Metoder til reducering af farvespild ved tømning og vask af farveværk er i dette
projekt hovedsageligt blevet undersøgt på et forsøgsanlæg
hos TRESU (se bilag G), men også i mindre grad på to fungerende
trykpresser på trykkeri A (se bilag C).
TRESUs forsøgsanlæg består af en kort
aniloxvalse med tilhørende pumpeenhed med farvefremføringssystem samt højtryksdysevaskesystem. Et tilsvarende anlæg (Pump Unit med højtryksdysevaskesystem) er kommercielt tilgængeligt
og beskrevet i bilag B. Forsøgsanlægget er detaljeret beskrevet i bilag G og afviger fra
det kommercielle anlæg bl.a. ved at være påmonteret en kammerrakel af plexiglas.
Den ene trykpresse på trykkeri A er en Göpfert
flexotrykpresse fra 1995 monteret med TRESU kammerrakel med indbygget højtryksvask. Trykmaskinen har to farveværker og en
valsebredde på 3,6 meter. Farvefremføring og -tilbageføring varetages af to pneumatisk
drevne membranpumper, og begge pumper
deltager i udpumpning af farve, når farveværket tømmes før vask. Højtryksdyserne, som
renser farveværket, bliver forsynet med varmt vand af en højtrykspumpe placeret over
farveværket, og der er ingen genbrug af dette vand.
Den anden trykpresse på trykkeri A er en Göpfert flexotrykpresse fra 1972 med en
åben farvebakke og en valsebredde på 4 meter.
Farvefremføringen sker med en enkelt membranpumpe, som pumper farven op i en
gravitationsbeholder, hvorfra det løber til farvebakken. Tømning sker ved passiv
gravitation, og afvaskningen foregår manuelt med vandslange og børste.
Den farvemængde, der står tilbage på et farveværk før vask, benævnes her residualfarvemængden (farvedødvolumenet)
og afhænger af farveværkets udformning, volumen, og af hvor godt det er tømt.
Residualfarvemængden er den maksimale mængde farve, der kan spildes under vask, og
derfor vil det altid være en fordel at minimere denne. Residualfarvemængden for TRESUs
forsøgsanlæg blev bestemt ved adskillige forsøg (se bilag G) udfra enten
differensvejninger som i forsøget illustreret i figur 9.1 eller ved at skylle
residualfarven ud med rent vand, måle tørstofindholdet og beregne mængden herudfra.
Resultaterne varierede mellem 0,56 og 1,0 kg. De resultater, som blev anset for mest
nøjagtige, lå omkring 0,6 kg, og det er derfor valgt at anvende denne værdi i alle
udregninger, f.eks. af relativ genvinding af farve.
Forsøgene viste endvidere, at omkring 85% af residualfarvemængden kan befinde sig i
pumper (farvefremførings- og tilbageføringspunper) og tilstødende, vandrette rør.
Der er grundlæggende to metoder til tømning før vask, passivt tilbageløb og tilbagepumpning, og på TRESUs forsøgsanlæg tømmes der
ved tilbagepumpning med to pumper. Der blev således gennemført et forsøg (se tabel G.1
i bilag G), hvor tilbagepumpningstiden blev varieret og residualfarvemængden blev
beregnet.
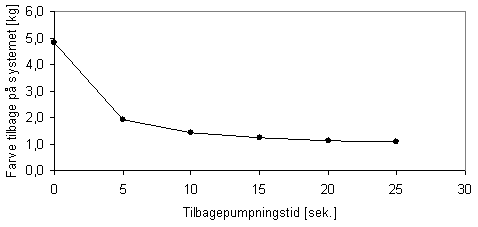
Figur 9.1
Betydningen af tilbagepumpningstid for tømningen af TRESUs forsøgsanlæg
Resultaterne af undersøgelsen indikerer, som det ses af figur 9.1, at uanset hvor lang
tid der pumpes tilbage, vil der være omkring 1 kg farve tilbage på dette anlæg. Under
trykningen er der ca. 5 kg farve på farveværket. Som det ses af figur 9.2 herunder,
pumpes der på de første 5 sekunder ca. 2,9 kg farve ud, mens der de næste 5 sekunder
pumpes yderligere ca. 0,5 kg farve ud.
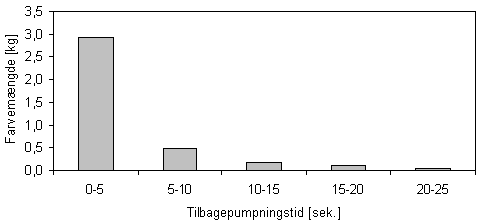
Figur 9.2
Betydningen af tilbagepumpningstid for tømningen af TRESUs forsøgsanlæg. Søjlerne
angiver hvor meget farve, der pumpes ud i det givne tidsinterval.
Betydningen af udpumpningstiden blev også undersøgt på
et fungerende full-size anlæg under normal drift på
trykkeri A (se tabel C.6 i bilag C). Anlægget var en Göpfert trykpresse fra 1995 med
TRESU kammerrakel. Farveværket blev også i dette tilfælde tømt ved, at begge pumper
pumpede farven ud. Undersøgelsen viste, at tømningen de første 4 minutter foregik i et
højt tempo ca. 1 kg/min., hvorefter hastigheden faldt til ca. 0,1 kg/min. Selv efter 11
minutter, hvor residualfarvemængden udgør ca. 3 kg,
kunne der stadig pumpes lidt farve ud.
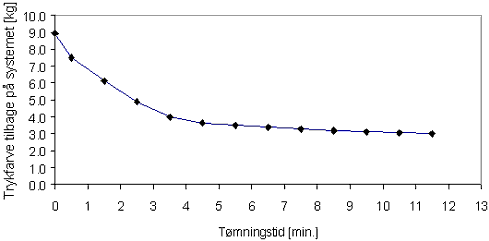
Figur 9.3
Betydningen af tilbagepumpningstid for tømningen af farveværk på en Göpfert 1995
trykpresse
Undersøgelserne viser, at selvom det meste farve kommer hurtigt ud, kan man med fordel
fortsætte så lang tid som muligt, eller til operatøren kan se, at der ikke kommer mere.
For TRESUs forsøgsanlæg er der ikke nogen ide i at fortsætte længere end ca. 25
sekunder. Forsøgene her illustrerer, at tilbagepumpningstiden/afløbstiden er kritisk for
hvor meget farve, der tømmes af farveværket. For at kunne optimere tilbagepumpnings-/afløbstiden er det
nødvendigt at måle på det konkrete anlæg på virksomheden. Målingen er ganske simpel (kræver spand, ur og
vægt) og kan udføres af virksomheden selv.
Når farveværket er tømt så meget som muligt for farve påbegyndes afvaskningen.
Farveværket vaskes normalt med vand ved skylning (flush) eller ved højtryksvask kombineret med flush. I begge
tilfælde vil det første vaskevand, der kommer igennem systemet, have en høj andel af
farve. Mulighederne for at genvinde farven ved at lade dette første vaskevand gå til
farvespanden, afhænger dels af fordelingen mellem farve og vand i vaskevandet, og dels af
hvordan en tilførsel af vaskevand påvirker farven. I dette afsnit gennemgås først
undersøgelser af fordeling mellem vand og farve i det første vaskevand ved forskellige
vaskemetoder og derefter betydningen for trykfarvens egenskaber.
