| Forside | | Indhold | | Forrige | | Næste |
Centralised Sorting of Municipal Solid Waste
Summary
A new study "Centralised Sorting of Municipal Solid Waste" shows that is technically possible to utilise the organic fraction of municipal solid waste (OFMSW) without source-sorting
or separate collection.
The study is based on a project presenting a three months test operation of a so-called Dewaster [3] installation placed at the MSW incineration plant in Odense, Denmark. The test
installation was supplied by the Danish company Ewoc A/S. During the project, app. 30 tests were carried out, covering a total of app. 400 tonnes of MSW.
The project was carried out in co-operation between the energy company Elsam A/S and the environmental company NLM Combineering ApS, the latter being project manager. Ewoc
A/S operated the equipment during the project. The Danish EPA has supported the study financially.
Project background
Over the years, many efforts have been made to recycle the OFMSW in Denmark into biogas fermentation, and subsequent spreading of the residues on farmland. For the purpose of
biogas production, the OFMSW must be cleaned for plastic, glass, metal and other foreign matter, and the use on farmland requires that the OFMSW meets a number of chemical
requirements. So far, the efforts have been focused on source-sorting and separate collection. In spite of this, the OFMSW is often not clean enough to be utilised directly in biogas
fermentors without prior mechanical treatment.
The Dewaster system was originally developed for removal of plastic and other unwanted substances from the source-sorted OFMSW prior to biogas fermentation. So far the system
has been tested or is in operation for this purpose in Aarhus, Aalborg and Holbæk (Denmark), Hamburg (Germany) and Kristianstad (Sweden).
The fact that source-sorting and separate collecting are relatively expensive and troublesome, and often gives a poor result, rendering mechanical treatment inevitable is most cases, gave
the idea to test the Dewaster process on non-sorted MSW.
The sorting plant and test procedures
The Dewaster installation used in this study is basically identical with prior Ewoc-plants for treatment of source-sorted waste for biogas fermentation. Only a few adjustments were made
to compensate for the lower content of organic material in the waste.
The principle of the treatment is based on a gentle tearing/opening of the collection bags. In this process, large items like bicycles (bulky refuse), which should not be in the MSW in the
first place, are also removed. A screen takes out a light fraction of plastic, paper and packaging material (screen fraction). By means of a magnet, a Ferro metal fraction is then removed,
and a special device (Desizer) removes hard items like bones and woodblocks. In the last step, the pre-sorted OFMSW is pressed in a two stage screw-press into a reject fraction
containing plastic, paper, glass and fibres, and a clean OFMSW fraction (biopulp).
Click here to The diagram.
The diagram shows the working principle of the sorting process and the six outgoing fractions. The fractions are automatically placed in separate containers.
Results and discussion
During the tests, all incoming and outgoing fractions were weighed, and for every app. 15 tonnes MSW a mass balance was calculated. The Technical University of Denmark,
Environment and Resources (M&R DTU) took part in the tests four times during the study for sample-taking and validation. During these test days, samples were taken from the screen
fraction, the reject and the biopulp. The diagram below shows the obtained fractions.
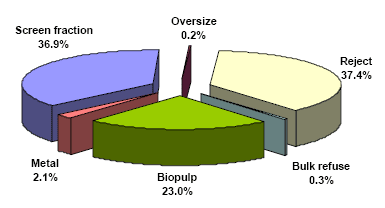
Biopulp
Generally, the pulp OFMSW can be described as a brown/grey pasty mush, which looks like sewage sludge, but does not have the characteristic smell of rotten material. Only in
connection with container discharge, a smell may arise, coming from anaerobic biological activity, otherwise the smell is a little sweet/sour. The biopulp is easily digestible in any existing
biogas plant.
From experience gained in a preliminary pilot test, a yield of OFMSW in the range of 20 – 25% (app. 28% dry matter) was expected. The pilot test gave a yield of 21%. The actual
average yield during the study was 23% (230 kg/tonne) with 29 – 34% DM, which fulfilled the expectations.
From the latest Danish study of the composition of MSW (published in 2003) we know that the OFMSW in Odense is app. 390 kg/tonne of the total MSW. The yield of 230 kg/tonne
in this study means that app. 59% of the organic material is sorted out of the MSW as biopulp. This is more than what is typically supplied to the biogas plant by sorting at the source
and separate collection.
According to the goals set, the level of heavy metals and other harmful substances in the biopulp should meet the requirements in Danish legislation at the time of the study. This goal has
been fulfilled, and in most cases with a good margin. Only the level of DEHP (Di(2-ethylhexyl) phthalate) is generally above the limit.
