| Forside | | Indhold | | Forrige | | Næste |
Behandlingsteknologier for batterier - Fase 1
4 Kortlægning af eksisterende behandlingsteknologier
I de følgende afsnit er mulighederne for sortering og kendte metoder til oparbejdning af de forskellige batterier beskrevet. Ved oparbejdningsmetoderne er der især fokuseret på alkali- og brunstensbatterier.
4.1 Sortering
De indsamlede batterier vil være en blanding af alle batterityper samt andet affald, som uundgåeligt også vil havne blandt batterierne. I de fleste tilfælde foregår sorteringen af batterierne i typer manuelt, da
det har været vanskeligt at udvikle en teknik der såvel økonomisk som teknisk kan konkurrere med manuel sortering.
Imidlertid har der gennem de senere år flere steder været gennemført udvikling af udstyr til automatisk sortering.
Nye kviksølvfrie alkali- og brunstensbatterier produceret i EU er påført en UV-markør, der betyder at et automatisk sorteringsanlæg let kan genkende disse batterier ved belysning med UV-lys. Det varer
dog en del år endnu før alle de gamle kviksølvholdige batterier er ude af affaldsstrømmen, ligesom man ikke kan være sikker på at batterier importeret til EU er mærket med UV-markør.
4.1.1 Automatisk sortering hos Trienekens AG /26/
Et af de nyeste og mest moderne automatiske sorteringsanlæg i Europa er placeret hos Trienekens AG i Düsseldorf. Anlægget er besøgt i august 2000.
Batterisorteringsanlægget hos Trienekens repræsenterer 3. generation inden for automatiske sorteringsanlæg, og er en videreudvikling af det anlæg, som står hos firmaet S.N.A.M. i Lyon.
Batterierne kommer fra den tyske indsamlingsordning, der administreres af GRS-Batterien. Trienekens AG er et at de 3 tyske firmaer der har kontrakt med GRS-Batterien, og i kontrakten forudsættes det,
at firmaerne etablerer automatiske sorteringsanlæg.
4.1.1.1 Princip
Anlægget består af 2 afsnit: Første afsnit er en manuel/mekanisk sortering og er udviklet af Trienekens selv. Dele af det har de patent på. Andet afsnit er udviklet af Euro Bat Tri, der er et datterselskab af
S.N.A.M, og består af vægt-, Tri-Mag- og UV-sensorer.
Første afsnit.
Anlægget fødes ved at batterierne hældes i en fødekasse med en rist, der tilbageholder store batterier. Herefter kører de ud på et transportbånd, hvor firkantede Ni-Cd, Ni-MeH og lithium batterier samt
militærbatterier og affald sorteres fra manuelt. Dernæst sker der en størrelsessortering på et ristesystem således at knapceller tages fra, og øvrige batterier deles i en strøm med store og små batterier.
Knapcellerne sorteres efter størrelse, i tre fraktioner, i et separat si-system. Størrelsen er specifik for de forskellige typer (zink-kviksølvoxid, zink-sølvoxid og zink-luft), og er således nok til at dele dem i
typer. Virksomheden har to anlæg, hvor bl.a. de kviksølvholdige knapceller destilleres.
De to strømme af de øvrige batterier føres videre til en anordning, hvor flade og firkantede batterier sorteres fra. Dette sker på skråtstillede roterende plader, således at runde batterier ruller af, mens flade
bliver ført med pladen. Det er nødvendigt at fjerne de firkantede og flade batterier her, da de ikke passer ind i teknikken på andet afsnit af anlægget.
Andet afsnit.
Her er der 2 linier til henholdsvis store og små runde batterier. Batterierne transporteres på "polycord belts", en slags runde plastkabler med ½-1½ cm mellemrum, således at batteriet ligger mellem kablerne
og hviler på disse. Dette sikrer at batteriet fastholdes i samme position.
Herefter registreres forskellige parametre for batterierne. Vægten registreres ved at batteriet, ved hjælp af overbånds kabler, løftes og vejes. Vægten lagres i en PLC. Alle batterier over en vis vægt
frasorteres herefter, da de enten indeholder bly eller kviksølv.
Dernæst passerer batterierne en såkaldt Tri-Mag-sensor, hvor der induceres et magnetisk felt i batteriet og detektorceller måler responsen. Dataene lagres ligeledes i PLC'en, og sammenholdt med
vægtregistreringerne kan der skelnes mellem brunstens-, alkali- og NiCd-batterier. NiCd batterier sorteres fra. Til slut passerer brunstens- og alkalibatterierne en UV-sensor, der registrerer eventuelle
UV-markører på batterierne. Nye kviksølvfrie batterier påføres hos de væsentligste producenter i Europa denne UV-markør for at lette sorteringen.
