| Bottom | | Front page |
Working Report no. 20, 2006
Substitution of cobalt driers in wood coatings
Contents
Sammenfatning og konklusioner
1 Introduction
2 Parameters with importance to drying
3 Contact to manufactures
4 Evaluation of drying properties as a function of alkyd and primary drier
5 Evaluation of drying properties in wood coating prototypes
6 Conclusion
7 References
Appendix A - Statistical analysis of 26-3 fractional factorial designs
Sammenfatning og konklusioner
Dette projekt er gennemført for at undersøge mulighederne for at erstatte koboltsikkativer i lufttørrende malinger til træ.
Baggrund og formål
Erfaring fra tidligere undersøgelser har vist, at substitution af kobolt sikkativ med alternative tørringsmidler er meget vanskeligt. Interessante resultater er opnået med mangan, men det er samtidig vist, at kobolt generelt er mere effektivt, og at alternativer udviser store begrænsninger, specielt når det gælder et helt produktsortiment.
Formålet med dette projekt var derfor ikke alene at undersøge muligheden for at substituere kobolt i eksisterende produkter, men også at opnå en bedre forståelse for, hvordan forskellige parametre i sikkativsystemet sammen med alkydens sammensætning påvirker tørreegenskaberne hos forskellige typer af overfaldebehandlinger.
I den sidste ende er hensigten at kunne basere udvikling og løsningsmodeller ikke alene på “trial and error” men også på en større forståelse for begrænsninger og muligheder ved forskellige systemer. Selvom alternative sikkativer ikke er ligeså effektive og universelle i deres brug som kobolt, kunne der være muligheder for gennem viden at vælge den rigtige type binder.
Undersøgelsen
Antallet af mulige alternativer til koboltsikkativer er begrænset. Der er indtil videre ikke blevet identificeret nogen ikke-metalliske forbindelser, som er i stand til at erstatte koboltsikkativer. Af metalliske forbindelser er det kun vanadium og mangan, der har tilstrækkelig katalytisk effekt til at blive betragtet som alternativer. I projektet er fjorten sikkativprodukter blevet testet som erstatning for koboltsikkativer inden for et bredt spektrum af oxidativt tørrende produkter. Tolv af sikkativerne er mangansikkativer, to er vanadiumsikkativer, og et enkelt er baseret på jern.
I undersøgelsen er der endvidere anvendt ni forskellige alkyder inklusive en standard alkyd produceret af Dyrup. Variationerne består af to standardalkyder med forskellig olietype, en af disse i en højmolekylær version samt to versioner modificeret med forskellige niveauer af konjugeret syre, tre ”high solid” alkyder og en urethan modificeret alkyd.
Denne undersøgelse omfatter evaluering af eksisterende alternativer til kobolt i oxidativt tørrende systemer af typen ren binder, transparente produkter, dækkende produkter i hvid og mørk nuance samt baser. Ved at undersøge indflydelsen af både sikkativ og alkyd vil muligheden for substitution ikke alene være et spørgsmål om at substituere kobolt i eksisterende produkter, men også muligheden for at modificere alkyden med henblik på at optimere tørringen så meget som muligt, når et alternativ sikkativ benyttes.
Undersøgelsen er udført i et samarbejde mellem Dyrup A/S og EnPro ApS, hvor råvarer er valgt i samarbejde med Sasol Servo og Cray Valley.
Hovedkonklusioner
Det har ikke været muligt at finde et sikkativ, der er lige så effektivt som kobolt. Generelt set har mangan ikke tilstrækkelig katalytisk effekt i træbeskyttelse. Anvendelse af mangansikkativ resulterer i en blød malingfilm, og desuden mister mangan sin effektivitet med tiden, når den våde maling står på lager.
Et vanadiumsikkativ gav gode resultater med hensyn til tørringsegenskaber. Ved tilsætning af en mængde der ligger midt i det anbefalede interval fra producenten var gulning egentlig ikke et problem i lyse transparente systemer. Desværre giver vanadium problemer med klæb, hvilket betyder, at vanadium ikke kan erstatte kobolt i en produktserie om end hårdheden opnås med tiden men med en lavere hastighed.
Generelle tørringsproblemer er observeret i nogle ganske få systemer, men dette kunne løses enten ved anvendelse af en modificeret alkyd med mindre behov for sikkativ eller ved øgning af sikkativ mængden. Dette ville betyde, at der ville være behov for at gå på kompromis med hensyn til for eksempel gulning i visse systemer. Hvis problemet med klæb kan løses, vil behovet for en modificeret alkyd kunne begrænses til nogle få kritiske systemer og dermed øge fleksibiliteten i produktudviklingen generelt.
Det har ikke været muligt at finde andre alternativer til kobolt sikkativ end vanadium og mangan.
Projektresultater
Undersøgelsen er delt op i en screening, hvor substitutter til kobolt er anvendt i rene bindemidler, andre råvarers indflydelse på tørring og film samt evaluering af de bedste substitutters funktion i færdige produkter.
På et tidligt tidspunkt i projektet blev det konstateret, at det af flere årsager var urealistisk at opnå en korrelation mellem sikkativets og alkydens egenskaber på et meget detaljeret niveau. Mange af alkydens egenskaber relaterer til hinanden, hvilket betyder, at ændringen af en vil påvirke flere andre. Arbejdet ville blive meget stort, og erfaringerne fra dette projekt er da også, at sådanne korrelationer er meget følsomme overfor små systemændringer.
I f.eks. rene bindemidler (alkyder) kan det anvendte salt af metalsyren påvirke tørretiden for en specifik binder. Til gengæld udligner tilstedeværelsen af andre råvarer tilsyneladende disse forskelle, hvilket betyder, at for eksempel mangan sikkativer stort set opfører sig ens, uanset hvilken producent de kommer fra. Om end der kan være små forskelle ved specifikke målinger, er de overordnede begrænsninger præcis de samme.
Screening
Udgangspunktet var at screene en række alternative sikkativer i udvalgte rene bindere af forskellig type og ud fra disse resultater udvælge relevante binder-/sikkativ systemer til videre test i diverse træbeskyttelsesprodukter.
Et vanadium sikkativ gav samme tørretider som kobolt, dog med det forbehold at den tørre film udviste klæb og at gulning forekom ved høj dosering.
Et enkelt mangan sikkativ kombineret med organisk accelerator udviste også gode egenskaber. Et par andre mangansikkativer kunne være af interesse, men dette ville kræve modificering af alkyden.
Alkyder modificeret med konjugerede syrer forbedrede generelt tørretiden. En af ”high solid” binderne var også lovende og udviste egenskaber svarende til eller bedre end de traditionelle alkyder.
Andre råvarers indflydelse på tørring og film
I den indledende screening klarede vanadium sig på niveau med kobolt i rene bindere mht. tørretiden. Det er kendt fra tidligere studier, at kobolt er mere effektivt i færdige produkter, hvilket tyder på, at de alternative sikkativer er mere følsomme overfor tilstedeværelsen af øvrige råvarer.
For at evaluere påvirkningen fra andre typiske råvarer, der anvendes i malevareindustrien, er et “26-3 fractional factorial” design anvendt, hvor parametrene er tilstedeværelse eller ikke tilstedeværelse af hhv. MEKO, pigment mix, thix-alkyd, UV-absorber, HALS og fungicid.
I forhold til pigmenterne er en medium pigmenteret transparent træbeskyttelsesfarve valgt.
Med undtagelse af thix-alkyden, der gav en hårdere film efter syv dage, har alle andre råvarer en negativ effekt.
Antioxidanten påvirker de initiale egenskaber efter påføring som tørretid og klæb, indtil den fordamper.
Pigmentet giver filmen farve, hvilket begrænser, at træet bliver mørkere og dermed også gulning. UV-absorber og HALS forventes ligeledes at begrænse gulning, men efter 28 dage er denne effekt ikke signifikant.
UV-absorber, HALS og fungicid reducerer alle hårdheden, og fungicidet har endvidere en negativ effekt på tørretiden.
Sikkativerne påvirker alle tørreegenskaber. Ulempen med vanadium i forhold til kobolt er reduceret hårdhed, klæb i lang tid og farvning af filmen. Ulemperne ved mangan er reduceret hårdhed, længere tørretid og forlænget tørretid efter lagring af det våde produkt.
Resultater fra den tekniske evaluering af produkter
De alternative sikkativer har nogle begrænsninger sammenlignet med kobolt, specielt når de anvendes i færdige produkter. Der er lavet en lang række forsøg på at optimere egenskaberne i forskellige typer af træbeskyttelse med alternative sikkativer.
Blandt andet er mængden af vanadium og mangan undersøgt i tre forskellige niveauer i hhv. rene bindere samt en transparent prototype. Dvs. udover maksimal og minimum anbefalet mængde er et niveau herimellem inkluderet.
Vanadium giver igen de bedste resultater, og en halvering af sikkativ mængden påvirker som udgangspunkt ikke tørretid, klæb eller hårdhed, mens farvning af filmen reduceres.
Dog udviser vanadium visse begrænsninger sammenlignet med kobolt i nogle få systemer, bl.a. en rød base og en hvid dækkende med højt indhold af titandioxid. Hvor en høj dosering af vanadium sikkativ ikke er tilstrækkelig, er et alternativ at erstatte binderen delvist med en binder, der er hurtigere tørrende, som f.eks. den urethan modificerede alkyd, der er testet i dette projekt.
Som nævnt er der imidlertid et generelt problem med klæb, hvilket udvider behovet for specielle bindere til praktisk taget hele produktserien og ikke kun nogle få kritiske systemer. Hvis ikke dette problem bliver løst, er anvendelsen af vanadium som alternativ mindre attraktiv.
Visse forbedringer er observeret i forbindelse med brug af “anti-blocking” additiver, og en tilgang kunne være at undersøge dette nærmere for at opnå en større fleksibilitet indenfor anvendelsesrammen.
