| Front page | | Contents | | Previous | | Next |
Use of Natural Refrigerants in Supermarkets
3 Component dimensioning
3.1 Pressure Equipment Directive
3.2 Design of pressure system
3.2.1 Comments
3.3 Main component summary - propane
3.4 Use of propane system
3.4.1 Machine card
3.5 CO2 system
3.6 Brine system
3.7 Safety
3.7.1 Safety – engine room
3.7.2 Safety – operation
3.7.3 Safety – standstill (CO2)
3.7.4 Safety – service
3.8 Servicing the system
3.8.1 Propane
3.8.2 CO2
3.8.3 Propane system
3.8.4 CO2 system
3.9 Control
3.9.1 Propane compressors
3.9.2 Propane condenser
3.9.3 Propane expansion valves
3.9.4 Brine pumps
3.9.5 CO2 compressor
3.9.6 Cascade heat exchanger adjustment
3.9.7 KA value
3.10 Daily operation
3.11 Zone division and electrical installations
3.11.1 Zone 2
3.11.2 Electrical installations
3.11.3 Propane
3.11.4 Inherent safety
3.11.5 Electrical components in Fakta Beder
3.12 ATEX directive
3.12.1 ATEX and Fakta Beder
3.12.2 Comments
Reference is made to appendices 3-6 for a list of the components used (parts lists).
3.1 Pressure Equipment Directive
The design of the propane system is based on Council Directive 97/23/EC, also known as the Pressure Equipment Directive (PED). The directive was implemented in Danish law by Order no. 743/99. However, the use of pressure equipment is a national matter, currently governed by Order no. 746.
The design can either be based on a calculation method such as AD-Merkblätter or on an experimental design method. In this case, the calculation method is used to support the important safety requirements, and thus to meet the provisions of the directive.
 Figure 5: Principle for order compliance".
3.2 Design of pressure system
- Classification of refrigerant
- Determination of type of refrigeration system
- Design of pipe system
- Determination of maximum allowable temperature/pressure
- Determination of design pressure P
d
- Determination of pipe dimensions
- Determination of method for calculating strength
- Categorisation of pipe system
- Categorisation of pressure vessels
- Determination of extent of documentation
- Determination of manufacture and material standards
- Requirements for fittings
- Requirements for components and valves
- Requirements for safety equipment, pressure switches and safety valves
- Requirements for assembling methods
- Determination of material documentation
- Conformity assessment
- Technical documentation
- Determination of control and quality management extent
- Final testing and verification
- Approval procedure
(Reference is made to the Danish EPA’s guide “Hydrocarbons in medium-sized systems”/1/)
Re 1. Propane is flammable and thus classified as Group 1.
Re 2. The system is located in a separate engine room with the door locked. This space is classified as person category C, which is permitted with propane.
Re 3. Pipe cross-section chosen on the basis of general requirements for pressure losses and then to ensure sufficient speed for the oil return.
Re 4. The maximum allowable pressure (PS) is fixed at 18 bar. A safety valve (SFV 15) ensures that the maximum pressure is not exceeded. The maximum temperature (TS) is fixed at 55°C.
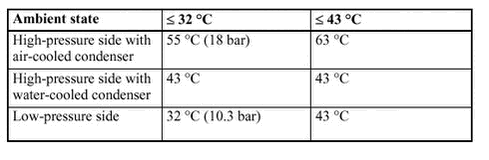 Ambient state".
Re 5. The design pressure is determined on the basis of EN 378-2: 2000, chp. 5 – ambient temperature <32°C High-pressure side: 18 bar (55°C) Low-pressure side: 10.3 bar (32°C)
Re 6. The propane system is a compact system with very short pipe lengths.
The gas and liquid pipes (to and from the condenser) are the two longest pipes (about 10 metres). The suction pipe is very short (about 2 metres). Single losses (valves and elbows) chiefly account for the pressure loss in this system. Pressure losses are about 0.01 bar (0.03K), 0.035 bar (0.8K) and 0.1 bar for the fluid, suction and pressure pipes, respectively.
Re 7. The calculations of pipe strength focus on the selection of material and wall thickness, with the aim of meeting the essential safety requirements in the Pressure Equipment Directive.
