| Front page | | Contents | | Previous |
Waste Strategy 2005-08
Appendix E
Fractions
E.1. Animal waste including food waste from industrial kitchens
Environmental problem |
Use of animal waste for feed has been banned, and alternative methods of recycling
must therefore be developed. |
Initiatives |
Studies of the possibility to add animal waste to biogas, especially waste
from abattoirs.
Examine the possibility of recovering phosphorus from the slag from incineration of meat-and-bone meal.
|
E 1.1 Status
Aims for 2008:
- increase the amount of animal waste for biogasification
- recover phosphorus from slag after incineration of meat-and-bone meal
Animal waste is produced at abattoirs, by the fish industry, and at industrial kitchens. A large amount of the animal waste has previously been considered as a homogenous by-product
and therefore it has not been included in the ISAG (the Information System for Waste and Recycling, see Appendix B), but it has been reprocessed into meat-and-bone meal and lard.
Industry produces 1.0-1.5 million tonnes animal waste per year. The waste is biologically degradable waste and often has a low dry matter content.
To date, most of the waste has been recycled, either through reprocessing into meat-and-bone meal and lard, or by adding it to biogas plants as an energy source. However, the
problems of the BSE and foot-and-mouth epidemics in Great Britain in 2001 have meant increased focus on recycling and management of animal waste. This led to a Regulation from
the EU on animal by-products in autumn 2002.
In future there will be severe restrictions or bans on using animal waste in meat-and-bone meal for feed for livestock. The approximately 800,000 tonnes of animal waste converted to
meat-and-bone meal and lard each year will in future be recycled as fertilizers after sanitation, or it will be incinerated. This will reduce recycling from the previous level of 95 per cent.
The content of phosphorus in meat-and-bone meal is an important resource and it should be exploited. The total phosphorus content in meat-and-bone meal could fertilise 400,000
hectares.
Food waste from industrial kitchens [1] has previously been reprocessed into animal feed. This is no longer allowed from 1 November 2002, and future management of waste from
industrial kitchens has been evaluated. This evaluation has led to a lifting of the requirement to collect food waste from industrial kitchens from 1 August 2003. In recent years,
approximately 22,000 tonnes waste from industrial kitchens has been collected each year.
Measures:
- trials with biogasification of animal waste and meat-and-bone meal have been carried out.
- extraction of phosphorus from meat-and-bone meal slag is being tested
E 1.2 Future initiatives
New regulations for recycling and disposal of animal waste, including waste from industrial kitchens were being prepared in spring 2003 in cooperation with the Danish Ministry of Food,
Agriculture and Fisheries. The reason for the change is that it is not permitted to use this waste in animal feed. The regulations are included in the Statutory Order on sludge and aim at
securing optimal treatment of animal waste on the basis of environmental considerations.
Studies are being carried out into the possibilities to increase the amounts of animal waste being recycled by agriculture through biogasification.
Trials are being carried out on recovering phosphorus from slag from incinerating meat-and-bone meal.
E 1.3 Regulation
In spring 2003, new regulations were prepared for managing animal waste and waste from industrial kitchens. These regulations were issued by the Ministry of Food, Agriculture and
Fisheries and the Danish EPA.
E 1.4 Capacity
Joint biogas plants and biogas plants on farms will be able to receive part of the organic waste products. However, for meat-and-bone meal it will not be possible to add the entire
amount, partly because of the high content of fertilizer in meat-and-bone meal, particularly phosphorus, and the problems associated with this when it is spread on fields.
Therefore, much of the production of meat-and-bone meal will continue to be incinerated in the future.
E 1.5 Environmental assessment
The ban on using meat-and-bone meal and waste from industrial kitchens in feed for livestock means significant reorganisation of the management of animal waste and a greater
proportion will have to be incinerated. Meat-and-bone meal has a positive calorific value (about 15-16 MJ/kg) but a lot of energy is used when the destruction installation treats the
animal waste. Therefore, the environmental advantages of burning animal waste directly should be considered.
E 1.6 Economic aspects
With the adoption of the EU Regulation on animal by-products [2] the use of meat-and-bone meal as feed has been banned until further notice. Similarly, it is banned to use waste from
industrial kitchens in feed.
In future, Danish production of meat-and-bone meal must therefore be incinerated in whole or in part. The amount has been assessed at about 200,000 tonnes per year. The Waste Tax
Act was amended in 2000 so that incineration of meat-and-bone meal and animal fat was exempted from waste taxes. Incineration of meat-and-bone meal takes place at incineration
plants and by the cement industry. The annual costs of incineration of meat-and-bone meal alone are about DKK 100 million. In addition to these, the costs of collection and treatment
amount to about the same figure.
Repealing the requirement to collect food waste from industrial kitchens [3] will imply less waste-management costs for restaurants and industrial kitchens.
E 1.7 Implications for national authorities
There will be significant follow-up work on the regulations introduced in 2003 as a result of the EU Regulation on animal by-products.
E 1.8 Implications for local authorities
None
E.2. Asphalt
Environmental problem |
Asphalt is a significant proportion of the total waste from building and construction,
and it will take up landfill capacity if it is not reused or recycled. |
Initiatives |
It must be ensured that asphalt is recycled appropriately in relation to the
environment and health. |
E 2.1 Status
Aims for 2008:
- ensure a high rate of recycling and/or reuse of broken-up asphalt
- ensure that recycling of broken-up asphalt takes place appropriately in relation to the environment and health
Asphalt is composed of stone, gravel, sand, filler, and an oil distillate (bitumen). Filler can be materials such as chalk, cement, and fly ash.
In 2001, asphalt comprised 11 per cent of the total amount of waste from building and construction. Most waste asphalt is either reused or recycled.
Recycling asphalt primarily takes place at stationery plants or semi-mobile plants, but some is reused directly by mobile plants. Stationery recycling is the most widespread type
and at these plants old, broken-up asphalt is crushed. After this it is transported for laying either as a bearing course in roads or as a replacement for granular sub-base material.
Semi-mobile plants are smaller units that can be relatively easily transported to new road projects where they act as stationery plants.
Mobile plants are used to mill-off and crush the asphalt, which is subsequently laid directly as new bearing course or wearing surface.
Asphalt treated at a mobile plant is not considered as waste and therefore it is not included in the amounts of waste registered in the ISAG. The amounts of asphalt registered in
the ISAG therefore comprise the recycled amounts at stationery asphalt factories and semi-stationery plants.
It has been estimated that the amount treated corresponds to 37 per cent of the total recycled amount treated at mobile plants (reuse).
The table below is an overview of the total waste amounts.
Treatment option |
1995 tonnes |
1996 tonnes |
1997 tonnes |
1998 tonnes |
1999 tonnes |
2000 tonnes |
2001 tonnes |
Reuse |
67,340 |
67,340 |
315,610 |
241,980 |
208,650 |
203,500 |
138,014 |
Recycling (ISAG) |
182,000 |
182,000 |
853,000 |
654,000 |
563,920 |
550,000 |
373,010 |
Total |
249,340 |
249,340 |
1168,610 |
895,980 |
772,570 |
753,500 |
511,024 |
Source: Waste Statistics
E 2.2 Future initiatives
- Measures:
- issue regulations or guidelines for recycling broken-up asphalt
It must be ensured that in future asphalt is recycled appropriately in relation to the environment and health.
The first step is to ensure that the health risks in laying crushed asphalt are minimised. This will take place by demanding that asphalt is compressed or stamped after laying so that dust
emissions are as low as possible.
In the long term it is expected that the Statutory Order on recycling residual products and soil in building and construction work will include guidelines on recycling asphalt.
E 2.3 Regulation
The guidelines for recycling broken-up asphalt appear today in the circular on use of broken-up asphalt for road-building purposes, etc. This states that recycling broken-up asphalt may
take place without restriction, and therefore recycling broken-up asphalt for cushion courses and surfacing in roads, paths, squares, etc. does not require a section 19 permit under the
Danish Environmental Protection Act. [4]. This applies irrespective of whether these applications are fitted with a waterproof bearing course/wearing surface.
On the other hand, establishment of permanent or temporary landfills of broken-up asphalt requires an environmental approval under part 5 of the Danish Environmental Protection Act.
[5].
E 2.4 Capacity
There is probably a lack of treatment capacity in Denmark.
E 2.5 Environmental assessment
After implementation of regulations to reduce dust emissions during laying of broken-up asphalt, the health risks will be reduced.
Waste indicators
The new waste indicators for saving resources, energy and landfill requirements [6] which are presented in chapter 2 have been calculated on the basis of the amount of the relevant
waste fraction and the factors shown below. The factors show savings per tonne for the relevant treatment option compared with 1 tonne of waste being landfilled.
Figure: Saving from reusing and recycling 1 tonne of asphalt waste compared to landfilling the same amount (in mPE)
Click here to see the Figure.
There is no LCA data for recycling by transporting for reprocessing or reuse at mobile plants. If there is a difference, this will probably be very small as transport distances are typically
very short. Therefore, the figure only shows the indicator for savings in landfilling of 1 tonne waste for recycling and reuse respectively. The saving compared to landfilling 1 tonne of
waste asphalt is the same for reuse and recycling as both reuse and recycling in this situation give rise to the same treatment.
E 2.6 Economic aspects
It is not expected that changes in the regulations will influence the costs of recycling broken-up asphalt.
E 2.7 Implications for national authorities
New guidelines will be prepared for recycling broken-up asphalt
In addition environmental economic assessments will be carried out of the consequences of allowing recycling of broken-up asphalt to be subject to the Statutory Order on residual
products.
E 2.8 Implications for local authorities
In their inspection, the municipalities must ensure compliance with the regulations and guidelines for recycling broken-up asphalt.
E.3. Lead batteries and accumulators
Environmental problem |
Batteries and accumulators can contain large amounts of heavy metals, especially
lead, but also mercury, cadmium and nickel.
Nickel-cadmium batteries not collected make up the most important source of cadmium in waste streams.
Mercury is the greatest barrier to effective treatment of batteries.
Many batteries also contain resources such as steel, zinc, manganese, and carbon that can be recovered.
|
Initiatives |
New initiatives are pending the revision of the EU Battery Directive. Denmark
will work to ensure batteries are collected and recovered.
New calculations will be prepared for the potential in nickel-cadmium batteries.
|
E 3.1 Status
Aims for 2008:
- the objective is awaiting the revision of the EU Battery Directive
Special collection schemes and suitable recycling methods exist for lead accumulators and nickel-cadmium batteries. The collection schemes work well.
In 2001, 16,963 tonnes of lead accumulators were sold in Denmark. According to estimates, accumulators mainly derive from the service sector, and from bulky waste. The figure
corresponds to the amount of accumulators that become waste each year on average. The collection rate for spent lead accumulators is 98.7 per cent.
Batteries may be subdivided roughly into two categories: single-use batteries and rechargeable batteries (see table).
Types of battery |
Single-use batteries:
alkaline batteries that previously contained mercury. Today, however most of these do not contain mercury
pyrolusite batteries that have not contained mercury for many years
lithium batteries
silver oxide
rechargeable batteries:
nickel-cadmium batteries
nickel-metalhydride batteries
lithium batteries
|
In 2001, 91 tonnes of nickel-cadmium batteries were collected and exported for reprocessing abroad. This figure does not correspond to the actual amount of discarded
nickel-cadmium batteries, as it is estimated that many batteries end in waste incineration, where their content of heavy metals contaminates the residues.
On the basis of models [7] it is possible to calculate the potential amount of nickel-cadmium batteries that could be collected. The collection potential can be described on the basis of
calculations of the number of batteries that are used up each year. This is combined with an estimate of the length of time spent batteries are stored by the consumer (storage effect), and
the length of time the batteries are in the collection system (pipeline effect). On the basis of these figures, the efficiency of collection schemes for batteries can be calculated.
An approximate calculation shows that the collection efficiency for 2001 was between 44 and 75 per cent. Correspondingly, in 2000 58 tonnes was collected, corresponding to a
collection efficiency of between 28 and 62 per cent. The variation in the figures is because the calculations are based on payments of allowances for collecting the batteries. The actual
collection of the batteries can take place in a year other than the year of registration.
Nickel-cadmium batteries and lead accumulators are reprocessed in Sweden or France.
Experience from many years' collection of batteries in Denmark shows that it is difficult for consumers to distinguish between different types of battery, despite the fact that recyclable
batteries carry a special recycling label. The result is that many consumers either collect all batteries regardless of type, or dispose of all types in domestic waste. As a consequence,
around half the discarded batteries are collected as a mixture of single-use and rechargeable batteries. The rest are disposed of in domestic waste.
Local authorities, municipal waste companies, and Kommunekemi A/S separate Ni-Cd batteries for recycling. The rest of the batteries collected are landfilled. Mercury-containing
batteries are normally landfilled at the Kommunekemi A/S special landfill site, and other types at conventional landfills.
The mercury content in batteries used to inhibit reprocessing. Today, the majority of single-use batteries do not contain mercury, and this makes recovery much easier. Internationally
there has been great progress in developing new technologies to recover the resources in batteries not containing mercury. It is therefore expected that far more batteries can be
recovered in future. Once they are completed, Danish studies initiated in 2002 will reveal opportunities to recover Danish batteries.
However, a prerequisite for efficient recycling is that reliable separation technologies are developed in addition to recovery technologies.
It is expected that the EU will revise the current Battery Directive during the period of this Waste Strategy. However, no timetable has yet been set for the revision.
Measures:
- influence EU negotiations
- preparation of new potential calculations
E 3.2 Future initiatives
At EU level, Denmark will continue its work to influence negotiations on the revision of the Battery Directive so that batteries are collected and recovered. Denmark will also place
priority on phasing out heavy metals including cadmium in rechargeable batteries as well as mercury in button batteries.
There will be a need to revise existing calculations for the collection potential of nickel-cadmium batteries as a basis for future efficiency calculations.
Other national initiatives on collection of batteries and phasing-out heavy metals are pending final adoption of the revised EU Battery Directive which is expected to place new
requirements for collection and reprocessing.
E 3.3 Regulation
Collection of batteries is regulated in the Statutory Order on Waste [8]. Nickel-cadmium batteries and lead accumulators, together with unseparated batteries are classified as hazardous
waste, while pure fractions of, for example batteries not containing heavy metals are generally not hazardous waste.
The collection of nickel-cadmium batteries and lead accumulators is also regulated by economic instruments, and collection is carried out by both private and public companies.
Collection of lead accumulators is ensured in an agreement between the Minister for the Environment and the battery industry (Returbat), under which Returbat is responsible for
collection of all spent lead accumulators in Denmark. The agreement is supplemented by two Statutory Orders. The first Statutory Order [9] lays down conditions for becoming
registered as a collector and eligible to receive subsidies. The second Statutory Order [10] forms the financial basis for the scheme.
Returbat administers the scheme and, on the basis of an approved budget, receives funds from the Danish EPA for payment of subsidies.
A maximum subsidy of DKK 0.9 per kg is available to collectors that deliver spent accumulators to approved recycling facilities.
