| Front page | | Contents | | Previous | | Next |
Waste Strategy 2005-08
Appendix D
Sectors
D.1. Waste incineration plants
Environmental
problem | Content of heavy metals in residues can limit recycling options Flue gas cleaning waste from waste incineration plants accounts for large volumes of hazardous waste
|
Initiatives | Investigate whether earlier initiatives have had a positive effect on the content of heavy metals in slag Investigate whether separation requirements should be introduced for fractions that can by recycled or that lead to environmental problems during incineration
New requirements for the recycling of slag in building and construction projects
On the basis of an environmental and cost-benefit analysis, an action plan will be prepared for the future management of flue gas cleaning products generated in
Denmark
Investigate the possibility of recovering phosphor from slag from incinerated meat-and-bone meal
|
D 1.1 Status
Aims for 2008
- reduce the volume of incinerated waste
- recycle 70 per cent of slag from waste incineration plants
- a Danish solution for the management of flue gas cleaning products
Waste incineration plants treat waste, but also generate waste.
1. In January 2003, there were a total of 32 waste incineration plants operating in Denmark, including a newly opened plant in Esbjerg. See Appendix C regarding capacity at
incineration plants.
In 2001, approx. 2.9 million tonnes of waste and approx. 300,000 tonnes of sludge were incinerated.
Residues from waste incineration plants consist of slag and flue gas cleaning waste, accounting for 20 per cent and 3 per cent, respectively, of the waste amounts treated.
Slag is separated, and 70-80 per cent is recycled. The remaining part is landfilled, primarily due to poor quality (heavy metal content too high).
The composition of the incinerated waste has a significant impact on the volume and quality of residues. As a result of Waste 21, requirements have been introduced stipulating
that a number of waste fractions containing environmental contaminants must, as far as possible, be prevented from reaching waste incineration plants. Examples of these fractions
include impregnated wood, electronic equipment, and PVC.
The volume of waste incinerated is shown in the table below.
`000 tonnes |
1995 |
1996 |
1997 |
1998 |
1999 |
2000 |
2001 |
Volume of waste incinerated |
2,306 |
2,507 |
2,622 |
2,740 |
2,929 |
3,064 |
3,221 |
Source: Waste Statistics 2001, Danish Environmental Protection Agency 2003.
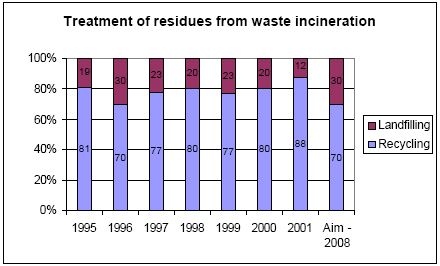
Source: Waste Statistics 2001, Danish Environmental Protection Agency 2003.
Measures
- documentation for the effectiveness of Waste 21 initiatives
- investigate the possibility of separating recyclable fractions or fractions leading to environmental problems
- requirements for management of residues
- action plan for the future management of flue gas cleaning products
D 1.3 Future initiatives
An investigation will be made into whether the content of heavy metals in slag has been reduced as a result of the initiatives in Waste 21.
Investigation will also be made into whether separation requirements should be introduced for fractions that can by recycled or that lead to environmental problems during incineration
This could lead to a reduction in the volume of waste incinerated.
The Statutory Order on recycling of residues and soil for building and construction purposes is to be revised. In the longer term, this Order will also cover the regulation of fractions
containing organic contaminants.
On the basis of an environmental and cost-benefit assessment, an action plan will be prepared for the future management of flue gas cleaning products. The plan will be prepared in
cooperation with waste incineration plants. The action plan will contain deadlines for when each problem with flue gas cleaning products has to be solved. The plan will also cover the
establishment of environmentally responsible reprocessing methods, leading to the recycling of flue gas cleaning products. The proximity principle will apply to all landfilling of flue gas
cleaning products, wherever this is environmentally and economically justifiable.
D. 1.2 Regulation
According to the Statutory Order on waste, municipalities must assign waste suitable for incineration - which is not recyclable - to incineration at a plant with energy recovery. Certain
types of waste are defined as waste not suitable for incineration, as incineration may lead to environmental problems. Examples of such waste include oil-contaminated soil, PVC waste,
electronic equipment, impregnated wood and waste containing heavy metals.
The recycling of slag is currently regulated under the Statutory Order on recycling residues and soil for building and construction purposes.
Flue gas cleaning waste is hazardous waste with a high leaching rate of environmental contaminants.
D 1.4 Environmental assessment
Keeping environmentally harmful fractions away from waste incineration plants would lead to a reduction in the heavy metals being added to slag or the flue gas cleaning product.
Keeping recyclable waste fractions away from waste incineration plants would lead to a reduction in the volumes of slag and flue gas cleaning products produced.
D 1.5 Implications for national authorities
Adjustments to the Statutory Order on Waste if it is practicable to separate out recyclable fractions or fractions that lead to environmental problems during incineration. However, this
will only have significance for the 2009-2012 plan period.
The national authorities will revise the Statutory Order on recycling residues and soil for building and construction purposes to also cover fractions contaminated with organic fractions.
The national authorities will be responsible for preparing an action plan for the future treatment of flue gas cleaning products from waste incineration plants.
D. 1.6 Implications for municipal authorities
If there is a need to keep other waste fractions away from waste incineration plants, municipalities must make allowances for this in their future waste planning. However, this will only
have significance for the 2009-2012 plan period.
D.2. Building and construction
Environmental
problem | Construction and demolition waste accounts for 28 per cent of the total volume of waste and would take up excessive landfill capacity if not recycled |
Initiatives | Prepare a guide for waste prevention during renovation
Analyse the level of contaminants in building and construction waste
Analyse the procedure for recycling building and construction waste
Enhance the foundation for the separation of hazardous waste fractions in construction waste
Adjust the foundation for recycling building and construction waste
Adjust the foundation for recycling residues, slag and soil in building and construction projects
Make specific proposals for a complete set of indicators for individual building projects and suggest principles for a benchmarking system to assess environmental
initiatives
Prepare an overview of where environmental considerations should be incorporated into the existing legal and regulatory base
Develop a tool for assessing and prioritising the use of chemicals in construction
Assess whether environmental and health impacts arise in connection with the use, renovation or demolition of buildings containing PCB
Ensure that asphalt, concrete and tiles are recycled in a manner that gives due consideration to the environment and health
Ensure that electrical and electronic equipment is managed in accordance with the EU Directive
Investigate whether the recycling rate for mineral wool can be increased
Increase the rate of recycling for wooden packaging
Prepare a strategy for hazardous waste
Increase the rate of recycling for transport packaging and certain retail packaging from trade and industry
Implement regulations on separate treatment of pre-insulated district heating pipes
Ensure that the treatment of waste from building and construction is organised in a cost-effective and environmentally responsible manner
|
D 2.1 Status
Aims for 2008
- 90 per cent recycling of building and construction waste
- ensure that recycling of building and construction waste gives maximum consideration to groundwater resources
- ensure that recycling of residues in the building and construction sector gives maximum consideration to groundwater resources
- develop indicators that make it possible to evaluate environmental initiatives in construction
Construction and demolition waste consists primarily of concrete, asphalt, stone, and other construction and demolition waste. In 2001, 3.4 million tonnes of such waste were produced.
The volume of construction and demolition waste has been increasing in recent years.
The high rate of recycling for construction and demolition waste will be maintained, as recycling this waste saves resources. It is important that recycling gives maximum consideration to
groundwater resources.
In 2001, 90 per cent of building and construction waste was recycled. Eight per cent of the total volume was landfilled, and two per cent of the waste was referred to special treatment
[1].
Since 1995, the total rate of recycling has risen by 5 per cent. The proportion of waste being landfilled has fallen by a corresponding 5 per cent. Since 1997, the distribution of waste
treatment has fulfilled the goal for treatment in 2004.
As well as generating waste, the building and construction sector extensively uses waste produced in other sectors, including residues from power plants and waste incineration plants.
An investigation has been carried out to describe the flow of problematic substances that can be expected to appear in building waste in the period 2001-2025. The investigation
concluded that there is a need for further technical investigations into the options for removing and managing building materials containing problematic substances. Initially, measures will
be undertaken to assess whether any health impacts arise from the use, renovation and demolition of buildings containing PCB's, see Appendix E 21.
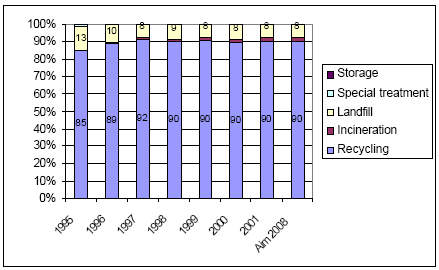
Source: Waste Statistics 2001, Danish Environmental Protection Agency 2003
There is a need to analyse whether waste from building and construction is being managed in an environmental and cost-effective manner. This analysis will be carried out by the task
force on waste appointed by the Minister for the Environment and will therefore not be described in further detail in this strategy.
D 2.2 Waste prevention
Waste from building and construction represents a particular problem. This waste constitutes a significant proportion (approx. 28 per cent in 2001) of the total volume of waste. Added
to this is the fact that the waste typically represents products – a building is seen as a product – marketed many years ago, as buildings have a very long lifetime. We therefore have to be
able to manage large volumes of waste from this sector – waste that has been impacted by the "sins of the past".
The building and construction sector can contribute to waste prevention by:
- supplying quality buildings with long lifetimes and using environmentally-friendly materials
- ensuring optimum material utilisation by avoiding wastage or damage to materials
- demanding high quality materials and products produced with waste prevention in mind and delivered in returnable packaging
- employing environmentally correct design or equivalent tools/methods
The building and construction sector is typically subject to a number of standards and norms governing how the work is carried out. For example, when a ventilation system is installed in
a building, there are requirements stipulating what proportion of fresh air must be recirculated. This can limit how much energy consumption can be reduced. Another example is a
motorway, where specifications govern how thick the road pavement should be. This places a limit on how low the resource input can be. There are thus a number of restrictions that
limit options for waste prevention, both in terms of practical implementation and price competition within the sector.
The instruments needed to promote these initiatives will primarily be of an administrative and financial character. One example might be the introduction of a system capable of evaluating
the environmental quality of a construction, and a corresponding reward system. This could be in the form of a declaration, or the possibility of favourable loan conditions.
Measures
- guide to waste prevention during renovation of buildings
- requirements to recycle building and construction waste in building and construction projects
- analyse the procedure for recycling building and construction waste in Denmark
- new requirements for recycling building and construction waste
- extend the regulations on recycling residues and soil to include organic contaminants
- prepare guidelines on moving soil and residues
- develop indicators designed to evaluate environmental initiatives
- investigate where environmental considerations are incorporated into existing laws and regulations
- develop tools to evaluate and prioritise chemicals in construction
- investigate whether there are environmental and health effects in connection with the use, renovation and demolition of buildings containing PCB.
- investigate the potential for recycling mineral wool
- requirements for separate treatment of pre-insulated district heating pipes
- requirements for the collection of iron and metal packaging
D 2.3 Future initiatives
Waste prevention
During the next few years, a guide to waste prevention will be prepared. During the renovation of older properties, it is constructive to re-use previously used building elements.
The guide will describe the activities that should be carried out during demolition to ensure the optimal re-use of building components. Renovation is an alternative to new
construction, and the scope of property renovation compared to demolition therefore needs to be analysed at a national level.
Other
Such high levels of contaminants have been recorded in building and construction waste that a nationwide investigation needs to be carried out to determine which contaminants
are present and in what concentrations. The sources of these contaminants must also be identified. On the basis of this study it may be necessary to adjust recycling aims.
