| Contents
|
Environmental and Health Assesment of Alternatives to Phthalates and to
flexible PVC
4.1 Use patterns of phthalates
4.1.1 Assessment of use of phthalate plasticisers
4.2 Selection of substitute substances
4.2.1 Assessed substitutes for phthalates - substances
4.2.2 Assessed substitutes for flexible PVC - materials
4.3 Proposed use pattern for substitutes
4.3.1 Substitution matrix for the 11 substances in tons
4.3.2 Substitution matrix for the two materials
4.4 Assessment of emission and exposure
4.4.1Considerations regarding specific uses of
phthalates/substitutes
4.4.2 Worker and consumer exposure
4.4.3 Exposure in environment
4.4.4 Migration potential
Many polymer products need to be flexible and soft so they can take on
a different shape and form depending on their application. This
plastification is often conducted using plasticisers such as phthalates,
adipates, trimelli-tates and citrates.
The major uses of flexible PVC in Western Europe is in the product
groups of film and sheet, wire and cable, floor covering, extrusions,
coated fabrics and plastisols (European Council for Plasticisers and
Intermediates, 2000).
PVC plasticisers
According to the European Council for Plasticisers and Intermediates
there are more than 300 different types of plasticisers of which about
50-100 are in commercial use (European Council for Plasticisers and
Intermediates, 2000). The most commonly used plasticisers are phthalates.
In
the Danish Product Register, close to 180 different plasticisers are
registered in a wide range of products. According to the European industry
95% of the plasticiser production is for PVC end-use. In Denmark phthalate
in PVC contributes with 90% of the turnover of phthalates (Hoffmann, 1996).
Plasticisers are used in a wide range of products from toys, babycare items,
medical devices, wall-coverings, electrical cables, automotive parts,
pack-aging, coatings and in the manufacture of clothing and footwear.
Smaller quantities of plasticisers are also used in paints, rubber products,
adhesives and some cosmetics. A small amount is used as denaturant in
cosmetics such as "sun-tan oil". In Denmark, phthalates are used
as plasticisers in various PVC-products for medical utilities, packaging,
cables, fittings, floor/wall covering, but there is still a an extensive,
not specified, consumption of phthalates in plasticised PVC products
(Hoffmann, 1996). This "Other application of PVC" covers e.g. the
use of phthalates in plastisol (coating materials) and toys. Artificial
leaders are e.g. produced by coating textile with plastisol. The plastisol
con-sists of a PVC-resin, solvent and a plasticiser e.g. phthalates. In
Denmark, phthalates are used as plasticisers in non-PVC materials such as
lacquer, paint, printing inks, adhesives, fillers and denaturants in
cosmet-ics. The unspecified consumption of phthalates in non-PVC
applications is small compared to the use in PVC (Hoffmann, 1996).
Capacitors with di-electric fluid may contain phthalates (notably DEHP), but
in Denmark most capacitors are dry and therefore without fluids. Another use
of phthalates in non-PVC products is in ceramics for electronic products. It
is assumed that the used amounts associated with these applications are
relatively small in Denmark. The use of phthalates as plasticisers a.o. in
1992 in Denmark was assessed in the Substance Flow Analysis (Hoffmann,
1996). This analysis indicates that the Danish distribution of the
applications of phthalates in 1992 can be illustrated as in Figure 4.1.
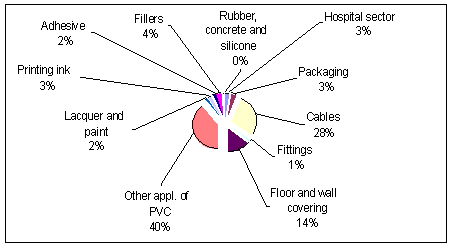
Figure 4.1 The distribution of phthalates for applications in Denmark
in 1992 (Hoffmann, 1996).
As mentioned earlier, the use of phthalates in PVC-toys is included
in "other applications of PVC". This amount is assumed equal to
the use of DEHP for flexible PVC-toys. This includes phthalates used for
toys for children both less and more that 3 years old ~ 380 ton/year. The
use of phthalates are now banned for the former category.
It appears that the amount of phthalates within certain applications is
de-creasing. This trend is illustrated in Table 4.1, where the development
in the use pattern is listed.
Table 4.1 Development in the use pattern of phthalates in different
applications in Denmark.
Application |
Subapplication |
Amount phthalate in 1992 in tonnesa |
Amount phthalate in 1994 in tonnesb |
Est. amount of phthalate in 2000 in tonnesc |
Trend |
PVC |
Medical utilities |
240-350 |
240 |
|
increasing a |
Packaging |
200-350 |
100 |
|
decreasing a |
Construction and installations:
- cables
- fittings
- floor and wall covering |
|
|
|
|
3,000 |
3,500 |
|
constant a |
80 |
700 |
|
constant a |
1,500 |
2,000 |
|
increasing a |
other application |
4190 |
3,100 |
|
e |
Subtotal |
9,200-9,500 |
9,640 |
|
d |
Non-PVC |
Lacquer and paint |
45-225 |
189g |
70 |
decreasing
a and c |
|
Printing ink |
90-270 |
|
50 |
decreasing
a and c |
|
Adhesives |
160-220 |
350g |
220 |
constant c |
|
Fillers |
< 400 |
|
100 |
decreasing c |
|
Denaturants |
< 5 |
|
|
? a |
|
Other non-PVC applications e.g. in rubber, concrete and silicone |
< 50f |
|
|
? a |
Total |
|
9,500-10,700 |
11,000 |
|
|
a Hoffmann (1996)
b The Danish Plastics Federation (1996)
c Hansen and Havelund (2000)
d At the moment increasing globally and constant on the Nordic
market, but decreasing a little on the Danish marked.
e According to SFA (Hoffmann, 1996) consumption is decreasing but
according to the Danish Plastics Federation (1996) it might be increasing.
f The application "other applications" under non-PVC
-products in Hoffmann (1996) is estimated to cover as a maximum 50 tons.
g Inventory for the Consumption in 1994 made by FDLF for The Danish
EPA.
