| Forside | | Indhold | | Forrige | | Næste |
Metoder til genanvendelse af farvede glasskår til produktion af tegl og beton og til vejbygning
3 Glas som fillermateriale i beton
Knust glas kan genanvendes i beton, både som tilslag og som filler.
Det største potentiale vurderes imidlertid at være til stede ved anvendelse af glas som fillermateriale. Dette har to
årsager. For det første er det som fillermateriale, at der kan afsættes de største mængder, fordi der af hensyn til
betonens holdbarhed, styrke mm. vil være nogle restriktioner ved brug af glas som tilslag. For det andet er det som
fillermateriale, at glasset mht. pris vil være mest konkurrencedygtigt. Sidstnævnte gælder især som filler til hvid
beton, hvor alternative fillermaterialer som hvid mikrosilica og hvid slagge både er dyre og svære at skaffe.
Det er derfor valgt at udføre pilotforsøg med anvendelse af glas som fillermateriale i beton, hvor glasset er formalet
til cementfinhed.
3.1 Forsøgsprogram
Forsøgsprogrammet er inddelt i forskellige faser:
- Forsøg med formaling af glas. Disse forsøg er foretaget for dels at kunne vurdere nogle af fillerens fysiske
egenskaber (primært kornkurven), dels for at kunne vurdere energiforbruget og dermed omkostningen ved
at formale glasset til filler.
- Indledende forsøg med pasta og mørtler. Ved disse forsøg vurderes glasfillerens indflydelse på styrke,
vandbehov og afbindingstid samt om glasfilleren vil gøre betonen mere eller mindre udsat for skadelige
alkali/kisel-reaktioner. Resultaterne af mørtelforsøgene benyttes desuden til at vælge en konkret glastype
samt formalingsgrad af glasset til betonforsøg.
- Betonforsøg. Der udføres parallelforsøg med en konventionel beton, der indeholder flyveaske, og en
tilsvarende beton, hvor flyveasken er erstattet af glasfiller. Ved disse forsøg undersøges den friske betons
egenskaber (bearbejdelighed, luftindhold mm.), den hærdnende betons egenskaber (varme- og
styrkeudvikling) samt den hærdnede betons holdbarhed.
- Måling af farveændringer ved anvendelse af glasfiller i hvid beton. Det er altafgørende for anvendelsen
af glasfiller i hvid beton og i beton med lyse nuancer i det hele taget, at fillerens betydning for det visuelle
indtryk af betonen er kendt. Derfor undersøges glasfillerens betydning for betonens farve specifikt.
Alle forsøgsfaser på nær betonforsøgene er udført med såvel grønt som klart glas. Der er udført forsøg med glas,
der er formalet til finheder på henholdsvis 350 m2/kg og 500 m2/kg (Blaine-værdier). Generelt gennem projektet
er der anvendt følgende benævnelser af prøveemner:
- REF: Referenceprøve uden glasfiller
- G350: Prøveemne med glasfiller af grønt glas formalet til en finhed på 350 m2/kg.
- G500: Prøveemne med glasfiller af grønt glas formalet til en finhed på 500 m2/kg.
- K350: Prøveemne med glasfiller af klart glas formalet til en finhed på 350 m2/kg.
- K500: Prøveemne med glasfiller af klart glas formalet til en finhed på 500 m2/kg.
De forskellige fillere er vist på Figur 3.1. Det er dog svært ud fra dette billede at se nogen forskel på pulverne.
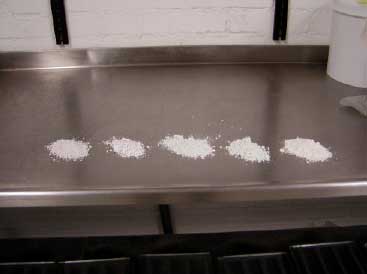
Figur 3.1: De fem glasfillere K350, K500, G500 og G350 samt Aalborg White cement
3.2 Formaling af glas
Glas til pilotforsøg er formalet på laboratoriemøller hos Aalborg Portland, der normalt anvendes til formaling af
cementklinker.
For såvel grønt som klart glas er der sket en formaling til to forskellige finheder, idet der er sigtet efter finheder på
henholdsvis 350 og 500 m2/kg (Blaine-værdier). De resulterende kornkurver ses i Bilag B, og mikroskopibilleder
fremgår af Bilag C.
Ved formalingen er der registreret et effektforbrug for
laboratoriemøllerne, der svarer til, at det ca. vil kræve 45 kWh at
formale 1 tons glas (lidt mindre ved formaling til 350 m2/kg, lidt
mere ved formaling til 500 m2/kg). Dette svarer til effektforbruget
ved formaling af cementklinker.