An investigation will be carried out to describe the normal procedure for managing building and construction waste in the municipalities. For example, this investigation will clarify
whether the individual fractions are mixed together before they are recycled, and whether the mixed fractions are recycled with the necessary Section 19 permission.
Consideration will be given to whether the recycling of building and construction waste should be regulated under the Statutory Order on residues and soil for building and
construction purposes, in the long term. The necessary basis for potentially revising the Statutory Order to also cover building and construction waste needs to be provided. It is
expected that the Statutory Order will be extended to also cover fractions containing organic contaminants (see Appendix E under the asphalt, concrete and tile fractions).
Guidelines on moving soil and residues will also be prepared (see Appendix E).
A proposal will be made for specific indicators for individual construction projects. Principles will also be proposed for a benchmarking system that makes it possible to evaluate
environmental initiatives.
An investigation will be initiated to provide an overview of where environmental considerations are incorporated into the existing legal and regulatory base. The existing
requirements need to be assessed to determine whether they support the environment goals presented in the Construction Panel's Action Plan.
Focus needs to be given to the use of chemicals in buildings and building products. A project will therefore be initiated with the aim of developing a simple tool to evaluate and
prioritise the use of chemicals in the building sector.
An investigation will be initiated examining whether environmental and health effects arise in connection with the use, renovation, and demolition of buildings containing PCB's. The
project will focus on evaluation of the PCB contribution from building dust, indoor air and soil close to buildings, in relation to the contribution from other sources, and TDI values
for PCB's (see Appendix E).
The potential for recycling mineral wool will be investigated, including the development of recycling methods and of the market for recyclable mineral wool (see Appendix E).
Regulations for separate treatment of pre-insulated district heating pipes will be implemented (see Appendix E).
PVC and impregnated wood will continue to be separated for either recycling or landfilling (see Appendix E).
Enterprises and municipalities will have to give greater focus to separating plastic film for recycling. Industry associations for waste producers need to be able to establish
nationwide collection schemes, and enterprises will be required to separate plastic containers for recycling (see Appendix E).
A strategy for hazardous waste will be prepared. The purpose of this strategy will be to identify whether the various regulations relating to hazardous waste represent barriers to
the best economic and environmental management of waste, and to identify potential initiatives to minimise these barriers (see Appendix E).
The new EU Directive on waste electrical and electronic equipment must be implemented in Danish legislation by the end of 2004. Implementation of this directive will mean
changes to requirements, and that more products will be subject to separate treatment (see Appendix E).
Under new EU regulations, Denmark must recycle 15 per cent of wooden packaging and 55 per cent of all packaging waste in 2008. In order to achieve this goal, an analysis
will initially be completed of the volume of wooden packaging waste, and potential buyers (see Appendix E).
The recycling rate for iron and metal packaging is to be increased (see Appendix E).
D 2.4 Regulation
In spring 1994, the Minister for the Environment, Local Government Denmark (LGDK), the City of Copenhagen, and the Municipality of Frederiksberg entered into an
agreement on waste suitable for incineration, construction and demolition waste, organic waste, and landfilling. In connection with this agreement, a Circular [2] was issued in
1995 on municipal regulations for the separation of construction and demolition waste for recycling. The Minister for the Environment also entered into an agreement with the
Danish Demolition Association [3] on selective demolition of building materials. This agreement ensured separation at source.
The Circular stipulates that waste from demolition works involving more than 1 tonne of construction and demolition waste must be separated at source into pure fractions, for
example, such that tiles and concrete are kept separate.
In pursuance of this Circular, municipalities have issued regulations containing requirements for separation. These regulations took effect no later than 1 January 1997.
The Statutory Order on recycling of residues and soil for building and construction purposes [4] regulates the recycling of residues and soil used as substitutes for primary raw
materials.
The waste tax has played a significant role in the regulation of construction and demolition waste, as recycled waste is not subject to the tax.
Government grants for recycling initiatives have also had a significant effect.
D 2.5 Capacity
A large proportion of building and construction waste is reprocessed using mobile and semi-mobile crushing plants, relocated according to needs. The capacity of these plants is
not considered to be a barrier to achieving the objective.
D 2.6 Environmental assessment
Subjecting the recycling of building and construction waste to the same requirements as residues will ensure that recycling takes place under the same terms and gives maximum
consideration to groundwater resources. Once the contamination levels in building and construction waste have been analysed, the actual consequences of the new initiatives will
be presented.
The establishment of indicators for a single building project will make it possible to compare building projects with the same purpose, e.g. constructing an office building. These
indicators will also make it possible to improve environmental initiatives in the sector.
D 2.7 Implications for national authorities
The national waste authorities will be responsible for issuing requirements for the recycling of building and construction waste.
The authorities will also be responsible for initiating projects to:
- Analyse the level of contaminants in building and construction waste
- Analyse the procedure for recycling building and construction waste
- Improve the basis for the separation of hazardous waste fractions in construction waste (project on PCB's in construction waste)
- Establish a complete set of indicators for individual building projects and suggest principles for a benchmarking system to assess environmental initiatives
- Prepare an overview of where environmental considerations are incorporated into the existing regulatory base
- Develop a tool for assessing and prioritising the use of chemicals in construction
The national authorities are also responsible for amending the Statutory Order on recycling residues and soil for building and construction purposes to cover fractions containing
organic contaminants. The authorities are also responsible for amending the regulations for the management of asphalt, concrete, and tiles.
The authorities are also responsible for implementing the Directive on waste electrical and electronic equipment.
Regulations will be laid down for the collection of iron and metal packaging.
Guidelines will be prepared on moving soil and residues.
Investigation of the recycling options for mineral wool may lead to the need for amendments to the regulations for landfilling this waste fraction (see Appendix E).
Regulations will be prepared for the management of waste containing ozone-depleting substances.
D 2.8 Implications for municipal authorities
Municipal authorities are responsible for ensuring, via supervision and municipal regulations, that building and construction waste is correctly sorted and used.
D 2.9 Economics
Before any new regulations are implemented, environmental and cost-benefit assessments of the consequences will be carried out.
D.3. Landfills
Environmental
problem | Whenever waste is landfilled, there will always be a risk of failure in one or more of the environmental protection systems established to ensure the environmentally
optimum operation of the landfill facility. |
Initiatives |
The potential to recycle/utilise waste must constantly be investigated so that in the future, waste will only be landfilled when it is environmentally appropriate and
responsible to do so
-{}-Requirements will be laid down governing the design and operation of landfill sites. For each of the four categories of landfill site (inert, mineral, mixed, and
hazardous waste), criteria and limit values for the content and leaching of environmental contaminants will also be set. These will aim to ensure, as far as possible, that
failure in the environmental protection systems does not lead to irreversible damage to nature and/or the environment surrounding a landfill site
As a result of the implementation of the EU Directive on the landfill of waste (including Annex harmonisation), new guidelines will be prepared on landfilling waste to
replace the guidelines from 1997, as the contents of the 1997 guidelines are out of date in a number of areas. The guidelines will especially focus on describing how
both the new requirements in the Statutory Order on landfilling and future requirements relating to waste characterisation should be tackled in order to ensure
"sustainable landfilling"
All employees at landfill sites will be required to hold a certificate confirming they have the necessary knowledge concerning the operation of a landfill facility. Training
plans, training material and various tests must therefore be prepared to provide a sufficient basis for employees to attain the required certificates before the deadlines,
cf. the requirements in Statutory Order no. 647 of 29 June 2001 on training of operations managers and personnel employed at landfill sites
|
D 3.1 Status
When waste can neither be recycled nor incinerated, it must be disposed of/treated at a landfill facility.
Volumes of waste landfilled
The total annual volumes of landfilled waste have generally been declining since the mid-1980's. In 1985, approx. 3.5 million tonnes of waste were landfilled, corresponding to
approx. 39 per cent of the total annual volume of waste. In 1993, approx. 2.5 million tonnes of waste were landfilled (26 per cent of the total volume of waste). In 1997, approx.
2.1 million tonnes of waste were landfilled (16 per cent of the total volume of waste). In 2001, approx. 1.3 million tonnes of waste were landfilled (10 per cent of the annual
volume of waste).
In step with the decline in the volume of landfilled waste, the number of landfill facilities has also reduced. However, the reduction in the number of landfill facilities has not matched
the rate of decline in the volume of landfilled waste. As a result, the average volume of waste currently landfilled at each facility is significantly less than it was previously.
As a consequence of Denmark's implementation of the EU Directive on the landfill of waste (see section A 2) [5], the number of landfill facilities in Denmark is expected to be
further reduced. The requirements laid down in the Statutory Order on landfill facilities [6] are expected to lead to the closure of 40-60 landfill facilities (out of the approx. 150
existing facilities) before 16 July 2009. This date is the deadline under the Order for when the operations of all Danish landfill facilities – both new and existing – are required to
fulfil the requirements of the Order.
Transition plans
The Statutory Order on landfill facilities stipulates that all existing landfill facilities must prepare and submit a transition plan to the approval authority by 16 July 2002. On the basis
of this transition plan, the approval authority will reassess the facility's environmental conditions and decide whether the facility can (or has the potential to) fulfil the requirements in
the Statutory Order on landfill facilities and hence be granted approval to continue operations after 16 July 2009. Alternatively – in cases where the facility does not fulfil the
requirements of the Order (and does not have the potential to do so) – the approval authority will have to issue an order for the facility to be closed by 15 July 2009.
Once the approval authorities have made their decisions on the basis of the submitted transition plans (this is expected to have happened before the end of 2004), each landfill
facility will receive an order in the form of a positive list specifying the waste types that the facility is permitted to receive for landfilling. The landfill facility operator will be required
to provide security for the obligations relating to the closure and post-treatment of the facility and will be informed of the terms of this requirement.
In 2002, the Danish Environmental Protection Agency issued Guideline no. 5, 2002 on the preparation of transition plans. This guideline explains, in a number of key areas, the
regulations relating to the preparation of transition plans laid down in the Statutory Order on landfill facilities, and should be seen as an aid and inspiration in the work of preparing
transition plans for existing landfill facilities.
Harmonisation of the Annexes to the Directive on the landfill of waste
In December 2002, the Danish presidency succeeded in gaining unanimous support from all 15 Member States for a number of amendments in relation to the Commission
proposal on harmonisation of the annexes to the Directive on the landfill of waste.
The annexes to the Directive on the landfill of waste must be implemented in Danish legislation by 16 July 2004. By 16 July 2005, there will be a general legislative requirement
that all waste must be characterised before it can be received for landfilling. This will mean that documentation for the waste's content and leaching of environmental contaminants
will be required. This documentation is aimed at ensuring that all landfilled waste fulfils the set limits for leaching for a number of environmental contaminants, and that each type of
waste is only landfilled together with other waste types with similar characteristics.
It is expected that the new requirements for waste characterisation will contribute to a further reduction in the annual volume of landfilled waste. The primary reason for this is that
as a result of the new requirements, it will become more expensive to landfill waste in the future, and waste producers can therefore be expected to make extra effort to find
treatment/utilisation options for the waste types (or parts thereof) that have previously been landfilled.
Expectations for landfilled waste during the plan period (2005-2008)
During the plan period it is expected that there will be:
- a new general requirement that waste must be characterised before it is received for landfilling
- a further reduction in the annual volume of landfilled waste
- a substantial increase in landfilling charges
- a reduction in the number of landfill facilities.
During the plan period, the development trend is expected to be towards fewer landfill facilities with greater average capacity. This will open the way for better/optimal
environmental and economic operation of each landfill facility, but will also (in certain regions) lead to greater transportation costs.
D 3.2 Future initiatives
The potential to recycle/utilise waste must constantly be investigated so that in the future, waste will only be landfilled when it is environmentally necessary and responsible to do
so.
