| Forside | | Indhold | | Forrige | | Næste |
LCA og kemikalier - forprojekt
Produktion af kemikalier foregår ofte i komplicerede procesanlæg, hvor kemiske
reaktioner, separationsprocesser, varme og køleprocesser finder sted i et optimeret
samspil. Derfor er det også naturligt, at der i forbindelse med udvikling af kemiske
procesanlæg og ved senere optimeringer anvendes analyseværktøjer
(simuleringsværktøjer), som kan håndtere de problemstillinger, der opstår i de
komplekse systemer, hvor ressourcer i form af energi og råvarer omsættes og genvindes.
I LCA sammenhæng er der inden for de seneste år udviklet metoder, der er rettet mod
"Environmental assessment" af kemiske processer. Et væsentligt element i LCA er
udarbejdelse af opgørelser. Disse kan specielt for stærkt integrerede processer
være svære at udarbejde. Antallet af ind- og udgående processtrømme kan være
stort, og sammensætningen kan være vanskelig eller umulig at måle direkte. Metoder for
systematiske LCA-opgørelser baseret på masse og energibalancer er foreslået (f.eks.
Jimenez-Gonzales, 2000).
En række metoder inkluderer LCA principper i et optimeringssystem (f.eks.
Pistikopoulos og Stefanis, 1998). Tilsvarende har de amerikanske miljømyndigheder
udviklet den såkaldte WAR algoritme (Cabezas 1999), som karakteriserer flowene og de
potentielle miljømæssige konsekvenser ved en kemisk proces. I WAR algoritmen benyttes ni
påvirkningskategorier, som går fra globale belastninger som f.eks. bidrag til
nedbrydning af ozonlaget til lokale belastninger som f.eks. human toksikologi. Bidraget
til påvirkningskategorierne beregnes ud fra de udgående processtrømmes kemiske
sammensætning. Da processimulatorer er i stand til at beregne disse sammensætninger
under alternative driftsforhold, vil det derfor være muligt at indarbejde
påvirkningskategorier umiddelbart. I det omfang, de forskellige påvirkningskategorier
kan vægtes, vil det umiddelbart være muligt at anvende optimeringsalgoritmer, der
systematisk kan optimere en given kemisk produktion.
I det følgende er nogle af de væsentligste simulerings- og optimerings-metoder, som
traditionelt har været anvendt til analyse og optimering af kemiske processer,
gennemgået. Ligeledes er der eksempler på, hvorledes værktøjerne i praksis anvendes og
illustrationer af, hvorledes de samme værktøjer kan anvendes i LCA-sammenhæng.
For at illustrere mulighederne for anvendelse af processimulering til udarbejdelse af
LCA opgørelser vil et eksempel på produktion af salpetersyre indledningsvis blive
gennemgået.
Salpetersyre hører til blandt verdens mest producerede kemikalier. De grundlæggende
mekanismer (reaktionsforløb) til produktion af salpetersyre har ligget fast de seneste 50
år. Alligevel er der mange muligheder for at tilpasse og optimere processen ud fra
forskellige kriterier. Der findes således på verdensplan salpetersyreanlæg med vidt
forskellige ydelser med hensyn til konverteringsgrad, energieffektivitet og
emissionsforhold. Figur 1 er et eksempel på et moderne salpetersyreanlæg. Det skal
bemærkes, at det kun er hovedstrømmene, der er medtaget på diagrammet. Udover de viste
komponenter er der et stort antal pumper og ventiler.
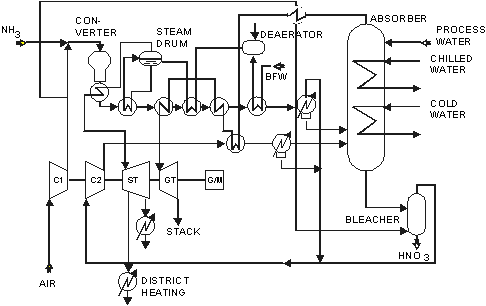
Figur 1.
Eksempel på moderne salpetersyreanlæg.
I processen omsættes ammoniak (NH3) til salpetersyre (HNO3) i
tre trin:
- Ammoniakforbrænding, hvor ammoniakken reagerer med ilt under dannelse af NO. Reaktionen
foregår katalytisk ved hjælp af en platinholdig katalysator.
- Oxidering af NO med ilt til NO2.
- Reaktion og absorption af NO2 og vand til dannelse af salpetersyre (HNO3)
Alle tre reaktioner er varmeafgivende (exoterme). Det betyder, at der samlet frigives
store energimængder i processerne. For at de enkelte reaktionstrin kan finde sted med
tilstrækkelig omsætningsgrad og reaktionshastighed, er der krav til temperaturer og
tryk. Således vil ammoniakforbrændingen (reaktion 1) have størst omsætningsgrad ved
høj temperatur, NO oxidationen (reaktion 2) foregå hurtigst under afkøling og
salpetersyreabsorptionen foregå bedst ved højt tryk og lav temperatur.
De specifikke forhold for reaktionerne er i høj grad afhængig af de ydre
omstændigheder som f.eks. råvarepriser, energipriser og miljøkrav. Typisk vil det
endelige design være underlagt et trade-off mellem bl.a. energiudgifter og
anlægsinvestering.
