| Front page | | Contents | | Previous | | Next |
EDIPTEX - Environmental assessment of textiles
Annex 2: Jogging suit of nylon and cotton
The jogging suit - summary and conclusions
The main scenario for the jogging suit shows that the most significant focus areas are toxicological environmental impacts and resource consumption. The contribution to the toxicological environmental impact potentials originates from fertilizer and insecticides for cotton in fibre production and from production of the artificial fertilizer used. The resource consumption and the contributions to the environmental impact potentials related to energy mainly originate from nylon production and washing and drying of the jogging suit during its use phase.
At an overall level, the scenarios indicate that there are good possibilities for influencing the environmental profile of the jogging suit for both the produce and the consumer.
The producer's options primarily lie in its choice of materials and chemicals. The former is made clear in the scenarios where organic cotton has been used. By living up to European and Scandinavian ecolabelling criteria and obtaining labelling approval, the producer can signal to the conscious consumer that the product in question has been produced in an environmentally sound manner. Moreover, there are a number of production-related improvements that only the producer can influence. This could be choices related to:
- use of organic materials
- development of hard-wearing materials
- choice of softener
- choice of fastness improver
- choice of knitting oil
- use of non-toxic dyes.
The individual consumer's consumption patterns and environmental awareness are also crucial for the jogging suit's environmental profile. Knowledge and choice of ecolabelled products may encourage the producer to produce environment-friendly products as described in brief above. In the use phase, good environmentally friendly habits allow the consumer to affect the overall profile. As the use phase is very dominant, this is an extremely important area.
- choice of the product that has been produced in the most environmentally friendly manner
- most environmentally friendly washing (40/60/90)
- minimal use of washing agent
- no use of fabric softeners
- no tumbler drying.
Thus, the conclusion is that focus should be on the fibre production phase, the production phase and the use phase.
Introduction
Lifecycle assessment is a method for identification and evaluation of environmental impact potentials of a product or a service from cradle to grave. This method enables the user to make an environmental assessment and focus on the most important environmental impacts.
Lifecycle assessment is an iterative process. The first definition of purpose and delimitations often need to be revised during work with lifecycle assessment. The amount of data available sets limits, and consequently the limits of the system are changed.
The method used in this case for assessment of products is "Environmental Design of Industrial Products" (EDIP) and the associated database and PC tool.
In the EDIPTEX project, sector-specific data have been prepared for the textiles sector in connection with the existing EDIP database. The reports contain environmental assessments for the following textile products:
- T-shirt
- Jogging suit
- Work jacket
- Floor covering
- Tablecloth
- Blouse.
These environmental assessments are intended to illustrate the scope for application of the EDIPTEX database by using the PC modelling tool and, at a more general level, application of the EDIP method.
Method
The six case stories vary a lot in scope. They can be divided into two main groups - with variations within these two main groups. The two main groups are:
- Group I: The T-shirt, the jogging suit and the work jacket.
- Group II: The floor covering, the tablecloth and the blouse.
The division into groups I and II relates to the scope of the collection of data as well as the quality of data.
For group I, it was possible to collect (and process) data for all significant processes. The data are of such quality that these three products have been selected to illustrate how far it is possible to take lifecycle assessment for textiles and to illustrate all relevant aspects of the EDIP method.
Each of the three group I cases contains:
- Definition of functional unit and reference product
- Modelling of main scenario
- Preparation of producer and consumer references
- Simulation of environmental impacts caused by choices made by producer and consumer respectively.
Work with these cases has been divided into phases as illustrated in figure 2.1.
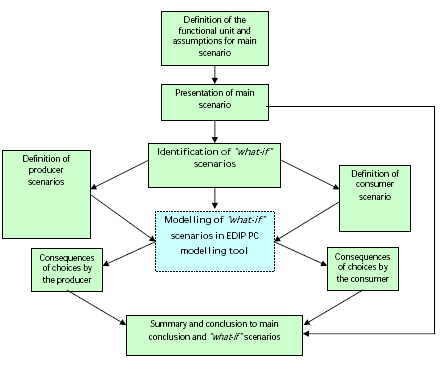
Figure 2.1 EDIPTEX case group I flow diagram
For group II, it was not possible to complete all sub-processes. Although only 1-2 sub-processes for each product have considerable lack of data, these processes are deemed potentially significant for the overall lifecycle assessment. The group II case stories are therefore of an entirely different character than those of group I.
The group II cases illustrate that it is possible to tell an interesting and exciting "environment story" based on lifecycle assessment (and EDIP) even though it has not been possible to analyse all aspects of lifecycle assessment data. This situation will arise very often in lifecycle assessment work. However, there is a significant difference in this EDIPTEX connection; it is possible to draw on results from the three lifecycle assessments from case group I (and this has been done), which improves the quality of the case stories.
Comments to the method
Product references
The "what-if" simulations were carried out to elucidate the consequences of possible changes in the product's lifecycle. A special product reference has been defined for the producer scenarios in some of the case stories. The producer only has limited influence on the use phase. In order to take this into account, a product reference has been prepared for the producer scenarios where only a limited part of the impacts from the use phase has been included in relation to the product reference from the main scenario. This was done in order to give producers a clearer picture of the influence of the production phase on the product's environmental profile in the "what-if" producer scenarios.
Data
With regard to data, it should be noted that the validity of the data in the database varies, depending on the processes considered. A global process like cultivation and harvest of cotton is subject to considerable uncertainty. This is because cotton is produced in countries with very different levels of development. For example, production varies a lot between South America and the US because of large differences in the use of pesticides, crop yields, etc.
This difference has not been taken directly into account in the EDIPTEX database, but a representative level for the data has been defined. Therefore, the data are very general and not necessarily representative for all lifecycle assessments. Other processes are more exact, such as extraction of crude oil for nylon. This process is well documented, both as regards industrial accidents and as regards resource consumption.
Production data primarily come from Danish enterprises. The number of enterprises involved represents limitations in this connection. For example, only one reactive dye and one acid dye have been studied thoroughly. These two substances represent the entire group of dyes, despite the major differences that may occur.
A large proportion of the environmental impacts come from the consumption of electrical energy. The data currently used in the database originate from the EDIP database, and the reference year is 1990. This area is being studied in order to update this part of the database. It is important to note that this lifecycle assessment was carried out using the 1990 data in all processes that consume electrical energy.
The jogging suit
Product description: two-piece jogging suit; trousers and top with outer covering of nylon and lining of uncoloured cotton. Elastic in trouser waist and legs and cuffs in top are not included.
Functional unit
The performance assessed can be described as a "functional unit", comprising a qualitative and a quantitative description, including the product's lifetime.
The qualitative description is to define the quality level for the performance, so that products can be compared at a somewhat uniform quality level. The quantitative description is to determine the size and duration of the performance.
In this project, the functional unit is defined as:
"24 days' use of jogging suit over the course of one year"
Reference product and main scenario
The jogging suit consists of two layers of textile; an outer shell of nylon (also called microfibre) and a lining of uncoloured cotton. Moreover, this assessment includes a zipper in the top. It is assumed that cotton and nylon represent equal parts of the jogging suit as regards weight. Elastic in trouser waist and legs and cuffs has been disregarded due to lack of data for materials and production processes. These assumptions are included in the discussion.
If the jogging suit is washed after each use, 24 days use of the jogging suit means that 1 jogging suit is completely used up in one year. The use of jogging suits varies a lot from consumer to consumer.
The reference product is assumed to meet the following criteria:
- Outer shell of woven nylon
- Nylon dyeing: acid dyes
- Lining of knitted cotton
- Cotton lining assumed to have been pre-washed, softened and bleached after knitting
- Two-piece; top and trousers
- Top includes zipper of polyester (both tape and teeth), approx. 60 cm long - zipper weights approx. 6 g, i.e. 0.1 g per cm.
- No print on the jogging suit
- Wash at 40°C
- Tumbler drying
- Ironing not necessary
- Weight: top weighs 406 g, of which 6 g is the zipper; trousers weigh 300 g. The lining weighs 50 per cent of the total weight, i.e. top: 200 g cotton, 200 g nylon. Trousers: 150 g cotton, 150 g nylon. Total: 350 g nylon and 350 g cotton. Total weight: 706 g.
A more detailed description of the processes, calculations of volumes, waste, etc. can be found in the section "Background data" at the end of this annex.
Product system
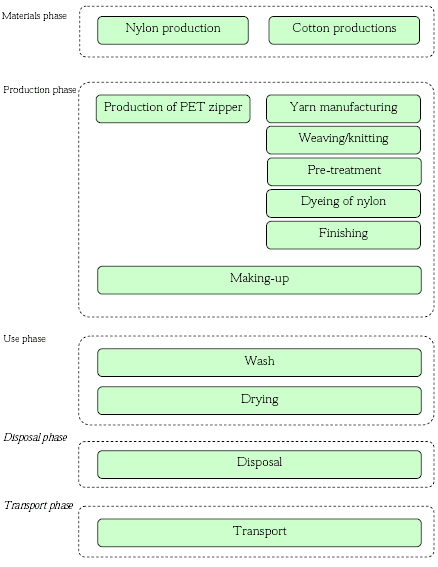
Figure 2.2 Lifecycle, flow and phases
Figure 2.2 describes the lifecycle of the jogging suit. From extraction of raw materials through production to the making-up of the finished jogging suit, the product has two parallel lifecycles due to the two layers of textile, cotton and microfibre.
The product's lifecycle phases from extraction of raw materials to disposal are described in the following.
Manufacture of raw materials
As mentioned, there are two main materials in the jogging suit assessed:
- Cotton
- Nylon (microfibre)
In the following, the lifecycle is described in more detail.
Cotton manufacture
Cotton is cultivated in many countries under different geographical and climatic conditions. Cultivation often entails a large consumption of artificial fertilizer, large water consumption and a large consumption of pesticides against insect attacks, diseases, worms and weeds. The extent of this depends largely on local conditions. The consumption of pesticides entails an important environmental problem for both human health and nature.
Irrigation and use of artificial fertilizer impact groundwater and surface water resources quantitatively as well as qualitatively. Before picking, it is common to use defoliating agents so that picking can be done mechanically.
Organic cotton
It is normally not permitted to use pesticides and artificial fertilizer in cultivation of organic cotton. Thus, it is only permitted to use a very limited selection of plant protection agents, and only when there is an acute danger for the crop. Organic production of cotton constitutes less than 1 per cent of total cotton production, but organic production is increasing and is expected to increase further due to increased demand.
Production of synthetic fibres
Nylon is produced on the basis of crude oil and natural gas that are converted to plastic through a number of chemical processes. The raw material is a limited resource, and production may lead to impacts on humans and the environment at local, regional and global levels. During processing of the materials into fibres, lubricants are usually added in the form of spindle oil and antistatic agents. Bactericides and fungicides may be added.
Production of the jogging suit
Production is divided into several sub-processes: yarn manufacturing, dyeing, finishing, making-up and distribution. Both cotton and nylon go through all these processes, although yarn manufacturing, dyeing and finishing are not the same for the two types of textile.
Yarn manufacturing
The cotton fibres are carded, combed and spun into yarns at a spinning mill. Before the cotton can be spun into yarn, the fibres need to be separated from the remaining plant material. One of the largest environmental risks in this process is inhalation of cotton dust. In just a few years, staff can develop the fatal disease Byssinosis (commonly called "Brown Lung"). It is therefore important that machines be closed in so that dust development is minimal. This also applies for the actual spinning process where the fibres are spun into yarns.
