| Front page | | Contents | | Previous | | Next |
EDIPTEX - Environmental assessment of textiles
Annex 5: Tablecloth - cotton and dirt-repelling
The tablecloth - summary and conclusions
Firstly, it is important to stress the following conditions with regard to lack of data for the model used as the basis for the environmental assessment of the tablecloth:
- Chemical emissions to the air while drying after pigment printing have been difficult to ascertain. Only emissions of formaldehyde have been included in the model.
- The same applies for chemical emissions to water when washing printing equipment.
- Furthermore, it has not been possible to obtain data to enable calculation of equivalency factors for an important finishing chemical.
As all relevant energy data have been included in the model, the lack of data has no significance for the appearance of the statements of consumption of primary energy and environmental impacts related to energy.
On the other hand the effect of the lack of data for amounts of human toxicity and ecotoxicity is somewhat uncertain for the statement of the environmental impacts related to chemicals. However, it has been estimated that fibre manufacture of cotton will be by far the most important for these impacts.
For general and non-product-specific aspects regarding quality of EDIPTEX data, see chapter 4.
In summary, and in comparison to the case for the T-shirt, it can be concluded that the tablecloth and the T-shirt belong in the same product family.
The overall conclusions for many of the scenarios for the T-shirt relating to consumption of energy and toxicological environmental impacts can therefore be transferred to the tablecloth.
The main scenario shows that the most significant contributions to the environmental impact potentials related to chemicals originate from cotton cultivation.
At an overall level, the results indicate that the consumer holds the best possibilities for influencing the product's overall environmental profile. This is due to the dominant use phase. The individual consumer's consumption patterns and environmental awareness are therefore crucial, i.e. awareness of ecolabelling of products in combination with good habits like:
- minimal use of washing agent
- no use of fabric softeners
- no ironing.
The producer is primarily able to affect the tablecloth's environmental profile through choice of materials. - choice of organic cotton. By living up to European and Scandinavian ecolabelling criteria and obtaining labelling approval, the producer can signal to the conscious consumer that the product in question has been produced in an environmentally sound manner.
Introduction
Lifecycle assessment is a method for identification and evaluation of environmental impact potentials of a product or a service from cradle to grave. This method enables the user to make an environmental assessment and focus on the most important environmental impacts.
Lifecycle assessment is an iterative process. The first definition of purpose and delimitations often need to be revised during work with lifecycle assessment. The amount of data available sets limits, and consequently the limits of the system are changed.
The method used in this case for assessment of products is "Environmental Design of Industrial Products" (EDIP) and the associated database and PC tool.
In the EDIPTEX project, sector-specific data have been prepared for the textiles sector in connection with the existing EDIP database. On the basis of the data collected, environmental assessments were prepared for the textile products.
- A T-shirt of 100 % cotton
- A jogging suit of nylon microfibres with cotton lining
- A work jacket of 65 per cent polyester and 35 per cent cotton
- A blouse of viscose, nylon and elastane
- A tablecloth of cotton
- A floor covering of nylon and polypropylene.
These environmental assessments are intended to illustrate the scope for application of the EDIPTEX database by using the PC modelling tool and, at a more general level, application of the EDIP method.
Method
The six case stories vary a lot in scope. They can be divided into two main groups - with variations within these two main groups. The two main groups are:
- Group I: The T-shirt, the jogging suit and the work jacket.
- Group II: The floor covering, the tablecloth and the blouse.
The division into groups I and II relates to the scope of the collection of data as well as the quality of data.
For group I, it was possible to collect (and process) data for all significant processes. The data are of such quality that these three products have been selected to illustrate how far it is possible to take lifecycle assessment for textiles and to illustrate all relevant aspects of the EDIP method.
Each of the three group I cases contains:
- Definition of functional unit and reference product
- Modelling of main scenario
- Preparation of producer and consumer references
- Simulation of environmental impacts caused by choices made by producer and consumer respectively.
