| Forside | | Indhold | | Forrige | | Næste |
Ressourceeffektivitet - forslag til definition samt praktiske eksempler på anvendelse af begrebet
6 Galvanisk overfladebehandling
6.1 Introduktion
Inden for galvanoområdet er det valgt at se på tre af de mest almindelige processer til overfladebehandling af stål, nemlig:
- Fornikling/forchromning
- Elektroforzinkning
- Varmforzinkning
Disse processer er ikke ligetil at indpasse i et livscyklusforløb som de foregående aktiviteter, hvor produktet og dets livsforløb kunne identificeres.
Her er valgt at se på processen i et livscyklusperspektiv som beskrevet i kapitel 2. Grafisk kan dette illustreres som vist i figur 6.1.
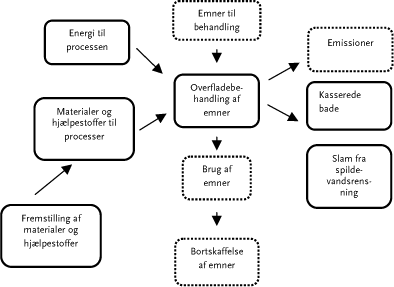
Figur 6.1 Galvanisk overfladebehandling i et livscyklusperspektiv
I det følgende er hver af processerne kortlagt.
6.2 Kortlægning af fornikling/forchromning
Fornikling/forchromning er efter elforzinkning den mest almindelige galvaniske proces i Danmark. Processen udføres af ca. 75 danske virksomheder i større eller mindre skala.
Der bruges årligt 125 ton nikkelanoder til fornikling, hvilket svarer til 1.170.000 m² overflade ved en lagtykkelse på 12 ìm. Der forkobres ca. 25 % af den behandlede overflade svarende til 295.000 m².
Omkring 80% af den samlede behandlede overflade bliver forchromet svarende til ca. 936.000 m².
Kortlægningen er gennemført ud fra en opgørelse baseret på 1.000 m² behandlet overflade. Der er taget udgangspunkt i, at det er stålplader, der er overfladebehandlet.
Procestrinnene ved en fornikling/forchromning er:
- Varm alkalisk affedtning
- Bejdsning i svovlsyre
- Elektrolytisk affedtning
- Forkobring
- Dekapering i svovlsyre
- Fornikling
- Forchromning
Processerne samt opgørelse af råvareforbrug, kemikalier, energi og andet er anført i bilag D.
6.2.1 Opgørelse af mængder for fornikling/forchromning
I det følgende er vist en opgørelse af forbruget af metaller, kemikalier, vand og energi til fornikling/forchromning. Data er beskrevet i bilag D.
Ved 1000 m² overfladebehandling med fornikling/forchromning findes der på emnerne efter overfladebehandlingen som et gennemsnit:
107,53 kg |
Nikkel |
27,04 kg |
Kobber |
1,48 kg |
Chrom |
Disse størrelser er opgjort ud fra en massebalance over forbrug og affaldsmængder ved processen.
6.2.1.1 Materialeforbrug ved fornikling/forchromning
Der er gennemført en opgørelse af, hvilke metaller og kemikalier der anvendes i de enkelte procesbade, og hvilke hovedbestanddele disse kemikalier har. Resultaterne er vist i Tabel 6.1.
Tabel 6.1 Kemikalieforbrug ved fornikling/forchromning
Kemikalie |
Samlet mængde |
Mængde pr.
1.000 m² overflade |
Nikkel |
130 ton |
111,1 kg |
Kobber |
33 ton |
28,2 kg |
Chrom |
10 ton |
8,5 kg |
Jern* |
9,5 ton |
8,1 kg |
Uorganiske syrer, primært svovlsyre |
110 ton |
94,0 kg |
Uorganiske baser, primært natriumhydroxid |
10 ton |
8,6 kg |
Organiske forbindelser som tensider og affedtersalte |
55 ton |
47,0 kg |
Cyanider |
30 ton |
25,6 kg |
Øvrige kemikalier, hvor sammensætningen ikke kendes |
65 ton |
55,6 kg |
* Da der ved renseprocesserne af stålpladerne sker en vis mængde afætsning af jern, som bl.a. findes i affaldsstrømmene, er disse medtaget i materialeforbruget.
Vandforbruget ligger på omkring 120.000 m³ pr. år svarende til ca. 100 m³ pr. 1.000 m² overflade.
6.2.1.2 Energiforbrug
Der anvendes energi til fremstilling af råvarer og til selve overfladebehandlingsprocessen. Det samlede energiforbrug i råvarefasen er vist i tabel 6.2.
Tabel 6.2 Energiforbrug ved fornikling/forchromning
|
Forbrug pr.
1000 m² (kg) |
Primært
energiforbrug
(MJ/kg) |
Primær energi
pr. 1000 m²
(MJ) |
Til metaller: |
Nikkel |
111,11 |
190,00 |
21.111,1 |
Kobber |
28,21 |
90 |
2.538,5 |
Chrom |
8,89 |
39 |
346,7 |
Stål |
8,12 |
40 |
324,8 |
Til kemikalier |
Uorg. syrer |
94,02 |
50 |
4.700,9 |
Uorg. baser |
8,55 |
38 |
324,8 |
Org. forbindelser |
47,01 |
60 |
2.820,5 |
Cyanider |
25,64 |
- |
- |
Andet |
55,56 |
- |
- |
Vand |
102.560,00 |
0,001 |
102,6 |
Til metaller, kemikalier og vand |
32.167 |
Energiforbruget til fremstilling af cyanider og andet er skønnet til i størrelsesordnen 4.000 MJ/1000 m². Det samlede energiforbrug i råvarefasen kan således opgøres til 36.000 MJ primær energi pr. 1.000
m².
Energiforbruget til overfladebehandlingsprocesserne er udelukkende elforbrug og opgjort til 29.400 kWh pr. 1.000 m² overflade. Dette energiforbrug svarer til 265.000 MJ pr. 1.000 m².
Der vil være et mindre energiforbrug ved behandling af affald i form af kasserede bade og slam, men dette er skønnet at udgøre meget lidt og er ikke medtaget.
Det samlede energiforbrug ligger på omkring 300.000 MJ primær energi pr. 1.000 m² behandlet overflade – 12 % i råvarefasen og 88% i produktionsfasen.
6.2.1.3 Godskrivning af materialer og energi
Da metallerne pålagt ved overfladebehandling ikke udvindes særskilt ved oparbejdning af stål, er genvinding ikke medtaget.
Der sker ikke noget oparbejdning af metallerne fra affaldsbehandlingen – slam og kasserede bade.
Da der ikke er nogen muligheder for genvinding af energi, især fra procesbadene, er dette ikke medtaget.
6.2.1.4 Råstofforbrug
Forbruget af råstoffer er estimeret ud fra forbruget af materialer. Opgørelsen er vist i tabel 6.3.
Tabel 6.3 Estimering af forbrug af råstoffer for fornikling/forchromning
Materiale
Behandlet overflade 1.170.000 m² |
Materiale-
forbrug
I alt |
Råstof-
forbrug
kg/kg |
Råstof-
forbrug
I alt |
Råstof-
forbrug
Pr. 1.000 m² |
Nikkel |
130 ton |
9,4 1) |
1.222 ton |
1.044 kg |
Kobber |
33 ton |
3,7 1) |
122 ton |
104 kg |
Chrom |
10 ton |
5,6 1) |
56 ton |
48 kg |
Uorganiske syrer, primært svovlsyre |
110 ton |
0,7 1) |
77 ton |
66 kg |
Uorganiske baser, primært natriumhydroxid |
10 ton |
1,2 1) |
12 ton |
10 kg |
Organiske forbindelser |
55 ton |
1,0 1) |
55 ton |
47 kg |
Cyanider |
30 ton |
2,0 1) |
60 ton |
51 kg |
Øvrige (ukendt sammensætning) |
65 ton |
3,0 2) |
195 ton |
167 kg |
I alt |
|
|
1.799 ton |
1.537 kg |
1): Data fra SigmaPro.
2): Tallet er anslået ud fra en antagelse om, at øvrige kemikalier indeholder en vis mængde metal og en vis mængde organiske forbindelser.
6.2.2 Opgørelse af vurderede mængder for fornikling/forchromning
I det følgende er materialer og energiforbrug omregnet til vurderede størrelse i mPR.