I forbindelse med udarbejdelse af opgørelser til brug i LCA antages de væsentligste
parametre at være:
 | Ammoniakforbrug |
 | NOx emission |
 | Vandforbrug |
 | Energiforbrug/overskud |
Det specifikke ammoniakforbrug hænger primært sammen med effektiviteten af
forbrændingen. Under forbrændingen omsættes ammoniak fortrinsvis til NO (primær
reaktion), mens en lille del omsættes til kvælstof og vand (sekundær reaktion). Derfor
givere højere konverteringsgrad (primær reaktion) mindre ammoniakforbrug.
NOx emissionen er primært afhængig af tryk og temperatur under
absorptionen. Højere tryk og lavere temperatur giver mindre NOx i restgassen,
som emitteres. Det skyldes, at omdannelse af NO2 og vand til salpetersyre er en
ligevægtsreaktion. Sammen med gas-/vandfase ligevægten bestemmer ligevægtsreaktionen
den aktuelle mængde NOx i restgassen (Figur 2).
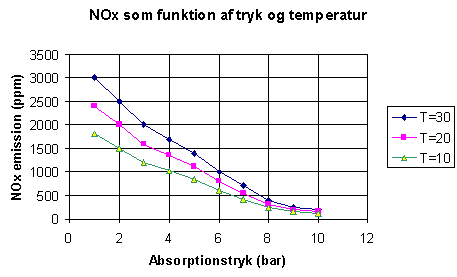
Figur 2.
Ligevægtsberegning for NOx koncentration i restgassen i et
salpetersyreanlæg (ved 10, 20 og 30 °C).
Vandforbruget til salpetersyreproduktion er stort set fastlagt på forhånd, jvf.
reaktionsforløbet
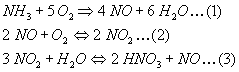
NO gassen recirkuleres således, at den samlede reaktion er:
,
hvilket giver en teoretisk salpetersyre koncentration på 78% (vægt). I praksis
produceres der salpetersyre med en koncentration på typisk 65% (vægt). Det betyder, at
der teoretisk skal tilføres 0.25 tons vand for hver produceret tons salpetersyre
(omregnet ren salpetersyre).
Mens de øvrige parametre (ammoniak, NOx og vand) primært er afhængige
af enkelte enhedsoperationer, er energiforbruget afhængig af samspillet mellem de enkelte
enhedsoperationer.
Da alle reaktionerne i processen er exoterme, er processen grundlæggende
energiproducerende. Den samlede energimængde, der frigives ved reaktionerne, er ca. 1800
kWh/ton syre. Hvis man ser på det udnyttede energioverskud fra reelle processer, varierer
dette typisk fra under 0 til 300 kWh. Energioverskuddet omsættes typisk til
dampproduktion.
I Tabel 23 er opgørelser for en række procesanlæg vist. Procesanlæggene er dels
eksisterende anlæg og dels simulerede anlæg. For de eksisterende anlæg er data baseret
på konkrete anlægsdata og verificeret ved simulering (energi og stofbalancer) (Nielsen,
1995). Herudover er der medtaget to procesanlæg, som ikke er bygget. Det første af dem
er et konventionelt anlæg tilbudt af en udbyder af procesanlæg (Contractor). Det sidste
anlæg er et konceptstudie med et anlægskoncept udarbejdet af dk-TEKNIK (Nielsen og
Hansen, 1995 og 1997). For Contractor processen er data opgivet direkte fra udbyderen og
herefter verificeret ved simuleringer. For dk-TEKNIKs proces er opgørelsen lavet
udelukkende på baggrund af simuleringer af processen.
Det væsentligste at bemærke ved opgørelserne i Tabel 23, er de store forskelle
mellem de bedste og de dårligste anlæg. Det er derfor vigtigt ved LCA opgørelser at
vide hvor produktet kommer fra. Det bemærkes iøvrigt, at de væsentligste forbedringer
ved fremtidige anlæg opnås gennem højere energieffektivitet.
Tabel 23
Opgørelse for forskellige salpetersyreanlæg per produceret tons
salpetersyre.
Parameter |
60er anlæg |
70er anlæg |
80er anlæg |
EFMA
BAT |
Contractor |
dk-TEKNIK |
Procestype |
1 bar
3 bar |
5 bar
10 bar |
5 bar
10.5 bar |
|
5 bar
11 bar |
5 bar
11 bar |
Inputs |
|
|
|
|
|
|
Ammoniak tons/tons |
0.280 |
0.282 |
0.283 |
|
0.280 |
0.280 |
Luft
tons/tons |
3.36 |
3.96 |
5.06 |
|
5.10 |
5.10 |
Vand
tons/tons |
0.266 |
0.263 |
0.265 |
|
0.265 |
0.545 |
Produkt |
|
|
|
|
|
|
Salpetersyre
tons/dag |
225 |
450 |
650 |
|
1150 |
1150 |
Dampeksport
Elforbrug |
0.07
22.5 |
0.11
25.2 |
0.80
25.0 |
|
0
-198.3 |
0
-247.8 |
Energi1
kWh/tons |
-5 |
-3 |
-159.2 |
|
-198.3 |
-247.8 |
Emissioner |
|
|
|
|
|
|
NOx ppm |
1000 |
100 |
80 |
100 |
80 |
80 |
NOx
kg/tons |
4.27 |
0.43 |
0.34 |
0.65 |
0.34 |
0.34 |
|
|
1 |
Energi overskud ved salpetersyreproduktion omregnes til
ækvivalent elproduktion. |
Det skal nævnes, at de to sidste (virtuelle) procesanlæg er baseret på
energioptimeret design. Det er således ikke nødvendigvis de anlæg, der bygges i dag.