TRESUs forsøgsanlæg kan indstilles således, at når vasken startes, er den
første aktion et kort tryk (boost) med vand fra højtryksdyserne i kammerraklen, og den
farve, som herved presses ud eller løber ud, går med vandet til farvespanden og
genbruges. Hvor stor en del af residualfarvemængden, som kommer tilbage i farvespanden,
afhænger af boosttiden, som er den tid, boostet varer.
I figur 9.4 er resultaterne vist for et forsøg med boosttidens betydning på TRESUs
forsøgsanlæg (se tabel G.2 i bilag G). Som det kunne forventes, betyder en øget boosttid, at en større del af residualfarvemængden går tilbage til
farvespanden, men også at farveandelen, af det som går tilbage i farvespanden, er
mindre. Under forsøget blev der opsamlet dels fra farvetilføringsstudsen og dels fra
farvetilbageføringsstudsen, og ca. 80% af det fjernede farve kom ud af
farvetilbageføringsstudsen, mens ca. 20% kom ud af farvetilføringsstudsen.
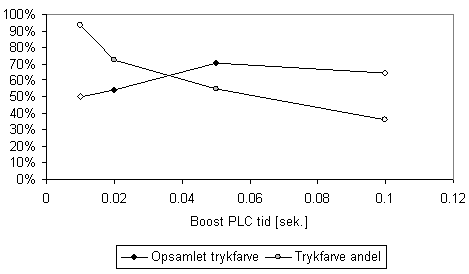
Figur 9.4
Boosttidens betydning for mængden af farve der går tilbage i farvespanden (opsamlet
trykfarve i procent af residualfarvemængden) og for fordeling mellem farve og vand i det
som går tilbage til farvespanden. Hvide målepunkter er korrigerede værdier.
Korrektionen var nødvendig, fordi der her kun er opsamlet fra
farvetilbageføringsstudsen. TRESUs forsøgsanlæg.
Forsøget viser, at der kan opnås en rimelig stor forøgelse i den farvemængde, der
genvindes ved at gå fra 0,01 sek. til 0,05 sek. Yderligere forlængelse af boosttiden
medfører ikke større farvegenvinding, men blot at der
går mere vand tilbage i farvespanden. Dette ses også tydeligt af figur 9.5. Det meget
høje farveindhold i det boostvand, som går tilbage i farvespanden ved meget korte boost,
skyldes antageligt, at boostet skaber et tryk (lufttryk) i systemet, der kan presse
trykfarve ud af slanger og pumper med meget lidt vand.
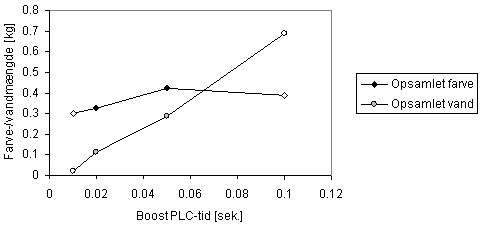
Figur 9.5
Mængden af farve og vand der går tilbage til farvespanden med boost af en given
længde. Hvide målepunkter indikerer, at tallene er korrigeret tilsvarende figur 9.4.
TRESUs forsøgsanlæg
Ved et andet forsøg (tabel G.4 i bilag G) hvor der blev boostet i 0,02 sek. blev der
genvundet 0,34 kg farve svarende til ca. 61% af residualfarvemængden bestemt til 0,56 kg.
I figur 9.6 er det vist, hvad de forskellige boosttider betyder for fortynding af 15
liter farve, som typisk er den mængde, der cirkuleres på farveværket under tryk (15-20
liters farvespand). Figuren viser, at man kan genvinde ca. 50% af
residualtrykfarvemængden med en fortynding af trykfarven på under 1% eller ca. 70% ved
en fortynding på under 2%.
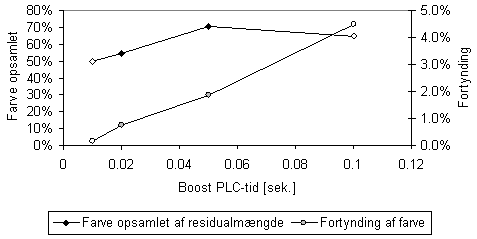
Figur 9.6
Fortynding af 15 liter trykfarve som funktion af opsamlet vand- og farvemængde ved
højtryksvask. Hvide målepunkter indikerer, at tallene er korrigeret tilsvarende figur
9.4. TRESUs forsøgsanlæg.
Når der boostes på TRESUs forsøgsanlæg, sker det ved,
at PLCen åbner for en ventil, således at der er forbindelse
mellem dyserne i kammerraklen og højtrykspumpen. Ved PLC-tid
forstås her den tid, PLCen (Programable Logic Controller, lille computer der her
styrer bl.a. vaskeanlæg) er programmeret til at holde dyserne åbne - svarer i princippet
til den reelle boosttid. Betydningen af boosttiden, dvs. den tid
ventilen er åben for mængden af vand, der kommer ud af dyserne, er blevet undersøgt ved
en forsøgsrække (tabel G.7 i bilag G). Resultatet af forsøget er vist i figur 9.7. For
de korte boosttider er der tilsyneladende en lineær sammenhæng mellem boosttid og
vandmængde, svarende til et konstant output fra dysen, men ved længere boosttider falder
output pr. tidsenhed.
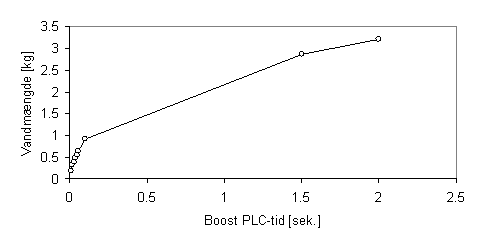
Figur 9.7
Boost PLC-tidens betydning for vandmængden der skylles med. TRESUs forsøgsanlæg.
I et andet forsøg (tabel G.9 i bilag G) blev det ved hjælp af monterede ventiler
muligt at udtage boost til farvespand fra både farvefremførings- og tilbageføringsstuds
samtidig. Resultatet af forsøget er vist i figur 9.8.
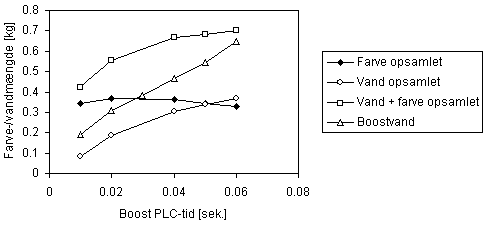
Figur 9.8
Boost PLC-tidens betydning for vandmængden der skylles med (forsøg med
fortrængning) og for farve og vand, der går i farvespanden (forsøg med opsamling med
ventil). TRESU forsøgsanlæg.
Som det fremgår af figur 9.8, går der en større mængde vand og farve til
farvespanden end den mængde vand, der boostes med, specielt for de korteste boosttider,
og det skyldes formodentlig, at det tryk, som boostet skaber, "skyder" farve ud.
