не извлекается [209] и рассеивается в окружающей среде
(главным образом, с выбросами в атмосферу и твердыми отходами). Так, в ежегодно
добываемых на Сафьяновском месторождении рудах содержится до 10 т ртути, которая при их
переработке теряется [169]. По оценке [41], на предприятиях цветной металлургии России в год
можно получать до 100 т попутной ртути.
Принято считать, что в 1970-80-х г.г. в СССР ежегодно производилось до 1200-1300 т
первичной ртути [41]. В то же время известно, что только Хайдарканский комбинат во времена
СССР давал около 1200 т ртути в год [240], а на Никитовском ртутном комбинате ежегодно
получали до 1000 т ртути (из которых 300-400 т - вторичная ртуть) [165]. Судя по всему,
приводимые в некоторых отечественных и зарубежных источниках сведения о производстве в
СССР первичной ртути по 1900-2200 т в год соответствуют действительности (табл. 2.4).
Таблица 2.4 Производство первичной ртути в бывшем СССР и России *
Год |
Страна |
Ртуть, т/год |
Источник |
1981 |
СССР |
2173 |
[396] |
1982 |
СССР |
1966 |
[396] |
1983-1989 г.г. |
СССР |
по 1500-1700 |
Metallgesellschaft, 1992, цит. по [406] |
1980-е г.г. |
СССР |
в среднем по 2200 |
[263] |
1991 |
СССР (СНГ) |
1330 |
[105] |
1989 |
Россия (РСФСР) |
27 |
[164] |
1990 |
Россия (РСФСР) |
32 |
[164] |
1991 |
Россия |
28-32 |
[105, 164] |
1992 |
Россия |
27 |
[164, 165] |
1993 |
Россия |
от 4 до 7 |
[164, 165] |
* В 1995 г. производство первичной ртути в России прекращено.
В настоящее время потенциальными производственными мощностями по выпуску
первичной ртути располагают ЗАО “Кубаньцветмет” на Сахалинском месторождении в
Краснодарском крае (до 50-60 т/год) и Акташское горно-металлургическое предприятие на
одноименном месторождении в Алтайском крае (до 100 т/год) [166]. Однако мелкий масштаб и
низкое качество ртутных руд Сахалинского месторождения и отсутствие собственной сырьевой
базы на Акташском предприятии не дают повода надеяться на возобновление работ на этих
объектах.
В настоящее время производство первичной или попутной ртути в России не
осуществляется. Шлам от переработки цинка, содержащий около 30% ртути, в небольших
объемах экспортировался в Киргизстан для дальнейшей переработки и получения ртути (см.
раздел 4.4).
Освоение крупных Тамватнейского и Западнопалянского месторождений в слабо
обжитых районах Чукотки невозможно без крупных инвестиций, на которые, учитывая узость
внутреннего и внешнего рынка ртути, рассчитывать трудно. К тому же разработка этих
месторождений может негативно сказаться на нерестилищах ценных пород рыб.
2.1.3 Производство вторичной ртути
Помимо производства первичной ртути, на рынок поступает вторичная ртуть.
Производство вторичной ртути в России осуществляется главным образом на двух
предприятиях. Подробное описание существующей ситуации, включая характеристику типов
отходов и технологических процессов можно найти в разделе 5.1. В данном разделе содержится
исторический обзор производства вторичной ртути в СССР и России. В 1966 г. Совет
Министров СССР особым распоряжением (№ 2155 от 10.9.1966 г.) обязал предприятия
химической и электротехнической промышленности страны отправлять образующиеся на них
ртутьсодержащие отходы на Никитовский ртутный комбинат для вторичной переработки.
Ежегодно (примерно до 1990 г.) на комбинат поступали отходы 12-ти наименований, из
которых получали до 400 т вторичной ртути [198]. По данным [263], производство вторичной
ртути в СССР составляло порядка 300 т/год.
В последние годы в России предпринимаются попытки организовать промышленное
производство вторичной ртути из различных отходов. Так, в феврале 1993 г. датская фирма
“Sovtrade” одобрила образование российско-датского совместного предприятия по переработке
ртутьсодержащих отходов. Проектная мощность планируемого на территории России завода по
выпуску вторичной ртути должна была составить 1000 т в год; как один из источников сырья
рассматривался импорт отходов [164]. В дальнейшем сведения по этому проекту не
публиковались. В мае 1997 г. было подписано “Соглашение между правительством Российской
Федерации и правительством Украины о сотрудничестве в области переработки
ртутьсодержащих отходов”, согласно которому на Никитовском ртутном комбинате (Украина,
г. Горловка) предполагалось осуществлять переработку отходов российских предприятий (до
500 т ежегодно, с получение их них 12-15 т ртути и ее соединений) [165]. Однако это
соглашение не было реализовано. Федеральная целевая программа “Отходы” на 1996-2000 г.г.,
утвержденная постановлением Правительством РФ (№ 1098 от 13.9.1996 г.), предусматривала
реконструкцию металлургического завода Краснодарского рудника для совместной
переработки вторичного и первичного ртутьсодержащего сырья (до 5 тыс. т отходов в год),
создание в Рязанской области установки по переработке ртутьсодержащих электрохимических
источников тока (500 т в год) и ряд других мероприятий по организации в стране системы
переработки ртутьсодержащих отходов.
Тем не менее, в первой половине 1990-х г.г. в небольших количества вторичную ртуть
получали на Акташском горно-металлургическом предприятии, во второй половине 1990-х г.г.
- на ЗАО “Кубаньцветмет”. В частности, есть сведения, что ртутьсодержащие отходы
некоторых российских химических заводов, целлюлозо-бумажных комбинатов и предприятий
по производству витамина В2 в конце 1990-х г.г. были переработаны на ЗАО “Кубаньцветмет”
и - в меньших объемах - на Акташском горно-металлургическом предприятии.
Объемы накопленных к настоящему времени на территории России ртутьсодержащих
отходов очень велики. Например, на конец 1990-х г.г., их общая масса оценивалась в 1,1 млн. т
[121, 198]. Основная часть таких отходов (58%) характеризуется содержаниями ртути в 0,001-0,003 %, около 30% - содержат ртуть в количестве более 0,5%, примерно 12% -
характеризуются концентрациями металла в 0,01-0,5% (по массе). По данным [96], на
территории страны складировано около 650 тыс. т отходов с содержанием ртути от 0,02 до
75%; ежегодно производится и складируется еще примерно 11 тыс. т. На предприятиях цветной
металлургии к настоящему времени накоплено более 63 тыс. т ртутно-селенового шлама, в
котором содержится порядка 155 т ртути [198]. Так называемая ртутная ступпа (с содержанием
ртути до 75-80%) - продукт переработки ртутьсодержащих изделий и приборов, по имеющимся
сведениям, хранится в специальных емкостях на станциях демеркуризации или на специальных
полигонах. Если это действительно так, то к настоящему времени количество ртути в такой
ступпе составляет - в масштабах страны - порядка 30 т.
Публикуемые оценочные данные о производстве вторичной ртути в современной России,
как правило, учитывают не только металл, полученный при переработке отходов, но и
рафинированную ртуть, основным источником которой являются ртутьсодержащие приборы
(игнитроны, манометры, термометры) и металлическая ртуть, хранящаяся в научно-
исследовательских институтах, на промышленных предприятиях и т. д. Количество такой
(“бесхозной”) ртути, в конечном счете вновь возвращаемой в производство, в настоящее время
не поддается точному учету, практически не контролируется, но, судя по имеющейся
информации, достаточно велико.
Например, по данным НПП “Экотром” и агентства “Ртутьсервис”, в конце 1990-х г.г. в
Москве в различных организациях ежегодно собиралось от 2,5 т до 8 т металлической ртути
(включая ртуть, извлекаемую из приборов), которая отправлялась на переработку (очистку) в
ЗАО .Кубаньцветмет.. В Санкт-Петербурге Инженерным центром экологических работ в 1992-
1998 г.г. было вывезено из различных организаций и извлечено из приборов более 6,5 т ртути (в
том числе, в 1997 г. – 1,5 т, в 1998 г. - более 1,6 т; за первое полугодие 2000 г. - более 0,5 т)
[133, 390]. В Самаре предприятием .Экология. в различных организациях города ежегодно
собирается до 0,4-0,5 т металлической ртути, которая по мере накопления передается
различным потребителям [258]. В Хабаровске Региональным экологическим центром
демеркуризации в 1996-2001 г.г. в организациях и на промышленных предприятиях города
было собрано 980 кг металлической ртути, которая, была вывезена “за пределы края” [369)]. В
Приморье на начало 2003 г. на складах краевого Управления ГО и ЧС хранилось около 600 кг
металлической ртути [353]. В 1992-2001 г.г. на ООО “Мерком” было рафинировано около 100 т
некондиционной ртути (в том числе в 1998 г. - 29 т), которая затем была отгружена
потребителям [96, 167]. В конце 1990-х - начале 2000-х г.г. определенное количество
некондиционной металлической ртути, а также ртутной ступпы, получаемой при переработке
главным образом люминесцентных ламп, поступало на ООО “Экос” (г. Казань), где имеется
шведская установка “MRT System” по переработке Hg-содержащих отходов и получению
чистой ртути марки Р2 (99,99%) [Охрана 204].
Отечественные и зарубежные авторы оценивают ежегодное производство вторичной
ртути в России в 1996-2001 г.г. в пределах 30-50 т, что, очевидно, соответствует
действительности (табл. 2.5).
Таблица 2.5 Производство вторичной ртути в России в 1992-2001 г.г. * [164, 165, 234, 314, с
добавлениями автора]
Год |
Масса ртути |
Примечание |
1992-1993 |
по 15-20 т/год |
Большая часть ртути была получена на Акташском предприятии |
1994 |
более 30 т |
Большую часть составляет рафинированная ртуть |
1995 |
более 20 т |
Большую часть составляет рафинированная ртуть |
1996-1998 |
по 50 т/год |
Включая рафинированную ртуть (от 10 до 60% общего количества) |
1999 |
около 25 т |
Около 7,5 т ртути получено ЗАО “Кубаньцветмет” из отходов |
2000 |
более 40 т |
Около 30 т ртути получено ЗАО “Кубаньцветмет” отходов |
2001 |
около 30 т |
Большую часть составляет рафинированная ртуть |
* Включая рафинированную ртуть, основная масса которой выпускается ООО “Мерком” (г.
Лыткарино, Московская область); его возможные производственные мощности по рафинированию ртути
составляют 100 т/год; объемы вторичной ртути, получаемой в конце 1990-х - начале 2000-х г.г.
предприятием “Экос” (г. Казань), не превышали 2 т/год. Есть сведения, что в последние годы в Сибири (в
частности, в Иркутской области) вторичную ртуть получают при переработке отходов
золотодобывающей промышленности, но какие-либо данные о масштабах производства не
публиковались (не исключено, что это первые тонны металлической ртути, поскольку говорилось даже
об ее экспорте в Китай). Количество некондиционной (“бесхозной”) металлической ртути, собираемой на
различных предприятиях и изъятой из приборов, часто вновь возвращаемой тем или иным способом в
производственный оборот, составляет (в масштабах всей страны) несколько тонн в год.
Ежегодное производство металлической ртути в СССР, начиная с середины 1970-х г.г.,
обычно превышало ее внутреннее годовое потребление на 200-400 т, из которых
формировались так называемые складские запасы ртути. В России (на начало 1990-х г.г.) они
измерялись тысячами тонн [Минеральные ресурсы мира на начало 1997 года, 1998]. С 1992 г.
они реализовывались для внутреннего потребления и на внешнем рынке. С 1999 г. Россия
отказалась от реализации ртути из своих стратегических запасов [169].
2.2 Экспорт и импорт ртути
В 1979 и 1980 г. на европейском рынке из СССР появлялось примерно по 9000 бутылей
ртути (по 310 т ртути) [396]. В 1981 г. СССР объявил политику не экспортирования ртути (ее
поставки осуществлялись только в страны-члены СЭВ и достигали порядка 100 т/год).
Сообщалось, что СССР не поставлял ртуть на внешний рынок вплоть до своего распада [165].
Однако, судя по всему, в конце 1980-х г.г. СССР возобновил продажу ртути в страны дальнего
зарубежья (есть сведения, что до 1992 г. экспорт ртути из СССР в указанные страны составлял
450-500 т/год [234]).
В 1992-1998 г.г. Россия реализовала часть своих складских запасов ртути на мировом
рынке. Так, в середине 1990-х г.г. значительную долю испанского импорта составляла ртуть из
российских складских запасов; компания “Minas de Almaden” закупала ее, рафинировала и
перепродавала [166], в том числе, российским предприятиям.
Динамика экспорта ртути Россией в страны дальнего зарубежья выглядит примерно
следующим образом (табл. 6). Доступные данные об импорте ртути Россией [169] единичны:
1997 г. - 30 т, 1998 г. - 46 т, 1999 г. - 11 т. В 2001-2002 г.г. одно из российских предприятий
ежегодно закупало в Испании (у “Minas de Almaden”) примерно по 15 т ртути.
Таблица 2.6 Экспорт ртути из России в 1992-2001 г.г. * [165-169].
Год |
Экспорт ртути, тонны |
1992 |
150 |
1993 |
535 |
1994 |
400 |
1995 |
926 ** |
1996 |
345,9 *** |
1997 |
1000 **** |
1998 |
70 |
1999 |
965 |
2000-2001 |
Нет данных ***** |
* В ежегодно публикуемых сборниках .Таможенная статистика внешней торговли Российской
Федерации. прямые сведения об экспорте и импорте ртути и ее соединений отсутствуют.
** 120 т российской ртути поступило в США [234].
*** Из России в США было экспортировано 79 т ртути [411]; по другим источникам [234], - 120 т
ртути.
**** Ртуть поступила в Роттердам, где к маю 1998 г. ее большая часть была продана, а оставшиеся
276 т - закуплены испанской компанией “Minas de Almaden” [167]; сообщается также [234], что из России
в США поступило 120 т ртути.
***** Определенное количество вторичной ртути, полученной из отходов золотодобывающей
промышленности одним из предприятий Иркутской области, в начале 2000-х г.г. было продано в Китай;
есть также сведения, что подмосковный “Мерком” в небольшом объеме экспортировал ртуть [96].
2.3 Внутренний рынок ртути в России
По одним оценкам, в 1980-х г.г. в СССР использовалось порядка 1000 т металлической
ртути в год (из которых - более 50% в химической промышленности, 20-25% - в
электротехнике и приборостроении, около 20% - в оборонной) [41]. По другим сведениям [322],
в 1980-х г.г. ежегодное потребление ртути в СССР составляло в среднем 1250 т. По данным
[320], в 1985 г. годовое использование ртути в СССР достигало 1307,5 т; в 1989 г. - 1030 т [198].
Не исключено, что в отдельные годы масштабы потребления металлической ртути в
СССР существенно превышали 1000-1200 т. Так, есть сведения [263], что в последние годы
существования Советского Союза ежегодное потребление ртути в стране составляло примерно
2000 т (что, кстати, хорошо соотносится с масштабами ежегодно производимого в стране
металла). Как правило, более 80% ртути, используемой в СССР, приходилось на долю
российских предприятий [198].
Имеющиеся данные следующим образом характеризуют потребление металлической
ртути в России в последнее десятилетие (табл. 2.7).
В табл. 2.8 дается структура потребления металлической ртути различными отраслями
промышленности в бывшем СССР и в России в 1980-1993 г.г. Ситуация по использованию
ртути в настоящий момент описана в следующих главах, в главе “Выводы и комментарии”
также приводится сравнительный анализ динамики использования ртути с показателями
прошлых лет.
Таблица 2.7 Потребление ртути в России 164, 234, 320]
Год |
Ртуть, тонны |
1989 (РСФСР) |
865,8 |
1993 |
538 |
1994 |
400-450 |
1995 |
400 |
1996-1998 |
по 300-400 |
1999-2001 |
по 280-300 * |
* Годовая потенциальная потребность российских предприятий в ртути (данные Департамента
финансов Министерства экономического развития и торговли РФ) [314]; реальное потребление - меньше.
Таблица 2.8 Структура потребления ртути в СССР и России в 1980-1993 г.г. [320*, 321**]
Промышленность, сфера использования |
СССР |
Россия |
1980** |
1985* |
1989* |
1993* |
% |
т |
% |
т |
% |
т |
% |
Химическая |
63,4 |
910,2 |
69,6 |
462 |
53,4 |
310 |
57,6 |
Медицина, фармацевтика |
2,1 |
35 |
2,7 |
12,5 |
1,4 |
9 |
1,7 |
Электротехника |
3,0 |
21,8 |
1,7 |
108,3 |
12,5 |
71 |
13,2 |
Приборостроение, электроника |
13,5 |
218 |
16,7 |
133 |
15,4 |
80 |
14,9 |
Цветная металлургия |
1,8 |
36 |
2,7 |
10 |
1,1 |
8 |
1,5 |
Агрохимия |
- |
- |
- |
50 |
5,8 |
10 |
1,8 |
Научные исследования, новая техника |
- |
30,5 |
2,3 |
25 |
2,9 |
10 |
1,9 |
Оборонная |
- |
- |
- |
40 |
4,6 |
20 |
3,7 |
Прочее |
16,2 |
56 |
4,3 |
25 |
2,9 |
20 |
3,7 |
Всего |
100 |
1307,5 |
100 |
865,8 |
100 |
538 |
100 |
3 Целевое использование ртути в России
3.1 Хлорно-щелочное производство
3.1.1 Производственный процесс и использование ртути
3.1.2 Основные статьи потерь ртути в производстве и ее поступления
в воздух, воду и грунты
3.1.3 Методы очистки продукции, стоков, отходов и газовых выбросов
от ртути
3.1.4 Анализ состояния производства каустической соды и потерь
ртути на действующих предприятиях
3.1.5 Оценка количества ртутных выбросов на производствах,
выведенных из эксплуатации
3.1.6 Заключение
3.2 Другое применение ртути в химической промышленности
3.2.1 Производство винилхлоридного мономера (ВХМ)
3.2.2 Производство витамина B2 в прошлом
3.2.3 Производство пигментов в прошлом
3.3 Добыча золота с использованием амальгамационного метода
3.3.1 История добычи золота в Российской Федерации
3.3.2 Добыча золота из техногенных россыпей и других отходов
золотодобычи
3.3.3 Использование ртути при добыче золота
3.3.4 Текущая ситуация
3.3.5 Ртутное загрязнение золотодобывающих регионов России
3.4 Зубные амальгамные пломбы
3.4.1 Использование ртути в зубных амальгамных пломбах
3.4.2 Поступление ртути в окружающую среду в составе зубных пломб
3.5 Ртутные термометры
3.5.1 Производство ртутных термометров
3.5.2 Распределение ртути при производстве термометров
3.5.3 Использование, экспорт и импорт ртутных термометров
3.5.4 Эмиссия ртути при использовании термометров
3.6 Барометры, манометры и другие измерительные приборы
3.6.1 Производство ртутьсодержащих измерительных приборов
3.6.2 Потребление ртути с измерительными приборами
3.6.3 Ртуть в отходах и ее поступление в атмосферу, грунты и водные
объекты
3.7 Гальванические элементы и батареи
3.7.1 Производство гальванических элементов и батарей
3.7.2 Экспорт и импорт гальванических элементов и батарей
3.7.3 Использование и утилизация гальванических элементов и
батарей
3.8 Источники освещения
3.8.1 Производство ртутьсодержащих источников освещения
3.8.2 Российский рынок ртутных ламп
3.9 Переключатели и другие электроприборы
3.10 Производство химикатов и лабораторное использование ртути в России
3.10.1 Производство ртутных химикатов
3.10.2. Использование ртутных соединений в лабораторной практике
3.11 Ртутьсодержащие пестициды
3.11.1 Производство
3.11.2 Действующие нормативные документы
3.11.3 Использование ртутьсодержащих пестицидов
3.11.4 Условия хранения ртутьсодержащих пестицидов
3.11.5 Места захоронения ртутьсодержащих пестицидов
3.11.6 Заключение
3.12 Другие области применения ртути
3.12.1 Производство изотопов лития
3.12.2 Производство полупроводников
3.12.3 Использование ртути для изготовления силовых
полупроводниковых приборов
3.12.4 Ртутьсодержащие биоциды
3.12.5 Другие сферы использования
3.1 Хлорно-щелочное производство
Около половины хлора в Российской Федерации производилось с использованием метода
ртутного электрода, остальная часть – с применением диафрагменного метода. В настоящее
время в России работают четыре производства по выпуску каустической соды и хлора ртутным
методом на следующих предприятиях[2]:
- ЗАО “Каустик” г. Стерлитамак, Республика Башкортостан (с 1977 г.);
- ОАО “Каустик” г. Волгоград, Волгоградская область (с 1968 г.);
- ОАО “Кирово-Чепецкий химкомбинат” Кирово-Чепецк, Кировская область (с 1955 г.),
- ОАО “Саянскхимпласт” г. Саянск, Иркутская область (с 1979 г.).
В 1980-90-х были закрыты следующие морально и физически устаревшие производства:
- ПО “Капролактам” (г. Дзержинск, Нижегородская область) мощностью ~10 тыс. т/год (в
1982 г.);
- ЗАО “Каустик”, производство .Кребс. (г. Стерлитамак, Республика Башкортостан)
мощностью 86 тыс. т/год (в 1988 г.);
- ОАО “Усольехимпром” (г. Усолье-Сибирское, Иркутская область)) мощностью 100 тыс.
т/год (в 1998 г.).
Кроме того, в 1990-х годах были закрыты небольшие производства и установки по получению
каустической соды и хлора, действовавшие на целлюлозно-бумажных комбинатах в г.г.
Светогорске (Ленинградская обл.), Новодвинске (Архангельская обл.), Коряжме
(Архангельская обл.) и Комсомольске-на-Амуре (Амурская обл.). Информация по содержанию
ртути в складированных здесь отходах, а также данные по ее концентрированию в грунтах
территорий указанных предприятий, представлены в разделе 3.1.5. Расположение российских
предприятий по производству хлора и каустической соды и хлорвинила приведено на рис. 3.1.
Рисунок 3.1 Расположение российских предприятий по производству хлора и каустической
соды и хлорвинила (указаны как .C.).
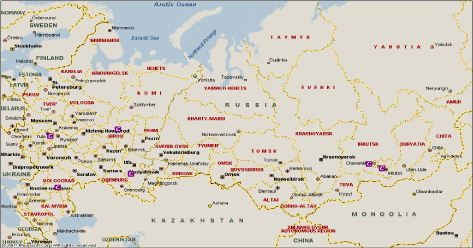
3.1.1 Производственный процесс и использование ртути
Каустическую соду, хлор и водород получают методом электролиза водного раствора
поваренной соли в горизонтальных ваннах с ртутным катодом[3]. Ванна состоит из
электролизера, разлагателя амальгамы и ртутного насоса. Ртуть в этом процессе является
промежуточным агентом и служит для переноса образующейся щелочи из электролизера в
разлагатель, что обеспечивает возможность получения ее концентрированного раствора с
минимальной примесью хлорида. Это преимущество ртутного метода перед диафрагменным и
даже мембранным оправдывает его применение, несмотря на связанные с ним экологические
проблемы.
Принципиальная схема производства с указанием основных потоков ртути и источников
ее выбросов представлена на рис. 3.2.
Раствор для электролиза готовят различными методами.
Выпарка подземного рассола после предварительной очистки его с последующим
использованием чистой выпаренной соли для донасыщения обедненного рассола после
электролиза с тонкой дофильтрацией последнего и возвратом его в электролиз (анолитный
цикл).
Преимуществом этого метода является обусловленное чистотой выпаренной соли
упрощение очистки рассола в анолитном цикле. Благодаря этому, ртуть, растворенная в
рассоле, выходящем из электролизеров, не выводится из цикла, а возвращается в
электролизеры. Недостатком метода является наличие стадии выпарки рассола.
Донасыщение анолитного цикла обратной солью, получаемой при упаривании щелоков
диафрагменного электролиза.
Использование этого метода возможно на предприятиях, в состав которых входят
производства, работающие как по ртутному, так и по диафрагменному методам. Он может
применяться в сочетании с методом, описанным выше. Его преимущества – минимальные
потери ртути с рассольными шламами, а также отсутствие или резкое сокращение затрат на
выпарку соли непосредственно в производстве.
Усредненные показатели потерь ртути в кг(Hg) /т(NaOH) представлены в таблицах 3,2., 3,3, 3,6
и 3,8.
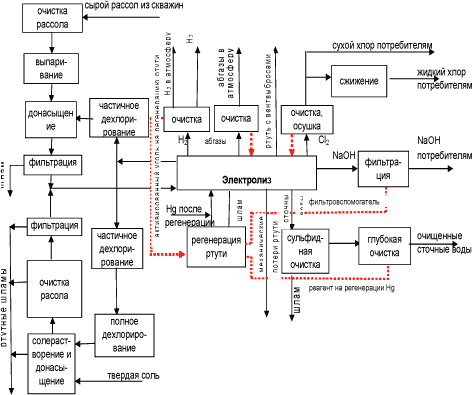
Рисунок 3.2 Принципиальная схема хлорно-щелочного производства с использование ртутных
электродов.
Растворение привозной самородной соли в резервуарах-растворителях с очисткой ее от
кальция, магния, железа и тяжелых металлов и подачей очищенного рассола после глубокой
фильтрации непосредственно в электролизеры, а из электролизеров - на донасыщение в
резервуары-растворители и последующую очистку от примесей.
Достоинством этого метода является исключение процесса выпарки, а также высокая
полнота очистки от примесей тяжелых металлов, что повышает эффективность протекания
процесса электролиза, недостатком - неизбежные потери уносимой из электролиза
растворенной ртути, вследствие осаждения ее на стадии очистки от тяжелых металлов в форме
нерастворимого сульфида, промышленная утилизация которого из бедных по ртути рассольных
шламов крайне затруднительна и поэтому нигде не производится.
В электролизере ведется электролиз раствора поваренной соли с образованием хлора и
амальгамы натрия. К качеству рассола, поступающего на электролиз, предъявляются высокие
требования, прежде всего по содержанию железа (не выше 0,1 мг/дм³) и тяжелых металлов
(сумма ванадия, молибдена и хрома - не более 0,01 мг/дм³). Эти ограничения связаны с тем, что
указанные химические элементы, восстанавливаясь на амальгамном катоде до металлов,
способствуют образованию так называемых “амальгамных масел” - вязкой массы, обладающей
ферромагнитными свойствами (в случае железа) и пенистой (в случае ванадия, молибдена,
хрома). Образование амальгамных масел серьезно нарушает работу электролизеров, что
вызывает необходимость частых чисток, связанных с неизбежными потерями ртути при
остановках электролиза. Масел образуется тем меньше, чем выше чистота рассола и полнота
разложения амальгамы в разлагателе.
Ртутным насосом осуществляется непрерывная циркуляция амальгамы в замкнутом
цикле.
В электролизере под действием электрического тока катионы натрия разряжаются на
ртутном катоде с образованием амальгамы натрия, а ионы хлора разряжаются на анодах с
образованием хлора. В разлагателе амальгама натрия разлагается умягченной водой с
образованием гидроксида натрия и водорода. Частичный унос ртути из разлагателей
происходит с водородом и щелочью, в результате чего требуется их очистка от ртути.
Существующие производства хлора и каустика оснащены электролизными ваннами
различного типа.
Объемы производства зависят от спроса на рынке каустической соды и химических
продуктов переработки хлора.
Из-за отсутствия оборотных средств, высокой стоимости ртути и ужесточения
требований к оформлению разрешения на ее закупку за последние 5 лет практически все
предприятия имели очень малые запасы ртути, а иногда они отсутствовали совсем. Вместе с
тем следует отметить, что неполная загрузка ртути в электролизеры крайне нежелательна ввиду
негативного влияния этого дефицита на показатели электролиза, что приводит к возрастанию
потерь ртути, т. е. к усугублению этого дефицита.
Производство каустической соды ртутным методом за последние 5 лет представлено в
табл. 3.1.
Электролизеры на всех предприятиях оснащены металлическими анодами с покрытием
на основе смешанных оксидов рутения и титана. Их межремонтный пробег составляет, в
зависимости от условий эксплуатации, от 1,5 до 5 лет. Его увеличение способствует
существенному снижению потерь ртути.
Очищенный рассол подается параллельно в каждый электролизер.
Хлоргаз из электролизеров поступает на охлаждение и сушку.
Амальгама вытекает из электролизера через ртутный затвор в выходной карман и оттуда
в разлагатель. Для входного и выходного карманов предусмотрена подводка умягченной воды
для промывки и охлаждения амальгамы, а также для уменьшения испарений ртути в воздух
производственных помещений. Отсасываемые из карманов абгазы, содержащие хлор и пары
ртути, поступают на очистку от них. В разлагатель амальгамы подается умягченная вода. На
графитовой насадке разлагателя происходит взаимодействие амальгамы и воды с получением
соды каустической и водорода.
Освобожденная от натрия ртуть перекачивается насосом из нижней части разлагателя во
входной карман электролизера по трубопроводу через холодильник, где охлаждается водой.
Массовая доля натрия в крепкой амальгаме не должна превышать 0,35%, в слабой амальгаме .
0,05%.
В ходе эксплуатации ванн количество ртути, циркулирующей в каждой из них,
постепенно сокращается вследствие потерь ее с выходящими потоками и в результате
периодических чисток. После того, как содержание ртути в электролизере сокращается
настолько, что это приводит к увеличению концентрации крепкой амальгамы выше нормы и
другим нарушениям режима работы, в ванну добавляют необходимое количество ртути.
Ртуть из электролизеров и разлагателей может теряться в результате течей (потерь) -
случайных и возникающих при разуплотнениях фланцевых соединений, в виде шламов при
чистках и в растворенном виде с анолитом. Количество этих потерь во многом зависит от
культуры эксплуатации электролизеров, особенностей их конструкции и продолжительности
работы без остановок.
Получившийся в результате разложения амальгамы водород охлаждается водой в
теплообменниках, установленных на крышках разлагателей. При этом большая часть уносимых
паров ртути конденсируется и возвращается в разлагатель. Водород после холодильников
для синтеза соляной кислоты или другой продукции, остальной водород - после очистки от
ртути - выбрасывается в атмосферу.
Раствор соды каустической с массовой долей 45-50% переливается из верхней части
разлагателя и поступает в сборник, откуда после охлаждения и фильтрации отгружается
потребителям.
Вода после промывки и дегазации полов зала электролиза собирается в емкость, из
которой откачивается на очистку от ртути.
Основными потребителями хлора, полученного в процессе электролиза поваренной соли,
являются производства поливинилхлорида, эпихлоргидрина, трихлорэтилена, дихлорэтана и
др. После выполнения Правительством РФ Монреальских соглашений и закрытия производств
по выпуску озоноразрушающих хладонов и четыреххлористого углерода значительно
снизилось хлоропотребление, что привело к снижению нагрузок на электролиз и уменьшению
выработки каустической соды как ртутным, так и диафрагменным методами.
Таблица 3.1 Производство каустической соды ртутным методом в РФ в 1998-2002 г.г.
Наименование предприятия |
Мощность на 01.1.03г, тыс. т |
Год ввода |
Выработка по годам, тыс. тонн |
1997 |
1998 |
1999 |
2000 |
2001 |
2002 |
ЗАО “Каустик”, г. Стерлитамак |
157 |
1997 |
88,9 |
78,3 |
103,6 |
122,9 |
109,3 |
110,8 |
ОАО “Каустик”, г. Волгоград |
110,4 |
1968 |
95,3 |
94,6 |
117,6 |
127,0 |
127,5 |
121,5 |
ОАО “Кирово-Чепецкий химкомбинат”, г. Кирово-Чепецк Кировской обл. |
205 |
1955 |
45,7 |
50,6 |
58,7 |
81,3 |
70,5 |
60,3 |
ОАО “Саянскхимпласт”, г. Саяны Иркутской обл. |
160 |
1979 |
51,8 |
58,4 |
79,1 |
101,2 |
112,6 |
114,5 |
ИТОГО |
573,4 |
281,7 |
281,9 |
359 |
432,4 |
419,9 |
407,1 |
3.1.2 Основные статьи потерь ртути в производстве и ее поступления в воздух, воду
и грунты
Как следует из приведенного выше описания производственного процесса, основными
источниками потерь ртути являются каустическая сода, водород, сточные воды, абгазы, хлор,
шламы, вентвыбросы, механические потери.
Потери ртути, как по отдельным статьям, так и в целом, различны как между собой, так и
по каждому из предприятий. Их величина определяется особенностями технологической
схемы, уровнем соблюдения технологического режима, общей культурой производства,
наличием и эффективностью работы узлов очистки от ртути.
Величины потерь по первым пяти позициям при наличии соответствующей очистки от
ртути, как правило, невелики и легко контролируются. При этом ртуть, теряемая с
каустической содой, хлором и водородом, распределяется в ничтожных количествах между
потребителями этих продуктов и, в конечном счете, поступает в окружающую среду или
отходы, при использовании или хранении продуктов.
Ртуть, теряемая с абгазами, частью водорода, не использованного в производстве, и
вентвыбросами, поступает в атмосферу, а уходящая со сточными водами, не используемыми в
замкнутом цикле, - в водоемы.
Потери ртути с рассольными шламами определяются существующим на производстве
методом очистки рассола. При использовании привозной соли без выпарки первичного рассола
они велики, при использовании чистой выпаренной соли - малы. Рассольные шламы с низкой
концентрацией ртути в них не подлежат переработке, а уплотняются и накапливаются на
специально оборудованных и контролируемых полигонах.
Величина потерь ртути с другими видами шламов - выбираемых из электролизеров при
чистках, образующихся при обратной промывке фильтров, после отстоя сточных вод, из
отработанного графита разлагателей, активированного угля, ионообменных смол и т. д., может
быть сведена до минимума за счет термической регенерации ртути из них.
Потери ртути с выбросами, образующимися в результате интенсивной вентиляции зала
электролиза, практически не могут быть сокращены иным путем, кроме поддержания высокой
культуры производства: герметизации ванн, и прежде всего, разлагателей амальгамы,
максимального сокращения частоты остановок и чисток ванн, предотвращения случайных
разливов и утечек ртути, организации своевременного сбора пролитой ртути. Пары ртути,
уходящие с вентвыбросами через аэрационные фонари зала электролиза, конденсируются и
оседают на строительные конструкции и почву в зоне, непосредственно прилегающей к
производству. Под воздействием атмосферных осадков и естественных процессов испарения-
конденсации эта ртуть может попадать в водоемы и разноситься за пределы зоны первичного
выброса.
Потери ртути могут происходить на электролизных или декомпозиционных установок при
утечках, случайных или вызванных негерметичностью фланцев, со шлаками или во время
очистки анолита. Ряд этих потерь зависит в большой степени от режима эксплуатации
электролизных установок, их конструктивных особенностей и периодов непрерывной работы
установок.
Потери ртути в производствах по вышеперечисленным статьям, поступающие в воздух,
водоемы и специальные хранилища, легко контролируются и, как показывает мировая
практика, отражаются в соответствующей отчетности предприятий. Однако при этом не
учитываются механические потери, возникающие в результате неполного улавливания и
возврата проливов ртути в ходе обслуживания и ремонтов электролизеров. Эти потери могут
составлять значительную долю общих потерь ртути в хлорно-щелочном производстве. В
технической отчетности предприятий бывшего СССР и Российской Федерации они
указываются в составе общего расхода ртути, что создает представление о чрезвычайно
высоких потерях металла по сравнению с зарубежными заводами. Механические потери могут
быть рассчитаны только как разность между количеством ртути, пошедшей со стороны на
восполнение ее убыли в работающих электролизерах, и зафиксированными потерями ртути по
другим статьям ее расхода в течение длительного периода (квартал, год).
Обобщенные показатели потерь с российских предприятий представлены в разделе 3.1.6,
где также приведено сравнение с показателями других стран (OSPAR 2002).
Снижения механических потерь можно добиться путем максимального сокращения
частоты остановок электролизеров на чистки и ремонты, строгого соблюдения норм
обслуживания и технологической дисциплины, повышения качества ремонтов, организации
постоянного сбора и возврата в электролизеры пролитой ртути с очисткой ее до требуемой
нормы, обеспечения герметичности полов в залах электролиза, организации лотков и приямков
для сбора сточных вод и пролитой ртути с вакуумным сбором последней.
Вместе с тем следует отметить неоднозначность вопроса об экологической роли ртути,
теряемой механическим путем. Просачиваясь в почву через неплотности полов
производственных зданий (прежде всего корпуса электролиза), она скапливается в подземных
пластах. Глубина ее проникновения и пути дальнейшей миграции, в том числе с возможным
попаданием в водоемы, определяются геологическими особенностями участка.
В связи с этим следует иметь в виду, что непосредственно под зданиями, где хлорно-
щелочное производство функционировало в течение нескольких десятилетий, и районе,
прилегающем к ним, возможно накапливание металлической ртути до нескольких сот тонн.
Поэтому вопросы локализации ее миграции и потенциального возврата в производство
представляются важными. Решение этих вопросов возможно лишь с привлечением
геологических служб.
3.1.3 Методы очистки продукции, стоков, отходов и газовых выбросов от ртути
Для предотвращения выделения ртути в атмосферу и попадания ее в водоемы на
предприятиях, выпускающих каустическую соду и хлор ртутным методом, используются
методы очистки газообразных, жидких и твердых отходов с сокращением содержания ртути в
них ниже утвержденных норм. Так, для предотвращения выделения вредных веществ в воздух
зала электролиза предусмотрена очистка от ртути абгазов, отсасываемых из выходных
карманов электролизеров с помощью вентиляторов. Далее их охлаждают до температуры не
более15°С с целью конденсации части ртутных и водяных паров. Охлажденные абгазы
проходят туманотделитель, служащий для удаления капельной ртути, затем они подаются на
фильтры с двойным слоем активированного угля для очистки от паров ртути. После фильтров
абгазы с массовой концентрацией ртути не более 0,01 мг/м³ выбрасываются в атмосферу.
Отработанная насадка направляется на регенерацию.
Абгазы, содержащие хлор и ртуть, отсасываемые из входных карманов, направляют на
очистку щелочным раствором гипохлорита натрия.
Конденсат ртутных и водяных паров из холодильника и фильтра собирается в приемник и
откачивается на установку для очистки его от ртути.
Водород после предварительной очистки от основной массы унесенной из разлагателя
ртути в холодильниках, установленных непосредственно на разлагателях, поступает на
финишную очистку от ртути. Ртуть, уносимая водородом, частично конденсируется в
гидрозатворах, установленных на водородном коллекторе, из которых ее собирают и
возвращают в электролизеры. Далее водород охлаждают до температуры не выше 15°С, подают
в фильтр, в котором задерживается основная часть капельной ртути, а затем он идет на
водородный компрессор. После компрессора водород охлаждается до температуры не более
40°С и поступает на заключительную стадию очистки от паров ртути в фильтры, заполненные
насадкой из активированного угля. Отработанную насадку из фильтров отправляют на
термическую регенерацию. Очищенный водород с массовой концентрацией ртути не более 0,01
мг/м³ поставляют потребителям или сбрасывают в атмосферу.
В производствах каустической соды и хлора ртутным методом предусмотрена
фильтрация раствора соды каустической от мелкодисперсной металлической ртути и
графитовой пыли, унесенных из разлагателей. Каустическая сода после разлагателей
охлаждается до температуры 55-75°С, после чего подается на фильтрацию. Очищенный раствор
с содержанием NaOH не менее 46% и массовой долей ртути не более 0,00007% направляется
потребителям или в складские емкости.
Ртутные шламы и амальгамное масло из зала электролиза в барабанах подаются в
отделение регенерации на переработку, включающую предварительный отстой или отбой
основной части ртути и последующую термическую регенерацию. Жидкая ртуть, отделенная от
шламов, сливается в металлические баллоны, а шламы направляются в отделение регенерации
ртути в печах с электронагревателями. Туда же поступают содержащие ртуть твердые отходы,
отработанные насадки фильтров очистки водорода и щелочи, сорбенты с установок очистки
сточных вод. Исключение составляют шламы рассолоочистки, объем которых велик, а
концентрация ртути - мала. Для демеркуризации отработанного крупногабаритного
оборудования перед отправкой его в лом используются специальные туннельные печи.
Абгазы из емкости, где обрабатывается шлам, отсасываются вентилятором и
направляются на санитарный фильтр - адсорбер для очистки, после которого выбрасываются в
атмосферу с содержанием ртути не более 0,01 мг/м³. Шламы загружают в печь, которая затем
плотно закрывается. Процесс регенерации ведется при температуре 500°С, при разрежении 10-20 мм водяного столба, создаваемого вентилятором. Образующаяся в печи смесь газов с парами
ртути проходит через трубчатый конденсатор, охлаждаемый оборотной водой.
Сконденсированная при этом металлическая ртуть поступает в сборник, откуда по мере
надобности заливается в электролизеры. Для предотвращения окисления ртути в печь подается
слабый поток азота.
Очистка сточных вод от ртути осуществляется методом сорбции на ионообменных
смолах с предварительным окислением металлической и одновалентной ртути, а также
газообразным хлором), либо в нерастворимый HgS (путем обработки гидросульфидом натрия).
После перевода ртути в нерастворимое соединение вода поступает на фильтрацию через
механические фильтры. В случае обработки хлорированием сточная вода после фильтрации
направляется на обесхлоривание в адсорбер, заполненный активированным углем. Это
производится с целью предупреждения проскока активного хлора в очищенные сточные воды.
Очищенная от основной массы ртути сточная вода насосами подается в абсорберы,
заполненные ионообменной смолой. Количество абсорберов – от 2 до 6. В них могут быть
загружены последовательно смолы различных марок. Из абсорберов очищенная вода с
содержанием ртути не более 0,005 мг/л сливается в емкость, из которой насосами подается в
сборники-осветлители. После очистки сточные воды, нейтрализованые щелочью, могут быть
направлены в баки для повторного их использования в производстве. При несоответствии
очищенной воды нормам она подается на повторную очистку.
Отработанная ионообменная смола с содержанием ртути 40% из первого абсорбера и до
10% из остальных отправляется на установку регенерации ртути или на
ртутьперерабатывающее предприятие.
3.1.4 Анализ состояния производства каустической соды и потерь ртути на
действующих предприятиях
ОАО “Кирово-Чепецкий химкомбинат”
Зал электролиза оснащен электролизерами Р-20М с разлагателями вертикального типа.
Всего установлено 92 электролизера, рассчитанных на нагрузку 200 кА и на выпуск 207 тыс. т
каустической соды.
В 1997 г. в работе находились 47 электролизеров при нагрузке 84 кА.
В 2002 г. - 63 электролизера при нагрузке 79 кА.
Приготовление и очистка рассола для электролиза производится путем донасыщения
анолитного цикла неочищенной твердой солью с последующей полной очисткой его от
примесей, включая сульфидную. Сырьем для получения хлора и каустической соды служит
привозная соль Баскунчакского месторождения.
Донасыщение циркулирующего в производстве рассола проводится непосредственно в
солерастворителях, а очистка содово-щелочным и сульфидным методом - в отстойниках Дорра
с последующей фильтрацией. Применяемая схема обеспечивает высокую степень очистки
рассола от вредных для процесса электролиза примесей, но одновременно сопровождается
потерей всей ртути, растворяющейся в анолите в процессе электролиза и поступающей на его
обесхлоривание и донасыщение.
Конструкция и качество обслуживания электролизеров, наряду с высокой чистотой
питающего рассола, обеспечивают минимальные механические потери ртути со сточными
водами и унос ее паров с вентилирующим воздухом.
Регенерацию ртути из шламов отделения электролиза после предварительного
отмешивания из них основной массы ртути в реакторе с мешалкой, а также из отработанных
реагентов с установок очистки водорода, соды каустической, сточных вод и т. д., проводят
методом термического восстановления в шахтной печи, после чего восстановленную ртуть
возвращают в электролиз. Заметные потери ртути на этой операции практически отсутствуют.
Производственные отходы, содержащие металлическую ртуть (отработавшие свой ресурс
днища электролизеров, холодильники водорода и ртути, разлагатели амальгамы, буферные
емкости и другое загрязненное оборудование, отработанная графитовая насадка из
разлагателей, насадка фильтров едкого натра) перед сдачей в металлолом или передачей на
участок захоронения отходов 3-4 класса опасности подвергаются термообработке.
Металлическая ртуть, образующаяся после конденсации паров, используется в производстве.
Загрязненный воздух перед выбросом в атмосферу подвергается очистке адсорбентом ХПР-2.
Потери ртути в производстве складываются из ее потерь со шламами очистки рассола и
сточных вод, со сточными водами, сбрасываемыми в систему водоотведения, с
вентиляционными выбросами, абгазами и водородом, сбрасываемым в атмосферу, с воздухом,
сбрасываемым с установки термической переработки отходов, с отходами после термической
регенерации ртутных шламов, с продукцией (содой каустической, хлором и частью водорода,
идущей на получение соляной кислоты) и с грунтовыми водами, куда входят потери,
возникающие в результате сброса ртути по системе ливневой канализации завода, фильтрации
неочищенных сточных вод через полы зала электролиза и дренирования со шламонакопителей.
Ниже приведена оценка этих потерь в 1997 и 2002 г.г.
Потери ртути со шламами солерастворения
До 1997 г. ртутьсодержащие шламы рассолоочистки с отстойников Дорра и после
регенерации песчаных фильтров фильтровали на барабанных вакуум-фильтрах, после чего
сбрасывали в шламонакопитель, представляющий собой контролируемый полигон площадью
4,5 га с дном и бортами, выполненными из влагонепроницаемой глины. Туда же поступала
отработанная серная кислота со стадии осушки хлора и сточные воды после сульфидного
осаждения ртути. Избыток осветленной воды из шламонакопителя с концентрацией ртути до
0,05 мг/л в количестве 10-15 м³/ч сбрасывался в систему водоотведения комбината. Шламы
солерастворения, содержащие нерастворимый сульфид ртути, складировались на
контролируемый участок захоронения отходов 3-4 класса опасности. По мере заполнения
шламом отдельных секторов участка, последние консервировались под слоем фторгипса.
В 1998 г. на заводе введена в эксплуатацию установка глубокой очистки сточных вод.
При этом увеличилась степень их очистки и уменьшился объем перерабатываемых вод, а
шламы рассолоочистки с отстойников Дорра были направлены в солерастворители с
последующим складированием совместно со шламами солерастворения на участке захоронения
отходов 3-4 класса опасности. Это позволило вывести из эксплуатации шламонакопитель с
полным прекращением сброса сточных вод из него.
С 2002 г. включена в работу установка разложения карбонатных шламов рассолоочистки
соляной кислотой с возвратом образующегося хлористого кальция на стадию растворения соли.
Это позволило сократить объемы складируемых шламов.
Потери ртути со шламами растворения и рассолоочистки составляли:
в 1997 г. – 12,4317 т (в том числе 3,85 т с установки очистки сточных вод),
в 2002 г. – 14,9403 т (в том числе 3,414 т с установки очистки сточных вод).
Потери ртути со сточными водами
До 1998 г. очистка сточных вод проводилась методом осаждения ртути в виде
нерастворимого сульфида с последующим его отстоем в шламонакопителе и сбросом
осветленной воды в систему водоотведения комбината.
С 1998 г. введена глубокая очистка сточных вод методом осаждения ртути в виде
сульфида, фильтрации через фильтр КМП-25 со складированием сульфидного шлама на
участке захоронения отходов 3-4 класса опасности и последующей доочисткой
отфильтрованной воды ионообменным способом.
Шламы фильтрации складируются на участке захоронения отходов 3-4 класса опасности.
Содержание ртути в сбрасываемой сточной воде составляет 0,0008-0,001 мг/дм³ при норме
0,001 мг/дм³.
Потери ртути с очищенными сточными водами составляли:
в 1997 г. - 1266 г,
в 2002 г. - 125 г.
Потери ртути с вентиляционными выбросами
Система вентиляции зала электролиза - приточная с выводом через аэрационные фонари.
Высота фонарей - 12 м. Расход нагнетаемого воздуха составляет 800-1000 тыс. м³/час.
Концентрация ртути в выбросах 0,012-0,017 мг/м³.
Выброс ртути через аэрационные фонари зала электролиза составлял:
в 1997 г. - 99 кг,
в 2002 г. - 139 кг.
С вентвыбросами отделения перекачки и очистки сточных вод потери ртути составляли:
в 1997 г. – 3,89 кг,
в 2002 г. – 5,1 кг.
Выброс ртути не превышал установленный норматив ПДВ.
Потери ртути с водородом
Из общего количества производимого водорода 75% сбрасывается в атмосферу через
трубу высотой 15 м. До 1998 г. двухступенчатая очистка водорода от ртути производилась
орошением хлоранолитом и щелочным рассолом. С 1998 г. введена глубокая очистка методом
адсорбции на активированном угле, что примерно на порядок повысило полноту очистки
водорода.
Потери ртути, выбрасываемой с водородом, составляли:
в 1997 г. – 0,42 кг,
в 2002 г. – 0,056 кг.
Выброс ртути не превышал установленный норматив ПДВ.
В 1997 г. с неочищенным водородом внутризаводским потребителям было передано 2,83
кг ртути.
Потери ртути с абгазами
Очистка абгазов от ртути и хлора производится поглощением последних щелочным
раствором гипохлорита натрия.
Выброс ртути с очищенными абгазами составлял:
в 1997 г. – 4,6 кг,
в 2002 г. – 2,65 кг.
Выброс не превышал установленный норматив ПДВ.
Отработанный поглотительный раствор направляется в анолитный цикл.
Потери ртути с грунтовыми водами
Потери ртути происходят в результате сброса ее по системе ливневой канализации завода
с поверхностным ливнестоком, фильтрации сточных вод через полы зала электролиза и
дренирования с участка захоронения отходов 3-4 класса опасности.
Они составляли:
в 1997 г. – 11,0 кг,
в 2002 г. – 11,5 кг.
Согласно своему происхождению, они включают в себя часть ртути, выбрасываемой в
атмосферу, оседающей затем на почву и уносимой ливневыми стоками, а также часть ртути,
выводимой с остаточной влагой ртутьсодержащих шламов, и, соответственно, должны быть
вычтены из этих потерь. Однако, поскольку в них входит еще и ртуть, присутствующая в
сточных водах, определенная часть которых теряется до их очистки, то количественно
разделить эти составляющие невозможно.
Потери ртути с продукцией
С синтетической соляной кислотой (HCl), содержащей 0,00001% ртути, потери
составляли:
в 1997 г. – 0,08 кг (масса полученной кислоты 760 т),
в 2002 г. – 0,1 кг (масса полученной кислоты 1002 т).
С содой каустической, содержащей 0,00005% ртути, потери составляли:
в 1997 г. - 23 кг,
в 2002 г. - 30 кг.
Потери ртути с выбросами установки химической переработки отходов
Потери с выбросами загрязненного воздуха после химической переработки
(демеркуризации) отходов составляли:
в 1997 г. – 0,0051 кг,
в 2002 г. - 0,0024 кг.
Выброс ртути не превышал установленный норматив ПДВ.
Потери ртути со шламами после их термической переработки составляли:
в 1997 г. – 0,89 кг,
в 2002 г. – 0,91 кг.
Механические потери ртути
Механические потери ртути включают в себя, прежде всего, металлическую ртуть,
проливаемую из электролизеров, разлагателей, насосов и коммуникаций в процессе
эксплуатации и ремонтных работ, и безвозвратно теряемую в результате фильтрации в почву
через дефекты полов. К ним следует причислить также ртуть, содержащуюся в той части
сточных вод, которые фильтруются сквозь неплотности полов.
Как указывалось в разделе 3.1.2, эти потери возможно определить только по разности
между известным количеством ртути, заливаемой в электролизеры со стороны в течение года, и
суммарными фиксированными потерями ее за этот период. В 2002 г. в общей сложности было
закуплено 15,1 т ртути. Посчитанные таким образом механические потери ртути в 2002 г.
составили 0,015 кг. Они на данном предприятии значительно ниже по сравнению с другими
аналогичными заводами, что обусловлено высокой культурой обслуживания производства
электролизеров, отсутствием дефекта полов в цехе электролиза, а также эффективной
организации системы сбора ртути.
Обобщенные показатели потерь ртути
Потери ртути, сброшенной в воздух, воду прудов-отстойников, захороненной и
складированной со шламами, а также потерянной механически и с товарной продукцией,
представлены в табл. 3.2.
Таблица 3.2 Потери ртути на ОАО “Кирово-Чепецкий химкомбинат”
Год |
1997г. |
2002г. |
Выпуск соды каустической, т |
45700 |
60300 |
Потери ртути: |
Абсолютны е, т |
Удельные, кг/т NаОН |
Абсолютн ые, т |
Удельные, кг/т NаОН |
- со шламами рассолоподготовки, рассолоочистки на захоронение в виде сульфида |
12,4317 |
0,272 |
14,9403 |
0,248 |
- в атмосферу с вентвыбросами, с очищенным водородом и абгазами |
0,108 |
2,4×10-3 |
0,147 |
2,4×10-3 |
- в систему водоотведения комбината со сточными и грунтовыми водами |
0,001266 |
2,8×10-5 |
0,000125 |
2,0×10-6 |
- с товарной продукцией |
0,0238 |
5,2×10-4 |
0,031 |
5,1×10-4 |
- с водородом потребителям |
0,00283 |
6,2×10-5 |
|
|
- механические |
н. д. |
|
0,015 |
2,5×10-4 |
ВСЕГО |
12,568 |
0,275 |
15,117 |
0,251 |
Из представленных данных видно, что в 2002 г. существенно сокращены абсолютные и
удельные выбросы ртути в систему водоотведения и удельные потери ртути со шламами
рассолоподготовки. Незначительное увеличение абсолютных потерь ртути в 2002 г. по
сравнению с 1997 г. связано с ростом выпуска товарной продукции.
Величина механических потерь ртути в Кирово-Чепецке (0,015 кг) мала вследствие высокого
качества эксплуатации и ремонтов оборудования, надежной защите полов, организации
постоянного сбора и регенерации проливаемой ртути.
Запасы ртути в производстве
Всего в цехе установлено 92 электролизера. Из них в работе 61 электролизер, а остальные
31 законсервированы.
Закладка ртути в один электролизер составляет 2,71 т. Таким образом, в работающих
электролизерах задействовано 165,3 т ртути.
Запас ртути в законсервированных электролизерах составляет 84 т. В настоящее время
этот запас начинают использовать для пополнения ртутью работающих электролизеров. Других
запасов ртути на комбинате нет.
Состояние окружающей среды
Согласно приближенным оценкам, в шламах, складированных за полувековой период
эксплуатации производства на контролируемых полигонах(шламонакопителе и участке
захоронения отходов 3-4 класса опасности), , содержится примерно от 300 до 700 т ртути (в
основном в форме сульфида ртути).
Значительное, но трудно поддающееся оценке количество сульфида ртути, вынесенного в
основном со сточными водами в период до перехода на глубокую очистку их, а также,
возможно, металлической ртути, оседающей из выбросов в воздушную среду и смываемой
атмосферными осадками, аккумулировано в донных отложениях водных систем в зоне,
примыкающей к ореолу рассеяния ртути, уходящей с жидкими и газовыми выбросами. Не
исключено также присутствие определенного количества металлической ртути, просочившейся
в глубинные слои грунтов и скапливающейся на локальных участках выше слоя пермских глин.
Согласно обследованию, проведенному в 1995 г. Государственным предприятием
экологических и геолого-географических исследований, Международным научным
экологическим центром и Экологическим фондом “Ртутная опасность” (г. Санкт-Петербург), на
Кирово-Чепецком химкомбинате обеспечивается максимально возможная для данной
технологии степень ртутной безопасности, а экологическая обстановка в районе, прилегающем
к предприятию, оценена как умеренно опасная. Потенциальным источником этой опасности
признано накопление ртути и ее соединений в донных илах водотоков, что не исключает ее
переход под воздействие речной биоты в легкорастворимые и высокотоксичные органические
соединения. Проведенное обследование не выявило случаев отравления людей, однако были
отмечены превышения ртутью уровней ПДК в печени хищных рыб, выловленных в пределах
ореола рассеяния ртутных выбросов. Содержания ртути в донных илах варьировались от 0,4 до
5,1 мг/кг, однако места отбора исследованных проб не указывались. Отмечены также
возможность просачивания ртути из шламохранилищ в грунтовые воды вследствие отсутствия
надежных систем гидроизоляции и вероятность попадания ртути и ее соединений в
хозяйственные и питьевые воды при водозаборе из колодцев и неглубоких скважин в
индивидуальных хозяйствах, расположенных в зоне ореола загрязнения. Делается также
прогноз о возможности дальнейшего распространения ртутного загрязнения вниз по реке,
особенно в периоды бурных паводков, при добыче песка из рек.
Согласно последним данным лаборатории охраны окружающей среды Кирово-Чепецкого
химкомбината, среднее содержание ртути в верхнем слое почвы в радиусе 1 км вокруг
производства составляет 0,2 мг/кг. Среднее содержание ртути в воде р. Просница (контрольный
створ расположен 500 м ниже сброса сточных вод комбината) составило: Hg (общее
содержание) – 0,0002 мг/дм³, Hg (растворенные формы)- 0,0001 мг/дм³, что не превышает
действующую ПДК. В воде р. Вятки ниже впадения в нее р. Просницы концентрация ртути
была менее 0,00003 мг/дм³. Среднее содержание ртути в донных отложениях р. Просницы в
районе контрольного створа составляло ~0,2 мг/кг.
Меры по сокращению загрязнения окружающей среды
- Предприятие характеризуется высокой культурой эксплуатации оборудования и
технологической дисциплиной. В течение последних 5 лет на нем введены в эксплуатацию
установки глубокой очистки сточных вод и водорода, усовершенствована система сброса и
консервации ртутьсодержащих рассольных шламов. Это привело к уменьшению потерь ртути в
расчете на единицу выпускаемой продукции с 0,275 кг/т до 0,250 кг/т. Действующие нормы
предельно допустимых выбросов ртути в воду и воздух соблюдаются.
- Потери ртути с рассольными шламами, вентвыбросами из зала электролиза и
грунтовыми водами, определяемые особенностями технологии и состоянием
шламонакопителей, составляют более 99,5% от ее общих потерь.
- Существующая технологическая схема не позволяет коренным образом сократить
потери ртути с рассольными шламами без серьезной реконструкции узла рассолоподготовки.
Проведение такой реконструкции крайне затруднено вследствие высоких капитальных затрат.
Имеются резервы некоторого сокращения общего количества ртути, теряемой в производстве,
и существенного сокращения ее потерь в водный и воздушный бассейны.
Снижение потерь ртути возможно при выполнении следующих мероприятий:
- реконструкции электролизеров с увеличением их пробега без вскрытий и ремонтов, что
будет способствовать сокращению потерь ртути с рассольными шламами и вентвыбросами;
- реконструкции системы сброса и улавливания сточных вод зала электролиза, что
обусловит сокращение инфильтрации неочищенных сточных вод зала электролиза в грунт;
- реконструкции узла солерастворения и участка захоронения отходов, что обеспечит
кардинальное сокращение проникновения ртути в грунт.
- Вместе с тем основным мероприятием, реализация которого позволила бы сократить на
99% количество ртути, теряемой в производстве, следует считать строительство узла
фильтрации анолита от ртути с реконструкцией существующей установки по термической
переработке ртутьсодержащих отходов.
ОАО “Каустик” (г. Волгоград)
Зал электролиза оснащен электролизерами Р-101 с разлагателями амальгамы
горизонтального типа, рассчитанными на нагрузку 100 кА. Всего установлено и работают 104
электролизера. Приготовление и очистка рассола для электролиза производится путем
донасыщения анолитного цикла чистой выпаренной солью с последующей фильтрацией на
насыпных фильтрах. Сырьем для получения хлора и каустической соды частично служит
выпаренная соль из подземного рассола, а частично - обратная соль выпарки щелоков
диафрагменного электролиза.
Оборудование узлов донасыщения и фильтрации рассола в анолитном цикле выполнено
из титана и допускает наличие в цикле до 20 мг/дм³ активного хлора. Благодаря этому
исключается полное обесхлоривание анолита путем обработки сульфидом, и ртуть,
содержащаяся в рассоле, сохраняется в нем без потерь с рассольными шламами. Рассол,
выходящий из электролизеров, после вакуумного обесхлоривания, подщелачивания и
донасыщения фильтруется через насыпные фильтры. Шлам после регенерации фильтров,
содержащий незначительные количества хлоридов ртути, направляется в секцию № 2 пруда-
накопителя. Более подробное описание системы контролируемых полигонов захоронения
отходов будет дано ниже в разделе “Потери ртути со сточными и грунтовыми водами”.
Конструкцию электролизеров, прежде всего из-за использования горизонтальных
разлагателей и ртутных насосов с конусным ротором, следует считать недостаточно
отвечающей современному уровню техники. Тем не менее вследствие регулярно проводимых
ремонтов и усовершенствований, качество их эксплуатации остается вполне
удовлетворительным, а использование металлооксидных анодов и высокая чистота рассола
позволяют иметь сравнительно низкие механические потери и потери с вентиляционными
выбросами.
В 2001 г. в основном была завершена реконструкция полов в корпусе электролиза, что
позволило существенно облегчить улавливание пролитой ртути, а также предотвратить
просачивание сточных вод и ртути через полы зала электролиза.
Регенерацию ртути из шламов, собираемых в корпусе электролиза, проводят методом
термического восстановления. Восстановленную ртуть возвращают в электролиз. В настоящее
время на предприятии приступили к регенерации ртути из твердых отходов, образовавшихся в
ходе работ по реконструкции полов зала электролиза. Эмиссия ртути на этой операции
практически отсутствует.
Общие потери ртути в хлорно-щелочном производстве рассматриваемого предприятия
складываются из ее потерь со шламами фильтрации анолита, сточными водами,
вентвыбросами, с продукцией (содой каустической и водородом) и механических потерь. Ниже
приведена оценка этих потерь в 1997 и 2002 г.г.
Потери ртути со шламами фильтрации анолита
При фильтрации подщелоченного анолита после его донасыщения выпаренной солью в
насадке песочных насыпных фильтров осаждаются микропримеси железа и тяжелых металлов,
присутствующие в основном в форме гидроксидов. По мере забивки фильтрующей насадки она
подвергается периодическим регенерациям обратным потоком промывного рассола. Затем
нерастворимые примеси из него отстаивают и фильтруют. Промывной рассол фильтруют и
возвращают в анолитный цикл, а шлам в специальных автомашинах, приспособленных для
перевозки пастообразных продуктов, вывозят на полигон захоронения отходов 2-4 класса
опасности (секция № 2 прудов-накопителей). Сбрасываемая с этим шламом ртуть находится в
форме растворимых в воде хлоридов.
Потери ртути со шламами фильтрации анолита составляли:
в 1997 г. – 112,3 кг,
в 2002 г. - 76,4 кг.
Потери ртути со сточными водами
Общее количество образующихся на предприятии ртутьсодержащих сточных вод
составляет примерно 100-130 тыс. м³/год. В состав сточных вод, помимо стоков цеха
электролиза и приготовления рассола, входят также содержащие FeCl3 отработанные растворы
отделения химической демеркуризации оборудования.
Очистка сточных вод проводится методом осаждения ртути в виде сульфида с
последующим отстоем и фильтрацией. Отфильтрованный шлам, содержащий в основном
сульфид ртути, временно складируется в контейнерах, которые размещаются на специально
оборудованной площадке. В дальнейшем его планируется отправлять на специализированное
ртутьперерабатывающее предприятие.
Сточные воды, содержащие после сульфидной очистки не более 0,05 мг/дм³ ртути,
направляют на вторую стадию очистки методом сорбции суспензией РЖ-1, после которой
содержание ртути в воде снижается до 0,005 мг/дм³. Очищенная вода подается в “грязную
секцию” прудов-испарителей, входящую в систему захоронения отходов производства, которая
состоит из 2-х прудов-накопителей (секции 1 и 2) и 5 прудов-испарителей. В первую секцию
(площадью 6,15 км²) поступают стоки (промышленные, ливневые и фекальные), прошедшие
биологическую очистку, а во вторую (площадью 2,11 км²) - жидкие и твердые отходы, включая
шламы рассолоочистки. В пруды-испарители (общей площадью 65,5 км²) откачивают по мере
наполнения отстоявшиеся стоки из прудов-накопителей, а также ртутьсодержащие сточные
воды после сорбционной очистки.
Пруды расположены в безлюдной местности на значительном удалении (несколько
десятков км) от предприятий, жилых зон и водных бассейнов и являются, согласно Водному
кодексу РФ, обособленными водными объектами. Берега и днища прудов защищены
водоупорными глинами толщиной 3-5 м. По периметру прудов расположена сеть скважин,
используемых для мониторинга состояния вод подземных горизонтов.
Существующая на предприятии двухстадийная система очистки сточных вод не
позволяет достичь требуемой нормы остаточного содержания ртути, равной 0,001 мг/дм³.
Общие потери ртути со сточными водами составляли (в т. ч. с очищенной водой):
в 1997 г. - 2783 кг (~1,7 кг),
в 2002 г. - 1320 кг (~0,81 кг).
Потери ртути с вентиляционными выбросами
Система вентиляции зала электролиза - приточная с выводом через аэрационные фонари.
Высота фонарей - 14 м. Расход нагнетаемого воздуха - 600 тыс.м³/ч.
Концентрация ртути в зале электролиза – 0,03-0,06 мг/м³. Кроме зала электролиза,
вентилируются также водородное отделение, операторная, насосное и печное отделения,
отделение регенерации шламов.
Общие потери ртути с вентвыбросами составляли:
в 1997 г. - 643 кг,
в 2002 г. - 387 кг.
Потери ртути с водородом
Весь производимый водород используется для внутризаводского потребления -
получения соляной кислоты и поливинилхлоридной смолы. С 1995 г. глубокая очистка
водорода, поступающего потребителям, производится в три стадии: орошением хлоранолитом,
щелочным рассолом и последующей сорбцией остаточной ртути на активированном угле.
Концентрация ртути в очищенном водороде, направляемом потребителям, - 0,01 мг/дм³.
Потери ртути с водородом (фактически - с выпускаемой продукцией) составляли:
в 1997 г. – 0,408 кг,
в 2002 г. – 0,327 кг.
Потери ртути с содой каустической
Каустическая сода фильтруется от примесей графита и диспергированной ртути.
Отработанный фильтрующий материал складируется вместе с ртутными шламами.
Потери ртути с содой каустической составляли:
в 1997 г. – 33,8 кг,
в 2002 г. – 28,4 кг.
Потери ртути с хлором
Уносимая с хлоргазом ртуть переходит в серную кислоту, используемую для его осушки.
Содержащая ртуть кислота распределяется между внутризаводскими потребителями.
Потери ртути составляли:
в 1997 г. – 56,2 кг,
в 2002 г. – 51,2 кг.
Потери ртути с абгазами
Очистка абгазов от ртути и хлора производится поглощением последних щелочным
раствором гипохлорита натрия.
Выброс ртути с очищенными абгазами составлял:
в 1997 г. – 2,80 кг,
в 2002 г. – 1,53 кг.
Потери ртути со сточными водами, исключая стоки цеха электролиза
Сточные воды, направляемые на установку биологической очистки, включают ливневые,
промышленные и фекальные стоки ОАО “Каустик” (1900-2500 тыс. м³/год), поступающие по
самотечной системе, и стоки, поступающие со стороны (3500-4000 тыс. м³/год) по напорной
системе.
Содержание ртути в сточных водах, равное в среднем 0,002-0,004 мг/дм³, определяется
прежде всего сбросом ртути, оседающей на почву, с поверхностным ливнестоком, а также
ртути, разносимой на колесах транспорта и подошвах людей по территории предприятия.
Возможен также вклад в эти стоки ртути, присутствующей в бытовых и промышленных
отходах (в основном, в отработанных люминесцентных лампах).
Общие потери ртути с этими стоками составляли:
в 1997 г. - 29 кг,
в 2002 г. - 18 кг.
Механические потери ртути
Механические потери, рассчитанные на основе количества закупленной ртути и общих
зарегистрированных потерь, составляли:
в 1997 г. - 24214 кг,
в 2002 г. - 4510 кг.
Столь значительное сокращение механических потерь в 2002 г. по сравнению с 1997 г.
обусловлено проведенной после 1997 г. реконструкцией полов корпуса электролиза, а также
повышением качества эксплуатации основного оборудования.
Обобщенные показатели по выбросам
Потери ртути, сброшенной в воздух, воду прудов-отстойников, захороненной и
складированной со шламами, а также потерянной механически и с товарной продукцией,
представлены в табл. 3.3.
Таблица 3.3 Потери ртути на ОАО “Каустик” (г. Волгоград)
Год |
1997 г. |
2002 г. |
Выпуск соды каустической, т |
45700 |
60300 |
Потери ртути: |
Абсолют ные, т |
Удельные, кг/т NаОН |
Абсолютн ые, т |
Удельные, кг/т NаОН |
- в атмосферу с вентвыбросами и абгазами |
0,648 |
5,8×10-3 |
0,389 |
3,2×10-3 |
- в систему захоронения отходов производства со шламами очистки сточных вод и фильтрации анолита, а также с очищенными сточными водами |
2,895 |
0,026 |
1,396 |
0,011 |
- с товарной продукцией, включая внутреннее потребление |
0,090 |
8,1×10-4 |
0,080 |
6,6×10-4 |
- в водные объекты |
0,0017 |
1,5×10-5 |
0,0008 |
6,6×10-6 |
- механические потери |
24,214 |
0,2174 |
4,51 |
0,0371 |
ВСЕГО |
27,845 |
0,25 |
6,375 |
0,0524 |
Значительное сокращение потерь ртути в 2002 г. по сравнению с 1997 г. обусловлено
повышением полноты улавливания ртути и ртутьсодержащих стоков в цехе электролиза за счет
выполнения мер по реконструкции полов, лотков и приямков.
Как видно из Таблицы 3,3, механические потери ртути на Волгоградском Каустике составили в
2002 году 4,51 тонны.
Унос ртути в атмосферу на производстве в Волгограде сокращено в 2002 году по
сравнению с 1997 г. в результате общего улучшения обслуживания и повышения технического
уровня производства – Отсутствие прямой корреляции между величиной этих потерь и уноса
ртути непосредственно из залов электролиза, рассчитываемых исходя из концентрации ртути в
воздухе, мощностью вентиляции, связано с тем, что вентилируются и другие помещения.
Динамика снижения среднегодового удельного расхода ртути в период с 1997 по 2002 г.
представлена в табл. 3.4.
Таблица 3.4 Удельный расход ртути с 1997 по 2002 г.г.
Год |
1997 |
1998 |
1999 |
2000 |
2001 |
2002 |
Удельный расход ртути, кг/т NaОН |
0,250 |
0,200 |
0,200 |
0,110 |
0,08 |
0,052 |
Как следует из представленных данных, снижение расхода ртути происходило
постепенно по мере проведения реконструкции полов зала электролиза и выполнения
мероприятий по повышению технологической дисциплины. Дальнейшее сокращение потерь
возможно прежде всего за счет полного завершения реконструкции полов, лотков и приямков,
увеличения безремонтного пробега электролизеров и дальнейшего повышения культуры
эксплуатации оборудования и технологической дисциплины. Сокращение потерь ртути со
сточными водами и шламами можно обеспечить в результате создания и освоения узлов
глубокой очистки сточных вод и регенерации ртути из сульфидных шламов и шламов
рассолоочистки.
Запасы ртути в производстве
Всего в производстве имеется 229 т ртути, находящейся в работающих электролизерах.
Ртуть, закупленная для пополнения электролизеров, практически сразу используется в
производстве. Других запасов ртути на предприятии нет.
Состояние окружающей среды
Постоянно проводимый мониторинг состояния воздушной среды на территории ОАО
“Каустик” и прилегающих промзон показывает, что среднее содержание ртути в воздухе, не
превышая в основном ПДК, в абсолютных величинах близко к рассчитанным величинам
выбросов ртути в атмосферу. Так, если по данным за 2002 г. количество ртути, выброшенное в
атмосферу с вентиляционным воздухом и абгазами хлорного производства, составило 0,389 т,
то общие выбросы ртути в воздух, оцененные на основании данных мониторинга ее
содержания в воздушном бассейне, составили 0,401 т.
Ртуть, направляемая со сточными водами очистки в систему прудов-отстойников и
прудов-испарителей, не вносит существенного вклада в общее содержание металла в
воздушном бассейне, главным образом вследствие присутствия его в составе шламов в форме
нерастворимых и нелетучих соединений. Инфильтрация ртути в подземные горизонты под
прудами, как показывают результаты постоянно проводимого исследования проб, отбираемых
из сети скважин, расположенных по периметру прудов, практически отсутствует вследствие
высокой водонепроницаемости так называемых “шоколадных” глин, слоем которых защищены
берега и днища прудов.
Вместе с тем, учитывая отмеченный выше факт наличия небольших количеств ртути и ее
соединений в стоках, не относящихся непосредственно к ртутьсодержащим, и принимая во
внимание существенную величину механических потерь металла в производстве, следует
признать возможным попадание ртути и ее соединений в водные бассейны и подземные
горизонты в зоне, примыкающей к ОАО “Каустик”.
По оценке, проведенной специализированными геологическими организациями в почве
под территорией хлорного цеха может находиться до 500 т ртути.
Строгая оценка количеств ртути, поступающей в водную и воздушную систему за счет
этого запаса, не представляется возможной.
Меры по сокращению загрязнения окружающей среды
- Производство характеризуется стабильностью режима и в целом высокой культурой
эксплуатации.
- Технологическая схема производства обеспечивает низкие потери ртути со шламами
рассолоочистки и дает предпосылки к дальнейшему снижению потерь ртути и ее выбросов в
атмосферу и водные бассейны за счет имеющихся резервов ее совершенствования.
- Сокращение потерь ртути и выбросов ртути может быть достигнуто за счет
выполнения следующих мероприятий:
- завершение проводимой реконструкции полов, лотков и приямков в зале электролиза;
- создание и освоение глубокой очистки сточных вод от ртути ионообменным методом с
целью достижения предельно допустимой нормы сброса;
- создание и освоение установки регенерации ртути из сульфидных шламов первой
стадии очистки сточных вод;
- увеличение мощности установки термической регенерации ртутьсодержащих шламов и
демеркуризации отходов с обеспечением возможности обработки всех ртутьсодержащих
шламов (кроме сульфидных);
- проведение комплекса мероприятий по увеличению сроков межремонтного пробега
электролизеров с целью сокращения механических потерь и потерь ртути с вентвыбросами.
ЗАО “Каустик” (г. Стерлитамак)
Зал электролиза оснащен электролизерами 30М2 (фирмы “О. De Nora”, Италия) с
разлагателями амальгамы вертикального типа, рассчитанными на нагрузку до 400 кА. Всего
установлено 34 электролизера. Эксплуатация электролизеров характеризуется значительными
колебаниями нагрузки на электролиз, связанными с нестабильностью потребления хлора и
каустической соды. В 1997 г. электролизеры работали при средней нагрузке 232 кА, в 2002 г. -
273 кА.
Приготовление и очистка рассола для электролиза производится путем донасыщения
анолитного цикла чистой выпаренной солью с последующей фильтрацией. Сырьем для
получения хлора и каустической соды частично служит соль из подземного рассола, а частично
- обратная соль выпарки щелоков диафрагменного электролиза.
Оборудование узлов донасыщения и фильтрации рассола в анолитном цикле, выполнено
из титана и стеклопластика, что допускает наличие в цикле 20-25 мг/дм³ активного хлора.
Благодаря этому исключается полное обесхлоривание анолита путем обработки сульфидом, и
ртуть, содержащаяся в рассоле, сохраняется в нем без потерь с рассольными шламами.
Рассол, выходящий из электролизеров, после вакуумного обесхлоривания,
подщелачивания и донасыщения фильтруется на листовых вертикальных фильтрах с
фильтрующим слоем на основе целлюлозы. Шлам после регенерации фильтров, содержащий
незначительные количества хлоридов ртути, направляется в сборник грязного рассола, куда
сливается также анолит из электролизеров, останавливаемых на ремонт. Шлам из сборника
выгружают и складируют на площадке временного хранения.
Электролиз ведут в электролизерах большой мощности, оснащенных металлооксидными
анодами. Конструкция, оснащение и техническое состояние электролизеров в целом отвечает
современному уровню техники. Однако проведение ремонтных работ на электролизерах
высокой единичной мощности приводит к повышенным выбросам ртутных паров в воздух и
капельной ртути на пол, что вызывает высокие механические потери последней и унос ее с
вентвыбросами. Поэтому актуальным для производства является максимальное увеличение
продолжительности работы электролизеров без вскрытия.
В период между 1997 и 2002 г.г. были проведены мероприятия по увеличению
межремонтного пробега электролизеров, который в настоящее время составляет около 500
суток. Отработанные технические решения по дальнейшему совершенствованию конструкции
рабочей части анодов, состава и количества активной массы анодных покрытий, созданию
автоматической системы регулирования напряжения позволяют увеличить этот срок еще в 2-3
раза, однако их освоение в полном объеме тормозится по причинам ограниченного
финансирования. Недостаточен также срок службы гуммировочных материалов деталей
электролизеров. Следствием недостаточной длительности межремонтного пробега
электролизеров является сравнительно высокий уровень механических потерь ртути и уноса ее
с вентиляционным воздухом.
В период между 1997 и 2002 г.г. проводились работы по реконструкции и
совершенствованию оборудования, а также повышению уровня технологической дисциплины
персонала. Это привело к сокращению потерь ртути на ряде стадий производства.
В 1998-2001 г.г. была проведена реконструкция лотков и приямков в полу зала
электролиза, что позволило сократить потери ртути со сточными водами и механические
потери ее за счет сбора и возврата пролитой ртути и шламов отделения электролиза.
Регенерацию ртути из шламов проводят методом термического восстановления в
специальной печи. Туда же направляют с площадки временного хранения смесь
ртутьсодержащих шламов фильтрации рассола и сточных вод, отработанные активированные
угли после очистки водорода, абгазов, обесхлоривания сточных вод и фильтрации соды
каустической, а также смолу после ионообменной очистки сточных вод. Перед отправкой на
регенерацию эти отходы, содержащие различное количество ртути, смешивают таким образом,
чтобы общая концентрация ртути в них была оптимальной для процесса термической
регенерации.
В 1997 г. в электролиз было возвращено 4,02 т, а в 2002 г. – 8,2 т вторичной ртути.
Потери ртути в производстве складываются из потерь со сточными водами,
вентвыбросами, шламами после регенерации из них ртути, с продукцией (содой каустической и
водородом) и механических потерь.
Потери ртути со сточными водами
Общее количество ртутьсодержащих сточных вод составляло в 1997 г. 48 тыс. м³, в 2002
г. - 73 тыс. м³. Все ртутьсодержащие сточные воды собирают в промежуточную емкость,
откуда непрерывно откачивают на предварительную грубую фильтрацию и отстой. После
отстоя вода, содержащая в среднем 3,5 мг/дм³ ртути, подвергается осветлению, хлорированию,
тонкой фильтрации на кварцевых фильтрах, обесхлориванию на активированном угле до
остаточного содержания активного хлора 30-50 мг/дм³ и направляется на ионообменную
очистку в трех последовательно соединенных адсорберах. Отработанная смола после промывки
водой и соляной кислотой складируется на площадке временного хранения ртутных отходов,
откуда периодически направляется на термическую регенерацию в смеси с другими шламами.
Концентрация ртути в очищенных сточных водах составляла:
в 1997 г. – 0,016 мг/дм³,
в 2002 г. – 0,019 мг/дм³.
Эти величины превышают существующую норму – 0,001 мг/дм³.
Очищенные воды поступают в общезаводскую систему минерально загрязненных стоков,
а из нее - в систему отстойников, расположенную за пределами предприятия. Кроме того, в эти
отстойники направляются условно чистые стоки ЗАО “Каустик”, включающие и ливневые
стоки, отдельный контроль содержания ртути в которых не проводится, а также стоки еще с
трех предприятий. Доля стоков ЗАО “Каустик” составляет примерно половину от общего
объема поступающих сточных вод.
Всего имеется два отстойника емкостью по 2,1 млн. м³ каждый. Они оснащены
перемешивающими устройствами и системой гидроизоляции.
Заливка и откачка сточных вод из обоих отстойников производится автономно из расчета
поддержания на выходе из каждого оптимального уровня выводимых примесей.
Сточные воды после отстоя сбрасываются в р. Белую.
Всего безвозвратные потери ртути со сточными водами составляли:
в 1997 г. – 0,768 кг,
в 2002 г. – 0,1387 кг.
Значительное снижение потерь в 2002 г. связано с переходом на более эффективный
сорбент (смола АВ17-8 вместо ВП1-АП).
Потери ртути с вентвыбросами
Система вентиляции зала электролиза - приточная с выводом через аэрационные фонари.
Высота фонарей - 18 м. Расход нагнетаемого воздуха – 1,2 млн. м³3/ч. Концентрация ртути в
зале электролиза составляла в 1997 г. – 0,018 мг/м³, в 2002 г. – 0,017 мг/м³.
Общие потери ртути с вентвыбросами составляли:
в 1997 г. - 882 кг,
в 2002 г. - 441 кг.
Снижение потерь ртути обусловлено проведением мероприятий по увеличению
межремонтного пробега электролизеров.
Потери ртути с водородом
Весь водород используется для внутризаводского потребления (синтез соляной кислоты,
печи подогрева пропилена в производстве эпихлоргидрина) или передается другим
потребителям (завод синтетического каучука, нефтехимическое производство).
Глубокая очистка водорода, поступающего потребителям, производится последовательно
орошением хлоранолитом, щелочным рассолом и последующей сорбцией остаточной ртути на
активированном угле ХПР-3П. Концентрация ртути в очищенном водороде, направляемом
потребителям – 0,003 мг/м³.
Потери ртути с водородом составляли:
в 1997 г. – 0,138 кг,
в 2002 г. – 0,08 кг.
Снижение потерь в 2002 г. связано с совершенствованием конструкции сорбционной
колонны.
Потери ртути с каустической содой
Каустическая сода фильтруется от примесей графита и диспергированной ртути через
слой активированного угля. Отработанный уголь направляется на площадку временного
хранения ртутьсодержащих отходов, а оттуда на термическую регенерацию. Остаточное
содержание ртути в отфильтрованной щелочи - 0,00002%масс.
Потери ртути с содой каустической составляли:
в 1997 г. – 242,8 кг,
в 2002 г. - 22,2 кг.
Резкое сокращение потерь в 2002 г. связано с выполнением мер по усилению
технологической дисциплины персонала.
Потери ртути с хлором
Эти потери не обнаруживаются, т. к. соединения ртути практически полностью
поглощаются водой при промывке влажного хлора.
Потери ртути с абгазами
Очистка абгазов от ртути производится сорбцией на активированном угле ХПР-3П.
Количество очищенных абгазов ~ 500 м³/ч, концентрация ртути в которых не превышает 0,0035
мг/м³.
Потери ртути с очищенными абгазами составляли:
в 1997 г. – 7,148 кг,
в 2002 г. – 0,015 кг.
Резкое сокращение ртути потерь в 2002 г. связано с повышением качества эксплуатации
электролизеров (в частности, нормализации температурного режима и промывки карманов) и
усовершенствованием конструкции адсорберов.
Потери ртути со шламами термической регенерации
Шламы, выгружаемые из печи термической регенерации ртути, содержат не более 0,01 %
масс. ртути. Эти шламы направляются на контролируемый полигон “Цветаевка”,
представляющий собой систему заглубленных в землю бетонных емкостей со специально
защитным покрытием.
Потери ртути со шламами составляли:
в 1997 г. - нет данных,
в 2002 г. – 6,5 кг.
Механические потери ртути
Они определяются по разности между количеством закупавшейся за год ртути и суммой
учтенных за тот же период потерь. При этом учитывается также изменение суммарной
закладки ртути в электролизеры по сравнению с предыдущим годом. Учет последнего фактора
для электролизеров 30М2 важен, поскольку их конструкция позволяет вести эксплуатацию в
широком интервале общего количества ртути в системе электролизер-разлагатель-насос,
однако технологические показатели работы электролизеров с уменьшением закладки ртути
ниже оптимального существенно ухудшаются. Указанные величины составляли (табл. 3.5).
Таблица 3.5 Расчет механических потерь ртути в 1997 и 2002 г.г. на ЗАО “Каустик” (г.
Стерлитамак)
Год |
Закупленная ртуть |
Изменение закладки ртути в электролизерах |
Учтенные потери ртути |
Механические потери ртути |
1997 |
5071,5 кг |
-4057 кг |
1133 кг |
7995,5 кг |
2002 |
10000 кг |
+5371 кг |
470 кг |
4157,82 кг |
Следует отметить, что рассчитанные таким образом механические потери ртути частично
входят в состав ртутьсодержащего шлама, накапливающего в сборнике загрязненного рассола и
отстойниках отделения очистки сточных вод. Эти шламы накапливаются в течение нескольких
лет, затем после плановых ревизий и чисток емкостного оборудования направляются на
термическую регенерацию. В связи с тем, что этот процесс растянут во времени, в течение
которого общие потери ртути меняются, раздельная оценка количества металла, выносимого из
электролизеров с осаждением в емкостях и теряемого в грунт через неплотности пола,
затруднительна.
Потери ртути, сброшенной в воздух, воду, захороненной и складированной со шламами, а
также потерянной механически, представлены в табл. 3.6.
Таблица 3.6 Потери ртути на ЗАО “Каустик” (г. Стерлитамак)
Год |
1997г. |
2002г. |
Выпуск соды каустической, т |
88940 |
110800 |
Потери ртути: |
Абсолютны е, т |
Удельные, кг/т NаОН |
Абсолютн ые, т |
Удельные, кг/т NаОН |
- в атмосферу с вентвыбросами и абгазами |
0,889 |
1,0×10-2 |
0,441 |
3,98×10-3 |
- в систему захоронения отходов |
Нет данных |
- |
0,0065 |
5,86×10-5 |
- в открытый водный бассейн |
0,000768 |
8,6×10-6 |
0,0001387 |
1,25×10-6 |
- с товарной продукцией, включая внутреннее потребление |
0,2423 |
2,72×10-3 |
0,02228 |
2,1×10-4 |
- вывод ртути с механическими потерями |
7,996 |
0,090 |
4,158 |
0,0375 |
ВСЕГО |
9,218 |
0,1026 |
4,629 |
0,0418 |
Значительное сокращение потерь ртути в 2002 г. по сравнению с 1997 г. произошло за
счет целенаправленного проведения мероприятий по совершенствованию технологии по
стадиям производства, повышению технологической дисциплины и контролю за качеством
ремонтных работ. Благодаря этому были в несколько раз снижены потери ртути с очищенными
сточными водами и с товарной продукцией, а также - вдвое - выбросы в атмосферу и
механические потери. Вместе с тем выбросы по двум последним позициям все еще остаются
значительными, а их сокращение позволит в дальнейшем существенно повлиять на величину
общих потерь ртути. Это может быть достигнуто прежде всего в результате существенного
увеличения длительности работы электролизеров без остановок и ремонтов.
Унос ртути в атмосферу на производстве в Стерлитамаке сокращено в 2002 году по сравнению
с 1997 г. в результате общего улучшения обслуживания и повышения технического уровня
производства – Отсутствие прямой корреляции между величиной этих потерь и уноса ртути
непосредственно из залов электролиза, рассчитываемых исходя из концентрации ртути в
воздухе, мощностью вентиляции, связано с тем, что вентилируются и другие помещения.
Запасы ртути в производстве
В производстве имеется 204 т ртути, находящейся в работающих электролизерах.
Ртуть, закупаемая для пополнения электролизеров, и вторичная ртуть, получаемая при
регенерации из шламов, практически сразу используются для пополнения убыли металла в
электролизерах.
Некоторое количество ртути, как металлической форме, так и в форме слаборастворимых
солей (сернокислой ртути и каломели) депонировано в осадках, скапливающихся на дне
отстойников и осветлителей сточных вод и бака-сборника загрязненного рассола. Средний срок
депонирования - примерно 3 года. Количественная оценка этих запасов затруднительна. Других
запасов ртути на предприятии нет.
Состояние окружающей среды
Содержание ртути в воздушном бассейне на территории предприятия и г. Стерлитамака,
а также в воде на контрольном створе в р. Белой, , куда сбрасываются очищенные стоки,
постоянно контролируются отделом охраны природы ЗАО “Каустик” и санитарными службами
города (табл. 3.7).
Таблица 3.7 Содержание ртути в воде р. Белой в районе контрольного поста на выходе из города
(после сброса сточных вод ЗАО “Каустик”) за период 1990-2002 г.г. *
Год |
Общее количеств о анализов |
Количество анализов, превышающих ПДК** для рыбохозяйственного водоема |
Доля анализов с превышением ПДК, % |
Максимальное содержание ртути, мг/дм³ |
Среднее содержание ртути, мг/дм³ |
1990 |
135 |
135 |
100 |
0,00542 |
0,0011 |
1991 |
102 |
102 |
100 |
0,0061 |
0,0013 |
1992 |
103 |
103 |
100 |
0,0026 |
0,00106 |
1993 |
130 |
129 |
99,2 |
0,00083 |
0,00029 |
1994 |
137 |
137 |
100 |
0,00044 |
0,00029 |
1995 |
138 |
138 |
100 |
0,00038 |
0,00020 |
1996 |
105 |
105 |
100 |
0,00026 |
0,00015 |
1997 |
109 |
5 |
4.,6 |
0,00004 |
0,000014 |
1998 |
76 |
3 |
3,9 |
0,00007 |
0,000002 |
1999 |
170 |
20 |
11,8 |
0,000092 |
0,000006 |
2000 |
324 |
4 |
1,2 |
0,00028 |
0,000002 |
2001 |
350 |
0 |
0 |
Не обнаружено |
Не обнаружено |
2002 |
354 |
1 |
0,3 |
0,00007 |
0,0000002 |
* Данные отдела охраны природы ЗАО “Каустик”.
** ПДК ртути составляют: для питьевой воды – 0,0005 мг/дм³; для рыбохозяйственных водоемов .
0,00001 мг/дм³.
Как видно из табл. 3.7, содержание ртути в воде р. Белой, начиная с 1998 г., не превышает
норм ПДК, принятых как для питьевой воды, так и для рыбохозяйственных водоемов.
На основании приближенной оценки величины механических потерь ртути за весь
период эксплуатации действующего производства можно предположить, что в почве под
территорией цеха электролиза аккумулировано примерно 200-300 т этого элемента.
Меры по сокращению загрязнения окружающей среды
- Производство характеризуется в целом высокой культурой эксплуатации при
значительной нестабильности режима работы по нагрузке на электролизеры.
- Технологическая схема производства обеспечивает низкие потери ртути со шламами
рассолоочистки, абгазами и продукцией, недостаточно низкие - с очищенными сточными
водами, сравнительно высокие механические потери и потери в атмосферу с вентвыбросами.
- Производство имеет предпосылки к дальнейшему существенному снижению потерь
ртути за счет выполнения следующих мероприятий:
- завершения комплекса мероприятий по увеличению межремонтного пробега
электролизеров, включающего полный перевод электролизеров на аноды с высокостойкими
активными покрытиями и усовершенствованной рабочей основой, полное оснащение
электролизеров системой автоматического поддержания и регулирования напряжения,
использование высокостойких гуммировочных материалов;
- повышения глубины очистки сточных вод за счет введения дополнительной стадии
предварительной химической очистки или усиления стадии ионообменной очистки.
ОАО “Саянскхимпласт” (г. Саянск)
Зал электролиза оснащен электролизерами СДМ-200/7,5 с металлооксидными анодами и
разлагателями вертикального типа. Всего установлено 96 электролизеров, рассчитанных на
нагрузку 200 кА. В 1997 г. в работе находилось 34 электролизера при нагрузке 140 кА, в 2002 г.
- 60 электролизеров при нагрузке 160 кА.
Приготовление и очистка рассола для электролиза производится путем донасыщения
анолитного цикла чистой выпаренной солью с последующей двухстадийной фильтрацией на
насыпных и рамных фильтрах. Сырьем для получения хлора и каустической соды служит соль
из подземного рассола, предварительно очищенная, а затем выпаренная.
Часть емкостей анолитного цикла выполнена из стали, футерованной кислотно-щелочной
плиткой, часть трубопроводов – из гуммированной стали. Состояние антикоррозийной защиты
оборудования анолитного цикла, включая состояние электролизеров, неудовлетворительно и не
позволяет обеспечить требуемое качество питающего рассола без полного химического
обесхлоривания всего потока анолита методом сульфидной обработки. Это приводит к потерям
ртути с рассольными шламами в виде сульфида ртути, а также к осложнениям в работе
электролизеров, следствием которых являются высокие механические потери ртути и унос ее
паров с вентиляционным воздухом.
Шламы, образующиеся в отделении электролиза, а также другие богатые ртутью шламы
направляются на термическую регенерацию ртути.
Проведенные в 1998-2002 г.г. мероприятия по сокращению потерь ртути носили частный
характер и не повлияли на их величину.
Ниже приведена оценка потерь ртути в 1997 и 2002 г.г.
Потери ртути со шламами фильтрации анолита
Рассольные шламы, содержащие сульфид ртути, направляются на захоронение в
специально оборудованный шламонакопитель совместно с другими ртутьсодержащими
отходами, включая сульфидные шламы очистки сточных вод. Полезный объем
шламонакопителя – 223 тыс. м³, площадь – 4,3 га, высота – 9 м. Днище шламонакопителя и
борта дамбы защищены полиэтиленовой пленкой с пригрузом из песка и гравия.
Потери ртути со шламами фильтрации анолита составляли:
в 1997 г. - 10360 кг,
в 2002 г. - 22908 кг.
Потери ртути со сточными водами
Общее количество ртутьсодержащих сточных вод составляло:
в 1997 г. - 78989 м³,
в 2002 г. - 127690 м³3.
Содержание ртути в неочищенной сточной воде варьировалось в пределах 15-20 мг/дм³.
Очистка сточных вод производится путем осаждения ртути сульфидным методом с
последующей выпаркой воды. Упаренный до концентрации NaCl, близкой к концентрации его
конденсат - на доочистку от остаточной ртути на угольном сорбенте. Очищенные сточные воды
возвращаются в производство и используются для промывки оборудования и приготовления
рабочих растворов. Избыток очищенного конденсата сбрасывается в промливневую
канализацию с последующим сбросом в р. Оку.
Сульфидный шлам очистки сточных вод направляется на захоронение вместе со
шламами рассолоочистки.
Концентрация ртути в очищенных сточных водах, спускаемых в водоем, составляла в
1997 г. – 0,016 мг/дм³, в 2002 г. – 0,0003 мг/дм³. Объемы очищенного конденсата,
сбрасываемого в водоемы, не фиксировались. Содержание ртути в речной воде на контрольном
створе р. Оки составляло 0,00001мг/дм³.
Потери ртути с очищенными сточными водами не поддаются оценке, но в целом,
учитывая особенности технологической схемы и глубину очистки, они невелики.
Относительно величин потерь со шламами на стадии сульфидной очистки сточных вод
прямой информации не имеется, однако, по всей вероятности, они входят в состав потерь с
сульфидными шламами рассолоочистки.
Потери ртути с вентиляционными выбросами
Система вентиляции зала электролиза приточная с выводом через аэрационные фонари.
Высота фонарей - 22 м. Расход нагнетаемого воздуха достигал в 1997 г. – 2,48 млн. м³/ч, в 2002
г. – 0,68 млн. м³3/ч.
Средняя концентрация ртути в воздухе зала электролиза изменялась в пределах:
в 1997 г. – 0,027-0,033 мг/м³,
в 2002 г. – 0,042-0,046 мг/м³.
Потери ртути с вентвыбросами составляли:
в 1997 г. - 652 кг,
в 2002 г. - 238 кг.
Потери ртути с водородом
Основная часть (~99%) выпускаемого водорода выбрасывается в атмосферу через трубу
высотой 22 м. Остальной водород используется для синтеза хлористого водорода.
Очистка водорода производится на сорбенте из активированного угля ХПР-3П.
Концентрация ртути в очищенном водороде составляла в 1997 г. – 0,048 мг/м³, в 2002г. –
0,0024 мг/м³ при норме 0,01 мг/м³3.
Всего потери ртути с водородом составляли:
в 1997 г. – 0,788 кг,
в 2002 г. – 0,083 кг.
Потери ртути с хлором
По информации предприятия эти потери практически отсутствуют.
Потери ртути с абгазами
Очистка абгазов от ртути и хлора производится на активированном угле ХПР-3П.
Содержание ртути в очищенных абгазах находится в пределах 0,003-0,0049 мг/м³ при
норме 0,01 мг/м³.
Потери ртути с абгазами составляли:
в 1997 г. – 0,181 кг,
в 2002 г. – 0,032 кг.
Потери ртути с содой каустической
Информация об этих потерях отсутствует. Однако, учитывая, что фильтрация соды
каустической на ОАО “Саянскхимпласт” аналогична имеющимся на других предприятиях,
указанные потери можно оценить, исходя из величин годового выпуска.
Оценочные величины потерь ртути составили:
в 1997 г. - ~0,08 кг,
в 2002 г. -~ 0,16 кг.
Механические потери ртути
Для заливки в электролизеры было закуплено ртути:
в 1997 г. - 24391 кг,
в 2002 г. – 70833,5 кг.
Механические потери ртути, рассчитанные по разности между количеством закупленного
металла и зафиксированными потерями его по вышеперечисленным позициям, составляли:
в 1997 г. - 13377 кг,
в 2002 г. - 47687 кг.
По данным предприятия, более чем за 20 лет работы производства в рыхлом чехле под
участком расположения цеха электролиза аккумулировано ориентировочно 800-1000 т
механически утерянной ртути.
Запасы ртути в производстве
Всего в электролизерах находится 171 т ртути.
Других запасов ртути на предприятии не имеется.
Потери ртути, сброшенной в воздух, складированной со шламами и поступившей
механически в грунт под корпусом электролиза, представлены в табл. 3.8.
Таблица 3.8 Потери ртути на ОАО .Саянскхимпласт. (г. Саянск)
Год |
1997 г. |
2002 г. |
Выпуск соды каустической, т |
51800 |
121500 |
Потери ртути: |
Абсолютн ые, т |
Удельные, кг/т NаОН |
Абсолютн ые, т |
Удельные, кг/т NаОН |
- в атмосферу с вентвыбросами и абгазами |
0,653 |
1,26•10-2 |
0,238 |
1,96×10-3 |
- в систему захоронения отходов производства со шламами очистки рассола и сточных вод |
10,360 |
0,20 |
22,908 |
0,189 |
- с товарной продукцией |
0,031 |
5,98×10-4 |
0,080 |
6,6×10-4 |
- в грунт с механическими потерями |
13,377 |
0,258 |
47,687 |
0,392 |
- в водоемы |
сведения отсутствуют |
сведения отсутствуют |
ВСЕГО |
24,421 |
0,471 |
70,913 |
0,583 |
Меры по сокращению загрязнения окружающей среды
Из представленных данных видно, что, несмотря на вполне удовлетворительные в
сравнении с другими действующими производствами величины выбросов ртути в воздух, воду
и потерь с товарной продукцией, и по всей вероятности, в воду, ее механические потери и
потери со шламами рассолоочистки неприемлемо высоки.
Общее состояние производства является неудовлетворительным, и в настоящее время
рассматривается вопрос о конверсии ртутного метода производства каустической соды и хлора
на метод электролиза с ионообменной мембраной, с последующей демеркуризацией зданий и
почвы, а также извлечением ртути из грунта.
3.1.5 Оценка количества ртутных выбросов на производствах, выведенных из
эксплуатации
Таких производств в России семь. За исключением двух крупнотоннажных производств
(ОАО “Усольехимпром” и производство “Кребс” на ЗАО “Каустик”), это - небольшие
установки мощностью от 1,3 до 20 тыс. т соды каустической в год, работавшие в основном в
составе целлюлозно-бумажных комбинатов (ЦБК). Все они, кроме производства “Кребс”,
использовали в качестве сырья привозную твердую соль. Химическое обесхлоривание анолита
проводилось обработкой сульфидом натрия с одновременным осаждением сульфида ртути.
Ртутные шламы с этих производств, содержащие более 1% ртути, отправлялись, как правило,
на регенерацию на Никитовский ртутный комбинат, рассольные шламы сбрасывались на
шламовые поля, огарки графитовых анодов - в отвалы, а сточные воды после сульфидной
очистки и отстоя - в общезаводскую канализацию. На всех производствах имели место высокие
механические потери ртути, которая просачивалась в грунт под зданием цеха электролиза.
Представленные в табл. 3.9 количества ртути, накопившейся в грунте, в отвалах и
шламонакопителях, а также поступившей в водоемы, являются приблизительными оценочными
величинами, рассчитанными на основании имеющейся информации о длительности
эксплуатации каждого из этих производств, особенностях технологической схемы на каждом из
них, данных об общем расходе ртути и потерях ее по отдельным статьям расхода,
определявшихся в ходе проведенных обследований. Точность этих оценок - ±20%.
Таблица 3.9 Содержание ртути в почвах, отходах и водных объектах на местах производств
каустической соды и хлора, выведенных из эксплуатации в 1982-1998 г.г.
Предприятие |
Мощность по NaOH, тыс. т/год |
Год пуска- остановки |
Приблизительное количество ртути, т |
в грунте |
в отвалах и шламонакопител ях |
в водоем ах |
ОАО “Усольехимпром”, г. Усолье- Сибирское, Иркутская область |
100 |
1970-1998 |
1500 |
800 |
70 |
ЗАО “Каустик”, производство “Кребс”, г. Стерлитамак, Башкортостан |
86 |
1964-1987 |
600 |
50 |
90 |
Котласский ЦБК, г. Коряжма, Архангельская область |
19,6 |
1964-1998 |
30 |
130 |
30 |
Архангельский ЦБК, г. Новодвинск, Архангельская область |
16,4 |
1962-1996 |
25 |
120 |
25 |
ОАО “Капролактам”, г. Дзержинск, Нижегородская область |
10 |
1948-1982 |
20 |
60 |
20 |
Амурский ЦБК, г. Комсомольск- на-Амуре, Хабаровский край |
7,35 |
1970-1997 |
18 |
56 |
15 |
Светогорский ЦБК, г. Светогорск, Ленинградская область |
1,3 |
1951-1993 |
25 |
11 |
25 |
Всего |
|
|
2218 |
1227 |
275 |
Проведенная оценка показала, что в зонах, примыкающих к производствам, выведенным
из эксплуатации, окружающая среда содержит значительные количества ртути,
распределенных в грунте под производственными зданиями (в основном в виде металлической
ртути), в шламонакопителях (в основном в виде сульфида ртути), в отвалах (в основном в виде
металлической ртути), в водоемах (в основном в виде сульфида ртути). Количество отходов
определяется мощностью производств, сроками их эксплуатации и уровнем потерь ртути.
Наибольшие загрязнения ртутью характерны для промзон г.г. Усолья-Сибирского,
Стерлитамака, Коряжмы и Новодвинска. По имеющейся информации, там ведутся
определенные работы по очистке от ртути грунтов в районе бывших производственных зданий.
С целью минимизации возможного ущерба от скопившихся в этих зонах ртутных отходов
и предотвращения дальнейшего рассеяния ртути представляется целесообразным расширение
обследований для уточнения карт размещения отходов, уровней заражения ртутью почв,
воздушной и водной сред, разработка мероприятий по локализации и консервации отходов.
3.1.6 Заключение
Ртуть, закупавшаяся в течение года, целиком использовалась в течение этого же периода для
пополнения электролизеров. Исключение составляет производство в Стерлитамаке, где
конструкция электролизеров допускает колебания среднегодовых закладок ртути в них.
Количественное определение этих колебаний возможно на основании сравнения
среднегодового уровня ртути в емкостях циркуляционных насосов.
В табл. 3.10 и 3.11 представлены итоговые сравнительные данные по результатам
инвентаризации поступления ртути в воздух, воду, грунт и продукцию от действующих в
Российской Федерации производств каустической соды и хлора по ртутному методу в 1997-
2002 г.
Таблица 3.10 Баланс ртути на хлорно-щелочных производствах РФ в 1997 г.
Предприятие |
Использова но ртути, т |
Выбросы в атмосферу , т |
Сбросы в водные объекты, т |
Механическ ие потери, т |
Размещен о на полигонах отходов, т |
Потери с товарной продукцие й, т |
ОАО “Кирово-Чепецкий химкомбинат” |
Нет данных |
0,11 |
0,0001 |
Нет данных |
12,4 |
0,03 |
ОАО “Каустик”, г. Волгоград |
27,8 |
0,65 |
0,001 |
24,2 |
2,9 |
0,09 |
ЗАО “«Каустик”, “0. Dе Nога”, г. Стерлитамак |
5,1 |
0,89 |
0,0008* |
8,0 |
n.a |
0,24 |
ОАО “Саянскхимпласт”, г. Саяны |
24,4 |
0,65 |
Нет данных |
13,4 |
10,4 |
0,03 |
Всего |
>57,3 |
2,30 |
>0,002 |
>45,5 |
>27,5 |
0,39 |
* В закрытые водные системы (пруды-испарители).
Таблица 3.11 Баланс ртути на хлорно-щелочных производствах РФ в 2002 г.
Предприятие |
Использова но ртути, т |
Выброс ы в атмосфе ру, т |
Сбросы в водные объекты, т |
Механиче ские потери, т |
Размещен о на полигонах отходов, т |
Потери с товарной продукцией , т |
ОАО “Кирово-Чепецкий химкомбинат” |
15,1 |
0,15 |
0,0001 |
0,015 |
14,9 |
0,03 |
ОАО “Каустик”, г. Волгоград |
7,3 |
0,39 |
0,0008* |
4,5 |
1,4 |
0,08 |
ЗАО “Каустик”, “0. Dе Nога”, г. Стерлитамак |
10,0 |
0,44 |
0,0001 |
4,2 |
0,007 |
0,02 |
ОАО “Саянскхимпласт”, г. Саяны |
70,8 |
0,24 |
Нет данных |
47,6 |
22,9 |
0,08 |
Всего |
103,2 |
1,22 |
>0,001 |
56,3 |
39,3 |
0,22 |
* В закрытые водные системы (пруды-испарители).
Из представленных данных видно, что за рассмотренное пятилетие на всех производствах
при повсеместном росте выпуска продукции значительно уменьшились поступления ртути в
воздух, воду и продукцию. Такое сокращение стало возможным благодаря проведению
соответствующих технических мероприятий, а также совершенствованию трудовой
дисциплина на предприятии.
На всех предприятиях, за исключением ОАО “Саянскхимпласт”, существенно снижены
поступления ртути в грунт за счет механических потерь и на контролируемые полигоны в
составе ртутьсодержащих шламов.
Вместе с тем, существующие на всех заводах потери ртути, равно как и ее выбросы в
воздух, требуют дальнейшего сокращения, причем у предприятий имеются конкретные
технические решения. Однако их скорейшая реализация тормозится отсутствием необходимых
финансовых вложений. Поэтому изыскание средств на проведение этих работ с контролем за
их целевым использованием на выполнение конкретных мероприятий, соблюдением
согласованных сроков их завершения и оценкой их эффективности, способствовало бы
дальнейшему значительному сокращению выбросов ртути с хлорных производств и
оздоровлению экологической обстановке в регионах.
Общий поток ртути в производстве хлора-щелочи в Российской Федерации в 2002 г.
показан на рис. 3.3.
Для сравнения с другими странами, данные по российским заводам вводятся в общую
таблицу OSPAR (OSPAR 2002) вместе с данными, полученными для предприятий Франции
(табл. 3.12). Это сравнение показывает, что удельный выброс ртути с очищенными сточными
водами и уходящими газами на российских предприятиях не превышают диапазона данных для
французских предприятий, что связано с использованием мер, направленных на измерение
глубины очистки таких выбросов.
Рисунок 3.3 Баланс ртути в хлорно-щелочном производстве, Российская Федерация, 1997 и 2002 г.г.

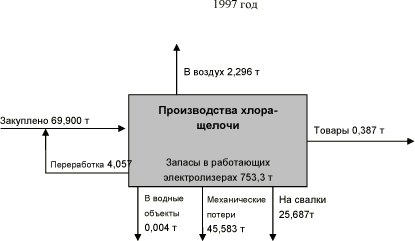
В то же время потери ртути с продукцией в 2-3 раза выше, чем на предприятиях Франции,
что свидетельствует о недостаточной очистке каустической соды от ртути на российских
предприятиях. Потери с вентиляционными выбросами также высокие в цехах электролиза. Эти
выбросы можно снизить только за счет максимально возможного уменьшения частоты и сроков
простоя электролизеров.
Механические потери ртути на российских предприятиях либо очень низкие (Кирово-
Чепецкий химический завод), либо в несколько раз превышают аналогичные показатели во
Франции (“Каустик”, г. Волгоград; “Каустик”, г. Стерлитамак) или же чрезвычайно высокие
(“Саянскхимпласт”). Потери ртути со шламом, который не годится для регенерации, на
предприятиях в Волгограде и Стерлитамаке аналогичны таким же потерям на предприятиях
Франции; в то же время такие потери на предприятиях Кирово-Чепецка и Саянска очень
высокие. Это связано с конкретными характеристиками применяемой здесь устаревшей
технологической схемы, что требует полного удаления хлора из анолита с использованием
сульфидной очистки (в Кирово-Чепецке), или неудовлетворительной защитой оборудования
анолитного цикла от коррозии (“Саянскхимпласт”).
Таблица 3.12 Потери на хлорно-щелочных предприятиях Франции в 2000 г. (OSPAR 2002) и Российской Федерации в 2002 г.
Нажмите сюда для просмотра Таблица 3.12
3.2 Другое применение ртути в химической промышленности
Хлористая ртуть используется для производства винилхлоридных мономеров (ВХМ) на
четырех предприятиях России (см. раздел 3.2.1).
До 1998-99 г.г. металлическая ртуть применялась в производстве витамина B2
(рибофлавина) на двух предприятиях. Информация о ртутьсодержащих отходах, хранящихся на
этих предприятиях, представлена в разделе 3.2.2.
Сульфат ртути (II) использовался до 2000 г. в качестве катализатора для изготовления
красок (1-аминоантрацен). Информация о ртутьсодержащих отходах представлена в разделе
3.2.3.
В СССР ртутные катализаторы использовались для производства ацетальдегида, но
данное предприятие было расположено в Казахстане (г. Темиртау, Карагандинская область).
Экологическая ситуация, сложившаяся в окрестностях этого предприятия, детально
рассмотрена в литературе [323].
3.2.1 Производство винилхлоридного мономера (ВХМ)
Углеводородное сырье для синтеза винилхлорида – ацетилен – получают из карбида
кальция или высокотемпературным пиролизом природного газа (либо углеводородов нефти).
Полученный очищенный и осушенный до остаточного содержания влаги менее 1,5 г/м³
ацетилен направляется в смеситель, куда подается также предварительно очищенный и
осушенный хлористый водород. Соотношение ацетилен: хлористый водород составляет обычно
1,0:1,1. Смесь газов далее поступает в верхнюю часть реактора, представляющего собой
кожухотрубный теплообменник, в межтрубном пространстве которого циркулирует
теплоноситель, а в трубках находится катализатор - активированный уголь с нанесенной на
него сулемой HgCI2 (10-15%). Реактор изготовлен из углеродистой стали; высота трубок 3-6 м,
диаметр 50-80 мм. Обычно в реактор загружают 6-12 м³ катализатора. Температура в
реакционной зоне поддерживается равной 150-180°С.
Реакционные газы после реактора проходят насадочную колонну, орошаемую соляной
кислотой для извлечения унесенной сулемы. Затем реакционный газ промывается водой и
раствором щёлочи в колоннах для удаления из газа хлористого водорода, ацетальдегида и
двуокиси углерода. Далее газ “захолаживается” в конденсаторе, охлаждаемом рассолом, для
удаления влаги, компримируется в компрессоре до 0,71.0,81 МПа и поступает на
ректификацию. Система ректификации состоит из двух тарельчатых колонн: на первой колонне
выводятся высококипящие примеси, в основном смесь 1,1- и 1,2-дихлорэтанов, на второй
колонне - низкокипящие примеси. Полученный ректификат проходит колонну осушки готового
продукта, заполненную твердым едким натром, для окончательной осушки и нейтрализации
винилхлорида.
Принципиальная схема получения винилхлорида из ацетилена с использованием
ртутного катализатора представлена рис. 3.4.
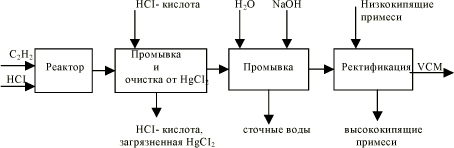
Рисунок 3.4 Производство ВХМ с использование ртутного катализатора.