Generelt set savner mangan sikkativerne, der er testet i dette projekt, tilstrækkelig katalytisk effekt for at være et reelt alternativ til kobolt i det testede produktsortiment. Om end anvendelse af sekundære sikkativ i enkelte tilfælde har vist en vis forbedring, er tørretider og hårdhed slet ikke på samme niveau som med kobolt eller vanadium sikkativ. Endvidere er den forlængede tørretid efter lagring et stort problem, der stiger med malingens alder.
En hurtigtørrende alkyd kan reducere disse problemer, men behovet er konsekvent sammenlignet med vanadium sikkativet, og derfor vil det reelle alternativ til kobolt være binderen selv. Overordnet set gælder den samme konklusion for mangan uafhængigt af, hvilket system det er testet i. En undtagelse er i et ”high solid” system, hvor den største hårdhed blev opnået med et mangan sikkativ. Profilen for udvikling af hårdhed er anderledes med denne type binder, og igen er årsagen mindre katalytisk effekt af mangan sikkativet.
Det understreges, at langtidsholdbarheden enten ved accelereret eller naturlig eksponering ikke er undersøgt. Alle konklusioner er kun baseret på mekaniske test af tørringsegenskaber.
Miljø og arbejdsmiljø spørgsmål
Dette projekt er initieret, da kobolt findes på listen over farlige stoffer grundet mistanken, at stoffet kan være cancerogent. Der forefindes meget lidt data tilgængelig vedrørende toksicitet og økotoksicitet for mangan og vanadium sikkativ, og hvis kobolt sikkativ bliver forbudt til maling, findes der ingen garanti for, at disse substitutter ikke bliver klassificeret tilsvarende med tiden.
Fremtiden
Med hensyn til VOC2010 kompatible systemer (lavt opløsningsmiddelsindhold) er situationen lidt speciel, da disse systemer endnu er eksperimentelle, og meget lidt erfaringsgrundlag med hensyn til egenskaber er tilgængeligt. Det kan dog konstateres, at disse systemer forventes at være en endnu større udfordring med hensyn til tørringsegenskaber. Endvidere er “high solid” bindere stadig under kraftig udvikling fra producenternes side, hvilket betyder, at malevareindustrien står overfor en stor opgave med hensyn til at opdatere deres produktsortiment uanset, hvilke sikkativer der bruges.
Det vil derfor være nødvendigt med videre udvikling af både oxidativt tørrende bindere og sikkativer for at kunne leve op til fremtidige lovgivningsmæssige og tekniske krav.
1 Introduction
Within the paint and varnish industry there is today a trend to reduce any use of dangerous substances. One issue is to reduce the use of cobalt driers in air-drying systems, due to cobalt in these compounds among others is appearing on the list of dangerous substances /1/ as being possible carcinogenic. The addition of driers to oxidative drying products, including alkyds, is essential in order to achieve satisfactory drying of these coatings. Today most oxidative drying products still contain cobalt driers, despite their environmental and health drawbacks, and even though there is a wide spread interest in the paint trade to substitute cobalt driers. The reason is that Co-driers are the most efficient driers available and that they are quite difficult to substitute.
Extensive substitution work has already been done to replace cobalt driers /2/. The work has shown that it is very difficult to find a general replacement for cobalt driers, but the work also indicated that some alternative drier products, especially manganese driers, could give a satisfactory drying time in some types of oxidative products. How successful a replacement of Co-driers will turn out depends partly on the alternative drier but also to a great extent on the nature and content of oxidative drying binder in the coating. The substitution of cobalt in high solids products is known to be especially problematic due to the high amount of oxidative drying binder. A thorough examination of the connection between drying time, binder type, and binder amount is desirable when using cobalt-free drier systems. This project was therefore initiated. The drying potential of several alternative driers, both manganese and vanadium based, has been evaluated in different alkyd binders with known variations.
By examining the influence on the drying of both the (alternative) driers and the alkyd, the possibilities in the substitution process of Co-driers will hopefully no longer only be a question of substituting the drier itself in existing coatings, but also modifying the alkyd binder to enhance the drying as much as possible when using alternatives driers.
The project and hence this report is divided into the following areas:
- Selection of raw materials, hereunder contact to suppliers
- Technical evaluation of the influence of the alkyds and the drier systems respectively on the technical properties
- Optimization of product properties based on the choice of alkyd and drier system respectively
A working committee including Dyrup, EnPro, Sasol Servo and Cray Valley was established in the beginning of this project. Before the practical work was started a meeting between Dyrup, EnPro, Sasol Servo and Cray Valley was arranged to discuss what variables with regard to drying that were relevant to investigate, what samples that were needed and to create a basis for a detailed project plan. A second meeting was held were the screening results were discussed. The industrial partners have thus been involved during the whole project.
The practical work and technical evaluations was performed by Dyrup and EnPro ApS.
The Danish Environmental Protection Agency has contributed to the costs of this project,
We thank all participants for their contributions with regard to samples, planning and discussions.
June 2005
2 Parameters with importance to drying
Drying of air-drying coatings consist of two steps. The first part is a physical drying where the solvent(s) evaporates. In the second part of the drying the paint film cures due to the introduction of oxygen from the air into the molecules, where a three dimensional network is formed.
Thus many parameters influence on the drying of an air-drying coating. Here the main focus will be on the binder (alkyds), the drier systems and the solvent. Other raw materials, which are not directly involved in the drying process, can also have an influence. During application and drying, factors like film thickness, relative humidity, temperature and air velocity will affect the drying process.
2.1 Solvent
The amount and type of solvent is important for the physical drying, where the solvent(s) evaporates.
The evaporation rate of the solvent will influence on the coating drying rate. The faster the evaporation rate, the faster an initial oxidative drying of the coating. The oxidative drying of the surface of the coating will influence on the evaporation of solvent, as the solvent in the film has to be transported up through the surface layer. Due to this transport phenomena the evaporation rate will to some extent vary with different drier systems.
2.1.1 Theoretical evaluation of Initial drying mechanisms
As the binder system contains solvents the first step of drying will be a physical drying were the evaporation of the solvent is dependent of temperature as well as air velocity. The humidity is a secondary parameter as the solvents used are not hygroscopic.
To describe the mechanisms of this first drying step modelling of the evaporation was done with a computer programme called dG /3/.
The solvent used for thinning the binders in the screening was Exxsol D60, which is a dearomatised high boiling naphtha (aliphatic hydrocarbons and cycloparaffines). Boiling interval 180-217 oC and flash point 62 oC.
As a model for Exxsol D60 a combination of undecane (90 wt-%) and butylcyclohexane (10 wt-%) was used. This composition represents a calculated boiling point of 194 oC and a calculated flash point of 62,3 oC, which is rather close to the commercial raw material. Still it should be noted that the composition is not at all accurate and should be regarded as an example to evaluate the climatic parameters in connection with evaporation.
In the calculations it is assumed that approximately 50 gram of solvent is applied on 1 m². In table 2.1 is the evaporation rate for a simplified solvent phase calculated under different conditions.
Table 2.1 Calculated evaporation rates for a solvent phase comparable to Exxsol D60 under different conditions.
Temperature
oC |
Air velocity
m/s |
Initial evaporation rate
g/m²/min |
Approx. time for 50 % evaporation from film in minutes |
Approx. time for 90 % evaporation from film in minutes |
23 |
0,1 |
0,16 |
170 |
320 |
23 |
0,2 |
0,26 |
110 |
200 |
23 |
0,3 |
0,34 |
80 |
150 |
30 |
0,1 |
0,27 |
100 |
185 |
30 |
0,2 |
0,44 |
60 |
115 |
30 |
0,3 |
0,58 |
46 |
87 |
It is obvious that both the temperature and the air velocity has a significant effect on the evaporation rate and thus on the drying time of the solvent. This also shows that it is necessary to have the same climate during drying tests when drying of paint films is compared. It is though assumed that air velocity has a much higher influence on solvent evaporation than on oxidative drying. The temperature will of course have an influence on both types of drying mechanisms.
2.2 Alkyds.
Alkyds are condensation products of polyols, polybasic acids and vegetable oils or fatty acids. The properties of the alkyd are dependent on the type and amount of the oil/fatty acid and on the used acid anhydride as well as the processing conditions.
Several parameters in an alkyd have influence on the oxidative drying properties of an air-drying paint. Many of these parameters are dependent on each other for which reason changing one of them will affect the other parameters as well.
2.2.1 Oil type
The oil part of the alkyd provides the air-drying properties, due to the presence of double bonds. Both the content and type of double bonds in the oil part influence on the drying. Higher content of double bonds and more conjugated double bonds reduces the drying time.
2.2.2 Oil length
The oil length expresses how large the oil content in percent w/w is in an alkyd. Shorter oil length reduces drying time of the alkyd but also the final cross linking as the oxidative drying is quite limited. The durability of the coating is thus also reduced. In decorative air-drying coating the alkyds usually have an oil length that exceeds 45 % w/w.
2.2.3 Molecular weight
Increasing molecule size promotes high viscosity and quick drying because less cross linking is necessary to form a coherent film.
2.2.4 Ortho- or isophthalic acid
The choice of ortho- or isophthalic acid leads to alkyds with different properties. The latter promotes longer molecule chains and thus higher viscosity. If the two is exchanged on a one to one basis the isophthalic acid gives a shorter drying time.
2.2.5 Hydroxyl- and acid value
The lower the acid value, the higher the degree of esterification and a low value is therefore preferred. The hydroxyl value is fixed for any given acid value by the hydroxyl excess employed at the beginning of the condensation process of alkyd manufacture.
A higher excess of OH groups in the manufacturing process results in shorter alkyd oil length but a noticeable effect on the drying time is not observed unless the residual hydroxyl value exceeds 60-70 mg KOH/g while the residual acid value is below 5 mg KOH/g.
2.3 Driers
Driers, also known as siccatives, are metallic soaps containing either alkaline earth metals or heavy metals combined with monobasic carboxylic acids.
The main influence of the acid is to ensure solubility in the coating medium and the binder itself. Different acids are used commercially and this could influence the drying properties due to compatibility issues with specific binders. Below a short general description is given of the different type of driers. For a more thorough description of driers consult the report “Substitution of Cobalt Driers and Methyl Ethyl Ketoxime” /2/.
