| Front page | | Contents | | Previous | | Next |
EDIPTEX - Environmental assessment of textiles
Annex 3: Work jacket of polyester/cotton
Work jacket – summary and conclusions
The main scenario for environmental assessment of the work jacket shows that the most significant focus areas are toxicological environmental impacts and resource consumption. The contribution to the toxicological environmental impact potentials originates from fertilizer and insecticides for cotton in fibre production and from production of the artificial fertilizer used. The resource consumption and the contributions to the environmental impact potentials related to energy mainly originate from production of steam for washing and drying at industrial laundries, i.e. during the use phase.
At an overall level, the scenarios indicate that the producer holds the best possibilities for influencing the product's overall environmental profile. This is primarily related to choice of materials and chemicals. The former is clear in the scenarios where organic cotton has been used. By living up to European and Scandinavian ecolabelling criteria and obtaining labelling approval, the producer can signal to the conscious consumer that the product in question has been produced in an environmentally sound manner. Moreover, there are a number of production-related improvements that only the producer can influence. This could be choices related to:
§ organic materials
§ hard-wearing materials
§ choice of carrier for the dyeing process
§ non-toxic reactive dyes.
The individual consumer's consumption patterns and environmental awareness are also crucial for the work jacket's environmental profile. Awareness of ecolabelling of products in combination with good habits like:
§ choice of the most environmentally friendly washing method (industry/household)
§ minimal use of washing agent
§ no use of fabric softeners
§ no tumbler drying.
Thus, the conclusion is that focus should be on the fibre production phase and the use phase.
Introduction
Lifecycle assessment is a method for identification and evaluation of environmental impact potentials of a product or a service from cradle to grave. This method enables the user to make an environmental assessment and focus on the most important environmental impacts.
lifecycle assessment is an iterative process. The first definition of purpose and delimitations often need to be revised during work with lifecycle assessment. The amount of data available sets limits, and consequently the limits of the system are changed.
The method used in this case for assessment of products is "Environmental Design of Industrial Products" (EDIP) and the associated database and PC tool.
In the EDIPTEX project, sector-specific data have been prepared for the textiles sector in connection with the existing EDIP database. The reports contain environmental assessments for the following textile products:
- T-shirt
- jogging suit
- Work jacket
- Floor covering
- Tablecloth
- Blouse
These environmental assessments are intended to illustrate the scope for application of the EDIPTEX database by using the PC modelling tool and, at a more general level, application of the EDIP method.
Method
The six case stories vary a lot in scope. They can be divided into two main groups - with variations within these two main groups. The two main groups are:
- Group I: The T-shirt, the jogging suit and the work jacket.
- Group II: The floor covering, the tablecloth and the blouse.
The division into groups I and II relates to the scope of the collection of data as well as the quality of data.
For group I, it was possible to collect (and process) data for all significant processes. The data are of such quality that these three products have been selected to illustrate how far it is possible to take lifecycle assessment for textiles and to illustrate all relevant aspects of the EDIP method.
Each of the three group I cases contains:
- Definition of functional unit and reference product
- Modelling of main scenario
- Preparation of producer and consumer references
- Simulation of environmental impacts caused by choices made by producer and consumer respectively.
Work with these cases has been divided into phases as illustrated in figure 3.1.
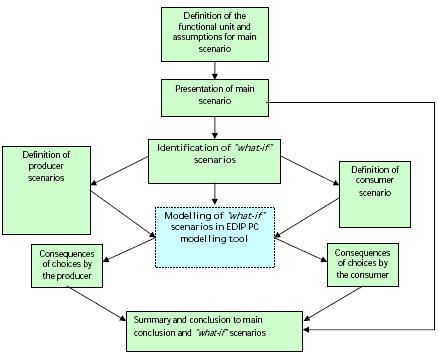
Figure 3.1 EDIPTEX case group I flow diagram
For group II, it was not possible to complete all sub-processes. Although only 1-2 sub-processes for each product have considerable lack of data, these processes are deemed potentially significant for the overall lifecycle assessment. The group II case stories are therefore of an entirely different character than those of group I. The group II cases illustrate that it is possible to tell an interesting and exciting "environment story" based on lifecycle assessment (and EDIP) even though it has not been possible to analyse all aspects of lifecycle assessment data. This situation will arise very often in lifecycle assessment work. However, there is a significant difference in this EDIPTEX connection; it is possible to draw on results from the three lifecycle assessments from case group I (and this has been done), which improves the quality of the case stories.
Comments to the method
Product references
The "what-if" simulations were carried out to elucidate the consequences of possible changes in the product's lifecycle. A special product reference has been defined for the producer scenarios in some of the case stories. The producer only has limited influence on the use phase. In order to take this into account, a product reference has been prepared for the producer scenarios where only a limited part of the impacts from the use phase has been included in relation to the product reference from the main scenario. This was done in order to give producers a clearer picture of the influence of the production phase on the product's environmental profile in the "what-if" producer scenarios.
Data
With regard to data, it should be noted that the validity of the data in the database varies, depending on the processes considered. A global process like cultivation and harvest of cotton is subject to considerable uncertainty. This is because cotton is produced in countries with very different levels of development. For example, production varies a lot between South America and the US because of large differences in the use of pesticides, crop yields, etc.
This difference has not been taken directly into account in the EDIPTEX database, but a representative level for the data has been defined. Therefore, the data are very general and not necessarily representative for all lifecycle assessments. Other processes are more exact, such as extraction of crude oil for nylon. This process is well documented, both as regards industrial accidents and as regards resource consumption.
Production data primarily come from Danish enterprises. The number of enterprises involved represents limitations in this connection. For example, only one reactive dye and one acid dye have been studied thoroughly. These two substances represent the entire group of dyes, despite the major differences that may occur.
A large proportion of the environmental impacts come from the consumption of electrical energy. The data currently used in the database originate from the EDIP database, and the reference year is 1990. This area is being studied in order to update this part of the database. It is important to note that this lifecycle assessment was carried out using the 1990 data in all processes that consume electrical energy.
The work jacket
Product description: work jacket of 65 per cent polyester and 35 per cent cotton. Ten brass buttons, one brass zipper and one polyester zipper in pocket are included.
Functional unit
The performance assessed can be described as a "functional unit", comprising a qualitative and a quantitative description, including the product's lifetime. The qualitative description is to define the quality level for the performance, so that products can be compared at a somewhat uniform quality level. The quantitative description is to determine the size and duration of the performance.
In this project, the functional unit is defined as:
"40 days' use of a work jacket washed each time after use, over three years"
Lifetime is defined as 3 years. It is assumed that the work jacket is washed 40 times in its lifetime. This corresponds to approx. 14 washes per year.
Reference product and main scenario
One work jacket is used as reference product. For the reference scenario, the functional unit corresponds to 1 work jacket being discarded every three years.
The following assumptions apply to the assessment and are thus included in the modelling of the main scenario.
