| Front page | | Contents | | Previous | | Next |
EDIPTEX - Environmental assessment of textiles
Annex 6: Floor covering of nylon and polypropylene
The floor covering – summary and conclusions
Firstly, it is important to stress the following conditions with regard to lack of data for the model used as the basis for the environmental assessment of the floor covering.
It has not been possible to procure enough data for:
- Production of face material of polypropylene fibres.
- Emissions of chemicals into air during production of the floor covering at the producer.
- Discharges of chemicals into water from dyeing the surface of the floor covering (face material).
However, it has been possible to collect energy data for all significant processes.
For general, and not product-specific conditions regarding quality of EDIPTEX data, see chapter 4.
It can be concluded that the energy profile for a floor covering is very different from that of garments. The use phase does not have the same importance at all. The consumer would have to vacuum the floor covering about 20 times per month for the use phase to outweigh the materials phase (fibre production).
The energy profile of the floor covering clearly shows that the floor covering producer holds the best possibilities for influencing the product's overall environmental profile. The producer should primarily focus on reuse of fibre material, as fibre materials represent a very large part of the total energy consumption during the lifetime of the floor covering.
Introduction
Lifecycle assessment is a method for identification and evaluation of environmental impact potentials of a product or a service from cradle to grave. This method enables the user to make an environmental assessment and focus on the most important environmental impacts.
Lifecycle assessment is an iterative process. The first definition of purpose and delimitations often need to be revised during work with lifecycle assessment. The amount of data available sets limits, and consequently the limits of the system are changed.
The method used in this case for assessment of products is "Environmental Design of Industrial Products" (EDIP) and the associated database and PC tool.
In the EDIPTEX project, sector-specific data have been prepared for the textiles sector in connection with the existing EDIP database. On the basis of the data collected, environmental assessments were prepared for the textile products.
- A T-shirt of 100 % cotton
- A jogging suit of nylon microfibres with cotton lining
- A work jacket of 65 per cent polyester and 35 per cent cotton
- A blouse of viscose, nylon and elastane
- A tablecloth of cotton
- A floor covering of nylon and polypropylene
These environmental assessments are intended to illustrate the scope for application of the EDIPTEX database by using the PC modelling tool and, at a more general level, application of the EDIP method.
Method
The six case stories vary a lot in scope. They can be divided into two main groups - with variations within these two main groups. The two main groups are:
- Group I: The T-shirt, the jogging suit and the work jacket.
- Group II: The floor covering, the tablecloth and the blouse.
The division into groups I and II relates to the scope of the collection of data as well as the quality of data.
For group I, it was possible to collect (and process) data for all significant processes. The data are of such quality that these three products have been selected to illustrate how far it is possible to take lifecycle assessment for textiles and to illustrate all relevant aspects of the EDIP method.
Each of the three group I cases contains:
- Definition of functional unit and reference product
- Modelling of main scenario
- Preparation of producer and consumer references
- Simulation of environmental impacts caused by choices made by producer and consumer respectively
Work with these cases has been divided into phases as illustrated in figure 6.1.
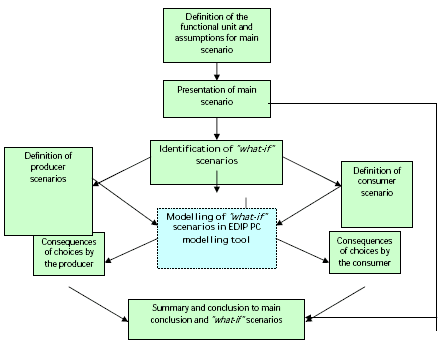
Figure 6.1 EDIPTEX case group I flow diagram
For group II, it was not possible to complete all sub-processes. Although only 1-2 sub-processes for each product have considerable lack of data, these processes are deemed potentially significant for the overall lifecycle assessment. The group II case stories are therefore of an entirely different character than those of group I. The group II cases illustrate that it is possible to tell an interesting and exciting "environment story" based on lifecycle assessment (and EDIP) even though it has not been possible to analyse all aspects of lifecycle assessment data. This situation will arise very often in lifecycle assessment work. However, there is a significant difference in this EDIPTEX connection; it is possible to draw on results from the three lifecycle assessments from case group I (and this has been done), which improves the quality of the case stories.
