| Главная страница | | Содержание | | Предыдущая страница | | Следующая страница |
Оценка поступлений ртути в окружающую среду с территории Российской Федерации
5 Оборот ртути при переработке отходов
5.1 Производство вторичной ртути
5.1.1 Ртутьсодержащие отходы
5.1.2 ЗАО “Научно-производственное предприятие
“Кубаньцветмет”
5.1.3 ООО “Мерком”
5.2 Оборот ртути с твердыми отходами
5.2.1 Образование твердых ртутьсодержащих отходов в России
5.2.2 Ртуть в промышленных отходах и отходах энергетики
5.2.3 Ртуть в твердых бытовых отходах
5.2.4 Ртуть в отходах медицинских учреждений
5.3 Ртуть в сточных водах
5.1 Производство вторичной ртути
5.1.1 Ртутьсодержащие отходы
Опубликованные в литературе данные о количестве образовавшихся к настоящему
времени на территории России ртутьсодержащих отходов (главным образом, промышленных)
свидетельствуют о том, что объемы последних очень велики.
Так, по оценкам [121, 198], общая масса таких отходов составляет 1,1 млн. т, причем
основная часть их (58% по массе) отличается содержаниями ртути в 10-30 мг/кг, около 30% -
содержат ртуть в количестве более 5000 мг/кг, примерно 12% - характеризуются
концентрациями металла в 100-5000 мг/кг. По другим сведениям [365], в России накоплено
750000 т ртутьсодержащих отходов, а по данным [96], - около 650 тыс. т (с содержанием ртути
от 200 до 750000 мг/кг), причем ежегодно образуется еще около 11 тыс. т. Наиболее
значительными объемами складированных ртутьсодержащих отходов и, соответственно,
высокими уровнями загрязнения среды обитания ртутью отличаются регионы страны, где
расположены крупные предприятия цветной металлургии, химической, целлюлозо-бумажной и
золотодобывающей промышленности.
Например, в районе Кирово-Чепецкого химического комбината (г. Кирово-Чепецк,
Пермская область) на временных свалках и полигоне глубинного захоронения размещено 409
тыс. т ртутьсодержащих отходов [218]. В Иркутской области в почвах промышленных
предприятий, производящих хлор и каустик, аккумулировано более 1000 т ртути и еще более
2000 т металла находится в шламонакопителях [85]. В прибрежной части устья р. Сев. Двины
недавно было захоронено 3,2 тыс. т ртутьсодержащих отходов Архангельского ЦБК, а на
полигоне Красный Бор (Ленинградская область) размещено более 100 т ртутьсодержащих
отходов [365]. На территории бывшего Амурского целлюлозо-картонного комбината (г.
Амурск, Хабаровский край) в контейнерах и на открытых площадках складировано порядка
300-500 т ртутьсодержащих шламов [378, 369]. По другим сведениям [206], на заброшенных
складах указанного комбината размещено 4400 т ртутьсодержащих отходов.
На территории российских предприятий цветной металлургии в конце 1990-х г.г.
размещалось более 63 тыс. т шламов, содержащих около 155 т ртути [198]. В Северной Осетии
(на полигонах площадью 250 га) к настоящему времени накоплено около 9 млн. т хвостов
обогащения Мизурской и Фиагдонской обогатительных фабрик и отходов металлургических
заводов “Электроцинк” и “Победит” (г. Владикавказ), в которых масса ртути оценивается в 110
т [252]. На территории Челябинского электролитного цинкового завода хранится 40 т ртутно-
селенового шлама [362].
Значительные объемы ртутьсодержащих отходов размещены в окрестностях
золотоизвлекательных фабрик. Например, в хвостохранилищах Семеновской фабрики (Южный
Урал) общая масса ртути составляет около 60 т [174]. В пос. Соловьевске (Тындинский район,
Амурская область) в районе шлихообогатительной установки складировано около 15 тыс. м³
ртутьсодержащих отходы [376], а в районе пос. Токур (Амурская область) в необслуживаемых
хранилищах размещено от 30 до 40 т ртути [54].
В России, согласно .Бизнес-книгам. и рекламным изданиям последних лет, известно
несколько предприятий, в той или иной мере занимающихся рафинированием отработанной
(“черновой”) ртути и переработкой промышленных ртутьсодержащих отходов. Однако
только два из них работают достаточно полномасштабно и регулярно поставляют на
внутренний рынок вторичную ртуть и ее соединения: это - ЗАО “НПП “Кубаньцветмет” и
ООО “Мерком”[8].
5.1.2 ЗАО .Научно-производственное предприятие .Кубаньцветмет.
ЗАО “НПП “Кубаньцветмет” расположено в пос. Холмский Абинского района
Краснодарского края. В 1998 г. ЗАО “Кубаньцветмет” в рамках Федеральной целевой
программы .Отходы. осуществило (за счет собственных средств) ремонтно-восстановительные
работы на металлургическом заводе, ранее принадлежавшего ООО “Краснодарский рудник”, и
разработало комплект технологических инструкций, регламентирующих процессы переработки
ртутьсодержащих отходов, рафинирования ртути и производства ртутных соединений.
В свое время “Краснодарский рудник” функционировал главным образом на базе
Сахалинского месторождения ртути (кварц-диккит-киноварного типа), расположенного
недалеко от пос. Холмский. В 1974-1992 г.г. из руд указанного месторождения было
произведено около 500 т металлической ртути. В 1990 г. подземная часть Сахалинского
месторождения (по причине экономической нецелесообразности ее разработки) была
законсервирована; в 1993 г. - прекращены работы на карьере, отрабатывавшем
приповерхностную часть месторождения. В 1993-1995 г.г. на металлургическом заводе
“Краснодарского рудника” осуществлялась переработка ранее добытых руд (получено около 30
т ртути), а начиная с 1992 г. эпизодически производился выпуск вторичной ртути (из
ртутьсодержащих отходов); в период с 1992 по 2001 г. здесь было получено более 98 т
вторичной ртути (в том числе около 65 т в 1999-2001 г.г.).
В настоящее время в сфере обращения с ртутьсодержащими отходами ЗАО
“Кубаньцветмет” осуществляет:
- переработку различных ртутьсодержащих промышленных отходов;
- переработку загрязненных ртутью почвогрунтов и строительных отходов;
- утилизацию ртутьсодержащего концентрата люминофора;
- демеркуризацию использованных ртутных ламп;
- утилизацию использованных и бракованных приборов с ртутным наполнением;
- рафинирование некондиционной (отработанной, черновой) металлической ртути;
- производство различных соединений ртути;
- получение особо чистой металлической ртути.
Деятельность ЗАО “Кубаньцветмет” предусматривает транспортировку отходов от мест
их образования (размещения) в специальных металлических контейнерах сортировку каждой
партии отходов с выделением групп материалов, пригодных для переработки или
обезвреживания в технологических аппаратах с извлечением товарной ртути, производство
соединений ртути, группировку образующихся в ходе собственной деятельности отходов с
целью их последующего безопасного захоронения и/или вторичного использования.
Технологические схемы переработки ртутьсодержащих отходов, используемые на ЗАО
“Кубаньцветмет”, позволяют рассматривать поступающие на утилизацию отходы как
своеобразное сырье, поскольку в большинстве случаев они являются основой для получения
товарных продуктов, а образующиеся в ходе их переработки побочные продукты, в свою
очередь, используются в качестве вторичного сырья в других производствах.
Технологические и производственные операции осуществляются с соблюдением условий
и требований нормативно-технических и санитарно-гигиенических документов [76-80, 155, 157,
244-246] и Технологических инструкций [285-290].
Деятельность предприятия также регламентируется:
- лицензией на право осуществления деятельности по обращению с опасными (в том
числе, ртутьсодержащими) отходами (сбор, использование, обезвреживание,
РФ;
- лицензией на право осуществления деятельности по заготовке, переработке и
реализации лома цветных металлов, выданной Комитетом по лицензированию
Краснодарского края;
- лицензией на право эксплуатации производственных объектов, на которых получают
расплавы черных и цветных металлов и сплавы на их основе, выданной Федеральным горным и
промышленным надзором России;
- лицензией на право осуществления перевозок грузов автотранспортом по Российской
Федерации, выданной Министерством транспорта РФ.
Химико-аналитическая лаборатория ЗАО “Кубаньцветмет” имеет Аттестат
(Сертификат) аккредитации, выданный Государственным комитетом РФ по стандартизации
и метрологии.
В структуре предприятия функционируют экологическая служба, отдел охраны труда и
техники безопасности, а также участок технического контроля переработки сырья.
В ходе переработки ртутьсодержащих отходов, получения товарной металлической ртути
и производства ртутных соединений осуществляется необходимый контроль технологических
процессов и режимов их протекания, состава перерабатываемого сырья, промежуточных
продуктов и конечной продукции, оцениваются материальный баланс производства и
технологические показатели работы печи ТВП-1 и другого оборудования.
Общая численность сотрудников ЗАО .Кубаньцветмет. составляет более 160 человек,
среди которых технологи и металлурги, имеющие многолетний опыт работы на крупнейших
ртутных и ртутно-сурьмяных комбинатах бывшего СССР.
Основные технологические схемы, оборудование и производственные операции,
связанные с переработкой ртутьсодержащего сырья
Производственная инфраструктура ЗАО “Кубаньцветмет” включает:
- административно-производственную базу (площадь территории около 6 га) с
примыкающим железнодорожным тупиком;
- промышленную зону (площадью около 39 га), основу которой составляют:
- металлургический завод, включающий две трубчатые вращающиеся печи, системы
газоходов и пылегазоочистки, устройства конденсации и рафинирования ртути,
ступпохранилище, отвал огарков; первая печь ТВП-1 - используется для переработки
ртутьсодержащего сырья путем его окислительного обжига с последующим выделением ртути
из газовой фазы (технологических газов); вторая печь ТВП-2 - для производства извести;
- участок по подготовке ртутьсодержащего сырья к металлургическому переделу;
- участок по производству соединений ртути;
- участок по производству особо чистой ртути (4 установки, в которых используется
многократная дистилляция с электроразрядной очисткой);
- участок демеркуризации трубчатых люминесцентных ламп;
- участок по утилизации ртутных ламп высокого давления;
- участок по утилизации металлических приборов с ртутным заполнением;
- участок по утилизации стеклянных приборов с ртутным заполнением;
- участок по обслуживанию и ремонту технологического оборудования;
- участок технического контроля переработки ртутьсодержащего сырья;
- химико-аналитическая лаборатория;
- склад готовой продукции.
Годовая производительность печи ТВП-1 (по сырью) составляет 36 тыс. т, установки по
демеркуризации трубчатых ртутных ламп - более 1 млн. шт., по очистке некондиционной
(отработанной) ртути - 240 т товарного металла, участка по производству соединений ртути -
30 т (в виде товарной продукции), установок по получению особо чистой ртути - 15 т металла.
ЗАО “Кубаньцветмет” располагает необходимыми оборудованием и технологиями для
обезвреживания и утилизации следующих видов ртутьсодержащих отходы производства и
потребление, которые по особенностям и условиям их переработки объединяются в несколько
групп (табл. 5.1). Основная масса отходов перерабатывается в трубчатой вращающейся печи ТВП-
1.
Конструкция трубчатой вращающейся печи
Печь ТВП-1 представляет собой металлический цилиндр (корпус) 6 диаметром 1,6 м и
длиной 14 м, установленный с уклоном 3-4° и футерованный огнеупорным кирпичом. Корпус
печи опирается бандажами 5 на ролики 13, на которых при помощи приводного механизма 14
он вращается со скоростью 0,6-2 об/мин, регулируемой с помощью 4-х скоростного
электродвигателя (рис. 5.1). В нижней части корпус примыкает к топочной камере 4, в верхней
- к пылевой камере 8. Камеры представляют собой металлические каркасы, футерованные
внутри огнеупорным кирпичом и имеющие проемы для подсоединения корпуса печи.
Топочная камера установлена над бункером огарков (обожженного сырья) 1. В ней через
форсунку 2 сжигается топливо (природный газ, расход которого составляет 26,6 м³ на 1 т
сырья), причем факел пламени поступает по центру в корпус печи. Верхняя (пылевая) камера
служит для сопряжения вращающегося корпуса печи со стационарным газоходом. Через проем
в торцовой стенке пылевой камеры в корпус пропущена труба питателя сырья 11, при помощи
которого сырье вводят в печь. Питатель установлен между бункером 10 сырья и печью. Печь
работает на противоточном режиме: подаваемое в печь сырье при вращении корпуса
перемещается от верхнего конца к нижнему, а газы, наоборот, движутся от топочной камеры к
верхнему концу корпуса и отводятся через верхнюю (пылевую) камеру 8 в газоход 9, по
которому поступают на очистку от пыли. При прохождении газов из печи в газоход через
пылевую камеру в последней оседает наиболее крупная пыль, вынесенная газовым потоком из
печи. В целях уменьшения выноса пыли из печи в газоходную систему в печи создается
минимальное разряжение, из-за чего в системе возникает опасность утечки технологических
газов через сопряжения между вращающимся корпусом печи и стационарными камерами. Для
предотвращения утечки газов сопряжения оборудованы особыми уплотнениями 12.
