| Bottom | | Front page |
Assessment of Mercury Releases from the Russian Federation
Contents
Preface
Symbols, Units and Acronyms
Executive Summary
1 Introduction
2 Production, Import and Export
3 Intentional use of Mercury
4 Mobilisation of Mercury Impurities
5 Turnover of Mercury by Waste Treatment
6 Summary and Discussion
7 References
ANNEX 1 Official Mercury Release Statistics
Annex 2 Storage of Mercury-containing Pesticides
Annex 3 Mercury in Coal from the Main Basins
Annex 4 Mercury Releases from Major Coal-fired Utility Plants
Preface
The results of the Arctic Monitoring and Assessment Programme summarising decades of environmental research in the Arctic region stressed the fact that humans and the environment in the Arctic region
currently experience alarming exposures to mercury, among a number of other toxic pollutants.
Within the framework of the Arctic Council, the eight Arctic Countries agreed on taking actions to contribute to the reduction of exposures to a number of priority pollutants, including mercury, in the Arctic
region. The Arctic Council issued an action plan including 6 projects on priority pollutants. Denmark is the co-ordinator for the project on mercury.
The overall objective of the project is to contribute to a reduction of mercury releases from the Arctic countries; partly by contributing to the development of a common regional framework for an action plan
or strategy for the reduction of mercury emissions, and partly by evaluating and selecting one or a few specific point sources for implementation of release reduction measures. In addition, the results of the
project may be used to improve the inputs for modelling of long-range transport of mercury. A part of the project is accordingly to prepare a comprehensive list of major point sources of mercury emission to
the atmosphere.
The present assessment of the releases of mercury from the Russian Federation has been prepared as part of the Arctic mercury project as a background document for the Russian reporting to a common
regional mercury assessment. The regional assessment summarises information on mercury release from all eight countries in the region.
This study has been undertaken by a group of Russian Experts coordinated by COWI in cooperation with the Ministry of Natural Resources of the Russian Federation (until April 2004) and the Russian
Federal Service for Environmental, Technological and Atomic Supervision (after April 2004). In the assessment official environmental data are combined with expert estimates to form a comprehensive view
of the circulation of mercury through the Russian technosphere as well as releases of mercury from the territory of the Russian Federation. All estimates are the sole responsibility of the editors and authors
and may be subject to change as more exact information is obtained.
Steering Group:
Mikala Klint (Denmark) - Chairman, Nikolai B. Nefediev (Russian Federation), Andrej Vl. Pechkurov (Russian Federation), Oxana Tsittser (Russian Federation), Marilyn Engle (USA), Douglas Steele
(USA), Stanley Durkee (USA), Grace Howland (Canada), Sjur Andersen (Norway), Bente Sleire (Norway), Magnus Nyström (Finland), Mats Ekenger (Sweden), John Munthe (Sweden), Halldor
Thorgeirsson (Iceland), Henrik Skov (Denmark), Gunnar Futsæter (ACAP Secretariat), Lars-Otto Reiersen (AMAP Secretariat), Simon Wilson (AMAP Secretariat), Garislav Shkolenok (UNEP
Chemicals), Husamudin Ahmadzai (NEFCO).
Coordinator:
Danish Environmental Agency, Mikala Klint.
Ministry of Natural Resources of the Russian Federation (MNR RF) (until April 2004) :
Nikolai B. Nefediev, Department of Methodological Provision of State Ecological Control;
Andrej Vl. Pechkurov, Department of Ecological Safety;
Yury Y. Alexandrovsky, Department of International Co-operation on Environment Protection.
Russian Federal Service for Environmental, Technological and Atomic Supervision (after April 2004):
Oxana Tsittser, Department of Control and Supervision in Environmental Protection;
Andrej Vl. Pechkurov, Department of Control and Supervision in Environmental Protection
Consultant:
COWI A/S (Denmark), Carsten Lassen (project manager, editor), Jakob Maag;
Moscow Representative Office of COWIconsult International Ltd., Tatyana V. Efimova (co-manager, editor), Irina Chernakova.
Russian Experts (main authors):
Yuri A. Treger, Scientific Research Institute "Syntez", the Design Bureau of the Ministry of Science and Industry of RF;
Eugeny P. Yanin, Institute of Geochemistry and Analytical Chemistry of V.I. Vernadskiy of RAS;
Boris A. Revich, Center for Demography and Human Ecology of Institute of Economic Forecasting of RAS;
Boris E. Shenfeld, Ural State Scientific Research Institute of Regional Ecological Problems of the Ministry of Natural Resources of RF;
Sergey V. Dutchak, Meteorological Synthesizing Centre East, EMEP MSC-E;
Nina A. Ozerova , Institute of Geology of Ore Deposits, Petrology, Mineralogy and Geochemistry of RAS;
Tatyana G. Laperdina, Institute of Geochemistry and Analytical Chemistry of V.I. Vernadskiy of RAS;
Vladimir L. Kubasov, State Scientific Research Institute of Nonferrous Metallurgy "Gintsvetmet".
Russian Technical Experts:
Elena Yu. Bykhovskaya, Valentin I. Eberilj, Anna Z. Oschepkova, Y.G. Dvoskin, M.I. Chubirko, N.M. Pichuzhkina, V.A. Sinoda, L.F. Mikhailovaà, V.A. Kataeva, V.L. Kovalsky.
International Expert:
John Munthe, IVL Swedish Environmental Research Institute Ltd. in cooperation with VTI, The All Russia Thermal Engineering Institute (project funded by USA).
Reviewers:
International reviewers: Mark Richardson (Canada), Leonard Surges (Canada), Jozef M. Pacyna (Norway), Edward M. Weiler (USA), Velu Senthil (USA), Frank Anscomb (USA), Alexander McBride
(USA), David Kirchgessner (USA), Mr. John Kinsey (USA), Mr. Russell Bullock (USA), Alexis Cain (USA), Stephen Hoffman (USA), Robert Stevens (USA), Richard Meyer (USA), Alan Kolker
(USA), John DeYoung (USA), William Brooks (USA), Richard Levine (USA), Thomas Goonan (USA), Dennis Kostick (USA), Richard Artz (USA), Mark Cohen (USA), James Ekmann (USA), Melissa
Chan (USA).
Financial support:
This study is financially supported by Denmark, Canada, USA and Norway.
Acknowledgement:
Special thanks are due to a large number of Russian enterprises who have contributed to this assessment by providing information on technologies and mercury releases.
Symbols, Units and Acronyms
ACAP Arctic Council Action Plan to Eliminate Pollution of the Arctic
AMAP Arctic Monitoring and Assessment Programme
ESP Electrostatic precipitator
GOST State standards
Hg Chemical symbol for mercury
INTAS International Association for the Promotion of Co-operation with Scientists from the New Independent States of the Former Soviet Union
JSC Joint Stock Company
MAC Maximum allowed concentration
MAD Maximum allowed dose
MCW Mercury containing waste
MSW Municipal solid waste
OSPAR The Convention for the Protection of the Marine Environment of the North-East Atlantic
PVC Poly vinyl chloride
RAS Russian Academy of Sciences
RF Russian Federation
USSR Union of Soviet Socialist Republics
VCM Vinyl chloride monomer
WWS Waste water sludge
Units
μg 10-6 g
ppm parts per million
Punctuation In accordance with English punctuation, dot (.) is used as decimal symbol and comma (,) as digit grouping symbol
t 1000 kg = metric ton
Tonne 1000 kg = metric ton = t
Executive Summary
The present assessment has been prepared as part of the ACAP (Arctic Council Action Plan to Eliminate Pollution of the Arctic) study "Reduction of atmospheric mercury releases from Arctic states". The
assessment of anthropogenic mercury releases from Russian sources has been prepared by combining official Russian environmental statistics with expert estimates obtained on the basis of an assessment of
mercury used intentionally or mobilised (as impurity) within different activity categories. For each activity category the flow of mercury is traced from production/extraction to final release or disposal. The
assessment does not cover eventual mercury consumption for defence industry applications.
Intentional uses of mercury in RF
The total intentional consumption of mercury in the Russian Federation in 2001/2002 is estimated at 151-160 t/year. Best estimates for consumption and releases of mercury to the air and waste is shown in
Table 1. Almost all the data in the table are subject to uncertainty, but the reader is referred to the extended summary and discussion in Chapter 6 for more detailed information on the uncertainties. The total
consumption has decreased significantly during the last decades (Figure 1). The reported total intentional mercury consumption in 1985 and 1993 was about 1,300 and 500 t/year, respectively. The trend in
mercury consumption in Russia thus follows the general trend in the world. According to the Financial Department of the Ministry of the Economic Development and Trade of RF the total potential demand
of mercury in Russian enterprises in 1999-2001 was 280-300/year. The discrepancy between these data and the result of the present assessment may be due to the facts that some facilities are operating
below their capacity, that mercury consumption is decreasing, that the consumption varies from year to year, and that the present assessment covers civilian applications only.
The main intentional application area is chlor-alkali production in which the mercury is used as electrode. The consumption for this application was about 103 t in 2002, but the amount varies from year to
year. All mercury used for this application ultimately ends up in the surroundings or waste dumps. The direct release to the air from the sector is estimated at 1.2 t/year. However, the unaccounted losses of
Hg in chlor-alkali production are estimated at more than 50 t year. A part of this amount may be lost to the ground at the production site, but a part of the unaccounted losses may actually directly or
indirectly be released to the air. Hg-containing solid wastes are mainly disposed of at the waste landfills and sludge storage facilities. At the moment some insignificant amount of mercury from the production
of chlor-alkali is recycled. The technologies used by the enterprises producing chlorine and caustic are very diverse and the specific losses from the individual enterprises vary considerably among enterprises.
The assessment indicates that there is a significant potential for reducing the releases by relatively simple improvements of management practices, although there is work and cost associated with these
changes.
Besides chlor-alkali production, mercury is used in the chemical industry as a catalyst for production of vinyl chlorine monomer for PVC production. Hg-containing waste from VCM production is mainly
recycled.
By today, the consumption of mercury in the chemical industry has decreased significantly from a level of about 900 t in 1985. A major part of this mercury used within this sector has been disposed of to
waste dumps or released to the ground below and around the facilities. The total amount of mercury in waste disposed at the landfills (operating or abandoned) by chemical enterprises is estimated at more
than 3,000 t. The historical consumption data indicate that the actual amount of the disposed Hg may be significantly more than the estimated amount.
The consumption of mercury for production of electrotechnical products and measuring equipment has also decreased markedly during the recent decade. In 1989 some 240 t mercury was used for
production of such products in the Russian Federation; in 2001 about 30-40 t was used for the production. Production of mercury thermometers and mercury light sources (mercury lamps) account for the
major part of the consumption of mercury for production of mercury-containing products. The consumption of mercury for the production of thermometers and light sources was in 2001 26 t and 7.5 t,
respectively. The mercury content of thermometers for the domestic market is estimated at about 10 t. The thermometers ultimately end up in solid waste and thermometers and other electrotechnical
equipment is estimated to be the major sources of mercury in municipal solid waste, and consequently, the major source of mercury emitted to the air from municipal waste incinerators. Mercury lamps are to
some extent processed for recycling of the mercury or temporary stored for possible future processing. The total amount of mercury actually recycled from the light sources accounted for less than ten
percent of the mercury content of disposed light sources (lamps) in 2001. The direct releases to the air from production of mercury-containing products are estimated to be very small compared to releases
from e.g. coal combustion or non-ferrous metal production.
Table 1 Summary of mercury consumption/mobilisation, releases to air and disposal to waste dumps in 2001/2002 (t/year)*
Activity category |
Mercury consumption /mobilisation |
Mercury releases to the air |
Mercury in waste disposed of for landfill/waste dumps |
Intentional use of mercury |
Chlor-alkali production |
103 |
1.2** |
39 |
Production of VCM |
7.5 |
0.02 |
0.0 |
Gold mining using the amalgamation method, mining of sec. placers |
5.5 |
3.1 |
1.1 |
Production of thermometers |
26 |
0.009 |
0.1 |
Production of light sources |
7.5 |
0.15 |
0.001 |
Other intentional uses |
5.8 (+ ?) |
0.06 (+ ?) |
2.4 (+ ?) |
Total assessed intentional uses |
155 |
4.5 |
43 |
Mobilisation of mercury impurities |
Coal - electricity producing sector |
10 |
8.0 |
2.0 |
Coal - other uses (incl. waste from extraction) |
12 |
6.3 |
3.6 |
Oil processing and use of petroleum products |
33 |
3.4 (+ ?) |
? |
Gas, oil-shale and bio-fuels |
8.0 |
1.0 |
? |
Zinc and lead production |
31 |
1.9 |
8.5 |
Nickel and copper production |
28 |
5.3 |
6.6 |
Production of other metals |
7.8 |
2.6 |
4.2 |
Cement and lime |
2.0 |
1.6 |
0.4 |
Total mobilisation as impurity |
132 |
30 |
22 |
Waste treatment |
Waste incineration |
|
3.5 |
|
Landfilling |
|
|
24 |
Sewage sludge |
|
< 0.1 |
5.7 |
Total waste treatment |
|
4 |
30 |
Grand total |
287 |
38 |
95 |
* Best estimates; "+ ?" indicates that the value only represents the assessed activities but some categories not been assessed may add significantly to the total. Note that the total may be equally higher than
indicated.
** Direct emissions from the chlor-alkali production processes. In 2002 totally 56 t lost from the process was unaccounted. A part of this may be emitted to the air.
The consumption of mercury for dental amalgams has decreased from about 6 t to about 0.8 t in 2001 during the last ten years. Because mercury amalgams fillings in Russia have been replaced with other
filling materials, the mercury consumption with dental amalgams in Russia is relatively low compared to the consumption for this application in other countries. The amount of mercury disposed of to solid
waste and discharged to waste water with amalgam, however, reflect the consumption ten years ago due to the life of the fillings, and it is estimated that this amount might reach 6 t/year. The discharged
amalgam is estimated most likely to be one of the major sources of mercury in municipal sewage.
The use of mercury for gold mining using the amalgamation method was prohibited in Russia more than 10 years ago. Nevertheless, the assessment indicates that some illegal activities may still take place in
remote areas of the country. Besides, today gold is legally extracted from waste material from former gold mining activities in which the amalgamation method was used. By the extraction a significant part of
the mercury in the waste is released to the air. The estimates indicate that 1.5-6.5 t mercury may be released to the air by such activities. As more that 6,000 t mercury has been used for gold production
during the history, the potential releases from mining of the waste could be very significant.
At present, there is no industrial production of mercury-containing pesticides and biocides in Russia, and their use is prohibited. Based on inventories made by the Ministry of Health it is estimated that 20-40
t mercury containing pesticides (about 0.6 t mercury) was, however, still used in 2001. The used pesticides most likely originate from stocks.
Figure 1 Consumption of mercury in the Russian Federation 1989, 1993 and 2001/02
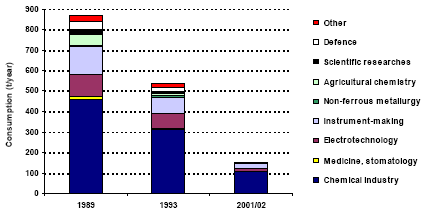
Production and recycling of mercury
Primary production of mercury does not take place in Russia today (stopped in 1995). About 5 t/year of mercury in residues from zinc production was in 2001 exported for refining abroad. By recycling of
mercury-containing waste products, among others from the production of vinyl chloride, about 30 t refined mercury was produced in 2001.
Mobilisation of mercury impurities
As the intentional consumption of mercury decreases, the mobilization of mercury impurities (trace element) increasingly account for a larger part of the total anthropogenic mercury flow. The total
mobilization of mercury impurities in Russia in 2001 is estimated at 138 t (66-198 t), and the major part is mobilized with coal, oil and non-ferrous metals ores (Table 1).
By the combustion of the fuels, a significant part of the mercury in the fuel is released to the air. For example total mercury release to the atmosphere due to the application of coal as a fuel (both upgrading
and combustion) was estimated for 2002 at 14.3 t, accounting for about 37 % of the total assessed atmospheric releases of mercury from Russia. At the same time for 2001, total mercury content in used
coal was estimated at 15.4 t out of which 13.2 t is emitted to the atmosphere and 2.2 tonnes is transferred to waste.
Based on a limited number of available analyses of mercury in Russian crude oils it is estimated that some 33 t mercury may be mobilized with crude oils refined in Russia. Globally, the mercury content of oil
and gas vary considerably from region to region and the available data indicates that the mercury content in Russian crude oil and gas may be relatively high. The data are, however, still too scarce to draw
any firm conclusions. Based on a few measurements of mercury in petroleum products the total release to the air by use (combustion) of the products is estimated at 3.4 t. In Russia, like in most other
countries, little is known about the fate of mercury by the initial processing and refining of the oil. The available data indicate that the processes may be significant sources of mercury releases to the air and
water, but the scarce data does not allow even a first rough estimate to be made. By the processing of natural gas, a considerable amount of mercury follows the stable condensate and sulphur, and
consequently the mercury content of the gas conducted to the consumers or exported is insignificant.
About 31-92 t mercury is estimated to be mobilized by extraction and processing of non-ferrous metals in Russia. The mercury will ultimately be released to the environment or end up in waste products. The
total release of mercury to the air from the sector is estimated at 8.2 t, and the sector account for about 22 % of the total accounted releases to air. These estimates are very uncertain and actual
measurements of mercury emission from the smelters should be carried out to validate the emission estimates.
Mercury releases to air
According to the official data the total emission of mercury from Russian enterprises that have the obligation to report on mercury emission was 2.9 t in 2001. Besides these sources, significant amounts of
mercury will be released from area sources and from processes in which mercury is present as a natural impurity in the raw materials. In the present assessment the total emission to the air in Russia is
estimated at 39 t, of which emission from processes where mercury is mobilised as impurity account for 77 %. Industrial processes in which mercury is intentionally used only accounted for about 3% of the
total assessed emission. The emissions to the air are mainly based on expert estimates using information on mercury in fuels and raw materials in combination with information on the fate of mercury by the
different processes. The estimated releases to air and other media are considered highly uncertain and there is an urgent need for further measurements of actual releases from the different processes in order
to reduce the uncertainty and thereby provide a more reliable basis for considerations regarding measures for release reduction.
The major sources are estimated to be combustion of coal and oil products, and non-ferrous metal production. Because of the limited data, the mercury emission from oil refineries and diffuse air emissions
from chlor-alkali production cannot be quantified and included in the inventory.
No data on the speciation of the mercury releases from Russian sources have been available. For the understanding of the atmospheric transport, fate and the potential environmental impact of the released
mercury it is essential to have more information on the speciation of mercury releases.
Mercury in waste water and releases to water bodies
Compared to the atmospheric emissions, direct release to water bodies is a minor pathway for mercury release from the technosphere to the environment. According to the official statistics the total
discharges of mercury from industrial activities to water bodies amount to 0.16 t. The major source category is being chemical industry i.e. production of chlor-alkali.
Based on data on mercury in municipal sewage sludge it is estimated in this assessment that the total discharges to water bodies from municipal sewage plants may constitute 3.4-11.9 t. The greater part of
mercury contained in the wastewater ends up in sewage sludge, which is mainly disposed of to sludge beds or dump sites. Besides the direct industrial discharges to the water bodies, industrial activities may
also be sources of mercury to the municipal sewer system. The major sources of mercury in the municipal sewage are probably mercury from dental clinics, mercury from broken thermometers and
electrotechnical equipment (e.g. broken switches). A significant part of the mercury-containing equipment produced ten years ago may still be in use, and when broken, a part of the mercury may end up in
the drain.
Mercury in process water from oil and gas extraction has not been assessed, but may be a significant source of direct mercury releases to water bodies.
Direct mercury releases to land
The major source of direct mercury releases to land (excluding releases to waste dumps) is releases to the ground from chlorine alkali production. A significant part of the 50 t/year of unaccounted losses
from the sector is assumed to be lost to the ground below and around the production facilities.
Up to 0.6 t tonne mercury was applied to land with pesticides (mainly Granosan) in 2001. The use of mercury-containing pesticides is prohibited, and the pesticides are no longer produced in Russia. Up to
20 t mercury in obsolete mercury-containing pesticides is stored around the country.
A few percent of the sewage sludge is used for agriculture. The typical concentration of mercury in the sludge is far below the maximum allowed concentration (MAC) of mercury in sludge used for
agricultural purposes. The amount of mercury spread on the fields with the sludge is less that 1 t per year.
Mercury disposal to waste dumps and emission from incineration
At least 95 t mercury contained in various waste categories each year ends up in landfills and waste dumps. This mercury may later to some extent be released to the air, to the soil, groundwater or surface
water bodies. As shown in Table 1, the estimated mobilised mercury exceeds the total of the releases to air and the mercury in waste products by about 80 t. The difference illustrate that the actual fate of the
mobilised mercury is still poorly understood, and the volumes that end up in waste products may be significantly higher than the indicated amounts.
As regards industrial activities with intentional use of mercury, chlor-alkali production is the major source of mercury to waste dumps. From gold mining using the amalgamation method in remote areas
roughly estimated 0.3-0.8 t may end up in tailings from the mining activities, which constitutes about 10% of the total Hg consumption for gold mining (3-8 t/year).
The majority of the mercury-containing products will ultimately be disposed of to waste dumps or incineration, and at the least 24 t mercury in products is disposed of with solid waste. The major sources are
thermometers, light sources, switches, batteries and dental amalgams. The amount of mercury in the present amount of waste partially reflect the consumption some years ago when the consumption of
mercury was significantly higher than today. Nationally, about 2-3 percent of the municipal solid waste is incinerated, giving rise to atmospheric emission of roughly estimated 3.5 t mercury per year.
Further development of the mercury assessment
In general the data on intentional uses of mercury is quite certain, as specific information have been obtained from most industrial users of mercury in the country. A few applications in the "Other applications"
section of the present document are only qualitatively described and the assessment could be made more comprehensive by obtaining more information on these applications.
As regards mobilisation of mercury impurities, the total mobilisation is for most applications estimated with high uncertainty. Combined with the uncertainty as to the fate of the mercury by
processing/combustion of the materials the uncertainty on the emission estimates are quite high. It should be noted that this is the case for mercury assessments in most countries.
The assessment indicates that extraction and processing of oil and use of oil products may be major sources of mercury to air in Russia, but the assessment is based on limited data. Further investigation of
the mercury content of crude oils and the fate of mercury by oil extraction and processing is needed in order to validate the estimates.
Non-ferrous metal smelters seem to be among the major point sources of mercury emission to the air. More exact information about the actual mercury content of the ores or concentrates used by the
individual enterprises and actual measurements of mercury emissions are required in order to obtain more exact estimates. The assessment indicates that extraction of gold from old mining waste (from mining
operations using the amalgamation method) could be a significant and increasing source of mercury releases to the air, but further investigations are needed to confirm the results.
1 Introduction
1.1 Previous Study on Mercury in the Environment
The Committee on Ecology of the State Duma of Russia and the Government of the Russian Federation issued the Order for the State Committee on Environment Protection in 1998 to develop a National
Report "On mercury pollution of the environment of the Russian Federation and its impact on population health". Unfortunately, this Order was not executed. Nevertheless, in 1999 Scientific Research
Institute on Problems of Resource Saving and Wastes Management under the Ministry of Economy if RF and Goscomecologia of RF together with the specialists from other institutions developed the report
titled "Analysis of mercury pollution of the environment of the Russian Federation". The main purposes of the report were to determine the main sources of mercury pollution and make recommendations for
potential development of the National Mercury Releases Investigation and Pollution Abatement Program.
In this report, the main sources of Hg pollution in Russian Federation were acknowledged to be production and consumption wastes. It was not possible to make comprehensive and accurate assessment of
the technogenic mercury releases from each of the sources, due to the lack of reported data concerning consumption and application of mercury and Hg-containing compounds.
Additionally it was determined that the distinctive features and conditions in Russia, which should be taken into account during elaboration of the National Mercury Releases Investigation and Pollution
Abatement Program, such as:
- Almost complete absence of large monometallic mercury deposits in the Russian Federation and trends for increase of accompanying mercury supplied in pyrite, zinc and copper concentrates;
- Sparseness and remoteness of many Hg consumers from Hg producers;
- Lack of continuous control over Hg consumption and recycling;
- Lack of high-effective sorbents for retention of Hg from gaseous and liquid releases at domestic market;
- Lack of standard reusable containers for collection, transportation and storage of Hg-containing wastes;
- Lack of technologies for processing of many types of Hg-containing wastes;
- Shortage of the existing capacities for Hg-containing wastes processing with application of the available technologies.
In other words, the bulleted information above might be posed as:
1. undefined user – producer relationships,
2. undefined recycling incentives,
3. insufficient data due to poor monitoring, and
4. insufficient knowledge regarding technological alternatives for treating mercury under varying circumstances.
Moreover the regulatory basis was reviewed and systematized to some extent. This regulatory basis for mercury pollution management was elaborated in 1970-80-ies. The existing regulations usually cover
general issues related to mercury contamination and Hg and Hg-waste management and do not include specific requirements.
It is the author's opinion, that one of the key causes of mercury pollution in Russia is a lack of the Hg-containing wastes management system, i.e. collection, storage, transportation and neutralization.
Collection, storage and transportation of Hg-containing wastes are acknowledged to be a bottleneck in the existing system of Hg-containing wastes utilization and neutralization. Lack of the agreed
documents and existence of contradictory requirements of various agencies and local authorities hamper the process of effective collection and delivery of Hg-containing wastes to the disposal site.
The authors of the document concluded that the problem of mercury pollution in the Russian Federation is strongly depends on the implementation on the "Wastes" Federal target Program. The following
activities were recommended for the Program' implementation targeted on Hg wastes management:
1. Forecasting on mercury consumption till 2010 and determination of the feedstock for the secondary mercury;
2. Elaboration and implementation of the Hg consumption and recycling control system (through environmental authorities);
3. Preparation of legal basis regarding Hg consumption and recycling (or regarding total losses);
4. The national inventory and certification of Hg-containing wastes covering all enterprises, which use mercury and process Hg-containing consumption wastes;
5. Design and manufacture of the reusable containers for collection, storage and transportation of Hg-containing wastes;
6. Elaboration of new utilization technologies for particular types of Hg-containing wastes.
1.2 Regulation of Mercury Releases
The content of mercury in different media is regulated by maximum allowed concentrations. The concentrations were fixed in the regulatory documents developed and adopted by the executive authorities of
the Russian Federation and/or the USSR (see tables 1.1 – 1.6).
Table 1.1 Main regulatory documents on environment and population protection from potentially dangerous pollutants including mercury and its compounds
Document |
Adopted |
1. Surface water protection |
Hygienic norms ÃÍ 2.1.5.689-98. Maximum allowable concentrations
(MAC) of chemical substances in drinking water sources and water bodies of cultural-recreational
application |
The Ministry of health of RF, 04.03.98,
No. 9.
|
Sanitary rules and norms of surface waters protection from pollution |
The Ministry of health of the USSR, July 09, 1988, No. 4630-88 |
Methodical guidelines on sanitary treatment of water bodies when non-ferrous
metals ores are extracted and dressed |
The Ministry of health of the USSR, No. 20-38-79 |
Methodical guidelines on detection of concentrations of dissolved mercury
in liquid mediums (natural, wastewater, water use facilities, drinking water,
solutions). |
The Ministry of health of RF, 16.02.94, No. 4.1.006 |
2. Atmospheric air protection |
Nature protection. Atmosphere. Rules on maximum allowable emissions of pollutants
by the industrial enterprises |
GOST 17.2.3.02-78 |
Temporary directive methodical guidelines on atmospheric air pollution assessment
|
The Ministry of health of the USSR, December 23, 1976 |
Methodical recommendations on hygienic assessment of atmospheric air pollution
in regions where mercury producing and consuming enterprises are located |
The Ministry of health of the USSR, July 13, 1989, No. 5050-89 |
Methodical recommendations on determination of one-time load of chemicals
emissions, water and foodstuff on population |
The Ministry of health of the USSR, No. 2983-84 |
Methodical guidelines on detection of Hg vapours concentration in the indoor
occupational air and the atmospheric air of settlements using the atomic-absorbtion
spectrometry |
The Ministry of health of RF, 16.02.94, No. 4.1.005 |
3. Soil protection, domestic and industrial wastes |
Nature protection. Soil. Indicators of sanitary state. |
GOST 17.4.2.01-81 |
Nature protection. Soil. Classification of chemicals for contamination control.
|
GOST 17.4.1.02-83 |
Scrap non-ferrous metals. General technical requirements |
GOST 1639-78 |
Maximum content of toxic compounds in industrial wastes for justification
of wastes as toxic. |
The Ministry of health of the USSR, December 12, 1984, No. 3170-84 |
Sanitary Rules CÏ 3183-84. Accumulation, transportation, neutralization
and burial of toxic industrial wastes |
The Ministry of health of the USSR, December 29, 1984, No. 3183-84 |
Maximum amount of accumulated toxic industrial wastes on the enterprise site |
The Ministry of health of the USSR, February 01, 1985, No. 3209-85 |
Maximum amount of toxic industrial wastes allowed for storage on dump-sites
of solid wastes |
The Ministry of health of the USSR, May 30, 1985, No. 3897-85 |
Maximum amount of toxic industrial wastes allowed for storage on dumps of
enterprises |
The Ministry of health of the USSR, November 19, 1985, No. 4015 |
Methodic guidelines for bodies of sanitary and epidemiological service on
control for sanitary protection of the environment from solid and liquid toxic
wastes pollution |
The Ministry of health of the USSR, July 12, 1985, No. 3912-85 |
Resource-saving. Waste management. Methods for Hg detection in Hg-containing
wastes. General requirements. |
GOST Ð 51768-2001 |
Resource-saving. Waste management. Wastes hazard classes certificate. General
requirements. |
GOST 30774-2001. |
Resource-saving. Waste management. Documentation and regulation of waste management
activity. General requirements. |
GOST Ð 51769-2001. |
Resource-saving. Waste management. Classification, identification and coding
of waste. General requirements. |
GOST 30775-2001. |
4. Protection of working areas |
Intersectoral Rules on occupational health and safety and mercury application.
ÏÎÒ ÐÌ-009-99 (valid since the 1st of
February 2000). |
The Ministry of Labour of RF, 14.09.99, No. 37 |
The Mercury. Technical requirements. |
GOST 4658-73 |
Work with mercury. Safety requirements. |
GOST 12.3.031-83 |
CÏ 4607-88. Sanitary rules for work with mercury, its compounds
and devices with mercury filling |
The Ministry of health of the USSR, April 04, 1988, No. 4687-88 |
Sanitary rules on design, equipment, operation and maintenance of enterprises
which produce mercury |
The Ministry of health of the USSR, December 27, 1979 No.2116-70 |
Hygienic norms ÃÍ 2.2.5.686-98. Maximum allowable concentrations
(MAC) of pollutants in the indoor occupational air. |
The Ministry of health of RF, 04.02.98, No. 4 |
Sanitary rules for non-ferrous metallurgy enterprises |
The Ministry of health of the USSR, February 24, 1982 No. 2528-82 |
Informational and methodical letter on hygienic activities and population
health risk assessment in places of mercury pollution |
The Ministry of health of the RSFSR, February 05, 1990, No. 23-01-2/101 |
Methodical recommendations on control for organization of current and final
de-mercurization and its efficiency assessment |
The Ministry of health of the USSR, December 31, 1987, No. 4545-87 |
Instruction on treatment of working clothes, metallic mercury or its compounds
pollution |
The Ministry of health of the USSR, July 20, 1976, No. 1442-76 |
5. Food products protection |
Medical and biological requirements and sanitary quality norms for food feed-stocks
and foodstuff |
The Ministry of health of the USSR, August 01, 1989 |
Temporary hygienic norms of toxic elements content (heavy metals) in cereals
products, supposed for children's food |
The Ministry of health of the USSR, No. 3091-84 |
Maximum allowable concentration of heavy metals and arsenic in production
feed-stocks and food products |
The Ministry of health of the USSR, No. 4089-86 |
Sanitary norms and rules. CàíÏèÍ 2.1.4.559-96.
Drinking Water. Hygienic requirements to the potable water quality in the centralized
water supply facilities. Quality control. |
The Ministry of health of RF, 24.10.96,
No. 26
|
6. Contamination assessment and demercuration activities |
Òåððèòîðèàëüíûé
gas-mercury monitoring of non-production facilities. Methodological Guidelines.
|
The Ministry of health of RF,
No. 2001/159.
|
Methodical guidelines on control over current and final demercuration activities
and effectiveness assessment |
The Ministry of health of the USSR, 31.12.87 No.4545-87 |
Methodical guidelines on demercuration activities arrangement and implementation |
The Ministry of Emergency of RF, 1998 |
Informational Letter on hygienic activities and assessment of health risk
in mercury contamination residues in residential and public buildings |
The Ministry of health of the RSFSR,
05.02.90, No. 23-01-2/101
|
Hygienic assessment of soil quality in the residential localities. Methodological
Guidelines. |
The Ministry of health of RF, 07.02.99, No. 2.1.7.730-99 |
Table 1.2 MAC of mercury and its compounds in the atmospheric air of the inhabited localities*
Substance** |
MAC, mg/m3 |
Maximum single |
Average daily |
Metallic mercury |
- |
0.0003 |
Diethyl mercury*** |
0.0003 |
- |
Mercury*** |
- |
0.0003 |
(II) dinitrate |
- |
0.0003 |
(I) nitrate |
- |
0.0003 |
(II) amidochloride |
- |
0.0003 |
(II) iodide |
- |
0.0003 |
(II) oxide |
- |
0.0003 |
(II) acetate |
- |
0.0003 |
(I) chloride |
- |
0.0003 |
(II) dichloride |
- |
0.0003 |
* Hygienic norms ÃÍ 2.1.6.695.98. Maximum allowable concentrations (MAC) in the atmospheric air of the inhabited localities. – Moscow: The Ministry of Health of RF, 1998.
** all regulated substances are related to the hazard class 1.
*** MAC for Hg compounds are presented in conversion to Hg.
Table 1.3 MAC of mercury and its compounds in the indoor occupational air*
Substance ** |
MAC, mg/m3 |
Prevailing aggregative state in occupational conditions |
|
Maximum |
Average per shift |
|
Metallic mercury |
0.01 |
0.005 |
Vapours |
Diethyl mercury |
- |
0.005 |
Vapours |
Inorganic compounds of mercury*** |
0.2 |
0.05 |
Aerosol |
Ethyl mercury phosphate *** |
- |
0.005 |
Mixture of vapours and aerosol |
Ethyl mercury chloride*** |
- |
0.005 |
Mixture of vapours and aerosol |
* Hygienic norms 2.1.6.686-98. Maximum allowable concentrations (MAC) in the occupational air. – Moscow: The Ministry of Health of RF, 1998. Mercury. Regulations and methodological guidelines.
Reference Book. Ò. 1. – Saint-Petersburg, 2001.
** All regulated substances are related to the hazard class 1.
*** MAC for Hg compounds are presented in corvension to Hg (influence of inorganic compounds requires special protection of eyes and skin).
Table 1.4 MAC of mercury and its compounds in potable water sources and cultural and recreational water bodies*
Substance** |
MAC, mg/l *** |
Diethyl mercury |
0.0001 |
Mercury (for inorganic compounds, given the gross content of all forms) |
0.0005 |
Ethyl mercury chloride |
0.0001 |
* Hygienic norms ÃÍ 2.1.5.690-98. Maximum allowable concentrations (MAC) of chemical substances in potable water sources and cultural and recreational water bodies. – Moscow: The Ministry of
Health of RF, 1998.
** All regulated substances are related to the hazard class 1.
*** Releases of inorganic mercury (Hg2+) and mercuric chloride into water bodies used for fishery are prohibited.
Table 1.5 MAC of gross concentration of mercury in soil and allowable content related to the hazard levels *
MAC,
mg/kg |
Hazard indicators and limitative concentrations values, mg/kg
** |
translocation |
Migratory |
General sanitary |
water |
air |
2.1 |
2.1 |
33.3 |
2.5 |
5 |
* Hygienic assessment of soil quality in the inhabited localities. Methodological Guidelines. – Moscow: the Ministry of Health of RF, 1999.
** Translocative indicator of hazard indicates ability of Hg to transit to agricultural plants and to accumulate in concentrations exceeding the established MAC. Migratory water hazard factor describes the
ability of Hg to migrate from soil to groundwater and surface water and to concentrate in the amounts exceeding the established MAC. Migratory air hazard factor indicates the ability of Hg to migrate from
soil to the atmospheric air reaching the concentrations exceeding MAC established for the atmospheric air. A general sanitary hazard factor indicates impact of Hg on the self-purifying capacity of soil and its
biological activity. Russian sanitary-hygienic legislation specifies, that this hazard factor having the lowest threshold value is selected as a limitative hazard factor and considered as the MAC of the particulate
chemical substance in soil. As regards mercury – this factor is translocative and equals to 2.1 mg/kg.
Table 1.6 Maximum allowable residues (MAR) of mercury in foodstuff
Allowable residues of mercury in foodstuff: |
MAR, mg/kg |
Fish |
0.5 |
Meat |
0.03 |
Milk products |
0.005 |
Vegetable |
0.02 |
Bread and cereals |
0.01 |
Fruits |
0.01 |
Juices |
0.05 |
Regulation on collection, package, transportation and utilization of mercury-containing wastes was given in the Instruction of the Ministry of Non-ferrous Metallurgy of the USSR, adopted in October 27,
1966. Many statements of the Instruction are outdated. Therefore regional rules on mercury-containing wastes management were developed in almost each region where a company dealing with collection
and treatment of mercury-containing wastes (mercury lamps first of all) is located.
1.3 Methodology of the Assessment
The present assessment of mercury releases in the Russian Federation has been undertaken by using a life-cycle approach. For each intentional application of mercury and each field of activity by which
mercury is mobilized as impurity the flow of mercury from its purchase/extraction to final release or disposal have been assessed.
The methodology is based on the principle of mass balance: al mercury brought into circulation (technosphere) will sooner or later be released to the environment of end up in waste products. For each area
of intentional application the use of mercury in production processes and in products is assessed on the basis of information obtained from enterprises or - in the case specific information could not be
obtained - from previous studies. Releases are estimated on the basis of direct information from the enterprises in combination with the official statistics on releases of mercury to air, water and waste
obtained from Goscomstat (see Annex 1). For the major uses of mercury, the enterprises have been visited in the frameworks of the present assessment.
For areas in which mercury is mobilized as impurity the total mobilization is estimated by multiplying raw material consumption (e.g. amount of coal used) with the concentration of mercury in the raw
materials.
In general terms it can be expressed as:

where the total amount of mobilized mercury (mobilization) is calculated by adding up the mercury content of all raw materials. The mercury content of each raw material is calculated by multiplying the
consumption of the raw material (consumptionx) with the mercury concentration of this material (concentrationx).
The releases from the processes (e.g. combustion of coal) to the different media are estimated by multiplying the total mobilized amount (mobilization) with media specific distribution factors (distribution)
using the following equation:
ReleaseAir = Mobilisation * DistributionAir
where distributionAir is the distribution factor expressing the share of the total mobilised mercury that is released to air by the process.
The distribution factors are either estimated on the basis of specific studies of the processes in the Russian Federation, or they are estimated on the basis of distribution factors obtained from other countries
using similar technology.
Almost all data used for the assessment are subject to a certain degree of uncertainty. To the extent possible the values are represented by "best estimate" and a range indicating the uncertainty. In most
cases it is not possible to estimate the uncertainty using standard statistical methods, but the uncertainty estimate is rather based on expert judgements. The ranges used in the assessment represent the range
within which the authors estimate that the right value will be with a probability of 90%. It means that for 10% of the estimates the true value may actually be beyond the indicated range. The probability
distribution is not necessarily a symmetric distribution around the mean e.g. can very uncertain estimates rather be assumed to be lognormal distributed (the probability that the true value is twice the "best
estimate" equal the probability that it is half the "best estimate").
Possible specific mercury consumption for the defence industry is not included in the assessment.
The object of the present assessment is to study the flow of mercury through the technosphere (see Figure 1.1). Mercury in the environment as well as environmental and health issues are briefly discussed in
a few chapters, but these issues have not been addressed uniformly through the report.
Figure 1.1 Schematic illustration of the overall flow of mercury through the technosphere
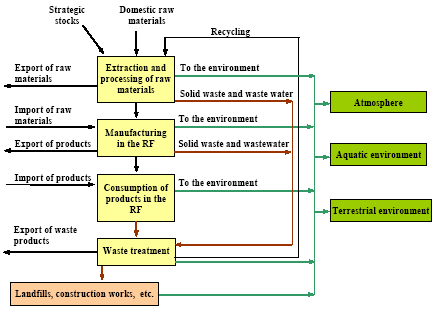
1.4 Mercury Chemistry
Mercury has been used since ancient times. The first record of mercury made by Aristotle dates back to 350 year B.C. Mercury was also found in writings of Aristotle's teacher, a founder of mineralogy;
Tirtamos from Eres, called Pheophrast. The chemical symbol of mercury "Hg" comes from Latin "hydrargyrum". It is believed that "hydrargyrum" (Greek words "hýdor" – water and "árgyros" – silver,
i.e. "liquid silver" or "silver water") was first mentioned by Pliniy the Senior (I c. A. D.).
Mercury was named by alchemists after the Roman god Mercury who was the god of commerce, profit and enrichment, custodian of roads, travelers and seafarers, patron of arts and crafts, connoisseur of
magic and astrology, guide of souls in the other world. The god Mercury was equated to the Greek god Hermes.
Origination of Russian name of mercury "“ðòóòü" is not known. The priority of adoption of mercury as an independent metal belongs to the famous Agricole. The solid mercury was first obtained in 1759 in
Petersburg by M.P. Braun and M.V. Lomonosov who managed to freeze the mercury in the mixture of snow and a concentrated nitric acid.
The following information has largely been extracted from the Global Mercury Assessment prepared by UNEP Chemicals (UNEP 2002), the Chemical Encyclopedia (Malaya Sovetskaya Encyclopedia, V.
2., pp. 1990. - 671), the reference book "the Properties of the Elements" (M. Metallurgia. 1997, p. 432) and the Geological Compendium on Mercury (V.P. Fedorchuk, E.F. Mintser, 1990, p. 215).
Mercury is a chemical element of the Group II in Mendeleyev periodical table; its atomic number is 80, the atomic weight - 200.59. Seven stable and more than 20 radioactive isotopes of mercury are
known. In normal conditions mercury is a heavy liquid metal. Textbooks specify such mercury as "elementary" or "metallic" (Hg(0) or Hg0). Mercury is relatively rarely found in nature in liquid (metallic)
form, but rather within organic and inorganic compounds, as monovalent and more often divalent Hg(I) and Hg(II) (or Hg2+) respectively. The elementary mercury contained in vapourous state in the
atmosphere, may transform into inorganic mercury compounds, thus providing possibility for precipitation of the technogenic mercury emitted to the atmosphere.
Mercury is rather rarely found in nature; its average content in the earth crust and main rocks is estimated within 3–9 * 10-6 % (by mass). The mass of mercury accumulated in the upper layer of the earth
crust of 1 km is estimated as 100,000,000,000 t (hundred billion tons), of which its natural deposits contain only 0.02%. The remaining part of mercury is extremely dispersed basically in rocks. Just this
dispersed mercury creates a natural geochemical background receiving mercury contamination caused by human activity.
By today more than 80 mercury minerals and dozens of mercury-containing minerals have been detected in nature. The basic ore mineral of industrial value is a cinnabar (vermilion, HgS). Globally there are
about 5000 mercury deposits, ore basins and ore-bearing sites which have their own names, about 500 of these have been developed in different times. Recently it has been detected, that mercury is
considerably concentrated not only in its native deposits, but in non-mercury ore deposits as well, such as pyrite, polymetallic, copper, gold and other, as well as in gas and gas-oil fields. Industrial production
of metallic mercury usually applies two Hg extraction technologies: distillate oxidizing roasting (basically cinnabar ores) under the temperature above 540°C with extraction of mercury from the gas phase and
(more seldom) a combined method including preliminary concentration of ores and further heating of the obtained concentrates.
Elemental mercury is a shiny, silver-white metal that is a liquid at room temperature and is traditionally used in thermometers and some electrical switches. The specific gravity of metallic mercury at 20°C is
13.5 g/cm3; the melting temperature is –39°C, the boiling temperature is +357°C. Frozen mercury (at –39°C) becomes solid and easy melt able. Having high ionization potential and high positive oxidability,
mercury is a relatively resistant chemical element. This conditions its ability to recover to the metal of various compounds and explains its existence in nature in its native state. Even under normal conditions,
the elemental mercury has an increased saturated vapour pressure and vapourizes rather rapidly – the faster the higher temperature is. This results in a mercury atmosphere hazardous for living organisms.
Impact of volt arc, electric spark and X-rays on mercury vapours creates the effects of luminescence, fluorescence and phosphorescence. The ultraviolet radiation is produced in vacuum tube between
mercury electrodes under electric discharges. This is used for mercury lamps designing. Dilution of metals in the elemental mercury provides formation of amalgams – metallic systems, which include mercury
as one of the components. They do not differ from the common alloys, although in case of a surplus Hg they are semi-fluid mixtures. Amalgamation is applied only for mercury wetted metals. The compounds
obtained in amalgamation are easily degradable below their melting temperature and release the excess mercury, which is widely applied at gold and silver extraction from ores.
Among inorganic mercuric compounds the most practically important are mercuric sulfide (HgS), mercuric oxides (HgO and Hg2O), iodic mercury (HgI), calomel (Hg2Cl2), and mercuric chloride (HgCl2).
These mercury compounds are also called mercury salts. The mercuric sulfide HgS is the most widespread Hg compound, which is known in three modifications: red (similar to cinnabar), black (black
mercuric sulfide or methacineabarite) and â-cinnabar (not found in nature). The iodic mercury exists in two modifications – red and yellow. The mercuric chloride is colorless rhombic crystals. Under
prolonged heating up to the temperatures close to the boiling temperature, the elemental mercury is combined with the atmospheric oxygen and creates red mercuric oxide (II) - HgO, with Hg ozidization
degree equal to +2. Yellow mercuric oxide (HgO) is obtained by adding alkaline to water solution of mercury salt (II). There is black mercurous oxide (Hg2O) – unstable compound with Hg oxidization
degree equal to +1. In all mercury compounds (I) its atoms are connected and create divalent groups –Hg2– or –Hg–Hg–. Such connection is kept in mercuric salts solutions (I). There are some other
inorganic mercury compounds such as fulminate of mercury Hg(ONC)2, mercuric nitrate Hg(NO3)2, mercuric sulfate HgSO4, mercuric sulfite HgSO3 etc. Impact of ammonia on the mercury salts creates
many complex compounds.
Some mercury salts (such as HgCl2) are sufficiently volatile to exist as an atmospheric gas. However, the water solubility and chemical reactivity of these inorganic (ionic) mercury gases lead to much more
rapid deposition from the atmosphere than for elemental mercury. This results in significantly shorter atmospheric lifetimes for these ionic (e.g. divalent) mercury gases than for the elemental mercury vapours.
There are many Hg-containing organic compounds, in which the atoms of metal are connected with the atoms of carbon. Chemical bond of carbon and mercury is very stable. It is not destroyed neither with
water nor weak acids nor bases. The most known are two types of Hg-containing organic compounds: R–Hg–R` and R–HgX, where R and R` - organic radicals, Õ – acid residual. The first group includes
apolar compounds which are almost insoluble in water and very volatile. The second group includes mercury compounds which are easily soluble in water and lipids and highly resistant in water, for instance
methyl mercury ion (CH3–Hg+). The well-known are such mercury organic compounds as dimethylmercury, phenylmercury, ethylmercury and methylmercury, however, by far the most common organic
mercury compound in the environment is methylmercury. The most toxic organic mercury compounds representing hazard for living organisms are alkylmercury compounds with a short chain in which
mercury is combined with the atom of carbon from methyl, ethyl and propyl groups (methyl mercury first of all).
Like the inorganic mercury compounds, both methylmercury and phenylmercury exist as "salts" (for example, methylmercuric chloride or phenylmercuric acetate). When pure, most forms of methylmercury
and phenylmercury are white crystalline solids. Eexceptionally toxic dimethylmercury, however, is a colorless liquid.
Methylmercury can be formed in the environment (especially in water bodies) by microbial metabolism (biotic processes) and by chemical processes that do not involve living organisms (abiotic
processes). It is generally believed that its formation in nature is predominantly due to biotic processes. Significant direct anthropogenic (or human-generated) sources of methylmercury are currently not
known, although some historic sources exist. Indirectly, however, anthropogenic releases contribute to the methylmercury levels found in nature because of the transformation from other mercury compounds
released to the environment. Examples of direct release of organic mercury compounds are the Minamata methylmercury-poisoning event that occurred in the 1950's where organic mercury by-products of
industrial-scale acetaldehyde production were discharged in the local bay, which caused accumulation of methyl mercury in marine food and mass poisoning and death of Japanese fishermen who at these
products; and the Iraqi poisoning events where wheat treated with a seed dressing containing organic mercury compounds were used for bread. The recent research has shown that methylmercury can be
released directly from municipal waste landfills and sewage treatment plants, but the general significance of this source is still uncertain.
Being a chemical element, mercury cannot be broken down or degraded into harmless substances. Mercury may change between different states and species in its cycle, but its simplest form is elemental
mercury, which itself is harmful to humans and the environment. Once mercury has been liberated from either ores or from fossil fuel and mineral deposits hidden in the earth's crust and released into the
biosphere, it can be highly mobile, cycling between the earth's surface and the atmosphere. The earth's surface soils, water bodies and bottom sediments are thought to be the primary biospheric sinks for
mercury.
1.5 Conceptual Model for Mercury Cycling
Conceptual models provide a clear written and graphical description, based on the current state of knowledge, of:
- the physical, biological, and chemical properties of a PBT that are significant for its fate, transport, and exposure; and,
- the causal linkages, to an appropriate level of detail, of sources, transport pathways, stressors, and human and wildlife receptors.
These models provide critical information about key monitoring targets (i.e., which sources, media, and receptors to monitor), as well as the temporal and spatial monitoring needs of a given compound. They
also provide information on relationships between media to give a complete multimedia perspective of the behaviour of substances in the environment.
The conceptual model for mercury is presented in Figure 1.2. As this figure depicts, mercury is emitted to the atmosphere from natural and anthropogenic sources, where it can cycle globally, constantly
moving among various environmental compartments through a complex combination of transport and transformation, ultimately resulting in human and wildlife exposure.
The most significant environmental releases of mercury are air emissions. In many countries, the largest emission sources of mercury are coal-fired electric utilities, coal-fired industrial boilers, and various
types of incinerators. There are also natural sources of air emissions, e.g., volcanoes. Mercury is released in other ways as well, including discharges from industrial sources to water bodies. Though releases
of mercury into water in most countries are believed to be small in comparison to atmospheric emissions, they can have significant local effects. For example, mercury discharges to surface waters from
abandoned gold and mercury mines often lead to high level of methylmercury in fish.
Figure 1.2 Conceptual model for mercury behaviour
Click here to see the figure.
2 Production, Import and Export
2.1 Production of Mercury in the Russian Federation
2.1.1 Historical View
First information on mercury production in Russia dates back to 1725, when a merchantman Peter Anisimov established a mercury factory, and the sources of feedstock were kept in secret (Kuzin, 1961).
The first commercial extraction of mercury ore (cinnabar) in Russia was initiated in 1759 at Ildikanskoye deposit in Transbaikalia and was occasionally carried out till 1853. (Korvatsky, 1907). The first
recovery of metallic mercury in Russia took place at this deposit. In the end of XIX – beginning of XX, minor amounts of cinnabar were extracted in alluvial deposits in Amur oblast. Approximately at the
same time, sections of Hg deposits were mined at Birksuisky ore deposit (South Fergana) and Khpek deposit (South Dagestan).
In 1879 Nikitovskoye mercury deposit (Ukraine) was discovered, the operation of which started (in parallel with metal smelting) in 1887 (Auerbach, 1888). In 1887-1908 annual volumes of Hg production
in Nikitovsky mine varied from 47.3 to 615.9 tonnes. The data-based estimations (Auerbach, 1888; Berling, 1928; Veber, Markov, 1917; Ore Industry..., 1922) show that since 1887 till 1917, 6,762 t of
metallic mercury was extracted at this mine, and a considerable part was exported (during 1889 - 1907 the exported was more than 5,145 t of Hg). In the beginning of XX century, Russia imported
cinnabar and mercury as well. For instance, in 1913, 56 t of cinnabar and 168 t of mercury were imported, in 1914 - 41 t of cinnabar and 129 t of mercury (Veber, Markov, 1917).
In 1900-1908, metallic mercury consumption in Russia varied within 49-118 t/year (Veber, Markov, 1917). At that time mercury was used in medicine and pharmaceutics, for production of mirrors and
paints, thermometers, barometers, manometers and other appliances, for rubbing pads of electrical machines, gold mining using the amalgamation method, copper and bronze gilding, felt treatment,
gold-embroidery and laboratory purposes.
2.1.2 Extraction and Primary Production of Mercury in the USSR and Russia
Before the USSR dissolution, metallic mercury was basically supplied to industrial enterprises from Ukraine (Nikitovka) and Kirgizia (Khaidarkan). Share of mercury annually produced in Russia usually did
not exceed 3-5% of total production in the former USSR. Totally, about 77,000 t of mercury was produced in the former USSR, including 7,300 t at Russia's enterprises [1].
For today, the State Inventory of Minerals of Russia has registered 24 mercury deposits, which in general have low quality ores (see Table 2.3). The most of the deposits are essentially mercury ones
(cinnabar) storing about not more than 2 th. t of the metal. Only four deposits are relatively large – Tamvanteyskoye (14 th. t), Zapadnopalyanskoye (10.1 th. t), Chagan-Uzunskoye (14 th. t), "Zvezdochka"
(3 th. t) (The Mineral Resources of the World by 1.01.2001..., 2002).
Table 2.1 Major mercury production sites in the former USSR*
Enterprise, deposit |
Operation period |
Mercury produced |
Note |
Ukraine |
Nikitovsky mercury combine,
Nikitovsky ore field (basically – Nikitovsky deposit)
|
1887-1995 |
More than 35,000 t |
In 1996 ã. ore extraction and production of mercury was stopped; in
the second half of 90-ies the combine reportedly recycled mercury from wastes,
as well as from previously extracted ores (20-50 t/year) |
Borkut Deposit,
Zakarpatskaya oblast
|
Middle of 60-ies – beginning of 80-ies |
About 500 t |
Underground mining |
Kirgizia |
Khardaykansky mining and smelting combine, Khardaykanskoye, Novoye, Chauvaiskoye,
Chonkoyskoye deposits |
Since 1942 up to now |
More than 32,000 t |
In 1995-2000 primary production of mercury amounted to 380-620 t/year |
Tadjikistan |
The concentrate produced at the concentrating plant of Anzobsky combineà
(Jijikrutskoye antimony deposit) was processed in Khaikardan |
End of 60-ies - 80-ies |
About 1,000 |
In 1993-2000 up to 9-80 t of mercury per year was produced from the concentrate;
it is planned to arrange internal mercury production in the country |
Azerbaijan |
Shorbulak and Agatyag deposits (Nagorny Karabakh) |
70-ies |
About 150 t |
The deposits are almost completely exhausted |
Kazahstan |
Lead-zinc combine, Ust-Kamenogorsk city (East Kazakhstan oblast), associated
mercury recycling from complex ores |
1970-80 |
About 130 t
(4-6 t/year in
average)
|
In 1996-2000, the associated mercury production amounted to 10-20
t/year ** |
Russia*** |
Aktash mining and smelting enterprise, Altai kray, Aktash deposit |
1941-1990 |
About 5 th. t (at annual volume from 30 to 130 t) |
In 90-ies the enterprise periodically melted the mercury from spent electrolyzers
of chlorine-alkali plants, mercury lamps, mercury oxides production wastes etc.).in
2002, the project on Hg-containing wastes recycling was elaborated (up to 15 th.
t/year with recovery of 120 t of recycled mercury); |
NPP Kubantsvetmet CJSC (former "Krasnodarsky Mine"), Sakhalin deposit,
Krasnodar Kray |
C 1970-õ ãã. äî1994 ã.. |
More than 500 t |
Due to economic difficulties the underground part of the mine was temporary
closed down in 1990, and the mine was abandoned in 1993; since 1995 the recycled
mercury production has been carried out from time to time |
Terluhaiskoye deposit, Tyva Republic |
1970-1972 |
40 t |
The dormant mine |
Plamennoye deposit, Chukotka |
70-ies |
About 150 t |
The deposit is exhausted; up to 30% of cinnabar reserves contained in dealluvial
deposit |
* in metallurgy and economy the distinguished are primary mercury (produced from mercury ores), accompanying mercury (obtained at extraction of ores of other metals, where mercury is contained as
impurity) and secondary mercury (recycled from waste).
**this estimation provided in various sources is obviously overvalued;
*** In Siberia (Altai, Kuznetsky Alatau, Zabaikailye, Khabarovsk kray) small mercury deposits (Soukhonkoye, Beloosipovskoye, Chuiskoye, Lanskoye etc.) were occasionally developed by prospectors
and small exploratory enterprises; the total mass of the metallic mercury amounts to about 150 t.
Sources: (Bagatayev, 1998; Butov et al, 1997; Reference Book..., 2002; the Mineral Resources of the World (at the beginning of 1994), 1995; the Mineral Resources of the World at the beginning of
1997, 1998; the Mineral Resources of the World at the beginning of 1998, 1999; the Mineral Resources of the World at the beginning of 1999, 2000; the Mineral Resources of the World at 1.01.2000,
2001, 2002; Obolensky et al., 1995; Mercury in environment of Siberia, 1995; Fedorchuk, 1983; Yagolnitser et al, 1995; http://www.rambler.ru/db/news/msg.html))
Considerable concentrations of mercury are observed in copper pyrite ores, polymetal, gold-silver and other types of ore deposits (Bobrova et. al., 1990; Ozerova, 1986; Pshenichny, 1975; Phedorchuk,
1983). The exceeded concentration (up to 88-800 mg/kg) of mercury is observed in copper pyrite deposits of the Southern Urals (Uchalinskoye, Uzelginskoye, Sibaiskoye, Buribaiskoye, Bakr-Tau,
Yubileynoye, Gaiskoye, etc.). Concentration of mercury in ores of gold-silver deposits in the north-east of Russia amounts to 8-75 mg/kg in average (up to 150-700 mg/kg max) (Sakharova et al., 1998).
The existing Russian technologies for processing e.g. copper pyrite ores do not employ mercury extraction (Permyakov, 1994). Therefore mercury is dispersed in the environment (basically with atmospheric
releases and solid waste streams). For instance the annual amount of ores mined in Safyanovskoye deposit contain up to 10 t of mercury which is lost during the ores processing (the Mineral Resources of
the World by 1.01.2001, 2000). According to the assessments (Butov et al, 1997), non-ferrous industries in Russia may ammually extract up to 100 t of accompanying mercury.
Table 2.2 Extraction and production of mercury in NIS countries, 1991 ( Rogovoy, 2000)
Country |
In % of total amount |
|
Extraction |
Production |
Kirgizia |
57 |
60 |
Ukraine |
31 |
37 |
Tadjikistan |
5 |
- |
Kazakhstan |
4 |
0.5 |
Russia |
3 |
2.5 |
Table 2.3 Mercury reserves in regions of the Russian Federation (Butov et al, 1997)
Region of RF |
Deposit |
Geological and industrial type |
Share in reserves (B+C1+C2), % * |
Hg content in ore, % ** |
Mercury deposits |
Altai kray |
Soukhonkoye |
Carbonate |
0.6 |
0.24 |
Kamchatka oblast |
Lyapganayskoye |
Opalite |
3.5 |
0.63 |
|
Alyutorskoye |
Opalite |
1.7 |
1.05 |
|
Chempurinskoye |
Opalite |
0.7 |
1.07 |
Kemerov oblast |
Kupriyanovskoye |
Quartz-dickite |
0.2 |
0.32 |
Krasnoyarsky kray |
Belokamennoye |
Quartz-dickite |
2.3 |
0.47 |
|
Salinskoye |
Quartz-dickite |
2.4 |
0.42 |
|
Dalneye |
Quartz-dickite |
1.8 |
0.31 |
|
Kaskadino |
Quartz-dickite |
0.1 |
0.14 |
Altai Republic |
Chagan-Uzunskoye |
Listvenite |
7.0 |
0.42 |
|
Cheremshnskoye |
Carbonate |
0.1 |
0.50 |
Saha Republic (Yakutiya) |
Zvezdochka |
Quartz-dickite |
6.2 |
1.59 |
|
Gal-Khaya |
Quartz-dickite |
1.1 |
0.60 |
|
Severnoye |
Quartz-dickite |
0.4 |
1.09 |
|
Sredneye |
Quartz-dickite |
0.3 |
3.40 |
|
Belgokakchan |
Quartz-dickite |
0.1 |
1.63 |
Tiva Republic |
Terlighaiskoye |
Polyargirite |
5.1 |
0.22 |
Northern Osetiya Republic- Alaniya |
Tibskoye |
Quartz-dickite |
1.6 |
0.25 |
Khabarovsk kray |
Lanskoye |
Polyargirite |
1.2 |
0.52 |
Chukotka Autonomous Okrug |
Tamvanteyskoye |
Listvenite |
33.1 |
0.70 |
|
Zapadnopalyanskoye |
Quartz-dickite |
24.0 |
0.53 |
Mercury containing deposits (associated mercury) |
Bashkortostan Republic |
Podolskoye |
Copper pyrite |
4.6 |
0.0025.0 |
Chelyabinsk oblast |
Talganskoye |
Copper pyrite |
0.6 |
0.0059 |
Sverdlovsk oblast |
Safyanovskoye |
Copper pyrite |
0.2 |
0.0014 |
* the revealed mercury stocks in Russia by 2001 are estimated as 45.3 th. t, including 15.6 th. t – industrial stocks;
** the average content of mercury in ores is equal to 0.453%.
The primary production of mercury in the former USSR in 1970-80 is considered to be up to 1,200-1,300 t per year (Butov et al, 1997). But at the same time, it is known that Khardaikansky combine in
the USSR time produced about 1,200 t of mercury per year (Mercury. Production and Processing// http...), and Nikitivsky ore factory annually produced up to 1,000 t of mercury (300-400 t of which is
recycled mercury) (The Mineral Resources of the World by 1997..., 1998). To all appearances, the data on primary production of mercury in the USSR provided in some domestic and foreign sources and
indicating production amounts equal to 1,900-2,200 t/year reflects the factual situation (see Table 2.4).
Table 2.4 Primary production of mercury in the former USSR and in Russia *
Year |
Country |
Mercury, t/year |
Source |
1981 |
USSR |
2,173 |
(Masters, 1983) |
1982 |
USSR |
1,966 |
(Masters, 1983) |
1983-1989 |
USSR |
By 1,500-1,700 |
(Metallgesellschaft, 1992), (Risk Reduction Monograph No. 4..., 1995) |
80-ies |
USSR |
In average by 2,200 |
(Skitskiy, Donskih, 1999) |
1991 |
USSR (NIS) |
1,330 |
(Reference Book..., 2002) |
1989 |
Russia (RSFSR) |
27 |
(the Mineral Resources of the World (at the beginning of 1994), 1995) |
1990 |
Russia (RSFSR) |
32 |
(The Mineral Resources of the World (at the beginning of 1994), 1995) |
1991 |
Russia |
28-32 |
(Reference Book ..., 2002; The Mineral Resources of the World (at the beginning
of 1994), 1995) |
1992 |
Russia |
27 |
(the Mineral Resources of the World (at the beginning of 1994), 1995; The
Mineral Resources of the World at the beginning of 1997, 1998) |
1993 |
Russia |
from 4 to 7 |
(the Mineral Resources of the World (at the beginning of 1994 ã.),
1995; the Mineral Resources of the World at the beginning of 1997, 1998) |
* In 1995 primary production of mercury in Russia was stopped (the Mineral Resources of the World at the beginning of 1998, 1999).
In present, the potential capacities for primary production of mercury are located at NPP Kubantsvetmet CJSC in Sakhalinskoye deposit of Krasnodarsky Kray (up to 50-60 t/year) and Aktash mining and
smelting factory in Altai Kray (up to 100 t/year). However, small scale and low quality of Hg ores of Sakhalin deposit and lack of own stocks of raw materials at Aktash mining factory make it impossible to
resume operations.
Today, primary production of mercury - neither from mercury ores nor as by-product - does not take place in Russia. Small amounts of sludge from processing of zinc containing about 30% mercury were
exported to Kyrgyzstan for further processing and mercury production. This is further discussed in section 4.4.
Development of large Tamvatneyskoye and Zapadnopolyanskoye deposits in scarcely populated areas of Chukotka is possible only with heavy capital investments, which can not be relied on given the
narrowness of internal and external mercury markets. Moreover, the development of these deposits can affect the spawning of valuable fish species.
2.1.3 Recycling of Mercury
Besides primary production of mercury, the market may be supplied with recycled mercury. Recycling of mercury takes place mainly in two enterprises. A detailed description of the actual situation including
waste types and processes can be found in section 5.1 whereas this section includes a historical view of recycling of mercury in the USSR and Russia. In 1966 the Council of Ministers of the USSR issued
the Special Resolution (No. 2155 dated 10.09.1966) obliging chemical and electro-technical industries to transport their mercury containing wastes to Nikitovsky Mercury Combine for recycling. Until
1990, the Combine had been receiving 12 types of wastes giving up to 400 t of recycled mercury (the Scientific Research Report..., 1999). The estimated (Skitskiy, Donskih, 1999) volumes of recycling of
mercury in the USSR amounted to 300 t/year.
Recently, some attempts were made towards arrangement of industrial recycling mercury from various types of wastes in Russia. E.g., in February 1993, the Sovtrade Danish Company agreed to set up a
joint Russia-Dutch enterprise for mercury containing wastes recycling. The design capacity of the enterprise on recycling of mercury planned to be built in Russia should have amounted to 1000 t/year; the
wastes import was considered as one of the raw materials sources (the Mineral Resources of the World (in the beginning of 1994), 1995). There was no information on this project published since that time.
In May 199, the Government of RF and the Government of Ukraine singed the Agreement on cooperation in the field of mercury containing wastes recycling, envisioning recycling of wastes (up to 500 t/year
with recovery of 12-15 t of mercury and its compounds) produced at Russian enterprises in Nikitovsky ore factory (Ukraine, Gorlovka town) (the Mineral Resources of the World in the beginning of 1997,
1998). However, this agreement had not been executed. The Federal Target Program "Wastes" for the period 1996-2000 adopted by RF Government Resolution No. 1098 dated 13.09.1996 envisaged
reconstruction of the metallurgical works of Krasnodarsky Mine for joint recycling of mercury containing raw materials (up to 5 th. t of wastes per year), installation of facility for recycling of mercury
containing electrochemical current sources in Ryazan oblast (500 t/year) and a number of other activities aimed at arrangement of mercury containing wastes recycling system in the country.
Nevertheless, in the first half of 1990-ies, minor amounts of recycled mercury were produced at Aktash mining factory; in the second half of 90-ies – at NPP Kubantsvetmet CJSC. In particular, according
to some information, the mercury containing wastes of some Russian chemical factories, paper-and-pulp factories and vitamin Â2 production facilities were recycled at NPP Kubantsvetmet CJSC, and in
smaller amounts at Aktash mining factory in the end of 90-ies.
Up to now, the great quantities of mercury containing wastes have been accumulated in Russia. For instance, by the end of 90-ies, their total mass was estimated at 1.1 million t (Klimov et al., 1999;
Scientific Research Report, 1999). The major part of such wastes (58%) contains 0.001-0.003 % of mercury, about 30% - more than 0.5% of Hg, about 12% - 0.01-0.5% (by mass). The available
information (Skitskiy, Donskih 1999) indicates that about 650,000 t of mercury containing (from 0.02 to 75%) wastes is stored in Russia; another 11,000 t is produced and stored annually. The non-ferrous
industries have accumulated more than 63,000 t of mercury-selenium slag containing about 155,000 t of mercury (Scientific Research Report, 1999). The so-called mercury stupp (up to 75-80% mercury
concentration) recycled from the mercury containing appliances is reported to be stored in special reservoirs at demercuration plants or specialised landfills. If it is true, the mercury concentration in such
stupp in Russia is equal to 30 t for the present.
The published estimations on the current production of mercury in Russia by recycling usually cover not only metal recycled from wastes, but the refined mercury as well, recovered from mercury containing
appliances (ignitions, manometers, thermometers) and the metallic mercury stored in scientific-research institutes, at industrial enterprises etc. The amount of such "ownerless" mercury, which is finally
returned to production process, can not be accurately estimated and is not controlled, but is reported to be very high.
For instance, according to Ecotrom SPE and Rtutservice Agency, in the end of 90-ies various companies in Moscow accumulated from 2.5 to 8 t/year of metallic mercury (including mercury extracted from
the appliances), which was recycled (treated) at NPP Kubantsvetmet CJSC. The Environmental Engineering Centre in Saint-Petersburg collected from various companies and extracted from the appliances
more than 6.5 t of mercury (including 1.5 t in 1997, more than 1.6 t in 1998; more than 0.5 t in the first half of 2000) during 1992-1998 (Korovotskiy, 1999; http://www.rambler.ru/db/news/msg.htm).
Ecologia Company in Samara annually collects up to 0.4-0.5 t of metallic mercury from various organisations, which is transferred to different users (Sedogin ). In 1996-2001 the Regional Environmental
Demercuration Center of Khabarovsk collected 980 kg of metallic mercury from industries and organizations, and took it outside the kray's borders (hhtp://www.khv.ru/MD/2001/12702/themel16.htm
(18.05.2001)). In the beginning of 2003, the warehouses of the Department of Civil Defence and Emergency of Primorsky Kray stored about 600 kg of metallic mercury (
http://novosti.vins.ru/?f=lf&t=010718c06 (01.02.2003)). In 1992-2001 Mercom JSC refined about 100 t of non-standard mercury (including 29 t in 1998), which is further shipped to the consumers
(Skitskiy, Donskih, 1999; the Mineral Resources of the World in the beginning of 1999, 2000). In the end of 90-ies – beginning of 2000, a certain amount of non-standard metallic mercury, as well as Hg
stupp, basically recycled from luminescent lamps, was transported to ECOS JSC (Kazan City) equipped with MRT System Swedish facility for recycling of mercury containing wastes and Ð2 (99.99%)pure
mercury recovery (Ref.: Environmental Protection. Kazan // http...).
According to estimations of Russian and foreign authors, mercury production by recycling in Russia in 1996-2001 varies between 30-50 t, which is presumed to reflect the real situation (Table 2.5).
Table 2.5 Recycling of mercury in Russia 1992-2001 * (Source: The Mineral Resources of the World (in the beginning of 1994 ã.), 1995; the Mineral Resources of the World in the beginning of
1997, 1998; Rogovoy, 2000; Sheveleva, 2001; additions of the author).
Year |
Mercury mass |
Note |
1992-1993 |
15-20 t/year |
Major part of mercury was produced at Aktash mining factory |
1994 |
More than 30 t |
The refined mercury constitutes the greater part |
1995 |
More than 20 t |
The refined mercury constitutes the greater part |
1996-1998 |
50 t/year |
Including the refined mercury (from 10 to 60% of the total amount) |
1999 |
About 25 t |
About 7.5 t was recycled at NPP Kubantsvetmet CJSC from mercury containing
wastes |
2000 |
More than 40 t |
About 30 t was recycled at NPP Kubantsvetmet CJSC from mercury containing
wastes |
2001 |
About 30 t |
The refined mercury constitutes the greater part |
* Including the refined mercury, the basic part of which is produced at Mercom JSC (Litkarino town, Moscow oblast); it's potential mercury refining capacity constitutes 100 t/year; the amount of recycled
mercury produced within end of 90-ies – beginning of 2000-ies by ECOS did not exceed 2 t/year. According to some data, the recycled mercury has recently being recycled from gold mining wastes in
Siberia (in Irkutskaya oblast in particulat), but there are no published data on production volumes (most probably that was the first metallic mercury, to some information it was even exported to China). The
amount of non-standard (ownerless) metallic mercury collected from different enterprises and extracted from the appliances and often returned to the production cycle (nationally) is equal to several t/year.
The annual production of metallic mercury in the USSR beginning with the middle of 70-ies usually 200-400 t exceed its internal annual consumption, this surplus created so called mercury stocks. In Russia
(in the beginning of 90-ies) the thousands tonnes of mercury were stored in stocks (the Mineral Resources of the World in the beginning of 1997, 1998). Since 1992 the stocks have been consumed for
internal purposes and sold in the foreign market. In 1999 Russia refused to sell mercury stored as strategic stocks (the Mineral Resources of the World by 1.01.2001, 2002).
2.2 Export and Import of Mercury
In 1979 - 1980 the USSR sold about 9,000 vessels of mercury on the European market (310 t of mercury annually) (Masters, 1983). In 1981 the USSR refused to export mercury (it was exported only to
COMECON countries and reached 100 t/year). The USSR has reportedly been exported mercury until the country's demolition (the Mineral Resources of the World in the beginning of 1997, 1998).
However, in the end of 80-ies the USSR apparently recommenced the sale of mercury to the foreign countries (according to some data, until 1992 the export of mercury from the USSR amounted to
450-500 t/year (Ðîãîâîé, 2000)).
In 1992-1998 Russia sold a part of its stocks of on the world market. E.g. in the middle of 90-ies, a greater part of Spanish import constituted of Russian stocks. Minas de Almaden company purchased,
refined and resold the mercury (the Mineral Resources of the World in the beginning of 1997, 1998), to the Russian enterprises as well.
The mercury export development in Russia is shown on the Table 2.6. The available data on mercury import in Russia (the Mineral Resources of the World 1.01.2001, 2002) are very scarce: 1997 - 30 t,
1998 - 46 t, 1999 - 11 t. In 2001-2002 one of Russian enterprises purchased annually about 15 t of mercury in Spain (Minas de Almaden).
Table 2.6. Mercury export from Russia 1992-2001 * (Source: The Mineral Resources of the World in the beginning of 1998, 1999; the Mineral Resources of the World by 1.01.2000, 2001; the
Mineral Resources of the World by 1.01.2001, 2002).
Year |
Export of mercury, tonnes |
1992 |
150 |
1993 |
535 |
1994 |
400 |
1995 |
926 ** |
1996 |
345.9 *** |
1997 |
1,000 **** |
1998 |
70 |
1999 |
965 |
2000-2001 |
N/A ***** |
* the Annual Compendiums "Customs statistics on foreign trade of the Russian Federation" do not contain direct information on export and import of mercury and its compounds;
** 120 t of Russian mercury was exported to the USA (Rogovoy, 2000);
*** Russia exported 79 t of mercury to the USA (The Materials flow of mercury in the Economies of the United States and the World); other sources (Rogovoy, 2000), say about 120 t of mercury;
**** Mercury was exported to Rotterdam, where it considerable part was sold by May 1998, and the rest 276 t – purchased by Minas de Almaden Spanish company (The Mineral Resources of the World
in the beginning of 1999, 2000); 120 t of mercury was reportedly exported from Russia to the USA (Rogovoy, 2000),;
***** The certain amount of mercury recycled from gold mining wastes by one of Irkutsk companies was sold to China in the beginning of 2000-ies; it was also reported that Mercom company exported
minor amounts of mercury (Donskih, Skitskiy 1999).
2.3 Domestic Mercury Market in Russia
Some estimations say about 1,000 t of metallic mercury annual consumption in 80-ies in the USSR (including more than 50% in chemical industry, 20-25% - in electronics and instrument-making, about 20%
- in defence industry) (Butov et. al, 1997). Other expert assessments (Yagoljnitser et al., 1993), indicates the average consumption of mercury equal to 1,250 t for the same period. According to some data
(Yusfin, Zaletin, 1998), the annual consumption of mercury in 1985 in the USSR amounted to 1,307.5 t; in 1989 – to 1,030 t (Scientific Research Report 1999). In particular years the metallic mercury
consumption the USSR was likely much more than 1,000-1,200 t. Some experts (Skitskiy, Donskih, 1999) say about 2,000 t of annual mercury consumption during the last years of the USSR existence
(which best corresponds to the annual production volumes by the way). As a rule, more than 80% of mercury used in the USSR was consumed by Russia's enterprises (Scientific Research Report, 1999).
The available data shown in Table 2.7 indicates the metallic mercury consumption in Russia during the latest decade.
Table 2.7 Mercury consumption in Russia (the Mineral Resources of the World (in the beginning of 1994), 1995; Rogovoy, 2000; Sheveleva, 2001; Yusfin, Zaletin, 1998)
Year | Mercury, tonnes |
1989 (RSFSR) | 866 |
1993 | 538 |
1994 | 400-450 |
1995 | 400 |
1996-1998 | 300-400/year |
1999-2001 | 280-300/year * |
* Annual potential mercury demand in Russian enterprises (according to the Financial Department of the Ministry of the Economic Development and Trade of RF) (Sheveleva, 2001); the actual consumption
is lower.
Table 2.8 presents the structure of metallic mercury consumption by various industrial sectors in the former USSR and in Russia within 1980-1993. The use of mercury today is described in the following
chapters and compared to the historical consumption figures in chapter "Summary and discussion".
Table 2.8 Mercury consumption in the USSR and Russia in 1980-1993 (Yusfin, Zaletin, 1998*; Yagoljnitser et al., 1993**)
Industry,
Field of application |
USSR |
Russia |
1980** |
1985* |
1989* |
1993* |
% |
t |
% |
t |
% |
t |
% |
Chemical |
63.4 |
910.2 |
69.6 |
462 |
53.4 |
310 |
57.6 |
Medicine, pharmaceutics |
2.1 |
35 |
2.7 |
12.5 |
1.4 |
9 |
1.7 |
Electrotechnology |
3.0 |
21.8 |
1.7 |
108.3 |
12.5 |
71 |
13.2 |
Instrument-making, electronics |
13.5 |
218 |
16.7 |
133 |
15.4 |
80 |
14.9 |
Non-ferrous metallurgy |
1.8 |
36 |
2.7 |
10 |
1.1 |
8 |
1.5 |
Agricultural chemistry |
- |
- |
- |
50 |
5.8 |
10 |
1.8 |
Scientific researches, novel techniques |
- |
30.5 |
2.3 |
25 |
2.9 |
10 |
1.9 |
Defence |
- |
- |
- |
40 |
4.6 |
20 |
3.7 |
Other |
16.2 |
56 |
4.3 |
25 |
2.9 |
20 |
3.7 |
Total |
100 |
1,307.5 |
100 |
865.8 |
100 |
538 |
100 |
3 Intentional use of Mercury
3.1 Chlor-alkali Production
About half of the chlorine produced in the Russian Federation is produced by using the mercury electrode method. The other part is produced by the diaphragm method. At present, there are four
chlor-alkali (chlorine and caustic soda) production facilities which use mercury in the Russian Federation [2]:
- CJSC "Kaustic", Sterlitamak City, Bashkortostan Republic (operated since 1977),
- JSC "Kaustic", Volgograd City, Volgograd oblast (operated since 1968),
- JSC "Kirovo-Chepetsky Chemical Combine", Kirovo-Chepetsk City, Kirov oblast (operated since 1955),
- JSC "Sayanskchimplast", Sayansk City, Irkutsk oblast (operated since 1979).
The following outdated production facilities were closed in 1980-s –1990-s:
- PA "Kaprolaktam", Dzherzhinsk City, Nizhegorodskaya oblast 10,000 t/y capacity – closed in 1982.
- CJSC "Kaustic", "Krebs" Plant, Sterlitamak City, Bshkortostan Republic 86,000 t/y capacity – closed in 1988.
- JSC "Usolyechimprom" (Usolie-Sibirskoye, Irkutsk oblast) 100,000 t/y capacity – closed in 1998.
Besides, in 1990-s small chlor-alkali production facilities operated in paper and pulp factories of Svetlogorsk (Leningrad oblast), Novodvinsk (Arkhangelsk oblast), Koryazhma (Arkhangelsk oblast) and
Komsomolsk-on-Amur (Amur oblast) were closed. Mercury in local waste dumps and the environment (soil in particular) around these closed down factories is further described in section 3.1.5. Location
of facilities for production of chlorine, caustic soda and vinyl chloride in the Russian Federation is shown on figure 3.1.
Figure 3.1 Location of facilities for production of chlorine, caustic soda and vinyl chloride in the Russian Federation (indicated by C)
Click here to see the figure.
3.1.1 Description of Production Process and Mercury Usage
The schematic process layout indicating the basic mercury flows and release sources is presented in figure 3.2 below.
Caustic soda (NaOH), chlorine and hydrogen are produced by electrolysis of a saturated water solution of sodium chloride (brine) [3] in a horizontal bath with a mercury cathode. The bath includes an
electrolyser, an amalgam decomposer and a mercury pump.
Figure 3.2 Process scheme of chlor-alkali production using mercury electrodes
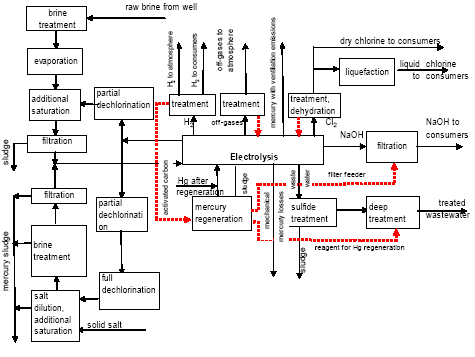
In the electrolyser, the electrolysis of the sodium chloride solution with formation of chlorine gas and a sodium amalgam (a sodium mercury alloy) takes place. The formed chlorine gas goes from the
electrolyser to cooling and drying (dehydration). Small amounts of mercury follow the chlorine gas.
The sodium amalgam is an intermediate product in the process and serves for the transfer of the generated NaOH from the electrolyser to the decomposer ensuring formation of a concentrated NaOH
solution with minimal impurity of chloride. The amalgam flows from the electrolyser through a mercury seal to the output pool and then to the decomposer. The decomposer is a short-circuited electrical cell
in which the sodium amalgam acts as the anode and graphite as the cathode in a sodium hydroxide solution. Softened water is added to the decomposer where it reacts with the sodium amalgam to produce
elemental mercury, sodium hydroxide, and by-product hydrogen gas. Mercury is partially released from the decomposer within hydrogen and NaOH, which consequently require mercury removal.
The input and output pools are supplied with softened water for the amalgam washing and cooling, as well as mercury evaporation decrease. Flue gases exhausted from the pools containing chlorine and Hg
vapours are directed to the treatment facilities.
Elemental mercury is recirculated back to the electrolyzer along a pipeline through a cooler, where is it cooled with water. The continuous circulation of mercury in the closed cycle is provided by a mercury
pump. When the mercury content of the electrolyser is decreased below established norms the necessary volume of mercury is added to the bath.
The hydrogen recovered from the amalgam decomposition is cooled with water in heat exchangers installed on the decomposer's covers. Most part of Hg vapours is condensed and returned to decomposer.
After cooling the hydrogen goes to a treatment and compression unit. A part of the recovered hydrogen is used for synthesis of hydrochloric acid or other products; the rest is released to the atmosphere
after mercury removal.
The caustic soda solution with 45-50% mass share flows from the decomposer's top to collection tank where it is cooled and filtered and then supplied to the consumers.
Water after washing and degassing of the electrolysis room's floors is collected to the container from where it is pumped to the mercury removal unit.
The quality of the brine fed to the electrolysis should be very high, first of all regarding iron content (not higher than 0.1 mg/dm3) and heavy metals (sum of vanadium, molybdenum and chrome - not more
than 0.01 mg/dm3). These requirements are concerned with the fact that by the recovering of the amalgam to elemental mercury mercury, the metals promote formation of so called "amalgam butter" – a
viscous mass with ferromagnetic properties (in case of iron) and a foamy mass (in case of vanadium, molybdenum, chrome). Generation of amalgam butter seriously destroys the electrolysers' performance
necessitating frequent cleansing connected with unavoidable losses of mercury at the electrolysis stops.
The electrolysis solution can be prepared by various methods and the selection of method has some influence on the formation of mercury-containing sludge:
(1) Evaporation of underground brine after its preliminary purification. Clean evaporated salt is then used for additional saturation of spent after-electrolysis brine which is returned to the electrolysis after fine
filtration (anolyte cycle). Simplicity of brine purification in anolyte cycle due to the use of clean evaporated salt is the main advantage of this method. It allows mercury dissolved in the brine coming out of the
electrolysers to return back to electrolysers rather than being removed from the cycle. Additional operation stage - brine evaporation - is the main disadvantage of this method.
(2) Additional saturation of spent brine with salt recovered from evaporation of alkaline solution at a diaphragm electrolysis plant. Application of this method is possible at those enterprises where both
mercury cell method and diaphragm method are used. It may be combined with the above-mentioned method. The advantages are: (a) minimum amount of mercury is lost with brine sludge; (b) within the
production cycle salt evaporation costs are significantly decreased if not eliminated at all.
(3) The dilution of halite deposit (or native sodium chloride as it is called in Russia), which is brought up to the site, takes place in solution tanks where calcium, magnesium, iron and heavy metals are removal
and the purified brine, after deep filtration, is pumped directly to electrolysers and from electrolysers it is fed back to the solution tanks for additional saturation and further removal of impurities. The
advantage of this method is that there is no need for brine evaporation, more over this method provides higher quality of purification and allows to remove more heavy metals, thus improving the efficiency of
electrolysis. Unavoidable loss of dissolved mercury, which is taken away from the electrolysis after its sedimentation as insoluble sulphide during the process of heavy metals removal, is a disadvantage
because industrial utilisation of such insoluble and Hg lean sulphide is very problematic and thus it is not practised.
Due to lack of current assets, high cost of mercury and tough requirements on issue of permits for its purchase, almost all enterprises had very limited stocks of mercury or had no stocks at all during the
latest 5 years. While it should be noted that incomplete charging of electrolysers with Hg is very undesirable due to a negative impact on electrolysis indicators resulting in Hg losses increase, i.e. this deficit
aggravation.
The caustic soda production by mercury method for the latest 5 years is presented in Table 3.1. The main consumers of chlorine produced in sodium chloride electrolysis are plants for production of
polyvinyl chloride, epichlorohydrins, trichloroethylene, dichloroethane, and other production plants. After fulfilment of RF Government of the engagements related to the Montreal agreements and closure of
ozone depleting coolants and carbon tetrachloride productions, chlorine consumption has considerably decreased resulting in lowering of electrolysis loads and caustic soda production, both by the mercury
and by the diaphragm method.
Table 3.1 Caustic soda production using mercury in RF, 1998-2002
Enterprise |
Capacity in 01.01.031000 tonnes |
Commissioning date |
Output by years, th. tonnes NaOH |
1997 |
1998 |
1999 |
2000 |
2001 |
2002 |
CJSC "Kaustic", Sterlitamak |
157 |
1997 |
88.9 |
78.3 |
103.6 |
122.9 |
109.3 |
110.8 |
JSC "Kaustic",
Volgograd |
110.4 |
1968 |
95.3 |
94.6 |
117.6 |
127.0 |
127.5 |
121.5 |
JSC "Kirovo-Chepetsk Chemical Enterprise", Kirovo-Chepetsk,
Kirovsk oblast |
205 |
1955 |
45.7 |
50.6 |
58.7 |
81.3 |
70.5 |
60.3 |
JSC "Sayanskchimplast", Sayani, Irkutsk oblast |
160 |
1979 |
51.8 |
58.4 |
79.1 |
101.2 |
112.6 |
114.5 |
TOTAL |
573.4 |
|
281.7 |
281.9 |
359 |
432.4 |
419.9 |
407.1 |
3.1.2 Pathways of Mercury Loss from Production Processes
As follows from the above description of the production process, the main pathways of mercury loss are caustic soda, hydrogen, wastewater, off-gases, chlorine, sludge, ventilation release, and mechanical
losses.
The magnitude of losses is determined by the applied technological process, how the technological conditions are observed, as well as by the general production culture, and availability and efficacy of
operation of mercury treatment units.
Magnitudes of losses according to the first five pathways are, as a rule, small and easy to adjust, provided the relevant mercury removal processes are used. Mercury lost with caustic soda, chlorine and
hydrogen is distributed, in negligible amounts, among users of such products and is ultimately released to the environment or waste by the use or disposal of the products.
Mercury lost with off-gases, a part of hydrogen, unused in production, and with ventilation release is emitted to the atmosphere, while mercury discharged with non-recycled wastewater is discharged to the
aquatic environment.
Losses of mercury with brine slurry are defined by the brine treatment methods used at production facilities. When salt is brought from outside without evaporation of the primary brine, such losses are big,
and when clean evaporated salt is used such losses are small. Brine slurry with a low concentration of mercury is not treated; rather it is compacted and accumulated at specially equipped and controlled
landfills at the production sites.
Magnitude of loss of mercury with other types of sludge, removed from electrolysers during treatment, or formed during backwash of filters, or after sedimentation of wastewater, or removed from spent
graphite in decomposers, activated carbon, ion-exchange resins, etc., can be minimized through thermal regeneration of mercury from them.
Losses of mercury as a result of release resultant from intensive ventilation of the electrolysis room cannot be, practically, reduced by any other means, but only through a high organization of production,
including sealing of bathtubs and, above all, amalgam decomposers, maximum decrease of stops and cleanups of bathtubs, accidental spilling and leakage of mercury, and through organization of proper
collection of spilled mercury. Mercury vapours released through ventilation by aeration lanterns in the electrolysis room are condensed and precipitated on the constructions and into the soil within the area
adjacent to the production facility. Under the impact of atmospheric precipitation and natural processes of evaporation and condensation such mercury may get into water bodies and hence beyond the
primary discharge area.
Mercury can be lost from the electrolysers and decomposers with leaks – occasional or caused by flanges unsealing, as slag and during cleansing with anolyte. Number of these losses significantly depends
on electrolysers operating procedures, their constructive features and non-stop functioning periods' duration.
Losses of mercury in production, as enumerated above, when it gets into air, water bodies or special storage facilities, are easy to control and, as the global experience shows, should be indicated in the
reports of the enterprises.
However, in such case they do not take into account mechanical losses resultant from incomplete catch and return of mercury spill during maintenance and repairs of electrolysers. Such losses may constitute
a significant part of the total losses of mercury in chlorine-alkali production. In the technical reports of enterprises of the former USSR and of the Russian Federation such losses are indicated as part of
general use of mercury, which gives an idea that such losses are extremely high as compared to similar indicators of other countries. Mechanical losses may be calculated only as a difference between the
quantity of mercury brought from outside so as to supplement for its losses through other causes during a long period of time (a three-month period or a year).
The losses from enterprises in the Russian Federation are in the summary, section 3.1.6, compared with losses reported from other countries (OSPAR 2002).
Reduction of mechanical losses can be reached through a maximum decrease of stops of electrolysers for cleanup and repairs, strict observing of maintenance standards and technological discipline,
improved quality of repair, organisation of permanent collection and return to electrolysers of spilt mercury treated additionally to the required standard, organisation of sealed floors in electrolysis room,
arrangement of trays and pits for collection of wastewater and spilt mercury and through vacuum collection of mercury.
At the same time it should be noted that the issue of environmental role played by mercury lost mechanically is ambiguous. Mercury can get into soil through unsealed floors of production buildings (above all,
from the electrolysis building) and then accumulated in underground layers. The depth of its penetration and ways of its further migration, including possible getting into water bodies, is defined by geological;
features of the area.
In view of this, it is necessary to keep in mind that directly under the buildings wherein chlor-alkali production facilities have been in place for several decades, as well as within the area adjacent to such
buildings metallic mercury may get accumulated in amounts up to several hundred tonnes. Therefore, issues of containment of mercury migration as well as issues of its possible return are very important.
Such issues can be resolved only with participation of geological services.
3.1.3 Methods of Mercury Removal from Products, Discharges, Waste and Off-gases
To prevent emission of mercury to atmosphere and it's getting into water bodies, enterprises producing caustic soda and chlorine using mercury methods apply methods for cleanup of gaseous, liquid and
solid waste, thereby reducing the content of mercury below the set standards.
Thus, to prevent emission of harmful gases to air in the electrolysis room, it is provided to clean off-gases from mercury – such gases are sucked from the outlet pockets of electrolysers by fans. Further, such
gases are cooled to a temperature not higher than 15 °C so as to condense part of mercury and water vapours. Cooled off-gases pass through a fog separator to remove mercury drops, and then through
filters with a double layer of activated carbon so as to remove mercury vapours. After the filter the off-gases with a mass concentration of mercury not more than 0.01 mg/m3 are released to atmosphere.
The spent packing is sent for regeneration.
Off-gases containing chlorine and mercury, sucked off the inlet boxes, are sent to be cleaned by an alkaline solution of sodium hypochlorite.
Condensate of mercury and water vapours from the cooler and the filter is collected to the receiver and pumped to the plant where it is cleaned from mercury.
After pre-treatment from the bulk mercury removed from the decomposer in the coolers, installed directly at the decomposers, hydrogen is fed for final cleanup from mercury. Mercury removed with
hydrogen is partially condensed in hydraulic valves installed on the hydrogen collector, wherefrom it is collected and returned to the electrolysers.
Then, hydrogen is cooled to temperature not more than 15 °C and fed to the filter wherein the bulk drops of mercury are retained. Then, hydrogen is fed to the suction side of the hydrogen collector.
After the compressor, hydrogen is cooled to temperature not more than 40 °C and fed for the final stage of mercury vapour clean to the filters packed with activated carbon. The spent packing of the filters is
sent for thermal regeneration. Cleaned hydrogen with the mass concentration of mercury not more than 0.01 mg/m3 is sent to users or released to atmosphere.
When caustic soda and chlorine are produced using a mercury method, caustic soda solution is filtered from fine-dispersion metallic mercury and graphite dust entrained from the decomposers. Caustic soda
after the decomposers is cooled to temperature 55-75 °C and then is fed for filtration. Cleaned solution with NaOH content not less than 46% and the mass share of mercury not more than 0.00007% is fed
to users or to storage tanks.
Mercury slurry and amalgam oil from the electrolysis room are fed in drums to the regeneration bay for treatment, including a preliminary settlement or separation of the bulk mercury portion followed by
thermal regeneration. Liquid mercury separated from slurry is fed to metal cylinders, while slurry is sent to the regeneration bay for mercury regeneration in electrically heated ovens. All solid waste containing
mercury, spent packing of the filters for hydrogen and alkaline cleanup, as well as sorbents from wastewater treatment plants are sent there; exception is brine cleanup slurry with small volumes and a low
concentration of mercury. For de-mercuration of spent bulky equipment before such equipment is processed as scrap, special tunnel ovens are used.
Off-gases are sucked from the tank wherein the slurry is treated by a fan and sent to the sanitation adsorbent filter for cleanup, and then they are released to atmosphere, provided the mercury concentration
is not higher than 0.01 mg/ m3.
Slurry is loaded to the oven, which is then tightly closed. Regeneration is done at a temperature of 500 C, with rarefaction of 10-20 mm of water column built by the fan. A mixture of gases with mercury
vapours is passed from the oven by the tubular condenser cooled by circulating water. The condensed metallic mercury is fed to the collector wherefrom it is fed to electrolysers as required. To prevent
oxidation of mercury, a low flow of nitrogen is fed to the oven.
Wastewater is cleaned from mercury by sorption method in ion-exchange resins, with pre-oxidation of metallic and monovalent mercury, as well as by transferring mercury compounds to water-insoluble
HgCl2_ through chlorination of wastewater by gaseous chlorine or to an insoluble HgS through treatment by sodium hydrosulphide. After the mercury has been transferred to insoluble state, water is fed for
filtration through mechanical filters. When chlorination treatment is used, wastewater is fed, after filtration, to the absorber filled with activated carbon – for de-chlorination. This is done to prevent active
chlorine getting into treated wastewater. Wastewater cleaned from the bulk mercury is fed by pumps to the absorbers filled with ion-exchange resin. The number of absorbers used is from 2 to 6 absorbers.
Resins of different brands can be fed into them sequentially. Treated water, with the mercury concentration not more than 0.005 mg/l, is fed to the tank, wherefrom it is pumped to clarification tanks. After
cleanup, wastewater neutralised by alkaline can be sent to tanks for their reuse in production. When cleaned water does not meet the standards, it is fed for a new cleanup.
Spent ion-exchange resin with the mercury concentration of 40% is fed, from the first absorber, as well as up to 10% from other absorbers, to the mercury regeneration plant or to the mercury processing
enterprise.
3.1.4 Production of Chlor-alkali and Mercury Loss at Operating Enterprises
3.1.4.1 Kirovo-Chepetsk Chemical Enterprise OJSC
The electrolysis room is equipped with electrolysers P-20M and vertical decomposers. Totally, 92 electrolysers are installed, rated 200 kA, and the output of caustic soda at 207,000 tonnes.
In 1997, there were 47 electrolysers in operation, rated 84 kA.
In 2002, there were 63 electrolysers, rated 79 kA.
Preparation and cleanup of brine for electrolysis is made by additional saturation of anolyte cycle with untreated solid salt, followed by its complete cleanup from admixtures, including sulphide. Raw materials
used for production of chlorine and caustic soda include salt transported from the Baskunchak fields.
Final saturation of brine, circulating in production, is done directly in salt solutions, while cleanup with soda and alkaline and sulphide method is done in Dorr settling tanks followed by filtration. The process
applied provides for a high degree of brine clarification from admixtures that are harmful for the process, but it also includes a loss of all mercury dissolved in the anolyte during electrolysis process and fed for
its dechlorination and final saturation.
The design and the quality of maintenance of the electrolysers ensures, in addition to a high cleanup of the feeding brine, minimum mechanical losses of mercury with wastewater and entrainment by ventilation
air.
Regeneration of mercury form slurry in the electrolysis bay, after a preliminary separation from them of the bulk mercury in a reactor with a stirrer, as well as from the spent reagents from the plants for
treatment of hydrogen, caustic soda, wastewater, etc., is done by the method of thermal recovery in a blast oven, following which the recovered mercury is returned for electrolysis. There are no any
noticeable losses of mercury during this operation.
Production waste containing metallic mercury (spent bottoms of the electrolysers, hydrogen and mercury coolers, amalgam decomposers, buffer tanks and other contaminated equipment) is thermally treated
before being used as scrap or transferred to the site for disposal of waste classified as 3 or 4 class hazard waste. Metallic mercury is used in production, after the vapours are condensed. Before releasing to
atmosphere, contaminated air is cleaned by adsorbent HPR-2 (in Russian – ÕÏÐ-2)
Losses of mercury during production process include losses with brine cleaning slurry, wastewater discharged to the wastewater removal system, with ventilation discharge, off-gases and hydrogen emitted to
atmosphere, with air released from the waste thermal treatment plant, with waste after thermal regeneration of mercury slurry, with products (chlorine, caustic soda and the part of hydrogen used to produce
hydrochloric acid), and with groundwater, including loss resultant from discharge of mercury through the enterprise rainwater discharge system, filtration of non-cleaned wastewater through the floors in the
electrolysis room and drainage from the slurry accumulators.
Below is given assessment of such losses for 1997 and 2002.
Losses of mercury with salt-dissolution slurry
Before 1997, mercury-containing slurry from brine cleanup at the Dorr settling basins and after regeneration of sand filters had been filtered at drum vacuum filters and then discharged to a slurry
accumulator, i.e. a banked controlled area of 4.5 hectares, whose bottom and banks were made from moisture impermeable clay. Also, spent sulphuric acid from the chlorine drying stage and the
wastewater after sulphide settling of mercury were discharged to the same area. Excessive clarified water from the slurry accumulator with mercury concentration up to 0.05 mg/l in the amount of 10-15 m3/h
was discharged to the wastewater removal system of the enterprise. Salt-dissolution slurry containing insoluble mercury sulphide was stored in the controlled area designed for storage of waste rated as
waste belonging to 3 or 4 hazard class. When sections of the site were filled with slurry, such areas were covered by a layer of fluorine gypsum.
In 1998, a unit for deep wastewater treatment was put into operation at the plant. This increased the degree of wastewater treatment and reduced the volume of treated wastewater; brine cleaning slurry from
the Dorr settling basins was fed to the salt dissolvers followed by its storage, together with the salt dissolution slurry, in the area designed for disposal of waste classified as 3-4 class hazard waste. This made
it possible to stop using the slurry accumulator and completely terminate discharge of wastewater from it.
Since 2002, the plant for decomposition of brine-cleaning carbonate slurry by means of hydrochloric acid was put into operation, which allows returning the generated chlorine calcium to the salt dissolution
stage. This made it possible to reduce volumes of stored slurry.
Losses of mercury with slurry generated during brine dissolution and cleaning were:
- In 1997: 12.432 t (including 3.85 tonnes from the wastewater treatment plant),
- In 2002: 14.940 t (including 3.414 tonnes from the wastewater treatment plant).
Losses of mercury with wastewater
Before 1998, wastewater had been treated by the method of mercury precipitation as an insoluble sulphide, followed by its settling in the slurry accumulator and discharge of the clarified water to the
wastewater discharge system of the enterprise. In 1998, the deep treatment of wastewater by precipitation of mercury as sulphide was started, including also filtration through KMP-25 filter, storage
of sulphide slurry in the area for disposal of waste classified as 3-4 class hazard waste, and followed by a final cleaning of filtered water by an ion-exchange method. Filtration slurry is stored in the site
designed for disposal of waste classified as 3-4 class hazard waste. The concentration of mercury in the discharged wastewater makes 0.0008-0.001 mg/dm³, while the norm is 0.001 mg/dm³.
Losses of mercury with wastewater were:
- In 1997: 1,266 g;
- In 2002: 125 g.
Losses of mercury with ventilation discharge
The system of ventilation in the electrolysis room is plenum, with outlet through aeration lanterns. The lantern height is 12 mother flow rate of pumped in air is 800-1000 thousand m3/h.
Concentration of mercury in discharge is 0.012-0.017 mg/m3.
Discharge of mercury through the aeration lanterns of the electrolysis room made:
- In 1997: 99 kg;
- In 2002: 139 kg.
Losses of mercury with ventilation discharge from the wastewater pumping and cleanup bay made:
- In 1997: 3.89 kg;
- In 2002: 5.1 kg.
The mercury discharge does not exceed the set standard MAD.
Losses of mercury with hydrogen
Out of the total amount of generated hydrogen, 75% is discharged to atmosphere through a stack 15 m high.
Before 1998, two-stage hydrogen cleaning from mercury had been organized through reflux with chloranolyte and alkaline brine. In 1998, deep cleanup method by adsorption in activated carbon was
started, which allowed increasing hydrogen cleaning degree by an order of magnitude.
Losses of mercury discharged with hydrogen made:
- In 1997: 0.42 kg,
- In 2002: 0.056 kg.
The mercury discharge does not exceed the set standard MAD.
In 1997, users inside the enterprise received 2.83 kg of mercury with untreated hydrogen.
Losses of mercury with off-gases
Cleaning of off-gases from mercury and chlorine is made by saturation of the latter by an alkaline solution of sodium hypochlorite.
Discharge of mercury with off-gases made:
- In 1997: 4.6 kg,
- In 2002: 2.65 kg.
The mercury discharge does not exceed the set standard MAD.
The spent saturating solution is fed to the anolyte cycle.
Losses of mercury with groundwater
Losses result from discharge of mercury by the rainwater system of the enterprise with the surface fun-off, filtration of wastewater through the floors in the electrolysis room and drainage from the site
for disposal of waste classified as 3-4-class hazard waste
They were:
- In 1997: 11.0 kg,
- In 2002: 11.5 kg.
By their origin, they include some part of mercury emitted to atmosphere that is later precipitated on the soil and carried away by rain water, as well as some part of mercury discharged with the
residual moisture of mercury-containing slurry and, hence, they must be subtracted from such losses. However, since they also include mercury-containing wastewater a particular part of which lost
before its treatment, it is impossible to divide these components in terms of quantity.
Losses of mercury with products
With synthetic hydrochloric acid (HCl) containing 0.00001% of mercury such losses made:
- In 1997: 0.08 kg (mass of the obtained acid – 760 t),
- In 2002: 0.1 kg (mass of the obtained acid – 1002 t).
With caustic soda containing 0.00005% of mercury, such losses made:
- In 1997: 23 kg,
- In 2002: 30 kg.
Losses of mercury with discharge from the waste chemical treatment plant
Losses with discharge of contaminated air after chemical processing (de-mercuration) of waste made:
- In 1997: 0.0051 kg,
- In 2002: 0.0024 kg.
The mercury discharge did not exceed the set standard MAD.
Losses of mercury with slurry after its thermal treatment were:
- In 1997: 0.89 kg,
- In 2002: 0.91 kg.
Mechanical losses of mercury
Mechanical losses of mercury include, above all, metallic mercury spilt from the electrolysers, decomposers, pumps and service lines in the process of operation and repair work and mercury lost
irrevocably through filtration into the soil through damaged floors. It also includes mercury contained in the part of wastewater filtered through non-tight joints in the floors.
As was indicated in section 3.1.2, that such losses can be determined only by the difference between the known amount of mercury filled into the electrolysers from outside during the year and the total
fixed losses over the same period of time. In total 15.1 t of mercury was purchased in 2002.
In 2002 mechanical losses of mercury calculated in this way made 0.015 kg.
The mechanical losses of mercury from the plant is significantly lower than the losses from the other plant due to a high culture of servicing the electrolysers, sealed floors in the electrolysis shop and
good organisation of mercury collection.
Summary on losses
Losses of mercury discharged into the air, water of the settling basins, buried or stored with slurry as well as mechanically lost mercury and lost with merchandise commodities are shown in Table 3.2.
Table 3.2 Losses from Kirovo-Chepetsk Chemical Enterprise OJSC
Year |
1997 |
2002 |
Caustic soda output, t |
45,700 |
60,300 |
|
|
|
|
|
Mercury losses: |
Absolute. tonnes |
Specific. Kg/t NàÎÍ |
Absolute. tonnes |
Specific. kg/t NàÎÍ |
With slags of brine preparation, treatment to burial as sulphide
|
12.4317 |
0.272 |
14.9403 |
0.248 |
To the atmosphere with ventilation emissions, with treated hydrogen
and flue gases |
0.108 |
2.4•10-3 |
0.147 |
2.4•10-3 |
To the plant's wastewater collection system with wastewater
and groundwater |
0.001266 |
2.8•10-5 |
0.000125 |
2.0•10-6 |
With commodity products |
0.0238 |
5.2•10-4 |
0.031 |
5.1•10-4 |
With hydrogen by consumers |
0.00283 |
6.2•10-5 |
|
|
Mechanical losses |
n.a. |
|
0.015 |
2.5•10-4 |
Total losses (purchased) |
12.568 |
0.275 |
15.117 |
0.251 |
The data shown demonstrate that in 2002 there were a significant reduction of absolute and specific discharge of mercury to the wastewater system and specific losses of mercury with slurry resultant
from brine preparation. An insignificant increase of absolute losses of mercury in 2002, as compared to 1997, was related to a growth in the merchandise product output.
For Kirovo-Chepetsk plant, relatively small amount of mercury losses from mechanical operations (0.015 kg) resulted from technical upgrading of equipment, high-quality operation of the equipment,
controlling equipment repair process, adequate protection of floors, continuous collection and recycling of mercury spills, etc. as described in the present section.
Production stocks of mercury
There are 92 electrolysers installed in the shop. Of this number, 61 electrolysers are in operations, while the remaining 31 electrolysers are removed from operation.
The amount of mercury placed into the electrolyser is 2.71 tethered are 165.3 tonnes of mercury used in the operating electrolysers.
The stock of mercury in the electrolysers removed from operation makes 84 tonnes. At present, this stock is already used so as to supplement mercury to the operating electrolysers. The enterprise
does not have any other stocks of mercury.
Environmental condition
By rough estimates, the slurry disposed at the controlled sites ( i.e. in the slurry accumulator and the site for disposal of waste classified as 3-4 class hazard waste) include about 300 to 700 tonnes of
mercury, accumulated here over fifty years of the enterprise operation, basically in the form of mercury sulphide.
A significant, though hard to quantify amount of mercury sulphide, discharged basically with wastewater during period preceding the transfer to its deep treatment, as well as, possibly, of metallic
mercury precipitated from emissions to atmosphere and washed off by atmospheric precipitations, accumulated in benthic sediments of the hydraulic systems within the area adjacent to the area of
mercury dissipation, or carried by liquid and gaseous discharge. Also, some quantity of metallic mercury may be present, penetrated into deep soil layers and accumulated in some isolated sections
above the Perm clay.
According to survey made in 1995 by the State enterprise of environmental and geologic and geographic research, the International Scientific Environmental Centre and the Environmental Fund
"Mercury Hazard" (St. Petersburg), Kirovo-Chepetsk Chemical Enterprise ensures maximum possible for this technology degree of mercury safety while environmental situation in the area adjacent
the enterprises was estimated as moderately dangerous. It was recognised that a potential source of this hazard was accumulation of mercury and its compounds in benthic slurry, because it can be
transferred, by the impact of river biota, into easily soluble and highly toxic organic compounds.
The survey did not show any cases of intoxication of people, however, there were cases when the concentration of mercury in liver of wild fish caught within the area of mercury dissipation was above
the standard. Concentration of mercury in benthic slurry, as demonstrated by analysis, made from 0.4 to 5.1 mg/kg. However, site for sampling were not indicated. Also, it is possible that mercury
may penetrate from the slurry storage sites into groundwater due to absence of safe hydraulic insulation systems; mercury and its compounds may also get into industrial and potable water when water
is taken from water wells and shallow wells in individual households located within the indicated dissipation area. It has been forecasted that mercury contamination could further spread downstream
during periods of high water or during extraction of sand from the rivers.
According to the latest analysis data received by the environmental laboratory of Kirovo-Chepetsk Enterprise, the average concentration of mercury in the surface layer of the soil, within 1 km radius
from the enterprise, was 0.2 mg/kg. The average concentration of mercury in water sampled at the control site in the river Prosnitsa (500 m downstream the point of wastewater discharge from the
enterprise) amounted to Hg total - 0.0002 mg/dm3, Hg soluble - 0.0001 mg/dm3, which corresponds to the current MAC standard. In the control site of the Vyatka River, downstream of its tributary
the Prosnitsa River, the mercury concentration was less than 0.00003 mg/dm3. The average concentration of mercury in benthic sediments at the control site on the Prosnitsa River made ~ 0.2 mg/kg.
Options for release reduction
1. The enterprise has a high culture of operation of equipment and a high technological discipline. Over the last 5 years, it has put into operation plants for deep treatment of water and hydrogen and
improved the system of discharge and preservation of mercury-containing brine slurry. This has resulted in decreased losses of mercury per unit of production from 0.275 kg/t to 0.250 kg/t. The
current norms for maximum allowed discharge of mercury to water and air are observed.
2. Losses of mercury with brine slurry, ventilation discharge from the electrolysis room and groundwater, defined by specific features of the technologies and the conditions of slurry accumulators,
make over 99.5% of its total losses.