2.3.1 Primary driers
Primary driers are soaps of metals, which exist in several oxidative states, and which undergoes redox reactions. The most common are Cobalt, Manganese, Vanadium, Iron and Cerium. The primary driers are essential for the drying of air-drying products as they act as catalysts for the drying process, but they differ in their ability to undergo oxidation from a lower to a higher state. Co-driers are far the most active of these driers promoting a rapid surface drying of the coating. The driers do also, in varying degree, possess some through-drying properties.
Iron and cerium driers are not efficient at ambient conditions and can therefore in most cases not be considered as alternatives to Co-driers. This means that the most probable alternatives are manganese and vanadium driers, which also in their traditional form are less active driers than Co-driers, especially with regard to surface drying.
2.3.2 Secondary driers
These are soaps of metals that exhibit no catalytic effect on their own while they only exist in a single oxidation state. However together with a primary drier they assist in the polymerisation process by the formation of coordination compounds with a consequent increase in the drying rate and an eventual improvement in drying properties.
The most important functions of secondary driers in coatings are better through drying and minimizing loss of dry. There is a spread of secondary driers for different purposes calcium, zirconium, zinc, aluminium and barium being the most important.
2.3.3 Drying accelerators
Drying accelerators are organic ligands, which are able to increase the activity of primary drier metals causing a more rapid drying of the coating film. They function by complexing with the metal atoms forming chelates.
The use of drying accelerators have been utilised by the drier manufactures to make a new generation of manganese and vanadium driers, combining the traditional salt with a drying accelerator in one product, and hereby increasing the activity of the driers making them more suitable alternatives to cobalt driers. Alternatively can the users themselves combine a traditional primary drier with a drying accelerator to obtain an increased drying effect.
3 Contact to manufactures
Different suppliers have been contacted in order to get samples of alkyds and driers and to get technical input to the project. The scope of the contacts was partly to find candidates that will participate in the project contributing with technical openness and knowledge.
To ensure continuity and to get most benefit out of the project, representatives from the coating industry, binder and driers manufactures have been involved in the planning and evaluation phase from the very beginning.
3.1 Binders
To be able to examine the influence of different aspects of the alkyd it was essential to find a supplier that was willing to produce model alkyds especially for the project.
Cray Valley has a long experience in the manufacturing of alkyds and agreed to participate and no further contact to suppliers of binders has been taken.
3.2 Driers
Different drier manufacturers have been contacted. The scope of the contacts has been to
- be updated technically in the drier area
- choose alternatives to cobalt to be tested
- find a supplier who would participate in the project
For the latter Sasol Servo now part of Elementis Specialties had some experience similar to the approach of this project and they agreed to participate. Sasol Servo contributed to the initial screening with technical input and assistance as well as samples of existing drier products.
4 Evaluation of drying properties as a function of alkyd and primary drier
The scope of this initial screening was to make a rough evaluation of the primary driers. Simple drying tests with selected binders combined with different driers were performed to reveal potential driers for further test in stains and to evaluate the consequence of different types of alkyds
4.1 Alkyds
As mentioned earlier the key parameters for an alkyd with respect to drying are oil length, oil type, molecular weight and whether the acid is iso- or orthophthalic. These parameters are not independent and it is hardly possible to evaluate each isolated.
Initially seven different alkyds with different variations produced by Cray Valley and a standard alkyd produced by Dyrup were included in the project.
Table 4.1 Types of alkyds included in the project
Product code |
Description |
A1 |
Standard long oil alkyd |
A2 |
High molecular version of A1 |
A3, A4 |
A1 modified with two levels of conjugated acids |
A5 |
High solids version of A1 for VOC < 300 g/l. |
A6 |
High solids for VOC < 250 g/l base on different oil type than A5 |
A7 |
Urethane modified alkyd. Standard long oil alkyd |
A8 |
Standard long oil alkyd produced by Dyrup. Different oil type than A1. |
Even though a systematic evaluation of the influence of every parameter not is achieved, the different types of alkyds were expected to give an indication of possibilities in combination with the primary drier.
4.2 Driers
In the initial screening it was investigated how the type and level of primary driers influence the drying of alkyd coatings.
4.2.1 Primary driers
The newest developed alternatives from the suppliers where tested. Most of these are mixtures of a primary drier and an organic accelerator. In some cases the drier products also contain some secondary driers.
Beside the drier products containing drying accelerator, common primary drier products, where the metal has been combined with different acids have also been tested, both alone and in combination with a variation of accelerators. In this way the influence of acids and accelerators was evaluated. Table 4.2 lists the driers tested in the project.
In earlier studies only vanadium and manganese has shown some potential as alternatives in wood coatings and as the drier manufactures are focusing on these metals they are also dominating in this project.
Table 4.2 Driers to be tested in the project.
Product code |
Metal |
Accelerator |
P1 |
Cobalt |
No |
P2 |
Vanadium |
Yes |
P3-P8 |
Manganese |
Yes |
P9 |
Vanadium |
No |
P10-P12 |
Manganese |
No |
4.2.2 Secondary driers
In a pre-evaluation of the test design it was concluded that secondary driers only have a limited influence on the drying time. This conclusion was confirmed by the participating drier producer and the secondary driers was therefore excluded in the initial screening. Later in the process, where the most promising systems are optimised, it is relevant to include these driers as they can enhance film hardness, gloss, stability of the drier system etc.
4.2.3 Organic accelerators
These are expected to have a pronounced influence on drying time and are already included in many of the commercial products.
However, to reduce the amount of tests they were postponed and tested later together with the best primary drier without accelerators from the first screening.
Two accelerators from two different suppliers were selected.
Product codes: AC1and AC2.
The active content in both is 2,2’-Bipyridyl only differing in solid content and solvent.
4.3 Screening tests
4.3.1 Test systems
Eight binders and fourteen primary driers were selected for the tests in the first screening. Besides a traditional alkyd from Dyrup, Cray Valley delivered seven alkyds of which most were made specifically for this project (4.1). The primary driers were delivered from Sasol Servo and other suppliers.
As other raw materials in the coating, such as pigments and additives, will affect the drying time their presence reduce the possibility to examine the influence of the variations in alkyd against different driers. Thus the driers were tested in the pure binder.
It is important how pigmentation, anti-skinning agents, co-solvents etc. affect the drying properties but it is aimed to reduce the selection of test system as much as possible before studying these aspects.
The alkyds were diluted to the same solid content with two exceptions due to viscosity issues with respect to application.
After the initial screening, selected driers were tested with accelerators in different combinations.
4.3.2 Tests
The criterion in the first screening was the drying time. Other properties like yellowing, hardness and loss of dry are of course also important, but they are more relevant in the testing of wood coating prototypes and thus evaluated at a later stage.
In real life there is a distinction between minimal, low and high build coatings and therefore it is relevant to test how the driers perform at different film thicknesses. To compare the alkyds directly it is also rational to test different systems at the same film thickness.
It was decided to measure the drying time of wet coating film applied with a hand-held applicator blade with a gap of 120 µm and 210 µm respectively, where the dry film thickness in advance has been estimated for each type of binder. It is assumed that different types of driers will not affect the film thickness.
In this way the measurements can be corrected theoretically to an equal film thickness, as variations can occur due to different solid contents and viscosities.
The application of the coating was made as a draw-down on a Letena card. A Letena card is a varnished card normally used for testing of the hiding power of a paint. The drying time was measured by drawing a line with a pen across the applied coating film every hour. When it is possible to write on the coating film it is dry. It is a fast method, which gives clear results and it is relative independent of the performer.
To evaluate the variation in film thickness achieved, when applying different alkyds (50 wt-% solid content) with a hand-held applicator at different gap sizes, the dry film thickness was measured for the draw-downs after drying, see table 4.3. The results showed acceptable variations.
Table 4.3 Dry film thickness measured on alkyds with 50 % solid content applied at different wet film thicknesses
Binder. |
Filmthickness [µm] |
|
120 |
150 |
180 |
210 |
A1 |
41 |
53 |
63 |
67 |
A2 |
42 |
54 |
64 |
72 |
A3 |
49 |
59 |
72 |
80 |
A4 |
50 |
62 |
72 |
80 |
A5 |
44 |
53 |
64 |
64 |
A6 |
43 |
52 |
68 |
80 |
A7 |
45 |
56 |
66 |
82 |
A8 |
44 |
52 |
58 |
68 |
Mean value |
46 |
|
|
73 |
4.4 Screening results
4.4.1 Handling of data
The method of measuring the drying time requires a manual evaluation every hour. Some systems will dry in a period of time (~10-15 hours) where such an hourly evaluation is not possible. In these cases the drying result is taken as an interval where the middle value is used as the drying time in the further handling of data.
Using intervals and middle values will affect the accuracy in the statistical treatment. The situation arises especially with slow drying systems but still the promising and thus most interesting systems will stand out, which is the purpose of this screening.
As mentioned above the tested binders differ in viscosity and thus the film thickness will differ too. Presuming that the correlation between drying time and film thickness is linear all results are adjusted to a middle dry film thickness at respectively 120 µm and 210 µm (wet film applied).
All driers were tested in two levels in each binder. Only the drier level with the best drying result is included in the evaluation.
An exception is cobalt, where the standard dosage used in Dyrup, calculated on solid binder is used.
4.4.2 Drying time - results
The experimental results have been treated by general linear statistic analyses (an example of a statistic analysis is given in the appendix A with reference to the results in chapter 5.3).
All conclusions refer only to the drying time and only as defined in this screening.
All parameters - binder, drier and film thickness - have a significant influence, and as expected the drying time is shorter at lower film thickness.
Diagram 4.1 Influence of film thickness on drying time
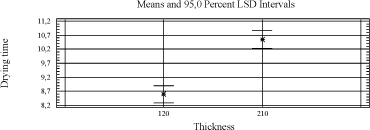
P02(V) is the best of the alternatives performing at the same level as cobalt. Among the manganese driers are P06(Mn) and P07(Mn) the most promising and the only ones that stand out from the driers without accelerator.