Nylon yarns are produced by extruding the heated nylon granulates into endless yarns; called filament yarns. Then the yarns are split into very thin fibres called microfibres. During the processing into yarn and microfibre, lubricants in the form of spindle oil and antistatic agents are usually added.
Manufacture of fabric
The cotton yarns are knitted on a circular knitting machine for fabric.
The nylon microfibres are woven into fabric, without the use of sizing agents. These are agents that make the yarn stronger. Microfibres give a light and strong textile with a silky, soft feel.
Pre-treatment
The cotton contains dirt and cotton wax that needs to be washed away in order to get a nice and uniform product. Remains of pesticides from cotton cultivation, mainly defoliation agents used in connection with the harvest, are also washed out in this process and end up in the wastewater.
The natural colour of the cotton fibres is removed by bleaching them. If chlorine bleaching is carried out, AOX compounds (adsorbable organic halogens) will be formed and subsequently discharged. They are harmful to the environment. It is also possible to bleach using hydrogen peroxide that does not cause discharges of AOX compounds.
Washing and bleaching with hydrogen peroxide, which is normal in Denmark, has been used as the basis for the environmental assessment of the jogging suit. Moreover, the environmental assessment includes limited discharges of pesticides (0.005 g defoliation agent per kg cotton).
Dyeing
The cotton lining is not dyed. The nylon microfibre textile is dyed with acid dyes. After dyeing, the nylon fabric is treated with fastness improvers. This ensures a good and lasting colour fastness and reduces colour loss when the textile is washed.
Dyes for dyeing textiles are chemically often based on azo groups and may contain heavy metals. Some dyes containing azo groups may release carcinogenic substances of the type arylamines.
A dye from the group of acid dyes without heavy metals and without arylamine problems has been selected for this environmental assessment. The nylon microfibre textile is dyed in a jigger dyeing machine. It has not been possible to collect enough data to carry out an environmental assessment of the fastness improver. Therefore, the properties of this chemical cannot be included in this environmental assessment.
Finishing
For cotton textiles, finishing will normally consist of treatment with a sewability improvement agent (softening) to facilitate the subsequent making-up stage.
The dyed nylon fabric is finished with two types of chemical. The objective is for the surface to become wind-proof as well as water-repellent and dirt-repellent. The chemicals also help improve sewability for the subsequent making-up process.
Chemicals are used to give many textiles specific functional properties in finishing, such as non-iron, water-repellent and fire-retardant. Auxiliary chemicals in these productions often have many extremely adverse properties, both for the environment and for occupational health and safety. Finishing with a fabric softener has been used as the basis for the environmental assessment of the jogging suit.
Making-up
In the making-up stage, there is waste from the cutting-to-size process for the final product. For the jogging suit, waste of 10 per cent is assumed.
Some of the waste products are reused for products of a lower quality, but the main part is sent to waste incineration with heat and energy recovery, which is set off against energy consumption by the production equipment.
Occupational health and safety
The supplier is obliged to reduce the amount of monotonous repetitive work and dust nuisance at work. Cotton dust may cause lung damage, for example.
Distribution
The jogging suit is packed in polyester bags and then on a wood pallet. Finally, it is distributed to retail suppliers.
Use phase
In this environmental assessment of the jogging suit, the main scenario is that it is washed at 40°C without prewash and then tumbler dried.
Disposal phase
Textiles may not be landfilled. On final disposal, they must be incinerated so that the energy content is recovered and replaces non-renewable energy sources like oil and natural gas. In some situations, the used jogging suit will be reused in a third-world country. In such situations, it is not possible to recover energy by incineration in Denmark.
Transport phase
In the environmental assessment of the jogging suit, transport scenarios are included to and from the different processing links in the production chain, and finally from the sewing factory to Danish retailers.
Main scenario - results
The results of the main scenario are presented according to processes. The negative contributions that occur in some processes are due to estimated reuse potentials, resource consumption and contribution to environmental impact potentials. In the processes in question, the contributions can be allocated to other products and thus appear as negative contributions in the jogging suit's environmental profile.
The values in the five figures are not immediately comparable, as the unit is not the same for the five categories. The consumption of primary energy is calculated in mega-joules (MJ), while the resource consumption is shown in the unit "person-reserves". Person-reserves take into account the supply horizon of the individual resources, calculated on the basis of the reserves available in the world in 1990. It should be noted that the data used here are more than ten years old, and therefore, new knowledge about the world's resources may have become available. The environmental impact potentials are presented as "milli-person equivalents" and are directly comparable. Milli-person equivalents are calculated as the direct impact for the year 2000. The weighting factors are based on global (w) or Danish (DK) discharges in the year 2000.
Consumption of primary energy
Figure 2.3 shows that the processes in the use phase represent the majority of the consumption of primary energy. The consumption of primary energy reflects the processes that require a lot of electrical energy or heating air or water. Fibre production consumes a lot of energy due to driving vehicles in the fields and production of artificial fertilizer and pesticides. In the use phase, particularly electricity consumption for washing and tumbler drying cause the impacts.
Resource consumption
The jogging suit consumes a relatively large amount of fossil fuels, partly because of the energy-intensive processes in its lifecycle, and partly because of the production of nylon for the outer shell - see figure 2.4. Nylon is produced from crude oil. As it is assumed that the jogging suit will be used in Denmark, electricity consumption is primarily based on burning coal at coal-fired power plants. In the disposal phase, some resources are credited because energy is recovered that would otherwise have come from burning fossil fuels.
Environmental impact potentials
Environmental impact potentials related to chemicals
Of the three environmental impact categories, those related to chemicals are dominant (see figure 2.5). This is due to the use of pesticides in cotton cultivation, softening of cotton fibres in connection with wet treatment, and use of knitting oil when processing the textiles. The nylon is dyed and surface-treated. Both processes contribute to environmental impact potentials related to chemicals.
In the use phase, primarily detergents in washing agents result in potential persistent toxicity. It is assumed that consumers do not add fabric softeners when washing, and therefore the impact potential probably does not tally completely with the actual conditions in Denmark.
Environmental impact potentials related to energy
The environmental impact potentials related to energy - illustrated in figure 2.6 - are caused by burning fossil fuels in the situations mentioned above.
Waste
The contributions to the waste categories mainly originate from electricity generation.
The conclusion of the lifecycle statement is that the product is resource-intensive primarily because of the large consumption of electrical energy in the use phase.
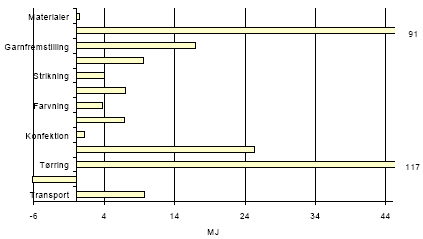
Figure 2.3 Result of main scenario; consumption of primary energy per functional unit – for translation of Danish terms see glossary in annex 11
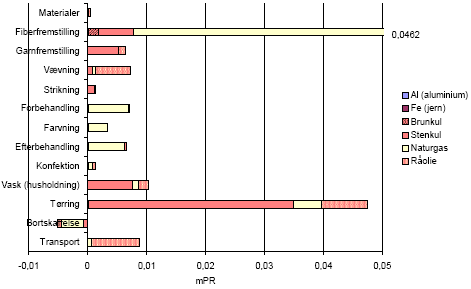
Figure 2.4 Result of main scenario; resource consumption per functional unit – for translation of Danish terms see glossary in annex 11
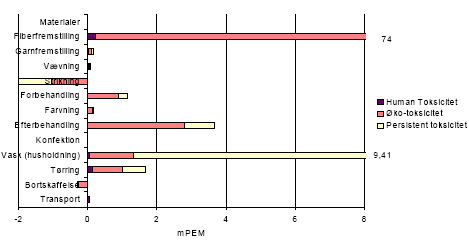
Figure 2.5 Result of main scenario; toxicological environmental impact potentials per functional unit – for translation of Danish terms see glossary in annex 11
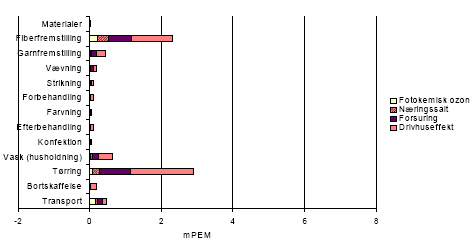
Figure 2.6 Result of main scenario; environmental impact potentials related to energy per functional unit – for translation of Danish terms see glossary in annex 11
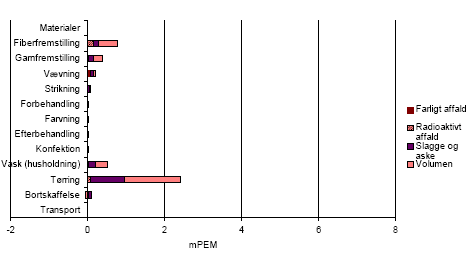
Figure 2.7 Result of main scenario; environmental impact potentials related to waste per functional unit – for translation of Danish terms see glossary in annex 11
Source identification
It is often necessary to study the large information volumes included in the results of a lifecycle assessment in order to achieve the best possible benefit of the assessment. Below is an overview of the most significant contributions to the categories:
- Primary energy
- Resource consumption.
The following three categories have the same unit, and are directly comparable:
- Toxicological environmental impacts
- Environmental impacts related to energy
- Environmental impacts related to waste.
The calculation of the consumption of primary energy does not include production of elastic or sewing of casings etc. for the jogging suit.
There are no data for the materials the elastic is made of.
Primary energy
The consumption of primary energy in the jogging suit's lifecycle phases is distributed as shown in figure 2.3 of the main scenario; consumption of primary energy per functional unit.
Table 2.1 Source identification, primary energy analysed by lifecycle phases
|
Consumption of primary energy/MJ |
Materials phase |
32 % of total primary energy consumption |
Materials |
No significant contributions from the production of the zipper. |
Fiber production |
Almost 100 % of this phase's contribution originates from fibre production. Primary consumption of electrical energy for production of nylon fibres approx. 70 %, while production of cotton fibres represents the remaining 30 %. This primarily originates from cotton cultivation, including transport with tractors etc. |
Production phase |
17 % of total primary energy consumption |
Yarn manufacturing |
Just less than 35 % of the production phase's consumption of primary energy originates from electricity consumption during yarn manufacturing for cotton lining. |
Weaving |
Approx. 20 % of the phase's primary energy consumption originates from the electricity consumption during weaving of nylon filament yarn for the jogging suit's outer shell. |
Knitting |
Consumption originates from the manufacture of cotton lining. Primarily from consumption of Danish electricity, corresponding to approx. 8 % of the phase's consumption from knitting cotton lining. |
Pre-treatment |
The consumption of primary energy in this process originates primarily from consumption of Danish electricity, approx. 14 %. Pre-treatment of cotton requires more energy than pre-treatment of nylon. |
Dyeing |
The consumption of primary energy in this process originates primarily from consumption of electricity in the process and natural gas to heat the process water, approx. 8 %. Only the microfibre is dyed. |
Finishing |
The consumption of primary energy in this process originates primarily from burning natural gas and consumption of Danish electricity, approx. 13 %, primarily from the cotton lining. |
Making-up |
Approx. 2 % of the phase's consumption of primary energy originates from this process. Primarily from production of plastic bags for packaging the jogging suit. |
Use phase |
50 % of total primary energy consumption |
Washing (households) |
18 % of this phase's consumption originates from electricity consumption for heating water in the washing machine |
Tumbler drying |
82 % of this phase's consumption is due to consumption of Danish electricity for tumbler dryers |
Disposal phase |
-2 % of total primary energy consumption |
Incineration |
Credit of the energy recovered by incineration of the jogging suit. |
Transport phase |
3 % of total primary energy consumption |
Transport |
Consumption of fossil fuels for petrol and diesel for various vehicles. |
Fibre production
The primary contribution originates from the production of nylon for the jogging suit's outer shell; raw materials and electricity for the processes. As regards the cotton lining, the most significant contribution originates from driving vehicles in the fields in connection with cultivation and harvest of cotton fibres. A small part originates from production of artificial fertilizer and pesticides. In the model for production of the cotton lining for the jogging suit, transport for spreading fertilizer and pesticides is not included.