Таблица 5.1 Виды перерабатываемых ЗАО “Кубаньцветмет” ртутьсодержащих отходов
Груп- па |
Вид отходов |
Основное оборудование |
Основные поставщики отходов в 2000-2002 г.г. |
1 |
Отработанный катализатор (отходы производства винилхлорида) |
Трубчатая вращающаяся печь ТВП-1 |
ОАО “Химпром” (г. Волгоград), ОАО “Пласткард” (г. Волгоград), НАК “Азот” (г. Новомосковск) |
1 |
Шлам производства 1-аминоантрахинона |
Трубчатая вращающаяся печь ТВП-1 |
ОАО “Химпром” (г. Новочебоксарск, Республика Чувашия) |
1 |
Ртутный сорбент (активированный уголь марки КПР и т. п.) |
Трубчатая вращающаяся печь ТВП-1 |
ОАО “Синтез” (г. Дзержинск), ОАО “Лисма” (г. Саранск), ЭП “Меркурий” (г. С.-Петербург), Химкомбинат им. Константинова (г. Кирово-Чепецк) |
1 |
Концентрат люминофора, образующийся при утилизации ртутных ламп |
Трубчатая вращающаяся печь ТВП-1 |
ООО “Экорецикл” (г. Ногинск, Московская обл.), ООО “НПП “Экотром” (г. Москва), ОАО “Волгохимторг” (г. Волгоград) |
1 |
Графит-отходы |
Трубчатая вращающаяся печь ТВП-1 |
ОАО “Усольехимпром” (г. Усолье-Сибирское, Иркутская обл.) |
1 |
Соединения ртути |
Трубчатая вращающаяся печь ТВП-1 |
В основном организации и предприятия Краснодарского края* |
1 |
Загрязненные ртутью почвогрунты и строительные отходы |
Трубчатая вращающаяся печь ТВП-1 |
Организации (преимущественно Краснодарского края), осуществляющие демеркуризацию строений и территорий** |
2 |
Гальванические элементы (отработанные и брак) |
Трубчатая вращающаяся печь ТВП-1 |
ОАО “Энергия” (г. Елец), ГП “Сигнал” (г. Челябинск) |
3 |
Трубчатые люминесцентные лампы |
Установка “Экотром-2” |
Предприятия и организации Краснодарского края |
4 |
Ртутные лампы высокого давления (типа ДРЛ) |
По принятой схеме |
Предприятия и организации Краснодарского края |
5 |
Металлические приборы с ртутным заполнением |
По принятой схеме |
Предприятия и организации Краснодарского края |
6 |
Стеклянные приборы с ртутным наполнением (отработанные и брак) |
По принятой схеме |
Предприятия и организации Краснодарского края |
7 |
Отработанные респираторы, использованная спецодежда, тканевые отходы фильтрования ртути |
Трубчатая вращающаяся печь ТВП-1 |
Отходы собственного производства |
8 |
Некондиционная (отработанная, черновая) металлическая ртуть |
Установка по рафинированию |
Различные организации и предприятия, в том числе Краснодарского края*** |
9 |
Пыль и шламы газоочистки |
Трубчатая вращающаяся печь ТВП-1 |
Очистка технологических газов |
10 |
Отходы картонной упаковки ртутных ламп |
Трубчатая вращающаяся печь ТВП-1 |
Организации и предприятия Краснодарского края |
* Например, в 2002 г. из Кубанской гидрогеологической мелиоративной партии поступило 217 кг
химических реактивов, содержащих ртуть.
** В 2002 г. от ООО ПАСФ “Ртутьсервис” (г. Краснодар) поступило 4,69 т ртутьсодержащего грунта.
*** В 2002 г. на переработку поступило 2775 кг некондиционной (“черновой”) ртути из Беларуси (УП
“Белцветмет”) и более 600 кг от различных предприятий Краснодарского края.
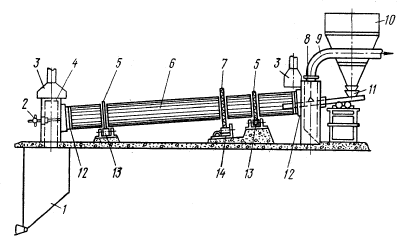
Рисунок 5,1 Схема устройства трубчатой печи:
1 - бункер для огарков; 2 - форсунка (горелка); 3 - зонты; 4 - топочная камера; 5 - бандажи; 6 - корпус печи; 7 - приводная шестерня; 8 - пылевая камера; 9 - газоход для отвода технологических газов; 10 - бункер для сырья; 11 - питатель; 12 - верхнее и нижнее уплотнения; 13 - опорные ролики; 14 - приводной механизм вращения печи
Температура перерабатываемого сырья по мере его продвижения в корпус печи
повышается, достигая максимума вблизи разгрузочного конца. Обожженное сырье (так
называемые огарки) поступает в расположенный под топочной камерой огарочный бункер, где
выдерживается определенное время, в течение которого выделяющиеся пары ртути вместе с
горячим воздухом отсасываются из бункера через топочную камеру обратно в печь. Для
предотвращения возможных потерь паров ртути конструкция соединения печи, топочной
камеры и бункера для огарков усиливаются путем установки нижнего уплотнения.
Общая схема пирометаллургического получения ртути
Металлургический передел сырья осуществляется по обычной схеме ртутного
производства (обжиг сырья - конденсация паров ртути - переработка ртутной ступпы), но
модернизированной специалистами ЗАО “Кубаньцветмет” для условий переработки тех или
иных групп ртутьсодержащих отходов (рис. 5.2).
Перед обжигом в печи сырье загружается в приемный бункер, откуда ленточным
питателем (длина ленты 3 м, ширина – 0,8 м, производительность 40 т/час) подается на
дробление (до кусков размерами 50-70 мм), которое осуществляется на щековой дробилке СМ-
741 (размер загрузочной щели 6 х 9 см; производительность дробилки - 40 т/час).
Образующаяся при этом пыль удаляется местной системой аспирации, накаливается в емкости
с водой и затем направляется на повторный обжиг в печь ТВП-1. Подготовленное сырье
ленточным конвейером (длина ленты 38,96 м, ширина – 0,65 м) направляется в расходный
бункер, откуда с помощью ленточного питателя (длина 1,8 м, ширина ленты 0,8 м,
производительность до 6 т/час) подается в печь ТВП-1.
Сырье подвергается обжигу при температуре не менее 500°С, при которой содержащаяся
в нем ртуть возгоняется и переходит в парообразное состояние (в технологические газы). Время
пребывания материала в печи составляет в среднем 1,5 часа. При необходимости
продолжительность обжига регулируется скоростью вращения печи. Процесс обжига
проводится в окислительной среде, т. е. в присутствие свободного кислорода. Окислительная
атмосфера в печи поддерживается за счет 30%-го избытка воздуха, необходимого для сжигания
топлива. Если в сырье присутствуют другие летучие элементы, то они также нацело или
частично возгоняются, как и влага, содержащаяся в обжигаемом сырье. Кроме того, в газы в
определенном количестве переходят пыль, газовые продукты, образующиеся при сжигании
топлива, а также избыток кислорода и азот, поступающие в технологический процесс с
воздухом.
Обожженное сырье, или огарки, имеющие на выходе из печи температуру порядка 500°С,
поступают в огарочный бункер. Выгрузка горячих огарков сопровождается образованием
восходящих потоков нагретого воздуха, а также пылением, для снижения которого огарки
обычно 4-6 часов выдерживаются в бункере, где охлаждаются до температуры ниже 180°С.
Выделяющаяся в этот период из огарков ртуть успевает поступить обратно в печь, а пыление
огарков значительно снижается. Опыт показывает, что в большинстве случаев содержание
ртути в огарках не превышает 25-26 мг/кг. Удаление огарков в отвалы осуществляется
самосвалами.
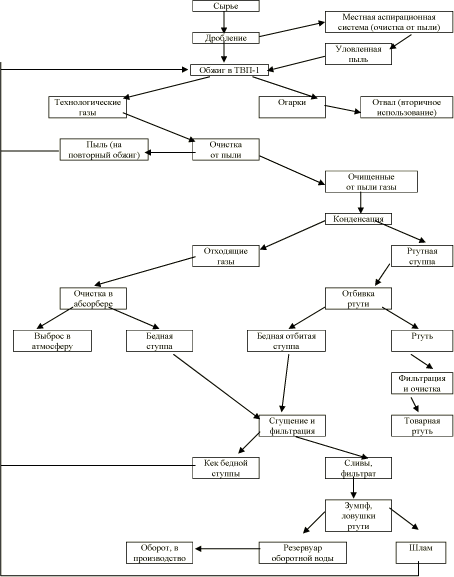
Рисунок 5.2 Принципиальная схема пирометаллургического процесса получения ртути.
Технологические газы, образующиеся при обжиге сырья и имеющие на выходе из печи
температуру не менее 500°С, по специальному газоходу поступают на групповой циклон, где
подвергаются очистке от пыли. При хорошо налаженной работе циклон улавливает до 90%
пыли, содержащейся в газах, которая затем возвращается на повторный обжиг. Все газоходы от
печи к аппаратам очистки от пыли, сами аппараты, а также газоходы от них оснащены
теплоизоляционными жаростойкими материалами.
После очистки от пыли технологические газы, несущие пары ртути, поступают на
охлаждение в трубчатый конденсатор-холодильник, где охлаждаются до 30оС и превращаются
в жидкость (рис. 5.3). Общий принцип действия конденсатора заключается в следующем.
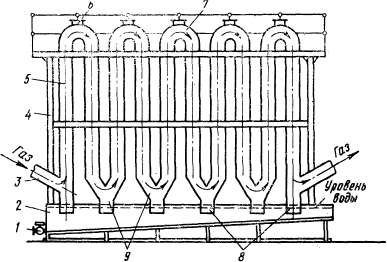
Рисунок 5.3 Схема устройства конденсатора-холодильника для конденсации ртути из технологических газов
1 - кран; 2 - приемник; 3 - газоход; 4 - рамная конструкция; 5 - металлические трубы (стояки); 6 - верхние люки (крышки); 7 - патрубки; 8 - нижние концы тройников (спуски); 9 - тройники
Очищенные от пыли технологические газы поступают по газоходу 3, из которого следуют
по ниткам конденсатора. Нитка конденсатора состоит из вертикальных металлических труб
(стояков) 5, укрепленных на рамной конструкции 4, установленных попарно и соединенных
сверху П-образными патрубками 7 (коленами). Внизу каждая пара соединена с соседней при
помощи тройников 9. Нижние концы тройников (спуски) 8 погружены в воду, наполняющую
приемник 2, установленный снизу вдоль всей нитки. Технологический газ, введенный в первый
стояк, под влиянием разрежения, создаваемого вентилятором, установленным за
конденсатором, поочередно проходит по системе труб, поднимаясь и опускаясь; затем
переходит в соседнюю пару и так до конца нитки. Для ускорения охлаждения технологических
газов в конденсаторе последние в ряду стояки орошаются водой, подаваемой через
разбрызгиватели, установленные в верхней части стояков. Кроме того, в конденсатор подается
определенное количество воды, что способствует более эффективному осаждению пыли,
содержащейся в технологических газах.
В процессе конденсации, начинающейся в пристенном слое, образуются капли ртути,
наиболее крупные из которых стекают в особые приемники (корыта конденсатора),
расположенные в нижней части охлаждающего аппарата, часть капель оседает на его
внутренних стенках, а наиболее мелкие капли (аэрозоли) покидают конденсатор с уходящим из
конденсатора потоком газов. В конденсаторе улавливается не только металлическая ртуть, но и
ее соединения, сконденсировавшиеся здесь вода, оксиды некоторых химических элементов, а
также существенная часть не уловленной ранее пыли. В результате в корытах конденсатора
собирается не чистая ртуть, а так называемая ступпа, представляющая собой смесь
металлической ртути, ее соединений, пыли, частиц несгоревшего топлива, воды. Количество
металлической ртути в ступпе колеблется от 20 до 80% и зависит от ряда факторов: содержания
металла в исходном сырье, коэффициента полезного действия системы пылеулавливания и др.
Образующаяся ступпа направляется (при помощи насоса) на так называемую отбивку
ртути, которая осуществляется в гидроциклоне, где под действием центробежных сил
происходит коагуляция и отделение (отбивка) металлической ртути от влаги и более легких
твердых продуктов обжига. В ходе отбивки металлической ртути образуется так называемая
бедная ступпа, которая поступает в сгуститель и затем на вакуумный фильтр, откуда
обезвоженная масса в виде кека бедной ступпы (влажностью 12-15%) направляется (после
шихтовки с известью) в печь на повторный обжиг с целью доизвлечения ртути.
