| Front page | | Contents | | Previous | | Next |
Use of Natural Refrigerants in Supermarkets
2 Natural refrigerants in Fakta Beder
2.1 System principle
2.2 Propane system
2.3 CO2 system
2.4 Display cases and heat exchangers
2.5 Compressor dimensioning
2.5.1 Summary of information
2.6 Refrigerants
2.6.1 Propane and CO
2.6.2 Brine
2.1 System principle
The system found in Fakta Beder was designed as a cascade system. Propane is used at high temperatures (-14/25°C), while CO2 is used at low temperatures (-32/-10°C). The two refrigerants exchange heat in the cascade heat exchanger, where propane evaporates through dry expansion and CO2 condenses. The CO2 is used directly in the supermarket’s freezer display cases and freezer rooms, while the propane exchanges heat with glycol in an indirect system.
The glycol is pumped in a closed system to the refrigerated display cases and the refrigerated rooms.
Suction gas-cooled, semi-hermetic compressors are used for both propane and CO2. Propane compressors have an oil pump, while CO2 compressors are splash-lubricated.
The refrigeration system itself is installed in a compressor rack, containing compressors, cascade heat exchangers, brine cooler, brine pumps, valves and vessels. The system is located in a separate engine room from which pipes and hoses connect the display cases to the system. The components containing propane are built into a ventilated enclosure.
2.2 Propane system
Propane as primary refrigerant:
- Flammable
- Properties comparable with those of HFCs, although
- heat transfer properties are better
- pressure drops are lower
- Copper pipes and soldering can be used
The propane system is designed as a compact indirect system, although the propane condenses directly in an air-cooled condenser. The condenser stands on the supermarket’s roof.
The propane system has two evaporators: one cascade heat exchanger and one brine cooler. Both are plate heat exchangers. Both heat exchangers use electronic expansion valves to inject the refrigerant. Also, the system has no oil separator. The system uses a mineral oil fully miscible with propane, so that the oil from the system returns to the compressors. Fitted balancing pipes ensure a uniform oil level in the compressors.
The internal heat exchanger (plate heat exchanger) ensures subcooling of the propane liquid before the expansion valves and superheating of the suction gas for the compressor. Compression with propane results in very low high-pressure gas temperatures, which allows the compressor to become relatively cold without an internal heat exchanger, thus making the refrigerant in the oil highly soluble. This may reduce the lubricating properties of the oil and increase the amount of oil transported from the compressor to the system.
Moreover, the compressor comes with a relatively big electrical heating element for the oil pan during standstill.
Finally, the system has a drying filter and a dirt filter in the fluid pipes, but no receiver.
2.3 CO2 system
Carbon dioxide as primary low-temperature refrigerant:
- Neither toxic nor flammable
- High COP (high isentropic efficiency for compressor, small pressure losses and good heat transfer properties)
- Good miscibility with ester oils like HFC refrigerants
- Acceptable high-pressure gas temperatures
- High-volumetric refrigeration capacity, generating small displacements for the compressor, and small suction and liquid lines identical to equipment used for HFC refrigerants
- Drying filter, sight glass and stop valves
- Copper pipes and soldering can be used
The system is designed as a conventional refrigeration system, although it has no internal heat exchanger.
The cascade heat exchanger functions as the CO2 system’s condenser, where CO2 condenses against evaporating propane. The condensate is not supercooled further. Next, the liquid circulates to the evaporators located in the outlet’s freezer display cases and rooms. Pulse-width modulating valves are used as injection valves, and 8K overheating is maintained. The gas is then sucked back into the compressor. The system has no oil separator.
The amount of oil entering the system will, due to high solubility with the refrigerant (esteroil/CO2) and relatively high gas velocities, be transported back into the compressor along with the refrigerant.
The compressor comes with an electrical heating element for the oil pan during standstill. Finally, the system is fitted with drying and dirt filters in the fluid pipe.
2.4 Display cases and heat exchangers
All the display cases used are standard models with evaporators adapted to the refrigerant (brine/CO2). Brine heat exchangers are already available in the market. In this case, ECO has supplied the air coolers for Arneg’s milk front and refrigerated room, where propylene glycol is used as brine. Arneg has supplied the brine heat exchangers contained in the islands. In terms of freezer islands, there are no immediate suppliers of evaporators in the market, and in this case, the Danish Technological Institute designed evaporators, which were subsequently manufactured by ECO. This goes for both the freezer room evaporators and the two evaporators for the freezer islands. All CO2 evaporators have been manufactured as conventional fine coils with 3/8” copper pipes and aluminium fins.