Herudover viser forsøget, at farvemængden, der går i farvespanden, i dette tilfælde
stort set er den samme uanset boosttiden, mens vandmængden naturligvis stiger med
længere boosttid. Dette indikerer sammen med de andre omtalte forsøg, at det er
fordelagtigt at anvende korte boosttider, hvis man vil
lade boostvand gå i farvespanden.
Undersøgelserne, som ovenfor beskrevet, viser, at der især ved meget korte boost
tages meget farve med i forhold til vand. Muligheden for at anvende serier af korte boost til at genvinde farve blev derfor
undersøgt ved samme forsøg. Der blev boostet først én gang og umiddelbart efter endnu
2 gange. Dette boostvand blev opsamlet ved hjælp af førnævnte ventil, hvorefter
vaskecyklussen blev fortsat. Forsøget viste, at man kan opnå et højere farveindhold i
det, som går til farvespanden, ved at benytte flere korte boost fremfor et længere.
Ligeledes opnår man en bedre farvegenvinding ved at køre
en serie af korte boost fremfor et langt. Det fremgår tydeligt af figur 9.9, 9.10 og
9.11. Figur 9.11 viser således, at der ved at booste 0,01 sek. 3 gange i serie kan opnås
en farvegenvinding på over 90% ved en samtidig fortynding
af farven i farvespanden på kun omkring 1%. At der, som det fremgår af figur 9.11,
tilsyneladende kan genvindes over 100% farve skyldes, at residualfarvemængden ved de
pågældende målinger har været lidt højere end 0,6 kg, som er anvendt ved
beregningerne.
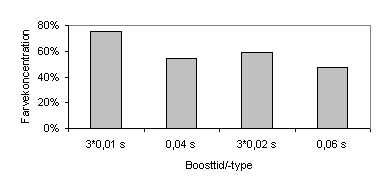
Figur 9.9
Andelen af farve i det boostvand som går til farvespanden efter første
boost/boostserie. TRESUs forsøgsanlæg.
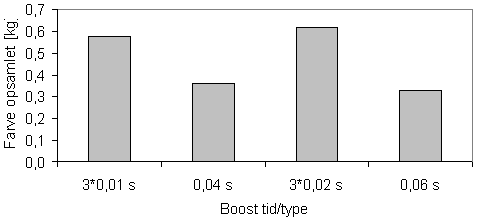
Figur 9.10
Mængden af farve som går med boostvandet tilbage til farvespanden efter første
boost/boostserie. TRESUs forsøgsanlæg.
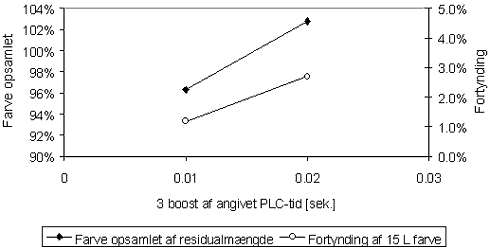
Figur 9.11
Fortynding af 15 L trykfarve som funktion af opsamlet vand- og farvemængde ved
tripelboost på 0,01 sek. og 0,02 sek. TRESUs forsøgsanlæg.
Muligheden for at genbruge det første skyllevand er også blevet undersøgt på en
stor flexotrykpresse (valsebredde 360 cm) under normal drift. Det drejer sig om forsøg
på et Göpfert 1995 anlæg med TRESU
kammerrakelrensesystem med højtryksdyser og opvarmet vand, se tabel C.4 og C.5 i bilag C.
Dette anlæg er ældre end forsøgsanlægget (Pump Unit) og således ikke optimeret med
hensyn til afvaskning. Vasken foregår her ved, at dyser spuler kammerraklen, mens
fremførings- og tilbageføringspumperne pumper skyllevandet ud, men der er ikke tale om
korte boost som på forsøgsanlægget. I dette tilfælde blev vaskevandet opsamlet i
fraktioner. I hver fraktion blev der målt tørstofindhold,
pH og temperatur. Resultaterne er vist på
figur 9.12-14.
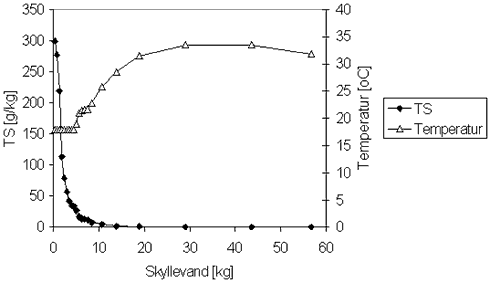
Figur 9.12
Opsamling af skyllevand fra Göpfert 1995, rød farve
Figur 9.12 viser, hvordan tørstofindholdet i skyllevandet falder med mængden der
pumpes ud. Grafen viser, hvordan stort set al farve kommer ud med de første 15 liter. På
grund af det opvarmede vaskevand stiger temperaturen af det udpumpede også efterhånden,
men de første ca. 5 liter har stuetemperatur ligesom trykfarven.
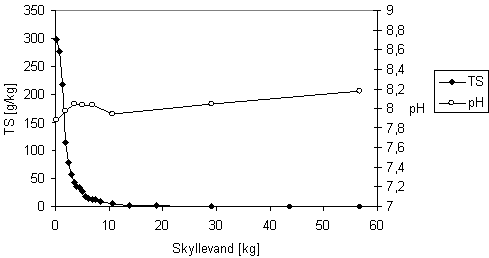
Figur 9.13
Opsamling af skyllevand fra Göpfert 1995, rød farve
Figur 9.13 viser, hvordan pH varierer i det opsamlede vaskevand. Det
ses, at pH varierer mellem ca. 7,9 og 8,2.
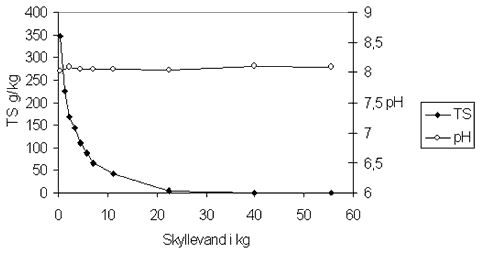
Figur 9.14
Opsamling af skyllevand fra Göpfert 1995, sort farve
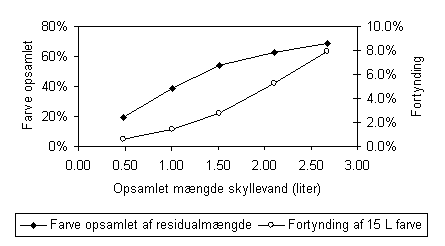
Figur 9.15
Fortynding af 15 L trykfarve som funktion af opsamlet vand- og farvemængde ved
højtryksvask. Göpfert 1995 trykpresse med TRESU kammerrakelrensesystem.
Figur 9.14 viser, hvordan pH og tørstof varierer i opsamlede
fraktioner for et forsøg med vask efter tryk med sort farve på Göpfert 1995. Også her
er næsten al farve vasket ud med de første ca. 15 liter. pH varierer
kun ganske lidt i vaskevandet og ligger omkring ca. 8,2.
