| Front page | | Contents | | Previous | | Next |
The Product, Functional Unit and Reference Flows in LCA
3. Procedure for determining the object of study, the functional unit and the
reference flows
Background
3.1 Determining the object of study
The object of a life cycle assessment is the environmental impacts of a potential product substitution, i.e. the choice of one product instead of another (or the choice of a specific product
instead of refraining from this product). The functional unit describes those properties of the product, which must be present for the studied product substitution to take place. These
properties are in turn determined by the requirements in the market in which the product is to be sold.
Step 1, 2 and 3
Therefore, the first steps in the five-step procedure are:
Step 1: Describe the product by its properties
Step 2: Determine the relevant market segment
At the same time, the identified product functions and the market segment delimit the products that may be involved in a product substitution, so that the next step can be a further
specification of the product alternatives to be included in the study:
Step 3: Determine the relevant product alternatives
3.1.1 Step 1: Describe the product by its properties
The purpose of this step is to identify - out of all the properties of the studied product – those properties that shall be included in the functional unit and/or in the determination of the
reference flow.
The product properties may be divided in three groups depending on their importance:
Three groups of product properties
- Obligatory properties that the product must have in order to be at all considered as a relevant alternative. These are the properties that are included in the functional unit. Example: A
beverage container must not leak.
- Positioning properties that are considered nice to have by the customer and which may therefore position the product more favourably with the customer, relative to other products
with the same obligatory properties. Example: A beverage container may be more or less easy to handle.
- Market-irrelevant properties that do not play a role for the customer's preferences. Example: A (refillable) beverage container may be more or less easy to clean.
Both positioning and market-irrelevant properties may be of importance to the reference flows (see section 3.3).
The same product property may be placed in different groups in different markets (see section 3.1.2). A company-internal study, comparing different options in the product
development, may define additional properties as obligatory for their own brand, although they are only regarded as a positioning properties on the general market (and would be
determined as such in a more generic life cycle assessment comparing this brand with other brands).
Properties
Properties may be related to:
- Functionality, related to the main function of the product
- Technical quality, such as stability, durability, ease of maintenance
- Additional services rendered during use and disposal
- Aesthetics, such as appearance and design
- Image (of the product or the producer)
- Costs related to purchase, use and disposal
- Specific environmental properties
Functionality, aesthetics, and image characterise the primary services provided to the user.
Technical quality and additional services ensure the primary services during the expected duration of these. Although durability may be included as part of the technical quality, it
should be noted that most of the mentioned properties have a time aspect.
Therefore, it is often important to specify the desired properties also in terms of the (minimum) period of time for which these properties are expected to last. For some products and/or
properties, there may be a gradual decline in the expectations over time. The time aspect is treated in more detail in Chapter 4.
Environmental properties may be included among the properties included in the functional unit. However, since the very purpose of a life cycle assessment is to study the
environmental impacts of the products, it is not meaningful to state in advance that the studied products should have such general properties as "environmentally friendly" or "non-toxic."
If environmental properties are included as obligatory, they must be expressed as specific properties, like "the seat and back rest must allow for recycling of the foam", so that it is
possible to judge - prior to the life cycle study - whether a product has the required property.
In developing more environmentally friendly products, it is important to understand the relationship between the individual properties and the environmental impact (see figure 4 for an
example). If the environmental impacts are particularly linked to specific properties, it is especially important to consider whether these "environmentally costly" properties are obligatory
or positioning, and whether it is possible to influence the trade-off
made by the customer between the properties in question and the environmental properties of the product, e.g. by environmental information to the customer.
Office chair example
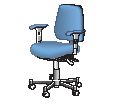
Figure 4:
The link between eight functional properties and two selected environmental impacts
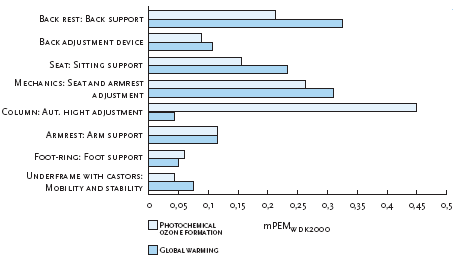
Information sources
Information on obligatory properties for a specific market segment can be obtained from:
- the marketing departments of the enterprises supplying products to the market segment,
- retailers,
- industrial organisations,
- industrial research institutions and industry consultants,
- regulating authorities and standardisation bodies,
- marketing and consumer research institutions.
