| Front page | | Contents | | Previous | | Next |
Development and use of screening methods to determine chromium (VI) and brominated flame retardants in electrical and electronic equipment
4 Screening method to determine hexavalent chromium in surfaces
In order to determine whether a piece contains chromium in a particular oxidation state (in this case hexavalent chromium, in the following referred to as chromium(VI)), it is necessary to use methods based on redox reactions that are specifically sensitive to the oxidation state in which chromium is present.
The International Electrotechnical Commission published an international standard in January 2009, including procedures for the determination of levels of regulated substances in electrotechnical products, IEC 62321.
This standard provides a method to determine levels of chromium(VI) (for further information about the method, see Chapter 5). The method is based on a colorimetric determination of the chromium(VI) content in a test liquid (colorimetry = determination by colour reaction). It is based on the reduction of chromium(VI) to chromium(III) in a reaction with 1.5 diphenylcarbazide oxidised to 1.5 diphenylcarbazone.
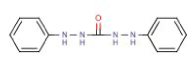
1.5 diphenylcarbazide
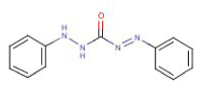
1.5 diphenylcarbazone
1.5 diphenylcarbazone yields a characteristic reddish purple colour with an absorption maximum of approx. 540 nm.
For a precise determination of the intensity of the red colour, and thus the chromium content in the test liquid, a spectrophotometer is required, but the red colour can also be observed with the naked eye, and the screening method developed is based on that principle.
The colorimetric method is also used to determine chromium(VI) in other media, and commercial test kits are available for drinking water and waste water analyses, among others, that are capable of testing for chromium(VI) in liquid volumes of 5-10 ml in special test tubes. An example is the Chromate Cell Test from Spectroquant®, which follows the US standards method 3500-Cr D. Spectroquant® test kits are available from VWR - Bie & Berntsen A/S, among others.
4.1 Development work
A number of experiments have been conducted in order to examine the possibilities and limitations of a screening test method based on visual colorimetric determination. The experiments, which are described in further detail in Annex 2, examine the sensitivity of the method in relation to different test materials. The test conditions most suited for a simple and quick screening method to be used without access to a fully equipped analysis laboratory have also been examined.
Based on the development work, the following section describes a test procedure and provides instructions as to the interpretation of test results.
4.2 Screening method procedure
The screening method can be used to determine chromium(VI) in passivation layers on metal pieces.
As mentioned above, the method is based on a colour reaction in a test liquid. In order to test for chromium(VI) in the passivation layer it is necessary to dissolve chromium(VI) in the test liquid and to ensure that chromium(VI) is not oxidised to chromium(III) before the colour reaction occurs.
Two methods are based on the corresponding methods described in IEC 62321.
- A spot test where chromium(VI) is dissolved in a drop of test liquid directly on the piece or in a white weighing boat.
- A screening boiling test where the piece is extracted for some time in de-ionised water at near-boiling point temperatures.
Neither test can be used to determine unambiguously whether the concentration in a homogeneous material is over 0.1%, but they can be used to detect the presence of chromium(VI). The screening boiling test can also be used to determine the concentration of chromium in a test liquid and thus yield a quantitative measurement. This can be used as an indirect indication of the concentration in the passivation layer under certain assumptions regarding the thickness of the passivation layer. It should be noted, however, that this also applies to the laboratory analyses described in IEC 62321. When testing for chromium(VI), the spot test should be performed first. If there is any doubt about the test result, it should be followed up with a screening boiling test.
As previously mentioned in section 1.4, it is possible to use an XRF instrument to determine whether there is chromium(VI) in a surface, but in practice, ideal measuring conditions can often not be obtained using a handheld instrument with a relatively large measuring window. Thus, the chromium content readout may well be under 0.1% even though the piece is coated with a thin chromium(VI) passivation layer. Proceeding directly to the spot test is therefore recommended.