An environmental tax has been introduced [11] on nickel-cadmium batteries. The tax is repaid through an allowance for collecting spent nickel-cadmium batteries. In connection with
the scheme, a Statutory Order has been issued [12], stating criteria to be met by collectors of spent nickel-cadmium batteries in order to achieve registration as a professional collector
and thereby be granted the allowance.
The scheme is administered by the Danish EPA.
An allowance of DKK 150 per kg is paid for collected spent Danish batteries delivered to an approved recycling facility.
E 3.4 Capacity
Capacity for recovery of lead, cadmium and nickel is available in Sweden and France.
Batteries containing mercury can be treated in Germany, the Netherlands, and Switzerland.
E 3.5 Environmental assessment
Establishment of a collection scheme for all batteries could lead to an even better collection rate, including for nickel-cadmium batteries. Furthermore, in the longer term, collection of all
types of battery will provide a better basis for financial exploitation of resources in more types of battery.
However, in order for resources to be exploited, the plastic and mercury content in batteries must not be so high that in causes problems for treatment.
E 3.6 Economic aspects
Exact treatment costs for all types of battery cannot be calculated before treatment methods have been developed. A final decision on requirements for treatment of batteries is pending
negotiations and initiatives in the EU, as well as a socio-economic analysis of the various alternatives.
E 3.7 Implications for national authorities
Once the EU Battery Directive has been revised and adopted, the Directive will be implemented in Danish legislation.
E 3.8 Implications for local authorities
Implementation of the Battery Directive in Danish legislation could lead to changes in municipal planning and regulations.
E.4. Concrete
Environmental problem |
Concrete is a significant proportion of the total waste from building and
construction, and it will take up landfill capacity if it is not recycled. |
Initiatives |
Efforts must ensure that concrete is recycled in an environmentally appropriate
manner. |
E 4.1 Status
Aims for 2008:
- ensure high recycling of concrete
- ensure that recycling of concrete takes place appropriately in relation to the environment
Concrete and tiles comprise the most significant part of building waste and could replace about 5 per cent of the total Danish gravel and stone consumption.
In 2001, concrete comprised 28 per cent of the total amount of waste from building and construction.
Concrete is crushed and recycled in road construction and as aggregate in new concrete. The distance to landfills and gravel quarries with virgin material determines how attractive
it is to recycle concrete.
The amount of pure concrete added to waste treatment plants appears in the table below.
Tonnes |
1995 |
1996 |
1997 |
1998 |
1999 |
2000 |
2001 |
Recycling |
|
|
|
780,000 |
750,000 |
1,054,000 |
949,480 |
Measures:
- changes in regulations for managing concrete
E 4.2 Future initiatives
In the long term, management of concrete will be included in the Statutory Order on recycling residual products and soil in building and construction work.
E 4.3 Regulation
Concrete in building and construction waste is managed primarily through the circular "Circular on municipal regulations on separation of building and construction waste with a view to
recycling", 1995, as well as the circular "Utilisation of pure, separated building waste for building and construction purposes", 1990.
The circular states that municipalities are to prepare a regulation for managing building and construction waste. Municipalities have two options in developing the scheme:
In the first option waste can either be assigned to recycling on-site or to a reprocessing plant.
In the second option waste can either be assigned to recycling on-site or the local council may decide that waste that is not recycled on-site is covered by a collection scheme for
recyclable building and construction waste.
In accordance with the circular from 1990, there is a free choice for recycling of pure fractions of concrete. This means that recycling of pure fractions of concrete does not require
authorisation under section 19 of the Danish Environmental Protection Act.
E 4.4 Capacity
There is considered to be adequate treatment capacity in Denmark.
E 4.5 Environmental assessment
By amending the Statutory Order on recycling of residual products and soil in building and construction work, a more uniform set of regulations will be prepared that ensures that
recycling of a number of larger waste fractions takes place on equal terms.
Waste indicators
The new waste indicators for saving resources, energy and landfill requirements [13] which are presented in chapter 2 have been calculated on the basis of the amount of the relevant
waste fraction and the factors shown below. The factors show savings per tonne for the relevant treatment option compared with 1 tonne of waste being landfilled.
Figure: Savings from recycling 1 tonne of concrete compared to landfilling the same amount of concrete (in 10 mPE)
Click here to see the Figure.
The figure shows the saving from recycling 1 tonne of concrete compared to landfilling the same amount of concrete. Recycling is the only treatment option included as recycling was the
only treatment option for concrete in 2000. It has not been possible to include crushing of concrete waste and transport, and therefore only the indicator value for landfills is included in
the figure. However, neither has the saving in extraction and transport of sand and gravel from recycling crushed concrete been included. Overall, these omissions will tend to cancel
each other out.
E 4.6 Economic aspects
An environmental economic assessment will be carried out of the consequences of allowing recycling of concrete to be subject to the Statutory Order on recycling residual products and
soil in building and construction work.
E 4.7 Implications for national authorities
The basis for preparing new guidelines for recycling concrete must be laid down.
The national authorities will be responsible for preparing the new guidelines and for carrying out the environmental-economic assessments of impacts.
E 4.8 Implications for local authorities
Through inspection, the municipalities ensure compliance with the regulations and guidelines for recycling concrete.
E.5. End-of-life vehicles
Environmental problem |
End-of-life vehicles contain a range of environmental contaminants, heavy
metals, oils etc. |
Initiatives |
Increased recycling of plastic components.
Development of new treatment technologies.
Mapping of existing treatment technologies for recovery of shredder waste.
Information on the end-of-life vehicle scrap scheme.
Implementation of producer responsibility for end-of-life motor vehicles (private cars and vans).
|
Goals for 2006:
- at least 80 per cent recycling achieved in the management of waste of private cars and vans
- increased recycling of glass and plastic
E 5.1 Status
The Statutory Order on scrapping of vehicles lays down rules on the management of end-of-life motor vehicles and derived waste fractions.
The revised Statutory Order on scrapping of vehicles, which entered into force on 1 July 2002, implements the EC Directive on end-of-life vehicles.
The Statutory Order on scrapping of vehicles provides for recycling of a number of waste fractions generated in connection with management of end-of-life vehicles and with
repair of vehicles.
The Order also lays down rules on payment of environmental premiums and reimbursement in connection with dismantling and scrapping of private cars and vans. These rules
motivate car owners to deliver end-of-life vehicles to authorised shredder plants that dismantle and scrap vehicles in accordance with the rules applying to such activities.
End-of-life private cars and vans must be delivered to enterprises that have been authorised and have set up certified environment or quality management systems. Other types of
end-of-life vehicles must be delivered to enterprises that have been approved for dismantling operations.
The rules ensure or contribute to efficient recycling of waste from vehicles, for instance used oil, lead accumulators, nickel-cadmium batteries, catalytic converters, tyres,
windscreens and plastic components. For used oil, tyres, lead accumulators and nickel-cadmium batteries, special arrangements have been set up, which are described in the
relevant sections of this Annex.
Shredding operations generate fractions such as iron and other metals, which are recycled. Today, the residual fraction (shredder waste) is deposited in landfills. See section E 28.
In 2002 a total of 119,000 private cars and vans were deregistered, and approx. 80,000 vehicles were delivered for dismantling in authorised plants. Moreover, a considerable
number of end-of-life private cars and vans are exported to Africa, Eastern Europe etc. According to data held by Statistics Denmark, a total of 15,000 end-of-life vehicles are
exported every year. An unknown number of private cars, vans and trucks are exported without notification to Statistics Denmark, because the exportation is in the hands of
private persons or small companies, which are exempt from the duty to report data to Statistics Denmark.
Beside the waste volumes generated in connection with dismantling and scrapping, car repair generates a similar volume of waste; mainly used tyres, lead accumulators, parts of
chassis, other components of metal and plastic, and used oil and other liquids resulting from repair and maintenance of motor vehicles.
For the overall volumes of waste generated in connection with dismantling and scrapping, the rates of recycling are estimated at approx. 75 per cent and landfilling at approx. 20
per cent. The remaining 5 per cent is incinerated. According to the goal for 2006, a minimum of 80 per cent of the waste volumes generated during dismantling and scrapping of
private cars and vans must be reused or recycled. This goal is to be achieved by increased recycling of plastic components and glass from end-of-life vehicles.
Data for waste volumes from repairs are not available at present, except data for the three fractions covered by special collection schemes, i.e. tyres, accumulators and used oil.
As regards abandoned cars, rules were stipulated in the amended legislation that the local authorities and the police may be reimbursed for the costs of disposal they incur,
provided other conditions specified for reimbursement are fulfilled. In connection with the egislative amendment, the Danish Parliament decided that special rules will not be
introduced for cars that have been abandoned on private property.
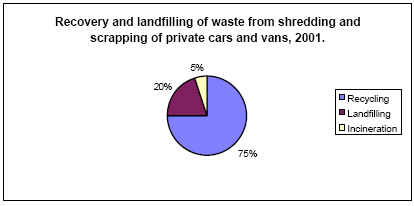
Measures:
- stricter requirements for management of waste from cars
- requirements for separation of recyclable components and materials
- information on the vehicle scrapping scheme
- producer responsibility
E 5.2 Future initiatives
In connection with an amendment to the Statutory Order on vehicle scrapping that will be made in the period covered by this plan, requirements will be laid down for increased recycling
of plastic components.
Initiatives to support the development of new separation technologies with the aim of increasing the rate of recycling of plastic and recovery of other organic fractions will be furthered.
Work has been done to map the treatment technologies, and work will continue, with a view to establishing plants for recovery of shredder waste generated during scrapping of vehicles
and of a number of other composite products.
Information material will be prepared, in order to inform about rules on scrapping of vehicles. The initiative will be financed by the proceeds resulting from the environment and scrapping
premiums.
Rules will be implemented in 2005-2006, providing for producer responsibility for private cars and vans, and to take effect from 1 January 2007.
E 5.3 Regulation
Management of end-of-life vehicles is regulated by Statutory Order on vehicle scrapping and in environmental approvals of plants authorised to carry out vehicle dismantling and
scrapping operations.
E 5.4 Capacity
Approx. 210 enterprises are authorised to carry out waste management operations for vehicles in accordance with the Statutory Order on vehicle scrapping. Further, a small number of
dismantling plants are in charge of breaking up other types of vehicles and end-of-life cars that have been subject to waste treatment in authorised dismantling plants. Finally, six shredder
plants work with shredding and separation of scrapped vehicles.
E 5.5 Environmental assessment
The proportion of car scrap to be disposed of in landfills will fall from 25 per cent to not more than 20 per cent. The rate of recycling of plastic components will increase from approx. 5
kg to approx. 25 kg/vehicle.
E 5.6 Economic aspects
It is estimated that the increased costs pertaining to dismantling and recycling of plastic components will amount to DKK 2-5 million.
E 5.7 Implications for national authorities
The Statutory Order on vehicle scrapping will be amended.
E 5.8 Implications for local authorities
None.
E.6. Tyres
Environmental problem |
Tyres contain rubber and steel, i.e. resources that should be utilised if
possible, by reuse or recycling. |
Initiatives |
Initiate information campaigns aiming at limiting faulty assembling of tyres
and promote the sale of retreaded tyres. |
E 6.1 Status
Goals for 2008:
- 90 per cent reuse or recycling of all discarded tyres
Collection and recovery of tyres is regulated by the Statutory Order on a fee on tyres and a recovery subsidy.
Tyres contain rubber, steel, and textiles. Rubber and steel can be recycled, and textile waste can be recovered by incineration.
In 2001 waste volumes amounted to approx. 42,800 tonnes, of which approx. 34,500 tonnes were reused or recycled. The remaining waste volumes were disposed of by incineration
or landfilling. Around 40 per cent of the total amounts of tyres is assessed to derive from private consumers, and 60 per cent is assessed to come from industry and business. Most of
the tyres are disposed of via the service sector, where tyres become waste in connection with renewal and repair.
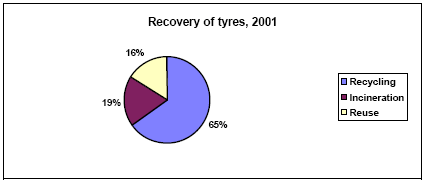
E 6.2 Future initiatives
Measures:
As part of the agreement with the Danish Tyre Trade Environmental Foundation information campaigns are being carried out, aiming at minimising waste volumes and promoting the use
of retreaded tyres
E 6.3 Regulation
On 20 February 1995, the Minister for Environment and Energy entered into an agreement with the tyre and motor trade associations, the Association of Danish Recycling Industries
and municipal associations on a take-back scheme for discarded tyres.
Through the agreement it is ensured that discarded tyres are collected and recycled or incinerated, thus avoiding landfilling and ensuring resource utilisation of waste tyres. The collection
and treatment scheme is organised on the basis of the following order of priority: retreading, rubber powder production, and incineration.
The agreement requests enterprises selling tyres to take back a corresponding number of discarded tyres without additional costs for the consumer.
Professional collectors are required to receive all tyres from enterprises collecting or receiving discarded tyres, including municipal collection schemes, and to deliver these for recycling
or incineration.
Further to the agreement, a fee was introduced on tyres [14] for financing of collection and treatment costs, administration of the scheme, and information campaigns [15].
Subsidies are paid to the tyre collectors that are registered in the Danish EPA. Registered enterprises must state in which municipalities tyres are collected. On certain conditions,
enterprises are required to collect tyres from waste producers. Subsidies for collection of tyres will only be given, if the tyres are delivered to a reprocessing plant.
No subsidies are granted for tyres delivered for reuse, including retreading.
An intermediary goal is that at least 80 per cent of all discarded tyres from private cars, vans, and motorbikes will be collected and recycled or incinerated before 1997. According to
the agreement, 80 per cent of all discarded tyres must be recycled or incinerated before 2000.
According to the goal at least 90 per cent should be reused or recycled in 2008.
E 6.4 Capacity
In Denmark there are around 10-15 reuse facilities working with retreading tyres. Furthermore, two reuse facilities are engaged in processes to produce rubber powder or rubber
granulate.
E 6.5 Environmental assessment
All tyres used on motor vehicles are covered by the Statutory Order. The collection scheme ensures that 98 per cent of all discarded tyres are collected. At least 80 per cent are reused
or recycled. For a minor part of the tyres, corresponding to 5-10 per cent, technical reasons prevent recycling, and the tyres are therefore recovered by incineration.
Possibilities exist for minimising the waste volumes by waste prevention and increased reuse (retreading) of tyres.
Waste indicators
The new waste indicators for saving resources, for energy and for landfill requirements [16] which are presented in chapter 2, have been calculated on the basis of the amount of the
relevant waste fraction and the factors shown below. The factors show savings per tonne for the relevant treatment option compared with one tonne of waste being landfilled.
Figure: Savings from incineration, recycling and reuse of one tonne of automobile rubber, compared to landfilling the same amount (in mPR, mPE, 10 mPE).
Click here to see the Figure.