Issues regulated in national and international legislation and standards will typically be obligatory properties.
Office chair example
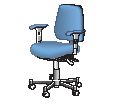
General obligatory properties of the office chair
ISO (and coming CEN) standards for office chairs comprise both technical properties such as strength (e.g. ISO 7173), stability (e.g. ISO 7174-1), and safety (e.g. prEN
1335) and functional properties such as adjustments of seat height, depth and width, seat inclination, backrest height, width and inclination and arm rests length and width
and more, see also Table 3.
The role of non- obligatory properties
The obligatory properties give a good description of what is required for products to substitute each other. However, the amount of substituted product or the interaction with other
product systems may be determined by other properties.
To ensure the equivalence between compared products, it is therefore necessary to analyse systematically all product properties and judge for each one whether it leads to differences in
the amount of substituted product or in the interaction with other product systems.
Office chair example
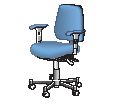
Non-obligatory properties of the office chairs
If the chairs have different lifetimes (beyond the obligatory minimum of 5-7 years), this may lead to a difference in the amount of chairs necessary to fulfil the main function
over time.
If the seat cover on one chair needs more maintenance while the other is maintenance-free - or if one of the chairs lead to a need for adjustments in other office equipment
while the other matches the existing office - additional functions of other systems (oil for maintenance, other office equipment) will have to be included to give a full
description of the consequences of the product substitution.
If several such additional properties can be identified, it is important to investigate whether one of the properties can be identified as the one determining the difference in performance.
Examples of determining properties:
In comparing different alternatives for hand drying, the technical properties of the tissue paper such as mass, absorption-power and tensile strength, may all influence the
number of tissue papers used. However, these properties may all turn out to be irrelevant if in practice it is the dispenser design that determines the amount of paper used.
Similarly, technical specifications of electrical hand driers, such as the volume of air and its temperature, may be irrelevant for comparing relative performance, if the
actual operating time and energy consumption of the devices are fixed by other factors, e.g. built-in timers that give a fixed time per hand-drying event to be multiplied with
the effect of the device.
In comparing alternative types of walls in buildings, the property that determines the material consumption will often vary with the specific type of wall, depending on the
chosen material or construction principle.This implies that it is not possible to identify a single determining property common to all the compared wall types. However, for
each individual wall alternative, a determining property may be identified. For one wall type, the determining parameter may be durability, for another it may be strength,
and for a third it may be sound or heat insulation.
It should be noted that differences in performance between the compared alternatives often appear when choosing a (too) narrow product perspective,
i.e. when studying intermediate products, components, or products that are otherwise very dependent on other products. Such performance differences, and the consequent need for
adjustments (see section 3.3), can often be avoided by choosing a broader function-based perspective, i.e. based on the needs fulfilled by the products (e.g. "lighting" and "cooling of
food") rather than based on the physical products themselves (e.g. "lamps" and "refrigerators"), see also the office chair example in section 3.1.2).
Price as a relevant property
It is normally assumed that the price (typically a positioning property), is approximately the same for all the compared alternatives, so that the overall economy of the buyer is not
affected. However, in some situations, there is a significant price difference between the different alternatives at the level of the end consumer, so that it is relevant to consider that the
money saved on the cheaper alternatives will eventually be liberated for alternative consumption in the customer segment affected by the price difference. If you wish to model the
environmental impacts of this situation correctly, the product systems of the cheaper alternatives may have to be adjusted to include this additional consumption, following the procedure
outlined in section 3.3.
3.1.2 Step 2: Determine the relevant market segment
The purpose of this step is to identify the market segment in which the potential product substitution is taking place.
Market segments
Markets are typically differentiated
<
- geographically,
- temporally, and
- in customer segments.
Geographical segmentation
The geographical segmentation of a market may be determined by differences in:
- natural geography (climate, landscape, transport distances etc.),
- regulation or administration (regulation of competition and market transparency, legislative product requirements, product standards, taxes, subsidies),
- consumer culture.
Office chair example
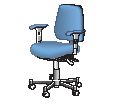
Geographical segmentation
The market for office chairs is regionally segmented, which means that chairs sold in Europe are almost exclusively produced in Europe, with additional national sub-
markets, so that the majority of chairs sold in Denmark are produced in Denmark.