Comments to the method
Product references
The "what-if" simulations were carried out to elucidate the consequences of possible changes in the product's lifecycle. A special product reference has been defined for the producer scenarios in some of the case stories. The producer only has limited influence on the use phase. In order to take this into account, a product reference has been prepared for the producer scenarios where only a limited part of the impacts from the use phase has been included in relation to the product reference from the main scenario. This was done in order to give producers a clearer picture of the influence of the production phase on the product's environmental profile in the "what-if" producer scenarios.
Data
With regard to data, it should be noted that the validity of the data in the database varies, depending on the processes considered.
Production data primarily come from Danish enterprises. The number of enterprises involved represents limitations in this connection. For example, only one acid dye has been studied thoroughly. This substance represents the entire group of acid dyes, despite the major differences that may occur.
A large proportion of the environmental impacts come from the consumption of electrical energy. The data currently used in the database originate from the EDIP database, and the reference year is 1990. This area is being studied in order to update this part of the database. It is important to note that this lifecycle assessment was carried out using the 1990 data in all processes that consume electrical energy.
Particularly for this product, it has not been possible to obtain data for production of the primary backing material of polypropylene fibres. At an overall level, this process corresponds to the process "weaving" for the tablecloth case. Therefore, the floor covering model is based of data for weaving, which seems to be a reasonable assumption.
Moreover, emissions of chemicals into the air during production of the floor covering have turned out to be difficult to ascertain, and have thus not been included in the model. However, energy consumption during the processes has been included. The same applies for discharges of chemicals into water from dyeing the surface of the floor covering. However, this is of less importance as the model assumes that a chemical precipitation system is connected (as is seen in the floor covering industry).
These aspects of data quality (particularly emissions of chemicals into air during production of the floor covering) mean that focus for this case is on primary energy and environmental impacts for the main scenario. The significance of the lack of data for the statement of results for the main scenario is discussed. Moreover relevant parallels have been drawn with the scenarios in the three group I cases.
The floor covering
Product description: The floor covering consists of pile (the surface) of 100 per cent nylon, a primary backing material of 100 per cent polypropylene (to which the pile is stitched), and the actual backing of latex foam.
Functional unit
The performance assessed can be described as a "functional unit", comprising a qualitative and a quantitative description, including the product's lifetime. The qualitative description is to define the quality level for the performance, so that products can be compared at a somewhat uniform quality level. The quantitative description is to determine the size and duration of the performance.
In this project, the functional unit is defined as:
"10 years' use of floor covering - corresponding to guaranteed lifetime"
It is assumed that the floor covering can be used for ten years before it is discarded.
It is assumed that the consumer vacuums the floor covering once per month, i.e. 120 times during the entire lifetime. No other maintenance is carried out.
Reference product and main scenario
The reference product is a product that meets the criteria of one functional unit.
Here, we have chosen a composite floor covering.
The calculations are carried out for "1 floor covering", these need to be converted in relation to lifetime, and the calculations need to be converted to "per year".
Quality floor coverings last longer than 10 years - up to 15 years is not unusual. Similarly, the lifetime of floor coverings of poorer quality can be significantly shorter.
Moreover, maintenance of floor coverings may also involve shampooing with an extraction cleaner (vacuum suction) - but this is not included in this project.
The following assumptions apply to the assessment and are thus included in the modelling of the main scenario.
- The floor covering is a composite - the pile is made of 100 per cent nylon, the primary backing material is made of 100 per cent polypropylene, and the back is made of latex foam.
- Lifetime is 10 years.