Ртуть в виде сулемы (HgCI2) используется только для приготовления катализатора.
Хлористая ртуть либо поставляется из-за границы (раньше из Испании, сейчас все больше из
Китая), либо российским предприятием ЗАО “НПП “Кубаньцветмет”. Производственные
процессы на данном предприятии описаны в разделе 5.1.
В табл. 3.13 представлены данные по производству винилхлорида из ацетилена, а также
ежегодному использованию катализатора и содержанию в нем металлической ртути. В общей
сложности для производства катализаторов в 2002 г. было израсходовано 15,5 т ртути.
Примерно половина этой ртути была получена в процессе переработки HCl, остальная часть
была закуплена у других предприятий.
Расход ртути складывается следующим образом: в отработанном катализаторе остается
около 30%; с соляной кислотой уходит практически все остальное (около 70%); с абгазами и
выбросами поступает около 0,1%; со сточными водами - около 0,1%
Отработанный катализатор по мере накопления отправляется в ЗАО “НПП
“Кубаньцветмет” (Краснодарский край, Россия) для полной переработки и получения
металлической ртути, часть которой превращают в сулему и отправляют обратно потребителю.
Таблица 3.13 Производство винилхлорида из ацетилена с использованием ртутного катализатора
Предприятие |
Винилхлорид, тыс. т/год |
Расход катализатора |
Мощн ость |
Производств о в 2001 г. |
Производств о в 2002 г. |
Катализат ора, т |
В пересчете на Hg, т |
ОАО Новомосковская Акционерная Компания “Азот” (НАК “Азот”), Тульская область |
45,0 |
12,0 |
19,6 |
60 |
4,5 |
ОАО “Пласткард”, г. Волгоград |
68,0 |
73,9 |
68,5 |
60 |
6,6 |
ОАО “Химпром” (г. Волгоград) |
27,0 |
24,3 |
22,1 |
30 |
2,2 |
ОАО “Усольехимпром” (г. Усолье-Сибирское, Иркутская область) |
26,0 |
20,0 |
17,5 |
30 |
2,2 |
Итого |
166 |
130,2 |
127,7 |
180 |
15,5 |
Соляная кислота с содержанием сулемы 0,05-0,1% возвращается в рецикл для
приготовления катализатора (около 8 т ртути). Частично она отправляется потребителям для
использования в металлургической или нефтяной и газовой промышленности для обработки
скважин. Использование такой соляной кислоты в пищевой и медицинской промышленности
категорически запрещено. При применении соляной кислоты при обработки скважин ртуть
остается в скважинах. Общее содержание ее в соляной кислоте, использованной для обработки
скважин, составило около 2,8 т.
Концентрация сулемы в абгазах и сточных водах находится в пределах разрешенных
норм.
Использование ртути при производстве ВХМ в Российской Федерации в 2002 г.
представлено на рис. 3.5.
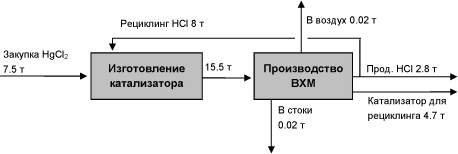
Рисунок 3.5 Использование ртути (в тоннах) при производстве ВХМ в 2002 г.
Использованный катализатор перед утилизацией хранится на территории предприятия. В
табл. 3.14 приведены приблизительные данные по количеству отработанного ртутного
катализатора на заводах, готового для переработки в ЗАО “Кубаньцветмет” Повышенное
скопившееся количество отработанного катализатора объясняется тем, что лицензия на
переработку ртутьсодержащих отходов в ЗАО “Кубаньцветмет” закончилась в 2001 г., и
понадобилось время для ее переоформления. С 2003 г. указанное предприятие приступает к
переработке отработанного катализатора.
Таблица 3.14 Ориентировочное количество отработанного ртутного катализатора,
находящегося на хранении к концу 2002 г.
Предприятие |
Катализатор винилхлорида |
Количество, т |
Содержание ртути, т |
ОАО Новомосковская Акционерная Компания “Азот” |
400 |
12 |
ОАО “Пласткард”, г. Волгоград |
250 |
7,5 |
ОАО “Химпром” (г. Волгоград) |
150 |
4,5 |
ОАО “Усольехимпром” (г. Усолье-Сибирское) |
120 |
7 |
Всего |
920 |
31 |
3.2.2 Производство витамина B2 в прошлом
Для производства витамина B2 (рибофлавина) использовалась металлическая ртуть с тем,
чтобы получить амальгаму натрия (Na), за счет чего имел место процесс получения алдозы из
альдонолактона.
В Российской Федерации синтез витамина B2 по этой технологии осуществляется на двух
предприятиях: ОАО “Белвитамины” (г. Белгород) и АК “Синтевита” (г. Болохов, Тульская
область). Оба предприятия были закрыты в период 1998-1999 г.г.
В общей сложности на ОАО “Белвитамины” и АК “Синтевита” было произведено около
150 т витамина B2. Коэффициент потребления ртути равен 0,036 кг металла на 1 кг витамина B2.
С учетом этого коэффициента общее потребление ртути в производственном процессе может
максимально составлять примерно 5,4 т.
Ртутьсодержащие отходы этих предприятий представляют собой шламы активных углей
с содержанием ртути до 5% мас. и отработанные сорбенты от установок газоочистки. В
качестве сорбента на АК “Синтевита” использовался активированный уголь,
модифицированный хлористым натрием, а на ОАО “Белвитамины” – пиролюзит. Объёмы
складирования ртутьсодержащих отходов на этих предприятиях в 1998 г. представлены в табл.
3.15.
Таблица 3.15 Объёмы образования ртутьсодержащих отходов при производстве витамина B2
Предприятие |
Вид ртутьсодержащих отходов |
Шламы |
Сорбент |
Тонны |
Содержание ртути, % |
Тонны |
Содержание ртути, % |
ОАО “Белвитамины”, г. Белгород |
70 |
1,2 – 1,5 |
50 |
0,1 – 6,0 |
АК “Синтевита”, Тульская область |
120 |
1,2 – 1,5 |
12 |
1,2 – 1,5 |
Итого |
190 |
|
62 |
|
В 1999 г. ЗАО “Кубаньцветмет” приняло от ОАО .Белвитамины. на утилизацию 22 т
шлама.
3.2.3 Производство пигментов в прошлом
Сульфат Hg (II) до 2000 г. применялся для производства красок (1-аминоантрацен) на
предприятии ОАО “Химпром” (г. Чебоксары, Республика Чувашия). Ежегодно на эти цели
использовалось несколько тонн ртути.
Отходы производства перерабатывались в ЗАО “НПП “Кубаньцветмет” (см. раздел 5.1).
3.3 Добыча золота с использованием амальгамационного метода
3.3.1 История добычи золота в Российской Федерации
Рождением золотодобывающей промышленности России считается 18-ый век: в 1737 г.
открыто золотомедное Воицкое месторождение в Карелии, в 1745 г – первое крупное
золоторудное Березовское месторождение на Урале [23]. К началу 19-го века было открыто
достаточно золоторудных месторождений, однако интенсивная промышленная добыча золота
началась после открытия в 1814 г. золотых россыпей Урала и Сибири. С 1816 по 1890 г. были
выявлены россыпи по всему югу Сибири от Урала до Приморья. В 70-х годах 19-го века
впервые в Сибири был применен гидравлический способ добычи золота при помощи
гидромониторов; в 1896 г. - построена первая драга. Добыча рудного золота возобновилась
после усовершенствования технологии переработки золотых руд и, в частности, применения
амальгамации.
В 40-х годах XIX столетия было добыто столько золота, что Россия вышла на первое
место в мире. Всего в дореволюционный период по официальным сведениям было добыто
2754,17 т золота [298], с учетом нелегальной добычи – около 3 т. Советский период добычи
золота формально начался с октября 1921 г., когда вышел Декрет Совнаркома “Про золотую и
платиновую промышленность”, в котором месторождения этих металлов объявили
государственной собственностью. В 1921-1925 г.г. создано 11 государственных
золотодобывающих трестов, а в 1927 г. организовано Всесоюзное акционерное общество
“Союззолото”. С тех пор информация, касающаяся объемов добычи, продажи этого металла на
мировом рынке и размеры его официального запаса, считалась государственной тайной,
поэтому по этим показателям существуют только экспертные оценки [107].
В 1991 г. произошла децентрализация и реформирование золотодобывающей
промышленности России. Были ликвидированы 12 крупных региональных объединений, а на
их базе сформировалось несколько тысяч (9000 в 1996 г.) различных золотодобывающих
предприятий. Их большая часть не выдержала работу в экономических условиях
постсоветского времени. В 2001 г. насчитывалось 639 предприятий разных форм
собственности; преимущественно это небольшие старательские артели; 584 из них (или 91%)
относится к “малым” предприятиям с добычей золота менее 500 кг/год и среднегодовой
численностью до 100 человек (суммарно они производят более 44 т золота). Свыше 1 т золота в
год добыли в 2001 г. 22 предприятия (суммарно 78,6 т или 55,6% от всего объема добычи) 102].
В 2000 г. двадцать предприятий, производящих в год более 1 т золота каждое, обеспечили 55%
российской добычи металла. В 2001 г. на эти же предприятия пришлось 80% роста добычи в
стране [82]. Такая организационная структура не способствует экономической эффективности
золотодобывающей отрасли. Мелкие артели не обладают достаточными финансовыми
ресурсами для приобретения современной техники, освоения новых технологий, проведения
геологоразведочных работ, выполнения природоохранных требований и мероприятий.
Динамика добычи золота в России с 1890 по 2000 г. приведена на рис. 3.6.
По разным источникам за 280 лет с 1719 г. (первые документальные сведения) количество
добытого золота составляет 11-12 тыс. т [23, 53, 298]. Экспертная оценка добычи золота в
разные временные периоды, включая коренное, россыпное и комплексное золота, приведена в
табл. 3.16 [23]. На рис. 3.7 приведены показатели общего производства и добычи золота за
последние 10 лет.
Таблица 3.16 Добыча золота в России [23]*
|
Периоды |
До 1900 |
1901-1916 |
1917-1945 |
1946-1954 |
1955-1964 |
1965-1975 |
1976-2001 |
Добыча, т |
1980 |
775 |
~1000-1500 |
880–1200 |
1600 |
1500 |
3755 |
ВСЕГО |
11490-12370 |
*Данные по 2001 г. добавлены автором отчета.
![Рисунок 3.6 Динамика добычи золота в России с 1890 по 2000 г. [23]](images/s063.gif)
Рисунок 3.6 Динамика добычи золота в России с 1890 по 2000 г. [23]
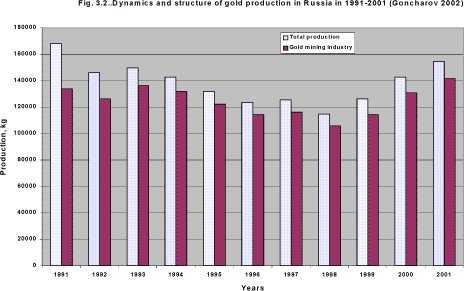
Рисунок 3.7 Динамика и структура добычи золота в России, 1991-2001 г.г.
По официальным данным в 2001 г. в России было добыто 154455 кг золота, из них
золотодобывающими предприятиями – 141449 кг. Однако по оценкам аналитиков компании
GFMS [344], в 2001 г. производство золота в России составило 168 тонн (пятое место в мировой
добыче металла). Расхождение с официальными данными объясняется тем, что эксперты GFMS
учитывают долю нелегального производства золота в России, оцениваемую ими в 10-15%
[344]. К такой же оценке доли нелегального золота склоняются и российские эксперты,
включая правоохранительные органы [2].
В настоящее время Россия занимает второе место в мире после ЮАР по прогнозным
ресурсам золота, по балансовым – третье место в мире после ЮАР и США, по
государственным резервным запасам золота к концу 2001 г. – 13-е место, на её долю
приходится 7-8% мировых запасов золота [82].
Месторождения золота расположены на значительной части территории России от
Балтийского щита на Западе до складчатых структур Восточной Чукотки (рис. 3.8)
Нажмите сюда для просмотра Таблица 3.12
Рисунок 3.8 Схема размещения основных месторождений золота, горнодобывающих предприятий
и золотороссыпных районов Российской Федерации [23]:
80% запасов российского золота в собственно золотосодержащих месторождениях
сосредоточены в коренных и около 20% – в россыпных месторождениях. Почти 29% запасов
золота заключено в комплексных месторождениях, преимущественно медно-колчеданных и
сульфидных медно-никелевых, реже – в полиметаллических. Россия является единственным в
мире крупным продуцентом золота, где большая часть металла добывалась ранее из россыпей,
хотя в них заключено лишь чуть более 17,5% запасов [71, 82].
Наблюдающийся в последние годы рост объема производства золота является прямым
следствием общего изменения структуры добычи его в России: перехода от отработки
преимущественно россыпных к активному вовлечению в освоение коренных месторождений.
До 1998 г. до 80 % драгоценного металла извлекалось именно из россыпей. В последующие
годы это соотношение стало кардинально меняться. Так, в 2001 г. доля добычи золота из
коренных месторождений достигла 40 % в общем объеме его добычи, а с 2002 г. рудные
объекты должны будут обеспечивать свыше половины добычи драгоценного металла в стране
[71]. В настоящее время в России разрабатываются более 1700 россыпей и свыше 1000
подготовлены к освоению.
3.3.2 Добыча золота из техногенных россыпей и других отходов золотодобычи
За всю историю добычи золота в России примерно 80-85 % (около 9 тыс. т) его получено
из россыпных месторождений [23]. В связи с интенсивной добычей россыпного золота,
истощением его запасов, а также сокращением объема выполняемых геологоразведочных
работ, за последние 10 лет разведанные запасы россыпного золота сократились на 15% [102].
Это явилось причиной того, что крупные золотодобывающие предприятия стали более активно
разрабатывать рудные месторождения, а мелкие недропользователи – добывать более дешевое
техногенное золото, т. е. золото, находящееся в отвалах, хвостохранилищах и шлихах,
громадное количество которых в старых золотодобывающих районах в ряде случаев являются
техногенными месторождениями. Себестоимость добываемого металла из техногенных
источников находится в диапазоне от 3,5 до 6,0 долларов за 1 грамм в золотом эквиваленте и
имеет тенденцию к снижению до своего минимума на 2-3-й год отработки отвала [21].
Актуальность переоценки техногенных россыпей и других золотосодержащих отходов
золотодобычи для компенсации реализуемых запасов россыпного золота подчеркнута в
Федеральной программе по воспроизводству минерально-сырьевой базы золота в 1994-2000 г.г.
[195]. Однако в настоящее время государственный статистический учет запасов техногенных
россыпей не ведется.
По разным экспертным оценкам, за время интенсивной добычи россыпного золота
промыто около 11,9 млрд. м³ горной массы, а суммарные прогнозные ресурсы золота в отвалах
составляют 3,3 тыс. т (с принятым средним содержанием 0,2 г/м³: галечные отвалы – 1,7 тыс. т,
эфельные отвалы – 0,2 и торфяные отвалы – 1,4. тыс. т [23]. В табл. 3.17 приведены отдельные
доступные данные по добыче золота из техногенных отвалов по некоторым
золотодобывающим субъектам РФ.
Таблица 3.17 Реализация техногенных золотосодержащих отвалов в некоторых субъектах РФ
[23]
Субъект РФ |
Объем промытых отвалов, тыс. м³ |
Добыча золота, кг |
Среднее содержание золота, мг/м³ |
Иркутская область |
1396 |
772 |
553 |
Республика Бурятия |
52 |
20 |
385 |
Читинская область |
704 |
67 |
95 |
Республика Саха (Якутия) |
1687 |
491 |
291 |
Амурская область |
809 |
177 |
219 |
Чукотский АО |
40296 |
22256 |
552 |
Примечание: Чукотский АО за 1970-1993 г.г., другие субъекты Федерации – за один год. Данные,
представленные в таблице 3,17 могут показаться неполными, однако это объясняется неполнотой
официальных статистических данных о золоторудных месторождениях и золотодобыче в Российской
Федерации. Поэтому в таблице представлена только частичная информация, которую удалось получить
из публикаций Беневольского В.И., 2002. Скудость сведений в информационных изданиях о добыче
техногенного золота объясняется следующей причиной. Если техногенные россыпи находятся на
участках горного отвода золотодобывающих предприятий, то эти предприятия могут без получения
лицензии перерабатывать золотосодержащие отвалы и хвосты, которые в этом случае являются для них
скрытым резервом добычи золота, афишировать который для предприятий невыгодно.
3.3.3 Использование ртути при добыче золота
Метод амальгамации золота, основанный на избирательном смачивании ртутью частиц
самородного металла, длительное время был обязательным звеном традиционных
технологических схем обогащения золотосодержащих руд и песков. В результате его
длительного и интенсивного применения на золотодобывающих территориях фиксировались
случаи сильной ртутной интоксикации работающего персонала и загрязнения окружающей
среды. В связи с этим приказом Главного управления драгоценных металлов и алмазов при
Кабинете Министров СССР № 124 от 29.2.88 г. ртуть официально запрещена к использованию
на драгах и промывочных приборах, начиная с 1989 г., а с 1990 г. – на ЗИФ и ШОУ [222]. Были
прекращены работы по усовершенствованию технологии амальгамации и созданию аппаратов
для демеркуризации золотосодержащих продуктов. Хотя проблема разработки таких аппаратов
и экологически безопасных технологий демеркуризации золотосодержащих продуктов
сохранилась в связи с наличием в них ртути, как техногенного (вторичная обработка россыпей
и лежалых хвостов ЗИФ), так и природного происхождения [173].
Затраты и безвозвратные потери ртути при амальгамации руд и песков в значительной
степени определялись типом месторождения, технологическими характеристиками
перерабатываемого сырья, методами добычи и обогащения. В истории российской
золотодобычи можно выделить пять этапов применения амальгамационных методов,
обусловленные техническим и технологическим переоснащением горно-обогатительной
отрасли и золотоизвлекательными фабриками в частности [248, 201, 298]:
- Широко распространенный в дореволюционной России и в первые годы советской
власти мускульный способ добычи золота, особенно из россыпей, сопровождался
неконтролируемыми значительными затратами и потерями ртути. Кустарные способы
амальгамации измельченного золотосодержащего сырья и отжига амальгамированного золота
на открытом огне без конденсации паров ртути близки к используемым в настоящее время в
южноамериканских странах, где потери ее в среднем составляют 1,32 кг на 1 кг добытого
золота [392].
- Второй период (с 1917 по 1930 г.г.) характеризуется расширением использования
амальгамации, созданием механизированной базы обогатительных фабрик, внедрением
процесса илового цианирования.
- Третий период (с 1930 по 1960 г.г.) сопровождается повсеместным использованием как
амальгамации, так и цианирования. Для повышения эффективности извлечения золота,
особенно из сложных руд и песков, разрабатываются комплексные схемы обогащения,
включающие гравитационные, амальгамационные, цианидные, флотационные методы.
Интенсивная промышленная разработка рудных месторождений, а также россыпей на северо-
востоке страны, начавшаяся с 1930 г., привела к усовершенствованию технологии
амальгамации золота с конденсацией ртути из амальгам при их отжиге, т. е. к уменьшению ее
удельных затрат за счет повторного использования. Однако рекуперация ртути обеспечивалась,
как правило, только на крупных предприятиях.
- Четвертый период (с 1960 г. по 1988 г.) характеризуется резким сокращением
применения амальгамации с переходом на внутреннюю схему амальгамирования сырья,
внедрения комплексных схем обогащения, использования ионообменной технологии.
- Пятый период (с 1989 г. по настоящее время) характеризуется официальным
запрещением применения ртути при добыче золота и внедрением новых технологий
обогащения. Однако нелегальное и поэтому трудно контролируемое использование ртути при
доводочных операциях, а также его применение небольшими артелями продолжаются до сих
пор.
Ранее, когда добыча золота в СССР была под строгим государственным контролем, на
предприятиях и в региональных управлениях велся учет расхода ртути на всех операциях по
обогащению золота. Существовали нормативы расхода ртути и её нормативные потери. Так,
например, при шлюзовом извлечении золота проектные потери ртути могли составлять 10 % за
счет смыва. При различных способах амальгамации (внутренней, внешней, на драгах,
промывочных приборах, золотоизвлекательных фабриках) расходы и потери ртути значительно
изменялись. Анализ реальных потерь ртути по архивным данным некоторых
золотодобывающих предприятий Дальнего Востока в 60-70-х годах показал, что они
варьируются в диапазоне 0,5-1 т на 1 т добытого золота [124, 260]. Как видно из табл. 3.18,
отношение затрат ртути к количеству добытого золота в разные годы изменялось в широком
диапазоне от (6-10):1 до 1:4. В годы, предшествующие запрету на использование ртути, когда
стали широко внедряться эффективные безртутные технологии, удельные затраты ртути были
значительно снижены. По официальным сведениям, в этот период общие безвозвратные потери
металлической ртути на драгах и промывочных приборах достигали 6 т/год, на
золотоизвлекательных фабриках – около 3 т/год [222]. Однако, по нашему мнению,
основанному на данных таблиц 3,18 и 3,19, официальные данные явно занижены.
Таблица 3.18 Затраты и потери ртути при амальгамировании золотосодержащего сырья
Типы сырья, методы добычи и обогащения |
Соотношение Hg : сырье |
Соотношение Hg : Au |
Потери Hg |
Кварцевые окисленные руды |
2-4 г/т5) |
|
|
Руды с высоким содержанием |
5-9 г/т5) |
|
|
сульфидов Руды с минералами |
10-15 г/т5) |
|
|
мышьяка и сурьмы |
|
|
|
Внутренняя амальгамация: |
15-20 г/т3) |
|
|
Бегунные фабрики |
6-10 г/т2) |
|
160-400 г/т2) |
для дробилок, мельниц, амальгаматоров |
5-20 г/т5) |
|
200-900 мг/т руды5) |
для мелкого золота |
|
(6-10):15) |
|
для крупного золота |
|
(4-6):15) |
|
для концентратов |
|
(10-15):15) |
|
Внешняя амальгамация: |
2-3 г/т3) |
|
|
шлюзовая амальгамация на драгах |
40-130 мг/м³песков4) |
|
55-70 мг/м³ песков4,6) |
|
70 мг/м³песков6) |
|
|
|
|
|
200 мг/м³ хвостов1) |
на гидромониторах |
290 мг/м³ песков6) |
|
10 % или 210 мг/м³ |
на ЗИФ |
2-7 г/т руды6) |
|
песков6) |
|
|
|
0,2-4,0 г/т концентратов1) |
Примечание. Источники информации – 1– [222]; 2– [175], 3 – [214], 4 – [101], 5 – [53]; 6 – [124].
Таблица 3.19 Содержание ртути и золота в отходах золотодобычи
Нажмите сюда для просмотра Таблица 3.19
Так, например, в конце 80-х годов ежегодное поступление ртути на объединение
“Забайкалзолото”, добывающее в то время около 8 т золота, составляло около 2-х т.
Следовательно, примерно столько же ртути безвозвратно терялось и поступало в окружающую
среду. Потери составляли 250 кг ртути на 1 т золота с учетом использования и других
технологий обогащения золота – гравитационного безамальгамационного концентрирования,
флотации и цианирования [143]. Государственные и экономические реформы, происшедшие в
России за последние 15 лет и приведшие к утрате или недоступности многих архивных
документов, не позволяют в настоящее время дать корректную статистическую оценку
суммарному количеству использованной ртути на золотодобывающих территориях этого
региона.
3.3.4 Текущая ситуация
Ртутное загрязнение зон традиционной золотодобычи в России, как и во всех
золотодобывающих регионах мира, является проблемой чрезвычайно актуальной, хотя и
малоизученной. Масштабы ртутного загрязнения и интенсивность его проявления на
отдельных территориях до сих пор не получили корректной оценки. Однако с уверенностью
можно утверждать, что регионы традиционной золотодобычи, указанные на рис. 3.7.
характеризуются ртутным загрязнением разной степени интенсивности. Необходимо отметить,
что загрязнение, как правило, носит нелокализованный характер. С внедрением более
эффективных методов добычи золота одни и те же участки богатых россыпей неоднократно
перемывались, поэтому ртутьсодержащие дражные и гидромониторные отвалы, как правило,
перемешивались с промываемой горной массой, что приводило к их пространственному
распределению по большей территории. К точечным источникам загрязнения относятся
сохранившиеся старые и действующие хвостохранилища, территории ЗИФ, ШОФ, ШОУ,
золотоприемных касс. Часто производственные и жилые зоны старых золотодобывающих
предприятий либо переносятся с отработанных территорий, либо со временем разрушаются.
Работы по рекультивации и консервации загрязненных участков золотодобычи ранее не
планировались и не проводились, поэтому содержимое разрушенных хвостохранилищ и
отработанные шлихи с высоким содержанием ртути являются источниками сильного
загрязнения окружающей среды. Поскольку местонахождение отработанных объектов
россыпной золотодобычи не всегда можно установить по архивным документам, оценка
ртутного загрязнения традиционных регионов золотодобычи требует дорогостоящих
экспедиционных и камеральных работ. Локальными, но оторванными от золотодобывающих
регионов источниками ртутного загрязнения являются аффинажные заводы.
В настоящее время можно выделить пять основных источников эмиссии ртути в
окружающую среду за счет золотодобычи, количественные характеристики которых зависят от
типа месторождения и запасов золота, длительности и интенсивности его отработки и
использования ртути в технологических процессах:
- Атмосферная эмиссия ртути с поверхности отвалов, хвостов обогащения,
загрязненных грунтов, а также их размывание и загрязнение водотоков, почвенного покрова,
водных и наземных экосистем.
- Широко практикуемая в настоящее время повторная отработка техногенных россыпей,
а также переработка хвостов обогащения и шлиховых концентратов рудного и россыпного
золота.
- Продолжающееся нелегальное использование ртути для обогащения
золотосодержащих концентратов и сырья.
- Отработка золотоносных месторождений с природным повышенным содержанием
ртути.
- Аффинаж золотосодержащих концентратов золота с повышенным природным или
техногенным содержанием ртути на аффинажных заводах.
Рассмотрим эти источники ртутного загрязнения более подробно и попытаемся оценить
их вклад.
Дражные и гидромониторные отвалы, хвосты обогащения, шлихи, загрязненные грунты
Отходы россыпной золотодобычи доминируют по их суммарному объему по сравнению с
другими источниками в этой группе. По экспертной оценке [23], за время интенсивной
россыпной золотодобычи промыто около 11,9 млрд. м³ горной массы. По имеющимся данным
(см. табл. 3.19), содержание ртути в отвалах находится в широком интервале от 0,05 до 2000
мг/кг. Участки сильного ртутного загрязнения отвалов более локальны и менее масштабны.
Поэтому ориентировочное среднее содержание ртути в отвалах значительно ниже и его можно
оценить как 0,2-0,5 г/м³. Исходя из этих показателей, общее количество ртути в отходах
россыпной золотодобычи может лежать в пределах от 3000 до 6000 т.
Оценить эмиссию в окружающую среду как техногенной, так и природной ртути,
попадающей в отвалы и хвостохранилища, чрезвычайно трудно, поскольку часть ее находится
в изолированном состоянии под слоем переработанной горной породы или в основании
дражных разрезов. Кроме того, при длительном хранении техногенная и природная ртуть
подвергается физико-химическим и химическим превращениям. Поэтому минеральный состав
ртутных соединений, состав и свойства амальгам золота и других металлов, содержание
жидкой ртути в отходах золотодобычи являются уникальными характеристиками для каждого
объекта, чрезвычайно важными для оценки эмиссии ртути и ее воздействия на окружающую
среду, а также для разработки экологически безопасных способов переработки золото- и
ртутьсодержащих отходов и очистки загрязненных территорий. Такого рода работы проводятся
в ряде российских организаций.
Так, например, сотрудниками ИРГИРЕДМЕТ изучается состав минеральных форм ртути
в перерабатываемом сырье для повышения эффективности извлечения золота и ртути из
перерабатываемой горной массы. Для одного из объектов был определен следующий состав (в
%): каломель (Hg2Cl2) - 51,8; оксид ртути (НgО - 1,1; самородная ртуть (Нg) в виде
амальгамированного золота - 25,1; киноварь (НgS) - 6,7; сулема (НgС12) и растворимые в воде
формы ртути - 1,4; селениды, теллуриды и другие “упорные” формы ртути -13,9 при общем
содержании ртути в сырье от 30 до 100 г/т [Муллов и др. 2002]. Сотрудниками Читинского
политехнического университета изучены состав и свойства золотосодержащих амальгам для
разработки эффективных магнитно-гравитационных технологий переработки техногенного
сырья [175, 176]. Список организаций, разрабатывающих технологии переработки золото- и
ртутьсодержащих техногенных отходов золотодобычи приведен в Приложении 1.
Отработка техногенных россыпей
Широкое вовлечение в повторную отработку техногенных россыпей, а также переработка
хвостов обогащения и шлиховых концентратов рудного и россыпного золота (табл. 3.19)
приводит к извлечению захороненной ртути в отвалах, разрезах, полигонах, ее переводу в
активное миграционное состояние и поступлению в окружающую среду с атмосферными
выбросами (термическая обработка концентратов, дегазация ртути из отвалов и др.) и сбросами
сточных вод. При выдаче лицензий на отработку таких россыпей, как правило, не учитывают
высокое техногенное содержание ртути в перерабатываемых песках и, следовательно, не
контролируют расширение ореолов ртутного загрязнения.
Несмотря на то, что в настоящее время разрабатываются и применяются технологии
переработки техногенного сырья с выделением как золота, так и ртути, небольшие
низкобюджетные предприятия, вероятнее всего, будут использовать более дешевые технологии
с выделением только золота, т. е. на конечной стадии использовать отжиг амальгамированного
золота без конденсации паров ртути. Если не будет усилен природоохранный контроль за
лицензированием и последующей отработкой таких золото- и ртутьсодержащих техногенных
месторождений, можно предположить, что половина количества ртути, находящейся в
настоящее время в отвалах и отходах (3000-6000 т), будет постепенно поступать в атмосферу и
водотоки.
По весьма ограниченным данным, приведенным в табл. 3.18, доля техногенного золота
для разных регионов в настоящее время составляет 1-5% от общего количества добытого
металла. В целом по России долю техногенного золота можно весьма грубо оценить в 2-4 %,
при этом количество техногенного золота, добытого в 2001 г., ориентировочно составляет
2800-5600 кг. Учитывая среднее содержание золота в техногенном сырье, равное 350 мг/м³
(табл. 3.18), объем переработанного техногенного сырья можно оценить следующим образом:
2800 кг : 350 мг/м³ = 8 млн. м³; 5600 кг : 350 мг/м³ = 16 млн. м³.
Исходя из объема переработанного техногенного сырья в 8-16 млн. м³ и среднего
содержания в нем ртути в 0,2-0,5 г/м³, общее количество техногенной ртути в этом объеме
может составить от 2 до 8 т. Часть ее (ориентировочно 15-20 %) могла быть утилизирована с
использованием современных технологий (Приложение 1), однако основное количество ранее
накопленной техногенной ртути (ориентировочно от 1,5 до 6,5 т) могло поступить в 2001 г. в
окружающую среду золотодобывающих регионов. Из этого количества около 60 % (0,9-3,9 т)
поступило в атмосферу, около 20 % (0,3-1,3 т) – в отходы , такое же количество (0,3-1,3 т) – в
водные объекты.
Добыча золота с применением метода амальгамации
Нелегальное и поэтому неконтролируемое использование амальгамации
золотосодержащих концентратов до сих пор продолжается, несмотря на официальное
запрещение [143, 201]. Основными потребителями ртути являются небольшие предприятия, не
имеющие необходимых средств для приобретения дорогостоящего обогатительного
оборудования и, как правило, повышающих эффективность выделения золота амальгамацией
его шлихов. Аналогичная ситуация наблюдается и в Казахстане, где процессы амальгамации
золота и отпарки ртути при нелегальной добыче золота отдельными жителями проводятся еще
более кустарно в домашних условиях [118].
Поскольку нелегальное использование ртути является нарушением природоохранного и
трудового законодательства и потому наказуемо, то количественная информация о
применении ртути в таких целях, естественно, является недоступной. Можно лишь произвести
очень грубый расчет современного применения ртути при амальгамации золота, используя
имеющиеся данные о структуре добычи российского золота в 1999 г. (см. табл. 3.20). В этом
году 639 предприятий занималось добычей золота, а в 2001 г. – 566. Можно предположить, что
структура золота в 2001 г. изменилась незначительно по сравнению с 1999 г. и
воспользоваться данными за этот год для последующих расчетов.
Таблица 3.20 Распределение золотодобывающих предприятий в 1999 г. [23, 130]
Добыча золота, кг/год |
Кол-во предприятий |
Доля в общем объеме, % |
От кол-ва предприятий |
От производства |
<100 |
389 |
68,7 |
11,2 |
100-300 |
99 |
17,5 |
14,8 |
>300 |
78 |
13,8 |
74,0 |
включая более 1.000 |
16 |
2,8 |
45,9 |
Всего |
566 |
100 |
100 |
Добыча золота золотодобывающими предприятиями в 2001 г. составила 141500 кг, из них
~ 26 % (11,2+14,8) или ~37 т золота добыто малыми предприятиями (<100-300 кг/год). Если
предположить, что при извлечении этого количества золота ртуть использовалась только на
доводочных операциях со шлихами и ее нормативные затраты при этом составляли, по оценке
[235], порядка 10 % от объема добытого золота, то общие затраты ртути на амальгамацию
составят примерно 3,7 т/год. Учитывая ориентировочную оценку объема добычи золота
малыми предприятиями с использованием ртути (20-40 т золота) и ее ориентировочные потери
при амальгамации шлихов (более 10-20 %), суммарные затраты ртути на амальгамацию золота
могут лежать в диапазоне 3-8 т. Вероятно, для этих же целей может использоваться и та ртуть,
которая выделяется при переработке золото- и ртутьсодержащего техногенного сырья. В
середине этого диапазона лежит оценочная величина – 6 т ртути в год, которая является
неофициальной информацией персоны, имеющей отношение к производству вторичной ртути
и не пожелавшей дать официальную информацию о поставках ртути золотодобывающим
предприятиям. Соответствие расчетного диапазона и неофициальной информации об объеме
используемой ртути для амальгамации золотосодержащего сырья подтверждает достоверность
выполненных расчетов.
Отработка золотоносных месторождений с природным повышенным содержанием
ртути в рудах, песках, вмещающих породах.
Содержание ртути в золотоносных рудах может достигать 300 г/т, при более часто
встречаемом содержание 1 г/т, а в эндогенных ореолах месторождений – 10-20 г/т при более
распространенных значениях 0,1-0,4 г/т [235]. При отработке таких месторождений отвалы
вмещающих пород содержат весьма высокие концентрации ртути, а сами отвалы служат
нелокализованными источниками ртутной эмиссии.
По экспертной оценке [235], при добыче 1 т золота примерно 100 кг природной ртути
попадает в отвалы и таким образом загрязняет окружающую среду. Используя соотношение
количеств добытого в 2001 г. рудного золота и ртути 1:10, ориентировочное количество
последней, совместно извлеченной из недр, можно оценить следующим образом: (141449 кг х
40%) : 10 – 5,6 т ртути. Учитывая ориентировочность проведенных расчетов, более корректно
использовать диапазон объемов поступления ртути в окружающую среду при переработке
золотосодержащего сырья, равный 4-8 т/год. Можно предположить, что 20 % от этого
количества (0,8-1,6 т/год) поступает в атмосферу, 10 % – в водные объекты, 70% (2,8-5,6 т/год)
– в отвалы и отходы обогащения.
В США 5-15 т попутной ртути получают при переработке комплексного золоторудного
сырья на нескольких (менее десятка) предприятиях в западной части страны – в штатах
Калифорния, Невада и Юта. Основная цель при этом не столько получение ртути, сколько
предотвращение её попадания в атмосферу и водный бассейн [226]. В России, к сожалению, вся
попутная ртуть поступает в окружающую среду с отходами горнодобывающих,
обогатительных и аффинажных производств.
Аффинаж золотосодержащих концентратов золота с повышенным природным
или техногенным содержанием ртути на аффинажных заводах
На 1 января 1999 г. право осуществлять аффинаж драгоценных металлов в России имели
следующие предприятия: Приокский завод цветных металлов (г. Касимов, Рязанская обл.);
Новосибирский аффинажный завод (г. Новосибирск); Щелковский завод вторичных
драгоценных металлов (г. Щелково, Московская обл.); Красноярский завод цветных металлов
(г. Красноярск); Екатеринбургский завод по обработке цветных металлов (г. Екатеринбург);
Кыштымский медеэлектролитный завод (г. Кыштым, Челябинская обл.); Колымский
аффинажный завод (пос. Хасын, Магаданская обл.); АО “Уралэлектромедь” (г. Верхняя
Пышна, Свердловская область); Норильский ГМК (г. Норильск, Красноярский край); Концерн
“ОНИКС” (г. Москва) [284].
По официальным данным содержание ртути в концентратах, посылаемых на
аффинажные заводы (до 1988 г.), составляло 0,2-4,0 г/т [222]. Наиболее сильным источником
ртутного загрязнения, скорее всего, был старейший из этих предприятий – Новосибирский
аффинажный завод, который до начала 90-х годов обеспечивал переработку около 60%
добытого золота [Терешина 2000]. В результате переработки золотосодержащих концентратов
и шлихового золота с повышенным содержанием ртути территория вокруг этого завода
характеризуется выраженным техногенным ореолом ртути в почвах (0,03-18,9 мг/кг). При этом
концентрация газообразной ртути в почвенном воздухе превышает местный фон в 100 раз
[235].
В настоящее время повышенное содержание ртути в концентратах, посылаемых на
аффинаж, может быть вызвано как природными факторами – увеличенное содержание ртути в
золотоносной руде, которое сохраняется в цианистых шламах, так и ее непосредственным
использованием ранее (отработка техногенных россыпей и хвостов) и нелегальным
применением сейчас. Оценить суммарную эмиссию ртути при аффинаже золотосодержащих
концентратов в настоящее время не представляется возможным, так как неизвестно
соотношение различных концентратов, поступающих на аффинаж (шлихи, слитки,
цианошламы и др.), и содержание в них ртути.
В последние годы предпринимались попытки оценить количество ртути, поступающее в
окружающую среду при современной добыче золота [235, 322]. Однако эти расчеты были
весьма приближенными и, кроме того, выполнены, исходя из ранее существовавшей структуры
и технологии добычи золота (доминировала разработка россыпных месторождений). Так,
например, ориентировочное ежегодное поступление ртути в окружающую среду Сибири
составляло по этим расчетам 34,4 т. При этом предполагалось, что доли атмосферной, водной и
наземной (отвалы, хвосты, почвы) эмиссии примерно одинаковы.
Заключение
Учитывая литературные, архивные и официальные данные, можно грубо оценить
суммарное поступление ртути в окружающую среду в разные временные периоды, в том числе
и в 2001 г. (табл. 3.21 и 3.22). За весь период добычи золота в России в окружающую среду
могло поступить 6350-6690 т ртути, из них 6125-6660 т за счет потерь при амальгамировании и
230-245 т в результате извлечения с золотосодержащими рудами и породами.
В 2001 г. в окружающую среду России за счет золотодобычи суммарно могло поступить
от 10 до 20 т ртути, из них природной ртути 4-6 т, за счет современной амальгамации сырья .
3-8 т и от 1,5 до 6,5 т ртути – при переработке техногенных отходов золотодобычи.
Представленная оценка является сугубо ориентировочной (в настоящее время у авторов нет
материалов для более корректной оценки).
Таблица 3.21 Ориентировочная оценка поступления ртути в окружающую среду при добыче
золота в России
Показатель |
Периоды |
до 1917 |
1917-1945* |
1946-1975 |
1976-1990 |
1991-2001 |
2001 |
Итого |
Суммарная добыча золота, т |
2755 |
~1000-1500 |
3980-4300 |
2292 |
1463 |
152 |
11490-12370 |
Ориентировочные соотношения потерь ртути (т) на добычу 1 т золота |
1:1 |
0,75:1 |
0,5:1 |
0,25:1 |
0,040:1 |
0,040:1 |
|
Ориентировочные суммарные потери ртути при амальгамировании, т |
2755 |
~750-1125 |
1990-2150 |
570 |
60 |
3-8 |
6125-6660 |
Ориентировочное суммарное извлечение ртути с золотосодержащими рудами и породами, т * |
55 |
20-30 |
80-85 |
45 |
30 |
5,6 |
230-245 |
Ориентировочное поступление ртути в окружающую среду при разработке техногенных россыпей |
|
|
|
|
|
1,5-6,5 |
|
ИТОГО |
|
|
|
|
|
10-20 |
6350-6690 |
*Расчет произведен, исходя из того, что ранее добыча коренного золота в среднем составляла 80 % от
общей добычи золота.
Таблица 3.22 Ориентировочная оценка поступления ртути в окружающую среду при добыче золота в России, 2001 г.
Источник |
Количество ртути, поступившей в окружающую среду, всего, т |
Эмиссия ртути в атмосферу, т |
Поступление в водные объекты, т |
Поступление в отвалы и отходы обогащения, т |
Вторичная отработка техногенных россыпей и отходов |
1,5-6,5 |
0,9-3,9 |
0,3-1,3 |
0,3-1,3 |
Амальгамация золотосодержащего сырья |
3-8 |
2,1-5,6 |
0,6-1,6 |
0,3-0,8 |
Мобилизация ртути в качестве микроэлемента * |
4-8 |
0,8-1,6 |
0,4-0,8 |
2,8-5,6 |
Аффинаж концентратов |
? |
? |
? |
? |
* Оценка включена в раздел 4.4, посвященный мобилизации ртути при производстве цветных
металлов.
Необходимо отметить, что в силу специфичности климатических условий основной части
золотодобывающих территорий России (низкие среднегодовые температуры, повсеместная
распространенность вечной мерзлоты, короткий период открытой воды и т.д.), весьма сложно
использовать коэффициенты распределения ртути, поступающей в объекты окружающей среды
(воздух, водные объекты, почвы), определенные для стран с тропическим климатом. Более
того, в отличие от таких стран, в России использовались и до сих пор используются более
производительные драги (с большей глубиной выемки и емкостью черпаков – до 600 м³) и
гидравлические горно-обогатительные установки, что в совокупности с более суровыми
климатическими условиями позволяет существенную часть ртути захоранивать
("консервировать") в анаэробных условиях под слоем переработанных песков. Мобилизация
захороненной ртути из таких техногенных россыпей возможна при их повторной отработке.
Принимая во внимание все вышеприведенные обстоятельства, довольно сложно оценить
соотношение эмиссии ртути в различные компоненты окружающей среды. На основе данных,
полученных для стран тропического климата [391, 392, 399], и учитывая специфические
климатические условия золотодобывающих территорий России, можно предположить, что в
период официально разрешенного использования амальгамирования при добыче золота с
рециклингом ртути ее эмиссия в атмосферу, воду, почвы и переработанные пески была примерно
одинакова. В настоящее время, когда ртуть используется нелегально в основном малыми
предприятиями и кустарными способами, количественные характеристики ее поступления в
окружающую среду могут быть близки к расчетным величинам для стран с тропическим
климатом: до 2/3 – в атмосферу, до 1/3 – в почвы и водные объекты, ~2-8 % – захораниваются с
переработанными песками. Для расчетов были выбраны следующие коэффициенты
распределения ртути в объекты окружающей среды: 70 % – в воздух, 20 % – в водные объекты,
10 % – в отходы с переработанными песками и шлихами. Необходимо отметить, что для
получения более достоверных показателей необходимы натурные исследования.
3.3.5 Ртутное загрязнение золотодобывающих регионов России
В настоящее время источниками ртутного загрязнения золотодобывающих регионов
являются отвалы и хвостохранилища, а также донные отложения загрязненных природных и
техногенных водных объектов. В результате наблюдается загрязнение природных экосистем и
селитебных зон в районах воздействия золотодобычи. Исследований по оценке степени
загрязнения территорий Сибири, Дальнего Востока и Урала, к сожалению, выполнено немного
[4, 142, 143, 201].
Как показывают результаты исследований, наиболее сильное ртутное загрязнение
наблюдается вблизи золотоизвлекательных фабрик, где ртуть непосредственно использовалась
в технологических процессах. Так, было установлено, что содержание ртути в объектах
окружающей среды может превышать ПДК в 4-100 раз. Зарегистрированы следующие
максимальные концентрации ртути: в почвах – 18,9 мг/кг (9 ПДК), общее содержание в
грунтовых водах - 32,8 мкг/л (65 ПДК для питьевых вод), в природных водотоках – 40 нг/л (4
ПДК для рыбохозяйственных водоёмов), в донных отложениях – 54,2 мг/кг. При шлюзовой
амальгамации на драгах и отпарке амальгам содержание паров ртути в воздухе может
превышать среднесменные ПДК в 50 раз (250000 нг/м³). Чрезвычайно высокие концентрации
ртути в 1000-2000 мг/кг (50-100 ПДК для почв) зарегистрированы в хвостах обогащения и
загрязненных грунтах вблизи установок по получению и переработке золотосодержащих
концентратов (ЗИФ, ШОУ и др.). В ряде районов (Красноярск, Чита, Благовещенск, Хабаровск)
разрабатываются и применяются технологии по утилизации такого сырья с выделением золота
и ртути. Следовательно, большая часть техногенных и селитебных территорий традиционной
золотодобычи характеризуются различной степенью ртутной загрязненности – от опасных до
допустимых.
Полученные данные показывают, что суровые климатические условия, характерные для
большей части уральских, сибирских и дальневосточных золотодобывающих территорий,
тормозят протекание некоторых химических, биохимических и биологических процессов, что
способствует большей локализации ртутного загрязнения по сравнению с аналогичными
очагами загрязнения в странах с тропическим климатом. Однако для изучения специфики
поведения ртути в наземных и водных экосистемах зон сезонной и вечной мерзлоты и,
особенно, процессов метилирования-деметилирования металла требуются дорогостоящие
экспедиционные и лабораторные исследования.
3.4 Зубные амальгамные пломбы
3.4.1 Использование ртути в зубных амальгамных пломбах
Амальгамы (серебряная и медная) применяют в стоматологии с 1819 г. С 1971 г. в
Минздравом СССР был запрещен выпуск медной амальгамы, содержащей до 65% ртути.
Причинами ее запрещения явились существенные клинические недостатки пломб из этого
материала и гигиеническая опасность ртути.
В российской стоматологической научной литературе постоянно идет дискуссия о новых
видах пломбировочного материала, но в определенном объеме серебряная амальгама
продолжает использоваться и даже ожидается увеличение этого вида пломб как надежного и
долговечного материала.
В настоящее время в целом по России ставится примерно 30 млн. пломб в год, из которых
7-8% составляют амальгамные (данные Отдела медико-экономических исследований в
стоматологической службе НИИ социальной гигиены, экономики и управления
здравоохранением им. Н.А. Семашко РАМН). Эти оценочные расчеты подтверждают и
специалисты Центрального научно-исследовательского стоматологического института
Минздрава России. Таким образом, число пломб из амальгамы, используемых ежегодно в
российской стоматологической практике, составляет 2,1-2,4 млн. в год. Расход ртути на одну
пломбу, согласно [398], составляет в среднем 350 мг, т. е. в год на изготовление 2 млн. пломб
расходуется примерно 700 кг ртути, которая в конечном счете попадет в окружающую среду.
Следует отметить, что доля амальгамных пломб в странах Западной Европы достигает 40-50%
[341].
Ртуть для изготовления амальгам производится как в России, так и импортируется.
Основным российским производителем амальгамы для стоматологии является ЗАО
“Стомахим” (г. Санкт-Петербург). Это предприятие поставляет в год до 500 тыс. упаковок
комплекта для приготовления амальгамы в капсулах “Амадент”. Такая амальгама готова к
использованию в стоматологических кабинетах и никаких дополнительных компонентов в неё
не добавляется. Остальное количество амальгамы импортируется.
3.4.2 Поступление ртути в окружающую среду в составе зубных пломб
Разогревание пломбировочного материала на открытом пламени, что практиковалось в
российских поликлиниках, всегда сопровождалось выделением паров ртути, содержание
которых значительно превышало ПДК в воздухе. В работах многих отечественных авторов
приведены данные о высоком содержании ртути в воздухе стоматологических кабинетов (от 20
до 440 мкг/м³), штукатурке стен, материалах основания пола. В качестве примера приведем
данные о содержании паров ртути в материалах из стоматологических кабинетов (табл. 3.23).
Таблица 3.23 Доля образцов строительных материалов из стоматологического кабинета с
содержанием ртути [В.А. Катаева, 2002]
Содержание ртути, мкг/г |
Линолеум |
Штукатурка стен |
Материал основания пола |
2-9 |
14 |
12 |
10 |
10 и более |
22 |
7 |
25 |
Не обнаружено |
14 |
28 |
17 |
Для защиты персонала стоматологических кабинетов от воздействия паров ртути
предусмотрен комплекс защитных мер, изложенный в соответствующих Санитарных правилах
Минздрава СССР (1984 г.). В этих правилах (п. 5,10) записано, что для предупреждения
загрязнения атмосферного воздуха от выбросов амальгамосмесителя должны быть установлены
устройства по очистке воздуха от паров ртути. Тем не менее таких установок нет, и в
настоящее время отсутствуют какие-либо локальные очистные сооружения в
стоматологических кабинетах и остатки пломб, содержащие ртуть, экстрагированные зубы
поступают в общие контейнеры с мусором, т. е. в итоге оказываются на свалках.
Учитывая, что 10 лет назад ртутные пломбы составляли примерно 60% от общего
количества пломб, а среднее время “жизни” одной пломбы 10 лет, в настоящее время с
экстрагированными зубами может поступать следующее количество ртути: 18 млн. пломб х 350
мг = 6,3 т/год. Стоматологические лечебные учреждения, как правило, не оборудованы
фильтрами, и основная часть экстрагированных зубов поступает в канализационную систему.
Часть амальгамы может быть размещена в составе ТБО.
Кроме того, определенное количество ртути выбрасывается при кремации. В России
крематории имеются только в 4-х городах – Москве, Петербурге, Екатеринбурге и Нижнем
Тагиле и строятся еще в 4-х городах. В год в России умирает до 2 млн. человек, из которых
кремируется примерно 7%, то есть 140 тыс. человек. По оценкам [341], при кремации 1 тела
выделяется до 350 мг ртути], т. е. общая ежегодная эмиссия ее может достигать 50 кг.
Оценку распределения ртути, поступающей в окружающую среду от пломб и из
крематориев, между атмосферным воздухом, почвой и водой можно дать в соответствие с
расчетами W.S. Atkins [1998], без ее эмиссии от поступающих на мусоросжигательные заводы
(их в России всего несколько) пломб. Крайне мало ртути поступает на рециклинг. Поэтому
можно предположить, что в настоящее время основное количество ртути – до 6 т/год -
поступает на свалки, причем оно будет ежегодно уменьшаться в связи со снижением числа
пломб с амальгамой. Как отмечалось выше, сейчас при кремации тел в атмосферный воздух
поступает около 50 кг ртути в год, а после начала работы новых крематориев это количество
увеличиться примерно на 10 кг.
3.5 Ртутные термометры
3.5.1 Производство ртутных термометров
Ртутные термометры представляют собой приборы для измерения температуры, действие
которых основано на изменении физических свойств металлической ртути, используемой в
качестве термометрической жидкости. Известно несколько групп ртутных термометров
(медицинский, лабораторные, технические, для испытания нефтепродуктов, для сельского
хозяйства, специальные, электроконтактные), которые рассчитаны на измерение температур в
диапазоне от –39 до +750оС. В некоторых разновидностях технических (специальных)
термометров в качестве термометрической жидкости используется сплав ртути и таллия, что
позволяет снизить нижний предел измеряемой температуры до –60°С. В табл. 3.24 приведена
краткая характеристика основных групп ртутных стеклянных термометров, производимых в
России.
Таблица 3.24 Основные группы ртутных термометров, производимых в России [182, 183, 199]
Группы термометров * |
Назначение и краткая характеристика |
Содержание Hg, г ** |
Термометр медицинский максимальный (типа ТБ-1Б) |
Для измерения температуры человеческого тела; снабжен максимальным приспособлением в виде специального щелевого пережима в нижней части капилляра, не допускающего перетекания ртути в резервуар после измерения температуры |
2 г (с 2001 г. – 1,85 г) |
Термометры метеорологические (типа ТМ) |
Для измерений, выполняемых главным образом на метеорологических станциях и постах; в зависимости от назначения отличаются размерами, устройством, пределами измерений и ценой деления шкалы (для измерения температуры воздуха, почвы, воды и др.) |
2-5 |
Термометры лабораторные (типа ТЛ, ТР, КШ) |
Для использования при выполнении лабораторных измерений и научных исследований; некоторые изготавливаются с вложенной шкалой неполного погружения, а также с конусными взаимозаменяемыми шлифами |
1,4 - 48 г |
Термометры для испытания нефтепродуктов (типа ТИН, ТН, ТН-М) |
Для измерения температуры при испытаниях нефтепродуктов в процессе их производства и использования |
0,3 – 2,2 г |
Термометры для сельского хозяйства (типа ТС, УРИ и др.) |
Для измерения температуры в лабораторных и производственных условиях различных отраслей сельского хозяйства и агропромышленного комплекса; изготавливаются с вложенной шкалой; |
2 - 4 |
Термометры технические (ТТ-П, ТТ-У, ТТ-МК) |
Используются в различных отраслях промышленности; изготавливаются в двух исполнениях - прямые и угловые (нижняя часть последних изогнута под углом 90о) |
3,9 – 5,8 |
Термометры электроконтактные (ТПК, ТПИ, ТК, ТРК, ТЗК и др.) |
Предназначены для сигнализации о заданной температуре и для включения или выключения соответствующего оборудования при достижении этой температуры; используются в системах для поддержания постоянной (заданной) температуры в промышленных, лабораторных, энергетических и других установках; изготавливаются термометры с переменной (устанавливаемой) температурой контактирования и с постоянной (заданной) температурой контактирования (термоконтакторы); термоконтакторы могут быть прямыми или угловыми, с одним или несколькими контактами, с подвижным контактом, виброустойчивые и др. |
1,8 – 14,4 |
Термометры специальные типа (СП, ТП) |
Для измерения температуры в установках или оборудовании специального назначения (газоанализаторы, рефрижераторы, хлебопекарные печи и др.); могут быть прямыми и угловыми |
2,6 – 7,4 |
* В каталоге продукции ОАО .Термоприбор. указано более 60 марок ртутных термометров, многие
из которых изготавливаются в нескольких исполнениях и(или) в виде комплекта изделий.
** Примерные пределы.
В настоящее время в России единственным производителем ртутных термометров
является ОАО “Термоприбор” (г. Клин Московской области) - правопреемник Клинского
термометрового завода, который свою первую продукцию выпустил в 1956 г.[4] В лучшие годы
Клинский завод серийно производил до 100 наименований (видов) ртутных термометров, а
также ртутные барометры и манометры, ртутные переключатели и выключатели, на
изготовление которых использовалось до 100-130 т ртути в год. В 1990 г. потребление ртути на
заводе составило 93,2 т [198]. В последующие годы объемы производства и, соответственно,
потребления ртути на ОАО “Термоприбор” снижались, но с конца 1990-х г.г. стали возрастать.
В 1998-2002 г.г. до 97-98% производимой здесь продукции составлял медицинский термометр;
остальная часть приходилась на долю промышленных (технических) термометров (табл. 3.25).
Производство ртутных барометров, манометров и переключателей на заводе полностью
прекращено.
Таблица 3.25 Производство термометров, использование ртути и образование отходов на ОАО
“Термоприбор” в 1998-2002 г.г. *
Год |
Производство медицинских термометров |
Производство прочих термометров |
Общая
масса ртути в продукци и, кг |
Количество, шт. |
Ртуть в продукц ии, кг |
Содержан ие ртути в одном изделии, г |
Количеств о, шт. |
Ртуть в продукци и, кг |
Среднее содержание ртути в одном в изделии, г |
1998 |
7 256 000 |
14 512 |
2 |
192 563 |
744,348 |
3,865 |
15 256,348 |
1999 |
8 430 550 |
16 861,1 |
2 |
197 428 |
783,166 |
3,967 |
17 644,266 |
2000 |
10 957 684 |
21 915,4 |
2 |
221 721 |
1 027,292 |
4,633 |
22 942,692 |
2001 |
11 695 500 |
21 636,7 |
1,85 |
280 322 |
2 397,314 |
8,552 |
24 034,014 |
2002 |
13 177 328 |
24 378,0 |
1,85 |
270 593 |
1 201,367 |
4,40 |
25 579,367 |
Продолжение табл. 3.25
Нажмите сюда для просмотра Продолжение табл. 3.25
Сейчас на заводе существует специальный цех по переработке бракованных изделий,
загрязненного стеклобоя, мягких отходов, демеркуризация которых осуществляется на
модернизированных установках УДЛ-2м. Если с утверждением, что ртуть, механически
теряемая в ходе технологических процессов, собирается форвакуумными насосами (из ртутных
ловушек) и затем - после очистки - вновь возвращается в производство, можно согласиться, то
утверждение, что “брак и мягкие отходы демеркуризируются, а образовавшаяся ртуть
возвращается в производство”, вызывает некоторые сомнения. Тем не менее в дальнейших
расчетах и оценках будем исходить из того, что модернизированная заводскими специалистами
демеркуризационная установка позволяет получать вторичную ртуть, которая - после очистки -
вновь возвращается в производство.
Изготовление термометров представляет собой массовое (конвейерное) или серийное
производство. В обоих видах производства в основу организации технологического процесса
положены целенаправленные дифференциация, отделение ртутных работ от нертутных и
механизация первых из них. На Клинском заводе для этих целей создан механизированный
ртутный комплекс, включающий участок очистки ртути, транспортировку ее к установкам
наполнения термометров ртутью и установки наполнения (УНР) высокой производительности[5].
Производство ртутных термометров сосредоточено в специальном - так называемом ртутном -
корпусе, в котором расположены участок очистки ртути, цех медицинских термометров и цех
промышленных термометров (цех специальных приборов в настоящее время не
функционирует). В общем случае процесс производства ртутных термометров состоит из трех
этапов. Первый этап включает очистку ртути, второй - изготовление стеклянной части
термометров и наполнение ее ртутью, третий - градуирование шкалы (термостатирование).
На участке очистки металлическая ртуть поступает в особую емкость, откуда по
трубопроводу подается в ванну химической очистки, далее, также по трубопроводу, идет на
вакуумную дистилляцию и затем на фильтрацию (используется система фильтров, что
позволяет осуществлять очень тонкую очистку металла). После такой подготовки ртуть по
трубопроводу (используются насосы) подается в цех изготовления термометров (в так
называемые приемные емкости, расположенные в отделении наполнения термометров). Из
приемных емкостей определенное количество металла (до 150 кг) самотеком поступает в УНР,
незначительная часть которого используется для одновременного наполнения нескольких
тысяч капиллярных трубок; остальная ртуть возвращается по трубопроводу в первоначальную
емкость, расположенную на участке очистки (для повторения рассмотренного цикла). В
наиболее активный период деятельности завода количество такой оборотной ртути, ежесуточно
участвующей в технологическом процессе, достигало 8 т.
В ходе технологического процесса изготовления термометров непосредственно
манипуляции с металлической (“открытой”, как принято говорить) ртутью сводятся к
следующим операциям: наполнение стеклянных капилляров ртутью, отливка излишних
количеств ртути, проверка масштаба, отпайка капилляра и цикл градуировочных операций,
построенных по принципу подборки готовых шкал по масштабу термометров. Затем все
термометры проходят испытания и проверки. После проверки кондиционные изделия
поступают на склад готовой продукции; бракованные - направляются в цех утилизации. Сюда
поступает загрязненный стеклобой и другие ртутьсодержащие отходы.
Технические операции с открытой ртутью сопровождаются поступлением ее паров в воз-
дух производственных помещений. В 1964 г. на Клинском заводе был пущен в эксплуатацию
цех очистки вентиляционных выбросов от паров ртути, основу которого составляют несколько
адсорберов (в каждом из которых размещено до 36 т пиролюзитовой руды). До его открытия
очистке подвергались только вентиляционные выбросы из цехов, где осуществлялись работы с
открытой ртутью, после - все выбросы данного производства [211]. Основной выброс цеха
очистки вентиляционных выбросов осуществляется через трубу, высота которой составляет 62
м. В настоящее время, если ориентироваться на данные табл. 3.25, эффективность работы
адсорберов составляет в среднем 83% (наполняющий адсорберы пиролюзит никогда не
заменялся, а только лишь периодически взрыхляется). Остаточный выброс ртути в атмосферу
(после очистки) в середине 1980-х г.г. составлял 150-190 г в сутки (55-69 кг/год), а
концентрации паров ртути в воздухе достигали 0,05-0,1 мг/м³ [162].
В первой половине 1990-х г.г. концентрации паров ртути в воздухе рабочих помещений
завода “Термоприбор” находились в пределах 0,02-0,05 мг/м³ [278]. Сейчас в 25 точках
ртутного корпуса примерно раз в неделю осуществляются измерения концентраций паров
ртути (около 1300 измерений в год); как правило, примерно в 10-20% случаев уровни паров
ртути превышают максимально разовую ПДК (предельно допустимую концентрацию) в
рабочей зоне (= 0,01 мг/м³). В свое время на упомянутом выше заводе в Голынках при
оптимальной температуре воздуха в рабочих помещениях (16-24оС) концентрации паров ртути
в 3 раза выше ПДК, по данным Центра Госсанэпиднадзора по Смоленской области,
наблюдались только на 5 технологических операциях из 20.
Значительная часть механически теряемой в ходе технологических процессов ртути
аккумулируется в ловушках ртутной канализации, откуда извлекается форвакуумными
насосами и затем поступает в особую емкость (после химической очистки, дистилляции и
фильтрации она вновь возвращается в производство). Заводы по изготовлению термометров
потребляют достаточно большое количество воды (до 1000 м³/сут.), которая расходуется на
системы кондиционирования воздуха и вентиляцию [292]. Обычно образующиеся сточные
воды содержат значительное количество пыли, которая сорбирует ртуть. В канализацию также
уходит существенное количество мелкодисперсной металлической ртути. Твердые отходы
производства ртутных термометров представляют собой в основном стеклобой (загрязненное
стекло), а также текстильные отходы (вата, хлопчатобумажная ткань).
3.5.2 Распределение ртути при производстве термометров
Оценка баланса использования ртути на приборостроительных заводах, выполненная в
1990 г. (основное потребление ртути тогда приходилось на производство термометров),
показывает, что в ходе технологических процессов примерно 97,38 % металла поступает в
конечную продукцию, 1,97% - представляет собой на так называемую вторичную ртуть
(возвращаемую в производство), а 0,65% - составляют безвозвратные потери [198]. Поскольку
кардинальных изменений в технологии производства термометров в последние 10 лет не
произошло, то указанные данные могут быть использованы для расчета баланса современного
использования ртути на ОАО “Термоприбор” (табл. 3.26).
Таблица 3.26 Использование ртути на ОАО .Термоприбор. в 1998-2002 г.г.
Год |
Общая масса использованной ртути |
Ртуть в конечной продукции * |
Технологические потери ртути-** |
кг |
% |
кг |
% |
кг |
% |
1998 |
15356,163 |
100 |
15256,348 |
99,35 |
99,815 |
0,65 |
1999 |
17759,704 |
100 |
17644,266 |
99,35 |
115,438 |
0,65 |
2000 |
23092,795 |
100 |
22942,692 |
99,35 |
150,103 |
0,65 |
2001 |
24191,257 |
100 |
24034,014 |
99,35 |
157,243 |
0,65 |
2002 |
25746,721 |
100 |
25579,367 |
99,35 |
167,354 |
0,65 |
* Выше отмечалось, что вторичная ртуть, получаемая на ОАО .Термоприбор. при утилизации
отходов, возвращается в производство (т. е. в конечном счете поступает в продукцию).
** Есть сведения, что в первой половине 1990-х г.г. Клинский завод термометров выбрасывал в
окружающую среду до 100 кг ртути в год [172].
В табл. 3.27 приведен расчетный баланс распределения потерь ртути при изготовлении
термометров. Так называемые неучтенные потери, которые по каким-то причинам не нашли
отражение в официальной заводской статистике (см. табл. 3.25), представляют собой потери
металла в канализацию (с взвесью стоков, а также в виде мелкодисперсной металлической
ртути, не улавливаемой ловушками ртутной канализации), неорганизованные выбросы паров
ртути (через дверные и оконные проемы), часть которых сорбируется строительными
конструкциями, оборудованием, одеждой и обувью рабочих и т. д.
Таблица 3.27 Баланс распределения потерь ртути на ОАО “Термоприбор” (общие потери =
100%)
Год |
Основные виды потерь ртути |
Уловлено адсорберами * |
Выброшено в атмосферу * |
Стеклобой * |
Со сточными водами * |
Неучтенные потери ** |
кг |
% |
кг |
% |
кг |
% |
кг |
% |
кг |
% |
1998 |
1,6 |
1,6 |
0,32 |
0,3 |
20,56 |
20,6 |
0,669 |
0,7 |
76,666 |
76,8 |
1999 |
6,2 |
5,4 |
0,26 |
0,2 |
0,075 |
0,1 |
0,627 |
0,5 |
108,276 |
93,8 |
2000 |
6,43 |
4,3 |
1,4 |
0,9 |
0,102 |
0,1 |
0,718 |
0,5 |
141,453 |
94,2 |
2001 |
6,97 |
4,4 |
1,4 |
0,9 |
0,104 |
0,1 |
0,605 |
0,4 |
148,164 |
94,2 |
2002 |
7,1 |
4,2 |
1,4 |
0,8 |
0,116 |
0,1 |
0,772 |
0,5 |
157,957 |
94,4 |
* Рассчитано на основе данных, предоставленных заводом (в сточных водах аналитически
учитываются только растворенные формы ртути).
** Главным образом потери в канализацию (сорбированная на взвеси ртуть, мелкодисперсная
металлическая ртуть, не улавливаемая ртутными ловушками), а также неорганизованные выбросы паров
ртути в атмосферу, их сорбция строительными конструкциями и оборудованием, одеждой рабочих и т. д.
Данные по другим объектам, использующим ртуть в технологическом процессе (прежде
всего, электроламповым заводам) свидетельствует о том, что до 95% от неучтенных потерь
приходятся на потери металла в канализацию (в виде мелкодисперсной ртути и в составе взвеси
сточных вод). Это позволяет детализировать баланс распределения ртути в ходе
технологических процессов изготовления термометров (табл. 3.28). Тот факт, что существенное
количество ртути теряется в канализацию, подтверждается следующими данными.
Таблица 3.28 Общий баланс распределения ртути на ОАО .Термоприбор. (общее потребление
=100%)
Нажмите сюда для просмотра Таблица 3.28
Сток ОАО “Термоприбор” поступает по канализации на общегородские очистные
сооружения, где совместно с бытовым стоком города подвергается очистки, в ходе которой
образуются осадки сточных вод (ОСВ), складируемые на иловых картах (площадках). Среднее
содержание ртути в ОСВ г. Клина очень велико и в середине 1980-х г.г. достигало 220 мг/кг
[15]. Установлено, что интенсивность образования осадков (на сухое вещество) на городских
очистных сооружениях составляет 80 г/чел. в сутки [98], В г. Клину проживает около 92,8 тыс.
чел. [57]. Таким образом, на очистных сооружениях города ежегодно образуется до 2800 т
осадков, в которых в середине 1980-х г.г. ежегодно накапливалось до 620 кг ртути, в основном
поступающей со стоком завода термометров. В то время потребление ртути на Клинском
заводе термометров составляло 100-130 т/год (в 4-5 раз больше, чем, например, в 2001 г.), а
потери ртути в канализацию (если исходить из их структуры, приведенной в табл. 5)
находились в пределах 580-755 кг/год[6]. Большая часть этой ртути в конечном счете поступала
на очистные сооружения города, а определенное количество аккумулировалась в
канализационной сети, протяженность которой (от завода до очистных сооружений) составляет
2 км. Естественно, что какая-то часть ртути сбрасывалась с очищенными стоками в р. Сестру,
что, в частности, обусловило ее накопление в речных отложениях. Так, выборочные
исследования показывают, что в донных отложениях р. Сестры ниже г. Клина концентрации
ртути достигают 1,55 мг/кг [301]. Это более чем в 50 раз выше типичного фонового уровня
металла в русловом аллювии незагрязненных рек (для рек Московской области он в среднем
составляет 0,03 мг/кг [332]).
Эффективность очистки сточных вод, особенно в отношении ртути, вряд ли превышает
90%; из этого следует, что в середине 1980-х г.г. ежегодно не менее 68 кг ртути уходило со
сточными водами, сбрасываемых с общегородских очистных сооружений в р. Сестру. Таким
образом, общие потери ртути на заводе в то время составляли, по крайней мере, 900 кг в год.
Есть сведения, согласно которым за период 1957-1993 г.г. завод “Термоприбор” выбросил в
окружающую среду не менее 35 т ртути [301], т. е. в среднем составляет примерно 945 кг в год.
Исследования распределения ртути в различных компонентах окружающей среды в зоне
влияния Клинского завода “Термоприбор”, выполненные главным образом в середине 1980-х
г.г., показали, что влияние выбросов в атмосферу достаточно локально. В частности, наиболее
высокие концентрации металла в почвах наблюдались непосредственно в промышленной зоне
завода, где они достигали 25 мг/кг (ПДК ртути в почвах = 2,1 мг/кг), а также в почвогрунтах
заводской свалки отходов - 20 мг/кг и в почвах у дороги, идущей к свалке – 0,9 мг/кг. За преде-
лами заводской территории и свалки уровней содержания ртути в почвах, превышающих ПДК,
обнаружено не было. Максимальные концентрации ртути в пыли, осажденной со снегом, также
фиксировались только вблизи завода (0,63 мг/кг). В атмосферном воздухе содержания паров
ртути превышали ПДК (для воздуха населенных мест, равную 0,3 мкг/м³) только в пределах
территории завода, в непосредственной близости от него они снижались до 0,25 мкг/м³ и на
удалении в 750-1000 м достигали фоновых концентраций (0,025-0,010 мкг/м³) [265]. Б.А. Ревич
установил, что дети работников Клинского завода термометров отличаются более высокими (в
среднем в 1,5 раза) концентрациями ртути в моче, нежели дети, родители которых работали на
других предприятиях города. Это свидетельствует о привносе ртути родителями (на одежде и
обуви) в жилые помещения.
В табл. 3.29 приведена эмиссии ртути в среду обитания в ходе изготовления термометров на
ОАО “Термоприбор”, подавляющая часть которой связана с потерями ртути в канализацию
(главным образом, в виде мелкодисперсной металлической ртути, а также с взвесью сточных
вод).
Таблица 3.29 Структура эмиссии ртути на ОАО .Термоприбор. (общие безвозвратные потери =
100%) *
Год |
Общие потери, кг |
В атмосферу |
В почву (на свалку) |
В канализацию |
кг |
% |
кг |
% |
кг |
% |
1998 |
98,215 |
4,153 |
4,23 |
20,56 |
20,93 |
73,502 |
74,84 |
1999 |
109,238 |
5,674 |
5,19 |
0,075 |
0,07 |
103,489 |
94,74 |
2000 |
143,673 |
8,473 |
5,90 |
0,102 |
0,07 |
135,098 |
94,03 |
2001 |
150,273 |
8,809 |
5,86 |
0,104 |
0,07 |
141,361 |
94,07 |
2002 |
160,245 |
9,298 |
5,80 |
0,116 |
0,07 |
150,831 |
94,13 |
* В США потери ртути при производстве термометров в 1995 г. составляли 9 кг на 1 т используемой
ртути [395].
3.5.3 Использование, экспорт и импорт ртутных термометров
В 2001 г. Клинский завод “Термоприбор” изготовил более 13,1 млн. медицинских термо-
метров и более 280,3 тыс. термометров промышленного (технического) назначения. Из этого
количества примерно 20% изделий было экспортировано в страны дальнего зарубежья и
примерно столько же - в страны СНГ (главным образом, в Украину и Казахстан). Оставшаяся
часть термометров (около 7,9 млн. шт. медицинских и 168,2 тыс. промышленных, содержащих
не менее 17 т ртути) поступило на внутренний российский рынок.
В последние годы в Россию завозятся (из Китая) ртутные термометры (главным образом,
медицинские - типа TVY-120 и TAYS-006) фирмы .Amrus Enterprises, Ltd. (США), имеющей
дочерние предприятия в КНР. По оценкам С.Г. Иткина (ОАО “Термоприбор”), импорт таких
термометров составляет примерно 1 млн. шт. в год. В небольшом количестве ртутные
термометры импортируются также из некоторых других стран. Общий объем российского
импорта ртутных термометров в 2001 г. может быть оценен в 1,3 млн. шт. (при среднем
количестве ртути в одном термометре около 1 г с ними в страну было завезено до 1,3 т ртути).
Таким образом, общее количество изделий, поступающих на внутренний рынок России,
достигает 9368 тыс. шт., из которых подавляющую часть (более 98%) составляют стандартные
медицинские термометры. Судя по всему, практически все они реализуются населению и
организациям в течение одного года.
3.5.4 Эмиссия ртути при использовании термометров
В России вышедшие из строя ртутные термометры практически всегда, в лучшем случае,
оказывались на свалках. Лишь в последние годы в некоторых городах предпринимаются
попытки организовать учет, сбор, хранение и утилизацию использованных изделий. В первую
очередь, организуются специальные пункты и емкости для вышедших из строя (разбившихся)
термометров в крупных больницах, а также осуществляются массовые мероприятия по изъятию
термометров из школ, детский дошкольных учреждений и т. д. Следует отметить, что особым
приказом Минобразования России (от 16 июня 1994 г.) использование в образовательных
учреждениях ртути и ртутьсодержащих приборов было запрещено.
Для расчета количества ртутных термометров, ежегодно используемых в стране,
приведем имеющиеся немногочисленные оценочные сведения.
По оценке В.В. Богатова (выступление на конференции “Ртуть. Комплексная система
безопасности”, 21-23 мая 1996 г.), в г. Санкт-Петербурге в середине 1990-х г.г. ежегодно
выбрасывалось (выходило из строя, разбивалось и т. п.) до 500 тыс. шт. ртутных термометров
(т. е. примерно одно изделие на 10 жителей города). По данным агентства .Ртутьсервис. и
НПП “Экотром”, в г. Москве в конце 1990-х г.г. ежегодно выходило из строя 0,5-0,8 млн.
ртутных термометров, т. е. в среднем примерно 650 тыс. шт. (1 термометр на 13 жителей
города.), из которых собиралось и утилизировалось не более 1%. В Республике Мордовии
(население 920 тыс. чел.) в 2000-2002 г.г. ежегодно поступало в продажу по 40 тыс. ртутных
термометров (1 термометр на 23 чел.); судя по всему, примерно такое же количество (или около
того) выходило из строя.
Таким образом, в зависимости от региона страны, ежегодно из строя выходит один
термометр в расчете на 10-23 жителей страны. Данные по Мордовии, где доля городского
населения не превышает 60%, безусловно, не совсем адекватно отражают реальную ситуацию,
существующую в стране (доля городского населения в России превышает 73%). Для расчета,
очевидно, следует ориентироваться на средний удельный показатель: 1 ртутный термометр на
16 жителей. В целом для страны это составит чуть более 9 млн. шт., что несколько меньше
количества изделий, поступивших в 2001 г. на внутренний рынок (это, впрочем, вполне
закономерно). В этих 9 млн. ртутных термометров содержится не менее 18,1 т ртути, которая в
настоящее время практически вся (до 90-95%) поступает - в лучшем случае - в канализацию, в
мусор, на свалки отходов.
3.6 Барометры, манометры и другие измерительные приборы
3.6.1 Производство ртутьсодержащих измерительных приборов
Ртуть длительное время использовалась при изготовлении ртутных переключателей,
ртутных вентилей, манометров, барометров, ртутных насосов и некоторых других приборов. В
настоящее время серийное, массовое производство большинства из них по различным
причинам прекращено. Тем не менее некоторые приборы, изготовленные в предыдущие годы,
все еще продолжают использоваться в различных сферах бытовой и производственной
деятельности. Есть сведения, что ртуть присутствует в мобильных телефонах, а также в
компьютерах (до 0,0022% от общей массы), где она используется в электронных ключах и
плоских мониторах [370…].
По оценкам МГУП “Промотходы”, только в г. Москве в настоящее время используется
более 6000 т изделий (приборов) радиоэлектронной, электротехнической и медицинской про-
мышленности, содержащих ртуть и ее соединения [91]. На предприятиях г. Омска
насчитывается более 16 тыс. различных приборов, содержащих более 250 кг ртути [384]. По
оценкам, в Краснодарском крае в ртутьсодержащих приборах (манометры, игнитроны и т. п.),
которые имеются у предприятий и организаций, находится около 20 т металлической ртути
[314]. В масштабах всей страны количество ртути, присутствующей в различных приборах, в
настоящее время эксплуатируемых на предприятиях и в организациях может, таким образом,
может достигать нескольких тысяч тонн.
Манометрические приборы (манометры) предназначены для измерений давления
жидкостей и газов. Для измерений атмосферного давления применяют барометры, для
измерений давления, близкого к нулю, - вакуумметры, для измерения артериального давления -
сфигмоманометры (аппараты Рива-Роччи).
В бывшем СССР основными производителями ртутных барометров и манометров
являлись Клинский завод термометров (ОАО “Термоприбор”), завод .Теплоконтроль. (г.
Казань), завод “Актюбрентген” (Казахстан), Тельшяйский завод счетных машин (Литва),
Лубенский завод счетных машин (Украина).
В настоящее время в России производство ртутных манометров (барометров, вакууммет-
ров, сфигмоманометров) прекращено (несколько лет назад).
3.6.2 Потребление ртути с измерительными приборами
В зависимости от формы сообщающихся сосудов ртутные барометры могут быть
чашечными, сифонными и сифонно-чашечными. Действие ртутных барометров основано на
уравновешивание атмосферного давления давлением ртутного столба, заключенного в
барометрической (из термометрического стекла) трубке (табл. 3.30).
Таблица 3.30 Содержание ртути в барометрах [199]
Наименование и марка |
Количество ртути в приборе, граммы |
Барометр СРА (станционный чашечный ртутный) |
586 |
Барометр СРБ (станционный чашечный ртутный) |
894,1 |
Барометр ИР (инспекторский ртутный, сифонно-чашечный) |
1257,1 |
Барометр КР (контрольный ртутный, сифонно-чашечный) |
2150 |
Ртутные барометры - очень точные приборы, ими оборудованы практически все
метеорологические станции и метеорологические службы аэродромов, по ним проверяется
работа других видов барометров. Они также применяются в научных и производственных
лабораториях. При осторожном обращении ртутные барометры работают многие десятки лет
(требуется лишь периодическое пополнение трубок ртутью). Только в самые последние годы на
метеорологических станциях начинает внедряться безртутный сетевой барометр БРС-1М, в
котором предусмотрена возможность его сопряжения с ПЭВМ.
Общее количество ртутных барометров, которые в настоящее время находятся в
эксплуатации, не поддается точному учету, но можно предполагать, что их число достигает
нескольких тысяч (в стране функционирует более 600 станций сети Росгидромета, около 400
гражданских аэродромов и т. д.). При среднем содержании в одном барометре до 1 кг ртути
общая ее масса, сосредоточенная в них, может измеряться несколькими тоннами (5-6 т).
Ежегодно некоторое количество ртути расходуется на пополнение барометров.
Сфигмоманометры в среднем содержат до 10% ртути (от общей массы прибора). Они по-
прежнему используются в медицинской практике, поскольку отличаются надежностью и
высокой точностью показаний. Определенное количество сфигмоманометров в свое время
было завезено в СССР и Россию в рамках так называемой гуманитарной помощи. В 2001 г.
число больничных учреждений в России составляло 10,6 тыс., число врачебных и амбулаторно-
поликлинических учреждений – 21,3 тыс. [228]. Если предположить, что хотя бы в одном из
таких учреждений имеется ртутный сфигмоманометр, то общее их количество составит более
30 тыс. шт. (они содержат не менее 300 кг ртути).
В ртутных манометрах МБП (манометр ртутный, бюро проверок) и МЧР-3 (манометр
чашечный ртутный) содержание ртути составляет 2111 и 1683 г соответственно [1980]. В свое
время достаточно распространены были ртутные (поплавковые) дифманометры (типа ДП-710Р,
ДТ-5, ДТ-50), промышленное производство которых было прекращено много лет назад. Тем не
менее некоторые из этих приборов все еще продолжают использоваться в бойлерных, на
газораспределительных станциях, в лабораториях и т. д. Следует отметить, что в Интернете
встречаются объявления о продаже дифманометров ртутных ДТ-50 (видимо, со складов), что
указывает на существование определенного спроса на эти изделия на российском рынке хотя
может предлагаться не столько сам прибор, сколько содержащаяся в нем ртуть).
3.6.3 Ртуть в отходах и ее поступление в атмосферу, грунты и водные объекты
По данным НПП “Экотром” (г. Москва), от различных предприятий и организаций
города в последние годы на утилизацию поступает несколько десятков дифманометров в год,
содержащих ртуть (например, в 2002 г. - 50 шт.). В масштабах всей России число подлежащих
утилизации ртутных манометров, с учетом сведений, приведенных в разделе 3.6.1, может,
очевидно, достигать нескольких сотен (до одной тысячи) в год (содержащих 300-500 кг ртути).
3.7 Гальванические элементы и батареи
3.7.1 Производство гальванических элементов и батарей
Гальванические элементы представляют собой единичные ячейки источников тока,
вырабатывающие электрическую энергию в результате прямого преобразования химической
энергии окислительно-восстановительных реакций и предназначенные для однократного
электрического разряда (они называются также первичными гальваническими элементами).
Группы однотипных первичных гальванических элементов могут быть соединены
электрически и конструктивно в электрическую батарею с целью получения такого
электрического напряжения (количества электричества), которое один элемент дать не может.
Главными составными частями гальванического элемента являются два электрода различной
природы и электролит. Обычно электроды представляют собой металлические пластинки или
сетки, на которые нанесены реагенты (“активные вещества”): на отрицательный электрод -
восстановитель (цинк, литий и др.), на положительный - окислитель (оксиды марганца, ртути,
другие металлы, а также различные соли). Гальванические элементы и батареи используются в
основном для питания переносной аппаратуры и поэтому изготавливаются преимущественно с
загущенным или твердым электролитом.
В бывшем СССР в 1980-х г.г. на производство гальванических элементов и батарей
(ртутно-цинковых, щелочных и солевых марганцево-цинковых, серебряно-цинковых) ежегодно
использовалось до 100-130 т ртути. Основными производителями указанных изделий были
Елец-кий элементный завод (ныне ОАО “Энергия”, г. Елец Липецкой области), НПО “Квант”
(г. Москва), заводы “Эластик” (пос. Лесной, Шиловский район Рязанской области), “Сигнал” (г.
Челябинск), “Сириус” (г. Клайпеда», Литва), “Уралэлемент” (г. Верхний Уфалей Челябинской
области), “Кузбассэлемент” (г. Новокузнецк), “Востсибэлемент” (г. Черемхово Иркутской об-
ласти), “Программатор” (г. Вязьма Смоленской области), конденсаторный (г. Новосибирск).
Для промышленных и научных целей в небольшом количестве изготавливались также
нормальные первичные элементы (ртутно-кадмиевые и ртутно-цинковые)
Общее производство гальванических элементов в СССР в конце 1980-х г.г. достигало 1
млрд. шт. в год. Например, только для электробытовых приборов в 1990 г. было изготовлено
683 млн. гальванических элементов, из которых более 333 млн. шт. - на Елецком элементном
заводе. С начала 1990-х г.г. в России наблюдается резкое сокращение их производства (табл.
3.31), причем на многих предприятиях оно полностью прекращено; на других - снижено на два
порядка; сейчас на некоторых заводах изготовление элементов и батарей носит разовый
характер (по заказам предприятий и организаций). Все это привело к существенному снижению
потребления ртути (табл. 3.32): в 2001 г. на эти цели в стране было затрачено примерно 0,8 т
ртути. Основными производителями гальванических элементов для бытовых электроприборов
являлись ФГУП “Уралэлемент”, г. Верхний Уфалей (марганцево-цинковые щелочные элементы
и батареи) и ОАО “Энергия”, г. Елец (ртутно-цинковые и щелочные марганцево-цинковые
элементы и батареи).
Таблица 3.31 Производство гальванических элементов всех типов для электробытовых приборов в
СССР и России, млн. шт. [147, 197, 237, с добавлениями автора]
Производство |
СССР |
Россия |
1980 |
1990 |
1995 |
1996 |
1997 |
1998 |
1999 |
2000 |
2001 |
2002 * |
Общее |
400 |
683 |
50,1 |
24,6 |
14,1 |
4,5 |
7 |
7,1 |
4,4 |
5,6 |
ОАО “Энергия”, г. Елец ** |
? |
333,1 |
14 |
4,4 |
3,5 |
1,4 |
1 |
2 |
1,6 |
2,8 |
* Завод .Уралэлемент. изготовил 2,8 млн. шт..
** В 1998 г. на ОАО “Энергия” разработана программа перехода на выпуск элементов воздушно-
цинковой и литиевой систем взамен ртутно-цинковой.
Содержание ртути в производимых батарейках
В ртутно-цинковых элементах (по отечественной номенклатуре - это элементы типа РЦ:
10РЦ53, 5РЦ83, 10РЦ85 и др.), выпускаемых в виде герметичных устройств малой емкости
дисковой (пуговичной, таблеточной) и цилиндрической конструкции, активная масса
положительного электрода состоит из оксида ртути HgO (он еще называется красным, или
желтым, оксидом ртути) с добавкой (5-15%) тонко очищенного графита; отрицательного - из
порошкообразного цинка с небольшим количеством ртути (амальгамированный цинк).
Таблица 3.32 Использование ртути на ОАО “Энергия”, г. Елец [147, 197, 198]
Год |
Потребление, кг/год |
Производство гальванических элементов всех типов, млн. шт. |
Ртуть металлическая |
HgО |
1996 |
34 |
1513 |
4,4 |
HgО |
1997 |
29,5 |
1720 |
3,5 |
HgО |
1998 |
16,5 |
725 |
1,4 |
HgО |
2001 |
18 * |
750 * |
1,6 |
* Оценка.
Активная масса положительного электрода запрессовывается в корпус элемента, а
отрицательная - в крышку. Перед сборкой гальванического элемента между корпусом и
крышкой помещается прокладка из пористой бумаги, пропитанная электролитом, состоящим из
раствора КОН (едкий кали) с оксидом цинка. Между корпусом и крышкой находится
изолирующая резиновая прокладка, одновременно являющаяся герметизирующим
уплотнением. Элементы типа РЦ в среднем содержат до 1% металлической ртути и до 37%
оксида ртути от их общей массы [199]. Масса этих элементов варьируется в пределах от
нескольких грамм (пуговичной конструкции) до 45-370 г (цилиндрической конструкции); масса
батареи “Прибой-2С” - 450 г. Саморазряд элементов ртутно-цинковой системы в процессе
хранения ничтожен: в период от 12 месяцев и до конца срока службы их работоспособность
снижается не более чем на 10%., что наряду с ударопрочностью, устойчивостью при
воздействии вибрации и способностью выдерживать значительный вакуум и повышенное
давление определило их применение в военной технике, полевой аппаратуре, радиозондах,
медицинских приборах, часах и т. д.
В щелочных марганцево-цинковых элементах цилиндрической конструкции (типа RL-
316, RL-332, RL-343) положительным электродом является оксид марганца с добавлением
графита, ацетиленовой сажи, электролита (в состав последнего входят едкий кали, оксид цинка,
бихромат калия, карбонаты). Отрицательный электрод изготовлен из однородной
пастообразной смеси: цинковый порошок - 1000 г, оксид ртути - 15 г, крахмал картофельный -
45 г, электролит - 340 мл [199]. Таким образом, в составе отрицательного электрода
присутствует до 1,1% оксида ртути (или 1,5% ртути от массы цинка). В частности, в элементе
RL-332 (его масса 35 г) содержится 66 мг оксида ртути; в элементе RL-343 (массой 70 г) - 154
мг оксида ртути; в элементах пуговичной конструкции - не более 20-25 мг ртути. В батарее
“Корунд” количество оксида ртути составляет 0,5%, (от их массы), в некоторых батареях серии
“Бакен” (их вес достигает 2,5 кг) - 18-25 г.
Содержание ртути в отходах и ее поступление в атмосферу, грунты и водные объекты
В общем случае технологическая схема изготовления гальванических элементов состоит
из трех основных групп операций: приготовление анодной массы, изготовление катода, сборка
элементов. Приготовление анодной массы включает очистку (фильтрацию) ртути, взвешивание
ртути, загрузку ртути в смеситель, перемешивание композиционных материалов, выгрузку
анодной массы, набивку дозаторов, чистку деталей смесителя. При изготовлении катода HgO,
MnO2 и графит из бункера загружаются в смеситель, полученная смесь направляется на
дополнительную обработку, в ходе которой она компактируется. Затем приготовленные катод и
анод поступают в отделение сборки гальванических элементов. Сборка элементов проводится
на автоматических (полуавтоматических) линиях, на которых осуществляют дозировку
анодной массы, заполнение корпуса элемента анодной массой, его герметизацию и т. д.
При изготовлении гальванических элементов ртуть эмитирует в воздух (в виде паров и
пыли оксидов ртути) при подготовке анодной массы и изготовлении катода, при сборке
элементов, при обслуживании и ремонте оборудования; механические потери металлической
ртути происходят при ее фильтрации, взвешивании, а также при приготовлении амальгамы.
Обычно во всех рабочих помещениях имеется общеобменная приточно-вытяжная вентиляция,
функционируют пылеулавливающие системы; фильтрация и взвешивание ртути
осуществляются в вытяжных шкафах, а остальные технологические операции, в том числе, на
автоматических линиях сборки, как правило, проводятся на оборудовании, не имеющего
местных вытяжных устройств. Сточные воды производства поступают на заводские локальные
очистные сооружения (на ОАО “Энергия”, например, используется реагентный способ
очистки), затем - по канализационной сети - на общегородские очистные сооружения, после
обработки на которых сбрасываются в водоток.
Данные, относящиеся к периоду относительно активной работы завода в г. Ельце,
свидетельствуют о высокой эмиссии паров ртути в воздух рабочих помещений на всех этапах
изготовления гальванических элементов [213]. Например, в воздухе цеха по производству
ртутно-цинковых элементов концентрации паров ртути и оксида ртути в воздухе превышали
предельно допустимую концентрацию (ПДК) в 25 раз; ртуть в высоких концентрациях
обнаруживалась также в водных смывах с рук и одежды рабочих, со стен и пола. В воздухе
цеха сборки марганцево-цинковых элементов концентрации паров ртути были намного меньше,
но, тем не менее, в среднем в 2 раза превышали ПДК. Наиболее высокие уровни паров ртути в
воздухе наблюдались при загрузке металла в смеситель (табл. 3.33), часто значительно
превышая ПДКMAX (максимально разовую ПДК в воздухе рабочей зоны), [114].
Технологические операции, осуществляемые при наполнении гальванических элементов
анодной массой и при их сборке, сопровождаются меньшей эмиссией ртути в воздух. Как
правило, наиболее опасной процедурой является техническое обслуживание и ремонт линии
сборки (табл. 3.34). Пары ртути в повышенных содержаниях фиксировались практически во
всех производственных помещениях Елецкого элементного завода [231]. У его работников
отмечены случаи хронической ртутной интоксикации, которые преобладали над другими
профессиональными заболеваниями. Повышенные концентрации ртути обнаруживаются в
почвах территории завода и его окрестностей, а также в других районах г. Ельца [269].
Таблица 3.33 Ртуть в воздухе помещения для изготовления анодной массы [114]
Технологическая операция |
Число измерений |
Концентрация ртути, мкг/м³ |
Средняя |
Максимальна я |
Фильтрация ртути |
13 |
1 |
50 |
Взвешивание ртути |
20 |
20 |
100 |
Загрузка ртути в смеситель |
8 |
212 |
760 |
Перемешивание анодной массы |
24 |
11 |
70 |
Выгрузка анодной массы |
13 |
10 |
100 |
Набивка дозаторов |
10 |
9 |
23 |
Мытье деталей смесителя |
12 |
5 |
52 |
ПДКСС (рабочая зона, среднесменная) |
|
5 |
ПДКMAX (рабочая зона, максимальная) |
|
10 |
ПДКА (атмосферный воздух населенных пунктов) |
|
0,3 |
Типичное фоновое содержание |
|
0,010-0,015 |
Таблица 3.34 Ртуть в воздухе помещений сборки элементов питания [114]
Технологическая операция |
Место наблюдения |
Количество наблюдений |
Концентрация ртути, мкг/м³ |
Средняя |
Максимальная |
Дозировка анодной массы и калибровка элементов |
Линии сборки элементов - А |
24 |
12 |
39 |
Линия сборки элементов - Б |
18 |
3 |
8 |
Кондиционер |
16 |
8 |
26 |
Дверь в коридор |
8 |
14 |
31 |
Ремонт механизмов линии сборки |
Линия сборки-А |
10 |
119 |
160 |
Кондиционер |
5 |
8 |
11 |
Дверь в коридор |
5 |
125 |
140 |
Резкое снижение объемов производства гальванических элементов на российских заводах
и, соответственно, существенное уменьшение потребления ими ртути обусловили резкое
снижение ее выбросов в атмосферу. Так, если в 1992 г. в г. Ельце в атмосферу поступало 107 кг
ртути, то в 1998 г. - 9 кг [269].
Баланс распределения ртути при производстве гальванических элементов
Оценка баланса распределения ртути при производстве гальванических элементов,
выполненная для промышленных предприятий СССР в 1990 г., показывает, что при их
изготовлении в конечную продукцию поступало 72,4% от общей массы использованного
металла, а 27,6% терялось (с бракованными изделиями и другими твердыми отходами, в
канализацию, в атмосферу) [198].
Данные (начало 1990-х г.г.) по заводам в городах Новосибирске и Новокузнецке, в то
время производившими гальванические элементы и батареи, свидетельствуют о том, что эти
предприятия суммарно выбрасывали в окружающую среду 770 кг ртути в год, из которых 40 кг
приходилось на ее эмиссию в атмосферу, 60 кг поступало в водную среду, а основная часть -
670 кг – концентрировалась в твердых отходах [241]. Таким образом, структура потерь ртути в
ходе изготовления гальванических элементов выглядит следующим образом: 5,2% - выбросы
металла в атмосферу, 7,8% - потери его в канализацию, 87% - связано с твердыми отходами.
Поскольку коренных изменений в технологии производства гальванических элементов на
российских предприятиях в последнее десятилетие не произошло, то указанные показатели
вполне могут использоваться для расчета баланса распределения и эмиссии ртути в
окружающую среду (табл. 3.35).
Таблица 3.35 Баланс распределения ртути при производстве гальванических элементов в России
в 2001 г.
Статьи баланса |
Ртуть, кг * |
% от общего количества |
Общее потребление ртути ** |
800 |
100 |
Поступило в конечную продукцию |
579,2 |
72,4 |
Технологические потери ***, в том числе: |
220,8 |
27,6 |
В атмосферу **** |
11,5 |
1,4 |
В канализацию ***** |
17,2 |
2,2 |
В твердые отходы ****** |
192,1 |
24 |
* Примерно 60% выбросов приходятся на ОАО .Энергия., г. Елец.
** Включая оксид ртути в пересчете на металлическую ртуть.
*** Высокие потери ртути во многом объяснялись массовым характером производства элементов на
заводах-изготовителях, не исключено, что в настоящее время технологические потери могут быть
меньше (это, впрочем, вряд ли существенно изменит общую картину).
**** Определенная часть ртути поступает в атмосферу в составе пыли в виде HgO.
***** Большая часть, судя по всему, это мелкодисперсная металлическая ртуть.
****** На многих российских заводах всегда был очень велик технологический брак (до 10% и более
от общего производства гальванических элементов); бракованные элементы составляли основную массу
твердых отходов, образующихся на таких предприятиях; по оценке М.Н. Борзых (личное сообщение), на
российских заводах, производивших марганцево-цинковые элементы, накопилось по 3-7 тыс. т твердых
отходов, содержащих до 3-7 т ртути; в частности, в районе завода “Эластик” (Рязанская область) на
открытой площадке складировано более 7 тыс. т бракованных марганцево-цинковых элементов с
содержанием ртути в одном элементе до 0,1% [154].
3.7.2 Экспорт и импорт гальванических элементов и батарей
В последние годы внутренний российский рынок первичных гальванических элементов и
батарей практически полностью формируется за счет импорта, объемы которого постоянно
увеличиваются и в настоящее время составляют не менее 11000 т (в таких единицах
таможенная статистика учитывает торговлю гальваническими элементами [280, 281]).
Основными импортерами гальванических элементов в Россию являются Польша, Китай и
Корея (суммарно до 65%), а также Япония, Бельгия, Тайвань, Германия и некоторые другие
страны. Российский экспорт гальванических элементов очень невелик и, например, в 1999 г.
составлял 24 т, в 2000 г. - 65 т (главным образом в Украину и Казахстан).
Известно, что в настоящее время в мире в наибольшем количестве производятся
первичные цинково-углеродные и особенно щелочные марганцево-цинковые элементы и
батареи. Например, щелочных элементов ежегодно продается более 10 млрд. шт., а их
удельный вес на рынках США и Канады составляет 80%, Японии - 65% [На мировом рынке
электрических…, 2001]. Согласно инструкции Европейского союза, с 1 января 2000 г.
запрещено производить и использовать все элементы и батареи, содержащие более 0,0005 %
ртути (по массе), а также щелочные марганцевые батареи с содержанием ртути более 0,025%
(по массе) [337]. Аналогичные ограничения на содержание ртути в первичных гальванических
элементах существуют в США, Японии и других странах.
Выборочный анализ предлагаемых к продаже гальванических элементов в магазинах
Москвы, Саранска, Смоленска и Пензы, некоторых небольших городов и поселков Московской
и Пензенской областей и Республики Мордовии, показывает, что среди имеющихся изделий (в
общей сложности до 200-250 типов) лишь единицы из них содержат указание о том, что они
включают ртуть (например, цилиндрические батарейки фирмы “Konnoc Battery Industrial Co.,
Ltd.”, содержащих 0,009% ртути); на многих гальванических элементах прямо указывается на
отсутствие в них ртути.
На сайте battery team, в каталоге предлагаемых к продаже гальванических элементов и
батарей, приведен перечень из 438 типов изделий (ведущих зарубежных фирм-
производителей), среди которых 35% представляют собой щелочные элементы, около 20% -
литиевые, 24% - серебряно-оксидные, 18% - цинково-углеродные, и только 4 вида названы
ртутными (фирмы “Energizer”). Показательно, что объемы предлагаемых к поставке, например,
щелочных элементов цилиндрической конструкции конкретного типа измеряются от 1000 до
100000 штук, а ртутных - всего лишь от 10 шт., что, безусловно, свидетельствует о
незначительном их завозе в Россию.
Для оценки массы ртути, поступающей в Россию с импортными гальваническими
элементами и батареями, предположим (с определенной степенью условности), что из 11000 т
завозимых изделий примерно 30% приходится на долю щелочных элементов и батарей с
содержанием ртути, исходя из принятых требований, не более 0,025% (по массе). Не сложные
расчеты показывают, что с таким количеством элементов в страну поступает примерно 0,8 т
ртути, а с учетом (предположительно) поставок ртутных и других ртутьсодержащих элементов
- порядка 1 т металла.
3.7.3 Использование и утилизация гальванических элементов и батарей
В бывшем СССР и сейчас в России первичные гальванические элементы и батареи в
массовом порядке никогда целенаправленно не собирались и, соответственно, не
утилизировались; они, в лучшем случае, вывозятся на свалки отходов [154, 326].
По данным НПП “Экотром”, в Москве в конце 1990-х г.г. в различных организациях и на
предприятиях ежегодно использовалось до 1 млн. шт. (общей массой около 100 т)
гальванических элементов и батарей (со средним содержанием ртути 0,1-1%), еще более 15
млн. шт. (около 1500 т) элементов и батарей образовывалось в бытовом секторе (у населения).
Из этого количества собиралось (на предприятиях) и затем утилизировалось не более 1%
(отправлялось на переработку в ЗАО “НПП “Кубаньцветмет”). В последние 2-3 года в Москве
только одна организация сдает в НПО “Экотром” на утилизацию ртутные батарейки (примерно
по 15 тыс. шт. в год). Есть сообщения, что недавно Гринпис России организовал в московских
магазинах IKEA пункты приема от населения отслуживших срок гальванических элементов и
батарей [347], хотя о дальнейшей судьбе их ничего не говорится.
Известно, что самые распространенные щелочные элементы обычно служат 1 год, после
чего 60% их переходит в отходы, 2 года служит только 20% из них, а 3 года - всего 10% [397].
Можно считать, что сейчас подавляющая часть всех производимых в России и завозимых в
страну гальванических элементов и батарей в течение года выходит из строя. К тому же,
нередки случаи поступления в продажу не совсем качественных батареек (возможно,
подделок), что значительно ускоряет их поступление в отходы. Общее количество ртути,
которое в конечном счете поступает на свалки (организованные и неорганизованные) с
использованными элементами и батарейками, с учетом выше сказанного, составляет примерно
1,6 т (рис. 3.9).
По-прежнему, серьезную проблему представляют твердые отходы (главным образом в
виде бракованных элементов), складированные в районе российских заводов-производителей
элементов и батарей.
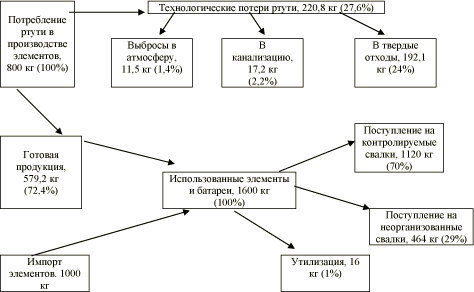
Рисунок 3.9 Распределения ртути при производстве и использовании гальванических
элементов и батарей в России в 2001 г.
Следует отметить, что в свое время в СССР были разработаны технологический процесс
и необходимое оборудование для термической демеркуризации ртутьсодержащих марганцево-
цинковых элементов [38, 39, 144, 145, 154]. Созданная и прошедшая опытные испытания
установка может также использоваться для утилизации других малогабаритных изделий
(например, боеприпасов, содержащих гремучую ртуть). В Федеральной программе “Отходы”,
утвержденной постановлением Правительства РФ (от 13 сентября 1996 г. № 1098),
планировалось создать в Рязанской области (на заводе “Эластик”) на базе указанной установки
соответствующее предприятие (мощность 500 т отходов в год) по переработке
ртутьсодержащих электрохимических источников тока. К сожалению, это решение так и не
было выполнено.
3.8 Источники освещения
Ртуть является составной частью газоразрядных ламп, в которых свечение создается от
электрического разряда в парах металла или в смеси газа и пара. Существуют три
разновидности ртутных ламп:
- лампы низкого давления (парциальное давление паров ртути при установившемся
режиме не превышает 102 Па),
- лампы высокого давления (от 105 до 106 Па),
- лампы сверхвысокого давления (106 Па и более).
Колбы ртутных ламп могут быть покрыты или непокрыты слоем люминофора.
3.8.1 Производство ртутьсодержащих источников освещения
В 2000-2002 г.г. российскими предприятиями производились следующие группы ртутных
ламп (табл. 3.36). Среди ламп низкого давления в массовом порядке выпускались трубчатые
люминесцентные лампы, в группе ламп высокого и сверхвысокого давления - лампы типа ДРЛ,
ДНаТ, ДНаЗ. Ежегодные объемы производства ламп низкого давления составляли 69-71 млн.
штук в год, ламп высокого и сверхвысокого давления – 6,5-7 млн. шт./год. Компактные
люминесцентные лампы (до 500-600 тыс. шт./год) изготавливались на ОАО “Лисма-ВНИИИС”
(150 тыс. шт./год) и Московском электроламповом заводе (ОАО .МЭЛЗ.) [223].
Таблица 3.36 Основные группы ртутных ламп, производимых в России [17, 108, 271]
Группа ламп |
Типы ламп, мощность, (маркировка) |
Количеств о типов ламп |
Средняя продолжительн ость горения, часы * |
Разрядные лампы низкого давления |
Люминесцентные |
Трубчатые, 4-80 Вт (ЛБ, ЛБЕ, ЛД, ЛДЦ, ЛЕЦ, ЛЕЦТ и др.) |
45 |
6000-12000 |
Фигурные, 22-60 Вт (ЛБК, ЛДК, ЛЕЦК, ЛТБЦЦК и др.) |
13 |
2000-15000 |
Цветные, 15-40 Вт (ЛГ, ЛК, ЛЗ, ЛЖ, ЛР, ЛС) |
15 |
7500-15000 |
Люминесцентные компактные |
7-36Вт (КЛ) |
12 |
8000-10000 |
Универсальные, 7-11 Вт (КЛУ) |
12 |
8000-10000 |
Цветные, 5-11 Вт (КЛ, КЛУ) |
30 |
5000 |
С электронным ПРА и цоколем Е27, 11-20 Вт (КЛЭ) |
19 |
8000 |
Люминесцентные ультрафиолетовог о излучения |
4-80Вт (ЛУФ, ЛУФТ, ЛУФК, КЛ) |
10 |
300-5000 |
Эритемные |
15-40 Вт (ЛЭ, ЛЭР) |
5 |
3000-5000 |
Бактерицидные |
4-60 Вт (ДБ, ДРБ, ДБК) |
7 |
3000-8000 |
Неоновые трубки |
Для световой рекламы |
- |
6000-8000 |
Разрядные лампы высокого и сверхвысокого давления |
Ртутные высокого и сверхвысокого давления |
50-Вт (ДРЛ, ДРТ, ДРТБ, ДРШ) |
38 |
500-24000 |
Металлогалогенн ые |
250-4000 Вт (ДРИ, ДРИЗ, ДРИФ, ДРИШ) |
24 |
200-10000 |
Натриевые высокого давления |
С прозрачной колбой, 50-1000 Вт (ДНаТ) |
9 |
10000-15000 |
Со светорассеивающей колбой, 50-1000 Вт (ДНаМт) |
9 |
10000-15000 |
Зеркальные “Рефлакс”, 50-600 Вт (ДНаЗ) |
9 |
10000-15000 |
Ртутно- ксеноновые |
500-1500 Вт (ДРКс) |
3 |
1200 |
Спектральные |
50-600 Вт (дугового разряда, ДРС), 12 (ртутно-гелиевая, ДРГ) |
4 |
50-500 |
* В режиме частых включений срок службы лампы заметно сокращается.
В 2001 г. основными производителями ртутных ламп и, соответственно, главными
потребителями ртути являлись ОАО “Лисма” (г. Саранск) и ОАО “Свет” (г. Смоленск).
Смоленский электроламповый завод (ОАО “Свет”) специализируется на изготовлении
люминесцентных ламп низкого давления, ежегодно выпуская до 50% отечественных ламп
подобного типа (в 2001 г. - более 35,6 млн. шт.). Саранское ОАО “Лисма” отличается
разнообразной номенклатурой продукции (более 700 наименований источников света
различного назначения, световые приборы, светильники и др.). Производство люминесцентных
ламп низкого давления сосредоточено на Саранском электроламповом заводе – “Лисма-СЭЛЗ”
(35 млн. шт. в 2001 г.). Выпуск ртутных ламп высокого и сверхвысокого давления (около 5,8
млн. шт. в 2001 г.) осуществлялся на Саранском заводе специальных источников света и
электровакуумного стекла (“Лисма-СИС-ЭВС”).
Указанные в Базе данных “Участники светотехнического рынка”, подготовленной
московским Домом Света [17], другие отечественные производители (5-6 предприятий)
ртутных ламп (в основном высокого давления и специального назначения) в 2001 г. обладали
незначительными производственными мощностями (до 100-150 тыс. ламп в год). На некоторых
из них производство ртутных ламп высокого давления осуществлялось с использованием
готовых разрядных трубок (ртутных горелок), поставляемых из-за рубежа. В целом их
деятельность оказывала незначительное влияние на российский рынок ртутных ламп и,
соответственно, на потребление ртути электроламповой промышленностью (табл. 3.37).
Таблица 3.37 Потребление ртути российской электроламповой промышленностью в 2001 г.
Потребители |
Масса ртути, кг |
Доля, % |
ОАО “Лисма”, г. Саранск |
4400 * |
58,7 |
ОАО “Свет”, г. Смоленск |
2600 |
34,7 |
Прочие производители |
350 |
4,6 |
Производство неоновых трубок |
150 |
2 |
Итого |
7500 ** |
100 |
* До 90% ртути потребляется Саранским электроламповым заводом (.Лисма-СЭЛЗ.).
** До 87% ртути используется в производстве люминесцентных ламп низкого давления.
В последние годы в России получило развитие производство неоновых трубок для
световой рекламы (в англоязычных странах оно именуется “bending”, по названию основной
операции - сгибанию стеклянных трубок). Например, только в г. Москве в 2001 г. существовало
более 20 производителей неоновых ламп. Как правило, это небольшие предприятия-
мастерские, весь комплект оборудования которых размещается на площади в 20 м²,
численность работников - 4-6 человек; потребление металлической ртути не превышает 8-10
кг/год.
Технологические процессы
Отечественные ламповые заводы в основном оснащены устаревшими
полуавтоматизированными линиями сборки люминесцентных ламп, изготовленными в свое
время в Венгрии (фирма Tungsram) и частично включающими отечественные машины
(проектная мощность одной линии - 1200 ламп/час). Основу некоторых линий сборки
составляют машины английской фирмы Badalex. В 2001 г. на Смоленском электроламповом
заводе эксплуатировалось 10 линий; на Саранском электроламповом заводе - 12 линий сборки
ламп.
Процесс сборки ламп начинается с мойки и сушки стеклянных трубок (колб ламп),
нанесения и сушки люминофорного слоя (рис. 3.10). Стеклянные трубки, изготовленные в
стекольном производстве, конвейером подаются в цех сборки ламп, где поступают на
специальные машины, на которых установлены сопла для мойки и сушки трубок, а также бачки
с люминофорной суспензией. В последние годы люминофорную суспензию готовят на водо-
растворимом полимере (на основе метилметакрилата), обеспечивающего закрепление
люминофорного слоя на стенках трубки в процессе его нанесения. В дальнейшем это
связующее вещество (биндер) удаляется (выжигается). Стеклянные трубки, подходя к бачку,
останавливаются над ним, после чего люминофорная суспензия с помощью создаваемого в
трубках вакуума втягивается в них. Установленные у верхнего конца трубки фотоэлементы
дают сигнал к выключению вакуума, когда суспензия поднимается до места их размещения.
После этого остатки суспензии стекает обратно в бачок, а трубки продвигаются на позиции
сушки люминофорного слоя. Теплый воздух (до 50-60°С) для сушки вымытых трубок подается
от печей выжигания биндера, для сушки люминофорного слоя - от калориферов. Затем трубки с
нанесенным и высушенным люминофором поступают на машины выжигания биндера, которые
состоят из 4-х частей: конвейера загрузки и маркировки трубок, печи выжигания, конвейера
подачи трубок к машине заварки с матовым экраном в конце конвейера (где осуществляется
проверка качества выжигания биндера), механизмов зачистки люминофорного слоя на концах
трубок.
Следующей операцией является заварка трубок, которая предваряется монтажом ножек и
оксидированием. Для этого на особую машину подаются стеклянные тарелки, штенгели и
металлические трехзвенные выводы. Выводы и штенгели заштамповываются в единое целое с
тарелкой и образуют так называемую стеклянную ножку, которая перемещается в печь отжига,
где постепенно остывает. Штенгель представляет собой стеклянный капилляр диаметром 5 мм,
с помощью которого внутренний объем лампы соединяется с откачной системой; он также
служит для введения в лампу ртути и инертного газа. Отверстие в штенгеле имеется лишь на
ножке для одного конца лампы (ножка с продутым штенгелем); другая ножка его не имеет
(ножка с непродутым штенгелем). На монтажно-оксидировочном автомате в крючки никелевых
частей выводов зажимаются триспиральные катоды, наносится слой оксидной суспензии,
который затем высушивается, а ножки автоматически подаются к машинам заварки трубок (на
газовых горелках).