The trend shown in Table 4.1 for the non-PVC-products, is a
decline in the consumption of phthalates. Concerning the PVC-products the
general trend is difficult to deduce from Table 4.1. According to the
suppliers the overall consumption is at the moment increasing but within
the near future it is ex-pected to decline. The consumption of phthalates
is slightly increasing in the EU as a whole, stagnant in northern Europe,
and decreasing slowly in Denmark (Hansen and Havelund, 2000).
In the following the background for the selection of the 11 substitutes
for phthalates is described. In Table 4.2 a total of 18 compounds are listed
that, in variable degree, all are potential substitutes for phthalates.
- 5 chemical compounds (substitutes), and
- 6 groups of substances.
Within each of the 6 groups, one specific substance has been
selected as marker for the group. The primary source of information
is the industry and the initial information from The Danish Product
Register. To get an impression of how the substitution will take
place selected indus-trial organisations have been contacted.
Suppliers and users of phthalates and/or have been contacted to give
an estimate of how a complete substitu-tion of phthalates 5 years
from here can be predicted. The same substance will not substitute
phthalates in all applications. The substitution will within the
different applications take place by a distribution of substitutes.
Estimates of this distribution are given in the substitution matrix
in Table 4.5 and Table 4.6. In Table 4.2, a short description of the
selection of substitutes for phthalates for various applications is
given.
Table 4.2 The plasticiser substitutes and suggestions for example
substances in the groups of plasticisers. Other possible substitutes are
shown in italics.
Group of
plasticiser |
Name of substance |
CAS No. |
Adipate |
Diethylhexyl adipate |
103-23-1 |
Diisodecyl adipate |
27178-16-1 |
Diisooctyl adipate |
1330-86-5 |
Citrate |
O-acetyltributyl citrate |
77-90-7 |
Phosphate |
Di(2-ethylhexyl) phosphate |
298-07-7 |
Tri(2-ethylhexyl) phosphate |
78-42-2 |
Mellitate |
Tri-2-ethylhexyl trimellitate |
3319-31-1 |
Alkylsulphonic acid esters |
o-Toluene sulfonamide
Toluene ethylsulfonamide |
88-19-7
8047-99-2 |
Butane esters |
2,2,4-trimetyl-1,3-pentanediole diisobutyate (TXIB) |
6846-50-0 |
Polyester |
No suggestion from industry |
- |
Epoxyester and epoxydised oils |
No suggestion from industry |
- |
Benzoate |
Dipropylene glycol dibenzoate |
27138-31-4 |
Diethylene glycol dibenzoate |
120-55-8 |
Triethylene glycol dibenzoate |
120-56-9 |
Sebacate
|
Dioctyl sebacate |
122-62-3 |
Dibutyl sebacate |
109-43-3 |
The Danish Product Register has conducted a search on these CAS No.s and
a general search to identify which CAS No.s are registered in Denmark as
plasticisers. The result of the general search was that approx. 180
different substances are registered as plasticisers. These were screened
with respect to their uses, and only a minority was found to be relevant
substitutes for phthalates. Reduction of the list in Table 4.2 has been
performed based on information from the industry, the result of
comprehensive information on use patterns from The Danish Product Register,
and assessment of the data availability regarding toxicological and
ecotoxicological information necessary for the assessment.
The plasticisers assessed are those for which most information is
expected to be available for the environmental and health assessment and
which have a use pattern involving high PVC volume and/or expected high
exposure of humans and/or the environment. The substances are listed in
Table 4.3.
Table 4.3 Substances used for the environmental and health
assessment.
Chemical group |
Name of substance |
CAS No. |
Suggested by DEPA |
Identified in Hansen and Havelund (2000) |
Plasticiser according to the PR |
Known actual application |
Adipates |
Diethylhexyl adipate |
103-23-1 |
Compound |
+ |
+ |
Broad application in PVC and non-PVC |
Citrates |
O-acetyl tributyl citrate |
77-90-7 |
Compound |
+ |
+ |
PVC, printing ink and concrete products |
Phosphates |
Di(2-ethylhexyl) phosphate |
298-07-7 |
Compound |
- |
- |
Broad application in PVC |
Tri(2-ethylhexyl) phosphate |
78-42-2 |
Compound |
+ |
+ |
Paint, glue and adhesive |
Mellitates |
Tri-2-ethylhexyl trimellitate |
3319-31-1 |
Compound |
- |
- |
Broad application in PVC |
Alkylsulphonic acid esters |
O-toluene sulfonamide |
88-19-7 |
Group |
- |
- |
Substance proposed by suppliers |
Butane esters |
2,2,4-trimethyl1,3-pentandioldiisobutyrate
(TXIB) |
6846-50-0 |
Group |
+ |
+ |
Printing ink, paint, glue, adhesive and concrete
products. |
Polyesters |
Polyadipates |
- |
Group |
- |
- |
Foils, substance proposed by Industry |
Epoxy esters and epoxidized oils |
Epoxidised soybean oil
|
8013-07-8 |
Group |
+ |
+ |
Printing ink, paint, glue and adhesive |
Benzoates |
Dipropylene glycol dibenzoate |
27138-31-4 |
Group |
+ |
+ |
Glue, adhesive |
Sebacates |
Dioctyl sebacate |
122-62-3 |
Group |
+ |
+ |
Printing ink and glue |
No specific substance to be used as a marker for
polyester-substitutes has been identified in PR or from suppliers. The
industry has emphasised that these substances may become important and
the branch organisation has suggested polyadipate as an example
substance. However, no information on health or environmental properties
has been identified on this substance or group during the present
project.
Polyethylene (PE) and polyurethane (PU) are both materials which
are identified as possible substitutes for flexible PVC in a number of
products and they thereby contribute to the overall substitution of
phthalates. The two materials polyurethane and polyethylene substitute the
PVC polymer as such and not only the plasticiser additive. Both materials
are polymers.