6.2.2.1 Vurdering af materialeforbrug ved fornikling/forchromning
Det væsentligste ressourceforbrug findes for metallerne. Opgørelsen herfor er vist i Tabel 6.4.
Tabel 6.4 Forbrug af metaller ved fornikling/forchromning
|
Nikkel |
Kobber |
Chrom |
Jern/stål |
pr. 1000 m² behandlet overflade |
Forbrug i alt (kg) |
111,11 |
28,21 |
8,89 |
8,12 |
Affald (kg) |
3,58 |
1,16 |
7,41 |
8,12 |
I produkt (kg) |
107,53 |
27,04 |
1,48 |
0,00 |
Ressourceforbrug |
mPR pr. kg |
106 |
16,5 |
12,8 |
Jern: 0,08
Mangan: 0,05 |
Ressourceforbrug |
11777,78 |
465,38 |
113,8 |
Jern: 0,65
Mangan: 0,48 |
I produktet |
11398,17 |
446,21 |
18,9 |
Jern: 0
Mangan: 0 |
Det samlede ressourceforbrug er på 12.358 mPR for metallerne, og i produktet findes 11.863 mPR. Tabet udgør 500 mPR svarende til 4% af ressourceforbruget.
Ressourceforbruget til kemikalierne er skønnet til at udgøre 340 mPR, da en eksakt beregning ikke kunne gennemføres.
Det samlede ressourceforbrug er derfor:
Samlet forbrug |
12.700 mPR |
I produktet |
11.860 mPR |
Tab ved råvareudvinding og produktion |
840 mPR |
Ressourcerne i produktet det vil sige overfladen tabes ligeledes ved oparbejdning af stålpladen.
6.2.2.2 Vurdering af energiforbrug ved fornikling/forchromning
Det samlede energiforbrug er opgjort til 300 GJ pr. 1.000 m² overflade. Fremstilles denne energimængde ud fra olie, svarer det til et forbrug på 289,5 mPR.
6.3 Ressourceeffektivitet for fornikling/forchromning
6.3.1 Ressourceeffektivitet på materialeniveau
6.3.1.1 Materialeforbrug, produktion og brug
Den samlede mængde materialer i form af metaller, der findes i produktet, overfladebehandling af 1.000 m² , er opgjort til 159,2 kg.
Det samlede forbrug af metaller og kemikalier udgør 182,9 kg metaller og 230,8 kg kemikalier.
Ressourceeffektiviteten kan derfor beregnes til:

Den beregnede effektivitet viser, at omkring 2/3 af de anvendte materialer tabes i processen. Tabet forekommer i selve overfladebehandlingsprocessen og udgør dels den samlede mængde kemikalier og dels
en del af metallerne.
Vandforbruget er opgjort til 100 m³ pr. 1.000 m² behandlet overflade.
6.3.1.2 Materialeforbrug, produktion, brug og bortskaffelse
Som tidligere nævnt sker der ingen genvinding af materialer. Effektiviteten
Mmat. P+B+A/N vil derfor være lig Mmat, P+B.
6.3.1.3 Materialeforbrug, hele livscyklus
Råstofforbruget er opgjort til 1.537 kg pr. 1.000 m² overflade. Ressourceeffektiviteten kan derfor beregnes til:

I råstofudvindingen bliver omkring 20-25% af den samlede mængde til anvendelige materialer. For metallerne er udnyttelsesgraden relativt lille (5-10%) og noget større for hjælpestofferne.
6.3.2 Ressourceeffektivitet baseret på vurderet opgørelse
6.3.2.1 Ressourceforbrug, materialer
Den mængde ressourcer, der findes i produktet – overfladebehandling af 1.000 m² stålplade med fornikling/forchromning, udgør 11.860 mPR.
Ressourceeffektiviteten opgjort som materialeeffektivitet, brutto kan beregnes til:

Den beregnede effektivitet afspejler, at det er de mindre knappe ressourcer i form af kemikalier, der tabes i udvinding og i processen.
6.3.2.2 Ressourceforbrug, materialer og energi
Hvis man ser på det samlede materiale og energiforbrug, udgør det samlede vurderede forbrug 12.700 mPR + 290 mPR = 13.000 mPR, og den samlede materiale- og energieffektivitet kan beregnes til:
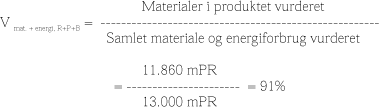
6.3.2.3 Ressourceforbrug, hele livscyklus
Der sker som tidligere nævnt ingen genvinding af materialer eller energi. Dette betyder, at effektiviteten for hele livscyklus, Vmat+energi, R+P+B+A/N vil være lig med Vmat+energi, R+P+B.
6.3.3 Fortolkning
De opgjorte ressourceeffektiviteter er vist i Tabel 6.5.
Tabel 6.5 Beregnede ressourceeffektiviteter for fornikling/forchromning
|
Betegnelse |
Ressource- effektivitet |
Materialeopgørelse |
|
|
• Materialer til produktion og brug |
Mmat, P+B |
39 % |
• Materialer, produktion, brug og bortskaffelse inkl. genanvendelse |
Mmat, P+B+A/N |
39 % |
• Råstoffer i hele livscyklus inkl. genanvendelse |
Mmat. R+P+B+A/N |
10% |
Ressourceopgørelse |
|
|
• Materialer vedrørende råstoffer, produktion og brug |
Vmat, R+P+B |
93 % |
• Materialer og energi vedrørende råstoffer, produktion og brug |
Vmat+energi, R+P+B |
91 % |
• Materialer og energi i hele livscyklus inkl. genvinding |
Vmat+energi, R+P+B+A/N |
91 % |
Af Tabel 6.5 ses det, at der tabes knapt 2/3 af de anvendte materialer i galvaniseringsprocessen (Mmat, P+B). Da beregningen er foretaget for en specifik proces, vil opgørelsen kunne bruges af branchens
virksomheder som sammenligningsgrundlag.
Den anden opgørelse på materialeniveau, Mmat. R+P+B+A/N omfatter dels materialetab i selve processen, men også tab ved udvinding af metaller og forarbejdning af kemikalier. Denne beregning vil
antageligt kun kunne anvendes på et mere overordnet plan.
Ses der på de effektiviteter, der er baseret på vurderede opgørelser (mPR), vil man få et fingerpeg, om det er knappe eller rigelige ressourcer, der tabes i livsforløbet. Metaller og især nikkel vægter højt i
denne opgørelse. Af de beregnede størrelser ses det, at effektiviteten er relativt høj, og at det er mindre knappe ressourcer, der primært tabes. En øget udnyttelse af primært nikkel, men også kobber og
chrom vil have en relativ stor indflydelse på ressourceeffektiviteten.
De to ressourceeffektiviteter, Vmat, R+P+B og Vmat+energi, R+P+B er meget lig hinanden, hvilket viser, at energiforbruget – både til udvinding af råstoffer og i galvaniseringsprocessen – ud fra et
ressourcesynspunkt er af mindre betydning.
Det er i opgørelserne forudsat, at der ikke finder genvinding sted af metallerne eller af hjælpestofferne. En genvinding af metallerne vil øge ressourceeffektiviteten – i mindre grad for de vægtbaserede
opgørelser og i højere grad for de vurderede opgørelser.
6.3.4 Affaldsminimering
Af de beregnede ressourceeffektiviteter ses det, at mængdemæssigt tabes der en stor del materiale i råstofudvindingen og i produktionen. Af de vurderede opgørelser ses det, at der tabes en mindre mængde
knappe ressourcer, og at energiforbruget i forhold til materialeforbruget er af mindre betydning. Lægges der vægt på knappe, miljøbelastende stoffer vil det være metallerne (nikkel, kobber og chrom), der
skal fokuserers på.
I det følgende trækkes en række væsentlige forhold frem.
6.3.4.1 Badkemikalier
I fornikling/forchromningsprocessen anvendes en række syrer, baser, cyanider og andre kemikalier. Disse kan ikke undværes, hvis overfladebehandlingen skal forløbe tilfredsstillende. Badene bliver sjældent
skiftet, da de løbende vedligeholdes, men der kan være behov for det efter uheld, driftsforstyrrelser og lignende. De kasserede bade vil i overvejende grad blive sendt til Kommunekemi, hvor de afgiftes ved,
at cyaniden omdannes, hvorefter metallerne fældes i alkalisk miljø som metalhydroxider. Det dannede slam afvandes og deponeres. Det er ikke i dag teknisk/økonomisk muligt at oparbejde slammet, da det
består af en blanding af en række metaller.