Diagram 4.2 Influence of drier on drying time
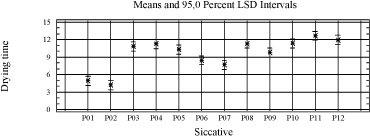
For the binders an improvement in drying is seen with higher content of conjugated acid. The high solid binder A5 is in general the most difficult to dry. The rest of the binders are at the same level.
Diagram 4.3 Influence of binder on drying time
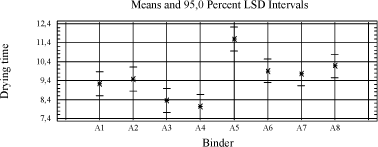
Splitting the data up in 120 µm and 210 µm respectively does not alter the conclusions, except for the standard from Dyrup (A8) that joins A5 as a slow drying binder at 210 µm.
In the statistical analyses the driers are evaluated with regard to their universality against different types of binders and visa versa, and particularly for the driers this is of course relevant to product development in general.
However as the conclusion from earlier studies has been that no alternatives have matched cobalt in this respect, one of the scopes in this project is to evaluate the influence of the properties of the alkyd to find a scenario for a cobalt free product range. Therefore it is also relevant to look at specific combinations of driers and alkyds.
Beside the driers P02, P06 and P07, which have already been estimated as promising cobalt alternatives in the statistical treatment, P09 is doing quite well within a few binders even without the presence of an accelerator.
A rough overview of the performance of the best driers with different binders is given in the table below.
Table 4.4 Overview of performance of best driers with binders
|
P01(Co) |
P02(V) |
P06(Mn) |
P07(Mn) |
P09(V) |
A1 |
|
|
|
|
|
A2 |
|
A3 |
|
A4 |
|
A5 |
|
|
|
|
A6 |
|
|
A7 |
|
|
A8 |
|
|
|
|
|
Dark grey: Drying time less or equal to 6 h at both 120 µm and 210 µm
Light grey: Drying time less or equal to 8 h at both 120 µm and 210 µm
4.4.3 Test with accelerators
Using the standard binder A8, the driers P09(V) and P10(Mn) have been tested together with the accelerators AC1 and AC2 in different combinations
Diagram 4.4 Test with organic accelerator
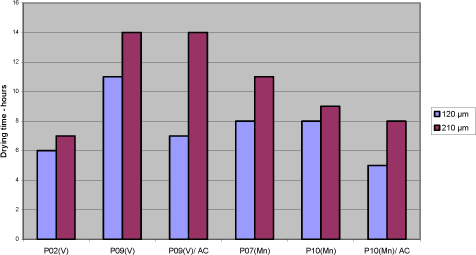
In both cases the drying is improved compared to when the driers are used with no accelerator, but only P10(Mn) reaches the level of P01(Co) and P02(V).
P10(Mn) is similar to P07(Mn) only without the accelerator. The results reflect a better combination of drier and accelerator than represented by P07(Mn) when used in A8.
4.4.4 Conclusions
The assumption for this screening was that no alternatives to Cobalt exhibit the same universality as cobalt driers. However looking at results obtained with the pure binders, P02(V) comes out as a clear candidate moving the focus against the influence of other raw materials. In the simple test of drying time it performs at the same level as cobalt but still there is a challenge with tackiness in specific binders and yellowing.
Among the Manganese driers P10(Mn) optimised with an accelerator might be a possible candidate. P07(Mn) and P06(Mn) are also of interest, but in these cases modification of the alkyd has to be considered to avoid compromising the drying time, compared to the performance of cobalt in standard binders.
With regard to the binders modified with conjugated acids, the modification improves the drying in general. Of the high solid binders A6 is performing best and is generally at the level or better than the traditional binders A1 and A8.
It is very different how the driers perform with the different types of alkyds. But besides the general observations it is not possible from the pool of data to relate drying times to connections between properties of respectively alkyd and drier.
The variety in the drying time, even among pure primary driers, indicates that not only the type of metal or combination with accelerator but also the type of salts plays a role.
5 Evaluation of drying properties in wood coating prototypes
With focus on the most promising drier and binder systems from the initial screening in pure binders the next step was to evaluate these raw materials in the different types of wood coatings and how the presence of pigments and additives influence on the drying properties.
5.1 Test methods
As a large number of systems where screened also in this part of the project simple reproducible tests has been used for evaluation of the drying properties.
Table 5.1 Test methods
|
Apparatus |
Conditions |
Method |
Demands* |
Drying time |
Applicator,
lenetacards, pen |
50 % HR, 23 °C,
120 µm wet film |
A pen is moved across a
draw-down every hour. When
its possible to draw a line
on the film it is dry. |
<8 hours |
Loss of dry |
Applicator,
lenetacards, pen,
oven |
2 weeks at 40 oC
or >6 weeks at RT |
As drying time but after
storage |
<8 hours |
Tackiness |
Applicator,
lenetacards |
50 % HR, 23 °C,
120 µm wet film |
Tackiness is measured by
pressing a finger against the
film after 6 and 24 hours |
Tack free
after one
day |
Hardness |
König Albert,
applicator, glass
plates |
50 % HR, 23 °C,
120 µm wet film |
The Kùnig hardness is
measured after 1, 7, 14 and
28(-55) days |
At the level
of cobalt
after 28
days |
Yellowing |
GretagMacbeth –
Color i5,
applicator
glas plates |
50 % HR, 23 °C,
120 µm wet film |
b-value is measured after 1
and 28 days. When
measuring on pure binders a
white cardboard is placed
behind the glass plate. |
At the level
of cobalt |
*The demands are indicating when an alternative drier is regarded as interesting in the project more than they are general product demands.
5.2 Choice of systems
Besides the selected driers and binders from the initial screening a few newcomers have been included.
Types of wood coatings as well as test systems have been chosen to target that the conclusions from this project can be related to a full product range.
Below is an overview as regards combinations of systems, binders, primary and secondary driers tested. Beside these combinations many primary and secondary driers are also tested in at least two concentrations.
Table 5.2 Complete overview as regards combinations of systems, binders, primary driers, and secondary driers tested.
System |
Binder |
P01(C0) |
P02(V) |
P06(Mn) |
P07(Mn) |
P10(Mn)/AC |
P13(Mn) |
P14(Mn) |
P15(Fe) |
Pure |
A1 |
Zr |
None |
None |
None |
A3 |
Zr |
None |
None |
None |
None |
A7 |
Zr |
None |
None |
A8 |
Zr |
Table 5.5, None, Zr/Ca, Zn/Ca, Zr/ Zn |
Table 5.5,
None,
Zr/Ca, Zn/Ca, Zr/ Zn |
None |
None, Zr/Ca |
None, Zr/Ca |
None,
Zr/Ca |
Trans-
parent |
A1 |
Zr |
None |
None |
A3 |
Zr |
None |
None |
None |
None |
None |
A7 |
Zr |
None |
None, Zr/Zn |
A8 |
Zr |
Table 5.5, None, Zr/Ca, Zn/Ca, Zr/ Zn |
Table 5.5, None, Zr/Ca, Zn/Ca, Zr/ Zn |
None |
None, Zr/Ca |
None, Zr/Ca |
None,
Zr/Ca |
A7/A8 |
Zr |
None |
None |
Opaque white |
A1/thix |
Zr |
None |
None |
A3/thix |
Zr |
None |
None |
A7/thix |
Zr |
None |
None, Zr/Zn |
A8/thix |
Zr |
None, Zr/Zn |
None, Zr/Ca, |
Zr,Ca |
Zr,Ca |
Opaque dark |
A1/thix |
Zr |
None |
None |
A3/thix |
Zr |
None |
None |
A7/thix |
Zr |
None |
None, Zr/Zn |
A8/thix |
Zr |
None, Zr/Zn |
None, Zr/Ca, |
Zr,Ca |
Zr,Ca |
Base red (T) |
A3 |
Zr |
None |
None |
None |
A8 |
Zr |
None |
None |
Base yellow (T) |
A3 |
Zr |
None |
None |
None |
A8 |
Zr |
None |
None |
Base red |
A3 |
Zr |
None |
None |
None |
A8 |
Zr |
None |
None |
Base blue |
A3 |
Zr |
None |
None |
None |
A8 |
Zr |
None |
None |
VOC2010 pure binder |
A8/
linseed |
Zr |
None, Zr/Ca |
None, Zr/Ca |
None, Zr/Ca |
A9 |
Zr |
None, Zr/Ca |
None, Zr/Ca |
None, Zr/Ca |
VOC2010 trans-
parent |
A7/
linseed |
Zr |
None |
None, Zr/Zn |
A8/
linseed |
Zr |
None, Zr/Ca |
None, Zr/Ca |
None, Zr/Ca |
A9 |
Zr |
None, Zr/Ca |
None, Zr/Ca |
None, Zr/Ca |
5.2.1 Driers
5.2.1.1 Primary driers
The main focus has been on the best candidates P02(V) and P07(Mn) from the initial screening in pure binders, and when going through the different drying properties (5.4) only these driers will be discussed.
P06(Mn) was tested in a few systems as it in pure binders showed good results with the modified binder A3, but no benefits compared to P07(Mn) has been observed. Also the expected advantages of A3 didn’t take place.
Table 5.3 Comparison of key drying properties of P06(Mn) and P07(Mn) in binder A3
Systems (5.2.4) |
Hardness 28 days* |
Drying time – hours |
Loss of dry - hours |
P06(Mn) |
P07(Mn) |
P06(Mn) |
P07(Mn) |
P06(Mn) |
P07(Mn) |
Pure binder |
15 |
15 |
5 |
4 |
- |
- |
Transparent |
11 |
12 |
6 |
6 |
- |
- |
Opaque dark |
18 |
20 |
10 |
18 |
25 |
30 |
Opaque white |
22 |
23 |
7 |
7 |
24 |
25 |
Base/Yellow(T) |
15 |
15 |
6 |
5 |
- |
- |
Base/Red(T) |
14 |
14 |
5 |
6 |
- |
- |
Base/Blue |
13 |
13 |
6 |
7 |
- |
- |
Base/Red |
12 |
11 |
8 |
7 |
- |
- |
* exceeds 28 days in some systems
P10(Mn) optimized with the organic accelerator AC2 showed some potential in the initial screening too, but again the behaviour in the later studies was very similar to P07(Mn).
