* excl. deposit-return bottles
Factors used for Model A in the calculation of indicators are shown in Table 4.3.
Factors are further illustrated in the following figures. The data basis for calculations
of the different factors for the three material fractions and relevant treatment options
is provided in Appendix D (not translated).
Resource values are stated in PR person reserves, expressing consumption
related to known reserves of a given resource per person in the world (see Glossary). The
calculation of the resource factor for a material fraction is based on a statement of
resource factors for each individual resource used in the production of a material
fraction. The contribution from each individual resource for each material fraction
appears from Appendix D (not translated). Comments on the following figures are based on
the underlying values.
Figure 5.1 shows that for paper the non-energy-related resource consumption has the
highest weight, which is mainly due to consumption of the resource sulphur for the
production of paper. The large weight attributed to sulphur in the statement is due to
sulphur having a short supply perspective, when only traditionally available sources are
taken into account. However, large sulphur resources are bound in fossil fuels, and they
are increasingly exploited today. Therefore, it may be argued that the resource statement
for sulphur should give a lower value, taking such sources into account (see Appendix C).
In the EDIP project, the normalisation of sulphur has been disregarded (setting the value
= 0), which does not seem correct either. The example thus indicates that the LCA
methodology is still under development.
For glass packaging, by contrast, energy-generating materials have the highest weight
(see Figure 5.2). The result is that from a resource perspective the difference between
recycling and landfilling glass is not very large, since there is considerable energy
consumption associated with glass remelting, whereas there is large benefit from reuse of
glass packaging without remelting. In terms of resources (and also energy) large benefits
can thus be obtained from reusing a large amount directly as glass packaging compared to
recycling glass from cullet.
Total resource consumption associated with the treatment of 1 tonne of aluminium
appears from Figure 5.3. Upon recycling or incineration secondary materials are generated,
thus saving virgin materials, aluminium and sand/gravel respectively. As the figure and
Table 4.3 shows, resource savings from incineration of aluminium are insignificant
compared to resource consumption for production of virgin aluminium for substitution of
what was lost. However, this is based on the assumption of aluminium being completely
incinerated (see Appendix C).
For resource factors (see Figures 5.1 to 5.3) it is evident that aluminium is markedly
different from the two other material fractions, as the factor per tonne is 30 times
higher than for paper and 150 times higher than for glass. The reason is that the use of
bauxite for aluminium production has a high weight despite a long supply perspective for
bauxite. The use of energy-generating materials only contributes little to the total
resource consumption associated with the production of aluminium, as hydropower is used
extensively, weighing very little in terms of resources (see Figure 5.3). The contribution
from the different raw materials to the resource factors can be seen in Appendix D (not
translated). Thus, it is also possible to break down contributions between renewable and
non-renewable resources, as in Figures 5.4 to 5.6. In general, renewable resources only
have low weight, which is due to the statement method (see Glossary).
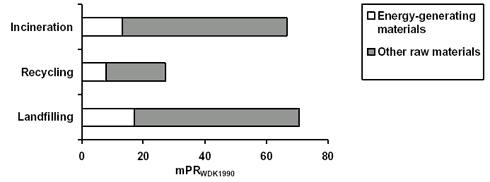
Figure 5.1
Total resource consumption associated with treatment of 1 tonne of paper
and production of substitute material for different waste treatment options.
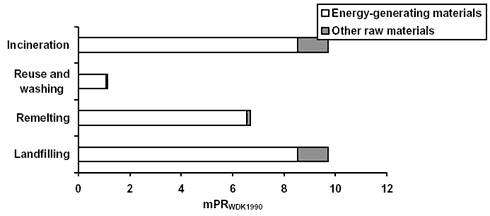
Figure 5.
2
Total resource consumption associated with treatment of 1 tonne of glass
and production of substitute material for different waste treatment options.
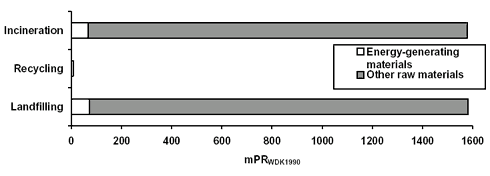
Figure 5.
