| Forside | | Indhold | | Forrige | | Næste |
Optimering af materialegenvinding af procesmaterialer af plast
3 Undersøgelse af muligheder for øget genanvendelse af kasseret procesmateriale
ved de deltagende virksomheder
3.1 Icopal
3.1.1 Præsentation af virksomheden
Icopal Gruppen er verdens førende producent af tagmaterialer og vandtætte membraner og er markedsleder i de nordiske lande inden for taglægning (www.icopal.com). Icopals
produktpalet omfatter også andre konstruktionsmaterialer til beskyttelse af bygninger og andre strukturer. Gruppen der har hovedsæde i Danmark, har ca. 3.400 ansatte og 29
forskellige produktionssteder. Udvikling og forskning inden for Icopal Gruppen vil også i fremtiden være koncentreret inden for Gruppens største og vigtigste produktområde, bitumen,
som man fortsat bedømmer som værende det mest unikke materiale i modificeret form til taglægning og andre applikationer der kræver tæthed over for vand.
Inden for miljøområdet er Icopals strategi fra og med 2003 at satse på en mere ensartet og fokuseret fremstillingspraksis omfattende tiltag til reduktion af energiforbrug og især til
reduktion af spild fra produktionen.
Icopal Plastic Membranes er et af produktionsstederne for Icopal Gruppen. Virksomheden er specialiseret i fremstilling af polyesterforstærkede polyethylenfolier til inddækning af
bygninger.
3.1.2 Problemstillinger
I forbindelse med produktionen af de polyesterforstærkede polyethylenfolier opstår der ganske betydelige mængder af produktionsspild i forbindelse med opstart og nedlukning og ved
konfektionering. Et eksempel på en sort indfarvet folie er vist på Figur 10. Der er ingen genanvendelsesmuligheder for affaldet i Icopal Plastic Membranes egen produktion på grund af
membranernes opbygning af to vidt forskellige plasttyper.
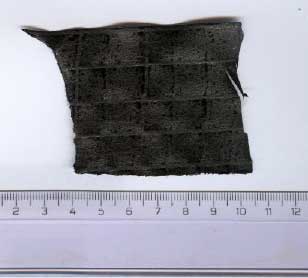
Figur 10 Sort plastfolieaffald
3.1.3 Løsningsmuligheder
Forskellige mulige løsninger er vurderet/undersøgt:
- Smeltefiltrering
- Oparbejdning ved neddeling med forskellig soldstørrelse
- Andre oparbejdningsmuligheder
3.1.4 Forsøgsarbejde
3.1.4.1 Oparbejdning ved smeltning
Smeltepunktet af polyethylenen varierer afhængigt af typen fra 104-120 °C, mens smeltepunktet af de polyesterbaserede fibre er 253 °C.
Ud fra smeltepunkter kan man se at det teoretisk er muligt at smeltefiltrere emnerne hvis man smelter en større portion af plastfolien ved temperaturer under fibrenes smeltepunkt og
presser det smeltede produkt gennem en si.
Et simpelt smelteforsøg ved 200 °C over en rist viser at polyethylenen hænger fast på fibrene, men ved smeltefiltrering under tryk bør der kunne frafiltreres en del polyethylen (se Figur
11).
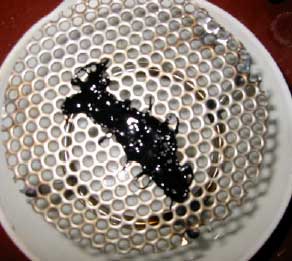
Figur 11 Smeltning af folie
3.1.4.2 Oparbejdning ved neddeling med fingranulator Affaldet er blevet neddelt ved Eldan med forskelligt udstyr hvoraf følgende producerer fraktioner med separerede fibre og
plastflager
Trin 1. Granulering med fingranulator FG475 og 10 mm sold. Der var ikke monteret støvafsugning i forsøget. Dette vil være nødvendigt ved etablering af et anlæg. Hvis dette udføres, vil
der mistes nogle af de fine partikler og fibre.
Trin 2. Sigtning med henholdsvis en laboratoriemodel og PC 600 med forskellige sold med nogenlunde samme resultat.
På Figur 12 ses at fraktionen > 4 mm langhul indeholder en blanding med en stor del af fibrene, men også med en del plastflager.
På Figur 13 ses at fraktionen fra 2 mm til 4 mm langhul indeholder plastflager med et lille indhold af fibre (< 1 % vægtmæssigt).
På Figur 14 ses at fraktionen < 2 mm indeholder en blanding af små fiberstykker som passerer soldet, samt plastflager.
Forsøgsmængderne var for små til at der kunne opnås tilstrækkelige mængder til bestemmelse af fordelingen mellem de tre fraktioner, ligesom det ikke er muligt at estimere den
kapacitet som det vil være muligt at opnå med det benyttede udstyr. Nye forsøg vil kunne afdække dette.
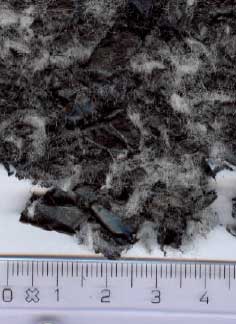
Figur 12 Fraktion > 4 mm langhul
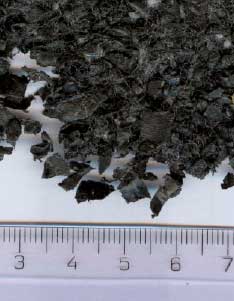
Figur 13 Fraktion mellem 2 mm og 4 mm langhul

Figur 14 Fraktion < 2 mm
Teknologisk Institut har peget på mulighederne for at anvende neddelte fraktioner af afdækningsfolierne i tætningsmasser til tage m.m. Det vil kræve et udviklingsarbejde i den division
hos Icopal der fremstiller denne type produkter, eller at man indleder et samarbejde uden for koncernen med andre producenter af tætningsmasser. Når det opfattes som en interessant
mulighed, skyldes det at man anvender en folie der er godt beskyttet mod vejrliget, og at polyesterfibrene kan bidrage til en bedre mekanisk styrke af tætningsmasserne.
Det skal påpeges at et af de fokuserede områder for Icopal Gruppen er udvikling af modificerede bitumenprodukter til vandtættende anvendelser. En udvikling af modificerede
bitumentyper med anvendelse af neddelt materiale i form af produktionsspildet der opstår ved produktionen af plastmembranerne, passer således ind i såvel Icopal Gruppens
overordnede strategi på udviklingssiden som med ønsket om at reducere spild.
3.1.4.3 Andre oparbejdningsmuligheder Plastfolien er sendt til vurdering af Result Technology i Schweitz som bedømmer at det er muligt at deres separationsteknologi kan separere
plast fra fibre. En nærmere vurdering kræver dog et forsøg til en pris af ca. 20.000 kr. hvilket ligger uden for projektets rammer.
3.1.5 Konklusion
Neddelingsforsøg på den polyesterforstærkede polyethylenmembran har vist at der kan frembringes en række fraktioner i forskellig størrelse. Det vil være mest nærliggende at Icopal
undersøger mulighederne for at bruge de neddelte fraktioner i forbindelse med virksomhedens bitumenbaserede tætningsprodukter.
3.2 Rosti OS og Smørum Gruppen
3.2.1 Præsentation af virksomheder
3.2.1.1 Præsentation af Rosti OS
Virksomheden Rosti OS er en de førende fremstillere af urtepotter af polypropylen, og man har en årelang tradition for at anvende kasseret procesmateriale i produktionen.
For at opnå en bedre intern og ekstern logistik blev der indledt et samarbejde mellem Rosti OS og Smørum Gruppen. Da Smørum Gruppen afsætter anden plast end PP, ville et
samarbejde endvidere kunne medføre at det blev muligt at afsætte den plast som ikke var PP.
Imidlertid blev det af ledelsen i Rosti OS i sommeren 2003 besluttet at gå bort fra genbrugsstrategien, jf. bl.a. de nævnte vanskeligheder med at skaffe tilstrækkelige mængder PP i god
kvalitet/egnet form.
3.2.1.2 Præsentation af Smørum Gruppen Smørum Gruppen er et 100 % familieejet aktieselskab som i over 30 år har haft som idégrundlag at servicere erhvervslivet med optimale
genbrugsløsninger.
Virksomheden består af en række underselskaber hvor Dansk Returpapir A/S har en landsdækkende logistik for håndtering og afhentning af genbrugspapir, pap og plast.
Fra sommeren 2003 er Smørum Gruppen indtrådt i projektet med deres ekspertise omkring håndtering af plastaffald.
3.2.2 Problemstilling
Ved sprøjtestøbning har man ved Rosti OS en årelang tradition for at bruge næsten 100% regenerat baseret på eksternt indkøbt materiale. Ved termoformning har man umiddelbart
kværnet opstået gitterspild og genanvendt dette i produktionen. Derudover er der suppleret med andet kasseret procesmateriale, fx sodavandskapsler.