The two alternative materials PE and PUR
In this study low density polyethylene (LDPE) rather than high density
polyethylene (HDPE) is selected for the environmental and health
assess-ment, since it is expected that LDPE will substitute plasticised PVC
in the main uses in toys and garden hoses.
PU is expected to substitute
plasticised PVC in waterproof cloths, shoes, boots and waders, and PUR based
on the diphenylmethane-4,4'-diisocyanate (MDI) monomer is selected for the
environmental and health assessment.
LDPE and HDPE
Industrial polyethylenes are thermoplastics, which exist in different
ver-sions. Low-density versions (LDPE and Linear LDPE) are produced in
branched forms in a structure with long and short branches respectively.
LDPE is therefore only partly crystalline and the polymer is highly
flexible. Principal uses include packaging film, waste bags and soft type
plastic bags, tubes, agricultural mulch, wire and cable insulation, squeeze
bottles, house-hold items, and toys. LDPE has already substituted flexible
PVC in the majority of household packaging products, and the potential for
substitution is therefore greater for other product groups like toys.
High density versions (HDPE) are produced in linear forms which allow the
polymer chains to pack closely together. This structure results in a dense
and highly crystalline material of high strength and moderate stiffness.
Principal uses include bottles, pails, bottle caps, packaging, household
appliances, and toys. Because of the strength and stiffness HDPE is more
commonly used for industrial products compared to household products and
consumers in general are more likely to be exposed to LDPE than HDPE. LDPE
and HDPE are assumed comparable with regard to effects on environment and
health.
HDPE is used for toys of rigid materials, but the proportion of toys
manu-factured from LDPE compared to HDPE is not known. It has been suggested
that the two PE polymers have an equal share of toy market, and it is
as-sumed that LDPE may lead to higher exposures than HDPE.
Polyurethanes
Polyurethanes cover a broad range of synthetic resinous, fibrous, or
elasto-meric compounds belonging to the family of organic polymers made by
the reaction of diisocyanates with other difunctional compounds such as
glycols (polyols). Polyurethanes are one of the most versatile of any group
of plas-tics, capable of an almost infinite number of variations in
chemistry, struc-ture and application. Polyurethanes can be produced as a
foam, in solid form, as an elastomer, coating, adhesive or binder. Foamed
polyurethanes form about 90% by weight of the total market for
polyurethanes, but there is also a wide range of solid polyurethanes used in
many diverse applications.
By itself, the polymerisation reaction produces a
solid polyurethane. Polyu-rethane foams are made by forming gas bubbles in
the polymerising mixture, which is achieved by using a blowing agent.
MDI
MDI is one of the most important raw materials to make polyurethane.
MDI can be grouped into polymeric MDI, which in the form of foam is
being used for several heat protection materials, motor car seats, etc.,
and mono-meric MDI, being used for shoe soles, coating materials,
synthetic leather, etc.
Because of the health risks ascribed to
monomeric diisocyanates, much at-tention is paid to the physico-chemical
and toxicological properties of the monomer in situations where
substitution with a polyurethane is required. MDI has a particularly low
vapour pressure compared to TDI (toluene diiso-cyanate), HDI
(hexamethylene diisocyanate) and IPDI (isophorone diiso-cyanate ) and is
under European legislation classified as harmful whereas the other
mentioned diisocyanates are classified as toxic. This often makes MDI a
better choice where it is technologically feasible. MDI is already used
in the production of PU for waterproof clothes, shoes, boots and waders,
application areas, which are suggested for substitution of flexible PVC
in the substitution matrix, and is therefore selected to the health and
environmental assessment.
The Danish Product Register (PR) has been used to establish an
overview of the function of phthalates in chemicals until now. The
Register mainly con-tains information about chemicals and to a lesser
extent about materials. The historical main use of phthalates in
Denmark, summarised in Table 4.1, forms the basis for the search for
relevant alternatives in the PR. The most important function of
phthalate has until now been plasticising, but besides this function
phthalates had have the function of being denatur-ants in cosmetics
(Hoffmann, 1996). The PR has conducted a search to identify the
plasticisers used in selected types of chemical products or materials.
The result is illustrated in Table 4.4 for the first 10 that are the
substances selected for the assessment. The Poly-ester was not included
due to lack of CAS no.
Table 4.4 The registered use of the selected substances as
plasticisers in the selected product groups. Data from the Danish
Product Register. The polyester plasticiser (polyadipate) was not
included due to lack of CAS no. Materials such as cables, profiles,
floor and wall covering are not covered by the PR.
CAS No. |
Name |
Fillers |
Paint and lacquers |
Adhesives |
Printing inks |
Plastic in Concrete |
Rubber products |
PVC packaging |
103-23-1 |
Di(ethylhexyl) adipate |
· |
· |
· |
|
· |
· |
|
77-90-7 |
O-acetyl tributyl citrate |
|
|
|
· |
· |
|
|
298-07-7 |
Di(2-ethylhexyl) phosphate |
|
|
|
|
|
|
|
78-42-2 |
Tri(2-ethylhexyl) phosphate |
· |
· |
· |
|
· |
|
|
3319-31-1 |
Tri-2-ethylhexyltrimellitatea |
|
|
|
|
|
|
|
88-19-7 |
Alkylsulfonic acid estera |
|
|
|
|
|
|
|
6846-50-0 |
2,2,4-trimethyl 1,3-pentanediol diisobutyrate (butane ester) |
· |
· |
|
· |
· |
|
· b |
8013-07-8 |
Epoxidised soybean oil |
· |
· |
· |
· |
|
|
· |
27138-31-4 |
Dipropylene glycol dibenzoate |
|
|
|
· |
|
|
|
122-62-3 |
Dioctyl sebacate |
|
|
· |
|
|
|
|
a Not found in the Product Register.
b Unclear whether 'plast' is PVC
Not all substances are registered as plasticisers in the selected
products. This has to be seen in the light of the fact that the register
only contains informa-tion about substances classified dangerous to the
environment or the health. The result of the search is therefore as
mentioned earlier supplemented with industrial information about the
development of plasticisers not containing phthalates.
