| Til bund | | Forside |
Miljøprojekt nr. 1053, 2005
Ressourceeffektivitet - forslag til definition samt praktiske eksempler på anvendelse af begrebet
Indholdsfortegnelse
Forord
Sammenfatning og konklusioner
Summary and conclusions
1 Introduktion
2 Metodegrundlag
3 Farmaceutiske virksomheder
4 Møbelfremstilling
5 Elektriske og elektroniske komponenter
6 Galvanisk overfladebehandling
7 Køle/smøremidler
8 Sammenfatning og konklusioner
Referencer
BILAGSSAMLING
Forord
Nærværende projekt har til formål at opstille et forslag til definition af ressourceeffektivitet, der kan anvendes af virksomheder, brancher og myndigheder samt illustrere anvendelsen af denne definition
gennem en række konkrete eksempler.
Projektet er gennemført af Teknologisk Institut, Miljø- og Affaldsteknik i perioden marts til december 2002. I projektet deltog akademiing. MS. Econ. Kirsten Pommer (projektleder), civ.ing., lic.tech. Bjørn
Malmgren-Hansen og teknikuming. Steen Olesen. Endvidere har cand. scient. Lennart Staal Olsen, Teknologisk Institut og Flemming Dahl, Wilson Engineering A/S medvirket i dele af projektet.
Nærværende projekt er 100% finansieret af Miljøstyrelsen under Program for renere produkter.
Sammenfatning og konklusioner
Baggrund og formål
Baggrunden for projektet er at sætte fokus på udnyttelse af ressourcer og nedbringelse af affaldsmængder og at knytte dette til produkter set i et livscyklusperspektiv.
Det er projektets sigte at opstille et så enkelt værktøj som muligt, der kan anvendes af virksomheder, brancheorganisationer, myndigheder og andre til at identificere ressourcetab ud fra eksisterende data.
Ved at identificere de væsentligste ressourcetab er det muligt at overveje affaldsforebyggelse, der hvor det er mest relevant.
Projektet har følgende delmål:
- Opstilling af konkrete eksempler på, hvorledes ressourceeffektiviteten kan opgøres på baggrund af en kortlægning af et typisk produkts livsforløb.
Kortlægningen af livsforløbet er sket med forskellig baggrund for de valgte eksempler med det formål at illustrere, hvilken betydning et givet datagrundlag har.
- Afklaring af mulighederne for reduktion af affaldsmængderne for de valgte eksempler.
Her vil blive taget udgangspunkt i affaldskortlægningen og den vurdering af ressourcer, der indgår i bestemmelse af ressourceeffektiviteten.
Projektets resultat er således primært at afklare, om en enkel operationel metode kan opstilles, udpege hvilket datagrundlag der er nødvendigt og skitsere hvad og hvem der kan anvende den udviklede
metode.
Konkrete anvisninger på, hvordan den enkelte virksomhed eller branche kan anvende metoden, og hvilket datagrundlag der er tilgængeligt for et bestemt område ligger uden for dette projekts rammer.
Nærværende projektrapports målgruppe er ikke virksomheder, men myndigheder, fagfolk inden for miljøvurderinger og affald samt andre med interesse for emnet. Praktisk arbejde med ressourceeffektivitet
i virksomheder vil kræve en mere konkret beskrivelse af, hvad man skal gøre, og især hvordan data bringes tilveje, - fx som i Håndbog i miljøvurderinger - en enkle metode (Pommer et al., 2001), hvor en
række data er givet i opslagstabeller.
Definition af begrebet
Overordnet defineres ressourceeffektivitet som forholdet i procent mellem materialeindholdet i produktet og de ressourcer, der medgår i hele produktets livscyklus.
Opgørelsen af ressourceforbruget sker ud fra livscyklusprincipper. I denne sammenhæng opfattes materialer og energi som ressourcer. Sammenhængen mellem de nævnte størrelser kan illustreres ved
følgende:

Et produkts livscyklus omfatter de 4 faser:
- Råstofudvinding og forarbejdning af råstoffer
- Produktion af produktet
- Brug af produktet
- Affaldsbehandling og oparbejdning
I livsforløbet fokuseres på indgående materiale- og energistrømme.
Selve produktet defineres som det produkt, der forlader produktionsvirksomheden, og ressourceeffektiviteten relateres i alle tilfælde til denne produktenhed.
Det er valgt at definere 2 typer af ressourceeffektivitet – en baseret på forbrug af materialer og råstoffer og en baseret på UMIP-metodens vægtede opgørelse af ressourceforbrug – her betegnet en vurderet
opgørelse. Den første type baseret på opgørelse af materialeforbrug (M) viser direkte tabet af råstoffer og materialer gennem livscyklus. Den anden type, der er baseret på vægtede opgørelser (V), viser,
hvilke ressourcer der er knappe og som der derfor skal fokuseres særligt på.
Der er blevet arbejdet med følgende 6 definitioner af ressourceeffektivitet som er vist i følgende tabel.
Tabel 0.1
Betegnelse |
Omfatter |
Bemærkninger |
1. MMat. P+B |
Materialeforbruget ved produktion og brug af produktet. |
Kan anvendes af produktionsvirksomheder, der ønsker at sammenligne sig med lignende virksomheder eller som
ønsker at vurdere en produktionsændring. |
2. MMat. P+B+A/N |
Materialeforbruget ved produktion og brug af produktet
modregnet genvundne materialer. |
Kan anvendes af virksomheder, der ønsker at vurdere en produktændring, der fører til bedre
genanvendelsesmuligheder. Sammenligning af genanvendelse inden for en produktgruppe eller mellem forskellige
produktgrupper. |
3. MMat. R+P+B+A/N |
Råstofudvinding, produktion og brug modregnet genvundne
materialer. |
Viser, hvilke produkter der kræver et stort forbrug af råstoffer. Kan anvendes til sammenligning inden for en
produktgruppe, hvor forskellige materialer anvendes. |
4. VMat. R+P+B |
Vurdering af materialer ved råstofudvinding, produktion og brug. |
Giver en virksomhed viden om, hvilke materialer der er knappe og dermed miljøbelastende. Sammenligning inden
for en produktgruppe, hvor forskellige materialer anvendes. |
5. VMat.+energi, R+P+B |
Vurdering af materialer og energi ved råstofudvinding,
produktion og brug. |
Giver mulighed for at sammenligne materiale- og energiforbrug for et produkt eller en produktgruppe, hvor
materialer og energiforbrug er forskellige. |
6. VMat.+energi, R+P+B+A/N |
Vurdering af materialer og energi ved råstofudvinding,
produktion og brug og modregnet genvundne materialer og
energi. |
Giver mulighed for udpege de materialer, der ud fra et knaphedssynspunkt er de væsentligste at genanvende.
Sammenligner genanvendelse inden for en gruppe af produkter, hvor mulighederne er forskellige. |
Note til ovenstående tabel:
R: Råstoffer
P: Produktion
B: Brugsfase
A/N: Affaldsbehandling/nyttiggørelse
Eksemplerne
Der blev valgt at arbejde med meget forskellige eksempler med henblik på at afprøve definitionen af selve produktet og krav til datagrundlaget. Eksemplerne dækker over meget forskellige produkter og
forskellige livsforløb. Nogle eksempler illustrerer produkter, hvor brugsfasen er væsentlig. Andre eksempler illustrerer produkter, hvor genanvendelse er væsentlig. Endelig er der eksempler, der omfatter
produkter, hvori kemikalier, som almindeligvis er vanskelige at håndtere i en LCA-sammenhæng, har væsentlig betydning.
Data til kortlægningen af produkternes livsforløb er baseret på forskelligt materiale. I nogle eksempler er der taget udgangspunkt i tidligere gennemførte miljøvurderinger, i andre er data hentet fra grønne
regnskaber, og i andre igen er der taget kontakt til brancheforeninger og virksomheder.
Følgende blev medtaget i projektet:
Tabel 0.2
Eksempel |
Bemærkninger |
Produktion af 1 ton medicin |
Et repræsentativt gennemsnitsprodukt for denne type er vanskeligt at udpege, og oplysninger om produktet er derfor mangelfuldt. Der blev taget udgangspunkt i grønne
regnskaber, hvilket ikke giver tilstrækkelige oplysninger. |
Produktion af 1 ton møbler |
Der blev taget udgangspunkt i 3 repræsentative produkter, for hvilke der var gennemført livscyklusvurderinger. |
Produktion af
1 kg bestykket print,
1 kg transformer |
Der blev valgt 2 produkter inden for elektronik. Datagrundlaget var dels gennemførte livscyklusvurderinger og dels oplysninger fra producenter. |
Galvanisk
overfladebehandling |
Produktet blev defineret som behandling af en given overflade/mængde gods. Kortlægningen blev gennemført i samarbejde med en brancheekspert. |
Køle/smøremidler |
Produktet blev defineret som fjernelse af 1 ton spåner. Kortlægningen var ikke tilstrækkelig, og definitionen af produktet er begrænset anvendelig. |
Det bedste grundlag for en vurdering af ressourceeffektivitet er, at:
- produktet, dets ydelse og livsforløb er klart defineret.
- der foreligger en relativ detaljeret kortlægning af livsforløbet samt forbrug af råstoffer, hjælpestoffer og energi i hele produktets livscyklus. Grønne regnskaber er ikke tilstrækkelige.
- produktet ikke indeholder store mængder kemiske stoffer, for hvilke data som regel er mangelfulde.
De beregnede ressourceeffektiviteter er vist i følgende Tabel 0.3.
Tabel 0.3 Ressourceeffektivitet
|
Medicin |
Møbler |
Trans- former |
Fornikling/
forchromning |
Materialeopgørelse |
|
|
|
|
MMat. P+B |
28 % |
83 % |
60% |
39 % |
MMat. P+B+A/N |
43 % |
91 % |
224% |
39 % |
MMat. R+P+B+A/N |
8 % |
32 % |
109% |
10% |
Vurderet opgørelse |
|
|
|
|
VMat. R+P+B |
27-52 % |
69 % |
96% |
93 % |
VMat.+energi R+P+B |
17-33 % |
24 % |
56% |
91 % |
VMat.+energi, R+P+B+A/N |
17-33 % |
40 % |
178% |
91 % |
Beregninger for printkort, elforzinkning og varmforzinkning er ikke vist i tabellen, da disse ligner andre eksempler. Beregningerne for køle/smøremidler er ligeledes udeladt her, da definitionen af produktet er
vanskelig at håndtere og datagrundlaget mangelfuldt (se i øvrigt kapitel 8).
- For fremstilling af medicin ses, at omkring 75% af materialerne tabes ved fremstilling af medicin. Også i råstofudvindingen tabes i størrelsesordnen 75%, således at den samlede ressourceeffektivitet ligger på 5-10%. Effektiviteterne opgjort som vurderede størrelser er meget usikre, da sammensætningen af medicin ikke er kendt.
- For møbler ses, at tabet er omkring 20%. Da en lille del af materialerne til møbelproduktion udgøres af metaller, finder der en begrænset genanvendelse sted. Ved udvinding af råstoffer, olieudvinding, skovning af træ og oparbejdning af jernmalm er der yderligere et tab på omkring 2/3. I de vurderede opgørelser er træ som en fornyelig ressource ikke medtaget. Medtages energiforbruget og energiindholdet (især i træ), falder effektiviteten væsentligt. Genvinding af stål samt udnyttelse af træets brændværdi har betydning.
- For transformere er det altafgørende, at kobberet genanvendes. Genanvendelse af det store jernindhold betyder meget mindre for VMat.+energi, R+P+B+A/N end en højere genanvendelse af det ganske lille tinindhold på 0,1%. Effekttabet har herudover en afgørende indflydelse på ressourceeffektiviteten. En højeffektiv transformer vil således kunne øge ressourceeffektiviteten med en faktor 2-3 i forhold til en ineffektiv (og billig) transformer.
- For overfladebehandlingsprocessen fornikling/forchromning er materialetabet omkring 60%. Der sker ingen genvinding af metaller og andet kasseret materiale fra processen. I udvindingen af metaller og hjælpestoffer tabes omkring 75%, således at den samlede effektivitet baseret på materialer er omkring 10%. Det er metallerne, der er de væsentligste i den vurderede opgørelse. Hjælpestofferne forbruges og ikke findes i produktet. Effektivieterne for de vurderede opgørelser er derfor højere end dem baseret på materialemængder. Energiforbruget betyder meget lidt ressourcemæssigt i forhold til materialeforbruget.
Overordnet kan det konkluderes at:
- De opstillede ressourceeffektiviteter for elektronik og overfladebehandling kan anvendes som benchmarking for virksomheder, der arbejder med de her valgte produkter.
- Når det er afklaret, om datagrundlaget for ressourceeffektiviteterne for møbelområdet er tidssvarende, kan de opstillede effektiviteter anvendes som benchmarking.
- Ressourceeffektiviteterne for medicinalprodukter og køle/smøremidler kan ikke anvendes. Medicinalindustrien er inhomogen, og for køle/smøremidler kunne et produkt ikke defineres.
Ressourceeffektiviteten MMat. P+B+A/N blev sammenlignet med statistiske oplysninger om Direkte MaterialeInput (DMI) for at se, om der her var overensstemmelse. DMI står for tilgangen af materialer,
der dels udgøres af dansk råstofudvinding og importerede varer. Oplysningerne er opdelt på varetyper og materialetyper.
Ressourceeffektiviteten MMat. R+P+B+A/N blev sammenlignet med Total MaterialeInput (TMI) baseret på data fra Wuppertal Institute for at se, om der her var overensstemmelse. Wuppertals
MIPS-begreb står for Material Input Per Unit Service og omfatter den samlede mængde råstoffer, der er medgået til at fremstille et produkt.
Som det ses, er de opgjorte effektiviteter meget forskellige for de enkelte eksempler. De opgjorte størrelser afspejler, at:
- Et kemisk produkt som medicin kræver detaljeret viden om sammensætningen, hvilket ikke var tilfældet. Det var derfor vanskeligt at sammenligne med DMI og TMI.
- Et produkt baseret på almindeligt kendte materialer som møbler giver nogle fornuftige resultater, der er sammenlignelige med DMI og TMI, når kortlægningen er god.
- For specifikke elektronikkomponenter som printplader og transformere findes ikke data for DMI. Det har ikke været muligt at gennemføre en beregning af TMI, da der mangler data for
ædelmetallerne, som anses for at have stor betydning for en sådan beregning.
- Overfladebehandlingsprocessernes resultater giver fornuftige effektiviteter. Der kan ikke foretages en sammenligning med DMI, da der for DMI tages udgangspunkt i produkter. En sammenligning med
TMI viser store forskelle grundet forskel i data for udvinding af nikkel og zink.
- For anvendelse af køle/smøremidler var det ikke muligt at opgøre operationelle effektiviteter, da ydelsen ”Fjernelse af 1 ton spåner” var vanskelig at relatere til et egentligt produkt. Dertil kommer, at
køle/smøremidler er et kemisk produkt, for hvilket datagrundlaget var mangelfuldt.
Affaldsforebyggelse
Ud fra den viden, der er opnået gennem kortlægning og opstilling af ressourceeffektiviteter for de enkelte eksempler, er der foretaget en vurdering af mulighederne for affaldsforebyggelse. De væsentligste
forhold, der blev udpeget, er vist i følgende Tabel 0.4:
Tabel 0.4
Medicin |
Kortlægningen er mangelfuld, og mulighederne for affaldsforebyggelse er derfor vanskelige at udpege. Det skal sikres, at alle materialer, herunder materialer af biologisk oprindelse, opløsningsmidler og kemiske forbindelser, der forekommer som affald og restprodukter i produktionen, genvindes, når der er mulighed for det. |
Møbler |
Forbrænding med energiudnyttelse af alt ikke forurenet affaldstræ.
Øget genvinding af stål og anvendelse af lav-legeret stål, hvor det er muligt.
Indsamling af plastaffald og kasserede produkter med henblik på oparbejdning, - alternativt forbrænding med energiudnyttelse. |
Transformere |
Sikring af at transformere sendes til behandling, hvor kobber frasepareres og oparbejdes i kobbersmelteværk. Øget fokus på genanvendelse af tin fra lodninger i kobbersmelteværket.
Separat omsmeltning af separeret blik, hvor kobberrester så vidt muligt undgås. |
Fornikling/for-chromning |
Nikkel er en knap ressource, og der bør sigtes mod at genvinde dette metal i affaldet fra produktionen og fra kasserede produkter. Chrom tabes især i produktionen, og her bør
genvindingsmetoder udvikles. |
Diskussion
Opgørelse af ressourceeffektivitet og dermed identifikation af, hvor i et produkts livscyklus, der tabes ressourcer, er anvendeligt som en del af beslutningsgrundlaget ved ressourceoptimering og
affaldsminimering, når tilstrækkelige data er til stede.
For produkter, hvor der allerede forligger livscyklusvurderinger eller -kort-lægninger (LCI), vil der kunne opstilles ressourceeffektiviteter, som den enkelte virksomhed kan bruge til at sammenligne egne tal
med.
Den enkelte virksomhed kan umiddelbart opstille ressourceeffektiviteten MMat. P+B, mens de øvrige definerede ressourceeffektiviteter kræver data om genvinding, råstofudvinding og omsætning til
vurderede opgørelser, som ikke alle virksomheder antages at have kendskab til.
På myndigheds- og/eller ekspertniveau vil alle de 6 definerede ressourceeffektiviteter give oplysninger om, hvor i livscyklus der tabes ressourcer, betydningen af genvinding, og hvilke materialer der ud fra et
knaphedssynspunkt, betyder mest.
Det anbefales derfor at arbejde videre med problematikken omkring ressourceeffektivitet, da det kan blive et enkelt og anvendeligt værktøj for virksomheder, brancheorganisationer, myndigheder og andre
beslutningstagere.
Et af målene for LCA-videncentret er at få skabt overblik over, hvilke relevante data der foreligger i form af gennemførte livscyklusvurderinger og -kort-lægninger. Når dette arbejde er nået et
stykke/gennemført, er det væsentligt at få etableret et mere fyldestgørende og lettilgængeligt datagrundlag til beregning af vurderede opgørelser. Heri skal også tages hensyn til ændrede programmel (Gabi),
der skal erstatte UMIP-metodens LCV-værktøj.
Det anbefales endvidere at få udarbejdet et let tilgængeligt informationsmateriale sammen med relevante brancheorganisationer inden for udvalgte produktgrupper/sektorer med henblik på, at virksomheder
kan opnå forståelse for begrebet og anvende det i deres udviklingsarbejde og produktion. Her er det også væsentligt at få samlet så mange "grunddata" som muligt, så arbejdet med opstilling af
effektiviteterne dels tager udgangspunkt i virksomhedens egne tal og dels i data, der er let tilgængelige.
Summary and conclusions
Background and Objective
The background of the project is to focus on the exploitation of resources in waste and the reduction of the volumes of waste and to relate this knowledge to products in a life cycle perspective.
The project aims to set-up a tool which is as simple as possible and can be used by companies, trade organisations, and authorities etc. to identify the loss of resources based on existing data. By identifying
the most significant losses of resources it is possible to consider waste prevention where it is most relevant.
The project has the following sub targets:
- To list specific examples of how resource efficiency can be assessed based on a survey of a typical life cycle of a product.
The survey of the life cycle has been made with different settings for the selected examples in order to illustrate the importance of the basis of the data.
- To identify the possibilities of reducing the volumes of waste for the selected examples.
This phase is based on the survey of waste and the assessment of resources included in the determination of the resource efficiency.
The project is therefore primarily to determine if a single operational method can be laid down, point out the necessary data basis, and outline for what and by whom the method developed can be used.
Specific instructions on how an individual company or trade can use the method and a description of the data and documentation available within a certain sector are outside the scope of the project.
The target group of the present project report is not companies but authorities, experts within environmental assessments and waste and others with interest in the subject. Working in practice with resource
efficiency in companies will require a more specific description of what to do and especially how to procure data e.g. as in the handbook on environmental assessments, "Håndbog i miljøvurderinger - en
enkel metode" (Pommer et al., 2001), in which several data are available in reference tables.
Definition of the Concept
Resource efficiency can generally be defined as the ratio in percentage of the material content in the product and the resources used in the entire life cycle of the product.
The specification of the consumption of resource is based on life cycle principles. In this context materials and energy are regarded as resources. The connection between the elements can be illustrated as
follows:

The life cycle of a product includes four phases:
- Extracting and processing raw materials
- Manufacturing the product
- Using the product
- Waste treatment and processing
In the life cycle, focus is on input material and energy flows.
The actual product is defined as the product leaving the production enterprise and the resource efficiency is related to the product unit in all cases.
It was decided to define two types of resource efficiency - one based on the consumption of materials and raw materials, and one based on the prioritised assessment of resource consumption under the
UMIP method - in this context determined as an estimated assessment. The first type is based on assessment of the consumption of materials (M) showing the direct loss of raw materials and materials
throughout the life cycle. The other type, based on prioritised assessments (V), shows the resources that are scarce and therefore need special attention.
The following six definitions on resource efficiency have been used, cf. table 0.1.
Table 0.1 Six definitions on resource efficiency
Description |
Includes |
Note |
1. MMat. P+B |
The consumption of materials in manufac-ture and use of the product. |
Can be used by production enterprises who wish to compare themselves with similar enterprises or who wish to asses a change in the manufacturing process. |
2. MMat. P+B+A/N |
The consumption of materials in manufac-ture and use of the product, deducting the recovered materials. |
Can be used by production enterprises who wish to asses a change in the manufacturing process leading to better possibilities for recycling. Comparison of recycling within a product group or between different product groups. |
3. MMat. R+P+B+A/N |
Extraction of raw materials, manufacture and use of the product, deducting the recovered materials. |
Show the products that require a large consumption of raw materials. Can be used for comparison within a product group in which different materials are used. |
4. VMat. R+P+B |
Assessment of materials at extraction and manufacture and use of the product. |
Gives companies information on which materials are scarce and therefore burden the environment. Comparison within a product group in which different materials are used. |
5. VMat.+energi, R+P+B |
Assessment of materials and energy at extraction and manufacture and use of the product. |
Gives an opportunity to compare consumption of material and energy for a product or a product group in which the consumption of materials and energy is different. |
6. VMat.+energi, R+P+B+A/N |
Assessment of materials and energy at extraction and manufacture and use of the product deducting the recovered materials and energy. |
Gives an opportunity to select the materials that, on the basis of scarcity can be significant to reuse. Compares recycling within a group of products for which the possibilities are different. |
Note for table 0.1:
R: Raw materials
P: Manufacture
B: Phase of utilization
A/N: Waste treatment/ recovery
Examples
It was decided to work with very different examples with a view to testing the definition of the product itself and the requirement for the data basis. The examples cover very different products and different
life cycles. Some examples illustrate products for which the user phase is important. Other examples illustrate products for which recycling is important. Finally, there are examples that include products in
which chemicals that are normally difficult to handle in an LCA context are important.
Data for the survey of the products' life cycle are based on different materials. Some examples are based on environmental assessments carried out previously; others on data retrieved from green accounts,
and finally some are based on contact with trade organisations and companies.
The following examples are included in the project:
Table 0.2
Example |
Note |
Manufacturing of 1 tonne of medicine |
A representative average product for this type of product is difficult to point out and the information on the products is therefore insufficient. The data used is based on green accounts, which do not give
sufficient information. |
Manufacturing of 1 tonne of furniture |
Three representative products have been used for which life cycle assessments have been carried out. |
Manufacturing of
1 kg of printed circuit boards,
1 kg of transformer |
Two products have been selected within the electronics sector. The data were partly based on life cycle assessments that have been carried out and partly on information from the manufacturers. |
Galvanic finishing surface treatment |
The product was defined as treatment of a certain surface/quantity of materials. The survey was carried out in co-operation with an expert from the trade. |
Cooling agents and lubricants |
The product has been defined as removal of 1 tonne of metal shavings. The survey was not sufficient and the definition of the product can only be used for limited purposes. |
The best basis for an assessment of resource efficiency is that:
- the product, its performance and life cycle is well defined.
- a rather detailed survey of the life cycle and consumption of raw materials, additives, and energy in the entire life cycle of the product is available. Green accounts are not sufficient.
- the product does not consist of large quantities of chemical substances, for which data are usually insufficient.
The calculated resource efficiencies are shown in Table 0.3.
Table 0.3 Resource efficiency
|
Medicine |
Furniture |
Trans- former |
Nickeling/ Chroming |
Material statement |
|
|
|
|
MMat. P+B |
28 % |
83 % |
60% |
39 % |
MMat. P+B+A/N |
43 % |
91 % |
224 % |
39 % |
MMat. R+P+B+A/N |
8 % |
32 % |
109 % |
10% |
Assessed statement |
|
|
|
|
VMat. R+P+B |
27-52 % |
69 % |
96% |
93 % |
VMat.+energi R+P+B |
17-33 % |
24 % |
56 % |
91 % |
VMat.+energi, R+P+B+A/N |
17-33 % |
40 % |
178 % |
91 % |
Calculations for printed circuit boards, zinc electroplating and hot-dip galvanizing are not shown in the table as they are similar to other examples. The calculations for cooling agents and lubricants are also
excluded as the definition of the product is difficult to manage and the data are insufficient. (cf. also chapter 8).
- When manufacturing medicine, about 75% of the materials are lost when the medicine is manufactured. When extracting raw materials in the area of the 75% is also lost so that the total resource efficiency is
about 5-10%. Efficiency assessed as estimated values is very uncertain as the composition of the medicine is unknown.
- For furniture the loss is about 20%. As a small part of the materials for manufacturing furniture consist of metals, only limited recycling takes place. When extracting raw materials and oil, felling forest and
processing of iron ore further losses are 2/3. In the estimated assessments wood is not included as a renewable resource. If the energy consumption and contents are included (especially in wood), the
efficiency declines significantly. Recycling of steel and exploitation of the thermal value of the wood are important.
- For transformers it is crucial that the copper is reused. Recycling of the large content of iron is less important to VMat.+energi, R+P+B+A/N than high recycling of the rather small content of tin of 0.1%.
The performance of the transformer also has a decisive influence on the resource efficiency. A highly efficient transformer will therefore be able to increase resource efficiency by a factor 2-3 compared to an
inefficient (and cheap) transformer.
- For the process of surface finishing with nickel/chrome, the loss of materials is about 60%. There is no recycling of metals and other rejected materials from the process. When extracting metals and auxiliary
constituents about 75% is lost so that the total efficiency based on materials is about 10%. The metals are most important in the estimated statement. The additives used up and are not present in the product.
The efficiency for the estimated statements is therefore larger than those based on quantities of materials. The energy consumption has less influence on the use of resources than the consumption of materials.
Generally speaking the following conclusion can be drawn:
- The resource efficiency for electronics and coating stated above can be used as benchmarking for companies working with the selected products.
- When it has been clarified whether the data for resource efficiency within the furniture sector are up-to-date, the efficiency above can be used as a benchmark.
- The resource efficiency of pharmaceutical products and cooling agents and lubricants cannot be used. The pharmaceutical industry is not homogenous and with regard to cooling agents and lubricants it has
not been possible to define a product.
The resource efficiency MMat. P+B+A/N was compared with statistical information on Direct Material Input (DMI) to examine whether they are in conformity with each other. DMI is the intake of
materials, partly from Denmark and partly imported goods. The information is divided into types of goods and materials.
The resource efficiency MMat. R+P+B+A/N was compared with Total Material Input (TMI) based on data from Wuppertal Institute to investigate whether they are in conformity with each other. The
Wuppertals MIPS-concept is Material Input Per Unit Service and includes the total quantity of raw materials used to manufacture a certain product.
As seen in Table 0.3 the calculated efficiencies differ a lot for the different examples. The calculated efficiency reflects that
- a chemical product like medicine requires detailed knowledge on composition, which was not the case in the study. It has therefore been difficult to compare with DMI and TMI.
- a product based on ordinary materials such as furniture yields reasonable results that are comparable with DMI and TMI, when the survey is good.
- as for specific electronic components such as circuit boards and transformers, data on DMI cannot be retrieved. It has not been possible to calculate TMI, as data on precious metals, which are
considered to have a large impact on such a calculation, are not available.
- the results of the coating processes provide reasonable efficiency. Comparison with DMI cannot be made as DMI is based on products. A comparison with TMI shows large differences due to
variance in data on extraction of nickel and zinc.
- when using cooling agents and lubricants it has not been possible to assess the operational efficiency as the output. "Removal of 1 tonne metal fillings" has been difficult to relate to an actual product.
Furthermore, cooling agents and lubricants are chemical products for which the data are insufficient.
Prevention of waste
Based on the knowledge achieved in the survey and the tables on resource efficiency of each single example, an assessment on the possibilities for prevention of waste has been made. The most significant
issues identified are shown in table 0.4.
Table 0.4
Pharmaceutical products |
The survey is insufficient and it is therefore difficult to point out the possibilities to prevent waste. Efforts should be made to ensure that all materials including materials from biological sources, solvents and chemical compounds, which are present in waste and in residues from the manufacture are recovered when ever possible. |
Furniture |
Incineration with the use of energy of not too polluted waste wood.
Increased recovery of steel and use of low-alloy steel whenever possible.
Collection of plastic waste and scrap products with a view to reprocessing, alternatively incineration with the use of energy. |
Transformers |
Ensuring that transformers are sent for treatment where copper is separated and processed in a copper melting plant. More focus on recovery of tin from solders in the copper melting plant.
Separate remelting of separated sheet metal where residues of copper are avoided as much as possible. |
Nickeling/chroming |
Nickel is a scarce resource and the aim should be to recover the material in waste from the manufacture and from scrap products. Chromium is especially lost in the manufacturing process and methods for recovering the materials should be developed. |
Discussion
A statement of the resource efficiency and thereby identification of the phases of a product's life cycle in which resources are lost, can be used as part of the basis for decisions to optimise the resources and
minimise the waste when sufficient data can be retrieved.
For products on which life cycle assessments or surveys (LCI) have already been prepared, the individual company can use resource efficiency for comparing the company's own figures.
The individual company can set-up the resource efficiency MMat. P+B immediately, while other defined resource efficiencies require data on recovery and extraction of raw materials which must be
transferred to analyses. Not all companies have this knowledge.
At the level of authorities and/or experts, all six defined types of resource efficiency give information on where in the life cycle resources are lost, the importance of recovery and which materials from a
scarcity perspective are most important.
It is therefore recommended to continue working on the problems concerning resource efficiency as it can become a simple and useful tool for companies, trades, authorities and other decision-makers.
One of the objectives of the LCA-knowledge centre is to build-up general knowledge encompassing relevant, existing data from life cycle assessments and surveys. When the work has been partly/fully
carried out it is essential to establish a more adequate and accessible basis of data for calculation of analyses. This should include considerations of changing software (Gabi) that will replace the LCV tool in
the UMIP method.
Furthermore, it is recommended to prepare accessible information materials together with trade organisations within the selected product groups/sectors so that companies can realise the concept and use it
in their development work and manufacturing. It is also essential to gather as many "basic data" as possible so that the work on setting-up and calculating the efficiencies is partly based on figures from the
company and partly on accessible data.
1 Introduktion
1.1 Baggrund
I Miljøstyrelsens Prioriteringsplan for program for renere produkter m.v. fra 2001 sættes der fokus på udnyttelse af ressourcer og nedbringelse af affaldsmængder. Det nævnes fx at:
- Reducere det samlede materialeinput med en faktor 4 i 2020/30.
- Nedsætte materialeinputtet med en faktor 10 på længere sigt.
- Sikre, at prisen på råvarer afspejler miljøbelastningen ved indvinding, fremstilling og anvendelse af den pågældende ressource.
- Stabilisere affaldsmængderne på kort sigt og nedbringe dem på længere sigt.
- Overvåge udviklingen i ressourceforbruget og at sikre, at ressourceeffektiviteten ses i et livscyklusperspektiv.
I forhold til Prioriteringsplanens mål er der således behov for at se affaldsgenereringen i forhold til et produkt og hele dets livscyklus.
Der er arbejde i gang, både på internationalt plan og herhjemme, for at se på ressourceeffektivitet – hvordan dette begreb skal defineres, og hvorledes det kan gøres operationelt.
Inden for visse brancher er der blevet arbejdet meget med livscyklusvurderinger, og i dag findes der et godt datamateriale for udvalgte produkter/produkttyper, men langt fra alle.
Det at gennemføre en livscyklusvurdering kræver en stor indsats. Der er derfor behov for at afklare, om enklere metoder, baseret et produkts livscyklus eller dele heraf, kan anvendes til at måle
ressourceudnyttelsen og bidrage til at udpege områder, hvor affaldsforebyggelse bør prioriteres set ud fra et ressourcesynspunkt.
1.2 Formål
Nærværende projekt er et af de første udviklingsprojekter, der fokuserer på udnyttelse af ressourcer set i forhold til fremstillede produkter. Det har til formål at opstille et forslag til definition af
ressourceeffektivitet og illustrere anvendelsen af denne definition gennem en række konkrete eksempler. Projektet skal endvidere komme med forslag til affaldsforebyggelse.
Projektet gennemføres parallelt med projektet ”Udvikling af indikatorsystem for materialestrømme, ressourceforbrug og effektivitet samt affaldsstrømme”.
I nærværende projekt tages udgangspunkt i 4 udvalgte industribrancher, hvor der tidligere er sket en kortlægning af affaldsmængder (Pommer et al., 2004). De udvalgte brancher er:
- Farmaceutisk industri
- Elektronisk industri
- Møbelindustri samt
- Jern- og metalområdet illustreret ved galvanisk overfladebehandling og anvendelse af køle/smøremidler.
Det er projektets sigte at opstille et så enkelt værktøj som muligt, der kan anvendes af virksomheder, brancheorganisationer, myndigheder og andre til at identificere ressourcetab ud fra eksisterende data.
Ved at identificere de væsentligste ressourcetab er det muligt at overveje affaldsforebyggelse, der hvor det er mest relevant.
Projektet har følgende delmål:
- For hver af disse områder er det målet at opstille konkrete eksempler på, hvorledes ressourceeffektiviteten kan opgøres på baggrund af en kortlægning af et typisk produkts livsforløb.
Kortlægningen af livsforløbet er sket med forskellig baggrund for de valgte eksempler med det formål at illustrere, hvilken betydning et givet datagrundlag har.
- Derudover er det hensigten at afklare mulighederne for reduktion af affaldsmængderne for de valgte eksempler.
Her vil blive taget udgangspunkt i affaldskortlægningen og den vurdering af ressourcer, der indgår i bestemmelse af ressourceeffektiviteten.
- Afslutningsvis er det målet at foretage en vurdering af om ressourceudnyttelsen i Danmark ligger på linie med andre vesteuropæiske lande.
Projektets resultat er således primært at afklare, om en enkel operationel metode kan opstilles, udpege hvilket datagrundlag der er nødvendigt og skitsere, hvad og hvem der kan anvende den udviklede
metode.
Konkrete anvisninger på, hvordan den enkelte virksomhed eller branche kan anvende metoden og hvilket datagrundlag, der er tilgængeligt for et bestemt område, ligger uden for dette projekts rammer.
Nærværende projektrapports målgruppe er ikke virksomheder, men myndigheder, fagfolk inden for miljøvurderinger og affald samt andre med interesse for emnet. Praktisk arbejde med ressourceeffektivitet
i virksomheder vil kræve en mere konkret beskrivelse af, hvad man skal gøre, og især hvordan data bringes tilveje, - fx som i Håndbog i miljøvurderinger - en enkle metode (Pommer et al., 2001), hvor en
række data er givet i opslagstabeller.
1.3 Gennemførelse
Projektet er gennemført af Teknologisk Institut, Miljø- og Affaldsteknik i perioden marts 2002 til marts 2003.
Gennem projektforløbet er der løbende sket en koordinering med projektet ”Udvikling af indikatorsystem for materialestrømme, ressourceforbrug og effektivitet samt affaldsstrømme” (”Indikatorprojektet”)
ved deltagelse i dette projekts følgegruppe. Dette projekt gennemføres af DHI, Institut for produktion og ledelse samt Danmarks Statistik.
1.4 Projektdeltagere
Projektet er blevet gennemført af en arbejdsgruppe inden for Miljø- og Affaldsteknik. I arbejdet med galvanisk overfladebehandling har Flemming Dahl fra Wilson Engineering A/S medvirket.
Til projektet har været knyttet et følgegruppe bestående af:
Lone Kielberg (formand) |
Miljøstyrelsen |
Lone Lykke Nielsen |
Miljøstyrelsen |
Lisbeth Hagelund Hansen |
Dansk Industri |
Uffe Juul Andersen I/S |
Amagerforbrænding |
Karsten Krog Andersen |
DHI, Projektleder for ”Indikatorprojektet” |
Kirsten Pommer (projektleder) |
Teknologisk Institut |
1.5 Rapportens opbygning
I rapportens kapitel 2 er samlet en beskrivelse af principper, antagelser og generelle forudsætninger for den anvendte metode.
I kapitlerne 3 til 7 er kortlægningen og opgørelse af ressourceeffektivitet anført for de 5 produkteksempler. Detaljer omkring kortlægningen, særlige forudsætninger, datagrundlag m.m. er anført i bilag A til E
– et bilag for hvert eksempel.
Kapitel 8 er en sammenstilling af projektets resultater. Den udviklede og anvendte metodik præsenteres i kort form, og de opnåede erfaringer med anvendelsen af den diskuteres.
2 Metodegrundlag
2.1 Introduktion
Set i lyset af et overordnet ønske om at udnytte tilgængelige ressourcer bedst muligt er det væsentligt at kunne opgøre ressourceeffektiviteten for et produkt.
Overordnet defineres ressourceeffektivitet som:
Ressourceeffektivitet = ressourcer i produktet/samlet ressourceforbrug
Med ressourcer i produktet menes her den mængde materialer, produktet består af. Det kan fx være en plastkop af 100 gram PE eller en vinduesramme af 1 kg aluminium.
Opgørelse af ressourceforbruget sker ud fra livscyklusprincipper. Effektiviteten i udnyttelsen af ressourcer til et givet produkt eller aktivitet vurderes ud fra nøgletallene:
- Materialer i produktet
- Samlet forbrug af materialer, hjælpestoffer og energi i hele livsforløbet
- Tab af materialer i form af affald for hver livscyklusfase
- Genvundet materiale og energi
I denne sammenhæng opfattes materialer og energi som ressourcer. Sammenhængen mellem de nævnte størrelser kan illustreres ved følgende

Det at opstille en definition af begrebet ressourceeffektivitet ud fra livscyklusprincipper og afprøve brugen af definitionen har to overordnede formål:
- Det første er at opstille klare og anvendelige definitioner for begrebet, få klarhed over begrænsninger og forudsætninger samt afdække databehovet.
- Det andet er at afprøve de opstillede begreber og skabe klarhed over, hvilke definitioner der kan give de ønskede opgørelser af ressourceudnyttelsen i konkrete praktiske situationer.
Disse mål er nået gennem opstilling og afprøvning af en række eksempler. En diskussion af dette findes i rapportens kapitel 8.
Generelle anvisninger på, hvordan og i hvilke situationer begrebet kan anvendes, er anført sidst i dette kapitel og kommenteret under de respektive eksempler i kapitlerne 3 til 7.
I nærværende projekt er taget udgangspunkt i principperne for livscyklusvurdering efter UMIP-metoden, som er beskrevet i ”Miljøvurdering af produkter” (Wenzel et al., 1996) og i Pommer et al., 2001.
Den forenklede metode er blandt andet baseret på, at der fokuseres på indgående strømme i produktets livsforløb.
2.2 Identifikation af produkt og livsforløb
Da begrebet ressourceeffektivitet er forankret i en livscyklustankegang, er det nødvendigt at dreje tilgangen fra en proces- og industrivinkel til en mere produktorienteret tilgang.
De udvalgte industribrancher er:
- Farmaceutiske virksomheder
- Montage og fremstilling af elektriske komponenter uden serieproduktion
- Møbelfremstilling
- Galvanisk overfladebehandling
- Brug af køle/smøremidler
For de tre første brancher er det muligt at udpege repræsentative produkter og opstille et livsforløb for disse.
De to sidstnævnte brancher repræsenterer processer/aktiviteter, og her er det nødvendigt at opstille en del afgrænsninger og tillempninger for at anskue disse ud fra en livscyklustankegang.
Som udgangspunkt søges det at vurdere produktet ud fra hele dets livscyklus –fra råstofferne udvindes og til affald og restprodukter genbruges eller slutdisponeres. Dette princip, der direkte kan anvendes
inden for de tre første industriområder, er vist i figur 2.1.
I relation til figur 2.1 vil der blive lagt vægt på fremstilling af råstoffer og produktionen, hvor der fokuseres på forbrug af ressourcer og fremkomsten af affald. Betegnelsen "Råstoffer" dækker i denne rapport
over råstofudvinding og råvarefremstilling.
Brugsfasen anses kun for væsentlig, når der er et betydeligt materiale- eller energiforbrug. Ved bortskaffelsen, herunder forstås affaldsbehandling og/eller nyttiggørelse, fokuseres der på, om der almindeligvis
fremkommer genanvendelige materialer.
Galvanisk overfladebehandling og brugen af køle/smøremidler kan ikke uden videre gå ind under principperne vist i figur 2.2, da der her er tale om processer, der påvirker et eller flere produkter. Den
principielle angrebsvinkel, der her ligger til grund er vist i figur 2.2.
Produktet, som det opfattes i figur 2.2, er en given mængde behandlet emne. Den mængde energi og de materialer, der medgår, kortlægges ligesom der ses på, hvordan materialer og hjælpestoffer er
fremstillet. I det omfang det er muligt, gås der helt tilbage i livscyklus.
Affaldsstrømmene fra processen, som de fremkommer i figur 2.2, kortlægges i forhold til de aktuelle forhold, og det vurderes, om der sker en genvinding af materialestrømmene.
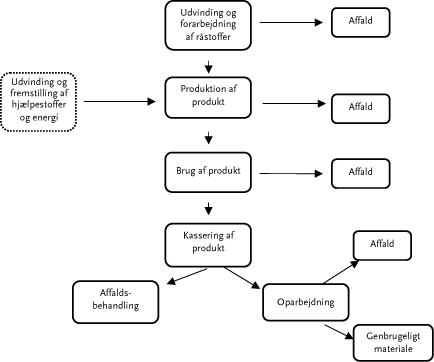
Figur 2.1 Principskitse for produkter set i et livscyklusperspektiv
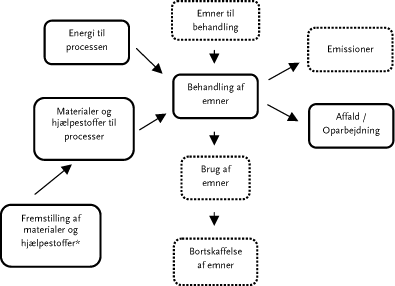
* Fremstilling af materialer og hjælpestoffer omfatter her materiale- og energiforbrug til udvinding, forarbejdning samt fremstilling herunder også de tab, der sker i form af affald.
Figur 2.2 Livscyklusperspektiv for processer
Fastlæggelse af en produktenhed er foretaget uafhængigt af hinanden inden for de 5 industrigrene.
- Inden for det farmaceutiske område er der taget udgangspunkt i formulering (blanding) og pakning af 1 ton medicinalprodukt.
- Inden for elektriske komponenter er der taget udgangspunkt i et printkort og en transformer.
- Inden for møbelområdet er der taget udgangspunkt i produktion af 1 ton møbler baseret på dansk gennemsnitsproduktion for branchen.
- Inden for galvanisk overfladebehandling er der taget udgangspunkt i behandling af henholdsvis 1.000 m² overflade og 1 ton gods ud fra en gennemsnitlig betragtning af danske aktiviteter på området.
- Brugen af køle/smøremidler tager udgangspunkt i skærende og spåntagende bearbejdning. Her er ”produktet” defineret som 1 ton fjernet materiale svarende til 1 ton spåner ud fra en gennemsnitlig
betragtning af danske aktiviteter på området.
2.3 Kortlægning
2.3.1 Fokus på indgående strømme
Den overordnede definition af ressourceeffektivitet tager udgangspunkt i forholdet mellem materialer i produktet og det samlede forbrug af ressourcer, hvilket begge er indgående strømme. Principper og data
fra den forenklede metode i Pommer et al., 2001 anvendes derfor.
Det principielle livsforløb med fokus på ressourceeffektivitet kan illustreres som vist i Figur 2.3. Begrebet Materialer i Figur 2.3 omfatter alle råvarer og materialer, der medgår til produktion af produktet.
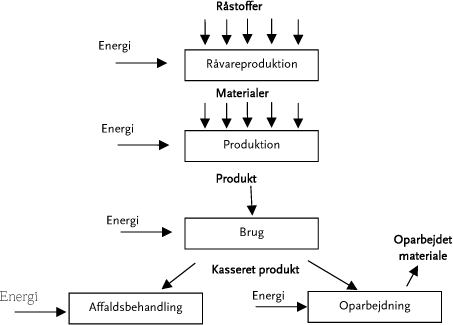
Figur 2.3 Livsforløb med fokus på ressourceforbrug
Affaldsstrømmene fremgår ikke af Figur 2.3, da affaldsmængderne beregnes indirekte ud fra antagelsen om at "Forbrug" - "Materialer i produktet" = "Affald".
En kortlægning kan illustreres ved følgende eksempel. Eksemplet er forenklet med henblik på at illustrere de væsentligste forhold. Der er ikke anvendt eksakte data, og eksemplet kan ikke anvendes i
praksis.
En vinduesramme består af aluminium. Vinduesrammen vejer 1 kg og defineres her som produktet. Kortlægningen er illustreret i Figur 2.4. Af figuren fremgår det, at der anvendes 3 kg råstoffer til fremstilling
af 1,1 kg aluminium. Af de 3 kg materialer, der indgår i udvinding og raffinering, bliver de 1,9 kg til affald. Under produktionen af vinduet fremkommer 0,1 kg affald, der i dette eksempel ikke kan
genanvendes. De kasserede vinduer indsamles og oparbejdes. Ved oparbejdningen kan 75% udnyttes, resten bliver til affald.
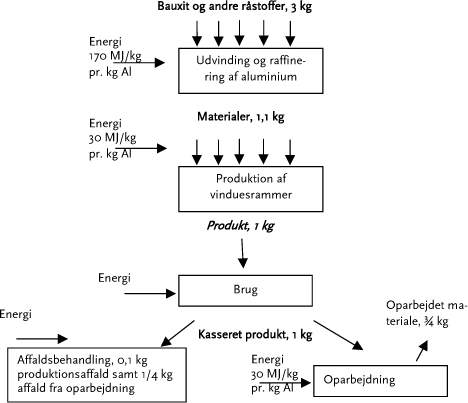
Figur 2.4 Eksempel på kortlægning af livsforløbet for en vinduesramme af aluminium
2.3.2 Afgrænsning og forudsætninger
2.3.2.1 Materialer
Materialeforbruget til produktionsvirksomheden er opgjort i mængde og type af materiale i forhold til en given mængde produceret produkt.
For de væsentligste materialer, der anvendes i et produkt, er det søgt at opgøre råstofforbruget. Det drejer sig fx om malm til fremstilling af metaller, skovet træ til træplanker eller råolie og naturgas til
fremstilling af basisplast.
For især kemikalier, der anvendes enten som hovedmaterialer (fx den farmaceutiske industri) eller som hjælpestoffer (fx lak til møbler eller glasmidler ved galvanisk overfladebehandling), er det ikke muligt at
opgøre forbruget af råstoffer og energi, da der ikke foreligger relevante data. I stedet er der anvendt estimater baseret på oplysninger om lignende kemikalietyper.
2.3.2.2 Energi
Energiforbruget i produktionsfase, ved brug og bortskaffelse er kortlagt med hensyn til mængde og energitype (kWh, kg olie, m³ naturgas). Alle energiforbrug omregnes til den fælles enhed primær energi,
hvor der er taget hensyn til energitab ved omdannelse til el eller varme.
Energiforbruget i råstoffasen er baseret på LCA-data fra Pommer et al., 2001.
Ved opstilling af en energibalance i en miljøvurdering medtages altid energiindholdet (brændværdien) af materialer. Dette gøres, for at der kan opnås balance i energiregnskabet, hvis materialet bortskaffes
ved forbrænding, hvor energiindholdet omsættes til forbrændingsvarme, der udnyttes.
2.3.2.3 Godskrivning
Materialer, der bliver genvundet ved indsamling og oparbejdning, opgøres og modregnes i materialeforbruget. Afhængig af de pågældende materiale vurderes indsamlingseffektivitet og tab ved oparbejdning.
Udvundne materialer, der er af samme kvalitet som de oprindelige, modregnes direkte. Er der en kvalitetsmæssig forskel på fx nyt og oparbejdet kobber, skal kvalitetsforringelsen vurderes, inden der kan
ske en modregning. I miljøvurderinger anvendes forskellige principper for modregning afhængig af, hvilke materialetyper det drejer sig om, og hvilken kvalitetsmæssig vurdering det er muligt at foretage.
Ved affaldsforbrænding udvikles energi. Udvundet energi, der kan anvendes, modregnes direkte i det samlede energiforbrug. Ved affaldsforbrænding regnes materialet som tab. Affald fra
forbrændingsprocessen opgøres ikke, da det er en udgående strøm.
2.3.2.4 Øvrige forhold
Ovenfor er nævnt de væsentligste afgrænsninger og forudsætninger. Generelt følges principperne i Pommer et al., 2001, hvor der fx er redegjort for, hvorledes energi opgøres og omregnes.
2.3.3 Former for opgørelse
Kortlægningen følger LCA-principper og medtager alle materialeforbrug – fra råstoffer udvindes, indirekte materialeforbrug til fx transport eller som proceshjælpemidler til produktet bortskaffes ved
affaldsbehandling eller oparbejdning.
Kortlægningens resultater præsenteres på to former. Først gives resultaterne af kortlægningen som en opgørelse af materiale- og energiforbrug. Dernæst fortages en omregning af mængdeopgørelserne, hvor
omregningen omfatter en skalering baseret på ressourcebelastningen.
2.3.3.1 Opgørelse af materialeforbrug
I den direkte opgørelse af materialeforbrug opgøres hvert betydende materiale med mængde og art. Energiforbruget opgøres i MJ primær energi. Vandforbruget opgøres særskilt.
2.3.3.2 En vurderet opgørelse
For hvert af de væsentlige materialer er der sket en omregning fra materialeforbrug til forbrug af råstoffer – en ”vurderet opgørelse”.
Omregningen til en ”vurderet opgørelse” er baseret på UMIP-metodens begreb vægtet opgørelse. Princippet i UMIP-metoden på dette punkt er, at alle materialer er tilegnet en faktor, der udtrykker
knapheden af den ressource, som materialet fremstilles ud fra. Knapheden er baseret på kendt forsyningshorisont og årligt forbrug. En vurderet opgørelse angives med enheden Person-Reserver (PR), og
faktoren har enheden PR/kg.
For et givet materialeforbrug, der indgår i produktionsprocessen, kan man således indregne råvarefasen, da dette ligger i den nævnte faktor. Eksempelvis fremstilles plast ud fra ressourcerne råolie og
naturgas. Når mængden og typen af plast er kendt, kan ressourceforbruget direkte beregnes. Efter UMIP-metoden medtages alle ressourceforbrug, også de indirekte forbrug til fx transport.
Fordelen ved at foretage denne omregning er dels, at man kan se, hvilke råstoffer der er knappe og derfor problematiske at bruge, og at forskellige råstofforbrug og energiforbrug kan lægges sammen.
Ofte anvendes enheden mPR i stedet for PR. Enheden mPR står for milli-Person-Reserver og er kun en operationel omregning for at kunne arbejde med passende talstørrelser.
Inden for metallerne er der meget stor forskel på de kendte reserver i verden og det årlige forbrug. Eksempelvis svarer 1 kg aluminium til 1,5 mPR og 1 kg jern til 0,08 mPR. Tallene for mPR viser, at
aluminium er en mere knap ressource end jern, og at det i en miljømæssig sammenhæng er mere problematisk at anvende aluminium end jern, hvis metallet ikke genanvendes. Ressourceforbruget opgjort i
mPR kan variere meget og ligger almindeligvis fra 0,001 mPR til 1.000 mPR pr. kg materiale.
Alle fornyelige ressourcer vil indgå med 0 i opgørelsen af mPR ud fra betragtningen om, at der ikke vil være knaphed på disse ressourcer. Vand betragtes i UMIP-metoden som en fornyelig ressource.
2.3.3.3 Datagrundlag
I Pommer et al., 2001 og i UMIP-værktøjet findes en række data for de mest almindelige materialer. Disse data er indsamlet under UMIP-projektet (Wenzel et al., 1996) suppleret med visse opdateringer.
Den væsentligste tabel i denne forbindelse er Håndbogens tabel B.1, der giver oplysninger om det samlede ressourceforbrug inklusive indirekte forbrug, der er medgået fra råstofudvinding og til materialet
kan anvendes på en produktionsvirksomhed.
De øvrige tabeller i Håndbogen giver oplysninger om energiforbrug ved udvinding, energiindhold i materialet og energiforbrug ved udvalgte processer.
Anvendelse af disse tabeller gør, at det ikke er nødvendigt at kortlægge materialets første livscyklustrin – råvarefasen.
2.3.3.4 Et eksempel
Fra eksemplet vist i Figur 2.4 kan det ses, at for at producere 1 kg vinduesramme (1 kg produkt) anvendes 1,1 kg materialer, som medfører et forbrug på 3 kg råstoffer. Ressourceeffektiviteten baseret på materialeforbrug kan således direkte udregnes i procent. Der regnes med, at 75% af materialet i vinduesrammen efter oparbejdning kan anvendes til samme eller andre formål. Nettoforbruget er således 0,25 kg + 0,1 kg (tab ved produktion) = 0,35 kg. Med udgangspunkt i nettoforbruget skal der bruges 0,35kg/1kg × 3 kg råstoffer = 1,05 kg råstoffer.
Omregnes data fra Figur 2.4 til en vurderet opgørelse haves, at materialeindholdet i vinduesrammen (produktet) udgør 1 kg × 1,5 mPR/kg = 1,5 mPR. Det samlede materialeforbrug er på 1,1 kg og udgør derfor 1,1 × 1,5 mPR/kg = 1,65 mPR. Energiforbruget medtages her. Der forbruges 170 MJ/kg til udvinding af 1 kg aluminium og 30 MJ i produktionen, hvilket svarer til 200 MJ/kg. For 1,1 kg svarer dette til 220 MJ/kg. Omregnes dette energiforbrug til forbrug af energiressourcer, svarer det til 220MJ / 1.025 MJ/mPR råolie = 0,21 mPR råolie. Det samlede ressourceforbrug til fremstilling af vinduesrammen er derfor 1,65 mPR + 0,21 mPR = 1,86 mPR i forhold til ressourceindholdet i produktet på 1,5 mPR.
Kortlægningen giver således mulighed for at opstille tal for ressourceindholdet i produktet og det samlede ressourceforbrug til brug for beregning af ressourceeffektiviteten.
2.4 Ressourceeffektivitet
Principielt opgøres ressourceeffektiviteten ud fra ressourcer i produktet i forhold til det samlede ressourceforbrug ved fremstilling af produktet.
Ressourceeffektiviteten kan opgøres på 2 principielt forskellige måder – enten på basis af vægtbaseret materialeforbrug (M) eller på basis af vurderede opgørelser (V).
Effektiviteten opgjort ud fra mængden af materialer i produktet i forhold til det samlede forbrug kan defineres forskelligt afhængig af, hvilke dele af produktets livscyklus der medtages. Her anvendes
forkortelserne R, P, B og A/N, der står for:
R: |
Råstoffase, der omfatter udvinding af råstoffer og forarbejdning af disse, så de fremtræder som de råvarer og hjælpestoffer en produktionsvirksomhed anvender. Aktiviteten omfatter fx udvinding af
malm og oparbejdning af disse til metaller eller udvinding af olie og gas samt forarbejdning af disse råstoffer til plast. |
P: |
Produktionsfase, der omfatter aktiviteter på den virksomhed, der fremstiller produktet. |
B: |
Brugsfase, der omfatter produktets livsforløb, fra det forlader produktionsvirksomheden, til produktets kasseres. Denne fase kan omfatte aktiviteter som vedligehold, energiforbrug eller ingen
aktiviteter. |
A/N: |
Affaldsbehandling og/eller nyttiggørelse omfatter produktets sidste livscyklustrin. Det kan være indsamling og deponering eller forbrænding med nyttiggørelse af energi afhængig af produktets karakter.
Det kan også omfatte indsamling og oparbejdning til genbrugelige materialer. Affaldsbehandling og/eller nyttiggørelse betegnes under et som bortskaffelse. |
Alle opstillede forhold mellem indhold i produktet og forbrug udtrykkes i procent.
De tre ressourceeffektiviteter baseret på mængde af materiale omfatter forskellige dele af produktets livscyklus og defineres som:
- Mmat. P+B, der betegnes ”Materialeforbrug, produktion og brug” og omfatter materiale i produktet sat i forhold til samlet materialemængde forbrugt ved produktion og brug.
- Mmat. P+B+A/N, der betegnes ”Materialeforbrug, produktion, brug og bortskaffelse” og omfatter materiale i produktet sat i forhold til samlet materialeforbrug ved produktion, brug, affaldsbehandling og modregnet oparbejdet materiale.
- Mmat. R+P+B+A/N, der betegnes ”Materialeforbrug, hele livscyklus” og omfatter materiale i produktet sat i forhold til det samlede materialeforbrug i råstoffasen, produktion, brug, affaldsbehandling og modregnet oparbejdet materiale.
De opstillede ressourceeffektiviteter baseret på mængden af materialer har indekset Mmat. for at understrege, at der kun er medtaget forbrug af materialer.
Endnu en definition af materialebaserede ressourceeffektiviteter er defineret:
- Mmat+energi, R+P+B+A/N, som betegnes ”Materiale- og energiforbrug, hele livscyklus” og omfatter materiale i produktet sat i forhold til det samlede materiale- og energiforbrug i råstoffasen, produktion, brug, affaldsbehandling og modregnet oparbejdet materiale samt genvundet energi.
Mmat+energi, R+P+B+O/A er relevant for produkter, hvor der i brugsfasen er et stort energiforbrug. Energiforbruget medtages ved at omregne energiforbruget i MJ til mængden af energiråstoffer, som er
forbrugt ved produktionen af energien. Mængden af forbrugte materialer og energiråstoffer kan så lægges sammen.
De vurderede opgørelser af ressourceeffektivitet (V) giver mulighed for at alene at medtage materialeforbruget eller at opgøre materialeforbrug og energiforbrug under et.
I opgørelsesmetoden ligger der, at ressourceforbruget i råvarefasen beregnes ud fra materialemængden, som går ind i produktionsfasen, ganget med en knaphedsfaktor. Dette betyder, at råvarefasen i den
vurderede opgørelse ikke behøver at blive kortlagt. Ressourceforbruget til selve materialet og hjælpestoffer er indregnet i faktoren.
De tre ressourceeffektiviteter baseret på vurderede opgørelser omfatter forskellige dele af livscyklus og er defineret som:
- Vmat., R+P+B, som betegnes ”Ressourceforbrug, materialer” og omfatter en vurderet opgørelse af materialemængden i produktet sat i forhold til en vurderet opgørelse af materialeforbruget i råvarefase, ved produktion og ved brug.
- Vmat.+energi, R+P+B, som betegnes ”Ressourceforbrug, materialer og energi” og omfatter en vurderet opgørelse af materialemængden i produktet sat i forhold til en vurderet opgørelse af materiale- og energiforbrug i råvarefase, ved produktion og ved brug.
- Vmat.+energi, R+P+B+A/N, som betegnes ”Ressourceforbrug, hele livscyklus” og således en vurderet opgørelse af materialemængden i produktet sat i forhold til en vurderet opgørelse af materiale- og energiforbrug i råvarefase, ved produktion og brug samt ved affaldsbehandling og modregnet oparbejdet materiale samt genvundet energi.
Kendes materialeforbruget til produktionen, kan råstofforbruget direkte slås op i tabeller angivet i mPR pr. kg materiale for almindeligt kendte materialer. I nærværende projekt er anvendt tabeller fra
Pommer et al., 2001.
For begge typer af opstillede ressourceeffektiviteter (M/V) gælder det, at for de effektiviteter, hvor oparbejdning ikke indgår, vil den beregnede effektivitet ligge på mellem 0 og 100%.
For de ressourceeffektiviteter (både M og V), hvor oparbejdning indgår, kan den beregnede effektivitet blive over 100%. Procenten bliver over 100, når forbrugt materiale minus oparbejdet materiale udgør
en mindre mængde end den mængde, der indgår i produktet.
Disse former for beregning af ressourceeffektivitet er defineret i det følgende og illustreret med et eksempel.
2.4.1 Materialeforbrug, produktion og brug
I forhold til en livscyklusbetragtning er det, der er medtaget i definitionen af
Mmat. P+B illustreret i figur 2.5. Det, der er angivet med grå skravering i figuren, er medtaget.

Figur 2.5 Materialestrømme i begrebet Mmat. P+B, Materialeforbrug, produktion og brug
De fleste produktionsvirksomheder har kendskab til, hvorledes deres produkter skal bruges, og en beregning af Mmat. P+B vil fx kunne anvendes af en virksomhed, der ønsker at sammenligne sig med
andre lignende virksomheder eller ønsker at vurdere en produktionsændring.
Ressourceeffektiviteten på materialeniveau tager udgangspunkt i opgjorte vægtenheder og defineres alene ud fra materialeopgørelsen som:
![M mat. P+B = Materialer i produktet [kg]/Samlet materialeforbrug [kg] × 100%](images/s037b.gif)
Mængden af materialer i produktet vil være 1 kg eller 1 ton. Det samlede materialeforbrug vil være materialeforbruget i produktionsfasen og eventuelt brugsfasen. Hjælpestoffer vil være taget med, hvor det
er relevant.
Hvor det er relevant, kan forbruget af vand og energi sættes i forhold til materialer i produktet. For strømforbrugende apparater vil brugsfasen have meget stor betydning. Energi udviklet ved fx forbrænding
vil blive opgjort særskilt i energiopgørelsen, hvis den udviklede energi erstatter andre energiforbrug.
Eksempelvis er vandforbruget i gennemsnit 80 m³ pr. ton farmaceutisk produkt, og tilsvarende er det primære energiforbrug til 1260 GJ pr. ton farmaceutisk produkt.
I kortlægningen af vinduesrammen (figur 2.4) er det vist, at produktet indeholder 1 kg materialer, og at materialeforbruget ved produktionen er 1,1 kg. Effektiviteten kan derfor beregnes til:
Mmat. P+B = 1 kg / 1,1 kg × 100% = 91 %
2.4.2 Materialeforbrug, produktion, brug og bortskaffelse
For en række produkter er det væsentligt at se på affaldsbortskaffelsen og mulighederne for at genanvende oparbejdede produkter. I definitionen af Mmat. P+B+A/N ligger en modregning af genanvendte
materialer fra produktets produktions-, brugs- og affaldsfase, hvis det er almindeligt. Dette er illustreret i figur 2.6.

Figur 2.6 Materialestrømme i begrebet Mmat. P+B+A/N , Materialeforbrug, produktion, brug og bortskaffelse
En beregning af Mmat. P+B+A/N i forhold til Mmat. P+B viser, hvilken betydning oparbejdning af kasserede produkter og genanvendelse af materialer har for et givet produkt.
Beregning af ressourceeffektiviteten Mmat. P+B+A/N er også relevant for andre end virksomheder. For produktionsvirksomheder kan beregningen fx anvendes i forbindelse med produktændringer, der
fører til bedre genanvendelsesmuligheder.
For andre, der ønsker at sammenligne genanvendelsesmulighederne inden for en produktgruppe eller sammenligne genanvendelsesmulighederne for forskellige produktgrupper, kan forskellen mellem Mmat.
P+B+A/N og Mmat. P+B give en god indikation.
Ressourceforbruget kan så defineres som:
![M mat. P+B+A/N = Materialer i produktet [kg]/Nettoforbrug af materialer [kg] × 100%](images/s038b.gif)
Ressourceeffektiviteten baseret på det samlede materialeforbrug vil altid være en procent mellem 1 og 100. Ressourceeffektiviteten baseret på nettoforbruget af materialer kan være en procent over 100.
I kortlægningen af vinduesrammen i Figur 2.4 er det vist, at 0,75 kg af materialet i vinduesrammen efter oparbejdning kan anvendes til samme eller andre formål. Nettoforbruget af materialer er således 1,1
kg – 0,75 kg = 0,35 kg. Effektiviteten kan derfor beregnes til:
Mmat. P+B+A/N = 1 kg / 0,35 kg × 100% = 286%
I nærværende eksempel er det antaget, at oparbejdet aluminium er af samme kvalitet som det, der bruges til fremstilling af produktet, og der kan ske en direkte modregning. I andre tilfælde vil oparbejdet
materiale ikke have den samme kvalitet – fx aluminium anvendt til elektromotorer – og her må så foretages en vurdering af det oparbejdede materiales "værdi" i forhold til nyt materiale.
2.4.3 Materialeforbrug, hele livscyklus
I forbindelse med udvinding og oparbejdning af råstoffer til materialer ligger ofte store tab af materialer. Dette er illustreret i opgørelsen af Mmat. R+P+B+A/N , hvor hele produktets livscyklus er medtaget.
Grafisk er det illustreret i figur 2.7.

Figur 2.7 Materialestrømme i begrebet Mmat. R+P+B+A/N , Materialeforbrug, hele livscyklus
En beregning af Mmat. R+P+B+A/N udtrykker det samlede forbrug af materialer i forhold til det fremstillede produkt og vil ud fra en livscyklustankegang være den mest korrekte definition at anvende.
Den vil dog for nogen være abstrakt, da det at tænke på forskellige materialers tilblivelse ikke altid er lige let. Samtidig er data for råvarefasen ikke umiddelbart tilgængelige. Råvarefasen kan dække over en
række produktionsprocesser. Det gælder især for kemiske produkter, og her vil det være en meget omfattende opgave at gennemføre en opgørelse af materialeforbrug.
Såfremt det er muligt at kortlægge råvarefasen for et konkret produkt eller en produkttype, vil det give et godt billede af, hvilke materialer der kræver mange råstoffer at fremstille, og hvilke der kræver få.
I de to ovenstående definitioner er ikke medtaget det første led i livscyklus, råstofudvindingen. Medtages dette for nettoforbruget af materialer, kan denne ressourceeffektivitet defineres som:
![M mat. R+P+B+A/N = Materialer i produktet [kg]/Nettoforbrug af råstoffer [kg] × 100%](images/s039b.gif)
Da der typisk bruges flere kg råstof til fremstilling af 1 kg materiale, kan Mmat. R+P+B+A/N udtrykt i procent blive et meget lille tal, hvis der ikke er nogen genanvendelse af materialer.
I kortlægningen af vinduesrammen i Figur 2.4 er det vist, at der til produktion af 1,1 kg materialer medgår en råstofmængde på 3 kg. Nettoforbruget er forbrug i produktionen - oparbejdet materiale
svarende til 1,1 kg - 0,75 kg = 0,35 kg. Til at fremstille 1 kg produkt skal der tages 3 kg råstoffer i arbejde. Nettomængden af råstoffer udgør derfor 0,35 kg materiale × 3 kg råstoffer/kg materiale = 1,05 kg
råstoffer. Effektiviteten kan derfor beregnes til:
Mmat. R+P+B+A/N = 1kg / 1,05 × 100 % = 95 %
Uden genanvendelse ville effektiviteten være 1 kg / 3 kg 100% = 33%.
2.4.4 Ressourceforbrug, materialer
I den vurderede opgørelse Vmat., R+P+B er alle materialeforbrug skaleret med en faktor, der udtrykker knapheden for de råstoffer, som materialet er fremstillet af.
I definitionen af Vmat., R+P+B er medtaget materialeforbrug i råvarefasen, i produktionsfasen og brugsfasen som illustreret i figur 2.8.

Figur 2.8 Ressourceforbrug baseret på begrebet Vmat., R+P+B , Ressourceforbrug, materialer
Det at opgøre materialeindholdet i produktet i mPR giver en indikation af, om et givet produkt indeholder få eller mange knappe ressourcer. Man får et sam-let tal for ressourceforbruget, men under
beregningen er det relativt let at se, hvilke materialer der betyder mest i opgørelsen. Dette er illustreret i eksemplerne i kapitel 3 til 7.
Ønsker en virksomhed at forbedre sin produktion og indlægge betragtninger om bæredygtighed, kan en beregning af Vmat., R+P+B bruges til at indikere, hvilke materialer man skal prioritere at bruge
mindst af.
Overordnet kan Vmat., R+P+B ligeledes bruges til at skabe klarhed over, inden for hvilke produktgrupper der anvendes væsentlige mængder af knappe ressourcer.
En vurderet opgørelse af materialer vil resultere i ressourceeffektiviteten defineret som:
![Vmat., R+P+B = Materialer i produktet vurderet [mPR]/Samlet materialeforbrug vurderet [mPR] × 100%](images/s040b.gif)
Et stort vandforbrug vil ikke kunne ses i den vurderede opgørelse, da ressourcen vand er defineret som 0 mPR.
I kortlægningen af vinduesrammen i Figur 2.4 består produktet af 1 kg aluminium. Materialeforbruget kan direkte omregnes til råstofforbrug opgjort i mPR ved at gange med knaphedsfaktoren 1,5 mPR/kg,
da denne rummer en opgørelse og vurdering af de råstoffer, der indgår i udvinding og forarbejdning af materialet – her aluminium. Faktoren 1,5 mPR/kg er slået op i tabel B.1 i Pommer et al., 2001 og er
givet i forhold til den mængde materiale, som en produktionsvirksomhed anvender.
Materialemængden i produktet vurderet er lig 1 kg × 1,5 mPR/kg = 1,5 mPR. Det samlede materialeforbrug vurderet er 1,1 kg × 1,5 mPR/kg = 1,65 mPR. Effektiviteten kan derfor beregnes til:
Vmat., R+P+B = 1,5 mPR / 1,65 mPR × 100% = 91 %
Der skal gøres opmærksom på, at det er den samme procent, der er beregnet her, som er vist for Mmat. P+B. Det vil kun være tilfældet, hvor et produkt består af et materiale. For andre situationer, hvor
der er tale om to eller flere materialer, vil de to beregninger vise forskellige resultater.
2.4.5 Ressourceforbrug, materialer og energi
Ofte betragtes materiale- og energiforbrug under et, da et energiforbrug kræver forbrug af energiressourcer i form af kul og olie til fremstilling af el og varme. For nogle materialer er der et stort energiforbrug
ved udvinding og bearbejdning og for andre et mindre.
Ressourceeffektiviteten Vmat.+energi, R+P+B viser det samlede energi- og materialeforbrug i råvarefase, ved produktion og brug i forhold til materialeindholdet i produktet og er illustreret i figur 2.9.

Figur 2.9 Ressourceforbrug baseret på materialer og energi i begrebet Vmat.+energi, R+P+B , Ressourceforbrug, materialer og energi
Ved en sammenligning af Vmat, R+P+B og Vmat.+energi, R+P+B kan man se energiforbrugets betydning i forhold til materialeforbruget ud fra en knaphedsvurdering.
For energiforbrugende produkter kan en sådan sammenligning fx anvendes til at indikere, om et øget materialeforbrug kan forsvares ved en optimering af energiforbruget.
Ressourceeffektiviteten for det totale ressourceforbrug – materialer og energi defineres som:
![V mat.+energi, R+P+B = Materialer i produktet vurderet [mPR]/Samlet materialeforbrug og energiforbrug [mPR] × 100%](images/s041b.gif)
Energiforbruget omregnes til forbrug af energiressourcer, udtrykkes i mPR og indgår i den samlede ressourceopgørelse. Valget af energiressource vil blive afgørende herfor. Det er almindeligt at anvende olie
som udgangspunkt, da denne energiressource betragtes som en marginal ressource de fleste steder i Europa. I andre sammenhænge, når den aktuelle energikilde kendes, fx kul, kan denne anvendes i
beregningen.
I kortlægningen af vinduesrammen i Figur 2.4 er der et primært energiforbrug ved udvinding på 170 MJ/kg aluminium og et energiforbrug ved produktion på 30 MJ/kg aluminium. Materialeforbruget er 1,1
kg og det samlede energiforbrug er derfor 1,1 kg × (170 MJ/kg + 30MJ/kg) = 220 MJ.
Antages det, at energiforbruget er baseret på forbrug af olie, kan forbruget af ressourcen olie beregnes ud fra, at 1.025 MJ svarer til 1 mPR (Pommer et al., 2001). Ressourceforbruget til energi er derfor
220 MJ / 1.025 MJ/mPR = 0,21 mPR. Det samlede materiale- og energiforbrug er således 1,65 mPR + 0,21 mPR = 1,86 mPR.
Effektiviteten kan beregnes til:
Vmat.+energi, R+P+B = 1,5 mPR / 1,86 mPR × 100% = 81 %
Den beregnede Vmat.R+P+B er på 91%, mens Vmat.+energi, R+P+B er på 81%. Energiforbruget udgør 11% (0,21/1,86 × 100) af det samlede ressourceforbrug.
2.4.6 Ressourceforbrug, hele livscyklus
Beregning af Vmat.+energi, R+P+B+A/N omfatter hele produktets livscyklus og medtager således materialer, der kan genvindes og udviklet energi, der kan nyttiggøres.

