Helstråkompositter er et nyudviklet pladeprodukt, der udnytter den høje styrke og
lave vægt af strå - naturens eget maste-materiale. På grund af kompositternes høje
styrke i forhold til vægt, er det sandsynligvis muligt at erstatte materialer med høje
funktionskrav - f.eks. lastbillad, togvogne og møllevinger. Møllevinger af
helstråkompositter udvikles og afprøves i et EU-projekt (JOULE-programmet). I
nærværende projekt er materialets egenskaber som byggemateriale blevet demonstreret og
testet.
Helstråkompositter er stadig under udvikling. Det er målet at udvikle et
miljøvenligt produkt med gode tekniske egenskaber. Pilotprodukter af forskellige
stråtyper og i forskellige former er udviklet og afprøvet i Tyskland ved
Frauenhofer-Institut für Holzforschung og ved Institut für
Bauforschung, FAL. Helstråkompositter fremstilles ved at samle strå i tætte
bundter og fylde hulrummene i bundtet ud med en skum. Ud af bundterne saves derefter
plader på tværs af stråenes længderetning, og der limes en tynd plade på top og bund
(se Fig. 1).
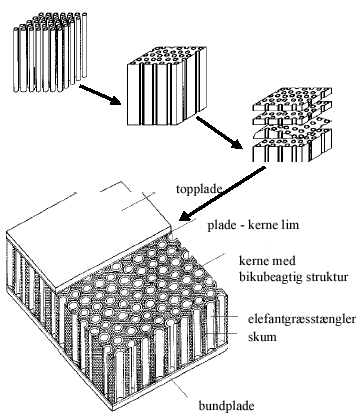
Figur 1.
Principskitse for fremstilling af helstråkomposit.
Principielt er det muligt at udnytte mange forskellige plantearters strå eller
stængler fx fra kornarter, tagrør, elefantgræs, hamp, bambus og kæmpetagrør (Arundo
donax). Det er dog vigtigt, at der ikke er løse bladskeder omkring strået, som
vanskeliggør skummets tilhæftning. Dette udgør et problem for tagrør og for visse
arter af elefantgræs. Stængler af hamp er ikke hule og er derfor forholdsvis tunge og
kan være vanskelige at tørre. Bambus kan give meget stor styrke, men har oftest stor
tyngde. Foreløbigt har interessen derfor samlet sig mest omkring strå fra almindelige
kornarter og fra arter af elefantgræs, som smider blade og bladskeder om vinteren. I et
igangværende EU-projekt (FAIR-programmet) undersøges egenskaber af en række ståtyper
dyrket under forskellige klimaforhold, og desuden indsamles nye genotyper med
tilsyneladende forbedrede egenskaber.
Rug og triticale (en krydsning mellem rug og hvede) er de kornarter, som giver de
bedste strå til helstråkompositter. Det skyldes en bedre længde (bør være over 1 m af
hensyn til rationel høst, bundtning og skumindblæsning), bedre bladtab og større styrke
end af hvede og byg. Fra forædlere i det tidligere Øst-tyskland og Polen er fremskaffet
rug-sorter, som har en særlig stor længde på stråene, og enkelte sorter, som er
forædlet specifikt mod en stor strådiameter (giver mulighed for mindre volumenvægt af
stråbundter). Disse er blevet prøvedyrket i Tyskland med henblik på test for
høstegnethed og styrke til fremstilling af helstråkompositter.
Strå fra elefantgræsarterne Miscanthus sinensis, M. Giganteus og M.
sacchariflorus er blevet afprøvet for egnethed til helstråkompositter. Sorter af M.
sinensis er mindre egnede på grund af at blade og bladskeder oftest bliver siddende
på stråene frem til høsttidspunktet i foråret. M. Giganteus er
blevet grundigt undersøgt for stråkvalitet som funktion af klimaforhold over Europa, og
under forskellige dyrkningssystemer, og arten har en god styrke og en rimelig afbladning
om vinteren.