Deoxidised copper pipes are used, with the copper content exceeding 99.9% and the phosphorous content amounting to 0.015-0.04%. Phosphorous counteracts copper oxidation, which makes the material brittle. The composition of material complies with DIN 1787 SF-Cu 2.0090. The minimum wall thickness is determined on the basis of AD-Merkblätter B1. The calculation pressure is the maximum allowable pressure (PS). The value of annealed copper is used as 0.2% stress; the value is given by the pipe supplier (the copper must be regarded as annealed after having been heated through soldering). Fittings are put on an equal footing with pipes, but the strength factor is based on AD-Merkblätter B9 diagram Bild 7d. The condenser is also put on an equal footing with pipes (heat exchangers in the form of pipes for cooling or heating air are put on an equal footing with pipe systems – PED, article 1 (2.1.2)). Current pipes appear from appendix 2. The pipe design as regards wall thickness is based on control calculations to meet the essential safety requirements of the Pressure Equipment Directive (article 1 (2.12) and article 3 (1.3-1.4)).
 Re 7: Calculation".
Re 8. Determination of pipe system safety category complies with the National Working Environment
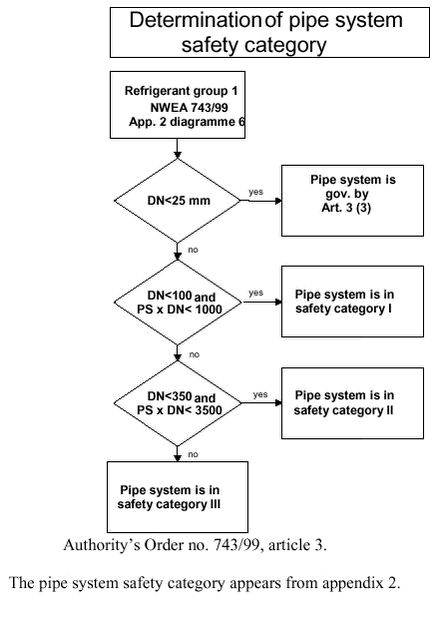 Determination of pipe system safety category".
Re 9. Determination of pressure vessel safety category complies with the PED, NWEA Order no. 743/99, article 3 (1.1) – plate heat exchanges are regarded as vessels. The plate heat exchanger safety category appears from appendix 3.
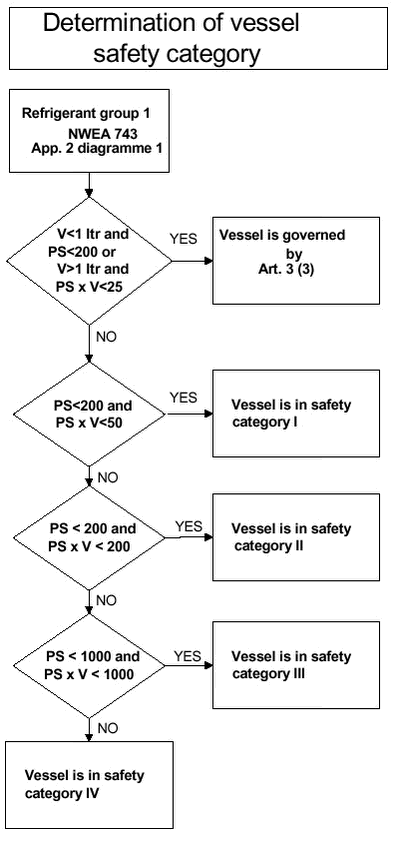 "Determination of vessel safety category".
Re 10. The extent of documentation is exclusively determined by the safety category to which the unit belongs. In this design, no components belong to a category higher than I. The documentation requirements of module A (Annex III to the PED) must be met to regard the design as being in compliance with Order no. 743.
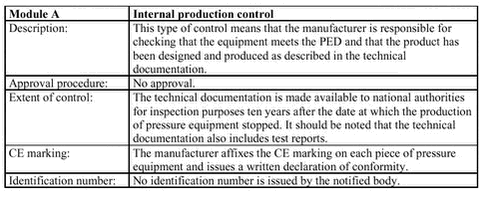 "Modul A Internal production control".
Re 11. The technical documentation contains material certificates and calculations supporting wall thickness and material conformity for copper pipes and heat exchangers.