Технологические газы, покидающие конденсатор-холодильник (отходящие, выбросные
газы), всегда содержат некоторое количество паров ртути, которое соответствует равновесному
содержанию, обусловленному температурой газов, т. е. чем она выше, тем больше в них
содержится ртути (табл. 5.2). Именно поэтому всегда стремятся охладить газы в конденсаторе
до возможно более низких температур (обычно ниже 30оС). Помимо паров ртути, в выбросных
газах, отводимых из конденсатора, присутствуют аэрозоли металлической ртути, пары воды,
тонкие частицы пыли, сажа и некоторые другие примеси.
Таблица 5.2 Содержание ртути в насыщенном паре в зависимости от температуры [157]
Температура, °С |
10 |
20 |
30 |
40 |
50 |
60 |
70 |
80 |
90 |
100 |
Ртуть, мг/м³ |
5,64 |
13,38 |
29,81 |
62,8 |
126,6 |
234,9 |
452 |
807 |
1396 |
2338 |
Отходящие (выбросные) газы поступают на дополнительную (санитарную) очистку,
которая осуществляется в двухступенчатом абсорбере. Первая ступень представляет собой
аппарат распылительного типа (АРТ), где улавливается основная масса пыли и частично ртуть.
Затем газы поступают в аппарат с шаровой насадкой (АШН), где в качестве орошающей
жидкости используется щелочной (известковый) раствор. Уловленная абсорберами пыль
(бедная ступпа) также направляется на повторный обжиг в печь.
Очищенные в абсорбере газы выводятся в атмосферу через заводскую трубу высотой 30
м (с учетом рельефа местности ее расположения - более 60 м), что обеспечивает необходимое
разбавление их воздухом. Обычно на каждую тонну переработанного сырья образуется в
среднем до 2400 м³ отходящих газов; при нормальных условиях протекания технологического
процесса содержание ртути в них составляет не более 25,4 мг/м³, т. е. в настоящее время
удельный выброс ртути в атмосферу на 1 т перерабатываемого сырья для печи ТВП-1
составляет 61 г. Предельно допустимый выброс ртути для металлургического завода ЗАО
.Кубаньцветмет. установлен в 80 кг в год. По данным [162], содержание пыли (после очистки)
в выбросных газах ртутного производства (переработка руды) обычно не превышает 5-6 мг/м³.
На металлургическом заводе ЗАО “Кубаньцветмет” применяется оборотная система
водоснабжения с ежедневной подпиткой (15 м³/сут. воды на технологические нужды и 5 м³/сут.
- на хозяйственно-бытовые нужды, которая поступает из специального металлического
резервуара). Производственные воды, участвующие в обороте, поступают в зумпф, проходят
через ртутные ловушки, затем идут в резервуар оборотной воды, откуда возвращаются в
технологический процесс. Образующийся шлам направляется на обжиг в ТВП-1.
Хозяйственно-бытовые стоки удаляются в канализацию.
Рафинирование ртути
В результате отбивки получается металлическая ртуть, которую затем фильтруют через
хлопчатобумажный бельтинг и шинельное сукно. Как правило, полученная таким образом
ртуть без какой-либо дополнительной обработки представляет собой товарный металл марки
Р3, который используется в производстве ртутных соединений и/или поставляется
потребителям. Необходимая дальнейшая очистка ртути осуществляется на установке по
рафинированию ртути, изготовленной специалистами ЗАО “Кубаньцветмет” и основанной на
использовании гидрохимического способа.
На очистку 1 т ртути расходуется 0,05 кг хлопчатобумажного бельтинга и 0,05 кг
шинельного сукна. Образующиеся после очистки и рафинирования ртути мягкие отходы (около
3 кг в год с содержанием ртути до 2%) накапливаются в кислотостойких, герметичных
емкостях и затем сжигаются в ТВП-1.
Состав, условия приемки, анализа, транспортировки и хранения ртути определяются
ГОСТ 4658-73, который распространяется на металл, предназначенный для производства
полупроводниковых материалов, для использования в вакуум-электротехнике, при
производстве контрольно-измерительных приборов, ртутно-цинковых источников тока,
различных реактивов и фармацевтических препаратов, а также в химической,
металлургической и в других отраслях промышленности (табл. 5.3).
В частности, ртуть марок Р1, Р2 и Р3 разливают в специальные стальные баллоны (марки
ЭР-2,75, изготавливаются Первоуральским новотрубным заводом), вмещающие по 34,5 кг
металла. Каждый баллон закрывают плотно завинчивающейся пробкой с прокладкой из
фторопластового материала толщиной не менее 0,15 мм. При длительном хранении баллоны
пломбируют.
Таблица 5.3 Химический состав ртути [80]
Требования к составу |
Марка ртути |
Р0 |
Р1 |
Р2 |
Р3 |
Ртуть, %, не менее |
99,9997 |
99,999 |
99,99 |
99,9 |
Нелетучий остаток, %, не более |
0,0003 |
0,001 |
0,01 |
0,1 |
Ртуть марки Р0 разливают в баллоны из толстостенного стекла, вмещающие 5 кг металла.
Розлив ртути марок Р1 и Р2 допускается осуществлять также в баллоны из толстостенного
стекла, которые закрывают металлической крышкой с прокладкой из пластиката. Ртуть марки
Р1, предназначенная для медицинских целей, разливают во флаконы, вмещающие 50 г металла
и которые закрывают полиэтиленовыми пробкой и крышкой. Каждый флакон помещают в
полимерную банку вместимостью 30 см³ и уплотняют алигнином. Гарантийный срок хранения
ртути марок Р1 и Р2 - два года, ртути марки Р0 - три года, марки Р3 - не ограничен.
Условия и особенности переработки ртутьсодержащих отходов
Технологическая схема переработки каждой группы ртутьсодержащих отходов имеет
свои особенности, зависящие от источника образования отходов, их вещественного состава и
консистенции (см. табл. 5.1).
Переработка отходов 1-й группы
Переработка отходов данной группы, в которую входят отработанный ртутный
катализатор (отходы производства винилхлорида), сорбенты (активированный уголь марки
КПР и т. п.), соединения ртути, шлам производства 1-аминоантрахинона, загрязненные ртутью
почвогрунты и строительные отходы, графит-отходы, концентрат люминофора и т. п., в общем
случае осуществляется по единой технологической схеме, которая включает следующие
основные технологические операции:
- шихтовка сырья, т. е. добавление к нему извести с целью нейтрализации кислотного
остатка в соотношении по массе 1,0:0,8 (сырье : известь);
- нагрев шихты в трубчатой вращающейся печи до температуры не менее 500°С
топочными газами для перевода ртути, содержащейся в исходном сырье, в газовую фазу;
- обеспыливание парогазовой смеси в групповом циклоне;
- конденсация ртути в холодильнике-конденсаторе;
- накопление ртутной ступпы в корытах конденсаторов;
- отбивка металлической ртути в гидроциклоне;
- очистка ртути от примесей с целью получения товарной металла;
- очистка отходящих (выбросных) газов от ртути в абсорбере;
- выгрузка огарков из печи в огарочный бункер (выход огарков составляет 94-96% от
массы обжигаемой шихты);
- вывоз огарков на огарочный отвал или на участок переработки свинцового лома в
отражательной печи, где они применяются в качестве восстановителя.
На рис. 5.4 в качестве примера приводится схема переработки отходов производства
винилхлорида (отработанного ртутного катализатора), среднее содержание ртути в которых
составляет 3000 мг/кг (30 кг металла в 1 т отходов).
С 2003 г. огарки, образующиеся при обжиге ртутного катализатора, шлама производства
1-аминоантрахинона и графит-отходов, предполагается передавать предприятиям,
осуществляющим металлургический передел лома цветных и черных металлов, где они будут
использоваться в качестве восстановителя и флюса. Огарки от обжига грунтов и строительных
материалов будут применяться при планировке дорог IV-V классов.
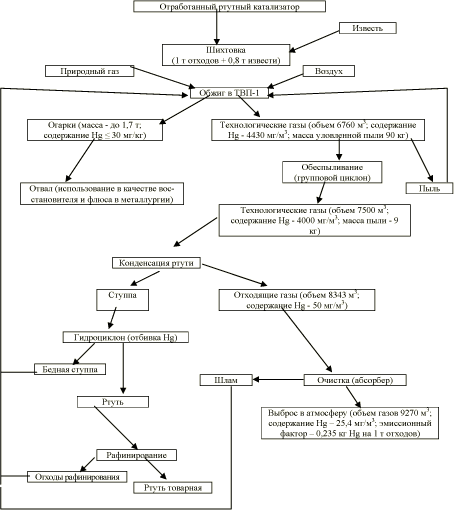
Рисунок 5.4 Схема переработки отходов производства винилхлорида (отработанного катализатора) в ТВП-1.
С 2003 г. на ЗАО “Кубаньцветмет” планируется ежегодная переработка 600 т отходов
производства винилхлорида, 50 т сорбентов ртути на основе активированных углей, 50 т
ртутьсодержащих почвогрунтов и строительных отходов, 60 т графит-отходов, 30 т шламов
производства 1-аминоантрахинона. Рассмотренная технологическая схема может
использоваться также для переработки отходов производства витамина В2 (шлам активного
угля), шламов хлорно-щелочных заводов и других близких по условиям образования, составу и
консистенции видов вторичного ртутьсодержащего сырья.
Утилизация гальванических элементов
Утилизация использованных и бракованных гальванических (ртутно-цинковых и
ртутьсодержащих) элементов и батарей производится по той же технологической схеме - обжиг
сырья в печи ТВП-1, но с раздельной загрузкой либо ртутных, либо ртутьсодержащих
элементов и батарей и без шихтовки сырья известью (рис. 5.5).
Отходами данного производственного процесса являются огарки (обожженные корпуса
элементов), содержащие около 45% железа и 55% цинка; концентрация в них ртути не
превышает 0,0002% (по массе). Огарки затариваются в металлические барабаны и реализуются
организациям, специализирующихся на сборе и переработке лома цветных и черных металлов.
Масса образующихся огарков составляла порядка 10-20 т/год.
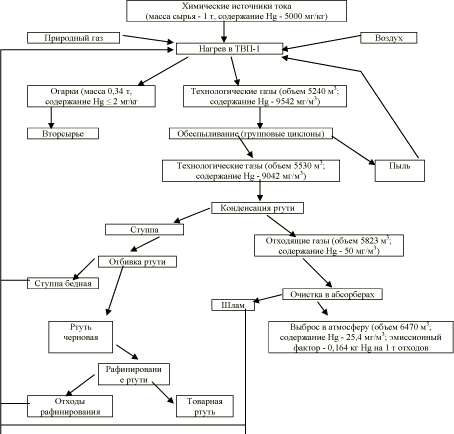
Рисунок 5.5 Схема утилизации химических источников тока в ТВП-1.
Демеркуризация трубчатых люминесцентных ламп
Переработка трубчатых люминесцентных ламп (типа ЛБ и т. п.), которая осуществляется
на вибропневматической установке “Экотром-2”, включает их механическое разрушение и
выделение под разряжением фракций стекломассы (стеклобоя), алюминиевых цоколей и
люминофора - основного концентратора ртути. Характеристика основных узлов установки
приведена в табл. 5.4, а технологическая схема процесса - на рис. 5.6. Перерабатываемые
изделия в среднем содержат (по массе): стекло 94,61%, алюминиевые цоколи – 2,39%,
люминофор - 3%, концентрация ртути в котором составляет 34400 мг/кг.
Таблица 5.4 Основные технические характеристики установки “Экотром-2”
Наименование аппарата и его характеристика |
Наименование и состав среды |
Расход на одну операцию |
Аппарат демеркуризации, 1200 ламп/час |
Измельченные компоненты ламп |
360 кг/час |
Циклон диметром 200 мм, длиной 800 мм |
Воздух, содержащий люминофор и стеклянную пыль |
360 нм³/час |
Рукавный фильтр, 9 рукавов, диаметр 180 мм, длина 2000 мм |
Воздух, содержащий люминофор и стеклянную пыль |
360 нм³/час |
Кассетный фильтр, 4 фильтра |
Воздух, содержащий люминофор и стеклянную пыль |
360 нм³/час |
Сборники люминофора, объем 50 л, диаметр 350 мм |
Ртутьсодержащий люминофор |
40 л |
Адсорбер рабочий, диаметр 800 мм, сорбент, содержащий активированный уголь |
Воздух, содержащий пары ртути |
360 нм³/час |
Емкость для сбора цоколей, объем 0,06 м³ |
Алюминиевые цоколи |
8,4 кг/час |
Бункер для сбора стеклобоя, объем 0,12 м³ |
Стеклобой |
10 м³ |
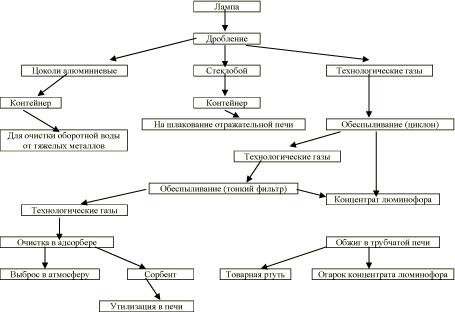
Рисунок 5.6 Схема утилизации трубчатых люминесцентных ламп (типа ЛБ, ЛД и т. п.).