The work jacket consists of 65 per cent polyester and 35 per cent cotton, corresponding to approx. 500 g and 270 g respectively. 10 brass buttons are included, each weighing 3.6 g, one brass zipper for the front, approx. 60 cm (40 g), and one polyester zipper in inner pocket, approx. 15 cm (4 g), a total of 80 g extra components.
The work jacket is washed after every use, corresponding to approx. 14 periods of use of the work jacket per year, i.e. approx. 40 times in 3 years, and then it is discarded. These are average data. Some work jackets last 10-12 years, corresponding to the 100-120 washes they can endure, while others are discarded because of damage that is too time-consuming to repair. A scenario will illustrate the consequence of maximum lifetime of the product.
The reference product is also assumed to meet the following criteria:
- The warps are treated with a sizing agent before the textile is woven.
- The woven textile is desized before being dyed.
- Reactive dyes are used for cotton and dispersion dyes are used for polyester.
- The textile is dyed in an atmospheric jigger using a solvent carrier based on dichlorobenzene.
- The textile is finished after dyeing with a sewability improvement agent (softener).
- There is no print on the work jacket.
- The work jacket has ten brass buttons, one brass zipper for the front and one polyester zipper in an inside pocket.
- Lifetime: Three years - key figures from the laundry sector.
- Number of washes during lifetime: 40 - key figures from the laundry sector.
- Washed at 80-95°C and tumbler dried at industrial laundry.
- Ironing not necessary.
A more detailed description of the processes, calculations of volumes, waste, etc. can be found in the section "Background data" at the end of annex 3.
Product system
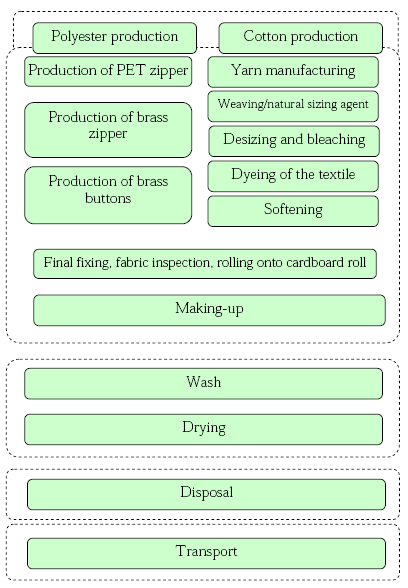
Figure 3.2 describes the lifecycle of the work jacket. From extraction of raw materials to yarn manufacturing, the product has two parallel lifecycles due to the textile composition; cotton and polyester. Manufacture of brass buttons and zipper has been included as secondary factors. This also applies to polyester buttons and zipper. The actual manufacture of buttons and zippers is not included.
The product's lifecycle phases from extraction of raw materials to disposal are described in the following.
Manufacture of raw materials
As mentioned, there are two main materials in the work jacket assessed:
Cotton manufacture
Cotton is cultivated in many countries under different geographical and climatic conditions. Cultivation often entails a large consumption of artificial fertilizer, large water consumption and a large consumption of pesticides against insect attacks, diseases, worms and weeds. The extent of this depends largely on local conditions. The consumption of pesticides entails an important environmental problem for both human health and nature.
Irrigation and use of artificial fertilizer impact groundwater and surface water resources quantitatively as well as qualitatively. Before picking, it is common to use defoliating agents so that picking can be done mechanically.
Organic cotton
It is normally not permitted to use pesticides and artificial fertilizer in cultivation of organic cotton. Thus, it is only permitted to use a very limited selection of plant protection agents, and only when there is an acute danger for the crop. Organic production of cotton constitutes less than 1 per cent of total cotton production, but organic production is increasing and is expected to increase further due to increased demand.
Production of synthetic fibres
Polyester is produced on the basis of crude oil and natural gas that are converted to plastic through a number of chemical processes. The raw material is a limited resource, and production may lead to impacts on humans and the environment at local, regional and global levels. During processing of the materials into fibres, lubricants are usually added in the form of spindle oil and antistatic agents. Bactericides and fungicides may be added.
Production of the work jacket
Production is divided into several processes: yarn manufacturing, weaving, pre-treatment, dyeing, finishing and making-up.
Yarn manufacturing
The cotton and polyester fibres are normally blended in the desired blending ratio as the first step of the process at the spinning mill. The fibres are then carded, combed and spun into yarns.
Before the cotton can be spun into yarn, the fibres need to be separated from the remaining plant material. One of the largest environmental risks in this process is inhalation of cotton dust. In just a few years, staff can develop the fatal disease Byssinosis (commonly called "Brown Lung"). It is therefore important that machines be closed in so that dust development is minimal. This also applies for the actual spinning process where the fibres are spun into yarns.
Weaving
All weaving mills use agents to reinforce the warp in the actual weaving process - these agents are called sizing agents. Sizing agents may be based on natural starch from e.g. corn, rice or potatoes. They may also be based on synthetic substances like polyvinyl alcohols (PVA) or carboxymethylcellulose (CMC). If synthetic sizing agents are used, they are sometimes reused. However, this requires the desizing process to be carried out near a weaving mill where the sizing agent can be reused.
In the environmental assessment of the work jacket, the assumption is that a natural sizing agent is used in the weaving process. This is because there are no enterprises in Denmark that can reuse the sizing agent. Moreover, the assessment applies data from modern weaving mills that use closed-off high-speed air jet looms.
Pre-treatment
In connection with the pre-treatment of woven products, the sizing agent is always washed out of the woven goods in a desizing process. The cotton also contains some cotton wax, and the polyester yarns contain lubricating oils from production that also need to be removed before it is possible to dye the textiles. Remains of pesticides from cotton cultivation, mainly defoliation agents, are also washed out in this process and then end up in the wastewater.
If the end product is to have a light colour, the natural colour of the fibres can be removed by bleaching them. If chlorine bleaching is used, AOX compounds (adsobable organic halogens) will be formed and subsequently discharged, and these are harmful to the environment. It is also possible to bleach using hydrogen peroxide that does not cause discharges of AOX compounds.
Desizing using enzymes and washing and bleaching with hydrogen peroxide, which are normal in Denmark, have been used as the basis for the environmental assessment of the work jacket. Moreover, the environmental assessment includes limited discharges of pesticides (0.005 g defoliation agent per kg cotton).
Dyeing
The different types of fibre are dyed separately. Cotton is typically dyed using vat or reactive dyes, and polyester is dyed using dispersion dyes.
The dyeing process for the reference product is defined as being carried out in an atmospheric jigger. In order to dye the polyester part, it is necessary to use carrier solvents to open the polyester fibres to the dispersion dyes. Dyeing with carriers is not normal in Denmark, as it has been ascertained that some of the substances are carcinogenic or harmful to the nervous system. However, carriers are still being used in several places in the world to dye polyester. Therefore, dyeing with carriers has been included to illustrate in a scenario the significance of transition to more environmentally friendly carrier types or of completely removing them from the process.
Dyes for dyeing textiles are chemically often based on azo groups and may contain heavy metals. Some dyes containing azo groups may release carcinogenic substances of the type arylamines.