Requirements will be laid down governing the design and operation of landfill sites. For each of the four categories of landfill site (inert, mineral, mixed, and hazardous waste),
criteria and limit values for the waste's leaching characteristics will also be set. These will aim to ensure, as far as possible, that failure in the environmental protection systems does
not lead to irreversible damage to nature and/or the environment surrounding a landfill site. Waste characterisation requirements will aim to ensure a high degree of environmental
protection, without placing unreasonable burden on waste producers.
As a result of the implementation of the EU Directive on the landfill of waste (including Annex harmonisation), new guidelines will be prepared on landfilling waste to replace the
guidelines from 1997, as the contents of the 1997 guidelines are out of date in a number of areas. The guidelines will especially focus on describing how both the new
requirements in the Statutory Order on landfilling and future requirements relating to waste characterisation should be tackled in order to ensure "sustainable landfilling".
All employees at landfill sites will be required to hold a certificate confirming they have the necessary knowledge concerning the operation of a landfill facility. Training plans,
training material and various tests must therefore be prepared to provide a sufficient basis for employees to attain the required certificates before the deadlines, cf. the
requirements in Statutory Order no. 647 of 29 June 2002 on training of operations managers and personnel employed at landfill sites.
D 3.3 Regulation
The design and operation of landfill facilities must conform to the requirements in the Statutory Order on landfill facilities.
The Statutory Order on training prescribes [7] compulsory examinations for both operations managers and staff employed at landfill facilities. Under the Order, existing operations
managers must hold an A certificate by 1 July 2004, and operations managers employed after 1 July 2003 must hold an A certificate within one year after commencing
employment. Existing staff involved in the daily operations of a landfill facility must hold a B certificate by 1 July 2005, and any staff employed after 1 July 2003 must hold a B
certificate within two years after commencing employment.
As a result of the Council's adoption of the harmonisation of the annexes to the EU Directive on the landfill of waste in December 2002, Denmark has to implement annex
harmonisation in national legislation by 16 July 2004.
Almost all drinking water in Denmark derives from groundwater. When the Danish criteria and limit values for waste characterisation are being determined, special focus will
therefore be given to protecting the scarce and vulnerable Danish drinking water resources. This is expected to result in more stringent limit values for a number of environmental
contaminants, compared to the limit values adopted by the EU under the annex harmonisation.
Once implementation is complete, more stringent requirements for the documentation of waste content and leaching of environmental contaminants will be laid down, to ensure
that in future, only waste that is suitable for disposal via landfilling is landfilled. Waste that does not comply with the set requirements may have to undergo further treatment before
it can be accepted for landfill.
D 3.4 Environmental assessment
Under the Statutory Order on landfill facilities, all existing landfill facilities had to submit a transition plan to the approval authority by 16 July 2002.
On the basis of the information in the transition plan, the approval authority will have the task of re-evaluating/environmentally assessing each facility's potential to continue
operation after 16 July 2009. This assessment will take into account all relevant environmental factors related to the design and operation of each facility, in order to ensure that
approval for continued operation is only granted to facilities that fulfil (or have the potential to fulfil) the requirements in the Statutory Order on landfill facilities.
Existing landfill facilities that cannot fulfil the requirements of the Statutory Order on landfill facilities must be ordered by the approval authority to be finally closed by 15 July
2009.
The Directive on the landfill of waste stipulates that a national strategy to reduce landfilling of biodegradable waste must be prepared by 16 July 2003. The overall goal of the
strategy is to ensure that the volume of landfilled biodegradable domestic waste (incl. waste that is similar to domestic waste) is reduced to a maximum of 35 per cent of the
volume of domestic waste produced in 1995. In contrast to many other EU Member States, Denmark already fulfils this requirement. As a result, Denmark is not required to
prepare a strategy (incl. the initiation of various measures) in relation to this EU requirement.
D 3.5 Economics
The total costs to waste producers of implementing basic characterisation for the waste types to be landfilled in the future is estimated to be of the order of DKK 100-200 million.
These expenses are expected to be incurred over approximately a two-year period (2004-2006), after the Annex of the Directive on the landfill of waste has been implemented in
Danish legislation (must be completed by 16 July 2004).
This estimate is based on a number of assumptions, as several factors will have crucial significance for how great these expenses end up being. These factors include:
- the actual requirements laid down in connection with the Danish implementation of the Annex to the Directive on the landfill of waste
- the content of a number of standards (CEN tests) currently under development
- the number of waste types that the Danish implementation stipulates are covered by the requirement for carrying out basic characterisation.
With regard to the latter point, the total number of waste types requiring characterisation will be directly dependent on how many waste types each landfill facility gains approval
for when the approval authority reassesses the transition plans for existing landfill facilities (see section D 3.1).
In addition to the costs of the basic characterisation of waste types for landfilling, there will be further costs incurred to carry out compliance tests. During the implementation of
the Annex to the Directive on the landfill of waste in Danish legislation, requirements for the scope (and frequency) of compliance tests will be laid down.
The total annual costs to waste producers for carrying out compliance tests are estimated to be in the order of DKK 5-10 million.
D 3.6 Implications for national authorities
There will continue to be a need to landfill waste in Denmark in the future – that is, waste that can neither be recycled nor incinerated.
With the adoption and implementation of the EU Directive on the landfill of waste, requirements have been laid down for the design and operation of both new and existing landfill
facilities to ensure that all facilities in operation after 16 July 2009 are subject to a uniform approval basis that ensures the environmentally responsible operation of all landfill
facilities. In particular, the implementation of the harmonisation of the Annex to the Directive on the landfill of waste will ensure that in the future, waste is only landfilled that is
deemed suitable for landfill based on an environmental assessment. If waste contains concentrations of substances that can lead to significant problems, for example, in the form of
unacceptable groundwater contamination resulting from leaching emissions from a facility, the waste in question will not be included on the facility's positive list. As a consequence,
the waste will either have to be treated (or further treated) before it can be landfilled, or disposed of in another way.
D 3.7 Implications for county authorities
According to the Planning Act [8], the county authorities are responsible for ensuring that there is adequate landfill capacity in their region. This is achieved by assessing future
landfill requirements – including the need to supply further landfill capacity during the plan period – in regular regional planning (see Appendix C2).
Under the Statutory Order on waste [9], municipalities are required to refer waste requiring landfill (that is neither recyclable nor suitable for incineration) for disposal/treatment at
a landfill facility.
Municipalities need to be very aware of which waste types a municipality can (or cannot immediately) refer to landfill in the future. This needs to be seen in the context of the
positive lists that all landfill facilities are obliged to observe once the approval authority has notified terms (for new facilities), or an order (existing facilities), to this effect. If a waste
type is not included on the positive list for a landfill facility, that type of waste cannot be landfilled at the facility until the waste type in question has been approved (by the approval
authority) and included on the facility's positive list. Since the inclusion of a waste type on a positive list requires a certain period of time to provide and assess the necessary
documentation, there may be a need for greater cooperation between municipalities across waste enterprises, etc., in order to ensure that municipalities can fulfil their referral
obligations under the Statutory Order on waste.
D.4. Households
Environmental
problem | The volume of waste from households has been increasing, but appears to now be stagnating. The recycling rate for household waste is unchanged compared to
earlier years. The energy resources in household waste are being utilised to a great extent
Household waste contains environmental contaminants, and these cause problems in waste treatment
|
Initiatives
Household waste
Domestic waste
Bulky waste
Hazardous waste
Garden waste
| Information campaign on the link between consumption and waste
Efforts to communicate information about the municipal schemes will be increased
Preparation of information and teaching materials for pre-schools, and primary and high schools
The Ministry of the Environment will develop a tool to be used to locally evaluate the environmentally and economically most appropriate management of organic
domestic waste
This will enable municipalities to assess whether two-part collection of the organic component of domestic waste should be locally introduced, and make a decision
about this
Focus on collection systems and the development of pre-treatment technologies to manage organic domestic waste
Investigate central sorting of combined domestic waste, with the aim of recycling the organic component
Increased collection and recycling of metal and plastic packaging
Increased re-use and recycling of bulky waste
Implementation of the EU Directive on waste electrical and electronic equipment by the end of 2004, including regulations for the management of refrigeration
equipment
Only wood impregnated with chromium, copper, and arsenic-containing substances may be treated as waste not suitable for incineration
Prepare new requirements for the management of PVC waste
Once the EU Directive on batteries has been adopted, the provisions of the Directive will be implemented
Improved information on hazardous household waste to increase collection
Maintain present initiatives for garden waste
|
D 4.1 Household waste
D 4.1.1 Status
Aims for 2008
- ensure that consumers have the opportunity to choose products that help prevent waste
- increased information about collection of hazardous waste from households
- 33 per cent recycling of household waste
- 60 per cent incineration of household waste
- 7 per cent landfilling of household waste
Household waste consists of domestic waste, bulky waste, and garden waste. In 2001, 29 per cent was recycled, 61 per cent was incinerated, 8 per cent was landfilled, and 1
per cent was stored temporarily. A small proportion of household waste is hazardous.
The volume of household waste was 3,083,000 tonnes in 2001. From 1995 to 2001, the volume of household waste increased by 473,000 tonnes. This increase was mainly
attributable to an increase in the volume of garden waste collected. But the volumes of domestic waste (including packaging waste), and bulky waste have also risen by 11 per
cent and 10 per cent, respectively, over the same six years.
Consumer habits have a crucial impact on the volumes of household waste. Purchasing goods with a long lifetime and high environmental quality would, all things being equal,
result in a lower volume of waste.
Household waste contains environmentally harmful waste fractions, causing problems in waste management. Residents have been given better opportunities to deliver these
fractions for separate treatment (PVC, impregnated wood, waste electrical and electronic equipment).
In most municipalities, management of household waste is financed via an overall waste collection fee. However, in recent years, a number of municipalities have introduced fees
that differentiate in relation to the amount of waste (weight or volume) in order to give households an extra incentive to make use of recycling schemes in the municipality.
Investigations have shown that it is important in municipalities with weight-based fees to monitor that the component of domestic waste that should be incinerated is not delivered
to recycling centres, rest areas, or incinerated in private boilers, etc.
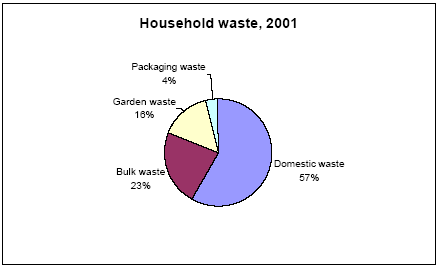
Hazardous household waste is found in both domestic waste and bulky waste. Such waste is typically residues from hazardous chemicals and products, paint residues, medicine
residues, batteries etc., which residents want to discard. Hazardous household waste must be collected separately by the municipality.
Various collection schemes currently exist in the various municipalities. The objective is to make it easy for residents to have their hazardous waste collected. Collection schemes
must be adapted to the prevailing conditions in urban and rural municipalities, and in single-family housing areas and housing estates. There will also be differences due to
variations in each municipality's structure.
Some municipalities have introduced green collection vehicles that collect hazardous waste in residential areas at certain intervals. Other municipalities have introduced kerbside
collection schemes for hazardous waste, using special containers.
Distributor schemes also exist whereby residents are able to deliver hazardous waste to shops that sell the products (medicine residues to pharmacies, paint and varnish residues
to paint shops, batteries to shops selling new batteries, etc.). In some municipalities, container schemes have been established, with collection containers placed at different urban
locations.
In addition, municipalities have established permanent recycling centres where other waste can be delivered.
Studies have shown that municipalities with kerbside collection schemes collect the largest volume of hazardous waste.
D 4.1.2 Waste prevention
Consumer waste consists primarily of end-of-life products and packaging. The volume of consumer waste is closely linked to how much is consumed and the nature of that
consumption (material products or immaterial services, products with short or long lifetimes etc). Reducing the volume of consumer waste is not an easy task.
