| Forside | | Indhold | | Forrige | | Næste |
Brancheorientering for varmforzinkning
6 BAT-løsninger
I dette afsnit findes der en samlet oversigt over anbefalede BAT-løsninger. Det skal dog tilføjes, at der foregår en løbende udvikling og forbedring, så listen bliver stadig længere. Derfor vil der godt kunne forekomme BAT-løsninger i praksis, som ikke findes på listen, lige som tiden efterhånden kan løbe fra nogle af de BAT-løsninger, som er anerkendte i dag.
6.1 Affedtning
6.1.1 Affedtning som separat proces
Affedtning bør altid foregå i en separat proces, medmindre emnerne er helt fri for fedt og olie. Fordelene er: hurtigere og mere ensartet bejdsning, mindre forbrug af bejdsesyre, mindre bejdseaffald, mindre brok og bedre overfladekvalitet. Det vil ofte være en dårlig miljøløsning at bejdse og affedte i samme kar.
Man foretrækker normalt en varm (50 - 70 °C) alkalisk affedtning; men flere virksomheder anvender en saltsyre affedter, mens nogle få anvender en phosphorsyre affedter med stor succes.
6.1.2 Optimal drift af affedterbad
Det er vigtigt med bevægelse i badet (fx. luftindblæsning). Spray affedtning, som det kendes ved sprøjtephosphatering, kunne også være en god løsning, da det giver både en mekanisk og en kemisk behandling af emneoverfladen. Ikke alle emner er dog egnede til denne form for affedtning. Dypning og spray kan evt. kombineres.
Badet bør løbende kontrolleres, så man kan sikre den optimale sammensætning. Det kan sikre maksimal effektivitet ved affedtningen og minimalt forbrug af affedtningskemikalier.
6.1.3 Rensning og genbrug
Den simpleste og letteste måde til rensning af affedterbadet er at skimme fri olie af overfladen og fjerne slam ved filtrering eller anden separationsmetode. Centrifugering kan være velegnet til at fjerne både olie og slam.
En stor del af olieindholdet i et affedterbad vil være emulgeret (opløst) og fjernes slet ikke med en olieskimmer og kun i begrænset omfang ved centrifugering. Den mest effektive metode til fjernelse af emulgeret olie er rensning i et ultra- eller mikrofilter. Ved denne metode fjernes olien og de bundne tensider, mens de fri tensider og de uorganiske komponenter i affedteren føres retur til badet og genanvendes. Membranerne skal vælges, så de passer til de anvendte affedterkemikalier. Badets levetid kan på den måde forøges 5 - 15 gange afhængig af forholdene.
6.1.4 Biologisk affedtning
Med denne løsning cirkuleres affedterbadet over et ”renseanlæg”, hvor mikroorganismer løbende nedbryder olien. Der tilsættes mikronæringsstoffer for at fremme den biologiske omdannelse af olie og fedt. Døde mikroorganismer og affaldsstoffer fjernes ved en mekanisk separation. Man kan gå direkte fra et biologisk affedterbad over i et bejdsebad uden mellemliggende skylning. Læs mere om biologisk affedtning i Case 5.
6.1.5 Ekstern behandling og oparbejdning
Ved den eksterne oparbejdning fjernes olie og andre forureninger fra affedterbadet, hvorefter badet kan returneres til virksomheden til genanvendelse efter tilsætning af de nødvendige affedtningskemikalier. Så vidt vides praktiseres metoden ikke i øjeblikket herhjemme. Der er flere firmaer, der modtager kasserede affedterbade; men alle destruerer badene ved at fjerne olie og fedt og neutralisere vandfasen før udledning til kloak.
6.2 Bejdsning og aftrækning
6.2.1 Adskillelse af bejdsning og aftrækning
Bejdsning og zinkaftrækning (stripning) bør holdes adskilt af hensyn til senere udnyttelse og oparbejdning af de kasserede bade.