3.3 Indledende forsøg med pasta og mørtler
Mørtel er i princippet en meget simpel beton, der kun består af sand, vand og cement samt eventuelt andet pulver,
hvor traditionel beton er et mere komplekst materiale. Pasta er endnu simplere, idet den kun består af pulver og
vand.
Resultater fra forsøg med mørtel kan ikke direkte overføres til beton, men for fx glasfiller-materialer vil de indikere
en række egenskaber, der vil kunne genfindes, når fillerne blandes i beton. Mørtelforsøgene er imidlertid nemmere
og billigere at udføre end tilsvarende forsøg med beton, og derfor egner de sig godt til at screene et større antal
fillermaterialer.
Mørtlerne med glasfiller i dette projekt er sammensat på samme måde som de mørtler, der benyttes til at teste
flyveaske, jf. DS/EN 450 [1], idet flyveasken blot erstattes med glas. Det betyder, at pulverkombinationen består
af 75% cement og 25% glasfiller, forholdet mellem vand og pulver er 1:2 og forholdet mellem pulver og sand er
1:3, se desuden Bilag D. Samme pulverkombination er anvendt i pasta.
Ved de indledende forsøg med pasta og mørtler er der målt styrkeudvikling, vandbehov og begyndende
afbindingstid. Der er desuden målt alkali/kisel-ekspansion for mørtelprismer med glasfiller.
3.3.1 Styrkeudvikling
Mørtlernes styrkeudvikling er registreret for mørtler med tre forskellige typer cement: Norsk Industricement, der
benyttes som referencecement ved test af flyveaske, samt Aalborg White® cement og Lavalkali Sulfatbestandig
cement fra Aalborg Portland, der er to danske cementtyper. Resultaterne fremgår af Figur 3.2, Figur 3.3 og Figur 3.4.
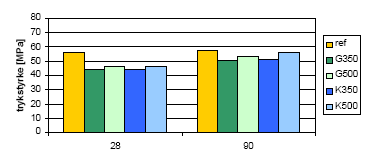
Figur 3.2: Styrkeudvikling for mørtel af Norsk Industricement og forskellige glasfillere (28 og 90 døgn).
Styrken for mørtler med Norsk Industricement er målt henholdsvis 28 og 90 døgn efter støbning. Ved 28 døgn
udgør styrken af mørtler med glasfiller 79-82% af styrken for en referencemørtel uden glasfiller (100% cement).
Ved 90 døgn har mørtel med glasfiller en styrke på 87-97% af referencemørtlens styrke.
For flyveaske er kravet, at styrken efter 28 og 90 døgn ikke må være mindre end henholdsvis 75% og 85% af
referencemørtlens styrke. De forskellige glasfillere ses alle at opfylde dette krav.
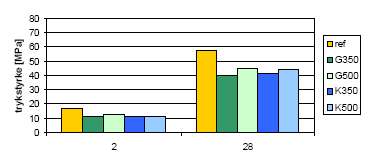
Figur 3.3: Styrkeudvikling for mørtel af Lavalkali Sulfatbestandig cement og forskellige glasfillere (2 og 28 døgn).
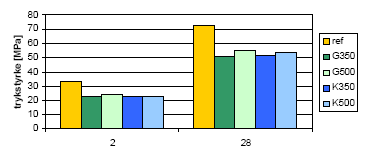
Figur 3.4: Styrkeudvikling for mørtel af Aalborg White® cement og forskellige glasfillere (2 og 28 døgn).
For mørtel med Lavalkali Sulfatbestandig cement og glasfiller er styrken efter 2 døgn på 67-72% af styrken for
mørtel med ren cement. Efter 28 døgn er styrken i forhold til den rene cementmørtel steget lidt til 70-78%. For
mørtel med Aalborg White® cement og glasfiller er de tilsvarende tal 69-76% og 70-76%.
For alle tre cementtyper ses der en tendens til, at der opnås lidt højere styrker ved den fine formaling på 500 m2/kg
end ved formalingen til 350 m2/kg. Der ses ikke nogen forskel afhængigt af glassets farve.
3.3.2 Vandbehov og tid til begyndende afbinding
Vandbehovet og det tidspunkt, hvor afbindingen sætter ind, måles vha. metoden beskrevet i DS/EN 196-3 [2].
Denne metode er udviklet til afprøvning af cement. I nærværende forsøg er cementen afløst af en
pulverkombination af 75% cement og 25% glas.