Table 5.4 Comparison of key drying properties of P10(Mn)/AC2 and P07(Mn)
Binder |
Systems (5.2.4) |
Hardness 40 days |
Drying time - hours |
P10(Mn)/AC2 |
P07(Mn) |
P10(Mn)/AC2 |
P07(Mn) |
A8 |
Pure binder |
23 |
23 |
5 |
5 |
A8 |
Transparent |
16 |
18 |
19* |
19* |
A1 |
Pure binder |
15 |
16 |
5 |
5 |
A1 |
Transparent |
12 |
12 |
23* |
25* |
*the drying time is unusually high in transparent systems compared to identically test with P07(Mn)
Two new manganese driers P13(Mn) and P14(Mn) have been included in the project and tested in a few relevant systems with and without recommended secondary driers but again the same limitations are observed as with P07(Mn)
Finally a drier based on Iron P15(Fe) was tested which, although interesting considering the type of metal, still cannot compete with vanadium and manganese. Main problems are drying times above 10 hours and after storage above 20 hours.
5.2.1.2 Secondary driers
To improve the drying properties the following secondary driers have been tested in minimum and maximum concentration recommended by supplier or literature. Relevant combinations of secondary driers are tested as well.
Table 5.5 Secondary driers tested in the project
Calcium |
Barium |
Potassium |
Zirconium |
Bismuth |
Cerium |
Aluminium |
Lithium |
Vanadium |
Strontium |
Zinc |
|
Cerium and Vanadium is in fact primary driers but are in this connection screened in combination with either P02(V) or P07(Mn).
5.2.2 Binders
5.2.2.1 VOC2007 compliant binders
The two long oil alkyds A1 and A8 are evaluated with most focus on A8 as it has a better hardness development.
In the initial screenings it was concluded that the binder A3 modified with conjugated acid reduces the drying times compared to the traditional binders.
However when the drying properties are examined in general no improvements of the drawbacks of the alternative driers are observed.
In pure binder, bases, opaque and transparent systems A3 behave very similar to A1 and do not reduce the problems with e.g. tackiness, hardness and loss of dry.
Table 5.6 examples of test results for A3 compared to A8 in the transparent prototype (6.1.4.1)
Drier |
Tackiness 1 day |
Hardness 55 days |
Loss of dry - hours |
A3 |
A8 |
A3 |
A8 |
A3 |
A8 |
P01(Co) |
1 |
1 |
17 |
24 |
|
7 |
P02(V) |
3 |
2,5 |
19 |
26 |
3 |
5 |
P07(Mn) |
1,5 |
1 |
12 |
12 |
24 |
24 |
Tackiness: 5 – bad, 1 – good/ tack-free
The urethane modified alkyd A7 is tested alone and in combination with other binders. It gives a harder film and has less need for driers in general (5.4).
5.2.2.2 VOC2010 compliant binders
The driers are tested in a high solid binder A9, which is new for the project as well as A8 and A7 combined with linseed oil.
5.2.3 Solvent
A few tests have been carried out using solvents with different boiling points to see the influence on mainly initial drying properties like tackiness.
As expected a lower boiling point reduces the drying time slightly but no effect is observed on e.g. the tackiness after one day which is a problem with P02(V)
5.2.4 Types of coatings
5.2.4.1 Pure binders
As in the initial screening the pure binder is evaluated with no other additives present.
5.2.4.2 Transparent high build coating
Beside binder and drier it contains UV-absorber, anti-skinning agent, fungicide and pigment mix (medium shaded wood colour). All screenings in transparent systems are based on this raw material mix with parallel tests in the pure binder.
Influence of the different raw materials is evaluated in chapter 5.3
5.2.4.3 Opaque high build coatings
A white coating highly loaded with titanium dioxide and a dark coating with a high level of carbon black are tested.
Both are Dyrup formulations.
The white coating is sensitive to yellowing, and high levels of pigments, especially carbon black, are suspected to affect the long-term stability of the driers (loss of dry).
5.2.4.4 Bases
A base for transparent colours and one for opaque colours each tinted with two different universal tinting pastes.
Bases together with universal tinting pastes have a higher level of especially surfactants to ensure compatibility and in some coincidences this causes a negative influence on drying properties even with cobalt
5.2.4.5 VOC2010 compliant coatings
VOC2010 compliant binders are tested alone and with the raw material mix mentioned above in the transparent prototype. These recipes are not optimised as coatings and are included to see how the alternative driers behave with these potentially more challenging binder systems.
5.3 Influence of additives and pigments
In order to evaluate the influence of typical raw materials used in the coating industry a 26-3 fractional factorial design is used where the parameters are the presence or non-presence of MEKO, pigment mix, thix-alkyd, UV-absorber, HALS and fungicide (appendix A).
For the pigments a combination corresponding to a medium pigmented transparent wood color is chosen.
In the 26-3 fractional factorial designs the primary driers Co, P02(V) and P07(Mn) are tested together with the two traditional long oil alkyds A1 and A8. The driers and binders are regarded as constants in the tests giving six combinations and thus six 26-3 fractional factorial designs.
Table 5.7 One out of six test designs - P01(Co) and A8.
Drier |
Binder |
Solid content |
Thix binder |
Color |
Meko |
UV abs. |
HALS |
Fungicide |
P01 |
A8 |
50 |
yes |
Trans |
yes |
no |
no |
no |
P01 |
A8 |
50 |
no |
Trans |
yes |
yes |
yes |
no |
P01 |
A8 |
50 |
yes |
no |
yes |
yes |
no |
yes |
P01 |
A8 |
50 |
no |
no |
yes |
no |
yes |
yes |
P01 |
A8 |
50 |
yes |
Trans |
no |
no |
yes |
yes |
P01 |
A8 |
50 |
no |
Trans |
no |
yes |
no |
yes |
P01 |
A8 |
50 |
yes |
no |
no |
yes |
yes |
no |
P01 |
A8 |
50 |
no |
no |
no |
no |
no |
no |
Table 5.8 Overview as regards which raw materials affects the drying properties significantly. A general linear model is used to estimate the factors with a significant influence at a 90 % confidence level.
|
Drying time |
Loss of dry |
Tackiness after 6 h |
Tackiness after 1 day |
Hardness after 1 day |
Hardness after 7 days |
Colour |
Yellowing 28 days |
MEKO |
X |
X |
X |
|
|
|
|
|
Pigment mix |
|
|
|
|
|
|
(X) |
X |
Thix-alkyd |
|
|
|
|
|
X |
X |
|
UV-abs |
|
|
|
|
|
X |
|
|
HALS |
|
|
|
|
|
X |
|
|
Fungicide |
X |
|
|
|
|
X |
|
|
Binder |
|
|
|
|
X |
X |
|
|
Drier |
X |
X |
X |
X |
X |
X |
X |
X |
With the exception of the thix-alkyd giving a harder film after seven days, the influence of other raw materials is always negative when significant.
The anti-skinning agent, before it evaporates, affects the initial properties after application like drying time and tackiness after six hours.
The pigments of course introduce colour to the film and therefore also prevent darkening of the wood and thus the yellowing. UV-absorber and HALS are also expected to prevent yellowing but after 28 days it is not significant.
UV-absorber, HALS and fungicide do all reduce the hardness and the fungicide has a negative influence on the drying time as well. As mentioned earlier the thix-alkyd gives a harder film and comparing the two traditional binders the one produced by Dyrup is the hardest.
The driers have influence on all properties. The drawbacks using P02(V) are reduced hardness, long term tackiness and colouring of the film. For P07(Mn) the drawbacks are reduced hardness, longer drying time and loss of dry.
5.4 Evaluation of drying properties
The alternative driers have some limitations compared to cobalt especially when moving from pure binder systems to wood coatings. Several initiatives have been carried out to optimise the performance of these driers in different types of wood coatings.
First the addition levels of P02(V) and P07(Mn) have been further investigated in pure binder and transparent prototype. Initially they were screened in just minimum and maximum recommended level and then a level in the middle of the interval was included.
P02(V) was earlier concluded to be most efficient at the high level but cutting the amount to the half does not affect drying time, tackiness or hardness and the colouring of the film is reduced. In the further tests this level was used where nothing else is mentioned.
The conclusion for P07(V) remains, it performs better at the lowest recommended addition.
5.4.1 Drying Time
In general the drying time using P02(V) is at the same level as with cobalt. Typically the drying time will be below five hours.
Only in the red tinted opaque base and the VOC2010 transparent system with high solid binder A9 it is not as efficient. In VOC2010 compliant system, using the highest recommended level reduces the difference bringing the drying time down to seven hours. This has not been tested in the base.
It should be noticed though that the VOC2010 systems in this project are very experimental and not satisfying even with cobalt looking at the drying properties in general.
Diagram 5.1 Drying times in tested systems with vanadium drier P02(V)
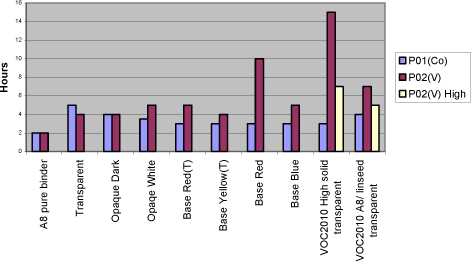
With P07(Mn) the drying times are typically between 5 and 7 hours although in the VOC2010 high solid system secondary driers are needed to keep this level. Except for this coincidence practically no reduction in drying time is observed from the use of secondary driers.
In the opaque dark system the drying time is quite long and the use of secondary driers or even faster drying binders like A7 does not reduce it to a satisfactory level.