3. The existing technological scheme does not allow a radical reduction of losses of mercury with brine slurry, without a serious reconstruction of the brine preparation unit. Such reconstruction is
extremely difficult because of high capital costs.
There are possibilities for further reduction of the total amount of mercury lost in production and a substantial reduction of its losses into water and air.
Mercury losses can be reduced through the following measures:
- Reduction of mercury losses with brine slurry and ventilation discharge – through reconstruction of electrolysers and increasing their running time without opening or repair;
- Reduced infiltration of untreated wastewater from the electrolysis room into the soil – through reconstruction of the system for discharge and catch of wastewater from the electrolysis room;
- Cardinal reduction of penetration of mercury into the ground – through reconstruction of the salt dissolution unit and the waste disposal site.
4. At the same time, the main action that could allow cutting down by 99% the amount of mercury lost in production should be the construction of a unit for filtration of anolyte from mercury and
reconstruction of the existing plant for thermal treatment of mercury-containing waste.
Kaustic OJSC (City of Volgograd)
The electrolysis room is equipped with electrolysers R-101 (in Russian P-101) and horizontal amalgam decomposers rated 100 kA. Totally, 104 electrolysers are in operation. Brine for electrolysis is
prepared and cleaned by additional saturation of the anolyte cycle by clean evaporated salt followed by filtration in bulk filters. Raw materials used for production of chlorine and caustic soda include
evaporated salt from the underground brine and also return salt from alkali evaporation during diaphragm electrolysis.
Equipment of saturation units and brine filtration in the anolyte cycle is made from titanium and allows presence of up to 20 mg/l of activated carbon in the cycle. This excludes complete dechlorination
of anolyte by treatment of with sulphide, and mercury contained in the brine is preserved in it without loss with brine slurry. Brine from the electrolysers, after vacuum dechlorination, alkalisation and
additional saturation, is filtered through bulk filters. After filter regeneration, slurry containing insignificant quantity of mercury chlorides is sent to section N2of the accumulation basin. A more detailed
description of the system of controlled sites for waste disposal will be given below, in the chapter "Losses of mercury with wastewater and groundwater".
The design of electrolysers should be considered as not completely meeting the modern level of technology development, because, above all, horizontal decomposers and mercury pumps with a cone
rotor are used. However, because of regular repair and improvements, quality of their operation remains quite satisfactory while the use of metal-oxide anodes and a high degree of cleanness of the
brine makes it possible to have comparatively low mechanical losses and losses with ventilation discharge.
In 2001, reconstruction of the floors in the electrolysis building was basically completed, which allowed a substantially simplified process of collection of spilt mercury and prevention of leaks of
wastewater and mercury through the floors of the electrolysis room.
Recovery of mercury from slurry, collected in the electrolysis building, is made by the thermal recovery method. Recovered mercury is returned back to electrolysis. Also, the enterprise started
recovery of mercury from solid waste, accumulated during reconstruction of the floors in the electrolysis building. There is no significant emission of mercury in this operation.
Total production losses of mercury in the chlor-alkali facilities include losses with anolyte filtration slurry, wastewater, ventilation discharge, losses with products (caustic soda and hydrogen) and
mechanical losses.
Below is given assessment of such losses in 1997 and 2002.
Losses of mercury with anolyte filtration slurry
During filtration of alkalised anolyte following its additional saturation with evaporated salt, micro admixtures of iron and heavy metals, present mainly as hydroxides, are precipitated in the packing of
the bulk filters. When the filtering packing becomes clogged, it is, from time to time, regenerated by a back flow of the wash brine. Then, insoluble admixtures are settled and filtered. The wash brine is
filtered and returned to the anolyte cycle, while slurry is transported in special motor vehicles, equipped for carrying paste products, to the sites for disposal of waste classified as 2-4 class hazard
(section N2 of the accumulation basins). Mercury discharged with such slurry is represented by water-soluble chlorides.
Losses of mercury with anolyte filtration slurry made:
- In 1997: 112.3 kg,
- In 2002: 76.4 kg.
Losses of mercury with wastewater
The total amount of mercury-containing wastewater generated at the enterprise makes about 100-130 thousand m3/year. In addition to wastewater from the electrolysis building and brine preparation
bay, the wastewater includes spent solution containing FeCl3 from the shop where chemical de-mercuration equipment is installed.
Wastewater is cleaned by the method of mercury precipitation as sulphide followed by settling and filtration. The filtered slurry containing basically mercury sulphide is stored temporarily into
containers on a specially equipped site. In future, it is planned to send such slurry to a specialised mercury processing enterprise.
Wastewater containing – after sulphide cleaning – not more than 0.05 mg/l of mercury is sent to the second stage of treatment by absorption with suspension RZh-1 (in Russian ÐÆ-1), after which
concentration of mercury in water reduces to 0.005 mg/l. Treated and cleaned water is sent to a "dirty section" of the evaporation basins which makes part of the production waste disposal system (2
accumulation basins (sections 1 and 2) and 5 evaporation basins). The first section (with the area of 6.15 km2) receives wastewater (industrial, rail and sanitarian wastewater) after biological
treatment, while the second (with the area of 2.11 km2) receives liquid and solid waste including brine treatment slurry. Evaporation basins (with the total area of 65.5 km2) receive wastewater from
the accumulation basins as well as mercury-containing wastewater after sorption cleanup.
The basins are located in uninhabited region, at a significant distance (several dozens of kilometres) from enterprises, dwelling houses and water basins, and represent – according to the RF Water
Code – individual water bodies. The basin banks and beds are lines with water-resistant clay, 3-5 m thick. Along the basin perimeters there is a network of wells where permanent monitoring of the
underground aquifers is organised.
The two-stage system for treatment of wastewater used by the enterprise does not allow attaining the required standard of residual mercury concentration, equal to 0.001 mg/l.
Total losses of mercury with wastewater to the ponds and with treated wastewater made:
- In 1997: 2,783 kg ; ca. 1.7 kg;
- In 2002: 1,329 kg ; ca. 0.81 kg.
Losses of mercury with ventilation emissions
The system of ventilation in the electrolysis building is plenum, with outlets through the aeration lanterns. The lanterns have a height of 14 m. The flow rate of pumped-in air is 600,000 m3/h.
The mercury concentration in the electrolysis building is 0.03-0.06 mg/m3. Beside the electrolysis room, also the hydrogen bay, the operator's room, the pump and the oven rooms as well as the slurry
regeneration room are ventilated.
The total losses of mercury with ventilation emissions from the electrolysis building and other premises made according to the enterprises official reports:
- In 1997: 643 kg,
- In 2002: 387 kg.
Losses of mercury with hydrogen
All generated hydrogen is used within the enterprise, for production of hydrochloric acid and polyvinyl chloride resin. Since 1995, deep treatment of hydrogen fed to users has been done in three
stages: sprinkling with chloranolyte, alkaline brine and followed by residual mercury sorption on activated carbon. Concentration of mercury in treated hydrogen fed to the users is 0.01 mg/l.
Losses of mercury with hydrogen (actually with the manufactured products) made:
- In 1997: 0.408 kg,
- In 2002: 0.327 kg.
Losses of mercury with caustic soda
Caustic soda is filtered from graphite and dispersed mercury. The spent filtration material is stored together with mercury slurry.
Losses of mercury with caustic soda made:
- In 1997: 33.8 kg,
- In 2002: 28.4 kg.
Losses of mercury with chlorine
Mercury entrained by chlorine gas is transferred to sulphuric acid used for its drying. The acid containing mercury is distributed among internal users of the enterprise.
Losses of mercury made:
- In 1997: 56.2 kg,
- In 2002: 51.2 kg.
Losses of mercury with off-gases
Treatment of off-gases from mercury and chlorine is made by absorbing the latter with an alkaline solution of sodium hypochlorite.
Discharge of mercury with treated off-gases made:
- In 1997: 2.80 kg,
- In 2002: 1.53 kg.
Losses of mercury with wastewater, excluding wastewater from the electrolysis shop
Wastewater sent to the biological treatment plant includes rain, industrial and sanitation wastewater of Kaustic OJSC (1900-2500 thousand m3/year), fed through a gravity system, and wastewater
from outside (3,500-4,000 thousand m3/year), fed through the pressurised system.
The content of mercury in the wastewater, equal, on the average, to 0.002-0.004 mg/l, is determined, above all, by the discharge of mercury settled in the soil, discharge with the surface rainwater as
well as mercury dissipated by the wheels of the motor vehicles and footwear of the people over the territory of the enterprise. Also, this may include housing and industrial mercury-containing waste
(basically luminescent lamps).
Total losses of mercury with such wastewater made:
- In 1997: 29 kg,
- In 2002: 18 kg.
Mechanical losses of mercury
Based on the amount of purchased mercury and the total recorded losses, mechanical losses of mercury calculated in this way made:
- In 1997: 24,214 kg,
- In 2002: 4,510 kg.
Such a significant reduction of mechanical losses in 2002, as compared to 1997, was due to reconstruction of the floors in the electrolysis building after 1997, as well as an improved quality of
operation of the basic equipment.
Summary on emissions
Losses of mercury discharged into the air, water of the settling basins, buried or stored with slurry as well as mechanically lost mercury and lost with merchandise commodities are shown in Table 3.3.
Table 3.3.Losses from Kaustic OJSC (City of Volgograd)
Year |
1997 |
2002 |
Caustic soda output, t |
111400 |
121500 |
Mercury losses: |
Absolute. tonnes |
Specific. kg/t NaOH |
Absolute. tonnes |
Specific. kg/t NaOH |
To the atmosphere with ventilation emissions and flue gases
|
0.648 |
5.8•10-3 |
0.389 |
3.2•10-3 |
To the production wastes burial system with slags of wastewater
treatment and è anolyte filtration, as well as with the effluent |
2.895 |
0.026 |
1.396 |
0.011 |
With commodity output, including internal consumption |
0.090 |
8.1•10-4 |
0.080 |
6.6•10-4 |
Water bodies |
0.0017 |
1.5•10-5 |
0.0008 |
6.6•10-6 |
Mechanical losses |
24.214 |
0.217 |
4.510 |
0.0371 |
Total losses (purchased mercury) |
27.845 |
0.250 |
6.375 |
0.0524 |
A significant reduction of losses of mercury in 2002, as compared to 1997, is also due to a higher level of catching of mercury and mercury-containing wastewater in the electrolysis shop after
reconstruction of the floor, trays and pits.
As it can be seen from the Table 3.3, mechanical losses of mercury for Kaustic Volgograd cell plant were 4.51 t.
Annual mercury emissions to the atmosphere at Kaustic Volgograd cell plant were reduced in 2002 compared to 1997 as a result of the improved equipment servicing and general technical
improvement of the facility. However there is no direct correlation between the values provided for 1997 and 2002 and the annual mercury emissions from the electrolysis shops calculated using
airborne concentration and the total ventilation air flow rate, because other rooms and shops are also ventilated.
Table 3.4 shows the dynamic of the average annual specific use of mercury over 1997 through 2002.
Table 3.4. Specific use of mercury over 1997 through 2002
Year |
1997 |
1998 |
1999 |
2000 |
2001 |
2002 |
Hg specific consumption, kg/t NaOH |
0.250 |
0.200 |
0.200 |
0.110 |
0.08 |
0.052 |
As can be seen from the shown data, reduction of the use of mercury was gradual – when the floors in the electrolysis building were rebuilt and measures were taken to improve technological
discipline. Further reduction of losses can be attained, above all, through complete reconstruction of floors, trays and pits, increasing the trouble-free run of the electrolysers and a further
improvement of the quality of operation of equipment and of the technological discipline. Reduction of losses of mercury with wastewater and slurry can be attained through organisation and
putting into operation of plant for deep treatment of wastewater and mercury recovery from sulphide slurry and brine treatment slurry.
Production stocks of mercury
The total production stock of mercury is 229 tonnes, kept in the operating electrolysers. Mercury purchased for supplementing the electrolysers is practically used immediately in the production.
The enterprise does not have any other stocks of mercury.
Environmental condition
Environmental monitoring of the condition of the air basin, made permanently at Kaustic OJSC and in the adjacent industrial areas, demonstrates that the average concentration of mercury in the
air is close, in terms of absolute values, to the rated values of mercury emission to atmosphere, thus it is not exceeding the existing maximum allowed concentration. Thus, while data of 2002
shoed that the amount of mercury released to atmosphere with ventilation air and off-gases from the chlorine production facilities was 0.389 tonnes, then the total emission of mercury to the air,
estimated on the basis of monitoring over its content in the air basin made 0.401 tonnes.
Mercury sent with wastewater to the settling basins and evaporation basins does not make any significant input into the total content of the metal in the air basin, mainly because it is present in
slurry as insoluble and non-volatile compounds. Infiltration of mercury into underground aquifers under the basins, as demonstrated by the results of the permanent monitoring of samples taken
from a network of boreholes located along the basins' perimeters, is not identifiable which can be explained by a high degree of water inpermeability of the so called "chocolate" clays, protecting
the basin banks and bottoms.
At the same time, given the above mentioned fact that small amounts of mercury and its compounds are present in wastewater as mercury-containing wastewater, as was indicated in par. 4.2.8,
and taking into account a significant magnitude of mercury losses in production, it should be acknowledged that mercury and its compounds can get into water basins and underground aquifers
in the area adjacent to Kaustic OJSC.
By assessment made by specialised geological organisations, there may be up to 500 tonnes of mercury inside the ground under the chlorine shop.
It is not possible to make a strict estimate of the mercury amounts discharged to the air and water system from such reserves.
Options for release reduction
1. The production enterprise is characterised by a stable condition and by a generally high operational discipline.
2. The technological production process ensures low losses of mercury with slurry from brine treatment and gives opportunities for further reduction of losses of mercury and its emissions to the
atmosphere and water basins at the expense of available reserves for improvement.
3. Reduction of losses and discharge/emission of mercury can be attained through implementation of the following actions:
- Completion of the reconstruction of the floors, trays and pits in the electrolysis building;
- Creation and putting into operation of a system for deep treatment of wastewater from mercury using ion-exchange method so as to attain the maximum allowed standard of discharge/emission;
- Creation and putting into operation of a plant for recovery of mercury from sulphide slurry at the first stage of wastewater treatment;
- Increasing the output of the plant for thermal regeneration of mercury-containing slurry and de-mercuration of waste, making it possible to treat all mercury-containing slurry (safe for sulphide
slurry);
- Implementing a range of actions to increase the period between repair of the electrolysers so as to reduce mechanical losses and losses of mercury with ventilation discharge.
Kaustic CJSC (Sterlitamak)
The electrolysis room is equipped with electrolysers 30M2 (manufactured by O. De Nora, Italy) and vertical amalgam decomposers, rated for 400 kA. Totally, 34 electrolysers are installed.
Operation of the electrolysers is characterised by insignificant variations of the load for the electrolysis, due to unstable use of chlorine and caustic soda. In 1997, the electrolysers worked under
the average load of 232 kA, while in 2002 this load was 273 kA.
Preparation and cleaning of the brine for electrolysis is done by additional saturation of the anolyte cycle with evaporated salt, followed by filtration. Raw material used to produce chlorine and
caustic soda includes salt from the underground brine and also return salt from the alkali evaporated during diaphragm electrolysis.
Equipment of the units designed for final saturation and filtration of brine in the anolyte cycle is made of titanium and fibreglass, which allows 20-25 mg/l of active chlorine in the cycle. This
excludes complete dechlorination of the anolyte through treatment by sulphide, and mercury in the brine is preserved without any loss with brine slurry.
Brine after the electrolysers – after vacuum dechlorination, alkalisation and final saturation – is filtered through vertical sheet filters with a filtering layer based on pulp. Slurry after filter
regeneration, containing insignificant amounts of mercury chlorides, is sent to the dirty brine collector, which also receives anolyte from the electrolysers shut down for repair. Slurry from the
collector is loaded out and stored in the temporary storage site.
Electrolysis is made in high-capacity electrolysers equipped with metal-oxide anodes. The design, equipment and technical conditions of the electrolysers on the whole meet the modern level of
technology. However, performance of repair work on the electrolysers with high individual power increases the discharge of mercury vapours intro the air and of the mercury drops on the floor,
which causes high mechanical losses of mercury and entrainment with the ventilated discharge. Therefore, maximum increase of the run period of the electrolysers without opening them is very
important for this production enterprise.
Over 1997 through 2002, actions were taken to increase the run time between repairs of the electrolysers, which now is 500 days. The technical decisions taken for further improvement of the
design of the anode working part, the composition and the amount of active anode coating, and the organisation of an automatic voltage control system allows extending this period 2-3 times,
however, their complete use is hindered by restricted funds. Also, the service life of gummed materials of the electrolysers' parts is not sufficient. Another result of insufficient run period between
repairs of the electrolysers is a relatively high level of mechanical mercury losses and its entrainment with the ventilated air.
Over 1997 through 2002, work was performed to reconstruct and improve the equipment, as well as to increase the technological discipline among personnel. This helped reduce losses of
mercury at several production stages.
In 1998-2002, trays and pits in the floor of the electrolysis building were reconstructed, which allowed reducing losses of mercury with wastewater and mechanical losses at the expense of
collection and return of spilt mercury and slurry in the electrolysis building.
Mercury is regenerated from slurry by thermal recovery methods in a special oven. There, a mixture of mercury-containing slurry of brine filtration and wastewater is sent, including also spent
activated carbon after hydrogen treatment, off-gases, dechlorination wastewater and caustic soda filtration wastewater, as well as resin from the ion-exchange treatment of wastewater. Before
this waste containing various amounts of mercury is sent for recovery, such waste is mixed in such a way that the total concentration of mercury in this waste should be optimum for the thermal
recovery process.
In 1997, the amount returned for electrolysis was 4.02 tonnes, while in 2002 about 8.2 tonnes of secondary mercury was returned.
Production losses of mercury include losses with wastewater, ventilated discharge, slurry after recovery of mercury, losses with products (caustic soda and hydrogen) and mechanical losses.
Losses of mercury with wastewater
The total amount of mercury-containing wastewater was 48,000 m3 in 1997 and 73,000 m3 in 2002. All mercury-containing wastewater is collected in the interim tank wherefrom it is pumped
for preliminary rough filtration and settling. After the settling, water containing 3.5 mg/l of mercury, on the average, is clarified, chlorinated, fine filtered in quartz filters, dechlorinated by activated
carbon till the residual content of active chlorine becomes 30-50 mg/l; then, it is sent to ion-exchange treatment at three sequentially-connected absorbers. Spent resin, after flushing with water
and hydrochloric acid, is stored on the site for temporary storage of mercury waste, wherefrom it is sent, from time to time, for thermal recovery in a mixture with other slurry.
Concentration of mercury in treated wastewater made:
- In 1997: 0.016 mg/l,
- In 2002: 0.019 mg/l.
These values exceed the current standard of 0.001 mg/l.
Treated wastewater is fed to the general in-house system for wastewater polluted with minerals, and then to the system of settling basins located outside the enterprise. These settling basins also
receive conventionally clean wastewater from Kaustic CJSC including rainwater with no separate control of mercury in it. They also receive wastewater from three other enterprises. The share
of wastewater from Kaustic CJSC makes about a half of its total amount.
Totally, there are two settling basins with the volume of 2.1 million m3 each. They are equipped with stirring devices and a system of hydraulic insulation.
Wastewater is filled into and pumped from both settling basins autonomously so as to maintain at the outlet of each of them an optimum level of outputted admixtures.
Wastewater is discharged, after settling, into the Belaya River.
The total amount of irrevocable losses of mercury with wastewater were:
- In 1997: 0.786 kg,
- In 2002: 0.139 kg.
This significant reduction of losses in 2002 was due to the use of a more effective sorbent (resin AB17-8 instead BP1-AP).
Losses of mercury with ventilation emissions
The system of ventilation in the electrolysis building is plenum, with outlets through the aeration lanterns. The lanterns have a height of 18 m. The flow rate of pumped-in air is 1.2 million m3/h.
The mercury concentration in the electrolysis building was 0.018 mg/m3 in 1997 and 0.017 mg/m3 in 2002.
The total losses of mercury with ventilation emissions from the electrolysis building and other premises made according to the enterprises official reports:
- In 1997: 882 kg,
- In 2002: 441 kg.
Reduction of losses of mercury was due to the use of measures aimed at increasing the run time between repairs of the electrolysers.
Losses of mercury with hydrogen
All generated hydrogen is used within the enterprise (for HCl synthesis, propylene heating ovens for epichlorohydrins production) or transferred to other users (the synthetic rubber enterprise, oil
and chemistry enterprise).
Deep treatment of hydrogen fed to the users is made by a sequential sprinkling with chlorine anolyte, alkaline brine and subsequent sorption of residual mercury by activated carbon HPR-3P.
Concentration of mercury in treated hydrogen fed to the users is 0.003 mg/ m3.
Losses of mercury with hydrogen made:
- In 1997: 0.138 kg,
- In 2002: 0.08 kg.
Reduction of losses of mercury in 2002 was due to improved design of the sorption column.
Losses of mercury with caustic soda
Caustic soda is filtered from graphite and dispersed mercury through a layer of activated carbon. The spent carbon is sent to the site for temporary storage of mercury-containing waste, and
then for thermal recovery. The residual content of mercury in the filtered alkaline is 0.00002% by weight.
Losses of mercury with caustic soda made:
- In 1997: 242.8 kg,
- In 2002: 22.2 kg.
A sharp reduction of losses of mercury in 2002 was due to introduction of measures enhancing technological discipline among personnel.
Losses of mercury with chlorine
No such loss is identified, since mercury compounds practically completely absorbed by water during flush of humid chlorine.
Losses of mercury with off-gases
Treatment of off-gases is made by sorption on activated carbon HPR-3P. The amount of treated off-gases was about 500 m3/h. Concentration of mercury in treated off-gases was not more
than 0.0035 mg/m3.
Losses of mercury with off-gases made:
- In 1997: 7.148 kg,
- In 2002: 0.015 kg.
A sharp reduction of losses of mercury in 2002 was due to improved quality of operation of the electrolysers (in particular, normalising the temperature conditions and flushing of boxes) and
improved design of absorbers.
Losses of mercury with thermal recovery slurry
Slurry loaded from the thermal mercury recovery oven contains not more than 0.01% by weight of mercury. Such slurry is sent to the controlled site "Tsvetayevka", which includes a system of
buried concrete containers with special protective coating.
Losses of mercury with slurry made:
- In 1997: no data available,
- In 2002: 6.5 kg.
Mechanical losses of mercury
They are determined by the difference between the amount of mercury purchased during the year and the amount of mercury losses accounted for the same year. Also take into account is the
change in the total load of mercury into the electrolysers in comparison to the previous year. The last factor is important for the electrolysers 30M2, since their design allows using a broad range
of mercury in the electrolyser-decomposer-pump system; however, when the load of mercury is below the optimum level it brings down technological indicators of the electrolyser operation.
The above values were as follows (see Table 3.5).
Table 3.5. Calculation of mechanical losses of mercury in 1997 - 2002 at Kaustik CJSC (Sterlitamak)
Year |
Purchased mercury |
Changing the load in the electrolysers |
Accounted losses |
Mechanical losses |
1997 |
5,071.5 kg |
-4,057 kg |
1,133 kg |
7,995.5 kg |
2002 |
10,000 kg |
+5,371 kg |
470 kg |
4,157.82 kg |
It should be noted that mechanical losses of mercury calculated as indicated above include also mercury-containing slurry accumulated in the contaminated brine collector and in settling
basins for treated wastewater. Such slurry is accumulated over several years and then is sent for thermal recovery after planned inspections and cleaning of tanks and containers. In view
of the fact that this process takes place within a time period when the total losses of mercury have also changed, separate estimation of amounts of mercury brought from the electrolysers
and settled in the tanks or lost in the ground through non-tight floors is difficult to make.
Losses of mercury emitted to the air, water, buried or stored with slurry as well as mechanically lost are shown in Table 3.6.
Table 3.6 Losses of mercury at Kaustic CJSC (Sterlitamak)
Year |
1997 |
2002 |
Caustic soda output, t |
88940 |
110800 |
Mercury losses: |
Absolute. tonnes |
Specific. Kg/t NaOH |
Absolute. tonnes |
Specific. kg/t NaOH |
To the atmosphere with ventilation emissions and flue gases
|
0.889 |
1.0•10-2 |
0.441 |
3.98•10-3 |
To the wastes burial system |
No. data |
- |
0.0065 |
5.86•10-5 |
To the open water basin |
0.000768 |
8.6•10-6 |
0.000139 |
1.25•10-6 |
With commodity output, including internal consumption |
0.2423 |
2.72•10-3 |
0.022 |
2.1•10-4 |
Mercury releases with mechanical losses |
7.996 |
0.090 |
4.158 |
0.0375 |
Total losses (purchased mercury) |
9.218 |
0.1026 |
4.629 |
0.0418 |
A significant reduction of losses of mercury in 2002 as compared to 1997 was due to a targeted implementation of actions aimed at improving technologies for different production stages,
increasing technological discipline and control of repair quality. This helped reduce several times losses of mercury with treated wastewater and merchandise products and reduce two
times emissions to atmosphere and mechanical losses. At the same time, discharge/emissions for the last two categories remain insignificant, while their reduction will make it possible, in
future, to exercise a significant impact on the value of the total mercury losses. This can be attained, above all, as a result of a substantial increase of the run time of the electrolysers
without stops and repairs.
At Kaustic-Sterlitamak cell plant annual mercury emissions to the atmosphere were reduced in 2002 compared to 1997 as a result of the improved equipment servicing and general
technical improvement of the facility. However there is no direct correlation between the values of mercury emissions to the atmosphere provided for 1997 and 2002 and the annual
mercury emissions from the electrolysis shops calculated using airborne concentration and the total ventilation air flow rate, because other rooms and shops were also ventilated.
Production mercury stocks
There is 204 tonnes of mercury in production – in the operated electrolysers.
Mercury accumulated for the electrolyser supplementation and secondary mercury after recovery from slurry is practically used immediately to supplement for its loss in the electrolysers.
Some amount of mercury, both as metallic mercury and as slowly soluble salts (sulphuric acid and calomel) is deposited in the precipitation accumulated on the bottom of the settling
basins and wastewater clarifiers and the tank for collection of contaminated brine. The average time of storage is about 3 years.
It is difficult to make a quantitative assessment of such stocks.
The enterprise does not have any other mercury stocks.
Environmental conditions
The environmental department of Kaustic CJSC and the sanitary services of the city permanently control the content of mercury in the air basin at the enterprises and in the city of
Sterlitamak as well as in water (at the control site in the Belaya River) where treated effluents are discharged (see table 3.7).
Table 3.7 Content of mercury at the control site on the Belaya River, after the city (downstream of the point of discharge form Kaustic CJSC ), over 1999-2002*
Year |
Total number of analyses |
Number of samples exceeding MAC** for fishery water bodies |
Share of MAC exceeding samples % |
Maximum Hg content. mg/dm3 |
Average Hg content. mg/dm3 |
1990 |
135 |
135 |
100 |
0.00542 |
0.0011 |
1991 |
102 |
102 |
100 |
0.0061 |
0.0013 |
1992 |
103 |
103 |
100 |
0.0026 |
0.00106 |
1993 |
130 |
129 |
99.2 |
0.00083 |
0.00029 |
1994 |
137 |
137 |
100 |
0.00044 |
0.00029 |
1995 |
138 |
138 |
100 |
0.00038 |
0.00020 |
1996 |
105 |
105 |
100 |
0.00026 |
0.00015 |
1997 |
109 |
5 |
4.6 |
0.00004 |
0.000014 |
1998 |
76 |
3 |
3.9 |
0.00007 |
0.000002 |
1999 |
170 |
20 |
11.8 |
0.000092 |
0.000006 |
2000 |
324 |
4 |
1.2 |
0.00028 |
0.000002 |
2001 |
350 |
0 |
0 |
Not detected |
Not detected |
2002 |
354 |
1 |
0.3 |
0.00007 |
0.0000002 |
* Data provided by the Environmental Department of Kaustik CJS
** Maximum allowed concentrations of mercury are: for potable water: 0.0005 mg/l; for fishery water bodes: 0.00001 mg/l.
As can be seen from Table 3.6, the concentration of mercury in the Belaya River, beginning from 1998, has not exceeded the MAC for potable water ands for fishery water bodies.
A rough estimate of the magnitude of mechanical losses of mercury over the entire period of operation of this enterprise suggests that the soil under the electrolysis building accumulates
about 200-300 tonnes of mercury.
Options for release reduction
1. The production enterprise is characterised by a generally high operational discipline with small variations of operational conditions at the electrolyser loads.
2. The technological production process ensures low losses of mercury with slurry from brine treatment, off-gases and products, insufficiently low losses with treated wastewater and
comparatively high mechanical losses and losses into atmosphere with ventilation discharge.
3. The enterprise has potential for a further reduction of losses of mercury that can be attained through implementation of the following actions:
- Completion of the actions for increasing the run time between repairs of the electrolysers, including full switching over of the electrolysers for anodes with high-resistance active coating
and improved working basis, a complete re-equipment of the electrolysers with a system for automatic maintenance and governing of voltage and the use of high-resistance gumming
materials;
- Improving the depth of treatment of wastewater through introduction of an additional stage of chemical pre-treatment or enhancing the ion-exchange treatment stage.
Sayanskchimplast OJSC (Sayansk City)
The electrolysis building is equipped with electrolysers SDM-200/7.5 (Russian abbreviation) with metal-oxide anodes and vertical decomposers. The total number of electrolysers is 96,
rated for 200 kA. In 1997, there were 34 electrolysers working, with the load of 140 kA; in 2002, this number was 60 with the load at 160 kA.
Brine for electrolysis is prepared and cleaned by additional saturation of the anolyte cycle with clean evaporated salt, followed by a two-stage filtration on bulk and frame filters. Raw
material used for production of chlorine and caustic soda is salt from the underground brine, which is first cleaned and then evaporated.
Some tanks of the anolyte cycle are made from steel lines with acid-alkaline lines; some pipelines are from gummed steel. Condition of anti-corrosion protection of the anolyte cycle
equipment, including the condition of the electrolysers, is unsatisfactory, and, thus, does not allow ensuring the required amount of feeding brine without a complete chemical
dechlorination of the whole anolyte flow using sulphide treatment method. This results in losses of mercury with brine slurry as mercury sulphides as well as in complications in the
operation of the electrolysers, bringing about high mechanical losses of mercury and its entrainment with ventilation as vapours.
Slurry generated in the electrolysis building as well as other slurry rich in mercury are sent for thermal recovery of mercury.
Actions performed during 1998 through 2002 to reduce losses of mercury were of partial nature and did not affect their magnitude.
Below is given assessment of losses of mercury in 1997 and 2002.
Losses of mercury with anolyte filtration slurry
Brine slurry containing mercury sulphide is sent for burial in a specially equipped slurry accumulator together with other mercury-containing waste, including sulphide slurry from
wastewater treatment.
The useful volume of the slurry accumulator is 223,000 m3, the area being 4.3 ha. The height is 9 metres. The slurry accumulator bottom and banks are lined with polyethylene film,
pressed by sand and gravel.
Losses of mercury with anolyte filtration slurry made:
- In 1997: 10,360 kg,
- In 2002: 22,908 kg.
Losses of mercury with wastewater
The total amount of mercury-containing wastewater was:
- In 1997: 78,989 m3,
- In 2002: 127,690 m3.
The content of mercury in untreated wastewater varied between 15-20 mg/dm³.
Wastewater treatment is made by precipitation of mercury using the sulphide method followed by water evaporation. The mother solution evaporated to the NaCl concentration close to
its concentration in a depleted anolyte is sent for supplement of the anolyte cycle while the water condensate is sent for additional treatment from residual mercury on the carbon sorbent.
Treated wastewater is returned to production and used for flushing of equipment and preparation of working solutions. Excessive treated condensate is discharged to the rainwater
sewerage system and then to the Oka River.
Sulphide slurry from wastewater treatment is sent for burial together with brine treatment slurry.
Concentration of mercury in treated wastewater, discharged to the sewerage system, made 0.016 mg/dm³ in 1997 and 0.0003 mg/dm³ in 2002. Volumes of treated condensate
discharged to water bodies were not recorded. Content of mercury in the control site in the Oka River water was 0.00001 mg/dm³.
Losses of mercury with treated wastewater cannot be estimated; however on the whole, given specific technological scheme and treatment depth, they are not high.
There is no relative information about values of losses with slurry at the stage of sulphide treatment of wastewater, however, most probably, they make part of the losses with sulphide
slurry of brine treatment.
Losses of mercury with ventilation emissions
The system of ventilation in the electrolysis building is plenum, with outlets through the aeration lanterns. The lanterns have a height of 22 m. The flow rate of pumped-in air in 1997 was
2.48 million m3/h, and in 2002 it was 0.68 million m3/h.
The average mercury concentration in the electrolysis building air varied between:
- In 1997: 0.027-0.33 mg/m3
- In 2000: 0.042-0.046 mg/m3.
The total losses of mercury with ventilation emissions from the electrolysis building and other premises made according to the enterprises official reports:
- In 1997: 652 kg,
- In 2002: 238 kg.
Losses of mercury with hydrogen
The bulk (ca. 99%) of discharged hydrogen is emitted into the atmosphere through a 22 m high pipe. The remaining hydrogen is used for synthesis of chlorine hydrogen.
Treatment of hydrogen is made on sorbent from activated carbon brand HPR-3P (Russian abbreviation).
Concentration of mercury in treated hydrogen fed was 0.048 mg/m3 in 1997 and 0.0024 mg/ in 2002; the standard rate is 0.01 mg/m3.
Total losses of mercury with hydrogen made:
- In 1997: 0.788 kg,
- In 2002: 0.083 kg.
Losses of mercury with chlorine
No information is available on such losses of the enterprise.
Losses of mercury with off-gases
Treatment of off-gases is made by sorption on activated carbon HPR-3P (Russian abbreviation).
Concentration of mercury in treated off-gases is within 0.003-0.0049 mg/m3, with the standard rate being 0.01 mg/m3.
Losses of mercury with off-gases made:
- In 1997: 0.181 kg,
- In 2002: 0.032 kg.
Losses of mercury with caustic soda
No information is available about such losses. However, given that filtration of caustic soda at the OJSC "Syanchimplast" is similar to other enterprises, it can be estimated on the basis of
annual output rate.
Estimated losses of mercury with caustic soda made:
- In 1997: ca. 0.08 kg,
- In 2002: ca. 0.18 kg.
Mechanical losses of mercury
The following amount of mercury was purchased for the electrolysers:
- In 1997: 24,391 kg,
- In 2002: 70,833.5 kg.
Mechanical losses, calculated by the difference between the amount of purchased mercury and losses recorded for the above-indicated causes, were:
- In 1997: 13,337 kg,
- In 2002: 47,687 kg.
Amounts of mechanically lost mercury accumulated over more than 20 years, according to the information of the enterprise, are contained within a loose cover under the electrolysis shop.
Tentatively, this amount is about 800-1000 tonnes.
Production mercury stocks
Total amount of mercury in the electrolysers is 171 tonnes.
The enterprise does not have any other stocks of mercury.
Losses of mercury emitted into the air, stored with slurry and mechanically lost into the ground under the electrolysis building, are shown in Table 3.8.
Table 3.8 Losses from Sayanskchimplast OJSC, Sayansk City
Year |
1997 |
2002 |
Caustic soda output, tonnes |
51,800 |
121,500 |
Mercury losses: |
Absolute,
t
|
Specific,
kg/t NaOH
|
Absolute,
t
|
Specific,
kg/t NaOH
|
to atmosphere with off-gases and ventilated discharge |
0.653 |
1.26•10-2 |
0.238 |
1.96•10-3 |
to the system of disposal of production waste with wastewater
and brine treatment slurry |
10.360 |
0.20 |
22.908 |
0.189 |
with merchandise products |
0.031 |
5.98•10-4 |
0.080 |
6.6•10-4 |
into the ground with mechanical losses |
13.377 |
0.258 |
47.687 |
0.392 |
to water bodies (tentative), not more than |
no data available |
no data available |
Total losses (purchased mercury) |
24.421 |
0.471 |
70.913 |
0.583 |
Options for release reduction
The data present show that, despite not quite satisfactory, as compared to other operating production facilities, values of discharge of mercury to air, water and losses with merchandise
products, and, most probably, discharge to water, mechanical losses and losses with brine treatment slurry are unacceptably high.
The total condition of production is unsatisfactory, and at present the issue is considered to convert the mercury method of production of caustic soda and chlorine into the electrolysis
method with an ion-exchange membrane, followed by de-mercuration of the buildings and the ground, as well as extracting mercury from the ground.
3.1.5 Waste Dumps and the Environment around Shut-Down Enterprises
There are seven shut-down production enterprises in Russia. With exception of two large enterprises (Usolyechimprom OJSC and Krebs at Kaustic OJSC), these are small installation
rated from 1.3 to 20 thousands of caustic soda per year; such enterprises operated basically as part of wood pulp and paper enterprises. All such enterprises, except for Krebs, used as
raw materials outside solid salt brought to the enterprises. Chemical dechlorination of anolyte was made by means of treatment of sodium sulphide with simultaneous precipitation of
mercury sulphide. Mercury slurry from such enterprises containing more than 1% of mercury were sent, as a rule, for recovery to the Nikitovsky Mercury Enterprise; brine slurry was
discharged to the slurry sites; graphite anode waste was disposed at the disposal sites; and wastewater after sulphide treatment and settling was discharged to the general sewerage
system of the enterprises. Mechanical losses of mercury were recorded at all enterprises: mercury infiltrated into the ground under the electrolysis building.
Amounts of mercury accumulated in the ground, on disposal sites and slurry accumulation sites, as well as discharged to water bodies are shown in Table 3.9; these are tentative values
calculated using available information about activities of every enterprise, specific data about technological process used at every enterprise, data about total use of mercury and its losses
through different causes, as determined during the surveys. The precision of such estimates is ±020%.
Table 3.9 Mercury in soils, waste dumps and water bodies by shut down enterprises produced caustic soda and chlorine (closed within 1982-1998)
Plant |
Capacity for NaOH
th. t/year
|
Commissioning date |
Shut-down date |
Approximate amount of Hg, t |
|
|
|
|
In soils |
In dumps and slag-heaps |
In water bodies |
Usolyechimprom JSC,
Usolye-Sibirskoye, Irkutsk oblast
|
100 |
1970 |
1998 |
1,500 |
800 |
70 |
JSC «Kaustic» «Krebs» Plant Sterlitamak City,
Bashkortostan |
86 |
1964 |
1987 |
600 |
50 |
90 |
Kotlass PPF
Koryazhma, Arkhangelsk oblast
|
19.6 |
1964 |
1998 |
30 |
130 |
30 |
Arkhangelsk PPFNovodvinsk,
Arkhangelsk oblast
|
16.4 |
1962 |
1996 |
25 |
120 |
25 |
Kaprolaktam JSC, dzherzhinsk, Nezhegorodskaya oblast |
10 |
1948 |
1982 |
20 |
60 |
20 |
Amursky PPF
Komsomolsk-na-Amure, Khabarovsk kray
|
7.4 |
1970 |
1997 |
18 |
56 |
15 |
Svetlogorsk PPF
Svetlogorsk, Leningrad oblast
|
1.3 |
1951 |
1993 |
25 |
11 |
25 |
Total |
|
|
|
2,218 |
1,227 |
275 |
The assessment made has demonstrated that within areas adjacent to the enterprises that are shut down the environment contains significant amounts of mercury dissipated inside the
ground under production buildings (basically as metallic mercury), in slurry accumulators (basically as mercury sulphide), in disposal sites (basically as metallic mercury) and in water
bodies (basically as mercury sulphides). The amount of such waste is determined by the production capacity, the period of their operations and the level of mercury losses. The highest
mercury pollution is typical of industrial areas in the towns of Usolye-Sibirskoye, Sterlitamak, Koryazhma and Novodvinsk. According to the available information, certain work is under
way there to clean up the grounds within the vicinity of former production buildings from mercury.
To minimise possible damage from mercury waste accumulated in these areas and prevent further dissipation of such waste, it is expedient to organise broader surveys to detail maps of
waste location, levels of soil, air and water pollution with mercury and design actions for containment and preservation of waste.
3.1.6 Summary
Tables 3.10 and 3.11 show summary comparative data based on the results of inventory of mercury discharge and emission to air, water, soil and products by the enterprises
manufacturing caustic soda and chlorine in the Russian Federation using the mercury methods in 1997-2002.
All mercury purchased during a year was used (for filling electrolyzers) during the same year at all the enterprises except Sterlytamak plant where electrolyzers are designed in such a way
that average annual fluctuations of mercury amount are possible.
Table 3.10 Mercury balance for chlor-alkali plants in the Russian Federation in 1997
Plant |
Mercury purchased, t |
Emissions to the atmosphere, t |
Discharged to water bodies, t |
Mechanical losses, t ** |
Disposed at the landfills, t |
Losses with commodity products, t |
Kirovo-Chepetsk combine JSC |
No data |
0.11 |
0.0001 |
n.a. |
12.4 |
0.03 |
Kaustik JSC (Volgograd) |
27.8 |
0.65 |
0.001 |
24.2 |
2.9 |
0.09 |
Kaustik CJSC, 0. De Nora (Sterlitamak) |
5.1 |
0.89 |
0.0008 |
8.0 |
n.a |
0.24 |
Sayanskhimplast JSC (Sayansk) |
24.4 |
0.65 |
No data |
13.4 |
10.4 |
0.03 |
Total |
>57.3 |
2.30 |
>0.002 |
>45.5 |
>27.5 |
0.39 |
* to closed water system (ponds-evaporators).
** the term "mechanical losses" is used here for all unaccounted losses
Table 3.11 Mercury balance for chlor-alkali plants in the Russian Federation in 2002
Plant |
Mercury purchased, t |
Emissions to the atmosphere, t |
Discharged to water bodies, t |
Mechanical losses, t * |
Disposed at the landfills, t |
Losses with commodity products, t |
Kirovo-Chepetsk combine JSC |
15.1 |
0.15 |
0.0001 |
0.015 |
14.9 |
0.03 |
Kaustik JSC (Volgograd) |
6.38 |
0.39 |
0.0008* |
4.5 |
1.4 |
0.08 |
Kaustik CJSC, 0. De Nora
(Sterlitamak) |
10.0 |
0.44 |
0.0001 |
4.2 |
0.007 |
0.02 |
Sayanskhimplast JSC (Sayansk) |
70.8 |
0.24 |
No data |
47.6 |
22.9 |
0.08 |
Total |
103.2 |
1.22 |
>0.001 |
56.3 |
39.3 |
0.22 |
* the term "mechanical losses" is used here for all unaccounted losses
The data presented shows that over the analysed 5-year period all these enterprises significantly reduced the amount of mercury emission/loss to air and products although all these
enterprises increased their production output. This reduction was possible due to the relevant targeted technological actions and improvement of general technological discipline among
personnel.
All enterprises, with exception of Sayanchimplast OJSC, substantially reduced discharge of mercury to the ground through mechanical losses and to the controlled sites used for disposal
of such waste as part of mercury-containing slurry.
At the same time, the mercury losses and emissions of mercury to the air at all enterprises should be further reduced. To do this, the enterprises have concrete technical solutions, but the
assessment also indicates that there is a significant potential for reducing the releases by relatively simple improvements of management practices. Expedient implementation of such
solutions is hindered only by a lack of required financial investments. Therefore, search of such funds to finance the above operations and to control the use of the funds for specific
actions, observation of the agreed terms for their completion and assessment of their efficacy would facilitate a further significant reduction of mercury discharge and emission from the
chlorine enterprises and improvement of the environmental conditions in the regions.
The overall flow of mercury by production of chlor-alkali in the Russian Federation in 2002 is illustrated in Figure 3.3.
Figure 3.3 Mercury balance for chlor-alkali production in the Russian Federation in 2002 and in 1997
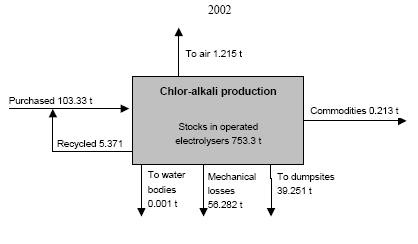
In order to compare the data of Russian enterprises with other countries the Russian data are entered into the common OSPAR reporting table (OSPAR 2002) along with the reported
data for French enterprises (see Table 3.12). This comparison shows that the specific release of mercury with treated wastewater and off-gases of the Russian enterprises are within the
range of the French. This is connected with the use of measures to increase the depth of purification of such release. At the same time, losses with products are 2-3 times higher than at
French enterprises. This indicates an insufficient purification of caustic soda from mercury in Russian enterprises. Losses with ventilation release are also high from electrolysis shops.
These releases can be reduced only by maximum possible decrease of frequency and duration of stoppage of the electrolysers.
Mechanical losses (unaccounted losses) of mercury at enterprises of the Russian Federation are either very low (Kirovo-Chepetsk chemical enterprise) or several times higher than in
France (Caustic, Volgograd; Caustic, Sterlitamak), or extremely high (Sayanskchimplast). Losses of mercury as slurry that is not fit for regeneration at enterprises in Volgograd and
Sterlitamak are similar to those in France, while in Kirovo-Chepetsk and Sayansk they are very high. This is related to specific features of outdated technological scheme that requires
complete dechlorination of anolyte using sulphide treatment (in Kirovo-Chepetsk) or unsatisfactory protection of the equipment of the anolyte cycle against corrosion (Sayanskchimplast).
Table 3.12 Losses form chlor-alkali plants in France in 2000, (OSPAR 2002) and the Russian Federation in 2002
Click here to see the table.
3.2 Other uses of Mercury in the Chemical Industry
Mercury chloride is used for production of vinyl chloride monomer (VCM) at four enterprises in the Russian Federation. The production is described in section 3.2.1.
Metallic mercury has until 1998-99 been used in the production of vitamin B-2 (riboflavin) at two enterprises. Mercury containing wastes stored at the enterprises is described in section
3.2.2.
Mercury sulfate (II) was until 2000 used as catalyst for production of cube (1-amino anthrachion) colours. Mercury-containing waste is briefly described in section 3.2.3.
In the former Soviet Union mercury catalysts were used for the production of acetaldehyde, but this production facility was situated in Kazakhstan (Termitau town, Karaganda oblast).
The environmental situation around this enterprise is discussed in details in the relevant references.
3.2.1 Production of Vinyl Chloride Monomer (VCM)
Hydrocarbon used as raw material for synthesis of vinyl chloride, i.e. acetylene, is generated from calcium carbide or by a high temperature pyrolysis of natural gas (or oil; hydrocarbons).
The produced purified acetylene dried to the residual moisture content less than 1.5 g/m3 is sent to the mixture where the pre-treated (purified) and dried hydrogen chloride is also fed.
The ratio of acetylene to hydrogen chloride usually is 1.0:1.1. This mixture of gases is fed to the upper part of the reactor represented by a shell-and-tube heat exchanger; inside the
inter-tubular space there is circulating a heat carrier while the tubes are filled with a catalysis represented by activated carbon with mercuric chloride HgCl2 (10-15%) deposited on it. The
reactor is made from carbon steel; the height of the tubes is 3-6 metres, and the diameter is 50-80 mm. Usually 6-12 m3 of catalyst are charged to the reactor. Temperature in the
reaction area is kept at 150-180 °C.
After the reactor the reaction gases are fed to the packed column sprayed with hydrochloric acid to extract the entrained mercuric chloride. Then, the reaction gas is flushed with water
and a solution of alkali in the columns to remove hydrogen chloride, acetaldehyde and carbon dioxide from the gas. After that, gas is "refrigerated" in the condenser cooled with brine so
as to remove moisture, compressed in the compressor to 0.071-0.81 MPa and fed for rectification. The rectification system includes two tray columns: the first column serves to extract
high-boiling admixtures, basically the mixture of 1.1- and 1.2-dichloroethane while the second column is used to remove high-boiling admixtures. The obtained rectification products
passes through the column for drying of the final product, filled with solid caustic soda for final drying and neutralisation of vinyl chloride.
The schematic diagram for production of vinyl chloride from acetylene using a mercury catalyst is shown below.
Figure 3.4 Production of VCM using a mercury catalyst
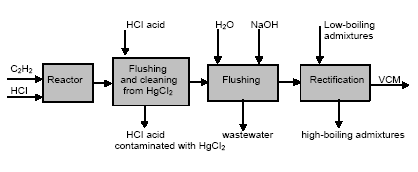
Mercury chloride (HgCl2) is used only for preparation of the catalyst. The mercury chloride is either purchased from abroad (earlier from Spain, but now more and more from China) or,
in part from the Russian enterprise NPP Kubantsvetmet CJSC. The production at this enterprise is further described in section 5.1.
Table 3.13 shows data on the capacity of production of vinyl chloride from acetylene as well as the use of catalyst per year as well as the content of metallic mercury in it. In total about
15.5 tonnes of mercury was used for the production of catalysts in 2002. About half of it was obtained from recycled HCl whereas the other half was purchased.
Table 3.13 Production of VCM from acetylene and use of catalyst
Enterprise |
Vinyl chloride, thousand tonnes/year |
Use of catalyst |
Capacity |
Production
2001 |
Production
2002 |
Catalyst
tonnes |
Calculated as Hg, tonnes |
Novomoskovsk Joint-stock Company Azo" OJSC (Tula oblast) |
45 |
12.0 |
19.6 |
60 |
4.5 |
Plastkard OJSC,City of Volgograd |
68 |
73.9 |
68.5 |
60 |
6.6 |
KHIMPROM OJSC,City of Volgograd |
27 |
24.3 |
22.1 |
30 |
2.2 |
Usolyekhimprom OJSC (Usolye-Sibirskoye, Irjutsk oblast) |
26 |
20.0 |
17.5 |
30 |
2.2 |
Total |
166 |
130.2 |
127.7 |
180 |
15.5 |
By the process the fate of the mercury is as follows: about 30% remains in the spent catalyst; practically all remaining amount goes with hydrochloric acid (about 70%); about 0.1% goes
with off-gases and emissions; about 0.1% goes with wastewater.
Spent catalyst is accumulated and then sent to Kubantsvetmet OJSC (Krasnodar kray, Russia) for complete treatment and extraction of metallic mercury. Part of it is turned into mercury
chloride and sent back to the user.
Hydrochloric acid with 0.05-0.1% of mercuric chloride is returned for recycling within the enterprises to make catalyst (about 8 tonne mercury). Partially, it is sent to users and used in
metallurgic or oil and gas industries for treatment of wells. It is absolutely prohibited to use such hydrochloric acid in food and medical industries. By the application of the hydrochloric
acid in the wells the mercury will end up in the wells. The hydrochloric acid used in well in total contained about 2.8 tonne mercury.
Concentration of mercuric chloride in off-gases and wastewater from the VCM production is within the allowed norms.
The overall flow of mercury by the production of VCM in the Russian Federation in 2002 is shown in Figure 3.5.
Figure 3.5 Use of mercury in production of VCM in 2002 ( t Hg)

Spent catalyst is stored at the enterprises before it is disposed of for recycling. Table 3.14 shows data about the approximate amount of spent mercury catalyst at the enterprises, ready
for processing at Kubantsvetmet OJSC. The elevated accumulated amount of spent catalyst is explained by the fact that the license for processing (treatment) of mercury-containing waste
at Kubantsvetmet OJSC expired in 2001 and it took time to arrange a new license. In 2003 Kubantsvetmet OJSC was to start to treat the spent catalyst.
Table 3.14 Approximate amount of spent mercury catalyst for reprocessing stored at the enterprises by the end of 2002
Enterprise |
Catalyst of vinyl chloride |
Amount,
tonnes |
Content of mercury in catalyst,
tonnes |
Novomoskovsk Joint-stock Company Azot OJSC |
400 |
12.0 |
Plastkard OJSC, City of Volgograd |
250 |
7.5 |
KHIMPROM OJSC, City of Volgograd |
150 |
4.5 |
UsolyekhimpromOJSC (Usolye-Sibirskoye, Irkutsk oblast) |
120 |
7.0 |
Total |
920 |
31 |
3.2.2 Former Production of Vitamin B-2
Metallic mercury was formerly used in a production of vitamin B-2 (riboflavin) in order to generate the amalgam of sodium (Na), by means of which there is carried out a process of
recovering the aldose from aldonolactone.
In the Russian Federation synthesis of vitamin B-2 under this technology was carried out at the two enterprises: Belvitamins JSC (Belgorod city) and Sintvita SC (Bolokhov, Tula region).
Both enterprises were closed within 1998-1999.
Totally at Belvitamins JSC and Sintvita SC there were produced about 150 tonnes of vitamin B-2. Mercury consumption coefficient is 0.036 kg per kg of vitamin B-2. Using this
coefficient, the total consumption of mercury for the process can be estimated at about 5.4 tonnes as a maximum.
Mercury containing wastes of these enterprises were sludge with mercury content up to 5% of mass, as well as used sorbents from gas purification facilities. Additionally, at Sintvita as a
sorbent there was used an activated carbon, modified by chlorinated sodium, and at Belvitamins JSC there was used a pyrolusite. Volumes of warehousing the mercury-containing wastes
at these enterprises in 1988 are presented in the table 3.15.
Table 3.15 Mercury-containing wastes from production of vitamin B-2 accumulated at the enterprises
Enterprises |
Type of mercury-containing wastes |
Sludge |
Sorbent |
Tonnes |
Mercury content,% |
Tonnes |
Mercury content,% |
Belvitamins JSC (Belgorod city) |
70 |
1-5 |
50 |
0.1-6.0 |
Sintvita SC (Bolokhov, Tula oblast) |
120 |
1-5 |
12 |
1.2-1.5 |
Total |
190 |
|
62 |
|
In 1999, Kubantsvetmet CJSC received from Belvitamins JSC 22 tonnes of sludge for utilization.
3.2.3 Former Production of Pigments
Mercury sulfate (II) was until 2000 used as catalyst for production of production of paints (1-amino anthrachion) by Khimprom JSC (City of Cheboksary, Republic of Chuvashia). The
annual use of metallic mercury for this purpose was several tonnes. Waste from the production was processed at Kubantsvetmet CJSC (section 5.1).
3.3 Gold Mining Using the Amalgamation Technology
3.3.1 History of Gold Mining in the Russian Federation
The gold mining industry came into being in Russia in the XVIII century. The first gold-copper Voitskoye deposit was discovered in 1737 in Karelia, and the first large ore gold deposit –
Berezovskoye was stricken in 1745 in Urals (Benevolsky, 2002). By the beginning of the XIX century more ore gold deposits had been discovered, however the intense commercial gold
mining started after striking of placer gold in Urals and Siberia in 1814. In the period 1816 to 1890, the placers have been found all over the south of Siberia and the Far East – between
Urals and the Littoral. In the 70-ies of XIX century, the use of hydraulic technology of gold mining by means of hydraulic monitors was pioneered in Siberia. In 1896 the first dredge was
constructed. Gold ore mining was recommenced after the improvement of gold ores processing technologies, in particular amalgamation technologies application.
In the 40-ies of XIX Russia mined as much gold that allowed it to be the first in the world. Totally, before the revolution Russia had officially extracted 2,754 tonnes of gold (Foss, 1963),
including approx. 3 tonnes mined illegally. In Soviet times gold mining was officially started in October 1921 pursuant to the Decree of Sovnarcom On Gold and Platinum Industry, which
declared the state ownership for the deposits of these metals. In 1921-1925, 11 state gold mining trusts were established. In 1927 All-Union Joint-Stock Association SoyuzZoloto was
set up. Since that time, all information concerning the gold production and sale on the world market and its official reserves had been considered to be the State secrete, and therefore
now is available only as the expert assessments (Gold History).
In 1991 the gold mining industry of Russia was decentralized and rearranged. 12 large regional associations were abolished and reorganized into several thousands (9,000 by 1996) gold
mining enterprises, most of which were not able to survive in difficult economic conditions, and therefore in 2001 there were 639 enterprises of various ownership, with prevalence of
small scale prospecting artels. 584 of these mines (or 91%) are small scale enterprises mining less than 500 kg/year with average year staff up to 100 people (totally extracting more than
44 t of gold). More than 1 t of gold was extracted in 2001 by 22 mines (totally - 78.6 t or 5.6% of total mining volume). (Gold - 2002). In 2000, 20 mines annually producing more that
1 t of gold each contributed 55% in Russian gold mining. In 2001 the same enterprises provided 80% growth of gold mining in the country (the State Report 2003). Such organizational
set-up is not able to promote the economic efficiency of the gold mining activity. Small scale mines don't have enough financial resources to purchase modern equipment, introduce novel
technologies, carry out the exploration works, and comply with the environmental requirements.
Development of gold mining in Russia within 1890 - 2000 is presented in Figure 3.6.
Click here to see the figure.
Figure 3.6 Development of gold mining in Russia within 1890 - 2000 (Benevolsky, 2002)
According to various sources, 11-12 th. t have been mined during 280 years since 1719 (the first documented data) (Foss 1963, Benevolsky 2002, Vyazelschikov 1963). The expert
assessments related to gold mining for the different time periods (incl. ore, placer and complex gold) are presented in Table 3.6 (Benevolsky, 2002). The Figure 3.7 includes the gold
mining data in Russian regions for the latest 10 years.
Table 3.16 Gold mining in Russia (Benevolsky 2002)*
|
Time periods |
|
before 1900 |
1901-1916 |
1917-1945 |
1946-1954 |
1955-1964 |
1965-1975 |
1976-2001 |
Gold production, t |
1980 |
775 |
~1,000-1,500 |
8801,200 |
1,600 |
1,500 |
3,755 |
TOTAL |
11,490-12,370 |
Note: the data for 2001 are entered by the author of the present report.
Figure 3.7 Dynamics and structure of gold production in Russia in 1991-2001
Click here to see the figure
The official data for 2001 says about 154,455 kg of gold mined in Russia, including 141,449 kg by gold-mining enterprises. However, according to the experts of GFMS (Gold Fields
Mineral Services), gold production in 2001 in Russia amounted to 168 tonnes, i.e. ranks fifth in the world gold production. The discrepancy with official data arise from the fact that
GFMS experts account a share of illegal gold production in Russia equal to their mind to 10-15% (GFMS 2002). The same amounts of illegal gold are confirmed by Russian experts,
including the law-enforcement authorities (Aivazov, 2001).
Presently, Russia comes second after Republic of South Africa with forecasted gold resources, and the third after Republic of South Africa and the USA with the balance reserves, and
the 13th place is taken by Russia with the state gold reserves by the end of 2001, Russia has 7-8% of the world reserves of gold (the State Report, 2003).
Gold deposits are situated on the considerable part of Russia – from the Baltic Gate in the west to the fold structure of the Eastern Chukotka (see Figure 3.8)
Click here to see the figure.
Figure 3.8 Location of main gold deposits, mining enterprises and gold placer areas of Russian Federation(Benevolsky 2002)
1 primary gold deposits; 2 gold-silver deposits; 3 enterprises located at the primary deposits; 4 enterprises located at the gold containing complex deposits; 5- enterprises located at the
gold-silver deposits; 6 gold placer deposits
80% of Russian gold reserves in gold deposits are contained in ore and about 20% in placer deposits. Almost 29% of gold reserves are located in complex deposits, basically in copper
pyrite and sulphide copper-nickel, and sometimes in polymetallic deposits. Russia is an only large producer of gold in the world, the greater part of the gold was formerly mined in placer
deposits, although they contain a little bit more than 17.5% of the reserves (the State Report 2003, Goncharov 2002.).
The recent growth of gold production volumes is conditioned by general change of gold mining structure in Russia: transition from development of placer deposits to the active placing of
the ore deposits into operation. Until 1998, the placer deposits provided up to 80 % of gold. During the following years this ratio has been changed fundamentally, in 2001 the share of
the ore gold deposits mining reached 40 % in the total gold mining volume, and since 2002 ore prospects are expected to provide more than a half of the gold output in the country
(Goncharov, 2002). Today, more than 1,700 placer deposits are developed and more than 1,000 are prepared for development in Russia.
3.3.2 Gold Production from Gold-mining Wastes
For the whole history of gold mining in Russia about 80-85 % (approx. 9 th. t) of gold has been mined from the placer deposits (Benevolsky 2002). Due to the intense mining of placer
gold, the reserves depletion, as well as decrease of the exploration works scope, the explored reserves of placer gold have 15% reduced during the latest 10 years (Gold, 2003). This
was the reason for the large gold-mining enterprises to more actively develop the ore deposits, and the small mining companies – to mine the cheaper "technogenic" gold, i.e. gold
contained in dumps, tailings and schliches, large number of which in the old gold-mining areas are the secondary industrial (technogenic) deposits in a number of cases. The prime cost of
the metal produced from the technogenic sources varies between 3.5 to 6.0 USD per 1 gram in gold equivalent and trends to cut down to its minimum at the 2nd – the 3rd year of dumps
operation (Bauer et al., 2001). The urgent need for the technogenic placers and other gold containing wastes of gold-mining reassessment for the compensation of realizable reserves of
placer gold is stressed in the Federal Program on Reproduction of the Gold Reserves in 1994-2000 (Orlov, 1993). However, today there is no state statistical inventory of potential
reserves in the technogenic placers.
According to different expert assessments, during the intense placer gold mining activity , about 11.9 billion m3 of rock mass has been being washed out. The overall forecasted reserves
of gold in dumps constitute 3,300 t (with the given average content equal to 0.2 g/m3: pebble dumps 1.7, gravel tailings 0.2 and peat dumps 1,400 t) (Benevolsky). Table 3.17 presents
the available data on gold production from technogenic dumps in several gold-miming regions of the Russian Federation.
Table 3.17 Reprocessing of technogenic gold containing dumps in some Russian constituents (Benevolsky 2002)
RF Constituent |
Volume of washed out dumps, th. m3 |
Gold production, kg |
Average gold content, mg/m3 |
Irkutsk oblast
Republic of Buryatia
Chita oblast Republic of Saha (Yakutia)
Amur oblast
Chukotka
|
1,396
52
704
1,687
809
40,296
|
772
20
67
491
177
22,256
|
553
385
95
291
219
552
|
Note: Chukotka – 1970-1993 period, other RF constituents – one year period. Data provided in this table may seem to look somewhat inconsistent due to the lack of official statistic
reporting on gold deposits and gold extraction rates in Russia. Therefore the above table presents only partial data that were available at Benevolsky B.I. 2002. Such inconsistency of
information on reprocessing of technogenic gold containing dumps can be explained very simple. In case a technogenic gold containing dump site is located at the territory of a gold mining
company then the latter does not need to obtain a licence for gold extraction from this dump site and consequently it would serve as a kind of additional gold extraction reserve and
companies prefer not to disclose such things.
3.3.3 Gold Mining with Mercury Amalgamation
The gold amalgamation technique based on selective wetting of the native metal particles with mercury has been an integral part of conventional technological flowsheet of gold ores and
sand concentration for a long time. The long and intense use of this technology in the gold-mining areas caused the severe Hg intoxication of employees and environment. In this
connection, the order of the Chief Department on precious metals and diamonds of Ministry Cabinet of the USSR, No. 124, December, 29, 1988, officially prohibited the application of
mercury in dredges and washing equipment since 1989, and since 1990 in gold-extracting plants (GEP) and schlich-concentrating plants (SCP) (The order of 1988). After this, all works
related to amalgamation technology improvement and design of equipment for gold containing products demercurization were stopped. Nevertheless, the need for such equipment and
environmentally sound technologies on Hg extraction from gold containing products still exists due to the mercury contained in these products has both technogenic (secondary processing
of placer deposits and stale tailings of GEF) and natural genesis (Mullov et al., 2001).
Mercury consumption and losses with ores and sands amalgamation to the great extent depended on deposit types, feedstock technological properties, mining and dressing technologies.
The Russian gold-mining history includes four phases of Hg-amalgamation technologies application, conditioned by technical and technological re-equipment of mining industry and gold
mining plants in particular (Foss 1963, Rukavishnikov 1984, Report 2002):
- A muscular gold mining (especially for the placer deposits) widely applied in pre-Revolutionary Russia and just after it was related with uncontrolled considerable Hg consumption and
losses. Artisanal operations of Hg-amalgamation of crushed gold-bearing ores and burning of the amalgamated gold on the open fire without Hg vapours condensation are similar to the
technologies presently applied in the South America, where mercury losses amount in average to 1.32 kg per 1 kg of the gold extracted (Lacerda 1998).
- The second period since 1917 till 1930 is distinguished for the extended use of Hg-amalgamation, mechanization of the dressing works, introduction of silt cyanidation process.
- The third period since 1930 till 1960 was notable for all-round application of both amalgamation and cyanidation. In order to improve the efficiency of gold extraction, especially from
the complex ores and sands, complex processing schemes were developed, including gravitational, amalgamation, cyanidation, flotation technologies. An intensive industrial gold ore
mining, as well as placer deposits in the north-east started in Russia in 1930 was followed by improvement of gold amalgamation technologies with Hg condensation from amalgams
burning, i.e. reduction of specific consumption due to its re-use. However, Hg recuperation was carried out only at large enterprises.
- The fourth period from 1960 till 1988 is notable for sharp decrease of amalgamation application with transition to the internal amalgamation of ores and sands, introduction of integrated
concentration systems, application of the ion-exchange technologies.
- The fifth period since 1989 up to now is remarkable for the official ban on Hg use -in gold mining, introduction of modern concentration technologies. However, the illegal and therefore
hard-to-control Hg use in the final refining process, as well as by small scale mines, is still going on.
In the former USSR times, when gold mining was under strict state control and management, the enterprises and regional administrative offices registered Hg consumption for all gold
concentration operations. There were norms for Hg consumption and losses established. For instance, the designed Hg losses at sluice gold extraction were equal to 10 % due to
amalgams washing away. Mercury consumption and losses at different amalgamation technologies (internal, external, on dredges, washing devices, and gold extraction factories) varied
considerably. Analysis of the real Hg losses based on the historical records of some gold mines of the Far East carried out in 60-70-ies showed the range of 0.5-1 t per 1 t of gold mined
(Koval at al 1997, Sidorov 1999).
As indicated in the Table 3.18, relation of Hg consumption to the amount of gold produced has been changed significantly from year to year from (6-10):1 to 1:4. Before
Hg-amalgamation ban, when the effective mercury-free technologies were widely introduced, Hg specific consumption was considerably reduced. According to official information, total
irreversible losses of metallic mercury on dredges and washing devices in this period reached 6 t/year, in GEF about 3 t/year (The order 1988). However, to our opinion based on the
tables 3.18 and 3.19 the official data is obviously underestimated. For instance, in the end of 80-ies the annual mercury delivery to Zabaikalzoloto Association (the Chita oblast)
producing about 8 t of gold constituted approx. 2 tonnes. Hence, almost the same amount of mercury is irreversible released to the environment. The losses amounted to 250 kg of
mercury per 1 t of gold, taking into account application of other gold concentration technologies mercury free gravity , flotation and cyanidation (Laperdina 1995). The state economic
reforms of the latest 15 years, which lead to loss and inaccessibility of many archival documents in Russia, do not allow to make a correct statistical estimation of total amount of mercury
used in the gold-mining regions.
Table 3.18 Mercury consumption and losses at gold-bearing rocks amalgamation
Rock types, mining and concentration technologies |
Hg : rock ratio |
Hg : Au ratio |
Hg losses |
Quartz oxidized ores
Ores with high content of sulfides
Ores with arsenic and antimony minerals
|
2-4 g/t5)
5-9 g/t5)
10-15 g/t5)
|
|
|
Internal amalgamation: |
15-20 g/t 3) |
|
|
Crusher-mill plants
For crushers, mills, amalgamators
For fine gold
For coarse gold
For concentrates
|
6-10 g/t2)
5-20 g/t5)
|
(6-10):15)
(4-6):15)
(10-15):15)
|
160-400 g/t 2)
200-900 mg/t ore5)
|
External amalgamation: |
2-3 g/t 3) |
|
|
sluice amalgamation on dredges
on hydraulic monitors
in extracting plants
|
40-130 mg/m3sands4)
70 mg/m3sands6)
290 mg/m3 sands6)
2-7 g/t ore6)
|
|
55-70 mg/m3 sands4, 6)
200 mg/m3 tailings 1)
10 % or 210 mg/m3 sands6)
0.2-4.0 g/t concentrates1)
|
Note: Information sources 1 Order of 1988; 2 Myazin et al 1997A, 3 Polkin 1987, 4 Zamyatin et al 1975, 5 Vyazelshchikov et al 1963; 6 Koval et al 1997.
Table 3.19 Hg and gold content in the gold mining wastes
Area |
Forecasted properties of the area |
Characteristics of processed wastes |
References |
amount of processed wastes |
Hg content |
gold content |
Hg : Au
ratio |
wastes (dumps, tailings, schliches) |
Hg |
Gold |
total
kg |
specific |
Amur Region
Verkhni Ingagli site
Aprelsky gold mine |
|
0.2 g/m³ |
0.5 g/m³ |
25 th. m3
53 th. m3 |
2.56 kg
15.5 kg |
0.6-2000 mg/kg |
6.83 kg
0.2 g/m3
10 kg |
|
MGGU Scientific & Research Center
Koval 1997 |
Krasnoyarsk Region
Tailing dump of schliches concentration plant |
|
40 kg |
3 kg |
20 m3 |
3.5 kg |
175 g/m3
(0-750 g/m3) |
8 g/m3
(0-18 g/m3) |
20 : 1 |
Makarov 1997 |
Republic of Bashkortostan
Mindyakskaya and Semyonovskaya GE"P, Uchalinskaya, Sibaiskaya, Buribayevskaya
concentration plants |
|
0.2 g/m³
1-3 g/t |
1.1 g/t
(tailings)
2.7 g/t
(dumps) |
|
|
|
|
|
Bashkortostan 1997
Kutliahmetov 2002 |
Republic of Buryatia, debris damp |
|
3-5 g/t |
|
|
|
|
|
|
Nikiforov, 1994 |
Khabarovsk Regoin
Wastes schliches concentration plantof
Kerbinsky, Sophyisky, Oktyabrsky gold deposits |
|
2-100 mg/kg |
|
200 t
92 m3 |
12 kg
52 kg |
60 ìã/kg |
|
|
Koval 1997 |
Chitia Region |
210 mil. t |
0.05-54.2 mg/kg |
149 T
0.3-3.5 g/t |
|
|
|
|
|
Haritonov 2002
Myazin 1997, Laperdina 1998, 2002 |
3.3.4 The Current Situation
Mercury contamination of traditional gold mining areas of Russia, as in all gold-mining areas of the world, is very urgent and poorly known problem. Scope of Hg contamination and its
effect in different territories are not thoroughly investigated. However, it can be stated with certainty, that all traditional gold mining areas shown in Figure 3.7 have different extent of
mercury contamination, which is not localized as a rule. With the introduction of the effective gold mining technologies, the same sites of rich placer deposits were repeatedly washed up
again, with subsequent mixing of mercury-containing dredges and hydraulic monitors dumps with the washed-out rocks, which resulted in their distribution all-over the bigger territory. The
point sources include abandoned and operating tailing dumps of extracting and concentrating plants, gold-receiving offices. The industrial and residential areas of old gold-mining
enterprises are often either transferred from the worked-out territories or gradually destroyed. Restoration and conservation of the contaminated gold-mining sites have not been planned
and carried out earlier, therefore the destroyed tailing dumps and exhaust schliches with high Hg content cause the severe environmental pollution. As the location of the old placer gold
mining sites can not always be found based on historical records, the assessment of mercury contamination of the traditional gold mining areas requires conduction of the expensive field
and desk studies. The local, but isolated from the gold-mining areas, sources of mercury contamination are the refining plants.
In present, there are five main sources of mercury release from gold mining activities, quantitative characteristics of which depend on deposit type and gold reserves, duration and intensity
of the deposit mining and mercury use in technological operations:
1. Atmospheric emission of Hg from dumps, tailings, contaminated soils, as well as its washing-out and contamination of watercourses, soils, water and terrestrial environment.
2. At present widely applied re-processing of the secondary industrial placers, as well as processing of tailings and schlich concentrates of ore and placer gold.
3. Continued illegal mercury use for gold-bearing concentrates and sands extraction.
4. Mining of the gold deposits with natural increased mercury concentration.
5. Refining of gold-bearing concentrates with the increased natural or industrial mercury content in the refining plants.
Let's consider these mercury release sources in detail and try to assess their impact:
Dredges and hydraulic dumps, tailings, schliches, contaminated soils.
The wastes of placer gold mining constitute the major share in this group of sources. According to the expert assessment (Benevolsky 2002), about 11.9 billion m3 of the rock has been
washed out during the period of intense placer gold mining. The available data (see Table 3.19) shows, that Hg content in dumps varies considerably from 0.05 to 2000 mg/kg. Dumps'
sites with severe mercury contamination are more localized and less scaled. Therefore, the approximate average Hg content in dumps is significantly lower and can be estimated as
0.2-0.5 g/m3. Given the above indicators, the total mercury amount in placer gold mining wastes ranges between 3,000 - 6,000 t.
It is very difficult to assess the release of both industrial and natural mercury contained in dumps and tailings, as it is partly isolated under the layer of the mined-out rock or in the
basement of dredge pits. Moreover during the long-term storage technogenic and natural mercury undergo physicochemical and chemical transformations. Therefore, the mineral
composition of mercury compounds, composition and properties of gold and other metals amalgams, concentration of liquid mercury in gold mining wastes are unique indicators for each
site, and they are extremely important for Hg environmental emission and impact assessment, as well as for development of the environmentally sound technologies of gold- and
mercury-containing wastes processing and remediation of the contaminated areas. Such kind of works are carried out in some Russian institutions. For example, IRGIREDMET staff
investigates the composition of mercury mineral forms in the re-processed rocks, in order to increase the efficiency of gold and mercury extraction. The following composition was
determined for one of the mining sites (in %): calomel (Hg2Cl2) - 51.8; mercury oxide (ÍgO - 1.1; native mercury (Íg) as the amalgamated gold - 25.1; cinnabar (ÍgS) - 6.7; mercuric
chloride (ÍgC12) and water-soluble mercury types - 1.4; selenides, tellurides and other "persistent" types of mercury -13.9 at the overall concentration of Hg in the rocks equal from 30
to 100 g/t. (Mullov et al., 2002). The specialists of Chita Polytechnic University have investigated the composition and properties of gold amalgams, in order to develop effective
magnetic-gravitational technologies of industrial wastes processing (Myazin et al., 1997A, 1997á).
Re-processing of secondary industrial placers
The extensive re-processing of secondary industrial placers, as well as processing of tailings and schlich concentrates of ore and placer gold (see Table 3,19) have lead to extraction of
Hg buried in dumps, pits, , its conversion into the active migrating state and release to the environment with atmospheric emissions (thermal treatment of concentrates, mercury degassing
from dumps etc.) and wastewater discharges. The licensing agreement on mining of such placers doesn't take into consideration a high industrial Hg content in the processed sands, and
therefore the dissemination and extension of mercury contamination scope is not controlled.
In spite of the currently developed and applied technologies of industrial feedstock processing with extraction of both gold and mercury, small scale enterprises with low revenues will
likely to use cheaper technologies with only gold extraction, i.e. use burning of the amalgamated gold without Hg vapours condensation at the final phase. In case the environmental control
over licensing and further mining of such gold- and mercury-bearing secondary industrial deposits is not strengthened, a half of mercury presently contained in dumps and wastes
(3,000-6,000 t) is supposed to be released gradually to the atmosphere and water bodies.
The scarce data presented in the table 3.18 indicates that a share of secondary industrial gold for various regions constitutes 1-5% of the total amount of the gold extracted. In general, a
share of technogenic gold in Russia can be approximately estimated as 2-4 %, therefore the amount of secondary industrial gold extracted in 2001 may be equal to about 2,800-5,600
kg. Taking into account the average content of gold in the industrial wastes equal to 350 mg/m3 (see Table 3.18), the volume of re-processed industrial wastes can be estimated as the
following:
2,800 kg : 350 mg/m3 = 8 million m3; 5,600 kg : 350 mg/m3 = 16 million m3.
Given the amount of the re-processed industrial wastes as 8-16 million m3 and average Hg content as 0.2-0.5 g/m3, the total share of industrial mercury in this volume might make up
from 2 to 8 t. About 15-20 % of this amount could have been utilized using modern technologies (see Annex 1), however the basic amount of previously accumulated industrial mercury
(approx. from 1.5 to 6.5 t) could be released in 2001 in the gold-mining sites and surrounding environments. It is roughly estimated that 60% of this amount was emitted to the
atmosphere, about 20% (0.3-1.3 t) accumulated in waste and the same amount, 0.3-1.3 t, released to water bodies.
Mining using the amalgamation method
The illegal and therefore uncontrolled mercury use in amalgamation operations of gold-bearing concentrates still persists, in spite of the official ban (Laperdina, 1995, Report 2002).
Major users of mercury are small-scale enterprises, which do not have enough finances to purchase the expensive processing equipment and use gold schliches amalgamation to increase
gold extraction efficiency. The similar picture is observed in Kazakhstan, where gold amalgamation and mercury burning at the illegal gold mining by individuals are carried out at homes
using much more primitive operations (Kirillova, 2002).
As an illegal use of mercury is punishable as violation of environmental and labour legislation, the information on such kind of Hg use is of course not available. Very rough estimation of
current Hg use in gold amalgamation process can be made using the existing data of Russian gold production structure in 1999 (see Table 3.20). In that year, the gold was produced by
639 enterprises, and in 2001 566. It is assumed that gold structure had been changed a little by 2001 compared to 1999 and the data for this year is used for further estimations.
Table 3.20 Distribution of gold miners in 1999 (Kolmogorov 2000, Benevolsky 2002)
Gold production,
kg/year |
Number of enterprises |
Share in total volume, % |
Of enterprises number |
Of production |
<100
100-300 >300
including more then 1,000
Total |
389
99
78
16
566 |
68.7
17.5
13.8
2.8
100 |
11.2
14.8
74.0
45.9
100 |
In 2001 gold mining enterprises produced 141,500 kg, including ~ 26 (11.2+14.8) % or ~ 37 t mined by small enterprises (<100-300 kg/year). In case the mercury was used in the final
refining of this gold, and Hg estimated (Roslyakov et al., 1995) norm consumption are equal to ~10 % per 1 kg of the mined gold, the total consumption of mercury in amalgamation will
be equal about 3.7 t/year. Taking into account the range of uncertainty of Hg use during gold production by small enterprises (20-40 t of gold) and loss percentage (10-20 % and more),
the total Hg consumption at gold amalgamation may vary between 3-8 t. The mercury extracted during gold- and mercury-containing industrial wastes can most probably be used for
these purposes. The value in the middle of the range 6 t of Hg/year was informally presented by a person related to secondary mercury production and by quite clear reasons not wished
to provide an official information on mercury supplies to gold mining enterprises.
Mining of gold-bearing deposits with the increased content of mercury in ores, sands, bearing stratum.
Mercury concentration in the gold ores can reach 300 g/t (the frequently occur level is 1 g/t), and 10-20 g/t in endogenous haloes of deposits (the frequently occur level is 0.1-0.4 g/t)
(Roslyakov et al., 1995). Due to mining of these deposits the dumps of bearing strata contain quite high concentrations of mercury, and are non-localized sources of mercury releases.
According to the expert assessment (Roslyakov et al., 1995), 1 tonne of gold mined gives about 100 kg of natural mercury contained in dumps and released to the environment. Given the
1:10 ratio of mercury and ore gold mined in 2001, the approximate amount of the extracted mercury can be estimated as the following: (141,449 kg õ 40%): 10 ≈; 5.6 t of Hg. Taking into
consideration an uncertainty of the calculated value, it would be more correctly to show a range of releases as 4 – 8 tonnes. It might be assumed that 20% (0.8-1.6 t/year) of this amount
is released to the atmosphere, 10% - to aquatic environment, 70% (2.8-5.6 t/year) – to tailings and waste.
In the USA, 5-15 t of the accompanying mercury was recovered during complex gold-ore rocks processing at several (below dozen) enterprises in the western part of the country – in
California, Nevada and Utah – with the key aim not to obtain mercury, but to prevent mercury releases to the atmospheric air and aquatic environment (Mercury production 2002).
Unfortunately in Russia all accompanying mercury is released in the environment with mining, processing and refining wastes.
Refining of the gold-containing concentrates with the increased natural or industrial concentration of mercury at refining plants.
By the 1st of January 1999 the following Russian enterprises were licensed to refine the precious metals: Prioksky non-ferrous metals plant (Kasimov town, Ryasan oblast Region);
Novosibirsk refining plant (Novosibirsk city); Schelkovsky secondary precious metals plant (Schelokovo town, Moscow Region); Krasnoyarsk non-ferrous metals plant (Krasnoyarsk
city); Yekaterinburg non-ferrous metals plant (Yekaterinburg city); Kishtim copper-electrolytic plant (Kishtim town, Chelyabinsk oblast Region); Kolimsky affinage plant (Hasin town,
Magadan oblast); Uralelectromed' JSC (Verkhnaya Pishan town, Sverdlovsk oblast); Norilsk Mining and Metallurgical Company (Norilsk city, Krasnoyarsk oblast); ONIX Concern
(Moscow) (Tereshina, 2000).
According to the official data, the Hg content in concentrates incoming at refining plants (up to 1988) was equal to 0.2-4.0 g/t (The order 1988). The severest mercury contamination
source was likely the oldest of the above enterprises – Novosibirsky affinage plant, which refined about 60% of the mined gold till the beginning of 90-ies (Tereshina, 2000). Taking into
account the refining of gold-containing concentrates and schlich gold with the increased mercury content, the surrounding environment of the plant has an industrial mercury halo in soils
(0.03-18.9 mg/kg). Concentration of gaseous mercury in the soil air 100 times exceeds the local background (Roslaykov, 1995).
In present, the increased Hg content in the concentrates incoming to refining might be caused both by natural factors – high Hg concentration in the gold ore, which is conserved just as in
cyanic sludge, and by its previous direct use (mining technogenic placers and tailings) and current illegal application. At present it is not possible to assess the total Hg release at the
refining of gold-containing concentrates, as the proportion of various concentrates to be refined (schliches, bullions, cyanic sludges etc.) and their Hg content is not known.
Recently the current amounts of Hg releases due to the gold mining have been assessed (Roslyakov et al., 1995, Yagolnitser et al., 1995). However these estimates were quite rough and
were performed based on the former gold-mining structure and technologies (gold placers mining prevailed). For example, the approximate annual mercury releases to the environment of
Siberia amounted to 34.4 t. Therefore the shares of atmospheric, water and terrestrial (dumps, tailings, soils) releases were supposed to be equal.
Summary
Based on historic records, references and official data, a rough estimation of total Hg releases to environment during different time periods, including 2001 can be made (see Table 3.21,
Table 3.22). For the whole history of gold mining in Russia, 6,350-6,690 t of Hg might have been released, including 6,125-6,660 t with losses during amalgamation and 230-245 t from
accompanying extraction with gold-bearing ores and rocks.
In 2001 Hg releases from gold mining in Russia could total from 10-20 t, including 4-6 t of natural mercury, 3-8 t from current amalgamation and 1.5 to 6.5 t from the gold mining
technogenic wastes treatment. The presented estimations are very approximate. Unfortunately the authors of the present report have no materials for more correct assessment.
Table 3.21 Approximate estimation of Hg releases from the gold mining in Russia
|
Time periods |
|
before 1917 |
1917-1945a |
1946-1975 |
1976-1990 |
1991-2001 |
2001 |
TOTAL |
Total gold production, t |
2,755 |
~1,000-1,500 |
3,980-4,300 |
2,292 |
1,463 |
152 |
11,490-12,370 |
Approximate relation of Hg losses (t) and 1 t of gold extracted |
1:1 |
0.75:1 |
0.5:1 |
0.25:1 |
0.040:1 |
0.040:1 |
|
Approximate total Hg losses at amalgamation, t |
2,755 |
~750-1,125 |
1,990-2,150 |
570 |
60 |
3-8 |
6,125-6,660 |
Approximate total Hg extraction with gold ores and rocks, t* |
55 |
20-30 |
80-85 |
45 |
30 |
5.6 |
230-245 |
Approximate Hg releases at secondary placers mining |
|
|
|
|
|
1.5-6.5 |
|
TOTAL |
|
|
|
|
|
10-20 |
6,350-6,690 |
*the estimation is based on average placer gold output formerly equal to 80 % of the total production of gold mines.
Table 3.22 Approximate estimation of Hg releases from the gold mining in Russia in 2001
|
Release, total, t |
Mercury emission to the atmosphere, t |
Mercury release to the aquatic environment ,t |
Mercury release to dumps and tailings, t |
Mining of secondary industrial placers |
1.5-6.5 |
0.9-3.9 |
0.3-1.3 |
0.3-1.3 |
Gold amalgamation |
3-8 |
2.1-5.6 |
0.6-1.6 |
0.3-0.8 |
Mercury mobilisation as microelement * |
4-8 |
0.8-1.6 |
0.4-0.8 |
2.8-5.6 |
Refining of concentrates |
? |
? |
? |
? |
* The estimate is included in the section of mobilisation of mercury by non-ferrous metallurgy in section 4.4.
Note, that due to specific climate conditions in the most of gold miming areas of Russia (low average annual temperatures, permafrost, short open water period etc.), it is rather difficult to
use Hg release ratios (atmospheric, water and terrestrial environments) determined for the tropical climate. Moreover, unlike these countries, Russia used and still uses more productive
dredges (with large digging depth and buckets capacity (up to 600 m3) and hydraulic processing facilities, which together with severer climate allows to bury ("conserve") a considerable
part of mercury in anaerobic conditions under a layer of processed sands. Mobilization of mercury from such secondary industrial placers is possibly during the re-mining.
Taking into account all above-mentioned, it is quite difficult to estimate ratio of Hg release to various environments. Based on the data obtained for tropical climate (Lacerda 1997,
MMSD 2002, Hylander 2001), and given the specific climatic conditions of Russian gold mining areas, it cab be concluded that during industrial use of mercury at gold mining and
recycling operations (before the official ban), Hg releases to aquatic, water, air and soil environments were almost equal. In our days, when mercury is mainly used by small enterprises,
the amounts of Hg releases may be close to the estimated values for tropical climate: 2/3 to the atmosphere, 1/3 to soils and water bodies, 2-8 % buried with the processed sands. The
estimations involved the following ratios of Hg distribution in the environment: 70% - air; 20% - water; 10% - process sands and slimes. It should be noted, that the reliable data can be
obtained only through field observations.
3.3.5 Mercury Contamination of Gold-mining Areas of Russia
Today the mercury contamination sources in the gold-mining areas are dumps and tailing dumps, as well as bottom sediments of natural and industrial water bodies. They cause pollution
of natural ecosystems and residential areas in the gold mining impact zones. The pollution level is very poorly investigated. Some data on gold mining areas of Siberia, Far East and Urals
are presented in (Alakayeva 1999, Laperdina 1999, Report 2002, Kutliahkmetov 2002).
According to the investigations results, the most severe mercury contamination is observed near gold extraction plants, where mercury was directly used in technological operations. For
example, it was determined, that Hg content in their surrounding environment might 4-100 times exceed maximum permissible concentration (MPC). The following maximum
concentrations of mercury have been detected: in soils – 18.9 mg/kg (9 MAC), total concentration in groundwater - 32.8 μg/l (65 MPC for drinking water), in natural watercourses – 40
ng/l (4 MPC for fishing water bodies), in bottom sediments – 54.2 mg/kg. At the sluice amalgamation on dredges and amalgam burning, Hg vapours content in the air might 50 times
exceed the mean-shift MPC (250,000 ng/m3). Extremely high concentrations of Hg - 1,000-2,000 mg/kg (50-100 MPC for soils) are registered in concentration tailings and
contaminated soils near processing and concentrating plants. In some regions (Krasnoyarsk, Chita, Blagoveschensk, Khabarovsk oblasts ) technologies on such industrial wastes
re-processing with gold and Hg extraction are developed and applied.
The obtained data shows, that severe climate typical for most Ural, Siberian and Far Eastern gold-mining areas inhibit some chemical, biochemical and biological processes promoting
more localized mercury contamination compared to similar pollution points in the countries with tropic climate. Nevertheless the investigation of specifics of Hg behaviour in terrestrial and
water ecosystems of seasonal frosts and permafrost zones, and metal methylation - demethylation processes in particular, requires execution of expensive laboratory and field studies.
3.4 Dental Amalgam Fillings
3.4.1 Use of Mercury for Dental Amalgams
Amalgams (silver and copper) have been applied in stomatology since 1819. In 1971 the Ministry of Health of the USSR prohibited to produce copper amalgam containing up to 65% of
mercury. This prohibition was caused by significant disadvantages of copper amalgam fillings and hygienic hazard of mercury.
New types of filling material are constantly discussed in Russian dental scientific publications, but the certain amount of silver amalgam is still used and is expected to be used wider as
durable and long-lived material.
Today in Russia about 30 million teeth are filled annually, 7-8% of which with amalgam fillings (data of the Department of medical and economic investigations in dental service of SRI of
social hygiene, economy and health management named after N.F. Semashko RAS). These estimations are confirmed by the experts of the Central Dental Scientific-Research Institute of
the Ministry of Health of RF. Some contradictory information has been obtained as regards the mercury content of the fillings. According to some experts the filling contain 7-8%
mercury, but the major mercury amalgam producing facility (mentioned below) states that the mercury content is about 50%. The mercury content of fillings used in Western Europe is
40-50% (Floyd et al. 2002). Thus, the mercury containing amalgam fillings annually used by Russian stomatologists amount to 2.1-2.4 million fillings a year. Consumption of mercury for
one filling is equal to 350 mg in average (based on information from Russian manufacturer and Floyd et. al. 2002), i.e. about 700 kg of mercury is annually used for 2 million Fillings,
which are finally release to the environment.
Mercury used for amalgams is both produced in Russia and imported. The major mercury amalgam production facility is Stomachim CJCS in Saint-Petersburg. This enterprise annually
supplies up to 500,000 capsules for amalgam making in "Amadent" capsules. Such amalgam is ready for use in dental clinics without additional components. The rest amalgam is
imported.
3.4.2 Mercury Releases from Fillings
Heating of the filling material on the open fire (that was plasticized in Russian clinics) always promoted evaporation of mercury, concentration of which was much higher than MAC. Many
Russian investigations indicate high concentration of mercury in the indoor air of dental clinics – from 20 to 440 μg/m3 – walls' plasters, floor base materials. Let's take for example the
data on mercury vapours concentration in dental rooms' construction materials (see Table 3.23).
Table 3.23 Mercury containing samples of construction materials of dental rooms (Kataeva V.A., 2002)
Mercury contents, μg/g |
Linoleum |
Walls' plasters |
Floor base materials |
2-9 |
14 |
12 |
10 |
10 and more |
22 |
7 |
25 |
Not detected |
14 |
28 |
17 |
A complex of measures aimed at dental clinics personnel protection from mercury vapours impact is envisioned in the relevant Sanitary Rules of the USSR Ministry of Health, 1984.
These Rules /p.5.10/ implicate installation of air treatment facilities for mercury removal to prevent atmospheric air pollution with amalgamator's emissions. Nevertheless, such facilities do
not exist, and presently there are no local treatment facilities installed in dental clinics, thus the mercury containing fillings' residuals and the extracted teeth go to the dumpsites with the
general flow of mixed wastes.
Taking into account that 10 years ago amalgam fillings constituted about 60% of the total amount of fillings, and the average lifetime of a filling is 10 years, the following releases with
extracted teeth are possible today: 18 million fillings õ 350 mg = 6.3 t/year. In general the dental clinics are not equipped with filters and the main part of the extracted fillings will end up in
the sewer. A part of the amalgams may be disposed of with municipal solid waste e.g. with lost teeth.
Besides, the certain amount of mercury is released during cremation. The crematoriums are available only in four Russian cities - Moscow, Saint-Petersburg, Ekaterinburg and Nizhny
Tagil, and are being built now in four more cities. Up to 2 million people die in Russia each year, 7% or 140,000 people are cremated. If it is assumed that the release by cremation is
similar to the amount released in Western Europe of 350 mg per person cremated (Floyd et. al 2002) up to 50 kg of mercury is released annually.
Assessment of distribution of mercury releases with cremation between atmospheric air, terrestrial and water environments can be presented in accordance with estimations of WS Atkins
/1998/, except releases with fillings incineration, as there are only several incineration plants in Russia. Very few amounts of mercury are recycled. Therefore, it is supposed that the major
quantities of mercury – up to 6 t/year - presently go to the sewer or to landfills/dumpsites, and this amount will decrease from year to year due to reduction of the number of amalgams
fillings. As it is mentioned above, the releases of mercury to the atmosphere with cremated people constitute about 50 kg of mercury per year and this amount will 10 kg increase when
new crematoria are operated.
3.5 Thermometers
3.5.1 Production of Mercury Thermometers
Mercury thermometers are devices used to measure temperature; their operation is based on alteration of properties of metallic mercury used as thermometer liquid. Several groups of
mercury thermometers are known (including medical, laboratory, technical thermometers, petroleum product testing thermometers, thermometers for agriculture, and special and
contact-free thermometers) that can be used to measure temperature from –39 to +750 °C. Some types of technical (special) thermometers use a fusion of mercury and thallium as
thermometric liquid, which allows decreasing the lower limit of measured temperature to –60 °C.
Table 3.24 gives a brief characterisation of the basic groups of glass mercury thermometers manufactured in Russia.
Table 3.24 Main groups of mercury thermometers manufactured in Russia (Nomenclature Reference Book ..., 1993; OJSC "Termopribor", Catalogue of Products ...; Report
on the Research Work on the Topic "Studying the Nomenclature ...", 2000)
Thermometer groups * |
Use and brief characterisation |
Content of Hg. g ** |
Maximum medical thermometer (type ÒÁ-1Á) |
Used for measuring human body temperature; has the maximum device represented
by a special slit in the lower part of the capillary, which does not allow flow
of mercury to the reservoir after measurement of temperature |
2 g
(from 2001
– 1.85 g)
|
Meteorological thermometers (type TM) |
Used for measurements, made mostly on meteorological stations and posts; depending
on their purpose of use they have different sizes, different structures, limits
of measurement and the division of the scale (for measuring temperature of air,
soil, water, etc.) |
2-5 |
Laboratory thermometers (type ÒË, ÒÐ, ÊØ) |
Used for laboratory measurements and scientific research; some of them have
an inserted incomplete immersion scale as well as cone interchangeable laps. |
1.4 - 48 g |
Thermometers for testing petroleum products (type ÒÈÍ, ÒÍ, ÒÍ-M) |
Used for measuring temperature for testing of petroleum products during their
production and use |
0.3 - 2.2 g |
Thermometers for agricultural use (type ÒÑ,ÓÐÈ,
etc.) |
Used for measuring temperature in laboratory and production conditions in
different agricultural sectors and agro-industrial complex; manufactured with
an inserted scale; |
2 - 4 |
Technical thermometers (ÒÒ-Ï, ÒÒ-Ó, ÒÒ-ÌÊ) |
Used in various industries; manufactured in two models – straight and
angular (the latter have their lower parts bent at 90O) |
3.9 – 5.8 |
Electrical contact thermometer ((ÒÏÊ, ÒÏÈ,
ÒÊ, ÒÐÊ, ÒÇÊ, etc.) |
Used to signal about specified temperature, and for switching on and off relevant
equipment when such temperature is reached; used in systems for maintaining permanent
(preset) temperature in industrial, laboratory, energy and other installations
and plants; manufactured with a variable (set) contact temperature and with permanent
(preset) contact temperature (thermal contactors); thermal contactors can be straight
and angular, with one or several contacts, with a movable contact, vibration-resistant,
etc. |
1.8 – 14.4 |
Special type thermometers (ÑÏ, ÒÏ) |
Used for measuring temperature in plants and equipment of special use (gas
analysers, refrigerators, bakeries, etc.); can be straight or angular |
2.6 – 7.4 |
* The Catalogue of Products of Termopribor OJSC includes more than 60 brands of mercury thermometers, many of which are made in different models and/or as a set of items;
** Approximate limits.
At present, the OJSC "Termopribor" is the only manufacturer of mercury thermometers in Russia (located in the town of Klin, Moscow Oblast), which is the successor of the Klin
Thermometer Plant, which manufactured its first products in 1956*. At its peak years, the Klin enterprise manufactured up to 100 names (types) of mercury thermometers on a mass
scale, as well as mercury switches and breakers, using up to 100-130 t/year. In 1990, the use of mercury at the plant was 93.2 tonnes (Report on Research on the Topic "Analysis ...".
1999).
In the recent years, the scope of production and, hence, the use of mercury at the OJSC "Termopribor" has bees permanently decreasing, however since late 1990's these figures started
to grow. In 1998-2002, up to 97-98% of products manufactured by the OJSC "Termopribor" included medical use thermometers; the remaining part included industrial (technical)
thermometers (Table 3.25). Manufacture of mercury barometers, manometers and switches at the enterprise has been terminated completely (due to lack of demand).
Now, the enterprise has a special shop for processing rejected products, contaminated broken glass, soft waste; they are subjected to de-mercuration at the modernised plants UDL-2m.
While it is possible to agree with the arguments that mercury mechanically lost in technological processes, collected by forepumps (from the mercury traps) and then – after cleaning –
returned to production, then the argument stating that "rejected products and soft waste are subjected to de-mercuration and the generated mercury is returned to production" is doubtful.
Nevertheless, we will assume in the following calculations and estimates that the de-mercuration plant modernised by the enterprise specialists allows producing secondary mercury that,
following its cleaning, is again returned to production.
Manufacture of thermometers is mass-scale (conveyor) or batch production. Both types of manufacture are based on technological process of targeted differentiation, separation of
mercury-related operations from non-mercury operations and mechanisation of mercury-relation operations. To this end, the Klin enterprise has special mechanised mercury facilities,
including a bay for mercury cleaning, its transportation to installations that fill mercury into thermometers, and high-capacity mercury filling installations (MFI).* Mercury thermometers are
mainly manufactured in the so-called special mercury building, which includes the bay for mercury cleaning, the shop of medical thermometers and the shop of industrial thermometers (at
present, the shop of special thermometers is not operated). Generally, the process of manufacture of mercury thermometers includes three stages. The first stage includes mercury
cleaning; the second stage includes manufacture of the glass part of the thermometers and filling of mercury; and the third stage includes graduation of the scale (thermostatic process).
Table 3.25 Manufacture of thermometers, use of mercury and generation of waste at the Termopribor OJSC in 1998-2002
Year |
Manufacture of medical thermometers |
Manufacture of other thermometers |
Total |
Quantity
pcs. |
Mercury in products
kg |
Content of mercury in one product
g |
Quantity
pcs. |
Mercury in products
kg |
Content of mercury in one product
g |
weight of mercury in products, kg |
1998 |
7 256 000 |
14 512 |
2 |
192 563 |
744.348 |
3.865 |
15 256.348 |
1999 |
8 430 550 |
16 861.1 |
2 |
197 428 |
783.166 |
3.967 |
17 644.266 |
2000 |
10 957 684 |
21 915.4 |
2 |
221 721 |
1 027.292 |
4.633 |
22 942.692 |
2001 |
11 695 500 |
21 636.7 |
1.85 |
280 322 |
2 397.314 |
8.552 |
24 034.014 |
2002 |
13 177 328 |
24 378.0 |
1.85 |
270 593 |
1 201.367 |
4.40 |
25 579.367 |
Table 3.25 (continued)
Click here to see the table.
* Primary actual data are given as provided by the Administration of Termopribor OJSC;
** Since 1999, the enterprise has been operating plants for de-mercuration of mercury waste (decontaminated broken glass is now taken to the municipal dumpsite; before, it was placed
at the enterprise waste field, now closed);
*** Dissolved mercury forms (other mercury is not identified by analysis);
**** Data marked "no confirmed data" (further only calculated data were used);
***** Cotton cloth, wool, etc. (first subjected to de-mercuration, then, probably, taken to the municipal dumpsite);
***** Data marked "metallic mercury is captured by mercury traps and then returned to production";
****** Data marked "rejected products are subjected to de-mercuration; the generated mercury is returned to production" (judging by the amount of generated broken glass, the share
of rejected products is rather high, probably making up to 15-20% of the total manufactured thermometers, which is about 1.2-1.6 million thermometers a year during the reported
period; it should be emphasised that Termopribor OJSC tests and checks each manufactured thermometer, unlike for example thermometers supplied to Russian from China where only 1
products per 1000 is tested).
At the cleanup bay, metallic mercury is fed to a special tank, wherefrom it is supplied, by a pipeline, to the chemical cleaning bath; then by a pipeline it is supplied fore vacuum distillation
and then to filtration (a system of filters is used, which allows a very fine cleaning of metal). After such preparation mercury is fed via a pipeline (suing pumps) to the shop of thermometers
(to the so-called reception tanks located in the thermometers filling bay). From the reception tanks, a predefined amount of metal (up to 150 kg) is fed by gravity to the MFI; an
insignificant part of it is used for parallel filling of several thousands capillary pipes; the rest of the mercury is returned by the pipeline to the initial tank located at the cleaning bay (for a
new cycle described). In the most active period at the enterprise, the amount of returnable mercury used daily in the technological process reached 8 tonnes.
During the technological process of manufacture of thermometers, direct manipulations with metallic (otherwise, "open" mercury) include the following operations: filling of thermal
ampoules with mercury; removal of excessive mercury; checking of the scale; soldering of capillary and the graduation operations cycle built on the principle of selection of ready scales
according to the thermometer scaling. Then all thermometers are tested and checked. Following checking, standard products are transported to the warehouse of finished products while
rejected products are sent to the disposal shop. This shop receives contaminated broken glass and other mercury-containing waste.
During technical operations with open (exposed) mercury its vapours get to air of the production rooms. In 1964, the Klin enterprise started the shop for cleanup of ventilation emissions
of mercury vapours; the main equipment of this shop includes several absorbers (each of them includes up to 36 tonnes of pyrolusite). Before this shop started its operation, only
ventilation emissions from the shops where "open" mercury operations were carried, had been cleaned; after this all emissions of this enterprise have been cleaned (Petukhov, Konovalov,
1973). The bulk of emissions from the shop of cleanup of ventilation emissions are emitted through the stack 62 m high. At present efficacy of operation of the absorbers is 83% on the
average (pyrolusite filled into the absorbers has never been replaced, but rather loosened from time to time). Residual emission of mercury to atmosphere (after cleaning) in the mid 1980's
was 150-190 g/day (55-69 kg/year), while concentrations of mercury vapours in air reached 0.05-0.1 mg/m3 (Methodological Recommendations ..., 1989).
In the first half of 1990's, concentration of mercury vapours in the air of the working room at the OJSC "Termopribor" was within 0.02-0.05 mg/m3 (Stepanova, 1994). Now,
concentrations of mercury vapours are measured in 25 points of the mercury building once a week (about 1,300 measurements a year); as a rule, in about 10-20% of cases the levels of
mercury vapours exceed the maximum single MAC (maximum allowed concentration) within the working area (= 0.01 mg/m3). Some year ago at the enterprise in Golynki,
concentrations of mercury vapours at the optimum temperature of the indoor air (16-24 °C) three times higher than MAC were recorded only in 5 technological operations out of 20 – the
data provided by the Centre of State Sanitary and Epidemiology Supervision of Smolensk Oblast.
A significant part of mercury mechanically lost during technological processes is accumulated in the mercury sewerage system traps, wherefrom it is extracted by the forepumps and then
is fed to a special tank (after chemical cleaning, distillation and filtration it is again returned to production). The enterprises manufacturing thermometers use a huge amount of water (up to
1000 m3/day), which is used in the air conditioning and ventilation systems (Enlarged Standards for Water Use ..., 1978). Usually, water contains a significant amount of dust absorbing
mercury. A substantial amount of fine-dispersion metallic mercury is also discharged to the sewerage system.
Solid waste from the manufacture of mercury thermometers includes primarily broken glass (contaminated glass) as well as textile waste (wool, cotton cloth).
3.5.2 Mercury consumption with thermometers
The estimation of the balance of mercury use at the instrument manufacturing enterprises, made in 1990 (the bulk use of mercury at that time was for manufacture of thermometers),
showed that in technological processes about 97.38% of metal is included into the final products, 1.97% represents the so-called secondary mercury (returned to production), and 0.65%
make irrecoverable loss {Report on Research Work on "Analysis ...", 1999). Since no cardinal changes have been made in the thermometers manufacturing technologies over the last 10
years, then the data provided were used to calculate the balance of modern use of mercury at the OJSC "Termopribor" (Table 3.26). Table 3.27 shows the rated (calculated) balance of
mercury distribution during manufacture of thermometers. The so-called unaccounted losses, which so some reasons were not reflected in the official statistical data of the enterprise (see
Table 3.25), include loss of metal discharged to the sewerage system (with suspended matter in the wastewater, as well as fine-dispersion metallic mercury not captured by the mercury
sewerage system traps), unorganised emission of mercury vapours (through doors and windows), some part of which is absorbed by construction elements, equipment, cloth and
footwear of personnel, etc.
Table 3.26 Use of mercury at Termopribor OJSC in 1998-2002
Year |
Total weight of used mercury |
Mercury in final products * |
Technological losses of mercury-** |
kg |
% |
kg |
% |
kg |
% |
1998 |
15,356.163 |
100 |
15,256.348 |
99.35 |
99.815 |
0.65 |
1999 |
17,759.704 |
100 |
17,644.266 |
99.35 |
115.438 |
0.65 |
2000 |
23,092.795 |
100 |
22,942.692 |
99.35 |
150.103 |
0.65 |
2001 |
24,191.257 |
100 |
24,034.014 |
99.35 |
157.243 |
0.65 |
2002 |
25,746.721 |
100 |
25,579.367 |
99.35 |
167.354 |
0.65 |
* It was mentioned above that secondary mercury generated at Termopribor OJSC during waste disposal (recycling) is returned to production (i.e. it is included ultimately into the
products);
** There are data showing that in the first half of 1990's the Klin thermometers enterprise emitted to the environment up to 100 kg of mercury (Moscow Regions Studies ..., 1996).
Data on other facilities using mercury in technological processes (above all these are electrical lamp enterprises) demonstrate that up to 95% of unaccounted losses include loss of metal to
the sewerage system (as fine-dispersion mercury and as part of wastewater suspended matter). This allows detailing of the balance of mercury distribution during technological processes
of thermometers manufacture (Table 3.28). The fact that a substantial amount of mercury is lost with discharge to the sewerage system is confirmed by the following data.
Table 3.27 Balance of mercury distribution at the OJSC "Termopribor" (total losses = 100%)
|
Main types of mercury losses |
Year |
Captured by absorbers * |
Emitted to atmosphere * |
Broken glass * |
Discharged with wastewater * |
Unaccounted losses ** |
|
kg |
% |
kg |
% |
kg |
% |
kg |
% |
kg |
% |
1998 |
1.6 |
1.6 |
0.32 |
0.3 |
20.56 |
20.6 |
0.669 |
0.7 |
76.666 |
76.8 |
1999 |
6.2 |
5.4 |
0.26 |
0.2 |
0.075 |
0.1 |
0.627 |
0.5 |
108.276 |
93.8 |
2000 |
6.43 |
4.3 |
1.4 |
0.9 |
0.102 |
0.1 |
0.718 |
0.5 |
141.453 |
94.2 |
2001 |
6.97 |
4.4 |
1.4 |
0.9 |
0.104 |
0.1 |
0.605 |
0.4 |
148.164 |
94.2 |
2002 |
7.1 |
4.2 |
1.4 |
0.8 |
0.116 |
0.1 |
0.772 |
0.5 |
157.957 |
94.4 |
* Calculated on the basis of data provided by the enterprise (in wastewater only dissolved forms of mercury are accounted by analysis);
** Mainly these are losses of mercury to the sewerage system (absorbed on the mercury suspension, fine-dispersion metallic mercury not captured by the mercury traps), as well as
unorganised emissions of mercury vapours to atmosphere, and their absorption by construction elements, equipment, clothes and footwear of personnel, etc.
Table 3.28 Total balance of mercury distribution at the OJSC "Termopribor" (total losses = 100%)
Click here to see the table.
Discharge from Termopribor OJSC is fed through the sewerage system to the communal treatment plants where it is treated, together with communal wastewater; as a result, wastewater
sludge (WWS) is generated that is stored at sludge sites. The average content of mercury in WWS in the town of Klin is very high, and in the mid 1990's it reached 220 mg/kg
(Achkasov, 1987). It was established that intensity of sludge generation (dry matter) at the municipal wastewater treatment plants made 80 g/man/day (Yevilevich, Yevilevich, 1988).
Population of the town of Klin is about 92,800 people (Geography of Russia ..., 1998). Thus, up to 2,800 tonnes of sludge is generated at the wastewater treatment plants of the town
every year; in mid 1980's, this sludge accumulated up to 620 kg of mercury a year, basically mercury coming with wastewater from the enterprise manufacturing thermometers. At that
time, the use of mercury at the Klin enterprise of thermometers made 100-130 t/year (4-5 times higher than, for example, in 2001), while losses of mercury with wastewater (if we judge
their structure, as given in Table 3.28) were within 580-755 kg/year.* Ultimately, major part of this mercury was fed to the municipal treatment plants while a define amount of mercury
was accumulated in the sewerage system whose length was 2 km (from the enterprise to the treatment plants). Naturally, some part of mercury was discharged with effluent to the Sestra
River, which, in particular, explains its accumulation in river sediments. Thus, selective surveys show that concentration of mercury in benthic sediments of the Sestra River, downstream of
the town of Klin, reach 1.55 mg/kg (Fursov, 1998). This is more than 50 times higher than the typical background level of metal in the riverbed alluvia in uncontaminated rivers (for
Moscow Oblast rivers it makes, on the average, 0.03 mg/kg (Yanin, 2002)).
Efficacy of treatment of wastewater, especially as regards mercury, hardly can exceed 90%; from this it follows that in mid 1990's at least 68 kg of mercury went to wastewater every
year; this wastewater was discharged to the Sestra River from the municipal wastewater treatment plants. Thus, total losses of mercury at the enterprise at that time were at least 900 kg a
year. There are data according to which over 1957-1993 the "Termopribor" enterprise emitted/discharged to the environment at least 35 tonnes (Fursov, 1997), i.e. 945 kg a year on the
average.
Survey of the distribution of mercury in different environmental components within the area of impact of Klin Termopribor enterprise, made mainly in mid 1980's, demonstrated that
impacts of emissions to atmosphere were rather local. In particular, highest concentrations of metal in soils were observed directly within the industrial area of the enterprise, reaching 25
mg/kg (MAC for mercury in soils = 2.1 mg/kg) as well as in ground in the enterprise dumpsite – 20 mg/kg and in soils near the road to the dumpsite – 0.9 mg/kg. Beyond the area of the
enterprise and the dumpsite area there were no concentrations of mercury in soils exceeding MAC. Maximum mercury concentrations in dust precipitated with snow also were found only
nearby the enterprise (0.63 mg/kg). Vapours of mercury in atmospheric air exceeded MAC (for populated centres MAC was 0.3 μg/m3) only within the enterprise area; they were lower
in the vicinity close to the enterprise area, 0.25 mg/kg, and reached background concentrations (0.025-0.010 g/m3) at a distance of 750-1000 m from the enterprise (Sokolov, 2000).