Først blandes pulveret med en given mængde vand, og pastaens konsistens registreres (målt som nedsynkningen af
et stempel). Dette gentages med mere eller mindre vand, indtil pastaen har en på forhånd defineret
standard-konsistens. Den mængde vand i forhold til pulvermængden, der lige netop giver pastaen den ønskede
standard-konsistens, kaldes vandbehovet. Vandbehovet udtrykker således noget om, hvordan glasfilleren påvirker
betons bearbejdelighed. Hvis vandbehovet er stort, vil glasfilleren forringe bearbejdeligheden, mens et lavt
vandbehov er til gavn for bearbejdeligheden.
Når der er opnået en pasta med standard-konsistens, anvendes denne til forsøg med afbindingstid. Med passende
mellemrum (dvs. mindst hvert 10. minut) stikkes en nål i pastaen, og modstanden måles. På et tidspunkt begynder
modstanden at stige som tegn på, at afbindingen er begyndt. Definitionen på det præcise tidspunkt for begyndende
afbinding er det tidspunkt, der svarer til en bestemt modstand.
Vandbehov og begyndende afbindingstid er målt ved anvendelse af tre forskellige cementtyper, se Figur 3.5 og Figur 3.6.
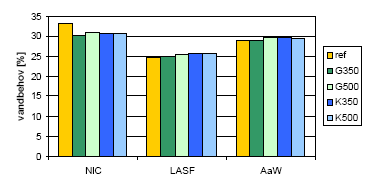
Figur 3.5: Målt vandbehov jf DS/EN 196-3. Forkortelser: NIC – Norsk Industricement; LASF – Lavalkali
Sulfatbestandig cement; AaW – Aalborg White® cement.
Det ses, at der ikke er noget entydigt billede, men derimod en afhængighed af hvilken type cement, glasfilleren
sammenlignes med. Ved anvendelse af en cement med højt vandbehov som fx Norsk Industricement, fås et lidt
lavere vandbehov, når en del af cementen erstattes med glasfiller. Anvendes der derimod en cement med lavt
vandbehov som fx Lavalkali Sulfatbestandig cement fra Aalborg Portland, øger glasfilleren vandbehovet.
Det kan således konkluderes, at de fire testede glasfillere nogenlunde bidrager til vandbehovet som en gennemsnitlig
cement. Der ses ikke nogen signifikante forskelle mellem de forskellige glasfillere, hverken mht. farve eller finhed.
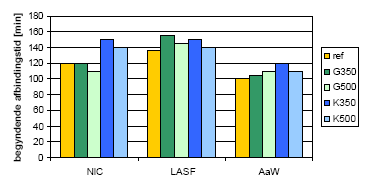
Figur 3.6: Begyndende afbindingstid jf DS/EN 196-3. Forkortelser: NIC – Norsk Industricement; LASF – Lavalkali
Sulfatbestandig cement; AaW – Aalborg White® cement.
Mht. afbindingstid ses det, at tilsætningen af glasfiller i stort set alle tilfælde forlænger tiden til afbindingen begynder.
Der er tale om forlængelser, der typisk er i størrelsesordenen 10-20 minutter.
Ved brug af Norsk Industricement og Aalborg White® cement ser det ud til, at det især er det klare glas, der
forlænger afbindingstiden. Ved brug af Lavalkali Sulfatbestandig cement, der i sig selv har en lidt længere
afbindingstid end de øvrige cementer, ses der dog ikke nogen effekt af glassets farve. I fem ud af seks tilfælde er
afbindingstiden længere ved brug af filler med finhed 350 m2/kg end ved brug af filler med finhed 500 m2/kg.
3.3.3 Alkali/kisel-reaktivitet
Som beskrevet i litteraturstudiet [3], er skadelige alkali/kisel-reaktioner et emne, der bør undersøges, før en
eventuel glasfiller anvendes til betonproduktion.
Når kisel (amorf SiO2) kommer i kontakt med en alkali-holdig væske, sker der en kemisk reaktion.
Reaktionsproduktet er en hygroskopisk gel, der tiltrækker vand og derfor sveller. Hvis reaktionen finder sted i
beton, vil alkali/kisel-gelen opbygge et tryk på det omgivende materiale, der kan få betonen til at revne.
Alkali stammer enten fra betonens delmaterialer (bl.a. cementen) eller trænger ind i betonen fra det omgivende miljø
(fx fra havvand og tø-salte). Kisel findes i forskellige sand- og stenmaterialer. I princippet er det tilstrækkeligt at
sikre ét af to, nemlig at der enten ikke er tilstrækkeligt alkali eller tilstrækkeligt kisel til at alkali/kisel-reaktionerne
kan få et skadeligt omfang. I DS 481 [4] stilles der dog for beton til fugtigt miljø både krav om, at der er et
begrænset alkali-indhold og at tilslagsmaterialerne ikke er alkali-reaktive.