Отходами демеркуризации трубчатых люминесцентных ламп являются:
- стеклобой (стекломасса), выход которого составляет 92% от массы перерабатываемого
изделия; он содержит не более 0,2% ртути, содержащейся в перерабатываемых изделий
(удельная концентрация ртути в стекломассе - не более 2,1 мг/кг);
- алюминиевые цоколи (их выход 2,33%);
- концентрат люминофора (выход 5,67%) с содержанием ртути (по массе) до 3,44%;
- выбросы (после очистки) отходящих газов в атмосферу (на 1 т утилизируемых изделий
выбрасывается порядка 0,69 мг ртути, или не более 0,07% от общего ее количества,
содержащегося в перерабатываемых лампах).
Стекломасса накапливается в металлических контейнерах и затем используется в
свинцовом производстве (для ошлакования в отражательной печи). Алюминиевые цоколи
люминесцентных ламп применяются в технологическом процессе пирометаллургического
передела ртутьсодержащего сырья в качестве восстановителя при очистке оборотной
технологической воды от растворимых солей тяжелых металлов. Концентрат люминофора,
получаемый при переработке ламп на установке “Экотром-2” (его образуется порядка 1 т/год),
хранится в герметичной упаковке и по мере накопления перерабатывается в трубчатой печи
ТВП-1 (вместе с поступающим от других организаций концентратом люминофора) по
рассмотренной выше схеме. Выход огарков от обжига концентрата люминофора составляет
порядка 96% от исходной массы перерабатываемого сырья; они используются для
рекультивации старых огарочных отвалов.
Утилизация ртутных ламп высокого давления
Переработка ртутных ламп высокого давления (типа ДРЛ) включает (рис. 5.7):
- разрушение колбы и накопление стекломассы (стеклобоя) с люминофором в
специальных контейнерах;
- отделение кварцевой горелки от цоколя с ножкой и раздельное их накопление в
контейнерах;
- измельчение горелок в молотковой дробилке и обжиг полученной массы в печи ТВП-1
вместе с другим ртутьсодержащим вторичным сырьем.
Отходами данного процесса являются стекломасса (используется в переработке
свинцового лома - для шлакования в отражательной печи) и лом черных и цветных металлов,
который реализуется (как вторсырье) соответствующим организациям.
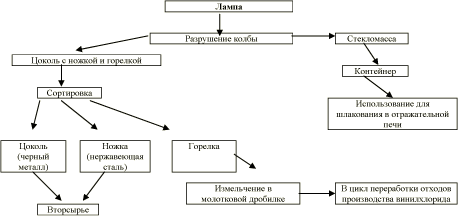
Рисунок 5.7 Схема утилизации ртутных ламп высокого давления (типа ДРЛ).
Утилизация металлических приборов с ртутным заполнением
Утилизация металлических приборов с ртутным заполнением осуществляется
следующим образом (рис. 5.8). Прибор помещается на специальный поддон; затем
механическим способом или электрогазосваркой в приборе вскрывается отсек, заполненный
металлической ртутью, которая сливается в стальной баллон. Корпуса приборов,
освобожденные таким образом от металлической ртути, помещаются в печь ТВП-1 и
прокаливаются в течение 3-4 час. при температуре не менее 500°С. Ртуть, сорбированная на
стенках корпусов, испаряется и вместе с технологическими газами поступает в систему
конденсации ТВП-1. Затем корпус прибора (содержание ртути ≤1 мг/кг) подвергается разборке
по видам металлолома.
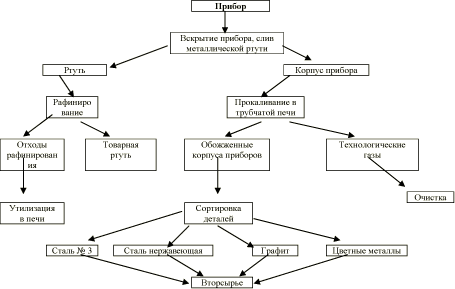
Рисунок 5.8 Схема утилизации металлических приборов с ртутным заполнением.
Утилизация стеклянных приборов с ртутным заполнением
Утилизация стеклянных приборов, содержащих металлическую ртуть (в среднем до 3,7%
от общей массы изделий), осуществляется следующим образом (рис. 5.9):
- разрушение стеклянной колбы (корпуса) прибора в ванне под слоем воды;
- слив металлической ртути в ванну;
- отделение металлических деталей;
- слив металлической ртути из ванны в специальную емкость;
- обжиг стеклобоя с целью отгонки остатков ртути;
- рафинирование металла по принятой на предприятии технологической схеме.
Степень извлечения ртути в данном технологическом процессе составляет более 99,9%.
Отходами процесса являются стекломасса (ее выход - порядка 89% от общей массы
утилизируемых изделий) и металлические фрагменты (до 6,53% от массы утилизируемых
изделий). Стекломасса применяется в свинцовом производстве (идет на ошлакование
отражательной печи), а металлические фрагменты реализуются как вторсырье.
Утилизация картонной тары
Данный вид отходов образуется на участке демеркуризации ртутных ламп, которые
поступают на переработку в картонной упаковке (средняя масса одной упаковки - 20 г). При
среднегодовом объеме перерабатываемых ламп в 145 тыс. шт. масса картонных отходов
составляет примерно 2,9 т. Они накапливаются в металлическом контейнере (объем - 1 м³) и
затем сжигаются в трубчатой вращающей печи ТВП-1.
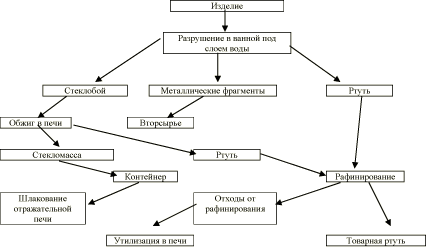
Рисунок 5.9 Схема утилизации стеклянных приборов с ртутным заполнением.
Утилизация использованных средств индивидуальной защиты и спецодежды
Отработанные респираторы (средний вес одного респиратора – 0,2 кг) и использованная
спецодежда собираются в металлический контейнер с крышкой и затем сжигаются в печи.
Ежегодно утилизируется около 580 кг отработанных респираторов и до 660 кг использованной
рабочей одежды и обуви.
Рафинирование некондиционной (отработанной) металлической ртути
Некондиционная (отработанная, черновая) ртуть, поступающая от различных
организаций, подвергается фильтрованию и очистки на установке рафинирования. Полученная
ртуть используется в производстве соединений ртути или поставляется различным
организациям и предприятиям.
Объемы переработки ртутьсодержащих отходов
В табл. 5.5 и 5,6 приведены сведения об объемах различных видов ртутьсодержащих
отходов производства и потребления, переработанных ЗАО “Кубаньцветмет” в 2001-2002 г.г., а
табл. 5.7 содержит обобщенные данные о переработке ртутьсодержащего сырья и производстве
вторичной ртути на ЗАО “Кубаньцветмет” в 1998-2002 г.г.
Таблица 5.5 Переработка ртутьсодержащих отходов, ЗАО “Кубаньцветмет”, 2001 г.
Вид отходов |
Масса отходов, кг |
Товарная Hg, кг |
Катализатор, сорбенты, шламы |
244312 |
9793 |
Некондиционная (отработанная, черновая) ртуть |
16113 |
16097 |
Ртутные лампы |
20610 |
7 |
Ртутьсодержащие приборы |
1784 |
131 |
Концентрат люминофора |
23700 |
78 |
Прочее (гальванические элементы, загрязненные ртутью строительные отходы и грунты, отходы собственного производства и др.) |
54800 |
343 |
Итого |
361319 |
26449 |
. Таблица 5.6 Переработка ртутьсодержащих отходов, ЗАО “Кубаньцветмет”, 2002 г.
Вид отходов |
Масса отходов, кг |
Товарная Hg, кг |
Некондиционная (отработанная, черновая) ртуть |
783,5 |
727 |
Ртутные лампы |
31200 |
10,5 |
Ртутьсодержащие приборы |
384 |
65,3 |
Концентрат люминофора |
59570 |
163,2 |
Прочее (гальванические элементы, реактивы, грунты и т. д.) |
2750 |
9,5 |
Итого |
94687,5 |
975,5 |
. Таблица 5.7 Переработка сырья и производство вторичной ртути ЗАО .Кубаньцветмет.
Год |
Масса отходов (всех видов), т |
Масса товарной ртути, кг |
1998 |
56,6 |
1459 |
1999 |
840,4 |
16020 |
2000 |
919,7 |
22061 |
2001 |
361,3 |
26449 |
2002 |
94,7 |
976 |
Итого |
2272,7 |
66965 |
Большая часть металлической ртути, полученной при переработке отходов производства
и потребления, использовалась в производстве ее различных соединений (марок ХЧ, ЧДА, Ч),
объемы и особенности изготовления которых рассмотрены в разделе 3.10. В 2000-2002 г.г. в
небольших количествах металлическая ртуть поставлялась (объемы поставок – по 2-4 т)
некоторым российским предприятиям (химические заводы в г. Волгограде, ОАО
“Термоприбор” в г. Клину, ОАО “Лисма’ в г. Саранске и др.). В 2003 г. порядка 150 кг
металлической ртути было отправлено на ОАО “Энергия” (г. Елец).
Производство особо чистой ртути
Как уже говорилось, ЗАО “Кубаньцветмет” располагает 4-мя установками по получению
особо чистой ртути (марок 5N, 6N и выше), основанных на использовании многократной
дистилляции металла с электроразрядной очисткой. Процессы дистилляционного
рафинирования осуществляются в аппаратах, плотно изолированных от рабочего пространства
участка. Упаковка ртути осуществляется в герметичные стеклянные ампулы, содержащие по 50
г или 75 г металла. В свое время указанная ртуть использовалась в научных исследованиях,
опытных производствах, в полупроводниковой промышленности. В последние годы заказов на
производство чистой ртути не поступало, что объясняется объективных и субъективных
причин (финансовые трудности, наличие на некоторых предприятиях собственных установок
по очистке ртути и др.).
Эмиссия ртути в ходе пирометаллургического передела сырья
В табл. 5.8 и 5,9 приведены основные показатели работы трубчатой вращающейся печи
ТВП-1 и характеристики образующихся отходов, а в табл. 5.10 дается баланс распределения
потерь ртути в ходе пирометаллургического передела ртутьсодержащего сырья. Существенное
снижение общих потерь ртути, начиная с 2000 г., обусловлено увеличением степени
пылеулавливания и переводом пыли, содержащей ртуть, в оборотные технологическое воды, с
повышением эффективности отбивки металлической ртути и с повторной переработкой ряда
промежуточных продуктов и отходов в печи. В частности, с 2000 г. внедрен обжиг
улавливаемой очистными установками пыли в печи вместе с сырьем. Определенную роль
играет и тот факт, что на переработку стали поступать отходы с более высоким содержанием
ртути. Хорошо известно, что на ртутных комбинатах практически все виды потерь ртути в ходе
технологических процессов, как правило, в значительной степени зависят от содержания ее в
исходном сырье: чем выше концентрация ртути в сырье, тем ниже ее потери [205].
Таблица 5.8 Основные показатели работы ТВП-1 металлургического завода ЗАО
“Кубаньцветмет” в 1999-2001 г.г.
Параметр |
1999 |
2000 |
2001 |
Переработано ртутьсодержащего сырья (сухая масса), кг |
840390 |
919744 |
361319 |
Количество ртути, содержащейся в сырье, кг |
16313,73 |
22302,56 |
26746,25 |
Получено металлической ртути, кг |
15803,11 |
22055 |
26625,89 |
Общие потери металла в ходе технологического процесса, кг |
510,6 |
247,6 |
120,4 |
Таблица 5.9 Характеристика отходов, образующихся при пирометаллургическом переделе
ртутьсодержащего сырья, ЗАО “Кубаньцветмет”
Год |
Огарки |
Отходящие газы |
Оборотная вода* |
Пыль циклонов** |
Масса, т |
Hg, мг/кг |
Объем, м³ |
Hg, мг/м³ |
Объем, м³ |
Hg, г/м³ |
Масса, т |
Hg, мг/кг |
1999 |
748 |
38 |
10449745 |
30,68 |
360 |
22,3 |
25 |
3400 |
2000 |
844 |
25 |
8182680 |
25,4 |
275 |
39 |
- |
- |
2001 |
129,9 |
26 |
2119487 |
24,3 |
250 |
259,4 |
- |
- |
* С ежедневной подпиткой свежей водой.