B.A. Raevich found that children of employees from the Klin thermometers manufacturing enterprise had higher (usually 1.5 times higher) concentrations of mercury in urine as compared
to children whose parents were employed at other enterprises. This testified to the fact that mercury was brought by parents to their living house (on clothes and footwear).
Table 3.29 shows the emissions of mercury to the habitat during manufacture of thermometers at Klin Termopribor OJSC; the overwhelming majority is connected with losses of mercury
to the sewerage system (mainly as fine-dispersion metallic mercury as well as wastewater suspended particles).
Table 3.29 Structure of mercury emissions/discharge at OJSC "Termopribor" (total irrecoverable losses = 100%) *
Year |
Total |
To atmosphere |
To soil (at dumpsite) |
To sewerage |
|
losses, kg |
kg |
% |
kg |
% |
kg |
% |
1998 |
98.215 |
4.153 |
4.23 |
20.56 |
20.93 |
73.502 |
74.84 |
1999 |
109.238 |
5.674 |
5.19 |
0.075 |
0.07 |
103.489 |
94.74 |
2000 |
143.673 |
8.473 |
5.90 |
0.102 |
0.07 |
135.098 |
94.03 |
2001 |
150.273 |
8.809 |
5.86 |
0.104 |
0.07 |
141.361 |
94.07 |
2002 |
160.245 |
9.298 |
5.80 |
0.116 |
0.07 |
150.831 |
94.13 |
* In USA, losses of mercury during production of thermometers in 1995 were 9 kg per tonne of used mercury (Locating and Estimating Air ..., 1997)
3.5.3 Use, Export and Import of Mercury Thermometers
In 2001, Klin's Termopribor OJSC manufactured more than 13.1 million medical thermometers and over 280.300 industrial (technical) thermometers. Of this number, about 20% of
products were exported to foreign countries other than CIS and about the same number to CIS countries (mainly to Ukraine and Kazakhstan). The rest of the thermometers (about 7.9
million medical thermometers and 168,200 industrial thermometers, cintained not less than 17 t of mercury) were supplied to the Russian domestic market.
In the recent years, mercury thermometers have been imported to Russia (from China) (mainly including methodical thermometers, TVY-120 and TAYS-006); they are manufactured by
the Asmus Enterprises Ltd. (USA) which has its subsidiaries in China. By estimates of S.G. Itkin (Termopribor OJSC), import of such thermometers makes about 1 million units a year. A
small number of mercury thermometers are imported also from some other countries. The total amount of Russian import of mercury thermometers in 2001 can be estimated at 1.3 million
pieces (the average content of mercury per thermometer being 1 g, so up to 1.3 tonnes of mercury was imported to our country).
Thus, the total number of products coming to the Russian domestic market reaches 9,368,000 thermometers, of which the overwhelming majority (over 98%) includes medical
thermometers. By all evidence, practically all of them are sold to population during one year.
3.5.4 Emission of Mercury When Using Thermometers
In Russia, faulty thermometers that are not used practically always are transported to dumpsites – this is the best case. Only in the recent years efforts have been seen in some towns to
organise account, collection, storage and disposal of used thermometers. First of all, special stations and tanks are organised for spent (broken) thermometers in large hospitals as well as
mass-scale actions aimed at collecting thermometers from schools, children's preschool institutions, etc. It should be noted that by a special order of the Ministry of Education of Russia
(of 16 June 1994) it was prohibited to use mercury and mercury-containing products in educational schools.
To calculate the number of mercury thermometers used in the country every year, we will give some limited estimates that are available.
By estimates of V.V. Bogatov (presentation at the conference "Mercury. Comprehensive Security System, 21-23 may 1996) in mid 1990's, in St. Petersburg, up to 500,000 mercury
thermometers were put out of use (faulty, broken, etc.) (i.e. about one thermometer per 10 citizens). By the data provided by the agency "Rtutservice" and NPP "Ecotrom", at the end of
1990's in Moscow, 0.05-0.8 million mercury thermometers were put out of use every year, i.e. about 650,000 (1 thermometer per 13 citizens), of which not more than 1% was collected
and disposed. In the republic of Mordovia (920,000 population), in 2000-2002, up to 40,000 mercury thermometers were supplied to the trade system every year (1 thermometer per
23 persons); by all evidence, about the same number of thermometers were put out of use.
Thus, depending on the region, every year one thermometer per 10-23 citizens of the country is put out of use. It is obvious that the data for Mordovia, where the share of urban
population does not exceed 60%, do not adequately reflect the real situation of the country (the share of urban population in Russia exceeds 73%). For calculation, it is probably
necessary to use the average specific indicator: 1 thermometer per 165 persons. For the whole country it will make just over 9 million thermometers, which is a little smaller than the
number of thermometers supplied to the domestic market in 2001 (which is however quite natural). These 9 million thermometers contain at least 18.1 tonnes of mercury; almost the entire
amount (up to 90-85%) is brought – at best – to the sewerage discharge, garbage or dumpsites.
3.6 Barometers, Manometers and Other Measuring Equipment
3.6.1 Production of Mercury-containing Measuring Equipment
Mercury has been used for a long time for manufacture of mercury switches, mercury valves, pressure gauges, barometers, mercury pumps and other devices. At present, mass-scale
manufacture of most of such devices has been terminated for various reasons. Nevertheless, some devices manufacture din the previous years are still used in different spheres, both
housing and industrial. There are data that mercury is present in mobile phones as well as in computers (up to 0.0022% of the total weight): it is used in electronic keys and flat monitors
(http://www.physfac.bspu.secta.ru/mirror/izone/izon...).
By estimates of Promotkhody MGUP (Industrial waste), only in Moscow more than 6,000 tonnes of radio-electronic, electrical engineering and medical products (devices) are used,
containing mercury and mercury compounds (Demina, 19999). Enterprises of the city of Omsk have more than 16,000 different devices containing over 250 kg of mercury
(http://www.rmx.ru/news/&news=295). By estimates, mercury-containing devices (pressure gauges, ignitrons, etc.) used by the enterprises and organizations in Krasnodar Krai include
about 20 tonnes of metallic mercury (Sheveleva, 2000). If we take the entire country, the amount of mercury in different devices that are used by enterprises and organisations nowadays
can reach several thousand tonnes.
Manometer devices (pressure gauges) are used to measure pressure of liquids and gases. Barometers are used to measure atmospheric pressure, vacuum meters are used to measure
pressure near zero, and sphygmomanometers are used to measure arterial pressure (Riva Rocci devices).
In the former USSR, the main manufacturers of mercury barometers and pressure gauges were: Klin Thermometer Plant (Termopribor OJSC), Teplocontrol enterprise (city of Kazan),
Aktryubrentgen enterprise (Kazakhstan), Telshai Plant of Computing Machines (Lithuania), and Lubenskiy Plant of Computing Machines (Ukraine).
Currently, Russian has stopped manufacture of mercury pressure gauges (barometers, vacuum meters, sphygmomanometers); it was terminated some years ago.
3.6.2 Mercury Consumption with Measuring Equipment
Depending on the form of communicating vessels, mercury barometers can be plate-type, siphon or siphon-plate barometers. Action of mercury barometers is based on equalising
atmospheric pressure by the mercury column pressure in the barometric (made from thermometer glass) tube (Table 3.30).
Table 3.30 Content of mercury in barometers (Report on Scientific Research devoted to the Topic "Study ..., 2000).
Name and brand |
Content of mercury in the device, g |
Barometer CPA (station, plate, mercury) |
586 |
Barometer ÑÐ (station, plate, mercury) |
894.1 |
Barometer ÈÐ (inspection, mercury, siphon-plate) |
1,257.1 |
Barometer ÊÐ (control, mercury, siphon-plate) |
2,150 |
Mercury barometers are highly precise devices; they are used practically in all meteorological stations and services of aerodromes; they are also used to check operation of other types of
barometers. They are used in scientific and production laboratories. When handled carefully, mercury barometers can operate several dozens years (to be filled from time to time with
mercury). Only in the recent years, meteorological stations have started using mercury-free network barometer ÁÐÑ-1M that can be interfaced with PC.
The total number of mercury barometers used nowadays cannot be counted precisely, however it can be assumed that their number can be several thousands (more than 600
meteorological stations operate in Russia; about 400 civil aerodromes, etc.). With the average content of mercury per barometer being up to 1 kg, the total weight in such devices can
make several tonnes (5-6 tonnes). Every year some amount of mercury is used to supplement barometers.
Sphygmomanometers contain up to 10% of mercury on the average (of the total weight). They are still used in medical practices since they are reliable and highly precise. A definite
number of sphygmomanometers were imported, some years ago, to USSR and Russia through the so-called humanitarian aid. In 2001, there were 10,600 hospital institutions in Russia,
while the number of medical and outpatient polyclinics was 21,300 (Industry of Russia..., 2002). If we assume that every such institution has at least one mercury sphygmomanometer,
then their total number will be more than 30,000 pieces (with at least 300 kg of mercury).
In mercury pressure gauges ÌÁÏ (mercury pressure gauges, checking bureau) and Ì×Ð-3 (mercury, plate-type pressure gauge) the content of mercury is 211 and 1,683 g, respectively
(Report on Scientific Research devoted to the Topic "Study ..., 2000). In the past, mercury float-type differential pressure gauges were very widely spread (types ÄÏ-710Ðá ÄÒ-5á ÄÒ-50), however their industrial manufacture was terminated several years ago. Nevertheless, some of these devices are still used in boiler houses, gas distribution stations, laboratories,
etc. It should be noted that one can find ads in Internet about sale of differential mercury pressure gauges ÄÒT-50 (probably, from store stocks), which indicates to some demand for these
items on the Russian market, although it is not the device itself can be offered for sale, but rather mercury in it.
3.6.3 Mercury in Waste Products and Releases of to Air, Soil and Water
By the data of the Exotrom NPP (Moscow), different enterprises and organizations of the city have supplied to this organization, in the recent years, several; dozens of differential mercury
pressure gauges containing mercury a year (for example, 50 items in 2002). If take the entire Russia, the number of mercury pressure gauges to be disposed (based on the data from
section 3.6.1) may, probably, constitute several hundreds (up to a thousand) a year (containing 300-500 kg of mercury).
3.7 Electrochemical Cells
3.7.1 Production of Mercury-containing Electrochemical Cells
Electrochemical cells are separate cells of current sources that generate electricity as a result of direct transformation of chemical energy of redox reactions; they are used for a single
electrical discharge (also called primary galvanic cells). Groups of identical electrochemical cells can be connected electrically and structurally into an electric battery so as to receive such
electrical current (quantity of electricity) that cannot be generated by a single cell. Basic components of an electrochemical cell are two electrodes of different nature and electrolyte.
Usually, electrodes are metal plates of meshes coated with reagents (active substance): a reducing agent (zinc, lithium, etc.) is deposited on the negative electrode, while oxidizing agent
(oxides of manganese, mercury or other metals) is deposited on the positive electrode. Electrochemical cells and batteries are used mainly for electrical supply to portable equipment and,
therefore, are manufactured mostly with thickened or solid electrolyte.
In the former USSR, in 1980's, up to 100-130 tonnes of mercury were used every year for manufacture of electrochemical cells and batteries (mercury-zinc, alkali and salt –
manganese-zinc and silver-zinc). The main manufacturers of these products were Yelets Cell Plant (now OJSC "Energia", town of Yelets, Lipetsk Oblast), NPO "Kvant" (Moscow
City), "Elastik" enterprise (town of Lesnoy, Shilovskiy District, Ryazan Oblast), "Signal" enterprise (town of Chelyabinsk), "Sirius" enterprise (town of Klaipeda, Lithuania),
"Uralelement" enterprise (town of Verkhny Ufaley, Chelyabinsk Oblast), "Kuzbaselement" enterprise (town of Novokuznetsk), "Vostsibelement" plant (town of Cheremkhovo, Irkutsk
Oblast), "Programmator" enterprise (town of Vyazma, Smolensk Oblast), and the Condenser Plant (town of Novosibirsk). Also, normal primary cells (mercury-cadmium and
mercury-zinc) were manufactured in small numbers for industrial and scientific use.
The total manufacture of electrochemical cells in the USSR at the end of 1980's was up to 1 billion cells a year. For example, in 1990 alone 683 million electrochemical cells were
manufactured for home electrical equipment; of them, over 333 million cells were manufactured at the Yelets Cell Plant. Since early 1990's, there has been a sharp reduction of their
manufacture in Russia (Table 3.31). Many enterprises discontinued their output all together; others halved their output; today, some enterprise manufacture electrochemical cells and
batteries only by orders from enterprises and organizations. All this resulted in a substantial decrease of the use of mercury (Table 3.32): in 2001 about 0.8 tonnes of mercury was used
for this purpose. The main manufacturers of electrochemical cells for home electrical appliances have been FGUP "Uralelement", town of Verkhny Ufaley (manganese-zinc alkali cells and
batteries) and OJSC "Energia", town of Yelets (mercury-zinc and alkali manganese-zinc cells and batteries).
Table 3.31 Manufacture of all types of electrochemical cells for home electrical appliances in the USSR and in Russia, in million pieces (Russian Statistical Yearbook ..., 2002;
Lipetsk Oblast in Figures for 2001 ..., 2002; Main Economic and Social Indicators of the Lipetsk Oblast ..., 2002; with amendments from the author)
Output |
USSR |
Russia |
|
1980 |
1990 |
1995 |
1996 |
1997 |
1998 |
1999 |
2000 |
2001 |
2002 * |
Total |
400 |
683 |
50.1 |
24.6 |
14.1 |
4.5 |
7.0 |
7.1 |
4.4 |
5.6 |
Energia OJSC, Yelets ** |
? |
333.1 |
14 |
4.4 |
3.5 |
1.4 |
1 |
2 |
1.6 |
2.8 |
* Uralelement enterprise manufactured 2.8 million pieces;
** In 1998, Energia OJSC developed a programme for transition to manufacture of cells for air-zinc and lithium systems replacing mercury-zinc systems.
Mercury in Produced Batteries
In mercury-zinc cells (according to the domestic nomenclature, these are cells of the type ÐÖ:
10ÐÖ53, 5ÐÖ83, 10ÐÖ85, etc.), manufactured as sealed low-capacity devices with a
disk (button or tablet) or cylindrical structure, the active mass of the positive electrode includes mercury oxide HgO (also called red or yellow mercury oxide) with a fine-refined graphite
added (5-15%); the negative electrode includes powder zinc with a small amount of mercury (amalgamated zinc).
Table 3.32 Use of mercury at Energia OJSC, town of Yelets (Report on Research ..., 1999; Lipetsk Oblast in Figures for 2001 ..., 2002; Main Economic and Social Indicators
of the Lipetsk Oblast ..., 2002)
Year |
Use, kg/year |
Output of all types electrochemical cells |
|
Metallic mercury |
HgO |
million a year |
1996 |
34 |
1,513 |
4.4 |
1997 |
29.5 |
1,720 |
3.5 |
1998 |
16.5 |
725 |
1.4 |
2001 |
18 * |
750 * |
1.6 |
* Estimates.
The active mass of the positive electrode is pressed into the cell body while the negative mass is pressed into its cover. Before the electrochemical cell is assembled, a gasket from porous
paper is placed between the body and the cover; this gasket is impregnated with electrolyte composed of a KOH (potassium hydroxide) solution with zinc oxide. An insulating rubber
gasket is placed between the body and the cover, which plays the role of the seal. Cells of the ÐÖ type contain on the average up to 1% of metallic mercury and up to 37% of mercury
oxide of their total weight (Report on Research of Topic "Study of Nomenclature ..., 2000). The weight of these elements varies from a few grams (button structure) to 45-370 g
(cylindrical structure); the weight of the battery "Priboy-2C" is 450 g. Self-discharge of the cells of a mercury-zinc system during their storage is negligible: it is decreased by not more
than 10% during a period from 12 months and till the end of their service life; alongside with high impact resistance, vibration stability and resistance to significant vacuum and high
pressure this property defined their use in military equipment, field devices, radiosondes, medical devices, watches and clocks, etc.
In alkali manganese-zinc elements of cylindrical structure (types RL-316, RL-332, RL-343), the positive electrode is manganese oxide with graphite, acetylene ash and electrolyte (the
latter includes potassium hydroxide, zinc oxide, potassium biochromate, and carbonates). The negative electrode is made from a homogeneous paste mixture: powder zinc – 1000 g,
mercury oxide – 15 g, potato starch – 45 g, and electrolyte – 340 ml (Report on Research of Topic "Study of Nomenclature ..., 2000). Thus, the negative electrode includes up to 1.1%
of mercury oxide (or 1.5% of the zinc weight). In particular, an RL-332 cell (its weight is 35 g) contains 66 mg of mercury oxide; an RL-343 cell (its weight is 70 g) contains 154 mg of
mercury oxide; and button-structure cells contain not more than 20-25 mg of mercury. Korund battery contains 0.5% (of its eight) of mercury oxide; some batteries of the series "Baken"
(their weight is up to 2.5 kg) contain 18-25 g of mercury oxide.
Mercury in Waste Products and Releases of to Air, Soil and Water
In the common case, the technological scheme for manufacture of electrochemical cells includes three main groups of operations: preparation of the anode mass; making of the cathode;
and assembly of cells. Preparation of the anode mass includes treatment (filtration) of mercury, weighing of mercury, filling of mercury into the mixer, mixing of component materials,
loading out of the anode mass, packing of feeders, and cleaning of the mixer parts. When the cathode is made, HgO, MnO2 and graphite are fed from the hopper to the mixer and the
resultant mixture is fed for additional treatment where it is compacted. Then the ready cathode and anode are fed to the shop for assembly of electrochemical cells. Cells are assembled
on automatic (semi-automatic) lines, which perform dose dispensing of the anode mass, fill the cell body with the anode mass, seal the cell, etc.
When electrochemical cells are produced, mercury is emitted to the air (as vapours or mercury oxide dust), during preparation of the anode mass and making of the cathode, assembly of
cells, and during maintenance and repair of equipment; mechanical losses of metallic mercury occur during its filtration, weighing and preparation of amalgam. Usually, all working rooms
have general exchange plenum and exhaust ventilation system as well as dust entraining systems; mercury filtration and weighing is made inside exhaust cabinets; the other technological
operations, including those performed on automatic assembly lines, as a rule, are made using equipment that has no local exhaust equipment. Production wastewater is fed to the
enterprise local wastewater treatment plants (for example, at Energia OJSC a reagent treatment method is used); then wastewater is fed, through the sewerage system, to communal
treatment facilities and, after them, it is discharged to water bodies.
Data related to the period of active operation of the Yelets enterprise indicate to a high emission of mercury vapours to air of the working rooms at all stages of preparation of
electrochemical cells (Pyatnitsky, 1994). For example, concentration of mercury vapours and of mercury oxide in the mercury-zinc cells shop 25 times exceeded the maximum allowed
concentration (MAC); high concentrations of mercury were also found in wastewater after washing of hands and special clothes, walls and floors. Concentration of mercury vapours in
the air of the manganese-zinc cells assembly shop was much smaller, however, on the average it was 2 times higher than MAC. The highest concentrations of mercury vapours in the air
were observed during filling of metal to the mixer (Table 3.33); very often they exceeded MACmax (maximum allowed single MAC in the air of the working area) (Karelin et al., 1992).
Technological operations performed during filling of electrochemical cells with anode mass and during their assembly emit less mercury vapours to the air. As a rule, the most dangerous
operation is maintenance and repair of assembly lines (Table 3.34). High concentration of mercury vapours were practically recorded in all production rooms at the Yelets Cell Plant
(Pyatnitsky, 1994). Cases of chronic mercury intoxication were recorded among the enterprise workers; these cases were dominant as compared to other occupational diseases. High
concentration of mercury vapours are also found in the soil in the enterprise area and in its surrounding, as well as in other areas of Yelets (Environmental Condition of the Lipetsk Oblast
in 1998..., 1999).
Table 3.33 Mercury in the air of the room wherein anode mass is prepared (Karelin et al., 1992).
Technological operation |
Number of measurements |
Mercury concentration, μg/m3 |
|
|
Average |
Maximum |
Mercury filtration |
13 |
1 |
50 |
Mercury weighing |
20 |
20 |
100 |
Filling of mercury to the mixer |
8 |
212 |
760 |
Mixing of the anode mass |
24 |
11 |
70 |
Unloading of the anode mass |
13 |
10 |
100 |
Packing of the feeders |
10 |
9 |
23 |
Washing of the mixer parts |
12 |
5 |
52 |
MACas (working area, average shift) |
|
5 |
MACmax (working area, maximum) |
|
10 |
MACA (atmospheric air in populated localities) |
|
0.3 |
Typical background content |
|
0.010-0.015 |
Table 3.34 Mercury in the air of the cell assembly shop (Karelin et al., 1992)
Technological operation |
Place ofobservation |
Number of observations |
Mercury concentration, μg/m3 |
Average |
Maximum |
Feeding of anode mass and calibration of cells |
Cell assembly line - A |
24 |
12 |
39 |
Cell assembly line - B |
18 |
3 |
8 |
Conditioner |
16 |
8 |
26 |
Door to the corridor |
8 |
14 |
31 |
Repair of mechanisms at the assembly line |
Cell assembly line -A |
10 |
119 |
160 |
Conditioner |
5 |
8 |
11 |
Door to the corridor |
5 |
125 |
140 |
A sharp decrease of output of electrochemical cells at Russian enterprises and, hence, respective decrease of mercury use at these enterprises has resulted in a sharp decrease of mercury
emission to atmosphere. Thus, while in 1992 in Yelets 107 kg of mercury was emitted to atmosphere, then in 1998 it made 9 kg (Environmental Condition of the Lipetsk Oblast in
1998..., 1999).
Balance of mercury distribution during manufacture of electrochemical cells
Assessment of the balance of mercury distribution during manufacture of electrochemical cells, made for industrial enterprises of the USSR in 1990-, showed that 72.4% of the total
weight of used metal was included into the final products while 27.6% was lost (with rejected products and other solid waste, discharged with wastewater or emitted to atmosphere)
(Report on Research ..., 1999).
Data (for early 1990's) for different enterprises in cities of Novosibirsk and Novokuznetsk, which at that time manufactured electrochemical cells and battaries, show that these
enterprises, taken together, released to the environment 770 kg of mercury a year; of this amount, 40 kg were emitted to atmosphere and 60 kg were discharged to water bodies, and the
remaining amount – 670 kg – was concentrated in solid waste (Mercury in Environment of Siberia: Estimates of the Input from Natural and Anthropogenic Sources ..., 1995). Thus, the
structure of mercury losses during manufacture of electrochemical cells is as follows: 5.2% is emissions of metal to atmosphere, 7.8% is lost to the sewerage system, and 87% is lost with
solid waste. Since in the recent decade no radical changes have been seen in the technologies applied for manufacture of electrochemical cells at Russian enterprises, then these indicators
can be quite safely used to calculate the balance of mercury distribution and mercury emission to the environment (Table 3.35).
Table 3.35 Balance of mercury distribution during manufacture of electrochemical cells in Russia, 2001
Items of the balance |
Mercury, kg * |
% of the total amount |
Total use of mercury ** |
800 |
100 |
Included into the finished products |
579.2 |
72.4 |
Technological losses ***, including: |
220.8 |
27.6 |
To atmosphere **** |
11.5 |
1.4 |
To wastewater ***** |
17.2 |
2.2 |
To solid waste ****** |
192.1 |
24 |
* About 60% include mercury from the OJSC "Energia", Yelets.
** Including mercury oxide as metallic mercury;
*** High losses of mercury were explained, in many respects, by a large-scale manufacture of cells at the enterprises; it cannot be ruled out that today technological losses might be
smaller (however, this can hardly change the total picture significantly);
**** Some mercury is emitted to atmosphere with dust as HgO;
***** Most probably, a greater part includes fine-dispersion metallic mercury;
****** Technological rejection rate has always been very high at many Russian enterprises (up to 10% or more of the total output of electrochemical cells); rejected cells made the bulk
of solid waste generated at these enterprises; by estimates of M.N. Borzykh (personal communication) Russian enterprises which manufactured manganese-zinc cells have accumulated
3-7,000 tonnes of solid waste each, containing up to 3-7 tonnes of mercury; in particular, in the vicinity of the "Elastik" enterprise (in Ryazan Oblast) more than 7,000 tonnes of rejected
manganese-zinc cells are stored in the open site, with the content of mercury in one cell up to 1.0% (Matsevich et al., 1994).
3.7.2 Export and Import of Electrochemical Cells
In the recent years, the Russian domestic market of electrochemical cells and batteries has been totally formed by import; the volumes of import has been permanently increasing and now
make at least 11,000 tonnes (this unit is used by the customs statistics to account trade in electrochemical cells (Customs Statistics ..., 2000; Customs Statistics ..., 2001)). The main
importers of electrochemical cells to Russia are Poland, China and Korea (up to 65% of the total import), as well as Japan, Belgium, Taiwan, Germany and some other countries. Russian
export of electrochemical cells is small, making, for example, 24 tonnes in 19999 ands 65 tonnes in 2000 (mainly to Ukraine and Kazakhstan).
It is known that at present the greatest amount of electrochemical cells in the world includes primary zinc-carbon and especially alkali manganese-zinc cells and batteries. For example,
more than 10 billion alkali cells are sold every year, while their share in the markets of USA and Canada is 80%, and in Japan it is 65% (The World Market of Electrical ..., 2001).
According to instruction of then European Union, since 1 January 2000 it is prohibited to manufacture and use all cells and batteries containing more than 0.0005% (weight percent) of
mercury as well as alkali manganese cells with the content of mercury over 0.025% (by weight) (Batterien mit zu ..., 2001). Similar restrictions on the content of mercury in primary
electrochemical cells exist in USA, Japan and other countries.
A selective analysis of electrochemical cells offered in the shops of Moscow, Saransk, Smolensk and Penza and in some small towns of Moscow and Penza Oblasts and in the Republic
of Mordovia demonstrates that only a few of such products on sale have an indication that they include mercury (for example, cylindrical batteries of the company Konnoc Battery
Industrial Co., Ltd., containing 0.009% of mercury); many of such cells have indication that that they do not include mercury.
The battery team site has a catalogue of electrochemical cells and batteries offered for sale, which includes a list of 438 types of products (manufactured by the leading foreign firms), of
which 35% include alkali cells, about 209% are lithium cells, 24% are silver oxide cells, 18% are zinc-carbon and only 4 types are named as mercury cells (Energizer firm). It is
indicative that the volumes of cells offered for sale, for example volumes of alkali cells of cylindrical structure vary from 1,000 to 100,000 cells, while volumes of mercury cells include
only up to 10 cells, which, undoubtedly, testifies to the fact that their import to Russia is very small.
To estimate the weight of mercury imported to Russia with electrochemical cells and batteries, we will assume (with a definite degree of convention) that out of 11,000 tonnes of imported
products about 30% include alkali cells and batteries with the content of mercury in them not more than 0.025% (by weight), calculated on the ground of general requirements. Simple
calculations show that such amount of cells imported to the country include about 0.8 tonnes of mercury, while if we take into account (possible) supply of mercury and other
mercury-containing cells, this amount may be about 1 tonne of metal.
3.7.3 Use and Disposal of Electrochemical Cells
In the former USSR and now in Russia, primary electrochemical cells and batteries have never been specially collected on a mass scale and, hence, never disposed; at best, they are
taken to waste dumpsites (Matsevich et al., 1994; Yanin, 1998).
By data of Ecotrom NPP, in Moscow, at the end of 1990's, different enterprises and organizations used up to 1 million electrochemical cells and batteries every year (the total weight
about 100 tonnes); over 15 million electrochemical cells and batteries (about 1,500 tonnes) were used by population. Of this amount, not more than 1% were collected (at enterprises)
and then sent to processing (at Kubantsvetmet CJSC).
In the recent 2-3 years, in Moscow, only one organization has sent used mercury batteries to Ecotrom SPE for disposal (about 15,000 batteries a year). There are data showing that
"Green Peace" of Russia has organised, in IKEA shops, points for collection of electrochemical cells and batteries from population
(http://eyge.narod.ru/Russian/List/08-10-200246.ht...), although nothing is mentioned about their work.
It is known that the most widely spread alkali cells usually have 1-year service life; after that 60% of them are discarded. Only 20% can be used for 2 years; and only 10% can be used
for 3 years (Matsui Yasuhiro, 1994). We can state that now the overwhelming majority of electrochemical cells and batteries manufactured in Russia and imported to this country are
discarded during one year. Also, very frequently we can find on sale batteries of substandard quality (probably, fakes), which significantly expedites the rates of their rejection with waste.
The total amount of mercury which is finally sent to dumpsites (both organized and unorganised) with used electrochemical cells and batteries, with due account of the above information,
makes about 1.6 tonnes (Fihure 3.9).
Figure 3.9 Distribution of mercury during manufacture and use of electrochemical cells and batteries in Russia in 2001
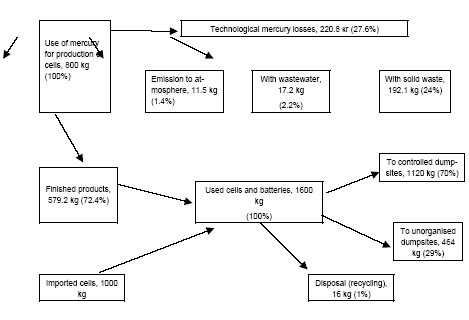
Still now, a very serious problem is solid waste (mainly as rejected cells), stored near the Russian manufacturers of electrochemical cells and batteries. It should be noted that in the former
USSR, technological processes and required equipment were developed for thermal treatment of mercury-containing manganese-zinc cells (Borzykh, 1989; Borzykh et al, 1988;
Levitskaya et al., 1987; Levitskaya et al., 1988; Matsevich et al, 1994). The plant that was designed and tested can also be used to recycle other small products (for example,
ammunitions containing detonating mercury). The federal programme "Waste" approved by resolution No. 1098 of the RF Government on 13 September 1996 planned to create in the
Ryazan Oblast (at Elastik enterprise), using the indicated plant, respective facilities (with the output of 500 tonnes of waster a year) for treatment (recycling) of mercury-containing
electrochemical cells. Unfortunately, this decision has never been fulfilled.
3.8 Light Sources
Mercury is a component of gas-discharge lamps in which glow is crated from electrical discharge in metal vapours or in a mixture of gas and vapour. There are three types of mercury
lamps:
- Low-pressure lamps (the partial pressure of mercury vapours in the steady condition does not exceed 102 Pa)
- High-pressure lamps (from 102 to 106 Pa)
- Ultrahigh pressure lamps (102 Pa or more).
Tubes of mercury lamps can be coated with a layer of luminophor or without such coating.
3.8.1 Production of Mercury-containing Light Sources
In 2000-2002, Russian enterprises manufactured the following groups of mercury lamps (Table 3.36). Mass-production low-pressure lamps included tubular luminescent lamps;
high-pressure and ultrahigh pressure lamps included lamps ÄÐË, ÄÍàÒ and ÄíàÇ (Russian designation letters). The annual production output of low-pressure lamps made 69-71 million
lamps, and the annual output of high-pressure and ultrahigh pressure lamps made 6.5-7 million lamps. Compact luminescent lamps (up to 500-600,000 lamps/year) were manufactured by
Lisma-VNIIIS OJSC (150,000 lamps/year) and Moscow Electrical Lamp Plant (MELZ OJSC). (Problems of modern ..., 2002).
Table 3.36 Basic groups of mercury lamps manufactured in Russia (Database ...., 2001; Sources of Light..., 2003; Reference Book on ..., 1995)).
Groups of lamps |
Types of lamps, power (marking) |
Quantity of lamps types
mg Hg/item |
Average duration of operation, hours * |
Low-pressure discharge lamps |
Luminescent lamps |
Tubular, 4-80 W (&(ËÁ, ËÁÅ, ËÄ, ËÄÖ, ËÅÖ,
ËÅÖÒ, etc. |
45 |
6,000-12,000 |
Shaped, 22-60 W (ËÁÊ, ËÄÊ, ËÅÖÊ, ËÒÁÖÖÊ, etc.) |
13 |
2,000-15,000 |
Colour, 15-40 W (ËÃ, ËÊ, ËÇ, ËÆ, ËÐ, ËÑ) |
15 |
7,500-15,000 |
Compact luminescent lamps |
7-36 W (ÊË) |
12 |
8,000-10,000 |
Universal, 7-11 W (ÊËÓ) |
12 |
8,000-10,000 |
Colour, 5-11 W (ÊË, ÊËÓ) |
30 |
5,000 |
With an electronic automatic controls and the base E27, 11-20 W (ÊËÝ) |
19 |
8,000 |
Luminescent ultraviolet lamps |
4-80 W (ËÓÔ, ËÓÔÒ, ËÓÔÊ. ÊË) |
10 |
300-5,000 |
Sunlamps |
15-40 W (ËÝ, ËÝÐ) |
5 |
3,000-5,000 |
Bactericidal lamps |
4-60 W (ÄÁ, ÄÐÁ, ÄÁÊ) |
7 |
3,000-8,000 |
Neon tube |
For light advertising |
- |
6,000-8,000 |
High-pressure and ultrahigh pressure
discharge lamps |
Mercury high-pressure and ultrahigh pressure discharge
lamps |
50 W (ÄÐË, ÄÐÒ, ÄÐÒÁ, ÄÐØ) |
38 |
500-24,000 |
Metal-halide lamps |
250-4000 W (ÄÐÈ, ÄÐÈÇ, ÄÐÈÔ, ÄÐÈØ) |
24 |
200-10,000 |
High-pressure sodium lamps |
With a transparent tube, 50-1000 W (ÄÍàÒ) |
9 |
10,000-15,000 |
With a light-dissipating tube, 50-1000 W (ÄÍàÌò) |
9 |
10,000-15,000 |
Mirror lamps "Reflax", 50-600 W (ÄÍàÇ) |
9 |
10,000-15,000 |
Mercury-xenon lamps |
500-1500 W (ÄÐÊñ) |
3 |
1,200 |
Spectral lamps |
50-600 W (arc discharge, ÄÐÑ), 12 (mercury-helium, ÄÐÃ) |
4 |
50-500 |
* In frequent switching conditions, the service life of the lamp notably reduces.
In 2001, the main manufacturers of mercury lamps and, hence, the main users of mercury were: Lisma OJSC (Saransk) and Svet OJSC (Smolensk). Smolensk Electrical Lamp Plant
(Svet OJSC) specialises in manufacture of low-pressure luminescent lamps – the annual output is up to 50% of domestic lamps of similar kinds (over 35.6 million lamps in 2001). Saransk
Lisma OJSC has a very diverse nomenclature of products (over 700 names of various-purpose light sources, lighting fixtures, luminaires, etc.). Luminescent low-pressure lamps are
basically manufactured by Saransk Electrical Lamp Plant "Lisma-SELZ" (35 million lamps in 2001). High-pressure and ultrahigh pressure lamps (about 5.8 million pieces in 2001) were
manufactured at the Saransk Plant of Special Light Sources and Electro-Vacuum Glass (Lisma-SIS-EVS).
Other domestic manufacturers (5-6 enterprises) of mercury lamps (basically high-pressure and special lamps), indicated in the Database "Participants of the Light Equipment Market",
prepared by the Moscow House of Light (Database ... 2001), had, in 2001, insignificant production capacities (up to 100-150,000 lamps a year). Some of them manufactured
high-pressure mercury lamps using ready discharge tubes supplied from abroad. On the whole, their operation had a very small impact on the Russian mercury lamps market and, hence,
on the use of mercury by electrical lamp manufacturers (Table 3.37).
Table 3.37 Use of mercury by Russian electrical lamp manufacturers in 2001
Users |
Weight of mercury, kg |
Share, % |
Lisma OJSC, Saransk |
4,400* |
58.7 |
Svet OJSC, Smolensk |
2,600 |
34.7 |
Other manufacturers |
350 |
4.6 |
Manufacturers of neon tubes |
150 |
2 |
Total |
7,500** |
100 |
* Up to 90% of mercury is used by the Saransk Electrical Lamp Plant (Lisma-SELZ);
** Up to 87% of mercury is used for production of low-pressure luminescent lamps
In the recent years, manufacture of neon tubes for light advertising has been developed in Russia (in English-speaking countries it is called "bending" by the name of the main operation,
which is bending of glass tubes). For example, in Moscow alone there were over 20 neon lamp manufactures in 2001. As a rule, these are small enterprises whose entire equipment is
located within 20 square metres, with 4-6 personnel members, and the use of metallic mercury not more than 8-10 kg/year.
3.8.1.1 Technological Processes
Domestic electrical lamp plants are mainly equipped with outdated semi-automated lines for assembly of luminescent lamps, manufactured in Hungary long time ago (by the Tungsram
company), with some domestic machines (the rated output of one line is 1,200 lamps/hour). The basis of some assembly lines is made by English machines manufactured by Badalex. In
2001, ten lines were in operation at the Smolensk Electrical Lamp Plant, and 12 assembly lines at the Saransk Electrical Lamp Plant.
The process of lamp assembly begins with washing and drying of glass tubes (lamp tubes), deposition and drying of the luminophor layer (Figure 3.10). The glass lamps manufactured by
the glass-making facility, are transported by a conveyor to the lamp assembly shop wherein they are fed to special machines with nozzles for tube washing and drying as well as with tanks
with luminophor suspension. In the recent years, luminophor suspension has been made by using a water-soluble polymer (based on methyl acrylate) that assures fixing of the luminophor
layer to the walls of the tubes in the process of deposition. Then, this binder is removed (burned out). Glass tubes are fed to the tank and are placed on it, following which the luminophor
suspension is sucked into them by the vacuum built in the tubes. Photo elements installed at the top end of the tube send a signal to switch off vacuum when suspension reaches up to the
point where they are placed. Afterwards, the residual suspension flows back into the tank, and the tubes are moved to the position for drying of the luminophor layer. Warm air (at 50-60
C) for drying of washes tubes is fed from the binder burnout stoves and for drying of the luminophor from air heaters. The, the tubes with the deposited and dried luminophor are fed to
the binder burnout machines made of four parts: a conveyor for loading and marking of tubes; a burnout stove; a conveyor for feeding of tubes to the soldering machine with a matted
screen at the end of the conveyor (where binder burnout quality is checked); and mechanisms for cleaning of the luminophor layer at the ends of the tubes.
The following operation includes welding of the tubes, preceded by installation of legs and oxidation. To this end, glass pans, exhaust tubes and metal three-link legs are fed to a special
machine. The legs and exhaust tubes are pressed as a single unit with the pan, thereby forming the so-called glass leg which is moved to the kiln wherein it gradually cools down. The
exhaust tube is a glass capillary 5 mm in diameter, which is used to connect the internal space of the lamp with the suction system; it is also used to introduce mercury and inert gas into the
lamp. The exhaust tube has a hole only on the leg for one end of the lamp (the leg with a purged exhaust tube); the second leg does not have it (the leg with the exhaust tube that was not
purged). The automated installation and oxidation machine is used to fix three-spiral cathodes into the hooks of the nickel sections of the legs and to deposit a layer of oxide suspension
that is then dried while the legs are fed automatically to the tube welding machines (using gas burners).
Figure 3.10 Technological process: assembly of luminescent lamps
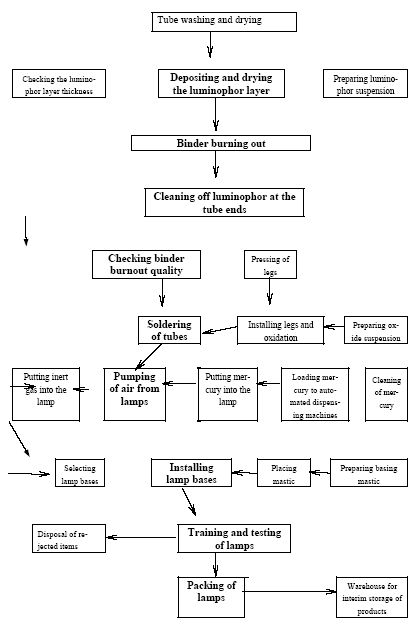
The main operation in the process of manufacture of luminescent lamps is their pumping at the semi-automated pumping machines: air is pumped from the lamp, the tubes are heated to
remove contamination from the glass and the luminophor layer; heat treatment of the electrodes is made by current (binder degradation products as well as oxide coating carbonates are
pumped off); mercury and inert gas is introduced into the lamp; electrodes are activated; lamps are unsoldered and placed onto the conveyor leading to the basing machine. Air is pumped
from the lamps by means of vacuum pumps. Metallic mercury used in the technological process is cleaned (distilled); then it is fed to the dispensing heads of the automated dispensing
machines used to feed metal to the lamp (as a drop with the defined weight).
Lamps with pumped air are fed by the conveyor to the basing machine. The exhaust tube that has not been purged is broken off automatically on the conveyor; the workers (making
basing operations), located in the middle of the conveyor, put (manually) bases with the mastic onto the lamps. After thermal treatment the basing mastic strongly binds the base with the
glass tube. Then lamps are fed by the conveyor to the training and testing machines, after which the products that meet technical specifications are packed and fed to the warehouse for
interim storage, while rejected products are sent for disposal.
The luminescent lamps assembly shop is equipped with general exchange ventilation, while the workplaces at the pumping semi-automatic machines are equipped with plenum and exhaust
ventilation. The shop includes a team for de-mercuration operations, who make periodical treatment (usually twice a shift) of the equipment and the floor, and collect broken exhaust
tubes, glass tubes and lamps. At the Smolensk Electrical Lamp Plant de-mercuration of the shop is made using 3% solution of sodium hypochlorite; at the Saransk Electrical Lamp Plant a
water solution of potassium permanganate oxidised with hydrochloric acid is used. After treatment, the de-mercuration solution is washed off by a jet of water towards the chutes of the
so-called mercury sewerage system equipped with traps for collecting metallic mercury (most of this mercury is the result of mechanical loss of metal during lamp assembly). Mercury is
removed from the traps by fore-vacuum pumps; then, it is sent for cleaning or recycling (reprocessing).
The technological process for production of mercury lamps, considered above, includes a great share of manual operations and is characterised by significant losses of mercury, especially
on the assembly lines, and by different unfavourable production factors (high concentrations of mercury vapours and some organic compounds, high air temperature, noise, infrared and
electromagnetic radiation). The basis of the majority lamp assembly lines, operated at the domestic enterprises, is made by equipment with practically 100% wear, which results in high
rejection rates, above all, because of braking of tubes and cracking of glass at the soldering joints (Bolokhontseva et al., 2002; Stepanov, 1997). In particular, while the share of the
so-called breakage of lamp tubes, as stipulated by the design, must not exceed 8%, then in reality it reaches 20-25%. The number of rejected lamps (that did not pass technical
inspection) is rather high (up to 7-9% of the total output).
Manufacture of high-pressure mercury lamps is organised on the assembly lines that are, in many aspects, similar to those considered above, however, they are, as a rule, characterised by
better quality of equipment (or, at least, less worn out equipment).
Specific Content of Mercury in Lamps
Domestic reference books and catalogues on lighting equipment include data showing that amounts of mercury in every low-pressure luminescent lamp manufactured by Russian
enterprises makes from 20 to 50 mg (see, for example (Light Sources. Catalogue of Lighting Equipment, 2003; Petrov, 19999; Rokhlin, 1991). However it is known that the technologies
used by Russian enterprises to manufacture luminescent lamps was based, initially, on introducing into each product from 80 to 120 mg of metallic mercury (without account of possible
losses). This was the amount of metal put into the ampoule part of the dispenser head of the automatic dispensing machine; ultimately, at least 50-80 mg of mercury was put into each
product. In the recent years, Svet OJSC (Smolensk) has organised technical actions for improving the dispensing heads, which allowed reducing the average dose of mercury put into
each luminescent lamp (without account of mercury losses): in 1998-2000 to 72.8-74.3 mg, in 2001 to 67.7 mg, in 2002 to 63.4 mg, and in 2003 to 52.6 mg. Of ten luminescent lamp
assembly lines in operation at the Smolensk Plant, two assembly lines have a smaller specific use of mercury put into the lamp (50 mg); two lines use titanium mercuride (getter-mercury
dose dispensers), however they are not effective lines, having low output capacity. In 2001, at the Saransk Electrical Lamp Plant, at least 100 mg of mercury were put into the ampoule
part of the automatic dispensing machines – of this amount, 60-70% were put into the lamp (66 mg on the average). Attempts to use in the production getter-mercury dispensing machines
in two production lines were not successful.
Table 3.38 shows data characterising the levels of concentration of mercury in the main types of lamps, manufactured by Russian enterprises.
Table 3.38 Concentration of mercury in main types of domestically produced discharge lamps, 2001
Groups of lamps |
Amount of mercury in one lamp, mg |
Luminescent lamps |
40-65 (52 on the average) |
Compact luminescent lamp |
3-5 |
High-pressure mercury lamps (type ) |
75-350 |
High-pressure mercury lamps (type ) |
50-600 |
Ultrahigh-pressure mercury lamps (type ) |
5 to 50% (by weight) |
Metal-halide lamps |
40-60 |
Sodium high-pressure lamps (type ) |
30-50 |
Neon tubes |
no data * |
* According to (Risk to health and the ..., 2002), one neon tube contains 10 mg of mercury; there are data showing that at Russian workshop enterprises mercury is put into neon tubes
manually, which a priori assumes a significantly higher amount.
Sources of Mercury Emission and its Content in the Work Area Air
Main losses of metallic mercury and intensive emission of its vapours into the air of the working rooms takes place at the pumping semi-automatic machine where metal is put into the
lamp. The device used to put mercury into the glass tube (the dispensing head) must provide simultaneously for the vacuum compaction and the correct dosing of metal. Ideally, a drop of
mercury, under its weight, must get into the lamp through the capillary of the exhaust tube, strictly vertically. In practice this does not happen always, and the mercury, colliding on the
walls of the capillary, remains partially in the exhaust tube and is partially lost. After the soldering the heated exhaust tube with residual mercury as well as mechanically lost mercury are
fed to the de-mercuration solution, spilt on the floor of the pumping room. From the time of soldering and until the time the exhaust tube is put into the solution, this tube represents a
source of intensive emission of mercury vapours into the air.
Mercury vapours are emitted to the production area during air pumping from the lamp, especially when the lamp, for some reason, is fed for a new cycle of pumping of air and filling of
mercury, as well as during soldering of lamps when the vacuum pumps are switched off. Glass tubes are often cracked or broken on the assembly lines, which results in the loss of
mercury and emission of its vapours into the air. Mechanical losses of metal and emission of its vapours into the air also take place in the process of cleaning (distillation) of mercury,
during filling of automatic dispensing machines and maintenance of dispensing heads, during collection of soldered or broken exhaust tubes and broken lamps, as well as during
maintenance of vacuum pumps and disposal of rejected lamps. High air temperature in the working rooms reaching in the warm seasons of the year 40 °C (18°C is the standard
temperature) during lamp assembly facilitates intensive degassing of mercury (Bolokhontseva et al., 2002). As a rule, the amount of mercury lost at Russian enterprises during assembly of
luminescent lamps (especially during pumping of air) makes from 30 to 40% of the total weight of the metal used.
The air in the lamp assembly shop includes high concentrations of mercury vapours. For example, of 856 measurements made during 2001 on the lamp assembly lines of the Smolensk
Electrical Lamp Plant, in 85% of cases the average concentration of mercury vapours exceeded 8 times the maximum single allowed concentration (MACmax) (this value varied from 4 to
15 MACmax) (Bolokhontseva et al., 2002). The highest concentrations of mercury vapours were recorded near the automatic pumping machines. During the subsequent operations
(basing, training, testing and packing of lamps), where there is no contact with metallic mercury, the concentration of its vapours in the air was smaller, however it was within 2 to 5
MACmax. As a rule, other rooms of the electrical lamp plants also have, stably, high concentration of mercury vapours (Table 3.39 and Table 3.40, Figure 3.11). The luminescent lamp
assembly shop is characterised by presence of secondary sources for mercury emission into the air (construction structures and technological equipment that deposit metal with time, to
different extent); such sources in high-temperature conditions, characteristic of such enterprises, constantly emit mercury to the environment.
Table 3.39 Concentration of the mercury vapours in the room air at Smolensk Electrical Lamp Plant *
Technological operation, the working room |
Concentration of mercury vapours in the air of the working area,
μg/m3 |
Average (maximum), 2001 |
Average (limit), first 3 months of 2003 |
Luminescent lamp assembly |
Washing of tubes and deposition of luminophor |
2.8 (5) |
2.1 (1.9-2.3) |
Soldering of tubes |
3 (7) |
2.3 (2.1-2.5) |
Cleaning of mercury |
16 (50) |
23.5 (21-27) |
Pumping of air from lamps |
66.3 (150) |
79.8 (37-110) |
Adjustment of semi-automatic pumping machine |
54.6 (180) |
79.4 (44-100) |
Maintenance of vacuum pumps |
50 (98) |
no data |
Lamps basing |
43.9 (74) |
58 (31-83) |
Lamps training |
32 (54) |
49.1 (19-76) |
Lamps testing |
15 (30) |
22 (8.7-32) |
Technical control department |
6 (16) |
no data |
Lamps packing |
1.5 (2) |
1.5 |
Auxiliary units |
Disposal of rejected lamps |
37 (57) |
22.3 (12-27) |
Compressor station |
4 (5) |
0.72 |
Hydrogen station |
2.5 (5) |
0.75 |
Oxygen station |
2.1 (4) |
0.4 |
Social facilities |
Laundry (for special clothes) |
6 (8) |
2 |
Special diet canteen |
4.8 (9) |
3.8 (2.8-5) |
Plant's polyclinic |
2.3 (4) |
2.3 (1.3-3) |
Standard and background concentration of metallic
mercury vapours in the air |
MACa (shift average) |
5 |
MACmax (working area, maximum) |
10 |
MACa (atmospheric air in populated localities) |
0.3 |
Typical background concentration |
0.010-0.015 |
* Hereinafter, the primary actual data for the Smolensk Plant, used as a base for calculations and assessments, were provided by the Centres of State Sanitary and Epidemiological
Surveillance of the Smolensk Oblast and the City of Smolensk.
Table 3.40 Dynamic of changes of the mercury vapour concentrations in the air at the semi-automatic pumping machine, Smolensk Electrical Lamp Plant *
18 December 2001 |
27 April 2002 |
21 February 2003 |
Time of the day |
Mercury, μg/m3 |
Time of the day |
Mercury, μg/m3 |
Time of the day |
Mercury, μg/m3 |
9:25-9:50 |
95 ± 23 |
10:00-10:25 |
100± 20 |
8:40-9:05 |
58± 15 |
- |
- |
10:30-10:55 |
117± 29 |
9:10-10:35 |
63± 16 |
- |
- |
11:00-11:25 |
100± 26 |
9:40-10:05 |
69± 17 |
- |
- |
11:30-11:55 |
89± 22 |
10:15-10:40 |
70± 17 |
12:30-12:55 |
54± 14 |
12:00-12:25 |
70± 18 |
10:45-11:10 |
78 ±18 |
- |
- |
12:30-12:55 |
56± 14 |
11:15-11:40 |
71± 17 |
- |
- |
13:00-13:25 |
270± 68 |
12:00-12:25 |
70± 17 |
- |
- |
13:30-13:55 |
75± 19 |
12:30-12:55 |
60± 15 |
14:00-14:25 |
110± 28 |
14:00-14:25 |
84± 21 |
13:00-13:25 |
100± 25 |
- |
- |
14:30-15:55 |
329± 80 |
- |
- |
Average |
86 |
Average |
129 |
Average |
71 |
Maximum |
110 |
Maximum |
329 |
Maximum |
100 |
Minimum |
54 |
Minimum |
70 |
Minimum |
58 |
* In the area of breathing of workers (1-2 m high above the floor).
Intensity of pollution of the enterprise rooms with mercury is illustrated by data on the frequency of occupational diseases of the workers (chronic mercury intoxication) (Figure 3.12).
Thus, at the Saransk Electrical Lamp Plant the diagnosis "occupational mercury intoxication" was made for 287 workers (86 workers in 1996-2001); among them 90% are women.
Basic professions are mostly susceptible to mercury intoxication: pumping workers (31%), soldering workers (15%), basing workers (14%). At the Smolensk Electrical Lamp Plant, 67
cases of chronic mercury intoxication were recorded during 1970-2001 (5 cases were recorded in 1997-2001) (Bolokhontseva et al., 2002). Annually, up to 30-90 cases of mercury
affect are recorded, i.e. workers with a high concentration of mercury in urine, 1-2 orders above the background (normal) level.
Figure 3.11 Distribution of average annual concentration of the mercury vapours in the air of the pumping room of the luminescent lamp assembly shop at the Saransk
Electrical Lamp Plant. (In 1988-1989, de-mercuration actions were organised here and many secondary sources of mercury were eliminated; routine de-mercuration of
rooms became regular). (Stepanov, 1997; with amendments)
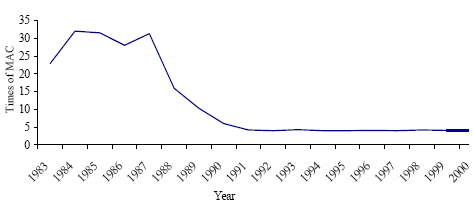
Figure 3.12 Dynamic of development of chronic mercury intoxication among workers, at the Saransk Electrical Lamp Plant (Stepanov, 1997, with amendments)
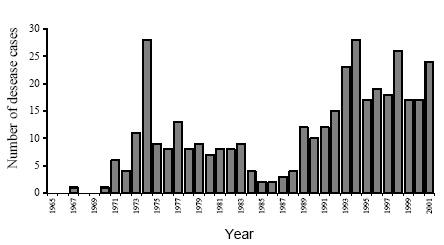
Distribution of Mercury by Manufacture of Luminescent Lamps
Table 3.41 shows data characterising manufacture of luminescent lamps, use of mercury and generation of waste at Smolensk Electrical Lamp Plant (Svet OJSC, Smolensk City) in
1998-2002 and for the first three months of 2003. They were used as the basis for calculations of the balance of distribution and loss of mercury during manufacture of such lamps (Table
3.42).
The process of manufacture of luminescent lamps at Smolensk Electrical Lamp Plant is characterised by high absolute and specific losses of mercury, which made, during the examined
period, 30-35% of the weight of used metal or 17-28 mg of mercury per conditioned lamp. Major losses take place on the luminescent lamps assembly lines, including mostly mechanical
loss of mercury that is accumulated in the sewerage system traps wherefrom it is collected by the vacuum pumps and sent for secondary recycling (cleaning), as well as mercury contained
in the de-mercuration slurry. Losses of mercury with broken glass and wastewater are not high. It should be noted that fine-dispersion metallic mercury fed to the mercury sewerage
system (up to 3.6% of the weight of used metal) is not recorded by the plant analytical laboratory. At the same time, drops of metallic mercury can be seen visually in wastewater
discharged to the city sewerage system; this mercury is lost irrecoverably, which may be due to the fact that the mercury traps are not efficient. At least 3-4% of the used amount of
mercury is emitted to atmosphere basically as vapours.
Table 3.41 Manufacture of luminescent lamps, use of mercury and generation of waste at the Smolensk Electrical Lamp Plant in 1998-2003
Year |
Output of lamps, ps. |
Total use of mercury, kg * |
Total loss of mercury, kg |
Captured mercury, kg |
Total |
Share of rejection, % |
By filters ** |
ÓÄË-750 (de-mercuration plant)*** |
1998 |
25 583 100 |
7.2 |
1,900.8 |
665.3 |
20.8 |
178.6 |
1999 |
29 373 300 |
7 |
2,177.65 |
740.4 |
25 |
198.7 |
2000 |
35 743 500 |
7.1 |
2,602.8 |
833 |
21.75 |
223.5 |
2001 |
38 333 500 |
7.1 |
2,596.09 |
830.75 |
22 |
223.0 |
2002 |
38 114 100 |
7 |
2,421.64 |
726.5 |
16.2 |
195.0 |
2003 (first 3 months) |
10 459 000 |
7 |
550 |
165 |
3.3 |
44.3 |
Table 3.41 (continued)
Year |
Emission of mercury to atmosphere, kg **** |
Broken glass ***** |
Lamp assembly shop wastewater |
t |
Mercury, g/t |
Total amount, m3 |
Mercury, g/l ****** |
1998 |
62.4 |
45 |
1.4 |
110 145 |
1.2 |
1999 |
75 |
48 |
1.4 |
88 025 |
0.95 |
2000 |
87 |
75 |
1.4 |
118 902 |
0.77 |
2001 |
88 |
75 |
1.5 |
156 385 |
1 |
2002 |
92 |
79 |
2 |
166 648 |
1.8 |
2003 (first 3 months) |
22.5 |
25 |
1.6 |
43 269 |
- |
* The shop for manufacture of luminescent lamps was commissioned in 1970; in 1970-1975 the amount of mercury used here reached 6 t/year;
** Filters of the general exchange ventilation of the lamp assembly shop (activated carbon modified with iodine potassium; the filters have never been replaced; today their efficacy is
20-25%);
*** The plant for de-mercuration (disposal) of rejected lamps, exhaust tubes, broken lamps, etc. (today, the product of their processing, i.e. mercury slurry with the concentration of
mercury 60-75%, is transported in polyethylene bags to the enterprise's waste field where it is placed into temporary storage bins);
**** After the filters of exchange ventilation;
***** After de-mercuration at the de-mercuration plant UDL-750 (broken glass is carried to the dumpsite where it is stored into temporary bins;
****** Only water-dissolved mercury (fine-dispersion metallic mercury fed finally to the sewerage system is not analysed); wastewater is discharged to the town sewerage system.
In 2001, the Smolensk Electrical Lamp Plant used 2,596.09 kg of mercury; of which 1,765.34 kg were included into the conditioned products, and 830.75 kg were technological losses
(68% and 32% of the total amount used, respectively). "Unaccounted losses" of mercury (33.7 kg) must, actually, be distributed pro rata among other kinds of metal loss. However, with
account of data obtained from the Saransk Electrical Lamp Plant (see below), the distribution of the above losses can be presented as follows: 1 kg of mercury is emitted to the
atmosphere as part of industrial dust; 3 kg of metal remains in the dust trapped by the treatment plants; 13.2 kg is accumulated in the mercury sewerage traps; 3.3 kg is lost in the
sewerage system as fine-dispersion mercury; 0.006 kg is discharged with the wastewater (dissolved and suspended forms of metal); and 13.2 kg is degassed into the air of the room and
(through door and window fenestrations, especially in warm seasons) emitted to the atmosphere, sorbed by construction elements, clothes and footwear of the workers, etc.
Table 3.42 Balance of mercury distribution at Smolensk Electrical Lamp Plant (total use of mercury = 100%)
Year |
Mercury losses |
Number of conditioned lamps, ps. |
Average concentration of mercury in one lamp, kg |
Mercury included into final products |
Total, kg |
Share of the used, % |
kg |
% of the used amount |
1998 |
665.3 |
35 |
23 732 000 |
52.06 |
1,235.5 |
65 |
1999 |
740.4 |
34 |
27 324 000 |
52.60 |
1,437.25 |
66 |
2000 |
833 |
32 |
33 188 000 |
53.33 |
1,769.8 |
68 |
2001 |
830.75 |
32 |
35 626 000 |
49.55 |
1,765.34 |
68 |
2002 |
726.5 |
30 |
35 455 000 |
47.81 |
1,695.14 |
70 |
2003, 1st quarter |
165 |
30 |
9 729 000 |
39.57 |
385 |
70 |
Table 3.42 (continued)
Year |
Mercury in de-mercuration slurry |
Mercury captured by the shop filters |
Technological loss of mercury |
kg |
% of the used amount |
kg |
% of the used amount |
Emission to atmosphere |
Wastewater * |
kg |
% of the used amount |
kg |
% of the used amount |
1998 |
178.6 |
9.4 |
20.8 |
1.09 |
62.4 |
3.28 |
0.132 |
0.006 |
1999 |
198.7 |
9.12 |
25 |
1.15 |
75 |
3.44 |
0.084 |
0.004 |
2000 |
223.5 |
8.59 |
21.75 |
0.84 |
87 |
3.34 |
0.095 |
0.004 |
2001 |
223 |
8.59 |
22 |
0.85 |
88 |
3.39 |
0.156 |
0.006 |
2002 |
195 |
8.05 |
16.2 |
0.67 |
92 |
3.80 |
0.3 |
0.012 |
2003, 1st quarter |
44.3 |
8.05 |
3.3 |
0.60 |
22.5 |
4.09 |
0.08 |
0.015 |
Table 3.42 (continued)
Year |
Technological mercury losses |
Broken glass |
To the sewerage system ** |
Other losses, kg*** |
Including: |
Kg |
% of the used amount |
kg |
% of the used amount |
Mechanical |
Unaccounted |
kg |
% of the used amount |
kg |
% of the used amount |
1998 |
0.063 |
0.003 |
68.4 |
3.6 |
335.2 |
310.05 |
16.33 |
24.7 |
1.3 |
1999 |
0.067 |
0.003 |
78.4 |
3.6 |
363.15 |
334.85 |
15.38 |
28.3 |
1.3 |
2000 |
0.105 |
0.004 |
93.7 |
3.6 |
406.85 |
373.05 |
14.33 |
33.8 |
1.3 |
2001 |
0.113 |
0.004 |
93.5 |
3.6 |
403.98 |
370.28 |
14.26 |
33.7 |
1.3 |
2002 |
0.158 |
0.007 |
87.2 |
3.6 |
335.64 |
304.14 |
12.56 |
31.5 |
1.3 |
2003, 1st quarter |
0.04 |
0.007 |
19.8 |
3.6 |
74.98 |
67.78 |
12.33 |
7.2 |
1.3 |
* Dissolved forms of mercury;
** Fine-dispersion metallic mercury fed to the sewerage system (calculations were made using data provided in (Stepanov, 1997));
*** Overwhelming majority (up to 95%, as shown below b)y the data for the Saransk Electrical Lamp Plant) is made by metallic mercury captured by the mercury sewerage traps (the
so-called mechanical mercury losses).
The rated balance of distribution of mercury losses at the Smolensk Electrical Lamp Plant for 2001 is given in Table 3.43. Major part of losses includes mechanical losses captured by the
mercury sewerage traps; a significant part of mercury is removed from rejected products; over 102 kg of mercury (3.9% of its total use) is emitted to the atmosphere; almost 97 kg
(3.7%) is fed to the sewerage system; more than 226 kg (8.7%) is carried to the plant's waste field (for temporary storage). Thus, eventually more than 425 kg of mercury is
emitted/discharged to the environment, i.e. almost 16.4% of the amount used in the technological process; more than 199 kg of mercury (about 7.7% of the total use) is dissipated in the
habitat and lost forever. Certain efforts on improvement of technology, first of all improvement of automatic dispensing machines, have been made in the recent years at Svet OJSC, which
facilitates a significant reduction of specific mercury losses (Table 3.44).
Saransk Electrical Lamp Plant (Lisma-SELZ), due to its technological processes, is characterised by a high use of mercury, higher absolute and specific losses of mercury and, hence, by
more complicated satiation and hygienic conditions [4]. At this enterprise, they manufactured 35,000,000 conditioned luminescent lamps in 2001, using 3,903 kg of mercury. Planned use
of metallic mercury for manufacture of one lamp, according to calculations based on the maximum allowed emissions/discharge (Draft Standards ..., 2000), makes 101.14 mg; of this
amount 30-40% of mercury (35% on the average) were lost during technological processes (mainly due to substandard operation of automatic dispensing machines). Thus, 65.74 mg of
mercury is used for one luminescent lamp, while losses of mercury metal during manufacture of lamps reach 1,366 kg. Additionally, 236 kg of metal are present in 3,590,000 rejected
lamps processed in 2001 at the installation de-mercuration plant UDL-750 (State Report on the Environmental Condition ... Republic of Mordovia..., 2002), i.e. total technological
losses of mercury at Saransk Electrical Lamp Plant make about 1,602 kg.
Table 3.43 Balance of technological losses of mercury at the Smolensk Electrical Lamp Plant, 2001
Types of mercury losses |
Technological mercury losses |
Notes |
kg |
Share, % |
Of total losses |
Of the used amount |
Solid waste to be processed |
Unconditioned metallic mercury (mechanical losses) |
383.48 |
46.16 |
14.77 |
By the data available they are sent for secondary processing |
Mercury contained in de-mercuration slurry, i.e. the product of de-mercuration
of rejected lamps and contaminated broken glass |
223 |
26.84 |
8.59 |
Today, de-mercuration slurry is carried in polyethylene bags to the enterprise
waste field and placed to the temporary storage bins |
Air-cleanup equipment filters in the luminescent lamps assembly shop |
22 |
2.65 |
0.85 |
Mercury is left on filters which have not been changed at the enterprise during
its entire operation period |
Mercury in dust captured by the cleaning installations |
3 |
0.36 |
0.12 |
Dust is carried to the dumpsite (?) |
Solid waste to be carried to the dumpsite |
Broken glass (after de-mercuration) |
0.113 |
0.01 |
0.004 |
Carried to the dumpsite |
Irrecoverable loss of mercury in the sewerage system |
Wastewater (with dissolved mercury) |
0.161 |
0.02 |
0.006 |
Discharged to the town sewerage system |
Fine-dispersion metallic mercury |
96.8 |
11.65 |
3.73 |
Fed to the sewerage system where it is, in part, accumulated and, in part,
discharged to the town sewerage system |
Irrecoverable loss of mercury in atmosphere |
Organised emission of mercury vapours (through the ventilation system of the
lamp assembly shop) |
88 |
10.6 |
3.37 |
Emitted to the external environment (atmosphere of the town) |
Unorganised emission of mercury vapours to air |
13.2 |
1.59 |
0.51 |
Emitted to atmosphere through doors and windows, sorbed by construction structures,
clothes and footwear of the workers, etc. |
Mercury in industrial dust |
1 |
0.12 |
0.04 |
Emitted to atmosphere with dust generated in the production cycle |
TOTAL |
830.75 |
100 |
32 |
|
Table 3.44 Specific losses of mercury at Smolensk Electrical Lamp Plant
Year |
Emission of mercury vapours to atmosphere (before cleaning of
emissions) * |
Specific losses of mercury |
kg |
share of the used amount, % |
per lamp, mg |
total |
mechanical |
to the sewerage system |
1998 |
83.2 |
4.38 |
3.51 |
28.03 |
13.45 |
2.98 |
1999 |
100 |
4.59 |
3.66 |
27.10 |
12.65 |
2.97 |
2000 |
108.75 |
4.18 |
3.28 |
25.10 |
11.64 |
2.92 |
2001 |
110 |
4.24 |
3.09 |
23.32 |
10.76 |
2.72 |
2002 |
108.2 |
4.47 |
3.05 |
20.49 |
8.92 |
2.55 |
2003, 1st quarter |
25.8 |
4.69 |
2.65 |
16.96 |
7.25 |
2.11 |
* Amount of mercury emitted to atmosphere is determined by the efficiency of the cleaning installations.
Data for Smolensk Electrical Lamp Plant show that during technological processes about 4.5% of the total used amount of mercury is emitted to air, which makes for Saransk enterprise
176 kg of metal. Of this amount 22 kg of mercury is emitted to the atmosphere in the town directly (Summary Report on Protection of Atmospheric Air for 2001...), and 154 kg are
captured by the carbon absorbers installed in the system of ventilation of the lamp assembly shop (over the last 10-15 years, the absorbers have been several times updated and even
replaced; for example, in 2001 a new absorber was put into operations). By the available data (The State Report on the Environmental Conditions of the Republic of Mordovia...,
2002), 1000 kg of spent mercury were collected and sent for recycling at Saransk Electrical Lamp Plant (basically, it was mercury lost mechanically during production processes and then
extracted from the mercury sewerage traps). According to N.A. Stepanov (1997), on the average 3.6% of mercury used in production at Saransk Electrical Lamp Plant is fed to the
sewerage system, bypassing the mercury traps, i.e. mainly as fine-dispersion metallic mercury. In 2001, such losses of mercury made 141 kg. Wastewater from the luminescent lamps
assembly shop of Saransk Electrical Lamp Plant is discharged to the plant treatment installations and then (through the municipal sewerage system) to the treatment plants of the town of
Saransk; after that, this wastewater id discharged to the Insar River. Annually, about 300 kg of sludge is generated at the local treatment plants of Saransk Electrical Lamp Plant; the
average concentration of mercury in the sludge reaches 300 mg/kg (Yanin, 1998; Yanin, 2000a), i.e. it accumulated up to 90 kg of mercury. The levels of mercury in the sediments of
wastewater generated at the municipal treatment plants (about 25,000 tonnes of dry substances a year) are 4 mg/kg on the average, i.e. it accumulated every year up to 100 kg of
mercury, the significant part of which, surely, is brought with wastewater from Electrical Lamp Plant (Yanin, 1996, 2000a). About 15 kg of mercury is discharged annually from the
municipal treatment plants to the Insar River
The data presented allow getting the following balance of mercury distribution at Saransk Electrical Lamp Plant (Table 3.45).
Table 3.45 The balance of mercury distribution at Saransk Electrical Lamp Plant in 2001 (the total use of mercury = 100%) *
Total use,
kg
| Total losses |
Mercury distribution in the technological processes |
Included into commodities |
Emission to the air |
Air in the working area (before cleaning) |
Including: |
Captured by absorbers |
To atmosphere |
|
kg |
% |
kg |
% |
kg |
% |
kg |
% |
kg |
% |
3,903** |
1,602 |
41.05 |
,2301 |
58.95 |
176 |
4.5 |
154 |
3.9 |
22 |
0.6 |
Table 3.45 (continued)
Mercury distribution in the technological processes |
Discharged to the sewerage system **** |
Mechanical losses ***** |
Captured by UDL-750 ****** |
Unaccounted losses |
kg |
% |
kg |
% |
kg |
% |
kg |
% |
141 |
3.6 |
1,000 |
25.6 |
236 |
6.1 |
49 |
1.3 |
* Such distribution of mercury is, mostly, typical of the enterprise operation in 1999-2002;
** In 1980's – early 1990's , the total use of mercury at the plant reached 5-5.5 t/year (Burenkov et al., 1993);
*** Cleaning equipment of the lamp assembly shop (W-shaped absorbers are used containing 1 t of activated carbon that is sprinkled with hydrochloric acid from time to time);
**** Mostly as fine-dispersion metallic mercury that is not captured by the mercury traps;
***** Mercury accumulated in the mercury sewerage traps;
****** De-mercuration slurry.
As has been noted before, unaccounted mercury losses represent balance discrepancies in the calculations, which must be distributed pro rata among basic metal losses. Nevertheless,
unaccounted losses of mercury can be related, to a significant degree, to unorganised emission of mercury vapours, sorption of vapours by the equipment and construction elements,
clothes and footwear of the workers, dust generated during technological processes, as well as to broken glass. Thus, Saransk Electrical Lamp Plant emits to atmosphere about 68-70
tonnes of solid substances (industrial dust) a year, and about 240 tonnes of dust are captured by the cleaning equipment. The average concentration of mercury in the industrial dust
generated by the enterprise makes 12 mg/kg (Yanin, 2003), i.e. it brings to the habitat up to 1 kg of mercury while about 3 kg of metal is present in dust captured by the cleaning plants;
24 kg of fine-dispersion mercury is lost to the sewerage system, 0.3 kg of dissolved mercury is discharged with wastewater, 0.2 kg is concentrated in broken glass, and 20.5 kg is
degassed to the air of the rooms and (through door and window fenestrations) is emitted to the adjacent rooms and outside environment, sorbed by construction elements, clothes of
workers, etc. Carrying of mercury on clothes and footwear of the workers is of certain hygienic importance. It has been established that children whose parents worked at Saransk
Electrical Lamp Plant had much higher (3-5 times) levels of mercury in their hair as compared to children of parents employed at other enterprises of the town (Yanin, 2000b, 2000b).
The calculated balance of mercury at Saransk Electrical Lamp Plant for 2001 in given in Table 3.46. As can be seen from the table, 43.5 kg of mercury (1.11% of the total weight of used
metal) was emitted to atmosphere; over 165 kg (4.24%) was discharged to the sewerage system; 239 kg of mercury (over 10%) was included into the de-mercuration slurry, dust and
broken glass and transported to the dumpsite; and 1,000 kg of unconditioned mercury was sent for recycling. Direct irrecoverable loss of metal (to atmosphere and the sewerage system)
made 208.8 kg (5.4% of the total amount of used mercury). A substantial part of mercury emitted to atmosphere is precipitated directly within the enterprise area, where over the 40-year
period of the plant operation up to 1 tonne of mercury has accumulated in the top level of the soil (Yanin, 1998). Specific losses of mercury and Saransk Electrical Lamp Plant are
naturally much higher than at Smolensk Plant (Table 3.47).
Table 3.46 Balance of technological losses of mercury at the Saransk Electrical Lamp Plant in 2001
Types of mercury losses |
Technological mercury losses |
Notes |
kg |
Share, % |
Of total losses |
Of the used amount |
Solid waste to be processed |
Unconditioned metallic mercury (mechanical losses) |
1,000 |
65.42 |
25.62 |
They are sent for recycling |
Mercury contained in de-mercuration slurry, i.e. the product
of de-mercuration of rejected lamps and contaminated broken glass |
236 |
14.73 |
6.05 |
Today, de-mercuration slurry is carried to the dumpsite, as can be judged
by available data |
Air-cleanup equipment filters in the luminescent lamps assembly
shop |
154 |
9.61 |
3.95 |
Mercury is left on filters |
Mercury in dust captured by the cleaning installations |
3 |
0.19 |
0.08 |
Dust is carried to the dumpsite |
Solid waste carried to the dumpsite |
Broken glass (after de-mercuration) |
0.2 |
0.01 |
0.005 |
Carried to the dumpsite |
Irrecoverable loss of mercury in the sewerage
system |
Wastewater (with dissolved mercury) |
0.3 |
0.02 |
0.008 |
Discharged to the local and to the town sewerage system |
Fine-dispersion metallic mercury |
165 |
10.3 |
4.23 |
Part of it is accumulated in the mercury sewerage system, part is precipitated
with slurry on the local cleaning facilities, and some part is discharged to the
town sewerage system |
Irrecoverable loss of mercury in atmosphere |
Organised emission of mercury vapours (through the ventilation
system of the lamp assembly shop) |
22 |
1.38 |
0.56 |
Emitted to the external environment (atmosphere of the town) |
Unorganised emission of mercury vapours to air |
20.5 |
1.28 |
0.53 |
Emitted to atmosphere through doors and windows, sorbed by construction structures,
clothes and footwear of the workers, etc. |
Mercury in industrial dust |
1 |
0.06 |
0.02 |
Emitted to atmosphere with dust generated in the production cycle |
TOTAL |
1,602 |
100 |
41.05 |
|
Table 3.47 Specific losses of mercury during manufacture of luminescent lamps
Mercury losses |
Mercury, mg/lamp |
|
Saransk Plant |
Smolensk Plant |
Total |
42.77 |
23.32 |
Mechanical losses |
33.29 |
10.76 |
To the sewerage system |
4.72 |
2.72 |
To air (before cleaning), mercury vapours |
5.61 |
3.09 |
Saransk and Smolensk Electrical Lamp Plants together used, in 2001, form manufacture of mercury lamps 6.5 tonnes of mercury, i.e. about 87% of the total amount of metal used by the
Russian electrical lamps enterprises. The remaining part of mercury was used for manufacture of mercury lamps at Saransk Plant of Special Sources of Light and Electro-vacuum Glass
("SIS-EVS") and the enterprise Lisma-VNIIIS (totally about 500 kg) and at some other enterprises (also about 500 kg of mercury). For assessment of the balance of mercury at these
enterprises the data on mercury distribution in the course of technological processes for Smolensk Plant were used (Table.3.48).
Table 3.49 shows data characterising the total balance of mercury used in 2001 by Russian electrical lamp enterprises. As can be seen here, technological losses of metal are high, making
2,753 kg (36.7% of the total amount); of the, more than 1,007 kg of mercury were lost irrecoverably (emission to atmosphere, discharge to the sewerage system, disposal of solid waste
at dumpsites) (Table 3.50). While solid waste carried to the dumpsites is placed, as a rule, in special bins that, to some extent, prevent migration of metal to the outside environment, then
mercury emitted to atmosphere of discharged to the sewerage systems (totally about 0.5 tonnes) ultimately is dissipated in the habitat.
Table 3.48 Balance of distribution of mercury at other Russian electrical lamps enterprises in 2001, kg
Distribution of mercury |
SIS-EVS and VNIIIS * |
Other |
To final products |
340 |
340 |
Total technological losses, including: |
160 |
160 |
Unconditioned metallic mercury (mechanical losses) |
73.9 |
73.9 |
Mercury contained in de-mercuration slurry |
42.9 |
42.9 |
Mercury captured by filters of the air cleaning equipment ** |
19.3 |
19.3 |
Mercury in the dust captured by cleaning plants |
0.6 |
0.6 |
Broken glass (after de-mercuration) |
0.01 |
0.01 |
Dissolved mercury (wastewater) |
0.03 |
0.03 |
Fine-dispersion metallic mercury (to the sewerage system) |
18.6 |
18.6 |
Organised emission of mercury vapours (after cleaning) ** |
2.2 |
2.2 |
Unorganised emission of mercury vapours to air |
2.6 |
2.6 |
Emission of mercury with dust to atmosphere |
0.2 |
0.2 |
* Located nearby in the northern industrial area of the town of Saransk, up to 90% of mercury is used at SIS-EVS;
** Calculated for cleaning efficacy of 90%.
Table 3.49 Balance of distribution of mercury among Russian electrical lamps enterprises in 2001, kg
Indicator |
kg |
% of the total use |
Total use of mercury, including: |
7,500 |
100 |
- In the final products: |
4,747 |
63.3 |
- Technological losses |
2,753 |
36.7 |
Structure of technological losses of mercury: |
|
kg |
% of the use |
% of the losses |
Solid waste to be processed |
Unconditioned metallic mercury (mechanical losses) * |
1,531 |
20.4 |
55.6 |
Mercury contained in de-mercuration slurry resultant from de-mercuration
of rejected products and broken glass ** |
544.8 |
7.3 |
19.8 |
Mercury captured by filters of the air cleaning equipment *** |
214.6 |
2.9 |
7.8 |
Mercury in the dust captured by cleaning plants **** |
7.2 |
0.1 |
0.3 |
Solid waste sent to dumpsites |
Broken glass (after de-mercuration) ***** |
0.3 |
0.004 |
0.01 |
Irrecoverable losses of mercury to the sewerage system |
Dissolved mercury (in wastewater) |
0.5 |
0.006 |
0.01 |
Fine-dispersion metallic mercury |
299 |
4 |
10.8 |
Irrecoverable losses of mercury to atmosphere |
Organised emission of mercury vapours (through the ventilation
system of the lamp assembly shop; after filtration) |
114.4 |
1.5 |
4.2 |
Unorganised emission of mercury vapours to
air *******
|
38.9 |
0.5 |
1.4 |
Emission of mercury with industrial dust to atmosphere |
2.4 |
0.02 |
0.08 |
* By available data, it is sent for recycling (cleaning);
** Today, basically placed to temporary storage bins at dumpsites;
*** At some enterprises sorbents capturing dust sometime are replaced; the spent ones are sent for recycling;
**** Captured dust is sent to dumpsites
***** Carried to the dumpsite where it is placed into temporary storage bins;
****** Mercury that is not captured by the mercury sewerage traps;
******* To the air of the working area and to outside environment
Table 3.50 Emission/discharge of mercury to the environment from the electrical lamp enterprises, 2001
Mercury emission/discharge |
Mercury, kg |
Share, % |
To atmosphere (as mercury vapours and with dust) * |
155.7 |
15.5 |
To the sewerage system (dissolved in wastewater and fine-dispersion metallic mercury) ** |
299.5 |
29.7 |
To soils (carrying of de-mercuration slurry, broken glass and captured dust to the dumpsites) *** |
552.3 |
54.8 |
Total |
1,007.5 |
100 |
* 98.5% is vapour and gas fraction;
** 99.8% is fine-dispersion metallic mercury;
*** 98.6% as part of the de-mercuration slurry.
3.8.2 Russian Market of Mercury Lamps
The main users of lighting equipment in Russia are estimated as follows: industry – 50-55%; agriculture – 7-8%; administrative, trade and other public buildings – 10-11%; housing sector
(including living houses) – 22-23%; outdoor lighting – about 1%; other – about 2% (Golembiovsky, Shemelin, 1997). Mercury lamps provide up to 60-65% of all artificial light generated
in Russia. If we stem from the data of the FSU (Aizenberg, Prytkov), then today about 140 million lighting fixtures with low-pressure luminescent lamps are used in Russia as well as up to
13 million high-pressure discharge lamp lighting fixtures.
In 2001, the share of domestic lamps made 40% in the retail trade, and the remaining part was imported (Problems of Contemporary Lighting, 2002). If we analyse the nomenclature of
products offered by large Russian trade companies working with imported electrical lamp products, then a substantial share will be made by luminescent, arc, metal-halide, high-pressure
sodium as well as compact luminescent lamps. Some foreign firms supply to Russia gas-discharge lamps for printing houses, television, etc. Electrical lamps are imported to Russia from
62 countries, including countries that do not have their own production facilities (like Australia, New Zeeland, Liechtenstein). Only in Moscow and in Moscow Region there are about
1900 commercial companies many of which practically sell only imported products and cover up to 50% of the local market (Aezenberg, Prytkov). In 2001, the Russian market selling
foreign lighting sources was essentially determined by such firms as: Osram, Tungsram, General Electric, Silvania (Barinova et al., 2002; Russia: Market of Electrical Lamps ...;
Problems of Contemporary Lighting ..., 2002) as well as Narva, OMS, BLV Licht, Vakuumtechnik, Aura, etc. It should be noted that efficacy of operation of mercury lamps
manufactured by leading foreign firms is much higher than those manufactured by local enterprises; in addition, imported lamps have much smaller content of mercury.
Precise data about Russian import and export of electrical lamps are not available. The annual reference books "Customs Statistics of Foreign Trade of the Russian Federation" do not
subdivide export and import of electrical lamps by their types and is assessed in monetary equivalent, which does not make it possible to determine the real number of products. It can be
only noted that the main importers to Russia of mercury lamps have been, in the recent years, Ukraine, Germany, Hungary, Poland, Taiwan and Finland (Customs Statistics ...,. 2001).
Major part of Russian export of mercury lamps covers Finland, Lithuania and Kazakhstan, which, probably, is equal to several million items a year (conventionally it is 10 million items in
2001, containing about 500 kg of mercury).
By the data of the association "Russian Light" which unites major part of Russian manufacturers of lighting equipment, supplies of foreign firms had exceeded, before August 1998, the
scope of production of the four middle-size Russian electrical lamps enterprises (Russia, Market of Electrical Lamps ...). At that time Russia had 6 electrical lamp manufacturers – only
two of them, in Saransk and Ufa (incandescent lamps), can be classified as large enterprises while the remaining four, Smolensk, Kalashnikov, Vladikavkaz and Tomsk, produced,
together, about 170 million pieces of all types of lamps a year. If we take the estimates of the association "Russian Light", then the volume of import of electrical lamps to Russia was
equal to this number. However, by the data of the same association, 42 million lamps were imported to Russian in 1998, and only 13 million pieces in 1999 (Russia: Market of Electrical
Lamps ...). It should be noted that at the end of 1990's, in Russia, up to 45-55% of the market of imported electrical lighting equipment included the so-called "black market", whose
substantial part was obvious smuggling (Golembiovsky, Shemelin). Moreover, the "black" import even now plays a great role on the Russian market of electrical lighting equipment
(Aizenberg, Prytkovb).
All stated above (with due account of the Russian demands) allows thinking that in 2001 several dozens of millions of mercury lamps of various types (up to 20-30 million items) were
imported to Russia. With the average content of mercury per lamp at 20 mg (calculated by (Risk to Health and..., 2002)), this gives about 400-600 kg of mercury (500 kg on the
average).
Disposal of Used Mercury Lamps
In 2001, less than 50 subjects of the Russian Federation had about 60 operating enterprises (de-mercuration stations or centres) which organised disposal of spent mercury lamps (first of
all, luminescent lamps). Some regions of the country had organisations specialising in collection and transportation of spent mercury lamps to the place of their recycling (usually to
neighbouring regions). About 30 Oblasts of Russia have regional and local regulatory acts determining the procedure for account, collection, storage, transportation and disposal of spent
or faulty mercury lamps. Nevertheless, many regions of the country did not have any system of collection and disposal of used mercury lamps (the Northern Caucasus, some regions of
the Central Russia, Republics of Karelia and Komi, Vologda, Kamchatka and Sakhalin oblasts, etc.).
Analysis of the today's Russian system of disposal of mercury lamps suggests the following (Kosorukova, Yanin, 2002).
Firstly, many Russian de-mercuration enterprises operate using not on a correct idea about the fact that all mercury in the spent luminescent lamps is in its elementary form. In particular, it
was found out that that up to 95% of mercury in a used lamp is connected with luminophor and about 3-5% of metal of the total amount is connected with glass (Makarchenko et al.,
2000; Doughty et al., 1995). In this case, luminophor acts as a sort of barrier, concentrating mercury in various forms, some of which are tightly connected with its matrix. Such behaviour
of mercury can be explained by electro-chemical effects and presence in the working lamp tube of plasma "mercury/rarefied gas".
Secondly, effectiveness of operation of de-mercuration stations is usually assessed in terms of prevention of possible mercury pollution of the habitat (simply speaking, the number of
processed products). At the same time, enterprises disposing (recycling) mercury lamps represent environmentally hazardous facilities and, therefore, are obliged to carry their operation
in conformity with the current requirements (Mercury. Standard ..., 1999, 2001). This demands regular analytical control (raw materials, production and environment control) to identify
mercury and other ingredients; filling of certificates for the final products and waste; statistical account, including on the balance of raw materials, other materials, mercury and other
pollutants. However, as a rule, all above conditions and requirements are not fulfilled in practice.
Thirdly, none of the domestic de-mercuration stations is not ready technologically to obtain secondary (recycled) mercury from mercury lamps, which is substantially due to a high cost of
the respective installation. The main final product obtained by recycling of mercury lamps is de-mercuration slurry (containing up to 60-75% of mercury), which is very rarely sent for
recycling so as to extract metal. In the majority of cases, by all judgement, it is carried to waste fields and kept in the so-called temporary bins.
In 2001, many domestic enterprises recycling mercury lamps used installations based on the thermal or thermo-vacuum method of processing (de-mercuration) of lamps – some of them
used a hydrometallurgical method and only one used "dry and cold" pneumatic vibration technology.
The hydrometallurgical method provides washing of mechanically ground luminescent lamps by a water solution and is based on redox reactions that theoretically explain transfer of
elementary mercury into hard-to-dissolve compounds or compounds that are easily recycled. In practice, they use a chlorine iron solution for this. From the chemical point of view, it
should result in hard-to-dissolve calomel. However, the chlorine iron solution is effective only in relation to elementary mercury, while the spent luminescent lamps contain mercury in
various compounds that are fixed mostly by means of luminophor and. partly, by glass. This defines the fact that the methods based on washing with water (which should be performed in
strict tight conditions, which is never done in practice) include some reaction rates and a low degree of cleaning of luminophor and glass from mercury. In view of this, it is recommended
that multiple washing of lamps should be done by solutions, which, however, does not preclude probability of redistribution of mercury between its three oxidation states (Hg0, Hg22+,
Hg2+). Moreover, when tight conditions for the process are not guaranteed, especially during multiple washing, mercury can oxidise to bivalent form (Hg2+), transfer in significant
amounts to the solution and form stable complexes, including bivalent mercuric chloride. All this demands creation of special systems for cleaning of washing water so as to obtain slurry
with concentrated mercury extracted from water. This slurry (together with hard-to-dissolve precipitation) must be sent for further recycling. However in practice, as a rule, no expensive
cleaning systems are used and the washing water with mercury is discharged into the municipal sewerage system. Residues of glass, luminophor and metal parts that were not properly
washed from mercury are carried to dumpsites. This practically ends the process, which in fact only imitates de-mercuration of mercury lamps.
The thermal method of recycling of mercury lamps is based on sublimation of mercury from a mixture of glass and metal scrap followed by capture and condensation of its vapours. It
makes the basis of the domestic installations UDL-100, UDL-15- and UDL-750 (designed by the former VNIIVMR, now NICPURO) and UDM-3000, UDMP-630 (NKP
"Merkuriy"). The thermo-vacuum method is used in the installation of the type URL-2m (firm "FID-DUBNA"), which operated using the principle of vacuum distillation of mercury and
its vapours are frozen on the surface of a cryogenic trap. Despite define advantages of both methods broadly promoted in Russia and the environmental cleanness of the technological
process and de-mercuration installations as a whole declared by their authors (Mercury. Catalogue of Products ..., 1999), the latter, nevertheless, are complicated for operation. They
require a lot of energy, high temperature, safe system for sorption of mercury from emitted gases, do not exclude probable emission of gases to atmosphere in case of loss of tightness in
the joints of technological lines, etc. They have one more disadvantage, i.e. not only de-mercury process slurry is formed, but also some other final products, which results in partial
dissipation of mercury extracted from lamps and its entering the habitat (Kosorukova, Yanin, 2002).
At present, many countries of the world make practical use of methods of disposal of mercury lamps based on the following principles: 1) non-use of high-temperature and "wet"
technologies, i.e. during lamp recycling no emission or discharge is made to the environment, which substantially reduces probability of secondary pollution of the habitat with mercury and
other pollutants; 2) getting as little as possible amount of final reprocessing products, which sharply reduced probability of "dissipation" of mercury by different materials; 30 taking into
account the fact that mercury in spent lamps is mostly bound with luminophor, which makes it necessary to separate it and transfer into a sort of raw material for obtaining secondary
mercury.
In our country, such "cold and dry" pneumatic vibration technology designed for recycling of luminescent lamps was developed and put into practice in the early 1990's at the
"Ecotrom-2" plant, whose principle of operation is based on separation of lamps into principal components: broken glass, aluminium bases and luminophor containing mercury. Separation
of luminophor – the main depositor of mercury – from glass is effected by blowing and suction of luminophor inside counter-moving systems "broken glass-air" in conditions of vibration.
Glass is fed to a special bin wherefrom it is removed by means of pneumatic transport to a special accumulating container. Air is cleaned, step-by-step, from luminophor (cyclone, sleeve
filter, cassette filter, enterprise absorber, shop absorber, sanitary absorber). Luminophor is blown off the sleeve filters by compressed air. Mercury-containing luminophor as well as spent
activated carbon from the cleaning systems, cleaning rugs, etc., are mixed with cement and water solutions (generated during the process of de-mercuration of the working areas for
sanitary and hygiene purposes and accumulated in a special container) and treated with a special substance that converts most of the mercury into its stable form, i.e. mercury sulphide.
Balance calculations demonstrate that this technology allows extracting up to 95-96% of mercury from the lamps and bind it reliably. By the data provided by the users of such plant, the
resultant cement and luminophor mixture, packed into polyethylene bags, is sent for recycling to obtain secondary mercury; ground glass is sent to enterprises making construction blocks;
and aluminium bases are used as secondary raw materials.
In 1999-2002, about 7 million mercury lamps (mainly luminescent lamps) were recycled in Moscow City and Moscow Oblast. Besides, this region has several thousands of small
enterprises and organisations that generate, annually, at least 2.5 million spent luminescent lamps that are not recycled due to the complex process of their assembly, but rather stored
indoors or carried to dumpsites (Kornitskaya, Rostokinskaya, 1999). Thus, at least 9.5 million mercury lamps are used during a year in the City of Moscow and Moscow Oblast (i.e.
about 0.7 lamp per urban dweller). If we calculate, using the same indicator, the annual number of mercury lamps out of use in Chuvashia, where, like in Moscow, the system of their
collection and disposal is well organised, then we get 673,000 lamps. It is indicative that, by the data available (Kartuzov, Shemanayev, 2000), here (in Cheboksary) up 700,000 lamps
are recycled every year (including a small number of lamps from the neighbouring regions). In Bashkiria, 1.5 million lamps were disposed over the first 9 months of 2001 (Sheveleva),
which gives, with such rates, about 1.9 million lamps a year (about 0.7 lamp per urban dweller of the republic). The obtained specific indictor (about 0.7 lamp per urban dweller) can,
probably, be used to calculate the number of spent lamps for other regions of the country and for Russia in general. Calculations show that in Russia, in the recent years, about 72 million
mercury lamps are used up (of them, about 3 million are high-pressure lamps). These lamps (basically domestically produced) contain at least 4 tonnes of mercury. Comparison of data on
the number of used mercury lamps, obtained buy calculations, with the real numbers of accounted, stored and disposed products (in about 30 Russian regions), shows that in 2001 about
40% of spent mercury lamps (mainly luminescent lamps) were recycled at de-mercuration station, 20% were placed into special stores at enterprises and in organisations, and the
remaining 40% were finally brought to landfills. It is assumed that the lamps break when they are disposed of to landfills and about 5% of the mercury (mercury in the gas phase) is
immediately released to the atmosphere. The remaining mercury may sooner or later be release to the environment from the landfills, but no data has been available on mercury releases
from landfills.
Location of major Russian plants producing mercury lamps, galvanic elements and thermometers is shown on Figure 3.13.
Click here to see the figure.
Figure 3.13 Location of facilities for production of lamps, batteries and thermometers
Summary
Therefore, in 2001 consumption of mercury for light sources production in Russia amounted to 7.5 t, of which more than 36% was lost during production. The summarized balance of
mercury distribution during production and use of mercury lamps is presented on Figure 3.13.
Figure 3.14 shows the scheme representing the balance of distribution of mercury during production and use of mercury lamps in Russia in 2001.
Figure 3.14 Balance of distribution of mercury during production and use of mercury lamps in Russia in 2001
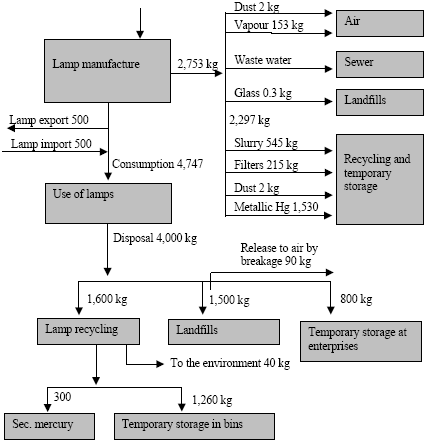
3.9 Switches and Other Electrical Equipment
Mercury switches
The electrical switch represents a device designed for switching of electrical circuits in carious installations, remote and automatic control systems, etc. In the USSR, mercury switches
were broadly used, i.e. glass cylinders with soldered-in contacts containing a definite amount of metallic mercury.
In the USSR (Russia), the main manufacturer of mercury switches was Klin Thermometer Enterprise; today it is called OJSC "Termopribor" (Table 3.51). In the second half of 1990's,
mass-scale manufacture of mercury switches was terminated in Russia.
Table 3.51 Content of mercury in basic types of switches manufactured in Russia (Nomenclature Reference Book ..., 1993; Report on Scientific Research devoted to the Topic
"Study ..., 2000).
Brand |
Content of mercury, g |
Switch ÏÐ-3A (five-contact) |
4.393 |
Switch ÏÐ-4 "Merkoid" (four-contact) |
6.249 |
Switch ÏÐ-5 (two-contact) |
3.365 |
Switch ÏÐ-8 (two-contact, plunger) |
4.807 |
Switch -ÏÐ-12 (plunger) |
23.46 |
Switch ÏÐ-13 |
14.73 |
Switch ÏÐ-15 (ring type) |
14.73 |
Switch ÏÐ-17, two-contact mercury-magnetic (for incubators) |
0.89 |
Special switch ÏÐ-18A (two-contact) |
11.89 |
Switch ÏÐ-20 (ring type) |
8.4 |
Switch ÂÐM-5 ÐÏ-7 (mercury-magnetic type), manufactured in two models |
0.879 |
Average |
8.526 |
At present, mercury switches are still used, differently, in different long-term operated devices, including home electrical rings. By data provided by Ecotrom NPP, in the recent years,
large enterprises and organisations (mainly from Moscow) have supplied up to 2000 mercury switches (sensors, pickups) a year for disposal. The number of such devices, used (and
discarded) every year by the private sector and small organisations, cannot be counted. It can be assumed, with a great degree of convention, that the number of spent (not longer used)
mercury switches in the country as a whole can reach several dozens thousands (containing at least 0.5 tonnes of mercury). Of this amount, not more than 10-15%, i.e. about 400 kg of
mercury are finally sent to waste dumpsites.
By the data available (Substances Flow Analysis of Mercury in Products, 2001), in 2001 in USA, practically every manufactured motor vehicle had mercury switches (located under the
bonnet and under the trunk cover); their number being 14 million pieces. The average amount of mercury in one motor vehicle switch is about 0.8 g. In 2002, import of cars to Russia was
127,000 (BIKI, 2003, No. 20). The share of motor vehicles delivered every year form USA does not exceed 5%. However, it cannot be excluded that motor vehicles imported from
other countries may also have mercury sensors (including the alarm. Hence, it follows that at least several dozens kilos of mercury can be brought to Russia with such products.
Mercury valves
The mercury valve is a generalised name for ion devices producing arc discharge, sending current one way only, having one cathode filled with liquid mercury, with one (single-anode
valve) or several (multi-anode valve) working anodes and one or several auxiliary electrodes used for igniting the arc. According to the method of control of arc discharge ignition mercury
valves are divided into ignitrons (with an auxiliary electrode controlling the ignition of the main arc discharge) and excitrons (with a single excitation of the cathode spot). Ignitrons are used
in ion electrical drives, pulsed modulators, electrical welding equipment, as well as in various switching devices. Excitrons are used for conversion of industrial and elevated frequency
current as well as switching devices in inductive accumulators of energy in linear modulators.
A multi-anode mercury valve or a set of anode mercury valves, made as a single structural unit designed for conversion of alternating current to direct current is called a mercury rectifier.
Before the 1980's mercury rectifiers had been widely use
d in industrial installations (rectifying units) of various power and various purpose, on transport traction substations (servicing tram and trolleybus lines, metro and railways), on
long-distance alternating current electrical locomotives, for switching and regulation of current in welding machines, for electrolysis in nonferrous metallurgy and chemical industry, etc.
The content of mercury in ignitrons varies from 10-250 g to 2-5 kg. For example, in ignitrons of types È-70, È-140, È-200 and È-350 the amount of mercury varies from 0.25 to 1 kg.
In the former USSR, mercury valves and mercury rectifiers were manufactured, at different times, at Togliatti Electrical Engineering Plant (the town of Togliatti), Tallinn Plant of Mercury
Rectifiers (town of Tallinn), Taganrog Metallurgy Plant (town of Taganrog), Electrosila plant (St. Petersburg), Electrovypryamitel (town of Saransk), Dynamo enterprise (Moscow),
Uralelectrotyazhmash (town of Yekaterinburg), etc.
At the end of 1970's, mass-scale (industrial) manufacture of mercury valves and rectifiers was terminated. In many respects, it was due to the fact that in 1960-1970's, in the USSR,
mercury rectifiers were replaced by solid semiconductor rectifiers in transport traction substations and in various industrial plants.
Nevertheless, some enterprise still continue to use installations with mercury valves (especially ignitrons). Moreover, according to data of the customs statistics (Customs Statistics ...,
2000), as early as in 1990 Russia imported some amounts of ignitrons and mercury rectifiers. Internet contains some ads, stating for example that a joint Belarusian-Lithuanian venture
"Bel-Oka" offers for sale in Russia mercury rectifiers with a liquid-metal cathode and mercury rectifiers with directly heated cathodes. There are also data stating that some Russian
enterprises manufacture mercury valves (ignitrons) by special orders in small amounts. However, judging by information available, the total output does not exceed several dozens devices
a year, using up to 150-200 kg of metallic mercury.
It should be noted that many enterprises store unused mercury valves in warehouses and from time to time submit them for disposal. For example, in 1999-2002, every year up to 300
ignitrons were received by Exotrom NPP (Moscow) from different Moscow organizations and enterprises, which gave up to 130-140 kg of spent mercury. For the country as a whole
this may make about 4,000 mercury valves a year, containing up to 3 tonnes of mercury, which is normally sent for treatment (purification) and then returned to production.
Vacuum pumps
In the past, mercury was widely used as a working liquid in vacuum mercury-vapour pumps, i.e. devices used for creation, increase and maintenance of vacuum. Vacuum mercury-vapour
pumps were used in pump and storage battery facilities of different enterprises, but mainly for pumping of mercury systems (for example, mercury rectifiers, as well as in research
laboratories. Amount of mercury contained in one vacuum mercury-vapour pump was up to 13-15 kg. Mercury if filled into pumps during their operation and use, manually through a
funnel. During operational use of vacuum mercury-vapour pumps incidents are often, which is accompanied by emission of metallic mercury to the environment; these facts were often
reported in the press (especially, in late 1980's). Usually, the content of mercury vapours in the air of the room where vacuum mercury-vapour pumps are used exceeds MAC.
At present, vacuum mercury-vapour pumps are still used at some Russian enterprises.
Summary
The table 3.52 summarises the available data on mercury use by switches and other electrical equipment.
Table 3.52 Hg consumption and release with production and use of other appliances, t
Hg-containing products |
Hg used in production of goods in 2001 |
Amount of mercury contained in goods in use (by 2001) |
Amount of Hg disposed at the dumpsites with the used goods in 2001 |
Switchers |
Not produced |
No data available |
Not less than 0.45 |
Valves |
0.15-0.20 |
No data available |
No data available |
Barometers |
Not produced |
5-6 |
No data available |
Sphygo-manometers |
Not produced |
Not less than 0.3 |
No data available |
Manometers* |
Not produced |
No data available |
No data available |
Vacuum pumps |
Not produced |
No data available |
No data available |
* A certain amount of Hg is used annually for filling of meteorological barometers and manometers (dozens of kilos?).
3.10 Production of Chemicals and Laboratory Use of Mercury in the Russian Federation
3.10.1 Production of Mercury Chemicals
There is no official statistical data on production and sale of mercury chemicals In Russia. The analysis of the existing Business-Books and advertisements indicates that the major mercury
compound producers, who supply them to the domestic market, include Altaykhimprom OJSC (Slavgorod town), Kubantsvetmet CJSC (Krasnodar kray) and Merkom Ltd. (Moscow
oblast) Mercury compunds are usually produced upon the direct requests from various enterprises and organizations. The Institute of Problems of Microelectronic Technologies and of
Special Purity Substances (IPMT RAS), together with Rtut CJSC, have developed technologies for production of pure mercury compounds, such as Hg2(NO3)2 • 2H2O, Hg(NO3)2 &bull
H2O, HgSO4, Hg2Cl2, HgO, etc. (http://extech.msk.su/expo/exibit/innov_98/org.texm...) At present, the existing capacities allow synthesizing up to 50 kg of the above compounds a
month. Bashkir innovation centre Sodeystviye (Assistance) (city of Ufa) offers services for production of various mercury compounds within 1-2 days, including those that have already
been marketed, like mercury nitrate Hg(II), mercury rodanite Hg(II), mercury sulphate Hg(II), acetic mercury Hg (II). Khimproyekt NPO (city of Ufa) offers for sale acetic mercury (II).
Mercury oxide (II) and mercury chloride (I) are used mainly in industrial production (vynilchloride and galvanic elements respectively); other Hg-containing chemicals are likely used in
laboratories.
Production of mercury compounds at Kubantsvetmet CJSC
Table 3.53 shows data about amounts of production of different mercury compounds at Kubantsvetmet CJSC, in 2001-2002. The bulk of these compounds is constituted by mercury
chloride delivered to enterprises producing vinyl chloride (city of Volgograd). In 2003, about 500 kg of red mercury oxide and 120 kg of mercury chloride were produced upon the
request of Energia OJSC (Yelets town).
Table 3.53 Production of mercury compounds at Kubantsvetmet CJSC in 2001 and 2002, kg*
Compound |
2001 kg compound |
2002 kg compound |
Main users |
Chlorine mercury (I)2 |
15,491 |
12,715 |
Enterprises producing vinyl chloride (city of Volgograd) |
Chlorine mercury (II) |
- |
2.6 |
Organisations selling reagents |
Bromine mercury (II) |
2 |
0.4 |
Organisations selling reagents |
Iodine mercury (II) |
5 |
7 |
Organisations selling reagents |
Mercury sulphate (II) |
10 |
51 |
Organisations selling reagents |
Mercury nitrate (I), 2H2O |
10 |
198.5 |
Organisations selling reagents |
Mercury nitrate (II), bivalent |
320 |
1,520 |
Organisations selling reagents (Reactive OJSC, city of Nevinnomyssk; Ekros
Ltd., City of St. Petersburg; etc.) |
Mercury rhodane, mercury thiocyanate (II) |
10 |
7.5 |
Organisations selling reagents |
Mercury acetate (II) |
10 |
- |
Organisations selling reagents |
Mercury oxide (II), yellow |
- |
8 |
Organisations selling reagents |
Mercury oxide (II), red |
- |
0.2 |
Organisations selling reagents |
Total |
15,858 |
14,510 |
|
* Besides compounds included into the table, the produced might also be amidochloride mercury (II), fluoric mercury (I), fluoric mercury (II), pyroalkaliantimonide mercury (II), mercury
sulphide (II).
Transportation of mercury to the areas of production of mercury compounds is made using special cylinders (by trucks). Mercury compounds are produced basically using hydrochemical
methods. Rooms at the facilities producing mercury compounds are equipped with carbon adsorbers, ARV and local mercury discharge system (with mercury traps). Spent sorbent and
collected metallic mercury are delivered for recycling. Soft waste is generated during production of mercury compounds. In particular, production of 1 t of the compound consumes 1 kg
of kapron or lavsan belting. Every year, about 20 kg of such waste is generated containing up to 2% of mercury (by weight). This waste is kept in acid-resistant and tight containers and is
incinerated in the oven TVP-1.
Production of mercury compounds at Merkom Ltd.
Table 3.54 shows data about production of mercury compounds at Merkom Ltd. in 2001-2002.
Table 3.54 Production of mercury compounds at the Merkom Ltd., kg
Year |
Hg oxide |
Nitrate, Hg (I) |
Nitrate, Hg (II) |
Sulphate, Hg |
Artificial cinnabar |
2001 |
75 |
30 |
0.3 |
0.3 |
0.8 |
2002 |
370 |
30 |
- |
- |
- |
Production of mercury compounds is made basically through direct orders of organisations and enterprises. In particular, a greater part of mercury oxide was delivered to Energia OJSC
(Yelets); other mercury compounds were produced mainly when ordered by organisations selling chemical reagents (including Moskhimreactiv). A small amount of artificial cinnabar was
synthesised for the association of artists (St. Petersburg).
3.10.2 Application of Mercury Chemicals for Laboratory Use
In Soviet times, all chemicals, including mercury-containing ones, were purchased through Soyuzreachim system, which included organizations dealing with production and sale of these
products. After the activity of this system had been stopped in 90-ies the domestic market was occupied by several dozens of companies reselling the chemicals.
Production of mercury-containing chemicals in Russia in 2002 that are used in laboratories, amounted to at least some 1.8 tonnes (Table 3.55). Besides, some chemicals may be
imported, but it has not been possible to obtain relyable information on imported chemicals. Total mercury content of mercury-containing laboratory chemicals produced in Russia in 2002
is about 1.2 tonnes. Mercury chemicals used as preservatives in vaccines are included in section 3.11.
Table 3.55 Production of mercury chemicals in Russia in 2002 to be used for laboratory application
Compound |
Production Kg compounds |
Mercury content, kg |
Mercury (II) chloride |
2.6 |
1.9 |
Mercury (II) bromide |
0.4 |
0.2 |
Mercury (II) iodide |
7 |
3 |
Mercury sulphate (II) |
51 |
35 |
Mercury (I) nitrate |
230 |
166 |
Mercury (II) nitrate |
1,520 |
942 |
Mercury thiocyanate |
7.5 |
5 |
Total |
1,818 |
1,153 |
In 2001 there was several dozens of companies dealing with chemicals resale. The largest companies were: Reachim JSC (Moscow), Chimmed JSC (Moscow), NevaReactive (Saint
Petersburg), and some other.
Mercury and its compounds are classic analytic and catalytic reagents and have been used for a large variety of purposes. It should be noted, that mercury is used in laboratories not only
as a chemical for analytical purposes, but also in diffusion vacuum pumps, mercury valves, thermometers, barometers, manometers, rheometers. These applications are included in the
sections dealing with the use of mercury in measuring equipment.
Below Table 3.56 presents a brief description of some of the uses of mercury chemicals in the laboratories and in analytical chemistry.
Table 3.56 Uses of mercury chemicals in the laboratories and in analytical chemistry *
Reagent |
Use |
Metallic mercury |
In polarography based on the use of mercury or amalgam dropping or jet indicator
electrodes; masking agent for quantitative determination of organic nitrates;
determining fluoride purity and its concentration in gases; creation of new superconducting
materials; development of new gas-discharge devices; mercury porometry (determination
of porosity of various materials and substances); laboratory electrochemistry
(mercury coulometry and electrochemical data converters); for preparation of reference
electrodes. |
Organic compounds of Hg |
For determination of organic disulphide; in laboratory organic synthesis;
in preparative chemistry |
Nessler's reagent
(alkaline solution of K2HgI4)**
|
For detection and photometric determination of ammonia (NH3), for detection
of alcohols and aldehydes, for identification (in paper and thin-layer chromatography)
of hydro amino acids *** |
Mercuric chloride, HgCl2 |
For identification of tyrrol, for nephelometric determination of dimethyl
sulphide, for quantitative determination of cysteine by potentiometer titration,
and as catalyst for hydro halogenation |
Mercury iodide, HgI2 |
Masking agent for quantitative determination of organic nitrates; component
of heavy liquids used in mineralogical analysis for distinction of minerals by
density, - Tule fluid (water solution of HgI2 + 2KI) and Shoushin-Rorbach fluid
(BaI2HgI2 x nH2O). |
Mercuric sulfate, HgSO4 |
Determination of chemical oxygen demand (COD) in wastewater; in laboratory
electrochemistry for creation of electrochemical chains. |
Mercury oxides |
Oxidizers in preparatory chemistry; for determination of acids titers; in
laboratory organic synthesis; for obtaining of some nitrose compounds, hypochlorides,
organic siloxanes; for preparation of reference electrodes. |
Mercury iodide |
For preparation of reference electrodes |
Mercury chloride, Hg2Cl2, calomel |
For preparation of reference electrodes |
Mercury fluoride, Hg2F2 |
For preparation of reference electrodes |
Mercury bromide, Hg2Br2 |
For preparation of electrolytes |
Mercury dibromide, HgBr+ |
In laboratory electrochemistry for preparation of cathodes for concetrate
current conversion |
Water solutions, Hg(NO3)2 or Hg(ClO4)2 |
As titrants for mercurimetry (titrimetric method of analysis of anions Cl-,
Br-, SCN-, CN-). |
Water solutions, Hg(NO3)2 |
As a titrant in mercurometry (titrimetric method halogenides detection). |
Mercuric nitrate, Hg(NO3)2 |
Catalyst for synthesis of tetra-nitro-methane |
Mercuric sulphate, HgSO4 or its mixture with CuS04 or Se02 |
Catalyst for detection of nitrogen in organic compounds using Kjeldahl method |
Mercuric thiocyanate, Hg(SCN)2 |
Analytical reagent in rodanometry and mercurimetry (also for determination
of halogenides, sulphides, tiosulphides and cyanides) |
Mercury fulminate, Hg(ONC)2 |
Synthesis of aromatic ketones using Hoesh reaction |
Millon's reagent (solution HgNO3 and Hg(NO3)2 in diluted
HNO3, containing admixture HNO2) |
Colour reaction for proteins and phenols |
Mercury acetate (CH3COO2)Hg |
Used in chinolisidine chemistry |
Hg(COOCH3)2, Hg(CN)2, HgO, HgBr2) |
Catalysts in Koenigs-Knorr reaction (synthesis of glycosides and oligosarides) |
*Mercury and its compounds are also used for in chemistry of cyclopropane, laboratory electrochemistry and research practices for creation of electrochemical conduits, detection of
unsaturation of organic compounds etc., some mercury compounds are used for analysis (amperometric titration) of thiocholine (sulphuric analogue of choline), quantitative determination
of glutamine;
** the main producer in Russia is Ural Plant of Chemical Reagents (town of Verkhnyaya Pyshma, Sverdlovsk Oblast);
An exact data on mercury-containing chemicals amount currently purchased by various companies for laboratory purposes in the particular year are not available, as in Russia there are no
strict reporting requirements for chemical and research laboratories regarding annual use of mercury-containing chemicals and their fate. The total use of mercury (including mercury
contained in chemicals) in laboratory practices in 2001 can be roughly estimated at 2-5 t/year with a best estimate of 3.5 t/year.
