| Forside | | Indhold | | Forrige | | Næste |
Ressourceeffektivitet - forslag til definition samt praktiske eksempler på anvendelse af begrebet
D Galvanisk overfladebehandling
D.1 Introduktion
Inden for galvanoområdet er det valgt at se på tre af de mest almindelige processer til overfladebehandling af stål, nemlig:
- Fornikling/forchromning
- Elektroforzinkning
- Varmforzinkning
Disse processer er ikke ligetil at indpasse i et livscyklusforløb som de øvrige aktiviteter, hvor det produkt og dets livsforløb kunne identificeres.
Her er valgt at se på processen i et livscyklusperspektiv som beskrevet i rapportens kapitel 2. Grafisk kan dette illustreres som vist i Figur D.1.
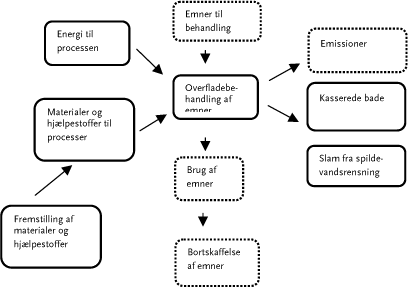
Figur D.1 Galvanisk overfladebehandling i et livscyklusperspektiv
I det følgende er hver af processerne kortlagt.
D.2 Kortlægning af fornikling/forchromning
Fornikling/forchromning er efter elforzinkning den mest almindelige galvaniske proces i Danmark. Processen udføres af ca. 75 danske virksomheder i større eller mindre skala. Ved fornikling/forchromning
foretages først en elektrolytisk pålægning af nikkel (8-15 m) efterfulgt af en elektrolytisk pålægning af chrom (0,2-0,3 m). Det kan undertiden være en teknisk og/eller økonomisk fordel at starte med at
pålægge et elektrolytisk kobberlag først.
Det skønnes, at kun 20-30% af virksomhederne anvender elektrolytisk kobber under nikkel. Man kan eventuelt også undlade at pålægge et chromlag før til sidst, og i så fald har man en ren forniklet
overflade. Det skønnes, at 80% af alle forniklede overflader i Danmark også forchromes.
Det skal bemærkes, at man langt fra altid anvender alle processer, som er vist i det komplette flow-sheet i Figur D.2.
Alle galvaniske processer starter normal med en såkaldt forbehandling, hvor emnerne renses og klargøres den elektrolytiske proces. Det er vigtigt for at opnå en overflade med høj kvalitet og pænt
udseende.
D.2.1 Processerne
D.2.1.1 Ludkogning
Første trin er normalt en varm alkalisk affedtning (ludkoger), hvor olie og fedt opløses og fjernes fra emnernes overflade. Badet indeholder et affedtersalt (natriumhydroxid, carbonater, phosphater, silikater
samt tensider og eventuelle kompleksdannere), der sørger for, at olie og fedt bliver delvis emulgeret i badet. Ofte kommer der efterhånden også fri olie på badoverfladen, og dette olie kan med fordel
skimmes af med mellemrum for at opnå længere levetid for badet.
Når badets indhold af olie og fedt er blevet så højt, at man ikke mere kan opnå en acceptabel affedtning af emnerne, selvom der tilsættes mere affedtersalt, må badet kasseres, og et nyt bad blandes op. Det
kasserede bad kan enten neutraliseres i eget renseanlæg, eller det afleveres til Kommunekemi eller anden godkendt modtager for kemikalieaffald. Badlevetiden afhænger af produktionens størrelse (m²/h),
emnernes tilsmudsning og virksomhedens evne og metode til at vedligeholde badet. Efter behandling i ludkogeren skylles emnerne i et eller flere skyllekar.
Input: |
Pålæsning af varer: |
Output: |
 |
Affedtersalt + vand Energi |
1. Varm alkalisk affedtning
(ludkogning), 70-80°C |
Kasseret bad
Varmeafgivelse |
 |
Vand |
Skyl |
Spildevand med udslæbte kemikalier |
 |
Svovlsyre + vand + Energi |
2. Bejdsning i svovlsyre 60°C |
|
 |
Vand |
Skyl |
Spildevand med udslæbte kemikalier |
 |
Affedtersalt + vand + energi |
3. Elektrolytisk affedtning
(el-affedter), 50°C |
|
 |
Vand |
Skyl |
Spildevand med udslæbte kemikalier |
 |
Kobberanode + natriumcyanid + Natriumhydroxid + kobbercyanid + vand + energi |
4. Forkobring
(Cyan kobber), 50-80°C |
|
 |
Vand |
Skyl |
Spildevand med udslæbte kemikalier |
 |
Svovlsyre + vand |
5. Dekapering i svovlsyre |
|
 |
Vand |
Skyl |
Spildevand med udslæbte kemikalier |
 |
Nikkelanoder + nikkelsulfat + nikkelchlorid + borsyre + svovlsyre/ saltsyre + glansmidler + vand + energi |
6. Fornikling 60°C |
Kasseret bad Varmeafgivelse |
 |
Vand |
Skyl |
Spildevand med udslæbte kemikalier |
 |
Chromsyre + svovlsyre + Dækvæske + vand + energi |
7. Forchromning
(Chromsyre), 35°C |
Kasseret bad
Varmeafgivelse |
 |
Vand |
Skyl |
Spildevand med udslæbte kemikalier |
 |
|
Aflæsning af varer |
|
Figur D.2 Flow-sheet for Kobber-Nikkel-Chrom metallisering
D.2.1.2 Bejdsning
Andet trin er rensning af emnerne i syre (bejdsebad), hvorved rust og glødeskaller opløses og fjernes fra emnernes overflade. Også det øverste lag af selve emnerne fjernes ved denne syrebehandling. Ofte
tilsættes badet en inhibitor, der skal forhindre angreb på grundmaterialet. Til bejdsning kan anvendes svovlsyre ved 50-60°C eller saltsyre ved stuetemperatur. Under bejdsningen forbruges syre til opløsning
af metaloxider, og noget af grundmateriale går også i opløsning. Der kan løbende spædes op med mere syre, men efterhånden bliver badets indhold af metal så højt, at badet må kasseret. Der kan eventuelt
kasseres mindre mængder lidt hyppigere, så man på den måde kan fastholde den ønskede syrekoncentration og en optimal metalkoncentration. Efter bejdsning skylles emnerne i et eller flere skyllekar.
Kasseret syre vil normalt afleveres til Kommunekemi, men det kan eventuelt også neutraliseres i virksomhedens eget renseanlæg, hvorved de opløste metaller udfældes som metalhydroxidslam, som senere
afleveres til Kommunekemi eller anden modtager. Badlevetiden kan forlænges, hvis man reducerer syreangrebet på grundmaterialet, og hvis man først kasserer badet, når metalkoncentrationen er kommet på
maksimum.
D.2.1.3 El-affedtning
Tredje trin er en alkalisk elektrolytisk affedtning (el-affedtning). Processen foregår varmt, og hovedformålet er en let rensning af emnets overflade enten anodisk eller katodisk. Emnerne indeholder normalt
ikke væsentlige mængder olie og fedt efter den forudgående behandling, og rust og glødeskaller er i princippet også væk. Der kan imidlertid være behov for at fjerne oxider, så overfladen bliver helt ren til
den efterfølgende metalpålægning (metallisering). Efter endt behandling skylles emnerne i et eller flere skyllekar.
El-affedteren har normalt længere levetid end ludkogeren, men efterhånden vil indhold af opløste metaller sætte en stopper for fortsat brug af badet selv ved tilsætning af mere affedtersalt. Kasseret bad kan
enten behandles i virksomhedens eget renseanlæg eller sendes til behandling hos Kommunekemi eller anden modtager af kemikalieaffald.
D.2.1.4 Forkobring
Fjerde trin er en elektrolytisk pålægning af kobber, men det er dog kun nødvendigt i enkelte tilfælde. Forkobring foregår som regel i et varmt cyanidholdigt kobberbad, der indeholder cyanid, hydroxid og
carbonat samt eventuelt glansmidler. Denne proces benyttes primært som forbehandling ved fornikling af stærkt blyholdige messinglegeringer, ved messing støbegods eller ved tromlefornikling, hvor man
ønsker at pålægge et tyndere nikkellag. Det er mest almindelig at undlade forkobring før fornikling, men i visse tilfælde kan det være teknisk eller økonomisk fordelagtigt at gøre det. Efter forkobring skylles i
et eller flere skyllekar.
Kobberbadet har forholdsvis lang levetid, men efterhånden vil der dannes mere og mere carbonat i badet, så det til sidst ikke kan fungere korrekt. Her vil man typisk fjerne carbonat (ved udfrysning eller
fældning) i stedet for at kassere hele badet, så det er absolut sjældent, at et cyanidholdigt kobberbad kasseres. Hvis badet skal kasseres, vil det normalt blive afleveret til Kommunekemi.
D.2.1.5 Dekapering
Femte trin er en syredekapering i svovlsyre. Eventuelle alkalirester på overfladen neutraliseres, og metaloxider opløses før forniklingen. Normalt skylles herefter i et enkelt skyllekar, men skylningen kan
eventuelt overspringes. Syrestyrken i dekaperingsbadet kan vedligeholdes ved passende tilsætning af ny syre, men det er ret almindeligt, at badet kasseres hyppigt. Denne badtype vil normalt altid behandles i
virksomhedens eget renseanlæg, da syreindholdet og metalkoncentrationen begge er lave.
D.2.1.6 Fornikling
Sjette trin er en elektrolytisk fornikling, som foregår i en varm nikkelholdig elektrolyt (50-60°C) med nikkelsulfat som hovedkomponent (Ni = 70 g/l). Badet indeholder også borsyre, lidt chlorid samt
glansmidler. Syreindholdet skal svare til pH = 3,5-4,5. Nikkel pålægges elektrolytisk, idet metallisk nikkel (nikkelanoder) opløses og udfældes på emnerne, der er forbundet som katode. Normalt skylles i et
eller flere skyllekar efter fornikling.
Nikkelbadet forurenes løbende med nedbrudte glasmidler, som kan fjernes ved filtrering med aktiv kul. Mange nikkelbade kører med kontinuert kulfiltrering, så badet hele tiden holdes rent. Badet kan også
forurenes med fremmedmetaller, og de kan som regel fjernes ved selektiv elektrolytisk udfældning uden for normal driftstid. Ved korrekt vedligeholdelse af badet har man normalt ikke behov for at kassere
et nikkelbad, men badet kan naturligvis ved et uheld blive så forurenet, at eneste udvej er at kassere det. I visse tilfælde vil det anodiske strømudbytte være større end det katodiske, og man opnår mere
opløsning af nikkel fra anoden, end der udfældes på varerne. I så fald må man med mellemrum kassere en del af badet for at holde nikkelkoncentrationen på den ønskede værdi. Kasseret nikkelbad vil
normalt afleveres til Kommunekemi.
D.2.1.7 Forchromning
Syvende trin er en elektrolytisk forchromning, men det er ikke alle forniklede emner, som man forchromer. Ca. 20% af de forniklede emner pålægges ikke chrom. Forchromning foregår i en kraftig
chromsyreopløsning (CrO3 = 200 g/l) tilsat lidt svovlsyre samt katalysator. Da chromlaget skal være meget tyndt (0,2-0,3 m), er procestiden kort. Badet er let opvarmet (ca. 35°C), men ofte er
overskudsvarmen ved den elektrolytiske proces nok til at holde temperaturen. I visse tilfælde kan afkøling ligefrem være påkrævet, idet kun 15% af strømmen udnyttes ved elektrolyseprocessen, mens resten
bliver til varme. Efter forchromning skal emnerne skylles grundigt i et eller flere skyllekar, før de aflæsses som færdige emner.
Det kan undertiden være nødvendigt at aktivere de forniklede emner, før de forchromes, og det kan foregå ved fordypning i halvkoncentreret chromsyre. Hvis emnerne skylles i afsaltet vand med meget lille
ledningsevne efter fornikling, vil man som regel få problemer ved forchromningen, idet emnerne bliver passive, og der kan ikke opnås en god forchromning. I så fald er en chromsyre aktivering før
forchromning helt nødvendigt. Passivering af de forniklede emner kan som regel undgås, hvis der skylles i postevand efter fornikling.
Den hyppigste forurening i badet er fremmedmetaller, Cr+3 og chlorider. Et vist indhold af Cr+3 er dog nødvendig af hensyn til den elektrolytiske proces, men for en høj koncentration giver problemer. Der
findes metoder til fjernelse af fremmedmetaller og Cr+3 men de er ikke vidt udbredt endnu, men chlorid fjernes rutinemæssigt ved fældning med AgO efterfulgt af filtrering/sedimentering. Et forurenet
chrombad afleveres normalt til Kommunekemi til behandling, men et chrombad kan normalt holde i 3-10 år – undertiden endnu længere. Levetiden afhænger blandt andet af de emner, der behandles samt
indslæb af nikkel fra foregående bad.
D.2.2 Skylning
Der anvendes normalt skylning efter hvert procesbad for at fjerne kemikalierester på emnernes overflade og stoppe den kemiske reaktion på emnerne, hvorved man også reducerer indslæb af fremmede
kemikalier i de efterfølgende procesbade. Skylning foregår ofte i flere kar, og der kan anvendes postevand, kemisk renset spildevand, ionbyttet vand eller afsaltet vand fra omvendt osmose (RO-vand).
Efter selve metalliseringsbadet kan med fordel anvendes et stillestående skyl (sparskyl) til opsamling af udslæbte badkemikalier. Det halvkoncentrerede sparskyl kan senere føres retur til procesbadet som
kompensation for fordampningstabet fra badet. Denne metode er en stor fordel ved varme procesbade, hvor man på den måde kan genvinde 50-90% af de udslæbte badkemikalier. Genvindingsgraden kan
øges ved at anvende 2 eller 3 sparskyl efter samme koncept, idet første skyl bruges til opspædning af procesbadet, 2. skyl bruges herefter til opspædning af 1. skyl osv. Systemet kan eventuelt
automatiseres, så det forløber kontinuert (low-flow skyllesystem med tilbageføring).
Efter forbehandlingsbadene (affedter, bejdse og dekapering) er der ikke samme fordel ved at anvende sparskyl, da man i disse bade løbende under driften får tilført forureninger, der er er med til at afkorte
badets levetid. Hvis disse forureninger føres tilbage ved opspædning med et sparskyl, vil levetiden forkortes yderligere, hvilket gør det til en tvivlsom fidus. Kun hvis man har udstyr til løbende oprensning og
regenerering af forbehandlingsbadene, vil det være en fordel at tilbageføre de udslæbte badkemikalier via et sparskyl.