Work with these cases has been divided into phases as illustrated in figure 5.1.
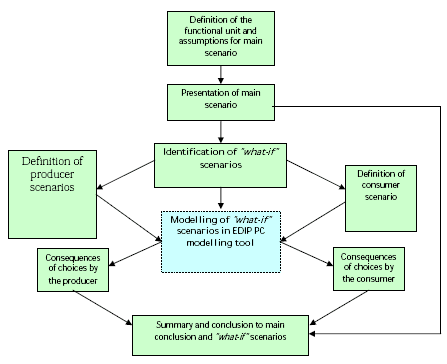
Figure 5.1 EDIPTEX case group I flow diagram
For group II, it was not possible to complete all sub-processes. Although only 1-2 sub-processes for each product have considerable lack of data, these processes are deemed potentially significant for the overall lifecycle assessment. The group II case stories are therefore of an entirely different character than those of group I. The group II cases illustrate that it is possible to tell an interesting and exciting "environment story" based on lifecycle assessment (and EDIP) even though it has not been possible to analyse all aspects of lifecycle assessment data. This situation will arise very often in lifecycle assessment work. However, there is a significant difference in this EDIPTEX connection; it is possible to draw on results from the three lifecycle assessments from case group I (and this has been done), which improves the quality of the case stories.
Comments to the method
Product references
The "what-if" simulations were carried out to elucidate the consequences of possible changes in the product's lifecycle. A special product reference has been defined for the producer scenarios in some of the case stories. The producer only has limited influence on the use phase. In order to take this into account, a product reference has been prepared for the producer scenarios where only a limited part of the impacts from the use phase has been included in relation to the product reference from the main scenario. This was done in order to give producers a clearer picture of the influence of the production phase on the product's environmental profile in the "what-if" producer scenarios.
Data
With regard to data, it should be noted that the validity of the data in the database varies, depending on the processes considered. A global process like cultivation and harvest of cotton is subject to considerable uncertainty. This is because cotton is produced in countries with very different levels of development. For example, production varies a lot between South America and the US because of large differences in the use of pesticides, crop yields, etc.
This difference has not been taken directly into account in the EDIPTEX database, but a representative level for the data has been defined. Therefore, the data are very general and not necessarily representative for all lifecycle assessments. Other processes are more exact, such as extraction of crude oil for nylon. This process is well documented, both as regards industrial accidents and as regards resource consumption.
Production data primarily come from Danish enterprises. The number of enterprises involved represents limitations in this connection. For example, only one reactive dye and one acid dye have been studied thoroughly. These two substances represent the entire group of dyes, despite the major differences that may occur.
A large proportion of the environmental impacts come from the consumption of electrical energy. The data currently used in the database originate from the EDIP database, and the reference year is 1990. This area is being studied in order to update this part of the database. It is important to note that this lifecycle assessment was carried out using the 1990 data in all processes that consume electrical energy.
For this product in particular, chemical emissions to the air during drying after pigment printing have been difficult to ascertain. Only emissions of formaldehyde have been included in the model. The same applies for chemical emissions to water when washing printing equipment. Furthermore, it has not been possible to obtain data to enable calculation of equivalency factors for an important finishing chemical.
These aspects of data quality mean that focus for this case is on primary energy and environmental impacts for the main scenario. The significance of the lack of data for the statement of results for the main scenario is discussed. Moreover relevant parallels have been drawn with the scenarios in the three group I cases.
Tablecloth
Product description: The tablecloth is made of 100 per cent cotton. The tablecloth is printed with pigments and has been finished to make it easier to maintain. The tablecloth can often be cleaned with just a wet cloth.
Functional unit
The performance assessed can be described as a "functional unit", comprising a qualitative and a quantitative description, including the product's lifetime. The qualitative description is to define the quality level for the performance, so that products can be compared at a somewhat uniform quality level. The quantitative description is to determine the size and duration of the performance.