Re 12. Category I fittings must have been produced from the same material as the pipes. The pipe supplier states the material’s conformity and coincidence in writing. The pipes’ conformity is confirmed by a material certificate - EN10204, type 3.1B. There are no fittings with a 3.1B certificate. The minimum wall thickness is determined on the basis of AD-Merkblätter. ANSI 16.22-89 (normal standard in Denmark) is the manufacturing standard for the fittings used.
Re 13. It is not yet possible to obtain PED declarations of conformity for valves. In this case, the supplier has declared in writing that the valves are suitable and usable in connection with propane.
Re 14. As regards safety category I components, sample pressure tests suffice. A pressure test certificate accompanies the plate heat exchangers. The safety valve (SFV) has been tested and sealed by TÜV NORD. The safety valve prevents the pressure from rising above 18 bar.
Re 15. Joints have been manufactured through hard-soldering – carried out by an experienced fitter. Visual inspection and test of soldering sample. Solder material: AGOP 15 with 15% Ag, 80% Cu and 5% P. The melting point is 600-800°C.
Re 16. The technical documentation made available by the supplier serves to document conformity The documentation contains information about the name of the manufacturer, allowable pressure and temperature, usability with propane, component materials, order number, pressure testing and, in some cases, the notified body.
Re 17. In order to assess the design’s conformity according to module A, the technical documentation must be available for assessing the design’s conformity with the relevant requirements ten years ahead. The documentation is contained in a ring binder.
Re 18. Furthermore, the technical documentation must provide diagrams, drawings and functional description – also contained in a ring binder.
Re 19. As the design belongs to safety category 1, the manufacturer does not need quality management approval. Internal production control suffices.
Re 20. Finally, the design is subjected to a leakage test at the maximum pressure possible during normal operation.
3.2.1 Comments
Declaration of conformity is a key phrase often associated with PED Order no. 743. The declaration confirms that the component meets the requirements of a specific safety category of the PED. Components carrying declarations of conformity are always difficult to find. The situation will change in time since products must carry the CE marking as at 29 May 2002. Until then, the documentation of conformity will be assessed on a component-by-component basis.
In this design of a propane/CO2 unit, the propane pipe design is what is interesting and assessed thoroughly. The CO2 pipe design is not subject to approval. CO2 belongs to gas group 2 and the threshold values for the product figure PxV are greater. The cross sections of CO2 pipes (½” and 3/8”) are small, meaning that the wall thickness of standard pipes is adequate even at very high pressures.
3.3 Main component summary - propane
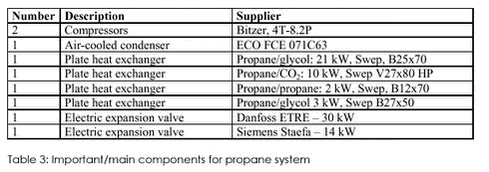 Table 3: Important/main components for propane system".
3.4 Use of propane system
As appears from the above, the use of pressure equipment is a national matter governed by Order no. 746. As a result, the unit must be registered with the National Working Environment Authority, which must also receive a copy of the design basis. Moreover, the following information must be provided with the system.
The system must come with an appropriate number of operational and maintenance manuals stating how to service the system.
Furthermore, the manuals must provide information about the measures to be taken in the event of breakdown or leakage. All manuals must be prepared in Danish by the manufacturer or the fitter. As a minimum, the manuals must provide the following information, if deemed relevant:
a) System purpose
b) Description of system and its equipment
c) Description and operational details of the entire system, including components, with a diagram of the refrigeration circuit and the electric circuit d) Instructions for system start, stop and standstill, or parts thereof e) Instructions for how to dispose of refrigerants and equipment
f) Causes of most common defects and measures to take, e.g. instructions regarding leakages discovered by authorised staff and the need to send for competent maintenance staff in the event of leakage or breakdown
g) Measures to be taken to prevent water from freezing in the condenser, evaporators, etc., at low ambient temperatures or if system pressure is reduced
h) Measures to be taken when lifting or transporting the system, or parts thereof
i) Information as it appears on summary machine cards or full machine cards, if need be
j) Preventive measures for first aid and procedures to be followed in the event of leakage, fire, explosion, etc.