Anvendes cirkulation af skyllevand over en ionbytter, eller hvis man cirkulerer kemisk renset vand, så er det ikke lige så vigtigt at minimere vandflowet ved at benytte flere skyllekar i modstrøm. Man kan
sige, at et højt flow er ”gratis”, og det er alene udslæbet af badkemikalier med emnerne, der belaster ionbytningsanlæg og renseanlæg. Det er dog klart, at et stort flow kræver enten en stor ionbytter eller et
stort renseanlæg, så derfor kan det normalt godt svare sig at holde flowet på et passende lavt niveau, så udstyret ikke bliver for stort og kostbart.
D.2.3 Ressourceforbrug
De væsentligste ressourcer, der forbruges ved fornikling/forchromning, er:
- Kemikalier bruges i procesbadene, til vandbehandling og til vandrensning.
- Metaller bruges primært som anoder (kobber og nikkel), der overføres til emnerne ved en elektrolytisk metaludfældning.
- Vand bruges til skylning og til opblanding af procesbade.
- Energi bruges til de elektrolytiske processer, til badopvarmning, til tørring, til ventilation og rumopvarmning samt til drift af produktionsudstyr som pumper og transportører samt renseanlæg.
D.2.3.1 Kemikalieforbrug og anodeforbrug
I Danmark bruges årligt ca. 125 ton nikkelanoder til fornikling, hvilket svarer til 1.170.000 m² overflade ved en lagtykkelse på 12 m. Heraf forkobres ca. 25% svarende til ca. 295.000 m². Af den samlede
forniklede overflade bliver ca. 80% eller 936.000 m² forchromet. Forbrug af hovedkemikalier til disse processer fremgår af Tabel D.1.
Tabel D.1 Kemikalieforbrug ved fornikling/forchromning
Procesbad |
Kemikalie |
% af branchen |
Produktion i 1000 m |
Typisk forbrug i kg pr. 1000 m² |
Kg/år |
Ludkoger |
Affedtersalt |
100 |
1.170 |
50,0 |
58.500 |
Bejdsebad |
Svovlsyre, 96% |
75 |
878 |
50,0 |
43.875 |
Bejdsebad |
Saltsyre, 30% |
25 |
293 |
75,0 |
21.938 |
El-affedter |
Affedtersalt |
100 |
1.170 |
40,0 |
46.800 |
Kobberbad |
Kobberanoder |
25 |
293 |
89,0 |
26.033 |
Kobberbad |
NaCN |
25 |
293 |
90,0 |
26.325 |
Kobberbad |
CuCN |
25 |
293 |
45,0 |
13.163 |
Kobberbad |
NaOH |
25 |
293 |
10,0 |
2.925 |
Dekapering |
Svovlsyre, 96% |
100 |
1.170 |
50,0 |
58.500 |
Nikkelbad |
Nikkelanoder |
100 |
1.170 |
107,0 |
125.190 |
Nikkelbad |
Nikkelsulfat |
100 |
1.170 |
7,5 |
8.775 |
Nikkelbad |
Nikkelchlorid |
100 |
1.170 |
2,0 |
2.340 |
Nikkelbad |
Borsyre |
100 |
1.170 |
1,0 |
1.170 |
Nikkelbad |
Glansmidler |
100 |
1.170 |
27,0 |
31.590 |
Chrombad |
Chromsyre |
80 |
936 |
21,1 |
19.750 |
For kobberbadet kan man groft regne med, at kobberanoderne ender som et kobberlag på varerne.
For nikkelbadet gælder som hovedregel, at de anvendte nikkelanoder ender som nikkellag på varerne, og der går i princippet ikke noget til spilde. Der udslæbes dog nikkel til skyllevandet, men en del af
denne nikkel (50-95%) føres retur til procesbadet og genanvendes, mens resten ender i spildevandet, hvor det omdannes til slam i renseanlægget. Man kan groft sige, at forbruget af nikkelsulfat,
nikkelchlorid og borsyre ender i spildevandet.
For chrombadet gælder, at en relativ stor del af chromsyreforbruget udslæbes med varerne, og kun en lille del bliver til et chromlag på emnerne, hvor man typisk kun har en lagtykkelse på 0,25 m. Ved hjælp
af et eller flere sparskyl kan man genvinde 25-90% af det chromsyre, som i første omgang udslæbes fra chrombadet med varerne, men man må nok regne med, at kun 50% af chromsyreforbruget ender som
chrom på varerne.
I Tabel D.2 er foretaget en vurdering af de i Tabel D.1 angivne kemikalieforbrug.
Tabel D.2 Bestanddele i kemikalier til fornikling/forchromning
Kemikalie |
Mængde |
Komponenter |
Affedtersalt |
59 ton |
Hydroxider, carbonater 5-25%
Tensider, kompleksdannere 5- 25%
Vand 50 – 90% |
3-15 ton
3-15 ton 30-50 ton |
Svovlsyre |
102 ton |
96% svovlsyre, regnes som ren syre |
Saltsyre |
22 ton |
30% syre svarer til 7 ton ren HCl |
Affedtersalt |
47 ton |
Syre eller base, - ikke oplyst |
Kobberanoder |
26 ton |
26 ton metallisk kobber |
Natriumcyanid |
26 ton |
Antagelig 100% natriumcyanid |
Kobbercyanid |
13 ton |
Antagelig 100% kobbercyanid, heraf 71 % kobber svarende til 9 ton Cu |
Natriumhydroxid |
3 ton |
Antagelig 100% NaOH |
Nikkelanoder |
125 ton |
125 ton metallisk nikkel |
Nikkelsulfat |
9 ton |
Antagelig 100 % NiSO4, heraf 38% nikkel svarende til 3,4 ton Ni |
Nikkelchlorid |
2,3 ton |
Antagelig 100% NiCl2, heraf 46% nikkel svarende til 1,1 ton nikkel |
Borsyre |
1,2 ton |
% borsyre ikke kendt |
Glansmidler |
32 ton |
Sammensætning ikke kendt |
Chromsyre |
20 ton |
Antagelig 100% CrO3, heraf 52% Chrom svarende til 10,4 ton |
På basis af antagelser og opgørelser kan følgende uddrages, at:
- der anvendes 475 ton kemikalier i alt, hvoraf vand antagelig udgør 30-50 ton.
- nikkelforbruget ligger på omkring 130 ton.
- kobberforbruget ligger på omkring 33 ton.
- chromforbruget ligger på omkring 10 ton.
- forbruget af uorganiske syrer, primært svovlsyre, ligger på omkring 110 ton.
- forbruget af uorganiske baser, primært natriumhydroxid, ligger på 5-15 ton.
- forbruget af organiske forbindelser som tensider, affedtersalt mv. udgør 50-60 ton.
- forbruget af cyanider udgør omkring 30 ton.
- for det øvrige forbrug på 60-70 ton kendes sammensætningen ikke.
Det samlede kemikalieforbrug udgør 0,42 kg pr. m² overflade. Metallerne udgør således ca. 35% af kemikaliemængden. Almindelige syrer og baser gør omkring 25%, organiske forbindelser omkring 18%
og uoplyste omkring 14%. De resterende 8% er primært vand, og for en mindre mængde salte/oxider, der følger med metallerne samt usikkerheder.
D.2.3.2 Råstofforbrug
Ud fra oplysninger i LCA-databaser som UMIP og SigmaPro er det søgt at opgøre råstofforbruget for de væsentligste materialeforbrug. Opgørelsen er vist i Tabel D.3.
Tabel D.3 Estimering af forbrug af råstoffer for fornikling/forchromning
Materiale
Behandlet overflade 1.170.000 m² |
Materiale-
forbrug I alt |
Råstof-
forbrug
kg/kg |
Råstof-
forbrug
I alt |
Råstof-
forbrug
Pr. 1.000 m² |
Nikkel |
130 ton |
9,4 1) |
1.222 ton |
1.044 kg |
Kobber |
33 ton |
3,7 1) |
122 ton |
104 kg |
Chrom |
10 ton |
5,6 1) |
56 ton |
48 kg |
Uorganiske syrer, primært svovlsyre |
110 ton |
0,7 1) |
77 ton |
66 kg |
Uorganiske baser, primært natriumhydroxid |
10 ton |
1,2 1) |
12 ton |
10 kg |
Organiske forbindelser |
55 ton |
1,0 1) |
55 ton |
47 kg |
Cyanider |
30 ton |
2,0 1) |
60 ton |
51 kg |
Øvrige (ukendt sammensætning) |
65 ton |
3,0 2) |
195 ton |
167 kg |
I alt |
1.799 ton |
1.537 kg |
1): Data fra SigmaPro.
2): Tallet er anslået ud fra en antagelse om, at øvrige kemikalier indeholder en vis mængde metal og en vis mængde organiske forbindelser.
Sammenlignes opgørelsen i med opgørelsen af materialeforbruget, ses det, at råstofforbruget er ca. 3,5 gange så stort (1,537/0,42).
D.2.3.3 Vandforbrug
Den galvaniske branche har nedsat vandforbruget voldsomt, siden der for alvor kom fokus på miljøet herhjemme i 1970’erne. Dengang var det ikke ualmindeligt med et vandforbrug på 1000 liter pr. m²
overflade – et tal som man stadigvæk kan møde i Østeuropa og andre lande, hvor vandprisen er lav, og hvor man endnu ikke for alvor har fokus på vandforbruget.
I dag er vandforbruget mere typisk på 50-250 liter pr. m² overflade, og det svarer til et samlet vandforbrug herhjemme på ca. 120.000 m³/år til fornikling/forchromning. Miljøstyrelsen mener, at man
efterhånden skal ned på et vandforbrug på 10 liter pr. m² overflade, og det er faktisk muligt ved brug af 3-trins modstrømsskyl eller andre lige så vandbesparende skyllemetoder (ionbytning, sprayskylning,
vandgenbrug), men det store problem er, at der helst skal bruges 2-4 skyllekar efter hvert proceskar, for at det skal lykkes. Det kan ofte være et problem at indsætte det fornødne antal skyllekar i
eksisterende produktionslinier, da det er uforholdsmæssigt dyrt sammenlignet med etablering af nye proceslinier. Ofte er der ikke plads i lokalet til at indføre mange ekstra skyllekar.
Der er ingen tvivl om, at tiden stadig arbejder for at opnå yderligere vandreduktioner i takt med de stigende vandpriser, men jo længere man kommer ned, jo færre kroner er der at hente på yderligere
vandbesparelser. Det skal dog også nævnes, at mindre vandforbrug kræver mindre renseanlæg, og der vil samtidig også være en vis besparelse i kemikalieforbrug til spildevandsrensning. Rent teknisk kan
virksomhederne stadig opnå store vandbesparelser ved i endnu højere grad at bruge de vandbesparende skyllemetoder og teknikker. Vandforbruget bør i løbet af de næste 5 år uden problemer kunne
komme ned på 30-40 liter pr. m² overflade svarende til ca. 40.000 m³/år fra al fornikling/forchromning i Danmark.
D.2.3.4 Energiforbrug
Energiforbruget til de elektrolytisk processer kan beregnes forholdsvis enkelt. Når man kender produktionens størrelse, kan man udregne strømforbruget ud fra de anvendte Volt, Amp og timer med tillæg
for strømtab i ensretter. Energiforbrug til badopvarmning afhænger af badtemperaturen, karisolering, rumtemperatur og udsugning. Energiforbrug til ventilation udgør også en betydelig post. Energiforbrug til
motorer, køling og trykluft – herunder renseanlæg – er af mindre betydning.
Det foreligger ikke mange publikationer og erfaring herhjemme om energiforbruget i galvanobranchen. Forbruget er derfor vurderet ud fra fornikling/forchromning dels ud fra overslagberegning og dels ud fra
konkrete tal og vurderingen fra en dansk virksomhed, der kun udfører fornikling/forchromning.
Tabel D.4 Energiforbrug ved fornikling/forchromning
|
Udvalgt virksomhed |
Hele Danmark |
kWh/år |
KWh/m² |
% |
Kwh/år |
Ensrettere |
13.000 |
1,01 |
3 |
1.176.425 |
Badvarme |
200.000 |
15,47 |
53 |
18.098.848 |
Tørring |
30.000 |
2,32 |
8 |
2.714.827 |
Ventilation |
43.000 |
3,33 |
11 |
3.891.252 |
Diverse |
94.000 |
7,27 |
25 |
8.506.458 |
Total |
380.000 |
29,39 |
100 |
34.387.810 |
Det samlede forbrug ligger således på 34.400 MWh pr. år og er udelukkende et elforbrug.
Det største forbrug går til badopvarmning, men denne post vil være forholdsvis mindre ved en mere intens udnyttelse af produktionsapparatet. Det forbruger jo også energi at have badene stående med
opvarmning om natten og i weekenden. Derfor vil der være mindre energispild, hvis der produceres hele tiden, så det specifikke energiforbrug (kWh/m²) til badopvarmning vil gå ned. Det skal også nævnes,
at man i ovenstående eksempel ikke anvender forkobring, som også vil kræve energiforbrug til badopvarmning og ensretter. Det er dog nok realistisk at regne med et total energiforbrug på 25-35 kWh pr.
produceret m².
D.2.4 Affald
De to væsentligste affaldsstrømme fra fornikling/forchromning er:
- Tungmetalslam fra spildevandsrensning
- Kasserede procesbade til ekstern behandling/oparbejdning
I Miljøprojekt 55/2000 vedrørende oparbejdning af galvanisk affald blev affaldsmængderne estimeret ud fra en beregningsmodel kombineret med data fra de største virksomheder i branchen. Dette er vist i
Tabel D.5.