Processpild som ikke har været gitterspild, blev før år 2000 ikke holdt tilstrækkeligt rent til anvendelse internt, men blev afsat til ekstern genanvendelse.
Fra år 2000 blev strategien ændret til at holde spildet bedre rent og tørt. Der blev investeret i et genanvendelsesanlæg med store kværne og regeneratekstruder, så genanvendelsen
kunne foretages ved Rosti. Endvidere blev det planlagt at opkøbe PP-affald til forarbejdning i anlægget til senere brug ved produktion af urtepotter.
Der opstod imidlertid problemer med at skaffe tilstrækkelige mængder PP i den rette kvalitet/form.
Således ønskede flere mulige samarbejdspartnere at afsætte al deres plastaffald og ikke blot PP. Et andet problem var at PP var opblandet med andet plastaffald, fx PP og POM. En
tredje faktor var at affaldet ikke var lagret på
en tilstrækkelig kompakt måde, dvs. at transportomkostningerne ville blive for høje til at det var rentabelt at transportere plastaffaldet.
3.2.3 Løsningsmuligheder
For at opnå tilstrækkelige mængder PP i god kvalitet kræves således enten:
- Bedre manuel sortering
- Maskinel sortering af blandet materiale
- Bedre logistik eller
- At man er aftager af alle typer plast
I det følgende beskrives forskellige muligheder for at opnå en afsættelig kvalitet af PP-plast med udgangspunkt i en affaldsfraktion stammende fra kasserede produktioner hvor der
indgår ca. 20 % POM. Mængden udgør < 300 ton årligt.
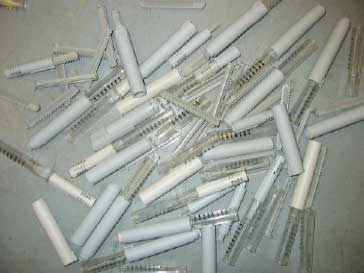
Figur 15 PP/POM-materiale
Som det ses, består affaldet af en række delkomponenter hvoraf nogle er indsat i hinanden. En stor del af komponenterne er dog også separeret fra hinanden.
Man kan forestille sig flere løsningsmuligheder på separationen af blandingen: 1: Der foretages en manuel separation i passende beholdere 2: Der foretages en maskinel separation internt
eller eksternt i virksomheden
3.2.3.1 Manuel separation Da affaldet består af en del separate dele af henholdsvis POM og PP, kunne man foretage en sortering hvor produktionsspildet opstår.
Her er det meget vigtigt at overveje hvordan man bedst kan foretage sorteringen, så den bliver nem i dagligdagen, og så der opnås så få fejl i sorteringen som muligt. Det kan her være
en fordel at tage en af de
professionelle indsamlere på markedet med på råd angående valg af de bedste systemer til opsamling af plastaffaldet. I det aktuelle eksempel kræver separation i virksomheden som
minimum at der opstilles mindst 3 typer beholdere til henholdsvis ren PP, ren POM og kasseret procesmateriale hvor PP- og POM-delene er samlet. Man kan endvidere vælge at
opdele PP efter de forskellige farver (klar, hvid, grå) hvorved PP-materialet efter kværning muligvis kan genanvendes til emner af disse farver i virksomheden hvis plasten lever op til de
materialekrav der stilles, herunder også krav til fødevaregodkendelse m.m.
Alternativt kan de rene fraktioner af PP afsættes til ekstern genanvendelse som blandet genbrugs-PP eller som separate PP-farver hvis man kan få en højere pris for de separerede
farver. Den rene fraktion af POM kan endvidere afsættes til ekstern genanvendelse til de gældende markedspriser.
For at opnå en god separation bør opsamlingssystemerne/opsamlingsposerne være mærkede eller have forskellig farve, så det er nemt for personalet at se hvilke emner der skal placeres
hvor. For plast som har en genkendelig fysisk form som i dette eksempel, kan man evt. også have en tavle ved beholderne med billeder af de emner som må lægges i beholderen. Hvis
den manuelle separation skal lykkes, kræves endvidere en grundig instruktion af personalet i virksomheden.
Eksempler på beholdere til opsamling af plast er vist på Figur 16.
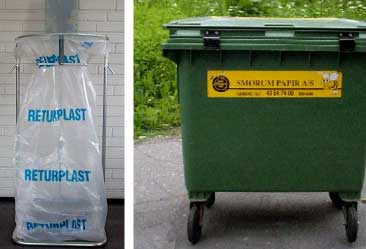
Figur 16 Beholdere til opsamling af plastaffald
Ved ekstern afsætning er det en forudsætning for opnåelse af en fornuftig pris at plastmaterialerne afsættes i partier, evt. sammen med andre genbrugsmaterialer som svarer til minimum
en lastbil/container ad gangen. Her har de professionelle indsamlere veludbyggede logistiske systemer som kan minimere omkostningerne til transport. En af fordelene ved at benytte de
professionelle indsamlere er at de kan samle tilstrækkelige mængder sammen fra forskellige kilder til at kunne afsætte en større mængde ad gangen til genanvendelse end den enkelte
virksomhed ellers ville kunne. Herved kan opnås en bedre samlet pris for det kasserede procesmateriale.
3.2.3.2 Maskinel separation af POM og PP PP og POM er to typer plast med meget forskellig vægtfylde henholdsvis ca. 0,9 g/cm3 for PP og 1,42 g/cm3 for POM. Hvis blandinger
af materialerne er neddelt, så de er separeret enkeltvis, vil det således være muligt at densitetsseparere dem. Hvis partikelstørrelsen kan bringes til at være næsten ens, kan benyttes tør
separation på et luftbord, alternativt kan separationen udføres i et synke-flydeanlæg med vand som separationsvæske.
På Figur 17 er vist materialet som er manuelt separeret nedsænket i et cylinderglas med vand. Materialet af POM synker til bunds (det grå, takkede materiale), mens forskelligt materiale
af PP flyder ovenpå.
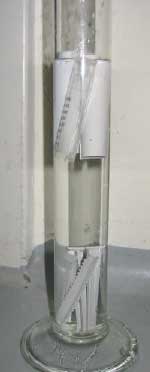
Figur 17 Separeret PP-/POM-materiale
Det vurderes at POM-inderdelen vil kunne befries ved neddeling til ca. 5 mm hvorefter POM og PP bør kunne separeres uden større problemer med flyde/synkeseparation.
Separationen kan sandsynligvis også lade sig gøre med tør massefyldeseparation. Her kan det dog være nødvendigt at indsnævre partikelstørrelsesfordelingen ved passende sigtning.
En god økonomi ved separationen forudsætter at der benyttes et anlæg hvor kapaciteten af anlægget udnyttes i tilstrækkelig grad. Da kapaciteten af anlæg til densitetsseparation af plast
typisk ligger fra ½-2 ton i timen svarende til ca. 800-3.000 ton/år i et skift, vil det være nødvendigt at anlægget kan behandle flere affaldsfraktioner end den nævnte for at udnytte
kapaciteten.
3.2.4 Konklusion
I en række af projektets eksempler er behandlet forskellige muligheder for øget genanvendelse af kasseret procesmateriale ved brug af en række neddelingsog sorteringsteknologier.
Nogle af metoderne kræver større mængder kasseret procesmateriale end der typisk er tilgængeligt fra de enkelte virksomheder, for at udføre en rentabel behandling og kræver derfor
at der er etableret oparbejdningsmuligheder ved eksterne aftagere. Mængderne, som bliver sendt til forbrænding fra de 25 virksomheder som svarede på spørgeskemaundersøgelsen i
afsnit 1.2, udgør som nævnt i afsnit 2.1 ca. 3.500 ton svarende til en udgift ved forbrænding på ca. 3,5 mio. kr., hvorfor der er en del penge at spare ved at finde egnede
genanvendelsesmuligheder.
Uanset om materialerne kan anvendes internt eller eksternt, kræves en fornuftig og logisk håndtering.
Ekstern genanvendelse
Genanvendelse af kasseret procesmateriale med afsætning til ekstern genanvendelse kræver, hvis der skal opnås en god pris, at materialet er separeret i de enkelte polymerer og fri for
det meste snavs og fremmedlegemer. Evt. separation i farver kan øge afsætningsprisen, men kræver at fraktionerne forekommer i tilstrækkeligt store mængder.
Den logistiske behandling af det kasserede procesmateriale stiller en række krav til opsamlingsbeholdere og indsamlingsmetode og skal både være velegnet til den interne håndtering,
transporten og til efterfølgende behandling ved ekstern behandler. Derudover kræves typisk instruktion/uddannelse af personalet.
For nogle fraktioner som fx nogle sammensatte plastfraktioner eller plastfraktioner i små mængder vil genanvendelse være mere vanskelig eller for dyr hvorfor disse fraktioner skal
sorteres til separat beholder til fx forbrænding eller alternativ oparbejdning. Når det skal vurderes hvilke fraktioner det er mest lønsomt at sortere i, og hvilke opsamlingsbeholdere og
metoder som er mest velegnede til opgaven, kan det være en fordel at kontakte professionelle indsamlere som ofte har erfaring fra lignende tilfælde, ligesom de kender
afsætningsmulighederne på verdensmarkedet og har veludbyggede logistiske systemer. Forbrænding bør således først vælges når mulighederne for genanvendelse er blevet undersøgt og
vurderet.