k) Maintenance instructions for the entire system with scheduled maintenance to prevent leakages
l) Instructions for adding, tapping and replacing refrigerants m) Instructions on refrigerant handling and associated risks
n) Need for periodic inspection of emergency lighting, including movable lighting
o) Instructions on function and maintenance of safety equipment, protective and first aid equipment, alarms and pilot light
p) Instructions for keeping a log
q) Required certificates
3.4.1 Machine card
The machine card must contain the following information:
a) Name, address and telephone number of fitter, service department, or other service partner or person responsible for the refrigeration system, and telephone numbers for the fire service, police, hospitals and burns centres
b) Indication of refrigerant, including its chemical name and number as indicated in the standards
c) Instructions for how to shut down the system in the event of emergency
d) Maximum pressures
e) Details about the flammability of the refrigerant
3.5 CO2 system
The standstill pressure (saturation pressure) at, for instance, 25°C will be about 64 bar, which is very high in terms of system dimensioning. The system can be dimensioned in different ways to achieve a lower design pressure. In this case, a system has been chosen where the refrigerant is merely blown off into the surroundings if pressures exceed allowed threshold values. The system is expected to be in constant operation to keep the pressure in the CO2 system below these values at all times.
 CO2 system pressure".
The maximum pressure at the suction side is 19 bar during operation. A starting pressure control (KVD) placed at the compressor’s suction end keeps the pressure below 19 bar when the compressor is started. Safety valves also protect the compressor against too high pressures (19/32 bar).
The maximum pressure at the high-pressure side is 32 bar. A high-pressure switch protects the compressor against too high outlet pressure. Safety valves also protect the compressor against too high pressures (19/32 bar).
Selection of components for CO2 system
- Semi-hermetic compressors from Bitzer (frequency transformer from Danfoss)
- Expansion valves from Danfoss, AKV
- Standard receiver/drying filter/sight glass
- Safety equipment (safety valves, pressure switches, pressure transmitters, gas sensors, etc.)
Selection of materials
- CO2 system made of soldered copper pipes
- Evaporators are made as conventional copper/aluminium heat exchangers (pipes/fins), but with 3/8" pipes
 CO2 compressor".
Other components appear from appendix 6.
The pressure losses are relatively significant, but small in terms of temperature. Pressure losses are about 0.11 bar (0.15K), 0.35 bar (0.8K) and 0.01 bar for the liquid, suction and pressure pipes, respectively. As can be seen, the pressure loss is small even when small pipe dimensions are used. However, the penetration of heat from the surroundings causes the biggest problems for the CO2 system.
The receiver and the liquid pipes function at about –10°C, which may cause problems regarding heat penetration and failing subcooling. In such systems with long pipe sections (e.g. 20 metres), pressure loss must be kept below 0.1K, and with 30 mm insulation, the heating of the CO2 liquid can be maintained at about 0.7K. This may be sufficient to avoid flash gas before the valves. Alternatively, an internal heat exchanger can be fitted into each case.
3.6 Brine system
The brine circuit is regulated by a pump currently operating at a constant flow. The total length of the main circuit is 30 metres. The inlet and return pressure losses are about 0.7 bar, while the pressure loss in the brine heat exchangers is 0.2-0.4 bar. The pressure loss in the part strings (pipes, valves and heat exchangers) is 0.3-0.5 bar.
The brine circuit has been fitted with string control valves – ASV-PV and ASV-I from Danfoss. The purpose of the valves is to secure uniform pressure loss in each part circuit. The problem with ”distorted” load on part strings becomes more pronounced in large brine systems. The connection between the brine heat exchanger in the engine room and the heat exchangers in the display cases is made up of hoses drawn through pipes in the floor. The cold hoses inside the cases have caused condensation problems on the underside of the cases during the warm summer months, resulting in water on the floor. The problem can be solved by increasing ventilation underneath the cases.
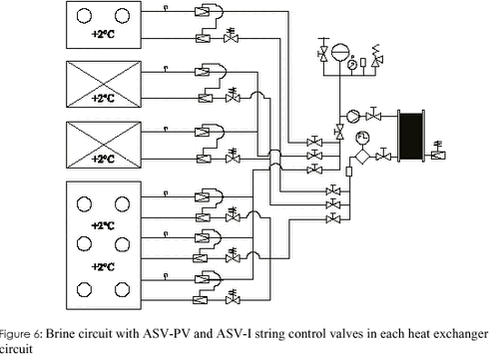 Se billede i fuld størrelse
3.7 Safety
3.7.1 Safety – engine room
The propane system stands in an engine room in a tight and ventilated enclosure. The enclosure’s constant mechanical ventilation ensures a constant negative pressure in the enclosure (compared with the surrounding engine room) of 10 Pa and a ventilated volume flow of 230 m3/h.