The markets are to a high extent regulated by legislative requirements.
Figure 5.
Geograhical market segments for the four examples in Figure 3
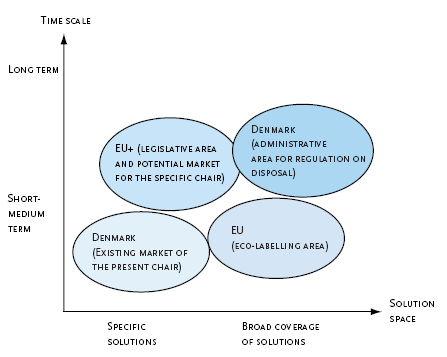
Temporal segmentation
Temporal segmentation of markets is common for service products (e.g. peak hours and night hours in electricity consumption, rush hours in traffic and telecommunication, seasons in the
tourist industry). For physical goods, markets are generally only segmented temporally when adequate supply or storage capacity is missing, either due to the nature of the product (e.g.
food products), or due to immature or unstable markets, as has been seen for some recycled materials. This temporal segmentation should be distinguished from the fact that markets
generally develop in time, e.g. governed by developments in fashion and technology, and that both geographical and temporal segmentation and customer segmentation therefore may
change over time. This latter issue is dealt with in chapter 4.
Each geographical market is typically divided into a number of customer segments.
Customer segments
Customer segments are generally defined in terms of clearly distinct function-based requirements, i.e. based on the needs fulfilled by the products rather than based on the physical
products themselves. Very similar products may serve different needs and hence serve different markets. And very different products may serve the same need, thus being in competition
on the same market.
Thus, in a life cycle study for a specific company, the product group "office chairs" could be too broad a market delimitation. Instead, a specific use situation (and customer group) for
office chairs must be identified. Alternatively, in more strategic contexts, the product group "chairs" may be seen as too narrow a definition, either because it excludes other ways of providing seating support, or because the chairs are only one component in a complete interior solution for the
office. This definition is not arbitrary, but depends on whether the results of the life cycle study is to be applied for a specific or a more broadly defined market.
Differences in customer requirements may be based on differences in the purchase situation, the use situation, customer scale, age, sex, education, status, "culture", attitudes etc.
To have a practical relevance, segments must be:
- of a size that can provide adequate revenue to support a separate product line.
- clearly distinct and with a minimum of overlap, so that all products targeted for a segment are considered substitutable by the customers of this segment, while there should be low
probability that a product targeted for another segment would be substitutable, implying that product substitution from segment to segment can be neglected.
Office chair example
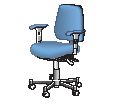
Customer segments
A small survey of the Danish office chair market has been made by acquiring marketing material from a number of suppliers, by telephone interviews with both suppliers
and purchasers and by personal interviews with two leading manufacturers.
From discussions with a Danish office chair manufacturer, it has become clear that at least four well distinguished customer segments exit, based on four different working
situations.These may be named after the working situation in question: 1) the labourer's chair, 2) the computer workstation chair, 3) the manager's chair, and
4) the 24-hour chair.The latter constitutes only a very limited market, and is not addressed further here.The other markets are shown in Figure 6 together with some
parameters that describe them.
Figure 6.
Segmentation of the office chair market, primarily based on the type of working situation
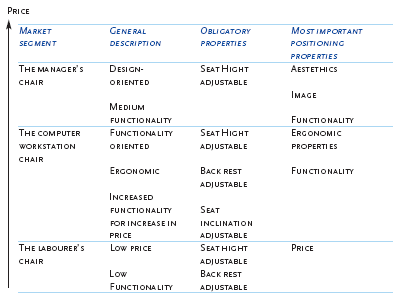
The labourer's chair is intended for the labourer, who is sitting on the chair at intervals only and not for many hours at the time, and who has intermittent standing and/or
walking working positions.The computer workstation chair is intended for the worker, who is primarily sitting, and who is working behind a visual display unit (VDU), e.g.
a computer, for a significant part of the day (at least two hours a day).The manager's chair is intended for the design-oriented person.This person is not working much on
computer, writing, or drawing, but rather reading, talking on the telephone and the like.This chair could typically be for the employer or senior employee, to whom design,
aestetics, and image/representativity to customers are important issues.