Et kasseret bejdsebad kan bruges til oparbejdning af jernchlorid, der er et hyppigt anvendt fældningsmiddel til spildevandsrensning. Det forudsætter, at indholdet af zink og andre metaller kun er til stede i små koncentrationer.
Kasserede bejdsebade med lavt indhold af zink kan oparbejdes på centrale anlæg i udlandet, hvor bejdsebadet omdannes til saltsyre og jernoxid ved høj temperatur.
Et kasseret bejdsebad indeholder ofte en høj koncentration af fri saltsyre. Den kasserede syre kan overføres til et separat kar og anvendes til aftrækning af zink fra værktøjer og fejlforzinkede emner, hvorved syreindholdet forbruges til opløsning af zink, før syren endelig kasseres. Her kan indholdet fx. være oppe på jern = 80 - 100 g/l og zink = 100 - 200 g/l
6.2.2 Minimering af aftræksmængden
Zink i bejdsebade og aftrækssyre stammer fra ophæng, værktøjer og omforzinkning. Mængden bør minimeres ved at benytte engangs-tråd til ophængning, så man undgår kroge og stativer, der forzinkes og kører med igennem bejdsebade igen og igen. Kroge og stativer bør faktisk aftrækkes i aftrækssyre, før de bruges igen. Enkelte danske virksomheder anvender i dag titankroge, fordi titan ikke optager zink og derfor kan genbruges mange gange. Titan er et dyrt materiale, og det er ikke helt problemfrit at arbejde med, så derfor har det endnu kun vundet begrænset udbredelse.
Fejlforzinkede emner skal laves om; men først fjerner man zink i aftrækssyre. Det er en af mange gode grunde til, at fejlprocenten skal holdes så lav som muligt. Det er netop også, hvad man opnår gennem flere af de præsenterede BAT-løsninger.
6.2.3 Oparbejdning af aftrækssyre
Det er vanskeligt at oparbejde en kasseret aftrækssyre, fordi den indeholder store koncentrationer af både jern og zink. Der kan dog udvindes flussalt af kasseret aftrækssyre ved først at fjerne jern, jf. metoden beskrevet under rensning og genvinding af flusbad. De fleste virksomheder producerer dog væsentlig mere aftrækssyre, end de kan udnytte til fremstilling af flusbad.
Tabel 5 er der foretaget en teoretisk beregning af, hvor meget flussalt, der kan udvindes ved behandling af 1 m³ kasseret aftrækssyre. Beregninger forudsætter, at aftrækssyren indeholder 150 g/l zink, 90 g/l jern og 20 g/l saltsyre. Ved behandling med brintperoxid og ammoniakvand vil 1 m³ aftrækssyre give 515 kg flussalt med 60,8 % zinkchlorid og 39,2 % ammoniumchlorid. Ved processen udskilles der 145 kg Fe(OH)3, hvilket giver 350 - 400 kg filterkage ved afvanding i en filterpresse.
Tabel 5. Beregning af udvundet flussalt fra aftrækssyre
|
g/l |
kg/m³ |
kg/m³ |
% |
Zink, Zn |
150 |
150 |
Zn |
313 |
ZnCl2 |
60,8 |
Saltsyre, HCl |
20 |
20 |
HCl |
29 |
NH4Cl |
39,2 |
Jern, Fe |
90 |
114 |
Cl |
172 |
NH4Cl |
Flussalt |
|
|
|
515 |
Flussalt |
|
Hvis man fremstiller aftrækssyren af frisk saltsyre, kan man næsten helt undgå jernforurening i badet, og når aftrækssyren kasseres, kan den meget let laves om til flusbad ved blot at neutralisere med ammoniakvand. Ved meget lave jernkoncentrationer behøver man ikke engang at ilte og udfælde jernet først.
I princippet kan kasseret aftrækssyre også oparbejdes til jern- og zinksalte, som kan anvendes inden for andre grene af industrien. Det er i øjeblikket ikke realistisk at gøre for den enkelte virksomhed, og i Danmark foregår der heller ingen central oparbejdning i øjeblikket.