** С 2000 г. внедрен обжиг пыли в печи вместе с сырьем (непосредственно в ходе осуществления
технологического процесса).
В 2001 г. доля безвозвратных потерь ртути в ходе пирометаллургического передела сырья
составляла 46,1% (или 55,5 кг), большая часть из которых приходилась на отходящие газы,
выбрасываемых в атмосферу (42,8% или 51,5 кг). Около 65 кг ртути (53,9% общих ее потерь) в
составе оборотной воды в конечном счете возвращалось в технологической процесс.
Таблица 5.10 Распределение потерь ртути в ходе пирометаллургического передела
ртутьсодержащего сырья в печи ТВП-1, ЗАО .Кубаньцветмет.
Вид потерь |
1999 |
2000 |
2001 |
кг |
доля, % |
кг |
доля, % |
кг |
доля, % |
С огарками* |
32,3 |
6,3 |
21,1 |
8,5 |
3,4 |
2,8 |
С отходящими газами** |
320,6 |
62,8 |
207,8 |
83,9 |
51,5 |
42,8 |
С оборотной водой*** |
8 |
1,6 |
10,7 |
4,3 |
64,9 |
53,9 |
С циклонной пылью**** |
85 |
16,6 |
- |
- |
- |
|
Неучтенные потери ***** |
64,7 |
12,7 |
8 |
3,3 |
0,6 |
0,5 |
Всего потерь |
510,6 |
100 |
247,6 |
100 |
120,4 |
100 |
* Безвозвратные потери (в отвал или вторичное использование).
** Безвозвратные потери, выброс в атмосферу через трубу.
*** Возвращаются в технологический процесс.
**** С 2000 г. внедрен обжиг пыли в печи вместе с сырьем (непосредственно в ходе осуществления
технологического процесса).
Данные наблюдений показывают, что воздух большинства рабочих помещений
предприятия характеризуется периодическим появлением концентраций паров ртути,
превышающих значения максимальной ПДК (табл. 5.11). Как правило, наиболее высокие
концентрации паров ртути наблюдались в воздухе участка розлива ртути и операторной
трубчатой вращающейся печи ТВП-1. На открытой площадке, около ТВП-1, уровни паров
ртути в воздухе обычно находятся около 0,01 мг/м³, снижаясь до 0,0001-0,0003 мг/м³ на
границе санитарно-защитной зоны.
Таблица 5.11 Уровни содержания ртути в воздухе рабочих помещений и в пределах санитарно-
защитной зоны (СЗЗ) металлургического завода ЗАО “Кубаньцветмет”, 2002 г.,
мг/м³
Участок |
Среднее |
Пределы |
Количество замеров в течение года* |
Операторная трубчатой печи |
0,019 |
0,010-0,025 |
12 |
Участок розлива ртути |
0,026 |
0,023-0,028 |
13 |
Склад готовой продукции |
0,010 |
0,001-0,014 |
10 |
Химико-аналитическая лаборатория |
0,007 |
0,002-0,010 |
13 |
Механический цех |
0,010 |
0,003-0,012 |
12 |
Административно-бытовой корпус |
0,011 |
0,007-0,012 |
14 |
Открытая площадка, около ТВП-1 |
в среднем около 0,01 |
- |
На границе СЗЗ** |
0,0001-0,0003 |
- |
ПДК в рабочей зоне, среднесменная |
0,005 |
- |
ПДК в рабочей зоне, максимальная |
0,010 |
- |
ПДК в воздухе насаленных мест |
0,0003 |
- |
Типичное фон содержание |
0,000010-0,000015 |
- |
* Примерно один раз в месяц.
** Размер СЗЗ - 1000 м.
Планируемое увеличение объемов переработки ртутьсодержащих отходов, безусловно,
приведет к заметному росту выбросов ртути в среду обитания, прежде всего, с отходящими
газами. Это обусловливает необходимость:
- проведения профилактических работ по увеличению надежности работы и
герметичности основных технологических трактов трубчатой вращающейся печи ТВП-1;
- модернизации (капитального ремонта) существующей системы пылегазоочистки;
- создания системы дополнительной очистки отходящих газов от ртути, которая должна
обеспечить многократное снижение в них содержания металла (по крайней мере, на порядок по
сравнению с существующим);
- проведения работ по полномасштабной демеркуризации основных рабочих,
административных и складских помещений промышленной зоны ЗАО “Кубаньцветмет” и
территории, прилегающей непосредственно к металлургическому заводу (с необходимым
комплексом натурных ртутометрических исследований);
- организации на предприятии постоянной службы текущей демеркуризации.
5.1.3 ООО “Мерком”
ООО “Мерком” организовано в 1992 г.; оно расположено на территории НИИ приборов
(г. Лыткарино, Московская область); общая численность сотрудников составляет более 40
человек.
В сфере обращения с ртутьсодержащими отходами ООО “Мерком” осуществляет
утилизацию:
- отработанной (некондиционной, черновой) металлической ртути (сбор, перевозка,
рафинирование, получение вторичного металла);
- соединений ртути (сбор, перевозка, очистка, переработка и производство различных
соединений ртути);
- приборов с ртутным наполнением - термометров, сфигмоманометров, игнитронов,
нормальных элементов, ртутных контактов и др. (сбор приборов, изъятие и очистка
металлической ртути, подготовка корпусов приборов и их транспортировка к местам
утилизации);
- ртутных ламп (сбор, транспортировка и утилизация);
- ртутно-цинковых гальванических элементов (сбор, упаковка и транспортировка к
местам переработки);
- твердых, пастообразных и жидких ртутьсодержащих отходов (сбор, упаковка,
транспортировка к местам переработки);
Рафинирование отработанной (некондиционной, черновой) металлической ртути с целью
получения товарного (вторичного) металла, очистка, переработка (перекристаллизация) и
производство соединений ртути осуществляются по технологиям, разработанным
специалистами ООО “Мерком”[96, 263]. Основной товарной продукцией предприятия
являются металлическая ртуть марок Р0 и Р1 и соединения ртути реактивной чистоты.
Основные технологические схемы и производственные операции
Производственная база ООО “Мерком” включает:
- участок рафинирования некондиционной (отработанной, черновой) ртути;
- участок по производству соединений ртути;
- участок утилизации приборов с ртутным наполнением;
- участок демеркуризации трубчатых люминесцентных ламп;
- участок приемки ртутьсодержащих сухих гальванических элементов.
Производственные (проектные) мощности по рафинированию некондиционной ртути и
получению вторичного металла составляют 100 т/год; по производству соединений ртути - 30
т/год; установки по демеркуризации трубчатых люминесцентных ламп - 1 млн. шт./год.
Технологические и производственные операции осуществляются с соблюдением условий
и требований нормативных документов [76-79, 155, 244-246].
Рафинирование некондиционной металлической ртути
Очистка некондиционного металла осуществляется на участке рафинирования ртути на
специальной установке, основанной на применении технологии, разработанной в ООО
“Мерком”. В основу технологии положен гидрохимический способ очистки, базирующийся на
многоступенчатой обработке некондиционной ртути различными растворами.
В общем случае технологическая схема рафинирования некондиционной металлической
ртути выглядит следующим образом (рис. 5.10).
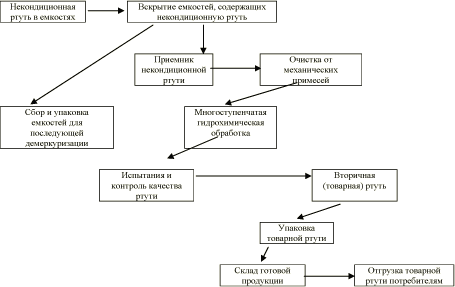
Рисунок 5.10 Технологическая схема рафинирования некондиционной ртути.
Испытания и контроль качества товарной ртути осуществляют по ГОСТ 4658-73 [80].
Конечной продукцией является ртуть марок Р0 и Р1, отвечающая требованиям указанного
ГОСТ.
Упаковка ртути марки Р1 производится в стандартные стальные баллоны, вмещающие по
34,5 кг ртути; ртути марки Р0 - в пластиковые емкости (по 3 кг металлической ртути в каждой)
под атмосферой инертного газа.
Производство соединений ртути
На участке по производству соединений ртути осуществляются следующие
технологические операции:
- производство различных соединений ртути из рафинированной металлической ртути
(синтез в химических реакторах гидрохимическими способами, разработанными в ООО
“Мерком”);
- перекристаллизация некондиционных соединений ртути, поступивших от различных
организаций, с целью получения товарных продуктов;
- очистка (от механических примесей) принятых от различных предприятий соединений
ртути с целью доведения их до необходимой кондиции.
Производство соединений ртути осуществляется по прямым заказам российских
промышленных предприятий и торговых организаций (см. раздел 3.10).
Утилизация приборов с ртутным наполнением
На участке утилизации приборов с ртутным наполнением осуществляются ручные
процедуры, связанные с вскрытием (под тягой) корпусов приборов (игнитронов,
сфигмоманометров и т. д.) и изъятием из них ртути в специальные емкости (ртуть отправляется
на участок рафинирования). Затем производится упаковка корпусов и прочих деталей приборов
для отправки их на демеркуризацию в фирму .ФИД-Дубна. (г. Дубна, Московская область).
В 2001 и 2002 г.г. большая часть собранных крупногабаритных приборов с ртутным
наполнением (после проверки на герметичность и соответствующей упаковки) была отправлена
на переработку в фирму “ФИД-Дубна”.
Демеркуризация ртутных ламп
В 2001 г. ООО “Мерком” осуществляло сбор и упаковку люминесцентных ламп низкого
давления (типа ЛБ, ЛД и т. п.) и ртутных ламп высокого давления (типа ДРЛ, ДНаТ), которые
затем были отправлены (около 50 тыс. шт.) на утилизацию в г. Дубну (“ФИД-Дубна”).
В 2002 г. была запущена в эксплуатацию собственная вибропневматическая установка
демеркуризации трубчатых люминесцентных ламп “Экотром-2”, основные принципы и
особенности функционирования которой описаны выше. В 2002 г. на установке было
утилизировано 241 тыс. люминесцентных ламп. Кроме того, 17 тыс. ртутных ламп высокого
давления (ДРЛ, ДНаТ) собрано и отправлено на переработку в г. Дубну. В планах ООО
“Мерком” - расширение объемов переработки трубчатых люминесцентных ламп до 1 млн. шт. в
год.
Участок приемки гальванических элементов
Здесь осуществляется упаковка (в полиэтиленовые мешки и затем в металлические
бочки) поступающих от различных предприятий нормальных и ртутно-цинковых
гальванических элементов. По мере накопления они направляются на вторичную переработку в
другие организации (в 2001 г. общий вес собранных гальванических элементов составил около
200 кг).
В 2002 г. было собрано (в организациях и на предприятиях г. Москвы и Московской
области) и утилизировано 1868 нормальных гальванических элементов (со стеклянным
корпусом), из которых извлечено 18 кг металлической ртути.
Прочие ртутьсодержащие отходы
ООО “Мерком” осуществляет сбор, упаковку и перевозку загрязненных ртутью
почвогрунтов, бытового и промышленного мусора, отработанных угольных сорбентов и
катализаторов, ртутьсодержащих шламов химического производства. Как правило, при
небольших объемах указанных отходов производится их безопасная упаковка и накопление на
специальном производственном участке, а затем они транспортируются к местам
непосредственной утилизации (в другие организации). Подготовка и упаковка
многотоннажных отходов для транспортировки производится непосредственно на месте их
образования.
Отходы, образующиеся в ходе технологических процессов и операций
В ходе технологических процессов и операция, связанных с переработкой
ртутьсодержащих изделий, рафинированием ртути и производством ее соединений,
осуществляемых ООО “Мерком”, образуются следующие виды ртутьсодержащих отходов,
требующие обезвреживания.
Сточные воды, большая часть которых (до 80%) образуется на участке очистки и
производства соединений ртути, характеризуются содержаниями ртути до 30-49 мг/л,
отличаются высокой минерализацией (до 300-400 г/л) и высокими концентрациями соединений
натрия, калия, азота, хлоридов, сульфатов. Они подвергаются на месте предварительной
очистке от ртути (используется химическое осаждение путем создания щелочной среды) и
затем накапливаются в специальных емкостях (накопительных баках). Объемы образующихся
сточных вод не очень велики. Так, к 1999 г. было накоплено и отправлено на утилизацию в
ЗАО “Кубаньцветмет” 5 м³ сточных вод; к настоящему времени объем сточных, хранящихся в
накопительных баках, составляет около 4 м³. Насущной проблемой для предприятия является
разработка и внедрение схемы глубокой очистки сточных вод непосредственной на месте, что
позволит существенно увеличить объемы рафинирования некондиционной ртути и
производства ртутных соединений.