Som det fremgår af figur 9.15, kan der på dette ikke optimerede afvaskningsanlæg
opnås genvinding af ca. 40% farve med en resulterende fortynding på ca. 1,5% af de 15 L
farve i farvespanden.
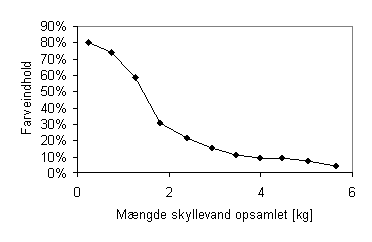
Figur 9.16
Opsamling af skyllevand fra Göpfert 1995, rød farve
Figur 9.16 viser, hvordan farveindholdet er i de første liter af skyllevandet, og det
ses, at farveindholdet i den første 0,5-1 liter er omkring 80%.
Som opsummering kan det anføres, at forsøgene beskrevet i dette afsnit tydeligt
viser, at man på trykpresser, hvor højtryksvask benyttes,
kan opnå stor genvinding af farve ved at opsamle det første skyllevand, og det vel at
mærke uden at der sker en større fortynding af farven i farvespanden end ca. 1-5%.
Specielt viser undersøgelserne, at den bedste genvinding og det bedste forhold mellem
farve og vand, som giver den mindste fortynding, hvis det går i farvespanden, opnås ved
at benytte korte boost. Forsøgene viste også, at det er mere fordelagtigt at anvende en
serie af korte boost end et langt.
Ved vask med flush vaskes farveværket ved, at der pumpes vand
rundt i systemet med farvefremførings- og farvetilbageføringspumpen, og her vil det
være muligt at lade det første skyllevand gå tilbage i farvespanden. Der blev
gennemført et forsøg på TRESUs forsøgsanlæg, hvor højtryksvasken blev frakoblet, og
systemet blev opereret som ved normal flush. Efter endt tømning af systemet for farve,
ved tilbagepumpning som normalt, blev der skyllet med rent vand fra vandspanden, og
skyllevandet blev opsamlet sekventielt. Mængden af farve, der blev opsamlet med det
første skyllevand, er vist i figur 9.17.
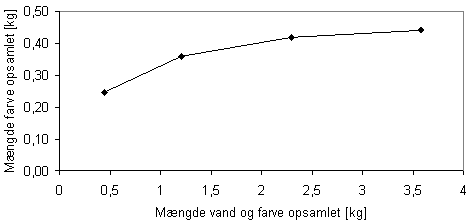
Figur 9.17
Mængden af farve i det første skyllevand ved flush. TRESU forsøgsanlæg.
Som det ses af figur 9.17, er der omkring 0,25 kg farve i den første halve liter
skyllevand, der kommer ud ved flush på TRESUs forsøgsanlæg.
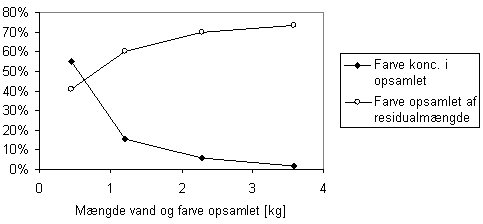
Figur 9.18
Den andel af trykfarvemængden, der er på anlægget efter tømning, og som opsamles
med den angivne mængde vand ved flush samt indholdet af trykfarve i skyllevandet. TRESUs
forsøgsanlæg.
Af figur 9.18 ses det, at man i den første liter skyllevand kan opsamle omkring 50% af
den trykfarve, der er tilbage på farveværket før vask. I denne første liter er omkring
25-30% trykfarve.
Det der er afgørende for hvor meget af skyllevandet, man kan lade gå til
farvespanden, er den fortynding af farven, der sker. Dette er illustreret i figur 9.19,
hvor det kan ses, at hvis man ved flush opsamler ca. den første liter vaskevand, opnår
man at genvinde ca. 50% af residualfarvemængden. Hvis
der er 15 liter farve i farvespanden, fortyndes farven 3-4%.
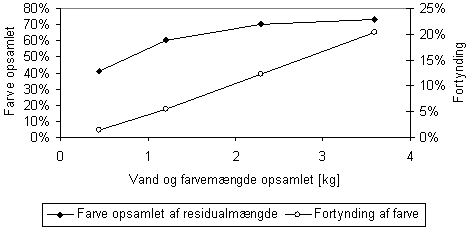
Figur 9.19
Fortynding af 15 liter trykfarve som funktion af opsamlet vand og farve
mængde ved flush. TRESUs forsøgsanlæg.
For at undersøge mulighederne for opsamling af det første skyllevand fra en stor
trykpresse (valsebredde 450 cm) med manuel vask under normal
drift, blev et forsøg med en ældre Göpfert 1972 trykpresse gennemført. Det drejer sig
her om en gammel trykpresse med åben farvebakke og manuel afvaskning (se tabel C.8 i
bilag C). Den manuelle vask foregik med vandslange og børste og metoden kan bedst
sammenlignes med flush. Forsøget viste, at i lighed med forsøget på Göpfert 1995
(kammerrakel med højtryksdysesystem) får man næsten al farven ud med de første 15
liter. Resultaterne er illustreret i figur 9.20.
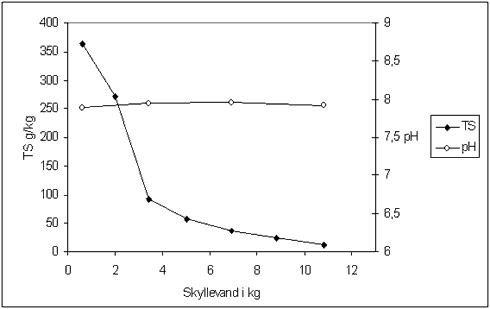
Figur 9.20
Opsamling af skyllevand fra Göpfert 1972, blå farve
På figur 9.21 er farveindholdet i skyllevandet vist, og det ses, at der er omkring 80%
farve i den første 0,5-1 liter skyllevand også ved manuel vask. Da residualfarvemængden
er omkring 3-4 kg, vil man ved at opsamle de første 1,3 kg skyllevand kunne opnå en
farvegenvinding på 26-35%.
Tilbageføres dette i en farvespand med 15 L farve, vil det medføre en fortynding på
godt 1%.
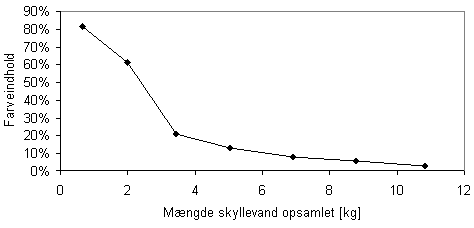
Figur 9.21
Opsamling af skyllevand fra Göpfert 1972, blå farve
Sammenlignes flush og højtryksvask for TRESUs forsøgsanlæg ser man, at der ved
højtryksvask, når der boostes i 0,05 sekunder (figur 9.4, 9.5 og 9.8), opsamles ca. 0,4
kg farve (i knap 0,3 kg vand) svarende til 70% af den farve, der er tilbage på anlægget.