Tabel D.5 Flydende kemikalieaffald fra fornikling/forchromning
Kasseret bad |
m² overflade
pr. år |
Kasseret bad
liter pr. 1000 m² |
Kasseret
bad, m³/år |
Metal i
bad, g/l |
Metal,
kg/år |
Ludkoger |
1.170.000 |
150 |
176 |
0 |
0 |
Bejdsebad |
1.170.000 |
45 |
53 |
40 |
2.106 |
El-affedter |
1.170.000 |
300 |
351 |
2 |
702 |
Kobberbad |
293.000 |
5 |
1 |
30 |
44 |
Dekaperingsbad |
1.170.000 |
500 |
585 |
2 |
1.170 |
Nikkelbad |
1.170.000 |
12 |
14 |
80 |
1.123 |
Chrombad |
936.000 |
16 |
15 |
110 |
1.647 |
Total |
6.793 |
Som det fremgår af Tabel D.5, er det langt fra alle affaldstyper, som indeholder væsentlige mængder tungmetaller. Det er oftest således, at virksomheder selv behandler de kasserede bade med lavt
metalindhold, mens mere koncentrerede bade som bejdsebade, kobberbade, nikkelbade og chrombade sendes til ekstern behandling (Kommunekemi). Bejdsebadene nedslides og kasseres forholdsvis ofte,
mens metalliseringsbadene kun meget sjældent kasseres på grund af forurening eller for høje koncentrationer.
Tabel D.6 Slam fra spildevandsrensning (filterkager med 30% tørstof)
Spildevand |
m² overflade
pr. år |
Metal i
bad, g/l |
Udslæb
af metal,
kg/år |
Genvin-
dings % |
Metal i
slam,
kg/år |
Filterkager
(30%TS)
ton/år |
Ludkoger |
1.170.000 |
0 |
0 |
0 |
0 |
0,0 |
Bejdsebad |
1.170.000 |
30 |
5.265 |
0 |
5.265 |
43,9 |
El-affedter |
1.170.000 |
0,5 |
88 |
0 |
88 |
0,7 |
Kobberbad |
293.000 |
30 |
1.319 |
0 |
1.319 |
11,0 |
Dekapering |
1.170.000 |
1 |
176 |
0 |
176 |
1,5 |
Nikkelbad |
1.170.000 |
70 |
12.285 |
75 |
3.071 |
25,6 |
Chrombad |
936.000 |
100 |
14.040 |
50 |
7.020 |
58,5 |
Total |
|
|
|
|
16.938 |
141,2 |
kg filterkage pr. m² produktion i gennemsnit: |
0,121 |
Produktion af filterkager pr. m² overflade er 0,121 kg, hvilket er lidt højere end for elforzinkning. Det skyldes blandt andet, at man ved fornikling/forchromning arbejder med flere og mere koncentrerede
metalliseringsbade.
Denne tabel omfatter ikke det slam, som dannes på de virksomheder, der selv neutraliserer kasserede procesbade, hvilket vil betyde en mindre stigning i slammængden. Sammenfattet kan følgende totale tal
opstilles, hvor slammængden er korrigeret med metalmængderne for de kasserede procesbade, som behandles af virksomhederne selv:
Metalmængde i kasserede bade til ekstern behandling: |
4.921 kg/år |
Metalmængde i spildevandsslam fra fældningsanlæg: |
18.810 kg/år |
Det fremgår, at der er næsten 4 gange mere metal i slammet end i det flydende kemikalieaffald, som levers til ekstern behandling (Kommunekemi).
Affald stammende fra ludkoger, bejdsebad, el-affedter samt dekaperingsbad indeholder metaller fra de emner, der behandles og udgøres derfor primært af jern. Affald fra kobberbadet er kobber, fra
nikkelbadet er det nikkel, og fra chrombadet er det trivalent og hexavalent chrom.
Ud fra affaldsopgørelserne for flydende kemikalieaffald (Tabel D.5)og slam fra spildevandsrensning (Tabel D.6) kan affaldet opdelt på de væsentligste metaller opgøres.
Tabel D.7 Affald opdelt på metaller i forhold til samlet mængde og ressourceforbrug
Materiale |
Affaldsmængde |
Del af den
samlede af- faldsmængde |
Ressource-
forbrug |
Affald i forhold
til ressourceforbrug |
Kobber |
1,36 ton |
5,7 % |
33 ton |
3-4 % |
Nikkel |
4,19 ton |
17,7 % |
130 ton |
3-4 % |
Chrom |
8,67 ton |
36,5 % |
10,4 ton |
83 % |
Andre metaller (primært jern) |
9.51 ton |
40,1 % |
Ikke relevant |
Ikke relevant |
Det fremgår af tabellen, at udnyttelsesprocenten for chrom er langt dårligere end for kobber og nikkel.
D.2.5 Hovedtal for fornikling/forchromning
Kortlægningen har vist, at der behandles 1,17 mio. m² overflade pr. år med lagtykkelse på 12 µm nikkel, og at 25% forkobres, mens 80% forchromes.
Der anvendes 475 ton kemikalier i alt, hvilket svarer til 0,42 kg pr. m² behandlet overflade. Nikkelforbruget ligger på omkring 130 ton, kobberforbruget ligger på omkring 33 ton og chromforbruget ligger på
omkring 10 ton. Dertil kommer omkring 270 ton øvrige kemikalier.
Der anvendes et vandforbrug på 120.000 m³/år og et energiforbrug i form af el på 34.400 MWh pr. år, svarende til 29.400 kWh pr. 1000 m² overflade.
Affald fra kasserede bade og slam udgør i alt 23.73 ton metal, hvoraf 1,36 ton er kobber, 4,19 ton er nikkel og 8,67 ton chrom. Omkring 9,5 ton er metaller fra den behandlede overflade og udgøres
primært af jern.
Forskellen i metalmængder mellem forbrug og affald antages at findes på emnerne. Ved kassering af emnerne vil metallerne tabes, selvom emnerne oparbejdes.
Omregnes materialeforbruget til forbrug af råstoffer ses det, at forbruget bliver omkring 3,5 gange større svarende til 1,54 kg pr. 1.000 m² overflade.
D.3 Kortlægning af elforzinkning
Elforzinkning den mest almindelige galvaniske proces i Danmark. Processen udføres af ca. 90 danske virksomheder i større eller mindre skala.
Ved elforzinkning foretages først en rengøring af emnerne (affedtning og bejdsning), hvorefter der elektrolytisk påføres er zinklag på 5-20 m. Lagtykkelsen er typisk mindst for tromlevarer (små emner), mens
større emner på stativer typisk påføres lagtykkelser på 12-20 m.
Behandlingen afsluttes med en passivering – det vil sige en kemisk behandling af overfladen i en chromatopløsning, hvorved overfladen bliver mere korrosionsbestandig.
D.3.1 Processerne
Den fulde proces er vist som flowsheet i Figur D.3. Det skal bemærkes, at man ikke altid anvender alle processer som vist på flowsheetet, da det kan afhænge af typen på zinkbadet (sur zink, cyan zink eller
alkalisk zink).
D.3.1.1 Ludkogning
Første trin er normalt en varm alkalisk affedtning (ludkoger), hvor olie og fedt opløses og fjernes fra emnernes overflade. Badet indeholder et affedtersalt (natriumhydroxid, carbonater, phosphater, silikater
samt tensider og eventuelle kompleksdannere), der sørger for, at olie og fedt bliver delvis emulgeret i badet. Ofte kommer der efterhånden også fri olie på badoverfladen, og denne olie kan med fordel
skimmes af med mellemrum for at opnå længere levetid for badet.
Når badets indhold af olie og fedt er blevet så højt, at man ikke mere kan opnå en acceptabel affedtning af emnerne, selvom der tilsættes mere affedtersalt, må badet kasseres, og et nyt bad blandes op. Det
kasserede bad kan enten neutraliseres i eget renseanlæg eller det afleveres til Kommunekemi eller anden godkendt modtager for kemikalieaffald. Badlevetiden afhænger af produktionens størrelse (m²/h),
emnernes tilsmudsning og virksomhedens evne og metode til at vedligeholde badet. Efter behandling i ludkogeren skylles emnerne i et eller flere skyllekar.
Input: |
Pålæsning af varer: |
Output: |
 |
Affedtersalt + vand Energi |
1. Varm alkalisk affedtning
(ludkogning), 70-80°C |
Kasseret bad
Varmeafgivelse |
 |
Vand |
Skyl |
Spildevand med udslæbte kemikalier |
 |
Svovlsyre + vand + energi |
2. Bejdsning i svovlsyre 60°C |
|
 |
Vand |
Skyl |
Spildevand med udslæbte kemikalier |
 |
Affedtersalt + vand + energi |
3. Elektrolytisk affedtning
(el-affedter), 50°C |
|
 |
Vand |
Skyl |
Spildevand med udslæbte kemikalier |
 |
Saltsyre + vand |
5. Dekapering i saltsyre |
|
 |
Vand |
Skyl |
Spildevand med udslæbte kemikalier |
 |
Zinkanoder + salte + glansmidler + vand + energi |
6. Forzinkning 20-35°C |
Kasseret bad |
 |
Vand |
Skyl |
Spildevand med udslæbte kemikalier |
 |
Chromsalte + syre + vand |
7. Passivering i chrom 20°C |
Kasseret bad |
 |
Vand |
Skyl |
Spildevand med udslæbte kemikalier |
 |
|
Aflæsning af varer |
|
Figur D.3 Flow-sheet for elforzinkning
D.3.1.2 El-affedtning
Tredje trin er en alkalisk elektrolytisk affedtning (el-affedtning). Processen foregår varmt, og hovedformålet er en let rensning af emnets overflade enten anodisk eller katodisk. Emnerne indeholder normalt
ikke væsentlige mængder olie og fedt efter den forudgående behandling, og rust og glødeskaller er i princippet også væk. Der kan imidlertid være behov for at fjerne oxider, så overfladen bliver helt ren til
den efterfølgende metalpålægning (metallisering). Efter endt behandling skylles emnerne i et eller flere skyllekar.
El-affedteren har normalt længere levetid end lugkogeren, men efterhånden vil indhold af opløste metaller sætte en stopper for fortsat brug af badet, selv ved tilsætning af mere affedtersalt. Kasseret bad kan
enten behandles i virksomhedens eget renseanlæg eller sendes til behandling hos Kommunekemi eller anden modtager af kemikalieaffald.
D.3.1.3 Dekapering
Fjerde trin er en syredekapering i saltsyre, og den anvendes fortrinsvis foran et surt zinkbad. Eventuelle alkalirester på overfladen neutraliseres, og metaloxider opløses før forzinkningen. Syrestyrken i
dekaperingsbadet kan vedligeholdes ved passende tilsætning af ny syre, men efter længere tids drift kasseres badet normalt helt. Det kasserede vil normalt altid behandles i virksomhedens eget renseanlæg,
da syreindholdet og metalkoncentrationen begge er lave. Dekaperingsbadet foran alkalisk zink vil normalt være en tynd opløsning af natronlud.
D.3.1.4 Forzinkning
Femte trin er elforzinkning. Der findes tre forskellige typer zinkbade. Det mest almindelige er sur zink (indeholder zinkchlorid, borsyre, kaliumchlorid og glansmidler). Dernæst kommer cyan zink (indeholder
zink, cyanid, NaOH og glansmidler), der tidligere var det mest almindelige bad. Endelig findes alkalisk zink (indeholder zink, NaOH og glansmidler), som har en begrænset udbredelse.
Et zinkbad arbejder normalt ved stuetemperatur, men sure zinkbade kan køre med lidt opvarmning (35°C), hvilket giver mulighed for direkte tilbageføring af udslæbte badkemikalier fra et sparskyl.
Anvendes varm sur zink, kan man ofte undgå en ekstern køling af badet. Med et strømudbytte på 90-100% er overskudsvarmen ved elektrolysen moderat. Det sure bad forurenes med jern og nedbrudte
glansmidler, hvilket stiller krav om rensning. Det er heller ikke ualmindeligt, at zinkkoncentrationen bliver for høj på grund af større anodisk strømudbytte ved elektrolysen.
Det cyanholdige zinkbad er meget robust og kan arbejde selv med store forureninger (olie, fedt, metal), men der dannes løbende carbonat, som må fjernes, når koncentrationen bliver for høj. Det kan enten
gøres ved udfældning med specialkemikalier eller ved udfrysning. Det cyanholdige zinkbad blev tidligere brugt af alle virksomheder, men nu er det på vej ud på grund af miljøproblematikken ved anvendelse
af giftige cyanforbindelser. Da badet kører ved stuetemperatur, er der normalt behov for køling for at fjerne overskudsvarmen fra elektrolyseprocessen, hvor strømudbyttet kun er på ca. 60%.
Det alkaliske zinkbad er et meget følsomt bad, der kræver en perfekt forbehandling for at opnå en god overfladekvalitet på emnerne. Strømudbyttet er kun 70%, hvilket betyder, at der skal bruges ekstern
køling for at fjerne overskudsvarmen fra elektrolysen. Badet kører med meget lavt zinkindhold (typisk 10 g/l), hvilket giver et lavt udslæb af zink til spildevandet.
Badene kasseres i princippet ikke, men det kan undtagelsesvis blive nødvendigt at kassere et forurenet bad. De kasserede bade sendes normalt til behandling hos Kommunekemi. Når cyanholdige bade skal
udskiftes med cyanfri bade, vil man normalt også sende de cyanholdige bade til Kommunekemi, da det er meget problematisk for den enkelte virksomhed at destruere opløsninger med så høje
cyanidkoncentrationer.
D.3.1.5 Passivering
Sjette trin er passivering i chromholdige opløsninger. I gamle dage brugte man udelukkede 6-gyldige chromforbindelser – de såkaldte chromater – og derfor kaldes processen også sommetider for en
chromatering (på engelsk: chromating). I dag anvendes der i Danmark udelukkende 3-gyldige chromforbindelse til blå passivering, mens der stadig anvendes chromater til gul-, sort- og oliven passivering.
Navnene angiver de farvenuancer, som overfladen får ved passiveringsprocessen. Undertiden kaldes blå passivering også for blank passivering, da overfladen ofte ønskes så blank som muligt, så det minder
om en forchromet overflade.
Ved passiveringsprocessen reagerer zinkoverfladen med kemikalierne i passiveringsbadet, hvorved der kommer opløst zink i badet. I de chromatholdige bade vil der efterhånden også dannes 3-gyldige
chromforbindelser. Zink og 3-gyldig chrom (i de chromatholdige bade) er forureninger, der enten må fjernes, eller badet må kasseres, når forureningerne er blevet for høje. Man spæder løbende badene op
med nye passiveringskemikalier og eventuelt syre i takt med, at kemikalierne forbruges. Ved passiveringsprocessen reagerer zinkoverfladen med chrom, så der dannes et kombineret zink-chrom lag, der er
mere korrosionsbestandig end selve zinklaget. Jo tykkere dette lag er, jo bedre korrosionsbestandighed.