Grunden til, at alkali/kisel-reaktioner særligt bør undersøges for materialer af glas, er, at hovedbestanddelen i glas
er amorf SiO2, men samtidigt har glasset et højt indhold af alkali (15-20%), så her tilsættes de to uønskede
komponenter samtidigt, og alkali/kisel-reaktioner er derfor uundgåelige. Det, der herefter afgør, om reaktionerne
rent faktisk fører til skader i betonen, er glassets partikelstørrelse.
For meget små partikler vil en stor del af kiselen blive omdannet til gel, fordi den specifikke overflade er stor og der
derfor er en stor flade med kontakt til en alkali-holdig porevæske, hvor reaktionerne kan foregå. Men selvom der
dannes meget gel, vil den være jævnt fordelt i form af meget små ansamlinger i betonens faststofstruktur. Mens
større ansamlinger lokalt kan give anledning til tryk, der overstiger betonens styrke, vil de små ansamlinger hver for
sig ikke være i stand til at opbygge et skadeligt tryk. På den måde kan tilsætningen af meget små, reaktive partikler
faktisk være en fordel, fordi de så at sige forbruger alkali, før det kan komme til at reagere med større partikler, og
dermed forebygger skadesudvikling, hvis fx sandpartiklerne er reaktive. Det samme gør sig gældende ved
anvendelsen af mikrosilica i beton.
I nærværende projekt er der udført to serier af mørtelforsøg i henhold til metoden DS 405.15 [5]. I begge tilfælde
erstattes 25% af cementen med glasfiller.
I den første serie er glasfilleren afprøvet sammen med ikke-reaktivt sand for at undersøge, om glasset i sig selv kan
give anledning til skadelige reaktioner. Det er valgt at gennemføre forsøgene med de to groveste fillere (finhed 350
m2/kg), for hvis disse to fillere ikke giver anledning til problemer, forventes der heller ikke at opstå problemer med
skadelige reaktioner ved anvendelse af endnu finere glaspartikler.
I den anden forsøgsserie er glasset afprøvet sammen med et reaktivt sand for at undersøge, om glasfilleren ligefrem
kan forebygge skadelige alkali-kiselreaktioner. I denne forsøgsserie indgår der også prøveemner, hvor 25% af
cementen er erstattet af flyveaske, idet flyveaske netop er kendt for at kunne have en sådan positiv effekt.
Prøveemnerne med flyveaske er mærket FA.
Resultaterne fra de to forsøgsserier er gengivet i Figur 3.7 og Figur 3.8.
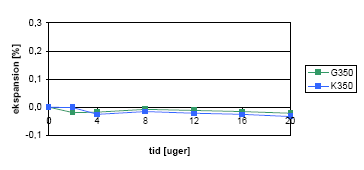
Figur 3.7: Alkali/kisel-ekspansion målt for prøveemner med ikke-reaktivt sand (Voervadsbro-sand).
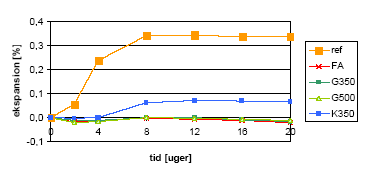
Figur 3.8: Alkali/kisel-ekspansion målt for prøveemner med reaktivt sand (Nymølle-sand).
Det ses af Figur 3.7, at selv ikke ved så store mængder som 25% af pulveret giver glasfilleren anledning til nævneværdig
ekspansion. I DS 481 [4] tillades der ved tilsvarende forsøg med sand, der skal godkendes til ekstra aggressivt
miljø, en ekspansion på 0,1% i løbet af 20 uger.
I Figur 3.8 ses det, at Nymølle-sandet er meget reaktivt, idet ekspansionen af referenceprismerne overstiger 0,1% efter
mindre end 4 ugers forsøg. De afprøvede glasfillere formår imidlertid at holde skadesudviklingen i skak på samme
vis som flyveaske og mikrosilica. Glassets farve eller formaling er tilsyneladende ikke afgørende.
3.4 Betonforsøg
Det er undersøgt, om glasfiller ændrer på forskellige væsentlige betonegenskaber så som bearbejdelighed, styrke
mm. Undersøgelserne er forløbet som parallelprøvning, hvor der er blandet en referencebeton med flyveaske og en
beton, der svarer til referencebetonen, men hvor flyveasken er erstattet af G350 glasfiller kg til kg.