Production phase
There are no data for electricity consumption during finishing of the microfibre. Finishing the cotton thus appears to contribute more in this process, but this is not necessarily the case in reality.
Drying
Electricity consumption for drying the jogging suit in a tumbler dryer represents the largest contribution in the entire lifecycle and is thus an important focal point. The consumption of primary energy for the washing machine also represents an important part of total consumption.
Resource consumption
The distribution of resource consumption in the processes in the jogging suit's lifecycle is shown in figure 2.4.
Table 2.2 Source identification of the most resource-intensive processes in the lifecycle of the jogging suit
|
Crude oil |
Natural gas |
Hard coal |
Materials phase |
50 % of total consumption |
70% of total consumption |
11 % of total consumption |
Materials |
1 % originates from extraction of oil for the plastic zipper |
1 % originates from extraction of oil for the plastic zipper, residual product |
No significant consumption |
Fibre production |
99 % of this phase's consumption of crude oil primarily originates from production of artificial fertilizer and pesticides, and transport of fibres |
99 %, primarily from production of artificial fertilizer and pesticides, and transport of fibres |
100 %, primarily from production of artificial fertilizer and pesticides |
Production phase |
16 % of total consumption |
26 % of total consumption |
14 % of total consumption |
Yarn manufacturing |
12 %, primarily for electricity generation for spinning the yarn |
No significant consumption |
66 %, primarily due to electricity consumption |
Knitting |
2 %, primarily due to electricity consumption |
No significant consumption |
15 %, primarily due to electricity consumption |
Weaving |
70 %, primarily due to electricity consumption |
3%, primarily due to electricity consumption |
11 %, primarily due to electricity consumption |
Pre-treatment |
3 %, primarily due to electricity consumption |
40 %, primarily due to electricity consumption |
2 %, primarily due to electricity consumption |
Dying |
2 %, primært til opvarmning af vand primarily for heating water |
18 %, primarily for heating water |
3 %, primarily due to electricity consumption |
Finishing |
3 %, primarily from electrical energy used for drying |
35 %, primarily from electrical energy used for drying the textiles |
1 %, primarily due to electricity consumption |
Making-up |
8 % of this phase's total crude oil consumption due to reuse of textile in another product |
4 % of this phase's total natural gas consumption due to reuse of textile in another product |
1 % of this phase's total coal consumption due to reuse of textile in another product |
Use phase |
19 % of total consumption |
8 % of total consumption |
76 % of total consumption |
Washing (households) |
18 % of this phase's contribution, primarily from consumption of Danish electricity |
18 % of this phase's contribution, primarily from consumption of Danish electricity |
18 % of this phase's contribution, primarily from consumption of Danish electricity |
Drying |
82 % of this phase's contribution primarily originates from electricity consumption from tumbler drying |
82 % of this phase's contribution primarily originates from electricity consumption from tumbler drying |
82 % of the phase's contribution, primarily from electricity consumption from tumbler drying |
Disposal phase |
1 % of total crude oil consumption can be credited |
5 % of the total natural gas consumption can be credited |
1 % of total coal consumption can be credited |
Incineration |
Incineration of the jogging suit recovers energy in the form of heat, and this replaces burning natural gas |
Incineration of the jogging suit recovers energy in the form of heat, and this replaces burning natural gas |
Incineration of the jogging suit recovers energy in the form of heat |
Transport phase |
16 % of total consumption |
1 % of total consumption |
No importance |
Transport |
Consumption of petrol and diesel |
Consumption of petrol and diesel |
|
The consumption of Fe, Al and lignite is very limited. This resource consumption has not been included here. The consumption of natural gas and coal is most important for the environmental profile of the jogging suit. Hard coal is burned in the generation of Danish electricity. Natural gas is primarily used during production of pesticides and artificial fertilizer, and for heating dye baths, while crude oil is used as a raw material for the zipper, but primarily as fuel for various vehicles.
Materials phase
In the fibre production process, primarily the production of pesticides and artificial fertilizer are energy-intensive, and thus represents most of the consumption of crude oil and natural gas. The assumption here is that European electricity is used, and therefore there is no large consumption of coal.
Production phase
Energy-intensive processes like heating water for dyeing and air for drying represent the main part of resource consumption in this phase. The dyeing and finishing processes are equally as energy-intensive. For finishing, this is primarily due to the drying process.
Use phase
The use phase is the most resource-intensive phase in the jogging suit's lifecycle. Electricity consumption represents most of the resource consumption. Washing in a washing machine in a normal household requires energy for heating the washing water. Tumbler drying requires a lot of electrical energy. Danish electricity is primarily based on burning coal, while space and water heating are often based on burning natural gas and oil.
Disposal phase
Energy is generated when the jogging suit is incinerated, and this replaces fossil fuels. However, resources for the operation of the plant are consumed at the same time.
Transport phase
The main contributions in this phase are small. They originate from consumption of crude oil for production of diesel and petrol. In this case, we have assumed that the jogging suit is transported to the private household by car, but that other goods are bought at the same time.
Toxicological environmental impacts
The background for the statement of the environmental impacts related to chemicals is not complete. The EDIPTEX database does not contain data for the chemicals used for surface treatment of the microfibre (nylon). The data basis as also limited for the acid dyes, and therefore, the environmental impacts related to chemicals will seem less than they actually are in the dyeing process.
Environmental impact potentials, toxicity, divided into the lifecycle phases of the jogging suit can be seen in figure 2.5 of the main scenario.
Table 2.3 Source identification for individual toxicity categories
|
Human toxicity |
Ecotoxicity |
Persistent toxicity |
Material phase |
Approx. 45 % of the total impact potential originates from this phase |
Approx. 98 % of the total impact potential originates from this phase |
Approx. 87 % of the total impact potential originates from this phase |
Fiber production |
Primarily from pesticides, emissions into the air. |
100 % of this phase's contribution originates from pesticides in cotton cultivation |
Approx. 90 % of this phase's contribution originates from pesticides in cotton cultivation |
Production phase |
Just under 10 % of the total impact potential can be attributed to this phase |
The negative contributions from knitting and making-up due to the reuse potential reduce this phase's total contribution to 0.1 %. |
In total, a negative contribution due to reuse potential for knitting and making-up |
Yarn manufacturing |
Approx. 50 % of this phase's contribution is due to electricity consumption for spinning cotton yarn |
Approx. 6 % of this phase's positive contribution is due to electricity consumption |
Approx. 10 % of this phase's positive contribution to the impact potential is due to electricity consumption when spinning the yarn |
Weaving |
27% |
2% |
|
Knitting |
6% |
Credit of impact potentials due to recycling options in this process |
Credit of impact potentials due to recycling options in this process |
Pre-treatment |
Approx. 6 % of this phase's contribution is due to electricity consumption |
78 % of this phase's total positive contribution originating from |
20 % of this phase's positive contribution originates from the washing agent used before the yarn is dyed |
Dying |
Approx. 4 % of this phase's contribution is due to electricity consumption |
Dyeing represents 13 % of this phase's total positive contribution originating from the use of acid dyes. |
2 % of this phase's positive contribution to the toxicity potential is due to the use of reactive dyes and electricity |
Finishing |
Approx. 4 % of this phase's contribution is due to electricity consumption |
This process contributes with the largest ecotoxicity potential, 1 % of the phase's positive contribution in this phase is due to the softening process. |
Approx. 65 % of this phase's positive contribution to the toxicity potential is due to the use of fabric softener. |
Making-up |
Credit of impact potentials due to recycling options in this process |
Credit of impact potentials due to recycling options in this process |
Credit of impact potentials due to recycling options in this process |
Use phase |
Approx. 37 % of total contribution |
Approx. 3 % of total contribution |
Approx. 15 % of total contribution |
Washing |
Approx. 82 % of this phase's impact potential originates from the washing agent |
Approx. 60 % of this phase's impact potential originates from the washing agent |
92 % of this phase's impact potential originates from detergents in the washing agent |
Tumbler drying |
Approx. 18 % of this phase's contribution is due to use of Danish electricity |
Approx. 40 % of this phase's impact potential is due to electricity consumption for tumbler dryers |
Approx. 7 % of this phase's contribution is due to electricity consumption for tumbler dryers |
Disposal phase |
Negative contribution due to recovery of energy |
Negative contribution due to recovery of energy |
Negative contribution due to recovery of energy |
Incineration |
|
|
|
Transport phase |
8 % of total impact potential |
No significant contribution |
No significant contribution |
Transport |
From burning fossil fuels |
|
|
In the production phase, knitting and making-up are assumed to contribute with a reuse potential that can be credited to fibre production. This means that the production phase has a net negative contribution to ecotoxicity and persistent toxicity impact potentials. In the table, the positive contribution from the production phase has only been calculated and used as a total value. The contribution from the actual phase is calculated on the basis of the total potential, i.e. including the negative contribution.
Materials phase
The most significant factors in this calculation are the ecotoxicity and the persistent toxicity from cotton cultivation. The high impact potentials are due to the use of pesticides: herbicides, insecticides, fungicides, growth regulators and defoliation agents.
Production phase
Pre-treatment of the nylon textile does not require the same amount of auxiliary chemicals, and therefore, pre-treatment should be regarded as two separate and different processes.
Use phase
Detergents in washing agents result in contributions primarily to human toxicity and persistent toxicity. Moreover, there is a small contribution to ecotoxicity (primarily from alcohol ethoxylate). However, it is important to mention that the contributions from this phase are small compared to the contributions from fibre production.
Electricity generation also contributes to the toxicity categories. Mining operations release some undesired substances to the environment, such as strontium.
Environmental impacts related to energy
The potential environmental impacts related to energy from the jogging suit's lifecycle phases are distributed as shown in figure 2.6 of the main scenario, toxicological environmental impact potentials per functional unit.