Koncentrationen af farve i dette første skyllevand bliver således ca. 60%. Ved flush
derimod skal man lade de første godt to liter af skyllevandet gå i farvespanden for at
opnå omtrent samme farvegenvinding (figur 9.17). Der ville altså i det tilfælde gå ca.
1,65 liter vand i farvespanden. Som illustreret i figur 9.22 er det altså muligt at opnå
en større farvegenvinding ved højtryksvask end ved flush, og med undtagelse af den
laveste farvegenvinding, går der langt mindre vand i farvespanden, når højtryksvask
anvendes. Ved højtryksvask med gentagne korte boost (f.eks. 3 · 0,01 sek.), er det
endvidere muligt at opnå i nærheden af 100% genvinding af farve ved en samtidig
fortynding af farven i farvespanden på kun ca. 1%. Er flush den eneste mulighed, kan der
dog på et anlæg som TRESUs forsøgsanlæg stadig genvindes omkring 40-50% af trykfarven
på anlægget, ved at lade de første ca. 0,7 liter vand gå i farvespanden. Forsøgene
udført på de to full-size trykpresser (Göpfert 1995 og 1972) under normal drift
bekræfter, at det på ikke optimerede anlæg i hvert fald er muligt at opnå 30-40%
genvinding af farven, og at den resulterende fortynding af 15 L farve kun vil udgøre
omkring 1%.
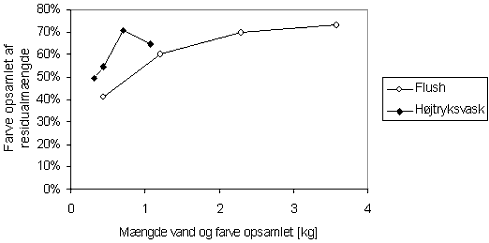
Figur 9.22
Sammenligning af trykfarveopsamlingen i procent af det som står på anlægget før
vask (residualmængden), som funktion af den mængde vand og trykfarve der opsamles.
TRESUs forsøgsanlæg.
Efter vask med vand vil en del vand stå tilbage på systemet og fortynde den nye
farve, der køres på farveværket. Denne mængde vand benævnes residualvandmængden (vanddødvolumenet).
Når det vurderes, hvor meget vand man kan lade gå med i farvespanden med den genvundne
farve, er det værd at huske, at der på alle anlæg, som vaskes med vand, allerede sker
en fortynding af farven med denne residualvandmængde. Er der 15 liter i farvespanden,
sker der for eksempel en fortynding på 1,9% på TRESUs forsøgsanlæg. På større anlæg
af samme type kan det forventes, at residualvandmængden er lidt større og fortyndingen
ligeledes lidt større.
Som de foregående afsnit viser, er der gode muligheder for at genvinde en del af
residualfarvemængden ved at opsamle/udtage det første boostvand eller skyllevand. Dette
afsnit omhandler hvilken indflydelse, en vandig fortynding af farven på 1-10% har på trykfarvens tryktekniske egenskaber. De
fire procesfarver sort, cyan, magenta og gul blev undersøgt,
og undersøgelserne er detaljeret beskrevet i bilag G (afsnit G.3).
Fortyndingens indvirkning på viskositeten
Betydningen af fortynding med
vand for viskositeten er undersøgt ved at måle gennemløbstider
med en DIN 4 kop, og resultaterne er vist på figur 9.23. Det ses,
at viskositeten, især for farver med høj viskositet,
falder kraftigst med det første vand. Ændringen i viskositet går fra lidt over 3
sekunder til ca. 1 sekund pr. procent fortynding.
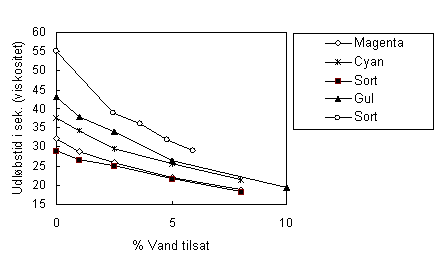
Figur 9.23
Fortyndingskurver for vandfortyndbare flexotrykfarver. % vand beregnes som: masse
vand/(masse vand+masse farve).
Fortyndingens betydning for overfladespændingen
Overfladespændingen har betydning for befugtningen af underlaget, og betydningen
af fortynding blev undersøgt for den sorte farve. En 5% fortynding gav en reduktion i
overfladespænding fra 35,4 mN/m til 34,8 mN/m, hvilket vurderes at ligge inden for
målemetodens usikkerhed og være uden betydning for trykfarvens befugtning
af underlaget.
Fortyndingens betydning for lagtykkelsen
Lagtykkelsen på en liner efter påføring af mere eller mindre
fortyndede farver med spiralapplikatorer blev uden held
forsøgt målt ved differensvejning. En teoretisk overvejelse viser imidlertid, at
lagtykkelsen af den tørre farve bliver reduceret svarende til fortyndingen af farve. For
eksempel giver 8% fortynding et 8% tyndere lag. For det tykkeste lag, påført med
applikator mrk. 10, vil en 8% fortynding således svare til, at laget reduceres fra 5,96
g/m2 til 5,48 g/m2.
Fortyndingens betydning for densiteten af det tørre tryk
Indvirkningen af fortynding på densiteten af det færdige tryk blev undersøgt for
sort farve. Densitet er en reflektionsmåling,
som anvendes i trykkerierne til vurdering og kontrol af farvestyrken.
Undersøgelsen viste, at der, uanset farvelagets tykkelse, ikke var nogen forskel på den
målte densitet for tryk, der var fortyndet med fra 0 til 8% vand.
Fortyndingens betydning for kuløren af det tørre tryk
Kuløren af tryk skabt ved påføring af mere eller mindre fortyndet, sort farve
blev undersøgt med et spektrofotometer, se figur 9.24.
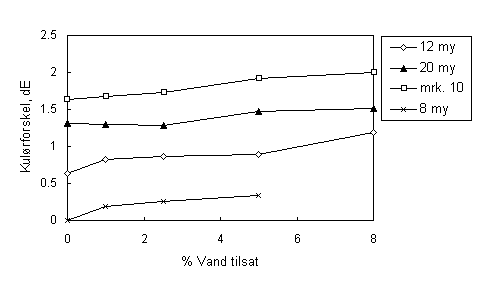
Figur 9.24
Kulørmåling på tørt tryk med ren og fortyndet sort farve
Som det ses af figuren, stiger kulørforskellen med fortynding, og forskellen i kulør på tryk med ufortyndet farve og farve fortyndet med 8% vand
ligger omkring 0,4-0,5 E enheder. Denne forskel er synlig for et trænet øje og svarer
til, at der er påført ca. 1 g mindre pr. m2.