6.3.4.2 Metallerne
Ud fra et ressourcesynspunkt er det mest problematisk at anvende nikkel. Målt i mPR ligger værdien for nikkel ca. 10 gange højere end for kobber og chrom.
Metallerne nikkel, kobber og chrom udnyttes ikke lige godt i processerne. Af tabel 6.6 ses det, at tabet af de enkelte metaller er meget forskelligt.
Tabel 6.6 Tab af metaller ved fornikling/forchromning
|
Mængde på emnet
pr. 1.000 m² |
Tab pr. 1.000 m² |
Tab i % af
mængde på emnet |
Nikkel |
107,53 kg |
3,57 kg |
3,3 % |
Kobber |
27,04 kg |
1,16 kg |
4,3 % |
Chrom |
1,48 kg |
7,02 kg |
474 % |
Som det ses af tabel 6.6, er der en relativ høj udnyttelse af nikkel og kobber i de galvaniske processer, hvorimod tabet ved pålægning af chrom er meget stort.
Det bør derfor overvejes af hensyn til ressourcetab og affaldsminimering, om chromateringen kan gøres mere effektiv, og/eller om anvendelse af chromatering kan minimeres.
Ved udvinding af metallerne tabes en del materiale. Metallerne i malmen findes som metaloxider eller –sulfider. Der kan være mere eller mindre jern i malmen. Ved oparbejdningen renses malmen ,og
metalionerne omdannes til metal. Tabet varierer fra malmtype til malmtype. Mulighederne for affaldsminimering kan dog ikke vurderes.
Ved kassering af produktet, - den overfladebehandlede plade eller genstand, tabes alt det pålagte metal. Stålet oparbejdes, men da nikkel, chrom og kobber udgør en meget lille del udnyttes dette ikke. I
Tabel 6.7 er vist, hvilke ressourcer der tabes ved oparbejdning af 1 m² stålplade med en godstykkelse på 5 mm.
Tabel 6.7 Ressourcer i en 1 m² jernplade der er forniklet/forchromet
|
Mængde pr. 1 m² |
Ressourceforbrug
pr. kg |
Ressourceforbrug
i 1 m² plade |
Jern* |
40 kg |
0,08 mPR |
3,200 mPR |
Nikkel |
107 gram |
116 mPR |
12,412 mPR |
Kobber |
27 gram |
16,5 mPR |
0,446 mPR |
Chrom |
1,5 gram |
12,8 mPR |
0,019 mPR |
* En jernplade på 1 m² med en godstykkelse på 5 mm har et volumen på 0,005 m³, og med en massefylde på 7,9 vejer pladen ca. 40 kg.
I forhold til Tabel 6.7 skal det bemærkes, at ressourcerne i jernpladen oparbejdes, og mere end 90% genvindes. Nikkel som ressource er af væsentlig større betydning, men tabes i oparbejdningen. Nikkel
kan måske til en vis grad udnyttes i det oparbejdede jern/stål som legeringsmetal, men bliver ikke med den i dag anvendte teknologi oparbejdet til rent metal.
6.3.4.3 Vandforbrug og spildevand
Vandforbruget til fornikling/forchroming bruges primært som skyllevand. Der bruges omkring 100 liter vand pr. m² behandlet overflade.
Der har gennem en del år været fokus på at nedsætte vandforbruget ved ændrede skylleteknikker. Det nævnes, at en af årsagerne til, at disse ikke er mere udbredt, er, at nyere teknikker er mere
pladskrævende og kræver mere styring.
Skyllevandet renses på virksomheden inden udledning, og hovedparten af metallerne findes i slam, der dannes ved rensningen. Slammet er en blanding af flere metalhydroxider og oparbejdes i dag ikke af
teknisk/økonomiske grunde, da slammet ud over de mere værdifulde metaller indeholder en hel del jern.
6.3.4.4 Energi
Energiforbruget til overfladebehandlingsprocessen udgør 88% af det samlede energiforbrug, - den resterende del går til udvinding af materialer.
Energiforbruget til processen er udelukkende el, hvor der forbruges 29 kWh pr. m² overflade, svarende til 300 MJ primær energi. Omregnes dette til forbrug af olieressourcer, udgør det omkring 0,29 mPR
pr. m². Da elektriciteten med sikkerhed produceres i Danmark, og der her hovedsagelig anvendes kul som energiressource, vil ressourcetrækket i stedet blive 1/5, da kul har en meget længere
forsyningshorisont end olie.
Til overfladebehandling af en jernplade bruges 7,5 MJ/kg. Da 1 m² jernplade vejer ca. 40 svarer det til et energiforbrug på 300 MJ. Til sammenligning kan anføres, at presning af stål kræver omkring 30
MJ/kg, og at trykstøbning ligger på mellem 20-50 MJ/kg.
Hvad enten el-forbruget baseres på kul eller olie, og det vurderes, at der bruges store mængder energi i processen, er energimængden i forhold til materialemængden meget lille.
6.3.4.5 Samlet prioritering
Ud fra et ressourcemæssigt synspunkt er nikkel et problematisk metal at anvende til overfladebehandling.
Fornikling/forchroming har en række fordele. Det giver en overflade af høj kvalitet og et pænt udseende, men
- Metallerne og især chrom, der forekommer som affald (primært slam)fra overfladebehandlingsprocessen, kan ikke genvindes.
- Metallerne og især nikkel, der findes på det kasserede produkt, kan ikke genvindes.
- Der anvendes en række hjælpekemikalier i processen, som tabes.
Der findes i dag ikke tekniske løsninger, som er økonomisk mulige for at genvinde metallerne.
6.3.5 Sammenligning med øvrige opgørelser
Overfladebehandlingsprocessen fornikling/forchromning, som den udføres i Danmark, er optimeret med hensyn til udnyttelse af metaller, energi- og vandforbrug og er således typisk for europæiske forhold.
6.3.5.1 Direkte materialeinput
Det er ikke muligt at foretage en sammenligning mellem de opgjorte mængder af materialer og data for DMI, da DMI ikke opgøres på procesniveau.
6.3.5.2 Totale materialeinput
I det følgende er søgt estimeret det totale materialeinput, baseret på Wuppertal's MIPS-data, se Tabel 6.8.
Tabel 6.8 Estimering af totalt materialeinput for fornikling/forchromning
Materiale
Behandlet overflade 1.170.000 m² |
Materiale-
forbrug
I alt |
Råstof-
forbrug
kg/kg |
Råstof-
forbrug
I alt |
Råstof-
forbrug
Pr. 1.000 m² |
Nikkel |
130 ton |
138,6 |
18.018 ton |
15.400 kg |
Kobber |
33 ton |
4,0 |
132 ton |
113 kg |
Chrom |
10 ton |
- 1) |
- |
- |
Uorganiske syrer, primært svovlsyre |
110 ton |
0,5 2) |
55 ton |
47 kg |
Uorganiske baser, primært natriumhydroxid |
10 ton |
1 2) |
10 ton |
9 kg |
Organiske forbindelser |
55 ton |
5 2) |
275 ton |
235 kg |
Cyanider |
30 ton |
10 2) |
300 ton |
256 kg |
Øvrige (ukendt sammensætning) |
65 ton |
10 2) |
650 ton |
556 kg |
I alt |
|
|
|
16.600 kg |
1): Ingen data.
2): Tallet er anslået ud fra forskellige kemiske forbindelser.
Som det fremgår af Tabel 6.8 mangler data for chrom. Materialeinputtet vil derfor være i størrelsesordnen 17.000 kg pr. 1.000 m² overflade.
I nærværende opgørelse er råstofforbruget opgjort til ca. 1/10 – 1.500 kg. Begge typer af opgørelser skulle i princippet være ens og medtage alle indirekte strømme.
Den væsentligste forskel ligger i opgørelsen for nikkel, hvor Wuppertal har opgjort materialeinputtet til at være mere end 10 gange så stort som data fra SigmaPro. Wuppertals data for de øvrige materialer
ligger også noget over de her anvendte LCA-data for de øvrige materialer.