Den endelige proces er baseret på et trade-off mellem de forskellige størrelser.
Med hensyn til fremskaffelse af de aktuelle procesdata til udarbejdelse af opgørelser
vil processimulering ofte være et uundværligt værktøj. Det gælder specielt processer
med emissioner, der enten ikke kan måles eller er meget bekostelige at måle. Her vil
modeller baseret på energi og massebalancer samt ligevægtsforhold kunne give oplysninger
om størrelser, som ellers ikke vil være tilgængelige.
Herudover vil det generelt for større procesanlæg være særdeles tidsbesparende at
benytte sig af processimulering ved udarbejdelse af opgørelser. Udover en systematik i
datahåndteringen er man sikker på, at de data, man anvender, er konsistente hvad angår
de primære masse- og energibalancer. Herudover vil man med en simuleringsmodel let kunne
udarbejde reviderede opgørelser på baggrund af ændrede procesbetingelser.
Figur 3 viser et uddrag af en simuleringsmodel for salpetersyreprocessen. Ved
anlægssimuleringer vil man umiddelbart se konsekvenserne i form af energiforbrug,
emissioner og ressourceforbrug ved ændrede driftsbetingelser. Simuleringsmodellen kan
således bruges interaktivt til optimering af processen og minimering af emissioner. I
Tabel 24 ses de procesmæssige udledninger, som simuleringsmodellen beregner.
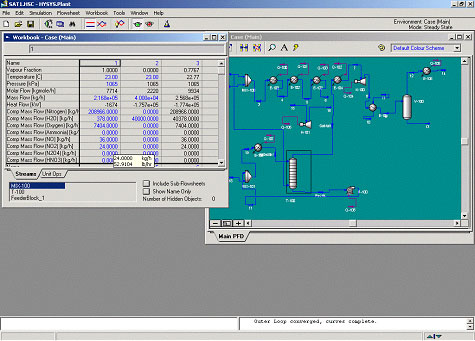
Figur 3
Uddrag af simuleringsmodel for salpetersyreanlæg.
For hver processtrøm kan der uddrages alle fysiske og termodynamisk beregnede
størrelser.
Tabel 24.
Sammensætning af restgas, som udledes fra skorsten.
Processtrøm |
|
Restgas til skorsten |
Tryk |
Bar |
1.05 |
Temperatur |
C |
85 |
Massefylde |
kg/m3 |
0.992 |
Komponentflow N2 |
kg/h |
104483 |
Komponentflow H2O |
kg/h |
189 |
Komponentflow O2 |
kg/h |
3702 |
Komponentflow NH3 |
kg/h |
0 |
Komponentflow NO |
kg/h |
18 |
Komponentflow NO2 |
kg/h |
12 |
I arbejdet med udarbejdelse af de i Tabel 23 udarbejdede opgørelser har det således
været forholdsvist enkelt at tilpasse generelle modeller til specifikke formål.
Generel anvendelse af simulerings- og optimeringsværktøjer bliver i stigende omfang
anvendt til udvikling og forbedring af kemiske processer. Fra starten af 60erne,
hvor de første computerbaserede analyseværktøjer blev udviklet, var de væsentligste
mål at kunne lave simuleringer af enkelte kemiske enhedsoperationer. I forbindelse med
computernes udvikling blev det muligt at foretage simuleringer af flere koblede
enhedsoperationer. I løbet af 70erne udviklede en række større
industrivirksomheder specialiserede simulatorer. Disse kunne gennemføre beregninger, der
hidtil havde været særdeles tidskrævende, på processerne. Simulatorerne blev udviklet
af større industrikoncerner som Union Carbide, Exxon m.fl. Også enkelte danske
virksomheder opbyggede simulatorer for kerneprocesserne, f.eks. De Danske Sukkerfabrikker
(nu Danisco Sugar). Sideløbende med de virksomhedsspecifikke simulatorer begyndte de
første kommercielle generelle processimulatorer at dukke op sidst i 70erne. Fælles
for såvel de virksomhedsspecifikke som for de generelle simulatorer var det, at de
stillede store krav til brugerne.
I løbet af 80erne blev simulatorerne udviklet yderligere, og der begyndte at
komme værktøjer målrettet til optimering af kemiske processer.
I 90erne var udbredelsen af simulatorerne forholdsvis stor, hvilket i høj grad
skyldes, at de blev væsentligt lettere tilgængelige. Udbredelsen af
optimeringsværktøjer har ikke været lige så stor som udbredelsen af de generelle
simuleringsværktøjer. Disse værktøjer stiller stadig store krav til brugerne.
Anvendelsen af simulerings- og optimeringsværktøjer i dag sker bl.a. til:
 | validering af målte procesdata, beregning af ikke målbare data, |
 | optimering af udbytte, |
 | energioptimering, f.eks. optimering af varmegenvinding, |
 | risikovurderinger, f.eks. simuleringer af konsekvenser ved fejlfunktion, |
 | beregning og minimering af emissioner, |
 | udvikling af nye kemiske stoffer. |
Udviklingen af værktøjer er primært sket for at dække et stadigt stigende behov for
at øge produktiviteten og minimere driftsomkostninger og anlægsudgifter. Dette har
været en bydende nødvendighed specielt i kemiske procesanlæg, som ofte er meget
kapitaltunge og har store driftsomkostninger.