Hence, the enclosure can be regarded as a zone 2, where the degree of protection must correspond to IP 54. The engine room surrounding the enclosure is specified as an unclassified area.
A pressure monitor (differential pressure transducer) constantly registers whether the negative pressure stated is maintained. If it is not, the power for all non-EEx equipment in the engine room will be cut off (all equipment, excluding emergency lighting, mechanical ventilation and pressure monitor). Pressure gas and liquid pipes have been connected to the condenser on the roof of the building through the ventilation channel from the enclosure to the surroundings. The CO2 system stands in the actual engine room from which fluid and suction pipes have been connected to the freezer display cases. The engine room has natural ventilation (grating next to the door). In the event of CO2 emission into the engine room, the gas will stand above the floor and be ventilated away automatically. The engine room also has a CO2 detector registering CO2 gas at 4,000 ppm.
CO2 below 5,000 ppm (0.1 kg/m3) does not affect humans – not even when they are exposed to this atmosphere for a long time. A load of 6 kg thus means that the volume must be higher than 27 28 60 m3 to be below this figure. The only rooms with a volume less than 60 m3 involving a risk of CO2 emission are the engine and freezer rooms. CO2 detectors and alarms have therefore been installed in these rooms.
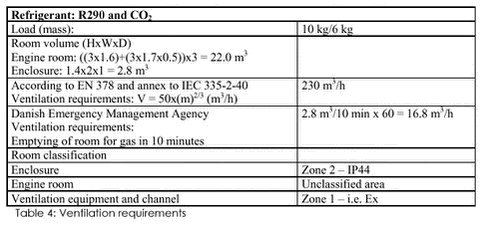 Table 4: Ventilation requirements".
3.7.2 Safety – operation
All compressors (propane and CO2) have high and low-pressure switches. The propane compressors also have an internal oil pump and therefore also oil differential switches. The propane system pressure switches are KP 17W with double bellows. The pressure switch bank has an inherently safe circuit as such circuits cannot produce sparks or heat capable of igniting a given explosive atmosphere.
Barriers and contactors are placed outside the propane enclosure (zone 2) in the electrical switchboard (unclassified area).
During operation, the propane system must maintain the pressure in the CO2 system below 32 bar. The CO2 compressor cannot run unless the propane system is running
3.7.3 Safety – standstill (CO2)
Refrigeration systems in supermarkets virtually never stand still – only in the event of failure (power failure). During standstill, the pressure in the CO2 system will rise slowly. The expansion valves for the CO2 evaporators will be shut, and the high-pressure side will therefore be blocked between the compressor’s pressure valve and the expansion valve. The pressure will rise slowly on account of the heat penetration.
The pressure will rise from the normal condensation pressure of 26.5 baro (-10°C) to 32 baro (-2°C) (safety valve setting) in three or four hours. The current system only has safety valves, meaning that CO2 will be blown off into the surroundings after three or four hours’ standstill of the propane system.
The blow-off occurs slowly and steadily, with the CO2 oozing from the safety valve at about 0.4 kg/h. Blow-off into the surroundings is the cheapest and most profitable method of reducing pressure in CO2 systems in supermarkets. Another solution is to use an expansion vessel, but the investment is simply too big.
3.7.4 Safety – service
When servicing the propane system, the fitter can disconnect the pressure monitor so that the enclosure can be opened without cutting off power to the engine room. The fitter does this at the main board in the storage room by using a key switch. Now he can service the propane system without stopping it. Since the fitter is now at risk in the event of a gas leakage (propane), he must bring a propane detector, which will warn him of any leakages (concentrations above 4,000 ppm) by producing sound and light signals. During servicing, the door into the engine room must be open. In the event that a leakage occurs while the system is being serviced, and the detector warns the fitter, he must leave the room immediately and cut off power to the engine room.
3.8 Servicing the system
The fitter must be aware of the special properties of propane and CO2 when servicing the refrigeration system:
 Table 5: Rules for servicing propane and CO2 systems - posted on the propane enclosure".
