| Forside | | Indhold | | Forrige | | Næste |
Udvikling af nye generationer fyldestationer, der muliggør påfyldning af CO2 i automobil- og køleindustrien
7 Projekt- & Produktspecifikationer
I det følgende beskrives de krav som har ligget til grund for udvikling af en mobil CO2 fyldestation til automobil industrien, baseret på de daværende sparsomme oplysninger som var givet fra BMW, AUDI
og VW.
Ref. Fragebogen og LV air-con CO2 (udkast)
7.1 Fragebogen
Deltager: AUDI: Hans Hammer, Diplom ingeniør, ansat i Versuch Kältekreislauf AGRAMKOW : Kai Kolbeck, Bjarne Lund
Besøget var specielt tilrettelagt med henblik på de teknologiske forhold i et CO2 anlæg, status på CO2 udvikling pt og fremover, hvordan AUDI og AGRAMKOW i vores gensidige samarbejde kan
bidrage til hinandens udvikling.
Tekniske afklaring:
- Skal CO2 anlæg evakueres: klart ja, da man ønsker så få fremmed partikler (luft og fugt) i kredsløbet som muligt
- Hvorfor er det vigtigt at kredsløbet ikke overfyldes: CO2 arbejder med et betydeligt højere tryk end 134a, hvorfor en stor overfyldning på fx 200g vil giv et øget tryk i kredsløbet med risiko for at
design trykket overstiges. LP siden er designet til 120 bar, HP siden til 160 bar (30 bar ved 134a). I meget varme landområder (fx Texas) vil der kunne opnås tryk af denne størrelse ved overfyldning.
Overfyldninger, vil grundet temperaturen på vores breddegrader, sandsynligvis ikke blive opdaget.
- Skal der gennemføres en tryktest før anlægget fyldes: det vil være meget tilrådeligt med en tryktest (montage test), da CO2 trykket ved 20 gr. er ca. 60 bar. Et prøvetryk på 20-30 vil efter al
sandsynlig hed være nok til at konstatere evt. montage fejl
- Med henblik på anlægget permeabilitet og garanti perioden, hvor stor skal overfyldningen være: pt ingen værdier
- Hvor meget CO2 kan anlægget miste før funktionen nedsættes: ca. 60%
- Er A/C med CO2 designet med henblik på udvidet diagnose funktioner: nej ikke udvidet i forhold til i dag
- Hvilken rolle spiller temperatur sensoren i kredsløbet: indført af hensyn til komfort regulering
- Hvornår regner man med at alle normer for CO2 ligger fast: skal være afsluttet i 2002 (gælder også spec på fyldestudser)
- Hvilken type kompressor olie skal anvendes: sikkert PAG med andre additiver
- Hvilken type kompressor anvendes for R&D test: LUK eller Valeo
- Hvilken afdeling af TÜV bruges: TÜV Sydtyskland München. Pt kun for normer og data
- Hvis CO2 kommer hvornår så: introduktion 2003, muligvis med Toyota som første
- Hvornår træffer AUDI sin afgørelse omkring CO2: afgørelse i 2001 (derfor indhentning af tilbud på CO2 fyldeanlæg). AUDI baserer sin afgørelse på det komfortmæssig område, da AUDI vil bruge
CO2 anlægget til både som aircon og varmepumpe (se også www.sae.org/misc/ac/presentations/hamwert.pdf). Det er af afgørende betydning at USA også går ind for CO2, en split løsning med 134a
i USA og CO2 i Europa er ikke tænkelig, med mindre der kommer en EU lov eller direktiv.
- Hvor stor er fyldevolumet: ca. det samme som i dag, men rør dimensioner er mindre LP Ø6 mm og HP Ø8 mm.
- Hvis AGRAMKOW skulle udvikle et fyldeudstyr for R&D test, hvilke processer skulle udstyret performe: tryktest – evakuering – fyldning – add on fyldning – kontrolleret afblæsning – muligvis
kontrolleret PAG fyldning
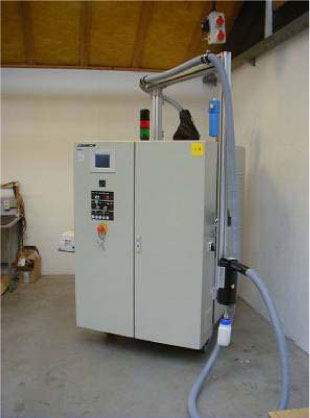
LV air-con CO2 (udkast)
7.2 Koncept
The equipment consists of a mobile unit which can be placed line side for continuously line production or be placed in the rectification area for repair work . The adapter (hereinafter called flex gun LP) is
connected to the CO2 circuit by the low pressure side nipple of the CO2 unit (hereinafter called LP) and performs the physical coupling between the CO2 unit and the mobile unit by a bundle of hoses
(hereinafter called hose management).