De miljømæssige aspekter er traditionelt behandlet som restriktioner i
procesoptimeringen. Det vil sige, at optimeringen er gennemført under hensyntagen til en
række af krav, der skal opfyldes (f.eks. lovmæssige restriktioner på udledninger af
VOCer).
Mange af værktøjerne kan dog umiddelbart anvendes til at inddrage miljøaspektet
direkte i optimeringerne. Bl.a. har energiforbruget i mange år spillet en central rolle i
den kemiske industris konkurrenceevne. Derfor vil der i forbindelse med etablering af nye
kemiske procesanlæg næsten altid blive taget specifikt fat på energiforholdene. Med
hensyn til de øvrige miljømæssige forhold inddrages disse i højere grad i
planlægningen af procesanlægget. Ofte er realiteten, at miljøforholdene er tæt knyttet
til energiforholdene, således at en stor omsætning af energi ofte udmønter sig i store
emissioner.
I LCA sammenhæng vil analyseværktøjer specielt kunne bidrage ved indsamling af data
for processer, der ikke er fuldt dokumenteret. En række af de værktøjer, der typisk
anvendes, er således velegnede til opstilling af konsistente energi- og massebalancer,
hvori der tages hensyn til de enkelte kemiske forbindelsers fysiske egenskaber.
Værktøjerne vil når tiden er moden også kunne bringes i anvendelse
til "LCA baseret optimering". Med det forstås en optimering, som producenterne
kan foretage i forsøget på at opnå en bedre "LCA-ydelse".
Som et eksempel betragtes en spildevandsrensningsproces, hvor der anvendes energi til
regenerering af spildevandets kontaminering. I eksemplet er der simuleret et system med
sprit (ethanol) i vand. Spildevandet renses ved en destillation (Figur 4), hvor der
anvendes energi i en reboiler.
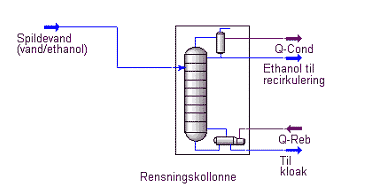
Figur 4
Model for destillationskolonne til rensning af spildevand.
Jo mere energi, der tilføres, jo mere sprit kan der sendes tilbage til processerne. I
simuleringsmodellen kan denne sammenhæng undersøges ved at variere på
designparametrene. I dette eksempel opsamles samhørende værdier for spritindhold i
spildevandet og energiforbruget (Figur 5).
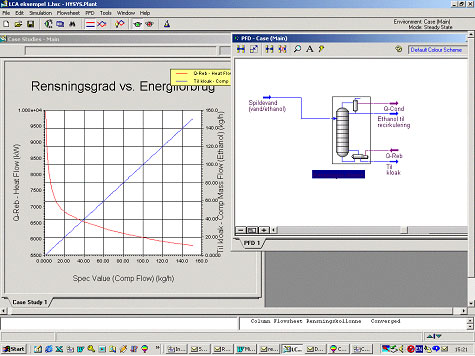
Figur 5
Brug af simuleringsmodel til systematisk afvejning af procesparametre.
Såfremt det er muligt at vægte de enkelte LCA parametre, vil det således være
muligt ved hjælp af simuleringsværktøjet at finde det design, der ud fra
en livscyklusbetragtning er bedst.
Ved at tillægge de enkelte parametre en "LCA-vægtning" er der i eksemplet
foretaget en simpel optimering, der angiver den optimale designkonfiguration af
rensningsprocessen (Figur 6).
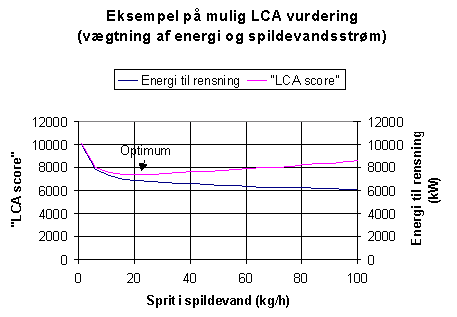
Figur 6
Optimering af "LCA ydelse". På baggrund af simuleringsresultater
kan der findes et optimum baseret på vægtning af energiforbrug og sprit i spildevandet.
Eksemplet viser en simpel simulering og optimering, hvor der optimeres på nogle få
driftsparametre. Det er derfor relativt nemt og overskueligt at finde et "LCA
optimum". I reelle kemiske processer vil der være betydelig flere driftsparametre,
som kan og skal indgå i optimeringen. Det betyder, at det næppe vil være
tilstrækkeligt at anvende simuleringsværktøjer. Der er også behov for at anvende
egentlige optimeringsmetoder, som er i stand til systematisk at optimere frihedsgraderne i
processerne.
Til den praktiske gennemførelse af processimulering og optimering findes en række
computer baserede værktøjer. Som udgangspunkt kan disse værktøjer deles op i
simuleringsværktøjer og synteseværktøjer (værktøjer til optimering af procesdesign).
Simuleringsværktøjer anvendes til at efterligne (beregne) virkelige processer
(tilstandsvariable eller tidsforløb i procesvariable) og er ofte knyttet sammen med
parameteroptimering.
Til dette kræves, at en række af procesanlæggets specifikationer og karakteristika
er kendte/antaget og indført i de modeller (komponenter), som simulatoren indeholder.