Brunstens og alkalibatteriene sorteres således i fire fraktioner: to garanterede kviksølvfrie alkali- og brunstens-fraktioner og to alkali- og brunstensfraktioner, hvor der kan forekomme kviksølv.
Endelig vil der være en fraktion, der ikke kan genkendes af nogle af systemerne og den udsorteres til sidst i anlægget. I dag er den ca. 2%, men mængden formindskes løbende, idet data for de ikke
genkendelige batterier efterfølgende lægges ind i systemet.
I alt sorteres i 11 fraktioner.
Vægt- og Tri-Mag-sensorerne er den mest kritiske del af systemet med hensyn til nøjagtighed og hastighed, mens UV-sensorerne er langt det hurtigste og mest stabile sensorsystem. Det samlede system kan
detektere 5-8 celler pr. sek.
4.1.1.2 Kvalitet.
Renheden af de enkelte fraktioner er bedre end ved manuel sortering. Med undtagelse af lithiumfraktionen er renheden over 99%. For lithiumfraktionen er den omkring 96%
4.1.1.3 Kapacitet.
Første afsnit: |
10.000 tons/år |
|
Andet afsnit: |
5.000 tons/år |
1 tons/time |
Der regnes med 5 tons/skift
Der regnes med en sortering af 2.500 tons batterier i 2000. Der arbejdes p.t. i 2 skift.
Prisen for sortering er ca. 1,50 kr. pr. kg
4.1.2 Automatisk sortering hos Uni-cyc GmbH (SORBAREC) /35, 36/
Hos firmaet Uni-cyc GmbH i Bremerhaven er der etableret et automatisk sorteringsanlæg kaldet SORBAREC. Anlægget anvender, som det første i verden, røntgen-gennemlysning til at identificere de
forskellige batterityper.
Først er der en manuel indgangskontrol af batterierne, hvor andet affald og store batterier sorteres fra. Herefter sker der en mekanisk sortering efter størrelse på en sigte, så batterierne opdeles i 5 fraktioner.
Knapceller og batterier med en diameter over 35 mm tages fra, mens de øvrige tre fraktioner, der udgør omkring 85%, går videre til røntgen-linien. Her bliver der taget et røntgenbillede, hvor gråtoningen er
forskellig på grund af metallernes forskellige evne til at absorbere røntgenstråler. Yderligere er der en UV-detektor, der kan udsortere kviksølvfrie batterier, der er UV-mærket.
Anlægget har en kapacitet på ca. 1 tons pr. time og kan sortere 12 batterier pr. sekund. Renheden af de sorterede fraktioner angives til at være over 99,75 %.
Prisen for sorteringen er opgivet til 1 - 1,50 kr. pr. kg.
4.2 Behandlingsteknologier
4.2.1 Blybatterier/blyakkumulatorer /21, 22/
Blyakkumulatorer fra biler og lignende indsamles i Danmark af foreningen ReturBat. Praktisk taget alle de indsamlede akkumulatorer behandles hos smelteværket, Boliden Bergsöe i Landskrona.
Akkumulatorerne leveres til smelteværket inklusive syre, og første trin er udtømning af syren. Denne opsamles, renses og neutraliseres, hvorefter den ledes ud i Øresund.
Efter tømning knuses akkumulatorerne, og det sønderdelte materiale blandes med koks og slaggedannerne jern, kalk og sand, hvorefter det hele føres til smelteovnene. Rester af svovlsyre fra de knuste
akkumulatorer bindes til jern i slaggen. Under processen forbrændes alle de organiske materialer, mens blyet smelter og kan aftappes. Herefter raffineres blyet, og anvendes til fremstilling af nye
akkumulatorer.
4.2.2 NiCd-batterier
I Europa er der identificeret 3 firmaer, der så vidt vides behandler alle de NiCd-batterier, der indsamles i Vesteuropa:
S.N.A.M. , Frankrig
SAFT NIFE AB, Oskarshamn, Sverige
ACCUREC GmbH, Tyskland
Disse virksomheder behandler til sammen ca. 8.000 tons NiCd-batterier pr. år, og princippet alle tre virksomheder benytter sig af, er en opvarmning af batterierne, således at cadmium destillerer af.
Industrielle batterier skilles ad og de negative plader, der indeholder cadmium, opvarmes hvorved cadmium fordamper og efterfølgende kondenseres. Små lukkede NiCd-batterier kan pyrolyseres, således
at plast og andet organisk materiale nedbrydes inden destillationen.
Det tilbageblevne stål/nikkelblanding kan herefter videreforarbejdes og anvendes til jern-nikkel legeringer.
4.2.3 NiMH-batterier
NiMH-batterier kan bl.a. behandles hos S.N.A.M. i Frankrig og hos NIREC - Nickel Recycling GmbH i Tyskland.