En forventet lagtykkelse i flexografi er
formentlig af størrelsesordenen 1-3 m m. Det betyder, at der
kan være en kulørforskel af størrelsesordenen 1 enhed, som
alene skyldes indstilling af flexomaskinen fra gang til gang. Det vil sige, at den
farveforskel, en 8% fortynding af farven afstedkommer, ligger inden for den usikkerhed,
som allerede eksisterer i påføringsmetode og målemetode. Normalt kan en farveforskel
på 1 enhed ses, om end denne farveforskel stort set altid vil ligge inden for den
tolerance, som defineres ved kvalitetsstyring. Det skal dog
understreges, at forskellige farver udviser forskellig følsomhed for fortynding, og at
øjet ikke er lige følsomt over for alle farver, hvilket betyder, at man typisk laver
individuelle tolerancer for de forskellige farver.
Undersøgelserne beskrevet ovenfor viste, at man ved at opsamle det første
skyllevand kan opnå en betydelig farvegenvinding. Desuden viser undersøgelserne, at hvis
dette skyllevand tilføres farvespanden (med 15 L farve i), vil den resulterende
fortynding stort set ikke ændre farvens tryktekniske egenskaber, se tabel 9.1.
Tabel 9.1
Undersøgelsesresultater
Man kan f.eks. ved at lade det første boost på 0,02 sekunder gå i farvespanden opnå en
genvinding på 65% eller ca. 0,4 kg farve på TRESUs forsøgsanlæg, og ved flush kan man
ved at lade den første liter af skyllevandet gå i farvespanden opnå en farvegenvinding
på 50%. Blot med en større fortynding af farven i farvespanden. Undersøgelserne viser,
at disse genvindinger kan opnås uden væsentlig effekt på trykfarvens egenskaber,
sålænge der ikke fortyndes mere end ca. 8%. Har anlægget mulighed for at generere en
serie af korte boost, kan man opnå en endnu højere genvinding, mere end 80%. Hvis der
spædes op med koncentreret farve, vil processen kunne gentages adskillige gange. Disse
tal stammer fra målinger på et forsøgsanlæg, men alle dele af forsøgsanlægget,
undtagen kammerraklen og farveslangerne, var i normal størrelse set i forhold til
bølgepap. At der kan genvindes farve svarende til i hvert fald 40% af residualfarvemængden resulterende i en fortynding med
vand på kun 1% i 15 liter trykfarve, bekræftes af forsøg på de to fungerende, ældre,
full-size trykpresser. Derfor viser resultaterne af de her udførte forsøg, at der endog
på ældre, ikke optimerede anlæg ved opsamling af det første skyllevand vil kunne
spares meget farve.
Genbrug af vand har til formål ikke kun at nedbringe
forbruget af friskvand men mere væsentligt at minimere volumenet af spildevand, der skal
renses eller afledes. Der skelnes mellem tre typer af vandgenbrug:
Direkte genbrug: Vandet genbruges
direkte fra én proces til en anden. Dette kan f.eks. gælde genbrug af vand fra sidste
skyl som skyllevand i nyt, første skyl.
Recirkulering: Vandet genbruges flere gange i den
samme proces. Dette kan f.eks. gælde recirkulering af
skyllevand fremfor direkte skyl til sump.
Genbrug via opgradering: Vandet genbruges
efter at have været gennem en rensningsproces. Dette kan gælde både direkte genbrug og
recirkulering.
I dette afsnit gennemgås de forskellige genbrugsmuligheder.
Som nævnt ovenfor er det væsentligste formål med reduktion at reducere mængden
af spildevand, som afledes fra vaskeprocessen til sumpen. Reduktionen bør i første
omgang sigte mod direkte genbrug af skyllevandet internt i skylleprocessen. Dette vil
opkoncentrere stofmængden i en mindre spildevandsmængde, hvorved den efterfølgende spildevandsrensning vil kunne forløbe mere effektivt ved
en mindre økonomisk og miljømæssig belastning.
Ved modstrømsskyl forstås en skylleprocedure, hvor skylningerne gennemføres i en
række batches. Skyllevandet fra hvert skyl opbevares indtil den næste afvaskning, hvor
skyllevandet genbruges i den umiddelbart foregående batch. Kun skyllevandet fra den
første batch ledes til sumpen, mens der kun anvendes friskvand i den sidste batch.
Modstrømsskyl sikrer et minimalt vandforbrug og en maksimal opkoncentrering af farve i
det vand, som ledes til sumpen. Princippet er illustreret i figur 9.25.
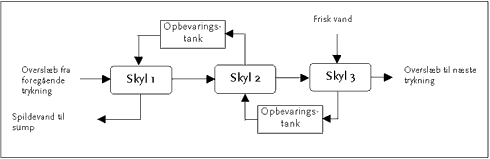
Figur 9.25
Princippet i et 3-trins modstrømsskyl
Et enkelt dansk anlæg (TRESUs Pump Unit, se bilag B) opererer i dag med direkte
genbrug af brugt skyllevand i skylleprocessen. I dette anlæg recirkuleres først brugt
skyllevand fra sidste vask. Dette vand føres efterfølgende til sump, og der skylles
afslutningsvis med friskvand. Vandet fra dette sidste skyl opsamles og genbruges som
første skyl i den næste afvaskning.
TRESUs Pump Unit opererer således med en kombination af recirkulering og
modstrømsskyl (2-trin). Et minimalt skyllevandsforbrug ved den nuværende teknologi vil
opnås ved omlægning til 3- eller 4-trins modstrømsskyl. Denne omlægning skal i givet
fald ske under hensyn til skyllekvaliteten, som ikke må forringes af hensynet til den
efterfølgende trykkeproces.
Der er gennemført en række målinger på det pågældende anlæg (dvs. TRESUs
forsøgsanlæg som omtalt i starten af dette kapitel) bl.a. med det formål at opstille en
massebalance for skylleprocessen og herved kunne regne på effekten af omlægninger til 3-
eller 4-trins modstrømsskyl. Baggrunden for beregningerne er gennemgået i bilag G
(afsnit G.5), hvor også en beskrivelse af udvalgte skylleprocedurer kan findes. I det
følgende gennemgås resultaterne ved sammenligning af følgende scenarier:
- Direkte skyl uden genbrug (3 trin)
- Direkte skyl med genbrug af sidste skyl (3 trin)
- 3-trins modstrømsskyl
- 4-trins modstrømsskyl
Det er ved beregningerne antaget, at farveværket kan rengøres tilfredsstillende med
ca. 14 L friskvand (4,6 L pr. batch). Det nødvendige skyllevandsforbrug er illustreret i
figur 9.26. Det fremgår, at genbrug af sidste skyl reducerer skyllevandsmængden med 1/3.
Såfremt der omlægges til fuldstændigt modstrømsskyl, kan dette forbrug yderligere
halveres og hermed kan opnås en besparelse på forbruget af friskvand. Det væsentligste
økonomiske og miljømæssige potentiale vurderes dog at ligge i reduktionen af
spildevand, som skal behandles.
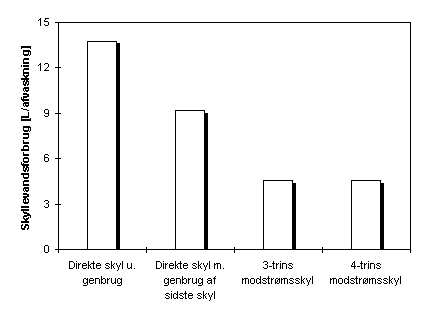
Figur 9.26
Nødvendigt skyllevandsforbrug ved de beregnede scenarier
Et vigtigt forhold ved omlægning af skylleproceduren er vandkvaliteten
af det sidste skyl, idet denne svarer til koncentrationen i den vandmængde, som efter
skyllet sidder i maskinen og overføres til næste trykkeproces. De beregnede
vandkvaliteter fremgår af figur 9.27.