Som referencebeton er valgt en beton til aggressiv miljøklasse med en karakteristisk styrke på 35 MPa. G350 er
valgt som glasfiller til betonforsøgene, fordi ingen af de foregående forsøg med mørtel har tydet på store forskelle
afhængigt af glassets farve og af om det er formalet til 350 eller 500 m2/kg. Det er derfor oplagt dels at bruge den
farve glas, der er størst interesse i at få nyttiggjort i beton, samt at anvende den formalingsgrad, der kræver det
mindste energiforbrug.
De to betoner benævnes henholdsvis Beton-ref og Beton-G350. Recepterne for de to betoner fremgår af Bilag D.
Rådata fra betonforsøgene fremgår af Bilag E.
3.4.1 Friskbetonegenskaber
Begge betontyper er blandet to gange, så nedenstående observationer af den friske betons egenskaber er
gennemsnittet for de to blandinger, se Tabel 3.1.
Tabel 3.1: Friskbetonegenskaber.
|
Beton-ref |
Beton-G350 |
sætmål, mm |
145 |
155 |
densitet, kg/m3 |
2249 |
2201 |
luftindhold1, volumen% |
6,8 |
9,2 |
1 Luftindholdet er beregnet på baggrund af den målte densitet og receptdata.
Det ses, at beton med glasfiller har en lidt bedre bearbejdelighed (målt som sætmål) end beton med flyveaske.
Dette skyldes muligvis, at beton med glasfiller også har et højere luftindhold end beton med flyveaske. En forklaring
på dette kan være, at luftindblandingsmidlet virker mere effektivt i beton med glasfiller, fordi der ikke er kulrester til
stede, der stammer fra flyveasken.
Ved udstøbning af beton til prøveemner til de øvrige undersøgelser, blev det vurderet, at beton med glasfiller
bevarede konsistensen længere, mens beton med flyveaske hurtigere tabte bearbejdeligheden. Der er imidlertid
ikke foretaget målinger af sætmålstabet som funktion af tid.
3.4.2 Varmeudvikling
Resultaterne for varmeudvikling fremgår af Figur 3.9 og Tabel 3.1.
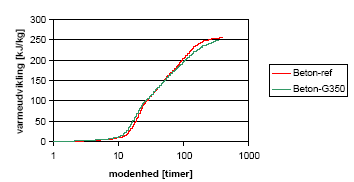
Figur 3.9: Målt varmeudvikling (kJ pr. kg pulver i blandingen).
Tabel 3.2: Parametre bestemt ved varmeudvikling.
|
Beton-ref |
Beton-G350 |
Q∞ - cement, kJ/kg |
347,1 |
349,5 |
Q∞ - pulver, kJ/kg |
277,5 |
279,4 |
α |
1,05 |
0,89 |
τ0, timer |
11,93 |
9,77 |
Varmeudviklingen er næsten identisk for de to typer beton, både med hensyn til den totale varmeudvikling Q∞ samt
de to parametre α og τ0,, der henholdsvis siger noget om, hvor hurtigt varmeudviklingen forløber, og hvornår betonen
begynder at udvikle varme. Man skal derfor være forsigtig med overfortolkning. Det ser dog ud til, at
varmeudviklingen starter en anelse tidligere for beton med glasfiller (muligvis pga. alkaliaktivering), men at
varmeudviklingen til gengæld forløber lidt langsommere. Det sidste gør, at der må forventes en lidt langsommere
styrkeudvikling for beton med glasfiller.
3.4.3 Styrkeudvikling
Betonens styrke er målt til fire terminer (2, 7, 28 og 56 døgn), se Figur 3.10.
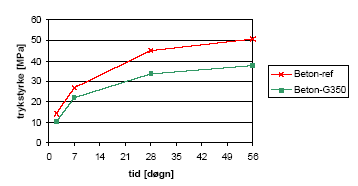
Figur 3.10: Styrkeudvikling.
Det ses, at beton med glasfiller har en lidt lavere styrke end beton med flyveaske. Dette kan til dels forklares med,
at beton med glasfiller har et luftindhold, der er 1-2% højere end luftindholdet i referencebetonen (dette ses af
målinger af den friske betons luftindhold samt analyse af luftporestrukturen i den hærdnede beton). Som
tommelfingerregel nedsætter hver % luft styrken med ca. 4%, og det må derfor forventes, at beton med glasfiller
har 4-8% lavere styrke.