3
Total resource consumption associated with treatment of 1 tonne of
aluminium and production of substitute material for different waste treatment options.
The energy factor expresses how much net primary energy (see Glossary) is used for
different treatments of the three waste fractions. The unit here is mPEDK98 per
1,000 tonnes of material. Primary energy consumption in Denmark in 1998 was 160 GJ per
person, and one mPE therefore equals 160 MJ. Energy consumption as an indicator is
particularly applicable as a total measurement of environmental impacts from use of
energy, and in contrast to the resource factor, it weighs renewable and non-renewable
resources against each other. Figures 5.4 to 5.6 therefore state which part of energy
consumption derives from renewable and which part derives from non-renewable energy
resources.
Virgin paper is primarily produced with renewable energy resources: wood and
hydropower. Figure 5.4 shows that paper upon incineration substitutes non-renewable energy
resources. Stated in person-equivalents the result upon incineration of paper is a primary
energy consumption in the form of renewable energy resources of over 100 mPE/tonne, which
is slightly more than upon recycling of paper.
Thus, the calculation shows that despite energy recovery upon waste incineration there
is a benefit in terms of energy from paper recycling, even though this benefit should be
compared to the larger consumption of non-renewable energy sources upon recycling. Energy
consumption upon recycling of paper, however, is in the range of 50% of energy consumption
of production of virgin paper.
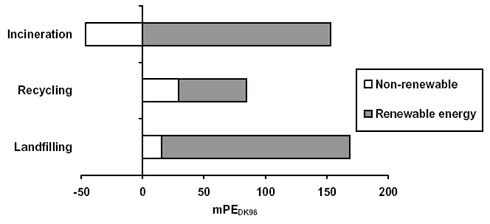
Figure 5.4
Total primary energy consumption associated with treatment of 1 tonne of
paper for different waste management options. Note that primary energy consumption is
calculated by deducting the left-hand side of the bar (the negative part) from the
right-hand side. Thus, incineration of paper rates worse in terms of energy than
recycling, and better than landfilling.
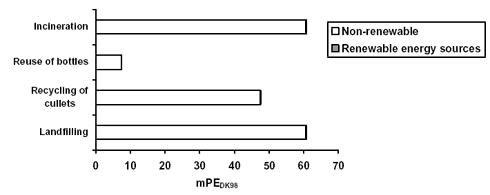
Figure 5.5
Total primary energy consumption associated with treatment of 1 tonne of
glass packaging for different waste management options.
Figure 5.5 shows that for glass packaging primary energy consumption upon reuse of
glass is markedly lower than upon remelting of cullet. However, remelting is slightly
better than landfilling, if only primary energy consumption is taken into account.
Figure 5.6 shows that primary energy consumption upon recycling of aluminium is
considerably lower than for other waste management options which is not surprising.
It is also seen that even if it is assumed that aluminium burns upon incineration (see
Appendix C), the energy benefit gained is relatively small compared to the benefit from
recycling.
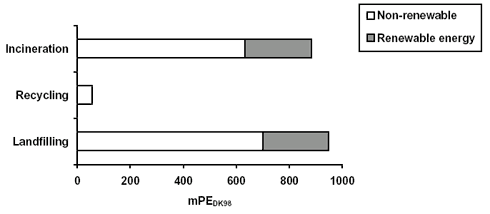
Figure 5.6
Total primary energy consumption associated with treatment of 1 tonne of
aluminium for different waste management options.
The landfill factor expresses how much waste for landfilling is generated upon
different management options for the three waste fractions. The unit is PEDK98 per
1,000 tonnes of material. The quantity of waste landfilled in Denmark in 1998 was 403
kg/capita, so one PE of waste for landfilling = 403 kg.
Figure 5.7 shows that upon landfilling of paper, the amount is just above the 2.5 PE
that paper for landfilling constitutes by itself. This is due to the fact that some waste
is landfilled in connection with production of paper. Upon recycling of paper, landfilling
of waste paper from the recycling process takes place particularly filler material
from paper often ends up in sludge for landfilling. Incineration of paper generates some
slag, which is mainly due to the contents of unburnable filler material in the paper. At
the same time, incineration also gives savings in primary energy such as coal, and thus
saves waste for landfilling from extraction and combustion of coal. Quantities are smaller
for incineration of paper compared to recycling mainly due to the fact that a very large
part of slag from incineration is used for building and construction purposes, thus
counting as recycling and not taking up space for landfilling.