Consumers should not be compelled to make particular consumption choices. Consumers must rather have the possibility of free choice, but this requires that each consumer be
given choices.
Private consumers need to be have the opportunity to contribute to waste prevention by:
- limiting unnecessary consumption and converting material consumption into immaterial consumption [10]
- acquiring products that are eco-labelled, have a proven, long lifetime and are easy to repair
- repairing/seeking repair for items
- participating in joint ownership schemes
- buying products in returnable packaging
- re-using products through purchase or sale
The actions of private consumers are largely controlled by external influences such as advertising, disposable income, access to relevant information, the range of goods available,
prices of goods, and the organisation of and service offered by the waste system. Private consumers are thus influenced by many of the other players in society. But there are
naturally a number of general basic needs, such as food, clothing, and housing, that must be met.
Examples of instruments that can be used to support prevention are: information campaigns, teaching materials on resource consumption and environmental problems from waste
to improve teaching in schools, promotion of products with long lifetimes, good repair opportunities for products, etc.
D 4.1.3 Future initiatives
Waste prevention
An information campaign will be carried out on the link between consumption and volumes of waste, giving specific recommendations on, for example, quality/durable products,
products manufactured from recycled materials, re-useable packaging, and packaged goods etc. The information campaign should ideally be carried out in cooperation between
the Danish Environmental Protection Agency and the National Consumer Agency of Denmark, and be coordinated with municipalities and waste enterprises. The effects from this
initiative should be seen from a long-term perspective.
Many consumption and behaviour patterns become established as children. To ensure that future residents are conscious of resource and waste problems, information and
teaching materials will be prepared for pre-schools, and primary and high schools. This material will highlight the link between increased material consumption and environmental
problems related to resource consumption and waste generation. Similarly, all children's and educational institutions should be encouraged to sort their own waste.
Product wastage at the consumer due to inappropriate packaging that is impossible or difficult to completely empty could be significantly reduced if packaging designers and
manufacturers developed packaging that it was possible to empty (see Appendix D5 Industry). This would lead to reductions in both the volume of packaging waste and organic
waste in the form of food items in domestic waste.
Other
In order to achieve the objectives for domestic waste, garden waste and bulky waste, it will be necessary for residents to be involved and to participate actively in the various
collection schemes. This means that municipal communication efforts will need to be increased in order to achieve the best possible awareness of the specific waste collection
schemes.
Residents need to be informed about what items are hazardous waste and how municipal schemes function.
D 4.1.4 Regulation
The management of household waste, including hazardous household waste is regulated by the Statutory Order on waste [11]. Waste must be collected by the municipality. Rules
on hazardous household waste have been clarified in a guideline on hazardous waste.
On 1 January 1997, a ban was introduced on the landfilling of waste suitable for incineration.
D 4.1.5 Environmental assessment
Waste prevention reduces resource consumption and the volume of waste requiring treatment.
Improved collection of hazardous waste will ensure environmentally appropriate management of waste.
D 4.1.6 Implications for national authorities
An information campaign on consumption and waste must be carried out.
Information and teaching materials will be prepared for pre-schools, and primary and high schools, with the aim of highlighting the link between increasing consumption and
environmental problems related to resource consumption and waste generation.
D 4.1.7 Implications for municipal authorities
It is important that municipalities focus their information initiatives on the link between residents' consumption and the increasing volumes of waste – and the behavioural changes
that might contribute to reducing the volume of waste.
Municipalities and counties should introduce waste separation in all their children's and educational institutions.
It is important that municipal authorities inform residents about the municipal schemes for hazardous waste.
D 4.2 Domestic waste from households
D 4.2.1 Status
Paper and glass are currently collected separately under the regulations in the Statutory Order on waste, while the separate collection of organic domestic waste is less
widespread.
A limited amount of metal and plastic packaging is currently collected for recycling in some municipalities.
Aims for 2008
- 20 per cent recycling of domestic waste
In 2001, the volume of domestic waste, including packaging waste, was 1,808,000 tonnes. Compared to 1995, the volume of domestic waste has risen 11 per cent. In 2001, the
recycling rate was 16 per cent [12]. The total volume of domestic waste for incineration and landfilling has been stable for a long period.
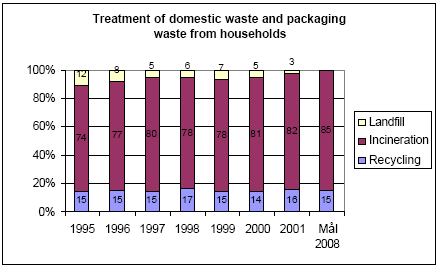
Source: Waste Statistics 2001, Danish Environmental Protection Agency 2003
Municipalities that do not have collection schemes for paper and cardboard have reported the collected volumes to the Danish Environmental Protection Agency for 2001. If the
ISAG figures for the municipalities that do have collection schemes are added, a total of 237,000 tonnes of paper and cardboard have been collected from households in 2001.
This is equivalent to 59 per cent of the potential for recyclable paper and cardboard from households.
Packaging waste accounts for around one quarter of domestic waste, corresponding to 425,000 tonnes, of which 30 per cent is materially recycled and the remaining 70 per cent
is incinerated.
Two thirds of the incinerated packaging is made up of cardboard, paper, and plastic. The rest is glass, tin-plate, and aluminium packaging. Glass is not suitable for incineration,
whereas a small proportion of aluminium packaging is recovered. Thin aluminium foil can be combusted, whereas aluminium cans do not combust in incineration plants. Tin-plate
packaging can be recovered after incineration. The iron is separated from the slag using magnets and sold as incineration scrap, but the loss of metal is very great.
The table below shows the total volume of domestic waste collected in 2001 via municipal collection schemes, amounting to approx. 1.14 million tonnes per annum from all
households in Denmark [13].
This figure has been derived from an analysis of the composition of domestic waste based on the collection of domestic waste from approx. 2,000 households in a number of
different municipalities. These figures therefore do not include glass/bottles and paper separated for recycling and collected separately. The calculations are based on 2,398,389
households nationwide, including permanently inhabited holiday houses.
In Waste Statistics, the total volume of domestic waste in 1998 was calculated to be 1.7 million tonnes. After a slight decrease in the volume of domestic waste in 1999 and 2000,
the figure for 2001 was calculated to be 1.8 million tonnes. These figures include glass and paper collected via separate collection schemes. These 1.8 million tonnes of waste
include a small, but unknown, volume of domestic waste from commercial enterprises. Recyclable paper and glass collected from households is calculated to be approx. 300,000
tonnes in ISAG. There is no equivalent calculation for how much waste from commercial enterprises is collected with domestic waste.
For the analysis of the composition of the collected domestic waste, the waste is sorted into 19 fractions, as shown in the table.
Generated domestic waste divided into type of residence per week and nationwide
Fraction | Apartments National avg.
Kg/household
Per week4)
| Single-family houses National avg. Kg/household
Per week5)
| Apartments1) Tonnes/year
| Single-family houses2) Tonnes/year
| All households3) Tonnes/year
| Relative distribution (%) Tonnes/year
|
Unprocessed vegetable | 1.69 | 2.32 | 83,803 | 174,298 | 258,101 | 22.6 |
Other vegetable waste | 0.65 | 0.93 | 32,232 | 69,870 | 102,102 | 8.9 |
Animal waste | 0.77 | 1.00 | 38,183 | 75,129 | 113,311 | 9.9 |
Recyclable paper | 0.96 | 0.98 | 47,604 | 73,626 | 121,230 | 10.6 |
Blotting paper | 0.32 | 0.29 | 15,868 | 21,787 | 37,655 | 3.3 |
Other clean, dry paper | 0.17 | 0.20 | 8,430 | 15,026 | 23,456 | 2.1 |
Other dirty paper | 0.45 | 0.76 | 22,314 | 57,098 | 79,412 | 7.0 |
Recyclable Plastic packaging
| 0.19 | 0.23 | 9,422 | 17,280 | 26,701 | 2.3 |
Other plastic | 0.54 | 0.68 | 26,777 | 51,087 | 77,865 | 6.8 |
Garden waste etc. | 0.24 | 0.51 | 11,901 | 38,316 | 50,217 | 4.4 |
Nappies etc. | 0.70 | 0.52 | 34,711 | 39,067 | 73,778 | 6.5 |
Other suitable for incineration | 0.43 | 0.50 | 21,323 | 37,564 | 58,887 | 5.2 |
Glass packaging | 0.21 | 0.25 | 10,413 | 18,782 | 29,196 | 2.6 |
Other glass items | 0.03 | 0.029 | 1,488 | 2,179 | 3,666 | 0.3 |
Metal packaging | 0.18 | 0.29 | 8,926 | 21,787 | 30,713 | 2.7 |
Other metal items | 0.07 | 0.045 | 3,471 | 3,381 | 6,852 | 0.6 |
Other not-suitable for incineration | 0.33 | 0.36 | 16,364 | 27,046 | 43,410 | 3.8 |
Composite products | 0.02 | 0.010 | 992 | 751 | 1,743 | 0.2 |
Hazardous waste | 0.01 | 0.018 | 496 | 1,352 | 1,848 | 0.2 |
Total waste | 7.96 | 9.94 | 394,718 | 746,778 | 1,141,496 | 100.0 |
Source: Petersen, Claus (2002): "Evaluation of home composting schemes and analysis of the composition of domestic waste" and Statistics Denmark 2002 – Households
divided by area, type of residence and time, as of 1 January 2001
Apartments include: multi-family buildings (924,609 households) and student residences (29,000 households). 953,609 households in total.
Single-family houses include: farmsteads (122,336 households), terrace houses and duplexes (311,974 households), detached houses (996,156 households) and (permanently
inhabited) holiday houses (14,314 households). 1,444,780 households in total.
Multi-family buildings (953,609 households) and single-family houses (1,444,780 households). 2,398,389 households in total.
The calculations do not include joint households (institutions, etc.) (13,497 households) and other permanent residences (13,699 households). As of 1 January 2001, 198,860
holiday houses were registered, of which only a small proportion were registered as permanently inhabited.
1) No. of people in household: 1.9.
2) No. of people in household: 2.4.
D 4.2.2 Future initiatives
Measures
- develop a tool to evaluate the significance of local factors on the management of organic domestic waste
- municipalities can make decisions on the management of organic domestic waste
- focus on collection costs and the development of pre-treatment technologies to manage organic domestic waste
- investigate central separation of combined domestic waste
- value other environmental effects relating to the management of organic domestic waste
- collect metal and plastic packaging for recycling
Recycling
A tool will be developed to help municipalities evaluate whether incineration, biogasification or composting of the organic component of domestic waste is best. This will enable
municipalities to assess which treatment for organic domestic waste is environmentally and economically most effective and make decisions accordingly.
Further work will also be done on developing cheaper collection methods and improving pre-treatment technology. As an alternative, the options for centrally sorting combined
domestic waste will be investigated. These investigations will focus on working environment conditions and the quality of the separated materials. Central sorting will only be
promoted if it is found to be a good idea in terms of the environment and the working procedure.
The collection of metal and plastic packaging for recycling will be increased.
From 2005, municipalities will be required to give residents the opportunity to separate certain items of plastic packaging and deliver them for recycling, for example at recycling
centres. Residents must also be given the opportunity to separate metal packaging for recycling, for example, by delivering it to recycling centres or via certain bulky waste
schemes.
The volume of paper collected for recycling will be maintained at the goal for 2004.
See also discussion of the separate fractions in Appendix E.
D 4.2.3 Regulation
In areas with more than 1,000 inhabitants, domestic waste must be collected [14]. In rural areas, waste must be assigned to treatment. Mixed domestic waste must be assigned to
incineration.