By using the amounts found within the different applications in the
sub-stance flow analyse (Hoffmann, 1996) and the proposed %-distribution of
the alternatives in Table 4.5, the following "amount-substitution
matrix" shown in Table 4.6 within the different applications can be
established.
Table 4.5 Substitution matrix for the 11 substances with anticipated
share given in %.
Note: It is only relevant to ad up the figures horizontal and not
vertically because each row describe the substitution within one
application. One column rep-resents non-comparable figures.
Based on information from the industry, Table 4.6 represents the best
pres-ent estimate on substitution of phthalates within different types of
products. The dominating amount is for each substance marked in bold. The
informa-tion is primarily based on interviews with industry sources rather
than trade bodies, since only little overview information is available. This
best present estimate has to be seen in the light of the situation in which
all phthalates in a product are substituted by only one substitute. The
actual substitution five years from now, will presumably not be exactly as
illustrated in Table 4.6, but the information indicates in which areas the
substances might be used extensively and in which areas the use is expected
to be negligible. It should be emphasised that a large portion of the
expected use is placed in "Other applications of PVC" (e.g. toys).
Another scenario is that one substance substitutes the phthalates 100%
within an application area (a 'worst worst case').
Table 4.6 Substitution matrix for the 11 substances (in tonnes)
Application |
Tons phthalates per year (1992) |
Diethylhexyl adipate, CAS no. 103-23-1 |
O-acetyltributylcitrate, CAS no. 77-90-7 |
Di(2-ethylhexyl)phosphat, CAS no. 298-07-7 |
Tri(2-ethylhexyl)phosphat, CAS no 78-42-2 |
Tri-2-ethyl trimellitate, CAS no. 3319-31-1 |
Toluene sulphonamide, CAS 88-19-7) |
2,2,4-trimethyl 1,3-pentanediol diisobutyrate, CAS no.
6846-50-0 |
Epoxidised soybean oil, CAS no. 8013-07-8 |
Polyester |
Dipropylene glycol dibenzoate, CAS no. 27138-31-4 |
Dioctyl sebacate, CAS no. 122-62-3 |
Other substanes and materials |
Hospital sector |
350 |
88 |
53 |
70 |
70 |
|
|
35 |
|
|
|
|
35 |
Packaging |
350 |
53 |
53 |
70 |
35 |
18 |
|
53 |
35 |
|
|
|
35 |
Cables |
3,000 |
90 |
|
750 |
900 |
840 |
30 |
120 |
30 |
|
|
|
240 |
Profiles |
80 |
16 |
|
12 |
12 |
8 |
|
12 |
|
|
|
12 |
8 |
Floor and wall covering |
1,500 |
450 |
|
300 |
300 |
150 |
|
150 |
|
|
|
|
150 |
Other application of PVC |
4,190 |
838 |
251 |
838 |
838 |
838 |
|
42 |
|
|
|
|
545 |
Lacquer and paint |
225 |
23 |
|
|
23 |
|
|
23 |
68 |
|
|
|
90 |
Printing ink |
270 |
54 |
81 |
|
|
|
|
27 |
54 |
|
|
54 |
|
Adhesive |
220 |
22 |
11 |
|
22 |
|
|
|
44 |
33 |
44 |
44 |
|
Filler |
400 |
40 |
80 |
|
40 |
|
|
|
20 |
60 |
160 |
|
|
Other applications e.g. in the following products: |
|
|
|
|
|
|
|
|
|
|
|
|
|
Rubber |
50 |
25 |
|
|
|
|
|
|
|
|
|
|
25 |
Concrete |
50 |
5 |
25 |
|
5 |
|
|
3 |
|
|
|
|
13 |
Silicone |
50 |
|
|
|
|
|
|
|
|
|
|
|
50 |
Sum (max.) |
10,735 |
1,704 |
554 |
2,040 |
2,245 |
1,854 |
30 |
465 |
251 |
93 |
204 |
110 |
1,190 |
In view of the general phase out policy for PVC the substitution of
phtha-lates may obviously take place exchanging the PVC-material by other
mate-rials that do not need to be plastified with phthalates. However, PE
and PU cannot substitute flexible PVC across-the-board, but as seen in
substitution matrix Table 4.7 PE and PU are possible substitutents for
flexible PVC in different kinds of products:
- PE will mainly substitute flexible PVC in toys
- PU will mainly substitute flexible PVC in waterproof clothes,
shoes, boots and waders.
Using the same procedure as for the 11 substances, but with the
1994-inventory from The Danish Plastics Federation of the consumption
of plasti-cised PVC, a substitution matrix for the PVC-substituting
materials can be established as in Table 4.8
Table 4.7 Substitution matrix for selected flexible PVC products in
% of the total amount plasticised PVC (tonnes).
Application |
Tons plasticised PVC |
Ethylene-vinyl-acetate (EVA) |
EPDM rubber |
Polyethylene (PE) |
Polypropylene (PP) |
Cardboard and paper |
Leather |
Polyurethane (PUR) |
Nylon |
Neoprene rubber |
Natural rubber |
Wood |
Other |
Sum (100%) |
Garden hose |
450 |
60 |
30 |
|
|
|
|
|
|
|
|
|
10 |
100 |
Office supplies |
3,500 |
|
|
|
75 |
20 |
5 |
|
|
|
|
|
|
100 |
Toys |
1,130 |
30 |
|
30 |
30 |
|
|
|
|
|
|
|
10 |
100 |
Waterproof clothes |
260 |
|
|
|
|
|
|
80 |
|
|
|
|
20 |
100 |
Shoes |
200 |
|
|
|
|
|
20 |
50 |
5 |
|
20 |
|
5 |
100 |
Boots and waders |
380 |
|
|
|
|
|
|
30 |
|
5 |
60 |
|
5 |
100 |
Sum |
5,920 |
* |
* |
* |
* |
* |
* |
* |
* |
* |
* |
* |
* |
* |
*: The vertical sum across different applications of PVC is not
relevant to cal-culate. It is only the horizontal sum within the same
application, which is relevant to calculate because it is describing
the situation within one spe-cific application and has to add up to
100%.