6.3 Bejdsning
6.3.1 Kontrol af badtemperatur
Temperaturen skal styres på den ønskede værdi for at opnå den rigtige bejdsetid. Forhøjet temperatur forøger bejdsehastigheden og kan derfor medføre ”overbejdsning”, hvis ikke opholdstiden i bejdsekarret nedsættes tilsvarende. Anvendelse af en passende inhibitor i bejdsebadet vil kunne forhindre angreb på grundmaterialet, når rust og glødeskaller er fjernet. Forhøjelse af temperaturen vil også medføre øget afgivelse af chlorbrintegas fra badet.
6.3.2 Kontrol af badkemi
Badsammensætningen skal følges nøje. De væsentligste parametre er indholdet af fri syre og jern. Også indholdet af zink kan have interesse. Badets sammensætning bør holdes nogenlunde konstant for at opnå en ensartet bejdsehastighed.
Et syreindhold på 80 - 100 g/l og et jernindhold på 70 - 90 g/l er normalt passende for en standard bejdse. Badet kan også køre med højere jernindhold og lavere syreindhold – en såkaldt aktiveret bejdse. Den har samme bejdsehastighed som den traditionelle bejdse og en typisk sammensætning på: Fri syre = 40 - 60 g/l, jern = 120 - 160 g/l.
Badet bør indeholde inhibitor i foreskrevet mængde for at undgå ”overbejdsning” af emnerne, da ”overbejdsning” medfører forøget forbrug af bejdsesyre samt øget produktion af kasseret bejdsebad.
6.3.3 Åbne bejdsekar uden udsugning
Anvendes der åbne bejdsekar uden udsugning, bør man normalt holde badtemperaturen under 25 °C for at undgå for stor chlorbrinteafgivelse til omgivelserne, hvis man anvender et ”standard” bejdsebad med 80 - 100 g/l fri syre. Chlorbrinteafgivelsen vil dog afhænge af luftbevægelse, emnernes afdrypning og bejdseprocessens udformning. En aktiveret bejdse indeholder lav syrekoncentration og kan derfor opvarmes, uden at det medfører øget chlorbrinteafgivelse sammenholdt med et traditionelt bejdsebad.
6.3.4 Udsugning fra bejdsekar
Udsugning fra bejdsekar medfører mindre chlorbrinteafgivelse til rumluften. Udsugning kan være nødvendig eller ønskelig under ugunstige produktionsforhold eller ved opvarmning af bejdsebadet. Udsugning kan etableres som en direkte randafsugning eller fra en flytbar overdækning af bejdsekarret. Man kan også samle de våde proceskar i et lukket rum med fælles afsugning, hvor kransystemet betjenes fra et lukket betjeningsrum. Det giver generelt et bedre arbejdsmiljø i den del af fabrikken, hvor folkene arbejder.
Når der etableres separat udsugning, kan det være nødvendigt at rense den chlorbrinteholdige udsugningsluft i en scrubber, hvor luften vaskes med vand, før den udsendes til atmosfæren. Vaskevæsken bliver efterhånden mere og mere koncentreret med syre, som kan bruges til opspædning af bejdsebad eller aftrækssyre, eller som kan neutraliseres og udledes til kloak.
6.3.5 Oparbejdning af brugt bejdsesyre
Brugt bejdsesyre bør oparbejdes, og her er flere muligheder, selv om man i Danmark savner den oplagte løsning, som alle med fordel kan anvende.
Der findes løsninger, hvor syren kan udvindes (inddampning, dialyse, ionbytning) og genanvendes internt. Disse løsninger har endnu ikke vundet indpas herhjemme, da de ikke markedsføres. De betragtes som dyre og urealistiske, da man ikke uden videre kan få tekniske data og erfaringer om dem.
Hvis syren er fri for zink, kan den oparbejdes til ferrichlorid hos Kemira, hvilket forekommer at være en fornuftig løsning, da ferrichlorid anvendes som fældningskemikalie på kommunale renseanlæg.