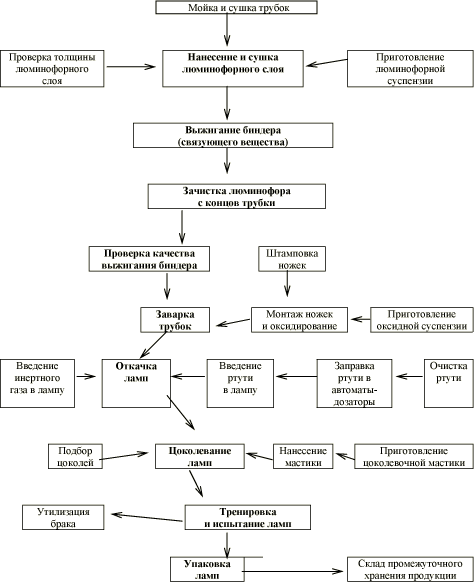
Рисунок 3.10 Схема технологического процесса сборки люминесцентных ламп.
Главной операцией процесса изготовления люминесцентных ламп является их откачка на
откачных полуавтоматах, в ходе которой из лампы удаляется воздух, производится прогрев
трубок для удаления из стекла и люминофорного слоя загрязнений, ведется тепловая обработка
электродов при пропускании по ним тока (с откачкой продуктов разложения биндера и
карбонатов оксидного покрытия), осуществляется введение в лампу ртути и инертного газа,
активирование электродов, отпаивание ламп и установка их в конвейер, идущий к машине
цоколевания. Откачка ламп осуществляется с помощью вакуумных насосов. Используемая в
технологическом процессе металлическая ртуть подвергается очистке (дистилляции); затем
осуществляется ее заправка в дозировочные головки автоматов-дозаторов, с помощью которых
производится подача металла в лампу (в виде капли определенной массы).
Откачанные лампы по конвейеру идут к машине цоколевания. На конвейере происходит
автоматическое обламывание непродутого штенгеля; работницы (цоколевщицы), находящиеся
в середине конвейера, надевают (вручную) на лампы цоколи с намазанной на них мастикой.
После термической обработки цоколевочная мастика прочно связывает цоколь со стеклянной
трубкой. Затем лампы подаются конвейером на машины тренировки и испытания, после
прохождения которых изделия, отвечающие техническим требованиям, упаковываются и
поступают на склад промежуточного хранения, а попавшие в категорию забракованных -
отправляются на утилизацию.
Цех сборки люминесцентных ламп оборудован общеобменной вентиляцией, рабочие
места у откачных полуавтоматов - местной приточно-вытяжной вентиляцией. В цехе работает
демеркуризационная бригада, осуществляющая периодическую обработку (обычно в течение
смены дважды) оборудования, пола, сбор разбитых штенгелей, стеклянных трубок и ламп. На
Смоленском электроламповом заводе для демеркуризации цеха используется 3%-ный раствор
гипохлорита натрия, на Саранском электроламповом заводе - водный раствор перманганата
калия, подкисленный соляной кислотой. После обработки демеркуризационный раствор
смывается струей воды по направлению к желобам ртутной канализации, оборудованной
ловушками металлической ртути (большая часть этой ртути является следствием механических
потерь металла в ходе сборки ламп). Извлечение ртути из ловушек осуществляется с помощью
форвакуумных насосов; в дальнейшем она отправляется на очистку или вторичную
переработку.
Технологический процесс производства люминесцентных ламп, рассмотренный выше,
включает большой удельный вес ручного труда, характеризуется значительными потерями
ртути, особенно на линиях сборки, и отличается наличием неблагоприятных производственных
факторов (высокие концентрации паров ртути и некоторых органических соединений,
повышенная температура воздуха, шум, инфракрасное и электромагнитное излучение). Основу
большинства линий сборки ламп, эксплуатируемых на отечественных электроламповых
заводах, составляет оборудование, характеризующееся практически 100%-ным сроком
амортизации, что предопределяет очень высокий брак, прежде всего, из-за разбивания трубок и
растрескивания стекла по шву заварки [36, 277]. В частности, если доля так называемого боя
трубок ламп, предусмотренная проектом, не должна превышать 8%, то в реальности она
достигает 20-25%. Достаточно велико также количество бракованных (не прошедших
технический контроль) ламп (до 7-9% от общего их производства).
Изготовление ртутных ламп высокого давления организовано на линиях сборки, во
многом аналогичных рассмотренным выше, но, как правило, характеризующимся более
качественным оборудованием (или, по крайней мере, менее изношенным).
Удельное содержание ртути в лампах
В отечественных справочниках по светотехнике и каталогах светотехнических изделий
приводятся сведения, что количество ртути в каждой люминесцентной лампе низкого давления,
изготовленной на российских заводах, составляет от 20 до 50 мг (см., например, [108, 212,
239]). Однако, известно, что используемая на российских предприятиях технология
изготовления люминесцентных ламп изначально базировалась на введении в каждое изделие от
80 до 120 мг металлической ртути (без учета ее возможных потерь). Именно такое количество
металла помещалось в ампульную часть дозировочной головки автомата-дозатора, причем в
каждое изделие в конечном счете попадало не менее 50-80 мг ртути. В последние годы на ОАО
“Свет” (г. Смоленск) были проведены технические мероприятия по усовершенствованию
дозировочных головок, позволившие уменьшить среднюю дозу вводимой в каждую
люминесцентную лампу ртути (без учета ее потерь) в 1998-2000 г.г. до 72,8-74,3 мг, в 2001 г. -
до 67,7 мг, в 2002 г. - до 63,4 мг, в 2003 г. - до 52,6 мг. Из 10 эксплуатируемых на Смоленском
заводе линий сборки люминесцентных ламп две отличаются меньшим удельным
меркурида титана (геттеро-ртутных дозаторов), однако работают они неэффективно, с малой
производительностью. В 2001 г. на Саранском электроламповом заводе в ампульную часть
автоматов-дозаторов помещалось не менее 100 мг ртути, из которых 60-70% попадали в лампу
(в среднем примерно 66 мг). Попытки внедрить в производство использование геттеро-ртутных
дозаторов на двух производственных линиях не увенчались успехом.
В табл. 3.38 приведены сведения, характеризующие уровни содержания ртути в основных
типах ламп, выпускаемых российскими предприятиями.
Таблица 3.38 Содержание ртути в основных типах отечественных разрядных ламп, 2001 г.
Группа ламп |
Количество ртути в одной лампе, мг |
Люминесцентные |
40 - 65 (среднее 52) |
Люминесцентные компактные |
3-5 |
Ртутные лампы высокого давления (типа ДРЛ) |
75 - 350 |
Ртутные лампы высокого давления (типа ДРТ) |
50 - 600 |
Ртутные лампы сверхвысокого давления (типа ДРШ) |
от 5 до 50% (по массе) |
Металлогалогенные |
40-60 |
Натриевые лампы высокого давления |
30-50 |
Неоновые трубки |
нет данных * |
* Согласно [341], одна неоновая трубка содержит 10 мг ртути; есть сведения, что на российских
предприятиях-мастерских ртуть вводится в неоновые трубки вручную, что априори предполагает ее
существенно больший расход.
Источники эмиссии ртути и ее содержание в воздухе рабочей зоны
Основные потери металлической ртути и интенсивная эмиссия ее паров в воздух рабочих
помещений происходят у откачного полуавтомата, где металл вводится в лампу. Устройство,
предназначенное для его введения в стеклянную трубку (дозировочная головка), обязано
обеспечивать одновременно вакуумное уплотнение и правильную дозировку металла. В идеале
капля ртути под своим весом должна поступать в лампу через капилляр штенгеля строго
вертикально. На практике это происходит не во всех случаях, и ртуть, ударяясь о стенки
капилляра, частично остается в штенгеле, частично теряется. После отпайки раскаленный
штенгель с остатками ртути, как и механически теряемая ртуть, поступают в
демеркуризационный раствор, которым заливается пол в откачном зале. От момента отпайки и
до поступления в раствор штенгель является источником интенсивного выделения паров ртути
в воздух.
Пары ртути поступают в производственную среду при откачке воздуха из лампы,
особенно в тех случаях, когда лампа по тем или иным причинам направляется на повторные
циклы откачки и введения ртути, а также при напаивании ламп, когда отключаются вакуумные
насосы. На линиях сборки нередко происходит растрескивание и разбивание стеклянных
трубок, что обусловливает потери ртути и выделение ее паров в воздух. Механические потери
металла и эмиссия его паров в воздух происходят также в ходе очистки (дистилляции) ртути,
при заправке автоматов-дозаторов и обслуживании дозировочных головок, при сборе
отпаянных и разбитых штенгелей, разбившихся ламп, а также при техническом обслуживании
вакуумных насосов и утилизации бракованных ламп. Интенсивной дегазации ртути
способствует повышенная температура воздуха в рабочих помещениях, достигающая на
линиях сборки ламп в теплое время года 40°С (при нормативной в 18°С) [36]. Как правило, на
российских заводах количество ртути, теряемой в ходе сборки люминесцентных ламп
(особенно при откачке ламп), составляет от 30 до 40% от общей массы потребляемого металла.
Воздух цеха сборки ламп отличается высокими концентрациями паров ртути. Например,
из 856 замеров, выполненных в течение 2001 г. на линиях сборки ламп Смоленского
электролампового завода, в 85% случаев фиксировались средние содержания паров ртути,
превышающие максимально разовую предельно допустимую концентрацию (ПДКmax) в 8 раз
(при вариациях от 4 до 15 ПДКmax) [36]. Наиболее высокие уровни паров ртути отмечались у
откачных полуавтоматов. На последующих операциях (цоколевание, тренировка, испытание,
упаковка ламп), где нет контакта с металлической ртутью, содержание ее паров в воздухе было
меньше, но тем не менее находилось в пределах 2-5 ПДКmax. Как правило, в других помещениях
электроламповых заводов также стабильно отмечаются высокие концентрации паров ртути
(табл. 3.39, 3,40, рис. 3.11). Цех сборки люминесцентных ламп характеризуется наличием
вторичных источников поступления ртути в воздух (строительные конструкции и
технологическое оборудование, в том или ином количестве со временем депонирующие
металл), которые в условиях повышенной температуры, свойственной данному производству,
постоянно эмитируют ртуть в окружающее пространство.
Таблица 3.39 Концентрация паров ртути в воздухе помещений Смоленского электролампового з-да*
Технологическая операция, рабочее помещение |
Концентрация паров ртути в воздухе рабочей зоны, мкг/м³ |
Средняя (максимальная), 2001 г. |
Средняя (пределы), I кв. 2003 г. |
Сборка люминесцентных ламп |
Мойка трубок и нанесение люминофора |
2,8 (5) |
2,1 (1,9-2,3) |
Заварка трубок |
3 (7) |
2,3 (2,1-2,5) |
Очистка ртути |
16 (50) |
23,5 (21-27) |
Откачка ламп |
66,3 (150) |
79,8 (37-110) |
Наладка откачного полуавтомата |
54,6 (180) |
79,4 (44-100) |
Обслуживание вакуумных насосов |
50 (98) |
нет данных |
Цоколевание ламп |
43,9 (74) |
58 (31-83) |
Тренировка ламп |
32 (54) |
49,1 (19-76) |
Испытание ламп |
15 (30) |
22 (8,7-32) |
Отдел технического контроля |
6 (16) |
нет данных |
Упаковка ламп |
1,5 (2) |
1,5 |
Вспомогательные подразделения |
Утилизация бракованных ламп |
37 (57) |
22,3 (12-27) |
Компрессорная станция |
4 (5) |
0,72 |
Водородная станция |
2,5 (5) |
0,75 |
Кислородная станция |
2,1 (4) |
0,4 |
Социальные объекты |
Прачечная (стирка спецодежды) |
6 (8) |
2 |
Столовая спецпитания |
4,8 (9) |
3,8 (2,8-5) |
Заводская поликлиника |
2,3 (4) |
2,3 (1,3-3) |
Нормативные и фоновые содержания паров металлической ртути в воздухе |
ПДКСС (рабочая зона, среднесменная) |
5 |
ПДКMAX (рабочая зона, максимальная) |
10 |
ПДКА (атмосферный воздух населенных мест) |
0,3 |
Типичное фоновое содержание |
0,010-0,015 |
* Здесь и далее первичные фактические данные по Смоленскому электроламповому заводу,
послужившие основой для расчетов и оценок, предоставлены Центрами Госсанэпиднадзора в
Смоленской области и г. Смоленске.
Таблица 3.40 Динамика изменения концентраций паров ртути в воздухе у откачного
полуавтомата, Смоленский электроламповый завод *
18 декабря 2001 г. |
27 апреля 2002 г. |
21 февраля 2003 г. |
Время суток |
Ртуть, мкг/м³ |
Время суток |
Ртуть, мкг/м³ |
Время суток |
Ртуть, мкг/м³ |
925-950 |
95 ± 23 |
1000-1025 |
100 ± 20 |
840-905 |
58 ± 15 |
- |
- |
1030-1055 |
117 ± 29 |
910-1035 |
63 ± 16 |
- |
- |
1100-1125 |
100 ± 26 |
940-1005 |
69 ± 17 |
- |
- |
1130-1155 |
89 ± 22 |
1015-1040 |
70 ± 17 |
1230-1255 |
54 ± 14 |
1200-1225 |
70 ± 18 |
1045-1110 |
78 ± 18 |
- |
- |
1230-1255 |
56 ± 14 |
1115-1140 |
71 ± 17 |
- |
- |
1300-1325 |
270 ± 68 |
1200-1225 |
70 ± 17 |
- |
- |
1330-1355 |
75 ± 19 |
1230-1255 |
60 ± 15 |
1400-1425 |
110 ± 28 |
1400-1425 |
84 ± 21 |
1300-1325 |
100 ± 25 |
- |
- |
1430-1555 |
329 ± 80 |
- |
- |
Средняя |
86 |
Средняя |
129 |
Средняя |
71 |
Максимальная |
110 |
Максимальная |
329 |
Максимальная |
100 |
Минимальная |
54 |
Минимальная |
70 |
Минимальная |
58 |
* В зоне дыхания рабочих (на высоте 1-2 м от пола).
Интенсивность загрязнения заводских помещений ртутью иллюстрируется данными о
частоте возникновения у рабочих профессиональных заболеваний (хронической ртутной
интоксикации) (рис. 3.12). Так, на Саранском электроламповом заводе диагноз
“профессиональная ртутная интоксикация” установлен 287 работникам (в том числе, в 1996-
2001 г.г. - 86 работникам), из которых более 90% составляют женщины. Наиболее подвержены
ртутной интоксикации работники основных профессий - откачницы (31%), заварщицы (15%),
цоколевщицы (14%). На Смоленском заводе с 1970 по 2001 г. у рабочих отмечено 67 случаев
возникновения хронической ртутной интоксикации (в том числе в 1997-2001 г.г. - 5 случаев)
[36]. Ежегодно фиксируется до 30-90 носителей ртути, т. е. работников, у которых ртуть в
повышенных концентрациях обнаруживается в моче, как правило, на один-два порядка выше
фонового (нормального) уровня.
![Рисунок 3.11 Распределение среднегодовых концентраций паров ртути в воздухе откачного зала цеха сборки люминесцентных ламп Саранского электролампового завода. (В 1988-1989 г.г. здесь были выполнены демекуризационные мероприятия, ликвидированы многие вторичные источники ртути; регулярно стала осуществляться текущая демеркуризация помещений.) [277, с дополнениями].](images/s102a.gif)
Рисунок 3.11 Распределение среднегодовых концентраций паров ртути в воздухе откачного зала цеха сборки люминесцентных ламп Саранского электролампового завода. (В 1988-1989 г.г. здесь были выполнены демекуризационные мероприятия, ликвидированы многие вторичные источники ртути; регулярно стала осуществляться текущая демеркуризация помещений.) [277, с дополнениями].
![Рисунок 3.12 Динамика возникновения хронической ртутной интоксикации у работников Саранского электролампового завода [277, с дополнениями].](images/s102b.gif)
Рисунок 3.12 Динамика возникновения хронической ртутной интоксикации у работников
Саранского электролампового завода [277, с дополнениями].
Распределение и потери ртути при производстве люминесцентных ламп
В табл. 3.41 приведены исходные данные, характеризующие производство
люминесцентных ламп, использование ртути и образование отходов на Смоленском
электроламповом заводе (ОАО “Свет”, г. Смоленск) в 1998-2002 г.г. и за первый квартал 2003
г. Они послужили основой для расчетов баланса распределения и потерь ртути при
производстве указанных ламп (табл. 3.42).
Процесс изготовления люминесцентных ламп на Смоленском заводе отличается
большими абсолютными и удельными потерями ртути, которые составляли в рассматриваемый
период 30-35% от массы используемого металла, или 17-28 мг на одну кондиционную лампу.
Большая часть потерь происходит на линиях сборки ламп и приходится на механически
теряемую металлическую ртуть, затем аккумулирующуюся в ловушках канализации, откуда
она извлекается форвакуумными насосами и отправляется на вторичную переработку
(очистку), а также на ртуть, содержащуюся в ртутной ступпе. Потери ртути со стеклобоем и
сточными водами невелики. Следует отметить, что мелкодисперсная металлическая ртуть,
поступающая в ртутную канализацию (до 3,6% от массы используемого металла), заводской
аналитической лабораторией в стоках не фиксируется. В то же время, в сточных водах,
отводимых в городскую канализацию, визуально наблюдаются капли металлической ртути,
которая в конечном счете теряется безвозвратно, что может быть связано с недостаточно
эффективной работой ртутных ловушек. Не менее 3-4% от применяемого количества ртути
выбрасывается в атмосферу, главным образом, в виде ее паров.
В 2001 г. на Смоленском заводе было использовано 2596,09 кг ртути, из которых 1765,34
кг поступили в кондиционную продукцию, а 830,75 кг составили технологические потери (68%
и 32% от общего потребления соответственно). “Неучтенные потери” ртути (33,7 кг) в
сущности должны быть распределены пропорционально среди других видов потерь металла.
Однако, с учетом данных, полученных для Саранского электролампового завода (см. ниже),
распределение указанных потерь можно представить следующим образом: 1 кг ртути поступает
в атмосферу в составе промышленной пыли, 3 кг металла остается в пыли, уловленной
очистными установками, 13,2 кг - аккумулируется в ловушках ртутной канализации, 3,3 кг - в
виде мелкодисперсной ртути теряется в канализацию, 0,006 кг сбрасывается со стоками
(растворенные и взвешенные формы металла), а около 13,2 кг дегазируется в воздух
помещений и (через дверные и оконные проемы, особенно в теплое время года) поступает в
атмосферу, сорбируется строительными конструкциями, одеждой и обувью рабочих и т. д.
Таблица 3.41 Производство люминесцентных ламп, использование ртути и образование отходов
на Смоленском электроламповом заводе в 1998-2003 г.г.
Год |
Производство ламп, шт. |
Общее потребление ртути, кг * |
Общие поте-ри ртути, кг |
Уловленная ртуть, кг |
всего |
доля брака, % |
фильт-рами ** |
УДЛ-750*** |
1998 |
25 583 100 |
7,2 |
1900,8 |
665,3 |
20,8 |
178,6 |
1999 |
29 373 300 |
7 |
2177,65 |
740,4 |
25 |
198,7 |
2000 |
35 743 500 |
7,1 |
2602,8 |
833 |
21,75 |
223,5 |
2001 |
38 333 500 |
7,1 |
2596,09 |
830,75 |
22 |
223,0 |
2002 |
38 114 100 |
7 |
2421,64 |
726,5 |
16,2 |
195,0 |
2003, I кв. |
10 459 000 |
7 |
550 |
165 |
3,3 |
44,3 |
Продолжение табл. 3.41
Год |
Выбросы ртути в атмосферу, кг **** |
Стеклобой***** |
Сточные воды цеха сборки ламп |
т |
Ртуть, г/т |
Общий объем, м³ |
Ртуть, мкг/л ****** |
1998 |
62,4 |
45 |
1,4 |
110 145 |
1,2 |
1999 |
75 |
48 |
1,4 |
88 025 |
0,95 |
2000 |
87 |
75 |
1,4 |
118 902 |
0,77 |
2001 |
88 |
75 |
1,5 |
156 385 |
1 |
2002 |
92 |
79 |
2 |
166 648 |
1,8 |
2003, I кв. |
22,5 |
25 |
1,6 |
43 269 |
- |
* Цех по изготовлению люминесцентных ламп пущен в эксплуатацию в 1970 г., в 1970-1975 г.г.
потребление ртути здесь достигало 6 т/год.
** Фильтры общеобменной вентиляции цеха сборки ламп (активированный угль, модифицированный
йодистым калием; они никогда не заменялись; их эффективность сейчас составляет 20-25%).
*** Установка демеркуризации (утилизации) бракованных ламп, штенгелей, разбитых ламп и др. (в
настоящее время продукт их переработки - ртутная ступпа с содержанием ртути 60-75% в
полиэтиленовых мешках вывозится на заводской полигон отходов, где размещается в бункере
временного хранения).
**** После фильтров общеобменной вентиляции.
***** После демеркуризации на УДЛ-750 (стеклобой вывозится на свалку).
****** Растворенная в воде ртуть (мелкодисперсная металлическая ртуть, поступающая в конечном
счете в канализацию, анализом не фиксируется); сточные воды сбрасываются в городскую канализацию.
Расчетный баланс распределения потерь ртути на Смоленском заводе в 2001 г. приведен в
табл. 3.43. Большая часть потерь - это механические потери ртути, которая перехватывается
ловушками ртутной канализации; значительная доля ртути извлекается из бракованных изделий;
более 102 кг ртути (3,9% общего ее потребления) выбрасывается в атмосферу, почти 97 кг (3,7%)
поступает в канализацию, более 226 кг (8,7%) вывозится на заводской полигон отходов (на
временное хранение). Таким образом, в окружающую среду, в конечном счете, поступает более
425 кг ртути, т. е. почти 16,4% от применяемой в технологическом процессе, более 199 кг ртути
(около 7,7% общего потребления), рассеиваясь в среде обитания, теряется безвозвратно. Усилия
по совершенствованию технологии, в первую очередь автоматов-дозаторов, в последние годы,
предпринимаемые на ОАО .Свет., способствует снижению удельных потерь ртути (табл. 3.44).
Таблица 3.42, Баланс распределения ртути на Смоленском заводе (общее потребление ртути =
100%)
Год |
Потери ртути |
Количе- ство конди- ционных ламп, шт. |
Среднее со- держание ртути в одной лампе, кг |
Ртуть, поступившая в конечную продукцию |
Общие, кг |
Доля от использов анной, % |
кг |
% от использованно й |
1998 |
665,3 |
35 |
23 73 2000 |
52,06 |
1235,5 |
65 |
1999 |
740,4 |
34 |
27 324 000 |
52,60 |
1437,25 |
66 |
2000 |
833 |
32 |
33 188 000 |
53,33 |
1769,8 |
68 |
2001 |
830,75 |
32 |
35 626 000 |
49,55 |
1765,34 |
68 |
2002 |
726,5 |
30 |
35 455 000 |
47,81 |
1695,14 |
70 |
2003, I кв. |
165 |
30 |
9 729 000 |
39,57 |
385 |
70 |
Продолжение табл. 3.42
Год |
Ртуть в ртутной ступпе |
Ртуть, уловленная фильтрами цеха |
Технологические потери ртути |
Выбросы в атмосферу |
Сточные воды * |
кг |
% от использов анной |
кг |
% от использов анной |
кг |
% от использова нной |
кг |
% от использова нной |
1998 |
178,6 |
9,4 |
20,8 |
1,09 |
62,4 |
3,28 |
0,132 |
0,006 |
1999 |
198,7 |
9,12 |
25 |
1,15 |
75 |
3,44 |
0,084 |
0,004 |
2000 |
223,5 |
8,59 |
21,75 |
0,84 |
87 |
3,34 |
0,095 |
0,004 |
2001 |
223 |
8,59 |
22 |
0,85 |
88 |
3,39 |
0,156 |
0,006 |
2002 |
195 |
8,05 |
16,2 |
0,67 |
92 |
3,80 |
0,3 |
0,012 |
2003, I кв. |
44,3 |
8,05 |
3,3 |
0,60 |
22,5 |
4,09 |
0,08 |
0,015 |
Окончание табл. 3.42
Год |
Технологические потери ртути |
Стеклобой |
В канализацию ** |
Прочи е потери , кг *** |
в том числе |
Механические |
Неучтенные |
кг |
% от использо ванной |
кг |
% от использо ванной |
кг |
% от использо ванной |
кг |
% от использо ванной |
1998 |
0,063 |
0,003 |
68,4 |
3,6 |
335,2 |
310,05 |
16,33 |
24,7 |
1,3 |
1999 |
0,067 |
0,003 |
78,4 |
3,6 |
363,15 |
334,85 |
15,38 |
28,3 |
1,3 |
2000 |
0,105 |
0,004 |
93,7 |
3,6 |
406,85 |
373,05 |
14,33 |
33,8 |
1,3 |
2001 |
0,113 |
0,004 |
93,5 |
3,6 |
403,98 |
370,28 |
14,26 |
33,7 |
1,3 |
2002 |
0,158 |
0,007 |
87,2 |
3,6 |
335,64 |
304,14 |
12,56 |
31,5 |
1,3 |
2003, I кв. |
0,04 |
0,007 |
19,8 |
3,6 |
74,98 |
67,78 |
12,33 |
7,2 |
1,3 |
* Растворенные формы ртути.
** Мелкодисперсная металлическая ртуть, поступающая в канализацию (расчет сделан на основе
данных, приводимых в [277]).
*** Подавляющую часть (до 95%, как свидетельствуют ниже приводимые данные по Саранскому
электроламповому заводу) составляет металлическая ртуть, которая улавливается ловушками ртутной
канализации (так называемые механические потери ртути).
Саранский электроламповый завод (.Лисма-СЭЛЗ.), в силу особенностей
технологического процесса, отличается большим потреблением ртути, более высокими
абсолютными и удельными ее потерями и, соответственно, более сложными санитарно-
гигиеническими условиями[7]. Здесь в 2001 г. изготовлено 35000000 кондиционных
затраты металлической ртути на производство одной люминесцентной лампы, согласно
расчетам, основанным на нормативах предельно допустимых выбросов [224], составляют
101,14 мг, из которых 30-40% ртути (в среднем 35%) терялось в ходе технологических
процессов (во многом из-за несовершенства автоматов-дозаторов). Таким образом, в одну
люминесцентную лампу в среднем поступает 65,74 мг ртути, а потери металла при
изготовлении ламп достигают 1366 кг. Еще 236 кг металла присутствует в 3590000
бракованных ламп, переработанных в 2001 г. на установке УДЛ-750 [84], т. е. общие
технологические потери ртути на Саранском электроламповом заводе составляют 1602 кг.
Таблица 3.43 Баланс технологических потерь ртути на Смоленском электроламповом заводе в
2001г.
Виды потерь ртути |
Потери ртути |
Примечание |
кг |
Доля, % |
от общих потерь |
от использо вания |
Твердые отходы, подлежащие переработке |
Некондиционная металлическая ртуть (механические потери) |
383,48 |
46,16 |
14,77 |
По имеющимся сведениям, отправляется на вторичную переработку |
Ртуть, содержащаяся в ртутной ступпе, - продукте демеркуризации брака и загрязненного стеклобоя |
223 |
26,84 |
8,59 |
В настоящее время ртутная ступпа в полиэтиленовых мешках вывозится на заводской полигон отходов и размещается в бункере временного хранения |
Фильтры воздухо-очистного оборудования цеха сборки люминесцентных ламп |
22 |
2,65 |
0,85 |
Ртуть остается на фильтрах, которые не менялись в течение всего времени функционирования завода |
Ртуть в пыли, уловленной очистными установками |
3 |
0,36 |
0,12 |
Пыль вывозится на свалку (?) |
Твердые отходы, направляемые на свалку |
Стеклобой (после демеркуризации) |
0,113 |
0,01 |
0,004 |
Вывозится на свалку |
Безвозвратные потери ртути в канализацию |
Сточные воды (растворенная ртуть) |
0,161 |
0,02 |
0,006 |
Сбрасываются в городскую канализацию |
Мелкодисперсная металлическая ртуть |
96,8 |
11,65 |
3,73 |
Поступает в канализацию, где частично аккумулируется, частично уходит в городскую канализацию |
Безвозвратные потери ртути в атмосферу |
Организованный выброс паров ртути (через вентиляционную систему цеха сборки ламп) |
88 |
10,6 |
3,38 |
Поступают во внешнюю среду (городскую атмосферу) |
Неорганизованный выброс паров ртути в воздух |
13,2 |
1,59 |
0,51 |
Поступают в атмосферу через дверные и оконные проемы, сорбируется строительными конструкциями, одеждой и обувью рабочих и т. п. |
Ртуть в промышленной пыли |
1 |
0,12 |
0,04 |
Поступает в атмосферу в составе пыли, образующейся в производстве |
ИТОГО |
830,75 |
100 |
32 |
|
Таблица 3.44 Удельные потери ртути на Смоленском электроламповом заводе
Год |
Эмиссия паров ртути в атмосферу (до очистки выбросов) * |
Удельные потери ртути, мг/лампа |
кг |
доля от используемой ртути, % |
на одну лампу, мг |
общие |
механическ ие |
в канализа цию |
1998 |
83,2 |
4,38 |
3,51 |
28,03 |
13,45 |
2,98 |
1999 |
100 |
4,59 |
3,66 |
27,10 |
12,65 |
2,97 |
2000 |
108,75 |
4,18 |
3,28 |
25,10 |
11,64 |
2,92 |
2001 |
110 |
4,24 |
3,09 |
23,32 |
10,76 |
2,72 |
2002 |
108,2 |
4,47 |
3,05 |
20,49 |
8,92 |
2,55 |
2003, I кв. |
25,8 |
4,69 |
2,65 |
16,96 |
7,25 |
2,11 |
* Количество ртути, поступающее в атмосферу, определяется эффективностью очистки выбросов.
Данные по Смоленскому заводу показывают, что в ходе технологических процессов
около 4,5% от общего количества потребляемой ртути эмитируется в воздух, что для
Саранского завода составляет 176 кг металла. Из этого количества 22 кг ртути непосредственно
поступает в атмосферу города [256], а 154 кг, таким образом, улавливается угольными
адсорберами, которыми оборудована вентиляционная система цеха сборки ламп (в течение
последних 10-15 лет адсорберы несколько раз модернизировались и даже заменялись;
например, в 2001 г. был введен в строй новый адсорбер). По данным [84], в 2001 г. на
Саранском электроламповом заводе было собрано и отправлено на вторичную утилизацию
1000 кг отработанной ртути (в основном это ртуть, механически теряемая в ходе производства
и затем извлекаемая из ловушек ртутной канализации). По Н.А. Степанову [277], на Саранском
заводе из общей массы используемой в производстве ртути в среднем 3,6% ее количества
уходит в канализацию, минуя ртутные ловушки, главным образом, в виде мелкодисперсной
металлической ртути. В 2001 г. такие потери ртути составили 141 кг. Сточные воды цеха
сборки люминесцентных ламп Саранского завода поступают на заводские локальные очистные
сооружения и затем (по городской канализации) подаются на очистные сооружения г.
Саранска, после чего сбрасываются в водоток (в р. Инсар). Ежегодно на локальных очистных
сооружениях Саранского электролампового завода образуется порядка 300 т шлама, средняя
концентрация ртути в котором достигает 300 мг/кг [325, 327], т. е. в нем накапливается до 90 кг
ртути. В осадках сточных вод, образующихся на городских очистных сооружениях (около 25
тыс. т сухого вещества в год), уровни ртути в среднем составляют 4 мг/кг, т. е. в них ежегодно
аккумулируется до 100 кг ртути, существенная часть которой, безусловно, поступает со
сточными водами электролампового завода [324, 330]. Около 15 кг ртути ежегодно
сбрасывается с общегородских очистных сооружений в р. Инсар.
Изложенные сведения позволяют следующим образом представить баланс распределения
ртути на Саранском электроламповом заводе (табл. 3.45).
Таблица 3.45 Баланс распределения ртути на Саранском электроламповом заводе в 2001 г. (общее
использование ртути = 100%) *
Общее потреб л ние, |
Общие потери |
Распределение ртути в ходе технологических процессов |
Поступило в товарную про- дукцию |
Выбросы в воздух |
В воздух рабочей зоны (до очистки) |
в том числе |
уловлено адсорберами *** |
в атмос- феру |
кг |
кг |
% |
кг |
% |
кг |
% |
кг |
% |
кг |
% |
3903 ** |
1602 |
41,05 |
2301 |
58,95 |
176 |
4,5 |
154 |
3,9 |
22 |
0,6 |
Продолжение табл. 3.45
Распределение ртути в ходе технологического процесса |
Ушло в кана- лизацию **** |
УМеханические потери ***** |
УУловлено УДЛ-750 ****** |
УНеучтенные потери |
кг |
% |
кг |
% |
кг |
% |
кг |
% |
141 |
3,6 |
1000 |
25,6 |
236 |
6,1 |
49 |
1,3 |
* Такое распределение ртути во многом типично для деятельности завода в 1999-2002 г.г..
** В 1980-х - начале 1990-х г.г. общее потребление ртути на заводе достигало 5-5,5 т/год [40].
*** Очистное оборудование цеха сборки ламп (используются W-образные адсорберы, содержащие по
1 т активированного угля, периодически орошаемого соляной кислотой).
**** Преимущественно в виде мелкодисперсной металлической ртути, не улавливаемой ртутными
ловушками.
***** Ртуть, аккумулирующаяся в ловушках ртутной канализации.
****** Ртутная ступпа.
Как уже отмечалось, неучтенные потери ртути представляют собой закономерную
балансовую неувязку подобных расчетов, которая, таким образом, должна быть распределена
пропорционально среди основных видов потерь металла. Тем не менее в значительной мере
неучтенные в данном случае потери ртути могут быть связаны с неорганизованными
выбросами ее паров, с сорбцией их оборудованием и строительными конструкциями, одеждой
и обувью рабочих, пылью, образующейся в ходе технологических процессов, а также со
стеклобоем. Так, Саранский электроламповый завод выбрасывает в атмосферу примерно 68-70
т/год твердых веществ (промышленной пыли), еще около 240 т пыли улавливается очистным
оборудованием. Среднее содержание ртути в промышленной пыли завода составляет 12 мг/кг
[333], т. е. с ней поступает в среду обитания до 1 кг ртути, а около 3 кг металла находится в
уловленной очистными установками пыли; 24 кг в виде мелкодисперсной ртути теряется в
канализацию, 0,3 кг в форме растворенной ртути сбрасывается со сточными водами, 0,2 кг
концентрируется в стеклобое, а 20,5 кг дегазируется в воздух помещений и (через дверные и
оконные проемы) поступает в соседние помещения и во внешнюю среду, сорбируется
строительными конструкциями, одеждой рабочих и т. п. Перенос ртути на одежде и обуви
рабочих имеет определенное гигиеническое значение. Установлено, что дети, родители
которых работали на Саранском электроламповом заводе, отличались более высокими (в 3-5
раз) уровнями ртути в волосах, нежели дети работников других предприятий города [323, 328,
331].
Расчетный баланс ртути на Саранском заводе в 2001 г. приведен в табл. 3.46.
Таблица 3.46 Баланс технологических потерь ртути на Саранском электроламповом заводе в 2001
г.
Виды потерь ртути |
Технологические потери ртути |
Примечание |
кг |
Доля, % |
от общих потерь |
от использовани я |
Твердые отходы, подлежащие переработке |
Некондиционная металлическая ртуть (механические потери) |
1000 |
62,42 |
25,62 |
Отправляется на вторичную переработку |
Ртуть, содержащаяся в ртутной ступпе, - продукте демеркуризации брака и загрязненного стеклобоя |
236 |
14,73 |
6,05 |
В настоящее время ртутная ступпа, судя по всему, вывозится на свалку |
Фильтры воздухо-очистного оборудования цеха сборки ламп |
154 |
9,61 |
3,95 |
Ртуть остается на фильтрах |
Ртуть в пыли, уловленной очистными установками |
3 |
0,19 |
0,08 |
Вывозится на свалку (?) |
Твердые отходы, направляемые на свалку |
Стеклобой (после демеркуризации) |
0,2 |
0,01 |
0,005 |
Вывозится на свалкуу |
Безвозвратные потери ртути в канализациюу |
Сточные воды (растворенная ртуть) |
0,3 |
0,02 |
0,008 |
Поступают на локальные очистные сооружения, затем - в городскую канализациюу |
Мелкодисперсная металлическая ртуть |
165 |
10,3 |
4,23 |
Частично аккумулируется в ртутной канализации, частично осаждается со шламами на локальных очистных сооружениях, частично уходит в городскую канализациюу |
Безвозвратные потери ртути в атмосферуу |
Организованный выброс паров ртути (через вентиляционную систему цеха сборки ламп) |
22 |
1,38 |
0,56 |
Поступают во внешнюю среду (городскую атмосферу)у |
Неорганизованный выброс паров ртути в воздух |
20,5 |
1,28 |
0,53 |
Поступают в атмосферу через дверные и оконные проемы, сорбируются строительными конструкциями и т. п.у |
Ртуть в промышленной пыли |
1 |
0,06 |
0,02 |
Поступает в атмосферу в составе пыли, образующейся в производствеу |
ИТОГО |
1602 |
100 |
41,05 |
|
Как видим, 43,5 кг ртути (1,11% от общей массы использованного металла) поступило в
атмосферу, более 165 кг (4,24%) ушло в канализацию; 239 кг ртути (более 10%) в составе
ступпы, пыли и стеклобоя вывезено на свалку, а 1000 кг некондиционной ртути отправлено на
вторичную переработку. Прямые безвозвратные потери металла (в атмосферу и в канализацию)
составили 208,8 кг (5,4% от общего количества использованной ртути). Существенная часть
ртути, выбрасываемой в атмосферу, осаждается непосредственно в пределах заводской
территории, где в верхнем слое почвогрунтов за 40-летний период функционирования завода
накопилось до 1 т ртути [325]. Удельные потери ртути на Саранском заводе закономерно
намного выше, нежели на Смоленском (табл. 3.47).
Таблица 3.47 Удельные потери ртути при производстве люминесцентных ламп
Потери ртути |
Ртуть, мг/на одну лампу |
Саранский завод |
Смоленский завод |
Общие |
45,77 |
23,32 |
Механические потери |
33,29 |
10,76 |
В канализацию |
4,72 |
2,72 |
В воздух (до очистки выбросов), пары ртути |
5,61 |
3,09 |
Смоленский и Саранский электроламповые заводы в 2001 г. использовали на
изготовление ртутных ламп в общей сложности 6,5 т ртути, т. е. около 87% общего
потребления металла российской электроламповой промышленностью. Остальное количество
его было использовано в производстве ртутных ламп на Саранском заводе специальных
источников света и электровакуумного стекла (“СИС-ЭВС”) и “Лисма-ВНИИИС” (в сумме
около 500 кг) и на ряде других предприятий (также 500 кг ртути). Для оценки баланса ртути на
этих предприятиях использовались данные по структуре распределения ртути в ходе
технологических процессов, установленные для Смоленского завода (табл. 3.48).
Таблица 3.48 Баланс распределения ртути на других российских электроламповых предприятиях
в 2001 г., кг
Распределение ртути |
СИС-ЭВС и ВНИИИС * |
Остальные |
В конечную продукцию |
340 |
340 |
Общие технологические потери, в том числе: |
160 |
160 |
Некондиционная металлическая ртуть (механические потери) |
73,9 |
73,9 |
Ртуть, содержащаяся в ртутной ступпе |
42,9 |
42,9 |
Ртуть, уловленная фильтрами воздухо-очистного оборудования ** |
19,3 |
19,3 |
Ртуть в пыли, уловленной очистными установками |
0,6 |
0,6 |
Стеклобой (после демеркуризации) |
0,01 |
0,01 |
Растворенная ртуть (сточные воды) |
0,03 |
0,03 |
Мелкодисперсная металлическая ртуть (в канализацию) |
18,6 |
18,6 |
Организованный выброс паров ртути (после очистки) ** |
2,2 |
2,2 |
Неорганизованный выброс паров ртути в воздух |
2,6 |
2,6 |
Поступление ртути с выбросами пыли в атмосферу |
0,2 |
0,2 |
* Расположены рядом в северной промышленной зоне г. Саранска, до 90% ртути используется на
“СИС-ЭВС”.
** Рассчитано при эффективности очистки в 90%.
В табл. 3.49 приводятся данные, характеризующие общий баланс ртути, использованной
в 2001 г. российской электроламповой промышленностью. Как видим, технологические потери
металла велики и составляют 2753 кг (36,7% от общего его количества), при этом более 1007 кг
ртути утеряно безвозвратно (выбросы в атмосферу, потери в канализацию, захоронение
твердых отходов на свалках) (табл. 3.50). Если твердые отходы, вывозимые на свалку,
размещаются, как правило, в особых бункерах, которые в определенной мере сдерживают
миграцию металла в окружающую среду, то ртуть, поступающая с выбросами в атмосферу и
сбросами в канализацию (в сумме около 0,5 т), в конечном счете рассеивается в среде обитания.
Таблица 3.49 Баланс распределения ртути в российской электроламповой промышленности в 2001
г.
Показатель |
кг |
% от общего потребления |
Общее потребление ртути, в том числе: |
7500 |
100 |
В конечную продукцию |
4747 |
63,3 |
Технологические потери |
2753 |
36,7 |
Структура технологических потерь ртути: |
|
кг |
% от потребл. |
% от потерь |
Твердые отходы, подлежащие переработке |
Некондиционная металлическая ртуть (механические потери) * |
1531 |
20,4 |
55,6 |
Ртуть, содержащаяся в ртутной ступпе, - продукте демеркуризации брака и загрязненного стеклобоя ** |
544,8 |
7,3 |
19,8 |
Ртуть, уловленная фильтрами воздухо-очистного оборудования *** |
214,6 |
2,9 |
7,8 |
Ртуть в пыли, уловленной очистным оборудованием **** |
7,2 |
0,1 |
0,3 |
Твердые отходы, направляемые на свалку |
Стеклобой (после демеркуризации) ***** |
0,3 |
0,004 |
0,01 |
Безвозвратные потери ртути в канализацию |
Ртуть, растворенная в сточных водах |
0,5 |
0,006 |
0,01 |
Мелкодисперсная металлическая ртуть ****** |
299 |
4 |
10,8 |
Безвозвратные потери ртути в атмосферу |
Организованный выброс паров ртути (через вентиляционную систему цеха сборки ламп; после прохождения фильтров) |
114,4 |
1,5 |
4,2 |
Неорганизованный выброс паров ртути в воздух ******* |
38,9 |
0,5 |
1,4 |
Ртуть в промышленной пыли, выбрасываемой в атмосферу |
2,4 |
0,02 |
0,08 |
* По имеющимся сведения, направляется на вторичную переработку (очистку).
** В настоящее время в основном размещается на свалках в бункерах временного хранения.
*** На некоторых предприятиях сорбенты, улавливающие ртуть, иногда заменяются, использованные
отправляются на вторичную переработку.
**** Уловленная пыль вывозится на свалку.
***** Вывозится на свалку, где размещается в бункерах временного хранения.
****** Ртуть, которая не улавливается ловушками ртутной канализации.
******* В воздух рабочей зоны и во внешнюю среду.
Таблица 3.50 Поступление ртути в окружающую среду от электроламповой промышленности,
2001г.
Поступление ртути |
Ртуть, кг |
Доля, % |
В атмосферу (в виде паров металла и в составе пыли) * |
155,7 |
15,5 |
В канализацию (растворенная ртуть сточных вод и мелкодисперсная металлическая ртуть) ** |
299,5 |
29,7 |
В почвы (вывоз на свалку ртутной ступпы, стеклобоя, уловленной пыли) *** |
552,3 |
54,8 |
Итого |
1007,5 |
100 |
* 98,5% - парогазовая фракция.
** 99,8% - мелкодисперсная металлическая ртуть.
*** 98,6% в составе ртутной ступпы.
3.8.2 Российский рынок ртутных ламп
Основные потребители светотехнической продукции в России оцениваются следующим
образом: промышленность - 50-55%; сельское хозяйство - 7-8%; административные, торговые и
др. общественные здания - 10-11%; бытовой сектор (в т. ч. жилые здания) - 22-23%; наружное
освещение - около 1%; прочие - около 2% [70]. Ртутные лампы дают до 60-65% всего
искусственного светового потока, генерируемого в России. Если основываться на данных для
бывшего СССР [3], то сейчас в России эксплуатируется около 140 млн. светильников с
люминесцентными лампами низкого давления и до 13 млн. - с разрядными лампами высокого
давления.
В 2001 г в ассортименте розничной торговли доля отечественных ламп составляла 40%,
остальное количество приходилось на импортную продукцию, [223]. Если ориентироваться на
номенклатуру изделий, предлагаемых крупными российскими торговыми компаниями,
работающими с импортной электроламповой продукцией, то существенную долю ее
составляют лампы люминесцентные, дуговые, металлогалогенные, натриевые высокого
давления, а также компактные люминесцентные лампы. Некоторые зарубежные фирмы
поставляют в Россию газоразрядные лампы для полиграфии, телевидения и пр. Электролампы в
Россию ввозят и продают 62 страны, в том числе даже не имеющие собственного производства
(например, Австралия, Новая Зеландия, Лихтенштейн). Только в Москве и Московском регионе
работает около 1900 коммерческих фирм, многие из которых практически полностью
ориентированы на зарубежного производителя и которые покрывают до 50% потребностей
местного рынка [3]. В 2001 г. российский рынок источников света зарубежного производства в
существенной мере определяли такие фирмы, как Osram, Philips, Tungosram, General Electric,
Silvania [19, 223, 238], а также Narva, OMS, BLV Licht, Vakuumtechnik, Aura и др. Следует
отметить, что эффективность работы ртутных ламп, выпускаемых ведущими зарубежными
фирмами, значительно выше, нежели изготавливаемых на отечественных заводах; к тому же,
импортные лампы отличаются намного меньшим содержанием ртути.
Точные данные о российском импорте и экспорте электроламп отсутствуют. В ежегодно
издаваемых сборниках “Таможенная статистика внешней торговли Российской Федерации”
импорт и экспорт электроламп не разделяется по их типам и оценивается в денежном
эквиваленте, что не позволяет определить реальное количество изделий. Можно лишь отметить,
что основными импортерами в России ртутных ламп в последние годы являлись Украина,
Германия, Венгрия, Польша, Тайвань и Финляндия [280, 281]. Большая часть российского
экспорт ртутных ламп приходится на Финляндию, Литву и Казахстан, объем которого достигает
нескольких миллионов штук в год (условно 10 млн. шт. в 2001 г., содержащих около 500 кг
ртути).
По данным ассоциации “Российский свет”, объединяющей большую часть российских
производителей светотехнической продукции, до августа 1998 г. поставки зарубежных фирм
перекрывали объемы производства четырех средних российских электроламповых заводов
[238]. В то время в России функционировало 6 электроламповых заводов, причем лишь два из
них - в Саранске и в Уфе (производство ламп накаливания) - могут быть отнесены к крупным
заводам, а остальные четыре - в Смоленске, Калашникове, Владикавказе и Томске - в общей
сложности производили около 170 млн. шт. всех типов ламп в год. Если ориентироваться на
оценку ассоциации “Российский свет”, то объем импорта электроламп в Россию был примерно
равен этому количеству. Однако, по данным той же ассоциации, в 1998 г. в Россию было
импортировано 42 млн. лампочек, а в 1999 г. - всего лишь 13 млн. шт. [238]. Необходимо
отметить, что в России конца 1990-х г.г. до 45-55% объема рынка импортного
светотехнического оборудования составлял так называемый “черный товар”, существенная
часть которого представляла собой явную контрабанду [70]. Более того, “черный” импорт и
сейчас продолжает играть большую роль на российском светотехническом рынке [3].
Сказанное (с учетом внутренних российских потребностей) позволяет считать, что в 2001
г. в страну было завезено несколько десятков миллионов ртутных ламп различного типа (до 20-
30 млн. шт.). При среднем содержании ртути в одной лампе в 20 мг (рассчитано по [341]) это
дает порядка 400-600 кг ртути (среднее 500 кг).
Утилизация использованных ртутных ламп
В 2001 г. не менее чем в 50 субъектах Российской Федерации функционировало около 60
предприятий (станций или центров демеркуризации), ориентированных на утилизацию
вышедших из строя ртутных (прежде всего, люминесцентных) ламп. В ряде областей страны
имелись организации, специализирующиеся на сборе и транспортировке отработанных
ртутных ламп к местам их переработки (обычно в соседние регионы). Примерно в 30 областях
России действуют региональные и местные нормативные акты, определяющие порядок учета,
сбора, хранения, транспортировки и утилизации вышедших из строя ртутных ламп. Тем не
менее, во многих районах страны отсутствовала какая-либо система сбора и утилизации
использованных ртутных ламп (регионы Северного Кавказа, некоторые области Центральной
России, Республики Карелия и Коми, Вологодская, Камчатская и Сахалинская области и др.).
Анализ состояния существующей в России системы утилизации ртутных ламп позволяет
отметить следующее [137].
Во-первых, деятельность многих российских демеркуризационных предприятий основана
на не совсем верном представлении о том, что вся ртуть в отработавших люминесцентных
лампах находится в элементарной форме. В частности, установлено, что до 95% ртути в лампе,
бывшей в эксплуатации, связано с люминофором и примерно 3-5% металла от общего его
количества - со стеклом [152, 338]. В данном случае люминофор выполняет функцию
своеобразного барьера, концентрируя ртуть в разнообразных формах, некоторые из которых
прочно связываются его матрицей. Такое поведение ртути объясняется электрохимическими
эффектами и наличием в колбе работающей лампы плазмы “ртуть/разряженный газ”.
Во-вторых, эффективность работы станций демеркуризации обычно оценивается с
позиций предотвращения возможного ртутного загрязнения среды обитания (говоря проще,
количеством переработанных изделий). В то же время предприятия по утилизации ртутных
ламп, являясь с экологической точки зрения объектами повышенной опасности, обязаны
осуществлять свою деятельность в соответствие с существующими требованиями [244-246].
Это предполагает проведение регулярного аналитического контроля (сырья, производственной
и окружающей среды) на ртуть и другие ингредиенты, ведение паспортов на конечную
продукцию и отходы, статистической отчетности, в том числе, по балансу сырья, материалов,
ртути, других поллютантов. Но, как правило, все названные условия и требования на практике
не выполняются.
В-третьих, практически ни одна из отечественных станций демеркуризации
технологически не готова получать из ртутных ламп вторичную ртуть, что в существенной
мере обусловлено высокой стоимостью соответствующих установок. Главный конечный
продукт, получаемый при переработке ртутных ламп, - ртутная ступпа (содержащая до 60-75%
ртути) лишь в исключительных случаях отправляется на вторичную переработку для
извлечения из нее металла. В большинстве случаев, судя по всему, она размещается на
полигонах отходов в так называемых бункерах временного хранения.
В 2001 г. на многих отечественных предприятий по утилизации ртутных ламп
использовались установки, в основу которых положены термический или термовакуумный
способы переработки (демеркуризации) ламп; на некоторых - применялся
гидрометаллургический способ, только на одном – “сухая и холодная” вибропневматическая
технология.
Гидрометаллургический метод предусматривает промывку предварительно механически
раздробленных люминесцентных ламп водным раствором и основан на реакциях окисления-
восстановления, теоретически обусловливающих перевод элементарной ртути в
труднорастворимые соединения или в соединения, легко поддающиеся дальнейшей
утилизации. На практике для этих целей используется раствор хлорного железа. С точки зрения
химии в данном случае должна образовываться труднорастворимая каломель. Однако раствор
хлорного железа эффективен в отношении только элементарной ртути, тогда как в
отработанных люминесцентных лампах ртуть находится в разнообразных соединениях,
фиксируясь преимущественно люминофором и отчасти стеклом. Это и определяет тот факт, что
способам, основанным на водной отмывке (которую следует осуществлять в строго
скорости реакции и невысокая степень очистки люминофора и стекла от ртути. В связи с этим
рекомендуют осуществлять многократную промывку ламп растворами, что, однако, не
исключает вероятности перераспределения ртути между тремя ее окислительными
состояниями (Hgo, Hg22+, Hg2+). Более того, при не соблюдении герметичности процесса,
особенно при многократной промывке, ртуть способна окисляться до двухвалентной формы
(Hg2+), в заметных количествах переходить в раствор и образовывать устойчивые комплексы, в
том числе хлорид двухвалентной ртути (сулему). Все это обусловливает необходимость
создания специальных систем очистки промывных вод с целью получения шлама,
концентрирующего извлеченную из ламп ртуть. Этот шлам (вместе с труднорастворимым
осадком) должен отправляться на дальнейшую переработку. Однако на практике, как правило,
никаких дорогостоящих систем очистки не применяется, а промывочные воды, содержащие
ртуть, сбрасываются в городскую канализацию. Остатки плохо отмытой от ртути смеси стекла,
люминофора и металлических деталей вывозятся на свалку. На этом процесс, в сущности лишь
имитирующий демеркуризацию ртутных ламп, завершается.
Термический способ утилизации ртутных ламп основан на возгонке ртути из смеси
стеклянного и металлического лома с последующим улавливанием и конденсацией ее паров.
Он положен в основу отечественных установок УДЛ-100, УДЛ-150, УДЛ-750 (разработки
бывшего ВНИИВМР, ныне НИЦПУРО) и УДМ-3000, УДМП-630 (НПК “Меркурий”).
Термовакуумный метод реализован в установке типа УРЛ-2м (фирма “ФИД-ДУБНА”),
принцип действия которой основан на вакуумной дистилляции ртути с вымораживанием ее
паров на поверхности криогенной ловушки. Несмотря на определенные достоинства обоих
широко используемых в России способов и на декларируемые их разработчиками
экологическую чистоту технологического процесса и демеркуризационных установок в целом
[242], последние, тем не менее, сложны в эксплуатации. Они достаточно энергоемки, требуют
высоких температур, надежных систем сорбции ртути из отходящих газов, не исключают
вероятности выброса газов в атмосферу при нарушении герметичности в стыках
технологических трактов и т. д. Еще один их недостаток заключается в образовании не только
ртутной ступпы, но и еще нескольких конечных продуктов, что обусловливает частичное
рассеивание извлекаемой из ламп ртути и ее поступление в среду обитания [137].
В настоящее время во многих странах мира находят практическое применение методы
утилизации ртутных ламп, основанные на следующих принципах: 1) на полном отказе от
применения высокотемпературных и «мокрых» технологий, т. е. в ходе переработки ламп не
образуются выбросы и стоки, поступающие в окружающую среду, что существенно снижает
вероятность вторичного загрязнения среды обитания ртутью и другими поллютантами; 2) на
получении как можно меньшего числа конечных продуктов переработки, что резко уменьшает
вероятность “распыления” ртути по различным материальным носителям; 3) на учете того
факта, что ртуть в отработанных лампах в наибольшем количестве связана с люминофором, что
обусловливает необходимость его отделения и перевода в своеобразное сырье для получения
вторичной ртути.
В нашей стране подобная “холодная и сухая”вибропневматическая технология
переработки люминесцентных ламп разработана и внедрена в практику в начале 1990-х г.г. на
установке “Экотром-2”, принцип действия которой основан на разделении ламп на главные
компоненты: стеклобой, алюминиевые цоколи, содержащий ртуть люминофор. Отделение
люминофора - главного депонента ртути - от стекла осуществляется за счет выдувания и
отсасывания его в противоточно движущихся системах “стеклобой-воздух” в условиях
вибрации. Стекло поступает в специальный бункер, откуда пневмотранспортом удаляется в
особый накопитель. Воздух поэтапно очищается от люминофора (циклон, рукавный фильтр,
кассетный фильтр, производственный адсорбер, цеховой адсорбер, санитарный адсорбер).
Обдувка люминофора с рукавных фильтров осуществляется сжатым воздухом.
Ртутьсодержащий люминофор, а также отработанный активированный уголь из систем
очистки, обтирочная ветошь и т. п. смешиваются с цементом и водными растворами
(образующихся в процессе периодически проводимой в санитарно-гигиенических целях
демеркуризации рабочего помещения и накапливаемых в специальном приемнике) и
обрабатывается особым веществом, переводящим большую часть ртути в ее устойчивую форму
- сульфид ртути. Балансовые расчеты показывают, что данная технология позволяет извлекать
из ламп и прочно фиксировать до 95-96% содержащейся в них ртути. По сведениям
пользователей указанной установки, образующаяся цементно-люминофорная смесь,
расфасованная в полиэтиленовые мешки, отправляется на переработку для получения
вторичной ртути; стеклянная крошка - на предприятия, производящие строительные блоки:
алюминиевые цоколи - используются как вторичное сырье.
В 1999-2002 г.г. в Москве и Московской области ежегодно перерабатывалось порядка 7
млн. ртутных (главным образом люминесцентных) ламп. Кроме того, в этом регионе на
десятках тысяч мелких предприятий и организаций в год образуется не менее 2,5 млн. шт.
отработанных люминесцентных ламп, которые из-за сложностей сбора не утилизируются, а
хранятся в помещениях или вывозятся на свалки [132]. Таким образом, в Москве и Московской
области в течение года используются (выходят из строя) не менее 9,5 млн. ртутных ламп (около
0,7 на одного городского жителя). Если рассчитать ежегодное количества ртутных ламп,
выходящих из строя в Чувашии, где, как и в Москве, достаточно хорошо организована система
их сбора и утилизации, с использование указанного показателя, то получается 673 тыс. ламп.
Показательно, что, по имеющимся сведениям [115], здесь (в Чебоксарах) ежегодно
перерабатывается до 700 тыс. ламп (включая незначительное количество ламп из соседних
регионов). В Башкирии за первые 9 месяцев 2001 г. было утилизировано 1,5 млн. ламп [314],
что при таких темпах дает 1,9 млн. ламп в год (примерно 0,7 лампы на одного городского
жителя республики).
Полученный удельный показатель (0,7 лампы на одного городского жителя) может,
очевидно, использоваться для расчета количества выходящих из строя ламп для других
регионов страны и для России в целом. Расчеты показывают, что в России в последние
несколько лет ежегодно выходит из строя порядка 72 млн. ртутных ламп (из которых около 3
млн. шт. - лампы высокого давления). В этих лампах (в основном отечественного производства)
содержится не менее 4 т ртути.
Сопоставление данных о количестве использованных ртутных ламп, полученных
расчетным путем, с реальными объемами учитываемых, складируемых и утилизируемых
изделий (примерно в 30 регионах России), показывает, что в 2001 г. в стране 40% вышедших из
строя ртутных (в основном, люминесцентных) ламп было переработано на станциях
демеркуризации, 20% размещено в специальных хранилищах на предприятиях и в
организациях, а остальные 40% в конченом счете были вывезены на свалки. Предполагается,
что при размещении боя люминесцентных ламп на полигонах ТБО 5% ртути (в газовой фазе)
незамедлительно выделяется в атмосферу. Оставшаяся ртуть может рано или поздно
высвободиться в окружающую среду с территории полигона, к сожалению, такие данные о
выбросах ртути с полигонов ТБО отсутствуют.
Расположение основных российских заводов по производству ртутных ламп,
гальванических элементов и термометров показано на рис. 3.13.
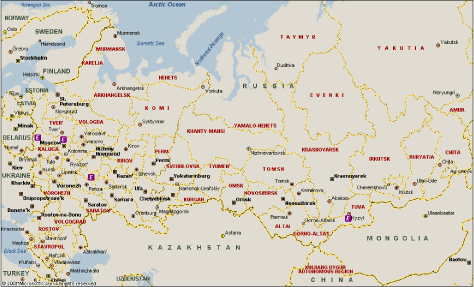
Рисунок 3.13 Расположение основных российских заводов по производству ртутных ламп,
гальванических элементов и термометров.
Заключение
Таким образом, в 2001 г. в России общее потребление ртути в производстве источников
света составило 7,5 т. Из этого количества металла более 36% было утеряно в ходе
технологических процессов.
Обобщенная схема баланса распределения ртути при производстве и использовании
ртутных ламп в 2001 году приведена на рис. 3.14.
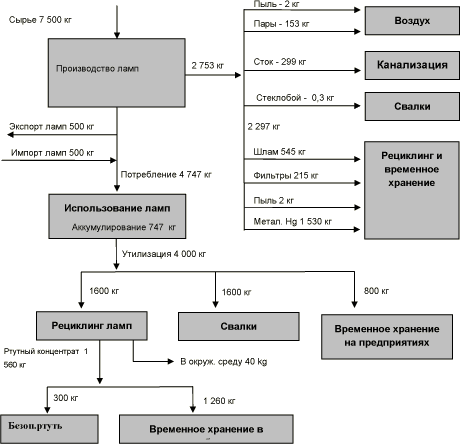
Рисунок 3.14 Баланс распределения ртути в производстве и использовании ртутных ламп в России
в 2001 г.
3.9 Переключатели и другие электроприборы
Ртутные переключатели
Электрический переключатель представляет собой устройство, предназначенное для
коммутации электрических цепей в различных установках, системах дистанционного и
автоматического управления и т. д. В СССР широким распространением пользовались ртутные
переключатели, представляющие собой стеклянные баллончики с впаянными в них контактами
и содержащими определенное количество металлической ртути.
В СССР (России) основным производителем ртутных переключателей являлся Клинский
завод термометров, ныне ОАО “Термоприбор“ (табл. 3.51). Во второй половине 1990-х г.г.
серийное изготовление ртутных переключателей в России было прекращено.
Таблица 3.51 Содержание ртути в основных типах выключателей, производимых в России [182,
199]
Марка |
Содержание ртути, граммы |
Переключатель ПР-3А (пятиконтактный) |
4,393 |
Переключатель ПР-4 “Меркойд” (четырехконтактный) |
6,249 |
Переключатель ПР-5 (двухконтактный) |
3,365 |
Переключатель ПР-8 (двухконтактный плунжерный) |
4,807 |
Переключатель-ПР-12 (плунжерный) |
23,46 |
Переключатель ПР-13 |
14,73 |
Переключатель ПР-15 (кольцевого типа) |
14,73 |
Переключатель ПР-17, ртутно-магнитный двухконтактный (для инкубаторов) |
0,89 |
Переключатель специальный ПР-18а (двухконтактный) |
11,89 |
Переключатель ПР-20 (кольцевого типа) |
8,4 |
Выключатель ВРМ-5 РП-7 (ртутно-магнитный), выпускался в 2-х исполнениях |
0,879 |
Среднее |
8,526 |
В настоящее время ртутные переключатели (выключатели) в той или иной мере по-
прежнему используются в различных длительно эксплуатируемых устройствах, в том числе, в
бытовых электрических звонках. По данным НПП “Экотром”, в последние годы на утилизацию
(главным образом от крупных предприятий и организаций г. Москвы) ежегодно поступало до
2000 ртутных переключателей (выключателей, датчиков). Количество таких изделий, ежегодно
используемых (выбрасываемых) в частном секторе и в небольших организациях учету не
поддается. Можно с большой долей условности предположить, что в целом по стране
количество ежегодно выводимых из строя ртутных переключателей достигает нескольких
десятков тысяч штук (содержащих не менее 0,5 т ртути). Из этого количества утилизируется не
более 10-15% процентов, т. е. примерно 400 кг ртути в конечном счете поступает на свалки
отходов.
По данным [409], в 2001 г. в США практически на каждом произведенном автомобиле
были установлены ртутные переключатели (размещаемые под капотом и под крышкой
багажника), число которых достигало 14 млн. шт. Среднее количество ртути в одном
автомобильном переключателе составляет примерно 0,8 г. В 2002 г. импорт легковых
автомобилей в Россию составил 127 тыс. штук [26]. Доля автомашин, поставляемых
непосредственно из США, не превышает 5%. Однако, не исключено, что на автомобилях,
завозимых из других стран, также установлены ртутные датчики (в том числе, в сигнально-
охранном оборудовании). Отсюда следует, что с такими изделиями на территорию России
завозится, по крайней мере, несколько десятков килограмм ртути.
Ртутные вентили
Ртутный вентиль - обобщенное название ионных приборов самостоятельного дугового
разряда, пропускающих ток только в одном направлении, с одним катодом, заполненным
жидкой ртутью, с одним (одноанодный вентиль) или несколькими (многоанодный вентиль)
рабочими анодами и с одним или несколькими вспомогательными электродами,
предназначенными для зажигания дуги. По методу управления моментом зажигания дугового
разряда ртутные вентили разделяются на игнитроны (со вспомогательным электродом,
управляющим моментом зажигания основного дугового разряда) и экситроны (с однократным
возбуждением катодного пятна). Игнитроны используются в ионных электроприводах,
импульсных модуляторах, электросварочной аппаратуре, а также в различной коммутационной
аппаратуре. Экситроны предназначены для преобразования тока промышленных и
повышенных частот, а также применяются в качестве коммутатора в индуктивных накопителях
энергии и в линейных модуляторах.
Многоанодный ртутный вентиль или комплект одноанодных ртутных вентилей,
объединенных в одно конструктивное целое и предназначенных для преобразования
переменного тока в постоянный, называют ртутным выпрямителем. В свое время (до начала
1980-х г.г.) ртутные выпрямители в массовом порядке использовались в промышленных
установках (выпрямительных агрегатах) разной мощности и различного назначения, на
транспортных тяговых подстанциях (обслуживающих трамвайные и троллейбусные линии,
метро, железные дороги), на магистральных электровозах переменного тока, для коммутации и
регулирования тока сварочных машин, для электролиза в цветной металлургии и химической
промышленности и др.
Содержание ртути в игнитронах изменяется от 10-250 г до 2-5 кг. Например, в
игнитронах типа И-70, И-140, И-200, И-350 количество ртути варьируется от 0,25 до 1 кг.
В бывшем СССР ртутные вентили и ртутные выпрямители в разное время серийно
производились на Тольяттинском электротехническом заводе (г. Тольятти), Таллинском заводе
ртутных выпрямителей (г. Таллин), Таганрогском металлургическом заводе (г. Таганрог), на
заводах “Электросила” (г. Санкт-Петербург), “Электровыпрямитель” (г. Саранск), “Динамо” (г.
Москва), “Уралэлектротяжмаш” (г. Екатеринбург) и др.
В конце 1970-х г.г. серийное (промышленное) производство ртутных вентилей и ртутных
выпрямителей было прекращено. Во многом это связано с тем, что в 1960-1970-х г.г. в СССР на
транспортных тяговых электростанциях и в промышленных установках различного назначения
ртутные выпрямители в массовом порядке были заменены выпрямителями на твердых
полупроводниках.
Тем не менее на некоторых предприятиях все еще эксплуатируются установки, в которых
применяются ртутные вентили (особенно игнитроны). Более того, согласно данным
таможенной статистики [281], еще в 1999 г. в Россию в определенном количестве
импортировались игнитроны и ртутные выпрямители. В Интернете встречаются объявления о
том, что, например, совместное белорусско-литовское предприятие “Бел-Ока” предлагает к
продаже на территории России выпрямители ртутные с жидкометаллическим катодом и
выпрямители ртутные с катодом прямого накала. Есть также сведения, что на некоторых
российских заводах осуществляется разовое (“штучное”) изготовление ртутных вентилей
(игнитронов). Общий объем их производства, судя по всему, не превышает нескольких
десятков приборов в год, на изготовление которых расходуется до 150-200 кг металлической
ртути.
Следует отметить, что на многих предприятиях не используемые в производстве ртутные
вентили хранятся на складах и периодически сдаются на утилизацию. Например, в 1999-2002
г.г. в НПП “Экотром” (г. Москва) из различных московских организаций и с предприятий
поступало до 300 игнитронов в год, из которых получали до 130-140 кг отработанной ртути. В
целом для страны это может составлять порядка 4 тыс. ртутных вентилей в год, содержащих до
3 т ртути, которая обычно отправляется на очистку и затем возвращается в производство.
Вакуумные насосы
В свое время ртуть широко использовалась как рабочая жидкость в вакуумных
парортутных насосах, т. е. устройствах, предназначенных для создания, повышения и
поддержания вакуума. Парортутные насосы применялись на насосно-аккумуляторных станциях
различных предприятий, но главным образом для откачки ртутных систем (например, ртутных
выпрямителей), а также в научно-исследовательских лабораториях. Количество ртути,
содержащееся в одном парортутном насосе, достигало 13-15 кг. Заливка ее в насосы в ходе их
эксплуатации производится вручную с помощью воронки. В процессе эксплуатации
пароструйных насосов нередки аварийные ситуации, что сопровождается выбросом
металлической ртути в окружающую среду, о чем в свое время (особенно в конце 1980-х г.г.)
часто сообщалось в печати. Обычно в помещениях, где работают паровакуумные насосы,
уровни содержания паров ртути в воздухе существенно превышают ПДК.
В настоящее время парортутные насосы по-прежнему используются на некоторых
российских предприятиях.
Заключение
В табл. 3.52 приводятся обобщенные данные по использованию ртути в выключателях и
других приборах.
Таблица 3.52 Потребление и выбросы ртути в процессе производства и использования других
приборов, т
Ртутьсодержащие изделия |
Количестко ртути, использованное для производства изделий в 2001 г. |
Количество ртути, содержащееся в используемых продуктах (на 2001 г.) |
Количество ртути, выбрасываемое на свалки с использованным и продуктами, 2001 г. |
Выключатели |
Не выпускались |
Данные отсутствуют |
Не менее 0,45 |
Вентили |
0,15-0,20 |
Данные отсутствуют |
Данные отсутствуют |
Барометры * |
Не выпускались |
5-6 |
Данные отсутствуют |
Сфигмоманометры |
Не выпускались |
Не менее 0,3 |
Данные отсутствуют |
Манометры * |
Не выпускались |
Данные отсутствуют |
Данные отсутствуют |
Вакуумные насосы |
Не выпускались |
Данные отсутствуют |
Данные отсутствуют |
* Определенное количество ртути используется ежегодно для заполнения метеорологических
барометров и манометров (десятки килограммов ?).
3.10 Производство химикатов и лабораторное использование ртути в
России
3.10.1 Производство ртутных химикатов
Официальная статистика о производстве и торговле ртутными химикатами в России
отсутствует. Анализ существующих “Бизнес-книг” и рекламных материалов свидетельствует о
том, что основными производителями ртутных соединений, которые поставляют эту
продукцию на российский рынок, являются ОАО “Алтайхимпром” (г. Славгород), ЗАО “НПП
“Кубаньцветмет” (Краснодарский край) и ООО .Мерком. (Московская область). Как правило,
производство ртутных соединений осуществляется по прямым заказам различных предприятий
и организаций. Есть сведения, что Институт проблем микроэлектронных технологий и особо
чистых веществ (ИПМТ РАН) совместно с ЗАО “Ртуть”, разработали технологию производства
чистых соединений ртути, таких, например, как Hg2(NO3)2 – 2H2О, Hg(NO3)2 – H2O, HgSО4,
Hg2Cl2, HgO и др. [345] В настоящее время имеющиеся производственные мощности позволяют
синтезировать до 50 кг указанных соединений в месяц. Башкирский инновационный центр
“«Содействие” (г. Уфа) предлагает услуги по изготовлению различных соединений ртути за 1-2
дня, включая те, которые уже поставляются на рынок, например, нитрат ртути Hg(II), роданид
ртути Hg(II), сульфат ртути Hg(II), ацетат ртути Hg (II). НПО “Химпроект” (г. Уфа) предлагает
для продажи ацетат ртути (II).
Оксид ртути (II) и хлорид ртути (I) используются в основном в промышленном
производстве (винилхлорида и гальванических элементов соответственно); прочие
ртутьсодержащие химикаты, судя по всему, - главным образом в лабораторной практике.
Выпуск соединений ртути ЗАО “НПП “Кубаньцветмет”
В табл. 3.53 приведены сведения об объемах производства различных соединений ртути
ЗАО “Кубаньцветмет” в 2001-2002 г.г. Основную массу изготовленных соединений составляет
хлорная ртуть, поставляемая предприятиям по производству винилхлорида (г. Волгоград). В
2003 г. по заказу ОАО “Энергия” (г. Елец) было произведено 500 кг красного оксида ртути и
120 кг хлорида ртути.
Таблица 3.53 Производство ртутных соединений ЗАО .НПП .Кубаньцветмет. в 2001-2002 г.г., кг *
Соединение |
2001 |
2002 |
Основной потребитель |
Хлорная ртуть (I)2 |
15491 |
12715 |
Предприятия, производящие винилхлорид (г. Волгоград) |
Хлорная ртуть (II) |
- |
2,6 |
Организации, торгующие реактивами |
Бромная ртуть (II) |
2 |
0,4 |
Организации, торгующие реактивами |
Йодная ртуть (II) |
5 |
7 |
Организации, торгующие реактивами |
Сернокислая ртуть (II) |
10 |
51 |
Организации, торгующие реактивами |
Азотнокислая ртуть (I), двухводная |
10 |
198,5 |
Организации, торгующие реактивами |
Азотнокислая ртуть (II) двухвалентная |
320 |
1520 |
Организации, торгующие реактивами (ООО “Реактив”, г. Невинномыск, ООО “Экрос”, г. С.-Петербург и др.) |
Роданистая ртуть, тиоционат ртути (II) |
10 |
7,5 |
Организации, торгующие реактивами |
Уксуснокислая ртуть (II) |
10 |
- |
Организации, торгующие реактивами |
Оксид ртути (II) желтый |
- |
8 |
Организации, торгующие реактивами |
Оксид ртути (II) красный |
- |
0,2 |
Организации, торгующие реактивами |
Итого |
15858 |
14510,2 |
|
* Кроме указанных в таблице соединений, могут производиться амидохлорная ртуть (II), фтористая
ртуть (I), фтористая ртуть (II), ртуть пиросурьмянокислая (II), сульфид ртути (II).
Транспортировка ртути на участок производства ее соединений осуществляется в
специальных баллонах (автомашинами). Производство соединений ртути основано главным
образом на использовании гидрохимических способов. Помещения участка по производству
соединений ртути оборудованы угольными адсорберами АРВ и местной ртутной канализацией
(с ртутными ловушками).
Отработанный сорбент и собранная металлическая ртуть направляются на вторичную
переработку.
При производстве соединений ртути образуются также мягкие отходы. В частности, на
изготовление 1 т ртутных соединений расходуется 1 кг капронового или лавсанового
бельтинга. В год образуется порядка 20 кг таких отходов с содержанием ртути до 2% (по
массе). Они хранятся в кислотостойких и герметичных емкостях и по мере накопления
сжигаются в печи ТВП-1.
Выпуск соединений ртути ООО “Мерком”
В табл. 3.54 приведены сведения о производстве соединений ртути ООО “Мерком” в
2001-2002 г.г.
Таблица 3.54 Производство соединений ртути ООО “Мерком”, кг
Год |
Окись ртути |
Нитрат, Hg (I) |
Нитрат, Hg (II) |
Сульфат Hg |
Искусственная киноварь |
2001 |
75 |
30 |
0,3 |
0,3 |
0,8 |
2002 |
370 |
30 |
- |
- |
- |
Производство соединений ртути осуществляется в основном по прямым заказам
организаций и предприятий. В частности, большая часть окиси ртути была поставлена на
предприятие ОАО “Энергия” (Елец); другие соединения ртути выпускались главным образом
по заказам организаций, продающих химреактивы (включая “Мосхимреактив”). Небольшое
количество искусственной киновари было синтезировано для объединения художников (г.
Санкт-Петербург).
3.10.2. Использование ртутных соединений в лабораторной практике
Во времена Советского Союза все химикаты, включая ртутьсодержащие, закупались
через системы “Союзреахим”, в которую входили организации, выпускающие и продающие
указанную продукцию. После того как в 1990-х годах эта система перестала существовать, на
внутреннем рынке страны появилось около десятка компаний, занимающихся в основном
перепродажей химикатов.
В 2002 г. в России было выпущено не менее 1,8 т ртутьсодержащих химикатов, которые
используются в лабораторной практике (табл. 3.55). Кроме того, некоторые химикаты могут
импортироваться, однако надежной информации об их поставке в Россию получить не
удалось.. Общее содержание ртути в ртутьсодержащих лабораторных химикатах,
производимых в России в 2002 г., составляет порядка 1,2 т. Ртутьсодержащие химикаты,
которые применяются в качестве консервантов для вакцин, рассматриваются в разделе 3.11.
Таблица 3.55 Производство ртутных соединений в России в 2002 г. для использования в
лабораторной практике
Соединение |
Производство соединения, кг |
Содержание ртути, кг |
Хлорид ртути (II) |
2,6 |
1,9 |
Бромид ртути (II) |
0,4 |
0,2 |
Йодид ртути (II) |
7 |
3 |
Сульфат ртути (II) |
51 |
35 |
Нитрат ртути (I) |
230 |
166 |
Нитрат ртути (II) |
1520 |
942 |
Тиоцианат ртути |
7,5 |
5 |
Всего |
1818 |
1153 |
В 2001 г. перепродажей химикатов занимались несколько десятков компаний,
крупнейшими из которых являлись АО “Реахим” (г. Москва), АО “Химмед” (г. Москва), “Нева-Реактив”. (г. Санкт-Петербург) и некоторые другие. .
Ртуть и ее соединения представляют собой классические аналитические реагенты,
которые применяются в самых различных целях. Следует отметить, что ртуть используется в
лабораториях не только в виде химического вещества для анализа, но также в диффузных
вакуумных насосах, ртутных клапанах, термометрах, барометрах, манометрах, реометрах.
Такое применение описано в разделах, касающихся использования ртути в измерительных
приборах.
В табл. 3.56 приводится краткое описание некоторых сфер применения ртутных
соединений в аналитической химии и лабораторных целях.
Точные сведения о количестве ртутьсодержащих химикатов, приобретаемых в настоящее
время различными компаниями для лабораторного применения, отсутствуют, поскольку в
России нет соответствующих строгих отчетных требований для химико-аналитических и
исследовательских лабораторий об ежегодном использовании указанных химикатов и их
дальнейшей судьбе. Общее применение ртути (включая ртуть в химикатах) в лабораторной
практике в 2001 г. может быть оценено примерно в 2-5 т (наилучшая оценка составляет 3,5 т).
Таблица 3.56 Использование ртути и ее соединений в аналитической химии и лабораторной практике
*
Вещество |
Использование |
Металлическая ртуть |
Полярография, основанная на применении ртутных или амальгамных
капающих или струйчатых индикаторных электродов; маскирующий
агент при количественном определении органических нитратов;
определение чистоты фтора и его концентраций в газах; создание
сверхпроводимых материалов; разработка газоразрядных приборов;
ртутная порометрия; ртутная кулонометрия и электрохимические
преобразователи информации; для приготовления электродов сравнения. |
Органические соединения
ртути |
Определение органических дисульфидов; в лабораторном
органическом синтезе; в препаративной химии |
Реактив Несслера (щелочной
раствор K2[HgI4]) ** |
Для обнаружения и фотометрического определения аммиака (NH3),
для обнаружения спиртов и альдегидов, для идентификации (в
бумажной и тонкослойной хроматографии) гидроксиаминокислот *** |
HgCl2 |
Для идентификации тиррола; при нефелометрическом определении
диметилсульфида; для количественного определения цистеина
потенциометрическим титрованием; как катализатор при
гидрогалогенировании и получении пиридана. |
HgI2 |
Маскирующий агент при количественном определении органических
нитратов; компонент тяжелых жидкостей, используемых в
минералогическом анализе для разделения минералов по плотности, -
жидкость Туле (водный раствор двойной соли йодида ртути HgI2 +
2KI) и жидкость Шушина-Рорбаха (BaI2HgI2 x nH2O). |
Сульфат ртути, HgSO4 |
Для определения химической потребности в кислороде (ХПК) в
сточных водах; в лабораторной электрохимии. |
Оксиды ртути |
Окислители в препаративной химии; для определения титра кислот; в
лабораторном органическом синтезе; для получения некоторых
нитрозосоединений, гипохлоритов, органосилоксанов; для
приготовления электродов сравнения. |
Йодид ртути |
Для приготовления электродов сравнения. |
Hg2Cl2, каломель |
Для приготовления электродов сравнения. |
Фторид ртути, Hg2F2 |
Для приготовления электродов сравнения. |
Бромид ртути, Hg2Br2 |
Для приготовления электролитов. |
Дибромид ртути. HgBr+ |
В лабораторной электрохимии для изготовления катодов
концентрационного преобразования тока. |
Водные растворы Hg(NO3)2
или Hg(Cl04)2 |
В качестве титрантов в меркуриметрии (титриметрический метод
анализа анионов Cl-, Br-, SCN-, CN-). |
Водные растворы Hg2(NO3) |
В качестве титранта в меркурометрия (титриметрический метод
определения галогенидов). |
Hg(NO3)2 |
Катализатор для синтеза тетранитрометана (нитрирующего агента) |
Сульфат ртути HgSO4 или его
смесь с CuS04 или Se02 |
В качестве катализатора при определении азота в органических
соединениях методом Кьельдаля. |
Роданид (тиоцианат) ртути,
Hg(SCN)2 |
Аналитический реагент в роданометрии и меркуриметрии (в том числе,
для определения галогенидов, сульфидов, тиосульфатов, цианидов). |
Hg(ONC)2 |
Получение ароматических кетонов с использованием реакции Хёша |
Реактив Миллона (раствор
HgNO3 и Hg(NO3)2 в
разбавленной HNO3,
содержащей примесь HNO2) |
Цветная реакция на белки и фенолы |
Ацетат ртути, (CH3COO2)Hg |
В химии хинолизидина |
Hg(COOCH3)2, Hg(CN)2, HgO,
HgBr2) |
Катализаторы в реакции Кёнигса-Кнорра (синтез гликозидов и
олигосаридов) |
* Ртуть и ее соединения используются также в химии циклопропана, при обнаружения
ненасыщенности органических соединений и др., с использованием некоторых соединений ртути
осуществляют анализ (амперометрическим титрованием) тиохолина (серного аналога холина),
количественное определение глутамина и др ** Oсновной производитель в России “Уральский завод
химических реактивов” (г. Верхняя Пышма, Свердловская область).
Утилизация использованных химикатов
В соответствии с Инструкцией по мерам безопасности в химических лабораториях,
последние обязаны проводить нейтрализацию ртутьсодержащих отходов (до перехода их с 1
класса опасности до 4-го). Затем они - без сортировки - помещаются в контейнеры (обычно с
пометкой “органические” или “неорганические” отходы), которые транспортируются на
свалки. Как правило, крупные аналитические центры применяют описанную выше процедуру.
Небольшие лаборатории после нейтрализации сбрасывают использованные реагенты в
виде сильно разбавленных растворов в городскую канализацию. Учитывая выше приведенные
сведения, можно предположить, что на свалки и (в меньшей степени) в канализацию ежегодно
выбрасывается от 2 до 5 т ртути.
3.11 Ртутьсодержащие пестициды
Ртутьорганические соединения используют как фунгициды и протравители семян,
например гранозан и его смеси с гексахлорбензолом (меркурбензол) и гексахлорциклогексаном
(меркургексан).
Всего в России использовалось 14 наименований ртутьсодержащих пестицидов (табл.
3.57).
Таблица 3.57 Ртутные протравители семян, использовавшиеся в быв. СССР и России
Соединение – действующее вещество |
Торговое название |
Содержание ртути, % |
Этилртутьхлорид |
Гранозан, меркуран, меркурбензол, меркургексан, НИИУиФ-2 |
1,8-2,3 |
Этилртутьфосфат |
НИИУиФ-1 новый церазан |
Нет данных |
β-Метоксиэтилмеркурхлорид |
Аретан, агалол, успулун, церазан-универсальнасебайце |
Нет данных |
β-Метоксиэтилмеркураацетат |
Радосан |
2,5 |
1-(3-(Хлормеркур)-2 метаксипропилмочевина |
Неогидрин |
Нет данных |
Дициандиалидметил ртути |
Паноген |
Нет данных |
N-Этилмеркур-N-фенил-n-толуол-сульфамид |
Гранозан М, церозан М |
1,8-2,3 |
Фенилмеркурбромид |
Агронал |
1,8 |
Фенилмеркурацетат |
Лейтозан, радосан, руберон, фализан – 2,5, агрозан, церозан |
1,0 |
2,3-Диоксипропил-меркаптидэтил ртути |
Церазан-75 |
Нет данных |
S-Этилртуть-тиосалицилат натрия |
Мертиолат |
Нет данных |
Оксихинолинат метил ртути |
Орто Л. М. |
Нет данных |
Фенилртуть-мочевина |
Лейтозан |
5,0 |
Оксиртутьхлорфенол |
Семазан |
Нет данных |
3.11.1 Производство
Производство ртутьорганических пестицидов в СССР было начато на химическом заводе
“Синтез” в г. Дзержинске Нижегородской области в 1955 г. (5 т); уже к 1960 г. производилось
до 200 т в год. Через 20 лет это производство стало сокращаться и в 1989 г. снизилось до 50 т.
Производство гранозана на этом заводе было закрыто в 1989 г.
3.11.2 Действующие нормативные документы
О случаях отравления населения ртутьсодержащими пестицидами сообщалось вплоть до
1970-х г.г. В 1958-1964 г.г. описаны случаи отравления гранозаном у 422 жителей Пермской
[259], Новосибирской [42] и Челябинской [65] областей.
В 2001г. в результате пожара на складе ядохимикатов в Оренбургской обл. произошло
отравление ртутью 26 человек. По официальной информации Минздрава Российской
Федерации, концентрации ртути в атмосферном воздухе на расстоянии 300.400 м от места
пожара составили 54–90 мкг/м³ при ПДК 0,3 мкг/м³, т.е. было превышение нормативных
величин в 300 раз.
О необходимости запрещения гранозана было сообщено на научных конференциях в
Киеве Л.И. Медведем еще в 1957 г. Впоследствии необходимость запрета гранозана, как
вещества, обладающего эмбриотоксическим, гонадотоксическим и цитогенетическим
действием была обоснована в диссертации В.И. Вашакидзе. Применение ртутьсодержащих
пестицидов окончательно было запрещено в 1991 г.
В соответствии с Законом Российской Федерации .О безопасном обращении с
пестицидами и агрохимикатами. (от 19 июля 1997 г. № 109-ФЗ), “не допускается оборот
агрохимикатов, которые не внесены в Государственный каталог пестицидов и агрохимикатов,
разрешенных к применению на территории Российской Федерации”. В Государственных
каталогах пестицидов и агрохимикатов, разрешенных к применению на территории России,
которые публикуются ежегодно, ртутьсодержащие пестициды отсутствуют [87].
В статье 12 указанного выше закона определен порядок государственной регистрации
пестицидов, который проводится Госхимкомиссией – межведомственным органом при
Минсельхозпроде Российской Федерации. Уничтожение и обезвреживание пестицидов и тары
из-под них проводятся в соответствии с “Временной инструкцией по подготовке к захоронению
запрещенных и непригодных к применению в сельском хозяйстве пестицидов и тары из-под
них”.
Нормативы содержания пестицидов в окружающей среде содержатся в нормативном
документе Минздрава России ГН 1,1,546-96 “Гигиенические нормативы содержания
пестицидов в объектах окружающей среды” [61]. В этом документе регламентированы
содержания этилмеркурхлорида (гранозана):
- допустимая суточная доза – не нормирована;
- ПДК в почве - не нормирована;
- ПДК в воде водоемов – 0,001мг/л по санитарно-токсикологическому показателю
вредности;
- ПДК в воздухе рабочей зоны – 0,005мг/м³ (по ртути) при применении этого вещества;
- ПДК в атмосферном воздухе -0,005мг/м³ (по ртути) при применении этого вещества;
- максимально допустимый уровень в пищевых продуктах и сырье - – полное отсутствие
данного вещества.
Минздравом России в 2002 г. введены новые “Санитарные правила и нормы” -
СанПиН 1,2,1077-01 “Гигиенические требования к хранению, применению и
транспортированию пестицидов и ядохимикатов”. Указанным министерством гранозан
включен в Перечень вредных производственных факторов (Приказ № 1010 от 10.2.2003 №
49 “Об утверждении перечня вредных производственных факторов, при воздействии
которых в профилактических целях рекомендуется употребление молока и ли других
равноценных пищевых продуктов”).
Специализированным институтом Минсельхоза России ВНИПИ по технологии и
экономике хранения, транспортировки и механизации внесения в почву удобрений
(ВНИПИагрохим, г. Рязань) в 1997 г. изданы “Рекомендации по подготовке запрещенных и
непригодных к использованию пестицидов к обеззараживанию и захоронению”. Согласно
этому документу, ртутьсодержащие пестициды по принятой в России классификации
относятся к веществам 1-го класса гигиенической опасности и подлежат захоронению в
металлических контейнерах.
3.11.3 Использование ртутьсодержащих пестицидов
По данным Ежегодника Института экспериментальной метеорологии Росгидромета [171],
применение гранозана на некоторых территориях России составило (в тоннах
этилмеркурхлорида): в 1995 г. – 6,17 т, в 1996 г. – 5,5 т.
Эти данные весьма неполные и не отражают действительный объем используемых
ртутьсодержащих пестицидов. В 2001 г. Федеральный центр Госсанэпиднадзора Минздрава
России провёл через территориальные органы сбор данных о количестве обращаемых
пестицидов, выделив в отдельную графу ртутьсодержащие пестициды. Установлено, что
ртутьсодержащие пестициды в 2000 г. продолжали использовать в 15 регионах страны (табл.
3.58). В частности, было применено примерно до 50 т гранозана, т. е. в окружающую среду
попала примерно 1 т ртути (при среднем содержании ртути в гранозане 2%). В 2001 г. только в
4-х областях страны было использовано около 17 т ртутьсодержащих пестицидов. Безусловно,
данные за 2000 г. по Пензенской и Читинской областям где применялось в год до 12 т
гранозана, требуют уточнения. Необходимо также получить сведения за 2001 г. по регионам,
где гранозан использовался в 2000 г.
Таблица 3.58 Количество применяемых ртутьсодержащих пестицидов в 2000.2001 г.г. (по
данным вопросника ФЦГСЭН Минздрава России “О состоянии государственного
санитарного надзора за обращением пестицидов и агрохимикатов”)
Территория |
Количество, т |
2000 г. |
2001 г. |
Орловская область |
2,65 |
0,1 |
Курская область |
0,09 |
не использовались |
Воронежская область |
3,78 |
не использовались |
Саратовская область |
1,28 |
Нет данных |
Псковская область |
4,53 |
Нет данных |
Томская область |
1,58 |
не использовались |
Пензенская область |
12,98 (необходимо уточнение) |
Нет данных |
Калининградская область |
1,0 |
Нет данных |
Читинская область |
12,0 (необходимо уточнение) |
8,5 |
Кировская область |
1,5 |
нет данных |
Костромская область |
1,0 |
нет данных |
Рязанская область |
0,7 |
нет данных |
Республика Дагестан |
6,2 |
5,6 |
Кабардино-Балкария |
0,9 |
Нет данных |
Липецкая область |
нет |
2,7 |
Всего |
50,2 (37,2 без Пензенской обл.) |
16,9 |
Наглядное представление о значительном снижении количества применяемых
ртутьсодержащих пестицидов дают данные по Воронежской области (письмо Главного врача
Центра Госсанэпиднадзора в Воронежской области М.И. Чубирко от 15 мая 2003 г.). Здесь в
1998 г. использовано 17,4 т гранозана, в 1999 г. – 26,89 т, в 2000 г. – 3,78 т и с 2001 г. этот
пестицид не применяется.
Несмотря на запрет использования гранозана и отсутствие ртутьсодержащих пестицидов
в Каталоге, в Интернете размещены предложения о продаже этого вещества, например, на
сайте Российского биотехнологического рынка и на сайте Деловых объявлений – .Предлагаю
удобрение гранозан., 15 т, фасовка бочки по 25 кг (medbionic 2003).
Анализ данных о количестве применённых пестицидов, представленный в табл. 3.58,
указывает на явное несоответствие данных за 2001 г. по сравнению с 2000 г. Это объясняется
отсутствием данных по 8 из 15 территорий России, включённых в таблицу. От использования
ртутьсодержащих пестицидов в 2001 г. отказались только 3 региона страны, причём только те,
где пестициды применялись в относительно небольших объёмах (до 4-х т в год). Можно
предположить, что в целом по стране продолжает использоваться примерно 20.40 т
ртутьсодержащих пестицидов в год.
3.11.4 Условия хранения ртутьсодержащих пестицидов
До 1990 г. основные количества пестицидов хранились на складах объединения
“Сельхозхимия”. По данным Научно-исследовательского центра по проблемам управления
ресурсосбережением и отходами (НИЦПУРО), в настоящее время на территории страны может
находиться до 750 т ртутьсодержащих пестицидов, что в пересчете на ртуть составляет
примерно 10 т. Анализ различных официальных источников о количестве ртутьсодержащих
пестицидов показывает, что эта цифра возможна занижена. Например, в Докладе о состоянии
окружающей природной среды в Ростовской области за 1998 г. сообщается, что на территории
области находится до 550 т этих веществ.
В табл. 3.59 приведены данные вопросника ФЦГСЭН Минздрава России .О состоянии
государственного санитарного надзора за обращением пестицидов и агрохимикатов. и
некоторых других организаций о количестве хранящихся на территории России
ртутьсодержащих пестицидов. Из них следует, что количество ртутьсодержащих пестицидов
превышает 1500 т, часть из которых хранится на специальных полигонах. Возможно, что и это
неполные данные. Например, в результате тщательной инвентаризации, проведенной в
Тверской области, количество хранящихся здесь ртутьсодержащих пестицидов возросло с 34,7,
зарегистрированных в 1999 г., до 43,8 т в 2003 г. Можно предположить, что на складах
количество ртутьсодержащих пестицидов (без учета полигонов), которые нуждаются в
уничтожении или размещению на специальных полигонах, превышает 1000 т, в которых
содержится примерно 20 т ртути.
В условиях рыночной экономики многие предприятия .Сельхозхимии. прекратили
деятельность, поэтому над условиями хранения пестицидов в определенной степени был
потерян государственный надзор. Сельскохозяйственные предприятия не были в состоянии
складировать пестициды должным образом и обеспечивать безопасность складских
помещений. В различных публикациях сообщается [10, 56, 104, 262, и др.], что наибольшие
объемы (более чем 10 т) вышедших из потребления ртутьсодержащих пестицидов хранятся на
территориях Алтайского и Краснодарского краев, Белгородской, Воронежской, Курской,
Курганской, Новосибирской, Омской, Псковской, Ростовской, Рязанской, Саратовской,
Свердловской, Смоленской, Тверской, Тульской, Ярославской областях, республик Мордовия,
Башкортостан и Татарстан. В то же время, на некоторых территориях северо-западной части (в
Мурманской, Новгородской областях, республиках Карелии и Коми), северной (Якутия) и
южной части России (Калмыкия, Ингушетия, Осетия), а также на Дальнем Востоке
(Сахалинская и Камчатская области), по официальным данным, в настоящее время
ртутьсодержащие пестициды отсутствуют.
Значительной проблемой является состояние складов хранения пестицидов. Очень
сложно точно определить количество хранящихся ртутьсодержащих пестицидов, поскольку
многие сельскохозяйственные предприятия обанкротились, что совершенно разрушило систему
какого-либо учета этих ядовитых веществ. Для уточнения количества устаревших пестицидов,
в т. ч. ртутьсодержащих, проводится их инвентаризация. Например, в 2001 г. с этой целью был
реализован проект UNEP Chemical, Госхимкомисии Министерства сельского хозяйства РФ и
Центра международных проектов в 5 регионах страны (Краснодарский край, Рязанская,
Тверская, Брянская, Воронежская области); в 2002 г. инвентаризация проводится по линии
АСАР совместно с Госхимкомисией Министерства сельского хозяйства РФ в 10 северных
регионах (Архангельская, Мурманская, Магаданская, Тюменская, Омская, Камчатская области,
Алтайский край, Красноярский край, республики Коми, Якутия-Саха), т. е. за 2 года
осуществлена инвентаризация пестицидов в 15 регионах России. В двух из этих областях .
Тверской и Воронежской - в мае 2003 г. получена дополнительная информация о
ртутьсодержащих пестицидах.
Таблица 3.59 Количество ртутьсодержащих пестицидов на складах или на полигонах на
территории некоторых регионов России
Регион |
Количество, т |
Место хранения |
Источник |
Ростовская обл. |
До 500, или 8 т в пересчете на ртуть
+52,2 |
На полигоне захоронения устаревших пестицидов На складах агропредприятий |
Доклад о состоянии окружающей природной среды в Ростовской области за 1998 г. Тот же, за 1999 г. |
Кемеровская обл. |
До 300 |
Нет сведений |
По материалам Ежедневных новостей Кузбасса от 06.1.2001 |
Пензенская обл. |
270,9 |
Нет сведений |
ЦГСЭН |
Иркутская обл. |
101 |
Нет сведений |
|
Волгоградская обл. |
Более 59 |
Склад бывшей “«Сельхозхимии” |
Газета Московский комсомолец в Волгограде, №34, 2002 |
Воронежская обл. |
49,2 |
Бо. льшая часть – на складах бывшего объединения “Агропромхимия” |
ЦГСЭН |
Псковская обл. |
38,3 + агрозан 0,1 |
Нет сведений |
ЦГСЭН |
Саратовская обл. |
32,6 |
Нет сведений |
ЦГСЭН |
Костромская обл. |
31,9 гранозан + 0,05 агрозан |
Нет сведений |
ЦГСЭН |
Тверская обл. |
2001г. – 28,9, в т. ч. гранозан – 27,3 2003 г.-42,8 |
Нет сведений |
Станция защиты растений |
Ярославская обл. |
21,0 +15 т вывезено на полигон Красный Бор в Ленинградской обл. |
Нет сведений |
(Боровицкий и др., 2000) |
Тульская обл. |
20,0 + 6,75 гранозан в смеси с другими препаратами |
Нет сведений |
ЦГСЭН |
Амурская область |
17,8 |
Нет сведений |
|
Краснодарский край |
17,7 сильно действующих ядовитых пестицидов |
Нет сведений |
ЦГСЭН, ГУПР, [56] |
Татарстан |
15,6 |
Нет сведений |
ЦГСЭН |
Мордовия |
14,5 |
Нет сведений |
ЦГСЭН |
Рязанская |
13,5 |
Нет сведений |
ЦГСЭН |
Московская обл. |
12,5 |
Нет сведений |
|
Читинская |
12,0 |
Нет сведений |
ЦГСЭН |
Волгоградская |
11,5 |
Нет сведений |
ЦГСЭН |
Омская область |
11,3 |
На полигоне захоронения устаревших пестицидов |
|
Свердловская |
11,0 |
|
ЦГСЭН |
Томская |
9,7 |
Сельскохозяйственные предприятия области |
Департамент экологии Администрации Томской области, 15.4.03 |
Удмуртия |
8,4 |
Нет сведений |
ЦГСЭН |
Оренбургская |
7,35 |
Нет сведений |
ЦГСЭН |
Томская |
3,6 |
Нет сведений |
ЦГСЭН |
Магаданская область |
3,55 |
Нет сведений |
ЦГСЭН |
Курская |
2,1 |
Нет сведений |
ЦГСЭН |
Приморский край |
1,4 |
Нет сведений |
ЦГСЭН |
Смоленская |
1,1 |
Нет сведений |
ЦГСЭН |
Челябинская |
0,6 |
Нет сведений |
ЦГСЭН |
Ленинградская |
0,43 |
Нет сведений |
ЦГСЭН |
Вологодская |
0,2 |
Нет сведений |
ЦГСЭН |
Липецкая |
0,2 |
Нет сведений |
ЦГСЭН |
Орловская |
0,1 |
Нет сведений |
ЦГСЭН |
Москва |
0,07 |
Нет сведений |
ЦГСЭН |
Кировская |
0,01 |
Нет сведений |
ЦГСЭН |
Для уточнения ситуации с условиями хранения ртутьсодержащих пестицидов экспертами
в мае 2003 г. были посещены г. Тверь и некоторые районы Тверской области (описание
количества ртутьсодержащих пестицидов и условий их хранения приведены в Приложении 2).
Тверская и Воронежская области – это примеры областей, где прошла инвентаризация
устаревших пестицидов, и условия их хранения можно характеризовать как относительно
хорошие. На семинаре по устаревшим пестицидам, который в мае 2003 г. проводил для стран
СНГ Центр международных проектов МПР в рамках проекта UNEP Chemical, отмечалась также
хорошая работа по инвентаризации устаревших пестицидов на территории Краснодарского
края – одного из основных аграрных центров России. Однако на большинстве других
территорий ситуация с хранением ртутьсодержащих пестицидов значительно хуже, причем в
ряде случаев ее можно характеризовать как катастрофическую. Несколько примеров.
Так, на территории Алтайского края, по данным Центра Госсанэпиднадзора, в отдельных
районах применялся гранозан. Сейчас из 429 складов пестицидов 56% не отвечают санитарным
требованиям, а в 318 хозяйствах такие хранилища отсутствуют.
В Тульской области протравливанием семян занимаются более трети хозяйств области. В
области скопилось 400 т пестицидов; 80% складских помещений не соответствует санитарным
требованиям (в 2001 г. органами Госсанэпиднадзора выдано только 18% санитарных паспортов
или 7% от общего количества складов). За последние годы разрушено более 20 складов. Новые
склады не строятся , а проблема утилизация устаревших пестицидов не решена [94].
В Камчатской области отмечается крайне неудовлетворительно состояние мест
захоронения гранозана на Козельском могильнике в 35 км северо-восточнее Петропавловска, в
окружении которого в грибах обнаруживается ртуть. В Алтайском крае неудовлетворительно
состояние Курьинского полигона в 20 км от с.Курья.
В Волгоградской области только на одном складе ядохимикатов хранится 59 т гранозана,
причем доступ на территорию склада свободный, металлическая тара проржавела.
В Ростовской области в 1976 г. вблизи г. Батайска был построен полигон для захоронения
непригодных к применению в сельском хозяйстве пестицидов. В 1977.1978 г.г. на этом
полигоне произведено санкционированное захоронение более 1500 т ядохимикатов, собранных
в сельскохозяйственных и других предприятиях Северо-Кавказского региона, в том числе более
500 т гранозана (около 8 т в пересчете на ртуть). В настоящее время полигон закрыт и
захоронение пестицидов на нём не проводится. В районе расположения полигона с начала
1990-х г.г. значительно повысился уровень грунтовых вод, в результате чего в отдельные
периоды года происходит подтопление его основания, что не исключает вероятности миграции
токсичных компонентов в подземные воды.
В Челябинской области подлежит утилизации 114,5 т ядохимикатов. По заключению
Центра Госсанэпиднадзора, в области проблема утилизации пестицидов чрезвычайно актуальна
и с каждым годом обостряется. Это связано с децентрализацией базисных и расходных складов,
отсутствием должного контроля за их состоянием и средств на их ремонт, а также
невозможностью отправить пестициды за пределы области для их уничтожения. Обычно
основная масса протравителей в течение 5.6 месяцев хранится на трех базисных складах в
удовлетворительном состоянии. Затем в предпосевной) период гранозан в герметичной
упаковке продается хозяйственным организациям, которые используют препарат по мере
необходимости. Во многих регионах страны на складах хранятся пестициды, на таре которых
утрачена маркировка. Например, по данным центров Госсанэпиднадзора, количество
обезличенных пестицидов, подлежащих уничтожению, составляет в Орловской области 250 т, в
Курской — 365 т, в Псковской – 244 т, в Республике Татарстан – 211 т. Не исключено, что
среди этих пестицидов присутствует, например, гранозан. Свободный доступ к гранозану в
ряде регионов России уже привёл к негативным последствиям. Существующий полигон для
захоронения непригодных пестицидов полностью заполнен. В 9 км от г. Кызыл – столицы
республики Тыва – по данным Департамента ветеринарии Правительства республики, 12 овец
отравились гранозаном. Есть опасность загрязнения ртутью и расположенного рядом
минерального источника Тос-Булак (Российское информационное агентство Новости.Сибирь
от 31 января 2003 г.).
3.11.5 Места захоронения ртутьсодержащих пестицидов
В России в организованном порядке ртутьсодержащие пестициды размещаются на
территории завода-изготовителя в г. Дзержинске (Нижегородская область), на полигоне
захоронения опасных отходов “Красный Бор” (Ленинградская область), а также на некоторых
других специализированных полигонах.
Проведённая в 2002 г. проверка условий хранения ртутьсодержащих отходов от
производства гранозана на заводе “Синтез” показала (Акт проверки Департаментом
государственного контроля МПР по Приволжскому региону выполнения природоохранного
законодательства ОАО “Синтез” от 16.4.2002 г.), что корпус производства гранозана и
локальные очистные сооружения находятся в разрушенном состоянии. Строительные
конструкции корпусов производства гранозана и очистных сооружений загрязнены ртутью.
Была отмечена необходимость проведения работ по демеркуризации оборудования
строительных конструкций производства гранозана. На асфальтированной площадке вблизи
корпуса производства гранозана размещены 22 контейнера (ёмкостью 1 м³ каждый) с
ртутьсодержащими отходами (активированный уголь с 5%-ным содержанием ртути). Всего в
контейнерах на момент проверки накоплено 0,02 тыс. т ртутьсодержащих отходов (т.е. до 1 т
ртути). Хранение отходов осуществляется с нарушением экологических требований, что
обусловлено разгерметизацией контейнеров. Вопрос по утилизации отходов находится в стадии
реализации. Имеется проект на перевозку контейнеров c ядохимикатами для их утилизации в
ЗАО “НПП “Кубаньцветмет”. Общественная экологическая организация СПЭС считает, что
металлических баллонах производились на территории предприятия с 1985 по 1989 г.г.,
возможно и в последующие годы), находящихся на территории ОАО “Синтез” (г. Дзержинск)
являются сильно заниженными (Письмо № 15 от 11.3.2003 г.).
На полигоне “Красный Бор” захоронение ртутьсодержащих пестицидов ведется с 1970 г.
По данным Администрации указанного полигона, захоронение ртутьсодержащих пестицидов
происходит следующим образом. Организация, желающая избавиться от опасных отходов,
обращается на полигон “Красный Бор” с соответствующим заявлением, указывая характер
отходов и класс опасности. После подписания договора о размещении отходов, организация
самостоятельно и за свой счет упаковывает отходы в соответствии с предусмотренными
правилами. Отходы помещаются в стандартный контейнер с толщиной стен не менее 10 мм
размером 1,7 м x 1,0 м x 1,0 м. Внутри стального контейнера на металлическую сетку наносится
бетонная оболочка толщиной не менее 5 см. Пестициды помещают на дно контейнера, а
пространство между тарой и стеками контейнера заливают бетоном. Внешняя металлическая
поверхность контейнера должна быть осмолена. На контейнере несмываемой краской делается
надпись: наименование предприятия, номер договора, тип отхода, вес нетто, вес брутто, дата
сдачи контейнера. Вес контейнера с отходами не должен быть более 3 т. На территории
полигона контейнеры с отходами размещаются в два яруса в слое кембрийской глины
толщиной 70 м. Вес отходов указывается в акте о приемке отходов. Для осуществления
контроля за состоянием почвы и грунтовых вод полигон “Красный Бор” оборудован
наблюдательными режимными скважинами, три из которых расположены непосредственно в
его пределах и еще три – по периметру полигона. Регулярно проводится взятие проб грунта и
воды из скважин для проведения комплексного анализа на наличие загрязняющих веществ, в
том числе ртути. За все историю функционирования полигона не было зафиксировано ни
одного случая превышения ПДК по ртути или тяжелым металлам в почве, грунтовых водах или
воздухе.
3.11.6 Заключение
На основе представленной выше информации, можно сделать следующие выводы:
1) Несмотря на официальный запрет, в Российской Федерации все еще имеет место
торговля ртутьсодержащими пестицидами. Ежегодно в сельском хозяйстве применяется около
20-40 т этих веществ.
2) Точный объем использованных пестицидов достаточно трудно оценить. В 2000 г. было
использовано примерно до 50 т ядохимикатов, содержащих около 1 т ртути, которая в конечном
счете поступила в окружающую среду.
3) Точное количество ртутьсодержащих пестицидов,
находящихся на складах и в хранилищах, неизвестно, но, согласно оценкам, может достигать 100-
1000 т, в которых содержится до 20 т ртути.
4) Большинство складских помещений в сельской местности находится в аварийном
состоянии, отходы хранятся с нарушением правил.
5) Существует реальная угроза загрязнения окружающей среды в местах хранения
ртутьсодержащих пестицидов; исследования распределения ртути в окрестностях складских
помещений и полигонов захоронения ртутьсодержащих отходов практически не проводятся.
3.12 Другие области применения ртути
В настоящем разделе дано краткое описание других областей применения ртути. По этой
теме была собрана менее подробная информация, либо по причине незначительного
использования ртути в этих областях, либо из-за сложности ее получения. В некоторых
случаях, например, при использовании продукции не только в гражданских, но и в оборонных
целях, информация является частично закрытой.
В данном разделе рассматриваются следующие аспекты:
- производство изотопов лития;
- производство полупроводников;
- производство силовых полупроводниковых приборов;
- ртутьсодержащие биоциды;
- другие сферы применения ртути.
3.12.1 Производство изотопов лития
Технологии получения чистых веществ (металлов), основанные на амальгамном способе,
известны достаточно давно [18, 22, 126, 127]. В свое время они применялись в промышленном
производстве цинка и кадмия высокой чистоты, при разделении стабильных изотопов, а также
использовались для получения сверхчистых металлов в опытных производствах, научных
исследованиях, лабораторном деле. Наиболее широкое промышленное применение
амальгамный способ, требующий значительных количеств ртути, нашел в технологии
разделения стабильных изотопов лития [10].
Изотопное разделение, т. е. выделение одного или нескольких изотопов данного элемента
из их смеси, осуществляют в специальных установках - противоточных колоннах. В таких
установках для достижения ступеней разделения больших, чем в единичной операции, часть
выходящего с последней ступени обогащенного целевым изотопом потока возвращают в
колонну и проводят так называемое обращение потока [304]. Для обращения потоков
применяют термическое или электрохимическое разложение либо реакции со
вспомогательными веществами. Накопление целевого изотопа начинается на конце колонны,
где вследствие обращения потока контактирующие фракции или потоки выводятся из
состояния равновесия. В результате в контакт с обогащенной фракцией данной ступени
приходит фракция, имеющая несколько более высокое содержание целевого изотопа, чем
обедненная фракция, уведенная с этой ступени. Последнее перераспределение изотопов
приводит к увеличению концентрации изотопа по сравнению с исходной в обеих покидающих
эту ступень фракциях. По мере протекания процесса обогащение на конце колоны
увеличивается, из состояния равновесия выводятся все более удаленные от места обращения
потока ступени, а протяженность обогащенной части колонны растет. После достижения на
конце колонны требуемой степени разделения начинают отбирать конечный продукт. Далее
колонна работает в стационарном режиме. Как правило, из-за низких исходных концентраций
целевого изотопа период накопления изотопа (так называемый пусковой период установки)
составляет сотни и тысячи часов.
![Рисунок 3.15 Схема процесса разделения изотопов лития амальгамным способом [10]](images/s134.gif)
1 - колонна изотопного обмена; 2 - колонна для
выделения лития из амальгамы; 3 - электролизер; 4 -
аппарат для растворения NaBr; 5 - разлагатель амальгамы;
6 - выпарка; 7 - ректификационная колонна
Рисунок 3.15 Схема процесса разделения изотопов
лития амальгамным способом [10]
На практике получило применение
разделение стабильных изотопов в системе
жидкость-жидкость методом химического обмена
(амальгамно-обменным методом) [10]. В данном
случае одной жидкостью является водный или
органический раствор соли какого-либо элемента,
в качестве второй жидкости используют
амальгаму этого элемента. В таких системах легко
осуществить противоток из-за большого различия
в плотностях, возможности физического
разделения двух жидкостей и относительной
простоты обращения потоков, т. к. амальгамы
легко получаются электрохимическим путем и
еще легче разлагаются или обменивают металл на
другой, находящийся в растворе. Именно
амальгамно-обменный метод и нашел
промышленное применение для разделения
стабильных изотопов лития (рис. 3.15).
В данном случае обращение потоков на верхнем конце каскада осуществляют
электролизом водных растворов солей лития на текущем ртутном катоде. Получаемая при этом
амальгама поступает в колонну изотопного обмена 1, а водный раствор органического
растворителя - на ректификацию в колонну 7, что позволяет использовать растворитель
многократно. Обращение потоков на нижнем конце колонны осуществляют различными
способами. Наиболее простой способ перевода лития из амальгамы в органический
растворитель состоит в разложении ее водой, подкисленной кислотой, упаривании водного
раствора соли, прокаливании и растворении ее в растворителе. Другой (непрерывный) способ
обращения потоков заключается в замене амальгамы лития натрием, стронцием или кадмием
по реакции:
Li(Hg) + MeX1(2) ↔ Me(Hg) + LiX,
где Ме - металл первой или второй группы периодической системы.
Реакцию осуществляют в отдельной колонне 2, за которой следуют аппараты 5 для
разложения Me(Hg), выпарки и растворения МеХ1(2) в органическом растворителе,
поступающем из системы верхнего обращения потоков. Ртуть, получаемая при разложении
Me(Hg), возвращается в электролизер. Для разложения амальгамы на богатом 6Li конце каскада
обычно используют разлагатели, заполненные графитом, чугуном или сплавами, а также
электрохимическое разложение путем приложения к амальгаме положительного потенциала
[10].
