| Front page | | Contents | | Previous | | Next |
Evaluation of Alternatives for Compounds under Risk Assessment in the EU, Bisphenol A
4 Bisphenol A in products in contact with food
Bisphenol A (BPA) containing products in contact with food mainly consist of coated food and beverage cans and vats (wine), coated lids for glass containers, besides some mineral
water bottles and food and beverage containers, such as jugs made of polycarbonate (PC).
4.1 Coated food and beverage containers
Due to the corrosive nature of much food and beverages, containers and lids made of metal (aluminium; iron with or without tin) are coated to ensure the integrity of the container and to
avoid metal migration into the food, attack on the metal substrate by the food or deleterious organoleptic effects. Some food is sterilised in the container by thermal processing (e.g.
120°C for 1 hour) and the coating thus needs to retain its resistance properties at these elevated temperatures and throughout the shelf-life of the canned food. The required properties of
can coatings can be summarised as:
- Resistance to content (i.e. foodstuffs)
- Chemical resistance
- Prevention of metal migration to the food content
- Thermal resistance during sterilisation of foodstuffs
- Compatibility with container manufacturing
Several materials can be used for coating food and beverage containers (epoxy-phenolics, polyester, PVC, epoxy-anhydrides and epoxy-aminos or epoxy-acrylic aminos) but the
choice of suitable coatings is limited for containers intended for very corrosive food.
4.1.1 Bisphenol A based epoxy coating
Epoxy-based coatings can withstand highly corrosive food and beverages (Glud & Marstrand, 2003; CEPE, 2003). Epoxy coatings are mainly thermoset, being based upon high
molecular weight epoxy resins. A thermoset polymeric material cannot be melted or dissolved in solvents. The final dried film of the epoxy coating is made by curing/hardening an epoxy
resin (pre-polymer) in the coating on the container or metal before can formation (Glud & Marstrand, 2003; CEPE, 2003).
Epoxy resins are characterised by molecules with more than one epoxy group. In the curing process, the epoxy resin molecules are linked by a curing compound, which establishes itself
as a permanent bridge (covalent bonds) between the epoxy and hydroxyl groups of the epoxy resin molecules (Figure 4.1). The curing renders the epoxy chemically resistant.
The most common epoxy resins used in coatings are the bisphenol A glydicylether epoxy resins, of which bisphenol A is a major constituent. Bisphenol A glycidylether resins or
prepolymers (Figure 4.1) are made from bisphenol A and epichlorhydrin of which the epichlorhydrin forms the glycidyl groups.
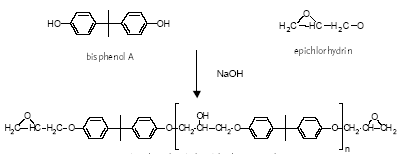
bisphenol A diglycidyl ether pre-polymer
CURING:
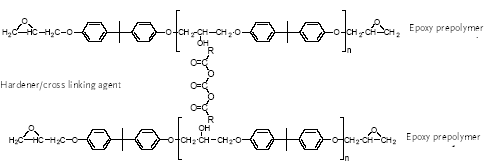
READY POLYMER:
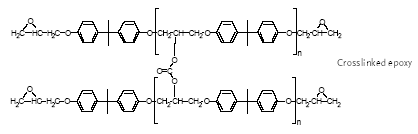
Figure 4.1 The process and structure of a bisphenol A glycidylether resin
For most purposes, n ranges from 0.2 to 13 (average numbers) and for can coatings, prepolymers with n = 2 to 30 are used (surface coatings). According to the EU risk assessment,
high molecular weight epoxy resins are used for can coating. If n is 0 or 1, the product is a viscous liquid while it is a brittle solid if n is larger than 1 (Polycondensation, 2003). Low
molecular weight epoxy resins are liquid while higher molecular weight epoxies are solid at room temperature (Ullmann, 2002). For can coatings and other uses, for which high molecular
weight prepolymers are required, short chain bisphenol A glydicylether epoxy resins (e.g. n = 0) are extended with additional bisphenol A an advancement process (EU, 2002 and
Polycondensation, 2003). The most widely used epoxy resins for can coating are based on bisphenol A diglycidylether (BADGE). BADGE is an intermediate for preparing all bisphenol
A/epichlorhydrin-based liquid epoxy resins (SPI, 2002B). The amount of `free' (residual) BADGE in the resin is dependent on many factors, of which molecular weight is one.