Extensive servicing of the propane system requires that the CO2 system be stopped and emptied before the propane system is stopped. When the propane system has been stopped, the pressure will rise above allowable values in two or three hours!
3.8.1 Propane
Propane is added and emptied outdoors on the roof at the drying filter. The system is sucked empty by pump-down and emptied at the filling valve. Propane can be emptied directly into the atmosphere, but at a price of DKK 250/kg.
Propane is added at the filling valve. The outlet end of the drying filter is shut by closing the stop valve. About 10 kg of propane is added to the system. During operation, the sight glass can be used to add the correct charge.
3.8.2 CO2
The CO2 system is stopped and emptied by slow blow-off into the atmosphere through a hose to the surroundings (outside the room). CO2 costs about DKK 15/kg and can be added again. The system must be emptied slowly to prevent the pressure from falling below 5.18 bar while there is still fluid. Otherwise, dry ice will form. CO2 can and may only be added to the system if the propane system is running properly (otherwise the pressure cannot be maintained below the threshold value). CO2 is added at the receiver in the engine room (the pressure here is lower than the saturation pressure of CO2 at room temperature). The refrigerant can be added during compressor standstill, but the compressor must be running to determine the correct amount to add. The sight glass at the receiver is also used in this case. If the refrigerant is added during operation, it must be added slowly to avoid too high pressures after the compressor.
Use a device with a pressure reducing valve and manometers from e.g. Hydro Gas.
Before starting the system, one must make sure that each refrigerant circuit is operational. The brine circuit is started first. Flushing and degassing are essential to system operation. Moreover, the pump and pump pressure must be checked (engine room).
The propane system can now be started. Evacuation of the system is important as is checking the oil level in the compressor. Once the propane compressor has been started, the system can be filled up. When the propane system has been started and is running properly, the CO2 system can be started. If the system has been without pressure, it must be evacuated and refrigerant added.
3.8.3 Propane system
- Service
- Use at least 97.5% pure propane.
- Use rear gas for welding/soldering and keep the system clean (vacuum must be maintained at 1.5 mbar).
- Less than 50 ppm moisture in the system (drying filter and moisture indicator).
- Ventilate room during service.
3.8.4 CO2 system
Service
2.
Use rear gas for soldering and keep the system clean (vacuum must be maintained at 1.5 mbar).
Less than 50 ppm moisture in the system (drying filter and moisture indicator).
Ventilate room during service.
3.9 Control
System control is based on separate control of compressors and display cases. Danfoss controls are used for both display cases and compressors. The compressors are controlled according to a constant suction pressure. The propane system operates at –14°C, generating an inlet brine temperature of about –10°C and a condensation temperature for the CO2 system of also –10°C.
Adap-Kool controllers control the display cases independently of the refrigeration system. Blowers, rim heat and defrosting can be controlled. Moreover, condenser blowers and the pump are controlled independently of the compressors.
The expansion valves for the two propane evaporators (brine cooler and cascade heat exchanger) use their own controller, controlling taking place exclusively after superheating.
3.9.1 Propane compressors
- The compressors are controlled by a Danfoss AKC 25H1 control.
- The compressors are exclusively controlled according to the evaporator pressure (initially set to 3 bar abs. -14°C).
- The propane system may not be started unless the brine pump is running.
- Safety in the form of oil differential pressure and high-pressure switches connected to AKC 25H1.
- Expansion valves (propane) are shut during compressor standstill.
3.9.2 Propane condenser
- ECO type FCE 071C63
- Three condenser blowers controlled by AKC 25H1 through pressure transmitter and neutral zone controller, with the set point being 25°C.
3.9.3 Propane expansion valves
-
A Danfoss AKC with ETRE expansion valve controls the brine heat exchanger.
-
A Siemens Steafa valve controls the cascade heat exchanger.
3.9.4 Brine pumps
The system has been equipped with a Grundfos CRE 5-4 brine pump. The pump comes with Grundfos’ own control. The pump can receive a control signal from the differential pressure transmitter mounted in the rack or above the brine heat exchanger.
3.9.5 CO2 compressor
- Controlled by AKC 25H5 with frequency transformer VLT 2800, with the set point for suction pressure set initially to 14 bar abs. ( -32°C).