Figur 2.10 Samlet ressourceforbrug inkl. genvinding og nyttiggørelse, Vmat.+energi, R+P+B+A/N , Ressourceforbrug, hele livscyklus
En sammenligning mellem Vmat.+energi, R+P+B og Vmat.+energi, R+P+B+A/N illustrerer betydningen af genvundne materialer og nyttiggørelse af energi ud fra en knaphedsbetragtning.
Ønsker man at fokusere på knappe ressourcer og hele produktets livsforløb, kan Vmat.+energi, R+P+B+A/N bruges til at sammenligne forskellige produkter.
Overordnet set må en ressourceeffektivitet beregnet som Vmat.+energi, R+P+B+A/N være at foretrække, da der her både tages hensyn til materialer og energi, herunder genanvendelse og til knaphed af de
anvendte ressourcer.
Sker der en genvinding af materialer, især de knappe ressourcer, vil det have stor betydning for ressourceeffektiviteten. Udvundet energi ved forbrænding, der nyttiggøres, vil ligeledes blive modregnet.
Ressourceeffektiviteten defineres som:
![V mat.+energi, R+P+B+A/N = Materialer i produktet vurderet [mPR]/Nettoforbrug af materialer og energi [mPR] × 100%](images/s042b.gif)
Ressourceeffektiviteten baseret på det samlede vurderede forbrug vil blive en procent mellem 1 og 100, hvorimod effektiviteten baseret på en nettoopgørelse kan give resultater, der er større end 100.
I kortlægningen af vinduesrammen i Figur 2.4 er nettoforbruget af materialer opgjort til 0,35 kg aluminium (1,1 kg – 0,75 kg) og svarer til 0,53 mPR.
Der medgår energi til udvinding af nettoforbruget af materialer på 170 MJ/kg. Der medgår energi til forarbejdning af 1,1 kg materialer på 30 MJ/kg, og der medgår energi til oparbejdning af 0,75 kg
aluminium på 30 MJ/kg.
Det samlede energiforbrug, når der tages hensyn til genvinding, er derfor:
0,35 kg × 170 MJ/kg + 1,1 kg × 30 MJ/kg + 0,75 kg × 30 MJ/kg = 115 MJ
Energiforbruget omregnet til forbrug af olieressourcer udgør 115 MJ / 1.025 MJ/mPR = 0,11 mPR.
Det samlede nettoforbrug af materialer og energi er derfor 0,53 mPR + 0,11 mPR = 0,64 mPR. Ud fra dette kan effektiviteten beregnes til:
Vmat.+energi, R+P+B+A/N = 1,5 mPR / 0,64 mPR × 100% = 234 %.
Af eksemplerne ses, at genanvendelsen har meget stor betydning og ændrer ressourceeffektiviteten fra 81% (Vmat.+energi, R+P+B) til 234% (Vmat.+energi, R+P+B+A/N ).
2.5 Sammenligning med øvrige opgørelser
Der har været ønske om at sammenligne de opstillede opgørelser og ressourceeffektiviteter med andre lignende opgørelser.
Her er valgt at sammenligne med opgørelser, der tager udgangspunkt i statistiske/økonomiske opgørelser for et land – de såkaldte MFA indikatorer (Material Flow Accounting). Der er nærmere redegjort
for disse begreber i projektet ”Udvikling af indikatorsystem for materialestrømme, ressourceforbrug og –effektivitet samt affaldsstrømme” (Andersen KK et al., 2003).
MFA princippet tager udgangspunkt i et lands økonomiske aktiviteter i form af produktion, forbrug og investeringer. I den forbindelse opererer man med to begreber, der er relevante i denne sammenhæng.
- DMI – direkte materialeinput for Danmark
Tilgangen af materialer udgøres dels af dansk råstofudvinding og af importerede varer.
- TMR – totalt materialebehov for Danmark
Her er medtaget alle indirekte materialestrømme – ubrugte ressourcer fra dansk råstofudvinding og ressourceforbrug knyttet til fremstilling af importerede varer i udlandet.
Hvor der findes opgørelser af DMI og TMR for produktgrupper, er det muligt at sammenligne med nærværende opgørelser baseret på LCA-betragtninger.
Opgørelser baseret på DMI kan sidestilles med opgørelser af materialeforbrug i kg baseret på produktion og brug for en produktgruppe, såfremt dansk råstofproduktion er ubetydelig.
Termen TMR oversættes af Det Europæiske Miljøagentur på dansk til samlet råstofforbrug og defineres som ”TMR udtrykker den samlede masse af primære materialer udvundet af naturen til at understøtte
menneskelige aktiviteter. TMR er en meget aggregeret indikator baseret på materialer for en økonomi.” (Egen oversættelse fra engelsk).
I definitionen af TMR nævnes ofte, at der medtages skjulte strømme. Bringezu og Schütz anfører i Technical Report no. 55, at TMR består af alle udvundne ressourcer, der forbruges ved produktets
fremstilling og transport, bortset fra luft og vand. Som eksempel angives, at skjulte strømme kan være mineralske materialer, der bliver til overs/fremkommer som affald fra udvinding af metaller eller energi,
der bruges ved transport.
I en livscyklusvurdering indgår disse nævnte skjulte strømme. Som eksempel kan nævnes, at der ved udvinding af råstoffer forbruges energi og materialer. Disse er medregnet, og de miljømæssige
påvirkninger i form af affald, emissioner, arealpåvirkning m.v. er medregnet i princippet, og hvor det er muligt, i praksis.
Opgørelser baseret på TMR kan sidestilles med opgørelser af materialeforbrug i kg baseret på råstofudvinding, produktion og brug baseret på LCA-principper.
Der findes ikke opgørelser, som kan sammenlignes med dette projekts opgørelser og ressourceeffektiviteter baseret på UMIP-metodens vurderede (vægtede) størrelser.
2.5.1 Direkte materialeinput
Der er udarbejdet en opgørelse af DMI for Danmark for 1997 opgjort for en række forskellige anvendelser (Gravgård Pedersen, 2002). Data herfra vil således være sammenlignelige med nærværende
opgørelse i de opstillede eksempler.
2.5.2 Totalt materialeforbrug
Suppleres DMI-opgørelsen med tal for de såkaldte indirekte materialestrømme i ind- og udland, fås indikatoren TMR. Denne indikator er et udtryk for den samlede mængde af materialer i naturen, der på
globalt plan påvirkes af den økonomiske aktivitet i landet.
Haves opgørelser af TMR for et produkt eller en snæver industrigren, vil det kunne sidestilles med råstofforbruget opgjort for produktets samlede livscyklus.
Det har dog ikke været muligt at finde data for TMR for afgrænsede produkter, der kan anvendes til sammenligning i nærværende projekt.
På Wuppertal Institute har man arbejdet med begrebet Material Input Per unit Service (MIPS) der omfatter den samlede mængde materialer, der er medgået til at fremstille og anvende et givet produkt. Det
er anført i rapporten ”Økologiske rygsække – ressourceeffektivitet, materialestrømme og globalisering” (Christensen et al., 2002), at MIPS kan sidestilles med LCA, hvor MIPS-tilgangens begreb Service
Unit modsvarer LCA-metodikkens funktionelle enhed.
Wuppertal Institute har opgjort en række data for forskellige materialer relation til MIPS, hvor materialeforbruget i form af abiotiske og biotiske materialer pr. ton er opgjort (Wuppertal Institute, 1998). Ud
fra disse opgørelser er det søgt at sammenligne med nærværende projekts opgørelser.
3 Farmaceutiske virksomheder
3.1 Introduktion
Medicinalindustrien i Danmark er karakteriseret ved to grupper af virksomheder. Den ene gruppe omfatter mindre virksomheder, der primært foretager formulering og pakning af medicinske produkter. Den
anden gruppe omfatter få store virksomheder, der beskæftiger sig med syntese og anden kemisk/biologisk produktion.
Medicinalindustrien (NACE kode 24.41.00 ”Fremstilling af farmaceutiske råvarer” og 24.42.00 ”Medicinalvarefabrikker”) består af ca. 190 selskaber med i alt omkring 30.000 ansatte. Halvdelen af
selskaberne er mindre virksomheder med i alt omkring 4.000 ansatte eller ca. 12-15% af de ansatte i branchen (Krak Direkt, 2002).
Novo Nordisk A/S' (Novo og Novozymes) andel udgør i underkanten af 45% af de ansatte i branchen og næsten 50% af omsætningen. De resterende ca. 40% ansatte er ansat i branchens øvrige store
virksomheder (Krak Direkt, 2002). De øvrige store virksomheder står for ca. 40% af omsætningen.
Medicinalindustrien i Danmark omsatte i 2000 for 26 mia. kr. og i 2001 for i underkanten af 32 mia. kr. (Danmarks Statistik, 2001). Produktionen i 2001 er af Danmarks Statistik opgjort til 38.306 ton.
Omsætningen for de store virksomheder udgør 90% målt i penge. Da gruppen af store virksomheder tegner sig for den største produktion, det største ressourceforbrug og de største affaldsmængder, er det
valgt i nærværende undersøgelse at fokusere på denne gruppe af virksomheder.
3.2 Et medicinalprodukts livsforløb
Medicinalprodukter kan generelt betragtes i et livscyklusperspektiv som vist i figur 3.1. Inputsiden er illustreret med bokse med dobbeltstreger, outputsiden ved bokse med kraftig enkeltstreg. De bokse, der
er mindre væsentlige, er illustreret med stiplede linier og udgangspunktet – produktion af produktet er illustreret med en skraveret boks.
Råvarer og kemikalier dækker over en bred gruppe af kemiske forbindelser og varierer meget fra produktion til produktion. I Figur 3.1 er der ikke vist, at hver af disse forbindelser har et livsforløb og
dermed et forbrug af råstoffer og energi samt generering af affald.
Alle virksomheder anvender emballager til deres produkter. Materialerne til emballagerne er primært papir/pap, plast og glas, men varierer meget fra produktion til produktion. Fremstilling af
emballagematerialerne er ikke vist i Figur 3.1.
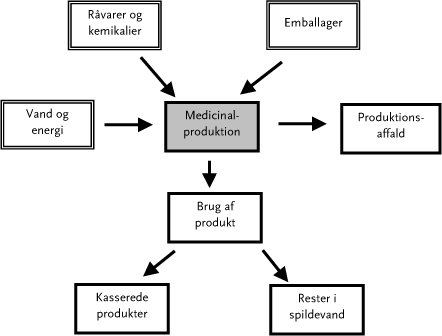
Figur 3.1 Principskitse for medicinalprodukter i et livscyklusperspektiv
Medicinalproduktion er karakteriseret ved, at der forbruges betydelige mængder vand og energi. Den største del af vandmængden afledes som spildevand. Energien er dels i form af olie og naturgas, dels
fjernvarme og dels el.
Affald fra produktionen er primært affald fra gæringstanke, farligt affald i form af blandt andet brugte opløsningsmidler, affald fra emballager og andet industriaffald.
Langt den overvejende del af produkterne bliver brugt af mennesker og dermed omsat. Rester kan forekomme i sanitært spildevand, men er ikke taget med i opgørelsen her.
Kassationen af produkter hos forbrugerne vurderes at være meget lille.
3.3 Kortlægning af farmaceutiske virksomheder
I nærværende projekt er det valgt at søge oplysninger gennem de grønne regnskaber, som denne gruppe af virksomheder har pligt til at udarbejde. Grønne regnskaber er gennemgået for en række af de
store medicinalvirksomheder, og på baggrund heraf er det valgt at anvende data fra virksomhederne:
- BASF Health & Nutrition A/S
- Ferring A/S
- H. Lundbeck A/S, Valby
- Novo Nordisk A/S
- Nycomed Danmark A/S
Disse virksomheder repræsenterer dels meget store og store virksomheder og er forskellige i deres produktion. En samlet beskrivelse af, hvad der er fundet i de grønne regnskaber, er beskrevet i bilag A.
3.3.1 Opgørelse af mængder (pr. ton produkt)
3.3.1.1 Materialer i kg
Input i form af råvarer og hjælpestoffer dækker over en meget bred vifte af kemiske forbindelser. Der vil dog være tre typer:
- Kemiske stoffer og produkter, som bruges direkte i produktet.
- Kemiske stoffer og produkter, der bruges ved en kemisk syntese eller anden omdannelse.
- Proceshjælpemidler som fx opløsningsmidler.
Emballager er indregnet i punkterne 1 til 3. Vand er opgjort særskilt og ikke medregnet i materialeforbruget.
De grønne regnskaber giver yderst sparsomme oplysninger om, hvilke typer og hvilke kemiske stoffer og produkter det drejer sig om.
Totalt forbrugte de farmaceutiske virksomheder ca. 140.000 ton råvarer inkl. emballager men ekskl. vand i 2000.
Det har ikke været muligt at finde eksakte tal for, hvor store mængder af fx stivelsesprodukter der indgår i produktionerne eller andre af de indgående materialer.
Derfor er der ud fra forfatternes erfaringer fra branchen, koblet med indikationer og fakta fra de grønne regnskaber, lavet en grov inddeling i 4 grupper af de kemiske stoffer og produkter, som indgår i
fremstillingsprocessen. Tallene er samlet i tabel 3.1 og viser, at der pr. ton farmaceutisk produkt i alt forbruges ca. 3.500 kg råvarer.
Tabel 3.1 Forbrug af råvarer og hjælpestoffer pr. ton produceret produkt (inkl. emballage)
Kemiske stoffer og produkter |
Råvareforbrug
(ton) |
Råvareforbrug
(kg/ton produkt) |
Stoffer baseret på stivelse, etc. |
69.509 (50%) |
1.815 |
Let bearbejdede kemiske forbindelser, råolie som eks. |
34.754 (25%) |
907 |
Meget bearbejdede kemiske forbindelser |
20.853 (15%) |
544 |
Organiske opløsningsmidler (regnes som ethanol) |
13.902 (10%) |
363 |
I alt |
139.017 (100%) |
3.629 |
Emballagerne udgør 10.615 ton af den samlede mængde råvarer og hjælpestoffer, hvilket svarer til omkring 8% af det totale råvareforbrug og 25% af den samlede mængde producerede produkt (inkl.
emballage). Råvarer og emballager regnes sammen under et.
Vandforbruget for hele branchen vurderes at være i størrelsesordenen 80 m³ pr. ton produkt. Vandforbruget indgår ikke i materialeopgørelsen. En del af vandet fordamper, men langt hovedparten ledes ud
som spildevand og indgår således ikke i de færdige produkter.
3.3.1.2 Estimering af råstofforbrug
På baggrund af de relativt sparsomme oplysninger er forbruget af råstoffer estimeret i tabel 3.2. Som det fremgår af tabellen, er det samlede forbrug af råstoffer estimeret til omkring 520.000 ton.
Tabel 3.2 Estimering af samlet råstofforbrug
Kemiske stoffer og produkter |
Råvareforbrug (ton) |
Råstofforbrug
pr. kg råvareforbrug |
Samlet råstof-
forbrug (ton) |
Stoffer baseret på stivelse etc. |
69.509 (50%) |
5 kg/kg |
350.000 ton |
Let bearbejdede kemiske forbindelser, råolie som eks. |
34.754 (25%) |
1,3kg/kg |
45.000 ton |
Meget bearbejdede kemiske forbindelser |
20.853 (15%) |
5 kg/kg |
105.000 ton |
Organiske opløsningsmidler (regnes som ethanol) |
13.902 (10%) |
1,3 kg/kg |
18.000 ton |
I alt for branchen |
139.017 (100%) |
|
520.000 ton |
Da opgørelsen bygger på en række antagelser grundet mangel på specifikke data, er opgørelsen meget usikker.
Råvareforbruget svarer til et forbrug på omkring 3,7 kg/kg materialer. Dette svarer til 13,5 kg/kg medicinalprodukt. Tages der hensyn til usikkerhederne i opgørelsen, skønnes det, at råstofforbruget ligger på
10-20 kg/kg produkt.
3.3.1.3 Energiforbrug i råvarer, produktion og brug
Det samlede primære energiforbrug i råvarefasen er opgjort til ca. 130 GJ pr. ton produkt i tabel 3.3.
Tabel 3.3 Primært energiforbrug i råvarefasen
Kemiske stoffer og produkter |
Råvareforbrug
(kg/ton produkt) |
Primært energi-
forbrug
(MJ/kg) |
Primært
energiforbrug
pr. ton
(MJ) |
Stoffer baseret på stivelse etc. |
1.815 |
0 |
0 |
Let bearbejdede kemiske forbindelser, råolie som eks. |
907 |
50 |
45.364 |
Meget bearbejdede kemiske forbindelser |
544 |
100 |
54.438 |
Organiske opløsningsmidler (regnes som ethanol) |
363 |
80 |
29.034 |
I alt |
3.629 |
|
128.835 |
Tilsvarende er energiforbruget i produktionsfasen opgjort til at udgøre ca. 230 GJ pr. ton produkt.
Energiforbruget i brugsfasen er minimalt og begrænser sig til transport, hvilket ikke medtages i opgørelsen.
Det samlede energiforbrug i råvare-, produktions- og brugsfasen er således ca. 360 GJ pr. ton farmaceutisk produkt.
3.3.1.4 Godskrivning af materialer og udviklet energi
Affaldet, som nyttiggøres, skal i princippet godskrives. Inden for den farmaceutiske branche vil noget affald i form af biomasse blive nyttiggjort og erstatte anden gødning. I bilag A er det anført, at ud af
stivelsesforbruget på 1,815 kg pr. kg produkt nyttiggøres 1,288 kg pr. kg produkt.
Da biomasse er en fornyelig ressource, som ressourcemæssigt er sat til at koste 0 mPR, kommer det ikke til at tælle i regnskabet for de vurderede opgørelser.
Industriaffald og farlige affald sendes til forbrænding. Den nyttiggjorte energi fra affaldsbehandlingen/forbrændingen godskrives, og ca. 5 GJ pr. ton produkt kan godskrives, se tabel 3.4.
Tabel 3.4 Energiindhold i affaldet som udnyttes
Affaldsopgørelse |
Affaldsproduktion
(kg/ton produkt) |
Energiindhol
(MJ/kg) |
Energiindhold
pr. ton produkt
(MJ) |
Genanvendelse, (nyttiggørelse) |
1.294 (61%) |
0 |
0 |
Forbrænding inkl. farligt affald |
509 (24%) |
10 |
5.100 |
Deponering |
318 (15%) |
0 |
0 |
I alt |
2.121 |
|
5.100 |
Der er ikke andre materialer, som kan godskrives.
3.3.2 Opgørelse af vurderede mængder (pr. ton produkt)
I det følgende er materialer og energiforbrug omregnet til vurderede størrelser i mPR.
3.3.2.1 Vurdering af materialeforbrug
Bruttoforbruget af materialer opgøres til at være 595 mPR pr. ton farmaceutisk produkt, se tabel 3.5.
Tabel 3.5 Bruttoforbrug af materialer
Kemiske stoffer og produkter |
Materialeforbrug
i fremstilling
(mPR/kg) |
Råvareforbrug
(kg/ton produkt) |
Ressourceforbrug
(mPR/ton produkt) |
Stoffer baseret på stivelse etc. |
0,00 |
1.815 |
0 |
Let bearbejdede kemiske forbindelser, råolie som eks. |
0,04 |
907 |
36 |
Meget bearbejdede kemiske forbindelser |
1,00 |
544 |
544 |
Organiske opløsningsmidler (regnes som ethanol) |
0,04 |
363 |
15 |
I alt |
|
3.629 |
595 |
Sammensætningen af de farmaceutiske produkter kendes ikke eksakt. Derfor opstilles der to scenarier.
Hvis sammensætningen af produktet er identisk med sammensætningen af udgangsmaterialerne, beregnes ressourceforbruget til 164 mPR pr. ton farmaceutisk produkt, se Tabel 3.6. Dette kaldes
produktsammensætning A.
Tabel 3.6 Ressourceindhold pr. ton farmaceutisk produkt hvis produktet har samme sammensætning som råvarerne – Produktsammensætning A
Kemiske stoffer og produkter |
Materialeforbrug
i fremstilling
(mPR/kg) |
Produktsam-
mensætning
(kg/ton) |
Ressourcer
i produkt
(mPR/ton) |
Stoffer baseret på stivelse etc. |
0,00 |
500 |
0 |
Let bearbejdede kemiske forbindelser, råolie som eks. |
0,04 |
250 |
10 |
Meget bearbejdede kemiske forbindelser |
1,00 |
150 |
150 |
Organiske opløsningsmidler (regnes som ethanol) |
0,04 |
100 |
4 |
I alt |
|
1.000 |
164 |
Hvis det derimod antages, at produkterne indeholder 5% stivelsesbaserede stoffer i stedet for 50%, som det er tilfældet i råvarerne beregnes ressourceforbruget til 312 mPR pr. ton farmaceutisk produkt –
se tabel 3.7. Dette kaldes produktsammensætning B.
Tabel 3.7 ressourceindhold pr. ton farmaceutisk produkt hvis produktet indeholder 5% stivelsesbaserede stoffer – Produktsammensætning B
Kemiske stoffer og produkter |
Materialeforbrug
i fremstilling
(mPR/kg) |
Produktsam-
mensætning
(kg/ton) |
Ressourcer
i produkt
(mPR/ton) |
Stoffer baseret på stivelse, etc. |
0,00 |
50 |
0 |
Let bearbejdede kemiske forbindelser, råolie som eks. |
0,04 |
475 |
19 |
Meget bearbejdede kemiske forbindelser |
1,00 |
285 |
285 |
Organiske opløsningsmidler (regnes som ethanol) |
0,04 |
190 |
8 |
I alt |
|
1.000 |
312 |
Der opstår store mængder biomasseaffald fra fremstillingen af farmaceutiske produkter. Derfor er der sandsynligt, at indholdet af stivelsesbaserede stoffer er nærmere de 50% end de 5%.
Produktsammensætning A vurderes at være mest sandsynlig.
Ingen af de forbrugte materialer kan godskrives rent ressourcemæssigt, hvorfor nettoforbruget af materialer er det samme som bruttoforbruget.
3.3.2.2 Vurdering af energiforbrug
Det samlede energiforbrug i råvare-, produktions- og brugsfasen opgjort til ca. 360 GJ pr. ton farmaceutisk produkt. Fremstilles denne mængde energi ud fra olie, svarer det til et forbrug på ca. 350 mPR pr.
ton fremstillet medicinalprodukt.
3.3.2.3 Vurdering af godskrivninger
Der kan godskrives 0,005 mPR pr. ton fremstillet medicinalprodukt i form af bortskaffelse af affald med energiudnyttelse.
3.4 Ressourceeffektivitet
3.4.1 Ressourceeffektivitet på materialeniveau
3.4.1.1 Materialeforbrug, produktion og brug
Det samlede mængde materialer i form af råvarer, hjælpestoffer og emballager er opgjort til 3.629 kg pr. ton farmaceutisk produkt.
Ressourceeffektiviteten kan derfor beregnes til:

Vandforbruget er opgjort til 80 m³ pr. 1.000 kg medicinalprodukt.
3.4.1.2 Materialeforbrug, produktion, brug og bortskaffelse
Nyttiggørelsen af biomasse udgør 1.288 kg pr. ton produceret produkt. Nettoforbrug af materialer udgør derfor 3.629 kg – 1.288 kg = 2.341 kg.
Ressourceeffektiviteten kan derfor beregnes til:

Det skal dog bemærkes, at den del af biomasseaffaldet, der modregnes, ikke kan anvendes i produktionen af medicin, men til andre formål. Det er stadig nødvendigt at fremstille den samlede mængde
stivelse.
3.4.1.3 Materialeforbrug, hele livscyklus
Til fremstilling af de 3.629 kg materialer, der medgår til fremstilling af 1 ton farmaceutisk produkt medgår i størrelsesordnen 13,6 ton råstoffer. Nyttiggørelsen af biomasse gør ikke, at der i produktionen kan
spares på stivelsesmængden. Den mængde biomasse, der nyttiggøres, modregnes derfor direkte i det samlede forbrug af råstoffer (13.600 – 1.288= 12.312 kg).
![M mat. R+P+B+A/N = Materialer i produktet [kg]/Nettoforbrug af råstoffer [kg] = 1.000 kg/12.312 kg = 8 %](images/s051c.gif)
Tages der hensyn til usikkerheder m.v., vil Mmat. R+P+B+A/N ligge på mellem 5 og 10%.
3.4.2 Ressourceeffektivitet baseret på vurderet opgørelse
3.4.2.1 Ressourceforbrug, materialer
Den samlede mængde materialer i form af råvarer, hjælpestoffer og emballager er opgjort til 595 mPR pr. ton farmaceutisk produkt.
Der kan opstilles to forskellige ressourceeffektiviteter afhængigt af, hvilken sammensætning produktet antages at have.
For produktsammensætning A beregnes ressourceeffektiviteten opgjort som materialeeffektivitet, brutto til:

Som det ses, findes ressourceeffektiviteten at være identisk med materialeeffektiviteten som beregnet ovenfor.
For produktsammensætning B beregnes ressourceeffektiviteten opgjort som materialeeffektivitet, brutto til:

Der mest sandsynlige er, at ressourceeffektiviteten, brutto skal findes et sted mellem de to beregnede materialeeffektiviteter.
3.4.2.2 Ressourceforbrug, materialer og energi
Hvis man ser på det samlede vurderede materiale og energiforbrug, udgør det 595 mPR + 350 mPR = 945 mPR pr. ton farmaceutisk produkt.
Der kan igen opstilles to forskellige ressourceeffektiviteter afhængigt af, hvilken sammensætning produktet antages at have.
For produktsammensætning A beregnes ressourceeffektiviteten opgjort som materiale- og energieffektivitet, brutto til:
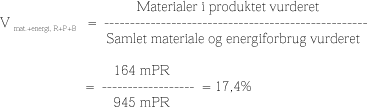
For produktsammensætning B beregnes ressourceeffektiviteten opgjort som materiale- og energieffektivitet, brutto til:
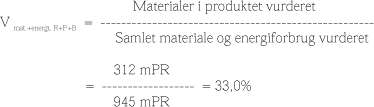
Det mest sandsynlige er igen, at ressourceeffektiviteten, brutto skal findes et sted mellem de to beregnede materiale- og energieffektiviteter.
3.4.2.3 Ressourceforbrug, hele livscyklus
Da nyttiggørelsen alene omfatter fornyelige ressourcer (stivelse udvundet af kartofler), vil dette ikke have betydning for den vurderede opgørelse, og der vil derfor ikke være forskel på, om det sidste led i
livscyklus tages med eller udelades. Den opgjorte størrelse Vmat.+energi, R+P+B vil derfor være lig Vmat.+energi, R+P+B+A/N, Ressourceforbrug, hele livscyklus.
3.4.3 Fortolkning
De opgjorte ressourceeffektiviteter er baseret på estimater over den gennemsnitlige danske medicinalproduktion. Da produktionsprocesser og materialer er meget forskellige fra virksomhed til virksomhed,
vil man kunne se meget store variationer i udnyttelsen af materialerne på de forskellige virksomheder i branchen.
Fremstilling af medicinalprodukter indebærer store tab af materialer, da der sker en intensiv bearbejdning af de indgående kemiske stoffer og materialer samtidig med, at der arbejdes efter høje krav til
renhed og hygiejne. Genvinding og/eller recirkulering af materialestrømme er derfor vanskelig.
De beregnede ressourceeffektiviteter afspejler dette, idet tallene viser, at der tabes omkring 3/4 af råstofferne ved fremstilling af materialerne til produktionen af produkterne. I gennemsnit vil ca. 1/3 af
materialerne i form af biomasse kunne nyttiggøres til andre og mindre værdifulde formål. Dog vil der være store variationer fra virksomhed til virksomhed. I udvinding og forarbejdning af råstoffer tabes
ligeledes omkring 3/4 af materialerne.
Ressourceopgørelserne baseret på de vurderede opgørelser (i mPR) ligger på et højere niveau, da en væsentligt del af råvarerne er fornyelige ressourcer (stivelse), som ikke tæller med i den vurderede
opgørelse.
De beregnede ressourceeffektiviteter er samlet i tabel 3.8.
Tabel 3.8 Beregnede ressourceeffektiviteter for den farmaceutiske industri
|
Betegnelse |
Ressourceeffektivitet |
Materialeopgørelse |
• Materialer til produktion og brug |
Mmat, P+B |
28 % |
• Materialer, produktion, brug og bortskaffelse inkl. genanvendelse |
Mmat, P+B+A/N |
43 % |
• Råstoffer i hele livscyklus inkl. genanvendelse |
Mmat. R+P+B+A/N |
8 % |
Ressourceopgørelse |
• Materialer vedrørende råstoffer, produktion og brug |
Vmat, R+P+B |
27-52% |
• Materialer og energi vedrørende råstoffer, produktion og brug |
Vmat+energi, R+P+B |
17-33 % |
• Materialer og energi i hele livscyklus inkl. genvinding |
Vmat+energi, R+P+B+A/N |
17-33 % |
De opstillede ressourceeffektiviteter er er baseret på en gennemsnitsproduktion. Da der er utroligt store produktions- og materialeforskelle inden for det farmaceutiske område, er det yderst vanskeligt at
vurdere, om de beregnede størrelser er repræsentative for branchen.
Anvendelse af begrebet ressourceeffektivitet inden for denne branche vil antageligt kun være relevant for en specifik produktion og kan så anvendes til at vurdere proces- og materialeoptimeringer.
Der skal gøres opmærksom på, at der generelt i farmaceutisk produktion indgår mange kemiske forbindelser, og det at kortlægge og vurdere fremstillingen af alle disse kemiske forbindelser vil være yderst
vanskeligt.
3.5 Affaldsforebyggelse
Det er yderst vanskeligt at udpege konkrete områder for affaldsminimering på basis af nærværende opgørelse for den farmaceutiske industri, da råvarer kun kendes i hovedgrupper, og fremstillingsmetoder
heller ikke er kendte.
Dertil kommer, at det er en branche, hvor fællestræk og generaliseringer er yderst vanskelige, da produktionerne på de enkelte virksomheder er meget forskellige.
Følgende overordnede forhold kan dog trækkes frem:
3.5.1.1 Stivelsesholdige materialer
Der anvendes mellem 10 og 50% materialer i produktionen, der er baseret på stivelse, sukkerstoffer eller lignende materialer af biologisk oprindelse.
Omkring 2/3 af den mængde stivelse, der anvendes, nyttiggøres og erstatter gødning. Den resterende del findes enten i produktet eller fremkommer som affald. Der kan ikke foretages en vurdering af denne
fordeling og dermed en vurdering af, om det er muligt at nyttiggøre mere stivelsesaffald.
Der er et stort tab af materialer ved fremstilling af ren stivelse. I beregningerne her er antaget, at 80% fremkommer som affald. Det vides ikke, om dette nyttiggøres under en eller anden form.
3.5.1.2 Opløsningsmidler
Der anvendes i produktionen af medicinalprodukter en række opløsningsmidler til oprensning og ekstraktion. Opløsningsmidlerne udgør 10-20% af materialeforbruget.
En væsentlig del af disse opløsningsmidler burde kunne indvindes. Det skønnes, at de ikke kan anvendes til samme formål igen, da renhedskravet inden for branchen er meget højt, men de indvundne
opløsningsmidler vil givet vis kunne anvendes til andre formål, hvor renhedskravet er mindre.
Det skal dog bemærkes, at der antagelig ikke er økonomisk incitament til dette, da de fleste almindelige opløsningsmidler i teknisk kvalitet er relativt billige.
Opløsningsmidler fremstilles ud fra de lette fraktioner ved destillation af råolie efterfulgt af kemiske omdannelser eller ud fra ethanol fremstillet ved gæring. Der er et tab i form af affald ved fremstilling af
opløsningsmidler, men dette skønnes at være relativt lille.
3.5.1.3 Kemiske forbindelser
Der anvendes en række kemiske forbindelser, der er mere eller mindre komplicerede at fremstille. Da de enkelte forbindelser ikke kendes, kan dette ikke vurderes.
Mængden, der anvendes, udgør mellem 20 og 75% af den samlede mængde materialer i produktionen. Der er et betydeligt tab i produktionen – i størrelsesordnen 75 %. Da selve fremstillingsmetoderne
ikke kendes, er det ikke muligt at påpege, hvilke processer/forhold der giver anledning til de største tab.
Selve fremstillingen af de kemiske forbindelser, der anvendes i en medicinalproduktion er antagelig forbundet med relativt store tab, da kravet om renhed er meget højt, og da de enkelte forbindelser kan
være yderst vanskelige/ressourcekrævende at fremstille.
I forhold til forbrug af ressourcer vil det være denne gruppe, der bør fokuseres på, såfremt man ønsker at forbedre ressourceeffektiviteten baseret på knappe ressourcer og på materialemængder.
3.5.1.4 Samlet prioritering
Ud fra det ret mangelfulde datagrundlag er det vanskeligt at komme med klare anbefalinger, men følgende skal dog trækkes frem:
- Det skal sikres, at alle stivelsesholdige og lignende materialer af biologisk oprindelse nyttiggøres, såfremt det medfører miljøbelastninger af de landbrugsjorde, hvor det udbringes på.
- Det bør undersøges, hvilke opløsningsmidler der anvendes, og om disse kan genvindes.
- Det største ressourcetab sker inden for gruppen ”Kemiske forbindelser”. De kemikalier, der anvendes, kendes ikke og vil antagelig variere meget fra virksomhed til virksomhed. Det vil derfor være
yderst vanskeligt at komme med generelle anbefalinger.
3.6 Sammenligning med øvrige opgørelser
De medicinalvirksomheder, der her er taget udgangspunkt i, er alle relativt store internationale virksomheder, hvor det må antages, at produktionsformer, teknologi og forbrug af materialer ligger på niveau
med de førende i den vestlige verden.
3.6.1 Direkte materialeinput
Det samlede materialeinput er i nærværende opgørelse estimeret til omkring 140.000 ton, som resulterer i en produktion på omkring 40.000 ton produkter.
Datagrundlaget er hentet fra Danmarks Statistik, da oplysningerne i virksomhedernes grønne regnskaber ikke var tilstrækkelige.
Opgørelse af det direkte materialeinput, DMI, for 1997 (Gravgård Pedersen, 2002) for Medicinalindustrien NACE kode 24.40.00 er opgjort til 330.000 ton.
DMI-opgørelsen antages dels at omfatte importeret medicinalprodukter og dels producerede produkter, og der er således ikke nogen umiddelbare uoverensstemmelser mellem de to opgørelser.
3.6.2 Totale materialeinput
Til fremstilling af de anvendte materialer er det estimeret, at der samlet skal anvendes en råstofmængde på 500.000 ton i alt svarende til 13 ton pr. ton fremstillet produkt.
De data, der er offentliggjort af Wuppertal Institute, er for specifikke kemiske forbindelser og materialer og ikke for grupper, som der arbejdes med for den farmaceutiske industri.
Ved en gennemgang af de af Wuppertal angivne data er der foretaget skøn for de materialegrupper, der arbejdes med, og en samlet opgørelse af niveauet for råstofforbruget er vist i tabel 3.9.
Tabel 3.9 Estimering af totalt materialeinput
Kemiske stoffer og produkter |
Råvareforbrug
(kg/ton produkt) |
Materialeinput
kg/kg |
Samlet
materialeinput |
Stoffer baseret på stivelse etc. |
1.815 |
0 1) |
0 |
Let bearbejdede kemiske forbindelser, råolie som eks. |
907 |
1,2 |
1.100 |
Meget bearbejdede kemiske forbindelser |
544 |
10 2) |
5.400 |
Organiske opløsningsmidler (regnes som ethanol) |
363 |
1 3) |
360 |
I alt |
3.629 |
|
6.900 |
1): Stivelse er kun medtaget med et energiforbrug.
2): Her er valgt at tage udgangspunkt i nogle af de stoffer med højt materialeinput som fx epoxyforbindelser.
3): Methanol er angivet med et materialeinput på 0,7 kg/kg, hvorfor ethanol skønsmæssigt er sat til 1 kg/kg.
Som det ses af tabel 3.9, ligger det samlede materialeinput på omkring 2 gange det opgjorte råvareforbrug hos medicinalproducenterne. Der skal gøres opmærksom på, at usikkerhederne er store, da
udgangspunktet – råvareforbruget – er usikkert.
I nærværende opgørelse ligger råvareforbruget på omkring det dobbelte af, hvad man kommer frem til med udgangspunkt i data fra Wuppertal. Årsagen hertil er primært, at data i nærværende opgørelse
inkluderer et stor råstofforbrug til fremstilling af stivelse på omkring 2/3 af det samlede råstofforbrug, og at dette ikke er med i Wuppertal's datasæt.
3.6.3 Samlet vurdering
Da de udarbejdede data er meget usikre, er det yderst vanskeligt at konkludere, om der er overensstemmelse mellem de sammenlignede størrelser (DMI og Wuppertal's data). Det kan dog konstateres, at
der ikke er nogen direkte modsætning.
Det totale materialeinput (DMI) indeholder mængder af importerede produkter, mens nærværende opgørelse alene omfatter en relativ usikker opgørelse af dansk produktion.
I relation til en sammenligning med Wuppertal's MIPS-data skal man tage udgangspunkt i specifikke stoffer og materialer for at få en meningsfuld sammenligning, og dette har ikke været muligt i nærværende
opgørelse.
4 Møbelfremstilling
4.1 Introduktion
Træ- og møbelindustrien i Danmark omsætter for omkring 25 mio. kr. årligt (Kvist KE et al., 2000). Dette omfatter skovbrug, byggevarer og møbelindustri. Møbelindustrien udgør 59% af den samlede
omsætning.
Møbelindustrien er kendetegnet ved mange mindre virksomheder. En gennemsnitsvirksomhed inden for dette område har i størrelsesordnen 15 ansatte. Inden for møbelindustrien findes omkring 2.300
virksomheder, der i større eller mindre grad beskæftiger sig med møbelproduktion.
Træ er møbelindustrien væsentligste råvare. I Miljøprojekt 561 (Kvist KE et al., 2000) er der opstillet en opgørelse af træproduktion og –forbrug i dansk møbelindustri og tilhørende aktiviteter. Med fokus
på møbelproduktion gengives denne opgørelse i figur 4.1.

Figur 4.1 Produktion og brug af træ (Kvist KE et al., 2000)
Af figur 4.1 ses det, at materialemængden i møbelprodukter udgør 500.000 ton, hvor den primære materialemængde er træ.
Tab på savværker, ved pladeproduktion og ved møbelproduktion kan ikke opgøres på basis af oplysningerne i figur 4.1, da mængden, der går til papirproduktion samt til byggevarer og andre produkter,
ikke er opgjort særskilt.
4.2 Produktvalg
4.2.1 Produktets livsforløb
Møbler generelt kan betragtes i et livscyklusperspektiv som vist i figur 4.2.
Inputsiden er illustreret ved bokse med dobbeltstreger, outputsiden ved bokse med kraftig enkelt streg. De bokse, der er mindre væsentlige er illustreret med stiplede linier og udgangspunktet – produktion af
produktet er illustreret med en skraveret boks.
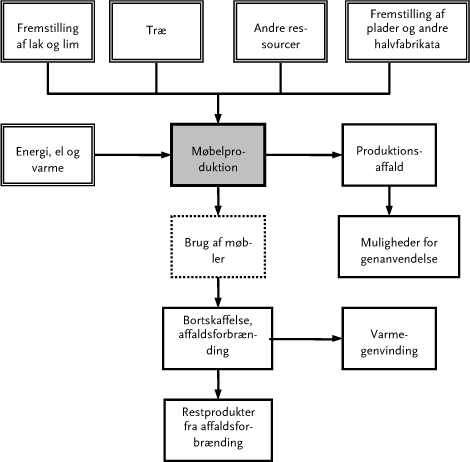
Figur 4.2 Principskitse for møbler i et livscyklusperspektiv
Af figur 4.2 fremgår det, at der hovedsageligt anvendes materialer i form af træ, plader og andre halvfabrikata, eventuelt andre materialer samt lak og lim. Hertil kommer energi i form af el og varme.
Fremstilling af disse materialer vil blive ført tilbage til råstoffer, i det omfang data er tilgængelige.
Det skal bemærkes, at figur 4.2 er en principskitse, hvor kun de overordnede elementer er vist. Fx dækker boksen fremstilling af plader og halvfabrikata en række procestrin inkl. energiudnyttelse af
affaldstræ.
Boksen ”Brug af møbler” i figur 4.2 er stiplet, da vedligeholdelse af møbler ikke er medtaget.
Energi til transport af materialer, produkter og affald er ikke medtaget.
På affaldssiden vil affaldsmængder, genanvendelige materialer samt udvundet energi ved affaldsforbrænding blive opgjort.
4.2.2 Produktudvælgelse
Den samlede produktion af møbler er på 473.000 ton. Heraf er den største del møbler fremstillet i træ med brug af små mængder metal, lak, lim og andre hjælpestoffer. Mængden af stålmøbler udgør
38.000 ton eller 8% af den samlede produktion.
Der er gennemført 3 livscyklusvurderinger inden for de seneste år af repræsentative produkter inden for møbelområdet:
- Det ene produkt er et sofabord af træ med klap af en størrelse på 1,4 m² og en forudsat levetid på 10 år. Dette produkt er repræsentativt ved, at det er fremstillet af træ og med meget små mængder
af andre materialer.
- Det andet produkt er en Montana-reol, der er fremstillet af møbelplade og finér med hængsler og skuffer af metal og plast. Ikke træ-baserede materialer udgør ca. 10% af produktet. Produktets
levetid er sat til 40 år.
- Som repræsentant for stålmøbler er det tredje produkt en kontorstol, der består af 84% stål, 12% træ og resten lak og plast. Stolens levetid er sat til 10 år.
Møbler fremstillet af tropisk træ udgør maksimalt 3% af den samlede produktion og medtages derfor ikke i nærværende vurdering (Kvist KE et al., 2000).
Det forudsættes, at disse tre produkttyper kan repræsentere dansk møbelproduktion. Dette er diskuteret med Træets Arbejdsgiverforening (Kofod CJ, pers. komm., maj 2002). Der findes ingen statistiske
opgørelser over typer af producerede møbler eller hvor stor en andel møbler, der primært består af møbelplade.
Fra miljøprojekt 281, Miljøprioritering af industriprodukter (Hansen et al., 1995) er det i den tilhørende database muligt at trække oplysninger ud om møbelproduktionen og -forbruget. Data er fra 1993,
men giver som vist i Tabel 4.1 en opdeling på typer af møbler for produktion og forbrug.
Som det fremgår af Tabel 4.1, er den samlede opgjorte møbelproduktion lavere i 1993 end opgørelsen i brancheanalysen fra 2000. Det er dog muligt at anvende oplysningerne i Miljøprojekt 281 til en
fordeling mellem de 3 produktkategorier; møbler af finér og møbelplade, møbler af massivt træ og møbler af stål. Hvor det ikke klart fremgår, om produkterne er af massivt træ eller finér og møbelplade, er
der antaget en fordeling på 50% til hver gruppe. Den lille mængde plastmøbler er udeladt af vurderingen.
Tabel 4.1 Opgørelse af produktion og forbrug af møbler (Hansen et al., 1995)
|
Data fra Miljøprojekt 281 |
Skøn over produktkategorier |
Opgørelse i ton pr. år |
Produktion |
Forbrug |
Finér/ Møbel- plade |
Massivt
træ |
Stål |
Træmøbler |
129.062 |
20.501 |
|
129.062 |
|
Møbler af træfiberplader o.l. |
181.343 |
89.278 |
181.343 |
|
|
Andre finerede eller laminerede træprodukter |
19.876 |
17.149 |
19.876 |
|
|
Møbler af spanskrør, bambus o.l. |
2.142 |
2.869 |
|
2.142 |
|
Møbler af metal |
42.568 |
43.913 |
|
|
42.568 |
Møbler af plastmaterialer |
2.287 |
3.694 |
|
|
|
Møbler til klinikker |
3.731 |
1.350 |
1.866 |
1.866 |
|
Andre møbler |
4.372 |
6.073 |
2.186 |
2.186 |
|
I alt |
385.381 |
184.827 |
205.271 |
135.256 |
42.568 |
Data i Tabel 4.1 indikerer, at fordelingen mellem de 3 produkttyper er:
- 50% reoler, baseret på møbelplade og finér med ca. 10% plast og metal
- 40% borde, baseret på massivt træ med ca. 2% metal
- 10% stålmøbler, baseret på 84% stål og 12% træ
Dette betyder, at der som udgangspunkt antages, at dansk møbelproduktion kan repræsenteres ved en årlig produktion som vist i tabel 4.2.
Tabel 4.2 Årlig dansk møbelproduktion repræsenteret ved 3 typer produkter
Møbeltype |
Skønnet andel |
Skønnet
mængde |
Vægt pr. enhed |
Skønnet antal enheder, |
Møbler af møbelplade og finér repræsenteret ved en reol |
50% |
240.000 ton |
122,4 kg |
1,96 mio. stk. |
Møbler af massivt træ repræsenteret ved et bord |
40% |
190.000 ton |
35,1 kg |
5,40 mio. stk. |
Møbler af stål repræsenteret ved en stol |
10% |
47.000 ton |
8,0 kg |
5,88 mio. stk. |
4.3 Kortlægning
Kortlægningen tager udgangspunkt i de tre møbeltyper som anført ovenfor. Kortlægningen er baseret på resultaterne fra 3 gennemførte livscyklusvurderinger. Selve kortlægningen er beskrevet i bilag B.
På basis af kortlægningen er det opgjort, hvilke materialer og mængden af disse der indgår i 1 ton møbler i gennemsnit. Dette er vist i Tabel 4.3.
Tabel 4.3 Materialeindhold i et gennemsnitsmøbel
|
Produkter af
møbelplade |
Produkter af
massivt træ |
Møbler
af stål |
Materialer
pr. ton møbel |
|
50 % |
40 % |
10 % |
|
Møbelplade |
105,1 kg |
|
|
429 kg |
Finér |
1,0 kg |
32,9 kg |
1,1 kg |
393 kg |
Bøg |
11,7 kg |
|
|
48 kg |
Stål |
1,8 kg |
0,8 kg |
6,5 kg |
98 kg |
Plast |
1,5 kg |
0,2 kg |
0,1 kg |
10 kg |
Lak og lim |
0,7 kg |
1,2 kg |
0,3 kg |
20 kg |
Fortynder |
0,6 kg |
|
|
2 kg |
Samlet vægt |
122,4 kg |
35,1 kg |
8,0 kg |
|
4.3.1 Opgørelse af mængder
4.3.1.1 Materialeforbrug
Forbruget af materialer er opgjort for gennemsnitsproduktet 1 ton møbler og vist i tabel 4.4.
Tabel 4.4 Materialeforbrug opgjort som ressourcer
Materiale |
Forbrug pr.
473.000 ton |
Forbrug pr. ton |
Møbelplade |
206.000 ton |
436 kg |
Finér |
8.460 ton |
18 kg |
Bøgetræ |
267.000 ton |
564 kg |
Stål |
73.700 ton |
156 kg |
Plast |
5.190 ton |
11 kg |
Lim |
2.400 ton |
5 kg |
Lak |
7.200 ton |
15 kg |
Lak og maling |
1.800 ton |
4 kg |
Fortynder |
1.200 ton |
3 kg |
I alt |
572.950 ton |
1.211 kg |
* Naturgasforbruget er omregnet efter 1.000 m³ = 1.205 ton
Som det ses af tabel 4.4, forbruges 1.211 kg materialer pr. 1.000 kg fremstillet produkt.
Det er antaget, at der ikke er noget materialeforbrug ved brug af produktet og ved bortskaffelse.
Stål genvindes, og i stedet for et forbrug på 73.700 ton anvendes netto et forbrug på 23.660 ton. Opgørelsen af dette er beskrevet i bilag B. Nettoforbruget svarer til 50 kg pr. ton møbler.
4.3.1.2 Råstofforbrug
Materialeforbruget opgjort som materialer, der anvendes på møbelvirksomheden, er regnet tilbage til forbrug af råmaterialer. Heri ligger en opgørelse af forbruget af råmaterialer til fremstilling af møbelplader,
finer, plast mv. Denne opgørelse er detaljeret beskrevet i bilag B.
Råstofforbruget er opgjort og vist i tabel 4.5 sammen med en omregning, der viser tabet ved udvinding af råstofferne. Betegnelsen Råstofforbrug pr. kg materiale dækker over den mængde råstof, der skal
udvindes for at få en given mængde råmateriale. Fx regnes der med, at der skal udvindes 2,4 kg jernmalm for at fremstille 1 kg råjern.
Tabel 4.5 Estimering af råstofforbrug
Materiale |
Mængde |
Råstofforbrug
pr. kg materiale |
Samlet
råstofforbrug |
Råstofforbrug
pr. ton møbler |
Træ |
679.000 ton |
2 kg/kg |
1.358.000 ton |
2.871 kg |
Jern |
23.660 ton |
2,4 kg/kg |
56.800 ton |
120 kg |
Kalk |
|
0,28 kg/kg |
6.600 ton |
14 kg |
Olie |
65.000 ton |
1,1 kg/kg |
71.500 ton |
151 kg |
Naturgas |
1.560 ton |
1,05 kg/kg |
1.600 ton |
3 kg |
I alt |
|
|
1.494.500 ton |
3.159 kg |
Den opgjorte mængde råstoffer svarer til et råstofforbrug på 3,16 ton pr. ton produkt, når genvinding er modregnet.
4.3.1.3 Energiforbrug
Energiforbruget til hele produktets livsforløb er opgjort i bilag B. Nøgletal herfra er vist i tabel 4.6.
Tabel 4.6 Nøgletal for energiforbrug
|
Forbrug pr.
473.000 ton |
Forbrug pr. ton |
Energi til råstoffer og halvfabrikata |
5.575 TJ |
11,79 GJ |
Energiindhold i materialer |
9.703 TJ |
20,51 GJ |
Energi til produktion |
3.812 TJ |
8,06 GJ |
Brutto-energiforbrug |
19.090 TJ |
40,36 GJ |
Energiudvikling ved affaldsbehandling |
7.169 TJ |
15.16 GJ |
Energiforbrug ved oparbejdning |
361 TJ |
0,76 GJ |
Netto-energiforbrug |
12.282 TJ |
25,97 GJ |
Som det ses af tabel 4.6, udgør energiindholdet i materialer en stor del af det samlede brutto-energiforbrug. Energiforbruget til fremstilling af råvarer, halvfabrikata og produktion udgør ca. 50%.
Energiforbruget i produktion af halvfabrikata er egentligt større, da en stor del af affaldstræet anvendes direkte som energikilde. Den mængde træ, der anvendes som energikilde, er opgjort i bilag B til
251.000 ton, svarende til 4.520 TJ, hvilket svarer til 9,6 GJ pr. ton producerede møbler. Denne energimængde er ikke medtaget i energiopgørelsen, men optræder alene som en materialemængde.
4.3.1.4 Godskrivning af materialer og energi
Det er blevet kortlagt, at der oparbejdes en del stålskrot fra stålmøbler og produktionsaffald. Der indsamles og oparbejdes 63.475 ton stålskrot, som bliver til 55.275 ton stål eller 116 kg pr. ton møbler.
For at fremstille 55.275 ton stål skal anvendes 60.936 ton råvarer. Denne mængde godskrives det samlede forbrug af stål.
Ved oparbejdningen af skrot forbruges energi. Det er regnet med, at der anvendes 20GJ/ton til oparbejdning, hvilket svarer til 1.270 TJ for 63.475 ton stålskrot eller 2,66 TJ pr. ton møbler.
Ved oparbejdning af skrot kan der spares fremstilling af en tilsvarende mængde materiale. Til fremstilling af sekundært stål anvendes 17,9 GJ/ton, hvilket svarer til besparelse på 909 TJ eller 1,91 TJ pr. ton
møbler.
Der genvindes energi fra forbrænding af kasserede møbler og fra affald frembragt ved produktion af råvarer, halvfabrikata og i produktionen.
Der er taget udgangspunkt i, at 75% af energiindholdet i de fleste materialer kan udnyttes. Energigenvindingen er vist i Tabel 4.7.
Tabel 4.7 Energigenvinding ved møbler
Materiale |
Mængde |
Energi-
indhold |
Udnyttel-
sesgrad |
Energi
udvikling |
Kasserede møbler |
430.000 ton |
18 GJ/ton |
75% |
5.805 TJ |
Lim og lak, affald fra fremstilling |
500 ton |
28 GJ/ton |
50% |
7 TJ |
Affaldstræ, produktion |
97.000 ton |
18 GJ |
75% |
1.310 TJ |
Lim og lak, affald fra produktion |
1.000 ton |
28 GJ/ton |
50 % |
14 TJ |
Andet affald fra produktion |
2.700 ton |
25 GJ/ton |
50 % |
34 TJ |
Energi fra oparbejdning |
|
|
|
-1.270 TJ |
Sparet energi ved materialegenbrug |
|
|
|
909 TJ |
Netto-enegiudvikling |
|
|
|
6.809 TJ |
Netto-udvikling pr. ton møbler |
|
|
|
14,40 GJ |
Som det ses af tabel 4.7, udvikles der 14,4 GJ primær energi pr. ton møbler.
4.3.2 Opgørelse af vurderede mængder
I det følgende er materialer og energiforbrug omregnet til vurderede størrelser i mPR.
Indholdet af materialer i 1 ton møbler er vist i tabel 4.3 og kan omregnes til forbrug af ressourcer som vist i tabel 4.8.
Tabel 4.8 Ressourcer i 1 ton møbler
|
Materialer
pr. ton møbel |
Ressourceforbrug
mPR/kg |
Samlet
ressourceforbrug |
|
|
|
|
Møbelplade |
429 kg |
0 mPR/kg |
0 mPR |
Finér |
393 kg |
0 mPR/kg |
0 mPR |
Bøg |
48 kg |
0 mPR/kg |
0 mPR |
Stål |
98 kg |
0,13 mPR |
12,74 mPR |
Plast |
10 kg |
0,04 mPR |
0,40 mPR |
Lak og lim |
20 kg |
0,04 mPR |
0,80 mPR |
Fortynder |
2 kg |
0,04 mPR |
0,08 mPR |
Samlet vægt |
|
|
14,02 mPR |
4.3.2.1 Vurdering af materialeforbrug
Ressourceforbruget til materialer er vist i Tabel 4.9.
Tabel 4.9 Materialeforbrug opgjort som ressourcer
Materiale |
Forbrug pr. ton |
Ressourcefor-
brug mPR/kg |
Ressource-
forbug mPR |
Træ |
1.435 kg |
0 mPR/ kg |
0 mPR |
Jern |
183 kg |
0,08 mPR/kg |
14,64 mPR |
Kalk |
9 kg |
0 mPR/kg |
0 mPR |
Råolie |
137 kg |
0,04 mPR/kg |
5,48 mPR |
Naturgas * |
3 kg |
0,06 mPR/kg |
0,18 mPR |
I alt |
1.767 kg |
|
20,30 mPR |
* Naturgasforbruget er omregnet efter 1.000 m³ = 1.205 ton
4.3.2.2 Vurdering af energiforbrug
Brutto-energiforbruget på 40,36 GJ pr. ton møbler svarer i ressourcer til 39,38 mPR baseret på olie.
Netto-energiforbruget på 25,97 GJ pr. ton møbler svarer i ressourcer til 25,34 mPR baseret på olie.
4.3.2.3 Vurdering af godskrivning
Ved genvinding spares der en mængde skrot i en mængde på 60.936 ton i forhold til den samlede produktion eller 127,7 kg pr. ton møbler.
Jern har et ressourcetræk på 0,08 mPR pr. kg. Ressourcebesparelsen pr. 1 ton møbler svarer til 10.22 mPR.
Energibesparelsen er opgjort til 14,40 GJ pr. ton, hvilket svarer til 14,05 mPR.
4.4 Ressourceeffektivitet
4.4.1 Ressourceeffektivitet på materialeniveau
4.4.1.1 Materialeforbrug, produktion og brug
Ved produktion af 1.000 kg møbler bruges til møbelproduktionen og i brugsleddet gennemsnitligt 1.211kg materialer, hovedsagelig træ samt mindre mængder jern og råolie til plast. Ressourceeffektiviteten
kan derfor beregnes til:

Den beregnede effektivitet viser, at der er et spild på 17% materialer i produktionen. Spildet er primært træ og stål samt små mængder plast og lim/lakrester.
Vandforbruget er estimeret til omkring 200.000 m³, hvilket svarer til omkring 0,5 m³ pr. ton produkt.
4.4.1.2 Materialeforbrug, produktion, brug og bortskaffelse
Stål genvindes, og i stedet for et forbrug på 156 kg pr. ton anvendes netto 50 kg pr. ton møbler. Netto, materialeforbrug bliver derfor 1.211-156+50 = 1.105 kg.
Ressourceeffektiviteten kan derfor beregnes til:

Genvinding af stål betyder en del for effektiviteten, og her er der taget udgangspunkt i, at 75% af det anvendte stål kan anvendes igen efter oparbejdning.
4.4.1.3 Materialeforbrug, hele livscyklus
Forbruget af råstoffer er opgjort ud fra materialeforbruget, når genvinding af stål er medregnet. Opgørelsen viser, at der forbruges 3,16 ton råstoffer pr. ton møbler.

Der er en betydelig forskel på materiale- og råstofforbrug. Der er regnet med, at der er 50% materialetab ved råstofudvinding for træ, der udgør den væsentligste mængde. Er tabet ved skovning af træ
mindre, vil effektiviteten for materialer og råstoffer nærme sig hinanden. For jern, olie og naturgas er der regnet med mindre tab.
4.4.2 Ressourceeffektivitet baseret på vurderet opgørelse
4.4.2.1 Ressourceforbrug, materialer
Den mængde ressourcer, der gennemsnitligt findes i 1 ton møbler, udgør 14,02 mPR. Af denne mængde ressourcer udgør stålet ca. 90 %.
I opgørelsen af ressourceforbruget er medtaget råstofudvinding, fremstilling af halvfabrikata, produktion af møbler samt brug. De ressourcer, der medgår til fremstilling af 1 ton møbler i gennemsnit, er opgjort
til 20,30 mPR.