Simuleringsværktøjer er velegnede til at undersøge og afprøve konsekvenserne af nye
driftsstrategier eller operationer på et anlæg på en økonomisk hensigtsmæssig måde,
idet det ikke kræves, at der står et virkeligt anlæg til rådighed, og der bruges ikke
råstoffer udover arbejdstid. Endvidere elimineres risici for uheld foranlediget af, at
anlægget er kommet ud i et driftsområde, hvor garantien ikke gælder for anlægget.
Synteseværktøjer retter sig mod design af anlæg. Der kan her være tale om
fastlæggelse af et overordnet systemdesign (konfiguration af systemet), eller designet
kan bestå i fastlæggelse af de enkelte komponenters kapacitet og fysiske størrelse.
Syntese af anlæg (i betydningen fastlæggelse af det overordnede systemdesign)
inddrager ofte komplekse problemstillinger, som udmynter sig i et væld af mulige
designkonfigurationer.
Værktøjerne kan benytte matematisk programmering til at finde frem til en optimal
konfiguration. En anden mulighed er anvendelse af heuristiske regler, som bygger på
erfaringer og ræsonnementer, der gør det muligt at reducere antallet af teoretiske
konfigurationer i en sådan grad, at det er muligt at overskue og undersøge de
tilbageværende konfigurationer.
Den ovennævnte opdeling i simulerings- og synteseværktøjer er dog ikke reel i
praksis, idet der ofte i simuleringsværktøjer er integreret en række
synteseværktøjer, som kan assistere brugeren i fastlæggelsen af enkeltkomponenters
specifikke design.
Forudsætningen for en god LCA opgørelse er bl.a., at alle væsentlige ind- og
udgående processtrømme for en produktionsproces er kendt.
For en lang række processer til fremstilling af kemiske produkter er forudsætningen,
om at alle ind- og udgående strømme er kendt, langt fra opfyldt. En total kortlægning
ved målinger og analyser af de ind og udgående strømme vil i mange tilfælde være
særdeles omfangsrig og behæftet med væsentlige fejl. Ved produktion af forskellige
produkter på samme procesanlæg, men med små driftsændringer, vil der være behov for
at gentage målingerne i fuldt omfang.
Ved at benytte sig af processimulering kombineret med målinger vil det
dels være muligt at lave opgørelserne væsentligt hurtigere og dels kunne give større
datasikkerhed, da processimulatorerne sikrer at alle stof- og energibalancer er i
overensstemmelse med de fysiske og termodynamiske love.
Såfremt en pålidelig processimuleringsmodel kan opstilles for en given
produktionsproces vil det endvidere være muligt hurtigt og nøjagtigt at lave opgørelser
for forskellige produktspecifikationer.
I praksis vil man for en given produktionsproces have opgørelse over en del af de ind-
og udgående processtrømme. Simuleringsmodellen kan herefter bruges til at beregne de
resterende data. Forudsætningen er at der er et tilstrækkeligt antal kendte størrelser.
Da processimulatorer baserer sig på løsning af ligningssystemer skal der være
overensstemmelse mellem antallet af ligninger og antallet af ubekendte størrelser. Hvis
der er for få oplysninger er det nødvendigt at anvende antagelser, hvilket giver
anledning til at usikkerheden på opgørelserne øges. Hvis der er færre ubekendte end
ligninger har man en situation hvor systemet siges at være overbestemt. Det betyder at
man har overskydende information. Her kan man vælge at anvende de overkydende data til at
checke om modellen og målinger stemmer overens. Såfremt målinger og balancer ikke
stemmer kan man med statistiske metoder finde frem til, hvilke data der må antages at
være mest troværdige. Jo mere systemet er overbestemt jo mere pålideligt bliver
resultatet. Da målinger ofte kan være behæftede med væsentlige fejl anbefales det
derfor altid at stræbe mod at få så mange målinger med som muligt.
Der findes en række alternative produkter til processimulering rettet mod kemisk og
beslægtet industri. Disse kan fordeles på kommercielle produkter og værktøjer udviklet
til forskningsmæssig brug på universiteter.
Markedet for kommerciel processimuleringssoftware er domineret af tre store udbydere,
som er:
 | Aspen Technology med produktet ASPENPLUS |
 | AEA Technology med HYSYS |
 | Simulation Science med PRO VISION |
Herudover er der en frodig underskov med talrige leverandører af generelle såvel som
produktionsspecifikke produkter.
For de generelle processimulatorer gælder, at de er designet til almene procestekniske
beregninger og bygget op af en række standardkomponenter. En standardkomponent kan
eksempelvis være en pumpe eller en varmeveksler. De enkelte standardkomponenters
karakteristika er hver især beskrevet med et sæt ligninger. Simulatoren består
endvidere af en beregningsdel (ligningsløser) og et interface (i dag typisk et grafisk
brugerinterface).
Det grafiske brugerinterface og den komponentorienterede opbygning giver mulighed for
direkte på en computerskærmen at opbygge et procesanlæg af enkeltkomponenter forbundet
og arrangeret som i virkeligheden, hvilket normalt øger forståelsen og overskueligheden.
Der kan opbygges ganske præcise modeller (specielt hvis der er mulighed for at
programmere/definere egne komponenter) af virkelige anlæg, hvor styrings- og
reguleringssystemet også er inddraget.