6.4 Kortlægning af elforzinkning
Elforzinkning er den mest almindelige galvaniske proces i Danmark. Processen udføres af ca. 90 danske virksomheder i større eller mindre skala.
Ved elforzinkning foretages først en rengøring af emnerne (affedtning og bejdsning), hvorefter der elektrolytisk påføres et zinklag på 5-20 m. Lagtykkelsen er typisk mindst for tromlevarer (små emner), mens
større emner på stativer typisk påføres lagtykkelser på 12-20 m. Der forbruges årligt ca. 600 ton zinkanoder, hvilket svarer til overfladebehandling af 8,5 mio. m² overflade.
Kortlægningen er baseret på en opgørelse ud fra 1.000 m² behandlet overflade. Der er taget udgangspunkt i, at det er stålplader, der er overfladebehandlet.
Procestrinnene ved en elforzinkning er:
- Alkalisk affedtning
- Bejdsning i svovlsyre
- Elektrolytisk affedtning
- Dekapering i saltsyre
- Forzinkning
- Passivering i chrom
Processerne samt opgørelse af råvareforbrug, kemikalier, energi og andet er anført i bilag D.
6.4.1 Opgørelse af mængder for elforzinkning
I det følgende er vist en opgørelse af metaller, kemikalier, vand og energi til elforzinkning. Data er beskrevet i bilag D.
Ved 1.000 m² overfladebehandling med elforzinkning findes der på emnerne efter overfladebehandling som gennemsnit:
70,01 kg |
zink |
0,35 kg |
chrom |
Disse størrelser er opgjort ud fra en massebalance over forbrug og affaldsmængder ved processen.
6.4.1.1 Materialeforbrug ved elforzinkning
Der er gennemført en opgørelse af, hvilke metaller og kemikalier der anvendes i de enkelte procesbade, og hvilke hovedbestanddele disse kemikalier har. Resultaterne er vist i Tabel 6.9.
Tabel 6.9 Kemikalieforbrug ved elforzinkning
Kemikalie |
Samlet
mængde |
Mængd
pr. 1.000 m²
overflade |
Zink |
630 ton |
74,1 kg |
Chrom |
14,1 ton |
1,7 kg |
Jern * |
74 ton |
8,7 kg |
Uorganiske syrer, primært svovlsyre |
310 ton |
36,5 kg |
Uorganiske baser, primært natriumhydroxid |
300 ton |
35,3 kg |
Borsyre |
13 ton |
1,5 kg |
Salte, primært kaliumchlorid |
100 ton |
11,8 kg |
Organiske forbindelser, som tensider og affedtersalte |
100 ton |
11,8 kg |
Cyanider |
80 ton |
9,4 kg |
Øvrige kemikalier, hvor sammensætningen ikke kendes |
167 ton |
19,6 kg |
* Da der ved renseprocesserne af stålpladerne sker en vis mængde afætsning af jern, som bl.a. findes i affaldsstrømmene, er disse medtaget i materialeopgørelsen.
Vandforbruget ligger på i størrelsesordnen 850.000 m³/år svarende til 100 m³ pr. 1.000 m² behandlet overflade.
6.4.1.2 Energiforbrug
Der anvendes energi til fremstilling af råvarer og til selve overfladebehandlingsprocessen. Det samlede energiforbrug i råvarefasen er vist i Tabel 6.8.
Tabel 6.10 Energiforbrug ved elforzinkning
|
Samlet
forbrug
pr. år (ton) |
Forbrug
pr. 1000 m²
(kg) |
Primært
Energiforbrug
(MJ/kg) |
Primær
energi
pr. 1000 m²
(MJ) |
Til metaller |
Zink |
630 |
74,12 |
70 |
5188,2 |
Chrom |
14,1 |
1,66 |
39 |
64,6 |
Stål |
74 |
8,71 |
40 |
348,2 |
Til kemikalier |
Uorg. syrer |
310 |
36,47 |
50 |
1823,5 |
Uorg. baser |
300 |
35,29 |
38 |
1341,2 |
Borsyre |
13 |
1,53 |
- |
- |
Salte |
100 |
11,76 |
5 |
58,8 |
Org. forbindelser |
100 |
11,76 |
60 |
705,9 |
Cyanider |
80 |
9,41 |
- |
- |
Andet |
167 |
19,65 |
- |
- |
Vand |
850.000 |
100.000 |
0,001 |
100 |
Til metaller, kemikalier og vand |
9.218 |
For de materialer, der ikke er medtaget i opgørelsen i, er energiforbruget skønnet til 1.500 MJ, hvilket betyder, at det samlede energiforbrug stiger til 10.700 MJ pr. 1.000 m² overflade.
Energiforbruget til processerne er udelukkende elforbrug og er opgjort til 2.677 kWh pr. m² overflade. Dette elforbrug svarer til 24.096 MJ primær energi pr. 1.000 m² overflade.
Der vil være et mindre energiforbrug ved behandling af affald i form af kasserede bade og slam, men dette er skønnet at udgøre meget lidt og er ikke medtaget.
Det samlede energiforbrug ligger på 34.800 MJ primær energi pr. m² behandlet overflade – ca. 30% i råvarefasen og ca. 70% i produktionsfasen.
6.4.1.3 Godskrivning af materialer og energi
Da metallerne pålagt ved overfladebehandling ikke udvindes særskilt ved oparbejdning af stål, er genvinding ikke medtaget.
Der er ingen oparbejdning af metallerne fra affaldsbehandlingen – slam og kasserede bade.
Da der ikke er nogen mulighed for genvinding af energi, især fra procesbadene, er dette ikke medtaget.
6.4.1.4 Opgørelse af råstofforbrug
Ud fra det materialeforbrug, der er opgjort i Tabel 6.9, er forbruget af råstoffer estimeret i Tabel 6.9.
Tabel 6.11 Estimering af forbrug af råstoffer for elforzinkning
Materiale
Behandlet overflade 8.500.00 m² |
Materiale-
forbrug
I alt |
Råstof-
forbrug
kg/kg |
Råstof-
forbrug
I alt |
Råstof-
forbrug
Pr. 1.000 m² |
Zink |
630 ton |
3,1 1) |
1.953 ton |
230 kg |
Chrom |
15 ton |
5,6 1) |
84 ton |
10 kg |
Uorganiske syrer, primært svovlsyre |
310 ton |
0,7 1) |
217 ton |
26 kg |
Uorganiske baser, primært natriumhydroxid |
300 ton |
1,2 1) |
360 ton |
42 kg |
Borsyre og salte |
113 ton |
1,0 3) |
113 ton |
13 kg |
Organiske forbindelser |
100 ton |
1,0 1) |
100 ton |
12 kg |
Cyanider |
80 ton |
2,0 1) |
160 ton |
19 kg |
Øvrige (ukendt sammensætning) |
167 ton |
3,0 2) |
501 ton |
59 kg |
I alt |
|
|
|
411 kg |
1): Data fra SigmaPro.
2): Tallet er anslået ud fra en antagelse om, at øvrige kemikalier indeholder en vis mængde metal og en vis mængde organiske forbindelser.
3) Data herfor er ukendt og derfor en anslået en værdi.
6.4.2 Opgørelse af vurderede mængder for elforzinkning
I det følgende er materiale- og energiforbrug omregnet til vurderede størrelser i mPR.
6.4.2.1 Vurdering af materialeforbrug ved elforzinkning
Det væsentligste ressourceforbrug findes for metallerne. Opgørelsen herfor er vist i Tabel 6.12.
Tabel 6.12 Forbrug af metaller ved elforzinkning
|
Zink |
Chrom |
Jern/stål |
Pr. 1000 m² overflade |
Forbrug (kg) |
74,12 |
1,66 |
8,71 |
Affald (kg) |
4,11 |
1,30 |
8,71 |
I produkt (kg) |
70,01 |
0,36 |
0,00 |
Ressourceforbrug |
mPR pr. kg |
33 |
12,8 |
Jern: 0,08
Mangan: 0,05 |
Ressourceforbrug |
2445,88 |
21,23 |
Jern: 0,70
Mangan: 0,44 |
I produkt |
2310,39 |
4,58 |
Jern: 0
Mangan: 0 |
Det samlede ressourceforbrug er på 2.468 mPR for metallerne, og i produktet findes 2.315 mPR. Tabet udgør 153 mPR svarende til 6 % af ressourceforbruget.