Common curing compounds (cross-linking compounds) are polyamines (ethylene diamine, diethylene triamine, triethylene tetraamine), polyamides, acid anhydrides, polymercaptans,
isocyanates, amino resins and phenolic resins. Among these, the polyamine and polyamide curing agents are used for heavy duty coatings (storage tanks, holds of ships, pipes etc.) and
normally not for can coatings (CEPE, 2003).
Epoxy resins reacted with an excess of polyamine yields an adduct, a polymer with amine functionality, which has certain advantages over aliphatic polyamines. Adducts can be made
from both solid and liquid epoxy resins. These adducts are used in heavy-duty coatings as curing agents for epoxy resin-based coatings.
For can coatings, high temperature cured coatings are used. As high molecular weight epoxy resin prepolymers are used, the hydroxyl groups become as important or even more
important than the epoxy groups for cross-linking and thus curing agents able to cross-link between hydroxyl groups are used. They are phenol formaldehyde resins (Figure 4.2),
melamine formaldehyde resins, urea formaldehyde resins and polyisocyanates (outside only).
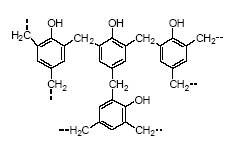
Figure 4.2 Phenol formaldehyde resin
Epoxy-anhydride coatings
The epoxy-anhydride coatings are high molecular weight epoxy resins cross-linked with anhydride hardeners. The epoxy-anhydrides are thermoset systems, which are normally
pigmented with titanium dioxide. With a good flexibility and a very good packing resistance, the BPA-containing epoxy-anhydride coatings are used for e.g. some drawn cans as the
white internal lacquer in some maize (sweet corn) cans (CEPE, 2003).
Epoxy-amino and epoxy-acrylic amino coatings
The epoxy-amino and epoxy-acrylic amino coatings are high molecular weight epoxy cross-linked with amino resins. With a good flexibility but a limited packing resistance, the
BPA-containing lacquers are used for e.g. beer and beverage cans (CEPE, 2003).
4.1.2 BPA-free alternatives in can linings
There are only few BPA-free alternatives available on the market today and these alternatives are limited for use in specific products.
Non-BPA containing epoxies are epoxy novolac resins and cycloaliphatic epoxy resins. Besides these, PVC is not containing epoxy, but most coatings using PVC contain
molecules/resins with some epoxy functionality (CEPE, 2003).
Phenolic resins
Phenolic resins (Figure 4.3) are reaction products of phenols and an aldehyde, usually formaldehyde (HCHO), in acid solution (surface coatings). Commercially used phenols are
bisphenols, phenol, cresols, xylenols, p-t-butylphenol, p-phenylphenol and resorcinol (SPI, 2002A). Many of the phenolic resins are made from mixed feedstock.
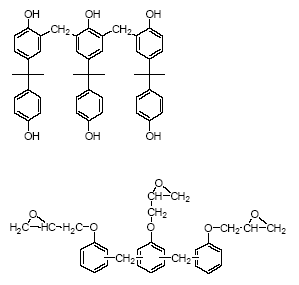
Figure 4.3 Phenolic resins
Epoxy resin esters are reaction products of epoxy resins and vegetable oil fatty acids.
Polyester-based coatings
Polyester resins are used for the interior coating of cans (Ullmann, 2002). The polyester systems can be based on either high molecular weight thermoplastic polyesters or on low
molecular weight thermoset polyesters. The ready-made polyester-based can coatings are delivered to the can producers as powders or liquids (CEPE, 2003).
Polyester-based coatings are not resistant to corrosive foods, i.e the packing resistance is limited. The polyester bonds tend eventually to hydrolyze, which results in coatings, that can
loose their resistance and performance properties, with can perforation being the worst case. However, the polyester-based coatings are generally more flexible compared to epoxy
coatings and their use is limited mainly to non-aggressive food (Glud & Marstrand, 2003). Newer polyester-based products are, however, suitable for a wider product range (CEPE,
2003).