Det er derfor muligt på ganske kort tid at opbygge en model af et procesanlæg, som
kan simulere driften af et virkeligt anlæg, og som samtidig er ret let at overskue og
forstå. Detaljer om processen kan specificeres i de enkelte komponenter, eller
komponenterne kan evt. skræddersyes til specielle processer. Simulatorerne giver mulighed
for at simulere stationære forhold såvel som dynamisk drift.
Når først en model af et procesanlæg er opbygget i en simulator, kan denne model
anvendes, hver gang konsekvensen af at ændre noget i anlæggets drift ønskes undersøgt.
Man kan vælge at fiksere nogle parametre, mens andre optimeres. Det kunne eksempelvis
være ønsket om at minimere det specifikke brændselsforbrug i en proces uden at ændre
på sammensætningen (kvaliteten) af produktet.
Ofte er det datagrundlag, som virksomhederne besidder om deres processer (endog egne
kærneprocesser), noget mangelfuldt. Her vil en model af processen opbygget i en simulator
normalt være til stor hjælp, hvis ukendte størrelser i processen ønskes estimeret
eller beregnet. Visse centrale procesdata kendes normalt, idet de måles løbende af
forskellige årsager.
Som et eksempel kan nævnes en proces, hvor træ tørres i et tørrekammer. I en sådan
proces vil man typisk under tørreprocessen løbende måle vandindholdet i træet, som
findes i tørrekammeret, idet dette er en central variabel, der skal ændres (nedbringes)
i tørreprocessen. Processen kan kontrolleres ved at måle på og styre en række variable
ved at regulere på andre variable. Styrevariable kan være temperatur og fugtindhold af
tørreluften, der sendes ind i tørrekammeret, mens en variabel, der reguleres på, kan
være damptilførsel.
En række parametre, som også har indflydelse på tørreprocessen, måles derimod ikke
enten fordi de ikke er så afgørende, eller fordi de ikke indgår som en
parameter, der styres efter. Eksempelvis kan det tænkes, at varmeforbruget i form af damp
ikke måles og dermed ikke registreres, men kun indgår som en variabel, der reguleres
på.
Hvis tørreprocessen opbygges i en simuleringsmodel, vil dampforbruget imidlertid kunne
beregnes udfra de registrerede måleværdier og er hermed et eksempel på, at
datagrundlaget i en proces kan udbygges ved anvendelse af simuleringsmodeller af
processen.
Med en god model af processen vil det ofte være muligt med ganske få målte eller
kendte størrelser som inddata at fastlægge (beregne) hele processen med en simulator.
Hvis den teoretiske model derimod er mere mangelfuld, er der behov for flere målte data
til at fiksere modelberegningerne.
Simulatoren kan dermed bruges til at beregne en lang række tilstandsstørrelser i
processen, som enten ikke kan måles eller er for dyre at måle.
En processimulator er et værdifuldt og effektivt værktøj til at udbygge et
mangelfuldt datagrundlag i procesindustrier, hvilket kan være yderst relevant i
forbindelse med udarbejdelse af LCA opgørelser.
En af de førende udbydere af processimulerings- og optimeringssoftware er Aspen
Technology, som udbyder et væld af produkter. Der er udover den generelle processimulator
ASPENPLUS, en række mere specifikke simulatorer og synteseværktøjer som kan integreres
med hinanden.
Udover simulatorer og optimeringsværktøjer i mere traditionel forstand til
procesindustrien er der på det seneste fremkommet produkter til optimering på et mere
overordnet plan, ved udnyttelse af informationer tilgængelige online. I princippet er der
ingen begrænsning i, hvilke informationer der her kan gøres brug af til optimering af en
produktion, f.eks. så den kan køre meget tæt på, hvad der er økonomisk optimalt.
Information om råvarepriser og kvalitet fra forskellige leverandører er et eksempel
herpå, hvor en processimulator vil kunne udregne konsekvenserne af at omstille og
optimere procesanlægget til en anden kvalitet af råvare og dermed finde frem til den
leverandør og råvare, der er mest fordelagtigt i øjeblikket.
Aspen Technology har sammensat nogle pakkeløsninger (Aspen Manufacturing Suite, Aspen
Engineering Suite og Aspen eSupply Chain Suite). Disse blokke kan kommunikere med
hinanden, så de udgør et totalsystem til styring og optimering af alle faser indenfor en
produktionsvirksomhed, fra indkøb af råvarer over produktionsprocessen til salg og
distribution af færdigvarer.
Firmaets fokusering på e-business området skal ses i sammenhæng med den voldsomme
vækst i internettets udbredelse og dermed mulighed for at få adgang til meget omfattende
og opdaterede data, både internt i verdensomspændende koncerner og mellem samhandlende
virksomheder.
Aspen Technology har integreret sin procesviden med internettet med det mål at blive
førende indefor internetbaserede produktions og supply-chain optimeringsværktøjer til
procesindustrien.
En sådan udvikling i retning af løbende at kunne håndtere dugfriske oplysninger om
næsten alt af relevans for en produktion og straks om muligt tilpasse produktionen, kan
på lang sigt have store perspektiver, idet det kan give mulighed for løbende at anvende
LCA i minimeringen af den samlede miljøbelastning i forbindelse med en given produktion.
Økonomi kan kobles på ved også at anvende LCA i reguleringen af miljøafgifter.
Ligesom Aspen Technology fokuserer også AEA og Simulation Science på pakkeløsninger
med bl.a. supply chain management, optimering, regulering m.m.