Dyes from the group of reactive dyes and dispersion dyes without heavy metals and without arylamine problems have been selected for this environmental assessment. The polyester part has been dyed using a carrier based on dichlorobenzene.
Finishing
Finishing the textiles for a work jacket will normally consist of a treatment with a sewability improvement agent (softening) to facilitate the subsequent making-up stage. Chemicals are also used to give many textiles specific functional properties, such as non-iron, water-repellent and fire-retardant. Auxiliary chemicals in these productions often have many extremely undesirable environmental properties, both for the environment and for occupational health and safety.
The environmental assessment of the work jacket is based on the textiles being finished with a fabric softener.
Making-up
In the making-up stage, there is waste from the cutting-to-size process for the final product. For the work jacket, waste of 10 per cent is assumed. Some of the waste products are reused for products of a lower quality. The main part is sent to waste incineration with heat and energy recovery, which is set off against energy consumption by the production equipment.
Occupational health and safety
The supplier is obliged to reduce the amount of monotonous repetitive work and dust nuisance at work. Cotton dust may cause lung damage, for example.
Distribution
The work jacket is packed in polyester bags and then on a wood pallet. Finally, it is distributed to retail suppliers.
Use phase
In this environmental assessment of the work jacket, the main scenario is that it is washed at 80°C and then tumbler dried at an industrial laundry.
Disposal phase
Textiles must not be landfilled. They must be incinerated at final disposal. In this way, the energy content is recovered and replaces energy sources like oil and natural gas. Incineration of cotton is CO2 neutral, because the cotton crop has absorbed the same quantity of CO2 as is released during incineration. The brass buttons and the zippers leave the incineration plant along with the slag, and have an insignificant impact on the environment.
Transport phase
In the environmental assessment of the work jacket, transport scenarios are included to and from the different processing links in the production chain, and finally from the sewing factory to Danish retailers.
Main scenario - results
The results of the main scenario are presented according to processes. The negative contributions that occur in some processes are due to estimated reuse potentials, resource consumption and contribution to environmental impact potentials. In the processes in question, the contributions can be allocated to other products and thus appear as negative contributions in the work jacket's environmental profile.
The values in the five figures are not immediately comparable, as the unit is not the same for the five categories. The consumption of primary energy is calculated in mega-joules (MJ), while the resource consumption is shown in the unit "person-reserves". Person-reserves take into account the supply horizon of the individual resources, calculated on the basis of the reserves available in the world in 1990. It should be noted that the data used here are more than ten years old, and therefore, new knowledge about the world's resources may have become available, but is not yet included in the database. The environmental impact potentials are presented in milli-person equivalents and are directly comparable. Milli-person equivalents are calculated as the direct impact for the year 2000. The weighting factors are based on global (w) or Danish (DK) discharges in the year 2000.
Consumption of primary energy
Figure 3.3 shows that the processes in the use phase represent the majority of the consumption of primary energy. The consumption of primary energy reflects the processes that require a lot of electrical energy or heating air or water. Clearly, washing and drying the work jacket in the use phase represents the main part of the primary energy consumed. The large consumption of electricity and steam at industrial laundries causes this impact. Fibre production is also an energy-consuming process because of the related production of artificial fertilizer and pesticides. Moreover, there is energy consumption for spreading artificial fertilizer and pesticides, but these are not included in the statement.
Resource consumption
The work jacket consumes a relatively large amount of fossil fuels (see figure 3.4), partly because of the energy-intensive processes in its lifecycle, and partly because of the production of 65 per cent polyester. Polyester is produced from crude oil. In the use phase, the large consumption of electricity and crude oil for the steam boilers at the industrial laundry causes the significant consumption of fossil fuels. As it is assumed that the work jacket will be used in Denmark, electricity consumption is primarily based on burning coal at coal-fired power plants. In the disposal phase, some resources are credited because energy is recovered that would otherwise have come from burning fossil fuels.
Environmental impact potentials
Environmental impact potentials related to toxicity
Of the three environmental impact categories, the ones related to toxicity are dominant (see figure 3.5). In the fibre production phase, the large contribution to ecotoxicity is primarily due to the use of pesticides in cotton cultivation. In the pre-treatment processes carriers, dyes and fabric softeners cause the contributions to ecotoxicity and persistent toxicity. The impact potentials in connection with wash of the work jacket primarily originate from detergents in washing agents, which result in potential human and persistent toxicity.
Environmental impact potentials related to energy
The environmental impact potentials related to energy (figure 3.6) are caused by burning fossil fuels in the situations mentioned above. As can be seen in the figure, the use phase impacts the environmental profile of the work jacket the most.
Environmental impact potentials related to waste
The contributions to the waste categories shown in figure 3.7 mainly originate from electricity generation. They are limited in size compared to the above impact categories.
The conclusion of the lifecycle statement is that the product is resource-intensive primarily because of the large consumption of electrical energy and crude oil for steam in the use phase.
Results from modelling and calculation of the main scenario
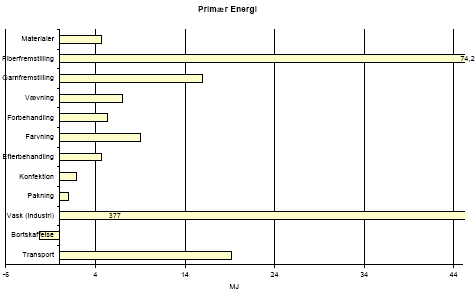
Figure 3.3 Results of main scenario; consumption of primary energy per
functional unit – for translation of Danish terms see glossary in annex 11
Click here to see the Figure.
Figure 3.4 Results of main scenario; resource consumption of primary
energy per functional unit – for translation of Danish terms see glossary
Click here to see the Figure.
Figure 3.5 Result of main scenario; toxicological environmental impact
potentials per functional unit – for translation of Danish terms see
glossary in annex 11
Click here to see the Figure.
Figure 3.6 Result of main scenario; environmental impact potentials
related to energy per functional unit – for translation of Danish terms
see glossary in annex 11
Click here to see the Figure.
Figure 3.7 Result of main scenario; environmental impact potentials
related to waste per functional unit – for translation of Danish terms
see glossary in annex 11
What-if simulations
The environmental profile for a given product - in this case a work jacket - can be affected by the choices made by the producer and by the consumer. In order to elucidate the consequences of possible changes in the product's lifecycle, a number of scenarios have been prepared that focus on the producer and consumer respectively.
By changing one or more of the reference conditions, it is possible to form a picture of the scope of the consequences based on the choices made. These changes are illustrated graphically by means of lifecycle statements within five categories, as described in section 5.
Consequences of choices by the producer
The producer influences all processes from extraction of raw materials until the finished product leaves the distribution phase. The producer can affect the processes in the use phase. However, it is not possible for the producer to affect all consumers of the product equally. Contrary to the product dealt with in annexes 1 and 2 - a T-shirt and a jogging suit - there is no producer reference for the work jacket. This is because the main scenario has been prepared on the basis of the producer and a consumer following a uniform and well-known consumption profile in the form of an industrial laundry. Therefore, consumer scenarios as well as producer scenarios will be compared with the same reference. The reference scenario is called the producer reference.