Det er dog indenfor arten M. sacchariflorus, at de bedste stråkvaliteter er
blevet fundet, idet stråene om foråret er totalt frie for blade og bladskeder. Endvidere
er fundet genotyper, som har større diameter og mindre volumenvægt (20-30 % mindre) end
strå af M. Giganteus. De mest lovende genotyper er under opformering
med henblik på at producere større mængder strå til kommende pilotproduktioner af
helstråkompositter.
Strå, som høstes til produktion af helstråkompositter, skal håndteres hele og
samles i ensartede bundter. Specielt til de høje (2-4 m) strå af elefantgræs findes
ingen gængse høstmaskiner, som kan gennemføre høsten tilfredsstillende. Derfor er en
specialmaskine blevet udviklet af firmaet Hvidsted Energiskov (Fig. 2), og den forventes
fra efteråret 2001 at kunne anvendes i praksis.
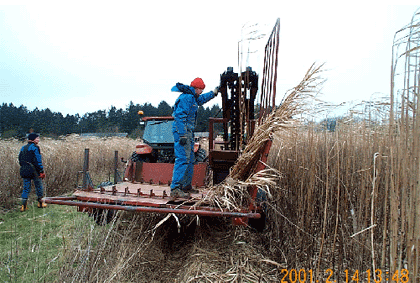
Figur 2.
Høst af strå af elefantgræs (M. Giganteus) med nyudviklet maskine fra
Hvidsted Energiskov.
Den skum, som indblæses mellem stråene, har primært til formål at fastholde
stråene under udsavning af de ønskede kernetykkelser og under pålimning af top- og
bundplader. Polyurethan fungerer glimrende rent teknisk, men matcher ikke målsætningen
om at udvikle et rent biologisk produkt med en lav miljøbelastning. Glutin (hudlim) har
vist sig at fungere godt under opskumning og ved den senere udsavning. Den skum, som
indblæses har dog et vandindhold på 60-70 %, og den efterfølgende tørring skal ske ved
maksimalt 30 oC, ellers smelter limen. Disse krav vanskeliggør en effektiv
proceslinje.
En række andre skumtyper er blevet afprøvet (bl.a. stivelse) og det bedste tekniske
resultat er opnået med en polyurethan fremstillet af planteolie, men dog stadig med brug
af isocyanat til hærdning. Sammenlignet med konventionel polyurethan er isocyanat-behovet
til opskumning af den biologiske olie dog reduceret fra 50 % til 30 %. Den biologisk
baserede polyurethanskum er vandfast og opskummes ved hjælp af luft.
Både glutinskum og biologisk baseret polyurethanskum kan opskummes, så der opnås
volumenvægte ned til 30 kg/m3.
Top- og bundpladerne på helstråkompositter (se Fig. 1) har oftest været af
krydsfiner. Det har dog været ønsket at afprøve nye pladematerialer, som er frie for
syntetisk lim, idet træfibrene er enzymatisk bundet sammen. Men disse plader, udviklet af
KVL i samarbejde med NOVO, har ikke kunnet leveres i tilstrækkelig størrelse til
produktion af helstråkompositter. Pladerne limes på stråkernen med en kaseinlim (et
biprodukt fra ostefremstilling).
Indtil videre er helstråkompositter alene blevet fremstillet manuelt i meget
begrænset skala, men i EU-projektet Optimisation of the production chain for high
performance Light Natural Sandwich materials as a basis for scaling up er skaffet
viden og erfaringer, som kan danne basis for en opskalering til pilot-skala. Figur 3
illustrerer en simpel proceslinje for fremstilling af kernemateriale.
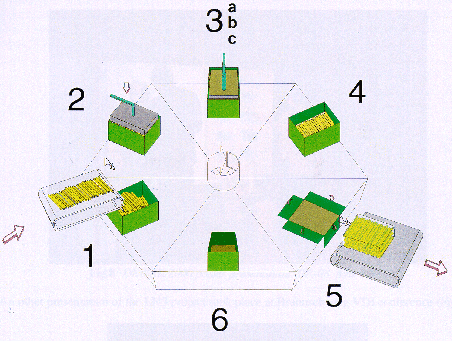
Figur 3.