Bisphenol A-based epoxy resins may also be used as a performance enhancer of polyester-based internal can coatings (Lyons, 2000). However, CEPE explains that the industry does
not use BPA for this purpose but may use an BPA-based epoxy resin to improve the performance of the polyester coating. Polyester resins are cross-linked with amino or phenolic
resins and may contain lower molecular weight epoxy resins to improve the resistance properties (CEPE, 2003).
PVC-based coatings
The PVC vinyl-based systems are thermoplastic (non-cross-linked) dispersed in a varnish. With a very good flexibility and packing resistance, the PVC systems are often used on top of
the epoxy-phenolic basecoat in e.g. drawn cans. As PVC can thermally degrade during stoving generating hydrochloric acid (HCl), epoxy or oxirane functional substances or resins are
often added as HCl scavengers (CEPE, 2003).
4.1.3 Coating properties influencing use and choice of coating
The can producers (e.g. Glud & Marstrand) receive ready-made can coatings from the coating producers (e.g. Valspar, PPG, ICI and Grace) whereas the coating producers receive
the epoxy resins from the resin producers (e.g. Dow, Resolution and Huntsman). The European epoxy resin producers are members of the Association of Plastics Manufacturers in
Europe (APME), about 95% of the European coating producers are members of the European Confederation of Paint, Printing Ink and Artists Colours Manufacturers (CEPE) and
many of the European can producers are members of the European Secretariat of Manufacturers of Light Metal Packaging (SEFEL). The food and beverage packers and fillers (food
industry) are members of the Confederation of the food and drink Industries of the EU (CIAA). APME, CEPE, SEFEL and CIAA are all members of the Joint Industry Group (JIG).
The BPA-based epoxy phenolic coatings, often called Phenolic Gold Lacquers due to their characteristic golden/yellowish colour, are used for the majority of applications including
highly corrosive foods such as fruit, vegetables, meat products etc.
While the adhesion of epoxy-based coatings is good for all materials, the polyester-based coatings may have varying adhesive properties depending on the type of substrate (e.g. tinplate
or aluminium) (Glud & Marstrand, 2003).
The polyester-based coatings are generally more expensive compared to the epoxy-based coatings, limiting their use mostly to cans or can components, in which their particular
properties (e.g. higher flexibility in drawn cans) are needed. Polyester-based coatings are used for non-corrosive food only, e.g. meat such as liver paste etc., in which the fat content of
the food protects the can coating against the aggressive food ingredients (Glud & Marstrand, 2003).
The packing resistance (shelf-life) of the polyester-based coatings will often be lower (e.g. 2-3 years) compared to the epoxy-based coatings, putting the integrity of the packaging at
risk and requiring extensive tests in order to establish the shelf-life of the various types of canned food. When using epoxy-based coatings, a shelf-life of up to 5 years can be assured for
a wide range of foods (Glud & Marstrand).
The same specification of cans with a given coating is often used for various end uses (e.g. different types of vegetables) under the can producers' guarantee. As a consequence of the
requirements to heat and corrosive resistance, durability and price, the can producers select coatings capable of withstanding the most severe requirements, i.e. epoxy coatings (Glud &
Marstrand, 2003).
In 2002, approx. 90% of the total use of coatings were based on epoxy (including PVC which frequently contains epoxy or oxirane functional species) while polyester-based coatings
only constitute one of the alternatives, which also include PVC (non-epoxy, non-oxirane containing) and to a lesser extent the acrylic resins.
For external coatings (non-food contact), epoxy resins may or may not be used. In many cases, a small amount of epoxy resin may be present even for acrylic and polyester resins in
order to improve performance. For internal can coatings (food contact), about 90% are based on BPA-based epoxy resins (CEPE, 2003).
4.1.4 Development of alternatives
The well-known bisphenol A-containing epoxy, i.e. BADGE-based coatings, has been used by the can coating industry for the past approx. 40 years (SPI, 2002B). Due to the focus on
bisphenol A, the reduction of release of free bisphenol A monomers from epoxy coatings and the development of bisphenol A-free can coating alternatives have progressed for the last
approx. 5 years (Glud & Marstrand, 2003; CEPE, 2003).