4.2.1 Test solution
A diphenylcarbazide solution for colorimetric testing is produced by dissolving 0.4 g 1.5 diphenylcarbazide in a mixture of 20 ml acetone and 20 ml 96% ethanol, adding 20 ml 75% H3PO4 and 20 ml de-ionised water after dissolution. The solution should be left for eight hours before use.
The diphenylcarbazide solution is used for both test methods and will be referred to as the "test solution" in the following text.
Experience shows that for spot tests, using a diluted spot test liquid for certain surfaces is also expedient. Such liquid is produced by mixing spot test liquid and de-ionised water in the ratio 1:6. This is referred to as the "diluted test solution" in the following text.
It is important not to let the solution get too old as it discolours in the course of time. This may yield incorrect positive results, i.e. a colour reaction incorrectly indicating the presence of chromium(+VI). Discarding the test liquid when it is more than two months old is recommended if a strong coloration/precipitation of brown particles is observed, or if contamination of the liquid is suspected.
4.2.2 Spot test
Perform the spot test as follows:
- Degrease the piece with alcohol (or another suitable solvent) to remove fingerprints, dirt, etc. Let the solvent evaporate.
- If there is a layer of enamel: Using grain size 800 sandpaper, carefully abrade the part of the surface on which the test is to be conducted without exposing the underlying iron surfaces. If the underlying iron surfaces are exposed, the exposed iron may react with the chromium(VI) during the test, thus yielding a false negative result. Chemical cleaning agents are not to be used as they would cause a chemical reaction with the chromium(VI) layer. Tests have shown that it is difficult to abrade just the right amount, so sending pieces that are clearly enamel-painted for laboratory analysis should be considered.
- Place 1-5 drops of test solution on the surface of the piece. For small pieces such as screws it is recommended to perform the test in a white weighing boat as this makes it easier to see the colour of the liquid. It is also possible to perform the test in a small test tube, holding the tube up against a white background. The pictures below show a positive and negative test result, respectively.
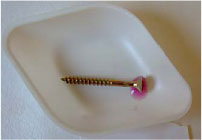
Yellow chromated screw with test solution. The characteristic reddish purple colour indicates the presence of chromium(VI).

Chromium(VI)-free screw. No colour reaction is seen in a test solution or diluted test solution.
- Compare the colour with a blank sample where a few drops of test solution are placed in a weighing boat without a metal piece. Before beginning the test, make sure the weighing boats give no colour reaction. The reddish purple colour should occur within 1-2 minutes and be stronger than the colour of the blank sample. The colour will bleach relatively quickly and should be registered within 2 minutes.
- If the result is negative, or in case of effervescence: Repeat the spot test using diluted spot test liquid. Strong effervescence indicates that the acid reacts with the metal layer, the underlying metal possibly releasing e.g. iron(II). The iron may reduce the chromium(VI) to chromium(III), thereby yielding a false negative result.
This is not described in the standard, but experiments have shown that for pieces with blue or clear chromium(VI) passivation layers it is often easier to see the colour reaction when using a diluted test solution. The results are illustrated in the photos below.
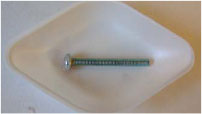
Spot test of blue chromated screw with normal test solution. The lack of reaction is probably due to the relatively quick dissolution of the chromate layer by the phosphorous acid and the associated release of iron(II) ions or zinc(II) from the underlying material. These ions will react with chromium(VI) and reduce it.
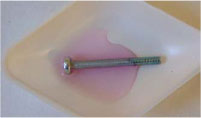
Spot test of the same type of screw with diluted test solution.
- If the result remains negative: To ensure there is no clear, transparent enamel on the piece, carefully abrade the part of the surface on which the test is to be performed using grain size 800 without exposing the underlying iron surfaces.
- Repeat the spot test.
If the result remains negative, the surface layer is not likely to contain any chromium(VI).
Risk of false positive results
The experiments yielded no false positive results. Chromium(III)-coated surfaces gave no colour reaction. However, the method is unsuitable for red-enamel painted pieces that may release colour to the test solution.