LCA data is not available for the granulation process, which is therefore not included in the calculation. Account has therefore not been taken of the fact that rubber powder and rubber
granulate replace new rubber raw material. Thus, the calculated benefits gained are a result of recycling the steel components of the tyres, and of the fact that landfilling is not required.
However, the calculation does not take account of the fact that steel ending up in the incineration slag will in practice be collected and utilised. For the purpose of reuse, new rubber
does not need to be produced, and this is included with LCA data for butadiene rubber.
From the figure it appears that the largest savings per tonne are achieved by incineration and reuse. And for these two treatment options, particular savings are gained for energy
resources and gross energy consumption. Further, it should be noted that by recycling, the savings achieved in energy resources, other resources and gross energy are quite modest.
Recycling of rubber is not possible after vulcanisation, because tyres cannot be vulcanised again. It is only when the tyres as such are reused by retreading, that considerable savings are
achieved in terms of energy and resources.
E 6.6 Economic aspects
Information activities will not trigger additional costs, since the funds required are allocated via the income deriving from fees.
E 6.7 Implications for national waste authorities
None
E 6.8 Implications for local waste authorities
Local authorities are to assign tyres to special treatment.
E.7. Waste electrical and electronic products
Environmental problem |
Waste electrical and electronic products contain many contaminants, especially
heavy metals. |
Initiatives |
The EU Directive on Waste Electrical and Electronic Equipment must be implemented
by the end of 2004.
Drafting of environmental guidelines for public procurement of a number of electrical and electronic products, and eco-labelling criteria for several products.
Improved resource utilisation by development of new technologies for reprocessing of the products.
|
Aims for 2008:
- increase the recycling rate for resources from electrical and electronic products
- make sure that waste from electrical and electronic products is not delivered to waste incineration plants and landfills
- environmentally sound disposal of electrical and electronic products
E 7.1 Status
Electrical and electronic products primarily include radio and television sets, IT products, regulation and monitoring equipment, white goods, refrigeration equipment, and office
equipment.
Collection and reprocessing of electrical and electronic products is currently based on Statutory Order no. 1067 of 22 December 1998 on management of waste from electrical
and electronic products. A special scheme has been set up for treatment of refrigeration equipment, see section E 15.
Under Statutory Order no. 1067, the local authorities have set up collection/assignment schemes for waste electrical and electronic products.
The Order requires that products listed in Annex 1 of the Order are reprocessed in accordance with Annex II and III. Moreover, under section 8 of the Order, anyone receiving
waste electrical and electronic products must remove the nickel-cadmium batteries and lead accumulators before reprocessing.
Total amounts of waste electrical and electronic products, excluding refrigeration equipment, which is discussed in Section E 15, have been calculated at 103,000 tonnes in 1997
[17]. The largest part is assessed to come from municipal bulky waste schemes (48 per cent). The remaining part is assumed to come from domestic waste (15 per cent), from
institutions, trade and offices, the service sector (20 per cent), and industry (15 per cent). Many discarded electrical and electronic products are disposed of by putting them away
in the attic. Moreover, many products are sold on second-hand markets. Therefore registration of the volumes of electrical and electronic products suffers from great uncertainty.
The volumes recorded here are considered somewhat overestimated.
In 2001, 21,200 tonnes of electronic waste and 11,940 tonnes of refrigeration equipment and freezers were collected and subjected to special treatment. To this should be added
the products delivered to shredding plants for the purpose of reprocessing. In 1997 the volume was calculated at 64,400 tonnes/year. These products are not registered in the
ISAG (Information System for Waste and Recycling), but the products seldom appear on second-hand markets, and are typically so large that they are not dumped. Estimates of
processed volumes at 50,000 tonnes in 2001 should therefore be considered a very conservative estimate.
According to estimates based on the above data, 75 per cent of the waste of all electrical and electronic products was delivered for reprocessing/recycling in 2001, approx. 15
per cent was disposed of in incineration plants, and 10 per cent was put on the market for second-hand products.
On 10 October 2002 the European Parliament and the EU Council of Ministers agreed on a directive regulating the future management of waste electrical and electronic
equipment. The Directive is due to be implemented in Danish legislation no later than December 2004.
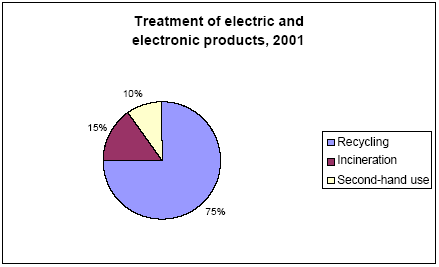
E 7.2 Future initiatives
- Measures:
- requirements for management and disposal of electrical and electronic products
- environmental guidelines for public procurement of electronic office equipment
- setting up product area panels
- development of improved reprocessing methods
The EU Directive on electrical and electronic equipment is to be implemented, with the purpose of securing minimum implementation of the provisions of the Directive. However, for
particularly dangerous fractions supplementary requirements for treatment will be laid down.
The EU Directive on management of waste from electrical and electronic equipment is based on producer responsibility. This means that within 30 months after the Directive comes into
force, the producers must take over responsibility for the management of the waste by environmentally sound methods, and they must finance management of the waste from the location
where it was collected.
The Directive lays down rules on reprocessing of the waste, and for the rates of recycling and recovery to be achieved before 31 December 2006. Reprocessing of the waste must only
take place in approved reprocessing facilities.
Implementation of the Directive implies that the requirements will be changed, and more products will have to be treated separately.
Moreover, within 30 months after the Directive comes into force, producers must label the products, stating the date of marketing, and inform the consumers of the possibilities available
for upgrading the product in order to give it a longer lifetime. Further, the producers must inform customers where they may dispose of the product free of charge.
Finally, the producers must inform the reprocessing facilities of the environmentally harmful substances/components contained in the products, and state their location.
Under the Directive, Member States must ensure that within 30 days after the Directive comes into force, collection schemes have been set up to minimise the risk that electrical and
electronic waste ends up in other municipal wastes.
Further, Member States must, before the end of 2006, ensure that a collection quota of no less than 4 kg per person per year has been achieved for electrical and electronic products
from households.
In connection with the action plan for environmentally conscious public procurement, guidelines have been prepared, aiming at assisting public procurers in purchasing a number of
electronic office products. Eco-labelling criteria will be worked out for several of the products.
Product-oriented environmental policies aim at improving the products and integrating waste disposal in the design of the products. In 1999 a product panel for electronic products was
established.
Among the initiatives launched by the product panel was a conference for designers, dealing with the design of products that are easy to reprocess, and with electronic tools assisting the
designers in their daily work.
Development of new technologies for reprocessing waste electrical and electronic products will be evaluated regularly. If there is a need for amending rules and regulations with a view to
using best available technology, this will be done on an ongoing basis.
E 7.3 Regulation
Management of waste electrical and electronic products has so far been regulated in general rules in the Statutory Order on waste, the Statutory Order on management of waste from
electrical and electronic products, and through environmental approvals of enterprises managing, reprocessing or disposing of this waste fraction.
E 7.4 Capacity
A further, estimated 10,000-20,000 tonnes of the total amount of electrical and electronic products will be collected and treated separately.
Around 20 disassembly enterprises exist today.
The total existing capacity is approx. 90,000 tonnes per year, and capacity problems are not expected in future.
E 7.5 Environmental assessment
The EU Directive on the management of electrical and electronic equipment will result in environmentally more sound management of this type of waste.
The Directive provides for separate treatment of a range of electrical and electronic equipment, which, today, are not covered by rules on separate treatment in the Danish Statutory
Order. Further, the Directive requires that a considerably larger number of substances/components must be removed from the products prior to mechanical treatment. Such selective
pretreatment will reduce the environmental impact resulting from subsequent reprocessing in for example incineration plants and in steel and metal works.
The rate of recycling/recovery of the heavy metals and the energy contained in the products will, to a smaller extent, increase as a result of the reprocessing and recovery requirements
set out in the EU Directive.
However, it is the Directive's requirements for selective pretreatment of the products that will trigger the most favourable effects on the environment. During pretreatment,
environmentally harmful components and substances are removed, for instance mercury, PCBs, lead and brominated flame retardants, which we know from experience present
environmental nuisances in connection with final recycling/recovery.
It is expected that the EU Directive will move approx. 15,000 tonnes of electrical and electronic waste from incineration and landfilling to recycling and recovery.
In the years to come, product-oriented environmental policies are expected to increase the market share for products that are easier to recycle, and also for products containing fewer
environmental contaminants.
E 7.6 Economic aspects
The costs pertaining to collection and processing of electrical and electronic products will amount to 0.2-3 per cent of the price of the products, and, thus, represent only a small fraction
of the costs of acquisition. This increase of the price of acquisition will/should be offset somewhat by the reduced municipal costs for waste collection.
E 7.7 Implications for local authorities
The local authorities can still collect electrical and electronic products, but the producers may establish their own alternative waste collection schemes.
When the EU Directive comes into force at the end of 2004, the local authorities will no longer be responsible for environmentally appropriate reprocessing of collected electrical and
electronic waste.
E 7.8 Implications for producers
When the EU Directive takes effect, responsibility for the collected products, including recycling/recovery of the products and the economic costs pertaining to these operations, is
vested in the producers. The producers may delegate the practical work relating to transportation and reprocessing to third parties acting on behalf of the producers.
In connection with the implementation of the Directive, the Danish EPA will cooperate with the associations of the electronics sector and with the local authorities to ensure that the
reprocessing requirements set out in Annexes II and III are met in a manner that is efficient and environmentally and economically sound.
E.8. Packaging waste
Environmental problem |
Packaging waste contains large quantities of reusable packaging and recyclable
materials. If environmentally and economically appropriate, packaging waste is
to be recycled instead of incinerated. |
Initiatives |
Increased recycling of metal and plastic packaging.
Retain the rate of recycling of glass and cardboard/paper packaging.
Mapping of quantities of volumes of wood packaging in 2004.
Report to the Danish Parliament in 2005 on the most appropriate action to be taken to reach the overall recycling goal of 55 per cent.
Report to the Danish Parliament in 2006 on experience gained with the Dansk Retursystem.
|
E 8.1 Status
Goals for 2008:
- cardboard/paper packaging - minimum 60 per cent recycling
- plastic packaging - 22.5 per cent recycling
- metal packaging - 50 per cent recycling
- glass packaging - 80 per cent recycling
- wood packaging - 15 per cent recycling
- packaging waste total - 55 per cent recycling
- rate of return for containers for beer and soft drinks in disposable packaging in 2005: no less than 95 per cent
- rate of return for containers for beer and soft drinks in refillable packaging to be retained at no less than 98 per cent
Volumes of packaging waste were assessed at approx. 1 million tonnes in 2000. This corresponds to 186 kg/per inhabitant in Denmark. However, 57 per cent of this amount
consists of transport packaging, of which only very limited amounts end up in private households. Sales packaging amounts to 43 per cent. Since 1997 volumes of packaging have
been slightly increasing. [18] Packaging waste represents approx. 8 per cent of total waste volumes in Denmark.
As opposed to a number of other countries, Denmark has decided not to establish separate management of all packaging waste, with the exception of collection of disposable
packaging for beer and carbonated soft drinks. Instead, focus is on how best to utilise various recyclable materials in waste from different sectors. This also applies to packaging
waste.
Packaging waste includes a large number of waste fractions, such as glass, paper and cardboard, metal, wood, and plastic. These fractions are described in the sections dealing
with the various fractions.
For 2001 the following recycling goals were set up: cardboard/paper packaging - 55 per cent, plastic packaging - 15 per cent, metal packaging - 15 per cent, and glass
packaging - 65 per cent.
All goals were achieved in 2001, except for plastic, where the rate of recycling reached 14 per cent. In 2001, the Danish Parliament adopted a report on recycling of plastic, in
which the goal was 22 per cent recycling by 2004, provided a number of conditions are fulfilled.
In 2000 the overall rate of recycling was 56 per cent for the four packaging materials (cardboard/paper, plastic, metal, and glass).
The national goals for recycling of waste packaging in 2008 have been adjusted to the objectives set in the revised EU Packaging Directive. The work to revise the Directive is
expected to be completed in 2003.
So far, the general rule has been not to include sales packaging of paper and cardboard, metal and plastic from households in the recycling systems. From a working-environment
and eco-environmental perspective, these types of sales packaging are considered less suitable for collection with the purpose of material recovery than transport packaging.
However, to achieve the goals in 2008, greater efforts should be made to include sales packaging in the recycling schemes.
The goal for recovery of paper and cardboard must be fulfilled primarily by recycling of cardboard packaging from industry and households. In 1994 a voluntary agreement on
recycling of transport packaging was made between the Minister for the Environment and Energy, the Confederation of Danish Industries, the Danish Plastics Federation, and the
Danish Packaging Industry. In 2000, the recycling percentage for transport packaging made from paper and cardboard was 83 per cent.
The recycling goal for plastic packaging is also expected to be fulfilled by transport packaging from industry. Therefore, the collection of packaging from industry must be
considerably strengthened. Moreover, selected sales packaging from industry and households must be collected in order to contribute to achieving the goal. Disposable packaging
collected via Dansk Retursystem will also contribute to achieving the goal.
Recycling of metal packaging includes both recycling of steel and tinplate packaging from industry, and a certain amount of recycling of the metal scrap ending up in incineration
plants after incineration of domestic waste. Finally, metal packaging collected via the Dansk Retursystem also contributes to recycling. In order to achieve the future goal, metal
packaging must be collected from households for the purpose of recycling, and possibilities of improving the management of waste at incineration plants must be investigated.
Recycling of glass packaging includes both recycling of discarded containers for beer and soft drinks, recycling of bottles for wine and spirits, and packaging glass collected via
municipal collection schemes. Finally, disposable packaging collected via the Dansk Retursystem also contributes to recycling.
The requirement for a 15 per cent recycling rate for wood packaging is new. This requirement will be achieved by repairing pallets and by recycling pallets for chipboards. It is
very difficult to assess the quantities of wood packaging waste in Denmark. It is very important to quantify the volumes of wood packaging waste, because it will influence the way
in which the goal of 15 per cent recycling of wood packaging waste, and the overall 15 per cent recycling goal, will be achieved.
The majority of remaining packaging waste is incinerated with energy recovery. In view of the ongoing and planned initiatives in the field of packaging, it is expected that in 2008 -
and if incineration at waste incineration plants is included - the overall recovery of packaging waste will exceed 90 per cent.
Dansk Retursystem A/S
When the Danish Government took office it decided that in the future the Danes must have a free choice of packaging for beer and carbonated soft drinks, and the Government
therefore lifted the ban on cans as of 23 January 2002. Moreover, Danish producers were given a general permission to use disposable packaging. It was also decided to
establish a common mandatory deposit and return system, in order to ensure that the cans and other disposable packaging are collected via the Dansk Retursystem A/S.