- The pile is dyed with acid dyes.
- Maintenance involves vacuuming.
- The total weight of the product is 2,633 g/m² - of which the pile weighs 1,100 g/m², the primary backing material weighs 133 g/m², the back weighs 1,400 g/m².
A more detailed description of the processes, calculations of volumes, waste, etc. can be found in the section "Background data".
Product system
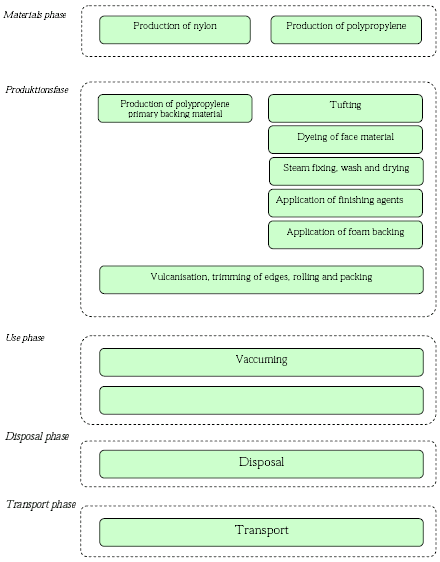
Figure 6.2 livscycle,, flow and phases
In the following, all phases of the floor covering's lifecycle will be described from extraction of raw materials through production to the cutting of the finished floor covering.
Manufacture of raw materials
Nylon and polypropylene fibres belong to the group of synthetic fibres and are produced on the basis of crude oil and natural gas that are converted to plastic through a number of chemical processes. The raw material is a limited resource, and production may lead to impacts on humans and the environment at local, regional and global levels. During processing of the materials into fibres, lubricants are usually added in the form of spindle oil and antistatic agents. Bactericides and fungicides may be added.
Production of the floor covering
Production is divided into several sub-processes:
- production of polypropylene backing (the primary backing material)
- tufting (nylon fibres that constitute the actual surface of the floor covering are stitched to the primary backing material)
- dyeing of face material (the nylon surface)
- steam fixing, wash and drying
- application of finishing agents
- application of foam backing (latex foam)
- vulcanisation (heat treatment)
- edge trimming, rolling and packing.
In principle, vulcanisation is treatment of crude rubber (caoutchouc) with sulphur which gives the rubber better elastic properties and improves its resistance to many chemicals, temperature fluctuations and influence by the air, makes it impenetrable by water, air (partly), and gives it good insulating properties.
It has not been possible to collect data for the production of the primary backing material of polypropylene fibres. At an overall level, this process corresponds to the process "weaving" for the tablecloth case. Therefore, the floor covering model is based of data for weaving, which seems to be a reasonable assumption.
Moreover, emissions of chemicals into the air during production of the floor covering have turned out to be difficult to ascertain, and have thus not been included in the model. However, energy consumption during the processes has been included.
The same applies for discharges of chemicals into water from dyeing the surface of the floor covering. However, this is of less importance as the model assumes that a chemical precipitation system is connected (as is seen in the floor covering industry).
Distribution
The floor covering is packed in polyethylene plastic foil and then it is distributed to retail suppliers throughout Denmark.
Use phase
It is assumed that maintenance only involves vacuuming - other possibilities would be shampooing with an extraction cleaner (vacuum suction).
Transport
The mode of transport when the floor covering is transported from the shop to the buyer's home is also important in connection with the overall environmental profile of the product. Options like driving a car or using public transport make a significant difference in this part of the product's lifecycle.
Disposal phase
Textiles may not be landfilled. On final disposal, they must be incinerated so that the energy content is recovered and replaces non-renewable energy sources like oil and natural gas.
Main scenario - results
The results of the main scenario are presented according to processes.
The production processes are collected in two main groups: own production and other production in Denmark, although the model divides them into more processes, cf. the overview in the section "Background data". Own production includes all production processes except production of polypropylene backing, which is referred to as other production in Denmark.