Hos NIREC sker behandlingen på den måde, at batterierne gennem en vakuumsluse tilføres en shredder, hvor batterierne neddeles under vakuum. Derved frigives der brint, der kontinuerligt fjernes fra
kammeret. Herefter sorteres kunststofdele fra, og tilbage haves et produkt med højt indhold af nikkel. Dette kan efter en yderligere bearbejdning anvendes som legeringsmiddel ved stålfremstilling.
4.2.4 Lithiumbatterier
Lithiumbatterier er forholdsvis nye på markedet og bl.a. derfor, er der ikke så mange oparbejdningsmuligheder i dag.
Et af problemerne ved oparbejdning af primære lithiumbatterier er, at de indeholder metallisk lithium, der kan reagere eksplosivt ved kontakt med fugtig luft. Det amerikanske firma ToxCo, Inc. har derfor
udviklet en metode, hvor både primære og sekundære lithiumbatterier kan oparbejdes, og er i dag verdens største lithiumbatteri-oparbejder i dag.
Ved ToxCo processen nedfryses de primære batterier i flydende nitrogen til -195 °C, hvorved lithiums reaktivitet reduceres meget betydeligt. Herefter neddeles batterierne nedsænket i en opløsning af
kaustisk lithiumhydroxid. Friktionsvarmen gør, at batteridelene tørrer, og lithium vil reagere med den vandige opløsning og bl.a. danne lithiumhydroxid, lithiumsulfater og lithiumcarbonater. Samtidig dannes
der hydrogen, der kontrolleret afbrændes på overfladen af badet. Herefter frasepareres de faste metaldele ligesom plastik og papir, der flyder ovenpå, tages fra. Kulstof og andet slam filtreres ud af
opløsningen, og ved tilsætning af natriumcarbonate udfælder lithiumcarbonat som et hvidt fast stof, der også kan filtreres fra.
Sekundære lithiumbatterier behandles på en tilsvarende måde, men det værdifulde cobalt oparbejdes også fra disse batterier /27/.
I Europa er der kendskab til tre processer til oparbejdning af lithiumbatterier hos:
- AEA Technology Batteries, England
- ACCUREC, Tyskland
- S.N.A.M. Frankrig
Disse teknikker er dog ikke fuldt udviklede til fuldskalaanlæg endnu.
Teknikken udviklet af AEA Technology Batteries bygger på en neddeling af batterierne i en inert tør atmosfære, således at reaktioner med metallisk lithium undgås. Herefter separeres elektrolytten og kan
evt. genanvendes. Elektroderne opløses i det samme opløsningsmiddel som anvendes ved fremstillingen af elektroderne. Herved kan plastik, stål, kobber m.v. tages fra, og de resterende elektrodepartikler er
lithium cobalt oxid og forskellige typer af carbon. Efterfølgende kan cobalt reduceres til cobalt(II)oxid ved elektrolyse hvorved der desuden dannes lithiumhydroxid. Cobalt(II)oxid og kulstof frafiltreres
opløsningen af lithiumhydroxid, og det faste stof separeres i cobalt(II)oxid og kulpulver /28/.
Hos S.N.A.M. behandles sekundære lithiumbatterier i et pilotanlæg ved hjælp af pyrolyse efterfulgt af en neddeling. Fra de neddelte batterier fjernes jern med en magnet, mens kobber og aluminium sigtes fra
den fine fraktion med lithium, cobalt og kul. Fra den fine fraktion kan cobalt efterfølgende oparbejdes /2, 8/.
4.2.5 Knapceller
Kviksølvholdige knapceller kan behandles ved at destillere kviksølv af. Dette gøres som regel ved at anbringe knapceller og evt. andet kviksølvholdigt affald i en destillationsbeholder, som herefter opvarmes.
Derved vil kviksølv fordampe, og dampene kan efterfølgende kondenseres som metallisk kviksølv med en renhedsgrad på over 99,9% Processen er således relativ enkel, men på grund af kviksølvs lave
damptryk og høje giftighed stiller processen høje krav til tætheden af anlægget.
Der findes flere virksomheder i Europa der udfører destillation af kviksølv fra batterier. Som eksempler kan her nævnes:
Batrec, Schweiz
Citron, Frankrig
NQR, Tyskland
Trienekens, Tyskland
4.2.6 Alkali- og brunstensbatterier
I dag, hvor der i Danmark ikke er en obligatorisk ordning, hvor alkali- og brunstensbatterier indsamles separat, bortskaffes langt de fleste af disse via dagrenovationen. Dette betyder at batterierne i stort
omfang ender i husholdningsforbrændingsanlæggene, hvor plast, papir og kul vil forbrændes, mens stål og mangan vil ende i slaggen og zink i flyveasken. Eventuelt kviksølv renses fra i røggasrensningen. Alle
ressourcerne går tabt ved denne løsning.