Principskitse for en mulig proceslinje til produktion af helstråkompositter. 1:
Ensartede strå fyldes i. 2: Injektion af skum. 3a: Presning af strå/skum-blanding. 3b:
Etablering af vakuum og opvarmning af boksen. 3c: Vakuum ophæves og stempel løftes. 4:
Hærdning af strå/skum-blanding. 5: Udformning for videre opsavning til kernemateriale.
6: Klargøring til ny produktion.
Der er tidligere fremstillet helstråkompositter af rug og elefantgræs, som har
ligeså gode tekniske data, som high-tech letvægtsmaterialer af glasfiber, letmetal eller
plastik fremstillet i en bikubestruktur (Tabel 1). Tryk- og bøjningsstyrke af
helstråkompositter afhænger dog meget af materialets dimensioner, specielt relationen
mellem strålængde og diameter. For at opnå de høje styrker angivet i tabel 1, må
forholdet mellem længde og diameter af strå holdes under 8.
Til byggematerialer er der normalt ikke så høje styrkekrav, mens til gengæld forhold
som lyd- og varmeisolering har stor betydning. Helstråkompositters evne til
varmeisolering afhænger meget af, hvilken type strå der anvendes, og hvordan de er
pakket i pladen. Termografiske billeder af helstråkompositter har vist, at der igennem
hule strå, som står på tværs af pladeoverfladen, sker en vis varmetransport. Hvis
stråene lægges ned, kan den isolerende evne blive på højde med cellulose- og
mineraluld, men til gengæld reduceres styrken.
Helstråkompositters lave densitet sandsynliggør en ringe evne til lydisolering.
Lydisoleringsevne og styrke af de aktuelle heltstråkompositter bygget ind i Hjortshøj er
blevet målt i projektet, se afsnit 3.
Tabel 1.
Sammenligning af densitet og styrkeværdier for forskellige pladematerialer. Data fra
Frank Möller.
Da helstråkompositter endnu ikke fremstilles i industriskala er det vanskeligt at
sige, hvad markedsprisen vil blive. Vurderinger i Tyskland af en sandsynlig markedspris
ligger på 1.300-2.600 kr/m3. Det er betydeligt billigere end
sandwichmaterialer af plastik og letmetal, men er dyrere end almindelige byggeplader af
gips eller træfibre.
Ideen bag udviklingen af helstråkompositter var at skabe et plademateriale, som er
meget let, stærkt og fremstillet af miljøvenlige råvarer. Den primære
produktmålgruppe var industriprodukter til erstatning af materialer af plast, letmetal og
specielle træprodukter såsom krydsfiner. Dermed opfylder helstråkompositter i deres
oprindelige udformning ikke nødvendigvis de krav, der kan stilles til byggematerialer, fx
med hensyn til lyddæmpning og brand.
Den forventede høje pris sammenlignet med billige pladematerialer til byggeri betyder
endvidere, at helstråkompositter ikke vil være konkurrencedygtige til almindelig
opbygning af indervægge o.l. Det vil være mere aktuelt at anvende helstråkompositter i
konstruktioner, hvor deres særlige egenskaber giver en fordel, hvilket kan være
tilfældet med gulve eller loftskonstruktioner med store spænd. Endelig kan letheden af
materialet udnyttes ved anvendelse til flytbare indervægge, hvor man ønsker mulighed for
fleksibel ruminddeling.
Ved produktion af nemt transporterbare barakker til nødområder eller til
fjerntliggende arbejdspladser vil letheden af helstråkompositter kunne udnyttes. At
produktet efter brug kan bortskaffes ved afbrænding eller kompostering kan yderligere
være en fordel.
I afsnit 6 har vi gennemgået mulige ændringer af produktet, som kan forbedre dets
egenskaber med henblik på anvendelse i byggeri.
| Forside | | Indhold | | Forrige | |
Næste | | Top
|