Ressourceforbruget til kemikalierne er skønnet til at udgøre 250 mPR, da en eksakt beregning ikke kunne gennemføres.
Det samlede ressourceforbrug er derfor:
Samlet forbrug |
2.720 mPR |
I produktet |
2.320 mPR |
Tab ved råvareudvinding og produktion |
500 mPR |
Ressourcerne i produktet – overfladen – tabes ligeledes ved oparbejdning af produktet – stålpladen.
6.4.2.2 Vurdering af energiforbrug ved elforzinkning
Det samlede energiforbrug er opgjort til 34,8 GJ pr. m² overflade. Fremstilles denne energimængde ud fra olie, svarer det til et forbrug på 34,0 mPR.
6.5 Ressourceeffektivitet for elforzinkning
6.5.1 Ressourceeffektivitet på materialeniveau
6.5.1.1 Materialeforbrug, produktion og brug
Den samlede mængde materialer i form af metaller til produktet, overfladebehandling af 1.000 m², er opgjort til 70,36 kg.
Det samlede forbrug af metaller og kemikalier udgør 84,5 kg metaller og 125,9 kg kemikalier. Ressourceeffektiviteten kan derfor beregnes til:

Den beregnede effektivitet afspejler, at alle kemikalierne og en del af metallerne tabes i galvaniseringsprocessen. En del vil findes i affald, og en del vil blive neutraliseret og ledt ud med spildevandet.
Vandforbruget er opgjort til 100 m³ pr. 1.000 m² behandlet overflade.
6.5.1.2 Materialeforbrug, produktion, brug og bortskaffelse
Som tidligere nævnt sker der ingen genvinding af materialer. Effektiviteten
MMat, P+B+A/N vil derfor være lig MMat, P+B.
6.5.1.3 Materialeforbrug, hele livscyklus
Råstofforbruget er opgjort til 411 kg pr. 1.000 m² overflade. Ressourceeffektiviteten kan derfor beregnes til:

Ved udvindingen udnyttes omkring 50% af råstofmængden – mindre for metallerne og mere for kemikalierne. Metallerne udgør i materialeopgørelsen omkring 1/3, mens de i råstofopgørelsen udgør mere end
50%.
6.5.2 Ressourceeffektivitet baseret på vurderet opgørelse
6.5.2.1 Ressourceforbrug, materialer
Den mængde ressourcer, der findes i produktet – overfladebehandling af 1.000 m² stålplade med elforzinkning udgør 2.320 mPR. Ressourceeffektiviteten opgjort som materialeeffektivitet, brutto kan
beregnes til:

Den opgjorte effektivitet afspejler, at det er de mindre knappe ressourcer i form af kemikalier, der tabes.
6.5.2.2 Ressourceforbrug, materialer og energi
Hvis man ser på det samlede materiale og energiforbrug, udgør det samlede vurderede forbrug 2.720 mPR + 34 mPR = 2.754 mPR, og den samlede materiale- og energieffektivitet, brutto kan beregnes til:
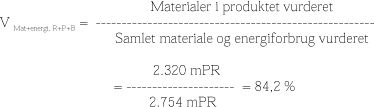
Den lille forskel i de to effektiviteter afspejler, at energiforbruget til både udvinding og overfladebehandlingsprocessen er relativ lille i forhold til materialeforbruget, når der anlægges en knaphedsbetragtning.
6.5.2.3 Ressourceforbrug, hele livscyklus
Der sker som tidligere nævnt ingen genvinding af materialer eller energi. Dette betyder, at effektiviteten for hele livscyklus Vmat+energi, R+P+B+A/N vil være lig Vmat+energi, R+P+A/N.
6.5.3 Fortolkning
De opgjorte ressourceeffektiviteter er vist i tabel 6.13.
Tabel 6.13 Beregnede ressourceeffektiviteter for elforzinkning
|
Betegnelse |
Ressource- effektivitet |
Materialeopgørelse |
|
|
• Materialer til produktion og brug |
Mmat, P+B |
33 % |
• Materialer, produktion, brug og bortskaffelse inkl. genanvendelse |
Mmat, P+B+A/N |
33 % |
• Råstoffer i hele livscyklus inkl. genanvendelse |
Mmat. R+P+B+A/N |
17 % |
Ressourceopgørelse |
|
|
• Materialer vedrørende råstoffer, produktion og brug |
Vmat, R+P+B |
85 % |
• Materialer og energi vedrørende råstoffer, produktion og brug |
Vmat+energi, R+P+B |
84 % |
• Materialer og energi i hele livscyklus inkl. genvinding |
Vmat+energi, R+P+B+A/N |
84 % |
Af tabel 6.13 ses det, at der tabes 2/3 af de anvendte materialer i galvaniseringsprocessen (Mmat, P+B ). Da beregningen er foretaget for en specifik proces, vil opgørelsen kunne bruges af branchens
virksomheder som sammenligningsgrundlag.
Den anden opgørelse på materialeniveau, Mmat. R+P+B+A/N, omfatter dels materialetab i selve processen, men også tab ved udvinding af metaller og forarbejdning af kemikalier. Denne beregning vil
antageligt kun kunne anvendes på et mere overordnet plan.
Ses der på de effektiviteter, der er baseret på vurderede opgørelser (mPR), vil man få et fingerpeg, om det er knappe eller rigelige ressourcer, der tabes i livsforløbet. Metaller og især zink vægter højt i
denne opgørelse. Af de beregnede størrelser ses det, at effektiviteten er relativt høj, og at det er mindre knappe ressourcer, der primært tabes. En øget udnyttelse af zink og til en vis grad chrom vil have en
relativ stor indflydelse på ressourceeffektiviteten.
De to ressourceeffektiviteter, Vmat, R+P+B og Vmat+energi, R+P+B er meget lig hinanden, hvilket viser, at energiforbruget både til udvinding af råstoffer og i galvaniseringsprocessen ud fra et
ressourcesynspunkt er af mindre betydning.
Det er i opgørelserne forudsat, at der ikke finder genvinding sted af metallerne eller af hjælpestofferne. En genvinding af metallerne vil øge ressourceeffektiviteten – i mindre grad for de vægtbaserede
opgørelser og i højere grad for de vurderede opgørelser.
6.5.4 Affaldsminimering
Af de beregnede ressourceeffektiviteter ses det at mængdemæssigt tabes der en stor del materiale i råstofudvindingen og i produktionen. Af de vurderede opgørelser ses det, at der tabes en mindre mængde
knappe ressourcer, og at energiforbruget i forhold til materialeforbruget er af mindre betydning. Lægges der vægt på knappe, miljøbelastende stoffer vil det være zink, der skal fokuserers på.
I det følgende trækkes en række væsentlige forhold frem.
6.5.4.1 Badkemikalier
Samme forhold som under fornikling/forchromning, se afsnit 6.3.4.1.
6.5.4.2 Zink og chrom
Til elforzinkning anvendes store mængder zink og små mængder chrom. Tabet af de to metaller er meget forskelligt, som det fremgår af tabel 6.14.
Tabel 6.14 Tab af metaller ved elforzinkning
|
Mængde på emnet pr. 1.000 m² |
Tab pr. 1.000 m² |
Tab i % af mængde på emnet |
Zink |
70,01 kg |
4,09 kg |
5,8 % |
Chrom |
0,35 kg |
1,35 kg |
385 % |
Som det ses af tabel 6.14, er der en relativ høj udnyttelse af zink, hvorimod tabet ved pålægning af chrom er meget stort.
Ved udvinding af metallerne tabes en del materiale. Metallerne i malmen er forbindelser af metallet som oxider eller sulfider. Ved oparbejdningen renses malmen, og metalionerne omdannes til metal. Tabet
varierer fra malmtype til malmtype. Mulighederne for affaldsminimering kan dog ikke vurderes.
Ved kassering af produktet, den overfladebehandlede plade eller genstand, tabes det pålagte metal. Stålet oparbejdes, men da zink udgør en meget lille del, udnyttes det ikke. I tabel 6.15 er vist hvilke
ressourcer, der tabes ved oparbejdning af 1 m² stålplade med en godstykkelse på 5 mm.