Blå passivering giver typisk et passiveringslag med ca. 0,03 g chrom pr. m². Gulpassivering giver typisk et passiveringslag med 0,40 g chrom pr. m², mens man ved sort og oliven passivering typisk har 0,95
g chrom pr. m². Alt afhænger naturligvis af badtype og procestiden.
Passiveringsbade kasseres ret hyppigt – især blå passiveringsbade. Kasserede passiveringsbade vil normalt behandles i virksomhedernes eget renseanlæg, da metalkoncentrationen og syreindholdet er
moderat. Enkelte virksomheder sender de mest koncentrerede bade (gul, sort og oliven) til Kommunekemi.
D.3.2 Skylning
Der anvendes normalt skylning efter hvert procesbad for at fjerne kemikalierester på emnernes overflade og stoppe den kemiske reaktion på emnerne, hvorved man også reducerer indslæb af fremmede
kemikalier i de efterfølgende procesbade. Skylning foregår ofte i flere kar, og der kan anvendes postevand, kemisk renset spildevand, ionbyttet vand eller afsaltet vand fra omvendt osmose (RO-vand).
Efter selve metalliseringsbadet kan med fordel anvendes et stillestående skyl (sparskyl) til opsamling af udslæbte badkemikalier. Det halvkoncentrerede sparskyl kan senere føres retur til procesbadet som
kompensation for fordampningstabet fra badet. Denne metode er en stor fordel ved varme procesbade – jo varmere, jo mere fordampning og jo større tilbageføring. Ved sur zink vil man dog næppe kunne
genvinde mere end 25-50% af de udslæbte badkemikalier på grund af den forholdsvis lave temperatur og dermed ringe fordampning. Genvindingsgraden kan øges ved at anvende 2 eller 3 sparskyl efter
samme koncept, idet første skyl bruges til opspædning af procesbadet, 2. skyl bruges herefter til opspædning af 1. skyl osv. Systemet kan eventuelt automatiseres, så det forløber kontinuert (low-flow
skyllesystem med tilbageføring). Tilbageføring ved kolde procesbade kan øges betydelig ved at skylle i sparskyllet både før og efter metalliseringsbadet. Det giver direkte 50% tilbageføring efter et koldt
metalliseringsbad.
Efter forbehandlingsbadene (affedter, bejdse og dekapering) er der ikke samme fordel ved at anvende sparskyl, da man i disse bade løbende under driften får tilført forureninger, der er er med til at afkorte
badets levetid. Hvis disse forureninger føres tilbage ved opspædning med et sparskyl, vil levetiden forkortes yderligere, hvilket gør det til en tvivlsom fidus. Kun hvis man har udstyr til løbende oprensning og
regenerering af forbehandlingsbadene, vil det være en fordel at tilbageføre de udslæbte badkemikalier via et sparskyl.
Anvendes cirkulation af skyllevand over en ionbytter, eller hvis man cirkulerer kemisk renset vand, så er det ikke lige så vigtigt at minimere vandflowet ved at benytte flere skyllekar i modstrøm. Man kan
sige, at flowet er ”gratis”, og det er alene udslæbet af badkemikalier med emnerne, der belastet ionbytningsanlægget og renseanlægget. Det er dog klart, at et stort flow kræver enten en stor ionbytter eller et
stort renseanlæg, så derfor kan det normalt godt svare sig at holde flowet på et passende lavt niveau, så udstyret ikke bliver for stort og kostbart.
D.3.3 Ressourceforbrug
De væsentligste ressourcer, der forbruges ved elforzinkning, er:
- Kemikalier bruges i procesbadene, til vandbehandling og til vandrensning.
- Metaller bruges primært som anoder (zink), der overføres til emnerne ved en elektrolytisk metaludfældning.
- Vand bruges til skylning og til opblanding af procesbade.
- Energi bruges til de elektrolytiske processer, til badopvarmning, til ventilation og rumopvarmning samt til drift af produktionsudstyr som pumper og transportører samt renseanlæg.
D.3.3.1 Kemikalieforbrug og anodeforbrug
Der bruges årligt ca. 600 ton zinkanoder, hvilket svarer til 8.500.000 m² overflade ved en lagtykkelse på 10 m. Forbrug af hovedkemikalier til disse processer fremgår af Tabel D.8.
Tabel D.8 Kemikalieforbrug ved elforzinkning
Procesbad |
Kemikalie |
% af
branchen |
Produktion
i 1000 m² |
Typisk forbrug
i kg pr. 1000
m² |
Ton/år |
Ludkoger |
Affedtersalt |
100 |
8.500 |
50,0 |
425,0 |
Bejdsebad |
Svovlsyre, 96% |
50 |
4.250 |
50,0 |
212,5 |
Bejdsebad |
Saltsyre, 30% |
50 |
4.250 |
75,0 |
318,8 |
El-affedter |
Affedtersalt |
100 |
8.500 |
40,0 |
340,0 |
Dekapering |
Saltsyre, 30% |
10 |
850 |
10,0 |
8,5 |
Zinkbad, surt |
Zinkanoder |
75 |
6.375 |
70,6 |
450,0 |
Zinkbad, surt |
Zinkchlorid |
75 |
6.375 |
3,5 |
22,3 |
Zinkbad, surt |
Kaliumchlorid |
75 |
6.375 |
15,0 |
95,6 |
Zinkbad, surt |
Borsyre |
75 |
6.375 |
2,0 |
12,8 |
Zinkbad, surt |
Glansmidler |
75 |
6.375 |
18,0 |
114,8 |
Zinkbad, cyan |
Zinkanoder |
15 |
1.275 |
70,6 |
90,0 |
Zinkbad, cyan |
Natriumcyanid |
15 |
1.275 |
64,0 |
81,6 |
Zinkbad, cyan |
Natriumhydroxid |
15 |
1.275 |
79,0 |
100,7 |
Zinkbad, cyan |
Zinkoxid |
15 |
1.275 |
1,5 |
1,9 |
Zinkbad, cyan |
Glansmidler |
15 |
1.275 |
14,0 |
17,9 |
Zinkbad, alkalisk |
Zinkanoder |
10 |
850 |
70,6 |
60,0 |
Zinkbad, alkalisk |
Natriumhydroxid |
10 |
850 |
150,0 |
127,5 |
Zinkbad, alkalisk |
Zinkoxid |
10 |
850 |
27,0 |
23,0 |
Zinkbad, alkalisk |
Glansmidler |
10 |
850 |
40,0 |
34,0 |
Blåpassivering |
Salt |
30,8 |
2.618 |
20,0 |
52,4 |
Gulpassivering |
Salt |
60,8 |
5.168 |
10,0 |
51,7 |
Oliven+sort pass. |
Salt |
8,4 |
714 |
15,0 |
10,7 |
For zinkbadet gælder som hovedregel, at de anvendte zinkanoder ender som zinklag på varerne, og der går i princippet ikke noget til spilde. Der udslæbes dog zink og andre salte fra badet til skyllevandet,
og disse kemikalier må løbende erstattes for at holde den optimale koncentration af kemikalier i badet. I den alkaliske cyanfri zinkbad skal der principielt tilsættes ZnO til erstatning af udslæbt zink, men flere
danske virksomheder har en separat opløsningstank, hvor badet løber igennem, og her kan man styre zinkkoncentrationen ved at lade badet opløse metallisk zink. Her bliver der således ikke behov for
tilsætning af ZnO, så derfor må forbruget af ZnO i tabellen tages med forbehold.
I det cyanidiske bad omdannes en del cyanid til carbonat ved en anodisk oxidation, ligesom der generelt i alkaliske bade dannes carbonat ved optagelse af luftens kuldioxid.
For passiveringsbadene gælder det, at der forbruges passiveringskemikalier og syre, som må erstattes løbende. Der ophobes efterhånden zink og 3-gyldig chrom (i chromatholdige passiveringsbade) som
forurening i badene, hvilket medfører, at disse bade må kasseres med passende mellemrum. Herved kasserer man også aktive kemikalier, hvilket er med til at øge forbruget af kemikalier.
I Tabel D.9 er foretaget en vurdering af de angivne kemikalieforbrug.
Tabel D.9 Bestanddele i kemikalier til elforzinkning
Kemikalie |
Mængde |
Komponenter |
Affedtersalt |
765 ton |
Hydroxider, carbonater 5-25% Tensider, kompleksdannere 5-25% Vand 50-90% |
40-190 ton 40-190 ton 400-700 ton |
Svovlsyre |
210 ton |
96 % svovlsyre, regnes som ren syre |
Saltsyre |
330 ton |
30 % syre svarer til 100 ton ren HCl |
Zink anoder |
600 ton |
Ren metallisk zink |
Zinkchlorid og zinkoxid |
47 ton |
ZnCl2 og ZnO, heraf 31 ton zink |
Natriumcyanid |
82 ton |
Antagelig 100% natriumcyanid |
Natriumhydroxid |
230 ton |
Antagelig 100% NaOH |
Kaliumchlorid |
96 ton |
Antagelig 100% KOH |
Borsyre |
13 ton |
Antagelig ren borsyre |
Glansmidler |
167 ton |
Sammensætning ikke kendt |
Blåpassivering, salt |
52 ton |
Indeholder Cr(III)-salte svarende til 1,2 ton Cr |
Gul, Oliven og sort passivering, salt |
62 ton |
Indeholder Cr(VI)-salte svarende til 14,128 ton Cr |
På basis af opgørelser og antagelser i Tabel D.9 kan følgende uddrages:
- der anvendes 2.650 ton kemikalier, hvoraf vand udgør i størrelsesordnen 1.000 ton.
- det samlede zinkforbrug ligger på omkring 630 ton.
- der anvendes omkring 15 ton chromforbindelser, hvoraf ca. 1 ton er Cr(III) og 14 ton er Cr(VI).
- forbruget af uorganiske syrer, primært svovlsyre, ligger på omkring 310 ton.
- forbruget af uorganiske baser, primært natriumhydroxid ligger på omkring 300 ton.
- forbruget af borsyre udgør 13 ton og salte (KCl) udgør omkring 100 ton.
- forbruget af organiske forbindelser som tensider, affedtersalt mv. udgør i størrelsesordnen 100 ton.
- forbruget af cyanider udgør omkring 80 ton.
- for det øvrige forbrug på 167 ton (glasmidler) kendes sammensætningen ikke.
Det samlede materialeforbrug er estimeret til 1.715 ton, hvilket svarer til 0,31 kg pr. m² behandlet overflade. Metalmængden udgør således ca. 26% af kemikaliemængden. Almindelige syrer, baser og salte
udgør ca. 27 %, organiske forbindelser omkring 7% og uoplyste omkring 6%. De resterende 33% er primært vand og for en mindre mængde salte/oxider, der følger med metallerne samt usikkerheder.
Ses der bort fra vandindholdet, er det samlede materialeforbrug 1.700 ton svarende til 0,20 kg pr. m².
D.3.3.2 Råstofforbrug
Ud fra oplysninger i LCA-databaser som UMIP og SigmaPro er det søgt at opgøre råstofforbruget for de væsentligste materialeforbrug. Opgørelsen er uden vand og vist i Tabel D.10.
Tabel D.10 Estimering af forbrug af råstoffer for elforzinkning
Materiale
Behandlet overflade 8.500.00 m² |
Materiale-
forbrug
I alt |
Råstof-
forbrug
kg/kg |
Råstof-
forbrug
I alt |
Råstof-
forbrug
Pr. 1.000 m² |
Zink |
630 ton |
3,1 1) |
1.953 ton |
230 kg |
Chrom |
15 ton |
5,6 1) |
84 ton |
10 kg |
Uorganiske syrer, primært svovlsyre |
310 ton |
0,7 1) |
217 ton |
26 kg |
Uorganiske baser, primært natriumhydroxid |
300 ton |
1,2 1) |
360 ton |
42 kg |
Borsyre og salte |
113 ton |
1,0 3) |
113 ton |
13 kg |
Organiske forbindelser |
100 ton |
1,0 1) |
100 ton |
12 kg |
Cyanider |
80 ton |
2,0 1) |
160 ton |
19 kg |
Øvrige (ukendt sammensætning) |
167 ton |
3,0 2) |
501 ton |
59 kg |
I alt |
411 kg |
1): Data fra SigmaPro.
2): Tallet er anslået ud fra en antagelse om, at øvrige kemikalier indeholder en vis mængde metal og en vis mængde organiske forbindelser.
3) Data herfor er ukendt, og derfor er der anslået en værdi.
Det samlede materialeforbrug excl. vand svarer til et forbrug på 0,20 kg pr. behandlet m², og når der ses på råstoffer, udgør forbruget 0,41kg pr. m².
D.3.3.3 Vandforbrug
Den galvaniske branche har nedsat vandforbruget voldsomt, siden der for alvor kom fokus på miljøet herhjemme i 1970'erne. Dengang var det ikke ualmindeligt med et vandforbrug på 1.000 liter pr. m²
overflade – et tal, som man stadigvæk kan møde i Østeuropa og andre lande, hvor vandprisen er lav, og hvor man endnu ikke for alvor har fokus på vandforbruget.
I dag er vandforbruget mere typisk på 50-250 liter pr. m² overflade, og det svarer til et samlet vandforbrug herhjemme på ca. 850.000 m³/år til elforzinkning. Miljøstyrelsen mener, at man efterhånden skal
ned på et vandforbrug på 10 liter pr. m² overflade, og det er faktisk muligt ved brug af 3-trins modstrømsskyl eller andre lige så vandbesparende skyllemetoder (ionbytning, sprayskylning, vandgenbrug),
men det store problem er, at der helst skal bruges 2-4 skyllekar efter hvert proceskar, for at det skal lykkes. Det kan ofte være et problem at indsætte det fornødne antal skyllekar i eksisterende
produktionslinier, da det er uforholdsmæssigt dyrt sammenlignet med etablering af nye proceslinier. Ofte er det et plads i lokalet til at indføre mange ekstra skyllekar.
Der er ingen tvivl om, at tiden stadig arbejder for at opnå yderligere vandreduktioner i takt med de stigende vandpriser, men jo længere man kommer ned, jo færre kroner er der at hente på yderligere
vandbesparelser. Det skal dog også nævnes, at mindre vandforbrug kræver mindre renseanlæg, og der vil samtidig også være en vis besparelse i kemikalieforbrug til spildevandsrensning. Rent teknisk kan
virksomhederne stadig opnå store vandbesparelser ved i endnu højere grad at bruge de vandbesparende skyllemetoder og teknikker. Vandforbruget bør i løbet af de næste 5 år uden problemer kunne
komme ned på 30-40 liter pr. m² overflade svarende til ca. 300.000 m³/år fra al elforzinkning i Danmark.