For glass (Figure 5.8) just about the same quantity is landfilled as for glass for
landfilling by itself so there is no significant contribution in connection with
the production of glass. Furthermore, the quantity for landfilling upon incineration
constitutes 40% of total quantities, as 60% of slag from incineration is recycled for
building and construction purposes. Recycling and reuse cause only a small amount for
landfilling.
Figure 5.9 shows landfilling of waste from the different waste management options for
aluminium. In addition to the quantity landfilled virgin aluminium must be produced,
causing very large quantities for landfilling. Also upon incineration, aluminium will have
to be substituted, and considerable quantities of slag are generated. Slag quantities are
around double the quantity of aluminium, under the assumption that incineration is
complete (see Appendix C). This is due to the fact that aluminium oxide is generated upon
incineration. In return, around 60% of slag is recycled as backfilling. The result is that
for landfill requirement there is no significant difference between direct landfilling and
incineration of aluminium. Only upon recycling is a substantial reduction in landfill
requirement achieved.
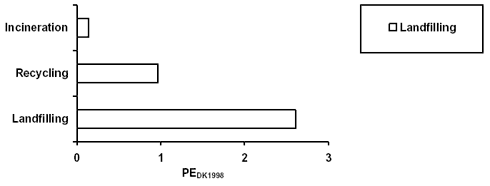
Figure 5.7
Total landfill requirement associated with treatment of 1 tonne of paper
and production of substitute material for different waste treatment options.
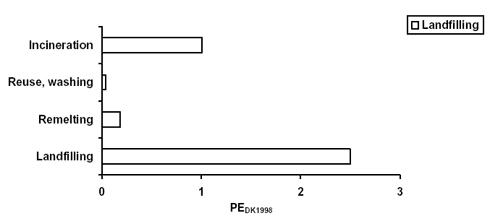
Figure 5.8
Total net landfill requirement associated with treatment of 1 tonne of
glass and production of substitute material for different waste treatment options.
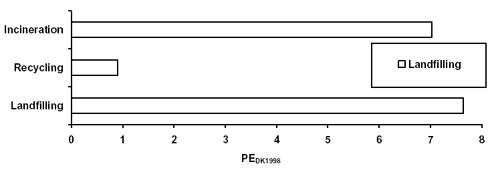
Figure 5.9
Total net landfill requirement associated with treatment of 1 tonne of
aluminium and production of substitute material for different waste treatment options.
There are significant differences for both energy and resource factors between
recycling and other treatment of aluminium. For paper just above half of the energy and
resource consumption is saved upon recycling compared to landfilling. For glass it is seen
that even if materials are recovered, there is considerable resource and energy
consumption in the range of 50-70% of consumption, if materials are landfilled. For energy
factors the difference between aluminium and the other materials is less marked, but still
significant (see Figures 5.4 to 5.6).
Naturally, the situation is different for the landfill factor, where there is a
significant effect of recycling (see Figures 5.7 to 5.9). The landfill factor is around
three times higher for aluminium for landfilling than for glass for landfilling. The
difference is due to the production of primary aluminium that generates considerable
quantities of waste included in the calculation. For paper, landfilling from recycling is
larger than landfilling from incineration, as filler material in paper is landfilled upon
recycling. Furthermore, incineration of paper leads to savings in coal, and thus there is
less waste for landfilling from coal extraction and combustion.
For aluminium the landfill factor is only slightly lower upon incineration than upon
landfilling, as part of aluminium oxidises upon incineration, thus generating considerable
waste quantities (see Appendix C). It may rightly be argued that similar oxidation will
take place in the long-term upon landfilling. But in order to simplify calculations,
long-term changes of materials upon landfilling have not been taken into account.
Recycling of slag from incineration for backfilling etc. constitutes 60% of slag and fly
ash generated /40/, which has been taken into account in
calculations.