Disposal of spent chemicals
According to the Instruction on safety measures in chemical laboratories, laboratories should neutralize the mercury-containing wastes. After getting the wastes of the 4th danger class
from hazardous wastes of the 1st danger class, the non sorted wastes are placed into containers (as a rule containers with names "organic" and "non-organic" waste) and then transported
to the landfills. As a rule, big analytical centers follow the above described way. The small laboratories after neutralization discharge the reagent wastes (in strongly diluted solution) to the
sewerage system. Based on the above mentioned information it could be roughly estimated that 2-5 t mercury per year is disposed of to landfills (less) and to the sewerage system.
3.11 Mercury-Containing Pesticides
Organomercuric compounds have been used as fungicides and seeds disinfectants, e.g. Granozan and its mixtures with hexachlorobenzene (mercurbenzene) and hexachlorocyclohexane
(mercurhexane). Fourteen types of mercury-containing pesticides were used in Russia (Table 3.57).
Table 3.57 Mercury seed disinfectants which were used in the USSR and Russia
Compound – active agent | Commercial name |
Hg content, % |
Ethyl mercury chloride | Granosan, mercuran, mercurbenzol, mercurhexane, NII UiF-2 |
1.8-2.3 |
Ethyl mercury phosphate | NII UiF-1 new cerazan |
N/A |
Â- methoxy ethyl mercury chloride | aretan, agalol, ust-pulun, universal cerazan |
N/A |
- methoxy ethyl mercury acetate | Radosan |
2.5 |
1-(3-(chlorinemercur)-2methoxypropilurea | Neogidrin |
N/A |
Dicyandialydmethilmercuric | Panogen |
N/A |
n-ethylmercur-N- phenyl –n- toluene sulfamide | Granosan-M, Cerozan-M |
1.8-2.3 |
Phenyl mercuriccurbomide | Agronal |
1.8 |
Phenylmercuricacetate | Leitosan, radosan, rubiron, falisan, agrosan, cerosan |
1.0 |
2,3-dixydroxy-propyl- mercaptide mercury ethyl | Cerosan-75 |
N/A |
S- mercury ethyl-hyosalicylate Na | Mertiolat |
N/A |
Oxyquinolinate mercury ethyl | Orto.-L.-T. |
N/A |
Phenylmercuric urea | Leitosan |
5.0 |
Oxymercuricchlorophenol | Semasan |
N/A |
3.11.1 Production.
Production of the organomercuric pesticides in the USSR was initiated at Sintez Chemical Plant in Dzerzhinsk Nizhegorodskaya oblast – beginning with 5 tonnes in 1955 and reaching
200 t/year by 1960. In 20 years the production started coming down and in 1989 decreased to 50 tonnes of mercury-containing pesticides. Production of Granosan at this plant was shut
down in 1989.
3.11.2 Current Regulations and Legal Acts
The cases of population poisoning with mercury containing pesticides had been reported till the 70-ies. Within 1958-1964, 422 persons have been reported to be poisoned with
Granosan in Perm oblast (Sivkov I.G., 1965), Novosibirsk oblast (Bychkova N.A., 1973) and Chelyabinsk oblast (Gisj Yu. F., Pozner Z.A., 1970).
In 2001 the fire at chemical pesticides warehouse in Orenbourg oblast caused mercury poisoning of 26 people. Mercury concentration in the atmospheric air 300 – 400 m far from the
fire point made up 54 – 90 μg/m3 (MAC is 0.3 μg/m3), i.e. the norms were 300 times exceeded (official information of RF Ministry of Health, 10.12. 2001).
The urgent need for Granosan prohibition was proclaimed at scientific conferences in Kiev by Mr. L.I. Medvedev as far back as 1957. The necessity for prohibition of Granosan being a
substance with embryotoxic, gonadotoxic and cytogenetic effects was further grounded in dissertation of Mr. V.I. Vashakidze. Application of mercury containing pesticides was finally
prohibited in 1991.
In compliance with the Law of the Russian Federation on Safe Handling of Pesticides and Agricultural Chemicals No. 109-FL dated July 19, 1997. "the turnover of agricultural chemicals
not included into the State Register of pesticides and agricultural chemicals permitted for application in the Russian Federation is prohibited. "The State Register of pesticides and
agricultural chemicals..." published annually doesn't contain mercury containing pesticides. The Article 12 of the Law implicates procedures of the state registration of pesticides to be
carried out by the State Chemical Commission – the interagency body under the Ministry of Agriculture. Destruction and neutralization of pesticides and pesticides containers is carried
out in compliance with the Temporary Instructions on preparatory measures for burial of prohibited and nonapplicable in agriculture pesticides and pesticides containers".
Pesticides allowable concentrations in the environment are presented in the Hygienic Norms of Pesticides Concentration in the Environment GN 1.1.546-96 issued by RF Ministry of
Health. The document regulates the following Granosan's concentrations:
- Permissible daily dose – not regulated
- MAC in soil - not regulated
- MAC in water bodies - 0.001 mg/l by sanitary-toxicological indicator of adverse health effect
- MAC in occupational air - 0.005 mg/m3 (for mercury) at the application
- MAC in the atmospheric air - 0.005 mg/m3 (for mercury) at the application
- MAC in foodstuffs and feedstock – not permitted.
In 2002, RF Ministry of Health put in force new SanPiN 1.2.1077-01 "Hygienic requirements for storage, application and transportation of pesticides and incecticides". RF Ministry of
Health has included Granosan into the List of occupational hazards adopted by the Resolution No. 1010 dated 10.02.2003 on Adoption of the List of occupational hazards under the
affect of which the employees are recommended to take milk and equivalent foodstuffs as the preventive measure.
The specialized institute on technology and economy of storage, transportation and mechanization of fertilizers application of RF Ministry of Agriculture (VNIPIagrochim, Ryazan city)
issued the Recommendations on preparation of prohibited and nonapplicable pesticides for neutralization and burial, 1997. This document refers the mercury containing pesticides to the
extremely hazardous class 1 (according to the ranking applied in Russia) and requires their burial in metallic containers.
3.11.3 Application of Mercury-containing pesticides
According to the data presented by the Yearbook of Rosgidromet Institute of Experimental Metheorology (Pesticides Monitoring..., 1999), the Granosan's application in several Russian
regions constituted (tonnes of ethyl mercury chloride):in 1995 – 6.1 7 tonnes, in 1996 – 5.5 tonnes.
This data is not comprehensive and doesn't reflect the actual scope of mercury containing pesticides application. In 2001 the Federal Center of the State Sanitary-Epidemiological Service
of RF Ministry of Health through its regional branches collected the data on quantities of pesticides turnover, had singled out the mercury containing pesticides as separate item. In 2000
the mercury containing pesticides were still used in 15 regions (see Table 3.58), about 50 tonnes of Granosan were applied meaning that about 1 tonne of mercury (at average Hg
concentration in Granosan equal to 2%) was released. In 2001, about 17 tonnes of Hg-containing pesticides were used in 4 areas of the country. There is no doubt, that the data for
2000 on Penza and Chita oblasts applied up to 12 tonnes of Granosan should be clarified. Besides, the data for 2001 on the regions where Granosan was applied in 2000 should be
obtained.
Table 3.58 Amounts of mercury containing pesticides applied in 2000 – 2001 (based on the data from the Questionnaire of FCGSEN of RF Ministry of Health "Status of the
state sanitary-epidemiological control over pesticides and agrochemicals turnover")
RF region |
Amount. tonnes |
|
2000 |
2001 |
Orlov oblast |
2.65 |
0.1 |
Kursk oblast |
0.09 |
Not used |
Voronezh oblast |
3.78 |
Not used |
Saratov oblast |
1.28 |
N/A |
Pskov oblast |
4.53 |
N/A |
Tomsk oblast |
1.58 |
Not used |
Penza oblast |
12.98 (requires clarification) |
N/A |
Kaliningrad oblast |
1.0 |
N/A |
Chita oblast |
12.00 (requires clarification) |
8.5 |
Kirovsk oblast |
1.5 |
N/A |
Kostroma oblast |
1.0 |
N/A |
Ryazan oblast |
0.7 |
N/A |
Dagestan Republic |
6.2 |
5.6 |
Kabardino-Balkaria |
0.9 |
N/A |
Lipetsk oblast |
non |
2.7 |
Total: |
50.2 (37.2 not incl. Penza oblast) |
16.9 |
N/A data not available
The clear picture confirming a considerable decrease of mercury containing pesticides application is presented based on the data for Voronezh oblast (The Letter of Mr. M.I. Chubriko
the Head Doctor of the State Sanitary-Epidemiological Service of Voronezh oblast dated May 15, 2003) where 17.4 tonnes of Granosan was used in 1998, 26.89 tonnes - in 1999,
3.78 tonnes - in 2000, and there have been no use since 2001.
In spite of the Granosan use prohibition and absence of the mercury containing pesticides in the Register, there are some advertisements regarding Granosan sale e.g. in the Internet Site of
the Russian biotechnological market and the Site of Business Advertisements - "Offer for sale - Granosan, 15 tonnes, in barrels 25 kg each) (medbiolink 2003).
Analysis of the data on amounts of used pesticides provided in Table 3.58 indicates a clear discrepancy between 2001 and 2000 data. This is caused by lack of data for 8 out of 15
territories of Russia included into the table. In 2001 mercury containing pesticides were net used only in 3 territories, which had applied relatively small amounts of pesticides (up to 4
t/year). Therefore, it is assumed that 20-40 of Hg containing pesticides are still used annually in the country.
3.11.4 Storage Conditions for Mercury-Containing Pesticides
Until 1990 the greater part of pesticides was stored in the warehouses of Selkhozchemia Association. The data of the Scientific-Research Center for Resource and Wastes Management
(NITsPURO) under RF Ministry of Economic Development and RF Ministry of Natural Resources indicate, that about 750 tonnes of mercury containing pesticides (about 10 tonnes of
Hg) can possibly be stored within RF territory in present. Compared to other official data regarding amounts of mercury containing pesticides used, this figure may be understated. For
instance, the Environmental Report of Rostov oblast for 1998 states that there are up to 550 tonnes of these substances in the oblast's territory.
Table 3.58 presents the data from the Questionnaire of FCGSEN of RF Ministry of Health "Status of the state sanitary surveillance over pesticides and agrochemicals turnover" and from
other organizations concerning amounts of the mercury containing pesticides stored in Russia. The data shows that a number of mercury containing pesticides exceeds 1,500 tonnes, a
part of which is stored on the specialized landfills. This data is probably also incomplete. For example, after the comprehensive inventory in Tver oblast amount of the stored mercury
containing pesticides increased from 34.7 registered in 1999 up to 43.8 tonnes in 2003. The amount of mercury containing pesticides stored in warehouses (except landfills) and requiring
destruction or storage at the special landfills is supposed to exceed 1,000 tonnes, which contain about 20 tonnes of mercury.
Table 3.59 Amount of mercury containing pesticides disposed in storage facilities and landfills in several regions of Russia
Region |
Amount. tonnes |
Storage site |
Source |
Rostov oblast |
Up to 500. or 8 tonnes of mercury
+52.2
|
The outdated pesticides landfill
Storehouses of agricultural enterprises
|
Environmental Report of Rostov oblast. 1998
Environmental Report of Rostov oblast. 1999
|
Kemerovo oblast |
Up to 300 |
No data avaiable |
Daily News of Kuzbass 06.11.2001 |
Penza oblast |
270.9 |
No data avaiable |
Center of the State Sanitary-Epidemiological Service (CSSES) |
Irkutsk oblast |
101 |
No data avaiable |
|
Volgograd oblast |
More than 59 |
Storehouse of the former Selkhozhimia Enterprise |
Moskovsky Komsomolets Newspapaer in Volgograd. No.34. 2002 |
Voronezh oblast |
49.2 |
The greatest part – at the storehouses of the former Agropromhimia Association |
CSSES |
Pskov oblast |
38.3 + agrosan 0.1 |
No data avaiable |
CSSES |
Saratov oblast |
32.6 |
No data avaiable |
CSSES |
Kostroma oblast |
31.9 Granosan + 0.05 agrosan |
No data avaiable |
CSSES |
Tver oblast |
2001ã. -- 28.9. inclusing Granosan – 27.3
2003ã.-42.8
|
No data avaiable |
CSSES |
Yaroslavl oblast |
21.0 +15 tonnes are disposed at Krasny Bor Landfill in Leningrad oblast |
No data avaiable |
Borovitsky and co-authors. 2000 |
Tula oblast |
20.0 + 6.75 Granosan mixed with other substances |
No data avaiable |
CSSES |
Amur oblast |
17.8 |
No data avaiable |
|
Krasnodar Kray |
17.7 of virulent poisonous pesticides |
No data avaiable |
CSSES. GUPR. Garkusha. Laugban. 2000 |
Tatarstan |
15.6 |
No data avaiable |
CSSES |
Mordovia |
14.5 |
No data avaiable |
CSSES |
Ryazanskaya oblast |
13.5 |
No data avaiable |
CSSES |
Moscow oblast |
12.5 |
No data avaiable |
|
Chita oblast |
12.0 |
No data avaiable |
CSSES |
Volgograd oblast |
11.5 |
No data avaiable |
CSSES |
Omsk oblast |
11.3 |
The outdated pesticides landfill |
|
Sverdlovsk oblast |
11.0 |
No data avaiable |
CSSES |
Tomsk oblast |
9.7 |
Agricultural enterprises of oblast |
Environmental Department of Tomsk oblast Administration 15.04.03 |
Udmutria |
8.4 |
No data avaiable |
CSSES |
Orenberg oblast |
7.35 |
No data avaiable |
CSSES |
Tomsk oblast |
3.6 |
No data avaiable |
CSSES |
Magadan oblast |
3.55 |
No data avaiable |
CSSES |
Kursk oblast |
2.1 |
No data avaiable |
CSSES |
Primorsky kray |
1.4 |
No data avaiable |
CSSES |
Smolensk oblast |
1.1 |
No data avaiable |
CSSES |
Chelyabinsk oblast |
0.6 |
No data avaiable |
CSSES |
Leningrad oblast |
0.43 |
No data avaiable |
CSSES |
Vologda oblast |
0.2 |
No data avaiable |
CSSES |
Lipetsk oblast |
0.2 |
No data avaiable |
CSSES |
Orlovskaya oblast |
0.1 |
No data avaiable |
CSSES |
Moscow |
0.07 |
No data avaiable |
CSSES |
Kirovsk oblast |
0.01 |
No data avaiable |
CSSES |
Under conditions of the market economy many agricultural chemistry enterprises ceased their activities, and the pesticides storage conditions therefore turned out to be out of the state
control. The agricultural enterprises were not able to store pesticides properly and to ensure safety of the storage facilities. Various publications (Andreeva 2000, Garkusha and Laubgan
2000, Ivanov 1999, Sinoda, Michailova 2000, et. al) inform, that the greatest volumes (i.e. more than 10 tonnes) of the outdated mercury containing pesticides are stored in Altai kray,
Krasnodar kray, Belgorodskaya, Voronezhskaya, Kurskaya, Kurganskaya, Novosibirskaya, Omskaya, Pskovskaya, Rostovskaya, Ryazanskaya, Saratovskaya, Sverdlovskaya,
Smolenskaya, Tverskaya, Tulskaya, Yroslavskaya oblasts and republics of Mordovia, Bashkortostan and Tatarstan. At the same time, some north-west (Murmanskaya and
Novgorodskaya oblasts, republics of Kerilia and Komi), north (Yakutia) and southern (Kalmikia, Ingushetia, Osetia) territories of Russia in the Far East (Sahalinskaya and
Kamchatskaya oblasts) officially do not have mercury containing pesticides.
A significant problem is the condition of pesticides storehouses and the clarification of exact number of stored mercury containing pesticides, as it is very difficult to take an inventory in
small companies, most of which have become bankrupts and do not properly register the poisonous substances. The more precise number of the outdated pesticides, including mercury
containing ones, is specified during inventories. For instance, in 2001 the UNEP Chemical Project of the State Chemical Commission of the Ministry of Agriculture and the Center of
International Projects was implemented in 5 regions (Krasnodarsky kray, Ryazanskaya, Tverskaya, Bryanskaya, Voronezhskaya oblasts). In 2002 the inventory was carried out within
ACAP in cooperation with the State Chemical Commission of the Ministry of Agriculture in 10 northern regions (Arhangelskaya, Murmanskaya, Magadanskaya, Tumenskaya,
Omskaya, Kamchatskaya oblasts, Altai Kray, Krasnoyarsk Kray, republics of Comi, Yakutia-Saha). I.e. 15 regions have been inventoried within 2 years. For the two of the above
oblasts – Tverskaya and Voronezhskaya - an additional information on mercury containing pesticides was obtained in May 2003.
In order to specify the conditions of mercury containing pesticides storage the centre of the oblast – Tver City and several oblast's regions – was visited by the experts in May 2003.
Description of mercury containing pesticides and their storage conditions in Tverskaya oblast are presented in the Annex 2.
Tverskaya and Voronezhskaya oblasts represent the cases of inventory of the outdated pesticides and their storage conditions can be considered as relatively good. Effective activity on
the outdated pesticides inventory in Krasnodar Kray (one of the main agricultural centers of Russia) was pointed out at the Seminar on the outdated pesticides, which was held for NIS
countries in May 2003 by the Center of International Projects in the frameworks of UNEP Chemical Project. However, the mercury containing pesticides storage conditions in most other
regions are much worse.
Examples
According to the State Sanitary-Epidemiological Service, Granosan was applied in several regions of Altai kray, 56% of 429 storehouses do not comply with sanitary requirements, 318
agricultural enterprises have no pesticides storehouses.
More than one third of agricultural enterprises in Tulskaya oblast carried out the seed treatment. 400 tonnes of pesticides are accumulated in the oblast. 80% of the storehouses do not
comply with sanitary requirements. In 2001 the State Sanitary-Epidemiological Service issued only 18% of sanitary certificates, i.e. 7% of the storehouses were certified. For the last
years about 20 storehouses had been destroyed resulted in chemicals, incl. Granosan, releases to terrestrial environment or being stolen. New storehouses are not built, therefore the
problem of the outdated pesticides utilization is not solved (the Sanitary Epidemiological Report of Tulskaya oblast, 2001).
Kamchatskaya oblast, Kozelsky Granosan burial site situated 35 km to the north-east from Petropavlovsk is in a very poor condition. The mercury is detected in the mushrooms growing
nearby. Kuryinsky Landfill situated 20 km from Kurya village in Altay Kray is in unsatisfactory condition.
One of the pesticides storehouses in Volgograd oblast store as much as 59 tonnes of Granosan, and this site is easily accessible; the metallic containers have been rusted through.
In 1976 the landfill for non-applicable pesticides was constructed near Bataisk city of Rostov oblast. In 1977 – 1978 this landfill legally accepted for the burial more than 1,500 tonnes of
pests-killers collected from agricultural and other enterprises of the Northern Caucasus, including more than 500 tonnes of mercury containing Granosan (about 8 tonnes of Hg). Today,
the landfill is closed. Moreover, since 90-ies the groundwater level in the landfill area had been considerably increased resulted in the landfill's basement flooding. This can cause migration
of mercury containing and other toxic components in the groundwater.
In total 114.5 tonnes of chemicals are subjected to utilization in Chelyabinsk oblast. According to the State Sanitary Epidemiological Service, the problem of pesticides utilization is
increasingly aggravating from year to year. This is caused by decentralization of the storehouses, lack of proper control activities and repair funds, as well as absence of posssibility to
deliver the pesticides for destruction outside oblast. The greater part of protectants is stored at three storehouses in due condition for 5–6 months. Then, during the preplant period
granosan in waterproof packing has been being sold to the relevant agricultural enterprises for futher application. Many storehouses store the unknown pesticides packed in non-labeled
containers. E.g., according to the State Sanitary-Epidemiological Service, amounts of such pesticides subjected to destruction constitute 250 tonnes in Orlovskaya oblast, 365 tonnes in
Kurskaya oblast, 244 tonnes in Pskovskaya oblast and 211 tonnes in Tatarstan. Such pesticides may also include Granosan. Free access to Granosan in a number of RF regions has lead
to the negative effects. The existing pesticides landfill is completely filled up. According to the Republican Veterinarian Department, 12 sheep were poisoned with Granosan 9 km from
Kizil City – a capital of Tiva Republic. The adjacent Tos-Bulak mineral spring is endangered to mercury contamination (Novosti Russian News Agency –Siberia, January 31, 2003).
3.11.5 Mercury containing pesticides burial sites
In Russia an authorized disposal of mercury containing pesticides takes place on the territories of manufacturing enterprise in Dzerzhinsk City ( Nizhegorodskaya oblast), Krasny Bor
Specialized Landfill in Leningrad oblast, some other specialized landfills.
Inspection of storage conditions of mercury containing wastes generated at Granosan production at Sintez Plant in 2002 (Ref.: the Statement on Environmental Compliance Monitoring in
Sintez JSC conducted in 16.04.2002 by the State Control Department of MNR, Privolzhsky Federal District) showed, that Granosan production building and local treatment facilities are
destroyed. The production buildings and treatment facilities are contaminated with mercury. The urgent need for degassing of the equipment installed in Granosan production facilities and
buildings had been stressed. The asphalted platform, near the Granosan production building, stores 22 containers (1 m3 each) with mercury containing wastes (activated carbon with 5%
mercury content). By the date of inspection, the containers hold 0.02 th. tonnes of mercury containing wastes, i.e. up to 1 tone of mercury. Wastes storage conditions do not correspond
with the environmental requirements related to the containers protection from leakage. The wastes are being utilized. The project on transportation of the containers for utilization at NPP
Kubantsvetmet CJSC has been elaborated. SPES Environmental NGO believes, that amounts of mercury containing wastes, as well as metallic mercury (which had been buried in
metallic containers at the enterprises's territory since 1985 till 1989, and most probably during the following years), stored at Sintez JSC (Dzerzhinsk City, Nizhegorodskaya oblast) are
significantly underestimated (Letter No.15 dated 11.03.2003).
The mercury containing pesticides have been disposed at Krasny Bor Specialized Landfill since 1970. According to the landfill's representatives it is done by the following way. Firstly,
a company should duly apply to Karsny Bor for the wastes disposal, indicating the wastes type and class of hazard. Having singed the agreement on wastes disposal, a company at own
expenses should pack the wastes into the standard containers in compliance with the established rules. A standard container for wastes has not less than 10 mm thick walls 1.7 m x 1.0 m
x 1.0 m. Inside the steel container there is a metallic grid covered with concrete layer over 5 am thick. Pesticides are placed on the container's bottom, and the space between package
and the walls in filled with concrete. The external surface of the container should be resinificated. The container should be marked with indelible paint specifying name of the company,
agreement No., waste type, net weight and gross weight, container hand over date. The weight of container with wastes should not exceed 3 tonnes. On the landfill the containers are
placed in two tires in 70 m thick Cambrian clay layer. Wastes weight is pointed out in the wastes acceptance certificate. Control over soil and groundwater quality is carried out by means
of three inspection wells located at the landfill and three wells outside (around the periphery) the landfill. The soil and water samples are taken from the wells regularly and analyzed for
presence of pollutants, including mercury. During the whole history of the landfill functioning there were no cases of MAC exceeding for mercury or heavy metals concentration in soil,
groundwater and air.
3.11.6 Summary
The present information on mercury-containing pesticides and be summarised as follows:
1. In spite of the official prohibition, trade with mercury containing pesticides still exists in the Russian Federation. Approximately 20-40 tonnes are used annually in agriculture.2. It is
difficult to estimate the exact volume of used pesticides. In 2000 approximately up to 50 tonnes of agrochemicals were used with a total mercury content of about 1 tonne which was
finally released to the environment.
3. The exact number of mercury containing pesticides located in the storehouses is not known, but may reach about 100-1,000 tonnes, containing up to 20 tonnes of mercury.
4. Most of the storehouses located in rural areas are in emergency condition, the wastes are stored improperly.
5. The environment is seriously endangered at mercury containing pesticides storage sites, mercury distribution in the areas adjacent to storehouses and mercury containing wastes landfills
is almost not controlled.
3.12 Other applications
In the following section other applications of mercury are briefly described. For these applications less detailed information have been obtained, either because the applications are
marginally or because the information was difficult to obtain. For some of the applications information is partly closed because the products are used for both civilian and military
purposes.
The section covers:
- Production of lithium isotopes;
- Production of semiconductors;
- Production of power semiconductor devices;
- Mercury containing biocides;
- Other uses.
3.12.1 Production of Lithium Isotopes
Technologies designed for production of pure substances (metals), based on the amalgam method, are known since rather long ago (Baymakov, Zhurin, 1977; Belyayev et al, 1969;
Kozin, 1970, 1973). They were used for the industrial production of zinc and cadmium of high purity, for split of stable isotopes, as well as for production of extra-pure metals in pilot
production facilities, scientific research and laboratories. The amalgam method requiring significant amounts of mercury was most widely used in industry for split of stable lithium isotopes
(Andreyev et el., 1982).
Isotope splitting, i.e. separation of one or several isotopes of a given element from their mixture, is performed in special installations – counter-flow columns. To obtain a degree of splitting
that is higher than in a single operation, in such installations a part of the flow (stream) going out from the last stage and enriched with the target isotope is returned to the column, i.e. the
so-called flow circulation is performed (Chemical Encyclopaedia ..., 1990). To circulate the flows, thermal or electro-chemical decomposition is used or reactions with auxiliary
substances. Accumulation of the target isotope begins at the end of the column, where the contacting fractions or streams are brought out of the equilibrium state due to stream circulation.
As a result, the enriched fraction of this stage contacts with a fraction that has somewhat higher content of the target isotope as compared to the depleted fraction carried away from this
stage. The last redistribution of isotopes results in an increased concentration of the isotope as compared to the initial concentration in both fractions leaving this stage. As the process
goes on, the enrichment at the end of the column becomes higher, and stages that are more remote from the stream circulation place are taken out of the equilibrium state, while the extent
of the enriched part of the column grows. When the required split degree is reached at the end of the column, the final products is taken up. As a rule, due to low initial concentrations of
the target isotope, the period of accumulation of the isotope (the so-called start-up period of the installation) makes hundreds and thousands of hours.
In practice, split of stable isotope in the liquid-liquid system is used by the chemical exchange method (amalgam exchange method) (Andreyev et al., 1982). In this case, one of the liquids
is a water or organic solution of any element salt, while the second liquid is an amalgam of the same element. Such systems allow easy counter-flow due to a large difference in density,
possibility to perform physical separation of two liquids and a relatively simple handling of streams, since amalgams are easily obtained by electrochemical methods and even more easily
degraded or exchange one metal for another metal available in the solution. It is precisely this amalgam exchange method has found its industrial use for separation of stable lithium
isotopes (see Figure 3.15).
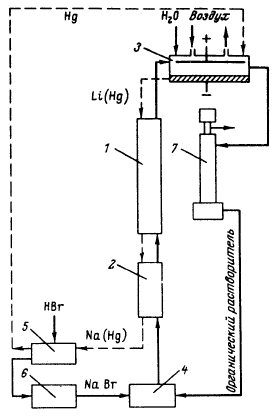
1 – Isotope exchange column; 2 – column for separation of lithium from amalgam; 3 - electrolyser; 4 – device for dissolution of NaBr; 5 – amalgam decomposer; 6 - evaporation; 7 –
rectification column
(Inscriptions in the diagram: Âîçäóõ = Air; Îðãàíè÷åñêèé ðàñòâîðèòåëü = Organic solvent)
Figure 3.15.
In this case, streams in the top end of the cascade are circulated by electrolysis of water solutions of lithium salts on the current mercury cathode. The obtained amalgam is fed to the
isotope exchange column 1, while the water solution of the organic solvent is fed to the rectification column 7, which allows using this solvent several times. Circulation of the streams at
the lower end of the column can be effected in different ways. The simplest method used for transfer of the lithium from the amalgam to the organic solvent is its decomposition by water
oxidized by an acid, evaporation of the water solution of the salt, incineration and dissolution in the solvent. Another (continuous) method of stream circulation includes replacement of the
lithium amalgam by the sodium, strontium or cadmium through the reaction:
Li(Hg) + MeX1(2) ↔ Me(Hg) + LiX,
where Me is the metal of the 1st or 2nd group of the periodic system.
The reaction is performed in a separate column 2, after which follow devices 5 for decomposition of Me(Hg), evaporation and dissolution of Me1(2) in the organic solvent fed from the
upper stream circulation system. Mercury obtained during decomposition of Me(Hg) is returned to the electrolyser. To decompose the amalgam at the end of the cascade right in 6Li,
usually decomposing agents are used filled with graphite, pig iron or alloys, as well as electrochemical decomposition by applying a positive potential to the amalgam (Andreyev et al.,
1982).
Production of lithium isotopes by the amalgam exchange method requires significant amounts of mercury. Thus, analysis of the technological cycle at one of such enterprises, located in the
city of Novosibirsk (the chemical concentrates plant)( demonstrated (Mercury in the Environment ..., 1995; Yagolnitser et al., 1995) that here, from mid 1990's, the total accounted
mercury loss during production of lithium isotopes by the amalgam-exchange method, had made about 35 t/year, while the unaccounted loss has reached 5 t (Fig. 3.16). Of all accounted
mercury loss about 1.6 tonnes were released to atmosphere, about 2 kg to the water environment and 33.5 t were in solid waste to be buried.
The data indicates that large amounts of mercury may be present in waste dumps around the enterprise.
Figure 3.16 Approximate structure of mercury loss in production of lithium isotopes by the amalgam-exchange method (Yagolnitser et al., 1995)
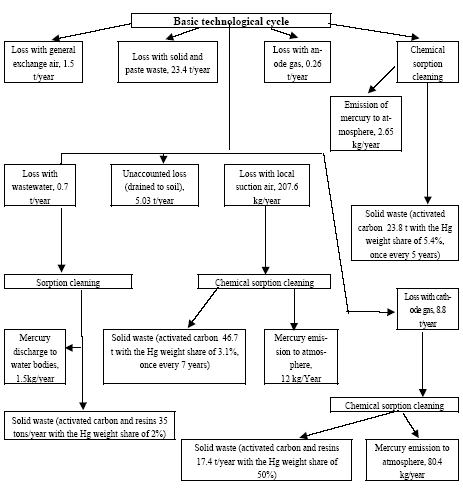
Data shown in Figure 3.16 allows calculations of relative mercury loss in the course of the above technological process (with the total loss about 40.2 t/year): with solid and pasty waste
about 58.2%, with spent activated carbon about 23.8%, with emissions to atmosphere about 4.6%, with wastewater about 0.004%; the share of unaccounted loss (drained to soil) about
12.5%.
Data on mercury consumption at the Novosibirsk enterprise of chemical concentrates in 2000-2002, as well as data on its emission to the habitat environment are not available in the
accessible information sources. However, it is know that the Institute of Chemistry of Solid State and Mechanical Chemistry of the Siberian Department of the RAS (city of Novosibirsk)
has developed (and by all evidence has put into practical use) a principally new method for separation of stable lithium isotopes that allowed reducing the production cycle, a substantial
decrease of electricity use and several-fold reduction of the volume of the used mercury ("Delovoy Novosibirsk ..."). This, undoubtedly, made it possible to reduce irrecoverable loss of
mercury, principally connected, most probably, with solid waste (spent activated carbon, resins, pasty waste), generated during the above production processes and subject to secondary
processing (or safe burial).
As reported (Shatalov, 2000), the Novosibirsk enterprise of chemical concentrates has recently made an agreement for processing of lithium waste from amalgam-exchange production in
USA and now intends to produce hydroxide, carbonate and waterless lithium chloride and pure metal.
3.12.2 Production of Semiconductors
Mercury is used for manufacture of semiconductor materials and using them to make a new generation of electronic and electronic-optical devices. The use of mercury in the technologies
designed for manufacture of semiconductor materials and as an acceptor admixture for germanium alloying (applied in infrared devices) to attribute to it a hole-type conductance was
started as early as in 1950's. Today, semiconductor materials based on compounds of the A2Â6 type that contain mercury are used to manufacture photo resistors, photodiodes, Hall
sensors, high-sensitivity receivers of optical light (photo receivers, photo receiving devise and sets), and semiconductor lasers.
Use of mercury for production of semiconductor materials
Until recently, mercury-containing semiconductor materials mostly were represented by HgS, SeHg and TeHg (Melikhov, Lazarev, 1987; Nashelskiy, 1987; Pasynkov, Sorokin, 1986,
Tairov, Tsvetkov). Then, it was established that compounds of the type A2B6 form, among themselves, a continuous series of solid solutions, the typical representatives of which were
CdXHg1-XTe, CdXHg1-XSe, CdTeXSe1-X, Hg1-XMnXTe, Hg3In2Te6, possessing unique electro-physical characteristics (Bovina et al, 1999; Varavin et al, 2002; Kurbatov, 1999;
Ponomarenko, Filachev, 2001; Sidorov et al, 2001). Of special interest among these compounds are solid solutions of cadmium and mercury telluride (Cd-Hg-Te), abbreviated in Russia
as CMT, that are used now widely for manufacture of semiconductor materials (Bovina, Stafeyev, 1999; Kurbatov, 1999). CMT semiconductors are widely applied world-wide for a
number of application among others thermal imaging, CO2 laser detection, FTIR spectroscopy, missile guidance and night vision.
A mixture Cd-Hg-Te (CMT) forms, in certain conditions, crystals with a sphalerite structure, where one sub-lattice is totally occupied by tellurium atoms, while the second houses atoms
of cadmium and mercury (Svitashev, Chikichev, 1996). Depending on the proportion in which atoms of cadmium and mercury are mixed in the metal sub-lattice, we can obtain crystals of
CMT with any given wide of forbidden area in the interval 0-1.6 eV (at 4.2 K). The most important among CMT, from the practical point of view, are solid solutions CdXHg1-XTe. In
the USSR, the semiconductor solid solution of CMT was for the first time (practically, in parallel with the scientists of Great Britain) synthesized and investigated by SA.D. Shnaider
(Lvov University) (XVI International Conference...).
In the USSR, methods for growth of CMT and making of photodiodes and photoresistors on its base were developed mainly in the NIIPF (today it is GNC "NPO Orion", Moscow)
(Stafeyev, 2001). Already in 1970, CMT was used to manufacture single-element photoresistors that were supplied to many organizations of the USSR. Some time later they started to
develop photoresistors at the enterprise "Sapfir", where they organized batch production of the USSR first photoreceiver based on CMT (Stafeyev, 2001). Rather quickly the methods
designed to grow CMT using the developments of the FTI of the USSR AS, NPO "Orion", NPO "GIPO" (city of Kazan), Institute of Semiconductors of the AS of Ukraine were
developed and used in the mass-scale production in the NPO "Giredmet" (Moscow) and also at the Plant of Pure Metals (town of Svetlovodsk, Ukraine) and the Experimental
Chemical-Metallurgical Plant (city of Podolsk) Kurbatov, 1999; Ponomarenko, Filachev, 2001). The Plant of Pure Metals in Ukraine, by mid 1980's, started to manufacture large-size
monocrystals of CMT of the required condition and in the required numbers. Today, this plant supplies its products basically to China and some other countries. The plant in the city of
Podolsk produces materials for bi-dimensional photoreceiver structures of the photodiode type and for photomatrixes (Kurbatov, 1999). In 1970's, the GOI of S.I. Vavilov (city of St.
Petersburg) manufactured photoreceivers and photoreceiving devices with sensitive elements from germanium alloyed with mercury (Kurbatov, 1999).
At present, CMT are used to make matrixes of photosensitive elements that are components of photoreceivers (PR), single, linear and matrix photoreceiving devices (PRD), sensitive
within the wave range of 1-20 μm (Bovina et al., 1999; Kurbatov, 1999; Ponomarenko, Filachev, 2001; Filachev et al., 2003). Photodiodes from CdXHg1-XTe are now the basic
photosensitive element in the modern IR-technologies, devices for receiving pulses from the CO2 laser, etc. semiconductor lasers and photoreceivers, based on CMT, are essential
components of the elemental base for fibre-optical communication lines. CdXHg1-XTe is used to manufacture uncooled photoresistors, range-finder IR imagers, heat direction- and
range-finders, etc. When Hall sensors are manufactured, the best results are attained when using solid solutions of HgSe è HgTe – as plates or thin films.
Mercury emission during production of semiconductor materials
Due to known circumstances, information about the scales of mercury use for manufacture of CMT and other semiconductor materials in Russia and in other countries of the worlds is not
published; at least, such information is not present in the available literature. The same reasons explain why there are no data on environmental aspects of production of
mercury-containing semiconductor materials. According to data, obtained from the workers of the mercury enterprises in the former USSR, one plant of pure metals for semiconductors
(city of Svetlovodsk, Ukraine) in 1980's ordered every month up to 300 kg of metallic mercury (i.e. up to 3.5 t/year). It should be noted that this period was a period of rather active
industrial production of volume CMT crystals and, evidently, of pilot work on improvement of technologies and introduction of new methods for CMT production.
Processes of production of such materials are highly technological, performed within a closed volume, and, as emphasized by authors of many publications, do not release harmful
substances. Besides, such production facilities have a high level of disposal and reuse of spent materials (which is due, to a significant degree, to their high cost), used in the technological
process. At the same time, some publications, for example, underline that "CMT epitaxy requires high use and disposal of toxic group" (Chikichev, 1996), although scales of such use of
metal are not reported. It is known, that CMT technologies depend very much not only on the growth of mercury-containing compounds, but also on post-growth thermal treatment of the
produced materials in the mercury vapours. Therefore, it cannot be ruled out that in the course of synthesis of semiconductor materials not only chambers are contaminated with the used
mercury, but that it is fed to the production environment, for example, due to un-tight equipment, to which indicate available indirect data. In particular, The Institute of Physics of
Semiconductors and the Design Technological Institute of Applied Microelectronics of the SB of the RSAS (Novosibirsk) have recently developed and patented a method for collection
of mercury in the technological chamber at the molecular beam epitaxy installation and also designed the respective plant (http://prometeus.nsc.ru/patent/1997/210.ssi). The above method
and the plant, as stated in the patent, increase efficiency of the technology designed for production of multi-layer fine-film coating, increase productivity of the process and secure
environmentally clean production.
In any case, out of the entire volume of mercury used for production of semiconductor materials an insignificant amount of mercury in included into the final products, a small amount is
emitted to the production environment, and the bulk is trapped, disposed, refined and reused in production. It cannot be precluded that main loss of mercury happens not so much during
production of semiconductor materials, but rather at the stage of its disposal and refining.
No data are at present available for quantification of the use of mercury for production of semiconductors or the releases from the production.
3.12.3 Power Semiconductor Devices
Several Russian enterprises of the semiconductor industry manufacture (by individual orders) power semiconductor devices that are not mass-produced anymore, but still used at
domestic enterprises. The use of such devices is due to the fact that electricity supply schemes of some enterprises do not allow, for different reasons (including technical ones), installation
of modern devices. Every device of the older generation, used to supply direct current to the electricity network, use up to 8 kg of metallic mercury (in the insulation jacket). For example,
one of the Russian enterprises manufacturing semiconductor devices used about 420 kg of metallic mercury (according to the material balance of raw materials) for manufacture of the
indicated power semiconductor devices in 2001-2002.
There are grounds to presume that similar products are also produced by some other domestic enterprises of the semiconductor industry. Hence, one can conclude that the total use of
metallic mercury in the country for such purposes may be about 0.5-2.5 t/year. Mercury loss during production process (in fact, individual and manual) of such products, evidently, bears
occasional nature and can hardly exceed 1-3% of the total used mercury (i.e. about 45-50 kg a year for the entire country). The majority of lost metal, by all judgment, finally ends in the
sewerage systems or dumpsites. The level of content of mercury vapours in the working area during production of the above devices may reach the level of MAC.
3.12.4 Mercury Containing Biocides
Mercury compounds have traditionally been used as desinfectants and preservatives for preparation of a number of medicines and vaccines and latex productsdisinfectants.
The concerned medicines included antiseptics (mercury amidochloride, diiodide, dichloride monochloride, oxide), oxicianide, salicylate amidochloride, mercurial yellow ointment,
mercurial grey ointment, mercurial - bismuthic ointment, mercury plaster and Sofradex nasal drops.
In persuance the Order of Russian Ministry of Health (No. 82 of 23.03.98 ã.) preparations and pharmaceutical substances containing mercury and its compounds have been excluded from
"the State Register of Medical Drugs allowed for medical use and industrial manufacture" (http://www.medin.ru/price/m1998_4.shtml).
Nevertheless, Internet sites include ads for sale of "medicines and preparations" including mercury amido-chloride (white precipitation mercury), mercury dichloride, mercury
monochloride (calomel), mercury oxy-cyanate, yellow mercury oxide (yellow precipitated mercury), mercury iodide (II) (pharm), which in the past were used as medicinal drugs and
antiseptics. Beginning from about early 1990's, they started to use in practice the so-called "vituride", i.e. preparation including mercury (dichloride), allegedly as a universal preparation
for treating a broad range of diseases. In particular, as stated by the inventors, it could be used for treating sugar diabetes, tumours, systemic lupus, psoriasis, bronchial asthma,
rheumatoid arthritis; it possesses antiviral activity against AIDS, hydrophobia, herpes and cytomegalovirus infections, etc. {Vituride ..., 1985). Despite the fact that the RF Ministry of
Health, in its special information letter of 31 March 1998, No. 2510/2871-98-32 "On the Vituride Preparation", not allowed for medical use, once again confirmed that this preparation
was prohibited for health uses (http://www.medin.ru/price/m1998_4.shtml (03.05.2003)), it is still advertised and, by all evidence, used for medical purposes (Vituride: Unique Domestic
Medicinal Preparation sodium 2-(ethylmercuriothio)benzoate
Ethylmercury thiosalicylate – marketed as "Merthiolat", "Temirosal" or "Thiomersal" - is added to the vaccines as a preservative. The problems of use of this substance for production of
diphtheria, tetanus toxoids, and pertussis vaccine (ÀÊÄÑ), diphtheria and tetanus toxoids, vaccine (ÀÄÑ) and ÀÄÑ-Ì or its analogue Imovax, as well as  hepatite and tetanus vaccines
was widely discussed in Russian scientific publications. For ÀÊÄÑ vaccine production 1 ml of whooping-cough suspension should be added with 100 μg of this compound. A Merthiolat
(0.005%) was used for production of Russian  hepatite vaccine by Combioteh company. Before use for vaccines production, the concentration of free Hg in Merthiolat should be
controlled. Most of the vaccines used in Russia contain mertiolat in 1: 10 000 proportion, in  hepatite vaccine – 1: 2.0 000. Thus, one inoculative dose contains small amount of
mertiolat. The total amount of mercury for preservation of vaccines has not been quantified, but is considered to be insignificant compared to other uses of ercury.
Information on mercury supplies from plants producing the vaccines is not available. By 6.08.2003 no information on current use of mercury containing biocides in Russia has been found
in related journals, statistical reference books and Internet. "Biocides for water-deluting paintwork materials review" prepared by specialists of SRI of Chemistry of Nizhny Novgorod
University named after Lobachevsky points out, that present production of such materials in Russia doesn't employ mercury and they are produced basically using imported materials
(www.snab.ru:8/01/lkm/02/06.html)
3.12.5 Other Uses
The following section includes scattered information on other uses of mercury, which have not been assessed in detail, but different information indicates that mercury is or has recently
been used for the applications.
Explosives
Mercury fulminate Hg (ONC)2 obtained by interaction between ethanol and solution of Hg(NO3)2 in HNO3, is used as the initiator explosive substance for blasting caps (which include
individual substance) and igniting caps (which include a mixture of initiator substances containing up to 16-28% of mercury fulminate).
Television and radio engineering
Small amounts of mercury are used in television and radio engineering. For example, in mid 1990's, the enterprise "Ekran" (city of Novosibirsk) emitted to the air system from the shop
where colour tubes were exposed (through the general exchange ventilation) up to 70 kg of mercury a year (Yagolnitser et al., 1995).
There are date showing that computers – electronic keys and flat monitors – include mercury (up to 0.0022% of their total weight)
(http://www.physfac.bspu.secta.ru/mirror/izone/izon...). The electronic key, i.e. the switch element, with a high electrical resistance in the closed state and a small electrical resistance in
the open state, is widely used in automatic devices, telemechanics, radio engineering, and computer equipment. It was recently reported that since 1 January 2006 it will be totally
prohibited to use mercury in Europe in production of electronic equipment (http://www.rambler.ru/db/news/msg.html?mid=1773229&s=12).
Paints
Now, Russia has more than a dozen large paint producers which produced, in 2001, about 351,135 tonnes of different paints, lacquers and varnishes. Concrete data on the use of
mercury for paint production are not published. Moreover, it is considered that at present mercury and its compounds are not used for production of paints and colours. Nevertheless,
there are indirect data showing that mercury and its compounds, most probably, are used, in different amounts, for production of paints, lacquers and varnishes. E.g. there is information
taht (Boratyrev et al., 1999) the largest Russian enterprise producing paints, lacquers and varnishes, annually discharges up to 60 kg of mercury salts together with wastewater to the
Volga River. A case is known when in Tver Oblast about 1,200 litres of mercury-containing waste was discharged to a quarry; this waste included secondary paint product used for
production of adhesive labels at Kamenka OJSC (Kouvshinovo town) (News. Battery. Ru – "Accumulator of News", 25.01.2001...). Also it was reported
(http://uuu.narod.ru/money.htm), that mercury-containing paintsrare used to print Russian paper banknotes; these paintsinclude the so-called active amalgams so as to protect
counterfeiting. It is thought that such protection is the best practical.
Mirrors
In recent years, data has been published in press about the use of mercury for production of mirrors, at least there can be seen ads on sale of domestic mirrors manufactured using the
amalgam method.
Hosehold application
A specific form of mercury use is its household application. Indeed, the available materials show that population has at homes a significant amount of metallic mercury and its compounds.
For example in 1999, in the city of Perm an environmental organization bought the metallic mercury from the citizens – within 6 months they bought from population about 0.3 tonnes of
this metal (Environmental Condition and People's Health in Perm ...). Given such situation as typical for most of 89 Russian regions, the weight of mercury being at households' disposal,
may constitute, at least, several tonnes. This mercury, by all evidence, not only kept by them, but also actively used for different purposes. Thus, for example, mass media regularly report
about attempts of illegal sale of metallic mercury on the "black" market in different regions of the country; the amount of seized metal varies from 10-60 kg to 1.5 tonnes. Internet sites
explain in details how to use metallic mercury to cover snoot hooks (different methods are offered to fishermen) or how to make mercury chloride. Internet as well as some known
magazines (see for example, "Radiolyubitel" (Radio Amateur"), 1991, No. 7, p. 43) recommend Gershtein amalgam (fine lead saw dust mixed with metallic mercury in the ratio of 1.5 kg
to 2 g) as a preparation fit for cold soldering of metals. The well known story about "red mercury" has been continued in the recent years, by different stories (especially through Internet)
about fantastic properties of the so-called mercury TV and radio antennas making of which requires substantial amounts of mercury (up to 10 kg of mercury per antenna). All this raises
new interest among people to metallic mercury and, hence, they are attempting to find it.
4 Mobilisation of Mercury Impurities
4.1 Coal
Globally coal combustion is the major anthropogenic source of mercury emission to the atmosphere (UNEP 2003).
The total extraction of coal in Russia in 2001 amounted 269 million tonnes. Of these 171 million t was bituminous coal, 98 million t was brown coal. The total consumption of coal broken
down on use category is shown in Table 4.1 The total domestic consumption in 2001 was according to this source 234 million t. According to the statistics from the International Energy
Agency the domestic supply should be a little higher; 251 million t. (IEA 2003). It should be noted that according to the IEA data the split between sectors is different as 32 million t
should be used for heat plants, whereas the consumption for other industrial uses should be only about 8 million t. However, the data of Table 4.1 will be used for the further calculations.
Table 4.1 Coal consumption in Russian Federation by use category2001 (calculated according to data from (Performance Results of Coal Sector in Russia ..., 2002))
Indicator |
million tonnes |
% |
Supply: |
Supply of Russian coal |
207.9 |
|
Import of power-generating coal from Kazakhstan (Ekibastuz) |
25.5 |
|
Import of coking coal from Kazakhstan (Karaganda) |
0.8 |
|
Total coal supplies to Russian coal users |
234.3 |
100 |
including: |
- for electricity generation sector |
124.3 |
53.1 |
- domestic heating |
7.6 |
3.2 |
- municipal boiler houses |
17.6 |
7.5 |
- for the agrarian-industrial complex |
0.9 |
0.4 |
- for coking |
41.7 |
17.8 |
- other industrial users* |
42.2 |
18.0 |
* In this case, by all evidence, it means basically the use of coal in industry, not only for direct combustion, but also for its processing (semi-coking, gasification, hydrogenation, production
of silisized carbon, calcium carbide, thermal anthracite, carbon sorbent, thermal graphite, etc.); most of these processes are based on high-temperature coal processing, which a priori
determines emissions of mercury from it to atmosphere.
4.1.1 Mercury in Coal from the Russian Federation
The mercury content in coal is very variable; both among coal basins and among the individual mines in each basin (see figure 4.1, Annex 3).
As an example, data for coal enterprises in Kuznetsk Basin ranked by mercury content is shown in Table 4.2. The Kuznetsk basin is the main basin in which 127 million t of coal was
extracted in 2001 (Table 4.3). The basin account for about 46% of all coal extracted in Russia and account for 78 % of all coking coal in the country. The mercury content expressed as
averages for each mine ranges from 0.01 mg/kg to 0.6 mg/kg. The simple average for all data from the basin is 0.09 mg/kg. Because of the large variation, in spite of the large number of
measurements (data representativeness n=39), the 90% confidence range on the average for the dataset (using the averages of each mine as data input) is still quite wide: 0.05-0.13
mg/kg.
Click here to see the figure.
Figure 4.1 Major coal basins in Russia (Source: International Coal & Methane Research Center http://www.uglemetan.ru)
The total mercury content of coal mined in Russia in 2001 was estimated by multiplying the coal mining by region by the estimated average mercury content of the coal for each region and
amounted to 22 t (Table 4.4). According to the Refference Book (Valuable and toxic elements in coals commercially available in Russia, 1996 – p. 238), the average mercury content of
the commercial coal from each region ranges a factor of 100 from 0.008 mg/kg in Buryatia Oblast to 0.85 mg/kg in the Amur Oblast. The weighted average content of mercury in Russian
coal is estimated as 0.08 mg/kg and is very dependent on the average Hg concentration in coal from Kemerovo Oblast (Kuznetsk Basin – a major coal supplier) that account for half of
the total mercury content in coal in Russia.
Considering that the estimate of the total mercury content in coal is dependent on its average concentrations used for a few of the regions, the uncertainty on the average is estimated to be
rather high in spite of the large number of available factual data. It is roughly estimated that the average mercury concentration in Russian coal is within the range of 0.07-0.09 mg/kg and
consequently it is supposed that the actual mercury mobilisation by extraction of coal in 2001 will be within the range 20-24 t/year. The coal consumption in Russia is growing and
accordingly the mercury mobilisation with coal will be increasing, the actual increase highly dependent on the coals that are mined.
Table 4.2 Average content of mercury in commercial coals from Kuznetsk Basin (based on Rugusol, 1996)
Coal field, deposit, enterprise |
Technological group (brand) of coal, coal brand |
Ash content Ad. % |
Humidity Wrt. % |
Hg. g/t of coal |
Kuznretskaya mine |
ã coking |
18.2 |
8.2 |
0.01 |
Novosergeevskiy OCC |
CC |
8.8 |
5.2 |
0.01 |
Cherkassovskaya mine |
K |
17.4 |
6.2 |
0.01 |
Sushtalepskaya mine |
T |
23.5 |
8.2 |
0.01 |
Tom-Usinskiy, Krasnogorskiy OCC |
T |
18.9 |
5.9 |
0.01 |
Kalinin mine |
K, KO, KC, CC |
22.1 |
5.3 |
0.02 |
Ziminka mine |
K, KO, KC |
15.1 |
6.7 |
0.02 |
Biryulinskaya mine |
K, KO |
32.2 |
7.4 |
0.03 |
Yuzhnaya mine |
CC |
14.5 |
7.2 |
0.03 |
Tyrganskaya mine |
CC |
10.4 |
6.5 |
0.03 |
Badayevskiy, Bolshevik mine |
ã coking |
13.1 |
7.1 |
0.03 |
Novokuznetskaya mine |
ã coking, ÃÆ |
14.9 |
7.1 |
0.03 |
Kolmogorovskiy OCC, Kolmogorovskiy unit 1 |
Ä, ã energy |
13 |
16.8 |
0.03 |
Zarechanaya mine |
ã energy |
13.1 |
11 |
0.03 |
Prokopyevsko-Kiselevskiy, Kiselevskoye, Krasnobrodskiy OCC |
T |
10.5 |
4.7 |
0.03 |
Kolmogorsovkiy 2 OCC |
Ä |
15.5 |
17.1 |
0.03 |
Arapichevskiy, Ordzhonikidze mine |
T |
27 |
6.5 |
0.03 |
Kondomskiy, Severny Kandysh mine |
T |
24.2 |
5.9 |
0.04 |
Vysokaya mine |
Æ |
32.5 |
5.9 |
0.04 |
Prokopyevsko-Kiselevskiy, Prokopyevskoye, Centralnaya mine |
T |
16.6 |
5.5 |
0.05 |
Prokopyevskiye OCC |
CC |
8.3 |
8.7 |
0.05 |
Zyryanovskaya mine |
ã coking, ãÆ |
23.5 |
7.6 |
0.05 |
Leninskiy, Signal mine |
ã energy |
13.9 |
1.4 |
0.05 |
Aparda mine |
K, KO, KC |
19.1 |
7 |
0.05 |
Tersinskiy, Badayevskiy OCC |
Äã, ã energy |
16.2 |
9.6 |
0.05 |
Belovskiy, Kolmogorskaya mine |
Äã, ã energy |
13.1 |
8.7 |
0.05 |
Berezovskaya mine |
K |
26.1 |
5.4 |
0.06 |
Dimitrov mine |
T |
21.2 |
6.7 |
0.06 |
Kemerovskiy, Volkov mine |
ãÆ |
26.5 |
7.5 |
0.08 |
Kedrovskiy OCC |
CC |
13.1 |
8.7 |
0.08 |
Anzherskiy, Sudzhenskaya mine |
TC |
18.1 |
2.3 |
0.08 |
M.m. Kolchuginskoye |
Ä |
17.8 |
8.6 |
0.08 |
OsinvskiyKapitalnaya mine |
Æ |
27.9 |
5.9 |
0.08 |
Mine named after 7th of November |
ã coking |
14.5 |
8.4 |
0.1 |
Shevyakov mine |
K, KO, KC, °C |
29.5 |
8.1 |
0.1 |
Raspadskaya mine |
ãÆ |
19.4 |
5.6 |
0.2 |
Olzherasskiy OCC |
CC |
22.5 |
6.4 |
0.3 |
Mrasskiy, Mezhdurechenskiy OCC |
K, KO, T |
18.4 |
4.2 |
0.5 |
Kaltansiy OCC |
T |
19.8 |
7.6 |
0.6 |
Tomusinkiy OCC |
°C |
17.8 |
5.1 |
0.6 |
Note: Kuznetsk basin is a large raw material facility for coke and chemical and fuel and energy industries; as regards balanced coal reserves it ranks first in the country; of especial
importance is coking coal; this coal makes about half of the total production in the basin; energy types of coal also include the following dominant brands Ä, CC, T, and, to some extent,
ã.
Table 4.3 Coal mining (in FR Ministry of Energy sector*) in 2001, million t (Performance Results of Coal Sector in Russia ..., 2002)
|
2001 |
Total |
266.32 |
Including: |
|
By the country economic districts |
|
Northern district |
19.07 |
Central district |
1.04 |
North Caucasian district |
9.46 |
Ural district |
5.09 |
West Siberian district |
127.96 |
East Siberian district |
75.69 |
Far East district |
28.01 |
By coal basins |
|
Kuznetsk |
127.44 |
Donetsk |
9.46 |
Pechora |
18.78 |
Kansko-Achinsk |
38.18 |
By methods of extraction |
|
Underground |
95.79 |
Open-cast |
170.53 |
Amount of coal extracted for coking |
62.33 |
Including in the coal basins |
|
Kuznetsk |
48.31 |
Donetsk |
0.39 |
Pechora |
8.81 |
Southern Yakutia |
4.82 |
* The remaining small part of coal is extracted by enterprises supervised by the RF Ministry of Natural Resources, local authorities, etc.
Table 4.4 Total mercury content of coal mined in
Russia by regions, 2001
Region, oblast |
Coal mining, million t * |
Mercury content in coal, average, mg/kg** |
Weight of mercury extracted from deposits with coal, tonnes |
Kaluga Oblast |
0.05 |
0.26 |
0.013 |
Tula Oblast |
1 |
0.26 |
0.26 |
Komi |
18.8 |
0.052 |
0.98 |
Murmansk Oblast |
0.3 |
0.05 |
0.015 |
Perm Oblast |
? |
0.44 |
? |
Rostov Oblast |
9.5 |
0.077 |
0.73 |
Bashkiria |
0.06 |
0.05 |
0.003 |
Sverdlovsk Oblast |
1.8 |
0.05 |
0.09 |
Chelyabinsk Oblast |
3.3 |
0.05 |
0.17 |
Buryatia |
3.9 |
0.0087 |
0.034 |
Tyva |
0.6 |
0.05 |
0.03 |
Khakasia |
6.8 |
0.05 |
0.34 |
Altai Krai |
0.01 |
0.05 |
0.0005 |
Krasnoyarsk Krai |
38.7 |
0.05 |
2 |
Irkutsk Oblast |
15.3 |
0.02 |
0.31 |
Kemerovo Oblast |
126 |
0.094 |
11.8 |
Novosibirsk Oblast |
0.5 |
0.05 |
0.25 |
Chita Oblast |
14.3 |
0.011 |
0.16 |
Sakha-Yakutia |
9.7 |
0.02 |
0.19 |
Primorskiy Krai |
9 |
0.11 |
0.99 |
Khabarovsk Krai |
2.3 |
0.4 |
0.92 |
Amur Oblast |
2.7 |
0.85 |
2.3 |
Sakhalin Oblast |
? |
0.11 |
? |
Russia, total |
~ 270 |
|
~ 22 |
* Source: Russian Statistical Annual Book. 2002: Statistical Book. - Moscow: State Committee of Statistics, Russia, 2002. - 690 p.
** Calculated on the basis of Rugusol, 1996 (Annex 3). Background data for each basin is shown in Annex 3. For fields where no data is available, the so-called average background
content of mercury in coal of the former USSR estimated at 0.05 mg/kg (By V.R. Kler et al. (1988) is used.
Pre-combustion processing of coal
A part of extracted coal is subjected to pre-processing, including operations of crushing (defragmentation), sorting, concentration, briquetting and drying (Kosinskiy et al., 1997).
Crushing of coal may be organised separately or as a preparatory operation for further concentration, briquetting, coking, etc. Sorting of coal is made to divide ordinary coal into classes,
containing lumps of specified size. Sorting is performed using sequential sifting of coal on screens, with the mesh sizes according to the size of commercial coal types. Sorting of coal is
also widely used for dividing concentration products into class by the size. Briquetting of coal is compulsory for small classes of commercial coal and concentrates that cannot be used in
their actual size. Briquetting is also required for long-distance transportation to exclude dusting and freezing of coal dust. Coal concentration is made using gravity processes (for large size
coal from 0.5 to 300 mm) and flotation (for concentration of small classes, <1 mm). Foam flotation is the most widely used method. Concentration products are: a concentrate containing
the highest purity coal; industrial products containing the highest quantity of coal aggregation with mineral formations; tailings (rocks) that are products with the highest content of inclusive
rocks (usually, tailings include a substantial part of pyrite contained in coals, i.e. the main carrier of mercury). By-products of the concentration process include: sifted part, i.e.
unconcentrated small-size coal; dust, i.e. coal particles smaller than 0.5-1 mm; slurry, i.e. dusty coal particles accumulated in washing and technological products. Depending on the ash
content, by-products are added to concentrate or industrial products. In the course of preliminary conditioning and concentration of coal, most frequently a notable reduction of mercury
content takes place, which is, to a substantial degree, caused by the forms of mercury present in coal and by technological specificities of their concentration process, during which pyrite
(the main mercury concentrator) is basically transferred to concentration waste (tailings).
Ya.E. Yudovich et al. (1985) having summarized the available data about the forms of mercury present in coal note that coal with background (normal) contents of this metal is dominated
by two forms: mercury bound with pyrite (Hgpyr) and mercury bound with organic matters (Hgorg). Hgorg, probably, include two forms of mercury: physically sorbed and in compounds
with organic matter like humus. In coal with higher content sulphur (with higher concentration of pyrite), the share of Hgorg in the mercury balance is more significant. Coal, abnormally
concentrated with mercury, also may include metallic mercury and cinnabar. Such forms of mercury present in coal predefine its distribution in coal concentration products: depletion of
commercial products and accumulation in tailings rich with pyrite (i.e. in waste). The above can be illustrated by data shown in Table 4.5, which indicate that concentrates (concentrated
coal) are characterized with a far lower concentrations of mercury as compared to ordinary coal. This fact should be taken into consideration when assessing mercury emissions
(especially, when using literature data about mercury content in coal).
Table 4.5 Average mercury content in commercial products of the Pechora coal basin (Yudovich, Zolotova, 1994)
Coal type | Hg, mg/kg of dry fuel | Field |
Coking | | |
Ordinary | 0.073 | Khalmeryuskoye, Vorkutskoye, Yunyaginskoye, Vorgashskoye |
Concentrate | 0.040 | Vorkutskoye and Vorgashskoye |
Sifted part | 0.039 | Vorkutskoye and Vorgashskoye |
Industrial product | 0.050 | Vorkutskoye |
Power-generating | | |
Ordinary | 0.08 | Vorkutskoye and Vorgashskoye |
Concentrate | 0.05 | Intinskoye |
Sifted part | 0.06 | Intinskoye |
It shall be understood that not all 270 mill. tonnes of coal extracted in 2001 were immediately combusted. In 2001, only 234 mill tonnes of coal were supplied to the consumer industries
but this includes also coal extracted during the preceding years and stored at mines and etc. It shall also benoted that pre-combustion treatment includes crushing (defragmentation),
sorting, concentration, briquetting and drying - meaning that some part of coal may only be crushed, another part may only be sorted and etc and etc. Unfortunateky no coresponding
statistics is available. From official statistics it is only known that in 2001 domestic concentration factories processed about 77.8 million tonnes of coal or more than 29% of the annual
production (Table 4.6). Besides, mechanized installations designed for selection of rocks processed 18.75 million tonnes of coal. Thus, the coal industry totally processed 96.55 million
tonnes of coal or over 36% of the total mined coal.
Table 4.6 Coal processing at concentration factories of Russia in 2000-2001 in million t (Performance Results of Coal Sector in Russia ..., 2002)
Indicator |
2001 |
Coal processing, total |
77.80 |
Including for coking |
52.63 |
Production of concentrate, total |
45.09 |
Including for coking |
35.54 |
Production of quality coal |
16.87 |
Including anthracite |
2.39 |
4.1.2 Releases of Mercury to the Environment and Wastes by Coal Mining
Mercury in waste
According to Table 4.6 about 77.8 million t coal was processed producing about 45 million t concentrate in 2002 in Russia. The remaining 32 million t was disposed of as waste from the
process. Assuming that the coal on average contained 0.08 mg mercury per kg and that half of the mercury content ended up in the waste, a total of 3.1 t mercury was disposed of with
waste of the concentartion process. Besides, some mercury may be disposed of with the rocks.
Discharge with waste water
The Russian coal industry annually discharges to surface water streams about 550-600 million m3 of wastewater (up to 75-80% of contaminated wastewater, of which, in turn, up to
80% are discharged without cleaning) and emit to atmosphere about 550 thousand tonnes of harmful substances (including up to 60-70 thousand tonnes of solids).
It is well known that extraction of coal is accompanied by generation of significant amounts of mining water that has extremely high concentrations of suspended substances (up to
2,000-4,000 mg/l), acid reaction (pH up to 2.5-4.0), increased mineralization varying within a broad range (from first hundreds to several thousands mg/l). For example, when coal was
extracted in Kuzbass in late 1990's, more than 100 million m3 polluted wastewater was discharged, containing up to 5-10 g/l of suspended matter, oil products, phenol, chlorides and
heavy metals (Zhdamirov, Kuznetsov, 1990). If we assume the average turbidity of discharged wastewater as 3,000 mg/l, then every year up to 1.5 million tonnes of solids will be
discharged with wastewater from coal mining enterprises in Russia. Let us assume that the average content of mercury in suspended particles in wastewater is 0.08 mg/kg, i.e.
correspondent to its level in coal. (This content is quite in line with the background content of mercury in natural river suspended matter. For example, the background (natural) content of
mercury in suspended matter in Moscow Oblast rivers makes 0.068 mg/kg (Yanin, 2003). The real content of mercury in suspended particles in wastewater discharged from coal mining
enterprises is presumably above this value). The simple calculations provide that the above amount of suspended matter discharged to water bodies will then contain about 120 kg of
mercury.
Let us assume that the content of mercury (in its dissolved forms) in wastewater from coal-mining enterprises makes 0.08 μg/l (the average content of this metal in the world's rivers
(Gordeyev. 1983)). It follows from the above that annually wastewater discharged to water bodies contains 48 kg of mercury.
Thus, the total supply of mercury together with wastewater discharged from coal mining facilities will be about 168 kg. It should be noted that this is a minimum estimate; the real emission
of mercury together with wastewater from coal-mining enterprises may be several fold higher.
Emission to the air
Mercury may be emitted to the atmosphere from the waste. According to data provided by S.V. Alistratov (1988), the average content of mercury in waste from Moscow region coal
basin varies from 0.24 to 1.3 mg/kg, reaching in some places the value of 3.3 mg/kg. Concentration of mercury in different waste banks may differ several times, depending on the waste
rock that constitute waste banks in different fields, on the time of their placement in waste banks and the intensity of hypergenic processing. The author of the quoted work noted that in
case of hypergenic changes in the waste bank ground, some part of mercury evaporates to atmosphere, which conditions the formation of its atmospheric and geochemical streams. Of
special importance is self-ignition of coal in mines, open casts, in natural fields and in waste piles, which can be accompanied by mercury release to atmosphere. When waste piles are
burning, temperature may be as high as 800-1000°C or more (in hidden cones), which results in destruction of sulphide and clay minerals and burnout of all organic matter. Mercury
contained in rocks is sublimed and evaporated to atmosphere. It cannot be ruled out that burning waste piles of coal concentration enterprises may be a significant source of mercury
vapour emission to atmosphere, since they have high contents of mercury in pyrite concentrates. According to calculations made by L.A. Dobryansky et al. (1992), out of the entire
amount of rocks fed to piles of the coal mines of Gorlovka (Donbass) in 1989, emission of mercury as a result of its degassing made 230 kg/year. Concentration of mercury in
atmosphere from waste piles was also confirmed by direct measurements. In particular, concentration of mercury vapours in the air at the waste pile of Gorlovka mines varied, in summer
of 1990, from 57 to 13,700 ng/m3; these measurements were made when the metallurgical shop of the Nikitovsky Mercury Enterprise was shut down, i.e., it could not exert any impact
on the measurements.
The available data indicates that the emission to air from the waste may be significant, but the information is considered to scarce for making an estimate of the emission of mercury from
the coal waste. Special investigations are needed.
4.1.3 Use of Coal for Power and Heat Production
In Russia in 2001 coal accounted for 34.1% of the energy input for combined heat-and-power plants and 45% of the input for municipal boiler houses.
Heat energy is supplied in Russia as follows (Reutov et al., 2002):
- 485 combined heat-and-power plants (CHP);
- about 6,500 boiler houses with the output over 20 Gcal/h (mainly municipal boiler houses);
- over 180,000 small boiler houses (mainly municipal boiler houses);
- about 600,000 autonomous individual heat generators.
According to the statistics from the International Energy Agency (EIA 2003) 127 million t was used for combined heat plants, 34 million t for heat plants (boiler houses) whereas
coal was not used for electricity plants without heat production.
Behaviour and emission of mercury during coal burning
At the high combustion temperatures mercury contained in coal is practically entirely transferred to the gaseous state and, finally, emitted to atmosphere with flue gas or adhered to
particles captured by the emission treatment systems.
Due to a high volatility of mercury, most existing emission treatment systems are not very efficient in retaining mercury. At present almost no reference data on the efficiency of the
different equipment of Russian power plants in retaining mercury exists.
Recently, there has been extensive testing of the mercury removable capabilities of various emission treatment systems on a wide range of coal-fired utility boilers in the USA (US
EPA 2002). The average results on mercury capture efficiency ranged from a capability of removing 0 to 96 percent dependent on a variety of factors as described in detail below
(see Table 4.7). In general the following have been stated:
- A specific technology, or combination of technologies, produced a range of mercury reduction for any coal type;
- The type of coal strongly affected the mercury control achieved, with average percent removal increasing as coal "rank" increased from lignite through subbituminous to bituminous.
Within any given rank of coal, a range of mercury removal was achieved. Note also that world coals represent a wider range of coal rank (e.g. brown coal) and characteristics (e.g.
sulfur, ash) than US coals.
Cyclones only are not included in the study, but the mercury capture efficiency must be expected to be lower that the result obtained with ESPs.
Table 4.7 Average mercury capture in % of mercury input to reduction device (based on US EPA 2002).
Post-combustion Control Strategy |
Post-combustion Emission Control Device Configuration
|
Average Mercury Capture by Control Configuration (no. of tests
in study in brackets) |
Coal Burned in Pulverized-coal-fired Boiler Unit |
Bituminous Coal |
Sub-bituminous Coal |
Lignite |
PM Control Only |
CS-ESP |
36 % (7) |
3 % (5) |
- 4 % (1) |
HS-ESP |
9 % (4) |
6 % (4) |
Not tested |
FF |
90 % (4) |
72 % (2) |
Not tested |
PS |
Not tested |
9 % (1) |
Not tested |
PM Control and Spray Dryer Adsorber |
SDA+ESP |
Not tested |
35 % (3) |
Not tested |
SDA+FF |
98 % (3) |
24 % (3) |
0 % (2) |
SDA+FF+SCR |
98 % (1?) |
Not tested |
Not tested |
PM Control and Wet FGD System (a) |
PS+FGD |
12 % (1) |
-8 % (4) |
33 % (1) |
CS-ESP+FGD |
74 % (1) |
29 % (3) |
44 % (2) |
HS-ESP+FGD |
50 % (1) |
29 % (5) |
Not tested |
FF+FGD |
98 % (2) |
Not tested |
Not tested |
(a) Estimated capture across both control devices;
SCR - Selective catalytic reduction; CS-ESP - Cold-side electrostatic precipitator;
HS-ESP - Hot-side electrostatic precipitator; FF - Fabric filter; PS - Particle scrubber;
SDA - Spray dryer adsorber system; FGD – Flue gas desulfurization.
The furnishes of Russian heat-and-power generating facilities devices can be divided into fuel-bed and chamber furnaces. In fuel-bed furnaces, the bulk of solid fuel is burned in the
fuel bed; in the chamber furnaces it is burned in the suspended condition. Chamber furnaces are divided into flare and vortex (cyclone) furnaces. In turn, flare furnaces used for
burning solid fuel – depending on removal of slag and ash – may be with dry (solid) slag removal and liquid slag removal. In Russia, the most widely spread are furnaces with solid
slag removal, wherein some part of ash (up to 10-15%) is removed to a slag hopper, while the rest is carried with flue gas to the boiler flue ducts. In furnaces with liquid slag
removal (single or two chambers) the share of fly ash is smaller than in furnaces with solid slag removal, though remaining rather significant. In single-chamber furnaces, it makes, on
the average, 30-40% while in two-chamber furnaces it is 50-60%.
At large (powerful) power generation plants (over 300 MW), they usually use chamber furnaces with solid slag removal, or, more rarely, open and semi-open furnaces with liquid
slag removal. In middle-rate power plants (50-300 MW), in addition to the above, they may also use cyclone furnaces. At smaller power plants and in boiler houses (less than 50
MW), cyclone furnaces are mostly used.
The Russian energy generation facilities make use of the following types of ash collectors: dry inertia ash collectors, wet ash collectors, electrical filters and combined ash collectors.
Cyclones and cyclone units are used to clean combustion products in low-capacity steam generators; battery-type cyclones provide a better removal of collected fly ash and a high
efficiency (82-90%). They are installed in boilers with the capacity from 25 to 320 t/h (tonne furnace steam per hour). In wet ash collectors, fly ash is collected by precipitating the
fly ash on the liquid film inside the device. For steam generators of low and middle capacity (90-100 t/h) they use centrifugal scrubbers which are vertical straight-through cyclones
whose interior system is continuously irrigated with water. For steam generators rated 120-150 t/h, the main type of wet ash collectors is an ash collector having a turbulent
coagulators located inside. They also use (usually for middle capacity boilers) vertical and horizontal dry and wet electrical filters. In mid 1990's, the average ash collection factor
for the Russian energy industry was estimated at 0.91. For Moscow CHPP this factor was 0.89; in communal sector and industry it was only 0.70 (Kakareka et al. 1998). Boilers
of low steam output capacity (< 50 MW), usually used in communal sector, agricultural and small industrial enterprises, are often not equipped with dust collecting devices.
In addition some power plants are equipped with SO2 controls including a variety of wet and dry scrubbers and NOx may be controlled by selective catalytic or selective
non-catalytic reduction.
The efficiency of the flue gas treatment controls of large Russian power plants for control of mercury emission is under evaluation.
Considering all stated above, as well as technological features of Russian heat and power generating facilities the relative mercury emissions (as part of its total quantity fed with
coal for combustion and/or processing) to the atmosphere is roughly estimated in the following way:
- use of coal for generation of electricity Munthe et al. (2004)
- plants equipped with cyclones – 95%
- plants equippend with ESP – 75%;
- plants equipped with wet scrubber – 75%;
- plants equipped with a combination of two of the mentioned air pollution controls – 60%
- use of coal for communal and housing needs – 95%;
- use of coal by population and the agro-industrial complex – 99%;
- use of coal by other users – 90%.
The remaining mercury is bound with ash and slag waste and ash collected by the cleaning installations.
The mobilisation and releases of mercury by use of coal for power and heat production in Russia in 2001 is summarised in Table 4.8 (emissions of mercury during coke production
are considered in a special section).
Large coal-fired power plants are among the major point sources of mercury emission. The emissions from the 129 largest plants of Russia have recently been evaluated (Munthe
et al. 2004). The location of the plants and the estimated mercury emission is shown on the maps below (see figure 4.2). Estimated emission from the utility plants is included in
Annex 4. As part of the study mercury emissions by major Russian power plants and the mercury content in coal from different coal fields in Russia has been reviewed (Munthe et
al., 2004). Averages for fields for which data have been identified are shown in Table 4.9. For other coal-fields a default value of 0.1 mg/kg is been applied in the study. Based on
coal amount of 74.4 Mtce (million t coal equivalent) and a breakdown of the coal types used at the 129 major coal-fired utility plants multiplied by the specific mercury content of
the coal, the total mercury content of the 74.4 Mtce coal used in the plants is estimated at 9.0 t/year as an average. Using maximum values for the mercury content, the total content
is estimated at 11 t. The average value corresponds to an average mercury concentration of the coal of 0.12 mg/kgce.
Table 4.8 The mobilisation and releases of mercury by use of coal for heat and power production in Russia in 2001
Activity |
Coal consumption
million tonnes |
Mercury content in used coal Tonnes (best estimate) |
Emission to atmosphere |
Transferred to waste
tonnes
best estimate |
Distribution factor, % * |
tonnes
best estimate |
Electricity generating sector |
124.3 |
9.9 |
80 |
8.0 |
2.0 |
Municipal use (boiler houses) |
7.6 |
0.6 |
95 |
0.6 |
0.03 |
Domestic heating and agro-industrial complex |
18.5 |
1.5 |
99 |
1.5 |
0.01 |
Other uses (mainly industry) |
42.2 ** |
3.4 |
90 |
3.1 |
0.3 |
Total, power and heat production |
|
15.4 (13.5-17.3) |
|
13.2 |
2.2 |
* The average share of the mercury fed with coal emitted to the atmosphere
** According to EIA (2003) 1.4 million t was used for non-energy applications.
Table 4.9 Average mercury content of coal used in Russian power plants ( Munthe et al. 2004)*
Coal field |
Average Hg content
mg/kg |
Irsha-Borodinsky |
0 |
Bashkirsky |
0.003 |
Gusinoozersky |
0.02 |
Kharanorsky |
0.02 |
Ekibastuzsky (Kazakhstan) |
0.02 |
Beryozovsky |
0.04 |
Karagandinsky (Kazakhstan) |
0.05 |
Vorkutinsky |
0.05 |
Intinsky |
0.05 |
Donetsky |
0.094 |
Kuznetsky |
0.11 |
Sakhalinsky |
0.11 |
Azeysky |
0.17 |
Cheremkhovsky |
0.17 |
Magadansky |
0.18 |
Podmoskovny |
0.2 |
Raychikhinsky |
0.4 |
Kizelovsky |
0.446 |
Ogodzhinsky |
0.9 |
* Only fields for which data are available are included in the table. For other fields a default figure of 0.1 mg/kg have been used.
Click here to see the figure.
Figure 4.2. Location and mercury emission of coal-fired utility plants in the Russian Federation (Munthe et al. 2004)
4.1.4 Production of Coke
In total 29,997 t coke was produced in Russia in 2001. The production of coke by enterprises is shown in Table 4.11. By the beginning of 2002, the Russian coke production
sector included 12 by-product coke enterprises, which had 62 operating coke-oven batteries (3,851 ovens) with the total rated output of 39,066 thousand tonnes of coke (6%
humidity) a year (In Russian By-product Coke ..., 2002). Of them, 59 batteries with the capacity of 36.9 million tonnes were permanently used (3 batteries were out of use). A
significant part of equipment used by by-product coke enterprises is outdated (in 2000, the average age of coke-oven batteries was 22 years). As a rule, practically all coke-oven
batteries are insufficiently equipped with efficacious dust and gas cleaning devices.
Modern by-product coke enterprises represent a production unit that produces not only coke, but also other materials. For example, the by-product coke enterprise Nosta OJSC
includes a coal-conditioning shop, two coke shops, a shop for production of ammonium sulphate (used in agriculture as fertiliser), coal tar (processed to obtain commodity
products) and raw coal benzene (for manufacture of benzene organic hydrocarbons), a biochemical installation for treatment of wastewater from facilities producing phenol,
rodanide and planide. By-product coke enterprises remain the main suppliers of raw materials for production of plastics, chemical fibres, paints and other synthetic materials. The
share of by-product coke enterprise products in the raw materials used by industries for base organic synthesis is up to 50%, and that of such important products as benzene is up
to 80%, of naphthalene and creosol almost 100%. The non-ferrous metallurgy is the user of low-ash caked coke and binders produced from coal tar. Coke is used for preparation
of anode mixtures used for making of aluminium. Hydrogen from coke gas and nitrogen from oxygen stations of metallurgical enterprises are used to produce nitric fertilizers.
Chemical coking products are also used for production of chemicals for protection of plants and animals.
Processes and technologies
Coke production includes the following stages: processing and storage of coal, loading of coal to coke ovens, quenching of coke, and cleaning of coke gas. Coke is produced by
dry distillation of coals in coke ovens collected in coke-oven batteries (40-70 ovens each). A coke oven represents a chamber with the width of 0.4-0.45 metres, length of 15
metres and height about 5 meters. The useful volume of the chamber is 30 m3, while the weight of fed blend is 22 tonnes. Coal blend, which frequently is a mixture of coal from
different blends, is fragmented in the disintegrator before caking, and then is loaded into coke ovens where it is heated to 1000°C (without air) and is kept for 15-16 hours. During
heating coal loses about 30% of its weight due to generation of gases and resin. Useful products of this process include coke and gas of an average calorific value. The capacity of
a modern battery reaches 1,500 t/day. The blend is fed to the ovens from the top. After the coking process is over, a special device pushes the coke (the cake) out of the oven to
the quenching car and then it is fed to the quenching tower. Here, coke is cooled with water (wet quenching) or inert gas (dry quenching).
Raw materials
The raw materials used for production of coke include special brands of coal. For coking processes, usually they use a mixture of coals in a predetermined ratio. Basically, they use
coking coal, steam fatty coal, steam caking coal and gas coal. One ton of a dry blend gives 750-800 kg of coke and 320-330 m3 of coke gas. The main source of raw materials
for the Russian coking enterprises is the Kuznetsk coal basin (85% of raw materials). For example, only in Kemerovo Oblast they extract up to 70% of all Russian coking coal,
while as regards specially valuable coking coal they produce here 100%. The average content of mercury in coal from the Kuznetsk basin, calculated according to data (Annex 3),
is 0.08 g/t. In coking coal from the Pechora basin the mercury content varies from 0.01 to 0.1 g/t (0.05 g/t on the average). Certain enterprises in Siberia sometime use coking coal
from the Karaganda coal basin. The content of mercury in the commercial concentrate is usually lower than in regular types of coal.
Sources and characteristics of dust and gas emission
The main sources of dust and gas emission are processing and storage of coal, coking of coal and its quenching. Coke dust is generated when coke is fed from oven chambers,
transported, sifted, fragmented and shipped; when dry quenching plants are used, such dust is generated from fore-chambers and smoke pipe bleeders. Ash can be released from
flue pipes; such ash is generated in heating systems of coke-oven batteries when they are not tight resulting in raw coke present inside heating channels (Pyrikov et al., 2000).
Unorganized release occurs when the coal blend is fed to oven chambers, or when coke is dispensed and quenched. Organized release occurs from exhaust pipes of the aspiration
systems at transport facilities, fragmentation, separation, and drying of blend, as well as during re-loading and sifting of coke. Maximum releases of dust occur during dry quenching
of coke, loading of coke to hoppers and from final combustion bleeders, as well as during unloading of hot coke into cars. Release during the process of caking occur due to
leakage through the doors of the oven chamber, hole lids, etc/ during coking the bulk amount of volatiles is generated. The content of dust in inert gas after the quenching hopper is
4-10 g/m3 (Stark, 1990). When coke is removed from the ovens and as a result of leaking doors, up to 35% of coking release occur on the coke side of the battery (Bondarenko
et al., 2002).
Dust and gas removal
Cleaning process is mandatory for coke gas if, during processing, vapours, resin and water are condensed, and ammonia and benzene hydrocarbons are trapped. Aspiration
systems of the coal-conditioning and coking shops, as a rule, are equipped with cyclones and wet dust traps, whose efficiency makes 96-98%. The most efficient method to reduce
release during the feeding of the blend is smoke-free loading: generated dust and gas are sucked by a steam or hydraulic injector to a feeder by which dust and gas are fed for
cleaning. When dry quenching is used, dust is first entrapped in the inertia dust trap, and then in the cyclone. When coke is unloaded, as a rule, the dust is not trapped.
On the average, when coke is produced, the content of coke and coal dust varies from 0.055 to 3.2 kg per tonne of products (Materials on Specific ..., 1987; Methodological
Instructions for determination ..., 1987). The specific release of coke dust proper varies from 0.05 to 2.5 kg/t of coke. Some time ago, the USSR Ministry of Ferrous Metallurgy
developed the average sectoral indicators for specific release of dust from by-product coke enterprises; they made 2 kg/t of coke (characterization of Specific ..., 1989). For
comparison, the coke enterprise of Western Europe have dust release from quenching process that does not exceed 10 g/t of coke, while the residual content of dust per enterprise
makes 5 g/t of coke (Kovalev et al., 2001).
Inventory of releases at a number of coke enterprises of Russia has demonstrated that dust releases from organized sources make 30% of the total release, while at enterprises
using dry quenching it is up to 70% (Pyrikov et al., 2000). Gas cleaning and aspiration systems usually use centrifugal inertia dust trapping devices, i.e. cylindrical and cone cyclones
(the degree of cleaning is 93-98%). Wet dust traps are used very often; they are applied to remove dust from aspiration air and coal-drying gases (which results in the problem
related to processing and disposal of slurry water). As regards wet dust traps, the most regularly used are centrifugal scrubbers with sprinkled rod lattice in the inlet pipe and
regular brands. The degree of removal of coal dust in centrifugal scrubbers varies from 85 to 98% (90% on the average); this rate for coke dust removal is 30-97% (90% on the
average). Also used are cyclones with a water film (the degree of coal dust removal 89-97%, of coke dust 88-90%), speedy scrubbers or straight-through wet cyclones (the
degree of coal dust removal 80-98%, of coke dust 85-95%). The scatter of indicators is due to different levels of maintenance of equipment at enterprises. At some domestic
enterprises they use gas scrubbers with Venturi pipes.
An the whole, the efficiency of dust and gas removal installations at coke production enterprises in CIS countries is estimated at about 90% (Emissions of Heavy Metals..., 1998).
Mercury in by-product coke production
Some years ago Ukrainian specialists studied distribution of mercury in coking products (Karasik, Dvornikov, 1968). Ordinary coal brought up to the surface from mines and
quarries is concentrated so as to remove rocks, eliminate high ash differences and pyrite concretions (usually, with a high mercury content). During concentration mercury is
distributed as follows (Figure 4.3): its bulk is converted to concentrate (up to 58-62%) and to waste, i.e. discarded rock and tailing (up to 24-26%). It is noteworthy that
according to data (Yudovich, Zolotova, 1994), the commercial products from the Pechora basin (Vorkuta and Vorgash deposits), the average mercury content was: in ordinary
coal – 0.073 g/t, in concentrated coal – 0.04 g/t, in sifted coal – 0.039 g/t, and in industrial products – 0.05 g/t. such (in this case specific) distribution of mercury, in fact, is
correlated with the above data (its content in concentrate is about 55% of its content in ordinary coal, and about 68% in industrial products).
As has bee stated, temperature in coking ovens is 1000°C or more, which results in practically complete transfer of mercury from the blend to direct coke gas, and then to different
products of solid, liquid or gaseous phases of by-product coking process (Karasik, Dvornikov, 1968). Mercury is accumulated in condensation products, generated during cooling
of raw coke gas, in particular in coal tar. Further, during distillation of resin it is deposited in the separator and the collector of light oil. As regards the sulphate compartment,
mercury was not found in ammonium sulphate; in the scrubber compartment, mercury was not found in the return gas, but it was present, in significant quantities, in the saturated
solutions from sulphur cleaning, in raw benzene, and in polymers; mercury also was found, in significant quantities, in a range of rectification products like heavy benzene, xylene,
toluene and in pure benzene. It was also present in some products and waste of resin distillation process (e.g. in naphthalene oil, anthracene fraction, and in pitch).
Figure 4.3 Mercury flow by coke production (according to data (Karasik, Dvornikov, 1968), with supplements and details).
Assuming the average content of mercury in the blend at 0.076 g/t, one million tonnes of blends will contain 76 kg of mercury. It is known that 1 ton of dry blend produced up to
800 kg of coke (i.e. one million tonnes of blends will give up 850 thousand tonnes of coke). During by-product coking process the above quantity of mercury is distributed
approximately as follows (see Table 4.10).
Table 4.10 Approximate distribution of mercury during coking process
|
% |
kg Hg/106 t blend |
g of Hg/t of coke |
Mercury amount in 2001, t |
To atmosphere during blending |
~ 5 |
3.8 |
0.0047 |
0.14 |
To slurry |
~ 2.5 |
1.9 |
0.0023 |
0.07 |
To industrial products |
~ 3.5 |
2.7 |
0.0033 |
0.10 |
To tailing |
~ 2.5 |
1.9 |
0.0023 |
0.07 |
To rock |
~ 22.5 |
17.1 |
0.0213 |
0.64 |
To atmosphere during coking |
~ 40.5 |
30.8 |
0.0385 |
1.15 |
To coke |
~ 0.5 |
0.4 |
0.0004 |
0.01 |
To water above resin |
~ 2.5 |
2.7 |
0.0033 |
0.10 |
To finished chemical products |
~ 17 |
12.9 |
0.0161 |
0.48 |
Total |
100 |
74 |
0.0922 |
2.8 |
In total 2.8 t mercury were in 2001 mobilised with coal for coke production. The specific mercury release to atmosphere will be, in general, at 0.043 g/t of produced coke,
including 0.0385 g/t during the coking process and 0.047 during blending. Thus, even at rather low mercury contents in coals, Russian coking producing enterprises receive a
notable quantity of this metal. Its substantial amount, 1.3 tonnes in 2001, is emitted to atmosphere, basically with flue gases of the coking process (Table 4.11). About 0.8 t ended
up in waste products, about 0.6 t followed the products, and 0.1 t was released with waste water.
Table 4.11 Mercury emission to atmosphere in Russia from coke production, 2001
Enterprise |
Location |
Production *1,000 t Coke |
Mercury emission t Hg |
OJSC "Altai-Koks" |
Zarinsk, Altai Krai |
3,176 ** |
0.137 |
OJSC "Koks" |
Kemerovo |
1,706 |
0.073 |
Moscow Coke-Oven Gas Plant |
Vidnoe, Moscow Oblast |
200*** |
0.009 |
OJSC «"Gubakhinsky Koks" |
Gubakha, Perm Oblast |
146 |
0.006 |
By-product coke enterprise OJSC "Zapadno-Sibirsky MK"
(metallurgical Combined Enterprise) |
Novokuznetsk, Kemerovo Oblast |
3,886 |
0.167 |
By-product coke enterprise OJSC «"Kuznetsk MK" |
Novokuznetsk, Kemerovo Oblast |
1,192 |
0.051 |
By-product coke enterprise OJSC "Magnitogorsk MK" |
Magnitogorsk, Chelyabinsk Oblast |
4,918 |
0.212 |
By-product coke enterprise OJSC "Nizhny Tagil MK" |
Nizhny Tagil, Sverdlovsk Oblast |
2,893 |
0.124 |
By-product coke enterprise OJSC «"Novolipetsk MK" |
Lipetsk |
4,349 |
0.187 |
By-product coke enterprise OJSC "Nosta"
(Orsko-Khalilovsky MK)
|
Novotroitsk, Orenburg Oblast |
1,311 |
0.056 |
By-product coke enterprise OJSC «"Mechel"
(Chelyabinsk MK)
|
Chelyabinsk |
2,257 |
0.097 |
By-product coke enterprise OJSC "Severostal" (Cherepovets
MK) |
Cherepovets, Vologda Oblast |
4,021 |
0.173 |
Total for Russia (rounded) |
30,000 |
1.3 |
* Source: (Annual Report of the "MMK" enterprise...;
"Metallurgist", 2002, No. 1; Novolipetsk Metallurgical Combined Enterprise.
Annual Report ...; Ferrous Metallurgy Urfo ...; http://metal.interfax.ru/test_metal....;
http://www.ako.ru/PRESS...; http://www.infogeo.ru;)
** In 2002.
*** Estimated by the authors.
4.1.5 Summary
The mobilisation and releases of mercury by use of coal in Russian in 2001 is summarised in Table 4.12. The total mercury mobilised in extracted coal amount to 22 t (20-24 t).
The total releases to the atmosphere and to coal extraction and consumption waste products are estimated at 19.8 t. Besides, some 0.5 t ends up in chemical products from coke
production. A part of mercury goes with coke and co-products and is among others included in the estimate for releases from ferrous metallurgy.
Table 4.12 Mobilisation of mercury by use of coal in the Russian Federation in 2001
Activity |
Coal extraction or consumption
million tonnes |
Mobilisation of Hg
Best estimate tonnes |
Emission to atmosphere |
Transferred to waste
tonnes
best estimate *** |
Distribution factor % * |
tonnes
best estimate |
Coal extraction and processing |
270 |
22 |
n.a. |
n.a. |
3.1 |
Power and heat production |
|
|
|
|
|
Electricity generating sector |
124.3 |
9.9 |
80 |
8.0 |
2.0 |
Municipal use (boiler houses) |
17.6 |
1.4 |
95 |
1.3 |
0.1 |
Residential heating and agro industrial complex |
8.5 |
0.7 |
99 |
0.7 |
0.0 |
Other uses (mainly industry) |
42.2* |
3.4 |
90 |
3.0 |
0.3 |
Coke production |
41.7 |
2.8 |
46** |
1.3 |
0.1* |
Total releases |
|
|
|
14.3 |
5.6 |
n.a. : not assessed
* Some of the mercury ending up in waste from the concentration of the coal is included in the estimate for "Coal extraction and processing"
** calculated on the basis of the unprocessed coal. By the processing of the concentrated coal 66% of the mercury content of the concentrate is estimated to be emitted to the air.
*** Do not include waste rock.
4.2 Oil, Natural Gas, Oil Shale and Biofuel
4.2.1 Introduction
Mercury content of crude oil and raw gas vary considerably. In order to obtain an accurate estimate of the total mobilisation of mercury by use of oil and gas in Russian it is
consequently necessary to obtain a large number of measurements of samples from the main oil and gas fields. Besides the mercury content of crude oils processed at the different
oil refineries may be very varying.
As background for the estimates of mercury mobilisation by use of oil and gas the following introduction discuss the distribution of mercury in oil and gas from a geological view.
The range of variations of the mercury content in raw gas and oil are rather considerable ( Table 4.13.)
Table 4.13 Range of mercury content in oil and gas fields in the world
Component |
Mercury concentration |
Oil | 0.003 – 21 mg/kg |
Condensate | <0.037 – 1.1 mg/kg |
Gas | 0.01•10-6 – 14,000•10-6 g/m3 |
This variation is caused by geological factors – the main reason is location of mercury-containing deposits in areas of mantle regional faults, wherefrom mercury as part of fluids
(mercury degassing of the Earth) is coming into areas of gas, oil and ore formation and takes part in these processes. One of such areas is the Karpinsky lineament (see figure 4.4),
extending from southeast to northwest, from Amu-Darya depression to North-German depression of the Middle European platform (Ozerova, Pikovsky 1985; Ozerova 1986;
Ozerova et al. 1989). This structure is related to known gas and gas-oil fields in Netherlands, Germany and Poland with a high content of mercury; within this structure the
mercury-containing deposits have also been found on the territory of the former USSR, however with smaller mercury concentrations. The Karpinsky lineament includes not only
deposits with high mercury concentrations, but also with rather low concentrations. This can be explained in terms of geology. What is important is the fact that identifying increased
contents of mercury in any oil-gas province field, the findings cannot be adapted for other deposits in the same province.
One more example of such structures similar to Karpinsky lineament is Pannonion-Volinian lineament (see Figure 4.5), controlling the disposition of mercury-bearing oil-gas, gas
and ore deposits on the territory of the Eastern Europe, including Ukraine (Pre-Carpathians depression). (Ozerova 1996; Ozerova et al. 1999).
Click here to see the figure.
Figure 4.4 Location of mercury-bearing gas and oil-gas deposits within Karpinsky lineament
Figure 4.5 Pannonion-Volinian lineament
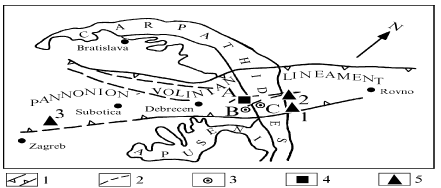
Another geological circumstance is that it has been established that the content of mercury vary in gas and gas-oil fields both within the province and in individual fields. This is
demonstrated in Table 4.14 and Table 4.15 (Ozerova 2002; Ozerova, Mashianov 1989; Ozerova, Dobryansky 2001). For us important is the latter fact which suggests that
mercury contents should not be assessed in the deposits by single mercury determinations, but rather must take into account from which level and in which proportions the samples
are taken from various depths.
Table 4.14. Content of mercury in gases from Mirnenskoye deposit Northern Caucasus (Karpinsky lineament)
Age of gas-bearing strata |
Difference in depth, m |
Number of samples |
Content of mercury,
10-6 g/m3
|
Palaeogene (Pg mkp3) |
2000 |
13 |
0.05 – 0.3 |
Chalky (K1) |
|
40 |
0.2 – 40 |
The third circumstance is that in the recent year at Mirnenskoye deposit (Russia) and Oposhnyanskoye deposit (Ukraine) a definite periodicity has been found (from several hours
to several days) in the change of the mercury concentrations in gases, related to the periods of movements of the Earth's proper rotation (Ryzhov, 2000; Ryzhov et al., 2003). The
interval of variations in the inspection wells changed from 10 to 80% of the average content of mercury in gases. And we do not know whether these are limit values or they may be
higher. Accordingly, this can have impact on the quality of testing.
Table 4.15 Content of mercury in gases from the Dnepr-Donetsk depression (Karpinsky lineament)
Nos. of wells |
Perforation interval, m |
Number of samples |
Mercury content,
10-6 g/m3 |
Oposhnyanskoye deposit |
23 |
2,952-2,990 |
8 |
0.2 – 2.1
average – 0.89 |
121 |
4,001-4,325 |
70 |
3.3 – 11,000
average – 67 |
111 |
average – 870 |
Yablunovskoye deposit |
11 |
3,744-3,801 |
6 |
0.11 –0.4
average – 0.26 |
61 |
4,680-4,978 |
8 |
0.61 – 2
average – 1.2 |
Long-term variations of the content of mercury in natural gases are of a higher importance. In particluar it has been detected taht concentrations of mercury may be different in
different years in the same wells – 15-20 times. And there are no clear reasons for that.
Analytical aspects are not less important. For instance, formerly used turbocolometric chemical methods of Hg microconcentrations detection (Saukov and co-authors, 1972 and
methods of direct differential atomic-absorption analysis of mercury in a flow of gas (Ganeev et. Al., 1995, Ganeev, Slyadnev, 1996) determine only the atomic mercury, while the
share of organic mercury and other mercury compounds was not known. Experiments using pyrolysis (temperature in the reactor was kept at the level of 750-800 °C) and
photolysis (temperature in the reactor was stabilised at about 50-60 °C) demonstrated (Table 4.16) that organic mercury when the compounds are decomposed by photolysis and
pyrolysis account for 30% of the total content (Ganeev, Maidurov et. al., 1996, Ozerova et al., 1999). These preliminary two experiments indicates that the actual content of
mercury in the gas is higher than previously measured, but the research should be continued.
Table 4.16 Content of atomic (HgO) and organic (HgR) mercury forms in natural gas
Gas fields |
HgO, 10-6 g/m3 |
HgR, 10-6 g/m3 |
|
|
Photolysis |
Pyrolysis |
Mirnenskoye (Northern Caucasus) |
19.1±0.3 |
5.8±1.5 |
|
Oposhnya (Dnepr-Donetsk depression) |
52.5±0.3 |
2.1±0.8 |
2.3±0.8 |
4.2.2 Mercury in Oil and Gas Raw Materials
Crude oil
Data on the content of mercury in oils in Russia are very scarce (Table 4.17). They do not include data about mercury concentration in oil of the main Russian oil fields. By today
forty-two sites have been investigated in more or less details ; the data on the content vary from 3•10-3 to 6.9 mg/kg. The average content is 0.30 mg/kg. For the samples from
Russian fields the average mercury content is estimated as 0.18 mg/kg. It should be noted that the oil samples from Russia are mostly from the southern part and includes fields with
known relatively high concentrations of mercury. However, it cannot be concluded that the measured average most probably will be higher than the actual average. In order to
obtain a more accurate estimate oil samples from the main Russian oil fields should be analysed.
Table 4.17 Content of mercury in crude oil from CIS countries
CIS countries |
Regions |
Field,
oil |
Mercury content.
mg/kg |
Number of samples |
Source |
Russia |
Prioralve |
Stepnoozerskoye |
0.032 |
1 |
(Saukov et al 1972) |
Ulyanovskaya area |
0.072 |
1 |
(Saukov et al 1972) |
Irkutsk Oblast |
Markovskoye |
0.32-0.36 |
4 |
(Foursov, 1977) |
Sakhalin |
Okhinskoye |
0.008 |
1 |
(Saukov et al 1972) |
|
0.4-0.46 |
2 |
(Foursov, 1977) |
Lysaya Sopka |
0.032 |
1 |
(Saukov et al 1972) |
Mukhto |
< 0.008 |
1 |
(Saukov et al 1972) |
Kovtovskaya area |
0.42 |
1 |
(Saukov et al 1972) |
Northern Caucasus |
Dysh |
0.14 |
1 |
(Saukov et al 1972) |
Datykh |
0.3-0.36 |
4 |
(Foursov, 1977) |
Russia-Ukraine |
Kerch-Taman |
|
0.27-0.51 |
20 |
(Foursov, 1977) |
Ukraine |
Dnepr-Donetsk depression |
Glinsko-Razbyshevskoye |
0.032-0.27 |
4 |
(Saukov et al 1972) |
|
0.35-0.41 |
2 |
(Foursov, 1977) |
Front Carpathian region |
Bytkovskoye |
1 |
1 |
(Saukov et al 1972) |
Gneditsy |
1.05-1.15 |
4 |
(Foursov, 1977) |
Kibinitsy |
0.24-0.3 |
5 |
(Foursov, 1977) |
Zachepilovka |
0.32-0.42 |
6 |
(Foursov, 1977) |
Belskoye |
0.33-0.41 |
2 |
(Foursov, 1977) |
Belarus |
|
Rechitskoye |
0.19 |
1 |
(Saukov et al 1972) |
Baltic region |
|
Krasnoborskoye |
0.34-0.48 |
3 |
(Foursov, 1977) |
Georgia |
South Ossetia Apsheron |
Lesevi |
0.19 |
1 |
(Saukov et al 1972) |
Gedeleti |
0.29 |
1 |
(Saukov et al 1972) |
Azerbaijan |
Baku |
0.11-0.15 |
2 |
(Saukov et al 1972) |
Kazakhstan |
|
Uzen |
0.34-0.44 |
8 |
(Foursov, 1977) |
|
0.003-0.05 |
6 |
* |
Kazakhstan |
|
Zhetybay |
0.023-0.09 |
2 |
* |
Zhetybay (collector) |
0.23-0.48 |
3 |
* |
Pridorozhnaya (well) |
1.6 |
1 |
* |
Burmasha |
0.007 |
1 |
* |
Asar |
0.019-0.096 |
2 |
* |
Karazhe |
0.115-0.85 |
2 |
* |
Akkar |
0.041 |
1 |
* |
Alatobe |
0.029-6.90 |
2 |
* |
Alatobe (collector) |
0.014-0.081 |
2 |
* |
Uzbekistan |
Fergana valley |
Mailisu |
0.19 |
1 |
(Saukov et al 1972) |
Northern Sokh |
0.11 |
1 |
(Saukov et al 1972) |
Chongara |
0.43 |
1 |
(Saukov et al 1972) |
Northern Ristan |
< 0.008 |
1 |
(Saukov et al 1972) |
Palvantash |
0.19 |
1 |
(Saukov et al 1972) |
Turkmenistan |
|
Cheleken |
< 0.008 |
1 |
(Saukov et al 1972) |
Central Asia |
|
Southern Alamyshek |
0.22-0.26 |
6 |
(Foursov, 1977) |
Sarytash |
0.28-0.32 |
2 |
(Foursov, 1977) |
* Data by Yu.I. Zherebtsov, V.V. Ryzhov, N.R. Mashvanov.
It should be stressed that the high concentrations of mercury are detected in those deposits related to regional zones of deep faults, in their activation sections – e.g. deposits
located on the territory of the former USSR and Russia, related to Karpinsky lineament and Pannonion-Volinian lineament – Dnieper-Donetsk depression, Pre-Carpathians flexure,
Belarus, Baltic countries, the Northern Caucasus, Kazakhstan etc. (see figures 4.4 and 4.5).
Another type of structures controlling the mercury-bearing oil deposits are global mercury belts with cinnabar deposits; the Table 4.17 presents the deposits of Sakhalin, which
constitute a part of the western framing of the global Pacific mercury belt.
The value of 0.3 mg/kg accepted as an average mercury concentration in oil is lower than the average content of 7.2 mg/kg proposed by V.V. Ivanov (Kakareka et al., 2000), but
significantly higher than the average applied for the USA in the most recent assessments where the average Hg content in oil is estimated to be within the range 0.005-0.05 mg/kg
(Wilhelm 2001). The difference may reflect real differences in mercury content of the crude oils.
Mercury content in hydrocarbon gases and condensate
The content of mercury in natural hydrocarbon gases of Russian gas fields is shown in Table 4.18, respectively for free gases (from gas wells) and casinghead gas (from oil wells).
The range of content of mercury in free gases are: 5•10-8 – 7•10-5 g/m3 (the average content 2.4•10-6) and in casinghead gases: 7•10-8 – 1.4•10-5 g/m3 (the average
3.4•10-6). The highest content of mercury – up to 20•10-6, 40•10-6 and 70•10-6 g/m3 is observed in some deposits of Stavropol arch (the metallic mercury was detected at one
of the technological units of PPP in Blagodarny town). This structure is a fragment of the Karpinsky liniament mentioned above.
In addition to values stated in the table 4.18, there are two more publications mentioning mercury in Russian gases: first, the article by L.M. Zorkin et al. (1974) in which only two
figures can be considered as authentic – for Stepnoye and Ravninnoye fields. The second mentioning was in the article by A.I. Gritsenko et al. (1993), which includes data on
mercury content in natural borehole gas in the Astrakhan field: (0.3-2.5 •10-6 g/m3). As regards other figures in this work, they are mistakenly overestimated. Table 4.18 shows
the contents of mercury in condensate from three large gas fields of Russia - Orenburg, Astrakhan and Karachaganakskoye fields, as well as from Ukrainian fields, so as to present
possible variation. The highest mercury concentrations were recorded for Oposhnya field - up to 1.95 mg/kg. As was shown above this field is characterised by rather high content
of mercury in gas. There are two types of condensate: raw (unstable) released from gas during field extraction and stable obtained at the gas processing plants GPP. A smaller
amount of condensate which is sent to GPP is also obtained in oil-gas-condensate fields.
Table 4.18 Content of mercury in free gas (without condensate) and casinghead gas in Russian fields *
Region |
Fields |
Number of samples |
Mercury content,
10-6 g/m3 |
Free gas of gas fields |
Azov-Kuban depression |
Anastasyevo-Troytskoye |
1 |
0.15 |
Takhta-Kugultinskoye |
12 |
0.4-70 |
Northern Stavropol |
10 |
0.4-20 |
Singeleevskoye |
1 |
<0.7 |
Stavropol arch |
Petrovsko-Blagodarnenskoye |
1 |
<0.3 |
Mirnenskoye: |
|
|
upper stratum (Pg2) |
13 |
0.05-0.03 |
lower stratut (K1) |
40 |
0.2-40 |
Pelagiadinskoye |
6 |
0.08-0.8 |
Southern Radykovskoye |
2 |
0.1 |
Northern Radykovskoy |
2 |
0.1 |
Tersko-Kumskaya depression |
Kamennaya Balka |
5 |
0.07-0.15 |
Kevsala |
1 |
0.2 |
Eki-Burulskoye |
6 |
0.1 |
Stepnoye** |
1 |
2 |
Ravninnoye** |
1 |
0.8 |
Tersko-Caspian depression |
Oktyabrskoye |
1 |
0.12 |
Astrakhan |
|
|
- wells |
8 |
0.3-2.5 |
|
|
average - 1.0 |
- raw separation gas |
3 |
0.3-3.5 |
|
|
average - 1.4 |
Caspian depression |
Orenburg |
|
|
- wells |
36 |
0.1-3.12 |
- raw separation gas |
|
average - 1.5 |
Karachaganakskoye |
|
|
- wells |
16 |
0.4-2.4 |
|
|
average - 1.6 |
- raw separation gas |
1 |
0.5 |
Ryazan-Saratov depression |
Lugovskoye |
2 |
0.07-0.66 |
Pervomayskoye |
|
|
|
Suslovskoye |
- wells |
|
0.07-0.4; 6.5 |
Furmanovskoye |
|
|
|
Casinghead gas from gas-oil fields |
Stavropol vault |
Southern Spasskoye |
1 |
11.5 |
Zhuravskoye |
1 |
14.1 |
Vorobyevskoye |
1 |
7.5 |
Ryazan-Saratov depression |
Sokolovogorskoye |
17 |
0.12-3.8 |
Uritskoye |
5 |
0.1-0.45 |
Yazykovskoye |
7 |
0.3-1.6 |
Zubovskoye |
1 |
0.5 |
Mechetkinskoye |
8 |
0.09-0.3 |
Eastern Suslovskoye |
4 |
0.07-0.4 |
Bashkir vault |
Kokuyskoye |
2 |
0.15-0.4 |
Eastern Kamchatka depression |
Bogachevskoye |
1 |
0.1 |
* By the data of N.A. Ozerova 1986; Ryzhov, Mashvanov;
**Stepanov (Zorkin and co-authors, 1974)
Table 4.19 Content of mercury in condensate from gas fields*
CIS countries |
Region |
Gas processing plants and fields |
Number of samples |
Content of mercury, mg/kg |
Russia |
Caspian depression |
Astrakhangazprom |
3
1 |
0.104- 0.377;
0.47** |
Orenburggazprom
Orenburg
Karachaganakskove |
1
1 |
0.08
0.066 |
Ukraine |
Dnepr-Donetsk depression |
Oposhnya
- wells |
5 |
0.624 – 1.95 |
5 fields
(Shebelinskoye, etc.)