For the past 5 years, the migration of BPA monomers from cured can coatings has been in focus and the industry strives for continuous improvement attempting to reduce the BPA
migration as well as other migrants (CEPE, 2003; Glud & Marstrand, 2003). Earlier, there existed some coating products with BPA monomers added as plasticizer but nowadays the
so-called "Clean Epoxy Technology" is used in which the polymerisation process is completed in order to reduce the content of free BPA monomers to a minimum (Grace, 2003).
Based on the measurements of BPA migration from epoxy resins into foodstuff, the concentrations of BPA from food contact applications are approx. 650 μg/l for wine and 100 μg/kg
from canned food (EU, 2003A). For adults the estimated daily ingestion of BPA is 500 μg/day from wine and 100 μg/day from canned food. The figures are used in the EU risk
characterisation (EU, 2003A).
The polyester-based coatings were developed in 1987 in order to replace the PVC organosols and were later considered as alternatives for BADGE-based coatings and later the BPA
containing coatings (CEPE, 2003).
Several can users, e.g. the military, demand long-lasting packing resistance with a durability of at least 5 years.
During recent years, the can coating industry has intensified the development of BPA-free alternatives. The development of a new can coating system takes approx. 10 years from the
testing and evaluation of the properties to the successful commercialisation including pack testing, which can last up to at least 5 years. During the development period, all information of
the new can coating system is kept strictly confidential.
Considering this 10-year time scale for developing and testing of new coatings, the contacted industries decided not to use the offer for "free" health and environmental evaluation of
BPA-free alternatives as the project period was considered to be unrealistically short for this purpose.
4.1.5 Other uses of coatings
To a lesser extent compared to the total use of bisphenol A in coatings, BPA-epoxy based systems are used for lid and cap coatings and for side seam stripes (CEPE, 2003; Metropak,
2003; Pelliconi, 2003).
Epoxy-based coatings are used as inside lid coatings in bottle lids, glass container lids, etc. It is estimated that all closing systems for glass jars today and most side seam stripes contain
at least one epoxy-based coating system (CEPE, 2003). Based on the experience from Pelliconi and their cooperation with coating suppliers, there are currently no alternatives to
epoxy-based coatings for lids (Pelliconi, 2003).
To a large extent (but not 100%) coatings for caps contain BPA-based resins, which are especially used when good substrate adhesion and protection against corrosion are needed
(Metropak, 2003).
The economical difference of the products depends not only on the price of the coating but also on its properties, etc. (e.g. what is the cost of a can with a shelf-life reduced from 1 year
compared to 5 years?). Therefore, no price examples comparing caps with BPA-based resins and BPA-free resins were given (Metropak, 2003).
4.1.6 Environmental and health screening of alternatives to bisphenol A in coatings for food and beverage purposes
During the search in the DPR, several polyester resins and polyacrylates were mentioned as possible alternatives to bisphenol A in coated food and beverage containers (Tables 3.3, 3.4
and 3.5). An internet search was performed in order to investigate the use of these substances. Some of the mentioned polyacrylates could be identified in coatings for floor, electrical
insulation (e.g. CAS No. 26376-86-3) etc. but not as ingredients in coatings for food or beverage purposes.
Among the polyester resins, mentioned on the internet one of the possible high molecular weight thermoplastic polyesters is based on polybutylene terephthalate (PBT). PBT is used in
heat resistant coatings on paper and board (e.g. for packaging of frozen food and oven-ready meals) as in the BASF product Ultradur B2550, where it might be in direct food contact.
No specific alternatives were pointed out by the industry (CEPE, 2003).
Very little information about the phenolic resins was available but many of the phenols are made from mixed feedstock of bisphenols, phenols etc. and are therefore not evaluated as
alternatives to the epoxy-based coatings. The PVC-based coatings are often used in a combination with the epoxy-phenolic coatings or resins and thus not evaluated as alternatives to
the epoxy-based coatings. The screening of the environmental and health properties of coatings for food or beverage purposes was thus based on the polyacrylate and polyester
properties in general.
Properties of polyacrylates
The properties of polyacrylates differ dependent on the specific substance. However, to some extent, acrylate monomers are likely to be released from the polyacrylate products. Some
of the acrylate monomers are classified with N; R51/53, i.e. toxic to aquatic organisms and may cause long-term effects in the aquatic environment (Danish EPA, 2002).