Already in May 2001, the Danish Parliament adopted an amendment to the Danish Environmental Protection Act, allowing for modernisation of the bottle return machines set up
in approx. 2,000 Danish supermarkets. Modernisation was required because sorting of refillable bottles, mainly of plastic, was becoming increasingly difficult, and also in order to
prepare for the reception of disposable packaging, in case this was to be permitted in Denmark. Total investments will amount to DKK 260 million. Furthermore, the shops will
be compensated for their handling of refillable bottles. In December 2002, Dansk Retursystem A/S was given the sole right to be in charge of this process to modernise and adjust
the return machines.
23 September 2002 was the first day Danish consumers could buy cans and other disposable packaging, labelled in accordance with the new requirements. Under the new
system, it is much easier for the consumers to dispose of non-refillable containers for beer and soft drinks. The about 2,000 shops with modern return machines are now able to
receive all kinds of disposable packaging, irrespective of whether the shops sell the product or not. Dansk Retursystem A/S has been given the sole right to be in charge of work
to operate the deposit and return system for disposable packaging.
Denmark is the only country in Europe that has set up a single-line mandatory return and deposit system for all types of disposable containers for beer and soft drinks. This paves
the way for high return percentages for disposable packaging, and for avoiding dumping in streets and nature. In addition to this, resources in the packaging waste are utilised, to
the benefit of the environment. According to objectives, Dansk Retursystem A/S will before 1 January 2004 have achieved a return rate for disposable packaging of no less than
90 per cent, increasing up to 1 January 2005 to no less than 95 per cent. The objective set for reuse of refillable packaging is 98 per cent.
According to assessments for the coming years, the future sale of beer and soft drinks in disposable packaging will amount to a minimum of 320 million containers. Thus, with a
return percentage of at least 95 per cent in 2005, 4,000 tonnes of metal waste, almost 1,000 tonnes of plastic waste, and just less than 5,000 tonnes of waste glass will be
recycled.
The sole right of operation of the return and deposit system vested in Dansk Retursystem A/S expires on 4 December 2008. No later than September 2006, the Minister for the
Environment will submit a report to the Danish Parliament, presenting experience gained with the system, and an evaluation of how the system may function most appropriately
after the sole right expires. This evaluation will also include an assessment of whether the scheme should be liberalised, if, it is assessed that the establishment of more deposit and
return systems will not weaken the scheme as such, in terms of both the environment and consumers.
Other specific Danish initiatives for prevention of packaging waste and reuse of packaging are described in Appendix A 2.2.9 on specific requirements for packaging and
packaging waste.
E 8.2 Future initiatives
Measures:
- increased recycling of metal and plastic packaging
- retain the rate of recycling for glass and cardboard/paper packaging
- mapping of quantities of wood packaging in 2004
- report to the Danish Parliament in 2005 on the most appropriate way to reach the 55 per cent recycling goal
- report to the Danish Parliament in 2006 on experience gained with the Dansk Retursystem A/S
- evaluate the deposit system for further types of packaging
In the individual sections on fractions, the initiatives to be taken to achieve the specific goals are described. The most important initiatives focus on increased recycling of
plastic, metal and wood packaging. Collection of plastic packaging from industry must be strengthened. In the future the citizens will be able to deliver metal packaging and
selected plastic packaging for recycling, for instance at recycling stations or via bulky waste collection schemes.
Volumes of wood packaging waste must be mapped in 2004, as part of a study of how the recycling of wood packaging waste might be organised. The size of wood
packaging waste volumes will be extremely important for possible further initiatives required to achieve the goal of 55 per cent recycling of all packaging waste in 2008.
A report will be prepared and submitted to the Danish Parliament in 2005, describing how the 55 per cent recycling goal can be achieved. Possible further initiatives must
be based on the most cost-effective solutions for society and the environment.
A study will be made to determine whether more types of beverage containers should be included in the deposit scheme. The Cleaner Products Council is currently
financing a project evaluating selected beverage containers. The project focuses on voluminous products and on products that have a consumer pattern similar to that of
beer and soft drinks.
For detailed information, see the sections on the fractions plastic, paper and cardboard, glass, metal and wood.
E 8.3 Regulation
Regulations pertaining to management and recovery of packaging waste have been laid down in Statutory Order no. 619 of 27 June 2000 on waste.
Requirements for manufacture and composition of packaging are laid down in Statutory Order no. 298 of 30 April 1997 on certain requirements for packaging.
Requirements for beverage containers are implemented by Lov nr. 475 af 7. juni 2001 om ændring af lov om miljøbeskyttelse (Pant- og retursystemer) (Act no. 475 of 7
June 2001 amending the Environmental Protection Act (Deposit and Return Systems)), and Statutory Order no. 713 of 24 August 2002.
E 8.4 Capacity, environmental assessment and economic aspects
It is estimated that the costs of the new initiatives launched to reach the specific goals for plastic and metal will amount to a total of approx. DKK 2 million per year. If
further initiatives have to be taken in order to reach the overall recycling goal, additional costs may be incurred. This will appear from the report to the Danish Parliament in
2005.
For detailed information, see the sections on the fractions plastic, paper and cardboard, glass, metal and wood.
E 8.5 Implications for local waste plans
According to the Statutory Order on waste, local authorities must report on initiatives for prevention and recycling packaging waste in their waste plans.
For detailed information, see the sections on the fractions plastic, paper and cardboard, glass, metal and wood.
E.9. Hazardous waste
Environmental problem |
By definition, hazardous waste implies risk of fire, or danger to health and
the environment, and it must therefore be managed in an environmentally appropriate
way. |
Initiatives |
Prepare a strategy for hazardous waste.
Promote recovery of hazardous waste.
Disseminate further the understanding of how the criteria for hazardous waste should be applied.
Implement criteria for hazardous waste (danger to the environment).
|
E 9.1 Status
Aims for 2008:
- optimised economic and environmental treatment of hazardous waste
- increased recycling of hazardous waste
- Hazardous waste is waste which is inflammable or constitutes a risk for health or the environment. Rules for hazardous waste are regulated in the EU and are
developed regularly.
Hazardous waste includes waste from both primary and from secondary sources (such as residual products from incineration plants). In 2001, waste generation from
primary sources amounted to 288,154 tonnes (equalling approx. 2 per cent of the total waste quantities) and 86,149 tonnes from secondary sources. Waste from
secondary sources is not included in the total waste production, since - if it were - it would be included in the calculation twice.
Hazardous waste includes many different waste fractions, originating from all sectors.
Some of these fractions are described in the relevant sections of this annex. For example batteries and accumulators, cars, electronic products, impregnated wood,
health-care risk waste, PCBs/PCTs and used oil. For these fractions, separate schemes have been established.
In addition to these, some residual products from waste incineration plants are classified as hazardous waste; namely acid flue-gas cleaning products. These fractions
are described in E25.
The table gives an overview of main sources of hazardous waste analysed by treatment option.
Hazardous waste 2001 (tonnes)
(Main sources) |
Recycling |
Incineration |
Special treatment |
Landfilling |
Total |
Primary sources |
|
|
|
|
|
- Lead batteries |
16,942 |
|
|
|
16,942 |
- Organic and inorganic compounds |
4,174 |
|
|
|
|
- Waste oil |
18,679 |
27,797 |
1,005 |
|
|
- Shredder waste |
|
|
|
92,101 |
92,101 |
- Dust-emitting asbestos |
|
|
|
9,336 |
9,336 |
- Health-care risk waste |
|
2,712 |
2,393 |
|
5,105 |
- Other hazardous waste |
31,995 |
13,179 |
1,405 |
1,678 |
48,257 |
|
|
|
|
|
|
Total |
71,790 |
87,142 |
15,162 |
106,980 |
281,074 |
- in per cent of total primary waste amounts |
25 |
30 |
5 |
37 |
97 |
|
|
|
|
|
|
Secondary sources |
|
|
|
|
|
- Flue-gas cleaning waste |
12,324 |
|
|
|
12,324 |
- Fly ash and flue-gas cleaning products from waste incineration plants |
0 |
0 |
0 |
73,825 |
73,825 |
Total secondary sources |
12,324 |
|
|
73,825 |
86,149 |
Source: Waste Statistics 2001; Danish EPA 2003
Apart from acid flue-gas cleaning products from waste incineration plants, Kommunekemi A/S generates residual products from its own facilities. These waste
residual products are likewise hazardous.
Criteria for hazardous waste more or less correspond to the EU Directive on hazardous waste [19] and the European waste catalogue [20].
Criteria have been adopted under the Basel Convention pertaining to what constitutes a danger to the environment.
Requirements for reporting of hazardous waste to the ISAG have been expanded so that in future the Danish EPA will receive information on hazardous waste stated
with EWC codes.
There are now several regulations regarding treatment of waste (landfilling, incineration), which use the term "hazardous waste" to delimit, how waste types may be
treated.
Hazardous waste is exempt from waste taxes. A study has been completed to examine whether it would be environmentally appropriate to continue this exemption
of hazardous waste from waste taxes, however, the study has not provided any clear answers. A more thorough assessment will be part of work on a national
hazardous waste strategy.
Flue-gas cleaning waste will not be dealt with in the national hazardous waste strategy, as the plan is to prepare a separate action plan for flue-gas cleaning waste.
E 9.2 Future initiatives
Measures:
- hazardous waste strategy
- development of new treatment methods
A hazardous waste strategy will be prepared. The purpose is, firstly, to clarify whether the different regulations pertaining to or referring to hazardous waste are an
impediment to economically and environmentally sound treatment of waste, secondly, to point to possible initiatives to reduce such impediment. There will be an
assessment of whether the QSAR classifications are to be used for assessment of the hazardousness of waste.
An ongoing task will be to disseminate knowledge about the use of hazardous waste criteria. Both to ascertain the environmentally sound management of waste and
to make sure that there are no unnecessary costs associated with treatment of waste, which in reality should not be managed as hazardous waste.
Initiatives to increase recovery of hazardous waste will be encouraged.
Work will be done to ensure that criteria for what constitutes a danger to the environment will be implemented in Danish legislation - preferably via adoption within
the EU.
E 9.3 Regulation
Hazardous waste is regulated via the Statutory Order on Waste [21] and special Statutory Orders pertaining to individual waste fractions. Rules for hazardous waste
were incorporated in Danish legislation in 1996 and by and large follow the rules on classification of chemical substances and products.
Enterprises are responsible for assessing whether their waste is hazardous and for notifying any such waste to the local authorities. Local authorities must collect all
hazardous waste.
E 9.4 Capacity
Today, 25 per cent of hazardous waste from primary sources is recycled:
- lead accumulators and Ni-Cd batteries are collected and recycled in Sweden or France
- waste oil is reprocessed at Dansk Oliegenbrug (Danish oil recycling company).
32 per cent is incinerated:
- used oil is treated at district heating plants and at Kommunekemi A/S
- health-care risk waste is mainly disposed of at Special Waste System A/S in Nørre Alslev, and at traditional waste incineration plants.
6 per cent is subject to special treatment:
- organic compounds without halogens are treated at Kommunekemi A/S and BOFA (municipal waste disposal centre on Bornholm).
37 per cent is landfilled:
- asbestos and contaminated soil are landfilled at special landfills
- shredder waste is landfilled at 4 different landfills in Denmark.
14 per cent of hazardous waste from secondary sources is recycled, whereas 86 per cent is landfilled.
A number of enterprises carry out pre-treatment of hazardous waste with a view to separating the non-hazardous fractions (oil filters, paint drums, and the aqueous
component in used oil).
Recycling enterprises exist for individual waste fractions (silver from the photographic sector and organic solvents), for example enterprises recovering silver or coolant.
Traditionally, however, not many methods of treatment have been developed for recovery or recycling of hazardous waste fractions.
Cars which have not been emptied of liquids, or other dangerous components, are classified as hazardous waste.
The Statutory Order on management of waste in the form of motor vehicles and derived waste fractions lays down rules on the management of end-of-life motor vehicles
and derived waste fractions.
End-of-life private cars and vans must be delivered to enterprises that have been authorised and have set up certified environment or quality management systems. Other
types of end-of-life vehicles must be delivered to enterprises that have been approved for dismantling operations.
Approx. 210 enterprises are authorised to carry out waste management operations for vehicles in accordance with the Statutory Order on management of waste in the form
of motor vehicles and derived waste fractions. In addition, a small number of dismantling plants is responsible for breaking up other types of vehicles and end-of-life cars
that have been subject to waste treatment in authorised dismantling plants. Finally, six shredder plants work with shredding and separation of vehicle scrap.
Electrical and electronic products
Collection and reprocessing of electrical and electronic products is currently based on Statutory Order no. 1067 of 22 December 1998 on management of waste from
electrical and electronic products.
In 2001, 21,200 tonnes of electronic scrap were collected and treated separately. A further, estimated 10,000-20,000 tonnes of the total amount of electrical and
electronic products will be collected and treated separately.
Around ten disassembly enterprises exist today.
The total existing capacity is around 90,000 tonnes per year, and capacity problems are not expected in future.
Filter dust and flue-gas cleaning products from waste incineration plants make up around 30 per cent of total hazardous waste amounts.
Flue-gas cleaning products are exported and landfilled pending the establishment of a permanent solution. Requirements for recycling of residual products will be adjusted
to take account of groundwater, see also E25.
E 9.5 Environmental assessment
Hazardous waste comprises many different waste types with many different environmental properties. Hazardous waste is classified due to its inherent properties, which
means management of the waste is potentially dangerous. The actual danger risk of hazardous waste, however, depends on conditions for management/treatment.
E 9.6 Implications for national authorities
A hazardous waste strategy will be prepared with the objective of ensuring economically and environmentally sound treatment of waste.
E 9.7 Implications for local authorities
Local authorities will inform citizens about municipal schemes for hazardous waste.
E.10. Glass
Environmental problem |
On recycling of glass and reuse of refillable glass bottles, energy consumption
is reduced compared to the manufacture of new glass. Moreover, this means the
raw material (the glass) is exploited more than one time. Collection of glass
for recycling must therefore as a minimum be kept at the present level. |
Initiatives |
Instigation of development work with a view to developing alternative methods
to recycle glass cullets. |
E 10.1 Status
Goals for 2008:
- 80 per cent recycling of glass packaging [22]
On recycling of glass, energy consumption in the manufacture of new glass is reduced. Furthermore, raw materials (glass) are exploited several times. Collection of
sheet glass, bottles, and glass packaging for recycling must therefore be kept at the present level and be improved.
The amount of waste sheet glass was estimated at around 35,000 tonnes in 2000. Of this, 27,000 tonnes, or 78 per cent, were recycled in Denmark, primarily for
insulating material. Part of the remaining amount is exported for recycling abroad, the rest is landfilled.
Technology for separation of recyclable sheet glass from frames exists and is in function at at least one facility in Jutland. The glass is recycled in e.g. mineral wool
production. According to a project not yet published entitled "Other problematic substances in building and demolition waste", separation of PCB filler may pose a
problem.
The amount of packaging glass marketed in Denmark in 2001 amounted to 184,000 tonnes.
A total of 132,000 tonnes of waste glass was collected from wine/ liquor bottles, glass packaging for food and medicines. Of this, 130,000 tonnes were recycled as
cullets or whole bottles for reuse. The rate of recycling has increased slightly in recent years [23].