Municipalities are required to collect paper, divided into a number of categories, for recycling, from private residential areas with more than 1,000 inhabitants, using permanent
collection equipment. Municipalities must also collect other paper and cardboard, including cardboard packaging, in residential areas with more than 1,000 inhabitants. However,
municipalities are not required to fulfil these regulations if they have collected 40 per cent and 55 per cent of the recyclable paper and cardboard potential from households in
2001 and 2002, respectively. In future, municipalities will only be required to fulfil the above regulations if the collected volume is less than 55 per cent of the recyclable paper and
cardboard potential for two consecutive calendar years, starting from 2003.
Municipal councils may establish collection schemes or other joint schemes for other fractions.
Residents, freeholders, enterprises, and institutions have a duty to use municipal schemes.
Municipal councils may assign waste suitable for incineration to temporary storage for a maximum period of one year. Domestic waste and other perishable waste may not be
assigned to temporary storage.
D 4.2.4 Environmental assessment
Increased recycling reduces resource consumption and volumes of waste for incineration.
Recycling plastic and metal ensures the resources in waste are utilised and reduces the total environmental impact from the management of these waste fractions.
D 4.2.5 Economic evaluation
It is estimated that collection schemes for metal and plastic packaging from households would cost approx. DKK 2 million per annum in increased expenses. If it becomes
necessary to implement further initiatives in order to achieve the goals in the Packaging Directive, the expenses for households may increase.
D 4.2.6 Implications for national authorities
The Ministry of the Environment is initiating the development of a model for local evaluation of which treatment for organic domestic waste is most appropriate, in terms of the
environment and costs.
Regulations will be formulated for the collection of iron and metal packaging.
D 4.2.7 Implications for municipal authorities
Municipalities can locally evaluate which treatment for organic domestic waste is environmentally and economically optimal.
Collection schemes will be established for metal and certain types of plastic packaging from households.
D 4.3 Bulky waste
D 4.3.1 Status
Aims for 2008
- 25 per cent recycling
- 50 per cent incineration
- 25 per cent landfilling
Recycling of bulky waste can be increased through improved separation of household waste.
Many municipalities have established manned recycling centres in recent years. However, there are big variations in which waste fractions (and how many) are separated.
Recycling centres are often supplemented by separate collection schemes.
With more stringent requirements for separation of waste fractions or special treatment for bulky waste schemes, residents can actively contribute to increasing recycling.
The volume of bulky waste has been increasing, in part due to the increased prevalence of separate collection schemes and manned recycling centres. A significant quantity
of waste is therefore no longer being disposed of in other ways. Between 1996 and 1998, the volume decreased by 67,000 tonnes. However, between 1998 and 2000,
the volume of bulky waste increased again by 158,000 tonnes.
In 2001, the volume of bulky waste was 680,000 tonnes. Of this, 18 per cent was recycled, 49 per cent incinerated, and 26 per cent landfilled. Six per cent was
temporarily stored.
Due to different methods of calculation in local administrations, figures for bulky waste are uncertain – in some administrations, bulky waste is included under industrial
waste. Aims for recycling, incineration, and landfilling should therefore be evaluated with caution [15].
The ban on landfilling of waste suitable for incineration introduced on 1 January 1997 has reduced the volume of bulky waste landfilled.
It is not feasible to calculate the environmental and cost-benefit effects of alternative forms of treatment for the many hundreds of different products that end up in bulky
waste. Municipalities will therefore have to base their evaluations of which types of products should be directed to recycling on the waste indicators for the various material
types, and on the potential markets for the various fractions.
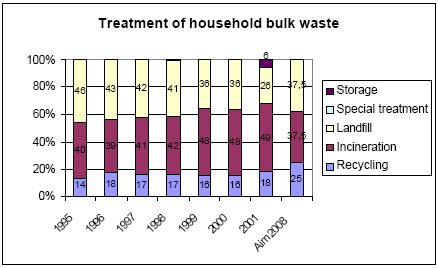
Source: Waste Statistics 2001
D 4.3.2 Future initiatives
Bulky waste is an area that requires local solutions and where there are advantages in building networks.
Waste prevention
The Ministry of the Environment will encourage municipalities to participate in establishing or improving existing re-use schemes. There are many examples of very
well-developed schemes that ensure that re-usable products do not end up in the waste system. These schemes are established by municipalities, often in cooperation with
charities, or by charities alone. Examples include: shops selling second-hand items – sometimes combined with repair workshops, second-hand markets on the Internet,
collection schemes for re-usable products from households, and an Internet-based repair guide. Setting aside a special area at municipal recycling centres for the collection
of re-usable items, in combination with marketing or sales, would significantly increase the re-use of bulky waste.
Measures
- encourage municipalities to increase the re-use of bulky waste
- promote the expansion of bulky waste schemes to include further recyclable waste fractions
- establish networks for personnel involved in bulky waste schemes
- disseminate experience from the re-use and recycling of bulky waste in apartment buildings
- implement the EU Directive on waste electrical and electronic equipment, including regulations for the management of refrigeration equipment
- new requirements for the management of PVC waste
Recycling
The Ministry of the Environment will encourage municipalities to extend municipal bulky waste schemes to cover many more recyclable waste fractions. A number of
municipalities have extended bulky waste schemes to cover more than 20 fractions, leading to a much greater proportion of bulky waste being separated for recycling, and
reducing the volumes of waste collected in the suitable for incineration and not suitable for incineration fractions.
Municipalities will be encouraged to establish networks for staff at recycling centres and involved in collection schemes for bulky waste, to allow them to share practical
experience with increasing the re-use and recycling of bulky waste, including knowledge of potential markets for the many material fractions and products in bulky waste.
The Ministry of the Environment will also encourage building associations and other apartment buildings to establish bulky waste schemes to ensure that re-usable items do
not end up in the waste system (exchange centres), and that recyclable waste fractions are separated for recycling. Experience from existing schemes should be collected
and disseminated to a wider circle of caretakers, property administrators and housing associations, e.g. via the Danish Centre for Urban Ecology.
Waste collection staff and property administrators should be in close contact with residents to inform them about correct separation of their waste, with the particular aim of
increasing the re-use and recycling of bulky waste. Municipalities will therefore need to take the initiative to train and instruct janitors, caretakers, waste collection staff and
staff at recycling centres, to equip them to give better advice to residents about waste separation.
The new EU Directive on waste electrical and electronic equipment must be implemented in Danish legislation by the end of 2004. Implementation of this directive will
mean changes to requirements, and that more products will be subject to separate treatment, including refrigeration equipment. The directive is based on producer
responsibility.
Impregnated wood containing chromium, copper and arsenic-containing substances will continue to be treated as waste not suitable for incineration, and landfilled. When
better treatment methods have been developed, these types of impregnated wood will be collected separately. Requirements for the management of certain types of
impregnated wood will be introduced on the basis of an environmental and cost-benefit assessment.
Efforts will be made to ensure that PVC waste is managed in an environmentally appropriate manner. This can be achieved by drafting requirements for the collection and
management of PVC waste.
D 4.3.3 Regulation
Municipalities must assign treatment methods for bulky waste and must ensure that residents separate waste suitable for incineration.
Management of waste electrical and electronic equipment has so far been regulated by general rules in the Statutory Order on waste, the Statutory Order on management
of waste from electrical and electronic products, and through environmental approvals for enterprises managing, reprocessing or disposing of this waste fraction.
Collection and management of CFC-containing refrigeration equipment is covered by an agreement between the Minister for the Environment and relevant associations on
the disposal of CFC-containing refrigeration equipment, as well as in a Circular [16] on municipal regulations on disposal of CFC-containing refrigeration equipment.
D 4.3.4 Environmental assessment
Efforts to increase re-use and recycling will ensure the utilisation of resources in waste and reduce the need for incineration and landfill capacity.
It is estimated that the initiatives for waste prevention can reduce the volume of bulky waste by 2-4 per cent.
D 4.3.5 Economic evaluation
No economic evaluations of initiatives to increase the re-use and recycling of bulky waste have been carried out.
D 4.3.6 Implications for national authorities
The Ministry of the Environment will ensure that material is sent to municipalities and housing associations, etc., on the options for increasing the re-use and recycling of
materials in household bulky waste. The Ministry of the Environment will encourage municipalities to establish networks for staff involved in bulky waste schemes.
D 4.3.7 Implications for municipal authorities
Municipalities must consider and implement possible improvements to bulky waste schemes, so that re-use and recycling can be significantly increased. Municipalities
should establish networks of personnel involved in bulky waste schemes/at recycling centres, with the aim of promoting experience exchange.
Municipalities should take the initiative to ensure that janitors, caretakers, waste collection staff and staff at recycling centres are trained and instructed, to equip them to
give better advice to residents about waste separation.
D 4.4 Garden waste
D 4.4.1 Status
Aims for 2008
- 95 per cent recycling of garden waste
A total of 99 per cent of garden waste was recycled in central composting plants in 2001, exceeding the aim of 95 per cent for 2004. As a consequence, landfilling
of garden waste decreased from 10 per cent in 1994 to one per cent in 2001. It is not expected to be possible to further increase the rate of recycling for garden
waste.
Home composting has been promoted for a number of years through information material and campaigns, and municipalities have voluntarily established schemes and
composting plants for garden waste. Garden waste initiatives are considered to have been a success.
In addition to home composting, garden waste is collected via municipal recycling schemes. Volumes have increased considerably in recent years, from 290,000
tonnes in 1994 to 458,000 tonnes in 2001. This is due to increased use of the schemes and improved collection of data on garden waste.
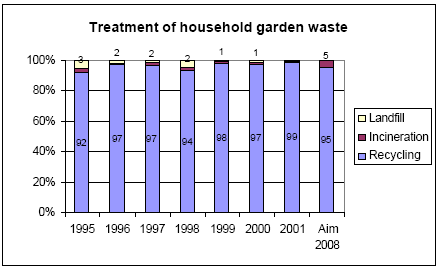
Source: Waste Statistics 2001
D 4.4.2 Future initiatives
Measures
- maintain present initiatives
Present efforts will be maintained, and no new initiatives are called for.
D 4.4.3 Regulation
Municipalities must assign garden waste to treatment. Garden waste can be treated in home composting without permission from municipal councils, as long as the relevant
regulations are complied with.
Incineration of waste is only permitted in approved plants. Municipalities may permit private burning of garden waste.
D 4.4.4 Implications for national authorities
None.
D 4.4.5 Implications for municipal waste authorities
Municipalities will continue their information initiatives regarding schemes for home composting and/or collection and central composting, and will ensure that the present
recycling rate for garden waste is maintained.
D.5. Industry
Environmental
problem | Increasing volumes of waste from industry – a large proportion of which is landfilled |
Initiatives | Guidelines on waste reduction conditions for enterprises both subject to and exempt from approval
Improved information on waste in green accounts, environmental management, environmental approvals, and through sector-specific briefings
Develop and improve tools to help enterprises and commercial waste consultants in relation to the analysis and minimisation of enterprise waste generation and
management
Develop recycling technologies that make it possible to recycle enterprise production waste internally within the enterprise
Establish a knowledge base for new treatment and recycling methods
Develop alternative recycling for packaging glass and plane glass
Develop reprocessing methods for problematic flows of waste, e.g. impregnated wood, PVC and shredder waste
Investigate the possibility of directing animal waste to biogasification, especially abattoir waste, and the possibility of recovering phosphor from slag from the
incineration of meat-and-bone meal
Lay down requirements for increased recycling of plastic components from vehicles and utilise a greater proportion of waste from end-of-life vehicles
Initiate information campaigns to limit damage during fitting, and promote the sale of retreaded tyres
Implement the EU Directive on waste electrical and electronic equipment, including regulations for the management of refrigeration equipment and producer
responsibility
Develop environmentally-friendly packaging and improve packaging design to allow complete emptying
Improve the collection of plastic packaging from trade and industry
Increase the recycling of wooden and metal packaging, hazardous waste, and waste with a high environmental impact
Increase the re-use and recycling of large plastic containers
Special initiatives aiming sectors that landfill large volumes of waste (for example foundries and scrap enterprises)
|
Aims for 2008
- 65 per cent recycling of waste from industry
- maximum of 15 per cent landfilling
- improved collection of hazardous waste
D 5.1 Status
Industrial waste in this connection refers to waste from discarded products and production waste from manufacturing enterprises.