In this project, the functional unit is defined as:
"150 times use of tablecloth over the course of 2½ years"
Cleaning/maintenance of the tablecloth are assumed to comprise only wiping with a cloth and (every six times) washing at 60°C. It is also assumed that the tablecloth is dried on a clothesline and it is ironed. Under these conditions, 150 times' usage (25 washes) is assumed to be a realistic lifetime. Other possible maintenance such as pressing and rolling has not been included in the project.
Reference product and main scenario
The reference product is a product that meets the criteria of one functional unit. Here, we have chosen a tablecloth.
The calculations are carried out for "1 tablecloth", these need to be converted in relation to lifetime, and the calculations need to be converted to "per year".
It is assumed that the tablecloth can be washed 25 times before it is discarded.
It is assumed that the tablecloth is used six times before each wash.
It is assumed that the tablecloth can be used 60 times each year.
If the tablecloth is used 60 times per year, and if the tablecloth is used six times before it is washed, the tablecloth will be washed 10 times per year. If the tablecloth can be washed 25 times before discarding, it will be completely worn out after 2½ years.
The following assumptions apply to the assessment and are thus included in the modelling of the main scenario.
- 100 per cent woven cotton.
- Printing with pigments.
- Washing 60°C.
- Drip drying on a clothesline.
- Ironed after each wash. It is assumed it takes about 10 min. to iron the tablecloth each time.
- Lifetime: 25 washes.
- Size and weight (based on company data): the tablecloth is assumed to measure 2.65 m². The tablecloth weighs 145 g per m². This means that the tablecloth weighs approx. 384 g.
A more detailed description of the processes, calculations of volumes, waste, etc. can be found in the section "Background data" at the end of this annex.
Product system
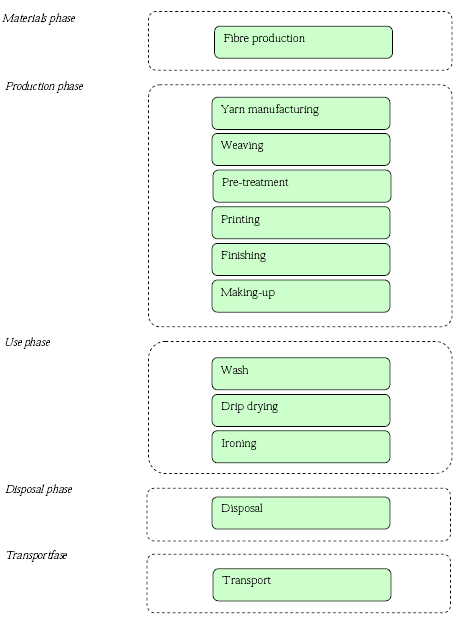
Figure 5.2 Livscycle, flow and phases
In the following, all phases of the tablecloth's lifecycle will be described from extraction of raw materials through production to the making-up of the finished tablecloth.
Manufacture of raw materials
The tablecloth consists solely of cotton. Cotton is cultivated in many countries under different geographical and climatic conditions. Cultivation often entails a large consumption of artificial fertilizer, large water consumption and a large consumption of pesticides against insect attacks, diseases, worms and weeds. The extent of this depends largely on local conditions. The consumption of pesticides entails an important environmental problem for both human health and nature.
Irrigation and use of artificial fertilizer impact groundwater and surface water resources quantitatively as well as qualitatively. Before picking, it is common to use defoliating agents so that picking can be done mechanically.
It is normally not permitted to use pesticides and artificial fertilizer in cultivation of organic cotton. Thus, it is only permitted to use a very limited selection of plant protection agents, and only when there is an acute danger for the crop. Organic production of cotton constitutes less than 1 per cent of total cotton production, but organic production is increasing and is expected to increase further due to increased demand.
Production of the tablecloth
Production is divided into several sub-processes: yarn manufacturing, weaving, pre-treatment, printing, finishing, making-up and distribution.
