| Front page | | Contents | | Previous |
Market information in life cycle assessment
Annex A. Avoiding co-product allocation in a simplified hypothetical refinery
22
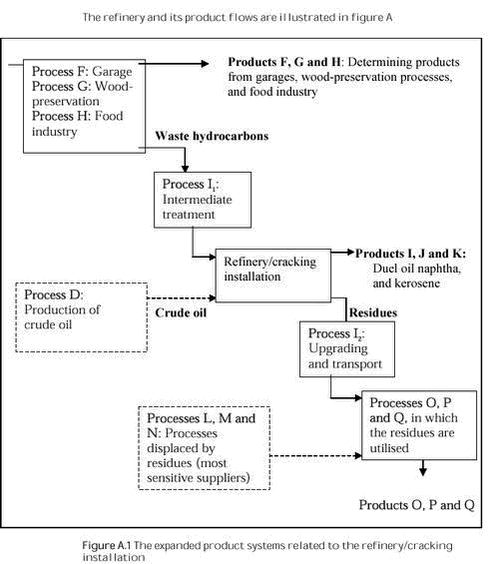
Click on the picture to see the html-version of: Figure A.1
A.1 Identification of the economic inputs and co-products
The refinery has:
- Three independently variable economic inputs:
- Waste lubricants from garages
- Waste hydrocarbons from wood preservation
- Waste hydrocarbons from food industry
These inputs are variable in the sense that they are not needed for the process and may therefore be varied depending on supply.
- One dependent economic input:
- Crude oil
This input is dependent in the sense that its volume depends on the volume of the variable inputs and outputs.
- Three independently variable economic outputs:
- Fuel oil
- Naphtha
- Kerosene
Within the technical limits, these outputs are variable depending on demand. If technical limits are encountered at the specific refinery investigated, the change in demand will lead to changes in the production of a similar refinery without these technical limits. When studying changes that are so large that the technical boundaries of the entire refinery industry are encountered, it is necessary to regard these outputs as dependent. We assume here, that the studied change is small.
- Three dependent economic outputs:
- Long residues
- Mixed residues for upgrading
- Mixed residues for incineration
These outputs are sought minimised and thus depend solely on the volume of the inputs and the variable outputs
A.2 Independently variable economic inputs
For the independently variable economic inputs (waste lubricants and other hydrocarbons) the following conditions apply (irrespectively of the economic value of the input):
- Upstream processes: The volume of these inputs depends on the volume of the upstream processes (processes F, G and H in figure A.1) of which these inputs are wastes, not on the volume of the refinery production. The refinery acts as a waste treatment for these inputs. The wastes are assumed fully utilised (since they are valuable as inputs to the refinery and the total amount available on the market does not exceed that which can be used by the refinery industry). Thus, the upstream processes are not relevant for the other refinery co-products, i.e. there is a clear cut-off at the incoming refinery gate.
- Avoided processes: The production of the crude oil displaced by the variable inputs (process D in figure A.1) is credited to the main products of the upstream processes of which these inputs are wastes (i.e. the products of the garages, wood preservation processes and food industry).
- Other effects on the refinery and downstream processes: If the input causes any changes in the environmental exchanges from the refinery or further downstream processes, compared to the use of crude oil as a raw material, these changes are ascribed to the main products of the upstream processes of which these inputs are wastes (i.e. the products of the garages, wood preservation processes and food industry). This may for example be due to the nature of the waste (the hydrocarbons from food industry may be vegetable, which e.g. may lead to lower VOC emissions than from comparable fossil raw materials) or due to contamination (e.g. heavy metals from the lubricant use or wood preservation).