Der findes et væld af ikke-kommercielle simulatorer i universitetssektoren, heriblandt
en par danske eksempler:
 | DNA (Dynamisk netværks analyse), Institut for Energiteknik, DTU |
 | ICAS (Integrated Computer Aided System) fra CAPEC (Computer Aided Process Engineering
Center), Institut for Kemiteknik, DTU |
De forskningsbaserede værktøjer er ofte lige så nøjagtige, som de kommercielle
værktøjer. Endvidere vil de ofte være billige eller endog gratis at erhverve. I praksis
lider programmerne dog af at være svært tilgængelige ligesom stabiliteten sjældent er
stor.
En væsentlig grund til, at der er og fortsat bliver udviklet mange simulatorer i
universitetsmiljøet, er at man her er interesseret i at have fuld adgang til
kildeteksten, så simulatoren kan skræddersyes til specifikke opgaver.
Dataindholdet til en simulator er i overvejende grad bestemt af formålet og dermed
detaljeringsgraden samt arten af analysen, og i mindre grad af hvilken specifik software
der anvendes til analysen. Eksempelvis vil de førnævnte tre generelle processimulatorer
typisk skulle have de samme informationer om processen og anlægskomponenter for at kunne
simulere samme driftssituation af anlægget.
Forskelle i indata kan bero på at de i simulatoren integrerede designværktøjer er
forskellige i omfang og detaljeringsniveau, og at der anvendes forskellige metoder til
løsning af ligningssystemet.
Eksempel: En varmeveksler kan specificeres udfra temperaturer før og efter
varmeveksleren og massestrømme af de to medier der indbyrdes udveksler varme i
komponenten. Udfra varmefylderne (Cp-værdier) af de to medier (der typisk er tilgængelig
via en stofdatabase med beregningsrutiner), kan størrelsen af varmeveksleren (UA-værdi)
bestemmes. A udtrykker arealet af det varmeoverførende areal og U er en størrelse der
udtrykker hvor effektiv varmeoverførslen skal være. Dimensioneringen af varmeveksleren
er her foretaget på et termodynamisk (energi-og temperaturmæssigt) niveau.
Et mere detaljeret niveau er hvor bl.a. også de strømningstekniske forhold i
varmeveksleren indgår i beregningerne af varmoverførsel (U). Til dette kræves adgang
til flere stofegenskaber for de to varmevekslende medier så som viskositet,
varmeledningsevne, emissionsforhold, densitet m.m. samt kendskab til geometri og materiale
af varmevekslerens strømningskanaler.
I relation til LCA vil et af de væsentligste formål med simulering af en proces være
at kunne opstille en energi- og massebalance for systemet, for at kunne fastlægge de
primære (direkte) behov for energi og råvarer til opretholdelse af en produktion.
I anden række kan en fastlæggelse af anlæggets detaljerede design bruges til
fastlæggelse af afledte ressourceforbrug, der medgår til fremstilling af selve
anlægget.
Endelig vil simulering kunne bruges i verifikation og dokumentation af nye alternative
fremstillingsprocesser.
Omfanget og præcisionskravene til datagrundlaget afspejles af formålet med
simuleringen af en proces. Således vil syntese, design og økonomisk optimering af et
procesanlæg kræve et betydelig mere omfattende datagrundlag end en procesberegning
(simulering), der blot har til formål at fastlægge energi- og massebalance.
Pålideligheden af en beregning afhænger dels af pålideligheden af inddata, dels af
modellens evne til at beskrive virkeligheden og endelig af præcisionen, hvormed
ligningsløseren løser ligningssystemet.
Det er klart, at kvaliteten af inddata er afgørende for hvor god en løsning
selv med en god model - der kan opnås. Dette følger devisen: garbage in
garbage out.
Hvis målinger af centrale inddata ikke er nogenlunde i overensstemmelse med
virkeligheden, er der derfor stor risiko for at resultatet af simuleringen heller ikke
stemmer blot nogenlunde overens med virkeligheden.
Ligeså afgørende for kvaliteten af en løsning er det, at modellen i simulatoren
beskriver de forhold, der ønskes undersøgt, på en måde, der stemmer godt overens med
virkeligheden. Ved udarbejdelsen af en model må man tilpasse detaljeringsgraden under
hensyn til behov, beregningstid, tilgængelighed af data, og teoretisk indsigt.
Her er en god model en model, der giver de nødvendige svar med tilstrækkelig
præcision, med så få og lettilgængelige inddata som mulig og med mindst mulig
beregningsarbejde.
Præcisionen på en beregning afhænger af flere typer af fejlkilder. Der er
fejlkilder/tilnærmelser i selve den teoretiske model, der er usikkerheder/fejl på
måledata og øvrigt datagrundlag, og endelig er der den numeriske præcision, hvormed et
problem bliver løst af ligningsløseren.
Den numeriske præcisionen på en beregning, dvs. hvor tæt den numeriske løsning
ligger på den sande løsning af det opstillede teoretiske problem, kan i mange
simulatorer justeres manuelt. Der gælder ofte, at jo bedre præcision, desto længere tid
tager beregningerne. I visse problemer, eksempelvis hvis der recirkuleres processtrømme,
kan det være vanskeligt at nå frem til en løsning, der opfylder meget høje
præcisionskrav. Normalt vil det dog være sådan, at fejlen på den numeriske løsning er
langt mindre end de fejlkilder og usikkerheder, der er mellem den teoretiske model og den
virkelige og usikkerheden på de målte inddata.