According to the office chair manufacturer, there is only very little overlap between these groups of customers.This is much in line with the findings of the market survey,
from which it is clear, that the chairs on the market are targeted to each of the outlined customer types. Furthermore, the grouping is emphasised by the specific legislative
requirements for seat inclination for the computer workstation chair.The probability that a chair targeted for one segment should sell to a customer in one of the other
segments is small, so that the product substitutability from segment to segment can be neglected.This implies that life cycle studies of office chairs should consider each of
the market segments separately and not allow for comparisons between them.
Information on market segmentation can typically be obtained from the marketing departments of the enterprises supplying products to the market. If information cannot be obtained
directly from the market suppliers, possible secondary sources are:
- retailers, which cover more than one segment,
- industrial associations,
- industrial research institutions and industrial consultants,>
- regulating authorities and standardisation bodies (with respect to differences between administrative areas),
- marketing and consumer research institutions,
- trade statistics (especially regarding geographical segmentation).
The importance of considering the market conditions
The above considerations of market segmentation and substitutability of products are of crucial importance in defining the scope of a life cycle study, when the compared products differ
in appearance and/or functionality. Since the environmental impacts to be assessed are a direct consequence of the product substitutions, only product substitutions that can be expected
to take place in practice should be included in the assessment. If the anticipated product substitutions do not occur in practice, the environmental impacts will be different from the ones
assessed by the study.
In parallel, the environmental impacts will also be different from the ones assessed by the study, if the assessment excludes product substitutions that can be expected to take place in
practice. Therefore, it is important to include in the study all relevant product alternatives. This is treated in further detail in the following section.
Due to the importance of these steps, the market segmentation is one of the places where it may be relevant to apply several alternative scenarios to reflect the limits of knowledge.
Table 3.
Selected technical properties of office chairs divided in obligatory (O) and positioning (P) in different market segments
Property |
Market segment |
|
Labourer's
chair |
Computer
workstation
chair |
Manager's
chair |
Seat height adjustable |
O |
O |
O |
Back rest adjustable |
O |
O |
|
Back rest inclination adjustable |
O |
O |
P |
Seat inclination adjustable |
|
O |
P |
Arm rest available |
P |
O |
O |
Arm rest adjustable |
P |
P |
|
Roller brakes and choice of soft and hard rollers |
P |
P |
P |
Angle between seat and back rest adjustable |
|
P |
P |
Sophistication of chair movement |
|
P |
P |
Seat depth adjustable and position lockable |
|
P |
|
3.1.3 Step 3: Determine the relevant product alternatives
The products that may be involved in a product substitution are delimited by the relevant market segment, as identified in the
procedure described in the previous sections. Whether all of the possible products also shall be included in the study, depends on the goal of the study.
Thus, the purpose of this step in the procedure is to determine what products shall be included in the study.
An enterprise internal study may be performed for a very specific purpose, which gives a large degree of freedom to define what is regarded as relevant alternatives. Public applications,
on the contrary, are typically aimed at influencing a predetermined market and must, therefore, relate to the products that are (expected to be) available on this market.
For example, to determine ecolabelling criteria for office chairs, a study should include a representative selection of the product alternatives, which can substitute each other in the
relevant market segment. A more narrow selection would be perceived as unfair to the excluded alternatives and not reflecting the true potential for environmental improvement. A
broader selection would be seen as suggesting irrelevant alternatives and thus also as an unfair comparison. An enterprise internal study of the same chairs may - without causing such
problems - be limited to study different alternatives within the product range of the enterprise itself or that of its closest competitors. Nevertheless, even enterprise internal studies should
seek to reflect the actual consequences of the decision to be supported, and should therefore include the product alternatives, which are expected to be involved.
Figure 7.
Relevant product alternatives for the four examples in Figure 3.
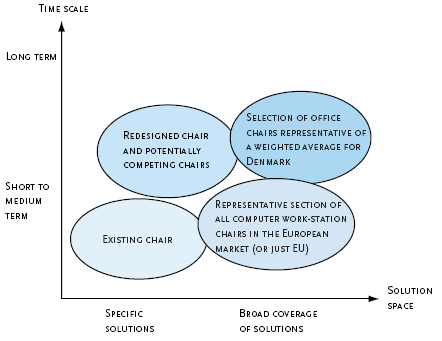
3.2 Step 4: Define the functional unit
The functional unit is the central hub of any life cycle assessment, since it provides the reference to which all other data in the assessment are normalised.