Da zink har et kogepunkt på omkring 900°C, vil zinken under oparbejdningen i overvejende grad findes i slagge og støv fra afgangsluften. Det vil derfor i nogen grad være muligt at oparbejde zinken. Om det
gøres vides ikke.
Tabel 6.15 Ressourcer i en 1 m² jernplade der er forniklet/forchromet
|
Mængde pr. 1 m² |
Ressourceforbrug pr. kg |
Ressourceforbrug i 1 m² plade |
Jern* |
40 kg |
0,08 mPR |
3,200 mPR |
Zink |
70,01 gram |
33 mPR |
2.310 mPR |
Chrom |
0,35 gram |
12,8 mPR |
0,004 mPR |
* En jernplade på 1 m² med en godstykkelse på 5 mm har et volumen på 0,005 m³ og med en massefylde på 7,9 vejer pladen ca. 40 kg
6.5.4.3 Vandforbrug og spildevand
Vandforbruget til elforzinkning bruges primært til skyllevand. Der bruges omkring 100 liter pr. m² behandlet overflade.
Se i øvrigt kommentater under fornikling/forchromning, afsnit 6.3.4.3.
6.5.4.4 Energi
Energiforbruget til overfladebehandlingsprocessen udgør 70% af det samlede energiforbrug. Den resterende del går til udvinding af materialer.
Energiforbruget til processen er udelukkende el, hvor der forbruges 2,7 kWh pr. m² overflade, svarende til 24 MJ primær energi. Energiforbruget til el-forzinkning ligger således på ca. 10% af
energiforbruget til fornikling/forchromning.
Også for elforzinkning er energiforbruget lille i forhold til materialeforbruget, når begge opgørelser omregnes til ressourceforbrug i mPR.
6.5.4.5 Samlet prioritering
Ud fra et ressourcemæssigt synspunkt kan det være noget problematisk at anvende zink til overfladebehandling, såfremt det ikke genvindes.
Elforzinkning har en række fordele. Det giver en overflade af høj kvalitet og et pænt udseende, men
- Zink og chrom, der forekommer som affald (primært slam) fra overfladebehandlingsprocessen, genvindes ikke.
- Zink fra det kasserede produkt bør genvindes i så høj grad som muligt.
- Der anvendes en række hjælpekemikalier i processen, som tabes.
Det vides ikke i, hvor høj grad zink genvindes fra oparbejdning af stål, og det er derfor et forhold, der bør fokuseres på.
6.5.5 Sammenligning med øvrige opgørelser
Overfladebehandlingsprocessen elforzinkning, som den udføres i Danmark, er optimeret med hensyn til udnyttelse af metaller, energi- og vandforbrug og er således typisk for europæiske forhold.
6.5.5.1 Direkte materialeinput
Det er ikke muligt at foretage en sammenligning mellem de opgjort mængder af materialer og data for DMI, da DMI ikke opgøres på procesniveau.
6.5.5.2 Totale materialeinput
I det følgende er søgt estimeret det totale materialeinput, baseret på Wuppertal's MIPS-data, se tabel 6.16.
Tabel 6.16 Estimering af materialeinput for elforzinkning
Materiale
Behandlet overflade 8.500.00 m² |
Materiale-
forbrug
I alt |
Råstof-
forbrug
kg/kg |
Råstof-
forbrug
I alt |
Råstof-
forbrug
Pr. 1.000 m² |
Zink |
630 ton |
23,1 |
14.553 ton |
1.712 kg |
Chrom |
15 ton |
- |
- |
- |
Uorganiske syrer, primært svovlsyre |
310 ton |
0,5 |
155 ton |
18 kg |
Uorganiske baser, primært natriumhydroxid |
300 ton |
1 |
300 ton |
35 kg |
Borsyre og salte |
113 ton |
1 1) |
113 ton |
13 kg |
Organiske forbindelser |
100 ton |
5 1) |
500 ton |
59 kg |
Cyanider |
80 ton |
10 1) |
800 ton |
94 kg |
Øvrige (ukendt sammensætning) |
167 ton |
10 1) |
1670 ton |
196 kg |
I alt |
|
|
|
2.127 kg |
1) Anslået ud fra data om andre kemiske forbindelser.
Som det fremgår af tabel 6.16, mangler der data for chrom. Materialeinputtet vil derfor være i størrelsesordnen 2.200 kg pr. 1.000 m² overflade.
I nærværende opgørelse er råstofforbruget opgjort til ca. 400 kg eller knapt 1/5 af det opgjorte materialeinput. Begge typer af opgørelser skulle i princippet være ens og medtage alle indirekte strømme. Den
væsentligste forskel ligger i opgørelsen for zink, hvor Wuppertal har opgjort materialeinputtet til at være omkring 8 gange så stort som data fra SigmaPro. Wuppertals data for de øvrige materialer ligger også
noget over de her anvendte LCA-data for de øvrige materialer.
6.6 Kortlægning af varmforzinkning
Ved varmforzinkning dyppes stålemner i et smeltet zinkbad ved ca. 460°C, hvorved der pålægges et zinklag med en lagtykkelse på 60-100 m, hvilket giver en langt bedre korrosionsbeskyttelse, end der
opnås ved elektrolytisk forzinkning, hvor man normalt arbejder med lagtykkelser på 5-20 m. Derfor anvendes varmforzinkning især til stålkonstruktioner, der anvendes udendørs, og metoden kan anvendes
på meget store emner op til 10-15 meters længde.
I Danmark findes 20 varmforzinkningsvirksomheder, men flere af virksomhederne har samme ejer. Det skønnes, at halvdelen af virksomhederne laver ca. 85% af produktionen. Der varmforzinkes
skønsmæssigt 120.000 ton gods årligt, og i 2001 var det samlede zinkforbrug for danske varmforzinkere på 9817 ton svarende til, at der i gennemsnit påføres ca. 8,2% zink i forhold til godsets vægt.
Kortlægningen er baseret på en opgørelse af 1 ton behandlet gods. Der er taget udgangspunkt i at det er stålplade, der er overfladebehandlet.
Procestrinnene ved varmforzinkning er:
- Alkalisk affedtning
- Bejdsning i saltsyre
- Flusning
- Tørring
- Forzinkning
- Køling
- Pudsning og afgratning
Processerne samt opgørelse af råvareforbrug, kemikalier, energi og andet er anført i bilag D.
6.6.1 Opgørelse af mængder for varmforzinkning
I det følgende er vist en opgørelse af metaller, kemikalier, vand og energi til varmforzinkning. Data er beskrevet i bilag D.
Ved behandling af 1 ton gods pålægges der i gennemsnit en zinkmængde på 64,4 kg. Denne mængde er opgjort ud fra data om forbrug og affaldsmængder.
6.6.1.1 Materialeforbrug ved varmforzinkning
Der er gennemført en opgørelse over forbruget af zink og kemikalier, der anvendes i de enkelte procesbade, og hvilke hovedbestanddele disse kemikalier har. Resultaterne er vist i tabel 6.17.
Tabel 6.17 Materialeforbrug ved varmforzinkning
Kemikalie |
Samlet mængde |
Mængde pr.
ton
behandlet
gods |
Zink |
9.830 ton |
81,9 kg |
Uorganiske syrer |
1.000 ton |
8,33 kg |
Uorganiske baser |
60 ton |
0,50 kg |
Ammoniak |
65 ton |
0,54 kg |
Hydrogenperoxid |
10 ton |
0,08 kg |
Organiske forbindelser |
25 ton |
0,21 kg |
Det samlede vandforbrug er opgjort til 15-20.000 m³ pr. år. Dette svarer til et forbrug på ca. 0,17 m³ pr. ton behandlet gods.
6.6.1.2 Energiforbrug
Der anvendes energi til fremstilling af råvarer og til selve overfladebehandlingsprocessen.
Det samlede energiforbrug i råvarefasen er vist i tabel 6.18.