Flere steder i udlandet (bla. i Tyskland) kan den brugte syre oparbejdes til ren saltsyre (15 - 18 %) og Fe2O3 ved en højtemperaturproces i meget stor skala. Processen er i øjeblikket ikke egnet til anskaffelse på den enkelte virksomhed; men den er udmærket at anvende som en fælles ekstern løsning for danske virksomheder.
Såfremt det kasserede bejdsebad indeholder meget zink, kan det oparbejdes til flusbad, såfremt virksomheden selv har et rensnings- og regenereringsanlæg for flusbade.
I dag afleverer de fleste danske virksomheder kasseret bejdsesyre til Kommunekemi. Kommunekemi har brug for store mængder bejdsesyre til det uorganiske behandlingsanlæg; men slutproduktet er slam, som deponeres på Kommunekemis depot. Metoden kan næppe siges at være en ren BAT-løsning, selv om de kasserede bejdsebade har deres mission på Kommunekemis uorganiske behandlingsanlæg.
Et brugt bejdsebad kan også anvendes i forbindelse med afgiftning af chromatholdigt spildevand på de varmforzinkningsvirksomheder, der også udfører elektrolytisk overfladebehandling med chromater. Også denne anvendelse har sin mission, selv om det ikke er en ren BAT-løsning.
6.4 Skylning
6.4.1 Skylning efter forbehandling
Der bør skylles efter de enkelte overfladebehandlingsprocesser for at minimere forureningen af de efterfølgende procesbade, medmindre denne forurening kan forhindres eller fjernes på anden vis. For at begrænse skyllevandsforbruget bør der anvendes modstrømsskyl eventuelt i kombination med statiske skyl, der kan føres retur til procesbadene. Også andre vandbesparende skyllemetoder kan komme på tale.
Skylning efter alkalisk affedtning kan foretages med postevand, renset spildevand eller med surt skyllevand fra bejdsning. Anvendes surt skyllevand fra bejdsning, opnås både vandbesparelser og en forneutralisering af affedterbadet, før det indslæbes med godset i bejdsebadet.
Skylning efter bejdsebadet vil minimere indslæb af saltsyre og jern i flusbadet. Jo bedre skylning, jo mindre forurening af flusbadet. Hvis skyllevandet iltes med brintperoxid og neutraliseres med ammoniakvand, kan det recirkuleres efter fraseparering af slampartikler. Vandet vil efterhånden indeholde store mængder ammoniumchlorid og en del zinkchlorid - afhængig af bejdsebadets zinkkoncentration - og disse flussalte vil slæbes med godset ind i flusbadet, hvor de udnyttes som fluskemikalier. Neutraliseres skyllevandet med natronlud, kan vandet fra den kemiske rensning også recirkuleres; men herved slæbes natriumchlorid ind i flusbadet i stedet for ammoniumchlorid. Mindre mængder natriumchlorid vil dog ikke give problemer i flusbadet.
Skylning efter bejdsning kan undgås; men uden skylning får man en meget hurtigere forurening af flusbadet. Det kan klares, hvis der etableres kontinuert rensning af flusbadet, hvorved en stor del af de indslæbte kemikalier omdannes til flusmidler, mens jernforureningen fjernes. Denne metode er lige så god som skylning ud fra en BAT vurdering, og den vil ofte være mere økonomisk.
Nogle varmforzinkningsvirksomheder har måttet etablere grundvandsrensning, fordi grundvandet er blevet forurenet med zinkchlorid, jernchlorid og saltsyre, der er sivet ud fra utætte bejdsekar. Dette vand kan genbruges til skylning efter forbehandling og renses derefter før udledning.
6.4.2 Minimering af overslæb
Man kan minimere udslæb af væske med godset fra procesbadene og dermed overslæbet til næste kar ved at sørge for en god afdrypning af emnerne, når de er trukket op af et proceskar. Derved reduceres forureningen af de efterfølgende procesbade, og behovet for skyllevand mellem de enkelte forbehandlingsprocesser minimeres.