In a comparative study, the functional unit shall be the same for all the compared product systems. This is a prerequisite for ensuring equivalence among the product systems (see also
section 3.3).
In general, it is a prerequisite for defining the functional unit that the relevant market segment and the obligatory product properties have been determined, as described in the previous
steps (section 3.1).
Thus, what remains in step 4 is mainly the quantification:
Step 4: Define and quantify the functional unit, in terms of the obligatory product properties required by the market segment.
The functional unit should as far as possible relate to the functions of the product rather than to the physical product. For example, rather "seating support for one person working at a
computer for one year" than "one computer workstation chair", rather "freezing capacity of 200 dm3 at -18ºC" than "one 200 dm3 refrigerator", rather "annual lighting of a work area
of 10 square metres with 30 lux" than "bulbs providing 30000 lumen for one year". In this way, it is ensured that all obligatory properties - as well as the duration of the product
performance - are addressed.
As a reference unit, the size of the functional unit is - in principle - arbitrary. In general, it does not matter whether the office-chair study is normalised to seating support for 0.28
persons, 1 person, 1000 persons or 1.4 million persons.
However, two concerns may be relevant when deciding on the size of the functional unit:
- the scale of the studied product substitution,
- the ease of comparison of the outcome of the study to other known quantities.
Scale of the study
The studied product substitution may be small or large. A large substitution is defined as one, which affects the determining parameters for the overall technology development. Thereby,
the studied substitution may in itself lead to new technologies being brought into focus. It can be a change so large that it affects the general trend in the market volume, e.g. from
decreasing to increasing, whereby a new technology comes into play. It may also be a change so large that it overcomes a constraint which otherwise prevents the use of a specific
technology. Further, a change may be so large that it affects the production costs of the involved technologies, e.g. through economies of scale. For such instances, it may be misleading
if the functional unit is chosen independently of the actual scale of the studied substitution. When studying substitutions involving the entire market of a major product or process, e.g.
studies dealing with the entire waste handling system of a region or studies dealing with legislation or standards for an entire sector, it is relevant to choose a functional unit of the same
size as the affected market.
Figure 8.
The basic functional unit of the 4 examples in Figure 3, taking into account the scale of the studied substitution
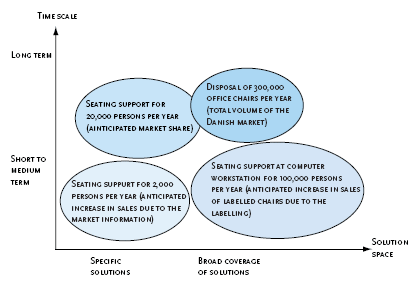
Often, however, life cycle studies deal with small substitutions, which do not affect the overall trends in market volumes, nor the constraints on and production costs of the involved
technologies. Therefore, the consequences of the substitution can be assumed linearly related to the size of the substitution so that the precise size of the functional unit will have no
importance for the interpretation of the results.
Ease of comparison
For such small substitutions, another concern may be relevant: When presenting the outcome of the study, it should be as easy as possible to compare the outcome to something
well-known to the reader. For this reason, the environmental exchanges are typically normalised to the annual exchanges from a region, from an average person living in this region
(person-equivalents as in the EDIP-method), or from the average monetary expenditure in this region. To ease this normalisation, and to present the results in an easily comprehensible
way, it may be an advantage to set the size of the functional unit equal or close to the annual per capita consumption of the studied product in the studied market segment.
Expanding the functional unit
In some instances, two products may be so closely linked that the separation of some of the processes in their life cycle may lead to an increase in uncertainty. If all the analysed product
systems provide the same amount of such linked products, this additional uncertainty may be avoided by including both products in the functional unit.
Example:
In a study comparing beverage containers, data for the distribution will relate to the beverage + container, and a separation would lead to an uncertainty in determining
how much of the transport to allocate to the container.This additional uncertainty can be avoided by expanding the functional unit to include the transport of the
beverage.The expanded systems are still comparable, since the functional unit for the containers will typically be related to the volume of beverage protected and
distributed, so that all the compared product systems will distribute the same amount of beverage.The same procedure may be used for other processes where the beverage
and the containers are treated together, e.g. pasteurisation.