In the following, the results of the producer-related scenarios are presented as summarised contributions over the entire lifecycle and compared with the producer reference scenario.
Scenarios - producer
Raw materials phase
Scenario 1: Choice of raw materials - organic cotton
Production phase
Scenario 2: Choice of chemicals - choice of carrier
Scenario 3: Choice of chemicals - choice of dyes, 10 per cent dyeing
Use phase:
Scenario 4: Influence of product quality - colour staining
Scenario 5: Influence of product quality - increased lifetime
Scenario 1: Choice of raw materials - organic cotton
The toxicological environmental impacts are the environmental impact potentials with the highest weight in the life of the work jacket. The contributions to this category have been ascertained as primarily due to use of pesticides and the energy consumption in production of artificial fertilizer for cotton cultivation.
For conventional cotton cultivation about 18 g pesticides are used per kg cotton in the worst case. The main scenario applies an average from cotton cultivation in the US and South America. The impact of pesticides on the environment has been assessed, and the factors have been included in the database. Pesticide residues can cause toxic impacts in humans during processing of the cotton fibres, as the oil used in this process is used for cooking in some countries. In this way, the pesticide residues end up in food and thus constitute a health threat to humans. The residues left in the cotton are assumed to be washed out during wet treatment.
In order to assess the toxicological environmental impacts in conventional cotton cultivation, the 35 per cent cotton in the work jacket is changed to organic cotton. In this way, the use of pesticides and artificial fertilizer is avoided and run-off of pesticides during cotton fibre processing is also eliminated. In production of organic cotton fibres, no chemicals are used for bleaching in pre-treatment, and this leads to another reduction of the toxicological environmental impact potentials.
The transport required to spread these substances on the field disappears for organic cultivation. On the other hand, there will often be some sort of mechanical weed control that contributes to the toxicity potentials. This transport is not, however, included in the reference scenario, due to the large differences between the cotton-producing countries and their ways of cultivating cotton. In some countries, vehicles only drive in the fields a few times per cultivation round. In other countries, typically South American countries, it is common to drive more in the fields to secure the crop yield. Generally, less transport reduces consumption of fossil fuels and is therefore also part of the energy-related and toxicological environmental impacts. For this calculation, please see annex 1 for the lifecycle assessment of a cotton T-shirt.
Result of changed choice of raw materials
Consumption of primary energy does not change significantly because of the changes choice of raw materials. This is because most of the energy consumption arises from processes in the production and use phases and these do not change. In total, energy consumption falls by 1 per cent for the changed choice of raw materials.
The toxicological environmental impacts are significantly reduced using organically cultivated cotton. Persistent toxicity and ecotoxicity is reduced by about 80 per cent compared with the reference scenario.
The environmental impacts related to energy, greenhouse effect, nutrient loading, and photochemical ozone formation are reduced by a small percentage, approx. 2-10 per cent. The reason is that there is no longer a contribution to these potentials from production of artificial fertilizer and pesticides. The same applies for the waste categories.
Conclusion to scenario 1
It can be concluded that the producer has great possibilities to influence the overall environmental profile of the textile, especially the toxicological impact potentials. It can be recommended to use organic cotton instead of conventionally cultivated cotton. It should also be considered that many of the agents used during cultivation of cotton are harmful to human health. Incorrect or careless use could mean that suppliers expose themselves and their employees to health hazards.
Pesticide residues washed out in several pre-treatment processes are yet another reason to avoid conventionally cultivated cotton.
Scenario 2: Choice of chemicals - choice of carrier
This scenario is to illustrate the impact of one of the choices of chemicals the producer can make in the production phase.
When polyester is dyed below approx. 130°C, which is the glass transition temperature or Tg for polyester, the polyester fibres are solid and are, at best, only dyed on the surface. By adding a solvent to the dye bath, the polyester fibres are partially softened, and the dyes can penetrate the polyester. When the solvent is removed, the polyester will become solid again, and the dyes are trapped inside the polyester fibres.
The solvent - the carrier of the dye - thus contributes to an even and deep colouring of the polyester and gives a very high degree of colour fastness. Carriers used are typically chlorinated aromates, phenols, benzenes, aromatic hydrocarbons and ethers, and aromatic esters. The substances are known for their harmful impacts on health. The majority are carcinogenic or harmful to the nervous system. A group of carriers that are more environment-friendly and, in particular, better for occupational health and safety has been developed. One of these is based on sodium benzoate, methanol and LAS, and in this case, it has been tested as an alternative to the carrier used in the reference product, which is based on 1,2 dichlorobenzene.
It is assumed that almost 100 per cent of the dose leaves the dye house via wastewater. Data for the manufacture of the carriers is not included, and therefore only the toxicological environmental impact potentials are changed in relation to the reference scenario.
Click here to see the Figure.
Figure 3.8. Result of scenario 2 shows reduced contribution to the toxicological environmental impact potentials – for translation of Danish terms see glossary in annex 11
The figure shows that the choice of a less toxic carrier has an impact of approx. 5 per cent for ecotoxicity, while it is approx. 1 per cent for persistent toxicity. The impact does not seem higher because of the very high contributions to these categories from cotton cultivation. If we only look at the dyeing process, the toxicological environmental impact potentials are reduced by up to 95 per cent, highest for ecotoxicity.
By choosing to use high-pressure machines, the use of carriers can be eliminated. By dyeing at a higher temperature than 130°C, typically just less than 140°C, and a similar pressure, Tg is exceeded and the polyester fibres are opened as if there had been a solvent, and the dye can thus be carried out without using a carrier.
Conclusion to scenario 2
The choice of carrier has a limited impact at an overall level, but the impact is large on the product's environmental profile, if the production phase is regarded separately. Thus, this is an area where the producer has a direct possibility of improving the product's environmental profile. The environmental profile of the dye house is improved considerably by using the least toxic carrier or none at all.
Legislation on ecolabelling indicates the substances that should be phased out, and those which should be avoided completely from an environmental perspective. This could be a guide for environmental work at the individual enterprise.
In this connection, it should also be noted that chlorinated carriers of the type mentioned here are no longer being used in Denmark because of their ecotoxicity and human toxicity impacts. The substances are not degraded in the municipalities' wastewater treatment plants, and therefore they are a potential contamination source that should be minimised or avoided.
Scenario 3: Choice of chemicals - choice of dyes, 10 per cent dyeing
In the reference, the work jacket is dyed with a blend of dispersion and reactive dyes for polyester and cotton. The 1 per cent dyeing corresponds to the amount of dyestuff used to dye in paler shades. This scenario illustrates the impact of a dark dye of 10 per cent.
