Modern Windships; Phase 2
15. Index & Tables
Index of Figures
Index of Tables
List of Equations
Index of Figures
Figure 1. Definitions used in the report.
Figure 2. Wind direction names.
Figure 3. Lift, drag etc,. definition of terms.
Figure 4. Range of angle of incidence
Figure 5. Modern WindShip balanced with thrusters and rudder.
Figure 6. Traditional sailing ships rig types.
Figure 7. Traditional square rig.
Figure 8. Different rig types, reproduced from WindShip report phase 1. Originals by Peter
Schenzle.
Figure 9. Coefficients for different rig types. Reproduced from WindShip report phase 1.
Originals by Peter Schenzle.
Figure 10. The rig type chosen in phase 1 of the WindShip project.
Figure 11. Brain storming, first idea.
Figure 12. Brainstorming, second idea.
Figure 13. High lift wing mast, stackable single profile.
Figure 14. The three types of profiles used for CFD calculations.
Figure 15. Profile 1, pressure distribution at a =9°.
Figure 16. Profile 2, pressure distribution at a =9°.
Figure 17. Profile 3 ,pressure distribution at a =9°.
Figure 18. The high lift wing mast.
Figure 19. Boundary layer suction principle. Reproduced from Ref. 27.
Figure 20. Thick profile lift coefficient, with boundary layer suction. Reproduced from
Ref. 27.
Figure 21. Mast sail and Wing Mast wind tunnel models.
Figure 22. Lift and drag compared when sailing upwind.
Figure 23. Performance comparison between the two different rig types.
Figure 24. Wing mast folded together.
Figure 25. Mast foot calculation.
Figure 26. Rotary vane engine flap turning mechanism.
Figure 27. Gear rim flap turning mechanism.
Figure 28. Flap turning through link mechanism.
Figure 29. Hydraulic flap mechanism.
Figure 30. Rotating the high lift wing profiles.
Figure 31. Fibre-glass panels
Figure 32. The WindShip stability curve.
Figure 33. Mast, general view.
Figure 34 Element plot no. 1 of flap with turning disc
Figure 35 Element plot no. 2 of flap with turning disc
Figure 36 Composite flap without the outer sandwich elements.
Figure 37. The mast with boundary conditions and loads
Figure 38. Detail of the mast foot boundary condition.
Figure 39 Wind pressure distributed on both sides of the composite flap.
Figure 40 The perimeter pressure load on the turning disc.
Figure 41 The flap boundary conditions. Note turning axis.
Figure 42 The overall deflection of the mast at full load, deflections in scale 1:1.
Figure 43. Von Mises effective stress in the mast.
Figure 44. Von Mises effective stress, outside of the mast foot.
Figure 45 Von Mises effective stress, backside of mast foot.
Figure 46 Von Mises effective stress, inside mast foot.
Figure 47 Von Mises effective stress, inside mast foot.
Figure 48 Shear stress under mast in mast foot.
Figure 49. The overall deformation of the flap at full load. Deformation scale 1:1.
Figure 50. Von Mises effective stress in the outer sandwich laminates, lower side.
Figure 51. Von Mises effective stress in the outer sandwich laminates, upper sides.
Figure 52. Von Mises effective stress in the solid laminates.
Figure 53. Core shear stress in the outer sandwich laminates.
Figure 54. Internal structure, von Mises effective stress.
Figure 55. The deckhouse design.
Figure 56. The modern WindShip wind tunnel model in the seven mast configuration.
Figure 57. Stability curves for the modern WindShip
Figure 58. Type A bow type.
Figure 59. Type B bow type.
Figure 60. Aft part of tested hull
Figure 61. The four tested underwater hull configurations.
Figure 62. An underwater hull model in the wind tunnel (configuration no. 2).
Figure 63. Photo of the aft of the model. Note the azimuth thruster and the relatively
small propeller.
Figure 64. Screenshot of the VPP user interface.
Figure 65. WindShip speed polar in 3 m/s true wind, varying the engine power between
0-100%.
Figure 66. WindShip speed polar in 16 m/s true wind, varying the engine power between
0-100%.
Figure 67. WindShip performance as 3D matrix plot instead of polar plot.
Figure 68 Trade routes in the two trade patterns used in the WindShip calculations.
Figure 69. Typical route-tree on leg 5. Optimal route marked with bold line.
Figure 70. Atlantic trade pattern fuel consumption.
Figure 71. Indian-Pacific trade pattern fuel consumption.
Figure 72. The variation of fuel oil prices since 1974.
Figure 73. Some of the possible profile improvements.
Figure 74. Five mast proposal.
Figure 75. Nomenclature
Figure 76. Flow between parallel plates
Figure 77. Schematic diagram of boundary-layer flow [SNAME vol II]
Figure 78. General view of PMM and model attached to the towing carriage. (Not the
WindShip model)
Figure 79. Examples of test executed in static mode of PMM operations.