Only one sample does not meet the requirements for heavy metals (mercury) for use of OFMSW on farmland. The quantity of mercury in the load indicates that it may have come from a
thermometer illegally disposed of in the MSW. In a longer perspective, mercury is not expected to be a problem, since it is prohibited in consumer goods in the EU. The list below
shows the levels of heavy metals in eight samples, the values are presented as percentages of the limit values.
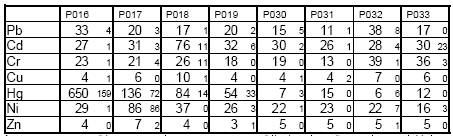
Average content of heavy metals as percentages of limit values for each metal. Values are based on two measurements (different laboratories). Small numbers indicate dispersion. In
sample P016 Hg is higher than allowed. In sample P017 the level of Hg is allowed when using the rule that some samples may exceed the limit by up to 50%.
The list below shows the results in real numbers and in percent of the limit values.

Values are displayed in mg/kg DM. The small numbers is the percentage of the limit value (NPE 10, PAH 3, DEHP 50, LAS 1300 mg/kg DM). LAS: Active component (anionic
detergent) in detergents and cleaning materials. NPE: Active component (non-ionic detergent) in detergents and cleaning materials, etc.
DEHP: Used as plasticiser in plastic products, e.g. PVC and Mac183. PAH: The sum of nine individual substances found in oil/tar products
The potential biogas production (of this 65% methane) is theoretically app. 193 Nm3/tonnes biopulp, based on 100% digestion of all VS (volatile substances). Analysis of the digestion
(EFOS – cattle) [4] shows that app. 93% of VS is digestible. The digestion has not been measured in a biogas reactor. Normally the EFOS analysis shows a somewhat higher yield than
what is practically obtainable. Compared to OFMSW obtained by source-sorting and separate collection, which typically gives a production of 100 – 150 Nm3 biogas/tonnes at 80%
digestion, the mechanically obtained biopulp is in the higher end.
Screen fraction
The screen fraction is very light and contains mainly plastic, paper, cardboard and textiles. The components are relatively large and intact and therefore easily recognisable. Some of the
common components are plastic bags, newspapers, food packaging and diapers.
One of the purposes of the study was to evaluate if this fraction could be used for co-burning in energy installations with higher electrical efficiency than waste incinerators. Or,
alternatively, if it could be utilised in industrial plants such as cement production. It was therefore the goal to increase the heat value and reduce the content of chloride, sulphur and alkali
metals. The list below shows a number of combustion parameters compared to the mixed MSW.

Average values, weighted average of the content in biopulp, oversize and reject
It is seen that the dry matter has a higher heat value than the average MSW. The removal of inorganic material and the high content of plastic can explain this. The dry matter content is
also increased but not as much as expected.
Reject
The reject is the dry fraction from the Dewaster screw-press. The fraction contains mainly paper- and plant fibres, plastic and inorganic components such as gravel, glass and aluminium.
There are basically three ways of disposing of this fraction: Incineration in a waste incinerator, co-burning in industrial plants or composting prior to landfill. The list below shows a
number of combustion parameters compared to the mixed MSW.

It is seen that the heat value is lower than for average MSW, which is explained by the higher ash content. The level of chloride is lower, while the level of alkali metals is higher than in
mixed MSW.
Metal
The metal fraction covers app. 2 per cent of the total MSW. The sorting quality was not optimised during the study, and the type of magnet used was not the best solution. Therefore,
visually, the metal was somewhat contaminated with organic material. Nevertheless, the company Uniscrap A/S has recycled the metal without problems. A previous study shows that
up to 70% of the sheet metal decomposes during incineration in a normal waste incineration plant. Most of the metal fraction is estimated to be sheet metal, which means that the
mechanical sorting plant has the potential of higher metal recycling.
ECONOMICAL EVALUATION
Capacity
During the tests, the average capacity of the test plant was app. 1.8 tonnes/hour on one Dewaster unit. The variation was 1.4 – 2.4 tonnes/hour (MSW). If the numbers are corrected
for the extra start-up and shut-down time, compared to a commercially operating plant, the capacity is estimated to be app. 2.0 tonnes MSW/hour. On a commercial plant in Århus for
treatment of source-sorted OFMSW, a number of improvements have been made, compared to the plant used in this study. The input to the Dewaster units on this plant is app. 2
tonnes/hour (after the screen fraction) even though the sorting quality is not optimal. It is estimated that a similar capacity can be obtained on mixed MSW, which means that the total
capacity should be up to 3 tonnes MSW/hour in a new installation.
Wear
The mechanical wear on the screw press is themost important cause of service and maintenance costs. During the construction of the plant in Århus, tfocus was on efforts to minimise
wear and tear. At the present stage of development, the screw press should be renovated for each app. 1000 tonnes.