- The compressor may not be started unless the propane system is running.
- High and low-pressure switches connected (the compressor has no oil pump).
The CO2 compressor starts by force a propane compressor at half capacity. The AKC 25H5 determines the number of revolutions of the compressor. An internal PI controller adjusts the number of revolutions, with the amplification and integration constant being set to achieve a moderate, bordering on small, adjustment in the number of revolutions. Slowly adjusting of the number of revolutions of the CO2 compressor slowly raises the condensation pressure, thus making it more possible for the injection valve to adjust superheating at the propane side of the cascade heat exchanger.
3.9.6 Cascade heat exchanger adjustment
In this case, the injection valve on the cascade heat exchanger is a Siemens Staefa valve – controlled by a Siemens PolyCool controller. The controller is a “pure” PID controller with overheating signal as process variable.

During start-up, pressure at the CO2 side increases quickly. The overheating signal at the propane side rises more slowly because of a large P-band, and the CO2 compressor stops at high pressure.
The broad P-band is required because the CO2 gas is +45°C on inlet and -10°C on outlet.
The differential element is set high to compensate for a broad P-band, meaning that relatively small changes in the process variable (superheat) cause a reaction in the valve. Unfortunately, the valve also reacts quickly and shuts when small amounts of liquid are primed.
The conclusion on this inaccurate start-up sequence is that the controller must control the valve with a start-up routine maintaining the opening of the valve during start-up for a pre-set period; the PID controller is subsequently released to control the valve. During normal operation, the controller is only to use proportional control.
In this case, the start-up routine has been fixed with a bypass as shown in figure 7; this will not be the only solution to the problem in future. Several suppliers are implementing a start-up routine in their software.
3.9.7 KA value
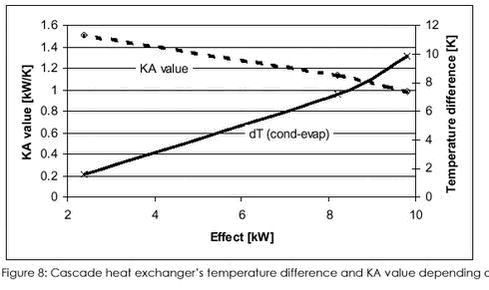 "KA value".
As can been seen from the figure, the temperature difference depends greatly on the effect. The relationship is even enhanced when the heat exchanger’s KA value falls as the effect increases.
3.10 Daily operation
Reference is made to file no. 731327/99-0199 for system operation: demonstration of natural refrigerants in supermarkets.
3.11 Zone division and electrical installations
Zone classification:
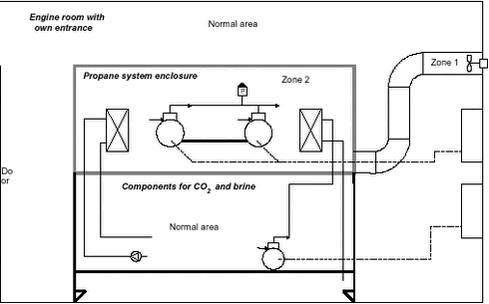 Se billede i fuld størrelse
The Danish Emergency Management Agency exclusively determines zone classification in Denmark. The agency has found that the ventilation of the enclosure is sufficient to maintain any gases at or below 25% of the lower explosion band, and that special safe ventilation ensures that all non-EEx equipment is disconnected in the event of ventilation failure. This means that the enclosure has been classified as zone 2 during normal operation and as zone 1 in the event of failure. The area outside the propane enclosure but inside the engine room is unclassified. The ventilation channel is zone 1, so the ventilator must comply with EEx (fire technology instructions no. 19).
In the event of ventilation failure, the main switch to the entire refrigeration installation will be switched off, i.e. display case controls, display case lights, etc. However, alarms can still be sent from the system.
A safety valve protects the system against too high design pressure at the high-pressure end. The area around the blow-off from the safety valve has also been classified as zone 2; the valve is located on the roof. The blow-off opening from the brine system air-escape valve has also been classified as zone 2.
3.11.1 Zone 2
Zone 2 areas are areas where an explosive atmosphere exists only in exceptional cases and then only for a short period of time. The 60079-10 harmonised standard defines short periods as no more than ten hours per year.