Intern genanvendelse
Her gælder de samme overvejelser som beskrevet ved ekstern genanvendelse, bortset fra at transport og afsætningsmuligheder ikke skal undersøges.
3.3 Superfos Packaging
3.3.1 Præsentation af virksomheden
Superfos er Europas største producent af sprøjtestøbt plastemballage. Virksomheden leverer kvalitetsemballage til virksomheder der fremstiller produkter til fødevare- og non
food-industrien. Superfos har sit hovedsæde i Danmark og har ca. 2.000 medarbejdere på 14 fabrikker spredt over hele Europa og i USA. Siden 1999 har firmaets kerneforretning
udelukkende været emballage.
Superfos arbejder udelukkende med plast af typerne polypropylen (PP) og polyethylen (PE). Disse plasttyper afgiver ingen uønskede stoffer og sikrer høj hygiejne. De leveres i
fødevaregodkendte kvaliteter. Efter brug kan PP og PE genbruges, genanvendes, forbrændes med energigenvinding eller bortskaffes på miljømæssig forsvarlig vis. Selve
sprøjtestøbningsprocessen sker ved at plastgranulatet opvarmes og smeltes hvorefter det sprøjtes ind i værktøjsformen. Formen åbnes når plastmaterialet er tilstrækkeligt afkølet, og
emnet kan udtages af formen.
Hensynet til miljøet er en integreret del af hverdagen i produktionen. Superfos har bl.a. succes med at reducere ressource- og energiforbruget og med at øge sin mulighed for
genanvendelse i produktionen. Af hygiejniske hensyn benyttes genanvendte materialer dog kun efter aftale med virksomhedens kunder. Superfos udvikler desuden løbende tyndere og
lettere emballager uden at gå på kompromis med emballagens egenskaber. Det er til fordel for miljøet, både når de lettere emballagetyper produceres, transporteres og bortskaffes.
3.3.2 Problemstilling
Superfos producerer et affaldsprodukt af PP som er et plastgranulat bestående af flager med en partikelstørrelse på ca. 2-12 mm og ca. 1 mm tykkelse. En stor del af flagerne er hvide,
men forefindes også i røde, orange, gule, grønne, blå og grå nuancer.
Flagerne har været forsøgt anvendt til produktion af brune plastspande, men der har været problemer med farveudtrædninger på overfladen af spandene (se Figur 18).
3.3.3 Løsningsmuligheder
Forskellige mulige løsninger af problem med farveudtrædninger er undersøgt:
- Separation af nogle kulører med densitetsseparation
- Separation af nogle kulører med mekanisk/optisk separationsudstyr
- Muligheder for forbedringer i fremstillingsprocessen
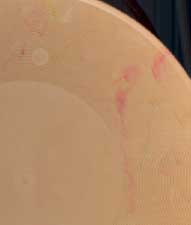
Figur 18 Spand produceret af Polypropylenproduktionsaffald
3.3.4 Forsøgsarbejde
3.3.4.1 Separation med densitetsseparation Når plast tilsættes pigment, vil den endelige densitet af den farvede plast være afhængig af densiteten af pigmenterne. Således har nogle
pigmenter en høj densitet, som fx TiO2 med en densitet på omkring 4 g/cm3 hvor PPs densitet er ca. 0,9 g/cm3. Tilsætning af Titandioxid som typisk bruges som hvidt pigment, vil således øge densiteten af den farvede polypropylenplast i forhold til den
ufarvede plast.
For at undersøge muligheden for en densitetsseparation blev lavet et simpelt forsøg i et cylinderglas med en blanding af 2 propanol og vand, således at der blev opnået en separation af
plastblandingen efter densitet. Glasset blev ultralydsbehandlet, og plasten blev omrørt for at opnå en passende separation. På Figur 19 ses separationen i glasset, og på Figur 20 er vist
de separerede plastblandinger. Der ses et tydeligt højere indhold af hvide flager i den tunge (nederste) fraktion.
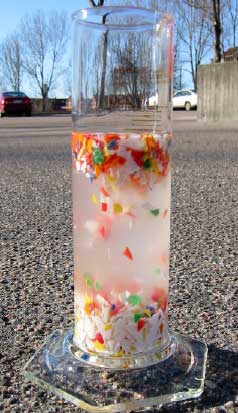
Figur 19 Separation i propanol/vand
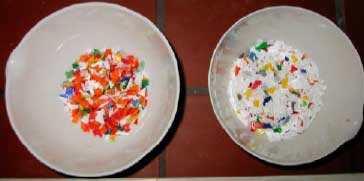
Figur 20 Separerede plastblandinger
Forsøget viser at der vil kunne opnås en delvis separation ved massefyldeseparation i væske med passende densitet.
Der findes en række typer separationsudstyr på markedet som er mere effektive end en simpel separation i et kar med væske af given densitet ved 1
G. Nogle af disse metoder bygger på centrifugeteknikker med G-påvirkninger fra 100-1.000 G og opnår derved en hurtig separation svarende til en høj kapacitet (ca. ½-1 ton/time).
3.3.4.2 Separation med mekanisk/optisk separationsudstyr Inden for de sidste 10 år er der sket en rivende udvikling inden for udstyr som er baseret på en sensorer der detekterer
ønskede partikler på et passerende transportbånd. Efterfølgende aktiveres en dyse hvor trykluft blæser den ønskede partikel over i en opsamlingsbeholder. Denne teknik er nu også
udviklet til optisk sortering efter farve til partikelstørrelse på omkring 2 mm og opefter.
Der er derfor udført et forsøg hvor en PP-plastblanding er søgt separeret i hvide og farvede partikler. Hvis separationen lykkes, vil der således kunne fremstilles hvide plastemner og
stærkt farvede emner af resten.
Blandingen er vist på Figur 21.
Inden farveseparation er de partikler frasigtet som er mindre end 2 mm (se Figur 22). Partiklerne udgør 3,5 % af input - se Tabel 3.1.
Herefter er de resterende 1.856 g prøve farvesepareret.
I den udvundne hvide fraktion (se Figur 23) opnås en renhed på 97,8 % bestemt ud fra et sorteringsforsøg, og udbyttet af de hvide partikler ved behandling i et trin er 78 %. Udbyttet er
beregnet ud fra det vejede indhold af hvide partikler i fraktionen 0-2 mm samt de producerede hvide og blandede fraktioner. Den farvede restfraktion er vist på Figur 24.
Herefter er udtaget en prøve af de hvide partikler, og på de resterende 925 g er kørt endnu en separation. Der opnås nu en hvid fraktion (se Figur 25) med en renhed på 99,9 %, og
udbyttet af de hvide partikler er nu faldet til 65 %, men til gengæld med en højere renhedsgrad end ved behandling i et trin. Den farvede restfraktion er vist på Figur 26.
Tabel 3.1 Resultater af farveseparation
Fraktion |
Vejet fraktion (g) |
Indhold af hvide partikler (g) |
Renhed % |
Input |
1.924 |
|
|
0-2 mm frasigtet |
68 |
33 |
|
Trin 1 input |
1.856 |
|
|
Hvid fraktion |
1.034 |
1.012 |
97,8 |
Farvet fraktion |
822 |
251 |
|
Trin2 input |
925 |
|
97,8 |
Hvid fraktion |
838,2 |
837,3 |
99,9 |
Farvet fraktion |
87 |
68 |
|
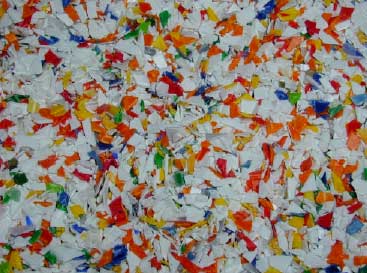
Figur 21 Input, 1.924 g
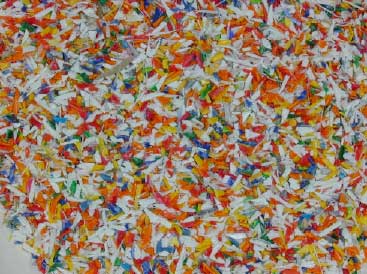
Figur 22 Frasigtede partikler 0-2 mm, 68 g
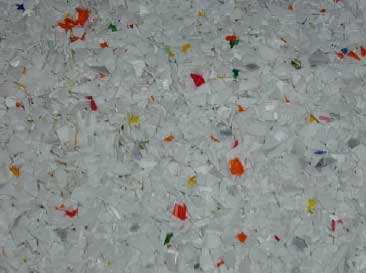
Figur 23 Trin 1 udvundet hvid fraktion, 1.034 g
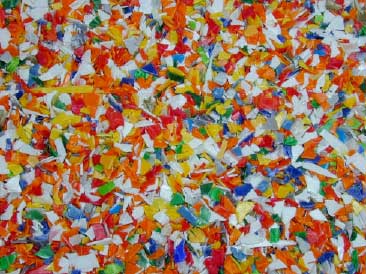
Figur 24 trin 1 restfraktion farvet, 822 g
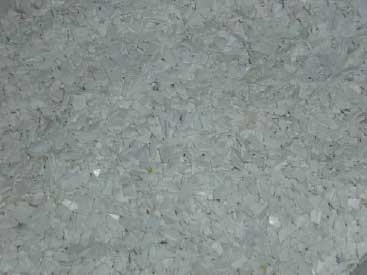
Figur 25 trin 2 udvundet hvid fraktion
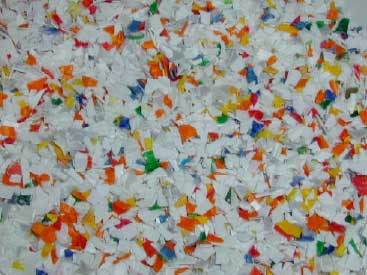
Figur 26 trin 2 restfraktion farvet
Økonomi
I Tabel 3.2 er vist beregninger af økonomien ved forskellige antagne afsætningspriser, driftstimer af udstyret per år og antal krævede gennemløb. Beregningerne er kun vejledende og
med en række forudsætninger, herunder:
Rentefod: 7 %
Forrentning over: 5 år
Bemanding: 0,2 mand per skift
Indhold af ønsket farve: 50 %
Der indgår endvidere data for processen vedrørende investering, energiforbrug, trykluftforbrug, vedligehold m.m.