Den tredjedel, der tabes af ressourcerne, udgøres dels af råjern og dels af olie til lak, lim og fortynder.
4.4.2.2 Ressourceforbrug, materialer og energi
Af energiopgørelsen ses det, at der forbruges 40,36 GJ/ton møbler produceret, når alle energiforbrug, - fra råstofudvinding til om med produktionen medtages. Et energiforbrug svarer til 39,38 mPR, når det
omregnes til forbrug af olie.
Det samlede forbrug af ressourcer til materialer og energi kan opgøres til 20,30 mPR + 39,38 mPR = 59,68 mPR.
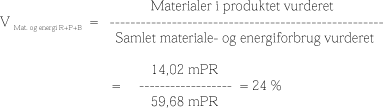
Det høje bidrag til det samlede materialeforbrug i form af energi, skyldes primært, at meget energi er bundet i træ. Af det samlede energiforbrug udgør ca. 50% energi bundet i materialer, godt 25% energi til
råstofudvinding og fremstilling af halvfabrikata og ca. 20% til møbelproduktion.
4.4.2.3 Ressourceforbrug, hele livscyklus
For kasserede møbler er det forudsat, at 75 % af stålet indsamles særskilt og oparbejdes. Endvidere er det forudsat, at 75% af energiindholdet i de kasserede møbler, og det fremkomne affald kan
nyttiggøres.
Det er opgjort, at ved genvinding af stål spares en ressourcemængde svarende til 10,22 mPR, hvilket udgør en væsentlig del af de ikke fornyelige ressourcer i produktet.
Der kan nyttiggøres en betydelig mængde energi, der primært stammer fra forbrænding af træet i møblerne. Besparelsen er opgjort til 14,40 GJ/ton produkt, hvilket i olieressourcer svarer til 14,05 mPR.
Under hensyntagen til genvinding og nyttiggørelse kan den vurderede ressourceeffektivitet for hele produktets livscyklus opgøres til:
![V mat. + energi, R+P+B+A/N = Materialer i produktet vurderet/Samlet nettoforbrug af materialer og energi vurderet = 14,02 mPR/[59,68 - 10,22 - 14,05] mPR = 40 %](images/s066b.gif)
4.4.3 Fortolkning
Datagrundlaget i form af en brancheanalyse samt livscyklusvurderinger for 3 repræsentative produkter har givet mulighed for at opstille nogle relativt sikre estimater for gennemsnitlige ressourceeffektiviteter.
Kortlægningen tager udgangspunkt i en gennemsnitlig produktion bestående af 50% produkter baseret på møbelplade, 40% baseret på massivt træ og 10% møbler primært udført i stål. En ændring fra
denne fordeling vil have stor betydning for de beregnede ressourceeffektiviteter.
4.4.3.1 Resultater
De opgjorte ressourceeffektiviteter er vist i Tabel 4.10.
Tabel 4.10 Beregnede ressourceeffektiviteter for møbelproduktion
|
Betegnelse |
Ressource- effektivitet |
Materialeopgørelse |
• Materialer til produktion og brug |
Mmat, P+B |
83 % |
• Materialer, produktion, brug og bortskaffelse inkl. genanvendelse |
Mmat, P+B+A/N |
91 % |
• Råstoffer i hele livscyklus inkl. genanvendelse |
Mmat. R+P+B+A/N |
32 % |
Ressourceopgørelse |
• Materialer vedrørende råstoffer, produktion og brug |
Vmat, R+P+B |
69 % |
• Materialer og energi vedrørende råstoffer, produktion og brug |
Vmat+energi, R+P+B |
24 % |
• Materialer og energi i hele livscyklus inkl. genvinding |
Vmat+energi, R+P+B+A/N |
40 % |
En forøgelse af ressourceeffektiviteten vil kunne ske, såfremt affaldsmængderne fra produktion af møbelplade, finér og anvendelsen af træ i selve møbelproduktionen kan optimeres. Tabet sker således dels
ved fremstilling af halvfabrikata og dels ved møbelproduktion.
Forskellen i ressourceeffektiviteten med og uden råstofudvinding skyldes primært tab ved skovning af træ. Der er regnet med et tab for træ alene på 50% i form af bark, fraskær og savsmuld.
I de vurderede opgørelser tæller træ ikke med, da det er en fornyelig ressource. Ressourcetabet (30%) udgøres således hovedsagelig af metalaffald fra produktionen samt affald fra lakering og limning.
Grunden til, at ressourceeffektiviteten er meget lav, når der ses på både materialer og energi, er, at energiindholdet i materialerne – primært træ – er meget højt. Af den energimængde, der indgår i
beregningen af det samlede forbrug, udgør energi til henholdsvis udvinding af råstoffer og produktion hver 20-30%, mens den resterende del er bundet i materialerne.
Ressourceeffektiviteten baseret på materialer og energi inkl. genvinding er 50% højere end uden genvinding. Genvinding af stål og forbrænding af kasserede produkter med energiudnyttelse har omtrent lige
stor betydning.
4.4.3.2 Anvendelse
Såfremt en virksomhed har en produktion af blandede produkter, der ligner nærværende opgørelse, vil den kunne sammenligne egne tal med ressourceeffektiviteten beregnet for materialer (MMat. P+B).
Ønsker man at vurdere bortskaffelsen af produkterne og fx fremme genanvendelse af materialer, kan MMat. P+B+A/N anvendes som sammenligningsgrundlag.
Fremstillere af halvfabrikata og andre materialer burde kunne få en indikation af ressourceeffektiviteten Mmat, R+P+B+A/N. Den er dog her opgjort samlet for alle typer af materialer, og skal der anvendes
en eller anden form for gennemsnitsmål, bør dette opgøres for hver materialetype.
Ressourceeffektiviteterne baseret på vurderede størrelser siger noget om, hvilke knappe ressourcer, der bør fokuseres mest på. En virksomhed, der producerer møbler, vil således kunne se, hvilke materialer
der først og fremmest bør prioriteres ved en indsats omkring ressourceminimering, – her metaller, dernæst plast og sidst træ.
Ressourceeffektiviteten opgjort i mPR for energi og materialer (VMat+nergi, R+P+B) giver et noget sløret billede af energiforbruget, da materialerne (især træ) i sig selv indeholder meget energi. En
formindskelse af energiforbruget ved fremstillingsprocessen vil således være vanskelig at se.
Ressourceeffektiviteten, der dækker hele livscyklus (VMat+nergi, R+P+B+A/N), viser betydningen af genvinding af materialer og udnyttelsen af energi i materialerne. En sådan beregning vil primært være
anvendelig på et overordnet plan, hvor man fx ønsker at sammenligne forskellige typer af produktioner/produkter.
4.5 Affaldsforebyggelse
Inden for møbelbranchen anvendes træ, halvfabrikata af træ i form af møbelplader og finér samt mindre mængder stål, plast samt lak og lim.
Meget træ og halvfabrikata importeres, ligesom stål og plast importeres og muligvis bearbejdes i Danmark inden anvendelse i møbelindustrien. Lak og lim fremstilles enten i Danmark af importerede
materialer eller importeres direkte.
Muligheder for minimering af affald, som ikke nyttiggøres, er beskrevet i det følgende.
4.5.1.1 Træ
Da træ indeholder relativt meget energi og i ikke forurenet form er velegnet til afbrænding, sker dette i stor udstrækning.
Træaffaldet i forbindelse med fremstilling af halvfabrikata er fra producenternes side ikke opgjort, da det oplyses, at alt træaffald forbrændes, og energien udnyttes i produktionen. I bilag B er det kortlagt, at
der til fremstilling af 160.500 ton møbelplader og finér forbrændes 251.000 ton træ. Dette giver en energimængde på 28 GJ/ ton møbelplade, og finér er er et meget væsentligt bidrag til det samlede
energiforbrug.
Træaffald i møbelproduktionen antages at blive forbrændt, såfremt det ikke er imprægneret eller på anden måde forurenet. Da andelen, der kan forbrændes, ikke er opgjort, er den energimængde, der kan
udvikles ikke opgjort. I tabel 4.3 og tabel 4.4 er materialeindholdet af træbaserede komponenter i produktet, og det der bruges i produktionen opgjort. Heraf fremgår det, at 1 ton gennemsnitsmøbler består
af 870 kg møbelplade, finér og massivt træ. Til produktionen anvendes 1.018 kg, hvilket betyder, at der fremkommer ca. 150 kg træaffald pr. ton møbler.
Såfremt alt dette træaffald kan brændes, vil det svarer til en energimængde på 2,7 GJ pr. ton produkt svarende til en energimængde på 1.260 TJ pr. år for den samlede produktion. Den energimængde
svarer til ca. 1/3 af den energimængde, der bruges i møbelproduktionen.
En stor del træaffald forbrændes i dag, og der bør fokuseres på, om mere kan forbrændes, uden det giver anledning til udledning af miljøbelastende emissioner.
4.5.1.2 Stål
Stål udgør den væsentligste ressource, når man anlægger et knaphedsperspektiv. I nærværende kortlægning er det vist, at genvinding af stålet har stor betydning for ressourceeffektiviteten.
Der findes knapt 100 kg stål i et ton gennemsnitsmøbler. Det dækker alt fra deciderede møbler fremstillet af stål til skruer, bolte og andet, der anvendes i træmøbler. På en møbelfabrik anvendes i gennemsnit
156 kg, hvilket vil sige, at omkring 1/3 eller 50 kg pr. ton møbler bliver til affald.
Meget stål fra produktionen bliver i dag indsamlet og genvundet. I gennemsnit ligger genvinding af stål på over 90%, men om dette også gælder for møbelproduktionen vides ikke.
Fra de kasserede møbler sker der antagelig en vis genvinding, men det kan ikke forventes, at alle skruer m.v. fjernes fra et træmøbel, inden det forbrændes.
Der bør dog sigtes mod en genvinding for stål fra møbler, og møbelproduktion der ligger på omkring 90%, da stålaffald fra produktionen, samt kasserede stålmøbler relativt let kan indsamles.
Et andet forhold, der bør fokuseres på er at anvende så lavlegeret stål som muligt. Rustfrit stål, der indeholder chrom og nikkel, er væsentligt mere ressourcebelastende end maskinstål, der er legeret med
små mængder mangan. Teknisk og kvalitetsmæssigt vil de forskellige producenter antagelig stille forskellige krav, der går på styrke, bearbejdelighed, udseende og holdbarhed, men det bør ud fra et
ressourcemæssigt hensyn overvejes, om der i nogle tilfælde kan bruges ståltyper med meget lidt legeringsmetaller.
Til at illustrere denne problematik er det opgjort, at:
- Maskinstål består af 99% jern og 1 % mangan og har et ressourcetræk på 0,99 × 0,08 mPR + 0,01 × 5 mPR = 0,13 mPR.
- Rustfrit stå består af 18% chrom, 8% nikkel og 74 % jern og har et ressourcetræk på 0,18 × 12,8 mPR + 0,08 × 106 mPR + 0,74 × 0,08 mPR = 10,8 mPR.
Heraf ses det, at rustrit stål er meget mere ressourcebelastende – næsten en faktor 100 efter UMIP-metodens principper – end maskinstål.
4.5.1.3 Plast
Plast anvendes som skuffer, til forskellige holdere m.v. Af opgørelsen fremgår det, at der i gennemsnit findes 10 kg plast i 1 ton møbler, og at 1 kg pr. ton fra møbelproduktionen fremkommer som affald.
Den samlede mængde plastaffald fra produktionen udgør derfor i størrelsesordnen 450-500 ton pr. år og fra de kasserede produkter 4.500 ton til 5.000 ton.
Den væsentligste mængde plast udgøres antagelig af polyestre (PE og PP) og vil forekomme i en række forskellige farver og kvaliteter.
Muligheder for indsamling og oparbejdning bør overvejes.
Alternativt kan forbrænding med energigenvinding overvejes. 1 ton plast har en brændværdi på 40 GJ. Udnyttes energiindholdet i affaldet fra produktionen vil det svare til en energimængde på 18 til 20 TJ
pr. år og 10 gange så meget for plasten i kasserede produkter.
4.5.1.4 Lim, lak og fortynder
Fra affaldskortlægningen (Pommer et al., 2003) er det opgjort, at der fremkommer 5-10% af de anvendte lak- og limprodukter som affald. Langt hovedparten behandles som farligt affald og forbrændes på
Kommunekemi eller andre affaldsbehandlingsanlæg. Det antages, at der i forbindelse med forbrændingen er energigenvinding.
4.5.1.5 Samlet prioritering
De forhold, der bør forkuseres på med hensyn til affaldsforebyggelse og ressourceminimering, er:
- Forbrænding med energiudnyttelse af alt ikke forurenet affaldstræ, der ikke kan anvendes som materialer.
- Øget indsamling af stål, både fra møbelproduktion og fra kasserede produkter.
- Anvendelse af ikke-legeret stål, hvor det er muligt.
- Indsamling af plastaffald fra møbelproduktion og kasserede produkter med henblik på oparbejdning – alternativt forbrænding med energiudnyttelse.
4.6 Sammenligning med øvrige opgørelser
En stor del af dansk møbelproduktion er gennem mange år blevet eksporteret til mange dele af verden. Det vurderes, at produktionsprocesser og anvendelse af materialer ligger på linie med eller på forkant
af europæisk møbelproduktion (per. komm. J Baadsgaard-Jensen, november 2002). Det må derfor antages, at udnyttelse af råvarer, materialer og energi i Danmark mindst ligger på linie med andre
europæiske lande.
4.6.1 Direkte materialeinput
DMI er for 1997 opgjort til 696.000 ton. Af opgørelsen fremgår det, at alt er opgjort som import og intet som danske ressourcer. Af opgørelsen fremgår det endvidere, at den største mængde (684.000 ton)
er opgjort som materialetypen ”Andet”. Med hensyn til anvendelsen af materialeinputtet er det anført for møbelindustrien, at omkring 2/3 eksporteres.
I nærværende opgørelse er der kommet frem til, at der til en produktion på 473.000 ton møbler anvendes 575.000 ton materialer. Heraf er de omkring 480.000 ton træ i form af planker og halvfabrikata.
De resterende udgøres stål samt olie og gas til plast.
En stor del af træ forarbejdes til møbelplader og finér mv. Ved fremstilling af disse halvfabrikata tabes materiale. Møbelplader og finér fremstilles dels i Danmark og importeres som halvfabrikata. Den
mængde materiale i form af træ, der skal anvendes til planker og halvfabrikata, jf. nærværende opgørelse, udgør 680.000 ton.
Såfremt en del af de træbaserede materialer importeres som halvfabrikata, vil nærværende opgørelse på 100.000 ton til stål, olie og gas samt mellem 480.000 ton og 680.000 ton til træbaserede produkter
kunne modsvare opgørelsen af DMI på 696.000 ton.
4.6.2 Totale materialeinput
Til fremstilling af 1 ton møbler anvendes gennemsnitligt 1,21 ton materialer pr. ton produkt eller 3,16 ton råstoffer pr. ton produkt.
For visse af de materialer, der anvendes, har Wuppertal angivet mængden af råstoffer. Der skal gøres opmærksom på, at det er antaget, at kalkforbruget, som er anført i tabel 4.5, er indregnet i
materialeforbruget for jern.
Tabel 4.11 Estimering af totalt materialeinput
Materiale |
Mængde |
Råstofforbrug
pr. kg materiale |
Samlet
råstofforbrug |
Råstofforbrug
pr. ton møbler |
Træ |
679000 ton |
5 kg/kg |
3.395.000 ton |
7,178 ton |
Jern |
23.660 ton |
4,7 kg/kg |
111.200 ton |
0,235 ton |
Olie |
65.000 ton |
1,2 kg/kg |
78.000 ton |
0,165 ton |
Naturgas |
1.560 ton |
1,2 kg/kg |
1.870 ton |
0,004 ton |
I alt |
|
|
3.586.000 ton |
7,582 ton |
Som det ses af tabel 4.11, er råstofforbruget baseret på Wuppertal's data væsentligt højere end det, der er kommet frem til i nærværende opgørelse. Det væsentligste bidrag til det totale materialeinput er
træ, hvor der er forudsat, at der anvendes 5 kg råtræ pr. kg. Dette er langt højere end de kilder, der i øvrigt er set på (SigmaPro, Tillman). Samtidig fremgår det ikke af MIPS-datasættet, hvilke
forudsætninger der er opstillet for de enkelte datasæt.
Materialeinputtet for jern er ligeledes højere, men dette er af mindre betydning, da den anvendte mængde er mindre. Materialeinputtet for olie og naturgas ligger på linie med andre LCA-data.
4.6.3 Samlet vurdering
Materialeforbruget til fremstilling af møbler stemmer nogenlunde overens med det direkte materialeinput, når der tages hensyn til, at en vis mængde af de træbaserede produkter importeres som halvfabrikata.
Forbruget af råtræ til træplanker eller forarbejdede produkter er opgjort meget forskelligt, og derfor ses der store forskelle i råstofforbruget opgjort i nærværende undersøgelse, og når der tages
udgangspunkt i Wuppertal's MIPS-data. For de øvrige råstofforbrug er der en rimelig overensstemmelse.
5 Elektriske og elektroniske komponenter
5.1 Introduktion
I Danmark produceres en række elektriske og elektroniske komponenter. I affaldskortlægning af udvalgte brancher (Pommer et al., 2003) er affaldsmængderne fra danske elektronikmontagevirksomheder,
samt komponentfremstillere med mindre end 200 ansatte kortlagt.
Affaldsproduktionen blev identificeret til at stamme fra følgende virksomheder:
- Elektronikmontagevirksomheder, som producerer bestykkede printkort, samt eventuelt færdige produkter
- Komponentfremstillingsvirksomheder som fremstiller
- transformere, spoler mv.
- komponenter baseret på keramiske bæremedier (hybridkredse, trimmere, pifiltre etc.)
- effektmodstande
- kondensatorer
- integrerede kredse fremstillet af udenlandske underleverandører, men som testes i Danmark
Affaldsundersøgelsen viste, at mængden af produktionsaffald fra virksomhederne var lille i forhold til gennemsnittet for fremstillingsvirksomheder. Der blev generelt konstateret en høj genanvendelse af de
metalholdige fraktioner i affaldet.
5.2 Produktvalg
Ved udvælgelse af produkter, som der skal foretages en vurdering af ressourceeffektiviteten for, tages der udgangspunkt i affaldskortlægningen, hvor affaldsproduktionen fra elektronikmontage virksomheder
og komponentfremstillere med mindre end 200 ansatte er undersøgt.
Et typisk elektronikprodukt, som fremstilles i mindre serier af elektronikmontagevirksomheder, kan fx være ladeapparater, laboratoriestrømforsyninger og måleudstyr, specialiseret audioudstyr etc. Denne
type udstyr består af et kabinet med påmonterede printkort og eventuelt løse komponenter monteret direkte i kabinettet som fx transformere og monitorer, se figur 5.1.
Det vil være meget vanskeligt at foretage en vurdering af ressourceeffektiviteten for alle produkter produceret af elektronikmontagevirksomheder med mindre end 200 ansatte, da der kun findes få data
vedrørende produkterne, og da disse varierer i mængde, størrelse og udformning fra uge til uge afhængigt af, hvilke ordrer elektronikmontagevirksomhederne modtager.
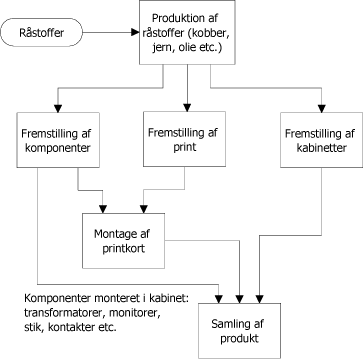
Figur 5.1 Fremstilling af typiske elektroniske produkter
Der indgår imidlertid bestykkede printkort i alle produkter, hvorfor det er relevant at vurdere ressourceeffektiviteten for produktionen af de printkort, der produceres af elektronikmontagevirksomhederne.
Komponentfremstillerne i Danmark fremstiller en række forskellige komponenter som vist ovenfor.
Ud fra supplerende oplysninger indhentet fra komponentfremstillere, som tidligere blev kontaktet og besøgt i affaldskortlægningen (tabel 5.1), udgør transformere langt den største del af komponenternes
samlede masse med ca. 96%, hvorfor det vil være relevant at udvælge denne komponent til at vurdere ressourceeffektiviteten for.
Tabel 5.1 Mængder af producerede samt testede komponenter i Danmark i virksomheder med mindre end 200 ansatte
Komponenter |
Ton |
% |
Sum passive komponenter + keramisk monterede hybridkredse |
210 |
3,5 |
Integrerede kredse (produceres i udland men testes i Danmark) |
28 |
0,5 |
Transformere |
5500 |
96 |
5.3 Kortlægning af printkort
Livsforløbet for et printkort, fra udvinding af råstoffer til bortskaffelse af de kasserede kort er vist i figur 5.2.
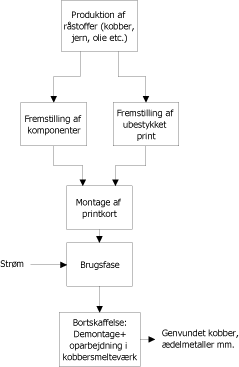
Figur 5.2 Livscyklus for et bestykket printkort
Råvarefasen omfatter udvinding og oparbejdning af metaller og materialer, som indgår i printkortet.
Produktionsfasen omfatter fremstilling af det ubestykkede printkort ved fremstilling af bæremateriale, pålægning af kobber, fremstilling af printmønster samt boring af huller. Hertil kommer fremstilling og
montage af komponenter.
Brugsfasen er karakteriseret ved tab af energi som varme i komponenterne på printkortet.
I bortskaffelsesfasen genvindes en del af metallerne via behandling i kobberværker samt eventuelt energiindhold af de organiske bestanddele. Denne model for bortskaffelse gælder kun for produkter på det
danske og til dels det europæiske marked.
Kortlægning af et printkorts livsforløb og de materialer og andre ressourcer, der anvendes, er beskrevet i bilag C.
Et typisk printkort består af en række metaller som vist tabel 5.2.
Tabel 5.2 Metaller i et typisk printkort
Materiale |
Vægt%
i print |
mPR/kg
print |
Metalmængde
pr. kg printkort |
Guld |
0,073 |
63,5 |
0,7 gram |
Palladium |
0,042 |
58,1 |
0,4 gram |
Sølv |
0,76 |
56,9 |
7,6 gram |
Tin |
1,02 |
24,7 |
10,2 gram |
Antimon |
0,23 |
7,79 |
2,3 gram |
Kobber |
22,43 |
5,05 |
224,3 gram |
Bly |
0,40 |
0,977 |
4,0 gram |
Nikkel |
0,18 |
0,266 |
1,8 gram |
Jern |
2,13 |
0,00473 |
21,3 gram |
Aluminium |
0,14 |
0,00298 |
1,4 gram |
Det ses, at de væsentligste bidrag udgøres af guld, palladium, sølv, tin, antimon og kobber, idet disse 6 grundstoffer står for over 99% af ressourceforbruget. Det er derfor ud fra et ressourcesynspunkt disse
stoffer, man bør forsøge at genvinde, mens resten af metallerne, plast mv. ikke tæller væsentligt set ud fra en ressourcebetragtning. I det følgende beregnes derfor kun for de 6 angivne grundstoffer.
I brugsfasen er effektforbruget afgørende for opgørelse af strømforbruget. Afhængig af hvilken form for elektronik printkortet anvendes i, vil effektforbruget variere i størrelsesordnen 1 W/kg til 250 W/kg. I
kortlægningen er der derfor foretaget en opgørelse af strømforbruget for lavt energiforbrug på1 W/kg, middel effektforbrug på 25 W/kg og et højt effektforbrug på 250 W/kg.
Levetiden af et printkort er sat til 10 år. For det varmetab, der sker under produktets levetid, er det antaget, at 50% udnyttes til rumopvarmning.
I bortskaffelsesfasen er det afgørende, om metallerne oparbejdes eller ej. Der er gennemregnet to tilfælde for middel effektforbrug, et med højere genanvendelse af metaller end i dag og et uden
genanvendelse.
5.3.1 Opgørelse af mængder (pr. kg produkt)
Ud fra oplysninger om et gennemsnitligt printkorts sammensætning er forbruget af råstoffer i livscyklus opgjort for en situation med et middel effektforbrug og typisk genanvendelse af metalindhold via
kobbersmelteanlæg. Resultatet er vist i tabel 5.3 og tabel 5.4. I tabel 5.4 er endvidere angivet det estimerede råstofforbrug i livscyklus for de printkort, der er estimeret produceret af danske virksomheder
med mindre end 200 ansatte (Pommer et al., 2003). Det skal bemærkes, at materiale- og råstofforbrug til fremstilling af komponenter og print ud fra råstoffer er negligeret. Dette gælder kun for opgørelser
baseret på vægtopgørelser og ikke opgørelser baseret på vurderede størrelser, hvor data stammer fra nøjagtige beregninger med alle procestrin.
Tabel 5.3 forbrug af materialer i livscyklus for printkort
Indhold |
Indhold af materiale/
grundstof pr. kg printkort |
Genvindings-
procent % |
Nettoforbrug af mate-
riale pr. kg printkort |
Kobber |
224,3 g |
98 |
4,486 g |
Jern |
21,3 g |
|
21,3 g |
Tin |
10,2 g |
20 |
8,16 g |
Sølv |
7,6 g |
90 |
0,76 g |
Bly |
4 g |
|
4 g |
Antimon |
2,3 g |
0 |
2,3 g |
Nikkel |
1,8 g |
|
1,8 g |
Aluminium |
1,4 g |
|
1,4 g |
Guld |
0,73 g |
98 |
0,0146 g |
Palladium |
0,42 g |
98 |
0,0084 g |
Plast |
363 g |
0 |
363 g |
Keramik/glas |
363 g |
0 |
363 g |
Tabel 5.4 Forbrug af råstoffer
Indhold |
Råstof Kg/kg |
Bruttoforbrug af råstoffer pr. kg |
Nettoforbrug af råstoffer pr. kg |
Bruttoforbrug af råstoffer pr. 1326 ton 3) |
Nettoforbrug af råstoffer pr. 1326 ton |
Kobber |
3,8 1) |
852 g |
17 g |
1130 ton |
22 ton |
Jern |
2 1) |
423 g |
42,6 g |
56 ton |
56 ton |
Tin |
10 2) |
102 g |
81,6 g |
135 ton |
108 ton |
Sølv |
10 2) |
76 g |
7,6 g |
101 ton |
10 ton |
Bly |
10 2) |
40 g |
40 g |
53 ton |
53 ton |
Antimon |
10 2) |
23 g |
23 g |
30 ton |
30 ton |
Nikkel |
7 1) |
12,6 g |
12,6 g |
17 ton |
17 ton |
Aluminium |
3 |
4,2 g |
4,2 g |
6 ton |
6 ton |
Guld |
10 2) |
7,3 g |
0,15 g |
10 ton |
0,2 ton |
Palladium |
10 2) |
4,2 g |
0,084 g |
6 ton |
0,1 ton |
Plast |
1,7 1) |
617 g |
617 g |
818 ton |
818 ton |
Keramik/glas |
1,3 1) |
472 g |
472 g |
626 ton |
626 ton |
|
|
|
|
|
|
Sum |
|
2,253 kg |
1,318 kg |
2.988 ton |
1.747 ton |
|
|
|
|
|
|
Energiforbrug i brugsfase som olie |
1,1 1) |
515,9 kg |
257,95 kg |
684.500 ton 4) |
342.250 ton 4) |
1) Råstofforbruget er estimeret ud fra oplysninger i UMIP database og omfatter forbrug af kemikalier, råstoffer og brændsel til energiproduktion, men ikke forbrug af vand. (Det forbrugte vand returneres til
biosfæren fra udvindingsprocessen med indhold af diverse stoffer).
2) Der haves ikke data fra UMIP for denne komponent, hvorfor forbruget er sat konservativt til maximalt en faktor 10 (excl. vandforbrug).
3) Produktionen af bestykkede printkort fra danske virksomheder med mindre end 200 ansatte er anslået til 1326 ton (Pommer et al., 2003).
4) Det beregnede nettoforbrug af energi forudsætter, at printkortene indgår i produkter i Danmark med 50% udnyttelse af spildvarmen til rumopvarmning. Det skal bemærkes, at der er tale om et
beregningseksempel, hvor der er antaget et middel energiforbrug på 25 W/kg bestykket printkort i 10 år.
Som det ses af tabel 5.4 forbruges omkring 2,3 kg råstoffer til fremstilling af 1 kg printkort brutto eller 1,3 kg netto, når der er taget hensyn til genvinding af ædelmetallerne. Forbruget af fossile brændsler til
produktion af energi i brugsfasen udgør dog en langt større vægt med 516 kg brutto eller 258 kg netto, idet der regnes med 50% udnyttelse af spildvarmen til rumopvarmning.
5.3.2 Opgørelse af vurderede mængder (mPR pr. kg produkt)
Materialeforbruget er opgjort i vurderede størrelser i tabel 5.5 for et middel effektforbrug på 25W/kg og typisk genanvendelse af metaller.
Tabel 5.5 Scenario 1 Middel effektforbrug med typisk genanvendelse af metaller
Materiale- og produktionsfase samt bortskaffelsesfase |
Indhold i færdigt produkt (gram) |
mPR i produkt |
MPR genvundet ved bortskaffelse |
Guld (Au) |
0,73 |
63,5 |
62,2 |
Palladium (Pd) |
0,42 |
58 |
56,8 |
Sølv (Ag) |
7,6 |
57 |
51,3 |
Tin (Sn) |
10,2 |
25 |
5 |
Antimon (Sb) |
2,3 |
7,8 |
0 |
Kobber (Cu) |
224,3 |
5,1 |
4,96 |
SUM |
|
216,9 |
180,5 |
Brugsfase |
Forbrug |
mPR forbrugt |
mPR genvundet |
Energiproduktion (kg olie) |
469,3 |
18,8 |
9,4 |
Der er i alt gennemregnet 5 forskellige scenarier, der illustrerer forskellige forudsætninger. Disse er vist i bilag C, ligesom en detaljeret beskrivelse af beregningsforudsætninger findes her.
Af tabel 5.5 fremgår
Samlet mængde forbrugte ressourcer: |
235,7 mPR |
Samlet mængde genvundne ressourcer: |
189,9 mPR |
Ressourcer i produkt: |
216,9 mPR |
5.4 Ressourceeffektivitet for et printkort
5.4.1 Ressourceeffektivitet på materialeniveau
5.4.1.1 Materialeforbrug, produktion, brug og bortskaffelse
Det har ikke med de foreliggende data været muligt at opgøre ressourceeffektiviteterne MMat, P+B materialeforbrug, produktion og brug samt MMat, P+B+A/N materialeforbrug, produktion, brug og
bortskaffelse på grund af manglende data.
5.4.1.2 Materialeforbrug, hele livscyklus
Ses der alene på den mængde materialer, der findes i produktet og de råstoffer, der medgår til fremstilling af disse materialer, kan råstofeffektiviteten opgøres (I opgørelsen indgår energi til råstofudvinding i form af fossile brændsler).
MMat. R+P+B = 1kg /2,253 kg × 100 =44 %
MMat. R+P+B+A/N = 1kg /(2,253-0,953) kg × 100 =76 %
Den del, der genvindes i forhold til det samlede råstofforbrug i livscyklus, udgør 0,953/2,253 × 100 =42%, hvilket er en relativ stor andel.
5.4.1.3 Materiale og energiforbrug
Da energiforbruget har meget stor betydning for det samlede forbrug af ressourcer, er det forsøgt at opgøre det materialeforbrug, der medgår til fremstilling af den energimængde, der medgår i produktets
levetid.
Med udgangspunkt i 1 kg bestykket printkort kan energiforbruget opgøres.
For et printkort, hvor effektforbruget sættes til middel (25 W/kg), kan følgende opgøres:
- I brugsfasen sker et energiforbrug på 7884 MJ/kg el over en levetid på 10 år. Omregnes elforbruget til primær energi svarer det til 19.710 MJ eller et olieforbrug på 469,3 kg.
- Hertil skal adderes forbruget til udvinding af olien anslået til 10% eller 46,9 kg.
I alt fås således et forbrug på 516,2 kg olie i brugsfasen, se tabel 5.4. Det antages, at halvdelen af spildvarmen genvindes som rumenergi, hvilket svarer til 258,1 kg olie til energiproduktion.
Forbruget af råstoffer til fremstillingen af printkortet er ligeledes opgjort i tabel 5.4 til 2,253 kg.
Nettoforbruget er opgjort til 1,318 kg svarende til en genvunden mængde på 2,253-1,318=0,935 kg
Vægtmængde i produktet: |
1 kg |
Samlet forbrug: |
518,5 kg |
Genvundet: |
259,0 kg |
Ressourceeffektiviteten kan derfor beregnes til:
MMat+energi, R+P+B = 1 kg / 518,5 kg 100 = 0,2 %
Tages der hensyn til genvundet energi, kan effektiviteten bestemmes til:
MMat+energi, R+P+B+A/N = 1 kg / (518,5 – 259,0) kg 100 = 0,4 %
Beregningerne med et lavt effektforbrug (1 W/kg) og højt effektforbrug (250 W/kg) illustrerer strømforbrugets store betydning. For et lavt effektforbrug er
MMat+energi, R+P+B+A/N = 8,6 % og for et højt effektforbrug er MMat + energi R+P+B+A/N = 0,04%.
Da den masse, der repræsenteres i selve materialerne, er meget mindre end den mængde, der medgår til energifremstilling, vil genvinding af materialer ikke ændre på ressourceeffektiviteten opgjort på
vægtbasis.
5.4.2 Ressourceeffektivitet baseret på vurderet opgørelse
5.4.2.1 Ressourceforbrug, materialer
Ud fra tabel 5.5 kan det opgøres, at indholdet af ressourcer i 1 kg gennemsnitsprintkort udgør 216,4 mPR.
Energiforbruget til udvinding af 1 kg materiale vil være under 200 MJ/kg, hvilket svarer til under 0,2 mPR. Dette ressourceforbrug kan derfor ikke ses af beregningerne. Tab af materialer i produktionen er
ikke opgjort og derfor kan VMat. R+P+B ikke bestemmes.
5.4.2.2 Ressourceforbrug, materialer og energi
Ved et middeleffektforbrug anvendes en energimængde svarende til 18,8 mPR, hvoraf det antages, at 50 % udnyttes til rumopvarmning.
Ved oparbejdning af kasserede printkort kan metaller svarende til 180,5 mPR genvindes.
For et printkort med et middeleffektforbrug kan effektiviteten for materiale- og energiforbrug opgøres til:
VMat+energi, R+P+B = 216, 9 / 235,7 = 92 %
5.4.2.3 Ressourceforbrug, hele livscyklus
Tages hensyn til genvinding, bliver effektiviteten
VMat+energi, R+P+B+A/N = 216, 9 / ( 235,7 – 9,4 – 180,5) = 473 %
En ændring af effektforbruget vil have væsentlig betydning for effektiviteten. Ændringerne er beregnet for:
VMat+energi, R+P+B+A/N = 589 % for lavt effektforbrug (1 W/kg)
VMat+energi, R+P+B+A/N = 167 % for højt effektforbrug (250 W/kg)
Udeladelse af udnyttelse af 50% af varmetabet vil have en meget lille betydning ved det lave effektforbrug, mens det for det høje effektforbrug vil reducere effektiviteten til omkring 95%.
I ovenstående beregninger er forudsat, at der sker en genvinding af metallerne guld, palladium, sølv og kobber samt genvinding af tin på 20 % og ingen genvinding af antimon. Ændres disse forudsætninger, vil
effektiviteten for et middeleffektforbrug kunne beregnes til:
VMat+energi, R+P+B+A/N = 96 %, når der ikke sker genvinding af nogen metaller, men kun udnyttelse af spildvarme til rumopvarmning.
VMat+energi, R+P+B+A/N = 893 %, når der sker genvinding af guld, palladium, sølv og kobber samt 80% tin og alt antimon samt udnyttelse af spildvarme til rumopvarmning.
Af de ovenstående beregninger ses det, at genvinding af metallerne har stor betydning for ressourceeffektiviteten. Det skal dog bemærkes, at en meget høj genvindingsgrad for tin samt genvinding af antimon i
dag ikke er økonomisk attraktiv.
Af ovenstående beregnede ressourceeffektiviteter ses det, at forudsætningerne har en afgørende betydning for resultaterne. På baggrund af de mange forskellige anvendelser, der er for bestykkede printkort,
kan følgende generelle forhold trækkes frem:
- Metallerne guld, palladium, sølv, kobber, tin og antimon er afgørende for ressourceforbruget.
- Et lavt effekttab giver en høj effektivitet.
- En lang levetid giver en høj effektivitet.
- En høj genvindingsgrad giver en høj effektivitet.
5.5 Kortlægning af transformere
Transformere består hovedsageligt af jern og kobber. Det er valgt kun at vurdere produktionsmetoden for traditionelle laminerede transformere med en jernkerne af blik og ikke de såkaldte
ringkernetransformere. Ringkernetransformere består dog ligeledes hovedsageligt af kobber og jern, hvorfor det vurderes, at indflydelsen i forskel af produktionsform ikke vil være så stor.
Livsforløbet for en transformer er vist i figur 5.3. Der tages udgangspunkt i, at levetiden for transformeren er 10 år.
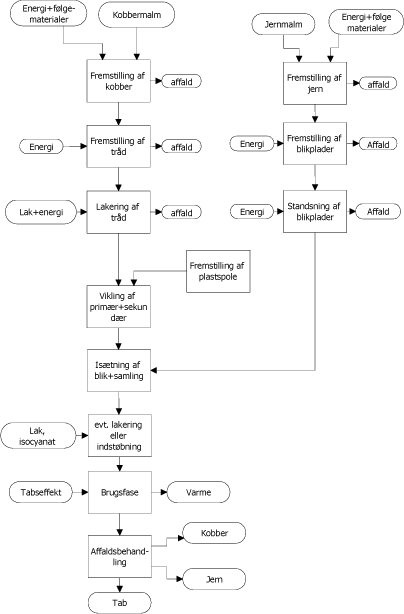
Figur 5.3 Livsforløbet for en transformer
I materialefasen indgår kobber til fremstilling af tråd, jern til blikplader m.v. samt energi. I produktionen indgår fremstilling af isoleret (lakeret) kobbertråd, udstandsning af plader, plast til spole, lak og den
egentlige fremstilling/montage af transformeren.
I brugsfasen har energiforbruget og dermed varmetabet en stor betydning.
I bortskaffelsen genvindes en del af materialerne samt eventuelt energiindholdet af de organiske bestanddele. Det antages, at kobberet oparbejdes.
Indholdet i en gennemsnitstransformer er vist i tabel 5.6.
Tabel 5.6 Materialer i gennemsnitstransformer
Materiale |
% |
Kobber |
32,5 |
Jern |
65 |
Lak, plast og andet organisk indhold |
3 |
Tin |
< 0,1% |
Selve kortlægningen af materiale og energiforbrug for en transformer er vist i bilag C, hvor detaljerede data og forudsætninger er anført.
I råvarefasen er det produktion af kobber og tin, der har betydning ressourcemæssigt.
Effekttabet i brugsfasen er helt afhængig af transformerens størrelse – små transformere har store tab, mens store transformere er langt mere effektive. Der er taget udgangspunkt i et effekttab på 12 %,
hvilket er typisk for en transformer med en størrelse på omkring 50 W.
I bortskaffelsesfasen er det genvinding af kobber og tin, der har betydning ressourcemæssigt.
5.5.1 Opgørelse af kortlagte mængder
Til fremstilling af 1 kg transformere anvendes følgende materialer:
Kobber |
332 gram, hvoraf der tabes 1 % i produktionen |
Jern |
1.313 gram, hvoraf der tabes 50% i produktionen |
Tin |
1 gram, hvoraf der tabes 1 % i produktionen |
Plast og lak |
31 gram, hvoraf der tabes 1 % i produktionen |
Samlet materialeforbrug: 1,676 kg pr. kg transformer.
Energiforbruget til fremstilling og brug af 1 kg transformer i 10 år er vist i Tabel 5.7.
Tabel 5.7 Energiforbrug for transformer
Fase |
Primær energi pr. kg |
Udvinding af materialer |
84,8 MJ 1) |
Fremstilling af kobbertråd |
24,9 MJ |
Fremstilling af blikplader |
131,3 MJ |
Fremstilling af lak og plast |
1,5 MJ |
Fremstilling af transformer |
17,9 MJ |
Brug af transformer, effekttab |
4.730,4 MJ |
Samlet forbrug |
4.991 MJ |
1) Energiforbrug er fra Pommer et al., (2001) se bilag C.
Ved omregning af energiforbruget til forbrug af olie svarer et energiforbrug på 4.991 MJ til et forbrug på 118,8 kg olie.
Under brugen antages det, at 50% af varmetabet kan udnyttes som rumopvarmning. Dette betyder, at energiforbruget reduceres til 2,626 MJ eller 62,5 kg olie.
Ved de forskellige procestrin er der endvidere antaget en række spildprocenter. Der er genvindes metaller svarende til 599 gr., se tabel 5.8.
Tabel 5.8 Genvundne materialer i procestrin
Produktion |
Forbrug af
materiale i gr. |
Genvundet i
procestrin i gr. |
Kobber |
332 |
5,9 |
Jern |
1.313 |
594 |
Tin |
1 |
0 |
Lak, plast m.v. |
31 |
0 |
Olie til energiproduktion |
4.182 |
0 |
I bortskaffelsen er det antaget, at der sker genvinding af metallerne, således at 95 % af kobberet, 50% af jernet og 20% af tinnet genvindes. Mængden af genvundne materialer i bortskaffelsesfasen udgør
635 gr. pr. kg transformer.
Ved en effekt på 50W er der forudsat et effekttab på 12%. Ved en levetid på 10 år svarer det til et samlet energiforbrug på 1892 MJ. Dette svarer til en forbrugt oliemængde på 112,6 kg, hvoraf 50%
godskrives, da noget af spildvarmes kan udnyttes. Nettoforbruget til energi svarer derfor til 56,3 kg.
Tabel 5.9 Genvundne materialer ved bortskaffelse
Bortskaffelse |
Indhold
pr. kg |
Genvindingsprocent
ved bortskaffelse |
Genvundet ved
bortskaffelse |
Kobber |
325 gram |
95 % |
308,75 gram |
Jern |
650 gram |
50 % |
325 gram |
Tin |
1 gram |
20 % |
0,2 gram |
Lak, plast m.v. |
30 gram |
0 % |
0 gram |
Råstofforbruget er opgjort på basis af materialeforbruget efter, at der er sket modregning af genanvendte materialer. Opgørelsen er vist i tabel 5.10.
Tabel 5.10 Forbrug af råstoffer
|
Råstof-
forbrug, kg/kg materiale |
Brutto
forbrug af råstoffer pr. kg |
Netto
forbrug af råstoffer pr. kg |
Brutto
forbrug af råstoffer pr.5.500 ton 1) |
Netto
forbrug af råstoffer pr. 5.500 ton 1) |
Kobber |
3,8 2) |
1.262 gram |
66 gram |
6.941 ton |
363 ton |
Jern |
2,0 2) |
2.626 gram |
788 gram |
14.443 ton |
4.334 ton |
Tin |
10 3) |
10 gram |
8 gram |
55 ton |
44 ton |
Lak, plast m.v. |
1,7 2) |
52,7 gram |
52,7 gram |
290 ton |
281 ton |
Olie til energi produktionsfaser |
1,1 2) |
4.600 gram |
4.600 gram |
25.300 ton |
25.300 ton |
Sum excl. Brugsfase |
|
8,55 kg |
5,52 kg |
47.028 ton |
30.322 ton |
Olie til energi forbrugsfase |
1,1 2) |
123,9 kg |
61,95 kg |
681.450 ton |
340.725
ton |
|
|
|
|
|
|
Sum inkl. forbrugsfase |
|
132,45 kg |
67,47 kg |
728.478 ton |
371.047
ton |
1) Produktionen af transformere fra danske virksomheder med mindre end 200 ansatte er anslået til 5.500 ton se bilag C (Pommer et al., 2003)
2) Råstofforbruget er estimeret ud fra oplysninger i UMIP database og omfatter forbrug af kemikalier, råstoffer og brændsel til energiproduktion men ikke forbrug af vand. (Det forbrugte vand returneres til
biosfæren fra udvindingsprocessen med indhold af diverse stoffer).
3) Der haves ikke data fra UMIP for denne komponent, hvorfor forbruget er sat konservativt til maximalt en faktor 10 (excl. vandforbrug).
5.5.2 Opgørelse af vurderede mængder
Materialerne i transformeren svarer til et ressourceforbrug på 6,32 mPR.
I tabel 5.11 er der angivet forbrug og genvundne mængder af materialer (kobber+jern+tin+plast/lak) og energi i form af olie i vurderede mængder mPR. Flere detaljer for de enkelte metaller kan findes i bilag
C.
Tabel 5.11 Forbrug og genvundne ressourcer i vurderede størrelser
Fase |
Forbrug
(Kobber, jern, tin,
plast/lak i mPR) |
Genvundet
(Kobber, jern, tin,
plast/lak i mPR) |
Forbrug
(Energi som
olie i mPR) |
Genvundet
(Energi som
olie i mPR) |
Råstofudvinding |
6,57 |
|
|
|
Produktionsfase |
|
0,1456 |
0,1673 |
|
Brugsfase |
|
|
4,51 |
2,25 |
Bortskaffelse |
|
5,296 |
|
|
Sum |
6,57 |
5,4416 |
4,677 |
2,25 |
Råvareforbruget til fremstilling af 1 kg transformer udgør 6,57 mPR.
Energiforbruget til fremstilling og brug af en transformer på 50W med 12% effekttab er opgjort til 4.906 MJ, hvilket svarer til ressourceforbrug på 4,68 mPR baseret på forbrug af olie.
En del af energiforbruget godskrives som erstatning for rumopvarmning. Herved spares ressourcer svarende til 2.365 MJ eller 2,25 mPR.
De genvundne metaller i produktionsfasen, der udgør 599 gr. pr. kg, svarer til 0,15 mPR, da størstedelen af den genvundne mængde udgøres af jern.
De genvundne metaller i bortskaffelsesfasen udgør næsten samme mængde på 635 gr. pr. kg transformer, men her opnås en langt højere ressourcemæssig gevinst på 5,296 mPR, idet der genvindes en stor
mængde kobber.
5.6 Ressourceeffektivitet for transformere
5.6.1 Ressourceeffektivitet på materialeniveau
5.6.1.1 Materialeforbrug, produktion og brug
Den samlede mængde materialer til fremstilling af 1 kg transformer er opgjort til 1,68 kg. Ressourceeffektiviteten kan derfor beregnes til:
MMat.P+B = 1,00 / 1,68 × 100 = 59,5 %
Der bruges således (100-59,5)/59,5 100= 68% flere materialer til fremstillingen, end der indgår i produktet.
5.6.1.2 Materialer, produktion, brug og bortskaffelse
Det er antaget, at der kan oparbejdes materialer i en mængde på 0,599 kg fra produktionsfaserne og 0,635 kg fra bortskaffelsesfasen pr. kg transformer. Nettoeffektiviteten for materialer kan derfor
opgøres til:
MMat. P+B+A/N = 1,00 / ( 1,68 – 1,234) × 100 = 224 %
5.6.1.3 Materialer og energi, produktion og brug
Tages der hensyn til, at der bruges energi i en mængde på 4.906 MJ svarende til 116,8 kg olie, kan effektiviteten beregnes til:
MMat.+energi P+B = 1,00 / 118,5 kg × 100 = 0,85 %
5.6.1.4 Materiale og energi, produktion, brug og bortskaffelse
Indregnes energiforbruget, og tages der hensyn til godskrivning af varmetabet, kan effektiviteten beregnes til:
MMat+energi, P+B+A/N = 1,00 / (118,5 – 56,3 – 1,234) kg × 100 = 1,6 %
Som det ses af ovenstående, har det stor betydning, om energiforbruget tages med eller ej.
5.6.1.5 Materialeforbrug, hele livscyklus
Hvis ressourceforbruget til udvinding af råstoffer medtages, fås
MMat. R+P+B = 1,00/3,95 × 100 =25%
Tages der hensyn til de materialer, der oparbejdes, og de ressourcer, der hermed spares, fås
MMat. R+P+B+A/N = 1,00/(3,95-3,03) × 100 =109 %
Da nettoforbruget af råstoffer excl. olie til energiproduktion i produktionsfasen, og brugsfasen er mindre end produktets vægt 1 kg, fås en effektivitet >100%.
Man kan beregne, at 3,03/3,95 100 =77% af det samlede råstofforbrug i livscyklus baseret på vægt genvindes i livscyklus (excl. energiforbrug i produktionsfaser + bortskaffelsesfasen).
5.6.1.6 Materiale- og energiforbrug, hele livscyklus
Endelig kan medtages energiforbruget og ressourcer forbundet med udvinding af dette.
MMat+energi, R+P+B = 1,00/132,45 × 100 =0,76 %
MMat.+energi, R+P+B+A/N = 1,00/(132,45-65) × 100 =1,5 %
I Bilag C er angivet resultater for henholdsvis højt effekttab og lavt effekttab, samt for en situation med højere genanvendelse af tin og en uden genanvendelse af metaller ved bortskaffelsen.
5.6.1.7 Fortolkning
Af opgørelserne ses det, at langt det væsentligste forbrug ligger i produktets brug og udgøres af energiforbruget.
Ressourceeffektiviteten (MMat, P+B+A/N) for materialer er høj, når der ses bort fra energiforbruget. Det er af meget stor betydning, at metallerne jern og kobber genvindes for denne opgørelsestype. Det
samme gør sig gældende for effektiviteten baseret på råstoffer (M Mat, R+P+B+A/N).
5.6.2 Ressourceeffektivitet baseret på vurderet opgørelse
5.6.2.1 Ressourceforbrug, materialer
Ressourceindholdet i 1 kg transformer er opgjort til 6,32 mPR og det samlede forbrug til 6,57 mPR. Effektiviteten er derfor:
VMat. R+P+B = 6,32 / 6,57 × 100 = 96 %
5.6.2.2 Ressourceforbrug, materialer og energi
Indregnes energiforbruget i ressourceeffektiviteten, fås:
VMat.+energi, R+P+B = 6,32 / ( 6,57 + 4,68) × 100 = 56 %
5.6.2.3 Ressourceforbrug, hele livscyklus
Tages der hensyn til genvinding af metaller svarende til 5,44 mPR og godskrivning af energi svarende til 2,25 mPR, kan nettoeffektiviteten beregnes til:
VMat+energi R+P+B+A/N = 6,32 / ( 6,57 – 5,44 + 4,68 – 2,25 ) × 100 = 178 %
For at illustrere betydningen af effekttabet og genanvendelse er der gennemført følsomhedsanalyser for disse parametre. Resultaterne er vist i tabel 5.12.
Tabel 5.12 Følsomhedsanalyser for effekttab og genanvendelse
Scenario |
Effekttab |
Genan-
vendelse
af kobber,
jern |
Genan-
vendelse
af tin |
VMat+energi R+P+B+A/N |
1: |
Middel effekttab, lav genanvendelse af tin og genanvendelse af kobber, jern |
12 W |
Ja |
20% |
178 % |
2: |
Lavt effekttab, lav genanvendelse af tin og genanvendelse af kobber, jern |
5 W |
Ja |
20% |
284 % |
3: |
Højt effekttab, lav genanvendelse af tin og genanvendelse af kobber, jern |
25 W |
Ja |
20% |
106 % |
4: |
Middel effekttab, høj genanvendelse af tin og genanvendelse kobber, jern |
12 W |
Ja |
80% |
210 % |
5: |
Middel effekttab, ingen genanvendelse af materialer ved bortskaffelse |
12 W |
Nej |
0% |
71 % |
I bilag C er angivet flere detaljer heriblandt netto ressourceforbruget for de 5 scenarier angivet i personressourcer for de danske virksomheder med mindre end 200 ansatte, der producerer transformere.
5.7 Fortolkning
Som under beregning af ressourceeffektiviteterne på vægtbasis ses det, at transformere med lavt effekttab er de mest ressourceeffektive, idet disse kun forbruger 100/284 × 100=35% af produktets
ressourceindhold i hele livscyklus, mens transformere med et effekttab på 25% næsten forbruger de samme ressourcer i livscyklus, som de indeholder =(100/106 × 100=94%). Det skal dog bemærkes, at en
mere effektiv transformer også kræver et noget større forbrug af kobber og jern, hvilket der ikke er korrigeret for.
Hvis man sammenligner scenario 5 med scenario 1, ses det, at genanvendelsen af metaller er meget vigtig, da ressourceeffektiviteten falder fra 178% til 71%, hvis metallerne ikke genvindes. Det er her
indholdet af kobber, der er dominerende for ressourceeffektiviteten. Hvis man således beregner for en situation, hvor man undlader genvinding af tin og jern, falder ressourceeffektiviteten kun fra 178 % til
168%. En manglende genanvendelse af de 650 gr. jern medfører kun et fald i ressourceeffektiviteten fra 178% til 177%, mens en højere genanvendelse af det ganske lille tinindhold på 1 gr. kan øge
ressourceeffektiviteten fra 178 til 210% i scenario 4. Det er således ud fra et ressourcesynspunkt vigtigere at gå efter det lille tinindhold end jernindholdet.
Genanvendelse af tin sker ikke i praksis, hvilket kan illustreres af en simpel økonomisk opstilling af værdien af metallerne.
Handelspriserne for jern er ca. 75 øre pr. kg, for kobber ca.10 kr. pr. kg og for tin ca. 40 kr./kg. Dette betyder, at indholdet af materialer i et kg transformer potentielt udgør værdier, inden oparbejdningen
påbegyndes som vist i tabel 5.13.
Tabel 5.13 værdi af metaller i transformer
Metal |
Vægt (gr.) |
Værdi (øre) |
Værdi % |
Jern |
650 |
49 |
13 |
Kobber |
325 |
325 |
86 |
Tin |
1 |
4 |
1 |
En oparbejder vil derfor altid gå efter kobberet, som repræsenterer 86% af produktets værdi, dernæst jern som repræsenterer 13 % af værdien og så tin.
I praksis vil tin følge kobberet, og det vil være op til kobbersmelteværkerne at udnytte det fra de forskellige restprodukter, det ender i. Årsagen til, at tin ikke tæller mere i den økonomiske nutidsbetragtning,
er, at der stadig er tin til en vis årrække, og at handelspriserne derfor ikke afspejler den langt højere pris, man vil nærme sig, når ressourcerne er næsten udtømte, forudsat man ikke har fundet en substitution.
Dette tages der i bedre grad hensyn til ved ressourcebetragtningen, og man kan derfor se, hvad man bør satse på at få genvundet over en årrække eller alternativt få udskiftet med et andet materiale.
5.8 Affaldsminimering
De undersøgte delprodukter printkort og transformere indgår i næsten alt elektronisk udstyr, som er drevet af 220 V.
Hvis man skal minimere mængden af affald for et givet produkt, er der nogle væsentlige faktorer, som har betydning for mængden af affald, der opstår. For en række elektroniske produkter bør man mere se
på minimering af affaldet for en given funktion. Fx funktionen "at kunne at tale i mobiltelefon" eller "have rådighed over en computer". For sådanne produkter vil den tid, der går til produktet kasseres, være
væsentligt lavere end levetiden, da der hele tiden sker en teknisk udvikling, som medfører, at de nye produkter kan mere.
Mængden af kasseret produkt pr. år er således afhængig af den årrække, som produktet er i anvendelse i, og mængden af anvendte materiale pr. produkt, som igen er afhængigt af det design, der er
anvendt.
5.8.1 Produktion
Ved montagen af printkort i Danmark forekommer en begrænset affaldsmængde, som for hovedparten af de knappe ressourcers vedkommende genanvendes (kobber, ædelmetaller fra kasserede printkort).
Selve fremstillingen af komponenter foregår for en stor dels vedkommende i udlandet, hvor det er svært at kontrollere, om produktionsaffaldet nyttiggøres.
Ved fremstilling af transformere i Danmark består det primære produktionsspild af blikplader, kobber og fejlproducerede transformere, hvor spildet af kobber og transformere er lille (1-2%). Hovedparten af
produktionsspildet af kobber, blik og transformere går til genanvendelse, men det er vurderet, at der vil kunne mistes noget metal ved oparbejdning af transformere afhængigt af den anvendte
oparbejdningsmetode. Da andelen af fejlproducerede transformere imidlertid er lille, er den totale mængde metal, som ikke genanvendes i forbindelse med produktion af transformere, lille. Det er beregnet, at
metallerne, der genvindes i produktionsfasen, svarer til 0,15 mPR for en transformator på 1 kg.
5.8.2 Affaldsbehandling og nyttiggørelse
Der, hvor indsatsen er vigtigst, er ved kasseringen af de elektriske og elektroniske produkter.
Med udgangspunkt i transformere er det således beregnet, at der under affaldsbehandlingen, hvor det antages, at 95% af kobberindholdet udvindes i kobbersmelteværk, genvindes ressourcer fra metallerne
svarende til 5,3 mPR eller 35 gange mere end i produktionsfasen. Tilsvarende betragtninger vil gælde for printkort.
Når produktet er kasseret, må det sikres, at det undgås, at printkort og transformere ender med affald til forbrænding eller deponering. I dag findes en veletableret ordning for indsamling af elektriske og
elektroniske produkter i Danmark og ligeledes snart i resten af EU, og større produkter som audio-video, computere mv. formodes stort set at blive korrekt indsamlet. Der er imidlertid en øget risiko for, at
mindre elektroniske produkter ryger i skraldespanden, og dette kan til en vis grad tænkes at blive et stigende problem for den stigende mængde af små elektriske og elektroniske produkter som fx
mp3afspillere, mobiltelefoner og løse transformere til fx computerudstyr (scanner, printer, modem mm), hvis ikke man opretholder en tilstrækkelig informationsindsats omkring dette. Ved forbrænding vil
produkternes indhold af kobber og tungmetaller stammende fra de bestykkede printkort have en negativ indflydelse på slaggens udvaskningsegenskaber og derved mulighed for genanvendelse af denne. Er
der tale om transformere, vurderes disse hovedsageligt at ende i jernfraktionen ved frasorteringen af metaller under slaggebehandlingen.
Udover at transformere fejlagtigt kan gå til forbrænding, vil nogle transformere formentlig også fejlagtigt blive bortskaffet med andet jernholdigt metal i industricontainere til jern og metal skrot. I sådanne
tilfælde vil transformerne blive delvist neddelt i shredderanlæggene, men da det er problem at opnå en god separation af kobber og jern ved behandling af transformere i de store shredderanlæg, vil en del
kobber kunne mistes sammen med jernfraktionen, idet kobbertrådene er viklet ind i jernblikket og derved frasorteres som jern ved den efterfølgende magnetseparation. Ved smeltningen af jern omviklet af
kobbertråde i stålværket enten fra shredderjern eller fra forbrændingsjern vil kobberet indgå som legeringsmetal i stålet, hvor det er et uønsket metal, hvis koncentrationen når over 0,1-0,2%.
Der vil således opstå et voldsomt lødighedstab for det kobber, som genvindes med jern. Det har ikke været muligt at skaffe tal for, hvor stor en del af transformere og printkort, der fejlagtigt sendes til
forbrænding, men der er lavet en beregning af worst case, hvor intet metal genanvendes. I så fald falder ressourceeffektiviteten for et printkort med en effekt på 25W med en faktor 5, mens
ressourceeffektiviteten for en transformer med et effekttab på 12W/kg falder en faktor 2,5. Dette svarer til tilsvarende stigninger i nettoforbruget af PR.
For de elektroniske produkter, som indsamles til korrekt behandling, vil en del produkter såsom computere og udstyr til disse blive kasseret, selvom produkterne stadig fungerer, idet udstyret hurtigt forældes
i forhold til den teknologiske udvikling. Dette medfører større mængder af affald og forbrug af ressourcer, end hvis produkterne er i brug i hele deres levetid. I nogle tilfælde kan man bedre lidt på dette ved
en passende sortering af produkterne. Derefter vil der ske videresalg eller demontage af de mest værdifulde komponenter som fx CPUer.
Når produkterne er endeligt udtjent, vil printkortene blive frasorteret og sendt til oparbejdning i kobbersmelteværkerne, hvor kobber og ædelmetaller (guld, palladium, sølv) udvindes. Indhold af plast og
organiske stoffer forbrændes i smelteprocessen, mens metaller som jern og aluminium mistes, da de oxideres og ender i en slagge. Jern og aluminium i printkortene tæller kun ganske lidt, når der laves en
vurdering baseret på indholdet af knappe ressourcer, mens de knappe ressourcer tin og antimon udgør et væsentligt bidrag, og disse stoffer udvindes kun i mindre grad i kobbersmelteværkerne, da dette ikke
er økonomisk favorabelt pt. Stofferne mistes således pt. sammen med røggasrenseprodukter og andre fraktioner. Hvis mere end 80% af disse to stoffer blev genvundet, ville den samlede ressourceeffektivitet
baseret på vurderede størrelser næsten kunne fordobles for printkort med et strømforbrug på 25 W/kg. Dette svarer til et fald i ressourceforbruget i hele livscyklus for bestykkede printkort stammende fra
danske virksomheder med <200 ansatte fra 61000 Pr til 32000 Pr. Det er ikke undersøgt i detaljer, om kobbersmelteværkerne vil være i stand til at opnå de antagne genvindingsgrader med den nuværende
teknologi, og hvad en større genvinding af tin og antimon i givet fald vil koste.
I kobberværkerne mistes pt. plast, keramik/glas, jern og aluminium. Alternative teknologier er under udvikling eller i brug, hvor printkortene udsættes for en neddeling, så kun kobber og ædelmetalindholdet
sendes til behandling i kobberværket. Herved kan der genvindes større mængder af jern og aluminium. Sådanne teknologier vil ikke betyde det store udfra en vurdering baseret på knappe ressourcer, men vil
mindske mængden af materialer, som ikke genvindes.
5.9 Sammenligning med øvrige opgørelser
Printkort og transformere produceres verden over i et meget konkurrencepræget marked. Med hensyn til produktionsforhold må det antages, at danske forhold ligger på linie med øvrige vesteuropæiske
lande, som Danmark naturligt sammenlignes med.
En stor del elektronik produceres i Østen under noget andre produktionsforhold, og her kan teknologiske og miljømæssige forhold ikke antages at være sammenlignelige med danske.
De opstillede ressourceeffektiviteter antages derfor kun at dække vesteuropæiske lande.
Det har været ønskeligt at sammenligne de opgjorte materialeforbrug med DMI og TMI. Disse sammenligninger har ikke været mulige at gennemføre, da:
- Opgørelse af DMI omfatter en produktgruppe som fx ”Elektronikindustri” og er ikke specifik i forhold til printkort og transformere. Det er ikke muligt at vurdere, hvor meget printkort og transformere
udgør af den samlede elektronikindustri.
- Opgørelse af TMI omfatter en opgørelse af det samlede råstofforbrug. I nærværende opgørelse var det vanskeligt at opgøre det samlede forbrug af råstoffer, da der ikke findes sikre opgørelser for
ædelmetallerne, som skønnes at have en stor betydning. Wuppertal's datasamling er ligeledes mangelfuld med hensyn til råstofforbrug pr. kg. ædelmetal.
6 Galvanisk overfladebehandling
6.1 Introduktion
Inden for galvanoområdet er det valgt at se på tre af de mest almindelige processer til overfladebehandling af stål, nemlig:
- Fornikling/forchromning
- Elektroforzinkning
- Varmforzinkning
Disse processer er ikke ligetil at indpasse i et livscyklusforløb som de foregående aktiviteter, hvor produktet og dets livsforløb kunne identificeres.
Her er valgt at se på processen i et livscyklusperspektiv som beskrevet i kapitel 2. Grafisk kan dette illustreres som vist i figur 6.1.
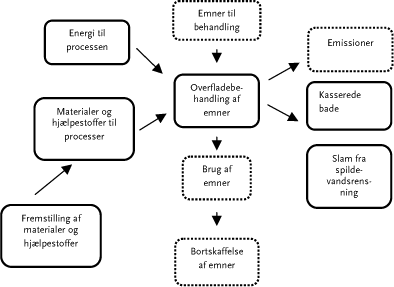
Figur 6.1 Galvanisk overfladebehandling i et livscyklusperspektiv
I det følgende er hver af processerne kortlagt.
6.2 Kortlægning af fornikling/forchromning
Fornikling/forchromning er efter elforzinkning den mest almindelige galvaniske proces i Danmark. Processen udføres af ca. 75 danske virksomheder i større eller mindre skala.
Der bruges årligt 125 ton nikkelanoder til fornikling, hvilket svarer til 1.170.000 m² overflade ved en lagtykkelse på 12 ìm. Der forkobres ca. 25 % af den behandlede overflade svarende til 295.000 m².
Omkring 80% af den samlede behandlede overflade bliver forchromet svarende til ca. 936.000 m².
Kortlægningen er gennemført ud fra en opgørelse baseret på 1.000 m² behandlet overflade. Der er taget udgangspunkt i, at det er stålplader, der er overfladebehandlet.
Procestrinnene ved en fornikling/forchromning er:
- Varm alkalisk affedtning
- Bejdsning i svovlsyre
- Elektrolytisk affedtning
- Forkobring
- Dekapering i svovlsyre
- Fornikling
- Forchromning
Processerne samt opgørelse af råvareforbrug, kemikalier, energi og andet er anført i bilag D.
6.2.1 Opgørelse af mængder for fornikling/forchromning
I det følgende er vist en opgørelse af forbruget af metaller, kemikalier, vand og energi til fornikling/forchromning. Data er beskrevet i bilag D.
Ved 1000 m² overfladebehandling med fornikling/forchromning findes der på emnerne efter overfladebehandlingen som et gennemsnit:
107,53 kg |
Nikkel |
27,04 kg |
Kobber |
1,48 kg |
Chrom |
Disse størrelser er opgjort ud fra en massebalance over forbrug og affaldsmængder ved processen.
6.2.1.1 Materialeforbrug ved fornikling/forchromning
Der er gennemført en opgørelse af, hvilke metaller og kemikalier der anvendes i de enkelte procesbade, og hvilke hovedbestanddele disse kemikalier har. Resultaterne er vist i Tabel 6.1.
Tabel 6.1 Kemikalieforbrug ved fornikling/forchromning
Kemikalie |
Samlet mængde |
Mængde pr.
1.000 m² overflade |
Nikkel |
130 ton |
111,1 kg |
Kobber |
33 ton |
28,2 kg |
Chrom |
10 ton |
8,5 kg |
Jern* |
9,5 ton |
8,1 kg |
Uorganiske syrer, primært svovlsyre |
110 ton |
94,0 kg |
Uorganiske baser, primært natriumhydroxid |
10 ton |
8,6 kg |
Organiske forbindelser som tensider og affedtersalte |
55 ton |
47,0 kg |
Cyanider |
30 ton |
25,6 kg |
Øvrige kemikalier, hvor sammensætningen ikke kendes |
65 ton |
55,6 kg |
* Da der ved renseprocesserne af stålpladerne sker en vis mængde afætsning af jern, som bl.a. findes i affaldsstrømmene, er disse medtaget i materialeforbruget.
Vandforbruget ligger på omkring 120.000 m³ pr. år svarende til ca. 100 m³ pr. 1.000 m² overflade.
6.2.1.2 Energiforbrug
Der anvendes energi til fremstilling af råvarer og til selve overfladebehandlingsprocessen. Det samlede energiforbrug i råvarefasen er vist i tabel 6.2.
Tabel 6.2 Energiforbrug ved fornikling/forchromning
|
Forbrug pr.
1000 m² (kg) |
Primært
energiforbrug
(MJ/kg) |
Primær energi
pr. 1000 m²
(MJ) |
Til metaller: |
Nikkel |
111,11 |
190,00 |
21.111,1 |
Kobber |
28,21 |
90 |
2.538,5 |
Chrom |
8,89 |
39 |
346,7 |
Stål |
8,12 |
40 |
324,8 |
Til kemikalier |
Uorg. syrer |
94,02 |
50 |
4.700,9 |
Uorg. baser |
8,55 |
38 |
324,8 |
Org. forbindelser |
47,01 |
60 |
2.820,5 |
Cyanider |
25,64 |
- |
- |
Andet |
55,56 |
- |
- |
Vand |
102.560,00 |
0,001 |
102,6 |
Til metaller, kemikalier og vand |
32.167 |
Energiforbruget til fremstilling af cyanider og andet er skønnet til i størrelsesordnen 4.000 MJ/1000 m². Det samlede energiforbrug i råvarefasen kan således opgøres til 36.000 MJ primær energi pr. 1.000
m².
Energiforbruget til overfladebehandlingsprocesserne er udelukkende elforbrug og opgjort til 29.400 kWh pr. 1.000 m² overflade. Dette energiforbrug svarer til 265.000 MJ pr. 1.000 m².
Der vil være et mindre energiforbrug ved behandling af affald i form af kasserede bade og slam, men dette er skønnet at udgøre meget lidt og er ikke medtaget.
Det samlede energiforbrug ligger på omkring 300.000 MJ primær energi pr. 1.000 m² behandlet overflade – 12 % i råvarefasen og 88% i produktionsfasen.
6.2.1.3 Godskrivning af materialer og energi
Da metallerne pålagt ved overfladebehandling ikke udvindes særskilt ved oparbejdning af stål, er genvinding ikke medtaget.
Der sker ikke noget oparbejdning af metallerne fra affaldsbehandlingen – slam og kasserede bade.
Da der ikke er nogen muligheder for genvinding af energi, især fra procesbadene, er dette ikke medtaget.
6.2.1.4 Råstofforbrug
Forbruget af råstoffer er estimeret ud fra forbruget af materialer. Opgørelsen er vist i tabel 6.3.
Tabel 6.3 Estimering af forbrug af råstoffer for fornikling/forchromning
Materiale
Behandlet overflade 1.170.000 m² |
Materiale-
forbrug
I alt |
Råstof-
forbrug
kg/kg |
Råstof-
forbrug
I alt |
Råstof-
forbrug
Pr. 1.000 m² |
Nikkel |
130 ton |
9,4 1) |
1.222 ton |
1.044 kg |
Kobber |
33 ton |
3,7 1) |
122 ton |
104 kg |
Chrom |
10 ton |
5,6 1) |
56 ton |
48 kg |
Uorganiske syrer, primært svovlsyre |
110 ton |
0,7 1) |
77 ton |
66 kg |
Uorganiske baser, primært natriumhydroxid |
10 ton |
1,2 1) |
12 ton |
10 kg |
Organiske forbindelser |
55 ton |
1,0 1) |
55 ton |
47 kg |
Cyanider |
30 ton |
2,0 1) |
60 ton |
51 kg |
Øvrige (ukendt sammensætning) |
65 ton |
3,0 2) |
195 ton |
167 kg |
I alt |
|
|
1.799 ton |
1.537 kg |
1): Data fra SigmaPro.
2): Tallet er anslået ud fra en antagelse om, at øvrige kemikalier indeholder en vis mængde metal og en vis mængde organiske forbindelser.
6.2.2 Opgørelse af vurderede mængder for fornikling/forchromning
I det følgende er materialer og energiforbrug omregnet til vurderede størrelse i mPR.
6.2.2.1 Vurdering af materialeforbrug ved fornikling/forchromning
Det væsentligste ressourceforbrug findes for metallerne. Opgørelsen herfor er vist i Tabel 6.4.
Tabel 6.4 Forbrug af metaller ved fornikling/forchromning
|
Nikkel |
Kobber |
Chrom |
Jern/stål |
pr. 1000 m² behandlet overflade |
Forbrug i alt (kg) |
111,11 |
28,21 |
8,89 |
8,12 |
Affald (kg) |
3,58 |
1,16 |
7,41 |
8,12 |
I produkt (kg) |
107,53 |
27,04 |
1,48 |
0,00 |
Ressourceforbrug |
mPR pr. kg |
106 |
16,5 |
12,8 |
Jern: 0,08
Mangan: 0,05 |
Ressourceforbrug |
11777,78 |
465,38 |
113,8 |
Jern: 0,65
Mangan: 0,48 |
I produktet |
11398,17 |
446,21 |
18,9 |
Jern: 0
Mangan: 0 |
Det samlede ressourceforbrug er på 12.358 mPR for metallerne, og i produktet findes 11.863 mPR. Tabet udgør 500 mPR svarende til 4% af ressourceforbruget.
Ressourceforbruget til kemikalierne er skønnet til at udgøre 340 mPR, da en eksakt beregning ikke kunne gennemføres.
Det samlede ressourceforbrug er derfor:
Samlet forbrug |
12.700 mPR |
I produktet |
11.860 mPR |
Tab ved råvareudvinding og produktion |
840 mPR |
Ressourcerne i produktet det vil sige overfladen tabes ligeledes ved oparbejdning af stålpladen.
6.2.2.2 Vurdering af energiforbrug ved fornikling/forchromning
Det samlede energiforbrug er opgjort til 300 GJ pr. 1.000 m² overflade. Fremstilles denne energimængde ud fra olie, svarer det til et forbrug på 289,5 mPR.
6.3 Ressourceeffektivitet for fornikling/forchromning
6.3.1 Ressourceeffektivitet på materialeniveau
6.3.1.1 Materialeforbrug, produktion og brug
Den samlede mængde materialer i form af metaller, der findes i produktet, overfladebehandling af 1.000 m² , er opgjort til 159,2 kg.
Det samlede forbrug af metaller og kemikalier udgør 182,9 kg metaller og 230,8 kg kemikalier.
Ressourceeffektiviteten kan derfor beregnes til:

Den beregnede effektivitet viser, at omkring 2/3 af de anvendte materialer tabes i processen. Tabet forekommer i selve overfladebehandlingsprocessen og udgør dels den samlede mængde kemikalier og dels
en del af metallerne.
Vandforbruget er opgjort til 100 m³ pr. 1.000 m² behandlet overflade.
6.3.1.2 Materialeforbrug, produktion, brug og bortskaffelse
Som tidligere nævnt sker der ingen genvinding af materialer. Effektiviteten
Mmat. P+B+A/N vil derfor være lig Mmat, P+B.
6.3.1.3 Materialeforbrug, hele livscyklus
Råstofforbruget er opgjort til 1.537 kg pr. 1.000 m² overflade. Ressourceeffektiviteten kan derfor beregnes til:

I råstofudvindingen bliver omkring 20-25% af den samlede mængde til anvendelige materialer. For metallerne er udnyttelsesgraden relativt lille (5-10%) og noget større for hjælpestofferne.
6.3.2 Ressourceeffektivitet baseret på vurderet opgørelse
6.3.2.1 Ressourceforbrug, materialer
Den mængde ressourcer, der findes i produktet – overfladebehandling af 1.000 m² stålplade med fornikling/forchromning, udgør 11.860 mPR.
Ressourceeffektiviteten opgjort som materialeeffektivitet, brutto kan beregnes til:

Den beregnede effektivitet afspejler, at det er de mindre knappe ressourcer i form af kemikalier, der tabes i udvinding og i processen.
6.3.2.2 Ressourceforbrug, materialer og energi
Hvis man ser på det samlede materiale og energiforbrug, udgør det samlede vurderede forbrug 12.700 mPR + 290 mPR = 13.000 mPR, og den samlede materiale- og energieffektivitet kan beregnes til:
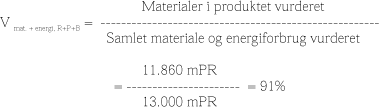
6.3.2.3 Ressourceforbrug, hele livscyklus
Der sker som tidligere nævnt ingen genvinding af materialer eller energi. Dette betyder, at effektiviteten for hele livscyklus, Vmat+energi, R+P+B+A/N vil være lig med Vmat+energi, R+P+B.
6.3.3 Fortolkning
De opgjorte ressourceeffektiviteter er vist i Tabel 6.5.
Tabel 6.5 Beregnede ressourceeffektiviteter for fornikling/forchromning
|
Betegnelse |
Ressource- effektivitet |
Materialeopgørelse |
|
|
• Materialer til produktion og brug |
Mmat, P+B |
39 % |
• Materialer, produktion, brug og bortskaffelse inkl. genanvendelse |
Mmat, P+B+A/N |
39 % |
• Råstoffer i hele livscyklus inkl. genanvendelse |
Mmat. R+P+B+A/N |
10% |
Ressourceopgørelse |
|
|
• Materialer vedrørende råstoffer, produktion og brug |
Vmat, R+P+B |
93 % |
• Materialer og energi vedrørende råstoffer, produktion og brug |
Vmat+energi, R+P+B |
91 % |
• Materialer og energi i hele livscyklus inkl. genvinding |
Vmat+energi, R+P+B+A/N |
91 % |
Af Tabel 6.5 ses det, at der tabes knapt 2/3 af de anvendte materialer i galvaniseringsprocessen (Mmat, P+B). Da beregningen er foretaget for en specifik proces, vil opgørelsen kunne bruges af branchens
virksomheder som sammenligningsgrundlag.
Den anden opgørelse på materialeniveau, Mmat. R+P+B+A/N omfatter dels materialetab i selve processen, men også tab ved udvinding af metaller og forarbejdning af kemikalier. Denne beregning vil
antageligt kun kunne anvendes på et mere overordnet plan.
Ses der på de effektiviteter, der er baseret på vurderede opgørelser (mPR), vil man få et fingerpeg, om det er knappe eller rigelige ressourcer, der tabes i livsforløbet. Metaller og især nikkel vægter højt i
denne opgørelse. Af de beregnede størrelser ses det, at effektiviteten er relativt høj, og at det er mindre knappe ressourcer, der primært tabes. En øget udnyttelse af primært nikkel, men også kobber og
chrom vil have en relativ stor indflydelse på ressourceeffektiviteten.
De to ressourceeffektiviteter, Vmat, R+P+B og Vmat+energi, R+P+B er meget lig hinanden, hvilket viser, at energiforbruget – både til udvinding af råstoffer og i galvaniseringsprocessen – ud fra et
ressourcesynspunkt er af mindre betydning.
Det er i opgørelserne forudsat, at der ikke finder genvinding sted af metallerne eller af hjælpestofferne. En genvinding af metallerne vil øge ressourceeffektiviteten – i mindre grad for de vægtbaserede
opgørelser og i højere grad for de vurderede opgørelser.
6.3.4 Affaldsminimering
Af de beregnede ressourceeffektiviteter ses det, at mængdemæssigt tabes der en stor del materiale i råstofudvindingen og i produktionen. Af de vurderede opgørelser ses det, at der tabes en mindre mængde
knappe ressourcer, og at energiforbruget i forhold til materialeforbruget er af mindre betydning. Lægges der vægt på knappe, miljøbelastende stoffer vil det være metallerne (nikkel, kobber og chrom), der
skal fokuserers på.
I det følgende trækkes en række væsentlige forhold frem.
6.3.4.1 Badkemikalier
I fornikling/forchromningsprocessen anvendes en række syrer, baser, cyanider og andre kemikalier. Disse kan ikke undværes, hvis overfladebehandlingen skal forløbe tilfredsstillende. Badene bliver sjældent
skiftet, da de løbende vedligeholdes, men der kan være behov for det efter uheld, driftsforstyrrelser og lignende. De kasserede bade vil i overvejende grad blive sendt til Kommunekemi, hvor de afgiftes ved,
at cyaniden omdannes, hvorefter metallerne fældes i alkalisk miljø som metalhydroxider. Det dannede slam afvandes og deponeres. Det er ikke i dag teknisk/økonomisk muligt at oparbejde slammet, da det
består af en blanding af en række metaller.
6.3.4.2 Metallerne
Ud fra et ressourcesynspunkt er det mest problematisk at anvende nikkel. Målt i mPR ligger værdien for nikkel ca. 10 gange højere end for kobber og chrom.
Metallerne nikkel, kobber og chrom udnyttes ikke lige godt i processerne. Af tabel 6.6 ses det, at tabet af de enkelte metaller er meget forskelligt.
Tabel 6.6 Tab af metaller ved fornikling/forchromning
|
Mængde på emnet
pr. 1.000 m² |
Tab pr. 1.000 m² |
Tab i % af
mængde på emnet |
Nikkel |
107,53 kg |
3,57 kg |
3,3 % |
Kobber |
27,04 kg |
1,16 kg |
4,3 % |
Chrom |
1,48 kg |
7,02 kg |
474 % |
Som det ses af tabel 6.6, er der en relativ høj udnyttelse af nikkel og kobber i de galvaniske processer, hvorimod tabet ved pålægning af chrom er meget stort.
Det bør derfor overvejes af hensyn til ressourcetab og affaldsminimering, om chromateringen kan gøres mere effektiv, og/eller om anvendelse af chromatering kan minimeres.
Ved udvinding af metallerne tabes en del materiale. Metallerne i malmen findes som metaloxider eller –sulfider. Der kan være mere eller mindre jern i malmen. Ved oparbejdningen renses malmen ,og
metalionerne omdannes til metal. Tabet varierer fra malmtype til malmtype. Mulighederne for affaldsminimering kan dog ikke vurderes.
Ved kassering af produktet, - den overfladebehandlede plade eller genstand, tabes alt det pålagte metal. Stålet oparbejdes, men da nikkel, chrom og kobber udgør en meget lille del udnyttes dette ikke. I
Tabel 6.7 er vist, hvilke ressourcer der tabes ved oparbejdning af 1 m² stålplade med en godstykkelse på 5 mm.
Tabel 6.7 Ressourcer i en 1 m² jernplade der er forniklet/forchromet
|
Mængde pr. 1 m² |
Ressourceforbrug
pr. kg |
Ressourceforbrug
i 1 m² plade |
Jern* |
40 kg |
0,08 mPR |
3,200 mPR |
Nikkel |
107 gram |
116 mPR |
12,412 mPR |
Kobber |
27 gram |
16,5 mPR |
0,446 mPR |
Chrom |
1,5 gram |
12,8 mPR |
0,019 mPR |
* En jernplade på 1 m² med en godstykkelse på 5 mm har et volumen på 0,005 m³, og med en massefylde på 7,9 vejer pladen ca. 40 kg.
I forhold til Tabel 6.7 skal det bemærkes, at ressourcerne i jernpladen oparbejdes, og mere end 90% genvindes. Nikkel som ressource er af væsentlig større betydning, men tabes i oparbejdningen. Nikkel
kan måske til en vis grad udnyttes i det oparbejdede jern/stål som legeringsmetal, men bliver ikke med den i dag anvendte teknologi oparbejdet til rent metal.
6.3.4.3 Vandforbrug og spildevand
Vandforbruget til fornikling/forchroming bruges primært som skyllevand. Der bruges omkring 100 liter vand pr. m² behandlet overflade.
Der har gennem en del år været fokus på at nedsætte vandforbruget ved ændrede skylleteknikker. Det nævnes, at en af årsagerne til, at disse ikke er mere udbredt, er, at nyere teknikker er mere
pladskrævende og kræver mere styring.
Skyllevandet renses på virksomheden inden udledning, og hovedparten af metallerne findes i slam, der dannes ved rensningen. Slammet er en blanding af flere metalhydroxider og oparbejdes i dag ikke af
teknisk/økonomiske grunde, da slammet ud over de mere værdifulde metaller indeholder en hel del jern.
6.3.4.4 Energi
Energiforbruget til overfladebehandlingsprocessen udgør 88% af det samlede energiforbrug, - den resterende del går til udvinding af materialer.
Energiforbruget til processen er udelukkende el, hvor der forbruges 29 kWh pr. m² overflade, svarende til 300 MJ primær energi. Omregnes dette til forbrug af olieressourcer, udgør det omkring 0,29 mPR
pr. m². Da elektriciteten med sikkerhed produceres i Danmark, og der her hovedsagelig anvendes kul som energiressource, vil ressourcetrækket i stedet blive 1/5, da kul har en meget længere
forsyningshorisont end olie.
Til overfladebehandling af en jernplade bruges 7,5 MJ/kg. Da 1 m² jernplade vejer ca. 40 svarer det til et energiforbrug på 300 MJ. Til sammenligning kan anføres, at presning af stål kræver omkring 30
MJ/kg, og at trykstøbning ligger på mellem 20-50 MJ/kg.
Hvad enten el-forbruget baseres på kul eller olie, og det vurderes, at der bruges store mængder energi i processen, er energimængden i forhold til materialemængden meget lille.
6.3.4.5 Samlet prioritering
Ud fra et ressourcemæssigt synspunkt er nikkel et problematisk metal at anvende til overfladebehandling.
Fornikling/forchroming har en række fordele. Det giver en overflade af høj kvalitet og et pænt udseende, men
- Metallerne og især chrom, der forekommer som affald (primært slam)fra overfladebehandlingsprocessen, kan ikke genvindes.
- Metallerne og især nikkel, der findes på det kasserede produkt, kan ikke genvindes.
- Der anvendes en række hjælpekemikalier i processen, som tabes.
Der findes i dag ikke tekniske løsninger, som er økonomisk mulige for at genvinde metallerne.
6.3.5 Sammenligning med øvrige opgørelser
Overfladebehandlingsprocessen fornikling/forchromning, som den udføres i Danmark, er optimeret med hensyn til udnyttelse af metaller, energi- og vandforbrug og er således typisk for europæiske forhold.
6.3.5.1 Direkte materialeinput
Det er ikke muligt at foretage en sammenligning mellem de opgjorte mængder af materialer og data for DMI, da DMI ikke opgøres på procesniveau.
6.3.5.2 Totale materialeinput
I det følgende er søgt estimeret det totale materialeinput, baseret på Wuppertal's MIPS-data, se Tabel 6.8.
Tabel 6.8 Estimering af totalt materialeinput for fornikling/forchromning
Materiale
Behandlet overflade 1.170.000 m² |
Materiale-
forbrug
I alt |
Råstof-
forbrug
kg/kg |
Råstof-
forbrug
I alt |
Råstof-
forbrug
Pr. 1.000 m² |
Nikkel |
130 ton |
138,6 |
18.018 ton |
15.400 kg |
Kobber |
33 ton |
4,0 |
132 ton |
113 kg |
Chrom |
10 ton |
- 1) |
- |
- |
Uorganiske syrer, primært svovlsyre |
110 ton |
0,5 2) |
55 ton |
47 kg |
Uorganiske baser, primært natriumhydroxid |
10 ton |
1 2) |
10 ton |
9 kg |
Organiske forbindelser |
55 ton |
5 2) |
275 ton |
235 kg |
Cyanider |
30 ton |
10 2) |
300 ton |
256 kg |
Øvrige (ukendt sammensætning) |
65 ton |
10 2) |
650 ton |
556 kg |
I alt |
|
|
|
16.600 kg |
1): Ingen data.
2): Tallet er anslået ud fra forskellige kemiske forbindelser.
Som det fremgår af Tabel 6.8 mangler data for chrom. Materialeinputtet vil derfor være i størrelsesordnen 17.000 kg pr. 1.000 m² overflade.
I nærværende opgørelse er råstofforbruget opgjort til ca. 1/10 – 1.500 kg. Begge typer af opgørelser skulle i princippet være ens og medtage alle indirekte strømme.
Den væsentligste forskel ligger i opgørelsen for nikkel, hvor Wuppertal har opgjort materialeinputtet til at være mere end 10 gange så stort som data fra SigmaPro. Wuppertals data for de øvrige materialer
ligger også noget over de her anvendte LCA-data for de øvrige materialer.
6.4 Kortlægning af elforzinkning
Elforzinkning er den mest almindelige galvaniske proces i Danmark. Processen udføres af ca. 90 danske virksomheder i større eller mindre skala.
Ved elforzinkning foretages først en rengøring af emnerne (affedtning og bejdsning), hvorefter der elektrolytisk påføres et zinklag på 5-20 m. Lagtykkelsen er typisk mindst for tromlevarer (små emner), mens
større emner på stativer typisk påføres lagtykkelser på 12-20 m. Der forbruges årligt ca. 600 ton zinkanoder, hvilket svarer til overfladebehandling af 8,5 mio. m² overflade.
Kortlægningen er baseret på en opgørelse ud fra 1.000 m² behandlet overflade. Der er taget udgangspunkt i, at det er stålplader, der er overfladebehandlet.
Procestrinnene ved en elforzinkning er:
- Alkalisk affedtning
- Bejdsning i svovlsyre
- Elektrolytisk affedtning
- Dekapering i saltsyre
- Forzinkning
- Passivering i chrom
Processerne samt opgørelse af råvareforbrug, kemikalier, energi og andet er anført i bilag D.
6.4.1 Opgørelse af mængder for elforzinkning
I det følgende er vist en opgørelse af metaller, kemikalier, vand og energi til elforzinkning. Data er beskrevet i bilag D.
Ved 1.000 m² overfladebehandling med elforzinkning findes der på emnerne efter overfladebehandling som gennemsnit:
70,01 kg |
zink |
0,35 kg |
chrom |
Disse størrelser er opgjort ud fra en massebalance over forbrug og affaldsmængder ved processen.
6.4.1.1 Materialeforbrug ved elforzinkning
Der er gennemført en opgørelse af, hvilke metaller og kemikalier der anvendes i de enkelte procesbade, og hvilke hovedbestanddele disse kemikalier har. Resultaterne er vist i Tabel 6.9.
Tabel 6.9 Kemikalieforbrug ved elforzinkning
Kemikalie |
Samlet
mængde |
Mængd
pr. 1.000 m²
overflade |
Zink |
630 ton |
74,1 kg |
Chrom |
14,1 ton |
1,7 kg |
Jern * |
74 ton |
8,7 kg |
Uorganiske syrer, primært svovlsyre |
310 ton |
36,5 kg |
Uorganiske baser, primært natriumhydroxid |
300 ton |
35,3 kg |
Borsyre |
13 ton |
1,5 kg |
Salte, primært kaliumchlorid |
100 ton |
11,8 kg |
Organiske forbindelser, som tensider og affedtersalte |
100 ton |
11,8 kg |
Cyanider |
80 ton |
9,4 kg |
Øvrige kemikalier, hvor sammensætningen ikke kendes |
167 ton |
19,6 kg |
* Da der ved renseprocesserne af stålpladerne sker en vis mængde afætsning af jern, som bl.a. findes i affaldsstrømmene, er disse medtaget i materialeopgørelsen.
Vandforbruget ligger på i størrelsesordnen 850.000 m³/år svarende til 100 m³ pr. 1.000 m² behandlet overflade.
6.4.1.2 Energiforbrug
Der anvendes energi til fremstilling af råvarer og til selve overfladebehandlingsprocessen. Det samlede energiforbrug i råvarefasen er vist i Tabel 6.8.
Tabel 6.10 Energiforbrug ved elforzinkning
|
Samlet
forbrug
pr. år (ton) |
Forbrug
pr. 1000 m²
(kg) |
Primært
Energiforbrug
(MJ/kg) |
Primær
energi
pr. 1000 m²
(MJ) |
Til metaller |
Zink |
630 |
74,12 |
70 |
5188,2 |
Chrom |
14,1 |
1,66 |
39 |
64,6 |
Stål |
74 |
8,71 |
40 |
348,2 |
Til kemikalier |
Uorg. syrer |
310 |
36,47 |
50 |
1823,5 |
Uorg. baser |
300 |
35,29 |
38 |
1341,2 |
Borsyre |
13 |
1,53 |
- |
- |
Salte |
100 |
11,76 |
5 |
58,8 |
Org. forbindelser |
100 |
11,76 |
60 |
705,9 |
Cyanider |
80 |
9,41 |
- |
- |
Andet |
167 |
19,65 |
- |
- |
Vand |
850.000 |
100.000 |
0,001 |
100 |
Til metaller, kemikalier og vand |
9.218 |
For de materialer, der ikke er medtaget i opgørelsen i, er energiforbruget skønnet til 1.500 MJ, hvilket betyder, at det samlede energiforbrug stiger til 10.700 MJ pr. 1.000 m² overflade.
Energiforbruget til processerne er udelukkende elforbrug og er opgjort til 2.677 kWh pr. m² overflade. Dette elforbrug svarer til 24.096 MJ primær energi pr. 1.000 m² overflade.
Der vil være et mindre energiforbrug ved behandling af affald i form af kasserede bade og slam, men dette er skønnet at udgøre meget lidt og er ikke medtaget.
Det samlede energiforbrug ligger på 34.800 MJ primær energi pr. m² behandlet overflade – ca. 30% i råvarefasen og ca. 70% i produktionsfasen.
6.4.1.3 Godskrivning af materialer og energi
Da metallerne pålagt ved overfladebehandling ikke udvindes særskilt ved oparbejdning af stål, er genvinding ikke medtaget.
Der er ingen oparbejdning af metallerne fra affaldsbehandlingen – slam og kasserede bade.
Da der ikke er nogen mulighed for genvinding af energi, især fra procesbadene, er dette ikke medtaget.
6.4.1.4 Opgørelse af råstofforbrug
Ud fra det materialeforbrug, der er opgjort i Tabel 6.9, er forbruget af råstoffer estimeret i Tabel 6.9.
Tabel 6.11 Estimering af forbrug af råstoffer for elforzinkning
Materiale
Behandlet overflade 8.500.00 m² |
Materiale-
forbrug
I alt |
Råstof-
forbrug
kg/kg |
Råstof-
forbrug
I alt |
Råstof-
forbrug
Pr. 1.000 m² |
Zink |
630 ton |
3,1 1) |
1.953 ton |
230 kg |
Chrom |
15 ton |
5,6 1) |
84 ton |
10 kg |
Uorganiske syrer, primært svovlsyre |
310 ton |
0,7 1) |
217 ton |
26 kg |
Uorganiske baser, primært natriumhydroxid |
300 ton |
1,2 1) |
360 ton |
42 kg |
Borsyre og salte |
113 ton |
1,0 3) |
113 ton |
13 kg |
Organiske forbindelser |
100 ton |
1,0 1) |
100 ton |
12 kg |
Cyanider |
80 ton |
2,0 1) |
160 ton |
19 kg |
Øvrige (ukendt sammensætning) |
167 ton |
3,0 2) |
501 ton |
59 kg |
I alt |
|
|
|
411 kg |
1): Data fra SigmaPro.
2): Tallet er anslået ud fra en antagelse om, at øvrige kemikalier indeholder en vis mængde metal og en vis mængde organiske forbindelser.
3) Data herfor er ukendt og derfor en anslået en værdi.
6.4.2 Opgørelse af vurderede mængder for elforzinkning
I det følgende er materiale- og energiforbrug omregnet til vurderede størrelser i mPR.
6.4.2.1 Vurdering af materialeforbrug ved elforzinkning
Det væsentligste ressourceforbrug findes for metallerne. Opgørelsen herfor er vist i Tabel 6.12.
Tabel 6.12 Forbrug af metaller ved elforzinkning
|
Zink |
Chrom |
Jern/stål |
Pr. 1000 m² overflade |
Forbrug (kg) |
74,12 |
1,66 |
8,71 |
Affald (kg) |
4,11 |
1,30 |
8,71 |
I produkt (kg) |
70,01 |
0,36 |
0,00 |
Ressourceforbrug |
mPR pr. kg |
33 |
12,8 |
Jern: 0,08
Mangan: 0,05 |
Ressourceforbrug |
2445,88 |
21,23 |
Jern: 0,70
Mangan: 0,44 |
I produkt |
2310,39 |
4,58 |
Jern: 0
Mangan: 0 |
Det samlede ressourceforbrug er på 2.468 mPR for metallerne, og i produktet findes 2.315 mPR. Tabet udgør 153 mPR svarende til 6 % af ressourceforbruget.
Ressourceforbruget til kemikalierne er skønnet til at udgøre 250 mPR, da en eksakt beregning ikke kunne gennemføres.
Det samlede ressourceforbrug er derfor:
Samlet forbrug |
2.720 mPR |
I produktet |
2.320 mPR |
Tab ved råvareudvinding og produktion |
500 mPR |
Ressourcerne i produktet – overfladen – tabes ligeledes ved oparbejdning af produktet – stålpladen.
6.4.2.2 Vurdering af energiforbrug ved elforzinkning
Det samlede energiforbrug er opgjort til 34,8 GJ pr. m² overflade. Fremstilles denne energimængde ud fra olie, svarer det til et forbrug på 34,0 mPR.
6.5 Ressourceeffektivitet for elforzinkning
6.5.1 Ressourceeffektivitet på materialeniveau
6.5.1.1 Materialeforbrug, produktion og brug
Den samlede mængde materialer i form af metaller til produktet, overfladebehandling af 1.000 m², er opgjort til 70,36 kg.
Det samlede forbrug af metaller og kemikalier udgør 84,5 kg metaller og 125,9 kg kemikalier. Ressourceeffektiviteten kan derfor beregnes til:

Den beregnede effektivitet afspejler, at alle kemikalierne og en del af metallerne tabes i galvaniseringsprocessen. En del vil findes i affald, og en del vil blive neutraliseret og ledt ud med spildevandet.
Vandforbruget er opgjort til 100 m³ pr. 1.000 m² behandlet overflade.
6.5.1.2 Materialeforbrug, produktion, brug og bortskaffelse
Som tidligere nævnt sker der ingen genvinding af materialer. Effektiviteten
MMat, P+B+A/N vil derfor være lig MMat, P+B.
6.5.1.3 Materialeforbrug, hele livscyklus
Råstofforbruget er opgjort til 411 kg pr. 1.000 m² overflade. Ressourceeffektiviteten kan derfor beregnes til:

Ved udvindingen udnyttes omkring 50% af råstofmængden – mindre for metallerne og mere for kemikalierne. Metallerne udgør i materialeopgørelsen omkring 1/3, mens de i råstofopgørelsen udgør mere end
50%.
6.5.2 Ressourceeffektivitet baseret på vurderet opgørelse
6.5.2.1 Ressourceforbrug, materialer
Den mængde ressourcer, der findes i produktet – overfladebehandling af 1.000 m² stålplade med elforzinkning udgør 2.320 mPR. Ressourceeffektiviteten opgjort som materialeeffektivitet, brutto kan
beregnes til:

Den opgjorte effektivitet afspejler, at det er de mindre knappe ressourcer i form af kemikalier, der tabes.
6.5.2.2 Ressourceforbrug, materialer og energi
Hvis man ser på det samlede materiale og energiforbrug, udgør det samlede vurderede forbrug 2.720 mPR + 34 mPR = 2.754 mPR, og den samlede materiale- og energieffektivitet, brutto kan beregnes til:
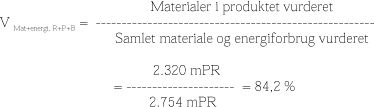
Den lille forskel i de to effektiviteter afspejler, at energiforbruget til både udvinding og overfladebehandlingsprocessen er relativ lille i forhold til materialeforbruget, når der anlægges en knaphedsbetragtning.
6.5.2.3 Ressourceforbrug, hele livscyklus
Der sker som tidligere nævnt ingen genvinding af materialer eller energi. Dette betyder, at effektiviteten for hele livscyklus Vmat+energi, R+P+B+A/N vil være lig Vmat+energi, R+P+A/N.
6.5.3 Fortolkning
De opgjorte ressourceeffektiviteter er vist i tabel 6.13.
Tabel 6.13 Beregnede ressourceeffektiviteter for elforzinkning
|
Betegnelse |
Ressource- effektivitet |
Materialeopgørelse |
|
|
• Materialer til produktion og brug |
Mmat, P+B |
33 % |
• Materialer, produktion, brug og bortskaffelse inkl. genanvendelse |
Mmat, P+B+A/N |
33 % |
• Råstoffer i hele livscyklus inkl. genanvendelse |
Mmat. R+P+B+A/N |
17 % |
Ressourceopgørelse |
|
|
• Materialer vedrørende råstoffer, produktion og brug |
Vmat, R+P+B |
85 % |
• Materialer og energi vedrørende råstoffer, produktion og brug |
Vmat+energi, R+P+B |
84 % |
• Materialer og energi i hele livscyklus inkl. genvinding |
Vmat+energi, R+P+B+A/N |
84 % |
Af tabel 6.13 ses det, at der tabes 2/3 af de anvendte materialer i galvaniseringsprocessen (Mmat, P+B ). Da beregningen er foretaget for en specifik proces, vil opgørelsen kunne bruges af branchens
virksomheder som sammenligningsgrundlag.
Den anden opgørelse på materialeniveau, Mmat. R+P+B+A/N, omfatter dels materialetab i selve processen, men også tab ved udvinding af metaller og forarbejdning af kemikalier. Denne beregning vil
antageligt kun kunne anvendes på et mere overordnet plan.
Ses der på de effektiviteter, der er baseret på vurderede opgørelser (mPR), vil man få et fingerpeg, om det er knappe eller rigelige ressourcer, der tabes i livsforløbet. Metaller og især zink vægter højt i
denne opgørelse. Af de beregnede størrelser ses det, at effektiviteten er relativt høj, og at det er mindre knappe ressourcer, der primært tabes. En øget udnyttelse af zink og til en vis grad chrom vil have en
relativ stor indflydelse på ressourceeffektiviteten.
De to ressourceeffektiviteter, Vmat, R+P+B og Vmat+energi, R+P+B er meget lig hinanden, hvilket viser, at energiforbruget både til udvinding af råstoffer og i galvaniseringsprocessen ud fra et
ressourcesynspunkt er af mindre betydning.
Det er i opgørelserne forudsat, at der ikke finder genvinding sted af metallerne eller af hjælpestofferne. En genvinding af metallerne vil øge ressourceeffektiviteten – i mindre grad for de vægtbaserede
opgørelser og i højere grad for de vurderede opgørelser.
6.5.4 Affaldsminimering
Af de beregnede ressourceeffektiviteter ses det at mængdemæssigt tabes der en stor del materiale i råstofudvindingen og i produktionen. Af de vurderede opgørelser ses det, at der tabes en mindre mængde
knappe ressourcer, og at energiforbruget i forhold til materialeforbruget er af mindre betydning. Lægges der vægt på knappe, miljøbelastende stoffer vil det være zink, der skal fokuserers på.
I det følgende trækkes en række væsentlige forhold frem.
6.5.4.1 Badkemikalier
Samme forhold som under fornikling/forchromning, se afsnit 6.3.4.1.
6.5.4.2 Zink og chrom
Til elforzinkning anvendes store mængder zink og små mængder chrom. Tabet af de to metaller er meget forskelligt, som det fremgår af tabel 6.14.
Tabel 6.14 Tab af metaller ved elforzinkning
|
Mængde på emnet pr. 1.000 m² |
Tab pr. 1.000 m² |
Tab i % af mængde på emnet |
Zink |
70,01 kg |
4,09 kg |
5,8 % |
Chrom |
0,35 kg |
1,35 kg |
385 % |
Som det ses af tabel 6.14, er der en relativ høj udnyttelse af zink, hvorimod tabet ved pålægning af chrom er meget stort.
Ved udvinding af metallerne tabes en del materiale. Metallerne i malmen er forbindelser af metallet som oxider eller sulfider. Ved oparbejdningen renses malmen, og metalionerne omdannes til metal. Tabet
varierer fra malmtype til malmtype. Mulighederne for affaldsminimering kan dog ikke vurderes.
Ved kassering af produktet, den overfladebehandlede plade eller genstand, tabes det pålagte metal. Stålet oparbejdes, men da zink udgør en meget lille del, udnyttes det ikke. I tabel 6.15 er vist hvilke
ressourcer, der tabes ved oparbejdning af 1 m² stålplade med en godstykkelse på 5 mm.
Da zink har et kogepunkt på omkring 900°C, vil zinken under oparbejdningen i overvejende grad findes i slagge og støv fra afgangsluften. Det vil derfor i nogen grad være muligt at oparbejde zinken. Om det
gøres vides ikke.
Tabel 6.15 Ressourcer i en 1 m² jernplade der er forniklet/forchromet
|
Mængde pr. 1 m² |
Ressourceforbrug pr. kg |
Ressourceforbrug i 1 m² plade |
Jern* |
40 kg |
0,08 mPR |
3,200 mPR |
Zink |
70,01 gram |
33 mPR |
2.310 mPR |
Chrom |
0,35 gram |
12,8 mPR |
0,004 mPR |
* En jernplade på 1 m² med en godstykkelse på 5 mm har et volumen på 0,005 m³ og med en massefylde på 7,9 vejer pladen ca. 40 kg
6.5.4.3 Vandforbrug og spildevand
Vandforbruget til elforzinkning bruges primært til skyllevand. Der bruges omkring 100 liter pr. m² behandlet overflade.
Se i øvrigt kommentater under fornikling/forchromning, afsnit 6.3.4.3.
6.5.4.4 Energi
Energiforbruget til overfladebehandlingsprocessen udgør 70% af det samlede energiforbrug. Den resterende del går til udvinding af materialer.
Energiforbruget til processen er udelukkende el, hvor der forbruges 2,7 kWh pr. m² overflade, svarende til 24 MJ primær energi. Energiforbruget til el-forzinkning ligger således på ca. 10% af
energiforbruget til fornikling/forchromning.
Også for elforzinkning er energiforbruget lille i forhold til materialeforbruget, når begge opgørelser omregnes til ressourceforbrug i mPR.
6.5.4.5 Samlet prioritering
Ud fra et ressourcemæssigt synspunkt kan det være noget problematisk at anvende zink til overfladebehandling, såfremt det ikke genvindes.
Elforzinkning har en række fordele. Det giver en overflade af høj kvalitet og et pænt udseende, men
- Zink og chrom, der forekommer som affald (primært slam) fra overfladebehandlingsprocessen, genvindes ikke.
- Zink fra det kasserede produkt bør genvindes i så høj grad som muligt.
- Der anvendes en række hjælpekemikalier i processen, som tabes.
Det vides ikke i, hvor høj grad zink genvindes fra oparbejdning af stål, og det er derfor et forhold, der bør fokuseres på.
6.5.5 Sammenligning med øvrige opgørelser
Overfladebehandlingsprocessen elforzinkning, som den udføres i Danmark, er optimeret med hensyn til udnyttelse af metaller, energi- og vandforbrug og er således typisk for europæiske forhold.
6.5.5.1 Direkte materialeinput
Det er ikke muligt at foretage en sammenligning mellem de opgjort mængder af materialer og data for DMI, da DMI ikke opgøres på procesniveau.
6.5.5.2 Totale materialeinput
I det følgende er søgt estimeret det totale materialeinput, baseret på Wuppertal's MIPS-data, se tabel 6.16.
Tabel 6.16 Estimering af materialeinput for elforzinkning
Materiale
Behandlet overflade 8.500.00 m² |
Materiale-
forbrug
I alt |
Råstof-
forbrug
kg/kg |
Råstof-
forbrug
I alt |
Råstof-
forbrug
Pr. 1.000 m² |
Zink |
630 ton |
23,1 |
14.553 ton |
1.712 kg |
Chrom |
15 ton |
- |
- |
- |
Uorganiske syrer, primært svovlsyre |
310 ton |
0,5 |
155 ton |
18 kg |
Uorganiske baser, primært natriumhydroxid |
300 ton |
1 |
300 ton |
35 kg |
Borsyre og salte |
113 ton |
1 1) |
113 ton |
13 kg |
Organiske forbindelser |
100 ton |
5 1) |
500 ton |
59 kg |
Cyanider |
80 ton |
10 1) |
800 ton |
94 kg |
Øvrige (ukendt sammensætning) |
167 ton |
10 1) |
1670 ton |
196 kg |
I alt |
|
|
|
2.127 kg |
1) Anslået ud fra data om andre kemiske forbindelser.
Som det fremgår af tabel 6.16, mangler der data for chrom. Materialeinputtet vil derfor være i størrelsesordnen 2.200 kg pr. 1.000 m² overflade.
I nærværende opgørelse er råstofforbruget opgjort til ca. 400 kg eller knapt 1/5 af det opgjorte materialeinput. Begge typer af opgørelser skulle i princippet være ens og medtage alle indirekte strømme. Den
væsentligste forskel ligger i opgørelsen for zink, hvor Wuppertal har opgjort materialeinputtet til at være omkring 8 gange så stort som data fra SigmaPro. Wuppertals data for de øvrige materialer ligger også
noget over de her anvendte LCA-data for de øvrige materialer.
6.6 Kortlægning af varmforzinkning
Ved varmforzinkning dyppes stålemner i et smeltet zinkbad ved ca. 460°C, hvorved der pålægges et zinklag med en lagtykkelse på 60-100 m, hvilket giver en langt bedre korrosionsbeskyttelse, end der
opnås ved elektrolytisk forzinkning, hvor man normalt arbejder med lagtykkelser på 5-20 m. Derfor anvendes varmforzinkning især til stålkonstruktioner, der anvendes udendørs, og metoden kan anvendes
på meget store emner op til 10-15 meters længde.
I Danmark findes 20 varmforzinkningsvirksomheder, men flere af virksomhederne har samme ejer. Det skønnes, at halvdelen af virksomhederne laver ca. 85% af produktionen. Der varmforzinkes
skønsmæssigt 120.000 ton gods årligt, og i 2001 var det samlede zinkforbrug for danske varmforzinkere på 9817 ton svarende til, at der i gennemsnit påføres ca. 8,2% zink i forhold til godsets vægt.
Kortlægningen er baseret på en opgørelse af 1 ton behandlet gods. Der er taget udgangspunkt i at det er stålplade, der er overfladebehandlet.
Procestrinnene ved varmforzinkning er:
- Alkalisk affedtning
- Bejdsning i saltsyre
- Flusning
- Tørring
- Forzinkning
- Køling
- Pudsning og afgratning
Processerne samt opgørelse af råvareforbrug, kemikalier, energi og andet er anført i bilag D.
6.6.1 Opgørelse af mængder for varmforzinkning
I det følgende er vist en opgørelse af metaller, kemikalier, vand og energi til varmforzinkning. Data er beskrevet i bilag D.
Ved behandling af 1 ton gods pålægges der i gennemsnit en zinkmængde på 64,4 kg. Denne mængde er opgjort ud fra data om forbrug og affaldsmængder.
6.6.1.1 Materialeforbrug ved varmforzinkning
Der er gennemført en opgørelse over forbruget af zink og kemikalier, der anvendes i de enkelte procesbade, og hvilke hovedbestanddele disse kemikalier har. Resultaterne er vist i tabel 6.17.
Tabel 6.17 Materialeforbrug ved varmforzinkning
Kemikalie |
Samlet mængde |
Mængde pr.
ton
behandlet
gods |
Zink |
9.830 ton |
81,9 kg |
Uorganiske syrer |
1.000 ton |
8,33 kg |
Uorganiske baser |
60 ton |
0,50 kg |
Ammoniak |
65 ton |
0,54 kg |
Hydrogenperoxid |
10 ton |
0,08 kg |
Organiske forbindelser |
25 ton |
0,21 kg |
Det samlede vandforbrug er opgjort til 15-20.000 m³ pr. år. Dette svarer til et forbrug på ca. 0,17 m³ pr. ton behandlet gods.
6.6.1.2 Energiforbrug
Der anvendes energi til fremstilling af råvarer og til selve overfladebehandlingsprocessen.
Det samlede energiforbrug i råvarefasen er vist i tabel 6.18.
Tabel 6.28 Energiforbrug ved varmforzinkning
|
Samlet forbrug
pr. år (ton) |
Forbrug pr. 1
ton gods (kg) |
Primært Energi
forbrug (MJ/kg) |
Primær energi
pr. ton gods (MJ) |
Til metaller |
Zink |
9.830 |
81,92 |
70 |
5.734,2 |
Til kemikalier |
Uorganiske syrer |
1.000 |
8,33 |
50 |
416,7 |
Uorganiske baser |
60 |
0,50 |
38 |
19,0 |
Ammoniak |
65 |
0,54 |
60 |
32,5 |
Hydrogenperoxid |
10 |
0,08 |
10 |
0,8 |
Organiske forbindelser |
25 |
0,21 |
60 |
12,5 |
Vand |
20.000 |
166,7 |
0,001 |
0,17 |
Til metaller, kemikalier og vand |
6.215,8 |
Til overfladebehandlingsprocessen bruges dels el og dels olie som energikilde. Pr. ton behandlet gods bruges i gennemsnit 240 kWh el og 15,2 kg olie.
Der kan også anvendes gas, og det forventes, at en del af olieforbruget med tiden vil blive erstattet af gas. Der haves dog ikke en opgørelse over, hvor stort gasforbruget er og alt vil i denne opgørelse blive
regnet som olie. Det skal bemærkes, at ressourcemæssigt vil forbrug af olie og gas vægte omtrent ens. Det der er væsentligt at skelne mellem er forbruget af elektricitet og olie/gas.
Omregnes procesenergien til primær energi kan forbruget opgøres til 2.160 MJ baseret på el og 576 MJ baseret på olie svarende til i alt 2.736 MJ pr. ton behandlet gods.
Det samlede energiforbrug ligger på 8.950 MJ primær energi pr. behandlet ton gods – ca. 70% fra råvarefasen og ca. 30% fra produktionsfasen.
6.6.1.3 Godskrivning af materialer og energi
Affaldsfraktionerne hårdzink og zinkaske indeholder store mængder zink, der kan oparbejdes og genanvendes. Zinkindholdet i disse fraktioner udgør 1.745 ton svarende til 14,5 kg pr. ton behandlet gods.
Her er ikke taget stilling til om oparbejdningen sker internt eller eksternt.
Ved oparbejdning sker et tab, antaget til 30%, således at der udvindes 10,2 kg zink. Det antages at have samme kvalitet som den zink, der anvendes i processen.
Ved oparbejdningen spares energi til fremstilling af ny zink, og der bruges energi til selve oparbejdningen. Energien til oparbejdningen er antaget at udgøre 50% af energiforbruget til fremstillingen.
Besparelsen kan derfor opgøres til:
Sparet udvinding |
10,2 kg × 70 MJ/kg |
= 712,5 MJ |
Energi til oparbejdning |
10,2 kg × 35 MJ/kg |
= 356,3 MJ |
Besparelse |
|
= 356,3 MJ |
6.6.1.4 Opgørelse af råstofforbrug
Forbruget af råstoffer er opgjort ud fra materialeforbrug og den mængde, der genvindes. Den mængde, der oparbejdes, udgør 1.745 ton zink. Ved oparbejdningen er der et tab, således at 1.142 ton zink
kan genanvendes (70%).
Tabel 6.19 Estimering af råstofforbrug for varmforzinkning
Materiale
120.000 ton gods |
Materiale-
mængde |
Råstof-
forbrug
Kg/kg |
Råstof-
forbrug
i alt |
Råstof-
forbrug
pr. ton gods |
Zink |
8.688 ton |
3,1 |
26.932 ton |
240 kg |
Uorganiske syrer |
1.000 ton |
0,7 |
700 ton |
6 kg |
Uorganiske baser |
60 ton |
1,2 |
72 ton |
0,6 kg |
Ammoniak og hydrogenperoxid |
75 ton |
2 1) |
150 ton |
1 kg |
Tensider m.v. |
25 ton |
2,0 1) |
50 ton |
0,4 kg |
|
|
|
|
248 kg |
1): Værdien er skønnet.
6.6.2 Opgørelse af vurderede mængder for varmforzinkning
I det følgende er materiale- og energiforbrug omregnet til vurderede størrelse i mPR.
6.6.2.1 Vurdering af materialeforbrug ved varmforzinkning
Det væsentligste ressourceforbrug ligger i forbruget af zink. Ressourceforbruget fra mindre mængder afætset jern/stål er ikke medtaget. Opgørelsen for zink er vist i tabel 6.20.
Tabel 6.20 Ressourceforbrug ved varmforzinkning
|
Mængde pr. be-
handlet ton gods |
Ressourceforbrug
33 mPR/kg zink |
Forbrug |
81,92 kg |
2.703 mPR |
Affald |
17,67 kg |
583 mPR |
I produktet |
64,25 kg |
2.120 mPR |
Som det ses af tabel 6.20, udgør indholdet af ressourcer i produktet – zinkpålægning af 1 ton gods 2.120 mPR. Tabet ved processen udgør 22 % af ressourceforbruget.
Ressourceforbruget til kemikalierne er skønnet til at udgøre 10 mPR, da en eksakt beregning ikke kunne gennemføres.
Det samlede ressourceforbrug udgør således 2.713 mPR.
Ressourcerne i produktet – overfladebehandlingen – tabes ved kassering af produktet, når stålpladen oparbejdes.
6.6.2.2 Vurdering af energiforbrug ved varmforzinkning
Det samlede energiforbrug er opgjort til 8.950 MJ primær energi pr. ton behandlet gods. Fremstilles denne energimængde ud fra olie, svarer det til et forbrug på 8,8 mPR.
6.6.2.3 Vurdering af genvundne mængder
Det er opgjort, at der genvindes 10,2 kg zink, hvilket svarer til en ressoucebesparelse på 336 mPR.
Det er opgjort, at der ved genvinding kan spares 356 MJ primær energi. Denne energimængde svarer til 0,3 mPR.
6.7 Ressourceeffektivitet for varmforzinkning
6.7.1 Ressourceeffektivitet på materialeniveau
6.7.1.1 Materialeforbrug, produktion og brug
Den samlede mængde zink i overfladebehandlingen udgør 64,42 kg. Det samlede forbrug af metal udgør 81,9 kg, og forbruget af kemikalier udgør 9,7 kg.
Ressourceeffektiviteten kan derfor beregnes til:

Tabet udgøres af kemikalierne samt en del zink, der fremkommer som affald i overfladebehandlingsprocesssen.
Vandforbruget er opgjort til 167 liter pr. ton behandlet gods.
6.7.1.2 Materialeforbrug, produktion, brug og bortskaffelse
Genvinding af zinkaffald fra overfladebehandlingen er opgjort til 10,2 kg. Netto-effektiviteten kan derfor beregnes til:

Genvinding af zink udgør omkring 50% af affaldsmængden og udgøres af zinkholdigt slagge. Genvindingen kan øges, men ikke til 100%, da der er et vist tab i genvindingsprocessen.
6.7.1.3 Materialeforbrug, hele livscyklus
Ses der på råstofforbruget, og tages der hensyn til genvinding af zink, kan effektiviteten beregnes til:

Råstofforbruget udgøres primært af zinkmalm, hvoraf omkring 1/3 af malmen bliver til zink.
6.7.2 Ressourceeffektivitet baseret på vurderet opgørelse
6.7.2.1 Ressourceforbrug, materialer
Den mængde ressourcer, der findes i produktet overfladebehandling af 1 ton gods –, udgør 2.120 mPR.
Ressourceeffektiviteten opgjort som materialeeffektivitet, brutto, kan beregnes til:

Tabet (de ca. 22%) udgøres af zink, da kemikalierne ikke tæller meget i den vurderede opgørelse.
6.7.2.2 Ressourceforbrug, materialer og energi
Hvis man ser på det samlede materiale- og energiforbrug, udgør det samlede vurderede forbrug 2.713 mPR + 8,8 mPR = 2.722 mPR, og den samlede materiale- og energieffektivitet kan beregnes til:
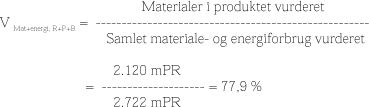
Som det kan ses af opgørelserne og af de beregnede effektiviteter, er energiforbruget til både udvindingen og til processen meget lille i forhold til ressourceforbruget af zink.
6.7.2.3 Ressourceforbrug, hele livscyklus
Tages der hensyn til genvinding, vil det samlede ressourceforbrug udgøre 2.722 mPR – 336 mPR = 2.386 mPR, og netto-effektiviteten kan beregnes til:
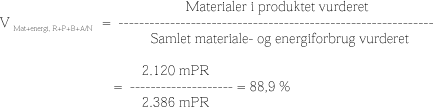
Effektiviteten baseret på vurderede opgørelser illustrerer også, at i størrelsesordnen 10% af den anvendte zink oparbejdes.
6.7.3 Fortolkning
De opgjorte ressourceeffektiviteter er vist i tabel 6.21.
Tabel 6.21 Beregnede ressourceeffektiviteter for varmforzinkning
|
Betegnelse |
Ressource- effektivitet |
Materialeopgørelse |
|
|
• Materialer til produktion og brug |
Mmat, P+B |
70 % |
• Materialer, produktion, brug og bortskaffelse inkl. genanvendelse |
Mmat, P+B+A/N |
79 % |
• Råstoffer i hele livscyklus inkl. genanvendelse |
Mmat. R+P+B+A/N |
26 % |
Ressourceopgørelse |
|
|
• Materialer vedrørende råstoffer, produktion og brug |
Vmat, R+P+B |
78 % |
• Materialer og energi vedrørende råstoffer, produktion og brug |
Vmat+energi, R+P+B |
78 % |
• Materialer og energi i hele livscyklus inkl. genvinding |
Vmat+energi, R+P+B+A/N |
89 % |
Af tabel 6.21 ses det, at der tabes omkring 30% i selve overfladebehandlingsprocessen (Mmat, P+B). Tabet udgøres af kemikalierne, der udgør ca. 1/3. Resten er zink. Da dette tal er opgjort specifikt for
denne proces, vil opgørelsen kunne bruges af branchens virksomheder som sammenligningsgrundlag.
Den næste effektivitet (Mmat, P+B+A/N) viser, at der sker en vis genvinding af zink. Omkring 50% af zinkaffaldet fra overfladebehandlingen oparbejdes. Det antages, at denne effektivitet kan forøges lidt,
men det vil ikke være muligt at oparbejde kemikalierne, der udgør lidt over 10%. Endvidere skal der tages højde for, at der altid vil være et vist tab af zink ved oparbejdningen.
Effektiviteten for råstoffer (Mmat. R+P+B+A/N) afspejler, at der ved udvinding af zink fra malm tabes omkring 2/3 af materialet. Denne beregning vil antageligt kun kunne anvendes på et mere overordnet
plan.
Ses der på beregningen af de vurderede opgørelser, fremgår det tydeligt, at zink er langt det vigtigste materiale, og at kemikalierne ikke betyder meget.
Af effektiviteten med og uden energi (Vmat, R+P+B og Vmat+energi, R+P+B) ses det tydeligt, at energiforbruget ikke betyder meget i forhold til forbruget af zink.
Effektiviteten Vmat+energi, R+P+B+A/N er højere end de to andre svarende til, at godt 10% af zinkmængden forudsættes oparbejdet.
6.7.4 Affaldsforebyggelse
Som for el-forzinkning ses det, at der mængdemæssigt tabes en relativ stor del materiale i råstofudvindingen og i produktionen. Af de vurderede opgørelser ses det, at der tabes en mindre mængde knappe
ressourcer, og at energiforbruget i forhold til materialeforbruget er af mindre betydning. Lægges der vægt på knappe, miljøbelastende stoffer, vil det være zink, der skal fokuserers på.
I det følgende trækkes en række væsentlige forhold frem.
6.7.4.1 Kemikalier
Til varmforzinkning anvendes en del kemikalier til rensning af godset inden forzinkningen. Dertil kommer flusmidler, der anvendes som en forbehandling inden dypning i zinksmelten.
Forbehandlingsbadene skiftes, når de er forurenende med jern, olie og andre urenheder. Se i øvrigt bemærkningerne under afsnit 6.3.4.1.
6.7.4.2 Zink
Til varmforzinkning pålægges i gennemsnit 64,4 kg pr. ton gods. I processen tabes 17,5 kg svarende til ca. 27 %. Der genvindes 10,2 kg zinkaske og en del andet affald, således at det egentlige tab udgør
7,3 kg eller 11 % af den mængde zink, der findes på emnet.
Det bør derfor overvejes, om de affaldsfraktioner, der i dag ikke oparbejdes, kan blive det, således at affaldsmængden reduceres, og zinken udnyttes bedre.
Ved kassering af produktet – det overfladebehandlede emne – tabes alt det pålagte metal. Her gør de samme forhold sig gældende som for elforzinkning. Zinken fordamper fra smelten inden jernet gør og
findes i slagge og støv fra afgangsluften. Den ressourcemængde jernet repræsenterer vil dog oftest være væsentlig større, end den mængde zinken repræsenterer, men det afhænger meget af emnets geometri.
6.7.4.3 Vandforbrug og spildevand
Der anvendes omkring 170 liter skyllevand til forbehandling af 1 ton gods. Skyllevandet vil være forurenet med olie, snavs, jern samt de anvendte kemikalier, herunder opløste zinksalte.
Se i øvrigt kommentarer under fornikling/forchromning, afsnit 6.3.4.3.
6.7.4.4 Energi
Energiforbruget er i alt på ca. 9.000 GJ/ton, fordelt på 70 % i råvarefasen og 30 % i overfladebehandlingsprocessen.
Typen af energiressourcer, der anvendes i råvarefasen kendes ikke.
Energiforbruget i varforzinkningen dækkes med 50% olie og ca. 50% el.
Ressourcemæssigt bruges der i alt i størrelsesordnen 9 mPR til energiforbruget baseret på olie. Til at dække materialebehovet anvendes 2700 mPR, og energiforbruget udgør således under 1 % af det
samlede ressourceforbrug.
6.7.4.5 Samlet prioritering
Ud fra et ressourcemæssigt synspunkt kan det være noget problematisk at anvende zink til overfladebehandling, såfremt det ikke genvindes.
Følgende forhold bør der fokuseres på:
- Zink fra det kasserede produkt bør genvindes i så høj grad som muligt.
- Zink, der forekommer som affald (primært slam, eventuelt spildevand) fra forbehandlingen genvindes ikke.
- Der anvendes en række hjælpekemikalier i processen, som tabes.
Det vides ikke, i hvor høj grad zink genvindes fra oparbejdning af stål og det er derfor et forhold, der bør fokuseres på.
6.7.5 Sammenligning med øvrige opgørelser
Overfladebehandlingsprocessen varmforzinkning, som den udføres i Danmark, er optimeret med hensyn til udnyttelse af metaller, energi- og vandforbrug og er således typisk for europæiske forhold.
6.7.5.1 Direkte materialeinput
Det er ikke muligt at foretage en sammenligning mellem de opgjort mængder af materialer og data for DMI, da DMI ikke opgøres på procesniveau.
6.7.5.2 Totale materialeinput
I det følgende er søgt estimeret det totale materialeinput, baseret på Wuppertal's MIPS-data, se tabel 6.22.
Tabel 6.22 Estimering af materialeinput for varmforzinkning
Materiale 120.000 ton gods |
Materiale- mængde |
Råstof- forbrug Kg/kg |
Råstof- forbrug i alt |
Råstof- forbrug pr. ton gods |
Zink |
8.688 ton |
23,1 |
200.693 ton |
1.672 kg |
Uorganiske syrer |
1.000 ton |
0,5 1) |
500 ton |
4 kg |
Uorganiske baser |
60 ton |
1 1) |
60 ton |
0,5 kg |
Ammoniak og hydrogenperoxid |
75 ton |
1 1) |
75 ton |
0,6 kg |
Tensider m.v. |
25 ton |
10 1) |
250 ton |
2 kg |
|
|
|
|
1.679 kg |
1) Værdien er skønnet fra oplysninger om lignende kemikalier.
I nærværende opgørelse er råstofforbruget opgjort til ca. 250 kg eller ca. 15% af det opgjorte materialeinput. Begge typer af opgørelser skulle i princippet være ens og medtage alle indirekte strømme. Den
væsentligste forskel ligger i opgørelsen for zink, hvor Wuppertal har opgjort materialeinputtet til at være omkring 8 gange så stort som data fra SigmaPro. Wuppertals data for de øvrige materialer ligger også
noget over der her anvendte LCA-data for de øvrige materialer.
7 Køle/smøremidler
7.1 Introduktion
Køle/smøremidler anvendes til køling og smøring ved skærende og spåntagende bearbejdning af emner af jern, stål og andre metaller.
Der findes to hovedtyper af produkter, den største er de vandbaserede produkter, hvor især køleeffekten er vigtig, og en mindre gruppe af vandfri produkter, hvor det især den smørende effekt der er vigtig.
Som ved den galvaniske overfladebehandling i kapitel 6 kan processen ”brug af køle/smøremidler” ikke sidestilles med et produkt. Her er valgt at se på processen i et livscyklusperspektiv som beskrevet i
kapitel 2. Grafisk kan dette illustreres som vist i figur 7.1.
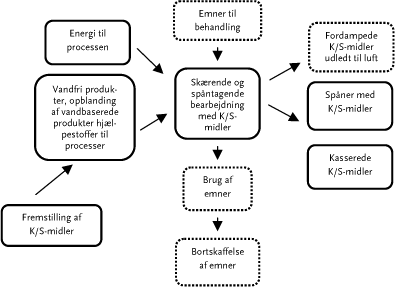
Figur 7.1 Skærende og spåntagende bearbejdning med anvendelse af køle/smøremidler (K/S-midler) i et livscyklusperspektiv
Det vanskelige ved vurdering af køle/smøremidler set i relation til ressourceeffektivitet er definition af en enhed, der er relevant i forhold til de forskellige skærende og spåntagende bearbejdninger i forskellige
materialer, og som samtidig siger noget om forbruget af køle/smøremidlerne.
Ved opslag i UMIP-databasen, SigmaPro samt forskellige håndbøger vedrørende metalbearbejdning er det valgt at tage udgangspunkt i mængden af fjernet materiale i form af spåner, slibestøv, fraskær og
andet.
Nyttevirkningen ved anvendelse af køle/smøremidler er, at en mængde materiale fra et givet emne fjernes. Derfor defineres produktet i denne sammenhæng som kg fjernet materiale.
7.2 Kortlægning
Skærende og spåntagende bearbejdning er udbredt over hele jern- og metalindustrien. En række metaller bearbejdes, og der fremkommer i størrelsesordnen 700.000 ton spåner årligt.
Kortlægningen af materiale- og energiforbrug ved fremstilling af køle/smøremidler og brug af disse i forhold til bearbejdning af metaller svarende til fremkomsten af 1 ton spåner er beskrevet i bilag E.
Der er gennemført en kortlægning dels af vandbaserede midler og dels af vandfri midler. For de vandbaserede midler er det forudsat, at brugsopløsningen er en 5% opblanding af koncentrat i vand.
7.2.1 Opgørelse af mængder
7.2.1.1 Materialeforbrug
Forbruget af køle/smøremidler er vist i tabel 7.1.
Tabel 7.1 Forbrug af Køle/smøremidler
|
Vandbaserede køle/
smøremidler |
Vandfri
smøremidler |
Køle/smøremiddel mængde pr. ton spåner |
1- 1,5 kg |
400-500 kg |
Totalt forbrug af køle/smøremidler |
700 ton |
500 ton |
Samlet mængde spåner |
500-700.000 ton |
1.000-1.300 ton |
Til fremstilling af 1,25 kg koncentrat til vandbaserede køle/smøremidler anvendes 1,0 kg kemikalier og 0,25 kg vand. Ved opblanding anvendes yderligere 23 liter vand.
Til fremstilling af 450 liter vandfri køle/smøremidler, der anvendes til fjernelse af 1 ton spåner, anvendes 450 kg kemikalier, der primært er organiske forbindelser.
Sammensætningen af de to typer køle/smøremidler er vist i bilag E. I tabel 7.2 er vist mængden og typerne af komponenter i de to midler.
Tabel 7.2 Indhold af hovedkomponenter i vanddige og vandfri køle/smøremidler
Komponent |
Vandbaserede køle/smøremidler |
Vandfri køle/smøremidler |
|
Indhold i
% |
Mængde
(ton) pr. år |
Mængde pr.
ton spåner |
Indhold i
% |
Mængde
(ton) pr. år |
Mængde pr.
ton spåner |
Vand |
20 |
140 ton |
0,25 kg |
0 |
0 |
|
Råoliedestillater og raffinerede olier |
25 |
185 ton |
0,31 kg |
18 |
90 ton |
81 kg |
Carbonhydrider med ilt |
15 |
105 ton |
0,19 kg |
10 |
50 ton |
45 kg |
Chlorerede organiske forbindelser |
3 |
21 ton |
0,04 kg |
3 |
15 ton |
13,5 kg |
Organiske kvælstofforbindelser |
17 |
119 ton |
0,21 kg |
12 |
60 ton |
54 kg |
Øvrige organiske forbindelser |
15 |
105 ton |
0,19 kg |
51 |
255 ton |
230 kg |
Uorganiske komponenter |
4 |
28 ton |
0,05 kg |
6 |
30 ton |
27 kg |
I alt |
|
703 ton |
1,24 kg |
|
500 ton |
450 kg |
Ved anvendelsen er der ikke medregnet tab ved opblandingen.
7.2.1.2 Energiforbrug
Der anvendes energi til fremstilling af råvarer, til blanding af råvarerne og til selve brugen af køle/smøremidlerne. Disse tab er vist i tabel 7.3.
Tabel 7.3 Energiforbrug pr. ton spåner
|
Vandbaserede
køle/smøremidler |
Vandfri
køle/smøremidler |
Energiforbrug til ressourcer |
73,1 MJ |
38.210 MJ |
Energiforbrug til blanding |
11,2 MJ |
4.050 MJ |
Energiforbrug ved brug |
3.000 MJ |
3.000 MJ |
Samlet energiforbrug |
3.084 MJ |
35.260 MJ |
7.2.1.3 Godskrivning af materialer og energi
Affald fra anvendelse af de vandbaserede køle/smøremidler indsamles, opkoncentreres, og koncentratet bortskaffes ved forbrænding. Det antages, at energiforbruget til opkoncentrering modsvarer
energiudviklingen ved forbrænding.
Affald fra vandfri køle/smøremidler forudsættes bortskaffet ved forbrænding med energigenvinding. Det er opgjort, at energiudviklingen er i størrelsesordnen 10.000 MJ pr. ton spåner.
7.2.1.4 Estimering af råstoffer
Der er ikke foretaget en estimering af råstofforbruget, da kendskabet til de indgående komponenter ikke er tilstrækkeligt.
7.2.2 Opgørelse af vurderede mængder
I det følgende er materialer og energiforbrug omregnet til vurderede størrelser i mPR.
Indholdet af ressourcer i produktet 1 ton spåner har betydning for fastsættelse af ressourceeffektiviteten. Spånerne har et forskelligt vurderet ressourceforbrug afhængig af, hvilken type spåner det er.
Følgende typer er medtaget:
Maskinstål |
130 mPR pr. ton |
Rustfrit stål |
12.300 mPR pr. ton |
Aluminium |
1.500 mPR pr. ton |
Kobber |
16.500 mPR pr. ton |
7.2.2.1 Vurdering af materialeforbrug
Ressourceforbruget til fremstilling af 1,24 kg vandbaserede køle/smøremidler er opgjort til 0,0376 mPR.
Ressourceforbruget til fremstilling af 450 kg vandfri køle/smøremidler er opgjort til 16,9 mPR.
7.2.2.2 Vurdering af energiforbrug
Energiforbruget pr. ton spåner ved anvendelse af vandbaserede midler er opgjort til 3.084 MJ primær energi. Fremstilles denne energimængde ud fra olie, svarer det til et forbrug på 3,0 mPR.
Energiforbruget pr. ton spåner ved anvendelse af de vandfri midler er opgjort til 35.260 MJ primær energi. Ved omregning til ressourceforbrug svarer det til 34,4 mPR.
7.2.2.3 Vurdering af genvinding
For de vandfri midler er det antaget, at energi udviklet ved affaldsbortskaffelse genvindes. Mængden udgør 10.000 MJ primær energi pr. ton spåner, hvilket svarer til 9,8 mPR.
7.3 Ressourceeffektivitet
7.3.1 Ressourceeffektivitet på materialeniveau
7.3.1.1 Materialeforbrug, produktion og brug
Mængden af materialer i produktet er det definerede produkt på 1 ton eller 1.000 kg. Den mængde materialer, der yderligere forbruges, udgøres af den anvendte mænge køle/smøremiddel.
For de vandbaserede midler vil ressourceeffektiviteten derfor kunne beregnes til:

For de vandbaserede midler er der et vandforbrug på omkring 23 kg pr. ton spåner.
For de ikke vandbaserede midler vil ressourceeffektiviteten kunne beregnes til:

7.3.1.2 Materialeforbrug, produktion, brug og bortskaffelse
Der sker ingen genvinding af materialer for de to typer køle/smøremidler. Effektiviteten M Mat, P+B+A/N er derfor lig M Mat, P+B.
7.3.1.3 Materialeforbrug, hele livscyklus
Der er ikke foretaget nogen beregning af effektiviteten M Mat, R+P+B+A/N baseret på råstofforbruget, da dette ikke er opgjort.
7.3.2 Ressourceeffektivitet baseret på vurderet opgørelse
7.3.2.1 Ressourceforbrug, materialer
Ressourceeffektiviteten baseret på materialer er opgjort som forholdet mellem materialer i produktet og samlet materialeforbrug. Begge materialeopgørelser er baseret på vurderede størrelser. Da materialer i
produktet, vurderet, afhænger af, hvilken type metal spånerne består af, er VMat, R+P+B vist i tabel 7.4.
Tabel 7.4 Ressourceeffektivitet, materialer, brutto
|
1 ton spåner af |
Maskinstål |
Rustfrit stål |
Aluminium |
Kobber |
Materialer i produktet, vurderet |
130 mPR |
12.300 mPR |
1.500 mPR |
16.500 mPR |
Vandbaserede køle/smøremidler |
|
|
|
|
Samlet materialeforbrug vurderet |
130,04 mPR |
12.300,04 mPR |
1.500,04 mPR |
16.500,04 mPR |
VMat, R+P+B |
100 |
100 |
100 |
100 |
Vandfri midler |
|
|
|
|
Samlet materialeforbrug, vurderet |
147 mPR |
12.317 mPR |
1.517 mPR |
16.517 mPR |
VMat, R+P+B |
88,4% |
99,9% |
98,9% |
99,9% |
7.3.2.2 Ressourceforbrug, materialer og energi
Medtages både materialeforbrug og energiforbrug, kan den samlede effektivitet beregnes som vist i tabel 7.5.
Tabel 7.5 Ressourceeffektivitet, materialer og energi
|
1 ton spåner af |
Maskinstål |
Rustfrit stål |
Aluminium |
Kobber |
Materialer i produktet, vurderet |
130 mPR |
12.300 mPR |
1.500 mPR |
16.500 mPR |
Vandbaserede køle/smøremidler |
|
|
|
|
Samlet materialeforbrug vurderet |
133 mPR |
12.303 mPR |
1.503 mPR |
16.503 mPR |
VMat+energi, R+P+B |
97,7 |
100 |
99,8 |
100 |
Vandfri midler |
|
|
|
|
Samlet materialeforbrug, vurderet |
164 mPR |
12.334 mPR |
1.534 mPR |
16.534 mPR |
VMat+energi, R+P+B |
79.2% |
99,7% |
97,8% |
99,8% |
7.3.2.3 Ressourceforbrug, hele livscyklus
Ved genvinding af energi ved forbrænding af vandfri midler vil der ”spares” 10 mPR. Dette vil betyde, at VMat+energi, R+P+B+A/N for maskinstål bliver på 84,4 % og for de andre meget tæt på 100%.
Der er ingen eller en meget lille energigenvinding ved bortskaffelse af de vandbaserede midler. Effektiviteten VMat+energi, R+P+B+A/N vil derfor være lig VMat+energi, R+P+B.
7.3.3 Fortolkning
Generelt er opstilling af ressourceeffektiviteter ikke egnede for delprocesser, hvor produktet er vanskeligt at definere.
Her er der taget udgangspunkt i det noget abstrakte begreb ”fjernelse af 1 ton spåner” fra skærende og spåntagende bearbejdning, og den mængde køle/smøremiddel, der bruges i den forbindelse, er blevet
vurderet.
Tab af køle/smøremiddel ved selve brugen er yderst begrænset. Det er antaget, at der ikke spildes noget af midlerne, men at der sker en vis udslæbning med emnerne. Det sammen med at kendskabet til
produktionen af køle/smøremidlerne ikke er tilstrækkeligt kendt, gør det uhyre vanskeligt at opstille et fornuftigt scenario.
De beregnede ressourceeffektiviteter ud fra vægtbaserede opgørelser udtrykker alene den mængde køle/smøremiddel, der slæbes ud med spånerne efter den skærende bearbejdning.
I de vurderede opgørelser er der taget hensyn den type metal, der bearbejdes og den mængde spåner, der fjernes er vurderet ud fra metaltypen. Eksemplet viser, at for relativt knappe ressourcer som rustfrit
stål og kobber betyder tabet af køle/smøremiddel mindre end for relativt rigelige metaller som maskinstål og aluminium.
Almindeligvis foreligger der kun yderst sparsomme data set ud fra en LCA-tilgang for produkter, der hovedsagelig består af kemikalier. Dette er også tilfældet for køle/smøremidler. Grundlaget har været
kendskab til en gennemsnitlig sammensætning baseret på nogle hovedtyper af kemiske forbindelser. På dette grundlag har det ikke været muligt at foretage en estimering af råstofforbruget.
Det har ikke været muligt at foretage sammenligning med andre opgørelser. Sammenligning med en opgørelse af det direkte materiale input (DMI) kunne ikke gennemføres, da DMI ikke opgøres for
specifikke processer. En sammenligning med det totale materiale input har heller ikke været muligt, da råstofforbruget ikke kunne estimeres.
7.4 Affaldsforebyggelse
På det foreliggende grundlag er det vanskeligt at foretage en vurdering af muligheden for affaldsforebyggelse i forbindelse med anvendelse af køle/-smøremidler.
Der har gennem en årrække været fokuseret på at forlænge levetiden for vandbaserede køle/smøremidler og for at nedsætte udslæbet af især vandfri midler med spånerne.
8 Sammenfatning og konklusioner
Formålet med projektet er at udvikle og afprøve en metode til ”måling” af ressourceeffektiviteten i vores forbrug af produkter og derigennem identificere tab af ressourcer og muligheder for
affaldsforebyggelse.
Der er opstillet forslag til definitioner for opgørelse af ressourceeffektivitet. De opstillede definitioner bygger på livscyklusprincipper og skal ses som en forenklet anvendelse af livscyklusvurderinger.
Når der arbejdes med livscyklusvurderinger, er udgangspunktet definition af et produkt og dets livsforløb. Her er ønskeligt at udvide begrebet så meget som mulig og afprøve, om det fx giver mening at
definere et ”gennemsnitsprodukt” for en branche eller en lidt mere snæver industrigren.
De opstillede definitioner er afprøvet på en række konkrete eksempler med forskelligt datagrundlag. På baggrund af dette er der nået frem til en række anbefalinger omkring anvendelsesmuligheder,
anvendelsesbegrænsninger og datakrav for metoden.
En sådan metode vil kunne anvendes i en indsats for at udpege væsentlige områder, hvor ressourceforbruget er stort, og/eller hvor en minimering er mulig. Det vil kunne anvendes for virksomheder,
industrigrene eller brancher, hvor de producerede produkter er rimelig ens med hensyn til forbrug af materialetyper og produktionsformer.
I det følgende er projektets væsentligste resultater, konklusioner og anbefalinger beskrevet.
8.1 Definition af ressourceeffektivitet
Overordnet defineres ressourceeffektivitet som ressourcer i produktet divideret med det samlet ressourceforbrug. Med ressourcer i produktet menes her den mængde materialer, produktet består af.
I denne sammenhæng opfattes materialer og energi som ressourcer. Sammenhængen mellem de nævnte størrelser kan illustreres ved følgende