Chemical emissions to the air during drying after pigment printing have been difficult to ascertain. Only emissions of formaldehyde have been included in the model. The same applies for chemical emissions to water when washing printing equipment. Furthermore, it has not been possible to obtain data to enable calculation of equivalency factors for an important finishing chemical.
Yarn manufacturing
By using long cotton fibres, a more durable product is obtained and thus it is possible to extend the lifetime of the product. Prior to weaving, the warp is covered with a sizing agent to reduce the friction in the weave. Sizing agents can be based on natural or synthetic substances.
Occupational health and safety
The supplier is obliged to reduce the amount of monotonous repetitive work and dust nuisance at work. Cotton dust may cause lung damage, for example.
Distribution
The tablecloth is packed in polyester bags and then on a wood pallet, after which it is distributed to retail suppliers throughout Denmark.
Use phase
The consumption of washing agents and fabric softeners and the consequential discharge of detergents and nutrient salts lead to possible local and regional impacts in the aquatic environment.
Transport
The mode of transport when the tablecloth is transported from the shop to the buyer's home is also important in connection with the overall environmental profile of the product. Options like driving a car, using public transport or a bike make a significant difference in this part of the product's lifecycle.
Disposal phase
Textiles may not be landfilled. On final disposal, they must be incinerated so that the energy content is recovered and replaces non-renewable energy sources like oil and natural gas.
Main scenario - results
The results of the main scenario are presented according to processes. The negative contributions that occur in some processes are due to estimated reuse potentials and contribution to environmental impact potentials. In the processes in question, the contributions can be allocated to other products and thus appear as negative contributions in the tablecloth's environmental profile.
The values in the four figures are not immediately comparable, as the unit is not the same for the four categories. The consumption of primary energy is calculated in mega-joules (MJ). The environmental impact potentials are presented as "milli-person equivalents" and are directly comparable. Milli-person equivalents are calculated as the direct impact for the year 2000. The weighting factors are based on global (w) or Danish (DK) discharges in the year 2000.
Consumption of primary energy
The consumption of primary energy reflects the processes that require a lot of electrical energy or energy to heat air or water.
Figure 5.3 (consumption of primary energy per functional unit) shows that the processes in the use phase (washing and ironing) represent most of the consumption of primary energy. In the use phase, the electricity consumption for washing and ironing cause the impacts. Manufacture of the cotton fibres accounts for the largest single contribution, however. Furthermore, processing into yarn makes a large contribution.
When the tablecloth is incinerated in an incineration plant, some energy is recovered and this is credited in the energy accounts.
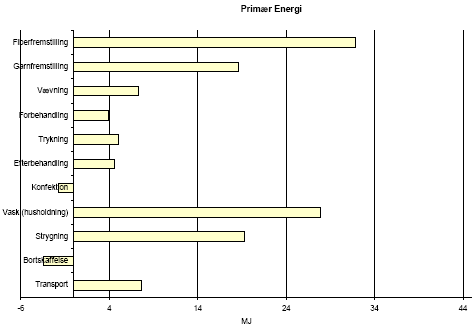
Figure 5.3 consumption of primary energy per functionl unit – for translation of Danish terms see glossary in annex 11
Environmental impact potentials
The problem with quality of data already mentioned (chemical emissions to the water and air from printing) means that there is some reservation regarding the results below. The comments to the figures are neutral, i.e. the comments are on the basis of what can be read from the figures, as they appear. The subsequent section (What-if) discusses the significance of the lack of data for the statement of results.
Figure 5.4 (Toxicological environmental impact potentials per functional unit), figure 5.5 (Environmental impacts related to energy per functional unit) and figure 5.6 (Environmental impacts, waste per functional unit) show that the contributions to the toxicological and environmental impact potentials dominate. Particularly ecotoxicity and persistence toxicity are very high, primarily because of the pesticides that are spread on the cotton fields during the cultivation process.