Table 4.8 Substitution matrix for alternative materials to flexible
PVC. The unit is tons.
Application |
Tons plasticised PVC |
Ethylene-vinyl-acetate (EVA) |
EPDM rubber |
Polyethylene (PE) |
Polypropylene (PP) |
Cardboard and paper |
Leather |
Polyurethane (PUR) |
Nylon |
Neoprene rubber |
Natural rubber |
Wood |
Other |
Sum (100%) |
Garden hose |
450 |
270 |
135 |
|
|
|
|
|
|
|
|
|
45 |
450 |
Office supplies |
3,500 |
|
|
|
2,625 |
700 |
175 |
|
|
|
|
|
|
3,500 |
Toys |
1,130 |
339 |
|
339 |
339 |
|
|
|
|
|
|
|
113 |
1,130 |
Waterproof clothes |
260 |
|
|
|
|
|
|
208 |
|
|
|
|
52 |
260 |
Shoes |
200 |
|
|
|
|
|
40 |
100 |
10 |
|
40 |
|
10 |
200 |
Boots and waders |
380 |
|
|
|
|
|
|
114 |
|
19 |
228 |
|
19 |
380 |
Sum |
5,920 |
609 |
135 |
339 |
2,964 |
700 |
215 |
422 |
10 |
19 |
268 |
|
239 |
5,920 |
As for the 11 substances, the information from the industry in
Table 4.8 rep-resents the most likely substitution of phthalates
within different types of PVC-products. The dominating amount for each
material is marked in bold. Again, the substitution five years from
now, will presumably not be exactly as illustrated in Table 4.8, but
the information indicates in which areas the materials might be used
extensively and in which areas the use is expected to be negligible.
The worst case scenario is when one material substitutes the
plasticised PVC 100% within an application area. As seen in Table 4.8,
polyethylene is most likely going to substitute 339 tons flexible PVC
in toys. With an average concentration of phthalates in soft-PVC toys,
similar to 34%, the 339 tons PVC represent 115 tons phthalates.
Polyurethane is, as shown in Table 4.8, the mayor substitute for PVC
in waterproof clothes. It is therefore of special interest to
undertake an EUSES-calculation on the 208 tons flexible PVC, which may
contain up to 100 tons phthalates.
Data compilation for substitution matrix
The qualitative information from suppliers of phthalates and the
alternative substances is based on an assumed complete substitution of
phthalate in the mentioned applications in the near future (a five year
perspective).
In Table 4.5 and Table 4.7 the qualitative information is
transferred to quantitative figures in percent. These figures form a
possible scenario for how the complete substitution can take place. It will
probably not corre-spond to the real situation in five years time, but it
illustrates where the use of a substance might be extensive and where the
use might be negligible. This overview is useful in connection with
evaluation of results from calcu-lations in EUSES and in connection with
priority of efforts of the environmental regulating authorities. The 11
substances and the 2 materials in this project are regarded as the main
basis for the complete substitution for phthalates. According to discussion
with the organisations listed in the Appendix, the most likely way to
substitute phthalates is illustrated in the following sub-stitution matrixes
Table 4.5 and Table 4.7.
Substitution matrix for the 11 substances in %
The consumption of phthalates within the relevant applications is
based on substance flow analyses covering the situation in 1992
(Hoffmann, 1996). In Table 4.5, the share of 11 substances for the
substitution of the phthalates within each application is estimated in
%.
According to the Danish Plastics Federation, flexible PVC is not used
in packaging, today. The actual consumption of phthalates for this
purpose is therefore estimated to be of minor importance. The first five
substances are expected to substitute phthalates directly. The next six
are selected as markers for chemical groups from which substitutes are
expected to be identified in the near future. Meanwhile the six markers
are used to calculate a scenario for substitution of phthalate. Other
substances and materials cover less important substitutions, conducted
by other means than the 11 substances. Examples could be substances not
covered by the 11 substances in Table 4.6, or new technology in the
produc-tion of the mentioned products. The new technology could be the
use of new materials without the need for plasticising with phthalates.
The point of origin of Table 4.5 is the Danish consumption of phthalates
in 1992 shown in Table 4.1 (Hoffmann, 1996). These data are selected
because they are the result of a comprehensive survey, and the studies
conducted later, confirm the amounts and the indicated development
trends within the different applications. For the non-PVC products a
decline in the use of phthalates has been identified (Hansen and
Havelund, 2000). For the PVC-products the suppliers expect a decline in
the near future. The background for the ratios in Table 4.5 is
information gathered in con-nection with one of the substitution
projects initiated by the Danish Envi-ronmental Protection Agency. It is
the general impression among suppliers and users of phthalates that a
complete substitution will be possible for both PVC and non-PVC
products. Available substitutes for non-PVC products have been
identified earlier (Hansen and Havelund, 2000).
Table 4.9 Estimated use of the substitutes. These volumes are used
for consumer expo-sure
Name of substitute |
Expected most relevant application |
Expected used amount for the substitution in
tons per year |
Di(2-ethylhexyl) phosphate, CAS No. 298-07-7 |
Cables |
750 |
Tri(2-ethylhexyl) phosphate. CAS No. 78-42-2 |
Cables |
900 |
Tri-2-ethylhexyltrimellitate, CAS No. 3319-31-1 |
Cables |
900 |
Alkylsulfonic acid ester (toluene sulphonamide, CAS 88-19-7) |
Cables |
30 |
Diethylhexyl adipate, CAS No. 103-23-1 |
Floor and wall covering |
450 |
Butane ester (2,2,4-trimethyl 1,3-pentanedioldiisobutyrate, CAS
No 6846-50-0) |
Floor and wall covering |
150 |
Epoxidised soybean oil (CAS No. 8013-07-8) |
Lacquer and paint |
70 |
o-Acetyl tributyl citrate, CAS No. 77-90-7 |
Toys |
250 |
Dioctyl sebacate (CAS No. 122-62-3) |
Printing ink |
50 |
Polyester |
Fillers |
60 |
Dipropylene glycol dibenzoate (CAS No. 27138-31-4 |
Fillers |
160 |
Industrial processes
There is no synthesis of phthalates or substitutes for phthalates in
Denmark.