Table 2.4 Source identification for environmental impact potentials related to energy
|
Greenhouse effect |
Acidification |
Nutrient loading |
Photochemical ozone formation |
Materials phase |
28 % of total contribution |
30 % of total contribution |
44 % of total contribution |
41 % of total contribution |
Materials |
No significant contribution |
No significant contribution |
No significant contribution |
3 per cent originates from extraction of crude oil for the zipper |
Fibre production |
100 %, originating primarily from burning fossil fuels and energy for production of N artificial fertilizer |
100 %, originating primarily from burning fossil fuels and energy for production of N artificial fertilizer |
100 %, originating from burning fossil fuels and energy for production of N artificial fertilizer |
97 %, originating from burning fossil fuels |
Production phase |
15 % of total contribution |
12 % af det samlede bidrag of total contribution |
10 % of total contribution |
11 % of total contribution |
Yarn manufacturing |
41 % of this phase's contribution originates from electricity consumption in this process |
51 % of this phase's contribution originates from electricity consumption in this process |
47 % of this phase's contribution originates from electricity consumption in this process |
The main part, approx. 20 %, of this phase's contribution originates from unburnt fuels in connection with transport |
Knitting |
9 % of this phase's contribution is due to electricity consumption |
10 % of this phase's contribution is due to electricity consumption |
9 % of this phase's contribution is due to electricity consumption |
Not significant |
Weaving |
19 % of this phase's contribution is due to electricity consumption |
24 % of this phase's contribution is due to electricity consumption |
19 % of this phase's contribution is due to electricity consumption |
20 % |
Pre-treatment |
10 % of this phase's contribution is due to electricity consumption |
5 % of this phase's contribution is due to electricity consumption |
8 % of this phase's contribution is due to electricity consumption |
16 % of this phase's contribution is due to incompletely burnt fuel in connection with transport |
Dying |
6 % of this phase's contribution is due to electricity consumption |
3 % of this phase's contribution is due to electricity consumption |
6 % of this phase's contribution is due to electricity consumption |
8 % of this phase's contribution, due to incompletely burnt fuel in connection with transport |
Finishing |
10 % of this phase's contribution is due to electricity consumption |
4 % of this phase's contribution is due to electricity consumption |
8 % of this phase's contribution is due to electricity consumption |
16 % of this phase's contribution is due to unburnt fuel in connection with transport |
Making-up |
5 % |
3 % |
3 % |
20 % due to incomplete burning fossil fuels |
Use phase |
50 % of total contribution |
51 % of total contribution |
36 % of total contribution |
16 % of total contribution |
Washing (households) |
18 % of this phase's impact contribution originates from electricity consumption for heating water in the washing machine |
18 % of this phase's impact contribution originates from electricity consumption for heating water in the washing machine |
18 % of this phase's impact contribution originates from electricity consumption for heating water in the washing machine |
18 % of this phase's impact contribution originates from electricity consumption for heating water in the washing machine |
Tumbler drying |
82 % of this phase's impact potential is due to the consumption of electricity for tumbler dryers |
82 % of this phase's impact potential is due to the consumption of electricity for tumbler dryers |
82 % of this phase's impact potential is due to the consumption of electricity for tumbler dryers |
82 % due to incomplete burning in connection with transport |
Disposal phase |
4 % of total |
No significant contribution or credit |
No significant contribution or credit |
Approx. 3 % of this phase's total contribution originates from incineration of the jogging suit |
Incineration |
|
|
|
|
Transport phase |
3 % of total contribution |
7 % of total contribution |
1 % of total contribution |
29 % of total contribution |
Transport |
Transport with diesel and petrol driven vehicles |
Burning fossil fuels |
Burning fossil fuels |
Burning fossil fuels |
Incomplete burning contributes to photochemical ozone formation, while burning fossil fuels generally contributes to all categories.
Materials phase
Burning fossil fuels for transport of the cotton fibres and electricity consumption in production of artificial fertilizer and pesticides are the main causes of the environmental impact contributions from this phase.
Production phase
In this phase, electricity consumption again represents the main part of the impact potentials. Especially the yarn manufacturing process is energy-intensive.
Use phase
The phase when the jogging suit is consumed is the absolute main contributor to the environmental impact potentials related to energy. This is caused by electricity for tumbler dryers and heating water for washing machines. Energy consumption from production of washing agents has not been included. If this had been included, the contribution from this phase would have been even larger. This result indicates that the consumer has considerable influence on the jogging suit's overall environmental profile.
What-if simulations
The environmental profile for a given product - in this case a jogging suit - can be affected by the choices made by the producer and by the consumer. In order to elucidate the consequences of possible changes in the product's lifecycle, a number of scenarios have been prepared that focus on the producer and consumer respectively.
By changing one or more of the reference conditions, it is possible to form a picture of the scope of the consequences based on the choices made. These changes are illustrated graphically by means of lifecycle statements within five categories, as described in the following section. The following scenarios have been prepared taking into account the producer's and the consumer's influence on the environmental profile of the product.
Consequences of choices by the producer
The producer influences all processes from extraction of raw materials until the finished product leaves the distribution phase. To some extent, the producer can affect the processes in the use phase. However, it is not possible for the producer to affect all consumers of the product equally. In order to take this into account, a product reference has been prepared for the producer scenarios where only a limited part of the impacts from the use phase has been included.
The revised use phase contains: washing after use as defined in the functional unit. No use of fabric softener when washing in private households, and tumbler drying after 50 per cent of washes. It is assumed that the jogging suit is drip-dried the remaining times.
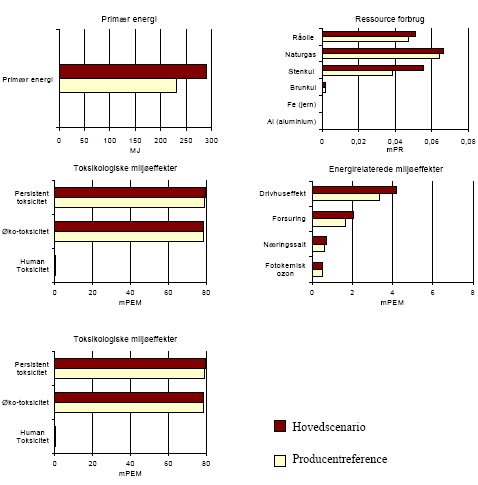
Figure 2.8 The producer reference in relation to the main scenario – for translation of Danish terms see glossary in annex 11
Figure 2.8 shows that the producer reference scenario has a 20 per cent lower consumption of primary energy per functional unit than the main scenario. This is due to lower consumption of electricity in the use phase, due to the reduced tumbler drying. For the same reason, the consumption of fossil fuels and the environmental impacts related to energy are reduced, both categories by between 10 and 30 per cent, the main part for coal.
The toxicological environmental impacts are only reduced by a few per cent, as cotton cultivation and use of softeners and dyes in the production of the jogging suit outweigh the contributions from coal-fired power plants.
In the following, the results of the producer-related scenarios are presented as summarised contributions over the entire lifecycle and compared with the producer reference scenario.
Scenarios - producer
Raw materials phase
Scenario 1: Choice of raw materials - Organic cotton lining
Production phase
Scenario 2: Choice of chemicals - dyes for cotton lining
Scenario 3: Choice of chemicals - choice of acid dyes
Scenario 4: Choice of chemicals - choice of dyes, 10 per cent dyeing
Scenario 5: Choice of chemicals - choice of fabric softener
Scenario 6: Choice of chemicals - use of fastness improver
Scenario 7: Choice of chemicals - use of extra knitting oil
Use phase
Scenario 8: Influence on product quality - 20 per cent colour loss
Scenario 9: Influence on product quality - colour staining
Scenario 10: Influence on product quality - reduced lifetime
Scenario 11: Influence on use phase - no tumbler drying
Scenario 1: Choice of raw materials - organic cotton
The toxicological environmental impacts are the environmental impact potentials with the highest weight in the life of the jogging suit. The contributions to this category have been ascertained as primarily due to use of pesticides and spreading artificial fertilizer during cotton cultivation.
For conventional cotton cultivation about 18 g pesticides are used per kg cotton in the worst case. The main scenario applies an estimated average of the pesticide volumes from cotton cultivation in the US and South America. The impact of pesticides on the environment has been assessed, and the factors have been included in the database. Pesticide residues can cause toxic impacts in humans during processing of the cotton fibres, as the oil used in this process is used for cooking in some countries. In this way, the pesticide residues end up in food and thus in people. The residues are assumed to be washed out of the cotton during wet treatment.
In order to assess the significance of the chemicals used in conventional cotton cultivation, the material is changed to organic cotton. In this way, the use of pesticides and artificial fertilizer is avoided and wash-out of pesticides during cotton fibre processing is also eliminated. In production of organic cotton fibres, no chemicals are used for bleaching in pre-treatment, and this leads to another reduction of the toxicological environmental impact potentials.
A further benefit is that the transport required to spread these substances on the field also disappears. This transport is not, however, included in either the main or the producer reference scenarios, due to the large differences between the cotton-producing countries. In some countries, vehicles only drive in the fields a few times per cultivation round. In other countries, typically South American countries, it is common to drive more in the fields to secure the crop yield. Less transport reduces consumption of fossil fuels and is therefore also part of the environmental impacts related to energy.
Consumption of primary energy does not change significantly because of the changed choice of raw materials. This is because most of the energy consumption arises from processes in the production and use phases and these do not change in this scenario. In total, energy consumption falls by 2-3 per cent for the changed choice of raw materials.
The toxicological environmental impacts are significantly reduced using organically cultivated cotton. Persistent toxicity is reduced by about 80-85 per cent, while ecotoxicity is reduced by up to 95 per cent compared with the reference scenario.
The environmental impacts related to energy, greenhouse effect, nutrient loading, and photochemical ozone formation are reduced by a small percentage, approx. 2-5 per cent. The reason is that there is no longer a contribution to these potentials from production of artificial fertilizer and pesticides. The same applies for the waste categories.
Conclusion to scenario 1 - organic cotton is recommended
It can be concluded that the producer has great possibilities to influence the overall environmental profile of the textile, especially the toxicological environmental impact potentials. Use of organic cotton rather than conventionally cultivated cotton to the greatest possible extent can clearly be recommended. It should also be considered that many of the agents used during cultivation of cotton are harmful to human health. Incorrect or careless use could mean that suppliers expose themselves and their employees to health hazards. Pesticide residues washed out in several pre-treatment processes are yet another reason to avoid conventionally cultivated cotton.
Scenario 2: Choice of chemicals - dyed cotton lining
The toxicological environmental impacts are the environmental impact potentials with the highest weight in the life of the jogging suit. The contributions to this category primarily originate from pesticides used in cotton cultivation, dyeing of textiles, and use of fabric softeners in the production and use phases.
In the reference scenario, it is assumed that the lining is not dyed. This scenario illustrates the environmental importance of dyeing the cotton lining.
The number of environmental equivalency factors for reactive dyes is limited in the EDIPTEX database. It is therefore important that the results of this scenario be regarded as a guide. There may be other equally common dyes that contribute more, or less, to the toxicological environmental impacts than those included here.
Cotton is dyed with reactive dyes. The model assumes that the cotton is dyed with 3 per cent dye, that 85 per cent of the dye dose is adsorbed to the textile, and that the remainder is discharged via treatment plants into water and soil. It is also assumed that the dyes are not washed out in the use phase.