To determine the environmental exchanges to be ascribed to the products of the garages, wood preservation processes and food industry (products F, G and H in figure A.1) the following information on the system is needed:
1) Changes in the economic outputs when changing the independently variable inputs (waste lubricants and other hydrocarbons): We assume that there is no change in the independently variable outputs (fuel oil, naphtha, kerosene), since such changes would be undesirable for the refinery, and would thus be avoided by reducing the variable inputs accordingly. We assume that the independently variable inputs (waste lubricants and other hydrocarbons) do not give rise to outputs of long residues and mixed residues for incineration, since these inputs have already been processed once. 2) The amount of crude oil displaced by the independently variable inputs (waste lubricants and other hydrocarbons): We assume that the hydrocarbon chains of these inputs are of similar composition as crude oil, with the exception mentioned under 1) that they do not contain the fractions that give rise to outputs of long residues and mixed residues for incineration. This leads to a slightly lower requirement of crude oil per input of waste hydrocarbons: 1 kton waste hydrocarbons yields 0.91 kton of the outputs fuel oil, naphtha, kerosene and mixed residues for upgrading (12 kton waste – 9.375% process loss), while 1 kton crude oil gives only 0.66 kton of these products (20 kton – 9.375% process loss – 5 kton long residues and mixed residues for incineration). Thus, 1 kton waste hydrocarbons displaces 1.38 kton crude oil. As can be seen from this calculation, we have assumed that the process loss (mainly feedstock used for fuel) does not depend on the type of input. If the waste hydrocarbons do not need as much processing as crude oil (or need more processing), this assumption should be changed accordingly, which will also lead to a change in the amount of crude oil displaced. 3) Changes in the environmental exchanges from the refinery when changing the independently variable inputs (waste lubricants and other hydrocarbons), compared to the use of crude oil as a raw material: The emissions from the refinery can largely be divided in emissions from combustion related to the use of process energy, emissions of VOC, and solid and liquid wastes. The combustion emissions depend on what processes the different raw materials require. We have assumed that there is no change in energy requirement (see point 2), and thus no change in combustion emissions. For VOC emissions from the from the waste hydrocarbons, it is reasonable to assume that there will be no emissions of methane (compared to 42 kg per kton crude oil) and fewer emissions of the lighter VOCs (we assume a 10% reduction from the 380 kg per kton crude oil), since these inputs have already been processed once. If it is assumed that any contaminants in the waste hydrocarbons are either degraded during processing or left in the product outputs (see point 4), also the solid and liquid wastes can be assumed linked to the crude oil only. 4f) Changes in the environmental exchanges from downstream processes when changing the input of waste lubricants from garages, compared to the use of crude oil as a raw material: Heavy metal contaminants (assumed 20 kg/kton) will be suspended in proportional amounts in all economic outputs, except the lightest fraction (mixed residues to incinerator). For the fuel fractions (fuel oil and kerosene) this will eventually end up as air pollution from the combustion. Heavy metal contaminants in the naphtha will end up in the products produced from this (plastics) and will be released from waste treatment of these products (we assume combustion). Heavy metal contaminants in the long residues will probably be fixed in the resulting products (asphalts etc.). 4g) Changes in the environmental exchanges from downstream processes when changing the input of waste hydrocarbons from wood preservation, compared to the use of crude oil as a raw material: If the waste contains any heavy metals, these will have the same fate as indicated under 4f). If the contaminants are organic, we assume that they are decomposed during the refinery processing. 4h) Changes in the environmental exchanges from downstream processes when changing the input of waste hydrocarbons from food industry, compared to the use of crude oil as a raw material: We assume that this will not cause any changes in downstream processes.
Furthermore, the following information on the environmental exchanges from each of the involved processes are needed:
Process F, G, H and I1: In this context, we do not use real data for these processes. Process D (crude oil production, incl. transport): For this, standard literature data (ETH) can be used. In this example, we limit the calculation to include the following emissions (per kton crude oil): CO2: 120 ton Methane: 10 ton NMVOC: 73 ton
The calculation to be made is (normalised to 1 kton of waste hydrocarbon input to the refinery): Environmental exchanges to be ascribed to products F, G and H, respectively = (Environmental exchanges from process F, G or H, respectively) – (Environmental exchanges from production of 1.38 kton crude oil) – (Refinery emissions of methane, lighter VOCs, solid and liquid wastes equivalent to 1.38 kton crude oil input) + (Downstream emissions of heavy metals equivalent to the difference in heavy metal content between the waste hydrocarbon and crude oil).
For waste hydrocarbons from wood preservation, the result is presented in table A.1 (not including the environmental exchanges from the wood preservation process itself).
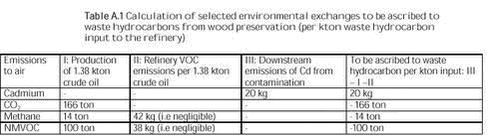
Click on the picture to see the html-version of: Table A.1
Provided more information on the different waste hydrocarbons, the above assumptions and the calculation result can be refined.
A.3 Independently variable economic outputs
For the independently variable economic outputs (fuel oil, naphtha, kerosene), the following conditions apply:
- Upstream processes: The dependent input (crude oil) will vary according to overall variations in the outputs.
- Refinery: The environmental exchanges of the refinery may vary according to the composition of the output, since different processing routes are involved.