D.3.3.4 Energiforbrug
Energiforbruget til de elektrolytisk processer kan beregnes forholdsvis enkelt. Når man kender produktionens størrelse, kan man udregne strømforbruget ud fra de anvendte Volt, Amp og timer med tillæg
for strømtab i ensretter. Energiforbrug til badopvarmning afhænger af badtemperaturen, karisolering, rumtemperatur og udsugning. Energiforbrug til ventilation udgør også en betydelig post. Energiforbrug til
motorer, køling og trykluft – herunder renseanlæg – er af mindre betydning.
Det foreligger ikke mange publikationer og erfaring herhjemme om energiforbruget i galvanobranchen. Forbruget er derfor vurderet ud fra elforzinkning dels ud fra overslagberegning og dels ud fra konkrete
tal og vurderingen fra en dansk virksomhed, der kun udfører elforzinkning.
Tabel D.11 Energiforbrug på en stor elforzinknings virksomhed med cyan zink
|
Udvalgt virksomhed |
Hele Danmark |
kWh/m² |
% |
kwh/år |
Ensrettere |
1,32 |
49 |
11.255.844 |
Badvarme |
0,23 |
8 |
1.925.572 |
Ventilation |
0,66 |
25 |
5.601.664 |
Køling |
0,05 |
2 |
437.630 |
Trykluft |
0,01 |
1 |
122.536 |
Motorer |
0,13 |
5 |
1.137.838 |
Belysning |
0,06 |
2 |
525.156 |
Diverse |
0,21 |
8 |
1.750.520 |
Total |
2,68 |
100 |
22.756.760 |
Det samlede forbrug ligger således 22.757 MWh pr. år og er udelukkende et elforbrug svarende til 2.677 kWh pr. 1000 m².
Der er indhentet tal fra en anden stor elforzinkningsvirksomhed, som kører primært med sur zink og sekundært alkalisk zink. Her er det totale energiforbruget opgjort til 2,98 kWh/m², hvilket ligger tæt på
værdien fra Tabel D.11 (2,68 kWh/m²). Man kan forvente, at små virksomheder, der udnytter produktionsapparatet mindre intens, vil bruge lidt mere energi pr. produceret m² overflade end store
virksomheder med meget stor produktion i flere skift.
Sammenholdes energiforbruget ved elforzinkning med energiforbruget ved fornikling/forchromning, så er energiforbruget pr. m² produceret overflade som ventet højere ved fornikling/forchromning, hvor man
anvender flere varme bade ved høje temperaturer.
De to væsentligste affaldsstrømme fra elforzinkning er:
- Tungmetalslam fra spildevandsrensning
- Kasserede procesbade til ekstern behandling/oparbejdning
I Miljøprojekt 55/2000 vedrørende oparbejdning af galvanisk affald blev affaldsmængderne estimeret ud fra en beregningsmodel kombineret med data fra de største virksomheder i branchen. Dette er vist i
Tabel D.12.
Tabel D.12 Flydende kemikalieaffald fra elforzinkning
Kasseret bad |
Overflade
m² pr. år |
Kasseret bad
liter pr. 1000 m² |
kasseret
bad, m³/år |
Metal i
bad, g/l |
Metal,
kg/år |
Ludkoger |
8.500.000 |
75 |
638 |
0 |
0 |
Bejdsebad |
8.500.000 |
45 |
383 |
40 |
15.300 |
El-affedter |
8.500.000 |
50 |
425 |
2 |
850 |
Dekaperingsbad |
4.000.000 |
25 |
100 |
2 |
200 |
Zinkbad, surt |
6.375.000 |
5 |
32 |
35 |
1.116 |
Zinkbad, cyan |
1.275.000 |
5 |
6 |
15 |
96 |
Zinkbad, alkalisk |
850.000 |
5 |
4 |
10 |
43 |
Blåpassivering |
2.618.000 |
20 |
52 |
3 |
157 |
Gulpassivering |
5.168.000 |
10 |
52 |
12 |
620 |
Oliven+sort pass. |
714.000 |
16 |
11 |
20 |
228 |
Total |
18.609 |
Som det fremgår af Tabel D.12, er det langt fra alle affaldstyper, som indeholder væsentlige mængder tungmetaller. Det er oftest således, at virksomheder selv behandler de kasserede bade med lavt
metalindhold, mens mere koncentrerede bade som bejdsebade, zinkbade samt eventuelt oliven og sort chromatering sendes til ekstern behandling (Kommunekemi). Bejdsebadene nedslides og kasseres
forholdsvis ofte, mens metalliseringsbadene kun meget sjældent kasseres på grund af forurening eller for høje koncentrationer.
Tabel D.13 Slam fra spildevandsrensning (filterkager med 30% tørstof)
Spildevand |
m² overflade
pr. år |
Metal i
bad, g/l |
Udslæb af
metal,
kg/år |
Genvin-
dings % |
Metal i
slam,
kg/år |
Filterkager (30%TS)
ton/år |
Ludkoger |
8.500.000 |
0 |
0 |
0 |
0 |
0,0 |
Bejdsebad |
8.500.000 |
30 |
38.250 |
0 |
38.250 |
318,8 |
El-affedter |
8.500.000 |
1 |
1.275 |
0 |
1.275 |
10,6 |
Dekaperingsbad |
4.000.000 |
30 |
18.000 |
0 |
18.000 |
150,0 |
Zinkbad, surt |
6.375.000 |
35 |
33.469 |
25 |
25.102 |
209,2 |
Zinkbad, cyan |
1.275.000 |
15 |
2.869 |
0 |
2.869 |
23,9 |
Zinkbad, alkalisk |
850.000 |
10 |
1.275 |
0 |
1.275 |
10,6 |
Blåpassivering |
2.618.000 |
2 |
1.047 |
0 |
1.047 |
8,7 |
Gulpassivering |
5.168.000 |
10 |
10.336 |
0 |
10.336 |
86,1 |
Oliven+sort passivering |
714.000 |
18 |
1.928 |
0 |
1.928 |
16,1 |
Total |
8.500.000 |
|
|
|
100.081 |
834,0 |
kg filterkage pr. m² produktion i gennemsnit |
0,098 |
Tabel D.13 omfatter ikke det slam, som dannes på de virksomheder, der selv neutraliserer kasserede procesbade, hvilket vil betyde en mindre stigning i slammængden. Sammenfattet er opstillet følgende
totale tal, hvor slammængden er korrigeret med metalmængderne for de kasserede procesbade, som behandles af virksomhederne selv:
Metalmængde i kasserede bade til ekstern behandling: |
18.609 kg/år |
Metalmængde i spildevandsslam fra fældningsanlæg: |
100.081 kg/år |
Metalmængden i de kasserede bade til ekstern behandling (Kommunekemi) er næsten 6 gange mindre end i det metalhydroxidslam, der dannes ved virksomhedernes egen spildevandsrensning.
Affald fra ludkoger, bejdsebad, el-affedter samt dekaperingsbad indeholder metaller fra de emner, der behandles og udgøres derfor primært af jern. Affald fra zinkbadenne indeholder zink. Affald fra
blåpassivering indeholder chrom(III) og zink, mens gul-, oliven og sortpassivering indeholder chrom(VI) og zink.
Ud fra affaldsopgørelserne for flydende kemikalieaffald (Tabel D.12) og slam fra spildevandsrensning (Tabel D.13) kan affaldet opdelt på de væsentligste metaller opgøres. Dette er vist i Tabel D.14.
Tabel D.14 Affald opdelt på metaller i forhold til samlet mængde og ressourceforbrug
Materiale |
Affaldsmængde |
Del af den
samlede af-
faldsmængde |
Ressource-
forbrug |
Affald i forhold
til ressource-
forbrug |
Zink |
34,9 ton |
29 % |
630 ton |
5,5 % |
Chrom |
11,06 ton |
9,3 % |
14,1 ton |
78 % |
Andre metaller (primært jern) |
72,7 ton |
61,3 % |
Ikke relevant |
Ikke relevant |
D.3.4 Hovedtal for elforzinkning
Kortlægningen har vist, at der behandles 8,5 mio. m² overflade ved elforzinkning pr. år.
Der anvendes 2.650 ton kemikalier, hvilket svarer til 0,31 kg pr. m² behandlet overflade. Zinkforbruget ligger på 630 ton, og chromforbruget ligger på 14 ton. I materialerne indgår en del vand. Fratrækkes
vandmængden, vil materialeforbruget ligge på 1.700 ton svarende til 0,20 kg pr. m².
Mængden af råstoffer, der skal udvindes for at dække materialebehovet, er opgjort til 3.500 ton svarende til 0,41 kg pr. m².
Der anvendes et vandforbrug på 850.000 m³/år og et energiforbrug i form af el på 22.757 MWh, svarende til 2.677 kWh pr. 1.000 m² overflade.
Affald fra kasserede bade og slam udgør i alt 119 ton, hvoraf 35 ton er zink og 11 ton er chrom. Omkring 73 ton er metaller fra den behandlede overflade og udgøres primært af jern.
Den mængde metal (zink og chrom), der anvendes og som ikke går i affaldsstrømmen, antages at blive på emnerne til de kasseres som affald.
D.4 Kortlægning af varmforzinkning
Ved varmforzinkning dyppes stålemner i et smeltet zinkbad ved ca. 460°C, hvorved der pålægges et zinklag med en lagtykkelse på 60-100 m. Dette giver en langt bedre korrosionsbeskyttelse, end der
opnås ved elektrolytisk forzinkning, hvor man normalt arbejder med lagtykkelser på 5-20 m. Derfor anvendes varmforzinkning især til stålkonstruktioner, der anvendes udendørs, og metoden kan anvendes
på meget store emner op til 10-15 meters længde.
I Danmark findes 20 varmforzinkningsvirksomheder, men flere af virksomhederne har samme ejer. Det skønnes, at halvdelen af virksomhederne laver ca. 85% af produktionen. Der varmforzinkes
skønsmæssigt 120.000 ton gods årligt, og i 2001 var det samlede zinkforbrug for danske varmforzinkere på 9817 ton svarende til, at der i gennemsnit påføres ca. 8,2% zink i forhold til godsets vægt.
D.4.1 Processerne
Den fulde proces er vist som flowsheet i Figur D.4. Det skal bemærkes, at man langt fra altid anvender alle processer, som er vist i det komplette flowsheet.
D.4.1.1 Alkalisk affedtning
Første trin er en varm alkalisk affedtning, hvor olie og fedt opløses og fjernes fra emnernes overflade. Badet indeholder et affedtersalt (natriumhydroxid, carbonater, phosphater, silikater samt tensider og
eventuelle kompleksdannere), der sørger for, at olie og fedt bliver delvis emulgeret i badet. Ofte kommer der efterhånden også fri olie på badoverfladen, og dette olie kan med fordel skimmes af med
mellemrum for at opnå længere levetid for badet. I Danmark springer man ofte dette trin over, hvis ikke emnerne er meget beskidte. Let olieret gods kan normalt renses i en bejdseaffedter – det vil sige en
sur bejdse med et mindre indhold af tensider til emulgering af olien.
Det skal nævnes, at enkelte virksomheder anvender en såkaldt biologisk affedter i stedet for en varm alkalisk affedter. I den biologiske affedter omdannes olie og fedt til slam af mikroorganismer, der
vedligeholdes ved tilsætning af mikronæringsstoffer.
Når badets indhold af olie og fedt er blevet så højt, at man ikke mere kan opnå en acceptabel affedtning af emnerne, selvom der tilsættes mere affedtersalt, må badet kasseres, og et nyt bad blandes op. Det
kasserede bad kan enten neutraliseres i eget renseanlæg eller det afleveres til Kommunekemi eller anden godkendt modtager for kemikalieaffald. Badlevetiden afhænger af produktionens størrelse (ton/time),
emnernes tilsmudsning og virksomhedens evne og metode til at vedligeholde badet. Efter behandling i affedteren skal emnerne skylles.
Input: |
Pålæsning af gods |
Output: |
 |
Affedtersalt + vand Energi |
1. Varm alkalisk affedtning 70-80°C |
Kasseret bad + slam Varmeafgivelse |
 |
Vand |
Skyl |
Spildevand med udslæbte kemikalier |
 |
Saltsyre + vand + Energi |
2. Bejdsning i saltsyre 20°C |
Kasseret bejdsebad + slam Syredampe |
 |
Vand |
Skyl |
Spildevand med udslæbte kemikalier |
 |
Flussalt + vand + energi |
3. Flusning, 50-70°C |
Kasseret flusbad + slam Varmeafgivelse |
 |
Energi |
Tørring |
Varrmeafgivelse |
 |
Zink + aluminium + bly + energi |
4. Forzinkning 460°C |
Zinkaske + hårdzink Varmeafgivelse Luftforurening |
 |
Vand/luft |
5. Køling (luft eller vand) |
Spildevand |
 |
|
6. Pudsning og afgratning |
Zinkstøv (på gulv) |
 |
|
Færdig gods |
|
Figur D.4 Flow-sheet for varmforzinkning
D.4.1.2 Bejdsning
Andet trin er rensning af emnerne i saltsyre (bejdsebad), hvorved rust og glødeskaller opløses og fjernes fra emnernes overflade. Det øverste lag af selve emnerne fjernes også ved denne syrebehandling.
Normalt tilsættes badet en inhibitor, der skal forhindre angreb på grundmaterialet. Bejdsningen foregår normalt ved stuetemperatur, men opvarmning vil øge bejdsehastigheden. Derfor har nogle
virksomheder opvarmning af bejdsebadet om vinteren, hvor temperaturen i produktionslokalet kan være ret lav.
Under bejdsningen forbruges syre, og grundmateriale går i opløsning. Der kan løbende spædes op med mere syre, men efterhånden bliver badets indhold af metal så højt, at badet må kasseret. De fleste
danske virksomheder foretrækker at udskifte badet gradvist, så man holder en nogenlunde konstant koncentration af syre og jern. En typisk sammensætning er: Fri syre = 90 g/l og jern = 80 /l. Enkelte
virksomheder anvender en såkaldt aktiveret bejdsning, hvor man kører med et jernindhold på 120-140 g/l. Ved dette høje jernindhold må man nøjes med et syreindhold på 50-60 g/l for at undgå udfældning
af ferrochlorid. Denne bejdse er næsten lige så effektiv som bejdsen med højere syreindhold, og så afgiver den færre syredampe.