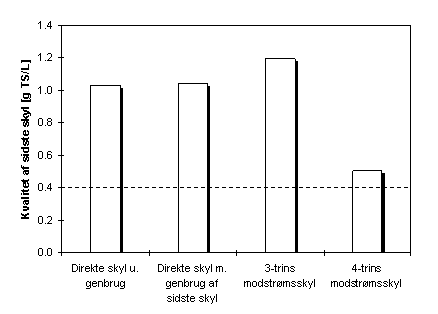
Figur 9.27
Vandkvalitet af sidste skyl ved de beregnede scenarier.
Den stiplede linie illustrerer vandkvaliteten af friskvand.
Det fremgår af figur 9.27, at der ved omlægning til 3-trins modstrømsskyl
sker en svag forringelse af vandkvaliteten i sidste skyl. Hvorvidt dette er acceptabelt,
må baseres på testskylninger på anlægget, men umiddelbart vurderes det ikke som noget
problem. Anvendes i stedet et 4-trins modstrømsskyl,
vil en meget effektiv skylning kunne opnås.
Vandkvaliteten af det spildevand, som ledes til sumpen, har interesse i forbindelse med
valg af rensningsteknologi.
Beregninger af dette fremgår af figur 9.28.
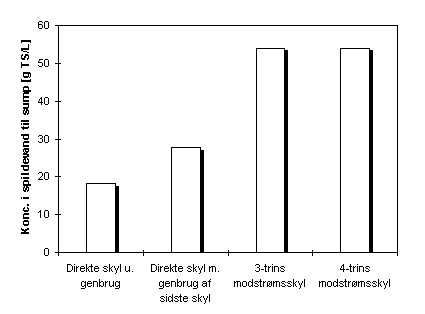
Figur 9.28
Forureningsgrad af brugt skyllevand som ledes til sump
Det fremgår af figur 9.28, at der opnås en væsentlig opkoncentrering ved brug af 3-
eller 4-trins modstrømsskyl fremfor direkte skyl. Betydningen af dette for valg af
rensningsteknologi vil blive gennemgået i afsnit 9.3.6.
Der vil således være en række tekniske og miljømæssige fordele forbundet med
omlægning til 3- eller 4-trins modstrømsskyl. Anlægsomkostningerne ved omlægning fra
genbrug af sidste skyl til 3- eller 4-trins modstrømsskyl forventes at være begrænsede.
Anlægget (Pump Uniten) har i dag én opbevaringstank til opbevaring af sidste skyl.
Ved omlægning til 3- eller 4-trins modstrømsskyl vil det være nødvendigt med 2 3
opbevaringstanke afhængigt af, om der vælges 3 eller 4 trin i skylleprocessen. Endvidere
vil det være nødvendigt med en mindre ombygning af pumpeenheden samt omprogrammering af
PLC-styringen. Det endelige antal af nødvendige opbevaringstanke må bestemmes ud fra en
statistisk vurdering af antallet af nødvendige skyl kombineret med yderligere
massebalanceberegninger samt på vurdering af de udgifter, der er forbundet med omlægning
til 3- eller 4-trins modstrømsskyl.
Direkte vandgenbrug i form af modstrømsskyl vil
således ikke reducere den samlede mængde stof, som ledes til sumpen, og som således
ikke kan nyttiggøres i trykkeprocessen med tab af råvare til følge. Dette vil kræve
tilbageføring af en del af skyllevandet til farvespanden, således at den udskyllede
farvemængde kan genbruges.
Som beskrevet i afsnit 9.2 er der udført forsøg med bl.a. at "booste" den
første skyllevandsmængde igennem systemet og returnere denne lille mængde til
farvespanden, her benævnt returskyl. Disse forsøg viste, at i hvert fald i
størrelsesordenen 40-60% af den farvemængde, som sidder tilbage i maskinen, kan
opsamles. Returskylningen kan således have den sidegevinst, at skyllevandsvolumenet kan
nedsættes. I det følgende præsenteres en række regneeksempler på effekten af at
returskylle farve til farvespanden efterfulgt af direkte skyl eller modstrømsskyl. Der
regnes med, at 50% af farven på anlægget går tilbage til farvespanden med returskyllet,
og følgende scenarier er analyseret:
2-trins skyl:
1. Direkte skyl uden genbrug
2. Direkte skyl med genbrug af sidste skyl (2-trins modstrømsskyl)
3-trins skyl
3. Direkte skyl uden genbrug
4. Direkte skyl med genbrug af sidste skyl
5. Modstrømsskyl
4-trins skyl
6. Modstrømsskyl
Som ved beregningerne i afsnit 9.3.2 er det her antaget, at farveværket kan
rengøres tilfredsstillende med ca. 14 L friskvand (4,6 L pr. batch). I figur 9.29 er
illustreret den beregnede vandkvalitet af det sidste skyl ved de beregnede scenarier. Det
fremgår tydeligt, at returskylningen ikke ændrer ved, at det er nødvendigt med tre skyl
for at opnå en tilstrækkelig god vandkvalitet i sidste skyl. Beregningerne viser dog
også, at returskylningen sikrer, at et 3-trins modstrømsskyl giver en tilfredsstillende
vandkvalitet i sidste skyl, hvorfor et 4. skyl ikke vurderes at være nødvendigt.
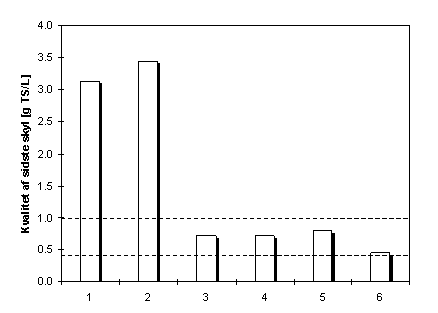
Figur 9.29
Vandkvalitet af sidste skyl ved de beregnede scenarier. Den øverste stiplede linie
illustrerer vandkvaliteten ved direkte skyl med genbrug af sidste skyl (3-trin) uden
returskylning, mens den nederste stiplede linie illustrerer vandkvaliteten af frisk vand.
Såfremt der gennemføres modstrømsskyl, vil spildevandet opkoncentreres
væsentligt (se figur 9.28). Dette kan muliggøre genbrug af spildevand uden opgradering ved at spæde det urensede spildevand til sort farve,
som i så fald skal leveres mere koncentreret fra leverandøren. En amerikansk virksomhed
har med succes gennemført dette og herigennem reduceret mængden af kemikalieaffald med 90%. Opspædning af sort farve med spildevand
havde ingen negativ effekt på kvaliteten af farven. Mindre mængder af spildevand vil
sandsynligvis også kun bruges til opspædning af andre farver, f.eks. grå /106/.