Det er antaget at blandingen inden sortering kan afsættes til 1.000 kr./ton, og at restfraktionen efter sortering kan afsættes til 1.000 kr./ton.
I scenarie 1 og 3 er regnet med fuld produktionstid (5 skift) og med henholdsvis en afsætningspris for den udsorterede farve på 2.000 kr./ton (scenarie 1) og den pris hvor processens
økonomi balancerer (1.130 kr./ton, scenarie 3). Dette svarer til at man blot skal opnå 13 % mere for den udsorterede farve end for blandingen for at processen løber rundt.
I scenarie 2 og 4 er tilsvarende regnet med et skift og 2 gange sortering svarende til at der opnås en højere renhed af den udsorterede farve. Her kræves at der kan opnås 62 % mere
for den udsorterede farve for at processens økonomi balancerer.
Tabel 3.2 Økonomi ved farveseparation
Scenarie |
1 |
2 |
3 |
4 |
Betingelser |
5 skift, 1 x sortering |
1 skift 2 x sortering |
5 skift, 1 x sortering, break even |
1 skift, 2 x sortering break even |
Driftstimer |
8.000 |
1.850 |
8.000 |
1.850 |
Behandlet mængde (ton) |
20.000 |
2.312 |
20.000 |
2.312 |
Fraktion 1 (produkt) % |
50 |
50 |
50 |
50 |
Afsætningspris, fraktion 1 (kr./kg) |
2 |
2 |
1,13 |
1,62 |
Fraktion 2 (rest) % |
50 |
50 |
50 |
50 |
Afsætningspris, fraktion 2 (kr./kg) |
1 |
1 |
1 |
1 |
Kapitalomkostninger (kr./ton) |
28 |
242 |
28 |
242 |
Driftsudgifter (kr./ton) |
35 |
67 |
35 |
67 |
Værdi af udvundne produkter (kr./ton) |
1.500 |
1.500 |
1.065 |
1.310 |
Værdi af mængde inden behandling (kr./ton) |
1.000 |
1.000 |
1.000 |
1.000 |
Nettobehandlingsudgift (kr./ton) |
-437 |
-191 |
-2 |
-1 |
3.3.4.3 Muligheder for forbedringer i fremstillingsprocessen Farveudtrædningerne i de producerede spande kan også skyldes at de forskelligt farvede plastpartikler ikke når at blive
tilstrækkeligt opblandet med hinanden i processen.
For at undersøge dette indledende blev udført et smelteforsøg i en ovn. Plasten var smeltet ved 193 °C som fremgår af Figur 27 og Figur 28. Et emne fremstillet ved sammenrøring af
plasten og yderligere opvarmet til 243 °C gav en homogen farvefordeling.
På Figur 30 er vist et forsøg hvor forskelligt farvede partikler opvarmes på en plade. Partiklerne var ikke smeltet ved 185 °C, mens alle var smeltet ved 193 °C som vist på Figur 31.
Noget tyder derfor på at de forskelligt farvede partikler bør kunne ekstruderes til et emne med ens farve ved ændrede driftsbetingelser hvor der sikres en bedre opblanding af den
smeltede plastmasse.
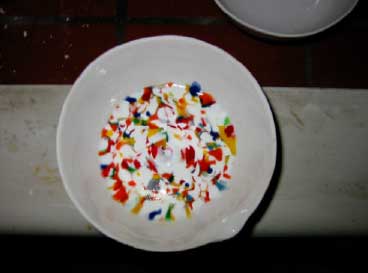
Figur 27 Plast ved 193 °C
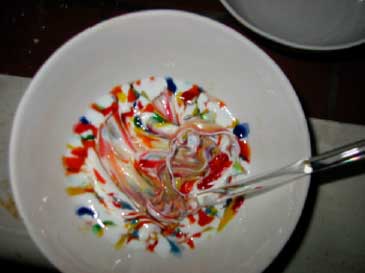
Figur 28 Smeltet plast
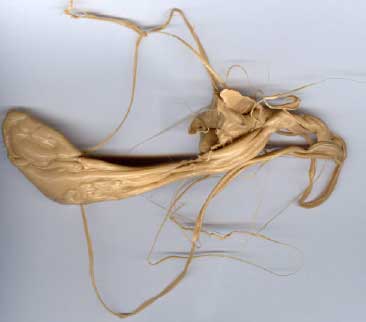
Figur 29 Sammenrørt emne
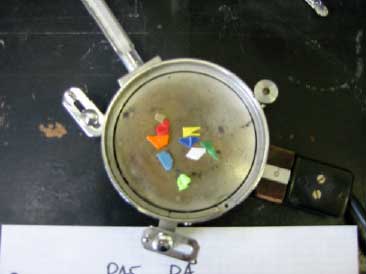
Figur 30 Smelteforsøg med forskelligt farvede PP-flager
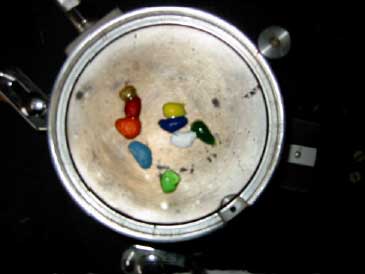
Figur 31 PP-flager smeltet ved 193 °C
Der er i oktober 2003 blevet gennemført forsøgskørsler med fremstilling af spande fra blandet fraktion hos Superfos i samarbejde med Teknologisk Institut for at se om man ved at
ændre på maskinindstillingerne kan få en bedre og fuldstændig opblanding direkte i sprøjtestøbemaskinen, eller om det er nødvendigt med et ekstra blandetrin via en ekstruder.
Forsøgene blev udført på en Klöckner ferromatic FM 320-350 sprøjtestøbemaskine med en maksimal lukkekraft på 350 kN. Maskinen var forsynet med mikserhoved og
barrieresnekke. Der blev anvendt en lukkekraft på 280 kN. Materialetemperaturen i tragt blev holdt på 50 °C og i snekken på 235 °C. Modtrykket blev varieret fra 6 bar til 12 bar.
Endvidere var det en forudsætning for lønsomheden af en evt. senere produktion at cyklustiden ikke blev længere end i den løbende produktion. Cyklustiden er et mål for hvor mange
spande der kan produceres pr. tidsenhed, og er en af de vigtigste optimeringsparametre inden for plaststøbning med henblik på at udnytte maskinparken mest optimalt. Cyklustiden skal
være så kort som muligt.
Problemstillingen med den blandede fraktion af PP i forskellige farver viste sig mere kompliceret end først opfattet. For det første har man en sæsonbetinget forskel i farvenuancer fra
forår til efterår. Om foråret er farverne på plastspandene mest pastelfarver, mens de om efteråret er meget varmere i farven (se Figur 32). Endvidere er en meget stor del af de hvide
spande der regranuleres, med farvetryk på ydersiden, således at de ikke kan sorteres i en ren hvid fraktion. Forholdene kompliceres yderligere ved at man inden for samme oktabin (en
oktabin er en stor ottekantet beholder med plastgranulat hvorfra granulatet suges op i tragten på sprøjtestøbemaskinen) kan have ændringer i farvenuancerne ned gennem oktabinen. Det
betyder at der vil ske et farveskift i spandene selv om det er muligt at opnå en fuldstændig opblanding af plastgranulatet under transporten frem til sprøjteværktøjet.