6.4.3 Genbrug af skyllevand
Modstrømsskylning efter en alkalisk affedter bruger så lidt vand, at alt vandet kan føres tilbage til affedterbadet som kompensation for fordampningstabet i det varme affedtningsbad. Metoden er primært velegnet, hvis affedterbadet løbende oprenses og genbruges, så man på den måde får fjernet olie og fedt fra systemet. Alternativt kan man skylle i et standskyl efterfulgt af et rindende skyl og benytte det halvkoncentrerede standskyl til opspædning af affedterbadet.
Der kan også anvendes et eller flere standskyl efter bejdsning. Når bejdsebadet udskiftes, kan man anvende det mest koncentrerede standskyl sammen med frisk koncentreret saltsyre til opblanding af en ny bejdse. De efterfølgende standskyl bruges til opspædning af de foregående, så man med mellemrum får tilsat frisk vand og derved holder en passende fortynding i skyllekarrene.
6.5 Flusning
6.5.1 Kontrol af temperatur
Badtemperaturen bør være mindst 70 °C for at sikre, at emnerne blive gennemvarme i flusbadet, så emnerne hurtigt tørrer, når de kommer op igen. Det er med til at sikre en optimal forzinkning. Ved tørring efter flusbadet er kravet betydeligt lavere: 35 – 40 °C.
6.5.2 Kontrol af badkemi
Den kemiske sammensætning af flusbadet påvirker forzinkningsprocessen. Flusbadet skal både indeholde tilstrækkelig flussalt (ammoniumchlorid + zinkchlorid), og forholdet mellem ammoniumchlorid og zinkchlorid skal afpasses efter produktionsforholdene for at give den optimale effekt. Ammoniumchlorid er den mest aktive komponent, og den er vigtig, hvis forbehandlingen ikke har været perfekt. Zinkchlorid er mindre aktiv og beskytter overfladen, og den er vigtig, hvis der er lang tørretid. Sammensætningen bør kontrolleres jævnligt, så badkemien kan fastholdes på de optimale værdier, der kan variere efter produktionsforholdene. Det kan forhindre overforbrug af flussalt og dermed holde luftforureningen fra zinksmelten så lav som mulig.
6.5.3 Rensning og genvinding
Jern er den værste forurening i et flusbad. Jern indslæbes i flusbadet som ferrochlorid sammen med syre og eventuelt zinkchlorid. Jern vil i første omgang foreligge som opløst jern, da flusbadets pH typisk ligger mellem 3,0 og 4,5. Efterhånden iltes noget jern af luftens ilt, og det udfælder som brune ferrihydroxidpartikler. Badets pH-værdi vil falde på grund af syreindslæb og udfældning af ferrihydroxid. Ved rensning af flusbadet skal man dels neutralisere syren og dels fjerne jern. Badet kan neutraliseres med ammoniakvand, hvorved der dannes ammoniumchlorid. Badet kan også neutraliseres med aske, hvor zink og zinkoxid reagerer med saltsyre og danner zinkchlorid. Begge de dannede stoffer er grundbestanddele af flusbadet.
Jern kan iltes med luft, med brintperoxid eller elektrolytisk. For at fremme iltning med luft kan der etableres en særlig luftindblæsning og et filter til fjernelse af det udfældede jernhydroxid. Denne simple løsning er kun egnet ved små forureninger. Ved store forureninger (uden skylning efter bejdsning) anbefales etablering af et egentligt flusrenseanlæg med kemisk eller elektrolytisk oxidation samt styring af pH ved tilsætning af ammoniakvand efterfulgt af fraseparering af jernhydroxid. Det vil normalt kunne svare sig at afvande jernhydroxidslammet i en filterpresse efter separering.