Via the recycling system for beer and softdrinks bottles, Danish brewers collected 9,000 tonnes of glass cullets for recycling in 2001.
Total recycling of glass in Denmark amounted to 140,000 tonnes in 2001, corresponding to 76 per cent. Private border trade accounted for about 20,000 tonnes. If
this trade is included in supply amounts, the recycling rate for glass packaging is 65 per cent.
The amount of glass packaging from Danish households, which ended up in the trash can, in 2001 amounted to about 29,000 tonnes. This amount is led to waste
incineration plants where the glass does not contribute to energy recovery, but ends up as slag.
A large number of whole bottles are separated from the collected amounts of glass packaging and reused as bottles. In 1999-2000, the Danish EPA carried out an
assessment of the market potential of reusable wine bottles in Denmark and of the environmental effects of export of wine bottles for reuse outside Denmark [24].
The study showed that there is an environmental benefit to be gained from reusing bottles, also in terms of exports to central Europe. Reuse of whole bottles can be
increased by applying "gentle" collection methods, which reduce the number of broken bottles. Municipal experience gained from different collection methods was
collected and disseminated in 2002.
Around 60 per cent of the amount of glass recycled is remelted to make new packaging.
There is not adequate capacity in Denmark to reprocess coloured cullets to make new packaging. There is therefore a need to come up with alternative ways of
recycling glass cullets.
There is capacity to reprocess more clear glass cullets in Denmark to make new glass packaging. However, for this end more cullets will have to be separated.
Today, cullets are separated at source in a select number of municipalities. Cullets from clear glass primarily originate from colour separation at bottle washing and
separation plants. According to assessments, around 70 per cent of cullets from municipal collection is separated by colour. Further clear cullets could be separated
from existing collection; however, the amount is probably limited.
The EU Packaging Directive is being revised. The expected goal for recycling glass in 2008 is 60 per cent.
E 10.2 Future initiatives
Measures:
- develop alternative ways of recycling packaging and sheet glass
A project to come up with alternative ways of recycling glass packaging waste was commenced in 2002. The project will survey amounts and assess possibilities for using
waste glass in cement, tiles, and road construction. There will be further needs for developing and testing methods for alternative recycling of glass.
E 10.3 Regulation
Municipalities are under obligation [25] to establish schemes for collection of glass from built-up areas with more than 2,000 households. The collection must be organised
so that essential parts of the glass are recycled. In most municipalities, bring-schemes have been introduced with bottle banks located at central places in the area, and at
recycling centres. Citizens have the duty to use collection schemes as described in municipal waste regulations.
Recyclable sheet glass and glass packaging from industry must be assigned to recycling.
E 10.4 Capacity
According to assessments, the total amount of glass collected for recycling could be sold to recovery in full, once alternative uses have been established.
E 10.5 Environmental assessment
A lower rate of cullets will reduce resource and energy consumption in connection with manufacturing glass. Reduction of the rate of cullets may lead to increased reuse of
whole bottles, ensuring a significant reduction in energy consumption. Reuse only requires around 15 per cent of the energy needed to produce a new bottle.
Waste indicators
The new waste indicators for saving resources, for energy and for landfill requirements [26] which are presented in chapter 2 have been calculated on the basis of the
amount of the relevant waste fraction and the factors shown below. The factors show savings per tonne for the relevant treatment option compared with 1 tonne of waste
being landfilled.
Glass packaging
The figure below shows savings gained for the five indicators via incineration, recycling, and reuse, respectively, of one tonne of glass packaging. Savings are calculated in
relation to landfilling. Benefits from recycling and reuse of glass are reduced energy consumption and landfill requirements.
Figure: Savings from incineration, recycling and reuse of one tonne of glass packaging, compared to landfilling the same amount (in mPR, mPE, and 10 mPE).
Click here to see the Figure.
The figure shows that the largest savings can be achieved from reuse of glass packaging. This applies to all indicators except "renewable gross energy", which for all three
treatment options is zero. Recycling provides savings of around the same amount of waste for landfilling, but gross energy is significantly lower due to a high consumption of
energy associated with manufacturing new glass from waste glass packaging.
Incineration shows negative marginal savings (-1 in the figure) for "non-renewable gross energy" and "waste for landfilling" respectively. This is because incineration of glass
packaging demands energy without in turn producing energy.
Sheet glass
The same LCA data has been used for treatment options for sheet glass as for glass packaging. However, energy consumption for washing processes in connection with
reuse has not been included in calculations. The figure below shows savings gained for the five indicators via incineration, recycling, and reuse, respectively, of one tonne of
waste sheet glass, compared to landfilling the same amount.
Figure: Savings from incineration, recycling and reuse of one tonne of sheet glass, compared to landfilling the same amount (in mPR, mPE, 10 mPE).
Click here to see the Figure.
Treatment of one tonne of sheet glass shows the same result as for glass packaging since the same data are used. Thus, the largest savings can be achieved from reuse.
E 10.6 Economic aspects
It is not expected that retention of the existing collection level for glass packaging will influence renovation fees.
E 10.7 Implications for national authorities
Development of alternative recycling technologies must be encouraged.
E 10.8 Implications for local authorities
In order to retain the present level of collection for glass packaging, it is important to regularly inform relevant actors about collection schemes and separation requirements.
It will be necessary to ensure a "gentle" collection system so that as many bottles as possible are reused.
E.11. Dredged material
Environmental problem |
Dredged material, which cannot be disposed of at sea, recovered or reused,
must be landfilled on land. This landfilling requirement is covered by the Statutory
Order on landfills [27], and at present
it is not yet clear how many of the existing landfills for disposal of dredged
material will be able to continue operations after July 2009.
It is not possible to estimate the amount of sediments that will require landfilling in future; including estimating whether there will be a capacity shortage. This is due to,
among other things, the current revision of the administrative basis for management of dredged material.
|
Initiatives |
To develop a tool which may help county councils and landfill owners to assess
whether existing landfills may be continued after 16 July 2009.
To create a new administrative basis for management of dredged material.
To initiate new initiatives as follow-up to the proposed new administrative basis.
|
Aims for 2008:
- to assess whether existing landfills for dredged material may continue operation after 16 July 2009
- to follow up on new administrative basis for management of dredged material
E 11.1 Status
Ports and harbours need to get rid of material which settles on the sea bed, both in the harbour and in shipping lanes. Such material is called sea-bed sediment or dredged
material/harbour sludge. The material may be disposed off either via landfills on land or via dumping the material outside harbour premises at sites, designated for such
purpose by the county. However, dredged material can also be recovered or recycled.
About 3 mill. tonnes of sediment (calculated in dry matter) are dredged each year to maintain harbours and shipping lanes. Of these, so far around 90 per cent has been
dumped at sea, while 10 per cent has been landfilled.
Many ports and harbours have experienced increasing problems in recent years in connection with the disposal of dredged material. This is primarily due to the enhanced
knowledge about the presence of a number of organic, environmental toxins in the sediments - in particular TBTs in anti-fouling boat paint. The counties have therefore
become more reluctant to permit dumping of dredged material.
Increased contents of acidifying substances in the sediments mean that more and more harbours have been denied permission to dump dredged material at sea. Instead,
they have had to choose the more expensive solution of landfilling. Today, however, the methods used by counties to assess contents of organic toxins in dredged material
vary greatly.
This very topical problem demands a solution that:
- will contribute to an environmentally appropriate management of dredged material
- will balance the economic aspects against the environmental aspects
- will ensure administration as uniformly as possible
- provides guidelines on good practice for management of dredged material on land
- is future-proofed.
In consultation with representatives from Danish Regions, Local Government Denmark, and the Association of Danish Ports, the Minister for the Environment is considering
a new administration basis for management of dredged material, which will be ready by autumn 2003 at the earliest.
Measures:
- developing a tool to help counties and landfill owners assess whether existing landfills can continue operation after 2009
- preparing a new administration basis
E 11.2 Future initiatives
In order to assess whether existing landfills for dredged material can continue operations after 16 July 2009, the Danish EPA has completed a project that was to facilitate
the assessment work of counties and landfill owners.
Further initiatives are pending the preparation of a new administration basis for management of dredged material.
E 11.3 Regulation
Under the Marine Environment Act, the counties [28] may, in most circumstances, grant permission for dumping of dredged material, if the material contains only
insignificant amounts of contaminants. Dumping of dredged material at sea is covered by the Marine Environment Protection Act and Statutory Order [29]on dumping
dredged material.
Sediments, which cannot be dumped at sea, recovered or recycled, must be brought on land and, today, are mainly placed in waste disposal sites near the coast. There are
a number of waste disposal sites and so-called hosing sites, including a number of smaller sites for disposal of contaminated dredged material.
Landfilling of dredged material is covered, in most cases, by the Statutory Order on landfills [30], which constitutes part of the implementation of the EU Directive on
landfill of waste [31]. This means that all new landfills must be designed and operated commensurate with the requirements of the Statutory Order. Existing landfills must
comply with the requirements laid down in the Statutory Order - or should be made to do so - and must otherwise be closed down no later than on 16 July 2009, cf. also
appendix D3.
It is uncertain, today, if any of the existing landfills for dredged material can continue operations after 16 July 2009, because of an insufficient data base for assessing
whether the landfills will be able to comply with certain requirements of the Statutory Order on landfills, e.g. regarding membrane and percolate collection systems. This
issue will be incorporated into the proposal for a new administration basis for management of dredged material.
E 11.4 Capacity
An estimated average of 3 mill. tonnes of sediments (calculated in dry matter) will have to be removed from harbours and shipping lanes annually. Of these, so far around
90 per cent has been dumped at sea, while 10 per cent has been landfilled.
Because the administration basis is currently being revised, it has not been possible to provide a qualified estimate as to the amounts of sediments that will have to be
landfilled in future. In a worst-case scenario, the new administration basis could lead to a shortage of capacity, if larger amounts of sediments than previously have to be
landfilled. A possible capacity shortage is, however, not likely to have effect until after 16 July 2009 when landfills for dredged material not complying with the Statutory
Order will be closed down.
E 11.5 Environmental assessment
Sea-bed sediments mainly comprise sand, clay, and organic material. In most Danish waters sea-bed sediments are moved about to a great extent - also from dredging
sites - and many ports and harbours serve has 'caches' for sediments, especially in the case of sediments of fine particulates, which contain most of the acidifying
substances. Pollutants are also added to the harbour from varying local sources dependent on the type of harbour. Dumping of dredged material first of all leads to
redistribution of the acidifying substances, and for a large part of the sediments, the substances are lead back to the marine environment.
In recent years ports and harbours have experienced incremental problems with management of contaminated dredged material. The problem became clear when more and
more samples of the sediments in the South Funen archipelago showed a high content of TBTs (organic tin compounds in anti-fouling paints).
The problem is thus especially prevalent in Danish coastal waters. This is the reason why many counties have not granted harbours permission to dump their dredged
material at sea, and why the harbours subsequently have been forced to manage the contaminated material otherwise - typically via landfilling - a substantially more costly
option.
As to contents of acidifying substances, chemical analyses have identified several heavy metals in the dredged material exceeding background level concentrations (mercury,
cadmium, lead, and copper, and to increasing extent dangerous substances such as TBTs and PAHs (poly aromatic hydrocarbons from incineration of fossil fuels)). The
Danish EPA has carried out a number of projects in which dredged material was screened for 113 different hazardous substances. Of these, 34 substances were found in
the sediments from all types of harbours, whereas the remaining substances were almost non-existent.
Certain heavy metals, TBTs and PAHs, pose a special problem. This is reflected in the occurrence of these substances among the acidifying substances in the sediments.
The occurrence of these groups of substances makes sediments especially toxic. Apart from the substances mentioned, other environmentally dangerous substances were
found among the 34 substances - for example nonylphenols and DEHPs (Di(2-ethylhexyl)phthalates)
In addition to being bioaccumulative, heavy metals are non-degradable and toxic to varying degrees. Heavy metals are found in varying concentrations in all types of
sea-bed sediments, however, most often they are found in concentrations less than two times the local background level. The background level is the level which can be
found in an area only subject to diffuse exposure to discharges from point sources.
TBT is a constituent in anti-fouling boat paints. Proven negative effects include androgenity and imposex in marine organisms at very low concentrations found in almost all
coastal Danish waters and in the open parts of Skagerrak and the North Sea.
Today, large amounts of TBTs are accumulated in the sediments in Danish waters, just as new TBTs are added daily from larger ships in transit or ships sailing into Danish
ports and harbours. An estimated 90 per cent of the TBTs added to the marine environment comes from ships, while the remaining 20 per cent can be attributed to
dumping at sea.
Other organic substances which are dangerous to the environment - including PAHs - are found in varying concentrations in sediments in Danish harbours and harbour
areas. PAHs are typically found in concentrations two times the background level. PAHs are mainly added via ambient air as fallout from incineration of fossil fuels and
from sources such as oil spills etc. Generally, there is no clear connection between operations in a harbour and the sediments' content of dangerous organic substances.
E 11.6 Economic aspects
Estimated annual costs for disposal of dredged material amount to DKK 160 mill. These costs are incurred by ships via harbour and goods taxes, which in reality are fees,
although they are termed taxes.
Changing the rules pertaining to disposal of contaminated dredged material, in the direction of prescribing more landfilling, will lead to increased costs. This area is entirely
user-financed, and harbour taxes will therefore have to be raised in step with increased costs. This will mean annual added costs of about DKK 60-110 mill. dependent on
landfill option requirements.
The Ministry of Finance has notified the Danish EPA that the increase in harbour taxes due to a restriction of the rules on disposal of contaminated dredged material will not
fall under the provisions regarding user financing under the Government's stop on tax increases. The argument is that taxes are raised due to increased costs in connection
with a restriction of legislative requirements and not due to the introduction of new user financing or an increase in the user share of existing user financing.
E 11.7 Implications for national authorities
A new administrative basis for management of dredged material will be ready by autumn 2003 at the earliest. As follow-up to the new administration basis, the Danish EPA
- in cooperation with the Danish Forest and Nature Agency - will prepare a draft statutory order (including guidelines) on management of dredged material. The draft
statutory order and guidelines will be sent out for consultation in the beginning of 2004.
E 11.8 Implications for local authorities
Possible implications for local authorities cannot be assessed until after the new administrative basis has been prepared. Considering that many Danish ports and harbours
are municipal-owned, restricted requirements for landfilling dredged material, and/or requirements, which lead to a greater amount of dredged material requiring landfilling,
will lead to significant additional costs, which will be covered, primarily, via harbour taxes.
E.12. Ferrous packaging
Environmental problem |
Metallic packaging is not adequately exploited as a resource. |
Initiatives |
Increased recycling of metallic packaging |
Goals for 2008:
- 50 per cent recycling of ferrous packaging
E 12.1 Status
The volume of ferrous packaging in Denmark in 2001 was 43,000 tonnes. Steel and tinplate packaging comprise a great part of the total volume.