The synthesis of phthalates for the Danish market is at the moment
mainly conducted in Sweden. The identified substitutes are expected also to
be synthesised in countries outside of Denmark. The main source to emissions
and exposures in Denmark is expected to be from formulation of products
containing plasticisers such as plasticised PVC, printing inks, adhesives
and fillers. For paints and lacquers there is also an emission and exposure
from the professional use of the products. Based on the substitution matrix
focus in this investigation has been set on the use of the eleven substances
with known potential application the fol-lowing process:
-
Use of di(2-ethylhexyl) phosphate (CAS
No. 298-07-7), tri(2-ethylhexyl) phosphate (CAS No. 78-42-2),
tri-2-ethylhexyltrimellitate (CAS No. 3319-31-1) and alkylsulfonic
acid ester (toluene sulphona-mide, CAS No 88-19-7) in the production
of cables
-
Use of butane ester diethylhexyl adipate
(CAS No. 103-23-1), (2,2,4-trimethyl 1,3-pentanediol diisobutyrate,
CAS No 6846-50-0) in the pro-duction of floor and wall covering
-
Professional use of epoxidised soybean
oil (CAS No. 8013-07-8) con-taining lacquer and paint products
-
Use of o-acetyl tributyl citrate (CAS
No. 77-90-7) and dioctyl sebacate (CAS No. 122-62-3) in the
production of printing inks.
-
Use of polyester and dipropylene glycol
dibenzoate (CAS No. 27138-31-4) in the production of fillers.
In general, uses of the products are
regarded as diffuse and as minor sources to emission, but concerning
consumer exposure of the 10 substances there are relevant scenarios that
are described in Section 5.4.
Human exposure is estimated mainly to take
place in connection with:
- Formulation process.
- Uses of the products
To illustrate the potential human exposure
from the 10 well defined sub-stances a calculation in EASE, which is
based on the principles in the TDG has been conducted. EASE calculates a
theoretical exposure of humans in the working environ-ment and private
consumers. The input data takes point of origin in the scenarios in
Table 4.10, which is assessed to represent the most extensive exposure.
Table 4.10 Exposure scenarios of the 11 substances
Name of
substance |
Scenarios |
Working environment |
Consumers |
Diethylhexyl adipate
(CAS 103-23-1) |
Production of follies to floor and wall coverings |
Use of floor and wall coverings in bathrooms |
o-acetyltributyl citrate
(CAS 77-90-7) |
Production of printed papers |
Daily use of printed papers |
Di(2-ethylhexyl)phosphate
(CAS 298-07-7) |
The well defined step in the production of cables which is the
exposure just after the extrusion of cables and before the cooling
in water |
Contact with cables in a private house |
Tri(2-ethyl)phosphate
(CAS 78-42-2) |
The well defined step in the production of cables which is the
exposure just after the extrusion of cables and before the cooling
in water |
Contact with cables in a private house |
Tri-2-ethylhexyltrimellitate
(CAS 3319-31-1) |
The well defined step in the production of cables which is the
exposure just after the extrusion of cables and before the cooling
in water |
Contact with cables in a private house |
o-Toluene sulphonamide
(CAS 88-19-7) |
The well defined step in the production of cables which is the
exposure just after the extrusion of cables and before the cooling
in water |
Contact with cables in a private house |
2,2,4-trimethyl 1,3-pentanediol diisobutyrate (CAS 6846-50-0) |
Production of follies to floor and wall coverings |
Use of floor and wall coverings in bathrooms |
Epoxidised soybean oil
(CAS 8016-11-3) |
Professional painting in a room without ventilation |
Stay in a painted house and conducting painting once a year |
Polyester |
Production of fillers |
Stay in a bathroom with fillers |
Dipropylene glycol dibenzoate
(CAS 27138-31-4) |
Production of fillers |
Stay in a bathroom with fillers |
Dioctyl Sebacate
(CAS 122-62-3) |
Production of printing inks |
Half an hour interior reading in printed papers |
To approach a situation five years from now the exposure calculation in
EUSES is therefore conducted for both the most likely situation
represented in bold figures and the 100%-scenario.
Assessment of the exposure of humans in the working environment and
con-sumers has been conducted using the model Estimation and Assessment of
Substances Exposure Physico-chemical Properties (EASE), which is a part of
the model European Union System for the Evaluation of Substances (EUSES).
Limitations and uncertainties of the EASE
The equations in EASE are intended to provide a simple description of
con-sumer exposure. Most equations give a worst case estimation of exposure,
by assuming that all of the compound in the product is at once available for
intake and uptake. Intake and uptake themselves are modelled as simple
fractions.
Workers exposure
EASE provides a general-purpose predictive model for exposure
assessment in the workplace. The model predicts external exposure only: it
does not take into account absorption and bioavailability. If reliable and
representative measured data are available these can be used to overwrite
the model results. The general-purpose model is called EASE (Estimation and
Assessment of Substance Exposure) which is described in details in Section
2.2 of the TGD. EASE was specifically developed for the purpose of modelling
inhalation and dermal workplace exposure across a wide range of
circumstances. EASE is an analogue model, i.e. it is based on measured data
which are as-signed to specific scenarios. The user can build scenarios by
choosing be-tween several options for each of the following variables:
physical proper-ties during processing (tendency to become airborne,
potential for dermal contact), use pattern and pattern of control. Numerical
ranges have been as-signed using measured data contained within the UK
National Exposure Database for inhalation exposure, and experimental data
and expert judge-ment for dermal exposure. The data used to assign ranges
within the model are all 8-hour time weighted averages and the numbers
generated by the model are only valid when the exposures being assessed can
be related to such averages. The output of EASE is numerical ranges of
concentrations or ppm. These are converted from ppm to kg.m-3 and can be
used as input for risk charac-terisation in which the exposure estimates are
compared to the results of the human effects assessment.