Risk of false negative results
False negative results may be obtained if iron parts are exposed which may release iron that reacts with chromium(VI). Make sure the test solution is only in contact with intact surfaces (except deliberately abraded surfaces).
It may be difficult to abrade the surface to remove enamel, and for enamelled pieces there is a great risk of not exposing the relatively thin layer of chromium(VI) because in most cases the chromium layer will be much thinner than the enamel layer. Laboratories performing tests according to the standard will have similar problems abrading the surface, however.
The method is destructive
After testing, the piece will not show that it has been tested, but because part of the passivation layer is removed, the piece will subsequently be more exposed to corrosion.
4.2.3 Screening boiling test
IEC 62321 recommends proceeding with a boiling test to verify the result of the spot test if there is any uncertainty about it, i.e. primarily
- if the colour reaction of the spot test is so weak that it is difficult to distinguish from a negative result, or
- in case of extensive effervescence in both the spot test liquid and the diluted spot test liquid.
A positive spot test is very likely to yield a positive result in a boiling test and therefore requires no further verification.
According to IEC 62321, the test requires a surface area of 50 ±5 cm². It takes a substantial number of screws and other small pieces to make up a surface area of 50 cm², and getting a sufficient number of identical pieces from one piece of electrical and electronic equipment will often not be possible. Furthermore, a boiling test requires the piece to boil for some time, which may be difficult in a screening test.
As a result, a screening test requiring less test liquid has been developed, as experiments have shown that the test can be performed on a surface of as little as 7-10 cm² and using a simpler extraction method. Experiments have shown that this method yields a satisfactory result when an exact quantification of chromium(VI) in the test liquid is not required. If sufficient material (50 ±5 cm²) and access to laboratory facilities are available, use of the standardised method described in IEC 62321 is recommended.
According to experiments, the method does not work if the piece contains exposed surfaces such as the fractured surface of a broken screw. This is probably due the iron released from the fractured surface reacting with chromium(VI). The same applies to tests performed in accordance with IEC 62321.
- Determine the surface of the pieces (using suitable geometric formulas) and select a number of pieces with a total surface of approx. 10 cm².
- Degrease the pieces with alcohol (or another suitable solvent) to remove fingerprints, dirt, etc. Let the solvent evaporate.
- If there is a layer of enamel: Using grain size 800 sandpaper, carefully abrade the part of the surface on which the test is to be performed without exposing the underlying iron surfaces. If the underlying iron surfaces are exposed, the exposed iron may react with the chromium(VI) during the test, thus yielding a false negative result. Chemical cleaning agents are not to be used as they would cause a chemical reaction with the chromium(VI) layer. Tests have shown that it is difficult to abrade just the right amount, and sending pieces that are clearly enamel-painted for laboratory analysis should be considered.
- Place the piece in a test tube with the following dimensions: internal diameter 14 mm, external diameter 16 mm, height 100 mm. Pour 10 ml de-ionised water into the test tube. Measure the distance to the edge of the tube.
- Place the test tube in a wire mesh holder, e.g. with white polycoating, a hole diameter of 18 mm/height 60 mm and 3*3 holes making it possible to test nine samples at the same time.
- Place the piece(s) in the test tube(s), transfer the wire mesh holder to a pot with boiling water reaching the liquid level in the tubes. Use a pair of tongs to transfer the holder. Extract for 10 minutes. Place a glass lid on the pot after making sure that chromium(+VI) is not released by any metal pieces (screws), etc. on the glass when spot testing the metal pieces.
- Remove the test tube from the pot and refill with liquid to distance a from the edge of the tube.
- Remove the piece from the tube and cool down the liquid to room temperature.
- Add 0.2 ml 75% phosphorous acid to the test tube, shake and distribute the liquid in two test tubes containing 5 ml each.
- Add 0.2 ml test solution to one test tube and shake. No test solution should be added to the other test tube, which acts as a blank sample.
- Compare the colour of the liquids in the two test tubes. If the test tube containing the test solution is clearly redder than the blank sample, the piece contains chromium(+VI).