Forskel i luftindhold kan dog ikke forklare hele forskellen på de målte styrker, og det ser således ud til, at beton
med glasfiller har en lavere styrke end beton med flyveaske.
3.4.4 Chloridmodstand
Chloridmodstanden er bestemt som chloridmigrationskoefficient jf. NT BUILD 492, dog er chloridmodstanden
bestemt 44 døgn efter støbning, hvor der normalt anvendes en prøvningstermin på 28 døgn. Dette har dog ingen
betydning for sammenligningen af resultater.
Beton-ref har en chloridmigrationskoefficient på 3,1·10-12 m2/s, mens Beton-G350 har en
chloridmigrationskoefficient på 2,5·10-12 m2/s. De lave koefficienter viser, at begge typer beton har god
chloridmodstand. Det kan se ud til, at glasset forbedrer chloridmodstanden en anelse. Det er dog problematisk at
drage nogen konklussion ved sammenligning af tal, der under alle omstændigheder er meget små.
3.4.5 Frostbestandighed
Frostbestandigheden kan dels vurderes på baggrund af en analyse af den hærdnede betons luftporestruktur, dels
ved direkte at måle skadesudviklingen i form af afskalning ved en accelereret test.
Resultaterne af luftporeanalysen fremgår af Figur 3.11 og Tabel 3.3.
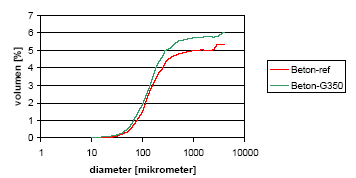
Figur 3.11: Luftporefordeling, jf. DS/EN 480-11.
Tabel 3.3: Parametre bestemt ved luftporeanalyse jf DS/EN 480-11.
|
Beton-ref |
Beton-G350 |
Totalt luftindhold, vol.% |
5,6 |
6,4 |
Specifik overflade, mm-1 |
51 |
55 |
Afstandsfaktor, mm |
0,09 |
0,08 |
Mikroluftindhold, vol.% |
4,5 |
5,0 |
Begge typer beton har meget tilfredsstillende luftporestrukturer. I DS 481 er der krav om, at afstandsfaktoren ikke
må overstige 0,20 mm. Begge typer beton opfylder dette krav, og det viser sig også, at begge typer beton klarer
sig godt i en accelereret frosttest, se Figur 3.12.
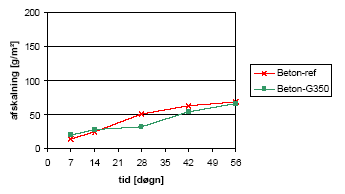
Figur 3.12: Resultat af accelereret frosttest jf. SS 13 72 44.
Iflg. DS 481 skal beton til aggressivt miljø have god frostbestandighed, hvilket betyder, at betonen i den
accelererede frosttest
· enten skal have en akkumuleret afskalning efter 56 døgn, der er mindre end 0,20 kg/m2
· eller skal have en akkumuleret afskalning efter 56 døgn, der er mindre end 0,50 kg/m2 samtidigt med at
afskalningen efter 56 døgn er mindre end det dobbelte af afskalningen efter 28 døgn (m56/m28<2).
Afskalningen for både Beton-ref og Beton-G350 er stort set negligerbar, og begge typer beton lever op til
DS 481s krav.
3.5 Måling af farveændringer ved anvendelse af glasfiller
Aalborg Portland har udviklet en standardiseret proCedure for måling af betons farve. Her udstøbes tre betonfliser
for hver prøve, og farven måles umiddelbart efter afformning (dvs. dagen efter støbning) samt 14 og 28 døgn efter
støbning. Ved farvemålingen anvendes en robot, der har en lyskilde og en farvescanner påmonteret. Målingerne
opsamles og bearbejdes af en computer. Opstillingen er vist på Figur 3.13 og skal blot give læseren en fornemmelse af,
hvordan farvemålingsudstyret ser ud.
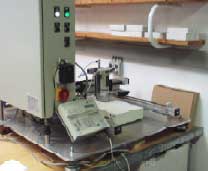
Figur 3.13: Farvemåler, Aalborg Portland.
Resultaterne præsenteres i form af tre forskellige værdier:
- Hunter L udtrykker fladens refleksion. En L-værdi på 100 svarer til en helt hvid flade, mens en L-værdi på
0 svarer til en helt sort flade.
- Hunter a udtrykker fladens rød/grøn-balance. Positive værdier angiver en rød toning, mens negative værdier
angiver en grøn toning.
- Hunter b udtrykker fladens gul/blå-balance. Positive værdier angiver en gul toning, mens negative værdier
angiver en blå toning.