- wells |
6 |
<0.065 |
* data of N.A. Ozerova, V.V. Ryzhov, N.R. Mashvanov
** Unstable condensate
Summary
The available data on mercury in hydrocarbon raw materials from Russia is summarised in Table 4.20.
Comparison with data on crude oil and condensate from some other countries (Table 4.21) shows that mercury content in the crude oils and condensate from Russian fields is
within the range of concentrations found other countries and also that there is a high variation in the content of mercury in the hydrocarbon raw materials from different parts of the
world. The variation of the data may beside the geographical variation be due to differences in sampling methods, handling techniques, analytical techniques, etc.
Table 4.20. Mercury content in hydrocarbon raw materials of Russia
Hydrocarbon raw material,
region
|
Number of sites |
Number of samples |
Unit |
Concentration range |
Simple average |
SD |
OIL |
Russia |
10 |
17 |
mg/kg |
<0.008-0.46 |
0.18 |
0.13 |
The former USSR republics |
42 |
117 |
-"- |
<0.008-6.9 |
0.3 |
1.4 |
FREE GAS |
Russia |
25 |
175 |
10-6 g/m3 |
0.05-70 |
2.4 |
12.9 |
CASINGHEAD GAS |
Russia |
11 |
48 |
10-6 g/m3 |
0.07-14.5 |
3.4 |
3.2 |
condensate |
Russia |
3 |
5 |
mg/kg |
0.06-0.47 |
0.27 |
0.18 |
Table 4.21 Mercury content distribution in some countries (summarized references) (based on Wilhelm 2001)
No. of samples |
Range ppm
(mg/kg)
|
Average ppm
(mg/kg)
|
SD |
Notes |
Cruide oil |
10 |
0.023-29.7 |
3.2 |
|
USA and import |
86 |
<0.002-0.399 |
0.022 |
0.063 |
Canada |
4 |
<0.004-23.1 |
5.8 |
|
USA and import |
6 |
0.0001-0.012 |
0.0031 |
0.0042 |
Libya |
26 |
<0.01-1.56 |
0.065 |
|
West Coast refineries |
76 |
no data available |
1.505 |
3.278 |
Origins not reported |
11 |
0.0016-0.0072 |
0.0044 |
0.001 |
Origins not reported |
23 |
0.0001-0.0122 |
0.0035 |
|
New Jersey refineries |
24 |
All <DL=0.015 |
0.008 |
|
Canada and import |
8 |
<0.002-0.009 |
0.0016 |
0.0016 |
Canadian refineries |
Gas condensate |
4 |
no data available |
0.015 |
|
Origins not reported |
18 |
no data available |
3.96 |
11.7 |
Mostly from Asia |
5 |
0.009-0.063 |
0.03 |
0.018 |
South-East Asia |
7 |
0.015-0.173 |
0.04 |
|
Asia |
4.2.3 Mercury Mobilisation with Oil
For a first highly tentative estimate of the total amount of mercury mobilized in oil produced in Russia in 2001, its average concentration of 0.18 mg/kg will be used It should be
noted that a significant part of the data presented in Table 4.17 relates to the fields containing oil with relatively high concentrations of mercury.
The total production of crude oil in Russia in 2001 amounted 336 million t. Assuming an average mercury content of 0.18 the total mercury content of the crude oil can be
estimated at 61 t (Table 4.22). It should be noted that this is a very tentative estimate. The average mercury content in the crude oils is used, i.e. before water and salts are
removed from it during primary treatment.
Primary phase separation
A significant amount of mercury may be removed from the crude oils before the oil is transported to oil refineries, however a very limited information exist on the fate of mercury by
the primary phase separation (Wilhelm 2001).
A significant share of oil produced in Russia is extracted from wells as a water emulsion. Such wells with high water content include more than 80% of the wells in operation in
2001. (The press release for the 8th International Exhibition of equipment for the oil and gas industry "Neftegaz-2000, 2000). When oil is produced, it always includes formation of
water (from less than 1% to 80-90% by weight) that is dispersed in oil, thereby forming a water-in-oil emulsion. The formation water, as a rule, contains high concentrations of
sodium, magnesium and calcium (up to 2500 mg/l of salts, even when oil contains only 1% of water), as well as sulphates and hydrocarbonates and also contains mechanical
admixtures. The typical content of water in crude oil is 200-300 kg/t, of mineral salt up to 10-15 kg/t; besides, crude oil contains associated gas (50-100 m3/t) (Bogomolov et al.,
1995). Probably, a part of mercury is present in the formation water and in mechanical admixtures. Before oil is transported to the refineries, it is required to remove gas,
mechanical admixtures, and the bulk of water and salt (Bogomolov et al., 1995; Levchenko et al., 1967). Some processes of the initial oil processing are carried out at high
temperatures. Using first stage separators, oil gas is separated from crude oil; then practically degassed oil is fed to oil conditioning units where the second and the third stages of
separation of gas from oil take place, as well as dewatering and removal of salt from oil. Dewatering of oil is performed in oil fields, usually by thermal and chemical; methods of
destruction (separation) of the water-oil emulsion using also de-emulsifying agents (i.e. carious surfactants) at the temperature of 50-80°C. During salt removal, salts and water left
after dewatering process are also removed from oil.
Salt removal includes mixing of oil with fresh water, destruction of the formed emulsion and followed by separation from oil of wash water together with salts and mechanical
admixtures that were transferred to it. Dewatered and de-salted oil is fed to sealed tanks, and then to the plant designed to estimate oil quantity and quality, after which it is fed to
commercial tanks wherefrom oil is pumped to the main oil pipelines.
Oil refineries and petroleum products
Almost a half of all Russian oil is exported to CIS and other countries, but its greater part is transported to Russian oil refineries (OR) for primary refining. According to data given
in Table 4.22 the total mercury content of oil delivered to the oil refineries can be estimated at 32 t. This amount will be used as representing the total mobilisation of mercury in the
xtracted oil in Russia in 2001. Based on a very rough estimate and considering the uncertainties on the average Hg concentration in Russian oil, the amount of the mercury mobilised
shall vary at 5-50 t/year. The mass of mercury actually transported to the oil refineries may, however, be less than this, as a part of the mercury most probably is released by the
first stage oil treatment.
Table 4.22 Mercury in oils of the Russian Federation, 2001
Oil distribution |
Hg volume
mil. t
|
Hg content, mg/kg |
Hg mass, tonnes |
Crude oil production |
336.47* |
0.18 |
61 |
Export to CIS countries |
22.68** |
0.18 |
4.1 |
Export to other countries |
137.06** |
0.18 |
25 |
Oil import (from CIS) |
5.03** |
0.3 **** |
1.5 |
Oil delivered to OR and PCE |
178.36*** |
0.19 |
33 |
Transformation to other energies; as a material for non-fuel
needs; for final use, losses |
3.4** |
0.18 |
0.6 |
*The State Balance... Oil, 2002
**Social and Economic Situation ... 2001
***Ratex
****The average have been applied based on the summarized dataset on former Soviet republics
The oil is refined at refineries, petroleum-chemical plants, Gazprom enterprises and some small oil. Refinery is a basic oil processing process. This is a physical process based on
difference of temperatures. It takes place in rectification columns wherein oil is fed under atmospheric pressure, heated to 300-350 °C. Obviously the bulk of mercury is released
from this oil and ends up in the refined products and waste or is released to the environment.
It has been possible to analyze Hg content in only single samples of petrol, diesel fuel and heavy oil. The samples was obtained in the Astrakhan gas and oil refinery (see section
"Mercury in gases"). The detected mercury concentrations were used for a first tentative estimate of the total content of mercury in oil refinery products. According to the estimates
in Table 4.23 the petrol, diesel fuel and heavy fuel oil (mazut) used in Russia (domestic supply) contained a total of 3.4 t mercury. It is assumed that almost all this amount will be
released to the atmosphere by the combustion of the products. Unfortunately, no data has been available on mercury in other refinery products like bitumen, petcoke, sulfur, etc.
These products may contain significant amounts of mercury. Available estimates are very uncertain and more analyses and call for further special studies of mercury content of
crude oils and refined products, the fate of mercury by oil refining and mercury in oil refinery products.
Comparing the mercury content of the refinery products with the content of mercury in the crude oils indicate that a major part of the mercury could released by the initial treatment,
be emitted from the refineries or end up in some waste products from the refineries. The uncertainty on the estimates, however, does not allow drawing any precise conclusions.
A study of the fate of mercury by oil refining in the USA indicates that about 3 % of mercury is released to the atmosphere and wastewater, 11 % goes to solid wastes, 67 % - to
the products burned as fuels, and 17 % - to the feedstock for chemical industry (Wilhelm 2001). According to the information obtained by the author of the present work,
investigations in Canada indicate that more than 90 % of mercury passed all feedstock processing stages is released to the atmosphere.
The mercury releases to air and wastewater significantly depend on the specific oil refinery technology e.g., mercury content in flue gases in Astrakhan Gas Processing Plant was
dependent on the performance of the installation with sulfrine (see section 4.2.4) - if it was not operated, Hg content in flue gases is 10 times increased which is consequently
followed by Hg air emissions increase. Use of zeolites for the flue gases treatment allows to dry the gas and remove mercury with the moisture.
Table 4.23 Mercury in basic oil refinery product in the Russian Federation, 2001
Basic oil refinery products |
Production
million t *
|
Domestic supply
million t *
|
Hg content, mg/kg |
Hg amount, tonnes |
Petrol |
27.6 |
24.9 |
0.013 |
0.3 |
Diesel fuel |
50.2 |
26.0 |
0.065 |
1.7 |
Heavy fuel oil |
50.2 |
27.5 |
0.05 |
1.4 |
Jet fuel |
9.0 |
9.0 |
N/A |
Gas |
20.0 |
20.0 |
N/A |
Other oil products (bitumen, pyrolysis feedstock, petcoke, sulfur,
etc.) |
15.7 |
15.7 |
N/A |
* EIA 2003. The difference between production and domestic supply is exported.
4.2.4 Fate of Mercury by Natural Gas Processing
In order to discuss the mobilisation of mercury with natural gas and the fate of the mercury in the gases, investigations of the fate of gas in gas processing plants is discussed in this
section. In the recent time gases from Astrakhan, Orenburg and Karachaganarskoye fields, being large fields in Russia, have been studied. Not only natural gas from these fields
has been studied, but also products of gas processing at Astrakhan and Orenburg gas-processing plants (GPP). They have been examined in details and we consider them as
standard reference, therefore, we provide complete factual data on these fields and plants (Table 4.24 and Table 4.25).
The feedstock for the gas processing plants is natural gas, unstable condensate (released from gas during field extraction) and condensate obtained in oil-gas fields. By the
processing stable condensate is produced. The stable condensate is used as feedstock for further processing and is widely used as motor oil.
Based on the tables (Table 4.24 and Table 4.25). the following aspects should be emphasised here. At Astrakhan GPP condensate generated during decomposition of the
mercury-containing gas-condensate mixture has a noticeable content of mercury (see Table 4.24). Gas is then processed to remove sulphur (de-sulphurised) and is noticeably
depleted in mercury while sulphur-containing gas is the raw material for production of sulphur. a similar picture can be seen at the Orenburg GPP (see Table 4.25). Finally, sulphur
contains mercury 1.5-2.0 times higher than the average of the earth's crust – 0.05 mg/kg. Hg concentration values vary from 0.01 up to 0.1 mg/kg; the average value is respectively
equal to 0.06 and 0.09 mg/kg for Astrakhan and Orenburg GPP. The mercury concentration is rather low in heavy fuel oil, diesel fuel and petrol. However, these are only single
determinations (sample number = 1) and may not be representative.
Table 4.24 Mercury content at the Astrakhan gas-processing plant
Samples |
Nos. in Fig. 4.6 |
Number of samples |
Mercury contents |
|
|
|
Units of measurement |
Limits and average |
Wells |
Gas (without condensate) |
|
8 |
10-6 g/m3 |
0.3-2.5 (8);
average: 1.0 |
Gas-processing plant |
Plastic gas-condensate mixture |
17 |
|
10-6 g/m3 |
54* |
Raw separation gas |
15 |
3 |
-"- |
0.3-3.5;
average: 1.4 |
Medium pressure gas |
14 |
2 |
-"- |
0.19-0.32 |
De-sulphurised gas |
8 |
3 |
-"- |
<0.05**-0.12 |
Commercial gas |
1 |
3 |
-"- |
<0.05-0.117 |
Unstable condensate |
18 |
1 |
mg/kg |
0.47 |
Stable condensate |
20 |
3 |
-"- |
0.106-0.386;
average: 0.279 |
Acid gas |
10
11 |
1
1 |
10-6 g/m3 |
0.8
1.4 |
Commercial sulphur |
|
19 |
mg/kg |
0.01-0.18;
average: 0.06 |
Petrol |
|
1 |
mg/kg |
0.013 |
Diesel fuel |
|
1 |
mg/kg |
0.065 |
Heavy fuel oil (mazut) |
|
1 |
-"- |
0.05 |
Flue gas |
21 |
3 |
10-6 r/M3 |
0.2-0.48 |
5 |
4 |
-"- |
0.1-0.35
3.4***; 1.7-0.38**** |
Ash from the stack |
|
3 |
10-2 mg/kg |
25-38 |
Stratum water |
19 |
2 |
10-3 mg/l |
<0.1-<0.2 |
Condensed water |
21 |
2 |
-"- |
<0.1 |
Atmospheric air in the area of the plant |
26 |
2 |
10-6 g/m3 |
0.006-<0.01 |
Spent catalyst |
7 |
8 |
10-2 mg/kg |
0.8-7 |
Zeolite |
6 |
2 |
-"- |
<1-6 |
* This is the calculated figure, since we analyse separately mercury in gas and in condensate and then, knowing the amount of condensate in m3 of gas, we estimate the total
content of mercury in the gas-condensate mixture.
** Limits of detection of equipment.
*** Content of mercury is increased when the plant with sulphrine is not operated.
****When there is a plant with sulphrine, the content of mercury is gradually decreasing.
Table 4.25 Mercury distribution at Orenburg gas-processing plant
Samples |
Number of samples |
Mercury contents |
|
|
Units of measurement |
Units of measurement |
Wells |
Gas from Orenburg field (without condensate) |
36 |
10-6 g/m3 |
0.1-3.12;
average - 1.5
|
Gas from Karachagakanskoye field |
16 |
-"- |
0.4-2.4;
average : 1.6
|
Gas-processing plant |
Raw separation gas fed to the plant from the Orenburg field |
11 |
10-6 g/m3 |
1.3-2.2;
average: 1.9
|
De-sulphurised gas from Orenburg field |
3 |
-"- |
0.05-0.7;
average: 0.4
|
Raw separation gas fed to the plant from the Karachaganakskoye
field |
2 |
-"- |
0.5-1.3 |
De-sulphurised gas from Karachaganakskoye field |
1 |
-"- |
0.07 |
Commercial gas |
|
|
|
Orenburg and Karachagakanskoye fields
(I+II stages)
|
7 |
-"- |
0.07-1.3;
average: 0.48
|
Karachaganakskoye field (III stage) |
1 |
|
0.15 |
Condensate from Orenburg field |
1 |
mg/kg |
0.08 |
Condensate from Karachaganakskoye field |
1 |
-"- |
0.066 |
Commercial sulphur |
4 |
10-2 mg/kg |
5-18;
average: 9.0
|
Flue gas |
6 |
10-6 g/m3 |
0.1-9.4;
average: 2.9
|
Stratum water |
1 |
10-3 mg/l |
0.08 |
Technological water |
8 |
-"- |
0.08 |
Atmospheric air in the Orenburg field (measures by profiles) |
5 |
10-6 g/m3 |
0.05 |
* Limits of detection of equipment
The commercial gas at Astrakhan GPP contains not more than 0.1•10-6 g/m3 of mercury; at Orenburg plant the average in commercial gas is 0.48 •10-6 g/m3.
At Astrakhan GPP, flue gas contains less mercury (close to MAC) than at Orenburg GPP, where on the average it is approximately 10 times higher than MAC (the reasons have
not been investigated).
It should be specially noted that the plant with sulphrine in Astrakhan GPP, is very effective for purification of flue gas from mercury (see Table 2.24 and the notes).
Technological water contains little mercury. Atmospheric air in the area of this field and at the area of the GPP is not polluted with mercury.
Balances for basic feedstock and basic products of Astrakhan GPP are set up in Table 4.26.
Gazprom JSC is the largest joint-stock company in Russia. In 2001 Gazprom developed 87 % of total Russian gas production volumes, supplied 90 % of gas to the United Gas
Supply System and exported 96 % of total Russia export to Europe. As it was mentioned above, investigations of mercury content have been done in three large fields – Orenburg,
Astrakhan and Karachaganakskoye, which are operated by Gazprom JSC; the main focus was given to Astrakhangazprom Production Complex as a typical model of Gazprom
branches in respect of structure of extraction and processing of the hydrocarbon feedstock (see table 4.25). The total amount of mercury in the feedstock supplied to
Astrakhangazprom in 2001 had totalled 2.4 t and 1.1 t in the output if we assume that the concentration in the feedstock resemble the average. The total volumes for Gazprom
GPP amounted to 5.8 t and 2.1 t respectively (see table 4.27). It is notable, that the main amount of mercury (0, 741 t – for Astrakhangazprom and 1,693 t – for all Gazprom
GPP) is connected with the condensates.
Figure 4.6 Scheme of processing of the gas and condensate mixture at the Astrakhan gas-processing plant
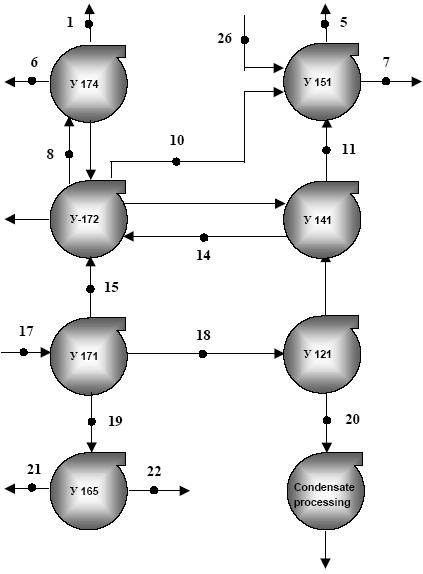
Ó 121-Ó 174 are the units for processing raw gas and condensate
Nos. 1-26 in the scheme are bays for sample taking for mercury analysis: gas stratum mixture – 17; gas separation – 15; middle pressure gas – 14; gas with sculpture removed – 8;
commercial gas – 1; unstable condensate – 18; stable condensate – 20; acid gas – 10 & 11; flue gas – 5 & 21; condensed water – 21; formation water - 19; zeolite – 6; spent
catalyst – 7.
Table 4.26 Amounts of mercury contained in gases, condensates and products of their processing at Astrakhan GPP, 2001. (Annual Report........., 2002)**
|
Volume of feedstock and output |
Hg content: |
Hg amount: |
|
Units |
Value |
Units |
Mean value |
kg |
% |
Feedstock |
Natural gas |
bil. m3 |
10.5 |
10-6 g/m3 |
1.4 |
14.7 |
0.6 |
Gas condensate
(oil)
|
1000 t |
2291.0 |
mg/kg |
0.27 |
618.57 |
26.25 |
Unstable gas
Condensate
|
1000 t |
3670.5 |
mg/kg |
0.47 |
1725.14 |
73.15 |
Total in the feedstock |
|
|
|
2435 |
100 |
Output |
Gas for consumers |
|
|
10-6 g/m3 |
0.05 |
|
|
Stable
Gas condensate
|
1000 t |
2743.0 |
mg/kg |
0.28 |
740.61 |
68.8 |
Motor gasoline |
1000 t |
959.1 |
mg/kg |
0.013 |
12.47 |
1.2 |
Diesel fuel |
1000 t |
794.6 |
mg/kg |
0.07 |
55.62 |
5.2 |
Fuel oil |
1000 t |
377.1 |
mg/kg |
0.05 |
18.86 |
1.7 |
Sulfur |
1000 t |
4151.0 |
mg/kg |
0.06 |
249.1 |
23.1 |
Total in the output |
9032 |
|
|
1077 |
100 |
Mercury in main pipelines
The content of mercury in main pipeline gas is compared to the mercury content of the gas feedstock very low (see Table 4.28). In 1990 the content was <0.03 – 0.1 μg/m3 and in
1991 it was <0.03-0.05 μg/m3. But these are not necessarely factual values of Hg content in gases from Urengoy and Yamburg from where they are delivered. According to
experience of Groningen (Holland) the gas is depleted in mercury by passing by pipelines through W. European countries; probably due to amalgamation of gas pipeline walls.
Probably, this takes place also in Russian gas pipelines, moreover as their length is much higher that the W. European, and the almost Hg-free gas is exported to other contries.
Table 4.28 Content of mercury in natural traded gas from main pipelines
Gas pipelines |
Content of mercury, μg/m3 |
|
1990 |
1991 |
Single union ring
(Davydovskaya gas distribution station, Tambov Oblast)
|
Gas pipeline "Urengoy-Uzhgorod" |
0.03 |
0.05 |
Gas pipeline "Urengoy-Centre 1" |
0.03 |
0.03 |
Gas pipeline "Urengoy-Centre 2" |
0.03 |
0.05 |
Gas pipeline "Yamburg-Yelets 1" |
0.1 |
0.05 |
Gas pipeline "Yamburg-Yelets 2" |
0.1 |
0.03 |
Gas pipeline "Yamburg-Moscow" |
0.09 |
0.05 |
Northern line, Moscow |
Gas pressure station, Mostransgaz |
0.03 |
N/A |
4.2.5 Mercury Mobilisation with Natural Gas and Gas Condensate
Based on the above, a rough estimate of mobilisation of mercury by the extraction and use of natural gas in Russia is summarised in Table 4.29. The estimate indicates that the main
source of mercury for the gas processing industry is mercury in gas condensates. As a best estimate some 8.2 t may be mobilised with natural gas and gas condensate. Considering
the high uncertainty, the range is estimate at 2-10 t mercury per year.
It is very certain that only a small amount, 0.03 t mercury, ends up in the gas for export and domestic consumption. Consuderable amount of mercury ends up in other products, in
particular stable gas condensate. The total mercury in products does not fully balance the estimated total in feedstock illustrating that all estimates on mercury in feedstocks and
products are very uncertain.
The obtained estimates indicate that a significant amount of mercury may be mobilised by production of natural gas and gas condensate and call for further studies of the fate of
mercury by processing and use of products.
There have been no estimates on the flared gas volumes obtained for all Russian fields, but for Western Siberia it was in 2001 about 19 billion m3. By using the average content of
mercury in casinghead gas, the flared gas would contain 65 kg of mercury. The mercury emission from flaring is most probably higher than from combustion of the processed gas.
Table 4.29 Mercury balance in RF gas industry in 2001
Feedstock/product |
Volume, bil. m³ |
Hg content, g/m3 |
Hg amount, t |
Basic feedstock |
Natural gas production |
573 * |
2.4 |
1.4 |
Gas condensates |
|
|
6.6 ** |
Processed gas |
Export (incl. to Europe) |
178 * |
0.05 |
0.009 |
Import (incl. from CIS) |
3.9 * |
0.05 |
0.0002 |
Domestic consumption *** |
398 * |
0.05 |
0.020 |
Other products |
Stable gas condensate |
|
|
2.0 ** |
Other products |
|
|
0.5 ** |
* Source: EIA 2003, Conversion factor: 38 TJ/million m3.
** Estrapolated from data in 4.26
***includes losses in the pipelines
4.2.6 Oil shale
In 2001, about 1.5 million of oil shale was produced; the overwhelming part in the Leningrad Oblast. This product mainly is sent to the oil shale processing plant (town of Slantsy,
Leningrad Oblast). Much smaller amounts are produced in the Kashpir deposit (Volga region) and some other places. Oil shale from the Kashpir deposit is dent for processing to
the Syzran shale processing plant. Oil shale is also used in Slantsy and Syzran as fuel for local CHPP; the main part is used in the town of Slantsy.
Content of mercury in oil shale of the Leningrad Oblast is estimated at 0.4 mg/kg on the average, similar to oil shale from Estonia (Table 4.30), since these two facilities belong to
the same Baltic basin of oil shale; conventionally – along the administrative border between Russian and Estonia, which separates these two deposits. Similar contents of oil shale as
in Estonia have been identified in the Kashpir deposit, the average being 0.44 mg/kg.
Table 4.30 Content of mercury in oil shale (Ozerova, Aidinyan, 1966)
Region |
Deposit |
Mercury content, mg/kg |
|
|
Range * |
Average |
Russia, Volga region |
Kashpir mining field, mine 1 |
0.2 – 1.6 (11) |
0.44 |
Estonia,
Baltic basin |
Ahtme mine |
0.17 – 0.38 (5) |
0.4 |
Kivyili mine |
0.2 – 1.5 (5) |
|
Note: in brackets the number of samples.
Using the value of 0.4 mg/kg and considering the uncertainty the total mercury content of the oil shale extracted in 2001 can be estimated at 0.6 (0.4-0.8 ) tonnes. In Russia, oil
shale is mainly used for energy production and is connected with its high temperature processing conditioning a greater part of the contained mercury to emit to the atmosphere and
the least part to be concentrated in the residues. As a first estimate it will roughly be assumed that 80% of the mercury is emitted to the atmosphere (0.5 t); 20% is deposited with
residues (0.1 t).
4.2.7 Wood
In 2001, about 5.7 million tonnes of conventional fuel units of wood were used for generating energy in Russia. If we take the factor for conversion of convention fuel units (by coal
equivalent) to tonnes wood that equal 0.266 (according to Methodological Regulations ..." of the State Committee of Statistics, 1999), we get 21.4 million tonnes wood.
It has not been possible to identify data on mercury in wood in Russia. According to Danish research (Skårup et al. 2003) the mercury content in burned wood and straw is within
the range 0.007-0.03 mg/kg of dry weight. According to American data (Friedly et al. 2001), mercury content in waste and green vegetation is 0.01-0.07 mg/kg of dry weight –
by results of surveys performed in 7 regions. For inventory of mercury emissions in the USA, the magnitude of the average factor of release for the burned wood was taken at
0.026 mg/kg – the typical release factor for combustion of wood waste in boiler houses (US EPA 1997). To calculate relevant figures for combustion of wood in houses, they also
used the factor 0.026 mg/kg. Swedish researchers ((Kindbom & Munthe 1998) established the concentration of mercury in firewood at 0.01-0.02 mg/kg of dry weight, willow
wood – 0.03-0.07 mg/kg of dry weight, in wood bark - 0.04 mg/kg of dry weight, and somewhat higher concentration in fir-tree needles at 0.3-0.5 mg/kg of dry weight.
On the basis of these data we used the value 0.01-0.03 mg/kg. To calculate the Hg emission with wood combustion we took the magnitude 0.02 mg/kg. In such case, the total
amount of mercury released to the atmosphere during burning of wood can be estimated for 2001 for Russia at 0.4 (0.2-0.4) tonnes.
Mercury released during wood fires, which may be very significant, is not included in this study.
4.2.8 Peat
In 2001, about 4.6 million tonnes of peat was extracted in Russia; of this amount, about 10% is used as fuel (i.e. 0.46 million tonnes), and the remaining part in agriculture.
In Tomsk Oblast (Yu.A. Golovatskiy, oral communication) the mercury content usually constitutes 0.02-0.5 mg/kg, however at deeper grounds there is a layer with a higher
concentration, i.e. 0.2-0.3 mg/kg.
In Tyumen Oblast, in the area of intensively used oil and gas fields, the background mercury content in peat soils is within 0.01-0.3 mg/kg, the average values being 0.2-0.25 mg/kg
(Dorozhukova et al. 2000). These data correspond to similar data for the above-mentioned Tomsk Oblast and for other regions. the USA – the average figures for peat soil are at
0.28 mg/kg. the summary report of D.S. Adriano indicates that Hg concentrations in peat soils of the world vary within 0.06-0.3 mg/kg (cited from the work of Dorozhukova et al.
2000). There are registered processes of mercury binding by organic substance from soils that are typical of peat bogs; the latter have a higher capacity to accumulate mercury
even in natural conditions.
By taking the average Hg content in peat soil as 0.2 mg/kg, the total amount of mercury released during use of peat as fuel in Russia can be estimated at 92 kg in 2001.
4.3 Cement and lime
The mercury content in clay rocks (beyond the border of deep faults and ore fields, where litho-chemical areoles of mercury are visible) that are used as raw material for
production of cement and lime is rather constant. Thus, for Russian platform (age - D2-K2), they are estimated on the average as follows: for limestone at 0.031 mg/kg (by 131
samples), for clay rocks at 0.035 mg/kg (58 samples), for sand and siltstone at 0.039 mg/kg (45 samples); Hg content in all these samples are close, irrespective of the conditions
of the sedimentary rocks formation. Special survey conducted in quarries in Russian platform (age - D3-K2), where limestone is extracted, showed that the average mercury
content in 19 combined samples including 3,117 individual samples, made 0.037 mg/kg (Ozerova, Adinyan, 1966). This figure is below the average mercury concentration of the
earth crust, i.e 0.045 mg/kg.
V.Z. Fursov (1977) gives a higher figure of the average mercury content in limestone, about 0.052 mg/kg, with the variation from 0.024 to 0.102 mg/kg (106 samples); this is due
to the fact that testing was organized in different USSR regions, including ore provinces and deep fault areas.
We take for calculations the average mercury concentration in the blends at 0.035 mg/kg with the following comments. Sometimes sand, siltstone and clay rocks with an admixture
of volcanic materials (effusion-deposition type of lithogenesis) are added to the initial raw material blend. In this case the mercury content in the blend is somewhat higher, since the
mercury concentration in the mentioned rocks is higher, on the average, than in rocks of deposition lithogenesis, making about 0.085 mg/kg in clay rocks and 0.097 mg/kg sand
and siltstone. In this case we take the mercury content in the blend at 0.05 mg/kg and then we should include certain comments in the final figures.
The main process that results in release of mercury during production of cement and lime is thermal – mercury is sublimed and released (emitted) with outgoing gases. In the work
(Fursov, 1977) it was shown that in conditions of experiment – during continuous heating of sample of limestone and clay rocks from the room temperature to 800° C – practically
all mercury is released at temperatures about 300 C. The process of roasting of raw cement mass, i.e. limestone and clay rocks goes on at high temperatures in the caking area:
1,450°C (in the blend) and about 2000 °C (in the gas stream). Therefore, we can assume that in such processes practically all mercury is emitted with flue gases.
It should be noted that during production of cement, when it is necessary to get a mixture with the required chemical composition, they use adjusting additives, usually not exceeding
0.09 tonnes per tonne of clinker (semi-finished cement). They include gypsum, iron ore, bauxite, quartz sand, tuf, diatomite, gaize, nepheline with rather low mercury content, i.e.
close to or higher than the percentage abundance (Saukov et al., 1971; Ozerova 1986) as well as fuel ash and pyrite cinders. According to the publications (Kakareka et al., 2000;
Yanin 2003), the mercury content in pyrite cinders used for production of cement at enterprises in Belarus and in the town of Novorossiysk are increased and equal to
0.116-0.121 mg/kg and 0.19-4.0 mg/kg, respectively. This allowed the authors of the research to assume that adding of pyrite cinders substantially increases the mercury
concentration in dust and gas emissions.
We can presume that some small amount of mercury is supplied to the area of the roasting oven together with fuel and then is released to atmosphere. This oven has a form of a
tilted cylinder; blend charge is loaded into its top end, while from the bottom a counter flow of hot gases is fed, which is generated as a result of combustion of fuel in the oven
bottom end.
There are two methods for production of cement: humid and dry, differing in the humidity of the initial blend from 32-45 % to 1-2 % respectively. the humid method requires a
higher fuel use, i.e. coal or gas, to produce clinker, and, hence, a higher amount of mercury is fed from the fuel (as compared to the dry method) to the oven. The use of coal is
connected with a much higher input of mercury to the oven and, therefore, in the releases as compared to gas (Table 4.31).
Table 4.31 Calculations of the mercury amount fed to the oven with fuel
|
Cement production |
|
Wet method |
Dry method |
Use per tonne of clinker:
gas
coal
|
200 m3
300 kg
|
110 m3
170 kg
|
Average mercury content in gases* |
2.4•10-6 g/m3 |
Average mercury content in coals (background)** |
0.045mg/g |
Amounts of mercury released from fuel during cement production
in 2001 (35,271 thousand tonnes)
- using gas
- using coal
|
16.9 kg
476 kg
|
9 kg
260 kg
|
* See the section "Mercury in Gases";
** (Saukov et al. 1972); in the mercury provinces the concentration of mercury in coals may increase to hundreds of a percent at the expense of development of mercury areoles;
the example is the province of Greater Donbass (Ozerova, 1962; Karasik, Dvornikov, 1968).
Taking all the above, we assume that all mercury, during roasting of limestone and clay rocks, is released with the gaseous phase. Respective figures for cement production and the
estimation of the mobilised mercury are given in Table 4.32. Emission of mercury are calculated on the basis of the average mercury content in the initial raw materials at 0.035
mg/kg and the volumes of the initial mixture with due account that 1.6 tonnes of the mixture is required per tonne of cement. The total cement production in 2001 in Russia was 35
million t.
Table 4.32 Amounts of mercury released from the blend during production of cement in 2001
Federal districts, federal subjects |
Share of cement production, % |
Mercury estimates,
t/year
|
Main cement producers |
Central federal district |
Belgorod Oblast |
9.8 |
0.193 |
Belgorod Cement,
City of Belgorod;
Oskolcement,
Town of Stary Oskol
|
Bryansk Oblast |
9.71 |
0.192 |
Maltsov Portland Cement, town of Fokino |
Voronezh Oblast |
0.87 |
0.017 |
|
Lipetsk Oblast |
4.54 |
0.090 |
Lipetskcement,
City of Lipetsk
|
Moscow Oblast |
6.49 |
0.128 |
Voskresenskcement,
Town of Voskresensk;
Schurovskcement,
Town of Kolomna
|
Ryazan Oblast |
4.11 |
0.081 |
Mikhailovcement,
Mikhailovsk District
|
North-western Federal District |
Komi Republic |
0.42 |
0.008 |
|
Archangelsk Oblast |
0.93 |
0.018 |
|
Leningrad Oblast |
4.57 |
0.090 |
Glinozem,
Town of Pikalevo
|
Southern Federal District |
Karachayevo-Cherkessk Republic |
2.94 |
0.058 |
Kavkazcement,
Town of Ust-Djeguta
|
Krasnodar Krai |
6.05 |
0.119 |
Novoroscement,
City of Novorossiysk
|
Volgograd Oblast |
6.02 |
0.119 |
Sebryakovcement,
Town of Mikhailovka
|
Rostov Oblast |
0.06 |
0.001 |
|
Privolzhsky Federal District |
Republic of Bashkortostan |
2.35 |
0.046 |
Soda,
Town of Sterlitamak
|
Republic of Mordovia |
5.83 |
0.115 |
Mordovcement,
Chamzinsky District
|
Orenburg Oblast |
1.58 |
0.031 |
|
Perm Oblast |
2.22 |
0.044 |
Gornozavodskcement,
Town of Gornozavodsk
|
Samara Oblast |
0.82 |
0.016 |
|
Saratov Oblast |
4.02 |
0.079 |
Volskcement,
Town of Volsk
|
Ulyanovsk Oblast |
2.79 |
0.055 |
Ulyanovskcemen,
City of Ulyanovsk
|
Federal districts, federal subjects |
Share of cement production, % |
Mercury estimates,
t/year
|
Main cement producers |
Ural Federal District |
Sverdlovsk Oblast |
7.19 |
0.142 |
Sukholozhskcement,
Town of Sukhoy Log;
Nevyansky Cement,
Nevyansky District
|
Chelyabinsk Oblast |
3.79 |
0.075 |
Uralcement,
Town of Korkino
|
Siberian Federal District |
Republic of Buryatia |
0.3 |
0.006 |
|
Altay Krai |
0.15 |
0.003 |
|
Krasnoyarsk Krai |
2.47 |
0.049 |
|
Irkutsk Oblast |
1.2 |
0.024 |
|
Kemerovo Oblast |
4.72 |
0.093 |
Topkinsky Cement,
Town of Topki
|
Novosibirsk Oblast |
1.45 |
0.029 |
|
Far East Federal District |
Republic of Saha (Yaklutia) |
0.58 |
0.011 |
|
Primorsky Krai |
1.01 |
0.020 |
|
Kamchatka Oblast |
0.04 |
0.001 |
|
Magadan Oblast |
0.04 |
0.001 |
|
Jewish Autonomous Oblast |
0.94 |
0.019 |
|
Russian Federation |
100.00 |
1.975 |
|
The total mercury amount, assumably released with gases and dust from the cement production facilities in 2001, is very optimally estimated at 2 tonnes and assuming
volcanic-sedimentary materials are introduced into the blend - 2.8 tonnes. The total released amount is consequently estimated at 2.0-2.8 t of which 1.3-2.1 t originates from
non-fuel raw materials. The main sources of dust in cement production are clinker roasting ovens and mills; the share of the roasting ovens includes up to 85% of all emissions from
the cement enterprises (Kolbasov et al., 1987; Varum, Izyumskaya, 1990). Dust from roasting ovens usually is polydispersion, with a high content of particles over 10 μm;
therefore, it is a good absorbent of heavy metals.
When cleaning systems are available, a part of the mercury is deposited on filters. In Russia, the cement enterprises use cyclones, hose filters, electrostatic filters (ESP) with the
dust catching efficacy of 80-99%; in most cases the factor of use of oven electrical filters at cement enterprises makes 80-84% (Chelnokov, Plyshevskiy, 1998, 2000). For
cleaning of off-gases from the rotary ovens, electrostatic filters are most commonly used (about 74% of the entire cleaning equipment), although only about one-third of this amount
is related to high efficacy equipment. At present, there is a need to modernize dust and gas cleaning equipment practically at all cement manufacturing enterprises of Russia
(Paionke, Mersmann, 2002).Dust and gas emissions contain up to 90-95% of the mercury engaged in the technological processes.
No data on the actual mercury catching efficiency of the filters applied in Russian have been identified. Contrary to other heavy metals, mercury is in general only partly captured by
the filters. It is in general very difficult to obtain an overview of the typical efficacy of different dust control measures for cement plants. A recent review of mercury speciation in
cement plants refers only scattered information of mass balances of mercury in cement kilns (Johansen, Hawkins 2003). The amount of mercury deposited on filters will among
other factors depend on the speciation of the mercury and the temperature above the filter. For a first estimate data from coal power plants can be applied.
The degree to which gaseous mercury adsorbs on the filter cake typically depends on the speciation of gaseous mercury in the flue gas; in general, gaseous Hg2+ is easier to
adsorb than gaseous Hg0 (US EPA 2001). Units that burn subbituminous coal or lignite typically have relatively low concentrations of Hg2+ and high concentrations of Hg0 at the
inlet to the control device compared to units that burn bituminous coal. Consequently the average mercury capture by ESP or bag filters in plants burning sub-bituminous coal is
lower. The average percentage that is captured by cold-side ESP is only 3%, whereas hot-side ESP and fabric filter capture 6% and 72%, respectively. No data on speciation of
mercury in gas from cement kilns have been identified. Considering the low efficiency of ESP when concentration of Hg0 is high and the fact that only about one-third of the ESPs
is related to high efficacy equipment the mercury capture efficiency may quite well only be 10-30%.
Assuming that 80% of the mercury in the raw materials are emitted to the air, the total air emission form cement kilns is estimated at 1.6 t/year corresponding to an emission factor
of 0.045 g/t cement produced. For comparison, average emission factors for cement kilns in the USA and Germany are 0.065 and 0.025 g/t cement, respectively (US EPA, 1997;
European Communities. 2001.)
The calculated average mercury content of the commercial cement calculated based on data (Emissions..1998; Plyshevsky and Chelnokov 2000; Chesnokov, Plyshevsky, 1998) is
estimated at 0.043 mg/kg. The value is slightly lower than the average value of 0.07 mg/kg in 416 samples reported from German cement plants (VDC 2000). Mercury content of
the final cement product will to some extent depend of the mercury content of other raw materials that are mixed with the clinker after the burning process.
Further improvement of the environmental situation in Russia, in regions where cement manufacturers are located, first of all is connected with modernizing the dust catching
systems, including heavy metals and mercury, and update of the respective equipment. The international association of cement and cement-based products producers (MGA
cement) has developed, together with the CJSC "Concern Cement" a programme for development of the Russian cement sector for 2001-2005. Special attention is paid to
reconstruction of electrical filters to reduce dust release to maximum allowed levels.
As regards lime, no estimates have been carried out in lack of information about relevant enterprises and lime production volumes. Based on the inventory experience of other
countries, it could be assumed that Hg emission at lime production would be considerably lower compared to cement production.
4.4 Non-ferrous Metallurgy
Mercury present as natural trace element of non-ferrous ores is mobilised by the extraction of the ores and may be released to the environment of by the processing of raw
materials and concentrates at metal production enterprises. The location of the nonferrous metal production enterprises in the Russian Federation is indicated in Figure 4.7.
Production of zinc, copper, nickel and lead is the most important (Table 4.33) and the most important besides gold from the point of view of potential mercury emission in 2001 in
Russia.
Figure 4.7 Location of nonferrous metal production enterprises in the Russian Federation
A – antimony, C – copper, L – lead, M - molybdenum, N -nickel, Z – zinc, T – tungsten
Click here to see the figure.
Table 4.33 Production of non-ferrous metals in Russia in 2001*
Metal |
T |
Main producers (share, %) |
Refined copper |
840,000 |
MMC Norilsk Nickel OJSC (> 54%) |
Refined zinc |
250,600 |
Chelyabinsk Zinc Works OJSC (> 62%) |
Primary nickel |
250,000 |
MMC Norilsk Nickel OJSC (> 89%) |
Refined lead |
34,000 |
Lead Works Dalpolymetall CJSC,
Electrozinc OJSC
|
Cobalt |
6,500 |
MMC Norilsk Nickel OJSC (70%),
Ufaleynickel OJSC
|
Refined tin |
4,500 |
Novosibirsk Tin Combined Enterprise OJSC (100%) |
Antimony |
1,500 |
Ryazantsvetmet OJSC (100%) |
* Production of bismuth, tungsten (wolfram) and other rare metals was few dozen t in most cases or few hundred t in rare cases.
Source: Analysis of financial ... BIKI, 2002; BIKI 2003; Gerasimchuk and others; Annual Report of Mining and Metallurgical Company (MMC) Norilsk Nickel ...; Kovalishina;
Global Mineral Resources as of 01.01.2001 ..., 2002; Polkin, Ponomariova ...; Cherniakova ...
The largest non-ferrous industry enterprises belong to the organization of MMC Norilsk Nickel OJSC. MMC Norilsk Nickel generates about 65-70 % of all atmospheric
emissions and up to 30-33 % of wastewater discharge from all Russian non-ferrous industry enterprises (including aluminium sector). The trans-polar Subdivision of MMC Norilsk
Nickel generates a major part of the said emissions and discharges. For example, in 1998 entire Russian industry generated 18,661,000 t of atmospheric emissions of hazardous
substances; within this amount, non-ferrous industry enterprises generated 3,292,000 t; within this, MMC Norilsk Nickel generated 2,436,000 t (within this amount, Zapolyarny
Subdivision of MMC Norilsk Nickel generated 2,140,000 t). Typical atmospheric emission of hazardous substances from any other Russian non-ferrous metallurgical works was
about few dozen thousand t.
4.4.1 Mercury in Non-Ferrous Metal Ores and Concentrates
Mercury is characterised by wide metallogenic connections. In the ore formation process, mercury is an element that accompanies mineral formation process in a wide range of
temperatures and physical and chemical conditions. (Ozerova, 1962, 1986; Rogovoi, 1989; Fedorchuk, 1983; Fedorchuk, Mintser, 1990). A large complex of deposits is known,
where mercury is represented in the proper mineral form (for example, copper and silver deposits), or is a part of complex minerals (platinoid type deposits), or exists in the
interspersed condition (copper pyrite, copper nickel, iron pyrite, complex ore deposits, etc.). Very high content of mercury is characteristic for ores from some stratimorphic
deposits. Minor scale aggregations of mercury in cupriferous sandstone are known (from a few tenths to a few mg/kg). Higher concentrations of mercury are characteristic for
some iron, manganese and aluminium (alunite and bauxite) ores.
Sulphide deposits are distinct with considerable scale of mercury yield, where sulphide zinc ores are most rich mercury (up to 10 - 100 mg/kg) (Fedorchuk, 1983). According to
N.A.Ozerova (1986), the overall quantity of mercury contained in pyrite deposits in Ural corresponds to a medium to large size commercial mercury deposit by its scale. Estimated
average content of mercury in pyrite deposit ores is 1 mg/kg (Ozerova, 1962); estimated average content of mercury in complex ores is 1.1 mg/kg (Korolev, Bobrova, 1963).
However, its level in commercial ore types has high variations (Table 4.34 and Table 4.35). As a rule, the maximum concentration of mercury is characteristic for copper-and-zinc
varieties, while the minimum concentration is characteristic for iron pyrite ores.
Sphalerite-chalcopyrite-pyrite ores from volcanogenic objects are characterised by especially high concentration of mercury. All copper pyrite deposits in South Ural (Uchalinskoe
deposit, Uzelginskoe deposit, Sibaiskoe deposit, Buribaiskoe deposit, Ubileinoe deposit, Gaiskoe deposit etc.) belong to this group. For example, mercury concentration varies
from some hundredth mg/kg to 800 mg/kg in ore from Uzelginskoe field, from 2 to 560 mg/kg in ore from Uchalinskoe field, and from 1 to 88 mg/kg in ore from Novouchalinskoe
deposit; all these ores being processed at Uchalinsky Mining and Concentration Combined enterprise (MCC). (Mineral Resources of Uchalinskoe ..., 1994).
Table 4.34 Mercury in ores and minerals in lead-zinc and copper deposits, mg/kg (Bobrova et al., 1990)
Commercial type of the deposit |
Ores |
Sphalerite |
Galenite |
Chalcopyrite |
Pyrite |
Fahlore |
Pyrite and complex (Altai type) |
0.1 - 20 |
0.2 - 26.1 |
0.01 - 16 |
0.4 - 3.4 |
0.2 - 10 |
traces - 300 |
Stratimorphic lead-zinc (Atasui type) |
0.9 - 406 |
23 - 7,600 |
0.6 - 530 |
1 - 240 |
2 - 50 |
below 12% |
Vein lead-zinc type |
?* |
0.4 - 1,000 |
0.075 - 25 |
?* |
0.1 - 100 |
80 - 800 |
Copper pyrite type |
0.6 - 900 |
70 - 250 (äî; 0.5-1.5%) |
?* |
?* |
?* |
below 3% |
* Here and hereinafter the mercury was not detected.
Table 4.35 Mercury in ores of sulfur deposits (Ozerova, 1962, 1986)
Deposit |
Mercury in ore, mg/kg |
Urals |
Mezhozernoe |
10-90 |
Komsomolskoe |
0.1-9 |
Sibaiskoe |
10-90 |
Gaiskoe |
1-90 |
Uchaly, Chadarskoe, Degtiarskoe, Krasnogvardeiskoe |
1-9 |
III International |
0.5-20 (average ~ 7) |
Maukskoe, Polevskoe, 50 Let Oktabrya |
0.1-0.9 |
Caucasus |
Filizchai |
10-90 |
Urup |
0.1-90 |
Vlasinchikhinskoe, Skalistoe |
0.4-15 |
Average content of mercury in sulphide copper-and-nickel ores is 1 mg/kg (Fedorchuk, 1983), though, for example, its concentration is as high as 9 mg/kg in ore from
Monchegorskoe copper-and-nickel deposit (Ozerova, 1962). Content of mercury in ores form copper pyrite complex deposits is 5 to 10 mg/kg; content of mercury in barite and
fluorite ores is 1 to 10 mg/kg (Fedorchuk, 1983). Exceeding concentration of mercury are also present in ore from other deposits (Table 4.36).
Table 4.36 Mercury content in ores from various deposits (Fursov, 1983)
Deposit |
Deposit type |
Average (range), mg/kg |
Tungsten |
Tyrnyauz, Caucasus |
Skarn type |
0.49 (0.25-0.87) |
Bom-Gorkhonskoe, Baikal Region |
Hydrothermal |
0.77 (0.38-1.51) |
Kholtosonskoe, Baikal Region |
Hydrothermal |
0.99 (0.73-1.35) |
Molybdenum |
Prvomaiskoe, Baikal Region |
Hydrothermal |
0.83 (0.72-0.98) |
Shakhtaminskoe, Baikal Region |
Hydrothermal |
1.27 (1.17-1.5) |
Tantal, niobium |
Deposits in the Far East and Baikal Region |
- |
(0.48-0.54) |
The main mass of mercury exists in the ore in the sulphide form as finely dispersed admixture in ore-forming minerals. Sphalerite is the main concentrator and media for mercury
(Ozerova, 1986). Fahlore, galenite, bornite, chalcopyrite, and pyrite are concentrators of mercury too. For example, 80-90 % of mercury is connected with sphalerite, 10 % of
mercury is connected with chalcopyrite, 5 % is connected with galenite, 3 % is connected with pyrite in ores from pyrite and complex ore deposits; about 70% of mercury is
connected with pyrite and up to 7 % of mercury is connected with chalcopyrite in ores from copper pyrite deposits in South Ural. (Bobrova et al., 1990). Accumulation of mercury
is observed in the areas of oxidizing of pyrite deposits (up to 80 mg/kg), sometimes mercury is found in metallic form in such areas (Kutliakhmetov, 2002).
Behaviour of mercury in the course of concentration of non-ferrous metal ore
Breaking and milling of ore and subsequent collective-and-selective or selective flotation and obtaining of various concentrates are the main techniques used in the concentration
works. In general, content of mercury in concentrate is very uneven, and it generally increases by one order of magnitude as compared to ore in zinc concentrate and (somewhat
less) in lead concentrate, making several dozen mg/kg on average. Concentration of mercury in the copper concentrate (for copper pyrite ores) increases by 2- 2.5 times, however
this is not observed in a number of cases (Table 4.37).
Table 4.37 Mercury content of industrial concentrates, g/t (Bobrova et al., 1990; Ozerova, 1986)
Commercial type of deposit |
Zinc |
Lead |
Copper |
Pyrite |
Molybdenum |
Tin |
Tungsten |
Pyrite and polymetal type |
0.3 - 175 |
0.3 - 390 |
0.22 - 65 |
0.2 – 11.4 |
- |
- |
- |
Stratiformic lead-and-zinc type |
8 - 1,700 |
0.6 - 520 |
2 - 290 |
2 - 90 |
1 - 4 |
- |
- |
Scarn and substitution lead-and-zinc type |
6.4 - 270 |
1 - 39 |
- |
- |
- |
- |
- |
Vein-type lead-and-zinc |
? |
5 |
- |
- |
- |
- |
- |
Copper pyrite type |
1 - 390 |
- |
0.3 - 150 |
0.1 – 26 |
- |
- |
- |
Cupriferous sandstone |
20 |
6 |
4 |
- |
- |
- |
- |
Vanadium-iron-copper type |
30 |
- |
70 |
90* |
- |
- |
- |
Copper-molybdenum type |
- |
- |
0.02 |
- |
0.1 |
- |
- |
Copper-nickel type |
- |
- |
0.14 – 0.4 |
0.45 - 2 |
18-36** |
- |
- |
Molybdenum-tungsten type |
- |
- |
- |
- |
0.2 – 0.5 |
- |
? |
Tin and tin-and-tungsten type |
- |
- |
- |
- |
- |
0.01 – 0.8 |
0.035 – 0.09 |
Antimony type |
- |
- |
- |
0.7 – 35*** |
- |
- |
- |
* Iron concentrate; ** Platinum concentrate; *** Antimony concentrate;
In the process of concentration of lead-zinc and pyrite-complex ore, main quantity of mercury (up to 70 - 80 %) in extracted into zinc concentrate. To large extent, this is explained
by connection of mercury with sphalerite and other minerals containing zinc (Table 4.38).
Table 4.38 Distribution of mercury (in percent of overall content in ore) to products of concentration of ore from lead-zinc and copper deposits, average value (range
of individual samples) (Bobrova et al., 1990)
Commercial type of deposit |
Concentrates |
Reject
material |
Zinc |
Lead |
Copper |
Pyrite |
Barite |
Pyrite and polymetallic type |
78.8 (78 – 79.5) |
1.1 (0.7 – 1.4) |
2.5 (0.7 – 4.4) |
? |
Is not extracted |
17.6 (16.8-18.4) |
Stratiformic lead-and-zinc type |
68.2 (66.8 – 93.1) |
20.4 (1.6 – 57.2) |
Is not extracted |
5 |
3.8 |
2.7 |
Copper pyrite type |
7.8 |
Is not extracted |
19.1 – 24.9 |
67.5 – 68.1 |
Is not extracted |
5.7 |
Vanadium-iron-copper type |
57 |
Is not extracted |
4.7 |
26.3* |
Is not extracted |
? |
Cupriferous sandstone |
Is not extracted |
9.2 |
28.8 |
Is not extracted |
Is not extracted |
? |
* Into iron concentrate.
In the course of concentration of copper pyrite ore, pyrite concentrate makes the main mass of product. Its output is measured in the range of 25 - 70 % (and up to 80 % for solid
ore). Therefore, it is pyrite concentrate where a considerable part of mercury (up to 40-60% of content in the ore) is lumped despite low content of mercury (usually a few mg/kg,
most often within 0.75 to 3 mg/kg).
Pyrite concentrates produced in the course of concentration of non-ferrous metal ore are used as feed for production of sulphuric acid in chemical sector plants; in so doing, only
selenium is produced from sulphuric acid sludge as by-product. Besides, some part of pyrite waste is processed it copper and lead-and-zinc combined works. Considerable
quantities of pyrite concentrates containing mercury have been accumulated by now in vicinity of many Russian ore concentration works. For example, 1 million t of pyrite
concentrates are piled in the area of Uchalinsky MCC, and 1.5 million t are piled in the vicinity of Bashkirsky Copper and Sulphur Combined enterprise (Magadeev et al., 1997).
Usually temperature in the cycle of ore processing in the ore concentration plant is not high (below 100 °C), that is why mercury virtually never goes to the atmosphere. For
instance, this is confirmed by results of gas and mercury observation at the industrial site of Uchalinsky MCC (Kutliakhmetov, 2002). Major part of mercury that is extracted along
with pyrite ore, goes into concentrate and moves to processing together with it; only small quantity (less that 2 -7 % of overall mass in ore) goes to concentration waste which is
piled in the reject material storage areas (see Table 4.39). As it is mentioned above, mercury is more intentsively joins pyrite concentrate (prevails by mass) and zinc concentrate
(has higher metal content). Mercury content in tails may also be rather high (up to 1-9 g/t). In the area of Uchalinsky MCC, weight of piled reject material from the concentration
works reaches 28 million t; weight of reject material piled in the vicinity of the concentration works of Bashkirsky Copper and Sulphur Combined enterprise is 480 million t;
(Magadeev et al., 1997); weight of piled reject material in the area of the concentration works belonging to Buribaiskoe Mining Administration is 6 million t; and, obviously, it
contains several hundred t of mercury.
Table 4.39 Distribution of mercury in ore concentration products at Uchalinsky MCC (Kutliakhmetov, 2002)
Ore, concentrate, waste |
Average , gram Hg / ton |
Relative quantity of mercury, % |
Ore * |
10-25 |
100 |
Pyrite concentrate |
5-15 |
36-50 |
Copper concentrate |
28-41 |
10-14 |
Zinc concentrate |
76-123 |
35-48 |
Reject materials |
1-9 |
2-9 |
* The concentration works of Uchalinsky MCC processes over 2 million t of copper pyrite ore per year.
Foreign data (Klimenko, Kiazimov, 1987) also show that mercury gets concentrated and accumulates chiefly in zinc concentrate (Table 4.40). Versus the concentration plant of
Gaisky MCC, the considerable rate of going into waste (up to 27 % of total quantity in ore) is noticeable; which is probably specific to the employed technology.
Table 4.40 Content of mercury in concentration products of Brunswik Works (Canada) (Klimenko, Kiazimov, 1987)
Product |
Quantity of processedore, t per day |
Content of Hg |
Extraction, |
|
|
Mg/kg |
Kg per day |
% |
Input ore |
8,575 |
2.1 |
18.24 |
100 |
Copper concentrate |
73.7 |
2.3 |
0.15 |
0.87 |
Lead concentrate |
400 |
2.7 |
1.09 |
5.97 |
Compound concentrate |
70 |
9.1 |
0.64 |
3.5 |
Zinc concentrate |
900 |
13.5 |
12.22 |
67.0 |
Reject material |
7,140 |
0.69 |
4.94 |
27.0 |
According to available overall estimates (Bobrova et al., 1990), distribution of potential total mercury resources in main industrial concentrates from lead-and-zinc and copper
deposits (percent) is as follows: zinc concentrate –42; pyrite concentrate 26; copper concentrate – 19; lead concentrate 13. In turn, considerable quantities of mercury are supplied
to national zinc (lead-and-zinc) and copper works together with concentrates of main metals; of which 65 % are connected with zinc concentrates, 20 % are connected with
copper concentrates and rich ores, 15 % are connected with lead concentrates.
Presence of considerable quantities of waste material containing some quantities of mercury in the area of concentration works predetermines potential engagement of mercury in
migration chains in the course of deterioration of waste piles due to hypergenic processes. In addition to that, mercury is released to the environment directly in the course of ore
mining. For instance, mercury concentrations were 20 and 13 microgram/l in mine water of Sibaiskoe and Oktyabrskoe fields, accordingly (Mustafin et al., 1998); and mercury
concentration in Buribaisky quarry water was 28.3 microgram/l, while the water was used for circulating water supply and discharged periodically into river Tanalyk (Zainullin,
Galimova, 1998), this was many times higher than the typical background level of this metal in natural water. Influx of pollutants to surface water streams is also connected with
wastewater leaking through dams and leaching products leaking from reject material storage areas. Degasification of mercury from waste piles generated by non-ferrous metal ore
mining and concentration during warm season is also possible.
4.4.2 Primary Production of Zinc
Primary production of zinc includes the following processes: concentration of zinc ore, oxidization (blend roasting) of zinc concentrate, production of zinc (by means of
electrochemical or thermal process), refining of zinc. Production of primary zinc is usually accompanied by production of sulphuric acid using standard processes.
Russian producers of zinc
In 2001 mainly two enterprises produced zinc in Russia: Chelyabinsk Zinc Works (town Chelyabinsk) and Electrozinc JSC (town Vladikavkaz). The third producer, Belovsky Zinc
Works, produces mainly zinc powder (Table 4.41). Several works belonging to Uralskaya Mining and Metallurgical Company and MMC Dalpolymetall JSC also produced some
small quantities of zinc (Kovalishina...). However in 2001 their total production was few dozen tonne of zinc. For example, in the 1st quarter of 2002 MMC Dalpolymetall JSC
produced 8.2 t of zinc (http://www.aviaport.ru/news/Markets/a1020229200.ht...). Thus, works in Chelyabinsk and Vladikavkaz were main sources of mercury emission to the
environment in 2001.
Table 4.41 Production of zinc by Russian works, th.. t
Enterprise |
Whereabouts |
1999 |
2000 |
2001 |
2002 |
Chelyabinsk Zinc Works |
Chelyabinsk |
138.3 |
145.7 |
155.5 |
165.8 |
Electrozinc* |
Vladikavkaz |
90.9 |
92.6 |
91.1 |
88.4 |
Belovsky Zinc Works |
Town of Belovo, Kemerovo
Oblast
|
2.8** |
2.2** |
4 |
2.84** |
Total in Russia |
232 |
241.9 |
250.6 |
257.1 |
* Operates under a tolling scheme (up to 85 - 90 % of produced metal; for example, it supplied just over 2 ,000 t of zinc to the internal market); ** zinc powder.
Source: Gerasimchuk et al.; Metallurgist, 2002, # 4; Polkin...; Polkin, Anisimov, 2002; Polkin, Ponomareva...; Russian zinc market...; http://www.aviaport.ru/news/...;
http:www.metalinform.com/...; http://www.zinc.ru/news.php3
Chelyabinsk Zinc Works (CZW) was established in 1935. It is located within town Chelyabinsk (dimension of the sanitary control area is about 1000 m). Besides metallic zinc it
produces zinc-aluminium alloys, foundry zinc alloy ingots, cadmium, metallic indium, technical grade zinc sulphate, zinc oxide, technical grade sulphuric acid. A process for
production of indium powder with particle size from 1 to 5 micrometer was implemented in the works in 2001 (http://metal.klimenko.ru/catalog/Detailed/21.html). There is some
information that Chelyabinsk Zinc Works have managed to `completely resolve the issue of mercury-and-selenium sludge' that is reportedly brought to Kyrgyzstan for processing,
and recently `the enterprise got close to resolving the issue of utilisation of mercury from gases' (Stepanov...). In particular, in order to reduce content of mercury in acid, the
enterprise planned to purchase a plant for utilisation of mercury from gases from Boliden Company. This would permit complete elimination of mercury emissions and considerable
decrease of sulphur oxide emission. In 2001 wastewater from the works were discharged to Miass River; and fresh water was taken from the same river.
Besides zinc, Electrozinc JSC (Vladikavkaz) produces lead, cadmium, sulphuric acid, copper sulphate, steel structures. Its share in total emission from stationary sources in the
Republic of Severnaya Osetia - Alania is about 70 %. Over 3.2 million t of solid waste was placed in the territory of the works by 1999; it contained several dozens t of mercury
(Satsaev, 2002). In 2001 Belovsky Zinc Works JSC completed reconstruction of a zinc powder plant and commenced production of commercial products.
Raw materials and mercury content in zinc concentrates
Zinc is mainly produced from polymetallic sulphide ores containing also compounds of lead, copper, cadmium and other metals. Polymetallic sulphide zinc ores could be divided
into lead-and-zinc, copper-and-zinc and lead-copper-zinc ore. Deposits in the Caucasus, Salairskoe and Sikhote-Alin deposits belong to the lead-and-zinc type. Copper-and-zinc
ores mainly come from Ural deposits. Major part of Altai ore is of lead-copper-zinc type. Lead-zinc and copper-lead-zinc ores are also raw materials for commercial production
of lead. Cadmium is extracted mainly as by-product along with zinc. In addition to that, copper-zinc pyrite ores and zinc pyrite ores are important for production of zinc. These are
available in varieties in zinc-and-copper pyrite deposits, and they are quite common in lead-and-copper deposits. There are pyrite polymetallic ores consisting predominantly of
pyrite and pirrhotine, and polymetallic ores, in which content of pyrite and pirrhotine does not exceed 2- 4 % (Gorzhevsky et al., 1997). Typical content of zinc in the ores being
processed is 1-3 % on average.
As mentioned above, due to low content of metals, first sulphide ore undergoes concentration process in order to extract concentrate. The concentration process (the enterprises
use fragmentation, initial concentration and floatation) produces zinc and other concentrates depending on composition of raw ore. For example, in the course of concentration of
pyrite-and-polymetallic ore the enterprises produce four concentrates: lead, zinc, copper and pyrite concentrate. Domestic zinc concentrates usually contain the following (percent):
zinc 45-51; lead 0.2-2.5; cadmium 0.1-0.25; iron 3-12; sulphur 30-38, gangue up to 10 (Gudima, Shein, 1975; Denisov, 1991; Basics of metallurgy..., 1962; Utkin, 1990).
In 2001 Chelyabinsk Zinc Works was oriented mainly to supplies of raw material from deposits in Ural region, which give more than 75% of total output of Russian zinc
concentrates. These supplies, from Uchalinsky, Gaisky and Sibaisky mining and concentration combines, provide about 95% of the works' demand of zinc concentrate. In 2001
MCC Uchaslinsky JSC was a main supplier of zinc concentrate for Chelyabinsk Zinc Works (providing up to one half of the overall quantity). Recently Chelyabinsk Zinc Works
purchased up to 20,000 t of concentrate (having zinc content 55-60 %) abroad every year.
In 2001 Chelyabinsk Zinc Works processed about 330,000 t of zinc concentrate. Electrozinc Works in Vladikavkaz was processing zinc concentrates coming, as one can guess,
mainly from Kazakhstan, China and Poland. Insignificant quantity of concentrate was supplied from Sadonsky lead-and-zinc works. In 2001 the works processed about 190,000 t
of zinc concentrate. Belovsky zinc works, presumably, received zinc concentrate from Ural and Sibertian (Altai) deposits. In 2001 weight of processed concentrate was 6,300 t.
Zinc concentrates, especially those produced by Ural concentration works that process ore from local copper-and-pyrite deposits, are characterised by high content of mercury
(Table 4.42, Table 4.43, Table 4.44). According to A.N. Kutliakhmetov (2002), mercury content in zinc concentrate produced by Uchalinsky MCC is 76 to 123 mg/kg.
Table 4.42 Composition of zinc concentrates (data of institute Gintsvetmet)
Mining and concentration combined enterprise |
Zinc, % |
Mercury, mg/kg |
Uchaslinsky |
45.5 |
20 |
Gaisky |
49.9 |
100 |
Baskirsky copper-and-sulphur combined enterprise |
44.1 |
30 |
Novoshiroksky mine |
54.0 |
10 |
Altaisky |
34.5 |
< 3 |
Dalpolymetall JSC |
49.1 |
3 |
Table 4.43 Mercury in zinc concentrates from pyrite and pyrite-and-polymetallic deposits (Ozerova, 1986)
Region |
Deposit |
Mercury in concentrate, mg/kg |
Average (estimated), mg/kg |
Middle Ural |
III International |
4.5 |
4.5 |
Lomovskoe, Levikhinskoe |
1-2 |
1.5 |
South Ural |
Gaiskoe |
10-25 |
17 |
Uchalinskoe |
10-75 |
42 |
XIX Party Congress |
25-75 |
50 |
Sibaevskoe |
1.8-7.5 |
4.7 |
Caucasus |
Filizchaiskoe |
18 |
18 |
Madneulskoe |
1.2 |
1.2 |
It seems that average content of mercury shown in Table 4.44 sufficiently correctly reflects mercury level in concentrates processed by Chelyabinsk Zinc Works in 2001. Similar
content may be assumed for Belovsky works. There is no direct information on content of mercury in concentrates supplied for processing to Electrozinc JSC. However it is
known that lead-and-zinc ores of Kazakhstan and zinc concentrates made of Kazakh ore usually have very high content of mercury (Bobrova et al., 1990).
Table 4.44 Mercury in zinc concentrates from Ural concentration works (Mustafin, 1998)
Concentration works |
Mercury, g/t |
Krasnouralskaya |
30 |
Kirovogradskaya |
20 |
Sredneuralskaya |
64 |
Gaiskaya* |
65 |
Uchalinskaya* |
53 |
Sibaiskaya* |
93 |
Karabashskaya |
91 |
Average |
59.4 |
* Main suppliers of zinc concentrates to Chelyabinsk Zinc Works.
Thus, in 2001 about 20 t of mercury was supplied with concentrates to Chelyabinsk Zinc Works for zinc production, 11 t of mercury was supplied to Electrozinc JSC, and 0.3 t of
mercury was supplied to Belovsky Zinc Works.
Processes and technologies
Hydrometallurgical (electrolytic) and pyrometallurgical (distillation) process systems are used for processing of zinc concentrates. The hydrometallurgical process is the main one
(works in Chelyabinsk and Vladikavkaz); the thermal process is used in Belovsky works.
Roasting of sulphide concentrates in order to convert sulphide compounds into oxidized compounds is the first operation in any process of zinc production from sulphide
concentrates. In the pyrometallurgical process, first the enterprises usually subject the initially dried concentrates (drying of the concentrates is done in drum-type kilns at the
temperature of incoming furnace gases, 700 - 800 °C) to incomplete oxidizing roasting process in multiple-bedded furnaces. This process produces powder. Then the powder is
sintered in agglomeration machines (at temperature 1,200°C). In the course of roasting, the purpose is to receive frying gases with high content of SO2 usable for production of
sulphuric acid and to catch evaporated useful metals. Ready agglomerate contains 0.5 - 0.8 % of sulphur. Physically it is roughly coked mass of porous material. It is subjected to
fragmentation and screening prior to going into distillation process. Then zinc oxide is deoxidised in retorts at temperatures above the boiling point of metallic zinc (above 906 °C).
This results in zinc sublimation as vapours which go into a condenser, where zinc is collected in liquid form. The zinc vapour is condensed, then the received crude zinc goes into
refining process.
Frying of zinc concentrate prior to hydrometallurgical processing is done in fluid-bed furnaces (the temperature of the flying bed is maintained at 900-950 °C, the temperature of
gas under the furnace roof is 800-850 °C). The fried product (cinder) contains about 55-65 % of zinc. Compounds of copper, lead, iron, cadmium, arsenic, antimony, cobalt,
noble and rate metals are also present in the cinder; content of sulphide sulphur is less than 1 %. The cinder is unloaded over the sill block by gravity flow and is transported to the
classification section. Dust is collected in cyclones; periodically they unload it and add to the cinder. Along with cinder and dust from cyclones they use dust from gas ducts of
electric filters. All these products are processed together. According to data from works Electrozinc, which may be regarded as typical data, output of frying products (percent) is
as follows: cinder – 65, dust from cyclones – 30, dust from gas ducts – 1.1, dust from electric filters – 3.3, ventilation dust 0.6 (Gudima, Shein, 1975). In Chelyabinsk Zinc Works
they sometimes add materials containing calcium oxide (sludge from treatment facilities) to the batch of concentrates being fried. This allows for processing of off-grade
concentrates with high content of silicon (Tarasov, 2001). Then zinc is leached from cinder using water solution of sulphuric acid. The enterprise carry out leaching in order to
completely transfer zinc and some components accompanying zinc into solution. Usually the enterprise manage to transfer about 90% of zinc into the solution (assuming that zinc in
cinder is 100%). Prior to electrolysis the enterprise remove admixtures from the solution. Then the solution is fed into electrolysis baths.
In the course of electrolysis zinc is plated on the cathode, while oxygen is released on the anode. In so doing, sulphuric acid is generated in the solution, which is necessary for
leaching of fresh portions of cinder. Cathode zinc deposits (cathode zinc) are melted in induction furnaces, and obtained zinc is cast into ingots using special machines.
Sources and characteristic of dust and gas generation
Flying-bed frying furnaces are main sources of dust and gas emissions at zinc works; flying bed furnace gases are characterised by high temperatures (up to 950 °C), considerable
dust content (up to 300 g/m3) and domination of small dust fractions (2.5 - 4.5 micrometer). Quantity of flue (frying) gases varies within the range of 1.3 to 3.1 thousand m3 per
tonne of concentrate. After cleaning flue gas goes into sulphuric acid production process. The flue gas cleaning system is comprised of cyclones (rough cleaning) and dry electric
filters (fine cleaning). In addition to that, the gas is treated in washer towers and wet electric filters immediately in the sulphuric acid production section. According to (Emission of
heavy metals..., 1998), in mid 1990-ties there were the following specific rates of dust emission in the course of production of zinc in CIS works: with cleaning efficiency 95 % –
57.2 kg kg/t of crude zinc; with cleaning efficiency 98 % – 17.2 kg/t; with cleaning efficiency 98 % – 2.29 kg/t of crude zinc.
According to (Denisov, 1991), cleaning efficiency of frying gas cleaning in enterprises if former USSR varied from 81.6 to 99.6 %. Average efficiency of the cleaning equipment
was estimated as 98.5 % (Savrayev, 1990). There are all grounds to assume that the latter figure corresponds to the level of 2001.
Emission and distribution of mercury in the course of zinc production
Behaviour of mercury in the primary production of zinc has been studies very little, therefore there are no reliable actual data regarding specifics of mercury distribution in main
products, waste and regarding emission to the environment.
It is known that about 35-40 t per year were supplied to Chelyabinsk Zinc Works together with zinc concentrates in 1988-1990 (Report on Research under title `Analysis of
Condition of Mercury ...', 1999). According to (Kamenev, Fadeeva, 1983), levels of mercury in zinc concentrates processed during 1970 - beginning of 80-ies reached 200
mg/kg. Authors of the cited publications believed that mercury was sublimated and went into sulphuric acid production process during frying of concentrates. As the technology of
flue gas cleaning used in the gas washing section of sulphuric acid production section of Chelyabinsk Zinc Works did not ensure complete entrapment of mercury, a considerable
quantity of mercury was going into produced sulphuric acid. According to (Report on research work under title `Analysis of condition of mercury ...', 1999), about 10-12 t per
year of mercury precipitated in the form of mercury-selenium sludge in the gas washing section, while other 25-30 t of mercury went into sulphuric acid. Annual sludge generation
reached 30-35 t at the time. Table 4.45 shows data of Ginstvetmet Institute that characterise quantities of mercury containing sludge generation in Russian zinc enterprises in 1985 -
2000.
Table 4.45 Quantities of mercury-selenetic sludge at non-ferrous metal works of Russia , tonnes
Enterprise |
1985-1990 |
1990-1995 |
1995-2000 |
sludge |
mercury |
sludge |
mercury |
sludge |
mercury |
Chelyabinsk Zinc Works* |
250 |
70 |
404 |
88 |
525 |
115 |
Belovsky Zinc Combined Enterprise |
850 |
27 |
850 |
27 |
850 |
27 |
* Until 1985, mercury and selenium sludge was supplied from Chelyabinsk Zinc Works to Ust-Kamenogorsk lead-and-zinc combined enterprise for processing; also there was a
production of by-product mercury from the said sludge in Chelyabinsk Zinc Works during an insignificant period.
The research conducted at the time in Chelyabinsk Zinc Works (Kamenev, Fadeeva, 1983), have shown that mercury transferred to the sulphuric acid production process
distributed as follows (it was assumed that content of mercury in frying gas equalled 100%): washing acid – 16.7%; sludge – 43.3%; product sulphuric acid – 36.6%; flue gases –
0.4%. Thus, 60% of mercury brought in together with gases was arrested in the washing section of the sulphuric acid production section and was removed with washing acid and
sludge. The remaining mercury went into drying and absorption section and contaminated product sulphuric acid. The authors of the cited publication had studied the balance of
distribution of forms of existence (conditions) of mercury in various products (Table 4.46).
Table 4.46 Balance of distribution of forms of existence (conditions) of mercury in various products of sulphuric acid production at Chelyabinsk Zinc Works, %
(Kamenev, Fadeeva, 1983)
Product |
Hgo |
Hg2h2 * |
HgS |
Hg2SO4 |
HgmSen |
HgSO4 |
Frying gas |
99.3 |
0.4 |
0.3 |
- |
- |
- |
Sludge |
4 |
9.5 |
50.5 |
- |
36 |
- |
Sulphuric acid |
- |
- |
- |
3.2 |
- |
96.8 |
* Mercury halides.
In publication (Bobrova et al., 1990) there is a diagram of distribution of mercury in process products generated in the course zinc production (Figure 4.8). The diagram is based
on data of (Kamenev, Fadeeva, 1983) and on authors' own estimates. In the course of frying of zinc concentrates, 94 % of mercury contained in the concentrate sublimates and
goes into frying gases in the form of metal vapours. The gases (having content of SO2 > 3.5 %) pass the dust arresting system (where up to 32 % of mercury is removed with dust)
and then go into sulphuric acid shops in order to produce sulphuric acid using the standard contact technique processes. Sulphuric gases get condensed in special washer towers in
the washing section of the sulphuric acid shop. The condensate goes to electric filters, from there the filtered condensate goes into the sulphuric acid production process, while
sludge enriched with selenium and mercury is transferred to a special plant. There sludge is processed to the commercial condition using floatation technique. Content of mercury in
lean sludge in settling tanks of the washer towers is 5-18%. Content of mercury in rich sludge of wet filters is 10-40%. An average Hg extraction from concentrates to sludge is
usually 27% (from mercury content in concentrates). A considerable quantity of mercury goes into commercial sulphuric acid and is arrested by washing acid. It is necessary to
note that the level of utilization of both mercury and mercury-selenium sludge was extremely low in Russian zinc works (Bobrova et al., 1990). For example, rate of mercury
extraction from zinc concentrates up to 99.5 % was achieved in Finland in late 1990-ties by three-stage cleaning of frying gases using the technology developed by Oytocumpu Oy
Company. This yielded over 70 t of commercial metal per year (Butov et al., 1997).
Firstly, all above estimates and diagrams of mercury distribution are relative to large extent (usually there are no data on absolute mercury distribution in products of zinc
production) and are characterised by some mismatch of mercury balance; secondly, all above estimates and diagrams of mercury distribution are based on the assumption that
atmospheric emission of mercury in the course of production of zinc and sulphuric acid either doesn't exist or, at least, is minimal (maximum 0.2% of the quantity of mercury
contained in concentrates), which certainly does not match the actual condition. In particular, mercury is capable of going into the environment when unloading the glowing cinder
from the furnace, during the periodical removal of dust from the cleaning system, or due to presence of various leakages (non-tight places) in the furnace, gas ducts and treatment
facilities, or together with ventilation emission, with aerosols and vapours generated in electrolysis processes, in the course of leaching, or mercury can emit directly in the rooms of
sulphuric acid production section (with steam and flue gases).
Certain amount of mercury is lost in the course of washing (goes into sewerage) and drying (goes to atmosphere) of mercury-and-selenium sludge. For example, content of mercury
in bottom sediments in river Kambileevka, that receives wastewater from Electrozinc Work in Vladikavkaz, is higher than the background values by several hundred times.
Intensive technogenic anomalies in river deposits are observed at distance 70 km below the works and are also registered in river Terek, where the River Kambileevka flows in
(Yanin, 2002). Concentration of mercury in atmospheric air in the vicinity of Electrozinc Works was higher by several hundred times than the background values (Volokh, 1998).
According to (Bobkov et al., 1997), specific emission of mercury to atmosphere in the primary zinc and cadmium production is 42 g of mercury per tonne of the product; the
authors of the cited publication estimate emission factor of zinc for the said production as 15,720 g/t. According to (Emission of heavy metals..., 1998), specific emission of zinc
for zinc works in CIS, depending on dust arresting efficiency , was 24,596 g/t with dust arresting efficiency 95 %; 7,396 g/t with dust arresting efficiency 98.5 % (this emission
treatment level is typical for works in CIS); and 984.7 g/t with dust arresting efficiency 99.8 %. If we assume emission treatment level of 98.5 %, then we can more or less
reasonably assume that specific mercury emission for such conditions was approximately 20 g/t.
In 1996 Chelyabinsk Zinc Works emitted 2.51 t of mercury to the air (Atmospheric air, waste, radiation ...). With annual production of zinc in the order of 115,000 t, specific
emission was 21.8 g/t (which is close to the above value). It is evident that these figures reflect the situation existing in the country's zinc industry at the time rather adequately. For
example, it is known that the quantities of zinc concentrate processing were considerably increased due to decrease of quality of supplied zinc concentrates, in the end of 1980-ties.
The flying-bed furnaces and the dust arresting systems were operated in boosted mode at the time.
Emission cleaning efficiency was low because of use of cleaning equipment beyond the normative service life and increased failure rate of the equipment. The capacity of electric
filters was used by 50% on average, because their operation was frequently interrupted by running repairs and overhauls. It was exactly in the mid 1990-ties that stable
concentrations of mercury vapours 1.5 to 2 times higher than the maximum allowed concentration (MAC) were observed in some areas of town Chelyabinsk
(http://www.chrab.chel.su/archive/17-10-97/1/RE12.D...). Concentration of mercury in the air was 5 times higher than MPC within the industrial zone of Chelyabinsk Zinc Works,
and concentration of mercury in the soil around the works was 100 times higher than the background values. It is also known that mercury-and-selenium sludge was dumped in the
territory of the works.
According to official information (Consolidated report on protection of ...), mercury emission from the non-ferrous metallurgy sector (that means from the zinc works) was as high
as 1,229 kg in Chelyabinsk in 2001. With annual zinc production at Chelyabinsk Zinc Works of 1,555,500 ton, specific mercury emission was 7.9 g of mercury per tonne of
produced zinc. It seems that the considerable decrease of specific mercury emission in 2001 compared to 1996 was a result of some improvements of technological processed in
Chelyabinsk Zinc Works in 2000-2001, and there are some references to this in press (Stepanov...; Tarasov, 2001, 2002).
Figure 4.8 Diagram of mercury distribution in processing products of zinc production (Bobrova et al., 1990)
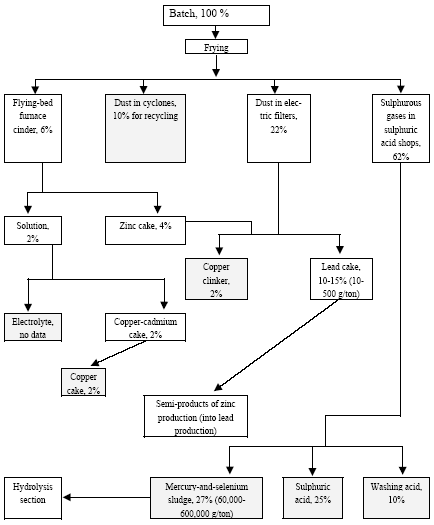
Thus we will assume that specific emission of mercury in the course of primary zinc production in Russian works was 7.9 g for 1 t of metal.
The data discussed above allow us to draw up a diagram of relative distribution of mercury in the course of zinc production using electrolysis process and in the accompanying
production of sulphuric acid (Figure 4.9).
Figure 4.9 Distribution of mercury in the course of zinc production using hydroelectric metallurgy technique
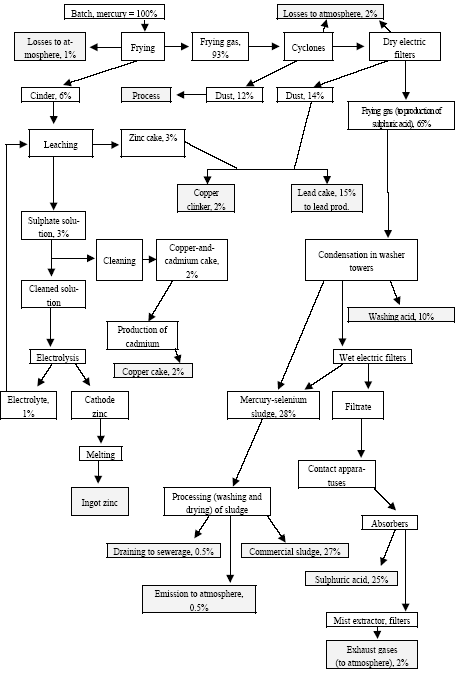
When drawing up this diagram, we took into account specific features of selenium behaviour in technological processes of sulphuric acid production in the course of
pyrometallurgical melting of cupreous pyrite. This process is based on frying of pyrite, processing of removed frying gas and production of sulphuric acid using the contact
technique. In practice this process is similar to production of sulphuric acid in the zinc works (Amelin, 1983; Sokolov, 2003).
Summary
Table 4.4 shows the estimated data characterising emission and distribution of mercury in the course of primary zinc production in Russia in 2001. Losses of mercury in the course
of technological processed mainly get to washing acid and product acid, mercury-and-selenium sludge, dust from flying-bed frying furnaces and atmospheric emissions. Some part
of mercury in latent form in transferred to the lead production section together with lead cake from the oxide leaching shop. (At all appearences, the lead cake is presently stored at
the enterprises' territories).
Table 4.47 Emission and losses of mercury in the course of primary zinc
production in Russian works in 2001
Enterprise |
Weight of Hg supplied intothe production with concentrates, ton |
Distribution of mercury, ton |
|
|
Atmospheric emission |
Sludge |
Sulphuric acid |
Goes to sewerage |
Lead cake * |
Copper cake |
Chelyabinsk Zinc Works |
20 |
1.2 |
5.4 |
5 |
0.1 |
3 |
0.4 |
Electrozinc Works |
11 |
0.7 |
3.0 |
2.8 |
0.06 |
1.7 |
0.2 |
Belovsky Zinc Works |
0.3 |
0.02 |
0.08 |
0.075 |
0.001 |
0.05 |
0.006 |
Total (round) |
31 |
1.9 |
8.5 |
7.8 |
0.16 |
4.7 |
0.6 |
* Was in 2001 deposited, in recent years the attempts to arrange the lead cakes processing have been being made in Chelyabinsk
4.4.3 Production of Primary Nickel
This section contains a characteristic of Russian producers of primary nickel and describes raw materials used for production of primary nickel, levels of mercury content in the raw
materials, a technological process of nickel production from silica (oxidised) ore, as well as emission of mercury in the course of processing of the ore in Russian works. Specialties
of production of nickel (and copper) from sulphide copper-and-nickel ores in works belonging to Mining and Metallurgical Company Norilsk Nickel and corresponding estimate of
mercury emission will be described in a special section. We adopted this approach because of a uniform technology used for processing of sulphide copper-and-nickel ore, existing
technological links between works belonging to MMC Norilsk Nickel OJSC and its dominating role in production of copper and nickel in Russia.
Russian producers of nickel
250,000 t of nickel was produced in Russia in 2001 (see Table 4.48). MMC Norilsk Nickel OJSC (hereinafter Norilsk Nickel) occupies a monopoly-like position in nickel
production sector in Russia for many years. Norilsk Nickel is one of leading producers of primary nickel in the world. Main commercial products (related to nickel) of Norilsk
Nickel are: metallic nickel (electrolytic), nickel carbonyl powder, and nickel carbonyl pellet. Other Russian producers of nickel, which are concentrated in Ural region, play an
insignificant role in the domestic market of this metal. Their products are: primary nickel, ferronickel, nickel hydroxide. In 2001 few other works produced nickel and products
containing nickel in small quantities, something like few hundreds t per year; for example, Uralelectromed OJSE (which produced about 900 t of nickel sulphate in 2001),
Kyshtymsky Medelectrolitny Zavod CJSE (copper electrolysis works) and other works.
Table 4.48 Production of primary nickel by Russian enterprises in 2000 and 2001, th. tonnes
Enterprise |
Deposits |
Production, t |
|
|
2000 |
2001 |
Zapolyarny Subdivision
of MMC Norilsk Nickel
|
City of Norilsk,
Krasnoyarsky Krai
|
116 |
120 |
Severonickel Combined Enterprise OJSE
(MMC Norilsk Nickel OJSC)
|
Town of Monchegorsk,
MurmanskOblast
|
101 |
103 |
Pechenganickel JSE |
Town of Zapolyarny,
Murmansk Oblast
|
Produces converter matte, which is processed by Severonickel Combined Enterprise |
Ufaleinickel OJSE |
Town of Verhny Ufalei,
Chelyabinsk Oblast
|
11 |
9.5 |
Rezhsky Nikelevy Zavod OJSE (nickel works) |
Town of Rezh, Sverdlovsk Oblast |
5 |
4.4 |
Yuzuralnickel OJSE |
Town of Orsk, Orenburg Oblast |
8.3 |
9.1 |
Total in Russia |
241.3 |
250 |
Source: BIKI, 2003, # 41; Gerasimchuk et al. Chernyakova...; http://www.aktex.ru/rus.news...; http://minamp.rbc.ru/ru/cp_on_commodity_marcet/ana...; with addenda
It is necessary to note that a part of technological basis of Ural exist since the first half of XX century. Works of MMC Norilsk Nickel in general have more advanced technology
and equipment.
Mercury content of raw materials
Magmatic sulphide copper-and-nickel deposits (Taimir, Kola Peninsula) and hypergenic silicate cobalt-and-nickel deposits in Middle and South Ural (Table 4.49) are main
sources of nickel in Russia. Processing of sulphide copper-and-nickel ore produces major part of nickel. Pentlandite, phyrrotine and magnetite are main minerals in
copper-and-nickel ores. The ores also contain pyrite, cubanite, talnakhite, platinum group minerals, gold, silver, galenite, sphalerite etc. A considerable part of nickel is related to
silicate minerals in the form of isomorphic mixes or fine grain sulphides, which are not extracted in the course of concentration. Major part of cobalt is related to silicates too.
Almost all copper in the ore exists in the form of sulphides. Sulphide ores can be divided into disseminated ore, breccia ore, massive ore, aggregated ore, and
vein-and-disseminated ore. From the angle of mineral composition, there are phyrrotine ore, cubanite ore, chalcopyrite ore, talnakhite ore, and other types of ore. From the angle
of nickel content, there are rich ore and lean ore; lean ore requires primary concentration. The primary concentration produces either combined copper and nickel concentrate or
separate nickel concentrate and copper concentrate.
Rich ore with nickel content over 1 % and nickel to copper ration at least 161 and low content of iron (less than 25%) goes straight to melting. Ores containing 8 - 20 % of iron, 6
- 12 % of sulphur, 18 -30 % of silica belong to self-melting type; they are processed without adding flux. Average content of nickel in ore is 1.6% (Chernyakova...). Major part of
nickel (about 80%) is extracted from rich ore that have average content of metal 2.6-2.9%.
Table 4.49 Main industrial types of Russian deposits of nickel (Krivtsov, Klimenko, 1997)
Type and subtype |
Content in ore, % |
Incidentalcomponents |
Examples ofdeposits |
Nickel |
Copper |
Nickel-and-copper (Norilsk type) |
0.5-3.5 |
1.0-7.5 |
Co, S, Pt and platinoids, Au, Ag, Se, Te |
Talnakhskoe deposit, Oktyabrskoe deposit |
Copper-and-nickel (Bushveldsk type) |
0.35 |
0.2 |
Platinum group metals |
Mochegorsk deposit |
Cupreous-and-nickel (Pechenegskk type) |
1.0 |
0.4 |
Co, S, ilmenite group metals |
Pechenegsk group of deposits |
Silicate-and-nickel crust of weathering |
0.7-1.3* |
- |
Cobalt (0.04-0.2%) |
Serovsk, Pokrovsk, Burtukalsk deposits |
* Estimated average content of nickel 0.9 % (Chernyakova...).
Silicate cobalt-and-nickel ores (in metallurgy they call them oxidized ores) related to weathering crusts of ultrabasic massive have very complex mineral composition and fine
disperse and amorphic and crystalline distribution of metal, which usually participates in various mineral phases. Residual weathering crusts are formed of hypergenic serpentine,
ferrosapolyte, nontronite, hetite-hydrohetite, cobalt-nickel asbolanes, hypergenic magnetite etc.
Nickel serpentine and nickel manganese serpentine, cerolite, pimelite and other minerals containing nickel are typical for filtration zones. Nickel berthierite, hypergenic magnetite
maghemite, millerite, etc. are well developed in converted weathering crusts. Major part of silicate ore belongs to the lean oxidized ore category. Content of nickel in the ore
0.4-1.7%, content of cobalt in the ore is 0.01-0.2%. Ores where cobalt content is more than 0.085-0.1% belong to cobalt ores by definition.
At least 85 % of confirmed nickel resources in the country reside in sulphide copper-and-nickel deposits of Norilsk region (Norilsk-1, Talnakhsk, Oktyabrsk and other deposits).
10 % of Russian nickel resources reside in sulphide deposits in Murmansk Oblast (Zhdanovsk, Zapolyarnoe, Kotselvaara, Semiletka and other deposits). Remaining 5 % are
connected with silicate nickel ores in deposits of Middle and Southern Ural, where Buruktalsk, Sakharinsk and Serovsk deposits are largest ones (Table 4.50). Table 4.51 shows
data available from literature on content of mercury in ores and concentrates from copper-and-nickel deposits. According to V. P. Fedorchuk's data (Fedorchuk, 1983), average
content of mercury in sulphide copper-and-nickel ore is 1 mg/kg. Weathering crusts of ultrabasic massive are the ore-yielding formation with which all silicate nickel deposits are
connected. Average content of mercury in ultrabasic rock is estimated as 0.09 mg/kg (Reference Book on Geochemistry, 1990). Let us assume that this concentration is an
average level of mercury content in silicate (oxidized) nickel ore. Let us also assume that this value accounts for the probability of mercury emission in production of nickel from
fuel, limestone and sulphidizing agents (gypsum, pyrite, kies) as well as from ore, in subsequent calculations.
Table 4.50 Main suppliers of raw materials to Russian nickel works in 2001
Enterprises |
Deposits |
Zapolyarny Subdivision of
MMC Norilsk Nickel
|
Norilsk-1, Talnakhsk, Oktyabrsk (Taimir Peninsula) |
Pechenganickel JSE (Kola Peninsula) |
Zhdanovsk, Zapolyarnoe, Kotselvaara, Semiletka
(Kola Peninsula)
|
Ufaleinickel OJSE |
Serovsk (SverdlovskOblast), Cheremshansk and Sinarsk (Chelyabinsk Oblast) |
Rezhsky Nickel Works |
Serovsk (Sverdlovsk Oblast) |
Yuzhuralnickel |
Buruktalskoe and Sakharinskoe (Orenburgskaya Oblast) |
Table 4.51 Mercury in ores and concentrates from copper-and-nickel deposits (Ozerova, 1986)
Deposit |
Component |
Average
(range), g/t |
Average (estimate**)
g/t |
Taimir Peninsula |
Talnakhsk |
Ore (run-of-mine) |
(0.01-2) |
1* ? |
Ore (massive) (Fursov, 1983)* |
1.3 (0.7-2) |
1.3 |
Pyrite concentrate |
(0.45 – 2) |
1.22** |
Chalcopyrite-pentlandite concentrate |
(0.14 – 0.4) |
0.27** |
Platinum metal minerals |
(18 – 36) |
27** |
Norilsk |
Ore (run-of-mine) |
(0.04-0.08) |
0.06** |
|
Ore (high-grade disseminated) (Fursov, 1983)* |
1.05 (0.79-1.38) |
1.05 |
Kola Peninsula |
Monchegorsk |
Ore |
0.05-0.11 |
0.08** |
Vostok |
Ore |
0.06-0.2 |
0.13** |
Allarechensk |
Ore (Fursov, 1983)* |
1.17 (0.97-1.43) |
1.17 |
Nittis-Kumuzhie |
Ore (Fursov, 1983)* |
1.65 (0.68-2.78) |
1.65 |
* Confidence interval for reliability 0.95. ** Estimated by the author of the present report
Specialties of processing of silicate (oxidized) ores
Pyrometallurgic techniques are used for extraction of nickel from silica ores in practice. These are melting with sulphidizing and reducing fusion in order to receive primary
ferronickel (Gudima, Shein, 1975; Basics of Metallurgy..., 1962). Two techniques are used in order to prepare ore for melting: briquetting (Rezhsky Nickel Works and
Ufaleinickel) and agglomeration (Yuzhuralnickel). Often ore is subjected to drying at temperature 700-800 °C in drying drums prior to briquetting. Black oil (mazoot) is used as fuel
for drying. Black oil consumption is 1-1.5 % of initial ore mass. The dried ore is mixed into batch with sulphidizing agent, and then the batch is briquetted in roll presses.
Agglomeration of oxidized ore is carried out in agglomerating machines. Necessary preparation of ore is carried out prior to agglomeration. This includes screening, milling
(reduction) and mixing with recycled agglomerate in order to increase gas permeability of batch. They do not dry out milled (reduced) ore prior to agglomeration. Essence of caking
in agglomerating machines is chemical and physical transformations of batch at high temperature (about 1,150 - 1,200 °C) achieved by burning breeze coke. Battery cyclones
(having design efficiency 99 %) are used for cleaning of flue gases. Output of good agglomerate is approximately 65-68 % of initial ore quantity.
Prepared oxidized nickel ore is mixed with additive containing sulphur (pyrite, gypsum, kies), flux (limestone) and fuel (coke). The mix is melted in pit-type furnaces to produce
matte. Walls of the furnaces usually have evaporation-type cooling system. (Generally, there are 5 such furnaces at each soviet works). In recent years the enterprise sometimes
added secondary raw materials containing nickel into ore batch. Consumption of sulphidizing agent is 7-9% of the part of batch that contains metal; consumption of limestone is
16-24%, consumption of natural coke is 21-33%. Temperature in the area of tuyeres of the pit-type furnace in focus reaches 1,450 - 1,500 °C, temperature at the throat is 400 -
500 °C. Output of dust carried away with gases is 6 - 18 % of mass of melted batch. It depends on velocity of gases, particle size distribution of batch and other factors.
Scrubbers and multiple cyclones having design efficiency 98-99 % are used for cleaning of flue gases.
Slag is released continuously from the pit-type furnaces through external crucibles and settlers where matte shots are installed. Slag output is 110-120 % of mass of melted
agglomerate or briquettes. Nickel matte is released from the crucible approximately every 2-3 hours. Composition of matte varies within the following ranges: nickel 12-20 %; iron
56-60 %; sulphur 17-23 %; slag impurities up to 4 %; copper and cobalt 0.4-0.6 %. Extraction of nickel to matte is 67-85%, extraction of cobalt to matte is 42-61% (the
maximum values are observed when ore is prepared by briquetting). Then nickel matte is processed in order to obtain metal. The process includes conversion of matte (at
temperature about 1,300 °C) that produces nickel converter matte, and burning of nickel converter matte, that is carried out in two stages (first in flying bed furnaces at temperature
1,000 - 1,150 °C, then in the tube furnace at temperature 750 - 800 °C). In order to reduce nickel protoxide, produced as a result of double burning, into metal, the enterprises
carry out reducing melting in electric furnaces. The enterprises use petroleum coke or pitch coke as reducing agent, and also they use small quantities of limestone. In this case they
produce ingot nickel or pellet nickel, or they produce nickel cathodes if further refining of metal is required. Sometimes they use alkali hydrometallurgic process in order to extract
nickel and cobalt from ore that passed reducing burning at temperature 580 - 780 °C (Krivtsov, Klimenko, 1997). Then they carry out calcination of carbonate solution cake in
tube furnaces to produce nickel protoxide.
Figure 4.10 Simplified diagram of processing of silicate (oxidized) nickel ore
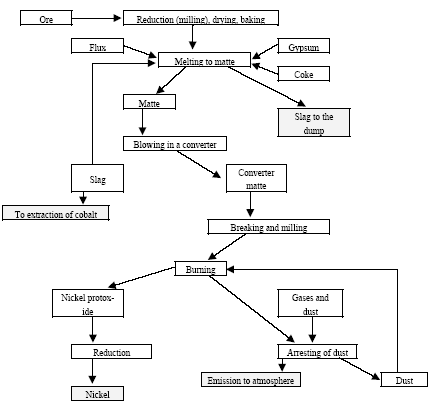
Table 4.52 Production of nickel and emission of mercury into the environment when processing silicate (oxidized) ore
Enterprise |
Production of nickel, 1000 t |
Nickel content in ore, % * |
Extraction of nickel to commercial product, %* |
Total quantity of nickel in ore, 1000 t |
Quantity of processed ore, 1000 t |
Quantity of nickel in ore, kg** |
Emission of mercury to atmosphere, kg*** |
Specific emission of mercury, g Hg/t of Ni |
Rezhnickel |
4.4 |
1.0 |
89.5 |
4.92 |
546 |
49 |
44 |
10 |
Ufaleinickel |
9.5 |
0.90 |
82.3 |
11.54 |
1,154 |
103 |
93 |
9.8 |
Yuzhuralnickel |
9.1 |
1.03 |
75.5 |
12.1 |
1,174 |
105 |
95 |
10.4 |
Other |
4.0 |
- |
- |
- |
- |
- |
40**** |
10.1 |
Total |
27 |
- |
- |
- |
- |
- |
272 |
- |
- (Krivtsov, Klimenko, 1997);
- ** average content in ore 0.09 mg/kg;
- *** on the basis of estimated mercury flue gas emission 90% of the quantity of mercury in raw materials being processed;
- **** with average specific emission 10.1 gram of mercury per one tonne of produced nickel.
4.4.4 Production of Copper
Production of crude copper from ore concentrate is of primary importance from the angle of supplying mercury to the environment; emission of mercury is considerably less when
processing waste and secondary materials and when refining crude copper. Usually processing of copper ore and concentrates is accompanied by producing of sulphur (sulphuric
acid) from frying (flue) gases. Mercury intensively concentrates in sludge of sulphuric acid production processes in the course of this.
A characteristic of Russian manufacturers of primary copper, of raw materials used for its production and of copper production process and mercury emission in works located in
Ural region is given below. Evaluation of mercury emission in the course of production of copper from copper-and-nickel ores in MMC Norilsk Nickel OJSE is given in a special
section.
Russian producers of copper
Russian enterprises producing copper are located in Taimir (Kransnoyarsk Krai), in Murmansk Oblast (MMC Norilsk Nickel OJSC) and in Ural region, where major part of them
belongs to Holding Uralsk Mining and Metallurgical Company. The exceptions are: Kishtimsky copper electrolysis works (Kishtimsky Medeelectrolitny Zavod CJSE) and
Karabashmed CJSE forming the 3rd group of Russian producers of copper (Table 4.53.)
Table 4.53 Production of copper in Russia in 2000-2001, th. tonnes *
Producer |
Location |
Copper |
|
|
|
|
2000 |
2001 |
2002 |
MMC Norilsk Nickel OJSC |
Taimir Peninsula (Krasnoyarsk Krai), Kola Peninsula (Murmansk
Oblast) |
Refined |
413 |
474 |
454 |
Karabashmed CJSE |
Karabash, Chelyabinsk Oblast |
Crude |
36.4 |
41.7 |
42.4 |
Kirovogradsky Medeplavilny Kombinat OJSE (Kirovogradsky copper
smelting combined works) |
Kirovograd, Sverdlovsk Oblast |
Crude |
50 |
46.6 |
46.9 |
Mednogorsky Mednoserny Kombinat OJSE (Mednogorsky copper and
sulphur combined works) |
Mednogorsk, Orenburg Oblast |
Crude |
16.3 |
23.9 |
31.2 |
Sviatogor OJSE |
Krasnouralsk, Sverdlovsk Oblast |
Crude |
56.5 |
55.3 |
62.2 |
Sredneuralsky Medeplavilny Zavod OJSE (Sredneuralsky copper smelting
works) |
Revda, Sverdlovsk Oblast |
Crude |
103.1 |
105.6 |
106.1 |
Kyshtymski Medeelectrolitny Zavod CJSE (Kyshtymski copper electrolyte
works) |
Kyshtym, Chelyabinsk Oblast |
Refined |
77.7 ò |
82.1 |
76.3 ò |
Uralelectromed OJSE |
Verkhnyaya Pyshma, Sverdlovsk Oblast |
Refined |
312.1 |
327.8 |
330.9 |
Crude |
- |
46.3 |
58.5 |
Total production of refined copper in Russia |
801 |
884 |
861 |
* Including secondary copper; according to data of Ministry of Economy and Development of RF (http://www.inves.ru/rus_china/4/pril_1.htm), 96.7 % of copper was produced
from domestic raw materials, including 23.1% from secondary raw materials (copper scrap, rock refuse and anode recrement of copper smelting production) in 2001.
Sources: (Metallurg, 2001, # 1; Mineral Resources of the World ..., 2002 ; Non-ferrous Metallurgy, 2002, # 6; http://www.aviaport.ru/news/Markets/21440.html;
http://metal-trade.ru/news/business/2002/12/index...; http://eurocopper.ru/stat%20ussr%20russ.htm; http://metall.klimenko.ru/arc.15-09-2002.html;
http://www.aktex.ru/rus/news/?year=2003&month...; http://www.kmez.ru; www.mineral.ru/Chapters/News/6016.html)
Mercury in raw materials
Currently in Russia major quantity of copper is produced from ores of copper-and-nickel deposits (content of copper in ore 0.2 - 0.5%) copper pyrite deposits (0.5 - 3 % of
copper) and copper-zinc-pyrite deposits (1-6 % of copper). (Krivtsov, Klimenko, 1997b).
Copper-and-iron deposits containing vanadium and titanium are of secondary importance (0.5% of copper). A characteristic of sulphide copper-and-nickel ores mined in Taimir
and Kola Peninsula has been given above. The enterprises produce up to 70% of primary copper from them in Russia. The remaining part comes from copper pyrite and
copper-and-zinc-and-pyrite deposits located in Ural region.
Ores from copper deposits can be divided into three groups by degree of oxidization: sulphide ore (virtually all Russian primary copper is produced from it), oxidized ore and
mixed ore. Main minerals in Ural sulphide ores are chalcopyrite, bornite and chalcocite. Sulphide ores usually contain 1-6% of copper, 8-40% of iron, 9-46% of sulphur, 1-6%
zinc, 5-55% silica, 2-12% alumina, 0.3-4% calcium oxide (Voskoboinikov et al., 1979).
Generally copper ores are complex and contain a large number of chemical elements, which are extracted in the course of their processing as much as possible.
In 2001 in Urals MCC Gaisky produced over 4.2 million copper ore and Safianovskaya Med OJSE produced 960,000 t (average content of copper 2.71 %). (Results of
production by Safianovskaya Med OJSE...). Main producers of copper concentrate were Gaisky MCC (440,000 t, average content of copper about 15 %), Uchalinsky OJSE,
Karabashmed CJSE (over 134,000 t), Kyshtymski Medeelectrolitny Zavod CJSE (Kyshtymski copper electrolyte works) (over 124,000 t), Sviatogor OJSE (about 180,000 t).
Baskirsky Mednoserny Kombinat OJSE (Baskirsky copper and sulphur combined works (21,000 t), Buribaevskoe mining administration (26,000 t), Turinsky mine and
Sredneuralsky Medeplavilny Kombinat OJSE (Sredneuralsky copper smelting combined works) (9- 12,000 t each) also produced copper concentrate. (According to some
estimates, Baskirsky copper-and-sulphur combined works produced 110,000 t of concentrate (http://www.mediatext.ru/docs/2417).)
Structure of raw materials basis of Ural copper works is rather complex; one works usually processes copper concentrates (both domestic and foreign ones), various copper
scrape and waste (refuse and anode recrement). An analysis of available information sources allowed us to systematize the structure of raw materials containing copper processed
by Ural works as follows (Table 4.54). An estimate of the structure of crude copper production by Ural copper smelting works in 2001 in presented in Table 4.55.
Table 4.54 Characteristic of raw materials containing copper processed by Ural works in 2001
Enterprise |
Main products and sources of raw materials |
Karabashmed CJSE |
Crude copper, processing of concentrate (Ural deposits) from own production
(134,400 t), and briquetted concentrate (Ural deposits) from Kyshtymski Medeelectrolitny
Zavod CJSE (125,100 t) |
Kyshtymski Medeelectrolitny Zavod CJSE (Kyshtymski copper electrolyte works) |
Refined copper, processing of crude copper supplied by Karabashmed CJSE and
copper scrap (on tolling basis). |
Mednogorsky Mednoserny Kombinat OJSE (Mednogorsky copper and sulphur combined
works) |
Crude copper, processing of copper concentrate from concern Erdenet in Mongolia
(about 40,000 t) and concentrate from Gaisky MCC |
Sviatogor OJSE |
Crude copper; processing of concentrate from own production (179,000 t) and
concentrate from Ural concentration plants. |
Sredneuralsky Medeplavilny Zavod OJSE (Sredneuralsky copper smelting works) |
Crude copper; processing of concentrates from Ural concentration plants (including
ore from Safianovskoe deposit); in 2001 commenced processing of recrement (in
the order of 1 million t per year) and, seemingly, copper scrap. |
Kirovogradsky Medeplavilny Kombinat OJSE (Kirovogradsky copper smelting combined
works) |
Crude copper; about 50% from copper concentrate (mainly from ore from Safianovskoe
deposit); the rest from copper scrap. |
Uralelectromed OJSE |
Refined copper; processing of crude copper from Ural works (a considerable
part of which is produced from concentrates from Krasnouralsk concentration works
and Sredneuralsk concentration works; these two works process ore from Safianovsk
deposit) and processing of own crude copper made from secondary raw materials
(own anode recrement and delivered copper scrape and bronze-and-tin scrape). |
Table 4.55 Structure of crude copper production in Ural,1000 t
Enterprise |
Total |
Raw materials from which copper is produced |
|
|
Domestic concentrates |
Concentrates from Erdenet |
Recrement |
Copper scrape |
Karabashmed CJSE |
41.7 |
41.7 |
- |
- |
- |
Mednogorsk Mednoserny Kombinat OJSE (Mednogorsky copper and sulphur
combined works) |
23.9 |
13.9 |
10 |
- |
- |
Sviatogor OJSE |
55.3 |
55.3 |
- |
- |
- |
Sredneuralsk Medeplavilny Zavod OJSE (Sredneuralsk copper smelting
works) |
105.6 |
90.6 |
- |
5 |
10 |
Kirovograd Medeplavilny Kombinat OJSE (Kirovograd copper smelting
combined works) |
46.6 |
26.6 |
- |
- |
20 |
Uralelectromed OJSE |
46.3 |
- |
- |
- |
46.6 |
Total |
319.4 |
173.1 |
10 |
5 |
76.6 |
There is little statistics in domestic literature on content of mercury in Ural copper ores and copper concentrates produced from them. Thus, ranges of determined mercury
concentrations are from 0.N to N x 100 mg/kg for ores from copper-and-pyrite deposits. Some authors estimate average content of mercury at few dozens mg/kg (Bobrova et al.,
1990). Content of mercury varies from less than 0.5 to 20 mg/kg in ores from III International deposit; content of mercury is 10-900 mg/kg in ores from Sibaiskoe deposit, 1-90
mg/kg in ores from Gaiskoe deposit; 1 - 9 mg/kg in ores from Uchalinskoe deposit, Degtyarskoe deposit and a number of other deposits (Ozerova, 1986).
According to (Mineral Resources of Uchalinskoe ..., 1994), concentration of mercury varies in wide range in all industrial sorts of ore and mineral types of ore processed by
Uchalinsky MCC: concentration of mercury is from some hundredth mg/kg to 800 gpt in ore from Uzelginskoe deposit, from 2 to 560 mg/kg in ore from Uchalinskoe deposit, from
1 to 88 mg/kg in ore from Novouchalinskoe deposit. Average content of mercury in ores from Uzelginskoe, Uchalinskoe and Novouchalinskoe deposits are usually few dozens
mg/kg. According to authors of the cited work, in general all sorts of ore from Uzelginskoe, Uchalinskoe and Novouchalinskoe deposits are high mercury types. In this respect they
are second only to ores from Safianovskoe deposit (Middle Ural). High content of mercury in ores from Safianovskoe deposit is confirmed in report 'State Balance of Mineral
Resources of the Russian Federation' (Mineral Resources of the World at early 1999 ..., 2000).
Actually, known data on mercury content in copper concentrates produced in various concentration works are rather inconsistent (Table 4.56). However it is accepted that content
of mercury in copper concentrate usually is higher by 2- 2.5 times (as compared to, for example, mercury content in ores), though such increase of mercury content is not observed
in a number of cases (Bobrova et al., 1990). According to (Bobrova et al., 1990), for example, from 19.1 to 24.9 % of all mercury present in ore goes into copper concentrate in
the course of concentration of ore from copper-and-pyrite deposits.
According to other source (Kutliakhmetov, 2002), from 10 to 14 % of all mercury present in ore goes into copper concentrate in the course of concentration of ore at Uchalinsky
MCC, and resulting content of mercury in concentrate is within 28 to 41 mg/kg.
In the course of ore concentration at Gaisky MCC in 2001, average output of copper concentrate was 9 %, average output of zinc concentrate was 1.47 %, average output of
pyrite concentrate was 45% (Krivtsov, Klimenko, 1997b).