In 2000, 8,400 tonnes of ferrous packaging was collected directly for recycling. The remaining amounts of ferrous packaging are led to waste incineration plants
where the iron is separated from the slag and recycled as incinerated iron. How much iron is lost in this process has not yet been assessed. However, experiments
from 2002 indicate that the loss of ferrous packaging is significant. For tinplate packaging, the estimated average loss is 76 per cent. The estimated minimum loss is
62 per cent and the estimated maximum loss is 90 per cent.
In 2002, collection of metallic packaging for beer and softdrinks was established via Dansk Retursystem. Amounts collected are not yet known. The scheme will
contribute to the recycling of aluminium.
Most of Danish metallic packaging comes from households. In 2001, the total amount of metallic packaging from Danish households came to about 31,000 tonnes.
Several opportunities exist for improving the management of metallic packaging in Denmark and thus reach the goal of the EU Packaging Directive. These include
increased separate collection of metallic packaging from industry and households, improved separation of metal from slag, and pre-separation of ferrous waste at
waste incineration plants.
Measures:
- separate collection of metallic packaging from households
- metallic packaging from industry assigned to recycling
- examination of opportunities for pre-separating waste and separating metal from slag
E 12.2 Future initiatives
There will be more requirements concerning increased collection of ferrous packaging from households, e.g. via recycling sites or as part of existing schemes for bulky
waste.
Examinations will be carried out into opportunities for pre-separating ferrous metals at waste incineration plants, and opportunities for improving the separation of ferrous
metals from slag.
The obligation of industry to assign metallic packaging to recycling will be clarified in the Statutory Order on waste.
E 12.3 Regulation
Regulations pertaining to management and recovery of packaging waste have been laid down in Statutory Order no. 619 of 27 June 2000 on waste.
Requirements for beverages packaging have been laid down in Lov nr. 475 af 7. juni 2001 om ændring af lov om miljøbeskyttelse (Pant- og retursystemer) (Act no. 475 of
7 June 2001, amending the Environmental Protection Act (Deposit and Return Systems)), and Statutory Order no. 713 of 24 August 2002.
E 12.4 Capacity
Ferrous metal waste, except aluminium, is exported for recycling abroad. Shortage of capacity is not likely to become a problem at the reprocessing plants, to which
Denmark exports ferrous metal waste.
E 12.5 Environmental assessment
Increased recycling will save energy and metal resources. The reduction of ferrous metals in household waste will lead to less caking in furnaces at waste incineration plants
and increased possibilities for recycling incineration slag.
Waste indicators
The new waste indicators for saving resources, energy and landfill requirements [32] which are presented in chapter 2 have been calculated on the basis of the amount of
the relevant waste fraction and the factors shown below. The factors show savings per tonne for the relevant treatment option compared with 1 tonne of waste being
landfilled.
b) Aluminium
Figure: Savings from incineration and recycling of one tonne of aluminium, compared to landfilling the same amount (in mPR, mPE, 10 mPE).
Click here to see the Figure.
The figure shows that recycling aluminium leads to significant savings in the indicator "other resources". Similarly, recycling leads to savings in gross energy and in waste
amounts requiring landfilling. The incineration option does not represent possible savings, which is due to the fact that incineration of aluminium is not considered to yield an
energy benefit. On the contrary, the incineration option consumes energy, as is also reflected in the value -1.
Iron and steel
The data basis for primary and secondary iron and steel is good, and the figure below therefore provides a picture of the savings gained from recycling one tonne of iron
and steel.
Figure: Savings from incineration and recycling of one tonne of iron and steel, compared to landfilling the same amount (in mPR, mPE, 10 mPE).
Click here to see the Figure.
The figure shows that great savings in waste for landfilling are achieved on recycling. Similarly, there are savings to be gained in total resources and non-renewable gross
energy. The figure shows that incineration apparently does not lead to any savings; however, this is not correct. In practice, iron and steel that end up at incineration plants,
will be separated from the slag and thus recycled. If this fact is included in the calculations, the figure would show savings from incineration similar to those gained from
recycling.
E 12.6 Economic aspects
The establishment of a collection scheme for ferrous packaging will mean additional costs for some local authorities. However, in most municipalities collection of ferrous
metals already takes place via recycling sites or bulky waste schemes.
Metallic packaging may be collected together with the remaining fraction of ferrous waste. If metallic packaging is collected separately, it will mean expenses saved with
regard to managing this type of packaging waste at waste incineration plants, and with regard to subsequent management of slag. It is therefore the assessment that only
very limited additional costs are associated with collecting metallic packaging via recycling sites.
E 12.7 Implications for national authorities
Rules regarding collection of metallic packaging will have to be laid down.
E 12.8 Implications for local authorities
Local authorities must ensure that metallic packaging waste is collected via bulky waste schemes or similar schemes. Moreover, local authorities must ensure that metallic
packaging waste from industry is assigned to recycling.
E.13. Soil
Environmental problem |
Large amounts of waste contaminated to varying degrees with heavy metals or
PAH or other organic compounds. |
Initiatives |
Prepare guidelines on recycling residual products and moving soil.
Revise Statutory Order no. 655 of 27 June 2000 on recycling residual products and soil in building and construction work.
|
Aims for 2008:
- recycling of soil contaminated with organic compounds to be covered by Statutory Order no. 655 of 27 June 2000
- prepare guidelines with clear, simple rules for recycling residual products and moving soil.
E 13.1 Status
Every day large amounts of soil are managed in connection with building and construction work and remediating contaminated properties.
In accordance with the ISAG, in 2001 about 588,000 tonnes of stone and soil was recycled, but this amount does not include soil used in connection with building
sound-absorbing barriers and other activities covered by Statutory Order no. 655 of 27 June 2000 on recycling of residual products and soil in building and
construction work.
Therefore, there is only limited knowledge about the total amount of soil moved, and about how this soil is managed.
With this background, elucidation work has been initiated to identify the amounts of soil currently being managed. The study will provide a snapshot picture of the
conditions, but it will not give ongoing statistics showing developments in the area.
Measures:
- revision of Statutory Order no. 655 of 27 June 2000
- guidelines on recycling residual products and moving soil
E 13.2 Future initiatives
Work is being carried out on guidelines regarding recycling residual products and moving soil.
Statutory Order no. 655 of 27 June 2000 on recycling residual products and soil in building and construction work is to be revised so that it also covers soil contaminated
with organic compounds.
E 13.3 Regulation
Contaminated soil is regulated by the Contaminated Soil Act no. 370 of 2 June 1999 and Statutory Order no. 655 of 27 June 2000 on recycling residual products and soil
in building and construction work.
No tax is due on waste that is recycled. On the other hand, tax is usually due on waste that is taken to an approved enterprise. All enterprises that landfill soil and residual
products must be registered and approved in accordance with the Waste Tax Act.
The most recent amendment to the Waste Tax Act has opened up for the possibility for limited amounts of contaminated soil to be used for day-to-day covering landfills
and in temporary roads at landfill sites, without being subject to waste tax.
E 13.4 Capacity
In connection with preparation of regional plans, counties are able to designate sites for landfilling contaminated soil.
E 13.5 Environmental assessment
Contaminated soil can affect the ground water and humans living on or using the sites.
E 13.6 Economic aspects
It is not expected that initiatives will have economic consequences.
E 13.7 Implications for national authorities
The Danish EPA will prepare guidelines on recycling and moving soil and residual products, and the Agency will revise Statutory Order no. 655 of 27 June 2000 on
recycling residual products and soil in building and construction work.
E 13.8 Implications for local authorities
The new regulations are expected to help municipal administration regarding recycling residual products and soil in connection with building and construction work.
E.14. Health-care risk waste
Environmental problem |
Health-care risk waste is infectious. |
Initiatives |
No new initiatives. |
E 14.1 Status
Aims for 2008:
Health-care risk waste is generated in both the primary and the secondary health sectors. The characteristic feature of health-care risk waste is that it may be infectious by
direct contact. According to the ISAG, 5,105 tonnes of health-care risk waste were generated in 2001. Health-care risk waste is classified as hazardous waste with
reference to the fact that it is infectious.
Almost all health-care risk waste is generated in the service sector.
Waste is incinerated both at special incineration plants and at conventional plants in compliance with special conditions reducing the risk of contact with waste. In
environmental terms, the incineration process is similar to incineration of, for example, domestic waste. Incineration means the waste becomes inactive, energy is recovered,
the volume is reduced, and the waste becomes unrecognisable. The latter is very appropriate for waste tissue.
Disposal requires a relatively large amount of packaging. To the extent improved separation will reduce the amount of health-care risk waste, it will also indirectly reduce
the total amount of waste and thus consumption of packaging will correspondingly be reduced.
Guidelines on health-care risk waste were issued in 1998 [33].
E 14.2 Future initiatives
No new initiatives are envisaged for health-care risk waste.
E 14.3 Regulation
Health-care risk Waste management is regulated in the Statutory Order on waste. Health-care risk waste is hazardous waste, and in accordance with the Statutory Order
on Waste, municipalities must therefore establish separate collection schemes for the waste.
E 14.4 Capacity
Disposal of health-care risk waste takes place at one special plant and seven conventional waste incineration plants.
E 14.5 Implications for national authorities
None.
E 14.6 Implications for local authorities
None.
E.15. Refrigeration equipment
Environmental problem |
Refrigeration equipment contains environmental contaminants, including CFC,,
that break down the ozone layer, as well as heavy metals and PCBs, which are extremely
harmful to the environment and health. |
Initiatives |
In a revised statutory order on managing waste from electrical and electronic
products, regulations will be added on managing refrigeration equipment. |
E 15.1 Status
Aims for 2008:
- 95 per cent collection of all discarded refrigeration equipment
The circular on municipal regulation of disposal of refrigeration equipment containing CFCs contains provisions that municipalities must lay down regulations on collection
and environmentally appropriate management of end-of-life fridges and freezers containing CFCs.
Refrigeration equipment manufactured before 1995 contains CFCs and other environmental-contaminant fractions.
The municipal regulations ensure that refrigeration equipment is collected and treated, and that environmental contaminants are extracted for special treatment. The
recyclable fractions (iron and metal components) are separated for recycling.
There is a special scheme (see appendix E7) for other types of waste electrical and electronic products.
In 2001, end-of-life refrigeration equipment amounted to about 300,000 units. In 2001, 266,000 pieces of refrigeration equipment were collected and treated,
corresponding to 89 per cent of the potential.
80 per cent of the refrigeration equipment collected is collected from households either through return schemes or through municipal bulky waste schemes. 15 per cent
comes from institutions, trade and offices. The remaining 5 per cent is collected from industry.
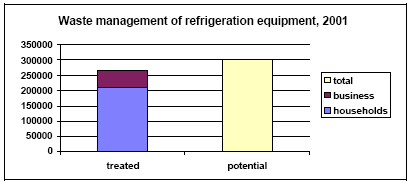
E 15.2 Future initiatives
The regulations for waste management of electrical and electronic equipment will be incorporated in a revised statutory order on management of waste from electrical and
electronic products, which is expected to be issued in 2004.
E 15.3 Regulation
Collection and management of refrigeration equipment containing CFCs is ensured by an agreement between the Minister and the organisations on disposal of refrigeration
equipment containing CFCs, as well as a circular [34] on municipal regulation regarding disposal of refrigeration equipment containing CFCs.
The goal of the agreement is to collect at least 90 per cent of the total discarded refrigeration equipment for treatment in accordance with the requirements laid down in the
circular.
At least 95 per cent of the content of the cooling agent CFC-12 must be extracted and collected. The frothing agent CFC-11 must be extracted at a rate of at least 80 per
cent. All CFC-12 collected must either be recycled or destroyed. All CFC-11 must be destroyed. In addition, mercury switches and condensers (PCBs) must be
extracted for environmentally appropriate management, see appendix E21.
E 15.4 Capacity
There is one special plant for treatment of refrigeration equipment. One-third of the refrigeration equipment collected is exported for treatment in Germany. Furthermore,
refrigeration equipment is treated at about five other Danish enterprises which can extract CFCs from refrigeration equipment.
E 15.5 Environmental assessment
250,000-300,000 pieces of refrigeration equipment (corresponding to 12,500 tonnes) are treated in accordance with the circular. About 100 tonnes of condensers
containing CFCs and PCBs are extracted and destroyed in an environmentally appropriate manner.
E 15.6 Implications for national waste authorities
None.
E 15.7 Implications for local waste authorities
None
E.16. Mineral wool
Environmental problem |
Mineral wool is a local irritant and in certain circumstances it is carcinogenic.
|
Initiatives |
The potential for recycling mineral wool will be examined, including development
and identification of methods of recycling, as well as the potential of developing
a market for recyclable mineral wool-
The opportunities for environmentally and economically appropriate landfilling of mineral wool waste will be investigated.
|
E 16.1 Status
Aims for 2008:
- increased recycling of mineral wool
- ensure environmentally appropriate and economically-effective disposal/recycling
Mineral wool is primarily used in the building and construction sector, but it is also widely used by nurseries as a growth medium.
There are no recent studies of the annual consumption or accumulated amounts of mineral wool in Denmark. Consumption is estimated at 40,000 tonnes per year for
stone wool and glass wool together.
Waste arises from the building and construction sector through cut-offs when cutting wool to shape in new construction and from demolition and conversion of
existing buildings.
Mineral wool was included in the official list of hazardous substances in 1999. Mineral wool must now be classified as hazardous waste. However, the Danish EPA
has recommended that municipalities wait for guidelines on the management of mineral wool waste in order to ensure uniform practices in the area. Therefore it is
likely that some waste mineral wool is currently sent for waste treatment with mixed building and construction waste.
There is not sufficient knowledge about the amount of used mineral wool from nurseries that ends as waste or is recycled by the nursery in other purposes.
A small amount of waste mineral wool is sent to waste treatment as hazardous waste, primarily by incineration. Mineral wool is not suitable for incineration, and the
reason it is incinerated is presumably that it is contaminated with other hazardous substances that can be incinerated at special incineration plants.
E 16.2 Future initiatives
Measures:
- study of the potential for recycling mineral wool
- study of the possibilities of environmentally and economically appropriate landfilling
There is a need for greater knowledge about management of mineral wool waste. Initiatives will be started to examine the potentials and barriers for recycling waste mineral
wool either as a replacement for virgin raw materials or for alternative purposes. Following the studies, suitable methods can be developed for recycling.
Furthermore there will be studies of how mineral wool, which is not suitable for recycling, can be landfilled in an environmentally and economically appropriate manner.
E 16.3 Regulation
Mineral wool is regulated by the Statutory Order on Waste [35] and classified as hazardous waste.
Moreover, a guideline has been prepared on how mineral wool should be classified and how it should be managed as waste.
E 16.4 Capacity
There is not sufficient knowledge of the possibilities to recycle mineral wool and the capacity available. Because of its classification, mineral wool must be landfilled at
special landfills for hazardous waste.
