| Front page | | Contents | | Previous | | Next |
Siloxanes - Consumption, Toxicity and Alternatives
1 Introduction
1.1 What are siloxanes and silicones?
Siloxanes are compounds in which silicon atoms (Si) are linked via oxygen atoms (O), each silicon atom bearing one or several organic groups. According to the main rules for classification of chemicals
(IUPAC) the compounds are designated siloxanes, but most often the term "silicones" are used. When talking about products and materials, "silicones" are nearly always used, and this term will be used here
as well. The term "siloxanes" will be used when we talk about single compounds, or when we have a more chemical approach to the subject. In other words: Siloxanes are building blocks for silicone
products.
The chemical names of the compounds most often include the string "siloxane", but in particular in cosmetics and toiletries names including methicone are used instead, e.g. dimethicone derived from dimethyl
silicone; synonymous with dimethylsiloxane. Another used synonym is poly(oxy(methylsilylene)). To add to the confusion about the terms, several of the compounds recorded in the Danish Product Register,
listed in Annex 3, are designated "silicones and siloxanes".
The alternating silicon and oxygen atoms form a backbone structure to which different side chains are linked. The side chains may form cross links which influence the properties of the polymer.
The silicon and oxygen atoms may be linked into cyclic or linear structures, and we distinguish between linear siloxanes and cyclic siloxanes.
Linear siloxanes
Linear polysiloxanes are characterised by the functional side chains attached to the Si-O backbone and the endgroups terminating the structure (illustrated by R5). The side groups may be the same group
or several different side groups may be attached (illustrated by R1-R4). |
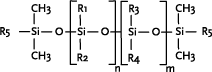 |
Linear polydimethyl siloxanes are the most important industrial polysiloxanes. In their most simple form they consist of methyl side-chains and methyl terminal groups, polydimethylsiloxane (PDMS).
The shorter linear polysiloxanes are, like some of the cyclic siloxanes mentioned below, volatile. The shortest, hexamethyldisiloxane, is volatile with a boiling point of 100°C, and is used in cosmetics among other applications. |
Polydimethylsiloxane
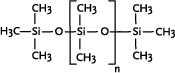
Hexamethyl disiloxane
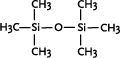 |
The endgroups determine the use of the polymer. Typical endgroups are methyl, hydroxyl, vinyl or hydrogen. For example are polydimethylsiloxanes typically silicone fluids, whereas vinyl- and
hydroxy-terminated polysiloxanes find major application in silicone elastomers. |
Vinyl-terminated dimethylsiloxane
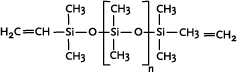 |
Major functional side groups are vinyl, aminopropyl, polyether, phenyl, trifluoropropyl, phenylethyl tetrachlorophenyl, and alkylene oxide. Hundreds of different compounds exist. In the Danish Product
Register about 175 different compounds (CAS no.) are registered as used in products in Denmark. |
The side groups determine together with the end-groups the properties of the siloxanes. Phenyl side groups provide e.g. oxidative stability.
Aminopropyl and polyether side groups provide water solubility, whereas the presence of alkyl groups enhances water repellancy and lubricity. |
Polyphenyldimethylsiloxane
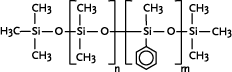 |
The presence of halogens in the side chains produces very stable polymers. Very high resistance to solvents can be obtained by using trifluoropropyl side chains, whereas lubricity at high temperatures is obtained by tetrachlorophenyl side groups. |
Polytrifluoropropylmethylsiloxane
 |
Cyclic siloxanes
Cyclic siloxanes are partly used as intermediates for the production of higher molecular weight linear siloxanes, partly used directly as fluids. In the cyclic siloxanes the Si-O backbone forms a cyclic structure with two substituents attached to each silicium atom.
The main compounds, octamethylcyclotetrasiloxane and decamethyl cyclopentasiloxane are used for a large number of applications. The two compounds are volatile, with boiling points of 176°C and 210°C respectively. |
Octamethylcyclotetrasiloxane
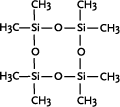 |
The cyclosiloxanes are often designated with reference to the number of silicium atoms: D3 (cyclotrisiloxane), D4 (cyclotetrasiloxane), D5 (cyclopentasiloxane) and D6 (cyclohexasiloxane).
Cyclic siloxanes with other functional groups, e.g. methylphenylcyclosiloxanes, are used for fewer applications. Among other applications, cyclic methylsiloxanes are widely used in cosmetic products, in
which cyclic siloxanes or mixtures of the compounds are known under the name "cyclomethicone". According to the 2000 version of the INCI list (Annex 1) cyclomethicone is synonymous with
octamethyltetrasiloxane. Producers, however, use the term more widely, e.g. the UK producer Basildon Chemicals has four types of cyclomethicone, either as pure D4 or D5 or as different mixtures of D4,
D5 and D6 (http://www.baschem.co.uk/downloads/cy56.pdf).