The values in the three figures are not immediately comparable, as the unit is not the same for the four categories. The consumption of primary energy is calculated in mega-joules (MJ). The environmental impact potentials are presented as "milli-person equivalents" and are directly comparable. Milli-person equivalents are calculated as the direct impact for the year 2000. The weighting factors are based on global (w) or Danish (DK) discharges in the year 2000.
Consumption of primary energy
The consumption of primary energy reflects the processes that require a lot of electrical energy or heating air or water.
Figure 6.3 (consumption of primary energy per functional unit) shows that manufacture of fibre is primarily responsible for large energy consumption because energy consumption in the manufacture of fibres is so large. In the use phase, the electricity consumption for vacuuming causes the impacts. The difference means that the consumer would have to vacuum the floor covering about 20 times per month for 10 years in order for the use phase to outweigh the fibre production.
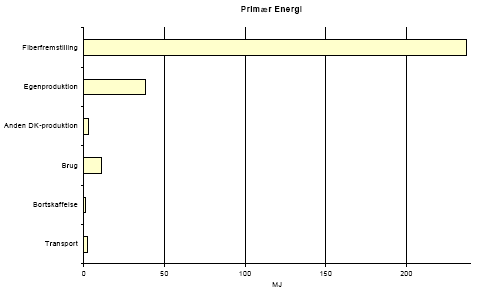
Figure 6.3 Consumption of primery nergi per functional unit – for translation of Danish terms see glossary in annex 11
Environmental impact potentials
The problem with quality of data already mentioned (particularly emissions of chemicals into the air during production of the floor covering) means that there is some reservation regarding the results in the text below. The comments to the figures are neutral, i.e. the comments are on the basis of what can be read from the figures, as they appear. The subsequent section (What-if) discusses the significance of the lack of data for the statement of results.
Figure 6.4 (Toxicological environmental impact potentials per functional unit), figure 6.5 (Environmental impacts related to energy per functional unit) show that the contributions to the environmental impact potentials primarily originate from the fibre-manufacturing process
Click here to see the Figure.
Figure 6.4 Toxicological environmental impact potentials per functional unit – for translation of Danish terms see glossary in annex 11
Click here to see the Figure.
Figure 6.5 Environmental impacts related to energy per functional unit – for translation of Danish terms see glossary in annex 11
The environmental impact potentials related to energy are primarily due to burning fossil fuels.
What-if discussion
This section will discuss the significance of the lack of data for the statement of results for the main scenario. Moreover relevant parallels have been drawn with the scenarios in the three group I cases.
The significance of lack of data for the statement of results
As all relevant energy data have been included in the model, it is deemed that the lack of data has no significance for the appearance of figure 6.3 - consumption of primary energy.
The same applies for figure 6.5, which for EDIPTEX primarily relates to environmental impacts related to energy.
However, the importance for figure 6.4 of lack of data for human toxicity and ecotoxicity from emissions of chemicals from the production of the floor covering is uncertain. In this connection, it is important to note that the floor covering's lifetime is 10 years, and any impacts measured as mPEM (milli person equivalents measured) should thus be distributed over a fairly long period of time.
However, there is no doubt that a similar lack of data for discharges of chemicals into water from dyeing (and washing) the floor covering does not mean so much. Firstly, the model includes a chemical precipitation system (as is common in the floor covering industry). Secondly, the environmental assessment of the jogging suit (where acid dyes are also used) shows that the effect of dyeing nylon with acid dyes is limited.
Parallels to case group I scenarios
The lifecycle of a floor covering is very different from that of garments.
As all the products in case group I are garments, the number of parallels it is possible to draw from their environmental assessments is limited.
This can be seen in the appearance of figure 6.3 - consumption of primary energy - which is very different from the corresponding case group I products (T-shirt, jogging suit and work jacket). Energy consumption in the manufacture of fibres is by far the most significant. Compared with the corresponding figures for the main scenarios for case group I products, it is apparent that although fibre manufacture is also very important here, the use phase (washing, drying and ironing) has an even greater significance.