It is assumed that 85 per cent of the dye does adsorbs to the textile and the remainder is led through wastewater treatment as in the reference scenario. As ten times as much dyestuff is used, ten times as much dyestuff is discharged than in the reference scenario. The calculations assume that dyestuff is not washed out during the use phase.
It is assumed that the same amount of textile as in the reference scenario can be reused directly from the knitting and making-up phases. There is data for one single acid dye, and therefore the scenario should not be regarded as representative for the whole group of acid dyes.
Click here to see the Figure.
Figure 3.9 Result of scenario 3 - increased contribution to environmental impact potentials related to chemicals – for translation of Danish terms see glossary in annex 11
The graphs show that the larger amount of dyestuff leads to an increase in the total contribution to the toxicological environmental impact potentials of about 1-4 per cent. This does not seem to be a lot, but it should be taken into account that this is solely due to an increase in the concentration of dyestuff. Seen in isolation, the dyeing process represents an increase of 12 per cent. The concentration of dyestuff should thus be a focus point for the producer.
In this scenario, production of the dyestuff is not included. Moreover, process variations in the dyeing process are not taken into account. On the basis of this, the environmental profile of a 10 per cent dyeing would be further impacted.
Conclusion to scenario 3 - large impact in dyeing process, less at overall level
It can be concluded that the amount of dyestuff per functional unit has an impact on the overall environmental profile for the product. If we look specifically at the production phase, we see increases of 10-85 per cent, which makes this an important focus point for the producer. The producer can affect the supplier of dyes in a more environmentally friendly direction by making environmental requirements for the dyes.
Scenario 4: Influence of product quality - colour staining
The quality of the dyeing, colour fastness, is important for the quality consumers perceive in the product. This scenario illustrates the impacts on the overall environmental profile of the work jacket if it ruins an entire machine wash once in its lifetime because the colour migrates to the other textiles in the wash. It is assumed that each wash included 4.5 kg textiles of the same composition as the work jacket, i.e. 35 per cent cotton and 65 per cent polyester. It is also assumed that all the washed textiles are unfit for use after the colour set-off, except the reference product.
The modelling is carried out by assuming that the wash is composed of 6 work jackets of the type described. Therefore, 6 work jackets of 877 g each must be produced, transported and disposed of. The use phase of the spoiled textiles is not included in the calculations, i.e. only the use phase for the reference product is included in the model, as it is assumed that it is not spoiled.
Production of the increased volume of textiles causes an increase in consumption of primary energy of approx. 130 per cent. The toxicological environmental impacts increase by about 500 per cent, and the same trend is apparent for the remaining categories.
Click here to see the Figure.
Figure 3.10 Result of scenario 4 – for translation of Danish terms see glossary in annex 11
Conclusion to scenario 4 - the contributions from the production processes outweigh the contributions from the use phase.
The scenario indicates that the use phase of the individual work jacket, otherwise dominant, is now outweighed by the processes in the production phase. On the basis of this, it can be concluded that the colour fastness of textiles of this type is very important. Alternatively, the producer can inform consumers about the risk of colour being transferred to other textiles, whereby the consumer is given the responsibility of washing the work jacket one or more times. This should be included in the product's overall environmental profile as a higher impact from wash in the use phase. If the work jacket is washed at an industrial laundry, there is also a risk that a blue work jacket is washed with light-coloured work clothes, and an entire wash can be spoiled there too. Such an error will probably not happen often. However, as the work clothes are sorted manually, it could occur on a busy day.
A similar scenario could be work jackets that are spoiled because pocket knives, ball-point pens or similar have been left in the pockets. The result could be that the individual work jacket must be disposed of or that other garments washed with the work jacket are damaged.
Scenario 5: Influence of product quality - increased lifetime
Product quality influences the lifetime of the product.
Colour fastness, durability of the fibre and stitching are examples of areas on which the durability and quality of the product can be judged. In connection with lifecycle assessments, the quality of the reference product will be important for the manufacture and disposal phases, as these are extended/reduced in order to meet the functional unit.
A work jacket is assessed to endure 100 washes, corresponding to approx. 10-12 years (Bang 2001). In practice however, the work jacket will often be discarded far earlier, namely after approx. 40 washes. This is typically because of damage that is too time-consuming to repair.
Scenario 5 assumes that the work jacket is washed 100 times - corresponding to the estimated maximum lifetime. This assumption means that approx. one-third fibre manufacture, production, disposal and transport is required to meet the functional unit.
Click here to see the Figure.
Figure 3.11 Result of scenario 5 – for translation of Danish terms see glossary in annex 11
The great importance of lifetime is clear. The consumption of primary energy is increased by approx. 110 %. Resource consumption is increased correspondingly, crude oil by 130 per cent, natural gas by 75 per cent, and coal by 10 per cent. This is due to the extra number of industrial washes and the increased transport volume. The contribution to the energy-related environmental impacts as a consequence of this, increases by 70-130 per cent. The waste categories increase by about 10-30 per cent for the same reasons.
The toxicological environmental impact potentials are affected differently by the increased lifetime of the work jacket. Persistent toxicity increases by 3 per cent, ecotoxicity is unchanged, while human toxicity increases by 100 per cent. Contributions from electricity generation to operation of the washing machines at the industrial laundry and the increased transport volume are the primary causes of the increased toxicological environmental impact potentials.
Conclusion to scenario 5 - lifetime is significant
The conclusion to this scenario is that the quality of the work jacket is an important focus point for the producer. However, it should be taken into account that fatal damage to the work jacket is often caused by external factors. A more wear-resistant material could probably limit such discards.
The quality of the textile is only determined by the producer, while the consumer has a great influence on how long the work jacket will last. There are sectors where work rarely leads to torn jackets or similar, and where the work jacket thus has a longer lifetime, while it must be discarded sooner in other places.
Consequences of choices by the consumer
The consumer is primarily able to influence the use phase and parts of the transport phase. The other phases can primarily be influenced by the producer. Secondly, the consumer is able to choose producer selectively through, e.g. ecolabel schemes.
The use phase for the reference scenario contains drying and washing at a laundry. Transport between producer and laundry as well as transport between consumer and laundry are included.
Scenarios – consumer
As mentioned in the introduction, the reference scenario for consumers and producers is the same.
Scenario 6: Choice of wash - dry cleaning vs. industrial wash
Scenario 7: Choice of wash - household wash vs. industrial wash
Scenario 8: Choice of wash - household wash 2
Scenario 6: Choice of wash - dry cleaning vs. industrial wash
Work clothes are often soiled much more than normal garments. In this scenario, the assumption is that the work clothes have stains after use that are difficult to remove in normal washing. Therefore, the work jacket is dry-cleaned. The dry-cleaning process is regarded as an industrial process organised similarly to the current industrial laundries.