Efter bejdsning er der enkelte virksomheder, der skyller godset før flusning, men de fleste danske virksomheder dypper direkte i flusbadet efter bejdsning, hvorved flusbadet forurenes kraftigt med jern og
syre fra bejdsen.
Brugt bejdsesyre anvendes ofte som såkaldt aftrækssyre til rensning af værktøj og fejlforsinket gods, før det endelig kasseres. Den kasserede syre kan afleveres til Kommunekemi, men flere danske
virksomheder sender den kasserede til oparbejdning i Tyskland, hvorfra man får regenereret syre retur. Kasseret syre kan principielt neutraliseres i virksomhedens eget renseanlæg, hvorved de opløste
metaller udfældes som metalhydroxidslam, men da det giver ekstremt meget slam og kræver et stort kemikalieforbrug, kan det ikke svare sig økonomisk. Enkelte virksomheder afleverer den kasserede syre
til Kemira Miljø, hvor bejdsebadet oparbejdes til et ferrichlorid fældningsmiddel. Badlevetiden kan forlænges, hvis man reducerer syreangrebet på grundmaterialet.
D.4.1.3 Flusning
Flusbadet er en blanding af zinkchlorid og ammoniumchlorid. Flussaltet kan være et dobbeltsalt (2 mol NH4Cl og 1 mol ZnCl2) med 44% NH4Cl, eller det kan være et trippelsalt (3 mol NH4Cl og 1 mol
ZnCl2) med 54% NH4Cl. Normalt foretrækkes trippelsaltet, da det er den mest aktive på grund af det højere indhold af NH4Cl. Koncentrationen af flussalt ligger typisk på 400-600 g/l. Ved dypning i
flusbadet bliver emnerne opvarmet og belagt med et lag af flussalt, når det atter trækkes op og tørres. Flussaltet har stor betydning for et godt resultat ved den efterfølgende forzinkning.
Flusbadet forurenes løbende med indslæb af jern og syre fra bejdsebadet, og forureningen foregår meget hurtigt, hvis godset ikke skylles mellem bejdsebadet og flusbadet. Jernforurening vil efterhånden
udfældes som brune partikler ferrihydroxid og ferrioxid i takt med, at ferro oxideres af luftens ilt til ferri. Oxidationen kan fremskyndes ved tilsætning af brintperoxid, hvorved oxidationen bliver momentan.
Det udnyttes i praksis til rensning og oparbejdning af flusbade, hvor man kan behandle badet løbende med brintperoxid og ammoniakvand for at holde pH på 3,5 -4,5 som er den optimale værdi. Udfældet
jern frasepareres og afleveres som kemikalieaffald.
Ved neutralisation af saltsyre dannes NH4Cl, som er den ene komponent i flusbadet. Bejdsebadet vil normalt også indeholde mere eller mindre zinkchlorid, og dette indslæb er et direkte tilskud til flusbadets
indhold af zinkchlorid. Skønsmæssigt 60% af de danske varmforzinkere har flusbadsgenvinding, og de bruger derfor meget lidt flussalt. Afhængig af det indslæbte bejdsebad vil disse virksomheder bruge
mindre mængder NH4Cl eller ZnCl2 for at fastholde den optimale sammensætning af badet. I yderste konsekvens kan indslæbet af zinkchlorid være så stort, at en del af badet må kasseres engang imellem.
Det skal sluttelig bemærkes, at flusbadet også kan neutraliseres med askeaffald, som indeholder zinkoxid, der giver zinkchlorid ved neutraliseringen. Det giver således et bidrag til badets indhold af
zinkchlorid.
D.4.1.4 Tørring
Det er vigtigt, at emnerne er tørre, før de nedsænkes i zinksmelten. Det kan gøres i en tørreovn eller en tørrezone med varm luft, men mange virksomheder lader simpelt hen emnerne hænge så længe i
lokalet, at de når at tørre før forzinkningen. Det hjælper godt her, at flusbadet kører ved så høj temperatur som muligt (helst 70°C).
D.4.1.5 Forzinkning
Selve forzinkningen foregå ved neddypning af godset i smeltet zink ved 460°C. Under processen reagerer smeltet zink med godsets overflade, hvor der i overgangszonen dannes forskellige jern-zink
legeringer. Yderst ligger det rene zinklag. Flussaltet på godsets overflade har stor betydning for processen i zinksmelten. Godsets sammensætning har også stor betydning for zinkoptagelsen og slutresultatet.
Silicium beroliget stål er uegnet til varmforzinkning, da zinkoptagelsen bliver ukontrollabel stor. Et lille indhold af aluminium (0,005 - 0,007 %) i smelten har en gunstig indflydelse på slutresultatet. En dårlig
flux og et lavt aluminiumindhold i smelten kan føre til små pletter på godset uden zinkbelægning.
I zinksmelten dannes løbende aske og hårdzink. Asken dannes på smeltens overflade og består primært af oxideret zink. Asken skal løbende skrabes væk fra godset under dypningen for at få en pæn
overflade. Hårdzink dannes som klumper i smelten, hvor jernforurening reagerer med zink og danner en jern-zink legering (3% Fe og 97% Zn), som man kalder hårdzink. Der skal altså kun små
jernmængder til at give meget hårdzink, så det betaler sig virkeligt at holde jernindslæbet fra flusbadet til smelten lavt, og det gør man ved at holde flusbadet rent (Fe < 2 g/l). Hårdzink er et affaldsprodukt,
som med mellemrum skal fjernes fra smelten.
Ved forzinkningsprocessen dannes støv med NH4Cl og zinkforbindelser. Jo mere ammoniumchlorid, der er på emnerne, jo mere røg dannes. Derfor holdes zinksmelten normalt indelukket, og der udsuges
store luftmængder under dyppeprocessen.
D.4.1.6 Køling
De varme emner skal køles efter zinksmelten, og de fleste danske virksomheder anvender luftkøling, hvor emnerne simpelt hen hænger til afkøling i produktionslokalet, indtil de kan videre bearbejdes.
Enkelte virksomheder ønsker en hurtigere køling ved dypning i et kar med stillestående vand, hvor der sker en kraftig fordampning af vandet og dermed en afkøling af emner. På mange udenlandske
virksomheder anvender man kølevand tilsat chromater, så man både opnår en hurtig køling og en let passivering af zinkoverfladen, som man kender fra elforzinkning. Det giver større korrosionsbestandighed
af godset og nedsætter dannelsen af hvidrust på godsets overflade.
D.4.1.7 Pudsning og afgratning
De færdige emner har ofte små knopper eller kanter, der skal fjernes ved pudsning, slibning eller filing. Dette er et manuelt arbejde, som udføres i produktionshallen, før emnerne går retur til kunderne.
D.4.2 Skylning
Generelt anvender danske varmforzinkere så lidt skylning som muligt for at undgå at skulle rense spildevand. En enkelt af de store virksomheder anvender dog skylning, hvilket betyder, at der anvendes
skylning ved ca. 40% af varmforzinkningen herhjemme. Anvender man ikke alkalisk affedtning, kan skyllevand helt undgås, hvis man går direkte fra bejdsebadet over i flusbadet, men det giver som nævnt en
kraftig forurening af flusbadet.
Da godset oftest er meget stort, kræves der store kar til forbehandlingen, og kar på 50-90 m³ er ikke ualmindelige. Da store kar er pladskrævende, er det ikke så almindeligt, at man anvender flere skyllekar
i modstrøm, hvilket ellers er den mest vandbesparende metode. En effektiv skylning efter bejdsning kan anbefales for at reducere forureningen af flusbadet, hvilket har mange fordele som beskrevet ovenfor.
Skylning efter affedtning er også vigtigt for at reducere indslæb af alkali i bejdsebadene.
D.4.3 Ressourceforbrug
De væsentligste ressourcer, der forbruges ved varmforzinkning, er:
- Kemikalier bruges i procesbadene og til vandrensning.
- Metaller bruges i zinksmelten.
- Vand bruges til skylning og til opblanding af procesbade.
- Energi bruges til zinksmelten, til badopvarmning, til ventilation og rumopvarmning samt til drift af produktionsudstyr som trykluft, pumper og kraner samt til renseanlæg.
D.4.3.1 Forbrug af kemikalier og metaller
Forbruget af de væsentligste kemikalier og metaller er vist i Tabel D.15. Opgørelsen er baseret på varmforzinkning af 120.000 ton gods pr. år.
Tabel D.15 Forbrug af kemikalier og metaller til proces og spildevand
Procesbad |
Kemikalie |
% af branchen |
Typisk forbrug
i kg pr. ton gods |
Total forbrug
i ton i DK |
Affedter |
Affedtersalt |
25 |
5,0 |
150 |
Bejdsebad |
Saltsyre, 30% |
100 |
30,0 |
3.600 |
Flusbad |
Flussalt |
40 |
1,5 |
72 |
Flusbad |
Ammoniakvand, 25% |
60 |
2,8 |
202 |
Flusbad |
Brintperoxid, 35% |
60 |
0,4 |
29 |
Zinksmelte |
Zink |
100 |
81,8 |
9.817 |
Spildevand |
Natronlud, 27% |
40 |
3,0 |
144 |
Forbrug af bly og aluminium i zinkbadet er ikke medtaget. De typiske forbrugstal i kg pr. ton gods er estimerede gennemsnitstal for branchen. Tallene er indsamlet gennem kontakt til udvalgte større
virksomheder, og de er løbende justeret ud fra nye oplysninger i Danmark og udlandet.
Det bemærkes, at forbruget af flussalt er beregnet ud fra et standardforbrug på 1,5 kg flussalt pr. ton gods for de virksomheder, der ikke har flusbadsregenerering, mens virksomheder med regenerering
bruger brintperoxid og ammoniakvand i stedet. For de sidstnævnte virksomheder vil der også være et mindre forbrug af flussalt (ammoniumchlorid og zinkchlorid), men det er vanskeligt at estimere dette
forbrug.
I Tabel D.16 er foretaget en vurdering af de i Tabel D.15 angivne kemikalieforbrug.
Tabel D.16 Bestanddele i kemikalier til varmforzinkning
Kemikalie |
Mængde |
Komponenter |
Affedtersalt |
150 ton |
Hydroxider, carbonater 5-25% Tensider, kompleksdannere 5-25% Vand 50-90 % |
10-35 ton
10-35 ton 80-130 ton |
Saltsyre |
3.600 ton |
30% syre svarer til 1000 ton ren HCl |
Flussalt |
72 ton |
Trippelsalt (ammoniumchlorid og zinkchlorid), - heraf 13 ton ammonium, 43 ton chlorid og 16 ton zink |
Ammoniakvand |
202 ton |
25 % ammonium svarende til 50 ton ren NH3 |
Brintperoxid |
29 ton |
35 % hydrogenperoxid svarende til 10 ton ren H2O2 |
Natriumhydroxid |
144 ton |
27% natriumhydroxid svarende til 40 ton ren NaOH |
Zink |
9.817 ton |
Metallisk zink |
På basis af opgørelser og antagelser i Tabel D.16 kan følgende hovedtal uddrages:
- der anvendes 14.000 ton kemikalier, hvoraf vand udgør omkring 3.000 ton.
- det samlede zinkforbrug udgør 9.830 ton.
- forbruget af uorganiske syrer ligger på omkring 1.000 ton.
- forbruget af uorganiske baser ligger på omkring 60 ton
- forbruget af ammoniak udgør omkring 65 ton, og forbruget af hydrogenperoxid udgør 10 ton.
- forbruget af organiske forbindelser som tensider m.v. udgør omkring 25 ton.
Det gennemsnitlige kemikalieforbrug ligger på 117 kg pr. ton behandlet gods. Metalmængden udgør således ca. 70% af kemikaliemængden. Almindelige syrer, baser og salte udgør ca. 8 % og organiske
forbindelser omkring 2%. De resterende 20% er primært vand samt usikkerheder.
D.4.3.2 Forbrug af vand
Hovedparten af de danske varmforzinkere bruger ikke egentligt skyllevand, men de anvender vand til opblanding af nye bade og til opspædning af bade med fordampningstab. De virksomheder, der
anvender alkalisk affedtning, er nødt til at skylle mellem affedteren og bejdsen. Enkelte virksomheder bruger også skyllevand efter bejdsen for at reducere indslæb af forurening i flusbadet. Andre
virksomheder skyller i forurenet grundvand i stedet for postevand, hvilket kan være hensigtsmæssigt, hvis grundvandet alligevel skal neutraliseres og renses. Det skønnes, at hele branchen anvender
15.000-20.000 m³ procesvand årligt.
D.4.3.3 Energiforbrug
Der foreligger ingen totale brancheanalyser vedrørende energiforbrug, men i Tabel D.17 er energiforbruget estimeret ud fra konkrete tal for to større danske varmforzinkningsvirksomheder, som anvender
el-opvarmet smelte og kører i 3 skift fem dage pr. uge.
Tabel D.17 Energiforbrug for udvalgt virksomhed samt estimeret forbrug for hele branchen baseret på en årlig produktion på 120.000 ton for hele branchen
|
Udvalgt virksomhed |
Hele Danmark |
kWh/ton |
% |
kWh/år |
Zinkgryde (el) |
132 |
61 |
15.840.000 |
Andet elforbrug |
84 |
39 |
10.080.000 |
Total |
216 |
100 |
25.920.000 |
Det største energiforbrug ligger på selve zinksmelten. Den kan opvarmes med elektricitet eller med olie/gas, og alle metoder anvendes herhjemme. Energiforbruget ved elopvarmning er dog betydeligt lavere
end ved olie/gas-opvarmning, og det kan derfor forventes, at det samlede energiforbrug i Danmark til varmforzinkning vil være betydeligt større end estimeret i Tabel D.17. Man kan dog forvente, at det
specifikke energiforbrug i kWh/ton er lidt lavere for virksomheder, der kører intens produktion i flere skift. Her er der kortere perioder, hvor smelten står ubenyttet hen og dermed mindre varmespild.