Waste prevention must be improved, and recycling of industrial waste must be increased - including hazardous waste. Environmentally harmful waste fractions must be
separated, and separate treatment technologies must be developed so that energy and raw material resources are utilised to a maximum extent.
The volume of industrial waste has reduced by 11 per cent from 2000 to 2001. In 2001, the volume of waste was 2,616,000 tonnes. The recycling aim for 2008 is 65 per
cent, and the volume of landfilled waste must not exceed 15 per cent [17].
Continued focus will therefore be given to industrial waste and the loss of resources connected with waste generation. In future, information on waste generation, waste
composition, and options for separating environmental contaminants from waste will be important elements in green accounting and environmental approvals, as well as in
environmental management.
The green accounts were evaluated in late 1999. On the basis of this evaluation, the regulatory base has been adjusted.
In 2001, 22 per cent of waste was landfilled, 65 per cent was recycled, and 12 per cent was incinerated [18]. The volume and composition of industrial waste vary greatly
and depend on the sector generating the waste, and the size and number of enterprises. The options for recycling or reducing volumes of waste are therefore very different
from one waste fraction to another, and from one sector to another.
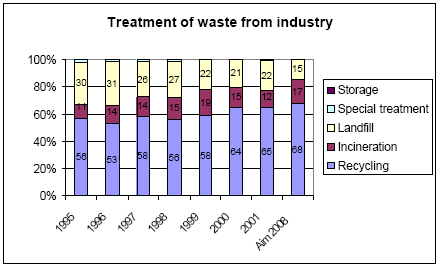
Source: Waste Statistics 2001, Danish Environmental Protection Agency 2003.
For sectors containing many small enterprises, it may be crucial to collect waste in larger units, to provide the necessary supply and economic basis for recycling.
The figure below shows a summary of industrial waste divided by form of treatment. The figures shows that the "iron and metal", "suitable for incineration", "not suitable for
incineration", and "beet soil" fractions account for the largest volumes of industrial waste.
Fig. 8. Waste from production, etc., 2001, divided into mixed and separated fractions
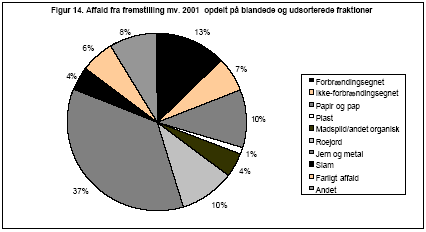
Summary of waste from manufacturing enterprises divided by form of treatment
Source: Waste Statistics 2001, Danish Environmental Protection Agency 2003
The "not suitable for incineration" fraction is mainly landfilled. This fraction primarily contains beet soil, foundry waste, and waste from scrap enterprises. Consideration
should be given to whether it is possible to recycle beet soil instead of landfilling this fraction.
A project has been carried out to identify where the largest and most important volumes of waste are generated in the industrial sector. Using a screening method, the most
important flows of waste produced by waste-intensive sectors have been identified. The sectors identified were: the pharmaceutical industry, the electronics industry, iron
and metal and the furniture industry. The volume and types of waste from these sectors have been analysed and the disposal channels have been evaluated.
The evaluation showed that the most harmful fractions come from the iron and metal industry. The volumes of waste analysed within the other sectors are estimated to
represent either small volumes, or waste with relatively low environmental impact. It was found that waste from these sectors is being disposed of in a responsible manner.
The volume of waste can possibly be reduced or recycled to a greater extent.
BAT – Best Available Techniques
Following up on the IPPC Directive, the European Commission, supported by national experts, regularly prepares "BAT Reference Documents" – or BAT notes –
containing information on best available techniques within a number of sectors. BAT refers to the technique that is technically possible and economically viable for a
particular type of enterprise. BAT notes are primarily issued for IPPC enterprises. The information for non-list enterprises is limited.
The aim of the BAT notes is to provide information about the level of contamination that can be achieved using the best available technology. Energy consumption and
waste generated from production are included as an integrated part of this assessment. The technology specified in the BAT notes becomes the standard within the
particular branch of enterprises.
The European Commission also intends to prepare BAT notes for reprocessing technologies.
D 5.2 Waste prevention
Waste from enterprises is largely process and packaging waste. Manufacturing enterprises play the role of both producer, and consumer of raw materials, components, and
semi-finished goods from suppliers. They can contribute to waste prevention by:
- analysing the enterprise's waste generation and resource consumption
- minimising wastage in the production process
- using quality management systems that contribute to reduced production errors
- demanding products for use in enterprise operations that have a long lifetime, are easy to repair, can be upgraded and are produced with waste prevention in mind
- demanding raw materials produced with waste prevention in mind
- purchasing raw materials and semi-finished goods in returnable packaging
- marketing products that have an eco-label or environmental declaration
- designing products that have a long lifetime, are easy to repair, can be upgraded and for which components can be re-used and packaging consumption minimised
When manufacturing products, enterprises need to take into account demand, market price, costs, technological factors in production, product quality and functionality, and
current laws, standards and codes. Thus there are many factors that have influence on an enterprise's decisions in relation to waste prevention initiatives.
A number of administrative tools can help to generate greater focus on waste from enterprises. These include: Part 5 conditions, green accounting, eco-management, and
environmental management. Economic mechanisms can also be brought into play in order to reduce volumes of waste from enterprises. Within this category, initiatives such
as changes to depreciation rules, duties on raw materials, reduced tax deductions for advertising, etc., can be considered.
D 5.3 Future initiatives
Waste prevention
Information on volumes of waste, composition, and potential for recycling will be improved in future preparation of environmental approvals, green accounts, and in the
establishment of environmental management in enterprises, or through sector agreements.
Environmental approvals will be improved in the area of waste management. With the implementation of the IPPC Directive [19] in Statutory Order no. 646 of 29 June
2001 on approval for specially polluting activities, the waste component has been given higher priority. Section 13(2)(4) of the Statutory Order states that enterprises must
take the necessary steps to avoid waste generation, and where this is not possible, to exploit the potential for recycling and recirculation.
Measures
- focus on waste in environmental approvals, green accounts, and environmental management
- guidelines and conditions for waste reduction or the establishment of sector agreements
- refine the existing waste analysis model
- promote internal recycling of waste from enterprises
- improve packaging design so that it can be emptied
- increase the re-use of large plastic containers
- establish a knowledge base for commercial waste consultants
- develop alternative recycling options for glass packaging and plane glass
- separate recyclable fractions from waste suitable for incineration
- requirements for increased recycling of a number of fractions
Assessment will be made as to whether increased use of environmental management in enterprises can be best achieved through sector agreements or whether guidelines on
conditions for waste reduction need to be prepared for enterprises subject to and exempt from approval. These guidelines could also describe BAT's to help reduce waste,
etc., for a number of waste-intensive enterprises, and the significance of BAT's in relation to the maximum waste volumes.
The existing waste analysis model will be refined so that it can also be used in large enterprises and in the service sector.
Recycling of enterprises' internal waste will be promoted.
In 2003, a sector initiative was launched for packaging, aimed at ensuring that better packaging systems are developed based on life-cycle analysis, including the
development of tools and documentation for minimising material consumption for each type of packaging, and practical tools for using life-cycle assessments in the design of
packaging and packaging systems.
Product wastage at the consumer due to inappropriate packaging that is impossible or difficult to completely empty could be significantly reduced if packaging designers
and manufacturers developed packaging that it was possible to empty. Packaging manufacturers and producers who fill packaging will therefore be encouraged to develop
and use better packaging that reduces wastage. This issue will also be incorporated into the sector initiative for packaging.
Based on an economic assessment, efforts should be made to ensure that large plastic containers (over 20 litres) from industrial enterprises are re-used. It is therefore
expected that regulations will be implemented, requiring large containers to be collected for re-use or recycling (see Appendix E).
Recycling
In 2001, "Description and assessment of consultancy schemes for industrial waste in local authorities and waste management companies" was published as Environment
Project no. 583. In response to one of the recommendations of the report, an electronic knowledge base will be established in the form of a website aimed at commercial
waste consultants, providing information that consultants can use in their daily work. The website will be set up under Waste Centre Denmark's website.
The agreement on transport packaging will be extended to include more materials and commercial packaging types. Commercial metal packaging must be referred to
recycling. The collection of plastic film from trade and industry will be improved. Enterprises and municipalities will have to give greater focus to separating plastic film for
recycling. Sector associations for waste producers must be able to establish nationwide collection schemes.
Development activities will be initiated aimed at developing alternative recycling processes for glass fragments.
Waste suitable for incineration contains recyclable fractions that must be separated because they can be recycled, or contain environmental contaminants. In future, industry
must separate paper and cardboard, plastic packaging, electrical and electronic equipment, PVC, iron and metal packaging, and impregnated wood (see Appendix E).
The EU Directive on waste electrical and electronic equipment, based on producer responsibility, must be implemented (see Appendix E).
An investigation will be carried out into the options for recycling greater volumes of animal waste for agricultural purposes through biogasification (see Appendix E).
Requirements will be laid down for increased recycling of plastic components from vehicles and utilising a greater proportion of waste from end-of-life vehicles (see
Appendix E).
An information campaign will be launched to limit damage during fitting and promote the sale of retreaded tyres (see Appendix E).
A strategy will be prepared for the management of hazardous waste (see Appendix E).
Landfilling
In general, too much industrial waste is landfilled. Specific initiatives will be carried out, targeting individual fractions and sectors. See Appendix E on foundry and shredder
waste, electronic equipment, refrigeration equipment, and end-of-life vehicles.
D 5.4 Regulation
Under Statutory Order no. 646 of 29 June 2001 on approval for specially polluting activities, before issuing approvals, authorities must assess whether an enterprise has
taken the necessary precautions to prevent contamination, including waste generation.
Management of industrial waste is regulated in the Statutory Order on waste [20]. Enterprises are responsible for knowing the composition of waste, assessing whether
waste is hazardous, and notifying the municipality if it is.
Municipalities must assign disposal options for industrial waste. Municipalities must also establish collection schemes for hazardous waste from enterprises.
Special Statutory Orders have also been prepared for the following specific flows of waste:
- Statutory Order no. 655 on recycling of residues and soil for building and construction purposes.
- Statutory Order no. 1067 of 22 December 1998 on management of waste from electrical and electronic products.
Enterprises are currently required to separate cardboard, paper, paper board, steel drums, electrical and electronic equipment, PVC, impregnated wood and plastic
transport packaging for recycling [21] and special treatment/landfilling.
D 5.5 Environmental assessment
Greater focus on enterprise production waste will increase opportunities for recycling, and minimise waste generation and landfilling.
The specific requirements laid down in relation to collection and reprocessing in the special Statutory Orders increase the opportunities for recycling some of the most
problematic flows of waste and minimise the environmental risks associated with disposal of the remaining waste.
Increased separation of environmentally harmful waste fractions will lead to better recycling opportunities for residues. Separation of recyclable fractions from the waste
suitable for incineration fraction will also mean that resources in waste are utilised, and that the need for incineration capacity is reduced.
D 5.6 Implications for national authorities
Packaging manufacturers and producers who fill packaging will be encouraged to develop and use better packaging that reduces wastage.
The EU Directive on waste electrical and electronic equipment must be implemented.
The collection of plastic and metal packaging from industry will be improved.
Requirements are expected to be laid down stipulating that large plastic containers must be collected for re-use or recycling.