It is assumed that industrial dry-cleaners will pick up the dirty work clothes and return the clean clothes in the same way as industrial laundries do today. There is an increased consumption of chemicals for dry cleaning textiles, while the consumption of other resources such as water is lower. Whereas industrial laundries use crude oil for steam production, the dry-cleaning process in the EDIPTEX database uses electricity. This would probably not be the case if an industrial dry cleaner were to function and compete on equal terms with the laundries. The data for the dry-cleaning process is based on dry-cleaners as they work in Denmark today. It is therefore conceivable that consumption of energy and chemicals could be reduced if the dry cleaning took place on a larger scale and under more uniform conditions, such as same textile type, type of dirt and regular volumes.
Data for the production of the chemical perchloroethylene for the dry-cleaning process has not been included in the lifecycle assessment, and environmental impact potentials have not been assessed. For the industrial washing agent, energy consumption for production of the washing agent has been included, while the environmental impact potentials have not yet been assessed.
Click here to see the Figure.
Figure 3.12. Result of scenario 6 – general increases in environmental impact potentials – for translation of Danish terms see glossary in annex 11
The total energy consumption is increased by 120 per cent. This is primarily due to increased consumption of electricity for heating steam. Transport is assumed to be the same for industrial wash and industrial dry cleaning, about 3,000 km during the lifetime of a work jacket. For industrial wash, energy consumption for production of the washing agent is included and this process represents 5 per cent of the total energy consumption in the main scenario.
The resource consumption for the two processes is very different. A lot of crude oil is used in industrial wash for the steam generator that delivers steam for the washing machines. In the dry-cleaning process, consumption of crude oil is reduced by 70 per cent, while consumption of coal is increased considerably. The reason is that Danish electricity is primarily generated at coal-fired power plants.
The toxicological environmental impacts are significantly increased when dry-cleaning is selected instead of industrial wash. Persistent toxicity is increased by about 170 per cent compared with the reference scenario, while ecotoxicity is increased by approx. 15 per cent, and human toxicity is increased by 800 per cent. The increase is merely due to consumption of electricity, as the environmental impact potentials for perchloroethylene have not been included.
For the environmental impacts related to energy, the result is that the greenhouse effect and acidification are increased by 180 per cent and 160 per cent respectively, while the nutrient loading and photochemical ozone formation are reduced by 5-30 per cent. The reason for this is the difference between using electrical energy generated by burning coal and energy generated by an oil-fired steam boiler.
Conclusion to scenario 6
It can be concluded that dry cleaning of work jackets/work clothes has an overall negative influence on the textile's overall environmental profile. The calculations are based on dry cleaning of textiles as the process is today. This means that there would probably be a reduction in some categories, if the process were optimised as an industrial process with associated economies of scale. The toxicity of washing agents and chemicals for dry-cleaning has not been assessed. This could change the size of the toxicological potentials.
Scenario 7: Choice of wash - household wash vs. industrial wash
The use of work clothes is primarily related to manual jobs. This includes all types of company, from one-man operations to large construction groups. Irrespective of the size of the enterprise, it will attempt to minimise all costs, including costs of washing work clothes. Therefore, it is assumed that the work clothes are only washed privately, when this is the most profitable way.
At industrial laundries, the clothes are washed and dried in the same process. For purposes of comparison, a 60°C wash without prewash and subsequent tumbler drying has thus been used.
It is assumed that large enterprises normally choose to use an industrial laundry and have clean work clothes delivered to the enterprise. Thus, this scenario is primarily aimed at small enterprises and one-man operations.
It is assumed that smaller enterprises with less than five employees will wash their work clothes themselves instead of having a laundry pick up and return work clothes for them.
It is assumed that the work jacket is washed with other clothes of the same material, probably several items of work clothing, so that the machine is full when the clothes are washed. In this scenario, the assumption is that there are 4.5 kg clothes in the machine.
The temperature is set at 60°C for household washes here, as washing agents and fabric softeners have been adapted to lower temperatures. It has also been taken into account that water and electricity constitute expenses for the households, and that most people will consequently try to minimise consumption of electricity and water.
Click here to see the Figure.
Figure 3.13 Result of scenario 7 – changed resource consumption, increased toxicological environmental impact potentials – for translation of Danish terms see glossary in annex 11
The total energy consumption is reduced by 20 per cent. Some of the explanation for this is the transport to and from the laundry in connection with industrial wash. Over the lifetime of a work jacket, this constitutes about 3,000 km. However, the primary reason is that household washing and tumbler drying is less energy-intensive than the process at an industrial laundry. For industrial wash, energy consumption for production of the washing agent is included, and this process represents 5 per cent. This is not the case with the washing agent used in households.
Resource consumption for the two processes is very different. The industrial wash uses a lot of crude oil for a steam boiler that supplies steam to the washing machines. Household wash and tumbler drying consumes 20 per cent of the amount of crude oil consumed by the industrial washing process. In the other hand, the household wash represents large consumption of coal; over 500 per cent more than industrial wash. Danish electricity is primarily produced at coal-fired power plants. Again, the production of the washing agent for the industrial laundry plays a role.
The toxicological environmental impacts are increased significantly reduced when household wash is chosen over industrial wash. Persistent toxicity is increased by about 30 per cent compared with the reference scenario, while ecotoxicity is increased by approx. 7 per cent, and human toxicity is unchanged.
The toxicity of the washing agent used in households is included in the statement. This is not the case for the industrial washing agent, but here energy consumption for production of the washing agent is included. The increase in toxicity and the changes in resource consumption should therefore be seen in this context.
For the environmental impacts related to energy, the result is that the greenhouse effect is unchanged while the nutrient loading and the photochemical ozone formation are reduced by 5-30 per cent. The reason for this is the difference between using electricity (households) generated by burning coal, and energy (industrial wash) generated by an oil-fired steam boiler.
Conclusion to scenario 7
It can be concluded that the consumer has great possibilities to influence the overall environmental profile of the textile, both as regards total energy consumption, resource consumption, toxicity categories and waste potentials.
Scenario 8: Choice of wash - household wash 2
This scenario builds on the results from scenario 7 where a normal 60-degree household wash followed by tumbler drying is assessed in relation to an industrial wash at a laundry. Instead of a normal 4.5 kg household wash, the work jacket in this scenario is washed alone with a pair of matching trousers, corresponding to a total weight of 1.54 kg. For calculation purposes, this means that the use phase has an extra consumption for the washing process, corresponding to a factor of 2.92 (4.5 kg divided by 1.54 kg). Other assumptions and considerations are the same as in scenario 7.
Click here to see the Figure.
Figure 3.14. Result of scenario 8 – large impact on resource consumption – for translation of Danish terms see glossary in annex 11
As can be seen from the graphs, this type of washing procedure places a strain on the overall environmental profile. However, we can see that consumption of natural gas and crude oil is larger in the reference scenario. Consumption of coal is the only resource increased compared with scenario 7. As described in scenario 7, this is partly due to the different methods of industrial washing and household washing (steam wash vs. electrical wash). Steam wash consumes a lot of crude oil compared to household wash that is powered by Danish electricity, primarily generated by burning coal.
Despite this, consumption of primary energy is increased by 10 per cent compared with the reference scenario. This is despite the fact that the work jacket is transported 3,000 km in a van between the enterprise and the laundry in the reference scenario.