Твердые отходы (пастообразной консистенции), в среднем содержащие 0,2-0,3% ртути,
образуются в ходе рафинирования некондиционной ртути и ее соединений от механических
примесей, а также при предварительной очистке сточных вод (шлам сточных вод). Отходы
упаковываются в полипропиленовый мешок (объемом 20-30 л) с полиэтиленовым вкладышем,
затем помещаются в металлическую бочку также с полиэтиленовым вкладышем. По мере
накопления они отправлялись на утилизацию в ОOО .Краснодарский рудник. (ЗАО
“Кубаньцветмет”). Удельное образование твердых отходов составляет примерно 1 кг на 1 т
полученной при рафинировании товарной ртути.
Емкости (тара) из стекла и пластика, в которых поступают на утилизацию
некондиционная металлическая ртуть и другие ртутьсодержащие отходы подвергаются
демеркуризации (демеркуризационные растворы идут в сточные воды). Металлическая тара
упаковывается и отправляется на утилизацию в фирму “ФИД-Дубна”. Обычно ежегодно
накапливается до 3-4 т такой тары.
Образующийся при утилизации ртутных ламп концентрат люминофора упаковывается (с
применением технологии ООО “Экотром”) в полиэтиленовые мешки; по мере накопления его
предполагается отправлять на переработку в ЗАО “Кубаньцветмет”; стеклобой вывозится на
свалку; алюминиевые части ламп сдаются организациям, занимающимся сбором цветного
металлолома.
Очистка выбросов в атмосферу
Участок рафинирования ртути оборудован угольными сорбентами (типа УПР), а участок
демеркуризации ламп, кроме того, фильтрами Петрянова; эффективность используемых систем
очистки выбросов составляет более 99%. Как правило, в воздухе рабочих помещений и на
выходе выбросов в атмосферу содержания паров ртути составляют не более 0,2-0,3 ПДК
рабочей зоны (среднесменной).
Все местные внутренние выбросы (включая отсосы от точечных источников) поступают
в промышленную общеобменную вентиляционную, проходят через три угольных адсорбера и
затем выбрасываются (3 тыс. м³/час) через трубу (высотой 120 м).
Установленный для ООО “Мерком” ПДВ (предельно допустимый выброс) паров ртути
составляет 800 мг в год.
Переработка ртутьсодержащих отходов и производство металлической ртути
В табл. 5.12 приведены сведения о сборе и переработке ртутьсодержащих отходов и
производстве (рафинировании) металлической (вторичной) ртути ООО “Мерком”в 2000-2002 г.г.
Таблица 5.12 Переработка некондиционной ртути и ртутьсодержащих отходов ООО “Мерком”
Год |
Неконди ционная
Hg, кг** |
Товарна я Hg, кг*** |
Некондицион ные соедине- ния Hg, кг |
Игнитроны, сфигмоманометры, термометры и др. |
Отходы (почвогрунты, мусор, сорбенты и т. п.), кг******* |
Общая масса, кг |
Изъятая Hg, кг |
2000 |
10990 |
9343 |
271 |
-**** |
- |
Нет данных |
2001 |
5766 |
5199 |
38 |
3137 |
395 ****** |
7460 |
2002* |
8987 |
8744 |
- |
110,5***** |
17,4 ****** |
2561 |
* В 2002 г. было утилизировано 287 ртутных контактов (извлечено 4,3 кг металлической ртути) и
1712 ртутных термометров (3,4 кг ртути).
** Масса дана вместе с тарой.
*** Металл, полученный при рафинировании некондиционной (черновой) ртути.
**** Приборы отправлялись на утилизацию в “ФИД-Дубна”.
***** Большая часть приборов отправлена в “ФИД-Дубна”.
****** Ртуть затем рафинировалась.
******* Отправлено в ЗАО “Кубаньцветмет”; за первые 7 месяцев 2003 г. ООО “Мерком” собрано,
упаковано и подготовлено к отправке на утилизацию 10 т загрязненных ртутью грунтов и строительных
отходов.
Металлическая ртуть, полученная ООО “Мерком” в 2000-2002 г.г., была поставлена
главным образом на отечественные электроламповые заводы (Смоленск и Саранск), на завод
ртутных термометров (г. Клин), на ОАО “Алтайхимпром” (г. Славгород) и в небольших
количествах - посредническим торговым организациям. Следует отметить, что в 2002 г. ООО
“Мерком” была приобретена партия металлической ртути в 8442 кг (у одного из заводов,
расположенного в г. Рязани, на котором в свое время изготавливали ртутные вентили). После
проведения необходимых технических испытаний, проверки тары и герметичности упаковки
ртуть была также поставлена на рынок (указанным выше предприятиям).
5.2 Оборот ртути с твердыми отходами
Для выявлении всех источников образования ртутьсодержащих отходов производства и
потребления (РСО) необходимо учесть те сферы практической деятельности, где ртуть и ее
соединения используются целенаправленно или присутствуют в значительных количествах в
качестве естественной примеси в перерабатываемом сырье и применяемых материалах и
изделиях. В соответствии с Законом Российской Федерации “Об отходах производства и
потребления” (от 24 июня 1998 г. № 89-ФЗ, статья 1) под РСО следует понимать содержащие
ртуть остатки сырья, материалов, полуфабрикатов, иных изделий или продуктов, которые
образовались в процессе производства или потребления, а также товары (продукцию),
утратившие свои потребительские свойства.
В общем случае образование РСО возможно при:
- добыче и производстве ртути;
- переработке природных материалов, содержащих ртуть;
- использовании ртути при добыче золота;
- использовании ртути и ее соединений при производстве химической продукции;
- производстве и использовании изделий, содержащих ртуть и ее соединения;
- переработке ртутьсодержащих отходов.
5.2.1 Образование твердых ртутьсодержащих отходов в России
В табл. 5.13 и 5,14 и на рис. 5.11 представлены официальные данные по накоплению,
образованию и обезвреживанию РСО в различных отраслях промышленности и основных
регионах России. Из них следует, что основные объемы РСО образуются в трех отраслях
промышленности - в химической, машиностроении и цветная металлургии. В отходах
машиностроения, вероятно, учитываются также ртутьсодержащие отходы потребления
(использованные и вышедшие из строя ртутные термометры, лампы, батарейки и т.д.),
описание которых дается в разделе 3.
Таблица 5.13 Накопление, образование и обезвреживание РСО в 2002 г. в различных отраслям
промышленности России (Госкомстат РФ, МПР РФ)
Наименование отрасли |
Накоплено РСО на конец 2001 г. |
Образовано РСО в 2002 г. |
Обезврежено РСО в 2002 г. |
т |
% |
т |
% |
т |
% |
Промышленность, в том числе: |
2.874 |
83,1 |
7.214 |
85,9 |
1.655 |
65,8 |
химическая |
1.159 |
33,5 |
1.200 |
14,3 |
536 |
21,3 |
машиностроение |
801 |
23,5 |
3.342 |
39,8 |
1.158 |
46,0 |
цветная металлургия |
691 |
20,0 |
2.075 |
24,7 |
1,9 |
0,08 |
целлюлозно-бумажная |
20 |
0,58 |
45 |
0,53 |
- |
- |
мукомольно-крупяная и комбикормовая |
|
|
|
|
|
|
электроэнергетика |
41 |
1,19 |
126 |
1,5 |
16 |
0,64 |
топливная промышленность |
30 |
0,87 |
85 |
1,0 |
- |
|
Промышленность строительных материалов |
108 |
3,1 |
145 |
1,7 |
- |
|
Жилищно-коммунальное хозяйство |
332 |
9,6 |
62 |
0,07 |
185 |
7,4 |
Всего по России |
3.458 |
100 |
8.396 |
100 |
2.517 |
100 |
Таблица 5.14 Распределение РСО по Федеральным округам РФ (по данным Госкомстата РФ и МПР
РФ)
Округ |
Накоплено РСО на конец 2001 г. |
Образовано РСО в 2002 г. |
Обезврежено РСО в 2002 г. |
т |
% |
т |
% |
т |
% |
Центральный |
376,9 |
10 |
2.184 |
26 |
950 |
38 |
Северо-западный |
88,4 |
2,6 |
145,2 |
1,7 |
44 |
1,8 |
Южный |
1.029,9 |
30 |
559 |
7 |
210 |
8 |
Приволжский |
287,1 |
8 |
936 |
11 |
747,4 |
30 |
Уральский |
213,3 |
6 |
2.422 |
29 |
54,8 |
2,1 |
Сибирский |
1.407,9 |
41 |
2.129,8 |
25 |
510,1 |
20 |
Дальневосточный |
54,6 |
1,6 |
19,4 |
0,2 |
0,135 |
0,0 |
Всего по России |
3.458 |
100 |
8.396 |
100 |
2.517 |
100 |
Самыми большими объемами образования РСО отличаются Сибирский, Уральский,
Приволжский и Центральный федеральные округа России. Это связано, в первую очередь, с
размещением здесь крупных промышленных предприятий, генерирующих указанные виды
отходов. Наибольшим объемом переработки РСО характеризуется Центральный федеральный
округ, хотя по количеству образованию их он находится на втором месте в стране. Наиболее
серьезная ситуация сложилась в Уральском федеральном округе: при доле ежегодного
образования РСО свыше 30%, объемы переработки их находятся на уровне 2%.
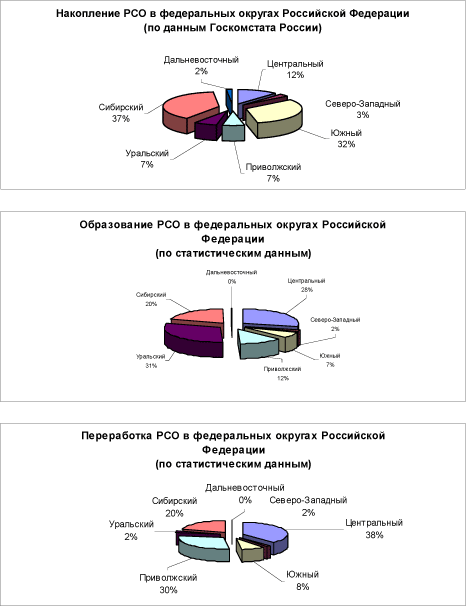
Рисунок 5.11 Образование, накопление и переработка РСО по регионам РФ в 2002 г.
Необходимо отметить, что в официальных источниках информации не указываются
концентрации ртути в накопленных и ежегодно образующихся РСО; отсутствует также
типизация отходов по уровням содержания в них ртути. Как было отмечено выше, из всей
массы накопленные к настоящему времени на территории России РСО примерно 58%
характеризуются уровнями содержания ртути в 10-100 мг/кг, около 12% - характеризуются ее
концентрациями в 100-5000 мг/кг, около 30% - содержат металл в количестве более 5000 мг/кг.
По другим сведениям [96], уровни содержания ртути в складированных и ежегодно
образующихся в России РСО варьируются от 0,02 до 75%. В России нормативно не установлен
нижний предел концентрации ртути в отходах, определяющий их отнесение к категории
ртутьсодержащих. Известно, что в практической деятельности в качестве такого минимального
уровня часто используется ПДК ртути в почве (2,1 мг/кг), что, очевидно, не всегда оправданно.
5.2.2 Ртуть в промышленных отходах и отходах энергетики
Оборот ртути с промышленными отходами и отходами энергетики рассматривается выше
в соответствующих разделах глав 3 и 4. Информация по указанным видам отходов,
размещенным на полигонах/свалках, систематизирована в табл. 5.15.
При целенаправленном использовании ртути в промышленности наибольшее количество
ее накапливается в отходах хлорно-щелочного производства, которые, как правило,
складируются вблизи заводов. Общая масса ртути в них ориентировочно оценивается в 39 т.
Количество ртути, содержащейся в отходах Новосибирского завода химконцентратов
(производство изотопов лития), накопленных к настоящему времени на территории
предприятия, оценивается в 100-500 т.
Таблица 5.15 Ртуть в промышленных отходах и отходах энергетики, поступивших на
полигоны/свалки, 2001/2002 г.г.