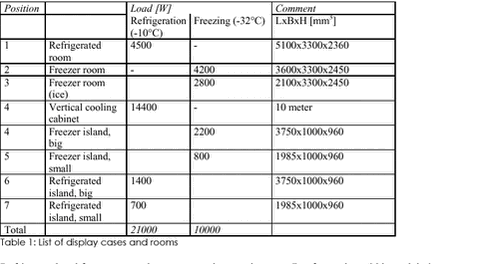 Table 1
Refrigerated and freezer rooms have separate heat exchangers. Danfoss pulse-width modulating valves control the injection of refrigerant in all heat exchangers. The CO2 injection valve has a period time of six seconds, while injection through the brine valve takes six minutes.
2.5 Compressor dimensioning
The above table shows that the refrigeration and freezing capacities are 21 and 10 kW, respectively. The system is dimensioned at about 21 kW (refrigeration) and 10 kW (freezing).
The dimensioning of refrigeration systems is based on information or calculations regarding refrigeration capacity. Moreover, the temperature level must be known. An outlet selling fresh (refrigerated) and frozen food operates with two different temperature levels. The temperature is between +1 and +3°C for refrigeration purposes, while it is between –25 and –18°C for freezing purposes.
These air temperatures can only be achieved if the refrigeration system for the refrigerated area operates at a temperature of about –14°C and the system for the freezing area operates at a temperature of about –32°C.
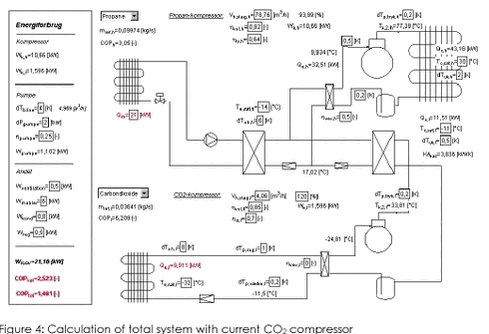 Se billede i fuld størrelse
In total, the propane compressors must be able to generate 32 kW. Bitzer’s catalogue only provides information about the compressor with various synthetic refrigerants. R22 comes closest to propane, so the R22 information is useful, and a recalculation will show capacity and energy consumption.
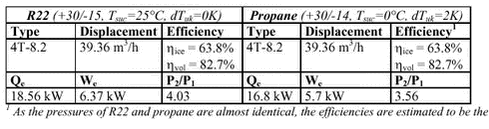 "R22 Propane".
Two Bitzers 4T – 8.2 are chosen.
Combined, they will generate refrigeration effect of about 33.6 kW. The system will have an internal heat exchanger, boosting capacity to about 34.6 kW. The freezing compressor has been selected, and the model available is a Bitzer X2KC of about 10 kW.
2.5.1 Summary of information
The following table contains a summary of information.
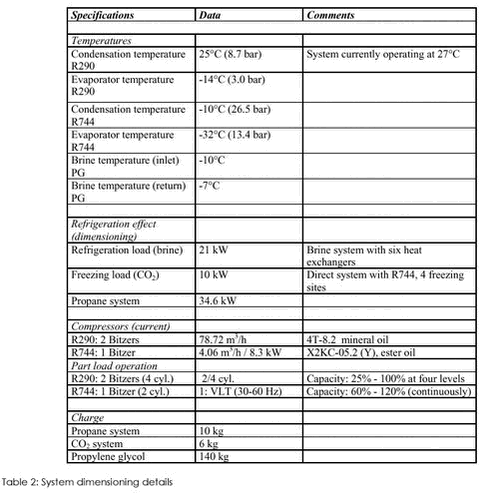 Table 2: System dimensioning details".
2.6 Refrigerants
The outlet’s refrigeration system uses the following refrigerants:
- Propane (R290)
- CO2 (R744)
- Technical propylene glycol (Dowcal N/ 40% wt.) – inhibited and approved for foods.
2.6.1 Propane and CO
Propane is an odourless and non-toxic gas. However, propane is an explosive gas with lower and upper explosive limits of 2.1-9.5 % v/v (0.038-0.171 kg/m3). The automatic flashpoint is 470°C. The gas is heavier than air and will therefore be at the lower level. CO2 is also odourless and non-toxic, but the gas can be hazardous to humans at concentrations higher than 0.5% v/v (5,000 ppm). The gas is heavier than air, and it should be noted that liquid expanding at pressures lower than 5.18 bar (-56.6°C – triple point) forms solid phase (dry ice). CO2 is also characterised by its very high saturation pressure. At 25°C, the saturation pressure is 64.4 bar. Finally, it should be noted that CO2’s low critical temperature and pressure (31°C and 73.8 bar) mean that a CO2 cycle becomes transcritical at high temperatures.
2.6.2 Brine
Technical propylene glycol Dowcal N is used. The concentration is 40% wt., ensuring a freezing point of –21°C.
The glycol is inhibited and approved for foods (by the FDA).
- Non-toxic, but should not be ingested
- Non-flammable
Dowcal N is compatible with generally used metals (copper, steel and brass) as well as plastic and elastomers (PE, PP, ABS, PVC, IIR, PTFE, EPDM, NBR and NR).
| Front page | | Contents | | Previous | | Next | | Top |
|