De kemiske processer ved flusbadsrensning er vist nedenfor. Først foretages samtidig en neutralisation med ammoniakvand (1) og en oxidation med brintperoxid (2), hvorved jern(III) udfældes som slam (3). Ved de processer dannes ammoniumchlorid (NH4Cl), som sammen med tilstedeværende zinkchlorid (ZnCl2) udgør flussalt. Mangler man zinkchlorid, kan det udvindes fra aftrækssyre, støv eller aske som beskrevet i beskrevne cases 2, 5 og 6.
Neutralisation og oxidation:
(1) HCl + NH4OH → NH4Cl + H2O
(2) 2 Fe+2 + H2O2 + 2 H+ → 2 Fe+3 + 2 H2O
Bundfældning af jern(III):
(3) FeCl3 + 3 NH4OH → Fe(OH)3 + 3 NH4Cl
I Tabel 6 er vist en realistisk beregning af, hvor meget flussalt der kan udvindes, når overslæb af bejdsebad til flusbad er 5 liter pr. ton gods uden mellemliggende skylning. Beregningerne viser, at der pr. ton gods dannes 1281 g flussalt med en sammensætning på 40,7 % zinkchlorid (ZnCl2) og 59,3 % ammoniumchlorid (NH4Cl). Ved beregningerne er der forudsat en sammensætning af bejdsebadet på 50 g/l zink, 90 g/l jern og 80 g/l saltsyre. Ændret sammensætning af bejdsebadet og overslæbets størrelse vil influere på, hvor meget flussalt der kan udvindes.
Tabel 6. Udvinding af fluskemikalier ved direkte udslæb af bejdsesyre fra bejdsebad til flusbad uden mellemliggende skyl.
|
g/l |
Udslæb l/ton |
g/ton gods |
g/ton gods |
% |
Zink |
50 |
5 |
250 |
Zn |
521 |
ZnCl2 |
40.7 |
Saltsyre |
80 |
5 |
400 |
HCl |
587 |
NH4Cl |
59.3 |
Jern |
90 |
5 |
114 |
Cl |
172 |
NH4Cl |
Flussalt |
|
|
|
|
1281 |
Flussalt |
100 |
Da man normalt anvender 1 - 2 kg flussalt pr. ton gods er det tæt på, at man med denne metode kan udvinde nok flussalt til at være "selvforsynende". Ønskes mere zinkchlorid, kan man udnytte zink fra aftrækssyre, støv eller aske for at få det ønskede blandingsforhold af ammoniumchlorid og zinkchlorid. I Figur 2 er der foretaget en grafisk afbildning af, hvorledes zinkkoncentrationen i bejdsebadet vil påvirke mængden og sammensætningen af det udvundne flussalt i eksemplet Tabel 6
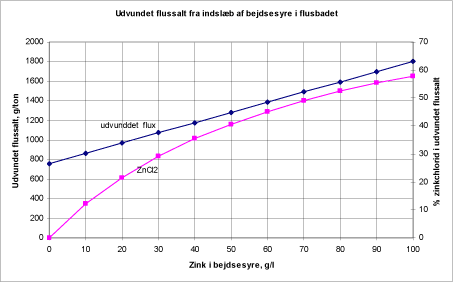
Figur 2. Beregning af udvundet mængde flussalt for en indslæbt bejdsesyre med HCl = 80 g/l, Fe= 90 g/l og variabel indhold af zink. Zinkkoncentrationen i det udvundne flussalt stiger fra 0 til 58 %, når zinkkoncentrationen i bejdsesyren stiger fra 0 til 100 g/l. Ved et zinkindhold på 70 g/l dannes der 1500 g flussalt pr. ton gods med et indhold af zinkchlorid på 50 % i flussaltet.
6.6 Forzinkning
6.6.1 Udsugning
Når emnerne dyppes i smeltet zink, udvikles der røg, der primært stammer fra flussaltet på emnernes overflade. Ammoniumchlorid giver en meget synlig røg; men det er røgens indhold af zink og zinkforbindelser, der udgør den største miljørisiko. Af hensyn til arbejdsmiljøet skal zinkgryden forsynes med en effektiv afsugning.