Figur 32 Billede af to efterårs- og en forårsfarveblanding
Det er på denne baggrund at resultaterne af sprøjtestøbningsforsøgene skal ses.
Det viste sig at man kunne opnå ensartede spande ved at anvende den hvide fraktion med farvetryk på den ene side. Ensartetheden øgedes som forventet ved at øge modtrykket fra 6
bar til 12 bar. Der blev endvidere tilsat dækfarve i størrelsesordenen 2 % af en grå masterbatch. Det øgede yderligere ensartetheden af udseendet.
Med hensyn til forsøg med den blandede fraktion af granulat fra spande i forskellige farver produceret i efteråret var det ikke selv med et modtryk på 12 bar muligt at opnå en
fuldstændig ensartethed af spandene. Spandene fik et rødbedefarvet udseende med farvemønstre her og der af farver der ikke var blevet blandet fuldstændig op.
På Figur 33 er vist eksempel på rødbedefarvede spande (til venstre), hvide spande fra fraktion med farvetryk på ydersiden og rødbedefarvet tilsat 2 % grå masterbatch.
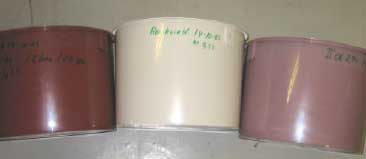
Figur 33 Diverse producerede spande
En anden problemstilling hos Superfos der blev diskuteret under forsøgskørslerne, var støv i granulatet fra genbrug af spandene. Støvet havde tendens til at sætte sig alle steder under
transport frem til sprøjtestøbemaskinen. Endvidere var der problemer med at fjerne hankene fra spande der var monteret med metalhanke, da det p.t. kan ske manuelt. Man havde
forsøgt sig hos en genbrugsvirksomhed med en maskinel løsning på hankeproblemet uden held.
3.3.5 Konklusion
Det er muligt at fremstille ensartede hvide spande ud fra granulat af hvide spande med farvetryk på den ene side ved anvendelse af eksisterende udstyr hos Superfos. Ensartetheden
stiger ved anvendelse af modtryk på 12 bar og ved tilsætning af grå farvemasterbatch på 2 %. Cyclustiden for fremstillingen af disse genbrugsspande er som for sædvanlig produktion.
Det er ikke muligt at fremstille ensartede spande ud fra de farvede fraktioner med mange ofte stærke farver sammenblandet. En delvis løsning på denne problemstilling kan være en
bedre udsortering på farver i produktionen.
Det er vist at man kan foretage en vellykket farveseparation ved eksempelvis at lade et anlæg med farvesensor vælge den hvide farve ud. Efter to gennemløb opnår man en meget ren
fraktion. Om det er en lønsom vej, afhænger af de samlede mængder hos Superfos, eller om man kan deles om et anlæg med andre virksomheder der har tilsvarende problemstilling.
Med hensyn til støvproblemet kan det oplyses at forskellige udstyrsleverandører som fx Kongskilde har udstyr (Combirenser) hvormed støvet kan suges bort. Udstyret er udviklet inden
for korn- og foderstofindustrien. Udstyret kaldes en evaporator og er baseret på en stigeluftsseparation.
Det bør undersøges nærmere om der findes neddelingsudstyr på markedet som kan grovneddele plastspande med metalhanke, så hankene befries fra plasten og efterfølgende kan
separeres med magnetseparation
3.4 Jysk Vakuum Plast A/S
3.4.1 Præsentation af virksomheden
Jysk Vacuum Plast er et selvstændigt selskab under Styropack A/S der ejes af den hollandske plastkoncern Synbra Group.
Jysk Vacuum Plast er en underleverandørvirksomhed der forarbejder mange forskellige termoplastiske materialer ved hjælp af vacuum og trykluftformning samt efter bearbejdning med
CNC-bearbejdningscenter.
Jysk Vacuum Plast udvikler og producerer emballager og tekniske artikler i samarbejde med sine kunder.
Emballageproduktionen foregår ved trykluft og vakuumformning af plastfolier til virksomheder inden for:
- Fødevarer og konfekture
- Medicinal
- Legetøj
- Elektronik
- Værktøj og reservedele
Produktionen af tekniske artikler foregår ved vacuumformning af plastplader til virksomheder som anvender:
- Kabinetter og dele til elektronik
- Plastkomponenter og konstruktionsdele til industrien
- Dele til hårde hvidevarer
- Isoleringsdele
- Display og skilte
- Plastpaller – plastmellemlæg samt kasser og bakker
Selve vakuumformningsprocessen består i at plastfolier eller plader ved hjælp af undertryk eller trykluft tager form efter et formværktøj - specielt udviklet efter kundens behov.
3.4.2 Problemstilling
Ved Jysk Vakuum Plast produceres et metalliseret folieprodukt som ikke umiddelbart kan genanvendes i egen produktion. Folien består af en 18-20 µm tyk PET-folie med et pådampet
lag af aluminium.
3.4.3 Løsningsmuligheder
En række muligheder er undersøgt/vurderet:
- Neddeling
- Smeltning
- Andre muligheder
3.4.4 Forsøgsarbejde
3.4.4.1 Neddeling
Folien er blevet neddelt ved Eldan til flager af ca. 3-5 mm størrelse som vist på Figur 34. Neddelingen blev udført på en granulator.
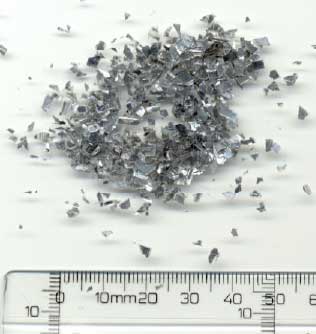
Figur 34 Neddelt folie
3.4.4.2 Smeltning
De neddelte plastflager er efterfølgende smeltet ved 260 °C, og der er rørt et par emner sammen med en spatel på smeltepladen (se Figur 35).
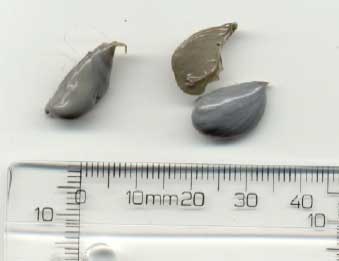
Figur 35 Smeltet folie
Som det ses, er aluminiumslaget tilstrækkeligt tyndt til at blive opløst i plasten som herved får en grålig farve.
3.4.4.3 Andre muligheder
Plastfolien er endvidere sendt til Result Technology i Schweiz for undersøgelse af om lagene af aluminium og PET kan adskilles. Undersøgelsen viste at det er ikke muligt at adskille så
tynde lag.
Man vil givetvis kunne fjerne laget med en mild sandblæsning.
Alternativt til omsmeltning kan overvejes afsætning af granulat til dekorationsformål hvor granulatet fx kan limes på papir som sølvglimmer. Inden salg bør de sundhedsmæssige
egenskaber ved brug til børn undersøges.
3.4.5 Konklusion
Det vurderes umidelbart mest interessant at undersøge de kommercielle muligheder for at afsætte det neddelte glimmerlignende materiale til hobby /legetøjssektoren. Da det drejer sig
om en neddelt levnedsmiddelgodkendt plastemballage, skulle der ikke være nogle sundhedsmæssige problemer i relation til denne brug.
3.5 SCA Packaging Flamingo
3.5.1 Præsentation af virksomheden
SCA Packaging Flamingo producerer emballager i ekspanderet polystyren (EPS), også kaldet Flamingoâ. Virksomheden opererer hovedsageligt i Danmark, og ca. 90 % af
produkterne er kundetilpassede løsninger. SCA Packaging Flamingo har fem fabrikker i Danmark, fordelt med 1 på Sjælland og 4 i Jylland. Der anvendes EPS som råvare.
EPS-perlerne opskummes med vanddamp hvorefter de formstøbes i aluminiumsforme. Produkterne er kendetegnet ved at være stødabsorberende, isolerende, vandafvisende og lette.
De giver optimal beskyttelse ved et meget lille råvareforbrug. Virksomheden er certificeret efter ISO 9001 og ISO 14001, og miljøcertificeringen omfatter arbejdsmiljø.
3.5.2 Problemstilling
I forbindelse med fremstilling af emner i EPS fremkommer en del produktionsspild i forbindelse med indstilling af maskiner og ved afskæring på glødeskæringsfabrikkerne (ca. 40 ton).
Alt internt skrot genanvendes så vidt muligt, men der er et stort ønske om at øge mængden af eksternt genbrugsmateriale som kan indgå i virksomhedens produkter (jf.
transportemballageaftalen).
Der er ikke den helt store omkostningsreducerende gevinst ved at øge mængden af eksternt genbrugsmateriale da der bruges ressourcer på at øge densiteten og på at runde kanterne,
men modsat spares der på anvendelsen af nye råvarer. Der er dog en betydelig miljømæssig gevinst da fremstilling af EPS-råvarer er meget energikrævende, og virksomheden har
forpligtet sig til at gøre en indsats for miljøet i forbindelse med miljøcertifikatet.