The message to a floor covering producer wanting to improve the environmental profile of the floor covering is therefore clear: work with reuse of the fibre material.
Background data
System structure in the EDIPTEX database for the floor covering
The figures in column on the right of the table refer to the ID numbers used in the original EDIP PC tool.
|
Ref. no. : EDIPTEX databasen |
1 floor covering, dyed
1 floor covering – Materials phase:
1.386 kg polyamide 6.6 fibres (nylon)
0.160 kg polypropylene fibres
1 floor covering – Production phase:
1.2 m² polypropylene backing (floor covering)
1.2 m² tufting face material, floor covering
1.2 m² dyeing and drying face material, floor covering
1.2 m² tip shearing, floor covering
1,2 m² application of Scotchgard and backing, floor covering
1 m² rolling, cutting and packing, floor covering
1 floor covering – Use phase:
120 m² Vacuum of floor covering
1 floor covering – Disposal phase:
0.133 kg waste incineration of polypropylene
1.1 kg waste incineration of polyamide (nylon)
1.4 kg waste incineration of latex foam
1 floor covering – Transport phase:740 kg km lorry > 16 t diesel out-of-town, terminated
740 kg km lorry > 16 t diesel urban traffic, terminated
740 kg km lorry > 16 t diesel motorway, terminated |
(TX0-06)
(TX6-1-09)
(TX1-06)
(TX1-07)
(TX6-2-22)
(TX1-07-2)
(TX24-2-80)
(TX25-80)
(TX27-2-80)
(TX27-2-81)
(TX28-1-08)
(TX6-3-07)
(TX34)
(TX6-4-07)
(TX41-1-08)
(TX41-1-05)
(TX41-1-09)
(TX6-5-07)
(O32694T98)
(O32695T98)
(O32693T98) |
Details of the floor covering model in the EDIPTEX database
Assumptions:
- The floor covering is a composite - the pile is made of 100 per cent nylon, the primary backing material is made of 100 per cent polypropylene, and the back is made of latex foam.
- Lifetime is 10 years.
- The pile is dyed with acid dyes.
- Maintenance involves vacuuming.
- The total weight of the product is 2,633 g /m² - of which the pile weighs 1,100 g/m², the primary backing material weighs 133 g/m², the back weighs 1,400 g/m².
Functional unit
For the floor covering, the functional unit is defined as:
"10 years' use of floor covering - corresponding to guaranteed lifetime"
It is assumed that the floor covering can be used for ten years before it is discarded.
It is assumed that the consumer vacuums the floor covering once per month, i.e. 120 times during the entire lifetime. No other maintenance is carried out.
The calculations are carried out for "1 floor covering", these need to be converted in relation to lifetime, and the calculations need to be converted to "per year".
Quality floor coverings last longer than 10 years - up to 15 years is not unusual. Similarly, the lifetime of floor coverings of poorer quality can be significantly shorter.
Moreover, maintenance of floor coverings may also involve shampooing with an extraction cleaner (vacuum suction) - but this is not included in this project.
Disposal:
It is assumed that the floor covering is sold in Denmark and disposed of through waste incineration. This means that 1,100 g/m² nylon, 133 g/m² polypropylene and 1,400 g/m² backing (latex foam) need to be incinerated.
Vacuuming:
It is assumed that the floor covering is vacuumed 120 times in its lifetime. This means that 120 m² must be vacuumed in the lifetime of the floor covering.
Rolling, cutting and packing, floor covering:
1 m² is used by this process (the volume is always based on outgoing volume for the process). During cutting (trimming of edges), there is waste of approx. 0.8 m² for every approx. 4.1 m² floor covering (company data), corresponding to approx. 0.2 m² for each square metre. The waste per m² of nylon, polypropylene and latex foam is thus 220 g (0.2 * 1,100), 26.6 g (0.2 * 133) and 280 g (0.2 * 1,400). It is assumed that the waste is disposed of via incineration. There is no data for volumes and types of packaging during further transport - this is not included in the model.