E 16.5 Environmental assessment
Mineral wool comprises a health problem when it is managed as waste. It is classified as hazardous waste because of its local irritant and carcinogenic effects.
More modern mineral wool (manufactured after 2000) can, however, only be regarded as a local irritant because the design of the fibres in the wool has been changed so
that they do not give rise to carcinogenic effects. The local-irritant effect still provides grounds to classify mineral wool as hazardous waste.
From a resource and environmental perspective there are indications that it is appropriate to recycle mineral wool fibres.
E 16.6 Economic aspects
It is not possible to forecast the profitability of recycling mineral wool products before new technologies have been developed.
Taxes and fees for landfilling mineral wool could be changed as a result of changes in landfilling practices.
Before implementing special regulations for management of waste mineral wool, an environmental and economic analysis of possible consequences will be carried out.
E 16.7 Implications for national authorities
The studies of landfilling possibilities could mean that regulations regarding landfilling waste mineral wool will have to be changed.
E 16.8 Implications for local authorities
Municipalities must be aware that there may be special regulations for landfilling waste mineral wool.
E.17. Organic domestic waste
Environmental problem |
Organic domestic waste constitutes a resource that can be utilised through
incineration, biogasification or composting. Local conditions determine how the
organic domestic waste is utilised optimally both environmentally and economically. |
Initiatives |
Focus on management technologies with a view to minimising collection costs.
Development of pretreatment technologies with a view to reducing separation of the organic proportion incinerated.
Development of a tool that can help make a local assessment of whether incineration, biogasification or composting is the most adequate solution environmentally
and economically.
This way the municipalities will have a chance to assess whether or not to initiate local two-tier collection of the organic part of domestic waste and to make a
decision in this respect.
Initiate studies regarding central separation of total domestic waste with a view to recycling the organic part.
Work with valuing environmental effects that have not yet been valued.
|
E 17.1 Status
Organic domestic waste constitutes a resource that is today primarily incinerated and only to a lesser extent utilised through composting or biogasification.
Biogasification is the form of recycling of organic domestic waste that has the highest priority because both energy content and fertiliser content of the waste are utilised.
Composting, including home composting, is still a suitable treatment option for recovery of the fertiliser content of the waste.
Organic domestic waste is defined as vegetable and animal food waste and other easily degradable organic material. The total amount of organic waste constitutes approx.
50 per cent of total domestic waste [36]. In 2001, around 60,000 tonnes of organic domestic waste were recycled through biological treatment [37] corresponding to
approx. 5 per cent of domestic waste. Of this amount, almost 40,000 tonnes were treated at central biogasification or composting plants while the rest was
home-composted. In pretreatment in central treatment, between 15 and 40 per cent of the collected amount is separated depending on the treatment technology. In 2001,
this entailed almost 55,000 tonnes organic domestic waste being collected separately.
Residues from the biological treatment of organic domestic waste are subject to the same requirements as sludge from public wastewater treatment plants with regard to
contents of heavy metal and xenobiotic substances in connection with agricultural use, see appendix E 29.
On the basis of the content of heavy metals and xenobiotic substances, it is assessed that there will not generally be problems with treated organic domestic waste
complying with limit and cut-off values. In addition, studies show that the composting process speeds up the degradation of xenobiotic organic substances.
In recent years, a large number of detailed tests and studies have been carried out illustrating various aspects of recycling organic domestic waste, primarily through
biogasification. The technical basis for assessment of relevant aspects of collection, management and recycling of organic domestic waste has thus been significantly
improved.
E 17.2 Future initiatives
Measures:
- focus on collection costs and development of pretreatment technology for
management of organic domestic waste
- clarify the significance of local conditions for waste management of organic domestic waste
- initiate studies regarding separation of total domestic waste value environmental impacts
The aim is to clarify what local conditions determine whether it is more appropriate to use incineration, biogasification or composting with regard to the organic part of
domestic waste. The Ministry of the Environment intends to develop a tool to assist the municipalities in their assessment. In this way, the municipalities will have a chance
to assess which method of waste management of organic domestic waste is optimal with regard to environmental economics and make a decision in this respect. Relevant
players will be invited to take part in the work.
In order to achieve an environmental assessment of the different uses of the organic part of the waste, it is necessary to work for a further valuation of a number of the side
effects resulting from incineration or recycling respectively.
So far, studies have shown that particularly the two-tier collection and pretreatment are very cost-intensive and crucial to the profitability of recycling organic waste.
Therefore, the aim is to minimise collection costs and to develop pretreatment technology.
As an alternative, the possibilities for central separation of total domestic waste with a view to recycling the organic part will be studied. The study will focus on potential
health and safety problems in a central separation plant and on the quality of the separated material.
E 17.3 Regulation
Under the Statutory Order on Waste (no. 619 of 27 June 2000), the municipalities must arrange collection of domestic waste from households in built-up areas with a
constant inhabitant count of more than 1,000. In municipal regulations, local councils may permit home composting of the vegetable fraction of domestic waste.
E 17.5 Economic aspects
Experience shows that it is relatively cost-intensive to establish two-tier collection of domestic waste with a view to recycling the organic fraction. The national additional
expense thus exceeds the cheaper treatment at biogasification and composting plants as well as the environmental advantages that it has been possible to price so far.
Recycling of degassed or composted organic domestic waste in agriculture requires very clean biomass. The pretreatment technologies already known meet the
requirement for clean biomass, but pretreatment is expensive, and a large part of the waste is filtered out in the pretreatment facilities and this has great influence on the
energy balance.
E 17.6 Environmental assessment
A comparison of the energy benefit from biogasification and incineration of the organic fraction of domestic waste at a national level shows that biogasification yields a
smaller energy benefit in relation to incineration. The calculations include transport, process energy, energy generation and energy consumption for substitution of chemical
fertiliser. Apart from the extensive separation process in pretreatment, the reason is that biogas potential in collected organic domestic waste is smaller than previously
assumed and that energy recovery at incineration plants has been significantly improved over the last 3-5 years.
With regard to energy, it cannot generally be ascertained that incineration is better than biogasification or vice versa. Local conditions such as collection systems, volumes
collected, pretreatment, etc. influence greatly which treatment option should be preferred from an environmental point of view.
Residues from biogasification of 1 tonne organic domestic waste have fertilising values in the range of 3-8 kg nitrogen, 0.5-1.1 kg phosphorous and 1.2-2.6 kg potassium.
Generally, composting does not yield an energy benefit, which is an important factor in the environmental assessment. Local and, in particular, home composting may,
however, still be beneficial, and composting is often cheaper than biogasification.
The environmental impacts of the different treatment options for organic domestic waste include a number of positive effects attached to the use of compost and waste
treated with biogasification which are not currently possible to include in the assessment. This is either because it is difficult to ascertain the effect or because the effect is not
easily priced.
Waste indicators
The new waste indicators for saving resources, energy and landfill requirements [38] which are presented in chapter 2 have been calculated on the basis of the amount of
the relevant waste fraction and the factors shown below. The factors show savings per tonne for the relevant treatment option compared with 1 tonne of waste being
landfilled.
The figure shows the savings achieved through incineration and recycling (biogasification) respectively.
In the LCA data used for biogas production, 4.5 MJ per kg organic waste is credited to natural gas supply. This figure includes both the calorific value of the gas and the
value of the nitrogen fertiliser in the degassed biomass. The value of the biomass as a soil-improving material may be significant but difficult to quantify and has not been
included.
In incineration of organic waste, a recovery figure of 4 MJ has been employed, and this is credited to other energy supply from waste incineration, ie. with a certain
proportion as electricity generation.
Reuse of food waste has not been included, since in 2002, it was prohibited to use food waste as animal feed. Reuse is therefore not a possible treatment option for food
waste today.
Figure: Savings from incineration and recycling in biogas production of one tonne food waste, compared to landfilling the same amount (in mPR, mPE or 10mPE).
Click here to see the Figure.
It appears from the figure that recycling through biogasification yields a slightly smaller energy benefit than does incineration.
Therefore, the balance is also affected by the assumption employed about energy recovery from waste incineration plants. A sensitivity calculation with halved energy
recovery in waste incineration therefore gives savings from biogasification rather than incineration.
There are, however, several conditions not included in the calculation; slag and ash from the incineration process and the soil-improving characteristics of recovery of
degassed biomass from biogas plant.
The figure shows the result that if the organic domestic waste is treated through biogasification (recycled), the energy saving is slightly smaller than for incineration. This
does, however, require that the benefit from incineration is as high as assumed, since the sensitivity calculation with a halved energy benefit in incineration gives the opposite
result.
The recently completed LCA study of treatment of food waste through incineration and biogasification (Danish EPA, 2003) shows the same trend. Slightly different
assumptions have, however, been used for eg. energy recovery. The indicator calculations shown are based on the assumption that energy recovery from incineration is 4
MJ/kg and that this is used for generation of electricity and heat. However, if the assumptions for the yield from incineration are changed, the picture will also change.
E 17.7 Implications for national authorities
The Ministry of the Environment will initiate the development of a model for local assessment of which method of waste management of organic domestic waste is optimal
environmentally and economically.
E 17.8 Implications for local waste authorities
The municipalities will assess locally which method of waste management of organic domestic waste is optimal with regard to environmental economics.
E.18. Organic waste from industry except animal waste and food waste
from industrial kitchens
Environmental problem |
Organic waste is a resource that should be utilised to an optimum extent.
|
Initiatives |
Status quo |
E 18.1 Status
Aims for 2008:
- recycling of no less than 90 per cent
Organic waste is generated both in industry and in industrial kitchens. Much waste from industry is homogeneous by-products and is therefore not included in the ISAG
(Information System for Waste and Recycling, see appendix B).
In industry, just less than 8.5 million tonnes of organic waste are generated each year. The waste is biologically degradable waste such as waste from abattoirs, dairy waste,
fisheries waste, etc., and often has a low dry matter content [39]. Animal waste primarily from slaughterhouses and the fisheries industry constitutes 1.0-1.5 million tonnes
per year and is dealt with in appendix E 1.
To date, most of the waste has been recycled. Some of the waste is used directly as fertiliser on agricultural soil and some substitutes raw materials. The remaining
one-tenth is used in biogas production [40]. Only about 1 per cent has been incinerated or landfilled. There are generally no disposal problems with residues of vegetable
origin.
E 18.2 Future initiatives
None.
E 18.3 Regulation
Recycling organic waste for agricultural purposes is regulated in the Statutory Order on sludge. [41]
E 18.4 Capacity
With regard to the fraction of the waste not recycled in other production, the waste may be used for agricultural purposes, possibly through a biogas plant, if the waste has
great biogas potential.
E 18.5 Environmental assessment
No significant changes in environmental aspects are expected for non-animal organic waste products and residues from industry.
E 18.6 Implications for national authorities
None.
E 18.7 Implications for local authorities
Local authorities will maintain their present efforts.
E.19. Ozone-depleting substances in waste fractions
Environmental problem |
Ozone depletion |
Initiatives |
Implementation of regulations pursuant to an EU directive on special treatment
of preinsulated district heating pipes. |
Goals for 2008:
- collection and destruction of no less than 50 per cent of ozone-depleting substances in waste
- collection and destruction of no less than 80 per cent of the CFC content in discarded district heating pipes
E 19.1 Status
In the 1990s, international regulations were implemented on phasing-out of the use of ozone-depleting substances through the Montreal Protocol and the EC
Regulation on substances that deplete the ozone layer.
Current regulations include bans on the use of all CFCs and HCFCs. These substances have been used for many years in foam production of polyurethane, which is
used as insulation material in fridges, freezers, refrigerated display cases, district heating pipes and refrigerated containers.
In 1996, regulations were laid down regarding collection and reprocessing of fridges and freezers with a view to environmentally appropriate handling of the CFC
content. Furthermore, a voluntary agreement was made on collection of CFCs during repair and discarding of large refrigeration systems (the KMO scheme).
In 2002, CFCs and HCFCs in waste were analysed. The analysis shows that from 2007 discarded district heating pipes will be the waste fraction that contains the
largest amount of CFCs. According to the analysis, the CFC volume in discarded district heating pipes was 57 tonnes in 2002, and the annual volume will continue
to increase until 2018 when it will be approx. 250 tonnes. After this, discards of district heating pipes with CFCs will fall gradually, and in 2040 CFCs will constitute
approx. 50 tonnes per year.
Ozone-depleting substances are also used in construction foam, insulation panels, insulated aluminium doors and building insulation. Apart from aluminium doors, it is
not assumed possible to establish special collection and treatment systems for these fractions.
Measures:
- lay down regulations regarding waste management of district heating pipes and doors containing ozone-depleting substances
E 19.2 Future initiatives
In accordance with the EU Regulation on substances that deplete the ozone layer, special regulations will be laid down regarding waste management of preinsulated district
heating pipes containing CFCs or HCFCs.
A study will be carried out of the possibilities for separate management of other waste fractions containing ozone-depleting substances. The study will also look into the
extent to which district heating pipes are dug up after the end of their useful life.
E 19.3 Regulation
Waste management of refrigeration equipment is regulated by the circular on municipal regulation of disposal of refrigeration equipment containing CFCs.
The voluntary KMO scheme was established in 1992 and includes environmentally appropriate handling of refrigerants from large refrigeration systems.
Waste management of other waste fractions containing ozone-depleting substances is regulated in the Statutory Order on Waste.
E 19.4 Capacity
It is assessed that existing plants will have sufficient capacity for reprocessing discarded district heating pipes. There may, however, prove to be a need to modify these
plants depending on the treatment requirements laid down.
E 19.5 Environmental assessment
Collection and destruction of the total amount of ozone-depleting substances in the waste are expected to increase from approx. 30 per cent to approx. 50 per cent.
E 19.6 Economic aspects
There is great uncertainty as to the number of district heating pipes dug up after the end of their useful lives. Therefore, there is a need for a study of this before the costs of
special treatment of district heating pipes containing ozone-depleting substances can be determined.
E 19.7 Implications for national authorities
The Statutory Order on Waste must be amended or a special statutory order on management of waste containing ozone-depleting substances must be prepared.
E 19.8 Implications for local authorities
None, except for supervision of compliance with the regulations.
E.20. Paper and cardboard
Environmental problem |
Paper and cardboard waste constitutes an important resource and should be
recycled. |
Initiatives |
Paper collection must be maintained at the 2004 level. |
Goals for 2008:
- 60 per cent recycling of all cardboard and paper waste
- 60 per cent recycling of cardboard and paper packaging waste
- maintain 60 per cent recycling of recyclable paper and cardboard waste from households
- maintain 75 per cent recycling of recyclable paper and cardboard waste from enterprises and public and private institutions
E 20.1 Status
In 2001, consumption of paper and cardboard was calculated at 1,360,000 tonnes. In the period 1997-2000, paper consumption has been at the same level.
In 2001, 721,000 tonnes of paper and cardboard were collected, corresponding to 53 per cent of paper consumption [42]. The amount collected increased steadily
from 1990 to 2001.
The amount of paper and cardboard suitable for recycling is smaller for households than for all the other sectors together. Tissue and soiled packaging (approx.