Another aspect that is also mentioned in scenario 7 is the data basis. There is data for the toxicological impacts of household washing agents, but no energy data for the production. Conversely, there is no data for the toxicological impacts of industrial washing agents, but there is energy data for the production of the washing agent. This makes the comparison less clear. An increase in persistent toxicity of 92 per cent is thus not a clear indication of the actual difference between the two washing methods, but merely an indication that there will be increased consumption of washing agent in this scenario and thus increased toxicity.
For the environmental impacts related to energy, the environmental impact is increased as regards greenhouse effect and acidification, but reduced as regards nutrient salts and photochemical ozone. The reason for this difference is the different nature of the resources and the way they are incinerated. It is clear that the changes to the impact potentials related to energy are due to resource distribution.
Conclusion to scenario 8
The conclusion to this scenario is that household wash with one set of work clothes places a strain on the work jacket's environmental profile compared to having it washed at an industrial laundry. If we compare scenarios 7 and 8, it is clear that this type of washing procedure is environmentally inappropriate. The number of clothes washed together is very important. It would probably be advantageous to invest in several sets of work clothes, if they are washed at home, and if the consumer does not wish to mix everyday clothes with work clothes. It is less clear what the picture would have looked like if the data bases for the two washing processes had been the same.
Background data
System structure in the EDIPTEX database for the work jacket
|
Ref. nr. UMIPTEX-databasen |
1 work jacket, dyed (cotton/polyester)
1 materials phase:
0.439 kg cotton fibres (incl. cultivation and harvest)
0.626 kg polyester fibres
0.04 kg zipper of brass
0.036 kg button of brass
0.004 kg zipper of plastic (polyester)
1 production phase:
0.877 kg yarn manufacturing (polyester/cotton - 65%/35%)
2.97 m² weaving, natural sizing agent
0.877 kg desizing and bleaching PET/CO, jigger
0.877 kg dyeing PET/CO in automatic jigger
0.877 kg softening PET/CO in jigger
0.868 kg drying, final fixing + set of m² weight (PET/CO)
2.9 m² fabric inspection + rolling onto cardboard roll (PET/CO)
1 work jacket- laying out, cutting and sewing
1 work jacket- packing
1 use phase:
10.78 kg industrial wash, 80 °C + mach. drying cotton
20.02 kg industrial wash, 80 °C + mach. drying polyester
1 disposal phase:
0.27 kg waste incineration of cotton
0.5 kg waste incineration of polyester
0.004 kg incineration of plastic zipper
1 transport phase:
8780 kg km container ship, 2-t, 28000DWT, terminated
1175 kg km lorry > 16 t diesel out-of-town, terminated
1175 kg km lorry > 16 t diesel urban traffic, terminated
1175 kg km lorry > 16 t diesel motorway, terminated
1148 kg km van < 3.5 t diesel, urban traffic, terminated
1148 kg km van < 3.5 t diesel, out-of-town, terminated
1148 kg km van < 3.5 t diesel, motorway, terminated |
(TX0-03)
(TX6-1-06)
(TX1-01-1)
(TX1-04)
(TX29-2-02)
(TX29-2-03)
(TX29-2-01)
(TX6-2-19)
(TX21-3)
(TX23-1)
(TX24-2-01-B)
(TX25-03)
(TX27-2-03)
(TX27-3-06-02)
(TX27-3-08-06-02)
(TX28-1-03)
(TX28-2-04)
(TX6-3-04)
(TX32-1-1)
(TX32-1-2)
(TX6-4-04)
(TX41-1-01)
(TX41-1-04)
(TX41-2-11)
(TX6-5-04)
(O32715T98)
(O32694T98)
(O32695T98)
(O32693T98)
(O32705T98)
(O32697T98)
(O32698T98) |
Details of the work jacket model in the EDIPTEX database
Assumptions:
- 65 per cent polyester/35 per cent cotton, total weight 850 g, of which textiles constitute approx. 770 g (295 g/m²) and extra components approx. 80 g. Approx. 500 g polyester and 270 g cotton.
- 10 buttons in 100 per cent brass - approx. 3.6 g each - total 36 g. In addition, 2 zippers - one brass zipper in front, approx. 60 cm (40 g) and one polyester zipper in inside pocket, approx. 15 cm (4 g). Total approx. 80 g extra components.
- Can be washed at 95°C and can be dry-cleaned chemically.
- Lifetime: the fabric quality used in the reference product in this case is strong enough to last for at least 100 washes; but in practice, the work jackets are discarded far earlier. 40 washes and a lifetime of 3 years is a key figure from the laundry industry. Some work jackets last 10-12 years, corresponding to the 100-120 washes they can actually tolerate. The early discard is typically caused by damage that is too time-consuming to repair.
·
Functional unit
The calculations are for "1 work jacket". This needs to be converted in relation to lifetime, and the calculations need to be converted to "per year".
It is assumed that the work jacket can be washed 40 times before it is discarded.
Lifetime is approx. 3 years - corresponding to approx. 14 washes per year.
It is assumed that the work jacket is used 1 working day of 8 hours and is then washed.
The functional unit for the work jacket is therefore:
"40 days' use of a work jacket washed each time after use over the course of 3 years".
It is assumed that 40 washes correspond to the number of days a consumer wears a work jacket over the course of 3 years.
For the reference scenario, this corresponds to 1 work jacket being discarded every three years.
Disposal:
It is assumed that the work jacket is sold in Denmark and disposed of through waste incineration. 0.50 kg polyester and 0.27 kg cotton and 76 g brass (buttons and zipper), 4 g polyester (pocket zipper). Extra components of brass are not included in the lifecycle assessment, as brass does not have a calorific value and will leave the incineration plant with the slag and have no significant impact on the environment.
Wash:
It is assumed that the work jacket can be washed 40 times in its lifetime. This means that 0.5 * 50 = 20 kg polyester and 0.27 * 40 = 10.8 kg cotton must be washed and dried. Industrial washing at 80°C and household washing at 90°C without prewash. The weight of extra components is not included in this context.
Drying:
For industrial wash, drying is part of the washing process. For households, it is assumed that the work jacket is dried in a tumbler dryer, i.e. 20 kg polyester (synthetic) and 10.8 kg cotton. The weight of extra components is not included in this context.
Packing the work jacket:
It is assumed that the work jacket is packed in a thin plastic bag. It is assumed the bag weighs 20 g (2 * T-shirt, see annex 1).
Making-up:
A new process has been set up: work jacket - laying out, cutting and sewing TX 28-1-01. The process is calculated "per work jacket". There is no data for energy consumption for a work jacket. It is assumed that energy consumption is approx. 10 times that of a tablecloth (approx. 35 minutes' sewing time vs. approx. 3).
Waste is estimated at approx. 10 per cent. This means approx. 0.77 kg / (1-0.10) = 0.855 kg polyester/cotton fabric, of which 0.555 kg is polyester and 0.300 kg is cotton, must be used. It is assumed that all the waste is discarded (incinerated at a waste incineration plant).