Hvis alkali- og brunstensbatterier blev indsamlet separat, ville der i dag principielt være tre muligheder for behandling:
- Deponering
- Oparbejdning i metalindustrien
- Oparbejdning i specialanlæg
Deponering er den væsentligste løsning der anvendes i dag for de alkali- og brunstensbatterier der indsamles i Danmark. Batterier uden kviksølv kan deponeres på almindelige kontrollerede lossepladser,
mens kviksølvholdige batterier er farligt affald og skal derfor deponeres på specialdepot.
De alkali- og brunstensbatterier som Kommunekemi modtager deponeres på Kommunekemis specialdepot ved Klintholm, hvor de indstøbes i beton for at immobilisere eventuelt kviksølv.
Ved en oparbejdningsløsning er det muligt at oparbejde batterierne i metalindustrien, hvor de kan indgå som en del af råmaterialet, eller i specialanlæg der er specielt konstrueret til behandling af batterier. I
tabel 4.1 er vist en oversigt over forskellige anlæg og processer der kan anvendes til oparbejdning, og i de følgende afsnit er der nærmere beskrivelse af de enkelte processer.
Genanvendelse
Produkter
Prisniveau for behandling
Metalindustrien
Stålværker
35-40%
Jern og zink genanvendes
Kullet bidrager i stålet eller som brændsel
Mangan går i slaggen
Jern indgår i stålet
Zink i flyveasken, der oparbejdes
Under 5 kr./kg
Waelzovn
20-25 %
Kun zink genanvendes.
Kul forbrændes
Støv med 65% zinkoxid til oparbejdning
Under 5 kr./kg
Zinksmelteovn
20-25 %
Kun zink genanvendes
Zink
(>99,99 % ren)
Under 5 kr./kg
Specialprocesser
Citron
60-70%
Jern, zink og mangan genanvendes
Kul anvendes som reduktionsmiddel/brændsel
Zinkoxidkoncentrat og manganoxid til oparbejdning
Stålskrot til oparbejdning
Kviksølv
5-10 kr./kg
Batrec
60-70%
Jern, zink og mangan genanvendes
Kul anvendes som reduktionsmiddel/brændsel
Ferromangan
Zink (99% ren)
Kviksølv (>99,99%)
Over 10 kr./kg
VALDI
60-70%
Jern, zink og mangan genanvendes
Kul anvendes som reduktionsmiddel/brændsel
Ferromangan
Støv med kviksølv og ca. 80% zinkoxid til oparbejdning
5-10 kr./kg
Ebs
60-70%
Jern, zink og mangan genanvendes
Kul anvendes som brændsel
Støv med jern (10%), zink (40%) og mangan(30%) til oparbejdning
Jernskrot til oparbejdning
5-10 kr./kg
Revatech /Erachem
60-70%
Jern, zink og mangan genanvendes
Stål og zinkskrot til genanvendelse
Pasta med zink og mangan til oparbejdning
?
Euro Dieuze Industrie
50-70%
Zink, mangan og måske jern genanvendes
?
Zimaval Technologies
60-70%
Benytter tilsyneladende samme teknik som Revatech / Erachem
?
Tabel 4.1. Oversigt over kortlagte processer til behandling af alkali- og brunstensbatterier
4.2.6.1 Oparbejdning i metalindustrien
Oparbejdning af alkali- og brunstensbatterier i metalindustrien er en løsning, som især den europæiske batteriorganisation, EPBA mener, bør fremmes. I metalindustrien er der mulighed for oparbejdning i
flere forskellige typer af industrier:
- I lysbueovne (EAF) på stålværker
- I Waelz-ovne til oparbejdning af stålværksstøv med zink
- I zinksmelteovne
- Ved fremstilling af ferromangan
- Ved jernfremstilling i højovne
Batterierne tilsættes som en delstrøm til råmaterialet, og et af problemerne ved dette er, at de kan kontaminere slutproduktet med uønskede stoffer. Ligeledes producerer disse termiske processer store
røggasmængder, og kritikerne fremhæver at eventuelt kviksølv, cadmium eller dannede dioxiner fra batterierne blot fortyndes væk. Der er således både et kvalitets- og miljømæssigt aspekt, der skal tages
højde for.
Ved oparbejdning i metalindustrien stilles der af miljøhensyn generelt krav om at batterierne maksimalt må indeholde 5-20 ppm kviksølv og maksimalt 5% organisk materiale (plastik etc.).