- Residues: The amount of residues are mainly determined by the raw material composition, but minor variations may be caused by changes in the output composition. The amount of residues may thus be calculated individually for each of the variable outputs. The residues are assumed fully utilised, so that any intermediate treatment (upgrading and transport) of the residues before they can displace other products are ascribed to the independently variable outputs in proportion to the amount of residues caused by each output (irrespectively of the economic value of the residues).
- Avoided processes: The processes displaced by the residues (processes L, M and N in figure A.1) are credited to the variable outputs in proportion to the amounts of residue caused by each output (irrespectively of the economic value of the residues).
To determine the environmental exchanges to be ascribed to the independently variable economic outputs (products I, J, and K in figure A.1), the following information on the system is needed: The amount of crude oil corresponding to a change in the independently variable economic outputs: We assume the same amount of crude oil input
irrespectively of the relative composition of the independently variable economic outputs. The environmental exchanges of the refinery corresponding to a change in the independently variable economic outputs: The combustion emissions will increase when additional processing is needed to produce more of a fraction than what is the result of one crude distillation and one cracking of the distillation residue. The processing requirement depends on the composition of the raw material input. The relations given in the ETH data can be used to calculate the emissions per type of refinery output, unless more specific data are available. The amount of residues caused by a change in the independently variable economic outputs: The amount of residues (especially the lighter residues) will increase slightly when additional processing is needed to produce more of a fraction than what is the result of one crude distillation and one cracking of the distillation residue. The processing requirement depends on the composition of the raw material input.
Furthermore, the following information on the environmental exchanges from each of the involved processes are needed: Process D: (as above) Process I2: We assume that upgrading of long and mixed residues will lead to emissions in the order of 20% of the general refinery emissions. For mixed residues for incineration, only the pumping to the incinerator is relevant (but assumed to be negligible). Process L: The displaced process is either a dedicated bitumen production, or a change in the composition of the raw material input at a refinery having bitumen as an important product, resulting in a similar change in bitumen output. We assume that 0.17 kton of bitumen is displaced per kton of the independently variable economic outputs. Process M: Parallel to process L, we assume the displacement to be accommodated by a change in the composition of the raw material input at a refinery having the upgraded product as an important product. We assume that 0.09 kton of other refinery products are displaced per kton of the independently variable economic outputs. Process N: The displaced process is production and supply of fuel oil or natural gas, depending on the local supply situation. We assume that 0.85 TJ of natural gas is displaced per kton of the independently variable economic outputs.
The calculation to be made is (normalised to 1 kton of the independently variable economic outputs (fuel oil, naphtha, kerosene): Environmental exchanges to be ascribed to fuel oil, naphtha and kerosene, respectively = (Environmental exchanges from production of 32/29 kton crude oil) + (Refinery emissions related to the output in question, cf. ETH) + (Environmental exchanges from upgrading of the amount of long and mixed residues that can be related to the output in question, cf. ETH) – (Environmental exchanges of the processes displaced by the residues that can be related to the output in question, cf. ETH).
For kerosene, the result is presented in table A.2 (not including the environmental exchanges from the wood preservation process itself).
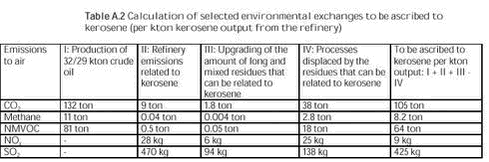
Click on the picture to see the html-version of: Table A.2
A.4 Dependent economic outputs
The dependent economic outputs (different residues) are utilised fully in other processes. Thus, a change in demand for these residues will affect the same processes as those displaced by the residues (processes L, M and N). These processes are therefore ascribed to the product in which the residues are utilised (irrespectively of the economic value of the residues).
To determine the environmental exchanges to be ascribed to the products in which the residues are used (products O, P and Q in figure A.1), the environmental exchanges from the following processes must be known: Process L, M and N: (as above) Process O, P and Q: In this context, we do not use real data for these processes.
The calculation to be made is (normalised to 1 kton of the residue): Environmental exchanges to be ascribed to the product in which the residue is utilised = (Environmental exchanges from process O, P or Q, respectively) + (Environmental exchanges of the process L, M or N, respectively).
____________________________________________________________ 22 The elaboration of this example was financed by the Dutch methodology project and originally published in their report (Guinée et al. 2001, part 2b, pp. 36-41).
| Front page | | Contents | | Previous | | Top |
|