The data used to determine the pesticide volumes per hectare are based on a worst-case assumption. The focus in this phase is to reduce pesticide consumption during cultivation of cotton.
Click here to see the Figure.
Figure 5.4 Toxicological environmental impact potentials per functional unit – for translation of Danish terms see glossary in annex 11
In the use phase, primarily detergents in washing agents result in potential persistent toxicity. It has been assumed that no users add fabric softener when washing, and therefore the figures probably do not tally with the actual conditions in private Danish households. The contributions to the waste categories (figure 5.6) mainly originate from electricity generation.
Click here to see the Figure.
Figure 5.5 Environmental impacts related to energy per functioanl unit – for translation of Danish terms see glossary in annex 11
The environmental impact potentials related to energy are primarily due to burning fossil fuels.
Click here to see the Figure.
Figure 5.6 Environmental impacts, waste per functional unit – for translation of Danish terms see glossary in annex 11
The contributions to the waste categories shown in the figure originate primarily from generation of electricity. Like the energy-related impacts, they are relatively limited in size compared with the toxicological impact categories.
What–if diskussion
This section will discuss the significance of the lack of data for the statement of results for the main scenario. Moreover relevant parallels will be drawn with the scenarios in the three group I cases.
The significance of lack of data for the statement of results
As mentioned above, the following conditions relating to the quality of data specifically for the tablecloth have been revealed:
- Chemical emissions to the air while drying after pigment printing have been difficult to ascertain. Only emissions of formaldehyde have been included in the model.
- The same applies for chemical emissions to water when washing printing equipment.
- Furthermore, it has not been possible to obtain data to enable calculation of equivalency factors for an important finishing chemical.
As all relevant energy data have been included in the model, it is deemed that the lack of data has no significance for the appearance of figure 5.3 - consumption of primary energy.
The same applies for figures 5.5 and 5.6, which primarily relate to environmental impacts resulting from consumption of energy.
On the other hand, there is some uncertainty of the significance of the lack of data for the above on the amount of human toxicity, ecotoxicity and persistent toxicity for the appearance of figure 5.4. However, it is estimated that manufacture of fibre will be dominant.
Parallels to case group I scenarios
As there was no lack of data on energy consumption in the assessment of the tablecloth, relatively certain comparisons can be made with environmental profiles for other textile products prepared using the same principles. Looking at the energy profile of the tablecloth in figure 5.3 and comparing this with the corresponding profile for a cotton T-shirt, for example, as in figure 5.7, the difference is remarkable.
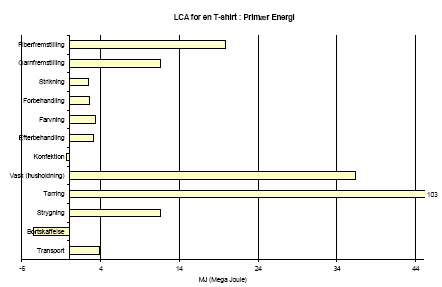
Figure 5.7 Consumption of primery energy per functional unit – for translation of Danish terms see glossary in annex 11
The use phase (washing and ironing for the tablecloth; washing and tumbler drying for the T-shirt) is the most important phase for the statement of primary energy. The drying process is dominant for the T-shirt, and this would also apply for the tablecloth, if drying were part of the model. The model does not include drying because it is assumed that the tablecloth has been finished to make maintenance easier (e.g. a wax tablecloth). This type of tablecloth dries very easily and tumbler drying is not necessary.
The statements of the toxicological environmental impacts (figure 5.4 for the tablecloth and 5.8 for the T-shirt below) are even more convergent (note that the scales on the x axes are very different). This is because both products are made of 100 per cent cotton. The toxicological impacts of the use of pesticides are extremely prominent.
Click here to see the Figure.
Figure 5.8 Toxicological environmental impact potentials per functional unit for a T-shirt – for translation of Danish terms see glossary in annex 11
The overall conclusions to the many scenarios for the T-shirt relating to consumption of energy and toxicological environmental impacts can therefore be transferred to the tablecloth. Therefore, it can be concluded that the products belong to the same product family.