Figure 80. Examples of Yaw tests executed in dynamic mode of planar-motion mechanism
operation.
Figure 81. Comparison of pure yawing motion generated with PMM and rotating arm.
Figure 82. Pierson-Moskowitz spectrum for the four sea-states.
Figure 83. The added resistance in head sea by strip theory for the four sea-states.
Figure 84. The WindShip speed at 100% power in increasing headwind.
Figure 85. A typical structural sandwich material.
Figure 86. The wind pressure dependence on wind speed
Figure 87. Profile plan with dimensions.
Figure 88. Square curve fit of the Cl-CN dependency. Linear
approximation CN(Cl) = 0.0774-0.07332*Cl.
Figure 89. Fuel consumption on the Atlantic trade pattern
Figure 90. Fuel consumption on the Indian-Pacific trade pattern
Figure 91. Speed for given thrust and 10 m/s wind
Figure 92. Thrust for given speed and 10 m/s wind.
Figure 93. Rudder angle for heading to true wind, 10 m/s.
Figure 94. Drift angle for given heading to true wind, 10 m/s of wind.
Index of Tables
Table 1. English phrases, definition
Table 2.Performance comparison between a wing mast and a sail mast.
Table 3. Wind statistics on the different trade routes.
Table 4. Extreme values of non-dimensional coefficients
Table 5 Forces and moments in the mast foot at 26.4 m/s of wind.
Table 6. Estimation of individual forces in the wing mast.
Table 7. Load cases to be considered.
Table 8. Wing mast estimated price and weight
Table 9. Modern WindShip hull main particulars
Table 10. Intact stability analysis of the WindShip
Table 11. Results of intact stability analysis according to IMO res. A.562(14).
Table 12. Model scale dimensions of the modern WindShip
Table 13. Test condition 01.
Table 14. The test matrix for 0% thrust trials
Table 15. The test matrix for 50% and 100% thrust trials.
Table 16. Note that the velocity and rudder angle were constant in this specific table.
Table 17. Note that the drift and rudder angle were constant in this specific table.
Table 18. Note that the velocity and drift angle were constant in this specific table.
Table 19. The modern WindShip speed at 100° true wind, 0% engine power.
Table 20. Trade routes in the Atlantic trade pattern
Table 21. Trade routes in the Indian-Pacific trade pattern
Table 22. Three year average wind speed along each route.
Table 23. Estimations of average fuel consumption at three speeds, conventional ship and
modern WindShip on the Atlantic trade pattern, fully laden.
Table 24. New-building price and capital costs. From Ref. 9, table 13, page 19.
Table 25. Dead weight and cubic metres. From Ref. 9, table 15, page 9.
Table 26. RFR per day, Atlantic and Indian-Pacific trade patterns. From Ref. 9, table 19,
page 25
Table 27. Parameters for the four spectra.
Table 28. Added resistance in heading waves (kN)
Table 29. Allowable stress levels for steel according to DNV.
Table 30. Dimensions for the individual profiles.
Table 31. Scaling the lift coefficient linearly with the depth of the profile
Table 32. Price and weight calculation for a25 m/s wing mast built in Denmark.
Table 33. Price and weight estimate for a 20 m/s wing mast built in Denmark
Table 34. Price and weight estimate for a 20 m/s wing mast built in a low-price country.
List of Equations
Equation 1 |
L = ½ r V2 S CL |
Equation 2 |
D = ½ r V2 S CD |
Equation 3 |
Re : Reynolds number : 
|
Equation 4 |
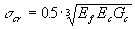 |
Equation 5 |
 |
Equation 6 |
CL = lift coefficient =
|
Equation 7 |
CD = drag coefficient = 
|
Equation 8 |
CK = bending moment coefficient = 
|
Equation 9 |
CN = rotating moment coefficient = 
|
Equation 10 |
Fvertical = 9.81 * m [N] (normal gravitational
load) |
Equation 11 |
Ftransverse = (2.95 + 0.044*(h-9.5))*m [N]
(transverse load with added rot.) |
Equation 12 |
Fvertical = 12.9 * m [N] (gravitation with
added acceleration) |
Equation 13 |
Flongitudinal = 4.51 * m [N] (longitudinal
acceleration) |
Equation 14 |
 |
Equation 15 |
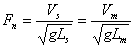 |
Equation 16 |
H1/3 = 0.6 + 0.15 U10 + 0.004 U10
2 |
Equation 17 |
T1 = 3.6 + 0.26 U10 |
Equation 18 |
S(w ) = 173 × HS2
× TS-4
× w -5 × exp(-692 × TS-4
× w -4) |
Equation 19 |
Raw(a ) = Raw(0)
× f(a ) |
Equation 20 |
f(a ) = 1 - 0.38 × (1 - cos(a )) - 0.44 sin2(a ) |
Equation 21 |
Raw (a ) = Raw (0)
f(a ) |
Equation 22 |
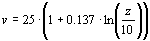 |
|