Der tilsættes i dag ca. 10 % skrottet materiale (blanding af internt + eksternt) til de produkter hvor der må tilsættes genbrugsmateriale (pga.
fødevarelovgivningen), men det er virksomhedens overbevisning at denne procentdel kunne være højere på visse produkter uden at det reducerer egenskaberne for det færdige produkt
(krav til sammensvejsning af perlerne, fald, tryk og udseende). Der modtages ca. 25 ton eksternt genbrugsmateriale hvoraf ca. 80 % kan genbruges i produktionen.
Resten er så snavset at det sendes direkte videre til forbrænding.
En vigtig forudsætning for at øge mængderne af eksternt genbrugsmateriale er at kunderne bliver bedre til at sortere, således at virksomheden ikke skal bruge unødige ressourcer på at
håndtere materialet når det modtages, men kan føre det direkte i knuseren og genbruge det med det samme. Tidligere har man kunnet afsætte neddelt EPS til isolering i huse, men dette
marked er forsvundet gennem de sidste par år. I Sverige genanvendes store mængder EPS i beton som isoleringsmateriale (ca. 215 ton/årligt) og en mindre del som løs isolering (ca. 2,7
ton) ifølge Svensk EPS Återvinning AB. Som indblanding i nye produkter genanvendes ca. 112,6 ton årligt.
Det er på nuværende tidspunkt ikke muligt at genanvende EPS fra affaldsselskaber, detailhandlere eller husstande da renheden af dette materiale ikke kan sikres, og det er af afgørende
betydning for genanvendelse hos produktionsvirksomhederne. Dette materiale kunne dog finde anvendelse i andre produkter hvor kravet om renhed ikke er så afgørende.
De mængder EPS-genbrugsmateriale som anvendes i Danmark, er sammenlignet med Sverige relativt små. Dog har det meget at sige at genbrugsordningen og mulighederne for
genanvendelse i Sverige er meget anderledes og gunstigere end i Danmark.
Der har ikke været de store muligheder for at finde nye veje for at genanvende EPS og derved øge genbrugsmængden i Danmark. Tidligere fandt EPS genanvendelse i beton eller som
løs hulmursisolering, men dette marked eksisterer som ovenfor nævnt ikke længere.
3.5.3 Løsningsmuligheder
Det er en forudsætning for øget genanvendelse af eksternt EPS at dette er ensartet i farve og absolut rent. Endvidere er det nødvendigt at dokumentere at de produkter som tilsættes
regenerat, bevarer deres mekaniske og isolerende egenskaber. Forsøgsarbejdet har taget udgangspunkt i disse nødvendige forudsætninger og har været tilrettelagt, så man for emner i
forskellige geometrier og godstykkelser har kunnet tilvejebringe den nødvendige dokumentation.
3.5.4 Forsøgsarbejde
3.5.4.1 Forsøg på øget genbrug af eksternt indsamlet EPS i nye produkter Der er på SCA Packaging Flamingo's fabrik i Hobro fremstillet en række forsøgsemner i forskellige
geometrier og godstykkelser med forskellig tilsætning af regenereret EPS. Der er fremstillet emner med op til 30 % tilsætning af regenerat.
Det har ikke været muligt at bestemme forholdet mellem det interne og eksterne regenerat i blandingen som er tilsat de producerede emner, hvilket kan have betydning for de undersøgte
egenskaber.
Der opleves ofte store produktionsmæssige problemer med tilsætning af regenerat, da dette materiale er "dødt", dvs. at det ikke indeholder pentan, som er ekspansionsmidlet i
EPS-perlerne. Der skal derfor være en god blanding mellem regenerat og ny råvare for at sammensvejsningen af perlerne i emnerne bliver fuldstændig – og emnet derved brugbart som
emballage. I alle de prøvede emner har sammensvejsningen været god.
Teknologisk Institut har på de fremstillede emner målt densitet (vægtfylde), Tryk E-modul og trykstyrke ved 10 % deformation. Densiteten er målt efter ISO 845 (1988) og trykstyrke
efter ISO 844 (1998) med en trykhastighed på 2,5 mm/min.
De fremkomne resultater er vist i nedenstående Tabel 3.4. Værdierne kan sammenlignes med de angivne værdier i Tabel 3.3, hvor råvareleverandørerne har angivet de intervaller som er
gældende for rene råvarer.
Tabel 3.4 forsøgsresultater fra Teknologisk Institut
Emne nr. |
%Tilsat Genbrugs EPS |
Densitet kg/m3 |
Tryk E-modulMPa |
Trykstyrke ved 10 % deformation MPa |
A |
10 |
22,3(0,5)1 |
5,5 (0,4) |
0,14(0,01) |
B |
25 |
21,8(0,4) |
5,2 (0,2) |
0,13(0,01) |
C |
30 |
24,2(0,7) |
5,0(1,0) |
0,13(0,02) |
D |
10 |
24,5(0,5) |
6,6(0,6) |
0,16(0,01) |
E |
10 |
20,9(1,0) |
5,4(0,6) |
0,14(0,01) |
F |
25 |
21,6(0,6) |
5,0(0,4) |
0,12(0,01) |
G |
30 |
24,1(1,2) |
6,1(0,2) |
0,15(0,01) |
H |
10 |
23,7(0,5) |
6,5(0,2) |
0,16(0,01) |
I |
18 |
23,7(0,5) |
5,9(0,3) |
0,15(0,01) |
J |
25 |
24,0(0,3) |
6,2(0,3) |
0,15(0,01) |
K |
10 |
24,5(1,0) |
5,6(1,1) |
0,16(0,02) |
L |
18 |
23,2(0,6) |
5,8(0,3) |
0,15(0,01) |
M |
25 |
23,1(0,4) |
5,5(0,2) |
0,15(0,01) |
N |
10 |
21,4(0,6) |
4,9(0,9) |
0,14(0,01) |
O |
30 |
21,2(0,5) |
4,7(0,6) |
0,13(0,01) |
P |
30 |
24,9(0,8) |
7,0(0,4) |
0,17(0,01) |
1 Tal i parentes angiver standardafvigelsen på målingen
Tabel 3.5 Virksomhedens råvareleverandører har opgivet følgende
værdier for densiteterne 20 og 25 kg/m3
|
20 kg/m3 |
25 kg/m3 |
Tryk E-modul MPa |
3,1-6,2 |
5,3-8,5 |
Trykstyrke ved 10 % deformation Mpa |
0,11-0,14 |
0,15-0,2 |
Det ses, at resultaterne, selv med meget høje genbrugsprocenter, ligger pænt inden for de af råvareleverandørerne angivne intervaller for tryk E-modul og trykstyrke ved 10 %
deformation. Dette betyder i realiteten at virksomheden godt kan øge genbrugsmængden med 15-20 % i forhold til de mængder som anvendes i dag. Det skal dog sikres at blandingen
mellem regenerat og ny råvare er optimal, og at blandingen mellem internt skrot og eksternt modtaget materiale er omkring 50:50 da internt skrot stadig indeholder en lille mængde
pentan og derved er betydeligt lettere at arbejde med da det ikke er helt "dødt", og en god sammensvejsning af perlerne kan sikres.
I dag er der kun ét regenereringsanlæg på virksomheden hvilket betyder at det produkt som procesmæssigt kan produceres med mindst regenereret materiale, er det som bestemmer
procenten i resten af produkterne i produktionslinien. Det er desværre ikke muligt at tilsætte 10 % regenerat til et produkt og 30 % til et andet, selvom det i realiteten ikke ville forringe
egenskaberne for det sidst nævnte produkt med 30 % regenerat.
3.5.5 Konklusion
Virksomheden skal overveje om det kan betale sig at lave et flerstrenget regenereringsanlæg, således at der kan optimeres på tilsætningen af regenerat i stedet for at det er det svageste
produkt som bestemmer genbrugsprocenten. Ligeledes kan tilsætningen af regenerat modtaget retur fra kunder øges hvis den interne skrotmængde reduceres.
Såfremt der skabes et nyt marked for EPS-genbrug som det ses i Sverige, kan mængden af genbrug øges betydeligt.
3.6 SP Group Tinby
3.6.1 Præsentation af virksomheden
Tinby A/S er et datterselskab under koncernen SP Group A/S som er en af Danmarks største producenter af plastprodukter.
Tinby A/S producerer tekniske emner i plastmaterialet polyurethan. Polyurethan er en hærdeplast hvilket betyder at det er en polymer som ikke kan smelte ved opvarmning, men kun vil
nedbrydes ved opvarmning. Det skyldes at der ved fremstillingen af polyurethan indgår to flydende materialer - en isocyanat og en polyol som efter en kemisk reaktion mellem de to
komponenter danner det færdige plastprodukt polyurethan.
3.6.2 Problemstilling
Konsekvensen af at polyurethan ikke kan smelte, er blandt andet at det er relativt vanskeligt at regenerere. Det gælder såvel produktionsspild som produkter i polyurethan der ender
som affald. Naturligvis kan man ved afbrænding af polyurethan i et forbrændingsanlæg nyttiggøre en del af energien fra polyurethanen.