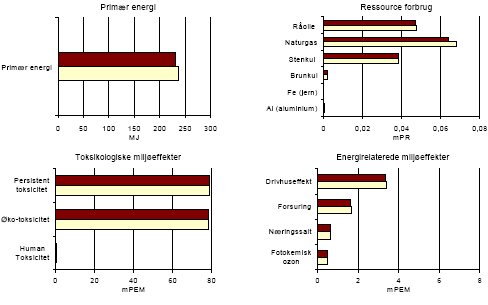
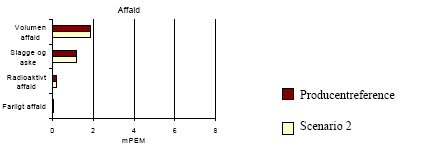
Figure 2.9 Result of scenario 2 – for translation of Danish terms see glossary in annex 11
The figure shows that the total impact is limited. The consumption of primary energy increases 2 per cent, as is the case for the environmental impacts related to energy. As regards resources, consumption of natural gas increases the most, by about 6 per cent. Natural gas is used to heat water etc. in the dyeing process.
Overall, the contributions to human toxicity increase by 0.5 per cent, while both persistent toxicity and ecotoxicity increase by less than 0.1 per cent if the lining is dyed. If only the contributions to toxicological environmental impacts from the dyeing process are considered, there is an increase of 130 per cent in human toxicity, 11 per cent in ecotoxicity and 50 per cent in persistent toxicity. Thus, dyeing the cotton lining of the jogging suit influences the product's environmental profile related to production greatly.
Conclusion to scenario 2 - impact on energy consumption and toxicological environmental impacts
Dyeing cotton has a toxicological impact on the environment. In this scenario, the assumption is that no dye is washed out during the use phase. In practice, this means that the washing out that does occur is disregarded. The production, distribution, storage and use of the dye have an undesired environmental impact on the product's environmental profile. These data are not available in the database, and therefore the impact of a cotton dye is larger than indicated by the results of this scenario.
In total, energy consumption increases by approx. 3 per cent when the cotton lining is dyed. This is a considerable increase, when we take into account that this is a single process in the production phase. It can be concluded that dyeing the lining should be avoided.
Scenario 3: Choice of chemicals - choice of acid dyes
The microfibre is dyed with acid dyes after the textile has been woven. Dyes add to the toxicological environmental impact potentials, although to a smaller extent than pesticides and artificial fertilizer from cultivating cotton. The database only includes equivalency factors for a single acid dye, and in the producer reference, the dyes are all allocated the same equivalency factors. Note that the limited knowledge on large parts of the dye range means that these models should not be regarded as representative for the whole group of dyes, but rather be seen as guides.
It is also assumed in the producer reference that 85 per cent of the dye dose adsorbs to the textile, the rest is discharged with wastewater to a treatment plant, where 13 per cent is discharged into water and 87 per cent into the soil. The dyes primarily contribute to ecotoxicity.
Click here to see the Figure.
Figure 2.10 Result of scenario 3 - small reduction of environmental impact potentials related to chemicals – for translation of Danish terms see glossary in annex 11
This scenario assumes that acid dyes do not add to the toxicological environmental impacts. As data for production is not included in the database, dyes do not appear in the model for this scenario.
It can be ascertained that the contributions of the dyes to toxicological environmental impact potentials are not very important at an overall level. Note that only one acid dye forms the basis for the contribution in the producer reference. Persistent toxicity is reduced by just less than 1 per cent, which is also the case for ecotoxicity. Human toxicity is unchanged.
In the dyeing process alone, the contributions are reduced by approx. 35 per cent. The remaining contribution from the process is due to consumption of electricity and heat.
Conclusion to scenario 3 - obtain more knowledge about acid dyes
Therefore, it can be concluded that the producer should focus on acquiring knowledge on the dyes used and their impact and degradability in the environment. The factors in this tool can be used as standards of reference and can thereby form the basis for choosing more environmentally friendly acid dyes.
Scenario 4: Choice of chemicals - choice of dye: 10 % dyeing
In the producer reference, the microfibre is dyed with 1 per cent acid dye, which corresponds to the amount of dyestuff used to dye in paler shades. This scenario illustrates the impact of a dark dye (worst case) of 10 per cent.
It is assumed that 85 per cent of the dye dose adsorbs to the textile and the remainder is led through wastewater treatment as in the reference scenario. As ten-times as much dyestuff is used in this scenario, ten-times as much dyestuff is discharged than in the reference scenario. The model assumes that dyestuff is not washed out during the use phase.
Click here to see the Figure.
Figure 2.11 Result of scenario 4 - increased contribution to toxicological environmental impact potentials – for translation of Danish terms see glossary in annex 11
It is assumed that the same amount of textile as in the reference scenario can be reused directly from the knitting and making-up phases. As in scenario 2, there is only data for one single acid dye, and therefore the scenario should not be regarded as representative for the whole group of acid dyes.
The graphs show that the larger amount of dyestuff leads to an increase in the total contribution to the toxicological environmental impact potentials of about 1-2 per cent. This does not seem to be a lot, but considering that this is solely due to an increase in the concentration of dyestuff in the outer shell of the jogging suit, this is an important focus point for the producer.
The production of 10 per cent more dyestuff per functional unit leads to an increase of 0.1 per cent in coal consumption. A similar increase is seen for the environmental impact potentials related to energy and for waste categories.
Conclusion to scenario 4 - large impact in dyeing process, less at overall level
It can be concluded that the amount of dyestuff per functional unit has an impact on the overall environmental profile for the product. If we look specifically at the production phase, we see increases of 5-50 per cent, which makes this an important focus point for the producer. The producer can encourage the supplier of acid dyes in a more environmentally friendly direction by making requirements for the environmental profile of the dyes.
Scenario 5: Choice of chemicals - choice of fabric softener
Both cotton and nylon are softened during the production phase. This scenario illustrates the impact of choice of fabric softener as well as the significance of any washing out of the fabric softener in the use phase. The producer reference includes the most commonly used fabric softener in the model for the lifecycle of the jogging suit. This chemical is the most toxic of the two fabric softeners in the EDIPTEX database. It is assumed that 85 per cent of the added amounts adsorbs to the textile and is not washed out in the use phase. It is also assumed that the two types of textiles are softened using the same chemical.
The producer is able to use fabric softeners of any toxicity. Therefore it is assumed that a less toxic chemical is used. Just as in the producer reference, it is assumed that 85 per cent of the chemical added adsorbs to the textile and that the fabric softener is not washed out during the use phase.
The producer has several possibilities to change the softening process, which can be carried out using different techniques.
- Addition of fabric softener in a wet treatment process.
- Fabric softener can be sprayed on the woven or knitted textile through nozzles.
- Lengths of textile can be led through a bath containing fabric softener that adsorbs to the material.
- Mechanical softening of the textile lengths where the fibres are softened through repeated mechanical treatment.
Data for the manufacture of fabric softeners is not included, and therefore only the toxicological environmental impact potentials are changed in relation to the reference scenario.
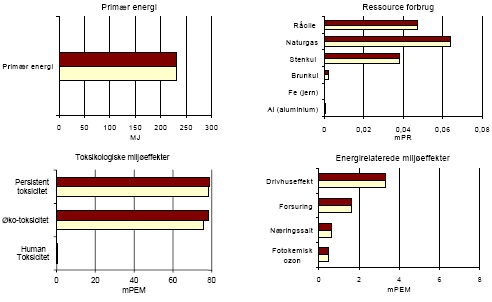
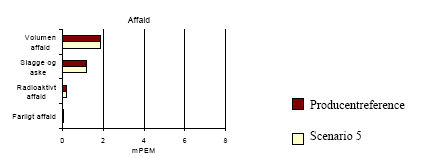
Figure 2.12 Result of scenario 5 - reduced toxicological environmental impact potentials – for translation of Danish terms see glossary in annex 11
The figure shows that the choice of a less toxic fabric softener has a total impact of 1-4 per cent, highest for ecotoxicity. This impact does not seem higher because of the very high contributions to these categories from cotton cultivation. If we only look at the production phase, the toxicological environmental impact potentials are reduced by more than 90 per cent, highest for ecotoxicity.
Conclusion to scenario 5 - choice of fabric softener is important
The choice of fabric softener has a limited effect at an overall level, but the effect is large on the product's environmental profile, if the production phase is regarded separately. Thus, this is an area where the producer has a direct possibility of improving the product's environmental profile.
Legislation on ecolabelling indicates the substances that should be phased out, and those which should be avoided completely from an environmental perspective. This could be a guide for environmental work at the individual enterprise. It should be noted that this scenario only deals with the amount of fabric softener used during the pre-treatment of the textile.
Scenario 6: Choice of chemicals - use of fastness improver
In order to achieve a better quality cotton jogging suit, the textile can be treated with fastness improvers in the same bath as the fabric softener. This process means that the coloured textile retains its colour better during washing than textiles that are not treated with fastness improvers.
In order to illustrate the significance of this process, this scenario includes the assumption that the fastness improver is allocated the same toxicity factors as the fabric softener used in the producer reference, as no equivalency factors have been prepared specifically for fastness improver. It is assumed that 85 per cent of the amounts added adsorbs to the textile, while the rest is led through a treatment plant and discharged into the environment.
It is also assumed that the same chemical can be used for colour fastening of cotton and nylon.
On the basis of previous models for a cotton T-shirt, the use of fastness improver is assessed to have less influence at an overall level, but significant influence in the production phase. Compared with the producer reference, the contribution to ecotoxicity increases by almost 2 per cent, while the contribution to persistent toxicity increases by almost 1 per cent.
As in scenario 3, the contributions are overshadowed by the large environmental impact potentials from fibre manufacture. If the jogging suit were manufactured from organic cotton, the contribution from the fastness improver would seem more significant.
Conclusion to scenario 6 - reduce use of fastness improvers
The conclusion to scenario 6 is that use of fastness improvers does not change the environmental profile of the jogging suit significantly. However, it should be noted that energy consumption in manufacture of the chemical has not been included in the calculations and therefore use of fastness improvers in industry will influence resource consumption and energy-related environmental impact potentials which are not illustrated here. For the production phase alone, the contribution to the toxicological environmental impact potentials is considerable, and therefore there should be special focus on minimal use of these auxiliary chemicals.
Scenario 7: Choice of chemical - use of knitting oil
In the knitting process for the cotton lining, an easily degradable, vegetable knitting oil is used for the reference product. This scenario will illustrate the influence it would have, if a mineral knitting oil that is difficult to degrade were used.
Data for the manufacture of knitting oils is not included, and therefore only the toxicological environmental impact potentials are changed in relation to the reference scenario.
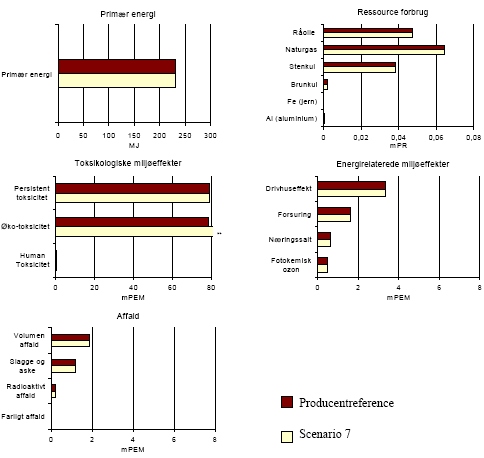
Figure 2.13 Result of scenario 7 – for translation of Danish terms see glossary in annex 11
The figure shows that the use of a mineral knitting oil that is difficult to degrade increases the overall toxicological environmental impact potential of ecotoxicity by 4 per cent. The impact does not seem higher because of the very high contributions to these categories from cotton cultivation. If we look at the production phase alone, the toxicological environmental impact potentials increase by just under 500 per cent for ecotoxicity.