Oparbejdning i stålværker (lysbueovn)
Ved en oparbejdning i stålværkernes lysbueovne tilsættes batterierne sammen med stålskrot. Herved vil jernet i batterierne blive genanvendt i det færdige stål. Zinken vil fordampe og blive oxideret til
zinkoxid, der opsamles i værkets røggasrensningssystem. Mangandioxid kan ikke reduceres i det smeltede stål, men vil i stedet flyde med op i slaggen. Mangandioxid fra batterier kan således ikke erstatte
den mangan der tilsættes ved stålproduktion. Organisk materiale og kul vil forbrændes ved processen.
Zinkstøv fra stålværker sendes som regel til oparbejdning i zinkværker (f.eks. Waelzovne), hvorved der også sker genbrug af zinken fra batterierne. Genanvendelsesprocenten vil således være noget større.
En af de kvalitetsmæssige indvendinger imod at anvende batterier i stålindustrien er batteriernes indhold af kobber, da kobber i stålet har en negativ indflydelse på kvaliteten. Hvorvidt stålværkerne kan
modtage batterier afhænger altså af hvilken stålkvalitet der fremstilles på de enkelte stålværker.
Miljømæssigt har det været anført, at der til trods for forbuddet mod et indhold af kviksølv på mere end 5 ppm i batterier, der fremstilles eller importeres til EU, stadig vil forekomme kviksølvholdige batterier
i affaldsstrømmen. Stålværkerne har normalt ikke udstyr til at rense afkastluften for kviksølv, men på grund af de store luftmængder vil der ske en fortynding af denne kviksølvmængde, således at mængden
der udledes vil synes meget lille. Cadmium fra NiCd-batterier der fejlagtigt ikke er sorteret fra, vil ligeledes emitteres.
Endelig har det været anført, at batteriernes indhold af organisk materiale kan være en kilde til dioxindannelse i stålværkerne.
Eksempler på stålværker i Europa der i dag har godkendelser og modtager batterier er:
- Nedstaal B.V., Holland
- Nervacero S.A., Spanien
- ASW Sherness Steel Ltd., England (kun test)
Waelz-ovn
Waelz-ovne benyttes især til oparbejdning af zinkholdigt støv fra stålværker, men processen kan også anvendes til andet zinkholdigt affald som batterier.
Waelz-processen går i korte træk ud på at opkoncentrere zinken ved at fordampe og oxidere zinken i affaldet og efterfølgende fange det zinkholdige støv i et filter.
Processen udføres i en Waelzovn - en ca. 40 m lang rotérovn - hvor det zinkholdige affald blandet med koks indføres i den ene ende (øverst), mens luft indblæses i den anden ende (nederst). Slaggen vil
således falde ud i den samme ende, som der indblæses luft. Undervejs i rotérovnen vil zinken fordampe og oxideres til zinkoxid, der føres med røggassen ud i samme ende som affaldet fyres ind i ovnen.
Røggassen og affaldsstrømmen er altså modsatrettede, hvilket bevirker at man gennem ovnen får en stigende opvarmning af affaldet.
Røggassen nedkøles kraftigt umiddelbart efter rotérovnen for at undgå dioxindannelse, hvorefter støvet med zinkoxid fjernes i et elektrofilter. Efterfølgende renses røggassen yderligere i filtre inden den ledes
ud.
Zinkstøvet, der kaldes Waelz-oxid, har et zinkindhold på ca. 65%, og sælges videre til zinkværker til yderligere oparbejdning /29/.
Batterier kan tilsættes som en delstrøm i det øvrige affald, og herved vil zinken fra batterierne kunne genvindes sammen med zink fra det øvrige affald. Organisk materiale og kul vil forbrændes, mens mangan
og jern vil blive tilbageholdt i slaggen, der eventuelt kan anvendes som fyld i forbindelse med anlægsarbejder. Ved processen er det således kun zink, der i egentlig forstand genanvendes.
Eksempel på en virksomhed i Europa der oparbejder batterier i Waelzovn er
- B.U.S. Berzelius Umwelt-Service AG, Tyskland.
Oparbejdning i zinksmelteovn
Batterier kan også oparbejdes i en zinksmelteovn - Imperial Smelting Process (ISP). Processen er udviklet til oparbejdning af zink og bly fra affaldsprodukter. Materialerne presses først til briketter,
hvorefter de sammen med koks indfødes i en skaktovn. Her opvarmes de til over 1.000 °C, hvorved slagge og metallisk bly kan aftappes i bunden, mens zink fordamper som metaldampe. Organisk
materiale og kul forbrændes i ovnen, og bidrager således til opvarmningen. Zinkdampene kondenseres efterfølgende som metal i en såkaldt bly "splash" kondensor. Princippet er, at flydende bly sprøjtes ind i
den varme gas, hvorved zink udkondenserer. Den flydende bly og zink fasedeler, hvorved zink kan tages fra og blyet kan genanvendes i kondensatoren. Efter separation og raffinering fås zink med en renhed
på mere end 99,990%
Ved anvendelse af batterier som fødemateriale er det, ligesom ved oparbejdning i Waelzovn, kun zinken fra batterierne der går til egentlig genanvendelse.