Производство изотопов лития амальгамно-обменным способом требует значительных
количеств ртути. Так, анализ технологического цикла одного из таких предприятий,
расположенного в г. Новосибирске (завод химических концентратов), показал [241, 322], что
здесь в середине 1990-х г.г. суммарные учтенные потери ртути при производстве изотопов
лития амальгамно-обменным способом составляли около 35 т в год, неучтенные потери -
достигали 5 т (рис 3,15.). Из всех учтенных потерь ртути в воздушную среду попадало 1,6 т
металла, около 2 кг поступало в водную среду и 33,5 т содержалось в твердых отходах,
подлежащих захоронению.
Приведенные данные свидетельствуют о том, что в местах размещения отходов,
расположенных вокруг предприятия, может содержаться большое количество ртути.
![Рисунок 3.16 Примерная структура потерь ртути в производстве изотопов лития амальгамно-обменным способом [322].](images/s135.gif)
Рисунок 3.16 Примерная структура потерь ртути в производстве изотопов лития амальгамно-
обменным способом [322].
Данные, приведенные на рис. 3.13, позволяют рассчитать относительные потери ртути в
ходе указанного технологического процесса (при ее общих потерях порядка 40,2 т/год): с
твердыми и пастообразными отходами – 58,2%, в составе отработанного активированного угля
– 23,8%, с выбросами в атмосферу – 4,6%, со сточными водами – 0,004%; на долю неучтенных
потерь (дренаж в почву) приходится 12,5%.
Сведения о потреблении ртути Новосибирским заводом химических концентратов в
2000-2002 г.г., как и данные о ее эмиссии в среду обитания, в доступных информационных
источниках отсутствуют. В то же время известно, что в Институте химии твердого тела и
механохимии СО РАН (г. Новосибирск) был разработан (и, судя по всему, уже внедрен в
практику) принципиально новый способ разделения стабильных изотопов лития, который
позволил сократить продолжительность производственного цикла, существенно уменьшить
затраты электроэнергии и многократно снизить объемы применяемой ртути [90]. Это,
безусловно, позволило существенно снизить безвозвратные потери ртути, связанные, судя по
всему, главным образом с твердыми отходами (отработанный активированный уголь, смолы,
пастообразные отходы), которые образуются в ходе указанного производства и подлежат
вторичной переработке (или безопасному захоронению).
По сообщению [313], Новосибирский завод химических концентратов недавно заключил
соглашение на переработку литиевых отходов амальгамно-обменного производства США (где
в свое время функционировали крупные предприятия по разделению изотопов лития) и
намерен производить гидроксид, карбонат и безводный хлорид лития и чистый металл.
3.12.2 Производство полупроводников
В настоящее время ртуть в полупроводниковой промышленности используется для
производства полупроводниковых материалов и создания на их основе электронных и
электронно-оптических приборов нового поколения. Применение ртути в технологии
производства полупроводниковых материалов и в качестве акцепторной примеси для
легирования германия (используемого в инфракрасной технике) с целью придания ему
дырочного типа проводимости началось еще в 1950-х г.г. Сейчас полупроводниковые
материалы на основе соединений типа А2В6, содержащих ртуть, используются при
изготовлении фоторезисторов, фотодиодов, датчиков Холла, высокочувствительных
приемников оптического излучения (фотоприемников, фотоприемных устройств и
комплексов), полупроводниковых лазеров.
Использование ртути в производстве полупроводниковых материалов
До недавних пор в качестве ртутьсодержащих полупроводниковых материалов чаще
всего употреблялись HgS, SeHg, TeHg [156, 179, 207, 279]. Затем было установлено, что многие
соединения типа А2В6 образуют между собой непрерывный ряд твердых растворов, типичными
представителями которых являются СdXHg1-XTe, CdXHg1-XSe, CdTeXSe1-X, Hg1-XMnXTe,
Hg3In2Te6, обладающие уникальными электрофизическими характеристиками [31, 43, 141, 219,
261]. Среди этих соединений особый интерес представляют твердые растворы теллуридов
кадмия и ртути (Cd-Hg-Te), получившие в России аббревиатуру КРТ и в настоящее время
широко применяющиеся для изготовления полупроводниковых материалов [30, 141].
Полупроводники КРТ широко применяются по всему миру в целом ряде областей, таких как
тепловидение, лазерное обнаружение CO2, инфракрасная спектроскопия с фурье-
преобразованием, отслеживание летящих предметов и ночное наблюдение.
Смесь Cd-Hg-Te (КРТ) при определенных условиях образует кристаллы со структурой
сфалерита, в которых одна подрешетка целиком занята атомами теллура, а в другой
располагаются атомы кадмия и ртути [255]. В зависимости от пропорции, в которой смешаны
атомы кадмия и ртути в подрешетке металла, могут быть получены кристаллы КРТ с любой
заданной шириной запрещенной зоны в интервале 0-1,6 эВ (при 4,2 К). Наиболее важное
практическое значение из КРТ имеют твердые растворы CdXHg1-XTe. В СССР
полупроводниковый твердый раствор КРТ был впервые (практически одновременно с учеными
Великобритании) синтезирован и исследован А.Д. Шнайдером (Львовский университет) [309].
В СССР разработка методов выращивания КРТ и изготовление фотодиодов и
фоторезисторов на его основе осуществлялись главным образом в НИИПФ (ныне ГНЦ .НПО
“Орион”, г. Москва) [275]. Уже в 1970 г. на основе КРТ производились одноэлементные
фоторезисторы, которые поставлялись во многие организации СССР. Несколько позже
начались разработки фоторезисторов на заводе .Сапфир., где затем было организовано
серийное производство первого в СССР фотоприемника на основе КРТ [275]. Достаточно
быстро методы выращивания КРТ с использованием разработок ФТИ АН СССР, НПО “Орион”,
НПО “ГИПО” (г. Казань), Института полупроводников АН Украины были развиты и доведены
до серийного производства в НПО “Гиредмет” (г. Москва) и внедрены на Заводе чистых
металлов (г. Светловодск, Украина) и Опытном химико-металлургическом заводе (г. Подольск)
[141, 219]. Завод чистых металлов в Украине к середине 1980-х г.г. производил объемные
монокристаллы КРТ нужной кондиции и в необходимом количестве; сейчас этот завод
поставляет свою продукцию главным образом в Китай и некоторые другие страны. Завод в г.
Подольске выпускает материал для двумерных фотоприемных структур фотодиодного типа и
фотоматриц, представляющих собой тонкие пленки КРТ на полупроводниковых подложках
[141]. В 1970-х г.г. в ГОИ им. С.И. Вавилова (г. Санкт-Петербург) были изготовлены
фотоприемники и фотоприемные устройства с чувствительными элементами из германия,
легированного ртутью [141].
В настоящее время на основе КРТ создаются матрицы фоточувствительных элементов,
являющихся составной частью фотоприемников (ФП), одиночных, линейных и матричных
фотоприемных устройств (ФПУ), чувствительных в диапазоне длин волн 1-20 мкм [29-31, 141,
219, 220, 297]. Фотодиоды из твердого раствора CdXHg1-XTe сейчас стали основным
фоточувствительным элементом современной ИК-техники, приборов для приема импульсов
СО2-лазера и др. Полупроводниковые лазеры и фотоприемники, на основе КРТ, являются
важнейшими составляющими элементной базы волоконно-оптических линий связи. На основе
CdXHg1-XTe изготавливаются неохлаждаемые фоторезисторы, тепловизоры-дальномеры,
теплопеленгаторы-дальномеры и т. д. При изготовлении датчиков Холла наилучшие
результаты достигаются при использовании твердых растворов HgSe и HgTe в виде пластинок
или тонких пленок.
Эмиссия ртути при производстве полупроводниковых материалов
В силу известных причин информация о масштабах использования ртути при
производстве КРТ и других полупроводниковых материалов, как в России, так и в других
странах мира не публикуется, по крайней мере, в доступной литературе она отсутствует. По
этим же причинам совершенно нет данных об экологических аспектах производства
ртутьсодержащих полупроводниковых материалов. По сведениям, полученным от работников
ртутных комбинатов быв. СССР, упомянутый выше Завод чистых металлов (г. Светловодск,
Украина) в 1980-х г.г. ежемесячно заказывал до 300 кг металлической ртути (т. е. до 3,5 т в
год). Следует отметить, что это был период достаточно активного промышленного
производства объемных кристаллов КРТ и, очевидно, опытных работ по совершенствованию
технологии и внедрению новых методов получения КРТ.
Априори можно предположить, что процессы изготовления указанных материалов
высокотехнологичны, проводятся в замкнутом объеме и, как подчеркивают авторы многих
публикаций, не имеют вредных выбросов. Кроме того, такие производства отличаются
высоким уровнем утилизации и повторного использования материалов (что в значительной
мере обусловлено их высокой стоимостью), участвующих в технологическом процессе. В то же
время в некоторых публикациях, например, подчеркивается, что “эпитаксия КРТ требует
больших расходов и утилизации токсичной ртути” [310], хотя масштабы указанных расходов
металла не сообщаются. Известно, что в технологии КРТ огромную роль играют не только
выращивание ртутьсодержащих соединений, но и послеростовые термообработки полученного
материала в атмосфере ртутного пара. Поэтому не исключено, что в ходе синтеза
полупроводниковых материалов происходит не только загрязнение камер используемой
системы ртутью, но и его поступление в производственную среду, например, из-за нарушений
герметичности используемого аппаратурного оборудования, на что указывают косвенные
данные. В частности, в Институте физики полупроводников и Конструкторско-
технологическом институте прикладной микроэлектроники СО РАН (г. Новосибирск) недавно
разработан и запатентован способ сбора ртути в технологической камере установки
молекулярно-лучевой эпитаксии и сконструирована соответствующая установка [354].
Указанные способ и используемая для его осуществления установка, как сказано в патенте,
повышают эффективность технологии получения многослойных тонкопленочных покрытий,
увеличивают производительность процесса и обеспечивают экологическую чистоту
производства.
В любом случае, из всего объема используемой при изготовлении полупроводниковых
материалов ртути незначительное количество ее входит в состав конечной продукции,
небольшое количество эмитируется в производственную среду, а основная масса улавливается,
утилизируется, рафинируется и повторно используется в производстве. Не исключено, что
основные потери ртути происходят не столько в ходе изготовления полупроводниковых
материалов, а сколько на стадии ее утилизации и рафинирования.
Данных о количестве ртути, используемой при производстве полупроводников, а также
поступающей в окружающую среду в результате производственных процессов, получить не
удалось.
3.12.3 Использование ртути для изготовления силовых полупроводниковых
приборов
На некоторых российских заводах полупроводниковой промышленности осуществляется
(по разовым заказам) изготовление силовых полупроводниковых приборов, уже снятых с
массового производства, но все еще использующихся на отечественных предприятиях.
Применение таких приборов обусловлено тем, что в схемах электроснабжения некоторых
предприятий, в силу различных (в том числе технических) причин, невозможно установить
современные приборы. В каждом приборе старого поколения, используемого для поддержания
постоянного тока в сети электроснабжения, в качестве теплоизолирующей рубашки
используется до 8 кг металлической ртути. Например, на одном российском заводе по
производству полупроводниковых приборов ежегодное использование металлической ртути
(согласно материально-сырьевому балансу) на изготовление указанных силовых
полупроводниковых приборов в 2001-2002 г.г. составляло порядка 420 кг.
Есть основания полагать, что аналогичную продукцию выпускают еще несколько
отечественных предприятий полупроводниковой промышленности. Отсюда следует, что общее
потребление металлической ртути в стране на такие цели может составлять порядка 2,2-2,5 т в
год. Потери ртути в ходе изготовления (в сущности, индивидуального, ручного) таких изделий,
очевидно, в основном случайны и вряд ли превышают 1-3% от общего количества
используемой ртути (т. е. порядка 45-50 кг в год в целом по стране). Большая часть теряемого
металла, судя по всему, в конечном счете попадает в канализацию и на свалки. Уровни
содержания паров ртути в рабочей зоне при изготовлении указанных приборов могут достигать
ПДК.
3.12.4 Ртутьсодержащие биоциды
Соединения ртути использовались при изготовлении ряда лекарств и вакцин, а также
латексных изделий и в качестве дезинфицирующих средств (ртути амидохлорид, дийодид,
дихлорид, монохлорид, оксид, а также оксицианид, салицилат амидохлорид, ртутная желтая
мазь, ртутная серная мазь, ртутно-висмутная мазь, ртутный пластырь, популярные капли
Софрадекс).
В настоящее время Приказом Минздрава РФ (№ 82 от 23.3.98 г.) ртутьсодержащие
медицинские препараты и лекарственные средства исключены из Государственного реестра
лекарственных средств, разрешенных к использованию в медицинских учреждениях и
промышленному производству [373]. Тем не менее на сайтах в Интернете, содержащих
объявления о продаже медицинских препаратов, встречаются предложения о продаже
аминохлорида ртути (белая осаждающая ртуть), дихлорида ртути, монохлорида ртути
(каломель), цианокиси ртути, оксида желтой ртути (желтая осажденная ртуть), йодида ртути
(II), которые ранее использовались в качестве лекарств и антисептиков. Начиная с 1990 г, было
начато практическое применение так называемого “витурида”, препарата имеющего в своем
составе ртуть (двухлористую), и как утверждают, универсального для лечения широкого ряда
заболеваний: сахарного диабета, опухолей, системной красной волчанки, псориаза,
бронхиальной астмы, ревматоидного артрита; он также, по утверждению изобретателей,
обладает антивирусной активностью простив СПИДа, водобоязни, герпеса и
цитомегаловирусных инфекций и т. д. [46]. Несмотря на официальное письмо Минздрава РФ от
31 марта 1998 г. № 2510/2871-98-32 “Об изготовлении витурида”, запрещающее использовать
этот препарат в лечебных целях, и повторное подтверждение данного запрета [373], до сих пор
можно встретить свидетельства применения витурида в медицине для лечения различных
заболеваний.
Соединение ртути (товарная марка “мертиолят” “тимеросал” или “тиомерсал”)
добавляется в вакцины в качестве консерванта. В российской научной печати широко
обсуждалась проблема использования этого препарата при производстве вакцины АКДС
(коклюшно-дифтерийная – столбнячная адсорбированная жидкая), вакцины АДС и АДС-М или
ее аналог Имовакс Д. Т. Адюльт (дифтерийно-столбнячная), широко используемых в
педиатрии, а также при изготовлении вакцины против гепатита “В” и столбняка. При
производстве вакцины АКДС на 1 мл. коклюшной взвеси добавляется 100 мкг этого
соединения, при производстве российской вакцины против гепатита “В” фирмой “Комбиотех”
в качестве консерванта применяется мертиолят в концентрации 0,005%. Перед употреблением в
производстве вакцин мертиолят должен контролироваться на содержание свободной ртути. В
большинстве используемых в России вакцинах мертиолят содержится в концентрациях 1: 10
000, в вакцинах против гепатита “В” – в концентрациях 1: 20 000. Таким образом, в одной
прививочной дозе содержится малое количество мертиолята. Общее количество ртути,
используемой для консервации вакцин, установить не удалось, но, по оценкам, оно
незначительно по сравнению с применением ртути на другие цели.
Информация о поступлении ртути на заводы, где производятся вакцины, отсутствует
полностью. По состоянию на 6.8.2003 г. не найдено информации в специализированных
журналах, статистических справочниках, Интернете о современном использовании в России
ртутьсодержащих биоцидов. В обзоре специалистов НИИ Химии Нижегородского
университета им. Н.И. Лобачевского “Биоциды для водоразбавляемых лакокрасочных
материалов” указывается, что в России на основе ртути такие материалы не производятся, а
используют в основном импортные материалы [385].
3.12.5 Другие сферы использования
В разделе содержится разрозненная информация, касающаяся других сфер использования
ртути, которые не оценивались детально, однако имеющиеся сведения указывают на то, что
ртуть применяли в этих целях еще совсем недавно или даже используют и сейчас.
Взрывчатые вещества
Гремучая ртуть, или фульминат ртути, Hg (ONC)2, которую получают взаимодействием
этанола с раствором Hg(NO3)2 в HNO3, используется в качестве инициирующего взрывчатого
вещества для капсюлей-детонаторов (в которых присутствует индивидуальное вещество) и
капсюлей-воспламенителей (присутствует смесь инициирующих веществ, содержащих до 16-28% гремучей ртути).
Теле- и радиотехника
Ртуть используется в небольших количествах в теле- и радиотехнике. Например, в
середине 1990-х годов предприятие “Экран” (г. Новосибирск) выбрасывало в воздушную
систему из цеха для экспонирования цветных трубок (через систему общей вентиляции) до 70
кг ртути в год [322].
Есть сведения, что в компьютерах - в электронных ключах и плоских мониторах -
содержится ртуть (до 0,0022% от общей массы) [370]. Электронный ключ, т. е. переключающий
элемент, имеющий высокое электрическое сопротивление в закрытом и малое - в открытом
состоянии, находят достаточно широкое применение в автоматике, телемеханике, радиотехнике
и вычислительной технике. Недавно сообщалось, что в Европе с 1 января 2006 г. будет
полностью запрещено использование ртути при производстве электронного оборудования
[382].
Краски
Сейчас в России функционируют более десятка крупных лакокрасочных предприятий,
которые в 2001 г. произвели 351 135 т различных лакокрасочных материалов. Конкретные
данные об использовании ртути в производстве красок не публикуются. Более того, считается,
что в настоящее время ртуть и ее соединения не применяются в производстве красителей и
красок. Тем не менее имеются косвенные сведения, показывающие, что ртуть и ее соединения,
судя по всему, в той или иной мере используются в лакокрасочном производстве. Так, по
данным [34], крупнейший российский производитель лакокрасочных материалов ОАО
“Лакокраска” (г. Ярославль) ежегодно сбрасывает в р. Волгу со сточными водами до 60 кг
солей ртути. Известен случай, когда в Тверской области в карьер было слито около 1200 л
ртутьсодержащих отходов, представляющих собой вторичный продукт от красок,
применяющихся на АО “Каменка” (г. Кувшиново) при изготовлении самоклеящихся этикеток
(News. Battery. Ru - Аккумулятор Новостей, 25.1.2001). Сообщалось также [356], что при
печатании российских денежных (бумажных) купюр используются ртутьсодержащие краски,
которые замешаны на так называемых активных амальгамах и призваны обеспечивать защиту
денег от подделок. Считается, что данная степень защиты на практике оказалась самой
надежной.
Зеркала
В последние годы в прессе появились сведения об использовании ртути в производстве
зеркал; по крайней мере, встречается реклама о продаже отечественных зеркал, изготовленных
с использованием амальгамного способа.
Использование ртути в быту
Своеобразной сферой применения ртути является ее использование в быту. Имеющиеся
материалы свидетельствуют о том, что на руках у населения находятся значительные
количества металлической ртути и ее соединений. Например, в 1999 г. в Перми одной
экологической организацией был организован выкуп металлической ртути у жителей города,
причем только за полгода было приобретено около 0,3 т металла [267]. Если такая ситуация
типична для большинства из 89 регионов России, то масса ртути, находящейся у населения
может измеряться, по крайней мере, несколькими тоннами, причем эта ртуть, судя по всему, не
просто хранится, но и достаточно активно используются в тех или иных целях. Так, в средствах
массовой информации регулярно сообщается о попытках незаконной продажи металлической
ртути на «черном рынке» в различных регионах страны, причем количество изъятого при этом
правоохранительными органами металла изменяется от 10-60 кг до 1,5 т.
На сайтах Интернета подробно рассказывается о том, как использовать металлическую
ртуть для покрытия блесны (рыбакам предлагается несколько рецептов) или как изготовить
сулему. Здесь же и в некоторых известных журналах (см., например, “Радиолюбитель”, 1991, №
7, с. 43) амальгаму Герштейна (мелконапиленные опилки свинца смешанные с металлической
ртуть в пропорции 1,5 г к 2 г) рекомендуют радиолюбителям применять в качестве препарата
для холодной пайки металлов.
Известная история с “красной ртутью” в последние годы получила продолжение в виде
многочисленных рассказов (особенно в Интернете) о фантастических свойствах так
называемых “ртутных теле- и радиоантенн”, на изготовление которых якобы требуются
существенные количества металла (до 10 кг ртути на одну антенну). Все это вызвало новый
интерес у населения к металлической ртути и, естественно, к ее поиску.
4 Мобилизация ртути в качестве примеси
4.1 Уголь
4.1.1 Содержание ртути в углях России
4.1.2 Поступление ртути в окружающую среду и отходы в процессе
угледобычи
4.1.3 Использование угля в электроэнергетике
4.1.4 Производство кокса
4.1.5 Заключение
4.2 Нефть, природный газ, горючие сланцы и биотопливо
4.2.1 Введение
4.2.2 Ртуть в нефтях и газоносном сырье
4.2.3 Мобилизация ртути в нефти
4.2.4 Поведение ртути при переработке природного газа
4.2.5 Мобилизация ртути с природным газом и газовым конденсатом
4.2.6 Горючие сланцы
4.2.7 Древесина
4.2.8 Торф
4.3 Цемент и известь
4.4 Цветная металлургия
4.4.1 Ртуть в рудах цветных металлов и концентратах
4.4.2 Первичное производство цинка
4.4.3 Первичное производство никеля
4.4.4 Производство меди
4.4.5 Производство меди и никеля ОАО “ГМК “Норильский никель”
4.4.6 Производство олова
4.4.7 Производство свинца
4.4.8 Производство других цветных металлов
4.4.9 Заключение
4.5 Черная металлургия
4.1 Уголь
В мировом масштабе сжигание угля является важнейшим источником антропогенной
эмиссии ртути в атмосферу [412].
Общий объем добычи угля в России в 2001 г. составил 269 млн. т, из них 171 млн. т -
каменный уголь и 98 млн. т – бурый уголь. Общее потребление угля в стране с разбивкой по
категориям применения показано в табл. 4.1. Согласно этим сведениям , общая поставка угля
российским потребителям в 2001 г. достигала 234 млн. т.
По статистическим данным Международного Энергетического Агентства [387], эта цифра
немного выше и равна 251 млн. т. Тем не менее в дальнейших расчетах использовались данные
табл. 4.1.
Таблица 4.1 Потребление угля в России по категориям применения, 2001 г. (подсчет произведен на
основе данных, приведенных в [110)
Показатель |
млн. тонн |
% |
Поставка: |
|
|
Поставка российских углей |
207,9 |
|
Импорт энергетических углей из Казахстана (Экибастуз) |
25,5 |
|
Импорт коксующихся углей из Казахстана (Караганда) |
0,8 |
|
Общая поставка угля российским потребителям |
234,3 |
100 |
в том числе: |
|
|
- на нужды электроэнергетики |
124,3 |
53,1 |
- на коммунально-бытовые нужды |
17,6 |
7,5 |
- для населения |
7,6 |
3,2 |
- аграрно-промышленный комплекс |
0,9 |
0,4 |
- для коксования |
41,7 |
17,8 |
- остальные промышленные потребители* |
42,2 |
18,0 |
* В этом случае, по всей видимости, имеется в виду использование угля в промышленности, не
только для непосредственного сжигания, а также для его переработки (полукоксование, газификация,
гидрогенизация, производство силисторного угля, карбида кальция, антрацита, сорбента, графита и т.д.);
большая часть этих процессов включает высокотемпературную обработку угля, что подразумевает
выбросы ртути в атмосферу.
4.1.1 Содержание ртути в углях России
Содержание ртути в углях значительно варьируется в зависимости от угольного бассейна,
а также в зависимости от шахт в пределах каждого бассейна (рис. 4.1; Приложение 3).
В качестве примера в табл. 4.2 приведены данные по содержанию ртути в углях
Кузнецкого бассейна, который является основным угольным бассейном России, где в 2001 г.
было добыто 127 млн. т угля (табл. 4.3). На его долю приходится около 46% от общей
угледобычи в России и 78 % коксующегося угля в стране. Среднее содержание ртути в углях
Кузнецкого бассейна, рассчитанное на основании табл. 4.2, составляет 0,09 мг/кг, варьируясь от
0,01 мг/кг до 0,6 мг/кг в зависимости от шахты или разреза. Указанная значительная вариация
концентраций ртути в углях, несмотря на представительность данных (n = 39), определяет тот
факт, что 90%-ный интервал достоверности в среднем по рассматриваемой выборке является
достаточно широким (0,05-0,13 мг/кг).
![Рисунок 4.1 Основные угольные бассейны России [388].](images/s142.gif)
Рисунок 4.1 Основные угольные бассейны России [388].
Общее количество ртути в угле, добытом в России в 2001 г., определялось путем
умножения объема его добычи в конкретном регионе страны на соответствующее оценочное
среднее содержание ртути в угле и составило 22 т (табл. 4.4.). По данным [312], cредние
содержания ртути в товарных углях России колеблются от 0,008 мг/кг (месторождения
Бурятской области) д. 0,85 мг/кг (месторождения Амурской области), т. е. различаются в 100
раз. Средневзвешенное содержание ртути в российских углях оценивается в 0,08 мг/кг, причем
оно в значительной степени зависит от средней концентрации ртути в углях Кемеровской
области (Кузнецкого бассейна – основного поставщика товарных углей), на которые
приходится половина общего количества ртути, содержащейся в добытых углях России.
Если принять, что общее оценочное содержание ртути в углях зависит от ее средних
концентраций, используемых для нескольких (незначительное число) регионов, то
неопределенность среднего значения можно определить как довольно высокую, невзирая на
большое число имеющихся фактических данных. По приближенным оценкам, средняя
концентрация ртути в российских углях варьируется в интервале 0,07-0,09 мг/кг.
Следовательно, можно предположить, что количество ртути, присутствующей в добытых в
2001 г. в России углях, находится в пределах 20-24 т. Поскольку потребление угля в России
растет, то увеличивается и количество ртути, присутствующей в углях, причем это увеличение
в значительной мере зависит от качества добываемых углей.
Предварительная подготовка угля
Существенную часть добытых углей подвергают предварительной подготовке, которая
включает операции дробления, сортировки, обогащения, брикетирования и сушки [136].
Дробление угля может представлять собой как самостоятельную, так и подготовительную
операцию для последующего обогащения, брикетирования, коксования и т. д. Сортировка
углей преследует цель разделения рядовых углей на классы, содержащие куски установленных
размеров. Она производится при помощи последовательного рассева углей на грохотах с
отверстиями сит размером, соответствующим крупности товарных углей. Сортировка углей
также широко используется для разделения продуктов обогащения на классы крупности.
Брикетирование углей является обязательным для мелких классов товарных углей и
концентратов, которые не могут использоваться в полученной крупности. Оно также
необходимо и при длительных перевозках для исключения пыления и смерзаемости угольной
пыли.
Таблица 4,2 Среднее содержание ртути в товарных углях Кузнецкого бассейна [312]
Угленосный р-н, месторождение, предприятие |
Технологическая группа (марка) угля, сорт угля |
Зольность Аd, % |
Влажность Wrt, % |
Hg, г/т угля |
Кузнецкая шахта |
Г кокс |
18,2 |
8,2 |
0,01 |
Новосергеевский разрез |
СС |
8,8 |
5,2 |
0,01 |
Черкассовская шахта |
К |
17,4 |
6,2 |
0,01 |
Шушталепская шахта |
Т |
23,5 |
8,2 |
0,01 |
Томь-Усинский, р-з Красногорский |
Т |
18,9 |
5,9 |
0,01 |
Шахта им. Калинина |
К, КО, КС, СС |
22,1 |
5,3 |
0,02 |
Шахта Зиминка |
К, КО, КС |
15,1 |
6,7 |
0,02 |
Шахта Бирюлинская |
К, КО |
32,2 |
7,4 |
0,03 |
Шахта Южная |
СС |
14,5 |
7,2 |
0,03 |
Шахта Тырганская |
СС |
10,4 |
6,5 |
0,03 |
Байдаевский, шахта Большевик |
Г кокс |
13,1 |
7,1 |
0,03 |
Шахта Новокузнекцкая |
Г кокс, ГЖ |
14,9 |
7,1 |
0,03 |
Колмогоровский разрез, уч-к Колмогоровский-1 |
Д, Г эн. |
13 |
16,8 |
0,03 |
Шахта Заречная |
Г эн. |
13,1 |
11 |
0,03 |
Прокопьевско-Киселевский, Киселевское, р-з Краснобродский |
Т |
10,5 |
4,7 |
0,03 |
Разрез Колмогоровский-2 |
Д |
15,5 |
17,1 |
0,03 |
Араличевский, шахта им. Орджоникидзе |
Т |
27 |
6,5 |
0,03 |
Кондомский, шахта Северный Кандыш |
Т |
24,2 |
5,9 |
0,04 |
Шахта Высокая |
Ж |
32,5 |
5,9 |
0,04 |
Прокопьевско-Киселевский, Прокопьевское, шахта Центральная |
Т |
16,6 |
5,5 |
0,05 |
Прокопьевский разрез |
СС |
8,3 |
8,7 |
0,05 |
Шахта Зыряновская |
Г кокс, ГЖ |
23,5 |
7,6 |
0,05 |
Ленинский, шахта Сигнал |
Г эн. |
13,9 |
1,4 |
0,05 |
Шахта Аларда |
К, КО, КС |
19,1 |
7 |
0,05 |
Терсинский, р-з Байдаевский |
ДГ, Г эн. |
16,2 |
9,6 |
0,05 |
Беловский, шахта Колмогосркая |
ДГ, Г эн. |
13,1 |
8,7 |
0,05 |
Шахта Березовская |
К |
26,1 |
5,4 |
0,06 |
Шахта им. Димитрова |
Т |
21,2 |
6,7 |
0,06 |
Кемеровский, шахта им. Волкова |
ГЖ |
26,5 |
7,5 |
0,08 |
Кедровский разрез |
СС |
13,1 |
8,7 |
0,08 |
Анжерский, шахта Судженская |
ТС |
18,1 |
2,3 |
0,08 |
Ш/у Кольчугинское |
Д |
17,8 |
8,6 |
0,08 |
Осиновский, Шахта Капитальная |
Ж |
27,9 |
5,9 |
0,08 |
Шахта им 7 Ноября |
Г кокс |
14,5 |
8,4 |
0,1 |
Шахта им. Шевякова |
К, КО, КС, ОС |
29,5 |
8,1 |
0,1 |
Шахта Распадская |
ГЖ |
19,4 |
5,6 |
0,2 |
Ольжерасский разрез |
СС |
22,5 |
6,4 |
0,3 |
Мрасский, разрез Междуреченский |
К, КО, Т |
18,4 |
4,2 |
0,5 |
Калтанский разрез |
Т |
19,8 |
7,6 |
0,6 |
Томусинский разрез |
ОС |
17,8 |
5,1 |
0,6 |
Примечание. Кузнецкий бассейн является крупнейшей сырьевой базой коксохимической и топливно-
энергетической промышленности; по балансовым запасам угля он занимает первое место в стране; особенно
важное значение имеют коксующиеся угли, добыча которых составляет около половины от общей добычи по
бассейну; в качестве энергетического топлива используются в основном угли марок Д, СС, Т, отчасти Г.
Таблица 4.3 Добыча угля (в системе Минэнерго РФ*) в 2001 г., млн. т [110]
Показатель |
2001 |
Всего, в т. ч.: |
266,32 |
по экономическим районам страны: |
|
Северный |
19,07 |
Центральный |
1,04 |
Северо-Кавказский |
9,46 |
Уральский |
5,09 |
Западно-Сибирский |
127,96 |
Восточно-Сибирский |
75,69 |
Дальневосточный |
28,01 |
по угольным бассейнам: |
|
Кузнецкий |
127,44 |
Донецкий |
9,46 |
Печорский |
18,78 |
Канско-Ачинский |
38,18 |
по способам добычи: |
|
Подземный |
95,79 |
Открытый |
170,53 |
Добыто угля для коксования |
62,33 |
в т. ч. по угольным бассейнам: |
|
Кузнецкий |
48,31 |
Донецкий |
0,39 |
Печорский |
8,81 |
Южно-Якутский |
4,82 |
* Оставшаяся незначительная часть угля добывается предприятиями, которые курируются МПР РФ,
местными органами власти и т. д.
Таблица 4.4 Общее содержание ртути в угле, добытом в России в 2001 году – по регионам
Регион, область |
Добыча угля, млн. тонн * |
Содержание ртути в угле, среднее, мг/кг** |
Масса ртути, изъятой из недр с углем, тонны |
Калужская область |
0,05 |
0,26 |
0,013 |
Тульская область |
1 |
0,26 |
0,26 |
Коми |
18,8 |
0,052 |
0,98 |
Мурманская область |
0,3 |
0,05 |
0,015 |
Пермская область |
? |
0,44 |
? |
Ростовская область |
9,5 |
0,077 |
0,73 |
Башкирия |
0,06 |
0,05 |
0,003 |
Свердловская |
1,8 |
0,05 |
0,09 |
Челябинская область |
3,3 |
0,05 |
0,17 |
Бурятия |
3,9 |
0,0087 |
0,034 |
Тыва |
0,6 |
0,05 |
0,03 |
Хакасия |
6,8 |
0,05 |
0,34 |
Алтайский край |
0,01 |
0,05 |
0,0005 |
Красноярский край |
38,7 |
0,05 |
2 |
Иркутская область |
15,3 |
0,02 |
0,31 |
Кемеровская область |
126 |
0,094 |
11,8 |
Новосибирская область |
0,5 |
0,05 |
0,25 |
Читинская область |
14,3 |
0,011 |
0,16 |
Саха-Якутия |
9,7 |
0,02 |
0,19 |
Приморский край |
9 |
0,11 |
0,99 |
Хабаровский край |
2,3 |
0,4 |
0,92 |
Амурская область |
2,7 |
0,85 |
2,3 |
Сахалинская область |
? |
0,11 |
? |
Всего по России |
~ 270 |
|
~ 22 |
* По [237].
** Рассчитано по [312]. Исходные данные по каждому бассейну приведены в Приложении 3. При
отсутствии данных использовалось среднее содержание ртути в углях быв. СССР, равное 0,05 мг/кг
[119].
При обогащении углей применяются гравитационные процессы (для углей крупностью от
0,5 до 300 мм) и флотация (для обогащения мелких классов, <1 мм). Наибольшее
распространение получила пенная флотация. Продуктами обогащения являются: концентрат,
содержащий наиболее чистый уголь; промпродукт, в котором содержится наибольшее
количество сростков углей с минеральными образованиями; хвосты (порода) – продукт с
наибольшим содержанием частиц вмещающих пород (обычно в хвосты переходит
существенная часть содержащегося в углях пирита – основного носителя ртути). Побочными
продуктами при обогащении являются: отсев – необогащенный мелкий уголь, пыль – частицы
угля менее 0,5-1 мм, шлам – частицы пылевидного угля, накапливающиеся в моечных и
технологических продуктах. В зависимости от зольности побочные продукты присаживаются к
концентрату или промпродукту. В ходе предварительной подготовки и обогащения углей в
обычно происходит заметное снижение уровней содержания в них ртути, что в существенной
мере обусловлено формами (видами) нахождения ртути в углях и технологическими
особенностями их обогащения, в ходе которого пирит (основной концентратор ртути) уходит
преимущественно в отходы (хвосты) обогащения.
Я.Э. Юдович и др. [319], обобщив известные данные по формам нахождения ртути в
углях, отмечают, что в углях с фоновыми (или, как иногда говорят, кларковыми) содержаниями
этого металла доминируют две формы: ртуть, связанная с пиритом (Hgпир) и ртуть, связанная с
органическим веществом (Hgорг). Обычно тяжелые фракции углей в 6-7 раз богаче ртутью, чем
легкие. В составе Hgорг, по-видимому, имеется две формы ртути: физически сорбированная и в
соединениях с органическим веществом типа гуматов. В более сернистых углях (с
повышенным содержанием пирита) вклад Hgпир в баланс ртути более значителен. В углях,
аномально обогащенных ртутью, встречаются также металлическая ртуть и киноварь. Такие
формы нахождения ртути в углях предопределяют ее распределение по продуктам обогащения
углей: обеднение товарных продуктов и накопление в богатых пиритом хвостах (отходах).
Сказанное иллюстрируется данными, приведенными в табл. 4.5, из которых следует, что
концентраты (обогащенный уголь) характеризуются заметно более низкими концентрациями
ртути, нежели рядовые угли. Этот факт следует учитывать при оценках эмиссии ртути
(особенно при использовании для этих целей литературных сведений о ее содержании в углях).
Таблица 4.5 Среднее содержание ртути в товарной продукции Печорского угольного бассейна
[318]
Тип угля |
Hg, мг/кг сухого топлива |
Месторождения |
Коксующиеся: |
|
|
Рядовой |
0,073 |
Хальмеръюское, Воркутское, Юньягинское, Воргашское |
Концентрат |
0,040 |
Воркутское и Воргашское |
Отсев |
0,039 |
Воркутское и Воргашское |
Промпродукт |
0,050 |
Воркутское |
Энергетические: |
|
|
Рядовой |
0,08 |
Воркутское |
Концентрат |
0,05 |
Интинское |
Отсев |
0,06 |
Интинское |
Необходимо отметить, что не все 270 миллионов тонн угля, добытого в РФ в 2001 году, были
сразу же сожжены. В 2001 г. российским потребителям г. было поставлено 234 млн. т угля (в
том числе, уголь, который поставлялся из ранее добытого – в предыдущие годы – угля,
который хранится на шахтах и т. п.). Кроме того, существенную часть добытых углей
подвергают предварительной подготовке, которая включает операции дробления, сортировки,
обогащения, брикетирования и сушки [136]. Очевидно, что часть углей может только
дробиться, часть сортироваться и т. д. Статистической информации о соотношении указанных
видов «предварительной обработки» углей найти не удалось. Из официальной статистики
известно только, что в 2001 г. отечественными обогатительными фабриками было
переработано 77,8 млн. т угля, или более 29% годовой добычи (табл. 4.6). Кроме того, на
установках механизированной породовыборки переработано 18,75 млн. т угля. Таким образом,
по угольной промышленности всего переработано 96,55 млн. т угля, или более 36% общего
объема поднятого угля.
Таблица 4.6 Переработка угля на обогатительных фабриках России в 2001 г., млн. т [110]
Показатель |
2001 |
Переработка угля, всего |
77,80 |
в т. ч. для коксования |
52,63 |
Выпуск концентрата, всего |
45,09 |
в т. ч. для коксования |
35,54 |
Выпуск сортовых углей |
16,87 |
в т. ч. антрацитов |
2,39 |
4.1.2 Поступление ртути в окружающую среду и отходы в процессе угледобычи
Ртуть в отходах
Как следует из табл. 4.6, в 2001 г. в России при переработке 77,8 млн. т угля было
получено около 45 млн. т концентрата. Остальные 32 млн. т составили отходы обогащения.
Если предположить, что в среднее содержание ртути в перерабатываемых углях составляет 0,08
мг/кг и что половина этой ртути поступает в отходы производства, то в них в общей сложности
содержится 3,1 т ртути. Кроме того, некоторое количество ртути может находиться в
отвальных породах.
Сбросы со сточными водами
Угольная промышленность России ежегодно сбрасывает в поверхностные водотоки
порядка 550-600 млн. м³ сточных вод (до 75-80% - загрязненных, из которых, в свою очередь,
до 80% сбрасываются без очистки) и выбрасывает в атмосферу порядка 550 тыс. т вредных
веществ (в том числе до 60-70 тыс. твердых веществ).
Хорошо известно, что угледобыча сопровождается образованием значительных объемов
шахтных (рудничных) вод, отличающихся экстремально высокими содержаниями взвешенных
веществ (до 2000-4000 мг/л), кислой реакцией (рН до 2,5-4,0), повышенной минерализацией,
колеблющейся в широких пределах (от первых сотен до нескольких тысяч мг/л). Например, при
угледобыче в Кузбассе в конце 1990-х г.г. ежегодно отводилось более 100 млн/м³ загрязненных
вод, содержащих до 5-10 г/л взвешенных веществ, нефтепродукты, фенолы, хлориды, тяжелые
металлы [99]. Если исходить из средней мутности сточных вод в 3000 мг/л, то с ежегодно
отводимыми стоками угледобычи в России будет сбрасывать до 1,5 млн. т твердых веществ.
Будем считать, что среднее содержание ртути во взвеси сточных вод составляет 0,08 мг/кг, т. е.
соответствует ее уровню в углях. (Это содержание вполне отвечает фоновому уровню ртути в
природной речной взвеси. Например, природное содержание ртути во взвеси рек Московской
области составляет 0,068 мг/кг [334]. Реальное содержание ртути во взвеси сточных вод
угольных предприятий, очевидно, выше указанной величины.) Простые расчеты показывают,
что со взвесью сточных вод угледобычи в водные объекты будет сбрасываться порядка 120 кг
ртути.
Предположим, что содержание ртути (ее растворенных форм) в сточных водах
угледобывающих предприятий составляет 0,08 мкг/л (это среднее содержание данного металла
в водах рек мира [72]). Отсюда следует, что ежегодно в составе сточных вод в поверхностные
водоемы поступает 48 кг ртути.
Таким образом, суммарная поставка ртути со сточными водами угледобычи составит
порядка 168 кг. Следует отметить, что это минимальная оценка; реальная эмиссия ртути со
сточными водами угледобывающих предприятий может быть, очевидно, увеличена в несколько
раз.
Выбросы в атмосферу
Источниками эмиссии ртути в атмосферу при угледобыче являются угольные и породные
отвалы. Например, по данным С.В. Алистратова [5], средние содержания ртути в отвалах
Подмосковного угольного бассейна варьируются от 0,24 до 1,3 мг/кг, достигая в отдельных
точках 3,3 мг/кг. Концентрация ртути в разных отвалах может различаться в несколько раз в
зависимости от пород, составляющих отвалы на том или ином месторождении, времени их
отсыпки и интенсивности гипергенной переработки. Автор цитируемой работы отмечает, что
при гипергенных изменениях грунтов отвалов часть ртути улетучивается в атмосферу, что
обусловливает формирование ее атмогеохимических потоков. Особое значение имеет
самовозгорание угля в шахтах, разрезах, в естественном залегании и в отвалах пород, которое
может сопровождаться поступлением ртути в атмосферу. При горении отвалов температуры
достигают 800-1000оС и более (в скрытых воронках), что приводит к разрушению сульфидных
и глинистых минералов, выгоранию всех органических веществ. Ртуть, содержащаяся в
породах, возгоняется и улетучивается в атмосферу. Не исключено, что горящие терриконы
углеобогатительных фабрик могут давать значительный выброс паров ртути в атмосферу,
поскольку отличаются повышенными содержаниями ртути в пиритном концентрате. По
расчетам Л.А. Добрянского и др. [93], от всей массы горных пород, поступившей на терриконы
угольных шахт Горловки (Донбасс) в 1989 г., эмиссия ртути в результате ее дегазации
составила 230 кг/год. Обогащение ртутью атмосферы на терриконах подтверждалось и
прямыми замерами. В частности, на породных терриконах шахт г. Горловки концентрации
паров ртути в воздухе летом 1990 г. варьировались от 57 до 13700 нг/м³, причем измерения
проводились в период остановки металлургического цеха Никитовского ртутного комбината, т.
е. влияние последнего практически исключалось.
Если ориентироваться на приведенные выше сведения, то с определенной долей
условности следует считать, что общая эмиссия ртути в ходе добычи и обогащения угля на
российских предприятиях может быть существенной. Однако этой информации не достаточно
для оценки эмиссии ртути из отходов угледобычи; необходимы специальные исследования.
4.1.3 Использование угля в электроэнергетике
В 2001 г. в России доля угля в общем объеме топлива для производства тепловой и
электрической энергии составила 34,1% на ТЭЦ и 45% в котельных ЖКХ.
Теплоснабжение России обеспечивают [232]:
- 485 теплоэлектроцентралей (ТЭЦ);
- около 6,5 тыс. котельных мощностью более 20 Гкал/час (в основном, муниципальные);
- более 180 тыс. мелких котельных (в основном, муниципальные);
- около 600 тыс. автономных индивидуальных теплогенераторов.
Согласно статистическим данным, приводимым Международным Энергетическим
Агентством [387], в России 127 млн. т угля было израсходовано на ТЭЦ, 34 млн. т – на
котельных установках, при этом уголь не использовался на электростанциях, не производящих
тепло.
Поведение и эмиссия ртути в процессе сжигания угля
Традиционно считается, что при высоких температурах сжигания ртуть, содержащаяся в
углях, практически вся переходит в газообразное состояние и, в конечном счете, выбрасывается
в атмосферу с отходящими газами или концентрируется на частицах, улавливаемым
специальными очистными установками.
Ввиду высокой летучести ртути большая часть наиболее распространенных систем
очистки выбросов не являются эффективными с точки зрения ее улавливания из отходящих
выбросов. В настоящее время в литературе практически отсутствуют сведения об
эффективности различного оборудования по улавливанию ртути, используемого на российских
энергоустановках.
Недавно в США были проведены широкомасштабные исследования по определению
эффективности различных систем очистки выбросов, используемых для улавливания ртути, на
большом количестве котельных, работающих на угле [415]. Средние показатели степени
очистки выбросов от ртути в зависимости от ряда факторов варьировались от 0 до 96% (табл.
4.7). В целом было установлено следующее:
- Применение определенной технологии или комбинации технологий позволяло
обеспечить различную эффективность с точки зрения снижения содержания ртути в
определенных типах угля.
- Эффективность контроля за выбросами ртутью во многом зависела от типа
используемого угля, при этом средний процент ее улавливания увеличивался по мере повышения
“ранга” используемого топлива, начиная от бурого угля и далее до полубитуминозного и
битуминозного угля. В рамках любого определенного “ранга” угля был обеспечен некий
диапазон удаления ртути. Здесь следует обратить внимание на то, что в глобальном масштабе
угли имеют более широкий ранг классификации (используется, например, бурый уголь) и
заметно различаются своими характеристиками (содержанием серы, зольностью и т. д.) по
сравнению с углями США.
Необходимо отметить, что в данном исследовании не анализировались циклоны, однако
можно предположить, что степень улавливание ртути ими окажется более низкой, нежели
электростатическими осадителями.
Таблица 4.7 Средний показатель улавливания ртути в виде % от ртути на входе в очистное
устройство (по данным [415]).
Стратегия контроля после процесса сгорания |
Конфигурация устройств для контроля эмиссии после сгорания |
Средний показатель улавливания ртути очистным оборудованием (в скобках число тестов, проведенных во время испытаний) |
Уголь, сжигаемый в котельных, работающих на угольной пыли |
Битуминозный уголь |
Полубитуминозный уголь |
Бурый уголь |
Только для контроля за СМЧ |
ХЭСО |
36 % (7) |
3 % (5) |
- 4 % (1) |
ГЭСО |
9 % (4) |
6 % (4) |
Испытания не проводились |
ТФ |
90 % (4) |
72 % (2) |
Испытания не проводились |
СМЧ |
Испытания не проводились |
9 % (1) |
Испытания не проводились |
Контроль за СМЧ и распыление- сушка- адсорбция |
РСА+ ЭСО |
Испытания не проводились |
35 % (3) |
Испытания не проводились |
РСА+ТФ |
98 % (3) |
24 % (3) |
0 % (2) |
РСА+ТФ+ИКВ |
98 % (1?) |
Испытания не проводились |
Испытания не проводились |
Контроль за СМЧ и влажная система ДТП (a) |
СМЧ+ДТГ |
12 % (1) |
-8 % (4) |
33 % (1) |
ХЭСО+ДТГ |
74 % (1) |
29 % (3) |
44 % (2) |
ГЭСО+ДТГ |
50 % (1) |
29 % (5) |
Испытания не проводились |
ТФ+ДТГ |
98 % (2) |
Испытания не проводились |
Испытания не проводились |
Примечание. (a) - Оценочный показатель улавливания на обоих устройствах; ИКВ – избирательное
каталитическое восстановление; ХЭСО – холодный электростатический осадитель; ГЭСО – горячий
электростатический осадитель; ТФ. тканевый фильтр; СМЧ – скруббер макрочастиц; РСА – система
“распылитель-сушитель-адсорбер”; ДТГ – десульфуризация топочного газа.
Топочные устройства (топки) разделяются на слоевые и камерные. В топках первого типа
основная масса твердого топлива сгорает в слое, в топках второго типа – во взвешенном
состоянии. Камерные топки делятся на факельные и вихревые (циклонные). В свою очередь,
факельные топки для сжигания твердых топлив в зависимости от отвода шлака и золы могут
быть с сухим (твердым) шлакоудалением и с жидким шлакоудалением. В России наибольшее
распространение имеют топки с твердым шлакоудалением, в которых часть золы (до 10-15%)
выпадает в шлаковый бункер, а остальная часть уносится топочными газами в газоходы котла.
В топках с жидким шлакоудалением (одно- или двухкамерных) доля летучей золы меньше,
нежели в топках с твердым шлакоудалением, но все же значительна. В однокамерных топках
она, в среднем, составляет 30-40%, в двухкамерных – 50-60%.
На крупных (мощных) электростанциях (более 300 МВт) обычно применяются камерные
топки с твердым шлакоудалением, реже – открытые и полуоткрытые топки с жидким
шлакоудалением. На ТЭЦ средней мощности (50-300 МВт), кроме указанных выше, могут
использоваться также циклонные топки. На небольших электростанциях и в котельных (менее
50 МВт) чаще других применяются циклонные топки.
На российских энергетических объектах применяют следующие виды золоуловителей:
сухие инерционные золоуловители, мокрые золоуловители, электрофильтры, комбинированные
золоуловители. Циклоны и блоки циклонов применяются для очистки продуктов сгорания
парогенераторов малой мощности; в батарейных циклонах достигается лучший отвод
уловленного уноса и повышенный КПД (82-90%). Они устанавливаются на котлах
производительностью от 25 до 320 т/ч. В мокрых золоуловителях улавливание уноса
производится путем осаждения его на пленку жидкости, находящейся внутри поверхности
аппарата. Для парогенераторов малой и средней производительности (90-100 т/ч) применяют
центробежные скрубберы, представляющие собой вертикальный прямоточный циклон,
внутренняя система которого непрерывно орошается водой. Для парогенераторов
производительностью 120-150 т/ч основным типом применяемых мокрых золоуловителей
является золоуловитель с турбулентными коагуляторами внутри. Используются также (обычно
для котлов средней мощности) вертикальные и горизонтальные сухие и мокрые
электрофильтры. В середине 1990-х г.г. средний коэффициент золоулавливания для российской
энергетики оценивался в 0,91. Для московских ТЭС он составлял 0,89; в коммунально-бытовом
хозяйстве и промышленности – только лишь 0,70 [52]. Котлы малой паропроизводительности
(< 50 МВт), используемые обычно в коммунальном хозяйстве, на сельскохозяйственных и
малых промышленных предприятиях, часто не оборудованы пылеулавливающими
устройствами.
Кроме того, некоторые энергоустановки оборудованы системами контроля SO2, включая
различные типы влажных и сухих скрубберов; для контроля за NOx могут применяться
избирательное каталитическое или избирательное некаталитическое восстановление.
В настоящее время проводится оценка эффективности работы оборудования,
используемого на крупных российских электростанциях для контроля и очистки топочного
газа. По предварительной оценке [339], первоначальный показатель улавливания (КПД очистки
выбросов) составляет 21%.
Учитывая сказанное, а также технологические особенности российских объектов
теплоэнергетики, можно, очевидно, следующим образом приблизительно оценить
относительный выброс ртути (от ее общего количества, поступившего с углем на сжигание
и/или переработку) в атмосферу:
- использование угля для нужд электроэнергетики – 80%;
- использование угля для коммунально-бытовых нужд – 95%;
- использование угля населением и в агропромышленном комплексе – 99%.
- использование угля остальными потребителями – 90%.
Остальная ртуть связывается с золошлаковыми отходами и с уловленной очистными
установками золой.
В табл. 4.8 приведена расчетная оценка баланса распределения ртути при использовании
углей для производства тепла и электроэнергии в России в 2001 г. (Эмиссия ртути при
производстве кокса рассматривается в специальном разделе.)
Таблица 4.8 Мобилизация и поступление ртути в окружающую среду при использовании угля
в России для выработки тепла и электроэнергии в 2001 г.
Область применения |
Потребл ение угля, млн. тонн |
Количество ртути в используемых углях, тонны (наилучшая оценка) |
Выбросы в атмосферу |
В отходы, тонны (наилучшая оценка) |
Коэффици ент распредел ения, % * |
тонны (наилучшая оценка) |
Электроэнергетика |
124,3 |
9,9 |
80 |
8,0 |
2,0 |
ЖКХ (котельные) |
17,6 |
1,4 |
95 |
1,3 |
0,1 |
Теплоснабжение населения и агропромышленный комплекс |
8,5 |
0,7 |
99 |
0,7 |
0,0 |
Другие (в основном промышленность) |
42,2 ** |
3,4 |
90 |
3,0 |
0,3 |
Общий объем производства тепла и энергии |
|
15,4 (13,5-17,3) |
|
13,0 |
2,4 |
* Средняя доля ртути, содержащаяся в угле и поступившая с выбросами в атмосферу.
** Согласно [387], 1,4 млн. т угля было использовано не для выработки энергии.
Крупные угольные электростанции являются одним из основных источников выброса
ртути. В настоящее время проводится оценка выбросов 129 крупнейших электростанций
России [339]. Ниже на карте (рис. 4.2) показано местоположение 50 из них. Расчетные
показатели выбросов с котельных ЖКХ представлены в Приложении 4.
В рамках указанного исследования выбросов ртути основными российскими угольными
электростанциями был также проведен обзорный анализ с целью определения содержания
ртути в угле, добываемом в России [339]. Средние концентрации ртути, полученные для
месторождений, где имеются фактические данные, приведены в табл. 4.9. Для других
месторождений было использовано условное значение в 0,1 мг/кг. С учетом количества углей
(74 420 000 т), их типов и удельного содержания в них ртути определена ее масса в углях,
использованных в 2002 г. на 129 российских электростанциях. При использовании средних
концентраций ртути она составила 6,3 т, при использовании максимальных значений –
примерно 8,8 т. Средняя масса ртути, присутствующей в использованных углях,
корреспондирует со средней концентрацией ртути в угле, равной 0,08 мг/кг, что, в свою
очередь, соответствует ее среднему содержанию в углях, указанному выше.
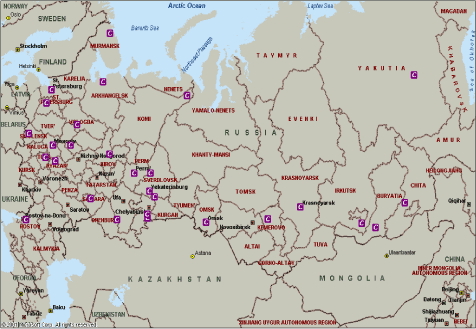
Рисунок 4.2 Местоположение 50 крупных российских угольных электростанций.
Крупные российские электростанции имеют системы для очистки топочного газа,
включая циклоны (КПД по удалению золы 75-80%), а также скрубберы (КПД 99%) [339].
Согласно авторам цитируемой работы, для первоначальной оценки применялся коэффициент
распределения выбросов ртути в атмосферу, равный 81%. При таком допущении выброс ртути
в воздух на 126 крупнейших российских электростанциях, где в 2002 г. было использовано 74,4
млн. т угля составляет, по оценке, в среднем 5 т (максимально 7 т), в то время как в остаточный
продукт сгорания поступает 1,3 т ртути (максимально 2,2 т). Таким образом, предварительные
расчеты, выполненные для 129 крупных угольных электростанций России, соответствуют
оценкам, полученным в ходе настоящего исследования.
Таблица 4.9 Среднее содержание ртути в углях России [339]
Угольное месторождение |
Среднее содержание ртути, мг/кг |
Ирша-Бородинское |
0 |
Башкирское |
0,003 |
Гусиноозерское |
0,02 |
Харанорское |
0,02 |
Экибазстуское (Казахстан) |
0,02 |
Березовское |
0,04 |
Карагандинское (Казахстан) |
0,05 |
Воркутинское |
0,05 |
Интышское |
0,05 |
Донецкое |
0,094 |
Кузнецкое |
0,11 |
Сахалинское |
0,11 |
Азейское |
0,17 |
Черемховское |
0,17 |
Магаданское |
0,18 |
Подмосковное |
0,2 |
Райчихинское |
0,4 |
Киселевское |
0,446 |
Огоджинское |
0,9 |
4.1.4 Производство кокса
В 2001 г. в России было получено 29 997 тыс. т кокса. (Объемы производства кокса
конкретными предприятиями приведены ниже, см. табл.4.11). К началу 2002 г. в российской
коксовой промышленности действовали 12 коксохимических предприятий, в составе которых
имелось 62 работоспособных коксовых батареи (3851 печь) общей проектной мощностью
39066 тыс. т кокса (6%-ной влажности) в год [51]. В постоянной эксплуатации находились 59
батарей мощностью 36,9 млн. т (3 батареи – на консервации). Значительная часть оборудования
коксохимических предприятий является устаревшим (средний возраст коксовых батарей в 2000
г. составил 22 года). Как правило, практически все батареи недостаточно оборудованы
эффективными пылегазоочистными устройствами.
Современное коксохимическое производство представляет собой сложный
производственный комплекс, продукцией которого является не только кокс, но ряд других
материалов. Например, коксохимическое производство ОАО “Носта” состоит из
углеподготовительного цеха, двух коксовых цехов, цеха по получению сульфата аммония
(применяемого в сельском хозяйстве в качестве удобрения), каменноугольной смолы (для
переработки ее в товарные продукты) и сырого каменноугольного бензола (для получения
органических углеводородов бензольного ряда), биохимической установки для очистки
сточных вод производства от фенолов, роданидов и планидов.
Коксохимия остается одним из основных поставщиков сырья для производства
пластмасс, химических волокон, красителей и других синтетических материалов. Доля
коксохимических продуктов в сырьевой базе промышленности основного органического
синтеза составляет до 50%, а таких важных продуктов, как бензол, достигает 80%, нафталин и
креозолы – почти 100%. Цветная металлургия является потребителем малозольного пекового
кокса и связующего, получаемых из каменноугольной смолы. Коксы используются для
приготовления анодной массы, применяемой при выплавке алюминия. На базе водорода
коксового газа и азота кислородных станций металлургических комбинатов производятся
азотистые удобрения. Химические продукты коксования используются также для изготовления
химических средств защиты растений и животных.
Процессы и технологии
Производство кокса включает следующие стадии: обработку и хранение угля, загрузку
угля в коксовую печь, тушение кокса, очистку коксового газа. Кокс получают сухой перегонкой
каменных углей в коксовых печах, собранных в коксовые батареи (в каждой из которых - по 40-
70 печей). Коксовая печь представляет собой камеру шириной 0,4-0,45, длиной около 15 и
высотой около 5 метров. Полезный объем камеры составляет 30 м³, а масса загружаемой шихты
– 22 т. Угольную шихту, нередко представляющую собой смесь углей из различных шахт,
перед спеканием измельчают в дезинтеграторе, затем загружают в коксовые печи, где
разогревают до 1000°С (без доступа воздуха) и выдерживают в течение 15-16 часов. В процессе
нагрева уголь теряет около 30% своей массы за счет образования газов и смолы. Полезными
продуктами процессы является кокс и газ средней калорийности. Производительность
современной батареи достигает 1500 т/сут. Шихту в печи загружают сверху. После коксования
коксовыталкиватель выгружает кокс (коксовый пирог) из печи в тушильный вагон для подачи
его в тушильную башню. Здесь кокс охлаждают водой (мокрое тушение) или инертным газом
(сухое тушение).
Сырье
Исходным сырьем для получения кокса являются особые сорта каменных углей. Для
коксования обычно используют смесь углей, взятую в определенном соотношении. В основном
применяют коксовые, паровично-жировые, паровично-спекающиеся и газовые угли. Из 1 т
сухой шихты получают 750-800 кг кокса и 320-330 м³ коксового газа. Основу угольной
сырьевой базы коксования России на 85% определяет Кузнецкий угольный бассейн. Например,
только в Кемеровской области добывается почти 70% всех российских коксующихся углей, а
по группе марок особо ценных коксующихся углей – 100%. Среднее содержание ртути в углях
Кузнецкого бассейна, рассчитанное по данным [312], составляет 0,08 г/т. В коксующихся угля
Печорского бассейна уровни содержания ртути изменяются от 0,01 до 0,1 г/т (среднее 0,05 г/т).
На некоторых производствах в Сибири иногда используются коксующиеся угли
Карагандинского угольного бассейна. Содержания ртути в товарном концентрате обычно ниже,
чем в рядовых углях.
Источники и характеристика пылегазовыделений
Основными источниками пылегазовыделений при производстве кокса являются
обработка и хранение угля, коксование угля и его гашение. Коксовая пыль образуется при
выдаче кокса из печных камер, транспортировке, рассеве, дроблении и отгрузке кокса, а при
наличии установок сухого тушения кокса - из свечей форкамеры и дымососа. Возможно
выделение сажи из дымовых труб, образование которой происходит в отопительных системах
коксовых батарей при их разгерметизации и попадании сырого коксового газа в отопительные
каналы [230]. Неорганизованные выбросы образуются при загрузке угольной шихты в печные
камеры, выдаче и тушении кокса. Организованные выбросы происходят из выхлопных труб
систем аспирации объектов транспортирования, измельчения, сепарации, сушки шихты, а
также при перегрузках и рассеве кокса. Максимальное выделение пыли отмечается при сухом
тушении кокса, при загрузке бункеров коксом и от свечи дожигания, а также при выгрузке
раскаленного кокса в вагон. Выбросы во время коксования возникают из-за утечек через двери
печной камеры, крышки люков и т.п. Во время коксования выделяется основная часть летучих
веществ. Запыленность инертного газа после тушильного бункера составляет 4-10 г/м³ [274].
При выгрузке кокса из печей и вследствие неплотности дверей в процессе эксплуатации на
коксовой стороне батареи выделяется до 35% от выбросов коксового цеха [37].
Пылегазоочистка
Обязательную очистку проходит коксовый газ, в процессе обработки которого
конденсируются пары и смол и воды, улавливаются аммиак и бензольные углеводороды.
Аспирационные системы углеподготовительного и коксового цехов, как правило, оборудованы
циклонами и мокрыми пылеуловителями, эффективность которых составляет 96-98%.
Наиболее эффективным методом снижения выбросов при загрузке шихты является бездымная
загрузка: образующиеся пылегазовыделения отсасываются с помощью парового или
гидравлического инжектора в коллектор, по которому направляются в газоочистку. При сухом
способе тушения кокса пыль улавливают сначала в инерционном пылеуловителе, а затем в
циклоне. При выгрузке кокса пыль, как правило, не улавливается.
В среднем при производстве кокса на тонну продукта выделяется от 0,055 до 3,2 кг
угольной и коксовой пыли [153, 163]. Удельные выбросы собственно коксовой пыли
варьируются от 0,05 до 2,5 кг/т кокса. В свое время Министерством черной металлургии СССР
были разработаны среднеотраслевые удельные выбросы пыли в коксохимическом
производстве, составившие 2 кг/т кокса [302]. Для сравнения, в Западной Европе на коксовых
предприятиях выбросы пыли при тушении кокса не превышают 10 г/т кокса, а остаточное
содержание пыли в целом по заводу составляет 5 г/т кокса [122].
Инвентаризация выбросов на ряде коксовых заводов России показала, что пылевые
выбросы от организованных источников составляют 30% всех выбросов, а на предприятиях с
сухим тушением – до 70% [230]. Широкое использование в системах газоочистки и аспирации
получили центробежные инерционные пылеуловители – цилиндрические и конические
циклоны (степень очистки 93-98%). Но особенно распространены мокрые пылеуловители,
которые часто применяются для обеспыливания аспирационного воздуха и газов сушки угля
(это создает проблему переработки и утилизации шламовых вод). Из мокрых пылеуловителей
наибольшее распространение получили центробежные скрубберы с орошаемой прутковой
решеткой во входном патрубке и обычного типа. Степень улавливания угольной пыли в
центробежных скрубберах составляет от 85 до 98% (в среднем 90%), при улавливании коксовой
пыли 30-97% (в среднем 90%). Применяются также циклоны с водяной пленкой (степень
улавливания угольной пыли 89-97%, коксовой 88-90%), скоростные промыватели, или
прямоточные мокрые циклоны (степень улавливания угольной пыли 80-98%, коксовой 85-
95%). Разброс показателей связан с разным уровнем обслуживания аппаратуры на заводах. На
ряде отечественных предприятий используются газопромыватели с трубами Вентури.
В целом эффективность пылегазоочистных сооружений в коксовом производстве стран
СНГ оценивается примерно в 90% [52].
Ртуть в коксохимическом производстве
Распределение ртути в продуктах коксования в свое время было изучено украинскими
специалистами [113]. Рядовой уголь, выдаваемый на поверхность из шахт и карьеров,
подвергается обогащению с целью удаления породы, высокозольных разностей и пиритных
конкреций (обычно отличающихся повышенным содержанием ртути). Ртуть в ходе обогащения
распределяется следующим образом (рис. 4.3): основное ее количество переходит в концентрат
(до 58-62%) и в отходы – в идущие в отвал породу и хвосты (до 24-26%). Показательно, что по
данным [318], в товарной продукции Печерского бассейна (месторождения Воркутское и
Воргашское) среднее содержание ртути составляло: в рядовом угле – 0,073 г/т, в концентрате .
0,04 г/т, в отсеве – 0,039 г/т, в промпродукте – 0,05 г/т. Такое (в данном случае удельное)
распределение ртути, в сущности, соотносится с выше приведенными сведениями (содержание
ее в концентрате составляет примерно 55% от содержания в рядовом угле, в промпродукте .
около 68%).
Как уже отмечалось, температура в печах коксования достигает 1000°С и более, что
приводит практически к полному переходу ртути из шихты в прямой коксовый газ, а затем в
разнообразные продукты твердой, жидкой и газовой фаз коксохимического процесса [113].
Накопление ртути происходит в продуктах конденсации, образующихся при охлаждении
сырого коксового газа, в частности в каменноугольной смоле. Далее, при разгонке смолы, она
осаждается в сепараторе и сборнике легкого масла. В сульфатном отделении ртуть не
обнаружена в сульфате аммония; в скрубберном отделении ртуть не обнаружена в обратном
газе, но в значимых количествах присутствовала в насыщенном растворе сероочистки, в сыром
бензоле, в полимерах; ртуть также была обнаружена в заметных количествах в целом ряде
продуктов ректификации – в тяжелом бензоле, в ксилоле, в толуоле, в чистом бензоле. Она
также присутствовала в некоторых продуктах и отходах процесса смолоразгонки (в фусах, в
нафталиновом масле, в антраценовой фракции, в пеке).
![Рисунок 4.3 Схема относительного распределения (баланса) ртути в продуктах переработки и отходах коксохимического производства (составлено по данным [113], с дополнениями и уточнениями).](images/s155.gif)
Рисунок 4.3 Схема относительного распределения (баланса) ртути в продуктах переработки и
отходах коксохимического производства (составлено по данным [113], с
дополнениями и уточнениями).
Среднее содержание ртути в шихте примем в 0,076 г/т. Таким образом, в 1 млн. т шихты
содержится 76 кг ртути. Известно, что из 1 т сухой шихты получают до 800 кг кокса (т. е. из 1
млн. т шихты будет получено 850 тыс. т кокса). В ходе коксохимического производства
указанное количество ртути распределяется примерно следующим образом (табл. 4.10).
Таблица 4.10 Примерное распределение ртути в ходе коксохимического производства
Поступление: |
% |
кг Hg/106 т шихты |
г Hg/т кокса |
Масса ртути, т, 2001 г. |
В атмосферу при шихтовке |
~ 5 |
3,8 |
0,0047 |
0,14 |
В шлам |
~ 2,5 |
1,9 |
0,0023 |
0,07 |
В промпродукт |
~ 3,5 |
2,7 |
0,0033 |
0,10 |
В хвосты |
~ 2,5 |
1,9 |
0,0023 |
0,07 |
В породу |
~ 22,5 |
17,1 |
0,0213 |
0,64 |
В атмосферу при коксовании |
~ 40,5 |
30,8 |
0,0385 |
1,15 |
В кокс |
~ 0,5 |
0,4 |
0,0004 |
0,01 |
В надсмольные воды |
~ 2,5 |
2,7 |
0,0033 |
0,10 |
В конечную химпродукцию |
~ 17 |
12,9 |
0,0161 |
0,48 |
Итого |
100 |
74 |
0,0922 |
2,8 |
Таким образом, всего в 2001 г. в процесс производства кокса было вовлечено 2,8 т ртути.
Удельный выброс ртути в атмосферу в целом составил 0,043 г/ на 1 т произведенного кокса, в
том числе 0,0385 г/т непосредственно в ходе коксования и 0,0047 в процессе смешивания
шихты. Таким образом, даже при относительно низких содержаниях ртути в углях на
российские коксовые заводы поступает заметное количество этого металла. Существенная
масса ее (1,3 т в 2001 г.) поступает в атмосферу главным образом с отходящими газами
коксования (табл. 4.11). Около 0,8 т в конечном итоге попадает в отходы, около 0,6 т- в
продукцию и 0,1 т в сточные воды.
Таблица 4.11 Эмиссия ртути в атмосферу в России при производстве кокса, 2001 г.
Предприятие |
Местоположение |
Кокс, тыс. т * |
Эмиссия Hg, т |
ОАО “Алтай-Кокс” |
г. Заринск, Алтайский край |
3176 ** |
0,137 |
ОАО “Кокс” |
г. Кемерово |
1706 |
0,073 |
Московский коксогазовый завод |
г. Видное, Московская обл. |
200*** |
0,009 |
ОАО “Губахинский кокс” |
г. Губаха, Пермская обл. |
146 |
0,006 |
Коксохимическое производство ОАО “Западно-Сибирский МК” |
г. Новокузнецк, Кемеровская обл. |
3886 |
0,167 |
Коксохимическое производство ОАО “Кузнецкий МК” |
г. Новокузнецк, Кемеровская обл. |
1192 |
0,051 |
Коксохимическое производство ОАО “Магнитогорский МК” |
г. Магнитогорск, Челябинская обл. |
4918 |
0,212 |
Коксохимическое производство ОАО “Нижнетагильский МК” |
г. Нижний Тагил, Свердловская обл. |
2893 |
0,124 |
Коксохимическое производство ОАО “Новолипецкий МК” |
г. Липецк |
4349 |
0,187 |
Коксохимическое производство ОАО “Носта” (Орско-Халиловский МК) |
г. Новотроицк, Оренбургская обл. |
1311 |
0,056 |
Коксохимическое производство ОАО “Мечел” (Челябинский МК) |
г. Челябинск |
2257 |
0,097 |
Коксохимическое производство ОАО “Северсталь” (Череповецкий МК) |
г. Череповец, Вологодская обл. |
4021 |
0,173 |
Всего по России (округленные данные) |
30000 |
1,3 |
* По [69, 160, 161, 181, 307, 357, 366].
** В 2002 г.
*** По оценке авторов.
4.1.5 Заключение
Обобщенные данные по мобилизации ртути при использовании угля в Российской
Федерации в 2001 г. представлены в табл. 4.12.
Общее количество ртути, содержащейся в добытом угле, оценивается в среднем в 22 т
(интервальная оценка составляет 20-24 т). Общий объем выбросов ртути в атмосферу и ее
поступления в отходы при добыче и использовании угля, согласно расчетам, составляет
примерно 19,8 т. Кроме того, около 0,5 т ртути содержится в химических продуктах,
получаемых при производстве и переработке кокса.
Определенная часть ртути содержится в коксе и побочных продуктах. Она учтена при
расчетах эмиссии ртути в окружающую среду предприятиями черной металлургии.
Таблица 4.12 Мобилизация ртути при использовании угля в Российской Федерации в 2001 г.
Область применения |
Добыча или потреблени е угля, млн. т |
Мобилизаци я ртути, т (наилучшая оценка) |
Выбросы в атмосферу |
В отходы, т (наилучша я оценка) *** |
Коэффицие нт распределен ия, % |
т (наилучшая оценка) |
Добыча и переработка угля |
270 |
22 |
нет данных |
нет данных |
3,1 |
Выработка тепла и энергии: |
|
|
|
|
|
электроэнергетика |
124,3 |
9,9 |
80 |
8,0 |
2,0 |
ЖКХ (котельные) |
17,6 |
1,4 |
95 |
1,3 |
0,1 |
теплоснабжение населения и агропромышленный комплекс |
8,5 |
0,7 |
99 |
0,7 |
0,0 |
Другие (в основном промышленность) |
42,2 * |
3,4 |
90 |
3,0 |
0,3 |
Производства кокса |
41,7 |
2,8 |
46** |
1,3 |
0,1 * |
Общий объем поступления в окружающую среду |
|
|
|
14,3 |
5,6 |
* Некоторое количество ртути, поступающее в отходы обогащения угля, включено в расчеты в
позицию “Добыча и переработка угля”.
** Расчет произведен на основе данных по необработанным углям; при переработке обогащенного
угля, в атмосферу поступает, согласно расчетам, 66% ртути, содержащейся в концентрате.
*** Не включает пустую породу.
4.2 Нефть, природный газ, горючие сланцы и биотопливо
4.2.1 Введение
Содержания ртути в сырой нефти и газе существенно различаются. С целью получения
точных расчетных данных по общему количеству ртути, мобилизованной при использовании
нефти и газа в России, необходимо получить данные анализа большого количества проб с
основных нефтяных и газовых месторождений. Кроме того, отличаться может количество
ртути, содержащееся в сырой нефти, перерабатываемой на различных НПЗ.
В качестве исходной информации для определения мобилизации ртути при
использовании нефти и газа, ее распределение в газонефтяном сырье рассматривается в данном
разделе в геологическом контексте.
Пределы колебаний содержания ртути в газонефтяном сырье весьма существенны (табл.
4.13). Эти колебания обусловлены геологическими причинами и главная из них .
приуроченность ртутьсодержащих месторождений к зонам региональных разломов мантийного
заложения, по которым ртуть в составе флюидов (ртутная дегазация Земли) поступает в зоны
газо-, нефте- и рудообразования и участвует в этих процессах.
Одной из таких зон является линеамент Карпинского (рис. 4.4) [188, 193, 194]. К этой
структуре приурочены все известные газовые и газонефтяные месторождения Нидерландов,
Германии и Польши с высокими содержаниями ртути. На территории бывшего СССР в
пределах линеамента Карпинского также установлены ртутьсодержащие месторождения, но со
значительно меньшими концентрациями ртути. Следует отметить, что здесь встречаются
месторождения не только с повышенными концентрациями ртути, но и с весьма низкими. И
тому есть тоже геологическое объяснение. Но для нас важно то обстоятельство, что, выявив
повышенные содержания ртути на месторождении в пределах какой-либо нефтегазовой
провинции, мы не можем адаптировать их на другие месторождения этой провинции.
Таблица 4.13 Пределы содержания ртути в нефтяных и газовых месторождениях мира
Компонент |
Концентрация ртути |
Нефть |
0,003 – 21 мг/кг |
Конденсат |
<0,037 – 1,1 мг/кг |
Газ |
0,01.10-6 – 14000.10-6 г/м³ |
Другим примером структур, подобных линеаменту Карпинского, является Паннонско-
Волынский линеамент (рис. 4.5), контролирующий размещение ртутьсодержащих
газонефтяных, газовых и рудных месторождений на территории Восточной Европы, включая
Украину (Предкарпатский прогиб) [401, 402].
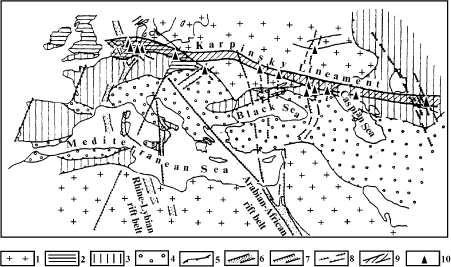
Рисунок 4.4 Расположение ртутоносных газовых и газонефтяных месторождений в
границах линеамента Карпинского
1-4 – складчатые области:1 – докембрийская, 2 – каледонская, 3 – герцинская, 4 – альпийская; 5 – границы
между складчатыми областями различного возраста; 6 – континентальные рифтовые пояса (Рейнско-Ливийский и
Аравийско-Африканский); 7 – крупные зоны поперечных нарушений; 8 – поперечные глубинные разломы; 9 .
линеамент Карпинского; 10 – газовые месторождения и проявления с содержанием ртути в газе более 1×10-6 г/м³
Другое геологическое обстоятельство: установлено увеличение содержаний ртути с
глубиной в газовых и газонефтяных месторождениях как в пределах провинции, так и на
отдельных месторождениях (табл. 4.14 и 4,15) [189, 191, 192]. Для нас важен последний факт,
указывающий на то, что мы не должны оценивать ртутоносность месторождений по отдельным
определениям ртути, а должны во время опробования учитывать – с каких горизонтов или в
какой пропорции производится добыча с разных глубин и т.д.
И третье обстоятельство. В последние годы на газовых месторождениях Мирненское
(Россия) и Опошнянское (Украина) установлена закономерная периодичность – от нескольких
часов до нескольких суток - в изменениях концентраций ртути в газах, связанная с периодами
собственных колебаний Земли [249, 407]. Размах колебаний при наблюдениях в скважинах
изменялся от 10 до 80% от величины среднего содержания ртути в газах. И мы не знаем,
предельные ли это значения, или они могут быть выше, что соответственно, может отразиться
на качестве опробования.
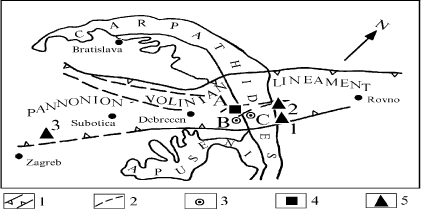
Рисунок 4.5 Паннонско-Волынский линеамент.
1 – разломы, окружающие линеамент; 2 – разломы; 3 – ртутные месторождения (B .
Вишковское, C – Углянское); 4 – Береговское полиметаллическое месторождение (A); 5
– нефтяные месторождения (1 – Битковское, 2 – Бориславское, 3 – Молве)
Таблица 4.14 Cодержание ртути в газах Мирненского месторождения на Северном Кавказе
(линеамент Карпинского)
Возраст газоносных пластов |
Разница в глубинах, м |
Число проб |
Содержание ртути, 10-6 г/м³ |
Палеогеновый (Pg mkp3) |
2000 |
13 |
0,05 – 0,3 |
Меловой (К1) |
40 |
0,2 – 40 |
Таблица 4.15 Содержание ртути в газах месторождений Днепрово-Донецкой впадины (линеамент
Карпинского)
№№ скважин |
Интервал перфорации, м |
Число проб |
Содержание ртути, 10-6 г/м³ |
Опошнянское месторождение |
23 |
2952-2990 |
8 |
0,2 – 2,1; среднее – 0,89 |
121 |
4001-4325 |
70 |
3,3 – 11000; среднее – 67 |
111 |
среднее – 870 |
Яблуновское месторождение |
11 |
3744-3801 |
6 |
0,11 – 0,4; среднее – 0,26 |
61 |
4680-4978 |
8 |
0,61 – 2; среднее – 1,2 |
Еще более существенна долговременная изменчивость содержания ртути в природных
газах. В частности, установлено, что концентрация ртути в разные годы может различаться в
одних и тех же скважинах в 15-20 раз. И причины тому достаточно полно не выяснены.
Не менее важны аналитические аспекты. Например, в используемых ранее
турбоколометрических химических методах определения микроколичеств ртути [253], а
позднее – в методиках прямого дифференциального атомно-абсорбционного анализа ртути в
потоке газа [343] определялась лишь атомарная ртуть, а доля ртутьорганических и других
соединений ртути была не известна.
Первые эксперименты были проведены с использованием пиролиза (температура в
реакторе поддерживалась на уровне 750-800 °С) и фотолиза (температура в реакторе
устанавливалась примерно в 50-60 °С). Показано (табл. 4.16), что вклад ртути в бюджет ее
валовой концентрации при разложении ртутных соединений фотолизом и пиролизом достигает
30 % [55, 402]. Эти два предварительных эксперимента показывают, что фактическое
содержание ртути в газе выше предварительно измеренного количества, но исследования
следует продолжить.
Таблица 4.16 Содержание атомарной (HgO) и органической (HgR) форм ртути в природном газе
Газовые месторождения |
HgO, 10-6 г/м³ |
HgR, 10-6 г/м³ |
Фотолиз |
Пиролиз |
Мирненское (Северный Кавказ) |
19,1±0,3 |
5,8±1,5 |
|
Опошня (Днепрово-Донецкая впадина) |
52,5±0,3 |
2,1±0,8 |
2,3±0,8 |
4.2.2 Ртуть в нефтях и газоносном сырье
Сырая нефть
Данные о содержании ртути в нефтях России весьма скудные (табл. 4.17). В частности,
отсутствуют сведения о концентрации ртути в нефтях основных российских месторождений. К
настоящему времени с разной степенью детальности изучено 42 объекта; содержания ртути в
нефтях изменяются от 3×10-3 до 6,9 мг/кг. Среднее содержание принято в 0,30 мг/кг.
Непосредственно в пределах России среднее содержание ртути оценивается в 0,18 мг/кг.
Следует отметить, что образцы нефти взяты в основном с месторождений южной части
территории России, отличающихся относительно высокими концентрациями ртути. Тем не
менее нельзя утверждать, что расчетное среднее значение будет выше фактического среднего
значения. Для получения более точных результатов, необходимо проанализировать образцы
нефти с главных нефтяных месторождений страны. Следует подчеркнуть, что повышенные
содержания ртути обнаружены месторождениях, приуроченных к региональным зонам
глубинных разломов, к участкам их активизации. Например, таковы месторождения,
приуроченные к линеаменту Карпинского и Паннонско-Волынскому линеаменту – Днепрово-
Донецкой впадине, Предкарпатскому прогибу, Белоруссии, Прибалтики, Северному Кавказу,
Казахстану и т.д. (см. рис. 4.4. и 4,5).
Другой тип структур, контролирующий ртутьсодержащие нефтяные месторождения .
глобальные ртутные пояса с киноварными месторождениями (в табл. 4.17 - это месторождения
острова Сахалин, представляющего собой фрагмент западного обрамления глобального
Тихоокеанского ртутного пояса).
Величина 0,3 мг/кг, принятая как средняя концентрация ртути в нефтях, меньше, чем
значение среднего содержания в 7,2 мг/кг, предложенное В.В. Ивановым (цит. по [111]), но
значительно выше среднего значение, использованного для недавней оценки мобилизации
ртути с нефтью в США, где среднее содержание находится в пределах 0,005-0,05 мг/кг [417].
Данный разброс может отражать фактическую разницу в содержании ртути в сырых нефтях.
Содержание ртути в углеводородных газах и конденсатах
Содержания ртути в природных углеводородных газах месторождений России
представлены в табл. 4.18, соответственно для свободных газов (из скважин) и попутного газа
нефтяных месторождений. Пределы содержаний ртути в свободных газах: 5×10-8 - 7×10-5 г/м³
(среднее – 2,4×10-6), а в попутных газах: 7×10-8 – 1,4×10-5 г/м³ (среднее – 3,4×10-6). Наиболее
высокие содержания ртути (до 20×10-6, 40.10-6 и 70×10-6 г/м³)установлены на ряде
месторождений Ставропольского свода (на НПЗ в г. Благодарный в одном из технологических
узлов была обнаружена даже металлическая ртуть). Эта структура представляет собой
фрагмент линеамента Карпинского, который, как указывалось выше, является ответственным
за появление ртутьсодержащих месторождений различного состава.
Таблица 4.17 Содержание ртути в нефтях (страны СНГ)
Страны СНГ |
Регион |
Месторождение, нефтепроявление |
Число проб |
Содержание ртути, мг/кг |
Источник |
Россия |
Приуралье |
Степноозерское |
1 |
0,032 |
[253] |
Ульяновская площадь |
1 |
0,072 |
[253] |
Иркутская область |
Марковское |
4 |
0,32-0,36 |
[299] |
Сахалин |
Охинское |
1 |
0,008 |
[253] |
2 |
0,4-0,46 |
[299] |
Лысая сопка |
1 |
0,032 |
[253] |
Мухто |
1 |
< 0,008 |
[253] |
Ковтовская площадь |
1 |
0,42 |
[253] |
Северный Кавказ |
Дыш |
1 |
0,14 |
[253] |
Датых |
4 |
0,3-0,36 |
[299] |
Россия-Украина |
Керчь-Тамань |
|
20 |
0,27-0,51 |
[299] |
Украина |
Днепрово-Донецкая впадина |
Глинско- Разбышевское |
4 |
0,032-0,27 |
[253] |
2 |
0,35-0,41 |
[299] |
Предкарпатье |
Битковское |
1 |
1 |
[253] |
Гнедицы |
4 |
1,05-1,15 |
[299] |
Кибиницы |
5 |
0,24-0,3 |
[299] |
Зачепиловка |
6 |
0,32-0,42 |
[299] |
Бельское |
2 |
0,33-0,41 |
[299] |
Белоруссия |
|
Речицкое |
1 |
0,19 |
[253] |
Прибалтика |
|
Красноборское |
3 |
0,34-0,48 |
[299] |
Грузия |
Южная Осетия |
Лесеви |
1 |
0,19 |
[253] |
Геделети |
1 |
0,29 |
[253] |
Азербайджан |
Апшерон |
Баку |
2 |
0,11-0,15 |
[253] |
Казахстан |
|
Узень |
8 |
0,34-0,44 |
[299] |
6 |
0,003-0,05 |
* |
Жетыбай |
2 |
0,023-0,09 |
* |
-"- (коллектор) |
3 |
0,23-0,48 |
* |
Казахстан |
|
Придорожная (скважина) |
1 |
1,6 |
* |
Бурмаша |
1 |
0,007 |
* |
Асар |
2 |
0,019-0,096 |
* |
Караже |
2 |
0,115-0,85 |
* |
Аккар |
1 |
0,041 |
* |
Алатобе |
2 |
0,029-6,90 |
* |
Там же (коллектор) |
2 |
0,014-0,081 |
* |
Узбекистан |
Ферганская долина |
Майлису |
1 |
0,19 |
[253] |
Северный Сох |
1 |
0,11 |
[253] |
Чонгара |
1 |
0,43 |
[253] |
Северный Ристан |
1 |
< 0,008 |
[253] |
Палванташ |
1 |
0,19 |
[253] |
Туркмения |
|
Челекен |
1 |
< 0,008 |
[253] |
Средняя Азия |
|
Южный Аламышик |
6 |
0,22-0,26 |
[299] |
Сарыташ |
2 |
0,28-0,32 |
[299] |
* Данные В.В. Рыжова, Н.Р. Машьянова и Ю.И. Жеребцова.
Кроме значений, приведенных в табл. 4.18, известны еще две опубликованные работы,
где есть упоминание о ртути в газах России. Это, во-первых, статья Л.М. Зорькина и др. [103],
где достоверными можно считать только две цифры по месторождениям Степное и Равнинное.
Во-вторых, статья А.И. Гриценко и др. [88], где приведены данные о содержании ртути в
природном газе из скважин Астраханского месторождения (0,3-2,5×10-6 г/м³); что касается
остальных цифр в этой работе, они ошибочно завышены.
Таблица 4.18 Ртуть в свободном (без конденсата) и попутном газах из месторождений России*
Регион |
Месторождения |
Число проб |
Содержание ртути, 10-6 г/м³ |
Свободный газ газовых месторождений |
Азово-Кубанский прогиб |
Анастасьевско-Троицкое |
1 |
0,15 |
Ставропольский свод |
Тахта-Кугультинское
Северо-Ставропольское
Сингелеевское
Петровско-Благодарненское
Мирненское:
верхний горизонт (Pg2)
нижний горизонт (К1) |
12 10 1 1
13 40 |
0,4-70 0,4-20 <0,7 <0,3
0,05-0,3 0,2-40 |
Терско-Кумская впадина |
Пелагиадинское
Южно-Радыковское
Северо-Радыковское
Каменная балка
Кевсала
Эки-Бурульское
Степное**
Равнинное** |
6 2 2 5 1 6 1 1 |
0,08-0,8 <0,1 <0,1 0,07-0,15 0,2 <0,1 2 0,8 |
Терско-Каспийский прогиб |
Октябрьское |
1 |
0,12 |
Прикаспийская впадина |
ПАстраханское
- скважины
- сырой газ сепарации |
8
3 |
0,3-2,5; среднее – 1,0 0,3-3,5; среднее – 1,4 |
Оренбургское - скважины - сырой газ сепарации |
36 |
<0,1-3,12; среднее – 1,5 |
Карачаганакское - скважины
- сырой газ сепарации |
16
1 |
0,4-2,4; среднее – 1,6 0,5 |
Рязано-Саратовский прогиб |
Луговское |
2 |
0,07-0,66 |
Первомайское Сусловское Фурмановское |
- скважины |
|
0,07-0,4; 6,5 |
Попутный газ газонефтяных месторождений |
Ставропольский свод |
Южно-Спасское Журавское Воробьевское |
1 1 1 |
11,5 14,1 7,5 |
Рязано-Саратовский прогиб |
Соколовогорское Урицкое Языковское Зубовское Мечеткинское Восточно-Сусловское |
17 5 7 1 8 4 |
0,12-3,8 <0,1-0,45 0,3-1,6 0,5 0,09-0,3 0,07-0,4 |
Башкирский свод |
Кокуйское |
2 |
0,15-0,4 |
Восточно-Камчатский прогиб |
Богачевское |
1 |
0,1 |
* [188, 249].
** Степанов (по [103]).
В табл. 4.19 представлены содержания ртути в конденсатах из трех крупных газовых
объектов России – Астраханского, Оренбургского и Карачаганакского месторождений, а также
из украинских месторождений, чтобы показать возможный разброс значений. Наиболее
высокие концентрации ртути отмечаются на месторождении Опошня – до 1,95 мг/кг. Как было
показано выше, это месторождение характеризуется весьма высокими содержаниями ртути и в
газе.
Существует два типа конденсатов: сырой (нестабильный), выделяющийся из газа в
процессе добычи, и стабильный, получаемый при переработке газа на ГПЗ. Небольшое
количество конденсата, который поступает на ГПЗ, получается также на газонефтяных
конденсатных месторождениях.
Таблица 4.19 Cодержание ртути в конденсатах газовых месторождений *
Страны СНГ |
Регион |
Газоперерабатывающие заводы и месторождения |
Число проб |
Содержание ртути, мг/кг |
Россия |
Прикаспийская впадина |
Астраханьгазпром |
3 1 |
0,104- 0,377; 0,47** |
Оренбурггазпром Оренбургское Карачаганакское |
1 1 |
0,08 0,066 |
Украина |
Днепрово- Донецкая впадина |
Опошнянское - по скважинам |
5 |
0,624 – 1,95 |
5 месторождений (Шебелинское и др.) - по скважинам |
6 |
<0,065 |
* По данным Н.А. Озеровой, В.В. Рыжова, Н.Р. Машьянова.
** Нестабильный конденсат.
Выводы
Имеющиеся данные по содержанию ртути в углеводородном сырье России, представлены
в табл. 4.20.
Сравнение с данными по сырой нефти и конденсату из других стран ) показывает (табл. 4.21),
что, во-первых, содержания ртути в сырых нефтях и конденсатах российских месторождений
находятся в пределах концентраций, типичных для других стран; во-вторых, наблюдается
существенная разница в содержании ртути в углеводородном сырье различных регионов мира.
Различие данных помимо географических условий вызвано разницей методов взятия проб, их
анализа и используемых аналитических методов исследований и т.п.
Таблица 4.20 Распределение ртути в углеводородном сырье России
Углеводородное сырье, регион |
Число объектов |
Число проб |
Единица измерения |
Пределы содержаний |
Среднее арифметическое |
SD |
НЕФТЬ |
Россия |
10 |
17 |
мг/кг |
<0,008-0,46 |
0,18 |
0,126 |
Страны бывшего СССР |
42 |
117 |
-"- |
0,008-6,9 |
0,3 |
1,365 |
СВОБОДНЫЙ ГАЗ |
Россия |
25 |
175 |
10-6 г/м³ |
0,05-70 |
2,4 |
12,94 |
ПОПУТНЫЙ ГАЗ |
Россия |
11 |
48 |
10-6 г/м³ |
0,07-14,5 |
3,4 |
3,175 |
КОНДЕНСАТ |
Россия |
3 |
5 |
10-2 мг/кг |
0,06-0,47 |
0,27 |
0,176 |
Таблица 4.21 Ртуть в сырой нефти и газоконденсате (обобщение литературных данных,
выполненное [417]
Число проб |
Пределы, pbb (мг/кг) |
Среднее, pbb (мг/кг) |
SD |
Примечания |
Сырая нефть |
10 |
23-29700 (0,023-29,7) |
3200 (3,2) |
- |
США и импорт |
86 |
2-399 (<0,002-0,399) |
22 (0,022) |
63,3 |
Канада |
4 |
4-23100 (<0,004-23,1) |
5803 (5,803) |
- |
США и импорт |
6 |
0,1-12,2 (0,0001-0,0122) |
3,1 (0,0031) |
4,2 |
Ливия |
26 |
<10-1560 (<0,01-1,56) |
65 (0,065) |
- |
НПЗ Западного побережья |
76 |
нет данных (1) |
1505 (1,505) |
3278 |
нет данных |
11 |
1,6-7,2 (0,0016-0,0072) |
4,4 (0,0044) |
1,0 |
нет данных |
23 |
0,1-12,2 (0,0001-0,0122) |
3,5 (0,0035) |
|
НПЗ Нью-Джерси |
24 |
< 15 (< 0,015) |
8 (0,008) |
|
Канада и импорт |
8 |
<2-9 (<0,002-0,009) |
1,6 (0,0016) |
1,6 |
НПЗ Канады |
Газоконденсат |
4 |
нет данных |
15 (0,015) |
|
нет информации об источниках |
18 |
нет данных |
3964 (3,96) |
11665 |
В большинстве из Азии |
5 |
9-63 |
30 (0,03) |
18,6 |
Юго-Восточная Азия |
7 |
15-173 |
40 (0,04) |
|
Азия |
4.2.3 Мобилизация ртути в нефти
Для первой и очень приблизительной оценки общего количества ртути, мобилизованной
с добытой в 2001 г. в России нефтью, будет использоваться ее средняя концентрация в 0,18
мг/кг. Необходимо отметить, что существенная доля сведений, представленных в табл. 4.17,
относится к месторождениям, нефть которых в силу геологических причин отличается
высокими концентрациями ртути.
Общий объем производства сырой нефти в России в 2001 г. составил 336 млн. т. Если
предположить, что среднее содержание ртути в ней составляет 0,18 мг/кг, то общая масса
металла, заключенного в сырой нефти, составит 61 т (табл. 4.22). Следует иметь в виду, что это
очень приблизительная оценка. К тому же, используется средняя концентрация ртути в сырой
нефти, , т. е. до удаления из нею воды и солей в процессе первичной нефтеподготовки.
Таблица 4.22 Ртуть в нефтях Российской Федерации, 2001 г.
Распределение нефти |
Объем нефти, млн. т |
Содержание ртути, мг/кг |
Масса ртути, т |
Добыча (сырая нефть) |
336,47* |
0,18 |
61 |
Экспорт в ближнее зарубежье |
22,68** |
0,18 |
4,1 |
Экспорт в дальнее зарубежье |
137,06** |
0,18 |
25 |
Импорт (все из СНГ) |
5,03** |
0,3**** |
1,5 |
Поставка на НПЗ и НХЗ |
178,36*** |
0,18 |
33 |
Преобразование в другие виды энергии; использование в качестве материала на нетопливные нужды, на конечное потребление, потери |
3,4** |
0,18 |
0,6 |
* [81].
** [270].
*** [405].
**** Используется среднее значение на основе обобщенных данных для республик СССР.
Первичное фазовое разделение
До транспортировки сырой нефти на перерабатывающий завод из нее может быть
удалено существенное количество ртути, однако о поведении ртути при первичной фазовой
сепарации сырья мало что известно [417]).
Значительная доля добываемой в России нефти поступает из скважин в виде водной
эмульсии. Таких сильно обводненных скважин насчитывается более 80% (из более чем 114 тыс.
скважин, которые эксплуатировались в 2001 г.) [221]. При добыче нефти неизбежный ее
спутник – пластовая вода (от менее 1 до 80-90% по массе), которая диспергируясь в нефти,
образует с ней эмульсии типа “вода в нефти” (дисперсионная фаза – нефть, дисперсная – вода).
Их формированию и стабилизации способствуют присутствующие в нефти природные
эмульгаторы (асфальтены, нафтены, смолы) и диспергирующие механические примеси
(частицы глины, песка, известняка, металлов). Пластовая вода, как правило, содержит высокие
концентрации натрия, магния, кальция (до 2500 мг/л солей даже при наличии в нефти всего 1%
воды), а также сульфаты и гидрокарбонаты и содержит механические примеси. Типичное
содержание воды в сырой нефти составляет 200-300 кг/т, минеральных солей – до 10-15 кг/т;
кроме того, сырая нефть содержит попутный газ (50-100 м³/т) [35]. Очевидно, что существенная
часть ртути присутствует именно в пластовой воде и механических примесях. Перед
транспортировкой нефти потребителям из нее должны быть удалены газ, механические
примеси, основная часть воды и солей [35, 146]. Некоторые процессы очистки нефти
осуществляют при повышенной температуре. Вначале от сырой нефти с помощью сепараторов
первой ступени отделяют нефтяной газ; затем частично дегазированная нефть поступает на
установки подготовки нефти, где происходят вторая и третья ступени сепарации газа от нефти,
а также обезвоживание и обессоливание нефти. Обезвоживание нефти осуществляют на
нефтепромыслах обычно термохимическим способом путем разрушения (расслоения) водно-
нефтяной эмульсии с применением деэмульгаторов (различных ПАВ) при 50-80°С. В ходе
обессоливания из нефти удаляют оставшиеся после обезвоживания соли и воду.
Обессоливание заключается в смешении нефти со свежей пресной водой, разрушении
образовавшейся эмульсии и последующим отделением от нефти промывной воды с
перешедшими в нее солями и механическими примесями. Обезвоженную и обессоленную
нефть подают в герметизированные резервуары, далее на установку, предназначенную для
оценки качества и количества нефти и после – в товарные резервуары, из которых насосами
нефть направляют в магистральный нефтепровод.
Нефтеперерабатывающие заводы и нефтепродукты
Почти половина всей российской нефти экспортируется в ближнее и дальнее зарубежье,
но бoльшая ее часть направляется на российские предприятия для первичной переработки. Из
табл. 4.22 можно видеть, что количество ртути, содержащейся в сырье, направляемом на НПЗ,
составляет 32 т. Данное количество будет использовано в качестве репрезентативного
показателя общей массы ртути, мобилизованной с добытой в 2001 г. в России нефтью. По
самой грубой оценке, с учетом неопределенностей, связанных с оценкой средней концентрации
ртути в российских нефтях, количество мобилизованной с ними ртути может изменяться в
пределах примерно 5-50 т/год. Масса ртути, фактически попадающей на НПЗ, может быть ниже
представленного значения, так как определенная часть металла, вероятнее всего,
высвобождается на первой стадии нефтеподготовки.
Переработка нефти осуществляется на нефтеперерабатывающих и нефтехимических
заводах, на предприятиях Газпрома и ряда мини-НПЗ. Главный процесс переработки нефти .
перегонка. Это физический процесс, основанный на различии температур. Он происходит в
ректификационных колоннах, куда при атмосферном давлении поступает нефть, нагретая до
300-350°С. Очевидно, что большая часть ртути содержится в этой нефти и поступает в
конечном итоге в продукцию нефтепереработки, отходы и в окружающую среду.
На содержание ртути удалось проанализировать только по одному образцу бензина,
дизельного топлива и мазута, отобранных на Астраханском НГПЗ (см. раздел “Ртуть в газах”).
Установленные концентрации ртути были использованы для приблизительной оценки общего
содержания ее в продуктах нефтепереработки. Согласно расчетам, представленным в табл.
4.23, бензин, дизельное топливо и мазут, используемые в России , содержали в общей
сложности 3,4 т ртути. Предполагается, что практически все это количество металла, в
конечном счете, поступает в атмосферу при их сжигании. К сожалению, не удалось получить
никаких данных по концентрации ртути в других продуктах нефтепереработки, таких как
битум, кокс, сера и т. д., которые также могут содержать значительное количество ртути. Все
полученные оценочные показатели имеют большую долю неопределенности. Безусловно,
необходимо проведение специальных исследований распределения ртути в сырой нефти и
продуктах ее переработки, поведения ртути при переработки нефти и использовании
нефтепродуктов.
Таблица 4.23 Ртуть в основных видах продукции переработки нефти в Российской Федерации, 2001
г.
Основные продукты нефтепереработки |
Производство, млн. т* |
Поставки на внутреннем рынке, млн. т* |
Содержание ртути, мг/кг |
Количество ртути, т |
Бензин |
27,6 |
24,9 |
0,013 |
0,3 |
Дизельное топливо |
50,2 |
26,0 |
0,065 |
1,7 |
Мазут |
50,2 |
27,5 |
0,05 |
1,4 |
Масла нефтяные, смазки |
9,0 |
9,0 |
Нет данных |
Сжиженные газы |
20,0 |
20,0 |
Нет данных |
Битум, пиролизное сырье, сера и другие виды продукции |
15,7 |
15,7 |
Нет данных |
* [387]. Разница между производством и внутренним потреблением идет на экспорт.
Если сравнить содержания ртути в продуктах нефтепереработки и в сырой нефти, то
можно увидеть, что основная доля ее высвобождается при первичной переработке сырья, с
выбросами НПЗ в атмосферу или поступает в отходы НПЗ. Однако сделать какие-либо
конкретные выводы не позволяет существующая неопределенность в оценках.
Изучение поведения ртути при переработке нефти в США показывает, что около 3%
ртути поступает в атмосферу и сточные воды, 11% - в твердые отходы, 67% - в сжигаемые
продукты и 17% - в сырье для химических предприятий [417]. По сведениям, приводимым
автором цитируемой работы, исследования, выполненные в Канаде, свидетельствуют о том, что
более 90% ртути, прошедшей все стадии переработки сырья, выбрасывается в атмосферу.
Поступление ртути в атмосферные выбросы и сточные воды очень сильно зависит от
применяемой технологии нефтепереработки. Например, содержание ртути в отходящих газах
на Астраханском ГПЗ определялось режимом работы установки с сульфином (см. раздел 4.2.4).
В частности, если она не функционировала, то концентрация ртути в отходящих газах была в
10 раз выше, что, соответственно, приводило к увеличению содержания ртути в выбросах.
Использование цеолитов для очистки отходящих газов позволяет высушивать их и удалять
ртуть вместе с влагой.
4.2.4 Поведение ртути при переработке природного газа
В качестве основы для обсуждения мобилизации ртути с природным газом и ее
поведения в процессе его переработки используются данные исследований, выполненных в
последнее время на Астраханском, Оренбургском и Карачаганакском месторождениях,
принадлежащих к числу крупных в России, а также на Астраханском и Оренбургском
газоперерабатывающих заводах (ГПЗ). В данном случае было изучено распределение ртути не
только в природных газах месторождений, но и в продуктах их переработки. Эти объекты были
исследованы весьма детально, мы их рассматриваем как эталонные, и поэтому приводим
полностью весь фактический материал по этим месторождениям и заводам (табл. 4.24 и 4,25).
Для Астраханского ГПЗ приведена технологическая схема переработки газоконденсатной
смеси и показаны участки опробования (рис. 4.6).
Содержания ртути в товарном газе Астраханского ГПЗ не превышают 0,1×10-6 г/м³, в
товарном газе Оренбургского ГПЗ составляют в среднем 0,48×10-6 г/м³. Дымовые газы на
Астраханском ГПЗ содержат меньше ртути (ее концентрации близки ПДК), чем на
Оренбургском, где в среднем ее концентрации примерно в 10 раз выше ПДК (причины этого
явления не изучались). Особо следует отметить, что установка с сульфрином, работающая на
Астраханском ГПЗ, весьма эффективна для очистки дымовых газов от ртути (см. табл. 4.23 и
примечание к ней). Технологические воды в целом отличаются невысокими содержаниями
ртути. Атмосферный воздух в районе месторождения и на территории ГПЗ также не загрязнен
ртутью. Баланс сырья и продукции на Астраханском ГПЗ представлен в табл. 4.26.
Таблица 4.24 Распределение ртути на Астраханском газоперерабатывающем заводе
Пробы |
№№ на рис. 4.6 |
Число проб |
Содержание ртути |
единицы измерения |
пределы и среднее |
Скважины |
Газ (без конденсата) |
|
8 |
10-6 г/м³ |
0,3-2,5; среднее – 1,0 |
Газоперерабатывающий завод |
Пластовая газоконденсатная смесь |
17 |
|
10-6 |
г/м³ 54* |
Сырой газ сепарации |
15 |
3 |
-"- |
0,3-3,5; среднее – 1,4 |
Газ среднего давления |
14 |
2 |
-"- |
0,19-0,32 |
Обессеренный газ |
8 |
3 |
-"- |
<0,05**-0,12 |
Товарный газ |
1 |
3 |
-"- |
<0,05-0,117 |
Нестабильный конденсат |
18 |
1 |
мг/кг |
0,47 |
Стабильный конденсат |
20 |
3 |
-"- |
0,106-0,386; среднее – 0,279 |
Кислый газ |
10 11 |
1 1 |
10-6 г/м³ |
0,8 1,4 |
Товарная сера |
|
19 |
мг/кг |
0,01-0,18; среднее – 0,06 |
Бензин |
|
1 |
мг/кг |
0,013 |
Дизельное топливо |
|
1 |
мг/кг |
0,065 |
Мазут |
|
1 |
-"- |
0,05 |
Дымовые газы |
21 |
3 |
10-6 г/м³ |
0,2-0,48 |
5 |
4 |
-"- |
0,1-0,35 3,4***; 1,7-0,38**** |
Зола из дымовой трубы |
|
3 |
10-2 мг/кг |
25-38 |
Пластовая вода |
19 |
2 |
10-3 мг/л |
<0,1-<0,2 |
Сконденсированная вода |
21 |
2 |
-"- |
<0,1 |
Атмосферный воздух на территории завода |
26 |
2 |
10-6 г/м³ |
0,006-<0,01 |
Отработанный катализатор |
7 |
8 |
10-2 мг/кг |
0,8-7 |
Цеолит |
6 |
2 |
-"- |
<1-6 |
* Цифра – расчетная, т. к. ртуть в газе и ртуть конденсате исследовались раздельно, затем, зная
количество конденсата в 1 м³ газа, оценивается общее содержание ртути в газоконденсатной смеси.
** Предел обнаружения аппаратуры.
*** Содержание ртути при выключенной установки с сульфрином повышено.
**** При включении установки с сульфрином содержание ртути постепенно снижается до
нормальных пределов.
Таблица 4.25 Распределение ртути на Оренбургском газоперерабатывающем заводе
Пробы |
Число проб |
Содержание ртути |
единицы измерения |
пределы и среднее |
Скважины |
Газ Оренбургского месторождения (без конденсата) |
36 |
10-6 г/м³ |
<0,1-3,12; среднее – 1,5 |
Газ Карачаганакского месторождения |
16 |
-"- |
0,4-2,4; среднее – 1,6 |
Газоперерабатывающий завод |
Сырой газ сепарации, поступающий на завод с Оренбургского месторождения |
11 |
10-6 г/м³ |
1,3-2,2; среднее – 1,9 |
Обессеренный газ Оренбургского месторождения |
3 |
-"- |
<0,05-0,7; среднее – 0,4 |
Сырой газ сепарации, поступающий на завод с Карачаганакского месторождения |
2 |
-"- |
0,5-1,3 |
Обессеренный газ Карачаганакского месторождения |
1 |
-"- |
0,07 |
Товарный газ Оренбургского и Карачаганакского месторождений (I+II очереди)
Карачаганакского месторождения (III очередь) |
7
1 |
-"- |
0,07-1,3; среднее – 0,48 0,15 |
Конденсат Оренбургского месторождения |
1 |
мг/кг |
0,08 |
Конденсат Карачаганакского месторождения |
1 |
-"- |
0,066 |
Товарная сера |
4 |
10-2 мг/кг |
5-18; среднее – 9,0 |
Дымовые газы |
6 |
10-6 г/м³ |
<0,1-9,4; среднее – 2,9 |
Пластовая вода |
1 |
10-3 мг/л |
<0,08 |
Технологические воды |
8 |
-"- |
<0,08 |
Атмосферный воздух в районе Оренбургского месторождения (измерения по профилям) |
5 |
10-6 г/м³ |
<0,05 |
* Предел обнаружения аппаратуры.
ОАО “Газпром”, крупнейшее в России акционерное общество, в 2001 г. освоил 87%
общероссийской добычи газа, поставил потребителям по Единой системе газоснабжения 90%
газа и обеспечил 96% общего экспорта России в Европу. Как указывалось выше, изучили
ртутоносность трех крупных месторождений – Астраханского, Оренбургского и
Карачаганакского, эксплуатируемых ОАО “Газпром”, причем наиболее детально
производственный комбинат “Астрахангазпром”, как характерный представитель дочерних
предприятий ОАО “Газпром” в отношении структуры добычи и переработки углеводородного
сырья (табл. 4.26). Общее количество ртути, заключенной в сырье, поставленном комбинату в
2001 г., составило 2,4 т, в произведенной продукции – 1,1 т. В целом по ГПЗ, принадлежащих
ОАО “Газпром”, эти объемы составили 5,8 т и 2,1 т соответственно (табл. 4.27). Обращает на
себя внимание, что основное количество ртути (0,741 т – по “Астрахангазпрому” и 1,693 т – по
всем ГПЗ “Газпрома”) связано с конденсатами.
Сырьем для ГПЗ являются природный газ, нестабильный конденсат (высвобождается из
газа в процессе добычи) и конденсат, полученные на нефтегазовых месторождениях. При
переработке производится стабильный конденсат, который используется в качестве сырья и
широко применяется как моторное топливо.
Анализ данных, приведенных в табл. 4.24 и 4,25, позволяет сделать следующие выводы.
На Астраханском ГПЗ конденсаты, образующиеся при разложении газоконденсатной смеси,
заметно обогащены ртутью (см. табл. 4.24). Газ далее подвергается процессу обессеривания и
обедняется ртутью, а серосодержащие газы являются сырьем для получения серы. Такая же
картина наблюдается и на Оренбургском ГПЗ (см. табл. 4.24).
В итоге сера содержит ртути в 1,5-2 раза выше, чем кларк ртути в земной коре (= 0,05
мг/кг). В целом концентрации ртути варьируются в пределах от 0,01 до.0,1 мг/кг; среднее
содержание для Астраханского ГПЗ составляет 0,06 мг/кг, для Оренбургского ГПЗ – 0,09 мг/кг.
В мазуте, дизельном топливе и бензине содержания ртути довольно низкие, но это только
единичные определения, а потому непредставительные.
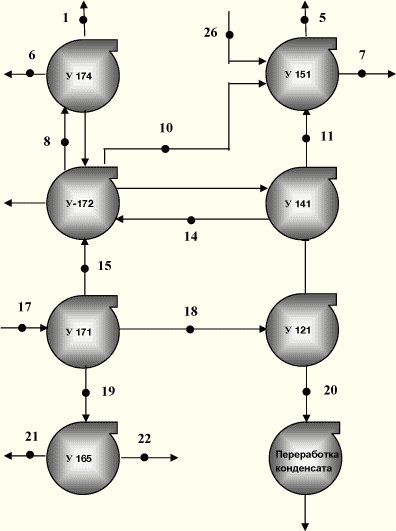
Рисунок 4.6 Схема переработки газоконденсатной смеси на Астраханском газоперерабатывающем
заводе
У 121 – У 174 - блоки, где перерабатывается газоконденсатное сырье; №№ 1-26 на схеме – участки
отбора проб для анализа на ртуть: газ пластовой смеси - 17; газ сепарации - 15; газ среднего давления .
14; обессеренный газ - 8; товарный газ - 1; нестабильный конденсат - 18; стабильный конденсат - 20;
кислый газ – 10 и 11; дымовые газы – 5 и 21; атмосферный воздух – 26; цеолиты – 6; отработанный
катализатор – 7.