Conclusion to scenario 7 - use easily degradable vegetable knitting oils
It can be concluded that the use of mineral knitting oils that are difficult to degrade should be limited as much as possible.
Scenario 8: Choice of chemicals - 20 per cent colour wash-out during use phase
A number of residual chemicals that are left in the textile from the production process will often be washed out during the use phase. This also includes dyestuffs. In the producer reference, the nylon microfibre is dyed with 1 per cent acid dye, which corresponds to a minimum of dye. However, there will often still be residual dye in the textile.
In this scenario, the assumption is that 20 per cent of the dyestuff is washed out during the use phase. This corresponds to 17 per cent of the total volume used.
There are only data for one single acid dye, and therefore the scenario should not be regarded as representative for the whole group of acid dyes. Similarly, it is uncertain how much the dye percentage used in production influences the percentage of colour washed out.
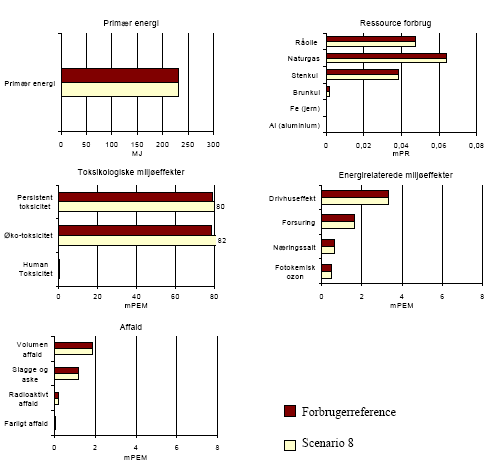
Figure 2.14 Result of scenario 8 - increased contribution to toxicological environmental impact potentials – for translation of Danish terms see glossary in annex 11
The graphs show that the larger amount of dyestuff washed out leads to an increase in the total contribution to the toxicological environmental impact potentials of about 1-2 per cent. This does not seem to be a lot, but considering that this is solely due to the dyeing method and the choice of dye for the outer shell of the jogging suit, this is an important focus point for the producer.
There are no other changes as the wash-out does not lead to further consumption. However, there will be further savings if the dose of dyestuff can be reduced by changing the production method - and give the same result.
Conclusion to scenario 8
It can be concluded that wash-out of dyestuff in the use phase per functional unit has an impact on the overall environmental profile. If we regard the production phase specifically, it is possible to reduce the use of dyestuffs, and this makes it an important focus point for the producer.
Scenario 9: Influence on product quality - colour staining
The quality of the dyeing, colour fastness, is important for the quality consumers perceive in the product.
This scenario illustrates the impacts on the overall environmental profile of the jogging suit if it ruins an entire machine wash once in its lifetime because the colour migrates to the other textiles in the wash. It is assumed that each wash includes 4.9 kg textiles of the same composition as the jogging suit, i.e. equal amounts of cotton and nylon plus a small amount of polyester. It is also assumed that all the washed textiles are unfit for use after the colour migrates.
The modelling is carried out by assuming that the wash is composed of 7 jogging suits of the type described. Therefore, 7 jogging suits of 706 g each must be produced, transported and disposed of. The use phase of the spoiled textiles is not included in the calculations, i.e. only the use phase for the reference product is included in the model, as it is assumed that it is not spoiled.
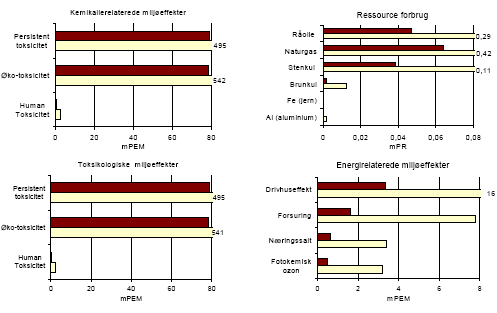
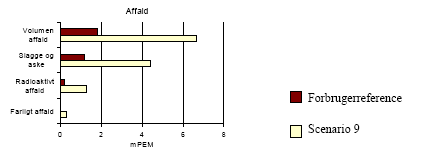
Figure 2.15 Result of scenario 9 – for translation of Danish terms see glossary in annex 11
Production of the increased volume of textiles causes an increase in consumption of primary energy of just under 500 per cent. The toxicological environmental impacts increase by 5-700 per cent, and the same trend is apparent for the remaining categories.
Conclusion to scenario 9 - the contributions from the production processes outweigh the contributions from the use phase.
The scenario indicates that the use phase of the individual jogging suit, otherwise dominant in connection with consumption of fossil fuels and environmental impacts related to energy and waste, is now outweighed by the processes in the production phase.
On the basis of this, it can be concluded that the colour fastness of textiles of this type is very important. Alternatively, the producer can inform consumers about the risk of colour being transferred to other textiles, whereby the consumer is given the responsibility of washing the jogging suit separately one or more times. Then, this should be included in the product's overall environmental profile as a higher impact from washing in the use phase.
Scenario 10: Influence of product quality - reduced lifetime
Product quality influences the lifetime of the product. Colour fastness, durability of the fibre and stitching are examples of areas on which the durability and quality of the product can be judged. In relation to lifecycle assessments, the quality of the product will be important for the manufacture and disposal phases, as these are extended/reduced in order to meet the functional unit.
Scenario 10 is based on halving the lifetime of the jogging suit compared with the producer reference. The assumption results in doubling fibre manufacture, production, disposal and transport as two jogging suits are now required to meet the functional unit.
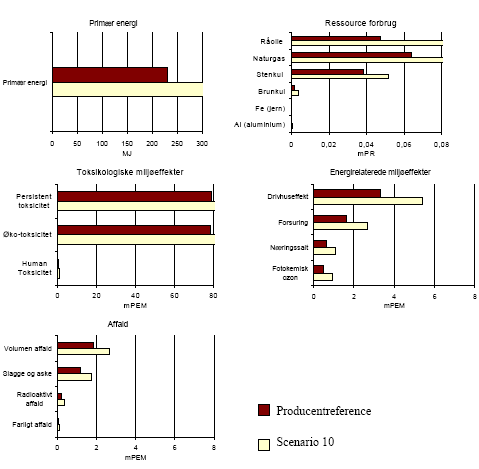
Figure 2.16 The producer reference in relation to the main scenario – for translation of Danish terms see glossary in annex 11
The great importance of lifetime is clear. The consumption of primary energy increases by approx. 30 per cent. Resource consumption is increased correspondingly, crude oil by 66 per cent, natural gas by 76 per cent, and coal by 11 per cent. This is due to increased consumption of electricity for production of the extra jogging suit. The contribution to the energy-related environmental impacts as a consequence of this increases by about 26 - 86 per cent. The waste categories increase by about 30 per cent for the same reasons.
The toxicological environmental impact potentials are increased by 40 per cent, and again the increased production of cotton is the determining factor in this context for the toxicity potentials, and the increased consumption of fabric softeners in the production phase. Contributions from electricity generation to toxicological environmental impact potentials are limited.
Conclusion to scenario 10 - lifetime is important
The conclusion to this scenario is that the quality of the jogging suit is an important focus point for the producer. It is decisive for the overall environmental profile, in particular with regard to consumption of primary energy and thus fossil fuels and the energy-related environmental impacts.
The toxicological environmental impacts also increase considerably, primarily because of the doubling of the amount of cotton per functional unit. One possibility to improve the environmental profile, despite reduced lifetime is organised reuse of the material. As the product consists of two types of textile, a high degree of recycling would require separation of the textile types.
The lifetime of the textile is not only determined by the producer, the consumer also has a great influence on this parameter.
Scenario 11: Influence of the use phase - no tumbler drying
The use phase has a great influence on the overall environmental profile of the jogging suit. Therefore, it is desirable that the producer improve the properties of the product to reduce the environmental impacts in this phase. As can be seen in the producer reference, electricity consumption has most significance, more specifically in the drying process. The producer reference assumes that the jogging suit is dried in a tumbler dryer for half of the washes.
This scenario assumes that the jogging suit is always hung up to dry on a clothesline and drip-dried. Emissions into the air from this process have not been included. The model simulates the change by setting the drying process at zero.
The possibilities for the producer to influence the drying method chosen by the consumer could include processing, weaving, or knitting the textile so that the textile retains less water after centrifuging in the washing machine. This will reduce the need for drying and more consumers will probably drip-dry the product.
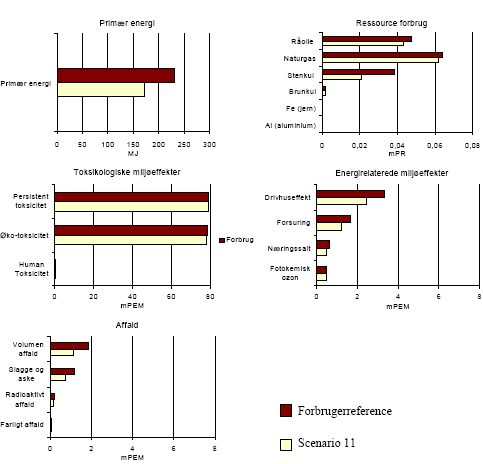
Figure 2.17 Result of scenario 11 - Significant reductions – for translation of Danish terms see glossary in annex 11
The figure shows that drying in a tumbler dryer has a great influence on the overall consumption of primary energy, and this is reduced by approx. 25 per cent. Consumption of resources is also reduced, consumption of crude oil by approx. 10 per cent, natural gas by approx. 5 per cent, and coal by about 50 per cent.
Eliminating drying in a tumbler dryer results in significantly less consumption of Danish electricity. Danish electricity is primarily produced at coal-fired power plants, and therefore consumption of coal is reduced more than crude oil and natural gas. The energy-related environmental impacts are correspondingly reduced.
The toxicological environmental impact potentials are reduced by just less than 1 per cent, which indicates that electricity consumption does not contribute significantly to this impact category.
Conclusion to scenario 11 - reducing drying needs has a positive impact on the environmental profile
It can be concluded that drying in a tumbler dryer during the use phase has a great influence on the overall environmental profile. It would therefore be an advantage if the producer processed the textile so that water is easier to centrifuge out of the jogging suit. It is necessary to consider the effect of any extra pre-treatment process in relation to savings in the use phase. Another weaving method or surface treatment will require energy, consumption of resources and add to the environmental impacts.
Consequences of choices by the consumer
The consumer reference is based on the main scenario for the lifecycle of 1 jogging suit. The assumptions for the model have previously been described.
The consumer is primarily able to influence the use phase and parts of the transport phase. The other phases can primarily be influenced by the producer. Secondly, the consumer is able to choose producer selectively through, e.g. ecolabel schemes, which can ensure an environmentally correct choice.
The use phase includes washes without prewash and at 40°C, 100 per cent drying. Transport home by car from the shop is included, and the impact is spread over 6 kg goods per jogging suit.