4.2.6.2 Oparbejdning i specialanlæg
Ved oparbejdning i specialanlæg forstås her anlæg, der er specielt udviklet med henblik på at oparbejde batterier i en separat proces. Der er ikke nogen klar skillelinie mellem processer, der kan henføres til
metalindustrien og specialprocesser, da mange af specialprocesserne bygger på i forvejen kendt teknologi fra metalindustrien.
Specialprocesserne kan opdeles i:
- Termiske processer
- Hydrokemiske processer
De termiske processer er langt de mest udbredte, men der findes enkelte firmaer i Europa der arbejder med hydrokemiske processer.
I det efterfølgende er der en kortere beskrivelse af de anlæg, der er identificeret i Europa. Nogle udvalgte anlæg er besøgt og analyseret mere indgående, og der er for disse en mere detaljeret beskrivelse i
bilag 1
Citron SA, Frankrig
Anlægget har en potentiel kapacitet på 130.000 tons pr. år, og kan behandle forskelligt tungmetalholdigt affald, herunder batterier med kviksølv. Der behandles pt. ca. 50.000 tons årligt, hvoraf batterier kun
udgør en mindre del. Det centrale i anlægget er den såkaldte Oxyreducer, hvor batterierne indfødes. Her opvarmes de til 1.000 - 1.200 °C ved hjælp af naturgasbrændere et stykke over affaldet. I bunden af
ovnen, hvor affaldet ligger, er der en reducerende atmosfære, således at metaloxider og -hydroxider reduceres, mens organiske dele pyrolyseres. Metaller som Zn, Pb, Cd og Hg med lavt
fordampningspunkt fordamper, og med undtagelse af Hg vil de re-oxideres når de når op i gasflammen.
Dette betyder at metallerne, med undtagelse af Hg, vil forlade ovnen som fine partikler. I et såkaldt gravitationskammer, hvor gashastigheden nedsættes på grund af kammerets størrelse vil partiklerne falde til
bunds, og kan tages ud. Hg og salte vil fortsætte med gassen, og renses ud i gasrensesystemet.
Fra gravitationskammeret fås således et pulverprodukt med et højt indhold af zinkoxid. Pulveret kan afsættes til yderligere oparbejdning, og en fordel ved processen er det lave indhold af chlorid i pulveret.
Kviksølv udkondenseres fra røggassen, og der fremstilles herved 99,995% rent kviksølv. Anlægget er nærmere beskrevet i bilag 1 A.
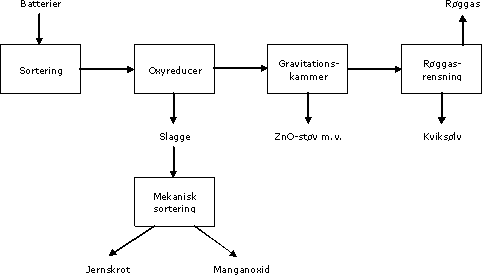
Figur 4.1. Citron SA. Skematisk procesdiagram.
Batrec Industrie AG, Schweiz
Dette anlæg med en årlig kapacitet på 3.000 tons, er specielt designet til behandling af batterier med kviksølv, og består først af en pyrolyse af batterierne ved ca. 600 °C. Herved pyrolyseres organisk
materiale og kviksølv fordamper. Batterierne overføres herefter til en induktions-smelteovn, hvor de opvarmes til 1.500 °C. Herved dannes der en slagge af ikke reducerbare metaller, en smelte af jern og
mangan (ferromangan) og en gas med zink på dampform. Gassen overføres til en splash-kondensor, hvor zinken kondenseres og aftappes i en renhed på 99%
Gassen fra pyrolysatoren renses for kviksølv, der efterfølgende destilleres til en renhed på 99,995%
Processen har en meget høj genanvendelsesgrad, idet praktisk taget alle metallerne oparbejdes. Anlægget er nærmere beskrevet i bilag 1 B.
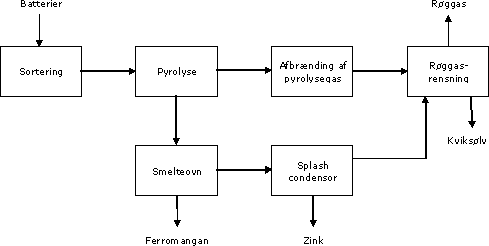
Figur 4.2. Batrec Industrie AG. Skematisk procesdiagram.
VALDI, Frankrig
Anlægget har en årlig kapacitet på 6.000 tons batterier med maksimalt 500 ppm kviksølv.