Det skal bemærkes, at vand ikke indgår i opgørelse af forbruget, med mindre det er en væsentlig bestanddel af produktet.
Ud fra en LCA-tankegang består et produkts livscyklus af faserne råvareproduktion (R), produktion (P), brug (B) og sidste led, der består af affaldsbehandling og nyttiggørelse (A/N).
I nærværende projekt er der taget udgangspunkt i principperne for livscyklusvurdering efter UMIP-metoden, som er beskrevet i Wenzel et al., 1996 og i Pommer et al., 2001. Denne metode er blandt
andet baseret på, at der fokuseres på indgående strømme.
Ressourceeffektiviteten kan defineres på forskellig vis afhængig af, hvilke data der er tilgængelige, og hvilket formål det har. I nærværende definitioner er der taget udgangspunkt i forbrug af
råstoffer/materialer og energi samt genvinding af materialer og nyttiggørelse af energi.
I projektet er det valgt at sætte fokus på knappe ressourcer og definere ressourceeffektivitet ud fra to forskellige tilgange:
- En opgørelse af materialeforbruget målt i vægtenheder i forhold til materialeindholdet i produktet.
- En opgørelse af materiale- og energiforbrug vurderet efter ressourcens knaphed (UMIP-metodens vægtningsbegreb). Det giver mulighed for at få et samlet mål for materiale- og energiforbrug.
Afhængig af hvilke data der er tilgængelige, kan man vælge at fokusere på hele produktets livscyklus eller dele heraf. Der er blevet defineret i alt 6 former for ressourceeffektivitet. De tre første er baseret på
vægtopgørelser, hvor der alene ses på materialer. De andre tre er baseret på vurderede opgørelser målt i mPR, der udtrykker de enkelte råstoffers knaphed ud fra forbrug af materialer og energi. De 6
definitioner og anvendelse af dem er vist i Figur 8.1.
I Figur 8.1 indeholder første kolonne en betegnelse for den pågældende ressourceeffektivitet. I anden kolonne er vist med sort, hvilke elementer der er medtaget.
Figur 8.1 Oversigt over ressourceeffektiviteter og deres anvendelse
Klik her for at se Figur 8.1
8.2 Eksempler og datagrundlag
I projektet er der gennemgået en del eksempler på brancheniveau for at illustrere begrebet ressourceeffektivitet og for at vurdere, hvilket datamateriale der er egnet.
Der blev valgt at arbejde med meget forskellige eksempler med henblik på at afprøve definitionen af selve produktet og krav til datagrundlaget. Eksemplerne dækker over meget forskellige produkter og
forskellige livsforløb. Nogle eksempler illustrerer produkter, hvor brugsfasen er væsentlig. Andre eksempler illustrerer produkter, hvor genanvendelse er væsentlig. Og andre igen omfatter produkter, hvori
kemikalier, som almindeligvis er vanskelige at håndtere i en livscyklusvurderings sammenhæng, har væsentlig betydning.
I det følgende er kort opridset de væsentligste forhold for hvert af eksemplerne. En detaljeret beskrivelse findes i kapitlerne 3 til 7 samt i bilagene.
Det første eksempel omfatter opgørelse af ressourceeffektivitet for produktion af 1 ton medicinalprodukt. Følgende skal fremhæves fra dette eksempel:
- Kortlægningen tog udgangspunkt i grønne regnskaber fra fem repræsentative medicinalvirksomheder, men oplysningerne herfra var mangelfulde til formålet.
- Der findes relevante statistiske oplysninger om emnet.
- Det var relativt entydigt af fastlægge produktets livscyklus.
- Det har været vanskeligt/umuligt at fastlægge indholdsstofferne i en mængde medicin.
- Bestemmelsen af forbrug af materialer og dermed råstoffer blev meget usikker.
Produktet 1 ton møbler blev kortlagt. Der blev taget udgangspunkt i tre repræsentative produkter, og følgende skal fremhæves fra dette eksempel:
- Der er blevet gennemført en brancheanalyse inden for området, som indeholdt relevante data.
- Der blev taget udgangspunkt i tre gennemførte livscyklusvurderinger. I dokumentationen af disse kunne mange men ikke alle relevante data findes.
- Bestemmelsen af forbrug af materialer er rimelig sikker og estimeringen af forbruget af råstoffer acceptabel.
Inden for elektronikområdet blev det valgt at se på et bestykket printkort og en transformer. Der er blevet taget udgangspunkt i en levetid på 10 år og en mængde på 1 kg henholdsvis printkort og
transformere. Følgende skal fremhæves fra dette eksempel:
- Der blev dels taget udgangspunkt i gennemførte livscyklusvurderinger og dels i dataindsamling fra producenter.
- Der er meget stor variation inden for området, og opgørelserne bygger på en del antagelser. For de væsentligste er der gennemført følsomhedsanalyser.
- De væsentligste materialer er metallerne, hvor dem med den væsentligste ressourcemæssige betydning udgøres af kobber, ædelmetaller, tin og antimon.
Inden for galvanisk overfladebehandling blev det valgt at se på tre typer overfladebehandling. Her kunne ikke tages udgangspunkt i 1 kg produkt som for de øvrige eksempler. For fornikling/forchromning og
elforzinkning blev det valgt at tage udgangspunkt i 1.000 m² behandlet overflade. For varmforzinkning blev det valgt at tage udgangspunkt i 1 ton behandlet gods. Følgende herfra skal fremhæves:
- Ressourceeffektivitet bygger på en livscyklustankegang og med fokus på en proces – overfladebehandling, skulle der ske visse metodemæssige tillempelser.
- Kortlægningen blev gennemført i samarbejde med en brancheekspert, hvilket gav et godt grundlag for vurdering af materialeforbrug og estimering af råstofforbrug.
Produktet ”Anvendelse af køle/smøremidler” er medtaget som et eksempel på en proces, der involverer en række kemiske stoffer. Anvendelse af 1 kg køle/smøremiddel repræsenterer ikke et produkt eller
en ydelse. Derfor blev det valgt at tage udgangspunkt i 1 ton fjernede spåner, hvor der er anvendt køle/smøremidler. Følgende herfra skal fremhæves:
- Det var vanskeligt at fastlægge en ”produkt-enhed” og dets livsforløb.
- Kortlægningen blev baseret på oplysninger om køle/smøremidlers sammensætning og en tidligere overordnet kortlægning af forbrug og affaldsmængder, som på visse punkter var mangelfuld.
- Bestemmelsen af forbrug af materialer og dermed råstoffer blev meget usikker.
Erfaringer fra arbejdet med de nævnte eksempler er primært:
- Det er nødvendigt, at produktet, dets bestanddele og dets livsforløber er klart defineret. Visse processer kan ”omskrives” til produkter, som fx galvanoprocesser, hvorimod andre ikke kan (brug af køle/smøremidler). Det væsentlige er, at der klart kan defineres en ydelse. Produkter med forskellig ydelse kan således ikke sammenlignes.
- For at opgørelsen skal dække mere end en virksomhed, fx en industrigren eller en hel branche er det nødvendigt, at der anvendes de samme typer af materialer og processer. Det er fx tilfældet inden for møbelindustrien og specifikke galvaniske overfladebehandlinger. Medicinalprodukter er et eksempel på det modsatte. Her anvendes forskellige materialer og processer på de enkelte virksomheder.
- Grønne regnskaber, miljøredegørelser og lignende materiale, som en virksomhed offentliggør indeholder ikke tilstrækkelige data om specifikke forbrug af materialer, energi, affald og produktionsformer.
- Ved opstilling af ressourceeffektiviteter, der dækker en branche eller et industriområde, er det væsentligt at have et godt teknisk kendskab til området for at kunne afgøre, hvilke virksomheder der ligner hinanden så meget, at fornuftige og repræsentative gennemsnitsdata kan opstilles.
- Det er væsentligt at der foreligger en relativ detaljeret kortlægning af produktets livsforløb samt forbrug af råstoffer, hjælpestoffer og energi i hele produktets livsforløb for at kunne opstille alle de foreslåede ressourceeffektiviteter.
- En virksomhed vil for det meste kunne opstille en effektivitet baseret på egne data om deres produkts materialeforbrug i produktions- og brugsfasen. Ønsker man at udvide opgørelsen til en industrigren eller en branche, kræves det, at der foreligger gennemsnitsdata.
- Ofte udelades en vurdering af anvendte hjælpestoffer i en livscyklusvurdering på grund af datamangel. Produkter, der indeholder store mængder kemiske stoffer, er derfor vanskelige at vurdere. Et eksempel på dette er medicinalprodukter, hvor det ville være vanskeligt at kortlægge alle de anvendte kemiske forbindelsers livscyklus tilbage til råstoffer.
8.3 Ressourceeffektivitet
I det følgende er samlet en oversigt over de ressourceeffektiviteter, der er opgjort for de enkelte eksempler. Da eksemplerne repræsenterer produkter, hver med meget forskellig ydelse, kan disse ikke
sammenlignes.
Der er ikke inden for dette projekts rammer opstillet en form/metodik, der kan anvendes til at sammenligne værdien af to produkter og deres ydelse.
8.3.1 Ressourceeffektiviteter på materialeniveau
I tabel 8.1 er samlet de resultater, der er baseret på en opgørelse af mængden af materialer og råstoffer, MMat. P+B, MMat. P+B+A/N og MMat. R+P+B+A/N.
I tabel 8.1 er der medtaget en sammenligning af materialeforbruget med DMI og for råstofforbruget med TMI baseret på MIPS-data fra Wuppertal Institute, hvor det har været muligt at gennemføre en
sådan sammenligning.
Af oplysningerne i tabel 8.1 kan det udledes, at:
- For medicinalprodukter tabes omkring 75% af materialerne ved fremstilling. Det er forudsat, at en del affald i form af biomasse kan nyttiggøres. I råstofudvindingen tabes også i størrelsesordnen 75%,
således at den samlede ressourceeffektivitet ligger på 5-10%.
Opgørelsen er meget usikker, dels på grund af datamangel og dels fordi de enkelte virksomheder er meget forskellige.
- For møbler er tabet 10-20%. Da en lille del af materialerne til møbelproduktion udgøres af metaller, finder der en vis genanvendelse sted. Ved udvinding af råstoffer, olieudvinding, skovning af træ og oparbejdning af jernmalm er der yderligere et tab på i størrelsesordnen 2/3.
Opgørelsen repræsenterer en relativ homogen branche, og de opstillede data vil være repræsentative for en virksomhed med en blandet produktion. De anvendte data er indsamlet i sidste halvdel af 90'erne,
hvorfor der kan være behov for en opdatering.
Tabel 8.1 Ressourceeffektivieter baseret på opgørelse af vægt
Klik her for at se Tabel 8.1
- For bestykkede printkort haves ikke en vægtbaseret opgørelse af forbruget i produktionsfasen. Dog er ressourceeffektiviteten estimeret for det samlede råstofforbrug til 76% under forudsætning af, at
forbruget til udvinding af råstofferne er væsentligt større end forbruget af andre materialer og spild i produktionsprocesserne af komponenter og printkort.
Tabet stammer hovedsageligt fra manglende genvinding af plast, keramik/glas samt nogle metaller i kobbersmelteværkerne og forventes ikke at kunne påvirkes, med mindre man anvender alternative
teknologier. Et eksempel kan være processer, der neddeler printkort og kan sende fraktioner af kobber og ædelmetaller til oparbejdning i kobbersmelteværket.
- For transformere viser brutto ressourceeffektiviteten for materialer (59,5%), at der bruges ca. 68 % flere materialer til produktionen, end de færdige transformere indeholder. Imidlertid genvindes en
stor del af spildet ved produktionen samt af metallerne i det kasserede produkt, således at netto ressourceeffektiviteten for materialer når 224% (excl. energiforbrug). Dette svarer til, at der bruges
under halvdelen af produktets indhold af materialer i livscyklus. Medtages råstofudvindingen, når ressourceeffektiviteten ned på 109% svarende til, at der bruges lidt mindre råstoffer i livscyklus end
produktets vægt (excl. energiforbrug).
Opgørelsen repræsenterer et mindre antal virksomheder med en relativ ensartet produktion. Data er dels baseret på en gennemført miljøvurdering af elektriske og elektroniske produkter samt
virksomhedsbesøg. De opstillede effektiviteter antages derfor at afspejle branchens forhold.
- For overfladebehandlingsprocessen fornikling/forchromning er materialetabet på omkring 60%. Der sker ingen genvinding af metaller og andet kasseret materiale fra processen. I udvindingen af metaller og hjælpestoffer tabes omkring 75%, således at den samlede effektivitet baseret på materialer er omkring 10%.
Opgørelsen er baseret på en detaljeret opgørelse dækkende de fleste virksomheder, der udfører den aktuelle overfladebehandlingsproces, og de opstillede effektiviteter vurderes derfor at være
repræsentative og kunne anvendes som benchmarking inden for branchen.
- For overfladebehandlingsprocessen el-forzinkning er materialetabet på omkring 67 %. Der sker ingen genvinding af metaller og andet kasseret materiale fra processen. I udvinding af metaller og hjælpestoffer tabes omkring 50%, således at den samlede effektivitet baseret på materialer er omkring 17 %.
Opgørelsen er baseret på en detaljeret opgørelse dækkende de fleste virksomheder, der udfører den aktuelle overfladebehandlingsproces, og de opstillede effektiviteter vurderes derfor at være repræsentative og kunne anvendes som benchmarking inden for branchen.
- For overfladebehandlingsprocessen varmforzinkning forbruges zink og relativt små mængder hjælpestoffer. I processen tabes ca. 30%, hvoraf en del zink kan oparbejdes. I udvinding af zink og hjælpestoffer tabes en væsentlig del, således at den samlede effektivitet baseret på materialer er omkring 26%.
Opgørelsen er baseret på en detaljeret opgørelse dækkende de fleste virksomheder, der udfører den aktuelle overfladebehandlingsproces, og de opstillede effektiviteter vurderes derfor at være repræsentative og kunne anvendes som benchmarking inden for branchen.
Ressourceeffektiviteten MMat. P+B+A/N blev sammenlignet med statistiske oplysninger om DMI for at se, om der her var overensstemmelse.
Ressourceeffektiviteten MMat. R+P+B+A/N blev sammenlignet med TMI baseret på data fra MIPS for at se, om der her var overensstemmelse.
Som det ses, er de opgjorte effektiviteter meget forskellige for de enkelte eksempler. De opgjorte størrelser afspejler, at:
- Et kemisk produkt som medicin kræver detaljeret viden om sammensætningen, hvilket ikke var tilfældet. Det var derfor vanskeligt at sammenligne med DMI og TMI.
- Et produkt baseret på almindeligt kendte materialer som møbler giver nogle fornuftige resultater, der er sammenlignelige med DMI og TMI, når kortlægningen er god.
- For specifikke elektronikkomponenter som printplader og transformere findes der ikke data for DMI. Det har ikke været muligt at gennemføre en beregning af TMI, da der mangler data for
ædelmetallerne, som anses for at have stor betydning for en sådan beregning.
- Overfladebehandlingsprocessernes resultater giver rimelige effektiviteter. Der kan ikke foretages en sammenligning med DMI, da der for DMI tages udgangspunkt i produkter. En sammenligning med
TMI viser store forskelle grundet forskel i data for udvinding af nikkel og zink.
- For anvendelse af køle/smøremidler var det ikke muligt at opgøre operationelle effektiviteter, da ydelsen ”fjernelse af 1 ton spåner” var vanskelig at relatere til et egentligt produkt. Dertil kommer, at
køle/smøremidler er et kemisk produkt, for hvilket datagrundlaget var mangelfuldt.
Overordnet kan det konkluderes ,at:
- De opstillede ressourceeffektiviteter for elektronik og overfladebehandling kan anvendes som benchmarking for virksomheder, der arbejder med de her valgte produkter.
- Når det er afklaret, om datagrundlaget for ressourceeffektiviteterne for møbelområdet er tidssvarende, kan de opstillede effektiviteter anvendes som benchmarking.
- Ressourceeffektiviteterne for medicinalprodukter og køle/smøremidler kan ikke anvendes. Medicinalindustrien er inhomogen og for køle/smøremidler kunne et produkt ikke defineres.
8.3.2 Ressourceeffektiviteter baseret på vurderet opgørelse
I Tabel 8.2 er samlet de resultater, der er baseret på vurderede opgørelser af forbruget af materialer og energi.
I de vurderede opgørelser er kun ikke-fornyelige ressourcer, der medtages i beregningerne. Fornyelige ressourcer som fx træ og stivelse er således ikke med i beregningerne. Ressourcer for hvilke
forsyningshorisonten er kort tæller relativt meget, det gælder fx ædelmetallerne.
I Tabel 8.2 står de anvendte forkortelser for ressourceeffektiviteter for:
VMat. R+P+B |
Vurderet opgørelse af materialeforbruget for råvarefase, produktion og brug |
VMat.+energi, R+P+B |
Vurderet opgørelse af materiale- og energiforbrug for råvarefase, produktion og brug |
VMat.+energi, R+P+B+A/N |
Vurderet opgørelse af materiale- og energiforbrug for råvarefase, produktion, brug samt affaldsbehandling og oparbejdning af materialer og nyttiggørelse af energi. |
Tabel 8.2 Ressourceeffektivieter baseret på en vurderet opgørelse
Produkt |
Ressourceeffektivitet |
Bemærkninger |
VMat. R+P+B |
VMat.+energi, R+P+B |
VMat.+energi, R+P+B+A/N |
Et ton medicinalprodukt |
27-52 % |
17-33 % |
17-33 % |
Da produktets sammensætning ikke er kendt er der
opstillet 2 scenarier |
Et ton møbler |
69 % |
24 % |
40 % |
|
Et ton printplader |
Ikke opgjort |
92 % |
473 % |
Varierer meget afhængig af antagelser, scenarier er
opstillet |
Et ton transformere |
96 % |
56 % |
178 % |
Varierer meget afhængig af antagelser, scenarier er
opstillet |
1000 m² overflade foniklet-forchromet |
93% |
91 % |
91 % |
Det er forudsat, at de metaller, der udgør
overfladebehandlingen, ikke kan genvindes. |
1000 m² overflade el-forzinket |
85 % |
84 % |
84 % |
Det er forudsat, at de metaller, der udgør
overfladebehandlingen, ikke kan genvindes. |
1 ton gods varmforzinket |
78 % |
78 % |
89 % |
Det er forudsat, at de metaller, der udgør
overfladebehandlingen, ikke kan genvindes. |
1 ton spåner fjernet ved skærende og spåntagende bearbejdning med
brug af køle/smøremidler, vandbaserede midler |
100% |
97-100 % |
Ikke opgjort |
Typen af spåner, der fjernes har en indflydelse |
1 ton spåner fjernet ved skærende og spåntagende bearbejdning med
brug af køle/smøremidler, vandfri midler |
88-99 % |
79-99 % |
Ikke opgjort |
Typen af spåner, der fjernes har en indflydelse |
Af oplysningerne i Tabel 8.2 ses det, at:
- Andelen af materialer af biologisk oprindelse er væsentlig for et medicinalprodukt, da denne type materialer (fornyelige) ikke medtages i en vurderet opgørelse. Da sammensætningen ikke kendes, er
der opstillet en række antagelser og gennemført nogle følsomhedsananlyser, som viser, at resultatet ligger inden for det givne interval. De beregnede effektiviteter viser, at 50–75% af materialerne set
ud fra et knaphedssynspunkt tabes i produktionsleddet. I udvinding af råstoffer og forarbejdning af disse tabes ligeledes i størrelsesordnen 50 %.
Opgørelsen er meget usikker, dels på grund af datamangel og dels fordi de enkelte virksomheder er meget forskellige.
- I de vurderede opgørelser for møbler er træ, som fornyelig ressource, ikke medtaget. Medtages energiforbruget og –indholdet (især i træ), falder effektiviteten væsentligt. Genvinding af stål samt udnyttelse af træets brændværdi har betydning for den sidstnævnte effektivitet.
Opgørelsen repræsenterer en relativ homogen branche, og de opstillede data vil være repræsentative for en virksomhed med en blandet produktion. De anvendte data er indsamlet i sidste halvdel af 90'erne, hvorfor der kan være behov for en opdatering.
- For printplader genvindes hovedparten af de væsentligste ressourcer kobber og ædelmetaller ved oparbejdning i kobbersmelteanlæg. Den totale netto ressourceeffektivitet er afhængig af effekttabet i elektronikken, men for moderate og lave strømforbrug fås en ressourceeffektivitet på omkring 500% svarende til, at 20% af produktets indhold af ressourcer bruges i livscyklus. Der kan dog opnås en halvering i ressourceforbruget ved at genvinde antimon og øge genanvendelsen af tin.
Opgørelsen repræsenterer et mindre antal virksomheder. Da sammensætningen af bestykkede printkort varierer en del med typen af elektronik, er der anvendt et opdateret modeleksempel fra IPU, som bør
være forholdsvis repræsentativt for en række produkter. Hvis man ønsker at anvende ressourceeffektiviteten til benchmarking, bør man imidlertid kun sammenligne produkter, som har samme funktion fx en
mobiltelefon eller en DVDafspiller, specielt hvis energiforbruget medtages, da dette kan variere med dekader for forskellige typer af produkter.
- For transformere er det altafgørende, at kobberet genanvendes. Genanvendelse af jernindholdet på 65% betyder næsten intet for ressourceeffektiviteten. En manglende genanvendelse medfører således et fald i ressourceeffektiviteten fra 178% til 177%, mens en højere genanvendelse af det ganske lille tinindhold på 0,1% kan øge ressourceeffektiviteten fra 178 til 210%.
Effekttabet har herudover en afgørende indflydelse på ressourceeffektiviteten. Således har en højeffektiv transformer med et effekttab på 5W en ressourceeffektivitet på 284%, mens ressourceeffektiviteten falder 106% for en ineffektiv transformer med effekttab på 25% til fx halogenlamper. Det skal dog bemærkes, at en mere effektiv transformer også kræver et noget større forbrug af kobber og jern, hvilket der ikke er korrigeret for.
Opgørelsen repræsenterer et mindre antal virksomheder med en relativ ensartet produktion. Data er dels baseret på en gennemført miljøvurdering af elektriske og elektroniske produkter samt virksomhedsbesøg. De opstillede effektiviteter antages derfor at afspejle branchens forhold.
- For de tre overfladebehandlingsprocesser er det metallerne, der er de væsentligste i den vurderede opgørelse. Hjælpestofferne forbruges og findes ikke i produktet. Effektiviteterne for de vurderede opgørelser er derfor højere end dem baseret på materialemængder. Energiforbruget betyder meget lidt ressourcemæssigt i forhold til materialeforbruget. Kun i forbindelse med varmforzinkning sker der genanvendelse, idet en del zinkaske oparbejdes og genbruges.
Opgørelserne er baseret på detaljerede opgørelser dækkende de fleste virksomheder, der udfører den aktuelle overfladebehandlingsproces, og de opstillede effektiviteter vurderes derfor at være
repræsentative og kunne anvendes som benchmarking inden for branchen.
- Beregning af ressourceeffektivitet for brug af køle/smøremidler giver ikke rigtigt nogen mening, da produktet ”fjernelse af 1 ton spåner” er en produktenhed, der er vaskelig at arbejde med.
Konklusionerne for anvendelse af resultaterne for de vurderede opgørelser er de samme som for de vægtbaserede opgørelser, se sidst i afsnit 8.3.1.
8.4 Anvendelse
I forbindelse med gennemgangen af de enkelte eksempler er der fremsat en række kommentarer om, hvor og hvordan de opgjorte effektiviteter kan anvendes. I det følgende er de væsentligste samlet.
Det skal indledningsvist bemærkes, at resultaterne fra de enkelte eksempler ikke kan sammenlignes. Et produkts værdi er her defineret som dets indhold af materialer, og det afspejler ikke nødvendigvis
produktets væsentlighed i forhold til en samfundsmæssig sammenhæng. Produkter, hvis ydelse kan sidestilles, kan sammenlignes.
8.4.1 Materialeforbrug
8.4.1.1 Materialeforbrug, produktion og brug
Ressourceeffektiviteten MMat. P+B viser primært materialetabet ved produktion.
For de eksempler, hvor datagrundlaget har været tilstrækkeligt, som fx for møbelproduktion og overfladebehandling, kan den opgjorte effektivitet anvendes som et udtryk for det gennemsnitlige niveau for
branchen, og den enkelte virksomhed kan sammenligne egne opgørelser hermed.
Eksemplerne viser ligeledes, at der er meget stor spredning mellem forskellige produkttyper, hvilket blandt andet kan forklares ved de meget forskellige produktionsprocesser, der ligger bag de enkelte
produkter.
8.4.1.2 Materialeforbrug, produktion, brug og bortskaffelse
Ressourceeffektiviteten MMat. P+B+A/N viser en højere værdi end bruttoopgørelsen, og forskellen afspejler den andel af materialer, der almindeligt genanvendes.
Eksemplerne viser, at der for nogle produkter naturligt ikke kan ske genvinding (medicin), for nogle sker det ikke, men i princippet kunne det godt lade sig gøre (overfladebehandling), og i nogle tilfælde sker
det (elektronik og møbler).
For de produkttyper, hvor genvinding er en realistisk mulighed, kan den opgjorte effektivitet anvendes af virksomheder til at sammenligne egne tal med gennemsnittet for branchen.
Beregning af MMat. P+B+A/N vil kunne anvendes til at vurdere effekten af nye genanvendelsesformer. Beregningen vil også kunne bruges til at vurdere den højeste realistiske effektivitet for en branche eller
et industriområde, såfremt branchen/industrien er homogen med hensyn til brug af materialer og processer.
8.4.1.3 Materialeforbrug, hele livscyklus
Ressourceeffektiviteten MMat. R+P+B+A/N udtrykker det samlede forbrug af råstoffer i forhold til indholdet i produktet, når der er taget hensyn til genanvendelse. Denne effektivitet udtrykker således i
forhold til opgørelsen af MMat. P+B+A/N den andel af materialer, der tabes i råstofudvindingen.
Såfremt data er tilgængelige, bør denne opgørelse anvendes, da der er stor forskel på, hvor meget der tabes i råstofudvindingen og -forarbejdningen.
BAT-noter, der beskriver eksempler på Best Available Technology, vil kunne vurderes ved beregning af MMat. R+P+B+A/N i forhold til en eksisterende teknologi. Det kræver dog, at et produkt og det
ydelse, dets livsforløb samt forbrug af materialer og energi i hele livsforløbet kan beskrives.
8.4.1.4 Sammenligning med andre opgørelser
Opgørelsen MMat. P+B+A/N kan sammenlignes med DMI, der står for det direkte materialeinput, når der er tale om klart definerede produkter, der består af importerede materialer. Af eksemplerne ses
det, at der er fundet rimelig overensstemmelse mellem de to opgørelser for møbler.
Opgørelse af effektiviteten MMat. R+P+B+A/N er søgt sammenlignet med Wuppertals opgørelse af totalt materiale input. Her er der ikke fundet nogen god overensstemmelse, da datagrundlaget som
udgangspunkt for de to typer opgørelser er relativt forskellige.
Især ved udvinding af metaller påvirkes store materialemængder, når metalindholdet i malmen er lille. Nogle datakilder medtager alt påvirket materiale, mens andre tager hensyn til, at store mængder materiale
lægges tilbage og dermed ikke forbruges.
Inden for LCA medtages i princippet alle strømme, der påvirkes og føres tilbage til råstoffer. Ligeledes medtages alle indirekte strømme, fx energiforbrug ved transport eller hjælpestoffer, der er nødvendige,
men som ikke findes i det færdige produkt. Således er principperne også bag UMIP, men i databasen er det ikke altid gennemført på grund af datamangel.
Opgørelser baseret på med Wuppertals opgørelse af totalt materiale input og UMIP's data er med hensyn til de overordnede principper ens, og begge indeholder skjulte strømme. Forskellene kommer
primært på grund af forskelligt datagrundlag.
8.4.1.5 Datamangel
For produkter, primært baseret på kemiske forbindelser, mangler der en række data. De råstoffer, der bruges i fremstillingen, udgør en stor mængde og giver derfor et mangelfuldt datagrundlag. Dette er
blandt andet tilfældet for eksemplerne medicin og køle/smøremidler samt tilsætningsstofferne til overfladebehandling.
8.4.2 Vurderede opgørelser
De vurderede opgørelser er baseret på UMIP-metodens vægtningsprincip, opgøres i mPR og udtrykker knapheden af indgående materialer.
I nogle tilfælde vil ressourceeffektiviteten baseret på de vurderede opgørelser være højere end de materialebaserede, da fornyelige ressourcer ikke bidrager til en vurderet opgørelse. Dette er fx tilfældet for
møbler, hvor hovedparten af materialeforbruget er træ.
Metaller og især ædelmetallerne har stor indflydelse på ressourceeffektiviteten. For produkter med et vist indhold af metaller vil disse vægte meget højt i forhold til andre materialer og være afgørende for
bestemmelse af effektiviteten. Da især ædelmetaller er værdifulde materialer, som udnyttes meget, vil produkter med ædelmetaller (og andre metaller) have en relativ høj effektivitet.
Beregning af ressourceeffektivitet baseret på vurderede størrelser vil ikke give nogen mening for produkter, der udelukkende består af fornyelige ressourcer.
8.4.2.1 Ressourceforbrug, materialer
Ressourceeffektiviteten VMat. R+P+B omfatter primært ressourceforbruget ved udvinding og produktion.
En virksomhed, der ikke ønsker at bruge knappe ressourcer, kan anvende VMat. R+P+B , når der overvejes at skifte mellem materialer. Endvidere kan opgørelsen anvendes inden for en produktgruppe,
hvor der anvendes forskellige typer materialer. Møbelområdet er her et eksempel, hvor der anvendes træ, plast og metal i forskelligt forhold.
8.4.2.2 Ressourceforbrug, materialer og energi
Ressourceeffektiviteten VMat.+energi, R+P+B omfatter forbruget af materialer og energi ved råstofudvinding, produktion og brug. Opgørelse af denne effektivitet er især relevant for energiforbrugende
produkter og produkter, der er meget energitunge i fremstillingen. Som eksempler herpå ses transformatorer.
Forskellen i effektiviteterne baseret på VMat. R+P+B og VMat.+energi, R+P+B viser andelen af ressourceforbruget, der går til energiforbruget.
Af eksemplerne kan det blandt andet ses, at energiforbruget i møbelproduktionen spiller en stor rolle. Det er dog ikke energi anvendt i processerne, der har den største betydning. Af det samlede
energiforbrug udgør ca. 50% energi bundet i materialerne (træ), 30% til råstofudvinding og 20% til møbelproduktion.
Det at regne energiforbruget med har mindre betydning for produkter, hvor der forbruges en del metaller. Dette kan blandt andet ses i eksemplerne fra overfladebehandling, hvor nikkel, chrom og zink er
knappe ressourcer og derfor 'tæller' meget i forhold til energiforbruget ud fra et knaphedssynspunkt.
8.4.2.3 Ressourceforbrug, hele livscyklus
Ressourceeffektiviteten VMat.+energi, R+P+B+A/N udtrykker det samlede forbrug af ressourcer, når der tages hensyn til genanvendelse. Den medtager således alle elementer i livscyklus og omfatter en
vurderet opgørelse af alle materiale- og energiforbrug.
For produkter, hvor der genanvendes en betydelig del af de knappe metaller, som fx ved elektronik, vil VMat.+energi, R+P+B+A/N blive langt over 100%, da metallerne i vurderingen har stor betydning i
forhold til energiforbruget.
For eksemplerne møbler og varmforzinkning sker der en vis genanvendelse af stål og zink, hvilket afspejles i en mindre stigning i effektiviteten mellem VMat.+energi, R+P+B og VMat.+energi, R+P+B+A/N.
8.5 Affaldsforebyggelse
8.5.1.1 Den farmaceutiske industri
Det er yderst vanskeligt at udpege konkrete områder for affaldsminimering på basis af nærværende opgørelse for den farmaceutiske industri, da råvarer kun kendes i hovedgrupper, og fremstillingsmetoderne
heller ikke er kendte. Dertil kommer, at det er en branche, hvor fællestræk og generaliseringer er yderst vanskelige, da produktionerne på de enkelte virksomheder er meget forskellige.
Ud fra de naturlige renheds- og kvalitetskrav, der stilles i medicinalindustrien, forventes det, at det er vanskeligt at forbedre de opstillede ressourceeffektiviteter væsentligt.
Ud fra det ret mangelfulde datagrundlag er det vanskeligt at komme med klare anbefalinger, men følgende skal dog trækkes frem:
- Det skal sikres, at alle stivelsesholdige og lignende materialer af biologisk oprindelse nyttiggøres, såfremt det ikke medfører miljøbelastninger af de landbrugsjorde, hvor det udbringes på.
- Det bør undersøges, hvilke opløsningsmidler der anvendes, og om disse kan genvindes.
- Det største ressourcetab sker inden for gruppen ”Kemiske forbindelser”. De kemikalier, der anvendes, kendes ikke og vil antagelig variere meget fra virksomhed til virksomhed. Det vil derfor være
yderst vanskeligt at komme med generelle anbefalinger.
8.5.1.2 Møbelindustri
De anvendte data til kortlægning og beregning af ressourceeffektiviteter er mellem 5 og 10 år gamle, og der kan derfor være behov for en opdatering.
De beregnede ressourceeffektiviteter er relativt høje og afspejler, at genanvendelse har en stor betydning. Det er forudsat, at 75 % af stålet oparbejdes, og at 75% af energien fra forbrænding af affaldstræ
nyttiggøres. Såfremt disse tal reelt er højere, vil de nogle af de beregnede ressourceeffektiviteter blive højere (MMat, P+B+A/N , MMat, R+P+B+A/N og VMat+energi, R+P+B+A/N).
De forhold, der bør fokuseres på inden for møbelindustrien med hensyn til affaldsforebyggelse og ressourceminimering, er:
- Forbrænding med energiudnyttelse af alt ikke forurenet affaldstræ, der ikke kan anvendes som materialer.
- Øget indsamling af stål, både fra møbelproduktion og fra kasserede produkter.
- Anvendelse af ikke-legeret stål, hvor det er muligt.
- Indsamling af plastaffald fra møbelproduktion og kasserede produkter med henblik på oparbejdning - alternativt forbrænding med energiudnyttelse.
8.5.1.3 Elektriske og elektroniske komponenter
De data, der er anvendt til kortlægning af de to eksempler inden for elektriske og elektroniske produkter, er mindre end 5 år gamle. De stammer dels fra andres kortlægninger og dels fra kontakt til
branchen.
De to produkteksempler, printkort og transformere, adskiller sig fra de øvrige produkter ved, at der er et betydeligt energiforbrug i brugsfasen, og at en del af energien tabes og delvist kan nyttiggøres til
rumopvarmning.
De opstillede ressourceeffektiviteter viser, at genvinding af kasserede produkter og oparbejdning af metallerne har meget stor betydning. De væsentligste forhold vedrørende affaldsminimering er derfor:
- Sortering og demontage af værdifulde komponenter med henblik på direkte genanvendelse
- Frasortering af komponenter med værdifulde og metalholdige komponenter, når komponenterne er udtjente
- Fokus på fraseparering af kobber med henblik på at kunne genvinde dette og undgå at det forurener jernfraktionen
- Fokus på mulige teknologier til oparbejdning af tin og antimon.
8.5.1.4 Galvanisk overfladebehandling
For de tre overfladebehandlingsprocesser fornikling/forchromning, elforzinkning og varmforzinkning viser ressourceeffektiviteterne opgjort som materialer relativt lave effektiviteter, da de anvendte
hjælpestoffer til rensning og behandling tabes. Effektiviteterne baseret på vurderede opgørelser er derimod relativt høje, fordi metallerne har stor betydning, og disse tabes i mindre grad.
For fornikling/forchromingsprocesser er det ud fra et ressourcemæssigt synspunkt problematisk at anvende nikkel til overfladebehandling.
Fornikling/forchroming har en række fordele. Det giver en overflade af høj kvalitet og et pænt udseende, men
- Metallerne og især chrom, der forekommer som affald (primært slam)fra overfladebehandlingsprocessen, kan ikke genvindes.
- Metallerne og især nikkel, der findes på det kasserede produkt, kan ikke genvindes.
- Der anvendes en række hjælpekemikalier i processen, som tabes.
Der findes i dag ikke tekniske løsninger, som er økonomisk mulige for at genvinde metallerne.
Ud fra et ressourcemæssigt synspunkt kan det være noget problematisk at anvende zink til el-forzinkning og varmforzinkning, såfremt det ikke genvindes.
Elforzinkning har en række fordel. Det giver en overflade af høj kvalitet og et pænt udseende, men
- Zink og chrom, der forekommer som affald (primært slam) fra overfladebehandlingsprocessen, genvindes ikke.
- Zink fra det kasserede produkt bør genvindes i så høj grad som muligt.
- Der anvendes en række hjælpekemikalier i processen, som tabes.
Følgende forhold bør der fokuseres på for varmforzinkning:
- Zink fra det kasserede produkt bør genvindes i så høj grad som muligt.
- Zink, der forekommer som affald (primært slam, eventuelt spildevand) fra forbehandlingen, genvindes ikke.
- Der anvendes en række hjælpekemikalier i processen, som tabes.
Det vides ikke, i hvor høj grad zink genvindes fra oparbejdning af stål, og det er derfor et forhold, der bør fokuseres på.
8.5.1.5 Køle/smøremidler
På det foreliggende grundlag er det vanskeligt at foretage en vurdering af muligheden for affaldsforebyggelse i forbindelse med anvendelse af køle/-smøremidler.
Der har gennem en årrække været fokuseret på at forlænge levetiden for vandbaserede køle/smøremidler og for at nedsætte udslæbet af især vandfri midler med spånerne.
8.6 Anbefalinger
Opgørelse af ressourceeffektivitet og dermed identifikation af, hvor i et produkts livscyklus der tabes ressourcer, er anvendeligt som en del af beslutningsgrundlaget ved ressourceoptimering og
affaldsminimering, når tilstrækkelige data er til stede.
For produkter, hvor der allerede forligger livscyklusvurderinger eller -kort-lægninger (LCI), vil der kunne opstilles ressourceeffektiviteter, som den enkelte virksomhed kan bruge til at sammenligne egne tal
med.
Den enkelte virksomhed kan umiddelbart opstille ressourceeffektiviteten MMat. P+B, mens de øvrige definerede ressourceeffektiviteter kræver data om genvinding, råstofudvinding og omsætning til
vurderede opgørelser, som ikke alle virksomheder antages at have kendskab til.
På myndigheds- og/eller ekspertniveau vil alle de 6 definerede ressourceeffektiviteter give oplysninger om, hvor i livscyklus der tabes ressourcer, betydningen af genvinding, og hvilke materialer der ud fra et
knaphedssynspunkt betyder mest.
Det anbefales derfor at arbejde videre med problematikken omkring ressourceeffektivitet, da det kan blive et enkelt og anvendeligt værktøj for virksomheder, brancheorganisationer, myndigheder og andre
beslutningstagere.
Et af målene for LCA-videncentret er at få skabt overblik over, hvilke relevante data der foreligger i form af gennemførte livscyklusvurderinger og –kortlægninger. Når dette arbejde er nået et
stykke/gennemført, er det væsentligt at få etableret et mere fyldestgørende og lettilgængeligt datagrundlag til beregning af vurderede opgørelser. Heri skal også tages hensyn til ændrede programmel (Gabi),
der skal erstatte UMIP-metodens LCV-værktøj.
Det anbefales endvidere at få udarbejdet noget let tilgængeligt informationsmateriale sammen med relevante brancheorganisationer inden for udvalgte produktgrupper/sektorer med henblik på, at
virksomheder kan opnå forståelse for begrebet og anvende det i deres udviklingsarbejde og produktion. Her er det også væsentligt at få samlet så mange "grunddata" som muligt, så arbejdet med opstilling af
effektiviteterne dels tager udgangspunkt i virksomhedens egen tal og dels i data, der er let tilgængelige.
Referencer
Andersen KK, Christensen TH, Jensen MS, Pedersen OG, Røpke I (2003) Udvikling af indikatorsystem for materialestrømme, ressourceforbrug og –effektivitet samt affaldsstrømme. (under udarbejdelse
jan. 2003) Miljøstyrelsen
Asger Mortensen, Dansk Apotekerforening. Personlig kommunikation.
Boliden, Personlig kontakt , august 2002
Baadsgaard-Jensen J . Teknologisk Institut, Centerchef Træteknik. Personlig kommunikation.
Bringezu Stefan, Schütz Helmut (2001) Total material requirement of the European Union, Technical Report No. 55. Prepared by Wuppetal Institute for EEA.
Christensen FM, Jørgensen T, Nielsen IR (2000) Environmental and technical characteristics of conductive adhesives versus soldering. Arbejdsrapport nr. 16/2000. Miljøstyrelsen
Christensen TE, Jørgensen H, Wejdling H (2002) Økologiske rygsække – ressourceeffektivitet, materialestrømme og globalisering. Arbejdsrapport fra Miljøstyrelsen Nr. 30, 2002.
Dahl F, Løkkegaard K (2000) Central oparbejdning af galvanisk affald. Miljøprojekt nr. 55, 2000 Miljøstyrelsen
Danmarks Statistik, 2002. www.statistikbanken.dk. Medicinalindustriens omsætning.
Elektronikaffald, 3. udkast 1995, Miljøstyrelsen
European Environmental Agency, http://glossary.eea.eu.int/EEAGlossary/T/total_material_requirement
Gravgård Pedersen O (2002) Opgørelse af DMI og TMR i Danmark 1997.
Hansen E (1995) Miljøprioritering af industriprodukter, Miljøprojekt 281, Miljøstyrelsen
Hansen OC, Bødker J, Pommer K, Vinten L (2003) Sporstoffer til benzin, diesel- og fyringsolie. Arbejdsrapport fra Miljøstyrelsen nr. 2, 2003
Karen Holst Duer, Danmarks statistik (2002). Personlig kommunikation og levering af data.
Kofod Christian J. Maj 2002, Træets Arbejdsgiverforening, personlig kommunikation
Kofod CJ, Kvist KE, Fox M (2000) Brancheanalyse af miljømæssige forhold i træ- og møbelindustrien: Enhedsprocesser. Miljøstyrelsen
Kreibe S (1996) Verwertung und Beseitigung von Leitenplattenschrott. BifA Texte Nr. 7, 1996
Kvist, K. E., Fox, M., Kofod, C.(2000): ”Brancheanalyse af Miljømæssige forhold i træ- og møbelindustrien”, Miljøprojekt 561, Miljøstyrelsen
Lassen J H og Nielsen P H (1998) Miljøvurdering og udvikling af et reolsystem. Miljøprojekt 376, Miljøstyrelsen
Legarth J, Gregersen J, Erichsen H (2001) Miljøspecifikationer for elektriske og elektroniske tele- og dataprodukter. Arbejdsrapport nr. 2/2001. Miljøstyrelsen.
Pommer K, Bech P, Wenzel H, Caspersen N, Olsen SI (2001) Håndbog i miljøvurdering af produkter - en enkel metode. Miljønyt nr. 58, 2001, Miljøstyrelsen.
Pommer K, Kofod C, Kvist KE, Malmgren-Hansen B, Olesen S, Jensen MS, Olsen LS (2004, in print) Udpegning og kortlægning af udvalgte affaldstunge industriområder. Miljøprojekt XX, Miljøstyrelsen
SAEFL (1998) Life Cycle Inventories for Packaging Environmental Series 250/I +II (BUWAL)
SigmaPro, PRE Consultants, version 5, 2001
tbl2001.novonordisk.com. Novo Nordisk A/S grønne regnskab m.v. kan findes på denne Internet adresse.
Tillman AM, Baumann H, Erikson E, Rydberg T (1991) Life-cycle analyses of selected packaging materials– quantification of environmental loadings. Chalmers Indutriteknik, Göteborg, Sweden.
UMIP 1998. PC-værktøj, Miljøstyrelsen, beta-version 2.11
Wenzel H, Hauschild M, Rasmussen E. (1996) Miljøvurdering af produkter, ISBN 87-7810-542-0 , Instituttet for Produktudvikling; Danmarks Tekniske Universitet. Institut for Teknologi og Samfund;
Dansk Industri, Genanvendelsesrådet.
Willum O (2002) Beregninger i UMIP ud fra data for elektronikkomponenter. Internt notat. IPU
Wuppertal Institute (1998) MI-Werte , 17.07.1998. Downloaded fra nettet under www.wupperinst.org/projekte/mipsonline/download/MIWerte oktober 2002.
BILAGSSAMLING
Forord
A Farmaceutiske virksomheder
B Møbelfremstilling
C Elektriske og elektroniske komponenter
D Galvanisk overfladebehandling
E Køle/smøremidler
Forord
Bilagene omfatter de grundlæggende data, beskrivelser og beregning af ressourceeffektivitet for de enkelte eksempler.
- Bilag A Farmaceutiske virksomheder er udarbejdet af Kirsten Pommer, Steen Olesen og Lennart Staal Olsen, Teknologisk Institut
- Bilag B Møbelfremstilling er udarbejdet af Kirsten Pommer, Teknologisk Institut
- Bilag C Elektriske og elektroniske komponenter er udarbejdet af Bjørn Malmgren-Hansen og Kirsten Pommer, Teknologisk Institut
- Bilag D Galvanisk overfladebehandling er udarbejdet af Flemming Dahl, Wilson Engineering og Kirsten Pommer, Teknologisk Institut
- Bilag E Køle/smøremidler er udarbejdet af Kirsten Pommer og Steen Olesen, Teknologisk Institut
A Farmaceutiske virksomheder
A.1 Introduktion
Medicinalindustrien i Danmark er karakteriseret ved to grupper af virksomheder. Den ene gruppe omfatter mindre virksomheder, der primært foretager formulering og pakning af medicinske produkter. Den
anden gruppe omfatter få store virksomheder, der beskæftiger sig med syntese og anden kemisk/biologisk produktion.
Medicinalindustrien (NACE kode 24.41.00 ”Fremstilling af farmaceutiske råvarer” og 24.42.00 ”Medicinalvarefabrikker”) består af ca. 190 selskaber med i alt omkring 30.000 ansatte. Halvdelen af
selskaberne er mindre virksomheder med i alt omkring 4.000 ansatte eller ca. 12-15% af de ansatte i branchen (Krak Direkt, 2002).
Novo Nordisk A/S (Novo og Novozymes) andel udgør i underkanten af 45% af de ansatte i branchen og næsten 50% af omsætningen. De resterende ca. 40% ansatte er ansat i branchens øvrige store
virksomheder (Krak Direkt, 2002). De øvrige store virksomheder står for ca. 40% af omsætningen.
Medicinalindustrien i Danmark omsatte i år 2000 for 26 mia. kr. og i år 2001 for i underkanten af 32 mia. kr. (Danmarks Statistik, 2001). Produktionen i 2001 er af Danmarks Statistik opgjort til 38.306
ton.
Omsætningen for de store virksomheder udgør 90% målt i penge. Da gruppen af store virksomheder tegner sig for den største produktion, det største ressourceforbrug og de største affaldsmængder, er det
valgt i nærværende undersøgelse at fokusere på denne gruppe af virksomheder.
A.2 Et medicinalprodukts livsforløb
Medicinalprodukter kan generelt betragtes i et livscyklusperspektiv som vist i. Inputsiden er illustreret med bokse med dobbeltstreger, outputsiden ved bokse med kraftig enkeltstreg. De bokse, der er
mindre væsentlige er illustreret med stiplede linier og udgangspunktet – produktion af produktet, er illustreret med en skraveret boks.
Råvarer og kemikalier dækker over en bred gruppe af kemiske forbindelser og varierer meget fra produktion til produktion. I Figur A.1 er ikke vist, at hver af disse forbindelser har et livsforløb og dermed
et forbrug af råstoffer og energi samt generering af affald.
Alle virksomheder anvender emballager til deres produkter. Materialerne til emballagerne er primært papir/pap, plast og glas, men varierer meget fra produktion til produktion. Fremstilling af
emballagematerialerne er ikke vist i Figur A.1.
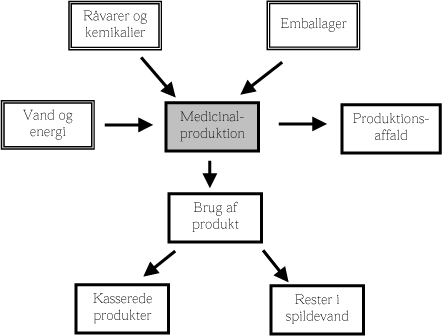
Figur A.1 Principskitse for medicinalprodukter i et livscyklusperspektiv
Medicinalproduktion er karakteriseret ved, at der forbruges betydelige mængder vand og energi. Den største del af vandmængden afledes som spildevand. Energien er i form af dels olie og naturgas, dels
fjernvarme og dels el.
Affald fra produktionen er primært affald fra gæringstanke, farligt affald i form af blandt andet brugte opløsningsmidler, affald fra emballager og andet industriaffald.
Langt den overvejende del af produkterne bliver brugt af mennesker og dermed omsat. Rester kan forekomme i sanitært spildevand, men er ikke taget med i opgørelsen her.
Kassationen af produkter hos forbrugerne vurderes at være meget lille.
A.3 Datagrundlag
Der er ikke tidligere blevet udarbejdet opgørelser over medicinalindustriens forbrug af ressourcer i relation til deres produktion.
I nærværende projekt er det derfor valgt at søge oplysninger gennem de grønne regnskaber, som denne gruppe af virksomheder har pligt til at udarbejde. Et grønt regnskab indeholder nøgletal for
virksomhedens produktion med hensyn til miljø- og arbejdsmiljø og giver således oplysninger om forbrug af ressourcer og udledninger samt affald.
En redegørelse efter EMAS-forordningen ville have været bedre, da der her stilles større krav til offentliggjorte informationer, men ingen virksomheder i Danmark inden for medicinalområdet er registreret
efter denne forordning.
Grønne regnskaber er gennemgået for en række af de store medicinalvirksomheder, og på baggrund heraf er det valgt at anvende data fra virksomhederne:
- BASF Health & Nutrition A/S
- Ferring A/S
- H. Lundbeck A/S, Valby
- Novo Nordisk A/S
- Nycomed Danmark A/S
Disse virksomheder repræsenterer dels meget store og store virksomheder og er forskellige i deres produktion.
De data, der ligger til grund for nærværende kortlægning for de 5 udvalgte virksomheder, er samlet i sidste kapitel i dette bilag.
Data for de 5 udvalgte virksomheder er vist i Tabel A.1. Resultaterne fra gennemgangen af virksomhedernes grønne regnskaber findes i under bilaget.
Tabel A.1 Størrelse af de 5 udvalgte medicinalvirksomheder (år 2001)
Virksomhed |
Ansatte |
Omsætning |
BASF Health & Nutrition A/S |
450 |
1% |
727 mio. kr. |
2% |
Ferring A/S |
250 |
1% |
417 mio. kr. |
1% |
H. Lundbeck A/S, Valby |
3.500 |
11% |
4.308 mio. kr. |
14% |
Novo Nordisk A/S |
14.000 |
45% |
15.725 mio. kr. |
49% |
Nycomed Danmark A/S |
5.50 |
2% |
784 mio. kr. |
2% |
Udvalgte virksomheder |
18.750 |
61% |
21.961 mio. kr. |
69% |
I alt for branchen |
30.000 |
100% |
31.688 mio. kr. |
100% |
Den væsentligste mangel ved de grønne regnskaber er, at produktionen i ton ikke er angivet, da det antageligt er følsomme virksomhedsoplysninger. Produktionen for hver af virksomhederne er dog forsøgt
estimeret, som en afledt af indgående materialer (råvarer og hjælpestoffer) minus udgående materialer (affald, spildevand, emissioner til luft).
Den samlede danske produktion i ton produkt kan alternativt beregnes ud fra Danmarks Statistiks tal for ”Eksport med vægtangivelse”. Der er strenge regler for, at virksomhederne skal oplyse Danmarks
Statistik om mængden af eksporterede varer. I år 2001 blev der således eksporteret 38.306 ton, se Tabel A.2.
Tabel A.2 Beregning af den farmaceutiske produktion i Danmark 2001 ud fra oplysninger fra Danmarks Statistik
Branche |
24.41.00 |
24.42.00 |
Ton |
1000 DKK |
Ton |
1000 DKK |
Salg af egne varer uden vægtangivelse |
|
884.799 |
|
26.175.982 |
Salg af egne varer med vægtangivelse |
14.516 |
1.240.474 |
1.284 |
1.674.009 |
Salg af egne varer i alt |
|
2.125.273 |
|
27.849.991 |
Eksport uden vægtangivelse |
|
51.803 |
|
1.777.709 |
Eksport med vægtangivelse |
17.858 |
1.895.001 |
15.730 |
23.967.641 |
Eksport i alt |
|
1.946.804 |
|
25.745.350 |
Enhedspris (1000 DKK/ton) |
1.895.001 / 17.858 = 106 |
23.967.641 / 15.730 = 1.524 |
Produktion i Danmark (ton) |
2.125.273 / 106 = 20.088 |
27.849.991 / 1.524 = 18.278 |
Samlet produktion i Danmark (ton) |
38.306 |
Ud fra tallene ”Salg af egne varer i alt” og ”Eksport med vægtangivelse” er der fundet henholdsvis 89% for branchekode 24.41.00 og 86% for branchekode 24.42.00 af det samlede salg af varer er opgjort i
mængder.
Tallet for ”Branchen i alt” fra Danmarks Statistik vurderes derfor at være pålideligt. Dels er talmaterialet baseret på hele branchens lovpligtige indberetninger, dels er mængderne for produceret mængde
produktbaseret på hver enkelt virksomheds eksakte oplysninger.
Den estimerede produktion for hver af de 5 virksomheder er vist i Tabel A.3. Mængden er beregnet ud fra henholdsvis talmateriale fra Danmarks Statistik og de grønne regnskaber. Produktionsmængden
indeholder al emballage på nær transportemballage.
Tabel A.3 Estimeret produktion opgivet i ton produkter
Virksomhed |
Kilde: Danmarks Stati- stik Produktion 2001. Fordelt efter % af omsætningen |
Kilde: Grønne regnskaber 1999-2001. ”Branchen i alt” er beregnet ud fra de udvalgte virksom- heders % af omsætningen |
BASF Health & Nutrition A/S |
2% |
766 |
687 |
Ferring A/S |
1% |
383 |
385 |
H. Lundbeck A/S, Valby |
14% |
5.363 |
945 |
Novo Nordisk A/S |
49% |
18.770 |
40.670 |
Nycomed Danmark A/S |
2% |
766 |
836 |
Udvalgte virksomheder |
69% |
26.431 |
43.523 |
I alt for branchen |
100% |
38.306 |
63.077 |
I det følgende anvendes dels data for de 5 virksomheder samlet og dels for hver enkelt for at belyse variationen i branchen. Råvaremængderne oplyst i de grønne regnskaber vurderes at være mest pålidelige,
hvorfor de anvendes til opskallering for hele branchen. For den producerede mængde produkt tages udgangspunkt i tallene fra Danmarks Statistik.
A.4 Ressourceforbrug
I det følgende foretages en opgørelse af de væsentligste ressourceforbrug omfattende, råvarer og hjælpestoffer, emballager, vand og energi.
A.4.1 Råvarer og hjælpestoffer
Input i form af råvarer og hjælpestoffer dækker over en meget bred vifte af kemiske forbindelser. Der vil dog være tre typer:
- Kemiske stoffer og produkter, som bruges direkte i produktet
- Kemiske stoffer og produkter, der bruges ved en kemisk syntese eller anden omdannelse
- Proceshjælpemidler som fx opløsningsmidler.
De grønne regnskaber giver yderst sparsomme oplysninger om, hvilke typer og hvilke kemiske stoffer og produkter det drejer sig om. De oplysninger, der kan anvendes fra de grønne regnskaber, er samlet i
Tabel A.4.
Tabel A.4 Oplysninger om råvarer og hjælpestoffer fra de grønne regnskaber. Tallene er inkl. emballageforbrug
Virksomhed |
Råvareforbrug
(ton) |
Bemærkninger til det samlede råvareforbrug - typer, arter, andel |
BASF Health &
Nutrition A/S |
5.495 |
En stor del af råvarerne (op mod 90%) er majsstivelse og forskellige sukkerarter. De øvrige råvarer er vand- og fedtopløselige vitaminer, syrer og baser. Det samlede
forbrug er beregnet på baggrund af de opgjorte affaldsmængder og nogle nøgletal som oplyses i regnskabet. Tallene er et gennemsnit af det grønne regnskab for 1999 og
2000. |
Ferring A/S |
416 |
Det væsentligste stof er lægemiddelstoffet 5-aminosalicylsyre, der indgår i alle afføringsmidlerne, som virksomheden producerer. I år 2000 var forbruget på 146 ton
svarende til 50% af råvareforbruget. Virksomheden anvendte samme år 136 ton opløsningsmidler. Endvidere havde virksomheden et væsentligt forbrug af natrium
dioctylsulfosuccinat. I år 2000 var forbruget af dette stof 289 kg. De resterende 133 ton bestod af emballage. Tallene er et gennemsnit af det grønne regnskab for 1999
og 2000. |
H. Lundbeck A/S,
Valby |
1.180 |
Virksomheden oplyser, at den i år 2000 anvendte 33 ton aktivstoffer, 154 ton hjælpestoffer og 12 ton opløsningsmidler ved fremstilling af produkterne. Endvidere blev
der i laboratorierne anvendt 25 ton opløsningsmidler og 3 ton øvrige kemikalier. Emballageforbruget var totalt på 845 ton, hvoraf pap og papir står for de 423 ton, plast
og gummi for 254 ton, 101 ton glas og 59 ton træ. De sidste 8 ton er anført som ”Andet”. |
Novo Nordisk
A/S |
87.995 |
Oplysningerne fra Novo Nordisk A/S er meget begrænsede, når det kommer til detaljer vedrørende indgående materialer. Det samme gør sig gældende for de udgående
materialer. Tallene er fra 2001. Mængden af indgående materialer er opgivet i det grønne regnskab som én post uden yderligere specificering. |
Nycomed
Danmark A/S |
836 |
For år 2000 er det oplyst, at virksomheden anvendte 584,3 ton aktivstoffer, 220 ton hjælpestoffer, ekskl. ethanol, 31,4 ton ethanol, 30 ton isopropanol og ca. 5 m³
rengøringsmidler. |
Udvalgte
virksomheder |
95.922 |
Sum af de 5 udvalgte virksomheders råvareforbrug. Råvareforbruget udgør 61%. |
I alt for
branchen |
139.017 |
|
Totalt forbrugte de farmaceutiske virksomheder ca. 140.000 ton råvarer inkl. emballager men ekskl. vand i år 2000.
Det har ikke været muligt at finde eksakte tal for, hvor store mængder af fx stivelsesprodukter, der indgår i produktionerne eller andre af de indgående materialer. Derfor er der ud fra forfatternes erfaringer
fra branchen, koblet med indikationer og fakta fra de grønne regnskaber, lavet en grov inddeling i 4 grupper af de kemiske stoffer og produkter, som indgår i fremstillingsprocessen, se Tabel A.5.
Tabel A.5 Gruppering af råvarer og hjælpestoffer (inkl. emballage)
Kemiske stoffer og produkter |
Råvareforbrug
(ton) |
Materiale-
forbrug ved
fremstilling
[mPR/kg] |
Primær
energiforbrug
[MJ/kg] |
Stoffer baseret på stivelse, etc. |
69.509 (50%) |
0,00 |
0 |
Let bearbejdede kemiske forbindelser, råolie som eks. |
34.754 (25%) |
0,04 |
50 |
Meget bearbejdede kemiske forbindelser*) |
20.853 (15%) |
1,00 |
100 |
Organiske opløsningsmidler (regnes som ethanol) |
13.902 (10%) |
0,04 |
80 |
I alt for branchen |
139.017 (100%) |
|
|
*) Tallet for materiale- og energiforbrug er sat konservativt ud fra oplysninger om fremstilling af bekæmpelsesmiddel.
En meget stor del af indgangsmaterialerne til branchen er substratstoffer til gæringsprocesserne, som især finder sted på Novo A/S insulinfabrik i Kalundborg. De øvrige virksomheder har, som det fremgår af
bemærkningerne i Tabel A.4, også et stort forbrug af denne gruppe af stoffer.
Det vurderes, at gruppen kan sidestilles med stivelse, herunder forskellige sukkerarter, papir og pap. Stivelse er en fornyelig ressource som i LCA sammenhæng normalt sættes til et ressourceforbrug på 0
mPR/kg (milli-Person-Reserver pr. kilo materiale) og et tilsvarende primær energiforbrug ved fremstilling på 0 MJ/kg.
Skønsmæssigt udgør stofferne baseret på stivelse 50% af den samlede mængde råvarer og hjælpestoffer (inkl. papir- og papemballage) svarende til 69.509 ton.
Tilsvarende er gruppen af let bearbejdede kemiske forbindelser, som skønsmæssigt er sat til at udgøre 25% af det samlede forbrug, associeret med fremstilling af råolie. I dette tilfælde benyttes data fra
UMIP (UMIP, 1998), hvor ressourceforbruget er 0,04 mPR/kg og det primære energiforbrug ved fremstilling er 50 MJ/kg. Til gruppen af let bearbejdede kemiske forbindelser hører plastemballager.
Hvad de meget bearbejdede forbindelser består af og i nøjagtig hvilke mængder oplyses ikke i de grønne regnskaber. Derimod oplyses, hvor store mængder farligt affald der frembringes fra de udvalgte
virksomheders produktioner. På baggrund heraf vurderes det, at de meget bearbejdede kemiske forbindelser udgør 15% svarende til 20.853 ton. Ressourceforbruget sættes konservativt i forhold til
oplysninger for fremstilling af bekæmpelsesmidler. Hvilket vil sige et ressourceforbrug på 1 mPR/kg med et primært energiforbrug ved fremstilling på 100 MJ/kg.
De organiske opløsningsmidler bruges i oprensningsprocesser og i laboratorierne. Denne gruppe af kemiske stoffer og produkter repræsenteres ved LCA-data for ethanol, som virksomhederne jf. de grønne
regnskaber benytter i stor udstrækning. Det fremgår blandt andet af Novo Nordisk A/S grønne regnskab, at de i 2001 afhændede mere end 4.000 ton ethanol i form af farligt affald svarende til 3% af
råvareforbruget. Ressourceforbruget ved brug af ethanol svarer til 0,04 mPR/kg med et primært energiforbrug ved fremstilling på 80 MJ/kg.
På baggrund heraf beregnes branchens materialeforbrug ved fremstilling til i alt 22.799 PR. I gennemsnit svarer dette til et ressourceforbrug på 595 mPR pr. ton fremstillet medicinalprodukt, se Tabel A.6.
Tabel A.6 Beregning af materialestrømmene er omsat til forbrug opgjort i person reserver
Kemiske stoffer og Produkter |
Materialeforbrug i fremstilling |
Råvare forbrug |
Produktsam- mensætning A |
Produktsam- mensætning B |
[mPR/kg] |
[ton] |
[PR] |
[ton] |
[PR] |
[ton] |
[PR] |
Stoffer baseret på stivelse, etc. |
0,00 |
69.509 (50%) |
0 |
19.153 (50%) |
0 |
1.915 (5%) |
0 |
Let bearbejdede kemiske forbindelser, råolie som eks. |
0,04 |
34.754 (25%) |
1.390 |
9.577 (25%) |
383 |
18.195 (47,5%) |
728 |
Meget bearbejdede kemiske forbindelser*) |
1,00 |
20.853 (15%) |
20.853 |
5.746 (15%) |
5.746 |
10.917 (28,5%) |
10.917 |
Organiske opløsningsmidler (regnes som ethanol) |
0,04 |
13.902 (10%) |
556 |
3.830 (10%) |
153 |
7.278 (19%) |
291 |
I alt for branchen |
|
139.017 (100%) |
22.799 |
38.306 (100%) |
6.282 |
38.306 (100%) |
11.936 |
*) Tallet for materialeforbrug er sat konservativt ud fra oplysninger om fremstilling af bekæmpelsesmiddel
Medicinalfabrikkerne i Danmark producerede og solgte i år 2001 38.306 ton produkter. Under forudsætning af at sammensætningen af produkterne er identisk med udgangsmaterialerne, ses det i kolonne
”Produktsammensætning A”, at ressourceindholdet i produkterne er 6.282 PR. Antages det derimod, at stoffer baseret på stivelse kun udgør 5% af produkterne, og at resten fordeles som før, ses det i
kolonne ”Produktsammensætning B”, at ressourceindholdet i produkterne er 11.936 PR.
A.4.2 Råstofforbrug
De råvarer og hjælpestoffer, der anvendes på medicinalfabrikkerne, er opgjort som grupper af stoffer, da det ikke var muligt at fremskaffe mere detaljerede oplysninger.
Det har derfor været nødvendigt at opstille en række antagelse for at nå frem til et estimat for de samlede forbrug af råstoffer.
For stivelsesbaserede produkter er det antaget, at råstofforbruget ligger på omkring 5 kg/kg, når stivelsen udvindes af kartofler og der medregnes gødning m.v. Oplysningerne stammer fra SigmaPro.
For letbearbejdede kemiske forbindelser er det antaget, at råstofforbruget svarer til forbruget af olie, hvor ressourceforbruget i UMIP er sat til 1,1 kg/kg. Tilsvarende data fra SigmaPro angiver et
råstofforbrug på 1,3 kg/kg.
For meget bearbejdede kemiske forbindelser har det ikke været muligt at finde data. I en opgørelse fra ETH/ESU 96 er det angivet, at råstofforbruget til organiske kemiske forbindelser ligger på 1,02 kg/kg.
Fremstilling af cyanider er i SigmaPro sat til 2,1 kg/kg. Da bearbejdede kemiske forbindelser kan rumme en række meget forskellige stoffer og materialer med en høj grad af forarbejdning, antages det, at
råstofforbruget ligger på 2 til 5 kg/kg. I beregningerne er det valgt at anvende 5 kg/kg.
For organiske opløsningsmidler er der taget udgangspunkt i ethanol, der er et almindeligt anvendt ekstrations- og oprensningsmiddel. Råstofforbruget til fremstilling af ethanol er estimeret til at ligge på linie
med let bearbejdede kemiske forbindelser og er derfor sat til 1,3 kg/kg.
Ud fra ovenstående er der i Tabel A.7 foretaget en estimering af råstofforbruget. Der skal gøres opmærksom på, at opgørelsen er baseret på et meget usikkert datamateriale.
Tabel A.7 Estimering af samlet råstofforbrug
Kemiske stoffer og produkter |
Råvareforbrug
(ton) |
Råstoffor-
brug pr. kg råvare- forbrug |
Samlet
råstoffor- brug (ton) |
Stoffer baseret på stivelse, etc. |
69.509 (50%) |
5 kg/kg |
350.000 |
Let bearbejdede kemiske forbindelser, råolie som eks. |
34.754 (25%) |
1,3kg/kg |
45.000 |
Meget bearbejdede kemiske forbindelser*) |
20.853 (15%) |
5 kg/kg |
105.000 |
Organiske opløsningsmidler (regnes som ethanol) |
13.902 (10%) |
1,3 kg/kg |
18.000 |
I alt for branchen |
139.017 (100%) |
|
520.000 |
A.4.3 Emballager
I de grønne regnskaber har 3 ud af de 5 virksomheder givet oplysninger om forbruget af emballager. Oplysningerne om forbrug af emballager findes i Tabel A.4. BASF Health & Nutrition A/S og Nycomed
Danmark A/S har ikke givet oplysninger om emballageforbrug.
Ferring A/S anvender noget mindre emballage, ca. 50% i forhold til mængden af produceret produkt. De oplyser i det grønne regnskab for år 2000, at forbruget i alt var på 154 ton emballage fordelt på 87
ton PE-plastgranulat, 21 ton tabletglas og 46 ton aluminiumsfolier.
For H. Lundbeck A/S er emballageforbruget mere end 8 gange større end den producerede mængde produkt. H. Lundbeck A/S oplyser, at de i 2000 anvendte 423 ton pap og papir, 254 ton plast og
gummi, 101 ton glas, 59 ton træ samt 8 ton uspecificeret emballage svarende til i alt 845 ton emballage.
Emballageforbruget hos Novo Nordisk A/S på 5.795 ton udgør i omegnen af 15% i forhold til den producerede mængde produkt. Grunden til dette kan meget vel skyldes, at Novo Nordisk A/S leverer
store dele af deres produkter i storemballage som halvfabrikata. Hvad emballagen består af oplyses ikke.
Det samlede forbrug i de 3 virksomheder udgør til sammen 6.794 ton. Tallet dækker over meget store udsving i forbruget. Endvidere er fordelingen mellem de materialer, som anvendes i emballeringen ikke
kendt til fulde.
Emballagerne antages at bestå af 50% pap og papir, 30% plast og gummi samt 20% glas og andet.
Ved opskallering ud fra virksomhedernes anslåede produktionsmængde beregnes branchens samlede forbrug af emballager til omkring 10.000 ton, hvilket svarer til ca. 25% af den samlede producerede
mængde produkt, se Tabel A.8.
Tabel A.8 Emballageforbrug
Virksomhed |
Kilde: Danmarks Statistik
Produktion 2001. Fordelt efter % af omsætningen |
Emballageforbrug
i alt fordelt efter |
Ferring A/S |
1% |
383 |
154 |
H. Lundbeck A/S, Valby |
14% |
5.363 |
845 |
Novo Nordisk A/S |
49% |
18.770 |
5.795 |
Udvalgte virksomheder |
64% |
24.516 |
6.794 |
I alt for branchen |
100% |
38.306 |
10.615 |
Tallet er temmelig usikkert og kan i virkeligheden lige så godt være 20%, som det kan være 30%.
I gennemsnit svarer dette til et emballageforbrug på 250 kg pr. ton fremstillet medicinalprodukt, hvoraf 125 kg er pap og papir, 75 kg er plast og gummi og 50 kg er glas og andet.
A.4.4 Vandforbrug
Vandforbruget er typisk stort inden for medicinalindustrien. Data fra de 5 virksomheder viser, at vandforbruget ligger på omkring 80 m³ pr. ton produkt, men med en stor variation mellem de enkelte
virksomheder. Vandforbruget svinger mellem ca. 20 og ca. 700 m³/ton produceret produkt, se Tabel A.9.
Tabel A.9 Beregning af vandforbrug
Virksomhed |
Vandforbrug |
Spildevand |
Differens |
Produceret produkt |
Vandforbrug pr. ton produkt |
(m³) |
(m³) |
(m³) |
(ton) |
(m³/ton) |
BASF Health & Nutrition A/S |
527.644 |
354.938 |
172.707 |
766 |
689 |
Ferring A/S |
11.103 |
10.697 |
406 |
383 |
29 |
H. Lundbeck A/S, Valby |
96.600 |
96.500 |
100 |
5.363 |
18 |
Novo Nordisk A/S |
1.429.381 |
1.120.660 |
308.721 |
18.770 |
76 |
Nycomed Danmark A/S |
20.485 |
20.086 |
399 |
766 |
27 |
Udvalgte virksomheder |
2.085.213 |
1.602.881 |
482.333 |
26.431 |
79 |
I alt for branchen |
3.022.048 |
2.323.015 |
699.033 |
38.306 |
79 |
Vandforbruget pr. ton produceret produkt er beregnet ud fra oplysninger fra de grønne regnskaber. Som det ses, er differencen, eller netto-vandforbruget, lille i forhold til vandforbruget. En stor del af dette
vand fordamper under produktionen, og en lille del indgår i de færdige produkter.
Vandforbruget for hele branchen vurderes at være i størrelsesordenen 80 m³ pr. ton produkt.
A.4.5 Energiforbrug
Af de grønne regnskaber for de udvalgte virksomheder var det ikke muligt at opgøre energiforbruget for Novo Nordisk A/S. Novo Nordisk A/S har valgt at omsætte energiforbruget til ton udledninger ud
fra procesrelaterede nøgletal. Det er ikke muligt ud fra de givne oplysninger at regne baglæns til fx ton naturgas.
Opgørelsen baseres derfor på de 4 øvrige udvalgte virksomheders oplysninger. De har oplyst, at de som energi anvender gasolie, råolie, naturgas samt fjernvarme og el. Det antages, at de 4 virksomheder er
repræsentative, og det samlede energiforbrug for branchen kan estimers på basis heraf. De fire virksomheder står for 20% af den samlede omsætning, hvorfor det samlede primære energiforbrug i branchen
beregnes til 8.820 TJ, se Tabel A.10 og Tabel A.11.
Tabel A.10 Energiforbrug opdelt efter energitype for 4 ud af de 5 udvalgte virksomheder
Virksomhed |
Produktion |
Gasolie og fyringsolie |
Naturgas |
Fjernvarme |
Elektricitet |
(ton) |
(ton) |
(Nm³) |
(GJ) |
(MWh) |
BASF Health & Nutrition A/S |
766 |
13.103 |
480.190 |
|
34.900 |
Ferring A/S |
383 |
534 |
|
1.888 |
20.894 |
H. Lundbeck A/S, Valby |
5.363 |
839 |
19.168 |
61.236 |
19.660 |
Nycomed Danmark A/S |
766 |
|
6.307 |
20.894 |
6.762 |
I alt for de 4 virksomheder |
7.278 |
14.476 |
505.665 |
84.018 |
82.216 |
Energiforbruget for hele branchen ses af første kolonne i Tabel A.11. I anden og tredje kolonne ses beregningen af det primære energiforbrug for de 4 virksomheder. Det samlede primære energiforbrug er
fundet ved opskallering fra 20% til 100%.
Tabel A.11 Estimering af det primære energiforbrug for energiforsyning
Energitype |
Energi-
Forbrug |
Enhed og omregningsfaktor (x/GJ) |
Primær energi-
forbrug i GJ |
Gasolie og Fyringsolie |
76.191 |
ton (50 MJ/kg *) |
3.809.547 |
Naturgas |
2.661.446 |
Nm³ (1,20 kg/Nm³, 3,4 MJ/kg *) |
10.859 |
Fjernvarme |
442.209 |
GJ (2,5 MJ/MJ *) |
1.105.521 |
Elektricitet |
432.724 |
MWh (9 kWh/MJ *) |
3.894.517 |
I alt for branchen |
8.820.444 |
* Pommer et al., 2001.
Energiforbruget ved fremstilling af råvarerne beregnes ud fra nøgletal herfor til i alt 4.240 TJ, se Tabel A.12.
Tabel A.12 Estimering af det primære energiforbrug for råvarer og hjælpestoffer (inkl. emballage)
Kemiske stoffer og produkter |
Råvareforbrug
(ton) |
Primær
energiforbrug [GJ/ton] |
Primær energi-
forbrug i GJ |
Stoffer baseret på stivelse, etc. |
69.509 (50%) |
0 |
- |
Let bearbejdede kemiske forbindelser, råolie som eks. |
34.754 (25%) |
50 |
1.737.700 |
Meget bearbejdede kemiske forbindelser*) |
20.853 (15%) |
100 |
2.085.255 |
Organiske opløsningsmidler (regnes som ethanol) |
13.902 (10%) |
80 |
1.112.136 |
I alt for branchen |
139.017 (100%) |
|
4.935.091 |
*) Tallet for energiforbrug er sat konservativt ud fra oplysninger om fremstilling af bekæmpelsesmiddel
I forbindelse med bortskaffelsen af det almindelige industriaffald og det farlige affald, som opstår i forbindelse med virksomhedernes produktion, skal den nyttiggjorte energi fra
affaldsbehandlingen/forbrændingen godskrives. I dette tilfælde kan 196 TJ godskrives som beregnet i Tabel A.15. Det netto primære energi- og ressourceforbrug i branchen er givet i Tabel A.13.
Tabel A.13 Det netto primære energiforbrug og ressourceforbrug i branchen
Kilde |
Primær energi-
forbrug i GJ |
Ressource-
forbrug |
Energiforbrug i produktionsfasen |
8.820.000 |
8.605 |
Råvarer og hjælpestoffer |
4.935.091 |
4.815 |
|
13.755.091 |
13.420 |
Affald (godskrives) |
- 196.220 |
-191 |
I alt for branchen |
13.558.871 |
13.228 PR |
Omsættes det netto primære energiforbrug til forbrug af olieressourcer (1.025 GJ/PR olie) svarer det til 13.228 PR eller ca. 350 mPR pr. ton fremstillet medicinalprodukt.
En del af affaldet forbrændes med energiudnyttelse, hvorfor der kan godskrives 191 PR eller 0,005 mPR pr. ton fremstillet medicinalprodukt.
A.5 Tabte materialer
A.5.1 Produktionsaffald
De grønne regnskaber giver oplysninger om de eksakte mængder og typer af affald fra produktionerne.
Affald fra produktionen er primært affald fra gæringstanke, farligt affald i form af blandt andet brugte opløsningsmidler, affald fra emballager og andet industriaffald.
Specielt Novo's produktion i Kalundborg genererer store mængder affald fra deres gæringstanke. Affalds-/biomasseproduktet sælges under navnet NovoGro og benyttes til gødskning af landbrugsjord. I
2001 producerede Novo 147.215 m³ biomasse svarende til 23.312 ton tørstof (tbl2001.novonordisk.com). Novo medtager ikke denne affaldsfraktion i deres opgørelser over affald. Da det af
virksomheden betragtes som et biprodukt fra produktionen, som har en særlig værdi.
Biproduktet medgår i form af ton tørstof i denne affaldsopgørelse.
Affaldsmængderne fra produktionerne er summeret til 81.254 ton i Tabel A.14. 61% af affaldet nyttiggøres, 24% forbrændes og de resterende 15% deponeres.
Tabel A.14 Produktionsaffald
Affaldsopgørelse (ton) |
BASF |
H. Lundb. |
Ferring |
Nycomed |
Novo |
Sum for 69% |
Total for hele branchen |
Genanvendelse til nyttiggørelse |
2.910 |
211 |
155 |
- |
30.771 |
34.047 |
49.343 (61%) |
Forbrænding inkl. farligt affald |
1.598 |
767 |
232 |
300 |
10.642 |
13.539 |
19.622 (24%) |
Deponering |
703 |
116 |
- |
67 |
7.593 |
8.479 |
12.288 (15%) |
Sum for de 5 virksomheder (69%) |
5.211 |
1.094 |
387 |
367 |
25.694 |
56.065 |
|
Total for hele branchen (ton) |
7.552 |
1.586 |
561 |
532 |
71.023 |
|
81.252 |
Det antages, at al affald til genanvendelse findes i form af biomasse. Biomassen regnes som værende baseret på stivelse og tæller derfor ikke i opgørelsen af det primære energiforbrug.
Ved forbrænding af det forbrændingsegnede affald inkl. det farlige affald kan godskrives en energimængde svarende til energiindholdet minus virkningsgraden på forbrændingsanlægget.
I dette tilfælde antages det, at affaldet, som forbrændes, har et energiindhold på 20 GJ/ton, hvilket svarer til energiindholdet for papir/pap og opløsningsmidler med oxygen. Det antages at, det er et
kraftværk, hvor 50% af energien udnyttes.
Alt i alt udnyttes et energiindhold på 10 GJ/ton, svarende til et energiindhold på 196.220 GJ, som beregnet i Tabel A.15.
Tabel A.15 Energiindhold i affaldet
Affaldsopgørelse |
Total affalds-
produktion for
hele branchen |
Energiindhold
(GJ/ton) |
Energiindhold
(GJ) |
Genanvendelse, (nyttiggørelse) |
49.343 (61%) |
0 |
0 |
Forbrænding inkl. farligt affald |
19.622 (24%) |
10 |
196.220 |
Deponering |
12.288 (15%) |
0 |
0 |
Total for hele branchen |
81.254 ton |
|
196.220 |
A.5.2 Spild af produkt
En mindre del af produkterne, som distribueres til kunderne, anvendes ikke (ca. 1%) og vil antageligt blive bortskaffet ved forbrænding (Pers. komm. Asger Mortensen, Dansk Apotekerforening).
Det har ikke været muligt at give nærmere beskrivelser af, hvordan produktet spildes.
A.6 Underbilag – Grønne regnskaber
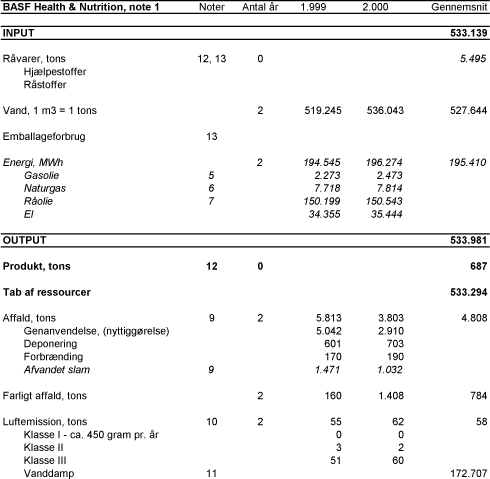
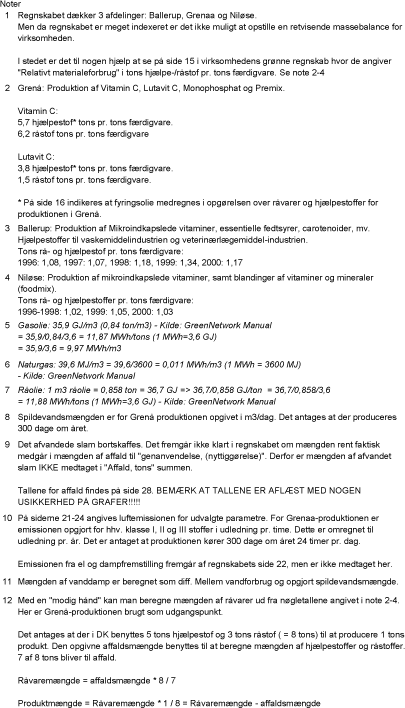
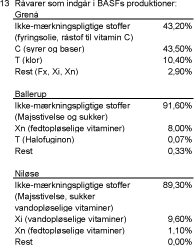
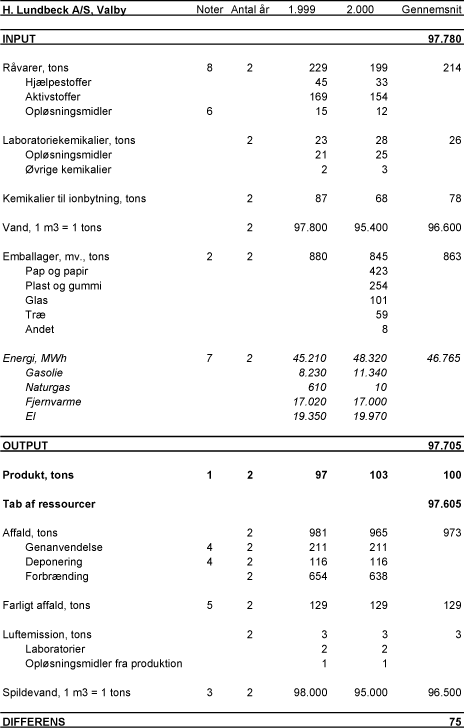
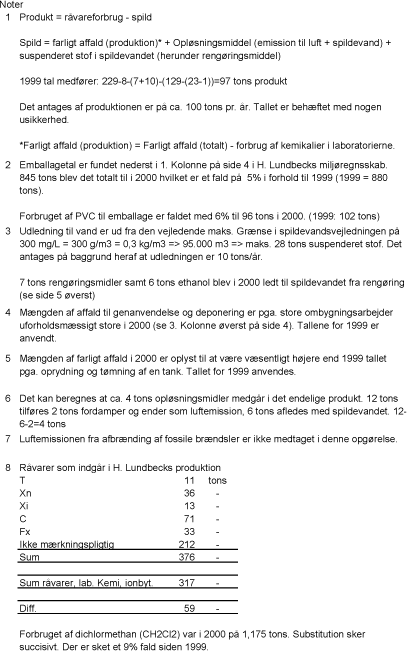
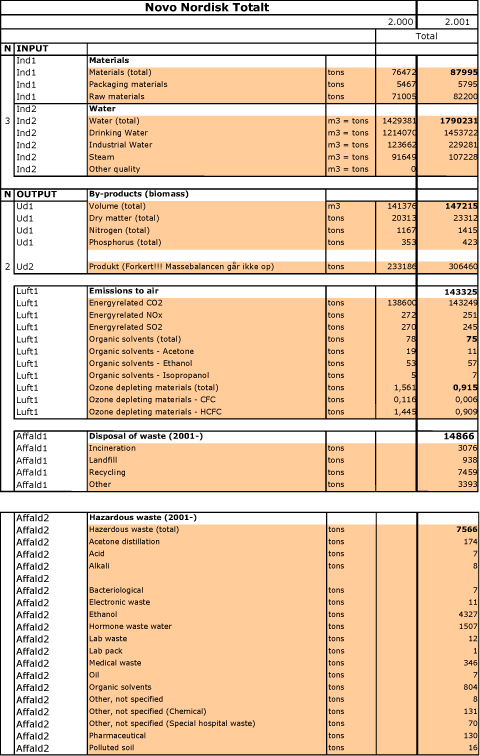


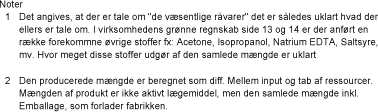

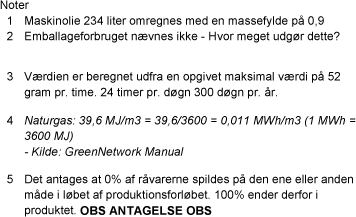
B Møbelfremstilling
B.1 Introduktion
Træ- og møbelindustrien i Danmark omsætter for omkring 25 mio. kr. årligt (Kvist KE et al., 2000). Dette omfatter skovbrug, byggevarer og møbelindustri. Møbelindustrien udgør 59% af den samlede
omsætning.
Møbelindustrien er kendetegnet ved mange mindre virksomheder. En gennemsnitsvirksomhed inden for dette område har i størrelsesordnen 15 personer. Inden for møbelindustrien findes omkring 2.300
virksomheder, der i større eller mindre grad beskæftiger sig med møbelproduktion.
Træ er møbelindustriens væsentligste råvare. I miljøprojekt 561 (Kvist KE et al., 2000) er der opstillet en opgørelse af træproduktion og –forbrug i dansk møbelindustri og tilhørende aktiviteter. Med fokus
på møbelproduktion gengives denne opgørelse i Figur B.1.