Consumer-exposure
The consumer, i.e. a member of the general public who may be of any
age, either sex, and in any stage of health may be exposed to chemical
substances by using consumer products.
A consumer product is one, which
can be purchased from retail outlets by members of the general public and
may be the substance itself, or a prepara-tion, or an article containing
the substance. The EASE equations for consumer exposure can be used to
estimate exter-nal exposure substances used as or in consumer products.
Absorption or bioavailability is not taken into account by the equations
implemented in EASE. The focus in EASE is on substances used indoors for a
relatively short pe-riod of time per event (such as e.g. a carrier/solvent
in a cosmetic formula-tion; a powder detergent). The equations in the
model apply to both volatile substances and airborne particulates. It is
assumed the substance is released as a vapour, gas, or air-borne
particulates, and the room is filled immediately and homogeneously with
the substance. Ventilation of the room is assumed to be absent. The
equations can also be adapted to estimate exposure arising from
'rea-sonably foreseeable misuse', i.e. when products are not used
according to the instructions, but as if they were other, allied products.
To adapt the equations, the values for the parameters used in the
equations are changed to reflect values foreseen in "reasonably
foreseeable misuse". For example, the volume of product or the area
of application is set to a dif-ferent value, reflecting reasonable
foreseeable misuse. If a substance is released relatively slowly from a
solid or liquid matrix (e.g. solvent in paint, plasticiser or monomer in a
polymer, fragrance in furniture polish), the equation in EASE acts as a
worst case estimation, estimating the maximum possible concentration.
Dermal
The calculation in EASE has in this investigation been operating with
two scenarios concerning dermal exposure: A and B
Dermal A: a substance contained in a medium. This dermal scenario also
applies to
- a non-volatile substance in a medium used without further dilution
(set dilution D=1), and
- a non-volatile substance in a volatile medium.
The assumption behind the equations in the calculations is that all of
the substance on the skin is potentially available for uptake. This is the
case when the medium is well mixed or only present as a thin film on the
skin. The dermal equations apply for:
- a non-volatile substance in a diluted product,
- a non-volatile substance in a medium used without further dilution,
and,
- a non-volatile substance in a volatile medium.
Dermal B: a non-volatile substance migrating from an article (e.g. dyed
clothing, residual fabric conditioner, dyestuff/newsprint from paper). The
assumption behind the equation is that only part of the substance will
migrate from the article (e.g. dyed clothing, residual fabric conditioner,
dye-stuff/newsprint from paper) and contact the skin. The migration is
assumed to be slow enough to be represented by a constant migration rate
multiplied by the time of contact. The exposure calculation will involve
estimating the amount of substance which will migrate from the area of the
article in contact with skin during the time of contact. Dyestuff amounts
in fabrics and paper are usually given as weight of product per unit area
(e.g. mg/m2).
Oral
The calculation concerning oral exposure has also been operating with
two scenarios: A and B.
Oral A: a substance in a product unintentionally
swallowed during normal use (e.g. toothpaste). The exposure equations may
also be used to estimate exposures arising from ingestion of the
non-respirable fraction of inhaled airborne particulates. The equations
may also be used to estimate exposures arising from ingestion of the
non-respirable fraction of inhaled airborne particulates. Oral B: a
substance migrating from an article into food or drink (e.g. plastic film,
plastic-coated cups/plates). It is assumed that the substance in a layer
of thickness of article (e.g. plastic film, plasticcoated cups/plates) in
contact with the food will migrate to the food. The migration rate is
assumed to be constant, and the migration rate multiplied by the contact
duration is the fraction of substance that is migrated to the food. The
equation can be used to give a conservative estimate of substance uptake
by a defined volume of food. The value of the migration rate will be
influenced by the type of food (e.g. fatty/dry/moist), the period of
exposure and the temperature at which it occurs. Consumer exposure level
will also be influenced by the proportion of contaminated food eaten.
Use pattern scenarios
Based contacts to the Danish industry and the substance flow analyse
(Hoffmann, 1996) relevant scenarios has been identified and are described
in section 4.3.
The background for choosing scenarios is the most likely
way of substitu-tion described by industrial actors and rendered in the
substitution matrix in Table 4.5. Within the substitution matrix the
application representing the largest estimated consumption of each
substitute is selected as the most relevant scenario. This application is
marked in bold figures in the substitu-tion matrix. The input data for the
calculation are the substitution matrix and scenarios with the largest
estimated consumption substitute for phthalate plasticisers. With point of
origin in the substitution matrix the substances are distributed in the
following most relevant application areas.
Plasticisers in the
"Cables"-application are expected to be:
- Di(2-ethylhexyl) phosphate, CAS No. 298-07-7
- Tri(2-ethylhexyl) phosphate. CAS No. 78-42-2
- Tri-2-ethylhexyltrimellitate, CAS No. 3319-31-1
- Alkylsulfonic acid ester (o-toluene sulphonamide, CAS No 88-19-7).
For the production of "floor and wall covering" the
following plasticisers are chosen:
- Diethylhexyl adipate, CAS No. 103-23-1
- Butane ester (2,2,4-trimethyl 1,3-pentanediol diisobutyrate, CAS
No 6846-50-0).
Concerning the production of lacquer and paint the focus is on:
- Epoxidised soybean oil (CAS No. 8013-07-8).
In connection with printing ink the relevant substances are estimated
as:
- O-acetyl tributyl citrate, CAS No. 77-90-7
- Dioctyl sebacate (CAS No. 122-62-3).
The production of "fillers" is assumed to include:
- Polyester
- Dipropylene glycol dibenzoate (CAS No. 27138-31-4).
The scenarios in EASE for the consumer exposure are based on the
amounts for these uses and the exposure characteristics for the
application.
Substance parameters
For each substance the required input parameters molecular weight,
octanol-water partition coefficient, water solubility, vapour pressure and
physical state were fed to the model in accordance with the data search
and evaluation.