Отрасль |
Масса ртути т/г Наилучшая оценка |
Глава |
Хлорно-щелочное производство |
39,3 |
3,1 |
Производство потребительских товаров: ламп, батареек и пр. |
0,3 |
3,5-3,9 |
Добыча золота с применением метода амальгамации |
0,55 |
3,3 |
Добыча и использование угля |
5,6 |
4,1 |
Нефть, газ и биотоплива |
? |
4,2 |
Производства меди и никеля |
6,6 |
4,3 |
Производство свинца и цинка |
8,5 |
4,3 |
Производство других цветных металлов |
4,2 |
3,3; 4,3 |
Производство цемента |
0,4 |
4,3 |
Всего |
65 |
|
В общей сложности в грунтах и отвалах на промплощадках предприятий, использующих ртуть,
накоплено более 3000 т этого металла. В Таблице 5.16 перечислены выявленные производственные
сооружения. Данный перечень достаточно представительный, принимая во внимание использование
ртути при производстве хлора (включая производство хлора на бумажных фабриках), но при этом , есть
основания полагать, что значительное количество ртути также накоплено на территориях предприятий,
производящих термометры, переключатели и другие электронные приборы.
За весь период добычи золота в России, около 6000 т ртути было использовано для амальгамационного
обогащения золота. Существенная часть использованной ртути содержится в техногенных россыпях
(отвалах, хвостах обогащения, отработанных дражных и гидромониторных полигонах и др.), при
повторной отработке которых эмиссия ртути в окружающую среду может быть очень значительной.
Отвалы предприятий цветной металлургии могут содержать существенные концентрации ртути, но
данных по общему содержанию ртути в отходах этих предприятий получено не было.
Таблица 5.15 Производства, на которых происходит накопление ртуть содержащих отходов
Предприятие |
Производство |
Период работы |
Примерное количество рутути (тонн) в отвалах и шлаконакоми телях |
Комментарии |
ОАО «Усольехимпром» Усолье-Сибирское |
Хлор-щелочное |
1970-1998 |
800 |
|
ОАО «Каустик», «Кребс», город Стерлитамак |
Хлор-щелочное |
1964-1987 |
50 |
|
ОАО «Капролактам», Дзержинск, Нижегородская область |
Хлор-щелочное |
1948-1982 |
60 |
|
ОАО “Кировочепецкий химический комбинат”, Кировочепецк, Кировская область |
Хлор-щелочное |
1955 -по сегодняшний день |
300-700 |
|
ОАО “Каустик”, Волгоград |
Хлор-щелочное |
1968 -по сегодняшний день |
<500 ? |
В почве под зданием В отвалах |
ЗАО «Каустик», Стерлитамак |
Хлор-щелочное |
1997 -по сегодняшний день |
200-300 ? |
В почве под зданием В отвалах |
ОАО «Саянскхимпласт», Саяны, Иркутская область |
Хлор-щелочное |
1979 -по сегодняшний день -today |
500 |
|
Котласский ЦБК, Коряжма, Архангельская область |
Хлор для производства бумаги |
1964-1998 |
130 |
|
Архангельский ЦБК, Новодвинск, Архангельской области |
Хлор для производства бумаги |
1962-1996 |
120 |
|
Амурский ЦБК, КОмсомольск-на-Амуре |
Хлор для производства бумаги |
1970-1997 |
56 |
|
Светлогорский ЦБК, Ленинградская область |
Хлор для производства бумаги |
1951-1993 |
11 |
|
Производство лития, Новосибирск |
Изотопы лития |
- |
100-500 |
35 т/год к серед. 90-х |
ИТОГО |
|
|
Более 3.000 |
|
5.2.3 Ртуть в твердых бытовых отходах
Основными источниками поступления ртути в твердые бытовые отходы (ТБО) являются
ртутные лампы, термометры, другие ртутьсодержащие приборы, используемые в быту, а также
элементы питания.
В 1997 г. в г. Санкт-Петербурге было установлено, что количество ртути в приборах,
находящихся у населения, составляет более 3 т [243]. Экстраполяция этих данных на всю
Российскую Федерацию позволяет говорить о 93 т ртути, находящейся в приборах, имеющихся
на руках у населения. Если допустить, что в каждой российской семье имеется два ртутных
термометра, то на руках у населения находится примерно 70 млн. шт. таких изделий,
содержащих в общей сложности 140 т ртути, что выше данных, полученных экстраполяцией
показателей по Санкт-Петербургу. Для дальнейшей оценки количества ртути, попадающие в
ТБО, были приняты допущения, что 1/6 всех находящихся на руках ртутьсодержащих приборов
ежегодно теряет свои потребительские свойства. В этом случае в ТБО ежегодно будет
поступать 15,5 т (по первому варианту) или 23,3 т (по второму варианту) ртути. В разделе 3.5
показано, что в России в вышедших в 2001 г. из строя термометрах содержится порядка 18 т
ртути, , основная доля которой поступила в составе твердых отходов на полигоны/свалки. В
целом, по расчетным данным, в составе использованных ртутьсодержащих приборов, в
конечном счете поступающих в отходы, может содержаться 16-23 т ртути. Кроме того, около
1,6 т ртути поступает в ТБО в составе ртутных люминесцентных ламп (см. раздел 3.8), 1,6 т в
составе батареек (см. раздел 3.7) и 0,4 т в составе переключателей (см. раздел 3.9).
Правильность оценки содержания ртути в батарейках сильно зависит от фактического срока их
службы, так как использование ртути постепенно снижается в течение последних лет. В 1980-х
г.г. ежегодно использовалось 100-130 т ртути для производства гальванических элементов и
батарей. Фактический срок использования/хранения батареек может быть значительно больше
срока их технической пригодности, поскольку они могут не сразу выбрасываться и попадать на
полигоны/свалки. По этой причине поступление ртути, связанной с указанными изделиями, в
ТБО может быть недооценено.
Поступление ртути, содержащейся в качестве примеси (рассеянного элемента) в
различных материалах, оказывающихся после их использования в ТБО, потенциально может
быть существенным, но трудно поддается оценке, главным образом, из-за отсутствия данных
по исходному уровню содержания ртути в отходах.
Среднее содержание ртути в ТБО, включающих использованные ртутьсодержащие
приборы и материалы, было определено на основе оценки источников (табл. 5.16) и анализа
общего объема ТБО, образующихся в Российской Федерации. Согласно оценкам, содержание
ртути в ТБО (за исключением случаев ее присутствия в различных материалах в качестве
примеси) может достигать 0,7-0,9 мг/кг, что ниже ПДК ртути в почвах, равной 2,1 мг/кг.
Таблица 5.16 Источники поступления ртути в ТБО
Источники попадания ртути в ТБО |
Примерное количество Hg, т/год |
Примечание |
Ртутьсодержащие приборы (в основном термометры) |
16-23 |
раздел 3.5 |
Батарейки |
1,6* |
раздел 3.6 |
Лампы |
2 |
раздел 3.8 |
Зубные амальгамные пробы |
6* |
раздел 3.4 |
Переключатели |
0,4 |
раздел 3.9 |
В качестве cледового микроэлемента во всех отходах |
? |
|
Всего |
26-33 |
|
* Точное количество ртути, поступающее в ТБО, не известно.
В Российской Федерации практически все ежегодно образующиеся ТБО размещаются на
свалках или полигонах. Мусоросжигательные заводы эксплуатируются в Москве, Пятигорске,
Сочи, Владивостоке, Мурманске (рис. 5.12, табл. 5.17). Доля ТБО, сжигаемых на этих
предприятиях, может быть оценена на уровне 2-3 % от их общего годового количества. На
основе вышеприведенных оценок, можно сделать вывод, что в сжигаемых отходах содержится
примерно 0,5 т ртути. Установлено, что выбросы ртути в атмосферу с установки по сжиганию
ТБО во Владивостоке в 1999 г. составили 0,5 т (согласно официальной статистической
отчетной форме “2 тп-Воздух”). Экстраполяция этих данных на другие предприятия, с учетом
их проектной мощности, позволяет приблизительно оценить выброс ртути с
мусоросжигательных установок в 3,5 т/год (для Пятигорска, Сочи, Владивостока и Мурманска).
Необходимо отметить, что результаты оценки бубуд выше, если учесть ожидаемый уровень
содержания ртути в сжигаемых отходах.
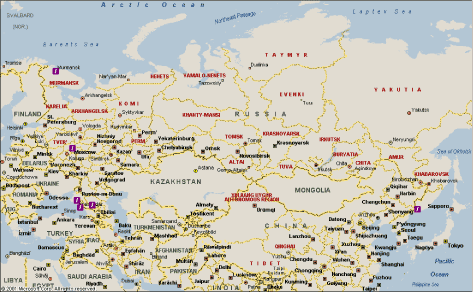
Рисунок 5.12 Расположение мусоросжигательных заводов в России (указаны как I).
Таблица 5.17 Мусоросжигательные заводы в Российской Федерации
Город |
Производительность, т/год |
Технология снижения загрязнений |
Москва (два завода) |
40000 |
Активный уголь |
Пятигорск |
150000 |
Данные отсутствуют |
Сочи |
Не работает |
Данные отсутствуют |
Владивосток |
Данные отсутствуют |
Данные отсутствуют |
Мурманск |
Данные отсутствуют |
Данные отсутствуют |
Всего |
Данные отсутствуют |
Данные отсутствуют |
На двух функционирующих в г. Москве мусоросжигательных заводах, общей мощностью
40.000 т отходов в год, в системах очистки отходящих газов используется активный уголь.
Аналитический контроль свидетельствует об отсутствии выбросов ртути в окружающую среду.
Выбросы завода соответствуют требованиями Directive-2000.
Мусоросжигательный завод в г. Сочи был закрыт, поскольку являлся существенным
источником загрязнения окружающей среды.
Производительность мусоросжигательного завода в г. Пятигорске составляет 150.000
т/год. Эмиссия ртути, определяемая аналитическим методом, достигает 0,000013 г/сек (старые
данные), расчетным путем – 0,000052 г/сек; концентрация ртути в золе – 4 мг/кг, в шлаке – 0,8
мг/кг, в водной вытяжке из золы - 0,003×10-3 % (масс.).
Разница между источниками и выбросами может в какой-то мере объясняться различием
в структуре бытового потребления между городским и сельским населением. В больших
городах, где расположены мусоросжигательные заводы, концентрации ртути в ТБО, по
сравнению со средними показателями, возможно, будут выше. Содержание ртути в сточных
водах также возможно выше в крупных городах (см. далее). Эта разница также может говорить
о том, что концентрация ртути в отходах может быть значительно выше, по сравнению с
вышеприведенными оценками. Причиной этого может быть тот факт, что большую долю ртути
в отходах составляет ртуть, содержащаяся в качестве примеси, а также и более длительное
использование батареек, переключателей и т.д. Потребление ртути для производства этих
изделий десять лет назад было значительно выше.
Согласно официальным данным, поступление ртути в окружающую среду от жилищно-
коммунального хозяйства составляет 3 кг/год (см. Приложение 1), но эта цифра, вероятно, не
учитывает сжигание ТБО.
5.2.4 Ртуть в отходах медицинских учреждений
К медицинским ртутьсодержащим отходам относятся ртутные лампы медицинского и
технического назначения (могут содержать до 500 мг ртути) и медицинские термометры.
В свое время в медицине использовали растворы хлорида ртути (II), или сулемы (HgCI2)
концентрацией от 1:1000 до 1:5000 (для дезинфекции медицинского инвентаря, лабораторной
посуды, поверхностного обеззараживания кожи). Сейчас применение сулемы для дезинфекции
строго ограничено.
Оценка количества медицинских отходов, находящихся в лечебных, детских дошкольных
учреждениях, выполнена по данным учета отходов в Пермской области в 2002 г. Здесь
масштабы накопления РСО достигают 175 т (без учета люминесцентных ламп), количество
ртути в которых составляет 29,9 кг, в том числе – 21,7 кг в термометрах, 7,9 кг – в приборах, 1,2
кг - в бактерицидных лампах, - 0,2 кг – в составе различных соединений ртути. Экстраполяция
этих данных на всю территорию Российской Федерации позволяет говорить о том, что в
непроизводственной сфере, не участвующей в отчетных кампаниях, накоплено 5750 т
приборов, содержащих 1,5 т ртути. Учитывая существенные объемы ртути, использованной для
производства других термометров и приборов, данный показатель довольно низок.
В Российской Федерации нет широкой практики сжигания опасных и медицинских
отходов. Приблизительный состав медицинских отходов, который могут сжигаться, выглядит
следующим образом [86]: 74,5% - перевязочные материалы, 9,3% - полимеры, 7,9% - пищевые
отходы, резина и металлы - по 3,1%, 1,09% - патологоанатомические отходы. Вероятность
содержания ртути в этих отходах очень невелика; они, как правило, поступают на захоронение
или сжигаются в котельных и крематориях.
РСО классифицируются как медицинские отходы класса D. Данная группа отходов также
включает просроченные лекарства и дезинфектанты, отходы диагностических препаратов и т.