Figur B.1 Produktion og brug af træ (Kvist KE et al., 2000)
Af Figur B.1 ses det, at materialemængden i møbelprodukter udgør 500.000 ton, hvor den primære materialemængde er træ.
Tab på savværker, ved pladeproduktion og ved møbelproduktion kan ikke opgøres på basis af oplysningerne i Figur B.1, da mængden, der går til papirproduktion samt til byggevarer og andre produkter,
ikke er opgjort særskilt.
B.2 Produktvalg
B.2.1 Produktets livsforløb
Møbler generelt kan betragtes i et livscyklusperspektiv som vist i Figur B.2. Inputsiden er illustreret ved bokse med dobbeltstreger, outputsiden ved bokse med kraftig enkelt streg. De bokse, der er mindre
væsentlige er illustreret med stiplede linier og udgangspunktet – produktion af produktet – er illustreret med en skraveret boks.
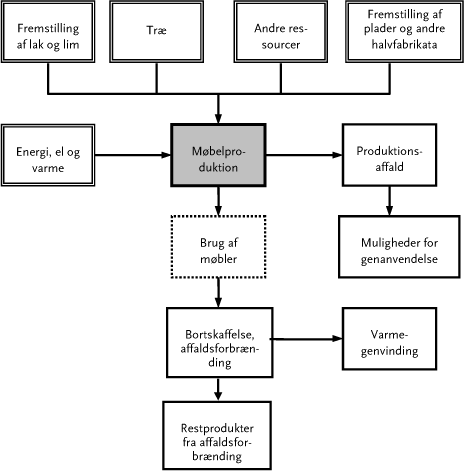
Figur B.2 Principskitse for møbler i et livscyklusperspektiv
Af Figur B.2 fremgår det, at der hovedsageligt anvendes materialer i form af træ, plader og andre halvfabrikata, eventuelt andre materialer samt lak og lim. Hertil kommer energi i form af el og varme.
Fremstilling af disse materialer vil blive ført tilbage til råstoffer, i det omfang data er tilgængelige.
Boksen ”Brug af møbler” i Figur B.2 er stiplet, da vedligeholdelse af møbler ikke er medtaget.
Energi til transport af materialer, produkter og affald er ikke medtaget.
På affaldssiden vil affaldsmængder, genanvendelige materialer og udvundet energi ved affaldsforbrænding blive opgjort.
B.2.2 Produktudvælgelse
Den samlede produktion af møbler er på 473.000 ton. Heraf er den største del møbler fremstillet i træ med brug af små mængder metal, lak, lim og andre hjælpestoffer. Mængden af stålmøbler udgør
38.000 ton eller 8% af den samlede produktion.
Der er gennemført 3 livscyklusvurderinger inden for de seneste år af repræsentative produkter inden for møbelområdet.
- Det andet produkt er en Montana-reol, der er fremstillet af møbelplade og finér med hængsler og skuffer af metal og plast. Ikke træ-baserede materialer udgør ca. 10% af produktet. Produktets
levetid er sat til 40 år.
- Det ene produkt er et sofabord af træ med klap af en størrelse på 1,4 m² og en forudsat levetid på 10 år. Dette produkt er repræsentativt ved, at det er fremstillet af træ og med meget små mængder
af andre materialer.
- Som repræsentant for stålmøbler er det tredje produkt en kontorstol, der består af 84% stål, 12% træ og resten lak og plast. Stolens levetid er sat til 10 år.
Møbler fremstillet af tropisk træ udgør maksimalt 3% af den samlede produktion og medtages derfor ikke i nærværende vurdering (Kvist KE et al., 2000).
Det forudsættes, at disse tre produkttyper kan repræsentere dansk møbelproduktion. Dette er diskuteret med Træets Arbejdsgiverforening (Kofod CJ, pers. komm., maj 2002). Der findes ingen statistiske
opgørelser over typer af producerede møbler, eller hvor stor en andel møbler der primært består af møbelplade.
Fra miljøprojekt 281, Miljøprioritering af industriprodukter (Hansen E, 1995) er det i den tilhørende database muligt at trække oplysninger ud om møbelproduktionen og -forbruget. Data er fra 1993, men
giver som vist i Tabel B.1 en opdeling på typer af møbler for produktion og forbrug.
Som det fremgår af Tabel B.1, er den samlede opgjorte møbelproduktion lavere i 1993 end opgørelsen i brancheanalysen fra 2000. Det er dog muligt at anvende oplysningerne i Miljøprojekt 281 til en
fordeling mellem de 3 produktkategorier: møbler af finér og møbelplade, møbler af massivt træ og møbler af stål. Hvor det ikke klart fremgår, om produkterne er af massivt træ eller finér og møbelplade, er
der antaget en fordeling på 50% til hver gruppe. Den lille mængde plastmøbler er udeladt af vurderingen.
Tabel B.1 Opgørelse af produktion og forbrug af møbler (Hansen et al., 1995)
Opgørelse i ton pr. år |
Data fra Miljøprojekt 281 |
Skøn over produktkategorier |
Produktion |
Forbrug |
Finér/ Møbelplade |
Massivt træ |
Stål |
Træmøbler |
129.062 |
20.501 |
|
129.062 |
|
Møbler af træfiberplader o.l. |
181.343 |
89.278 |
181.343 |
|
|
Andre finerede eller laminerede træproduktion |
19.876 |
17.149 |
19.876 |
|
|
Møbler af spanskrør, bambus o.l. |
2.142 |
2.869 |
|
2.142 |
|
Møbler af metal |
42.568 |
43.913 |
|
|
42.568 |
Møbler af plast-materialer |
2.287 |
3.694 |
|
|
|
Møbler til klinikker |
3.731 |
1.350 |
1.866 |
1.866 |
|
Andre møbler |
4.372 |
6.073 |
2.186 |
2.186 |
|
I alt |
385.381 |
184.827 |
205.271 |
135.256 |
42.568 |
Data i Tabel B.1 indikerer, at fordelingen mellem de 3 produkttyper er:
- 50% reoler, baseret på møbelplade og finér med ca. 10% plast og metal
- 40% borde, baseret på massivt træ med ca. 2% metal
- 10% stålmøbler, baseret på 84% stål og 12% træ
Dette betyder, at det som udgangspunkt antages, at dansk møbelproduktion kan repræsenteres ved en årlig produktion som vist i Tabel B.2.
Tabel B.2 Årlig dansk møbelproduktion repræsenteret ved 3 typer produkter
Møbeltype |
Skønnet andel |
Skønnet mængde |
Vægt pr. enhed |
Skønnet antal enheder |
Møbler af møbelplade og finér repræsenteret ved en reol |
50% |
240.000 ton |
122,4 kg |
1,96 mio. stk. |
Møbler af massivt træ repræsenteret ved et bord |
40% |
190.000 ton |
35,1 kg |
5,40 mio. stk. |
Møbler af stål repræsenteret ved en stol |
10% |
47.000 ton |
8,0 kg |
5,88 mio. stk. |
B.3 Kortlægning
For hver af de 3 valgte produkttyper er der gennemført livscyklusvurderinger. Det betyder, at der findes data for materiale og energiforbrug dækkende hele produktets livscyklus.
De data, der er relevante for nærværende projekt, er gengivet i det efterfølgende. Der er ikke medtaget data baseret på emissioner, da der alene er fokuseret på materialestrømme og energiforbrug/udvikling.
De tre udvalgte møbeltyper har forskellig levetid, hvilket vil sige, at kassering af produkterne vil ske til forskellig tid efter produktionsåret. I nærværende undersøgelse er antages det dog, at produktionen ikke
har ændret sig væsentligt over den årrække, der er aktuel for de relevante produkter. Dette betyder, at det antages, at den mængde produkter, der produceres årligt, også antages at forfalde som kasserede
produkter og dermed fremstå som affald.
B.3.1 Materiale- og energistrømme for en reol
I Miljøprojekt 376 er gengivet et eksempel på en livscyklusvurdering af et reolsystem fremstillet af Montana Møbler A/S (Lassen JH og Nielsen PH, 1998).
Produktet er en Montana reol med de mest almindelige funktioner for reolsystemet så som hylder, skuffer og låger. Reolen kan rumme et volumen på 1/8 m³ og har en levetid på 40 år.
Som udgangspunkt for livscyklusvurderingen er der opstillet en meget detaljeret stykliste. En forenkling og sammenstilling af denne er vist i Tabel B.3.
Tabel B.3 Materialer i en reol
Materialer – forbrug pr. reol |
Vægt |
Møbelplade |
105,1 kg |
Finér |
1,0 kg |
Stål |
11,7 kg |
Plast |
1,8 kg |
Lak |
1,5 kg |
Lim |
0,1 kg |
Fortynder |
0,6 kg |
Samlet vægt |
122,4 kg |
Ved produktionen af reolen er der angivet et forbrug af energi og vand som vist i Tabel B.4.
Tabel B.4 Forbrug af energi og vand til produktion af 1 reol
Benzin |
0,232 kg |
Diesel |
0,111 kg |
El |
31,0 kWh |
Naturgas |
2,64 kg |
Vand |
27,7 liter |
Der er opgivet, hvor meget affald der fremkommer ved fremstilling af reolen. Dette er opgjort pr. reol til:
Træaffald |
3,98 kg |
Lak-affald |
0,10 kg |
Andet affald |
1,39 kg |
I Tabel B.5 er vist de samlede materiale- og energiforbrug fra produktion af reoler samt de affaldsmængder, der fremkommer ved produktionen. Der er regnet med et antal reoler på 1,96 mio. stk.
Tabel B.5 Input og output fra produktionen af 1,96 mio. reoler
Input/output fra produktionen |
Samlet mængde
pr. 1,96 mio. stk. i
produktets levetid |
Materialeforbrug |
Møbelplade |
206.000 ton |
Finér |
1.960 ton |
Stål |
22.900 ton |
Plast |
3.500 ton |
Lak |
2,900 ton |
Lim |
200 ton |
Fortynder |
1.200 ton |
Energi |
Benzin |
455 ton |
Diesel |
220 ton |
El |
60.760 MWh |
Naturgas |
5.200 ton |
Affald |
Træaffald |
7.800 ton |
Lakaffald |
200 ton |
Andet affald |
2.700 ton |
B.3.2 Materiale- og energistrømme for et bord
I Miljøprojekt 561 er gengivet et eksempel på en livscyklusvurdering af et bord (Kvist K et al., 2000). Det valgte eksempel er et sofabord af massivt bøgetræ med en anslået levetid på 10 år.
Produktet er typisk for møbler af massivt træ. Der er anvendt ganske få skuer og små mængder plast. Dertil kommer mindre mængder lak og lim.
De anvendte materialer, der indgår i bordet fremgår af Tabel B.6.
Tabel B.6 Materialer i et bord
Bøgetræ |
32,9 kg |
Stål |
0,8 kg |
Plast |
0,2 kg |
Lak |
0,8 kg |
Lim |
0,4 kg |
Samlet vægt |
35,1 kg |
Af det opstillede materialeflow (Kvist K et al., 2000) fremgår det endvidere, at forbruget af bøgetræ er 0,09 m³ svarende til 49,4 kg, og at 1/3 bliver til affald. Affaldsmængder fra limning og lakering er ikke
medtaget. Ud fra kortlægningen af møbelområdet i projektet "Udpegning og kortlægning af udvalgte affaldstunge industriområder" (Pommer K et al., 2003) antages affaldsmængden af lak og lim at udgøre
10% af forbruget.
I forbindelse med produktionen bruges 41,1 kWh el og 0,10 kg naturgas pr. produceret bord.
Dertil kommer et forbrug af materialer til emballering af produktet i form af 3,3 kg pap og 0,5 kg plast. Disse materialer bortskaffes ved affaldsforbrænding umiddelbart før brug.
I Tabel B.7 er vist de samlede materiale- og energiforbrug fra produktion af borde samt de affaldsmængder, der fremkommer ved produktionen. Der er regnet med et antal borde på 5,4 mio. stk. med en
levetid på 10 år.
Tabel B.7 Input og output fra produktionen af 5,4 mio. borde
Input/output fra
produktionen |
Materialeforbrug
pr. 1 stk. produkt |
Samlet mængde
pr.5,4 mio. stk. i
produktets levetid |
Materialeforbrug |
Bøgetræ |
49,4 kg |
267.000 ton |
Stål |
0,8 kg |
4.300 ton |
Plast |
0,2 kg |
1.100 ton |
Lak |
0,8 kg |
4.300 ton |
Lim |
0,4 kg |
2.200 ton |
Energi |
El |
41,1 kWh |
222.000 MWh |
Naturgas |
0,10 kg |
540 ton |
Affald |
Træaffald |
16,5 kg |
89.000 ton |
Lim og lak rester |
0,12 kg |
650 ton |
B.3.3 Materiale og energistrømme for en stol
I miljøprojekt 561 er gengivet et eksempel på en livscyklusvurdering af en stol, der hovedsagelig består af stål (Kvist K et al., 2000). Stolen er tiltænkt til undervisningsbrug og har en anslået levetid på 10 år.
Det valgte eksempel repræsenterer møbler af stål. Der er ud over stål anvendt lidt træ samt mindre mængder lak og plast.
De materialer, der indgår i stolen er vist i Tabel B.8.
Tabel B.8 Materialer i en stål-stol
Bøgefinér |
1,1 kg |
Stål |
6,5 kg |
Plast |
0,1 kg |
Lak og maling |
0,3 kg |
Samlet vægt |
8,0 kg |
Af det opstillede materialeflow (Kvist K et al., 2000) fremgår det endvidere, at der fremkommer stålaffald fra bearbejdning af stålet på 1,4 kg pr. enhed. Da der ikke er givet oplysninger om affald fra
lakering og maling, antages det, at 10% fremkommer som affald svarende til 0,03 kg pr. enhed.
Der er ikke givet oplysninger om energiforbrug til bearbejdning af stålet eller til formgivning af træ samt lakering og maling.
I tillæg til brancheanalysen er der udarbejdet et sæt enhedsprocesser, hvor blandt andet energi og materialeforbrug for en række processer inden for møbelområdet er opgjort (Kofod et al., 2000). Fra disse
enhedsprocesser er oplysninger om energiforbrug hentet.
Bearbejdning af stålet omfatter:
Formgivning |
0,1 kWh pr. kg |
Svejsning |
0,179 kWh pr. kg |
Lakering |
0,343 kWh pr. kg samt 0,21 kg naturgas pr. kg |
Samlet energiforbrug bliver derfor 0,622 kWh el og 0,21 kg naturgas pr. kg stål svarende til 4,0 kWh el og 1,4 kg naturgas pr. produceret enhed.
Til overfladebehandling af træ forbruges 4,4 kWh el pr. kg produkt samt 0,5 kg fuelolie. Dette svarer til et forbrug pr. produceret enhed på 4,8 kWh og 0,55 kg fuelolie.
Det samlede energiforbrug opgøres derfor til:
El: |
8,4 kWh |
Naturgas |
1,4 kg |
Fuelolie |
0,55 kg |
I Tabel B.9 er vist de samlede materiale- og energiforbrug fra produktion af stålstole samt de affaldsmængder, der fremkommer ved produktionen. Der er regnet med et antal stole på 5,88 mio. stk. med en
levetid på 10 år.
Tabel B.9 Input og output fra produktion af 5,88 mio. stålstole
Input/output fra produktionen |
Materialeforbrug
pr. 1 stk. produkt |
Samlet mængde
pr.5,88 mio. stk. i produktets levetid |
Materialeforbrug |
Bøgefinér |
1,1 kg |
6.500 ton |
Stål |
7,9 kg |
46.500 ton |
Plast |
0,1 kg |
590 ton |
Lak og maling |
0,3 kg |
1.800 ton |
Energi |
El |
8,4 kWh |
50.000MWh |
Naturgas |
1,4 kg |
8.200 ton |
Fuelolie |
0,55 kg |
3.200 ton |
Affald |
Stålaffald |
1,4 kg |
8.200 ton |
Lak og malingsrester |
0,03 kg |
200 ton |
B.3.4 Samlede materiale- og energistrømme
De samlede materiale- og energistrømme for de tre produkttyper, der antages at repræsentere hele møbelproduktionen i Danmark pr. år er vist i Tabel B.10.
Tabel B.10 Input og output fra produktion af møbler pr. år
|
Produkter af mø-
belplade, 50%,
1,96 mio. reoler |
Produkter af
massivt træ,
40%,
5,4 mio. borde |
Produkter af
stål, 10 %, 5,88
mio. stålstole |
Samlet |
Materialer |
Møbelplade |
206.000 ton |
|
|
206.000 ton |
Finér |
1.960 ton |
|
6.500 ton |
8.460 ton |
Bøgetræ |
|
267.00 ton |
|
267.000 ton |
Stål |
22.900 ton |
4.300 ton |
46.500 ton |
73.700 ton |
Plast |
3.500 ton |
1.100 ton |
590 ton |
5.190 ton |
Lim |
200 ton |
2.200 ton |
|
2.400 ton |
Lak |
2.900 ton |
4.300 ton |
|
7.200 ton |
Lak og maling |
|
|
1.800 ton |
1.800 ton |
Fortynder |
1.200 ton |
|
|
1.200 ton |
Energi |
El |
60.760 MWh |
222.000 MWh |
50.000 MWh |
330 GWh |
Naturgas |
5.200 ton |
540 ton |
8.200 ton |
14.000 ton |
Diesel og fuelolie |
220 ton |
|
3.200 ton |
3.420 ton |
Benzin |
455 ton |
|
|
455 ton |
Affald |
Træaffald |
7.800 ton |
89.000 ton |
|
97.000 ton |
Stålaffald |
|
|
8.200 ton |
8.200 ton |
Lak og limrester |
200 ton |
650 ton |
200 ton |
1.000 ton |
Andet affald |
2.700 ton |
|
|
2.700 ton |
Vandforbruget til den samlede produktion er ikke opgjort, da vandforbruget kun var oplyst for fremstilling af reoler. Vandforbruget til reolerne udgør omkring 50.000 m³.
B.4 Ressourceopgørelse
Livsforløbet for møbler repræsenteret ved de 3 valgte møbletyper kan illustreres som vist i Figur B.3.
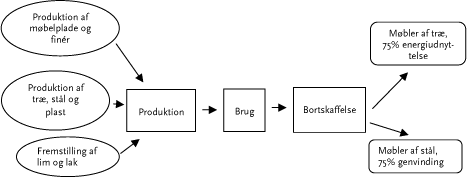
Figur B.3 Livsforløbet for de 3 valgte møbeltyper
De mængder materialer, der anvendes i produktionen, er vist i Tabel B.10. Ligeledes er der i denne tabel angivet affaldsmængder fra produktionen.
I det efterfølgende fokuseres der på materialestrømmene ind i produktionen – fra råstofferne udvindes til materialerne anvendes i produktionen. Dernæst opstilles en opgørelse over de samlede
affaldsmængder og en energibalance.
B.4.1 Lak og lim
Fra projektet om udpegning og kortlægning af industriområder (Pommer et al., 2003) er det opgjort, hvilke hovedbestanddele lak og lim består af, samt hvilke affaldsmængder der forekommer. I Tabel
B.11 er vist den kortlagte mængde lak og i Tabel B.12 er vist den kortlagte mængde lim.
Tabel B.11 Affald fra brug af lak i møbelindustrien
Laktype |
Årligt
forbrug |
Affalds-
mængde |
Typiske komponenter |
Syrehærdende lak |
3.150 ton |
315 ton |
Bindemiddel 1/3, opløsningsmidler 2/3 |
Celluloselak |
900 ton |
90 ton |
Bindemiddel ¼, opløsningsmidler ¾ |
Polyurethanlak |
100 ton |
10 ton |
Polyoler og isocyanater ca. ½, opløsningsmidler ½ |
UV-hærdende lak |
1.050 ton |
50 ton |
Præplymere acrylater, monomer acrylat og initiator |
Vandbaseret lak |
1.600 ton |
160 ton |
Acryldispersioner, glycoler og vand |
Fortyndere |
2.000 ton |
200 ton |
opløsningsmidler |
I alt |
8.800 ton |
825 ton |
|
Tabel B.12 Affaldsmængder fra forbrug af lim til møbelfremstilling
Produktgruppe |
Årligt
forbrug |
Affalds-
mængde |
Typiske komponenter |
Polymerdispersioner og emulsioner |
3.000 ton |
150 ton |
2/3 polyvinylacetat, 1/3 vand |
Hotmelt inkl. fugt-hærdende typer |
1.000 ton |
50 ton |
Co-polymere af vinylacatat, polyamid og/eller urethan |
Reaktiv (polymeriserende) systemer |
3.000 ton |
150 ton |
Ureaformaldehyd-præpolymere |
I alt |
7.000 ton |
350 ton |
|
Ud fra en samlet opgørelse over materiale- og energiforbrug samt fremkomsten af affald for de 3 typeprodukter er mængden af lak- og limaffald opgjort til omkring 1.000 ton (Tabel B.10). Dette stemmer
overens med de mængder, der er opgjort ud fra kortlægning af affaldsmængderne.
Ud fra Tabel B.11 og Tabel B12 kan de samlede mængder forbrug og affaldsmængder på typer af komponenter i lak og lim opgøres. Disse er vist i Tabel B.13.
Tabel B.13 Komponenter i lak og lim
Komponent |
I affaldet pr. år |
Årligt forbrug |
Bindemiddel |
130 ton |
1.275 ton |
Polyol og isocyanater |
5 ton |
50 ton |
Acrylater |
50 ton |
1.050 ton |
Acryl og vinylacatat co-polymere |
230 ton |
3.800 ton |
Ureaformaldehyd-præpolymer |
150 ton |
3.000 ton |
Opløsningsmidler |
480 ton |
4.800 ton |
Vand |
130 ton |
1.800 ton |
I alt |
1.175 ton |
15.775 ton |
Som det ses af Tabel B.13, udgør det samlede forbrug omkring 14.000 ton excl. vand. Heraf er 1/3 opløsningsmidler og den resterende del mere eller mindre komplekse kemiske forbindelser.
Opløsningsmidlerne og de kemiske forbindelser antages fremstillet i udlandet. Opløsningsmidlerne vil typisk være baseret på råolieprodukter. De øvrige vil have en blandet oprindelse – dels baseret på
råolieprodukter og dels på andre basiskemikalier så som cellulose, kvælstofforbindelser og organiske forbindelser.
Da der ikke haves specifikke oplysninger om råvareforbrug, energiforbrug og affaldsmængder for fremstilling af disse kemikalier anslås forbruget som anført i Tabel B.14.
Tabel B.14 Ressourcer og affald til fremstilling af lim og lak
Type |
Estimat for |
Materialeforbrug |
Energiforbrug |
Energiindhold |
Affaldsmængde |
Opløsningsmidler, pr. 1 ton |
1,05 ton råolie(1) |
80 GJ(2) |
25 GJ(2) |
0,05 ton(1) |
Råoliebaserede kemikalier, pr. 1 ton |
1,05 ton råolie(1) |
14 GJ(2) |
30 GJ(2) |
0,05 ton(1) |
Ikke råoliebaserede kemikalier, pr. 1 ton |
Ikke opgjort |
24 GJ(3) |
5 GJ(3) |
ikke opgjort |
Pr. 4.800 ton opløsningsmidler |
5.040 ton |
384.000 GJ |
120.000 GJ |
240 ton |
Pr. 4.600 ton råoliebaserede kemikalier |
4.830 ton |
64.400 GJ |
138.000 GJ |
230 ton |
Pr. 4.600 ton ikke råoliebaserede kemikalier |
Ikke opgjort |
110.400 GJ |
23.000 GJ |
Ikke opgjort |
Samlet estimat |
10.000 ton |
560.000 GJ |
280.000 GJ |
500 ton |
1) Materialemængden er taget fra Pommer et al., 2001 med en anslået affaldsmængde på 5 %.
2) Energiforbruget er taget fra Pommer et al., 2001 for opløsningmiddelbaserede malinger
3) Energiforbruget er taget fra Pommer et al., 2001 for vandbaserede malinger
B.4.2 Møbelplade og finér
Fremstilling af en møbelplade, MDF, er ikke beskrevet i rapporten om Montana-reolen. Data er derimod givet i brancheanalysen - side 55 i Kvist et al., 2000.
De fleste opgørelser for materialeforbrug tager udgangspunkt i antal m³ plade. Den gennemsnitlige massefylde for en MDF-plade er 650 kg/m³ med en variation fra 600 til 700 kg/m³.
Produktionen af MDF-plader omfatter en forarbejdning af træflis, der koges, defibreres, tilsættes lim og voks og tørres. Det oplyses i brancheanalysen, at resttræ og kasserede produkter forbrændes på
virksomheden, hvor energien udnyttes. Der er således ingen opgørelser af affaldsmængder, men alene en opgørelse af materiale- og energiforbrug. Disse er vist i Tabel B.15.
I Materiale- og energiforbrug til MDF-plader er estimeret en fordeling af det anvendte træ på anvendelserne ”i produktet”, til ”energiudnyttelse” og som ”overskudstræ”. Oplysninger om overskudstræ
stammer fra brancheanalysen. Mængden af træ i produktet er beregnet ud fra antagelsen om, at 1 ton MDF-plade indeholder lim, urea og andre tilsætningsstoffer samt træ. Mængden af træ til
energiudnyttelse er differencen ”samlet mængde træ” – ”træ i produktet og overskudstræ”.
Tabel B.15 Materiale- og energiforbrug til MDF-plader
|
Forbrug til
fremstilling af 1 m³ MDF-plade |
Forbrug til
fremstilling af 1 ton MDF-plade |
Fremstilling af
206.000 ton MDF-plade |
Materialer |
Bøgetræ |
1,42 ton |
2,18 ton |
450.000 ton |
- heraf i produktet |
|
737 kg |
152.000 ton |
- heraf til energiudnyttelse |
|
1.146 kg |
237.000 ton |
Melamin-ureaformaldehydlim |
150 kg |
230 kg |
47.400 ton |
Urea |
8,47 kg |
13,0 kg |
2.680 ton |
Ammoniumsulfat |
1,71 kg |
2,6 kg |
540 ton |
Vokstørstof |
11,55 kg |
17,8 kg |
3.670 ton |
Vand |
365 kg |
561 kg |
116.000 ton |
Energi |
Fuelolie |
11,9 liter |
18,3 liter |
3.800 m³ |
Elektricitet |
271,8 kWh |
418 kWh |
86.100 MWh |
Overskudstræ |
193 kg |
297 kg |
61.000 ton |
Fremstilling af finér er medtaget i brancheanalysen. Her findes en opgørelse af materiale- og energiforbrug for bøgefinér. Massefylde for finér er gennemsnitligt 500 kg/m³ med en variation fra 450 til 550
kg/m³. Opgørelsen er vist i Tabel B.16.
Her er ligeledes ikke i brancheanalysen opgiver, hvor stor en andel af træet der indgår i selve produktet, og hvor stor en del der anvendes som energikilde. Mængden, der anvendes som energikilde, er
beregnet ud fra antagelsen om, at der indgår 1 ton træ i 1 ton finér og oplysningen om mængden af resttræ.
Tabel B.16 Materiale- og energiforbrug til finér-fremstilling
|
Forbrug til fremstil-
ling af 1 m³ finér |
Forbrug til fremstil-
ling af 1 ton finér |
Fremstilling af
8.460 ton finér |
Materialer |
Bøgetræ |
1,46 ton |
2,91 ton |
24.600 ton |
- heraf i produktet |
|
1, 0 ton |
8.460 ton |
- heraf til energiudnyttelse |
|
1,91 ton |
14.080 ton |
Lim |
0,041 liter |
0,082 liter |
0,690 m³ |
Smøreolie |
0,082 liter |
0,16 liter |
1,350 m³ |
Energi |
Elektricitet |
362 kWh |
724 kWh |
6.125 MWh |
Fuelolie |
24,5 kg |
49 kg |
415 ton |
Træ |
838 kg |
1,68 ton |
14.200 ton |
Affald |
Slagge og aske |
8,38 kg |
16,7 kg |
141 ton |
Resttræ |
122 kg |
244 kg |
2.060 ton |
Ud fra oplysningerne om ressourceforbrug til finér og møbelplader er det samlede forbrug til fremstilling opgjort på hovedkomponenter og vist i Tabel B.17.
Ved skovning af træ anvendes energi, som ikke er medtaget i Tabel B.15 og Tabel B16. Den energimængde, der forbruges ved skovning, udgør 0,52 kg benzin og 2,06 kg diesel pr. ton træ og udgør for det
samlede forbrug af træ 273 ton benzin og 1.080 ton dieselolie. Dette energiforbrug er medtaget i Tabel B.17.
Opgørelsen for lim og øvrige hjælpestoffer føres tilbage til råstofforbrug ved at anvende opgørelserne fra Tabel B.14 med hensyn til lim.
Tabel B.17 Ressourcer til Møbelplader og Finér
Materialer |
|
Bøgetræ |
475.000 ton |
Lim, 48.000 ton |
|
- råoliebaserede kemikalier |
50.400 ton råolie |
Øvrige hjælpestoffer, 7.000 ton |
|
- ikke råoliebaserede kemikalier |
Ikke opgjort |
Energi |
|
Elektricitet |
92.225 MWh |
Fuelolie (1) |
4.915 ton |
Benzin |
273 ton |
Overskudstræ |
75.000 ton |
Primær energi til fremstilling af råvarer til lim og øvrige hjælpestoffer |
840.000 GJ |
Affald |
|
Slagge og akse |
141 ton |
Andet affald |
2.400 ton |
Resttræ |
2.060 ton |
|
|
(1) Fuelolie antages at have en massefylde på 0,90 (Hansen et al., 2002)
Energiindholdet i materialerne, der forbruges, udgør:
- Bøgetræ:
Energiindhold pr. 1 ton: 18 GJ/ton
Af træforbruget på 475.000 ton anvendes 160.500 ton i produkterne, 251.000 ton til energiudnyttelse og 63.000 ton til andre formål
Energiindholdet i det træ, der findes i produkterne, udgør 160.500 ton × 18 GJ/ton = 2.900.000 GJ
Energiindholdet i det træ, der bruges som energikilde i produktionen, udgør 251.000 ton × 18 GJ = 4.520.000 GJ
- Råoliebaserede kemikalier
Energiindhold pr. 1 ton: 30 GJ/ton
Energiindhold i 48.000 ton: 1.440.000 GJ
- Ikke råoliebaserede kemikalier
Energiindhold i 1 ton: 5 GJ/ton
Energiindhold i 7.000 ton: 35.000 GJ
Det samlede energiindhold i de forbrugte materialer til fremstilling af plader og finér er 4.375.000 GJ.
Træmængden, der bruges som energikilde i produktionen, opgøres som ét materialeforbrug.
B.4.3 Træ, stål og plast
B.4.3.1 Træ
Fældning af træ af forskellige sorter er medtaget i brancheanalysens enhedsprocesser. Her er medtaget 4 almindelige danske træsorter og energiforbruget ved skovningen er opgjort.
Til skovning af 1 m³ træ bruges typisk 0,34 kg benzin og 1,34 kg dieselolie. Da træet har en massefylde på omkring 0,65 ton/m³, vil forbruget pr. ton blive 0,52 kg benzin og 2,06 kg dieselolie. Der er ikke
anført nogle affaldsmængder, men det antages heller ikke, at der forekommer affald af væsentlig betydning.
For forbruget på 267.000 ton træ forbruges følgende energimængder til skovning:
- 91 ton benzin
- 550 ton dieselolie
De anførte energiressourcer skal medregnes ved forbrug af træ.
Energiindholdet i træet, der følger med materialet, sættes til 18 MJ/kg, hvilket for den samlede mængde svarer til 4.800.000 GJ.
B.4.3.2 Stål
Stål til fremstilling af møbler stiller ikke væsentlige kvalitetskrav, som ikke kan honoreres ved anvendelse af oparbejdet stål.
Til fremstilling af 1 kg oparbejdet stål anvendes 1,2 kg stålskrot samt små mængder andre metaller (SAEFL, 1998).
Her tages derfor udgangspunkt i stål, der udgøres af 80% oparbejdet skrot og 20% nyt stål.
Forbrug af materialer og primær energi samt fremkomne affaldsmængder er opgjort for stålplader i. Data er hentet fra SAEFL (1998) Life Cycle Inventories for Packaging og vist i Tabel B.18. I datasættet
fra SAEFL er angivet en række meget små materialeforbrug i form af hjælpestoffer. Disse er ikke medtaget her.
Tabel B.18 Ressource og energiforbrug til fremstilling af stål
|
1 ton primært
stål |
1 ton sekundært
stål |
1 ton, 80%
sekundært og 20% primært stål |
73.700 ton,
80% sekundært og 20 % pri- mært stål |
Komponent |
Jernmalm |
2,4 ton |
|
0,48 ton |
35.400 ton |
Skrot |
0,1 ton |
1,2 ton |
0,98 ton |
72.200 ton |
Kalk |
0,28 ton |
|
0,06 ton |
4.130 ton |
Primær energi |
35,7 GJ |
17,9 GJ |
21,5 GJ |
1.582.000 GJ |
Affald |
Metal og kemikalieaffald |
42,1 kg |
23 kg |
26,8 kg |
1.980 ton |
Slagge og aske |
476 kg |
80 kg |
102 kg |
7.500 ton |
B.4.3.3 Plast
For de mest almindelige plasttyper – PE og PP – er de grundlæggende LCA-data meget ens. Her er det valgt at anvende data for polypropylen (PP). Data er hentet fra SAEFL (1998) Life Cycle
Inventories for Packaging. I datasættet fra SAEFL er angivet en række meget små materialeforbrug i form af hjælpestoffer. Disse er ikke medtaget her.
Tabel B.19 Ressource og energiforbrug til fremstilling af plast
|
1 ton plast
(PP-granulat) |
5.190 ton plast
(PP-granulat) |
Komponent |
Naturgas |
250 m³ |
1.300.000 m³ |
Råolie |
830 kg |
4.310 ton |
Primær energi |
32,3 GJ |
167.600 GJ |
Energi indhold |
47,7 GJ |
248.000 GJ |
Affald |
Ikke specificeret affald |
31,2 kg |
162 ton |
B.4.4 Samlet materialeforbrug
I de forrige afsnit er opgjort, hvilke råmaterialer der forbruges til fremstilling af materialer til møbelproduktionen. Disse er samlet i Tabel B.20.
Tabel B.20 Forbrug af råmaterialer til møbelfremstilling
Råmaterialer |
Mængde |
Lim og lak |
- råolie |
10.000 ton |
Møbelplader og finér |
- træ |
475.000 ton |
- råolie |
50.400 ton |
- resttræ til andre formål |
- 63.000 ton |
Træ |
- træ |
267.000 ton |
Stål |
- skrot |
72.200 ton |
- jernmalm |
35.400 ton |
- kalk |
4.130 ton |
Plast |
- naturgas |
1.300.000 m³ |
Til fremstilling af 1 ton råjern medgår 2,85 ton jernmalm (SAEFL, 1998). Forbruget af jernmalm på 35.400 ton svarer således til 12.400 ton råjern, hvilket i denne forbindelse sidestilles ressourcemæssigt
med jernskrot. Det samlede forbrug af skrot er derfor 72.200 ton + 12.400 ton = 84.600 ton.
I kortlægningen er der anført 2 væsentlige vandforbrug – det ene ved fremstilling af reoler på omkring 50.000 m³ og det andet ved fremstilling af MDF-plader på 116.000 m³. Det samlede vandforbrug
estimeres i omkring 200.000 m³.
Samles de forbrug af ressourcer, der er nævnt i Tabel B20, vil der samlede forbrug blive:
Træ: |
679.000 ton |
Jernskrot: |
84.600 ton |
Kalk: |
4.310 ton |
Råolie: |
65.000 ton |
Naturgas: |
1.300.000 m³ svarende til 1.560 ton |
Vand |
200.000 m³ |
B.4.5 Råstofforbrug
For at udvinde de materialer, der er nævnt i afsnit B.4.4, skal udvindes nogle råstoffer. Mængden af disse er søgt opgjort ud fra følgende forudsætninger:
For træ er angivet 1 kg/kg i UMIP. Dette er i overensstemmelse med angivelser i SAELF (1998) for skovning af træ til papirproduktion. I SigmaPro er der dog anført, at der pr. kg træ skoves 3,8 kg råtræ.
I rapporten Lifecycle analyses of selected packaging materials (Tillman et al., 1991) er der redegjort for skovning, afbarkning og opsavning af træ. Her anføres det, at der er en udnyttelse af råstoffet træ på
ca. 50%, hvilket svarer til, at der anvendes 2 kg træ pr. kg opskåret træ. I det følgende anvendes dette nøgletal.
For jern er der opgjort, at der som råstof anvendes jernmalm samt kalk. I UMIP-databasen er angivet, at råstofforbruget er 0,69 kg/kg jern. Her er ikke nærmere givet detaljer for processen. Det er der
derimod i SAELF, hvor det er angivet, at der anvendes 2,4 kg jernmalm og 0,28 kg kalk pr. kg produceret råjern. Det vælges derfor at anvende angivelserne i SAELF. Det opgjorte materialeforbrug af kalk
antages at modsvare angivelserne i SAELF.
For forbruget af olie regnes med et tab i råstofudvindingen på 10% som anført i UMIP, således at udvinding af olie svarer til 1,1 kg råolie.
Der er ikke fundet data for naturgas. Ud fra en konservativ betragtning regnes med et tab på 5 %.
Det samlede forbrug af råstoffer er estimeret i Tabel B.21.
En del af stålet oparbejdes, hvorfor der kun vil være behov for udvinding af råstoffer til nettoforbruget. I afsnit B4.8 er det opgjort, at der oparbejdes 50.780 ton stål, som modsvarer et forbrug af jern på
60.936 ton. Nettoforbruget af jern er derfor 23.660 ton.
Tabel B.21 Estimering af råstofforbrug
Materiale |
Mængde |
Råstofforbrug pr. kg
materiale |
Samlet råstofforbrug |
Træ |
679.000 ton |
2 kg/kg |
1.358.000 ton |
Jern |
23.660 ton |
2,4 kg/kg |
56.800 ton |
Kalk |
|
0,28 kg/kg |
6.600 ton |
Olie |
65.000 ton |
1,1 kg/kg |
71.500 ton |
Naturgas |
1.560 ton |
1,05 kg/kg |
1.600 ton |
I alt |
1.494.500 ton |
Som det ses af Tabel B.21, ligger råstofforbruget på i størrelsesordnen 1,5 mio. ton.
B.4.6 Energi
Under opgørelsen af materialer og energiforbrug for de enkelte materialer til møbelproduktion er energien dels opgjort som primær energi ved udvinding af ressourcer, energi brugt til processer og
energiindhold i materialer. Disse opgørelser er omregnet til primær energi og til energi i materialer og vist i Tabel B.22.
Tabel B.22 Samlet opgørelse af energiforbrug
|
Forbrugt energi |
Omregning |
Primær energi |
Mængde |
Enhed |
Faktor |
Enhed |
Mængde |
Enhed |
Energi til råstoffer og halvfabrikata |
|
|
|
|
|
|
Lak og lim |
|
|
|
|
560 |
TJ |
Møbelplader og finér |
|
|
|
|
|
|
Elektricitet |
92.225 |
MWh |
9 |
MJ/kWh |
830 |
TJ |
Fuelolie |
4.915 |
ton |
42 |
GJ/ton |
206 |
TJ |
Benzin |
273 |
ton |
43 |
GJ/ton |
12 |
TJ |
Overskudstræ |
75.000 |
ton |
18 |
GJ/ton |
1.350 |
TJ |
Til lim og hjælpestoffer |
|
|
|
|
840 |
TJ |
Træ |
|
|
|
|
|
|
Benzin |
91 |
ton |
43 |
GJ/ton |
4 |
TJ |
Dieselolie |
550 |
ton |
42 |
GJ/ton |
23 |
TJ |
Stål |
|
|
|
|
1.582 |
TJ |
Plast |
|
|
|
|
168 |
TJ |
Samlet for råstoffer og materialer |
|
|
|
|
5.575 |
TJ |
|
|
|
|
|
|
|
Energi-indhold i materialer |
|
|
|
|
|
|
Lak og lim |
|
|
|
|
280 |
TJ |
Møbelplader og finér |
|
|
|
|
4.375 |
TJ |
Træ |
|
|
|
|
4.800 |
TJ |
Stål |
|
|
|
|
0 |
TJ |
Plast |
|
|
|
|
248 |
TJ |
Samlet energi-indhold |
|
|
|
|
9.703 |
TJ |
|
|
|
|
|
|
|
Energi til produktion |
|
|
|
|
|
|
Elektricitet |
330 |
GWh |
9 |
MJ/kWh |
2.970 |
TJ |
Naturgas |
14.000 |
ton |
48,5 |
GJ/ton |
679 |
TJ |
Diesel og fuelolie |
3420 |
ton |
42 |
GJ/ton |
144 |
TJ |
Benzin |
455 |
ton |
43 |
GJ/ton |
20 |
TJ |
Samlet energiforbrug til produktion |
|
|
|
|
3.812 |
TJ |
|
|
|
|
|
|
|
Brutto-forbrug |
473.000 |
ton |
|
|
19.090 |
TJ |
Bruttoforbrug pr. ton møbler |
|
|
|
|
40,36 |
GJ |
Opgørelsen opstilles ud fra følgende forudsætninger:
- Det antages, at energiforbruget ved udvinding af råstoffer er opgjort som primær energi.
- Dertil kommer opgørelse af energiindhold i materialer.
- Elforbrug fra produktion og andet omregnes til primær energi: 1 kWh × 9 = MJ.
- Energiindholdet i energiressourcer (olie, gas etc.) omregnes efter nedre brændværdi.
- Energi udviklet ved forbrænding er primær energi.
- Energi, der medgår til oparbejdning af materialer, skal medregnes.
- Samlet energiregnskab opstilles efter: Energiindhold i materialer + energiforbrug - udviklet energi = nettoforbrug.
B.4.7 Samlede affaldsmængder
Affald fremkommer ved udvinding af råstoffer og fremstilling af halvfabrikata, ved produktion af produkter og ved bortskaffelse af produkterne. Affald er tab af ressourcer, såfremt der ikke sker genvinding.
Affald fra udvinding af råstoffer og fremstilling af halvfabrikata har været vanskeligt at kortlægge på grund af sparsomme oplysninger. I det følgende er de tilgængelige oplysninger samlet.
Tabel B.23 Oversigt over affaldsmængder
Art |
Mængde |
Fra råstofudvinding og halvfabrikata |
Fremstilling af lak og lim |
500 ton |
Plader og finér |
|
- slagge og aske |
141 ton |
- resttræ, - er modregnet i forbrug |
|
- andet affald |
2.400 ton |
Træ – intet opgjort |
|
Stål |
|
- metal og kemikalieaffald |
1.980 ton |
- slagge og aske |
7.500 ton |
Plast |
|
-ikke specificeret affald |
162 ton |
Fra produktionen |
Træ-affald, er modregnet i forbrug |
|
Stålaffald, er modregnet i forbrug |
|
Lak- og limrester |
1.000 ton |
Andet affald |
2.700 ton |
Kasserede produkter |
- Af massivt træ (borde) |
190.000 ton |
- af plade og finér (reoler) |
240.000 ton |
- af stål (stole) 75% oparbejdning |
11.750 ton |
I opgørelsen er medregnet affald fra udvinding og oparbejdning af stål og plast, men ikke for de mængder råolie, naturgas og kul der dels indgår som basismaterialer og dels forbruges som energiressourcer.
Træ som råstof til fremstilling af halvfabrikata (MDF-plader og finér), der ikke findes i produkterne brændes, og energien udnyttes i produktionen. Træaffald forekommer derfor ikke.
B.4.8 Oparbejdede materialer og genvundet energi
B.4.8.1 Stål
Der anvendes 73.700 ton stål, primært til produktion af stålmøbler og en mindre del til skruer og lignende til de andre møbeltyper. Det antages, at det anvendte stål indsamles og oparbejdes. Ved indsamling
sættes det samlede tab til 25% svarende til en oparbejdet mængde på 55.275 ton.
Dertil kommer, at der fremkommer stålaffald ved fremstilling af stålmøbler i en mængde på 8.200 ton. Her antages det, at 100% oparbejdes.
Den samlede mængde stål, der oparbejdes, er således 63.475 ton. Ved oparbejdningen antages et tab på 20%, således at den mængde materiale, der kan genbruges udgør 50.780 ton.
Til oparbejdningen anvendes energi. Til omsmeltning af stål anvendes 20 GJ/ton (Pommer et al., 2001). Det samlede primære energiforbrug bliver derfor:
63.475 ton × 20 GJ = 1.270 TJ
Når en vis mængde materiale kan genbruges, spares dels selve råstoffet, men også den energimængde, der medgår til udvinding af råstoffet.
Til fremstilling af sekundært stål anvendes, se Tabel B.18, 1,2 ton stålskrot og 17,9 GJ primær energi pr. ton. De sparede ressourcer udgør derfor 60,936 ton skrot og 909 TJ.
Der vil i alt være en besparelse af ressourcer på 60.936 ton skrot og et netto-energiforbrug på 361 TJ.
B.4.8.2 Genvundet energi
Det antages, at møbel af møbelplader og massivt træ bortskaffes ved forbrænding med energigenvinding.
Træbaserede møbler udgør i alt 430.000 ton, og det antages, at 75% af energiindholdet kan udnyttes.
Den udviklede energi udgør:
430.000 ton × 0,75 × 18 GJ/ton = 5.805 TJ.
Fra produktionen af lim fremkommer affald, der naturligt vil bortskaffes ved forbrænding. Da det antages, at ikke alt affald indsamles, antages den samlede energiudnyttelse at være 50%.
Den udviklede energi udgør:
500 ton × 0,5 × 28 GJ/ton = 7 TJ
Fra produktionen fremkommer en del affaldsfraktioner, der vil blive bortskaffet ved forbrænding. Disse er:
- affaldstræ, 97.000 ton, hvor energiudnyttelsen antages at være 75 %
- lak og limaffald, 1.000 ton, hvor energiudnyttelsen antages at være 50%
- andet affald, 2.700 ton, hvor energiudnyttelsen antages at være 50%
Den udviklede energi fra disse affaldsfraktioner vil være:
97.000 ton × 0,75 18GJ/ton + 1.000 ton × 0,5 × 28 GJ/ton + 2.700 ton × 0,5 × 25 GJ/ton = 1.357 TJ
Den samlede energi fra affaldsforbrænding vil være 7.169 TJ.
B.5 Ressourceforbrug
B.5.1 Produktet
Produktet 1 ton møbler er i denne sammenhæng repræsenteret ved
- 50 % produkter, bestående af møbelplader og finér
- 40% produkter bestående af massivt træ og
- 10% produkter, hovedsagelig bestående af stål.
Materialerne i produktet er vist i Tabel B.24.
Tabel B.24 Materialeindhold i et gennemsnitsmøbel
|
Produkter af møbelplade |
Produkter af massivt træ |
Møbler af stål |
Materialer pr. ton møbel |
50 % |
40 % |
10 % |
|
Møbelplade |
105,1 kg |
|
|
429 kg |
Finér |
1,0 kg |
32,9 kg |
1,1 kg |
393 kg |
Bøg |
11,7 kg |
|
|
48 kg |
Stål |
1,8 kg |
0,8 kg |
6,5 kg |
98 kg |
Plast |
1,5 kg |
0,2 kg |
0,1 kg |
10 kg |
Lak og lim |
0,7 kg |
1,2 kg |
0,3 kg |
20 kg |
Fortynder |
0,6 kg |
|
|
2 kg |
Samlet vægt |
122,4 kg |
35,1 kg |
8,0 kg |
|
Omregnes disse materialer til ressourcetræk i mPR, anvendes følgende antagelser:
- møbelplade, finér og bøg regnes som træ, en fornyelig ressource, hvor mPR=0
- Stål regnes som maskinstål, for hvilket gælder at 1 kg = 0,130 mPR
- Plast regnes til at bestå af polyethylen, for hvilket gælder et ressourcetræk på 0,02 mPR råolie og 0,02 mPR naturgas svarende til 0,04 mPR/kg
- Lim, lak og fortynder regnes at stamme fra råolie med et ressourcetræ på 0,04 mPR/kg
På baggrund af ovenstående kan ressourceindholdet i 1 ton møbler beregnes til:
98 kg × 0,130 mPR/kg + 10 kg × 0,04 mPR/kg + 22 kg × 0,04 mPR/kg = 14,02 mPR pr. ton.
B.5.2 Materialer
Omregning af opgørelsen af det samlede materialeforbrug i Tabel B.20 til forbrug af ressourcer er vist i Tabel B.25.
Tabel B.25 Materialeforbrug opgjort som ressourcer
Materiale |
Forbrug pr.
473.000 ton |
Forbrug pr. ton |
Ressource-
forbrug mPR/kg |
Ressource-
forbug mPR |
Træ |
679.000 ton |
1.435 kg |
0 mPR/ kg |
0 mPR |
Jern |
86.400 ton |
183 kg |
0,08 mPR/kg |
14,64 mPR |
Kalk |
4.310 ton |
9 kg |
0 mPR/kg |
0 mPR |
Råolie |
65.000 ton |
137 kg |
0,04 mPR/kg |
5,48 mPR |
Naturgas * |
1.566 ton |
3 kg |
0,06 mPR/kg |
0,18 mPR |
I alt |
|
1.767 kg |
|
20,30 mPR |
* Naturgasforbruget er omregnet efter 1.000 m³ = 1.205 ton
B.5.3 Energi
Energiforbruget til hele produktets livsforløb er opgjort i Tabel B.22. Nøgletal herfra er vist i Tabel B.26.
Tabel B.26 Nøgletal for energiforbrug
|
Forbrug pr. 473.000 ton |
Forbrug pr. ton |
Energi til råstoffer og halvfabrikata |
5.575 TJ |
11,79 GJ |
Energiindhold i materialer |
9.703 TJ |
20,51 GJ |
Energi til produktion |
3.812 TJ |
8,06 GJ |
Brutto-energiforbrug |
19.090 TJ |
40,36 GJ |
Energiudvikling ved affaldsbehandling |
7.169 TJ |
15.16 GJ |
Energiforbrug ved oparbejdning |
361 TJ |
0,76 GJ |
Netto-energiforbrug |
12.282 TJ |
25,97 GJ |
Brutto-energiforbruget på 40,36 GJ pr. ton møbler svarer i ressourcer til 39,38 mPR baseret på olie.
Netto-energiforbruget på 25,97 GJ pr. ton møbler svarer i ressourcer til 25,34 mPR baseret på olie.
B.5.4 Godskrivning
Den mængde jernskrot, der spares ved oparbejdning af skrotaffald og kasserede møbler, udgør 60.936 ton svarende til 127,75 kg pr. ton møbler.
For jern er der et ressourcetræk på 0,08 mPR pr. kg. Godskrivningen for jernskrot udgør derfor 10,22 mPR.
Som opgjort i afsnit B.5.3 udgør brutto-energiforbruget 40,36 GJ pr. ton møbler svarende til 39,38 mPR. Netto-energiforbruget udgør 25,97 GJ pr. ton møbler svarende til 25,34 mPR.
Besparelsen i energiressourcer kan derfor opgøres til 14,39 GJ pr. ton eller 14,04 mPR.
C Elektriske og elektroniske komponenter
C.1 Introduktion
I Danmark produceres en række elektriske og elektroniske komponenter. I affaldskortlægning af udvalgte brancher (Pommer et al., 2003) er affaldsmængderne fra danske elektronikmontagevirksomheder,
samt komponentfremstillere med mindre end 200 ansatte kortlagt.
Affaldsproduktionen blev identificeret til at stamme fra følgende virksomheder:
- Elektronikmontagevirksomheder, som producerer bestykkede printkort, samt eventuelt færdige produkter
- Komponentfremstillingsvirksomheder, som fremstiller
- transformere, spoler mv.
- komponenter baseret på keramiske bæremedier (hybridkredse, trimmere, pifiltre etc.)
- effektmodstande
- kondensatorer
- integrerede kredse fremstillet af udenlandske underleverandører, men som testes i Danmark
Affaldsundersøgelsen viste, at mængden af produktionsaffald fra virksomhederne var lille i forhold til gennemsnittet for fremstillingsvirksomheder. Der blev generelt konstateret en høj genanvendelse af de
metalholdige fraktioner i affaldet.
C.2 Produktvalg
Ved udvælgelse af produkter, er der taget udgangspunkt i en tidligere affaldskortlægning. Denne kortlægning omfattede affaldsproduktionen fra elektronikmontage virksomheder og komponentfremstillere
med mindre end 200 ansatte er undersøgt. For disse produkter er ressourceeffektivteten vurderet.
Et typisk elektronikprodukt, som fremstilles i mindre serier af elektronikmontagevirksomheder, kan fx være ladeapparater, laboratoriestrømforsyninger og -måleudstyr, specialiseret audioudstyr etc. Denne
type udstyr består af et kabinet med påmonterede printkort og eventuelle løse komponenter monteret direkte i kabinettet som fx transformere og monitorer, se Figur C.1.
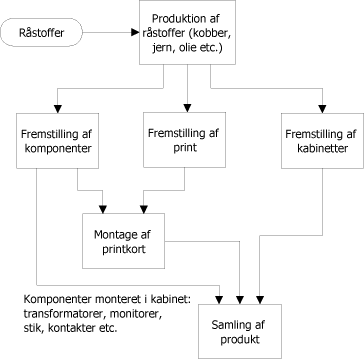
Figur C.1 Fremstilling af typiske elektroniske produkter
Det vil være meget vanskeligt at foretage en vurdering af ressourceeffektiviteten for alle produkter produceret af elektronikmontagevirksomheder med mindre end 200 ansatte, da der kun haves få data
vedrørende produkterne, og da disse varierer i mængde, størrelse og udformning fra uge til uge afhængigt af, hvilke ordrer elektronikmontagevirksomhederne modtager.
Der indgår imidlertid bestykkede printkort i alle produkter, hvorfor det er relevant at vurdere ressourceeffektiviteten for produktionen af de printkort, der produceres af elektronikmontagevirksomhederne.
Komponentfremstillerne i Danmark fremstiller en række forskellige komponenter som vist i Figur C.1.
Ud fra supplerende oplysninger indhentet fra komponentfremstillere, som tidligere blev kontaktet og besøgt i affaldskortlægningen, se Tabel C.1, udgør transformere langt den største del af komponenternes
samlede masse med ca. 96%, hvorfor det vil være relevant at udvælge denne komponent til at vurdere ressourceeffektiviteten for.
Tabel C.1 Mængder af producerede samt testede komponenter i Danmark i virksomheder med mindre end 200 ansatte
Komponenter |
Ton |
% |
Sum passive komponenter + keramisk monterede hybridkredse |
210 |
3,5 |
Integrerede kredse (produceres i udland men testes i Danmark) |
28 |
0,5 |
Transformere |
5500 |
96 |
De valgte produkter indeholder begge væsentlige mængder kobber og vil derfor delvis eller fuldstændigt blive oparbejdet via udenlandske kobbersmelteværker. Det er derfor af væsentlig betydning, hvilke
genanvendelsesgrader der er for kobber og andre værdifulde metaller i produkterne, når mængden af ressourcer, som genvindes, skal beregnes.
Der er indhentet data for genanvendelsesprocenter af metaller for de to mest nærliggende aftagere for affald fra danske kobberholdige produkter. Data er skaffet ved kontakt til Boliden samt oplysninger for
Norddeutsche affinerie/Hüttenwerke Kaiser (Kreibe, 1996).
Tabel C.2 Genanvendelsesprocenter for metaller
Metal |
Boliden % udbytte |
Norddeutsche
affinerie % udbytte |
Kobber (Cu) |
98 |
>95 |
Platin (Pt) |
0 |
>90 |
Paladium (Pd) |
98 |
>90 |
Guld (Au) |
98 |
>90 |
Sølv (Ag) |
>90 |
>90 |
Nikkel (Ni) |
80 |
>70 |
Bismut (Bi) |
0 |
|
Tin (Sn) |
0-20 |
45 |
Antimon (Sb) |
0 |
0? |
Bly (Pb) |
80 |
80 |
Zink (Zn) |
85 |
|
C.3 Kortlægning af printkort
C.3.1 Materiale- og energistrømme
I det følgende er vist en kortlægning for fremstilling af bestykkede printkort i elektronikmontagevirksomheder med mindre end 200 ansatte. Livscyklus for et bestykket printkort fremgår af Figur C.2.
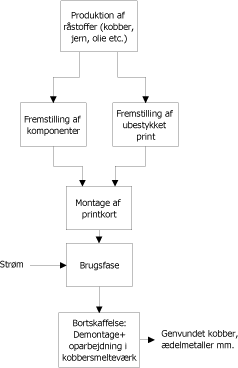
Figur C.2 Livscyklus for et bestykket printkort
I materialefasen indgår
- fremstilling af alle metaller og materialer, som indgår i printkort
- olie, naturgas og andre
Der indgår produktionsfaser for
- fremstilling af det ubestykkede printkort, som igen kan opdeles i en række procestrin
- fremstilling af bærematerialet, der fx er epoxy-glasfiberbaseret
- pålægning af kobberlag
- fremstilling af det ønskede printmønster
- hulboring
- fremstilling af komponenter (Her vil være en masse procestrin)
- montage af komponenter
I brugsfasen indgår
- tab af energi som varme i komponenterne i printkortet
I bortskaffelsesfasen genvindes en del af metallerne via behandling i kobberværker samt eventuelt energiindhold af de organiske bestanddele. Denne model for bortskaffelse gælder kun for produkter på det
danske og til dels det europæiske marked.
C.3.2 Sammensætning af bestykkede printkort samt mængde produceret af danske virksomheder
Bestykkede kredsløbskort består af en lang række komponenter. Typiske sammensætninger fra forskellige kilder er vist i Tabel C.3.
Tabel C.3 Sammensætning af bestykkede printkort
|
Elektronik-
affald (1996)
indhold i % |
Legarth et al.,
2001
Indhold i % |
Willum, 2002
Indhold i % |
Kobber (Cu) |
9,6 |
11 |
22 |
Jern (Fe) |
9,2 |
4 |
2,1 |
Aluminium (Al) |
5,8 |
3,8 |
0,15 |
Bly (Pb) |
2,2 |
1,6 |
0,40 |
Tin (Sn) |
2,1 |
1,4 |
1,0 |
Brom (Br) |
2 |
|
|
Zink (Zn) |
1,2 |
0,7 |
|
Nikkel (Ni) |
0,69 |
0,6 |
0,18 |
Chrom (Cr) |
0,52 |
|
0,0006 |
Antimon (Sb) |
0,35 |
|
0,23 |
Chlor (Cl) |
0,24 |
|
|
Sølv (Ag) |
0,059 |
0,1 |
0,76 |
Guld (Au) |
0,023 |
0,03 |
0,07 |
Cadmium (Cd) |
0,014 |
|
|
Paladium (Pd) |
0,01 |
0,02 |
0,04 |
Berylium (Be) |
0,0029 |
0,004 |
|
Kviksølv (Hg) |
0,0009 |
|
|
Arsen (As) |
0 |
|
|
Sum |
34,0098 |
|
|
Rest |
|
|
|
Keramik, glas |
32,50 |
|
|
Plast |
32,50 |
|
|
Papir, væske |
1 |
|
|
Da data i kilderne Elektronikaffald og Legarth et al. er en del år gamle, er det valgt at indhente de nyeste oplysninger vedrørende en typisk sammensætning af et gennemsnitsprint med den
komponentbestykning, som man anvender i dagens typisk producerede printkort (Willum, 2002).
Mængden af producerede bestykkede kredsløbskort fra virksomheder i Danmark med mindre end 200 ansatte er bestemt ud fra indhentede oplysninger fra virksomheder, der ligeledes blev kontaktet i
Affaldsprojektet (Pommer et al., 2003).
Ud fra tal over produceret mængde og antal ansatte er den producerede mængde bestykkede printkort pr. ansat bestemt til i størrelsesordenen 0,4 ton/ansat. Ud fra et samlet antal ansatte i branchen på
mellem minimum 2621 og maksimum 3743 (Pommer et al., 2003) fås en produceret mængde bestykkede printkort på:
- minimum 1092 ton
- maksimum 1560 ton
- middelværdi 1326 ton
C.3.3 Data for de enkelte livscyklusfaser af bestykkede printkort
For at få så opdaterede tal for ressource- og energiforbrug som muligt benyttes nyindhentede data for et gennemsnitsprintkort med komponentsammensætning som angivet i Tabel C.4.
Tabel C.4 Indhold i 1 g printkort
0,000105 stk.. Snap-in-Kondensator |
0,594 stk.. SMT-Induktivit„t SIMID 1210A |
0,00915 stk. SMD dioder i glashus-MELF |
0,00104 stk. Lav og medium krafttransistorer |
0,0599 stk. Opto-elektronik – Lysdioder |
0,0329 stk. Integrerede kredse PLCC20-84 |
0,170 stk. Integrerede kredse SO8-44 |
0,0166 stk. Integrerede kredse TSOP28-56 |
6,05E-5 kg Plast, ABS |
7,33E-6 kg Tin-bly legering Sn60Pb40 |
3,66E-6 kg Filter - EMI/EMC - Ferrit perler, kerner |
0,0665 g Kondensatorer - FIXED – Keramiske – HI-PER,SMD |
0,114 g Konnektorer - Rektangulære |
0,000137 m² Printplade, FR4, Standard komponent |
0,0128 g Relæer |
0,0550 g Modstand - Fixeret – Netværk |
0,0326 g Modstand - Fixeret – Lineær, Fortinnet |
Sammensætningen af printkort i Tabel C.3 (Willum, 2002) er fremkommet ved beregning for komponentsammensætningen i Tabel C.4.
Sammenlignes tallene for den nyeste opgørelse (Willum, 2002) (Tabel C.3) med de tidligere estimater (Elektronikaffald, 1996 og Legarth, 2001) ses det, at koncentrationen af kobber er højere i de moderne
printkort. Den højere kobberkoncentration formodes at skyldes, at komponenterne er blevet meget mindre (overflademonterede integrerede kredse og passive komponenter) og derfor ikke tæller
vægtmæssigt så meget i forhold til det ubestykkede printkort og dettes indhold af kobber. Det skal bemærkes, at de dansk producerede printkorts sammensætning formodes at kunne variere en del
afhængigt af, hvilket produkt der fremstilles. Fx vil en konstruktion med elektrolytkondensatorer hæve indholdet af aluminium væsentligt i forhold til Willum's opgørelse.
For de angivne komponenter i Tabel C.4 er IPU i besiddelse af livscyklusdata, som er benyttet til en beregning af ressourceforbruget i PR i UMIP for materiale- og produktionsfasen.
C.3.3.1 Materiale og produktionsfase
Bestykkede kredsløbskort indeholder som vist i Tabel C.3 en lang række grundstoffer, hvoraf en del er sjældne og begrænsede ressourcer. De sjældne grundstoffer tæller således meget kraftigt i et
regnskab, hvor PRforbruget for hver grundstof opgøres, selvom de sjældne grundstoffer indgår i elektronikken i lille mængde. Guld, palladium har således ressourceforbrug på ca. 100.000 mPR/kg, mens
jern har et ressourceforbrug på 0,08 mPR/kg, se Pommer et al., 2001.
Beregningerne af ressourceforbrug er udført af Ole Willum, IPU i UMIP med de nyeste tal for ressourceforbrug af grundstofferne. De beregnede ressourceforbrug er opstillet for de i printkortet indgående
grundstoffer med angivelse af de største ressourceforbrug i Tabel C.5.
Tabel C.5 Materiale og produktionsfase
Materiale |
Vægt% i print |
mPR/kg print |
Au (guld) |
0,073 |
63,5 |
Pd (palladium) |
0,042 |
58,1 |
Ag (sølv) |
0,76 |
56,9 |
Sn (tin) |
1,02 |
24,7 |
Sb (antimon) |
0,23 |
7,79 |
Cu (kobber) |
22,43 |
5,05 |
Pb (bly) |
0,40 |
0,977 |
Ni (nikkel) |
0,18 |
0,266 |
Co (kobalt) |
|
0,101 |
Fe (jern) |
2,13 |
0,00473 |
Al (aluminium) |
0,14 |
0,00298 |
Det ses, at de væsentligste bidrag udgøres af guld, palladium, sølv, tin, antimon og kobber, idet disse 6 grundstoffer står for over 99% af ressourceforbruget. Det er derfor ud fra et ressourcesynspunkt disse
stoffer, som man bør forsøge at genvinde, mens resten af metallerne, plast mv. ikke tæller væsentligt ud fra en ressourcebetragtning. I det følgende beregnes derfor kun for de 6 angivne grundstoffer.
C.3.3.2 Brugsfase
De færdigproducerede bestykkede printkort monteres enten i færdige elektroniske produkter i montagevirksomhederne eller sælges som et delprodukt til andre virksomheder i ind- og udland, som
færdigmonterer produkterne. De færdige produkter vil herefter blive solgt til brug i ind- og udland.
Tabel C.6 Brugsfase 1 kg bestykket printkort
Emne |
Enhed |
Kilde/antagelser |
Indhold guld |
0,00073kg |
|
Indhold palladium |
0,00042 kg |
|
Indhold sølv |
0,0076 kg |
|
Indhold tin |
0,01 kg |
|
Indhold antimon |
0,0023 kg |
|
Indhold kobber |
0,220 kg |
|
Effekt |
25 W |
Effektforbruget er meget afhængigt af valgt produkt 1) |
Udnyttelse af varme til rumopvarmning |
50% |
Det antages, at spildvarmen erstatter forbrug af fossile brændsler i vinterperioden (6 måneder). |
Levetid |
5-15 år |
Afhængigt af produkt. Der antages 10 års levetid. |
1) Da de behandlede montagevirksomheder producerer meget forskellige produkter, som varierer fra uge til uge, alt efter hvilke ordrer der indløber, kan et realistisk gennemsnitseffektforbrug ikke vurderes.
Man kan beregne nogle eksempler for typiske effektforbrug af forskellige typer elektronik. Med udgangspunkt i at 0,139 m² bestykket printkort vejer 1 kg (Willum, 2002), er der i Tabel C.7 vist nogle
eksempler på effektforbrug. Ud fra tabellen vurderes et middeleffektforbrug at være ca. 25 W/kg. Et højt effektforbrug på 250 W/kg opnås ved udstyr med processorer eller effektelektronik og et lavt
energiforbrug på ca. 1W/kg ved fx batteridrevet udstyr.
Tabel C.7 Effektforbrug af bestykkede printkort i forskellig elektronik
Type |
Areal (m²) |
Vægt (Kg) |
Effektforbrug (W) |
Effektforbrug (W/kg) |
Audio-videoudstyr |
0,045 |
0,32 |
5 |
15 |
Indstikskort med processor |
0,025 |
0,18 |
5-50 |
25-250 |
Signalbehandlingsudstyr uden effektelektronik |
0,012 |
0,090 |
0,1-1 |
1-10 |
Batteridreven elektronik (fx røgalarm) |
0,003 |
0,002 |
|
0,02 |
C.3.3.3 Bortskaffelse
Da produkterne, som printkortene indgår i, vil blive solgt til aftagere i hele verden, vil effektiviteten af bortskaffelsen være afhængig af regler og traditioner for de enkelte lande.
I udlandet vil en del vil blive bortskaffet med affald til deponering eller affald til forbrænding, men der vil også være en del, der vil blive oparbejdet via de enkelte landes metaloparbejdningskredsløb. Her vil
kobber og ædelmetalholdige fraktioner typisk ende i kobbersmelteværker. For den del, der bliver genvundet, er de typiske genanvendelseseffektiviteter som angivet i Tabel C.8.
Tabel C.8 Bortskaffelse
Emne |
Enhed |
Kilde/antagelser |
Genvundet guld |
98% |
(Boliden) |
Genvundet palladium |
98% |
(Boliden) |
Genvundet sølv |
90% |
(Boliden) |
Genvundet tin |
0-20% |
(Boliden) Noget tin genvindes fra filterstøv |
Genvundet antimon |
0% |
(Boliden) |
Genvundet kobber |
98% |
(Boliden) |
C.4 Ressourceeffektivitet for printkort
C.4.1 Råstofforbrug
Ud fra de i afsnit C.3 opstillede data er materialeforbruget estimeret for 1 kg bestykket printkort. Hovedbestanddelene er metaller, keramik/glas og plast. Metallerne udgør 274 gram pr. kg, mens resten
udgøres af lige dele keramik/glas og plast, svarende til 363 gram.
Tabel C.9 Indhold af stoffer i et typisk printkort
Indhold |
Indhold af ma-
teriale/ grund-
stof pr. kg
printkort |
Genvindings-
procent |
Nettoforbrug af
materiale pr. kg
printkort |
Kobber |
224,3 g |
98 |
4,486 g |
Jern |
21,3 g |
|
21,3 g |
Tin |
10,2 g |
20 |
8,16 g |
Sølv |
7,6 g |
90 |
0,76 g |
Bly |
4 g |
|
4 g |
Antimon |
2,3 g |
0 |
2,3 g |
Nikkel |
1,8 g |
|
1,8 g |
Aluminium |
1,4 g |
|
1,4 g |
Guld |
0,73 g |
98 |
0,0146 g |
Palladium |
0,42 g |
98 |
0,0084 g |
Plast |
363 g |
0 |
363 g |
Keramik/glas |
363 g |
0 |
363 g |
Energiforbruget i hele produktets levetid ved en effekt på 25W og en levetid på 10 år er opgjort til 7884 MJ. Ved beregningen er det antaget, at der kun benyttes fossile brændsler i elproduktionen svarende
til olie, og at der opnås en virkningsgrad i elproduktionen på 40% svarende til et primær energiforbrug på 78842,5 = 19710 MJ eller 470kg olie med brændværdi på 42MJ/kg. I dette tal indgår ikke
energiforbruget til produktion af olien eller tilsvarende fossile brændstoffer. Dette forbrug estimeres Tabel C.10. Der regnes med, at 50% af energien kan genanvendes som varme til rumopvarmning, og at
det reelle tab derfor udgør 50% svarende til 3942 MJ eller 235 kg olie.
Det har ikke været muligt inden for projektets rammer at skaffe data til estimering af råstofforbruget baseret på vægt til fremstilling af komponenter og print, ligesom der ikke haves præcise data for nogle
grundstoffer vedrørende forbrug af råstoffer/kg udvundet grundstof. Med disse forudsætninger er råstofforbruget estimeret i Tabel C.10.
Tabel C.10 Råstofforbrug i et printkorts livscyklus
Indhold |
Råstof
kg/kg |
Bruttoforbrug af
råstoffer pr. kg |
Nettoforbrug af
råstoffer pr. kg |
Kobber |
3,8 1) |
852 g |
17 g |
Jern |
2 1) |
423 g |
42,6 g |
Tin |
10 2) |
102 g |
81,6 g |
Sølv |
10 2) |
76 g |
7,6 g |
Bly |
10 2) |
40 g |
40 g |
Antimon |
10 2) |
23 g |
23 g |
Nikkel |
7 1) |
12,6 g |
12,6 g |
Aluminium |
3 |
4,2 g |
4,2 g |
Guld |
10 2) |
7,3 g |
0,15 g |
Palladium |
10 2) |
4,2 g |
0,084 g |
Plast |
1,7 1) |
617 g |
617 g |
Keramik/glas |
1,3 1) |
472 g |
472 g |
|
|
|
|
Sum |
|
2,253 kg |
1,318 kg |
|
|
|
|
Energiforbrug i brugsfase som olie |
1,1 1) |
515,9 kg |
257,95 kg |
1) Råstofforbruget er estimeret ud fra oplysninger i UMIP-databasen og omfatter forbrug af kemikalier, råstoffer og brændsel til energiproduktion, men ikke forbrug af vand. (Det forbrugte vand kommer returneres til biosfæren fra udvindingsprocessen med indhold af diverse stoffer).
2) Der haves ikke data fra UMIP for denne komponent, hvorfor forbruget er sat konservativt til maximalt en faktor 10 (excl. vandforbrug).
Som det ses af Tabel C.10, forbruges omkring 2,3 kg råstoffer brutto til fremstilling råstofferne i 1 kg printkort eller 1,3 kg netto, når der er taget hensyn til genvinding af ædelmetallerne. Massen af fossilt
brændstof i form af olie til dækning af forbruget af elenergi i brugsfasen inkl. forbrug af brændsel til fremstilling af olien på ca. 10% (råolie + naturgas) udgør 516 kg brutto eller 258 kg netto. Forbruget af
fossile brændstoffer til elproduktion er således langt større end forbruget af råstoffer i printkortet. Det skal bemærkes, at forbruget af ressourcer til fremstilling af printkortet ud fra råstofferne er negligeret.
C.4.2 Ressourceforbrug
Ud fra data i kapitel 3 er der foretaget en beregning af ressourceeffektiviteten for en række scenarier med udgangspunkt i 1kg bestykket printkort.
Effektforbrug er illustreret gennem 3 gennemregnede scenarier for ressourceeffektivitet svarende til
- Middeleffektforbrug (25 W/kg)
- Højt effektforbrug (250W/kg)
- Lavt effektforbrug (1W/kg) (se Tabel C.6).
Genanvendelsen af materialer er illustreret gennem et scenario uden genanvendelse, hvis fx en småelektronik som røgalarmer, fjernbetjeninger etc. bortskaffes med restaffald, og et scenario med høj
genanvendelse af tin og antimon.
Vedrørende de vægtbaserede ressourceeffektiviteter MMat+energi, R+P+B og MMat+energi, R+P+B+A/N haves ikke data til nøjagtig beregning af disse. Derfor benyttes estimaterne i Tabel C.10. For de
fleste scenarier vil forbruget af fossile brændstoffer til energiproduktion i produktets levetid være langt større end materialeforbruget til råstoffer og produktion, hvorfor usikkerheden i bestemmelse af
råstofforbruget baseret på masseandel har mindre betydning.
Ved beregning af ressourceeffektiviteterne for materialer og energi VMat+energi, R+P+B og VMat+energi, R+P+B+A/N er disse baseret på de beregnede mPR fra UMIP for materiale- og
produktionsfaser af komponenter/printkort (se Tabel C.5). Hertil er adderet forbrug af PR til fossile brændstoffer til produktion af energi i brugsfasen. Endelig genvindes en del af ressourcerne i form af de
værdifulde metaller i bortskaffelsesfasen.
Scenarierne omfatter
Scenario 1: Middel effektforbrug, ressourcegenanvendelse excl. antimon
Scenario 2: Lavt effektforbrug, ressourcegenanvendelse excl. antimon
Scenario 3: Højt effektforbrug, ressourcegenanvendelse excl. antimon
Scenario 4: Middel effektforbrug, ingen ressourcegenanvendelse
Scenario 5: Middel effektforbrug, ressourcegenanvendelse høj genanvendelse af tin og antimon
Detaljer er vist for scenario 1 i Tabel C.11.
Tabel C.11 Scenario 1 Middel effektforbrug med ressourcegenanvendelse excl. Antimon
Materiale og produktionsfase
Beregnet ressourceforbrug for materiale og produktionsfase (UMIP) |
Guld (Au) |
Palladium (Pd) |
Sølv (Ag) |
Tin (Sn) |
Antimon
(Sb) |
Kobber
(Cu) |
Indhold i færdigt produkt (kg) |
1 |
0,00073 |
0,00042 |
0,0076 |
0,01 |
0,0023 |
0,22 |
mPR i produkt |
|
63,5 |
58,0 |
57,0 |
25,0 |
7,8 |
5,1 |
Brugsfase
Effekt 1 kg print |
25 W |
Varmetab |
788,4 MJ/kg/år |
Genudnyttelse af varme til opvarmning rum |
50 % |
Brug (år) |
10 år |
Forbrug af elenergi i levetid (MJ/kg) |
7884 MJ/kg |
Energiforbrug af olie omregnet til primær energi (faktor=2,5) |
469,3 kg |
mPR brugt |
18,8 |
mPR genvundet |
9,4 |
Bortskaffelse
|
Guld
(Au) |
Palladium
(Pd) |
Sølv
(Ag) |
Tin
(Sn) |
Antimon
(Sb) |
Kobber
(Cu) |
% genvundet |
98 |
98 |
90 |
20 |
0 |
98 |
Mængde genvundet |
0,000715 |
0,000412 |
0,0068 |
0,002 |
0 |
0,216 |
mPR genvundet |
62,2 |
56,8 |
51,3 |
5 |
0 |
4,96 |
Opgørelse af ressourceforbrug baseret på vægt for scenario 1:
Forbrug af råstoffer materialefase (fra Tabel C.10) |
2,253 kg |
Forbrug af råstoffer i brugsfase (olie) |
469,3 kg |
Forbrug af råstoffer til fremstilling af olie i brugsfase |
46,9 kg |
Genvundne råstoffer ved bortskaffelse:
fra Tabel C.10 :2,253kg-1,318kg |
0,935 kg |
Genvunden energi i form af sparet rumopvarmning |
|
50% af forbrug af råstoffer i brugsfase |
234,6 kg |
50% af forbrug af råstoffer til fremstilling af olie i brugsfase |
23,5 kg |
Som nøgletal for scenario 1 til beregning af ressourceeffektiviteter fås herefter
Sum af forbrugt masse i livscyklus |
518,5 kg |
Sum af genvundet masse i livscyklus |
259,0 kg |
Sum mPR brugt |
235,7 mPR |
Sum mPR genvundet |
189,9 mPR |
Sum mPR produkt |
216,9 mPR |
Ressourceeffektiviteterne ud fra samlet forbrug af materialer og energi baseret på vægt:
MMat+energi, R+P+B |
=1/518,5 × 100 =0,193% |
MMat+energi, R+P+B+A/N |
=1/(518,5-259,0) × 100 =0,386% |
Ressourceeffektiviteterne ud fra samlede forbrug af materialer og energi baseret på PR:
VMat+energi, R+P+B |
=216,9/235,7 × 100 =92,0% |
VMat+energi, R+P+B+A/N |
=216,9/(235,7-189,9) × 100 =473% |
De forskellige scenarier er vist i Tabel C.12.
Tabel C.12 Beregnede ressourceeffektiviteter
|
Scenario 1 |
Scenario 2 |
Scenario 3 |
Scenario 4 |
Scenario 5 |
Effekttab (W) |
25 |
1 |
250 |
25 |
25 |
Genanvendelse Au,Pd,Ag,Cu |
Ja |
Ja |
Ja |
Nej |
Ja |
Genanvendelse tin % |
20 |
20 |
20 |
0 |
80 |
Genanvendelse antimon % |
0 |
0 |
0 |
0 |
80 |
MMat+energi, R+P+B |
0,19 |
4,4 |
0,02 |
0,19 |
0,19 |
MMat+energi, R+P+B+A/N |
0,39 |
8,6 |
0,04 |
0,39 |
0,39 |
VMat+energi, R+P+B |
92 |
99,7 |
54 |
92,0 |
92,0 |
VMat+energi, R+P+B+A/N |
473 |
589 |
167 |
95,8 |
893 |
Netto Ressource-forbrug DK (virksomheder <200 ansatte) Pr |
60780 |
48800 |
173000 |
300000 |
32000 |
Scenario 1-3 illustrerer betydningen af effektforbruget.
MMat+energi, R+P+B+A/N er mellem 0,04% og 8,6 % VMat+energi, R+P+B+A/N er mellem 167% og 589%, hvilket svarer til et forbrug af PR fra 48800-173000. Den høje ressourceeffektivitet for
produktet med lavt energiforbrug i scenario 3 VMat+energi, R+P+B+A/N = 589% betyder et kun 1/6 af produktets indhold af ressourcer forbruges netto i produktets levetid.
Scenario 4 viser effekten af at indsamle elektronik med bestykkede printkort til genanvendelse. Her falder netto ressourceeffektiviteten baseret på PR VMat+energi, R+P+B+A/N fra 473% til 96%, hvis
produktet bortskaffes til forbrænding eller deponering i stedet for at genanvende dette.
Scenario 5 viser effekten af at genvinde tin og antimon med høj genvindingsgrad, hvilket der pt. ikke er tilstrækkeligt økonomisk incitament til. Herved stiger ressourceeffektiviteten VMat+energi,
R+P+B+A/N for et produkt med et effektforbrug på 25 W/kg fra 473% til 893% (Der bruges således kun 1/9 af produktets ressourceindhold i produktets levetid).
C.5 Kortlægning af transformere
I det følgende er vist en kortlægning af transformere i komponentfremstillingsvirksomheder med mindre end 200 ansatte.
C.5.1 Materiale- og energistrømme
Transformere består hovedsageligt af jern og kobber. Det er valgt kun at vurdere produktionsmetoden for traditionelle laminerede transformere med en jernkerne af blik og ikke de såkaldte
ringkernetransformere. Ringkernetransformere består dog ligeledes hovedsageligt af kobber og jern, hvorfor det vurderes, at indflydelsen i forskel af produktionsform ikke vil være så stor.
Livsforløbet for en transformer er vist i Figur C.3.
I materialefasen indgår
- kobber til fremstilling af kobbertråd
- jern til fremstilling af blikplader, skruer mm.
- olie, naturgas og andre
Der indgår produktionsfaser for
- fremstilling af isoleret (lakeret) kobbertråd
- fremstilling af udstandsede blikplader
- plast til spole
- lak
- eventuelt isocyanatstøbemasse (kun til små printtransformere)
- fremstilling af transformer
I brugsfasen indgår
- tab af energi som varme i transformeren
I bortskaffelsesfasen genvindes en del af materialerne samt eventuelt energiindhold af de organiske bestanddele. Det antages, at kobberindholdet grundet værdien altid oparbejdes via et kobbersmelteværk.
Dette tyder forespørgsler i forbindelse med affaldskortlægningen på (Pommer et al., 2003).
Enten vil transformere kunne blive behandlet direkte i kobberværk, hvorved jernindholdet mistes med slaggen, eller der kan foretages en mekanisk separation inden oparbejdning af kobberindholdet i
smelteværk. En sådan oparbejdning antages at omfatte neddeling, magnetsortering af jern og efterfølgende oparbejdning af resten, det vil sige kobber, tin, lak, plast mv. i kobbersmelteværk.
Hvis der separeres mekanisk, vil noget af kobberet teoretisk kunne mistes med jernfraktionen, hvis trådene fx hænger fast i det neddelte jern. Det er vigtigt at undgå dette, fordi det kan få konsekvenser for
stålfremstillingen, da kobber kun er acceptabel i en meget lille koncentration sammen med jern til oparbejdning i stålværk.
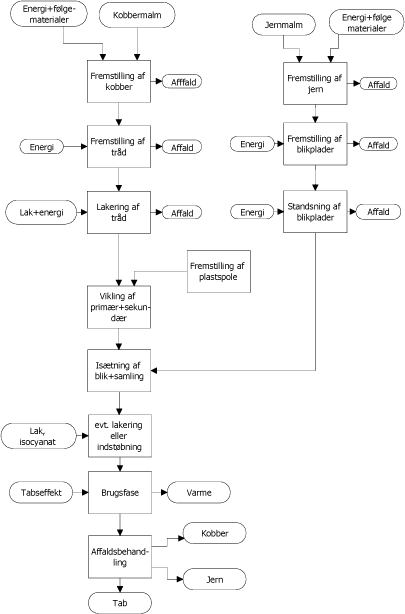
Figur C.3 Livsforløbet for en transformer