Den sydafrikanske varmforzinkerforening er i gang med at samle energidata ind fra deres medlemmer, og de har oplyst følgende typiske gennemsnitstal for virksomheder, der producerer i 2 skift 5 dage pr.
uge:
Opvarmning af zinkbad: |
245 kWh pr. ton gods |
Andet energiforbrug: |
112 kWh pr. ton gods |
Total energiforbrug: |
357 kWh pr. ton gods |
Opgørelsen er excl. energiforbrug til rumopvarmning.
De sydafrikanske tal er lidt højere end de danske, men tallene er af samme størrelsesorden. Det bemærkes, at den danske virksomhed arbejder i 3 skift, hvilket typisk betyder mindre energiforbrug pr. ton
gods, da der er korte stilstandsperioder. Sydafrikanerne oplyser i øvrigt, at det samlede energiforbrug under stilstand er 70-90 kWh pr. ton gods.
Sammenfattet må der forventes et samlet energiforbrug hos de danske varmforzinkere på 300-500 kWh pr. ton gods svarende til et årsforbrug på 36-60 mill. kWh for hele branchen. Her tages
udgangspunkt i et gennemsnit på 400 kWh pr. ton gods.
Da zinksmelten bliver opvarmet dels med el og dels med olie/gas, antages det i denne forbindelse, at 40% af det samlede energiforbrug dækkes af olie, mens resten er el. Ved et energiforbrug på 48.000
MWh dækkes de 19.200 MWh af olie/gas. Ved en energiudnyttelse på 90% og et energiindhold i olie på 42 MJ/kg svarer 19.200 MWh til:
19.200 MWh × 3600 MJ/MWh / (0,90 × 42 MJ/kg × 1000 kg/ton) = 1.829 ton
Det samlede gennemsnitlige energiforbrug udgøres derfor til varmforzinkning af:
- 28.800 MWh el
- 1.829 ton råolie
D.4.3.4 Råstofforbrug
På baggrund af materialeopgørelsen i Tabel D.16 er forbruget af råstoffer opgjort i Tabel D.18. Data er baseret på oplysninger fra SigmaPro.
I opgørelsen er taget højde for, at 1.745 ton zink oparbejdes. Ved oparbejdningen er der et tab, således at 1.142 ton zink kan genanvendes (70%).
Tabel D.18 Estimering af råstofforbrug for varmforzinkning
Materiale
120.000 ton gods |
Materiale-
mængde |
Råstof-
forbrug Kg/kg |
Råstof-
forbrug i alt |
Råstof-
forbrug pr. ton gods |
Zink |
8.688 ton |
3,1 |
26.932 ton |
240 kg |
Uorganiske syrer |
1.000 ton |
0,7 |
700 ton |
6 kg |
Uorganiske baser |
60 ton |
1,2 |
72 ton |
0,6 kg |
Ammoniak og hydrogenperoxid |
75 ton |
2 1) |
150 ton |
1 kg |
Tensider m.v. |
25 ton |
2,0 1) |
50 ton |
0,4 kg |
|
248 kg |
1): Værdien er skønnet.
Som det fremgår af Tabel D.18, udgør hovedparten af råstofforbruget af zink. Det samlede forbrug pr. ton behandlet gods udgør 248 kg.
D.4.4 Affald
De væsentligste affaldstyper og –mængder fremgår af Tabel D.19.
Tabel D.19 Affald fra varmforzinkning
Affald |
% af branchen |
kg/ton |
ton total i DK |
Hårdzink |
100 |
6,5 |
780 |
Aske |
100 |
10,0 |
1200 |
Kasseret bejdsesyre |
100 |
30,0 |
3600 |
Kasseret affedter |
25 |
5,0 |
150 |
Filterkager (flus) |
60 |
4,0 |
288 |
Filterkager (spildevand) |
40 |
5,0 |
240 |
Diverse slam og flydende affald |
100 |
2,0 |
240 |
Hårdzink indeholder 97% zink, og alle danske virksomheder sender dette affald til oparbejdning i udlandet. Virksomhederne får dog kun refunderet 60% af zinkværdien for dette affald, så der er alt mulig
grund til at reducere mængden af hårdzink.
Asken er en anden vigtig affaldstype, og ligesom hårdzink indeholder asken meget zink. De fleste større virksomheder har anskaffet en smelteovn til behandling af asken. Ved smeltning får man fjernet det
metalliske zink fra asken (40-70%), så kun zinkoxiden bliver tilbage. Zinkoxidresten sendes til oparbejdning i udlandet, men den kunne også oparbejdes internt ved at opløse zinkoxid i saltsyre og bruge
opløsningen i flusbadet. I Sydafrika benytter flere virksomheden simpelthen selve zinksmelten til at udvinde det metalliske zink af asken, og det kræver kun lidt ”know-how” for at gøre det rigtigt. Resten af
asken kan eventuelt fyldes direkte i flusbadet til neutralisation af overskudssyre.
Kasseret bejdsesyre indeholder ofte store mængder zink ved siden af jern (Typisk: Fe=80-140 g/l, Zn=20-200 g/l). Specielt de brugte bejdsebade, som har været anvendt som aftrækssyre, indeholder
meget zink og kun lidt fri syre. Enkelte virksomheder holder zinkindholdet meget lavt (1-2 g/l), da det så kan bruges direkte til fremstilling af ferrichlorid fældningsmiddel.
Kasseret affedter indeholder ikke væsentlige mængder metal, og de kan principielt neutraliseres i virksomhedens eget renseanlæg. Det kan eventuelt give for meget olie i spildevandet, og derfor vil nogle
virksomheder bortskaffe de kasserede affedterbade til ekstern behandling.
Filterkagerne fra flusbadsrensning indeholder primært udfældet jernhydroxid med opløste flussalte i porevandet. Tørstofindholdet er derfor usædvanlig højt – ca. 60% mod normalt 30% i filterkager.
Filterkagernes indhold af ammoniak gør, at Kommunekemi må brænde disse kager, og afleveringsprisen er derfor næsten tre gange højere end normalt.
Der dannes lidt mere filterkage pr. ton gods ved rensning af skyllevand end ved rensning af flusbad. Det er principielt den samme jernmængde, der skal fjernes fra henholdsvis skyllevandet og flusbadet, men
fra skyllevand udfældes også zinkhydroxid, idet zink tilføres med den udslæbte bejdse. I flusbadet udfældes zink derimod ikke på grund af den lave fældnings pH-værdi (ca. 4,5) og det store indhold af
ammonium, som kompleksbinder zink.
Andre affaldstyper dækker over slam fra affedterbade og bejdsebade samt kasseret flusbad. Mængderne svinger meget fra virksomhed til virksomhed afhængig af produktionsforholdene.
Af ovenstående fremgår det, at affaldet fra hårdzink, aske og kasseret bejdsesyre primært består af zink, mens de øvrige affaldsfraktioner primært indeholder metaller fra godset og andet.
Den samlede zinkmængde, der tabes, kan opgøres til:
Hårdzink, antaget 100% zink |
780 ton |
Aske, antaget zinkoxid, 80% zink |
965 ton |
Bejdsesyre, 100 g Zn/liter |
360 ton |
Filterkager fra spildevand, 5% zink |
12 ton |
Kasseret flusbad med 15% zink |
8 ton |
Samlet |
2.120 ton |
Da der anvendes 9.830 ton zink i alt, udgør affaldsmængden ca. 20%.
D.4.5 Hovedtal for varmforzinkning
Kortlægningen har vist, at der behandles 120.000 ton gods pr. år med varmforzinkning.
Der anvendes 14.000 ton kemikalier, hvilket svarer til 117 kg pr. behandlet ton gods. Zinkforbruget ligger på 9.830 ton. Råstofforbruget svarer til 248 kg pr. ton behandlet gods.
Der anvendes et vandforbrug på i størrelsesordnen 15-20.000 m³/år.
Det samlede energiforbrug er estimeret til 36-60.000 MWh. Det er antaget, at 40% stammer fra olie/gas og resten fra el. Energiforbruget kan derfor opgøres til et elforbrug på 28.800 MWh og 1.829 ton
råolie.
Affald fra kasserede bade og slam udgør i alt 6.500 ton, hvoraf det er estimeret at zinkmængden udgør 2.100 ton.
Den mængde zink, der anvendes, og som ikke går i affaldsstrømmen, antages at blive på emnerne, indtil de kasseres som affald.
D.5 Ressourceopgørelse
I afsnit D.2-D.4 er gennemført en kortlægning af de procesrelaterede forhold ved de tre overfladebehandlingsformer. Der er opgjort mængden af materialer, hjælpestoffer og energi, der går til processerne
og hvilke tab, der forekommer.
Som basis for kortlægningen er taget udgangspunkt i behandling af det antal m² overflade, der behandles ved fornikling/forchromning og elforzinkning i Danmark og for varmforzinkning for den mængde gods
målt i ton, der behandles i Danmark.
Med henblik på at gennemføre en beregning af ressourceeffektivitet er det nødvendigt, hvor det er muligt, at foretage en vurdering af forbruget af råstoffer og energi til fremstilling af opgjorte forbrug.
D.5.1 Metaller
De metaller, der er relevante ved de 3 overfladebehandlingsprocesser, er
- nikkel
- kobber
- chrom
- zink
- jern
For disse metaller er ressourcetræk opgjort i mPR og primær energi ved udvinding og fremstilling opgjort i Miljønyt nr. 58 (Pommer et al., 2001). Data herfra er vist i Tabel D.20.
Tabel D.20 Ressourceforbrug for metaller
Metal |
Ressource-
forbrug |
Primær energi
til fremstilling |
Nikkel |
106 mPR/kg |
190 MJ/kg |
Kobber |
16,5 mPR/kg |
90 MJ/kg |
Chrom |
12,8 mPR/kg |
39 MJ/kg |
Zink |
33 mPR/kg |
70 MJ/kg |
Jern/stål |
0,08 mPR Fe
og 0,05 mPR Mn |
40 MJ/kg |
I det følgende er vist forbruget af metaller for de tre overfladebehandlingsprocesser. For fornikling/forchromning og for elforzinkning er der foretaget en omregning til enheden 1.000 m² behandlet overflade.
For varmforzinkning er der foretaget en omregning til 1 ton behandlet gods. Omregningerne er foretaget for at kunne sammenligne de forskellige overfladebehandlingstyper.
Tabel D.21 Fornikling/forchromning, Samlet behandlet areal 170.000 m²
|
Nikkel |
Kobber |
Chrom |
Jern/stål |
Forbrug i alt (ton) |
130 |
33 |
10,4 |
9,5 |
Affald (ton) |
4,19 |
1,36 |
8,67 |
9,5 |
I produkt (ton) |
125,81 |
31,64 |
1,73 |
0 |
pr. 1000 m² behandlet overflade |
Forbrug i alt (kg) |
111,11 |
28,21 |
2,99 |
8,12 |
Affald (kg) |
3,58 |
1,16 |
0,00 |
8,12 |
I produkt (kg) |
107,53 |
27,04 |
2,99 |
0,00 |
Ressourceforbrug |
mPR pr. kg |
106 |
16,5 |
12,8 |
Jern: 0,08
Mangan: 0,05 |
Ressourceforbrug |
11777,78 |
465,38 |
38,29 |
Jern: 0,65
Mangan: 0,48 |
I produktet |
11398,17 |
446,21 |
38,29 |
Jern: 0
Mangan: 0 |
Det samlede ressourceforbrug er på 12.358 mPR for metallerne, og i produktet findes 11.863 mPR. Tabet udgør 500 mPR svarende til 4% af ressourceforbruget.
Tabel D.22 Elforzinkning , Samlet behandlet areal 8.500.000 m²
|
Zink |
Chrom |
Jern/stål |
Forbrug i alt (ton) |
630,00 |
14,1 |
74 |
Affald (ton) |
34,90 |
11,06 |
74 |
I produkt (ton) |
595,10 |
3,04 |
0 |
Pr. 1000 m² overflade |
Forbrug (kg) |
74,12 |
1,66 |
8,71 |
Affald (kg) |
4,11 |
1,30 |
8,71 |
I produkt (kg) |
70,01 |
0,36 |
0,00 |
Ressourceforbrug |
mPR pr. kg |
33 |
12,8 |
Jern: 0,08
Mangan: 0,05 |
Ressourceforbrug |
2445,88 |
21,23 |
Jern: 0,70
Mangan: 0,44 |
I produkt |
2310,39 |
4,58 |
Jern: 0
Mangan: 0 |
Det samlede ressourceforbrug er på 2.468 mPR for metallerne, og i produktet findes 2.315 mPR. Tabet udgør 153 mPR svarende til 6,2% af ressourceforbruget.
Tabel D.23 Varmforzinkning, Behandlet godsmængde 120.000
|
Zink |
Forbrug i alt (ton) |
9830 |
Affald (ton) |
2120 |
I produkt (ton) |
7710 |
Pr. 1 ton behandlet gods |
Forbrug i alt (kg) |
81,92 |
Affald (kg) |
17,67 |
I produkt (kg) |
64,25 |
Ressourceforbrug |
mPR pr. kg |
33 |
Ressourceforbrug |
2703,3 |
I produkt |
2120,3 |
Af Tabel D.23 kan det beregnes, at tabet udgør 583 mPR, hvilket udgør 21,6% af det ressourceforbruget.
D.5.2 Kemikalier
Der anvendes en række kemikalier i forbindelse med de 3 overfladebehandlingsprocesser. I Tabel D.24 er skitseret, hvilke der kan fastlægges et ressourceforbrug for, og hvilke forudsætninger der er gjort.
Ved affaldsbehandlingen sker en fældning af metallerne som metalhydroxider. Ved fældningen vil der blive tilsat hydroxider antagelig i form af natriumhydroxid samt flokuleringsmidler for at effektivisere
fældningen. Disse ressourceforbrug er ikke medtaget i opgørelsen.