In the calculation of indicator values, factors for the three waste fractions (see
Table 4.3) are multiplied by waste quantities for the different treatment options (see
Table 5.1). The calculation is described in more detail in Chapter 4. Results are
presented and commented on below.
As seen from Figure 5.10, indicator values give slightly different pictures of the
relative importance in terms of waste of material fractions upon the relevant waste
treatment option. It is seen that the three indicators give significantly different
results that supplement each other.
For reasons of simplification, in this and the other figures on indicator values no
distinction has been made between resources in energy resources and other resources.
Neither has a distinction been made between primary energy in renewable and non-renewable
sources. The distinction can be found in Figures 5.1 to 5.6, or in Appendix D, stating
detailed results (not translated).
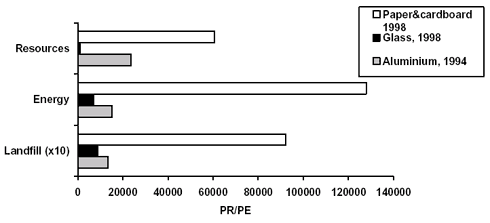
Figure 5.
10
Consumption of resources, energy and landfill requirement from treatment of
waste and production of substitute materials.
The following units have been used: Resource consumption: PRWDK90
,Energy consumption: PEDK98 , landfill requirement: PEwaste DK98.
Values for landfill requirement must be multiplied by 10. Note that the three indicators
have only been shown on the same figure for practical reasons. Each indicator should be
studied separately.
Results can also be illustrated relatively, as in Figure 5.11, where the three
materials have been interrelated. The figure shows how much each material fraction makes
up of total indicator value. Figure 5.11 shows that despite the far smaller waste
quantities compared to the two other material fractions, aluminium gives a considerable
contribution in terms of resource consumption. Paper gives the most significant
contribution to energy, which may not be surprising. Paper also gives a significant
contribution to resource consumption, this is mainly due to the large weight in terms of
resources that has been attributed to sulphur in the statement. This is discussed in
Chapter 5.2.1.
Figure 5.11 gives an idea of the focus of the three indicators, and it shows that waste
quantities by themselves give a markedly different picture. Thus, there may be good
reasons to operate with several indicators to gain an adequate picture of the waste
management situation.
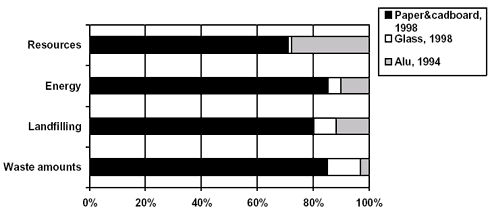
Figure 5.11
Relative contribution of the three waste fractions studied, in relation to
the three indicators and waste quantities.
As one of the purposes of indicators is to illustrate effects from initiatives in the
waste management field, it is important that indicators can be used to follow
developments.
Figure 5.12 shows waste quantities and the three indicators for glass stated for 1991,
1995 and 1998 and indexed on 1991. Total quantities of glass waste in the period increased
by around 20%, and similarly energy and resource indicators increased by 10-15%. The lower
increase in indicators is the result of increased recycling, but results show that total
resource and energy consumption associated with the use of glass increased in the period
despite initiatives in the waste management field. The landfill factor, by contrast,
decreased by 20%, which reflects the fact that glass for incineration is partly recycled
together with slag from the incineration plants.
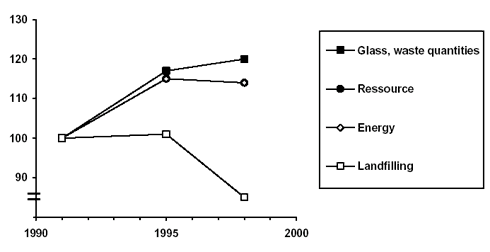
Figure 5.12
Developments in waste quantities and the three indicators for glass in 1991,
1995 and 1998, with 1991 = index 100. Note that resource and energy indicators are
coincidental for the three years.
For aluminium, a detailed material flow analysis is only available for 1994 (see
Appendix C), and therefore it is not possible to make a statement where developments are
followed, for example from 1991 to 1998. It is likely that increased use of civic amenity
sites and schemes for collection of waste electronic and electrical equipment have led to
an increase in collection of aluminium, but it is also likely that waste quantities have
increased. However, without an update of the available mass-flow analysis it is not
possible to reflect this development.