C.5.2 Sammensætning af transformer samt mængde produceret af danske virksomheder
Indholdet af materialer i transformere varierer en del. Ud fra data fra kontaktede producenter er indhentet data, som er vist i Tabel C.13.
Tabel C.13 Sammensætning af transformere
Spænding (V) |
Effekt (W) |
Cu/Fe 1) |
% spole |
% andet 2) |
W/kg |
|
100 |
0,70 |
|
|
54 |
12 |
180 |
0,26 |
1,6 |
9 |
42 |
24 |
20000 |
0,52 |
1,3 |
1,9 |
390 |
80 |
4800 |
0,35 |
1,3 |
2,2 |
104 |
1) : Cu/Fe er forholdet mellem kobbertråd og blikplader af jern.
2) : % andet er indhold af bolte, lak, loddeben mm., hvor en væsentlig del af vægten udgøres af bolte (jern).
Det ses, at indholdet af kobber og jern varierer meget med et forhold fra 0,26 til 0,7. Indholdet af plast, lak mm. formodes ud fra tallene over ”% spole” og ”% andet” at være mindre end 3%.
Ud fra ovenstående data antages en gennemsnitstransformer at bestå af mindre end 3% organisk og et forhold mellem kobber og jern på 0,5. Heraf fås en sammensætning af en gennemsnitstransformer som
angivet i Tabel C.14.
Til montering af transformeren benyttes typisk lodning. For at anslå mængden af loddetin til en 1 kg transformer, er der udført et forsøg. En tråd blev loddet på et loddeøje, og tinforbruget blev bestemt til ca.
200 mg. Antallet af lodninger af terminaler på en transformer varierer fra 4-8 afhængigt af, om primær og sekundær er opdelt i to kredse. Endvidere skal der påloddes ledninger på terminalerne. Således
vurderes det, at loddetinforbruget for en 1kg transformer er mindre end 8 0,2g=1,6 g. Indholdet af tin udgør ifølge Christensen et al., 2000, ca. 63% svarende til 1 g pr. kg transformer. For større
transformere vil tinforbruget udgøre en mindre del, mens forbruget vil være større for mindre transformere.
Tabel C.14 Materialer i gennemsnitstransformer
Materiale |
% |
Kobber |
32,5 |
Jern |
65 |
Lak, plast og andet organisk indhold |
3 |
Tin |
< 0,1% |
Mængden af producerede transformere fra virksomheder i Danmark med mindre end 200 ansatte er bestemt ud fra indhentede oplysninger fra virksomheder, der ligeledes blev kontaktet i (Pommer et al.,
2003). Ud fra tal over produceret mængde og antal ansatte er den producerede mængde transformere pr. ansat bestemt til i størrelsesordenen 7-9 ton/ansat. Ud fra et samlet antal ansatte i branchen på
mellem minimum 587 og maksimum 803 (Pommer et al., 2003) fås en produceret mængde transformere (både laminerede og ringkerne) på
- minimum 4865 ton
- maksimum 6255 ton
- middelværdi 5560 ton
C.5.3 Data for de enkelte livscyklusfaser af en transformer
I tabellerne C.15-C.23 er angivet indhentede og beregnede forbrug af materialeressourcer og energiforbrug i de enkelte faser i livscyklus for en transformer.
For at kunne identificere de væsentlige bidrag til forbruget af PR er der lavet en række overslag over forbrug af ressourcer til de forskellige procestrin. Hvis bidragene ved en beregning af det samlede
ressourceforbrug er af væsentlig betydning (>2%), er der forsøgt skaffet supplerende information til en bedre opgørelse af ressourceforbruget for det pågældende trin i livscyklussen.
C.5.3.1 Materialefase
Tabel C.15 Materialefase
Emne |
Ressource-
forbrug
mPR/kg |
Energiforbrug fremstilling
(MJ/kg) |
Kilde/antagelser |
Kobber |
16,5 |
90 |
Pommer et al. (2001) |
Jern |
0,08 |
40 |
Pommer et al. (2001) |
Plast, lak mm. |
0,04 |
80 (antaget) |
Pommer et al. (2001), Antaget ressource + energiforbrug som PE mm. |
Tin |
900 |
90 |
Pommer et al. (2001), Energiforbruget er antaget som for kobber. |
C.5.3.2 Produktionsfase
Tabel C.16 Produktionsfase kobbertråd
Emne |
Enhed |
Kilde/antagelser |
Tab |
1% |
Tabet er antaget lille. |
Genvundet |
0,9% |
Mindst 90% af kobber antages genanvendt. |
Energiforbrug fremstilling |
30 MJ/kg |
Pommer et al. (2001). Energiforbruget er antaget i samme størrelsesorden som andre fremstillingsprocesser fx drejning, fræsning, presning. |
Tabel C.17 Produktionsfase Blikplader
Emne |
Enhed |
Kilde/antagelser |
Tab |
50% |
Kun en mindre del af pladearealet kan bruges. |
Genvundet |
45% |
90% af jernaffaldet antages genanvendt. |
Energiforbrug fremstilling |
1 MJ/m snitlængde |
Pommer et al. (2001). |
Antal plader |
100 |
Vurderet ud fra besigtigelse af transformer på ca. 1kg. |
Snitlængde |
0,4 |
Vurderet ud fra besigtigelse af transformer på ca. 1kg. |
Tabel C.18 Produktionsfase plast/lak mm.
Emne |
Enhed |
Kilde/antagelser |
Tab |
1% |
Tabet kendes, ikke men er antaget lille. |
Genvundet |
0% |
0% antages genanvendt. |
Energiforbrug fremstilling |
20MJ/kg |
Energiforbrug til plaststøbning Pommer et al. (2001). |
Tabel C.19 Produktionsfase loddetin
Emne |
Enhed |
Kilde/antagelser |
Indhold af tin |
Ca.50% |
(Antaget ud fra sammensætning af printkort). |
Ressourceforbrug bly |
80
mPR/kg |
Pommer et al. (2001) Ressourceforbruget til fremstilling af bly er negligeabelt i forhold til tin (900 mPR/kg), hvorfor kun ressourceforbruget til tin er medtaget i
produktionsfasen for loddetin. |
Tab |
1% |
Tabet er ukendt, men antages lille. |
Genvundet |
0,9% |
90% antages genanvendt. |
Energiforbrug
fremstilling |
Neg. |
Energiforbruget til smeltning antages negligeabelt i forhold til ressourceforbruget for tin. |
Tabel C.20 Produktion af transformer
Emne |
Enhed |
Kilde/antagelser |
Vikling |
20 MJ/kg |
Antaget energiforbrug som for typiske andre forarbejdningsprocesser Pommer et al. (2001). |
Varmlakering |
20 MJ/kg |
Antaget energiforbrug som ved plaststøbning. |
Tab kobber 1) |
1% |
Pommer et al. (2003). |
Genvundet kobber |
0,9% |
90% antages genanvendt. |
Tab jern 1) |
1% |
Pommer et al. (2003). |
Genvundet jern |
0,5% |
50% antages genanvendt Pommer et al. (2003). |
Tab plast, lak 1) |
1% |
Pommer et al. (2003). |
Genvundet plast, lak |
0% |
0% antages genanvendt dog lidt som energibidrag til smelteværker Pommer et al. (2003). |
Tab tin |
1% |
Pommer et al. (2003). |
Genvundet tin |
0% |
Afhænger af hvilket kobbersmelteværk der benyttes. |
1) Vedrørende produktionsspild ved fremstilling af transformere er dette vurderet til <1% i Pommer et al. (2003).
C.5.3.3 Brugsfase
De færdigproducerede transformere monteres enten i færdige elektroniske produkter i montagevirksomhederne eller sælges som en komponent til andre virksomheder i ind- og udland, som monterer
komponenter i deres elektronikprodukter. De færdige produkter vil herefter blive solgt til brug i ind- og udland.
Tabel C.21 Brugsfase 1 kg transformer
Emne |
Enhed |
Kilde/antagelser |
Indhold kobber |
0,325 kg |
|
Indhold Jern |
0,65 kg |
|
Indhold plast, lak mm. |
0,03 kg |
|
Indhold tin |
0,001 kg |
|
Effekt |
50 W |
Vurderet ud fra indhentede leverandøroplysninger for transformere på ca. 1 kg. |
Effekttab |
5-25% |
Effekttabet varierer med størrelse og design Se 1) |
Udnyttelse af varme til rumopvarmning |
50% |
Det antages, at spildvarmen erstatter forbrug af fossile brændsler i vinterperioden (6 måneder). |
Levetid |
5-15 år |
Afhængigt af produkt. |
1) Effekttabet fra transformere er typisk afhængigt af størrelse, således at større transformere har et lavt effekttab. Tabet ved maksimal belastning er afhængigt af kobbertrådens og jernkernens egenskaber.
Der kan godt opnås et lille effekttab, men så kræves et højt materialeforbrug af jern og kobber. Fra leverandørside påpeges, at billige transformere, som importeres fx sammen med halogensæt, af hensyn til
størrelse typisk er meget pressede og derfor med har et stort effekttab og udviklet varme. Følgende tal er fra leverandører oplyst som eksempler på tab som funktion af effekt for almindelige transformere
produceret af dansk industri (Tabene vil kunne variere en del afhængigt af transformernes opbygning).
Tabel C.22 Effekttab af transformer
Effekt |
Tab |
% |
Maksimal effekt (W) |
Tab ved max. Effekt (W) |
Tab % |
2,5 |
3,3 |
132 1) |
48 |
12 |
25 |
250 |
30 |
12 |
3000 |
146 |
4,9 |
1) Tab for de helt småtransformere fx til printmontage ses at kunne blive meget store. Disse vægtmæssigt små transformere vurderes dog at udgøre en mindre del af den samlede vægt af producerede
transformere.
C.5.3.4 Bortskaffelse
Da produkterne, som transformere indgår i, vil blive solgt til aftagere i hele verden, vil effektiviteten af bortskaffelsen være afhængig af regler og traditioner for de enkelte lande.
I udlandet vil en del vil blive bortskaffet med affald til deponering eller affald til forbrænding, men der vil også være en del, der vil blive oparbejdet via de enkelte landes metaloparbejdningskredsløb. Her vil
kobberholdige fraktioner typisk ende i kobbersmelteværker. For den del, der bliver genvundet, er de typiske genanvendelseseffektiviteter som angivet Tabel C.23.
Tabel C.23 Bortskaffelse
Emne |
Enhed |
Kilde/antagelser |
Genvundet kobber |
95% |
|
Genvundet jern |
50% |
Se 1) |
Genvundet lak, plast |
0% |
0% antages genanvendt dog lidt som energibidrag til smelteværker Pommer et al. (2003). |
Genvundet tin |
0-20% |
Afhængigt af anvendt kobbersmelteværk og verdens markedspriser. |
1) I Pommer et al. (2003) blev fundet en række bortskaffelsesveje, som alle genvinder den væsentlige komponent kobber. Ved nogle behandlingsmetoder mistes jern dog. Dette har dog ikke den store
betydning for ressourceforbruget, da kobber tæller meget mere ressourcemæssigt.
C.6 Ressourceeffektivitet for transformere
Ud fra data i kapitel 5 er foretaget en beregning af ressourceeffektiviteten for en række scenarier med udgangspunkt i 1 kg færdigsamlet transformer. Der er først lavet et overslag for at se, hvilke
delprocesser der betyder mest for forbruget af PR. For de små bidrag er det således af mindre betydning, hvilken usikkerhed data er omfattet af.
I tabellerne Tabel C.25 til Tabel C.31 er beregningerne for scenario 1 vist, som er en beregning med middelværdien af de parametre, der er indhentet oplysninger om fra de omfattede virksomheder. De
bidrag til PR, som udgør >2% (0,2 mPR) af det totale ressourceforbrug =(11 mPR), er vist med kursiv og fed. Resten af bidragene er af mindre betydning, og her betyder det ikke så meget, om
usikkerheden på værdien er 50%.
Det ses, at de parametre, der har væsentlig betydning, udgøres af 5 parametre:
Ressourceforbrug:
- Produktion af kobber
- Produktion af tin
- Effekttab i brugsfase (regnet som netto effekttab efter)
Genvundet ressourceforbrug:
Til at fastlægge ressourceforbruget baseret på vægtandel benyttes de samme faktorer som i Tabel C.10.
Tabel C.24 Råstofforbrug til fremstilling af ressourcer i transformere
Indhold |
Råstof
kg/kg |
Kobber |
3,8 |
Jern |
2 |
Tin |
10 |
Plast |
1,7 |
Olie |
1,1 |
Tabel C.25 Scenario 1, middel effekttab, høj genanvendelse af tin, genanvendelse af kobber
Materialefase |
Udvinding råstoffer |
Kobber |
Jern |
Tin |
plast, lak |
Mængde (kg) |
0,3316 |
1,3131 |
0,0010 |
0,0306 |
Ressourceforbrug mPR/kg |
16,5 |
0,08 |
900 |
0,04 |
Forbrug af ressourcer (mPR) |
5,47 |
0,105 |
0,909 |
0,0012 |
Forbrug af ressourcer (kg) 1) |
1,26 |
2,63 |
0,01 |
0,05 |
1) Beregnes ud fra Tabel C.24.
Tabel C.26 Scenario 1, middel effekttab, høj genanvendelse af tin, genanvendelse af kobber
Produktionsfase (1) |
Fremstilling af kobbertråd |
Kobber |
Jern |
Tin |
plast, lak |
Olie, andet fossilt |
Mængde (kg) |
0,3316 |
1,3131 |
0,0010 |
0,0306 |
|
Mængde forbrugt i denne fase (kg) |
|
|
|
|
0,5921 |
Tab (%) |
1 |
|
|
|
|
Genvundet (%) |
0,9 |
|
|
|
|
Energiforbrug fremstilling MJ/kg |
30 |
|
|
|
|
Energifaktor |
2,5 |
|
|
|
|
Som primær energi i aktuel mængde MJ |
24,87 |
|
|
|
|
Forbrug af ressourcer (mPR) |
|
|
|
|
0,0237 |
Genvundne ressourcer (mPR) |
0,0492 |
|
|
|
|
Forbrug ressourcer (kg) 1) |
|
|
|
|
0,651 |
Genvundne ressourcer (kg) 1) |
0,011 |
|
|
|
|
1) Beregnes ud fra Tabel C.24.
Tabel C.27 Scenario 1, middel effekttab, høj genanvendelse af tin, genanvendelse af kobber
Produktionsfase (2) |
Fremstilling af blikplader |
Kobber |
Jern |
Tin * |
Plast, lak |
Olie, andet fossilt |
Indhold (kg) |
0,3283 |
1,3131 |
0,0010 |
0,0306 |
|
Mængde forbrugt i denne fase (kg) |
|
|
|
|
3,127 |
Tab (%) |
|
50 |
|
|
|
Genvundet (%) |
|
45 |
|
|
|
Energiforbrug standsning MJ/m |
|
1 |
|
|
|
Antal plader ved 1kg transformer |
|
100 |
|
|
|
Snitlængde (m) |
|
0,4 |
|
|
|
Energiforbrug fremstilling MJ/kg |
|
40 |
|
|
|
Energifaktor |
|
2,5 |
|
|
|
Som primær energi i aktuel mængde MJ |
|
131,3 |
|
|
|
Forbrug af ressourcer (mPR) |
|
|
|
|
0,125 |
Genvundne ressourcer (mPR) |
|
0,0473 |
|
|
|
Forbrug ressourcer (kg) 1) |
|
|
|
|
3,44 |
Genvundne ressourcer (kg) 1) |
|
1,18 |
|
|
|
1) Beregnes ud fra Tabel C.24.
Tabel C.28 Scenario 1, middel effekttab, høj genanvendelse af tin, genanvendelse af kobber
Produktionsfase (3) |
Fremstilling plast, lak |
Kobber |
Jern |
Tin |
Plast, lak |
Olie, andet fossilt |
Indhold (kg) |
0,3283 |
0,6566 |
0,0010 |
0,0306 |
|
Mængde forbrugt i denne fase (kg) |
|
|
|
|
0,0364 |
Tab (%) |
|
|
|
1 |
|
Genvundet (%) |
|
|
|
0 |
|
Energiforbrug fremstilling MJ/kg |
0 |
|
|
20 |
|
Energifaktor |
|
|
|
2,5 |
|
Som primær energi i aktuel mængde MJ |
|
|
|
1,53 |
|
Forbrug af ressourcer (mPR) |
|
|
|
|
0,0015 |
Genvundne ressourcer (mPR) |
|
|
|
|
|
Forbrug ressourcer (kg) 1) |
|
|
|
|
0,040 |
Genvundne ressourcer (kg) 1) |
|
|
|
|
|
1) Beregnes ud fra Tabel C.24.
Tabel C.29 Scenario 1, middel effekttab, høj genanvendelse af tin, genanvendelse af kobber
Produktionsfase (4) |
Vikling af transformer + varmlakering + pålodning af klemmer |
Kobber |
Jern |
Tin |
Lak, plast etc. |
Olie, andet fossilt |
Indhold (kg) |
0,3283 |
0,6566 |
0,0010 |
0,0303 |
|
Mængde forbrugt i denne fase (kg) |
|
|
|
|
0,4269 |
Tab (%) |
1 |
1 |
1 |
1 |
|
Genvundet (%) |
0,9 |
0,5 |
0 |
0 |
|
Energiforbrug fremstilling MJ/kg |
20 |
|
|
20 |
|
Energifaktor |
2,5 |
|
|
2,5 |
|
Som primær energi i aktuel mængde MJ |
16,4 |
0.0000 |
0.0000 |
1,52 |
|
Forbrug af ressourcer (mPR) |
|
|
|
|
0,0171 |
Genvundne ressourcer (mPR) |
0,0488 |
0,0003 |
0,0000 |
0,0000 |
|
Forbrug ressourcer (kg) 1) |
|
|
|
|
0,47 |
Genvundne ressourcer (kg) 1) |
0,011 |
0,007 |
|
|
|
|
|
|
|
|
|
Færdigt produkt (kg) |
0,325 |
0,65 |
0,001 |
0,03 |
|
mPR i produkt |
5,363 |
0,052 |
0,9 |
0,0012 |
|
1) Beregnes ud fra Tabel C.24.
Tabel C.30 Scenario 1, middel effekttab, høj genanvendelse af tin, genanvendelse af kobber
Brugsfase |
|
Effekt 1 kg transformer |
50 W |
Effekttab i transformer =spildvarme |
12 % |
Effekttab |
0,0216 MJ pr. time |
Varmetab |
189,2 MJ/kg/år |
Genudnyttelse af varme til opvarmning rum |
50 % |
Brug |
10 år |
Forbrug i levetid |
1892 MJ/kg |
Energifaktor |
2,5 |
Som primær energi i aktuel mængde MJ |
4730,4 |
Mængde forbrugt i denne fase(kg) |
112,6 |
Forbrug af ressourcer (mPR) |
4,51 |
Genvundne ressourcer (mPR) |
2,25 |
Forbrug ressourcer (kg) 1) |
123,9 |
Genvundne ressourcer (kg) 1) |
62,0 |
1) Beregnes ud fra Tabel C.24.
Tabel C.31 Scenario 1, middel effekttab, høj genanvendelse af tin, genanvendelse af kobber
Bortskaffelse |
Kobber |
Jern |
Tin |
plast, lak |
% genvundet |
95 |
50 |
20 |
0 |
mPR værdi af genvundet |
16,5 |
0,08 |
900 |
100 |
Mængde genvundet |
0,309 |
0,325 |
0,0002 |
0 |
Forbrug af ressourcer (mPR) |
|
|
|
|
Genvundne ressourcer (mPR) |
5,09 |
0,026 |
0,18 |
0 |
Forbrug ressourcer (kg) 1) |
|
|
|
|
Genvundne ressourcer (kg) 1) |
1,17 |
0,65 |
0,002 |
|
1) Beregnes ud fra Tabel C.24.
De samlede bidrag, som er opgjort i tabellerne C.24-C.31, kan opgøres til:
Sum af masse i produkt |
1,0 kg |
Sum af forbrugt masse i livscyklus |
132,4 kg |
Sum af genvundet masse i livscyklus |
65,0 kg |
Sum forbrugte ressourcer i livscyklus |
11,2 mPR |
Sum genvundne ressourcer i livscyklus |
7,7 mPR |
Sum af ressourcer i produkt |
6,32 mPR |
Ressourceeffektiviteterne ud fra samlet forbrug af materialer og energi baseret på vægt:
MMat+energi, R+P+B |
=1/132,4 100 =0,76% |
MMat+energi, R+P+B+A/N |
=1/(132,4-65,0) 100 =1,48% |
Ressourceeffektiviteten ud fra samlet nettoforbrug af materialer og energi baseret på PR:
VMat+energi, R+P+B |
=6,32/11,2 100 =56% |
VMat+energi, R+P+B+A/N |
=6,32/(11,2-7,7) 100 =178% |
Den vægtbaserede ressourceeffektiviteter MMat+energi, R+P+B og MMat+energi, R+P+B+A/N bliver lave, idet der bruges en meget større mængde brændsel til produktion af strøm i produktets levetid
end produktets vægt.
Ressourceeffektiviteten baseret på PR VMat+energi, R+P+B+A/N bliver større end 100%, idet der genvindes en så stor del af produktets PR i form af metaller i produktets levetid, at nettoforbruget i
levetiden er mindre end indholdet i produktet (der bruges 100/178 100=56% af produktets indhold af PR i dets levetid).
Da der er en stor variation med hensyn til effekttab og usikkerhed med hensyn til genanvendelse, er følgende scenarier opstillet:
Scenario 1: Middel effekt tab, lav genanvendelse af tin, genanv. kobber
Scenario 2 Lavt effekttab, lav genanvendelse af tin, genanv. kobber
Scenario 3 Højt effekttab, lav genanvendelse af tin, genanv. kobber
Scenario 4 Middel effekttab, høj genanvendelse af tin, genanv. kobber
Scenario 5: Middel effekt tab, ingen genanvendelse af tin, kobber, jern
I Tabel C.32 er vist ressourceeffektiviteterne baseret på vægt og PR for alle beregnede scenarier.
Endvidere er vist nettoressourceforbruget i livscyklus for de transformere, der produceres af danske virksomheder med <200 ansatte (5500 ton) i PR =1000 mPR.
Tabel C.32 Beregnede ressourceeffektiviteter
|
Scenario 1 |
Scenario 2 |
Scenario 3 |
Scenario 4 |
Scenario 5 |
Effekttab (W) |
12 |
5 |
25 |
12 |
12 |
Genanvendelse af kobber |
Ja |
Ja |
Ja |
Ja |
Nej |
Genanvendelse tin % |
20 |
20 |
20 |
80 |
0 |
MMat+energi, R+P+B |
0,76 |
1,7 |
0,38 |
0,76 |
0,76 |
MMat+energi, R+P+B+A/N |
1,48 |
3,2 |
0,74 |
1,48 |
1,44 |
VMat+energi, R+P+B |
56 |
73 |
39 |
56 |
56 |
VMat+energi, R+P+B+A/N |
178 |
284 |
106 |
210 |
71 |
Netto Ressourceforbrug DK (virksomheder <200 ansatte) PR |
19700 |
12400 |
33300 |
16700 |
49160 |
Tabel C.32 viser, at det er meget væsentligt at begrænse effekttabet, idet der ved lavt effekttab på 5% og 20% tingenanvendelse kun forbruges 12.400 PR eller VMat+energi, R+P+B+A/N =284%
(scenario 2), mens der ved et effekttab på 25% forbruges 33.000 PR eller VMat+energi, R+P+B+A/N =106% (scenario 3).
Vedrørende betydningen af genanvendelse af tin medfører en oparbejdning med lav tin genanvendelse et ressourceforbrug på 19.700 Pr (scenario 1) VMat+energi, R+P+B+A/N =178% eller ca. 3.000 PR
mere, end hvis tinnet genanvendes med høj genvindingsgrad (scenario 4).
Hvis der er højt effekttab og lav genvinding af tin, er ressourceeffektiviteten for produktet er VMat+energi, R+P+B+A/N = 106% svarende til, at der netto bruges ligeså mange ressourcer i produktets
livscyklus, som produktet indeholder. Samtidig er ressourceeffektiviteten baseret på vægt kun 0,68%, hvilket skyldes det høje energiforbrug og dermed et højt forbrug af fossile brændstoffer.
Ved lavt effekttab (scenario 2) er ressourceeffektiviteten for produktet 284% svarende til, at der netto bruges 100/284 × 100=35% så mange ressourcer i produktets livscyklus, som produktet indeholder ved
salg. Samtidig er ressourceeffektiviteten baseret på masse steget fra 0,68% til 3 %.
En del transformere vil indgå i produkter, som bruges og bortskaffes i lande, hvor der ikke er en genanvendelse af elektronikprodukter med samme effektivitet som i Danmark. Hvis alle produkter med
danske transformere blev forbrændt eller deponeret, fås en ressourceeffektivitet på 71% (scenario 5) og et ressourceforbrug på ca. 50.000 PR, hvilket svarer til, at der forbruges 2,5 gange så mange PR,
som hvis metallerne genvindes (scenario 1).
D Galvanisk overfladebehandling
D.1 Introduktion
Inden for galvanoområdet er det valgt at se på tre af de mest almindelige processer til overfladebehandling af stål, nemlig:
- Fornikling/forchromning
- Elektroforzinkning
- Varmforzinkning
Disse processer er ikke ligetil at indpasse i et livscyklusforløb som de øvrige aktiviteter, hvor det produkt og dets livsforløb kunne identificeres.
Her er valgt at se på processen i et livscyklusperspektiv som beskrevet i rapportens kapitel 2. Grafisk kan dette illustreres som vist i Figur D.1.
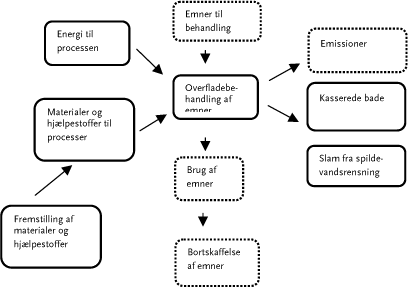
Figur D.1 Galvanisk overfladebehandling i et livscyklusperspektiv
I det følgende er hver af processerne kortlagt.
D.2 Kortlægning af fornikling/forchromning
Fornikling/forchromning er efter elforzinkning den mest almindelige galvaniske proces i Danmark. Processen udføres af ca. 75 danske virksomheder i større eller mindre skala. Ved fornikling/forchromning
foretages først en elektrolytisk pålægning af nikkel (8-15 m) efterfulgt af en elektrolytisk pålægning af chrom (0,2-0,3 m). Det kan undertiden være en teknisk og/eller økonomisk fordel at starte med at
pålægge et elektrolytisk kobberlag først.
Det skønnes, at kun 20-30% af virksomhederne anvender elektrolytisk kobber under nikkel. Man kan eventuelt også undlade at pålægge et chromlag før til sidst, og i så fald har man en ren forniklet
overflade. Det skønnes, at 80% af alle forniklede overflader i Danmark også forchromes.
Det skal bemærkes, at man langt fra altid anvender alle processer, som er vist i det komplette flow-sheet i Figur D.2.
Alle galvaniske processer starter normal med en såkaldt forbehandling, hvor emnerne renses og klargøres den elektrolytiske proces. Det er vigtigt for at opnå en overflade med høj kvalitet og pænt
udseende.
D.2.1 Processerne
D.2.1.1 Ludkogning
Første trin er normalt en varm alkalisk affedtning (ludkoger), hvor olie og fedt opløses og fjernes fra emnernes overflade. Badet indeholder et affedtersalt (natriumhydroxid, carbonater, phosphater, silikater
samt tensider og eventuelle kompleksdannere), der sørger for, at olie og fedt bliver delvis emulgeret i badet. Ofte kommer der efterhånden også fri olie på badoverfladen, og dette olie kan med fordel
skimmes af med mellemrum for at opnå længere levetid for badet.
Når badets indhold af olie og fedt er blevet så højt, at man ikke mere kan opnå en acceptabel affedtning af emnerne, selvom der tilsættes mere affedtersalt, må badet kasseres, og et nyt bad blandes op. Det
kasserede bad kan enten neutraliseres i eget renseanlæg, eller det afleveres til Kommunekemi eller anden godkendt modtager for kemikalieaffald. Badlevetiden afhænger af produktionens størrelse (m²/h),
emnernes tilsmudsning og virksomhedens evne og metode til at vedligeholde badet. Efter behandling i ludkogeren skylles emnerne i et eller flere skyllekar.
Input: |
Pålæsning af varer: |
Output: |
 |
Affedtersalt + vand Energi |
1. Varm alkalisk affedtning
(ludkogning), 70-80°C |
Kasseret bad
Varmeafgivelse |
 |
Vand |
Skyl |
Spildevand med udslæbte kemikalier |
 |
Svovlsyre + vand + Energi |
2. Bejdsning i svovlsyre 60°C |
|
 |
Vand |
Skyl |
Spildevand med udslæbte kemikalier |
 |
Affedtersalt + vand + energi |
3. Elektrolytisk affedtning
(el-affedter), 50°C |
|
 |
Vand |
Skyl |
Spildevand med udslæbte kemikalier |
 |
Kobberanode + natriumcyanid + Natriumhydroxid + kobbercyanid + vand + energi |
4. Forkobring
(Cyan kobber), 50-80°C |
|
 |
Vand |
Skyl |
Spildevand med udslæbte kemikalier |
 |
Svovlsyre + vand |
5. Dekapering i svovlsyre |
|
 |
Vand |
Skyl |
Spildevand med udslæbte kemikalier |
 |
Nikkelanoder + nikkelsulfat + nikkelchlorid + borsyre + svovlsyre/ saltsyre + glansmidler + vand + energi |
6. Fornikling 60°C |
Kasseret bad Varmeafgivelse |
 |
Vand |
Skyl |
Spildevand med udslæbte kemikalier |
 |
Chromsyre + svovlsyre + Dækvæske + vand + energi |
7. Forchromning
(Chromsyre), 35°C |
Kasseret bad
Varmeafgivelse |
 |
Vand |
Skyl |
Spildevand med udslæbte kemikalier |
 |
|
Aflæsning af varer |
|
Figur D.2 Flow-sheet for Kobber-Nikkel-Chrom metallisering
D.2.1.2 Bejdsning
Andet trin er rensning af emnerne i syre (bejdsebad), hvorved rust og glødeskaller opløses og fjernes fra emnernes overflade. Også det øverste lag af selve emnerne fjernes ved denne syrebehandling. Ofte
tilsættes badet en inhibitor, der skal forhindre angreb på grundmaterialet. Til bejdsning kan anvendes svovlsyre ved 50-60°C eller saltsyre ved stuetemperatur. Under bejdsningen forbruges syre til opløsning
af metaloxider, og noget af grundmateriale går også i opløsning. Der kan løbende spædes op med mere syre, men efterhånden bliver badets indhold af metal så højt, at badet må kasseret. Der kan eventuelt
kasseres mindre mængder lidt hyppigere, så man på den måde kan fastholde den ønskede syrekoncentration og en optimal metalkoncentration. Efter bejdsning skylles emnerne i et eller flere skyllekar.
Kasseret syre vil normalt afleveres til Kommunekemi, men det kan eventuelt også neutraliseres i virksomhedens eget renseanlæg, hvorved de opløste metaller udfældes som metalhydroxidslam, som senere
afleveres til Kommunekemi eller anden modtager. Badlevetiden kan forlænges, hvis man reducerer syreangrebet på grundmaterialet, og hvis man først kasserer badet, når metalkoncentrationen er kommet på
maksimum.
D.2.1.3 El-affedtning
Tredje trin er en alkalisk elektrolytisk affedtning (el-affedtning). Processen foregår varmt, og hovedformålet er en let rensning af emnets overflade enten anodisk eller katodisk. Emnerne indeholder normalt
ikke væsentlige mængder olie og fedt efter den forudgående behandling, og rust og glødeskaller er i princippet også væk. Der kan imidlertid være behov for at fjerne oxider, så overfladen bliver helt ren til
den efterfølgende metalpålægning (metallisering). Efter endt behandling skylles emnerne i et eller flere skyllekar.
El-affedteren har normalt længere levetid end ludkogeren, men efterhånden vil indhold af opløste metaller sætte en stopper for fortsat brug af badet selv ved tilsætning af mere affedtersalt. Kasseret bad kan
enten behandles i virksomhedens eget renseanlæg eller sendes til behandling hos Kommunekemi eller anden modtager af kemikalieaffald.
D.2.1.4 Forkobring
Fjerde trin er en elektrolytisk pålægning af kobber, men det er dog kun nødvendigt i enkelte tilfælde. Forkobring foregår som regel i et varmt cyanidholdigt kobberbad, der indeholder cyanid, hydroxid og
carbonat samt eventuelt glansmidler. Denne proces benyttes primært som forbehandling ved fornikling af stærkt blyholdige messinglegeringer, ved messing støbegods eller ved tromlefornikling, hvor man
ønsker at pålægge et tyndere nikkellag. Det er mest almindelig at undlade forkobring før fornikling, men i visse tilfælde kan det være teknisk eller økonomisk fordelagtigt at gøre det. Efter forkobring skylles i
et eller flere skyllekar.
Kobberbadet har forholdsvis lang levetid, men efterhånden vil der dannes mere og mere carbonat i badet, så det til sidst ikke kan fungere korrekt. Her vil man typisk fjerne carbonat (ved udfrysning eller
fældning) i stedet for at kassere hele badet, så det er absolut sjældent, at et cyanidholdigt kobberbad kasseres. Hvis badet skal kasseres, vil det normalt blive afleveret til Kommunekemi.
D.2.1.5 Dekapering
Femte trin er en syredekapering i svovlsyre. Eventuelle alkalirester på overfladen neutraliseres, og metaloxider opløses før forniklingen. Normalt skylles herefter i et enkelt skyllekar, men skylningen kan
eventuelt overspringes. Syrestyrken i dekaperingsbadet kan vedligeholdes ved passende tilsætning af ny syre, men det er ret almindeligt, at badet kasseres hyppigt. Denne badtype vil normalt altid behandles i
virksomhedens eget renseanlæg, da syreindholdet og metalkoncentrationen begge er lave.
D.2.1.6 Fornikling
Sjette trin er en elektrolytisk fornikling, som foregår i en varm nikkelholdig elektrolyt (50-60°C) med nikkelsulfat som hovedkomponent (Ni = 70 g/l). Badet indeholder også borsyre, lidt chlorid samt
glansmidler. Syreindholdet skal svare til pH = 3,5-4,5. Nikkel pålægges elektrolytisk, idet metallisk nikkel (nikkelanoder) opløses og udfældes på emnerne, der er forbundet som katode. Normalt skylles i et
eller flere skyllekar efter fornikling.
Nikkelbadet forurenes løbende med nedbrudte glasmidler, som kan fjernes ved filtrering med aktiv kul. Mange nikkelbade kører med kontinuert kulfiltrering, så badet hele tiden holdes rent. Badet kan også
forurenes med fremmedmetaller, og de kan som regel fjernes ved selektiv elektrolytisk udfældning uden for normal driftstid. Ved korrekt vedligeholdelse af badet har man normalt ikke behov for at kassere
et nikkelbad, men badet kan naturligvis ved et uheld blive så forurenet, at eneste udvej er at kassere det. I visse tilfælde vil det anodiske strømudbytte være større end det katodiske, og man opnår mere
opløsning af nikkel fra anoden, end der udfældes på varerne. I så fald må man med mellemrum kassere en del af badet for at holde nikkelkoncentrationen på den ønskede værdi. Kasseret nikkelbad vil
normalt afleveres til Kommunekemi.
D.2.1.7 Forchromning
Syvende trin er en elektrolytisk forchromning, men det er ikke alle forniklede emner, som man forchromer. Ca. 20% af de forniklede emner pålægges ikke chrom. Forchromning foregår i en kraftig
chromsyreopløsning (CrO3 = 200 g/l) tilsat lidt svovlsyre samt katalysator. Da chromlaget skal være meget tyndt (0,2-0,3 m), er procestiden kort. Badet er let opvarmet (ca. 35°C), men ofte er
overskudsvarmen ved den elektrolytiske proces nok til at holde temperaturen. I visse tilfælde kan afkøling ligefrem være påkrævet, idet kun 15% af strømmen udnyttes ved elektrolyseprocessen, mens resten
bliver til varme. Efter forchromning skal emnerne skylles grundigt i et eller flere skyllekar, før de aflæsses som færdige emner.
Det kan undertiden være nødvendigt at aktivere de forniklede emner, før de forchromes, og det kan foregå ved fordypning i halvkoncentreret chromsyre. Hvis emnerne skylles i afsaltet vand med meget lille
ledningsevne efter fornikling, vil man som regel få problemer ved forchromningen, idet emnerne bliver passive, og der kan ikke opnås en god forchromning. I så fald er en chromsyre aktivering før
forchromning helt nødvendigt. Passivering af de forniklede emner kan som regel undgås, hvis der skylles i postevand efter fornikling.
Den hyppigste forurening i badet er fremmedmetaller, Cr+3 og chlorider. Et vist indhold af Cr+3 er dog nødvendig af hensyn til den elektrolytiske proces, men for en høj koncentration giver problemer. Der
findes metoder til fjernelse af fremmedmetaller og Cr+3 men de er ikke vidt udbredt endnu, men chlorid fjernes rutinemæssigt ved fældning med AgO efterfulgt af filtrering/sedimentering. Et forurenet
chrombad afleveres normalt til Kommunekemi til behandling, men et chrombad kan normalt holde i 3-10 år – undertiden endnu længere. Levetiden afhænger blandt andet af de emner, der behandles samt
indslæb af nikkel fra foregående bad.
D.2.2 Skylning
Der anvendes normalt skylning efter hvert procesbad for at fjerne kemikalierester på emnernes overflade og stoppe den kemiske reaktion på emnerne, hvorved man også reducerer indslæb af fremmede
kemikalier i de efterfølgende procesbade. Skylning foregår ofte i flere kar, og der kan anvendes postevand, kemisk renset spildevand, ionbyttet vand eller afsaltet vand fra omvendt osmose (RO-vand).
Efter selve metalliseringsbadet kan med fordel anvendes et stillestående skyl (sparskyl) til opsamling af udslæbte badkemikalier. Det halvkoncentrerede sparskyl kan senere føres retur til procesbadet som
kompensation for fordampningstabet fra badet. Denne metode er en stor fordel ved varme procesbade, hvor man på den måde kan genvinde 50-90% af de udslæbte badkemikalier. Genvindingsgraden kan
øges ved at anvende 2 eller 3 sparskyl efter samme koncept, idet første skyl bruges til opspædning af procesbadet, 2. skyl bruges herefter til opspædning af 1. skyl osv. Systemet kan eventuelt
automatiseres, så det forløber kontinuert (low-flow skyllesystem med tilbageføring).
Efter forbehandlingsbadene (affedter, bejdse og dekapering) er der ikke samme fordel ved at anvende sparskyl, da man i disse bade løbende under driften får tilført forureninger, der er er med til at afkorte
badets levetid. Hvis disse forureninger føres tilbage ved opspædning med et sparskyl, vil levetiden forkortes yderligere, hvilket gør det til en tvivlsom fidus. Kun hvis man har udstyr til løbende oprensning og
regenerering af forbehandlingsbadene, vil det være en fordel at tilbageføre de udslæbte badkemikalier via et sparskyl.
Anvendes cirkulation af skyllevand over en ionbytter, eller hvis man cirkulerer kemisk renset vand, så er det ikke lige så vigtigt at minimere vandflowet ved at benytte flere skyllekar i modstrøm. Man kan
sige, at et højt flow er ”gratis”, og det er alene udslæbet af badkemikalier med emnerne, der belaster ionbytningsanlæg og renseanlæg. Det er dog klart, at et stort flow kræver enten en stor ionbytter eller et
stort renseanlæg, så derfor kan det normalt godt svare sig at holde flowet på et passende lavt niveau, så udstyret ikke bliver for stort og kostbart.
D.2.3 Ressourceforbrug
De væsentligste ressourcer, der forbruges ved fornikling/forchromning, er:
- Kemikalier bruges i procesbadene, til vandbehandling og til vandrensning.
- Metaller bruges primært som anoder (kobber og nikkel), der overføres til emnerne ved en elektrolytisk metaludfældning.
- Vand bruges til skylning og til opblanding af procesbade.
- Energi bruges til de elektrolytiske processer, til badopvarmning, til tørring, til ventilation og rumopvarmning samt til drift af produktionsudstyr som pumper og transportører samt renseanlæg.
D.2.3.1 Kemikalieforbrug og anodeforbrug
I Danmark bruges årligt ca. 125 ton nikkelanoder til fornikling, hvilket svarer til 1.170.000 m² overflade ved en lagtykkelse på 12 m. Heraf forkobres ca. 25% svarende til ca. 295.000 m². Af den samlede
forniklede overflade bliver ca. 80% eller 936.000 m² forchromet. Forbrug af hovedkemikalier til disse processer fremgår af Tabel D.1.
Tabel D.1 Kemikalieforbrug ved fornikling/forchromning
Procesbad |
Kemikalie |
% af branchen |
Produktion i 1000 m |
Typisk forbrug i kg pr. 1000 m² |
Kg/år |
Ludkoger |
Affedtersalt |
100 |
1.170 |
50,0 |
58.500 |
Bejdsebad |
Svovlsyre, 96% |
75 |
878 |
50,0 |
43.875 |
Bejdsebad |
Saltsyre, 30% |
25 |
293 |
75,0 |
21.938 |
El-affedter |
Affedtersalt |
100 |
1.170 |
40,0 |
46.800 |
Kobberbad |
Kobberanoder |
25 |
293 |
89,0 |
26.033 |
Kobberbad |
NaCN |
25 |
293 |
90,0 |
26.325 |
Kobberbad |
CuCN |
25 |
293 |
45,0 |
13.163 |
Kobberbad |
NaOH |
25 |
293 |
10,0 |
2.925 |
Dekapering |
Svovlsyre, 96% |
100 |
1.170 |
50,0 |
58.500 |
Nikkelbad |
Nikkelanoder |
100 |
1.170 |
107,0 |
125.190 |
Nikkelbad |
Nikkelsulfat |
100 |
1.170 |
7,5 |
8.775 |
Nikkelbad |
Nikkelchlorid |
100 |
1.170 |
2,0 |
2.340 |
Nikkelbad |
Borsyre |
100 |
1.170 |
1,0 |
1.170 |
Nikkelbad |
Glansmidler |
100 |
1.170 |
27,0 |
31.590 |
Chrombad |
Chromsyre |
80 |
936 |
21,1 |
19.750 |
For kobberbadet kan man groft regne med, at kobberanoderne ender som et kobberlag på varerne.
For nikkelbadet gælder som hovedregel, at de anvendte nikkelanoder ender som nikkellag på varerne, og der går i princippet ikke noget til spilde. Der udslæbes dog nikkel til skyllevandet, men en del af
denne nikkel (50-95%) føres retur til procesbadet og genanvendes, mens resten ender i spildevandet, hvor det omdannes til slam i renseanlægget. Man kan groft sige, at forbruget af nikkelsulfat,
nikkelchlorid og borsyre ender i spildevandet.
For chrombadet gælder, at en relativ stor del af chromsyreforbruget udslæbes med varerne, og kun en lille del bliver til et chromlag på emnerne, hvor man typisk kun har en lagtykkelse på 0,25 m. Ved hjælp
af et eller flere sparskyl kan man genvinde 25-90% af det chromsyre, som i første omgang udslæbes fra chrombadet med varerne, men man må nok regne med, at kun 50% af chromsyreforbruget ender som
chrom på varerne.
I Tabel D.2 er foretaget en vurdering af de i Tabel D.1 angivne kemikalieforbrug.
Tabel D.2 Bestanddele i kemikalier til fornikling/forchromning
Kemikalie |
Mængde |
Komponenter |
Affedtersalt |
59 ton |
Hydroxider, carbonater 5-25%
Tensider, kompleksdannere 5- 25%
Vand 50 – 90% |
3-15 ton
3-15 ton 30-50 ton |
Svovlsyre |
102 ton |
96% svovlsyre, regnes som ren syre |
Saltsyre |
22 ton |
30% syre svarer til 7 ton ren HCl |
Affedtersalt |
47 ton |
Syre eller base, - ikke oplyst |
Kobberanoder |
26 ton |
26 ton metallisk kobber |
Natriumcyanid |
26 ton |
Antagelig 100% natriumcyanid |
Kobbercyanid |
13 ton |
Antagelig 100% kobbercyanid, heraf 71 % kobber svarende til 9 ton Cu |
Natriumhydroxid |
3 ton |
Antagelig 100% NaOH |
Nikkelanoder |
125 ton |
125 ton metallisk nikkel |
Nikkelsulfat |
9 ton |
Antagelig 100 % NiSO4, heraf 38% nikkel svarende til 3,4 ton Ni |
Nikkelchlorid |
2,3 ton |
Antagelig 100% NiCl2, heraf 46% nikkel svarende til 1,1 ton nikkel |
Borsyre |
1,2 ton |
% borsyre ikke kendt |
Glansmidler |
32 ton |
Sammensætning ikke kendt |
Chromsyre |
20 ton |
Antagelig 100% CrO3, heraf 52% Chrom svarende til 10,4 ton |
På basis af antagelser og opgørelser kan følgende uddrages, at:
- der anvendes 475 ton kemikalier i alt, hvoraf vand antagelig udgør 30-50 ton.
- nikkelforbruget ligger på omkring 130 ton.
- kobberforbruget ligger på omkring 33 ton.
- chromforbruget ligger på omkring 10 ton.
- forbruget af uorganiske syrer, primært svovlsyre, ligger på omkring 110 ton.
- forbruget af uorganiske baser, primært natriumhydroxid, ligger på 5-15 ton.
- forbruget af organiske forbindelser som tensider, affedtersalt mv. udgør 50-60 ton.
- forbruget af cyanider udgør omkring 30 ton.
- for det øvrige forbrug på 60-70 ton kendes sammensætningen ikke.
Det samlede kemikalieforbrug udgør 0,42 kg pr. m² overflade. Metallerne udgør således ca. 35% af kemikaliemængden. Almindelige syrer og baser gør omkring 25%, organiske forbindelser omkring 18%
og uoplyste omkring 14%. De resterende 8% er primært vand, og for en mindre mængde salte/oxider, der følger med metallerne samt usikkerheder.
D.2.3.2 Råstofforbrug
Ud fra oplysninger i LCA-databaser som UMIP og SigmaPro er det søgt at opgøre råstofforbruget for de væsentligste materialeforbrug. Opgørelsen er vist i Tabel D.3.
Tabel D.3 Estimering af forbrug af råstoffer for fornikling/forchromning
Materiale
Behandlet overflade 1.170.000 m² |
Materiale-
forbrug I alt |
Råstof-
forbrug
kg/kg |
Råstof-
forbrug
I alt |
Råstof-
forbrug
Pr. 1.000 m² |
Nikkel |
130 ton |
9,4 1) |
1.222 ton |
1.044 kg |
Kobber |
33 ton |
3,7 1) |
122 ton |
104 kg |
Chrom |
10 ton |
5,6 1) |
56 ton |
48 kg |
Uorganiske syrer, primært svovlsyre |
110 ton |
0,7 1) |
77 ton |
66 kg |
Uorganiske baser, primært natriumhydroxid |
10 ton |
1,2 1) |
12 ton |
10 kg |
Organiske forbindelser |
55 ton |
1,0 1) |
55 ton |
47 kg |
Cyanider |
30 ton |
2,0 1) |
60 ton |
51 kg |
Øvrige (ukendt sammensætning) |
65 ton |
3,0 2) |
195 ton |
167 kg |
I alt |
1.799 ton |
1.537 kg |
1): Data fra SigmaPro.
2): Tallet er anslået ud fra en antagelse om, at øvrige kemikalier indeholder en vis mængde metal og en vis mængde organiske forbindelser.
Sammenlignes opgørelsen i med opgørelsen af materialeforbruget, ses det, at råstofforbruget er ca. 3,5 gange så stort (1,537/0,42).
D.2.3.3 Vandforbrug
Den galvaniske branche har nedsat vandforbruget voldsomt, siden der for alvor kom fokus på miljøet herhjemme i 1970’erne. Dengang var det ikke ualmindeligt med et vandforbrug på 1000 liter pr. m²
overflade – et tal som man stadigvæk kan møde i Østeuropa og andre lande, hvor vandprisen er lav, og hvor man endnu ikke for alvor har fokus på vandforbruget.
I dag er vandforbruget mere typisk på 50-250 liter pr. m² overflade, og det svarer til et samlet vandforbrug herhjemme på ca. 120.000 m³/år til fornikling/forchromning. Miljøstyrelsen mener, at man
efterhånden skal ned på et vandforbrug på 10 liter pr. m² overflade, og det er faktisk muligt ved brug af 3-trins modstrømsskyl eller andre lige så vandbesparende skyllemetoder (ionbytning, sprayskylning,
vandgenbrug), men det store problem er, at der helst skal bruges 2-4 skyllekar efter hvert proceskar, for at det skal lykkes. Det kan ofte være et problem at indsætte det fornødne antal skyllekar i
eksisterende produktionslinier, da det er uforholdsmæssigt dyrt sammenlignet med etablering af nye proceslinier. Ofte er der ikke plads i lokalet til at indføre mange ekstra skyllekar.
Der er ingen tvivl om, at tiden stadig arbejder for at opnå yderligere vandreduktioner i takt med de stigende vandpriser, men jo længere man kommer ned, jo færre kroner er der at hente på yderligere
vandbesparelser. Det skal dog også nævnes, at mindre vandforbrug kræver mindre renseanlæg, og der vil samtidig også være en vis besparelse i kemikalieforbrug til spildevandsrensning. Rent teknisk kan
virksomhederne stadig opnå store vandbesparelser ved i endnu højere grad at bruge de vandbesparende skyllemetoder og teknikker. Vandforbruget bør i løbet af de næste 5 år uden problemer kunne
komme ned på 30-40 liter pr. m² overflade svarende til ca. 40.000 m³/år fra al fornikling/forchromning i Danmark.
D.2.3.4 Energiforbrug
Energiforbruget til de elektrolytisk processer kan beregnes forholdsvis enkelt. Når man kender produktionens størrelse, kan man udregne strømforbruget ud fra de anvendte Volt, Amp og timer med tillæg
for strømtab i ensretter. Energiforbrug til badopvarmning afhænger af badtemperaturen, karisolering, rumtemperatur og udsugning. Energiforbrug til ventilation udgør også en betydelig post. Energiforbrug til
motorer, køling og trykluft – herunder renseanlæg – er af mindre betydning.
Det foreligger ikke mange publikationer og erfaring herhjemme om energiforbruget i galvanobranchen. Forbruget er derfor vurderet ud fra fornikling/forchromning dels ud fra overslagberegning og dels ud fra
konkrete tal og vurderingen fra en dansk virksomhed, der kun udfører fornikling/forchromning.
Tabel D.4 Energiforbrug ved fornikling/forchromning
|
Udvalgt virksomhed |
Hele Danmark |
kWh/år |
KWh/m² |
% |
Kwh/år |
Ensrettere |
13.000 |
1,01 |
3 |
1.176.425 |
Badvarme |
200.000 |
15,47 |
53 |
18.098.848 |
Tørring |
30.000 |
2,32 |
8 |
2.714.827 |
Ventilation |
43.000 |
3,33 |
11 |
3.891.252 |
Diverse |
94.000 |
7,27 |
25 |
8.506.458 |
Total |
380.000 |
29,39 |
100 |
34.387.810 |
Det samlede forbrug ligger således på 34.400 MWh pr. år og er udelukkende et elforbrug.
Det største forbrug går til badopvarmning, men denne post vil være forholdsvis mindre ved en mere intens udnyttelse af produktionsapparatet. Det forbruger jo også energi at have badene stående med
opvarmning om natten og i weekenden. Derfor vil der være mindre energispild, hvis der produceres hele tiden, så det specifikke energiforbrug (kWh/m²) til badopvarmning vil gå ned. Det skal også nævnes,
at man i ovenstående eksempel ikke anvender forkobring, som også vil kræve energiforbrug til badopvarmning og ensretter. Det er dog nok realistisk at regne med et total energiforbrug på 25-35 kWh pr.
produceret m².
D.2.4 Affald
De to væsentligste affaldsstrømme fra fornikling/forchromning er:
- Tungmetalslam fra spildevandsrensning
- Kasserede procesbade til ekstern behandling/oparbejdning
I Miljøprojekt 55/2000 vedrørende oparbejdning af galvanisk affald blev affaldsmængderne estimeret ud fra en beregningsmodel kombineret med data fra de største virksomheder i branchen. Dette er vist i
Tabel D.5.
Tabel D.5 Flydende kemikalieaffald fra fornikling/forchromning
Kasseret bad |
m² overflade
pr. år |
Kasseret bad
liter pr. 1000 m² |
Kasseret
bad, m³/år |
Metal i
bad, g/l |
Metal,
kg/år |
Ludkoger |
1.170.000 |
150 |
176 |
0 |
0 |
Bejdsebad |
1.170.000 |
45 |
53 |
40 |
2.106 |
El-affedter |
1.170.000 |
300 |
351 |
2 |
702 |
Kobberbad |
293.000 |
5 |
1 |
30 |
44 |
Dekaperingsbad |
1.170.000 |
500 |
585 |
2 |
1.170 |
Nikkelbad |
1.170.000 |
12 |
14 |
80 |
1.123 |
Chrombad |
936.000 |
16 |
15 |
110 |
1.647 |
Total |
6.793 |
Som det fremgår af Tabel D.5, er det langt fra alle affaldstyper, som indeholder væsentlige mængder tungmetaller. Det er oftest således, at virksomheder selv behandler de kasserede bade med lavt
metalindhold, mens mere koncentrerede bade som bejdsebade, kobberbade, nikkelbade og chrombade sendes til ekstern behandling (Kommunekemi). Bejdsebadene nedslides og kasseres forholdsvis ofte,
mens metalliseringsbadene kun meget sjældent kasseres på grund af forurening eller for høje koncentrationer.
Tabel D.6 Slam fra spildevandsrensning (filterkager med 30% tørstof)
Spildevand |
m² overflade
pr. år |
Metal i
bad, g/l |
Udslæb
af metal,
kg/år |
Genvin-
dings % |
Metal i
slam,
kg/år |
Filterkager
(30%TS)
ton/år |
Ludkoger |
1.170.000 |
0 |
0 |
0 |
0 |
0,0 |
Bejdsebad |
1.170.000 |
30 |
5.265 |
0 |
5.265 |
43,9 |
El-affedter |
1.170.000 |
0,5 |
88 |
0 |
88 |
0,7 |
Kobberbad |
293.000 |
30 |
1.319 |
0 |
1.319 |
11,0 |
Dekapering |
1.170.000 |
1 |
176 |
0 |
176 |
1,5 |
Nikkelbad |
1.170.000 |
70 |
12.285 |
75 |
3.071 |
25,6 |
Chrombad |
936.000 |
100 |
14.040 |
50 |
7.020 |
58,5 |
Total |
|
|
|
|
16.938 |
141,2 |
kg filterkage pr. m² produktion i gennemsnit: |
0,121 |
Produktion af filterkager pr. m² overflade er 0,121 kg, hvilket er lidt højere end for elforzinkning. Det skyldes blandt andet, at man ved fornikling/forchromning arbejder med flere og mere koncentrerede
metalliseringsbade.
Denne tabel omfatter ikke det slam, som dannes på de virksomheder, der selv neutraliserer kasserede procesbade, hvilket vil betyde en mindre stigning i slammængden. Sammenfattet kan følgende totale tal
opstilles, hvor slammængden er korrigeret med metalmængderne for de kasserede procesbade, som behandles af virksomhederne selv:
Metalmængde i kasserede bade til ekstern behandling: |
4.921 kg/år |
Metalmængde i spildevandsslam fra fældningsanlæg: |
18.810 kg/år |
Det fremgår, at der er næsten 4 gange mere metal i slammet end i det flydende kemikalieaffald, som levers til ekstern behandling (Kommunekemi).
Affald stammende fra ludkoger, bejdsebad, el-affedter samt dekaperingsbad indeholder metaller fra de emner, der behandles og udgøres derfor primært af jern. Affald fra kobberbadet er kobber, fra
nikkelbadet er det nikkel, og fra chrombadet er det trivalent og hexavalent chrom.
Ud fra affaldsopgørelserne for flydende kemikalieaffald (Tabel D.5)og slam fra spildevandsrensning (Tabel D.6) kan affaldet opdelt på de væsentligste metaller opgøres.
Tabel D.7 Affald opdelt på metaller i forhold til samlet mængde og ressourceforbrug
Materiale |
Affaldsmængde |
Del af den
samlede af- faldsmængde |
Ressource-
forbrug |
Affald i forhold
til ressourceforbrug |
Kobber |
1,36 ton |
5,7 % |
33 ton |
3-4 % |
Nikkel |
4,19 ton |
17,7 % |
130 ton |
3-4 % |
Chrom |
8,67 ton |
36,5 % |
10,4 ton |
83 % |
Andre metaller (primært jern) |
9.51 ton |
40,1 % |
Ikke relevant |
Ikke relevant |
Det fremgår af tabellen, at udnyttelsesprocenten for chrom er langt dårligere end for kobber og nikkel.
D.2.5 Hovedtal for fornikling/forchromning
Kortlægningen har vist, at der behandles 1,17 mio. m² overflade pr. år med lagtykkelse på 12 µm nikkel, og at 25% forkobres, mens 80% forchromes.
Der anvendes 475 ton kemikalier i alt, hvilket svarer til 0,42 kg pr. m² behandlet overflade. Nikkelforbruget ligger på omkring 130 ton, kobberforbruget ligger på omkring 33 ton og chromforbruget ligger på
omkring 10 ton. Dertil kommer omkring 270 ton øvrige kemikalier.
Der anvendes et vandforbrug på 120.000 m³/år og et energiforbrug i form af el på 34.400 MWh pr. år, svarende til 29.400 kWh pr. 1000 m² overflade.
Affald fra kasserede bade og slam udgør i alt 23.73 ton metal, hvoraf 1,36 ton er kobber, 4,19 ton er nikkel og 8,67 ton chrom. Omkring 9,5 ton er metaller fra den behandlede overflade og udgøres
primært af jern.
Forskellen i metalmængder mellem forbrug og affald antages at findes på emnerne. Ved kassering af emnerne vil metallerne tabes, selvom emnerne oparbejdes.
Omregnes materialeforbruget til forbrug af råstoffer ses det, at forbruget bliver omkring 3,5 gange større svarende til 1,54 kg pr. 1.000 m² overflade.
D.3 Kortlægning af elforzinkning
Elforzinkning den mest almindelige galvaniske proces i Danmark. Processen udføres af ca. 90 danske virksomheder i større eller mindre skala.
Ved elforzinkning foretages først en rengøring af emnerne (affedtning og bejdsning), hvorefter der elektrolytisk påføres er zinklag på 5-20 m. Lagtykkelsen er typisk mindst for tromlevarer (små emner), mens
større emner på stativer typisk påføres lagtykkelser på 12-20 m.
Behandlingen afsluttes med en passivering – det vil sige en kemisk behandling af overfladen i en chromatopløsning, hvorved overfladen bliver mere korrosionsbestandig.
D.3.1 Processerne
Den fulde proces er vist som flowsheet i Figur D.3. Det skal bemærkes, at man ikke altid anvender alle processer som vist på flowsheetet, da det kan afhænge af typen på zinkbadet (sur zink, cyan zink eller
alkalisk zink).
D.3.1.1 Ludkogning
Første trin er normalt en varm alkalisk affedtning (ludkoger), hvor olie og fedt opløses og fjernes fra emnernes overflade. Badet indeholder et affedtersalt (natriumhydroxid, carbonater, phosphater, silikater
samt tensider og eventuelle kompleksdannere), der sørger for, at olie og fedt bliver delvis emulgeret i badet. Ofte kommer der efterhånden også fri olie på badoverfladen, og denne olie kan med fordel
skimmes af med mellemrum for at opnå længere levetid for badet.
Når badets indhold af olie og fedt er blevet så højt, at man ikke mere kan opnå en acceptabel affedtning af emnerne, selvom der tilsættes mere affedtersalt, må badet kasseres, og et nyt bad blandes op. Det
kasserede bad kan enten neutraliseres i eget renseanlæg eller det afleveres til Kommunekemi eller anden godkendt modtager for kemikalieaffald. Badlevetiden afhænger af produktionens størrelse (m²/h),
emnernes tilsmudsning og virksomhedens evne og metode til at vedligeholde badet. Efter behandling i ludkogeren skylles emnerne i et eller flere skyllekar.
Input: |
Pålæsning af varer: |
Output: |
 |
Affedtersalt + vand Energi |
1. Varm alkalisk affedtning
(ludkogning), 70-80°C |
Kasseret bad
Varmeafgivelse |
 |
Vand |
Skyl |
Spildevand med udslæbte kemikalier |
 |
Svovlsyre + vand + energi |
2. Bejdsning i svovlsyre 60°C |
|
 |
Vand |
Skyl |
Spildevand med udslæbte kemikalier |
 |
Affedtersalt + vand + energi |
3. Elektrolytisk affedtning
(el-affedter), 50°C |
|
 |
Vand |
Skyl |
Spildevand med udslæbte kemikalier |
 |
Saltsyre + vand |
5. Dekapering i saltsyre |
|
 |
Vand |
Skyl |
Spildevand med udslæbte kemikalier |
 |
Zinkanoder + salte + glansmidler + vand + energi |
6. Forzinkning 20-35°C |
Kasseret bad |
 |
Vand |
Skyl |
Spildevand med udslæbte kemikalier |
 |
Chromsalte + syre + vand |
7. Passivering i chrom 20°C |
Kasseret bad |
 |
Vand |
Skyl |
Spildevand med udslæbte kemikalier |
 |
|
Aflæsning af varer |
|
Figur D.3 Flow-sheet for elforzinkning
D.3.1.2 El-affedtning
Tredje trin er en alkalisk elektrolytisk affedtning (el-affedtning). Processen foregår varmt, og hovedformålet er en let rensning af emnets overflade enten anodisk eller katodisk. Emnerne indeholder normalt
ikke væsentlige mængder olie og fedt efter den forudgående behandling, og rust og glødeskaller er i princippet også væk. Der kan imidlertid være behov for at fjerne oxider, så overfladen bliver helt ren til
den efterfølgende metalpålægning (metallisering). Efter endt behandling skylles emnerne i et eller flere skyllekar.
El-affedteren har normalt længere levetid end lugkogeren, men efterhånden vil indhold af opløste metaller sætte en stopper for fortsat brug af badet, selv ved tilsætning af mere affedtersalt. Kasseret bad kan
enten behandles i virksomhedens eget renseanlæg eller sendes til behandling hos Kommunekemi eller anden modtager af kemikalieaffald.
D.3.1.3 Dekapering
Fjerde trin er en syredekapering i saltsyre, og den anvendes fortrinsvis foran et surt zinkbad. Eventuelle alkalirester på overfladen neutraliseres, og metaloxider opløses før forzinkningen. Syrestyrken i
dekaperingsbadet kan vedligeholdes ved passende tilsætning af ny syre, men efter længere tids drift kasseres badet normalt helt. Det kasserede vil normalt altid behandles i virksomhedens eget renseanlæg,
da syreindholdet og metalkoncentrationen begge er lave. Dekaperingsbadet foran alkalisk zink vil normalt være en tynd opløsning af natronlud.
D.3.1.4 Forzinkning
Femte trin er elforzinkning. Der findes tre forskellige typer zinkbade. Det mest almindelige er sur zink (indeholder zinkchlorid, borsyre, kaliumchlorid og glansmidler). Dernæst kommer cyan zink (indeholder
zink, cyanid, NaOH og glansmidler), der tidligere var det mest almindelige bad. Endelig findes alkalisk zink (indeholder zink, NaOH og glansmidler), som har en begrænset udbredelse.
Et zinkbad arbejder normalt ved stuetemperatur, men sure zinkbade kan køre med lidt opvarmning (35°C), hvilket giver mulighed for direkte tilbageføring af udslæbte badkemikalier fra et sparskyl.
Anvendes varm sur zink, kan man ofte undgå en ekstern køling af badet. Med et strømudbytte på 90-100% er overskudsvarmen ved elektrolysen moderat. Det sure bad forurenes med jern og nedbrudte
glansmidler, hvilket stiller krav om rensning. Det er heller ikke ualmindeligt, at zinkkoncentrationen bliver for høj på grund af større anodisk strømudbytte ved elektrolysen.
Det cyanholdige zinkbad er meget robust og kan arbejde selv med store forureninger (olie, fedt, metal), men der dannes løbende carbonat, som må fjernes, når koncentrationen bliver for høj. Det kan enten
gøres ved udfældning med specialkemikalier eller ved udfrysning. Det cyanholdige zinkbad blev tidligere brugt af alle virksomheder, men nu er det på vej ud på grund af miljøproblematikken ved anvendelse
af giftige cyanforbindelser. Da badet kører ved stuetemperatur, er der normalt behov for køling for at fjerne overskudsvarmen fra elektrolyseprocessen, hvor strømudbyttet kun er på ca. 60%.
Det alkaliske zinkbad er et meget følsomt bad, der kræver en perfekt forbehandling for at opnå en god overfladekvalitet på emnerne. Strømudbyttet er kun 70%, hvilket betyder, at der skal bruges ekstern
køling for at fjerne overskudsvarmen fra elektrolysen. Badet kører med meget lavt zinkindhold (typisk 10 g/l), hvilket giver et lavt udslæb af zink til spildevandet.
Badene kasseres i princippet ikke, men det kan undtagelsesvis blive nødvendigt at kassere et forurenet bad. De kasserede bade sendes normalt til behandling hos Kommunekemi. Når cyanholdige bade skal
udskiftes med cyanfri bade, vil man normalt også sende de cyanholdige bade til Kommunekemi, da det er meget problematisk for den enkelte virksomhed at destruere opløsninger med så høje
cyanidkoncentrationer.
D.3.1.5 Passivering
Sjette trin er passivering i chromholdige opløsninger. I gamle dage brugte man udelukkede 6-gyldige chromforbindelser – de såkaldte chromater – og derfor kaldes processen også sommetider for en
chromatering (på engelsk: chromating). I dag anvendes der i Danmark udelukkende 3-gyldige chromforbindelse til blå passivering, mens der stadig anvendes chromater til gul-, sort- og oliven passivering.
Navnene angiver de farvenuancer, som overfladen får ved passiveringsprocessen. Undertiden kaldes blå passivering også for blank passivering, da overfladen ofte ønskes så blank som muligt, så det minder
om en forchromet overflade.
Ved passiveringsprocessen reagerer zinkoverfladen med kemikalierne i passiveringsbadet, hvorved der kommer opløst zink i badet. I de chromatholdige bade vil der efterhånden også dannes 3-gyldige
chromforbindelser. Zink og 3-gyldig chrom (i de chromatholdige bade) er forureninger, der enten må fjernes, eller badet må kasseres, når forureningerne er blevet for høje. Man spæder løbende badene op
med nye passiveringskemikalier og eventuelt syre i takt med, at kemikalierne forbruges. Ved passiveringsprocessen reagerer zinkoverfladen med chrom, så der dannes et kombineret zink-chrom lag, der er
mere korrosionsbestandig end selve zinklaget. Jo tykkere dette lag er, jo bedre korrosionsbestandighed.
Blå passivering giver typisk et passiveringslag med ca. 0,03 g chrom pr. m². Gulpassivering giver typisk et passiveringslag med 0,40 g chrom pr. m², mens man ved sort og oliven passivering typisk har 0,95
g chrom pr. m². Alt afhænger naturligvis af badtype og procestiden.
Passiveringsbade kasseres ret hyppigt – især blå passiveringsbade. Kasserede passiveringsbade vil normalt behandles i virksomhedernes eget renseanlæg, da metalkoncentrationen og syreindholdet er
moderat. Enkelte virksomheder sender de mest koncentrerede bade (gul, sort og oliven) til Kommunekemi.
D.3.2 Skylning
Der anvendes normalt skylning efter hvert procesbad for at fjerne kemikalierester på emnernes overflade og stoppe den kemiske reaktion på emnerne, hvorved man også reducerer indslæb af fremmede
kemikalier i de efterfølgende procesbade. Skylning foregår ofte i flere kar, og der kan anvendes postevand, kemisk renset spildevand, ionbyttet vand eller afsaltet vand fra omvendt osmose (RO-vand).
Efter selve metalliseringsbadet kan med fordel anvendes et stillestående skyl (sparskyl) til opsamling af udslæbte badkemikalier. Det halvkoncentrerede sparskyl kan senere føres retur til procesbadet som
kompensation for fordampningstabet fra badet. Denne metode er en stor fordel ved varme procesbade – jo varmere, jo mere fordampning og jo større tilbageføring. Ved sur zink vil man dog næppe kunne
genvinde mere end 25-50% af de udslæbte badkemikalier på grund af den forholdsvis lave temperatur og dermed ringe fordampning. Genvindingsgraden kan øges ved at anvende 2 eller 3 sparskyl efter
samme koncept, idet første skyl bruges til opspædning af procesbadet, 2. skyl bruges herefter til opspædning af 1. skyl osv. Systemet kan eventuelt automatiseres, så det forløber kontinuert (low-flow
skyllesystem med tilbageføring). Tilbageføring ved kolde procesbade kan øges betydelig ved at skylle i sparskyllet både før og efter metalliseringsbadet. Det giver direkte 50% tilbageføring efter et koldt
metalliseringsbad.
Efter forbehandlingsbadene (affedter, bejdse og dekapering) er der ikke samme fordel ved at anvende sparskyl, da man i disse bade løbende under driften får tilført forureninger, der er er med til at afkorte
badets levetid. Hvis disse forureninger føres tilbage ved opspædning med et sparskyl, vil levetiden forkortes yderligere, hvilket gør det til en tvivlsom fidus. Kun hvis man har udstyr til løbende oprensning og
regenerering af forbehandlingsbadene, vil det være en fordel at tilbageføre de udslæbte badkemikalier via et sparskyl.
Anvendes cirkulation af skyllevand over en ionbytter, eller hvis man cirkulerer kemisk renset vand, så er det ikke lige så vigtigt at minimere vandflowet ved at benytte flere skyllekar i modstrøm. Man kan
sige, at flowet er ”gratis”, og det er alene udslæbet af badkemikalier med emnerne, der belastet ionbytningsanlægget og renseanlægget. Det er dog klart, at et stort flow kræver enten en stor ionbytter eller et
stort renseanlæg, så derfor kan det normalt godt svare sig at holde flowet på et passende lavt niveau, så udstyret ikke bliver for stort og kostbart.
D.3.3 Ressourceforbrug
De væsentligste ressourcer, der forbruges ved elforzinkning, er:
- Kemikalier bruges i procesbadene, til vandbehandling og til vandrensning.
- Metaller bruges primært som anoder (zink), der overføres til emnerne ved en elektrolytisk metaludfældning.
- Vand bruges til skylning og til opblanding af procesbade.
- Energi bruges til de elektrolytiske processer, til badopvarmning, til ventilation og rumopvarmning samt til drift af produktionsudstyr som pumper og transportører samt renseanlæg.
D.3.3.1 Kemikalieforbrug og anodeforbrug
Der bruges årligt ca. 600 ton zinkanoder, hvilket svarer til 8.500.000 m² overflade ved en lagtykkelse på 10 m. Forbrug af hovedkemikalier til disse processer fremgår af Tabel D.8.
Tabel D.8 Kemikalieforbrug ved elforzinkning
Procesbad |
Kemikalie |
% af
branchen |
Produktion
i 1000 m² |
Typisk forbrug
i kg pr. 1000
m² |
Ton/år |
Ludkoger |
Affedtersalt |
100 |
8.500 |
50,0 |
425,0 |
Bejdsebad |
Svovlsyre, 96% |
50 |
4.250 |
50,0 |
212,5 |
Bejdsebad |
Saltsyre, 30% |
50 |
4.250 |
75,0 |
318,8 |
El-affedter |
Affedtersalt |
100 |
8.500 |
40,0 |
340,0 |
Dekapering |
Saltsyre, 30% |
10 |
850 |
10,0 |
8,5 |
Zinkbad, surt |
Zinkanoder |
75 |
6.375 |
70,6 |
450,0 |
Zinkbad, surt |
Zinkchlorid |
75 |
6.375 |
3,5 |
22,3 |
Zinkbad, surt |
Kaliumchlorid |
75 |
6.375 |
15,0 |
95,6 |
Zinkbad, surt |
Borsyre |
75 |
6.375 |
2,0 |
12,8 |
Zinkbad, surt |
Glansmidler |
75 |
6.375 |
18,0 |
114,8 |
Zinkbad, cyan |
Zinkanoder |
15 |
1.275 |
70,6 |
90,0 |
Zinkbad, cyan |
Natriumcyanid |
15 |
1.275 |
64,0 |
81,6 |
Zinkbad, cyan |
Natriumhydroxid |
15 |
1.275 |
79,0 |
100,7 |
Zinkbad, cyan |
Zinkoxid |
15 |
1.275 |
1,5 |
1,9 |
Zinkbad, cyan |
Glansmidler |
15 |
1.275 |
14,0 |
17,9 |
Zinkbad, alkalisk |
Zinkanoder |
10 |
850 |
70,6 |
60,0 |
Zinkbad, alkalisk |
Natriumhydroxid |
10 |
850 |
150,0 |
127,5 |
Zinkbad, alkalisk |
Zinkoxid |
10 |
850 |
27,0 |
23,0 |
Zinkbad, alkalisk |
Glansmidler |
10 |
850 |
40,0 |
34,0 |
Blåpassivering |
Salt |
30,8 |
2.618 |
20,0 |
52,4 |
Gulpassivering |
Salt |
60,8 |
5.168 |
10,0 |
51,7 |
Oliven+sort pass. |
Salt |
8,4 |
714 |
15,0 |
10,7 |
For zinkbadet gælder som hovedregel, at de anvendte zinkanoder ender som zinklag på varerne, og der går i princippet ikke noget til spilde. Der udslæbes dog zink og andre salte fra badet til skyllevandet,
og disse kemikalier må løbende erstattes for at holde den optimale koncentration af kemikalier i badet. I den alkaliske cyanfri zinkbad skal der principielt tilsættes ZnO til erstatning af udslæbt zink, men flere
danske virksomheder har en separat opløsningstank, hvor badet løber igennem, og her kan man styre zinkkoncentrationen ved at lade badet opløse metallisk zink. Her bliver der således ikke behov for
tilsætning af ZnO, så derfor må forbruget af ZnO i tabellen tages med forbehold.
I det cyanidiske bad omdannes en del cyanid til carbonat ved en anodisk oxidation, ligesom der generelt i alkaliske bade dannes carbonat ved optagelse af luftens kuldioxid.
For passiveringsbadene gælder det, at der forbruges passiveringskemikalier og syre, som må erstattes løbende. Der ophobes efterhånden zink og 3-gyldig chrom (i chromatholdige passiveringsbade) som
forurening i badene, hvilket medfører, at disse bade må kasseres med passende mellemrum. Herved kasserer man også aktive kemikalier, hvilket er med til at øge forbruget af kemikalier.
I Tabel D.9 er foretaget en vurdering af de angivne kemikalieforbrug.
Tabel D.9 Bestanddele i kemikalier til elforzinkning
Kemikalie |
Mængde |
Komponenter |
Affedtersalt |
765 ton |
Hydroxider, carbonater 5-25% Tensider, kompleksdannere 5-25% Vand 50-90% |
40-190 ton 40-190 ton 400-700 ton |
Svovlsyre |
210 ton |
96 % svovlsyre, regnes som ren syre |
Saltsyre |
330 ton |
30 % syre svarer til 100 ton ren HCl |
Zink anoder |
600 ton |
Ren metallisk zink |
Zinkchlorid og zinkoxid |
47 ton |
ZnCl2 og ZnO, heraf 31 ton zink |
Natriumcyanid |
82 ton |
Antagelig 100% natriumcyanid |
Natriumhydroxid |
230 ton |
Antagelig 100% NaOH |
Kaliumchlorid |
96 ton |
Antagelig 100% KOH |
Borsyre |
13 ton |
Antagelig ren borsyre |
Glansmidler |
167 ton |
Sammensætning ikke kendt |
Blåpassivering, salt |
52 ton |
Indeholder Cr(III)-salte svarende til 1,2 ton Cr |
Gul, Oliven og sort passivering, salt |
62 ton |
Indeholder Cr(VI)-salte svarende til 14,128 ton Cr |
På basis af opgørelser og antagelser i Tabel D.9 kan følgende uddrages:
- der anvendes 2.650 ton kemikalier, hvoraf vand udgør i størrelsesordnen 1.000 ton.
- det samlede zinkforbrug ligger på omkring 630 ton.
- der anvendes omkring 15 ton chromforbindelser, hvoraf ca. 1 ton er Cr(III) og 14 ton er Cr(VI).
- forbruget af uorganiske syrer, primært svovlsyre, ligger på omkring 310 ton.
- forbruget af uorganiske baser, primært natriumhydroxid ligger på omkring 300 ton.
- forbruget af borsyre udgør 13 ton og salte (KCl) udgør omkring 100 ton.
- forbruget af organiske forbindelser som tensider, affedtersalt mv. udgør i størrelsesordnen 100 ton.
- forbruget af cyanider udgør omkring 80 ton.
- for det øvrige forbrug på 167 ton (glasmidler) kendes sammensætningen ikke.
Det samlede materialeforbrug er estimeret til 1.715 ton, hvilket svarer til 0,31 kg pr. m² behandlet overflade. Metalmængden udgør således ca. 26% af kemikaliemængden. Almindelige syrer, baser og salte
udgør ca. 27 %, organiske forbindelser omkring 7% og uoplyste omkring 6%. De resterende 33% er primært vand og for en mindre mængde salte/oxider, der følger med metallerne samt usikkerheder.
Ses der bort fra vandindholdet, er det samlede materialeforbrug 1.700 ton svarende til 0,20 kg pr. m².
D.3.3.2 Råstofforbrug
Ud fra oplysninger i LCA-databaser som UMIP og SigmaPro er det søgt at opgøre råstofforbruget for de væsentligste materialeforbrug. Opgørelsen er uden vand og vist i Tabel D.10.
Tabel D.10 Estimering af forbrug af råstoffer for elforzinkning
Materiale
Behandlet overflade 8.500.00 m² |
Materiale-
forbrug
I alt |
Råstof-
forbrug
kg/kg |
Råstof-
forbrug
I alt |
Råstof-
forbrug