Diagram 5.2 Drying times in tested systems with Manganese drier P07(Mn)
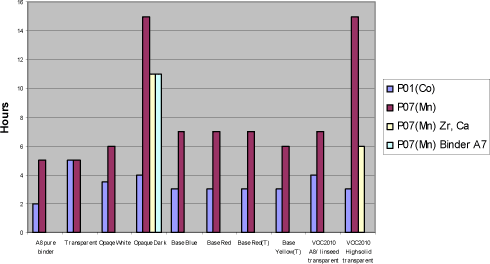
5.4.2 Loss of dry
In transparent systems P02(V) is stable and perform at the same level as cobalt but in the red bases, opaque systems and the VOC2010 compliant systems the drying time is increased to 14 to 24 hours. Using the highest recommendable dosage brings the drying time down to an acceptable level in some systems but introduces other problem like colouring of the film in the opaque white. Another option is to partly introduce the modified alkyd A7. Combination of A7 and high dosage of P02(V) should reduce the drying time further.
Diagram 5.3 Drying times after storage with vanadium drier P02(V).
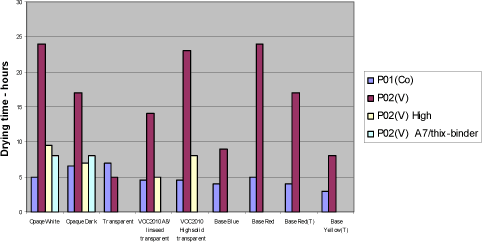
The bases have not been optimised due to lack of time and material. Beside the dosage and use of special alkyds it would be natural to look at the tinting pastes as different technologies for ensuring compatibility is available.
Any use of secondary siccatives has a negative influence together with P02(V) on loss of dry as well as other drying properties.
Loss of dry is a problem in general when using P07(Mn). The drying times exceed 20 hours no matter dosage level or use of secondary driers alone or in combinations.
Using the alkyd A7 alone in transparent systems has solved the problem reducing the drying time to 6 hours after storage. Substituting the binder partly is not efficient when tested in the transparent and opaque systems.
Diagram 5.4 Examples of drying times after storage with manganese drier P07(Mn).
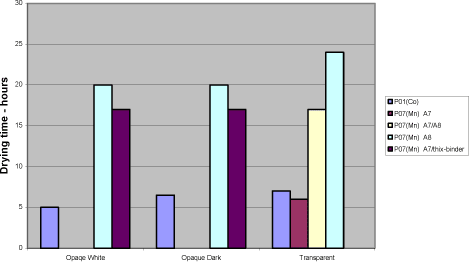
5.4.3 Tackiness
The main issue with P02(V) is tackiness. Except for the opaque dark all other systems stays tacky even one day after the film was applied. Again secondary siccatives make no difference and the only way for improvement is the binder.
Using pure urethane modified binder A7 eliminates the tackiness at least after one day and a one to one combination with A8 reduces it to a level that could be acceptable.
Also a few tests have been carried out with anti-blocking agents and although it does not solve the problem the tackiness is reduced.
Still these improvements are only seen after one day where cobalt normally is almost tack-free after 6 hours.
With P07(Mn) tackiness is not a problem. When the film is dry it gets tack-free within a few hours. In other words – if the film stays tacky for a long time it is due to a long drying time!
5.4.4 Hardness
In general the same hardness is gained with P02(V) as with cobalt no matter the type of coating but it takes longer time to get there. Cobalt reaches its final hardness faster but after 3 and more often 4 weeks the hardness is the same.
As seen before white opaque causes some problems and here the above is only true if P02(V) is dosed in the highest recommended amount resulting in some colouring of the film.
Again secondary driers should be avoided.
Diagram 5.5 Examples of hardness development with vanadium drier P02(V)
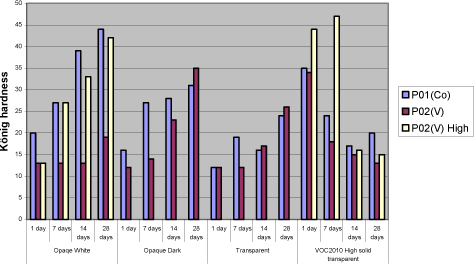
In systems with P07(V) the development of hardness almost stops after 1 to 7 days and never reaches the level of cobalt. High dosage of secondary driers like Zirconium, Zinc and Calcium improve the hardness in transparent system and pure binder, but only in the latter it is to the same level as P02(V) and Cobalt. Combinations of either zinc or zirconium in combination with calcium have been tried in opaque systems with no success.
Aluminium is very efficient but causes a serious viscosity rise or even jellification of the liquid.
In VOC2010 compliant systems the situation is somehow turned around. As regards binder A8 combined with linseed oil the hardness development is very poor with all driers. But when it comes to the high solid binder after 28 days the systems with P07(Mn) are superior to the ones with Cobalt and P02(V). For the two latter the hardness develops very fast but soon it drops again and the result is a rather soft film. With P07(Mn) however the hardness stays at a level which is rather high compared to other systems with this drier.
This is hardly a result of P07(Mn) being more efficient with this type of binder, as the drop in hardness seen with the other driers, most like is due to catalytic activity.
Diagram 5.6 Examples of hardness development with manganese drier P07(Mn)
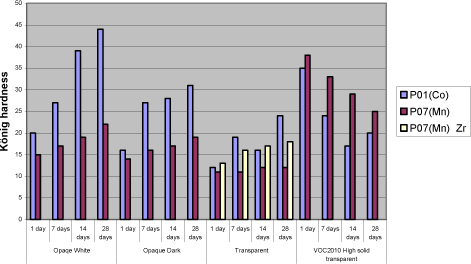
Using harder binders like A7 improves the hardness overall no matter the drier.
Diagram 5.7 Hardness development using binder A7 in transparent prototype
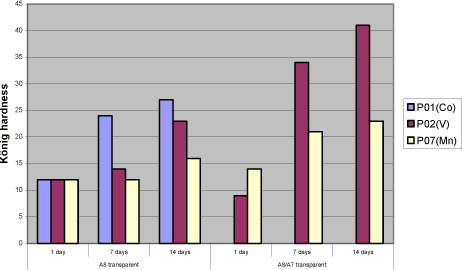
5.4.5 Yellowing – colouring of the film
P02(V) contribute to colouring of the film and the only way to reduce this is to keep the dosage level as low as possible. It will only be a problem in light coloured opaque systems when the need of P02(V) is high as seen with the opaque white system. Here the only option revealed in this project is to introduce a faster drying alkyd, which in this system is also necessary for other drying properties.
Some secondary driers reduces the colouring but as mentioned above together with P02(V) they have a negative influence on properties like drying time, hardness and loss of dry.
Compared to cobalt yellowing, this is not an issue when using P07(Mn)
6 Conclusion
Experiences from earlier studies have shown that substitution of cobalt with alternative driers is very difficult. Although interesting results have been achieved especially with manganese driers, it is clear that cobalt is more efficient and the alternatives reveal strong limitations when it comes to substitution in a whole product range.
Thus the scope of this project was not only to look into substitution of the drier in existing products but also to get a better understanding of how different aspects of the drier systems together with different parameters of the alkyds affect the drying properties in various types of coatings.
Optimally this would lead to solution scenarios not based on trial and error but a stronger understanding of limitations and possibilities.
When alternative driers are not as efficient or “universal” as cobalt there could be possibilities through the knowledge to choose the right types of binders.
Early in the project it was clarified that looking into correlations between parameters of driers and alkyds respectively on a very detailed level was unrealistic for several reasons. Many of the parameters of the alkyds are related to each other and changing one will affect several others. The work would be enormous and the clear feeling from this project is that these correlations are very sensitive to small system changes.
In e.g. pure binders just the salt of the metal acid shows an influence on drying time with specific binders. However with the presence of other raw materials these differences seem to smoothen out and for example manganese driers, from different suppliers, behaves almost identically. Maybe there are small differences in specific measurements but overall the limitations are exactly the same.
The best candidate for a substitute to cobalt is P02(V). If it was not for the tackiness it could replace cobalt in the major part of a product range. Overall good drying properties are achieved and at a medium dosage level yellowing is not really an issue even in light opaque systems. Hardness is not developed as fast as with cobalt but ends up at the same level in 3 to 4 weeks.
In a few systems however like the red opaque base and the white opaque system with high amounts of titanium dioxide it shows some limitations compared to cobalt. Where a high dosage level of P02(V) is not a solution replacing part of the binder with a faster drying alkyd, as e.g. the urethane modified A7 tested in this project, is a possibility.
Anyway the problem with tackiness is a reality for both the vanadium driers tested in this project. The only real solution has been to partly replace the traditional binder with A7. It is a possibility for sure, but P02(V) is less attractive as a substitute when the need of special binders is necessary in all products and not only a few critical systems.
Some improvements are observed using anti-blocking agents and an approach could be to evaluate this further to get more flexibility in this scenario.
In general P07(Mn) and other manganese driers tested in this project simply lacks catalytic efficacy to be a real option as an alternative. Although the use of secondary siccatives have shown limited improvement, drying times and hardness are not at the level of Cobalt or P02(V) and especially loss of dry is a pronounced problem.
Again a fast drying alkyd like A7 can reduce these problems but the need is very consequent compared to P02(V) and the real alternative to cobalt is arguable the binder itself.
As concerns VOC2010 compliant systems it is a special situation, because these are experimental and relatively few experiences is available as regards the properties in general. Also the high solid binders are still under heavy development from the suppliers and the coating industry is facing a challenge updating the product range no matter the driers.
Overall the conclusions is the same as with other systems only with the high solid binder the hardest film is achieved with P07(Mn). As explained (5.4.4) it is probably still because of less drying efficacy and how this affects the durability is to be tested.
To summarize it has not been possible to find a drier system as efficient as cobalt. However if a modified alkyd with less need of drier is introduced a replacement seems possible although with the technologies available today some compromises will be necessary. This could e.g. be acceptance of more yellowing in some systems. The better efficacy of the drier the more the use of a special alkyd can be limited to critical systems which is a plus for the flexibility in product development in general.
It should be emphasized that at this stage durability tests, artificial or natural exposure, has not been performed and the conclusions are only based on mechanical tests of drying properties.