Tabel 6.28 Energiforbrug ved varmforzinkning
|
Samlet forbrug
pr. år (ton) |
Forbrug pr. 1
ton gods (kg) |
Primært Energi
forbrug (MJ/kg) |
Primær energi
pr. ton gods (MJ) |
Til metaller |
Zink |
9.830 |
81,92 |
70 |
5.734,2 |
Til kemikalier |
Uorganiske syrer |
1.000 |
8,33 |
50 |
416,7 |
Uorganiske baser |
60 |
0,50 |
38 |
19,0 |
Ammoniak |
65 |
0,54 |
60 |
32,5 |
Hydrogenperoxid |
10 |
0,08 |
10 |
0,8 |
Organiske forbindelser |
25 |
0,21 |
60 |
12,5 |
Vand |
20.000 |
166,7 |
0,001 |
0,17 |
Til metaller, kemikalier og vand |
6.215,8 |
Til overfladebehandlingsprocessen bruges dels el og dels olie som energikilde. Pr. ton behandlet gods bruges i gennemsnit 240 kWh el og 15,2 kg olie.
Der kan også anvendes gas, og det forventes, at en del af olieforbruget med tiden vil blive erstattet af gas. Der haves dog ikke en opgørelse over, hvor stort gasforbruget er og alt vil i denne opgørelse blive
regnet som olie. Det skal bemærkes, at ressourcemæssigt vil forbrug af olie og gas vægte omtrent ens. Det der er væsentligt at skelne mellem er forbruget af elektricitet og olie/gas.
Omregnes procesenergien til primær energi kan forbruget opgøres til 2.160 MJ baseret på el og 576 MJ baseret på olie svarende til i alt 2.736 MJ pr. ton behandlet gods.
Det samlede energiforbrug ligger på 8.950 MJ primær energi pr. behandlet ton gods – ca. 70% fra råvarefasen og ca. 30% fra produktionsfasen.
6.6.1.3 Godskrivning af materialer og energi
Affaldsfraktionerne hårdzink og zinkaske indeholder store mængder zink, der kan oparbejdes og genanvendes. Zinkindholdet i disse fraktioner udgør 1.745 ton svarende til 14,5 kg pr. ton behandlet gods.
Her er ikke taget stilling til om oparbejdningen sker internt eller eksternt.
Ved oparbejdning sker et tab, antaget til 30%, således at der udvindes 10,2 kg zink. Det antages at have samme kvalitet som den zink, der anvendes i processen.
Ved oparbejdningen spares energi til fremstilling af ny zink, og der bruges energi til selve oparbejdningen. Energien til oparbejdningen er antaget at udgøre 50% af energiforbruget til fremstillingen.
Besparelsen kan derfor opgøres til:
Sparet udvinding |
10,2 kg × 70 MJ/kg |
= 712,5 MJ |
Energi til oparbejdning |
10,2 kg × 35 MJ/kg |
= 356,3 MJ |
Besparelse |
|
= 356,3 MJ |
6.6.1.4 Opgørelse af råstofforbrug
Forbruget af råstoffer er opgjort ud fra materialeforbrug og den mængde, der genvindes. Den mængde, der oparbejdes, udgør 1.745 ton zink. Ved oparbejdningen er der et tab, således at 1.142 ton zink
kan genanvendes (70%).
Tabel 6.19 Estimering af råstofforbrug for varmforzinkning
Materiale
120.000 ton gods |
Materiale-
mængde |
Råstof-
forbrug
Kg/kg |
Råstof-
forbrug
i alt |
Råstof-
forbrug
pr. ton gods |
Zink |
8.688 ton |
3,1 |
26.932 ton |
240 kg |
Uorganiske syrer |
1.000 ton |
0,7 |
700 ton |
6 kg |
Uorganiske baser |
60 ton |
1,2 |
72 ton |
0,6 kg |
Ammoniak og hydrogenperoxid |
75 ton |
2 1) |
150 ton |
1 kg |
Tensider m.v. |
25 ton |
2,0 1) |
50 ton |
0,4 kg |
|
|
|
|
248 kg |
1): Værdien er skønnet.
6.6.2 Opgørelse af vurderede mængder for varmforzinkning
I det følgende er materiale- og energiforbrug omregnet til vurderede størrelse i mPR.
6.6.2.1 Vurdering af materialeforbrug ved varmforzinkning
Det væsentligste ressourceforbrug ligger i forbruget af zink. Ressourceforbruget fra mindre mængder afætset jern/stål er ikke medtaget. Opgørelsen for zink er vist i tabel 6.20.
Tabel 6.20 Ressourceforbrug ved varmforzinkning
|
td>
Mængde pr. be-
handlet ton gods |
Ressourceforbrug
33 mPR/kg zink |
Forbrug |
81,92 kg |
2.703 mPR |
Affald |
17,67 kg |
583 mPR |
I produktet |
64,25 kg |
2.120 mPR |
Som det ses af tabel 6.20, udgør indholdet af ressourcer i produktet – zinkpålægning af 1 ton gods 2.120 mPR. Tabet ved processen udgør 22 % af ressourceforbruget.
Ressourceforbruget til kemikalierne er skønnet til at udgøre 10 mPR, da en eksakt beregning ikke kunne gennemføres.
Det samlede ressourceforbrug udgør således 2.713 mPR.
Ressourcerne i produktet – overfladebehandlingen – tabes ved kassering af produktet, når stålpladen oparbejdes.
6.6.2.2 Vurdering af energiforbrug ved varmforzinkning
Det samlede energiforbrug er opgjort til 8.950 MJ primær energi pr. ton behandlet gods. Fremstilles denne energimængde ud fra olie, svarer det til et forbrug på 8,8 mPR.
6.6.2.3 Vurdering af genvundne mængder
Det er opgjort, at der genvindes 10,2 kg zink, hvilket svarer til en ressoucebesparelse på 336 mPR.
Det er opgjort, at der ved genvinding kan spares 356 MJ primær energi. Denne energimængde svarer til 0,3 mPR.
6.7 Ressourceeffektivitet for varmforzinkning
6.7.1 Ressourceeffektivitet på materialeniveau
6.7.1.1 Materialeforbrug, produktion og brug
Den samlede mængde zink i overfladebehandlingen udgør 64,42 kg. Det samlede forbrug af metal udgør 81,9 kg, og forbruget af kemikalier udgør 9,7 kg.
Ressourceeffektiviteten kan derfor beregnes til:

Tabet udgøres af kemikalierne samt en del zink, der fremkommer som affald i overfladebehandlingsprocesssen.
Vandforbruget er opgjort til 167 liter pr. ton behandlet gods.
6.7.1.2 Materialeforbrug, produktion, brug og bortskaffelse
Genvinding af zinkaffald fra overfladebehandlingen er opgjort til 10,2 kg. Netto-effektiviteten kan derfor beregnes til:

Genvinding af zink udgør omkring 50% af affaldsmængden og udgøres af zinkholdigt slagge. Genvindingen kan øges, men ikke til 100%, da der er et vist tab i genvindingsprocessen.
6.7.1.3 Materialeforbrug, hele livscyklus
Ses der på råstofforbruget, og tages der hensyn til genvinding af zink, kan effektiviteten beregnes til:

Råstofforbruget udgøres primært af zinkmalm, hvoraf omkring 1/3 af malmen bliver til zink.
6.7.2 Ressourceeffektivitet baseret på vurderet opgørelse
6.7.2.1 Ressourceforbrug, materialer
Den mængde ressourcer, der findes i produktet overfladebehandling af 1 ton gods –, udgør 2.120 mPR.
Ressourceeffektiviteten opgjort som materialeeffektivitet, brutto, kan beregnes til:

Tabet (de ca. 22%) udgøres af zink, da kemikalierne ikke tæller meget i den vurderede opgørelse.
6.7.2.2 Ressourceforbrug, materialer og energi
Hvis man ser på det samlede materiale- og energiforbrug, udgør det samlede vurderede forbrug 2.713 mPR + 8,8 mPR = 2.722 mPR, og den samlede materiale- og energieffektivitet kan beregnes til:
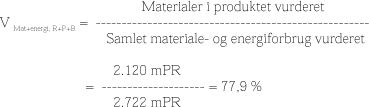
Som det kan ses af opgørelserne og af de beregnede effektiviteter, er energiforbruget til både udvindingen og til processen meget lille i forhold til ressourceforbruget af zink.
6.7.2.3 Ressourceforbrug, hele livscyklus
Tages der hensyn til genvinding, vil det samlede ressourceforbrug udgøre 2.722 mPR – 336 mPR = 2.386 mPR, og netto-effektiviteten kan beregnes til:
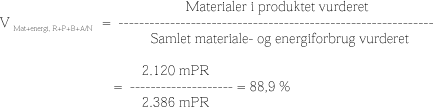
Effektiviteten baseret på vurderede opgørelser illustrerer også, at i størrelsesordnen 10% af den anvendte zink oparbejdes.