Batterierne tilføres en lysbueovn, hvor de smeltes i et stålbad ved ca. 1.600 °C. Herved vil jern og mangan indgå i en legering med stålbadet. Der tilføres samtidig forskellige additiver for at reducere MnO2 i
batterierne og for at neutralisere den udviklede gas. Ferromangan-legeringen aftappes og udstøbes i barrer der sælges.
Zink fra batterierne vil fordampe og efterfølgende oxideres i ovnen. Ligeledes vil kviksølv og salte fordampe, og under transporten til det efterfølgende filter vil kviksølvet reagere med zinken og danne en
stabil amalgamforbindelse. For at modvirke dannelse af dioxiner chokkøles gassen umiddelbart efter ovnen, og der tilsættes aktivt kul. I et posefilter udtages støvet fra gassen, og dette støv indeholder
75-86% zinkoxid og op til 0,06% kviksølv.
Zinkstøvet sendes til hydrokemisk oparbejdning hos et firma i Belgien, der også udvinder kviksølvet.
Ved processen sker der således en genanvendelse af både jern, mangan, zink og kviksølv fra batterierne. Anlægget er nærmere beskrevet i bilag 1 C.
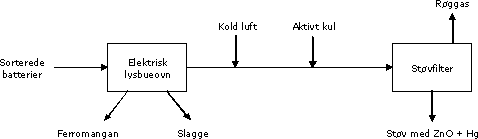
Figur 4.3. VALDI. Skematisk procesdiagram.
Entsorgungsbereich Simmering, EbS, Østrig
Anlægget har en kapacitet på 3.000 tons batterier pr. år, og er designet specielt til kviksølvholdige batterier indsamlet i Østrig.
Batterierne indfyres i en rotérovn, hvor de opvarmes til 600 °C. Herved åbner batterierne sig og kviksølv vil fordampe, mens organiske dele vil forbrændes. Røggassen afkøles efterfølgende og ledes igennem
en vådscrubber med NaOH, hvor kviksølv vaskes ud. Vaskevandet behandles kemisk således at kviksølvet fældes og det rensede vand udledes til Donau.
Røggassen fra skrubberen ledes til EbS' øvrige forbrændingsanlæg til forbrænding af farligt affald, således at røggasrensningen herfra sikrer at EU's emissionskrav er overholdt.
De "afgiftede" batterier udledes fra ovnen ved hjælp af en vandkølet snegl til en shredder. Efter shredningen deles materialet i en fin (< 1 mm) og en grov fraktion. Den fine fraktion, der indeholder en stor
mængde zink og mangan sendes til oparbejdning i metalindustrien, mens den jernholdige separeres fra den grove fraktion ved hjælp af en magnetseparation. Både den ikke jernholdige fraktion, der
indeholder en del kobber, og jernfraktionen sendes til oparbejdning i metalindustrien. Det har ikke været muligt at få detaljerede oplysninger om hvordan metallerne oparbejdes i metalindustrien, men på
baggrund af den separation der sker hos EbS må der forventes en høj grad af genanvendelse. Anlægget er nærmere beskrevet i bilag 1 D.
Klik her for at se Figur 4.4.
Figur 4.4. Entsorgungsbereich Simmering, EbS,. Skematisk procesdiagram.
Revatech - Erachem Europe, Belgien
Processen hos de to belgiske firmaer Revatech og Erachem Europe er designet til at behandle kviksølvholdige batterier mekanisk og hydrokemisk.
Ravatech står for den mekaniske behandling, mens Erachem Europe fra Revatech modtager et mellemprodukt og behandler dette hydrokemisk.
Kapaciteten hos Revatech er 3.000 - 4.000 tons batterier pr. år.
Processen starter hos Revatech med en mekanisk behandling, hvor batterierne knuses. Restenergien i batterierne gør, at der udvikles varme ved knusningen, hvilket betyder afdampning af kviksølv. Luft,
afsuget fra knusningen, ledes gennem et kulfilter. Plastik og metaldele (stål og zink) fjernes og plasticdelen sendes til cementindustrien, hvor energiindholdet udnyttes, mens metaldelen sendes til oparbejdning i
metalindustrien.
Den resterende del af batterierne udgør ca. 2/3 af vægten og benævnes som "black mass" på grund af den sorte farve. Denne del sendes til Erachem Europe og behandles hydrokemisk. Der startes med en
alkalisk vask for at fjerne elektrolytten efterfulgt af en filtrering. Spildevandet med elektrolytten renses og udledes, mens resten behandles med svovlsyre og additiver og filtreres, således at der fremstilles en
blanding af ZnSO4 og MnSO4, og en fast restfraktion der deponeres.