Table 4.1 Properties of polyacrylates
Name |
Polyacrylate |
Synonym |
Data not available |
CAS No. |
9003-01-4; 51142-25-7 |
Formula |
Data not available |
Classification |
Not present on the list4
Some acrylate monomers: N;R51/534 |
Ready biodegradability |
Data not available |
Bioaccumulation |
Data not available |
Ecotoxicity |
Data not available |
Endocrine disruption |
Not present on the list5 |
Acute toxicity |
LD50 (rat, oral) 2500 mg/kg1 |
Irritation/corrosion |
Data not available |
Sensitization |
Data not available |
Toxicity by repeated exposure |
Data not available |
Carcinogenicity |
Inadequate animal and human data for assessment of carcinogenicity. Group
3.2 |
Reproductive toxicity |
No developmental toxicity was demonstrated when acrylic acid polymers cross-linked
with allyl ethers of pentaerythritol and/or sucrose were tested in a rat study
at high doses.3 |
Genotoxicity |
Data not available |
- Sheftel (2000)
- IARC (1999)
- Reprotext (2003)
- Danish EPA (2002).
- Danish EPA (2003)
Polymers have little specific toxicological activity. The biological effects of polymers may be attributed to residual monomers, oligomers or low-molecular-weight by-products that are
incorporated into the polymer, additives or molecular changes during the curing process. Polyacrylates are a large group of resins produced from a large number of feedstock and to
which a large number of additives are added. It is thus not possible to make any general assessments regarding toxicological properties, although the polyacrylates themselves are not
dangerous to health.
Regarding the effects on health, the possible content of the residual monomers in polymers, monoalkyl, monoaryl or monoalkylaryl esters of acrylic acid are included in the Annex 1 of
the EU directive on classification and labelling of dangerous substances with a classification as irritating to eyes, skin and respiratory organs. The influence from these monomers should
be considered regarding releases from the finished product and regarding the environment and working environment related to the production and manufacture.
Properties of polyester
Polyester consists of long-chain polymers chemically composed of at least 85% by weight of an ester of a dihydric alcohol and a terephthalic acid. Esters are formed when alcohol reacts
with a carboxylic acid. Polyesters can consist of any hydrocarbon chemical group. The properties of the polyester compound will depend on the influence of the specific hydrocarbon
chemical group.
As the polyester compounds used in coatings for food or beverage purposes could not be specified, the general properties of the polyester are included in the Table 4.2.
Table 4.2 Properties of polyester
Name |
Polyester |
Synonym |
|
CAS No. |
63148-69-61 |
Formula |
Data not available |
Classification |
Not present on the list5 |
Readily biodegradable |
Data not available |
Bioaccumulation |
Data not available |
Ecotoxicity |
EC50 (fish, 96h): >560 mg/l2 |
Endocrine disruption |
Not present on the list6 |
Acute toxicity |
LD50 (rat): > 5000 mg/kg3 |
Irritation/corrosion |
Essentially innocuous to the skin (basic polyethylene terephthalate)4
Dust and fibers may irritate the respiratory system.4 |
Sensitization |
Data not available |
Toxicity by repeated exposure |
No pathological evidence of toxicity observed in 90-day feeding studies with
rats and dogs.4 |
Carcinogenicity |
Data not available |
Reproductive toxicity |
Data not available |
Genotoxicity |
Data not available |
- Chemfinder (2003)
- US EPA (2003)
- RTECS (2003)
- Sheftel (2000)
- Danish EPA (2002)
- Danish EPA (2003)
Based on the available data, polyester cannot be classified as dangerous to the environment. However, as the properties depend on the specific substance, it is not possible to make a
general assessment of the environmental hazard of polyester-based alternatives.
The biological effects of polymers may be attributable to residual monomers; oligomers or low-molecular-weight by-products that become incorporated into the polymer, additives or
molecular changes form the curing process. Polyesters are a large group of resins produced from a large number of feedstock and added a large number of additives. It is thus not
possible to make any general assessments regarding toxicological properties. However, the polyesters themselves are not classified as dangerous to health.
4.1.7 Legislation related to coating of cans
Within the EU, the European Scientific Committee for Food (SCF) is the responsible for assessing materials intended to come into contact with food (SPI, 2002B).