Inventory result relates to the result of adding or subtracting one functional unit
The outcome of the study, as e.g. presented in the inventory tables, represents the environmental exchanges resulting from adding or subtracting one functional unit compared to the other
systems studied, or by fulfilling the performance described by the functional unit compared to not fulfilling this performance. It should not be understood to represent the environmental
exchanges of the functional unit in itself, since the result may to a larger or minor degree come from interactions with other product systems (see also the text on system expansion in
section 3.3)
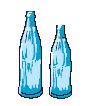
Example:
In a comparison of 0.5-litres one-way bottles with 0.4-litres returnable bottles, the difference in volume may have been determined to affect the consumption of the
beverage (see more on this in the example in section 3.3), so that the introduction of the returnable bottles is expected to lead to a decrease in consumption, e.g. from 4
million litres (in 8 million 0.5-litre bottles) to 3.6 million litres (in 9 million 0.4-litre bottles).Thus, the amount of beverage is expected to decrease even though the number of
bottles increases. In this case, the product system of the 0.5-litre bottles will have to be expanded with the production of 0.4 million litres of beverage, in order to give a
complete description of the consequences of a product substitution with the 0.4-litre bottles-system. In this case, the functional unit of the study is still "containment of xx
litres of beverage" while the large part of the environmental exchanges reported for the 0.5-litre bottles-system will come from the production of beverage.This means that
these data cannot be taken and uncritically used in another study, not even in a study with the same functional unit, unless the described system expansion is equally
relevant in the other study.
3.3 Step 5: Determine the reference flows The final step in the procedure is:
Step 5: Determine the reference flow for each of the product systems.
A reference flow is a quantified amount of the product(s), including product parts, necessary for a specific product system to deliver the performance described by the functional unit.
For a composite product, the reference flow will typically be identical to the parts list of the product, multiplied by a factor to scale it to the functional unit.
The purpose of the reference flows is to translate the abstract functional unit into specific product flows for each of the compared systems, so that product alternatives are compared on
an equivalent basis, reflecting the actual consequences of the potential product substitution.
The reference flows must take into account all those properties (whether obligatory, positioning, or market-irrelevant), which were identified in step 1 (section 3.1.1) as determining for a
performance difference. It is not just the obligatory product properties that determine the amount of substituted product or the interaction with other product systems. For example, the
ease of handling and cleaning a beverage container (positioning and non-market relevant properties, respectively) can influence the amount of car-driving on behalf of the consumer and
the type and amount of cleaning agent, respectively.
A relative measure of the substitution
For each of the properties identified as having a determining influence on the amount of product necessary, a relative measure must be determined of the extent to which the studied
products are expected to substitute each other.
Examples:
In a comparison of lighting alternatives, 3 bulbs of 3000 lumen may be substituted by 2 bulbs of 4500 lumen if the bulbs can be placed so that the distribution of light is
equal (or so that the difference is acceptable to the user). If the bulbs have different lifetimes, the comparison must be further adjusted to take this into account, resulting in
reference flows of e.g.
• 5 times 3 bulbs of 3000 lumen with a lifetime of 10000 hours each, equal to
• 10 times 2 bulbs of 4500 lumen with a lifetime of 5000 hours each.
When comparing paints with the same obligatory product properties (e.g. minimum 98% opacity and minimum 5 years durability), differences in covering ability (a
positioning property) will determine the reference flow of the different paints, e.g. a ratio of 2.3 litres of paint A to 1.9 litres of paint B to 1.7 litres of paint C etc.
In comparing different alternatives for hand drying, the dispenser design may determine the size of the reference flow of tissue paper.
In comparing 0.5-litres one-way bottles with 0.4-litres returnable bottles, the amount of bottles needed to fulfil the same function of protecting a certain amount of beverage
is determined by two properties: the volume and the return rate of the returnable bottles (with a return rate of 90%, a reference flow of 125 returnable bottles would protect
the same amount of beverage as the reference flow of 1000 one-way bottles).
Appropriate tests and measures
When determining the relative performance of different products, test conditions and measurement methods should be appropriate to the intended comparison. It may not always be
adequate to use the information from the producer.
Examples:
It should be ensured that the test of the covering ability of the paints have been performed on a surface with similar properties as the surface for which the paint is intended
in the specific life cycle assessment.