En total indkapsling af gryden med udsugning i siden eller toppen er det mest effektive, og den forhindrer samtidig, at små zinkklumper sprøjtes ud i lokalet. Udsugningen bør indrettes med variabel hastighed, så der suges særlig kraftigt under og efter dypning.
En transportabel overdækning med udsugning, der følger emnerne, vil også være en effektiv måde til at opfange og fjerne røgen. En kantafsugning er noget mindre effektiv, og den er ikke særlig velegnet på store gryder, hvor der skal suges over en meget stor overflade.
6.6.2 Luftrensning
I en røgsvag flux er en del ammoniumchlorid erstattet med natrium- eller kaliumchlorid. Den giver mindre røg, men ikke mindre zink i røgen, og zinkindholdet er den kritiske faktor. Det antages, at en røgsvag flux giver mere hårdzink. Derfor synes der ikke at være nogen afgørende miljømæssig fordel ved at benytte en røgsvag flux i stedet for en traditionel.
Hovedparten af de forurenende stoffer i luften foreligger som støv, og derfor vil en effektiv støvfjernelse i textilfiltre (posefiltre) normalt være fuldt tilstrækkelig. Luften kan også renses i en vådscrubber, der både fjerner støv og gasser, og det vil give en lidt bedre rensning; men det er normalt også den dyreste metode. Ifølge BREF-dokumentet kan man med den rette BAT-løsning rense udsugningsluften til et støvindhold < 5 mg/m³. Det stemmer også godt med danske erfaringer.
Støv fra luftrensning indeholder store mængder zink og ammoniumchlorid. Støvet kan derfor forholdsvis let oparbejdes til flussalt; men virksomhederne kan have svært ved at udnytte de store mængder flussalt, der fås, når man både regenererer selve flusbadet samt oparbejder aftrækssyre og støv til flussalt.
Læs mere om luftrensning i Case 1 og 6.
6.6.3 Aske
Aske er en blanding af zink (60 - 85 %) og zinkoxid. Under dypning af emnerne iltes zinkoverfladen under dannelse af mørkt zinkoxid, som løbende skimmes af og opsamles. Asken er således et spildprodukt, som man skal søge at begrænse. Askedannelsen påvirkes af mange forhold, bla. flusbadets sammensætning, jernforurening i flusbadet og aluminiumindholdet i zinksmelten.
Asken er værdifuld og skal oparbejdes. Dette kan foregå eksternt, men der er også flere muligheder for en intern oparbejdning:
- Smeltning i speciel smelteovn og genanvendelse af zink i gryden (restproduktet
er ZnO, som oparbejdes eksternt)
- Kan anvendes til fremstilling eller neutralisering af flusbad
- Zink kan med en særlig teknik udvindes direkte på selve
zinksmelten (restprodukt ZnO oparbejdes herefter eksternt)
Zinkoxid kan opløses i saltsyre (1), hvorved dannes zinkchlorid (ZnCl2). Herefter neutraliseres overskud af saltsyre med ammoniakvand (2) og danner ammoniumchlorid (NH4Cl). På den måde får vi dannet flussalt, som er en blanding af zinkchlorid og ammoniumchlorid
(1) ZnO + 2 HCl → ZnCl2 + H2O
(2) HCl + NH4OH → NH4Cl + H2O
I Tabel 7 findes en beregning af, hvor meget flussalt, der kan dannes af 325 g zinkoxid, som er dannet ved smeltning af 1 kg aske. Ved beregningen er det endvidere forudsat, at der dannes 10 kg aske pr. ton gods. Dette tal er nok i underkanten for en del virksomheder, da flere virksomheder producerer op til 25 kg aske pr. ton gods, idet der er stor forskel på askedannelse ved lav temperatur og centrifugegods.