The European Commission (Directorate General of Health and Consumer Protection) has published legislation (2002/16/EC) on the use of BADGE, bisphenol-F diglydicyl ether
(BFDGE) and the wider family of novolac glycidyl ethers (NOGE).
The use of BADGE as monomer and as reaction intermediate or additive in food cans coatings is permitted until 1 January, 2005. Until then, the sum of the migration levels of BADGE
and BADGE derivatives must not exceed 1 mg/kg foodstuff. The EU is currently processing the first amendment to 2002/16/EC. This amendment will extend the deadline until
31/12/2005 in order to enable the European Food Safety Authority (EFSA) to give their opinion on a toxicological dossier for BADGE due to be submitted at the end of the first
quarter of 2004 (CEPE, 2003).
The same goes for BFDGE (also the sum of BFDGE + BFDGE derivatives + BADGE + BADGE derivatives < 1 mg/kg).
NOGE was allowed only until 1 December 2002. It is therefore currently being phased out (Times food, 2003).
BPA is permitted under the Directive 2002/72/EC and due to a recent opinion from the SCF, the Specific Migration Limit (SML) is expected to be 0.6 mg/kg. According to CEPE, the
typical BPA migration levels in foodstuffs are up to about 0.05 mg/kg (CEPE, 2003).
BADGE is included in current danish legislation regarding materials and subjects intended for foodcontact (Retsinfo, 2003). BADGE may only be released to the food from plastic
materials, surface coatings and adhesives. BADGE must not exceed 1 mg/kg in the food or 1 mg/dm2 for cans etc. (Retsinfo, 2003).
4.2 Polycarbonate food and beverage containers
Polycarbonate products are used in food contact materials such as mineral water bottles, infant feeding bottles, returnable beverage bottles (e.g. used in water cooler machines),
tableware (plates and mugs), jugs, beakers, microwave ovenware and storage containers (EC, 2002; EU 2003A).
Polycarbonate is a hard clear lightweight thermoplast, which is often based on bisphenol A. Approximately 487,000 tonnes bisphenol A is used in the production of polycarbonates per
year within the EU (EU, 2003A). It can be made in three different ways:
- Phosgenation of dihydric phenols, usually bisphenol A
- Ester exchange between diaryl carbonates and dihydric phenols, usually between diphenyl carbonate (C5H5O)2CO and bisphenol A
- Interfacial polycondensation of bisphenol A and phosgene COCl2 (Figure 4.4) (SPI, 2002A)
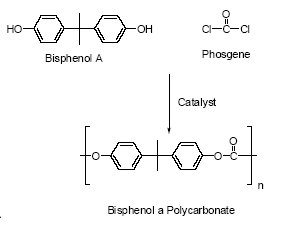
Figure 4.4 Interfacial polycondensation of bisphenol A and phosgene
Polycarbonate is a very stable hard heat-tolerant material with high electrical insulating properties, impact resistance, ductility and optical clarity (Bisphenol A org., 2003; EU, 2003A).
Polycarbonate resins readily undergo hydrolysis under alkaline conditions leading to the release of bisphenol A, e.g. in paper recycling plants (Fukazawa et al., 2002). It is a well-known
fact that polycarbonate hydrolyses after prolonged contact with hot water (>60°C) hydrolyses (Pedersen, 2001). However, short sterilisation with water at 120°C is not considered to
lead to hydrolysis of polycarbonate (Leisewitz & Schwarz, 1997).
The maximum residual content of bisphenol A in polycarbonates is reported to be 50 mg/kg but the typical residual content is < 10 mg/kg (EU, 2003A).
The amount of unreacted monomers in polycarbonate is less than 100-150 mg/kg and, in general, it is <25 mg/kg according to the polycarbonate producers, Bayer and Dow (Leisewitz
& Schwarz, 1997).
In a European-wide survey, migration of BPA from the bottles into food simulants was not detectable at <3 μg/kg (EC, 2002). For used bottles BPA was detected in water and/or
acetic acid samples from five of twelve bottles, the levels measured ranging from 20-50 μg/l, i.e.20-50 ppb. 50 μg/l is considered to represent the realistic worst-case exposure
conditions of BPA migration from polycarbonates into food (EU, 2003A). The estimated daily ingestion of BPA for infants is 35-50 μg/day from polycarbonate feeding bottles, which is
used in the EU risk characterisation (EU, 2003A).