Pr. 1.000 m² |
Zink |
630 ton |
3,1 1) |
1.953 ton |
230 kg |
Chrom |
15 ton |
5,6 1) |
84 ton |
10 kg |
Uorganiske syrer, primært svovlsyre |
310 ton |
0,7 1) |
217 ton |
26 kg |
Uorganiske baser, primært natriumhydroxid |
300 ton |
1,2 1) |
360 ton |
42 kg |
Borsyre og salte |
113 ton |
1,0 3) |
113 ton |
13 kg |
Organiske forbindelser |
100 ton |
1,0 1) |
100 ton |
12 kg |
Cyanider |
80 ton |
2,0 1) |
160 ton |
19 kg |
Øvrige (ukendt sammensætning) |
167 ton |
3,0 2) |
501 ton |
59 kg |
I alt |
411 kg |
1): Data fra SigmaPro.
2): Tallet er anslået ud fra en antagelse om, at øvrige kemikalier indeholder en vis mængde metal og en vis mængde organiske forbindelser.
3) Data herfor er ukendt, og derfor er der anslået en værdi.
Det samlede materialeforbrug excl. vand svarer til et forbrug på 0,20 kg pr. behandlet m², og når der ses på råstoffer, udgør forbruget 0,41kg pr. m².
D.3.3.3 Vandforbrug
Den galvaniske branche har nedsat vandforbruget voldsomt, siden der for alvor kom fokus på miljøet herhjemme i 1970'erne. Dengang var det ikke ualmindeligt med et vandforbrug på 1.000 liter pr. m²
overflade – et tal, som man stadigvæk kan møde i Østeuropa og andre lande, hvor vandprisen er lav, og hvor man endnu ikke for alvor har fokus på vandforbruget.
I dag er vandforbruget mere typisk på 50-250 liter pr. m² overflade, og det svarer til et samlet vandforbrug herhjemme på ca. 850.000 m³/år til elforzinkning. Miljøstyrelsen mener, at man efterhånden skal
ned på et vandforbrug på 10 liter pr. m² overflade, og det er faktisk muligt ved brug af 3-trins modstrømsskyl eller andre lige så vandbesparende skyllemetoder (ionbytning, sprayskylning, vandgenbrug),
men det store problem er, at der helst skal bruges 2-4 skyllekar efter hvert proceskar, for at det skal lykkes. Det kan ofte være et problem at indsætte det fornødne antal skyllekar i eksisterende
produktionslinier, da det er uforholdsmæssigt dyrt sammenlignet med etablering af nye proceslinier. Ofte er det et plads i lokalet til at indføre mange ekstra skyllekar.
Der er ingen tvivl om, at tiden stadig arbejder for at opnå yderligere vandreduktioner i takt med de stigende vandpriser, men jo længere man kommer ned, jo færre kroner er der at hente på yderligere
vandbesparelser. Det skal dog også nævnes, at mindre vandforbrug kræver mindre renseanlæg, og der vil samtidig også være en vis besparelse i kemikalieforbrug til spildevandsrensning. Rent teknisk kan
virksomhederne stadig opnå store vandbesparelser ved i endnu højere grad at bruge de vandbesparende skyllemetoder og teknikker. Vandforbruget bør i løbet af de næste 5 år uden problemer kunne
komme ned på 30-40 liter pr. m² overflade svarende til ca. 300.000 m³/år fra al elforzinkning i Danmark.
D.3.3.4 Energiforbrug
Energiforbruget til de elektrolytisk processer kan beregnes forholdsvis enkelt. Når man kender produktionens størrelse, kan man udregne strømforbruget ud fra de anvendte Volt, Amp og timer med tillæg
for strømtab i ensretter. Energiforbrug til badopvarmning afhænger af badtemperaturen, karisolering, rumtemperatur og udsugning. Energiforbrug til ventilation udgør også en betydelig post. Energiforbrug til
motorer, køling og trykluft – herunder renseanlæg – er af mindre betydning.
Det foreligger ikke mange publikationer og erfaring herhjemme om energiforbruget i galvanobranchen. Forbruget er derfor vurderet ud fra elforzinkning dels ud fra overslagberegning og dels ud fra konkrete
tal og vurderingen fra en dansk virksomhed, der kun udfører elforzinkning.
Tabel D.11 Energiforbrug på en stor elforzinknings virksomhed med cyan zink
|
Udvalgt virksomhed |
Hele Danmark |
kWh/m² |
% |
kwh/år |
Ensrettere |
1,32 |
49 |
11.255.844 |
Badvarme |
0,23 |
8 |
1.925.572 |
Ventilation |
0,66 |
25 |
5.601.664 |
Køling |
0,05 |
2 |
437.630 |
Trykluft |
0,01 |
1 |
122.536 |
Motorer |
0,13 |
5 |
1.137.838 |
Belysning |
0,06 |
2 |
525.156 |
Diverse |
0,21 |
8 |
1.750.520 |
Total |
2,68 |
100 |
22.756.760 |
Det samlede forbrug ligger således 22.757 MWh pr. år og er udelukkende et elforbrug svarende til 2.677 kWh pr. 1000 m².
Der er indhentet tal fra en anden stor elforzinkningsvirksomhed, som kører primært med sur zink og sekundært alkalisk zink. Her er det totale energiforbruget opgjort til 2,98 kWh/m², hvilket ligger tæt på
værdien fra Tabel D.11 (2,68 kWh/m²). Man kan forvente, at små virksomheder, der udnytter produktionsapparatet mindre intens, vil bruge lidt mere energi pr. produceret m² overflade end store
virksomheder med meget stor produktion i flere skift.
Sammenholdes energiforbruget ved elforzinkning med energiforbruget ved fornikling/forchromning, så er energiforbruget pr. m² produceret overflade som ventet højere ved fornikling/forchromning, hvor man
anvender flere varme bade ved høje temperaturer.
De to væsentligste affaldsstrømme fra elforzinkning er:
- Tungmetalslam fra spildevandsrensning
- Kasserede procesbade til ekstern behandling/oparbejdning
I Miljøprojekt 55/2000 vedrørende oparbejdning af galvanisk affald blev affaldsmængderne estimeret ud fra en beregningsmodel kombineret med data fra de største virksomheder i branchen. Dette er vist i
Tabel D.12.
Tabel D.12 Flydende kemikalieaffald fra elforzinkning
Kasseret bad |
Overflade
m² pr. år |
Kasseret bad
liter pr. 1000 m² |
kasseret
bad, m³/år |
Metal i
bad, g/l |
Metal,
kg/år |
Ludkoger |
8.500.000 |
75 |
638 |
0 |
0 |
Bejdsebad |
8.500.000 |
45 |
383 |
40 |
15.300 |
El-affedter |
8.500.000 |
50 |
425 |
2 |
850 |
Dekaperingsbad |
4.000.000 |
25 |
100 |
2 |
200 |
Zinkbad, surt |
6.375.000 |
5 |
32 |
35 |
1.116 |
Zinkbad, cyan |
1.275.000 |
5 |
6 |
15 |
96 |
Zinkbad, alkalisk |
850.000 |
5 |
4 |
10 |
43 |
Blåpassivering |
2.618.000 |
20 |
52 |
3 |
157 |
Gulpassivering |
5.168.000 |
10 |
52 |
12 |
620 |
Oliven+sort pass. |
714.000 |
16 |
11 |
20 |
228 |
Total |
18.609 |
Som det fremgår af Tabel D.12, er det langt fra alle affaldstyper, som indeholder væsentlige mængder tungmetaller. Det er oftest således, at virksomheder selv behandler de kasserede bade med lavt
metalindhold, mens mere koncentrerede bade som bejdsebade, zinkbade samt eventuelt oliven og sort chromatering sendes til ekstern behandling (Kommunekemi). Bejdsebadene nedslides og kasseres
forholdsvis ofte, mens metalliseringsbadene kun meget sjældent kasseres på grund af forurening eller for høje koncentrationer.
Tabel D.13 Slam fra spildevandsrensning (filterkager med 30% tørstof)
Spildevand |
m² overflade
pr. år |
Metal i
bad, g/l |
Udslæb af
metal,
kg/år |
Genvin-
dings % |
Metal i
slam,
kg/år |
Filterkager (30%TS)
ton/år |
Ludkoger |
8.500.000 |
0 |
0 |
0 |
0 |
0,0 |
Bejdsebad |
8.500.000 |
30 |
38.250 |
0 |
38.250 |
318,8 |
El-affedter |
8.500.000 |
1 |
1.275 |
0 |
1.275 |
10,6 |
Dekaperingsbad |
4.000.000 |
30 |
18.000 |
0 |
18.000 |
150,0 |
Zinkbad, surt |
6.375.000 |
35 |
33.469 |
25 |
25.102 |
209,2 |
Zinkbad, cyan |
1.275.000 |
15 |
2.869 |
0 |
2.869 |
23,9 |
Zinkbad, alkalisk |
850.000 |
10 |
1.275 |
0 |
1.275 |
10,6 |
Blåpassivering |
2.618.000 |
2 |
1.047 |
0 |
1.047 |
8,7 |
Gulpassivering |
5.168.000 |
10 |
10.336 |
0 |
10.336 |
86,1 |
Oliven+sort passivering |
714.000 |
18 |
1.928 |
0 |
1.928 |
16,1 |
Total |
8.500.000 |
|
|
|
100.081 |
834,0 |
kg filterkage pr. m² produktion i gennemsnit |
0,098 |
Tabel D.13 omfatter ikke det slam, som dannes på de virksomheder, der selv neutraliserer kasserede procesbade, hvilket vil betyde en mindre stigning i slammængden. Sammenfattet er opstillet følgende
totale tal, hvor slammængden er korrigeret med metalmængderne for de kasserede procesbade, som behandles af virksomhederne selv:
Metalmængde i kasserede bade til ekstern behandling: |
18.609 kg/år |
Metalmængde i spildevandsslam fra fældningsanlæg: |
100.081 kg/år |
Metalmængden i de kasserede bade til ekstern behandling (Kommunekemi) er næsten 6 gange mindre end i det metalhydroxidslam, der dannes ved virksomhedernes egen spildevandsrensning.
Affald fra ludkoger, bejdsebad, el-affedter samt dekaperingsbad indeholder metaller fra de emner, der behandles og udgøres derfor primært af jern. Affald fra zinkbadenne indeholder zink. Affald fra
blåpassivering indeholder chrom(III) og zink, mens gul-, oliven og sortpassivering indeholder chrom(VI) og zink.
Ud fra affaldsopgørelserne for flydende kemikalieaffald (Tabel D.12) og slam fra spildevandsrensning (Tabel D.13) kan affaldet opdelt på de væsentligste metaller opgøres. Dette er vist i Tabel D.14.
Tabel D.14 Affald opdelt på metaller i forhold til samlet mængde og ressourceforbrug
Materiale |
Affaldsmængde |
Del af den
samlede af-
faldsmængde |
Ressource-
forbrug |
Affald i forhold
til ressource-
forbrug |
Zink |
34,9 ton |
29 % |
630 ton |
5,5 % |
Chrom |
11,06 ton |
9,3 % |
14,1 ton |
78 % |
Andre metaller (primært jern) |
72,7 ton |
61,3 % |
Ikke relevant |
Ikke relevant |
D.3.4 Hovedtal for elforzinkning
Kortlægningen har vist, at der behandles 8,5 mio. m² overflade ved elforzinkning pr. år.
Der anvendes 2.650 ton kemikalier, hvilket svarer til 0,31 kg pr. m² behandlet overflade. Zinkforbruget ligger på 630 ton, og chromforbruget ligger på 14 ton. I materialerne indgår en del vand. Fratrækkes
vandmængden, vil materialeforbruget ligge på 1.700 ton svarende til 0,20 kg pr. m².
Mængden af råstoffer, der skal udvindes for at dække materialebehovet, er opgjort til 3.500 ton svarende til 0,41 kg pr. m².
Der anvendes et vandforbrug på 850.000 m³/år og et energiforbrug i form af el på 22.757 MWh, svarende til 2.677 kWh pr. 1.000 m² overflade.
Affald fra kasserede bade og slam udgør i alt 119 ton, hvoraf 35 ton er zink og 11 ton er chrom. Omkring 73 ton er metaller fra den behandlede overflade og udgøres primært af jern.
Den mængde metal (zink og chrom), der anvendes og som ikke går i affaldsstrømmen, antages at blive på emnerne til de kasseres som affald.
D.4 Kortlægning af varmforzinkning
Ved varmforzinkning dyppes stålemner i et smeltet zinkbad ved ca. 460°C, hvorved der pålægges et zinklag med en lagtykkelse på 60-100 m. Dette giver en langt bedre korrosionsbeskyttelse, end der
opnås ved elektrolytisk forzinkning, hvor man normalt arbejder med lagtykkelser på 5-20 m. Derfor anvendes varmforzinkning især til stålkonstruktioner, der anvendes udendørs, og metoden kan anvendes
på meget store emner op til 10-15 meters længde.
I Danmark findes 20 varmforzinkningsvirksomheder, men flere af virksomhederne har samme ejer. Det skønnes, at halvdelen af virksomhederne laver ca. 85% af produktionen. Der varmforzinkes
skønsmæssigt 120.000 ton gods årligt, og i 2001 var det samlede zinkforbrug for danske varmforzinkere på 9817 ton svarende til, at der i gennemsnit påføres ca. 8,2% zink i forhold til godsets vægt.
D.4.1 Processerne
Den fulde proces er vist som flowsheet i Figur D.4. Det skal bemærkes, at man langt fra altid anvender alle processer, som er vist i det komplette flowsheet.
D.4.1.1 Alkalisk affedtning
Første trin er en varm alkalisk affedtning, hvor olie og fedt opløses og fjernes fra emnernes overflade. Badet indeholder et affedtersalt (natriumhydroxid, carbonater, phosphater, silikater samt tensider og
eventuelle kompleksdannere), der sørger for, at olie og fedt bliver delvis emulgeret i badet. Ofte kommer der efterhånden også fri olie på badoverfladen, og dette olie kan med fordel skimmes af med
mellemrum for at opnå længere levetid for badet. I Danmark springer man ofte dette trin over, hvis ikke emnerne er meget beskidte. Let olieret gods kan normalt renses i en bejdseaffedter – det vil sige en
sur bejdse med et mindre indhold af tensider til emulgering af olien.
Det skal nævnes, at enkelte virksomheder anvender en såkaldt biologisk affedter i stedet for en varm alkalisk affedter. I den biologiske affedter omdannes olie og fedt til slam af mikroorganismer, der
vedligeholdes ved tilsætning af mikronæringsstoffer.
Når badets indhold af olie og fedt er blevet så højt, at man ikke mere kan opnå en acceptabel affedtning af emnerne, selvom der tilsættes mere affedtersalt, må badet kasseres, og et nyt bad blandes op. Det
kasserede bad kan enten neutraliseres i eget renseanlæg eller det afleveres til Kommunekemi eller anden godkendt modtager for kemikalieaffald. Badlevetiden afhænger af produktionens størrelse (ton/time),
emnernes tilsmudsning og virksomhedens evne og metode til at vedligeholde badet. Efter behandling i affedteren skal emnerne skylles.
Input: |
Pålæsning af gods |
Output: |
 |
Affedtersalt + vand Energi |
1. Varm alkalisk affedtning 70-80°C |
Kasseret bad + slam Varmeafgivelse |
 |
Vand |
Skyl |
Spildevand med udslæbte kemikalier |
 |
Saltsyre + vand + Energi |
2. Bejdsning i saltsyre 20°C |
Kasseret bejdsebad + slam Syredampe |
 |
Vand |
Skyl |
Spildevand med udslæbte kemikalier |
 |
Flussalt + vand + energi |
3. Flusning, 50-70°C |
Kasseret flusbad + slam Varmeafgivelse |
 |
Energi |
Tørring |
Varrmeafgivelse |
 |
Zink + aluminium + bly + energi |
4. Forzinkning 460°C |
Zinkaske + hårdzink Varmeafgivelse Luftforurening |
 |
Vand/luft |
5. Køling (luft eller vand) |
Spildevand |
 |
|
6. Pudsning og afgratning |
Zinkstøv (på gulv) |
 |
|
Færdig gods |
|
Figur D.4 Flow-sheet for varmforzinkning
D.4.1.2 Bejdsning
Andet trin er rensning af emnerne i saltsyre (bejdsebad), hvorved rust og glødeskaller opløses og fjernes fra emnernes overflade. Det øverste lag af selve emnerne fjernes også ved denne syrebehandling.
Normalt tilsættes badet en inhibitor, der skal forhindre angreb på grundmaterialet. Bejdsningen foregår normalt ved stuetemperatur, men opvarmning vil øge bejdsehastigheden. Derfor har nogle
virksomheder opvarmning af bejdsebadet om vinteren, hvor temperaturen i produktionslokalet kan være ret lav.
Under bejdsningen forbruges syre, og grundmateriale går i opløsning. Der kan løbende spædes op med mere syre, men efterhånden bliver badets indhold af metal så højt, at badet må kasseret. De fleste
danske virksomheder foretrækker at udskifte badet gradvist, så man holder en nogenlunde konstant koncentration af syre og jern. En typisk sammensætning er: Fri syre = 90 g/l og jern = 80 /l. Enkelte
virksomheder anvender en såkaldt aktiveret bejdsning, hvor man kører med et jernindhold på 120-140 g/l. Ved dette høje jernindhold må man nøjes med et syreindhold på 50-60 g/l for at undgå udfældning
af ferrochlorid. Denne bejdse er næsten lige så effektiv som bejdsen med højere syreindhold, og så afgiver den færre syredampe.
Efter bejdsning er der enkelte virksomheder, der skyller godset før flusning, men de fleste danske virksomheder dypper direkte i flusbadet efter bejdsning, hvorved flusbadet forurenes kraftigt med jern og
syre fra bejdsen.
Brugt bejdsesyre anvendes ofte som såkaldt aftrækssyre til rensning af værktøj og fejlforsinket gods, før det endelig kasseres. Den kasserede syre kan afleveres til Kommunekemi, men flere danske
virksomheder sender den kasserede til oparbejdning i Tyskland, hvorfra man får regenereret syre retur. Kasseret syre kan principielt neutraliseres i virksomhedens eget renseanlæg, hvorved de opløste
metaller udfældes som metalhydroxidslam, men da det giver ekstremt meget slam og kræver et stort kemikalieforbrug, kan det ikke svare sig økonomisk. Enkelte virksomheder afleverer den kasserede syre
til Kemira Miljø, hvor bejdsebadet oparbejdes til et ferrichlorid fældningsmiddel. Badlevetiden kan forlænges, hvis man reducerer syreangrebet på grundmaterialet.
D.4.1.3 Flusning
Flusbadet er en blanding af zinkchlorid og ammoniumchlorid. Flussaltet kan være et dobbeltsalt (2 mol NH4Cl og 1 mol ZnCl2) med 44% NH4Cl, eller det kan være et trippelsalt (3 mol NH4Cl og 1 mol
ZnCl2) med 54% NH4Cl. Normalt foretrækkes trippelsaltet, da det er den mest aktive på grund af det højere indhold af NH4Cl. Koncentrationen af flussalt ligger typisk på 400-600 g/l. Ved dypning i
flusbadet bliver emnerne opvarmet og belagt med et lag af flussalt, når det atter trækkes op og tørres. Flussaltet har stor betydning for et godt resultat ved den efterfølgende forzinkning.
Flusbadet forurenes løbende med indslæb af jern og syre fra bejdsebadet, og forureningen foregår meget hurtigt, hvis godset ikke skylles mellem bejdsebadet og flusbadet. Jernforurening vil efterhånden
udfældes som brune partikler ferrihydroxid og ferrioxid i takt med, at ferro oxideres af luftens ilt til ferri. Oxidationen kan fremskyndes ved tilsætning af brintperoxid, hvorved oxidationen bliver momentan.
Det udnyttes i praksis til rensning og oparbejdning af flusbade, hvor man kan behandle badet løbende med brintperoxid og ammoniakvand for at holde pH på 3,5 -4,5 som er den optimale værdi. Udfældet
jern frasepareres og afleveres som kemikalieaffald.
Ved neutralisation af saltsyre dannes NH4Cl, som er den ene komponent i flusbadet. Bejdsebadet vil normalt også indeholde mere eller mindre zinkchlorid, og dette indslæb er et direkte tilskud til flusbadets
indhold af zinkchlorid. Skønsmæssigt 60% af de danske varmforzinkere har flusbadsgenvinding, og de bruger derfor meget lidt flussalt. Afhængig af det indslæbte bejdsebad vil disse virksomheder bruge
mindre mængder NH4Cl eller ZnCl2 for at fastholde den optimale sammensætning af badet. I yderste konsekvens kan indslæbet af zinkchlorid være så stort, at en del af badet må kasseres engang imellem.
Det skal sluttelig bemærkes, at flusbadet også kan neutraliseres med askeaffald, som indeholder zinkoxid, der giver zinkchlorid ved neutraliseringen. Det giver således et bidrag til badets indhold af
zinkchlorid.
D.4.1.4 Tørring
Det er vigtigt, at emnerne er tørre, før de nedsænkes i zinksmelten. Det kan gøres i en tørreovn eller en tørrezone med varm luft, men mange virksomheder lader simpelt hen emnerne hænge så længe i
lokalet, at de når at tørre før forzinkningen. Det hjælper godt her, at flusbadet kører ved så høj temperatur som muligt (helst 70°C).
D.4.1.5 Forzinkning
Selve forzinkningen foregå ved neddypning af godset i smeltet zink ved 460°C. Under processen reagerer smeltet zink med godsets overflade, hvor der i overgangszonen dannes forskellige jern-zink
legeringer. Yderst ligger det rene zinklag. Flussaltet på godsets overflade har stor betydning for processen i zinksmelten. Godsets sammensætning har også stor betydning for zinkoptagelsen og slutresultatet.
Silicium beroliget stål er uegnet til varmforzinkning, da zinkoptagelsen bliver ukontrollabel stor. Et lille indhold af aluminium (0,005 - 0,007 %) i smelten har en gunstig indflydelse på slutresultatet. En dårlig
flux og et lavt aluminiumindhold i smelten kan føre til små pletter på godset uden zinkbelægning.
I zinksmelten dannes løbende aske og hårdzink. Asken dannes på smeltens overflade og består primært af oxideret zink. Asken skal løbende skrabes væk fra godset under dypningen for at få en pæn
overflade. Hårdzink dannes som klumper i smelten, hvor jernforurening reagerer med zink og danner en jern-zink legering (3% Fe og 97% Zn), som man kalder hårdzink. Der skal altså kun små
jernmængder til at give meget hårdzink, så det betaler sig virkeligt at holde jernindslæbet fra flusbadet til smelten lavt, og det gør man ved at holde flusbadet rent (Fe < 2 g/l). Hårdzink er et affaldsprodukt,
som med mellemrum skal fjernes fra smelten.
Ved forzinkningsprocessen dannes støv med NH4Cl og zinkforbindelser. Jo mere ammoniumchlorid, der er på emnerne, jo mere røg dannes. Derfor holdes zinksmelten normalt indelukket, og der udsuges
store luftmængder under dyppeprocessen.
D.4.1.6 Køling
De varme emner skal køles efter zinksmelten, og de fleste danske virksomheder anvender luftkøling, hvor emnerne simpelt hen hænger til afkøling i produktionslokalet, indtil de kan videre bearbejdes.
Enkelte virksomheder ønsker en hurtigere køling ved dypning i et kar med stillestående vand, hvor der sker en kraftig fordampning af vandet og dermed en afkøling af emner. På mange udenlandske
virksomheder anvender man kølevand tilsat chromater, så man både opnår en hurtig køling og en let passivering af zinkoverfladen, som man kender fra elforzinkning. Det giver større korrosionsbestandighed
af godset og nedsætter dannelsen af hvidrust på godsets overflade.
D.4.1.7 Pudsning og afgratning
De færdige emner har ofte små knopper eller kanter, der skal fjernes ved pudsning, slibning eller filing. Dette er et manuelt arbejde, som udføres i produktionshallen, før emnerne går retur til kunderne.
D.4.2 Skylning
Generelt anvender danske varmforzinkere så lidt skylning som muligt for at undgå at skulle rense spildevand. En enkelt af de store virksomheder anvender dog skylning, hvilket betyder, at der anvendes
skylning ved ca. 40% af varmforzinkningen herhjemme. Anvender man ikke alkalisk affedtning, kan skyllevand helt undgås, hvis man går direkte fra bejdsebadet over i flusbadet, men det giver som nævnt en
kraftig forurening af flusbadet.
Da godset oftest er meget stort, kræves der store kar til forbehandlingen, og kar på 50-90 m³ er ikke ualmindelige. Da store kar er pladskrævende, er det ikke så almindeligt, at man anvender flere skyllekar
i modstrøm, hvilket ellers er den mest vandbesparende metode. En effektiv skylning efter bejdsning kan anbefales for at reducere forureningen af flusbadet, hvilket har mange fordele som beskrevet ovenfor.
Skylning efter affedtning er også vigtigt for at reducere indslæb af alkali i bejdsebadene.
D.4.3 Ressourceforbrug
De væsentligste ressourcer, der forbruges ved varmforzinkning, er:
- Kemikalier bruges i procesbadene og til vandrensning.
- Metaller bruges i zinksmelten.
- Vand bruges til skylning og til opblanding af procesbade.
- Energi bruges til zinksmelten, til badopvarmning, til ventilation og rumopvarmning samt til drift af produktionsudstyr som trykluft, pumper og kraner samt til renseanlæg.
D.4.3.1 Forbrug af kemikalier og metaller
Forbruget af de væsentligste kemikalier og metaller er vist i Tabel D.15. Opgørelsen er baseret på varmforzinkning af 120.000 ton gods pr. år.
Tabel D.15 Forbrug af kemikalier og metaller til proces og spildevand
Procesbad |
Kemikalie |
% af branchen |
Typisk forbrug
i kg pr. ton gods |
Total forbrug
i ton i DK |
Affedter |
Affedtersalt |
25 |
5,0 |
150 |
Bejdsebad |
Saltsyre, 30% |
100 |
30,0 |
3.600 |
Flusbad |
Flussalt |
40 |
1,5 |
72 |
Flusbad |
Ammoniakvand, 25% |
60 |
2,8 |
202 |
Flusbad |
Brintperoxid, 35% |
60 |
0,4 |
29 |
Zinksmelte |
Zink |
100 |
81,8 |
9.817 |
Spildevand |
Natronlud, 27% |
40 |
3,0 |
144 |
Forbrug af bly og aluminium i zinkbadet er ikke medtaget. De typiske forbrugstal i kg pr. ton gods er estimerede gennemsnitstal for branchen. Tallene er indsamlet gennem kontakt til udvalgte større
virksomheder, og de er løbende justeret ud fra nye oplysninger i Danmark og udlandet.
Det bemærkes, at forbruget af flussalt er beregnet ud fra et standardforbrug på 1,5 kg flussalt pr. ton gods for de virksomheder, der ikke har flusbadsregenerering, mens virksomheder med regenerering
bruger brintperoxid og ammoniakvand i stedet. For de sidstnævnte virksomheder vil der også være et mindre forbrug af flussalt (ammoniumchlorid og zinkchlorid), men det er vanskeligt at estimere dette
forbrug.
I Tabel D.16 er foretaget en vurdering af de i Tabel D.15 angivne kemikalieforbrug.
Tabel D.16 Bestanddele i kemikalier til varmforzinkning
Kemikalie |
Mængde |
Komponenter |
Affedtersalt |
150 ton |
Hydroxider, carbonater 5-25% Tensider, kompleksdannere 5-25% Vand 50-90 % |
10-35 ton
10-35 ton 80-130 ton |
Saltsyre |
3.600 ton |
30% syre svarer til 1000 ton ren HCl |
Flussalt |
72 ton |
Trippelsalt (ammoniumchlorid og zinkchlorid), - heraf 13 ton ammonium, 43 ton chlorid og 16 ton zink |
Ammoniakvand |
202 ton |
25 % ammonium svarende til 50 ton ren NH3 |
Brintperoxid |
29 ton |
35 % hydrogenperoxid svarende til 10 ton ren H2O2 |
Natriumhydroxid |
144 ton |
27% natriumhydroxid svarende til 40 ton ren NaOH |
Zink |
9.817 ton |
Metallisk zink |
På basis af opgørelser og antagelser i Tabel D.16 kan følgende hovedtal uddrages:
- der anvendes 14.000 ton kemikalier, hvoraf vand udgør omkring 3.000 ton.
- det samlede zinkforbrug udgør 9.830 ton.
- forbruget af uorganiske syrer ligger på omkring 1.000 ton.
- forbruget af uorganiske baser ligger på omkring 60 ton
- forbruget af ammoniak udgør omkring 65 ton, og forbruget af hydrogenperoxid udgør 10 ton.
- forbruget af organiske forbindelser som tensider m.v. udgør omkring 25 ton.
Det gennemsnitlige kemikalieforbrug ligger på 117 kg pr. ton behandlet gods. Metalmængden udgør således ca. 70% af kemikaliemængden. Almindelige syrer, baser og salte udgør ca. 8 % og organiske
forbindelser omkring 2%. De resterende 20% er primært vand samt usikkerheder.
D.4.3.2 Forbrug af vand
Hovedparten af de danske varmforzinkere bruger ikke egentligt skyllevand, men de anvender vand til opblanding af nye bade og til opspædning af bade med fordampningstab. De virksomheder, der
anvender alkalisk affedtning, er nødt til at skylle mellem affedteren og bejdsen. Enkelte virksomheder bruger også skyllevand efter bejdsen for at reducere indslæb af forurening i flusbadet. Andre
virksomheder skyller i forurenet grundvand i stedet for postevand, hvilket kan være hensigtsmæssigt, hvis grundvandet alligevel skal neutraliseres og renses. Det skønnes, at hele branchen anvender
15.000-20.000 m³ procesvand årligt.
D.4.3.3 Energiforbrug
Der foreligger ingen totale brancheanalyser vedrørende energiforbrug, men i Tabel D.17 er energiforbruget estimeret ud fra konkrete tal for to større danske varmforzinkningsvirksomheder, som anvender
el-opvarmet smelte og kører i 3 skift fem dage pr. uge.
Tabel D.17 Energiforbrug for udvalgt virksomhed samt estimeret forbrug for hele branchen baseret på en årlig produktion på 120.000 ton for hele branchen
|
Udvalgt virksomhed |
Hele Danmark |
kWh/ton |
% |
kWh/år |
Zinkgryde (el) |
132 |
61 |
15.840.000 |
Andet elforbrug |
84 |
39 |
10.080.000 |
Total |
216 |
100 |
25.920.000 |
Det største energiforbrug ligger på selve zinksmelten. Den kan opvarmes med elektricitet eller med olie/gas, og alle metoder anvendes herhjemme. Energiforbruget ved elopvarmning er dog betydeligt lavere
end ved olie/gas-opvarmning, og det kan derfor forventes, at det samlede energiforbrug i Danmark til varmforzinkning vil være betydeligt større end estimeret i Tabel D.17. Man kan dog forvente, at det
specifikke energiforbrug i kWh/ton er lidt lavere for virksomheder, der kører intens produktion i flere skift. Her er der kortere perioder, hvor smelten står ubenyttet hen og dermed mindre varmespild.
Den sydafrikanske varmforzinkerforening er i gang med at samle energidata ind fra deres medlemmer, og de har oplyst følgende typiske gennemsnitstal for virksomheder, der producerer i 2 skift 5 dage pr.
uge:
Opvarmning af zinkbad: |
245 kWh pr. ton gods |
Andet energiforbrug: |
112 kWh pr. ton gods |
Total energiforbrug: |
357 kWh pr. ton gods |
Opgørelsen er excl. energiforbrug til rumopvarmning.
De sydafrikanske tal er lidt højere end de danske, men tallene er af samme størrelsesorden. Det bemærkes, at den danske virksomhed arbejder i 3 skift, hvilket typisk betyder mindre energiforbrug pr. ton
gods, da der er korte stilstandsperioder. Sydafrikanerne oplyser i øvrigt, at det samlede energiforbrug under stilstand er 70-90 kWh pr. ton gods.
Sammenfattet må der forventes et samlet energiforbrug hos de danske varmforzinkere på 300-500 kWh pr. ton gods svarende til et årsforbrug på 36-60 mill. kWh for hele branchen. Her tages
udgangspunkt i et gennemsnit på 400 kWh pr. ton gods.
Da zinksmelten bliver opvarmet dels med el og dels med olie/gas, antages det i denne forbindelse, at 40% af det samlede energiforbrug dækkes af olie, mens resten er el. Ved et energiforbrug på 48.000
MWh dækkes de 19.200 MWh af olie/gas. Ved en energiudnyttelse på 90% og et energiindhold i olie på 42 MJ/kg svarer 19.200 MWh til:
19.200 MWh × 3600 MJ/MWh / (0,90 × 42 MJ/kg × 1000 kg/ton) = 1.829 ton
Det samlede gennemsnitlige energiforbrug udgøres derfor til varmforzinkning af:
- 28.800 MWh el
- 1.829 ton råolie
D.4.3.4 Råstofforbrug
På baggrund af materialeopgørelsen i Tabel D.16 er forbruget af råstoffer opgjort i Tabel D.18. Data er baseret på oplysninger fra SigmaPro.
I opgørelsen er taget højde for, at 1.745 ton zink oparbejdes. Ved oparbejdningen er der et tab, således at 1.142 ton zink kan genanvendes (70%).
Tabel D.18 Estimering af råstofforbrug for varmforzinkning
Materiale
120.000 ton gods |
Materiale-
mængde |
Råstof-
forbrug Kg/kg |
Råstof-
forbrug i alt |
Råstof-
forbrug pr. ton gods |
Zink |
8.688 ton |
3,1 |
26.932 ton |
240 kg |
Uorganiske syrer |
1.000 ton |
0,7 |
700 ton |
6 kg |
Uorganiske baser |
60 ton |
1,2 |
72 ton |
0,6 kg |
Ammoniak og hydrogenperoxid |
75 ton |
2 1) |
150 ton |
1 kg |
Tensider m.v. |
25 ton |
2,0 1) |
50 ton |
0,4 kg |
|
248 kg |
1): Værdien er skønnet.
Som det fremgår af Tabel D.18, udgør hovedparten af råstofforbruget af zink. Det samlede forbrug pr. ton behandlet gods udgør 248 kg.
D.4.4 Affald
De væsentligste affaldstyper og –mængder fremgår af Tabel D.19.
Tabel D.19 Affald fra varmforzinkning
Affald |
% af branchen |
kg/ton |
ton total i DK |
Hårdzink |
100 |
6,5 |
780 |
Aske |
100 |
10,0 |
1200 |
Kasseret bejdsesyre |
100 |
30,0 |
3600 |
Kasseret affedter |
25 |
5,0 |
150 |
Filterkager (flus) |
60 |
4,0 |
288 |
Filterkager (spildevand) |
40 |
5,0 |
240 |
Diverse slam og flydende affald |
100 |
2,0 |
240 |
Hårdzink indeholder 97% zink, og alle danske virksomheder sender dette affald til oparbejdning i udlandet. Virksomhederne får dog kun refunderet 60% af zinkværdien for dette affald, så der er alt mulig
grund til at reducere mængden af hårdzink.
Asken er en anden vigtig affaldstype, og ligesom hårdzink indeholder asken meget zink. De fleste større virksomheder har anskaffet en smelteovn til behandling af asken. Ved smeltning får man fjernet det
metalliske zink fra asken (40-70%), så kun zinkoxiden bliver tilbage. Zinkoxidresten sendes til oparbejdning i udlandet, men den kunne også oparbejdes internt ved at opløse zinkoxid i saltsyre og bruge
opløsningen i flusbadet. I Sydafrika benytter flere virksomheden simpelthen selve zinksmelten til at udvinde det metalliske zink af asken, og det kræver kun lidt ”know-how” for at gøre det rigtigt. Resten af
asken kan eventuelt fyldes direkte i flusbadet til neutralisation af overskudssyre.
Kasseret bejdsesyre indeholder ofte store mængder zink ved siden af jern (Typisk: Fe=80-140 g/l, Zn=20-200 g/l). Specielt de brugte bejdsebade, som har været anvendt som aftrækssyre, indeholder
meget zink og kun lidt fri syre. Enkelte virksomheder holder zinkindholdet meget lavt (1-2 g/l), da det så kan bruges direkte til fremstilling af ferrichlorid fældningsmiddel.
Kasseret affedter indeholder ikke væsentlige mængder metal, og de kan principielt neutraliseres i virksomhedens eget renseanlæg. Det kan eventuelt give for meget olie i spildevandet, og derfor vil nogle
virksomheder bortskaffe de kasserede affedterbade til ekstern behandling.
Filterkagerne fra flusbadsrensning indeholder primært udfældet jernhydroxid med opløste flussalte i porevandet. Tørstofindholdet er derfor usædvanlig højt – ca. 60% mod normalt 30% i filterkager.
Filterkagernes indhold af ammoniak gør, at Kommunekemi må brænde disse kager, og afleveringsprisen er derfor næsten tre gange højere end normalt.
Der dannes lidt mere filterkage pr. ton gods ved rensning af skyllevand end ved rensning af flusbad. Det er principielt den samme jernmængde, der skal fjernes fra henholdsvis skyllevandet og flusbadet, men
fra skyllevand udfældes også zinkhydroxid, idet zink tilføres med den udslæbte bejdse. I flusbadet udfældes zink derimod ikke på grund af den lave fældnings pH-værdi (ca. 4,5) og det store indhold af
ammonium, som kompleksbinder zink.
Andre affaldstyper dækker over slam fra affedterbade og bejdsebade samt kasseret flusbad. Mængderne svinger meget fra virksomhed til virksomhed afhængig af produktionsforholdene.
Af ovenstående fremgår det, at affaldet fra hårdzink, aske og kasseret bejdsesyre primært består af zink, mens de øvrige affaldsfraktioner primært indeholder metaller fra godset og andet.
Den samlede zinkmængde, der tabes, kan opgøres til:
Hårdzink, antaget 100% zink |
780 ton |
Aske, antaget zinkoxid, 80% zink |
965 ton |
Bejdsesyre, 100 g Zn/liter |
360 ton |
Filterkager fra spildevand, 5% zink |
12 ton |
Kasseret flusbad med 15% zink |
8 ton |
Samlet |
2.120 ton |
Da der anvendes 9.830 ton zink i alt, udgør affaldsmængden ca. 20%.
D.4.5 Hovedtal for varmforzinkning
Kortlægningen har vist, at der behandles 120.000 ton gods pr. år med varmforzinkning.
Der anvendes 14.000 ton kemikalier, hvilket svarer til 117 kg pr. behandlet ton gods. Zinkforbruget ligger på 9.830 ton. Råstofforbruget svarer til 248 kg pr. ton behandlet gods.
Der anvendes et vandforbrug på i størrelsesordnen 15-20.000 m³/år.
Det samlede energiforbrug er estimeret til 36-60.000 MWh. Det er antaget, at 40% stammer fra olie/gas og resten fra el. Energiforbruget kan derfor opgøres til et elforbrug på 28.800 MWh og 1.829 ton
råolie.
Affald fra kasserede bade og slam udgør i alt 6.500 ton, hvoraf det er estimeret at zinkmængden udgør 2.100 ton.
Den mængde zink, der anvendes, og som ikke går i affaldsstrømmen, antages at blive på emnerne, indtil de kasseres som affald.
D.5 Ressourceopgørelse
I afsnit D.2-D.4 er gennemført en kortlægning af de procesrelaterede forhold ved de tre overfladebehandlingsformer. Der er opgjort mængden af materialer, hjælpestoffer og energi, der går til processerne
og hvilke tab, der forekommer.
Som basis for kortlægningen er taget udgangspunkt i behandling af det antal m² overflade, der behandles ved fornikling/forchromning og elforzinkning i Danmark og for varmforzinkning for den mængde gods
målt i ton, der behandles i Danmark.
Med henblik på at gennemføre en beregning af ressourceeffektivitet er det nødvendigt, hvor det er muligt, at foretage en vurdering af forbruget af råstoffer og energi til fremstilling af opgjorte forbrug.
D.5.1 Metaller
De metaller, der er relevante ved de 3 overfladebehandlingsprocesser, er
- nikkel
- kobber
- chrom
- zink
- jern
For disse metaller er ressourcetræk opgjort i mPR og primær energi ved udvinding og fremstilling opgjort i Miljønyt nr. 58 (Pommer et al., 2001). Data herfra er vist i Tabel D.20.
Tabel D.20 Ressourceforbrug for metaller
Metal |
Ressource-
forbrug |
Primær energi
til fremstilling |
Nikkel |
106 mPR/kg |
190 MJ/kg |
Kobber |
16,5 mPR/kg |
90 MJ/kg |
Chrom |
12,8 mPR/kg |
39 MJ/kg |
Zink |
33 mPR/kg |
70 MJ/kg |
Jern/stål |
0,08 mPR Fe
og 0,05 mPR Mn |
40 MJ/kg |
I det følgende er vist forbruget af metaller for de tre overfladebehandlingsprocesser. For fornikling/forchromning og for elforzinkning er der foretaget en omregning til enheden 1.000 m² behandlet overflade.
For varmforzinkning er der foretaget en omregning til 1 ton behandlet gods. Omregningerne er foretaget for at kunne sammenligne de forskellige overfladebehandlingstyper.
Tabel D.21 Fornikling/forchromning, Samlet behandlet areal 170.000 m²
|
Nikkel |
Kobber |
Chrom |
Jern/stål |
Forbrug i alt (ton) |
130 |
33 |
10,4 |
9,5 |
Affald (ton) |
4,19 |
1,36 |
8,67 |
9,5 |
I produkt (ton) |
125,81 |
31,64 |
1,73 |
0 |
pr. 1000 m² behandlet overflade |
Forbrug i alt (kg) |
111,11 |
28,21 |
2,99 |
8,12 |
Affald (kg) |
3,58 |
1,16 |
0,00 |
8,12 |
I produkt (kg) |
107,53 |
27,04 |
2,99 |
0,00 |
Ressourceforbrug |
mPR pr. kg |
106 |
16,5 |
12,8 |
Jern: 0,08
Mangan: 0,05 |
Ressourceforbrug |
11777,78 |
465,38 |
38,29 |
Jern: 0,65
Mangan: 0,48 |
I produktet |
11398,17 |
446,21 |
38,29 |
Jern: 0
Mangan: 0 |
Det samlede ressourceforbrug er på 12.358 mPR for metallerne, og i produktet findes 11.863 mPR. Tabet udgør 500 mPR svarende til 4% af ressourceforbruget.
Tabel D.22 Elforzinkning , Samlet behandlet areal 8.500.000 m²
|
Zink |
Chrom |
Jern/stål |
Forbrug i alt (ton) |
630,00 |
14,1 |
74 |
Affald (ton) |
34,90 |
11,06 |
74 |
I produkt (ton) |
595,10 |
3,04 |
0 |
Pr. 1000 m² overflade |
Forbrug (kg) |
74,12 |
1,66 |
8,71 |
Affald (kg) |
4,11 |
1,30 |
8,71 |
I produkt (kg) |
70,01 |
0,36 |
0,00 |
Ressourceforbrug |
mPR pr. kg |
33 |
12,8 |
Jern: 0,08
Mangan: 0,05 |
Ressourceforbrug |
2445,88 |
21,23 |
Jern: 0,70
Mangan: 0,44 |
I produkt |
2310,39 |
4,58 |
Jern: 0
Mangan: 0 |
Det samlede ressourceforbrug er på 2.468 mPR for metallerne, og i produktet findes 2.315 mPR. Tabet udgør 153 mPR svarende til 6,2% af ressourceforbruget.
Tabel D.23 Varmforzinkning, Behandlet godsmængde 120.000
|
Zink |
Forbrug i alt (ton) |
9830 |
Affald (ton) |
2120 |
I produkt (ton) |
7710 |
Pr. 1 ton behandlet gods |
Forbrug i alt (kg) |
81,92 |
Affald (kg) |
17,67 |
I produkt (kg) |
64,25 |
Ressourceforbrug |
mPR pr. kg |
33 |
Ressourceforbrug |
2703,3 |
I produkt |
2120,3 |
Af Tabel D.23 kan det beregnes, at tabet udgør 583 mPR, hvilket udgør 21,6% af det ressourceforbruget.
D.5.2 Kemikalier
Der anvendes en række kemikalier i forbindelse med de 3 overfladebehandlingsprocesser. I Tabel D.24 er skitseret, hvilke der kan fastlægges et ressourceforbrug for, og hvilke forudsætninger der er gjort.
Ved affaldsbehandlingen sker en fældning af metallerne som metalhydroxider. Ved fældningen vil der blive tilsat hydroxider antagelig i form af natriumhydroxid samt flokuleringsmidler for at effektivisere
fældningen. Disse ressourceforbrug er ikke medtaget i opgørelsen.
Tabel D.24 Ressourcetræk og energiforbrug for kemikalier
Kemikalier |
Ressource-
forbrug |
Primært energi-
forbrug til
fremstilling |
Forudsætninger og antagelser |
Uorganiske syrer |
0 da rigelig ressource |
50 MJ/kg |
Anslået. |
Uorganiske baser |
0 da rigelig ressource |
38 MJ/kg |
Som natriumhydroxid |
Organiske forbindelser, Tensider |
0,04 mPR |
60 MJ/kg |
Ressourcetræk vurderet som stammende fra olieprodukter, energiforbrug fra Miljønyt nr. 58 |
Cyanider |
|
|
Kan ikke vurderes og medtages |
Borsyre |
|
|
Kan ikke vurderes og medtages |
Salte (KCl) |
0 da rigelig ressource |
5 MJ/kg |
Anslået ud fra natriumhydroxid på 1,2 MJ/kg |
Glansmidler |
|
|
Kan ikke vurderes og medtages |
Ammoniak |
0 da rigelig ressource |
60 MJ/kg |
Ressourcetræk anslået, energiforbrug fra Miljønyt nr. 58 |
Brintperoxid |
0 da rigelig ressource |
10 MJ/kg |
Anslået |
Vand regnes efter UMIP-metoden som en rigelig ressource. Den eneste miljømæssige belastning, der er medtaget i UMIP-metoden, er energiforbrug til oppumpning af vand, der udgør 0,001 MJ/kg
svarende til 1 MJ/m³. I det følgende er vist ressourceforbruget for de tre processer i de grupper, som det er valgt at opgøre kemikalierne i.
D.5.2.1 Fornikling/forchromning
Forbruget af kemikalier og vand samt omregning til ressourceforbrug er vist i Tabel D.25.
Tabel D.25 Kemikalie- og vandforbrug ved fornikling, forchromning, årlig behandling af 170.000 m²
Kemikalietype |
Årligt forbrug
(ton) |
Forbrug pr.
1.000 m² (kg) |
MPR pr. kg |
mPR
pr. 1.000 m² |
Uorganiske syrer |
110 |
94,02 |
0 |
0 |
Uorganiske baser |
10 |
8,55 |
0 |
0 |
Organiske forbindelser |
55 |
47,01 |
0,04 |
1,88 |
Cyanider |
30 |
25,64 |
- |
0 |
Andet |
65 |
55,56 |
- |
0 |
Vandforbrug |
40.000 |
34.188 |
0 |
0 |
I alt |
1,88 |
Ressourceforbruget for uorganiske syrer, uorganiske baser og vand er sat til 0 mPR, da disse ressourcer betragtes som rigelige. Ressourceforbruget til fremstilling af cyanider og andet, herunder glansmidler,
er ikke medtaget på grund af manglende oplysninger.
Udeladelserne kan vurderes ud fra:
- ressourceforbruget for cyanid kan ligge på niveau med ressourceforbruget til fremstilling af tensider, uden disse 2 stoftyper i øvrigt kan sammenlignes.
- ressourceforbruget til glansmidler kan vanskeligt vurderes, da sammensætningen ikke kendes. Det antages, at op til 50% af mængden af glansmidler på 32 ton udgøres af metaller med et gennemsnitligt
ressourceforbrug på 25 mPR/kg.
Disse antagelser vil viser, at udeladelsen af cyanider ikke har væsentlig betydning, da ressourceforbruget hertil er omkring 1 mPR. Ressourceforbruget til glansmidler kan derimod være af stor betydning, da
32 ton glansmidler svarer til et metalindhold på 13,7 kg, hvis 50% af glansmidlerne er metaller. Ved et gennemsnitligt ressourceforbrug på 25 mPR pr. kg betyder dette et ressourceforbrug på 340 mPR for
glansmidlerne. Tages der hensyn til andre indholdsstoffer, vil ressourceforbruget kunne komme op på 500 mPR ved en konservativ vurdering.
Overordnet må det dog konkluderes, at ressourceforbruget til kemikalier og vand er meget lille – op til 500 mPR i forhold til ressourceforbruget til metaller på i størrelsesordnen 12.000 mPR.
D.5.2.2 Elforzinkning
I Tabel D.26 er vist kemikalie- og vandforbruget for elforzinkning samt opgjort ressourceforbruget hertil.
Tabel D.26 Kemikalie- og vandforbrug ved elforzinkning, årlig behandling af 8.500.000 m²
Kemikalietype |
Årligt forbrug
(ton) |
Forbrug pr. ton
(kg) |
mPR pr. kg |
mPR
Pr. 1000 m² |
Uorganiske syrer |
310 |
36,47 |
0 |
0 |
Uorganiske baser |
300 |
35,29 |
0 |
0 |
Borsyre |
13 |
1,53 |
- |
- |
Salte |
100 |
11,76 |
0 |
0 |
Organiske forbindelser |
100 |
11,76 |
0,04 |
0,47 |
Cyanider |
80 |
9,41 |
- |
- |
Andet |
167 |
19,64 |
- |
- |
Vandforbrug |
300.000 |
35.294 |
0 |
0 |
I alt |
0,008 |
I denne opgørelse er der ligesom for fornikling/forchromning udeladt ressourceforbrug til glansmidler, cyanider og borsyre. Ressourceforbrug til cyanider og borsyre antages at være beskedent. Af
glansmidler anvendes 167 ton på årsbasis svarende til 19,6 kg pr. 1.000 m². Regnes der ligesom for fornikling/forchromning med et ressourceforbrug på i størrelsesordnen 25 mPR pr. kg glansmidler, vil
ressourceforbruget udgøre 250 mPR.
Ressourceforbruget til metaller udgør omkring 2.500 mPR, og da en konservativ vurdering af ressourceforbruget til kemikalier kan udgøre op til 500 mPR, er denne andel ikke uvæsentlig.
D.5.2.3 Varmforzinkning
I Tabel D.27 er vist kemikalie- og vandforbruget for varmforzinkning samt opgjort ressourceforbruget hertil.
Tabel D.27 Kemikalie- og vandforbrug ved varmforzinkning, årlig behandling af 120.000ton
Kemikalietype |
Årligt forbrug
(ton) |
Forbrug pr. ton
(kg) |
mPR pr. kg |
mPR
Pr. ton |
Uorganiske syrer |
1.000 |
8,33 |
0 |
0 |
Uorganiske baser |
60 |
0,50 |
0 |
0 |
Ammoniak |
65 |
0,54 |
0 |
- |
Hydrogenperoxid |
10 |
0,08 |
0 |
0 |
Organiske forbindelser |
25 |
0,21 |
0,04 |
0,008 |
Vandforbrug |
20.000 |
167 |
0 |
0 |
I alt |
0,008 |
I denne opgørelse af ressourceforbrug for kemikalier er der ikke stofgrupper, for hvilke sammensætningen er ukendt. Muligvis vil der være et ganske lille ressourceforbrug ved nogle af de kemikalietyper, der
er sat til 0, men samlet vurderes det, at ressourceforbruget for kemikalierne ikke vil være højere end 10 mPR.
Ressourceforbruget til kemikalier og vand vil således udgøre en meget lille del i forhold til ressourceforbruget til metaller, der udgør omkring 2700 mPR.
D.5.3 Energi
Ved opstilling af en energiopgørelse skal energiforbrug og eventuelt udviklet energi opgøres.
For de tre overfladebehandlingsprocesser skal der medtages energiforbrug til fremstilling af materialer og hjælpestoffer samt energiforbrug ved selve processen.
Energiforbrug til spildevandsrensning på virksomheden er medtaget i energiforbruget under processen. Energiforbrug til affaldsbehandling af kasserede bade og slam er derimod ikke medtaget.
Affaldsbehandlingen består principielt i en fældning af metallerne som hydroxider, presning af slam og efterfølgende deponering. Energiforbruget vurderes til at udgøre i størrelsesordnen 1 til 5 MJ pr. kg.
D.5.3.1 Fornikling/forchromning
Energiforbruget til fremstilling af metaller, kemikalier og vand er opgjort i Tabel D.28. Opgørelsen udtrykker energiforbruget i primær energi.
Tabel D.28 Energiforbrug ved fornikling/forchromning
|
Samlet for-
brug pr. år (ton) |
Forbrug pr.
1000 m² (kg) |
Primært
energiforbrug (MJ/kg) |
Primær energi
pr. 1000 m² (MJ) |
Til metaller |
Nikkel |
130,00 |
111,11 |
190,00 |
21.111,1 |
Kobber |
33 |
28,21 |
90 |
2.538,5 |
Chrom |
10,4 |
8,89 |
39 |
346,7 |
Stål |
9,5 |
8,12 |
40 |
324,8 |
Til kemikalier |
Uorganiske syrer |
110,00 |
94,02 |
50 |
4.700,9 |
Uorganiske baser |
10,00 |
8,55 |
38 |
324,8 |
Org. forbindelser |
55,00 |
47,01 |
60 |
2.820,5 |
Cyanider |
30,00 |
25,64 |
- |
- |
Andet |
65,00 |
55,56 |
- |
- |
Vand |
120.000,00 |
102.560,00 |
0,001 |
102,6 |
Til metaller, kemikalier og vand |
32.167 |
Af Tabel D.29 fremgår det, at det samlede energiforbrug er på 32.200 MJ pr. 1000 m². Langt det største energiforbrug går til udvinding af nikkel.
I opgørelsen mangler energiforbrug til fremstilling af cyanider og andre materialer. Energiforbruget hertil vil antagelig skønsmæssigt ligge på omkring 50 MJ/kg. Er denne antagelse korrekt, vil energiforbruget
til fremstilling af cyanider og andet udgøre i størrelsesordnen 4.000 MJ pr. 1000 m², hvilket vil betyde, at det samlede energiforbrug stiger til 36.000 MJ pr. 1000 m².
Energiforbruget til processen er opgjort til 34.400 MWh for den samlede årlige produktion svarende til 29.400 kWh pr. 1000 m². Hele energiforbruget er elenergi og kan omregnes til primær energi. (1
kWh = 9 MJ). Energiforbruget til processen udgør således 265.000 MJ pr. 1000 m².
Det samlede energiforbrug kan sættes til 300.000 MJ pr. 1.000 m² behandlet overflade.
Der fremkommer omkring 1.200 m³ kasserede bade pr. år. Dette svarer til i størrelsesordnen 1 m³ bad pr. 1000 m² behandlet overflade. Energiforbruget hertil vil ligge på mellem 1.000 og 5.000 MJ og vil
derfor ikke være af væsentlig betydning.
D.5.3.2 Elforzinkning
Energiforbruget til fremstilling af metaller, kemikalier og vand er opgjort i Tabel D.29. Opgørelsen udtrykker energiforbruget i primær energi.
Tabel D.29 Energiforbrug ved elforzinkning
|
Samlet forbrug pr. år (ton) |
Forbrug pr. 1000 m² (kg) |
Primært Energiforbrug (MJ/kg) |
Primær energi pr. 1000 m² (MJ) |
Til metaller |
Zink |
630 |
74,12 |
70 |
5188,2 |
Chrom |
14,1 |
1,66 |
39 |
64,7 |
Stål |
74 |
8,71 |
40 |
348,2 |
Til kemikalier |
Uorganiske syrer |
310 |
36,47 |
50 |
1823,5 |
Uorganiske baser |
300 |
35,29 |
38 |
1341,2 |
Borsyre |
13 |
1,53 |
- |
- |
Salte |
100 |
11,76 |
5 |
58,8 |
Org. forbindelser |
100 |
11,76 |
60 |
705,9 |
Cyanider |
80 |
9,41 |
- |
- |
Andet |
167 |
19,65 |
- |
- |
Vand |
850.000 |
100.000 |
0,001 |
100 |
Til metaller, kemikalier og vand |
9.218 |
Af Tabel D.29 fremgår det, at det samlede energiforbrug er på 9.200 MJ pr. 1000 m². Langt det største energiforbrug går til fremstilling af zink.
I opgørelsen mangler energiforbrug til fremstilling af borsyre, cyanider og andet. Energiforbruget hertil vil antagelig skønsmæssigt ligge på omkring 50 MJ/kg. Er denne antagelse korrekt, vil energiforbruget til
fremstilling af disse materialer udgøre 1.500 MJ pr. 1000 m², hvilket vil betyde, at det samlede energiforbrug stiger til 10.700 MJ pr. 1000 m².
Energiforbruget til processen er opgjort til 22.757 MWh for den samlede årlige produktion svarende til 2.677 kWh pr. 1000 m². Hele energiforbruget er elenergi og kan omregnes til primær energi.
Energiforbruget til processen udgør således 24.096 MJ pr. 1000 m².
Det samlede energiforbrug kan sættes til omkring 35.000 MJ pr. 1000 m².
I Tabel D.1 er vist, at der fremkommer omkring 1.700 m³ kasserede bade pr. år. Dette svarer til i størrelsesordnen 0,2 m³ pr. 1.000 m² behandlet overflade. Energiforbruget hertil vil ligge på mellem 200 til
1.000 MJ pr. 1.000 m² og vil derfor ikke være af væsentlig betydning.
D.5.3.3 Varmforzinkning
Energiforbruget til fremstilling af metaller, kemikalier og vand er opgjort i Tabel D.30. Opgørelsen udtrykker energiforbruget i primær energi.
Tabel D.30. Energiforbrug ved varmforzinkning
|
Samlet for- brug pr. år (ton) |
Forbrug pr. 1 ton gods (kg) |
Primært Energiforbrug (MJ/kg) |
Primær energi pr. ton gods (MJ) |
Til metaller |
Zink |
9.830 |
81,92 |
70 |
5.734,2 |
Til kemikalier |
Uorganiske syrer |
1.000 |
8,33 |
50 |
416,7 |
Uorganiske baser |
60 |
0,50 |
38 |
19,0 |
Ammoniak |
65 |
0,54 |
60 |
32,5 |
Hydrogenperoxid |
10 |
0,08 |
10 |
0,8 |
Organiske forbindelser |
25 |
0,21 |
60 |
12,5 |
Vand |
20.000 |
166,7 |
0,001 |
0,17 |
Til metaller, kemikalier og vand |
6.215,8 |
Af Tabel D.30 fremgår det, at det samlede energiforbrug er på 6.200 MJ pr. ton gods. Langt det største energiforbrug går til udvinding af zink.
Energiforbruget til processen består dels af et elforbrug og dels af et forbrug af råolie. Energiforbruget for 120.000 ton er opgjort til 28.800 MWh el og 1.829 ton råolie svarende til 240 kWh el og 15,2 kg
olie pr. ton gods.
Omregnes procesenergien til primær energi, fås 2.160 MJ fra elforbruget og 576 MJ fra olieforbruget, svarende til i alt 2.736 MJ. I beregningen er forudsat en udnyttelse af olien på 90% og et energiindhold
på 42 MJ/kg.
Det samlede forbrug af primær energi udgør 8.950 MJ pr. ton behandlet gods.
Der vil være et energiforbrug i forbindelse med affaldsbehandlingen, men dette kan ikke estimeres.
E Køle/smøremidler
E.1 Introduktion
Køle/smøremidler anvendes til køling og smøring ved skærende og spåntagende bearbejdning af emner af jern, stål og andre metaller.
Der findes to hovedtyper af produkter, - den største er de vandbaserede produkter, hvor især køleeffekten er vigtig, og en mindre gruppe af vandfri produkter, hvor den især den smørende effekt er vigtig.
Som ved den galvaniske overfladebehandling i kapitel 6 kan processen ”brug af køle/smøremidler” ikke sidestilles med et produkt. Her er valgt at se på processen i et livscyklusperspektiv som beskrevet i
kapitel 2. Grafisk kan dette illustreres som vist i Figur E.1.
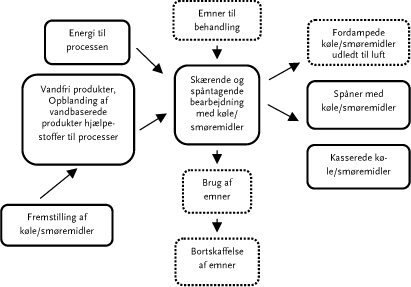
Figur E.1 Skærende og spåntagende bearbejdning med anvendelse af Køle/smøremidler i et livscyklusperspektiv
Det vanskelige ved vurdering af køle/smøremidler set i relation til ressourceeffektivitet er definition af en enhed, der er relevant i forhold til de forskellige skærende og spåntagende bearbejdninger i forskellige
materialer, og som samtidig siger noget om forbruget af køle/smøremidlerne.
Ved opslag i UMIP-databasen, SigmaPro samt forskellige håndbøger vedrørende metalbearbejdning er det valgt at tage udgangspunkt i mængden af fjernet materiale i form af spåner, slibestøv, fraskær og
andet.
Nyttevirkningen ved anvendelse af køle/smøremidler er, at en mængde materiale fra et givet emne fjernes. Derfor defineres produktet i denne sammenhæng som kg fjernet materiale.
Til at opnå den ønskede nyttevirkning anvendes køle/smøremidler, energi og vand, og der fremkommer affald som skitseret i Figur E.1.
Skærende og spåntagende bearbejdning af metaller dækker over en række forskellige processer, hvis formål er at fjerne dele af emnet.
De mest benyttede processer er:
- drejning
- fræsning
- genvindskæring
- boring
- savning
hvor man overvejende anvender vandbaserede midler.
E.2 Mængder
E.2.1 Forbrug af køle/smøremidler
Forbruget af køle/smøremidler afhænger af procestype, af anlæggets type og udnyttelsesgrad.
Her er taget udgangspunkt i forbruget på Danfoss, som beskrevet i Udpegning og kortlægning af affaldstunge industriområder (Pommer et al., 2003), da det antages, at man på denne virksomhed har et
bredt udsnit af processer og materialer.
I ovennævnte kortlægning blev det estimeret, at der anvendes 24 kg vandbaserede køle/smøremidler pr. ton spåner. Det antages derfor, at forbruget ligger på mellem 20-30 kg pr. ton fjernede spåner.
Antages det, at køle/smøremidlerne er en 5% opblanding af koncentrat, vil koncentratforbruget ligge på omkring 1 til 1,5 kg pr. ton fjernede spåner.
For de vandfri midler følger der i eksemplet omkring 450 kg vandfri smøremidler med 1 ton spåner. En stor del af denne mængde drænes, men kan ikke anvendes igen, da den er forurenet.
Ud fra det samlede forbrug, der er estimeret i kortlægningsprojektet kan forbrug og mængden af spåner estimeres (Pommer et al., 2003). Der skal gøres opmærksom på, at tallene er behæftet med en
betydelig usikkerhed.
Tabel E.1 Forbrug af køle/smøremidler
|
Vandbaserede køle/ smøremidler |
Vandfri smøremidler |
Køle/smøremiddel mængde pr. ton spåner |
1- 1,5 kg |
400-500 kg |
Totalt forbrug af køle/smøremidler |
700 ton |
500 ton |
Samlet mængde spåner |
500-700.000 ton |
1.000-1.300 ton |
E.2.2 Forbrug af vand
Til de vandbaserede køle/smøremidler anvendes vand anvendes vand ved opblanding af emulsionen. Ellers er der ikke noget vandforbrug. Til opblanding af 1 kg køle/smøremiddel antages anvendt 0,95 kg
svarende til 19 til 28,5 kg vand pr. ton spåner.
Det samlede vandforbrug kan estimeres til i størrelsesordnen 15.000 m³. Ved anvendelse af vandfri smøremidler er der ikke noget vandforbrug.
E.2.3 Forbrug af energi
Der er et energi ved:
- Udvinding og bearbejdning af råstoffer
- Fremstilling af køle/smøremidlerne
- Brug af køle/smøremidlerne
- Bortskaffelse af køle/smøremidlerne
Energiforbruget til udvinding og bearbejdning af råstoffer er søgt opgjort i forbindelse med vurdering af indholdsstofferne, se kapitel 3.
E.2.3.1 Energiforbrug ved fremstilling
Energiforbruget til fremstilling af køle/smøremidlerne omfatter en blanding af komponenterne. En almindelig blandeproces har et meget lavt energiforbrug og sættes i denne forbindelse konservativt til 1 MJ/kg
køle/smøremiddel produceret opgjort som elforbrug. Dette svarer til 9 MJ primær energi.
For de vandbaserede midler anvendes 1,24 kg køle/smøremidler pr. ton spåner, hvilket betyder, at der er et energiforbrug på 9 1,24 MJ = 11,2 MJ primær energi.
For de vandfri midler anvendes 450 kg køle/smøremidler pr. ton spåner, hvilket betyder, at der er et energiforbrug på 9 450 MJ = 4.050 MJ primær energi.
E.2.3.2 Energiforbrug ved anvendelse
Energiforbruget til skærende og spåntagende bearbejdning er meget varierende. Det afhænger af procestype og materialetype.
I UMIP-databasen er nævnt forskellige former for skærende og spåntagende bearbejdning. For bearbejdning af jern og stål, der er det mest almindelige, ligger energiforbruget på 1 til 5 MJ/kg fjernet
materiale. I det følgende vælges derfor at tage udgangspunkt i et energiforbrug på 3 MJ/kg spåner opgjort som primær energi.
Ved bearbejdning udgør dette i størrelsesordnen 3 GJ pr. ton spåner eller 20.000.000 GJ for 700.000 ton spåner.
E.2.4 Affald
Spåner med køle/smøremidler drænes, før de sendes til oparbejdning – direkte eller via skrothandler.
Affald i form af drænede køle/smøremidler vil derfor forkomme
- på virksomheder, der anvendes køle/smøremidler
- hos skrothandlere, der oplagre spåner, på virksomheder
- hos oparbejdere af spåner
- samt som diffus forurening
Opsamlede køle/smøremidler vil blive opkoncenteret og derefter bortskaffet ved forbrænding.
I affaldskortlægningen (Pommer et al., 2003) er det anslået, at omkring 5% af de vandbaserede køle/smøremidler spredes som diffus forurening. Den resterede del forbrændes enten efter behandling af
kasserede køle/smøremidler eller ved oparbejdning af spånerne.
For de vandfri midler er det antaget, at omkring 20% tabes som olietage. Den resterende del forbrændes, enten ved affaldsforbrænding eller ved oparbejdning af spånerne.
Ved affaldsbehandling af de vandbaserede midler sker dels en filtrering og en opkoncentrering inden forbrænding. Det antages, at energiforbruget til behandling i størrelsesordnen modsvarer den udviklede
energi ved affaldsforbrændingen.
For de vandfri midler vil der ske en energiudvikling ved forbrænding. Det antages, at 80% svarende til 400 ton forbrændes. Med et energiindhold på niveau med råolie, der er omkring 40MJ/kg og en
udnyttelse på 75%, svarer dette til en energiudvikling på i størrelsesordnen 12.000 GJ. Med en mængde spåner med vandfri midler på 1.000 til 1.300 ton svarer dette til 9 til 12 GJ pr. ton spåner.
E.3 Indholdsstoffer i køle/smøremidler
I affaldskortlægningen (Pommer et al., 2003) er gengivet en opgørelse fra Produktregistret, der er foretaget i september 2001. I denne opgørelse er det samlede forbrug af køle/smøremidler opgjort til
omkring 1.000 ton. I opgørelsen er det ikke skelnet klart mellem midler til emulsioner – de vandbaserede midler – og midler der anvendes direkte – de vandfri midler.
Opgørelsen er anvendt i det følgende med antagelse om, at følgende midler er vandbaserede midler:
K6000 |
Køle/smøremidler til metalbearbejdning |
771,0 ton |
K6014 |
Gevindskæremidler |
70,0 ton |
K6016 |
Køle/smøremidler til rømning |
0,1 ton |
K6020 |
Slibevæsker |
60,0 ton |
K6025 |
Andre køle/smøremidler til spåntagende metalbearbejdning |
68,0 ton |
K6035 |
Andre køle/smøremidler til plastisk bearbejdning |
3,2 ton |
K6045 |
Andre køle/smøremidler til klippende bearbejdning |
0,5 ton |
Følgende midler er antaget som vandfri midler:
K6010 |
Boreolier |
40,5 ton |
K6040 |
Udstandsningsolier |
13,8 ton |
Af denne opgørelse ses det, at de vandbaserede midler udgør i alt 973 ton med de væsentligste mængder inden for grupperne K6000, K6014, K6020 og K6025. For de vandfri midler omfatter opgørelsen
kun to væsentlige typer olier.
Mængderne stemmer ikke helt overens med de mængder, der er antaget som forbrugt i dag. Dette kan forklares ved, at nogle af de registrerede midler ikke anvendes i det omfang, som det var forventet. De
indholdsstoffer opgørelsen viser, antages det dog at kunne give et billede af, hvilke stoftyper der indgår i dels de vandbaserede og dels de vandfri midler.
E.3.1 Vandbaserede midler
Opgørelsen er gennemgået og de enkelte indholdsstoffer er grupperet efter deres type rent kemisk. Opgørelsen er vist i Tabel E.2.
Tabel E.2 Indholdsstoffer i vandige køle/smøremidler
Alle angivelser er i ton pr. år |
K 6000
Metalbear- bejdning |
K 6014
Gevindskæ- remidler |
K 6020
Slibevæsker |
K 6025
Andre midler til spånta- gende be- arbejdning |
Sum |
Råoliedestillater |
209,3 |
9,15 |
12,57 |
4,13 |
235,16 |
Olier, raffinerede, diverse |
22,1 |
0,51 |
0,18 |
0,66 |
23,45 |
Fedtsyrer |
26,9 |
5,96 |
0,56 |
0,00 |
33,42 |
Aromater |
0,6 |
0 |
0 |
0 |
0,60 |
alkoholer |
2,7 |
0 |
0 |
0,23 |
2,93 |
Aldehyder, ketoner og ethere |
5,5 |
0 |
0 |
0,15 |
5,65 |
Estere og acetater |
1 |
0 |
0 |
0,07 |
1,07 |
Organiske syrer |
18,3 |
0 |
0 |
0 |
18,30 |
Glycoler |
57,6 |
4,99 |
1,55 |
10,56 |
74,70 |
Aminer og andre kvælstofforbindelser |
99,5 |
3,52 |
42,16 |
20,43 |
165,61 |
Chlorerede forbindelser, organiske |
27,2 |
0,54 |
|
0,00 |
27,74 |
Svovlforbindelser, organiske |
17,1 |
3,01 |
1,04 |
5,01 |
26,16 |
Phosporforbindelser, organiske |
3,1 |
0 |
0 |
0 |
3,10 |
Kvælstof- og svovlforbindelser, organiske |
1,6 |
0 |
0 |
0 |
1,60 |
Diverse organiske forbindelser |
40,5 |
42,47 |
0,00 |
25,85 |
108,83 |
Bor-forbindelser |
24,7 |
0,00 |
2,02 |
0,01 |
26,73 |
Hydroxider, silikater og salte |
4,43 |
0,00 |
0,36 |
0 |
4,79 |
Gasser |
2,4 |
0,00 |
0 |
0 |
2,40 |
Vand |
206,9 |
0,00 |
0,00 |
0,42 |
207,33 |
I alt |
771,43 |
70,16 |
60,45 |
67,53 |
969,57 |
Som det fremgår af Tabel E.2, udgør vand i køle/smøremidlerne omkring 20 % af indholdsstofferne. Råoliedestillater og raffinerede olier udgør omkring 25 %. Gruppen af organiske carbonhydrider med ilt,
der omfatter fedtsyrer, aromater, alkoholer, aldehyder, ketoner og ethere, estre og acetater, organiske syrer samt glycoler udgør omkring 15 %. Chlorerede organiske forbindelser udgør 3%, mens aminer
og andre kvælstofholdige forbindelser udgør 17 %. Øvrige organiske forbindelser udgør omkring 15%, og uorganiske komponenter udgør ca. 4 %.
I affaldskortlægningen er det opgjort, at der forbruges omkring 700 ton køle/smøremiddel pr. år. I Tabel E.3 viser det årlige forbrug af en række hovedkomponenter. Endvidere er forbrug pr. 1 ton spåner
opgjort, underforudsætning af, at der bruges 1,25 kg køle/smøremiddel pr. ton.
Tabel E.3 Indhold af hovedkomponenter i vanddige køle/smøremidler
Komponent |
Indhold i % |
Mængde (ton) pr. år |
Mængde pr. ton spåner |
Ressourceforbrug pr. ton spåner |
Energiforbrug pr. ton spåner |
mPR /kg |
mPR |
MJ/kg |
MJ |
Vand |
20 |
140 |
0,25 kg |
0 |
0 |
0,001 |
0 |
Råoliedestillater og raffinerede olier |
25 |
185 |
0,31 kg |
0,04 |
0,0124 |
50 |
15,5 |
Carbonhydrider med ilt |
15 |
105 |
0,19 kg |
0,04 |
0,0076 |
80 |
15,2 |
Chlorerede orga-niske forbindelser |
3 |
21 |
0,04 kg |
0,04 |
0,0016 |
60 |
2,4 |
Organiske kvælstofforbindelser |
17 |
119 |
0,21 kg |
0,04 |
0,0084 |
100 |
21,0 |
Øvrige organiske forbindelser |
15 |
105 |
0,19 kg |
0,04 |
0,0076 |
100 |
19,0 |
Uorganiske komponenter |
4 |
28 |
0,05 kg |
0 |
0 |
50 |
2,5 |
I alt |
0,0376 |
|
73,1 |
I Tabel E.3 er det antaget, at alle de organiske komponenter har et ressourceforbrug svarende til råolie, da det ikke har været muligt at skaffe mere detaljerede oplysninger.
Med hensyn til det primære energiforbrug ved fremstilling er de fleste data taget fra Pommer et al., 2001. Det er antaget, at råoliedestillater og raffinerede olier kan sidestilles med olieprodukter, raffinerede,
flydende, og at carbonhydrider med ilt kan sidestilles med opløsningsmidler med oxygen. Chlorerede organiske forbindelser er sidestillet med chlorerede opløsningsmidler. For organiske kvælstofforbindelser
og øvrige organiske forbindelser har det ikke været muligt at finde data, hvorfor der er antaget en konservativ værdi. Det samme gør sig gældende for de uorganiske komponenter.
E.3.2 Vandfri midler
Opgørelsen er gennemgået og de enkelte indholdsstoffer er grupperet efter deres type rent kemisk.
Tabel E.4 Indholdsstoffer i vandfri køle/smøremidler
Alle angivelser er i ton pr. år |
K 6010
Boreolier |
K 6040
Udstandsningsolier |
Sum |
Råoliedestillater |
3,82 |
1,42 |
5,24 |
Olier, raffinerede, diverse |
0,10 |
4,56 |
4,66 |
Fedtsyrer |
0,25 |
|
0,25 |
Estere og acetater |
0,65 |
|
0,65 |
Glycoler |
4,64 |
|
4,64 |
Chlorerede forbindelser, organiske |
1,09 |
0,25 |
1,34 |
Svovlforbindelser, organiske |
1,21 |
5,30 |
6,51 |
Diverse organiske forbindelser |
25,72 |
2,00 |
27,72 |
Gasser |
2,98 |
|
2,98 |
Vand |
0,08 |
0,22 |
0,30 |
|
40,54 |
13,76 |
54,29 |
Da det i affaldskortlægningen er er opgjort, at der forbruges omkring 500 ton smøremidler pr. år, er der i vist, hvilket årligt forbrug der svarer til delt op på hovedkomponenter som for de vandbaserede
midler.
Tabel E.5 Indhold af hovedkomponenter i vandfri smøremidler
Komponent |
Indhold i % |
Mængde (ton) pr. år |
Mængde pr. ton spåner |
Ressourceforbrug pr. ton spåner |
Energiforbrug pr. ton spåner |
mPR /kg |
mPR |
MJ/kg |
MJ |
Råoliedestillater og raffinerede olier |
18 |
90 |
81 kg |
0,04 |
3,24 |
50 |
4.050 |
Carbonhydrider med ilt |
10 |
50 |
45 kg |
0,04 |
1,80 |
80 |
3.600 |
Chlorerede organiske forbindelser |
3 |
15 |
13,5 kg |
0,04 |
0,54 |
60 |
810 |
Organiske kvælstofforbindelser |
12 |
60 |
54 kg |
0,04 |
2,16 |
100 |
5.400 |
Øvrige organiske forbindelser |
51 |
255 |
230 kg |
0,04 |
9,20 |
100 |
23.000 |
Uorganiske komponenter |
6 |
30 |
27 kg |
0 |
0 |
50 |
1.350 |
I alt |
16,94 |
|
38.210 |
E.4 Ressourceopgørelse
Som basis for kortlægningen er taget udgangspunkt i forbruget af køle/smøremidler ved ydelsen ”Fjernelse af 1 ton spåner”. Produktet sættes derfor lig med 1 ton metalspåner.
Det er tidligere opgjort, at der fremkommer i størrelsesordnen 700.000 spåner i Danmark pr. år.
E.4.1 Produktet spåner
Typen af spåner afhænger af det materiale, der bearbejdes, og kan derfor være jern, stål, aluminium, kobber eller andre metaller. Mængdemæssigt vil de forskellige metalspåner ”tælle” det samme, men ses
der på ressourceforbruget opgjort som mPR, vil disse metaller blive vurderet forskelligt.
Maskinstål er et meget almindeligt materialer ved skærende og spåntagende bearbejdning. Det er ligeledes valgt at se på rustfrit stål, aluminium og kobber.
Maskinstål består af jern og mangan, og ressourceforbruget er på 0,08 mPR jern og 0,05 mPR mangan svarende til i alt 0,13 mPR/kg.
Rustfrit stål består af jern, chrom og nikkel, og her er ressourceforbruget 0,06 mPR jern, 2,3 mPR chrom og 9,9 mPR nikkel, svarende til i alt 12,3 mPR/kg.
Aluminium medfører et ressourceforbrug på 1,5 mPR/kg og kobber et ressourceforbrug på 16,5 mPR.
E.4.2 Køle/smøremidler
For de vandbaserede midler anvendes 1,24 kg koncentrat pr. ton spåner. Ressourceforbruget til fremstilling af dette er opgjort til 0,0376 mPR/ton spåner. Det årlige forbrug ligger på ca. 700 ton.
For de vandfri midler anvendes der 450 kg køle/smøremiddel pr. ton spåner. Ressourceforbruget til fremstilling af dette er opgjort til 16,94 mPR/ton spåner. Det årlige forbrug ligger på omkring 500 ton.
E.4.3 Energi
Nøgletal for energiforbruget for de to typer køle/smøremidler er vist i Tabel E.6.
Tabel E.6 Energiforbrug pr. ton spåner
|
Vandbaserede
køle/smøremidler |
Vandfri køle/
smøremidler |
Energiforbrug til ressourcer |
73,1 MJ |
38.210 MJ |
Energiforbrug til blanding |
11,2 MJ |
4.050 MJ |
Energiforbrug ved brug |
3.000 MJ |
3.000 MJ |
Energiforbrug ved bortskaffelse |
˜ 0 MJ |
-10.000 MJ |
Samlet energiforbrug |
3.084 MJ |
35.260 MJ |
Omregnet til mPR |
3,0 mPR |
34,4 mPR |
| Til Top | | Forside |
Version 1.0 December 2005 • © Miljøstyrelsen.
|