Scenarios - consumer
Scenario 12: Choice of wash - halved washing frequency
Scenario 13: Choice of wash - increased washing temperature from 40°C to 60°C and no prewash
Scenario 14: Choice of wash - use of fabric softener
Drying
Scenario 15: No tumbler drying
- the green consumer's jogging suit
Scenario 16: Half the number of washes, no drying in a tumbler dryer, and produced in organic cotton.
Scenario 12: Choice of wash - halved washing frequency
In the functional unit, the jogging suit is deemed to be used 24 times and washed after each use, i.e. 24 washes. The washing frequency can be affected by the consumer, as this involves consumer habits and consumption patterns. This scenario is to show how much consumer habits influence the overall environmental profile. The following assumes that the jogging suit is washed after being used twice, i.e. half as many washes in private households, resulting in half as many dryings in a tumbler dryer and ironing compared to the consumer reference scenario.
The changes are expected to influence environmental impacts related to energy, resource consumption, as well as toxicological impact types, where use of washing agent has an impact.
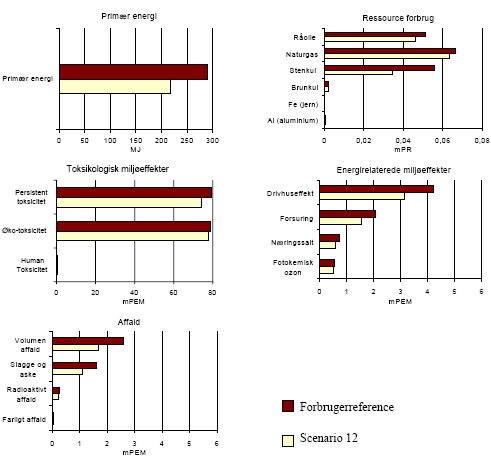
Figure 2.18 Result of scenario 12 - great consumer influence – for translation of Danish terms see glossary in annex 11
Consumption of primary energy is reduced by 24 per cent as a result of lower electricity consumption, primarily for drying. With regard to resources, consumption of fossil fuels is also reduced. The largest reduction is consumption of coal (about 38 per cent). Furthermore, the environmental impacts related to energy are reduced by 7-25 per cent due to a reduction of electricity consumption. As a result of the lower number of washes and consequent lower use of washing agent, there is a slight reduction in the toxicological environmental impacts.
Conclusion to scenario 12
The conclusion to this scenario is that the consumer has a large influence on the overall environmental profile of the jogging suit. A lower number of washes saves the environment from a number of impacts and also increases the lifetime of the jogging suit, provided the assumption that the number of washes wears out the jogging suit is correct. The increased lifetime is not taken into account. This would mean a reduction in the environmental impacts in the manufacturing and production phase.
Scenario 13: Choice of wash - increased washing temperature
Over the last few years, the washing temperature has become a less important parameter for washing effectiveness. Modern washing machines often achieve the same cleanness at low temperatures. Textiles that are washed at high temperatures for hygiene reasons should be disregarded in this context.
This scenario looks at the consequences of an increased washing temperature. The reference scenario has been prepared on the basis of a 40°C wash programme. In the scenario below, a 60°C washing temperature has been selected on the assumption that it will not affect the quality of the wash.
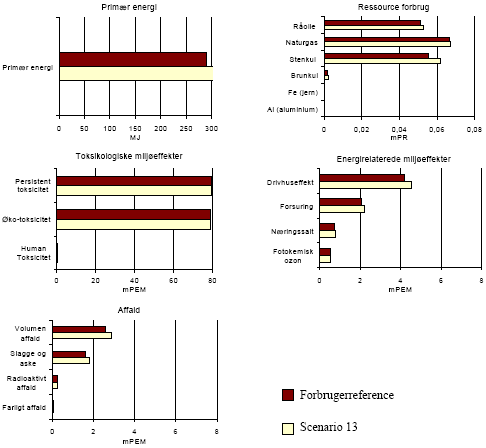
Figure 2.19 Result of scenario 13 - great consumer influence – for translation of Danish terms see glossary in annex 11
The figure shows that the primary energy consumption is increased by approx. 7 per cent when the washing temperature is increased in the use phase. This is due to the energy consumption for hotter washing water. The remaining changes in the environmental profile are directly related to this increased electricity consumption.
As shown before, it is also mainly consumption of coal that increases here, due to Danish electricity generation. Thus, there are also more energy-related impacts and a larger waste volume from incineration. There is also a slight increase in toxicological environmental impacts.
Conclusion to scenario 13
As shown, the consumer holds a large part of the responsibility for the overall environmental profile of a product like the jogging suit. An increased washing temperature would lead to large increases in the environmental impacts related to increased energy consumption, and it is very clear that the consumer has every opportunity to limit the environmental impacts in the use phase by thinking in an environment-friendly manner and by choosing a frugal consumption pattern.
Scenario 14: Choice of wash - use of fabric softener
Fabric softener is primarily used in the production phase, which uses large amounts after dyeing to achieve the quality required for further processing. Moreover, fabric softener is used in many homes as part of an ordinary machine wash. Consumer surveys show that 60 per cent of the Danish population use fabric softener. Fabric softeners in households are not the same as those used by industry, so it is not possible to compare the two processes directly. This scenario has been prepared in order to demonstrate the use of fabric softeners in the home. It is assumed that 3 g of active substance are used per wash. This dosage is different from product to product, but is based on an average. Therefore, it is also assumed that the consumer uses the recommended dose. The database does not include production of the fabric softener, packaging or transport home. Therefore, the only difference is that the toxicological environmental impacts are increased.
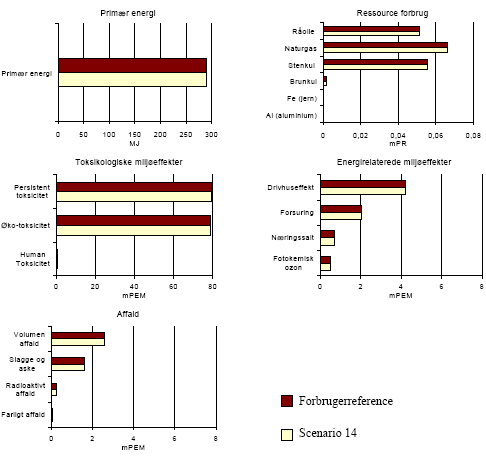
Figure 2.20 Result of scenario 14 - great consumer influence – for translation of Danish terms see glossary in annex 11
There seems to be no significant increase for the persistent toxicity nor for ecotoxicity (0.1 per cent and 0.04 per cent respectively), and human toxicity is unchanged compared with the consumer reference scenario.
If the use of fabric softener is considered in relation to a jogging suit of organic cotton and nylon, the conclusion is very different. Here, the fabric softener contributes with just under 10 per cent to ecotoxicity and 0.7 per cent to persistent toxicity.
Conclusion to scenario 14
The conclusion to this scenario is that the environmental impact from a fabric softener is important. In per cent, the impact seems smallest when the material contains conventional cotton, as this has very high toxicity factors (see scenario 1).
It is recommended that the consumer does not use fabric softeners. Furthermore, if overdoses are applied there will be greater consequences for the environmental profile and thus even greater toxicological environmental impacts.
Scenario 15: Choice of wash - no use of tumbler dryer
Drying in the home can primarily use two methods. Drip drying on a clothesline and tumbler drying. Often simple factors such a space, time, and economics determine the method used. A clothesline requires a lot of space, and it may be time demanding in some seasons, e.g. if clothes dry outdoors. Tumbler drying does not require much space in the home and has a constant and short drying time. Conversely, the electricity need is large.
This scenario ignores any wear on the jogging suit from using a tumbler dryer. In such a situation, the scenario would also have to include lifetime and quality. The reference scenario is based on the jogging suit being 100 per cent tumbler dried after washing. This scenario is intended to show the importance of the choice of drying method, and therefore tumbler drying has been excluded. It is assumed that the jogging suit is air-dried.
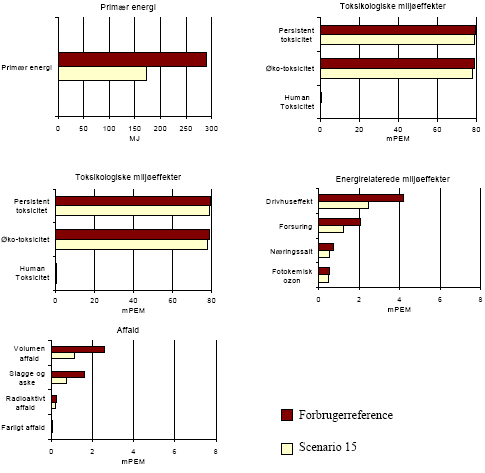
Figure 2.21 Result of scenario 15 - great consumer influence – for translation of Danish terms see glossary in annex 11
The clearest change here is the reduction of primary energy by approx. 40 per cent. Thus, the mechanical drying process contributes considerably to the consumption of primary energy. As a consequence of reduced energy consumption, there is a corresponding fall in the use of coal, which is the primary energy source in Denmark. This fall is approx. 60 per cent. There is a smaller fall for natural gas and crude oil. When energy consumption is reduced, there will be a similar fall in the environmental impacts related to energy like greenhouse effect and acidification. There is a fall of 10-40 per cent.
Conclusion to scenario 15
Of all the consumer scenarios in this report, this best illustrates the consumer's possibility of significantly affecting the environmental profile of a textile product, in this case, a jogging suit. The mechanical drying process uses a lot of electrical energy and is therefore resource-intensive and environmentally harmful. The energy saving is up to 40 per cent, and the other factors are reduced by 10-40 per cent. In addition, the lifetime of a product may be extended by avoiding tumbler drying. Increased lifetime has not been taken into account in this scenario, but extended lifetime would mean further reductions for all impacts. When choosing drying method, the consumer has a great influence on the environmental impacts throughout the lifecycle.
Scenario 16: Optimised use phase - organic cotton, half the number of washes, no drying in a tumbler dryer and double lifetime
This scenario attempts to illustrate an optimised use phase, where it is assumed that the consumer takes the greatest possible consideration for the environment, and that the jogging suit is of good quality that increases its lifetime. This optimised scenario includes organic cotton in the materials phase, good product quality, and a use phase that involves less washes and no tumbler drying.
In the preceding scenarios, we have seen how the individual processes contribute to the overall environmental profile. Each scenario elucidates the importance of individual processes in the use phase and of the choice of raw materials. This scenario is intended to show the consumer's overall possibility of influencing the overall environmental profile when selecting materials and an optimal consumption pattern.
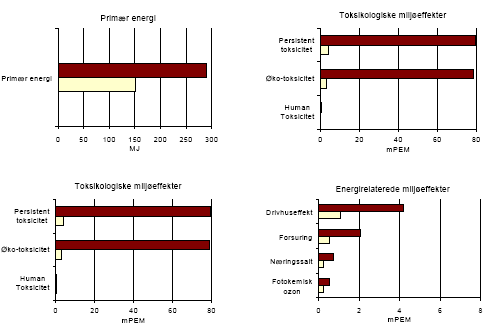
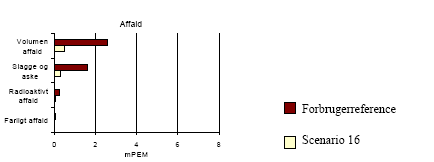
Figure 2.22 Result of scenario 16 - great consumer influence – for translation of Danish terms see glossary in annex 11
The figure shows that the consumer's choices have major consequences for the overall environmental profile. The reduction of primary energy of almost 50 per cent is due to air-drying and a halved number of washes. Moreover, lifetime plays an overall role, as the jogging suit will last two years instead of the one year in the functional unit. This means there is one-half jogging suit per functional unit. As a consequence of reduced energy consumption, there are similar reductions in resources and environmental impacts related to energy. The reduction of toxicological environmental impacts originates from the use of organic cotton instead of conventionally cultivated cotton, which contributes to the environmental profile with its large pesticide consumption. This reduction corresponds to almost 98 per cent of the jogging suit's overall contribution to the toxicological environmental impacts. Finally, there is reduced waste generation as a consequence of reduced energy consumption.