This project has been initiated because of the appearance of cobalt on the list of dangerous substances /1/ as being possible carcinogenic.
Very little data concerning toxicity and ecotoxicity is available for manganese and vanadium and if cobalt is forbidden as a drier in coatings there is no guarantee that these will not follow sooner or later.
Also the binder systems compliant with VOC2010 seem to be even more challenging as regards drying properties.
Thus to meet future demands development is necessary both in the binder and the drier area.
7 References
/1/ List of dangerous substances. 3rd June 2002. Available at the Danish EPA www.mst.dk.
/2/ Pilemand C., Wallstrùm E., Hoffmann L. and Poulsen P.B. „Substitution of Cobalt Driers and Methyl Ethyl Ketoxime“; Environmental project no. 884, Danish EPA, 2003.
/3/ Rasmussen, D. & Wallstrùm E.: Computer calculation of component and mixture properties: an introduction to dG (a PC program for prediction of mixture behaviour and retrieval of solvent properties). - JOCCA 1994(3): p. 87-94.
Appendix A - Statistical analysis of 26-3 fractional factorial designs.
1 Design and results
Click here to see table with design and results
2 Statistic analysis
General Linear Models
---------------------
Number of dependent variables: 7
Number of categorical factors: 8
Number of quantitative factors: 0
Analysis of Variance for YellowingOne
Source |
Sum of Squares |
Df |
Mean Square |
F-Ratio |
P-Value |
Model |
14871,5 |
9 |
1652,39 |
1015,40 |
0,0000 |
Residual |
61,8388 |
38 |
1,62734 |
Total (Corr.) |
14933,4 |
47 |
|
|
|
|
Type III Sums of Squares |
Source |
Sum of Squares |
Df |
Mean Square |
F-Ratio |
P-Value |
Anti skin |
0,259602 |
1 |
0,259602 |
0,16 |
0,6918 |
Binder |
0,0462521 |
1 |
0,0462521 |
0,03 |
0,8670 |
Color |
14790,8 |
1 |
14790,8 |
9088,95 |
0,0000 |
Drier |
28,1515 |
2 |
14,0758 |
8,65 |
0,0008 |
Fungicide |
0,0910021 |
1 |
0,0910021 |
0,06 |
0,8143 |
HALS |
2,47975 |
1 |
2,47975 |
1,52 |
0,2246 |
Thix binder |
49,5524 |
1 |
49,5524 |
30,45 |
0,0000 |
UV abs |
0,155269 |
1 |
0,155269 |
0,10 |
0,7591 |
Residual |
61,8388 |
38 |
1,62734 |
|
|
Total (corrected) |
14933,4 |
47 |
|
|
|
All F-ratios are based on the residual mean square error.
R-Squared = 99,5859 percent
R-Squared (adjusted for d.f.) = 99,4878 percent
Standard Error of Est. = 1,27567
Mean absolute error = 0,92467
Durbin-Watson statistic = 2,28349
Residual Analysis
|
Estimation |
Validation |
N |
48 |
|
MSE |
1,62734 |
|
MAE |
0,92467 |
|
MAPE |
7,60461 |
|
ME |
-5,71765E-15 |
|
MPE |
-1,41698 |
|
Analysis of Variance for Yellowing28
Source |
Sum of Squares |
Df |
Mean Square |
F-Ratio |
P-Value |
Model |
14318,0 |
9 |
1590,89 |
1033,84 |
0,0000 |
Residual |
58,475 |
38 |
1,53881 |
|
|
Total (Corr.) |
14376,5 |
47 |
|
|
|
|
Type III Sums of Squares |
Source |
Sum of Squares |
Df |
Mean Square |
F-Ratio |
P-Value |
Anti skin |
0,0229688 |
1 |
0,0229688 |
0,01 |
0,9034 |
Binder |
0,00016875 |
1 |
0,00016875 |
0,00 |
0,9917 |
Color |
14242,0 |
1 |
14242,0 |
9255,16 |
0,0000 |
Drier |
37,1699 |
2 |
18,5849 |
12,08 |
0,0001 |
Fungicide |
0,188752 |
1 |
0,188752 |
0,12 |
0,7281 |
HALS |
2,31002 |
1 |
2,31002 |
1,50 |
0,2280 |
Thix binder |
36,3138 |
1 |
36,3138 |
23,60 |
0,0000 |
UV abs |
0,00175208 |
1 |
0,00175208 |
0,00 |
0,9733 |
Residual |
58,475 |
38 |
1,53881 |
|
|
Total (corrected) |
14376,5 |
47 |
|
|
|
All F-ratios are based on the residual mean square error.
R-Squared = 99,5933 percent
R-Squared (adjusted for d.f.) = 99,4969 percent
Standard Error of Est. = 1,24049
Mean absolute error = 0,908741
Durbin-Watson statistic = 1,87598
Residual Analysis
|
Estimation |
Validation |
N |
48 |
|
MSE |
1,53881 |
|
MAE |
0,908741 |
|
MAPE |
6,32946 |
|
ME |
-5,71765E-15 |
|
MPE |
-1,25901 |
Analysis of Variance for Tack6
Source |
Sum of Squares |
Df |
Mean Square |
F-Ratio |
P-Value |
Model |
45,3281 |
9 |
5,03646 |
10,39 |
0,0000 |
Residual |
18,4167 |
38 |
0,484649 |
|
|
Total (Corr.) |
63,7448 |
47 |
|
|
|
|
Type III Sums of Squares |
Source |
Sum of Squares |
Df |
Mean Square |
F-Ratio |
P-Value |
Anti skin |
3,25521 |
1 |
3,25521 |
6,72 |
0,0135 |
Binder |
0,130208 |
1 |
0,130208 |
0,27 |
0,6072 |
Color |
0,046875 |
1 |
0,046875 |
0,10 |
0,7575 |
Drier |
39,5417 |
2 |
19,7708 |
40,79 |
0,0000 |
Fungicide |
1,17188 |
1 |
1,17188 |
2,42 |
0,1282 |
HALS |
1,17188 |
1 |
1,17188 |
2,42 |
0,1282 |
Thix binder |
0,00520833 |
1 |
0,00520833 |
0,01 |
0,9180 |
UV abs |
0,00520833 |
1 |
0,00520833 |
0,01 |
0,9180 |
Residual |
18,4167 |
38 |
0,484649 |
|
|
Total (corrected) |
63,7448 |
47 |
|
|
|
All F-ratios are based on the residual mean square error.
R-Squared = 71,1088 percent
R-Squared (adjusted for d.f.) = 64,2661 percent
Standard Error of Est. = 0,696167
Mean absolute error = 0,471354
Durbin-Watson statistic = 1,44214
Residual Analysis
|
Estimation |
Validation |
N |
48 |
|
MSE |
0,484649 |
|
MAE |
0,471354 |
|
MAPE |
27,0263 |
|
ME |
0,0 |
|
MPE |
-9,77203 |
|
Analysis of Variance for Tack24
Source |
Sum of Squares |
Df |
Mean Square |
F-Ratio |
P-Value |
Model |
11,6667 |
9 |
1,2963 |
5,59 |
0,0001 |
Residual |
8,8125 |
38 |
0,231908 |
|
|
Total (Corr.) |
20,4792 |
47 |
|
|
|
|
Type III Sums of Squares |
Source |
Sum of Squares |
Df |
Mean Square |
F-Ratio |
P-Value |
Anti skin |
0,1875 |
1 |
0,1875 |
0,81 |
0,3742 |
Binder |
0,0833333 |
1 |
0,0833333 |
0,36 |
0,5524 |
Color |
0,0208333 |
1 |
0,0208333 |
0,09 |
0,7660 |
Drier |
10,2917 |
2 |
5,14583 |
22,19 |
0,0000 |
Fungicide |
0,1875 |
1 |
0,1875 |
0,81 |
0,3742 |
HALS |
0,520833 |
1 |
0,520833 |
2,25 |
0,1422 |
Thix binder |
0,1875 |
1 |
0,1875 |
0,81 |
0,3742 |
UV abs |
0,1875 |
1 |
0,1875 |
0,81 |
0,3742 |
Residual |
8,8125 |
38 |
0,231908 |
|
|
Total (corrected) |
20,4792 |
47 |
|
|
|
All F-ratios are based on the residual mean square error.
R-Squared = 56,9685 percent
R-Squared (adjusted for d.f.) = 46,7768 percent
Standard Error of Est. = 0,481568
Mean absolute error = 0,365451
Durbin-Watson statistic = 1,91465
Residual Analysis
|
Estimation |
Validation |
N |
48 |
|
MSE |
0,231908 |
|
MAE |
0,365451 |
|
MAPE |
8,79998 |
|
ME |
2,59052E-16 |
|
MPE |
-1,10805 |
|
Analysis of Variance for HardnessOne
Source |
Sum of Squares |
Df |
Mean Square |
F-Ratio |
P-Value |
Source |
Sum of Squares |
Df |
Mean Square |
F-Ratio |
P-Value |
Model |
133,833 |
9 |
14,8704 |
24,13 |
0,0000 |
Residual |
23,4167 |
38 |
0,616228 |
|
|
Total (Corr.) |
157,25 |
47 |
|
|
|
|
Type III Sums of Squares |
Source |
Sum of Squares |
Df |
Mean Square |
F-Ratio |
P-Value |
Anti skin |
0,0 |
1 |
0,0 |
0,00 |
1,0000 |
Binder |
18,75 |
1 |
18,75 |
30,43 |
0,0000 |
Color |
0,333333 |
1 |
0,333333 |
0,54 |
0,4666 |
Drier |
112,5 |
2 |
56,25 |
91,28 |
0,0000 |
Fungicide |
0,0833333 |
1 |
0,0833333 |
0,14 |
0,7151 |
HALS |
0,0833333 |
1 |
0,0833333 |
0,14 |
0,7151 |
Thix binder |
1,33333 |
1 |
1,33333 |
2,16 |
0,1495 |
UV abs |
0,75 |
1 |
0,75 |
1,22 |
0,2769 |
Residual |
23,4167 |
38 |
0,616228 |
|
|
Total (corrected) |
157,25 |
47 |
|
|
|
All F-ratios are based on the residual mean square error.