Таблица 4.26 Количества ртути, заключенной в газах, конденсатах и продукции их переработки
на Астраханском газоперерабатывающем заводе, 2001 г. [68]
Продукт |
Объем сырья и продукции: |
Содержание ртути: |
Количества ртути: |
Единицы измерения |
Значение |
Единицы измерения |
Среднее значение |
кг |
% |
Сырье |
Природный газ |
млрд. м³ |
10,5 |
10-6 г/м³ |
1,4 |
14,7 |
0,6 |
Газовый конденсат (нефть) |
1000 т |
2291,0 |
мг/кг |
0,27 |
618,57 |
26,25 |
Нестабильный газовый конденсат |
1000 т |
3670,5 |
мг/кг |
0,47 |
1725,14 |
73,15 |
Всего в сырье |
|
|
|
2435 |
100 |
Продукция |
Газ для потребителей |
|
|
10-6 г/м³ |
0,05 |
|
|
Стабильный газовый конденсат |
1000 т |
2743,0 |
мг/кг |
0,28 |
740,61 |
68,8 |
Бензин автомобильный |
1000 т |
959,1 |
мг/кг |
0,013 |
12,47 |
1,2 |
Дизельное топливо |
1000 т |
794,6 |
мг/кг |
0,07 |
55,62 |
5,2 |
Мазут топочный |
1000 т |
377,1 |
мг/кг |
0,05 |
18,86 |
1,7 |
Сера |
1000 т |
4151,0 |
мг/кг |
0,06 |
249,1 |
23,1 |
Всего в продукции |
9032 |
|
|
1077 |
100 |
Таблица 4.27 Расчетные количества ртути, заключенной в основных видах сырья и основной
продукции ОАО “Газпром”, 2001 г. [68]
Продукт |
Объем сырья и продукции: |
Содержание ртути: |
Количества ртути: |
единицы измерения |
значение |
единицы измерения |
среднее значение |
кг |
% |
Сырье |
Природный газ |
млрд. м³ |
34,6 |
10-6 г/м³ |
1,4 |
48,44 |
0,84 |
Газовый конденсат (нефть) |
1000 т |
4965,9 |
мг/кг |
0,27 |
1340,8 |
23,19 |
Нестабильный газовый конденсат |
1000 т |
9347,8 |
мг/кг |
0,47 |
4393,47 |
75,97 |
Всего в сырье |
|
|
|
5782,71 |
100 |
Продукция |
Газ для потребителей |
|
|
10-6 г/м³ |
0,05 |
|
|
Стабильный газовый конденсат |
1000 т |
6047,5 |
мг/кг |
0,28 |
1693,3 |
79,76 |
Бензин автомобильный |
1000 т |
1215,8 |
мг/кг |
0,013 |
15,8 |
0,74 |
Дизельное топливо |
1000 т |
1617,4 |
мг/кг |
0,07 |
113,22 |
5,33 |
Мазут топочный |
1000 т |
384,4 |
мг/кг |
0,05 |
19,22 |
0,9 |
Сера |
1000 т |
4694,7 |
мг/кг |
0,06 |
281,68 |
13,27 |
Всего в продукции |
13985 |
|
|
2123 |
100 |
Содержание ртути в газах магистральных трубопроводов
Содержания ртути в газе магистральных газопроводов – исключительно низкие, по
сравнению с содержанием ртути в сыром газе (табл. 4.28). Но это не истинные содержания ртути
в газах Уренгоя и Ямбурга, откуда их качают. Дело в том, что по опыту Гронингена (Нидерланды)
известно, что газ, проходя по трубопроводу через европейские страны, теряет ртуть (вероятно, из-за
амальгамации стенок газопровода). Очевидно, это имеет место и в случае российских газопроводов,
тем более, что длина их несоизмеримо больше, и газ, практически чистый от ртути, экспортируется
в другие страны.
Таблица 4.28 Содержание ртути в природном (товарном) газе из магистральных трубопроводов
Газопроводы |
Содержание ртути, 10-6 г/м³ |
1990 г. |
1991 г. |
Единое союзное кольцо
(Давыдовская газораспределительная станция, Тамбовская обл.) |
Газопровод “Уренгой –Ужгород” |
<0,03 |
0,05 |
Газопровод “Уренгой –Центр-1” |
<0,03 |
<0,03 |
Газопровод “Уренгой –Центр-2” |
<0,03 |
0,05 |
Газопровод “Ямбург-Елец-1” |
0,1 |
0,05 |
Газопровод “Ямбург-Елец-2” |
0,1 |
<0,03 |
Газопровод “Ямбург-Москва |
0,09 |
0,05 |
Северная ветвь, г. Москва |
Газонапорная станция, “Мострансгаз” |
<0,03 |
Нет данных |
4.2.5 Мобилизация ртути с природным газом и газовым конденсатом
На основании вышеизложенного была сделана приближенная оценка мобилизации ртути
в составе добываемого и используемого природного газа в России (табл. 4.29). , Эти оценочные
данные указывают на то, что основным носителем ртути в данном секторе является газовый
конденсат. Согласно наилучшим оценкам, с природным газом и газовым конденсатом может
быть мобилизовано около 8,2 т ртути. С учетом высокой степени неопределенности, интервал
оценки составляет 2-10 т ртути в год.
Таблица 4.29 Баланс ртути в газовой промышленности России в 2001 г.
Исходный материал/продукция |
Объем, млрд. м³ |
Содержание Hg, 10-6 г/м³ |
Количество Hg, т |
Исходное сырье |
Природный газ |
573 * |
2,4 |
1,4 |
Газовый конденсат |
|
|
6,6 ** |
Очищенный газ |
Экспорт (в том числе в Европу) |
178 * |
0,05 |
0,009 |
Импорт (в том числе из СНГ) |
3,9 * |
0,05 |
0,0002 |
Внутреннее потребление *** |
398 * |
0,05 |
0,020 |
Другие продукты |
Стабильный газовый конденсат |
|
|
2,0 ** |
Другие продукты |
|
|
0,5 ** |
* Источник [387], фактор преобразования: 38 TДж/млн. м³.
** Экстраполировано по данным табл. 4.26 при допущении, что объемы продукции, приведенные в
указанной таблице, составляют 87% от общего их российского производства.
***Включает потери в трубопроводах.
Совершенно определенно, что лишь небольшое количество ртути (0,03 т) попадает в газ,
который идет на экспорт и используется внутри страны. Ртуть, прежде всего, в значительных
содержаниях попадает в другие продукты, в частности, в стабильный газовый конденсат.
Общее количество ртути в продуктах не уравновешивает в полной мере оценочное общее
количество ее в исходном сырье. Это свидетельствует о том, что все оценочные данные
относительно содержания ртути в исходном сырье и продуктах его переработки весьма
неопределенны. Полученные оценочные данные показывают, что значительное количество
ртути потенциально может мобилизоваться в результате добычи природного газа и газового
конденсата. Безусловно, необходимы дальнейшие исследования поведения ртути при
переработке природного газа и использовании полученных продуктов.
Не удалось получить полных сведений об объемах газа, сжигаемого в факелах на всех
месторождениях России. Для Западной Сибири этот объем в 2001 г. составил 19 млрд. м³.
Используя среднее содержание ртути в попутном газе, можно рассчитать количество ртути в
газе, сжигаемом в факелах, которое составит 65 кг. Не исключено, что выбросы ртути при
сжигании попутного газа в факелах могут быть выше ее эмиссии в результате сжигания
очищенного газа.
4.2.6 Горючие сланцы
В 2001 г. добыто 1,5 млн. т горючих сланцев; подавляющая часть – в Ленинградской
области; добытый продукт, в основном, направляется на сланцевый перерабатывающий завод
(г. Сланцы, Ленинградская область). В очень небольших объемах добыча горючих сланцев
производится на Кашпирском месторождении (Поволжье) и некоторых других. Сланцы с
Кашпирского месторождения направляются на переработку на Сызраньский сланцевый
перерабатывающий завод. В г. Сланцы и г. Сызрани они используются как топливо на местных
ТЭЦ, причем основная часть реализуется в г. Сланцы.
Содержания ртути в горючих сланцах Ленинградской области оценивается, в среднем, в
0.4 мг/кг по аналогии со сланцами Эстонии (табл. 4.30), поскольку эти два объекта
принадлежат единому Прибалтийскому бассейну горючих сланцев, условно - по
административной границе между Россией и Эстонией - разделяемых на два месторождения.
Такие же содержания, как в Эстонии, установлены в сланцах Кашпирского месторождения
(среднее – 0,44 мг/кг).
Таблица 4.30 Содержание ртути в горючих сланцах [190]
Район |
Месторождение |
Содержание ртути, мг/кг |
Пределы * |
среднее |
Россия, Поволжье |
Рудник Кашпир, шахта 1 |
0,2 – 1,6 (11) |
0,44 |
Эстония, Прибалтийский бассейн |
Шахта Ахтме |
0,17 – 0,38 (5) |
0,4 |
Шахта Кивыили |
0,2 – 1,5 (5) |
* В скобках - число проб.
Используя значение в 0,4 мг/кг и принимая во внимание неопределенность, общее
содержание ртути в горючих сланцах, добытых в 2001 г согласно расчетам, может составить
примерно 0,6 (0,4-0,8) тонн. В России горючие сланцы в основном используются для
производства энергии, что предопределяет их переработку при высоких температурах, в ходе
которой большая часть содержащейся в них ртути эмитирует в атмосферу, , а небольшая часть
- концентрируется в отходы. В качестве первичной оценки предполагается, что 80% ртути
поступает в атмосферу (0,5 т), а 20% размещается в составе отходов (0,1 т).
4.2.7 Древесина
В 2001 г. в России для производства энергоресурсов было использовано 5,7 млн. т
условного топлива (тут) древесины, или 21,4 млн. т в натуральном (согласно “Методическим
положениям…” Госкомстата, 1999) коэффициент пересчета условного топлива равен 0,266).
Данные о содержании ртути в древесине на территории России получить не удалось. В Дании
содержания ртути в сжигаемой древесине и соломе находятся в пределах 0,007-0,03 мг/кг
сухого веса [408]. По американским данным [342], концентрации ртути в мусоре и зеленой
растительности, по результатам обследования 7 регионов США, составляют 0,01-0,07 мг/кг
сухого веса. При инвентаризации выбросов ртути с территории США величина среднего
коэффициента ее выбросов при сжигании древесины принята в 0,026 мг/кг как типичный
коэффициент выбросов при сжигании древесных отходов в котельных [413]. При сжигании
древесины в быту также использовался коэффициент эмиссии ртути в 0,026 мг/кг. Шведские
исследователи [390] установили в топливной древесине концентрацию ртути в 0,01-0,02 мг/кг
сухого веса, в ивовой древесине – 0,03-0,07 мг/кг сухого веса), в коре – 0,04 мг/кг сухого веса, а
в иголках пихты более высокую концентрацию – 0,3-0,5 мг/кг сухого веса.
На основании приведенных данных использовалось значение 0,01-0,03 мг/кг. Нами для
расчетов эмиссии ртути при сжигании древесины использовался эмиссионный фактор в 0,02
мг/кг. Расчеты показывают, что количество ртути, выделившейся в атмосферу при сжигании
древесины в 2001 г. в России, может быть оценено в 0,4 (0,2-0,4) тонны. Здесь не учтено
количество ртути, высвободившееся при лесных пожарах, которое может быть очень
значительным.
4.2.8 Торф
В 2001 г. в России было добыто 4,6 млн. т торфа, из которых примерно 10% (т. е. 0,46
млн. т) обычно используется как топливо, остальное – в сельском хозяйстве.
По данным Ю.А. Головатского (устное сообщение), в торфяных почвах Томской области
содержания ртути обычно составляют 0,02-0,05 мг/кг, но на глубине выделяется горизонт с
более высоким содержанием в 0,2-0,3 мг/кг.
В Тюменской области – на территории интенсивно эксплуатируемых и находящихся на
стадии проектирования нефтегазоносных месторождений - фоновые содержания ртути в
торфяных почвах находятся в пределах 0,01-0,3 мг/кг, при средних значениях 0,2-0,25 мг/кг
[97]. Эти данные согласуются с аналогичными сведениями по упомянутой выше Томской
области и по другим районам. Так, в торфяных почвах США средние уровни ртути составляют
до 0,28 мг/кг, по данным Д.С. Адриано, концентрации ртути в торфяных почвах мира
варьируются в пределах 0,06-0,3 мг/кг (цит. по [97]). Отмечаются процессы фиксации ртути
органическим веществом почв, которые типичны для болотно-торфяных почв; последние даже
в естественных условиях отличаются повышенной способностью к аккумулированию ртути.
Если считать, что среднее содержание ртути в торфе составляет 0,2 мг/кг, то при его
сжигании в 2001 г. в России в атмосферу поступило 92 кг ртути.
4.3 Цемент и известь
Содержания ртути в карбонатных и глинистых породах (вне зон глубинных разломов и
рудных месторождений, где проявляются литохимические ореолы ртути), которые являются
сырьем для производства цемента и извести весьма стабильны. Так, для Русской платформы
(возраст D2-K2) они оценены в среднем для известняков – в 0,031 мг/кг (по данным 131 пробы),
для глинистых пород – в 0,035 мг/кг (58 проб), для песков и алевролитов – 0,039 мг/кг (45
проб), причем содержания ртути близки независимо от фациальных и климатических условий
формирования осадочных пород. Специальное исследование, проведенное на карьерах в
пределах Русской платформы (возраст D3-K2), где добывается известняк, показало, что среднее
содержание ртути по 19 объединенным пробам, составленным из 3117 отдельных проб,
составляет 0,037 мг/кг [190], т. е. ниже кларка земной коры (0,05 мг/кг). Более высокая цифра
среднего содержания ртути в известняках представлена в работе В.З. Фурсова [299] – 0,052
мг/кг при разбросе от 0,024 до 0,102 мг/кг (106 проб); это связано с тем, что опробование
проводилось в различных районах СССР, включая рудные провинции и зоны глубинных
разломов.
Мы принимаем для расчетов среднюю концентрацию ртути в шихте в 0,035 мг/кг со
следующими комментариями. Иногда в исходную шихту добавляют песчано-алевролитовые и
глинистые породы с примесью вулканического материала (эффузивно-осадочный тип
литогенеза), тогда содержание ртути в шихте несколько повышается, т. к. концентрация ртути в
указанных породах в среднем несколько выше, чем в породах осадочного литогенеза, и
составляет – 0,085 мг/кг в глинистых и 0,097 мг/кг в песчано-алевролитовых разностях. В этом
случае содержание ртути в шихте примем в 0,05 мг/кг и в итоговых цифрах сделаем
определенные примечания.
Основной процесс, который приводит к выделению ртути при производстве цемента и
извести, это термический, при котором происходит возгонка ртути и выделение ее с
отходящими газами. В работе [299] показано, что в условиях эксперимента – при непрерывном
нагревании проб известняков и глинистых пород от комнатной температуры до 800°С .
практически вся ртуть выделяется при температурах около 300°С. Процесс обжига цементной
сырьевой массы - известняка и глинистых пород – осуществляется при высоких температурах в
зоне спекания: 1450°С (по шихте) и около 2000°С (по газовому потоку). Поэтому можно
полагать, что в этих процессах практически вся ртуть уходит с дымовыми газами.
Следует заметить, что при производстве цемента для получения смеси необходимого
химического состава используются корректирующие добавки, обычно не превышающие 0,09 т
на 1 т клинкера (полуфабрикат цемента). К ним относятся гипс, железная руда, бокситы,
кварцевые пески, туфы, диатомит, опока, нефелин с весьма низкими – близкларковыми и
закларковыми содержаниями ртути [253, 188], топливные золы и пиритные огарки. Судя по
работам [111, 335], содержание ртути в пиритных огарках, используемых при производстве
цемента на заводах Белоруссии и в г. Новороссийске, повышены и составляют 0,116-.,121 мг/кг
и 0,19-4,0 мг/кг соответственно. Это позволило авторам исследования полагать, что добавка
пиритных огарков существенно повышают концентрацию ртути в пылегазовых выбросах.
Можно предположить, что небольшое количество ртути поступает в зону обжиговой
печи вместе с топливом, а затем эмигрирует в атмосферу. Печь имеет форму наклонного
цилиндра, в верхний торец которого загружается шихта, а снизу поступает встречный поток
горячих газов, который образуется от сгорания топлива в нижнем торце печи.
Существуют два способа производства цемента: мокрый и сухой, различающиеся
влажностью исходной шихты – 32-45 % и 1-2 % соответственно. Мокрый способ требует более
высокого расхода топлива – угля или газа - для получения клинкера, и таким образом, большее
количество ртути за счет топлива (по сравнению с сухим способом) поступает в печь. Но в
любом случае использование угля привносит значительно большую порцию ртути в печь, а
потом и в атмосферу, чем газ (табл. 4.31).
Таблица 4.31 Расчет количества ртути, поступающей с топливом в печь
Показатель |
Производство цемента |
Мокрый способ |
Сухой способ |
Расход на 1 тонну клинкера: - газа - угля |
200 м³ 300 кг |
110 м³ 170 кг |
Среднее содержание ртути в газах* |
2,4×10-6 г/м³ |
Среднее содержание ртути в углях (фоновые)** |
0,045мг/г |
Количество ртути, выделившейся из топлива при
производстве цемента за 2001 г. (35271 тыс. т)
- при использовании газа
- при использовании угля |
16,9 кг 476 кг |
9 кг 260 кг |
* См. раздел .Ртуть в газах..
** [253]; в ртутных провинциях концентрация ртути в углях может возрасти до сотых долей процента
за счет развития ртутных ореолов ; пример - угольная провинция Большого Донбасса [187, 113].
На основе всего вышеизложенного принимаем, что вся ртуть при обжиге известняка и
глинистых пород выделяется с газовой фазой. Соответствующие цифры для предприятий по
производству цемента и оценка выделяющейся ртути приведены в табл. 4.32. Эмиссия ртути
рассчитана на основе среднего содержания ее в исходном сырье – 0,035 мг/кг и объемов
исходной смеси с учетом того, что на одну тонну цемента требуется 1,6 т смеси. В 2001 г.
производство цемента в России составило 35 млн. т.
Таблица 4.32 Количество ртути, выделившейся из шихты при производстве цемента в России в 2001 г.
Федеральные округа, субъекты федерации |
Доля производства цемента, % |
Оценка ртути, т/год |
Предприятия - основные производители цемента |
Центральный федеральный округ |
Белгородская область |
9,8 |
0,193 |
“Белгородский цемент”, г. Белгород; “Осколцемент”, г. Старый Оскол |
Брянская область |
9,71 |
0,192 |
“Мальцовский портландцемент”, г. Фокино |
Воронежская область |
0,87 |
0,017 |
|
Липецкая область |
4,54 |
0,090 |
“Липецкцемент”, г. Липецк |
Московская область |
6,49 |
0,128 |
“Воскресенскцемент”, г. Воскресенск; “Щуровский цемент”, г. Коломна |
Рязанская область |
4,11 |
0,081 |
“Михайловцемент”, Михайловский район |
Северо-Западный федеральный округ |
Республика Коми |
0,42 |
0,008 |
|
Архангельская область |
0,93 |
0,018 |
|
Ленинградская область |
4,57 |
0,090 |
“Глинозем”, г. Пикалево |
Южный федеральный округ |
Карачаево-Черкесская Республика |
2,94 |
0,058 |
“Кавказцемент”, г. Усть-Джегута |
Краснодарский край |
6,05 |
0,119 |
“Новоросцемент”, г. Новороссийск |
Волгоградская область |
6,02 |
0,119 |
“Себряковцемент”, г. Михайловка |
Ростовская область |
0,06 |
0,001 |
|
Приволжский федеральный округ |
Республика Башкортостан |
2,35 |
0,046 |
“Сода”, г. Стерлитамак |
Республика Мордовия |
5,83 |
0,115 |
“Мордовцемент”, Чамзинский район |
Оренбургская область |
1,58 |
0,031 |
|
Пермская область |
2,22 |
0,044 |
“Горнозаводскцемент”, г. Горнозаводск |
Самарская область |
0,82 |
0,016 |
|
Саратовская область |
4,02 |
0,079 |
“Вольскцемент”, г. Вольск |
Ульяновская область |
2,79 |
0,055 |
“Ульяновскцемент”, г. Новоульяновск |
Уральский федеральный округ |
Свердловская область |
7,19 |
0,142 |
“Сухоложскцемент”, г. Сухой лог; “Невьянский цементник”, Невьянский район |
Челябинская область |
3,79 |
0,075 |
“Уралцемент”, г. Коркино |
Сибирский федеральный округ |
Республика Бурятия |
0,3 |
0,006 |
|
Алтайский край |
0,15 |
0,003 |
|
Красноярский край |
2,47 |
0,049 |
|
Иркутская область |
1,2 |
0,024 |
|
Кемеровская область |
4,72 |
0,093 |
“Топкинский цемент”, г. Топки |
Новосибирская область |
1,45 |
0,029 |
|
Дальневосточный федеральный округ |
Республика Саха (Якутия) |
0,58 |
0,011 |
|
Приморский край |
1,01 |
0,020 |
|
Камчатская область |
0,04 |
0,001 |
|
Магаданская область |
0,04 |
0,001 |
|
Еврейская АО |
0,94 |
0,019 |
|
Российская Федерация |
100 |
1,975 |
|
Суммарное количество ртути, которое, как, мы полагаем, эмигрировало с отходящими
газами и пылью в цементном производстве в 2001 г., составило почти 2 т и в самом
оптимальном случае, при введении в шихту вулканогенно-осадочного материала, – 2,8 т.
Общее количество ртути, поступившее в окружающую среду, согласно оценкам, составило 2,0-
2,8 тонн, из которых 1,3-2,1 тонны – из негорючего сырья. Основными источниками пыли в
цементном производстве являются печи обжига клинкера и мельницы помола, причем на долю
обжиговых печей приходится до 85% всех выбросов цементных заводов [44, 129]. Пыль
обжиговых печей обычно полидисперсная, с высоким содержанием частиц размером менее 10
мкм, поэтому является хорошим сорбентом по отношению к тяжелым металлам, в том числе и
ко ртути.
При наличии систем очистки значительное количество ртути осаждается на фильтрах. В
России на цементных заводах используются циклоны, рукавные фильтры, электрофильтры с
эффективностью улавливания пыли 80-99%; в большинстве случаев коэффициент
использования печных электрофильтров на цементных заводах составляет 80-84% [305, 306].
Для очистки отходящих газов от вращающихся печей обжига чаще всего применяются
электрофильтры (около 74% от всего очистного оборудования), хотя из них только одна треть
приходится на высокоэффективные аппараты. В настоящее время назрела необходимость в
модернизации пылегазоочистного оборудования практически на всех цементных заводах
России [204]. В пылегазовых выбросах находится до 90-95% ртути, участвующей в
технологическом процессе.
Не было найдено никаких данных по фактической эффективности улавливания ртути
фильтрами, используемыми в России. В отличие от других тяжелых металлов, ртуть только
частично улавливается фильтрами. В целом очень сложно получить представление об
эффективности различных методов контроля пыли на цементных заводах. Существует лишь
скудная информация о масс-балансе ртути в цементных печах [389]. Количество ртути,
осажденной на фильтрах, помимо других факторов зависит от вида ртути и температуры над
фильтром. Для первичной оценки, видимо, можно использовать информацию, полученную по
угольным ТЭЦ.
Степень адсорбции газообразной ртути на фильтрах как правило зависит от типа
газообразной ртути, содержащейся в отходящем газе; газообразная Hg2+ легче адсорбируется по
сравнению с газообразной Hg0 [414]. Установки, работающие на полубитуминозном угле или
лигните, обычно имеют относительно низкие концентрации Hg2+ и высокие концентрации Hg0
на входе контрольной аппаратуры по сравнению с установками, работающими на каменном
угле. Следовательно, средняя эффективность улавливания ртути ЭФ или мешочными
фильтрами на установках, сжигающих полубитуминозный уголь, ниже. Средний процент
ртути, улавливаемой холодной стороной ЭФ, равен лишь 3%, тогда как осаждение на горячей
стороне ЭФ и тканевом фильтре составляет 6% и 72% соответственно. Данные по содержанию
ртути в газах цементных печей получить не удалось. Учитывая низкую эффективность ЭФ
(высокая концентрация Hg0 и возможность использования только одной трети ЭФ на
высокоэффективном оборудовании), эффективность улавливания ртути может быть только на
уровне 10-30%. Если предположить, что 80% ртути, содержащейся в сырье, поступает в
атмосферу, общий объем выбросов цементных печей, по расчетам, составляет 1,6 т/год, что
соответствует коэффициенту выбросов равному 0,045 г/т произведенного цемента. Для
сравнения, средние коэффициенты выбросов цементных печей в США и Германии составляют
0,065 и 0,026 г/т цемента соответственно [340, 413]
Среднее содержание ртути в товарном цементе, рассчитанное по данным [52, 213, 305)],
оценивается в 0,043 мг/кг Эта величина немного ниже среднего значения - 0,07 мг/кг для 416
образцов, взятых с цементных заводов Германии [416]. Содержание ртути в конечном продукте
в некоторой степени зависит от содержания ртути в сырье, добавляемом в клинкер уже после
термического процесса.
Дальнейшее улучшение экологической обстановки на территории России в районах
цементных заводов в первую очередь связано с модернизацией систем пылеулавливания
тяжелых металлов, включая ртуть, и обновлением соответствующего оборудования.
Международная ассоциация производителей цемента и изделий на его основе (МГА цемент)
разработала совместно с ЗАО “Концерн Цемент” программу развития российской цементной
промышленности на 2001-2005 г.г. Особое внимание при этом уделяется реконструкции
электрофильтров для снижения пылевыбросов до предельно допустимых норм.
По извести экспертную оценку произвести не удалось, поскольку в нашем распоряжении
не было информации о соответствующих предприятиях и объемах ее производства. По опыту
инвентаризации в других странах можно предположить, что при производстве извести эмиссия
ртути в атмосферу будет, по крайней мере, на порядок меньше, нежели ее выбросы при
производстве цемента.
4.4 Цветная металлургия
Ртуть, присутствующая в качестве естественной примеси в рудах цветных металлов,
мобилизуется при их добыче и может поступать в окружающую среду в процессе переработки
сырья и концентратов на металлургических заводах. Расположение предприятий цветной
металлургии на территории Российской Федерации представлено на рис. 4.7.
В 2001 г. в России с точки зрения потенциальной эмиссии ртути в окружающую среду
наибольшее значение имело первичное производство цинка, меди, никеля; объемы выпуска
других цветных металлов были на один-два порядка меньше (табл. 4.33).
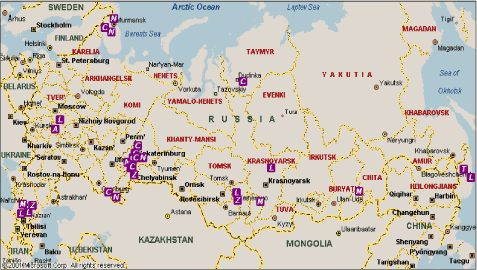
Рисунок 4.7 Расположение предприятий цветной металлургии на территории Российской
Федерации (A – сурьма, C – медь, L – свинец, M – молибден, N - никель, Z – цинк, T .
вольфрам).
Таблица 4.33 Производство цветных металлов в России, 2001 г. [7, 25, 27, 58, 59, 66, 67, 123, 169, 217,
308]*
Металл |
тыс. т |
Основные производители (доля в %) |
Медь рафинированная |
840 |
ОАО “ГМК “Норильский никель” (> 54%) |
Цинк рафинированный |
250,6 |
ОАО “Челябинский цинковый завод” (> 62%) |
Никель первичный |
250 |
ОАО “ГМК “Норильский никель” (> 89%) |
Свинец рафинированный |
34 |
ЗАО “Свинцовый завод- Дальполиметалл“, ОАО “Электроцинк” |
Кобальт |
6,5 |
ОАО “ГМК «Норильский никель. (70%), ОАО “Уфалейникель” |
Олово рафинированное |
4,5 |
ОАО “Новосибирский оловянный комбинат” (100%) |
Сурьма |
1,5 |
ОАО “Рязцветмет” (100%) |
* Производство висмута, вольфрама, молибдена и других редких металлов составляло первые десятки
(чаще) – первые сотни (реже) тонн в год.
Самые крупные предприятия цветной металлургии входят в структуру ОАО “ГМК
“Норильский никель”, на долю которого ежегодно приходится до 65-70% выбросов в
атмосферу и до 30-33% объема сбрасываемых сточных вод всех российских предприятий
цветной металлургии (включая алюминиевую промышленность). В свою очередь,
подавляющая часть указанных выбросов и сбросов осуществляется Заполярным филиалом
“ГМК “Норильский никель”. Например, в 1998 г. всей промышленностью России было
выброшено в атмосферу 18661,82 тыс. т вредных веществ, из них предприятиями цветной
металлургии – 3291,79 тыс. т, в том числе “ГМК “Норильский никель” – 2436,2 тыс. т (из них
Заполярным филиалом “ГМК “Норильский никель” – 2139,5 тыс. т). Типичные объемы
выбросов вредных веществ в атмосферу любым другим российским заводом цветной
металлургии в 2001 г. составляли первые десятки тысяч тонн.
4.4.1 Ртуть в рудах цветных металлов и концентратах
Ртуть отличается широкими металлогеническими связями и является в процессе
рудообразования элементом, сопровождающим процесс минералообразования в широком
диапазоне температур и физико-химических условий [187, 188, 233, 295, 296]. Известен
широкий комплекс месторождений, в рудах которых ртуть представлена в собственно
минеральной форме (например, медно-серебряные месторождения), входит в состав сложных
минералов (тип платиноидных месторождений) или же находится в рассеянном состоянии
(медно-колчеданные, медно-никелевые, серно-колчеданные, полиметаллические
месторождения и др.). Очень высокие содержания ртути характерны для руд некоторых
стратиформных месторождений. Незначительные по масштабам скопления ртути известны в
медистых песчаниках (от десятых долей до первых граммов на тонну). Повышенными
концентрациями ртути характеризуются также некоторые железные, марганцевые и
алюминиевые (алуниты и бокситы) руды.
Значительными масштабами ртутноносности отличаются сульфидные месторождения,
причем наиболее обогащены ртутью сульфидные руды цинка (до 10-100 г/т) [295]. По Н.А.
Озеровой [188], для колчеданных месторождений Урала общее количество заключенной в них
ртути соответствует по масштабу промышленным ртутным месторождениям средних и
крупных размеров. Среднее содержание ртути в рудах колчеданных месторождений
оценивается примерно в 1 г/т [187], в полиметаллических рудах - в 1,1 г/т [134]. Однако в
конкретных случаях ее уровни в промышленных сортах (типах) рудах отличаются высокой
вариацией (табл. 4.34, 4,35). Как правило, максимальные концентрации ртути характерны для
медно-цинковых, минимальные - для серно-колчеданных руд.
Таблица 4.34 Ртуть в рудах и минералах свинцово-цинковых и медных месторождений, г/т [33]
Промышленный тип месторождений |
Руды |
Сфалерит |
Галенит |
Халькопи рит |
Пирит |
Блекла я руда |
Колчеданно- полиметаллический (алтайский) |
0,1 - 20 |
0,2 – 26,1 |
0,01 - 16 |
0,4 – 3,4 |
0,2 - 10 |
следы - 300 |
Стратиформный свинцово- цинковый (атасуйский) |
0,9 - 406 |
23 - 7600 |
0,6 - 530 |
1 - 240 |
2 - 50 |
до 12% |
Жильный свинцово- цинковый |
?* |
0,4 - 1000 |
0,075 - 25 |
?* |
0,1 - 100 |
80- 800 |
Медно-колчеданный |
0,6 - 900 |
70 - 250 (до 0,5-1,5%) |
?* |
?* |
?* |
до 3% |
* Здесь и далее в таблицах – ртуть не определялась; прочерк означает, что данные отсутствуют.
Сфалерит-халькопирит-пиритовые руды вулканогенных объектов, к группе которых
относятся все медно-колчеданные месторождения Южного Урала - Учалинское, Узельгинское,
Сибайское, Бурибайское, Юбилейное, Гайское и др. – характеризуются особенно высокими
концентрациями ртути. Так, в перерабатываемых Учалинским ГОКом рудах Узельгинского
месторождения ее концентрации изменяются от сотых долей г/т до 800 г/т, Учалинского
месторождения - от 2 до 560 г/т, Новоучалинского – 1-88 г/т [170].
Таблица 4.35 Ртуть в рудах колчеданных месторождений [187, 188]
Месторождение |
Ртуть в рудах, г/т |
Урал |
Межозерное |
10-90 |
Комсомольское |
0,1-9 |
Сибайское |
10-90 |
Гайское |
1-90 |
Учалы, Чадарское, Дегтярьское, Красногвардейское |
1-9 |
Имени III Интернационала |
0,5-20 (среднее ~ 7) |
Маукское, Полевское, 50 лет Октября |
0,1-0,9 |
Кавказ |
Филизчай |
10-90 |
Уруп |
0,1-90 |
Власинчихинское, Скалистое |
0,4-15 |
Среднее содержание ртути в сульфидных медно-никелевых рудах составляет 1 г/т [295],
хотя, например, в рудах Мончегорского медно-никелевого месторождения ее концентрации
иногда достигают 9 г/т [187]. В рудах медно-колчеданно-полиметаллических месторождений
ртути содержится 5-10 г/т; в баритовых и флюоритовых рудах - 1-10 г/т [295]. Ртуть в
повышенных концентрациях присутствует также в рудах других месторождений (табл. 4.36).
Таблица 4.36 Содержание ртути в рудах различных месторождений [300]
Месторождение |
Тип месторождения |
Среднее (пределы), г/т |
Вольфрамовые |
Тырныауз, Кавказ Скарновый |
0,49 |
(0,25-0,87) |
Бом-Горхонское, Забайкалье Гидротермальное |
0,77 |
(0,38-1,51) |
Холтосонское, Забайкалье Гидротермальное |
0,99 |
(0,73-1,35) |
Молибденовые |
Первомайское, Забайкалье Гидротермальный |
0,83 |
(0,72-0,98) |
Шахтаминское, Забайкалье Гидротермальный |
1,27 |
(1,17-1,5) |
Тантала и ниобия |
Месторождения Забайкалья и Дальнего Востока |
- |
(0,48-0,54) |
Основная масса ртути в рудах находится в сульфидной форме в виде тонкодисперсной
примеси в рудообразующих минералах. Главный концентратор и носитель ртути – сфалерит
[188]. Концентраторами ртути являются также блеклые руды, галенит, борнит, халькопирит,
пирит. Например, в рудах колчеданно-полиметаллических месторождений со сфалеритом
связано 80-90% ртути, с халькопиритом – 10%, галенитом – 5%, пиритом – 3%; в рудах медно-
колчеданных месторождений Южного Урала с пиритом связано около 70% ртути, с
халькопиритом – до 7% [33]. Накопление ртути наблюдается в зоне окисления колчеданных
месторождений (до 80 г/т), где она встречается в металлическом виде [142].
Поведение ртути при обогащении руд цветных металлов
Основными способами, применяемыми на обогатительных фабриках, являются
дробление и измельчение руд с последующей коллективно-селективной или селективной
флотацией и получением различных концентратов. В общем случае содержание ртути в
концентратах крайне неравномерно и, обычно, по сравнению с рудой, возрастает на порядок в
цинковом и (в меньшей степени) свинцовом, составляя в среднем несколько десятков грамм на
тонну; степень концентрирования ртути в медном концентрате (из медно-колчеданных руд)
повышается в 2-2,5 раза, что, однако, в ряде случаев не наблюдается (табл. 4.37).
Таблица 4.37 Пределы содержаний ртути в промышленных концентратах, г/т [33, 188]
Промышленный тип месторождений |
Цинко вый |
Свинц овый |
Медный |
Пиритн ый |
Молибде новый |
Оловя нный |
Вольфра мовый |
Колчеданно- полиметаллический |
0,3 - 175 |
0,3 - 390 |
0,22 - 65 |
0,2 – 11,4 |
- |
- |
- |
Стратиформный свинцово-цинковый |
8 - 1700 |
0,6 - 520 |
2 - 290 |
2 - 90 |
1 - 4 |
- |
- |
Скарновый и метасоматический свинцово-цинковый |
6,4 - 270 |
1 - 39 |
- |
- |
- |
- |
- |
Жильный свинцово-цинковый |
? |
5 |
- |
- |
- |
- |
- |
Медно-колчеданный |
1 - 390 |
- |
0,3 - 150 |
0,1 – 26 |
- |
- |
- |
Медистые песчаники |
20 |
6 |
4 |
- |
- |
- |
- |
Ванадиево-железо-медный |
30 |
- |
70 |
90* |
- |
- |
- |
Медно-молибденовый |
- |
- |
0,02 |
- |
0,1 |
- |
- |
Медно-никелевый |
- |
- |
0,14 – 0,4 |
0,45 - 2 |
18-36** |
- |
- |
Молибденово-вольфрамовый |
- |
- |
- |
- |
0,2 – 0,5 |
- |
? |
Оловянный и оловянно-вольфрамовый |
- |
- |
- |
- |
- |
0,01 – 0,8 |
0,035 – 0,09 |
Сурьмяный |
- |
- |
- |
0,7 – 35*** |
- |
- |
- |
* Железный концентрат.
** Платиновый концентрат.
*** Сурьмяный концентрат.
При обогащении свинцово-цинковых и колчеданно-полиметаллических руд основное
количество ртути (до 70-80%) извлекается в цинковый концентрат, что в существенной степени
объясняется ее связью со сфалеритом и другими цинксодержащими минералами (табл. 4.38).
Таблица 4.38 Распределение ртути (в % от общего содержания в руде) по продуктам обогащения
руд свинцово-цинковых и медных месторождений, среднее (пределы) [33]
Промышленный тип месторождений |
Концентраты |
Хвосты |
Цинковый |
Свинцовый |
Медный |
Пиритный |
Баритовый |
Колчеданно-поли-металлический |
78,8 (78 – 79,5) |
1,1 (0,7 – 1,4) |
2,5 (0,7 – 4,4) |
? |
Не извлекается |
17,6 (16,8-18,4) |
Стратиформный свинцово-цинковый |
68,2 (66,8 – 93,1) |
20,4 (1,6 – 57,2) |
Не извлекается |
5 |
3,8 |
2,7 |
Медно-колчеданный |
7,8 |
Не извлекается |
19,1 – 24,9 |
67,5 – 68,1 |
Не извлекается |
5,7 |
Ванадиево-железо-медный |
57 |
Не извлекается |
4,7 |
26,3* |
Не извлекается |
? |
Медистые песчаники |
Не извлекает ся |
9,2 |
28,8 |
Не извлекается |
Не извлекается |
? |
* В железный концентрат.
При обогащении медно-колчеданных руд основную массу продуктов составляет
пиритный концентрат, выход которого изменяется в пределах 25-70% (до 80% для сплошных
руд). Поэтому, несмотря на низкие содержания ртути (обычно первые г/т, чаще всего в
пределах 0,75-3 г/т), значительная ее часть (до 40-60% от содержания в руде) обычно переходит
именно в пиритный концентрат.
Пиритные концентраты, получаемые при обогащении руд цветных металлов, служат
сырьем для производства серной кислоты на предприятиях химической промышленности,
причем в качестве попутной продукции здесь получают только селен из сернокислотных
шламов. Кроме того, часть пиритных огарков перерабатывается на медеплавильных и
свинцово-цинковых комбинатах. В настоящее время в окрестностях многих российских
обогатительных фабрик накопились значительные объемы пиритных концентратов,
содержащих ртуть. Например, в районе Учалинского ГОКа их складировано 1 млн. т, вблизи
Башкирского медно-серного комбината – 1,5 млн. [150].
Температура в технологическом цикле переработки руд на обогатительных фабриках
обычно невысока (менее 100°С), поэтому ртуть практически не поступает в атмосферу, что,
например, подтверждается результатами газо-ртутных наблюдений на промышленной
площадки Учалинского ГОКа [142]. Подавляющая часть ртути, извлекаемой с колчеданными
рудами, переходит в концентраты и вывозится в их составе на переработку; лишь
незначительное ее количество (до 2-7% от общей массы в рудах) уходит в отходы обогащения,
которые складируются в хвостохранилищах (табл. 4.39). Как уже отмечалось, наиболее
интенсивно ртуть переходит в пиритный концентрат (преобладает по массе) и цинковый
концентрат (отличается наиболее высокими содержаниями металла). Содержания ртути в
хвостах могут быть также достаточно высокими (до 1-9 г/т). В районе Учалинского ГОКа масса
отвальных хвостов обогатительной фабрики достигает 28 млн. т, вблизи обогатительной
фабрики Башкирского медно-серного комбината – 480 млн. т [150], в районе обогатительной
фабрики Бурибайского рудоуправления – 6 млн. т, в которых, очевидно, содержится несколько
сотен тонн ртути.
Таблица 4.39 Распределение ртути в продуктах переработки руд, Учалинский ГОК [142]
Руда, концентрат, отходы |
Среднее, г/т |
Относительное количество ртути, % |
Руда * |
10-25 |
100 |
Пиритный концентрат |
5-15 |
36-50 |
Медный концентрат |
28-41 |
10-14 |
Цинковый концентрат |
76-123 |
35-48 |
Хвосты |
1-9 |
2-9 |
* Учалинский ГОК ежегодно перерабатывает на обогатительной фабрике более 2 млн. т медно-
колчеданных руд.
Зарубежные данные также показывают [120], что при переработке колчеданных руд ртуть
особенно интенсивно концентрируется и накапливается в цинковом концентрате (табл. 4.40).
Обращает на себя внимание существенный ее переход, в отличие от обогатительной фабрики
Гайского ГОКа, в отходы (до 27% от общего количества в руде), что, возможно, обусловлено
особенностями применяемой технологии.
Таблица 4.40 Содержание ртути в продуктах обогащения фабрики предприятия .Брансуик. (Канада)
[120]
Продукт |
Количество перерабатыва- емой руды, т/сут |
Содержание Hg |
Извлечение, % |
г/т |
кг/сут |
Исходная руда |
8575 |
2,1 |
18,24 |
100 |
Медный концентрат |
73,7 |
2,3 |
0,15 |
0,87 |
Свинцовый концентрат |
400 |
2,7 |
1,09 |
5,97 |
Коллективный концентрат |
70 |
9,1 |
0,64 |
3,5 |
Цинковый концентрат |
900 |
13,5 |
12,22 |
67,0 |
Хвосты |
7140 |
0,69 |
4,94 |
27,0 |
Согласно обобщенным оценкам [33], потенциальные суммарные ресурсы ртути в
основных промышленных концентратах свинцово-цинковых и медных месторождений
распределяются следующим образом (в %): цинковый – 42, пиритный – 26, медный – 19,
свинцовый – 13. В свою очередь, на цинковые (свинцово-цинковые) и медные предприятия
страны с концентратами основных металлов ежегодно поступает весьма значительные
количества ртути, из которых 65% связано с цинковыми концентратами, 20% - с медными
концентратами и богатыми рудами, 15% - со свинцовыми концентратами.
Наличие в районах обогатительных фабрик значительных объемов отходов, в том или
ином количестве содержащих ртуть, предопределяет потенциальную возможность включению
ее в миграционные цепи в ходе разрушения отвалов гипергенными процессами. Кроме того,
ртуть поступает в окружающую среду непосредственно при добыче руд. В частности, в
шахтных водах Сибайского и Октябрьского месторождений ее концентрации составляли 20 и
13 мкг/л соответственно, [174], а в воде Бурибайского карьера, используемой для оборотного
водоснабжения и периодически сбрасываемой в р. Таналык, – 28,3 мкг/л [100], что многократно
превышает типичные фоновые уровни этого металла в природных водах. Поступление
поллютантов в поверхностные водотоки связано также с утечками сточных вод через дамбы и
фильтрата с хвостохранилищ. В теплое время года не исключена дегазация ртути из отвалов
отходов добычи и обогащения руд цветных металлов.
4.4.2 Первичное производство цинка
Первичное производство цинка включает в себя следующие процессы: обогащение
цинковых руд, окисление (обжиг) цинкового концентрата, производство цинка
(электрохимическим или термическим методом), рафинирование цинка. Производство
первичного цинка обычно сопровождается получением серной кислоты по стандартной
технологической схеме.
Российские производители цинка
В 2001 г. цинк в России производился в основном двумя предприятиями: ОАО
“Челябинский цинковый завод” (г. Челябинск) и ОАО “Электроцинк” (г. Владикавказ). Третий
производитель - ОАО “Беловский цинковый завод” выпускает в небольшом объеме
преимущественно цинковый порошок (табл. 4.41). В очень небольших количествах первичный
цинк производили предприятия, входящие в Уральскую горно-металлургическую компанию, и
ОАО “ГМК “Дальполиметалл” [123]. Однако общие объемы их производства в 2001 г.
составили первые десятки тонн цинка. Например, в 1-м квартале 2002 г. в ОАО “ГМК
“Дальполиметалл” было получено 8,2 т цинка [361]. Таким образом, основными источниками
эмиссии ртути в окружающую среду в 2001 г. являлись заводы в г. Челябинске и в г.
Владикавказе.
Таблица 4.41 Производство цинка российскими заводами, тыс. т [58, 59, 161, 215-217, 236, 360, 374,
386]
Предприятие |
Местонахождение |
1999 |
2000 |
2001 |
2002 |
ОАО “Челябинский цинковый завод” |
г. Челябинск |
138,3 |
145,7 |
155,5 |
165,8 |
ОАО “Электроцинк”* |
г. Владикавказ |
90,9 |
92,6 |
91,1 |
88,4 |
ОАО “Беловский цинковый завод” |
г. Белово, Кемеровская обл. |
2,8** |
2,2** |
4 |
2,84** |
Всего в России |
232 |
241,9 |
250,6 |
257,1 |
* Работает (до 85-90% выпускаемого металла) по толлинговой схеме; (например, в 2002 г. на
внутренний рынок поставил чуть больше 2 тыс. т цинка).
** Цинковый порошок.
Челябинский цинковый завод (ЧЦЗ), основанный в 1935 г. и расположенный в черте г.
Челябинска (размер санитарно-защитной зоны составляет 1000 м), выпускает, кроме
металлического цинка, сплавы цинк-алюминиевые, сплавы цинковые литейные в чушках,
кадмий, индий металлический, сульфат цинка технический, оксид цинка, кислоту серную
техническую. В 2001 г на заводе внедрена технология получения индиевого порошка с
размером частиц от 1 до 5 мкм [349]. Есть сведения, что ЧЦЗ удалось “полностью решить
проблему ртутно-селенистого шлама”, который якобы вывозится на переработку в Киргизию, а
в последнее время “предприятие в плотную подошло к решению проблемы утилизации ртути
из газов” [276]. В частности, для снижения содержания ртути в кислоте планируется
приобрести у фирмы “Boliden” установку по утилизации ртути из газов, что позволит свести к
нулю выбросы ртути и значительно сократить выбросы оксидов серы. В 2001 г. сточные воды
завода сбрасывались в р. Миасс; отсюда же бралась свежая вода.
ОАО “Электроцинк” (г. Владикавказ), кроме цинка, производит также свинец, кадмий,
кислоту серную, сульфат меди, металлоконструкции. На его долю приходится около 70% всех
выбросов от стационарных источников в Республике Северная Осетия – Алания. К 1999 г. на
территории предприятия было размещено более 3,2 млн. т твердых отходов, в которых
присутствуют десятки тонн ртути [252]. В 2001 г. на ОАО “Беловский цинковый завод” была
завершена реконструкция установки по производству цинкового порошка, и завод приступил к
выпуску товарной продукции.
Сырье и содержание ртути в цинковых концентратах
Сырьем для получения цинка в основном служат полиметаллические сульфидные руды,
содержащие также соединения свинца, меди, кадмия и других металлов. Полиметаллические
сульфидные цинковые руды можно разделить на свинцово-цинковые, медно-цинковые и
свинцово-медно-цинковые. К типу свинцово-цинковых относятся месторождения Кавказа, а
также Салаирское и Сихотэ-Алинское. Медно-цинковые руды наиболее ярко представлены
месторождениями Урала. Большинство руд Алтая являются свинцово-медно-цинковыми.
Свинцово-цинковые и медно-свинцово-цинковые руды являются также сырьем для
промышленного получения свинца. Кадмий извлекается в основном попутно с цинком. Кроме
того, в производстве цинка большое значение имеют колчеданные медно-цинковые и цинковые
колчеданные руды. Они широко представлены на цинково-медных колчеданных
месторождениях, но нередко встречаются и в свинцово-цинковых. Различают колчеданно-
полиметаллические руды, основная масса которых сложена пиритом или пирротином, и
полиметаллические, в которых содержание пирита и пирротина не превышает 2-4% [73].
Типичное содержание цинка в перерабатываемых рудах составляет в среднем 1-3%.
Как отмечалось выше, из-за низкого содержания полезных металлов сульфидные руды
предварительно обогащают с целью выделения концентратов. В процессе обогащения
(используются дробление, предварительное обогащение и флотация) в зависимости от состава
исходной руды получают цинковые и другие концентраты. Например, при обогащении
колчеданно-полиметаллических руд получают четыре концентрата: свинцовый, цинковый,
медный и пиритный. В отечественных цинковых концентратах обычно содержится (в %): цинк
45-51, свинец 0,2-2,5, медь 0,4-3, кадмий 0,1-0,25, железо 3-12, сера 30-38, пустой породы до 10
[89, 92, 196, 294].
Челябинский цинковый завод в 2001 г. был основном ориентирован на поставки сырья с
месторождений уральского региона, на долю которых приходится более 75% объема выпуска
российских цинковых концентратов. Эти поставки - с Учалинского, Гайского и Сибайского
ГОКов, Башкирского медно-серного комбината - обеспечивают завод цинковым концентратом
примерно на 95%. В 2001 г. ОАО “Учалинский ГОК” являлся основным поставщиком на ЧЦЗ
цинкового концентрата (до половины от всего количества). В последнее время ЧЦЗ также
ежегодно закупал за рубежом до 20 тыс. т концентрата (с содержанием цинка 55-60%).
В 2001 г. ЦЧЗ переработал порядка 330 тыс. т цинкового концентрата. Владикавказский
“Электроцинк” перерабатывал цинковые концентраты, поставляемые, судя по всему, главным
образом из Казахстана, Китая и Польши. Незначительное количество концентрата поступило с
Садонского свинцово-цинкового комбината. В 2001 г. на заводе было переработано около 190
тыс. т цинкового концентрата. Беловский цинковый завод, очевидно, получал цинковые
концентраты с уральских и сибирских (алтайских) месторождений. Масса переработанного в
2001 г. концентрата составила 6,3 тыс. т.
Цинковые концентраты, особенно уральских обогатительных фабрик, перерабатывающих
руды медно-колчеданных месторождений, характеризуются высокими содержаниями ртути
(табл. 4.42-4,44). По данным А.Н. Кутлиахметова [142], содержания ртути в цинковом
концентрате, производимого Учалинским ГОКом, составляют 76-123 г/т.
Таблица 4.42 Состав цинковых концентратов (данные института Гинцветмет)
Горно-обогатительный комбинат |
Цинк, % |
Ртуть, г/т |
Учалинский |
45,5 |
20 |
Гайский |
49,9 |
100 |
Башкирский медно-серный комбинат |
44,1 |
30 |
Новоширокинский рудник |
54,0 |
10 |
Алтайский |
34,5 |
< 3 |
ОАО “Дальполиметалл” |
49,1 |
3 |
Таблица 4.43 Ртуть в концентратах колчеданных и колчеданно-полиметаллических месторождений, г/т
[188]
Регион |
Месторождение |
Ртуть в концентрате, г/т |
Среднее (оценка), г/т |
Средний Урал |
имени III Интернационала |
4,5 |
4,5 |
Ломовское, Левихинское |
1-2 |
1,5 |
Южный Урал |
Гайское |
10-25 |
17 |
Учалинское |
10-75 |
42 |
имени XIX партсъезда |
25-75 |
50 |
Сибаевское |
1,8-7,5 |
4,7 |
Кавказ |
Филизчайское |
18 |
18 |
Маднеульское |
1,2 |
1,2 |
Таблица 4.44 Ртуть в цинковых концентратах уральских обогатительных фабрик [174]
Обогатительная фабрика |
Ртуть, г/т |
Красноуральская |
30 |
Кировоградская |
20 |
Среднеуральская |
64 |
Гайская* |
65 |
Учалинская* |
53 |
Сибайская* |
93 |
Карабашская |
91 |
Среднее |
59,4 |
* Основные поставщики цинковых концентратов на Челябинский цинковый завод.
Приводимое в табл. 4.43 среднее содержание ртути, очевидно, достаточно реально
отражает ее уровень в концентратах, переработанных в 2001 г. Челябинским цинковым
заводом. Аналогичное содержание может быть принято и для Беловского завода. Прямые
сведения о содержании ртути в концентратах, поступивших на переработку на ОАО
“Электроцинк”, отсутствуют, но известно, что свинцово-цинковые руды Казахстана и
производимые их них цинковые концентраты также отличаются очень высокими ее
содержаниями [33].
Таким образом, в цинковое производство в 2001 г. с концентратами на Челябинский
завод поступило примерно 20 т ртути, на ОАО “Электроцинк” – 11 т ртути, на Беловский
цинковый завод – 0,3 т ртути.
Процессы и технологии
Для переработки цинковых концентратов применяются гидрометаллургические
(электролитические) и пирометаллургические (дистилляционные) технологические схемы.
Гидрометаллургический способ является основным (заводы в Челябинске и Владикавказе);
термический способ - используется на Беловском цинковом заводе.
Первой операцией в любом способе производства цинка из сульфидных концентратов
является их обжиг с целью перевода сульфидных соединений в окисленные. В
пирометаллургическом производстве предварительно высушенные (во вращающихся
барабанных печах при температуре поступающих топочных газов 700-800°С) концентраты
вначале подвергают неполному окислительному обжигу на порошок в многоподовых печах, а
затем спекают (при 1200°С) на агломерационных машинах. При обжиге стремятся получить
концентрированные по содержанию SO2 обжиговые газы, пригодные для производства серной
кислоты, и уловить возгоняемые полезные металлы. Готовый агломерат содержит 0,5-0,8%
серы и представляет собой плохо спеченные куски пористого материала. Перед подачей на
дистилляцию его подвергают дроблению и грохочению. Затем оксид цинка восстанавливают в
ретортах при температурах выше точки кипени металлического цинка (>906°С), что
обеспечивает его возгонку в виде паров, которые поступают в конденсатор, где собираются в
жидком виде. Пары цинка в дальнейшем конденсируются, а полученный черновой цинк
направляют на рафинирование.
Обжиг цинковых концентратов перед гидрометаллургической переработкой проводят в
печах кипящего слоя (температура кипящего слоя поддерживается в пределах 900-950°С;
температура газов под сводом печи 800-850°С). В обожженном продукте (огарке) содержится
55-65% цинка, а также присутствуют соединения меди, свинца, железа, кадмия, мышьяка,
сурьмы, кобальта, благородных и редких металлов; содержание сульфидной серы составляет
менее 1%. Огарок самотеком выгружается через сливной порог и доставляется в
классификационное отделение. Пыль собирается в циклонах; периодически ее выгружают и
присоединяют к огарку. Наряду с огарком и пылью из циклонов получают пыль из газоходов
электрофильтров. Все перечисленные продукты подвергаются совместной переработке. По
данным завода “Электроцинк”, которые можно считать типичными, выход продуктов обжига
составляет (в %): огарок – 65, пыль из циклонов – 30, пыль из газоходов – 1,1, пыль из
электрофильтров – 3,3, вентиляционная пыль – 0,6 [89]. В цинковом производстве на ЧЦЗ в
шихту обжигаемых концентратов иногда вводят содержащие оксид кальция добавки (шламы
очистных сооружений), что позволяет перерабатывать некондиционные концентраты с
повышенным содержанием кремния [282]. Из огарка цинк выщелачивают водным раствором
серной кислоты. Выщелачивание проводят с целью наиболее полного перевода цинка и
некоторых сопутствующих ему компонентов в раствор. Обычно в раствор удается перевести до
90% цинка, считая цинк в огарке за 100%. Перед электролизом раствор тщательно очищают от
примесей, после чего подают в электролизные ванны.
Цинк при электролизе осаждается на катоде, на аноде выделяется кислород. При этом в
растворе регенерируется серная кислота, необходимая для выщелачивания свежих порций
огарка. Катодные осадки цинка (катодный цинк) переплавляют в индукционных печах, а
полученный цинк разливают с помощью специальных машин в слитки.
Источники и характеристика пылегазовыделения
Основными источниками пылегазовых выбросов на цинковых заводах являются
обжиговые печи кипящего слоя. Газы печей кипящего слоя характеризуются высокими
температурами (до 950°С), значительной запыленностью (до 300 г/м³) и преобладанием мелких
фракций пыли (2,5-4,5 мкм). Объем отходящих (обжиговых) газов колеблется в пределах 1,3-
3,1 тыс. м³ на тонну концентрата. Схема очистки обжиговых газов, поступающих затем в
сернокислотное производство, включает циклоны (грубая очистка) и сухие электрофильтры
(тонкая очистка). Кроме того, непосредственно в сернокислотном отделении газы
обрабатываются в промывных башнях и на мокрых электрофильтрах. По данным [52], в
середине 1990-х г.г. удельные показатели выбросов пыли при производстве цинка на заводах
СНГ составляли: при эффективности очистки 95% - 57,2 кг, при очистке 98,5% - 17,2 кг, при
очистке 99,8% - 2,29 кг на тонну чернового цинка.
Согласно [92], степень очистки обжиговых газов на предприятиях быв. СССР
варьировалась от 81,6 до 99,6%. Средняя эффективность работы очистного оборудования
оценивалась в 98,5% [250]. Есть все основания считать, что последний показатель
соответствует уровню 2001 г.
Эмиссия и распределение ртути при производстве цинка
Поведение ртути в первичном производстве цинка изучено крайне слабо, что
обусловливает отсутствие надежных фактических данных об особенностях ее распределения в
основных продуктах, отходах и об эмиссии в окружающую среду.
Известно, что в 1988-1990 г.г. на Челябинский цинковый завод с цинковыми
концентратами поступало порядка 35-40 т ртути в год [198]. По данным [112], уровни
содержания ртути в перерабатываемых в 1970-х – начале 1980-х г.г. на ЧЦЗ цинковых
концентратах достигали 200 г/т. Авторы цитируемых работ считают, что при обжиге
концентратов ртуть возгоняется и в составе обжиговых газов переходит в сернокислотное
производство. Поскольку используемая технология очистки обжиговых газов в промывном
отделении сернокислотного производства ЧЦЗ не обеспечивала полного улавливания ртути, то
значительное ее количество поступало в продукционную (техническую) серную кислоту. По
данным [198], около 10-12 т ртути в год выпадало в составе ртутно-селенистых шламов в
промывном отделении, остальные 25-30 т ртути поступали в серную кислоту. Ежегодное
образование шламов тогда достигало 30-35 т. В табл. 4.45 приведены данные института
Гинцветмет, характеризующие объемы образования ртутьсодержащих шламов на российских
цинковых предприятиях в 1985-2000 г.г.
Таблица 4.45 Масса ртутно-селенистых шламов на предприятиях цветной металлургии РФ, тP
Предприятие |
1985-1990 |
1990-1995 |
1995-2000 |
шлам |
ртуть |
шлам |
ртуть |
шлам |
ртуть |
Челябинский цинковый завод* |
250 |
70 |
404 |
88 |
525 |
115 |
Беловский цинковый комбинат |
850 |
27 |
850 |
27 |
850 |
27 |
* До 1985 г. ртутно-селенистые шламы ЧЦЗ в небольшом объеме поступали на переработку на Усть-
Каменогорский свинцово-цинковый комбинат; в течение незначительного периода времени на ЧЦЗ
существовало также производство попутной ртути из указанных шламов.
Исследования, в свое время выполненные на ЧЦЗ [112], показали, что поступавшая в
сернокислотное производство в составе обжиговых газов ртуть распределялась следующим
образом (содержание ртути в обжиговом газе = 100%): промывная кислота – 16,7%; шлам –
43,3%; продукционная серная кислота – 36,6%; отходящие газы – 0,4%. Таким образом, 60%
поступившей с газами ртути улавливалось в промывном отделении сернокислотного
производства и выводилось с промывной кислотой и шламом. Оставшаяся ртуть поступала в
сушильно-абсорбционное отделение и загрязняла продукционную серную кислоту. Авторами
цитируемой работы был изучен также баланс распределения форм нахождения (состояния)
ртути в различной продукции (табл. 4.46).
Таблица 4.46 Баланс распределения форм нахождения (состояния) ртути в различных продуктах сернокислотного производства ЧЦЗ, % [112]
Продукт |
Hgo |
Hg2Г2 * |
HgS |
Hg2SO4 |
HgmSen |
HgSO4 |
Обжиговый газ |
99,3 |
0,4 |
0,3 |
- |
- |
- |
Шлам |
4 |
9,5 |
50,5 |
- |
36 |
- |
Серная кислота |
- |
- |
- |
3,2 |
- |
96,8 |
* Галогениды ртути.
В работе [33] приводится схема распределения ртути в продуктах переработки цинкового
производства, основанная на данных [112] и на собственных расчетах авторов (рис. 4.8). При
обжиге цинковых концентратов ртуть, содержащаяся в концентрате, возгоняется (на 94%) и в
виде паров металла переходит в обжиговые газы. Газы (с содержанием SO2 > 3,5%) проходят
систему пылеулавливания (с пылью выводится до 32% ртути) и поступают в сернокислотные
цеха (СКЦ) для получения серной кислоты контактным способом по стандартной
технологической схеме. В промывном отделении СКЦ сернистые газы конденсируются в
специальных промывных башнях, затем конденсат поступает на электрофильтры, откуда
фильтрат идет на получение серной кислоты, а обогащенный селеном и ртутью шлам подается
на специализированную установку и доводится до товарной кондиции методом флотации. В
бедных шламах отстойников промывных башен содержание ртути составляет 5-18%; в богатых
шламах мокрых электрофильтров - 10-40%. Как правило, среднее сквозное извлечение ртути из
концентратов в шлам составляет 27% (от ее содержания в концентратах). Значительное
количество ртути поступает в товарную серную кислоту, а также связывается с промывной
кислотой. Необходимо отметить, что уровень утилизации как ртути, так и ртутно-селенистых
шламов на российских цинковых заводах был крайне низким [33]. Например, в Финляндии из
цинковых концентратов путем трехступенчатой очистки обжиговых газов по технологии
компании “Oytocumpu Oy” в конце 1990-х г.г. достигалось извлечение ртути до 99,5%, что в год
составляло более 70 т товарного металла [41].
![Рисунок 4.8 Схема распределения ртути в продуктах переработки цинкового производства [33].](images/s191.gif)
Рисунок 4.8 Схема распределения ртути в продуктах переработки цинкового производства [33].
Все приводимые выше оценки и схемы распределения ртути, во-первых, в существенной
мере относительны (обычно отсутствуют сведения об абсолютном распределении ртути в
продуктах цинкового производства) и характеризуются определенной нестыковкой баланса
ртути; во-вторых, основаны на том, что при производстве цинка и серной кислоты выброс
металла в атмосферу отсутствует или, по крайне мере, минимален (не более 0,2% от количества
ртути, содержащейся в концентратах), что, безусловно, не соответствует действительности. В
частности, ртуть способна поступать в окружающую среду при выгрузке раскаленного огарка
из печи, при периодическом удалении пыли из систем очистки, из-за наличия в печи, газоходах
и очистных устройствах различных неплотностей, с вентиляционными выбросами, с
аэрозолями и испарениями, образующимися в процессах электролиза, при выщелачивании, а
также эмитировать непосредственно в помещениях сернокислотного производства (с паром,
отходящими газами). Определенное ее количество теряется при промывке (в канализацию) и
сушке (в атмосферу) ртутно-селенистого шлама. Например, в донных отложениях р.
Камбилеевки, принимающей стоки завода “Электроцинк” (г. Владикавказ), содержания ртути в
сотни раз превышают фоновый уровень. Интенсивные техногенные аномалии ртути в речных
отложениях прослеживаются на расстоянии в 70 км ниже завода и фиксируются в Тереке, в
который впадает Камбилеевка [332]. В атмосферном воздухе вблизи завода “Электроцинк”
концентрации ртути в сотни раз превышали ее фоновые содержания [47].
По [33], удельная эмиссия ртути в атмосферу в первичном цинково-кадмиевом
производстве составляет 42 г Hg/т продукции; эмиссионный фактор цинка для указанного
производства авторы цитируемой работы оценивают в 15720 г/т. Согласно [52], удельный
выброс цинка для цинковых заводов СНГ при эффективности пылеулавливания 95% составляет
24596 г/т продукции, при 98,5% - 7396 г/т (типичный для заводов СНГ уровень очистки
выбросов), при очистке выбросов в 99,8% - 984,7 г/т. Если исходить из степени очистки
выбросов в 98,5%, то с определенной долей условности можно допустить, что удельный
выброс ртути для таких условий составит примерно 20 г/т.
В 1996 г. ЧЦЗ выбросил в воздух 2,51 т ртути [12]. При годовом производстве цинка
порядка 115000 т удельная эмиссия составила 21,8 г/т (что близко выше приводимому
значению). Очевидно, что эти показатели достаточно адекватно отражают существовавшую
тогда в цинковой промышленности страны ситуацию. В частности, известно, что в конце 1980-
х г.г. из-за ухудшения качества поступающих цинковых концентратов заметно были увеличены
объемы их переработки с форсированным режимом эксплуатации как самих печей кипящего
слоя, так и систем пылеулавливания.
Степень очистки выбросов была невысока из-за превышения нормативного срока службы
очистных аппаратов и ускоренного их выхода из строя; мощность электрофильтров
использовалась в среднем на 50%, поскольку их работа постоянно прерывалась текущим или
капитальным ремонтом. Именно в середине 1990-х г.г. в отдельных районах г. Челябинска в
воздухе стабильно наблюдались концентрации паров ртути, в 1,5-2 превышающие ПДК [362]. В
пределах промзоны ЧЦЗ концентрации ртути в воздухе были в 5 раз выше ПДК, а в почве возле
завода уровни ртути в 100 раз превышали ее фоновые концентрации. Известно также, что
ртутно-селенистые шламы складировались на территории предприятия.
Согласно официальным сведениям [256], в 2001 г. в г. Челябинске выброс ртути от
цветной металлургии (т. е. от цинкового завода) достигал 1229 кг. При годовом производстве
цинка на ЧЦЗ в 155500 т удельный выброс ртути составил 7,9 г Hg/т полученного цинка.
Существенное снижение удельного выброса ртути в 2001 г. по сравнению с 1996 г. отчасти,
видимо, обусловлено определенными улучшениями технологических процессов на ЧЦЗ в 2000-
2001 г.г., на что уже указывалось в печати [276, 282, 283].
Таким образом, будем считать, что удельная эмиссия ртути при производстве первичного
цинка на российских заводах в 2001 г. составляла 7,9 г на 1 т металла.
Рассмотренные выше данные позволяют составить схему относительного распределения
ртути в ходе получения цинка электролитным способом и в сопутствующем сернокислотном
производстве (рис. 4.9).
При составлении данной схемы учтены также особенности поведения селена в
технологических процессах получения серной кислоты при пирометаллургической плавке
медистого колчедана. Указанный процесс, основанный на обжиге колчедана, переработке
отводимого обжигового газа и получении серной кислоты контактным способом практически
аналогичен производству кислоты на цинковых заводах [6, 266].
Заключение
В табл. 4.47 приведены расчетные данные, характеризующие эмиссию и распределение
ртути при производстве первичного цинка в России в 2001 г. Потери ртути в ходе
технологических процессов приходятся в основном на промывную и продукционную кислоту,
ртутно-селенистый шлам, пыль обжиговых печей кипящего слоя, а также на выбросы в
атмосферу. Частично ртуть в латентной форме передается вместе со свинцовым кеком цеха
выщелачивания оксидов в свинцовое производство (судя по всему, в настоящее время
свинцовый кек в основном складируется на территории предприятий).
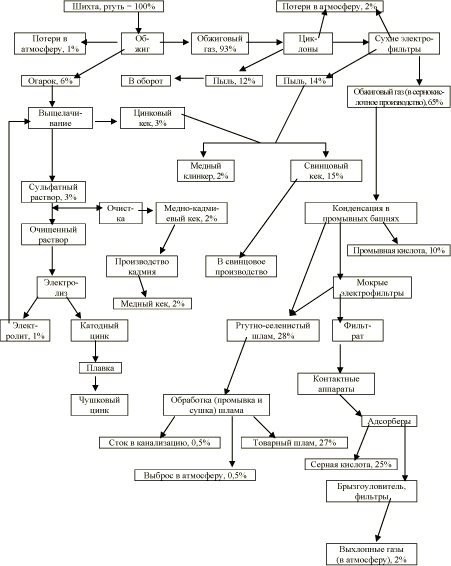
Рисунок 4.9 Распределение ртути при производстве цинка гидроэлектрометаллургическим
способом.
Таблица 4.47 Эмиссия и потери ртути при производстве первичного цинка на российских заводах в 2001 г.
Предприятие |
Масса Hg, поступив- шей с концентратами в производство, т |
Распределение ртути, т |
Выброс в атмосферу |
Шлам |
Серная кислот а |
В канали зацию |
Свинцо- вый кек* |
Медны й кек |
“Челябинский цинковый завод” |
20 |
1,229 |
5,4 |
5 |
0,1 |
3 |
0,4 |
“Электроцинк” |
11 |
0,72 |
2,97 |
2,75 |
0,055 |
1,65 |
0,22 |
“Беловский цинковый завод” |
0,3 |
0,024 |
0,081 |
0,075 |
0,001 |
0,045 |
0,006 |
Всего |
31 |
1,9 |
8,5 |
7,8 |
0,16 |
4,7 |
0,6 |
* Складирован в 2001 г.; в последние годы в Челябинске предпринимались попытки по организации
переработки свинцового кека
4.4.3 Первичное производство никеля
В данном разделе дается характеристика российских производителей первичного никеля,
а также используемого для его получения сырья, уровней содержания в нем ртути,
технологической схемы получения никеля из силикатных (окисленных) руд и оценивается
эмиссия ртути при переработке указанных руд на российских заводах. Особенности
производства никеля (и меди) из сульфидных медно-никелевых руд на предприятиях ОАО
“ГМК “Норильский никель” и соответствующая оценка эмиссии ртути будут рассмотрены в
специальном разделе. Необходимость этого обусловлена единством используемой
технологической схемы переработки сульфидных медно-никелевых руд, существующими
технологическими связями между предприятиями, входящими в ОАО “ГМК “Норильский
никель”, и его доминирующей ролью в производстве никеля и меди в России.
Российские производители никеля
В 2001 г. в России было произведено 250 тыс. т никеля (табл. 4.48). Монопольное
положение в его производстве уже многие годы занимает ОАО “ГМК “Норильский никель”
(далее – “Норильский никель”), который является одним из ведущих мировых производителей
первичного никеля.
Таблица 4.48 Производство первичного никеля российскими предприятиями в 2000 и 2001 г.г.,
тыс. т [27, 58, 59, 308, 352, 358, с дополнениями]
Предприятие |
Местонахождение |
2000 |
2001 |
ОАО Заполярный филиал “ГМК “Норильский никель” |
г. Норильск, Красноярский край |
116 |
120 |
ОАО “Комбинат «Североникель” (РАО “Норильский никель”) |
г. Мончегорск, Мурманская обл. |
101 |
103 |
АО “Печенганикель” (РАО “Норильский никель”) |
г. Заполярный, Мурманская обл. |
Производит файнштейн, который перерабатывается на “Североникель” |
ОАО “Уфалейникель” |
г. Верхний Уфалей, Челябинская обл. |
11 |
9,5 |
ОАО “Режский никелевый завод” |
г. Реж, Свердловская обл. |
5 |
4,4 |
ОАО “Южуралникель” |
г. Орск, Оренбургская обл. |
8,3 |
9,1 |
Всего в России |
241,3 |
250 |
Основная товарная (никелевая) продукция .Норильского никеля. - металлический
(электролитный) никель, никелевый карбонильный порошок, никелевая карбонильная дробь.
Другие российские производители никеля, сосредоточенные в Уральском регионе, играют
несущественную роль на внутреннем рынке этого металла. Их продукцией является первичный
никель, гранулированный никель, ферроникель, гидроокись никеля. В 2001 г. в небольших
объемах – первые сотни тонн в год – никель и никельсодержащая продукция эпизодически
выпускались еще несколькими заводами, например, ОАО “Уралэлектромедь” (~ 900 т
сернокислого никеля в 2001 г.), ЗАО “Кыштымский медеэлектролитный завод” и др.
Необходимо отметить, что часть технологической базы уральских заводов сохранилась
еще с первой половины ХХ в. Предприятия “Норильского никеля” в целом отличаются более
совершенными технологиями и оборудованием.
Сырье и содержание в нем ртути
В России основными источниками никеля являются магматические сульфидные медно-
никелевые месторождения (Таймыр, Кольский полуостров) и гипергенные силикатные кобальт-
никелевые месторождения Среднего и Южного Урала (табл. 4.49). Подавляющее количество
никеля получают при переработке сульфидных медно-никелевых руд, главными минералами
которых являются пентландит, пирротин, магнетит. Руды содержат также пирит, кубанит,
талнахит, минералы группы платины, золото, серебро, галенит, сфалерит и др. Значительная
часть никеля связана с силикатными минералами в форме изоморфных смесей или
тонкозернистых сульфидов, не извлекаемых при обогащении. С силикатами связана также
подавляющая часть кобальта. Почти вся медь в рудах находится в виде сульфидов.
Сульфидные руды подразделяются на вкрапленные, брекчевидные, сплошные и массивные и
прожилково-вкрапленные. По минеральному составу различают пирротиновые, кубанитовые,
халькопиритовые, талнахитовые и др. типы руд. По содержанию никеля выделяются богатые
руды и руды, требующие предварительного обогащения с получением коллективного медно-
никелевого концентрата или раздельно никелевого и медного концентратов.
Таблица 4.49 Основные промышленные типы российских месторождений никеля [139]
Тип или подтип месторождений |
Содержание в рудах, % |
Попутные компоненты |
Примеры месторождений |
Никель |
Медь |
Никель-медный (норильский) |
0,5-3,5 |
1,0-7,5 |
Co, S, Pt и платиноиды, Au, Ag, Se, Te |
Талнахское, Октябрьское |
Медно-никелевый (бушвельдский) |
0,35 |
0,2 |
Металлы платиновой группы |
Мочегорское |
Медисто-никелевый (печенгский) |
1,0 |
0,4 |
Co, S, металлы ильменитовой группы |
Печенгская группа месторождений |
Силикатный кобальт-никелевый кор выветривания |
0,7-1,3* |
- |
Кобальт (0,04-0,2%) |
Серовское, Покровское, Буртукальское |
* Среднее содержание никеля оценивается в 0,9% [308].
Богатые руды с содержанием никеля более 1% при отношении никеля к меди не менее
161 и с пониженным содержанием железа (менее 25%) направляются непосредственно в
плавку. Руды, содержащие 8-20% железа, 6-12 серы, 18-30% кремнезема, относятся к
самоплавким, они перерабатываются без добавки флюсов. Среднее содержание никеля в рудах
составляет 1,6% [308]. Основная часть никеля (около 80%) добывается из богатых руд со
средним содержанием металла 2,6-2,9%.
Силикатные кобальт-никелевые руды (в металлургии их называют окисленными),
связанные с корами выветривания ультраосновных массивов, обладают весьма сложным
минеральным составом при тонкодисперсном и аморфно-кристаллическом распределении
металла, обычно входящего в различные минеральные фазы. Остаточные коры выветривания
образованы гипергенным серпентином, ферросаполитом, нонтронитом, гетитом-гидрогетитом,
кобальт-никелевыми асболанами, гипергенным магнетитом и др. Для зон фильтрации
характерны никелевые и магний-никелевые серпентины, керолит, пимеит и другие
никельсодержащие минералы. В преобразованных корах выветривания развиты никелевый
бертьерит, гипергенный магнетит, маггемит, миллерит и др. Большинство силикатных руд
относится к категории бедных окисленных. Содержание никеля в рудах составляет 0,4-1,7%,
кобальта 0,01-0,2%. К кобальтовым принадлежат руды, в которых его содержание превышает
0,085-0,1%.
На долю сульфидных медно-никелевых месторождений Норильского района (Норильск-
1, Талнахское, Октябрьское и др.) приходится не менее 85% подтвержденных запасов никеля
страны [308]. В сульфидных месторождениях Мурманской области (Ждановское, Заполярное,
Котсельваара, Семилетка и др.) сосредоточено 10% российских запасов никеля. Остальные 5%
связаны с силикатными никелевыми рудами месторождений Среднего и Южного Урала, среди
которых наиболее крупными являются Буруктальское, Сахаринское и Серовское (табл. 4.50). В
табл. 4.51 приведены известные в литературе сведения о содержании ртути в рудах и
концентратах медно-никелевых месторождений. Среднее содержание ртути в сульфидных
медно-никелевых рудах, по данным В.П. Федорчука [295], составляет 1 г/т. Рудоносной
геологической формацией, с которой связаны силикатные никелевые месторождения, являются
коры выветривания ультраосновных массивов. Средние содержание ртути в ультраосновных
породах оценивается в 0,09 г/т [272]. Примем эту концентрацию за средний уровень
содержания ртути в силикатных (окисленных) никелевых рудах и условимся, что в дальнейших
расчетах он учитывает вероятность эмиссии ртути при использовании в производстве никеля не
только из руд, но и из топлива, известняка и сульфидизаторов (гипса, пирита, колчедана).
Таблица 4.50 Основные поставщики сырья на российские никелевые заводы в 2001 г.
Предприятия |
Месторождения |
ОАО Заполярный филиал “ГМК “Норильский никель” |
Норильск-1, Талнахское, Октябрьское (Таймырский полуостров) |
АО “Печенганикель” (Кольский полуостров) |
Ждановское, Заполярное, Котсельваара. Семилетка (Кольский полуостров) |
ОАО “Уфалейникель” |
Серовское (Свердловская обл.), Черемшанское и Синарское (Челябинская обл.) |
ОАО “Режский никелевый завод” |
Серовское (Свердловская область) |
ОАО “Южуралникель” |
Буруктальское и Сахаринское (Оренбургская обл.) |
Таблица 4.51 Ртуть в рудах и концентратах медно-никелевых месторождений [188]
Месторождение |
Компонент |
Среднее (пределы), г/т |
Среднее (оценка**), г/т |
Таймырский полуостров |
Талнахское |
Руда (рядовая) |
(0,01-2) |
1* (?) |
Руда (сплошная) [183]* |
1,3 (0,7-2) |
1,3 |
Пиритовый концентрат |
(0,45 – 2) |
1,22** |
Халькопирит-пентландитовый концентрат |
(0,14 – 0,4) |
0,27** |
Платиновые минералы |
(18 – 36) |
27** |
Норильское |
Руда (рядовая) |
(0,04-0,08) |
0,06** |
Руда (богатая вкрапленная) [183]* |
1,05 (0,79-1,38) |
1,05 |
Кольский полуостров |
Мончегорское |
Руда |
0,05-0,11 |
0,08** |
Восток |
Руда |
0,06-0,2 |
0,13** |
Аллареченское |
Руда [183]* |
1,17 (0,97-1,43) |
1,17 |
Ниттис-Кумужье |
Руда [183]* |
1,65 (0,68-2,78) |
1,65 |
* Доверительные интервалы надежностью 0,95.
** Оценки автора настоящего отчета.
Особенности переработки силикатных (окисленных) руд
В практике извлечения никеля из силикатных руд используются пирометаллургические
способы – плавка с сульфидированием и восстановительная плавка на первичный ферроникель
(рис. 4.10) [89, 196]. Для подготовки руды к плавке используют два способа: брикетирование
(“Режский никелевый завод” и “Уфалейникель”) и агломерацию (“Южуралникель”).
Брикетированию руды часто предшествует ее сушка при температуре 700-800°С в сушильных
барабанах. В качестве топлива при сушке используют мазут, расход которого составляет 1-
1,5% от массы исходной руды. Подсушенную руду шихтуют с сульфидизатором – пиритом или
гипсом и брикетируют на валковых прессах. Агломерацию окисленных руд осуществляют на
ленточных агломашинах. Перед агломерацией проводят необходимую подготовку руды:
грохочение, дробление и смешение с оборотным агломератом для повышения
газопроницаемости шихты. Перед агломерацией сушку измельченной руды не производят.
Сущность спекания на агломашинах заключается в химических и физических превращениях
шихты под воздействием температуры (порядка 1150-1200°С), развиваемой при горении
коксика. Высокая температура приводит к окускованию шихты. Для очистки отходящих газов
используют батарейные циклоны (с проектной эффективностью 99%). Выход годного
агломерата составляет примерно 65-68% от исходной руды.
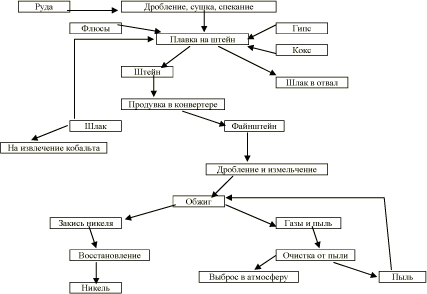
Рисунок 4.10 Упрощенная схема переработки силикатных (окисленных) никелевых руд.
Подготовленную окисленную никелевую руду плавят в смеси с серосодержащей
добавкой (колчеданом, гипсом, пиритом), флюсом (известняком) и топливом (коксом) в
шахтных печах, стены которых обычно имеют испарительную систему охлаждения, с
получением штейна. (Как правило, на каждом российском заводе имеется по 5 таких печей.) В
последние годы в рудную шихту иногда добавляют вторичное никелевое сырье. Расход
сульфидизатора составляет 7-9% от металлосодержащей части шихты, известняка – 16-24%,
кокса натурального – 21-33%. Температура в области фурм шахтной печи в фокусе достигает
1450-1500°С, а на колошнике – 400-500°С. Выход пыли, уносимой с газами, составляет 6-18%
от массы проплавленной шихты и определяется скоростью газов, гранулометрического состава
шихты и других факторов. Для очистки отходящих газов используются скрубберы и
мультициклоны, проектный КПД которых составляет 98-99%.
Шлак из шахтных печей выпускается непрерывно через выносные горны и отстойники, в
которых улавливаются корольки штейна. Выход шлака составляет 110-120% от массы
проплавленного агломерата или брикетов. Никелевый штейн выпускается из горна примерно
каждые 2-3 часа. Состав штейна колеблется в следующих пределах (в %): 12-20 никеля, 56-60
железа, 17-23 серы, до 4 - шлаковых включений, 0,4-0,6 меди и кобальта. Извлечение никеля в
штейн составляет 67-85%, кобальта – 42-61% (максимальные значения наблюдаются при
подготовке руды брикетированием). Затем осуществляется передел никелевых штейнов на
металл, включающий их конвертирование (при температуре около 1300°С) и получение
никелевого файнштейна, обжиг никелевого файнштейна, который осуществляют в две стадии
(сперва в печах кипящего слоя при температуре 1000-1150°С, затем в трубчатой печи при 750-
800°С). Для восстановления полученной в результате двойного обжига закиси никеля в металл
применяют восстановительную плавку в электропечах. В качестве восстановителя используется
нефтяной или пековый кокс, а также - в небольшом количестве - известняк. В этом случае
получают чушковый или гранулированный никель или никелевые катоды, если требуется
дальнейшее рафинирование металла. Иногда для извлечения никеля и кобальта из руд,
прошедших восстановительный обжиг при температурах 580-780°С, применяют щелочной
гидрометаллургический процесс [139]. Кеки карбонатных растворов затем кальцинируются в
трубчатых печах с получением закиси никеля.
Эмиссия ртути при переработке силикатных (окисленных) руд
В ходе получения металлического никеля исходная руда и другие используемые
материалы подвергаются неоднократной высокотемпературной обработке, что предопределяет
практически полный переход ртути из них в парогазовое состояние. Очевидно, что
значительная часть ртути, присутствующей в сырье, возгоняется уже либо при сушке руды,
либо на стадии агломерации, а после шахтной плавки вся ртуть улетучивается с отходящими
газами. Можно предположить, ориентируясь на особенности распределения ртути при обжиге
цинкового концентрата, что примерно 8% ртути (от поступающей с сырьем в технологические
процессы) концентрируется в пыли, улавливаемой циклонами агломерационного отделения,
скрубберами и мультициклонами плавильного цеха (пыль возвращается в производственный
процесс), порядка 2% ртути (от поступившей в технологический процесс) - остается в шлаке, а
90% ее в конечном счете поступает в атмосферу с отходящими газами никелевого производства
(табл. 4.52).
Таблица 4.52 Производство никеля и эмиссия ртути в окружающую среду при переработке
силикатных (окисленных) руд в России в 2001 г.
Предприятие |
Произв од-ство никеля, тыс. т |
Ни- кель в руде, % * |
Извлечение никеля в товарный продукт, %* |
Всего никеля в руде, тыс. т |
Перера - ботано руды, тыс. т |
Количес тво ртути в руде, кг** |
Эмиссия Hg в ат- мосферу , кг*** |
Удель- ная эми- ссия, г Hg/т Ni |
“Режникель” |
4,4 |
1,0 |
89,5 |
4,92 |
546 |
49 |
44 |
10 |
“Уфалейникель” |
9,5 |
0,90 |
82,3 |
11,54 |
1154 |
103 |
93 |
9,8 |
“Южуралникель” |
9,1 |
1,03 |
75,5 |
12,1 |
1174 |
105 |
95 |
10,4 |
Прочие |
4,0 |
- |
- |
- |
- |
- |
40**** |
10,1 |
Всего |
27 |
- |
- |
- |
- |
- |
272 |
- |
* [139].
** При ее среднем содержании в руде 0,09 г/т.
*** Из расчета поступления с отходящими газами 90% ртути, присутствующей в перерабатываемом
сырье.
**** При средней удельной эмиссии 10,1 г Hg/т полученного никеля.
4.4.4 Производство меди
С точки зрения поступления ртути в окружающую среду главное значение имеет
производство черновой меди из рудного концентрата; ее эмиссия при переделе отходов и
вторичного сырья и при рафинировании черновой меди существенно меньше. Переработка
медных руд и концентратов обычно сопровождается получением серы (серной кислоты) из
обжиговых (отходящих) газов, в ходе которого ртуть интенсивно концентрируется в шламах
сернокислотного производства.
Ниже дается характеристика российских производителей первичной меди, используемого
для ее получения сырья, технологии получения меди и эмиссии ртути на заводах,
расположенных в Уральском регионе. Оценка эмиссии ртути при производстве меди из медно-
никелевых руд в ОАО “ГМК “Норильский никель” приводится в специальном разделе.
Российские производители меди
Российские предприятия, производящие медь, расположены на Таймыре (Красноярский
край) и в Мурманской области (ОАО “ГМК “Норильский никель”), а также в Уральском
регионе, где большая часть из них входит в состав холдинга .Уральская горно-
металлургическая компания.. Исключение составляют ЗАО .Кыштымский медеэлектролитный
завод. и ЗАО .Карабашмедь., образующие 3-ю группу российских производителей меди (табл.
4.53).
Таблица 4.53 Производство меди в России в 2000-2001 г.г., тыс. т * [159, 169, 311, 346, 347, 350,
358, 360, 371, 377]
Производитель |
Местонахождение |
Медь |
2000 |
2001 |
2002 |
ОАО “ГМК “Норильский никель” |
Таймырский п-ов (Красноярский край), Кольский п-ов (Мурманская обл.) |
Рафинир ованная |
413 |
474 |
454 |
ЗАО “Карабашмедь” |
г. Карабаш, Челябинская обл. |
Черновая |
36,4 |
41,7 |
42,4 |
ОАО “Кировградский медеплавильный комбинат” |
г. Кировград, Свердловская обл. |
Черновая |
50 |
46,6 |
46,9 |
АООТ “Медногорский медно-серный комбинат” |
г. Медногорск, Оренбургская обл. |
Черновая |
16,3 |
23,9 |
31,2 |
ОАО “Святогор” |
г. Красноуральск, Свердловская обл. |
Черновая |
56,5 |
55,3 |
62,2 |
ОАО “Среднеуральский медеплавильный завод” |
г. Ревда, Свердловская обл. |
Черновая |
103,1 |
105,6 |
106,1 |
ЗАО “Кыштымский медеэлектролитный завод” |
г. Кыштым, Челябинская обл. |
Рафинир ованная |
77,7 т |
82,1 |
76,3 т |
ОАО “Уралэлектромедь” |
г. Верхняя Пышма, |
Рафиниро ванная |
312,1 |
327,8 |
330,9 |
Свердловская обл. |
Черновая |
- |
46,3 |
58,5 |
Общее производство рафинированной меди в России |
802,8 |
883,9 |
861,2 |
* Включая вторичную медь; по данным Минэкономразвития РФ [368], в 2001 г. из отечественного
сырья было произведено 96,7% меди, в том числе 23,1% из вторичного сырья (медного лома, отвальных
и анодных шлаков медеплавильного производства).
Сырье и уровни содержания в нем ртути
В настоящее время в России основное количество меди получают из руд медно-
никелевых месторождений (содержание меди в рудах 0,2-3,5%), медно-колчеданных
месторождений (меди 0,5-3%) и медно-цинково-колчеданных (меди 1-6%) [138].
Второстепенное значение имеют железо-медные ванадий-титансодержащие
месторождения (меди 0,5%). Характеристика сульфидных медно-никелевых руд, добываемых
на Таймыре и Кольском полуострове, была дана выше. Из них в России получают до 70%
первичной меди. Остальная часть приходится на медно-колчеданные и медно-цинково-
колчеданные месторождения, расположенные в Уральском регионе.
По степени окисления руды медных месторождений разделяются на три группы:
сульфидные (из которых производится практически вся российская первичная медь),
окисленные и смешанные. Главные минералы меди в уральских сульфидных рудах .
халькопирит, борнит, халькозин. Сульфидные руды обычно содержат 1-6% меди, 8-40%
железа, 9-46% серы, 1-6% цинка, 5-55% кремнезема, 2-12% глинозема, 0,3-4% оксида кальция
[49].
Медные руды, как правило, являются комплексными и содержат широкий круг
химических элементов, которые, по возможности, извлекаются при их переработке.
В 2001 г. на Урале более 4,2 млн. т медной руды было добыто Гайским ГОКом, 960 тыс. т
(среднее содержание меди 2,71%) – ОАО “Сафьяновская медь” [109]. Основными
производителями медного концентрата являлись Гайский ГОК (440 тыс. т, среднее содержание
меди ~ 15%), ОАО “Учалинский ГОК”, ЗАО “Карабашмедь” (> 134 тыс. т), ЗАО “Кыштымский
медеэлектролитный завод” (более 124 тыс. т), ОАО “Святогор” (~ 180 тыс. т).
Медный концентрат производили также ОАО .Башкирский медно-серный комбинат. (21
тыс. т; по некоторым сведениям, комбинат в 2001 г. произвел 110 тыс. т концентрата [372]),
Бурибаевское рудоуправление (26 тыс. т), Туринский рудник и ОАО “Среднеуральский
медеплавильный комбинат” (по 9-12 тыс. т).
Структура сырьевой базы медных заводов Урала достаточна сложна; на одном и том же
заводе одновременно перерабатываются медные концентраты (отечественные и зарубежные),
различный медный лом и отходы (отвальные и анодные шлаки). Анализ доступных
информационных источников позволил следующим образом систематизировать структуру
перерабатываемого уральскими заводами сырья медьсодержащего сырья (табл. 4.54). В табл.
4.55 дается оценка структуры производства черновой меди уральскими медеплавильными
заводами в 2001 г.
Таблица 4.54 Характеристика медьсодержащего сырья, переработанного в 2001 г. на уральских
заводах
Предприятие |
Основная продукция и источники сырья |
ЗАО “Карабашмедь” |
Черновая медь; переработка концентрата (уральские месторождения)
собственного производства (134,4 тыс. т), и брикетированного
концентрата (уральские месторождения) с ЗАО “Кыштымский
медеэлектролитный завод” (125,1 тыс. т) |
ЗАО .Кыштымский
медеэлектролитный завод. |
Рафинированная медь; переработка черновой меди, поставляемой ЗАО
.Карабашмедь., а также (по толлингу) медный лом |
АООТ “Медногорский
медно-серный комбинат” |
Черновая медь; переработка медного концентрата из концерна
“Эрденет”, Монголия (около 40 тыс. т), а также концентрат с Гайского
ГОКа |
ОАО “Святогор” |
Черновая медь; переработка концентрата собственного
производства (179 тыс. т), а также концентратов уральских
обогатительных фабрик |
ОАО “Среднеуральский
медеплавильный завод” |
Черновая медь; переработка концентрата уральских обогатительных
фабрик (в том числе, из руды Сафьяновского месторождения); в 2001 г.
приступил к переработке отвальных шлаков (порядка 1 млн. т в год) и,
судя по всему, медного лома |
ОАО “Кировоградский
медеплавильный комбинат” |
Черновая медь; ~ 50% из медного концентрата (главным образом из
руды Сафьяновского месторождения), оставшаяся часть – из медного
лома |
ОАО “Уралэлектромедь” |
Рафинированная медь; переработка черновой меди уральских заводов
(значительная часть которой производится из концентратов
Красноуральской и Среднеуральской обогатительных фабрик,
перерабатывающих руду Сафьяновского месторождения) и
собственной черновой меди из вторичного сырья (собственного
анодного шлака и привозного медного и бронзолатунного лома) |
Таблица 4.55 Структура производства черновой меди на уральских заводах, тыс. т
Предприятие |
Всего |
Сырье, из которого получена медь |
Отечественные концентраты |
Концентраты “Эрденет” |
Отвальные шлаки |
Медный лом |
ЗАО “Карабашмедь” |
41,7 |
41,7 |
- |
- |
- |
АООТ “Медногорский медно-серный комбинат” |
23,9 |
13,9 |
10 |
- |
- |
ОАО “Святогор” |
55,3 |
55,3 |
- |
- |
- |
ОАО “Среднеуральский медеплавильный завод” |
105,6 |
90,6 |
- |
5 |
10 |
ОАО “Кировоградский медеплавильный комбинат” |
46,6 |
26,6 |
- |
- |
20 |
ОАО “Уралэлектромедь” |
46,3 |
- |
- |
- |
46,6 |
Итого |
319,4 |
173,1 |
10 |
5 |
76,6 |
В отечественной литературе имеется немного статистически обоснованных данных о
содержании ртути в уральских медных рудах и получаемых из них медных концентратах. Так,
для руд медно-колчеданных месторождений интервалы установленных концентраций ртути
составляют от 0.n до n х 100 г/т, среднее содержание некоторыми авторами оценивается на
уровне первых десятков г/т [33]. В рудах медно-колчеданного месторождения им. III
Интернационала содержания ртути варьируются от менее 0,5 до 20 г/т; в рудах Сибайского
месторождения - составляют 10-900 г/т, Гайского – 1-90 г/т, Учалинского, Дегтярского и ряда
других – 1-9 г/т [188].
По данным [170], во всех промышленных сортах и минералогических типах руд,
перерабатываемых Учалинским ГОКом, концентрации ртути варьируются в широких пределах:
в рудах Узельгинского месторождения – от сотых долей г/т до 800 г/т, Учалинского – от 2 до
560, Новоучалинского – от 1 до 88 г/т. Средние содержания ртути в рудах Узельгинского,
Учалинского и Новоучалинского месторождений обычно составляют первые десятки г/т. В
целом, как утверждают авторы цитируемой работы, все сорта и типы руд Узельгинского,
Учалинского и Новоучалинского месторождений являются высокортутистыми, причем по
этому показателю они уступают лишь рудам Сафьяновского месторождения (Средний Урал),
высокие концентрации ртути в которых подтверждены .Государственным балансом запасов
полезных ископаемых Российской Федерации. [167].
В сущности, достаточно противоречивы и известные сведения о содержании ртути в
медных концентратах, получаемых на различных обогатительных фабриках (табл. 4.56). Тем не
менее считается, что ее уровни в медном концентрате обычно в 2-2,5 раза выше (относительно,
например, ее содержания в медно-колчеданных рудах), хотя в ряде случаев такого повышения
содержания и не наблюдается [33]. По данным [33], в медный концентрат при обогащении,
например, руд медно-колчеданных месторождений переходит 19,1-24,9% от всей ртути,
присутствующей в рудах.
Таблица 4.56 Содержания ртути в медных концентратах [33, 188]
Промышленный тип месторождений |
Ртуть в медном концентрате, г/т |
Колчеданно-полиметаллический |
0,22 - 65 |
Стратиформный свинцово-цинковый |
2 - 290 |
Медно-колчеданный |
0,3 - 150 |
Медистые песчаники |
4 |
Ванадиево-железо-медный |
70 |
Медно-молибденовый |
0,02 |
По другим сведениям [142], в медный концентрат при переработке руд на Учалинском
ГОКе переходит 10-14% ртути от ее общего количества в рудах, причем ее содержания в
концентрате находятся в пределах 28-41 г/т. Выход медного концентрата при обогащении руд
на Гайском ГОКе в среднем составляет 9%, цинкового – 1,47%, пиритного – 45% [138].
В 2001 г. Гайским ГОКом было переработано более 4222 тыс. т медной руды, из которого
произведено 440 тыс. т медного концентрата, т. е. выход медного концентрата составил
примерно 10,5%. Отсюда следует, что при обогащении медных руд не происходит, по крайне
мере, обеднения медного концентрата ртутью по сравнению с ее содержаниями в исходной
руде. Следует также отметить, что уральские медные концентраты, как правило, являются
высокоцинковистыми, что косвенно указывает на повышенные в них содержания ртути.
В то же время есть сведения, показывающие, что ртуть, с одной стороны, практически не
концентрируется в медном и даже в цинковом концентратах, получаемых при обогащении руд
многих колчеданных и медно-колчеданных месторождений (табл. 4.57). Особенно наглядно это
демонстрируется данными по Сибайскому месторождению, при обогащении руд которого
уровни содержания ртути в медном и цинковом концентратах практически на один-два порядок
ниже, нежели в обогащаемой руде. Таким образом, получается, что основные промышленные
минералы цинка и меди, одновременно являющиеся главными носителями ртути, в рудные
концентраты не переходит. С другой стороны, например, в цинковом концентрате Учалинского
месторождения уровни ртути превышают ее концентрации в сфалерите, а медный концентрат
месторождения имени XIX партсъезда содержит в несколько раз больше ртути, нежели
цинковый (см. табл. 4.57). Противоречивость рассмотренных данных о содержании ртути в
рудах и концентратах в существенной мере связана с тем, что они, как правило, были получены
при аналитическом исследовании одной-двух (реже трех-четырех) проб руды или концентрата
и, таким образом, вряд ли могут считаться репрезентативными.
Таблица 4.57 Ртуть в рудах, концентратах и минералах месторождений Урала, г/т [188]
Месторождение |
Руда |
Концентраты |
Минералы |
Медны й |
Цинковы й |
Пиритны й |
Пи- рит |
Сфале рит |
Халькоп ирит |
Сибайское |
10-900 |
0,3-1,8 |
1,8-7,5 |
0,15-1,5 |
2,8 |
160 |
22 |
Гайское |
1-90 |
1,7-2,7 |
10-25 |
- |
- |
85-220 |
- |
Учалинское |
1-9 |
5-10 |
10-75 |
0,75-3 |
0,72-2,5 |
10-55 |
0,5 |
Им. III Интернационала |
1-9 |
2,5 |
4,5 |
0,3-3 |
6 |
- |
- |
Ломовское, Левихинское |
- |
1 |
1-2 |
0,1 |
- |
- |
- |
Им. XIX партсъезда |
- |
50-150 |
25-75 |
1,1 |
- |
- |
- |
С этой точки зрения интерес представляют результаты исследований распределения
ртути в рудах широкой группы медных месторождений, полученные В.З. Фурсовым [300].
Указанные исследования основывались, как правило, на относительно представительных
выборках и осуществлялись с использованием достаточно надежного аналитического метода
(табл. 4.58). С высокой долей вероятности можно считать, что данные, приводимые в табл. 4.58,
достаточно адекватно отражают средние содержания ртути в перерабатываемых медных рудах
Южного Урала, варьируясь в среднем в пределах 9,8-13 г/т (общее среднее 11,5 г/т). По данным
документа “Государственный баланс запасов полезных ископаемых Российской Федерации.
Ртуть” (1998 г.), в медных рудах, ежегодно добываемых на Сафьяновском месторождении в
Свердловской области, содержится до 10-12 т ртути [167], что (например, при добыче руды в
960 тыс. т в 2001 г.) дает среднее содержание ртути в рудах в пределах 10,4-12,5 г/т, что
соответствует выше приведенным значениям.
Таким образом, можно рассчитать среднее содержания ртути в медном концентрате,
который перерабатывается уральскими медеплавильными заводами. Допустим, что на
обогатительные фабрики поступают руды со средним содержанием ртути 11,5 г/т, выход
медного концентрата составляет 10%, в него переходит 12% ртути, содержащейся в рудах.
Простые расчеты показываю, что при таких допущениях среднее содержание ртути в медном
концентрате составит 13,8 г/т. Это значение и будет использоваться в дальнейших расчетах.
Таблица 4.58 Средние содержания ртути в рудах медных месторождений (доверительные
интервалы надежностью 0.95) [300]
Тип, месторождение, регион |
Характеристика руд |
Кол-во проб |
Hg, среднее (пределы), г/т |
Медно-колчеданный |
Учалы, Южный Урал |
Сплошные |
7 |
9,8 (3,2-19,75) |
Им. XIX партсъезда, Южный Урал |
Сплошные |
9 |
12 (4-27) |
Сибай, Южный Урал |
Сплошные |
8 |
11,2 (3,7-23,10) |
Гайское, Южный Урал |
Сплошные |
14 |
13 (5-27) |
Урупское, Северный Кавказ |
Сплошные |
13 |
8,95 (6,34-13,76) |
Им. 50 лет октября, Зап. Казахстан |
Вкрапленные |
7 |
1,35 (0,92-2,04) |
Кусмурун, Западный Казахстан |
Сплошные |
11 |
9,2 (4,3-16,70) |
Медистых песчаников |
Джезгазган, Центральный Казахстан |
Массивные (халькопиритовые) |
15 |
3,15 (2,8-3,68) |
Там же |
Вкрапленные (борнитовые) |
11 |
1,45 (1,23-1,87) |
Там же |
Вкрапленные (халькозиновые) |
17 |
1,57 (1,08-2,20) |
Удокан, Забайкалье |
Вкрапленные |
11 |
1,13 (0,77-1,68) |
Медно-порфировый |
Коунрад, Центральный Казахстан |
Вкрапленные (первичные) |
8 |
0,87 (0,76-1,02) |
Процессы и технологии
При обогащении медных руд основным продуктом являются медные концентраты,
содержащие чаще всего, за редким исключением, 10-30% меди. Например, в медном
концентрате Гайского комбината среднее содержание меди составляет 15,8% [138]. При
обогащении сульфидных руд главным образом используется флотация.
Основное количество меди производится пирометаллургическим способом, который
включает следующие технологические операции: сушка медных концентратов, обжиг
концентратов, агломерация концентратов, плавка подготовленной шихты в плавильных печах,
конвертирование медных штейнов и огневое рафинирование черновой меди [49, 89, 196, 294].
В конкретных случаях некоторые технологические операции могут пропускаться или
заменяться другими. Например, окислительный обжиг применяется, как правило, при
переработке бедных по меди высокосернистых концентратов или руд. На одном и том же
заводе могут одновременно применяться разные варианты пирометаллургического передела
рудного сырья (табл. 4.59, рис. 4.11).
Целью окислительного обжига в пирометаллургии меди является частичное удаление
серы, перевод части железа из сульфидов в оксиды, получение 25-30%-ного штейна и газов,
пригодных для производства серной кислоты.
Окислительный обжиг медных концентратов (или приготовленной шихты) чаще всего
проводят в обжиговой печи. В основном применяют обжиг в многоподовых печах или печах
кипящего слоя. При обжиге (580-850°С) в многоподовых печах частично удаляется сера,
хорошо перемешивается концентрат с флюсами и оборотами, вводимыми, как правило, в шихту
обжига. При обжиге образуется пыль, унос которой с отходящими газами составляет 10-12%
(иногда больше) от веса шихты.
При высокой запыленности газов система пылеулавливания обычно состоит из циклонов
(грубая очистка) и электрофильтров (тонкая очистка). Уловленную грубую пыль возвращают в
шихту обжига, тонкую пыль чаще всего направляют на специальную переработку с целью
извлечения цинка, свинца, кадмия и некоторых редких металлов. Содержание SO2 в обжиговых
газах перед электрофильтром колеблется в пределах 12-13%.
Большую часть меди выплавляют в отражательных печах, в которых перерабатывают три
вида шихты: сырую, подсушенную или обожженную. Кроме твердой шихты в отражательной
печь заливают конвертерный шлак, который принимает участие в окончательном
формировании штейна и отвального шлака (на 1 т черновой меди образуется 6,5-9,5 т шлака с
типичным содержанием меди 0,3-0,35%).
Таблица 4.59 Особенности технологических процессов на уральских заводах по производству меди
Производитель |
Особенности технологического процесса |
ЗАО
“Карабашмедь” |
Для переработки рудного сырья применяют плавку в шахтных печах (три печи) с
последующим конвертированием (три конвертера) полученного штейна. В мае
2001 г. была пущена первая очередь комплекса по утилизации технологических
газов медеплавильного цеха – кислородная станция, позволяющая улучшить
экологические показатели шахтной плавки. |
ОАО
“Кировградский
медеплавильный
комбинат” |
Для переработки рудного (и/или вторичного) сырья используют шахтную плавку
или плавку шихты на штейн в отражательных печах с последующим
конвертированием; имеются рукавные фильтры для очистки газов передела
вторичной меди; конвертерные газы очищаются от пыли на специальной
установке с выделением сернистого газа и передачи его на химический завод. |
АООТ
“Медногорский
медно-серный
комбинат” |
Для переработки рудного сырья применяют плавку в шахтных печах с
последующим конвертированием полученного штейна. Технологическая схема
предусматривает получение элементарной серы из газов шахтных печей. Для
очистки газов сократительной плавки и конвертеров используются
электрофильтры. |
ОАО “Святогор” |
Один из вариантов предусматривает обжиг сырья в многоподовых печах, затем
плавку огарка на штейн в отражательной печи с последующим
конвертированием полученного штейна. По второму варианту плавка сырья на
штейн осуществляется непосредственно в отражательных печах с последующим
конвертированием штейна (4 конвертера типа «Пирс-Смит», работают 3, один – в
резерве или ремонте). Отходящие газы направляются на очистку от пыли и затем
в сернокислотное производство. Имеются электрофильтры для очистки газов
обжиговых печей; для удаления из конвертерных газов тонкой пыли
используется установка гидроочистки; для улавливания пыли из газов фьюминг-
печей применяются рукавные фильтры. |
ОАО
“Среднеуральский
медеплавильный
завод” |
Медные концентраты в основном перерабатываются по схеме обжига (в печах
кипящего слоя), затем осуществляют плавку огарка на штейн в отражательных
печах и конвертирование штейна; плавка сырья на штейн иногда осуществляется
непосредственно в отражательных печах с последующим конвертированием
штейна; эксплуатируется также печь Ванюкова (плавка меди в жидкой ванне). На
серосодержащих газах медеплавильного производства и конвертирования
работает сернокислотный цех; на местной серной кислоте функционирует цех
двойного суперфосфата. Грубая очистка обжиговых газов от пыли
осуществляется в циклонах, тонкая – в сухих электрофильтрах; для очистки
конвертерных газов применяют циклоны и гидроочистку; для газов фьюминг-
печей – очистку в рукавных фильтрах. |
ОАО
“Уралэлектромедь” |
Завод ориентирован на получение рафинированной меди. Для производства
черновой меди из вторичного сырья в конце 2000 г. пущен в строй специальный
металлургический комплекс (шахтная печь, электроотстойник, конвертер,
система газоочистных сооружений). В 1999-2000 г.г. введены в строй две
очереди системы очистки отходящих газов медерафинировочных печей. |
Основной целью плавки является расплавление шихты, сульфидирование меди с
переводом ее в штейн и одновременное ошлакование большей части железа. Это достигается
переплавом обожженного концентрата с флюсом в слабоокислительной атмосфере при
температурах 1200-1550°С. На отражательных печах применяют два вида горелок:
турбулентные газо-мазутные внешнего смешивания и газовые внутреннего смешивания. Расход
условного топлива - 120-180 кг/т шихты. Медные штейны в зависимости от состава
перерабатываемого сырья и метода плавки содержат (в %): медь 15-60, цинк 1-6, никель до 0,5,
свинец до 1.
Шахтная плавка медных руд - наиболее старый способ плавки на штейн. В шахтных
печах плавят кусковой материал крупностью 20-100 мм, поэтому в случае переработки мелкой
шихты (руды или концентратов) ее подвергают предварительному окускованию методами
агломерации или брикетирования.
Медные штейны повсеместно перерабатывают методом конвертирования (продувки
сжатым воздухом) в горизонтальных конвертерах. Основная цель процесса конвертирования .
окисление сульфидов с выделением серы в виде сернистого ангидрида, ошлакование железа и
получение черновой меди. Штейн заливают в конвертер в расплавленном состоянии при
температуре 1100-1200°С. После начала продувки температура быстро повышается до 1250-1300°С. Отвод газов из конвертеров осуществляется через газоходы.
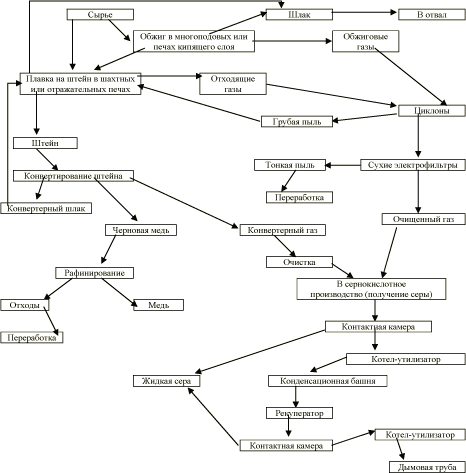
Рисунок 4.11 Обобщенная схема пирометаллургического передела медного сырья.
Готовую черновую медь сливают из конвертера и в зависимости от места последующего
рафинирования либо заливают в жидком виде в миксер (копильник) и далее по мере
надобности в рафинировочную печь, либо разливают в слитки массой от 2 т и отправляют на
специальные рафинировочные заводы. Конвертерные шлаки с содержанием меди 1,5-2%
возвращают (с целью их обеднения) в плавку на штейн. Извлечение меди из штейна в черновую
медь (с учетом переработки конвертерных шлаков) обычно составляет 98-99% (извлечение
меди из концентрата в черновую медь ~ 93%).
Рафинирование черновой меди проводят в две стадии. Сначала очистку меди ведут
методом огневого (окислительного) рафинирования, а затем электролитическим способом.
Цель огневого рафинирования – удаление ряда примесей и получение плотных анодов для
процесса электролитического рафинирования меди. Для огневого рафинирования меди
используют печи двух типов: стационарные отражательные и наклоняющиеся. Анодная медь
содержит 99,4-99,6% меди; остальное приходится на долю оставшихся после огневого
рафинирования примесей, включая золото, серебро, селен и теллур. Медь после огневого
рафинирования разливают в слитки (аноды) пластинчатой формы с ушками. Аноды затем
направляют в электролизный цех, где анодную медь подвергают электролитическому
рафинированию с целью получения металла высокой чистоты, извлечения золота, серебра,
селена и теллура, иногда никеля и кобальта. Процесс ведут в электролизных ваннах, в которых
аноды электрохимически растворяют в сернокислом электролите, на катоде осаждают чистую
медь, а примеси выпадают в осадок.
Источники и характеристика пылегазовыделения
Основными источниками пылегазовыбросов на заводах по выплавке меди из первичного
сырья являются обжиговые печи (многоподовые и кипящего слоя), шахтные и отражательные
печи, конвертеры, а также сушилки концентратов. Наибольшее количество пыли и тяжелых
металлов выносится с газами отражательных печей и конвертеров (табл. 4.60).
Таблица 4.60 Основные параметры выбросов на уральских медеплавильных заводах [95]
Предприятие |
Источник выбросов |
Объем отходящих газов, м³/ч |
Запыленность, г/м³ |
“Среднеуральский |
Отражательная печь |
300000 |
0,6-0,8 |
медеплавильный завод” |
Конвертеры |
50000 |
0,2 |
“Святогор” |
Отражательная печь |
210000 |
0,5-1,3 |
|
Конвертеры |
130000 |
0,3 |
“Кировоградский |
Отражательная печь |
230000 |
1,38 |
медеплавильный |
Конвертеры |
503000 |
0,033 |
комбинат” |
Шахтные печи |
168000 |
0,08 |
По данным [95], на уральских медеплавильных заводах с выбросами отражательных
печей поступало в атмосферу 90-95% пыли и 57% свинца, с выбросами конвертеров – 5-8%
пыли и 37% свинца. Среднее количество образующихся технологических газов оценивается в
50 тыс. м³ на тонну цветных металлов [208]. Отходящие газы большинства операций получения
меди имеют высокую температуру: от обжиговых печей – 500-800°С, от отражательных печей .