Silanes
Silanes are used as precursors in the production of siloxanes and are used as cross-linking agents for formation of silicone elastomers and resins (described later in this section).
Silanes are silicon compounds, both organic and inorganic. The siloxanes are actually one of five subgroups of silanes, but often the term "silanes" is used for designating the other groups. The other groups
are those containing Si–H bonds (hydride functional silanes), Si–X (halosilanes), Si–C (organosilanes), and Si–OR (silicon esters).
Both linear and cyclic polysiloxanes are generally produced by reacting organodichlorosilanes with water (Ullmann 2003). Besides their use in production processes, organodichlorosilanes may also be present in products for polymerisation of silicones by the users. |
Dichlorodimethylsilane
 |
Silsesquioxanes
The silsesquioxanes are a subgroup of the siloxanes. The term silsesquioxanes denotes a polymer in which the ratio of silicon and oxygen in each moiety (sequence) is 1.5 (latin: sesqui). Many commercial
silicones include silsesquioxanes.
The polysilsesquioxanes are highly branched polymers and difficult to describe. In their most simple form they can be described by a ladder structure, more complex structures are designated "cage
structures" and "random structures".
They are mainly used for silicon resins, in particular for paints and coatings. |
Polymethyl silsesquioxane
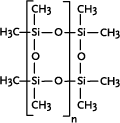 |
Fluids, elastomers and resins
Silicones can be classified into three types depending on the length of the backbone, the extent of crosslinking and the type and number of organic groups attached to the silicon atoms:
- Fluids;
- Elastomers;
- Resins.
Silicone fluids
Silicones generally increase in viscosity with increasing chain length. In silicone fluids, the number of dimethylsiloxane moieties (indicated by the "n" in the chemical formulae) is up to 4000 (Ullmann 2003).
Silicone fluids are distinguished from common organic fluids by a number of unique properties (Ullmann 2003):
- Good thermal stability (150-200°C);
- Good low-temperature performance (<-70°C);
- Strong hydrophobicity;
- Excellent release properties;
- Antifriction and lubricating properties;
- Pronounced surface activity;
- Good dielectric properties;
- Very good damping behaviour;
- Good radiation resistance;
- High solubility of gases;
- Physiological inertness;
- Low temperature dependence of physical properties.
Because of these properties silicone fluids are widely applied as release agents for moulding operations, medical and cosmetic applications, polishes, coolants and dielectric fluids for electrical systems, metal
processing fluids and agents for foam control.
The silicone fluid may be formulated into emulsions, dispersions, greases and compounds.
Silicone elastomers
Silicone elastomers, or silicone rubbers, are formed from fluid siloxanes by the formation of cross links between the linear polymers by use of cross-linking agents. The process is designated "curing" or
"vulcanization".
In general is distinguished between four main systems:
- One component RTV (room temperature vulcanizing) elastomers;
- Two component RTV elastomers;
- HTV (high temperature vulcanizing) elastomers;
- LSR (liquid silicone rubber) elastomers.
Different cross-linking agents are used depending on temperature and other conditions for the curing process. The marketed products, e.g. silicone sealants, thus both contain the siloxanes and cross-linking
agents.
The principle is here illustrated by the release of compounds when one-component room-temperature-vulcanising (RTV) silicone sealants are applied. The products are widely applied by both private and
professional users.
Curing of one-component RTV silicones starts when the compounds are exposed to atmospheric moisture during application. The cross-linking agents are tri- or tetrafunctional silanes containing hydrolyseable Si-O or Si-N bonds.
Depending on the used cross-linking agent different compounds are formed as cleavage product and will be released during the curing process (see Table 1.1) |
Ethyltriacetoxysilane
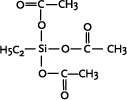 |
Well known is the smell of acetic acid, when silicone sealants with ethyltriacetoxysilane as cross-linking agent are applied. The acetic acid is formed by the curing process.
Table 1.1 Crosslinking agents and cleavage products for curing of silicone elastomers ( based on Ullmann 2003)
Cross-linking agent |
Cleavage product |
Alkoxysilanes |
Alcohols |
Methyl- or ethyltriacetoxysilane |
Acetic acid |
Tris(cyclohexylamino)methylsilane and others |
Amines |
Methyl(tributanone oximo)silane |
Butanonoxime |
Benzamide silanes |
N-butylbenzamide and ethanol |
Silicone elastomers are characterised by excellent electrical insulating properties, inertness, low toxicity and resistance to ozone, weathering, oil and moisture. Some grades have the ability to perform at very
low temperatures, whereas others retain elastomeric properties at very high temperatures.