The volume of wooden packaging will be analysed and an estimate will be made for how the goal of 15 per cent recycling will be achieved.
A number of sector-specific briefings will be prepared.
D 5.7 Implications for municipal and county authorities
Use of Chapter 5 approvals in connection with waste minimisation and increased recycling of enterprise production waste will place greater demands on county
competence in particular.
Municipalities must extend the collection and source separation of cardboard, plastic, impregnated wood, and waste electrical and electronic equipment, and must assign
separated waste fractions for recycling, landfilling, or special treatment.
D.6. Institutions, trade and offices
Environmental
problem | Volumes of waste are increasing dramatically. Currently, less waste is recycled than desired, and consequently resources are lost.
Waste from the trade and service sector contains environmental contaminants that must be separated for separate treatment
|
Initiatives | Encourage the trade and repair sector to use re-usable boxes in transport and logistic systems
Develop and improve tools to help enterprises and commercial waste consultants in relation to the analysis and minimisation of enterprise waste generation and
management
The management of organic waste from the trade of convenience goods will be evaluated
The collection of plastic packaging will be improved
Investigate how the recycling of wooden packaging can be organised
Prepare draft requirements for the management of PVC waste
The EU Directive on waste electrical and electronic equipment must be implemented by the end of 2004
Prepare environmental guidelines for public purchasers of a number of electrical and electronic products and eco-labelling criteria for several products
Regulations for the management of refrigeration equipment will be included in a revised Statutory Order on management of waste electrical and electronic
equipment
More stringent requirements for the management of waste from vehicles and the separation of recyclable and environmentally harmful fractions
Information campaign to promote the use of retreaded tyres
|
D 6.1 Status
Aims for 2008
- 50 per cent recycling
- 45 per cent incineration
- 5 per cent landfilling
This sector covers waste from institutions, trade, and private and public offices, i.e. the trade and service sector.
The volume of waste from the trade and service sector is increasing dramatically. Recycling of waste from this sector must be increased, and environmentally harmful
fractions must be separated for special treatment. Enterprises and public and private institutions play an important role in increasing the separation of recyclable materials
and environmentally harmful fractions.
In 2001, the total volume of waste was 1,307,000 tonnes [22]. The volume of waste from the trade and service sector increased dramatically by over 25 per cent from
1994 to 1995, but has only risen by between one and two per cent per annum between 1995 and 1997. Between 1999 and 2001, there was again a dramatic increase of
17 per cent per annum.
In 2001, the rate of recycling was 36 per cent, which is below the objective of 50 per cent for 2004. 49 per cent of waste was incinerated, and 12 per cent landfilled. A
further three per cent was stored temporarily. Since there has been a significant increase in the volume of waste from the trade and service sector, it is not expected to be
possible to increase the rate of recycling. The aim for recycling has therefore been maintained at 50 per cent. It is still the case that it is not expected that landfilling can be
completely avoided.
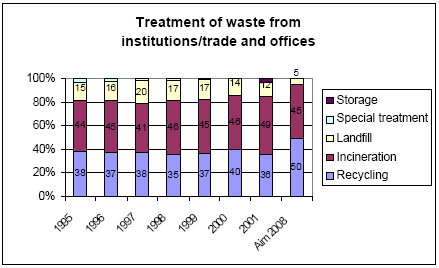
Source: Waste Statistics 2001
Waste consists of many different waste fractions. With the aim of supporting targeted initiatives for the sector as a whole, an investigation has been carried out into the
composition of waste in a number of industries within the service sector: trade of convenience goods, other retail trade, garages, hotels, etc., schools and institutions, and
office enterprises. An analysis of the volume of waste from the trade of convenience goods has been carried out using classifications in a number of shops. If the volumes
found are extrapolated to the national level, there are approx. 212,000 tonnes of waste annually. Of this amount, approx. 38 per cent was cardboard, approx. 22 per cent
was organic waste, and approx. 39 per cent was waste suitable for incineration [23]. An investigation of the volume of waste in a number of other sub-sectors within the
area of trade, offices and institutions has also been carried out. This analysis showed that there was a significant potential for recycling larger quantities. But there are large
variations in the volume of waste between sectors and between enterprises in the same sector [24].
Many municipalities and waste enterprises have established schemes involving waste consultants, with the aim of increasing information on municipal regulations and guiding
enterprises towards more appropriate waste management. An evaluation of the schemes revealed that approx. 200 municipalities were covered by a consultant scheme in
2000. The evaluation also showed that the schemes are successful in drawing attention to waste from enterprises, leading to better separation of environmental
contaminants and the movement of waste from landfilling and incineration to recycling.
D 6.2 Waste prevention
Measures
- encourage the trade and repair sectors to use re-usable boxes for transport packaging
- refine the existing waste analysis model
- evaluate the management of organic waste from the trade of convenience goods
- increase the collection and recycling of plastic packaging
- sector associations for waste producers must be able to establish nationwide collection schemes for plastic film
Waste from the trade and service sector consists mainly of end-of-life products. Initiatives in this sector should be targeted at helping the service sector to be better at
providing immaterial services, so that the population can shift from material consumption to immaterial consumption. It is important that the sector is able to provide services
that can increase product lifetimes, e.g. repair services. The volume of waste from the sector can be further reduced by using standardised re-usable packaging within the
sector.
Service enterprises and the trade sector play an important role in waste prevention since they both purchase goods (and can hence place demands on suppliers) and offer
goods/services for sale to consumers (and can thus influence demand).
Service enterprises can contribute to waste prevention by:
- providing services (e.g. repair services ) that ensure that product lifetimes are increased
- demanding and consuming products that have a long lifetime, are easy to repair, and are produced with waste prevention in mind
- using products shipped in returnable packaging
- introducing administration procedures to prevent waste generation
- marketing leasing schemes in which product lifetimes are optimised through component re-use and maintenance
The trade sector can contribute to waste prevention by:
- purchasing and selling eco-labelled products, produced with waste prevention in mind, shipped in packaging that has been minimised or is returnable
- demanding products for use in enterprise operations that have a long lifetime, are easy to repair, and are produced with waste prevention in mind
- providing storage and transport systems that minimise packaging and using return systems for transport packaging
- participating in deposit and return systems for retail sales packaging
- carrying out information campaigns that promote the sale of environmentally-friendly products
D 6.3 Future initiatives
A number of the initiatives launched in this sector will be targeted towards specific fractions.
Waste prevention
Steps need to be taken to encourage the trade and repair sectors to make greater use of re-usable transport packaging and extend, improve and optimise the use of
returnable transport packaging, as, for example, is seen today for milk crates and boxes for fruit and vegetables. These are used for transportation and can be directly use
in shops to present goods. Another example is Toyota Denmark, who have begun using specially-produced re-usable boxes for smaller items. These items were previously
transported in cardboard boxes that were discarded after being used once. This initiative has achieved savings in excess of DKK 1 million in the transport and logistics
system.
- Investigate how the recycling of wooden packaging can be organised
- collect PVC in an environmentally appropriate manner
- regulations for the treatment of refrigeration equipment will be incorporated into the Statutory Order on management of waste from electrical and
electronic products
- more stringent requirements on the management of waste from vehicles
- requirements for the management and disposal of electrical and electronic equipment, environmental guidelines for public purchasers of electronic office
equipment, and the appointment of a product panel
- information campaign to promote the use of retreaded tyres
The existing waste analysis model will be refined so that it can also be used in large enterprises and in the service sector.
The Danish Environmental Council for Cleaner Products appointed a Retail Trade Panel in 2002. The aim of the panel is to generate activities to change attitudes and
behaviour, with the aim of reducing the total environmental impact from retail trade. The panel also aims to promote the range of and market for cleaner products in the area
of convenience goods. The panel will also examine the indirect environmental impact from associated transport and packaging, and the operational waste and resources
linked to the sale of products. In the area of waste management, the panel will initiate activities relating to organic waste, packaging waste, shop personnel training and
packaging systems.
Recycling
There are large quantities of organic waste in convenience stores. The best way of managing organic waste from the trade of convenience goods is to be determined in
cooperation with the Retail Trade Panel and the food authorities. Ways of making it easier for retail chains to organise nationwide collection of organic waste will also be
investigated.
The collection of plastic packaging from trade and industry will be enhanced by improving the separation of transport packaging film. Waste producers will have to
participate more actively in the organisation of effective schemes. It needs to be easier for sector associations that represent waste producers/retail chains to establish
nationwide collection schemes. Separation of other plastic packaging from trade and industry must also be increased. These initiatives are described in more detail in
Appendix E22.
Investigation will be made into how the recycling of wooden packaging can be organised.
Efforts will be made to ensure that PVC waste is managed in an environmentally appropriate manner. This can be achieved by drawing up requirements for the collection
and management of PVC waste, and providing tax exemption for products that are managed in an environmentally responsible manner.
Regulations on the waste treatment of refrigeration equipment will be incorporated in a revised Statutory Order on management of waste electrical and electronic
equipment, expected to be issued in 2004.
An amendment to the Statutory Order on end-of-life vehicles will lay down requirements for increased recycling of plastic components.
The EU Directive on waste electrical and electronic equipment must be implemented in Danish legislation, in requirements governing the management and disposal of
electrical and electronic equipment. Environmental guidelines will also be prepared for public purchasers of electronic office equipment. Finally, a product panel will be
appointed, focusing on electronic equipment.
An information campaign will be carried out to promote the use of retreaded tyres.
D 6.4 Regulation
Municipalities must assign treatment or disposal options for waste generated in this sector.
Enterprises, institutions, offices, etc., are currently required to separate cardboard, paper, paper board, steel drums, and plastic transport packaging for recycling.
As of 1 August 2003, in the Statutory Order on sludge, new regulations for the recycling and disposal of animal waste, including commercial kitchen waste, have been
drawn up in cooperation with the Ministry of Food, Agriculture and Fisheries. The scheme for food waste from commercial kitchens has been evaluated and discontinued
against the background of the prohibition against use in pig food.
In 1994, an agreement was made between the Ministry of the Environment and Energy, the Confederation of Danish Industries, the Danish Plastics Federation and the
Packaging Industry on transport packaging. The agreement set goals for the recycling of paper/cardboard and plastic transport packaging. The committee for the
Agreement on Transport Packaging continues to monitor the agreement to ensure future recycling goals are fulfilled for packaging made from plastic, paper and cardboard,
metal and wood.
D 6.5 Capacity
There is no shortage of treatment capacity for the majority of recyclable fractions. For several environmentally harmful fractions, treatment methods have not yet been fully
developed.
D 6.6 Environmental assessment
Initiatives to increase recycling will reduce the need for incineration and landfill capacity and ensure the utilisation of resources in waste.
It is not possible to estimate how much the volume of waste can be reduced through these waste prevention initiatives.
D 6.7 Implications for national authorities
The trade and repair sectors must be encouraged to increase the re-use of transport packaging.
D 6.8 Implications for municipal authorities
Municipalities must improve the information on existing schemes and the supervision of enterprises and institutions in this sector, especially in relation to the obligation to use
assignment schemes for recyclable waste.
D.7. Power plants
Aims for 2008
- 90 per cent recycling of residues from coal-fired power plants
- reduce coal-based energy generation
- ensure that recycling of bioash takes place in an environmentally responsible manner
Environmental problem |
The use of coal as an energy source leads to the emission of large quantities of CO2. Under initiatives to
counter climate changes, the use of coal as a fuel must cease
|
Initiatives
|
Implementation of Energy 21
Re-evaluation of current regulations for the recycling of bioash
for agricultural purposes
|
D 7.1 Status
The Danish power supply has been largely based on coal. In 1996, the Danish Government presented a comprehensive plan of action for energy - Energy 21 –
aimed at ensuring that Denmark contributed to reducing CO2 emissions by 20 per cent in year 2005 compared to 1988 levels.