300-400°С, от шахтных печей – 350-550°С, от конвертеров – 900-1000°С [203].
Для грубой очистки выделяющихся (обжиговых и конвертерных) газов чаще всего
используют циклоны; основными аппаратами тонкой очистки являются сухие электрофильтры.
Проектная эффективность улавливания пыли сухими электрофильтрами составляет 98,9-99,9%.
Однако на данном этапе оценить хотя бы в среднем эффективность очистки отходящих газов на
медеплавильных заводах России не представляется возможным, поскольку на многих из них
используются устаревшие технологии (износ основных фондов на некоторых заводах достигает
100%), а отдельные технологические процессы не обеспечены очистным оборудованием.
Например, до недавнего времени отходящие газы отражательных печей на
Среднеуральском, Красноуральском (ОАО “Святогор”) и Кировоградском медеплавильных
заводах поступали в атмосферу без очистки [95], что приводило к существенному выбросу
сернистого ангидрида, преобладающего в выбросах заводов, и пыли. Большой пылевыброс
обусловливает существенную эмиссию тяжелых металлов, особенно свинца.
Так, все предприятия, входящие в Уральскую горно-металлургическую компанию, в
последние годы (2000-2002 г.г.) ежегодно выбрасывали в атмосферу более 575 т свинца, в том
числе Среднеуральский медеплавильный завод -170 т (общий выброс вредных веществ – > 79
тыс. т), Кировоградский медеплавильный комбинат - 114 т (общий выброс > 110 тыс. т),
“Святогор” - 291 т (общий выброс > 87 тыс. т); ЗАО “Карабашмедь” в 2002 г. выбросило в
атмосферу 79 т свинца (общий выброс вредных веществ > 97 тыс. т) [351, 355]:
В табл. 4.61 приведены обобщенные данные по удельным выбросам пыли в атмосферу
некоторыми заводами, которые свидетельствуют о существенной их вариации. По оценке [52],
среднее значение удельных выбросов пыли при первичном производстве меди составляет 46,4
кг/т черновой меди.
Таблица 4.61 Удельные выбросы пыли, кг/т продукции* [52]
Предприятие |
Вид продукции |
Пыль, кг/т |
Кировоградский медеплавильный комбинат |
Черновая медь |
12,4 |
“Уралэлектромедь” |
Медь электролитическая |
0,41 |
Среднеуральский медеплавильный завод |
Черновая медь |
320,1 ** |
“Печенганикель” |
Черновая медь |
42,0 |
* В 2002 г на ЗАО .Карабашмедь. удельный выброс вредных веществ составил свыше 2 т на 1 т
черновой меди.
** В 2002 г. на ОАО .Среднеуральский МПЗ. удельный выброс вредных веществ в атмосферу
составил около 600 кг на 1 т черновой меди [351];
Эмиссия и особенности поведения ртути
Поведение ртути в медеплавильном производстве изучено слабо. Аналитическое
исследование содержаний ртути в исходном сырье, а также в продуктах переделов в
лабораторных службах медных комбинатов, как правило, не производится.
При обжиге медных концентратов ртуть на 80-90% возгоняется [33]. При очистке
отходящих сернистых газов она частично улавливается в пыли (содержание ртути в пыли
достигает 15-560 г/т), частично поступает с газами в сернокислотный цех (СКЦ.) Здесь в
промывном отделении ртуть концентрируется в шламах, которые не используются и, судя по
всему, просто складируются в отвалах. Грубая пыль поступает в оборот (добавляется в шихту).
В случае переработки тонкой пыли ртуть накапливается в свинцовом кеке (до 1100 г/т),
который поступает на дальнейшую переработку на свинцовые заводы, и отвальном арсенатном
кеке (он обычно идет на захоронение) [33]. Есть все основания считать, что поведение ртути в
ходе получения меди на медеплавильных заводах во многом аналогично ее распределению ее
при производстве цинка. Следует лишь отметить, что в медеплавильном производстве, с одной
стороны, несколько большее количество ртути концентрируется в пыли, улавливаемой
очистными установками (в силу более высокого пылевыноса из печей и конвертеров). В то же
время, из-за менее совершенной технологии и устаревшего оборудования на медеплавильных
заводах будет несколько выше относительный выброс ртути в атмосферу.
На основании выше рассмотренных сведений (с учетом особенностей технологических
процессов, функционирования пылегазоочистного оборудования и поведения ртути в
производстве цинка) можно, с определенной долей условности (для некоторых материальных
потоков), следующим образом оценить распределение ртути при переработке медьсодержащего
сырья (рис. 4.12). Для оценки эмиссии и определения удельных потерь ртути при производстве
черновой меди из отечественных (уральских) медных концентратов рассмотрим условное
предприятие, мощность которого составляет 100000 т черновой меди в год.
Выше было показано, что содержание ртути в поступающем на металлургический
передел медном концентрате составляет 13,8 г/т, меди – 15%, извлечение меди из концентрата
93%.
Таким образом, масса перерабатываемого на данном предприятии концентрата составит
716667 т. Общая масса ртути в концентрате, поступающем в передел, - 9,89 т, т. е. на каждую
полученную тонну черновой меди в производство вовлекается 98,9 г ртути.
При производстве 100000 т черновой меди в атмосферу будет выброшено порядка 840 кг
ртути (удельный выброс – 8,4 г Hg/т меди), в шламах сернокислотного производства
аккумулируется 2670 кг ртути (26,7 г Hg/т меди), в отвальных шлаках – ~ 198 кг ртути (~ 2 г
Hg/т меди), уйдет в канализацию – 148,4 кг ртути (1,48 г Hg/т меди). Будем также считать, что
все эти показатели учитывают эмиссию ртути из других материалов, использующихся при
производстве черновой меди (топливо, флюсы и т. д.).
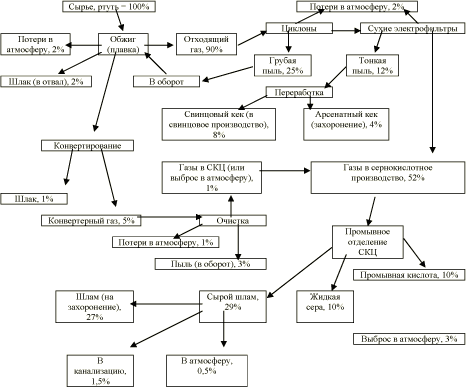
Рисунок 4.12 Распределение ртути при переработке медьсодержащего сырья.
Среднее содержание ртути в рудах медно-порфировых месторождений установлено в
0,87 г/т (см. табл. 4.58). Примем, что такая же концентрация ртути характерна и для руд
(аналогичного по типу) месторождения Эрдэнэтийн-Обо в Монголии (разрабатываемого
концерном “Эрденет”). В концентрате, полученного при обогащении руд указанного
месторождения, содержания ртути составят примерно 1,2 г/т. Нетрудно рассчитать, что
удельный выброс ртути в атмосферу при пирометаллургической переработке такого
концентрата будет равен 0,73 г Hg/т черновой меди, для шламов – 2,3 г/т, для отвальных
шлаков – 0,17 г/т, в канализацию уйдет 0,13 г Hg на 1 т полученной черновой меди.
В 2001 г. Среднеуральский медеплавильный завод в 2001 г. переработал около 1 млн. т
шлаков, содержащих примерно 200 кг ртути, из которых 17 кг поступило в атмосферу, 54 кг – в
шламы сернокислотного производства, 3 кг – в канализацию, 4 кг – в твердые отходы;
остальная ртуть перераспределилась в оборотных продуктах.
Если ориентироваться на соотношении выбросов пыли при производстве черновой меди
и при производстве рафинированной меди (см. табл. 4.61), то можно утверждать, что удельный
выброс ртути при рафинировании меди будет меньше аналогичного показателя при
производстве черновой меди как минимум в 100 раз. Утверждение достаточно условное, но тем
не менее примем (с учетом улавливания части ртути очистными установками, где она главным
образом концентрируется в пыли), что удельный выброс ртути в атмосферу при рафинировании
черновой меди составит 0,06 г Hg/т продукции.
В табл. 4.62 приведены расчетные сведения, оценивающие эмиссию ртути в атмосферу и
ее распределение в основных отходах медеплавильных заводов Урала, производящих черновую
медь. Кроме того, примерно 10% (2,3 т) поступает в серную кислоту.
Таблица 4.62 Производство черновой меди заводами Урала из концентратов и эмиссия ртути в
2001 г.
Производитель |
Чернова я медь, тыс. т |
Hg, поступившая с сырьем в производство, т |
Эмиссия Hg в атмосферу , т |
Hg в шлама х, т |
Hg в шлаках , т |
Hg, поступивш ая в канализаци ю, т |
ЗАО “Карабашмедь” |
41,7 |
4,12 |
0,350 |
1,11 |
0,083 |
0,062 |
ОАО “Кировградский медеплавильный комбинат” |
26,6 |
2,63 |
0,223 |
0,710 |
0,053 |
0,039 |
АООТ “Медногорский медно-серный комбинат” |
23,9 |
1,43 |
0,124 |
0,394 |
0,029 |
0,022 |
ОАО “Святогор” |
55,3 |
5,45 |
0,465 |
1,48 |
0,111 |
0,082 |
ОАО “Среднеуральский медеплавильный завод” |
90,6 |
8,96 |
0,761 |
2,42 |
0,181 |
0,134 |
Всего, черновая медь |
238,1 |
22,59 |
1,923 |
6,114 |
0,456 |
0,339 |
4.4.5 Производство меди и никеля ОАО .ГМК .Норильский никель.
ОАО “ГМК “Норильский никель” (далее – “Норильский никель”) - крупнейший
российский и мировой производитель меди, никеля, кобальта, некоторых редких и
драгоценных металлов. В его состав входят ОАО Заполярный филиал “ГМК “Норильский
никель” (Красноярский край, п-ов Таймыр), Кольская ГМК, включающая АО “Комбинат
“Печенганикель” и ОАО “Комбинат “Североникель” (Мурманская обл., Кольский п-ов) и ряд
других предприятий.
Объемы производства меди и никеля
Доля “Норильского никеля” в российском производстве никеля стабильно составляет 95-
96%, рафинированной меди - 55-57% (табл. 4.63 и 4,64); на месторождениях Таймыра и
Кольском п-ова в последние годы ежегодно добывалось и затем перерабатывалось до 18,5-19,8
млн. т сульфидных медно-никелевых руд (табл. 4.65). Предприятия “Норильского никеля”
ежегодно вовлекают в переработку образовавшиеся в текущем году или накопленные ранее,
так называемые, оборотные материалы и “лежалое сырье” (руды, концентраты, отвальные
шлаки и т. п.), из которого извлекаются десятки тысяч тонн меди и до 10-15 тыс. никеля.
Перерабатывается также цветной лом и другое сырье, в том числе поступающее из-за рубежа.
Таблица 4.63 Производство первичного никеля предприятиями РАО «ГМК «Норильский никель» в
2000-2002 г.г., тыс. т [27, 58, 59, 308, 350, 367]
Предприятие |
Местонахождение |
2000 |
2001 |
2002 |
ОАО Заполярный филиал “ГМК “Норильский никель” |
г. Норильск, Красноярский край |
116 |
120 |
120 |
АО “Комбинат “Печенганикель” |
г. Заполярный, Мурманская обл. |
Производит файнштейн, который перерабатывается на комбинате “Североникель” |
ОАО “Комбинат “Североникель” |
г. Мончегорск, Мурманская обл. |
101 |
103 |
98 |
Всего |
217 |
223 |
218 |
Таблица 4.64 Производство меди предприятиями РАО «ГМК «Норильский никель» в 2000-2002 г.г.,
тыс. т * [347, 350, 367, 377]
Производитель |
Местонахождение |
2001 |
2002 |
ОАО Заполярный филиал “ГМК “Норильский никель” |
г. Норильск, Красноярский край |
341,3 |
357 |
АО “Комбинат “Печенганикель” |
г. Заполярный, Мурманская обл. |
Производит файнштейн, который перерабатывается на комбинате “Североникель” |
ОАО “Комбинат “Североникель” |
г. Мончегорск, Мурманская обл. |
132,7 |
97 |
Всего |
474 |
454 |
* Включая вторичную медь.
Таблица 4.65 Добыча сульфидных медно-никелевых руд ГМК «Норильский никель», млн. т [66] *
Год АО “Печенганикель” (Кольский п-ов) |
Заполярный филиал (Таймыр) |
Всего |
1996 |
7,8 |
9 |
16,8 |
1997 |
7,7 |
9,8 |
17,5 |
1998 |
7,95 |
10,2 |
18,15 |
1999 |
7,65 |
11 |
18,65 |
2000 |
7,65 |
11,2 |
18,85 |
2001 |
7,72 |
12,1 |
19,82 |
* Рассчитано по графику, который приведен в указанном документе.
Основой производственного функционирования “Норильского никеля” в существенной
мере является общая схема переработки сульфидных медно-никелевых руд и технологическая
связь между входящими в его состав предприятиями. Так, АО “Комбинат “Печенганикель”
железной дорогой поставляет ОАО “Комбинат “Североникель” медно-никелевый файнштейн;
ОАО Заполярный филиал “ГМК “Норильский никель” поставляет предприятиям,
расположенным на Кольском п-ове, богатую руду, файнштейн, иногда вторичное сырье.
Аффинаж драгоценных металлов, производимых Заполярным филиалом, Кольской ГМК и ЗАО
“Полюс”, осуществляется на Красноярском, Приокском и Екатеринбургском заводах цветных
металлов [66, 67].
Добыча руд
Руды месторождений, разрабатываемых .Норильским никелем., делятся на богатые
(сплошные), вкрапленные и медистые. Богатые руды характеризуются повышенным
содержанием цветных и драгоценных металлов, а медистые руды отличаются более высокими
концентрациями меди. Как отмечалось выше, богатые руды с содержанием никеля более 1%
при отношении никеля к меди не менее 1:1 и с пониженным содержанием железа (менее 25%)
направляются непосредственно в плавку. Более бедные по содержанию никеля руды требуют
предварительного обогащения с получением коллективного медно-никелевого концентрата или
раздельно никелевого, медного и пирротинового концентратов [139].
Обогащение руд
На Норильском комбинате обогащение руд (по схемам коллективно-селективной
флотации) осуществлялось на двух обогатительных фабриках (ОФ) [66]. Талнахская ОФ
перерабатывала часть богатых и медистых руд Талнахско-Октябрьского месторождения с
получением никелевого, медного и пирротинового концентратов; Норильская ОФ - весь объем
вкрапленных руд месторождения Норильск-1 и Талнахско-Октябрьского месторождения, часть
богатых и медистых руд Талнахско-Октябрьского месторождения, а также так называемый
лежалый пирротиновый концентрат с получением никелевого и медного концентрата.
Никелевый концентрат содержит 5,67% Ni и 2,9% Cu, медный – 23,6% Cu и 1,7% Ni,
пирротиновый – 3,7% Ni и 3,4% Cu. Извлечение никеля в концентрат составляет 88-97%, меди
– 89-98%, кобальта – 66% [139]. При обогащении руды применяется дробильное,
измельчительное, флотационное, сгустительное и насосное оборудование. Затем по системе
гидротранспорта полученные концентраты отправляются на заводы; отходы обогащения –
хвосты - размещаются в специальных хранилищах. С 1995 г. в обогатительное производство
вовлекается складированное ранее минеральное сырье, в том числе вкрапленные и медистые
руды, пирротиновый концентрат, материал отстойников и др. В 1997 г. на Норильской и
Талнахской ОФ внедрена технология обогащения богатых руд с выводом в хвосты большей
части пирротинов (60-80%) и получением богатого никелевого концентрата (содержание Ni 9-
14%), а с 1999 г. используется технология получения богатых медных концентратов с
содержанием меди 27-29% [315]. В 1997 г. на Норильской ОФ внедрена гравитационно-
флотационная технология обогащения вкрапленных и медистых руд, позволяющая выделять
концентрат, обогащенный металлами платиновой группы.
На Кольском п-ове обогатительная фабрика (в г. Заполярный), входящая в состав
комбината .Печенганикель., осуществляла переработку местных вкрапленных руд (среднее
содержание Ni 0,75%, Cu 0,42%) с получением коллективного медно-никелевого концентрата,
содержащего 5-6% никеля и 2-3% меди [139]. Извлечение никеля в концентрат – 78-81%, меди –
73-76%.
Принципиальная схема переработки сульфидного медно-никелевого сырья
Подготовка сульфидного медно-никелевого сырья к плавке предусматривает его
окускование агломерацией или окатыванием (или сочетанием этих процессов) с
одновременным обжигом [89, 196]. Концентрат окатывают в чашевых грануляторах, а затем
полученные окатыши подвергают упрочняющему обжигу на агломашинах с десульфуризацией
до 30-40%, имеющих три зоны – сушки, частичного обжига и охлаждения окатышей, выход
которых составляет 90%. Как правило, в состав шихты агломерации входят концентрат и
обороты (возвратные продукты предприятия) в соотношении 1:1. Помимо этого, в количестве
3-4% от их массы в шихту добавляют обожженный известняк. Топливо (коксик) обычно вводят
в уже готовый агломерат перед его электроплавкой в рудотермических печах (рис. 4.13).
Шихта загружается в электропечи через отверстия в своде, штейн и шлак выпускаются
через шпуры. Штейн содержит 9-12% никеля, 5-10% меди; отвальный шлак - 0,078-0,098%
никеля, 0,063-0,01% меди; извлечение в штейн – никель 96-97%, медь 96%, кобальт 75-82%.
Конвертирование (продувка) медно-никелевых штейнов (с целью получения медно-никелевого
файнштейна) аналогична по организации процесса и аппаратурному оформлению продувке
никелевых штейнов. Для более полного извлечения кобальта конвертеры работают в замкнутом
цикле с электропечами обеднения. С этой целью шлаки конвертеров проходят обеднение в
специальных электропечах для доизвлечения цветных металлов бедной сульфидной рудой или
бедным штейном. При этом получаются отвальные шлаки и штейн, обогащенный кобальтом,
направляемый также на конвертирование. Состав файнштейна, получаемого на отечественных
заводах, примерно следующий: 37-42% Ni и 35-37% Cu. В файнштейне концентрируются
металлы платиновой группы. Предельное извлечение цветных металлов в файнштейн составляет
96-97%.
Для разделения файнштейна на никелевый и медный концентраты используется способ
флотации (механического обогащения). Охлаждение файнштейна ведут, разливая его в
шамотные или графитовые изложницы, врытые в землю для замедленного охлаждения. В
каждой застывает слиток массой примерно 25 т. Метод флотационного разделения файнштейна
не дает отвальных продуктов, так как все металлы распределяются между концентратами,
направляемыми в дальнейшую переработку. Потери металлов на этом переделе минимальные и
составляют не более 0,1-0,2%.
Никелевый концентрат от разделения файнштейна направляется на никелевую линию,
где его обжигают в печах кипящего слоя при температуре порядка 1150°С, что обеспечивает
некоторое укрупнение обжигаемого материала и снижает вынос мелкой фракции. При анодной
плавке используется известняк в количестве до 20 кг/т анода; в качестве восстановителя
применяют мелочь каменного угля или коксовый штыб. Извлечение никеля в закись составляет
при обжиге 97-99%, закись никеля затем поступает на восстановительную плавку в
электропечи типа сталеплавильных, в ходе которой получают анодный никель. Он имеет
примерно следующий состав: Ni 88,4-89%, Cu 4,5-6,5%, Co 1,2-2,2%, Fe 2,5-2,6%, S 0,4-0,5%,
As 0,001%.
При электролизе (электролитическом рафинировании) из анодного никеля в раствор
переходят, помимо никеля, сопутствующие примеси. Электролиз ведется с разобщенным
анодным и катодным пространством. Выход от загруженных анодов составляет – скрапа 16-
18%, шлама – 4-5%. В катодном никеле должно содержаться не менее 99,99% суммы никеля и
кобальта (в том числе кобальта не более 0,005%).
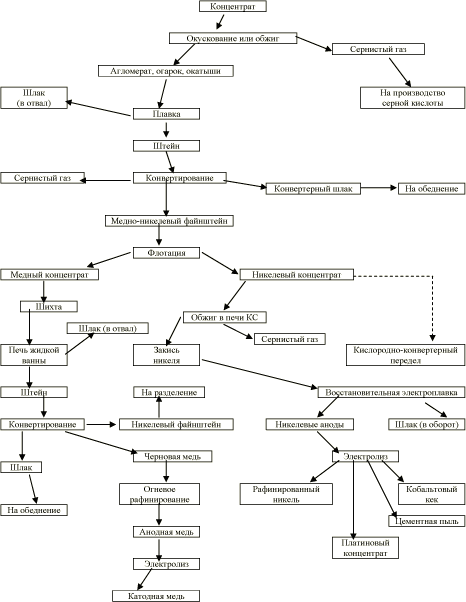
Рисунок 4.13 Принципиальная схема переработки сульфидного медно-никелевого сырья.
В шламе, образующемся в процессе электролитического растворения никелевых анодов,
концентрируются не переходящие в электролит металлы платиновой группы, золото, серебро,
селен, теллур. Переработка шлама с целью обогащения его указанными элементами
осуществляется в отдельном цикле, в результате чего получается обогащенный концентрат
драгоценных металлов и никель, возвращаемый обратно в основное производство. Концентрат
драгоценных металлов подвергается переработке по сложной технологической схеме для
раздельного получения каждого из металлов в товарном виде.
Для извлечения никеля из сырья (например, из пентландит-пирротинового концентрата)
применяют также плавку во взвешенном состоянии. Шихта для плавки состоит из концентрата,
остатков от выщелачивания при извлечении никеля, а также кварцевого флюса. После
предварительной сушки во вращающейся печи шихта поступает в печь, где сульфиды
окисляются, образуется штейн и шлак. Штейн направляют на конвертирование, шлак,
содержащий 0,8% Ni и 0,6% Cu, в специальную электропечь на обеднение. Отвальный шлак
электропечи содержит 0,10% Ni и 0,25% Cu.
Медный концентрат от разделения файнштейна направляют в медную линию
производства, где его обжигают в печах жидкой ванны (печах Ванюкова). Полученный штейн
подвергается конвертированию, а черновая медь поступает на огневое рафинирование, затем
анодная медь идет в цех электролитического рафинирования для получения катодной меди.
Шламы, образующиеся при электролизе, направляются на переработку.
В 2001 г. на Норильском комбинате (п-ов Таймыр) получаемые при обогащении руд
концентраты перерабатывались (пиро- и гидрометаллургическими способами) на трех
металлургических заводах: Надеждинском, Никелевом и Медном; работал также цех по
производству концентратов драгоценных металлов [66].
Надеждинский металлургический завод Норильского комбината перерабатывал весь
объем никелевого и пирротинового концентрата Талнахской ОФ, весь объем медного
концентрата цеха рафинирования файнштейна Никелевого завода с получением файнштейна и
медных анодов.
Аглофабрика и Никелевый завод перерабатывали весь объем никелевого концентрата
Норильской ОФ, весь объем обогащенного лежалого пирротинового концентрата, часть
файнштейна Надеждинского металлургического завода с получением товарного никеля и
кобальта.
Медный завод перерабатывал весь объем медных концентратов Норильской и
Талнахской ОФ и медные аноды Надеждинского металлургического завода с получением
товарной меди. Металлургический цех производства концентрата драгоценных металлов
перерабатывал шламы цеха электролиза никеля и цеха электролиза меди с последующим
получением концентратов драгоценных металлов и металлического серебра.
Ртуть в сульфидных медно-никелевых рудах, минералах и концентратах
В литературе известно немного сведений о содержании ртути в сульфидных медно-
никелевых рудах и минералах месторождений Таймыра и Кольского полуострова, а также в
продуктах их обогащения (табл. 4.66). В большинстве случаев приводимые данные
основываются на единичных химико-аналитических измерениях, что не позволяет
рассматривать их в качестве репрезентативных. Тем не менее, считается [264], что при
образовании медно-никелевых месторождений существенную роль играли постмагматические
процессы и сульфуризация, а сера, как известно [188], является основным осадителем ртути в
земной коре, что априори должно было способствовать накоплению ртути в сульфидных
медно-никелевых рудах [300].
По оценке В.П. Федорчука [295], среднее содержание ртути в сульфидных медно-
никелевых рудах составляет 1 г/т. Близкие результаты получены В.З. Фурсовым [300], который
достаточно детально изучил распределение ртути в рудах некоторых медно-никелевых
месторождений Таймыра и Кольского п-ова (табл. 4.67).
Основываясь на данных табл. 4.66, примем для сульфидных медно-никелевых руд
Таймыра среднее содержание ртути в 1,18 г/т; для руд Кольского п-ова – 1,41 г/т.
Таблица 4.66 Ртуть в рудах и концентратах сульфидных медно-никелевых месторождений [184,
188]
Месторождение |
Руда, минерал, концентрат |
Количество проб |
Ртуть, г/т |
Таймырский полуостров |
Талнахское |
Пирротин |
- |
0,05-0,2 |
Пентландит |
- |
0,15-6 |
Халькопирит |
- |
0,06-0,4 |
Кубанит |
- |
0,4 |
Халькозин |
- |
0,3-0,7 |
Руда |
- |
0,01-2 |
Пиритовый концентрат* |
4 |
0,45-2 |
Халькопирит-пентландитовый концентрат |
2 |
0,14-0,4 |
Платиновый концентрат ** |
2 |
18-36 |
Норильское |
Сфалерит |
- |
1,5 |
Руда |
- |
0,04-0,08 |
Октябрьское |
Сфалерит |
- |
0,2 |
Концентраты *** |
- |
0,3-1 |
Кольский полуостров |
Мончегорское **** |
Руда |
- |
0,05-0,11 |
Восток |
Руда |
- |
0,06-0,2 |
* Насколько известно [66, 139], на обогатительных фабриках Норильского комбината пиритовый
концентрат не получают; возможно, что в данном случае речь идет о пирротиновом концентрате.
** В цитируемой работе не указывается на какой стадии переработки руд был получен данный
концентрат; дело в том, что платиновый концентрат на Норильском комбинате всегда был конечным
продуктом сложного и многостадийного металлургического передела (в том числе, неоднократного
высокотемпературного) медно-никелевых руд, после которого трудно ожидать столь высоких
содержаний ртути в конечном продукте; если же этот концентрат является продуктом
полупромышленных испытаний на стадии обогащения руд, то указанные высокие концентрации ртути в
нем вполне могут реальными (в том числе, например, из-за присутствия амальгам).
*** Интервальная оценка содержания ртути в концентратах, перерабатываемых Норильским
комбинатом [Ягольницер и др., 1995].
**** Согласно [187], содержание ртути в рудах Мончегорского месторождения (по единичным
анализам) составляет 9 г/т, в пентландите – 46 г/т в пирротине – 1,8 г/т, в магнетите – 3 г/т.
Таблица 4.67 Средние содержания ртути в рудах медных месторождений (доверительные
интервалы надежностью 0.95) [300]
Месторождение, регион |
Характеристика руд |
Кол-во проб |
Hg, среднее (пределы), г/т |
Норильск, Таймыр |
Вкрапленные |
22 |
1,05 (0,79-1,38) |
Талнах, Таймыр |
Сплошные |
15 |
1,30 (0,7-2,0) |
Аллареченское, Кольский п-ов |
Сплошные |
16 |
1,17 (0,97-1,43) |
Ниттис-Кумужье, Кольский п-ов |
Сплошные |
9 |
1,65 (0,68-2,78) |
Эмиссия ртути
Сведения о распределении ртути при производстве цветных металлов на предприятиях
ОАО “ГМК “Норильский никель” в доступной литературе отсутствуют. Известна в сущности
лишь одна работа, в которой дается экспертная оценка выбросов ртути в атмосферу
предприятиями Норильского комбината (п-ов Таймыр) в первой половине 1990-х г.г., которая
варьировалась в пределах 0,75-2,5 т Hg/год (среднее значение – 1,63 т/год) [322]. Указанная
оценка эмиссии в последствие повторялась авторами цитируемой работы в ряде их других
публикаций.
Отсутствие необходимой информации не позволяет с высокой степенью достоверности
оценить современную эмиссию ртути предприятиями .Норильского никеля.. Ориентируясь на
особенности поведения ртути при пирометаллургическом переделе сырья, которые были
рассмотрены в предыдущих разделах, можно, очевидно, лишь установить порядок эмиссии
ртути на указанных предприятиях (главным образом в атмосферу).
Данные по комбинату “Печенганикель” показывают, что здесь в 2001 г. было
переработано примерно 7,5 млн. т руды (в том числе до 500 тыс. т полученного рудного
концентрата). При средней концентрации ртути в рудах 1,41 г/т общее ее количество в
переработанном в 2001 г. сырье составило ~10,5 т. Будем считать (основываясь на
особенностях поведения ртути при обогащении руд), что 15% от массы содержащегося в рудах
металла переходило при обогащении в коллективный концентрат (~1575 кг ртути). Концентрат,
содержащий указанное количество ртути, поступал в цех обжига, где до 95% присутствующей
в нем ртути (1496 кг) возгоняется и переходит в обжиговые газы, которые после очистки от
пыли выбрасывались в атмосферу. Выше было показано, что обычно 25-37% ртути (в данном
случае 374-554 кг) выводится из обжиговых газов с грубой и тонкой пыль, осаждающейся в
очистных установках. Таким образом, остальное количество ртути (942-1122 кг)
выбрасывалось в атмосферу. Незначительная часть металла (~ 50-60 кг) в составе окатышей
поступала в плавильный цех (на рудную электроплавку). Кроме того, примерно 300 тыс. т
руды, добываемой комбинатом “Печенганикель”, относится к категории богатой и
непосредственно поступало на переработку в плавильный цех. В этой руде содержится ~0,42 т
ртути. В указанный цех поступает также 300 тыс. т богатой норильской руды (~0,35 т ртути). В
небольшом количестве ртуть присутствует также в цветном ломе и другом сырье. Будем
считать, что в общей сложности на пирометаллургический передел (рудную электроплавку)
поступало порядка 0,8 т ртути, из которых незначительное количество переходило в отвальный
шлак, еще меньше - в штейн, а большая часть ртути (до 95-97%) возгонялась и выводилась с
отходящими газами, судя по всему, в сернокислотное производство, где перераспределялась
между различными продуктами (серной кислотой, шламами, кеком нейтрализации промывной
соляной кислоты). Примерно 2-4% от поступившей ртути выбрасывается с отходящими газами
сернокислотного цеха (~16-32 кг).
Таким образом, в 2001 г. на комбинате “Печенганикель” 0,95-1,15 т ртути (39-47% от
общей ее массы, поступившей с сырьем) было выброшено в атмосферу, 0,37-0,55 т (15-23%)
накопилось в улавливаемой пыли (которая, судя по всему, является оборотным продуктом),
~0,75 т (31-32%) поступило в отходы и конечную продукцию сернокислотного производства.
Количество ртути, поступающей в составе файнштейна (с комбината “Печенганикель” и
Норильского комбината) на комбинат “Североникель”, невелико (судя по всему, первые
килограммы). В плавильном цеху комбината “Североникель” ежегодно перерабатывается до
100-150 тыс. т руды с Норильского комбината, а также (судя по всему, примерно в таком же
количестве) лом и другое сырье. Общее количество ртути, поступившей в 2001 г. в плавильный
цех указанного комбината оценим примерно в 300 кг, из которых, с учетом технологической
схемы производства, незначительная часть (4-6 кг) ушла со шлаком в отвалы шлака, еще
меньше - в штейн, 75-111 кг осадилось вместе с пылью в очистных установках, а 180-220 кг
поступило в атмосферу. Сернокислотное производство комбината функционирует на
конвертерных газах, содержания ртути в которых явно невелики, поэтому она вряд ли
накапливается в значительных количествах в шламах и других продуктах сернокислотного
цеха.
На Норильском комбинате в 2001 г. в производство были вовлечены не только рудные
(никелевый, медный и пирротиновый) концентраты, но и продукты обогащения (никелевый и
медный концентраты) так называемого лежалого пирротинового концентрата (в прошлые годы
он складировался в отвалах). Информация об объемах переработки лежалого пирротинового
концентрата на обогатительной фабрике отсутствует. Кроме того, на Норильском комбинате в
производство вовлекались ранее накопленные оборотные материалы, количество которых
также неизвестно. В то же время, например, в 2002 г. в целом по ОАО “ГМК “Норильский
никель” из ранее накопленных оборотных материалов и лежалого сырья было получено около
6% никеля и более 8% меди (от общего их производства) [Годовой отчет «ГМК «Норильский
никель» -2002]. Отсюда следует, что указанные материалы и сырье обычно составляют
незначительную часть от добытых и переработанных сульфидных медно-никелевых руд.
Общее количество ртути, содержащееся в добытых в 2001 г. рудах, достигает 14,3 т (при
средней концентрации ртути в рудах 1,18 г/т). Будем считать, что ~30% от этого количества
(~4,3 т) перешло в рудные концентраты (никелевый, медный и пирротиновый), которые затем
были переработаны на металлургических заводах Норильского комбината. Приведенные выше
технологические схемы переработки сырья на этих заводах позволяют отметить следующее.
Так, на Никелевом заводе (при агломерации и электроплавке) подавляющая часть ртути должна
уходить с отходящими газами, которые после очистки от пыли (ртуть частично
концентрируется в пыли), выбрасываются в атмосферу; незначительное количество ртути
поступит в отвальные шлаки. На Медном заводе (при сушке и особенно при плавке сырья)
ртуть также должна улетучиваться с отходящими газами в атмосферу (частично
концентрируясь при очистке в уловленной пыли). На Надеждинском заводе ртуть будет
уходить в хвосты флотации (судя по всему, в существенных количествах), частично должна
поступать в серный концентрат, который идет на выплавку серы в автоклавах (при этом ртуть
частично улетучивается в атмосферу с выбросами данного производства), а также
выбрасываться с отходящими газами пирометаллургического передела сульфидного и
никелевого концентратов (с определенным накоплением в пыли, осаждающейся в очистном
оборудовании).
Основываясь на структуре потерь ртути, рассчитанной выше для комбината
“Печенганикель”, можно с определенной долей условности оценить эмиссию ртути на
Норильском комбинате. Так, выброс ртути в атмосферу с отходящими газами
пирометаллургического передела сырья составит 1,7-2,02 т, порядка 0,65-0,99 т ртути будет
осаждаться в составе пыли в очистных установках. Оставшееся количество ртути,
поступающей в производство в составе сырья, в той или иной мере распределяется среди
других продуктов (отвальные шлаки, хвосты флотации, оборотные сливы и т. д.), а также,
очевидно, отчасти теряться в окружающую среду с неорганизованными выбросами и
неучтенными источниками, в том числе, с выбросами производства серной кислоты. Из-за
отсутствия необходимой информации оценить все эти потоки ртути на данном этапе не
представляется возможным. В табл. 4.68 дается ориентировочно-расчетная оценка эмиссии
ртути в атмосферу на предприятиях ОАО “ГМК “Норильский никель”.
Таблица 4.68 Оценка эмиссии ртути на предприятиях ОАО .ГМК .Норильский никель. в 2001 г,т
Предприятие |
Поступило в атмосферу |
Накопилось в уловленной пыли |
“Печенганикель” |
0,95-1,15 |
0,37-0,55 |
“Североникель” |
0,18-0,22 |
0,075-0,111 |
Заполярный филиал |
1,7-2,02 |
0,65-0,99 |
Всего |
2,83-3,39 |
1,095-1,651 |
4.4.6 Производство олова
В 2001 г. практически единственным производителем олова в России являлось ОАО
“Новосибирский оловянный комбинат” (г. Новосибирск), на долю которого приходилось 99,9%
российского рафинированного олова (табл. 4.69), причем мощности комбината были загружены
только на 27,5% [58, 59].
Таблица 4.69 Производство олова в России, тыс. т [58, 59, 167-169]
Производство олова |
1997 |
1998 |
1999 |
2000 |
2001 |
В концентратах |
9 |
5,53 |
4,72 |
5,0 |
Нет сведений |
Рафинированного |
6,7 |
7,7 |
4,09 |
5,2 |
4,5 |
Вторичного * |
1 |
1 |
0,45 |
0,5 |
0,5 |
* Оценка.
Особенности технологии
Принципиальная технологическая схема переработки оловянных концентратов
предусматривает подготовку концентратов, магнитную сепарацию, доводку (на доводочной
фабрике), обжиг (при температуре порядка 700°С с целью удаления серы и мышьяка),
выщелачивание (крепкой соляной кислотой с целью очистки концентратов от железа, свинца,
трехокиси вольфрама и других кислоторастворимых примесей), плавку (богатых
маложелезистых концентратов – в электропечах, остальных – в отражательных печах) с целью
получения чернового олова.
Черновой металл, содержащий 93-99% олова, подвергается рафинированию (огневому,
вакуумному или электролитическому). Олово высокой чистоты получают путем зонной плавки
обычного марочного металла. Шлаки отражательной плавки и электроплавки подвергаются
вторичной переработке в фьюминг-печах. Наряду с оловом при фьюминговании отгоняются
мышьяк, цинк, свинец и редкие металлы.
Съемы рафинирования также вторично плавятся в электропечах, возгоны
(оловосодержащие пыли) подвергаются грануляции в чашах и поступают в переплавку. Бедные
оловосодержащие материалы (шламы доводочных фабрик и др.) перерабатывают методом
хлорирования. Возгоны летучего хлористого олова переводятся затем в сернокислые
соединения и подвергаются электролизу с нерастворимым анодом.
На Новосибирском оловянном комбинате применяется комплекс технологических
процессов и установок, позволяющих перерабатывать различные виды оловосодержащего
сырья и извлекать многие попутные металлы (свинец, висмут, мышьяк, индий и др.).
Предприятие выпускает олово различной степени чистоты, припои на основе олова, свинца,
сурьмы, висмута, индия, бессвинцовые припои, оловянные и припойные порошки,
легкоплавкие припои и сплавы; паяльные пасты с флюсами для пайки сталей и цветных
металлов; баббиты различных марок на основе олова, свинца, меди и сурьмы; висмут
различных марок; галлий и индий высокой чистоты [149]. Комбинат обладает комплексом
очистных установок, обеспечивающим на 99,9% обеспыливание отходящих технологических
газов и практически 100%-ный водооборот, исключающий промышленные стоки.
Сырье
Новосибирский комбинат имеет собственную сырьевую базу на основе ГОКов
.Хинганское олово. (Еврейская автономная область), “Дальолово” (Солнечный ГОК,
Хабаровский край), “Тяшь-Шаньолово”, обладает крупным пакетом акций оловодобывающего
предприятия ОАО “Депутатсколово” (Якутия). Среднее содержание олова в коренных рудах
разрабатываемых месторождений оценивается в 0,47% [167].
Среднее содержание олова в перерабатываемых концентратах составляет 52%. На основе
руд Хинганского месторождения производятся оловянные концентраты марки с содержанием
олова около 63% [363]. В конце 1990-х г.г. доля отечественных оловянных концентратов,
перерабатываемых на Новосибирском комбинате, составляла около 60%; остальное
приходилось на концентраты, импортируемые из Китая, Нигерии, Перу, Португалии и
Великобритании [166]. В настоящее время, судя по всему, основная часть олова производится
из отечественных концентратов; в небольших объемах используется вторичное сырье.
Эмиссия ртути при производстве олова
В рудах оловорудных месторождений среднее содержание ртути составляет 0,1 г/т [187].
В оловянных концентратах (месторождения Приморья, Якутии, Забайкалья) содержания ртути
варьируются в пределах 0,01-0,5 г/т, в оловянных концентратах с сульфидами – 0,7-0,8 г/т
[188]. По данным В.З. Фурсова [300], уровни содержания ртути в рудах оловянных
месторождений выше и в среднем варьируются от 0,86 до 1,89 г/т (табл. 4.70). Общее среднее
составляет ~ 1,3 г/т. Будем считать, что такое количество ртути содержится и в оловянных
концентратах. Относительно повышенные содержания ртути в пределах оловорудных зон (в
том числе, на месторождениях Приморья) в свое время отмечались в ряде других работ (см.,
например, [135]).
Согласно [322], в первой половине 1990-х г.г. эмиссия ртути при производстве олова на
Новосибирском заводе (судя по всему, в то время он работал практически на полную
мощность) варьировалась в пределах 9-33 кг/год (непосредственно из оловянных концентратов
1-25 кг/год). Указанную оценку авторы цитируемой работы осуществили на основе содержания
ртути в перерабатываемых оловянных концентратах в пределах 0,01 – 0,5 мг/кг и ежегодного
использования на заводе 8 тыс. т поступавшего с Урала серного колчедана (1 г/т). Если
ориентироваться на подход авторов к расчету эмиссии и исходить из того, что в 2001 г.
производственные мощности завода были загружены на 27,5%, то в указанном году эмиссия
ртути при переработке оловянных концентратов должна составить 0,3-7 кг.
Таблица 4.70 Средние содержание ртути в рудах оловянных месторождений (доверительные
интервалы надежности 0.95) [300]
Месторождение, регион |
Количество проб |
Ртуть, г/т |
Валькумей, Чукотка |
5 |
0,86 (0,40-1,85) |
Фестивальное, Дальний Восток |
4 |
1,89 (1,27-2,64) |
Хрустальное, Приморье |
6 |
1,34 (0,98-1,87) |
Учкошкон, Киргизия |
8 |
1,2 (0,87-1,76) |
Будем считать, что в 2001 г. среднее содержание олова в концентратах составляло ~ 50%.
Отсюда следует, что для получения 4,5 тыс. т олова (с учетом степени его извлечения в
товарный продукт) необходимо было переработать ~ 10 тыс. т концентратов, с которыми (при
среднем содержании в них ртути 1,3 г/т) на передел поступило 13 кг ртути. Большая часть
ртути возгоняется из концентратов уже на стадии их обжига; оставшаяся ртуть (~5% от общей
массы) удаляется из сырья при выщелачивании и плавке. Как отмечалось выше, на комбинате
используется эффективная система пылеулавливания. Это позволяет считать, что не менее 60%
ртути, содержащейся в отходящих газах, осаждается в составе пыли на фильтрах очистных
установок. Таким образом, непосредственно в атмосферу поступило примерно 5 кг ртути.
4.4.7 Производство свинца
В России производится первичный и вторичный свинец, причем в различных (в том
числе, в официальных) источниках информации обычно сообщаются данные только о
рафинированном свинце, независимо от сырья, из которого он был получен (табл. 4.71).
Таблица 4.71 Производство и потребление свинца в России, тыс. т * [83, 106, 167, 169]
Показатель |
1999 |
2000 |
2001 |
Производство свинца в концентратах (по металлу) |
13 |
12,2 |
16,1 |
Производство рафинированного свинца |
68,8 |
55,4 |
60 |
Импорт рафинированного свинца |
27,2 |
- |
40 |
Импорт свинца в концентратах |
-** |
10 |
20 |
Экспорт свинца в концентратах |
15 |
20 |
9 |
Экспорт рафинированного свинца |
3,4 |
- |
8 |
Потребление рафинированного свинца |
95 |
83 |
90 |
* Анализ имеющейся информации позволяет считать, что производство вторичного свинца (из
свинцового лома) в России примерно равно его получению из рудных концентратов и совместно
перерабатываемых оборотных продуктов свинцового и полупродуктов цинкового, медного и
редкометального производств.
По данным Министерства природных ресурсов РФ, в 2001 г. большая часть свинца в руде
(и свинцовых концентратов) была добыта на месторождениях Приморского и Красноярского
краев (41% и 34% соответственно) [83].
Производство свинцовых концентратов осуществляли ОАО “Дальполиметалл”
(Приморский край, месторождения Николаевское, Партизанское, Верхнее, Южное; в 2000 г.
было добыто более 800 тыс. т полиметаллической руды, получено 23-24 тыс. т концентрата, из
которых 70% было экспортировано), АО “Горевский ГОК” (Красноярский край, разрабатывает
Горевское месторождение; в 2001 г. добыто 67,5 тыс. т руды, получено 5,53 тыс. т свинцового
концентрата) В небольших объемах свинцовый концентрат производился Садонским свинцово
цинковым комбинатом (Северная Осетия-Алания; первые сотни тонн свинца в концентрате) и
АО “Салаирский ГОК”. Свинцовые концентраты поступали также из Казахстана [48, 83, 158,
359, 364, 383].
Переработка концентратов и производство рафинированного свинца осуществлялась на
ЗАО “Свинцовый завод – Дальполиметалл” (пос. Рудная Пристань, Приморский край,
производит свинец из концентратов, проектная мощность по свинцу 14,5 тыс. т в год, в
меньшей степени – вторичный свинец), Верхне-Нейвинском заводе (пос. Верхне-Нейвинск,
Свердловская область, вторичный свинец, проектная мощность 10,7 тыс. т), на ОАО
“Рязцветмет” (свинец из вторичного сырья, мощность 11,4 тыс. т в год), ОАО “Электроцинк”
(из свинцовых концентратов и попутно при переработке цинковых концентратов, мощность
38,6 тыс. т) [83].
В небольшом количестве (очевидно, первые сотни кг) свинец получали на ОАО
“Новосибирский оловянный комбинат” (главным образом, попутно при переработке оловянных
концентратов). В ЗАО “Свинцовый завод - Дальполиметалл” осуществляется переработка
способом горновой плавки только богатых концентратов (содержащих не менее 73% свинца),
производимых в ОАО “Дальполиметалл”. В 2000 г. на свинцовом заводе “Дальполиметалл”
было переработано около 8,5 тыс. т свинцового концентрата, получено примерно 6 тыс. т
рафинированного свинца; еще около 2 тыс. т свинца произведено из вторичного сырья
(свинцовый лом, отработавшие аккумуляторные батареи подводных лодок и т. п.).
Производство свинца в ЗАО “Свинцовый завод - Дальполиметалл” из концентратов в 2001 г.
может быть оценено в 5 тыс. т, из вторичного сырья – 2-2,5 тыс. т.
В 1998 г. ОАО “Рязцветмет” вышло на первое место в России по объемам производства
свинца и сплавов на его основе из вторичного сырья; в этом году им было получено 25 тыс. т
свинца (~50% всего российского металла) [166]. Здесь в производстве свинца используется
технология переработки аккумуляторного лома с применением электропечей [282]. Плавку
свинцового сырья осуществляют в электротермической печи плавильного цеха по технологии,
отличающейся от действующих тем, что не применяется в качестве флюсующего агента сода,
процесс ведется без образования штейна и количество шлака сокращено до минимума, так как
его образование определяется только зольностью кокса и качеством разделки лома. Данная
технология имеет существенные преимущества по сравнению с шахтной плавкой и плавкой в
короткобарабанных печах. В частности, уменьшено количество образующихся технологических
газов, снижены пылевынос, количество оборотных продуктов и шлака, уменьшен расход кокса.
Рафинирование чернового свинца осуществляется по известной технологии, но на ряд приемов
рафинирования имеется ноу-хау. Переработка продуктов электроплавки свинцового вторичного
сырья (шлаки, шликеры, съемы) и эбонитовой фракции осуществляется в возгоночной печи.
Сырье и особенности его переработки
Основным сырьем для производства свинца являются сульфидные руды с содержанием
металла не более 8-9%. В металлургическую переработку на свинцовые заводы обычно
поступают концентраты, содержащие 30-80% свинца, 1-14% цинка до 10% меди [294]. Шихту
для агломерационного обжига составляют из сульфидных концентратов, богатых окисленных
руд, пыли и возгонов сернокислотных установок медеплавильных и цинковых заводов и
флюсов – железной руды или пиритного огарка, известняка и кварца.
Свинец из рудных концентратов производится преимущественно пирометаллургическим
способом – восстановительной плавкой свинца в шахтных печах. Сульфидный концентрат,
полученный после флотационного обогащения руд, совместно с флюсами подвергается
окислительному обжигу (спеканию). Спекание свинцовых концентратов осуществляют на
агломашинах. В процессе обжига сульфиды металлов окисляются до оксидов, мелкие частицы
руды металлических спекаются в агломерат. Плавку агломерата проводят в шахтной печи в
восстановительной атмосфере. Продуктами плавки являются: черновой свинец, штейн,
содержащий медь, сульфиды меди и свинца. Жидкие продукты плавки собираются во
внутреннем горне печи, где отстаиваются по плотности. Черновой свинец выпускают из горна
и направляют на рафинирование. Шлак со штейном выпускают из печи в два наружных
отстойника. Черновой свинец содержит 90-97% Pb и многочисленные примеси. При
рафинировании чернового свинца получают чистый свинец, сплав золота с серебром и другие
продукты.
Поведение и эмиссия ртути
В процессе окислительного агломерирующего обжига и шахтной плавки свинцовых
концентратов, в которых концентрация ртути варьируется в пределах от 0,3 до 520 г/т, большая
часть ее (> 90%) возгоняется и улавливается в пыли электрофильтров, рукавных фильтрах и
при очистке вентиляционных газов [33] (рис. 4.14).
![Рисунок 4.14 Схема распределения ртути в продуктах переработки свинцового производства [33].](images/s223.gif)
Рисунок 4.14 Схема распределения ртути в продуктах переработки свинцового производства
[33].
Из газовой фазы, в случае получения серной кислоты, в промывных башнях осаждается
около 5,5% ртути, поступающей в технологический процесс с сырьем. Основная масса пыли,
образующейся при спекании и плавке сырья (60-80%), является оборотным продуктом, что
ведет к увеличению потерь металлов (и ртути) за счет возрастания выхода пыли и непрерывной
циркуляции значительного ее количества.
Фактически с различными разновидностями пыли в редкометальное производство
поступает около 20-25% ртути, содержащейся в шихте. Здесь пыль подвергается
сульфатизирующему обжигу, при котором такие элементы, как ртуть, селен, мышьяк, фтор и
другие переходят в газы. Содержание ртути в шламе достигает 1,71%. Шлам проходит очистку
от мышьяка и ртути, при этом образуется арсенит кальция, идущий на захоронение. Из
сульфатного продукта ртуть практически полностью переходит в свинцовый кек, являющийся
оборотным продуктом.
По данным [32], среднее значение фактора эмиссии ртути при первичном производстве
свинца составляет 2 г Hg/т полученного металла. Поведение ртути при производстве
вторичного свинца на российских заводах не изучалось; отсутствуют также какие-либо
сведения о значениях ее эмиссионного фактора для этого производства. С высокой степенью
условности примем, что этот показатель, как минимум, на порядок ниже, нежели при
производстве первичного свинца, и составляет 0,2 г Hg/т полученного металла.
Имеющиеся сведения позволяют оценить эмиссию ртути в атмосферу при производстве
свинца в целом для всей страны, которая составит: при производстве (30 тыс. т) первичного
свинца – 60 кг, при производстве (30 тыс. т) вторичного свинца – 6 кг.
Как показано выше, только относительно небольшая часть ртути выводится из
технологического процесса с выбросами, товарными и поступающими на захоронение
полупродуктами, а основное количество ее накапливается в оборотных полупродуктах.
4.4.8 Производство других цветных металлов
Вопросы, связанные с производством золота, освещены в разделе 3.3 Согласно оценкам,
в рудах, переработанных в 2001 г., содержится 4-8 т ртути, которая в основном остается в
отвалах и отходах обогащения. Можно предположить, что около 20% от количества попутно
извлекаемой из недр ртути может поступать в атмосферу на разных стадиях добычи и
переработки золотосодержащего сырья, а также хранения отходов. Данные, необходимые для
оценки эмиссии ртути при аффинаже золота, получить не удалось.
В России в 2000-2001 г.г. из рудного сырья (рудных концентратов) в очень
незначительных объемах производились сурьма, молибден, вольфрам и некоторые (в основном
попутно) редкие металлы. Годовые объемы производства концентратов указанных металлов
были очень невелики и составляли первые тысячи тонн. Существенная часть сурьмяного,
молибденового и вольфрамового концентратов экспортировалась, и лишь незначительное их
количество перерабатывалось на отечественных заводах.
Сурьма из рудного сырья производилась в основном на ОАО “Рязцветмет“ (г. Рязань),
где перерабатывался концентрат (1-2 тыс. т/год), поступающий с золотосурьмяного
Сарылахского месторождения (Якутия). Производство сурьмы, созданное на заводе в 1995 г.,
позволяет эффективно перерабатывать золотосурьмяные концентраты с получением
триоксида сурьмы (металлической сурьмы) и золотосурьмяного сплава, пригодного для
получения золотых слитков [282]. На этом же заводе осуществлялось производство
вторичной сурьмы в виде сплавов (первые сотни тонн в год). Есть сведения, что в очень
небольших количествах якутский концентрат поступал также на Новосибирский оловянный
завод. В 2000 г. в России производство сурьмы в концентратах оценивалось в 4,7 тыс. т.,
металлической сурьмы - в 1-2 тыс. т. [169].
Одним из основных экспортеров вольфрамового концентрата из России является АО
“Лермонтовская горнорудная компания” (Приморский край) [166, 210], производство которого
в последнее время составляло примерно 4-5 тыс. т/год.
Молибденовый концентрат также в основном идет на экспорт [210]. Объемы
производства молибденового концентрата в России в последние годы составляли 3-5 тыс. т/год,
большая часть из которых приходилась на долю ОАО “Молибден” (Сорский комбинат,
Хакассия, до 90% российской добычи); в очень малых объемах концентрат производили
Тырныаузский комбинат (Кабардино-Балкария) и ОАО “Жирекенский молибден” (Читинская
область) [28].
Учитывая очень незначительные объемы перерабатываемых на российских заводах
сурьмяных, молибденовых и вольфрамовых концентратов, уровни содержания в них (или
рудах) ртути, редко превышающие, как указывают немногочисленные литературные данные
[188, 300], 1 г/т, можно считать, что эмиссия ртути в атмосферу при производстве сурьмы,
молибдена и вольфрама невелика и в целом для всей страны может быть оценена в 3-5 кг/год.
4.4.9 Заключение
Имеющиеся данные по выбросам ртути в атмосферу и ее поступлению в отходы при
добыче и переработке цветных металлов в Российской Федерации обобщены в табл. 4.72. К
сожалению, отсутствие необходимой информации не позволило оценить все возможные
источники мобилизации ртути при производстве цветных металлов. Данные о количестве
ртути, присутствующей в отходах обогащения сульфидных медно-никелевых руд, указывают
на вероятность ее концентрирования в значительных объемах в аналогичных отходах,
образующихся на уральских обогатительных фабриках (при получении медного и цинкового
концентратов). Для дальнейшего уточнения необходимо проведение специальных
исследований непосредственно на предприятиях.
Таблица 4.72 Выбросы ртути в атмосферу и ее поступление в отходы при добыче и переработке
цветных металлов в Российской Федерации, 2001 г., наилучшая оценка, тонны
Производство |
Hg в рудах |
Hg в концентра тах |
Эмиссия Hg в атмосферу |
Hg в хвоста х |
Hg в других твердых отходах |
Сбросы в канализац ию |
Цинка |
н. д. * |
31 |
1,9 |
н. д. |
8,5 |
0,2 |
Никеля (из силикатных руд), уральские заводы |
0,3 |
Плавка из руд |
0,3 |
Нет хвосто в |
0,006 |
н. д. |
Никеля и меди (предприятия “ГМК “Норильский никель”) |
24,8 |
5,9 |
3,1 |
18,9 |
н. д. |
н. д. |
Меди (уральские заводы) |
н. д. |
23 |
2,0 |
н. д. |
6,6 |
0,4 |
Олова |
н. д. |
0,01 |
0,005 |
н. д. |
н. д. |
н. д. |
Свинца |
н. д. |
н. д. |
0,06 |
н. д. |
н. д. |
н. д. |
Добыча золота |
6 |
н. д. |
1,2 |
4,2 |
н. д. |
0,6 |
Другие цветные металлы |
н. д. |
< 1 |
0,005 |
н. д. |
н. д. |
н. д. |
Итого |
> 31,2 |
> 60 |
> 8,6 |
> 23 |
> 15 |
> 0,6 |
* “н. д.” – оценка отсутствует, поскольку не удалось получить необходимой информации.
4.5 Черная металлургия
В табл. 4.73 приведены сведения, характеризующие объемы производства основных
видов продукции черной металлургии в России в 1999-2002 г.г.
Таблица 4.73 Производство основных видов продукции черной металлургии в России в 1999-2002 г.г.,
млн. т [8, 117, 128, 227, с дополнениями]
Год |
Железная руда |
Кокс (6% влажности) |
Чугун |
Сталь |
Прокат готовый |
Трубы стальные |
1999 |
82,2 |
28,1 |
40,9 |
52,5 |
40,9 |
3,3 |
2000 |
87,1 |
30 |
44,8 |
59,1 |
46,7 |
4,8 |
2001 |
82,8 |
29,9 |
47,1 |
59 |
47,1 |
5,4 |
2002 |
84,2 |
30,9 |
46,3 |
59,8 |
48,7 |
5,1 |
Крупнейшие металлургические комбинаты, функционирующие в России, представляют
собой промышленные комплексы, как правило, с полным технологическим циклом,
включающим в себя горнорудные предприятия, коксохимическое и огнеупорное производства,
доменный (от 2 до 7 домн), сталеплавильный и прокатный переделы, а также строительные,
ремонтные, энергетические, транспортные и другие подразделения; численность рабочих на
каждом предприятии достигает 20-40 тыс. человек
В табл. 4.74 приведены поставщики железорудного сырья на основные металлургические
предприятия России. Сырьевой базой небольших предприятий Северного и Среднего Урала
являются в основном Качканарская группа месторождений и месторождения Тагило-
Кувшинского, Серовско-Ивдельского и Богословского районов; аналогичные предприятия
Южного Урала получают руды в основном с месторождений горы Магнитной и Халиловской
группы.
Таблица 4.74 Поставщики железорудного сырья на основные металлургические заводы России [8,
14, 166-168, 313]
Предприятие |
Основные поставщики железорудного сырья |
ОАО “Магнитогорский МК” |
На 50-70% - поставки из Центрально-Черноземного и Северного районов
России: ОАО “Михайловский ГОК” (Михайловское месторождение КМА),
ОАО “Стойленский ГОК” (Стойленское месторождение КМА); остальная часть
с местных железорудных предприятий (месторождения Магнитогорское и
Малый Куйбас) либо импортируется (Соколовско-Сарбайское железорудной
месторождение, Казахстан) |
ОАО “Новолипецкий МК” |
ОАО “Лебединский ГОК” (Лебединское и Стойло-Лебединское месторождения
КМА), ОАО “Стойленский ГОК” (Стойленское месторождение КМА), ОАО
“Михайловский ГОК” (Михайловское месторождение КМА) |
ОАО “Северсталь” (Череповецкий МК) |
ОАО “Оленегорский ГОК” (месторождения Оленегорское, Кировогорское, им.
проф. Баумана, XV лет Октября, Комсомольское), ОАО “Ковдорский ГОК”
(Ковдорское месторождение), ОАО “Карельский окатыш” (Костомукшское
месторождение); ОАО “Лебединский ГОК” (Лебединское и Стойло-
Лебединское месторождения КМА); ОАО “Стойленский ГОК” (Стойленское
месторождение КМА) |
ОАО “Нижнетагильский МК” |
На 50-70% - поставки из Центрально-Черноземного и Северного районов
России; остальная часть с местных месторождений (Качканарское и Тагило-
Кувшинские) и предприятий (ОАО “Качканарский ГОК”) либо импортируется |
ОАО “Западно-Сибирский МК” |
ОАО “Коршуновский ГОК” (Коршуновское месторождение), ОАО “Сибруда”,
“Лебединский ГОК”, местные месторождения (Ташгальское, Шерегешское,
Казское, Сухаринское), Качканарский ГОК (месторождение Гусевогорское), а
также привозное сырье |
ОАО “Мечел” (Челябинский МК) |
Бакальское месторождение (частично), сырье из центрального и северного
районов России (на 50-70%); местные предприятия (“Качканарский ГОК”),
незначительный импорт |
ОАО “Кузнецкий МК” |
ОАО “Коршуновский ГОК” (Коршуновское месторождение), местные
месторождения (Ташгальское, Шерегешское, Казское), привозное сырье
ОАО “Тулачермет” Месторождения КМА |
ОАО “Носта” (Орско-Халиловский МК) |
Бакальское месторождение (частично), сырье из центрального и северного
районов России (на 50-70%), частично - импорт |
Особенности доменного производства
Процесс выплавки чугуна в доменной печи осуществляется непрерывно. В качестве
сырьевых материалов используются агломерат, флюсы, кокс, окатыши, дутье, природный газ.
Доменная печь работает по схеме противоточного процесса. Агломерат, флюсы, окатыши и
кокс периодически загружаются в домну сверху. Подогретый до 1050-1300°С воздух подается в
домну снизу и проходит через опускающуюся шихту, которая нагревается, восстанавливается и
плавится. Чугун - основной продукт доменного производства – представляет собой сплав
железа с углеродом, содержащий определенные количества Si, Mn, P, S. По своему назначению
чугун подразделяются на три группы: 1) передельный, предназначенный для последующего
передела в сталь; 2) литейный, применяемый для отливок (в чугунолитейном производстве); 3)
специальный (доменные ферросплавы, употребляемые в качестве раскислителей при
производстве стали) [196].
Отработанный доменный газ является горючим, поэтому он выводится из домны и после
предварительной очистки направляется в кауперы (доменные воздухонагреватели), где
сжигается совместно с природным или коксовым газом, подогревая дутьевой воздух для
домны. На выходе из печи температура доменного газа составляет 300-500°С; количество его .
от 2000-2500 до 3800-4000 м³ на тонну чугуна (в зависимости от вида давления и дутья);
запыленность доменного газа при работе печи с нормальным давлением на колошнике (верхней
части доменной печи) – 50-60 г/м³ (иногда до 100 г/м³); при работе с повышенным давлением .
35-40 г/м³ [274]. Как правило, для улавливания пыли применяют многоступенчатую очистку. В
качестве пылегазоочистного оборудования на 1-й степени используют сухие системы (циклоны
с поворотом потока газа на 180°), затем – мокрые (форсуночный скруббер, труба Вентури с
каплеуловителем и дроссельная группа или мокрые трубчатые электрофильтры). Обычно
эффективность грубой очистки составляет не более 65-70%. На некоторых заводах дроссельные
группы очистного оборудования в последние годы были заменены газовыми утилизационными
бескомпрессорными турбинами. В среднем эффективность пылегазоочистных устройств на
предприятиях СНГ оценивается в 98% [52].
Эмиссия ртути при доменном производстве чугуна
Содержания ртути в концентратах месторождений Курской магнитной аномалии (КМА),
являющихся основным источником сырья для многих российских заводов, находятся в
пределах 0,01-0,1 мг/кг (месторождения Стойленское, Коробовское), в концентрате
Коршуновского месторождения (Сибирь) – 0,02-0,085 мг/кг [188]. Будем считать, что среднее
содержание ртути в железной доменной руде и окатышах составляет 0,06 мг/кг, в агломерате,
металлодобавках и коксе – 0,0004 мг/кг; в природном газе – 0,1 мкг/м³, в известняках – 0,05
мг/кг, в марганцевой руде – 0,06 мг/кг. Основываясь на данных табл. 4.75, рассчитаем удельное
количество ртути, поступающей в доменный процесс (на 1 т произведенного чугуна). Оно
составит 39,86 мг/т чугуна (0,03986 г/т чугуна). Допустим, что 99% ртути, поступающей в
доменное производство, возгоняется и в конечном счете эмитирует в атмосферу. Таким
образом, удельная эмиссия ртути составляет 0,0395 г/т чугуна. Этот показатель соответствует
известному эмиссионному фактору ртути, рассчитанного J. Pacyna and E. Pacyna [404], который
равен 0,039 г Hg/т чугуна и который, очевидно, может использоваться для оценки выбросов
ртути при производстве чугуна в России (табл. 4.76).
Таблица 4.75 Удельный расход основных материалов (в кг) на производство 1 т чугуна
Материалы |
2000 г. |
2001 г. |
Средняя концен- трация Hg, мг/кг * |
Масса Hg, поступаю-
|
[117] |
Железорудная часть шихты |
1674 |
1660 |
|
|
в том числе: |
|
|
|
|
железная доменная руда |
17 |
16 |
0,06 |
0,96 |
агломерат |
1137 |
1141 |
0,0004 |
0,456 |
окатыши |
520 |
502 |
0,06 |
30,12 |
металлодобавки |
15 |
20 |
0,0004 |
0,008 |
Скиповый кокс |
468 |
457 |
0,0004 |
0,183 |
Природный газ, м³ |
92 |
92 |
0,1 мкг/м³ |
0,009 |
Кислород, м³ |
85 |
81 |
- |
|
Известняк |
161 |
158 |
0,05 |
8,05 |
Марганцевая руда |
1,3 |
1,3 |
0,06 |
0,078 |
Итого |
39,9 |
* Для 2001 г; используются минимальные концентрации ртути; в реальности на отдельных
предприятиях используются, например, известняки и железные руды, в которых ртуть присутствует в
более высоких концентрациях.
Общее количество ртути, мобилизованной и выброшенной, согласно оценкам, составляет
примерно 1,8 т/год. Учитывая разброс значений, общее количество мобилизованной ртути по
грубым подсчетам может составить 1,2-2,4 т/год.
Таблица 4.76 Эмиссия ртути в атмосферу при производстве доменного чугуна в России, 2001 г.
Предприятие |
Местоположение |
Чугун, тыс. т/год |
Эмиссия Hg, т/год |
ОАО “Магнитогорский МК” |
г. Магнитогорск, Челябинская обл. |
8662 |
0,338 |
ОАО “Новолипецкий МК” |
г. Липецк |
7464 |
0,291 |
ОАО “Северосталь” (Череповецкий МК) |
г. Череповец, Вологодская обл. |
7447,9 |
0,290 |
ОАО “Нижнетагильский МК” |
г. Нижний Тагил, Свердловская обл. |
4628,7 |
0,181 |
ОАО “Западно-Сибирский МК” |
г. Новокузнецк, Кемеровская обл. |
4546 |
0,177 |
ОАО “Мечел” (Челябинский МК) |
г. Челябинск |
2905,79 |
0,113 |
ОАО “Кузнецкий МК” |
г. Новокузнецк, Кемеровская обл. |
2750,7 |
0,107 |
ОАО “Тулачермет” |
г. Тула |
2200 |
0,086 |
ОАО “Носта” (Орско-Халиловский МК) |
г. Новотроицк, Оренбургская обл. |
1786 |
0,070 |
ОАО “Чусовской металлургический завод” |
г. Чусовой, Пермская обл. |
678,7 |
0,027 |
ОАО “Свободный сокол” |
г. Липецк |
580 |
0,023 |
ОАО “Косогорский металлургический завод” |
г. Тула |
403 |
0,016 |
ОАО “Металлургический завод им. А.К. Серова” |
г. Серов, Свердловская обл. |
341,7 |
0,013 |
ОАО “Саткинский чугуноплавильный завод» |
г. Сатка, Челябинская обл. |
180,8 |
0,007 |
Верхне-Синячихинский металлургический завод |
Свердловская обл. |
112,5 |
0,004 |
Белорецкий металлургический комбинат |
г. Белорецк, Башкортостан |
109,2 |
0,004 |
Алапаевская ферросплавная компания |
г. Алапаевск, Свердловская обл. |
14,9 |
0,001 |
Итого |
|
44811,9 |
1,748 |
Всего по России |
|
47100 |
1,837 |
Эмиссия ртути в чугунолитейном производстве
В России существует несколько сотен чугунолитейных (получение отливок) производств
(главным образом, на машиностроительных предприятиях). Ведущее место среди плавильных
печей литейного производства занимают вагранки (около 90% общего объема выплавки), около
10% отливок получают в дуговых печах; на некоторых заводах применяются индукционные
печи. Вагранка – печь шахтного типа для плавки чугуна в литейных цехах. Шихтовые
материалы загружаются в шахту с колошниковой площадки послойно (колошами): чушковый
доменный чугун, металлолом, флюсы, кокс. Расплавленный чугун собирается в горне и
перетекает в копильник. Производительность таких печей – от 1 до 60 т в час. В среднем на
тонну готового литься расходуется около 18% кокса, 2-3% флюсов, до 20% металлолома, 40-
45% чушковых чугунов, 15-20% возврата собственного производства.
В литейных цехах пылегазовые выбросы выделяются при выплавке металла, заливке его
в формы при формовке, выбивке и очистке литья, при производстве стержней, приготовлении
формовочной смеси, погрузочно-разгрузочных операциях на шихтовом дворе. Основным
источником пылегазовых выбросов являются плавильные отделения, на долю которых
приходится до 50-80% всех выбросов твердых частиц. При выплавке 1 т жидкого металла из
вагранки выбрасывается 1000 м³ газа; концентрация пыли составляет 1-10 г/м³. Средняя
эффективность очистки выбросов при плавке чугуна в открытых вагранках для предприятий
СНГ оценивается в 90% [52].
Установлено [52], что удельный выброс ртути в чугунолитейном производстве составляет
0,001 г Hg/т литья (при эффективности пылеулавливания 90%). Ежегодно в чугунолитейных
цехах российских предприятий производится порядка 9-10 млн. т литья. Таким образом, в
целом для страны эмиссия ртути может быть оценена в 9-10 кг/год.
Эмиссия ртути при производстве стали
Производство стали в России осуществляется кислородно-конвертерным процессом
(около 63% общего объема производства), электродуговой плавкой (около 14%) и
мартеновским процессом (около 24%) [317]. Таким образом, можно считать, что в 2001 г. в
России примерно 8 млн. т стали произведено электродуговой плавкой, 37 млн. т – кислородно-
конвертерным процессом , 14 млн. т – мартеновским процессом.
Данные об удельных выбросах ртути при производстве стали на отечественных
предприятиях отсутствуют. Белорусские исследователи на основе экспериментальных работ,
проведенных на Белорусском металлургическом комбинате, установили, что в пыли
электросталеплавильных печей концентрации ртути (из рукавного фильтра) варьировались в
пределах 2,241-15,333 мг/кг (среднее – 8,446 мг/кг) [52]. Удельная эмиссия ртути с учетом
неорганизованных выбросов при производстве стали в электродуговых печах в странах СНГ
оценивается авторами цитируемой работы в 0,012 г Hg/т стали, без учета неорганизованных
выбросов – 0,007 г Hg/т стали. Таким образом, общая эмиссия ртути в ходе этого производства
может быть оценена в целом для всей России (в 2001 г.) примерно в 98 кг ртути.
Относительно высокие концентрации ртути в пыли и повышенная эмиссия ее
объясняются широким использованием в качестве исходного сырья для
электросталеплавильного производства металлического лома, в составе которого присутствуют
материалы, содержащие ртуть. Для повышения содержания углерода в шихте применят чугун,
кокс и электродный бой. Легирование стали и раскисление осуществляются с помощью
стандартных ферросплавов и легирующих добавок.
По данным [52], в мартеновской пыли (завод “Запорожсталь”, Украина) содержание
ртути составляло 0,098 мг/кг, что практически на два порядка меньше, нежели в пыли
электросталеплавильных печей. С определенной долей условности можно предположить, что
удельные выбросы ртути при производстве стали мартеновским и кислородно-конвертерным
способами не превышают аналогичный показатель для чугунолитейного производства, т. е.
составляют порядка 0,001 г Hg/т стали. Отсюда следует, что эмиссия ртути при производстве
стали указанными процессами в целом для России в 2001 г. составила примерно 51 кг.
Таким образом, общая эмиссия ртути в атмосферу при производстве стали в России в
2001 г. может быть оценена в 149 кг (0,15 т).
5 Оборот ртути при переработке отходов
5.1 Производство вторичной ртути
5.1.1 Ртутьсодержащие отходы
5.1.2 ЗАО “Научно-производственное предприятие
“Кубаньцветмет”
5.1.3 ООО “Мерком”
5.2 Оборот ртути с твердыми отходами
5.2.1 Образование твердых ртутьсодержащих отходов в России
5.2.2 Ртуть в промышленных отходах и отходах энергетики
5.2.3 Ртуть в твердых бытовых отходах
5.2.4 Ртуть в отходах медицинских учреждений
5.3 Ртуть в сточных водах
5.1 Производство вторичной ртути
5.1.1 Ртутьсодержащие отходы
Опубликованные в литературе данные о количестве образовавшихся к настоящему
времени на территории России ртутьсодержащих отходов (главным образом, промышленных)
свидетельствуют о том, что объемы последних очень велики.
Так, по оценкам [121, 198], общая масса таких отходов составляет 1,1 млн. т, причем
основная часть их (58% по массе) отличается содержаниями ртути в 10-30 мг/кг, около 30% -
содержат ртуть в количестве более 5000 мг/кг, примерно 12% - характеризуются
концентрациями металла в 100-5000 мг/кг. По другим сведениям [365], в России накоплено
750000 т ртутьсодержащих отходов, а по данным [96], - около 650 тыс. т (с содержанием ртути
от 200 до 750000 мг/кг), причем ежегодно образуется еще около 11 тыс. т. Наиболее
значительными объемами складированных ртутьсодержащих отходов и, соответственно,
высокими уровнями загрязнения среды обитания ртутью отличаются регионы страны, где
расположены крупные предприятия цветной металлургии, химической, целлюлозо-бумажной и
золотодобывающей промышленности.
Например, в районе Кирово-Чепецкого химического комбината (г. Кирово-Чепецк,
Пермская область) на временных свалках и полигоне глубинного захоронения размещено 409
тыс. т ртутьсодержащих отходов [218]. В Иркутской области в почвах промышленных
предприятий, производящих хлор и каустик, аккумулировано более 1000 т ртути и еще более
2000 т металла находится в шламонакопителях [85]. В прибрежной части устья р. Сев. Двины
недавно было захоронено 3,2 тыс. т ртутьсодержащих отходов Архангельского ЦБК, а на
полигоне Красный Бор (Ленинградская область) размещено более 100 т ртутьсодержащих
отходов [365]. На территории бывшего Амурского целлюлозо-картонного комбината (г.
Амурск, Хабаровский край) в контейнерах и на открытых площадках складировано порядка
300-500 т ртутьсодержащих шламов [378, 369]. По другим сведениям [206], на заброшенных
складах указанного комбината размещено 4400 т ртутьсодержащих отходов.
На территории российских предприятий цветной металлургии в конце 1990-х г.г.
размещалось более 63 тыс. т шламов, содержащих около 155 т ртути [198]. В Северной Осетии
(на полигонах площадью 250 га) к настоящему времени накоплено около 9 млн. т хвостов
обогащения Мизурской и Фиагдонской обогатительных фабрик и отходов металлургических
заводов “Электроцинк” и “Победит” (г. Владикавказ), в которых масса ртути оценивается в 110
т [252]. На территории Челябинского электролитного цинкового завода хранится 40 т ртутно-
селенового шлама [362].
Значительные объемы ртутьсодержащих отходов размещены в окрестностях
золотоизвлекательных фабрик. Например, в хвостохранилищах Семеновской фабрики (Южный
Урал) общая масса ртути составляет около 60 т [174]. В пос. Соловьевске (Тындинский район,
Амурская область) в районе шлихообогатительной установки складировано около 15 тыс. м³
ртутьсодержащих отходы [376], а в районе пос. Токур (Амурская область) в необслуживаемых
хранилищах размещено от 30 до 40 т ртути [54].
В России, согласно .Бизнес-книгам. и рекламным изданиям последних лет, известно
несколько предприятий, в той или иной мере занимающихся рафинированием отработанной
(“черновой”) ртути и переработкой промышленных ртутьсодержащих отходов. Однако
только два из них работают достаточно полномасштабно и регулярно поставляют на
внутренний рынок вторичную ртуть и ее соединения: это - ЗАО “НПП “Кубаньцветмет” и
ООО “Мерком”[8].
5.1.2 ЗАО .Научно-производственное предприятие .Кубаньцветмет.
ЗАО “НПП “Кубаньцветмет” расположено в пос. Холмский Абинского района
Краснодарского края. В 1998 г. ЗАО “Кубаньцветмет” в рамках Федеральной целевой
программы .Отходы. осуществило (за счет собственных средств) ремонтно-восстановительные
работы на металлургическом заводе, ранее принадлежавшего ООО “Краснодарский рудник”, и
разработало комплект технологических инструкций, регламентирующих процессы переработки
ртутьсодержащих отходов, рафинирования ртути и производства ртутных соединений.
В свое время “Краснодарский рудник” функционировал главным образом на базе
Сахалинского месторождения ртути (кварц-диккит-киноварного типа), расположенного
недалеко от пос. Холмский. В 1974-1992 г.г. из руд указанного месторождения было
произведено около 500 т металлической ртути. В 1990 г. подземная часть Сахалинского
месторождения (по причине экономической нецелесообразности ее разработки) была
законсервирована; в 1993 г. - прекращены работы на карьере, отрабатывавшем
приповерхностную часть месторождения. В 1993-1995 г.г. на металлургическом заводе
“Краснодарского рудника” осуществлялась переработка ранее добытых руд (получено около 30
т ртути), а начиная с 1992 г. эпизодически производился выпуск вторичной ртути (из
ртутьсодержащих отходов); в период с 1992 по 2001 г. здесь было получено более 98 т
вторичной ртути (в том числе около 65 т в 1999-2001 г.г.).
В настоящее время в сфере обращения с ртутьсодержащими отходами ЗАО
“Кубаньцветмет” осуществляет:
- переработку различных ртутьсодержащих промышленных отходов;
- переработку загрязненных ртутью почвогрунтов и строительных отходов;
- утилизацию ртутьсодержащего концентрата люминофора;
- демеркуризацию использованных ртутных ламп;
- утилизацию использованных и бракованных приборов с ртутным наполнением;
- рафинирование некондиционной (отработанной, черновой) металлической ртути;
- производство различных соединений ртути;
- получение особо чистой металлической ртути.
Деятельность ЗАО “Кубаньцветмет” предусматривает транспортировку отходов от мест
их образования (размещения) в специальных металлических контейнерах сортировку каждой
партии отходов с выделением групп материалов, пригодных для переработки или
обезвреживания в технологических аппаратах с извлечением товарной ртути, производство
соединений ртути, группировку образующихся в ходе собственной деятельности отходов с
целью их последующего безопасного захоронения и/или вторичного использования.
Технологические схемы переработки ртутьсодержащих отходов, используемые на ЗАО
“Кубаньцветмет”, позволяют рассматривать поступающие на утилизацию отходы как
своеобразное сырье, поскольку в большинстве случаев они являются основой для получения
товарных продуктов, а образующиеся в ходе их переработки побочные продукты, в свою
очередь, используются в качестве вторичного сырья в других производствах.
Технологические и производственные операции осуществляются с соблюдением условий
и требований нормативно-технических и санитарно-гигиенических документов [76-80, 155, 157,
244-246] и Технологических инструкций [285-290].
Деятельность предприятия также регламентируется:
- лицензией на право осуществления деятельности по обращению с опасными (в том
числе, ртутьсодержащими) отходами (сбор, использование, обезвреживание,
РФ;
- лицензией на право осуществления деятельности по заготовке, переработке и
реализации лома цветных металлов, выданной Комитетом по лицензированию
Краснодарского края;
- лицензией на право эксплуатации производственных объектов, на которых получают
расплавы черных и цветных металлов и сплавы на их основе, выданной Федеральным горным и
промышленным надзором России;
- лицензией на право осуществления перевозок грузов автотранспортом по Российской
Федерации, выданной Министерством транспорта РФ.
Химико-аналитическая лаборатория ЗАО “Кубаньцветмет” имеет Аттестат
(Сертификат) аккредитации, выданный Государственным комитетом РФ по стандартизации
и метрологии.
В структуре предприятия функционируют экологическая служба, отдел охраны труда и
техники безопасности, а также участок технического контроля переработки сырья.
В ходе переработки ртутьсодержащих отходов, получения товарной металлической ртути
и производства ртутных соединений осуществляется необходимый контроль технологических
процессов и режимов их протекания, состава перерабатываемого сырья, промежуточных
продуктов и конечной продукции, оцениваются материальный баланс производства и
технологические показатели работы печи ТВП-1 и другого оборудования.
Общая численность сотрудников ЗАО .Кубаньцветмет. составляет более 160 человек,
среди которых технологи и металлурги, имеющие многолетний опыт работы на крупнейших
ртутных и ртутно-сурьмяных комбинатах бывшего СССР.
Основные технологические схемы, оборудование и производственные операции,
связанные с переработкой ртутьсодержащего сырья
Производственная инфраструктура ЗАО “Кубаньцветмет” включает:
- административно-производственную базу (площадь территории около 6 га) с
примыкающим железнодорожным тупиком;
- промышленную зону (площадью около 39 га), основу которой составляют:
- металлургический завод, включающий две трубчатые вращающиеся печи, системы
газоходов и пылегазоочистки, устройства конденсации и рафинирования ртути,
ступпохранилище, отвал огарков; первая печь ТВП-1 - используется для переработки
ртутьсодержащего сырья путем его окислительного обжига с последующим выделением ртути
из газовой фазы (технологических газов); вторая печь ТВП-2 - для производства извести;
- участок по подготовке ртутьсодержащего сырья к металлургическому переделу;
- участок по производству соединений ртути;
- участок по производству особо чистой ртути (4 установки, в которых используется
многократная дистилляция с электроразрядной очисткой);
- участок демеркуризации трубчатых люминесцентных ламп;
- участок по утилизации ртутных ламп высокого давления;
- участок по утилизации металлических приборов с ртутным заполнением;
- участок по утилизации стеклянных приборов с ртутным заполнением;
- участок по обслуживанию и ремонту технологического оборудования;
- участок технического контроля переработки ртутьсодержащего сырья;
- химико-аналитическая лаборатория;
- склад готовой продукции.
Годовая производительность печи ТВП-1 (по сырью) составляет 36 тыс. т, установки по
демеркуризации трубчатых ртутных ламп - более 1 млн. шт., по очистке некондиционной
(отработанной) ртути - 240 т товарного металла, участка по производству соединений ртути -
30 т (в виде товарной продукции), установок по получению особо чистой ртути - 15 т металла.
ЗАО “Кубаньцветмет” располагает необходимыми оборудованием и технологиями для
обезвреживания и утилизации следующих видов ртутьсодержащих отходы производства и
потребление, которые по особенностям и условиям их переработки объединяются в несколько
групп (табл. 5.1). Основная масса отходов перерабатывается в трубчатой вращающейся печи ТВП-
1.
Конструкция трубчатой вращающейся печи
Печь ТВП-1 представляет собой металлический цилиндр (корпус) 6 диаметром 1,6 м и
длиной 14 м, установленный с уклоном 3-4° и футерованный огнеупорным кирпичом. Корпус
печи опирается бандажами 5 на ролики 13, на которых при помощи приводного механизма 14
он вращается со скоростью 0,6-2 об/мин, регулируемой с помощью 4-х скоростного
электродвигателя (рис. 5.1). В нижней части корпус примыкает к топочной камере 4, в верхней
- к пылевой камере 8. Камеры представляют собой металлические каркасы, футерованные
внутри огнеупорным кирпичом и имеющие проемы для подсоединения корпуса печи.
Топочная камера установлена над бункером огарков (обожженного сырья) 1. В ней через
форсунку 2 сжигается топливо (природный газ, расход которого составляет 26,6 м³ на 1 т
сырья), причем факел пламени поступает по центру в корпус печи. Верхняя (пылевая) камера
служит для сопряжения вращающегося корпуса печи со стационарным газоходом. Через проем
в торцовой стенке пылевой камеры в корпус пропущена труба питателя сырья 11, при помощи
которого сырье вводят в печь. Питатель установлен между бункером 10 сырья и печью. Печь
работает на противоточном режиме: подаваемое в печь сырье при вращении корпуса
перемещается от верхнего конца к нижнему, а газы, наоборот, движутся от топочной камеры к
верхнему концу корпуса и отводятся через верхнюю (пылевую) камеру 8 в газоход 9, по
которому поступают на очистку от пыли. При прохождении газов из печи в газоход через
пылевую камеру в последней оседает наиболее крупная пыль, вынесенная газовым потоком из
печи. В целях уменьшения выноса пыли из печи в газоходную систему в печи создается
минимальное разряжение, из-за чего в системе возникает опасность утечки технологических
газов через сопряжения между вращающимся корпусом печи и стационарными камерами. Для
предотвращения утечки газов сопряжения оборудованы особыми уплотнениями 12.
Таблица 5.1 Виды перерабатываемых ЗАО “Кубаньцветмет” ртутьсодержащих отходов
Груп- па |
Вид отходов |
Основное оборудование |
Основные поставщики отходов в 2000-2002 г.г. |
1 |
Отработанный катализатор (отходы производства винилхлорида) |
Трубчатая вращающаяся печь ТВП-1 |
ОАО “Химпром” (г. Волгоград), ОАО “Пласткард” (г. Волгоград), НАК “Азот” (г. Новомосковск) |
1 |
Шлам производства 1-аминоантрахинона |
Трубчатая вращающаяся печь ТВП-1 |
ОАО “Химпром” (г. Новочебоксарск, Республика Чувашия) |
1 |
Ртутный сорбент (активированный уголь марки КПР и т. п.) |
Трубчатая вращающаяся печь ТВП-1 |
ОАО “Синтез” (г. Дзержинск), ОАО “Лисма” (г. Саранск), ЭП “Меркурий” (г. С.-Петербург), Химкомбинат им. Константинова (г. Кирово-Чепецк) |
1 |
Концентрат люминофора, образующийся при утилизации ртутных ламп |
Трубчатая вращающаяся печь ТВП-1 |
ООО “Экорецикл” (г. Ногинск, Московская обл.), ООО “НПП “Экотром” (г. Москва), ОАО “Волгохимторг” (г. Волгоград) |
1 |
Графит-отходы |
Трубчатая вращающаяся печь ТВП-1 |
ОАО “Усольехимпром” (г. Усолье-Сибирское, Иркутская обл.) |
1 |
Соединения ртути |
Трубчатая вращающаяся печь ТВП-1 |
В основном организации и предприятия Краснодарского края* |
1 |
Загрязненные ртутью почвогрунты и строительные отходы |
Трубчатая вращающаяся печь ТВП-1 |
Организации (преимущественно Краснодарского края), осуществляющие демеркуризацию строений и территорий** |
2 |
Гальванические элементы (отработанные и брак) |
Трубчатая вращающаяся печь ТВП-1 |
ОАО “Энергия” (г. Елец), ГП “Сигнал” (г. Челябинск) |
3 |
Трубчатые люминесцентные лампы |
Установка “Экотром-2” |
Предприятия и организации Краснодарского края |
4 |
Ртутные лампы высокого давления (типа ДРЛ) |
По принятой схеме |
Предприятия и организации Краснодарского края |
5 |
Металлические приборы с ртутным заполнением |
По принятой схеме |
Предприятия и организации Краснодарского края |
6 |
Стеклянные приборы с ртутным наполнением (отработанные и брак) |
По принятой схеме |
Предприятия и организации Краснодарского края |
7 |
Отработанные респираторы, использованная спецодежда, тканевые отходы фильтрования ртути |
Трубчатая вращающаяся печь ТВП-1 |
Отходы собственного производства |
8 |
Некондиционная (отработанная, черновая) металлическая ртуть |
Установка по рафинированию |
Различные организации и предприятия, в том числе Краснодарского края*** |
9 |
Пыль и шламы газоочистки |
Трубчатая вращающаяся печь ТВП-1 |
Очистка технологических газов |
10 |
Отходы картонной упаковки ртутных ламп |
Трубчатая вращающаяся печь ТВП-1 |
Организации и предприятия Краснодарского края |
* Например, в 2002 г. из Кубанской гидрогеологической мелиоративной партии поступило 217 кг
химических реактивов, содержащих ртуть.
** В 2002 г. от ООО ПАСФ “Ртутьсервис” (г. Краснодар) поступило 4,69 т ртутьсодержащего грунта.
*** В 2002 г. на переработку поступило 2775 кг некондиционной (“черновой”) ртути из Беларуси (УП
“Белцветмет”) и более 600 кг от различных предприятий Краснодарского края.
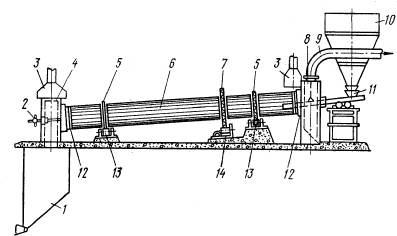
Рисунок 5,1 Схема устройства трубчатой печи:
1 - бункер для огарков; 2 - форсунка (горелка); 3 - зонты; 4 - топочная камера; 5 - бандажи; 6 - корпус печи; 7 - приводная шестерня; 8 - пылевая камера; 9 - газоход для отвода технологических газов; 10 - бункер для сырья; 11 - питатель; 12 - верхнее и нижнее уплотнения; 13 - опорные ролики; 14 - приводной механизм вращения печи
Температура перерабатываемого сырья по мере его продвижения в корпус печи
повышается, достигая максимума вблизи разгрузочного конца. Обожженное сырье (так
называемые огарки) поступает в расположенный под топочной камерой огарочный бункер, где
выдерживается определенное время, в течение которого выделяющиеся пары ртути вместе с
горячим воздухом отсасываются из бункера через топочную камеру обратно в печь. Для
предотвращения возможных потерь паров ртути конструкция соединения печи, топочной
камеры и бункера для огарков усиливаются путем установки нижнего уплотнения.
Общая схема пирометаллургического получения ртути
Металлургический передел сырья осуществляется по обычной схеме ртутного
производства (обжиг сырья - конденсация паров ртути - переработка ртутной ступпы), но
модернизированной специалистами ЗАО “Кубаньцветмет” для условий переработки тех или
иных групп ртутьсодержащих отходов (рис. 5.2).
Перед обжигом в печи сырье загружается в приемный бункер, откуда ленточным
питателем (длина ленты 3 м, ширина – 0,8 м, производительность 40 т/час) подается на
дробление (до кусков размерами 50-70 мм), которое осуществляется на щековой дробилке СМ-
741 (размер загрузочной щели 6 х 9 см; производительность дробилки - 40 т/час).
Образующаяся при этом пыль удаляется местной системой аспирации, накаливается в емкости
с водой и затем направляется на повторный обжиг в печь ТВП-1. Подготовленное сырье
ленточным конвейером (длина ленты 38,96 м, ширина – 0,65 м) направляется в расходный
бункер, откуда с помощью ленточного питателя (длина 1,8 м, ширина ленты 0,8 м,
производительность до 6 т/час) подается в печь ТВП-1.
Сырье подвергается обжигу при температуре не менее 500°С, при которой содержащаяся
в нем ртуть возгоняется и переходит в парообразное состояние (в технологические газы). Время
пребывания материала в печи составляет в среднем 1,5 часа. При необходимости
продолжительность обжига регулируется скоростью вращения печи. Процесс обжига
проводится в окислительной среде, т. е. в присутствие свободного кислорода. Окислительная
атмосфера в печи поддерживается за счет 30%-го избытка воздуха, необходимого для сжигания
топлива. Если в сырье присутствуют другие летучие элементы, то они также нацело или
частично возгоняются, как и влага, содержащаяся в обжигаемом сырье. Кроме того, в газы в
определенном количестве переходят пыль, газовые продукты, образующиеся при сжигании
топлива, а также избыток кислорода и азот, поступающие в технологический процесс с
воздухом.
Обожженное сырье, или огарки, имеющие на выходе из печи температуру порядка 500°С,
поступают в огарочный бункер. Выгрузка горячих огарков сопровождается образованием
восходящих потоков нагретого воздуха, а также пылением, для снижения которого огарки
обычно 4-6 часов выдерживаются в бункере, где охлаждаются до температуры ниже 180°С.
Выделяющаяся в этот период из огарков ртуть успевает поступить обратно в печь, а пыление
огарков значительно снижается. Опыт показывает, что в большинстве случаев содержание
ртути в огарках не превышает 25-26 мг/кг. Удаление огарков в отвалы осуществляется
самосвалами.
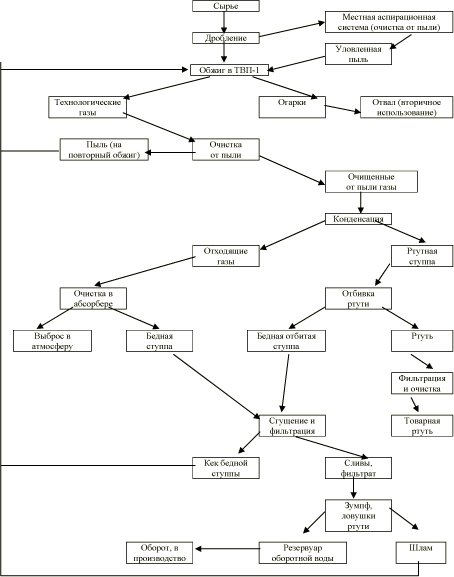
Рисунок 5.2 Принципиальная схема пирометаллургического процесса получения ртути.
Технологические газы, образующиеся при обжиге сырья и имеющие на выходе из печи
температуру не менее 500°С, по специальному газоходу поступают на групповой циклон, где
подвергаются очистке от пыли. При хорошо налаженной работе циклон улавливает до 90%
пыли, содержащейся в газах, которая затем возвращается на повторный обжиг. Все газоходы от
печи к аппаратам очистки от пыли, сами аппараты, а также газоходы от них оснащены
теплоизоляционными жаростойкими материалами.
После очистки от пыли технологические газы, несущие пары ртути, поступают на
охлаждение в трубчатый конденсатор-холодильник, где охлаждаются до 30оС и превращаются
в жидкость (рис. 5.3). Общий принцип действия конденсатора заключается в следующем.
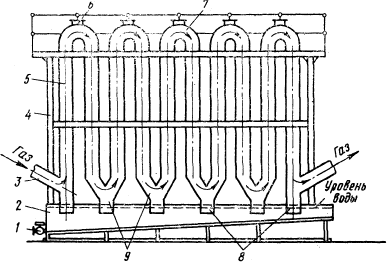
Рисунок 5.3 Схема устройства конденсатора-холодильника для конденсации ртути из технологических газов
1 - кран; 2 - приемник; 3 - газоход; 4 - рамная конструкция; 5 - металлические трубы (стояки); 6 - верхние люки (крышки); 7 - патрубки; 8 - нижние концы тройников (спуски); 9 - тройники
Очищенные от пыли технологические газы поступают по газоходу 3, из которого следуют
по ниткам конденсатора. Нитка конденсатора состоит из вертикальных металлических труб
(стояков) 5, укрепленных на рамной конструкции 4, установленных попарно и соединенных
сверху П-образными патрубками 7 (коленами). Внизу каждая пара соединена с соседней при
помощи тройников 9. Нижние концы тройников (спуски) 8 погружены в воду, наполняющую
приемник 2, установленный снизу вдоль всей нитки. Технологический газ, введенный в первый
стояк, под влиянием разрежения, создаваемого вентилятором, установленным за
конденсатором, поочередно проходит по системе труб, поднимаясь и опускаясь; затем
переходит в соседнюю пару и так до конца нитки. Для ускорения охлаждения технологических
газов в конденсаторе последние в ряду стояки орошаются водой, подаваемой через
разбрызгиватели, установленные в верхней части стояков. Кроме того, в конденсатор подается
определенное количество воды, что способствует более эффективному осаждению пыли,
содержащейся в технологических газах.
В процессе конденсации, начинающейся в пристенном слое, образуются капли ртути,
наиболее крупные из которых стекают в особые приемники (корыта конденсатора),
расположенные в нижней части охлаждающего аппарата, часть капель оседает на его
внутренних стенках, а наиболее мелкие капли (аэрозоли) покидают конденсатор с уходящим из
конденсатора потоком газов. В конденсаторе улавливается не только металлическая ртуть, но и
ее соединения, сконденсировавшиеся здесь вода, оксиды некоторых химических элементов, а
также существенная часть не уловленной ранее пыли. В результате в корытах конденсатора
собирается не чистая ртуть, а так называемая ступпа, представляющая собой смесь
металлической ртути, ее соединений, пыли, частиц несгоревшего топлива, воды. Количество
металлической ртути в ступпе колеблется от 20 до 80% и зависит от ряда факторов: содержания
металла в исходном сырье, коэффициента полезного действия системы пылеулавливания и др.
Образующаяся ступпа направляется (при помощи насоса) на так называемую отбивку
ртути, которая осуществляется в гидроциклоне, где под действием центробежных сил
происходит коагуляция и отделение (отбивка) металлической ртути от влаги и более легких
твердых продуктов обжига. В ходе отбивки металлической ртути образуется так называемая
бедная ступпа, которая поступает в сгуститель и затем на вакуумный фильтр, откуда
обезвоженная масса в виде кека бедной ступпы (влажностью 12-15%) направляется (после
шихтовки с известью) в печь на повторный обжиг с целью доизвлечения ртути.
Технологические газы, покидающие конденсатор-холодильник (отходящие, выбросные
газы), всегда содержат некоторое количество паров ртути, которое соответствует равновесному
содержанию, обусловленному температурой газов, т. е. чем она выше, тем больше в них
содержится ртути (табл. 5.2). Именно поэтому всегда стремятся охладить газы в конденсаторе
до возможно более низких температур (обычно ниже 30оС). Помимо паров ртути, в выбросных
газах, отводимых из конденсатора, присутствуют аэрозоли металлической ртути, пары воды,
тонкие частицы пыли, сажа и некоторые другие примеси.
Таблица 5.2 Содержание ртути в насыщенном паре в зависимости от температуры [157]
Температура, °С |
10 |
20 |
30 |
40 |
50 |
60 |
70 |
80 |
90 |
100 |
Ртуть, мг/м³ |
5,64 |
13,38 |
29,81 |
62,8 |
126,6 |
234,9 |
452 |
807 |
1396 |
2338 |
Отходящие (выбросные) газы поступают на дополнительную (санитарную) очистку,
которая осуществляется в двухступенчатом абсорбере. Первая ступень представляет собой
аппарат распылительного типа (АРТ), где улавливается основная масса пыли и частично ртуть.
Затем газы поступают в аппарат с шаровой насадкой (АШН), где в качестве орошающей
жидкости используется щелочной (известковый) раствор. Уловленная абсорберами пыль
(бедная ступпа) также направляется на повторный обжиг в печь.
Очищенные в абсорбере газы выводятся в атмосферу через заводскую трубу высотой 30
м (с учетом рельефа местности ее расположения - более 60 м), что обеспечивает необходимое
разбавление их воздухом. Обычно на каждую тонну переработанного сырья образуется в
среднем до 2400 м³ отходящих газов; при нормальных условиях протекания технологического
процесса содержание ртути в них составляет не более 25,4 мг/м³, т. е. в настоящее время
удельный выброс ртути в атмосферу на 1 т перерабатываемого сырья для печи ТВП-1
составляет 61 г. Предельно допустимый выброс ртути для металлургического завода ЗАО
.Кубаньцветмет. установлен в 80 кг в год. По данным [162], содержание пыли (после очистки)
в выбросных газах ртутного производства (переработка руды) обычно не превышает 5-6 мг/м³.
На металлургическом заводе ЗАО “Кубаньцветмет” применяется оборотная система
водоснабжения с ежедневной подпиткой (15 м³/сут. воды на технологические нужды и 5 м³/сут.
- на хозяйственно-бытовые нужды, которая поступает из специального металлического
резервуара). Производственные воды, участвующие в обороте, поступают в зумпф, проходят
через ртутные ловушки, затем идут в резервуар оборотной воды, откуда возвращаются в
технологический процесс. Образующийся шлам направляется на обжиг в ТВП-1.
Хозяйственно-бытовые стоки удаляются в канализацию.
Рафинирование ртути
В результате отбивки получается металлическая ртуть, которую затем фильтруют через
хлопчатобумажный бельтинг и шинельное сукно. Как правило, полученная таким образом
ртуть без какой-либо дополнительной обработки представляет собой товарный металл марки
Р3, который используется в производстве ртутных соединений и/или поставляется
потребителям. Необходимая дальнейшая очистка ртути осуществляется на установке по
рафинированию ртути, изготовленной специалистами ЗАО “Кубаньцветмет” и основанной на
использовании гидрохимического способа.
На очистку 1 т ртути расходуется 0,05 кг хлопчатобумажного бельтинга и 0,05 кг
шинельного сукна. Образующиеся после очистки и рафинирования ртути мягкие отходы (около
3 кг в год с содержанием ртути до 2%) накапливаются в кислотостойких, герметичных
емкостях и затем сжигаются в ТВП-1.
Состав, условия приемки, анализа, транспортировки и хранения ртути определяются
ГОСТ 4658-73, который распространяется на металл, предназначенный для производства
полупроводниковых материалов, для использования в вакуум-электротехнике, при
производстве контрольно-измерительных приборов, ртутно-цинковых источников тока,
различных реактивов и фармацевтических препаратов, а также в химической,
металлургической и в других отраслях промышленности (табл. 5.3).
В частности, ртуть марок Р1, Р2 и Р3 разливают в специальные стальные баллоны (марки
ЭР-2,75, изготавливаются Первоуральским новотрубным заводом), вмещающие по 34,5 кг
металла. Каждый баллон закрывают плотно завинчивающейся пробкой с прокладкой из
фторопластового материала толщиной не менее 0,15 мм. При длительном хранении баллоны
пломбируют.
Таблица 5.3 Химический состав ртути [80]
Требования к составу |
Марка ртути |
Р0 |
Р1 |
Р2 |
Р3 |
Ртуть, %, не менее |
99,9997 |
99,999 |
99,99 |
99,9 |
Нелетучий остаток, %, не более |
0,0003 |
0,001 |
0,01 |
0,1 |
Ртуть марки Р0 разливают в баллоны из толстостенного стекла, вмещающие 5 кг металла.
Розлив ртути марок Р1 и Р2 допускается осуществлять также в баллоны из толстостенного
стекла, которые закрывают металлической крышкой с прокладкой из пластиката. Ртуть марки
Р1, предназначенная для медицинских целей, разливают во флаконы, вмещающие 50 г металла
и которые закрывают полиэтиленовыми пробкой и крышкой. Каждый флакон помещают в
полимерную банку вместимостью 30 см³ и уплотняют алигнином. Гарантийный срок хранения
ртути марок Р1 и Р2 - два года, ртути марки Р0 - три года, марки Р3 - не ограничен.
Условия и особенности переработки ртутьсодержащих отходов
Технологическая схема переработки каждой группы ртутьсодержащих отходов имеет
свои особенности, зависящие от источника образования отходов, их вещественного состава и
консистенции (см. табл. 5.1).
Переработка отходов 1-й группы
Переработка отходов данной группы, в которую входят отработанный ртутный
катализатор (отходы производства винилхлорида), сорбенты (активированный уголь марки
КПР и т. п.), соединения ртути, шлам производства 1-аминоантрахинона, загрязненные ртутью
почвогрунты и строительные отходы, графит-отходы, концентрат люминофора и т. п., в общем
случае осуществляется по единой технологической схеме, которая включает следующие
основные технологические операции:
- шихтовка сырья, т. е. добавление к нему извести с целью нейтрализации кислотного
остатка в соотношении по массе 1,0:0,8 (сырье : известь);
- нагрев шихты в трубчатой вращающейся печи до температуры не менее 500°С
топочными газами для перевода ртути, содержащейся в исходном сырье, в газовую фазу;
- обеспыливание парогазовой смеси в групповом циклоне;
- конденсация ртути в холодильнике-конденсаторе;
- накопление ртутной ступпы в корытах конденсаторов;
- отбивка металлической ртути в гидроциклоне;
- очистка ртути от примесей с целью получения товарной металла;
- очистка отходящих (выбросных) газов от ртути в абсорбере;
- выгрузка огарков из печи в огарочный бункер (выход огарков составляет 94-96% от
массы обжигаемой шихты);
- вывоз огарков на огарочный отвал или на участок переработки свинцового лома в
отражательной печи, где они применяются в качестве восстановителя.
На рис. 5.4 в качестве примера приводится схема переработки отходов производства
винилхлорида (отработанного ртутного катализатора), среднее содержание ртути в которых
составляет 3000 мг/кг (30 кг металла в 1 т отходов).
С 2003 г. огарки, образующиеся при обжиге ртутного катализатора, шлама производства
1-аминоантрахинона и графит-отходов, предполагается передавать предприятиям,
осуществляющим металлургический передел лома цветных и черных металлов, где они будут
использоваться в качестве восстановителя и флюса. Огарки от обжига грунтов и строительных
материалов будут применяться при планировке дорог IV-V классов.
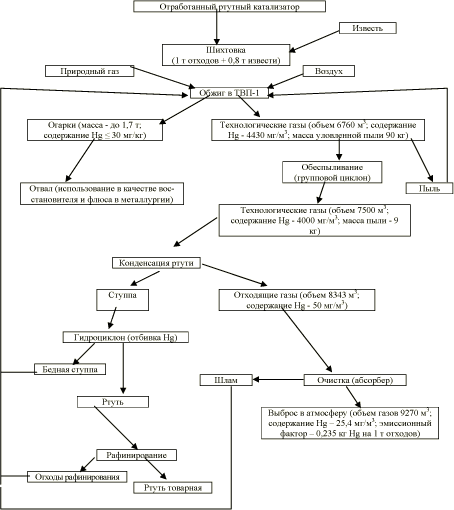
Рисунок 5.4 Схема переработки отходов производства винилхлорида (отработанного катализатора) в ТВП-1.
С 2003 г. на ЗАО “Кубаньцветмет” планируется ежегодная переработка 600 т отходов
производства винилхлорида, 50 т сорбентов ртути на основе активированных углей, 50 т
ртутьсодержащих почвогрунтов и строительных отходов, 60 т графит-отходов, 30 т шламов
производства 1-аминоантрахинона. Рассмотренная технологическая схема может
использоваться также для переработки отходов производства витамина В2 (шлам активного
угля), шламов хлорно-щелочных заводов и других близких по условиям образования, составу и
консистенции видов вторичного ртутьсодержащего сырья.
Утилизация гальванических элементов
Утилизация использованных и бракованных гальванических (ртутно-цинковых и
ртутьсодержащих) элементов и батарей производится по той же технологической схеме - обжиг
сырья в печи ТВП-1, но с раздельной загрузкой либо ртутных, либо ртутьсодержащих
элементов и батарей и без шихтовки сырья известью (рис. 5.5).
Отходами данного производственного процесса являются огарки (обожженные корпуса
элементов), содержащие около 45% железа и 55% цинка; концентрация в них ртути не
превышает 0,0002% (по массе). Огарки затариваются в металлические барабаны и реализуются
организациям, специализирующихся на сборе и переработке лома цветных и черных металлов.
Масса образующихся огарков составляла порядка 10-20 т/год.
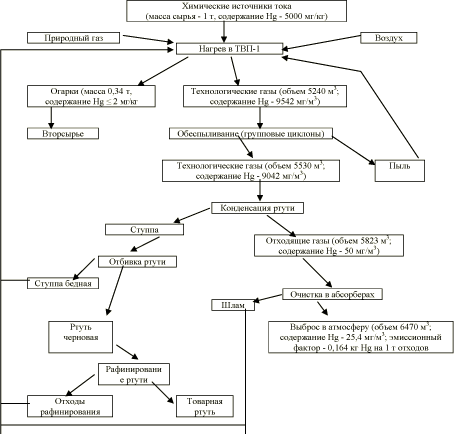
Рисунок 5.5 Схема утилизации химических источников тока в ТВП-1.
Демеркуризация трубчатых люминесцентных ламп
Переработка трубчатых люминесцентных ламп (типа ЛБ и т. п.), которая осуществляется
на вибропневматической установке “Экотром-2”, включает их механическое разрушение и
выделение под разряжением фракций стекломассы (стеклобоя), алюминиевых цоколей и
люминофора - основного концентратора ртути. Характеристика основных узлов установки
приведена в табл. 5.4, а технологическая схема процесса - на рис. 5.6. Перерабатываемые
изделия в среднем содержат (по массе): стекло 94,61%, алюминиевые цоколи – 2,39%,
люминофор - 3%, концентрация ртути в котором составляет 34400 мг/кг.
Таблица 5.4 Основные технические характеристики установки “Экотром-2”
Наименование аппарата и его характеристика |
Наименование и состав среды |
Расход на одну операцию |
Аппарат демеркуризации, 1200 ламп/час |
Измельченные компоненты ламп |
360 кг/час |
Циклон диметром 200 мм, длиной 800 мм |
Воздух, содержащий люминофор и стеклянную пыль |
360 нм³/час |
Рукавный фильтр, 9 рукавов, диаметр 180 мм, длина 2000 мм |
Воздух, содержащий люминофор и стеклянную пыль |
360 нм³/час |
Кассетный фильтр, 4 фильтра |
Воздух, содержащий люминофор и стеклянную пыль |
360 нм³/час |
Сборники люминофора, объем 50 л, диаметр 350 мм |
Ртутьсодержащий люминофор |
40 л |
Адсорбер рабочий, диаметр 800 мм, сорбент, содержащий активированный уголь |
Воздух, содержащий пары ртути |
360 нм³/час |
Емкость для сбора цоколей, объем 0,06 м³ |
Алюминиевые цоколи |
8,4 кг/час |
Бункер для сбора стеклобоя, объем 0,12 м³ |
Стеклобой |
10 м³ |
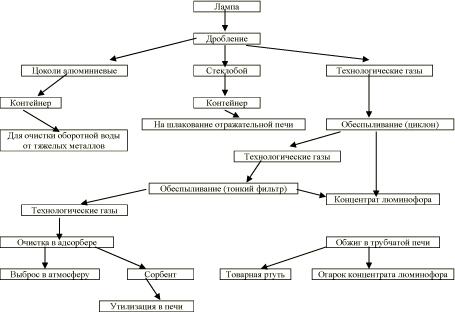
Рисунок 5.6 Схема утилизации трубчатых люминесцентных ламп (типа ЛБ, ЛД и т. п.).
Отходами демеркуризации трубчатых люминесцентных ламп являются:
- стеклобой (стекломасса), выход которого составляет 92% от массы перерабатываемого
изделия; он содержит не более 0,2% ртути, содержащейся в перерабатываемых изделий
(удельная концентрация ртути в стекломассе - не более 2,1 мг/кг);
- алюминиевые цоколи (их выход 2,33%);
- концентрат люминофора (выход 5,67%) с содержанием ртути (по массе) до 3,44%;
- выбросы (после очистки) отходящих газов в атмосферу (на 1 т утилизируемых изделий
выбрасывается порядка 0,69 мг ртути, или не более 0,07% от общего ее количества,
содержащегося в перерабатываемых лампах).
Стекломасса накапливается в металлических контейнерах и затем используется в
свинцовом производстве (для ошлакования в отражательной печи). Алюминиевые цоколи
люминесцентных ламп применяются в технологическом процессе пирометаллургического
передела ртутьсодержащего сырья в качестве восстановителя при очистке оборотной
технологической воды от растворимых солей тяжелых металлов. Концентрат люминофора,
получаемый при переработке ламп на установке “Экотром-2” (его образуется порядка 1 т/год),
хранится в герметичной упаковке и по мере накопления перерабатывается в трубчатой печи
ТВП-1 (вместе с поступающим от других организаций концентратом люминофора) по
рассмотренной выше схеме. Выход огарков от обжига концентрата люминофора составляет
порядка 96% от исходной массы перерабатываемого сырья; они используются для
рекультивации старых огарочных отвалов.
Утилизация ртутных ламп высокого давления
Переработка ртутных ламп высокого давления (типа ДРЛ) включает (рис. 5.7):
- разрушение колбы и накопление стекломассы (стеклобоя) с люминофором в
специальных контейнерах;
- отделение кварцевой горелки от цоколя с ножкой и раздельное их накопление в
контейнерах;
- измельчение горелок в молотковой дробилке и обжиг полученной массы в печи ТВП-1
вместе с другим ртутьсодержащим вторичным сырьем.
Отходами данного процесса являются стекломасса (используется в переработке
свинцового лома - для шлакования в отражательной печи) и лом черных и цветных металлов,
который реализуется (как вторсырье) соответствующим организациям.
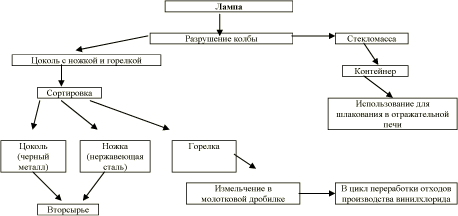
Рисунок 5.7 Схема утилизации ртутных ламп высокого давления (типа ДРЛ).