The trial shows that it is very relevant to include metals, if the life-cycle-based
indicators are to be applied to the entire waste management field. For the indicator for
resource consumption a number of other metals will probably contribute considerably,
similar to aluminium. In the normalisation of world resources for the different metals,
even metals consumed in small amounts, but having a low rate of recycling, will contribute
significantly to the weighted resource consumption. For energy consumption, aluminium
weighs heavily, and other metals apart from iron and steel will probably
contribute significantly less than aluminium.
The difference between presentations A and B is primarily in the focus of the
presentation. Whereas A focuses on total waste quantities, B focuses on savings realised
in resources, energy consumption and landfilling upon the waste treatment option in
question compared to 100% landfilling.
The basic calculation principles for life-cycle data and quantitative data are similar
for the two models. In principle, indicator values for presentation Model B can be
calculated on the basis of two scenarios, one of which is the calculation for Model A,
showing indicator values for the waste management option in question. The second waste
treatment scenario is calculated, assuming that all waste is landfilled. Indicator values
for the presentation of Model B are then found by calculating the difference between the
two scenarios. This results in indicator values for resource, energy and landfill
advantages realised upon the current waste management compared to 100% landfilling.
Finally, a third scenario can be added where a full optimisation of waste management is
assumed. The difference between this scenario and current waste management shows the
potential from optimising waste management. This is also included in the presentation
Model B below.
In the calculation, however, the procedure has been simplified by converting factors
from Model A (Table 5.1) into a set of factors for Model B (Table 5.2). The conversion has
been made by calculating the difference between landfilling and other options for each
individual factor and material. Basic data is thus similar to data described for Model A.
The column for landfilling in Table 5.2 is 0 for all fields, and positive or zero for
other treatment options. It shows that landfilling is always the poorest alternative in
the examples calculated.
Table 5.2
Calculated factors, Model B. Savings from different treatment options
compared to landfilling.
Units used::
mPR (milli person reserves), mPE (milli person equivalents), and PE (person equivalents)
The presentation of data in Model B matches well with the data found for waste
management in waste statistics. It first and foremost shows indicator values for waste
collected for reprocessing, whereas waste led to landfill does not contribute to the
indicator. If the potential from an optimisation of waste management is to be calculated,
data must be supplemented from other statistics than the waste statistics. In addition, it
is necessary to assess how much material it is possible to collect from a waste fraction.
This is discussed in the following chapters.
Below the principles of the current optimal recycling and how they can be
calculated in an indicator calculation are discussed.
For example, for aluminium normal practice in connection with recycling is that a
number of aluminium alloys are mixed, and that upon recycling almost exclusively
high-alloy cast aluminium is produced. Opportunities for future recycling of this cast
aluminium will be significantly more limited than recycling of low-alloy aluminium types.
The latter constitutes the major part of aluminium disposed of today through recycling.
Thus, in a long-term perspective it will be optimal to keep aluminium alloys separate in
the recycling process.
In the recycling process some aluminium oxidises and is landfilled in the form of
aluminium oxide. In some Norwegian melting works treatment and recycling of this aluminium
oxide takes place. In relation to resource savings this process will be optimal compared
to the more usual melting process. The optimal recycling thus differs from the form of
recycling that is generally used today.
If a detailed analysis is to be made for each disposal option of the best available
technique, the task of data collection and assessment would be very extensive. Therefore,
it is proposed that the definition of the optimal form of recycling is handled more
pragmatically, so that for example in relation to aluminium average data from European
recycling industries is used, provided by the EDIP PC tool database. In addition to
simplifying data collection this has the advantage of avoiding very extensive explanations
of calculation assumptions.
When direct recycling as a metal is compared to energy recovery upon incineration or
recycling of aluminium oxide in the form of slag from waste incineration, recycling as a
metal will be the optimal choice in all circumstances.
In relation to current recycling the problem is more than the impacts associated with
recycling; these can be determined in relation to the actual recycling (to the extent that
data is available). The problem is also to determine what is actually substituted upon
recycling, and what quality (value) to attribute to the recycled material.