In 2001 Gaisky MCC have processed over 4,222,000 t of copper ore and produced 440,000 t of copper concentrate; i.e. output of copper concentrate was approximately 10.5
%. Hence, at least there is no depletion of mercury content in ore concentrate as compared to mercury content in initial ore. It is noteworthy that Ural copper concentrates usually
have high content of zinc. This is an indirect indication that these ores have high content of mercury in them.
Table 4.56 Content of mercury in copper concentrates (Bobrova et al., 1990; Ozerova, 1986)
Commercial type of deposit |
Mercury in copper concentrate, g/t |
Pyrite and complex metallic |
0.22 - 65 |
Stratimorphic lead-and-zinc |
2 - 290 |
Copper-and-pyrite |
0.3 - 150 |
Cupreous limestone |
4 |
Vanadium-iron-copper |
70 |
Copper-and-molybdenum |
0.02 |
At the same time there are some data showing that, on one hand, mercury virtually does not concentrate in copper concentrate nor even in zinc concentrate produced by
concentrating ores from many pyrite and copper-and-pyrite deposits (Table 4.57). This is especially visible from data for Sibaiskoe deposit. When concentrating ore from
Sibaiskoe deposit, content of mercury in copper concentrate and zinc concentrate is actually lower than mercury content in the ore being concentrated by one or two orders of
magnitude. It follows from the above that mercury does not go into ore concentrates when processing the main commercial zinc and copper minerals, which are also main mercury
yielding minerals. On the other hand, for example, level of mercury content in zinc concentrate from Uchalinskoe deposit is higher than mercury concentration in sphalerite, and
copper concentrate from XIX Party Congress deposit contains more mercury than zinc concentrate by several times (Table 4.57) Inconsistency of the discussed data on content of
mercury in ores and concentrates to large extent is connected with that usually these data were obtained through analytical research of one or two (less often three or four) samples
of ore and concentrate and, therefore, can't be regarded as representative data.
Table 4.57 Mercury in ores, concentrates and minerals from Ural deposits, g/t (Ozerova, 1986)
Deposit |
Ore |
Concentrates |
Minerals |
Copper concentrate |
Zinc concentrate |
Pyrite concentrate |
Pyrite |
Sphalerite |
Chalcopyrite |
Sibaiskoe deposit |
10-900 |
0.3-1.8 |
1.8-7.5 |
0.15-1.5 |
2.8 |
160 |
22 |
Gaiskoe deposit |
1-90 |
1.7-2.7 |
10-25 |
- |
- |
85-220 |
- |
Uchalinskoe deposit |
1-9 |
5-10 |
10-75 |
0.75-3 |
0.72-2.5 |
10-55 |
0.5 |
III International deposit |
1-9 |
2.5 |
4.5 |
0.3-3 |
6 |
- |
- |
Lomovskoe deposit, Levikhinskoe deposit |
|
1 |
1-2 |
0.1 |
- |
- |
- |
XIX Party Congress deposit |
|
50-150 |
25-75 |
1.1 |
- |
- |
- |
From this angle, interesting are results of research of mercury distribution in ores from a wide group of copper deposits obtained by V.Z. Fursov (1983). Generally, the research
was based on relatively representative sample and was carried out using rather reliable analytical method (Table 4.58). One can assume with high degree of probability that data
shown in Table 4.58 do adequately represent average content of mercury in copper ores processed from South Ural. The data vary within limits of 9.8 - 13 mg/kg on average
(total average value is 11.5 mg/kg). According to document 'State Balance of Mineral Resources of the Russian Federation. Mercury.' (1998), there is 10-12 t of mercury in
copper ores produced at Safianovsk deposit in Sverdlovsk Oblast (Mineral Resources of the World at early 1999 ..., 2000). This results in average content of mercury in ore
within 10.4 - 12.5 mg/kg (with ore production 960,000 t in 2001), which corresponds to the above values.
Table 4.58 Average content of mercury in ores from copper deposits (confidence intervals for reliability 0.95) (Fursov, 1983)
Type, deposit, region |
Ore characteristic |
Nr. of samples |
Mercury, average (limits), mg/kg |
Copper-and-pyrite |
Uchalinskoe deposit. South Ural |
Massive |
7 |
9.8 (3.2-19.75) |
XIX Party Congress deposit. South Ural |
Massive |
9 |
12 (4-27) |
Sibaiskoe deposit, South Ural |
Massive |
8 |
11.2 (3.7-23.10) |
Gaiskoe deposit, South Ural |
Massive |
14 |
13 (5-27) |
Urupskoe deposit, Northern Caucasus |
Massive |
13 |
8.95 (6.34-13.76) |
%0 Let Oktyabrya deposit, Western Kazachstan |
Disseminated |
7 |
1.35 (0.92-2.04) |
Kusmurun, Western Kazachstan |
Massive |
11 |
9.2 (4.3-16.70) |
Cupreous limestones |
Dzhezgazgan, Central Kazachstan |
Massive (chalcopyrite) |
15 |
3.15 (2.8-3.68) |
Dzhezgazgan, Central Kazachstan |
Disseminated (bornite) |
11 |
1.45 (1.23-1.87) |
Dzhezgazgan, Central Kazachstan |
Disseminated (chalcopyrite) |
17 |
1.57 (1.08-2.20) |
Udokan, Baikal Region |
Disseminated |
11 |
1.13 (0.77-1.68) |
Copper-and-porphyry |
Counrad, Central Kazachstan |
Disseminated (primary) |
8 |
0.87 (0.76-1.02) |
Thus, one can calculate average content of mercury in copper concentrate, which is processed by Ural copper smelting works. Let's assume that concentration works receive ore
with average content of mercury 11.5 mg/kg, output of copper concentrate is 10 % and 12 % of mercury contained in ore goes to concentrate. Simple calculations show that, with
the above assumptions, average content of mercury in copper concentrate will be 13.8 mg/kg. This is the value that we will use in subsequent calculations.
Processes and technologies
When concentrating copper ore, copper concentrates most often containing 10-30 % of copper, with rare exceptions, are usually the main product of copper ore concentration.
For example, average content of copper in concentrate from Gaisky combined works is 15.8 % (Krivtsov, Klimenko, 1997b). It is floatation process that is mainly used when
concentrating sulphide ore.
The main quantity of ore is produced by pyrometallurgical process which includes the following process operations: drying of copper concentrates, frying of concentrates,
agglomeration of concentrates, melting of prepared batch in melting furnaces, conversion of copper matte and fire refining of crude copper (Voskoboinikov et al., 1979; Gudima,
Shein, 1975; Basics of Metallurgy..., 1962; Utkin, 1990). Some operations can be excluded or substituted with other operations in specific cases. For example, oxidizing frying is
used generally when processing hugh-sulphur ore or concentrates lean of copper. Various options of pyrometallurgical processing of ore raw materials can be used at one works
simultaneously (Table 4.59, Figure 4.11).
Table 4.59 Specialties of technological processes for copper production in Ural
Producer |
Specialties of technological process |
Karabashmed CJSE |
The enterprise use melting in pit-type furnaces (three furnaces) with subsequent
converting (three converters) of produced matte for processing of ore raw materials.
The first phase of a complex for utilisation of flue gases from copper smelting
shop was started in May 2001. It includes an oxygen station which allows improving
environmental indicators of melting in pit-type furnaces. |
Kirovograd Medeplavilny Kombinat OJSE (Kirovograd copper smelting combined
works) |
The enterprise use melting in pit-type furnaces or melting of batch to matter
in reflection furnaces with subsequent conversion for processing of ore raw materials.
There are bag filters for cleaning of gas after processing of secondary copper.
Converter gas is cleaned from dust in a special plant where sulphurous gas in
extracted. Subsequently sulphurous gas is transferred to a chemical plant. |
Mednogorsk Mednoserny Kombinat OJSE (Mednogorsk copper and sulphur combined
works) |
The enterprise use melting in pit-type furnaces with subsequent conversion
of produced matte for processing of ore raw materials. The process includes production
of elementary sulphur from pit-type furnace gas. Electric filters are used for
cleaning of gas from reduction melting and converter gas. |
Sviatogor OJSE |
One of options includes frying of raw materials in multiple-hearth furnaces,
melting of cinder to matte in a reflection furnace and subsequent conversion of
produced matte. In the second option, melting of raw materials to matte is carried
out directly in reflection furnaces, then matte is converted (4 converters, type
Pierse-Smith(?), 3 are operative and one in repair or stand by). Flue gases go
to the process of cleaning from dust and then to production of sulphuric acid.
There are electric filters for cleaning of gas from frying furnaces; hydraulic
cleaning plant is used for removal of fine dust from converter gas; bag filters
are used for arresting dust from fuming furnace gases. |
Sredneuralsk Medeplavilny Zavod OJSE (Sredneuralsk copper smelting works) |
Copper concentrates are mainly processed using frying technology (in flying
bed furnaces). Then the enterprise carries out melting of cinder to matte in reflection
furnaces and conversion of matte. Sometimes melting of raw materials to matte
is carried out directly in the reflection furnaces, after that matte is converted.
Also a Vaniukov furnace is operated (smelting of copper in liquid bath). A sulphuric
acid production shop uses gases containing sulphur from the copper production.
A shop for production of double superfosphate utilises locally produced sulphuric
acid. Rough cleaning of frying gas from dust is carried out in cyclones, fine
cleaning of frying gas is carried out in dry electric filters. The enterprise
use cyclones and hydraulic cleaning for cleaning of converter gas; cleaning of
fuming furnace gas is done in bag filters. |
Uralelectromed OJSE |
The works is focused on production of refined copper. A special metallurgical
complex for production of crude copper from secondary raw materials was started
up in late 2000 (comprised of a pit-type furnace, a settling tank, a converter
and a system of gas cleaning equipment). Two stages of a system for cleaning of
flue gases from copper refining furnaces were commissioned in 1999 and 2000. |
The following are purposes or oxidizing frying in the pyrometallurgy of copper: partial removal of sulphur, transfer of a part of iron to oxides from sulphides, production of 25- 30
% matte and gases usable for production of sulphuric acid.
Most often the enterprise carries out oxidizing frying of copper concentrates (or prepared batch) in the frying furnace. Sulfur is partly removed, the concentrate gets well mixed with
fluxes and returns that are usually added to frying batch, when carrying out frying (at 580- 850 °C) in multiple hearth furnaces.
Frying produces dust. Carry over of dust with flue gases in 10-12 % (sometimes more) of weight of batch.
When there is high content of dust in flue gas, the cleaning system is usually comprised of cyclones (rough cleaning) and electric filters (fine cleaning). Arrested rough dust is
returned to frying batch. Fine dust is usually sent for special treatment in order to extract zinc, lead, cadmium and some rare metals. Content of SO2 in frying gases before the
electric filter varies within 12-13 %.
A major part of copper is smelted in reflection furnaces where three types of batch is processed: raw, dried or fried. In addition to solid batch, they pour converter slag to the
reflection furnace. Converter slag participates in final formation of converter matte and recrement. (The process generates 6.5-9.5 t of recrement with typical copper content 0.3 -
0.35 % per 1 tonne of crude copper.)
Main purposes or smelting are: melting of batch, sulphidizing of copper and transfer of sulphidized copper to matte, and simultaneous slagging of major part of iron. This is achieved
by melting of fried concentrate together with flux in lean oxidizing atmosphere at temperature 1200 - 1550 °C. They use two types of burners in reflection furnaces: external mixing
turbulence gas-and-mazoot (fuel oil) burners and internal mixing gas burners. Consumption of coal equivalent is 120 - 180 kg/tonne of batch. Depending on composition or
processed raw materials and used melting technology, content of copper matte is the following: copper 15-60 %, zinc 1-6 %, nickel up to 0.5 %, lead up to 1 %.
Pit melting of copper ore is the oldest technique of melting to matte. The melt materials with particle size 20 - 100 mm in pit-type furnaces, so small-particle batch (of ore and
concentrates) is subjected to agglomeration or briquetting prior to melting.
Everywhere copper matte is processed by conversion (blowing with compressed air) in horizontal converters. Main purposes of conversion process are: oxidizing of sulphides with
extraction of sulphur in the form of sulphur angidride, slagging of iron and production of crude copper. Matte is poured to the converter in liquid condition at temperature 1100 -
1200 °C. The temperature quickly increases to 1200- 1300 °C after start of blowing. Gases are removed from converters through gas ducts.
Depending on the place of subsequent refining, product crude copper is either poured down from the converter to the mixer (accumulator) and then, as much as needed, to refining
furnace in liquid condition, it is cast to to ingots weighing 2 t or more to be sent to special refining works. Converter slag having copper content 1.5 - 2 % is returned to matte
melting process in order to deplete it. Extraction of copper to crude copper from matte (taking into account processing of converter slag) is usually 98 - 99 % (extraction of copper
from concentrate to crude copper is approximately 93 %).
Refining of crude oil is carried out in two stages. First copper is refined using a fire (oxidization) refining technique, after that copper is refined using an electrolysis technique.
Removal of a number of admixtures and production of dense anodes for electrolysis copper refining process is the purpose of fire refining process. They use two types of furnaces
fire refining of copper: stationary reflection furnaces and tilting furnaces. Anode mix contains 99.4 - 99.6 % of copper; other parts are admixtures remaining after fire refining,
including gold, silver, selenium and tellurium. They pour copper to ingots (anodes) having a flat form and lugs after fire refining. Then anodes are sent to electrolysis shop. There
anode copper undergoes electrolytic refining in order to produce high purity metal and extract gold, silver, selenium and tellurium, and sometimes nickel and cobalt. The process is
carried out in electrolysis baths where anodes are electrically and chemically dissolved in sulphuric acid electrolyte. Pure copper plate on the cathode, admixtures precipitate.
Figure 4.11 General diagram of pyrometallurgical processing of copper raw materials
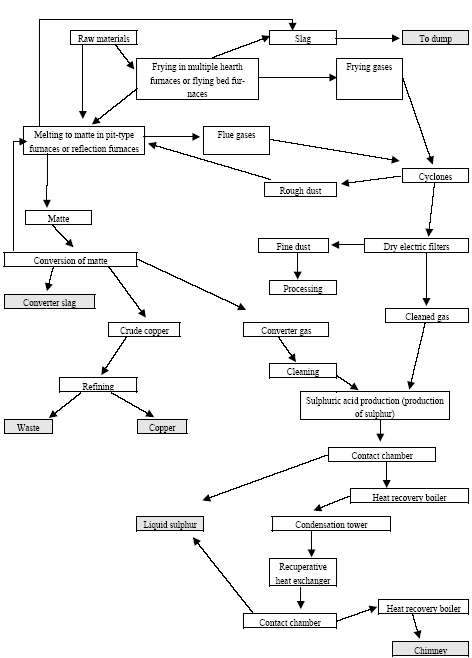
Sources and characteristics of dust and gas emission
Frying furnaces (multiple hearth and flying bed), pit-type furnaces and reflector furnaces, converters and concentrate dryers are main sources of dust and gas emission at copper
smelting works using primary raw materials. Major part of dust and heavy metals is carried away together with gases from reflection furnaces and converters (Table 4.60).
According to (Paper on Lead ..., 1997), 90-95 % of dust and 57 % of lead were released to atmosphere along with emission from reflection furnaces and 5-8 % of dust and 37 %
of lead were emitted from converters at Ural copper smelting works. Average quantity of generated process gases is estimated as 50,000 m3 per tonne of non-ferrous metals
(Perederij, Mishkevich, 1991). Flue gases generated by a major part of copper production operations have high temperature. Flue gas from frying furnaces has temperature
500-800 °C, flue gas from reflection furnaces has temperature 300-400 °C, flue gas from pit-type furnaces has temperature 350-550 °C, flue gas from converters has temperature
900-1000 °C (Cleaning of Industrial Gases ..., 1992).
Table 4.60 Main parameters of emission at copper smelting works in Urals (Paper on Lead ..., 1997)
Enterprise |
Source of emission |
Quantity of flue gas, m3/h |
Dust rate, g/m3 |
Sredneuralsk Medeplavilny Zavod OJSE (Sredneuralsk
copper smelting works) |
Reflection furnace |
300000 |
0.6-0.8 |
Converters |
50000 |
0.2 |
Sviatogor OJSE |
Reflection furnace |
210000 |
0.5-1.3 |
Converters |
130000 |
0.3 |
Kirovograd Medeplavilny Kombinat OJSE (Kirovograd
copper smelting combined works) |
Reflection furnace |
230000 |
1.38 |
Converters |
503000 |
0.033 |
Pit-type furnace |
168000 |
0.08 |
Cyclones are most often used for rough cleaning of escaping gases (frying gas and converter gas); dry electric filters are main equipment for fine cleaning. Design efficiency of
arresting dust by dry electric filters is 98.9 - 99.9 %. However, it is not possible to estimate even average efficiency of flue gas cleaning at copper smelting works in Russia at this
stage, because many works use outdated technology, and some technological processed are not fitted with cleaning equipment.
For example, until recent time flue gases from reflection furnaces at Sredneuralsky copper smelting works, Krasnouralsky copper smelting works (Sviatogor OJSE) and
Kirovogradsky copper smelting combined works had been released to the atmosphere without cleaning (Paper on Lead ..., 1997). This caused sufficient emission of sulphurous
anhydride, which is predominant in works' emissions, and dust. High emission of dust causes considerable emission of heavy metals, especially lead.
Thus, all enterprises belonging to Uralskaya Mining and Metallurgical Company emitted to atmosphere over 575 t of lead in recent years (2000-2002). This included: Sredneuralsk
copper smelting works emitted 170 t (total emission of hazardous substances 79,000 t); Kirovograd copper smelting combined works emitted 114 t (total emission of hazardous
substances over 110,000 t); OJSE Sviatogor emitted 291 t (total emission of hazardous substances over 87,000 t); CJSE Karabashmed emitted 79 t of lead to atmosphere in
2002 (total emission of hazardous substances over 97,000 t) (http://metal-trade.ru/news/business/2003/03/1337.s...; http://uralnep.ru/news/view_article.php?newsid=422...).
Summary data on specific emission of dust to the atmosphere by some works are shown in Table 4.61. The data shows that there is a substantial variation in specific emission.
According to (Emission of Heavy Metals ..., 1998), average value of specific emission of dust in the course of primary production of copper is 46.4 kg/tonne of crude copper.
Table 4.61 Specific emission of dust, kg/tonne of products* (Emission of Heavy Metals ..., 1998),
Enterprise |
Type of product |
Dust, kg/t |
Kirovograd copper smelting combined works |
Crude copper |
12.4 |
Uralelectromed OJSE |
Electrolytic copper |
0.41 |
Sredneuralsk copper smelting works |
Crude copper |
320.1 ** |
Pechenganickel |
Crude copper |
42.0 |
* Specific emission of hazardous substances was over 2 t per 1 t of crude copper at Karabashmed CJSE in 2002.
** Specific emission of hazardous substances to atmosphere was about 600 kg per 1 t of crude copper at Sredneuralsky Medeplavilny Zavod OJSE (Sredneuralsky copper
smelting works) (http://metal-trade.ru/news/business/2003/03/1337.s...);
Mercury emission and specialties of behaviour of mercury
Behaviour of mercury in copper smelting production is little researched. Analytical research of content of mercury in raw materials and in products of processing is not generally
carried out in laboratories of copper smelting combined works.
Mercury sublimates by 80-90 % in the course of of frying of copper concentrates (Bobrova et al., 1990). In the course of cleaning of sulphurous flue gases mercury is partly
arrested together with dust (content of mercury in dust reaches 15-560 g/t) and partly goes to the sulphuric acid production shop together with gas. There mercury is concentrated
in slurry in the washing section. The slurry is not used anywhere and, most probably, is simply dumped. Rough dust is circulated (they add it to batch). If fine dust is processed, the
it is collected in lead cake (up to 1,100 kg/ton), which then goes to lead works for further processing. Otherwise fine dust is collected in dump arsenate cake (and it usually goes to
burial ground disposal) (Bobrova et al., 1990).
There are all grounds to believe that behaviour of mercury in the course of production of copper at copper smelting works is similar in many aspects to distribution of mercury in the
course of production of zinc. It just has to be mentioned that, on one hand, somewhat more quantity of mercury concentrates in dust arrested by cleaning equipment (due to higher
carrying out of dust from furnaces and converters). On the other hand, relative emission of mercury to the atmosphere by copper smelting works is somewhat higher because of
less sophisticated technology and outdated equipment.
Based on the above information (and taking into account specialties of technological processes, functioning of dust arresting and gas cleaning equipment and behaviour of mercury
in the zinc production), one can estimate distribution of mercury in the course of processing of raw materials containing copper as follows (with some conditions and for some
material flows) (Figure 4.12). In order to estimate emission and determine specific losses of mercury in the course of production of crude copper from domestic (Ural) copper
concentrates, let's consider a fictional enterprise with production capacity 100,000 t of crude copper per year.
Above we have demonstrated that content of mercury in copper concentrate coming for metallurgical processing is 13.8 mg/kg, content of copper is 15%, and rate of extraction of
copper from concentrate is 93 %.
Thus, mass of concentrate processed at the works will be 716,667 t. Total mass of mercury in the concentrate coming for processing is 9.89 t, that means that 98.9 g of mercury is
involved per each tonne of produced crude copper.
Figure 4.12 Estimated distribution of mercury in the course of processing of raw materials containing copper
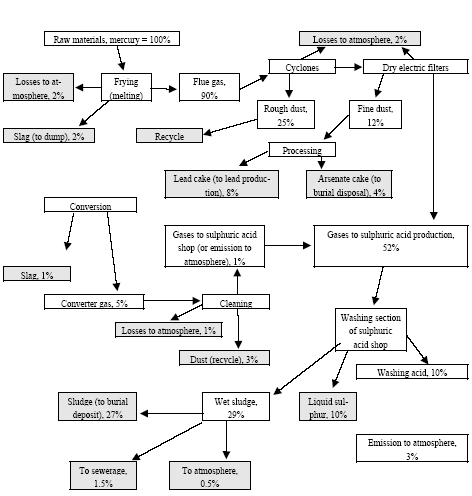
When producing 100,000 t of crude copper, about 840 kg of mercury will be emitted to the atmosphere (specific emission 8.4 g of mercury per tonne of copper), 2,670 kg of
mercury will be accumulated in sulphuric acid production sludge (26.7 g of mercury per tonne of copper), 198 kg of mercury will go to dump slag (approximately 2 kg of mercury
per tonne of copper) and 148.4 kg of mercury will go to sewerage (1.48 g of mercury per tonne of copper). Let's also assume that all these indicators include emission of mercury
from other materials used in the course of production of crude copper (such as fuel, flux, etc.).
Determined average content of mercury in ore from copper-and-porphyry deposits is 0.87 mg/kg (ref. Table 4.58). Let's assume that the same concentration is characteristic for
ore (of similar type) from Erdenetiyn-Obo in Mongolia (developed by concern Erdenet). Content of mercury in concentrate produced by concentration of ore from this deposit will
be approximately 1.2 mg/kg. It is easy to calculate that specific emission of mercury to the atmosphere from pyrometallurgic processing of such concentrate will be as follows 0.73
g of mercury per tonne of produced crude copper; quantity of mercury going into sludge will be 2.3 g/t, quantity of mercury going to dump slag will be 0.17 g/t, and 0.13 g of
mercury per tonne of produced copper will be discharged to sewerage.
In 2001 Sredneuralsky copper smelting works processed about 1 million t of scrap containing about 200 kg of mercury. From this quantity, 17 kg were emitted to the atmosphere,
54 kg went to sulphuric acid production sludge, 3 kg were discharged to sewerage and 4 kg went to solid waste; remaining mercury was redistributed in return products.
Based on relation of dust emission in the course of production of crude copper and in the course of production of refined copper (see Table 4.61), one can state that specific
emission of mercury in the course of copper refining will be less than similar indicator for crude copper production by 100 times minimum. This statement is rather conditional,
however, (taking into account that part of mercury is arrested by gas cleaning facilities, where it mainly concentrates in dust) let's assume that specific emission of mercury to the
atmosphere in the course of refining of crude copper is be 0.06 g of mercury per tonne of product.
Estimated figures for emission of mercury to the atmosphere and mercury distribution in main waste materials from Ural copper smelting works producing crude copper are shown
in Table 4.62. Besides some 10%, 2.3 t , goes to sulphuric acid.
Table 4.62. Production of crude copper at Ural works from ore concentrates and estimated mercury emission in 2001
Producer |
Crude copper, 1000 t |
Mercury supplied to the production with raw materials, t |
Emission of mercury to the atmosphere, t |
Mercury in sludge, t |
Mercury in slag, t |
Mercury discharged to sewerage, t |
Karabashmed CJSE |
41.7 |
4.12 |
0.350 |
1.11 |
0.083 |
0.062 |
Kirovogradsky Medeplavilny Kombinat OJSE (Kirovograd copper smelting
combined works) |
26.6 |
2.63 |
0.223 |
0.710 |
0.053 |
0.039 |
Mednogorsk Mednoserny Kombinat OJSE (Mednogorsk copper and sulphur
combined works) |
23.9 |
1.43 |
0.124 |
0.394 |
0.029 |
0.022 |
Sviatogor OJSE |
55.3 |
5.45 |
0.465 |
1.48 |
0.111 |
0.082 |
Sredneuralsk Medeplavilny Zavod OJSE (Sredneuralsk copper smelting
works) |
90.6 |
8.96 |
0.761 |
2.42 |
0.181 |
0.134 |
Total, crude copper |
238.1 |
22.59 |
1.923 |
6.114 |
0.456 |
0.339 |
4.4.5 Copper and Nickel Production at MMC Norilsk Nickel OJSC
MMC Norilsk Nickel OJSC (hereinafter – MMC Norilsk Nickel) is the largest Russian and world manufacturer of copper, nickel, cobalt, some rare and precious metals. The
enterprise includes Trans-polar Branch of MMC Norilsk NickelOJSC (Krasnoyarsk Region, Taimyr Peninsula), Kolsk GMK, including Pechenganickel Combine Joint-Stock
Company (JSC) and Severonickel Combine OJSC (Murmansk Region, Kola Peninsula) and a number of other enterprises.
Volumes of production of copper and nickel
The share of MMC Norilsk Nickelin the total Russian output of nickel is stably making 95-96 %, of refined copper – 55-57 % (Table 4.63, Table 4.64); up to 18.5-19.8 million t
of sulphide copper-nickel ores have been per year mined and then refined during the recent years from deposits of Taimyr and Kola Peninsula (Table 4.65). The enterprises of
MMC Norilsk Nickelare per year involving into processing all the so-called "circulating" materials and "stale" raw materials (ores, concentrates, dump slag, etc.), produced during
the current year or stored earlier, from which 10,000 t of copper and up to 10-15,000 t of nickel are extracted. They are also processing non-ferrous scrap and other raw
materials, including those arriving from abroad.
Table 4.63 Production of primary nickel by the enterprises of MMC Norilsk Nickel OJSC in 2000 and 2002
Enterprise |
Location |
Production, 1000 t |
|
|
2000 |
2001 |
2002 |
Trans-polar Branch of MMC Norilsk Nickel OJSC |
Norilsk, Krasnoyarsk Region |
116 |
120 |
120 |
Pechenganickel OJSC |
Zapolyarny, Murmansk Region |
Produces converter matte, which is refined at Severonickel Combine |
Severonickel Combine OJSC |
Monchegorsk, Murmansk Region |
101 |
103 |
98 |
Total |
217 |
223 |
218 |
Source: (BIKI, 2003, No. 41; Gerasimchuk et al.; Chernyakova ...; http://metal-trade.ru/news/business/2002/12/index...; http://www.infoline.spb.ru/metall.html)
Table 4.64 Production of copper by the enterprises of MMC Norilsk Nickel OJSC in 2000 and 2002 *
Enterprise |
Location |
Production, 1000 t |
|
|
2001 |
2002 |
Trans-polar Zapolyarny Branch of MMC Norilsk NickelOJSC |
Norilsk, Krasnoyarsk Region |
341.3 |
357 |
Pechenganickel OJSC |
Zapolyarny, Murmansk Region |
Produces converter matte, which is refined at Severonickel Combine |
Severonickel Combine OJSC |
Monchegorsk, Murmansk Region |
132.7 |
97 |
Total |
474 |
454 |
* Including secondary copper.
Source: (http://metal-trade.ru/news/business/2002/12/index...; http://metall.klimenko.ru/arc.15-09-2002.html; http://www.infoline.spb.ru/metall.html;
http://www.mineral.ru/Chapters/News/6016.html)
Table 4.65 Mining volumes of sulphide copper-nickel ores by MMC Norilsk Nickel, million t (Annual Report of MMC Norilsk Nickel-2001) *
Year |
Pechenganickel JSC
(Kola Peninsula)
|
Trans-polar Branch (Taimyr) |
Total |
1996 |
7.8 |
9 |
16.8 |
1997 |
7.7 |
9.8 |
17.5 |
1998 |
7.95 |
10.2 |
18.15 |
1999 |
7.65 |
11 |
18.65 |
2000 |
7.65 |
11.2 |
18.85 |
2001 |
7.72 |
12.1 |
19.82 |
* Calculated from the schedule, which is given in the quoted document.
The basis of manufacturing operation of MMC Norilsk Nickelis essentially made up by a unified processing technology of sulphide copper-nickel ores and technological links
between the enterprises, which the company includes. Thus, Pechenganickel Combine JSC delivers copper-nickel converter matte by railway to Severonickel Combine OJSC;
Trans-polar Branch of MMC Norilsk NickelOJSC delivers rich ore, converter matte, sometimes secondary raw materials to the enterprises situated in Kola Peninsula. The
affinage of precious metals produced by Trans-polar Branch, Kolsk GMK and Polyus Closed Joint-Stock Company (CJSC) is made at the Krasnoyarsk, Prioksky and
Yekaterinburg plants of non-ferrous metals (Annual Report of MMC Norilsk Nickel2001; Annual Report of MMC Norilsk Nickel-2002).
Ore mining
The ores of the deposits developed by MMC Norilsk Nickelare divided into rich (compact), ingrained and cupriferous ones. The rich ores are characterized by increased contents
of non-ferrous and precious metals and cupriferous ores are notable for higher concentrations of copper. As it was marked above, the rich ores with the contents of nickel of more
than 1 % at nickel to copper ratio of at least 1:1 and with a decreased contents of iron (below 25 %) go directly into melting. The ores, which are poorer in nickel contents, require
a preliminary enrichment with obtaining of a collective copper-nickel concentrate or separate nickel, copper and pyrrhotine concentrates (Krivtsov, Klimenko, 1997).
Ore Dressing
At MMC Norilsk Nickelthe ore dressing (by the method of collective-selective flotation) was made at two concentrating mills (CM) (Annual Report of MMC Norilsk
Nickel-2001). Talnakh CM refined a part of the rich and cupriferous ores of Talnakh-Oktiabrskoye deposit with obtaining nickel, copper and pyrrhotine concentrates; Norilsk
CM – the whole volume of ingrained ores of Norilsk-1 and Talnakh-Oktiabrskoye deposits, a part of the rich and cupriferous ores of Talnakh-Oktiabrskoye deposit, and also the
so-called stale pyrrhotine concentrate with obtaining of nickel and copper concentrates. The nickel concentrate contains 5.67 % Ni and 2.9 % Cu, the copper one – 23.6 % Cu
and 1.7 % Ni, the pyrrhotine one – 3.7 % Ni and 3.4 % Cu. Extraction of nickel into concentrate makes 88-97 %, of copper – 89-98 %, of cobalt – 66 % (Krivtsov, Klimenko,
1997). At ore dressing they use crushing, grinding, floatation, thickening and pumping equipment. Then, via the hydraulic transportation system the obtained concentrates arrive to
the plants; the dressing wastes – the tailings – are placed into special storehouses. Since 1995, they started to involve the mineral raw materials, which were warehoused earlier,
into the dressing process, including the ingrained and cupriferous ores, pyrrhotine concentrate, materials from sumps, etc. In 1997, Norilsk and Talnakh CMs implemented the
technology of rich ore dressing with extracting the greater part of the pyrrhotines (60-80 %) into the tailings and obtaining of a rich nickel concentrate (9-14 % of Ni contents), and
since 1999 the technology of obtaining rich copper concentrates with the 27-29 % contents of copper has been used (Economy and Life-Siberia, 2000). In 1997 Norilsk CM
implemented the gravitation-floatation technology of dressing ingrained and cupriferous ores, which allows extracting the concentrate, enriched by platinum metals.
The concentrating mill in Kola Peninsula (in Zapolyarny), which is a part of Pechenganickel Combine, was processing local ingrained ores (the average contents of Ni 0.75 %, Cu
0.42 %) with obtaining of a collective copper-nickel concentrate containing 5-6 % of nickel and 2-3 % of copper (Krivtsov, Klimenko, 1997). Extraction of nickel into
concentrate was 78-81 %, of copper – 73-76 %.
Main diagram of processing sulphide copper-nickel raw materials
The preparation of sulphide copper-nickel raw materials to melting envisages agglomeration or pelletization (or combination of these processes) with simultaneous roasting
(Goudima, Shein, 1975; Fundamentals of Metallurgy ..., 1962). The concentrate is nodulized in cup granulating machines, and then the obtained pellets undergo hardening roasting
in sintering machines with desulphurization down to 30-40 %; the machines have three zones – drying, partial roasting and cooling of pellets, the yield thereof making 90 %. As a
rule, the agglomeration charge comprises the concentrate and the returns (recurrent products of the plant) in 1:1 ratio. Apart from it, some burnt chalkstone is added into the charge
volume in the quantity of weight 3-4 %. The fuel (charge coke) is usually added to the finished agglomerate before its electric melting in ore heat-treating furnaces (Fig. 4.13).
The charge is loaded into electric furnaces through the openings in the dome; the matte and slag are drained through blast-holes. The matte contains 9-12 % of nickel, 5-10 % of
copper; the dump slag – 0.078-0.098 % of nickel, 0.063-0.01 % of copper; extraction into the matte – nickel 96-97 %, copper 96 %, cobalt 75-82 %. Converting (purging) of
copper-nickel mattes (with the aim to obtain copper-nickel converter matte) is similar by its process and hardware to purging of nickel mattes. For a more complete extraction of
cobalt the converters work in the looped cycle with depletion electric furnaces. With this aim the converter slag undergoes depletion in special electric furnaces for recovery of
non-ferrous metals by poor sulphide ore or low-grade matte. In this way they obtain the dump slag and the matte enriched with cobalt, which is also directed to converting. The
composition of the converter matte obtained at domestic plants is approximately as follows: 37-42 % Ni and 35-37 % Cu. In the converter matte the platinum group metals are
concentrating. The limit extraction of non-ferrous metals into the converter matte makes 96-97 %.
For division of the converter matte into nickel and copper concentrates they use the flotation (mechanical dressing) method. Cooling of the converter matte is carried out by means
of pouring it into chamotte or graphitic moulds dug into ground for slow cooling. In each mould an ingot of about 25 t of weight compactifies. The method of floatation separation of
converter matte yields no dump products, as all the metals are distributed among the concentrates, directed to further processing. The losses of metals at this operation are minimal
and make at most 0.1-0.2 %.
The nickel concentrate is directed, after division of the converter matte, to the nickel line, where it is burnt in fluidized bed furnaces at the temperature of about 1,150 °C, which
ensures some amalgamation of the burnt material and reduces the removal of the small-sized fraction. At anodic melting the chalkstone is used in the quantity of up to 20 kg/t of
anode; as a reducing agent they apply small fractions of hard coal or coking dust. Extraction of nickel into monoxide makes at roasting 97-99 %, the nickel monoxide then arrives
for the reduction melting in electric furnaces such as steel-melting ones, during which they obtain anodic nickel. It has the following approximate composition: Ni 88.4-89 %, Cu
4.5-6.5 %, Co 1.2-2.2 %, Fe 2.5-2.6 %, S 0.4-0.5 %, As 0.001 %.
At electrolysis (electrolytic refinement), apart from nickel, also the concomitant impurities pass over from the anodic nickel into the solution. The electrolysis is carried out with
disconnected anode and cathode compartments. The yield from loaded anodes makes: scrap 16-18 %, sludge – 4-5 %. The cathode nickel should contain at least 99.99 % of the
sum of nickel and cobalt (including cobalt at most 0.005 %).
In the sludge, which is generated during electrolytic dissolution of nickel anodes, the metals of platinum group concentrate, which do not pass into the electrolyte, namely, gold,
silver, selenium, and tellurium? Sludge processing with the aim to enrich it with the said elements is made in a separate cycle, as a result of which we obtain enriched concentrate of
precious metals and nickel, which is returned back into the basic production. The concentrate of precious metals undergoes a complicated processing cycle to obtain each of metals
separately in the marketable form.
To extract nickel from raw materials (for example, from pentlandite-pyrrhotine concentrate) the also apply melting in suspended condition. The melting charge comprises the
concentrate, residues after leaching at nickel extraction, and also quartz flux. After preliminary drying in a rotated furnace, the charge arrives into the furnace, where the sulphides
get oxidized forming matte and slag. The matte is directed to converting, while the slag containing 0.8 % Ni and 0.6 % Cu – to a special electric furnace for depletion. The dump
slag of the electric furnace contains 0.10 % Ni and 0.25 % Cu.
Figure 4.13. Functional block chart of processing sulphide copper-nickel raw materials
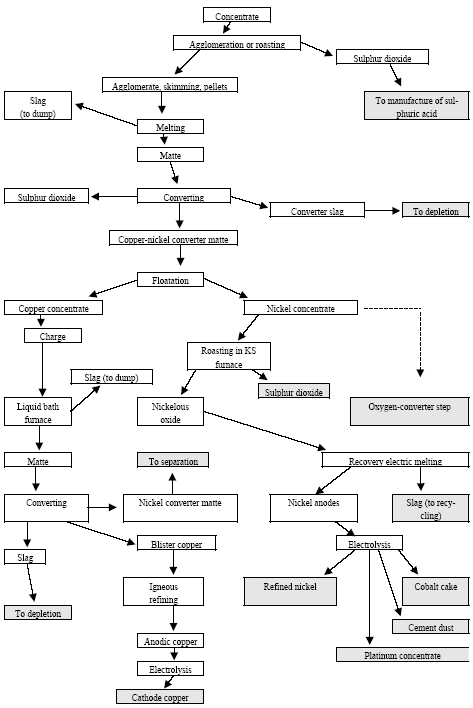
The copper concentrate from converter matte separation arrives to the copper production line, where it is annealed in liquid bath furnaces (Vanyukov furnaces). The resulting matte
is subject to converting, and the blister copper arrives to igneous concentration, then the anodic copper arrives to the shop of electrolytic refinement for obtaining of cathode
copper. The sludge generated at electrolysis is sent to recycling.
In 2001, MMC Norilsk Nickel (Taimyr Peninsula) processed the concentrates, obtained after ore dressing (by pyro- and hydrometallurgical methods), at three metallurgical plants:
Nadezhdinsky, Nickel and Copper; a shop for production of precious metals concentrates was also operated (Annual Report of MMC Norilsk Nickel-2001). Nadezhdinsky
Metallurgical Plant of MMC Norilsk Nickelrefined the whole volume of nickel and pyrrhotine concentrates of Talnakh CM, the whole volume of copper concentrate of the shop of
converter matte refinement of Nickel Plant with the yield of converter matte and copper anodes. The Agglomeration Factory and the Nickel Plant refined the whole volume of
nickel concentrate of Norilsk CM, the whole volume of enriched stale pyrrhotine concentrate, a part of converter matte of Nadezhdinsky Metallurgical Plant with obtaining of
marketable nickel and cobalt. The Copper Plant refined the whole volume of copper concentrate of Norilsk and Talnakh CM and the copper anodes of Nadezhdinsky
Metallurgical Plant with obtaining of marketable copper. The metallurgical shop of the production facility of precious metals concentrate was processing the sludge from the nickel
and copper electrolysis shops with subsequent production of concentrates of precious metals and metal silver.
Mercury in sulphide copper-nickel ores, minerals and concentrates
In literature little data may be found on mercury contents in sulphide copper-nickel ores and minerals of the deposits of Taimyr and Kola Peninsula, and also in products of their
dressing (Table 4.66). In most cases the presented data is based on occasional single chemical and analytical measurements, which does not allow considering them to be
representative. Nevertheless, it is considered (Smirnov et al., 1968) that at formation of copper-nickel deposits, an essential role was played by post-abyssal processes and
sulphurization, and sulphur, as it is well-known (Ozerova, 1986), is the basic precipitant of mercury in the earth's crust, which a priori should have promoted accumulation of
mercury in sulphide copper-nickel ores (Fursov, 1983). By an estimation of V. P. Fyodorchuk (1983), the average mercury contents in sulphide copper-nickel ores makes 1
mg/kg. The close results have been obtained by V. Z. Fursov (1983), who studied the distribution of mercury in ores of some copper-nickel deposits of Taimyr and Kola Peninsula
in quite detail (Table 4.67).
Table 4.66 Mercury in ores and concentrates of sulphide copper-nickel deposits (Obolensky et al., 1995; Ozerova, 1986)
Deposit |
Ore, Mineral, Concentrate |
Number of samples |
Mercury, mg/kg |
Taimyr Peninsula |
Talnakh |
Pyrrhotine |
- |
0.05-0.2 |
|
Pentlandite |
- |
0.15-6 |
|
Yellow copper ore |
- |
0.06-0.4 |
|
Cubanite |
- |
0.4 |
|
Chalkosine |
- |
0.3-0.7 |
|
Ore |
- |
0.01-2 |
|
Pyrite concentrate* |
4 |
0.45-2 |
|
Yellow copper ore-pentlandite concentrate |
2 |
0.14-0.4 |
|
Platinum concentrate |
2 |
18-36 |
Norilsk |
Black jack |
- |
1.5 |
|
Ore |
- |
0.04-0.08 |
Octiabrskoye |
Black jack |
- |
0.2 |
|
Concentrates** |
- |
0.3-1 |
Kola Peninsula |
Monchegorsk*** |
Ore |
- |
0.05-0.11 |
"Vostok" |
Ore |
- |
0.06-0.2 |
* As far as it is known (Annual Report of MMC Norilsk Nickel-2001; Krivtsov, Klimenko, 1997), at the concentrating mills of MMC Norilsk Nickelthey do not obtain the pyrite
concentrate; it is possible that in this case the pyrrhotine concentrate is meant.
** The quoted work does not state at what stage of processing of ores the said concentrate was obtained; as a matter of fact, the platinum concentrate at the Norilsk Combine has
always been a finished product of a composite and multistage metallurgical processing (including, multiple high-temperature steps) of copper-nickel ores, after which it is difficult to
expect such high mercury contents in the finished product; if this concentrate is a product semi-industrial tests at the stage of ore dressing, then the said high concentrations of
mercury in it may quite be realistic (including, for example, because of the presence of amalgams). ** An interval estimation of mercury contents in concentrates processed by
MMC Norilsk Nickel (Yagolnitser et al., 1995).
*** According to (Ozerova, 1962), the mercury contents in the ores of Monchegorsk deposit (under single analyses) makes 9 mg/kg, in pentlandite – 46 mg/kg, in pyrrhotine –
1.8 mg/kg, in magnetite – 3 mg/kg.
Based on the data of Table 4.67, let us accept for the sulphide copper-nickel ores of Taimyr the average mercury contents of 1.18 mg/kg; for the ores of Kola Peninsula – 1.41
mg/kg.
Table 4.67 The average mercury contents in ores of copper deposits (0.95 confidence reliability interval) (Fursov, 1983)
Deposit, Region |
Ore Characteristic |
Number of samples |
Hg, average (limits), mg/kg |
Norilsk, Taimyr |
Ingrained |
22 |
1.05 (0.79-1.38) |
Talnakh, Taimyr |
Compact |
15 |
1.30 (0.7-2.0) |
Allarechenskoye, Kola Peninsula |
Compact |
16 |
1.17 (0.97-1.43) |
Nattis-Kumuzhye, Kola Peninsula |
Compact |
9 |
1.65 (0.68-2.78) |
Emission of Mercury
The information on distribution of mercury at production of non-ferrous metals by the enterprises of MMC Norilsk Nickel OJSC is missing in the accessible literature sources. Only
one work is known in fact only, in which an expert estimation is made of mercury emissions into the atmosphere by the enterprises of Norilsk Combine (Taimyr Peninsula) in the
first half of the 1990s; the value varied within the limits of 0.75-2.5 t Hg/year (the average value – 1.63 t/year) (Yagolnitser et al., 1995). The said estimation of mercury emission
was later repeated by the authors of the quoted work in a number of their subsequent publications.
The absence of the necessary information does not allow us to evaluate, with a high degree of veracity, the current mercury emission by the enterprises of MMC Norilsk Nickel. In
view of the peculiarities of mercury behaviour during the pyro-metallurgical processing of raw materials, which were reviewed in the previous sections, it is possible, apparently,
only to establish the order of mercury emission by the said enterprises (mainly into the atmosphere).
The data for Pechenganickel Combine demonstrate that in 2001 they processed approximately 7.5 million t of ore (including up to 500,000 t of the received ore concentrate).
Under the average concentration of mercury in ores being 1.41 mg/kg, its total amount in the raw materials, processed in 2001, would make ~10.5 t. Let us consider (basing on the
peculiarities of mercury behaviour at ore dressing) that 15 % of the metal weight, contained in the ores, passed over at the dressing into the bulk concentrate (~1575 kg of
mercury). The concentrate, which contained the said quantity of mercury, arrived to the roasting shop, where up to 95 % of mercury, present in it (1496 kg), got sublimated and
passed over into the roast gases, which after dust removal were emitted into the atmosphere. It was shown above that customary some 25-37 % of mercury (in this case 374-554
kg) is ejected out of roast gases with rough and fine dust, stopped by purification facilities. Thus, the remaining amount of mercury (942-1122 kg) was emitted into the atmosphere.
A minor part of the metal (~ 50-60 kg) inside the pellets arrived to the melting shop (to the ore electric melting). Besides, about 300,000 t of ore extracted by Pechenganickel
Combine fell into the category of rich ore and arrived directly to the melting shop for further processing. This ore contained ~0.42 t of mercury. The said shop also received
300,000 t of rich Norilsk ore (~0.35 t of mercury). In minor amounts mercury is also present in a non-ferrous scrap and other raw materials. Let us consider that in general some
0.8 t of mercury arrived to the pyro-metallurgical process step (to the ore electric melting), of which a minor amount passed over into the dumped slag, still less – into the matte,
and the greatest portion of mercury (up to 95-97 %) got sublimated and was removed together with end gases, most probably, into the sulphuric acid production, where it was
redistributed among different products (sulphuric acid, sludge, cake of neutralization of the flush hydrochloric acid). Approximately 2-4 % of the arriving mercury was emitted with
the end gases of the sulphuric acid shop (~16-32 kg).
Thus, in 2001 Pechenganickel Combine emitted some 0.95-1.15 t of mercury (39-47 % of its total weight, which arrived with raw materials) into the atmosphere, 0.37-0.55 t
(15-23 %) was accumulated in entrapped dust (which is, as far as we know, a recycled product), ~0.75 t (31-32 %) joined the wastes and the end product of sulphuric acid
facility.
The amount of mercury arriving in converter matte (from Pechenganickel Combine and Norilsk Combine) to Severonickel Combine is insignificant (it appears to be a couple of
kilograms). The melting shop of Severonickel Combine is annually processing up to 100-150,000 t of ore received from Norilsk Combine, and also (about the same quantity) of
scrap and other raw materials. The total amount of mercury, which arrived in 2001 into the melting shop of the said Combine may be estimated approximately as 300 kg, from
which, in view of the production flow chart, a minor portion (some 4-6 kg) left with the slag into the dump, even a lesser amount – into the matte, some 75-111 kg got captured
together with dust in the purification facilities, and some 180-220 kg was emitted into the atmosphere. The sulphuric acid production of the Combine is based on the converter
waste gases, the mercury contents in then is obviously insignificant; therefore, it is hardly ever accumulating in significant amounts in the sludge and other products of the sulphuric
acid shop.
In 2001, Norilsk Combine engaged into its production not only the ore (nickel, copper and pyrrhotine) concentrates, but also the products of dressing (nickel and copper
concentrates) of the so-called stale pyrrhotine concentrate (during the previous years it was stored in dumps). The information on the volumes of processed stale pyrrhotine
concentrate by the concentrating mill is missing. Besides, Norilsk Combine also involved into production some earlier stored recycling materials, the amount of which is also
unknown. At the same time, for example, in 2002 as a whole, MMC Norilsk Nickel produced, from earlier stored recycling materials and stale raw materials, about 6 % of nickel
and more than 8 % of copper (of the total output thereof) (Annual Report of MMC Norilsk Nickel-2002). From here it follows that the said stock and raw materials usually made
a minor part of the extracted and processed sulphide copper-nickel ores.
The total amount of mercury, contained in ores, extracted in 2001, reached 14.3 t (at the average concentration of mercury in ores of 1.18 mg/kg). Let us consider that ~30 % of
this amount (~4.3 t) has passed over into the ore concentrates (nickel, copper and pyrrhotine), which then was processed at the metallurgical plants of Norilsk Combine. The
above process flow charts of raw materials at these plants allow us to conclude the following. Thus, at Nickel Plant (at agglomeration and electric melting) the overwhelming part of
mercury should leave with the end gases, which after dust removal (the mercury partially concentrating in the dust) is emitted into the atmosphere; a minor amount of mercury will
go into the dumped slag. At Copper Plant (at drying and especially at melting of raw materials), mercury should also fly away with the end gases into the atmosphere (while partially
concentrating at purification in the trapped dust). At Nadezhdinsky Plant mercury would leave into floatation tailings (most probably, in essential amounts); it should also arrive
partially into the sulphuric concentrate, which goes to sulphur melting in autoclaves (in this event mercury is partially emitted into the atmosphere with the effluents of this production
facility), and also should be rejected with the end gases of the pyro-metallurgical operation step of the sulphide and nickel concentrates (with a definite accumulation in the dust
deposited in purification refining equipment).
Basing on the structure of mercury losses, calculated above for Pechenganickel Combine, we may estimate, with a certain degree of conventionality, the mercury emission of
Norilsk Combine. Thus, the mercury emission into the atmosphere with the end gases of the pyro-metallurgical processing step of raw materials will make 1.7-2.02 t, about
0.65-0.99 t of mercury will be deposited with the dust in the air-treating equipment. The remaining amount of mercury, arriving into production together with raw materials, will be
distributed, to this or that extent, among other products (dumped slag, floatation tailings, recycling drains, etc.), and also, apparently, partially lost in the environment with
unorganized emissions and unaccounted sources, including the emissions of sulphuric acid production. Because of absence of the necessary information, it is not obviously possible
to evaluate all these mercury flows at the given stage. In Table 4.68 the approximate-calculated estimation of mercury emission into the atmosphere by the enterprises of MMC
Norilsk Nickel is given.
Table 4.68 Estimation of mercury emissions by the enterprises of MMC Norilsk Nickel OJSC in 2001, t
Enterprise |
Emitted into atmosphere |
Accumulated in captured dust |
Pechenganickel |
0.95-1.15 |
0.37-0.55 |
Severonickel |
0.18-0.22 |
0.075-0.111 |
Trans-polar Branch |
1.7-2.02 |
0.65-0.99 |
Total (round) |
2.8-3.4 |
1.1-1.7 |
4.4.6 Production of Tin
Novosibirsky Olovianny Kombinat OJSE (Novosibirsky tin combined works) (located in Novosibirsk) was virtually the only producer of tin in Russia in 2001. It produced 99.9 %
of Russian refined tin (Table 4.69), while the combined works' capacity was used to 27.5 % only (Gerasimchuk et al, ...)
Table 4.69 Production of tin in Russia, 1,000 t
Production of tin |
1997 |
1998 |
1999 |
2000 |
2001 |
In concentrates |
9 |
5.53 |
4.72 |
5.0 |
No data |
Refined tin |
6.7 |
7.7 |
4.09 |
5.2 |
4.5 |
Secondary tin * |
1 |
1 |
0.45 |
0.5 |
0.5 |
* Estimate.
Source: (Gerasimchuk et al, ...; Mineral Resources of the World at early 1998 ..., 1999; Mineral resources of the World at early 1999 ..., 2000; Mineral Resources of the World
on 01.01.2001 ..., 2002;)
Technology
Principal technology of processing of tin concentrates includes preparation of concentrates, magnetic separation, finishing (at finishing works), frying (at t about 700 °C in order to
remove sulphur and arsenic), leaching (using strong hydrochloric acid in order to remove iron, lead, tungsten trioxide and other acid soluble admixtures from concentrates), melting
(melting of low iron concentrates is carried out in electric furnaces, melting of other concentrates is carried out in reflection furnaces) in order to produce crude tin.
Crude metal containing 93 - 99 % of tin is subjected to refining (fare refining, vacuum refining or electrolytic refining). High purity tin is produced by zone melting of ordinary grade
metal. Slag generated by melting in reflection furnaces and electric furnaces undergoes secondary processing in fuming furnaces. Arsenic, zinc, lead and rare metals are stripped
along with tin in the course of fuming.
Materials skimmed in the course of melting are again melted in electric furnaces, sublimated tin chloride materials (dust containing tin) undergo granulation and in bowls and return to
melting process. Lean materials containing tin (sludge from finishing works, etc.) are processed using chlorination technique. Sublimated volatile tin chloride is transferred to
sulphuric acid compounds and undergoes electrolysis with an insoluble anode.
At Novosibirsky tin combined works they use a complex of technological processes and equipment permitting processing of various types of raw materials containing tin and
extract many incident metals (lead, bismuth, arsenic, indium and other metals). The enterprise produces tin of various degrees of purity, solder alloys based on tin, lead, antimony,
bismuth, indium, lead-free solder alloys, tin powder and solder powder, low-melting-point solders and alloys; soldering paste and fluxes for soldering of steel and non-ferrous
metals, babbites of various grades on the basis of tin, lead, copper and antimony; various grades of bismuth, high purity gallium and indium (People of Action ...). The works has a
complex of cleaning plants that ensure 99.9 % removal of dust from flue process gases and virtually 100 % cycling of water, excluding any industrial effluents.
Raw materials
Novosibirsky combined works has its own raw materials basis comprised of mining and concentration combined works Khinganskoe Olovo (Evreiskaya Autonomous oblast),
Dalolovo (Solnechny mining and concentration combined works, Khabarovsky Krai), Tyash-Shan-olovo. Novosibirsky combined works owns a large stock package in tin mining
enterprise Deputatskolovo OJSE (Yakutia). Average content of tin in ledge ore in developed deposits is estimated as 0.47% (Mineral Resources of the World in Early 1998 ...,
1999).
Average content of tin in the concentrates being processed is 52 %. They produce graded tin concentrates having tin content about 63 % from ores from Khinganskoe deposit
(http://www.eao.ru/in_olovo.html). In late 1990ties a share of domestic tin concentrates processed at Novosibirsky combined works was about 60 %; the rest were concentrates
imported from China, Nigeria, Peru, Portugal and UK (Mineral Resources of the World in Early 1998 ..., 1999). Seemingly, at present the main part of tin is produced from
domestic concentrates; secondary raw materials is used in small quantities.
Emission of mercury in the course of production of tin
Average content of tin in ores from tin ore deposits is 0.1 mg/kg (Ozerova, 1962). Content of mercury in tin concentrates (deposits in Primorie region, Yakutia, Baikal region)
varies within limits of 0.01 - 0.5 mg/kg. Content of mercury in tin concentrates with sulphides is within 0.7 - 0.8 mg/kg (Ozerova, 1986). According to V. Z. Fursov (1983), levels
of mercury content in ores from tin deposits are higher and vary from 0.866 to 1.89 mg/kg on average (Table 4.70). Overall average value is approximately 1.3 mg/kg. Let's
assume that this quantity of mercury is contained in tin concentrates. Relatively high content of mercury within boundaries of tin ore areas (including deposits in Primorie region)
were also pointed out in a number of other works (ref., for example, (Korostelev, 1968)).
Table 4.70 Average content of mercury in ores from tin deposits (confidence interval 0.95) (Fursov, 1983)
Deposit, region |
Number of samples |
Mercury, mg/kg |
Valkumei, Chuckchee |
5 |
0.86 (0.40-1.85) |
Festivalnoe, Far East |
4 |
1.89 (1.27-2.64) |
Khrustalnoe, Primorie |
6 |
1.34 (0.98-1.87) |
Uchkoshkon, Kyrgyzstan |
8 |
1.2 (0.87-1.76) |
According to (Yagolnitser et al., 1995), in the first half of 1990-ties mercury emission in the course of production of tin at Novosibirsky combined works varied within 9-33 kg per
year. Novosibirsky combined works generated 1-25 t per year directly from tin concentrates (it seems that Novosibirsky combined works was operated to its full capacity at the
time). Authors of the cited work arrived at this estimate on the basis that mercury content in the tin concentrates being processed is within 0.01 - 0.5 mg per kg and annually the
works used 8,000 t of sulphur ore (pyrite) delivered from Ural (1 mg/kg).
If we accept the authors' approach to calculation of emission and, and take into account that production capacities of the works were employed to 27.5 % in 2001, we arrive at a
conclusion that mercury emission in the course of processing of tin concentrates should have been 0.3 - 7 kg in year 2001.
Let's assume that average content of tin in concentrates was approximately 50 %. Hence, in order to produce 4,500 t of tin (taking into account the rate of tin extraction to
commercial product), it was necessary to process approximately 10,000 t of concentrates. Assuming average content of mercury in concentrates 1.3 mg/kg, it was 13 kg of
mercury that came into processing with concentrates. A major part of mercury sublimates from concentrates as early as in the frying stage; remaining mercury (approximately 5 %
of overall mass) is removed from raw materials in the course of leaching and melting. As we noted above, an efficient dust arresting system is operated at Novosibirsky combined
works. This permits us to assume that at least 60 % of mercury contained in flue gases precipitates on filters of cleaning facilities together with dust. Thus, approximately 5 kg of
mercury was emitted directly to atmosphere.
4.4.7 Production of Lead
In Russia they produce primary and secondary lead. Usually various information sources (including official ones) only give data on refined lead irrespectively of from what raw
materials it is produced (Table 4.71).
Table 4.71 Production and consumption of lead in Russia, th. t
Indicator |
|
1999 |
2000 |
2001 |
Production of lead in concentrates (metal) |
13 |
12.2 |
16.1 |
Production of refined lead |
68.8 |
55.4 |
60 |
Import of refined lead |
27.2 |
-** |
40 |
Import of lead in concentrates |
-** |
10 |
20 |
Export of lead in concentrates |
15 |
20 |
9 |
Export of refined lead |
3.4 |
-** |
8 |
Consumption of refined lead |
95 |
83 |
90 |
* Analysis of available information permits to believe that production of secondary lead in Russia (from lead scrape) is approximately equal to production of lead from ore
concentrates and jointly processed return products of lead production and semi-finished products of zinc, copper and rare metal production; ** no data is available.
Source: (State Report 'On condition of Mineral Raw Materials ...'; Information and analytical ... Lead and Zinc, 2002; Mineral Resources of the World at 01.01.2001 ..., 2002).
According to Ministry of Natural Resources of RF, in 2001 major part of lead in ore was mined at deposits in Primorsky Krai and Krasnoyarski Krai (41 % and 34 %,
correspondingly). (State Report 'On Condition of Mineral Raw Materials ...').
Main producers of lead concentrates were OJSE Dalpolimetall (Primorski Krai, deposits Nikolaevskoe, Partizanskoe, Verkhnee, Yuzhnoe; over 800,000 t of complex ore was
mined and 23,000 - 24,000 t of concentrate was produced in 2001, of which 70% of concentrate was exported) and JSE Gorevsky GOK (mining and concentration combined
works) (Krasnoyarski Krai, develops Gorskoe, 67,500 t of ore was mined and 5,530 t of concentrate was produced in 2001).
Some small quantity of lead concentrate was produced by Sadonsky lead and zinc combined works (Northern Osetia-Alania, few hundred t of lead in concentrate) and Salairsky
GOK JSE (mining and concentration combined works). Lead concentrates were supplied also from Kazakhstan (Vorontsova ..., Geological Service of Primorie ..., 2000; State
Report 'On condition of Mineral Raw Materials ...'; Metal Supply and Sales, 2001, #12; http://www.aktex.ru/rus/analytics/equimpent;
http://www.enicey.ktk.ru/nature/13.cfm?nid=200; http://www.rambler.ru/db/news/msg.html?mid=1449831...).
Processing of concentrates and production of refined lead was carried out at Svintsovy Zavod Dalpolimetall CJSE (Dalpolimetal lead works) (town Rudnaya Pristan, Primorski
Krai, produces lead from concentrates, design lead production capacity 14,500 t per year, and produces some lesser quantities of secondary lead), Verkhne-Nevijsky Zavod
(town Verkhne-Nevijsk, Sverdlovskaya Oblast, secondary lead, design capacity 10,700 t), Ryaztsvetmet OJSE (production of lead from secondary raw materials, capacity
11,400 t per year), Electrotsink OJSE (production of lead from lead concentrates and as a by-product in the course of of processing or zinc concentrates, capacity 38,600 t)
(State Report 'On Condition of Mineral Raw Materials ...').
Novosibirski Olovyanny Kombinat OJSE (Novosibirski tin combined works) produced some small quantities of tin, seemingly, few hundred t, mainly as a by product in the course
of production of tin concentrates. Svintsovy Zavod Dalpolimetall CJSE (Dalpolimetall lead works) only carries out processing of rich concentrates (containing at least 73 % of lead)
produced by Dalpolimetall OJSE, by crucible melting.
In 2000 Dalpolimetall lead works processed about 8,500 t of lead concentrates and produced about 6,000 t of refined lead; in addition to that, approximately 2,000 t was
produced from secondary raw materials (lead scrape, spent submarine batteries, etc.). Production of lead by Svintsovy Zavod Dalpolimetall CJSE (Dalpolimetall lead works) in
2001 can be estimated as 5,000 t, production of lead from secondary raw materials can be estimated as 2,000 - 2,500 t.
In 1998 Ryazttsvetmet OJSE took the first place in Russia regarding quantity of lead and lead-based alloy production from secondary raw materials. It produced about 25,000 t of
lead (about 50 % of all Russian metal) in that year (Mineral Resources of the World at early 1998 ..., 2000). At Ryaztsvetmet OJSE they use a technology of processing of battery
scrape using electric furnaces for lead production (Tarasov, 2001). Melting of lead raw materials is carried out in an electrothermal furnace in the melting shop using a special
technology. The difference of the used technology from common processes is that soda is not used as flux agent, the process is carried out without formation of matte, and quantity
of slag is reduced to the minimum, because formation of slag depends on ash content in coke and on quality of preparation of scrap. This technology provides sufficient advantages
compared to melting in pit-type furnaces or melting in short drum furnaces. In particular, quantity of generated process gases is reduced, carry out of dust is reduced, quantities of
return products and slag are reduced and consumption of coke is reduced. Refining of crude lead is carried out using a known technology. However, there is know-how for a
number of refining techniques. Processing of products of electric melting of secondary lead raw materials (slag, dross, skimming) and ebonite fraction is carried out in a sublimation
furnace.
Raw materials and specialties of its processing
Sulphide ores having content of metal maximum 8 - 9 % are the main raw material for lead production. Concentrates supplied to lead works for processing usually contain 30- 80
% of lead, 1 - 14% of zinc and up to 10 % of copper (Utkin, 1990). Batch for agglomeration frying is composed of sulphide concentrates, rich oxidized ores, dust, sublimation
materials from sulphuric acid production plants at copper smelting and zinc works and fluxes: iron ore or pyrite cinder, limestone and quartz.
Lead is produced form ore concentrates mainly using pyrometallurgy technique, by reduction melting of lead in pit-type furnaces. Sulphide concentrate produced by floatation
concentration of ore is subjected to oxidizing frying (sintering) together with fluxes. Sintering of lead concentrates is carried out in agglomeration machines. Sulphides of metals are
oxidized to oxides, and small particles of ore are sintered to agglomerate in the course of frying. Melting of agglomerate is carried out in a pit-type furnace in reducing atmosphere.
Products of melting are: crude lead, copper-containing matte, copper sulphide and lead sulphide. Liquid products of melting are collected in the internal crucible of the furnace,
where they settle down according to their density. Crude lead is released from the crucible and is transferred to the refining process. Slag and matte are released into two outside
settling reservoirs. Crude lead contains 90- 97 % of pure lead and multiple admixtures. They produce pure lead, alloy of gold with silver and other products in the course of
refining.
Behaviour and emission of mercury
In the course of oxidizing agglomeration frying and pit-type furnace melting of lead concentrates, in which content of mercury varies within limits 0.3 to 520 mg/kg, major part of
mercury (over 90 %) sublimates and it is arrested together with dust in electric filters, bag filters and in the course of cleaning of ventilation gases (Bobrova et al., 1990).
If sulphuric acid is produced, about 5.5 % of mercury (fed with raw materials) precipitates from gas phase in washing towers. The main mass of dust that is produced in the course
of sintering and melting of raw materials (60 - 80 %) is a returned product. This causes increase of losses of metals (and mercury) because of increasing output of dust and constant
circulation of considerable quantity of dust.
Actually, about 20 -25 % of mercury contained in batch goes to rare metal production processes together with various types of dust. Here dust is subjected to sulphidizing frying.
Such elements as mercury, selenium, arsenic, fluorine and other go into gases in the course of sulphidizing frying. Content of mercury in sludge reaches 1.17 %. Sludge undergoes
cleaning in order to remove arsenic and mercury, in so doing, calcium arsenite is formed. It goes to burial disposal. Mercury transfers from sulphate product to lead cake virtually
completely. Lead cake is a return product (Figure 4.14).
According to (Bobkov et al., 1997), average value of mercury emission factor in the course of primary production of lead is 2 g of mercury per tonne of produced metal.
Behaviour of mercury in the course of production of secondary lead at Russian works has not been studied; there are no data on mercury emission factor for this type of
production. Let's assume, on a very conditional basis, that this emission factor is less than mercury emission factor for primary production of lead by at least by one of magnitude,
and that it equals 0.2 g of mercury per tonne of produced metal.
Available data permit to estimate mercury emission to the atmosphere in the course of lead production in general for entire country. This estimated general mercury emission to the
atmosphere: 60 kg in the course of primary lead production (30,000 t); 6 kg in the course of secondary lead production (30,000 t).
As it is shown above, only a relatively small part of mercury is removed from the technological process together with emissions, commercial products and materials going to burial
disposal. Major part of mercury is accumulated in return semi-processed products.
4.4.8 Production of Other Non-ferrous Metals
The production of gold has been described in section 3.3. According to the estimates the ores processed in 2001 contained 4-8 tonnes of mercury, which mainly ended up in the
tailings by production of concentrates. It is assumed that about 20% of the amount of the mercury extracted as a coproduct might be emitted to the atmosphere at the different
stages of extraction and processing of gold ore, as well as waste storage. No data has been available for estimating emission to the environment from the refining of the gold.
Antimony, molybdenum, tungsten and some other (mainly incidental) rare metals were produced from ore raw materials (ore concentrates) in very small quantities in 2000-2001 in
Russia. Annual production of concentrates of these metals was rather small, in the order of few thousand t. A considerable part of antimony concentrate, molybdenum and tungsten
concentrates were exported, and only a small part was processed at domestic works.
Antimony was produced from ore raw materials mainly at Ryaztsvetmet OJSE (in Ryazan), where concentrate supplied from gold and Sarylykhanskoe antimony deposit (in
Yakutia) was processed (1,000 -2,000 t per year). Facilities for production of antimony, established in the works in 1995, allow for efficient processing on gold-and-antimony
concentrates in order to produce antimony trioxide (metallic antimony) and gold-and-antimony alloy usable for production of gold bars (Tarasov, 2001). The same works
produced secondary antimony in the form of alloys (few thousand t per year). There is information that concentrates from Yakutia was also supplied to Novosibirsky tin works in
very small quantities. Production of antimony in concentrates in Russia in 2000 was estimated as 4,700 t, production of metallic antimony in Russia in 2000 was estimated as
1,000-2,000 t (Mineral Resources of the World on 01.01.2001 ..., 2002).
Lermontovskaya Gornorudnaya Kompania JSE (Lermontovskaya Ore Mining Company), located in Primorski Krai, is one of main exporters on tungsten concentrate from
Russia (Mineral Resources of the World in Early 1998 ..., 1999; Petrov et al. ...). Recently production of the enterprise was approximately 4,000-5,000 t per year.
Figure 4.14 Diagram of mercury distribution in processing products of lead production (Bobrova et al., 1990)
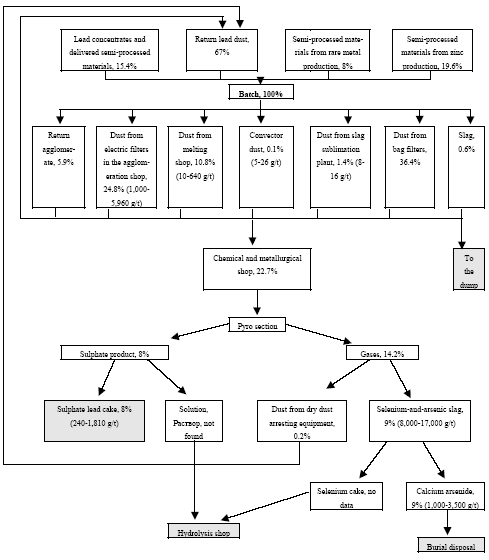
Molybdenum concentrate also mainly goes to export (Petrov et al. ...). In recent years in Russia production of molybdenum concentrate was 3,000-5,000 t per year. A major
part of this production belongs to Molibden OJSE (Sorsky combined works, Khakasia, up to 90 % of Russian mining production). Also Tyrnyauzski combined works
(Kabardino-Balkaria) and Zhirekensky Molibden OJSE (Chitinskaya Oblast) produced molybdenum concentrate in very small quantities (Blagutin).
Taking into account minor quantities of antimony concentrates, molybdenum concentrates and tungsten concentrates processed at Russian works, and taking into account content
of mercury in concentrates or in ores, whish are seldom higher that 1 mg/kg, according to scarce data available from literature (Ozerova, 1986; Fursov, 1983); one can assume that
mercury emission to the atmosphere in the course of production of antimony, molybdenum and tungsten is small. It can be estimated as 3-5 kg per year in the entire country.
4.4.9 Summary
The present information on mercury emission to the air and mercury in waste and products from nonferrous metal production in the Russian Federation is summarised in Table
4.72. It has within the present inventory not been possible to investigate all parts of the mobilisation of mercury by non-ferrous metal production. The estimate on mercury on
tailings from combined nickel and copper production indicates that very high amounts of mercury may also be disposed of with tailing form copper (Ural enterprises) and zinc
production. For further development of the inventory it will be necessary to obtain more specific information directly from the enterprises.
Table 4.72 Mercury emission and mercury in waste and products from nonferrous metal production in theRussian Federation, 2001, best estimates, tonnes
Sector |
Mercury in ores |
Mercury in concen-trates |
Hg emission to air |
Hg in tailings |
Hg in other solid waste |
Discharge to sewerage |
Zinc production |
n.a |
31 |
1,9 |
n.a. |
8.5 |
0.2 |
Nickel production from silicate ore (Ural enterprises) |
0.3 |
Direct ore processing |
0,3 |
no tailings |
0.006 |
n.a. |
Combined nickel/copper production (MMC Norilsk Nickel) |
24.8 |
5.9 |
3,1 |
18.9 |
n.a. |
n.a. |
Copper production (Ural enterprises) |
n.a. |
23 |
2,0 |
n.a. |
6.6 |
0.4 |
Tin production |
n.a. |
0.01 |
0,005 |
n.a. |
n.a. |
n.a. |
Lead production |
n.a. |
n.a. |
0,06 |
n.a. |
n.a. |
n.a. |
Gold mining |
6 |
n.a. |
1,2 |
4.2 |
n.a. |
0.6 |
Other nonferrous metallurgy |
n.a. |
<1 |
0,005 |
n.a. |
n.a. |
n.a. |
Total (round) |
> 31.2 |
> 60 |
8.6 |
> 23 |
> 15 |
> 0.6 |
n.a. not assessed bacause data have not been available
4.5 Ferrous Metallurgy
Table 4.73 shows data that characterize outputs of main ferrous metallurgy products in Russia in 1999-2002.
Table 4.73 Production of main types of ferrous metallurgy products in Russia, 1999-2002, million t
Year |
Iron ore |
Coke (6% humidity) |
Pig iron |
Steel |
Finished rolled metal |
Steel pipes |
1999 |
82.2 |
28.1 |
40.9 |
52.5 |
40.9 |
3.3 |
2000 |
87.1 |
30 |
44.8 |
59.1 |
46.7 |
4.8 |
2001 |
82.8 |
29.9 |
47.1 |
59 |
47.1 |
5.4 |
2002 |
84.2 |
30.9 |
46.3 |
59.8 |
48.7 |
5.1 |
Source: (Analytical Record on the Condition ...; Katunin, 2001; Kozyrev, 2002; with supplements)
Largest metallurgical combined enterprises operating in Russia represent industrial complexes, as a rule, with a complete technological cycle, including mining enterprises, coke and
chemistry and refractory production facilities, blast furnaces (2 to 7 blast furnaces), steel melting and rolled metal facilities, as well as construction, repair, energy, transport and
other units; the number of employees at each such enterprise is up to 20-40,000 persons.
Features of blast furnace production
The process of pig iron melting in blast furnaces is continuous. Raw materials include sinter, flux, coke, pellets, blown materials, natural gas. Blast furnaces operate using
counter-flow process. Sinter, flux, pellets and coke are loaded, from time to time into the blast furnace from the top. Air heated to 1,050-1,300°C is fed to the blast furnace from
the bottom and passes through the ascending blend, that is heated, recovered and melted. Pig iron, the main product of blast furnace production, is an alloy of iron with carbon,
containing certain quantities of Si, Mn, P, S. According to its purpose, pig iron is divided into three groups: 1) conversion pig iron, i.e. designed for processing into steel; 2) casting
pig iron, i.e. pig iron used for castings (pig iron castings); 3) special (blast furnace ferrous alloys used as deoxidizer for steel production) (Principles of Metallurgy ..., 1962).
Spent blast furnace gas is a fuel; therefore, it is removed from the blast furnace and, after pre-treatment, is sent to blast furnace (Cawper) stoves (blast furnace air heater), wherein
it is incinerated together with natural gas or coke gas, thus heating blow air for the blast furnace. At the outlet of the stove, temperature of the blast furnace gas makes 300-500°C;
its quantities are from 2,000-2,500 to 3,800-4,000 m3 per tonne of pig iron (depending on the type of melting and pressure); dust content in the blast furnace gas when the oven
works with the normal pressure in the upper part of the blast furnace) is 50-60 g/m3 (sometime up to 100 g/m3); when increased pressure is used, it is 35-40 g/m3 (Stark, 1990).
As a rule, a multi-stage cleaning process sis used to entrap dust. Gas and dust removal equipment of the 1st stage includes dry systems (cyclones with the flow turning of 180°),
then wet systems are used (nozzle scrubber, Venturi pipe with a drop trap and throttle group or wet tubular electrical filters). Usually, coarse cleaning efficacy is not more than
65-70%. At some enterprises throttle groups of cleaning equipment have been replaced, in recent years, by gas utilization turbines without compressors. The average efficacy of
gas and dust removal systems at CIS enterprises is estimated at 98 % (Emissions of Heavy Metals ..., 1998).
Table 4.74 shows the suppliers of raw materials for the main metallurgical enterprises in Russia. Raw materials for small enterprises of the Northern and Middle Ural regions are
mainly supplied from Kachkanar group of deposits and deposits of Tagil-Kuvshinskiy, Serov-Ivdelsky and Bogoslovsky regions; similar enterprises of Southern Ural receive ore
mainly from deposits in the Magnitnaya Mountain and Khalilovskaya group.
Table 4.74 Suppliers of unprocessed iron raw materials to main metallurgical enterprises of Russia
Enterprise |
Main suppliers of unprocessed iron ore |
MC (metallurgical company) Magnitogorsk OJSC " |
50-70% are supplied from Central Chernozem and Northern regions of Russia:
Mikhailovskiy GOK OJSC; the remaining part is supplied from local iron ore mining
enterprises (Magnitigorsk and Maly (Minor) Kuzbas deposits), or is imported (Sokolovsk-Sarbaysk
iron ore deposit, Kazakhstan) |
MC Novolipetsk OJSC |
Lebedinsky GOK OJSC(Lebedinsk and Stoylo-Lebedinsk deposit, KMA),
Stoylensk GOK OJSC (Stoylensk deposit, KMA), Mikhaylovsk GOK
OJSC (Mikhailovsk deposit, KMA) |
Severostal OJSC (Cherepovetsk MC) |
Olenegorsk GOK OJSC (Olenegorsk, Kirovogorsk, Bauman, XV Let Oktyabrya, Komsomolsk
deposits), Kovdorsk GOK OJSC (Kovdorsk deposit), Karelsky Okatysh OJSC (Kostomuksha
deposit); Lebedinsk GOK OJSC (Lebedinsk and Stoylo-Lebedinsk deposits, KMA);
Stoylensk GOK OJSC (Stoylensk deposit, KMA) |
MC Nizhny Tagil OJSC |
50-70% are supplied from Central Chernozem and Northern regions of Russia;
the remaining part is supplied from local deposits (Kachkanarsk and Tagil-Kuvshinsk)
and from enterprises (Kachkanarsk GOK OJSC) or imported |
Zapadno-Sibirsk MC OJSC " |
Korshunovsk GOK OJSC (Korshunovsk deposit), Sibruda OJSC, Lebedinsk GOK, local
deposits (Tashgalsk, Sheregersk, Kazsk, Sukharinsk), Kachkanarsk GOK (Gusevogorsk
deposit), and imported raw materials |
Mechel OJSC (Chelyabinsk MC) |
Bakalsk deposit (in part), raw materials from central and northern regions
of Russia (50-70%); local enterprises (Kachkanarsk GOK), and a small amount of
import |
MC Kuznetsk MK OJSC |
Korshunovsk GOK OJSC (Korshunovsk deposit), local deposits (Tashgalsk, Sheregersk,
Kazsk), and imported raw materials |
Tulachermet OJSC |
KMA deposits |
Nosta OJSC(Orsk-Khalilovsky MC) |
Bakalsk deposit (part), raw materials from central and northern regions of
Russia (50-70%), and some raw materials are imported |
Source: Analytical Record on the Condition of ferrous...; Afanasyev et al., 1997; Gobal Mineral Resources at the Beginning of 1998..., 1999; bal Mineral Resources at the
Beginning of 1999..., 2000; Sharov et al., 1997.
Mercury emissions during blast furnace production of pig iron
The content of mercury in concentrates from Kursk Magnetic Anomaly (KMA) deposits, the main source of raw materials for Russian enterprises, is within 0.01-0.1 mg/kg
(Stoylensk and Korobovsk deposits); concentrates from Korshunovsk deposit (Siberia) include 0.02-0.085 mg/kg (Ozerova, 1986). We presume that the average mercury
content in blast furnace iron ore and in pellets is 0.06 mg/kg, in sinter, metal additives and in coke it is 0.0004 mg/kg; in natural gas it is 0.1 μg/m3, in limestone it is 0.05 mg/kg, and
in manganese ore it is 0.06 mg/kg. based on data of Table 4.75, we calculate the specific quantity of mercury fed to the blast furnace process (per tonne of produced pig iron). It
will be 39.86 mg/t of pig iron (0.03986 mg/kg of pig iron). Presuming that 99% of mercury, used for blast furnace process, is sublimed and, eventually, emitted to atmosphere the
specific emission of mercury makes 0.0395 mg/kg of pig iron. This indicator corresponds to the known mercury emission factor, calculated by J. Pacyna and E. Pacyna (2000),
which is equal to 0.039 g of Hg/t of pig iron, which probably can be used for estimating mercury emissions during production of pig iron in Russia (Table 4.76).
The total amount of mercury mobilised and emitted is estimated at 1.8 t/year. Considering the uncertainty the range of the total amount mobilised is roughly estimated at 1.2-2.4
t/year.
Table 4.75 Specific consumption of main materials (kg) for production of one t of pig iron
Materials |
2000 |
2001 |
Average concentration
of Hg, mg/kg * |
Weight of Hg, fed to
production, mg/t fed |
(Katunin, 2001) |
Iron ore part of the blend including: |
1,674 |
1,660 |
|
|
iron blast furnace ore |
17 |
16 |
0.06 |
0.96 |
sinter |
1,137 |
1,141 |
0.0004 |
0.456 |
pellets |
520 |
502 |
0.06 |
30.12 |
metal additives |
15 |
20 |
0.0004 |
0.008 |
Skip coke |
468 |
457 |
0.0004 |
0.183 |
Natural gas, m3 |
92 |
92 |
0.1 g/m3 |
0.009 |
Oxygen, m3 |
85 |
81 |
- |
|
Limestone |
161 |
158 |
0.05 |
8.05 |
Manganese ore |
1.3 |
1.3 |
0.06 |
0.078 |
Total |
39.9 |
* For 2001, minimum mercury concentrations are used; in reality, some enterprises use, for instance, limestone and iron ore with higher mercury concentrations.
Table 4.76 Mercury emission during production of blast furnace iron in Russia, 2001
Enterprise |
location |
Pig iron, 1000 t/year |
Hg emission, t/year |
OJSC "Magnitogorsk MK" |
City of Magnitogorsk, Chelyabinsk Oblast |
8,662 |
0.338 |
Novolipetsk MC OJSC |
City of Lipetsk |
7,464 |
0.291 |
Severostal OJSC (Cherepovets MC) |
City of Cherepovets, Vologda Oblast. |
7,447.9 |
0.290 |
Nizhny Tagil MC OJSC |
City of Nizhny Tagil, Sverdlovsk Oblast |
4,628.7 |
0.181 |
Zapadno-Sibirskiy MC OJSC |
City of Novokuznetsk, Kemerovo Oblast |
4,546 |
0.177 |
Mechel OJSC (Chelyabinsk MC) |
City of Chelyabinsk |
2,905.8 |
0.113 |
Kuznetsk MC OJSC |
City of Novokuznetsk, Kemerovo Oblast |
2,750.7 |
0.107 |
Tulachermet OJSC |
City of Tula |
2,200 |
0.086 |
Nosta OJSC (Orsko-Khalilovsky MC) |
Town of Novotroitsk, Orenburg Oblast |
1,786 |
0.070 |
Chusovoy MC OJSC |
Town of Chusovoy, Perm Oblast |
678.7 |
0.027 |
Svobodny Sokol OJSC |
City of Lipetsk |
580 |
0.023 |
Kosogorsky Metallurgical Plant OJSC |
City of Tula |
403 |
0.016 |
Metallurgical Plant named after A.K. Serov OJSC |
Town of Serov, Sverdlovsk Oblast |
341.7 |
0.013 |
Satka Pig Iron Plant OJSC |
Town of Satka, Chelyabinsk Oblast |
180.8 |
0.007 |
Verkhne-Sinyachikhinsky Metallurgical Plant |
Sverdlovsk Oblast |
112.5 |
0.004 |
Beloretsk Metallurgical Combined Enterprise |
Town of Beloretsk, Bashkortostan |
109.2 |
0.004 |
Alapayevsk Ferrous Alloy Company |
Town of Alapayevsk, Sverdlovsk Oblast |
14.9 |
0.001 |
Total |
|
4,4811.9 |
1.75 |
Mercury emission from ironworks
In Russia, there are several hundreds of ironworks (production of casting) (mainly, at machine-building enterprises). The leading place among iron foundry facilities is taken by blast
cupolas (about 90% of the total melt); about 10% of castings are made in arc furnaces; some enterprises use induction furnaces. The cupola is a shaft furnace designed for melting
pig iron in foundries. Blend materials are loaded to the shaft from the blast furnace top in layers (charges): blast furnace iron in pellets, metal scrap, flux and coke. Melted coke is
collected in a hearth and is fed to the receiver. The output efficiency of such furnaces is from 1 to 60 t/hour. On the average, about 18% of coke, 2-3% of flux, up to 20% of scrap
iron, 40-45% of pellets and 15-20% of recycled materials from its own production are used per tonne of finished casting products.
In foundries, dust and gas emissions occur when melting metals, pouring metals into moulds, during shaking and clearing of castings, during manufacture of cores, preparation of
mounding sand, loading and unloading operations in the blend area. The main source of dust and gas emission is melting shops (foundries), which give up to 50-80% of all solid
emissions. For melting one t of liquid metal, 1000 m3 of gas are emitted from the cupola; dust concentration is about 1-10 g/m3. the average efficacy of emission cleaning when pig
iron is melted in open cupolas at CIS enterprises is estimated at 90% (Emissions of Heavy Metals ..., 1998).
It was found (Emissions of Heavy Metals ..., 1998), that the specific emission of mercury in ironworks makes 0.001 g Hg/t of casting (at 90% dust entrapment efficacy). Annually,
about 9-10 million t of castings are produced in ironworks by Russian enterprises. Thus, for the whole country the mercury emissions can be estimated at 9-10 kg/year.
Mercury emission from steel production facilities
Steel is produced in Russia by means of the basic oxygen furnaces (about 63% of the total production output), electrical arc melting (about 14%) and open-hearth furnaces (about
24%) (Yugov, 2002). Thus, we can presume that in 2001, in Russia, about 8 million t of steel were produced by electrical arc melting; 37 million t by basic oxygen furnaces and 14
million t by open-hearth furnaces.
Data about specific mercury emission during production of steel at domestic enterprises are not available. Belarusian researchers organised experimental work at Belarusian
Metallurgical Combined Enterprise; they found that mercury concentrations in dust of electrical steel-making furnaces (from the hose filters) caries within 2.241-15.333 g/t (the
average figure was 8.446 g/t) (Emissions of Heavy Metals ..., 1998). Specific mercury emission, taking into account unorganized emissions during steel making in electrical arc
furnaces in CIS countries, is estimated by the authors of the mentioned work at 0.012 ã Hg/t of steel, neglecting unorganised emissions, i.e. 0.007 g of Hg/t of steel. Thus, total
emission of mercury during this process can be estimated for the whole of Russia (in 2001) at about 98 kg of mercury.
Relatively high concentrations of mercury in dust and increased emission of mercury can be explained by a wide use of scrap iron, including mercury-containing materials, as the
initial raw material for electrical steel making. To increase the content of carbon in the blend they use pig iron, coke and broken electrodes. Steel alloying and oxidizing is performed
using standard ferrous alloys and alloy additives.
According the data (Emissions of Heavy Metals ..., 1998), the open-hearth furnace dust (Zaporozhstal enterprise, Ukraine) had the mercury content of 0.098 mg/kg, which in fact
2 orders lower than in dust from electrical steel-making furnaces. With some degree of conventionality we can presume that specific emissions of mercury in steel making facilities
using open-hearth furnaces and oxygen converters do not exceed a similar indicator for ironworks making pig iron castings, i.e. about 0.001 g Hg/t of steel. Hence, we can draw a
conclusion that mercury emission in Russia during making of steel using the above processes was about 51 kg in 2001.
Thus, total mercury emission to atmosphere during making of steel in Russia in 2001 can be estimated at 149 kg (0.15 t).
5 Turnover of Mercury by Waste Treatment
5.1 Mercury Recycling
5.1.1 Mercury-containing waste
Data on the amounts of mercury-containing waste (manly industrial waste) generated by now in Russia, as published in literature, testify that such amounts are very high.
Thus, by different assessments (Klimov et al, 1999; Report on Research Work ..., 1999), the total amount of such waste makes 1.1 million tonnes. Among such waste, the bulk of
mercury-containing waste (58% by weight) has the mercury content of 10-30 mg/kg; 30% of the waste has the mercury content of over 5000 mg/kg; and about 125 have metal
concentrations at 100-5000 mg/kg. According to other data (http://www.greenpeace.ru/gpeace/43520/gp_article_t...), in Russia there is about 750,000 tonnes of
mercury-containing waste; according to (Donskykh, Skitskiy), this content is about 650,000 (with the mercury content from 200 to 750,000 mg/kg); annually about 11,000
thousands new waste are generated. The most significant volumes of stored mercury-containing waste and, hence, high levels of habitat pollutions are in the regions of the country
where large nonferrous metallurgy, chemical, wood pulp and paper and gold mining enterprises are located.
For example, near Kirovo-Chepetsk Chemical Enterprise (the city of Kirovo-Chepetsk, Perm Oblast) there are temporary dumpsites and deep-burial dump fields which house
409,000 tonnes of mercury-containing waste (Polskykh ...). In Irkutsk Oblast, soils at industrial enterprises producing chlorine and caustic accumulate over 1,000 tonnes of
mercury, and more than 2,000 tonnes of metal can be found in slurry accumulating sites (the State Report "On Environmental Condition in the Russian Federation in 2002"). In the
coastal area of the Northern Dvina River mouth, 3,200 tonnes of mercury-containing waste from Archangelsk Wood Pulp and Paper Enterprise have been recently dumped;
Krasny Bor dumpsite (Leningrad Oblast) located over 100 tonnes of mercury-containing waste (http://www.greenpeace.ru/gpeace/43520/gp_article_t...). In the territory of the
former Amur Wood Pulp and Paperboard Enterprise (city of Amursk, Khabarovsk Krai) about 300-500 tonnes of mercury-containing waste are kept in containers and on open
sites (http://www.3e.opec.ru/news; http://www.khv.ru/MD/2001/12720/ob.htm). According to other data (Parliament Gazette ...), the old (now unused) stores of this enterprise
house about 4,400 tonnes of mercury-containing waste.
At the end of 1990's, Russian nonferrous metallurgy enterprises houses in their territories over 63,000 tonnes of slurry containing about 155 tonnes of mercury (Report on the
Research Work ..., 1999). In Northern Osetia (the area of dumpsites of 250 ha) now accumulate about 9 million tonnes of enrichment rejections (tailings) from Mizurskaya and
Fiagdonskaya enrichment enterprises and waste from the metallurgical enterprises Electrozink and Pobedit (the city of Vladikavkaz), in which the estimated weight of mercury is
about 110 tonnes (Satsayev, 2002). Chelyabinsk electrolyte sink enterprise houses, in its territory, about 40 tonnes of mercury and selenium slurry
(http://www.chrab.chel.su/archive/17-10-97/1/RE12.D... (16.10.1997)).
Significant amounts of mercury-containing slurry are located in the vicinity of gold-extracting enterprises. For example, the rejection stores at Semenovskaya factory (Southern
Ural) contain totally about 60 tonnes of mercury (Mustafin et al., 1998). In the township of Solovyovka (Tynda District, Amur Oblast), the heavy concentrate enrichment
installation houses, in its stores, about 15,000 m3 of mercury-containing slurry (http://www.mhg.ru/proekt/doklad/99/region/am/chapt...); in the township of Tokur (Amur Oblast),
about 30 to tonnes of mercury are stored in unattended store facilities (The Priamurskiye Vedomosti Newspaper ...).
According to Business Books and advertising publications of the recent years, in Russia there are several enterprises that are engaged, to different degrees, in refining of spent
mercury and processing of industrial mercury-containing waste. However, only two of such enterprises operate at a rather full scale and regularly supply secondary mercury and its
compounds to the local markets: they are NPP Kubantsvetmet CJSC and Mercom Ltd.*
5.1.2 Scientific and Production Enterprise Kubantsvetmet CJSC
NPP Kubantsvetmet CJSC is located in the township of Kholmsky (Abinsk District, Krasnodar Krai). In 1998, NPP Kubantsvetmet CJSC performed (using its own resources)
repair and rehabilitation work at the metallurgy plant, which, in the past, belonged to Krasnodarsky Rudnik Ltd. and developed a range of technological instructions regulating
processes for processing of mercury-containing waste, mercury refining and production of mercury compounds. This work was done within the Federal targeted programme
"Waste".
Some time ago, Krasnodarsky Rudnik Ltd. operated, basically, in the area of Sakhalin mercury deposits (quartz-dikkit-cinnabar type), located not far from the township of
Kholmsky. In 1974-1992, about 500 tonnes of metallic mercury was produced from ores extracted in this deposit field. In 1990, the underground part of Sakhalin deposit was
removed from use (due to economic inexpediency of its further development); in 1993 work on the quarry processing the ground-surface part of the deposit was terminated. In
1993-1995, Krasnodarsky Rudnik enterprise was processing ore extracted in the previous years (about 30 tonnes of mercury was produced); beginning from 1992, there has
been sporadic production of secondary mercury (from mercury-containing waste); during 1992-2001, this enterprise produced over 98 tonnes of secondary mercury (including
about 65 tonnes over the period of 1999-2001).
At present, NPP Kubantsvetmet CJSC performs the following operations with mercury-containing waste:
- processing of different mercury-containing industrial waste;
- processing mercury-polluted soils and construction waste;
- disposal of mercury-containing luminophor concentrate;
- de-mercuration of spent mercury lamps;
- disposal of spent and rejected mercury-filled devices;
- refining of unconditioned (spent or black) metallic mercury;
- production of different mercury compounds;
- production of special highly clean metallic mercury.
Activities of NPP Kubantsvetmet CJSC include transportation of waste from places of its generation (placement) in special metal containers for sorting of every waste batch,
separation of groups of metals fit for processing or decontamination in technological devices and extraction of commercial mercury, production of mercury compounds,
grouping of waste generated during activities of the enterprise for its further safe disposal (burial) and/or reuse.
Technological schemes applied to process mercury-containing waste, used at NPP Kubantsvetmet CJSC, make it possible to consider all waste delivered for disposal as a
sort of raw material, while by-products generated as a result of their processing, in turn, are used as secondary raw materials in other production facilities.
Technological and production operations are performed observing conditions and requirements contained in regulatory, technical, sanitary and hygienic documents (State
Standard GOCST 30772-2001; GOST 30773-2001; GOST 30774-2001; GOST 30775-2001; GOST 4658-73; Inter-sectoral rules on protection ...; Melnikov, 1974;
Mercury. Regulatory ..., 2001; Mercury. Specifications ..., 1977) and technological instructions (Technological Instructions ...).
Activities of enterprises are also regulated by:
- Licenses giving the right perform activities on handling hazardous (including mercury-containing waste) waste (like collection, use, decontamination, transportation,
placement, storage), issued by RF Ministry of Natural Resources;
- Licenses giving the right to perform activities on collection, processing and sale of ferrous scrap metals, issued by the Committee on Licensing of Krasnodar Krai;
- Licenses giving the right to use and operate production facilities producing melted ferrous and nonferrous metals and alloys of them, issued by the Federal Mining and
Industrial Supervision Committee of Russia;
- Licenses giving the right to transport cargo by motor vehicles in the Russian Federation, issued by RF Ministry of Transport.
The chemical analytical laboratory of NPP Kubantsvetmet CJSC has the Certification of Accreditation, issued by the State Committee on Standardisation and Metrology of
the Russian Federation.
The enterprise also includes the environmental service, the labour protection and safety department, as well as the section on technical control over raw material processing.
In the course of processing of mercury-containing waste, production of commercial metallic mercury and mercury compounds, there is performed relevant technological
control over processes and their parameters, the composition of processed raw materials, interim products ands final products, the material production balance is assessed
as well as technological performance indicators of the TVP-1 furnace and other equipment.
The total number of personnel at NPP Kubantsvetmet CJSC is more than 160 persons, including technologists and metallurgists who have long-standing experience of work
at large mercury and enterprises and mercury and antimony enterprises of the FSU.
Main technological schemes, equipment and production operations related to processing of mercury-containing raw materials
The production structure of NPP Kubantsvetmet CJSC includes the following:
1) The administrative and production facilities (with the total area of about 6 ha) and the adjacent railway dead-end track;
2) The industrial area (about 39 ha), including the following main facilities:
- a metallurgic plant, including two tubular rotary ovens, gas release and dust cleanup systems, mercury condensation and refining devices, slurry storage places, cinder sites;
the first TVP-1 oven is used for processing the mercury-containing raw materials by oxidation roasting, followed by release of mercury from the gaseous phase
(technological gases); the second TVP-2 oven is used for production of lime;
- an area for conditioning of mercury-containing raw materials for metallurgic processing;
- an area for production of mercury compounds;
- an area for production of highly cleaned mercury (4 plants using multiple-stage distillation with electrical discharge cleaning);
- an area for de-mercuration of high-pressure mercury lamps;
- an area for disposal of metal mercury-filled devices;
- an area for disposal of metal mercury-filled devices;
- an area for disposal of glass mercury-filled devices;
- an area for maintenance and repair of technological equipment;
- an area for technical control of mercury-containing raw material processing;
- a chemical analytical laboratory; and
- a finished products warehouse.
The annual production capacity of the TVP-1 oven (as regards raw material) is 36,000 tonnes; of the plant for de-mercuration of tubular mercury lamps is more than 1 million
pieces; of the plant for cleaning of unconditioned (spent) mercury I 240 tonnes of commercial metal; of the area for production of mercury compounds is 30 tonnes (as commercial
products); and of the plant for production of highly clean mercury is 15 tonnes of metal.
NPP Kubantsvetmet CJSC has the following required equipment and technologies for decontamination and disposal of the following types of mercury-containing production and
consumption waste that are included into several groups as regards their features and conditions of their processing (Table 5.1). The bulk of waste is processed by means of the
tubular rotary oven TVP-1.
The design of the tubular rotary oven
The tubular rotary oven TVP-1 is a metal cylinder (body) 6 with the diameter 1.6 m and the length 14 m, installed at a gradient of 3-4 and lined with refractory bricks. The body of
the oven is supported by bandage elements 5 on rollers 13, on which it is rotated at the velocity of 0.6-2 RPM, by means of the driving mechanism 14; this velocity is regulated by
means of a 4-speed electrical motor (Fig. 5.1). In the bottom part, the body abuts the furnace chamber 4, and in the top part it abuts the dust chamber 8. These chambers
represent metal frames, lines on inside with refractory bricks and having openings for connection of the oven body.
Table 5.1 Types of mercury-containing waste processed at NPP Kubantsvetmet CJSC
Group |
Type of waste |
Basic equipment |
Main waste suppliers in 200-2002 |
1 |
Spent catalyst (vinyl chloride production waste) |
Tubular rotary oven TVP-1 |
Khimprom OJSC (City of Volgograd); Plastcard OJSC (City of Volgograd); Azot
NAK (City of Novomoskovsk) |
1 |
Slurry from 1-amino anthrachion production (production terminated in 2000)
|
Tubular rotary oven TVP-1 |
Khimprom JSC (City of Cheboksary, Republic of Chuvashia) |
1 |
Mercury sorbent (activated carbon, KPR brand, etc.) |
Tubular rotary oven TVP-1 |
Sintez OJSC (City of Dzerzhinsk); Lisma OJSC (City of Saransk); Merkuriy EP
(City of St. Petersburg); Chemical enterprise named after Konstantinov (City of
Kirovo-Chepetsk) |
1 |
Concentrate of luminophor generated during mercury lamp disposal |
Tubular rotary oven TVP-1 |
Ecorecycle Ltd. (Town of Noginsk, Moscow Oblast); NPP Ecotrom Ltd. (City of
Moscow); Volgokhimtorg OJSC (City of Volgograd) |
1 |
Graphite waste |
Tubular rotary oven TVP |
Usolyekhimprom OJSC (City of Usolye-Sibirskoye, Irkutsk Oblast) |
1 |
Mercury compounds |
Tubular rotary oven TVP |
Mainly organisations and enterprises of Krasnodar Krai* |
1 |
Soils and construction materials contaminated with mercury |
Tubular rotary oven TVP |
Mainly organisations and enterprises of Krasnodar Krai* performing de-mercuration
of buildings and areas ** |
2 |
Galvanic elements (spent and rejected) |
Tubular rotary oven TVP |
Energia OJDSC (City of Yelets); Signal (City of Chelyabinsk) |
3 |
Tubular luminescent lamps (types LB, LD, etc.) |
Ecotrom-2 plant |
Organisations and enterprises of Krasnodar Krai |
4 |
High-pressure mercury lamps (DRL types) |
According to the adopted scheme |
Organisations and enterprises of Krasnodar Krai |
5 |
Metal devices filled with mercury |
According to the adopted scheme |
Organisations and enterprises of Krasnodar Krai |
6 |
Glass devices filled with mercury (spent and rejected) |
According to the adopted scheme |
Organisations and enterprises of Krasnodar Krai |
7 |
Spent respirators, used special clothes, fabric waste of mercury filtration |
Tubular rotary oven TVP-1 |
Organisations and enterprises of Krasnodar Krai |
8 |
Unconditioned metallic mercury (spent or black) |
Refining installation |
Different organisations and enterprises, including from Krasnodar Krai |
9 |
Gas-cleaning dust and slurry |
Tubular rotary oven TVP-1 |
Cleaning of technological waste |
10 |
Paperboard waste from mercury lamp packages |
Tubular rotary oven TVP-1 |
Organisations and enterprises of Krasnodar Krai |
- For example, in 2002, about 217 kg of chemical reagents containing mercury were received form the Kuban hydrometeorological land-reclamation party;
- ** in 2002, the PASF "Rtutservice" Ltd. (City of Krasnodar) generated 4.69 tonnes of mercury-containing soils;
- *** in 2002, about 2775 kg of unconditioned (black) mercury for received for processing from Belarus (UP "Beltsvetmet") and more than 600 kg from different enterprises
of Krasnodar Krai.
The furnace chamber is installed above the hopper for cinders (roasted raw materials) 1. In it, fuel (natural gas with the flow rate of 26.6 m3 per 1 ton of raw materials) is burned
through the nozzle 2; the flame is fed through the centre to the oven body. The upper (dust) chamber is used for interface of the rotary body of the oven with the stationary gas
duct. The pipe feeder of raw material 11 is laid through a hole in the end wall of the dust chamber into the body; it is used to feed raw material to the oven. The feeder is installed
between the hopper 10 of raw material and the oven. The oven is counter-flow oven: the raw material fed to the oven is moved, during rotation of the body, from the upper end to
the lower end, while gases, on the contrary, are moved from the furnace chamber to the upper end of the body and are released through the upper (dust) chamber 8 to the gas duct
9, whereby they are fed to de-dusting area. When gases pass from the oven to the gas duct through the dust chamber, the large dust particles are precipitated in the latter (the dust
brought out of the oven by the gas flow). To reduce the removal of dust from the oven to the gas system, a minimum pressure is built in the oven, which creates a danger of leakage
of technological gases through adjacent elements between the rotating oven body and the stationary chambers. To prevent gas leakage, these adjacent elements has special seals
12.
Figure 5.1 The layout of the tubular oven
Click here to see the figure.
1 – hopper for cinders; 2 – nozzle (burner); 3 - umbrellas; 4 - furnace; 5 – bandage elements; 6 – oven body; 7 – driving gear; 8 – dust chamber; 9 – gas duct for removal of
technological gases; 10 – hopper for raw materials; 11 - feeder; 12 – upper and lower seals; 13 – supporting rollers; 14 – driving mechanism for oven rotation
Temperature of processed raw material, when it is moved to the oven body, is increased, reaching its maximum near the unload end. Roasted raw material (the so-called cinders) is
fed to the cinder hopper located under the furnace chamber, where it is kept for a definite time, dur8ing which the released mercury vapours together with the hot air are sucked
from the hopper via the furnace chamber back into the oven. To prevent possible loss of vapours, the structure of the connections between the oven, the furnace and the hopper
fore cinders is reinforced by placing the lower seals.
General layout of the pyrometallurgical mercury production
The metallurgical processing of raw materials is effected by means of a regular scheme used in mercury production (raw material roasting – mercury vapour condensation –
mercury slurry processing), which was modernised by specialists of NPP Kubantsvetmet CJSC keeping in mind the conditions for processing of different groups of
mercury-containing waste (Fig. 5.2).
Before roasting in the oven, the raw material is loaded to the receiving hopper, wherefrom it is fed by a tape conveyor (3 m long, 0.8 m wide, 40 t/h capacity) for defragmentation
(to get pieces of 50-70 mm), performed using a special type crusher CM-741 (with the size of the loading slit 6 x 9 cm and the capacity 40 t/h). Dust generated during this process
is removed by means of the local ventilation system, accumulated in a tank with water and then fed for renewed roasting to the TVP-1 oven. The thus prepared raw materials is fed
by means of a tape conveyor (the tape length is 38.96 m and the width is 0.65 m) to the dispenser hopper, wherefrom it is fed by means of a tape feeder (1.8 m long; the tape
width 0.8 m, the capacity up to 6 t/h) to the TVP-1 oven.
Raw material is roasted at a temperature not less than 500 C, at which mercury contained in raw material is sublimed and transferred to vapour condition (technological gases). The
duration of material in the oven is 1.5 hours on the average. When required, the period of roasting can be regulated by the oven rotation velocity. Roasting is going on in an
oxidising environment, i.e. when free oxygen is present. Oxidising conditions in the oven are maintained by means of 30% air excess, as required for fuel combustion. If the raw
material includes other volatiles, then they are sublimed, fully or partially, as well as moisture contained in the roasted raw material. Besides, dust is also turned into gases, in a
definite quantity, just as gas products generated during fuel combustion, and the excessive oxygen and nitrogen fed to the technological process with the air.
Figure 5.2 Principal diagram of the pyrometallurgical mercury-production process
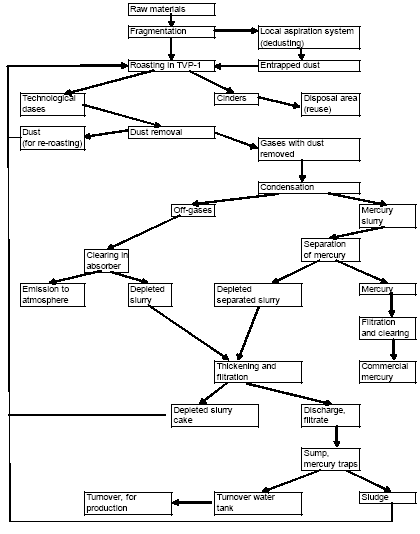
Roasted raw materials or cinders with the temperature at the oven exit at about 500 are fed to the cinder hopper. During unloading of hot cinders ascending hot air flows are
generated as well as dusting; to reduce this phenomenon, cinders are normally are kept in the hopper for 4-6 hours to bring their temperature below 800 C. Experience shows that
in most cases the mercury content in cinders does not exceed 25-26 mg/kg. Cinders are removed to dumpsites by dump trucks.
Technological gases generated during roasting of raw materials with the temperature at the oven exit not less than 500 C are fed, via a special gas duct, to a group cyclone, where
they are cleaned from dust. When cyclones operate efficiently, they entrap up to 90% of dust from gases, after which this dust is returned back for a new roasting. All gas ducts
from the oven to the devices used to remove dust, the devices themselves as well as gas ducts thereof are equipped with heat-insulation and heat-resistant materials.
After removal of dust, technological gases carrying mercury vapours are fed for cooling to the tubular condenser refrigerator where they are cooled down to 30 C and turned into
liquid (Fig. 5.3). The general principle of the condenser operation is as follows:
Figure 5.3. Diagram of the condenser refrigerator for condensation of mercury from technological gases
1 - tap; 2 - receiver; 3 – gas duct; 4 – frame structure; 5 – metal pipes (standpipes); 6 – upper holes (lids); 7 - piping; 8 – lower ends of T-pipes (discharge); 9 – T-pipes
Click here to see the figure.
Technological gases with dust removed are fed via the gas duct 3 and further along the condenser loops. Condenser loops include vertical metal pipes (standpipes) 5, fixed to the
frame structure 4, arranged in pairs and connected in the top area by means of U-shaped piping 7 (elbows). In the lower part, every pair is connected to the neighbouring pair by
means of T-pipes 9. Lower ends of T-pipes (discharge pipes) 8 are immersed into water in the receiver 2, installed in the bottom along the entire loop. Technological gas, fed to
the first standpipe, under impact of rarefaction generated by the fan installed after the condenser, passes stage-by-stage through the entire pipe system, ascending and descending;
then it passes to the neighbouring pair, and further on, till the end of the loop. To speed up cooling of technological gases inside the condenser, the standpipes that are the last in the
row are sprinkled with water fed through sprinklers (sprays) installed in the upper section of the standpipes. Besides, a definite amount of water is also fed to the standpipes, which
facilitates effective cooling of the dust contained in technological gases.
In the process of condensation, starting in the layer near the walls, mercury drops are generated; the largest drops flow down to special receivers (condenser troughs), located in
the lower part of the cooling device; part of the drops precipitate on its inside walls while the finest drops (aerosols) quite from the condenser with the outgoing gas flows exiting the
condenser. Condenser entraps not only metallic mercury, but also its compounds, the water that is accumulated here, oxides of some chemicals as well as a substantial part of dust
that has not been entrapped earlier. As a result, the condenser trough collects not clean mercury but the so-called slurry, i.e. a mixture of metallic mercury, its compounds, dust,
particles of unburned fuel and water. The amount of metallic mercury in the slurry varies from 20 to 80%, depending on a range of factors, like: the content of metal in the initial raw
material, the efficiency of the dust-entrapment system, etc.
The generated slurry is fed (by pumps) to the so-called mercury separation, which is effected in a hydraulic cyclone, wherein centrifugal forces result in coagulation and separation)
of metallic mercury from moisture and lighter solid products of roasting. During separation of metallic mercury the so-called depleted slurry is generated which is fed to the
thickener and then to the vacuum filter, wherefrom the dewatered mass, i.e. the depleted slurry cake (12-15% of humidity) is fed (after blending with lime) to the oven for a new
roasting so as to remove the remaining mercury.
Technological gases exiting from the condenser refrigerator (emitted off-gases) always contain some quantity of mercury vapours which corresponds to the equilibrium content
predetermined by the gas temperature, i.e. the higher the temperature, the greater the amount of mercury in them (Table 5.2). It is precisely for this reason that it is always
preferable to cool down the gases in the condenser to lowest possible temperatures (normally below 30 C). Beside mercury vapours, the released gases, removed from the
condenser, include also aerosols of metallic mercury, water steam, fine dust particles, ash and some other admixtures.
Table 5.2 Content of mercury in saturated vapour depending on the temperature (Melnikov, 1974)
Temperature, °C |
10 |
20 |
30 |
40 |
50 |
60 |
70 |
80 |
90 |
100 |
Mercury, mg/m3 |
5.64 |
13.38 |
29.81 |
62.8 |
126.6 |
234.9 |
452 |
807 |
1,396 |
2,338 |
Emitted off-gases are fed for additional (sanitary) cleaning, performed in a two-stage absorber. The first stage represents a spraying device (SD), wherein the bulk amount of dust
and some mercury are entrapped. Then the gases are fed to the ball-packing device (BPD), wherein an alkaline (lime) solution is used as a spray liquid. Dust entrapped by the
absorbers (depleted slurry) also is fed to the oven for a new roasting.