Tabel 7: Udvinding af flussalt ved behandling af restprodukt fra askesmeltningsproces.
|
g/kg aske |
kg aske/ton gods |
g/ton gods |
g/ton gods |
% |
ZnO |
325 |
10 |
3250 |
ZnO |
5447 |
ZnCl2 |
88.1 |
HCl |
50 |
10 |
500 |
HCl |
734 |
NH4Cl |
11.9 |
Flussalt |
|
|
|
|
6181 |
Flussalt |
|
Ifølge Tabel 7 dannes 6,2 kg flussalt pr. ton gods, hvilket er 3 - 6 gange mere end det normale forbrug af flussalt. Flussaltet indeholder mere zinkchlorid og mindre ammoniumchlorid end et standard flussalt, og der skal derfor tilsættes mere ammoniumchlorid for at få et blandingsforhold på 50:50. Der kan fx. bruges større overskud af saltsyre, hvorved der dannes mere ammoniumchlorid. Metoden kan også kombineres med andre flusgenvindingsmetoder.
Læs mere om askebehandling i Case 2 og 6.
6.6.4 Hårdzink
Hårdzink dannes, når zinksmelten tilføres jern, der reagerer med zink. Hårdzink indeholder ca. 94 % zink og 6 % jern, så en lille jernforurening i zinksmelten kan binde store mængder zink. Hårdzinken bliver til klumper, der synker til bunds i zinksmelten, og disse klumper er affald, der må fjernes med mellemrum. Det er derfor vigtigt at minimere jernforureningen i zinksmelten, og nøglen hertil er at styre flusbadet optimalt – dvs. med lavt jernindhold og optimalt saltindhold. Også jern fra stålgryden vil efterhånden gå i opløsning og danne hårdzink. Hårdzink oparbejdes eksternt til zink.
6.6.5 Additiver i zinksmelten
I zinksmelten anvendes ofte et eller flere legeringsmetaller i lav koncentration for at opnå bestemte egenskaber, hvilket kan have både produktionsmæssige og miljømæssige konsekvenser. De mest almindelige additiver er:
- Blyindholdet blev tidligere holdt på ca. 1 % for at sænke overfladespændingen af zinksmelten og derved øge afdrypningen af smeltet zink fra emnerne, når de blev trukket op. Ofte tilsatte man bly ud over mætningspunktet (1,4 %), så man fik et lag smeltet bly på bunden af gryden. Hårdzinken vil flyde på dette blylag, så man lettere kan få fat i hårdzink-klumperne og tage dem op. I dag vil man ofte nøjes med et noget lavere blyindhold og eventuelt samtidig benytte andre additiver.
- Ved traditionel varmforzinkning bør aluminiumindholdet ligge på 0,005 - 0,007 %. Herved opnås minimal askedannelse, blank overflade, lavere zinkforbrug, bedre afdrypning og mindre lagtykkelse på reaktive ståltyper. Aluminium bør tilsættes som en zink-aluminium-legering flere gange daglig for at få optimalt udbytte.
6.6.6 Energiforbrug
Zinkgryden kan opvarmes elektrisk eller med en olie/gas-brænder, og begge dele anvendes i Danmark. Generelt er energiforbruget pr. ton gods lavere ved en el-opvarmet gryde (120 - 250 kWh/ton) end ved olie/gas-opvarmning (500 - 800 kWh/ton). I begge tilfælde kan der spares energi ved at minimere varmeafgivelsen fra smelten bla. gennem indkapsling og ventilation.
Der bruges også energi til at holde smelten opvarmet, når der ikke produceres, så derfor vil det specifikke energiforbrug normalt være lavest på virksomheder, der producerer i døgndrift. For en olie/gas-opvarmet gryde skal brænderen være korrekt justeret, og der skal være perfekte varmeovergangsforhold mellem flamme og gryde. Energiindholdet i den varme røggas bør udnyttes andre steder i virksomheden.
| Forside | | Indhold | | Forrige | | Næste | | Top |
Version 1.0 Januar 2011, © Miljøstyrelsen.
|