Direkte genanvendelse af polyurethan kan tænkes ved granulering af polyurethan hvorefter granulatet kan genanvendes som fyldstof i et nyt produkt hvor polyurethanens egenskaber kan
udnyttes.
I projektet er denne tankegang forsøgt efterprøvet i et konkret produkt. Et af Tinby A/S' store produktområder er Ergonomiske arbejdspladsmåtter i et flexibelt opskummet
polyurethan. Her opstår dels under støbningen og dels under efterfølgende sammenlimning og afskæring et produktionsspild på mellem 10 og 15 %. Hele denne mængde bliver i dag
bortskaffet som affald til forbrænding.
Det omtalte produktionsspild har en rimeligt ensartet sammensætning og vil således kunne indgå som et ensartet granulat i et nyt produkt.
Måtterne er fremstillet som et integralskum, dvs. de har en hud med højere densitet på overfladen som følge af at overfladen af værktøjet er koldt i modsætning til kernen der kan opnå
temperaturer på 130 °C som følge af den exoterme reaktion mellem isocyanat og polyol.
Ved Tinby forekommer forskellige typer produktionsaffald i forbindelse med måtteproduktionen.
Et eksempel er rester som sidder i produktionsudstyret i form af en "Andefod", er vist på Figur 36.
Et andet eksempel er afskær af måtteproduktionen fremgår af Figur 37.
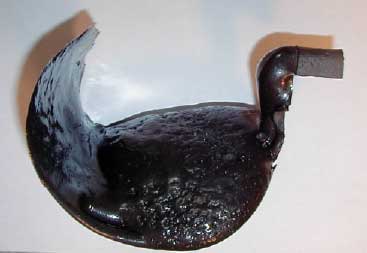
Figur 36 Udluftningsmateriale
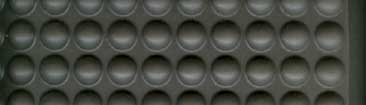
Figur 37 Afskær af måtte
Produktionsaffaldet findes enten i form af polyester eller polyether, PUR.
3.6.3 Løsningsmuligheder
Der er undersøgt/vurderet en række muligheder for genanvendelse under følgende delemner:
- Neddelingsforsøg
- Genanvendelse af granuleret PUR i "recycle gummimåtte"
- Genanvendelse af granuleret PUR i "recycle PUR-måtte"
- Øvrige anvendelsesmuligheder
3.6.4 Forsøgsarbejde
3.6.4.1 Neddelingsforsøg Der er foretaget en neddeling af affaldet ved Eldan Scandinavian Recycling A/S. Neddelingen er udført på en fingranulator.
På Figur 38 er vist resultatet af første trin hvor integralskum i polyurethan neddeles til 10 mm.
På Figur 39 er vist neddeling af materialet til 2 mm. Det ses at en del af materialet neddeles til væsentligt lavere kornstørrelse (< 1 mm).
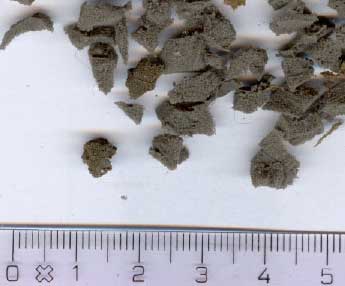
Figur 38 10 mm fraktion
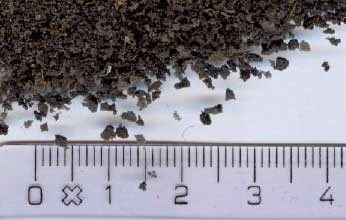
Figur 39 2 mm fraktion
Ved neddeling til mindre partikelstørrelse kræves højere energiforbrug, ligesom der opstår fare for antænding hvorved det kan være påkrævet med neddeling i inert atmosfære.
3.6.4.2 Genanvendelse af granuleret PUR i "Recycle gummimåtte" Da salgsafdelingen Ergomat A/S under Tinby A/S ønskede en gummimåtte produceret på basis af "recycle"
materialer til erstatning for et "recycle"
produkt som var baseret på en gummi med indarbejdet "recycle" bildæk, var det oplagt at forsøge at indarbejde granuleret PUR i en gummiblanding.
Udviklingsforsøgene blev udført hos AVK GUMMI A/S som i forvejen producerer gummimåtter i nitril til Tinby A/S.
Det lykkedes at indarbejde en forholdsvis stor del regenereret PUR i en gummiblanding baseret på naturgummi. De første måtter blev trykstøbt (se Figur 40).
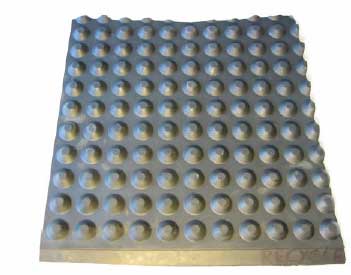
Figur 40 Indarbejdet PUR i naturgummiemne
Da der senere blev udført forsøg med sprøjtestøbning af gummiblandingen, viste det sig at være vanskeligt at indarbejde PUR'en godt nok i gummimassen til at det kunne lade sig gøre at
opnå tilstrækkeligt gode flydeegenskaber i gummimassen til at sprøjteprocessen kunne anvendes.
Det er således ikke muligt at opnå en rentabilitet i produktet da den besparelse i råvareomkostninger man kan opnå ved anvendelse af regenereret PUR i gummimassen, ikke opvejer de
ekstra omkostninger der er ved at skulle trykstøbe måtterne frem for at sprøjtestøbe måtterne.
3.6.4.3 Genanvendelse af granuleret PUR i "recycle PUR-måtte" Det er sideløbende forsøgt at indarbejde granuleret PUR i en polyurethanmåtte. Dette kunne give mulighed for at
fremstille en "recycle PUR måtte" som endnu et produkt i Tinby A/S' måtteprogram Ergomat.
I laboratoriet lykkedes det at indarbejde en stor del granuleret PUR i polyolkomponenten. Denne masse bliver meget højviskøs og grødet på grund af det høje volumenindhold (70-80
%) af faststof. Polyolkomponenten skal blandes ensartet med en isocyanat i et bestemt blandingsforhold og under den kemiske reaktion mellem de to komponenter skal PUR'en flyde
ind og danne det færdige emne.
På grund af den høje viskositet er det meget vanskeligt at opnå tilstrækkeligt gode flydeegenskaber til at opnå et homogent emne hvilket skal opnås inden for reaktionstiden på ca. 6
sekunder. På Figur 41 ses et emne hvor det granulerede PUR er homogent fordelt i emnet, men en måtte med dimensionerne 600x900 mm er langt vanskeligere at få fuldstøbt med en
tilfredsstillende vægtfylde.
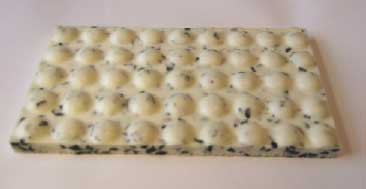
Figur 41 Produceret testemne med granuleret PUR uden tilsat farve
Det er ikke rentabelt i det eksisterende produktprogram at producere en "recycle PUR-måtte" da besparelsen på råvarerne ved anvendelse af granuleret PUR ikke opvejer de ekstra
omkostninger der er til procesteknisk at fremstille en sådan måtte.
Efterfølgende er der planlagt ekstra forsøg med fremstilling af "recycle PUR-måtte ved anvendelse af præpolymeriseret isocyanatteknologi i samarbejde med en anden dansk
virksomhed. Resultaterne fra disse forsøg har vist sig så lovende at man ønsker at fortsætte dem med henblik på en kommerciel løsning.
3.6.4.4 Øvrige anvendelsesmuligheder
I udlandet findes processer til genanvendelse af PUR-skum til produktion af byggeprodukter med varme eller lydisolerende egenskaber, men disse processer er på nuværende tidspunkt
ikke etableret i Danmark.
PUR-granulatets fleksible "touch" og elasticitet kan tænkes udnyttet i en række produkter hvor en sådan egenskab ønskes.
Man kan pege på mulighederne for at bruge løst granulat i staldmåtter af plastfolie til grise og køer, idet der her ikke stilles strenge krav til udseende. Denne type produkter findes
allerede på basis af gummigranulat fra kasserede bildæk.
Det er også muligt at anvende PUR-granulat som tilsætning til gummicompounds hvor trykstøbning stadig er rentabelt. Denne type processer anvendes endnu i stor stil i fjernøsten på
grund af den billige arbejdskraft.
3.6.5 Konklusion
Tinby har undersøgt en række muligheder for at genanvende neddelt PUR fra virksomhedens produktionsspild i forbindelse med fremstilling og konfektionering af Ergomat måtter. Det
har vist sig mest lovende at genanvende granulatet ved indstøbning i præpolymeriseret polyurethan.