Gases purified in the absorber are emitted to atmosphere through the enterprise stack 30 m high (it may be over 60 m depending on the terrain), which secures the required dilution
of gases with air. Normally, up to 2,400 m3 of such gases are generated per tonne of processed raw materials, on the average; in normal conditions of the technological process,
the mercury content in the gases makes not more than 25.4 mg/m3, i.e. at present the specific emission of mercury to atmosphere makes 61 g per 1 tonnes of raw materials
processed in the TVP-1 oven. Maximum allowed emission of mercury for the metallurgical enterprise NPP Kubantsvetmet CJSC " is set at 80 kg/year. According to data
(Methodological ..., 1989), the content of dust (after cleaning) in emitted gases of mercury production (ore processing) usually does not exceed 5-6 g/m3.
At the metallurgical enterprise NPP Kubantsvetmet CJSC, they use a circulating water-supply system with the daily water makeup (15 m3/day for technological needs, and 5
m3/day for communal and other needs; the water if supplied from a special metal tank). Production circulation water is fed to the sump, passing through mercury traps, and then is
fed to the return water tank, wherefrom it is returned to the technological process. The generated sludge is fed to the roasting oven TVP-1. Communal and other non-production
wastewater is discharged to the sewerage system.
Mercury refining
The separation process allows getting metallic mercury that is filtered through a cotton belting and military cloth. As a rule, mercury obtained in this way is, without any additional
processing, a commercial product, P3 brand (Russian abbreviation), used for production of mercury compounds and/or supplied to users. Further required mercury cleaning is
performed at the mercury refining plant, manufactured by specialists of NPP Kubantsvetmet CJSC, which is based on using a hydrochemical method.
About 0.05 kg of cotton belting and 0.05 kg of military cloth are used to clean 1 ton of mercury. Soft waste generated after the cleaning and refining of mercury (about 3 kg per
year, with the mercury content up to 2%) is accumulated in acid-resistant, tight vessels and then burned in the oven TVP-1.
The composition, conditions of acceptance, analysis, transportation and storage of mercury are defined in the State Standard GOST 4658-73, which specifies metals used for
production of semiconductor materials, for use in vacuum electrical engineering, manufacture of instruments, mercury and zinc current supply sources, various reagents and
pharmaceutical preparations, as well as in chemical, metallurgical and other sectors of industries (Table 5.3).
Table 5.3 Chemical composition of mercury (GOST 4658-73)
Requirements to the composition |
Mercury brand |
|
P0 |
P1 |
P2 |
P3 |
Mercury, %, minimum |
99.9997 |
99.999 |
99.99 |
99.9 |
Non-volatile residue, %, maximum |
0.0003 |
0.001 |
0.01 |
0.1 |
In particular, mercury of brands P1, P2 and P3 (Russian designation letters) is poured into special steel cylinders (ER-2,75; manufactured at Pervouralskiy pipe manufacturing
enterprise), rated 34.5 kg of metal. Each cylinder is tightly closed by a screwed cap with a gasket from fluoride plastic material of at least 0.15 mm thick. When cylinders are
stored for a long time, seals are attached to them. P0 mercury is poured into cylinders made from thick-wall glass with a capacity of 5 kg of metal. Mercury P1 and P2 can be
poured into cylinders made from thick-wall glass, after which these cylinders are closed with a metal lid and a gasket from plastic material. P1 mercury, designed for medical use, is
poured into vials containing 50 g of metal; these vials are plugged with polyethylene plugs and lids. Each vial is placed into a polymer can 30 cm3 and sealed with alignine. The
warranty storage period for P1 and P2 mercury is two years, for P0 mercury – three years, for P0 mercury – unlimited.
Conditions and specific features of processing of mercury-containing waste
The technological scheme for processing of each group of mercury-containing waste has its specific features, depending on the waste generation source, and its substances and
consistency (see Table 5.1).
Processing 1st group waste
Processing of this waste, which includes spent mercury catalysts (waste from vinyl chloride production), sorbent (activated carbon KPR brand, etc.), mercury compounds,
production sludge from 1-amine anthrachion, soils and construction materials polluted with mercury, graphite waste, luminophor concentrate, etc., is generally performed using the
single technological scheme, which includes the following main technological operations:
- blending of raw materials, i.e. adding of lime for neutralizing the acid residue, in the weight ratio of 1.0:0.8 (raw material : lime);
- heating of the blend in a tubular rotary oven to the temperature of at least 500 °C by flue gases so as to convert mercury contained in the initial raw material into a gaseous
phase;
- dedusting of the vapour and gas mixture in a group cyclone;
- condensation of mercury in a condenser refrigerator;
- accumulation of mercury slurry in condenser troughs;
- separation of metallic mercury in a hydraulic cyclone;
- cleaning of mercury from admixtures so as to obtain commercial metal;
- cleaning of off-gases from mercury in absorber;
- unloading of cinders from the oven to the cinder hopper (cinder output makes 94-96% of the roasted blend weight);
- removal of cinders to the cinder dump or the area for processing of scrap lead in a reflector oven wherein they are used as reducer agents.
Fig. 5.4 shows, as an example, the scheme for processing of waste from vinyl chloride production (spent mercury catalyst), with the average mercury content being 3,000
mg/kg (30 kg of metal per tonne of waste).
It was planned that since January 2003 cinders generated during roasting of mercury catalyst, sludge generated during production of 1-amino anthrachion and graphite waste
would be transferred to enterprises processing scrap ferrous and nonferrous metals, where they would be used as reducing agents and flux. Cinders from roasting of soils
and construction mater8ials would be used for levelling of roads of IV and V classes.
Figure 5.4 Scheme of processing of waste generated from vinyl chloride production facilities (spent catalyst) in TVP-1
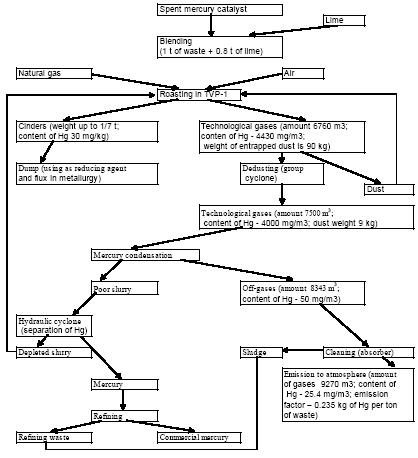
It is planned that from 2003 NPP Kubantsvetmet CJSC will be processing annually 600 tonnes of waste from vinyl chloride production, 50 tonnes of mercury sorbent
based on activated carbon, 50 tonnes of mercury-containing soils and construction waste, 60 tonnes of graphite waste, 30 tonnes of sludge from 1-amine anthrachion
production. The considered technological scheme can be used also for processing waste generated at facilities producing V2 vitamins (activated carbon sludge),
sludge from chlorine and alkaline enterprises and other types of secondary mercury-containing raw materials that have similar conditions of generation, compositions
and consistency.
Disposal of galvanic elements
Disposal of spent and rejected galvanic elements (mercury-zinc and mercury-containing elements) and batteries is performed using the same technological scheme, i.e.
roasting in the oven TVP-1, but with separate loading of mercury elements or mercury-containing elements and batteries and without blending of raw materials with
lime (Fig. 5.5).
Waste from such production process includes cinders (roasted element bodies), containing about 45% of iron and 55% of zinc; concentration of mercury in such
elements does not exceed 0.0002% by weight. Cinders are placed into metal drums and sold to organisations that are specialised in collection and processing of scrap
ferrous and nonferrous metal. The weight of generated cinders is about 10-20 t/year.
Figure 5.5 Scheme of disposal of chemical current supply elements in TVP-1
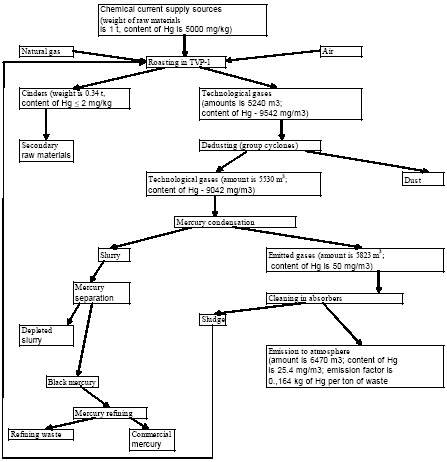
De-mercuration of tubular luminescent lamps
Processing of mercury luminescent lamps (types LB, etc.), performed by using the vibration pneumatic plant Ecotrom-2, includes their mechanical destruction and
separation under discharge of glass fractions (broken glass), aluminium bases and luminophor, i.e. the basic mercury concentrates. Characterisation of the basic units
of this plant is given in Table 5.4, while the technological process scheme is given in Fig. 5.6.
Table 5.4 Basic technical characteristics of the plant Ecotrom-2
Name of the device and its characteristics |
Name and composition of the environment |
Flow rate per operation |
De-mercuration device, 1200 lamps/hour |
Fragmented lamp components |
360 kg/hour |
Cyclone, diameter 200 mm, length 800 mm |
Air containing luminophor and glass dust |
360 nm3/hour |
Sleeve filter, 9 sleeves, diameter 180 mm, length 2000 mm |
Air containing luminophor and glass dust |
360 nm3/hour |
Cassette filter, 4 filters |
Air containing luminophor and glass dust |
360 nm3/hour |
Luminophor collectors, volume 50 l, diameter 350 mm |
Mercury-containing luminophor |
40 l |
Working absorber, diameter 800 mm, sorbent, containing activated carbon |
Air containing mercury vapours |
360 nm3/hour |
Base collection container, volume 0.06 m3 |
Aluminium bases |
8.4 kg/hour |
Hopper fore collection of broken glass, volume 0.12 m3 |
Broken glass |
10 m3 |
Processed products contain on the average (by weight): glass – 94.61%, aluminium bases – 2.39%, luminophor – 3%, with mercury concentration is 34,400 mg/kg.
Figure 5.6 Scheme of disposal of tubular luminescent lamps (types LB, LD, etc.)
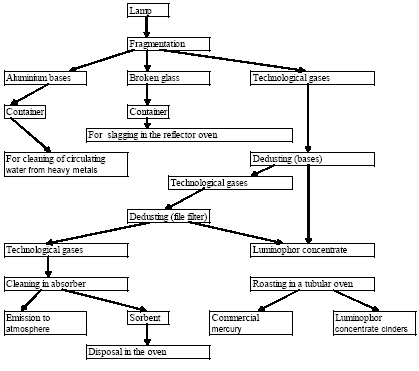
Waste from de-mercuration of tubular luminescent lamps includes:
- broken glass, the output of which makes 92% of the weight of the processes products; it contains not more than 0.2% of mercury included into processed products (the
specific mercury concentration in broken glass is not more than 2.1 mg/kg);
- aluminium bases (their output is 2.33%0;
- luminophor concentrate (their output is 5.67%) with mercury concentration up to 3.44% (by weight);
- emission (after cleaning) of off-gases to atmosphere (about 0.69 mg of mercury from its total quantity contained in processed lamps is emitted per tonne of disposable
products).
Broken glass is accumulated in metal containers and then used in lead production (for slagging of the reflector oven). Aluminium bases of luminescent lamps are used in
technological processes for pyrometallurgical; processing of mercury-containing raw materials as reducing agents during cleaning of circulating technological water from
soluble heavy metal salts. Luminophor concentrate produced during lamp processing at Ecoptrom-2 plant (about 1 t/year) is stored in tight packs and is processed in a
tubular oven TVP-1 (together with luminophor concentrate delivered from other organisations), using the above described scheme. Output of cinders from luminophor
concentrate roasting makes about 96% of the initial freight of processed raw materials; they are used for reclamation of old cinder dumpsites.
Disposal of high-pressure mercury lamps
Processing of high-pressure mercury lamps (DRL type) includes (Fig. 5.7):
- destruction of the lamp tubes and accumulation of broken glass with luminophor in special containers;
- separation of the quartz burner from the base with the lug and their separately accumulation in containers;
- defragmentation of burners in a hammer crusher and roasting of the obtained mass in the oven TVP-1 together with other mercury-containing secondary raw materials.
Waste of this process includes broken glass (used for processing of scrap lead, for slagging of the reflector oven) and scrap nonferrous and ferrous metal that is sold (as
secondary raw materials) to respective organisations.
Figure 5.7 Scheme of disposal of high-pressure mercury lamps (DRL type)
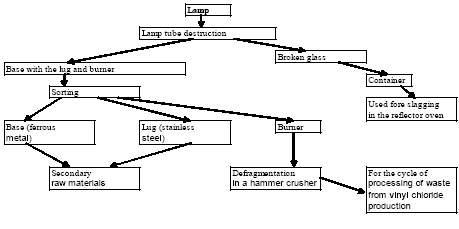
Disposal of metal mercury-filled devices
Disposal of metal devices with mercury fill is performed as follows (Fig. 5.8). The device is placed into a special tray; then a mechanical method or electrical gas welding is
used to open a section in the device filled with mercury; this mercury is poured into a steel cylinder. Bodies of devices with mercury removed as described above are placed
into the oven TVP-1 and are roasted for 3-4 hours at temperature of at least 500 °C. Mercury sorbed on the walls of the bodies is evaporated and is fed together with
technological gases to the system of condensation in the TVP-1. Then the body of the device (with mercury content ≤ 1 mg/kg) is disassembled into different types of scrap
metals.
Figure 5.8 Scheme of disposal of metal mercury-filled devices
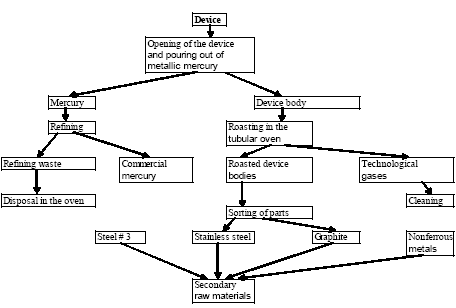
Disposal of glass mercury-filled devices
Disposal of glass devices filled with metallic mercury (on the average up to 3.7% of the total weight of the product) is performed as follows (Fig. 5.9):
- destruction of the glass tube (body) of the device in a bathtub under a water layer;
- pouring of metallic mercury into a tub;
- separation of metal parts; <
- pouring of metallic mercury from the tub into a special container;
- roasting of broken glass to remove residual mercury;
- refining of metal using the technological scheme adopted at the enterprise.
The degree of removal of mercury in this technological process makes over 99.9%. Waste of the process includes broken glass (up to 89% of the total weight of disposable
products) and metal fragments (up to 6.53% of the weight of disposable products). Broken glass is used in production of lead (for slagging of the reflector oven) and metal
fragments are sold as secondary raw materials.
Figure 5.9 Scheme of disposal of glass mercury-filled devices
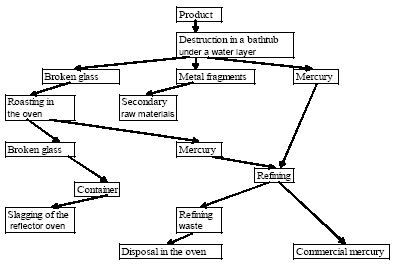
Disposal of paperboard packs
This type of waste is generated in the area of de-mercuration of mercury lamps delivered to processing in paperboard packs (the average weight of one pack is 20 g). With
the average annual number of processed lamps at 145,000 lamps, the weight of paper waste makes about 2.9 tonnes. This waste is accumulated in a metal container (1 m3)
and then incinerated in a tubular rotary oven TVP-1.
Disposal of spent personal protection equipment and special clothes
Spent respirators (one respirator is about 0.2 kg) and used special clothes are collected in a metal container with a lid and then incinerated in an oven. Annually, about 580
kg of spent respirators and up to 660 kg of used working clothes and footwear are disposed.
Refining of unconditioned (spent) metallic mercury
Unconditioned (spent or black) mercury delivered from different organisations is filtered and cleaned at the refining plant. The thus obtained mercury is used in production of
mercury compounds or supplied to different organisations and enterprises.
Amounts of processed mercury-containing waste
Tables 5.5 and 5.6 show data about amounts of different types of mercury-containing waste from production and consumption, processed at NPP Kubantsvetmet CJSC in
2001-2002; Table 5.7 includes summarised data about processed mercury-containing raw materials and production of secondary mercury at NPP Kubantsvetmet CJSC in
1998-2002.
Table 5.5 Processing of mercury-containing waste at NPP Kubantsvetmet CJSC, 2001
Type of waste |
Weight of waste, kg |
Commercial Hg, kg |
Catalyst, sorbent, sludge |
244312 |
9793 |
Unconditioned (spent, black) mercury |
16113 |
16097 |
Mercury lamps |
20610 |
7 |
Mercury-containing devices |
1784 |
131 |
Luminophor concentrate |
23700 |
78 |
Other (galvanic elements, mercury-contaminated construction waste
and soils, proper production waste, etc.) |
54800 |
343 |
Total |
361319 |
26449 |
Table 5.6 Processing of mercury-containing waste at NPP Kubantsvetmet CJSC , 2002
Type of waste |
Weight of waste, kg |
Commercial Hg, kg |
Unconditioned (spent, black) mercury |
783.5 |
727 |
Mercury lamps |
31200 |
10.5 |
Mercury-containing devices |
384 |
65.3 |
Luminophor concentrate |
59570 |
163.2 |
Other (galvanic elements, mercury-contaminated construction waste
and soils, proper production waste, etc.) |
2750 |
9.5 |
Total |
94687.5 |
975.5 |
Table 5.7 Processing of raw materials and production of secondary mercury at NPP Kubantsvetmet CJSC, 2002
Year |
Weight of waste, t |
Commercial Hg, kg |
1998 |
56.6 |
1459 |
1999 |
840.4 |
16020 |
2000 |
919.7 |
22061 |
2001 |
361.3 |
26449 |
2002 |
94.7 |
976 |
Total |
2272.7 |
66965 |
Greater part of metallic mercury produced during processing of production and consumption waste was used for production of different mercury compounds (brands HCh,
ChDA, Ch) (Russian abbreviation) production of which is described in section 3.10. In 2000-2002, metallic mercury was supplied in small amounts (2-4 t/year) to some
Russian enterprises (chemical enterprises in Volgograd, Termopribor OJSC in Klin, Lisma OJSVC in the city of Saransk, etc.). In 2003, about 150 tonnes of metallic
mercury was delivered to Energia OJSC (city of Yelets).
Production of highly pure mercury
As mentioned above, NPP Kubantsvetmet CJSC has 4 areas for production of special pure mercury (brands 5N, 6N or higher), based on the use of multiple distillation of
metal with electrical discharge cleaning. Processes of distillation refining are performed in the devices that are tightly isolated from the working space of the production area.
Mercury is packed into tight glass ampoules, containing 50 g or 75 g of metal. Some year ago, this mercury was used for scientific research, pilot production and in
semiconductor industry. In the recent years, no orders have been received for production of pure mercury, which can be explained by objective and subjective reasons
(financial problems, some enterprises have their own mercury refining plants, etc.).
Emission of mercury in the course of pyrometallurgical processing of raw materials
Table 5.8 and Table 5.9 show the basic indicators of operation of the tubular rotary oven TVP-1 and characteristics of the generated waste; Table 5.10 shows the balance
of distribution of mercury loss in the course of pyrometallurgical processing of mercury-containing raw materials. Since 2000, there has been a substantial reduction of total
mercury loss, due to increased degree of dust entrapment and conversion of the dust containing mercury into recycling technological water, increased efficacy of metallic
mercury separation and reprocessing of a range of interim products and waste in the ovens. In particular, in 2002 roasting of entrapped dust (entrapped by cleaning facilities)
in the oven together with the raw materials was started. A certain role is played by the factor that waste with high concentrations of mercury is now delivered for processing.
It is well known that practically all losses of mercury at mercury enterprises in the course of technological processes, as a rule, greatly depend on its content in the initial raw
materials: the higher the mercury concentration in the initial raw materials, the lower its loss (Pak et al., 1984).
Table 5.8 Basic characterisations of operation of the oven TVP-1 at the metallurgical plant NPP Kubantsvetmet CJSC for 1999-2001
Parameter |
1999 |
2000 |
2001 |
Processes mercury-containing raw materials (dry weight), kg |
840,390 |
919,744 |
361,319 |
Quantity of mercury in raw materials, kg |
16,313.73 |
22,302.56 |
26,746.25 |
Amount of metallic mercury produced, kg |
15,803.11 |
22,055 |
26,625.89 |
Total loss of mercury during technological processes, kg |
510.6 |
247.6 |
120.4 |
Table 5.9 Characterisation of waste generated during pyrometallurgical processing of mercury-containing raw materials, NPP Kubantsvetmet CJSC
Year |
Cinders |
Off-gases |
Circulating water * |
Dust of cyclones ** |
|
Weight, t |
Hg, mg/kg |
Volume, m3 |
Hg, mg/m3 |
Volume, m3 |
Hg, mg/m3 |
Weight, t |
Hg, mg/kg |
1999 |
748 |
38 |
10,449,745 |
30.68 |
360 |
22.3 |
25 |
3,400 |
2000 |
844 |
25 |
8,182,680 |
25.4 |
275 |
39 |
- |
- |
2001 |
129.9 |
26 |
2,119,487 |
24.3 |
250 |
259.4 |
- |
- |
- With annual fresh water makeup;
- ** From 2000, dust has been burned in the oven together with the raw materials (during the technological process).
In 2001, the share of irrecoverable mercury loss in the course of pyrometallurgical processing of raw materials made 46.1% (or 55.5 kg); the majority of this amount
included emitted off-gases emitted to atmosphere (42.8% or 51.5 kg). About 65 kg of mercury (53.9% of the total mercur4y loss) was finally returned together with
the circulating water to the technological process.
Table 5.10 Distribution of mercury loss in the course of the pyrometallurgical processing of raw materials in the oven TVP-1, at NPP
Kubantsvetmet CJSC
Types of loss |
1999 |
2000 |
2001 |
|
kg |
share, % |
kg |
share, % |
kg |
share, % |
With cinder * |
32.3 |
6.3 |
21.1 |
8.5 |
3.4 |
2.8 |
With off-gases ** |
320.6 |
62.8 |
207.8 |
83.9 |
51.5 |
42.8 |
With circulating water *** |
8 |
1.6 |
10.7 |
4.3 |
64.9 |
53.9 |
With cyclone dust **** |
85 |
16.6 |
- |
- |
- |
|
Unaccounted loss ***** |
64.7 |
12.7 |
8 |
3.3 |
0.6 |
0.5 |
Total loss |
510.6 |
100 |
247.6 |
100 |
120.4 |
100 |
- Unaccounted loss (into dumps or secondary use);
- ** Irrecoverable loss, emission to atmosphere via the stack;
- *** returned to the technological process;
- **** From 2000, dust has been burned in the oven together with the raw materials (during the technological process).
These observation data demonstrate that air in most working rooms at the enterprise from time to time includes mercury vapour concentrations exceeding the MAC
(Table 5.11). As a rule, the highest mercury vapour concentrations have been observed in the areas of mercury pouring into containers and in the operator room of
the tubular rotary oven TVP-1. In the open site, near the oven TVP-1, levels of mercury vapours in the air usually are about 0.01 mg/m3, going down to
0.0001-0.0003 mg/m3 on the border of the sanitary protection area.
Table 5.11 Levels of mercury concentrations in the air of the working rooms and within the sanitary protection area (SPA) at the metallurgical plant
of NPP Kubantsvetmet CJSC , 2002, in mg/m3
Area |
Average |
Limits |
Number of measurements per year * |
Operator's room of the tubular rotary oven |
0.019 |
0.010-0.025 |
12 |
Area for mercury pouring into containers |
0.026 |
0.023-0.028 |
13 |
Finished products warehouse |
0.010 |
0.001-0.014 |
10 |
Chemical analytical laboratory |
0.007 |
0.002-0.010 |
13 |
Mechanical shop |
0.010 |
0.003-0.012 |
12 |
Administrative and auxiliary building |
0.011 |
0.007-0.012 |
14 |
Open site, near TVP-1 |
Average about 0.01 |
- |
On the border of the SPA ** |
0.0001-0.0003 |
- |
MAC *** in the working area, average per shift |
0.005 |
- |
MAC in the working area, maximum |
0.010 |
- |
MAC in the air of populated localities |
0.0003 |
- |
Typical background content |
0.000010-0.000015 |
- |
- Approximately once a month;
- ** Size of the SPA is 100 m;
- *** Maximum allowed concentrations
The planned increase of mercury-containing waste amounts will, no doubt, lead to a noticeable growth in mercury emission to the habitat; above all, together with emitted
gases. This makes it necessary to:
- perform preventive operations to increase reliability of work and tightness of basic technological lines in the tubular rotary oven TVP-1;
- update (overhaul) the existing dust-and-gas cleaning system;
- create a system for additional cleaning of emitted gases from mercury, which must secure several-fold reduction of metal in them (at least, by one order as compared
to the excising);
- perform full-scale operations for de-mercuration of the basic working, administrative and warehouse rooms in the industrial area at NPP Kubantsvetmet CJSC and in
the area adjacent directly to the metallurgical plant (including the required range of full-scale mercury research);
- organise at the enterprise a permanent service for current de0mercuration.
5.1.3 Merkom Ltd.
Merkom Ltd. was organised in 1992; it is located in the research Institute of Instruments and devices (town of Lytkarino, Moscow Oblast); the total personnel includes over
40 persons.
Merkom performs disposal of the following mercury-containing waste:
- spent (unconditioned or black) metallic mercury (collection, transportation, refining, obtaining of secondary metal);
- mercury compounds (collection, transportation, processing and production of different mercury compounds);
- instruments filled with mercury, like thermometers, sphygmomanometers, ignitrons, normal elements, mercury contacts, etc. (collection of instruments and devices,
removal and cleaning of metallic mercury, preparation of instruments' bodies and their transportation to places of disposal);
- mercury lamps (collection, transportation and disposal);
- mercury-zinc galvanic elements (collection, packing and transportation to places of processing);
- hard, paste and liquid mercury-containing waste (collection, packing and transportation to places of processing).
Refining of spent (unconditioned, black) metallic mercury so as to produce commercial (secondary) metal; cleaning, processing (re-crystallisation) and production of
mercury compounds are performed using technologies developed by specialists of Merkom Ltd. (Donskykh, Skitskiy ...; Skitskiy, Donskykh, 1999). The basic
commercial products of the enterprise include metallic mercury P0 and P1 and mercury compounds of reactive purity.
Basic technological schemes and production operations
- Production facilities of the Merkom Ltd. include:
- the area for refining of the unconditioned (spent, black) mercury;
- the area for production of mercury compounds;
- the area for disposal of mercury-filled instruments and devices;
- the area for de-mercuration of tubular luminescent lamps;
- the area for receiving mercury-containing dry galvanic elements.
Production output for refining of unconditioned mercury and producing secondary metal is 100 t/year; for production of mercury compounds – 30 t/year; plants for
de-mercuration of tubular luminescent lamps – 1 million lamps/year.
Technological and production operations are performed observing conditions and requirements of the existing regulatory and technical as well as sanitary and hygienic
documents (GOST 30772-2001; GOST 30773-2001; GOST 30774-2001; GOST 30775-2001; GOST 4658-73; Inter-sectoral Rules on Protection ...; Mercury.
Regulatory ..., 2001; Mercury. Specifications ..., 1997).
Refining of the unconditioned metallic mercury
Cleaning of unconditioned metal is performed at the area for refining mercury at a special plant, based on the use of technology developed at Merkom Ltd. This
technology is based on a hydrochemical cleaning method, including multiple-stage processing of unconditioned mercury by different solutions.
In a general case, the technological scheme for refining of unconditioned metallic mercury is as is shown in Fig 5.10. Testing and quality control of commercial mercury
are effected according to GOST 4657-73 (GOST 4658-73). The final product is mercury of brands P0 and P1 that meet the requirements of the indicated State
Standard.
Figure 5.10 Technological scheme of substandard mercury refinement

Packing of P1 mercury is made into standard steel cylinders containing 34.5 kg of mercury; P0 mercury is packed into plastic containers (3 kg of metallic mercury in
each container) in inert gas atmosphere.
Production of mercury compounds
The following technological operations are performed at the area for production of mercury compounds:
Disposal of instruments and devices filled with mercury
The area designed for disposal of mercury-filled instruments and devices includes different manual operations related to opening of the devices' bodies (ignitrons,
sphygmomanometers, etc.) and removal of mercury from them into special containers (mercury is delivered to the refining area). Then bodies and other parts of the
instruments and devices are packed and sent to FID-Dubna de-mercuration company (town of Dubna, Moscow Oblast).
In 2001 and 2002, a greater part of collected large-size instruments and de3vices filled with mercury (after verification of their tightness and respective packaging)
were sent to FID-Dubna for processing.
De-mercuration of mercury lamps
In 2001, Merkom Ltd. collected and packed low-pressure luminescent lamps (LD, LB and other types) and high-pressure mercury lamps (DRL, DNaT types),
which were then sent to Dubna, FID-Dubna, for disposal (about 50,000 lamps).
In 2002, the enterprise started its own vibration and pneumatic plant for de-mercuration of tubular luminescent lamps Ecotrom-2; its basic principles and features
were described above. In 2002, this plant was used to dispose of 214,000 luminescent lamps. In addition, 17,000 high-pressure mercury lamps (DRL, DNaT) were
collected and sent to Dubna for processing. Plans of Merkom Ltd. include expansion of the scopes of processing of tubular luminescent lamps up to 1 million lamps a
year.
The site for receiving galvanic elements
In this area, regular and mercury-zinc galvanic elements are packed which are delivered from different enterprises (they are packed into polyethylene bags ands then
into metal barrels). When these lamps are collected in large amounts, they are sent for secondary processing to other organisations (in 2001, the total weight of
collected galvanic elements was about 200 kg).
In 2002, the collected and disposed elements included 1,868 regular galvanic elements (with glass bodies), producing 18 kg of metallic mercury from them (they were
collected from organisations and enterprises of Moscow City and Moscow Oblast).
Other mercury-containing waste
Merkom Ltd. collects, packs and transports mercury-contaminated soils, communal and industrial waste, spent carbon sorbent and catalysts, mercury-containing
chemical sludge. As a rule, when the above waste is in small amounts, the company secures its safe packing and accumulation in the special production area, and then
it is transported to places of its direct disposal (to other organisations). Preparation and packing of large volumes of waste for its transportation is performed directly
at its source.
Waste generated during technological processes and operations
In the course of technological processes and operations connected with processing of mercury-containing products, mercury refining and production of mercury
compounds at Merkom Ltd. the following types of mercury-containing waste are generated that should be decontaminated.
Wastewater, the majority of which (up to 80%) is generated at the area of cleaning and production of mercury compounds, is characterised by the content of mercury
up to 30-49 mg/l; ts has high content of minerals (up to 300-400 g/l) and high concentrations of sodium, potassium, nitrogen, chloride and sulphate compounds. Such
wastewater is pre-treated on the site from mercury (using chemical deposition by creating an alkaline environment) and then accumulated in special containers (tanks).
The volumes of generated wastewater are not great. Thus, in 1999, 5 m3 of wastewater was accumulated and sent for disposal to NPP Kubantsvetmet CJSC; by
now, the volume of wastewater stored in accumulation tanks is about 4 m3. An urgent problem for the enterprise is development and using of a scheme for in-depth
treatment of wastewater directly on the site, which would allow a substantial increase of the volumes of refined unconditioned mercury and production of mercury
compounds.
Solid waste (pasty) contain, on the average, 0.2-0.3% of mercury generated during refining of unconditioned mercury and of its compounds from mechanical
admixtures, as well as during pre-treatment of wastewater (wastewater sludge). Waste is packed into polyethylene bags (20-30 l) with a polyethylene insert; then it is
placed into a metal barrel also having a polyethylene insert. When waste is accumulated it is sent to Karsnodardsky Rudnik enterprise for disposal (NPP
Kubantsvetmet CJSC). The specific generation of solid waste makes about 1 g per tonne of refined commercial mercury.
Containers from glass and plastics used to deliver unconditioned metallic mercury for disposal and other mercury-containing waste are de-mercurised (de-mercuration
solutions are drained to wastewater). Metal containers are packed and delivered to disposal to FID-Dubna. Usually, up to 3-4 tonnes of such containers are collected
every year.
Luminophor concentrate generated during disposal of mercury lamps is packed (using technology of Ecotrom Ltd.) into polyethylene bags; when Luminophor
concentrate is accumulated it is planned to deliver it form processing to NPP Kubantsvetmet CJSC; broken glass is removed to dumpsites; aluminium parts of lamps
are delivered to organisations that collect nonferrous scarp metals.
Cleaning emission to atmosphere
The area of mercury refining is equipped with carbon sorbent (UPR type); the area for lamp de-mercuration is also equipped with Pertyanov filters; efficiency of used
emission cleaning systems is over 90%. As a rule, the content of mercury vapours in the air of the working rooms and at the exit of emissions to atmosphere is not
more than 0.2-0.3 MAC for the working area (average monthly).
All local emissions (including suctions from point sources) are fed to industrial general exchange ventilation system, pass through three carbon absorbers and then
released (3,000 m3/h) through the stack (120 m high).
The maximum allowed emission of mercury vapours set for Merkom Ltd. is 800 mg a year.
Processing of mercury-containing waste and production of metallic mercury
Table 5.12 shows data about collection and processing of mercury-containing waste and production (refining) of metallic (secondary) mercury at Merkom Ltd., in
200-2002.
Metallic mercury obtained by Merkom Ltd. in 2000-2002 was delivered, mainly, to domestic electrical lamp manufacturers (Smolensk and Saransk), the plant of
mercury thermometers (Klin), Altaykhimprom OJSC (Slavgorod) and, in small amounts, to intermediary trade organisations. It should be noted that in 2002 Merkom
Ltd. purchased a batch of metallic mercury of 8,442 kg (from an enterprise located in the city of Ryazan which in the past manufactured mercury valves). After the
required technical tests, containers preparation and checking of the packages tightness, mercury was also delivered to the market (to the above enterprises).
Table 5.12 Processing of unconditioned mercury and mercury-containing waste at Merkom Ltd.
Year |
Unconditioned Hg, kg ** |
Commercial Hg, kg *** |
Unconditioned Hg compounds, kg |
Ignitrons, sphygmomanometers, thermometers, etc. |
Waste (soils, garbage, sorbent, etc.), kg ******* |
Total weight, kg |
Extracted Hg, kg |
2000 |
10,990 |
9,343 |
271 |
-**** |
- |
No data |
2001 |
5,766 |
5,199 |
38 |
3,137 |
395 ****** |
7,460 |
2002* |
8,987 |
8,744 |
- |
110.5***** |
17.4 ****** |
2,561 |
- In 2002, the number of disposed mercury contacts was 287 (removing 4.3 kg of metallic mercury) and 1,721 mercury thermometers (3.4 kg of ,mercury);
- ** Weight together with the containers;
- *** Metal obtained during refining of unconditioned (black) mercury);
- **** Devices were sent for disposal to FID-Dubna;
- ***** The greater part of devices was sent to FID-Dubna;
- ****** Mercury was refined;
- ******* Sent to NPP Kubantsvetmet CJSC; during first 7 months of 2003 Merkom Ltd. collected, packed and prepared for deliver to disposal about 10
tonnes of mercury-contaminated soils and construction waste.
5.2 Mercury Turnover with Solid Waste
To identify all sources of mercury-containing consumption and production wastes (MCW) generation, it's important to take into consideration the spheres where
mercury or its compounds are used intentionally or mercury is present in considerable quantities as natural impurity in the raw materials and products. According to the
Article 1 of the Law of the Russian Federation On Production and Consumption Waste No. 89-FL dated June 24, 1998, u mercury-containing waste are
mercury-containing residual raw materials, semi-products and products generated as a result of production or consumption and as well as goods that have lost their
consuming properties.
Generation of mercury-containing solid waste could be in:
- Extraction and production of mercury;
- Processing of natural materials, containing mercury;
- Use of mercury in gold mining;
- Use of mercury and its compounds in production of chemical products;
- Production and use of goods containing mercury and its compounds;
- Reprocessing of mercury-containing wastes (MCW).
5.2.1 Generation of Mercury-containing Solid Waste in Russia
Official data on MCW accumulation, generation and neutralization in various sectors and main regions of Russia is shown in Table 5.13 and Table 5.14. As it can be
seen the three industrial sectors - chemical, machine-building and non-ferrous metallurgy - are accounted for the major part of generated mercury-containing waste.
Machine-building waste which most probably covers the mercury-containing consumption waste (used and outdated thermometers, lamps, batteries, etc.) are
described in chapter 3.
Siberian, Ural, Volga and Central Federal Districts of the Russian Federation account for a major part of generated mercury-containing waste. The reason is the
location of large industrial enterprises generating mercury-containing waste. Central Federal District is characterized by the biggest volume of MCW processing,
though the District holds the second place with MCW generation in Russia. The most urging situation is in Ural Federal District: having MCW annual generation share
as 30 %, wastes treatment volumes are as 2 %.
A consideration should be given to the fact that official informational sources do not mention Hg concentrations in accumulated and annually generated MCW, as well
as typification of waste by Hg concentration level. As mentioned above, the whole amount of MCW accumulated in Russia by tiday includes about 58% waste with
Hg content of 10-100 mg/kg, about 12% - 100-5,000 mg/kg, about 30% - above 5,000 mg/kg. According to information from other sources, Hg content in stored
and annually generated MCW varies from 0.02 to 75%. In Russia there is no lower limit of mercury concentration in waste according to which the waste could be
included into the mercury-containing waste category. It is known that in practice such lower limit is considered as MAC of mercury in soil (2,1 mg/kg) which is
obviously not always relevant.
Table 5.13 Accumulated, generated and neutralised mercury-containing waste in 2002 (Goscomstat RF, Ministry of Natural Resources RF)
Sector |
Accumulated mercury-containing wastes by the end of 2001 |
Generated mercury-containing wastes in 2002 |
Neutralized mercury-containing wastes in 2002 |
t |
% |
t |
% |
t |
% |
Industry, including: |
2,874 |
83.1 |
7,214 |
85.9 |
1,655 |
65.8 |
Chemical |
1,159 |
33.5 |
1,200 |
14.3 |
536 |
21.3 |
Machine-building |
801 |
23.5 |
3,342 |
39.8 |
1,158 |
46.0 |
Non-ferrous metallurgy |
691 |
20.0 |
2,075 |
24.7 |
1.9 |
0.08 |
Pulp and paper |
20 |
0.58 |
45 |
0.53 |
- |
|
Flour-and-cereals and feed mill |
|
|
|
|
|
|
Power industry |
41 |
1.19 |
126 |
1.5 |
16 |
0.64 |
Fuel industry |
30 |
0.87 |
85 |
1.0 |
- |
|
Construction materials industry |
108 |
3.1 |
145 |
1.7 |
- |
|
Municipal housing economy |
332 |
9.6 |
62 |
0.07 |
185 |
7.4 |
Totally in Russia |
3,458 |
100 |
8,396 |
100 |
2,517 |
100 |
Table 5.14 Mercury-containing wastes distribution by the federal districts of RF (Goscomstat and Ministry of Natural Resources)
District |
Accumulated mercury-containing wastes at the end of 2001 |
Generated mercury-containing wastes in 2002 |
Neutralized mercury-containing wastes in 2002 |
t |
% |
t |
% |
t |
% |
Central |
376.9 |
10 |
2,184 |
26 |
950 |
38 |
North-West |
88.4 |
2.6 |
145.2 |
1.7 |
44 |
1.8 |
South |
1,029.9 |
30 |
559 |
7 |
210 |
8 |
Privolzhskij |
287.1 |
8 |
936 |
11 |
747.4 |
30 |
Ural |
213.3 |
6 |
2,422 |
29 |
54.8 |
2.1 |
Siberia |
1,407.9 |
41 |
2,129.8 |
25 |
510.1 |
20 |
Far east |
54.6 |
1.6 |
19.4 |
0.2 |
0.135 |
0.0 |
Totally in Russia |
3,458 |
100 |
8,396 |
100 |
2,517 |
100 |
Figure 5.11 Accumulation, generation and treatment of mercury-containing solid waste in RF regions in 2002.
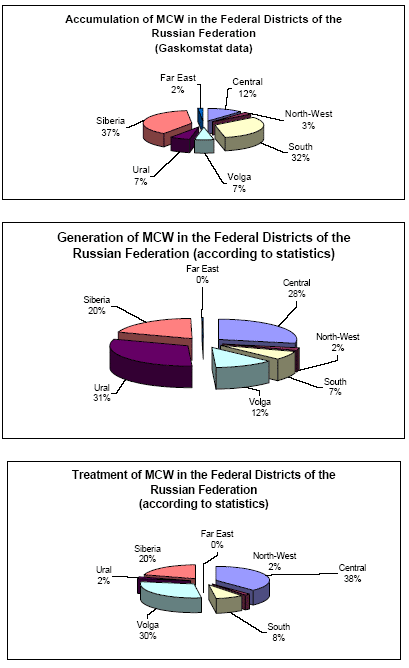
5.2.2 Mercury in Industrial Waste and Waste from Energy Production
Mercury in industrial waste and waste from energy production has been described in the different sections in Chapter 3 and 4. The information on the waste that is
disposed of to landfills/waste dumps is summarized in Table 5.15.
As regards intentional industrial uses of mercury, chlor-alkali production account by far for the major part of mercury in the waste, which is in general disposed of in
dumps close to the production sites. The total amount of mercury in the waste is tentatively estimated to be equal to 39 tonnes. Mercury contained in waste generated
at the territory of Novosibirsky Chemical Concentrates Production Facility (production of lithium isotopes) by now amounts to 100-500 tonnes.
Table 5.15 Mercury in industrial waste and waste from energy production disposed on to landfill/waste dumps 2001/2002
Activity |
Mercury masstonnes/year Best estimate |
Section |
Chlor-alkali production |
39,3 |
3.1 |
Production of consumer products: lamps, batteries, etc. |
0,3 |
3.5- 3.9 |
Gold mining using amalgamation method |
0,55 |
3.3 |
Coal extraction and use |
5,6 |
4.1 |
Oil, gas and biofuels |
? |
4.2 |
Copper/nickel production * |
6,6 |
4.3 |
Lead and zinc production |
8,5 |
4.3 |
Other non-ferrous metal production |
4,2 |
3.3; 4.3 |
Cement production |
0,4 |
4.3 |
Total |
65 |
|
* Exclusive tailings
In total more than 3000 t mercury is accumulated in the soil and at dumpsites around production facilities in which mercury has been used. Table 5.16 lists the
identified production facilities. The list is considered comprehensive as regards the use of mercury for production of chlorine (inclusive chlorine production in paper
plants), but significant amounts of mercury may also be accumulated around facilities for production of thermometers, switches and other eletrotechnical products.
For the whole history of gold mining in Russia, about 6,000 t mercury has been used for gold mining by the amalgamation method. The major part of this mercury is
accumulated in tailings and other wastes. A significant amount of mercury may be released by mining of these waste heaps and tailings.
Tailings from production of non-ferrous metals may contain significant amounts of mercury, but no data has been available on total mercury content of tailings.
Table 5.16 Sites with accumulation of mercury containing waste
Plant |
Activity |
Period of activity |
Approximate amount of Hg, t In dumps and slag-heaps |
Comment |
JSC «Usolyechimprom»,
Usolye-Sibirskoye
|
Chlor-alkali |
1970-1998 |
800 |
|
JSC «Kaustic» «Krebs» Plant Sterlitamak City |
Chlor-alkali |
1964-1987 |
50 |
|
OAO «Kaprolaktam», dzherzhinsk,
Nezhegorodskaya oblast |
Chlor-alkali |
1948-1982 |
60 |
|
JSC "Kirovo-Chepetsk Chemical Enterprise", Kirovo-Chepetsk,
Kirovsk oblast |
Chlor-alkali |
1955-today |
300-700 |
|
JSC "Kaustic",
Volgograd
|
Chlor-alkali |
1968-today |
<500? |
In soil under building
In waste dumps
|
CJSC "Kaustic", Sterlitamak |
Chlor-alkali |
1997- today |
200-300? |
In soil under building
In waste dumps
|
JSC "Sayanskchimplast", Sayani, Irkutsk oblast |
Chlor-alkali |
1979-today |
500 |
|
Kotlass PPF Koryazhma, Arkhangelsk oblast |
Cl for paper production |
1964- 1998 |
130 |
|
Arkhangelsk PPF Novodvinsk,
Arkhangelsk oblast
|
Cl for paper production |
1962-1996 |
120 |
|
Amursky PPF
Komsomolsk-na-Amure
|
Cl for paper production |
1970-1997 |
56 |
|
Svetlogorsk PPF
Svetlogorsk, Leningrad oblast
|
Cl for paper production |
1951-1993 |
11 |
|
Lithium production, Novosibirsk |
Lithium isotopes |
- |
100-500 |
35 t/year by mid 1990's |
Total |
|
|
more than 3,000 |
|
5.2.3 Mercury in Municipal Solid Waste
Mercury lamps, thermometers, batteries and other mercury-containing devices used at homes as well as batteries can be considered as major sources of mercury in
municipal solid waste (MSW).
In 1997, it was established that in St. Petersburg the amount of mercury in devices used by the population contained more than 3 tonnes mercury (Mercury. Complex
safety system...., 1996). Extrapolation of these data on the Russian Federation suggests that about 93 tonnes of mercury is in the devices used by population of the
country. If every Russian family has two mercury thermometers, then the total number of thermometers used by population makes about 70 million pieces (140 tonnes
of mercury), which is much higher than the data obtained by extrapolation of the indicators for St. Petersburg. To estimate the amount of mercury that goes into waste
from population, we used the presumption that 1/6 of all devices used by population loss their consumer properties every year. In this case, 15.5 tonnes of mercury
(using the St. Petersburg data) or 23.3 tonnes of mercury (using the thermometer approach) will be lost with MSW. In section 3.5 it is described that in the outadted
thermometers for the domestic market in 2001 contained about 9.3 t mercury of which the major part was disposed of with solid waste. All in all it is estimated that
some 16-23 t may be disposed of with mercury-containing devices. Besides, about 1.6 t of mercury is included into MSW with spent luminescent lamps (see section
3.8), 1.6 with batteries (section 3.7) and 0.4 t with switches (section 3.9). The estimate for batteries is very dependent on the actual life of batteries, as the
consumption of mercury has decreased steeply the last years. In the 1980's, up to 100-130 tonnes of mercury were used every year for manufacture of galvanic
elements and batteries. The actual life-time of batteries may be significantly longer than their technical life as it may take some time before the batteries are disposed of.
For this reason these products as a source of mercury in MSW may be underestimated.
The releases of mercury contained as a trace element (impurity) in MSW may be significant, but is difucult to estimate as no data on the background level of mercury
in the waste exist.
The average content of mercury in MSW from mercury-containing devices and materials was determined on basis of the source estimate (see Table 5.17), and the
total amount of MSW generated in the Russian Federation. According to the estimates, mercury content in MSW (except as impurity) may reach 0.7-0.9 mg/kg of
MSW, which is lower than mercury MAC for soils of 2.1 mg/kg.
Table 5.17 Sources of mercury in municipal solid wastes
Source of Hg releases with wastes |
Approximate amount of Hg, t/year |
Note |
Hg-containing devices (mainly thermometers) |
16-23 |
Section 3.5 |
Batteries |
1.6* |
Section 3.6 |
Lamps |
2 |
Section 3.8 |
Dental amalgam fillings |
6* |
Section 3.4 |
Switchers |
0.4 |
Section 3.9 |
As trace element/impurity in all waste |
? |
|
Total |
26-33 |
|
* It is unclear how much of this exactly ends up in solid waste.
In the Russian Federation, almost all annually generated MSW are disposed on dumpsites or landfills. MSW incinerating plants operate in Moscow, Pyatigorsk,
Sochi, Vladivostok and Murmansk (see Table 5.18 and Figure 5.12). The share of MSW incinerated by these enterprises may be assessed at 2-3% of the total
annual amount of MSW. Using the above estimate some 0.5 t mercury should be contained in the incinerated MSW. It is known ("Reference materials...,1999) that
Hg emissions to the atmosphere from MSW incineration plant of Vladivostok in 1999 amounted to 0.5 t (according to the official state statistical observation 2
TP-air). Extrapolation of these data to other enterprises taking into account their design capacity allows to obtain the approximate amount of Hg emissions from
garbage incineration plants 3.5 t/year (for Pyatigorsk, Sochi, Vladivostok and Murmansk). It should be noted that the estimate seems to be quite high if the expected
mercury content of the incinerated waste is considered.
Two plants are operated in Moscow with total capacity 40,000 tonnes of wastes/year. Cleaning system is carried out by activated carbon. Mercury emissions were
not detected by analytical control. Emissions of the plant are in a compliance with regulatory requirements of the Directive dated year 2000.
The plant in Sochi was closed because of significant impact on the environment
The plant in Pyatigorsk is operated with annual capacity 150,000 tonnes/year. Mercury emissions detected by analytical method is 0.000013 g/second (old data), by
calculations is 0.000052 g/second. Mercury content in ashes is 4 mg/kg., in slag is 0.8 mg/kg, in aqueous extract of ashes is 0.003*10-3 % mass.
Figure 5.12 Location of municipal waste incinerators in the Russian Federation (indicated as I)
Click here to see the figure.
The difference between sources and emissions may to some extent be explained by differences in domestic consumption structure between urban and rural population.
In big cities, where garbage incineration plants are located, mercury concentration in MSW will most probably be higher than the average values. Mercury content of
waste water seems also to be higher in big cities (discussed below). The difference may also indicate that the mercury content of waste could be significantly higher
than estimated above. The reason could be that mercury as trace element account for a major part of the mercury in the waste or that the life-time of batteries,
switches, etc. is longer than assumed. The consumption of mercury for production of these products ten years ago was several times higher than the consumption
today.
According to official data, emissions from housing and communal sector make 3 kg of mercury a year (see Annex 1), but this includes most probably not MSW
incineration.
Table 5.18 Municipal solid waste incinerators in the Russian Federation
Town |
Capacitytonnes |
Emission abatement technology |
Moscow |
40,000 |
Activated carbon |
Pyatigorsk |
150,000 |
no data |
Sochi |
"closed" |
no data |
Vladivostok |
no data |
no data |
Murmansk |
no data |
no data |
Total |
no data |
no data |
5.2.4 Mercury in Medical Waste
Medical mercury-containing waste includes luminescent lamps used for medical and technical porpoises (they may contain up to 500 mg of mercury) and medical
thermometers.
In medicine mercuric chloride solutions (II) or HgCI2 with concentrations from 1:1000 to 1:5000, were formerly used for disinfecting medical equipment, laboratory
vessels and decontamination of skin. Today, use of mercuric compounds for disinfections is strictly restricted.
An investigation of the amount of medical waste in health and children's preschool institutions was performed in 2002, using data on the account of waste in Perm
Oblast, where the accumulated mercury-containing waste reached 175 tonnes (without luminescent lamps). The content of mercury in this mercury-containing waste
made 29.9 kg, including 21.7 kg in thermometers, 7.9 kg in devices, 1.2 kg in bactericidal lamps and 0.2 kg in different mercury compounds. Extrapolation of these
data for the entire Russian Federation suggests that the non-productive sectors, not involved into reporting campaigns, have accumulated 5,750 tonnes of devices,
containing 1.5 tonnes of mercury. Considering the significant amounts of mercury that have been used for production of other thermometers and other devices the
estimate, however, seems very low.
In the Russian Federation, there is no broad practice of incineration of hazardous waste, and hospital waste. An approximate composition of medical wastes which
may be incinerated looks like the following (The State Report... 2002): 74.5% - bandaging material, 9.3% - polymers, 7.9% - food waste, resin and metal - by 3.1%
each, 1.09% - pathologoanatomic waste. The probability of Hg content in these wastes is very low. These wastes are buried and incinerated in boiler houses and
crematoriums.
Hg-containing wastes are classified as medical wastes Class D. This group also includes the outdated medicines and disinfectants, wastes of diagnostic medications
etc.
The inventory carried out in 2000 in Novokuznetsk revealed, that a share of Class D wastes constitutes 6.3% of the total amount of medical wastes (4,249,052 t)
(Economical and social geography of Russia. Moscow,2001). Inventory in Yeraterinburg indicated 6.6%.
The total amount of medical wastes was calculated by extrapolation of medical wastes inventory data in Kaluga oblast (999.457 t) and Novokuznetsk city to Russian
Federation dimension, with the given specific amount of wastes per capita. Thus, the obtained amount of medical wastes constitutes 461,000 t.
5.3 Mercury in Waste Water
Data on the content of mercury in organized wastewater discharge and its subsequent entering water bodies are included into Form 2 of the water sector (Form
òï-Âîäõîç). Below are given data of the state statistics on discharge of contaminants to water bodies in 2001 (see Tables 5.19 and 5.20 and Annex 1).
Table 5.19 Discharge of mercury in surface water sources by regions of the Russian Federation in 2001
Territory name |
Volume of polluted discharges
million m3
|
Mercury discharge,
kg
|
Note |
Russian Federation (in total) |
22,370 |
177 |
|
Saint-Petersburg |
1,244 |
19 |
|
Leningrad region |
413 |
2 |
|
Moscow |
2,185 |
2 |
|
Kirov region |
183 |
2 |
Chemical industry |
Republic of Bashkortostan |
449 |
16 |
Chemical industry |
Novosibirsk region |
385 |
1 |
|
Krasnoyarsk krai |
644 |
1 |
|
Irkutsk region |
911 |
129 |
Chemical industry |
Sakhs Republic (Yakutia) |
93 |
4 |
|
Amur region |
109 |
1 |
|
Table 5.20 Discharge of mercury into surface water sources by industrial sector in 2001
Sector |
Volume of polluted discharges, mln cub m |
Mercury discharge, kg |
Russian Federation (in total) |
22,370 |
177 |
Industry |
7,273 |
156 |
Non-ferrous metallurgy |
593 |
6 |
Chemical |
855 |
146 |
Pulp and paper |
1,421 |
1 |
Flour-and-cereals and feed mill |
23 |
2 |
Municipal housing economy |
13,474 |
20 |
Chemical industry accounts for the major part of the industrial sources. According to official data, the total discharge from chemical industry was 146 kg mercury.
According to the assessment in section 3.2 about 20 kg mercury is discharged from VCM production. Most probably the remaining part of Hg is discharged from
chlor-alkali industry. However, according to the assessment in section 3.1, only about 1 kg should be discharged with waste water from such facilities. Thus, the
official statistics indicate that this amount most probably is underestimated.
Wastewater from housing and communal facilities brings according to the statistic 20 kg of mercury into water bodies. It is not clear which activities are included in
"municipal housing economy". Most likely we are talking about waste water discharge from waste water treatment facilities operated by local municipalities and city
administrations.
The total discharge of mercury with municipal wastewater may be estimated based on it concentration in sewage sludge from wastewater treatment facilities. Data on
mercury concentration of sewage sludge from a number of towns obtained from different sources is shown in Table 5.21. As it can be seen, the mercury concentration
varies considerably. The higher concentration of mercury is found in sludge from towns where large volumes of mercury is used in industrial enterprises (e.g. Klin and
Saransk), but high concentrations may be found in other towns as well.
In the major cities, e.g., St. Petersburg and Moscow, the measured concentration is within 1-2 mg/kg dry weight whereas it seems to be lower in the smaller towns.
The established norms for mercury content of sludge to be used as fertilizer is 15 mg/kg dry weight (SanPiN 2.1.7.573-96).
The number of data is too limited to make an exact estimate of the total annual mercury content in sewage sludge in Russia, but they can be used for a first rough
estimate.
The total amount of sewage sludge generated can be estimated from the volume of waste water using general experience on the amount of sludge generated by the
water treatment.
Most Russian cities have centralized municipal sewage treatment plants where household and industrial wastewater is treated. Usually, a 2-stage treatment system is
used, including mechanical and biological treatment. In the course of treatment, significant sewage sludge is generated, i.e. colloidal sludge mixture of mineral and
organic substances that has a specific chemical composition and the average humidity of 96.2% (Turovsky, 1988).
To remove water and decontaminate the sludge, it is usually placed to the sludge beds or (less frequently) to filtration fields located near the municipal sewage
treatment plants. In most cases, sludge is fed (poured) onto sludge beds from time to time, in separate layers (up to 20-25 cm thick). When it dries, the sludge loses
moisture, mainly through evaporation; some water is filtered through ground. Some mercury in the sludge may be released from the fields but no data exists.
At technical calculations the sludge content (the average humidity of 96.2%) is usually considered as equal to 0.5-1.0% of the wastewater volume (Turovsky, 1988);
a density of sludge is 949 kg/m3 on the average (Disposal of solid wastes, 1985) - this corresponds to 0.18-0.36 kg dry weight per m3 wastewater. The capacity of
sewage treatment facilities in the Russian Federation constitutes 57.2 million m3/day / (The State Catalogue on pesticides and agricultural chemicals allowed for
application in Russia – M. 2002), i.e. about 20,878 million m3/year of water passes trough the wastewater treatment facilities in Russia. If all wastewater is biologically
treated, the sludge generation volume will amount to 3.8-7.5 million t dry weight.
Using these data the total mercury content of municipal sewage sludge can be estimated at 3.4-11.9 t/year (table 5.22).
It is assumed that the wastewater treatment efficiency for mercury is 50 %. For comparison the treatment efficiency of Danish treatment plants is about 65% (Skaarup
et al 2003). Assuming a 50% efficiency, the estimates indicate that in Russia 3.4-11.9 t mercury is discharged to the water bodies from municipal sewage treatment
plants; more that 20 times more than the total registered discharges from industrial sources. It should be kept in mind, that the municipal sewage treatment plants
receive not only household but industrial wastewater as well, which might input a considerable amount of mercury. Official statistics on industrial mercury discharges to
water obviously covers only the wastewater directly discharged to water bodies from the treatment facilities of the enterprises (avoiding municipal sewage treatment
plants).
Table 5.21 Mercury in municipal sewage sludge
locality |
Mercury content mg/kg dry weight |
Moscow oblast (Achkasov) |
Klin (mercury thermometer enterprise) |
220 |
Kolomna |
10 |
Aprelevka |
3.6 |
Zagorsk |
2.8 |
Orekhovo-Zuyevo |
2.4 |
Bronnitsy |
0.8 |
Serpukhov |
0.4 |
Zaraysk |
0.4 |
Voskresensk |
0.3 |
Domodedovo |
0.2 |
Pavlovsky Posad |
0.2 |
Podolsk |
0.2 |
Shatura |
0.2 |
Elektrostal |
0.1 |
Belozersky |
0.1 |
Istra |
0.1 |
Naro-Fominsk |
0.1 |
Ramenskoye |
0.03 |
Moscow (Achkasov) |
Lubertsy wastewater treatment plant |
1.8 |
Kuryanovo wastewater treatment plant |
1.3 |
Republic of Mordovia (Yanin, 1995) |
Saransk, municipal wastewater treatment plant (mercury lamp enterprise) |
4 (3-5) |
Perm oblast (the Analytical Center, 1998) |
Gubakha (industrial enterprises) |
14.1 |
Kungur |
0.6 |
St. Petersburg (Waste generation and utilization........) |
Treatment facilities of St. Petersburg |
1.6 |
Table 5.22 Mercury in the municipal wastewater sludge
City type * |
Share in population of Russia, % |
Amount of dry Hg-containing sludge,
million tonnes dry weight
|
Average mercury content
mg/kg dry weight
|
Mercury in sludge
tonnes
|
Small and medium |
30 |
1.1-2.3 |
0.2-0.6 |
0.2-1.4 |
Big |
70 |
2.64-5.27 |
1.2-2.0 |
3.2-10.5 |
Total (round) |
100 |
3.8-7.5 |
|
3.4-11.9 |
* Small and medium cities are the cities with population number up to 100,000 people and more than 100,000 people respectively.
Thus in Russia in total the untreated municipal waste water contains 7-24 t mercury per year. In some Russian localities (towns of Klin, Saransk, etc.) industrial
enterprises which use mercury intentionally in technological processes may be significant sources of mercury to wastewater delivered and treated at the centralized
municipal treatment plants together with the domestic sewage. Nevertheless, on a national scale, such enterprises input an insignificant share of mercury in
wastewater/effluents discharged to water bodies. Some part of mercury may be delivered to water bodies with the surface run-off (rain and melted water) from urban
territories which don't undergo the necessary treatment in most Russian cities. A detailed analysis of sources of mercury to waste water in Denmark indicated that rain
water may account for about 10% of the total sources (average mercury content in sludge was 1.2 mg/kg (Skaarup et al 2003)).
A major source may be dental amalgams from dental clinics discharging it to the centralized municipal sewerage (up to 6 tonnes of mercury as indicated in section
3.4). Besides, mercury from broken thermometers and measuring equipment may be significant sources. If only a small part of the 18 t used annually with
thermometers ends up in the sewage it would be significant.
Infiltration water from landfills for municipal solid waste which include used\broken mercury-containing appliances can be considered as a source of mercury in water
bodies. According to data (EIA of MSW landfill in Perm), the content of mercury in the landfill leachate can be 2 microgram/l in the average (with the range from
0.055 microgram/l to 1.46 microgram/l).
A practical example can be given using data of control of underground water in St. Petersburg (Report on wastes management, 2002). Only in one field mercury was
found in samples in the amount of 0.0007 mg/l.
Disposal of sewage sludge
Out of the total sewage sludge generated every year in Russia, about only 10-15% is treated according to modern requirements, i.e. compacted, stabilised, dewatered
and used as fertilisers or transported to special fields (Agranovich, 1992). According to other data, the level of practical use of sewage sludge today is about 1-1.5%
(Lotosh, 2002). In any case, the overwhelming majority of sewage sludge is placed (for a rather long period of time) to sludge beds (filter beds) and then, as a rule,
brought to waste dumpsites (or to quarries). In Russia, the content of mercury in WWS that can be used as fertilizers must not exceed 15 mg/kg of dry weight
(SanPiN ...). In soils with middle and heavy granulometric compositions, to avoid accumulation of metal, it is not allowed to use more than 10 t/ha of dry sludge in its
pure substance or as part of compost (the frequency of application at least 5 years). In light sand and clay sand soils, the norm of application is limited to 7 t/ha with
the frequency of use 3 years minimum. It is prohibited to use WWS and composts based on WWS in soils with pH below 5.5, without liming of such soils, if the
content of calcium in the sludge or compost does not maintain pH at 5.5 or higher. It should be noted that Hg concentration in WWS are as usual considerably higher
than in standard mineral fertilizers in which it is equal to 0.05 mg/kg (Kovda,1985).
6 Summary and Discussion
6.1 Use and Mobilisation of Mercury in the Russian Federation
The intentional use of mercury in the Russian Federation and the mobilization of mercury impurities are summarized in table 6.1. The assessment does not include
possible applications within the defence industry.
Intentional uses of mercury
The total intentional use of mercury in 2001/2002 is estimated at 155 t/year. The estimate is quite certain as actual information on mercury use have been obtained
from the major mercury consuming enterprises. According to the Financial Department of the Ministry of the Economic Development and Trade of RF the potential
annual demand of mercury in Russian enterprises in 1999-2001 was 280-300/year (section 2.3). The discrepancy between these data and the result of the present
assessment may be due to the following reasons: (1) potential demand is based on the design capacities of the facilities which are not fully loaded in the latest years;
(2) within the mentioned period some of Russian enterprises using considerable amounts of mercury have been closed; (3) mercury consumption is decreasing or
varies from year to year at some enterprises; (4) mercury consumption for "other applications" may be significant and (5) the present assessment covers civilian
applications only.
The main application area is still chlor-alkali production in which the mercury is used as electrode. The consumption (the amount purchased) for this application was in
2002 about 103 t, but the amount varies from year to year and the consumption may be higher in some years. Another 7.5 t of mercury in the form of mercury
chloride was used as catalyst for the production of vinyl chlorine monomer (VCM that is used for production of PVC). For both applications the mercury is used as
process chemical and a very small part of the used mercury follows the final products. Until recently mercury was also used as catalyst for production of vitamin B2
and some dyes, but this production has ceased.
Mercury used for production of thermometers and lamps accounted for the major part of mercury consumption for production of consumer products. As concerns
mercury-containing consumer products, Table 6.1 indicates the amount of mercury used for production of these products. The amount of mercury in products sold on
Russian market is different from the amount used for production. This is a consequesce of different technological losses of mercury, as well as export and import of
mercury-containing goods. The total content of mercury in consumer products sold on the Russian market is estimated at about 18 t (Table 6.2). The consumption of
mercury for production of thermometers, galvanic cells and batteries and other measuring and electrotechnical equipment has decreased several times during the last
decade, and the production of some appliances (such as mercury switches, valves, manometers, barometers etc.) has with a few exceptions ceased. Mercury may still
be present in some imported products, e.g. blood pressure gauges and switches in some cars; mainly manufactured in America). The total import of mercury with this
equipment is estimated to be less than 2 t. Contrary to many Western countries mercury use in stomatology has almost completely been ceased in Russia.
Table 6.1 Use and mobilization of mercury in the Russian Federation, 2001/2002
Activity category |
Consumption/mobilisation |
|
Best estimate (t/year) |
Range (t/year) |
% of grand total |
Intentional use of mercury |
Chlor-alkali production |
103 |
103 |
36 |
Production of VCM |
7.5 |
7.5 |
2.6 |
Gold mining using the amalgamation method |
5.5 |
3-8 |
1.9 |
Stomatology (dental amalgams) |
0.7 |
0.6-0.8 |
0.2 |
Prod. of thermometers |
26 |
26 |
9.1 |
Prod. of barometers, manometers and other measuring equipment |
0.2 |
0.2-1 |
0.1 |
Prod. of galvanic cells and batteries |
0.8 |
0.8 |
0.28 |
Prod. of light sources |
7.5 |
7.5 |
2.6 |
Laboratory use |
3.5 |
2-5 |
1.2 |
Biocides and pesticides |
0.6 |
0.4-0.8 |
0.2 |
Other intentional uses |
? |
|
|
Total intentional uses |
155 |
151-160 |
54 |
Mobilisation of mercury impurities |
Coal |
22 |
20-24 |
7.7 |
Oil * |
33 |
5-50 |
11 |
Gas, condensate, oil-shale and biofuels |
8 |
2-12 |
2.8 |
Zinc and lead production ** |
31 |
16-47 |
11 |
Copper and nickel production ** |
28 |
14-42 |
9.8 |
Other non-ferrous metallurgy ** |
6 |
4-8 |
2.1 |
Iron and steel production |
1.8 |
1.2-2.4 |
0.6 |
Cement production |
2 |
1.6-2.8 |
0.7 |
Total mobilisation as impurity |
132 |
66-198 |
46 |
Grand total |
287 |
217-358 |
100 |
* Mercury in oil refined in RF
** Includes mercury in concentrates. The total mercury content of mined ores may be considerably higher.
Table 6.2 Mercury in consumer products supplied to Russian market, 2001
Mercury-containing goods |
Mercury consumption for production t/year |
Mercury content of produced productst/year |
Mercury content of products sold on the Russian markett/year* |
Thermometers |
24.2 |
24.0 |
9.4 |
Light sources |
7.5 |
4.7 |
4.7 |
Batteries |
0.8 |
0.6 |
1.6 |
Switches, manometers, etc. |
0.2 |
0.2 |
<2 |
Total (round) |
33 |
30 |
18 |
* Including import/export
Gold mining using the amalgamation method is prohibited in Russia. It is, however, estimated that some illegal activities take place in remote areas, and the total use of
mercury for gold mining in 2001 is roughly estimated at 3-8 t. As the activities are illegal it has not been possible to confirm this expert estimate with official statistics.
The amount is ten-fold lower than the approximately 40 t/year used for gold mining in the period 1976-1990. "Other uses" column in Table 6.1 includes production of
semiconductors, production of ultra-pure metals by amalgamation and other possible mercury uses. For these uses it has not been possible to obtain information on
actual mercury consumption.
Mobilisation of mercury impurities
The total mobilization of natural mercury impurities (mercury as a trace element) in processed and used materials and products is of the same magnitude as the
intentional uses. The total mobilization of mercury is estimated at 138 t with a range of 66-198 t indicating that the estimates are quite uncertain. The major categories
are coal, oil and nonferrous metallurgy.
In total, about 20-24 t of mercury is mobilized with coal; mainly used for power and heat production and production of coke. The mercury content of coal from
different coal fields of Russia may twofold differs, and the uncertainty on the estimate of the total mobilization is a consequence of the uncertainty on the mercury
content of the coal actually used. Compared to mercury in other fossil fuels and in ores mercury in Russian coal is well-investigated.
The content of mercury in crude oil and natural gas is as well very variable depending on the geology of the oil and gas fields. Based on the available data on mercury
in crude oil it is estimated that about 33 t is mobilized with oil processed in RF. Besides, nearly the same amount would be present in the crude oil exported for
processing abroad. As mentioned above, these estimates are based on the mercury concentration in crude oils, but it is unknown how much of this that actually goes
with the oil for refinery/export after the initial processing of the oils. Due to the high variability of the mercury content of the crude oil (range by a factor of 50) and a
limited dataset, the total mercury mobilised is encumbered with high uncertainty and the range of uncertainty is roughly estimated at 5-50 t. Compared to the data
reported from other countries the average mercury concentration of the Russian crude oils are quite high, this may reflect actual geological differences in formation and
localization of oil fields, but may also reflect that more data is available on mercury in oil and gas from fields located within mercury provinces, hyper tectonism zones
etc. In order to reduce the uncertainty on the estimate, crude oil samples from the major Russian oil fields and samples of refinery feedstock should be analyzed. The
total mobilization of mercury with natural gas, gas-condensate, oil-shale and bio-fuels is estimated at 9 t, broken down into 8 t with gas and condensate, 0.6 t with
oil-shale and 0.4 t with bio-fuels. The mercury in natural gas mainly follows the stable condensate from the purification, and the mercury content in the purified gas
conducted to the consumers or exported is insignificant.
The mobilization of mercury by use of bio-fuels differs form the other categories by the fact that this mercury in any case would be released when the biomass was
decomposed.
A significant amount of mercury is mobilized by extraction of ores, in particular ores of zinc, copper, nickel, lead and gold. The table 6.1 shows the mercury content of
metal concentrates processed by Russian metal smelters.
The major part of mercury is mobilized with zinc and copper concentrates. By the processing the mercury is either emitted to the air, ends up in waste or ends up in
co-products like sulphuric acid. An insignificant part follows the refined metals to the consumers. By-extraction of mercury at gold production is estimated at 4-8
t/year. The greater part of it ends up in tailings and dumps and about 20 % may be emitted to the atmosphere.
Mercury mobilization by production of cement is estimated at 1.6-2.8 t originating from the mineral raw materials and fuels. Mercury in lime will also be mobilized by
the burning of the lime for production of quick lime. In the lack of data, this activity is not included in the assessment, but the mobilization will be significantly lower that
the mobilization by cement production.
Development in intentional use of mercury
The total consumption of mercury for intentional uses in the Russian Federation has decreased significantly from 866 t/year in 1989 to 155 t/year in 2001 (see table
6.3). The trend in mercury consumption in Russia thus follows the general trend in the world of decreased use of mercury for most intentional applications. The per
capita consumption of 1.1 g/capita in Russia in 2001 was slightly lower than the consumption in the USA, 1.2 g/capita in 1998 (based on "reported consumption" in
Sznopek, Goonan, 2000).
Table 6.3 Consumption of mercury in the Russian Federation 1989-2001
Industry,
Field of application |
1989 * |
1993 * |
2001 |
t/year |
% |
t/year |
% |
t/year |
% |
Chemical industry |
462 |
53.4 |
310 |
57.6 |
111 |
72 |
Medicine, pharmaceutics, stomatology |
12.5 |
1.4 |
9 |
1.7 |
0.7 |
0.5 |
Electrotechnics |
108.3 |
12.5 |
71 |
13.2 |
8.3 |
5 |
Instrument-making, electronics |
133 |
15.4 |
80 |
14.9 |
26 |
17 |
Non-ferrous metallurgy |
10 |
1.1 |
8 |
1.5 |
5.5 |
2.9 |
Agricultural chemistry |
50 |
5.8 |
10 |
1.8 |
0.6 |
0.4 |
Scientific researches, novel techniques |
25 |
2.9 |
10 |
1.9 |
3.5 |
2.3 |
Defence industry |
40 |
4.6 |
20 |
3.7 |
n.i. |
n.i. |
Other |
25 |
2.9 |
20 |
3.7 |
? |
- |
Total |
865.8 |
100 |
538 |
100 |
155 |
100 |
n.i.: not included
* Source: Yusfin, Zaletin, 1998
6.2 Releases of Mercury from the Russian Federation
Judged from the available data, the main direct pathway for releases of mercury from the technosphere to the environment is atmospheric releases. Mercury releases
to the atmosphere in Russia are summarized in Table 6.4. The table shows best estimates and an indication of the uncertainty on the emission estimates. The amount of
mercury mobilised with fossil fuels and ores is, as indicated in the previous Table 6.1, quite uncertain and to this uncertainty adds the uncertainty on the fate of the
mercury by the combustion or processing. There are almost no data available of measurements of actual mercury emissions especially in the sectors and activities
where mercury is mobilised as a natural impurity. Whereas data for emission have been obtained from enterprises intentionally using mercury e.g. in the chemical
industry.
No data on the speciation of the mercury releases from Russian sources have been available. For the understanding of the atmospheric transport, fate and the potential
environmental impact of the released mercury it is essential to have more information on the speciation of the mercury releases.
Intentional uses
Based on the available data, the atmospheric release of mercury from chlor-alkali and caustic soda production in 2002 is estimated at 1.2 tonnes. This represents the
direct releases with ventilation air and flue gas. Besides, some mercury releases may take place from the territory of the enterprises; either from mercury mechanically
lost or from on-site Hg-containing waste dumps. In the present assessment more than 50 t mercury is unaccounted in the balances and this mercury is assumed
primarily to be lost to structural building parts and the ground below and around the facilities. The presented estimates of air emission from the chlor-alkali processes
are identical with the enterprises' reporting to the environmental authorities and the official mercury emission inventory (Annex 1). How much of the unaccounted
losses that sooner or later is emitted to the air is an open question, not only as regards Russia, but in international reporting like the reporting on the European chlorine
industry to the OSPAR commission (OSPAR 2001). In the OSPAR reporting the "difference to balance" is not further interpreted, but it should be noted that this
"difference to balance" in most countries represent a significant part of the total mercury flow though the chlor-alkali sector. It should further be noted that the releases
and unaccounted losses vary very much among the enterprises.
Atmospheric emissions of mercury from the production of mercury-containing consumer products are described in detail in the report (see above). The emission may
create local technogenic pollution zones in the environment and have impact on the working environment, but in the national inventory they account for less that 1% of
the total mercury emission to the atmosphere.
Re-mobilisation of mercury
The assessment indicates that releases of mercury by gold mining of secondary placers, i.e. tailings from former mining activities using the amalgamation method, is a
significant source of mercury emission to the air. The atmospheric releases from the activities may amount to 0.9-3.9 t/year or about 60% of the total Hg content in the
processed placers (1.5-6.5 t/year). During the history of gold mining some 6,000 t of mercury has been used for gold mining in Russia. The main part of this may still
be present in the waste heaps and a part of this is emitted to the air as the tailings are heated for extraction of the residual gold. Newly developed equipment and
technologies exist for condensation of mercury evaporized from the process, but the use of the equipment is not widespread.
By the mining activities the re-mobilisation of mercury from the wastes is accelerated, but the mercury releases from all kind of mercury-containing waste may in fact
be significant. Only very limited is known on the release rates of mercury from waste and other secondary releases has not been quantified.
Mobilisation of mercury impurities
Mobilisation of mercury in fossil fuels, ores and other minerals account for the major part of the air emission from the Russian territory. The major part of this is
released from point sources: power plants, metal smelters, coke plants, cement plants, etc. Due to the volatile nature of mercury much emission abatement control
equipment - efficient in dust releases control - is only to a minor degree able to retain the mercury released from the raw materials by combustion or heating
processes. Consequently a significant part of the mercury mobilised will be released to the atmosphere.
By the use of coal, a total of about 14 t of mercury was released in 2001, broken down into 8 t from the electricity producing sector (combined power and heat
plants), 1.3 t from coke production, 2 t from municipal (boiler houses) and domestic heating and 3 t from other uses of coal. Combined power and heat plants are
equipped with controls for dust releases and to some extent equipment for desulphurization, but it is roughly estimated that still some 80% of the mercury content of
the coal is emitted to the atmosphere.
A part of the mercury present in crude oil will by the refining end up in the oil refinery products and ultimately be released to the air by the combustion of the products.
Comparing the total mercury content of crude oil for refining in Russia with the total emission by combustion of the petroleum products indicates that a significant part
of the mercury is released either by the initial treatment of crude oil or by the refinery process. Due to the lack of information about the fate of mercury by the
processes, no attempt has been done to estimate the potential releases from these processes. The knowledge on the fate of mercury in oil refinery activities is in
general very limited all over the world and it has not been possible to obtain a first estimate by using distribution factors adapted from other countries.
Table 6.4 Releases of mercury to the atmosphere in the Russian Federation, 2001/2002
Activity category |
Mercury emission to the atmosphere |
|
Best estimate (t/year) |
% of grand total |
Uncertainty category**** |
Intentional use of mercury |
Chlor-alkali production |
1.2*** |
3.0 |
3.0 |
Production of VCM |
0.02 |
0.05 |
0.05 |
Gold mining using the amalgamation method and mining of secondary
placers |
3.1 |
8.0 |
8.0 |
Stomatology (dental amalgams) |
0.05 |
0.1 |
0.1 |
Production of thermometers |
0.009 |
0.02 |
0.02 |
Production of batteries, barometers, manometers and other measuring
equipment |
0.01 |
0.03 |
0.03 |
Production of light sources |
0.15 |
0.4 |
0.4 |
Other intentional uses |
? |
- |
- |
Total intentional uses |
5.3 |
12 |
12 |
Mobilisation of mercury impurities |
Coal - electricity generating sector |
8.0 |
21 |
21 |
Coal - municipal and domestic heating |
2.1 |
6.0 |
6.0 |
Coal - Coke production |
1.3 |
3.0 |
3.0 |
Coal - other uses |
3.0 |
8.0 |
8.0 |
Oil processing |
? |
- |
- |
Use of gasoline, diesel and heavy fuel oil |
3.4 |
9.0 |
9.0 |
Gas, oil-shale and biofuels |
1.0 |
2.6 |
2.6 |
Zinc production |
1.9 |
5.0 |
5.0 |
Nickel and copper production |
5.3 |
14 |
14 |
Other non-ferrous metallurgy |
1.2 |
3.0 |
3.0 |
Iron and steel production |
1.4 |
4.0 |
- |
Cement production |
1.6 |
4.0 |
79 |
Use of by-products ** |
? |
- |
|
Total mobilisation as impurity |
30 |
79 |
0.1 |
Waste treatment |
Recycling of mercury |
0.05 |
0.1 |
9.0 |
Recycling of iron and steel |
? |
- |
- |
Waste incineration |
3.5 |
9.0 |
0.3 |
Disposal at landfills and dumpsites |
? |
- |
0.3 |
Light sources utilization |
0.1 |
0.3 |
10 |
Sewage sludge incineration |
<0.1 |
0.3 |
3.0 |
Total waste treatment |
3.8 |
10 |
0.05 |
Grand total |
42.6 |
100 |
|
* Secondary mobilisation of mercury previously used for gold mining using the amalgamation method
** Air emission from use of by-products like sulphuric acid, hydrochloric acid, bitumen, etc. has not been assessed but may be significant
*** Direct emissions from the processes. A certain amount of mercury may be emitted to the atmosphere in the so-called unaccounted losses of mercury which in
2002 were equal to 50 tonnes.
**** Uncertainty categories:
A: Based on specific information from enterprises - uncertainty connected to unaccounted releases
B: Experts estimates - the true value is most probably within a range of ± 50% of the best estimate
C: Expert estimates - the true value may quite well be beyond the a range of ± 50% of the best estimate
In the non-ferrous metal sector a smaller part of the mercury present in the concentrates is emitted to air as a significant part of the mercury is captured, in particular in
the controls for sulphur emission. It is estimated that in Russia about 8 t/year in total is emitted to the atmosphere, mainly from zinc, copper and nickel production.
The emission to the atmosphere from incineration of solid waste is roughly estimated at 3.5 t. Only a small part of the country's municipal solid waste is incinerated at 4
incinerators. The main source of mercury in the waste for incineration is anticipated to be mercury thermometers, batteries, light sources and switches.
Comparison with other inventories
According to the official Russian environmental statistics about 2.9 t mercury was released to the atmosphere from technogenic sources in 2001. These data are based
on the reporting of the individual enterprises to the environmental authorities. As a rule in Russia the enterprises and organizations report only on emission of pollutants
included into MAE regulations or certificates for technological equipment, i.e. in case particular mercury emission is not covered in the mentioned special documents
and regulations its release to the environment is not registered. Besides, only enterprises intentionally using mercury (chlor-alkali facilities, production of lamps,
thermometers etc.) have the obligation to report mercury emissions. For these activity categories the estimates of the present assessment is in due accordance with the
official data. In some cases the official data include information from a few metal smelters, but in general mobilised mercury impurities are not included into the
environmental reporting as the enterprises, utility plants, etc. have no obligation to report on the emissions of mercury.
Inventories of mercury emissions from Russia and other countries have recently been carried out as a part of the international INTAS project "Development of
methods for trace metal emission evaluation and their implementation for flux estimates in NIS territory, including economic aspects of flux reduction" (Pacyna 2003a).
Based on the INTAS data, updated estimates of the mercury emission from Russia has been done as part of the EU MERCYMS project (Pacyna 2003b). The data
are in Table 6.5.compared with the estimates of the present project. The estimates of the MERCYMS projects are quite well in line with the results of the present
assessment as regards coal combustion, pig iron and cement productions and non-ferrous metals production. The release from coal combustion is higher in the
MERCYMS inventory - in particular as regards residential heating. In total the release from coal combustion is twice as high in the MERCYMS inventory. The
release from waste incineration is significantly lower in the MERCYMS inventory. In the current assessment, the release of mercury from waste incinerators is
compared to the estimated mercury content of the waste and on this background it is estimated that the emission from waste incineration most probably is
underestimated in the MERCYMS inventory. According to the MERCYMS inventory mercury emission from chlor-alkali production is very high and is the main
source of mercury emission to the atmosphere in Russia. The high estimates are based on the assumption that unaccounted mercury losses are included into bulk
atmospheric emissions of mercury, which is probably not correct. More probably the greater part of mercury included into the category "unaccounted losses" (which
is determined based on the difference in balance – see Section 3.1 of the present report) is released to the terrestrial environment in the industrial zone of the
enterprise. And the air emissions estimates are based on the measured emission with ventilation air and flue gasses. These estimates of air emission from the processes
are in accordance with the enterprises' reporting to the environmental authorities and the official mercury emission inventory (Annex 1). It is worth mentioning once
again that in the international reporting like the reporting on the European chlorine industry to the OSPAR commission (OSPAR 2001) the "difference to balance"
(which is similar to "unaccounted losses") is noted without further interpretation, whereas the unaccounted differences in most countries account for a significant part of
the total mercury flux through the process at chlor-alkali facilities. As time goes by a particular part of this mercury is probably released to the atmosphere, but the
quantitative assessment of this source requires special investigations. According to the authors the reported emission from lead production actually represents the total
emission from the nonferrous metal sector and is of same magnitude as estimated in this project.
Table 6.5 Emission of mercury to atmosphere from Russia in 2000 according to the estimates done within the MERCYMS project (based on Pacyna,
2003b)
Source category |
MERCYMS data, 2000 |
This inventory, 2001/2002* |
Emission to air t/year |
% of total |
Emission to air t/year |
% of total |
Chlor-alkali production |
28 |
42 |
1,2 ** |
4 |
Coal combustion - large power plants |
15.5 |
23 |
8 |
27 |
Coal combustion - residential heating |
11 |
17 |
2 |
7 |
Other use of coal |
not included |
- |
4,3 |
|
Oil, gas and biofuels combustion |
no data not included |
- |
4,4 |
12 |
Non-ferrous metals production |
5.9 |
9 |
8,4 |
28 |
Pig & iron production |
1.9 |
3 |
1,4 |
5 |
Cement production |
3.7 |
6 |
1,6 |
5 |
Waste disposal |
0.1 |
0.2 |
3,5 |
12 |
Gold mining using the amalgamation method, use of secondary placers |
not included |
- |
3,1 |
|
Total |
66.1 |
100 |
38 |
100 |
* Best estimate
** In addition a part of the 56 t unaccounted losses may directly or indirectly be releases to the atmosphere.
Mercury in waste water and releases to water bodies
Compared to the atmospheric emissions, direct release to water bodies appears to be a minor pathway for mercury releases from the technosphere to the
environment. According to the official statistics, the total discharges of mercury with industrial wastewater to water bodies amounted to 0.16 t in 2001. The major
source category is chemical industry, production of chlor-alkali first of all.
Based on data on mercury in municipal sewage sludge it is estimated that the total discharges from municipal sewage plants may constitute 3.4-11.9 t. A similar
amount may end up in sewage sludge which is mainly disposed of to sludge beds and dump sites. In many Russian cities the industrial discharges are delivered directly
to the municipal sewer system and then together with municipal sewage treated at municipal wastewater treatment plants. The major sources of mercury in the
municipal sewage is probably mercury from dental clinics, mercury from broken thermometers and electrotechnical equipment (e.g. broken switches), and rain water.
A significant part of the mercury-containing appliances produced ten to twenty years ago may still be in use and, when broken, a part of the mercury may end up in
the drain.
Direct mercury releases to land
The major source of direct mercury releases to land (excluding waste dumps) is releases to the ground from chlor-alkali production. A significant part of the 50 t/year
of unaccounted losses is assumed to be directly lost to the ground below and around the production facilities. Mercury may as well accidentally be lost to the ground
by other types of production involving mercury. A number of the most mercury contaminated sites around production facilities - closed or still in operation - are listed
in the assessment.
The use of mercury-containing pesticides is prohibited in Russia. Nevertheless in 2001 mercury-containing pesticides (basically Granosan) were still used in agriculture
and might be a source of about 0.6 t of mercury released to terrestrial environment. Today, up to 20 t mercury in obsolete mercury-containing pesticides is stored
around the country. Many of the storehouses located in rural areas are in inadequate condition and there is a risk of releases of the pesticides to the surroundings.
In Russia a few percent of the sewage sludge is used for agriculture and less than a tonne of mercury may be spread with sewage sludge on the fields. The typical
concentration of mercury in the sludge is far below the MAC of mercury in sludge used for agricultural purposes in Russia. The mercury content of mineral and organic
fertilisers applied in Russia has not been quantified as part of this inventory.
By burials the mercury content of the dental amalgams will sooner or later be released to the ground on the cemeteries. Mercury in dental amalgams in buried corpses
may be several tonnes per year.
Indirect releases via products
During various technological processes mercury may end up as occasional impurity in the finished products or by-products (see Table 6.6). It is estimated that more
than 16 t/year ends up in these products. The fate of this mercury has not been investigated, but it is assumed that it will be released to the environment or end up in
waste products. The mercury content of oil refinery products - apart from petrol, diesel and heavy fuel oil - has not been assessed, but the total mercury content may
be significant.
Table 6.6 Mercury impurities in products and by-products not further assessed, 2001
Activity category |
By-product |
Mercury mass Best estimate
t/year
|
Application |
Ultimate fate |
VCM production |
Hydrochloric acid |
2.8 |
Injection in oil- and gas wells |
n.a |
Chorine-alkali |
Caustic soda, chlorine, hydrogen |
0.2 |
Production of PVC;Chemical industry |
n.a |
Coke production |
Different chemical products |
0.6 |
Different applications |
n.a |
Zinc production |
Sulphuric acid |
7.8 |
n.a. |
n.a |
Copper production |
Sulphuric acid |
2.3 |
n.a. |
n.a. |
Oil refinery |
Petcoke, bitumen, sulphur |
n.a |
n.a |
n.a |
Gas processing |
Sulphur Stable gas condensate |
0.32.0 |
n.a |
n.a |
Total |
|
>16 |
|
|
n.a Not assessed
6.3 Mercury in Solid Waste
Mercury in waste products is summarised in Table 6.7. In total at least 98 t mercury ended up in waste products disposed of for landfills/dumpsites whereas about 32
t was recycled (waste and ferrous metals processing). It should be noted that mercury in the waste products will be at various chemical forms and by this have
different mobility. As for atmospheric emission only best estimates are shown with an indication of the uncertainties.
In total 39 t mercury was disposed of with waste from chlor-alkali production. The waste was mainly stored in waste dumps at the production sites. At present no
external recycling of mercury from chlor-alkali production waste takes place. Contrary to this, the main part of the waste from the production of VCM was recycled
for production of new catalysts. Mercury waste disposed of to waste dumps from production of mercury-containing products was insignificant (in total 0.3 t).
Mercury compounds which have been used in analytical and scientific laboratories are typically neutralized and disposed of to landfills.
Of the estimated 3-8 t mercury used for illegal gold mining 0.6-1.6 might have ended up in the tailings from the mining process.
About 5.6 t mercury ended up in bottom ash and fly ash from coal combustion. A minor part of the fly ash is used for cement production, but the major part is
disposed of to landfills.
A total of about 11 tonnes of mercury accumulated in waste from smelting in non-ferrous metallurgy. A very significant amount of mercury ends up in tailings from ore
processing and is disposed of to waste dumps, but it has not been possible to quantify the amount in this inventory. It is unclear to what extent mercury in the mining
waste is mobile and released to the surroundings. Some investigations indicate that mercury in tailings from coal concentrate production may to some extent be mobile
and emitted to the atmosphere.
If the data of Table 6.1, Table 6.4 and Table 6.7 are combined, the estimated mobilised mercury exceeds the total of the releases to air and the mercury in waste
products by about 75 t. The difference illustrates that the actual fate of the mobilised mercury is still poorly understood, and the volumes that end up in waste products
may be significantly higher than the indicated amounts.
The content of mercury in municipal solid waste is estimated at 24 t at the least. Almost no data are available on the mercury content as natural trace element in all
types of waste. The major source of mercury in the waste is deemed to be broken mercury thermometers. A part of the mercury in thermometers may be discharged
with waste water when thermometers break by use. Other sources of mercury to the waste are mercury lamps, switches, batteries and dental amalgams. Considering
the high amounts of mercury that was used for production of batteries, switches, measuring equipment and other electrotechnical equipment 10 years ago, the amount
of mercury ending up in solid waste with these products may be highly underestimated. The amount of mercury in the waste can be estimated by investigating mercury
in flue gas and residues from waste incinerators, but such measurements have not been available from Russian incinerators.
Recycling and mercury co-product production
About 30 t refined mercury was produced in 2001 at two main recycling enterprises by recycling of mercury-containing waste products. In general the amount
recycled varies very much from year to year and in 2002 only about 10 t mercury was recycled. About 9.8 t of the recycled mercury in 2001 originated from the
production of vinyl chloride monomer (VCM) although the actual amount disposed of from the production in 2001 amounted to 4.7 t. The difference reflects the fact
that the waste may be stored for some time before treatment. About 24 t of the recycled mercury was spent mercury metal that might originate from different
measuring equipment, switches, old mercury stocks at the enterprises, etc. Less than 100 kg of mercury was refined from discarded mercury lamps in 2001 although
the mercury content of treated lamps was significantly higher.
About 5 t of mercury in sludge from zinc production was exported for refining abroad.
Table 6.7 Mercury in solid waste products in the Russian Federation, 2001/2002
Activity category |
Mercury in waste products |
|
for landfills/dumpsites |
for recycling/refining |
|
Best estimate (t/year) |
% of grand total |
Uncertainty category |
Best estimate (t/year) |
Intentional use of mercury |
Chlor-alkali production |
39 |
41 |
A |
|
Production of VCM |
0.0 |
0.0 |
A |
4.7 |
Gold mining using the amalgamation method |
1,1 |
1 |
B |
|
Production of thermometers |
0.1 |
0.1 |
A |
|
Production of batteries, barometers, manometers and other measuring
equipment |
0.2 |
0.2 |
A |
|
Production of light sources |
0.001 |
0.0 |
A |
2.3 |
Laboratory use |
2.2 |
2.3 |
B |
|
Other intentional uses |
? |
- |
- |
|
Total intentional uses |
43 |
45 |
|
7 |
Mobilisation of mercury impurities |
Coal - extraction and processing |
3.1 |
3.0 |
B |
|
Coal - electricity generating sector |
2 |
2.1 |
B |
|
Coal - other uses |
0.5 |
0.5 |
B |
|
Oil processing |
? |
- |
C |
|
Gas and biofuels |
? |
0 |
C |
|
Zinc |
8.5 |
9 |
C |
5.4 |
Copper and nickel production |
6.6 |
7.0 |
C |
|
Other non-ferrous metallurgy (incl. gold) |
4.2 |
4.0 |
C |
|
Cement production |
0.4 |
0.4 |
B |
|
Use of by-products |
? |
- |
|
|
Total mobilisation as impurity |
22 |
23 |
|
5.4 |
Waste treatment |
Recycling of mercury |
0.003 |
0.0 |
A |
|
Recycling of iron and steel |
? |
- |
- |
|
Municipal and hospital solid waste |
0.8 |
0.8 |
C |
|
Secondary production of gold from placers |
24 |
25.5 |
B |
|
- thermometers |
19.5 |
21 |
B |
|
- batteries |
1.6 |
1.7 |
B |
0.02 |
- light sources |
1.6 |
1.7 |
B |
|
- measuring equipment, switches, etc. |
0.04 |
0.0 |
C |
0.5 |
- amalgams |
1.0 |
1.1 |
C |
|
- other solid waste |
? |
- |
- |
|
Sewage sludge |
5.7 |
6.0 |
B |
|
Mercury metal of unknown origin*** |
? |
- |
A |
21 |
Total waste treatment |
30 |
32 |
|
22 |
Grand total |
94 |
100 |
|
34 |
Notes: see next page
* By-product mercury exported for refinery abroad.
** Indicates the amount disposed of for recycling from the process. The actual amount recycled in 2001 was 9.8 t
*** Mercury metal for recycling with no information on origin; may originate from measuring equipment, switches, stocks, etc.
**** A part of this may be discharged with waste water.
*** Uncertainty categories:
A: Based on actual information from enterprises - uncertainty connected to unaccounted releases
B: Experts estimates - the true value is most probably within a range of ± 50% of the best estimate
C: Expert estimates - the true value may quite well be beyond the a range of ± 50% of the best estimate
7 References
If nothing else is indicated the sources are in Russian.
References to Internet sites refer if nothing else is mentioned to the sites in spring 2003.
Achkasov A.I. Distribution of Microelements in Agrarian Landscapes of Moscow Oblast: Author's Abstract of the Dissertation ... Candidate of Geographical
Sciences. Moscow, 1987. 24 p.
Achtenberg A., Zaanen J.J. 1972. Sporen kwik in het Groninger aardgas. Chem. weekbl., Bd. 68, N 8. (In Dutch)
Afanasyev, B. V., Bichuk, N. I., Dain, A. D. et al. Mineral and Raw Material Resources of the Murmansk Region//Mineral Resources of Russia, 1997, No. 3, p.
16-22.
Aivazov G. 2001. It is time to tame wild gold. The newspaper "Krasnoyarsky rabochy", February, 21. Available at
http://krasrab.krsn.ru/archive/2001/02/21/06/view_article
Aizenberg Yu.B., Prytkov A.A. Review of Development of Russian Lighting Equipment Market at the Modern Stage //http://www.lta.ru/marketing/review-01.shml.
Alakaeva R.A. 1999. Some aspects of the environmental mercury contamination danger on gold concentration from ores by direct cyanidation technique. In:
Proceedings from IIIrd Scientific-technical conference. Mercury. Complex safety system. St. Petersburg, pp. 62-66.
Amelin A.G. Technology of Sulphuric Acid. – Moscow: Khimia, 1983. – 360 p.
Analysis of Financial Market... // http:www.analitika.fis.ru/article/?id=992 (12.08.2003).
Analysis of state of mercury pollution of the environment in the Russian Federation. NITsPURO, Mytischy, 1999
Analytical Record on the Condition of ferrous Metallurgy in Russia// Bulletin of the Accounting Chamber of the Russian Federation, 2002, No. 9 (57) // Materials of the
official site of the Accounting Chamber of RF.
Andreeva V. State of affairs with non-applicable pesticides in Voronezh oblast. The materials of the Russian seminar "Inventory of stocks of obsolete pesticides".
Center of International projects, Voronezh, 2000, p. 133-135.
Andreyev B.M., Zelvensky Ya.D., Katalnikov S.G. Splitting of Stable Isotopes by Physico-Chemical Methods. – Moscow: "Energoatomizdat" Publishers, 1982. –
208 p.
Annual Report 2001 "Gazprom JSC", 2002 www.gazprom.ru
Annual Report of MMC Norilsk Nickel - 2001. (Official website of MCC Norilsk Nickel).
Annual Report of OJSC "MMK" of 2002 for Investors // www.mmk.ru.
Annual Report of OJSC "MMK" of 2002, for Investors// www.mmk.ru.
Annual Report of MMC Norilsk Nickel-2002 (Official web-site of the GMK "Norilsky Nickel"//www.nornik.ru).
Annual Report of MMC Norilsk Nickel-2001 (Official web-site of MMC Norilsk Nickel//www.nornik.ru).
Antipov E.V., Putilin S.N. Superconductive Mercury Complex Copper Oxides // http://elibrary.ru/books/janus/antip.htm (25.05.1998).
Atmospheric Air, Waste, Radiation – Chelyabinskaya oblast... // www.grenpeace.ru/default/8300 (10.01.2003).
Atmospheric Emission Inventory Guidebook. A joint EMER/CORINAIR Production Prepared by the EMER Task Force on Emission Inventories, 1996. (In English)
Auerbah A. Description of mercury mine and plant which is owned by Auerbah and CO // Mine journal, 1888, v. 2, April-June, p. 1-12.
Bagataev R.M. Mercury deposits of quartz-dikkit type, geological industrial model, forecasting and assessment (Example of Donbass and the Northern Caucasus): -
M.: IMGRE, 1998. - 46 p.
Bailey E.H., Snavely P.D., White D.E. 1961. Chemical analyses of brines and oil, Cymric field, Kern Country, California. Geol. Surv. Profess. Pap. D., N 424. (In
English)
Balagutin Yu, L. // http://www.gornymir.ru/SEMENAR/usl_licenz6.htm (15.04.2002).
Bank of natural technologies and equipment. FSU UralNII "Ecology".
Barinova I.A., Sinitsina A.V., Kharitonov A.A. Energy Saving in the Housing Light System of the Town of Saransk (Market Situation) // "Svetotekhnika", 2002, No.
5., p. 21-23.
Bashkortostan. Brief Encyclopedia. 1997. Available at (http://www.uic.bashedu.ru/encikl/maintitle.htm )
Basics of Metallurgy. V.2. Heavy Metals. Moscow: Metallurgizdat Publishers, 1962. 792 c.
Bauer B., Karpov S. 2001. Creation reserves of the gold Russian market. RCB. Goods market No 0 (Pilot issue). Available at
(http://www.investor.ru/Archive/articlestr.asp?aid=1844 )
Baymakov Yu.V., Zhurin A.I. Electrolysis in Hydrometallurgy. - Moscow: "Metallurgia" Publishers, 1977. - 335 p.
Belyayev A.I., Zhemchuzhina E.A., Firsanova L..A. Metallurgy of Pure Metals and Elemental Semiconductors. - Moscow: "Metallurgia" Publishers, 1969. - 504 c.
Benevolsky B.I. 2002. Gold of Russia. ZAO Geoinformmark, Moscow.
Berling N.I. Dagestan and mercury problem // Planning economy of Dagestan, 1928, No. 5-6, p. 32-35.
BIKI, 2002, # 148.
BIKI, 2003, # 41.
Bobkov A.C., Blinov A.A., Rozdin I.A., Khabarova E.I. Labour Protection and Environmental Safety in Chemical Industry. Moscow: Khimia, 1997. – 400 p.
Bobrova L.V., Kondrashova O.V., Fedorchuk N.V. Economy of Geological Survey of Mercury, Antimony and bBismuth. - Moscow. Nedra, 1990.
Bobrova L.V., Kondrashova O.V., Phedorchuk N.V. The Economy of geological exploration works on mercury, antimony and bismuth. - M.: Nedra 1990. - 156 p.
Bogatyrev V.P., Galay N.N., Belogub M.F., Yudina I.M. Resource Study. Part 1. Main Types of resources in the Nizhniy Novgorod Oblast. Nizhniy Novgorod:
Publisher's House of the Volgo-Vyatka Academy of State Service, 1999. - 183 p.
Bogomolov A.I., Gayle A.A., Gromova V.V. et al. Oil and Gas Chemistry. St. Petersburg: Chemistry, 1995. 448 c.
Bolokhontseva R.V., Koshlek T.I., Savelyeva L.F. et al. Sanitary and technical Characterisation of Labour Conditions at the OJSC "Svet" // Proceedings of the
Scientific and Practical Conference "Relevant Issues of Ensuring Sanitary and Epidemiological Welfare and Protection of Health of Population in the Central Region of
Russia" Devoted to 80th Anniversary of the State Sanitary and Epidemiological Service of Russia (Smolensk, 26-29 November 2002). Smolensk: SGMA, 2002, p.
234-236.
Bondarenko V.N., Kolesnikov A.G., Bondarev V.G. Equipment of Environmental Protection // "Koks i Khimia" (Coke and Chemistry), 2002, No. 1, p. 32-35.
Bovina L.A., Boltar KO., Burlakov I.D. et al. Matrix Receivers 128x128 and 384x288 Based on Photodiodes from CdXHg1-XTe // Applied Physics, 1999, No. 3, p.
32-41.
Bovina L.A., Stafeyev V.I. Photodiodes and Photodiode Materials Based on CdXHg1-XTe // Applied Physics, 1999, No. 6, p. 59-69.
Bovina L.A., Stafeyev V.I., Boltar K.O. Research into Stability of Characteristics of Photodiodes from CdXHg1-XTe // Applied Physics, 1999, No. 3, p. 41-46.
Burenkov E.K., Yanin E.P., Kizhapkin S.A. et al. Ecological and Geochemical Assessment of the Environment of the Town of Saransk. Moscow: IMGRE, 1993,
115 p.
Butov V.A., Ivanov V.S., Kremenitskiy A.A., Usova T.Yu. Mercury of Russia: problems and perspectives // Mineral resources of Russia. Economics and
management, 1997, No. 5, p. 9-13.
Byshkova N.A. Clinic and medical treatment of children intoxication by granosan. – Abstract. – Novosibirsk, Omsk; 1973. – 15 p.
CADASTRE. Conditions and Outlooks of Waste Formation in Mining and Metallurgical Production//http://www.murman.ru/ecology/cadastre/3-1.html (09.02/2003).
Characterisation of Specific Release of Pollutants from Some Enterprises and Their Use for Expertise of Air Protection Actions. – Moscow: USSR Ministry of
Ferrous Metallurgy, 1989
Chelnokov, A.A., S.V. Plishevsky 2000. Regarding air emissions of heavy metals from cement production facilities//Cement and its use, No. 6, p. 41-45.
Chelnokov, A.A., S.V. Plishevsky, 1998. Application options of "Manual on air emissions inventory" at the assessment of emissions from building materials
enterprises//Issues related to pollutants emissions inventory. Materials of the International Symposium on Pollutants Air Emissions Inventory and EMER/CORINAIR
Manual Application. Minsk-Raubichi, Republic of Belarus, 1997. – Minsk: Institute of Natural Resources Use and Ecology of Belarus AS, p. 91-102.
Chemical Encyclopaedia. Vol. 2. – Moscow: "Soviet Encyclopaedia" Publsihers, 1990. - 671 p.
Cherniakova N. Strength Margin? Overview of Nickel Industry (Securities Market, 2002, # 24) // http://www.rcb.ru/Archive/articlesrcb.asp?aid=3002
(13.08.2003).
Chikichev S.I. Hetero-structures CdXHg1-XTe /.../ Si: Yesterday, Today and Tomorrow // Autometry, 1996, No. 4, p. 6-31.
Cleaning of Process Gases in Non-ferrous Metallurgy. Moscow, 1992.
Consolidated Report on Protection of Atmospheric air for 2001. Goskomstat (State Statistical Committee) of Russia, GMC of Goskomstat of Russia.
Criteria of classification as hazardous wastes for the environment. Appr. by the Order of the Ministry of Natural Resources of Russia, dated June 15, 2001, No.511.
Customs Statistics of Foreign Trade of the Russian Federation. Book for 2000. Moscow: GTK RF, 2001. 450 p.
Database "Participants of the Lighting Equipment Market. Issue 1.; Moscow, "Dom Sveta", 2001. 152 p.
Delovoy Novosibirsk (21.11.2002) // http://www.dnsk.ru/2002/korp/1121_litiy.htm (11.03.2003).
Denisov S.I. Arresting and Utilization of Dust and Gases. Moscow: Metallurgy, 1991.
Dickenstein G.Ch., Cluschko W.W., Goldbecher K., Müller E.P. et al. 1973. Zum Auftreten von Quecksilber in Erdgasen am Beispiel der
Rotliegenderdgaslagerstatten. Stschr. angew. Geol., Bd. 19, H. 10. (In German)
Donskih D.K., Skitskiy V.L. Problems of mercury-containing wastes utilization and paths to solve it // http://recyclers.ru/text/037.html (03.01.2003).
Dorozhukova, S.L., Y.P. Yanin, A.A. Volokh 2000. Natural concentrations of mercury in some types of soils of oil and gas bearing areas of Tyumen oblast. Bulletin
on ecology, dendrology and landscaping. Issue 1. Tyumen.
Doughty D.A., Wilson R.H., Thaler E.G. Mercury-Glass Interaction in Fluorescent Lamps // J. Electrochem. Soc., 1995, 142, No. 10, p. 3542-5351.
Draft of Regulations on Maximum Allowed Emission for Industrial Site No. 1 ("Lisma-SELZ"). Saransk: VNIIISM-Lisma, 2000. 295 p.
Drilling and oil, 2003. No. 3.
Eco-bulletin No. 3 (62) March, 2001.
Economical and social geography of Russia. Moscow,2001.Informational and analytical collection «World and national markets of non-ferrous and rare metals» (state
on July 1, 2002) Fascicle 14. Mercury. Informational and analytical center JSC «Informmetgeo», Moscow , 2002.
Economy and Life-Siberia, 2000. No. 8 // http://www.ecolife.krsk.ru/old/Arh/2000/122/14.asp (05.07.2003).
Electrical Engineering Industry and Environment (Ecological and Geochemical Aspects). Moscow: Dialogue-MGU, 1998. 281 p.
EMAS of MSW landfill for Perm city.
Enlarged Forms of Waste Use and Waste Conditioning for Different Industrial Branches. Moscow: "Stroyizdat" Publishers, 1978. 590 p.
Environmental Condition and Human health in Perm in 1999: Reference Information Materials / Edit Board: V.A. Sedina, O. P. Volk-Leonovich / Municipal
Administration on Environment and Nature Use. Perm, 2000. - 74 p. // http://www.ecology.permregion.ru/doc/1999/ (11.02.2003).
Environmental situation in Saint-Petersburg city and Leningrad oblast in 1997. Reference review (7 edition). Saint-Petersburg city, 1998.
European Communities. 2001. Ambient mercury pollution by mercury - Position Paper. Office for Official Publications of the European Communities, Luxembourg.
(In English)
Fedorchuk V.P. Geology of Mercury. Moscow, "Nedra" Publishers, 1983. 270 p.
Fedorchuk V.P., Mintser E.F., Geological Reference Book on Mercury, Antimony, Bismuth. Moscow, "Nedra" Publishers, 1990. – 215 p.
Ferrous Metallurgy Urfo // http://www.econ.epn.ru/articles/cher_met.asp (28.06.2003).
Filachev A.M., Ponomarenko V.P., Taubin I.I., Ushakova M.B. Infrared Matrixes and Trends in Their Development. Part 1 // Applied Physics, 2003, No. 3, p.
105-120.
Floyd, P., Zarogiannis, P., Crane, M., Tarkowski, S. Bencko, V. 2002. Risk to Health and the Environment Related to the Use of Mercury Products. Final Report,
prepared for the European Commission, DG Enterprise by Risk & Policy Analysts Limited, London, 2002. 119 p.
Foss G.V. 1963. Gold. Gosgeoltechizdat, Moscow
Friedli, H.R., Radke L.F. & Lu J.Y. 2001. Mercury in Smoke from Biomass Fires. Geophysical Research Letter, 28: 3223-3226. (In English)
Fursov ,V.Z., 1977. The mercury as an indicator at geochemical methods of ore deposits searching. M., The Subsurface.
Fursov V.Z. Gas-and-Mercury Method for Mineral Products. Moscow, "Nauka" Publishers, 1983. – 205 p.
Fursov V.Z. Mercury Atmosphere of Natural and Man-Made Areas // Geochemistry ("Geokhimia"), 1997, No. 6, p. 644-652.
Ganeev A.A., Pogarev S.E., Ryzhov V.V., Sholupov S.E., Dreval T.V. 1995. The new method for direct and express determination of mercury in oil, gascondensate
and biological samples. J. Ecol. Chem., 4, 122.
Ganeev, A.A., V.V. Ryzhov, A.D. Maidurov, N.R. Mashyanov, S.Y. Sholupov, N.A. Ozerova, A.E. Chernova, 1966. Direct detection of Hg-containing
compounds in natural gas and air through pyrolisys and photolysis. Bulletin of Saint-Petersburg University, ser. 4, issue 1(4).
Garkusha F., Laubgan T. Control of storage of pesticides in Krasnodar krai and problem of disabled pesticides. The materials of the Russian seminar "Inventory of
stocks of obsolete pesticides". Center of International projects, Voronezh, 2000, p151-153.
Geography of Russia. Encyclopaedic Dictionary. Moscow: Big Russian Encyclopaedia, 1998. 800 p.
Geological Service of Primorie (50th anniversary of establishment). Vladivistok: Dalnauka Publishers, 2000 – 159 p.
Gerasimchuk I., Simonov K., Gosudareva V. et al. Current and Perspective Consumption of Metals in Russia and Ukraine //
http://www.marketing.cfin.ru/mr/industry/consuptio... (16.05.2003).
Global Mineral Resources at the Beginning of 1998 (official publication). Moscow: FGUNNP "Aerogeologia", 1999. - 870 p.
Global Mineral Resources at the Beginning of 1999 (official publication). Moscow: FGUNNP "Aerogeologia", 2000. - 911 p.
Glogoczowsky J.J., Karpinski T., Streetelski J., Zuk W. 1977. Zwazki genetyczne miedzy naftova gasem siemnym i substancya organiozna, rozproszona wutworach
permu Monokyly Pezedsudeckiej. Nafta, N 2.
Gold Fields Mineral Services (GFMS). January, 2002. Available at http://www.aurum79.ru/
Gold-2002. From deposit to jewelry. 4th International exhibition. Available at http://www.rusexpo.com/gold/otchot02.htm)
Golembiovsky S.A., Shemelin Yu. A. Russian Market of Light Engineering Products Designed for Houses and Offices. Inside View // "Svetotekhika", 1997, p.
39-43; No. 6, p. 38-40, 1997.