3.11.2 Electrical installations
The electrical installations comply with the Danish Electricity Council’s Danish Heavy Current Executive Order, chapter 704 – Potentially explosive areas. According to the order, the material used in zone 2 must be at least IP 44, the surface temperature must not exceed 100°C, and sockets must have covers. General rules also apply to dangerous sparks and inherent safety requirements for the use of material in connection with gas groups IIA, IIB and IIC.
The requirements contained in the order regarding installations in potentially explosive areas resemble those contained in EN 60079-14.
3.11.3 Propane
Propane belongs to the IIA gas group and T1 temperature class – identical to NH3.
3.11.4 Inherent safety
Inherent safety is understood as: a circuit that both during normal operation and during failure cannot produce any sparks or heat of such a nature that a given potentially explosive atmosphere can be ignited.
3.11.5 Electrical components in Fakta Beder
The propane system in Fakta Beder contains pressure switches for high and low-pressure monitoring, pressure transmitters for controlling compressors and oil-pressure monitoring. All these components are in direct contact with propane. The components are fitted in a zone 2 area (the propane enclosure). The common provisions on potentially explosive areas comprise these components. Therefore, the requirements include inherent safety for pressure transmitters and protection against dangerous sparks between banks in pressure switches. PLC replaces the timer function of the oil differential pressure monitor.
The pressure switches have double bellows, gold switches and IP 54 encapsulation (KP17W). Where the voltage to the bank does not exceed 8 v, EEx-approved impulse isolators (from PR) offer protection against sparks.
The oil differential pressure monitor on the compressors is undertaken by conventional MP54s, where the heating element has been replaced by a small PLC located outside zone 2 in an electric cabinet.
Pressure transmitters for compressor control have an inherently safe circuit with an EEx-approved Zener barrier (from PR).
The compressor terminal box complies with IP54 and has a special terminal block. An anchor pipe separates the coils for solenoid valves from the gas. The coils meet IP67 and the voltage is 24 v AC.
Whether chapter 704 of the Danish Heavy Current Executive Order requires the use of an inherently safe circuit in connection with pressure transmitters is debatable.
3.12 ATEX directive
The implementation of the ATEX Directive by Orders nos. 696 and 697 with effect as from 30 June 2003 means that chapter 704 of the Danish Heavy Current Executive Order can no longer be used as a foundation. The directive covers electrical and mechanical equipment used in potentially explosive atmospheres. The implementation of the directive means that the harmonised standards will provide the foundation for meeting the ATEX Directive.
The harmonised standards for electrical equipment are EN 60079-10 - 17 and EN 50014-50021.
All electrical and mechanical equipment to be used in an EEx area must be approved and certificated according to EN 500014 - 20.
The following applies to zone 2 equipment: equipment suitable for zone 0 or 1 or equipment particularly suited for zone 2 may be used. For instance, ”n” protection or equipment encapsulated according to IP54 and that does not produce sparks. Equipment potentially producing sparks must meet the requirements set out in IEC 79-11.
Implementation of the ATEX Directive ensures uniform safety and health conditions through joint European rules and guidelines.
3.12.1 ATEX and Fakta Beder
However, the implementation of the ATEX Directive will not tighten electrical installations requirements. The rules may be less ambiguous and clearer.
Manufacturers of components for EEx installations must document compliance with the directive and the harmonised standards. The product must be CE-marked according to ATEX.
After 30 June 2003, pressure transmitters must comply with EEx and bear the CE marking and the “EEx” stamp showing compliance with “ia” or “ib” standards, which indicates IIA protection, the gas group for propane, etc., and T1 for the temperature class. The marking will be ”better” in practice. In general, components are classified for higher gas groups and temperature classes than the ones mentioned here.
The pressure switches must also bear the CE marking and be protected by Zener barriers. Chapter 704 of the Danish Heavy Current Executive Order often relies on the harmonised standards applicable from 30 June 2003. Therefore, the fitter will find no significant differences.
3.12.2 Comments
The implementation of the ATEX Directive means that the “new” method of approving installations will also cover the electric part , i.e. the manufacturer must document compliance with the directive and put the CE marking on the unit in keeping with the PED. The unit supplied (the refrigeration system) must also bear the CE marking as regards ATEX.
| Front page | | Contents | | Previous | | Next | | Top |
|