Ved processer, som er velkendte, og hvor der i lang tid har været anvendt
processimulering i optimeringer, er der et godt erfaringsgrundlag for, hvorledes processen
skal modelleres (modelopbygning) for at de teoretiske beregninger stemmer godt overens med
praksis. I denne type af procesindustri kan man derfor forvente høj præcision og
troværdighed af resultaterne, hvor usikkerheden hovedsagelig relaterer sig til
usikkerheden på målte inddata. Dvs. her kan man i bedste fald forvente usikkerheder ned
til en størrelse omkring 1%.
I andre procestyper, hvor erfaring med modellering er sparsom, kan der imidlertid være
betydelig større usikkerhed på resultater.
For de kommercielle processimulatorer og specialværktøjer til syntese og
optimering gælder at priserne afspejles i markedet for denne type af produkter. Det
totale produktsalg kan typisk opgøres i nogle få hundrede enheder eller mindre. Priserne
på produkterne vil derfor være ganske høje, for at de ret store udviklingsomkostninger
kan dækkes.
Det høje prisniveau implicerer en reduktion af det potentielle marked og virker dermed
selvforstærkende.
Til de meget omfattende og komplette simuleringspakker er køberne derfor primært
internationale kemikoncerner, konsulentvirksomheder med speciale i processimulering eller
universiteter, der ofte får programmerne stillet tilrådighed på en ikke-kommerciel,
undervisningsbaseret licensaftale til favorable priser.
Som eksempel på priser kan nævnes at HYSYS Proces (processimulator der kan foretage
statisk men ikke dynamisk simulering) koster cirka 25 000 $ som et engangsbeløb i
erhvervelse. Løbende opdateringer af programmet kan fås ved oprettelse af en
licensaftale, hvor der betales et årligt beløb på omkring 15-20% af grundprisen for
programmet dvs. i dette tilfælde omkring 4-5000 dollars om året.
Fra samme softwareudbyder kan synteseværktøjet HX-NET (værktøj til syntese og
design af varmevekslernetværk) fås for omkring 15 000 $.
Prisen på AspenTechs processimulator er noget højere end HYSYS Process.
Andre simulatorer og synteseværktøjer kan være meget billige eller evt. gratis
men i en del tilfælde er brugen af denne type produkter begrænset med en
restriktion om at de ikke må anvendes i professionel eller kommerciel sammenhæng.
Mange simuleringsværktøjer er beskrevet, så de kan anvendes med blot ganske få
dages træning. For at kunne arbejde effektivt tidsmæssigt med processimulatorer kræves
dog normalt betydeligt længere tid. Kun hvis brugeren har almen erfaring i brugen af
andre processimuleringsværktøjer vil det sandsynligvis være tilstrækkeligt med få
dages træning.
Årsagen til den vanskelige indlæring er primært, at simuleringssystemerne er
komplicerede. Det skal nævnes at der ved blot simple processimuleringer, som f.eks. det
indledende eksempel på rensning af sprit fra spildevand, let kan være flere hundrede
variable og et tilsvarende antal ligninger, der skal løses. Så, selvom udviklerne af de
kommercielle simuleringsværktøjer har gjort sig store anstrengelser med at pakke
ligningsløserne godt ind, er det i mange tilfælde meget vigtigt for brugeren af
simuleringssystemerne at have et godt kendskab til hvordan ligningsløserne fungerer. For
de ikke-kommercielle værktøjer er dette problem som regel endnu mere udtalt. Her er
systemerne ofte udviklet af et få antal personer til primært egne forskningsmæssige
formål.
Udover en forholdsvis lang indlæringstid for brugere uden forudgående erfaring
kræves det også at brugeren benytter simuleringsprogrammerne med jævne mellemrum. Det
skyldes at programmerne indeholder temmelig mange detaljer.
For at kunne simulere og beskrive en proces realistisk er det endvidere en stor fordel
at man har et godt kendskab til både den grundlæggende proces, simulatoren samt almen
simuleringserfaring, for at kunne foretage nødvendige genveje uden at miste
troværdigheden af simuleringsresultatet.
For anvendelse af egentlige optimeringsprogrammer (synteseværktøjer) er det om muligt
endnu mere nødvendigt at have en forholdsvis stor indsigt i programmernes virkemåde.
Disse værktøjer er i mange tilfælde udviklet til specifikke formål, hvilket kan give
anledning til problemer når de forsøges anvendt til generelle formål. Derfor er
anvendelse af synteseværktøjer i industrien forholdsvist begrænset.
Der er i øjeblikket to trends, der kan have stor indflydelse på antallet af brugere.
Den første er, at primært simulatorerne - men også synteseværktøjerne - bliver
udvidet med endnu flere detaljer. Det gør det muligt at gennemføre endnu mere
detaljerede analyser, men betyder samtidig også, at programmerne for ikke-trænede bruger
bliver endnu mere uoverskuelige. Den anden trend er, at de indbyggede ligningsløsere
bliver mere robuste, hvilket alt andet lige vil gøre det lettere for nye brugere at gøre
brug af værktøjerne.
Det skal sluttelig pointeres, at når man har opnået fortrolighed med
processimulatorerne, så kan der opnås store tidsmæssige besparelser ved at anvende
disse f.eks. ved opgørelser til LCA. Denne fordel er specielt udtalt hvis man
arbejder med snært beslægtede industrielle processer.
| Forside | | Indhold | | Forrige | | Næste | | Top
| |