д. Инвентаризация, проведенная в 2000 г. в Новокузнецке, показала, что доля отходов класса D
достигает 6,3% от общего количества медицинских отходов (4249.052 т) [316]. По данным
инвентаризации в Екатеринбурге, этот показатель составляет 6,6%.
Общее количество медицинских отходов определялась путем экстраполяции данных
инвентаризации медицинских отходов в Калужской области (999,457 т) и г. Новокузнецке на
всю территорию Российской Федерации (с учетом удельного количества отходов на душу
населения). Рассчитанный таким образом объем медицинских отходов составил 461000 т.
5.3 Ртуть в сточных водах
Сведения по содержанию ртути в организованных сбросах сточных водах и ее
последующему попаданию в водные объекты содержаться в форме “2 тп-Водхоз”. Ниже
представлены данные государственной статистической отчетности по сбросу загрязняющих
веществ в водные объекты в 2001 г. (табл. 5.18, 5,19, см. также Приложение 1).
Химическая промышленность является основным источником сброса ртути со сточными
водами, который, по официальным данным, составляет 146 кг. Согласно оценке, приведенной в
разделе 3.2, около 20 кг ртути сбрасывается со стоками предприятий по производству ВХМ.
Вполне вероятно, что оставшаяся часть металла поступает со стоками хлорно-щелочных
производств. Однако. согласно оценке в разделе 3.1, со сточными водами таких производств
должно поступать только лишь около 1 кг ртути. Таким образом, официальная статистика
указывает на то, что этот показатель завышен.
Таблица 5.18 Сброс ртути в поверхностные водные источники по регионам России в 2001 г.
Наименование территории |
Объем загрязненных стоков, млн. м³ |
Сброс ртути, кг |
Примечание |
Российская Федерация (в целом) |
22370 |
177 |
|
г. Санкт-Петербург |
1244 |
19 |
|
Ленинградская обл. |
413 |
2 |
|
г. Москва |
2185 |
2 |
|
Кировская обл. |
183 |
2 |
Химическая промышленность |
Республика Башкортостан |
449 |
16 |
Химическая промышленность |
Новосибирская обл. |
385 |
1 |
|
Красноярский край |
644 |
1 |
|
Иркутская обл. |
911 |
129 |
Химическая промышленность |
Республика Саха (Якутия) |
93 |
4 |
|
Амурская обл. |
109 |
1 |
|
Таблица 5.19 Сброс ртути в поверхностные водные источники по отраслям промышленности в
2001г.
Наименование отрасли |
Объем загрязненных стоков, млн. м³ |
Сброс ртути, кг |
Российская Федерация (в целом) |
22370 |
177 |
Промышленность: |
7273 |
156 |
Цветная металлургия |
593 |
6 |
Химическая |
855 |
146 |
Целлюлозно-бумажная |
1421 |
1 |
Мукомольно-крупяная и комбикормовая |
23 |
2 |
Жилищно-коммунальное хозяйство |
13474 |
20 |
Согласно статистическим данным, со стоками ЖКХ в водные объекты поступает 20 кг
ртути. Не совсем ясно - какие области деятельности подразумеваются под .ЖКХ.. Судя по
всему, речь идет о сбросе сточных вод с очистных сооружений, эксплуатируемых жилищно-
коммунальными хозяйствами российских городов и поселков.
Поступление ртути с городскими сточными водами может быть оценено на основе ее
концентраций в осадках сточных вод (ОСВ), образующихся на очистных сооружениях.
Данные о содержании ртути в ОСВ некоторых городов России, полученные из различных
источников, приведены в табл. 5.20. Как видим, концентрация ртути в ОСВ сильно
колеблется. Наиболее высокие содержания металла были установлены в ОСВ в тех городах,
где ртуть в значительных количествах используется на промышленных предприятиях
(например, в Клину и Саранске). Однако высокие концентрации ртути в ОСВ могут быть
обнаружены и в других городах.
В крупных городах, например в Санкт-Петербурге и Москве, установленные уровни
ртути в ОСВ колеблются в пределах 1-2 мг/кг сухого веса, в то же время в малых городах ее
концентрации, вероятно, ниже. Установленная норма содержания ртути в ОСВ,
предполагаемых для использования в сельском хозяйстве в качестве агломелиорантов,
составляет 15 мг/кг сухого веса [251].
Объем данных слишком ограничен, чтобы достаточно точно оценить общее количества
ртути, ежегодно аккумулирующейся в ОСВ в целом по всей России, тем не менее, эти данные
можно использовать для первой приближенной оценки.
Таблица 5.20 Ртуть в осадках городских сточных вод
Город |
Ртуть, мг/кг сухого веса |
Московская область [15] |
Клин (поступают стоки завода ртутных термометров) |
220 |
Коломна |
10 |
Апрелевка |
3,6 |
Загорск |
2,8 |
Орехово-Зуево |
2,4 |
Бронницы |
0,8 |
Серпухов |
0,4 |
Зарайск |
0,4 |
Воскресенск |
0,3 |
Домодедово |
0,2 |
Павловский посад |
0,2 |
Подольск |
0,2 |
Шатура |
0,2 |
Электросталь |
0,1 |
Белозерский |
0,1 |
Истра |
0,1 |
Наро-Фоминск |
0,1 |
Раменское |
0,03 |
Город Москва [15] |
Люберецкая станция аэрации |
1,8 |
Курьяновская станция аэрации |
1,3 |
Республика Мордовия [324] |
Саранск, городские очистные сооружения (поступают стоки завода ртутных ламп) |
4 (3-5) |
Пермская область [9] |
Губаха (промышленные предприятия) |
14,1 |
Кунгур |
0,6 |
Санкт-Петербург [185] |
Очистные сооружения города |
1,6 |
В большинстве российских городов имеются общегородские очистные сооружения, на
которых осуществляется совместная очистка бытовых и промышленных сточных вод. Обычно
применяется 2-хступенчатая система очистки - механическая и биологическая. В ходе очистки
образуются значительные массы ОСВ, представляющих собой илисто-коллоидную смесь
минеральных и органических веществ, обладающую специфическим химическим составом и
средней влажностью 96,2% [291].
Для обезвоживания и обезараживания ОСВ обычно практикуется их размещение на
иловых площадках (иловых картах) или (реже) на полях фильтрации, расположенных, как
правило, вблизи комплекса городских очистных сооружений. В большинстве случаев ОСВ
поступают (наливаются) на иловые площадки периодически, отдельными слоями (мощностью
до 20-25 см). По мере высыхания они частично теряет влагу, в основном за счет испарения;
часть воды фильтруется через грунт. В ходе указанных явлений и процессов определенное
количество ртути может эмитировать в окружающую среду, однако какие-либо данные
отсутствуют.
При технических расчетах количество образующихся ОСВ (при средней влажности
96,2%) обычно принимается равным 0,5-1% от объема очищаемых сточных вод [291];
плотность ОСВ в среднем составляет 949 кг/м3 [293], что соответствует 0,18-0,36 кг сухого веса
на м3 жидкого стока. Производительность канализационных очистных сооружений в
Российской Федерации составляет 57,2 млн. м3/сутки ([86], или около 20 878 млн. м3 сточных
вод в год. Если биологической очистке подвергаются все сточные воды, то в таком случае
объем образующихся ОСВ (на сухое вещество) будет составлять 3,8-7,5 млн. т. Используя эти
данные, можно оценить общее содержание ртути в муниципальном жидком стоке (иле) на
уровне около 3,4-11,9 т/год (табл. 5.21).
Таблица 5.21 Ртуть в осадках городских сточных вод
Тип городов * |
Доля населения России, % |
Количество ОСВ, млн. т сухого веса |
Среднее содержание ртути, мг/ кг сухого веса |
Ртуть в ОСВ, т |
Малые и средние |
30 |
1,1-2,3 |
0,2-0,6 |
0,2-1,4 |
Крупные |
70 |
2,64-5,27 |
1,2-2,0 |
3,2-10,5 |
Всего (округлено) |
100 |
3,8-7,5 |
0,2-2,0 |
3,4-11,9 |
* Малые и средние города - соответственно с населением до 100000 и населением свыше 100000 чел.
По оценкам, КПД очистки сточных вод от ртути составляет около 50%. Например,
указанный показатель на канализационных очистных сооружениях Дании составляет около
65% [408]. Если принять исходить из значения КПД в 50%, то можно рассчитать, что в России
3,4-11,9 т ртути сбрасывается в водные объекты с городских очистных сооружения; это более
чем в 20 раз превышает общий официально учитываемый ее сброс со сточными водами
промышленных предприятий. Следует напомнить, что на общегородские очистные сооружения
поступают не только бытовые, но и промышленные сточные воды, которые и могут являться
существенным источником поступления ртути. Очевидно, что в официальной статистике по
сбросу ртути в водные объекты промышленными предприятиями учитывается только те
промышленные сточные воды, которые сбрасываются непосредственно в водотоки и водоемы с
заводских очистных сооружений (минуя общегородские канализационные сооружения).
Таким образом, в целом в городах России в муниципальные сточные воды до процесса
очистки попадает 7-24 т ртути в год. В ряде городов промышленные предприятия,
целенаправленно использующие ртуть в своих технологических процессах (Клин, Саранск и
др.), могут представлять собой значительный источник ее поступления в сточные воды,
которые очищаются на общегородских очистных сооружениях совместно с бытовым стоком.
Тем не менее в масштабе страны на долю таких предприятий приходится небольшая часть
ртути, поступающей со сточными водами в водотоки и водоемы. Определенным источником
поступления ртути в водотоки и водоемы может быть поверхностный (дождевой и талый) сток
с городских территорий, который в подавляющем большинстве городов России отводится без
необходимой очистке. Детальный анализ источников поступления ртути в сточные воды в
Дании показал, что на дождевые воды может приходиться около 10% всего количества ртути
(среднее содержание ртути в жидком осадке составляло 1,2 мг/кг [408]).
Серьезным источником ртути может быть также зубная амальгама, которая в
стоматологических клинках сбрасывается в муниципальные канализационные системы (как
показано в разделе 3.4, до 6 т). Кроме того, значительными источником может быть ртуть из
разбитых термометров и измерительного оборудования. Даже если небольшая часть от 18 т
ртути, которая присутствует в ежегодно выходящих из строя термометрах, попадает в сточные
воды, то это составит значительное количество.
Инфильтрация воды с территории свалок ТБО, в которых присутствуют использованные
ртутьсодержащие изделия, также может рассматриваться как источник поступления ртути в
водные объекты. Согласно данным [186], содержание ртути в свалочном фильтрате может
составлять в среднем 2 мкг/л при вариации от 0,055 до 1,46 мкг/л.
Можно привести практический пример с использованием данных контроля за
грунтовыми водами в Санкт-Петербурге [200]. Только в одном месте анализ показал
содержание ртути в пробе около 0,0007 мг/л.
Утилизация осадков городских сточных вод
Из всей ежегодно образующейся в пределах России массы ОСВ лишь около 10-15%
обрабатывается в соответствии с современными требованиями, т. е. уплотняется,
стабилизируется, обезвоживается и используется в качестве удобрения, либо вывозится на
специальные полигоны [1]. По другим сведениям, уровень практического использования ОСВ в
настоящее время составляет 1-1,5% [148]. В любом случае подавляющая часть ОСВ
размещается (на довольно длительный срок) на иловых площадках (полях фильтрации) и затем,
как правило, вывозится на свалки отходов (или просто в карьеры). В России содержание ртути
в ОСВ, предполагаемых использоваться как удобрение, не должно превышать 15 мг/кг сухой
массы [251]. При этом на почвах среднего и тяжелого гранулометрического состава во
избежание накопления металла не допускается внесение более 10 т/га сухой массы ОСВ в
чистом виде или в составе компостов (при периодичности внесения не менее 5 лет). На легких
песчаных и супесчаных почвах норма внесения ограничивается 7 т/га с периодичностью
внесения не менее 3 лет. Использование ОСВ на торфяных почвах по агрономическим
соображениям не рекомендуется. Запрещается применение ОСВ и компостов из них на почвах
с рН ниже 5,5 без предварительного известкования последних, если содержания кальция в
осадке или компосте не обеспечивает поддержание рН на уровне 5,5 и более. Необходимо
отметить, что уровни ртути в ОСВ, как правило, заметно превышают концентрации ее в
стандартных минеральных удобрениях, в которых среднее содержание этого металла
оценивается в 0,05 мг/кг [125].
Fodnoter
[8] Большая часть информации и первичные статистические данные, положенные в основу ниже приводимых материалов о деятельности ЗАО “Кубаньцветмет” и ООО “Мерком” в сфере переработки ртутьсодержащих отходов и производства ртути и ее соединений, были получены непосредственно на указанных предприятиях.
| Главная страница | | Содержание | | Предыдущая страница | | Следующая страница | | Верх |
Версия 1.0 март 2005, © Датское агентство по охране окружающей среды
|