The starting point is that we wish to make a calculation covering all material
recovered. How would all the aluminium produced today from recycling have been produced if
there had been no recycling? And how would the district heating provided today from waste
incineration have been generated if there had been no energy recovery from incineration?
We actually do not know this, and particularly in the field of energy, developments
will not only be governed by market economy mechanisms. Similar to the approach used for
determining the optimal form of recycling we will therefore use a pragmatic approach,
based on average considerations. However, for heating generation from incineration we have
carried out a more detailed study in Appendix C. This means for the example of aluminium
that data is used representing in the EDIP PC tool database the average for aluminium
produced in Europe. For power and heating generated in Denmark we have made a specific
assessment of the impact from incineration of waste at Danish waste incineration plants on
consumption of coal.
The indicators in calculation Model B have the purpose of showing realised and
potential savings in relation to the three parameters. Realised savings can be based on
quite reliable quantitative data and are altogether not very debatable, whereas it is
necessary to make more assumptions for potential savings.
In the calculation examples used, potential savings have been calculated as follows:
For paper and cardboard a theoretical potential has been used, where 87% of total paper
consumption is recycled in a way similar to present recycling of paper and cardboard. It
will not be possible to reach a higher rate of collection, as some paper is tissue ending
up in domestic waste or in the sewer. In waste statistics /39/
the realistic potential of recycling of paper is assessed at 80%. See also Appendix C.
Furthermore, it has been taken into account that paper material loses utility value
upon recycling. Thus the potential is an expression of theoretical maximum limit. Further
savings can be realised if paper and cardboard are reused directly, but this will probably
only be practicable for a small part of transport packaging, and the amount of paper and
cardboard directly that is reusable has not been estimated.
For glass packaging two theoretical potentials have been stated. One level presupposes
the recycling by washing glass which is reused today, whereas the rest is recovered by
remelting. However, there will probably be a minor part of glass packaging that cannot be
collected for recycling because of different kinds of contamination, so 100% recycling
will be unachievable in practice. It should be noted that reuse of bottles for beer and
soft drinks is not included in the calculation, which covers other forms of glass
packaging.
At the other potential level it is assumed that 100% of glass waste can be potentially
reused as bottle / glass packaging including glass currently remelted. To achieve
such a high degree of reuse will probably require significant changes in the use of glass
for packaging as well as a collection system where glass is not broken (for example
standard packaging types as known from beer and soft drinks). Today, a significant part is
broken upon collection. Thus, the potential is theoretical, but it is not possible offhand
to assess the extent of a realistic potential.
For aluminium 100% recovery is assumed in the calculation. In the recycling process
there will be a loss in the range of 5%, which has been taken into account in this
process. Thus, virgin aluminium will be added on a continuous basis, and it will be
possible to have a cycle without losses due to material deterioration upon recycling. In
practice, with the present use of aluminium for packaging it will be difficult (or
impossible) to achieve such high rates of recycling, as part of it will end up in domestic
waste.
Realised and theoretical potential savings in resources, energy and landfill
requirement are shown in Figures 5.13 to 5.15. For comparison, realised and potential
savings stated in waste quantities are shown in Figure 5.16.
Compared to paper and cardboard, and aluminium, realised savings from recycling of
glass are relatively modest both in terms of resources and energy. It should be noted that
reuse of bottles for beer and soft drinks is not included in the calculation. However, in
terms of energy there is a potential for savings, if glass packaging is reused directly.
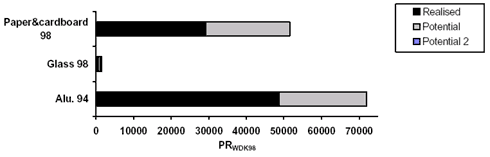
Figure 5.13
Realised savings from present waste management and possible potentials for
savings in resource consumption associated with treatment of the three material
fractions. "potential 2" is reuse of all glass packaging by washing.