For at denne strategi kan lykkes og have en reel betydning, skal en væsentlig del af
den anvendte trykfarve være sort, samtidig med at vandforbruget skal reduceres til et
minimum via direkte genbrug. Beregningerne på opkoncentreringsgraden
ved introduktion af modstrømsskyl viser, at der kan opnås et tørstofindhold i
størrelsesordenen 50 g/L. Dette er dog stadig kun godt 1/10 af tørstofkoncentration i
brugsklar farve.
Opkoncentrering af spildevandet ved membranfiltrering
eller inddampning vil væsentligt øge
genanvendelsespotentialet af stoffraktionerne i spildevandet. Herigennem forventes det
muligt at opnå tørstofkoncentrationer i samme størrelsesorden som brugsklar farve.
På virksomhed A foregår godt 30% af samtlige kørsler med sort
farve, og forbruget af sort farve udgør tilsvarende godt 30% af det årlige
farveforbrug. På denne baggrund ses der et væsentligt potentiale i genbrug af farve fra
afvaskningen med eller uden opkoncentrering af skyllevandet.
Genbrug af spildevand/koncentrater i farverecepterne er både økonomisk og
miljømæssigt en optimal løsning, idet stofferne genbruges på det højest mulige niveau
som et fyldestgørende produkt. Råvareforbruget vil optimeres, og kemikalieaffaldsmængden
vil reduceres til et minimum. Hvorvidt
løsningen er teknisk mulig, er endnu uafklaret. Bl.a. vil løsningen sandsynligvis ikke
være mulig, hvis der anvendes afvaskningskemikalier i skylleprocessen.
Renset skyllevand kan i mange tilfælde ledes tilbage i processen og genbruges som
skyllevand, såfremt rensningsteknologien er tilstrækkeligt effektiv. Dette vil typisk
gælde vand fra membranfiltrering og inddampning men også vand fra koagulering/flokkulering efterfulgt af en efterpolering.
Incitamentet til genbrug af vandet ligger i besparelser på vandforbruget og dermed
vandafgift og afledningsafgift. Der kan ved fuldstændigt genbrug af spildevandet opnås
spildevandsfri drift, hvor vandforbruget kun skal substituere vand, der tabes som følge
af fordampning mm.
I tilfælde af inddampning kan der eventuelt ske udnyttelse af vandets energiindhold
til forbedring af skylleeffektiviteten. Såfremt der anvendes afvaskningskemikalier, kan
der eventuelt samtidig ske et genbrug af disse, såfremt overskydende kemikalier kan
genfindes i det rensede vand. Dette vil typisk gælde for membranfiltrering.
Det væsentligste økonomiske potentiale i rensningsteknologierne ligger dog ikke i
vandbesparelsen men på besparelsen i mængden af kemikalieaffald, idet de
miljøproblematiske stoffer koncentreres i en mindre vandmængde.
Teknisk set kan der i visse tilfælde opstå problemer i forbindelse med meget lukkede vandkredsløb. Stoffer, som ikke frasepareres ved
rensningen, vil opbygges i vandsystemet. Dette kan føre til problemer såsom
udfældninger, biologisk vækst, lugt mm. En nærmere analyse er nødvendig for at
afgøre, hvorvidt sådanne problemer kan forventes at opstå.
Ved ændring af skylleproceduren til modstrømsskyl vil det reducerede
skyllevandsvolumen resultere i, at koncentrationen af stof i det spildevand, som skal
behandles, vil stige væsentligt (se figur 9.28). Baseret på en teknisk, økonomisk og
miljømæssig vurdering har både mængden og sammensætningen af spildevandet betydning
for valget af rensningsteknologi. Derfor vil ændringer i skylleproceduren have væsentlig
betydning for hvilken teknologi, som vælges.
Et publiceret eksempel på dette er membranfiltrering af pigmenter stammende fra
vandfortyndbare flexotrykfarver /107/. Dette studie
viste, at ved lave pigmentkoncentrationer (< 10 g/L) forekom en betydelig tilsætning
af membranerne (fouling), mens dette ikke forekom ved højere
koncentrationer. Opkoncentrering af skyllevandet ved direkte genbrug kan således have
væsentlig, positiv effekt på membranernes driftsøkonomi.
Uanset hvilken teknologi der vælges, vil reduktionen af skyllevandsvolumen føre til
økonomiske og effektivitetsmæssige forbedringer af renseprocessen. Betydningen vil være
størst på udstyrstunge teknologier som
membranfiltrering og inddampning og mindre på koagulering/flokkulering samt adsorptions- og oxidationsprocesser.
Modsat vil de udstyrstunge teknologier ikke være rentable under en vis vandmængde,
hvor koagulering/flokkulering vil være den økonomisk mest attraktive løsning. I hvert
enkelt tilfælde må således foretages en individuel vurdering af hvilken
rensningsteknologi, som er mest fordelagtig ud fra en teknisk, økonomisk og miljømæssig
vurdering.
Ved reduktion af skyllevandsvolumen og samtidig valg af rensningsteknologi skal der
tages forbehold for eventuelle begrænsninger på baggrund af den offentlige regulering,
som virksomheden er underlagt. Som før nævnt, forventes det reducerede
skyllevandsvolumen at forøge renseprocessens effektivitet over for mængden af stof, som
frasepareres i processen og dermed den stofmængde, som udledes til offentlig kloak. Da
mængden af stof samtidig findes i en mindre vandmængde, kan det dog ikke udelukkes, at
koncentrationen af stof vil stige i afløbsvandet. Dette vil være en begrænsning for
indførelse af renere teknologi, såfremt virksomheden
reguleres efter koncentrationen af stof i afløbet og ikke den samlede mængde af stof
udledt. Denne begrænsning kan forventes at gælde ved både koagulering/flokkulering, membranprocesser, adsorptionsprocesser
og oxidationsprocesser. Derimod kan der i den henseende
ikke forventes begrænsninger ved valg af inddampning som
rensningsproces. I dette tilfælde må det dog også forventes, at kondensatet
vil blive genbrugt i skylleprocessen eller andre steder og ikke afledt til kloak.
Det er meget vanskeligt at beregne de økonomiske konsekvenser ved implementering af renere teknologi og forbedret rensning af spildevand.
Sammenlignet med andre brancher, er vandforbruget generelt relativt begrænset, hvorfor
individuelle forhold på virksomhederne vil have væsentlig betydning for rentabiliteten
af løsningerne.
For illustration af de økonomiske potentialer ved implementering af renere teknologi
og forbedret spildevandsrensning er det i stedet valgt at vise besparelsespotentialerne
ved de nævnte løsninger, mens de yderligere omkostninger til anlæg og drift, som
teknologierne omfatter, er udeladt. Herefter må en individuel analyse på de enkelte
virksomheder afdække, om besparelsespotentialerne er tilstrækkelige til at dække de
udgifter, der er forbundet med implementering og drift.
Beregning af besparelsespotentialerne er eksemplificeret ved to virksomheder, A og B.
Nøgletal for de to virksomheder er givet i tabel 9.2.
Tabel 9.2
Nøgletal for virksomhed A og B til beregning af besparelsespotentialer