Утилизация металлических приборов с ртутным заполнением
Утилизация металлических приборов с ртутным заполнением осуществляется
следующим образом (рис. 5.8). Прибор помещается на специальный поддон; затем
механическим способом или электрогазосваркой в приборе вскрывается отсек, заполненный
металлической ртутью, которая сливается в стальной баллон. Корпуса приборов,
освобожденные таким образом от металлической ртути, помещаются в печь ТВП-1 и
прокаливаются в течение 3-4 час. при температуре не менее 500°С. Ртуть, сорбированная на
стенках корпусов, испаряется и вместе с технологическими газами поступает в систему
конденсации ТВП-1. Затем корпус прибора (содержание ртути ≤1 мг/кг) подвергается разборке
по видам металлолома.
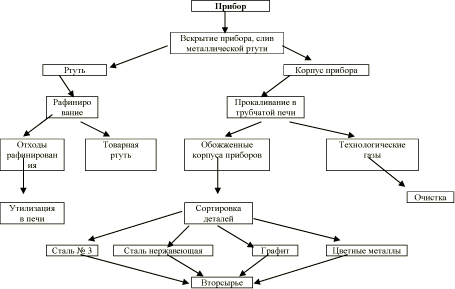
Рисунок 5.8 Схема утилизации металлических приборов с ртутным заполнением.
Утилизация стеклянных приборов с ртутным заполнением
Утилизация стеклянных приборов, содержащих металлическую ртуть (в среднем до 3,7%
от общей массы изделий), осуществляется следующим образом (рис. 5.9):
- разрушение стеклянной колбы (корпуса) прибора в ванне под слоем воды;
- слив металлической ртути в ванну;
- отделение металлических деталей;
- слив металлической ртути из ванны в специальную емкость;
- обжиг стеклобоя с целью отгонки остатков ртути;
- рафинирование металла по принятой на предприятии технологической схеме.
Степень извлечения ртути в данном технологическом процессе составляет более 99,9%.
Отходами процесса являются стекломасса (ее выход - порядка 89% от общей массы
утилизируемых изделий) и металлические фрагменты (до 6,53% от массы утилизируемых
изделий). Стекломасса применяется в свинцовом производстве (идет на ошлакование
отражательной печи), а металлические фрагменты реализуются как вторсырье.
Утилизация картонной тары
Данный вид отходов образуется на участке демеркуризации ртутных ламп, которые
поступают на переработку в картонной упаковке (средняя масса одной упаковки - 20 г). При
среднегодовом объеме перерабатываемых ламп в 145 тыс. шт. масса картонных отходов
составляет примерно 2,9 т. Они накапливаются в металлическом контейнере (объем - 1 м³) и
затем сжигаются в трубчатой вращающей печи ТВП-1.
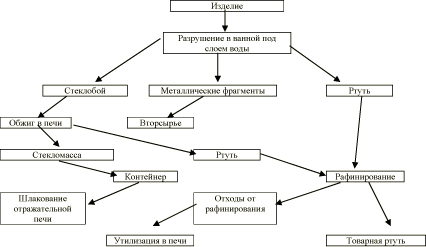
Рисунок 5.9 Схема утилизации стеклянных приборов с ртутным заполнением.
Утилизация использованных средств индивидуальной защиты и спецодежды
Отработанные респираторы (средний вес одного респиратора – 0,2 кг) и использованная
спецодежда собираются в металлический контейнер с крышкой и затем сжигаются в печи.
Ежегодно утилизируется около 580 кг отработанных респираторов и до 660 кг использованной
рабочей одежды и обуви.
Рафинирование некондиционной (отработанной) металлической ртути
Некондиционная (отработанная, черновая) ртуть, поступающая от различных
организаций, подвергается фильтрованию и очистки на установке рафинирования. Полученная
ртуть используется в производстве соединений ртути или поставляется различным
организациям и предприятиям.
Объемы переработки ртутьсодержащих отходов
В табл. 5.5 и 5,6 приведены сведения об объемах различных видов ртутьсодержащих
отходов производства и потребления, переработанных ЗАО “Кубаньцветмет” в 2001-2002 г.г., а
табл. 5.7 содержит обобщенные данные о переработке ртутьсодержащего сырья и производстве
вторичной ртути на ЗАО “Кубаньцветмет” в 1998-2002 г.г.
Таблица 5.5 Переработка ртутьсодержащих отходов, ЗАО “Кубаньцветмет”, 2001 г.
Вид отходов |
Масса отходов, кг |
Товарная Hg, кг |
Катализатор, сорбенты, шламы |
244312 |
9793 |
Некондиционная (отработанная, черновая) ртуть |
16113 |
16097 |
Ртутные лампы |
20610 |
7 |
Ртутьсодержащие приборы |
1784 |
131 |
Концентрат люминофора |
23700 |
78 |
Прочее (гальванические элементы, загрязненные ртутью строительные отходы и грунты, отходы собственного производства и др.) |
54800 |
343 |
Итого |
361319 |
26449 |
. Таблица 5.6 Переработка ртутьсодержащих отходов, ЗАО “Кубаньцветмет”, 2002 г.
Вид отходов |
Масса отходов, кг |
Товарная Hg, кг |
Некондиционная (отработанная, черновая) ртуть |
783,5 |
727 |
Ртутные лампы |
31200 |
10,5 |
Ртутьсодержащие приборы |
384 |
65,3 |
Концентрат люминофора |
59570 |
163,2 |
Прочее (гальванические элементы, реактивы, грунты и т. д.) |
2750 |
9,5 |
Итого |
94687,5 |
975,5 |
. Таблица 5.7 Переработка сырья и производство вторичной ртути ЗАО .Кубаньцветмет.
Год |
Масса отходов (всех видов), т |
Масса товарной ртути, кг |
1998 |
56,6 |
1459 |
1999 |
840,4 |
16020 |
2000 |
919,7 |
22061 |
2001 |
361,3 |
26449 |
2002 |
94,7 |
976 |
Итого |
2272,7 |
66965 |
Большая часть металлической ртути, полученной при переработке отходов производства
и потребления, использовалась в производстве ее различных соединений (марок ХЧ, ЧДА, Ч),
объемы и особенности изготовления которых рассмотрены в разделе 3.10. В 2000-2002 г.г. в
небольших количествах металлическая ртуть поставлялась (объемы поставок – по 2-4 т)
некоторым российским предприятиям (химические заводы в г. Волгограде, ОАО
“Термоприбор” в г. Клину, ОАО “Лисма’ в г. Саранске и др.). В 2003 г. порядка 150 кг
металлической ртути было отправлено на ОАО “Энергия” (г. Елец).
Производство особо чистой ртути
Как уже говорилось, ЗАО “Кубаньцветмет” располагает 4-мя установками по получению
особо чистой ртути (марок 5N, 6N и выше), основанных на использовании многократной
дистилляции металла с электроразрядной очисткой. Процессы дистилляционного
рафинирования осуществляются в аппаратах, плотно изолированных от рабочего пространства
участка. Упаковка ртути осуществляется в герметичные стеклянные ампулы, содержащие по 50
г или 75 г металла. В свое время указанная ртуть использовалась в научных исследованиях,
опытных производствах, в полупроводниковой промышленности. В последние годы заказов на
производство чистой ртути не поступало, что объясняется объективных и субъективных
причин (финансовые трудности, наличие на некоторых предприятиях собственных установок
по очистке ртути и др.).
Эмиссия ртути в ходе пирометаллургического передела сырья
В табл. 5.8 и 5,9 приведены основные показатели работы трубчатой вращающейся печи
ТВП-1 и характеристики образующихся отходов, а в табл. 5.10 дается баланс распределения
потерь ртути в ходе пирометаллургического передела ртутьсодержащего сырья. Существенное
снижение общих потерь ртути, начиная с 2000 г., обусловлено увеличением степени
пылеулавливания и переводом пыли, содержащей ртуть, в оборотные технологическое воды, с
повышением эффективности отбивки металлической ртути и с повторной переработкой ряда
промежуточных продуктов и отходов в печи. В частности, с 2000 г. внедрен обжиг
улавливаемой очистными установками пыли в печи вместе с сырьем. Определенную роль
играет и тот факт, что на переработку стали поступать отходы с более высоким содержанием
ртути. Хорошо известно, что на ртутных комбинатах практически все виды потерь ртути в ходе
технологических процессов, как правило, в значительной степени зависят от содержания ее в
исходном сырье: чем выше концентрация ртути в сырье, тем ниже ее потери [205].
Таблица 5.8 Основные показатели работы ТВП-1 металлургического завода ЗАО
“Кубаньцветмет” в 1999-2001 г.г.
Параметр |
1999 |
2000 |
2001 |
Переработано ртутьсодержащего сырья (сухая масса), кг |
840390 |
919744 |
361319 |
Количество ртути, содержащейся в сырье, кг |
16313,73 |
22302,56 |
26746,25 |
Получено металлической ртути, кг |
15803,11 |
22055 |
26625,89 |
Общие потери металла в ходе технологического процесса, кг |
510,6 |
247,6 |
120,4 |
Таблица 5.9 Характеристика отходов, образующихся при пирометаллургическом переделе
ртутьсодержащего сырья, ЗАО “Кубаньцветмет”
Год |
Огарки |
Отходящие газы |
Оборотная вода* |
Пыль циклонов** |
Масса, т |
Hg, мг/кг |
Объем, м³ |
Hg, мг/м³ |
Объем, м³ |
Hg, г/м³ |
Масса, т |
Hg, мг/кг |
1999 |
748 |
38 |
10449745 |
30,68 |
360 |
22,3 |
25 |
3400 |
2000 |
844 |
25 |
8182680 |
25,4 |
275 |
39 |
- |
- |
2001 |
129,9 |
26 |
2119487 |
24,3 |
250 |
259,4 |
- |
- |
* С ежедневной подпиткой свежей водой.
** С 2000 г. внедрен обжиг пыли в печи вместе с сырьем (непосредственно в ходе осуществления
технологического процесса).
В 2001 г. доля безвозвратных потерь ртути в ходе пирометаллургического передела сырья
составляла 46,1% (или 55,5 кг), большая часть из которых приходилась на отходящие газы,
выбрасываемых в атмосферу (42,8% или 51,5 кг). Около 65 кг ртути (53,9% общих ее потерь) в
составе оборотной воды в конечном счете возвращалось в технологической процесс.
Таблица 5.10 Распределение потерь ртути в ходе пирометаллургического передела
ртутьсодержащего сырья в печи ТВП-1, ЗАО .Кубаньцветмет.
Вид потерь |
1999 |
2000 |
2001 |
кг |
доля, % |
кг |
доля, % |
кг |
доля, % |
С огарками* |
32,3 |
6,3 |
21,1 |
8,5 |
3,4 |
2,8 |
С отходящими газами** |
320,6 |
62,8 |
207,8 |
83,9 |
51,5 |
42,8 |
С оборотной водой*** |
8 |
1,6 |
10,7 |
4,3 |
64,9 |
53,9 |
С циклонной пылью**** |
85 |
16,6 |
- |
- |
- |
|
Неучтенные потери ***** |
64,7 |
12,7 |
8 |
3,3 |
0,6 |
0,5 |
Всего потерь |
510,6 |
100 |
247,6 |
100 |
120,4 |
100 |
* Безвозвратные потери (в отвал или вторичное использование).
** Безвозвратные потери, выброс в атмосферу через трубу.
*** Возвращаются в технологический процесс.
**** С 2000 г. внедрен обжиг пыли в печи вместе с сырьем (непосредственно в ходе осуществления
технологического процесса).
Данные наблюдений показывают, что воздух большинства рабочих помещений
предприятия характеризуется периодическим появлением концентраций паров ртути,
превышающих значения максимальной ПДК (табл. 5.11). Как правило, наиболее высокие
концентрации паров ртути наблюдались в воздухе участка розлива ртути и операторной
трубчатой вращающейся печи ТВП-1. На открытой площадке, около ТВП-1, уровни паров
ртути в воздухе обычно находятся около 0,01 мг/м³, снижаясь до 0,0001-0,0003 мг/м³ на
границе санитарно-защитной зоны.
Таблица 5.11 Уровни содержания ртути в воздухе рабочих помещений и в пределах санитарно-
защитной зоны (СЗЗ) металлургического завода ЗАО “Кубаньцветмет”, 2002 г.,
мг/м³
Участок |
Среднее |
Пределы |
Количество замеров в течение года* |
Операторная трубчатой печи |
0,019 |
0,010-0,025 |
12 |
Участок розлива ртути |
0,026 |
0,023-0,028 |
13 |
Склад готовой продукции |
0,010 |
0,001-0,014 |
10 |
Химико-аналитическая лаборатория |
0,007 |
0,002-0,010 |
13 |
Механический цех |
0,010 |
0,003-0,012 |
12 |
Административно-бытовой корпус |
0,011 |
0,007-0,012 |
14 |
Открытая площадка, около ТВП-1 |
в среднем около 0,01 |
- |
На границе СЗЗ** |
0,0001-0,0003 |
- |
ПДК в рабочей зоне, среднесменная |
0,005 |
- |
ПДК в рабочей зоне, максимальная |
0,010 |
- |
ПДК в воздухе насаленных мест |
0,0003 |
- |
Типичное фон содержание |
0,000010-0,000015 |
- |
* Примерно один раз в месяц.
** Размер СЗЗ - 1000 м.
Планируемое увеличение объемов переработки ртутьсодержащих отходов, безусловно,
приведет к заметному росту выбросов ртути в среду обитания, прежде всего, с отходящими
газами. Это обусловливает необходимость:
- проведения профилактических работ по увеличению надежности работы и
герметичности основных технологических трактов трубчатой вращающейся печи ТВП-1;
- модернизации (капитального ремонта) существующей системы пылегазоочистки;
- создания системы дополнительной очистки отходящих газов от ртути, которая должна
обеспечить многократное снижение в них содержания металла (по крайней мере, на порядок по
сравнению с существующим);
- проведения работ по полномасштабной демеркуризации основных рабочих,
административных и складских помещений промышленной зоны ЗАО “Кубаньцветмет” и
территории, прилегающей непосредственно к металлургическому заводу (с необходимым
комплексом натурных ртутометрических исследований);
- организации на предприятии постоянной службы текущей демеркуризации.
5.1.3 ООО “Мерком”
ООО “Мерком” организовано в 1992 г.; оно расположено на территории НИИ приборов
(г. Лыткарино, Московская область); общая численность сотрудников составляет более 40
человек.
В сфере обращения с ртутьсодержащими отходами ООО “Мерком” осуществляет
утилизацию:
- отработанной (некондиционной, черновой) металлической ртути (сбор, перевозка,
рафинирование, получение вторичного металла);
- соединений ртути (сбор, перевозка, очистка, переработка и производство различных
соединений ртути);
- приборов с ртутным наполнением - термометров, сфигмоманометров, игнитронов,
нормальных элементов, ртутных контактов и др. (сбор приборов, изъятие и очистка
металлической ртути, подготовка корпусов приборов и их транспортировка к местам
утилизации);
- ртутных ламп (сбор, транспортировка и утилизация);
- ртутно-цинковых гальванических элементов (сбор, упаковка и транспортировка к
местам переработки);
- твердых, пастообразных и жидких ртутьсодержащих отходов (сбор, упаковка,
транспортировка к местам переработки);
Рафинирование отработанной (некондиционной, черновой) металлической ртути с целью
получения товарного (вторичного) металла, очистка, переработка (перекристаллизация) и
производство соединений ртути осуществляются по технологиям, разработанным
специалистами ООО “Мерком”[96, 263]. Основной товарной продукцией предприятия
являются металлическая ртуть марок Р0 и Р1 и соединения ртути реактивной чистоты.
Основные технологические схемы и производственные операции
Производственная база ООО “Мерком” включает:
- участок рафинирования некондиционной (отработанной, черновой) ртути;
- участок по производству соединений ртути;
- участок утилизации приборов с ртутным наполнением;
- участок демеркуризации трубчатых люминесцентных ламп;
- участок приемки ртутьсодержащих сухих гальванических элементов.
Производственные (проектные) мощности по рафинированию некондиционной ртути и
получению вторичного металла составляют 100 т/год; по производству соединений ртути - 30
т/год; установки по демеркуризации трубчатых люминесцентных ламп - 1 млн. шт./год.
Технологические и производственные операции осуществляются с соблюдением условий
и требований нормативных документов [76-79, 155, 244-246].
Рафинирование некондиционной металлической ртути
Очистка некондиционного металла осуществляется на участке рафинирования ртути на
специальной установке, основанной на применении технологии, разработанной в ООО
“Мерком”. В основу технологии положен гидрохимический способ очистки, базирующийся на
многоступенчатой обработке некондиционной ртути различными растворами.
В общем случае технологическая схема рафинирования некондиционной металлической
ртути выглядит следующим образом (рис. 5.10).
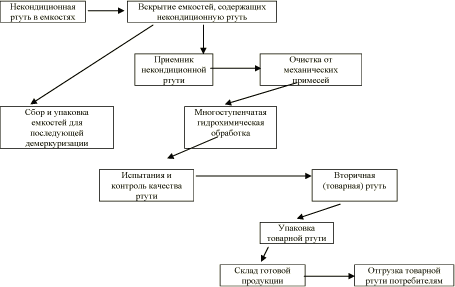
Рисунок 5.10 Технологическая схема рафинирования некондиционной ртути.
Испытания и контроль качества товарной ртути осуществляют по ГОСТ 4658-73 [80].
Конечной продукцией является ртуть марок Р0 и Р1, отвечающая требованиям указанного
ГОСТ.
Упаковка ртути марки Р1 производится в стандартные стальные баллоны, вмещающие по
34,5 кг ртути; ртути марки Р0 - в пластиковые емкости (по 3 кг металлической ртути в каждой)
под атмосферой инертного газа.
Производство соединений ртути
На участке по производству соединений ртути осуществляются следующие
технологические операции:
- производство различных соединений ртути из рафинированной металлической ртути
(синтез в химических реакторах гидрохимическими способами, разработанными в ООО
“Мерком”);
- перекристаллизация некондиционных соединений ртути, поступивших от различных
организаций, с целью получения товарных продуктов;
- очистка (от механических примесей) принятых от различных предприятий соединений
ртути с целью доведения их до необходимой кондиции.
Производство соединений ртути осуществляется по прямым заказам российских
промышленных предприятий и торговых организаций (см. раздел 3.10).
Утилизация приборов с ртутным наполнением
На участке утилизации приборов с ртутным наполнением осуществляются ручные
процедуры, связанные с вскрытием (под тягой) корпусов приборов (игнитронов,
сфигмоманометров и т. д.) и изъятием из них ртути в специальные емкости (ртуть отправляется
на участок рафинирования). Затем производится упаковка корпусов и прочих деталей приборов
для отправки их на демеркуризацию в фирму .ФИД-Дубна. (г. Дубна, Московская область).
В 2001 и 2002 г.г. большая часть собранных крупногабаритных приборов с ртутным
наполнением (после проверки на герметичность и соответствующей упаковки) была отправлена
на переработку в фирму “ФИД-Дубна”.
Демеркуризация ртутных ламп
В 2001 г. ООО “Мерком” осуществляло сбор и упаковку люминесцентных ламп низкого
давления (типа ЛБ, ЛД и т. п.) и ртутных ламп высокого давления (типа ДРЛ, ДНаТ), которые
затем были отправлены (около 50 тыс. шт.) на утилизацию в г. Дубну (“ФИД-Дубна”).
В 2002 г. была запущена в эксплуатацию собственная вибропневматическая установка
демеркуризации трубчатых люминесцентных ламп “Экотром-2”, основные принципы и
особенности функционирования которой описаны выше. В 2002 г. на установке было
утилизировано 241 тыс. люминесцентных ламп. Кроме того, 17 тыс. ртутных ламп высокого
давления (ДРЛ, ДНаТ) собрано и отправлено на переработку в г. Дубну. В планах ООО
“Мерком” - расширение объемов переработки трубчатых люминесцентных ламп до 1 млн. шт. в
год.
Участок приемки гальванических элементов
Здесь осуществляется упаковка (в полиэтиленовые мешки и затем в металлические
бочки) поступающих от различных предприятий нормальных и ртутно-цинковых
гальванических элементов. По мере накопления они направляются на вторичную переработку в
другие организации (в 2001 г. общий вес собранных гальванических элементов составил около
200 кг).
В 2002 г. было собрано (в организациях и на предприятиях г. Москвы и Московской
области) и утилизировано 1868 нормальных гальванических элементов (со стеклянным
корпусом), из которых извлечено 18 кг металлической ртути.
Прочие ртутьсодержащие отходы
ООО “Мерком” осуществляет сбор, упаковку и перевозку загрязненных ртутью
почвогрунтов, бытового и промышленного мусора, отработанных угольных сорбентов и
катализаторов, ртутьсодержащих шламов химического производства. Как правило, при
небольших объемах указанных отходов производится их безопасная упаковка и накопление на
специальном производственном участке, а затем они транспортируются к местам
непосредственной утилизации (в другие организации). Подготовка и упаковка
многотоннажных отходов для транспортировки производится непосредственно на месте их
образования.
Отходы, образующиеся в ходе технологических процессов и операций
В ходе технологических процессов и операция, связанных с переработкой
ртутьсодержащих изделий, рафинированием ртути и производством ее соединений,
осуществляемых ООО “Мерком”, образуются следующие виды ртутьсодержащих отходов,
требующие обезвреживания.
Сточные воды, большая часть которых (до 80%) образуется на участке очистки и
производства соединений ртути, характеризуются содержаниями ртути до 30-49 мг/л,
отличаются высокой минерализацией (до 300-400 г/л) и высокими концентрациями соединений
натрия, калия, азота, хлоридов, сульфатов. Они подвергаются на месте предварительной
очистке от ртути (используется химическое осаждение путем создания щелочной среды) и
затем накапливаются в специальных емкостях (накопительных баках). Объемы образующихся
сточных вод не очень велики. Так, к 1999 г. было накоплено и отправлено на утилизацию в
ЗАО “Кубаньцветмет” 5 м³ сточных вод; к настоящему времени объем сточных, хранящихся в
накопительных баках, составляет около 4 м³. Насущной проблемой для предприятия является
разработка и внедрение схемы глубокой очистки сточных вод непосредственной на месте, что
позволит существенно увеличить объемы рафинирования некондиционной ртути и
производства ртутных соединений.
Твердые отходы (пастообразной консистенции), в среднем содержащие 0,2-0,3% ртути,
образуются в ходе рафинирования некондиционной ртути и ее соединений от механических
примесей, а также при предварительной очистке сточных вод (шлам сточных вод). Отходы
упаковываются в полипропиленовый мешок (объемом 20-30 л) с полиэтиленовым вкладышем,
затем помещаются в металлическую бочку также с полиэтиленовым вкладышем. По мере
накопления они отправлялись на утилизацию в ОOО .Краснодарский рудник. (ЗАО
“Кубаньцветмет”). Удельное образование твердых отходов составляет примерно 1 кг на 1 т
полученной при рафинировании товарной ртути.
Емкости (тара) из стекла и пластика, в которых поступают на утилизацию
некондиционная металлическая ртуть и другие ртутьсодержащие отходы подвергаются
демеркуризации (демеркуризационные растворы идут в сточные воды). Металлическая тара
упаковывается и отправляется на утилизацию в фирму “ФИД-Дубна”. Обычно ежегодно
накапливается до 3-4 т такой тары.
Образующийся при утилизации ртутных ламп концентрат люминофора упаковывается (с
применением технологии ООО “Экотром”) в полиэтиленовые мешки; по мере накопления его
предполагается отправлять на переработку в ЗАО “Кубаньцветмет”; стеклобой вывозится на
свалку; алюминиевые части ламп сдаются организациям, занимающимся сбором цветного
металлолома.
Очистка выбросов в атмосферу
Участок рафинирования ртути оборудован угольными сорбентами (типа УПР), а участок
демеркуризации ламп, кроме того, фильтрами Петрянова; эффективность используемых систем
очистки выбросов составляет более 99%. Как правило, в воздухе рабочих помещений и на
выходе выбросов в атмосферу содержания паров ртути составляют не более 0,2-0,3 ПДК
рабочей зоны (среднесменной).
Все местные внутренние выбросы (включая отсосы от точечных источников) поступают
в промышленную общеобменную вентиляционную, проходят через три угольных адсорбера и
затем выбрасываются (3 тыс. м³/час) через трубу (высотой 120 м).
Установленный для ООО “Мерком” ПДВ (предельно допустимый выброс) паров ртути
составляет 800 мг в год.
Переработка ртутьсодержащих отходов и производство металлической ртути
В табл. 5.12 приведены сведения о сборе и переработке ртутьсодержащих отходов и
производстве (рафинировании) металлической (вторичной) ртути ООО “Мерком”в 2000-2002 г.г.
Таблица 5.12 Переработка некондиционной ртути и ртутьсодержащих отходов ООО “Мерком”
Год |
Неконди ционная
Hg, кг** |
Товарна я Hg, кг*** |
Некондицион ные соедине- ния Hg, кг |
Игнитроны, сфигмоманометры, термометры и др. |
Отходы (почвогрунты, мусор, сорбенты и т. п.), кг******* |
Общая масса, кг |
Изъятая Hg, кг |
2000 |
10990 |
9343 |
271 |
-**** |
- |
Нет данных |
2001 |
5766 |
5199 |
38 |
3137 |
395 ****** |
7460 |
2002* |
8987 |
8744 |
- |
110,5***** |
17,4 ****** |
2561 |
* В 2002 г. было утилизировано 287 ртутных контактов (извлечено 4,3 кг металлической ртути) и
1712 ртутных термометров (3,4 кг ртути).
** Масса дана вместе с тарой.
*** Металл, полученный при рафинировании некондиционной (черновой) ртути.
**** Приборы отправлялись на утилизацию в “ФИД-Дубна”.
***** Большая часть приборов отправлена в “ФИД-Дубна”.
****** Ртуть затем рафинировалась.
******* Отправлено в ЗАО “Кубаньцветмет”; за первые 7 месяцев 2003 г. ООО “Мерком” собрано,
упаковано и подготовлено к отправке на утилизацию 10 т загрязненных ртутью грунтов и строительных
отходов.
Металлическая ртуть, полученная ООО “Мерком” в 2000-2002 г.г., была поставлена
главным образом на отечественные электроламповые заводы (Смоленск и Саранск), на завод
ртутных термометров (г. Клин), на ОАО “Алтайхимпром” (г. Славгород) и в небольших
количествах - посредническим торговым организациям. Следует отметить, что в 2002 г. ООО
“Мерком” была приобретена партия металлической ртути в 8442 кг (у одного из заводов,
расположенного в г. Рязани, на котором в свое время изготавливали ртутные вентили). После
проведения необходимых технических испытаний, проверки тары и герметичности упаковки
ртуть была также поставлена на рынок (указанным выше предприятиям).
5.2 Оборот ртути с твердыми отходами
Для выявлении всех источников образования ртутьсодержащих отходов производства и
потребления (РСО) необходимо учесть те сферы практической деятельности, где ртуть и ее
соединения используются целенаправленно или присутствуют в значительных количествах в
качестве естественной примеси в перерабатываемом сырье и применяемых материалах и
изделиях. В соответствии с Законом Российской Федерации “Об отходах производства и
потребления” (от 24 июня 1998 г. № 89-ФЗ, статья 1) под РСО следует понимать содержащие
ртуть остатки сырья, материалов, полуфабрикатов, иных изделий или продуктов, которые
образовались в процессе производства или потребления, а также товары (продукцию),
утратившие свои потребительские свойства.
В общем случае образование РСО возможно при:
- добыче и производстве ртути;
- переработке природных материалов, содержащих ртуть;
- использовании ртути при добыче золота;
- использовании ртути и ее соединений при производстве химической продукции;
- производстве и использовании изделий, содержащих ртуть и ее соединения;
- переработке ртутьсодержащих отходов.
5.2.1 Образование твердых ртутьсодержащих отходов в России
В табл. 5.13 и 5,14 и на рис. 5.11 представлены официальные данные по накоплению,
образованию и обезвреживанию РСО в различных отраслях промышленности и основных
регионах России. Из них следует, что основные объемы РСО образуются в трех отраслях
промышленности - в химической, машиностроении и цветная металлургии. В отходах
машиностроения, вероятно, учитываются также ртутьсодержащие отходы потребления
(использованные и вышедшие из строя ртутные термометры, лампы, батарейки и т.д.),
описание которых дается в разделе 3.
Таблица 5.13 Накопление, образование и обезвреживание РСО в 2002 г. в различных отраслям
промышленности России (Госкомстат РФ, МПР РФ)
Наименование отрасли |
Накоплено РСО на конец 2001 г. |
Образовано РСО в 2002 г. |
Обезврежено РСО в 2002 г. |
т |
% |
т |
% |
т |
% |
Промышленность, в том числе: |
2.874 |
83,1 |
7.214 |
85,9 |
1.655 |
65,8 |
химическая |
1.159 |
33,5 |
1.200 |
14,3 |
536 |
21,3 |
машиностроение |
801 |
23,5 |
3.342 |
39,8 |
1.158 |
46,0 |
цветная металлургия |
691 |
20,0 |
2.075 |
24,7 |
1,9 |
0,08 |
целлюлозно-бумажная |
20 |
0,58 |
45 |
0,53 |
- |
- |
мукомольно-крупяная и комбикормовая |
|
|
|
|
|
|
электроэнергетика |
41 |
1,19 |
126 |
1,5 |
16 |
0,64 |
топливная промышленность |
30 |
0,87 |
85 |
1,0 |
- |
|
Промышленность строительных материалов |
108 |
3,1 |
145 |
1,7 |
- |
|
Жилищно-коммунальное хозяйство |
332 |
9,6 |
62 |
0,07 |
185 |
7,4 |
Всего по России |
3.458 |
100 |
8.396 |
100 |
2.517 |
100 |
Таблица 5.14 Распределение РСО по Федеральным округам РФ (по данным Госкомстата РФ и МПР
РФ)
Округ |
Накоплено РСО на конец 2001 г. |
Образовано РСО в 2002 г. |
Обезврежено РСО в 2002 г. |
т |
% |
т |
% |
т |
% |
Центральный |
376,9 |
10 |
2.184 |
26 |
950 |
38 |
Северо-западный |
88,4 |
2,6 |
145,2 |
1,7 |
44 |
1,8 |
Южный |
1.029,9 |
30 |
559 |
7 |
210 |
8 |
Приволжский |
287,1 |
8 |
936 |
11 |
747,4 |
30 |
Уральский |
213,3 |
6 |
2.422 |
29 |
54,8 |
2,1 |
Сибирский |
1.407,9 |
41 |
2.129,8 |
25 |
510,1 |
20 |
Дальневосточный |
54,6 |
1,6 |
19,4 |
0,2 |
0,135 |
0,0 |
Всего по России |
3.458 |
100 |
8.396 |
100 |
2.517 |
100 |
Самыми большими объемами образования РСО отличаются Сибирский, Уральский,
Приволжский и Центральный федеральные округа России. Это связано, в первую очередь, с
размещением здесь крупных промышленных предприятий, генерирующих указанные виды
отходов. Наибольшим объемом переработки РСО характеризуется Центральный федеральный
округ, хотя по количеству образованию их он находится на втором месте в стране. Наиболее
серьезная ситуация сложилась в Уральском федеральном округе: при доле ежегодного
образования РСО свыше 30%, объемы переработки их находятся на уровне 2%.
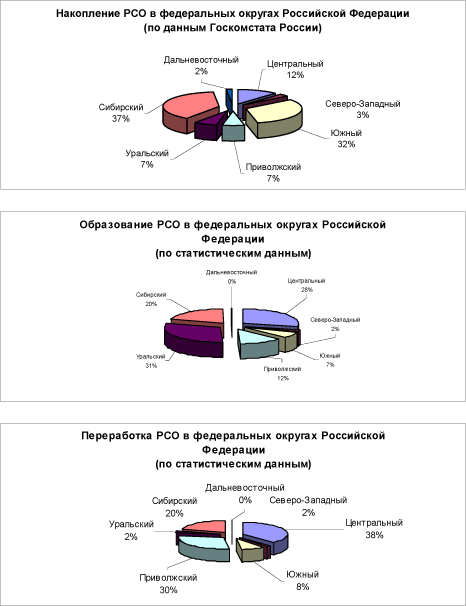
Рисунок 5.11 Образование, накопление и переработка РСО по регионам РФ в 2002 г.
Необходимо отметить, что в официальных источниках информации не указываются
концентрации ртути в накопленных и ежегодно образующихся РСО; отсутствует также
типизация отходов по уровням содержания в них ртути. Как было отмечено выше, из всей
массы накопленные к настоящему времени на территории России РСО примерно 58%
характеризуются уровнями содержания ртути в 10-100 мг/кг, около 12% - характеризуются ее
концентрациями в 100-5000 мг/кг, около 30% - содержат металл в количестве более 5000 мг/кг.
По другим сведениям [96], уровни содержания ртути в складированных и ежегодно
образующихся в России РСО варьируются от 0,02 до 75%. В России нормативно не установлен
нижний предел концентрации ртути в отходах, определяющий их отнесение к категории
ртутьсодержащих. Известно, что в практической деятельности в качестве такого минимального
уровня часто используется ПДК ртути в почве (2,1 мг/кг), что, очевидно, не всегда оправданно.
5.2.2 Ртуть в промышленных отходах и отходах энергетики
Оборот ртути с промышленными отходами и отходами энергетики рассматривается выше
в соответствующих разделах глав 3 и 4. Информация по указанным видам отходов,
размещенным на полигонах/свалках, систематизирована в табл. 5.15.
При целенаправленном использовании ртути в промышленности наибольшее количество
ее накапливается в отходах хлорно-щелочного производства, которые, как правило,
складируются вблизи заводов. Общая масса ртути в них ориентировочно оценивается в 39 т.
Количество ртути, содержащейся в отходах Новосибирского завода химконцентратов
(производство изотопов лития), накопленных к настоящему времени на территории
предприятия, оценивается в 100-500 т.
Таблица 5.15 Ртуть в промышленных отходах и отходах энергетики, поступивших на
полигоны/свалки, 2001/2002 г.г.
Отрасль |
Масса ртути т/г Наилучшая оценка |
Глава |
Хлорно-щелочное производство |
39,3 |
3,1 |
Производство потребительских товаров: ламп, батареек и пр. |
0,3 |
3,5-3,9 |
Добыча золота с применением метода амальгамации |
0,55 |
3,3 |
Добыча и использование угля |
5,6 |
4,1 |
Нефть, газ и биотоплива |
? |
4,2 |
Производства меди и никеля |
6,6 |
4,3 |
Производство свинца и цинка |
8,5 |
4,3 |
Производство других цветных металлов |
4,2 |
3,3; 4,3 |
Производство цемента |
0,4 |
4,3 |
Всего |
65 |
|
В общей сложности в грунтах и отвалах на промплощадках предприятий, использующих ртуть,
накоплено более 3000 т этого металла. В Таблице 5.16 перечислены выявленные производственные
сооружения. Данный перечень достаточно представительный, принимая во внимание использование
ртути при производстве хлора (включая производство хлора на бумажных фабриках), но при этом , есть
основания полагать, что значительное количество ртути также накоплено на территориях предприятий,
производящих термометры, переключатели и другие электронные приборы.
За весь период добычи золота в России, около 6000 т ртути было использовано для амальгамационного
обогащения золота. Существенная часть использованной ртути содержится в техногенных россыпях
(отвалах, хвостах обогащения, отработанных дражных и гидромониторных полигонах и др.), при
повторной отработке которых эмиссия ртути в окружающую среду может быть очень значительной.
Отвалы предприятий цветной металлургии могут содержать существенные концентрации ртути, но
данных по общему содержанию ртути в отходах этих предприятий получено не было.
Таблица 5.15 Производства, на которых происходит накопление ртуть содержащих отходов
Предприятие |
Производство |
Период работы |
Примерное количество рутути (тонн) в отвалах и шлаконакоми телях |
Комментарии |
ОАО «Усольехимпром» Усолье-Сибирское |
Хлор-щелочное |
1970-1998 |
800 |
|
ОАО «Каустик», «Кребс», город Стерлитамак |
Хлор-щелочное |
1964-1987 |
50 |
|
ОАО «Капролактам», Дзержинск, Нижегородская область |
Хлор-щелочное |
1948-1982 |
60 |
|
ОАО “Кировочепецкий химический комбинат”, Кировочепецк, Кировская область |
Хлор-щелочное |
1955 -по сегодняшний день |
300-700 |
|
ОАО “Каустик”, Волгоград |
Хлор-щелочное |
1968 -по сегодняшний день |
<500 ? |
В почве под зданием В отвалах |
ЗАО «Каустик», Стерлитамак |
Хлор-щелочное |
1997 -по сегодняшний день |
200-300 ? |
В почве под зданием В отвалах |
ОАО «Саянскхимпласт», Саяны, Иркутская область |
Хлор-щелочное |
1979 -по сегодняшний день -today |
500 |
|
Котласский ЦБК, Коряжма, Архангельская область |
Хлор для производства бумаги |
1964-1998 |
130 |
|
Архангельский ЦБК, Новодвинск, Архангельской области |
Хлор для производства бумаги |
1962-1996 |
120 |
|
Амурский ЦБК, КОмсомольск-на-Амуре |
Хлор для производства бумаги |
1970-1997 |
56 |
|
Светлогорский ЦБК, Ленинградская область |
Хлор для производства бумаги |
1951-1993 |
11 |
|
Производство лития, Новосибирск |
Изотопы лития |
- |
100-500 |
35 т/год к серед. 90-х |
ИТОГО |
|
|
Более 3.000 |
|
5.2.3 Ртуть в твердых бытовых отходах
Основными источниками поступления ртути в твердые бытовые отходы (ТБО) являются
ртутные лампы, термометры, другие ртутьсодержащие приборы, используемые в быту, а также
элементы питания.
В 1997 г. в г. Санкт-Петербурге было установлено, что количество ртути в приборах,
находящихся у населения, составляет более 3 т [243]. Экстраполяция этих данных на всю
Российскую Федерацию позволяет говорить о 93 т ртути, находящейся в приборах, имеющихся
на руках у населения. Если допустить, что в каждой российской семье имеется два ртутных
термометра, то на руках у населения находится примерно 70 млн. шт. таких изделий,
содержащих в общей сложности 140 т ртути, что выше данных, полученных экстраполяцией
показателей по Санкт-Петербургу. Для дальнейшей оценки количества ртути, попадающие в
ТБО, были приняты допущения, что 1/6 всех находящихся на руках ртутьсодержащих приборов
ежегодно теряет свои потребительские свойства. В этом случае в ТБО ежегодно будет
поступать 15,5 т (по первому варианту) или 23,3 т (по второму варианту) ртути. В разделе 3.5
показано, что в России в вышедших в 2001 г. из строя термометрах содержится порядка 18 т
ртути, , основная доля которой поступила в составе твердых отходов на полигоны/свалки. В
целом, по расчетным данным, в составе использованных ртутьсодержащих приборов, в
конечном счете поступающих в отходы, может содержаться 16-23 т ртути. Кроме того, около
1,6 т ртути поступает в ТБО в составе ртутных люминесцентных ламп (см. раздел 3.8), 1,6 т в
составе батареек (см. раздел 3.7) и 0,4 т в составе переключателей (см. раздел 3.9).
Правильность оценки содержания ртути в батарейках сильно зависит от фактического срока их
службы, так как использование ртути постепенно снижается в течение последних лет. В 1980-х
г.г. ежегодно использовалось 100-130 т ртути для производства гальванических элементов и
батарей. Фактический срок использования/хранения батареек может быть значительно больше
срока их технической пригодности, поскольку они могут не сразу выбрасываться и попадать на
полигоны/свалки. По этой причине поступление ртути, связанной с указанными изделиями, в
ТБО может быть недооценено.
Поступление ртути, содержащейся в качестве примеси (рассеянного элемента) в
различных материалах, оказывающихся после их использования в ТБО, потенциально может
быть существенным, но трудно поддается оценке, главным образом, из-за отсутствия данных
по исходному уровню содержания ртути в отходах.
Среднее содержание ртути в ТБО, включающих использованные ртутьсодержащие
приборы и материалы, было определено на основе оценки источников (табл. 5.16) и анализа
общего объема ТБО, образующихся в Российской Федерации. Согласно оценкам, содержание
ртути в ТБО (за исключением случаев ее присутствия в различных материалах в качестве
примеси) может достигать 0,7-0,9 мг/кг, что ниже ПДК ртути в почвах, равной 2,1 мг/кг.
Таблица 5.16 Источники поступления ртути в ТБО
Источники попадания ртути в ТБО |
Примерное количество Hg, т/год |
Примечание |
Ртутьсодержащие приборы (в основном термометры) |
16-23 |
раздел 3.5 |
Батарейки |
1,6* |
раздел 3.6 |
Лампы |
2 |
раздел 3.8 |
Зубные амальгамные пробы |
6* |
раздел 3.4 |
Переключатели |
0,4 |
раздел 3.9 |
В качестве cледового микроэлемента во всех отходах |
? |
|
Всего |
26-33 |
|
* Точное количество ртути, поступающее в ТБО, не известно.
В Российской Федерации практически все ежегодно образующиеся ТБО размещаются на
свалках или полигонах. Мусоросжигательные заводы эксплуатируются в Москве, Пятигорске,
Сочи, Владивостоке, Мурманске (рис. 5.12, табл. 5.17). Доля ТБО, сжигаемых на этих
предприятиях, может быть оценена на уровне 2-3 % от их общего годового количества. На
основе вышеприведенных оценок, можно сделать вывод, что в сжигаемых отходах содержится
примерно 0,5 т ртути. Установлено, что выбросы ртути в атмосферу с установки по сжиганию
ТБО во Владивостоке в 1999 г. составили 0,5 т (согласно официальной статистической
отчетной форме “2 тп-Воздух”). Экстраполяция этих данных на другие предприятия, с учетом
их проектной мощности, позволяет приблизительно оценить выброс ртути с
мусоросжигательных установок в 3,5 т/год (для Пятигорска, Сочи, Владивостока и Мурманска).
Необходимо отметить, что результаты оценки бубуд выше, если учесть ожидаемый уровень
содержания ртути в сжигаемых отходах.
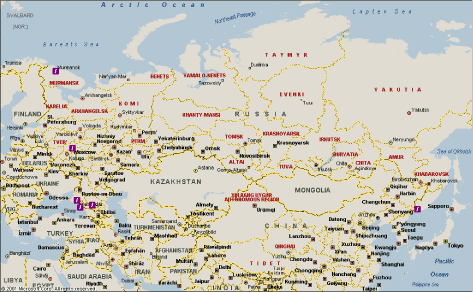
Рисунок 5.12 Расположение мусоросжигательных заводов в России (указаны как I).
Таблица 5.17 Мусоросжигательные заводы в Российской Федерации
Город |
Производительность, т/год |
Технология снижения загрязнений |
Москва (два завода) |
40000 |
Активный уголь |
Пятигорск |
150000 |
Данные отсутствуют |
Сочи |
Не работает |
Данные отсутствуют |
Владивосток |
Данные отсутствуют |
Данные отсутствуют |
Мурманск |
Данные отсутствуют |
Данные отсутствуют |
Всего |
Данные отсутствуют |
Данные отсутствуют |
На двух функционирующих в г. Москве мусоросжигательных заводах, общей мощностью
40.000 т отходов в год, в системах очистки отходящих газов используется активный уголь.
Аналитический контроль свидетельствует об отсутствии выбросов ртути в окружающую среду.
Выбросы завода соответствуют требованиями Directive-2000.
Мусоросжигательный завод в г. Сочи был закрыт, поскольку являлся существенным
источником загрязнения окружающей среды.
Производительность мусоросжигательного завода в г. Пятигорске составляет 150.000
т/год. Эмиссия ртути, определяемая аналитическим методом, достигает 0,000013 г/сек (старые
данные), расчетным путем – 0,000052 г/сек; концентрация ртути в золе – 4 мг/кг, в шлаке – 0,8
мг/кг, в водной вытяжке из золы - 0,003×10-3 % (масс.).
Разница между источниками и выбросами может в какой-то мере объясняться различием
в структуре бытового потребления между городским и сельским населением. В больших
городах, где расположены мусоросжигательные заводы, концентрации ртути в ТБО, по
сравнению со средними показателями, возможно, будут выше. Содержание ртути в сточных
водах также возможно выше в крупных городах (см. далее). Эта разница также может говорить
о том, что концентрация ртути в отходах может быть значительно выше, по сравнению с
вышеприведенными оценками. Причиной этого может быть тот факт, что большую долю ртути
в отходах составляет ртуть, содержащаяся в качестве примеси, а также и более длительное
использование батареек, переключателей и т.д. Потребление ртути для производства этих
изделий десять лет назад было значительно выше.
Согласно официальным данным, поступление ртути в окружающую среду от жилищно-
коммунального хозяйства составляет 3 кг/год (см. Приложение 1), но эта цифра, вероятно, не
учитывает сжигание ТБО.
5.2.4 Ртуть в отходах медицинских учреждений
К медицинским ртутьсодержащим отходам относятся ртутные лампы медицинского и
технического назначения (могут содержать до 500 мг ртути) и медицинские термометры.
В свое время в медицине использовали растворы хлорида ртути (II), или сулемы (HgCI2)
концентрацией от 1:1000 до 1:5000 (для дезинфекции медицинского инвентаря, лабораторной
посуды, поверхностного обеззараживания кожи). Сейчас применение сулемы для дезинфекции
строго ограничено.
Оценка количества медицинских отходов, находящихся в лечебных, детских дошкольных
учреждениях, выполнена по данным учета отходов в Пермской области в 2002 г. Здесь
масштабы накопления РСО достигают 175 т (без учета люминесцентных ламп), количество
ртути в которых составляет 29,9 кг, в том числе – 21,7 кг в термометрах, 7,9 кг – в приборах, 1,2
кг - в бактерицидных лампах, - 0,2 кг – в составе различных соединений ртути. Экстраполяция
этих данных на всю территорию Российской Федерации позволяет говорить о том, что в
непроизводственной сфере, не участвующей в отчетных кампаниях, накоплено 5750 т
приборов, содержащих 1,5 т ртути. Учитывая существенные объемы ртути, использованной для
производства других термометров и приборов, данный показатель довольно низок.
В Российской Федерации нет широкой практики сжигания опасных и медицинских
отходов. Приблизительный состав медицинских отходов, который могут сжигаться, выглядит
следующим образом [86]: 74,5% - перевязочные материалы, 9,3% - полимеры, 7,9% - пищевые
отходы, резина и металлы - по 3,1%, 1,09% - патологоанатомические отходы. Вероятность
содержания ртути в этих отходах очень невелика; они, как правило, поступают на захоронение
или сжигаются в котельных и крематориях.
РСО классифицируются как медицинские отходы класса D. Данная группа отходов также
включает просроченные лекарства и дезинфектанты, отходы диагностических препаратов и т.
д. Инвентаризация, проведенная в 2000 г. в Новокузнецке, показала, что доля отходов класса D
достигает 6,3% от общего количества медицинских отходов (4249.052 т) [316]. По данным
инвентаризации в Екатеринбурге, этот показатель составляет 6,6%.
Общее количество медицинских отходов определялась путем экстраполяции данных
инвентаризации медицинских отходов в Калужской области (999,457 т) и г. Новокузнецке на
всю территорию Российской Федерации (с учетом удельного количества отходов на душу
населения). Рассчитанный таким образом объем медицинских отходов составил 461000 т.
5.3 Ртуть в сточных водах
Сведения по содержанию ртути в организованных сбросах сточных водах и ее
последующему попаданию в водные объекты содержаться в форме “2 тп-Водхоз”. Ниже
представлены данные государственной статистической отчетности по сбросу загрязняющих
веществ в водные объекты в 2001 г. (табл. 5.18, 5,19, см. также Приложение 1).
Химическая промышленность является основным источником сброса ртути со сточными
водами, который, по официальным данным, составляет 146 кг. Согласно оценке, приведенной в
разделе 3.2, около 20 кг ртути сбрасывается со стоками предприятий по производству ВХМ.
Вполне вероятно, что оставшаяся часть металла поступает со стоками хлорно-щелочных
производств. Однако. согласно оценке в разделе 3.1, со сточными водами таких производств
должно поступать только лишь около 1 кг ртути. Таким образом, официальная статистика
указывает на то, что этот показатель завышен.
Таблица 5.18 Сброс ртути в поверхностные водные источники по регионам России в 2001 г.
Наименование территории |
Объем загрязненных стоков, млн. м³ |
Сброс ртути, кг |
Примечание |
Российская Федерация (в целом) |
22370 |
177 |
|
г. Санкт-Петербург |
1244 |
19 |
|
Ленинградская обл. |
413 |
2 |
|
г. Москва |
2185 |
2 |
|
Кировская обл. |
183 |
2 |
Химическая промышленность |
Республика Башкортостан |
449 |
16 |
Химическая промышленность |
Новосибирская обл. |
385 |
1 |
|
Красноярский край |
644 |
1 |
|
Иркутская обл. |
911 |
129 |
Химическая промышленность |
Республика Саха (Якутия) |
93 |
4 |
|
Амурская обл. |
109 |
1 |
|
Таблица 5.19 Сброс ртути в поверхностные водные источники по отраслям промышленности в
2001г.
Наименование отрасли |
Объем загрязненных стоков, млн. м³ |
Сброс ртути, кг |
Российская Федерация (в целом) |
22370 |
177 |
Промышленность: |
7273 |
156 |
Цветная металлургия |
593 |
6 |
Химическая |
855 |
146 |
Целлюлозно-бумажная |
1421 |
1 |
Мукомольно-крупяная и комбикормовая |
23 |
2 |
Жилищно-коммунальное хозяйство |
13474 |
20 |
Согласно статистическим данным, со стоками ЖКХ в водные объекты поступает 20 кг
ртути. Не совсем ясно - какие области деятельности подразумеваются под .ЖКХ.. Судя по
всему, речь идет о сбросе сточных вод с очистных сооружений, эксплуатируемых жилищно-
коммунальными хозяйствами российских городов и поселков.
Поступление ртути с городскими сточными водами может быть оценено на основе ее
концентраций в осадках сточных вод (ОСВ), образующихся на очистных сооружениях.
Данные о содержании ртути в ОСВ некоторых городов России, полученные из различных
источников, приведены в табл. 5.20. Как видим, концентрация ртути в ОСВ сильно
колеблется. Наиболее высокие содержания металла были установлены в ОСВ в тех городах,
где ртуть в значительных количествах используется на промышленных предприятиях
(например, в Клину и Саранске). Однако высокие концентрации ртути в ОСВ могут быть
обнаружены и в других городах.
В крупных городах, например в Санкт-Петербурге и Москве, установленные уровни
ртути в ОСВ колеблются в пределах 1-2 мг/кг сухого веса, в то же время в малых городах ее
концентрации, вероятно, ниже. Установленная норма содержания ртути в ОСВ,
предполагаемых для использования в сельском хозяйстве в качестве агломелиорантов,
составляет 15 мг/кг сухого веса [251].
Объем данных слишком ограничен, чтобы достаточно точно оценить общее количества
ртути, ежегодно аккумулирующейся в ОСВ в целом по всей России, тем не менее, эти данные
можно использовать для первой приближенной оценки.
Таблица 5.20 Ртуть в осадках городских сточных вод
Город |
Ртуть, мг/кг сухого веса |
Московская область [15] |
Клин (поступают стоки завода ртутных термометров) |
220 |
Коломна |
10 |
Апрелевка |
3,6 |
Загорск |
2,8 |
Орехово-Зуево |
2,4 |
Бронницы |
0,8 |
Серпухов |
0,4 |
Зарайск |
0,4 |
Воскресенск |
0,3 |
Домодедово |
0,2 |
Павловский посад |
0,2 |
Подольск |
0,2 |
Шатура |
0,2 |
Электросталь |
0,1 |
Белозерский |
0,1 |
Истра |
0,1 |
Наро-Фоминск |
0,1 |
Раменское |
0,03 |
Город Москва [15] |
Люберецкая станция аэрации |
1,8 |
Курьяновская станция аэрации |
1,3 |
Республика Мордовия [324] |
Саранск, городские очистные сооружения (поступают стоки завода ртутных ламп) |
4 (3-5) |
Пермская область [9] |
Губаха (промышленные предприятия) |
14,1 |
Кунгур |
0,6 |
Санкт-Петербург [185] |
Очистные сооружения города |
1,6 |
В большинстве российских городов имеются общегородские очистные сооружения, на
которых осуществляется совместная очистка бытовых и промышленных сточных вод. Обычно
применяется 2-хступенчатая система очистки - механическая и биологическая. В ходе очистки
образуются значительные массы ОСВ, представляющих собой илисто-коллоидную смесь
минеральных и органических веществ, обладающую специфическим химическим составом и
средней влажностью 96,2% [291].
Для обезвоживания и обезараживания ОСВ обычно практикуется их размещение на
иловых площадках (иловых картах) или (реже) на полях фильтрации, расположенных, как
правило, вблизи комплекса городских очистных сооружений. В большинстве случаев ОСВ
поступают (наливаются) на иловые площадки периодически, отдельными слоями (мощностью
до 20-25 см). По мере высыхания они частично теряет влагу, в основном за счет испарения;
часть воды фильтруется через грунт. В ходе указанных явлений и процессов определенное
количество ртути может эмитировать в окружающую среду, однако какие-либо данные
отсутствуют.
При технических расчетах количество образующихся ОСВ (при средней влажности
96,2%) обычно принимается равным 0,5-1% от объема очищаемых сточных вод [291];
плотность ОСВ в среднем составляет 949 кг/м3 [293], что соответствует 0,18-0,36 кг сухого веса
на м3 жидкого стока. Производительность канализационных очистных сооружений в
Российской Федерации составляет 57,2 млн. м3/сутки ([86], или около 20 878 млн. м3 сточных
вод в год. Если биологической очистке подвергаются все сточные воды, то в таком случае
объем образующихся ОСВ (на сухое вещество) будет составлять 3,8-7,5 млн. т. Используя эти
данные, можно оценить общее содержание ртути в муниципальном жидком стоке (иле) на
уровне около 3,4-11,9 т/год (табл. 5.21).
Таблица 5.21 Ртуть в осадках городских сточных вод
Тип городов * |
Доля населения России, % |
Количество ОСВ, млн. т сухого веса |
Среднее содержание ртути, мг/ кг сухого веса |
Ртуть в ОСВ, т |
Малые и средние |
30 |
1,1-2,3 |
0,2-0,6 |
0,2-1,4 |
Крупные |
70 |
2,64-5,27 |
1,2-2,0 |
3,2-10,5 |
Всего (округлено) |
100 |
3,8-7,5 |
0,2-2,0 |
3,4-11,9 |
* Малые и средние города - соответственно с населением до 100000 и населением свыше 100000 чел.
По оценкам, КПД очистки сточных вод от ртути составляет около 50%. Например,
указанный показатель на канализационных очистных сооружениях Дании составляет около
65% [408]. Если принять исходить из значения КПД в 50%, то можно рассчитать, что в России
3,4-11,9 т ртути сбрасывается в водные объекты с городских очистных сооружения; это более
чем в 20 раз превышает общий официально учитываемый ее сброс со сточными водами
промышленных предприятий. Следует напомнить, что на общегородские очистные сооружения
поступают не только бытовые, но и промышленные сточные воды, которые и могут являться
существенным источником поступления ртути. Очевидно, что в официальной статистике по
сбросу ртути в водные объекты промышленными предприятиями учитывается только те
промышленные сточные воды, которые сбрасываются непосредственно в водотоки и водоемы с
заводских очистных сооружений (минуя общегородские канализационные сооружения).
Таким образом, в целом в городах России в муниципальные сточные воды до процесса
очистки попадает 7-24 т ртути в год. В ряде городов промышленные предприятия,
целенаправленно использующие ртуть в своих технологических процессах (Клин, Саранск и
др.), могут представлять собой значительный источник ее поступления в сточные воды,
которые очищаются на общегородских очистных сооружениях совместно с бытовым стоком.
Тем не менее в масштабе страны на долю таких предприятий приходится небольшая часть
ртути, поступающей со сточными водами в водотоки и водоемы. Определенным источником
поступления ртути в водотоки и водоемы может быть поверхностный (дождевой и талый) сток
с городских территорий, который в подавляющем большинстве городов России отводится без
необходимой очистке. Детальный анализ источников поступления ртути в сточные воды в
Дании показал, что на дождевые воды может приходиться около 10% всего количества ртути
(среднее содержание ртути в жидком осадке составляло 1,2 мг/кг [408]).
Серьезным источником ртути может быть также зубная амальгама, которая в
стоматологических клинках сбрасывается в муниципальные канализационные системы (как
показано в разделе 3.4, до 6 т). Кроме того, значительными источником может быть ртуть из
разбитых термометров и измерительного оборудования. Даже если небольшая часть от 18 т
ртути, которая присутствует в ежегодно выходящих из строя термометрах, попадает в сточные
воды, то это составит значительное количество.
Инфильтрация воды с территории свалок ТБО, в которых присутствуют использованные
ртутьсодержащие изделия, также может рассматриваться как источник поступления ртути в
водные объекты. Согласно данным [186], содержание ртути в свалочном фильтрате может
составлять в среднем 2 мкг/л при вариации от 0,055 до 1,46 мкг/л.
Можно привести практический пример с использованием данных контроля за
грунтовыми водами в Санкт-Петербурге [200]. Только в одном месте анализ показал
содержание ртути в пробе около 0,0007 мг/л.
Утилизация осадков городских сточных вод
Из всей ежегодно образующейся в пределах России массы ОСВ лишь около 10-15%
обрабатывается в соответствии с современными требованиями, т. е. уплотняется,
стабилизируется, обезвоживается и используется в качестве удобрения, либо вывозится на
специальные полигоны [1]. По другим сведениям, уровень практического использования ОСВ в
настоящее время составляет 1-1,5% [148]. В любом случае подавляющая часть ОСВ
размещается (на довольно длительный срок) на иловых площадках (полях фильтрации) и затем,
как правило, вывозится на свалки отходов (или просто в карьеры). В России содержание ртути
в ОСВ, предполагаемых использоваться как удобрение, не должно превышать 15 мг/кг сухой
массы [251]. При этом на почвах среднего и тяжелого гранулометрического состава во
избежание накопления металла не допускается внесение более 10 т/га сухой массы ОСВ в
чистом виде или в составе компостов (при периодичности внесения не менее 5 лет). На легких
песчаных и супесчаных почвах норма внесения ограничивается 7 т/га с периодичностью
внесения не менее 3 лет. Использование ОСВ на торфяных почвах по агрономическим
соображениям не рекомендуется. Запрещается применение ОСВ и компостов из них на почвах
с рН ниже 5,5 без предварительного известкования последних, если содержания кальция в
осадке или компосте не обеспечивает поддержание рН на уровне 5,5 и более. Необходимо
отметить, что уровни ртути в ОСВ, как правило, заметно превышают концентрации ее в
стандартных минеральных удобрениях, в которых среднее содержание этого металла
оценивается в 0,05 мг/кг [125].
6 Выводы
6.1 Использование и мобилизация ртути в Российской Федерации
6.2 Эмиссия ртути в Российской Федерации
6.3 Ртуть в твердых отходах
6.1 Использование и мобилизация ртути в Российской Федерации
Обобщенные сведения о целевом использовании ртути в Российской Федерации и
мобилизация металла как примеси представлены в табл. 6.1. Эти сведения не включают
возможное применение ртути в оборонной промышленности.
Целевое использование ртути
Общее целевое использование ртути в России в 2001/2002 г.г. оценивается на уровне 155
т/год. Данная оценка вполне определенная, поскольку основывается на конкретных сведениях,
полученных от предприятий, являющихся основными потребителями ртути в стране. По
данным Департамента финансов Министерства экономического развития и торговли РФ,
годовая потенциальная потребность российских предприятий в ртути в 1999-2001 г.г.
оценивалась в 280-300 т/год (см. раздел 2.3). Расхождение между этими данными и
результатами настоящей оценки обусловлены следующими причинами: 1) потенциальная
потребность основывается на учете плановых производственных мощностей предприятий,
которые в последние годы не используются полностью; 2) в указанный период в России были
закрыты некоторые производства, где в значительных количествах применялась ртуть; 3) на
ряде предприятий потребление ртути постоянно снижается или варьируется год от года; 4)
потребление ртути для “«других целей” может быть существенным; 5) настоящая оценка
распространяется только на целевое применение ртути в гражданском секторе.
Хлорно-щелочное производство по-прежнему остается основной сферой использования
ртути, где она применяется в качестве электрода. В 2002 г. потребление ртути на эти цели
составило около 103 т, однако ее использование в этом секторе варьируется из года в год,
причем в определенные годы оно может возрастать. Еще около 7,5 т ртути (в виде хлорида
ртути) было использовано в качестве катализатора для производства хлорвинилового
мономера (ХВМ), используемого для получения ПВХ. В обоих случаях ртуть используется в
качестве технологического химического вещества, при этом лишь незначительная часть ее
попадает в конечную продукцию. До недавнего времени ртуть использовалась в качестве
катализатора для получения витамина В-2, и некоторых красителей, однако сейчас такое
производство прекращено.
Основная часть ртути, используемой для изготовления потребительских товаров,
применялась в производстве ртутных термометров и ламп. В табл. 6.1 приведено общее
количество ртути, используемой для производства указанной продукции. Количество ртути,
присутствующей в потребительских ртутьсодержащих товарах, продаваемых на российском
рынке, отличается от ее объемов, использованных при их производстве. Это обусловлено
определенными технологическими потерями металлами, а также импортом и экспортом
ртутьсодержащих изделий. Общее количество ртути в потребительских товарах, поступающих
на внутренний рынок страны, оценивается примерно на уровне 18 т (табл. 6.2).
Следует отметить, что в России потребление ртути для производства термометров,
гальванических элементов и батарей, другого измерительного и электротехнического
оборудования за последнее десятилетие уменьшилось в несколько раз, а выпуск некоторых
приборов и изделий (ртутные переключатели, ртутные вентили, манометры, барометры и т.
п.) прекращен практически полностью. Ртуть по-прежнему может присутствовать в
некоторых видах импортируемого оборудования, например в выключателях, используемых в
некоторых легковых автомобилях в основном американского производства. Общее
поступление ртути в Россию с таким оборудованием оценивается на уровне менее 2 т. В
отличие от многих западных стран в России практически полностью прекращено
использование ртути в стоматологии.
Таблица 6.1 Использование и мобилизация ртути в Российской Федерации, 2001/2002 г.г.
Категория деятельности |
Потребление/мобилизация |
Оптимальная оценка, т/год |
Интервал, т/год |
% от общего суммарного количества |
Целевое использование ртути |
Хлорно-щелочное производство |
103 |
103 |
36 |
Производство ХВМ |
7,5 |
7,5 |
2,6 |
Добыча с использованием метода амальгамации |
5,5 |
3-8 |
1,9 |
Стоматология (зубные амальгамы) |
0,7 |
0,6-0,8 |
0,2 |
Производство термометров |
26 |
26 |
9,1 |
Производство барометров, манометров и другого измерительного оборудования |
0,2 |
0,2-1 |
0,1 |
Производство гальванических элементов и батарей |
0,8 |
0,8 |
0,28 |
Производство источников света |
7,5 |
7,5 |
2,6 |
Лабораторное применение |
3,5 |
2-5 |
1,2 |
Биоциды и пестициды |
0,6 |
0,4-0,8 |
0,2 |
Другие целевое применение |
? |
|
|
ИТОГО |
155 |
151-160 |
54 |
Мобилизация ртути в качестве примеси |
Уголь |
22 |
20-24 |
7,7 |
Нефть * |
33 |
5-50 |
11 |
Газ, кондесат, горючие сланцы и биотопливо |
8 |
2-12 |
2,8 |
Производство цинка и свинца ** |
31 |
16-47 |
11 |
Производство меди и никеля ** |
28 |
14-42 |
9,8 |
Другие цветные металлы ** |
6 |
4-8 |
2,1 |
Производство чугуна и стали |
1,8 |
1,2-2,4 |
0,6 |
Производство цемента |
2 |
1,6-2,8 |
0,7 |
Итого, мобилизация в качетсве примесей |
132 |
66-198 |
46 |
Всего |
287 |
217-358 |
100 |
* Ртуть в продуктах переработки нефти в РФ.
** Включает ртуть в концентратах. Общее содержание ртути в добываемых рудах может быть
значительно выше.
Таблица 6.2 Ртуть в потребительских товарах, поступивших на российский рынок, 2001 г.
Ртутьсодержащие изделия |
Потребление ртути для производства, т/год |
Содержание ртути в получаемой продукции, т/год |
Содержание ртути в продукции, поставляемой на рынок, т/год* |
Термометры |
24,2 |
24,0 |
9,4 |
Источники света |
7,5 |
4,7 |
4,7 |
Батареи |
0,8 |
0,6 |
1,6 |
Выключатели, манометры и т. д. |
0,2 |
0,2 |
< 2 |
Всего (округлено) |
33 |
30 |
18 |
* С учетом импорта/экспорта.
Применение ртути для обогащения золотодсодержащего сырья в России запрещено.
Однако по имеющемся сведениям амальгамационный способ обогащения сырья до сих пор
нелегально используется малыми предприятиями в районах, удаленных от природоохранного
контроля. Ориентировочное суммарное потребления ртути при добыче золота в 2001 г.
находится в интервале 3-8 тонн. Поскольку такое использование ртути является незаконным, в
официальной статистике отсутствуют необходимые сведения, которые могли бы подтвердить
приведенную экспертную оценку. Следует отметить, что в 2001 г. количество ртути,
использованной в золотодобывающей промышленности, уменьшилось приблизительно в 10 раз
по сравнению с периодом 1976-1990 г.г., когда затраты ртути могли составлять около 40 т/год.
В табл. 6.1. строка “другое целевое применение” включает производство полупроводников,
сверхчистых металлов методом амальгамации и прочее возможное использование ртути.
Однако не удалось получить информации о фактическом потреблении ее в этих целях.
Мобилизация ртути в качестве примеси
Общая мобилизация ртути, присутствующей в качестве естественной примеси
(рассеянного, следового элемента) в перерабатываемых и используемых сырье и материалах,
составляет примерно столько же, что и ее целевое использование. Общая мобилизация ртути
оценивается на уровне 138 т с интервалом 66-198 т, что свидетельствует о значительной
неопределенности оценочных данных. Основное количество ртути мобилизуется при добыче и
использовании угля и нефти и в цветной металлургии.
В целом мобилизация ртути с углем составляет около 20-24 т, который используется
главным образом для производства тепла и электричества и получения кокса. Содержания
ртути в углях, добываемых в различных угольных бассейнах страны, могут различаться на два
порядка, при этом неопределенность оценочных данных, касающихся общего объема
мобилизации ртути, является следствием неопределенности данных относительно ее
содержания в непосредственно использованном угле. Тем не менее распределение ртути в
товарных углях России изучено достаточно хорошо, чем в других видах ископаемого топлива и
рудах.
Содержание ртути в сырой нефти и природном газе также в значительной степени
варьируется в зависимости от геологии нефтяных и газовых месторождений. По оценке,
основанных на содержаниях ртути в сырой нефти, при переработке последней в России
мобилизуется около 33 т ртути. Помимо этого, почти такое же количество, вероятно,
присутствует в сырой нефти, экспортируемой для переработки в другие страны. Как уже
сказано, эти оценки основываются на данных о концентрации ртути в сырой нефти, однако
неизвестно, какая доля непосредственно поступает с нефтью на переработку или
экспортируется после первичной переработки нефти. Вследствие высокой вариабельности
содержания ртути в сырой нефти (в пределах множителя 50) и ограниченного числа данных,
общее количество мобилизуемой ртути определить очень трудно, при этом интервал
неопределенности приблизительно составляет порядка 5-50 т. По сравнению с данными,
известными для других стран, средняя концентрация ртути в российской сырой нефти
достаточно высока. Это, возможно,, является следствием фактических геологических условий
формирования и локализации нефтяных месторождений, но также может отражать тот факт,
что большая часть имеющихся данных получена на месторождениях нефти и газа,
территориально расположенных в пределах ртутных провинций, в зонах повышенной
тектонической активности и т. д. Для того чтобы уменьшить степень неопределенности
полученных оценочных данных, необходимо выполнить анализ проб сырой нефти на основных
российских нефтяных месторождениях, а также проб нефти, имеющейся в хранилищах на
нефтеперерабатывающих предприятиях.
Общая мобилизация ртути с природным газом, газовым конденсатом, горючими
сланцами и биотопливом, по оценкам, составляет 9 т (8 т в газе и конденсате, 0,6 т в горючих
сланцах и 0,4 т в биотопливе). Ртуть, содержащаяся в природном газе, в процессе его
ректификации в основном переходит в стабильный конденсат;, содержание ртути в очищенном
газе, поставляемом потребителям или на экспорт, незначительно.
Объем мобилизации ртути в результате использования биотоплива отличается от объема
мобилизации ртути по другим категориям по той причине, что такая ртуть в любом случае
будет выбрасываться при разложении биомассы.
Значительное количество ртути мобилизуется при добыче руд, особенно содержащих
цинк, медь, никель, свинец и золото. В табл. 6.1 показано количество ртути в концентратах
металлов, перерабатываемых на российских металлургических предприятиях. Общее
содержание ртути в руде, содержащей цветные металлы, оценивается на уровне xx-xx т/год. Из
этого количества xx-xx т уходит в хвосты, а остальная часть – 31-92 т/год (как указано в табл.
6.1) попадает в концентрат, который подвергается дальнейшей переработке.
Основная часть ртути мобилизуется с цинковым и медным концентратами. В процессе их
переработки ртуть либо выбрасывается в воздух, либо попадает в отходы или же в побочные
продукты, например в техническую серную кислоту. Очень незначительная часть ртути
поступает с полученными металлами потребителям.
Попутное извлечение ртути при добыче золота по ориентировочной оценке может
составлять 4-8 т/год. Ее основное количество поступает в отвалы и хвосты и около 20 % может
поступать в атмосферу.
Мобилизация ртути в производстве цемента оценивается в пределах 1,6-2,8 т; здесь
источником ртути являются используемые минеральное сырье и топливо. Эмиссия ртути
происходит также в ходе получения гашеной извести, однако из-за отсутствия данных такая
производственная деятельность не включена в оценку. Можно ожидать, что в данном случае
мобилизация ртути будет значительно ниже, чем в цементном производстве.
Динамика целевого потребления ртути
В последнее десятилетие общее целевое потребление ртути в Российской Федерации
значительно сократилось: с 866 т в 1989 г. до 155 т в 2001 г. (табл. 6.3). Таким образом,
динамика использования ртути в России соответствует общемировой тенденции,
проявляющейся в снижении потребления ртути в большинстве сфер ее целевого применения.
Потребление ртути на душу населения, составившее в 2001 г. 1,1 г на одного жителя России,
оказалось несколько ниже аналогичного показателя в США - 1,2 г на одного жителя страны в
1998 г. (рассчитан на основании сведений, приводимых в [Sznopek, Goonan, 2000].
Таблица 6.3 Потребление ртути в Российской Федерации, 1989-2001 г.г.
Отрасль, сфера применения |
1989 |
1993 |
2001 |
т/год |
% |
т/год |
% |
т/год |
% |
Химическая промышленность |
462 |
53,4 |
310 |
57,6 |
111 |
72 |
Медицина, фармацевтика, стоматология |
12,5 |
1,4 |
9 |
1,7 |
0,7 |
0,5 |
Электротехника |
108,3 |
12,5 |
71 |
13,2 |
8,3 |
5 |
Приборостроение, электроника |
133 |
15,4 |
80 |
14,9 |
26 |
17 |
Цветная металлургия |
10 |
1,1 |
8 |
1,5 |
5,5 |
2,9 |
Агрохимия |
50 |
5,8 |
10 |
1,8 |
0,6 |
0,4 |
Научные исследования, новейшие технологии |
25 |
2,9 |
10 |
1,9 |
3,5 |
2,3 |
Оборонная промышленность |
40 |
4,6 |
20 |
3,7 |
- |
- |
Другое |
25 |
2,9 |
20 |
3,7 |
? |
- |
Всего |
865,8 |
100 |
538 |
100 |
155 |
100 |
6.2 Эмиссия ртути в Российской Федерации
Основной прямой путь эмиссии ртути из техносферы в окружающую среду это ее
поступление в атмосферу. Выбросы ртути в атмосферу в России в общем виде представлены в
табл. 6.4, в которой приведены наиболее точные оценочные данные, а также указана степень их
неопределенности. Количество ртути, мобилизуемой с ископаемым топливом и рудами,
показанное ранее в табл. 6.1, достаточно неопределенно; кроме того, такая оценка осложняется
неясностью в плане дальнейшего состояния и поведения ртути в ходе процессов сгорания
топлива и переработки руд и концентратов. Практически отсутствуют данные, полученные при
инструментальном измерении фактических выбросов ртути, что особенно характерно для тех
сфер деятельности, в ходе которых происходит ее мобилизация в качестве естественной
примеси. В то же время имеются данные по выбросам ртути предприятиями, целенаправленно
использующими ртуть в своих технологических процессах (например, для химических
заводов).
Таблица 6.4 Эмиссия ртути в атмосферу в Российской Федерации, 2001/2002 г.г.
Категория деятельности |
Эмиссия ртути в атмосферу |
Оптимальная оценка, т/год |
% от общего суммарного количества |
Категория неопределенн ости**** |
Целевое использование ртути |
Хлорно-щелочное производство |
1,2*** |
3,0 |
3,0 |
Производство ХВМ |
0,02 |
0,05 |
0,05 |
Добыча золота с использованием метода амальгамации и переработка отходов золотодобычи |
3,1 |
8,0 |
8,0 |
Стоматология (зубные амальгамы) |
0,05 |
0,1 |
0,1 |
Производство термометров |
0,009 |
0,02 |
0,02 |
Производство барометров, манометров и другого измерительного оборудования |
0,01 |
0,03 |
0,03 |
Производство источников света |
0,15 |
0,4 |
0,4 |
Другое плановое применение |
? |
- |
- |
ИТОГО |
5,3 |
12 |
12 |
Мобилизация ртути в качестве примеси |
Уголь – для выработки электроэнергии |
8,0 |
21 |
21 |
Уголь – муниципальное и бытовое отопление |
2,1 |
6,0 |
6,0 |
Уголь – производство кокса |
1,3 |
3,0 |
3,0 |
Уголь – другое применение |
3,0 |
8,0 |
8,0 |
Переработка нефти |
? |
- |
- |
Использование бензина, дизельного топлива и мазута |
3,4 |
9,0 |
9,0 |
Газ, горючие сланцы и биотопливо |
1,0 |
2,6 |
2,6 |
Производство цинка |
1,9 |
5,0 |
5,0 |
Производство никеля и меди |
5,3 |
14 |
14 |
Производство других цветных металлов |
1,2 |
3,0 |
3,0 |
Производство железа и стали |
1,4 |
4,0 |
- |
Производство цемента |
1,6 |
4,0 |
79 |
Использование побочных продуктов ** |
? |
- |
|
ИТОГО |
30 |
79 |
0,1 |
Переработка отходов |
Производство вторичной ртути |
0,05 |
0,1 |
9,0 |
Переработка железа и стали |
? |
- |
- |
Сжигание отходов |
3,5 |
9,0 |
0,3 |
Размещение отходов на свалках/полигонах |
? |
- |
0,3 |
Утилизация источников света |
0,1 |
0,3 |
10 |
Сжигания осадков городских сточных вод |
<0,1 |
0,3 |
3,0 |
ИТОГО |
3,8 |
10 |
0,05 |
ОБЩЕЕ СУММАРНОЕ КОЛИЧЕСТВО |
42,6 |
100 |
|
* Вторичная мобилизация ртути, ранее использованной в золотодобывающей промышленности для
амальгамационного обогащения сырья.
** Выбросы ртути в атмосферу из побочных продуктов, таких как серная кислота, азотная кислота,
битума и т. д., не оценивались, однако они могут быть значительными.
*** Прямая эмиссия в ходе технологических процессов. Определенное количество ртути может
поступать в атмосферу из ее так называемых неучтенных потерь, которые в 2002 г. оценивались в 50 т.
**** Категории неопределенности: A: на основании фактических данных предприятий -
неопределенность в связи с неучтенными потерями; B: оценки экспертов - подлинное значение скорее
всего будет в диапазоне ± 50% от наиболее точной оценки; C: оценки экспертов - подлинное значение
может значительно превышать диапазон ± 50% от наиболее точной оценки.
Целевое использование ртути
Выбросы ртути в атмосферу в результате производства хлора и каустической соды в 2002
г. оцениваются на уровне 1,2 т. Это прямые выбросы поллютанта с воздухом систем
вентиляции и топочными газами. Помимо этого, определенное количество ртути может
выбрасываться с территорий предприятий (при дегазации механически теряемой ртути,
поступлении ее с мест размещения ртутьсодержащих отходов и т. д.). В настоящей оценке
изначально принято допущение о том, что неучтенные потери ртути в хлорно-щелочном
производстве России составляют более 50 т, причем ртуть главным образом аккумулируется в
строительных конструкции, в почвогрунтах промплощадок и окрестностей предприятий.
Представленные оценки по выбросам ртути в воздух на хлорно-щелочных заводах
соответствуют сведениям, которые предприятия направляют органам охраны окружающей
среды, и данным, включенным в официальные документы инвентаризации выбросов ртути (см.
Приложение 1). Какое количество ртути из ее так называемых неучтенных потерь рано или
поздно поступает в атмосферный воздух, точно не известно. Данная ситуация типична не
только для России, но и для других стран. Например, в отчетах, предоставляемых
предприятиями по выпуску хлора в Европе в комиссию OSPAR [OSPAR 2001] указывается на
“различие в балансе” (что соответствует российским “неучтенным потерям”) без дальнейшей
интерпретации, однако следует отметить, что в большинстве стран такие потери ртути
составляют значительную долю ее общего количества, используемого в технологических
процессах.
Выбросы ртути в атмосферу в результате производства потребительских товаров,
содержащих ртуть, описаны подробно в отчете (см. выше). Они могут обусловливать
формирование в окружающей среде локальных зон техногенного загрязнения, а также
воздействовать на рабочую среду, однако в национальных документах по инвентаризации на
них в целом приходится менее 1% от общей эмиссии ртути в атмосферу.
Вторичная мобилизация
Проведенная оценка показывает, что добыча золота из техногенных россыпей (отвалы,
хвосты и др.), отрабатываемых ранее с использованием амальгамационного метода , является
значительным источником поступления ртути в окружающую среду. Эмиссия ртути в
атмосферу при этом может составлять 0,9-3,9 т/год или около 60 % от ее общего содержания в
перерабатываемом техногенном сырье (1,5-6,5 т/год). За всю историю добычи золота в России
было использовано около 6000 тонн ртути. Ее значительная часть до сих пор остается в
техногенных россыпях , а часть поступает в воздух при их повторной переработке и извлечении
золота. Разрабатываемые технологии и оборудование переработки золото- и ртутьсодержащего
техногенного сырья позволяют количественно извлекать различные формы ртути и выделять
металлическую ртуть путем термического нагрева концентратов и конденсации паров ртути.
Однако такое оборудование используется редко.
Добыча золота из техногенных отходов существенно ускоряет процесс вторичной
мобилизации ртути из отходов, в то же время выбросы ртути их всех видов отходов,
содержащих ртуть, могут быть значительными. Существует очень мало информации
относительно объемов выброса ртути из отходов; другие вторичные источники выбросов не
анализировались в количественном отношении.
Мобилизация ртути в качестве примеси
Переработка и использование ископаемого топлива, руд и другого минерального сырья, в
которых ртуть присутствует в качестве естественной примеси, являются основными
источниками ее выбросов в атмосферу на территории России. Значительная часть такой ртути
поступает из точечных источников (электростанции, металлоплавильное производство,
коксовые установки, цементные предприятия и т. д.). В большинстве случаев оборудование,
используемое главным образом для снижения выбросов пыли, лишь в незначительной степени
обеспечивает улавливание летучей ртути, выделяющейся из сырья или ископаемого топлива в
ходе их высокотемпературной переработки. Следовательно, значительная часть мобилизуемой
в этом секторе ртути будет выбрасываться в атмосферу.
В результате использования угля общее количество выбросов ртути в атмосферу
составило около 14 т: 8 т приходится на выработку электроэнергии (теплоэлектроцентрали), 1,3
т - на производство кокса, 2 т – муниципальные котельные и бытовые отопительные системы, 3
т – на другие виды использования угля. Теплоэлектроцентрали имеют средства контроля за
выбросами пыли, а также – в определенной мере – оборудование для удаления серы, однако, по
приблизительным оценкам, по-прежнему около 80% ртути, содержащейся в угле, поступает в
атмосферный воздух.
Определенная часть ртути, присутствующей в сырой нефти, в ходе переработки попадает
в нефтепродукты и в конечном итоге выбрасывается в воздух в результате их сжигания. Если
сравнить общее количество ртути в нефти, поступающей на переработку в России, с общими
выбросами при сжигании нефтепродуктов, можно отметить, что значительная часть металла
выбрасывается либо в результате первоначальной переработки сырой нефти, либо в ходе
процесса очистки нефти. Ввиду отсутствия информации о дальнейшем состоянии ртути, оценка
ее потенциальных выбросов в результате таких технологических процессов не проводилась.
Данные о дальнейшей судьбе ртути, поступающей на переработку в составе сырой нефти на
соответствующие заводы, в целом очень ограничены во всем мире; нам не удалось получить
первую оценку, используя факторы распределения, адаптируемые по данным для других стран.
В цветной металлургии меньшая доля ртути, присутствующей в перерабатываемых
концентратах, выбрасывается в воздух, поскольку значительная часть ее улавливается, в
частности, оборудованием, предназначенным для контроля за выбросами серы. По оценкам, в
России ежегодно в атмосферу поступает около 8 т ртути, главным образом при производстве
цинка, меди и никеля.
Выбросы ртути в атмосферу в результате сжигания твердых бытовых отходов (ТБО)
оцениваются на уровне 3,5 т. В России функционирую 4 мусоросжигательных завода, на
которых сжигается лишь незначительная часть ТБО, ежегодно образующихся в стране.
Основными источниками поступления ртути в сжигаемых ТБО, по оценкам, являются ртутные
термометры, батарейки, источники света и выключатели.
Сравнение с данными других документов по инвентаризации
Согласно официальной статистике, в России в 2001 г. в атмосферу от техногенных
источников поступило около 2,9 т ртути. Эти данные основаны на информации, которая
приводится в соответствующих отчетах , направляемых предприятиями и организациями в
государственные органы защиты окружающей среды. В России, как правило, предприятия и
организации отчитываются только за выбросы тех вредных веществ, эмиссия которых
предусматривается документом ПДВ (предельно допустимых выбросов) или паспортами
технологического оборудования, т. е. если эмиссия ртути не определена указанными
техническими документами, то ее выбросы в окружающую среду не регистрируются. В
отношении ртути информацию о ее выбросах предоставляют лишь те предприятия, которые
используют ртуть в основных технологических процессах (хлорно-щелочные заводы,
электроламповые, термометровые и т. д.). Для таких категорий деятельности данные,
полученные при проведении настоящей оценки, хорошо соотносятся с официальной
статистикой. В некоторых случаях официальные данные включают информацию, полученную
от небольшого количества металлоплавильных предприятий, однако в целом мобилизация
ртути, присутствующей в виде естественной примеси в перерабатываемых и используемых
сырье и материалах, не включается в экологическую отчетность предприятий и организаций,
поскольку они формально не обязаны декларировать эмиссию ртути.
Недавно была проведена оценка техногенных выбросов ртути в России и странах СНГ,
выполненная в рамках международного проекта INTAS “Разработка методов оценки выбросов
рассеянных металлов и их практическое применение для оценки потоков в CНГ, включая
экономические аспекты снижения потоков” (Development of methods for trace metal emission
evaluation and their implementation for flux estimates in NIS territory, including economic aspects of
flux reduction) [Пацина 2003a]. В соответствии с информацией INTAS, последние оценки
поступления ртути в окружающую среду с территории России были выполнены в рамках
проекта ЕС MERCYMS (Pacyna 2003b). Результаты этих оценок представлены в Таблице 6,5.,
где также приводятся результаты оценок, полученные по данному проекту. Данные,
полученные в ходе выполнения указанного проекта, относительно неплохо согласуются с
результатами нашей инвентаризации эмиссии ртути при сжигании угля, производстве чугуна,
цемента, цветных металлов. Выбросы ртути при сжигания отходов оказались значительно
выше, чем по результатам оценок MERCYMS. Следует отметить, что в ходе нашей оценки
выбросы ртути из установок для сжигания отходов сравнивались с содержанием ртути в
отходах; эти данные свидетельствуют том, что оценки, касающиеся выбросов при сжигании
отходов, указанные в документах инвентаризации MERCYMS, занижены. Согласно
результатам проекта MERCYMS, в России выбросы ртути в хлорно-щелочном производстве
очень велики и являются основным источником ее эмиссии в атмосферу. Столь высокие
оценочные данные были получены авторами отчета по проекту MERCYMS на основании
включения, так называемых, неучтенных потерь ртути в общую ее эмиссию в атмосферный
воздух, что не совсем соответствует действительности. Дело в том, что ртуть, включаемая в
категорию .неучтенные потери. (которые формируются в основном за счет механических
потерь металла и определяются по разнице баланса – см. раздел 3.1 настоящего отчета),
главным образом поступает в почвогрунты промзоны предприятий. Оценки, касающиеся
выбросов ртути в воздух, были получены нами на основании данных измерений ее выбросов с
воздухом вентиляционных систем и отходящими газами. Представленные оценочные данные
по выбросам в воздух в ходе различных процессов соответствуют данным предприятий,
которые направляются органам охраны окружающей среды, и сведениям, включенным в
официальные документы по контролю за выбросами ртути (см. Приложение 1). Еще раз
следует отметить, что в отчетах, предоставляемых предприятиями по выпуску хлора в Европе в
комиссию OSPAR (OSPAR 2001), указывается на .«различие в балансе. (что аналогично
.неучтенным потерям.) без дальнейшей интерпретации, причем неучтенные различия в
большинстве стран составляют значительную долю общего количества ртути, используемой в
технологических процессах на хлорно-щелочных заводах. Не исключено, что со временем
определенная часть этой ртути поступает в атмосферной воздух, однако для количественной
оценке этого источника необходимо проведение специальных исследований.
Таблица 6.5 Выбросы ртути в атмосферу в России в 2000 году по данным проекта INTAS [403]
Категория источника |
Проект MERCYMS |
Проект АСАР* |
Выбросы в воздух, т/год |
Доля, % |
Выбросы в воздух, т/год |
Доля, % |
Хлорщелочное производство |
28 |
42 |
1,2 ** |
4 |
Сжигание угля – крупные ТЭЦ |
15,5 |
23 |
8 |
27 |
Сжигание угля – районные котельные |
11 |
17 |
2 |
7 |
Другое использование угля |
Не рассм. |
- |
4,3 |
|
Сжигание мазута, газа и биотоплива |
Нет данных, не рассм. |
- |
4,4 |
12 |
Производство цветных металлов |
5,9 |
9 |
8,4 |
28 |
Производство железа и чугунных чушек |
1,9 |
3 |
1,4 |
5 |
Производство цемента |
3,7 |
6 |
1,6 |
5 |
Размещение отходов |
0,1 |
0,2 |
3,5 |
12 |
* Оценочные данные.
**Кроме того, некоторая часть из этих 56 тонн может прямо или косвенно поступить в атмосферу
Ртуть в сточных водах и ее поступление в водные объекты
По сравнению с выбросами в атмосферу прямое поступление ртути в водные объекты
составляет незначительную часть ее эмиссии из техносферы в окружающую среду. Согласно
официальной статистике, общий сброс ртути с сточными водами промышленных предприятий
в водные объекты в 2001 г. составил 0,16 т. Основная категория источников включает
химическую промышленность (главным образом хлорно-щелочное производство.
На основании данных о содержании ртути в осадках сточных вод было определено, что
общие сбросы ее с городских очистных сооружений могут составлять 3,4-11,89 т. Аналогичное
количество ртути может концентрироваться в осадках городских сточных вод, которые обычно
складируются на иловых площадках и вывозятся на свалки. Во многих городах России сточные
воды промышленных предприятий непосредственно поступают в городскую канализацию и
затем совместно с бытовым стоком очищаются на общегородских очистных сооружениях.
Существенным источником поступления ртути в городские системы канализации, вероятно,
являются стоки стоматологических поликлиник, ртуть из разбитых термометром и ртуть из
электротехнического оборудования (например, разбитые выключатели). Значительная часть
ртутьсодержащих изделий и приборов, выпущенных десять лет назад, может по-прежнему
находиться в эксплуатации и, таким образом, являться потенциальным источником
поступления ртути в сточные воды.
Поступление ртути в почву
Одним из основных источников прямого поступления ртути в почву (не считая свалок
отходов) являются предприятия по выпуску хлора и каустической соды, на которых.
значительная часть от общего количества неучтенных потерь – 50 тонн/год – поступает
непосредственно в почвогрунты на территории или вблизи производственных предприятий.
Ртуть также может случайно попадать в почву с других производств, где она используется. В
отчете приводится перечень наиболее интенсивно загрязненных ртутью промышленных
площадок (как закрытых производств, так и ныне действующих).
. Применение и производство ртутьсодержащих в России запрещено. Тем не менее в 2001
г. в сельском хозяйстве продолжали использоваться ртутьсодержащие пестициды (в основном
гранозан), с которыми в почву поступило до 0,6 т ртути. В настоящее время в стране на складах
хранятся ртутьсодержащие пестициды, количество ртути в которых достигает 20 т. Многие
хранилища, расположенные в сельской местности, находятся в неприемлемом состоянии, что
не исключает вероятность поступления пестицидов в окружающую среду.
В России лишь незначительная часть ежегодно образующихся осадков городских
сточных вод используется в качестве агломелиорантов, с которыми в сельскохозяйственные
почвы может поступать около 1 т ртути. Типичные концентрации ртути в осадках сточных вод
обычно намного ниже существующей ПДК. Настоящая оценка не включала количественную
оценку содержания ртути в используемых в сельском хозяйстве России минеральных и
органических удобрениях.
Ртуть, содержащаяся в зубной амальгаме, рано или поздно будет попадать в почву в
местах захоронения (на кладбищах), где ее количество может составлять до нескольких
тонн/год.
Косвенное поступление ртути с различными продуктами
В ходе различных промышленных процессов ртуть может попадать в качестве
нежелательной (случайной) примеси в ту или иную конечную продукцию или побочные
продукты (табл. 6.6). Как видим, по оценкам, более 16 т ртути в год поступает в виде
нежелательной примеси в различную конечную продукцию и побочные продукты. Дальнейшая
судьба этой ртути не оценивалась, но можно полагать, что в конечном счете она поступает в
окружающую среду или в отходы. Количество ртути в продуктах переработки нефти – за
исключением бензина, дизельного топлива и мазута – не оценивалось, однако общее
содержание ее может быть значительным.
Таблица 6.6 Ртуть в основной продукции и побочных продуктах (дополнительно не оценивались), 2001 г.
Категория деятельности |
Побочный продукт |
Масса ртути (наиболее точная оценка), т/год |
Применение |
Конечная судьба |
Производство ХВМ |
Азотная кислота |
2,8 |
Для заливки нефтяных скважин |
н. о. * |
Производство хлора-щелочи |
Каустическая сода, хлор, водород |
0,2 |
Производство ПВХ; химическая промышленность |
н. о. |
Производство кокса |
Различные химические продукты |
0,6 |
Различное применение |
н. о. |
Производство цинка |
Серная кислота |
7,8 |
н. о. |
н. о. |
Производство меди |
Серная кислота |
2,3 |
н. о. |
н. о. |
Переработка нефти |
Коксовый остаток нефтехимии, битум, сера |
н.о |
н. о. |
н. о. |
Переработка газа |
Сера Устойчивый газоконденсат |
0,3 2,0 |
н. о. |
н. о. |
Всего |
|
>16 |
|
|
* .н. о.. - не оценивалась.
6.3 Ртуть в твердых отходах
Общая масса ртути, присутствующей в ежегодно вывозимых в России на свалки и
полигоны твердых отходах, составляет около 98 т; около 32 т вторичной ртути получают при
переработке различных отходов и рафинировании чернового металла (табл. 6.7). Следует
отметить, что ртуть в отходах находится в разнообразных химических формах, обладающих
различной подвижностью. В отношении эмиссии ртути в атмосферный воздух приводятся
наиболее точные оценки с указанием степени их неопределенности.
С отходами предприятий по выпуску хлора и каустической соды на полигоны поступило
39 т ртути. В настоящее время утилизация указанных отходов с целью извлечения их них
ртути, не проводится, тогда как основная часть отходов производства ХВМ была переработана
для получения новых катализаторов. Количество ртути в отходах, вывезенных на полигоны
предприятиями, выпускающими продукцию, содержащую ртуть, оказалось незначительным
(всего около 0,3 т).
Соединения ртути, используемые в аналитических и научных лабораториях, обычно
нейтрализуются и затем вывозятся на полигоны.
По оценкам, около 3-8 тонн ртути нелегально использовано золотодобывающими
предприятиями, из них 0,6-1,6 (~20%) могло попасть в отвалы и хвосты.
Около 5,6 т ртути попало в зольный остаток и летучую золу при сжигании угля. Малая
часть угольной золы используется для производства цемента, а основная часть ее вывозится на
свалки.
В общей сложности в отходах плавильных предприятий цветной металлургии
аккумулировано примерно 11 т ртути. Кроме того, около xx-xx тонн ртути поступило в отходы
горнодобывающей промышленности и хвосты обогащения. Неясно, какова степень
подвижности ртути, содержащейся в отходах добывающих предприятий, и какое ее количество
в конченом счете поступает в окружающую среду. Результаты некоторых исследований
указывают на то, что ртуть, концентрирующая в хвостах угольных обогатительных фабрик,
является относительно мобильной и может эмитировать в атмосферный воздух.
Если объединить данные таблиц 6,1, 6,4 и 6,5, то количество мобилизуемой ртути превысит
общее количество ртути, поступившей в атмосферный воздух и отходы производста, на 75
тонн. Данная разница иллюстрирует факт, что судьба мобилизуемой ртути до сих пор до конца
неизвестна, и количество ртути в конечных отходах производства может быть существенно
выше указанного количества.
Количество ртути, присутствующей в твердых бытовых отходах, оценивается, как
минимум, в 24 т. Практически отсутствуют данные о содержаниях ртути в виде природной
примеси (следового элемента) в отходах всех видов. Основным источником поступления ртути
в твердые бытовые отходы являются, вероятно, выходящие из строя (разбитые) ртутные
термометры.
Определенная часть ртути, содержащаяся в разбитых термометрах, может поступать в
канализацию. Другими источниками поступления ртути в ТБО являются ртутные лампы,
выключатели, батарейки и зубная амальгама. Если учитывать, что большие количества ртути,
использовавшейся 10 лет тому назад для производства батареек, выключателей, измерительных
приборов и другого электротехнического оборудования, попадали в твердые отходы вместе с
этими продуктами, то такая оценка, вероятно, является слишком заниженной. Количество
ртути в отходах можно оценить путем анализа ее содержания в отходящих газах и остатке
установок, применяемых в России для сжигания отходов, однако результаты таких измерений
отсутствуют.
Рециклинг ртути и получение побочных продуктов
В 2001 г. на двух основных российских предприятиях в результате рециклинга
ртутьсодержащих отходов было получено около 30 т вторичной ртути. В целом производство
вторичной ртути сильно колеблется из года в год. Например, в 2002 г. объем ее производства
составил лишь около 10 т. В 2001 г. около 9,8 т вторичной ртути было получено при
переработке отходов производства хлорвинила (ХВМ), хотя фактическое количество ртути,
содержащейся в образовавшихся в этом году таких отходов, составляло 4,7 т. Эта разница
указывает на то, что отходы могут накапливаться в течение некоторого времени до их
переработки. Около 24 т вторичной ртути было получено при рафинировании чернового
(отработанного) металла, источником которого могли быть различные измерительные приборы,
выключатели, старые запасы ртути на предприятиях и т. д. Менее 100 кг ртути в 2001 г. было
получено при утилизации использованных ртутных ламп, хотя содержание ртути в
переработанных лампах было значительно выше.
Около 5 т ртути в составе шлама предприятий по выпуску цинка было экспортировано
для переработки за рубежом.
Таблица 6.7 ых отходах в Российской Федерации, 2001/2002 г.г.
Категория деятельности |
Ртуть в твердых отходах |
размещение на свалках/полигонах |
рециклинг ртути, наиболее точные оценки, т/год |
наиболее точные оценки, т/год |
% от общего суммарног о количества |
категория неопределен ности |
Целевое использование ртути |
Хлорно-щелочное производство |
39 |
41 |
A |
|
Производство ХВМ |
0,0 |
0,0 |
A |
4,7 |
Добыча золота с использованием амальгамационного метода |
1,1 |
1 |
B |
|
Производство термометров |
0,1 |
0,1 |
A |
|
Производство батареек, барометров, манометров и других измерительных приборов |
0,2 |
0,2 |
A |
|
Производство источников света |
0,001 |
0,0 |
A |
2,3 |
Лабораторное применение |
2,2 |
2,3 |
B |
|
Другое плановое использование |
? |
- |
- |
|
ИТОГО |
43 |
45 |
|
7 |
Мобилизация ртути в виде примеси |
Уголь – добыча и переработка |
3,1 |
3,0 |
B |
|
Уголь – для выработки электроэнергии |
2 |
2,1 |
B |
|
Уголь – другое применение |
0,5 |
0,5 |
B |
|
Переработка нефти |
? |
- |
C |
|
Газ и биотопливо |
? |
0 |
C |
|
Цинк |
8,5 |
9 |
C |
5,4 |
Производство меди и никеля |
6,6 |
7,0 |
C |
|
Производство других цветных металлов (включая золото) |
4,2 |
4,0 |
C |
|
Производство цемента |
0,4 |
0,4 |
В |
|
Использование побочных продуктов |
? |
- |
|
|
ИТОГО |
22 |
23 |
|
5,4 |
Переработка отходов |
Переработка ртути |
0,003 |
0,0 |
A |
|
Переработка железа и стали |
? |
- |
- |
|
Муниципальные и больничные отходы |
24 |
25 |
B |
|
- термометры |
20 |
21 |
B |
|
- батарейки |
1,6 |
1,7 |
C |
0,02 |
- источники света |
1,6 |
1,7 |
B |
|
- измерительные приборы, выключатели и т .д. |
0,04 |
0,0 |
C |
0,5 |
- амальгама |
1 |
1,1 |
C |
|
- другие твердые отходы |
? |
- |
- |
|
Осадки сточных вод |
5,7 |
6,0 |
B |
|
Металлическая ртуть неизвестного происхождения*** |
? |
- |
A |
21 |
ИТОГО |
30 |
32 |
|
22 |
Общее суммарное количество |
95 |
100 |
|
34 |
* Ртуть в побочных продуктах, экспортируемых за рубеж для переработки.
** Показывает количество, утилизируемое для рециклинга в ходе производственного процесса.
Фактический объем рециклинга в 2001 г. составил 9,8 т.
*** Металлическая ртуть для рециклинга без указания на источник ее происхождения; источником
может быть измерительное оборудование, выключатели, запасы и т.д.
**** Часть этого объема может сбрасываться со сточными водами.
*** Категория неопределенности: A: на основании фактических данных предприятий -
неопределенность в связи с неучтенными потерями; B: оценки экспертов - подлинное значение, скорее
всего, будет в диапазоне ± 50% от наиболее точной оценки; C: оценки экспертов - подлинное значение
может значительно превышать диапазон ± 50% от наиболее точной оценки.
7 Источники информации и использованная литература
If nothing else is indicated the sources are in Russian.
References to Internet sites refer if nothing else is mentioned to the sites in spring 2003.
1. Агранович Р.Я. Проблемы обработки осадков городских сточных вод // Водоснабжение
и санитарная техника, 1992, № 4, с. 2-3.
2. Айвазов Г. Пора приручить дикое золото // Красноярский рабочий, 21.2.01.
3. Айзенберг Ю.Б., Прытков А.А. Очерк развития российского светотехнического рынка
на современном этапе // http://www.lta.ru/marketing/review-01.shml.
4. Алакаева Р.А. Некоторые аспекты опасности ртутного загрязнения среды при
извлечении золота из руды методом прямого цианирования // Ртуть. Комплексная система
безопасности. Сборник материалов 3-й научно-технической конференции. – СПБ., 1999, с. 62-
66.
5. Алистратов С.В. Загрязнение почв ртутью в Подмосковном угольном бассейне //
Теория и практика геохимических поисков в современных условиях: Тез. докл. к IV Всес. сов.
(Ужгород, 10-12 октября, 1988). - М.: ИМГРЭ, 1988, с. 10.
6. Амелин А.Г. Технология серной кислоты. – М.: Химия, 1983. – 360 с.
7. Анализ финансового рынка. // http:www.analitika.fis.ru/article/?id=992 (12.8.2003).
8. Аналитическая записка о состоянии черной металлургии в России // Бюллетень
Счетной палаты Российской Федерации, 2002, № 9 (57) // Материалы с официального сайта
Счетной палаты РФ.
9. Анатитцентр, 1998
10. Андреев Б.М., Зельвенский Я.Д., Катальников С.Г. Разделение стабильных изотопов
физико-химическими методами. - М.: Энергоатомиздат, 1982. - 208 с.
11. Андреева В. Состояние дел с непригодными пестицидами в Воронежской области //
Материалы Российского семинара “Инвентаризация запасов устаревших пестицидов”. –
Воронеж: ЦПР, 2000, с. 133-135.
12. Атмосферный воздух, отходы, радиация – Челябинская область. //
www.grenpeace.ru/default/8300 (10.1.2003).
13. Ауэрбах А. Описание ртутного рудника и завода, принадлежащих товариществу А.
Ауэрбаху и Ко // Горный журнал, 1888, т. 2, апрель-июнь, с. 1-12.
14. Афанасьев Б.В., Бичук Н.И., Даин А.Д. и др. Минерально-сырьевая база Мурманской
области // Минеральные ресурсы России, 1997, № 3, с. 16-22.
15. Ачкасов А.И. Распределение микроэлементов в агроландшафтах Московской области:
Автореф. дис…. канд. географ. наук. - М., 1987. - 24 с.
16. Багатаев Р.М. Ртутные месторождения кварц-диккитового типа, геолого-
промышленная модель, прогнозирование и оценка (на примере Донбасса и Северного Кавказа):
Автореф. дис. … доктора геол.-мин. наук. - М., 1998. - 46 с.
17. База данных “Участники светотехнического рынка”. Вып. 1. - М.: Дом Света, 2001. -
152 с.
18. Баймаков Ю.В., Журин А.И. Электролиз в гидрометаллургии. - М.: Металлургия, 1977.
- 335 с.
19. Баринова И.А., Синицына А.В., Харитонов А.А. Энергосбережение в бытовом
освещении г. Саранска (рыночная ситуация) // Светотехника, 2002, № 5, с. 21-23.
20. Башкортостан. Краткая энциклопедия // http://www.uic.bashedu.ru/encikl/maintitle.htm.
21. Бауэр В., Карпов С. Резервы формирования российского рынка золота // .РЦБ.
Товарный рынок., 2001, (пилотный выпуск) //
http://www.investor.ru/Archive/articlestr.asp?aid=1844.
22. Беляев А.И., Жемчужина Е.А., Фирсанова Л.А. Металлургия чистых металлов и
элементарных полупроводников. - М.: Металлургия, 1969. - 504 с.
23. Беневольский Б.И. Золото России. - М.: Геоинформмарк, 2002. - 464 с.
24. Берлинг Н.И. Дагестан и проблема ртути // Плановое хозяйство Дагестана, 1928, № 5-
6, с. 32-35.
25. БИКИ, 2002, № 148.
26. БИКИ, 2003, № 20.
27. БИКИ, 2003, № 41.
28. Благутин Ю.Л. // http://www.gornymir.ru/SEMENAR/usl_licenz6.htm (15.4.2002).
29. Бовина Л.А., Болтарь К.О., Бурлаков И.Д. и др. Матричные приемники формата
128х128 и 384х288 на основе фотодиодов из CdXHg1-XTe // Прикладная физика, 1999, № 3, с.
32-41.
30. Бовина Л.А., Стафеев В.И. Фотодиоды и фотодиодные матрицы на основе CdXHg1-
XTe // Прикладная физика, 1999, № 6, с. 59-69.
31. Бовина Л.А., Стафеев В.И., Болтарь К.О. Исследования стабильности характеристик
фотодиодов из CdXHg1-XTe // Прикладная физика, 1999, № 3, с. 41-46.
32. Бобков А.С., Блинов А.А., Роздин И.А., Хабарова Е.И. Охрана труда и экологическая
безопасность в химической промышленности. – М.: Химия, 1997. – 400 с.
33. Боброва Л.В., Кондрашова О.В., Федорчук Н.В. Экономика геологоразведочных работ
на ртуть, сурьму и висмут. – М.: Недра, 1990. – 156 с.
34. Богатырев В.Р., Галай Н.Н., Белогуб М.Ф., Юдина И.М. Ресурсология. Ч. 1. Основные
виды ресурсов Нижегородской области. - Нижний Новгород: Изд-во Волго-Вятской академии
государственной службы, 1999. - 183 с.
35. Богомолов А.И., Гайле А.А., Громова В.В. и др. Химия нефти и газа. – СПб.: Химия,
1995. – 448 с.
36. Болохонцева Р.В., Кошлек Т.И., Савельева Л.Ф. и др. Санитарно-гигиеническая
характеристика условий труда на ОАО .Свет. // Материалы научно-практической конференции
“Актуальные вопросы обеспечения санитарно-эпидемиологического благополучия и охраны
здоровья населения центрального региона России”, посв. 80-летию Государственной сан.-эпид.
Службы России (Смоленск, 26-29 ноября 2002 г.). - Смоленск: СГМА, 2002, с. 234-236.
37. Бондаренко В.Н., Колесников А.Г., Бондарев В.Г. Оборудование и охрана окружающей
среды // Кокс и химия, 2002, № 1, с. 32-35.
38. Борзых М.Н. Проблемы обезвреживания и утилизации ртутьсодержащих
гальванических элементов // Передовой производственный опыт, 1989, № 3, с. 46-47.
39. Борзых М.Н., Михайлов В.К., Пустильник А.И. и др. Переработка отходов
производства гальванических элементов // Цветные металлы, 1988, № 4, с. 47-49.
40. Буренков Э.К., Янин Е.П., Кижапкин С.А. и др. Эколого-геохимическая оценка
состояния окружающей среды г. Саранска. - М.: ИМГРЭ, 1993. - 115 с.
41. Бутов В.А., Иванов В.С., Кременецкий А.А., Усова Т.Ю. Ртуть России: проблемы и
перспективы // Минеральные ресурсы России. Экономика и управление, 1997, № 5, с. 9-13.
42. Бычкова Н.А. Клиника и лечение интоксикации гранозаном у детей: Автореф. дис..
канд. мед. наук. – Новосибирск, 1973. – 15 с.
43. Варавин В.С., Гутаковский А.К., Дворецкий С.А. Состояние и перспективы
молекулярно-лучевой эпитаксии CdXHg1-XTe // Прикладная физика, 2002, № 6, с. 25-41.
44. Варум Я.И., Изюмская Л.А. Эффективность печных электрофильтров // Цемент, 1990,
№ 4, c. 5-6.
45. Вебер В., Марков К. Ртуть // Естественные производительные силы России, 1917, вып.
9, с. 1-17.
46. Витурид. Роль ртути в жизнедеятельности организма. - Петрозаводск: АОЗТ “Фирма
“Витурид”, 1995. - 116 с.
47. Волох А.А. Опыт контроля за загрязнением атмосферного воздуха металлами и
летучими органическими соединениями на городских и фоновых территориях // Геохимические
исследования городских агломераций. – М.: ИМГРЭ, 1998, с. 40-58.
48. Воронцова Н. Дальневосточная кладовая ждет своего Алладина // kapital.zrpress.ru
(18.X.2003).
49. Воскобойников В.Г., Кудрин В.А., Якушев А.М. Общая металлургия. – М.:
Металлургия, 1979. – 487 с.
50. Временная инструкция по подготовке к захоронению запрещенных и непригодных к
применению в сельском хозяйстве пестицидов и тары из-под них. – Рязань: ВНИПИагрохим,
1989.
51. В Российской коксохимической теплотехстанции // Кокс и химия, 2002, № 5, с. 11-21.
52. Выбросы тяжелых металлов в атмосферу: Опыт оценки удельных показателей. .
Минск: ИПИПРиЭ НАН Беларуси, 1998. – 156 с.
53. Вязельщиков В.П., Парицкий З.Н. Справочник по обогащению золотосодержащих руд
и песков. - М.: ГОНТИ, 1963.
54. Газета “Приамурские ведомости”, 13 августа 2002 г.. № 144 (2785) //
http://pv.leased.redcom.ru/archive/02/08/13/a7.htm (29.3.2003).
55. Ганеев А.А., Рыжов В.В., Майдуров А.Д. и др. Прямое определение ртутьорганических
соединений в природном газе и воздухе с использованием пиролиза и фотолиза // Вестник
Санкт-Петербургского Университета, 1996, сер. 4, вып. 1(4).
56. Гаркуша Ф., Лаубган Т. Контроль хранения пестицидов в Краснодарском крае и
проблема пестицидов, пришедших в негодность // Материалы Российского семинара
“Инвентаризация запасов устаревших пестицидов”. – Воронеж: ЦПР, 2000, c. 151-153.
57. География России. Энциклопедический словарь. - М.: Большая Российская
энциклопедия, 1998. - 800 с.
58. Герасимчук И., Симонов К., Государева В. и др. Текущее и перспективное
потребление металлов в России и Украине // http://www.marketing.cfin.ru/mr/industry/consuptio.
(16.5.2003).
59. Герасимчук И., Симонов К., Государева В. и др. Текущее и перспективное
потребление металлов в России и Украине // http://www.marketing.cfin.ru/mr/industry/consuptio.
(11.7.2003).
60. Гигиеническая оценка качества почвы населенных мест. Методические указания. –
Москва: Минздрав России, 1999.
61. Гигиенические нормативы. ГН 1,1,546-96. Гигиенические нормативы содержания
пестицидов в объектах окружающей среды.
62. Гигиенические нормативы ГН 2,1,6,695,98. Предельно допустимые концентрации
(ПДК) загрязняющих веществ в атмосферном воздухе населенных мест. – Москва: Минздрав
России, 1998.
63. Гигиенические нормативы ГН 2,1,6,686-98. Предельно допустимые концентрации
(ПДК) вредных веществ в воздухе рабочей зоны. – Москва: Минздрав России, 1998
64. Гигиенические нормативы ГН 2,1,5,690-98. Предельно допустимые концентрации
(ПДК) химических веществ в воде водных объектов хозяйственно-питьевого и культурно-
бытового водопользования. – Москва: Минздрав России, 1998
65. Гись Ю.Ф., Познер З.А., 1970
66. Годовой отчет “ГМК “Норильский никель” -2001 г. (Официальный веб-сайт “ГМК
“Норильский никель” // www.nornik.ru.
67. Годовой отчет “ГМК “Норильский никель” – 2002 г. (Официальный веб-сайт “ГМК
“Норильский никель” //www.nornik.ru.
68. Годовой отчет за 2001 г. ОАО “Газпром” // www.gazprom.ru.
69. Годовой отчет ОАО “ММК” за 2002 год для инвесторов // www.mmk.ru.
70. Голембиовский С.А., Шемелин Ю.А. Российский рынок светотехнической товарной
продукции бытового и офисного назначения. Взгляд изнутри // Светотехника, 1997, № 4, с. 39-
43, № 6, с. 38-40, 1997
71. Гончаров В.Г. Золотодобывающая промышленность России. Итоги 2001 г. //
Минеральные ресурсы России, 2002, № 1-2, с. 40-45.
72. Гордеев В.В. Речной сток в океан и черты его геохимии. – М.: Наука, 1983. – 160 с.
73. Горжевский Д.И., Ручкин Г.В., Клименко Н.Г. Минеральное сырье. Свинец и цинк.
Справочник. – М.: Геоинформмарк, 1997. – 47 с.
74. Госкомстат РФ. Постановление об утверждении .Методологических положений по
расчету топливно-энергетического баланса Российской Федерации в соответствии с
международной практикой. от 23 июня 1999 г. № 46.
75. Госкомстат РФ. Производство продукции в отдельных отраслях промышленности
(открытые информационные фонды) // http://www.gks.ru
76. ГОСТ 30772-2001. Ресурсосбережение. Обращение с отходами: Термины и
определения. - М.: Изд-во стандартов, 2002. - 15 с.
77. ГОСТ 30773-2001. Ресурсосбережение. Обращение с отходами. Этапы
технологического цикла: Основные положения. - М.: Изд-во стандартов, 2002. - 11 с.
78. ГОСТ 30774-2001. Ресурсосбережение. Обращение с отходами. Паспорт опасности
отходов: основные требования. - М.: Изд-во стандартов, 2001. - 21 с.