The result can be compared with the colour scale shown in Figure 3. If the result matches the colour of 0.2 ppm (mg/L) or more, the piece can be regarded as containing chromium(+VI) exceeding the limit value (unless the blank sample is also coloured). Multiply the limit of detection to be seen with the naked eye of approx. 0.1 mg/L by an uncertainty factor 2 to make the determination fairly certain. If the colour is below that level, a laboratory spectrophotometer test is required to obtain a more certain determination.
The test liquid concentration can be converted to chromium(VI) per m² surface. If the pieces have a total surface of 10 cm², 0.2 ppm in the test liquid will correspond to approx. 2 mg chromium(VI)/m², if all the chromium(VI) has been dissolved in the test liquid. The screening test gives only a rough indication of the amount of chromium(VI) per m². If a more exact determination is required, a laboratory analysis in accordance with the standard is necessary.
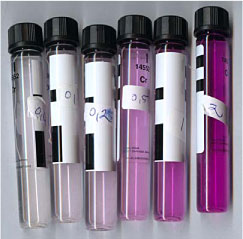
Figure 3 Colour scale - liquids for calibration: Concentrations in ppm from left: 0.05/0.1/0.2/0.5/1/2.
Neither the screening boiling test nor the laboratory analyses can be used to determine whether the concentration of Cr(VI) is over 0.1%; they can only be used to indicate the amount of CR(VI) per m² of the tested piece. Chapter 5 describes how to interpret the result of a laboratory analysis.
Risk of false positive results
The experiments have yielded no false positive results. However, the method is unsuitable for red-enamel painted pieces that may release colour to the test solution.
Risk of false negative results
False negative results may be obtained if iron parts are exposed which may release iron that reacts with chromium(VI). Make sure all pieces have intact surfaces (except deliberately abraded surfaces).
It may be difficult to abrade the surface to remove enamel, and for enamel-painted pieces there is a great risk of not exposing the relatively thin layer of chromium(VI) because in most cases the chromium layer will be much thinner than the enamel layer. Laboratories performing tests according to the standard will have similar problems abrading the surface, however.
The method is destructive
After testing, the piece will not show that it has been tested, but because part of the passivation layer is removed, the piece will subsequently be more exposed to corrosion.
It should be noted that a test kit (e.g. the Spectroquant Chromate cell test) can be used for screening boiling tests, but this may require a new colour scale, because in terms of chemicals the test kit is not completely identical with the spot test liquid in the IEC test. IEC 62321, 2008 also describes a test liquid more durable than the spot test liquid based on a solution of diphenylcarbazide in acetone.
4.2.4 Decision tree
The decisions to be taken in connection with the screening test are illustrated in Figure 4.
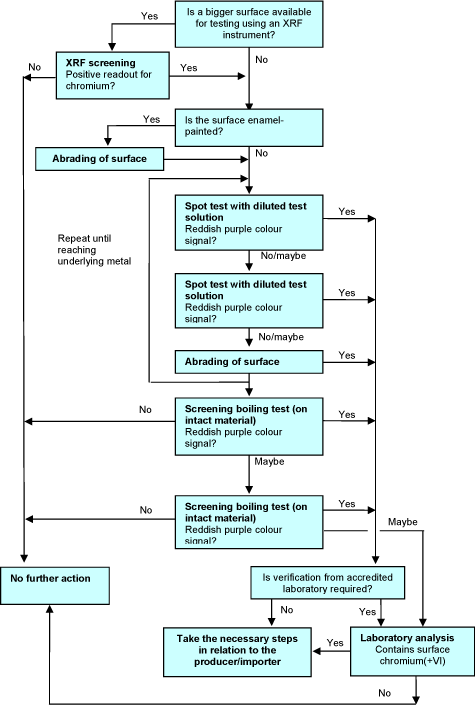
Figure 4 Decision tree for chromium(VI) screening test.
| Front page | | Contents | | Previous | | Next | | Top |
Version 1.0 May 2009, © Danish Environmental Protection Agency
|