Se desuden 3.14

Figur Figur 3.14: Hunters farvepræsentation.
Som tommelfingerregel er farvedifferencer synlige, når
- Hunter L-værdier afviger 1,0 eller mere (i området 75-85)
- Hunter a-værdier afviger 0,2 eller mere (i området –1 til 1)
- Hunter b-værdier afviger mere end 0,5 (i området 0 til 6)
Resultaterne for de aktuelle farvemålinger, hvor 10% af den hvide cement i den oprindelige recept er udskiftet med
glasfiller, er vist i Figur 3.15, Figur 3.16 og Figur 3.17.
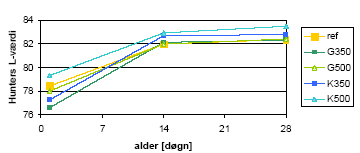
Figur 3.15: Målinger af refleksion.
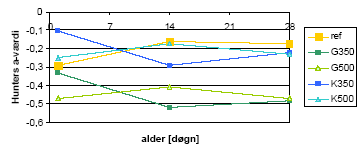
Figur 3.16: Målinger af rød/grøn-balance.
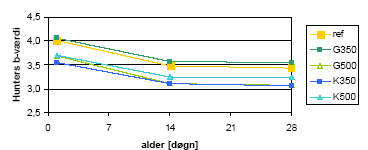
Figur 3.17: Målinger af gul/blå-balance.
Det ses, at refleksionen stiger, når betonen bliver ældre. Refleksionen for beton med grøn glasfiller er helt på linie
med refleksionen for referencen, hvorimod refleksionen for beton med filler fremstillet af klart glas er lidt højere.
Differencen ved de sene terminer er på grænsen til det synlige.
Ikke overraskende forskyder det grønne glas den rød/grønne balance. Forskellen i forhold til beton med klart glas
og referencen uden glas er i størrelsesordenen 0,2 til 0,3 og vil sandsynligvis kunne skelnes med det blotte øje, hvis
to prøver holdes op mod hinanden.
Alle betonerne har en gul nuance, men ved anvendelse af glas bliver tonen en anelse mere blå. Forskellene målt
med Hunters b-værdi er dog mindre end 0,5 og vil derfor sandsynligvis ikke være synlig.
Farveindtrykket af hvid beton afhænger af en række faktorer, så som anvendte tilslagsmaterialer, additiver,
udstøbningsmetoder mm. På baggrund af de foretagne farvemålinger vurderes glasfilleren ikke at influere væsentligt
på den endelige farve.
Generelt vurderes det, at de anvendte glastyper og størrelsesfraktioner alle kan anvendes til fremstilling af hvid
beton, uden det går ud over farveindtrykket, og ændringerne er således acceptable. Tilsvarende farveændringer
kendes fra andre fillermaterialer til hvid beton som fx hvid mikrosilica, der også ændrer betonens nuance i retning af
mere grønt og blåt [6].
Ved fremstilling af betonfliser til farvemålinger blev der desuden målt sætmål og luftindhold for betonen, og der blev
efterfølgende målt styrke 2 og 28 døgn efter støbning. Både luftindhold og sætmål for beton med glasfiller er på
niveau med det, der er registreret for referencen (indenfor måleusikkerheden). Der er dog for alle betoner tale om
ret stiv beton med et meget ringe luftindhold, og det er derfor ikke sikkert, at disse observationer også gælder for
beton med mere gængs sætmål og luftindhold.
Styrkemålingerne for den hvide beton er vist i Figur 3.18.
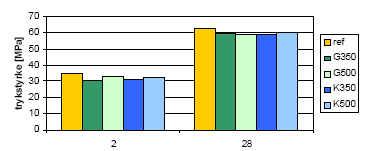
Figur 3.18: Styrkeudvikling for hvid beton til farvemålinger.
Det ses, at styrkereduktionen ved anvendelse af glasfiller i de hvide betoner er mindre end den styrkereduktion, der
blev konstateret ved mørtelforsøg, se afsnit . Dette var forventeligt, da kun 10% af cementen er substitueret ved
fremstilling af beton til farvemåling, mens substitutionsgraden i mørtelforsøgene var 25%.
På baggrund af de foreliggende målinger er det muligt at beregne glasfillernes aktivitetsfaktorer. Aktivitetsfaktoren
er et mål for et puzzolansk materiales styrkepotentiale i forhold til cement, idet den benyttes til at omregne
mængden af puzzolan til ækvivalent cementmængde. De beregnede aktivitetsfaktorer er vist i Tabel 3.4. En aktivitetsfaktor
på fx 0,5 betyder, at 1 kg af den pågældende puzzolan kan erstattes af 0,5 kg cement.