Unfilled silicone elastomers achieve only low mechanical strength when cured. Adequate strength is obtained by incorporating reinforcing fillers. Small-particle-size, silicas are used almost exclusively for this
purpose. Because of the small particle size elastomers with high transparency can be produced.
The major application of silicone elastomers is as sealant, but they are also widely used for other applications like electrical fittings, textile coating, paints and rubbers for automotive, medical and dental
purposes.
Silicone resins
Whereas silicone fluids and elastomers are based on cyclic or linear polymers, silicone resins are highly branched polymers. Compared to the fluids and elastomers, the market of silicone resins is limited.
The major market for silicone resins is surface coatings, mainly water-repellant coatings for masonry and high-performance paints. For these purposes the silicone resin is often reacted with other polymers to
form copolymers. Silicone/alkyd and silicone/polyester are the most frequently used.
1.2 International market
Globally the consumption of siloxanes totals about 0.85 million tonnes (Will et al 2003). The main producer countries are the USA, Germany, Japan, France and the UK. The American producer DOW
Corning Corporation is by far the largest producer of the World with production facilities in many countries. In Western Europe Wacker Group (Germany), Degussa AG (Germany) and Rhodia S.A.
(France) are main producers.
The total consumption of silicones in Western Europe is according to Will et al. about 296,000 t. The breakdown by application is shown in Table 1.2. The consumption breakdown is by the authors of the
report designated "somewhat tentative", but is considered to provide a general view of the market.
In this report the breakdown of the Western European consumption will be used as basis for a first rough estimate on the use of silicones in Denmark if nothing more specific is known. Denmark accounts for
1.2% of the W. European population, but for 1.4% of the total industry-related GDP (Gross Domestic Product). For the first estimate the per-capita ratio of 1.2% will be used. For most consumer products
and products used in the building industry the consumption pattern of siloxanes in Denmark is most probably not very different from the common W. European market. Differently, the consumption of
siloxanes in industrial processes will be very dependent on the extent to which the industrial processes, in which siloxanes are used as processing aids, take place in Denmark. The actual consumption may
thus be quite different from the common W. European use pattern.
The information on the W. European market will be combined with information about siloxanes registered in the Danish Product Register and information obtained from providers and users of silicones in
Denmark.
Table 1.2 Consumption of silicones in Western Europe in 2002 (Will et al. 2003)
Silicone category |
Applications |
Consumption |
|
|
1000 t |
% |
Fluids |
Processing aids |
40 |
14 |
|
Surfactants for PUR foam production |
25 |
8 |
|
Primary polymer production aids and various defoamer uses |
15 |
5 |
|
Textile applications |
28.4 |
10 |
|
Softeners |
22 |
7 |
|
Defoamers/antifoaming agents |
4 |
1.4 |
|
Water repellents |
1.2 |
0.4 |
|
Other |
1.2 |
0.4 |
|
Cosmetics, toiletries and medical/pharmaceutical preparations |
25 |
8 |
|
Emollients, moisturizers, hair conditioning polymers |
19 |
6 |
|
Medicals/pharmaceuticals |
4 |
1.4 |
|
Other |
2 |
0.7 |
|
Papercoatings and defoamers (mainly backing for self-adhesives) |
17.5 |
6 |
|
Thermal curing, mainly for paper backing |
12.2 |
4 |
|
UV curing mainly for foils backing |
3.2 |
1.1 |
|
EB (electron beam) curing, mainly for foils backing |
2.1 |
0.7 |
|
Paints, coatings and waxes |
11 |
4 |
|
Mechnical fluids (hydraulic fluids and lubricants/greases) |
9 |
3 |
|
Other |
26 |
9 |
Subtotal |
|
156.9 |
53 |
Elastomers |
General-purpose sealants (construction) |
78 |
26 |
|
Special-purpose sealants and rubber |
43 |
15 |
|
Automotive |
11 |
4 |
|
Electrical fittings |
7 |
2.4 |
|
Medical/health |
5 |
1.7 |
|
Domestic appliances |
4 |
1.4 |
|
Consumer goods |
4 |
1.4 |
|
Textile coating |
3 |
1.0 |
|
Business machines |
2 |
0.7 |
|
Paints and coatings |
2 |
0.7 |
|
Mouldmaking |
2 |
0.7 |
|
Other |
3 |
1.0 |
Subtotal |
|
121 |
41 |
Resins |
All applications |
18 |
6 |
Grand total |
|
295.9 |
100 |
| Front page | | Contents | | Previous | | Next | | Top |
Version 1.0 September 2005, © Danish Environmental Protection Agency
|