Two types of assessments were performed for each
substance substituting phthalates. One scenario simulates the best
educated guess for the future share that this particular substance would
gain in the market based on inter-views with the industry. The second
assessment simulates the hypothetical situation where only one of the
alternatives (100% substitution case) sub-stitutes the entire tonnage of
phthalates. In the 100% substitution case it is chosen to base the
estimates on the most recent inventory of the phthalates in PVC and use
the sum used in 1992 (10,735 tons). In various applications substitutes
may be used in different volumes than the phthalates - if 1 kg new
substance can substitute 2 kg phthalate or vice versa. Since the available
information on this is very in-complete it has been decided not to try to
include such information in the calculations. The physical parameters of
some of the compounds are out of the advised range in which EUSES
operates. In the cases where the physical parameters are out of the
pre-set range (e.g. logPow > 6) or unknown as melting and boiling point
sometimes are, it has been chosen to use the nearest maximum or minimum
value as suggested in EU TDG or use a worst case approach. All results are
presented in the report with two significant digits rounded off from the
EUSES calculations with three significant digits (given in appen-dix). The
assessment of emission to the environment and exposure of man and biota
from environmental concentrations of phthalate alternatives are based on
the procedures outlined in the EU TGD (EU Commission 1996). The actual
concentrations are calculated by using the PC program EUSES (European
Chemicals Bureau 1996), which is designed to provide decision support for
the evaluation of the risks of substances to man and the envi-ronment
based directly on the EU TGD. In the present evaluation EUSES is operated
in three of the possible five modes. Parameters are entered for:
- Environmental assessment,
- Predators exposed via the environment and
- Humans exposed via the environment.
EUSES will calculate concentrations and doses for the assessment on
three spatial scales: the local (point source), the regional (small and
densely in-habited country) and the continental (Europe). The default
regional scale has been changed to suit Danish conditions (see below). The
local and conti-nental scenarios are included in the calculations, but no
specific values have been entered. The EUSES program calculates
environmental exposure based on 1) a physical scale where the use and
emission takes place, 2) the use and emis-sion pattern of the substance
and 3) on substance specific parameters. The specific parameters for each
substance are provided for each exposure esti-mation. To assist the
comparison between substances the physical dimen-sions of the scenario and
the overall industrial use and emission pattern has been set identical for
all substances.
Use and emission scenarios
The use and emission scenarios rely on the database of emission
scenario documents for a number of industrial uses included in EUSES. The
follow-ing settings have been used to represent the primary use of
phthalate alter-natives:
Emission input data |
No. |
Name |
Industry category |
11 |
Polymers industry |
Use category |
47 |
Softeners |
Main category (production) |
III |
Multi-purpose equipment |
Main category (formulation) |
III |
Multi-purpose equipment |
Main category (processing) |
IV |
Wide dispersive use |
Danish regional scenario
The physical dimensions of the regional scenario have been set at
values representative for Denmark, those changed are shown in Table 4.11
(a com-plete list of parameters can be found in the Appendix). The values
were taken from the evaluation of the SimpleBox Model for Danish
conditions (Miljostyrelsen 1995).
Table 4.11 Parameters of the EUSES model, which were adapted to Danish
conditions
Parameter |
Value |
Units |
Fraction of EU production volume for region |
0.05 |
[-] |
Fraction connected to sewer systems |
0.9 |
[-] |
Environmental temperature |
7.7 |
[oC] |
Volume fraction water in soil |
0.4 |
[m3.m-3] |
Weight fraction of organic carbon in soil |
0.025 |
[kg.kg-1] |
Number of inhabitants of region |
5.30E+06 |
[eq] |
Wind speed in the system |
5 |
[m.s-1] |
Area of regional system |
4.30E+04 |
[km2] |
Area fraction of water of the regional system |
0.011 |
[-] |
Area fraction of natural soil |
0.332 |
[-] |
Area fraction of agricultural soil |
0.647 |
[-] |
Area fraction of industrial/urban soil |
0.01 |
[-] |
Suspended solids concentration of regional system |
17.7 |
[mg.l-1] |
Net sedimentation rate |
8.22 |
[mm.yr-1] |
Average annual precipitation |
735 |
[mm.yr-1] |
Fraction of rain water infiltrating soil |
0.46 |
[-] |
Calculate dilution from river flow rate |
No |
|
Mixing depth of grassland soil |
0.05 |
[m] |
Mixing depth agricultural soil |
0.2 |
[m] |
A key parameter in comparing various plasticisers is their potential
for mi-grating out of the PVC polymer. Only few data has been identified
on mi-gration potential for the substitutes. The information on migration
potential will be used in the expert assessment process, but is not used
in the exposure calculation model. To determine the total migration
potential various reference methods are used which all are available as
CEN standards (ENV 1186-1 - ENV 1186-12). Several new standards in this
area are in preparation. In general the methods are divided in two
categories: Migration from plastic to an oily extractant and migration
from plastic to an aqueous solution. To determine the total migration
potential using the two groups of methods either a double sided test
(total submergence of plastic piece) or a single sided test (using a
migration cell or by incorporating the plastic piece into a bag) is
performed. The total migration potential is determined as the difference
in weight be-fore and after extraction or as weight of the evaporation
residue of the ex-tractant. The 3 commonly water based extractants are
distilled water, 3% acetic acid and 10 % ethanol. Since most plasticisers
are lipophilic it is most relevant to express the migration as migration
from plastic to fat containing food. As fat simulator olive oil is the
commonly used. The amount of plasticiser extracted is extractant
dependent and usually the extraction time of olive oil and 95% ethanol is
10 days at 40 °C and for iso-octane 2 days at 20 °C. The difference in extraction
time is due the extraction power of each ex-tractant and the ability of
the extractant to make the plastic swell. When the plastic swells the dept
of the layer in contact with the extractant increases and the amount of
platisicer extracted increases. The extraction power of the
extractant types depends on the plastic type that is investigated, but
usually, when considering plastics that contains lipo-philic plasticisers
the order extraction power is: isooctane > olive oil > etha-nol..
|