Application of Scotchgard and backing, floor covering:
As mentioned above, this process requires 1.2 m². This process adds weight to the product (the latex backing), but as calculations are made in m², 1.2 m² is still needed from the preceding process. This is allowed as long as the weight increase has been taken into account in other data for the process.
Tip shearing, floor covering:
As mentioned above, this process requires 1.2 m². This process removes some weight from the product (tip shearing of nylon pile), but as calculations are made in m², 1.2 m² is still needed from the preceding process. There is no company data for the pile waste - it is assumed to be approx. 5 per cent of nylon for the finished floor covering. The estimated nylon waste is thus (1.2 * 1.1) * 0.05 = 66 g.
Dyeing and drying face material, floor covering:
This process requires 1.2 m². It is assumed there is no significant waste from this process.
Tufting of face material, floor covering:
This process requires 1.2 m². It is assumed there is no significant waste from this process.
Polypropylene backing, face material (floor covering):
There is no data for this process. At an overall level, this process corresponds to the process "weaving" for the tablecloth. Therefore, the floor covering model is based on data for weaving, which seems to be a reasonable assumption. It is assumed there is no significant waste from this process. This process requires 1.2 m².
Polyamide 6.6 fibres (nylon):
This process is calculated per kg. Calculation of the volume of nylon fibres for production of 1 m² finished floor covering is done by adding up the waste from the above production processes and then adding the figure to the volume of nylon in 1 m² finished floor covering:
1,100 g nylon is included in each m² finished floor covering.
For the process "Rolling, cutting and packing, floor covering", waste is 220 g.
For the process, "Tip shearing, floor covering", waste is 66 g.
Thus, this process requires 1.386 kg.
Polypropylene fibres:
As for nylon, this process is calculated per kg.
133 g polypropylene is included in each m² finished floor covering.
For the process "Rolling, cutting and packing, floor covering", waste is 26.6 g.
Thus, this process requires about 0.160 kg.
Transport:
All transport distances are estimated. Calculations are per m² floor covering. See table below.
Transport |
Quantity for one floor covering |
Kg km |
Transport of nylon fibres from fibre producer in Germany to floor covering producer in Denmark |
1,386 kg transported 1000 km by lorry |
1386 kg km by lorry |
Transport of polypropylene fibres from fibre producer in Germany to producer of polypropylene backing in Denmark |
0,160 kg transported 1000 km by lorry |
160 kg km by lorry |
Transport of polypropylene backing from producer to floor covering producer, both in Denmark |
0,160 kg transported 100 km by lorry |
16 kg km by lorry |
Transport from floor covering producer to shop in Denmark, lorry |
2,633 kg transported 100 km by lorry |
263,3 kg km by lorry |
Consumer transport - from shop to consumer |
2,633 kg transported 100 km by lorry |
263,3 kg km by lorry |
Transport of discarded floor covering (with household refuse) |
2,633 kg transported 50 km by lorry |
131,6 kg km by lorry |
Lorry, total: 2220.02 kg km (assumed 33 per cent urban, 33 per cent out-of-town, 33 per cent motorway). I.e. total transport:
Proces no. in EPIPTEX database |
Name of process |
Transport need |
O32695T98 |
Lorry > 16 t, diesel urban traffic, TERMINATED |
740 kg km by lorry |
O32694T98 |
Lorry > 16 t diesel out-of-town, TERMINATED |
740 kg km by lorry |
O32693T98 |
Lorry > 16 t diesel motorway, TERMINATED |
740 kg km by lorry |
| Front page | | Contents | | Previous | | Next | | Top |
Version 1.0 July 2007, © Danish Environmental Protection Agency
|