Two CO2 bottles can be connected to the mobile unit simultaneously.
Option: application with assembly test, the mobile unit is supplied with i.e. nitrogen by a bottle.
Option: applications with two side evacuation and one side charging the CO2 circuit of the CO2 unit is connected to an additional adapter (hereinafter called flex gun HP) by the high side nipple (hereinafter
called HP).
CO2 Process sequence
The unit performs an evacuation and a pressure charging of the CO2 circuit of the CO2 unit according to the following sequence (pls. note two side evacuation and one side charging):
- Option: Pressure increasing with i.e. nitrogen typically to 10-13 bar incl. continued control of major leakage. Typical process time 8-15 sec.
- Pressure equalization and pressure test (pressure drop) typical to less than 0,1 bar/sec. Typical process time 5-10 sec.
- Venting typical down to 0,5 bar. Typical process time 2-5 sec.
- 1.evacuation typically to less than 3-5 mbar incl. continued control of vacuum leakage (major and minor leakage). Typical process time 35-45 sec.
- Vacuum control for 5–10 sec. typical to less than 10-8 mbar incl. control of vacuum (pressure rise).
- 2. Evacuation typically to less than 3-5 mbar incl. continued control of vacuum leakage (minor leakage). Typical process time 5 sec.
- Charging incl. control of blocked nipple, charging time and amount. Typical process time 7-10 sec. (charging speed 80 gram/ sec.)
The times depend on the applications therefore the times mentioned are only directive. Furthermore the operator's handling time and the on-line units return time must be added to these times.
Operator sequence
When a CO2 unit arrives in the charging area the following operator sequence must be performed (pls. note two side evacuation and one side charging):
Lift the ergonomic designed flex guns out of the holsters and connect them to the CO2 nipples. Press gently at the start button of the flex gun LP to start the process.
The process runs automatically. The operator can monitor the process on the operator panel on the control cabinet. The operator can interrupt the process by pressing the stop button at the flex gun LP and
restart the process by pressing the start button at the flex gun LP or he can remove the flex guns from the nipples and place them into the holsters.
An acoustic sound indicates the end of the process.
The operator removes the flex guns from the nipples and places them into the holsters.
7.3 Teknisk løsning
Pump Cabinet
The hydraulic cabinet with integrated drip-tray contains a vacuum pump, a mass-flow, a mass-flow controller, accumulator, sensors, a valve terminal and process valves, and a internal pump with automatic
change over facility by empty bottle (including alarm warning).
All components fulfil the technical performance during evacuation and charging of CO2.
Option: applications with assembly test, the mobile unit is supplied with i.e. nitrogen by a bottle. All pressure relief device and safety valves are built-in incl. alarm for empty bottle.
Filling head
The flex guns are provided by a hose management consisting of evacuation and charging hoses.
The flex guns are made of light and operator friendly materials, environmental designed and with automatic clamping quick couplings.
The hose management is connected to the pump cabinet with a quick-connector for quick exchange.
Control cabinet (standard)
Cabinet built together with the main unit mechanical cabinet with all electrical switch gear and control modules including PLC.
The cabinet is built according to EN60204-1. The control cabinet has general control modules as control on/off, main switch etc. The configuration of the unit is also made for remote I/O connection
including the pneumatic control part. All sensors are connected with M8/12 approved remote plug terminals if possible.
The control cabinet has an operator panel (hereinafter called HMI) visualizing the process parameter, the process sequence with actual and pre-set units, the process faults, the unit faults and alarms that can
be modified through password protection.
The process technically related operator controls as manual, automatic operation, push buttons, pilot lamps etc. are placed at the HMI.
7.4 Specifikationer
PLC Control
PLC S7-315-2DP with ET200S/200X and TB170B (5,7”) operator touch panel for parameter settings, monitoring sequence steps with measured scaled values, process faults, equipment faults and alarms.
The following Siemens S7 versions will be used for the application software.
