| Forside | | Indhold | | Forrige | | Næste |
Substitution af diffundérbare råvarer i UV-hærdende lakker til træmøbler
Summary and conclusions
Background and purpose
Danish furniture manufacturers use lacquers that cure by means of ultraviolet radiation as the most frequent surface treatment of wooden furnitures – in particular of plane products. UV curing primers and finishes are being applied by rollers or by spray guns, and are subsequently cured in special ovens with UV light. The advantage of the UV lacquers is their fast curing following the application, which allows handling and packaging after less than 10 seconds.
When UV-cured lacquers are applied, the part of the lacquer having the lowest viscosity will penetrate into the wood and become inaccessible to the UVradiation, thus remain un-cured. Additionally, the lacquer may contain monomers and binders that do not completely polymerize from the UV radiation. In this way, all these un-cured components may fairly easily emit from the wood and lacquer when the furniture is introduced at the end-user and will deteriorate the indoor climate.
One monomer used for UV-furniture lacquers is 1,6 hexandiolacrylate (HDDA, CAS 13048-33-4). According to the Nordic SPIN database, 31.8 tons of HDDA were used in Denmark in 2007. This monomer is classified as a local irritant with the risk designations R36/38 (Irritating to eyes and skin) and R43 (Irritant. May cause sensitization by skin contact). Accordingly it must be regarded as an allergenic.
Nordic environmental regulations consider the health impact of such allergic and/or carcinogenic residual monomers to be so large that separate requirements exist for the maximum content of residual monomers, e.g. the Ecolabel criteria for chemical building products.
The aim of the project was to eliminate or sharply reduce emitting substances in UVcuring furniture lacquers and thereby decrease allergens in the home environment. The examined primary component was HDDA.
The project
In cooperation with the paint manufacturer Teknos, FORCE Technology has carried out this project on reducing emitting substances in UV curing furniture lacquers.
A number of suppliers of monomers, oligomers and binders for UV-lacquers were contacted to obtain information on possible alternatives. In order to evaluate the alternatives forwarded a testing regime was created to search for the best possible combinations. The tests were carried out by FORCE Technology’s department of Chemical Analysis.
Based on the laboratory tests the best combinations were formulated to UV lacquers, and applied and tested at a professional workshop.
Conclusion
The project has shown that UV-curing furniture lacquers contain more or less un-reacted monomers after UV curing and also their amount. However the varnish manufacturer can reduce such emissions by a careful choice of appropriate materials. The choice can be made by a thoroughly environmentally-related study of the ingredients included in the varnish. The study should primarily focus on the monomer and binder, since they contribute most to the varnish composition. Monomers’ and binders’ content of chemical compounds will be reflected in their statutory safety data sheet and will give an indication of their reactivity: Lower reactivity leads to more un-reacted compounds in the varnish and results in higher diffusion.
In the same literature study commodities with genuine health and environment-damaging components are discarded.
Later, when the furniture varnish is further developed – i.e. achieves its desired technical and commercial properties (curing, gloss, hardness, price, etc.) - chemical analysis could show comparative emission levels from the lacquers after UV curing.
Project results
Besides the review of safety data sheets of approx. 40 monomers/oligomers and binders for UV lacquers, the investigation showed that there were significant differences between the mentioned raw materials’ tendency to diffusion after UV curing. For example, the chemical analysis showed that the lacquer manufacturer simply by changing his commercially used monomer HDDA to DPGDA (Dipropylene diacrylat - CAS 57472-68-1) or TPGDA (Tripropyleneglycol diacrylat - CAS 42978-66-5) could reduce emissions significantly, Figure 0-1.
A shift from HDDA to TPGDA means at the same time a change to acrylates with a higher molecular weight, and thereby to less acute toxic acrylates.
Figure 0-1 Extractable monomer-emission mg/m² - indexed
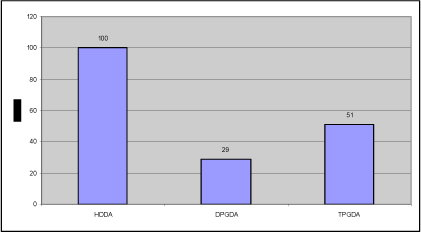
This optimisation - along with a replacement of the used binder - gave a 2 / 3 reduction in the diffusion of a random primer, Figure 0-2.
Figure 0-2 Extractable monomer-emission mg/m² from a furniture primer
varnish - indexed
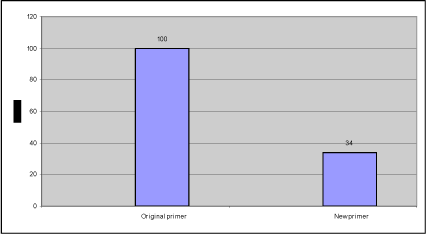
A change in primer - acrylates with much higher molecular weight at the same time means that the acute toxicity of the UV lacquers is reduced.
The monomer and binder replacements could be performed without considerable technical or financial consequences for the varnish manufacturer - and from this - at the end user. Actually, Teknos began the process of changing the composition of their UV-curing coatings to be marketed during the course of the project. This product optimisation process is still ongoing when this project ended.
Even though the final formulation of the UV lacquers was not available when this project ended, all results indicates that the new formulations consists of more pure raw materials, i.e. fewer constituents in the final product. This must be regarded as an advantage, as there is not complete knowledge about the health and environmental properties of the different constituents.
Acrylates are in general regarded as causing sensitisation. Changing to other acrylates does therefore not remove this risk. The results of the project do however, show that the achieved optimisation will lead to less diffusion of monomers from lacquered wooden furniture, and thereby help improve the indoor environment at the end user.
| Forside | | Indhold | | Forrige | | Næste | | Top |
Version 1.0 Januar 2011, © Miljøstyrelsen.
|