Dobbeltsulfatblandingen oprenses yderligere, idet den indeholder op til 500 ppm kviksølv samt nikkel, cadmium og andre urenheder. Herefter kan der fremstilles og sælges forskellige salte og oxider af
mangan og zink.
Ved processen er der en udnyttelse af jern, zink og mangan i batterierne, og Revatech angiver genanvendelsesgraden til 70%
Klik her for at se Figur 4.5.
Figur 4.5. Revatech – Erachem. Skematisk procesdiagram.
Euro Dieuze Industrie, Frankrig
Euro Dieuze Industrie, der ejes af det franske Vivendi, behandler batterier ved en mekanisk/hydrokemisk proces. Det har ikke været muligt at få oplysninger direkte fra virksomheden om deres proces,
hvorfor beskrivelsen bygger på andenhånds oplysninger. Processen minder tilsyneladende om processen hos Revatech/Erachem Europe.
Først neddeles batterierne mekanisk, hvorefter pulver og metal/plastik adskilles ved sigtning. Metallet består især af stål og zink. Pulveret behandles med svovlsyre, hvorefter kulstof frafiltreres. Filtratet, der
indeholder opløst zink og mangan, behandles således at kviksølv udfældes, hvorefter der fremstilles mangan- og sulfatforbindelser til salg.
Zimaval Technologies, Frankrig
Zimaval har en kapacitet på behandling af 4.000 tons batterier årligt, og processen bygger på den samme teknik som hos Revatech, der tilsyneladende også har en aktieandel i Zimaval. Det har ikke været
muligt at fremskaffe flere oplysninger om processen.
4.3 Vurdering af behandlingsteknologierne
Som det fremgår af forrige afsnit, er der med hensyn til alkali- og brunstensbatterier, mulighed for at oparbejde dem som en delstrøm i metalindustrien eller i specialiserede anlæg.
Generelt er priserne de laveste ved oparbejdning i metalindustrien, men til gengæld er genanvendelsesprocenten også lavere. Ofte er det kun zinken der oparbejdes til egentlig genanvendelse, hvilket giver en
genanvendelsesgrad på op til 25%. På stålværkerne er det dog jerndelen der genanvendes direkte og zinken genanvendes ved efterfølgende oparbejdning af flyveasken. På stålværkerne kan således opnås
en genanvendelsesgrad på op til 40% /34/.
Et andet problem, der har været nævnt ved behandling i metalindustrien er, at disse anlæg generelt ikke har røgrensningsudstyr til at fange cadmium og bly fra fejlsorterede batterier og kviksølv fra gamle
alkalibatterier. Endvidere kan der fra batteriernes organiske dele (plastik etc.) dannes dioxiner under forbrændingen, og normalt har anlæggene ikke udstyr til at rense for dette. Ved emissionsmålinger på
anlæggene vil det dog ofte ikke være muligt at måle en øget emission i røggassen, hvilket kan skyldes at den evt. øgede emission fortyndes bort i den store røggasmængde.
Eneste mulighed for behandling i metalindustrien i Danmark er Det Danske Stålvalseværk A/S. Her har man dog af kvalitetsmæssige årsager ikke hidtil haft mulighed for at modtage batterier, da bl.a.
kobberindholdet overstiger den mængde som værket kan acceptere. Hvis batterierne skal oparbejdes i metalindustrien, er man således nødt til at sende dem til udlandet. Herved bliver der ud over udgifterne
til behandling også en transportudgift, der naturligvis afhænger af den aktuelle afstand.
Som nævnt er behandlingen på de specialiserede anlæg dyrere, men til gengæld er genanvendelsesgraden også op til 70%. Endvidere er nogle af anlæggene specielt designet til at behandle kviksølvholdige
batterier, og samtidig tage hånd om f.eks. cadmium og bly fra fejlsorterede batterier.
Inden for specialanlæggene er der stor forskel på de produkter der fremstilles, og i hvor høj grad der skal ske en yderligere oparbejdning på andre anlæg efterfølgende.
Hos f.eks. Batrec fremstilles der udelukkende salgbare produkter, der kan anvendes uden yderligere oparbejdning. Hos de øvrige anlæg skal en større eller mindre del af produkterne - specielt zink - sendes
til yderligere oparbejdning inden de bliver anvendelige.
Kort kan det konkluderes, at fordelen ved oparbejdning i metalindustrien er de lave omkostninger, mens oparbejdningsgraden er højere i de specialiserede anlæg. Endvidere er disse også i højere grad
indrettet til at kunne håndtere evt. kviksølv, cadmium og dioxiner/furaner.
I afsnit 4.2.6 er i tabel 4.1 vist en oversigt over genanvendelsesgrad og prisniveau for de undersøgte processer.
| Forside | | Indhold | | Forrige | | Næste | | Top |
|