R-Squared = 85,1086 percent
R-Squared (adjusted for d.f.) = 81,5817 percent
Standard Error of Est. = 0,785002
Mean absolute error = 0,586806
Durbin-Watson statistic = 2,70544
Residual Analysis
|
Estimation |
Validation |
N |
48 |
|
MSE |
0,616228 |
|
MAE |
0,586806 |
|
MAPE |
6,17109 |
|
ME |
0,0 |
|
MPE |
-0,591566 |
|
Analysis of Variance for Hardness7
Source |
Sum of Squares |
Df |
Mean Square |
F-Ratio |
P-Value |
Model |
919,146 |
9 |
102,127 |
31,47 |
0,0000 |
Residual |
123,333 |
38 |
3,24561 |
|
|
Total (Corr.) |
1042,48 |
47 |
|
|
|
|
Type III Sums of Squares |
Source |
Sum of Squares |
Df |
Mean Square |
F-Ratio |
P-Value |
Anti skin |
1,02083 |
1 |
1,02083 |
0,31 |
0,5782 |
Binder |
63,0208 |
1 |
63,0208 |
19,42 |
0,0001 |
Color |
2,52083 |
1 |
2,52083 |
0,78 |
0,3837 |
Drier |
592,667 |
2 |
296,333 |
91,30 |
0,0000 |
Fungicide |
42,1875 |
1 |
42,1875 |
13,00 |
0,0009 |
HALS |
105,021 |
1 |
105,021 |
32,36 |
0,0000 |
Thix binder |
54,1875 |
1 |
54,1875 |
16,70 |
0,0002 |
UV abs |
58,5208 |
1 |
58,5208 |
18,03 |
0,0001 |
Residual |
123,333 |
38 |
3,24561 |
|
|
Total (corrected) |
1042,48 |
47 |
|
|
|
All F-ratios are based on the residual mean square error.
R-Squared = 88,1692 percent
R-Squared (adjusted for d.f.) = 85,3672 percent
Standard Error of Est. = 1,80156
Mean absolute error = 1,30903
Durbin-Watson statistic = 2,34626
Residual Analysis
|
Estimation |
Validation |
N |
48 |
|
MSE |
3,24561 |
|
MAE |
1,30903 |
|
MAPE |
10,5103 |
|
ME |
-7,03141E-16 |
|
MPE |
-1,12406 |
|
Analysis of Variance for Drying time
Source |
Sum of Squares |
Df |
Mean Square |
F-Ratio |
P-Value |
Model |
141,904 |
9 |
15,7671 |
14,10 |
0,0000 |
Residual |
41,3728 |
37 |
1,11818 |
|
|
Total (Corr.) |
183,277 |
46 |
|
|
|
|
Type III Sums of Squares |
Source |
Sum of Squares |
Df |
Mean Square |
F-Ratio |
P-Value |
Anti skin |
10,6892 |
1 |
10,6892 |
9,56 |
0,0038 |
Binder |
2,0086 |
1 |
2,0086 |
1,80 |
0,1883 |
Color |
1,28211 |
1 |
1,28211 |
1,15 |
0,2912 |
Drier |
118,325 |
2 |
59,1626 |
52,91 |
0,0000 |
Fungicid |
7,36865 |
1 |
7,36865 |
6,59 |
0,0144 |
HALS |
1,3163 |
1 |
1,3163 |
1,18 |
0,2850 |
Thix binder |
1,62506 |
1 |
1,62506 |
1,45 |
0,2357 |
UV abs |
0,0224921 |
1 |
0,0224921 |
0,02 |
0,8880 |
Residual |
41,3728 |
37 |
1,11818 |
|
|
Total (corrected) |
183,277 |
46 |
|
|
|
All F-ratios are based on the residual mean square error.
R-Squared = 77,426 percent
R-Squared (adjusted for d.f.) = 71,9351 percent
Standard Error of Est. = 1,05744
Mean absolute error = 0,714632
Durbin-Watson statistic = 1,76075
Residual Analysis
|
Estimation |
Validation |
N 47 |
|
MSE |
1,11818
| |
MAE |
0,714632
| |
MAPE |
14,817
| |
ME |
0,0
| |
MPE |
-3,2546 |
|
The StatAdvisor
--------------------
This pane summarizes the results of fitting 7 general linear statistical model relating 7 dependent variables to 8 predictive factors. Since the P-value in the first ANOVA table for YellowingOne is less than 0.01, there is a statistically significant relationship between YellowingOne and the predictor variables at the 99% confidence level.
The R-Squared statistic indicates that the model as fitted explains 77,426% of the variability in YellowingOne. The adjusted R-squared statistic, which is more suitable for comparing models with different numbers of independent variables, is 71,9351%. The standard error of the estimate shows the standard deviation of the residuals to be 1,05744. This value can be used to construct prediction limits for new observations by selecting the Reports option from the text menu. The mean absolute error (MAE) of 0,92467 is the average value of the residuals. The Durbin-Watson (DW) statistic tests the residuals to determine if there is any significant correlation based on the order in which they occur in your data file. Since the DW value is greater than 1.4, there is probably not any serious autocorrelation in the residuals.
The output also summarizes the performance of the model in fitting the data, and in predicting any values withheld from the fitting process. It displays:
(1) the mean squared error (MSE)
(2) the mean absolute error (MAE)
(3) the mean absolute percentage error (MAPE)
(4) the mean error (ME)
(5) the mean percentage error (MPE)
Each of the statistics is based on the residuals. The first three statistics measure the magnitude of the errors. A better model will give a smaller value. The last two statistics measure bias. A better model will give a value close to 0.0.
Below is a graphical presentation of the significant factors
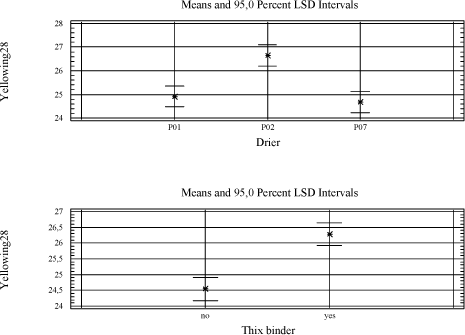
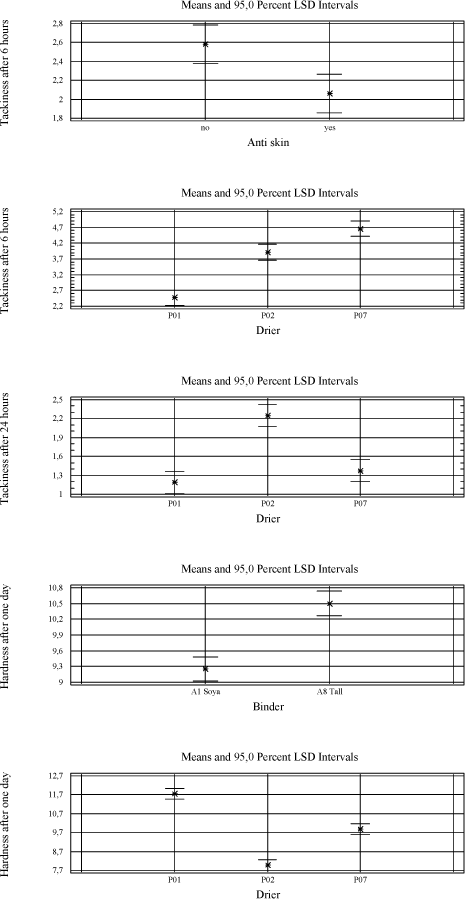
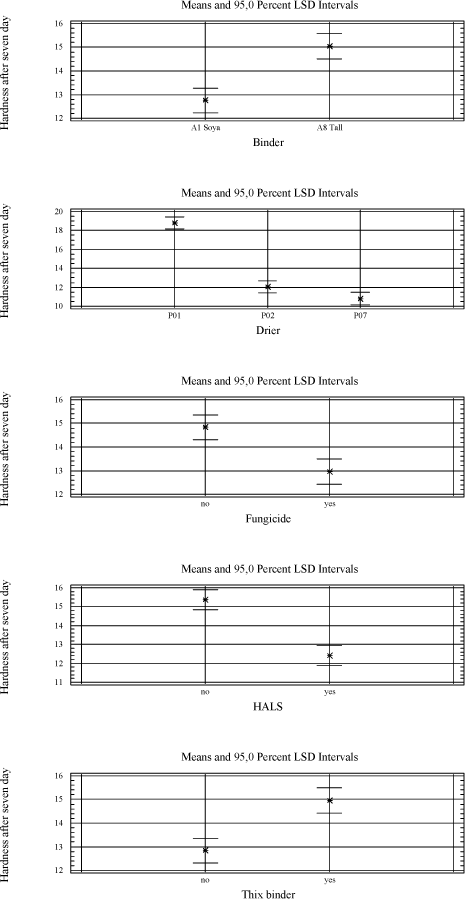
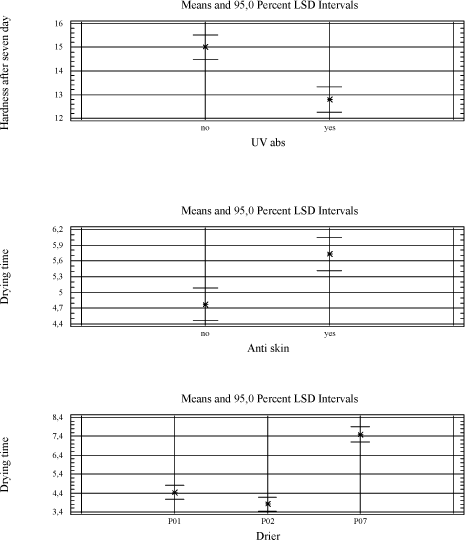
| Top | | Front page |
Version 1.0 August 2006, © Danish Environmental Protection Agency
|