Fabric - inspection and rolling onto a cardboard roll:
There is no company data for woven fabric for a work jacket. It is assumed that data is the same as for woven fabric for a tablecloth (annex 5). Therefore process no. TX 27-3-08-06 is used. Volume: The process is calculated per m². 0.855 kg polyester/cotton fabric is used for making-up the work jacket. An m² weight of 295 g/m² is assumed - this means that 2.90 m² approved textile must be used after the fabric inspection, and this means that the process must use 2.90 m².
Fabric inspection uses 1.015 kg textile per kg approved textile after the fabric inspection. Therefore 1.015 * 0.855 = 0.868 kg textile must be produced (dried and fixed).
Drying, final fixing and setting square-metre weight:
As mentioned above, 0.868 kg textile must be used per work jacket. This corresponds to 2.94 m² textile (dried and fixed) per work jacket weighing 295 g per m².
As there is waste in drying and final fixing, 1010 g dyed fabric per kg dried fabric are used. This means 1.01 kg * 0.868 = 0.877 kg softened textile must be used. This corresponds to approx. 2.97 m² (this figure is needed for weaving, natural sizing agent).
Softening polyester/cotton in jigger:
The process requires 0.877 kg - there is no waste - this means that 0.877 kg coloured textile is needed. This corresponds to approx. 2.97 m² (this figure is needed for weaving, natural sizing agent).
Dyeing polyester/cotton in atmospheric jigger:
0.877 kg is used by this process per work jacket. There is no waste of textile in this process. This corresponds to approx. 2.97 m² (this figure is needed for weaving, natural sizing agent).
Desizing and bleaching of polyester/cotton, jigger:
0.877 kg is used by this process per.
Although the textile loses weight when the sizing agent is washed out (added during weaving process), it is not necessary to adjust for this in the following calculations, as the process weaving, natural sizing agent is calculated as m² - the amount of textile in m² is unchanged. Therefore 2.97 kg woven textile, natural sizing agent is required.
Weaving, natural sizing agent:
This process is calculated per m². As the amount of textile in m² is not changed in this process, although the textile does take up sizing agent during the process, 2.97 m² is required for this process.
As the two processes "weaving, natural sizing agent" and "desizing and bleaching of polyester/cotton, jigger" add and remove the same amount of sizing agent, the start weight of the yarns is 0.877 kg. Thus, 0.877 kg is required for the process "yarn manufacturing (polyester/cotton 65%/35%)".
Yarn manufacturing:
0.877 kg polyester/cotton yarn must be used per work jacket. 0.877 kg textile is required per work jacket for this process - 0.570 kg polyester and 0.307 kg cotton.
For synthetic fibres, waste is approx. 9 per cent. As the yarn contains 65 per cent polyester, 0.570 kg/0.91 = 0.626 kg polyester fibres is required. For carded cotton, waste is approx. 30 per cent (of the raw cotton weight). This means that 0.307 kg * 0.7 = 0.439 kg cotton fibres are required per kg yarn. The waste of polyester fibres is 0.626-0.570 kg = 0.056 kg, and waste of cotton is 0.439-0.307 = 0.132.
In: 0.626 kg polyester fibres + 0.439 kg cotton fibres = 1.065 kg total
Out: 0.877 kg yarn + 0.056 kg polyester fibres (waste) + 0.132 kg cotton fibres (waste) = 1.065 kg total.
Cotton fibres (incl. cultivation and harvest):
0.439 kg is used by this process per work jacket.
Polyester fibres:
0.626 kg is used by this process per work jacket.
Extra components
Plastic zipper:
0.004 kg polyester zipper is used.
Brass zipper:
0.040 kg brass zipper is used.
Brass button:
0.036 kg brass buttons is used (10 of 3.6 g each).
Transport:
All transport distances are estimated. See table below.
Transport |
Quantity for one work jacket |
Kg km |
Materials |
|
|
Transport of polyester fibres from Germany to spinning mill in Poland |
0,626 kg transported 1.000 km by lorry |
626 kg km by lorry |
Transport of cotton from cultivator in China to spinning mill in Poland |
0,439 kg transported 20.000 km by ship |
8.780 kg km by ship |
Transport of 2 zippers from Germany to making-up enterprise in Poland |
0,044 kg transported 1.000 km by lorry |
44 kg km by lorry |
Transport of buttons from Germany to making-up enterprise in Poland |
0,036 kg transported 1.000 km by lorry |
36 kg km by lorry |
Semi-finished goods |
|
|
Transport of yarn from spinning mill in Poland to weaving mill in Denmark |
0,877 kg transported 1.000 km by lorry |
877 kg km by lorry |
Transport of woven fabric from weaving mill to pre-treater and dye house, both in Denmark |
0,877 kg transported 200 km by lorry |
175 kg km by lorry |
Transport of dyed fabric from Denmark to making-up enterprise in Poland |
0,855 kg transported 1.000 km by lorry |
855 kg km by lorry |
Transport from making-up enterprise in Poland to shop in Denmark, lorry (jacket+packaging) |
0,870 kg transported 1.000 km by lorry |
870 kg km by lorry |
Use phase |
|
|
Consumer transport* |
|
3.443 kg km by van |
Disposal phase |
|
|
Transport of discarded work jacket (with household refuse) |
0,850 kg transported 50 km by lorry |
43 kg km by lorry |
’Consumer transport: It is assumed that the consumer has the work jacket delivered by van. It is assumed the supplier drives 50 km (50 km * 0.850 kg = 42.5 kg km by van). As the work jacket is used and washed 40 times during its lifetime, 40 times 50 km transport each way of a work jacket from enterprise to laundry are included (40 * 50 * 2 km = 3,400 kg km by van). Total 3,443 kg km by van.
Lorry, total: 3,526 kg km (assumed 33 per cent urban, 33 per cent out-of-town, 33 per cent motorway). Van, total: 3,443 kg km (assumed 33 per cent urban, 33 per cent out-of-town, 33 per cent motorway).
I.e. total transport:
Process no. in EPIDEX database |
Name of process |
Transport need |
O32715T98 |
Container ship, 2-t 28000 DWT, terminated |
8.780 kg km by ship |
O32695T98 |
Lorry > 16 t, diesel urban traffic, terminated |
1.175 kg km by lorry |
O32694T98 |
Lorry > 16 t diesel out-of-town, terminated |
1.175 kg km by lorry |
O32693T98 |
Lorry > 16 t diesel motorway, terminated |
1.175 kg km by lorry |
O32705T98 |
Van < 3.5 t diesel, urban, terminated |
1.148 kg km by van |
O32697T98 |
Van < 3.5 t diesel, out-of-town, terminated |
1.148 kg km by van |
O32698T98 |
Van < 3.5 t diesel, motorway, terminated |
1.148 kg km by van |
| Front page | | Contents | | Previous | | Next | | Top |
Version 1.0 July 2007, © Danish Environmental Protection Agency
|