System expansion
For each of the properties identified as leading to differences in the way that the compared systems interact with other systems, the system boundaries must be modified to avoid this
difference.
This is parallel to the procedure for handling co-products, which also lead to a need for modifying the system boundaries to include the processes affected by the differences in amounts
of co-products from the analysed systems (see also the technical report: "Market information in LCA").
What is important in this step, is the description of the difference between the analysed products and a general description of the system modifications necessary to avoid this difference.
The description must include any difference, which leads to additional processes in one or more of the analysed product systems. Also future processes, such as additional needs for
maintenance, replacements, waste treatment, or recycling of raw materials must be included in the description, whenever these processes are planned or can be foreseen to be
necessary. This is one of the places where it may be relevant to apply several alternative scenarios to reflect the limits of knowledge.
Examples:
In the comparison of 3 light bulbs of 3000 lumen to 2 bulbs of 4500 lumen, it may be necessary to include the sockets and other fixtures which may be affected by the
choice. Furthermore, if the heat given off from the bulbs (which would normally be a market-irrelevant property) is not equal, this will affect the need for room heating
and/or cooling (unless it is an outdoor lighting).Thus, the reduction in heating requirement and/or increase in cooling requirement must be included in the comparison.
In the above example, the difference in lifetime of the two bulbs was simply taken into account when calculating the relative performance of the two light bulbs.While this
adjustment may be an acceptable procedure for a comparison of light bulbs, more long-lived products, such as refrigerators with life times of 10 or 20 years it require that
technology development is taken into account. One refrigerator with a lifetime of 20 years cannot simply be compared to two successive, present-day refrigerators with a
lifetime of 10 years.The refrigerators available 10 years from now are certain to be more energy efficient (i.e. having lower energy input per functional unit) than the
present, so the energy efficiency of the second refrigerator of the 10 + 10 years alternative must be determined by forecasting, while the energy efficiency of the 20 years
alternative is fixed.
Including changes in customer behaviour
It should be noted that the behaviour of the customer may be affected differently by the different product alternatives. This is especially relevant when studying consumer products and
may often significantly affect the outcome of the study. Thus, it is necessary to include the entire change in consumer behaviour in the reference flow.
Examples:
A comparison of refrigerators may be based on their internal and/or external volume.The primary function is obviously related to their internal volume, but the external
volume may be an obligatory property, if the refrigerator is to be fitted into an existing kitchen. If the external volume is required to be equal, the internal volume may
differ because of differences in insulation thickness.This may cause differences in behaviour of the user (e.g. shopping more often, storing certain items outside the
refrigerator, or adding another secondary refrigerator elsewhere in the house). Each of these changes in behaviour will involve changes in different processes, which then
have to be included in the study. If, on the other hand, the internal volume is required to be equal (i.e. is an obligatory property), a change in insulation thickness may
require adjustments in the physical surroundings of the refrigerator (the other kitchen furniture). If both the internal and the external volumes are regarded as obligatory
properties, obviously no adjustment is possible that can accommodate the change in isolation thickness.This illustrates that the obligatory properties also determine which
products it is possible to include in the study.
In the comparison of 0.5-litres one-way bottles with 0.4-litres returnable bottles, it may - as mentioned in section 3.2 - be necessary to investigate how the difference in
volume affects the consumption of the beverage. If the consumer regards 1 bottle equal to 1 bottle, the total consumption of beverage will decrease when the returnable
bottles are introduced. In this case, the packaging cannot be studied independent of its contents.The goal of the study may then have to be redefined to allow a comparison
of beverage plus packaging taking into account the changes in consumption.
Including effects of price differences
If there is a large price difference between different product alternatives at the end consumer level, and you wish to model the environmental impacts of this situation correctly, the
reference flow of the cheaper alternatives may - as mentioned in section 3.1.1 - have to be adjusted to include the alternative spending of the money saved. This addition should ideally
model the marginal spending by utilising information on what products increase their market volume when the spending increases, as presented in figure 9.
Figure 9.
The distribution of 1% growth in private consumption in the period 1977-1997 in Denmark. Calculated by the Copenhagen

Note that this is generally only relevant for price differences at the end consumers, since at enterprises the price differences seldom have any lasting effects due to the tendency of
marginal profits and wages to level out across all industries.