4.2.1 Alternatives to polycarbonate
There are different types of non-bisphenol A plastic products on the market. Compared to the properties of polycarbonate, the bisphenol A-free nylon products e.g. Grilamid TR, are
considered to have similar properties and may be seen as an alternative to polycarbonate.
A few companies produce nylon (polyamide) that can be used for baby bottles as a replacement for polycarbonate bottles. The companies are EMS-Grivory in Germany and Sumter in
the USA. Grilamid TR grades are transparent thermoplastic polyamides based on aliphatic and cycloaliphatic blocks. Grilamid TR is characterised by its UV resistance, high chemical
and stress crack resistance etc. (Grivory, 2003).
Polyamide (nylon)
The high molecular weight polyamide, hexamethylene adipamide, is formed from adipic acid and hexamethylene diamine in a polymerisation process, and is also known as nylon 66.
Polyamide has puncture resistance and thermoformability with very good barrier properties and is therefore used for food packaging for e.g. meat and cheese products (BASF, 2003).
BASF is one of the major resin suppliers to the manufacturers of polyamide. The manufactured quantity of nylon 66 in the EU by e.g. BASF, Rhone-Poulenc and Du Pont is
>1,000,000 tonnes/year (Iuclid, 2003).
Polyamide was thus considered as a possible alternative to polycarbonates and the environmental and health assessments were based on data available for polyamide.
4.2.2 Environmental and health screening of alternatives to polycarbonates
The environmental and health screening of polyamide are based on the properties listed in Table 4.3.
Table 4.3 Properties of the polyamide, nylon 66
Name |
Hexamethylene adipamide |
Synonym |
Nylon 66; polyamide |
CAS No. |
32131-17-2 or 3323-53-3 |
Formula |
C6H16N2.C6H10O4 |
Classification |
Not present on the list5 |
Ready biodegradability |
No
61% after 5 days (BOD5 test)1
BOD5/COD: 0.611
|
Bioaccumulation |
Data not available |
Ecotoxicity |
LC50 (Fish, 96h): 10,000 mg/l1
EC50 (Daphnia, 48h): 99 mg/l1
EC50 (Algae, 72h): 292 mg/l1
|
Endocrine disruption |
Not present on the list2 |
Acute toxicity |
LD50 (rat, oral): 5900 mg/kg3 |
Irritation/corrosion |
Data not available |
Sensitization |
Data not available |
General toxicity by repeated exposure |
Rats were dosed with 300 and 500 mg/kg bw for 40 days. Behavioural, biochemical
and pathological changes were observed.4
Administration of 5 mg/kg bw to rabbits for 7 months resulted in changes in blood chemistry. No morphological changes in the visceral organs.4
|
Carcinogenicity |
Data not available |
Reproductive toxicity |
Data not available |
Genotoxicity |
Data not available |
- Iuclid (2003)
- Danish EPA (2003)
- RTECS (2003)
- Sheftel (2000)
- Danish EPA (2002)
The degree of degradability will depend on the aliphatic and cycloaliphatic blocks in the polyamide. Polyamide is degradable, and with a BOD/COD ratio above 0.5 it seems to fulfil the
criteria for ready biodegradability. The acute toxicity to aquatic organisms is about 100 mg/l for daphnia, which is considered to be the most sensitive group. There are no data
describing the bioaccumulation of polyamide. Based on the available data it is, however likely that polyamide should not be classified as dangerous to the environment.
Polymers have as such little specific toxicological activity. The biological effects of polymers may be attributable to residual monomers, oligomers or low-molecular-weight by-products
that are incorporated into the polymer, additives or molecular changes of the polymer during the curing process. It is not possible to make any general assessments regarding
toxicological properties of polyamides. However, the polymer itself is not classified as dangerous to health.
4.2.3 Legislation related to plastic materials
The limit to migration of bisphenol A from plastic materials used for food contact materials is 3 mg/kg (Retsinfo, 2001). At present, there are no legal restrictions on the amount of
bisphenol A that can be present in the final plastic product (EU, 2003A).
| Front page | | Contents | | Previous | | Next | | Top |
Version 1.0 March 2004, © Danish Environmental Protection Agency
|