This applies as a minimum to the overall conclusions in the following T-shirt producer scenarios:
Choice of raw materials:
Scenario 1: Choice of raw materials - organic cotton
Scenario 2: Choice of raw materials - halved cotton waste
The use phase:
Scenario 6: Use phase - extended textile lifetime
Scenario 7: Use phase - colour staining
And as a minimum the following T-shirt consumer scenarios:
Scenario 10: Choice of wash - halving wash frequency
Scenario 12: Choice of wash - use of fabric softener
Scenario 14: No ironing
Scenario 15: Transport home - car with shopping.
This observation leads to the overall conclusion that the consumer holds the best possibilities for influencing the product's overall environmental profile. This is due to the dominant use phase. The individual consumer's consumption patterns and environmental awareness are therefore crucial, i.e. awareness of ecolabelling of products in combination with good habits like:
- minimal use of washing agent
- no use of fabric softeners
- no ironing.
The producer is primarily able to affect the T-shirt's environmental profile through choice of materials - choice of organic cotton.
Background data
System structure in the EDIPTEX database for the tablecloth
The figures in column on the right of the table refer to the ID numbers used in the original EDIP PC tool.
|
Ref. no.: EDIPTEX database |
1 Tablecloth, pigment printed (cotton)
1 Tablecloth – Materials phase:
0.644 kg Cotton fibres (incl. cultivation and harvest)
1 Tablecloth – Production phase:
1 Tablecloth – Yarn manufacture
0.45 kg Yarn manufacture (cotton yarn)
1 stk. Tablecloth – Weaving
3.103 m² Weaving, natural sizing
1 stk. Tablecloth – Pre-treatment
0.446 kg Desizing (persulphate) of woven cotton
1 stk. Tablecloth – Printing
3.075 m² Application and fixing printing paste
3.075 m² Wash 9 templates incl. auxiliary eqt.
3.075 m² Overhead use for printing
1 Tablecloth – Finishing
3.075 m² Finishing and drying on stretching frame
3.075 m² Pressing
3.075 m² Condensation of impregnation on stretching frame
3.03 m² Fabric – inspection and rolling onto cardboard roll
1 Tablecloth – Making-up
1 Laying out, cutting and sewing the tablecloth
1 Tablecloth, pigment printed – Packing
1 Tablecloth – Use phase:
9.6 kg Household wash, 60 °C with prewash
9.6 kg Hang/drip/lay dry after wash
250 minutes ironing cotton and other cellulose
1 Tablecloth – Disposal:
0.384 kg Waste incineration of cotton
1 Tablecloth – Transport phase:
12880 kg km Container ship, 2-t, 28000DWT, Terminated
470 kg km Lorry > 16 t diesel out-of-town Terminated
470 kg km Lorry > 16 t diesel urban Terminated
470 kg km Lorry > 16 t diesel motorway Terminated
0.04 Petrol combusted in petrol engine |
(TX0-05)
(TX6-1-08)
(TX1-01-1)
(TX6-2-21)
(TX-2-23)
(TX21-1)
(TX6-2-24)
(TX23-1)
(TX6-2-25)
(TX24-2-02)
(TX6-2-26)
(TX26-2-01)
(TX26-2-02)
(TX26-2-03)
(TX6-2-27)
(TX27-2-30-1)
(TX27-1-01)
(TX27-2-30-2)
(TX27-3-08-06)
(TX6-2-28)
(TX28-1-06)
(TX-28-2-03-06)
(TX6-3-06)
(TX-1-202)
(TX33-2-9)
(TX33-3-01)
(TX6-4-06)
(TX41-1-01)
(TX6-5-06)
(O32715T98)
(O32694T98)
(O32695T98)
(O32693T98)
(E32751) |
Details of the tablecloth model in the EDIPTEX database
Assumptions:
- 100 per cent woven cotton.