Conclusion to scenario 16
As was said in the introduction to this scenario, the preceding scenarios have helped illustrate how the individual processes are related to environmental impacts. This scenario has shown how far it is possible to go by combining the many possibilities of reducing impacts. The conclusion is that the use phase represents a significant proportion of the overall impact during a lifecycle. This scenario has shown that savings have been achieved for all significant impacts of 45-98 per cent. It shows that the consumer can make large environmental savings by influencing the market towards ecology and quality and by thinking environment-friendly during the use phase. No mechanical drying, fewer washes and purchasing environmentally friendly products.
Background data
System structure in the EDIPTEX database for the jogging suit
|
Ref. no.: EDIPTEX database |
1 jogging suit, dyed (nylon/cotton)
1 materials phase:
0.402 kg polyamide 6.6 fibres (nylon)
0.006 kg plastic zipper (polyester)
0.583 kg cotton fibres (incl. cultivation and harvest)
1 production phase:
(Nylon outer shell)
4.02 m weaving, no sizing agents
0.398 pre-treatment of woven fabric (nylon)
0.398 kg softening nylon
0.394 kg drying, final fixing + set of m² weight (nylon)
3.88 m² fabric inspection + rolling onto cardboard roll (nylon)
0.398 kg dyeing nylon (acid dye %)
(Cotton lining)
0.408 kg yarn manufacturing (cotton yarn)
0.402 kg circular knitting, general data
0.398 kg pre-bleaching with H2O2 (knitted cotton)
0.398 kg softening cotton textile
0.394 kg drying, final fixing + setting m² weight
2.59 m² fabric inspection + rolling onto cardboard rolls
(Making-up)
1 jogging suit – laying out and cutting
1 jogging suit – packing
1 use phase
16.8 kg household wash, 40°C, normal, no prewash
8.4 kg tumbler drying (vent) cotton, cupboard-dry
8.4 kg tumbler drying (vent) synthetic
1 disposal phase
0.35 kg waste incineration of cotton
0.35 kg waste incineration of polyamide (nylon)
0.006 kg incineration of plastic zipper
1 Transport phase
0.07 kg petrol combusted in petrol engine
11660 kg km container ship, 2-t, 28000DWT, terminated
830 kg km lorry > 16 t diesel out-of-town, terminated
830 kg km lorry > 16 t diesel urban traffic, terminated
830 kg km lorry > 16 t diesel motorway, terminated 1 stk. Træningsdragt, farvet (Nylon/Bomuld) |
(TX0-04)
(TX6-1-07)
(TX1-06)
(TX29-2-01)
(TX1-01-1)
(TX6-2-20)
(TX23-2)
(TX24-2-03)
(TX27-2-02)
(TX27-3-01)
(TX27-3-08-06-01)
(TX25-06-01)
(TX21-1)
(TX22-1-01)
(TX24-1-03)
(TX27-2-01)
(TX27-3-06)
(TX27-3-08-06)
(TX28-1-01)
(TX28-2-03-01)
(TX6-3-05)
(TX33-1-101)
(TX33-2-11)
(TX33-2-13)
(TX6-4-05)
(TX41-1-05)
(TX41-1-01)
(TX41-2-11)
(TX6-5-05)
(E32751)
(O3715T98)
(O32694T98)
(O32695T98)
(O32693T98) |
Details of the jogging suit model in the EDIPTEX database
Assumptions:
- 100 % nylon, microfibre, woven
- 100 % cotton lining (knitted)
- Consists of both top and trousers
- Top includes zipper of polyester (both tape and teeth), 60 cm, zipper weighs approx. 6 g, i.e. 0.1 g per cm
- Dyeing nylon: acid dyes
- Cotton lining is assumed to be prewashed and bleached after knitting
- Washing 40°C
- Tumbler drying
- Ironing not necessary
- Lifetime: 24 washes
- Weight: Top weighs 406 g, of which 6 g is zipper, trousers weigh 300 g. Lining weighs 50 % of total weight, i.e. top: 200 g cotton, 200 g nylon. Trousers: 150 g cotton, 150 g nylon. Total 350 g nylon and 350 g cotton.
Functional unit
The calculations are for "1 jogging suit".
This needs to be converted in relation to lifetime, and the calculations need to be converted to "per year".
It is assumed that the jogging suit can be washed 24 times before it is discarded.
It is assumed that the consumer wears the jogging suit approx. twice per month.
It is assumed that the jogging suit is used once and is then washed.
The lifetime is thus 12 months or approx. 1 year.
The functional unit for a jogging suit is therefore:
"24 days' use of jogging suit washed each time after use".
It is assumed that 24 days correspond to the number of days a consumer wears a jogging suit over the course of 1 year.
For the scenario, this corresponds to 1 jogging suit being completely worn out (in that it is assumed that the jogging suit is washed after use for 1 day).
Disposal:
It is assumed that the jogging suit is sold in Denmark and disposed of through waste incineration. 0.35 kg cotton and 0.35 kg nylon and 6 g polyester (zipper).
Household wash:
It is assumed that the jogging suit can be washed 24 times in its lifetime. This means that 0.35 kg * 24 = 8.4 kg cotton + 0.35 kg * 24 = 8.4 kg nylon (synthetic), total 0.7 kg * 24 = 16.8 kg must be washed. Washing at 40°C, normal, no prewash.
Drying:
It is assumed that the jogging suit is dried in a tumbler dryer. 8.4 kg cotton and 8.4 kg nylon (synthetic).
Packing the jogging suit:
It is assumed that the jogging suit is packed in a thin plastic bag. It is assumed the bag weighs 20 g (twice that of a T-shirt, see annex 1).
Making-up the jogging suit:
A new process has been set up: jogging suit - laying out, cutting and sewing TX 28-1-01. The process is calculated "per jogging suit". It is assumed that energy consumption is approx. twice of what is consumed for a tablecloth, see annex 5.
Waste is estimated at approx. 10 per cent for outer shell, nylon and cotton lining. This means approx. 0.35 kg / (1-0.10) = 0.388 kg nylon and cotton must be used. It is assumed that all the waste is discarded (incinerated at a waste incineration plant).
Nylon outer shell
Dyeing nylon (acid dye) 1 %:
0.388 kg textile must be used per jogging suit for this process. There is no waste of textile in this process.
Pre-treatment of synthetic woven fabric:
Only washing. No bleaching. 0.388 kg textile must be used for this process.
There is waste in the process, and therefore 1010 g woven textile must be used per kg pre-treated textile. Therefore, 1.01 kg * 0.388 = 0.392 woven fabric must be used per jogging suit. The waste is incinerated.
Weaving, no sizing agent:
0.388 kg textile must be used for this process.
Polyamide 6.6 fibre (nylon):
0.388 kg textile must be used for this process. Note that in relation to cotton there is no yarn manufacturing, as filament yarns are used and they come directly from the fibre producer.
Cotton lining
Bleaching with H2O2 (knitted cotton):
0.388 kg textile must be used for this process.
There is waste in the process, and therefore 1010 g knitted textile must be used per kg bleached textile. Therefore, 1.01 * 0.388 = 0.392 kg knitted textile is used.
Knitting:
0.392 kg textile must be knitted.
1.015 kg yarn is used per kg circular-knitted textile. Therefore, 1.015 * 0.392 = 0.398 kg yarn is used.
Yarn manufacturing:
0.398 kg yarn must be used per jogging suit.
1.43 kg cotton fibre is used per kg cotton yarn. Therefore, 1.43 * 0.398 = 0.569 kg cotton yarn is used for one jogging suit.
Cotton fibre:
0.569 kg cotton fibre is used for one jogging suit.
Standard components, zipper
Plastic zipper:
0.006 kg polyester zipper is used.
Transport:
All transport distances are estimated. See table below.
Transport |
Quantity for one jogging suit |
Kg km |
Nylon outer shell: |
|
|
Transport of nylon fibres (filaments) to weaving mill from Germany to Denmark |
0.388 kg transported 1000 km by lorry |
388 kg km by lorry |
Transport of woven fabric from weaving mill to pre-treater and dye house, both in Denmark |
0.388 kg transported 1000 km by lorry |
77,6 kg km by lorry |
Transport of dyed fabric from Denmark to making-up enterprise in Poland |
0.388 kg transported 1000 km by lorry |
388 kg km by lorry |
Cotton lining: |
|
|
Transport of cotton from cultivator in China to spinning mill in Poland |
0,569 kg transported 20000 km by ship |
11380 kg km by ship |
Transport of yarn from spinning mill in Poland to knitting mill in Denmark |
0,398 kg transported 1000 km by lorry |
398 kg km by lorry |
Transport of fabric from knitting mill to pre-treater, both in Denmark |
0,392 kg transported 200 km by lorry |
78,4 kg km by lorry |
Transport of fabric from pre-treater in Denmark to making-up enterprise in Poland |
0,388 kg transported 1000 km by lorry |
388 kg km by lorry |
Jogging suit: |
|
|
Transport from making-up enterprise in Poland to shop in Denmark, lorry |
0,706 kg transported 1000 km by lorry |
706 kg km by lorry |
Consumer transport* |
|
0,07 kg petrol |
Transport of discarded jogging suit (with household refuse) |
0,706 kg transported 50 km by lorry |
35,3 kg km by lorry |
Lorry, total: 2459.3 kg km (assumed 33 per cent urban, 33 per cent out-of-town, 33 per cent motorway).
* Consumer transport: It is assumed that the consumer drives in town by car to buy 1 jogging suit and 5.294 kg other goods. It is assumed the consumer drives 10 km and the car goes 12 km per litre. This means 0.83 l petrol is used (= 0.61 kg petrol, as petrol weighs 0.73 kg per litre). Of this, 0.61 * 0.706/6 is allocated to the jogging suit, i.e. 0.07 kg petrol.
I.e. total transport:
Process no. in EDIPTEX database |
Name of the process |
Transport need |
O32715T98 |
Container ship, 2-t 28000 DWT, TERMINATED |
11.660 kg km by ship |
O32695T98 |
Lorry > 16 t, diesel urban traffic, TERMINATED |
830 kg km by lorry |
O32694T98 |
Lorry > 16 t diesel out-of-town, TERMINATED |
830 kg km by lorry |
O32693T98 |
Lorry > 16 t diesel motorway, TERMINATED |
830 kg km by lorry |
E32751 |
Petrol consumed in petrol engine |
0,07 kg petrol |
| Front page | | Contents | | Previous | | Next | | Top |
Version 1.0 July 2007, © Danish Environmental Protection Agency
|