The objective of Energy 21 is to reduce energy consumption by utilising energy more efficiently, and to convert the energy supply from fossil fuel to renewable energy
sources.
As a consequence, the use of coal as a fuel will be phased out almost completely within the next 30 years, in parallel with an increase in energy generation based on
renewable energy, including biofuel.
Biofuels are currently being used at both heat and electricity generating plants.
Energy generation produces varying amounts of residues. For example, oil and natural gas-fired power plants generate hardly any residues.
The volume of residues generated depends on how much electricity is generated and electricity imports and exports. The volume of waste from power plants can
therefore only be reduced by reducing how much electricity is generated, increasing power plant energy efficiency, or by phasing out fuels that generate waste, such
as coal.
Phasing out coal-based energy generation will have a crucial impact on the volume of residues generated. These are expected to fall significantly over the next 30
years. On the other hand, increasing the use of biofuel will lead to an increase in the volume of bioash. Recycling this waste fraction will be given high priority in the
years ahead.
To date, residues from coal-fired power plants have accounted for the largest waste fraction from power plants. Residues from coal-fired power plants include slag,
fly ash, gypsum, TASP and sulphuric acid. Residues contain a number of heavy metals, limiting recycling options.
The Waste 21 objective of 90 per cent recycling of residues from coal-fired power plants has been reached. In 2001, the registered recycling rate was 99 per cent.
The volume of residues has fallen since 1996. This is due to the decline in the export of electricity from Denmark in recent years, and the stated objective in the
former Government's energy plan, Energy 21, that the use of coal should be discontinued in the long-term and be replaced by natural gas and renewable energy,
including biofuel.
In 2000, the Statutory Order on the recycling of bioash was issued. This Order makes it possible for the nutrients in bioash, primarily potassium and phosphor, to be
recycled as fertiliser in agriculture and forestry. Calculations have shown that 64 per cent of bioash was recycled in 2000.
Measures
- implementation of Energy 21
D 7.2 Future initiatives
Energy 21 will be implemented. The Plan of Action is particularly part of initiatives to combat climate change. However, phasing out coal-fired power plants will also lead
to a reduction in residues.
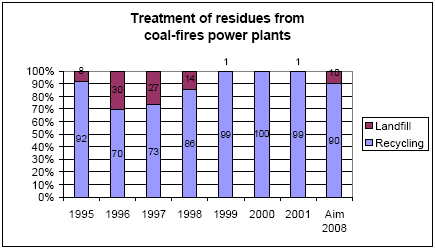
Source: Waste Statistics 2001, Danish Environmental Protection Agency 2003.
The Statutory Order on bioash will be revised to incorporate the latest knowledge on the availability of nutrients in hardened bioash.
D 7.3 Regulation
The waste tax was restructured in December 1998 to include the landfilling of residues under the higher charge for landfilling. This provides a further incentive to reduce the
volume of residues or to recycle them.
Energy 21 will lead to a conversion from the use of fossil fuel to renewable energy sources.
The recycling of bioash for agricultural purposes is regulated in Statutory Order no. 39 of 20 January 2000 on the use of ash from the gasification and incineration of
biomass and biomass waste for agricultural purposes.
D 7.4 Environmental assessment
In the long term, residues from coal-based energy generation will disappear as energy generation based on coal is phased out. As a consequence, leaching of metals and
salts from such residues will cease. The value of bioash as a fertiliser will be utilised. The regulation is based on a recirculation principle, such that each forest and piece of
farmland cannot have more heavy metals added (especially cadmium) than were taken away in the original biomass (straw or wood).
D 7.5 Implications for national waste authorities
None.
D 7.6 Implications for municipal authorities
None.
D.8. Public wastewater treatment plants
Environmental problem | Sewage sludge represents a resource that can be utilised for agricultural purposes |
Initiatives | General phase out of environmental contaminants |
D 8.1 Status
Aims for 2008
- 50 per cent recycling of sludge for agricultural purposes
- 25 per cent incineration of sludge with recycling of the ash in industrial processes
- 20 per cent incineration
- 5 per cent landfilling
- influence the EU's revision of the Sludge Directive
In 1987, the Danish Folketing adopted an Action Plan for the Aquatic Environment. Under this plan, wastewater treatment from all wastewater treatment plants larger than
5,000 person equivalents was to be improved before 1 January 1993. Extensions to the wastewater treatment plants were completed in the beginning of 1996.
Waste from wastewater treatment plants consists of sludge, sand, and screenings. There has been stable production of between 150,000 and 160,000 tonnes of sludge dry
matter annually in recent years. For a typical dry matter content of 20 per cent, this is equivalent to 750-800,000 tonnes of wet sludge. In 2001, a further approx.
100-200,000 tonnes of waste in the form of sand and screenings was generated at municipal wastewater treatment plants, with a dry matter content of 25 per cent. No
significant changes are expected in these volumes in future in terms of dry matter. However, sludge treatment technologies will significantly change the dry matter content at
the time sludge is recorded, leading to a significant increase in the total volume in terms of wet weight.
Of the total volume of waste from wastewater treatment plants in 1999, 61 per cent was recycled, 9 per cent was incinerated with the ash recycled in industrial process, 21
per cent was incinerated, and 9 per cent was landfilled. This means that the Waste 21 objective of 50 per cent recycling of sludge in 2004 has been fulfilled.
In 1997, requirements governing the content of certain organic environmental contaminants in sludge were introduced, and these were made more stringent in 2000 and
2002. These requirements, together with the increased pressure on soil from livestock manure, are expected to lead to a continuing decline in the recycling of sludge for
agricultural purposes.
An increased proportion of sludge is expected to be used in thermal industrial processes in the years ahead, primarily the production of sandblasting sand and cement.
Under these processes, the sludge is incinerated and the inorganic component, typically 30-40 per cent of the sludge's dry matter, is incorporated into the products.
Incineration processes in which the ash is used, for example, to produce sandblasting sand or cement, are not considered to be recycling, but rather disposal with intelligent
utilisation of the inorganic residue. Proper recycling would require that the nutrient contents of the sludge were utilised.
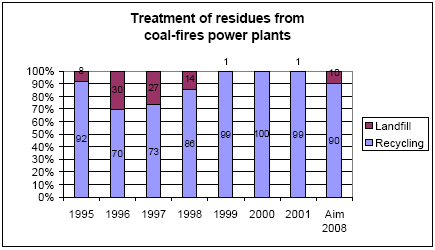
Source: Waste Statistics 2001, Danish Environmental Protection Agency 2003, Briefing from the Environmental Protection Agency no. 3, 2001. The percentages given are
based on dry matter figures.
D 8.2 Future initiatives
In the long term, it is expected that the quality of sludge and its recycling potential will be improved through the general policy of phasing-out environmental contaminants.
The levels of these substances in sludge are thus expected to be further reduced.
Denmark hopes to influence the revision of the EU Sludge Directive so that it contains more stringent requirements on the levels of heavy metals, in line with the Danish
limits, and introduces requirements for certain organic environmental contaminants.
D 8.3 Regulation
The application of sludge to farmland is regulated in the Statutory Order on sludge [25], and the Statutory Order of the Ministry of Food, Agriculture and Fisheries on
inspection of the quality of municipal sewage sludge and composted household waste applied to farmland [26]. The Statutory Order on sludge lays down limit values for a
number of heavy metals and cut-off values for these organic xenobiotic substances: NPE, DEHP, LAS, and certain PAH's.
The Statutory Order on sludge is being revised in spring 2003 as a result of the EU Animal By-products Regulation.
D 8.4 Environmental assessment
The levels of environmental contaminants in sludge are expected to be reduced in the long term, making it possible for sludge to continue to be recycled for agricultural
purposes, thus allowing the nutrient contents of sludge, especially phosphor, a limited world resource, to be recycled.
For sludge that is not recycled for agricultural purposes, it is important that the inorganic contents (the ash) can be recycled in industrial processes such as the production of
cement and sandblasting sand.
D 8.5 Implications for national waste authorities
None.
D 8.6 Implications for municipal authorities
None.
Footnotes
[1] The Plan of action for waste and recycling 1993-1997 states that the goal for 2000 is a recycling rate of 60 per cent. The goal was revised in 1993 and set to 85 per
cent recycling before 2000. The action plan highlights building and construction waste as an important focus area, and a Sub-action plan for cleaner technology and
recycling initiatives in the building and construction sector 1993-97 has therefore been prepared. The goal in Waste 21 was to recycle 90 per cent in 2004.
[2] Circular no. 94 of 21 June 1995
[3] Demolition Industry Environmental Control Scheme NMK 96
[4] Statutory Order no. 655 of 27 June 2000
[5] Council Directive no. 99/31/EC of 26 April 1999 on landfilling of waste, Official Journal of the European Communities 1999 L 182, p. 1.
[6] Statutory Order no. 650 of 29 June 2001 on landfill facilities.
[7] Statutory Order no 647 of 29 June 2001 on training of operations managers and personnel employed at landfill sites.
[8] Consolidated Act no. 518 of 11 June 2000 on planning.
[9] Statutory Order no. 619 of 27 June 2000 on waste, as most recently amended by Statutory Order no. 616 of 22 July 2002.
[10] "Immaterial consumption" refers to the consumption of non-physical products, such as services. Immaterial consumption will often involve a certain level of
consumption of energy or other materials, but this will typically be lower than for the consumption of physical products. One example of such a service is the service
whereby a telephone enterprise takes messages, instead of each consumer having to purchase an answering machine.
[11] The Ministry of the Environment and Energy's Statutory Order no. 619 of 27 June 2000 on waste, as most recently amended by Statutory Order no. 616 of 22 July
2002.
[12] The goal for recycling of domestic waste in Waste 21 is 30 per cent in 2004. This was intended to be achieved through increased recycling of paper and the organic
component of domestic waste. According to the objectives, the remaining volume of domestic waste is to be incinerated with energy recovery. The recycling rate has risen
from 15 per cent in 1995 to 16 per cent in 2001.
[13] Petersen, Claus (2002): "Evaluation of home composting schemes and analysis of the composition of domestic waste".
[14] Under the Ministry of the Environment and Energy Statutory Order no. 619 of 27 June 2000 on waste, as most recently amended by Statutory Order no. 616 of 22
July 2002.
[15] Waste 21: Goals in 2000 for forms of treatment: 25 per cent recycling, 37.5 per cent incineration, and 37.5 per cent landfill.
[16] Circular no. 132 of 13 June 1996 on municipal regulations on disposal of CFC-containing refrigeration equipment
[17] Waste 21 1998-2004: the goal for 2004 was that industry should recycle 65 per cent, and that no more than 15 per cent of waste should be landfilled.
[18] The rise in landfilling and the decline in incineration is partly due to the separation of PVC, impregnated wood, and electrical and electronic equipment.
[19] Industrial Prevention Pollution Control Directive no. 96/61/EC, 24 September 1996.
[20] The Ministry of the Environment's Statutory Order no. 619 of 27 June 2000, on waste.
[21] Section 36 of the Statutory Order on Waste.
[22] In Waste 21, the Government's waste plan 1998-2004, the goal was to recycle 50 per cent of the waste from institutions, trade and offices, to incinerate 45 per cent,
and to landfill 5 per cent.
[23] Environment Project no. 671 2002: Analysis of waste from the trade of convenience goods in Denmark.
[24] Environment project no. 723 2002: Detailed analysis of the composition of waste in the service sector.
[25] Statutory Order no. 49 of 20 January 2000 on the use of waste products for agricultural purposes.
[26] Statutory Order no. 56 of 24 January 2000 on inspection of sewage sludge used for agricultural purposes.
| Front page | | Contents | | Previous | | Next | | Top |
Version 1.0 June 2004, © Danish Environmental Protection Agency
|