- Printing with pigment.
- Washing 60°C.
- Drip drying on a clothesline.
- Ironed after each wash. It is assumed that it takes about 10 min. to iron the tablecloth each time.
- Lifetime: 25 washes.
- Size and weight (based on company data): the tablecloth is assumed to measure 2.65 m². The tablecloth weighs 145 g per m². This means the tablecloth weighs 384 g.
Functional unit
For the tablecloth, the functional unit is defined as:
"150 day’s' use of tablecloth over the course of 2½ years"
Cleaning/maintenance of the tablecloth are assumed to include drying (every six washes) and washing at 60 0C. It is also assumed that the tablecloth is dried on a clothesline and it is ironed. Under these conditions it is estimated that 150 times' usage (25 washes) is realistic for a lifetime. Other possible types of maintenance such as pressing and rolling have not been included in this project.
The calculations are carried out for "1 tablecloth", these need to be converted in relation to lifetime, and the calculations need to be converted to "per year".
It is assumed that the tablecloth can be washed 25 times before it is discarded.
It is assumed that the tablecloth is used six times before each wash.
It is assumed that the tablecloth is used 60 times per year.
If the tablecloth is used 60 times each year, and if the tablecloth is used six times before it is washed, the tablecloth will be washed 10 times a year. If the tablecloth can be washed 25 times before discarding, it will be completely worn out in 2½ years.
Disposal:
It is assumed that the tablecloth is sold in Denmark and disposed of through waste incineration. This means that 384 g cotton must be incinerated (the weight of the tablecloth).
Household washing:
It is assumed that the tablecloth can be washed about 25 times in its lifetime. This means that 0.384 kg * 25 = 9.6 kg cotton must be washed in the lifetime of the tablecloth.
Drying:
It is assumed that the tablecloth is dried on a clothesline. This is also 9.6 kg cotton.
Ironing:
The tablecloth must be ironed after each wash. It is assumed that it takes 10 minutes each time to iron the tablecloth. 10 minutes * 25 = 250 minutes.
Packing the pigment-printed tablecloth:
The tablecloth measures 2.65 m². A pigment-printed tablecloth weighs 145 g per m². This means that the tablecloth weighs about 384 g.
Laying out, cutting and sewing the tablecloth:
OUT: The process is calculated "per tablecloth" out of the process.
IN: During the process "laying out, cutting and sewing of tablecloth" there is waste from cutting and mistakes. This means that 3.03 m² fabric is required per tablecloth.
Fabric - inspection and rolling onto a cardboard roll:
OUT: The process is calculated "per m² inspected and approved textile" (i.e. the amount out of the process). As mentioned above, "3.03 m² inspected and approved textile" must be used per tablecloth.
IN: During the inspection of fabric about 0.015 m² textile are discarded to waste. This means that 1.915 m² textile must be used within the process for each 1 m² inspected and approved textile, corresponding to 3.03 m² * 1.015 m² per m² = 3.076 m² in.
Condensation of impregnation on steamer:
As mentioned above, 3.075 m² textile must be used from this process for one tablecloth. The process involves neither shrinking, waste, nor discarding of textile, and therefore the same number of m² go out as come in.
Pressing:
As mentioned above, 3.075 m² textile must be used from this process for one tablecloth. The process involves neither shrinking, waste, nor discarding of textile, and therefore the same number of m² go out as come in.
Finishing and drying on stretching frame:
The textile shrinks by about 4.5 per cent in this process. This is because the material is stretched in the other processes. There is max. 5 per cent stretching and shrinking and overall the material shrinks by less than 2 per cent from when the goods go into the printers to when they are inspected in the fabric inspection. This stretching and shrinking has been ignored as it is relatively little, and as it is estimated that it is within the uncertainties always connected with data for lifecycle assessments. This means that the calculations have not included adjustments for stretching and shrinking the textile. As there is no waste of the textile in this process, it is assumed that just as many m² enter the process as come out.