6.7.3 Fortolkning
De opgjorte ressourceeffektiviteter er vist i tabel 6.21.
Tabel 6.21 Beregnede ressourceeffektiviteter for varmforzinkning
|
Betegnelse |
Ressource- effektivitet |
Materialeopgørelse |
|
|
• Materialer til produktion og brug |
Mmat, P+B |
70 % |
• Materialer, produktion, brug og bortskaffelse inkl. genanvendelse |
Mmat, P+B+A/N |
79 % |
• Råstoffer i hele livscyklus inkl. genanvendelse |
Mmat. R+P+B+A/N |
26 % |
Ressourceopgørelse |
|
|
• Materialer vedrørende råstoffer, produktion og brug |
Vmat, R+P+B |
78 % |
• Materialer og energi vedrørende råstoffer, produktion og brug |
Vmat+energi, R+P+B |
78 % |
• Materialer og energi i hele livscyklus inkl. genvinding |
Vmat+energi, R+P+B+A/N |
89 % |
Af tabel 6.21 ses det, at der tabes omkring 30% i selve overfladebehandlingsprocessen (Mmat, P+B). Tabet udgøres af kemikalierne, der udgør ca. 1/3. Resten er zink. Da dette tal er opgjort specifikt for
denne proces, vil opgørelsen kunne bruges af branchens virksomheder som sammenligningsgrundlag.
Den næste effektivitet (Mmat, P+B+A/N) viser, at der sker en vis genvinding af zink. Omkring 50% af zinkaffaldet fra overfladebehandlingen oparbejdes. Det antages, at denne effektivitet kan forøges lidt,
men det vil ikke være muligt at oparbejde kemikalierne, der udgør lidt over 10%. Endvidere skal der tages højde for, at der altid vil være et vist tab af zink ved oparbejdningen.
Effektiviteten for råstoffer (Mmat. R+P+B+A/N) afspejler, at der ved udvinding af zink fra malm tabes omkring 2/3 af materialet. Denne beregning vil antageligt kun kunne anvendes på et mere overordnet
plan.
Ses der på beregningen af de vurderede opgørelser, fremgår det tydeligt, at zink er langt det vigtigste materiale, og at kemikalierne ikke betyder meget.
Af effektiviteten med og uden energi (Vmat, R+P+B og Vmat+energi, R+P+B) ses det tydeligt, at energiforbruget ikke betyder meget i forhold til forbruget af zink.
Effektiviteten Vmat+energi, R+P+B+A/N er højere end de to andre svarende til, at godt 10% af zinkmængden forudsættes oparbejdet.
6.7.4 Affaldsforebyggelse
Som for el-forzinkning ses det, at der mængdemæssigt tabes en relativ stor del materiale i råstofudvindingen og i produktionen. Af de vurderede opgørelser ses det, at der tabes en mindre mængde knappe
ressourcer, og at energiforbruget i forhold til materialeforbruget er af mindre betydning. Lægges der vægt på knappe, miljøbelastende stoffer, vil det være zink, der skal fokuserers på.
I det følgende trækkes en række væsentlige forhold frem.
6.7.4.1 Kemikalier
Til varmforzinkning anvendes en del kemikalier til rensning af godset inden forzinkningen. Dertil kommer flusmidler, der anvendes som en forbehandling inden dypning i zinksmelten.
Forbehandlingsbadene skiftes, når de er forurenende med jern, olie og andre urenheder. Se i øvrigt bemærkningerne under afsnit 6.3.4.1.
6.7.4.2 Zink
Til varmforzinkning pålægges i gennemsnit 64,4 kg pr. ton gods. I processen tabes 17,5 kg svarende til ca. 27 %. Der genvindes 10,2 kg zinkaske og en del andet affald, således at det egentlige tab udgør
7,3 kg eller 11 % af den mængde zink, der findes på emnet.
Det bør derfor overvejes, om de affaldsfraktioner, der i dag ikke oparbejdes, kan blive det, således at affaldsmængden reduceres, og zinken udnyttes bedre.
Ved kassering af produktet – det overfladebehandlede emne – tabes alt det pålagte metal. Her gør de samme forhold sig gældende som for elforzinkning. Zinken fordamper fra smelten inden jernet gør og
findes i slagge og støv fra afgangsluften. Den ressourcemængde jernet repræsenterer vil dog oftest være væsentlig større, end den mængde zinken repræsenterer, men det afhænger meget af emnets geometri.
6.7.4.3 Vandforbrug og spildevand
Der anvendes omkring 170 liter skyllevand til forbehandling af 1 ton gods. Skyllevandet vil være forurenet med olie, snavs, jern samt de anvendte kemikalier, herunder opløste zinksalte.
Se i øvrigt kommentarer under fornikling/forchromning, afsnit 6.3.4.3.
6.7.4.4 Energi
Energiforbruget er i alt på ca. 9.000 GJ/ton, fordelt på 70 % i råvarefasen og 30 % i overfladebehandlingsprocessen.
Typen af energiressourcer, der anvendes i råvarefasen kendes ikke.
Energiforbruget i varforzinkningen dækkes med 50% olie og ca. 50% el.
Ressourcemæssigt bruges der i alt i størrelsesordnen 9 mPR til energiforbruget baseret på olie. Til at dække materialebehovet anvendes 2700 mPR, og energiforbruget udgør således under 1 % af det
samlede ressourceforbrug.
6.7.4.5 Samlet prioritering
Ud fra et ressourcemæssigt synspunkt kan det være noget problematisk at anvende zink til overfladebehandling, såfremt det ikke genvindes.
Følgende forhold bør der fokuseres på:
- Zink fra det kasserede produkt bør genvindes i så høj grad som muligt.
- Zink, der forekommer som affald (primært slam, eventuelt spildevand) fra forbehandlingen genvindes ikke.
- Der anvendes en række hjælpekemikalier i processen, som tabes.
Det vides ikke, i hvor høj grad zink genvindes fra oparbejdning af stål og det er derfor et forhold, der bør fokuseres på.
6.7.5 Sammenligning med øvrige opgørelser
Overfladebehandlingsprocessen varmforzinkning, som den udføres i Danmark, er optimeret med hensyn til udnyttelse af metaller, energi- og vandforbrug og er således typisk for europæiske forhold.
6.7.5.1 Direkte materialeinput
Det er ikke muligt at foretage en sammenligning mellem de opgjort mængder af materialer og data for DMI, da DMI ikke opgøres på procesniveau.
6.7.5.2 Totale materialeinput
I det følgende er søgt estimeret det totale materialeinput, baseret på Wuppertal's MIPS-data, se tabel 6.22.
Tabel 6.22 Estimering af materialeinput for varmforzinkning
Materiale 120.000 ton gods |
Materiale- mængde |
Råstof- forbrug Kg/kg |
Råstof- forbrug i alt |
Råstof- forbrug pr. ton gods |
Zink |
8.688 ton |
23,1 |
200.693 ton |
1.672 kg |
Uorganiske syrer |
1.000 ton |
0,5 1) |
500 ton |
4 kg |
Uorganiske baser |
60 ton |
1 1) |
60 ton |
0,5 kg |
Ammoniak og hydrogenperoxid |
75 ton |
1 1) |
75 ton |
0,6 kg |
Tensider m.v. |
25 ton |
10 1) |
250 ton |
2 kg |
|
|
|
|
1.679 kg |
1) Værdien er skønnet fra oplysninger om lignende kemikalier.
I nærværende opgørelse er råstofforbruget opgjort til ca. 250 kg eller ca. 15% af det opgjorte materialeinput. Begge typer af opgørelser skulle i princippet være ens og medtage alle indirekte strømme. Den
væsentligste forskel ligger i opgørelsen for zink, hvor Wuppertal har opgjort materialeinputtet til at være omkring 8 gange så stort som data fra SigmaPro. Wuppertals data for de øvrige materialer ligger også
noget over der her anvendte LCA-data for de øvrige materialer.
| Forside | | Indhold | | Forrige | | Næste | | Top |
Version 1.0 December 2005, © Miljøstyrelsen.
|