Tabel D.24 Ressourcetræk og energiforbrug for kemikalier
Kemikalier |
Ressource-
forbrug |
Primært energi-
forbrug til
fremstilling |
Forudsætninger og antagelser |
Uorganiske syrer |
0 da rigelig ressource |
50 MJ/kg |
Anslået. |
Uorganiske baser |
0 da rigelig ressource |
38 MJ/kg |
Som natriumhydroxid |
Organiske forbindelser, Tensider |
0,04 mPR |
60 MJ/kg |
Ressourcetræk vurderet som stammende fra olieprodukter, energiforbrug fra Miljønyt nr. 58 |
Cyanider |
|
|
Kan ikke vurderes og medtages |
Borsyre |
|
|
Kan ikke vurderes og medtages |
Salte (KCl) |
0 da rigelig ressource |
5 MJ/kg |
Anslået ud fra natriumhydroxid på 1,2 MJ/kg |
Glansmidler |
|
|
Kan ikke vurderes og medtages |
Ammoniak |
0 da rigelig ressource |
60 MJ/kg |
Ressourcetræk anslået, energiforbrug fra Miljønyt nr. 58 |
Brintperoxid |
0 da rigelig ressource |
10 MJ/kg |
Anslået |
Vand regnes efter UMIP-metoden som en rigelig ressource. Den eneste miljømæssige belastning, der er medtaget i UMIP-metoden, er energiforbrug til oppumpning af vand, der udgør 0,001 MJ/kg
svarende til 1 MJ/m³. I det følgende er vist ressourceforbruget for de tre processer i de grupper, som det er valgt at opgøre kemikalierne i.
D.5.2.1 Fornikling/forchromning
Forbruget af kemikalier og vand samt omregning til ressourceforbrug er vist i Tabel D.25.
Tabel D.25 Kemikalie- og vandforbrug ved fornikling, forchromning, årlig behandling af 170.000 m²
Kemikalietype |
Årligt forbrug
(ton) |
Forbrug pr.
1.000 m² (kg) |
MPR pr. kg |
mPR
pr. 1.000 m² |
Uorganiske syrer |
110 |
94,02 |
0 |
0 |
Uorganiske baser |
10 |
8,55 |
0 |
0 |
Organiske forbindelser |
55 |
47,01 |
0,04 |
1,88 |
Cyanider |
30 |
25,64 |
- |
0 |
Andet |
65 |
55,56 |
- |
0 |
Vandforbrug |
40.000 |
34.188 |
0 |
0 |
I alt |
1,88 |
Ressourceforbruget for uorganiske syrer, uorganiske baser og vand er sat til 0 mPR, da disse ressourcer betragtes som rigelige. Ressourceforbruget til fremstilling af cyanider og andet, herunder glansmidler,
er ikke medtaget på grund af manglende oplysninger.
Udeladelserne kan vurderes ud fra:
- ressourceforbruget for cyanid kan ligge på niveau med ressourceforbruget til fremstilling af tensider, uden disse 2 stoftyper i øvrigt kan sammenlignes.
- ressourceforbruget til glansmidler kan vanskeligt vurderes, da sammensætningen ikke kendes. Det antages, at op til 50% af mængden af glansmidler på 32 ton udgøres af metaller med et gennemsnitligt
ressourceforbrug på 25 mPR/kg.
Disse antagelser vil viser, at udeladelsen af cyanider ikke har væsentlig betydning, da ressourceforbruget hertil er omkring 1 mPR. Ressourceforbruget til glansmidler kan derimod være af stor betydning, da
32 ton glansmidler svarer til et metalindhold på 13,7 kg, hvis 50% af glansmidlerne er metaller. Ved et gennemsnitligt ressourceforbrug på 25 mPR pr. kg betyder dette et ressourceforbrug på 340 mPR for
glansmidlerne. Tages der hensyn til andre indholdsstoffer, vil ressourceforbruget kunne komme op på 500 mPR ved en konservativ vurdering.
Overordnet må det dog konkluderes, at ressourceforbruget til kemikalier og vand er meget lille – op til 500 mPR i forhold til ressourceforbruget til metaller på i størrelsesordnen 12.000 mPR.
D.5.2.2 Elforzinkning
I Tabel D.26 er vist kemikalie- og vandforbruget for elforzinkning samt opgjort ressourceforbruget hertil.
Tabel D.26 Kemikalie- og vandforbrug ved elforzinkning, årlig behandling af 8.500.000 m²
Kemikalietype |
Årligt forbrug
(ton) |
Forbrug pr. ton
(kg) |
mPR pr. kg |
mPR
Pr. 1000 m² |
Uorganiske syrer |
310 |
36,47 |
0 |
0 |
Uorganiske baser |
300 |
35,29 |
0 |
0 |
Borsyre |
13 |
1,53 |
- |
- |
Salte |
100 |
11,76 |
0 |
0 |
Organiske forbindelser |
100 |
11,76 |
0,04 |
0,47 |
Cyanider |
80 |
9,41 |
- |
- |
Andet |
167 |
19,64 |
- |
- |
Vandforbrug |
300.000 |
35.294 |
0 |
0 |
I alt |
0,008 |
I denne opgørelse er der ligesom for fornikling/forchromning udeladt ressourceforbrug til glansmidler, cyanider og borsyre. Ressourceforbrug til cyanider og borsyre antages at være beskedent. Af
glansmidler anvendes 167 ton på årsbasis svarende til 19,6 kg pr. 1.000 m². Regnes der ligesom for fornikling/forchromning med et ressourceforbrug på i størrelsesordnen 25 mPR pr. kg glansmidler, vil
ressourceforbruget udgøre 250 mPR.
Ressourceforbruget til metaller udgør omkring 2.500 mPR, og da en konservativ vurdering af ressourceforbruget til kemikalier kan udgøre op til 500 mPR, er denne andel ikke uvæsentlig.
D.5.2.3 Varmforzinkning
I Tabel D.27 er vist kemikalie- og vandforbruget for varmforzinkning samt opgjort ressourceforbruget hertil.
Tabel D.27 Kemikalie- og vandforbrug ved varmforzinkning, årlig behandling af 120.000ton
Kemikalietype |
Årligt forbrug
(ton) |
Forbrug pr. ton
(kg) |
mPR pr. kg |
mPR
Pr. ton |
Uorganiske syrer |
1.000 |
8,33 |
0 |
0 |
Uorganiske baser |
60 |
0,50 |
0 |
0 |
Ammoniak |
65 |
0,54 |
0 |
- |
Hydrogenperoxid |
10 |
0,08 |
0 |
0 |
Organiske forbindelser |
25 |
0,21 |
0,04 |
0,008 |
Vandforbrug |
20.000 |
167 |
0 |
0 |
I alt |
0,008 |
I denne opgørelse af ressourceforbrug for kemikalier er der ikke stofgrupper, for hvilke sammensætningen er ukendt. Muligvis vil der være et ganske lille ressourceforbrug ved nogle af de kemikalietyper, der
er sat til 0, men samlet vurderes det, at ressourceforbruget for kemikalierne ikke vil være højere end 10 mPR.
Ressourceforbruget til kemikalier og vand vil således udgøre en meget lille del i forhold til ressourceforbruget til metaller, der udgør omkring 2700 mPR.
D.5.3 Energi
Ved opstilling af en energiopgørelse skal energiforbrug og eventuelt udviklet energi opgøres.
For de tre overfladebehandlingsprocesser skal der medtages energiforbrug til fremstilling af materialer og hjælpestoffer samt energiforbrug ved selve processen.
Energiforbrug til spildevandsrensning på virksomheden er medtaget i energiforbruget under processen. Energiforbrug til affaldsbehandling af kasserede bade og slam er derimod ikke medtaget.
Affaldsbehandlingen består principielt i en fældning af metallerne som hydroxider, presning af slam og efterfølgende deponering. Energiforbruget vurderes til at udgøre i størrelsesordnen 1 til 5 MJ pr. kg.
D.5.3.1 Fornikling/forchromning
Energiforbruget til fremstilling af metaller, kemikalier og vand er opgjort i Tabel D.28. Opgørelsen udtrykker energiforbruget i primær energi.
Tabel D.28 Energiforbrug ved fornikling/forchromning
|
Samlet for-
brug pr. år (ton) |
Forbrug pr.
1000 m² (kg) |
Primært
energiforbrug (MJ/kg) |
Primær energi
pr. 1000 m² (MJ) |
Til metaller |
Nikkel |
130,00 |
111,11 |
190,00 |
21.111,1 |
Kobber |
33 |
28,21 |
90 |
2.538,5 |
Chrom |
10,4 |
8,89 |
39 |
346,7 |
Stål |
9,5 |
8,12 |
40 |
324,8 |
Til kemikalier |
Uorganiske syrer |
110,00 |
94,02 |
50 |
4.700,9 |
Uorganiske baser |
10,00 |
8,55 |
38 |
324,8 |
Org. forbindelser |
55,00 |
47,01 |
60 |
2.820,5 |
Cyanider |
30,00 |
25,64 |
- |
- |
Andet |
65,00 |
55,56 |
- |
- |
Vand |
120.000,00 |
102.560,00 |
0,001 |
102,6 |
Til metaller, kemikalier og vand |
32.167 |
Af Tabel D.29 fremgår det, at det samlede energiforbrug er på 32.200 MJ pr. 1000 m². Langt det største energiforbrug går til udvinding af nikkel.
I opgørelsen mangler energiforbrug til fremstilling af cyanider og andre materialer. Energiforbruget hertil vil antagelig skønsmæssigt ligge på omkring 50 MJ/kg. Er denne antagelse korrekt, vil energiforbruget
til fremstilling af cyanider og andet udgøre i størrelsesordnen 4.000 MJ pr. 1000 m², hvilket vil betyde, at det samlede energiforbrug stiger til 36.000 MJ pr. 1000 m².
Energiforbruget til processen er opgjort til 34.400 MWh for den samlede årlige produktion svarende til 29.400 kWh pr. 1000 m². Hele energiforbruget er elenergi og kan omregnes til primær energi. (1
kWh = 9 MJ). Energiforbruget til processen udgør således 265.000 MJ pr. 1000 m².
Det samlede energiforbrug kan sættes til 300.000 MJ pr. 1.000 m² behandlet overflade.
Der fremkommer omkring 1.200 m³ kasserede bade pr. år. Dette svarer til i størrelsesordnen 1 m³ bad pr. 1000 m² behandlet overflade. Energiforbruget hertil vil ligge på mellem 1.000 og 5.000 MJ og vil
derfor ikke være af væsentlig betydning.
D.5.3.2 Elforzinkning
Energiforbruget til fremstilling af metaller, kemikalier og vand er opgjort i Tabel D.29. Opgørelsen udtrykker energiforbruget i primær energi.
Tabel D.29 Energiforbrug ved elforzinkning
|
Samlet forbrug pr. år (ton) |
Forbrug pr. 1000 m² (kg) |
Primært Energiforbrug (MJ/kg) |
Primær energi pr. 1000 m² (MJ) |
Til metaller |
Zink |
630 |
74,12 |
70 |
5188,2 |
Chrom |
14,1 |
1,66 |
39 |
64,7 |
Stål |
74 |
8,71 |
40 |
348,2 |
Til kemikalier |
Uorganiske syrer |
310 |
36,47 |
50 |
1823,5 |
Uorganiske baser |
300 |
35,29 |
38 |
1341,2 |
Borsyre |
13 |
1,53 |
- |
- |
Salte |
100 |
11,76 |
5 |
58,8 |
Org. forbindelser |
100 |
11,76 |
60 |
705,9 |
Cyanider |
80 |
9,41 |
- |
- |
Andet |
167 |
19,65 |
- |
- |
Vand |
850.000 |
100.000 |
0,001 |
100 |
Til metaller, kemikalier og vand |
9.218 |
Af Tabel D.29 fremgår det, at det samlede energiforbrug er på 9.200 MJ pr. 1000 m². Langt det største energiforbrug går til fremstilling af zink.
I opgørelsen mangler energiforbrug til fremstilling af borsyre, cyanider og andet. Energiforbruget hertil vil antagelig skønsmæssigt ligge på omkring 50 MJ/kg. Er denne antagelse korrekt, vil energiforbruget til
fremstilling af disse materialer udgøre 1.500 MJ pr. 1000 m², hvilket vil betyde, at det samlede energiforbrug stiger til 10.700 MJ pr. 1000 m².
Energiforbruget til processen er opgjort til 22.757 MWh for den samlede årlige produktion svarende til 2.677 kWh pr. 1000 m². Hele energiforbruget er elenergi og kan omregnes til primær energi.
Energiforbruget til processen udgør således 24.096 MJ pr. 1000 m².
Det samlede energiforbrug kan sættes til omkring 35.000 MJ pr. 1000 m².
I Tabel D.1 er vist, at der fremkommer omkring 1.700 m³ kasserede bade pr. år. Dette svarer til i størrelsesordnen 0,2 m³ pr. 1.000 m² behandlet overflade. Energiforbruget hertil vil ligge på mellem 200 til
1.000 MJ pr. 1.000 m² og vil derfor ikke være af væsentlig betydning.
D.5.3.3 Varmforzinkning
Energiforbruget til fremstilling af metaller, kemikalier og vand er opgjort i Tabel D.30. Opgørelsen udtrykker energiforbruget i primær energi.
Tabel D.30. Energiforbrug ved varmforzinkning
|
Samlet for- brug pr. år (ton) |
Forbrug pr. 1 ton gods (kg) |
Primært Energiforbrug (MJ/kg) |
Primær energi pr. ton gods (MJ) |
Til metaller |
Zink |
9.830 |
81,92 |
70 |
5.734,2 |
Til kemikalier |
Uorganiske syrer |
1.000 |
8,33 |
50 |
416,7 |
Uorganiske baser |
60 |
0,50 |
38 |
19,0 |
Ammoniak |
65 |
0,54 |
60 |
32,5 |
Hydrogenperoxid |
10 |
0,08 |
10 |
0,8 |
Organiske forbindelser |
25 |
0,21 |
60 |
12,5 |
Vand |
20.000 |
166,7 |
0,001 |
0,17 |
Til metaller, kemikalier og vand |
6.215,8 |
Af Tabel D.30 fremgår det, at det samlede energiforbrug er på 6.200 MJ pr. ton gods. Langt det største energiforbrug går til udvinding af zink.
Energiforbruget til processen består dels af et elforbrug og dels af et forbrug af råolie. Energiforbruget for 120.000 ton er opgjort til 28.800 MWh el og 1.829 ton råolie svarende til 240 kWh el og 15,2 kg
olie pr. ton gods.
Omregnes procesenergien til primær energi, fås 2.160 MJ fra elforbruget og 576 MJ fra olieforbruget, svarende til i alt 2.736 MJ. I beregningen er forudsat en udnyttelse af olien på 90% og et energiindhold
på 42 MJ/kg.
Det samlede forbrug af primær energi udgør 8.950 MJ pr. ton behandlet gods.
Der vil være et energiforbrug i forbindelse med affaldsbehandlingen, men dette kan ikke estimeres.
| Forside | | Indhold | | Forrige | | Næste | | Top |
Version 1.0 December 2005, © Miljøstyrelsen.
|