Application and fixing printing paste, washing nine templates incl. auxiliary equipment, and overheads from printing:
All these processes are calculated per m² pigment-printed textile (after application and fix of printing paste). As there is no waste of textile in the process, just as many m² enter the process as come out. With a m² weight of 145 g/m², this corresponds to 3.075 m² * 145 g/m² = 446 g textile per tablecloth.
Desizing (persulphate) woven cotton:
Data for this process is calculated per kg desized textile.
Because of waste, 1010 g woven cotton textile is used per kg washed woven goods. This means that for one tablecloth 446 g * 1.01 = 450 g woven textile must be used. 450 g / 145 g per m² = 3.103 m² textile.
Weaving:
This process is calculated per m² woven textile. According to Grenaa Danpvæveri, the waste of yarn, plastics, cardboard, paper, and iron totals 1.89 g per m². Assuming that 1 m² weighs 145 g, this gives a max. waste of yarn of 1.89 g / 145 g = 1.3 per cent. From this, it is assumed that the waste is insignificant and ignored. Therefore, 3.103 m² is used in this process.
Spinning:
This process is calculated per kg finished yarn. 450 g yarn is required for a tablecloth. Therefore, 450 g is used in this process.
Cotton fibres:
Because of waste, 1.43 kg cotton fibre is used per kg finished yarn. This means 450 g * 1.43 = 644 g cotton fibres are required for one tablecloth.
Transport:
All transport distances are estimated. See table below.
Transport |
Quantity for one tablecloth |
Kg km |
Transport of cotton from cultivator in China to spinning mill in Poland |
0,644 kg transported 20000 km by ship |
12880 kg km by ship |
Transport of yarn from spinning mill in Poland to weaving mill in Denmark |
0,45 kg transported 1000 km med lorry |
450 kg km by lorry |
Transport of fabric from weaving mill to pre-treater, both in Denmark |
0,45 kg transported 200 km by lorry |
90 kg km by lorry |
Transport of fabric from pre-treater and printer, both in Denmark |
0,45 kg transported 200 km by lastbil |
90 kg km by lorry |
Transport of printed fabric from printer in Denmark to making-up enterprise in Poland |
0,384 kg transported 1000 km by lorry |
384 kg km by lorry |
Transport from making-up enterprise in Poland to shop in Denmark, lorry |
0,384 kg transported 1000 km by lorry |
384 kg km by lorry |
Consumer transport* |
|
0,04 kg petrol |
Transport of discarded tablecloth (with household refuse) |
0,384 kg transported 50 km by lorry |
19,2 kg km by lorry |
* Consumer transport: It is assumed that the consumer drives in town by car to buy 1 tablecloth and 5.616 kg other goods. It is assumed the consumer drives 10 km and the car goes 12 km per litre. This means 0.83 l petrol is used (= 0.61 kg petrol, as petrol weighs 0.73 kg per litre). Of this, 0.61 * 0.384/6 is allocated to the tablecloth, i.e. 0.04 kg petrol.
Lorry, total: 1417.2 kg km (assumed 33 per cent urban, 33 per cent out-of-town, 33 per cent motorway).
I.e. total transport:
Process no. in ediptex-database |
Name of process |
Transport need |
O32715T98 |
Container ship, 2-t 28000 DWT, TERMINATED |
12880 kg km by ship |
O32695T98 |
Lorry > 16 t, diesel urban traffic, TERMINATED |
470 kg km by lorry |
O32694T98 |
Lorry > 16 t diesel out-of-town, TERMINATED |
470 kg km by lorry |
O32693T98 |
Lorry > 16 t diesel motorway, TERMINATED |
470 kg km by lorry |
E32751 |
Petrol consumed in petrol engine |
0,04 kg petrol |
| Front page | | Contents | | Previous | | Next | | Top |
Version 1.0 July 2007, © Danish Environmental Protection Agency
|