A similar adjustment may be required if the there is a large difference between the product alternatives in terms of time consumption at the end consumer level. In this case, the
timesaving alternatives may have to be adjusted to include the changes in overall behaviour as a result of the additional time available in these alternatives.
Details of system expansion can be postponed
To determine exactly what additional processes are to be included as a result of differences between the analysed systems often requires more detailed investigation. This investigation,
which follows the same procedure as for determining the system expansions related to co-products, does not have to be finalised as part of the procedure described here.
Similarly, the detailed description of the additional processes may be referred to the general description of what is included in and excluded from the analysed systems.
Reporting of system expansions
For the final reporting, it is appropriate to report all system expansions in one place, both those relating to product properties and those related to co-products. In order to avoid
misunderstandings as to the extent of the systems described by the functional unit, the appropriate place for reporting
all system expansions (including those from handling of co-products) is in close conjunction with the description of the functional unit. Also, it is recommended that in the presentation of
the outcome of the study (inventory tables etc.), the influences of system expansions should be presented separately.
3.4 Summary of the procedure in checklist form
Figure 10.
Information flow between the five steps in the procedure
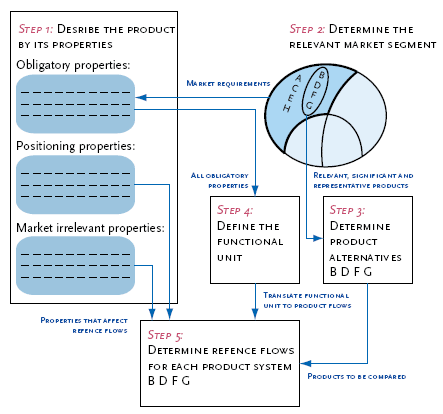
Step 1: Describe the product by its properties
- Identify - out of all the properties of the studied product – those properties that the product must have in order to be at all considered as a relevant alternative. These, so-called
obligatory product properties - are the properties that are to be included in the functional unit.
- Analyse systematically all product properties and judge for each one whether it leads to differences in the amount of substituted product or in t he interaction with other product
systems. If several such additional properties can be identified, investi-gate whether one of the properties can be identified as the one determining the difference in performance.
- Use a broad function-based perspective, i.e. based on the needs fulfilled by the products (e.g. "seating support during one year") rather than based on
the physical products themselves (e.g. "chairs") to avoid a (too) narrow product perspective, i.e. when studying intermediate products, components, or products that are otherwise very
dependent on other products.
Step 2: Determine the relevant market segment
- Identify the market segment in which the potential product substitution is taking place (geographically, temporally, and in terms of customer segment).
Step 3: Determine the relevant product alternatives
- Out of the products that may be involved in a product substitution
(as identified in the previous steps), determine what products shall be included in the study. This depends on the goal of the study.
Step 4: Define and quantify the functional unit, in terms of the obligatory product properties required by the market segment.
- The relevant market segment and the obligatory product properties were already determined in the previous steps. Thus, what remains to be done in this step is the quantification.
- As a reference unit, the size of the functional unit is - in principle - arbitrary. However, two rules of thumb may be applied:
- When studying substitutions involving the entire market of a major product or process, choose a functional unit of the same magnitude as the affected market.
- For small substitutions, set the size of the functional unit equal or close to the annual per capita consumption of the studied product (facilitates the comparison of the outcome of the
study to other known quantities).
Step 5: Determine the reference flow for each of the product systems.
- Translate the abstract functional unit into specific product flows for each of the compared systems.
- Take into account all those properties, which were identified in step 1 as determining for a performance difference.
- For each of the properties identified as having a determining influence on the amount of product consumed, determine a relative measure of the extent to which the studied products are
expected to substitute each other. Relate this to the functional unit.
- For a composite product, the reference flow will typically be identical to the parts list of the product, multiplied by the relevant factors to scale it to the functional unit.
- For each of the properties identified as leading to differences in the way that the compared systems interact with other systems, modify the system boundaries to avoid these
differences. Include all significant changes in consumer behaviour. More detailed investigation, to determine exactly what additional processes are to be included as a result of differences
between the analysed systems, does not have to be finalised as part of the procedure described here, but may be postponed to the general description of what is included in and
excluded from the analysed systems.
| Front page | | Contents | | Previous | | Next | | Top |
Version 1.0 November 2004, © Danish Environmental Protection Agency
|