STEP 7 V. 5.2 + SP1, S7-GRAPH V. 5.1 + SP1, S7-PDIAG V. 5.1, Simatic ProTool/Pro V 6.0 + SP2, Simatic ProAgent V. 6.0 +SP2, NCM S7 Industrial Ethernet V. 5. + SP1, NCM S7 PROFIBUS
V. 5.2 + SP1, CP PtP Param V. 5. + SP2, FM 350-1/450-1 V. 5.1, FM 350-2 V 4.0.1, Simatic Net PC software V 6.1 + SP1.
Please note that AGRAMKOW reserves the right to use the latest versions at project start
Process capability
Cmk > 1,67 calculated by 50 samples of vacuum level as a function of fixed time (typical 30-40 sec.), and 50 samples of charged CO2. Vacuum range 5 – 2 mbar abs. ± 2 mbar. CO2 amount 400-3000
gram ± 1%
Pls note: the sample is not a normal distribution.
Calculation
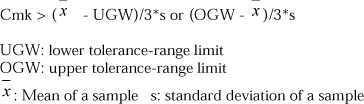
Technical performance rev. 18-9-02
General Data
Placing: The equipment must be placed indoors.
Ambient air temperature: 12 to 45°C
Atmospheric humidity: 30-90% (not condensing)
Transportation and storage: -25 to +55°C
Colour: RAL 7032 (light grey)
Electrical performance: According to IEC 204-1 or EN 60204-1
PUMP CABINET
1 Dimensions incl control panel (l x h x w): 1375 x 1650 x 8/0 mm
2 Weight: abt. 400 kg
3 Evacuation capacity: 16 m³/h
3.1 End vacuum (abs.): 0.5 mbar
3.2 Make: Leybold (2-stage)
3.3 Vacuum sensor type: ceramic diaphragm
3.3.1 Range (abs.): 0,1-200 mbar
3.3.2 Accuracy: ± 0,2% FS
4 Charging amount: 400 - 3,000 g
4.1 Charging speed: approx 50-100 g/s
4.2 Accuracy approx: ± 1%
4.3 Temperature compensation: 10 - 50° C
5 Refrigerant connection: ? male
5.1 Refrigerant: CO2
5.2 Inlet filter: Particle filter
5.3 Inlet pressure: max 100 bar
5.4 Pump capacity: 50-100 g/s at 20 °C
5.5 Max pressure: typical 70 bar
6 Refrigerant bottle: ? litre
7 Emptying level of bottle: tara + 2 kg (20° C)
8 Air connection: TEMA 1800 male
8.1 Allowable inlet pressure: 5-10 bar
8.2 Air consumption: 500 Nl/min. (NON lubricated)
9 Ventilation connection: NW16
9 Nitrogen/air pressure test (OPTION)
Allowable inlet pressure: max 20 bar
Nitrogen/air consumption: (A/C volume * pressure) litre (typical 240Nltr/min)
Pressure sensor type: ceramic diaphragm (IFM)
Range (abs.): 0-10bar
CONTROL PANEL (STANDARD)
Power consumption: abt. 4.0 kVA
Supply voltage: 3 x phase + N + PE
Frequency: 50 Hz or 60 Hz
Please note: Supply voltage and frequency in accordance with IEC 204-1 or EN 60204-1.
7.5 Opgavebeskrivelse DTI
AGRAMKOW Fluid Systems A/S ønsker at udvikle et færdigt prototypeanlæg til semiautomatisk fyldning af automobilklimaanlæg med CO2 som kølemiddel. Princippet bag den semiautomatiske
prototype, som er et mobilt udstyr med automatisk proces, skal være udgangspunkt for en videreudvikling af et on-line udstyr med automatisk proces til bilfabrikker.
Løsning af opgaven baseres på et system, hvor CO2 fra flaske påfyldes køleanlægget på en nippel mellem kompressor og receiver.
Fyldesekvensen er som standard: Trykprøvning, evakuering og fyldning. Standarden kan afviges, hvis det findes fordelagtigt i relation til en given konceptudformning for fyldeudstyret. For nærværende
opgave fokuseres dog kun på selve fyldeprocessen efter evakuering.
Proceskrav DTI
Fyldemængden på køleanlæg med et volumen på 1 til 2 liter er 400 g ± 1% med en CPK>1,67, og det er ønskeligt med en fyldehastighed omkring 100 g/s. Tilstanden i køleanlægget efter fyldning vil have
en densitet på minimum 200 til 400 kg/m³.
I gasform svarer dette til en tilstand i umiddelbar nærhed af det kritiske punkt (se figur 3).
Prototypen og det fremtidige fuldautomatiske udstyr skal kunne fungere ved omgivelsestemperaturer mellem 5°C (12°C?) og 40°C.