It has during the study not been possible to gain precise data of the wear and tear when running on mixed MSW, but it is estimated that the wear is not significantly higher than when
running on source-sorted waste. On this basis all the economic estimates are based on the consumption of spare parts estimated for source-sorted waste.
Economy scenarios
During three scenarios, the economical basis on commercial mechanical waste separation was studied. The scenarios only focus on the costs directly connected to the sorting equipment
installation, operation and maintenance. Costs for buildings, administration and transportation etc. are not included in the scenarios. Also the potential value of the different fractions is not
included in the scenarios.
Scenario 1 is based on a new plant including two Dewaster units. The total capacity is set to 4 tonnes MSW/hour. The plant is operated in one-shift, app. 2100 hours per year. The
depreciation is made over five years at 6%. The plant price is estimated to be 7,500,000.00 DKK. It is estimated that the operator does not have other assignments.
The total cost of the operation is calculated to be app. 324.00 DKK/tonnes MSW
Scenario 2 is based on the same plant as scenario 1, but the plant is operated in two-shift, app. 4200 hours/year. The operator is assigned to other tasks during 50% of the time of
operation.
The total costs of the operation are calculated to be app. 192.00 DKK/tonnes MSW
Scenario 3 is based on the treatment of 100,000 tonnes MSW per year. The operation is based on two-shift on 8 Dewaster unit plants. The total capacity is 20 tonnes MSW/hour. The
depreciation time is raised to eight years at 6%. The plant price is estimated to be 23 mill. DKK. Two operators are estimated to be on the plant during operation.
The total cost of the operation is calculated to be app. 117.00 DKK/tonnes MSW
It is estimated that if only metal and biopulp are recycled, a decrease of 25% in waste for incineration is obtained. At an estimated cost of incineration of DKK 500.00/tonnes (incl.
environmental taxes), savings of DKK 125.00 are obtained, based on cost-free disposal of metal.
The biopulp generates a theoretical biogas yield of 194 Nm3/tonnes. Based on 70% digestion efficiency a realistic outcome is 136 Nm3 biogas. Based on biogas data from the Danish
Energy Authority (December 2001 and June 2002) an average profit from selling biogas energy can be estimated at app. DKK 2.00per Nm3 biogas, although there are large variations
between the different biogas plants.
The theoretical profit from selling biogas produced on biopulp is DKK 272 per tonne biopulp. If the expenses at the biogas plant for operation and spreading of the residues are
estimtated at DKK 70.00, the net energy value of the biopulp is app. DKK 202.00 per tonne. Giving 230 kg of biopulp per tonne of MSW (23%), one tonne of MSW has a biogas
value of app. DKK 46.00
In total, the mechanical sorting generates "savings" of DKK 125.00 and a "profit" of DKK 46.00, in total a margin of DKK 171.00 per tonnes MSW compared to incineration. This is
more than the expenses in scenario 3, and gives reason to assume that mechanical sorting of household waste with the Dewaster system can be profitable at large scale.
The above calculations and estimations are based on the financial conditions of the companies, and, thus, include savings of incineration taxes. Further, the calculations do not cover the
expenses relating to buildings, administration and transport etc. In a more specific evaluation of the economic consequences, the actual obtainable disposal price at the biogas producers,
the possible use of other fractions and the costs and benefits not quantified in the scenarios should be taken into consideration.
The environmental perspective of the project
The evaluation of previous projects regarding utilisation of OFMSW, all by source-sorting, shows that the environmental benefit is very small and very expensive to obtain. There are
two main reasons for this. The separate collection of "green" and "black" bags is expensive and energy-demanding, and it is only the organic fraction that is recycled, while the rest is
incinerated. Further, organic material is lost during the source-sorting when it is put into the wrong bag.
Collection of mixed MSW followed by mechanical separation of the waste into a number of fractions can possibly change this picture. The OFMSW can be obtained without costs of
installation, operation and environmental costs of the separate collection. Further, the potential quantity of organic material is increased, since nothing is lost in the wrong fraction.
Source-sorting is often just a question of using the organic fraction, while the mechanical sorting presented in this study has the potential of metal recycling and co-incineration.
In connection with the installation of new incineration plants, both environmental and economic benefit may be obtained by mechanical sorting of MSW combined with a smaller
incineration plant – or no incineration plant at all. In Denmark this has limited relevance since Denmark already has sufficient incineration capacity for the produced MSW, but in the UK
and the southern part of Europe it may be most relevant when MSW is no longer permitted on the landfills.
Referencer:
[3] The names Dewaster and Desizer is registered trademarks owned by EWOC A/S
[4] EFOS – cattle determines the content of enzymatic digestible biological material as simulation of the digestion in cattle.
| Forside | | Indhold | | Forrige | | Næste | | Top |
Version 1.0 August 2004, © Miljøstyrelsen.
|