79. ГОСТ 30775-2001. Ресурсосбережение. Обращение с отходами. Классификация и
кодирование отходов: Основные положения. - М.: Изд-во стандартов, 2002. - 37 с.
80. ГОСТ 4658-73. Ртуть. Технические условия. - М.: ИПК Издательство стандартов,
1997. - 11 с.
81. Государственный баланс запасов полезных ископаемых Российской Федерации.
Нефть. 2002. Росгеолфонд.
82. Государственный доклад о состоянии и использовании минерально-сырьевых
ресурсов Российской Федерации в 2001 году. Золотодобывающая промышленность. - М. 2003 //
http://www.mineral.ru/Chapters/Production/Issues/35/Issue_Files.html.
83. Государственный доклад .О состоянии минерально-сырьевой базы Российской
Федерации. // http://www.mineral.ru.
84. Государственный доклад о состоянии окружающей природной среды Республики
Мордовия в 2001 году. - Саранск: Комитет природных ресурсов по Республике Мордовия,
2002. - 264 с.
85. Государственный доклад “О состоянии окружающей природной среды Российской
Федерации в 2000 году”. – М., 2001.
86. Государственный доклад “О состоянии и об охране окружающей среды Российской
Федерации в 2001 году”. – М., 2002.
87. Государственный каталог пестицидов и агрохимикатов, разрешенных к применению
на территории Российской Федерации. – М., 2002.
88. Гриценко А.И., Босняцкий Г.П., Шилов Ю.С., Седых А.Д. Экологические проблемы
газовой промышленности. – М., 1993.
89. Гудима Н.В., Шейн Я.П. Краткий справочник по металлургии цветных металлов. – М.:
Металлургия, 1975. – 536 с.
90. Деловой Новосибирск (21.1.2002) // http://www.dnsk.ru/2002/korp/1121_litiy.htm
(11.3.2003).
91. Демина Л.А. Ртуть вокруг нас // Энергия: Экономика, техника, экология, 1999, № 4, с.
65-68.
92. Денисов С.И. Улавливание и утилизация пылей и газов. – М.: Металлургия, 1991.
93. Добрянский Л.А., Артеменко В.М., Морозов В.И. Ртуть в окружающей среде
некоторых городов Украины. - Киев: ИГН АН Украины, 1992. - 44 с.
94. Доклад о санитарно-эпидемиологическом благополучии Тульской области за 2001
год.
95. Доклад о свинцовом загрязнении окружающей среды Российской Федерации и его
влиянии на здоровье населения. – М., 1997.
96. Донских Д.К., Скитский В.Л. Проблемы утилизации ртутьсодержащих отходов и пути
их решения // http://recyclers.ru/text/037.html (03.1.2003).
97. Дорожукова С.Л., Янин Е.П., Волох А.А. Природные уровни ртути в некоторых типах
почв нефтегазоносных районов Тюменской области // Вестник экологии, лесоведения и
ландшафтоведения, 2000, вып. 1.
98. Евилевич А.З., Евилевич М.А. Утилизация осадков сточных вод. - Л.: Стройиздат, 1988.
- 248 с.
99. Ждамиров В.М., Кузнецов В.И. Экологические проблемы угольных разрезов Кузбасса
// Уголь, 1990, № 9, с. 25-29.
100. Зайнуллин Х.Н., Галимова Е.Ж. Оценка влияния отходов и сточных вод
Бурибаевского рудоуправления на загрязнение реки Таналык // Экологические проблемы
промышленных зон Урала. Т. 1. – Магнитогорск: МГМА, 1998, с. 137-142.
101. Замятин О.В., Лопатин А.Г. Обогащение золотосодержащих песков и
конгломератов. - М.: Недра, 1975. - 264 с.
102. “Золото-2002” От месторождения до ювелирного изделия.. 4-я Международная
выставка // http://www.rusexpo.com/gold/otchot02.htm.
103. Зорькин Л.М., Стадник Е.В., Юрин Г.А., Сошников В.Х. Содержание ртути в ртути
некоторых газовых и газоконденсатных месторождений СССР // Геология нефти и газа, 1974,
№ 10.
104. Иванов А.А. Результаты мониторинга загрязнения рыбы и рыбопродуктов
пестицидами // Здоровье населения и среда обитания, 1999, № 11, с. 19-21.
105. Информационно-аналитический сборник “Мировой и внутренний рынок цветных и
редких металлов” (по состоянию на 1.7.2002 г.). Вып. 14. Ртуть. - М.: ИАЦ ООО “Инфометгео”,
2002. - 16 с.
106. Информационно-аналитический обзор “Состояние и перспективы мирового и
внутреннего рынков цветных, редких и благородный металлов”. Вып. 3. Свинец и цинк. – М.:
ООО “Инфометгео”, 2002. – 66 с.
107. История золота. Банк .Финансы и Кредит., Украина //
http://www.fc.kiev.ua/metals/history.html.
108. Источники света. Каталог светотехнических изделий. - М.: Московский “Дом
Света”, 2003. - 124 с.
109. Итоги производства ОАО “Сафьяновская медь” за 1 квартал 2003 года //
http://www.mineral.ru/Chapters/News/7460.html (16.5.2003).
110. Итоги работы угольной промышленности России за 2001 г. // Уголь, 2002, № 3, с. 54-
62.
111. Какарека С.В., Кухарчик Т.И., Хомич В.С., Янин Е.П. О состоянии и проблемах
инвентаризации выбросов ртути в атмосферу // Эколого-геохимические проблемы ртути. - М.:
ИМГРЭ, 2000, с. 12-37.
112. Каменев В.Ф., Фадеева Л.В. Распределение ртути в сернокислом производстве //
Цветные металлы, 1983, № 8, с. 35-36.
113. Карасик М.А., Дворников А.Г. Ртутоносность углей Донецкого бассейна и продуктов
его переработки. – М.: ОНТИ ВИЭМС, 1968. – 45 с.
114. Карелин О.Н., Константинова Л.Н., Ксенофонтов В.Н. и др. Загрязнение воздуха
ртутью при производстве элементов питания электроприборов // Гигиена и санитария, 1992, №
7-8, с. 3
115. Картузов В.М., Шеманаев С.А. Утилизация ртутьсодержащих отходов // Экология и
промышленность России, 2000, апрель, с. 14-16, 49.
116. Катаева В.А., 2002
117. Катунин В.В. Итоги работы черной металлургии России за 2001 г. // Черная
металлургия, 2002, № 2, с. 3-16.
118. Кириллова Т. Павлодарская лихорадка // Новости недели (Казахстан), 2002, № 1 (67)
от 0,9.1.02 // (http://hghltd.yandex.ru/yandbtm?url=http://www.nn.kz/cgi-bin/newsweek.cgi.
119. Клер В.Р., Ненахова В.Ф., Сапрыкин Ф.Я. и др. Металлогения и геохимия
угленосных и сланцесодержащих толщ СССР. Закономерности концентрации элементов и
методы их изучения. - М.: Наука, 1988. - 256 с.
120. Клименко Н.Г., Кязимов Р.А. Анализ современного состояния переработки
колчеданных руд. - М.: ВИЭМС, 1987. - 51 с.
121. Климов О.М., Мельниченко А.С., Голубин А.К. К вопросу загрязнения окружающей
среды ртутью отходами производства // Ртуть. Комплексная система безопасности. Сборник
материалов III-й научно-технической конференции. - СПб., 1999, с. 14-18.
122. Ковалев Е.Т., Рудыка В.И., Малина В.П. Охрана окружающей среды в
коксохимической промышленности Европы и США // Углехимический журнал, 2001, № 1-2, с.
63-65.
123. Ковалишина Г. Тенденции на рынках основных цветных металлов //
http://www.tdvtb.ru/news/nonferruus/review.xsp (13.6.2003).
124. Коваль А.Т., Сидоров Ю.Ф., Нагорный В.А., Остапчук В.И. Техногенное загрязнение
металлической ртутью районов золотодобычи Амурской области и Хабаровского края //
Сборник докладов семинара “Добыча золота. Проблемы и перспективы”. – Хабаровск, 1997, c.
347-352.
125. Ковда В.А. Биогеохимия почвенного покрова. - М.: Наука, 1985. - 263 с.
126. Козин Л.Ф. Амальгамная металлургия. - Киев: Технiка. 1970. - 272 с.
127. Козин Л.Ф. Амальгамная пирометаллургия. Физико-химические основы. - Алма-Ата:
Наука, 1973. - 269 с.
128. Козырев В. Металлургия СНГ: десять лет спустя // Металлы Евразии, 2002, № 3, с.
30-33.
129. Колбасов В.М., Леонов И.И., Султменко Л.М. Технология вяжущих материалов. М.,
Стройиздат, 1987.
130. Колмогоров Н.К. Золотодобывающая промышленность России. Проблемы и
перспективы // Минеральные ресурсы России, 2000, №2.
131. Корвацкий В. Ильдиканское месторождение киновари в Нерчинском округе //
Горный журнал, 1907, т. 2, кн. 6 (июнь), с. 347-356.
132. Корницкая В.М., Ростокинская Н.В. Кто остановит “Меркурий”? // Экология и
жизнь, 1999, № 1, с. 58-60.
133. Коровицкий С.Л. Изъятие не используемой ртути и ртутьсодержащих изделий как
фактор уменьшения опасности ртутных загрязнений // Ртуть. Комплексная система
безопасности. Сборник материалов III-й научно-технической конференции. - СПб., 1999, с. 33-
35.
134. Королев Ю.Н., Боброва Л.В. Роль попутных компонентов при оценке промышленной
значимости комплексных руд цветных металлов. – М.: ВИЭМС, 1963.
135. Коростелев П.Г. Геохимические связи формирования оловянной и ртутной
минерализации // Вопросы металлогении ртути (по материалам Сибири и Дальнего Востока). .
М.: Наука, 1968, , с. 142-148.
136. Косинский В.А., Корнилов Ю.Н., Поляковская Е.И., Черников А.Б. Минеральное
сырье. Уголь: Справочник. – М.: Геоинформарк, 1997. – 63 с.
137. Косорукова Н.В., Янин Е.П. Утилизация отходов ртутьсодержащих изделий:
состояние и проблемы // Светотехника, 2002, № 3, с. 25-29.
138. Кривцов А.И. Клименко Н.Г. Минеральное сырье. Медь. Справочник. – М.:
Геоинформмарк, 1997. – 51 с.
139. Кривцов А.И., Клименко Н.Г. Минеральное сырье. Никель и кобальт. Справочник. –
М.: Геоинформмарк, 1997. – 52 с.
140. Кузин А.А. История открытий рудных месторождений в России. - М.: Изд-во АН
СССР, 1961. - 360 с.
141. Курбатов Л.Н. Основные направления разработок фотоприемников и фотоприемных
устройств для тепловидения в период 1970-1998 г.г. // Прикладная физика, 1999, № 3, с. 5-18.
142. Кутлиахметов А.Н. Ртутное загрязнение ландшафтов горнорудными предприятиями
Башкирского Зауралья: Автореф. дисс…. канд. геогр. н. - Екатеринбург, 2002. – 25 с.
143. Лапердина Т.Г. Ртутное загрязнение окружающей среды в зонах влияния
золотодобывающих предприятий Забайкалья // Химия в интересах устойчивого развития, 1995,
№ 3, c. 57-67.
144. Левицкая Т.Д., Буркина С.К., Пустильник А.И. и др. Авторское свидетельство №
1334734 на изобретение “Способ переработки ртутьсодержащих гальванических элементов”,
1987.
145. Левицкая Т.Д., Пустильник А.И., Гуськов В.И. и др. Авторское свидетельство №
1434781 на изобретение “Способ переработки ртутьсодержащих гальванических элементов”,
1988.
146. Левченко Д.Н., Бергштейн Н.В., Худякова А.Д., Николаева Н.М. Эмульсии нефти с
водой и методы их разрушения. – М.: Химия, 1967.
147. Липецкая область в цифрах за 2001 год. - Липецк: Липецкий облкомстат, 2002. - 200 с.
148. Лотош В.Е. Утилизация канализационных стоков и осадков // Ресурсосберегающие
технологии. Межотраслевой выпуск. Экспресс-информация, 2002, № 24, с. 7-24.
149. “Люди-Дела” (Российский аналитический журнал для деловых людей, 2002, № 27 //
http://www.ludidela.ru/0206/0206-33-01.html (13.7.2003).
150. Магадеев Б.Д., Грешилов А.И., Антонов К.В., Чернов А.Л. Минерально-сырьевая база
Республики Башкортостан // Минеральные ресурсы России, 1997, № 6, с. 15-21.
151. Макаров В.А., Шрайнер А.Д., Бурлаков А.А., Цыкин С.Р. Опыт решения
геологических, технологических и экологических задач при переоценке техногенных россыпей
и хвостохранилищ Енисейского кряжа // Cборник материалов отраслевой научно-технической
конференции.ю посвященной 125-летию со дня основания института Иргиредмет. – Иркутск,
1997.
152. Макарченко Г.В., Косорукова Н.В., Волох А.А. Демеркуризация объектов городской
среды // Эколого-геохимические проблемы ртути. - М.: ИМГРЭ, 2000, с. 153-160.
153. Материалы по удельным выбросам веществ в атмосферу коксохимических произ-
водств востока и Центра СССР. – М.: Минчермет СССР, 1987.
154. Мацевич В.В., Борзых М.Н., Доморощин В.П. Установка утилизации
ртутьсодержащих щелочных марганцево-цинковых гальванических элементов // Ртутная
опасность - проблема ХХ века. - СПб., 1994, с. 93-98.
155. Межотраслевые правила по охране труда при производстве и применении ртути.
ПОТ РМ-009-99. - СПб.: Изд-во ДЕАН, 2001. - 64 с.
156. Мейлихов Е.З., Лазарев С.Д. Электрофизические свойства полупроводников. - М.:
ЦНИИатоминформ, 1987. - 87 с.
157. Мельников С.М. Техника безопасности в металлургии ртути. - М.: Металлургия,
1974. - 184 с.
158. Металлоснабжение и сбыт, 2001, № 12.
159. Металлург, 2001, № 1
160. Металлург, 2002, № 1
161. Металлург, 2002, № 4.
162. Методические рекомендации по гигиенической оценке загрязнения атмосферного
воздуха в районах размещения предприятий по производству и применению ртути. - М.:
Минздрав СССР, 1989. - 17 с.
163. Методические указания по определению неорганизованных выбросов. - Свердловск,
1987.
164. Минеральные ресурсы мира (на начало 1994 г.). - М.: ВНИИзарубежгеология, 1995. -
575 с.
165. Минеральные ресурсы мира на начало 1997 года (издание официальное). - М.:
ФГУНПП “Аэрогеология”, 1998. - 738 с.
166. Минеральные ресурсы мира на начало 1998 года (издание официальное). - М.:
ФГУНПП “Аэрогеология”, 1999. - 870 с.
167. Минеральные ресурсы мира на начало 1999 года (издание официальное). - М.:
ФГУНПП “Аэрогеология”, 2000. - 911 с.
168. Минеральные ресурсы мира на 1.1.2000 г. Статистический справочник (издание
офици-альное). - М.: ФГУНПП «Аэрогеология», 2001. - 477 с.
169. Минеральные ресурсы мира на 1.1.2001 г. Статистический справочник (издание
офици-альное). - М.: ФГУНПП “Аэрогеология”, 2002. - 475 с.
170. Минеральные ресурсы Учалинского горно-обогатительного комбината. – Уфа:
Башкирское книжное издательство, 1994. – 328 с.
171. Мониторинг пестицидов в объектах природной среды Российской Федерации.
Ежегодник Института экспериментальной метеорологии Росгидромета. - С.-Петербург, 1999,
Приложение 3, с. 31.
172. Москвоведение: Экология Московского региона. Пособие для учащихся 8-9 классов
г. Москвы и Московской области. - М.: Экопрос, 1996. - 208 с.
173. Муллов В.М., Чикина Т.В., Альперт В.А. Решение проблемы охраны среды при
переработке золото-ртутьсодержащих руд по ионообменной технологии // Cборник материалов
III Конгресса обогатителей стран СНГ, 2001.
174. Мустафин С.К., Минигазимов Н.С., Зайнуллин Х.Н. и др. Проблемы ртутной
безопасности Южного Урала // Экологические проблемы промышленных зон Урала. Т. 1. -
Магнитогорск: МГМА, 1998, с. 148-154.
175. Мязин В.П., Татауров С.Б. Разработка и совершенствование технологий и
оборудования по извлечению золотосодержащей амальгамы и токсичных соединений ртути из
техногенных образований // Горный информационно-аналитический бюллетень, 1997a, № 1, с.
61-70.
176. Мязин В.П., Татауров С.Б. О некоторых направлениях к разработке технологических
схем утилизации золотосодержащей амальгамы из техногенных месторождений // Сборник
докладов семинара “Добыча золота. Проблемы и перспективы”. - Хабаровск, 1997б, с. 315-325.
177. На мировом рынке электрических батарей // БИКИ, 2001, № 125, с. 10-11.
178. Научно-Технический Центр “Горнообогатительные модульные установки”
Московского Государственного Горного Университета (НТЦ МГГУ). 2000 //
http://stc.msmu.ru/index.htm.
179. Нашельский А.Я. Технология полупроводниковых материалов. - М.: Металлургия,
1987. - 336 с.
180. Никифоров К.А., Хантургаева Г.И., Шатуев И.Н., Будаева Н.Р. Обогащение
ртутьсодержащих отходов золотодобывающих предприятий // Физико-технические проблемы
разработки полезных ископаемых, 1994, № 5, c.113-115.
181. Новолипецкий металлургический комбинат. Годовой отчет. 2001 г. // www.nlmk.ru.
182. Номенклатурный справочник изделий приборостроительных предприятий России. -
М.: ИН-ФОРМПРИБОР, 1993. - 75 с.
183. ОАО “Термоприбор”_Каталог продукции // http://www.thermopribor.com/kat_1.htm.
184. Оболенский А.А., Озерова Н.А., Васильев В.И. Природные источники ртути в Сибири
// Химия в интересах устойчивого развития, 1995, 3, № 1-2, с. 11-22.
185. Образование, поступление, использование и размещение отходов //
http://www.ecolog.nw.ru/REVIEW97/15.htm (29.7.2002).
186. ОВОС полигона ТБО г. Перми.
187. Озерова Н.А. Первичные ореолы рассеяния ртути. – М.: Изд-во АН СССР, 1962. –
135 с.
188. Озерова Н.А. Ртуть и эндогенное рудообразование. - М.: Наука, 1986. - 232 с.
189. Озерова Н.А. Ртутоносность газовых и газонефтяных месторождений // Новые идеи в
геологии и геохимии нефти и газа. К созданию общей теории нефтегазоносности недр.
Материалы шестой международной конференции. Кн. 2. - М.: ГЕОС, 2002.
190. Озерова Н.А., Айдиньян Н.Х. Ртуть в осадочном процессе // Очерки геохимии
эндогенных и гипергенных процессов. - М.: Наука, 1966.
191. Озерова Н.А., Добрянский Л.А. Опыт прогнозирования ртутоносности газовых
месторождений (на примере газоконденсатного месторождения Опошня, ДДВ) // Геохimiчнi
методы пошукiв – стан i перспективи розвитку. - Киев, 2000.
192. Озерова Н.А., Машьянов Н.Р. Новое в ртутометрии // Геохимические методы и
научно-технический прогресс в геологическом изучении недр. - М.: Наука, 1989.
193. Озерова Н.А., Машьянов Н.Р., Пиковский Ю.И. и др. Линеамент Карпинского –
сквозная ртутьконцентрирующая структура // Сквозные рудоконцентрирующие структуры. -
М.: Наука, 1989, с. 52-58.
194. Озерова Н.А., Пиковский Ю.И. Региональные закономерности размещения
ртутьсодержащих углеводородных газов // Природные газы Земли и их роль в формировании
земной коры и месторождений полезных ископаемых. – Киев: Наукова думка, 1985, c. 144-155.
195. Орлов В.П. О Федеральной программе воспроизводства минерально-сырьевой базы
России // Минеральные ресурсы России, 1993, № 4, с. 4-7.
196. Основы металлургии. Т. 2. Тяжелые металлы. – М.: Металлургиздат, 1962. – 792 с.
197. Основные экономические и социальные показатели Липецкой области за 1998-2001
г.г. - Липецк: Облкомгосстат, 2002. - 118 с.
198. Отчет о научно-исследовательской работе по теме “Анализ состояния ртутного
загрязнения окружающей среды в Российской Федерации”. - Мытищи: НИЦПУРО, 1999. - 47 с.
199. Отчет о научно-исследовательской работе по теме “Изучение номенклатуры
ртутьсодержащих отходов в Российской Федерации с целью их паспортизации”. - Мытищи:
НИЦПУРО, 2000. - 49 с.
200. Отчет по обращению с отходами. ООО “Экологическая фирма “Оскар”, 2002 г.,
Пермская область.
201. Отчет по теме НИР “Составление комплекта карт антропогенного загрязнения
территории Амурской области м-ба 1:500 000 и крупнее” (объект “Антропогенный”). Отв. исп.
Сидоров Ю.Ф. – Благовещенск: ГПЦ при КПР по Амурской области, 2002.
202. Охрана окружающей среды. Казань // http://kazadmin.narod.ru/ocrsred.htm (23.8.2002).
203. Очистка технологических газов в цветной металлургии. – М., 1992.
204. Пайонке В., Мерсманн М. Реконструкция печных линий в условиях работы
российской цементной промышленности // Цемент и его применение, 2002, № 3, с. 11-13.
205. Пак Н.Т., Клопотовский И.С., Нагний В.А. Обогащение и металлургическая
переработка полиметаллического сырья // Сборник научных трудов Среднеазиатского
НИИПИцветмет. - Ташкент, 1984, с. 97-101.
206. Парламентская газета, 8 февраля 2003 г., № 1155 //
http://www.pnp.ru/pg.nomers/10868.htm.
207. Пасынков В.В., Сорокин В.С. Материалы электронной техники. - М.: Высшая школа.
1986. - 367 с.
208. Передерий О.Г., Микшевич Н.В. Охрана окружающей среды на предприятиях
цветной металлургии. – М., 1991.
209. Пермяков Т.А. Ртуть // Сырьевые рынки России, 1994, № 10, с. 9-12.
210. Петров И., Троицкий В., Гришаев С. Разработка методических основ анализа
товарных рынков минерального сырья и продуктов его переработки // Практический маркетинг,
1999, № 10 (http://www.cfin.ru/press/practical/1999-10/01.shtml).
211. Петухов А.Г., Коновалов А.И. Опыт работы Клинского термометрового завода по
оздоровлению атмосферного воздуха // Гигиена и санитария, 1973, № 10, с. 98-99.
212. Петров В.И. Азбука освещения. - М.: ВИГМА, 1999. - 84 с.
213. Плышевский С.В., Челноков А.А. Эмиссия тяжелых металлов в атмосферу при
производстве цемента // 2-е Международное совещание по химии и технологии цемента,
Москва, 2000: Стендовые доклады. Т. 3. – М., Изд-во РХТУ, 2000, с. 262-265.
214. Полькин С.И. Обогащение руд и россыпей редких и благородных металлов. - М.:
Недра, 1987.
215. Полькин В.И. Рынок цинк содержащей продукции и технологий на подъеме
(“Металлоснабжение и сбыт”, 2003, № 2) // http://www.zinc.ru/pub_view.php?gid=1&id=8
(10.9.2003).
216. Полькин В., Анисимов С. Металл больших возможностей // Металлы Евразии, 2002,
№ 1, с. 50-53.
217. Полькин В.И., Пономарева Н.П. Обзор рынка цинка и оцинкованной продукции //
http://www.zdc.ru/pablic_7.htm (30.6.20030.
218. Польских Е. Анчар региональной индустрии // Всем, 30 марта 2001 г., № 13 (382).
219. Пономаренко В.П., Филачев А.М. Фотоприемники и фотоприемные модули нового
поколения (к 55-летию НИИ-801 - НПО “Орион”) // Прикладная физика, 2001, № 6, с. 20-38.
220. Пономаренко В.П., Филачев А.М. Фотоэлектроника для нового поколения оптико-
электронной аппаратуры // Прикладная физика, 2002, № 6, с. 13-24.
221. Пресс-релиз к пресс-конференции на 8-й Международной выставке оборудования
для нефтяной и газовой промышленности “Нефтегаз-2000”. – М.: Экспоцентр, 2000.
222. Приказ Главдрагмета при Кабинете Министров СССР № 124 от 29.2.88 г. “О
прекращении применения ртути (амальгамации) в технологических процессах при обогащении
золотосодержащих руд и песков”.
223. Проблемы современного светотехнического рынка России // Светотехника, 2002, №
2, с. 28-31.
224. Проект нормативов предельно допустимых выбросов для промплощадки № 1
(“Лисма-СЭЛЗ”). - Саранск: ВНИИИС-Лисма, 2000. - 295 с.
225. Проект 1 очереди расширения Саранского завода специальных источников света и
электровакуумного стекла – АО “Лисма СИС и ЭВС” со строительством корпуса
люминесцентных ламп и стекольного корпуса № 1. Корректировка проекта с выделением
пускового комплекса. Раздел 6. Технические условия и документы согласований. - М.:
ГИПРОНИИЭЛЕКТРО, 1993.
226. Производство ртути в США // http:// www.mineral.ru/Chapters/News/2855.html 2002-
май/22.
227. Производство чугуна в России в 2001 г. // http://www.netro.ru/profilescompany.
shtml?05_07_2. (21.3.2003).
228. Промышленность России. 2002: Статистический сборник. – М.: Госкомстат России,
2002. – 453 с.
229. Пшеничный Г.Н. Гайское медно-колчеданное месторождение Южного Урала
(минералогия, геохимия, строение и условия формирования руд). - М.: Наука, 1975. - 187 с.
230. Пыриков А.Н., Васнин С.В., Боранбаев Б.М., Козлов В.Д. Защита окружающей среды
на коксохимических предприятиях. - М.: Интермет Инжиниринг, 2000. - 182 с.
231. Пятницкий О.В. Ртутная опасность в производстве химических источников тока //
Ртутная опасность - проблема ХХ века. - СПб.: Экофонд "Ртутная опасность", 1994, с. 92-93..
232. Реутов Б.Ф., Именов В.Г., Наумов А.В. и др. Теплоснабжение страны на грани. //
Энергия: экономика, техника, экология, 2002, № 1, с. 3-8.
233. Роговой В.М. Ртутоносные провинции СССР (Региональные закономерности
размещения, прогнозирование и оценка ртутного оруденения). - М.: Наука, 1989. - 96 с.
234. Роговой В.М. Редкометальный комплекс России и стран СНГ (минерально-сырьевая
база, производство, состояние рынка редких металлов). - М.: ВИЭМС, 2000. - 40 с.
235. Росляков Н.А., Кириллова О.В. Ртутное загрязнение окружающей среды при добыче
золота в России // Химия в интересах устойчивого развития, 1995, № 3, c. 43-55.
236. Российский рынок цинка: проблемы и перспективы // http://www.zdc.ru/pablic_2.htm
(25.7.2003).
237. Российский статистический ежегодник. 2002: Статистический сборник. - М.:
Госкомстат России, 2002. - 690 с.
238. Россия: рынок электроламп // http://subscribe.ru/archive/business.marketnews/20…
239. Рохлин Г.Г. Разрядные источники света. - М.: Энергоатомиздат, 1991. - 720 с.
240. Ртуть (добыча и переработка) // http://rus.gateway.kg/ind_merc.
241. Ртуть в окружающей среде Сибири: оценка вклада природных и антропогенных
источников. Итоговый доклад Временного научного коллектива Сибирского отделения РАН по
проекту СКОПЕ “Оценка распределения ртути и ее роли в экосистемах”. - Новосибирск: СО
РАН, 1995. - 30 с.
242. Ртуть. Каталог продукции и услуг. Приложение к материалам 3-й науч.-техн. конф.
“Ртуть. Комплексная система безопасности”. - СПб., 1999. - 24 с.
243. Ртуть. Комплексная система безопасности. Сборник материалов научно-технической
конференции. - СПб., 1996.
244. Ртуть. Нормативные и методические документы. Справочник. - СПб.: Мониторинг,
1999. - 235 с.
245. Ртуть. Нормативные и методические документы. Справочник. - СПб.: Мониторинг,
2001. – Т. 1 - 242 с.; Т. 2. - 80 с.
246. Ртуть. Технические условия (Mercury. Specifications). ГОСТ 4658-73. Издание
официальное. - М.: ИПК Издательство стандартов, 1997. - 11 с.
247. Рудная промышленность на территории РСФСР за 1914-1921 г.г. // Горный журнал,
1922, № 6-9, с. 320-321.
248. Рукавишников В.С. Санитарно-гигиеническая оценка условий труда и состояния
здоровья работающих на золототзвлекательных фабриках // Вопросы гигиены труда и
профпатологии в золотодобывающей промышленности Востока страны. - М.: НИИ гигиены
труда им. Ф.Ф. Эрисмана, 1984, c. 29-36.
249. Рыжов В.В., Машьянов Н.Р., Озерова Н.А. Пространственно-временная
изменчивость содержания ртути в углеводородных газах // Эколого-геохимические проблемы
ртути. – М.: ИМГРЭ, 2000.
250. Савраев О.В. Состояние и возможности совершенствования очистки газов
свинцовых и цинковых заводов от пыли. – М.: Металлургия, 1990.
251. Санитарные правила и нормы. СанПиН 2,1,7,573-96 Гигиенические требования к
использованию сточных вод и их осадков для орошения и удобрения (Утверждены
постановлением Госкомсанэпиднадзора России от 31 октября 1996 г. № 46).
252. Сатцаев А.М. Комбинированное выщелачивание металлов при утилизации хвостов
// Цветная металлургия, 2002, № 7, с. 40-43.
253. Сауков А.А., Айдиньян Н.Х., Озерова Н.А. Очерки геохимии ртути. - М., Наука, 1972.
254. Сахарова М.С., Китаенко А.Э., Кривицкая Н.Н. и др. Формы нахождения и
особенности накопления токсичных элементов в золотосеребряных рудах Северо-Востока
России // Минералогические исследования в решении экологических проблем. - М.: ИГЕМ
РАН, 1998, с. 61-72.
255. Свиташев К.К., Чикичев С.И. Некоторые проблемы создания многоэлементных
фотоприемных устройств на основе твердых растворов теллуридов кадмия и ртути //
Автометрия, 1996, № 4, с. 3-5.
256. Сводный отчет об охране атмосферного воздуха за 2001 год. - М.: Госкомстат
России, 2002. -
257. Свойства элементов: Справочник. Кн. 1. – М.: Металлургия. 1997. – 432 с.
258. Седогин М.П. Система профилактики ртутных загрязнений и утилизация ртутных
отходов в г. Самаре // http://ecoport.narod.ru/mercury3.htm.
259. Сивков И.Г. Алиментарный гранозановый токсикоз и его предупреждение: Автореф.
дисс.. канд. мед. наук. – Л., 1965. – 20 с.
260. Сидоров Ю.Ф. Проблемы техногенного загрязнения ртутью территории Амурской
области (актуальность и пути решения) // Ртуть. Комплексная система безопасности. Cб.
материалов III научно-технической конференции. – СПб, 1999, c. 57-61.
261. Сидоров Ю.Г., Дворецкий С.А., Варавин В.С. и др. Молекулярно-лучевая эпитаксия
твердых растворов кадмий-ртуть-теллур на .альтернативных» подложках. // Физика и техника
полупроводников, 2001, 35, вып. 8. С. 1092-1101.
262. Синода В.А., Михайлова Л. Ф. О состоянии хранения и утилизации устаревших
пестицидов в Тверской области // Материалы Российского семинара .Инвентаризация запасов
устаревших пестицидов.. – Воронеж: ЦПР, 2000, c. 157-159.
263. Скитский В.Л., Донских Д.К. Современное состояние рынка металлической ртути и
ртуть-содержащих отходов в России и СНГ // Ртуть. Комплексная система безопасности. Сб.
мат-рол III-й научн.-техн. конференции. - СПб., 1999, с. 22-26.
264. Смирнов В.И., Годлевский М.Н., Никитин В.Д. и др. Генезис эндогенных
месторождений. – М.: Недра, 1968. – 719 с.
265. Соколов Л.С. Ртуть в окружающей среде Московского региона // Эколого-
геохимические проблемы ртути. - М.: ИМГРЭ, 2000, с. 90-95.
266. Соколов Р.С. Химическая технология: Т. 1. – М.: Гуманитарный издательский центр
ВЛАДОС, 2003. – 368 с.
267. Состояние окружающей среды и здоровья населения Перми в 1999 г.: Справочно-
информационные материалы / Ред. коллегия: В. А. Сединина, О. П. Волк-Леонович /
Муниципаль-ное управление по экологии и природопользованию. Пермь, 2000. - 74 с. //
http://www.ecology.permregion.ru/doc/1999/ (11.2.2003).
268. Состояние окружающей среды Московской области в 1999 году: Государственный
доклад. - М.: Мособлкомприрода, 2000. - 148 с.
269. Состояние окружающей природной среды Липецкой области в 1998 году: Доклад. -
Липецк: Изд-во ЛЭГИ, 1999. - 182 с.
270. Социально-экономическое положение России. 2001. Госкомстат РФ, № 12.
271. Справочная книга по светотехнике. - М.: Энергоатомиздат, 1995. - 528 с.
272. Справочник по геохимии. – М.: Недра, 1990. – 480 с.
273. Справочник.,1999
274. Старк С.Б. Газоочистные аппараты и установки в металлургическом производстве. .
М., 1990.
275. Стафеев В.И. Становление разработки и производства фотоприемников на основе
КРТ в НИ-ИПФ (НПО “Орион”) и в СССР // Прикладная физика, 2001, № 6, с. 39-43.
276. Степанов И. Экологический эффект Larox. Челябинский цинковый завод
ликвидировал “свинцовые” выбросы в окружающую среду (Деловой Урал, 2002, № 33) //
http://www.infoural.ru/delur/2002/33-8.html. (17.9.2002).
277. Степанов Н.А. Гигиеническое исследование опасности для здоровья человека в
связи загрязнением заводской и окружающей среды ртутью от производства люминесцентных
ламп: Диссертация, представленная на соискание ученой степени кандидата медицинских наук.
- СПб.: С.-Петербургская Академия последипломного образования, 1997. - 134 с.
278. Степанова Н.И. Демеркуризация озонированием // Медицина труда и
промышленная экология, 1994, № 2, с. 34-36.
279. Таиров Ю.М., Цветков В.Ф. Технология полупроводниковых и диэлектрических
материалов. - СПб.: Изд-во .Лань., 2002. - 424 с.
280. Таможенная статистика внешней торговли Российской Федерации. Сборник 1999
года. - М.: ГТК РФ, 2000. - 450 с.
281. Таможенная статистика внешней торговли Российской Федерации. Сборник 2000
года. - М.: ГТК РФ, 2001. - 450 с.
282. Тарасов А.В. Развитие технологий в цветной металлургии России // Цветные
металлы, 2001, № 6, с. 70-75.
283. Тарасов А.В. Экологические проблемы цветной металлургии – пути решения //
Электрометаллургия, 2002, № 1, с. 14-19.
284. Терешина Т.О. География золотопромышленности России // Вестник Московского
университета. Сер. 5. География, 2000, № 4, c. 27-33.
285. Технологическая инструкция на обжиг графит-отходов. ТИ-01-01-02.
286. Технологическая инструкция на обжиг отработанного ртутного катализатора. ТИ-01-
01-02.
287. Технологическая инструкция на переработку люминесцентных ламп. ТИ-01-05-99.
288. Технологическая инструкция на переработку ртутных ламп высокого давления. ТИ-01-06-99
289. Технологическая инструкция на переработку стеклянных приборов с ртутным
заполнением. ТИ-01-03-99.
290. Технологическая инструкция на переработку химических источников тока. ТИ 01-07-01.
291. Туровский И.С. Обработка осадков сточных вод. - М.: Стройиздат, 1988. - 256 с.
292. Укрупненные нормы водопотребления и водоподготовки для различных отраслей
промышленности. - М.: Стройиздат, 1978. - 590 с.
293. Утилизация твердых отходов: Пер. с англ.: В 2-х т. - М.: Стройиздат, 1985, т. 1. - 336
с.; т. 2 - 348 с.
294. Уткин Н.И. Цветная металлургия. – М., 1990.
295. Федорчук В.П. Геология ртути. - М.: Недра, 1983. - 270 с.
296. Федорчук В.П., Минцер Э.Ф. Геологический справочник по ртути, сурьме, висмуту. .
М.: Недра, 1990. – 215 с.
297. Филачев А.М., Пономаренко В.П., Таубин И.И., Ушакова М.Б. Инфракрасные
матрицы и тен-денции их развития. Часть 1 // Прикладная физика, 2003, № 3, с. 105-120.
298. Фосс Г.В. Золото. – М.: Госгеолтехиздат, 1963.
299. Фурсов В.З. Ртуть – индикатор при геохимических поисках рудных месторождений. -
М.: Недра, 1977.
300. Фурсов В. З. Газортутный метод месторождений полезных ископаемых. – М.: Наука,
1983. – 205 с.
301. Фурсов В.З. Ртутная атмосфера природных и антропогенных зон // Геохимия, 1997,
№ 6, с. 644-652.
302. Характеристика удельных выбросов загрязняющих веществ от отдельных произ-
водств и их использование при экспертизе воздухо-охранных мероприятий. – М.: Минчермет
СССР, 1989
303. Харитонов Ю.Ф., Васильев В.Г., Андрейчук Д.А., Глазунов А.П. Эколого-
экономическая оценка отходов горнопромышленного комплекса Читинской области // Ресурсы
Забайкалья, 2002, cпец. выпуск.
304. Химическая энциклопедия. Т. 2. - М.: Сов. энциклопедия, 1990. - 671 с.
304. Химическая энциклопедия. Т. 4. - М.: Большая Российская энциклопедия, 1995. - 639 с.
305. Челноков А.А., Плышевский С.В. О возможности использования “Руководства по
инвентаризации выбросов в атмосферу” при оценке выбросов предприятий строительных
материалов // Проблемы инвентаризации выбросов загрязняющих веществ в атмосферу.
Материалы международного симпозиума по инвентаризации выбросов загрязняющих веществ
в атмосферу и использованию справочного руководства EMER/CORINAIR. Минск-Раубичи,
Республика Беларусь, 1997. – Минск: Институт проблем использования природных ресурсов и
экологии НАН Беларуси, 1998, с. 91-102.
306. Челноков А.А., Плышевский С.В. К вопросу об эмиссии тяжелых металлов в
атмосферу при производстве цемента // Цемент и его применение, 2000, № 6, с. 41-45.
307. Черная металлургия Урфо // http://www.econ.epn.ru/articles/cher_met.asp (28.6.2003).
308. Чернякова Н. Запас прочности? Обзор никелевой промышленности («Рынок ценных
бумаг», 2002, № 24) // http://www.rcb.ru/Archive/articlesrcb.asp?aid=3002 (13.8.2003).
309. XVI Международная конференция по фотоэлектронике и приборам ночного
видения; тезисы // http://www.vimi.ru/confer/orion/16-ts-r.htm (11.8.2000).
310. Чикичев С.И. Гетероструктуры CdXHg1-XTe /./ Si: вчера, сегодня, завтра //
Автометрия, 1996, № 4, с. 6-31.
311. Цветная металлургия, 2002, № 6
312. Ценные и токсичные элементы в товарных углях России. Справочник. – М.: Недра,
1996. – 238 с.
313. Шаров Г.Н., Трибунский Е.Н., Николаев С.Л. Минерально-сырьевая база
Кемеровской области // Минеральные ресурсы России, 1997, № 2, с. 12-15.
313. Шаталов В.В. Сырьевые проблемы ЯТЦ // Атомная энергия, 2000, 89, вып. 4,
октябрь, с. 334-338.
314. Шевелева О. Мифы и легенды российской ртути // Спасение, 2001, № 20, с. 5.
315. ЭиЖ-Сибирь, 2000, № 8 // http://www.ecolife.krsk.ru/old/Arh/2000/122/14.asp
(05.7.2003).
316. Экономическая и социальная география России. – М., 2001.
317. Югов П. Конверторный модуль // Металлы Евразии, 2002, № 1, с. 64-67.
318. Юдович Я.Э., Золотова В.В. Элементы-примеси в углях Печорского бассейна //
Народное хозяйство Республики Коми, 1994, 3, № 1, с. 16-25.
319. Юдович Я.Э., Кетрис М.П., Мерц А.В. Элементы-примеси в ископаемых углях. - Л.:
Наука, 1985. - 239 с.
320. Юсфин Ю., Залетин В. Бомба замедленного действия. Составляющие .ртутного
вопроса. в России // Металлы Евразии, 1998, № 3, с. 72-76.
321. Ягольницер М.А., Оболенский А.А., Бабич В.В. и др. Выбор эффективной стратегии
развития горно-металлургического предприятия в новых условиях хозяйствования
(моделирование, имитация, принятие решений, охрана окружающей среды). - Новосибирск:
ИЭиОПП СО РАН, 1993. - 123 с.
322. Ягольницер М.А., Соколов В.М., Рябцев А.Д. и др. Оценка промышленной эмиссии
ртути в Сибири // Химия в интересах устойчивого развития, 1995, 3. № 1-2. С. 23-35.
323. Янин Е.П. Ртуть в окружающей среде промышленного города. - М.: ИМГРЭ, 1992. -
169 с.
324. Янин Е.П. Геохимические особенности осадков сточных вод промышленного города
(на примере Саранска). - М.: ИМГРЭ, 1996. - 41 с.
325. Янин Е.П. Электротехническая промышленность и окружающая среда (эколого-
геохимические аспекты). - М.: Диалог-МГУ, 1998. - 281 с.
326. Янин Е.П. Экологические аспекты производства и использования бытовых
химических источников тока // Геохимические исследования городских агломераций. - М.:
ИМГРЭ, 1998, с. 113-126.
327. Янин Е.П. Ртуть в осадках городских сточных вод // Эколого-геохимические
проблемы ртути. - М.: ИМГРЭ, 2000, с. 143-152.
328. Янин Е.П. Химические элементы в пылевых выбросах электротехнических
предприятий // Медицина труда и промышленная экология, 2000, № 8, с. 24-27.
329. Янин Е.П. Добыча и производство ртути в СНГ как источник загрязнения
окружающей среды // Эколого-геохимические проблемы ртути. - М.: ИМГРЭ, 2000, с. 38-59.
330. Янин Е.П. Техногенные илы в зоне влияния промышленного города (формирование,
состав, геохимические особенности). - М.: ИМГРЭ, 2002. - 100 с.
331. Янин Е.П. Ртуть в пылевых выбросах промышленных предприятий // Экологическая
экспертиза. Обзорная информация. - М.: ВИНИТИ, 2002, вып. 4, с. 10-29.
332. Янин Е.П. Техногенные геохимические ассоциации в донных отложениях малых рек
(состав, особенности, методы оценки). - М.: ИМГРЭ, 2002. - 52 с.
333. Янин Е.П. Промышленная пыль в городской среде (геохимические особенности и
экологическая оценка). - М.: ИМГРЭ, 2003. - 82 с.
334. Янин Е.П. Тяжелые металлы в малой реке в зоне влияния промышленного города. .
М.: ИМГРЭ, 2003. – 89 с.
335. Янин Е.П. Эмиссия ртути при производстве цемента в России, 2003 (рукопись в
печати).
336. Atkins W.S., 1998
337. Batterien mit zu viel Quecksilber verbieten // Galvanotechnik, 2001, 92, № 11, s. 3108.
338. Doughty D.A., Wilson R.H., Thaler E.G. Mercury-glass interaction in fluorescent lamps //
J. Electrochem. Soc., 1995, 142, № 10, р. 3542-5351.
339. Emissions of mercury from coal fired power plants in Russia - preliminary estimated for
ACAP. Munthe J.; Wängberg I.; Chugaeva A.N.; Kiseleva N.V.; Smigol I.N.; Bragina O.N., Anichkov
S.N.; Tumanovsky A.G. .IVL Swedish Environmental Research Institute, Sweden and VTI All Russia
Thermal Engineering Institute, 2003.
340. European Communities. 2001. Ambient mercury pollution by mercury - Position Paper.
Office for Official Publications of the European Communities, Luxembourg.
341. Floyd P., Zarogiannis P., Crane M., Tarkowski S. Bencko V. Risk to Health and the Environment
Related to the Use of Mercury Products. Final Report, prepared for the European Commission,
DG Enterprise by Risk & Policy Analysts Limited, London, 2002. - 119 p.
342. Friedli, H.R., Radke L.F., Lu J.Y. Mercury in Smoke from Biomass Fires // Geophysical
Research Letter, 2001, 28, p. 3223-3226.
343. Ganeev A.A., Pogarev S.E., Ryzhov V.V. et al. The new method for direct and express determination
of mercury in oil, gascondensate and biological samples // J. Ecol. Chem., 1995, 4, 122.
344. Gold Fields Mineral Services (GFMS). January 2002 // http://www.aurum79.ru/.
345. http://extech.msk.su/expo/exibit/innov_98/org.texm.
346. http://eurocopper.ru/stat%20ussr%20russ.htm (12.6.2003).
347. http://eyge.narod.ru/Russian/List/08-10-200246.ht.
347. http://metall.klimenko.ru/arc.15-09-2002.html (29.8.2003).
349. http://metal.klimenko.ru/catalog/Detailed/21.html (17.8.2003).
350. http://metal-trade.ru/news/business/2002/12/index (05.9.2003).
351. http://metal-trade.ru/news/business/2003/03/1337.s. (29.8.2003).
352. http://minamp.rbc.ru/ru/cp_on_commodity_marcet/ana. (17.7.2003).
353. http://novosti.vins.ru/?f=lf&t=010718c06 (01.2.2003).
354. http://prometeus.nsc.ru/patent/1997/210.ssi (12.7.2003).
355. http://uralnep.ru/news/view_article.php?newsid=422. (10.8.2003).
356. http://uuu.narod.ru/money.htm.
357. http://www.ako.ru/PRESS/viewtext.asp?C8688=On (08.7.2003).
358. http://www.aktex.ru/rus.news/?year=2003&month=1&da… (17.8.2003).
359. http://www.aktex.ru/rus/analytics/equimpent (18.9.2003).
360. http://www.aviaport.ru/news/Markets/21440.html (17.1.2002).
361. http://www.aviaport.ru/news/Markets/a1020229200.ht. (18.3.2003).
362. http://www.chrab.chel.su/archive/17-10-97/1/RE12.D. (16.0.1997).
363. http://www.eao.ru/in_olovo.html (31.3.2003).
364. http://www.enicey.ktk.ru/nature/13.cfm?nid=200 (06.9.2003).
365. http://www.greenpeace.ru/gpeace/43520/gp_article_t. (21.5.2003).
366. http://www.infogeo.ru.
367. http://www.infoline.spb.ru/metall.html (27.1.2003).
368. http://www.inves.ru/rus_china/4/pril_1.htm (12.5.2003)
369. http://www.khv.ru/MD/2001/12720/ob.htm (21.9.2001).
370. http://www.physfac.bspu.secta.ru/mirror/izone/izon.
371. http://www.kmez.ru.
372. http://www.mediatext.ru/docs/2417 (30.3.2003).
373. http://www.medin.ru/price/m1998_4.shtml (03.5.2003).
374. http://www.metalinform.com/?op=news&lang=ru&idstr=– (05.9.2003).
375. http://metal.interfax.ru/test_metal….
376. http://www.mhg.ru/proekt/doklad/99/region/am/chapt… (29.0.2000).
377. http://www.mineral.ru/Chapters/News (15.4.2003).
378. http://www.3e.opec.ru/news_doc.asp?d_no=172 (29.4.2003).
379. http://www.rambler.ru/db/news/msg.html?mid=1449831. (24.1.2001).
380. http://www.rambler.ru/db/news/msg.htm (26.8.2002).
381. http://www.rambler.ru/db/news/msg.html (12.9.2002)
382. http://www.rambler.ru/db/news/msg.html?mid=1773229&s=12.
383. http://www.rambler.ru/db/news/msg.html?mid=1449831.
384. http://www.rmx.ru/news/&news=295.
385. http://www.snab.ru:8/01/lkm/02/06.html.
386. http://www.zinc.ru/news.php3 (07.7.2003).
387. IEA. 2003. Energy Statistics of non-OECD countries. International Energy Agency, Paris.
388. International Coal & Methane Research Center // http://www.uglemetan.ru.
389. Johansen, V.C., Hawkins, G.J. Mercury speciation in cement Kilns: A literature review //
R&D Serial, 2003, – 2567, Portland Cement Association, Skokie, USA.
390. Kindbom K., Munthe J. Hur påverkas kvicksilver i miljön av olika energialternativ? IVL
Svenska Miljöinstitutttet, 1998.
391. Hylander L.D. Global mercury pollution and its expected decrease after a mercury trade
ban // Water, Air and Soil Pollution, 2001, 125, p. 331-344.
392. Lacerda L. D., Salomons W. Mercury from gold and silver mining: a chemical time bomb?
- Berlin, Heidelberg, Springer-Verlag, 1998.
393. Laperdina T.G., Melnikova M.V., Khvostova T.E. Gold mining in Siberia as a source of
mercury contamination of the environment // Mercury Contaminated Sites: Characterization, Risk Assessment
and Remediation, R. Ebinghaus, R.R. Turner, D. Lacerda, O. Vasiliev, W. Salomons (eds),
Springer Environmental Science, Springer Verlag Heidelberg, 1999, p. 357-374.
394. Laperdina T.G. Estimation of mercury and other heavy metal contamination in traditional
gold mining areas of Transbaikalia // Geochemistry, Exploration, Environment, Analysis, 2002, 2, №
3, p. 219-223.
395. Locating and Estimating air emissins from sources of mercury and mercury compounds.
EPA-454/R-97-012, 1997.
396. Masters H.B. Electrinic metals and minerals mercury // Mining Annal Review, 1983, – № 6,
p. 90-92.
397. Matsui Yasuhiro // KOSHU EISEI KENKYU.= Bull. Inst. Public Health., 1994, 43, – № 3,
p. 365-366.
398. Mercury Products-risk to Health and the Environment
399. MMSD. Breaking New Ground: Mining, Minerals, and Sustainable Development. International
Institute for Environment and Development, 2002.
(http://www.iied.org/mmsd/finalreport/index.html per September 2002).
400. OSPAR. 2001. Mercury losses from the chlor-alkali industry in 1999. OSPAR Commission,
London. (in English)
401. Ozerova N.A. Mercury in geological systems. // Regional and Global Mercury Cycles:
Fluxes and Mass Balances. Kluwer Academic Publishers, Dortrecht, The Nitherlands, 1996.
402. Ozerova N.A., Mashyanov N.R., Pikovsky Yu.J. et al. Mercury in Gas and Oil Deposits //
Mercury Contaminated Sites. Springer, 1999.
403. Pacyna J. Development of methods for trace metal emission evaluation and their implementation
for flux estimates in NIS territory, including economic aspects of flux reduction - INTAS №‚
97-31581, 2003.
404. Pacyna J., Pacyna E., 2000
405. Ratex (Агенство экономической информации) // www.ratex.ru.
406. Risk Reductio Monograph No. 4: Mercury. Background and National Experience with Reducing
Risk / OECD Environment Monograph Series No. 103. - Paris, OECD, 1995. - 159 p.
407. Ryshov V.V., Mashyanov N.R., Ozerova N.A., Pogarev S.E. Regular variations of the mercury
concentration in natural gas // The Science of the Total Environment, 2003, 304, №‚ 1-3.
408. Skårup S., Christensen C.L., Maag J., Jensen S.H. Massestrømsanalyse for kviksølv 2001
[Substance flow analysis for mercury 2001]. Environmental Report 808, Danish EPA, Copenhagen,
2003. (In Danish).
409. Substances Flow Analysis of Mercury on Product, 2001
410. Sznopek. J.L., Goonan, T.G. The materials flow of mercury in the economies of the United
States and the World. U.S. Geological Survey Circular 1197. U.S. Department of the Interior; U.S.
Geological Survey; Denver, 2000.
411. The Materials flow of mercury in the Economies of the United States and the World / J.L.
Sznopek, T.G. Goonan / U.S. Geological Survey Circular 1197. - 28 p. //
http://greenwood.cr.usgs.gov./pub/circulars/c1197/.
412. UNEP 2003
413. US EPA 1997. Mercury study report to Congress volume II: An inventory of anthropogenic
mercury emissions in the United States. US EPA, Washington DC.
414. US EPA. 2001. Kilgroe J.D., Sedman, C. B., Srivastava R.K., Ryan J.V., Lee C.W., Thorneloe,
S.A. Control of mercury emissions from coal- fired electric utility boilers: Interim Report. U.S.
Environmental Protection Agency Office of Research and Development.
415. US EPA. 2002. Control of Mercury Emissions from Coal-fired Electric Utility Boilers, Interim
Report Including errata Data 3-21-02. EPA-600/R-01-109, National Risk Management Research
Laboratory, Research Triangle Park, NC.
416. VDZ 2000. Environmental data on the German cement industry. Verein Deutscher Zementwerke
e. V.
417. Wilhelm S.M. Mercury in petroleum and natural gas: Estimation of emissions from production,
processing, and combustion. U.S. EPA, Office of Air Quality Planning and Standards, Washington
D.C., 2001.
418. Pacyna, J. 2003b. Personal communication.
419. “Reference materials on indicators of specific production and consumption wastes generation
” prepared by the Scientific and Research Center on Problems of Resource Saving and Wastes
Management (NITsPURO),1999.
420. UNEP. 2002. Global mercury assessment. UNEP Chemicals, Geneva.
http://www.chem.unep.ch/mercury/Report/Final%20Assessment%20report.htm
Приложение 1. Официальная статистика по поступлению ртути в окружающую среду
Выбросы ртути в атмосферу
Сбросы ртути со сточными водами в поверхностные водные объекты, 2001 г.
Образование, накопление, использование и обезвреживание ртутьсодержащих отходов в 2001 г.
Выбросы ртути в атмосферу
Информация, содержащаяся в .Сводном отчете об охране атмосферного воздуха за 2001
год. ГМЦ Госкомстата России, основана на данных по выбросам ртути, представляемых
предприятиями. Предприятия обязаны отчитываться только о выбросах поллютантов,
включенных в утвержденный для каждого предприятия список и имеющих нормы ПДК,
установленные природоохранными органами. Это означает, что официальные статистические
данные не затрагивают все источники выбросов ртути. В большинстве случаев данные по
выбросам ртути, предоставляемые предприятиями, основаны на расчетах, а не на фактических
измерениях ее эмиссии.
В ниже приводимой таблице указаны регионы и названия предприятий или отраслей
промышленности (курсивом), являвшиеся в России в 2001 г., по официальным сведениям,
основными источниками эмиссии ртути в атмосферу.
Выбросы ртути в атмосферный воздух в 2001 г. |
Тонны |
Российская Федерация (в целом) |
2,022 |
Центральный федеральный округ (всего) |
1,105 |
Владимирская область |
0,003 |
Липецкая обл. |
0,003 |
Московская обл. |
0,001 |
Рязанская обл. |
0,002 |
Смоленская обл. |
0,088 |
г. Смоленск ФГУ “Аналитприбор” |
0,088 |
Тульская обл. |
0,004 |
г. Новомосковск НАК “Азот” |
0,004 |
г. Москва |
0,005 |
ОАО Московский электроламповый завод |
0,003 |
Северо-Западный федеральный округ (всего) |
0,003 |
Вологодская область |
0,003 |
г. Череповец |
0,003 |
Жилищно-коммунальное хозяйство |
0,003 |
Южный Федеральный округ (всего) |
0,502 |
Краснодарский край |
0,114 |
г. Новороссийск |
0,05 |
Промышленность строительных материалов АО “Новоросцемент” |
0,05 |
Волгоградская обл. |
0,388 |
г. Волгоград |
0,385 |
Химическая промышленность АО “Химпром”, АО “Пласткард” |
0,385 |
г. Волжский |
0,003 |
химическая промышленность |
0,003 |
Приволжский Федеральный округ (всего) |
0,637 |
Республика Башкортостан |
0,457 |
г. Стерлитамак |
0,451 |
основная химия АО “Сода”, АО “Каустик” |
0,451 |
Республика Мордовия |
0,022 |
г. Саранск |
0,022 |
машиностроение Электроламповый завод |
0,022 |
Республика Татарстан |
0,032 |
АО “Нижнекамскнефтехим” |
0,126 |
Кировская обл. |
0,126 |
г. Кирово-Чепецк |
0,126 |
Кирово-Чепецкий химический комбинат |
1,22 |
Уральский Федеральный округ (всего) |
1,229 |
Челябинская область |
1,229 |
г. Челябинск |
1,229 |
цветная металлургия |
1,229 |
Сибирский федеральный округ (всего) |
0,445 |
Иркутская область |
0,24 |
г. Усолье Сибирское |
0,13 |
АО “Усольехимпром” |
0,13 |
Новосибирская область |
0,205 |
г. Новосибирск |
0,205 |
цветная металлургия |
0,205 |
Сбросы ртути со сточными водами в поверхностные водные объекты,
2001 г.
Официальная статистическая информация по сбросам ртути основана на данных,
представляемых предприятиями. Предприятия обязаны отчитываться только о сбросах
поллютантов, включенных в утвержденный для каждого предприятия список имеющих нормы
ПДК, установленные природоохранными органами. Следовательно, эта статистика не отражает
полную картину сбросов ртути точечными источниками. Кроме того, существует значительное
количество неточечных источников, территорий, имеющих грунты, загрязненные ртутью
(например, в результате добычи золота), которые также являются источниками проникновения
ртути в водные объекты. Такого рода неточечное загрязнение не учитывается в официальной
статистике, приведенной в следующей таблице.
Сбросы ртути со сточными водами в поверхностные водные объекты |
Ртуть, кг |
По отраслям |
|
Всего по России |
177 |
Промышленность |
157 |
Цветная металлургия |
6 |
Химическая и нефтехимическая |
148 |
Целлюлозно-бумажная |
1 |
Мукомольно-крупяная и комбикормовая |
2 |
Жилищное хозяйство |
1 |
Коммунальное хозяйство |
19 |
По регионам |
|
Всего по России |
177 |
Центральный федеральный округ |
2 |
г. Москва |
2 |
Северо-западный федеральный округ |
21 |
г. Санкт-Петербург |
19 |
Ленинградская область |
2 |
Приволжский федеральный округ |
18 |
Республика Башкортостан |
16 |
Кировская обл. |
2 |
Сибирский федеральный округ |
131 |
Красноярский край |
1 |
Иркутская обл. |
129 |
Новосибирская обл. |
1 |
Дальневосточный федеральный округ |
5 |
Республика Саха-Якутия |
4 |
Амурская обл. |
1 |
По бассейнам рек и морей |
|
Всего по России |
177 |
Балтийское море |
21 |
Река Нева |
16 |
Ладожское озеро |
1 |
Каспийское море |
20 |
Река Волга |
20 |
Река Ока |
2 |
Река Москва |
2 |
Река Кама |
17 |
Река Белая |
16 |
Река Вятка |
2 |
Карское море |
131 |
Река Енисей |
130 |
Река Ангара |
130 |
Река Обь |
1 |
Охотское море |
1 |
Река Амур |
1 |
Река Зея |
1 |
Море Лаптевых |
4 |
Река Лена |
4 |
Река Алдан |
4 |
Сброс ртути с ливневыми водами |
|
Всего по России |
11 |
Северо-Западный федеральный округ |
11 |
г. Санкт-Петербург |
11 |
Образование, накопление, использование и обезвреживание
ртутьсодержащих отходов в 2001 г.
Данные из “Отчета об образовании и удалении токсичных отходов” Госкомстат России,
ГМЦ Госкомстата России.
Официальная статистическая информация по образованию, утилизации и размещению
отходов основана на данных, представляемых предприятиями. Предприятия обязаны
отчитываться об образовании, накоплении, использовании и обезвреживании отходов (по
классам опасности и по видам отходов). Ртутьсодержащие отходы (как один из видов отходов)
относятся к 1-му классу опасности (наиболее опасные отходы). Несмотря на то, что система
регистрации и учета отходов была внедрена еще в 1994 г., не все предприятия регулярно
предоставляют необходимые данные.
Представленные в таблице данные касаются только промышленных опасных отходов,
поскольку официальные статистические данные по составу промышленных неопасных отходов
и бытовых отходов отсутствуют. Следовательно, здесь нет данных о ртутьсодержащих
бытовых отходах, также о количестве ртути, содержащейся в других представленных видах
отходов.
Ртутьсодержащие промышленные опасные отходы (тонны) |
|
Наличие на предприятии на начало года |
Образов а- лось |
Использовано и обезврежено |
Наличие на предприятии конец года |
Россия в целом |
2586,957 |
10887,16 |
138,54 |
26.9.25 |
Белгородская обл. |
18,684 |
0,002 |
|
18,684 |
Брянская обл. |
13,715 |
13,69 |
0,03 |
15,388 |
Владимирская обл. |
53,975 |
50,696 |
|
47,273 |
Воронежская обл. |
4,632 |
13,323 |
|
3,923 |
Ивановская обл. |
7,649 |
6,576 |
|
6,333 |
Калужская обл. |
1,686 |
4,875 |
0,012 |
3,89 |
Костромская обл. |
2,726 |
5,057 |
|
3,367 |
Курская обл. |
0,004 |
0,008 |
|
0,007 |
Липецкая обл. |
15,883 |
41,112 |
0,002 |
18,834 |
Московская обл. |
57,023 |
181,912 |
51,427 |
50,084 |
Орловская обл. |
0,702 |
7,045 |
|
2,968 |
Рязанская обл. |
27,64 |
105,334 |
0,079 |
27,523 |
Смоленская обл. |
24,821 |
121,562 |
44,367 |
22,787 |
Ярославская обл. |
2,776 |
3,734 |
0,004 |
1,568 |
Тамбовская обл. |
3,239 |
1,613 |
0,002 |
3,012 |
Тверская обл. |
4,236 |
37,883 |
|
3,342 |
Тульская обл. |
98,9 |
0,166 |
|
98,253 |
г. Москва |
6,872 |
267,352 |
|
11,625 |
Республика Коми |
5,463 |
7,437 |
|
8,692 |
Архангельская обл. |
252,374 |
37,761 |
|
88,673 |
Ненецкий а.о. |
0,902 |
0,515 |
|
1,394 |
Вологодская обл. |
8,516 |
72,955 |
41,185 |
6,976 |
Калининградская обл. |
0,002 |
0,007 |
|
0,002 |
Ленинградская обл. |
92,149 |
49,47 |
320,609 |
62,231 |
Мурманская обл. |
23,331 |
19,173 |
0,018 |
15,894 |
Новгородская обл. |
7,065 |
34,571 |
0,015 |
5 |
Псковская обл. |
0,333 |
6,472 |
|
0,396 |
г. Санкт-Петербург |
31,957 |
134,287 |
|
23,293 |
Республика Башкортостан |
30,568 |
562,245 |
15,58 |
33,38 |
Республика Марий-Эл |
0 |
1,352 |
|
|
Республика Мордовия |
0,318 |
69,283 |
|
64,379 |
Республика Татарстан |
12,855 |
66,788 |
12,184 |
11,939 |
Удмуртская Республика |
53,539 |
92,306 |
0,164 |
67,505 |
Чувашская Республика |
27,269 |
54,696 |
217,68 |
30,371 |
Кировская обл. |
37,775 |
0 |
3,41 |
28,64 |
Нижегородская обл. |
116,39 |
121,904 |
68,572 |
128,042 |
Оренбургская обл. |
1,279 |
2,365 |
|
0,492 |
Пензенская обл. |
4,225 |
24,466 |
9,015 |
4,521 |
Пермская обл. |
19,372 |
38,797 |
|
21,261 |
Самарская обл. |
34,328 |
147,784 |
|
43,253 |
Саратовская обл. |
50,974 |
64,373 |
|
41,07 |
Ульяновская обл. |
21,999 |
51,628 |
3,652 |
18,975 |
Республика Адыгея |
0,725 |
0,313 |
|
0,373 |
Республика Дагестан |
0,313 |
0,021 |
|
0,002 |
Кабардино-Балкарская Республика |
0,102 |
0 |
|
0,102 |
Карачаево-Черкесская Республика |
1,305 |
1,601 |
|
1,238 |
Республика Северная Осетия - Алания |
11,817 |
4,015 |
20,247 |
11,321 |
Краснодарский край |
18,391 |
13,902 |
298,559 |
18,946 |
Ставропольский край |
0,021 |
0,037 |
|
0,037 |
Астраханская обл. |
3,321 |
12,458 |
|
3,225 |
Волгоградская обл. |
294,816 |
262,26 |
145,301 |
391,707 |
Ростовская обл. |
21,85 |
51,936 |
0,04 |
22,378 |
Курганская обл. |
16,81 |
19,918 |
63,3 |
7,933 |
Свердловская обл. |
25,224 |
6999,772 |
2,025 |
23,51 |
Тюменская обл. |
3,987 |
3,594 |
|
2,744 |
Ханты-Мансийский а. о. |
0,505 |
2,848 |
|
2,101 |
Ямало-Ненецкий а. о. |
0,285 |
0,537 |
|
0,55 |
Республика Бурятия |
3,6 |
6,575 |
0,236 |
3,085 |
Республика Тыва |
14,7 |
0 |
|
14,7 |
Республика Хакассия |
8,18 |
8,446 |
|
9,169 |
Алтайский край |
84,271 |
1,616 |
|
83,286 |
Красноярский край |
448,058 |
52,909 |
|
456,019 |
Иркутская обл. |
149,848 |
223,414 |
122 |
232,335 |
Кемеровская обл. |
64,08 |
30,151 |
|
24,494 |
Новосибирская обл. |
32,473 |
466,669 |
1,244 |
38,577 |
Омская обл. |
27,28 |
42,044 |
0,006 |
51,736 |
Томская обл. |
11,705 |
14,854 |
8,787 |
17,749 |
Читинская обл. |
0,667 |
0,007 |
|
0,636 |
Республика Саха-Якутия |
4,722 |
6,832 |
0,018 |
9,17 |
Приморский край |
69,878 |
9,203 |
0,501 |
66,349 |
Хабаровский край |
0,001 |
0,004 |
|
0 |
Амурская обл. |
1,803 |
0,002 |
|
1,804 |
Камчатская обл. |
2,316 |
1,278 |
0,02 |
0,831 |
Магаданская обл. |
0,081 |
0,288 |
0,1 |
0,226 |
Сахалинская обл. |
0,663 |
0,073 |
0,6 |
0,114 |
Приложение 2. Хранение ртутьсодержащих пестицидов
В данном приложении рассматриваются вопросы хранения устаревших ртутьсодержащих
пестицидов в некоторых областях и районах Российской Федерации.
Ртутьсодержащие пестициды в Тверской области
Тверская область расположена в северо-западной части России. На севере она граничит с
Вологодской, на северо-западе - с Новгородской, на западе - с Псковской, на юге - со
Смоленской и Московской и на востоке - с Ярославской областями.
Площадь области составляет 84,23 тыс. км². Леса, кустарники, реки, озера и болота
занимают около 48% площади, сельскохозяйственные угодья - около 44%.
По территории области проходит главный водораздел между бассейнами Каспийского и
Балтийского морей. Большинство рек тяготеет к Верхней Волге, и лишь на северо-западе реки
Мета, Цна и Шлина относятся к бассейну озера Ильмень, а на юго-западе берут начало реки
бассейна р. Западной Двины. Речная сеть густо и равномерно покрывает территорию области, в
ней насчитывается около 450 рек длиной более 10 км, из которых 55 - протяженностью свыше
50 км и 19 -свыше 100 км.
В области много озер и торфяных болот. Первые сосредоточены на северо-западе, вторые
на юго-востоке и в центре. Естественные водоемы представлены большим количеством
ледниковых озер в северо-западном холмистом районе. Всего, включая многочисленные
одиночные озера, в Тверской области насчитывается около 600 водоемов, самый большой из
которых оз. Селигер с площадью зеркала воды 208 км². Мелкие озера - глухие, бессточные, с
заболоченными берегами и илистым дном - находятся в стадии зарастания.
Тверская область отличается уникальными природными ресурсами. Общая площадь
особоохраняемых территорий 403,8 тыс. га, в т.ч. заповедники федерального значения 42,2 тыс.
га, госкомплекс “Завидово” - 68,7 тыс. га, заказники областного значения 292,9 тыс. га.
В связи с этим серьезную проблему и угрозу для окружающей среды составляет
накопленное значительное количество запрещенных и непригодных пестицидов, которые
хранятся, в основным, в приспособленных складах и лишь 4 из них - типовые. Кроме этого 72%
складов построены из деревянных конструкций еще в 70-80 годы и находятся в ветхом
состоянии и поэтому количество складов, подлежащих паспортизации, ежегодно уменьшается:
с 51% в 2000 г. до 44% в 2001 г.. На 02.6.03 года паспортизировано лишь 34% имеющихся
складов. Следствием этого является неудовлетворительное состояние хранения пестицидов, в т.
ч. ртутьорганических препаратов (агрозан, агронал, гранозан, радосан, фунгитокс), в условиях,
не соответствующих санитарным нормам и правилам (СанПиН 1,2,1077-01). .Данные о
количестве ртутьсодержащих пестицидов представлены в табл. 1.
Таблица 1. Наличие ртутьсодержащих пестицидов в Тверской области с 1999 г. по 2003 г.
Год |
1999 |
2000 |
2001 |
2002 |
2003 |
Количество, т |
34,676 |
31,214 |
30,760 |
42,843* |
42,798* |
* - с 1999 г. по 2001 г. сведения даны только по ртутьсодержащим препаратам (агрозан, агронал,
гранозан, радосан, фунгитокс); 2002 г. - 2003 г. - с учетом ртутьсодержащих смесей, определенных в ходе
пилотного проекта, т. к. при перезатарке все смеси ТХА натрия, симазина и других препаратов, хотя бы
содержащие следы ртути, были отнесены к ртутьсодержащим.
Дальнейшее хранение запрещенных пестицидов, пришедших в негодность, представляет
большую опасность для окружающей среды и людей, требует немедленного решения.
Опасность ситуации связана также с тем, что хозяйства не в состоянии вовремя оплатить
ремонт и охрану обветшалых складов. В результате ежегодно происходят пожары в период
весеннего пала травы. Только в апреле–мае текущего года произошло 5 возгораний складов
пестицидов (Лихославльский, Калязинский, Селижаровский, Спировский районы).
Периодически устаревшие конструкции (шифер, двери, доски, кирпич) расхищаются. По
результатам проверок условий хранения пестицидов выявленные нарушения устранялись
(проводился ремонт складов, навешивались замки, проводилась уборка складов, обновлялись
этикетки). Но склады снова подвергались взломам, происходило хищение стройматериалов. В
результате тара перезатаренных и маркированных пестицидов подвергалась порче,
образовывались просыпи препаратов, что создает угрозу для окружающей среды.
В последние годы сельскохозяйственные предприятия дробятся и реструктуризируются.
В результате после этого хозяйства прекращают свое существование и склады для хранения
химических средств защиты растений остаются бесхозными (Рамешковский район, хозяйства
“Тучевский”, “Бэман”).
В соответствии с постановлением Губернатора области от 24.4.2000 г. № 195 .Об
инвентаризации и утилизации устаревших, запрещенных пестицидов. в 2000-2001 годах был
реализован первый этап работ в рамках пилотного проекта, проведена инвентаризация
устаревших, запрещенных пестицидов в хозяйствах области, а также идентификация
обезличенных пестицидов, в ходе которой выявлено большое количество ртутьсодержащих
смесей (2003 г. - 14.036 т), а также наличие мышьяксодержащих пестицидов - арсенит натрия,
парижская зелень (всего 0,6 т).
Однако последующие этапы утилизации пестицидов, пришедших негодность, полностью
приостановлены из-за отсутствия финансовых средств.
В Тверской области имеется 556 складов ядохимикатов, но типовых только в
объединении “Агропромхимия” – 5 штук, остальные приспособленные [262]. 19-20 мая 2003 г.
состоялась поездка в область. На областной станции защиты растений получены данные о
содержании ртутьсодержащих пестицидов в 36 районах области. Из 426 складов ядохимикатов,
подлежащих паспортизации, положительное санитарно-эпидемиологическое заключение в 2002
г. получили 203 склада или 47,6% (в 2000 г. – 47,4%, в 2001 г. – 50,2%).
Государственной санитарно-эпидемиологической службой ведется контроль за оборотом
пестицидов и агрохимикатов. Разрешены для применения только те препараты, которые
включены в “Государственный каталог пестицидов и агрохимикатов, разрешенных к
применению на территории Российской Федерации, 2002”, согласованный с Минздравом
России [87]. Из более 80 заявленных областной станцией защиты растений наименований
пестицидов и агрохимикатов разрешены к применению только 74 препарата.
Остается нерешенной проблема утилизации устаревших, запрещенных и непригодных
для использования пестицидов и агрохимикатов. Совместными усилиями администраций 9
районов области и учреждений Госсанэпиднадзора, агрохимическими службами удалось
вывезти для захоронения за пределы области 41,8 тонны непригодных пестицидов. На
сегодняшний день требуется утилизация 388,2 т, из них 151,1 т - пестициды 1 класса опасности,
в т. ч. ртутьсодержащие.
За нарушение санитарных норм и правил при работе с пестицидами Центрами
Госсанэпиднадзора в городах и районах области было вынесено 181 постановление о
приостановлении эксплуатации складов ядохимикатов, наложено 19 штрафов, выдано 202
предписания, составлен 261 акт санитарно-эпидемиологического обследования условий
хранения ядохимикатов.
По предложению Центра Госсанэпиднадзора в Тверской области Департаментом по
социально-экономическому развитию села Администрации области были разработаны
“Мероприятия по соблюдению регламентов применения и хранения средств защиты растений в
сельхозорганизациях Тверской области на 2002-2004 г.г.”.
В области в рамках проекта UNEP Chemical на средства областной администрации была
проведена инвентаризация устаревших пестицидов. С этой целью в 2000.2001 г.г.
сотрудниками Тверской областной станции защиты растений был выполнен анализ 1200
образцов пестицидов. В настоящее время имеется информация о количестве 5
ртутьсодержащих пестицидов, находящихся на территориях 26 районов области, в 6 районах
эти пестициды не применялись (Табл. 2).
Таблица 2. Перечень территорий Тверской области, где находятся ртутьорганические пестициды по
состоянию на 01. 3.2003 г.
Наименование района |
СДЯВ |
Итого |
Гранозан |
Агрозан |
Агронал |
Радосан |
Фунгитокс |
|
Андреапольский |
380 |
– |
– |
– |
– |
380 |
Бологовский |
100 |
– |
– |
– |
– |
100 |
Весьегонский |
455 |
60 |
125 |
– |
– |
640 |
Вышневолоцкий |
876 |
– |
– |
– |
– |
876 |
Западнодвинский |
936 |
– |
– |
– |
– |
936 |
Зубцовский |
910 |
50 |
– |
– |
– |
960 |
Калининский |
2068 |
– |
– |
– |
– |
2068 |
Калязинский |
600 |
– |
– |
– |
– |
600 |
Кашинский |
420 |
– |
– |
– |
– |
420 |
Кесовогорский |
150 |
– |
– |
– |
– |
150 |
Кимрский |
25 |
– |
– |
– |
– |
25 |
Краснохолмский |
735 |
150 |
– |
– |
– |
885 |
Кувшиновский |
125 |
– |
– |
– |
– |
125 |
Лесной |
1900 |
– |
– |
– |
– |
1900 |
Лихославльский |
400 |
– |
– |
– |
– |
400 |
Максатихинский |
958 |
– |
– |
– |
160 |
1118 |
Молоковский |
1810 |
– |
– |
– |
– |
1810 |
Нелидовский |
678 |
– |
– |
375 |
– |
1053 |
Оленинский |
180 |
– |
– |
– |
– |
180 |
Рамешковский |
1452 |
350 |
– |
– |
– |
1802 |
Ржевский |
1261 |
– |
50 |
– |
– |
1311 |
Сандовский |
230 |
– |
– |
– |
– |
230 |
Селижаровский |
2446 |
200 |
– |
– |
– |
2646 |
Сонковский |
1900 |
– |
– |
– |
– |
1900 |
Спировский |
– |
60 |
– |
– |
– |
60 |
Старицкий |
320 |
– |
– |
– |
– |
320 |
Торжокский |
3817 |
35 |
– |
– |
– |
3852 |
Торопецкий |
1945 |
– |
– |
– |
– |
1945 |
Удомельский |
70 |
– |
– |
– |
– |
70 |
Фировский |
100 |
– |
– |
– |
– |
100 |
Итого |
27247 |
905 |
175 |
375 |
160 |
28862 |
Примечание. В 6 районах области ртутьсодержащие пестициды не применялись.
Всего на территории области находится 27,2 т ртутьсодержащих пестицидов, причем
большая их часть находится на полигоне в Торжокском районе – 3,8 т. Поэтому приведем более
подробную информацию по этому полигону.
Полигон захоронения пестицидов в Торжокском районе
Полигон площадью 0,8 га находится в 600 м от дороги. Проект полигона 1976 г.
разработан по заказу областного объединения .Сельхозтехника. в соответствии с временной
Инструкцией по уничтожению ядохимикатов, признанных непригодными к использованию, и
тары из под них. Грунты на площадке слабо фильтрующие, воды залегают на глубине 21 м.
Захоронение ядохимикатов и тары производилось в траншеи глубиной 5 м. Гидроизоляция дна
и стен выполнена из глины. Покрытие дна - сборные железобетонные плиты, глиняный замок
толщиной 1 м. После окончания заполнения траншеи ядохимикатами и тарой сверху насыпался
слой глины толщиной 1 м.
Согласно проекту, отметка верха гидроизоляционного слоя должна быть выше отметки
прилегающей территории на 0,5 м, но на момент осмотра этого видно не было. Территория
заросла лесом, огранка сломана, ворота не установлены. Наблюдательная скважина, из которой
ранее брались пробы подземных вод для определения ртути, не функционирует. В проекте на
бурение наблюдательной скважины указано на возможность загрязнения водоносного
горизонта. По данным Станции защиты растений, в поверхностной воде ртуть не
обнаруживается, но данных о состоянии подземных вод в настоящее время нет.
Расстояние от полигона: до реки Тверца - примерно 2 км, до дачных посёлков - 3,5 км, до
деревни Добрынино - 6 км.
Примером успешной инвентаризации пестицидов, в т. ч. и ртутьсодержащих пестицидов,
являются агрохозяйства Старицкого района.
Старицкий район
В районе расположено централизованное захоронение пестицидов на складе,
организованное в 2000 г. в рамках пилотного проекта UNEP Chemical. Проведена
идентификация пестицидов. Обнаружены россыпи гранозана примерно до 100 кг. Старицкий
склад является одним из лучших в области. В 2000 г. произошло перезатаривание пестицидов и
их маркировка. На станции “Старица” расположены склады быв. объединения
“Агропромхимия”. Вывезено из колхозов 16 бочек с гранозаном по 20 кг, итого 320 кг + смеси
~ 100 кг , всего 420 кг. Кирпичный склад может вместить 300 тонн пестицидов, высота 4 м.
Охрана имеется.
Ржевский район - 130 км от г. Тверь
Всего хранится 1,3 т гранозана на 12 складах, которые приведены в порядок, крыши не
текут, двери, замки имеются. На каждый склад имеется санитарный паспорт. Склады .
приспособленные помещения.
Все склады расположены на расстоянии не менее 1 км от открытых источников
водоснабжения и соответствуют санитарным нормативам.
Приложение 3. Содержание ртути в углях основных угольных
бассейнов России
Ниже в табл. 1-14 приведены данные из работы “Ценные и токсичные элементы в
товарных углях России: Справочник. – М.: Недра, 1996. – 238 с. (Российская государственная
компания “Росуголь”; Российский комитет по геологии и использованию недр)”.
Этот справочник является итогом специальных работ и в существенной мере составлен на
материалах ревизионного опробования товарной продукции предприятий угольной
промышленности страны в 1988-1991 г.г. Для обоснования и контроля полученных результатов
привлекались данные опробования 1960-1970-х г.г. В общей сложности банк данных включает
анализы 13,5 тыс. проб товарных углей не только на ртуть, а на 25-50 химических элементов.
Опробование углей осуществлялось в соответствии с номенклатурой товарной продукции
угольных предприятий. При прочих равных условиях предпочтение отдавалось рядовым углям.
На предприятиях, выпускающих только сортовые угли, исследовался доминирующий в
шахтовыдаче сорт. Работа основана на исследовании специально составленных групповых
проб, характеризующих продукцию конкретного угольного предприятия за максимально
длительный период. На предприятии отбиралось не менее трех групповых проб,
принадлежащих одной технологической группе (марке) и соответствующих качеству
продукции не менее чем за календарный месяц. В свою очередь, каждая групповая проба
составлена из 3-15 и более первичных проб угля (в зависимости от конкретной геологической и
производственной ситуации и ряда других условий). В качестве первичных проб были
использованы дубликаты проб, отбираемых Отделом технического контроля и
углехимическими лабораториями соответствующих угольных предприятий с целью оценки
качества угля, отгружаемого потребителю (в частности, использовались: дубликаты проб,
характеризующих текущую выдачу угля угольным предприятием; пробы, среднемесячных
проб, составленные из проб текущей выдачи и характеризующие продукцию, выдаваемую
предприятием за месяц; суточные, сменные и другие пробы, оценивающие текущую работу
предприятия). При формировании групповых проб учитывалось количество угля, отгружаемого
потребителю, долевое участие рабочих пластов угля в шахтовыдаче и другие показатели).
Периоды опробования (формирования групповой пробы) составляли от 3 до 12 месяцев. При
опробовании товарных углей использовалась система контроля, предусматривающая
выбраковку непредставительных по зольности первичных проб угля. Первичная проба
исключалась из массива, если ее зольность отличалась на ±10% (относительных) от зольности
среднемесячной расчетной пробы. Распределение ртути в пробах осуществлялось атомно-
абсорбционным методом. Сказанное позволяет считать, что представленные в справочнике
сведения о содержании ртути в товарных угля России являются репрезентативными, в высокой
степени объективно отражающие реальное распределение ртути в основных типах (марках)
углей России.
Mercury content was determined on a dry basis. The detection limit for mercury by atomic absorption
method (% to coal) was 0,00001. Non-detects were treated as 0.s.
Таблица 1. Среднее содержание ртути в товарных углях Печорского бассейна
Угленосный р-н, месторождение, предприятие |
Технологическая группа (марка) угля, сорт угля |
Зольность Аd, % (на сухое топливо) |
Влажность Wrt, % (на рабочее топливо) |
Hg, г/т угля |
Воркутинский |
2 ж конц. кокс. |
8,5 |
5,0 |
0,04 |
Воркутское |
Отс. |
21,6 |
7,3 |
0,05 |
ОФ ш. Северная |
Пр. |
29,9 |
4,4 |
0,07 |
|
Отх. |
89,0 |
|
0,01 |
|
Шл. |
31* |
|
0,03 |
ОФ ш. Воркутинская |
2ж конц. кокс. |
8,5 |
6,3 |
0,01 |
|
Отс. |
23,7 |
7,9 |
0,02 |
|
Пр. |
28,4 |
4,5 |
0,03 |
|
Отх. |
82,6 |
|
0,04 |
|
Шл. |
31* |
|
0,02 |
ОФ ш. Южная |
1Ж Р эн. |
34,2 |
7,0 |
0,07 |
|
Отх. |
81* |
|
0,1 |
|
шл. |
31* |
|
0,06 |
ОФ ш. Аяч-Яга |
1 Ж Р эн. |
31,3* |
7,5 |
0,07 |
|
Отх. |
81* |
|
0,02 |
|
Шл. |
31* |
|
0,07 |
ОФ ш. Октябрьская |
1 Ж конц. кокс. |
13,6 |
4,8 |
0,03 |
|
Отс. |
17,1 |
7,3 |
0,04 |
|
Отх. |
76,2 |
|
0,3 |
ОФ ш. Заполярная |
1 Ж конц. кокс. |
10,2 |
|
0,04 |
|
Отс. |
24,2 |
8,1 |
0,04 |
|
Пр. |
29,1 |
4,9 |
0,04 |
|
Отх. |
70,0 |
|
0,05 |
|
Шл. |
31* |
|
0,04 |
ОФ ш. Юр-Шор |
1 Ж конц. кокс. |
11,7 |
7,3 |
0,03 |
|
Отс. |
24,3 |
7,9 |
0,05 |
|
Отх. |
75,0 |
|
|
|
Шл. |
31* |
|
0,02 |
ОФ ш. Центральная |
1 Ж конц. кокс. |
10,9 |
6,4 |
0,03 |
|
Отс. |
18,9 |
7,9 |
0,03 |
|
Отх. |
81* |
|
0,1 |
|
Шл. |
31* |
|
0,02 |
ОФ ш. Промышленная |
1 Ж конц. кокс. |
11,2 |
6,8 |
0,1 |
|
Отс. |
17,7 |
7,6 |
0,04 |
|
Отх. |
72,4 |
|
0,1 |
|
Шл. |
31* |
|
0,2 |
ОФ ш. Комсомолькая |
2 Ж Р, кокс. |
20,9 |
6,8 |
0,04 |
|
Отх. |
81* |
|
0,2 |
|
Шл. |
31* |
|
0,02 |
Юньягинское, |
1 К Р, кокс. |
22,7 |
7,6 |
0,04 |
ОФ ш. Юнь-Яга |
Отх. |
81* |
|
0,08 |
|
Шл. |
31* |
|
0,03 |
Воргашорское, |
ГЖО К, кокс. |
19,6 |
5,7 |
0,08 |
Ш. Воргашорская |
ГЖО ОМСШ, кокс. |
18,9 |
7,7 |
0,07 |
Хальмеръюский, |
1 К Р, кокс. |
29,7 |
5,3 |
0,1 |
Хальмеръюское, |
|
|
|
|
Ш. Хальмер-Ю |
|
|
|
|
Интинский, |
Д конц |
23,1 |
9,7 |
0,05 |
Интинское, |
Отс. |
32,2 |
11,4 |
0,06 |
ГОФ Интинская, цех 1 |
Шл. |
31* |
|
0,05 |
ГОФ Интинская, цех 2 |
Д конц. |
24,3 |
10,5 |
0,03 |
|
Отс. |
32,5 |
11,8 |
0,04 |
|
Отх. |
60* |
|
0,7 |
|
Шл. |
31* |
|
0,02 |
ГОФ Капитальная |
Д конц. |
24,0 |
9,3 |
0,06 |
|
Отс. |
32,6 |
11,7 |
0,06 |
|
Шл. |
31* |
|
0,04 |
|
Отх. |
60* |
|
0,1 |
Примечание. Печорский угольный бассейн является крупным сырьевым источником для развития
энергетической и коксохимической промышленности, значительная его часть находится севернее
Полярного круга; кокс. – коксующийся, эн. – энергетический; технол. – технологический; ш/у –
шахтоуправление,; р-з – разрез; уч-к – участок; ОФ – обогатительная фабрика; ЦОФ – центральная
обогатительная фабрика; ГОФ – групповая обогатительная фабрика; УОФ – углеобогатительная
фабрика; конц. – концентрат; отс. – отсев; шл. – шлам; отх. – отходы; Р – рядовой; П – плитный, К – крупный; О – орех; М – мелкий; С – семечко; Ш – штыб.
Таблица 2. Среднее содержание ртути в товарных углях Подмосковного бассейна
Угленосный р-н, месторождение, предприятие |
Технологическая группа (марка) угля, сорт угля |
Зольность Аd, % |
Влажность Wrt, % |
Hg, г/т угля |
Б. Нелидовское, ш. Нелидовская, № 4 |
2Б Р |
36,8 |
33,6 |
0,7 |
Сафоновское, ш. Сафоновская № 7 |
2Б Р |
36,7 |
36,0 |
0,82 |
Середейское, ш. Середейская № 1 |
2Б Р |
36,0 |
32,9 |
0,33 |
Липковское, ш. Сеченская |
2Б Р |
38,0 |
31,0 |
0,18 |
Ш. Липковская № 9 |
2Б Р |
40,6 |
30,8 |
0,23 |
Ш. Бородинская № 17 |
2Б Р |
37,8 |
30,4 |
0,18 |
Ш. Сеченская № 15 |
2Б Р |
38,0 |
30,8 |
0,11 |
ОФ ш. Владимирская |
2Б конц. отх. |
39,8 64,3 |
30,9 |
0,09 0,25 |
Уч-к Дедиловский, ш. Комсомольская |
2Б Р |
38,6 |
31,2 |
0,14 |
Грызловское, ш. Подмосковная |
2Б Р |
40,7 |
29,5 |
0,15 |
Р-з Грызловский |
2Б Р |
41,2 |
31,2 |
0,12 |
ОФ ш. Бельковская |
2Б конц. отх. |
39,8 78,1 |
30,9 |
0,6 0,05 |
Березовское, ОФ ш. Прогресс |
2Б конц. отх. |
43,3 75,4 |
31,5 |
0,2 4,5 |
Смородинское, ш. Донская (Смородинская) |
2Б Р |
35,8 |
32,0 |
0,1 |
Ш. Майская |
2Б Р |
34,4 |
32,2 |
0,06 |
Львовское, ш. Львлвская |
2Б МСШ |
35,1 |
32,7 |
0,22 |
Никулинское, ОФ ш. Никулинская |
2Б конц. 38,4 отх. |
32,6 61,7 |
|
0,25 0,75 |
Примечание. Буроугольный бассейн, расположен в пределах пяти административных областей:
тверской, Смоленской, Калужской, Тульской и Рязанской; здесь распространены окисленные угли,
характеризующиеся повышенными зольностью, влажностью, низкими прочностными показателями.
Таблица 3. Среднее содержание ртути в товарной продукции угледобывающих и
углеобогатительных предприятий Восточного Донбасса
Угленосный р-н, месторождение, предприятие |
Технологическая группа (марка) угля, сорт угля |
Зольность Аd, % |
Hg, г/т угля |
АО “Гуковуголь”, ш. Западная |
К |
31,7* |
0,07 |
Ш. Изваринская |
К |
33,9* |
0,06 |
Ш. Центральная |
К |
39,3* |
0,09 |
ЦОФ Донецкая |
К конц. |
8,9* |
0,1 |
|
шл. |
48,8 |
0,05 |
|
пр. |
43,0* |
0,04 |
Ш. Бургустинская |
А Р |
32,0* |
0,03 |
Ш. Замчаловская |
А Р |
30,6* |
0,02 |
Ш. им. 50-летия Октября |
А |
25,6* |
0,02 |
Ш. Гуковская |
А Р |
26,6* |
0,03 |
Ш. Антрацит |
А Р |
24,7* |
0,01 |
Ш. Обуховская |
А К |
5,0 |
0,02 |
Ш. Алмазная |
А |
11,8 |
0,02 |
|
А Ш |
24,1 |
0,07 |
|
А М |
11,6 |
0,02 |
|
А О |
8,6 |
0,03 |
|
А К |
7,8 |
0,06 |
|
А П |
6,7 |
0,05 |
|
А С |
11,9 |
0,03 |
Ш. Ростовская |
А М |
13,2 |
0,02 |
|
А К |
5,8 |
0,02 |
|
А С |
14,1 |
0,01 |
|
А Ш |
25,3 |
0,004 |
|
А О |
10,8 |
0,02 |
ПО “Ростовуголь”, ш. им. Ленина |
А |
29,9* |
0,11 |
Ш. им. Кирова |
А |
36,0* |
0,13 |
Ш. Соколовская |
А |
27,5* |
0,06 |
Ш. им. газеты Комсомольская правда |
А |
25,6* |
0,01 |
Ш. им. Красина |
А |
34,0* |
0,13 |
Ш. Зап. Капитальная |
А |
30,1* |
0,07 |
Ш. Краснодонецкая |
А |
34,0* |
0,04 |
Ш. Наклонная |
А |
26,5* |
0,14 |
Ш. Самбековская |
А |
34,0* |
0,11 |
Ш. Несветаевская |
А |
29,6* |
0,06 |
Ш. Майская |
А |
25,6* |
0,04 |
Ш. им. Окт. Революции |
А |
33,1* |
0,07 |
Ш. Юилейная |
А |
25,8* |
0,15 |
Ш. Мирная |
А |
26,5* |
0,10 |
Ш. Аютинская |
А |
29,7* |
0,09 |
ЦОФ Аютинская |
А Ш |
29,1 |
0,11 |
Ш. Южная |
А |
23,2* |
? |
ОФ Южная |
А С |
12,3 |
0,19 |
|
А О |
12,8 |
0,22 |
|
А П |
14,8 |
0,15 |
ГОФ им. Артема |
А Ш |
29,8 |
1,13 |
ГОФ Соколовская |
А СМШ |
18,7 |
0,16 |
ПО “Шахтуголь”, ш. № 410 |
А М |
11,1 |
0,02 |
Ш. Калиновская № 5 |
А Р |
35,5 |
0,02 |
Ш. № 10 |
А Ш |
26,0 |
0,07 |
Ш. № 19 |
А Ш |
23,8 |
0,02 |
Ш. Сулинская № 3 |
А М |
38,2 |
0,03 |
Ш. № 56 |
А С |
32,2 |
0,10
|
Ш. Сулинская № ; |
А М |
28,9 |
0,06 |
Ш. № 57 |
А Р |
37,9 |
0,04 |
Ш. № 40 |
А С |
18,6 |
0,01 |
ЦОФ Гуковская |
А М |
9,2 |
0,03 |
|
А С |
15,7 |
0,01 |
|
А КО |
7,3 |
0,002 |
|
А Ш |
22,6 |
0,02 |
|
А П |
6,2 |
0,002 |
Примечание. В пределах Ростовской области Донецкий бассейн представлен своей восточной частью,
куда входят преимущественно районы распространения антрацитов: Гуково-Зверевский,
Краснодонецкий, Сулино-Садкинский, Цимлянский, Шахтинско-Несветаевский, Задонский угленосные
районы; меньшая роль принадлежит районам распространения спекающихся и тощих углей: Каменско-
Гундоровскому, Белокалитвенскому и Тацинскому.
Таблица 4. Среднее содержание ртути в товарной продукции угледобывающих предприятий
Угленосный р-н, месторождение, предприятие |
Технологическая группа (марка) угля, сорт угля |
Зольность Аd, % |
Hg, г/т угля |
Кизеловский, ш. им. 40-летия ВЛКСМ |
Г, ГЖ Р |
36,2* |
0,35 |
Ш. Северная |
ГЖ Р |
28,5* |
0,45 |
Ш. им. Ленина |
ГЖ Р |
32,9* |
0,48 |
Губахинский, ш. Ключевская |
Г, ГЖ Р |
32,4* |
0,48 |
Ш. Нагорная |
Г Р |
29,0* |
0,41 |
Гремячинский, ш. им. 40-летия Октября |
ГЖ, Р |
23,9* |
0,54 |
Ш. Скальная |
Г Р |
31,3* |
0,48 |
Ш. Шумихинская |
ГКО Г МСШ |
18-24,7 42,6-44,4 |
0,41 0,34 |
Примечание. Бассейн расположен между р. Яйва на севере и р. Вильва на юге и имеет длину около 150
км при ширине 5-20 км; в угленосной толще содержится до 25 пластов и прослоев угля, из них рабочей
мощности достигают лишь пять пластов; угли марок Г, ГЖО, ГЖ и Ж используются как энергетическое
и технологическое сырье.
Таблица 5. Среднее содержание ртути в товарной продукции предприятий Буланаш-Елкинского
угленосного бассейна
Угленосный р-н, месторождение, предприятие |
Технологическая группа (марка) угля, сорт угля |
Зольность Аd, % |
Hg, г/т угля |
Буланашское, ш. Буланаш 2/5, Буланаш-3, Буланаш-4 |
Г Р |
24-25* |
? |
Примечание. Здесь известно два месторождения – Буланашское и Дальне- Буланашское
верхнетриасового возраста; промышленностью осваивается только Буланашское месторождение,
которое занимает северную часть Буланаш-Елкинской депрессии; на месторождении зафиксировано
более 40 угольных пластов, из которых 29 имеют рабочую мощность от 0,9 до 48 м.
Таблица 6. Среднее содержание ртути в товарной продукции угледобывающих предприятий
Челябинского бассейна
Угленосный р-н, месторождение, предприятие |
Технологическая группа (марка) угля, сорт угля |
Зольность Аd, % |
Влажность Wrt, % |
Hg, г/т угля |
Камышинский, ш. Капитальная, Октябрьская, Комсомольская, Подозерная |
3Б Р |
41,5-44,4* |
12-14** |
? |
Коркинский, р-з Коркинский, ш. Коркинская, Калачаевская |
3Б Р |
37,9-45,5* |
11-14** |
? |
Примечание. Челябинский буроугольный бассейн расположен на восточном склоне Южного Урала в
пределах Челябинской области и представляет собой узкую полосу шириной до 15 км, протягивающуюся
почти параллельно Уральскому хребту на протяжении 170 км от р. Теча на севере до р. Уй на юге.
Таблица 7. Среднее содержание ртути в товарной продукции угледобывающих предприятий Южно-Уральского бассейна
Угленосный р-н, месторождение, предприятие |
Технологическая группа (марка) угля, сорт угля |
Зольность Аd, %
|
Влажность Wrt, % |
Hg, г/т угля |
Бабаевское, р-з Кумертауский № 1 |
1Б Р |
24,2* |
55** |
? |
Примечание. Южно-Уральский бассейн объединяет многочисленные месторождения бурых углей
третичного возраста, расположенные на территории Республики Башкортостан и Оренбургской области;
бассейн вытянут в меридиональном направлении на 350 км при ширине 70-80 км.
Таблица 8. Среднее содержание ртути в товарных углях Кузнецкого бассейна
Угленосный р-н, месторождение, предприятие |
Технологическая группа (марка) угля, сорт угля |
Зольность Аd, % |
Влажнос ть Wrt, % |
Hg, г/т угля |
Кемеровский, ш. им. Волкова |
ГЖ |
26,5 |
7,5 |
0,08 |
Ш. Бирюлинская |
К, КО |
32,2 |
7,4 |
0,03 |
Ш. Березовская |
К |
26,1 |
5,4 |
0,06 |
Ш. Южная |
СС |
14,5 |
7,2 |
0,03 |
Р-з Кедровский |
СС |
13,1 |
8,7 |
0,08 |
Анжерский, ш. Судженская |
ТС |
18,1 |
2,3 |
0,08 |
Прокопьевско-Киселевский, Прокопьевское, ш. Центральная |
Т |
16,6 |
5,5 |
0,05 |
Ш. им. Калинина |
К, КО, КС, СС |
22,1 |
5,3 |
0,02 |
Ш. Зиминка |
К, КО, КС |
15,1 |
6,7 |
0,02 |
Ш. Тырганская |
СС |
10,4 |
6,5 |
0,03 |
Р-з Прокопьевский |
СС |
8,3 |
8,7 |
0,05 |
Байдаевский, ш. Большевик |
Г кокс |
13,1 |
7,1 |
0,03 |
Ш. Зыряновская |
Г кокс, ГЖ |
23,5 |
7,6 |
0,05 |
Ш. Новокузнецкая |
Г кокс, ГЖ |
14,9 |
7,1 |
0,03 |
Ленинский, ш. Сигнал |
Г эн. |
13,9 |
1,4 |
0,05 |
Р-з Колмогоровский, уч-к Колмогоровский-1 |
Д, Г эн. |
13,0 |
16,8 |
0,03 |
Ш/у Кольчугинское |
Д |
17,8 |
8,6 |
0,08 |
Ш. им 7 Ноября |
Г кокс. |
14,5 |
8,4 |
0,1 |
Ш. Кузнецкая |
Г кокс. |
18,2 |
8,2 |
0,01 |
Ш. Заречная |
Г эн. |
13,1 |
11,0 |
0,03 |
Прокопьевско-Киселевский, Киселевское, р-з Краснобродский |
Т |
10,5 |
4,7 |
0,03 |
Р-з Новосергеевский |
СС |
8,8 |
5,2 |
0,01 |
Ш. Черкасовская |
К |
17,4 |
6,2 |
0,01 |
Кондомский, ш. Северный Кандыш |
Т |
24,2 |
5,9 |
0,04 |
Р-з Калтанский |
Т |
19,8 |
7,6 |
0,6 |
Ш. Аларда |
К, КО, КС |
19,1 |
7,0 |
0,05 |
Ш. Шушталепская |
Т |
23,5 |
8,2 |
0,01 |
Р-з Колмогоровский-2 |
Д |
15,5 |
17,1 |
0,03 |
Терсинский, р-з Байдаевский |
ДГ, Г эн. |
16,2 |
9,6 |
0,05 |
Томь-Усинский, р-з Красногорский |
Т |
18,9 |
5,9 |
0,01 |
Р-з Томусинский |
ОС |
17,8 |
5,1 |
0,6 |
Р-з Ольжерасский |
СС |
22,5 |
6,4 |
0,3 |
Ш. им. Шевякова |
К, КО, КС, ОС |
29,5 |
8,1 |
0,1 |
Ш. Распадская |
ГЖ |
19,4 |
5,6 |
0,2 |
Мрасский, р-з Междуреченский |
К, КО, Т |
18,4 |
4,2 |
0,5
|
Беловский, ш. Колмогосркая |
ДГ, Г эн. |
13,1 |
8,7 |
0,05 |
Араличевский, ш. им. Орджоникидзе |
Т |
27,0 |
6,5 |
0,03 |
Ш. им. Димитрова |
Т |
21,2 |
6,7 |
0,06 |
Осиновский, ш. Капитальная |
Ж |
27,9 |
5,9 |
0,08 |
Ш. Высокая |
Ж |
32,5 |
5,9 |
0,04 |
Примечание. Кузнецкий бассейн является крупнейшей сырьевой базой коксохимической и топливно-
энергетической промышленности; по балансовым запасам угля он занимает первое место в стране;
особенно важное значение имеют коксующиеся угли, добыча которых составляет около половины от
общей добычи по бассейну; в качестве энергетического топлива используются угли преимущественно
марок Д, СС, Т, отчасти Г.
Таблица 9. Среднее содержание ртути в товарной продукции угледобывающих предприятий Республики Бурятии
Угленосный р-н, месторождение, предприятие |
Технологическая группа (марка) угля, сорт угля |
Зольность Аd, % |
Влажность Wrt, % |
Hg, г/т угля |
Гусиноозерское, ш. Гусиноозерская |
3Б Р |
26,9* |
20,0** |
0,005 |
Р-з Холбольджинский |
3Б Р |
24,8* |
25** |
0,006 |
Сангинское, р-з Сангинский |
3Б Р |
23,0* |
23,0?? |
0,015 |
Примечание. В Бурятии преобладают буроугольные месторождения, 11 месторождений с
балансовыми запасами угля.
Таблица 10. Среднее содержание ртути в товарной продукции угледобывающих предприятий
Читинской области
Угленосный р-н, месторождение, предприятие |
Технологическая группа (марка) угля, сорт угля |
Зольность Аd, % |
Влажность Wrt, % |
Hg, г/т угля |
Тарбагатайское, р-з Тигнинский |
Б Р |
17,8* |
30-31** |
0,012 |
Букачачинское, ш. Букачача |
Г Р |
18,4* |
|
0,007 |
Харанорское, р-з Харанорский |
2Б Р |
17,3* |
40** |
0,02 |
Татауровское, р-з Восточный |
2Б Р |
14,5* |
32-34** |
0,006 |
Примечание. Угли северной группы месторождений каменные, марок Г – Т, угли Чикойской впадины
– переходные от бурых к каменным, зольностью 10-20%; бурые угли большинства площадей
характеризуются зольностью 8-25%.
Таблица 11. Среднее содержание ртути в товарных углях Ленского бассейна
Угленосный р-н, месторождение, предприятие |
Технологическая группа (марка) угля, сорт угля |
Зольность Аd, % |
Влажность Wrt, % |
Hg, г/т угля |
Кангаласское, р-з Кангаласский |
3Б Р |
13,6 |
29,0 |
0,03 |
Уч-к Восточный |
3Б |
12,4 |
|
0,02 |
Джебарики-Хая, ш. Джебарики-Хая № 2 |
Д Р |
10,0 |
9,0 |
0,01 |
Примечание. Угольные месторождения бассейна расположены в основном на территории Республики
Саха; не разрабатываемое м-ние Юрунг-Тумус (Нордвик) относится к Красноярскому краю); запасы
оценены в 19 месторождениях, три наиболее крупных (Кангаласское, Джебарики-Хая, Сангарское)
интенсивно разрабатываются.
Таблица 12. Среднее содержание ртути в товарных углях Северо-Востока и Камчатки
Угленосный р-н, месторождение, предприятие |
Технологическая группа (марка) угля, сорт угля |
Зольность Аd, % |
Влажность Wrt, % |
Hg, г/т угля |
Харанга, р-з Харанга |
Т Р |
15,0 |
12,0 |
0,5 |
Анадырское, ш. Анадырская |
3Б Р |
17,0 |
22,0 |
0,03 |
Нижн.-Аркагалинское, ш. Кедровская № 7 |
Д Р |
13,3 |
16,0 |
0,1 |
Ш. Кадыкчанская № 10 |
Д Р |
12,8 |
16,0 |
0,06 |
Верх.-Аркагалинское, р-з Тал-Юрях |
Д Р |
14,1 |
17,0 |
0,2 |
Примечание. Промышленная угленосность связана с крупными геологическими структурами .
Зырянским (Республика Саха), Аркагалинским (Магаданская обл.) угольными бассейнами и с
обширными угленосными площадями Магаданской, Камчатской областей – Анадырской, Омсукчанской,
Эльгенской, Камчатской. С последними связаны эксплуатируемые месторождения бурых и каменных
углей – Анадырское, бухты Угольной, Галимовское, Кэнское, Эльгенское (лигниты), Корфское.
Таблица 13. Среднее содержание ртути в товарных углях месторождений Хабаровского края и
Амурской области
Угленосный р-н, месторождение, предприятие |
Технологическая группа (марка) угля, сорт угля |
Зольность Аd, % |
Влажность Wrt, % |
Hg, г/т угля |
Райчихинское, р-з Северо-Восточный. Р-з Широкий, р-з Юго-Западный |
2Б Р |
11,7 |
36,8 |
0,4 |
Архаро-Богучанское, уч-к Богучан |
Б Р |
14,4 |
37,1 |
1,3 |
Огоджинское, р-з Контактовый |
ГЖ |
28,0 |
17,0 |
0,9 |
Примечание. В пределах этих регионов известно более 100 месторождений и углепроявлений
каменных и бурых углей; на территории Хабаровского края разрабатывается Ургальское м-ние
(восточная часть Буреинского бассейна); угли каменные, марки Г; Райчихинское и Архаро-Богучанское
м-ния находятся в Амурской области в пределах современной Нижне-Зейской впадины; Райчихинское м-
ние эксплуатировалось разрезами, угли бурые, технологической группы 2Б; на Архаро-Богучанском м-
нии угли бурые, по степени углефикации от 1Б до 3Б.
Таблица 14. Среднее содержание ртути в товарных углях и продуктах углеобогащения Сахалинской
области
Угленосный р-н, месторождение, предприятие |
Технологическая группа (марка) угля, сорт угля |
Зольность Аd, % |
Влажность Wrt, % |
Hg, г/т угля |
Мгачинское, ш. Мгачи |
ДГ Р |
15,8 |
7,5 |
0,08 |
Александровское, ш. Арково |
Д р |
14,5 |
8,1 |
0,07 |
Бошняковское, ш. Бошняково |
ДГ Р |
18,8 |
9,7 |
0,1 |
Лесогорское, ОФ ш. Тельновская |
ДГ ОМСШ |
17,9 |
11,4 |
0,04 |
Углегорское, ш. Углегорская |
Г Р эн. |
27,4 |
6,5 |
0,11 |
Ш. Ударновская |
Д Р |
26,7 |
9,3 |
0,08 |
Солнцевское, р-з Солнцевский |
Д Р |
16,2 |
19,8 |
0,03 |
Тихменевское, ш. Тихменевская |
3Б Р |
17,4 |
21,3 |
0,04 |
Вахрушевское, ОФ ш/у Лермонтовское |
Д КОМ |
19,5 |
16,2 |
0.07 |
|
Д СШ |
18,8 |
19,1 |
0,09 |
|
Д МСШ |
35,9 |
19,2 |
0,12 |
Макаровское, ш. Макаровская |
Д Р |
26,3 |
16,9 |
0,1 |
Лопатинское, ОФ ш. Долинская |
Д ОМ |
17,1 |
9,4 |
0,08 |
|
Д СШ |
21,7 |
9,9 |
0,09 |
|
отх. |
61,5 |
|
0,03 |
Ш. Южно-Сахалинская |
Д Р |
25,9 |
8,4 |
0,3 |
Горнозаводское, ОФ ш. Горнозаводская |
3б ОМ |
9,1 |
18,2 |
0,21 |
|
3Б СШ |
15,2 |
20,2 |
0,2 |
Ш. Шебунино |
Б Р |
20,4 |
22,0 |
0,06 |
Новиковское, р-з Новиковский |
Д Р |
31,4 |
16,6 |
0,3 |
Примечание. Основные угольные месторождения расположены в западной части острова; по степени
углефикации угли относятся к бурым технологической группы 3Б и каменным марок Д, Г, Ж, Т;
каменные угли распространены в основном на западном побережье острова в Александровском и
Углегорском угленосных районах, бурые угли . в основном в Центральном и Южном угленосных
районах; угли характеризуются высоким качеством и разнообразными свойствами, они малосернистые,
мало- и среднезольные (15-25%), рабочая влага бурых углей не превышает 18-20%, каменных . 9-10%;
все промышленные месторождения угля Сахалина сосредоточены в четырех угленосных районах:
Александровском, Углегорском, Центральном и Южном.
Сноски
[1] С распадом СССР практически полностью была нарушена существовавшая в стране система
контроля и статистического учета производства и потребления ртути [234]. Оценка и учет техногенной
эмиссии ртути в странах СНГ также находятся в крайне неудовлетворительном состоянии [111].
[2] Необходимо учитывать что значительное количество диафрагменных хлор-щелочных производств осталось в других странах СНГ - на Украине (4 завода), в Узбекистане, Азербайджане и Армении, в то время как большинство руттных производств осталось на территории России. По сравнению с бывшим СССР, объемы производства хлора в России существенно упали. На ОАО Каустик, г. Волгоград, ртутное производство хлора было организовано в 1968, а диафрагменное производство было создано в 1984 году, и в настоящее время функционируют оба производства.
[3] В качестве сырья в производствах хлора по ртутному методу на предприятиях Волгограда, Стерлитамака и Саянска используется выпаренная соль из рассола, а Кирово-Чепецке – твердая привозная соль, растворяемая в отработанном анолите.
[4] С 1971 г. и примерно до середины 1990-х г.г. производство ртутных термометров осуществля-лось также на заводе “Стеклоприбор” (ныне ЗАО “ЕВРОГЛАСС”) в пос. Голынки (Руднянский район Смоленской области). Здесь (в последние годы функционирования производства) ежегодно использовалось до 19 т ртути.
[5] Все технологическое оборудование в свое время было разработано и изготовлено непосредственно на предприятии (автоматические стеклоформирующие машины для изготовления деталей и сборки заготовок термометров, высокоточные термостаты для отметки основных точек шкал, вакуумные установки для наполнения термометров ртутью и др.) Именно поэтому доступная литература, в которой содержатся детальные описания технологического процесса изготовления ртутных термометров, в библиотеках отсутствует. По имеющимся сведениям, техническая документация хранится на заводе в виде машинописных рукописей. Большая часть изделий изготавливается по техническим условиям (ТУ) завода.
[6] При потреблении ртути в 130 т/год потери ее в канализацию составляют 755 кг; можно
предположить, что при уменьшении потребления металла до 24.191 т (уровень 2001 г.), т. е. в 5.27 раз, потери его также уменьшатся примерно во столько же (они составят 140.6 кг, что практически равно расчетному количеству потерь для 2001 г., приведенные в табл. 3.28).
[7] В настоящее время решается вопрос о закрытии производства люминесцентных ламп на Саранском электроламповом заводе и демонтаже цеха их сборки с проведением демеркуризационных мероприятий. Новое производство ламп, во многом в соответствие с ранее разработанным проектом [225], более мощное, но основанное на технологии с намного меньшим потреблением ртути, предполагается организоваться на другой промышленной площадке.
[8] Большая часть информации и первичные статистические данные, положенные в основу ниже приводимых материалов о деятельности ЗАО “Кубаньцветмет” и ООО “Мерком” в сфере переработки ртутьсодержащих отходов и производства ртути и ее соединений, были получены непосредственно на указанных предприятиях.
| Главная страница | | Верх |
Версия 1.0 март 2005, © Датское агентство по охране окружающей среды
|