A/C-anlæggene, som skal fyldes, antages før fyldning at have samme temperatur som omgivelserne.
Fyldeanlægget skal kunne stå strømløs i en længere periode, og et system skal identificere, når CO2-flasken er tom og automatisk omskifte til en ny flaske.
7.6 Foranalyse, konceptbeskrivelse
Foranalyse
Udformningsvariable
Som princip kan der varieres på flaskens tilstand, som kan svinge frit med omgivelserne eller påtrykkes en fastlagt tilstand. Udtaget fra flasken kan være fastdefineret (væske, gas eller overkritisk) eller
variere frit med omgivelserne og flaskens fyldningsgrad.
Endelig kan udtag til fyldning kontrolleres uafhængigt af flasken ved at indskyde en afspændingsbeholder, som udligner svingninger i flaskeudtagets fasetilstande eller transformerer udtagets fase til en ny en
fase (f.eks. gas til væske).
Flaske ved:
Variable konditioner (5°C / (12°C?) til 40°C)
Fastpåtrykte konditioner (f.eks. 5°C eller 50°C)
Udtag fra flasken:
Gasfase (kræver fastpåtrykte flaskebetingelser) med topudtag
Væskefase (kræver fastpåtrykte flaskebetingelser) med dykrør
Overkritisk fase (kræver fastpåtrykte flaskebetingelser)
Gas/væske/overkritisk (variable flaskebetingelser) dykrør eller topudtag
OBS: Tilstanden C) Overkritisk fase i flasken kan kun opretholdes for en vis (begrænset) fyldningsgrad af flasken (se eksempelvis figur 3 og 4).
Udtag fra gasfasen resulterer i, at flasken afkøles under aftapning. Kvalitativt udtrykt kan det beskrives ved, at udtag af en given masse fra gasfasen skal modsvares af en tilsvarende fordampning fra
væskefasen. Normalt er varmetilførslen til fordampning begrænsende, og derved falder temperatur og tryk i flasken. Udtryk ved termodynamikkens 1. hovedsætning kan tappeprocessen fra flasken
(forenklet) beskrives som:
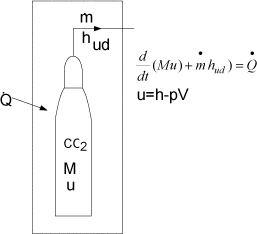
Ud fra denne lidt forenklede betragtning vil energitransporten ud af flasken være mindst, når tilstanden af CO2 på afgangen svarer mest mulig til den makroskopiske tilstand i flasken, dvs. som væske eller
overkritisk gas i de fleste tilfælde.
Uafhængig af flaskens konditioner og flaskens udtag kan til A/C-unitten påtvinges tre fastlagte tilstande:
Gasfase
Væskefase
Overkritisk fase
Tilstande i CO2-flasken under fyldning
Ved de specificerede omgivelsestemperaturer vil tilstanden i en helt fyldt flaske i nogle tilfælde være overkritisk eller en ligevægt mellem væske og gas.
![Figur 1: Faser i en fuld CO2-flaske ved forskellige omgivelsestemperaturer [Kilde: Hydrogas]](images/s23a.gif)
Figur 1: Faser i en fuld CO2-flaske ved forskellige omgivelsestemperaturer [Kilde: Hydrogas]
Fyldningsgraden af flasken bestemmer sammen med flaskens temperatur den tilstand, der hersker i flasken. Det bemærkes i figur 2, at kurven A ikke rammer mætningskurven, før temperaturen er mindre end
22,2°C. I dette tilfælde haves en flaske med høj fyldningsmængde, hvor densiteten ikke nødvendigvis er fastlagt af mætningskurven. I de fleste tilfælde leveres flasken dog kun 80% væskefyldt, og da kan
man regne med, at mætningskurven følges ved temperaturer under 31°C.