Goncharov V.G. 2002. The gold-mining industry of Russia. 2001 Results. Mineral resources of Russia. Economy and management 1-2: 40-45 (in Russian and
English).
Gordeyev V.V. River Flow to Oceans and Its Geochemistry Features. Moscow: "Nauka" Publishers, 1983. 160 p.
Gorzhevsky D.I., Ruchkin G.V., Klimenko N.G. Mineral Raw Materials. Lead and Zinc. Reference Book. Moscow: Geoinformmark, 1997. - 47 p.
GOST 30772-2001. Resource Saving. Terms and Definitions. Moscow, Standard Editing House, 2002, 15 p.
GOST 30773-2001. Resource Saving. Handling of Waste. Stages of Technological Cycle: Basic Provisions. Moscow, Standard Editing House, 2002, 11 p.
GOST 30774-2001. Resource Saving. Handling of Waste. Certificate on Waste Hazard: Basic Requirements. Moscow, Standard Editing House, 2001, 21 p.
GOST 30775-2001. Resource Saving. Handling of Waste. Classification and Coding of Waste: Basic Provisions. Moscow, Standard Editing House, 2002, 37 p.
GOST 4658-73. Mercury. Specifications. Moscow, Standard Editing House, 1997, 11 p.
Gritsenko, A.I., G.P. Bosnyatsky, Y.S. Shilov, A.D. Sedikh, 1993. Environmental problems of gas industry.
Gudima. N.V., Shein Ya.P. Brief Reference Book on Metallurgy of Non-ferrous Metals. Moscow: Metallurgy, 1975. – 536 p.
History of gold. Bank "Finances and Credit" Ukraine. Available at http://www.fc.kiev.ua/metals/history.html
http://bo.torg-center.ru/925.html.
http://doklad.ru/monika/doklad/view/zip-1375.html (05.09.2003).
http://eurocopper.ru/stat%20ussr%20russ.htm (12.06.2003).
http://extech.msk.su/expo/exibit/innov_98/org.texm... (28.05.2002).
http://mcm.anod.net.
http://metal.interfax.ru/test_metal_show.html?tz=0... (07.07.2003).
http://metal.klimenko.ru/catalog/Detailed/21.html (17.08.2003).
http://metall.klimenko.ru/arc.15-09-2002.html (29.08.2003).
http://metal-trade.ru/news/business/2002/12/index (05.09.2003).
http://metal-trade.ru/news/business/2003/03/1337.s... (29.08.2003).
http://minamp.rbc.ru/ru/cp_on_commodity_marcet/ana... (17.07.2003).
http://novosti.vins.ru/?f=lf&t=010718c06 (01.02.2003).
http://prometeus.nsc.ru/patent/1997/210.ssi (12.07.2003)
http://uralnep.ru/news/view_article.php?newsid=422... (10.08.2003).
http://uuu.narod.ru/money.htm (09.09.2002).
http://web-lab.dvgu.ru/~gke/monitor/mon2.htm
http://www.3e.opec.ru/news_doc.asp?d_no=172 (29.04.2003).
http://www.ako.ru/PRESS/viewtext.asp?C8688=On (08.07.2003).
http://www.aktex.ru/rus.news/?year=2003&month=1&da... (17.08.2003).
http://www.aktex.ru/rus/analytics/equimpent (18.09.2003).
http://www.aviaport.ru/news/Markets/21440.html (17.01.2002).
http://www.aviaport.ru/news/Markets/a1020229200.ht... (18.03.2003).
http://www.chrab.chel.su/archive/17-10-97/1/RE12.D... (16.10.1997)
http://www.chrab.chel.su/archive/17-10-97/1/RE12.D... (16.10.1997)
http://www.eao.ru/in_olovo.html (31.03.2003).
http://www.enicey.ktk.ru/nature/13.cfm?nid=200 (06.09.2003).
http://www.giredmet.ru/segodnya1.html.
http://www.greenpeace.ru/gpeace/43520/gp_article_t... (21.05.2003).
http://www.infogeo.ru.
http://www.infogeo.ru.
http://www.infoline.spb.ru/metall.html (27.01.2003).
http://www.infoural.ru/infoural/delur/1999/r2/14-1... (04.02.2000).
http://www.inves.ru/rus_china/4/pril_1.htm (12.05.2003)
http://www.khv.ru/MD/2001/12720/ob.htm (21.09.2001)
http://www.kmez.ru.
http://www.mediatext.ru/docs/2417 (30.03.2003).
http://www.medin.ru/price/m1998_4.shtml (03.05.2003).
http://www.metalinform.com/?op=news&lang=ru&idstr=... (05.09.2003).
http://www.mhg.ru/proekt/doklad/99/region/am/chapt... (date of the original document: 29.10.2000).
http://www.mineral.ru/Chapters/News (15.04.2003).
http://www.mineral.ru/Chapters/News/7460.html (16.05.2003).
http://www.physfac.bspu.secta.ru/mirror/izone/izon...
http://www.rambler.ru/db/news/msg.htm (26.08.2002).
http://www.rambler.ru/db/news/msg.html (12.09.2002)
http://www.rambler.ru/db/news/msg.html?mid=1449831... (24.01.2001).
http://www.rambler.ru/db/news/msg.html?mid=1773229&s=12.
http://www.waste.ru/modules/news/article.php?storyid=59
http://www.zinc.ru/news.php3 (07.07.2003).
IEA. 2003. Energy Statistics of non-OECD countries. International Energy Agency, Paris.
In a Russian Coking Heating Technological Station // "Koks i Khimia" (Coke and Chemistry), 2002, No.No. 5, p. 11-21.
Information and Analytical Review 'Condition and Prospects of World and Domestic Markets for Non-ferrous, Rare and Noble Metals'. Issue 3. Lead ans Zinc.
Moscow: OOO Infometgeo Publishers, 2002 - 66 p.
Informational and analytical brochure «Global and national market of non-ferrous and scarce metals» (as on 1.07.2002). Iss.14. Mercury. - M.: IATs «Infometgeo»,
2002. - 16 p.
InfoTEC 2003. Monthly Analytical Bulletin, No. 1.
Inter-sectoral Rules on Protection of Labour during Production and Use of Mercury. POT RM-009-99. St. Petersburg; Edition of the DEAN; 2001. 64 p.
Ivanov A.A. Results of monitoring of fish and fish products intoxication with pesticides //Population health and habitat, 1999, No.11, p.19-21
Johansen, V.C., Hawkins, G.J. 2003. Mercury speciation in cement Kilns: A literature review. R&D Serial No. 2567, Portland Cement Association, Skokie, USA.
(In English)
JSC «Lisma» http://www.lisma-lighting.ru
Kakareka S.V., Kukharchik T.I., Khomich V.S., Yanin E.P. On state and problems of mercury emissions inventory // Ecologo-geochemical problems of mercury. -
M.: IMGRE, 2000, p. 12-37.
Kakareka, S., V. Khomich, T. Kukharchyk et al.Heavy metals emission factors assessement for the CIS countries. 1998. – Minsk: Institute for Problems of Natural
Resources Use and Ecology of the National Axademy of Sciences of Belarus. 159 p.
Kakareka, S.V., T.I. Kukharchik, V.S. Khomich, Y.P. Yanin 2000. The status and problems of Hg air emissions inventory. Environmental and geochemical mercury
related problems.
Kamenev V.F., Fadeeva L.V. Distribution of Mercury in Sulphuric Acid Production // Non-ferrous metals, 1983, # 8, p. 35-36.
Karasik M.A., Dvornikov A.G. Mercury Contents in Coal from Donetsk Basin and in Its Processing Products. – Moscow: ONIT VIEMS, 1968. – 45 p.
Karasik, M.A., A.G. Dvornikov. 1968. Mercury content in coals of Donetsk basin and products of coals processing. M., VIEMS.
Kartuzov V.M., Shemanayev S.A. Disposal of Mercury-Containing Waste // Ecology and Industry of Russia, 2000, April. p. 14-16, 49.
Katunin V.V. Results of Ferrous Metallurgy Operation in Russian in 2001 // "Chernaya Metallurgia" (Ferrous Metallurgy) , 2002, No. 2, C. 3-16.
Kharitonov Y.F., Vasiliev V.G., Andreichuk D.A., Glazunov A.P. 2002. Ecological-economical assessment of wastes of gold mining industry of the Chita Region.
Resources of Transbaikalie. Ad hoc issue. Available at http://www.zabnii.ru/publications/index.php?article=11
Kindbom, K & Munthe J. 1998. Hur påverkas kvicksilver i miljön av olika energialternativ? IVL Svenska Miljöinstitutttet. (In Swedish).
Kirillova T. 2002. Pavlodar gold-rush. Newsweek (Kazakhstan) 1(67), January, 9 http://www.nn.kz/cgi-bin/newsweek.cgi?menu=view&id=A1UHux1Pxv
Kler V.R., Nenakhova V.F., Saprykin F.Ya. et al. Metallogenics and Geochemistry of Coal-Bearing and Coal Shale Containing Regions of USSR. Justified
Concentrations of Elements and Methods of Their Study. Moscow: "Nauka" Publishers, 1988. 256 p.
Klimenko N.G., Kiazimov R.A. Analysis of Contemporary Condition of Pyrite Ore Processing. Moscow: VIEMS, 1987. - 51 p.
Klimov O.M., Meljnichenko A.S., Golubin A.K. Industrial mercury wastes pollution of the environment // Mercury. Complex safety system. Materials for the 3rd
scientific conference. - SPb., 1999, p. 14-118.
Kolbasov, V.M., I.I. Leonov, L.M. Sultmenko, 1987. Technology of binding material. M., Striizdat.
Kolmogorov N.K. 2000. The gold-mining industry of Russia. The problems and outlooks. Mineral resources of Russia. Economy and management 2.. Available at
http://www.geoinform.ru/mrr.files/issues/articles/kolm2.html#null
Kopin L.F. Amalgam Hydrometallurgy. Physico-Chemical Principles. – Alma-Ata: "Nauka" Publishers, 1973. - 269 p.
Kopin L.F. Amalgam Metallurgy. – Kiev: "Tekhnika" Publishers. 1970. - 272 p.
Kornitskaya V.M., Rostokinskaya N.V. Who Will Stop "Merkuruy"? // Ecology and Life, 1999, No. 1. p. 58-60.
Korolev U.N., Bobrova L.V. Role of By-components in Evaluation of Industrial Importance of Complex Ores of Non-ferrous Metals. Moscow: VIEMS, 1963.
Korostelev P. G., Geochemical Connections in Formation of Tin and Mercury Mineralisation // Issues of metallogeny of mercury (based on materials on Siberia and
Far East). Moscow: Nauka Publishers, 1968, pp. 142- 148.
Korovitskiy S.L. Taking away of non-usable mercury and mercury-containing products as a factor of decreasing the mercury pollution danger // Mercury. Complex
safety system. Materials for the 3rd scientific conference. - SPb., 1999, p. 33-35.
Korvatskiy V. Iljdikanskoe deposit of cinnabar in Nerchinsk region // Mine journal 1907, v. 2, ch. 6 (June), p. 347-356.
Kosinsky V.A., Kornilov Yu.N., Poliakovskaya E.I., Chernikov A.B. Mineral Raw Materials. Coal: Reference Book. Moscow: "Geoinfomark" Publishers, 1997. 63
p.
Kosorukova N.V., Yanin E.P. Disposal of Mercury-Containing Product Waste" Condition and Problems // "Svetotekhika", 2002, No. 3, p. 25-29.
Koval A. T., Sidorov Y. F., Nagorny V. A., Ostapchuk V. I. 1997. Technogenic pollution of metallic mercury in gold-mining areas of Amur and Khabarovsk
Regions. Proceedings from Seminar: Gold mining. The problems and outlooks. Vol. 2. Khabarovsk, pp. 347-352.
Kovalev E.T., Rudyka V.I., Malina V.P. Environmental Protection in By-product Coke Sector B in Europe and USA // "Uglekhimicheskiy Zhurnal" (Coal and
Chemistry Magazine), 2001, No. 1-2, p. 63-65.
Kovalishina G. Trends in Markets of Main Non-ferrous Metals // http://www.tdvtb.ru/news/nonferruus/review.xsp (13.06.2003).
Kozyrev V. CIS Metallurgy: Ten Years After // Metals of Eurasia, 2002, No. 3, p. 30-33.
Krivtsov A.I., Klimenko N. G., Mineral Raw Materials. Copper. Reference Book. Moscow: Geoinformmark Publishers, 1997. – 51 p. (b)
Krivtsov A.I., Klimenko N.G., Mineral Raw Materials. Nickel and Cobalt. Reference Book. Moscow.: Geoinformmakr Publishers, 1997. – 52 p.
Kurbatov L.N. Main Lines for Development of Photoreceivers and Photoreceiving Devices for Heat Imaging during 1970-1998 rr. // Applied Physics, 1999, No. 3, p.
5-18.
Kusin A.A. History of mercury deposits discovery in Russia. - M.: AS USSR, 1961. - 360 p.
Kutliahkmetov A.N. 2002. Mercury pollution of landscapes by mining enterprises of Bashkirian Zauralie. Author's abstract. FGUP, RosNIIVH, Ekaterinburg.
Kutliakhmetov A.N. Mercury Contamination of Landscapes by Mining Enterprises of Bashkirian East-of-Ural Region. Autoref. Thesis of Cand. Geogr. Sc. –
Yekaterinburg, 2002. 25 p.
L.M. Zorkin, Y.V. Stadnik, G.A. Yurin, V.K. Soshnikov, 1974. Mercury content in some gas and gas-condensate fields of the USSR. Geology of oil and gas, No.
10.
Lacerda L. D., Salomons W. 1998. Mercury from gold and silver mining: a chemical time bomb? Heidelberg, Springer-Verlag. Berlin.
Laperdina T G, Tupyakov A B, Yegorov A I. Melnikova M.V., Askarova O.B., Banshchikov V.A., Khvostova T.E., Tsybikdopzhiev Z., Bochko O.K. 1995.
Environment pollution by mercury in the zones of influence of Transbaikalian gold mining plants. Chemistry for Sustainable Development 3:53-62.
Laperdina T.G. 2002. Estimation of mercury and other heavy metal contamination in traditional gold mining areas of Transbaikalia. Geochemistry, Exploration,
Environment, Analysis, 2, No. 3: 219-223.
Laperdina T.G., Melnikova M.V., Khvostova T.E. 1999. Gold mining in Siberia as a source of mercury contamination of the environment. - In Mercury
Contaminated Sites: Characterization, Risk Assessment and Remediation, R.Ebinghaus, R.R.Turner, D.Lacerda, O.Vasiliev, W.Salomons (eds), Springer
Environmental Science, Springer Verlag Heidelberg. pp.357-374. (In English)
Lean D., O'Driscoll N., Siciliano S., Aldameary M., Draper L. and Trip L. 2000. Significance of Petroleum Products to Global Mercury Budgets.
Levchenko D.N., Bergshtein R.V., Khudyakova A.D., Nikolayeva N.M. Emulsions of Oil with Water and Methods of Their Destruction. Moscow: "Khimia"
Publishers, 1967.
Light Sources. Catalogue of Lighting Equipment. Moscow: Moscow "House of Light" ("Dom Sveta"), 2003. 124 p.
Locating and Estimating Air Emissions from Sources of Mercury and Mercury Compounds. EPA-454/R-97-012, 1997. (In English)
Lubas J. 1984. Geochemiczne aspekty wystepowania rteci w gazie ziemnym na Nizu Polskim. Nafta. Vol. 40, N 11/12.
Magadeev B.D., Greshilov A.I., Antonov K.V., Chernov A.L. Mineral and Raw Material Resources of the Republic of Bashkortostan // Mineral Resources of
Russia, 1997, # 6, p. 15-21.
Makarchenko G.V., Kosorukova N.V., Volokh A.A. De-mercuration of Urban Facilities // Ecological and Geochemical Problems of Mercury. Modscow: IMGRE,
2000, p. 153-160.
Makarov V.A., Shrainer A.D., Burlakov A.A., Tsykin S.R. 1997. Experience of the solving of geological, technological and ecological problems at reassessment of
technogenic placers and òåõíîãåííûõ looses and tailings dumps of the Yenisei range. Proceedings from Branch-wise scientific-technical conference devoted 125th
anniversary of the Institute IRGIREDMET foundation. Irkutsk, pp. 18-28.
Makarov, A.A., T.Y. Makarova, L.M. Shevchuk 2003. Priority directions of RF gas industry development. Proceedings of the Academy of Sciences, Energy, No.2.
Mashianov, N.R., S.E. Pogarev, V.V. Ryzhov et al. 1998. Use of PA-915 mercury spectrometer in environmental and geochemical researches//Minerals, No. 1. P.
70-72.
Masters H.B. Electrinic metals and minerals mercury // Mining Annal Review, 1983, No. 6, P. 90-92.
Materials on Specific Emissions of Substances to Atmosphere from By-product Coke Enterprises of Russian east and central Regions. – Moscow: USSR Ministry of
Ferrous Metallurgy, 1987.
Medbiolink 2003. Internet addresses: http://www.medbiolink.ru/search.php and http://www.calculate.ru/bbs-chemistry_agricultural-1029501409.html .
Meilikhov E.Z., Lazarev S.D. Electrophysical Properties of Semiconductors. – Moscow: CNIIatominform, 1987. - 87 p.
Melnikov S.M. Safety Measures in Mercury Metallurgy. Moscow, "Metallurgia" Publishers, 1974. 184 p.
Mercury (extraction and processing) // http://rus.gateway.kg/ind_merc.
Mercury in the environment of Siberia: assessment of natural and anthropogenic sources input. Final report of the Temporary scientific group of the Siberian office of
the RAS under the project SKOPE "Assessment of mercury diffusion and its role in ecosystems". - Novosibirsk, 1995. - 30 p.
Mercury pollution in Irkutsk region. E. Rikhvanov. «Baikal ecological wave». http://www.baikalwave.eu.org/mercury.html
Mercury production in USA. Mineral, 2002. May/22. Available at http://www.mineral.ru/Chapters/News/2855.html )
Mercury Usolje http://www.greenpeace.ru/gpeace/43520
Mercury. Catalogue of Products and Services. Attachment to Materials of the 3rd Scientific-Technical Conference "Mercury. Complex Security System". St.
Petersburg, 1999. 24 p.
Mercury. Complex safety system. Collection of materials from the scientific-technical conference. Saint-Petersburg, 1996.
Mercury. Regulatory and Methodological Document. Reference Book. Vol. 1 and 2. St. Petersburg, 2001, Vol. 1. 242 p; Vol. 2, 80 p.
Mercury. Regulatory and Methodological Documents. Reference Book. St. Petersburg: Monotoring, 1999. 253 p.
Mercury. Regulatory and Methodological Documents. Reference Book. St. Petersburg: Monotoring, 2001, Volume 1. 242 p.; Volume 2, 80 p.
Mercury. Specifications. GOST 4658-73. Official Edition. Moscow: IPK "Standard Publishers". 1997. 11 p.
Metal Supply and Sales, 2001, # 12.
Metallurgist, 2001, # 1
Methodological Instruction for determination of Unorganised Release. - Sverdlovsk, 1987;
Methodological recommendations on calculation of quantity and quality of incoming wastewater and polluted substances to sewerage systems. Appr. by the Order of
Gosstroy of Russia, dated April 6, 2001, N 75
Methodological Recommendations on Hygienic Assessment of Atmospheric Air Pollution within Areas of Location of Enterprises Producing or Using Mercury.
Moscow: Ministry of Health of USSR, 1989. 17 p.
Mineral Resources of the World at early 1998 (Official Edition). Moscow.: FGUNPP Aerologia, 1999. - 870 p.
Mineral Resources of the World at Early 1999 (official edition). - Moscow: FGUNPP Aerologia Publishers , 2000. - 911 p.
Mineral Resources of the World on 01.01.2001. Statistical Reference Book (Official Edition). Moscow: FGUNPP Aerologia, 2002. 475 p.
Mineral Resources of Uchalinsky Mining and Concentration Combined enterprise. – Ufa: Baskirskoe Knizhnoe Izdatelstvo, 1994. – 328 p.
Monitoring of pesticides in the environment objects of the Russian Federation. Yearbook of the Institute of experimental meteorology of Roshydromet, S.Petersburg,
1999, Annex 3, p. 31
Morrison J. 1972. NAM recovers mercury produced with Dutch natural gas. J. Oil and Gas. Vol. 70.
Moscow Region Studies: Environment of Moscow Region. Manual for 8- and 9-Grade Schoolchildren of the City of Moscow and Moscow Oblast. Moscow:
"Ecopross" Publishers, 1996. 208 p.
Mullov V.M., Chikina T.V. Alpert V.A. 2001. The solving of a environment protection problem at reprocessing gold- and mercury-bearing ores by ion-exchanging
technology. Proceedings from IIIrd Congress of CIS dressers. Moscow. Available at http://www.minproc.ru/congress2001.html
Munthe, J., Wängberg, I., Chugaeva, A.N., Kiseleva, N.V., Smigol I.N., Bragina O.N., Anichkov, S.N., Tumanovsky, A.G. 2004. Emissions of mercury from coal
fired power plants in Russia - final report to ACAP.. IVL Swedish Environmental Research Institute, Sweden and VTI All Russia Thermal Engineering Institute. (In
English)
Mustafin S.K., Minigazimov N.S., Zainulin H.N. et al. Problems of Mercury-Related Safety of Southern Ural // Environmental Problems of Industrial Areas of Ural.
V. 1 Magnitogorsk: MGMA, 1998, p. 148-154.
Myazin V.P., Tataurov S.B. 1997b. Some directions on development of technological flow sheets of recycling gold-bearing amalgams from industry secondary
deposits. Proceedings from Seminar: Gold mining. The problems and outlooks. Vol. 2. Khabarovsk, pp. 315-325.
Myazin V.P., Tataurov S.B. 1997A. Development and improvement of technologies and equipment on extraction gold-bearing amalgams and toxic mercury
compounds from technogenic tailings. Mining information analytical bulletin 1: 61-70.
Nashelskiy A.Ya. Technology of Semiconductor Materials. - Moscow: "Metallurgia" Publishers, 1987. - 336 p.
News. Battery.Ru – Accumulator of News, 25.01.2001 // http://green.bn.by/ecoinform/2001/Ein1-01.htm (01.07.2003).
Newspaper "Priamurskiye Vedomosti", 13 August 2002, No. 144 (2785) // http://pv.leased.redcom.ru/archive/02/08/13/a7.htm (29.03.2003).
Nikiforov K.A., Khanturgaeva G. I., Shatuev I.N., Budaeva N.R. 1994. Concentration of mercury-bearing wastes of gold-mining enterprises. Physicotechnical
problems of mineral resources 5:113-115.
Nomenclature Reference Book of Products Manufactured by Instrument Making Enterprises of Russia. Moscow: INFORMPRIBOR, 1993. 75 p.
Non-ferrous Metallurgy, 2002, # 6
Non-ferrous Metals, 2001, # 12.
Novolipetsk Metallurgical Combined Enterprise. Annual Report. 2001 // www.nlmk.ru.
NTC MGGU. 2000. Scientific and Technical Center "Mining and processing module equipments" of Moscow State Mining University. Available at
http://stc.msmu.ru/kpmf4.htm
O.V. Braginsky, 2002. Production, consumption and export of condensed gases of Russia. Oil, gas and business.
Obolenskiy A.A., Ozerova N.A., Vasiljev V.I . Natural sources of mercury in Siberia // Chemistry for sustainable development, 1995, 3, No. 1-2, p. 11-22.
Oil-and-gas vertical 2002. No. 3.
OJSC "Termopribor". Catalogue of Products // http://www.thermopribor.com/kat_1.htm.
Ore industry on the territory of the RSFSR for 1914-1921 // Mine journal, 1922, No. 6-9, p. 320-321.
Orlov V.P. 1993. The Reproduction Federal Program of mineral resources of Russia. Mineral resources of Russia 4: 4-7.
OSPAR. 2001. Mercury losses from the chlor-alkali industry in 1999. OSPAR Commission, London. (in English)
Ozerova N.A. 1996. Mercury in geological systems. In: Bayes W., Ebinghaus R., Vasiliev O (eds). Regional and Global Mercury Cycles: Fluxes and Mass Balances.
Kluwer Academic Publishers, Dortrecht, The Nitherlands.
Ozerova N.A. Mercury and Endogenic Ore Formation. Moscow: "Nauka" Publishers, 1986. 232 p.
Ozerova N.A. Mercury and endogenous ore formation. - M.: Nauka, 1986. - 232 p.
Ozerova N.A. Primary Oreols of Dispersal of Mercury. Moscow: Publishing House of AN USSR, 1962. 135 c.
Ozerova N.A., Mashyanov N.R., Pikovsky Yu.J., Ryzhov V.V., Chernova A.E., Ganeev A.A., Sholupov S.E. and Dobryansky Z.A. 1999. Mercury in Gas and Oil
Deposits. Mercury Contaminated Sites. Springer.
Ozerova, N.A. 1981. New mercury belt in Western Europe//Geology of ore deposits, No. 6. p. 45-56 (translation: Ozerova N.A. 1983. Mercury Ore Belt in West
Europe//J. Inter. Geol. Rev., 25. P.1095-1100).
Ozerova, N.A. , 1975. Mercury in gas fields of the Central Europe//Soviet Geology, No. 6. P. 72-79.
Ozerova, N.A. , L.A. Dobryansky, 2000. Experience of forecasting of mercury content in gas fields (based on the case of gas-condensate deposit Oposhnya, DDV).
Ãåîõimi÷íi ìåòîäû
ïîøóêiâ – ñòàí i ïåðñïåêòèâè ðîçâèòêó.. Kiev.
Ozerova, N.A. , N.H. Aidinyan, 1966. Mercury in the sedimentation process. Reviews of geochemistry of endogenous and supergene processes. M., "Science"
Publishing House.
Ozerova, N.A. , N.R. Mashianov, 1989. New ideas in mercury measurement. Geochemical methods and scientific and technological changes in geological research
of subsurface. M., Science.
Ozerova, N.A. , N.R. Mashianov, Y.I. Pikovsky, V.V. Rizov, L.A. Dobryansky, M.A. Gruzdeva 1989. Kerpinsky lineament – through mercury concentrating
structure//The through mercury concentrating structures. M., Science. P. 52-58.
Ozerova, N.A. , N.R. Mashianov, Z. Shpirich, M. Dragash, 1998. Mercury content in gas and oil-gas deposits of Pannonion-Volinian lineament (Ukrainian and
Croatian sites). The Fifth International Conference "Oil-Gas Ukraine-98". Poltava. Vol. 1.
Ozerova, N.A. , Y.I. Pikovsky 1985. Regional regularities of mercury containing hydrocarbon gases allocation//The natural gases of the Earth and their participation
on formation of the earth's crust and mineral deposits. Kiev, Naukova Dumka. p. 144-155.
Ozerova, N.A. , Y.I. Pikovsky, N.D. Shikina, M.A. Gruzdeva, A.D. Fedin, 1974. Mercury in oil and gas fields of the USSR. Geology of ore deposits, No. 4.
Ozerova, N.A. , M.A. Gruzdeva, L.A. Dobryansky, Y.I. Pikovsky et al., 1998. Mercury content in gas fields of Dneiper-Donetsk depression. The Fifth International
Conference "Oil-Gas Ukraine-98". Poltava. Vol. 1.
Ozerova, N.A. 1962. Primary Dispersion Halos of Mercury. Geochemical issues, IV. Proceedings of the Institute of Geochemistry of Ore Deposits, Petrology,
Mineralogy and Geochemistry, RAS, Issue 72. USSR Academy of Sciences publishing house. (the translated material was published by American Geological
Institute).
Ozerova, N.A. 1986. Mercury and endogenous ore formations. M., Science.
Ozerova, N.A. 2002. Mercury content in gas and oil-and-gas deposits. New concepts in geology and geochemistry of oil and gas. Related to elaboration of common
theory of oil and gas presence in subsurface. Materials of the VI International Conference. Book 2. M., GEOS.
Pacyna, J. 2003a. Development of methods for trace metal emission evaluation and their implementation for flux estimates in NIS territory, including economic aspects
of flux reduction. INTAS No. 97-31581 (in English)
Pacyna, J. 2003b. Personal communication.
Painoke, V., M. Mersman, 2002. Reconstruction of furnace lines in Russian cement industries//Cement and its use, No. 3, p. 11-13.
Pak N.T., Klopotosvkiy I.S., Nagniy V.A. Enrichment and Metallurgical Processing of Polymetal Raw Materials // Collection of Scientific Works of the Middle Asian
NIIPItsvetmet. Tashkent, 1984, p. 97-101.
Paper on Lead Contamination of Environment in the Russian Federation and its Effect on Public Health. Moscow, 1997.
Parliament Gazette, 8 February 2003, no. 1155 // http://www.pnp.ru/pg.nomers/10868.htm
Pasynkov V.V., Sorokin V.S. Materials of Electronic Technologies. – Moscow: "Vysshaya Shkola" Publishers. 1986. - 367 p.
People of Action, Russian analytical magazine for business people, 2002, # 27, // http://www.ludidela.ru/0206/0206-33-01.html (13.07.2003).
Perederij O.G., Mikshevich N.V., Environmental Protection at Non-ferrous Metallurgy Enterprises. Moscow, 1991.
Performance Results of Coal Sector in Russia in 2001 ã. // Coal, 2002, No. 3, p. 54-62.
Permyakov T.A.. Mercury // Raw materials markets of Russia, 1994. No. 10, p. 9-12.
Petrov I. Troistsky V., Grishaev C. Development of Mineral Raw Materials and Products of their Processing // Practical Marketing, 1996, # 10
(http://www.cfin.ru/press/practical/1999-10/01.shtml).
Petrov V.I. ABC of Lighting. Moscow: VIGMA, 1999. 84 p.
Petukhov A.G., Konovalov A.I. Experience of Operation of the Klin Thermometers Enterprise Related to Rehabilitation of the Atmospheric Air // Hygiene and
Sanitation ("Gigiena i Sanitaria"), 1973, No. 10, p. 98-99.
Phedorchuk V.P. Mercury geology. - M.: Nedra, 1983. - 270 p.
Plishevsky, S.V., A.A. Chelnokov, 2000. Heavy metals releases to the atmosphere from cement production facilities//II International Conference on Chemistry and
Technology of Cement, Moscow, 2000: Test-bench reports. T. 3. – M., RCTU Publishing House, C. 262-265.
Polkin S.I. 1987. Concentration of ores and placers of Rare and precious metals. Nedra, Moscow.
Polkin V., Anisimov S. Metal of high possibilities // Metals of Eurasia, 2002, # 1, p. 50-53.
Polkin V.I. The Raising Market of Products Containing Zinc and Zinc Technologies (Metal Supply and Sales, 2003, # 2) //
http://www.zinc.ru/pub_view.php?gid=1&id=8 (10.09.2003).
Polkin V.I., Ponomariova N.P. Overview of Zinc and Zinc Products Market // http://www.zdc.ru/pablic_7.htm (30.06.20030.
Polskykh E. Antiar of Regional Industry // "Vsem", 30 March 2001, No. 13 (382).
Ponomarenko V.P, Filachev A.M. Photoelectronics for the New Generation of Optico-Electronic Devices // Applied Physics, 2002, No. 6, p. 13-24.
Ponomarenko V.P, Filachev A.M. Photoreceivers and Photoreceiving Devices of the New generation (top 55th anniversary of the NII-801 – NPO "Orion" // Applied
Physics, 2001, No. 6, p. 20-38.
Principles of Metallurgy. Volume 2. Moscow: State Scientific and Technical Publishers on Ferrous and Nonferrous Metallurgy, 1962. – 792 p.
Problems of chemical safety. Chemistry and life. Information of UCS-INFO.979, April,18 , 2003 ã.
Problems of mercury-containing wastes utilization and paths of its solution. D.Donskikh, V.Skitsky JSC «Merkom» Lytkarino, Moscow region.
http://www.recyclers.ru/text/037.html
Problems of Modern Light Engineering Market of Russia // "Svetotekhika", 2002, No. 2, p. 28-31.
Production of Pig Iron in Russia in 2001 // http://www.netro.ru/profiles-company.shtml?05_07_2... (21.03.2003).
Production of Pig Iron in Russia in 2001 // http://www.netro.ru/profiles-company.shtml?05_07_2... (21.03.2003).
Project of the 1st Stage of Expansion of the Saransk Plant of Special Sources of Light and Electro-vacuum Glass – JSC "Lisma SIS & EVS", Including Construction
of a Building for Manufacture of Luminescent Lamps and Glass Manufacturing Building No. 1. Adjustment of the Project, Including Separate Specification of the
Start-up Facility. Section 6. Specifications and Agreement Documents. Moscow: GIPRONIIELECTRO, 1993.
Properties of Elements: Reference Book, Vol. 1. Moscow: Metallurgy. 1997 - 432 p.
Pshenichny G.N. Gayskoe copper pyrites deposit pf the Southern Ural (mineralogy, geochemistry, structure and conditions of ore formation) - M.: Nauka, 1975. -
187 p.
Pyrikov A.N., Vasnin S.V., Boranbaeyv B.N., Kozlov V.D. Environmental Protection in By-product Coke Enterprises. - Moscow: Intermet Engineering, 2000. -
182 p.
Ratex (Agency for Economic Information) www.ratex.ru
Reference Book on Geochemistry. Moscow.: Nedra Publishers, 1990. – 480 p.
Reference Book on Lighting Products. Moscow: "Energoatomizdat", 1995. 528 p.
"Reference materials on indicators of specific production and consumption wastes generation" prepared by the Scientific and Research Center on Problems of
Resource Saving and Wastes Management (NITsPURO),1999.
Report on Research Work Devoted to "Analysis of Environmental Pollution with Mercury in the Russian Federation". Mytischi: NICPURO, 1999. 47 p.
Report on scientific and research work «Analysis of mercury pollution state of the environment in the Russian Federation ». - Mytischy NITsPURO, 1999. - 47 p.
Report on Scientific Research Work on Theme `Analysis of the Condition of Mercury Contamination of the Environment in Russian Federation'. Mytischy:
NITsPURO, 1999. 47 p.
Report on the Environmental Condition in the Republic of Mordovia in 2001. Saransk: Committee on natural Resources for the Republic of Mordovia, 2002. 264 p.
Report on the scientific-research works. 2002. Preparation of the maps set of anthropogenous pollution of the Amur region territory, scale 1 to 500,000 and is larger
" (object "Anthropogenous"). Responsible Executor Sidorov Y.F. GPC, CNR of Amur Region, Blagoveshchensk.
Report on wastes management, JSC "Ecological company "Oskar", 2002, Perm' region.
Reports on Research Work on the Topic "Analysis of the Environmental Mercury Pollution in the Russian Federation". Mytisctchi: NICPURO, 1999. 47 p.
Reports on Research Work on the Topic "Studying the Nomenclature of Mercury-Containing Waste in the Russian Federation for the Purpose of Certification and
Registration". Mytisctchi: NICPURO, 2000. 49 p.
Results of Production of OJSE Safianovskaya Med in 1st Quarter of 2003
Reutov B.F., Imenov V.G., Naumov A.V et al. Heat Supply in the Country is on the Brink... // Energy: Economy, technology, Environment, 2002, No. 1, p. 3-8.
RF Committee for Statistics. Production output in some industrial sectors (open information), http://www.gks.ru
Risk Reductio Monograph No. 4: Mercury. Background and National Experience with Reducing Risk / OECD Environment Monograph Series No. 103. - Paris,
OECD, 1995. - 159 p.
Rizhov, V.V., N.R. Mashianov, N.A. Ozerova. 2000. The space-time changeability of mercury content in hydrocarbon gases. Compendium "Environmental and
geochemical mercury related problems". Institute of Mineralogy, Geochemistry and Crystallography of rare elements. Moscow.
Rogovoi V.M. Mercury-Yielding Provinces of USSR (Regional Logic of Placement, Prognosis and Estimation of Mercury Presence in Ore): "Nauka" Publishers,
1989. – 96 p.
Rogovoy V.M. Rare-metal complex of Russia and CIS countries (mineral and raw materials base, production, market status) - M.: VIEMS, 2000. – 40 p.
Rokhlin G.G. Discharge Light Sources. Moscow""Energoatomizdat", 1991. 720 p.
Roslyakov N. A. & Kirillova O. V. 1995. Environmental contamination by mercury owing to gold production in Russia. Chemistry for sustainable development 3:
41-52 (in Russian and English).
Rukavishnikov V. S. 1984. Sanitary estimation of labour conditions and health of attendants at gold extraction plants. In: Problems of labour hygiene and professional
pathology in gold mining in the East of the country. Ministry of public health, Moscow. pp. 29-36.
Russia: Market of Electrical lamps // http://subscribe.ru/archive/business.marketnews/20 ...
Russian Statistical Year-Book, 2002. RF Committee on Statistics
Russian Zinc Market: Problems and Perspectives // http://www.zdc.ru/pablic_2.htm (25.07.2003).
Rusugol. 1996. Valuable and toxic elements in commercial coal of Russia: Reference Book. – Moscow: "Nedra" Publishers, 1996. – 238 p. (Russian State Company
"Rosugol"; Russian Committee on Geology and Use of Subterranean Resources).
Ryshov V.V., Mashyanov N.R., Ozerova N.A., Pogarev S.E. 2003. Regular variations of the mercury concentration in natural gas. The Science of the Total
Environment, V. 304/1-3.
Sakharova M.S., Kitaenko A.E., Krivitskaya N.N. and oth Forms of finding and peculiarities of accumulating the toxic elements in gold and silver ores of the North
and East of Russia. // Mineralogical investigations in solving of ecological problems. - M: IGEM RAN, 1998, p. 61-72.
Sanitary rules and norms SanPiN 2.1.7.573-96 "Hygienic requirements to use of wastewater and its sediments for irrigation and fertilizing". Appr. by the resolution of
Goskomsanepidnadzor of Russia, October 31,1996 N 46
Satsaev A.M. Combined Leaching of Metals in the Course of Utilization of Reject Materials. // Non-ferrous Metallurgy, 2002, #7, p. 40-43.
Satsayev A.M. Combined Leaching of Metals during Disposal of Waste Tails // "Nonferrous Metallurgy", 2002, No. 7, p. 40-43.
Saukov, A.A., N.K. Aidinyan, N.A. Ozerova 1972. Geochemistry of mercury. M., Science.
Savina A.G. Significance of data on electrocardiography for acute toxic exposure // Acute toxic exposure: diagnosis, clinic and medical treatment. – M., 1970. –
p.111 – 118.
Savraev O.V., Current Condition and Possibilities of Improvement of Lead and Zinc Works Gas Cleaning from Dust. Moscow: Metallurgy, 1990.
Sedogin M.P. System of preventive measures from mercury pollution and utilization of mercury wastes in Samara city // http://ecoport.narod.ru/mercury3.htm.
Sharov G.N., Tribunsky E.N., Nikolaev S.L. Raw Mineral Resources of Kemerovo Oblast. Mineral Resources of Russia, 1997, No. 2, p. 12-15.
Shatalov V.V. Raw Material Problems of the YaTC (ßTÖ) // "Atomnaya Energia" (Atomic Energy), 2000, 89, issue 4, October, p. 334-338.
Sheveleva O. Myths and legends of the Russian mercury // Rescue, 2001, No. 20, p. 5.
Sidorov Y.F. 1999. Problems of technogenic mercury pollution of the Amur Region territory (Urgency and solving ways) Proceedings from IIIrd Scientific-technical
conference. Mercury. Complex safety system. St. Petersburg. pp. 57-61.
Sinoda V.A., Mikhailova L.F. On state of storage and utilization of obsolete pesticides in Tver oblast. The materials of the Russian seminar "Inventory of stocks of
obsolete pesticides". Center of International projects, Voronezh, 2000, p.157-159.
Sivkov I.G. Alimentary granosan toxicosis and its prevention: Abstract. – L., 1965. – 20 p.
Skårup, S., C.L. Christensen, J. Maag & S.H. Jensen. 2003. Massestrømsanalyse for kviksølv 2001 (Substance flow analysis for mercury 2001). Environmental
Report 808, Danish EPA, Copenhagen. (In Danish).
Skitskiy V.L., Donskykh D.K. Contemporary Condition of the Metallic Mercury and Mercury-Containing Waste Market in Russian and CIS // Mercury.
Comprehensive Safety System. Collection of Proceedings of 3rd Scientific and Technical Conference. St. Petersburg, 1999, p. 22-26.
Skitskiy V.L., Donslih D.K. Metallic mercury and mercury containing wastes market state in Russia and CIS countries // Mercury. Mercury. Complex safety system.
Materials for the 3rd scientific conference. - SPb., 1999, p.. 22-26.
Smirnov, V. I., Godlevsky, M. N., Nikitin, V. D. et al. Genesis of Endogenic Deposits. - M.: "Nerda", 1968 - 719 p.
Social and Economic Situation in Russia 2001. RF Committee on Statistics, No. 12.
Social and Economic Situation in Russia 2002. RF Committee on Statistics, No. 1.
Sokolov L.S. Mercury in the Environment of the Moscow Region // Environmental and Geochemical Problems of Mercury ("Ecologo-geokhimitcheskiye problemy
rtuti"). Moscow: IMGRE, 2000, p. 90-95. Environmental Condition of the Moscow region in 1999: State Report. Moscow: Moscow Oblast Committee on Natural
Resources, 2000. 148 p.
Sokolov R.S. Chemical technology: V. 1. Moscow: Humanitarian Publishing Centre VLADOS, 2003. - 368 p.
Sokolov, V.A. 1971. Geochemistry of natural gases. M., Subseface.
Spiric, Z., M. Dragas, J. Vadunec, N. Mashjanov, V. Ryzhov, S. Pogarev, N. Ozerova, S. Sholupov. 1999. Investigation of mercury content in Podravina gas fields
and environment. Proc. Internat. Conf. "The Use of Remote Imagery Analysis in Environment Impact Assessment". Houston, USA.
Sriric Z. 1996. Mercury removal from natural gas with sulphur impregnated activated carbon – our experience. Addition and Revised Abstracts 4th Int. Conference
on Mercury as a Global Pollutant, 1996. Gamburg.
Stafeyev V.I. Development and Production of Photoreceivers Based on CMT in the NIIPF (NPO "Orion") and in the USSR // Applied Physics, 2001, No. 6, p. 39-43.
Stark S.B. Gas Cleaning Devices and Installations in Metallurgical Production. – M., 1990.
Stark S.B. Gas Cleaning Devices and Installations in Metallurgical Production. – Moscow, 1990.
State Report "On Environmental Condition in the Russian Federation in 2000".
State Report 'On Condition of Mineral Raw Materials Basis of Russian Federation' // http://www.mineral.ru.
State Report. 2003. On Current State of Mineral Resources Base in the Russian Federation as of 01.01.2002. Gold mining industry
(http://www.mineral.ru/Chapters/Production/Issues/35/Issue_Files.html )
Stepanov N.A. Hygienic Research of the Hazard for Human Health in View of Pollution of Enterprise and Outside Environments with Mercury from Manufacture of
Luminescent Lamps: Dissertation Submitted for Scientific degree of the Candidate of Medical Sciences. St. Petersburg Post-Diploma Studies Academy, 1997. 134
p.
Stepanov. I. Environmental Effect of Larox. Chelyabinsk Zinc Works Eliminated Lead Emission to the Environment (Delovoi Ural, 2002, # 33) //
http://www.infoural.ru/delur/2002/33-8.ht... (17.09.2002).
Stepanova N.I. De-mercuration by Ozonation // Occupational medicine and Industrial Ecology ("Meditsina truda i promyshlennaya ekologia"), 1994, No. 2, p.
34-36.
Summary Report on Protection of Atmospheric Air for 2001. Moscow: "Goskomizdat", Rissia, 2002.
Svoitashev K.K., Chikichev S.I. Some Problems of Creation of Multi-elemental Photoreceiving Devices Based on Solid Solutions of Cadmium and Mercury Telluride
// Autometry, 1996, No. 4, p. 3-5.
Sznopek. J.L., Goonan, T.G. 2000. The materials flow of mercury in the economies of the United States and the World. U.S. Geological Survey Circular 1197. U.S.
Department of the Interior; U.S. Geological Survey; Denver. (In English)
Tarasov A.V. Development of Technologies in Non-ferrous Metallurgy in Russia // Non-ferrous Metals, 2001, # 6, p. 70-75.
Tarasov A.V. Environmental Problems in Non-ferrous Metallurgy, Ways of Solving // Electric Metallurgy, 2002, # 1, p. 14-19.
Technological Instruction for Processing of Chemical Current Sources. TI-01-07-01.
Technological Instruction for Processing of High-Pressure Mercury Lamps. TI-01-06-99.
Technological Instruction for Processing of Mercury Lamps. TI-01-05-99.
Technological Instruction for Processing of Mercury-Filled Glass devices. TI-01-03-99.
Technological Instruction for Roasting of Graphite Waste. TI-01-01-02.
Technological Instruction for Roasting of Spent Mercury Catalyst. TI-01-01-02.
Temporary instruction on preparation for burial of prohibited and non-applicable in agriculture pesticides and its tares. VNIPIagrochim, Ryazanj, 1989
Tereshina T.O. 2000. Geography of gold mining industry of Russia. Bulletin of Moscow University. Ser. 5. Geography 4: 27-33.
The Environment Protection Kazanj city // http://kazadmin.narod.ru/ocrsred.htm (23.08.2002).
The Mineral Resources of the World (in the beginning of 1994). - M.: VNIIzarubezhgeologia, 1995. - 575 p.
The Mineral Resources of the World at 1.01.2000 Statistical reference-book (official publication). - M.: FGUNPP «Aerogeology», 2001. - 477 p.
The Mineral Resources of the World at 1.01.2001 Statistical reference-book (official publication).- M.: FGUNPP «Aerogeology», 2002. - 475 p.
The Mineral Resources of the World in the beginning of 1997 (official publication). - M.: FGUNPP «Aerogeology», 1998. - 738 p.
The Mineral Resources of the World in the beginning of 1998 (official publication). - M.: FGUNPP «Aerogeology», 1999. - 870 p.
The Mineral Resources of the World in the beginning of 1999 (official publication) - M.: FGUNPP «Aerogeology», 2000. - 911 p.
The Ministry of Health of Russia. Hygienic norms. HN 1.1.546-96 «Hygienic norms of pesticides keeping in the environment».
The order of the Chief Department on precious metals and diamonds of Ministry Cabinet of the USSR No. 124, December, 29, 1988. "On the prohibition of mercury
(amalgamation) in the technological processes during concentration of gold-bearing ores and sands".
The State Balance of Minerals Reserves in Russian Federation. Burning gases. 2002. Rosgeolfund.
The State Balance of Minerals Reserves in Russian Federation. Condensate. 2002. Rosgeolfund.
The State Balance of Minerals Reserves in Russian Federation. Petroleum. 2002. Rosgeolfund.
The State Catalogue of pesticides and agrochemicals, permitted for application on the territory of the Russian Federation, M, 2002
The State Committee for statistics of RF. Resolution on Adoption of "Methodological provisions for calculation of RF energy budget calculation in compliance with
international practices" dated June 23, 1999 No. 46.
The state of environment and population health of Permj city in 1999: Reference informational materials Municipal department on ecology and nature use. Perm city,
2000. - 74 p. // http://www.ecology.permregion.ru/doc/1999/ (11.02.2003).
The State Report «On state and protection of the environment of the Russian Federation in 2001», Moscow 2002 .
The State Report «On state and protection of the environment of the Russian Federation in 2001», Moscow 2002.
Tunn W. 1973. Quecksilberspuren in Erdgasen aus deutchen Erdgasfelden und ihr Einfluss auf die Luft. Erdöl und Kohle-Erdgas-Petrochem. ver Brennst.-Chem. Bd.
26, N 9.
Tunn W. 1976. Untersuchungen Ûber Spurenelement in Gasen aus deutchen Erdgas und Erdölfelden. Ibid. Bd. 29, N 5. (In German)
UNEP. 2002. Global mercury assessment. UNEP Chemicals, Geneva. (In English) http://www.chem.unep.ch/mercury/Report/Final%20Assessment%20report.htm
US EPA 1997. Mercury study report to Congress volume II: An inventory of anthropogenic mercury emissions in the United States. US EPA, Washington DC. (In
English)
US EPA. 2001. Kilgroe J.D., Sedman, C. B., Srivastava R.K., Ryan J.V., Lee C.W., Thorneloe, S.A. Control of mercury emissions from coal- fired electric utility
boilers: Interim Report. U.S. Environmental Protection Agency Office of Research and Development. (In English)
US EPA. 2002. Control of Mercury Emissions from Coal-fired Electric Utility Boilers, Interim Report Including errata Data 3-21-02. EPA-600/R-01-109, National
Risk Management Research Laboratory, Research Triangle Park, NC. (in English)
Utkin N.I. Non-ferrous Metallurgy. . Moscow, 1990.
Valuable and Toxic Elements in Commercial Coal in Russia. Reference Book. – Moscow, "Nedra" Publishers, 1996. – 238 p.
Varum, Y.I., L.A. Izumskaya, 1990. Efficiency of furnace electrofilters//Cement, No. 4. C. 5-6.
Vasiljeva L.D. Improvement of medical wastes management system in Ekaterinburg city. Materials of the 3rd international congress on wastes management
WASTETEC -2003. Moscow, June 3-6, 2003.
VDZ 2000. Environmental data on the German cement industry. Verein Deutscher Zementwerke e. V. (In German)
Veber V., Markov K. Mercury // Natural productive forces of Russia, 1917, iss. 9, p. 1-17.
Vituride: Role of mercury in Human Bodies. - Petrozavodsk: AOZT "Firm "Vituride", 1995. - 116 p.
Vituride: Unique Domestic Medical Preparation
// http://www.bazar.vtc.ru/medicine/med003.htm (03.01.2003).
Volokh A.A. Experience of Checking of Atmospheric Air Contamination with Metals and Volatile Organic Compounds in Urban and Background Territories //
Geochemical research of urban agglomerations. – Moscow: IMGRE, 1998, p. 40-58.
Vorontsova N. Far East Storeroom is Waiting for its Alladin // kapital.zrpress.ru (18.X.2003).
Voskoboinikov V. G., Kudrin V. A., Yakushev A. M. General Metallurgy. Moscow: Metallurgia Publishers, 1979. - 487 p.
Vyazelshchikov V.P., Paritzky V.P. 1963. Handbook on processing of gold-bearing ores and placers. GONTI, Moscow.
Wilhelm S. Mark, Bloom Nicolas. 2000. Mercury in petroleum. Fuel Processing Technology 63 1-27. (In English)
Wilhelm S.M. 2001. Mercury in petroleum and natural gas: Estimation of emissions from production, processing, and combustion. U.S. EPA, Office of Air Quality
Planning and Standards, Washington D.C. (In English)
XVI International Conference on Photoelectronics and Night-sighting Devices; Theses // http://www.vimi.ru/confer/orion/16-ts-r.htm (11.08.2000).
Yagolnitser M.A., Obolenskiy A.A., Babich V.V. et al. Choice of effective strategy of development of mining metallurgical plant in frame of new conditions of
economy (modeling, imitation, decision making, environment protection ). - Novosibirsk: IEiOPP SO RAS, 1993. - 123 p.
Yagolnitser M.A., Sokolov V.M., Ryabtsev A.D. et al. Assessment of Industrial Emission of Mercury in Siberia // "Chemistry in the Interests of Sustainable
Development", 1995, 3, Nos. 1-2, p. 23-35.
Yagolnitser M.A., Sokolov V.M., Ryabtsev A.D., Obolenskii A.A., Ozerova N.A., Dvurechinskaya S.Ya. and Sukhenko S.A. 1995. Industrial mercury sources in
Siberia. Global and Regional Mercury Cycles: Sources, Fluxes and Massbalances. (In English)
Yanin E.P. (a) Mercury in Precipitations of the Urban Wastewater // Ecological and Geochemical Problems of Mercury. Moscow: IMGRE, 2000, p. 143-152.
Yanin E.P. (a) Man-Made Sludge within the Area of Impact of an Industrial Town (Formation, Composition and Geochemical Features). Moscow: IMGRE, 2002.
100 p.
Yanin E.P. (b) Chemical Elements in Dust Emission from Electrical Engineering Enterprises // Occupational Medicine and Industrial Ecology, 2000, No. 8, p. 24-27.
Yanin E.P. (b) Mercury in Dust Emission from Industrial Enterprises // Environmental Expertise, Review Information. Moscow: VINITI, 2002, Issue 4, p. 10-29.
Yanin E.P. Extraction and production of mercury in CIS as a source of environment pollution // Ecological geochemical problems of mercury. - M.: IMGRE, 2000, p.
38-59.
Yanin E.P. Geochemical Features of Wastewater Precipitations in an Industrial Town (Using Example of Samara). Moscow: IMGRE, 1996. 41 p.
Yanin E.P. Heavy Metals in Small Rivers within Industrial Enterprise Impact Area. Moscow: IMGRE, 2003. – 89 p.
Yanin E.P. Industrial Dust in Urban Environment (Geochemical Features and Environmental Assessment). Moscow: IMGRE, 2003. 82 p.
Yanin E.P. Man-Made Geochemical Associations in Benthic Sediments of Small Rivers (Composition, Features, Methods of Evaluation). Moscow: IMGRE, 2002.
52 p.
Yanin E.P. Technogenic Geochemical Associations in Bottom Deposits of Small Rivers (Composition, Specifics, Evaluation Methods). Moscow: IMGRE, 2002. - 52
p.
Yanin, Y.P., 1992. Mercury in the environment of industrial cities. M., IMGRE. 169 p.
Yevlevich A.Z., Yevlevich M.A. Disposal of Wastewater Sludge. Leningrad. "Stroyizdat" Publishers, 1988. 248 p.
Yudovich Ya.E., Ketris M.P., Merts A.V. Admixture Elements in Fossil Coal. Leningrad: "Nauka" Publishers. 1985. 239 p.
Yudovich Ya.E., Zolotova V.V. Admixture Elements in Coal from Pechora Basin // Economy of the republic of Komi, 1994, 3, No.No. 1, p. 16-25.
Yugov P. Converter Module // Metals of Eurasia, 2002, No. 1, p. 64-67.
Yusfin Yu., Zaletin V. Bomb of delayed action. Components of mercury issue in Russia. // Euroasia metals, 1998, No. 3, p. 72-76.
Zainullin H.N., Galimova E.Zh. Evaluation of Effect of Waste Materials and Wastewater of Buribaevskoe Mining Administration on Contamination of Tanalyk River //
Environmental Problems of Industrial Areas of Ural. V. 1. Magnitogorsk: MGMA, 1998, p. 137-142.
Zakharova E.M. Mineralogy of Placers. – Moscow: "Nedra" Publishers, 1994. - 271 p.
Zamyatin O.V., Lopatin A.G. 1975. Concentration of gold-bearing sands and conglomerates. Nedra, Moscow.
Zhdamirov V.M., Kuznetsov V.I. Environmental Problems of Kuzbass Open-Cast Coal Fields // Coal, 1990, No. 9, p. 25-29.
ANNEX 1
Official Mercury Release Statistics
Mercury Emissions to the Atmosphere
The official statistics (Report on Air Protection in 2001 of Goscomstat of RF) on mercury emissions is based on emissions data reported by individual enterprises. The
enterprises are obliged to report only on the emissions of pollutants which are included in the official list of emitted pollutants for each individual enterprise and
restricted by standards (Maximum Allowable Emissions) issued by environmental authorities. It means the official statistics does not cover all sources of mercury
emissions. In most cases, the data on mercury emissions reported by the enterprises are based on calculations, not on actual measurements.
In the table the name on enterprises or a sector that in 2001 officially accounted for a significant part of the emission from Russia's region is indicated with italics below
the region.
Mercury emissions to air in 2001 |
Tonnes |
Russian Federation total |
2.922 |
Central Federal District total |
0.106 |
Vladimir Oblast |
0.003 |
Lipetsk Oblast |
0.003 |
Moscow Oblast |
0.001 |
Ryazan Oblast |
0.002 |
Smolensk Oblast |
0.088 |
Smolensk Federal State Institution "Analitpribor"
|
0.088 |
Tula Oblast |
0.004 |
Novomoskovsk "Azot" |
0.004 |
Moscow |
0.005 |
Moscow electric lamp plant JSC |
0.003 |
North-West Federal District total |
0.003 |
Vologda Oblast |
0.003 |
Cherepovets |
0.003 |
Municipal housing sector |
0.003 |
South Federal District total |
0.502 |
Krasnodarskiy Krai |
0.114 |
Novorossiysk, |
0.050 |
Construction materials industry, Novoroscement JSC |
0.050 |
Volgograd Oblast |
0.388 |
Volgograd , |
0.385 |
Chemical industry Khimprom JSC, Plastcard JSC |
0.385 |
Volzhskiy, |
0.003 |
Chemical industry |
0.003 |
Privolzhskiy Federal District total |
0.637 |
Bashkortastan Republic |
0.457 |
Sterlitamak, |
0.451 |
Chemical industry: Soda JSC, Kaustik JSC |
0.451 |
Mordovia Republic |
0.022 |
Saransk, |
0.022 |
Machine building industry, Electric Lamp Plant |
0.022 |
Tatarstan Republic |
0.032 |
Nizhnekamskneft JSC |
0.126 |
Kirovsk Oblast |
0.126 |
Kirovo-Chepetsk |
0.126 |
Kirovo-Chepetskiy chemical plant |
0.122 |
Ural Federal District total |
1.229 |
Chelyabinsk Oblast |
1.229 |
Chelyabinsk, |
1.229 |
Non-ferrous metallurgy |
1.229 |
Siberian Federal District total |
0.445 |
Irkutsk Oblast |
0.240 |
Usole-Sibirskoe, |
0.130 |
Usolekhimprom JSC |
0.130 |
Novosibirsk Oblast |
0.205 |
Novosibirsk |
0.205 |
, Non -ferrous metallurgy |
0.205 |
Mercury Discharges to Surface Water Bodies in 2001
The official statistics on mercury discharges is based on discharges data reported by individual enterprises. The enterprises are obliged to report only on the
discharges of pollutants which are included in the official list of discharged pollutants for each individual enterprise and restricted by standards (Maximum Allowable
Emissions) issued by environmental authorities. Therefore, the official statistics does not cover all mercury discharges even from point sources. Additionally, there a
significant number of non-point sources, areas with soils contaminated by mercury (e.g., due to gold mining activities), which contribute to mercury releases to water.
This non-point contamination is not taken into account by official statistics presented in the table below.
Mercury releases to surface water bodies |
Mercury, kg |
By sectors |
Russia – total |
177 |
Industry
non-ferrous metallurgy
chemistry and petrochemistry
pulp and paper
flour-and-cereals and feed mill
housing economy
communal economy
|
157
6
148
1
2
1
19
|
By regions |
|
Russia – total |
177 |
Central Federal District |
2 |
Moscow |
2 |
North-West Federal District |
21 |
Saint-Petersburg |
19 |
Leningrad Oblast |
2 |
Privilzhsky Federal District |
18 |
Bashkortostan Republic |
15 |
Kirovskaya Oblast |
2 |
Siberian Federal District |
131 |
Krasnoyarsky Kray |
1 |
Irkutskaya Oblast |
129 |
Novosibirskaya Oblast |
1 |
Far East Federal District |
5 |
Sakha-Yakutiya Republic |
4 |
Amurskaya Oblast |
1 |
By rivers and seas basins |
|
Russia – total |
177 |
The Baltic Sea |
21 |
The Neva River |
16 |
Ladoga Lake |
1 |
The Caspian Sea |
20 |
The Volga River |
20 |
The Oka River |
2 |
The Moscow River |
2 |
The Kama River |
17 |
The Belaya River |
16 |
The Vyatka River |
2 |
The Karskoye Sea |
131 |
The Yenissey River |
130 |
The Angara River |
130 |
The Ob River |
1 |
The Sea of Okhotsk |
1 |
The Amur River |
1 |
The Zeya River |
1 |
The Laptev Sea |
4 |
The Lena River |
4 |
The Aldan River |
4 |
Mercury releases with storm water |
|
Russia – total |
11 |
North-West Federal District |
11 |
Saint-Petersburg |
11 |
Accumulation, Generation, Use and Decontamination of Mercury-containing Waste in 2001
- Data from the Report on Hazardous Wastes Generation and Disposal of Goscomstat of RF
Official statistics on mercury-containing waste generation, handling and disposal is based on data reported by individual enterprises. Any enterprise is obliged to report
on generation, accumulation, use and decontamination of waste (in total, by hazard class and by generic waste type). Mercury-containing waste (as a generic waste
type) belongs to Class 1 (the most hazardous class). Although the system of waste reporting was established in 1994, not all enterprises submit their waste-related
data regularly.
This information relates only to industrial hazardous waste as there is no official statistical data on the composition of industrial non-hazardous waste and municipal
waste. Therefore, mercury containing in municipal waste is not included. The data does not reflect the content of mercury in the waste.
Mercury containing industrial hazardous waste (tonnes waste) |
|
Accumulated at the enterprise by the beginning of the year |
Generated |
Used at source and decontaminated |
Accumulated at the enterprise by the end of the year |
Russian Federation |
2586.957 |
10887.160 |
1385.40 |
2629.250 |
Belgorod oblast |
18.684 |
0.002 |
|
18.684 |
Bryansk oblast |
13.715 |
13.690 |
|
15.388 |
Vladimir oblast |
53.975 |
50.696 |
0.030 |
47.273 |
Voronezh oblast |
4.632 |
13.323 |
|
3.923 |
Ivanovo oblast |
7.649 |
6.576 |
|
6.333 |
Kaluga oblast |
1.686 |
4.875 |
|
3.890 |
Kostroma oblast |
2.726 |
5.057 |
0.012 |
3.367 |
Kursk oblast |
0.004 |
0.008 |
|
0.007 |
Lipetsk oblast |
15.883 |
41.112 |
|
18.834 |
Moscow oblast |
57.023 |
181.912 |
0.002 |
50.084 |
Orlyel oblast |
0.702 |
7.045 |
51.427 |
2.968 |
Ryazan oblast |
27.64 |
105.334 |
|
27.523 |
Smolensk oblast |
24.821 |
121.562 |
0.079 |
22.787 |
Yaroslavl oblast |
2.776 |
3.734 |
44.367 |
1.568 |
Tambov oblast |
3.239 |
1.613 |
0.004 |
3.012 |
Tver oblast |
4.236 |
37.883 |
0.002 |
3.342 |
Tula oblast |
98.900 |
0.166 |
|
98.253 |
Moscow City |
6.872 |
267.352 |
|
11.625 |
Comi Republic |
5.463 |
7.437 |
|
8.692 |
Arkhangelsk oblast |
252.374 |
37.761 |
|
88.673 |
Nenetsky Autonomous Okrug |
0.902 |
0.515 |
|
1.394 |
Vologda oblast |
8.516 |
72.955 |
|
6.976 |
Kalinigrad oblast |
0.002 |
0.007 |
41.185 |
0.002 |
Leningrad oblast |
92.149 |
49.470 |
|
62.231 |
Murmansk oblast |
23.331 |
19.173 |
320.609 |
15.894 |
Novgorod oblast |
7.065 |
34.571 |
0.018 |
5.000 |
Pskov oblast |
0.333 |
6.472 |
0.015 |
0.396 |
Saint-Petersburg City |
31.957 |
134.287 |
|
23.293 |
Bashkortostan Republic |
30.568 |
562.245 |
|
33.380 |
Mariy-El Republic |
0 |
1.352 |
15.580 |
|
Mordoviya Republic |
0.318 |
69.283 |
|
64.379 |
Tatrstan Republic |
12.855 |
66.788 |
|
11.939 |
Udmurtia Republic |
53.539 |
92.306 |
12.184 |
67.505 |
Chuvash Republic |
27.269 |
54.696 |
0.164 |
30.371 |
Kirov oblast |
37.775 |
0 |
217.680 |
28.640 |
Nezhegorodskaya oblast |
116.39 |
121.904 |
0.341 |
128.042 |
Orenburg oblast |
1.279 |
2.365 |
68.572 |
0.492 |
Penza oblast |
4.225 |
24.466 |
|
4.521 |
Perm oblast |
19.372 |
38.797 |
9.015 |
21.261 |
Samara oblast |
34.328 |
147.784 |
|
43.253 |
Saratov oblast |
50.974 |
64.373 |
|
41.070 |
Ulyanovsk oblast |
21.999 |
51.628 |
|
18.975 |
Adigeya Republic |
0.725 |
0.313 |
0.365 |
0.373 |
Dagestan Republic |
0.313 |
0.021 |
|
0.002 |
Cabardino Balkaria Republic |
0.102 |
0 |
|
0.102 |
Carachayevo-Cherkessiya Republic |
1.305 |
1.601 |
|
1.238 |
Northern Osetiya Republuc – Alaniya |
11.817 |
4.015 |
|
11.321 |
Krasnodar Kray |
18.391 |
13.902 |
20.247 |
18.946 |
Stavropol Kray |
0.021 |
0.037 |
298.559 |
0.037 |
Astrakhan oblast |
3.321 |
12.458 |
|
3.225 |
Volgograd oblast |
294.816 |
262.26 |
|
391.707 |
Rostov oblast |
21.850 |
51.936 |
145.301 |
22.378 |
Kurgan oblast |
16.810 |
19.918 |
0.040 |
7.933 |
Sverdlovsk oblast |
25.224 |
6999.772 |
6.330 |
23.510 |
Tyumen oblast |
3.987 |
3.594 |
0.202 |
2.744 |
Khanty-Mansy Autonomous Okrug |
0.505 |
2.848 |
|
2.101 |
Yamalo-Nenetsky Autonomous Okrug |
0.285 |
0.537 |
|
0.550 |
Buryatya Republic |
3.600 |
6.575 |
|
3.085 |
Tiva Republic |
14.700 |
0 |
0.236 |
14.700 |
Khakassiya Republic |
8.180 |
8.446 |
|
9.169 |
Altay Kray |
84.271 |
1.616 |
|
83.286 |
Krasnoyarsk Kray |
448.058 |
52.909 |
|
456.019 |
Irkutsk oblast |
149.848 |
223.414 |
|
232.335 |
Kemerovo oblast |
64.080 |
30.151 |
122.000 |
24.494 |
Novosibirsk oblast |
32.473 |
466.669 |
|
38.577 |
Omsk oblast |
27.280 |
42.044 |
1.244 |
51.736 |
Tomsk oblast |
11.705 |
14.854 |
0.006 |
17.749 |
Chita oblast |
0.667 |
0.007 |
8.787 |
0.636 |
Sakha Yakutiya Republic |
4.722 |
6.832 |
|
9.170 |
Primorsky Kray |
69.878 |
9.203 |
0.018 |
66.349 |
Khabarovsk Kray |
0.001 |
0.004 |
0.501 |
0 |
Amur oblast |
1.803 |
0.002 |
|
1.804 |
Kamchatskaya oblast |
2.316 |
1.278 |
|
0.831 |
Magadan oblast |
0.081 |
0.288 |
0.020 |
0.226 |
Sakhalin oblst |
0.663 |
0.073 |
0.100 |
0.114 |
Annex 2
Storage of Mercury-containing Pesticides
The following annex include examples of storage of obsolete mercury-containing pesticides in certain regions.
Mercury containing pesticides in Tverskaya oblast
Tverskaya oblast is located in the north-west of Russia. It is contiguous with Vologodskaya oblast in the north, Novgorodskaya oblast in the north-west, Pskovskaya
oblast in the west, Smolenskyay and Moscow oblasts in the south and Yaroslavskaya oblast in the east.
The oblast's area is 84.23 th. km2. Forests, bushes, rivers, lakes and bogs occupy 48% of the area, and agricultural lands constitute about 44%.
The main watershed between basins of the Caspian Sea and the Baltic Sea runs along the oblast territory. Most rivers gravitate to the Upper Volga, and the Meta,
Tsna and Shlina rivers in the north-west belong to Ilmen Lake basin, and the rivers of the Zadandaya Dvina basin spring from the south-west of oblast. The river
network densely and evenly covers the oblast's territory and includes about 450 rivers more than 10 km long, including 55 rivers – more than 50 km long and 19 –
more than 100 km.
There are many lakes and peatbogs in the north-west, east-west and center of the oblast. Natural water reservoirs are represented by many glacial lakes in the
north-west hilly area. Tverskaya oblast totally includes about 600 water bodies (including large number of individual lakes), the biggest of which is Seliger Lake with
208 km2 water-surface area. Small lakes (blind, closed lakes with waterlogged banks and sludgy bottoms) are overgrowing.
Tverskaya oblast is distinguished for unique natural resources. The total area of the specially protected areas is 403.8 th. hectares, including zapovednics of federal
significance - 42.2 th. hectares, Zavidovo state reservoir - 68.7 th. hectares, preserves of regional significance - 292.9 th. hectares.
The accumulated considerable amounts of prohibited and outdated pesticides stored basically in storehouses (only 4 of which are standard ones) seriously endanger
the environment. Moreover, 72% of the storehouses are build of wood in 70-80-ies and now are tumbledown, and therefore the number of the storehouses
appropriate for certification has been decreasing from year to year: from 51% in 2000 down to 44% in 2001. Only 34% of available storehouses have been certified
by 02.06.03. Such situation has resulted in poor conditions of pesticides storage, including organomercuric chemicals (agrosan, agronal, granosan, radosan, fungotox)
not complying with sanitary requirements (SanPiN 1.2.1077-01). Data on mercury containing pesticides quantities is presented in the Table 1.
Table 1 Inventory of mercury containing pesticides in Tverskaya oblast since 1999 to 2003
Year |
1999 |
2000 |
2001 |
2002 |
2003 |
Amount |
34,676 |
31,214 |
30,760 |
42,843* |
42,798* |
Note: * - the data for 1999 – 2001 covers only mercury containing chemicals (agrosan, agronal, granosan, radosan, fungotox); 2002 – 2003 data includes mercury
containing mixtures determined during the pilot project implementation, as after re-packing all sodium TÕA, simazin and other mixtures containing just even traces of
mercury were related to mercury containing ones.
Further storage of prohibited outdated pesticides is very dangerous for environment and health and requires taking the urgent measures. The danger is also connected
with inability of companies and enterprises to pay for repair and guarding of the dilapidated storehouses in time. Such situation leads to fires caused by grass firing in
spring time. In April – May of the current year 5 pesticides storehouses were ignited in Lihoslavlsky, Kalyazinsky, Selizharovsky and Spirovsky regions. The
worn-out installations (roofing slate, doors, wood boards, brick) are plundered. The damaged pesticides storehouses had been repaired, locked, tidied up, re-labeled,
but after a time were broken in and robbed again, re-packed and labeled pesticides were damaged, the chemicals spilled endangering the environmental health.
During the latest years the agricultural enterprises have been being split up and restructured. Some companies cease their activity, and the chemicals storehouses
become ownerless (Rameshkovsky region, Tuchevsky and Beman enterprises).
In compliance with the Resolution of the Oblast Governor No. 195 dated 24.04.2000 On Inventory and utilization of the outdated and prohibited pesticides, in
2000-2001 the first phase of the pilot project was implemented, the outdated and prohibited pesticides available in the oblast enterprises were inventoried, and the
identification of unknown pesticides was carried out showing large amount of mercury containing mixtures (14,036 t in 2003), as well as availability of
arsenic-containing pesticides - sodium arsenite, Paris green (0.46 t in total).
Unfortunately the next phases of the outdated pesticides utilization activities were not implemented due to lack of financing.
Tverskaya oblast has 556 chemical pest-killers storehouses, only 5 of them (in Agropromchemia Association) are of standard parameters (Ref.: Â.À. Ñèíîäà, Ë.Ô. Ìèõàéëîâà,, 2000). The oblast was visited on May 19-20, 2003. The oblast plants protection point has collected data on mercury containing pesticides in 36 oblast's
regions. In 2002, 203 storehouses or 47.6% (47.4% - in 2000, 50.2% - in 2001) out of 426 pesticides storehouses subjected to certification obtained the
sanitary-epidemiological certificates.
The State Sanitary-Epidemiological Service controls pesticides and agrochemicals turnover. The applied may be only the chemicals included into the State Register of
pesticides and agricultural chemicals permitted for application in Russian Federation in 2002 agreed with RF Ministry of Health. 74 of more than 80 titles of pesticides
and agrochemicals declared by the oblast plants protection point were permitted for application.
The problem concerning utilization of the outdated and prohibited pesticides and agrochemicals is still exists. The administrations of 9 oblast's regions and centers of
the State Sanitary-Epidemiological Service, agrochemical services all together managed to delivery more than 41.8 tonnes of the outdated pesticides for burial outside
the oblast's borders. For today, 388.2 tonnes require utilization, including 151.1 tonnes of Class 1 pesticides (incl. mercury containing ones).
The State Sanitary-Epidemiological Service suspended operation of 181 pesticides storehouses in towns and regions of the oblast, imposed 19 fines, issued 202
prescriptions, drawn up 261 statements of sanitary-epidemiological inspection of the chemical pest-killers storage conditions.
Following the proposal of the Center of the State Sanitary-Epidemiological Service in Tversakay oblast, the Department on Social and Economic Development of
Rural Areas under the administration prepared Practical Guidelines on use and storage of plant protection chemicals in agricultural enterprises of Tverskaya oblast for
2002-2004.
In the frameworks of UNEP Chemical Project the inventory of the outdated pesticides financed by the administration was carried out in the oblast. With this
purpose, in 2000 – 2001 Tver oblast plants protection point analyzed 1200 samples of pesticides. Presently there is information on 5 mercury containing pesticides
available in 26 regions and not used in 6 regions of the oblast (see Table 2).
Table 2 List of regions in Tverskaya oblast storing organomercuric pesticides (by 01.03.2003).
Region |
Substance |
Total |
Granosan |
Agrosan |
Agronal |
Radosan |
Fungitox |
Andreapolsky |
380 |
– |
– |
– |
– |
380 |
Bologovsky |
100 |
– |
– |
– |
– |
100 |
Vesyegonsky |
455 |
60 |
125 |
– |
– |
640 |
Vishnevolotsky |
876 |
– |
– |
– |
– |
876 |
Zapadnodvinsky |
936 |
– |
– |
– |
– |
936 |
Zubtsovsky |
910 |
50 |
– |
– |
– |
960 |
Kalininsky |
2068 |
– |
– |
– |
– |
2068 |
Kalyazinsky |
600 |
– |
– |
– |
– |
600 |
Kashinsky |
420 |
– |
– |
– |
– |
420 |
Kesovogorsky |
150 |
– |
– |
– |
– |
150 |
Kimrsky |
25 |
– |
– |
– |
– |
25 |
Krasnoholmsky |
735 |
150 |
– |
– |
– |
885 |
Kuvshinovsky |
125 |
– |
– |
– |
– |
125 |
Lesnoy |
1900 |
– |
– |
– |
– |
1900 |
Lihoslavlsky |
400 |
– |
– |
– |
– |
400 |
Maxatihinsky |
958 |
– |
– |
– |
160 |
1118 |
Molokovsky |
1810 |
– |
– |
– |
– |
1810 |
Nelidovsky |
678 |
– |
– |
375 |
– |
1053 |
Oleninsky |
180 |
– |
– |
– |
– |
180 |
Rameshkovsky |
1452 |
350 |
– |
– |
– |
1802 |
Rzhevsky |
1261 |
– |
50 |
– |
– |
1311 |
Sandovsky |
230 |
– |
– |
– |
– |
230 |
Selizharovsky |
2446 |
200 |
– |
– |
– |
2646 |
Sonkovsky |
1900 |
– |
– |
– |
– |
1900 |
Spirovsky |
– |
60 |
– |
– |
– |
60 |
Staritsky |
320 |
– |
– |
– |
– |
320 |
Torzhoksky |
3817 |
35 |
– |
– |
– |
3852 |
Toropetsky |
1945 |
– |
– |
– |
– |
1945 |
Udomelsky |
70 |
– |
– |
– |
– |
70 |
Firovsky |
100 |
– |
– |
– |
– |
100 |
Total |
27247 |
905 |
175 |
375 |
160 |
28862 |
Note: the mercury containing pesticides were not used in 6 regions.
The oblast has 27.2 tonnes of mercury containing pesticides, the greater part of which is stored on the landfill in Torzhoksky region – 3.8 tonnes. Taking this into
account, Torzhoksky region has been investigated more comprehensively.
Pesticides landfill in Torzhoksky region.
The landfill area is equal to 0.8 hectares, it is located in 600 m from the road. The landfill was designed in 1976 by request of Selkhoztehnica oblast association and in
compliance with the Temporary Instructions on nonapplicable pesticides and pesticides containers destruction. The soil of the landfill is poorly filtering with 21 m deep
groundwater. Pesticides and containers are buried in 5 m deep trenches with clay insulated bottom and walls. The bottom is covered with prefabricated concrete iron
slabs, the clay lock is 1 m thick. The trench filled with pesticides is covered with 1 m thick clay layer.
The designed top of the waterproofing cover should be 0.5 m higher than the adjoining territory top level, but this was not confirmed during the inspection. The
territory is overgrown with woods, the gates are not installed. The inspection well formerly used from groundwater sampling for mercury detection is not operated.
The design of the inspection well's drilling envisages possibility of the aquifer contamination. According to the data of the plants protection point, the surface water
doesn't contain mercury, but there are no data on the groundwater composition.
The distance from the landfill to: the Tvertsa River is about 2 km, to summer houses — 3.5 km, to Dobrinino village — 6.0 km.
The inventory of pesticides, including mercury containing ones, was successfully carried out in agricultural enterprises of Staritsky region.
Staritsky region
This region has a specialized pesticides burial at the storehouse arranged in 2000 in the frameworks of UNEP Chemical Pilot Project. The pesticides have been
identified. Up to 100 kg of granosan were revealed. The Staritsky storehouse is one of the best in the oblast. In 2000 the pesticides were repacked and labeled.
Storehouses of the former Agropromhimia association are located in Staritsa Station. 16 barrels with granosan (20 kg each), total - 320 kh + mixtures ~ 100 kg =
420 kg were collected from the collective farms. The brick storehouse 4 m height can contain 300 tonnes of pesticides. The storehouse is guarded.
Rzhevsky region — 130 km from Tver
1.3 t of granosan are stored in 12 storehouses, which are in good condition (they have doors and locks, the roofs don't spring leaks). Each storehouse has a sanitary
certificate and is appropriate for storage.
All storehouses are located not closer than 1 km from open water supply sources and comply with sanitary requirements.
Annex 3
Mercury in Coal from the Main Basins
The data presented in Tables 1-14 below are taken from: Valuable and Toxic Elements in Commercial Coal of Russia: Reference Book. – Moscow: "Nedra"
Publishers, 1996. – 238 p. (Russian State Company "Rosugol"; Russian Committee on Geology and Use of Subterranean Resources).
This Reference Book is the outcome of specialized work and is based on materials of revision testing of commercial products of coal sector enterprises in the country
over 1988-1991. To justify and control the obtained results, testing data were used for the period of 1960-1970. Totally, this databank includes analyses of 13,500
samples of commercial coal not only for mercury, but also for other 25-50 chemical elements. Testing of coal was effected in conformity with the nomenclature of
commercial products of coal enterprises. With all other conditions being equal, ordinary coal types were preferred. At enterprises producing only quality coal, the
investigation included the sorts of coal that were dominant among the coal types brought from the mines. This work was based on survey of specially supplied group
samples characterizing products of the specific coal enterprises over a maximum possible period of time. At such enterprise, they took at least three group samples
belonging to the same technological group (brand) and correspondent to the product quality for at least one calendar month. In turn, each group sample includes 3-15
or even more primary coal samples (depending on the specific geological and production situation and other conditions). Primary samples included sample duplicates
taken by the Technical Control Department and by coal and chemistry laboratories of respective coal enterprises so as to assess quality of coal shipped to the user (in
particular, they used: sample duplicates characterizing the current provision of coal to coal enterprises; samples taken from average monthly samples made p of
samples of current provision and characterizing products produced by the enterprise during the month; daily, shift and other samples evaluating current performance of
the enterprise). When group samples were compiled, they took into consideration amount of coal shipped to the user, the shares of working coal strata in the mine
output and other indicators). The testing periods (periods of formation of the group samples (were from 3 to 12 months. When commercial coal was tested, they used
the system of control with rejection of primary coal samples whose ash content was not representative. The primary sample was excluded from the array, if its ash
content varied by 10% (relative) from the ash content of the average monthly rated sample. Distribution of mercury in samples was determined using atomic
adsorption methods. The above stated allows us to think that data presented in the reference Book about the content of mercury in commercial coal of Russia are
representative and very objectively reflect the real distribution of mercury in the main types (brands) of coal in Russia.
Mercury content was determined on a dry basis. The detection limit for mercury by atomic absorption method (% to coal) was 0.00001. Non-detects were treated as
0's.
Table 1 Average content of mercury in commercial coal from Pechora Basin
Coal field, deposit, enterprise |
Technological group (brand) of coal, coal brand |
Ash content Ad, % (as dry fuel) |
Humidity Wrt, % (in working fuel) |
Hg, g/t of coal |
Vorkutinskiy |
2 æ coking concentrate |
8.5 |
5.0 |
0.04 |
Vorkutskoye |
Screenings |
21.6 |
7.3 |
0.05 |
CCE CD. Severnaya |
ÏP. |
29.9 |
4.4 |
0.07 |
|
Waste |
89.0 |
|
0.01 |
|
Slurry |
31* |
|
0.03 |
CE Vorkutinskaya mine |
2æ coking concentrate |
8.5 |
6.3 |
0.01 |
|
Screenings. |
23.7 |
7.9 |
0.02 |
|
ÏP. |
28.4 |
4.5 |
0.03 |
|
Waste |
82.6 |
|
0.04 |
|
Slurry |
31* |
|
0.02 |
CE Yuzhnaya mine |
1Æ R energy |
34.2 |
7.0 |
0.07 |
|
Waste |
81* |
|
0.1 |
|
Slurry |
31* |
|
0.06 |
CE Ayach-Yaga mine |
1 Æ R energy |
31.3* |
7.5 |
0.07 |
|
Waste |
81* |
|
0.02 |
|
Slurry |
31* |
|
0.07 |
CE Oktyabrskaya mine |
1 Æ coking concentrate |
13.6 |
4.8 |
0.03 |
|
Screenings |
17.1 |
7.3 |
0.04 |
|
Waste |
76.2 |
|
0.3 |
CE Zapolyarnaya mine |
1 Æ coking concentrate |
10.2 |
|
0.04 |
|
Screenings |
24.2 |
8.1 |
0.04 |
|
ÏP. |
29.1 |
4.9 |
0.04 |
|
Waste |
70.0 |
|
0.05 |
|
Slurry |
31* |
|
0.04 |
CE Yur-Shor mine |
1 Æ coking concentrate |
11.7 |
7.3 |
0.03 |
|
Screenings |
24.3 |
7.9 |
0.05 |
|
Waste |
75.0 |
|
0.05 |
|
Slurry |
31* |
|
0.02 |
CE Centralnaya mine |
1 Æ conc. Coking |
10.9 |
6.4 |
0.03 |
|
Screenings |
18.9 |
7.9 |
0.03 |
|
Waste |
81* |
|
0.1 |
|
Slurry |
31* |
|
0.02 |
CE Promyshlennaya mine |
1 Æ coking concentrate |
11.2 |
6.8 |
0.1 |
|
Screenings |
17.7 |
7.6 |
0.04 |
|
Waste |
72.4 |
|
0.1 |
|
Slurry |
31* |
|
0.2 |
CE Komsomolskaya mine |
2 Æ P, coking |
20.9 |
6.8 |
0.04 |
|
Waste |
81* |
|
0.2 |
|
Slurry |
31* |
|
0.02 |
Yunyaglindskoye |
1 L P, coking |
22.7 |
7.6 |
0.04 |
CE Yun-Yaga mine |
Waste |
81* |
|
0.08 |
|
Slurry |
31* |
|
0.03 |
Vorgashorskoye |
ÃÆÎ Ê, coking |
19.6 |
5.7 |
0.08 |
Vorgashorskaya mine |
ÃÆÎ ÎÌÑØ, coking |
18.9 |
7.7 |
0.07 |
Khalmeryuskiy, |
1 L P, coking |
29.7 |
5.3 |
0.1 |
Khalmeryuskoye |
|
|
|
|
Khalmer-U mine |
|
|
|
|
Intinskiy, |
Ä concentrate |
23.1 |
9.7 |
0.05 |
Intinskoye, |
Screenings |
32.2 |
11.4 |
0.06 |
GCE Intinskaya, shop 1 |
Slurry |
31* |
|
0.05 |
GCE Intinskaya, shop 2 |
Ä concentrate. |
24.3 |
10.5 |
0.03 |
|
Screenings |
32.5 |
11.8 |
0.04 |
|
Waste |
60* |
|
0.7 |
|
Slurry |
31* |
|
0.02 |
GCE Kapitalnaya |
Ä concentrate |
24.0 |
9.3 |
0.06 |
|
Screenings |
32.6 |
11.7 |
0.06 |
|
Slurry |
31* |
|
0.04 |
|
Waste |
60* |
|
0.1 |
Notes: Pechora coal basin is a large raw material source for the development of the energy and coke-and-chemical industries; its significant part is located to the north
of the Polar Circle; coking means coking coal, en. means energy; technol. means technological; m.m. means mine management; OCC means opencast colliery; unit
means mining unit; CE means cleaning (concentrating) enterprise; CCE means central cleaning enterprise; GCE means group cleaning enterprise; CCE means coal
cleaning enterprise; conc .means concentrate; scr. means screenings; slr. means slurry; wst. means waste; P means regular; Ï means plate, K means large-size; O means
nuts; M means small-size; C – seeds; Ø means coal dust.
Table 2 Average content of mercury in commercial coal from Moskovskiy Basin
Coal field, deposit, enterprise |
Technological group (brand) of coal, coal brand |
Ash content Ad, % |
Humidity Wrt, % |
Hg, g/t of coal |
B. Nelidovskoye, Nelidovskaya mine, No. 4 |
2Á P |
36.8 |
33.6 |
0.7 |
Safonovskoye, Safobovskaya mine No. 7 |
2Á P |
36.7 |
36.0 |
0.82 |
Seredeyskoye, Seredeyskaya ,mine No. 1 |
2Á P |
36.0 |
32.9 |
0.33 |
Lipkovskoye, Sechensjaya mine |
2Á P |
38.0 |
31.0 |
0.18 |
Lipkovskaya mine No. 9 |
2Á P |
40.6 |
30.8 |
0.23 |
Borodinskaya mine No. 17 |
2Á P |
37.8 |
30.4 |
0.18 |
Sechenskaya mine No. 15 |
2Á P |
38.0 |
30.8 |
0.11 |
CE Vladimirskaya mine |
2Á concentrate. |
39.8 |
30.9 |
0.09 |
|
Waste |
64.3 |
|
0.25 |
Dedilovskiy unit, Komsomolskaya mine |
2Á P |
38.6 |
31.2 |
0.14 |
Gryzlovskoye, Podmiskovskaya mine |
2Á P |
40.7 |
29.5 |
0.15 |
Gryzlovskiy OCC |
2Á P |
41.2 |
31.2 |
0.12 |
CE Belkovskaya mine |
2Á concentrate |
39.8 |
30.9 |
0.16 |
|
Waste |
78.1 |
|
0.05 |
Berezovskoye, CE Progress mine |
2Á coking concentrate |
43.3 |
31.5 |
0.2 |
|
Waste |
75.4 |
|
4.5 |
Smorodinskoye, Donskaya mine (Smorodinskaya) |
2Á P |
35.8 |
32.0 |
0.1 |
Mayskaya mine |
2Á P |
34.4 |
32.2 |
0.06 |
Lvovskoye, Lvovskaya mine |
2Á MCØ |
35.1 |
32.7 |
0.22 |
Nikulinskoye, CE Nikulinskaya mine |
2Á conc. 38.4 |
32.6 |
0.25 |
|
|
Waste |
61.7 |
|
0.75 |
Note: Brown coal basin is located in five administrative regions: Tver, Smolensk, Kaluga, Tula and Ryazan. They include mostly oxidized coal with a high ash content,
humidity and low strength indicators.
Table 3 Average content of mercury in commercial products from coal-mining and coal-cleaning enterprises of the Eastern Donbass
Coal field, deposit, enterprise |
Technological group (brand) of coal, coal brand |
Ash content Ad, % |
Hg, g/t of coal |
JSC "Gukovugol", Zapadnaya mine |
K |
31.7* |
0.07 |
Izvarinskaya mine |
K |
33.9* |
0.06 |
Centralnaya mine |
K |
39.3* |
0.09 |
CCE Donetskaya |
L conc. |
8.9* |
0.1 |
|
slurry |
48.8 |
0.05 |
|
AP. |
43.0* |
0.04 |
Burgustinskaya mine |
A P |
32.0* |
0.03 |
Zamchalovskaya mine |
A P |
30.6* |
0.02 |
Mine named after 50th anniversary of October |
A |
25.6* |
0.02 |
Gukovskaya mine |
A P |
26.6* |
0.03 |
Anthracite mine |
A P |
24.7* |
0.01 |
Obukhovskaya mine |
A K |
5.0 |
0.02 |
Almaznaya mine |
A |
11.8 |
0.02 |
|
A Ø |
24.1 |
0.07 |
|
A M |
11.6 |
0.02 |
|
A O |
8.6 |
0.03 |
|
A K |
7.8 |
0.06 |
|
A Ï |
6.7 |
0.05 |
|
A C |
11.9 |
0.03 |
Rostovskaya mine |
A M |
13.2 |
0.02 |
|
A K |
5.8 |
0.02 |
|
A C |
14.1 |
0.01 |
|
A Ø |
25.3 |
0.004 |
|
A O |
10.8 |
0.02 |
PA "Rostovugol", Lenin mine |
A |
29.9* |
0.11 |
Kirov mine |
A |
36.0* |
0.13 |
Sokolovskaya mine |
A |
27.5* |
0.06 |
Mine named after Komsomolskaya Pravda newspaper |
A |
25.6* |
0.01 |
Krasin mine |
A |
34.0* |
0.13 |
Zapadnaya Kapitalnaya mine |
A |
30.1* |
0.07 |
Krasnodonetskaya mine |
A |
34.0* |
0.04 |
Naklonnaya mine |
A |
26.5* |
0.14 |
Sambekovskaya mine |
A |
34.0* |
0.11 |
Nesvetayevskaya mine |
A |
29.6* |
0.06 |
Mayskaya mine |
A |
25.6* |
0.04 |
October Revolution mine |
A |
33.1* |
0.07 |
Yubileynaya mine |
A |
25.8* |
0.15 |
Mirnaya mine |
A |
26.5* |
0.10 |
Ayutinskaya mine |
A |
29.7* |
0.09 |
CCE Ayutinskaya |
A Ø |
29.1 |
0.11 |
Yuzhnaya mine |
A |
23.2* |
? |
CE Yuzhnaya |
A C |
12.3 |
0.19 |
|
A O |
12.8 |
0.22 |
|
A Ï |
14.8 |
0.15 |
GCE named after Artem |
A Ø |
29.8 |
1.13 |
GCE Sokolovskaya |
A CMØ |
18.7 |
0.16 |
PA "Shakhtugol", mine No. 410 |
A M |
11.1 |
0.02 |
Kalinovskaya mine No. 5 |
A P |
35.5 |
0.02 |
Mine No. 10 |
A Ø |
26.0 |
0.07 |
Mine No. 19 |
A Ø |
23.8 |
0.02 |
Sulinskaya mine No. 3 |
A M |
38.2 |
0.03 |
Mine No. 56 |
A C |
32.2 |
0.10 |
Sulinskaya mine No. ; |
A M |
28.9 |
0.06 |
Mine No. 57 |
A P |
37.9 |
0.04 |
Mine No. 40 |
A C |
18.6 |
0.01 |
CCE Gukovskaya |
AM |
9.2 |
0.03 |
|
A C |
15.7 |
0.01 |
|
A KO |
7.3 |
0.002 |
|
A Ø |
22.6 |
0.02 |
|
A Ï |
6.2 |
0.002 |
Note: In Rostov Oblast the Donetsk Basin includes its eastern area, basically anthracite regions: Gukovo-Zverevskiy, Krasnodonetskiy, Sulino-Sadkinsjiy,
Tsymlyanskiy, Shakhtinsko-Nesvetayevskiy, Zadonskiy coal fields; a smaller role is played by caking and thin coal regions: Kamensko-Gundorovskiy,
Belokalitvesnkiy and Tatsinskiy.
Table 4 Average content of mercury in commercial products from coal-mining of the Kizelovsky Basin
Coal field, deposit, enterprise |
Technological group (brand) of coal, coal brand |
Ash content Ad, % |
Hg, g/t of coal |
Kizelovskiy, mine named after 40th anniversary of VLKSM, |
Ã, ÃÆ Ð |
36.2* |
0.35 |
Severnaya mine |
ÃÆ Ð |
28.5* |
0.45 |
Lenin mine |
ÃÆ Ð |
32.9* |
0.48 |
Gubakhinskiy, Klyuchevskaya mine |
Ã, ÃÆ Ð |
32.4* |
0.48 |
Nagornaya mine |
à Р|
29.0* |
0.41 |
Gremachinskiy, mine named after 40th anniversary of October |
ÃÆ, Ð |
23.9* |
0.54 |
Skalnaya mine |
à R |
31.3* |
0.48 |
Shumikhinskaya mine |
ÃÊÎ |
18-24.7 |
0.41 |
|
à ÌÑØ |
42.6-44.4 |
0.34 |
Note: The basin is located between rivers Yayva in the north and Vilva in the south, is about 2150 km long and 5-20 km wide; the coal stratum includes 5 layers and
interim layers of coal; of them, only 5 layers are of working thickness; coal brands Ã, ÃÆÎ, ÃÆ and Æ are used as energy and technological raw materials.
Table 5. Average content of mercury in commercial products from coal-mining enterprises of Bulanash-Yelkinskiy coal basin
Coal field, deposit, enterprise |
Technological group (brand) of coal, coal brand |
Ash content Ad, % |
Hg, g/t of coal |
Bulanashkoye, Bulanash 2/5, Bulanash-3, Bulanash-4 mines |
à P |
24-25* |
? |
Note: This basin includes 2 coal fields: Bulanash and Dalne-Bulanash of the upper Triassic age; industrial use is made only of Bulanash field, which occupies the
northern part of the Bulanash-Yekinskiy depression; this field includes over 40 coal layers that have been identified; of them, 29 have the working thickness of 0.9 to
4.8 km.
Table 6 Average content of mercury in commercial products from coal-mining enterprises of Chelyabinsk basin
Coal field, deposit, enterprise |
Technological group (brand) of coal, coal brand |
Ash content Ad, % |
Humidity Wrt, % |
Hg, g/t of coal |
Kamyshinskiy, Kapitalnaya, Oktyabrskaya, Komsomolskaya and Poozernaya
mines |
3Á P |
41.5-44.4* |
12-14** |
? |
Korkinskiy, Korskinskiy OCC, Korkinskaya and Kalachayevskaya
mines |
3Á P |
37.9-45.5* |
11-14** |
? |
Note: Chelyabinsk brown coal basin is located on the eastern slope of the South Urals within Chelyabinsk Oblast, representing a narrow strip with the width up to 15
km, expended almost parallel to the Ural ridge over 170 km, from Techa River in the north to Uy River in the south.
Table 7 Average content of mercury in commercial products from coal-mining enterprises of South-Ural basin
Coal field, deposit, enterprise |
Technological group (brand) of coal, coal brand |
Ash content Ad, % |
Humidity Wrt, % |
Hg, g/t of coal |
Babayevskoye, Kamertauskiy OCC No. 1 |
1Á P |
24.2* |
55** |
? |
Note: The South-Ural basin integrates multiple brown coal fields of the tertiary age; located in the Republic of Bashkortostan and Orenburg Oblast; the basin extends
along the meridian for 350 km and has the width of 70-80 km.
Table 8 Average content of mercury in commercial products from coal-mining enterprises from Kuznetsk basin
Coal field, deposit, enterprise |
Technological group (brand) of coal, coal brand |
Ash content Ad, % |
Humidity Wrt, % |
Hg, g/t of coal |
Kemerovskiy, Volkov mine |
ÃÆ |
26.5 |
7.5 |
0.08 |
Biryulinskaya mine |
K, KO |
32.2 |
7.4 |
0.03 |
Berezovskaya mine |
K |
26.1 |
5.4 |
0.06 |
Yuzhnaya mine |
CC |
14.5 |
7.2 |
0.03 |
Kedrovskiy OCC |
CC |
13.1 |
8.7 |
0.08 |
Anzherskiy, Sudzhenskaya mine |
TC |
18.1 |
2.3 |
0.08 |
Prokopyevsko-Kiselevskiy, Prokopyevskoye, Centralnaya mine |
T |
16.6 |
5.5 |
0.05 |
Kalinin mine |
K, KO, KC, CC |
22.1 |
5.3 |
0.02 |
Ziminka mine |
K, KO, KC |
15.1 |
6.7 |
0.02 |
Tyrganskaya mine |
CC |
10.4 |
6.5 |
0.03 |
Prokopyevskiye OCC |
CC |
8.3 |
8.7 |
0.05 |
Badayevskiy, Bolshevik mine |
à coking |
13.1 |
7.1 |
0.03 |
Zyryanovskaya mine |
à coking, ÃÆ |
23.5 |
7.6 |
0.05 |
Novokuznetskaya mine |
à coking, ÃÆ |
14.9 |
7.1 |
0.03 |
Leninskiy, Signal mine |
à energy |
13.9 |
1.4 |
0.05 |
Kolmogorovskiy OCC, Kolmogorovskiy unit 1 |
Ä, Ã energy |
13.0 |
16.8 |
0.03 |
M.m. Kolchuginskoye |
Ä |
17.8 |
8.6 |
0.08 |
Mine named after 7th of November |
Ä coking |
14.5 |
8.4 |
0.1 |
Kuznretskaya mine |
Ä coking |
18.2 |
8.2 |
0.01 |
Zarechanaya mine |
Ä energy |
13.1 |
11.0 |
0.03 |
Prokopyevsko-Kiselevskiy, Kiselevskoye, Krasnobrodskiy OCC |
T |
10.5 |
4.7 |
0.03 |
Novosergeevskiy OCC |
CC |
8.8 |
5.2 |
0.01 |
Cherkassovskaya mine |
K |
17.4 |
6.2 |
0.01 |
Kondomskiy, Severny Kandysh mine |
T |
24.2 |
5.9 |
0.04 |
Kaltansiy OCC |
T |
19.8 |
7.6 |
0.6 |
Aparda mine |
K, KO, KC |
19.1 |
7.0 |
0.05 |
Sushtalepskaya mine |
T |
23.5 |
8.2 |
0.01 |
Kolmogorsovkiy 2 OCC |
Ä |
15.5 |
17.1 |
0.03 |
Tersinskiy, Badayevskiy OCC |
ÄÃ, Ã energy |
16.2 |
9.6 |
0.05 |
Tom-Usinskiy, Krasnogorskiy OCC |
T |
18.9 |
5.9 |
0.01 |
Tomusinkiy OCC |
OC |
17.8 |
5.1 |
0.6 |
Olzherasskiy OCC |
CC |
22.5 |
6.4 |
0.3 |
Shevyakov mine |
K, KO, KC, °C |
29.5 |
8.1 |
0.1 |
Raspadskaya mine |
ÃÆ |
19.4 |
5.6 |
0.2 |
Mrasskiy, Mezhdurechenskiy OCC |
K, KO, T |
18.4 |
4.2 |
0.5 |
Belovskiy, Kolmogorskaya mine |
ÄÃ, Ã energy |
13.1 |
8.7 |
0.05 |
Arapichevskiy, Ordzhonikidze mine |
T |
27.0 |
6.5 |
0.03 |
Dimitrov mine |
T |
21.2 |
6.7 |
0.06 |
OsinvskiyKapitalnaya mine |
Æ |
27.9 |
5.9 |
0.08 |
Vysokaya mine |
Æ |
32.5 |
5.9 |
0.04 |
Note: Kuznetsk basin is a large raw material facility for coke and chemical and fuel and energy industries; as regards balanced coal reserves it ranks first in the
country; of especial importance is coking coal; this coal makes about half of the total production in the basis; energy types of coal also include the following dominant
brands Ä, CC, T, and, to some extent, Ã.
Table 9 Average content of mercury in commercial products from coal-mining enterprises of Buryatia Republic
Coal field, deposit, enterprise |
Technological group (brand) of coal, coal brand |
Ash content Ad, % |
Humidity Wrt, % |
Hg, g/t of coal |
Gusinozerskoye, Gusinozerskaya mine |
3Á P |
26.9* |
20.0** |
0.005 |
Kholboldzhinskiy OCC |
3Á P |
24.8* |
25** |
0.006 |
Sanginskoye, Sanginskiy OCC |
3Á P |
23.0* |
23.0?? |
0.015 |
Note: Brown coal fields are dominant in Buryatia, 11 deposits are known with the balance coal reserves.
Table 10 Average content of mercury in commercial products from coal-mining enterprises in Chita Oblast
Coal field, deposit, enterprise |
Technological group (brand) of coal, coal brand |
Ash content Ad. % |
Humidity Wrt. % |
Hg. g/t of coal |
Tarbagatayskoy, Tignisnkiy OCC |
Á P |
17.8* |
30-31** |
0.012 |
Bukachachinskoye, Bukachacha mine |
Á P |
18.4* |
Á |
0.007 |
Kharanorskoy, Kharanorskiy OCC |
2Á P |
17.3* |
40** |
0.02 |
Tataurovskoy, Vostochniy OCC |
2Á P |
14.5* |
32-34** |
0.006 |
Note: The northern coal group includes bituminous coal, brands à – T, Chikoyskaya depression coal is transient, between brown coal and bituminous coal; ash
content is 10-20%; brown coal in the majority of regions have the ash content of 8-25%.
Table 11 Average content of mercury in commercial products from Lenskiy basin
Coal field, deposit, enterprise |
Technological group (brand) of coal, coal brand |
Ash content Ad, % |
Humidity Wrt, % |
Hg,
ã g/t of coal
|
Kangalasskoy, Kangalasskiy OCC |
3Á P |
13.6 |
29.0 |
0.03 |
Vostochny Unit |
3Á |
12.4 |
|
0.02 |
Djebariki-Hah, Djebariki-Hah mine No. 2 |
Ä P |
10.0 |
9.0 |
0.01 |
Note: Coal fields of the basin are located basically in Republic of Sakha; undeveloped field Yurung-Tumus (Nordvik) is in Krasnoyarsk Krai; reserves are estimated
in 19 deposits; three largest (Kangalasskopye, Djebariki-Hah and Sangarskoy) are developed intensively.
Table 12 Average content of mercury in commercial coal of North-Eastern and Kamchatka regions
Coal field, deposit, enterprise |
Technological group (brand) of coal, coal brand |
Ash content Ad, % |
Humidity Wrt, % |
Hg,
g/t of coal
|
Kharanga, Kharanga OCC |
Á P |
15.0 |
12.0 |
0.5 |
Anadyrskoye. Anadyrskaya mine |
à P |
17.0 |
22.0 |
0.03 |
Nizhne-Arkagalinskoye, Kedrovskaya mineNo. 7 |
2Á P |
13.3 |
16.0 |
0.1 |
Kadykchanskaya mine No. 10 |
2Á P |
12.8 |
16.0 |
0.06 |
Verkhne-Arkagalinskoye, Tal-Yuryah OCC |
Á P |
14.1 |
17.0 |
0.2 |
Note: Industrial coal regions are related to large geological structures: Zyryanskiy (Sakha Republic) and Arkagalinskiy (Magadan Oblast) coal basins, and vast coal
fields of Magadan and Kamchatka Oblasts, i.e. Anadyrskiy, Omsukchanskiy, Elgenskiy and Kamchatskiy. The latter are related to the operated brown and
bituminous coal fields, i.e. Anadyrskiy, Ugolanaya, Gapivskoye, Kenskoye, Elgenskoye (lignite) and Korfskoye.
Table 13 Average content of mercury in commercial coal from Khabarovsk Krai and Amur Oblast
Coal field, deposit, enterprise |
Technological group (brand) of coal, coal brand |
Ash content Ad, % |
Humidity Wrt, % |
Hg,
g/t of coal
|
Raychikhinskoye, North-Eastern OCC. Shirokiy OCC, South-Western
OCC |
2Á PR |
11.7 |
36.8 |
0.4 |
Arkharo-Boguchanskoye, Boguchan unit |
Á PR |
14.4 |
37.1 |
1.3 |
Ogodzhinskoye, Kontaktoviy OCC |
ÃÆ |
28.0 |
17.0 |
0.9 |
Note: These regions include more than 100 known fields and deposits of brown and bituminous coal; in Khabarovsk Krai, the Urgalskoye field is operated (in the
eastern part of Bureynskiy basin); bituminous coal, brand Ã; Raychitinskoye and Arkharo-Boguchanskoye fields are located in Amur Oblast, within contemporary
Nizhne-Zeyskoaya depression, Raychitinskoye field included operated opencast colliers, brown coal, technological group 2Á; Arkharo-Boguchanskoye field includes
brown coal, with the carbonation degree from 1Á to 3Á.
Table 14 Average content of mercury in commercial coal and coal-cleaning products form Sakhalin Oblast
Coal field, deposit, enterprise |
Technological group (brand) of coal, coal brand |
Ash content Ad, % |
Humidity Wrt, % |
Hg,
g/t of coal
|
Mgachinskoye, Mgachi mine |
ÄÃ P |
15.8 |
7.5 |
0.08 |
Aleksandrovskoye. Arkovo mine |
Ä P |
14.5 |
8.1 |
0.07 |
Boshnyakovskoye. Boshnyakovo mine |
ÄÃ P |
18.8 |
9.7 |
0.1 |
Lesogorskoye, CE, Telnovskaya mine |
ÄÃ ÎÌÑØ |
17.9 |
11.4 |
0.04 |
Uglegorskoye. Uglegorskaya mine |
à P energy |
27.4 |
6.5 |
0.11 |
Udarnoskaya mine |
Ä P |
26.7 |
9.3 |
0.08 |
Solntsevskoye, Solntsevskiy OCC |
Ä P |
16.2 |
19.8 |
0.03 |
Tikhminevskoye, Tikhminevskaya mine |
3Á P |
17.4 |
21.3 |
0.04 |
Vakhroschevskoye, CE, m.m. Lermonstovdkoye |
Ä KOM |
19.5 |
16.2 |
0.07 |
|
Ä CØ |
18.8 |
19.1 |
0.09 |
|
Ä MCØ |
35.9 |
19.2 |
0.12 |
Makarovskoye. Makarovskaya mine |
Ä P |
26.3 |
16.9 |
0.1 |
Lopatinskoye, CE, Dolinskaya mine |
Ä OM |
17.1 |
9.4 |
0.08 |
|
Ä CØ |
21.7 |
9.9 |
0.09 |
|
Waste |
61.5 |
|
0.03 |
Uzhno-Sakhalinskaya mine |
Ä R |
25.9 |
8.4 |
0.3 |
Gornozavodskoye, CE, Gornozavodskaya mine |
3Á OM |
9.1 |
18.2 |
0.21 |
|
3Á CCD |
15.2 |
20.2 |
0.2 |
Shebunino mine |
ÁR |
20.4 |
22.0 |
0.06 |
Novikovskoye, Novikovskiy OCC |
ÄR |
31.4 |
16.6 |
0.3 |
Note: Main coal fields are located in the western part of the island; as regards the degree of carbonation, this coal is brown coal of the technological group 3Á and
bituminous coal brands Ä, Ã, Æ,, T; bituminous coal brands are located basically on the western coast of the island, in Aleksandrovskiy and Uglegorskiy coal fields;
brown coal is located basically in the central and Southern coal fields; this coal has high quality and diverse properties; it includes a low concentration of sulfur; little or
average content of ash (15-25%), the working humidity of brown coal does not exceed 18-20%, of bituminous coal 9-10%; all industrial coal fields in Sakhalin are
concentrated in four coal bearing fields: Aleksandrovskiy, Uglegorskiy, Central and Southern.
Annex 4
Mercury Releases from Major Coal-fired Utility Plants
Estimated releases of mercury from major coal-fired utility plants in the Russian Federation (Munthe et. al 2004)
Click here to see the table.
Footnotes
[1] After the USSR demolition, the applied system of control and inventory of Hg production and consumption has been almost completely destroyed (Rogovoy,
2000). Systems of assessment of registration of the technogenic emission of mercury in NIS countries are also in very poor condition (Kakareka and oth., 2000).
[2] It shall be understood that a number of diaphragm chlor-alkali production facilities remained in other CIS countries, for instance in Ukraine (4 diaphragm facilities),
Uzbekistan, Azerbaijan and Armenia. At the same time most of the mercury cell facilities except one small in Azerbaijan and one in Ukraine, remained in Russia. More
over, compared to the former USSR, chlorine production rates were decreased at the remaining facilities in Russia, including the diaphragm ones. The JSC "Kaustic"
in Volgograd was established as a mercury cell facility in 1968 and a diaphragm plant was established there in addition in 1984. Currently both plants are functioning.
[3] Volgograd, Sterlitamak and Sayansk mercury cell plants use sodium chloride evaporated form the brine as a feedstock and at Kirovo-Chepetsk plant halite
deposit salt dissolved in a spent anolyte is used as a feedstock.
* Since 1976 and till about mid 1990's, mercury thermometers were also manufactured at the "Steklopribor" Plant (today CJSC "EUROGLASS") in the town of
Golynki (Rudnyansky District, Smolensk Oblast). This enterprise used (during the last years of its operation) up to 19 tonnes of mercury annually.
* All technological equipment was designed and manufactured directly at the enterprise (automatic glass-polishing machines for manufacture of parts and assembly of
blank thermometers; high precision thermostats to mark basic points of the scale; vacuum plants for filling mercury to thermometers; etc.). Therefore, the literature,
which contains detailed description of the technological process of manufacture of mercury thermometers, is not present in the library. According to available data,
technical documents are kept at the enterprise in typewritten copies. Most of the products are manufactured according to specifications of the enterprise.
* With the amount of mercury used at 130 t/year, losses of mercury to the sewerage system make 755 kg; we can assume that when use of mercury is decreased to
24.191 t (the level of 2001). i.e. 5.27 times, losses of metal will also decrease by the same number of times (they will be 140.6 kg, which is actually equal to the
amount of losses in 2001, as given in 28).
[4] Now, the issues are under consideration to shut down the facility for manufacture of luminescent lamps at the Saransk Electrical Lamp Plant and dismantling of the
lamps assembly shop, including de-mercuration procedures. It is planned to organise at another industrial site a new facility for manufacture of lamps, which will be, in
many aspects, meeting the earlier design (Design, 1st stage..., 1993), of a higher capacity, however based on technologies with much smaller use of mercury.
* The majority of information and primary statistical data used as the basis for the below materials about activities of NPP Kubantsvetmet CJSC and Mercom Ltd. In
the field of processing of mercury-containing waste and production of mercury and its compounds were obtained directly from the above enterpreises.
| Top | | Front page |
Version 1.0 March 2005, © Danish Environmental Protection Agency
|