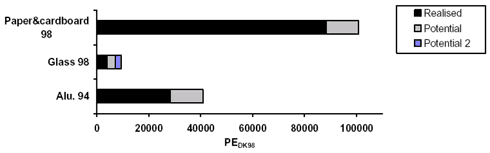
Figure 5.14
Realised savings from current waste management and possible potentials for
savings in primary energy consumption associated with treatment of the three
material fractions. "Potential 2" is reuse of all glass packaging by washing.
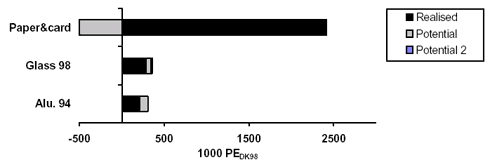
Figure 5.15
Realised savings from current waste management and possible potentials for
savings in landfill requirement associated with treatment of the three material
fractions. "Potential 2" is reuse of all glass packaging by washing. Note that
the potential of increased recycling of paper and cardboard gives increased landfill
requirement for residuals from recycling (the negative part of the bar). See also Figure
5.4.
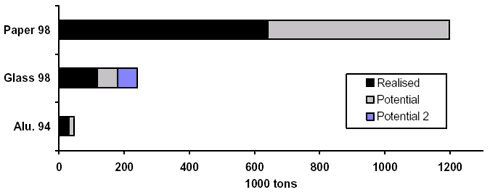
Figure 5.16
Realised savings from present waste management and possible potentials for
savings stated as waste quantities associated with treatment of the three material
fractions. "Potential 2" is reuse of all glass packaging by washing.
Figure 5.17 shows developments in realised savings associated with disposal of glass
waste in the period 1991-1998. The figure is based only on calculated factors and data
from the ISAG. The pattern seen is a reflection of the pattern seen in Figure 5.12, as
here total savings to some extent are a function of larger waste quantities. However,
there is also an effect from improved treatment options, as savings measured by the three
indicators increase more than waste quantities.
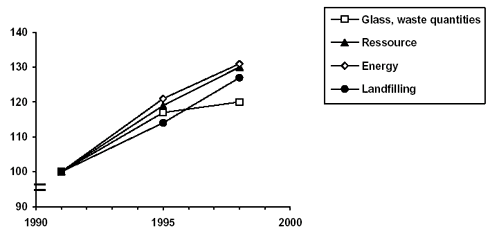
Figure 5.17
Realised savings from recycling of glass in the period 1991-1998 shown as
indexed values for the three indicators compared to developments in glass waste
quantities.
For aluminium, developments in realised savings are shown in Figure 5.18. In Appendix C
a method is described based on information from Statistics Denmark for
estimating amounts of aluminium treated upon recycling. In order to test whether the
method is reliable and actually visualises developments, collected amounts have been
calculated for a number of years and are shown as indexed values in Figure 5.18. Only
developments in resource savings have been calculated.
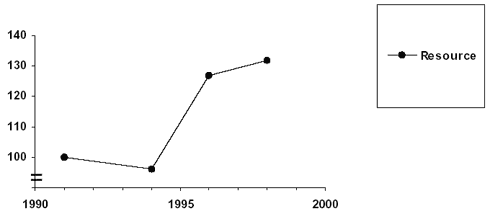
Figure 5.
18
Realised resource savings from recycling aluminium in the period
1991-1998.
To illustrate how the different material fractions contribute to total savings, Figure
5.19 shows data for 1991, 1995 and 1998 for energy savings realised from the actual waste
treatment compared to 100% landfilling of waste. Overall, savings have increased by around
40% through the 90s.
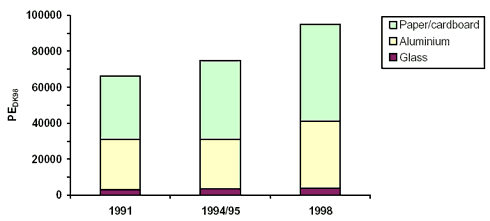
Figure 5.
19
Realised energy savings from recycling of paper and cardboard, glass
and aluminium in 1991, 1994/95 (Alu:1994, others 1995) and 1998.
The different ways of presenting indicators focus on different aspects of waste
treatment. One of the essential arguments for preferring presentation B to presentation A
is the possibility of collecting and updating data. This is discussed in Chapter 6.
| Front page | | Contents | | Previous
| | Next | | Top |