![Figur 2: Tilstande i en 100% fuld CO<sub>2</sub>-flaske ved forskellige omgivelsestemperaturer [Kilde: Hydrogas]](images/s23b.gif)
Figur 2: Tilstande i en 100% fuld CO2-flaske ved forskellige omgivelsestemperaturer [Kilde: Hydrogas]
Til vurdering af alternative fyldeprocesser er relevante tilstand indtegnet i nedenstående
log p-h diagram, som viser:
Starttilstand i flasken (røde kurver)
Tømning ved isoterme konditioner (grønne kurver)
Isochorer (konstant densitet) (blå kurver)
Isenthalpe ekspansionslinier (blågrønne kurver)
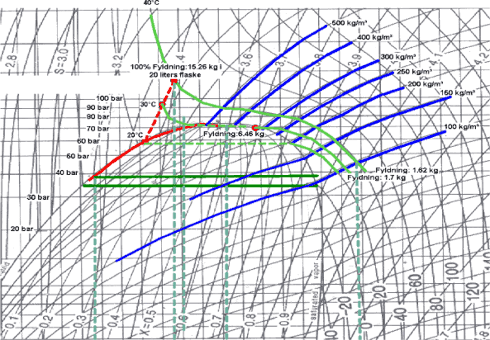
Figur 3: Tilstande angivet i log p-h diagram CO2-flaske
Baseret på kurverne i figur 3 kan alle løsninger baseret på fyldning direkte fra gasfasen i praksis udelukkes, da kravet til densiteten i den fyldte A/C-unit (400 kg/m³ ved 400 gram i et anlægsvolumen på 1
liter) kun kan opfyldes i et yderst snævert område umiddelbart under det kritiske punkt.
Fyldningen til A/C-unitten må altså - ud fra dette krav – nødvendigvis foregå fra væskefase eller en overkritisk tilstand.
Uden en afspændingsbeholder indskudt mellem flaske og A/C-unit angiver de grønne isotermer fyldeprocessen direkte fra en flaske med dykrør, hvor CO2 i udgangspunktet tages fra flasken i enten en
overkritisk tilstand eller fra væskefasen. I figur 4 er eksempler på trykket i flasken angivet under tømning gennem dykrør langs isotermerne 20°C, 30°C og 40°C.
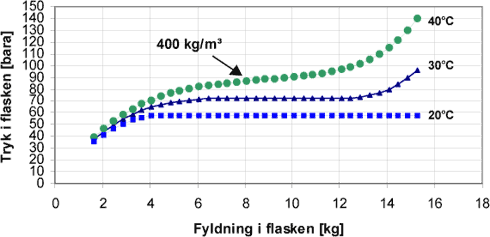
Figur 4: Tryk i CO2-flaske under isotermtappeproces med dykrør (Langs grønne kurver i figur 3)
De vandrette områder af kurverne angiver fyldning fra væskefase. I figur 4 er for isotermen 40°C angivet en pil ved en fyldning på ca. 8 kg, hvor densiteten falder under 400 kg/m³. Dette er i henhold til
kravene grænsen for fyldning direkte fra flaske. Et system som Behrs kan derfor ikke tømme CO2-flasken mere en 40-60% afhængig af CO2-flaskens fyldningsgrad og A/C-unittens tilstand (volumen og
temperatur).
Forsøg med fyldning fra flaske
Til vurdering af fyldning direkte fra flaske - uden afspændingsbeholder, pumpe, kompressor og andet udstyr - er der udført screeningsforsøg med fyldning fra flaske til en evakueret beholder ved 20°C med
volumen på 1,1 liter. Resultaterne er vist i tabel 1.
Udtag fra |
Flasketryk |
Indfyldt mængde |
Slutdensitet |
Gasdensitet på mætningskurven |
Væske |
35 bar / 0°C |
157 gram |
141 kg/m³ |
97,7 kg/m³ |
Gas |
35 bar / 0°C |
56 gram |
50 kg/m³ |
97,7 kg/m³ |
Væske |
45 bar / 10°C |
103 gram |
93 kg/m³ |
135,2 kg/m³ |
Overkritisk |
80 bar / 40°C |
200 gram |
182 kg/m³ |
277,7* kg/m³ |
Tabel 1: Fyldning direkte fra CO2-flaske til evakueret beholder (1,1 liter)
*) Tilstand ikke fastlagt på mætningskurven
Under ekspansion fra 45 bar er mængden af flashgas større end ved 35 bar, og fyldningsmængden er derfor mindre. Ved fyldningen fra væskefase kunne tøris ikke konstateres i prøvebeholderen. Trykket
opbygges momentant af flashgassen, som optager stort set hele volumenet i beholderen ved 5,2 bar. Det vurderes, at fyldning fra væske eller overkritisk tilstand bør afprøves i praksis før løsninger, hvor
A/C-anlægget forfyldes fra gasfasen.
Ekspansionstryktabet bør dog af hensyn til snedannelse i rør placeres så tæt på nippeltilslutningen som muligt.
| Forside | | Indhold | | Forrige | | Næste | | Top |
Version 1.0 November 2005, © Miljøstyrelsen.
|