3.7 Primo Danmark A/S
3.7.1 Præsentation af virksomheden
Primo Danmark A/S fremstiller som underleverandør ekstruderede profiler i termoplastiske materialer. Profilerne bruges blandt andet i vinduesindustrien, hårde hvidevare-industrien,
byggeindustrien samt diverse brancher. PRIMO DANMARK A/S har kunder i såvel indland som udland.
I produktionen er de primære ressourceparametre plast af typerne: polyvinylklorid, polyolefiner, styrenbaseret plast, termoplastiske elastomer, polymethylmethacrylat og
farve-masterbatch.
3.7.2 Problemstilling
Processpild som kan genanvendes internt, udgjorde 10 % i 2002 – og stammer hovedsagligt fra opstart og indkøring.
Plastaffaldet, dvs. processpild, som ikke kan genanvendes internt, udgjorde 2 % i 2002 – og består fortrinsvis af større "klumper" fra opstart, materiale indeholdende stop-mix og
profiler der består af et materiale-mix: coektruderede typer, profiler med forstærkning og konfektionerede profiler med fx tape.
I dette projekt er det plastaffaldet som er undersøgt med henblik på at kunne genanvende mere internt eller eksternt som et led i Primos miljøstyringssystem.
3.7.3 Løsningsmuligheder
Ud fra en affaldsanalyse er forskellige muligheder for øget genanvendelse vurderet.
3.7.4 Forsøgsarbejde
3.7.4.1 Affaldsanalyse af mængder af kasseret procesmateriale I april 2003 er lavet en uges indsamlingsforsøg af kasseret procesmateriale fra de forskellige produktionslinier ved
Primo Danmark.
Fordeling mellem plasttyperne er vist i Tabel 3.6.
Tabel 3.6 Affaldsanalyse af fordelingen mellem kasserede plasttyper
Plastfraktion | % |
Øvrige | 47,5 1 |
PVC, hård | 23,1 |
PVC, blød | 7,1 |
ABS | 4,5 |
ABS, coeks. | 4,2 |
PP, coeks. | 3,6 |
PP | 3,3 |
TPE | 3,2 |
PVC, coeks | 2,4 |
PE | 0,9 |
PS | 0,3 |
1 indeholder mere end 85 % hård PVC
Mængderne af kasseret procesmateriale i Tabel 3.6 svarer til ca. 2,3 % af råvareforbruget ved Primo. Det skal bemærkes at der allerede genanvendes procesmateriale internt svarende
til ca. 10 % af råvareforbruget ved Primo.
På Figur 42 til Figur 46 er vist eksempler på de største affaldsfraktioner som udgøres af hård PVC, blød PVC og ABS.
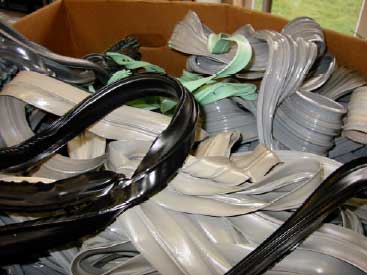
Figur 42 Hård PVC
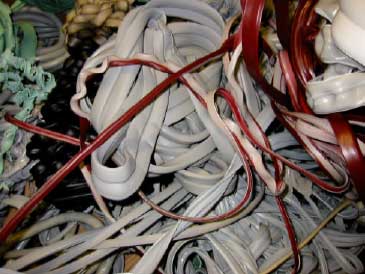
Figur 43 Hård PVC (opskummet)
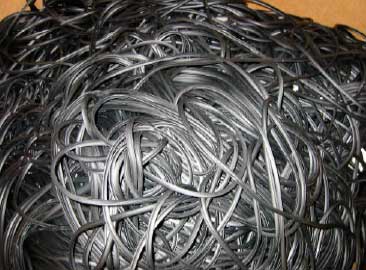
Figur 44 Blød PVC med polyesterkord.
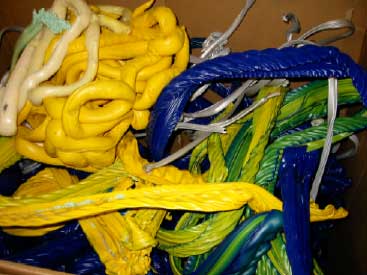
Figur 45 ABS
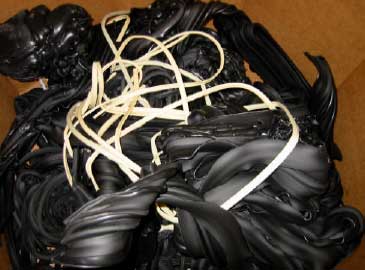
Figur 46 TPE
3.7.4.2 Muligheder for øget genvinding af kasseret procesmateriale Ud fra affaldsanalysen kan beregnes at 63,5 % af det procesmateriale der endnu ikke genanvendes internt
udgøres af hård PVC når indholdet i fraktionen "øvrige" medtages, mens resten er enkeltfraktioner af plasttyper som hver især udgør < 7 %. Det vil derfor være oplagt at koncentrere
indsatsen om den hårde PVC. Den hårde PVC forventes at kunne genanvendes efter passende neddeling hvilket enten kræver køb af udstyr eller afsætning til eksisterende oparbejdere.
I projektforløbet er herefter arbejdet videre med muligheder for øget intern genanvendelse.
Nogle af de blandede fraktioner er vanskelige at oparbejde. Eksempler er vist på Figur 47.
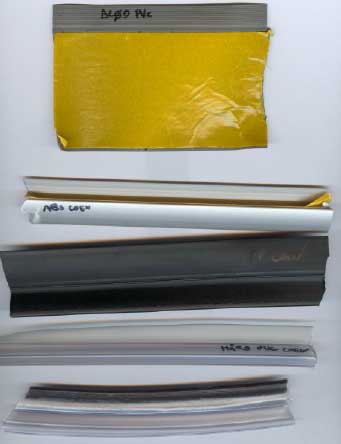
Figur 47 Laminater og coekstruderede emner
Øverst er vist blød PVC med påklistret tape, dernæst følger coekstruderede emner i ABS med blød overkant, PP med blød overkant, Hård PVC med blød overkant og en hård plast
fra fraktionen øvrige hvor der både er en blød coekstruderet del øverst og en indsat hård plastliste.
En simpel test er udført for blød PVC med pålimede papirtape. Strimlerne blev forsøgt fjernet ved opvarmning med damp og varm luft samt frysning til -18 °C. Ingen af metoderne
medførte tilfredsstillende frigørelse af tapen.
Ved neddeling vil man formentlig få problemer med fastsiddende PVC i neddelingsanlægget. Man vil muligvis kunne opløse limen med passende opløsningsmidler, men det forventes at
være en dyr løsning.
Den bløde PVC vil formentlig kunne blive behandlet termisk når der bliver etableret en vådpyrolyseproces ved Stigsnæs (RGS90) hvorved man vil undgå hovedparten af
restprodukterne da klorindholdet omdannes til salte.
Med hensyn til oparbejdning af de coekstruderede emner til plast af næsten virgin kvalitet vil der være potentiel mulighed for oparbejdning af emner hvor den coekstruderede bløde
plastdel har forskellig massefylde fra den hårde plast. Hvis man neddeler disse plasttyper til fx et par mm kornstørrelse, vil de to typer plast efterfølgende kunne separeres med
massefyldeseparation. Der vil så opstå en mindre forurening af de separerede fraktioner med de partikler som indeholder både den bløde og hårde plastdel.
På figuren er også vist et emne med indsat sort plastliste. Det forventes realistisk at en neddeling til 3-4 mm vil frigøre den sorte liste hvorefter det vil være muligt at fraseparere de sorte
partikler med farveseparation eller med massefyldeseparation hvis massefylden er forskellig af den sorte og klare plast. Da mængderne er små, vil separationen kun være relevant hvis
der benyttes eksisterende anlæg hvor separationen af en containerfuld kan udføres som lønarbejde.
Alternativt til separation kan de forskellige coekstruderede plasttyper forsøges afsat som en blandet plastfraktion som der kan fremstilles større emner af der ikke kræver så høj
mekanisk styrke som emner fremstillet i virgine plastmaterialer.
3.7.5 Konklusion
Primo Danmark genbruger allerede en meget stor del af det interne produktionsspild ved at have opstillet kværne direkte ved ekstruderingslinierne. Affaldsanalysen af det spild der ved
projektets start ikke kunne genanvendes internt, viser at ca. 2/3 udgøres af hård PVC som derfor er et af de områder hvor der efter affaldsanalysen har været gjort en indsats for øget
intern genanvendelse. Affaldsanalysen har generelt øget fokus på hvad der kan genanvendes internt og tallene fra 2002 til 2003 viser også en tydelig effekt. Intern genanvendelse er
således ændret fra 10,3% i 2002 til 11,8 % i 2003. Materiale til ekstern genanvendelse er ændret fra 2,66 % i 2002 til 0,57% i 2003 og kasseret materiale er reduceret fra 2,53 % i
2002 til 2,26 % i 2003.
| Forside | | Indhold | | Forrige | | Næste | | Top |
Version 1.0 Juni 2004, © Miljøstyrelsen.
|