Tabel 3.4: Aktivitetsfaktorer bestemt for forskellige glasfillere på baggrund af målte 28-døgnsstyrker.
|
G350 |
G500 |
K350 |
K500 |
aktivitetsfaktor |
0,58 |
0,51 |
0,45 |
0,66 |
Det ses, at aktivitetsfaktorerne for glasfillere er på samme niveau som aktivitetsfaktoren for flyveaske, der ifølge
DS 481 [4] kan sættes til 0,5. Aktivitetsfaktoren for glasfilleren er imidlertid meget mindre end aktivitetsfaktoren for
mikrosilica, der ifølge samme standard kan sættes til 2,0.
3.6 Konklusion
Sammenfattes resultaterne i de forskellige forsøg beskrevet i afsnit - kan det konkluderes:
- Glas kan formales til filler med samme udstyr som det, der benyttes til cementformaling. Energiforbruget er
omtrent det samme som ved formaling af cement, hvilket kan være med til at indikere, hvad prisen er på
fremstilling af glasfiller.
- Det er muligt at fremstille beton med glasfiller med god bearbejdelighed. Om glasfilleren giver bedre eller
ringere bearbejdelighed afhænger af, hvad den substituerer (typen af cement eller flyveaske), men generelt er
bearbejdeligheden på niveau med tilsvarende typer beton med samme pulverindhold.
- Tilsætning af glasfiller betyder muligvis en mindre styrkereduktion. Vurderingen afhænger af, hvad glasfilleren
substituerer (cement eller flyveaske). Det afhænger givetvis også af i hvor store mængder, filleren tilsættes.
Således er fillerens aktivitetsfaktor ca. 0,5 i forsøg med betonens farve, hvor glasfiller erstatter 10% af
cementvægten, mens den er tæt på 0 i mørtelforsøgene, hvor glasfiller erstatter 25% af cementen.
- Hvis glasfiller erstatter flyveaske, er det muligt at opnå samme luftindhold med en lavere dosering af
luftindblandingsmiddel. Glasfilleren ser ikke ud til at påvirke luftporestrukturen negativt, og beton med
glasfiller har god frostbestandighed, når ellers kravene til luftporestrukturen er opfyldt.
- Beton med glasfiller i stedet for flyveaske har en chloridmodstand, der er lige så god som chloridmodstanden
for beton med flyveaske.
- Glasfilleren giver ikke i sig selv anledning til alkali/kisel-skader, selvom glas indeholder både alkali og reaktivt
kisel. Tværtimod ser det ud til, at glasfilleren kan undertrykke en skadelig reaktion, hvis der anvendes
reaktivt sand, på samme måde som flyveaske gør det.
- Anvendt i moderate mængder betyder anvendelsen af glasfiller en ændring af betonens farve, der knapt kan
skelnes med det blotte øje. Farveændringen i hvid beton er på niveau med hvad der kendes fra andre hvide
fillermaterialer som fx hvid mikrosilica.
De foreliggende resultater tyder således ikke på, at der ud fra et betonteknologisk synspunkt er noget til hinder for,
at glasfiller kan anvendes til fremstilling af beton. Der må dog tages forbehold for det forholdsvis begrænsede
forsøgsomfang.
Det bør desuden bemærkes, at i forhold til det nuværende regelgrundlag (standarden DS 481) er det kun tilladt at
anvende glasfiller i større mængder i beton til passivt miljø, idet det i denne miljøkasse kun er nødvendigt at
dokumentere, at glasfilleren ikke skader betonens egenskaber.
Det forventes, at DS 481 inden for en relativ kort tidshorisont afløses af EN 206 samt et nationalt tillægsdokument
til denne fælles europæiske standard. Her vil det være muligt at anvende puzzolanske tilsætninger ud over flyveaske
og mikrosilica i alle miljøklasser, hvis det er specificeret i projektoplægget. Dette kan både betyde en stramning og
en lempelse for glasfilleren. Det er en lempelse, at der ikke er noget, der hindrer anvendelsen af glasfilleren i alle
miljøklasser. Men i praksis vil det nemt komme til at virke som en stramning, at anvendelsen af glasfiller skal
specificeres i det enkelte projekt. Betonproducenten kan således ikke uden videre indarbejde glasfiller i sine
standardrecepter.
| Forside | | Indhold | | Forrige | | Næste | | Top |
Version 1.0 Januar 2004, © Miljøstyrelsen.
|