200,000 tonnes) is seen more frequently in household waste and is not suitable for recycling. The goal for households of 60 per cent recycling of recyclable paper
and cardboard waste corresponds to approx. 48 per cent of the total amount of paper and cardboard waste in households. The goal for enterprises of 75 per cent
recycling of recyclable paper and cardboard waste corresponds to approx. 68 per cent of the total amount of paper and cardboard waste from industry.
According to the ISAG, 192,000 tonnes of paper and cardboard waste from households and 516,000 tonnes from enterprises, institutions, trade and offices were
collected in 2001 [43]. Municipalities that do not have collection schemes have reported their total collected amounts for 2001 to the Danish EPA.
If ISAG figures are added for municipalities with collection schemes, a total of 237,000 tonnes paper and cardboard were collected from households in 2001. This
corresponds to 59 per cent of the potential for recyclable paper and cardboard from households.
The remaining volume of paper and cardboard waste of approx. 639,000 tonnes is primarily taken to waste incineration plants and energy recovered. There are
approx. 262,000 tonnes of paper and cardboard in the residual waste of households. Approx. 46 per cent of this is estimated to be suitable for recycling.
E 20.2 Future initiatives
It may become necessary to increase the volume of packaging waste from paper and cardboard used for recycling in order to reach the goal of 55 per cent recycling
of all packaging waste in 2008. This may necessitate the introduction of collection schemes for cardboard from households. This will be clarified in the white paper to
the Danish Parliament in 2005 mentioned in appendix E 8.
E 20.3 Regulation
The regulations regarding collection and recycling of paper and cardboard can be found in the Statutory Order on Waste [44]. Under the Statutory Order on Waste,
the municipalities are under an obligation to ensure recycling of transport packaging of paper and cardboard from enterprises and public and private institutions. This
duty is to be seen as an extension of the agreement on transport packaging between the Ministry of the Environment and the Confederation of Danish Industries, the
Danish Plastics Federation, and the Danish Packaging Industry in 1994.
The municipalities are under an obligation to collect a number of types of paper for recycling from private built-up areas with more than 1,000 inhabitants. This must
be done by means of fixed collection equipment. Furthermore, the municipalities must collect other paper and cardboard including cardboard packaging from private
built-up areas with more than 1,000 inhabitants. However, the municipalities do not have to meet these requirements if they collected 40 and 55 per cent respectively
in 2001 and 2002 of recyclable paper and of cardboard potential from households. In future, the municipalities only have to meet the above requirements if the
volume collected is less than 55 per cent of recyclable paper and cardboard potentials in two successive calendar years from 2003 onwards.
E 20.4 Capacity
Marketing possibilities for collected waste paper are good both on the national as well as the international market, but prices vary.
Today, around 20 enterprises in Denmark deal in waste paper, and four enterprises that consume collected waste paper recycle this into new products.
The treatment capacity is adequate for recycling of all collected waste paper.
E 20.5 Environmental assessment
Recycling waste paper is environmentally superior to manufacturing new paper. Increased recycling of paper will give a total CO2 reduction and reduced impacts
from wastewater discharges. In addition, the volume of domestic waste to be treated at incineration plants is limited and this frees capacity.
Waste indicators
The new waste indicators for saving resources, energy and landfill requirements [45] which are presented in chapter 2 have been calculated on the basis of the
amount of the relevant waste fraction and the factors shown below. The factors show savings per tonne for the relevant treatment option compared with 1 tonne of
waste being landfilled.
The figure below shows the savings from using incineration and recycling respectively of 1 tonne of paper and cardboard compared to landfilling 1 tonne of paper
and cardboard. The five columns for each treatment option thus show the savings for energy resources, other resources, gross energy and landfilling of waste. So,
the higher the columns are the greater the saving achieved compared to a landfilling solution.
Figure: Savings from treatment of 1 tonne of paper and cardboard by incineration and recycling respectively. The values are:
mPR per tonne for the two resource factors,
mPE per tonne (1 PE=160 GJ) for the two energy indicators and
10 mPE per tonne (1 PE=403 kg) for the landfill factor
Click here to see the Figure.
Thus it appears from the figure that the greatest saving in renewable gross energy is achieved by recycling 1 tonne paper and cardboard instead of incinerating it, and
this is also reflected in the indicator for energy resources. For the other three indicators, the saving from recycling is only marginal.
The crediting of the energy from waste incineration is an important condition for this conclusion. A sensitivity calculation assuming a halved energy benefit in
incineration shows increased saving in recycling. The reason that the energy benefit in incineration may be smaller in future is that it is to be expected that the
efficiency of the total electricity generation system is constantly improving and to an increasing extent based on renewable energy.
However, there are significant differences in the energy and environmental advantages in recycling different paper types. In particular, a total assessment of what the
individual waste paper qualities in practice replace is still needed. A project has been initiated and the results will give a differentiated picture of what paper qualities
can be recycled with the greatest energy and environment advantage.
E 20.6 Economic aspects
Maintaining the goal of 60 per cent recycling of paper and cardboard is not expected to lead to extra costs.
E 20.7 Implications for national authorities
The Danish EPA will assess whether there is a need for further initiatives regarding paper and cardboard packaging.
E 20.8 Implications for local authorities
In future planning, the municipalities must provide ongoing information on collection schemes and separation requirements in order to maintain the level of paper
collection.
E.21. PCBs and PCTs
Environmental problem |
PCBs/PCTs are hazardous to human health and the environment. |
Initiatives |
Assess whether environmental or health effects arise in connection with using,
renovating, or demolishing buildings containing PCBs. |
E 21.1 Status
Aims for 2008:
- status quo with regard to the goal that oils containing PCBs/PCTs (>0.05 per cent by weight) in transformers should be phased out before 2000
- assessment of whether there are environmental or health effects from using, renovating, or demolishing buildings containing PCBs
PCBs are a group of chlorinated biphenyls, and PCTs are a group of chlorinated terphenyls. These substances do not readily decompose and accumulate in the food chain.
PCBs and PCTs are teratogenetic, carcinogenic, and are suspected of demonstrating hormone-like effects on reptiles and mammals. High concentrations of PCBs and
PCTs have been found in fat tissues of, for example, polar bears, seals, and birds of prey.
PCBs are one of the 12 substances on the Stockholm Convention list of substances where a stop on production, use and consumption should be ensured as well as
environmentally sound destruction.
PCBs and PCTs have been used as refrigerants and insulation fluids in electrical equipment such as transformers and condensers. Furthermore they have been used in heat
pumps, gas turbines, hydraulic systems, glue, fire inhibitors, sealing and filling compounds etc.
Special measures have been initiated in Denmark and internationally to phase out the use of the substances. There has been a ban in Denmark on importing and selling
PCBs/PCTs, as well as equipment containing these substances since 31 October 1986.
Furthermore, since 1 January 1995 the use of PCB/PCT-containing condensers and transformers above a certain limit (total weight > 1 kg or effect > 2kW) has been
banned. Therefore, large transformers (>5 l PCB) do not exist in Denmark. Small condensers and transformers may be used until the end of their useful life.
Since 1 January 1999 there has been a requirement that transformers with a PCB concentration above a certain limit (>0.05 per cent by weight) should be decontaminated
as soon as possible.
PCBs were used in fillers and sealing materials for sealed glazing units for window panes between 1950 and 1976. Studies indicate that consumption of PCBs in fillers
during the period was 110 tonnes PCBs and 200 tonnes PCBs in sealing glues.
The technical lifetime of fillers is usually 25 years. In practice fillers are replaced less often and a screening survey indicates that there is still a large amount of old filler
remaining in existing buildings. According to estimates, 75 tonnes of PCBs remain in fillers today.
Similarly, surveys from Norway and Sweden show that only few sealed window panes are replaced. It is estimated that 160 tonnes PCBs remain in sealed double-glazing.
Measures:
- examine whether there are environmental and health effects in connection with using, renovating, or demolishing buildings containing PCBs
E 21.2 Future initiatives
A study will be initiated to examine whether there are environmental and health effects in connection with using, renovating, or demolishing buildings containing PCBs. The
project will focus on assessing PCBs in house dust, indoor air, and soil close to buildings, as well as making comparisons with other sources and TDI values for selected
PCBs.
E 21.3 Regulation
In the Statutory Order on waste, PCB/PCT waste is regulated as hazardous waste. As a consequence, local authorities are responsible for collecting such waste.
In 1998 a Statutory Order on PCBs, PCTs and substitute substances was issued. [46]. The Statutory Order entered into force on 1 January 1999.
In the Statutory Order on electrical and electronic products [47] condensers containing PCBs are further regulated.
E 21.4 Capacity
In Denmark, Kommunekemi A/S is the only enterprise authorised to destroy PCB/PCT condenser and transformer oils with a PCB/PCT content above 50 ppm.
E 21.5 Environmental assessment
New requirements will ensure controlled disposal of remaining PCBs/PCTs.
E 21.6 Economic aspects
If the project on PCBs in building and construction waste gives rise to changes in legislation, an environmental-economic analysis will be carried out of the consequences.
E 21.7 Implications for local authorities
In parallel to the decontamination of transformers with PCB-containing oils, local authorities must collect waste.
E.22. Plastic
Environmental problem |
Plastic waste constitutes a non-renewable resource that can be utilised better
than it is at present. |
Initiatives |
Increased recycling of transport packaging and certain sales packaging from
business and households. |
E 22.1 Status
Goal for 2008:
- increase recycling of plastic packaging to 22.5 per cent
The Danish plastic requirement in 2000 amounted to about 604,000 tonnes, and waste amounts were around 345,000 tonnes. According to estimates, the amount
of plastic in waste was lower than consumption because plastic is part of products with a long lifetime such as water, sewage, and district heating pipes, electricity
and telephone cables, and components in wind turbines. Consumption of plastic and the amount of waste increased by about 40 per cent between 1996 and 2000.
Consumption of plastic packaging in 2001 has been calculated at some 150,000 tonnes. This amount has remained constant from 1997-2000 [48].
In 2001, 43,000 tonnes of plastic were collected and recycled in Denmark. This figure includes both production and packaging waste that is reprocessed in
Denmark. About 21,000 tonnes of plastic packaging was collected for recycling, and about 10,000 tonnes of this amount was exported for recycling abroad [49].
Plastic comprises about 9 per cent of the contents of households' dustbins. This corresponded to about 155,000 tonnes in 2001, and of this the most dominant
fraction was plastic packaging. The recyclable proportion of the plastic packaging amounted to about 27,000 tonnes. More or less all plastic ending in domestic
waste goes to waste incineration plants where heat and electricity are produced.
It is likely that there is a lot of the plastic in the combustible part of the waste from business enterprises (institutions, trade and offices, as well as manufacturing
industries), but there are no analyses of the plastic content in these fractions. Estimates indicate that about 280,000 tonnes of plastic are incinerated each year.
Finally there is plastic in three environmental contaminant waste fractions – PVC, electronic products, and end-of-life vehicles. See appendices E 23, E 7, and E 5.
Denmark has primarily aimed at meeting the minimum requirement of 15 per cent recycling contained in the Packaging Directive of 2001 by recycling transport
packaging plastic from business, as there are typically large, clean and more homogenous fractions. In contrast plastic waste from households occurs in small, soiled
amounts comprising many types of plastic. In 2001, transport packaging plastic amounted to about 50 per cent of the total supply of packaging.
Denmark expected to meet the minimum requirement in the Packaging Directive so that no less than 15 per cent of plastic packaging was recycled in 2001. Data for
2001 show that Denmark recycled 14 per cent in 2001; just under the goal for 2001.
In 2001, the Danish Parliament adopted a report on recycling plastic packaging, in which the goal was 22 per cent recycling by 2004. However, this assumes high
price levels and constant amounts, and that a number of initiatives are started.
At the moment there are negotiations on revising the Packaging Directive. It is expected that the new goal for recycling plastic packaging will be 22.5 per cent in
2008. This corresponds 35,000 tonnes, on the basis of the amounts of waste plastic packaging in 2000.
In 2002 a collection scheme for single-use bottles for carbonated soft drinks was established via Dansk Retursystem. Recycling of these bottles will contribute to
meeting the goal with about 1,000 tonnes.
A lot of waste plastic is not suitable for recycling and is therefore incinerated with energy recovery. Therefore, it should be considered whether it would be more
beneficial to separate mechanically this type of plastic waste with a view to energy recovery of the calorific value in the plastic at special plants so that the only loss of
resources is the conversion from oil into plastic. In 2002 a project was initiated to assess the environmental conditions involved in the various forms of energy
recovery from plastic.
Measures:
- enterprises and municipalities to have greater focus on separating plastic film for recycling
- the sector organisations for waste producers to be able to establish nationwide collection schemes
- enterprises to separate plastic containers for recycling
- compulsory schemes for collection of plastic containers and bottles from households
E 22.2 Future initiatives
Increased separation of transport packaging film from industry, building, trade, etc.
Municipalities will prioritise supervision by seeing that transport packaging is collected for recycling.
Waste producers will play a greater part in organising effective schemes. It will be easier for sector organisations representing waste producers/chains to establish collection
schemes covering the whole of Denmark. Legislative changes will be examined so that amended legislation in 2004 can allow new schemes to work from 2005.
It is most appropriate environmentally and economically that enterprises with large amounts carry out separation. Estimates indicate that about 42,000 tonnes plastic foil
waste comes from enterprises with more than 10 employees each year. [50]. Therefore there will be more focus on enterprises with large amounts in industry, trade and
service.
It may be necessary to extend the requirements for collection to smaller enterprises. A project currently in progress is examining collection systems for transport packaging
made of plastic from small and medium-sized enterprises.
Increased separation of other plastic packaging from industry, trade, etc.
In 2002, a project was initiated to assess the potential to recycle and reuse plastic drums and containers from business with special focus on identifying relevant sectors.
Environmental and economic aspects will also be investigated. When the project is completed in mid 2003, a decision will be made regarding the types of packaging to be
separated.
Compulsory schemes for collecting plastic containers and bottles from households.
From 1999 to 2001 three projects were completed to assess whether it is possible to collect plastic bottles and containers from households for recycling and achieve good
quality plastic in the recycled material. Assessments were made of the potential, collection systems, separation criteria, and sales possibilities, including a collection trial in
Nyborg [51].
In addition an environmental assessment has been completed of recycling compared with incineration of plastic bottles and containers from households. It is environmentally
appropriate to recycle, if the product can easily be emptied from the packaging [52].
Finally, an environmental economic assessment of recycling compared with incineration of plastic bottles and containers has been completed [53]. Two collection systems
for recycling were compared; a voluntary bring scheme to containers, and collection at recycling stations. The results showed that it is most expensive in terms of
socio-economics to establish a bring scheme in containers, cheaper to collect at recycling stations, and cheapest to incinerate this type of packaging. Recycling is
particularly affected by the costs of manual separation.
On the basis of these surveys, from 2005 municipalities will be subject to providing citizens with the possibility to separate relevant packaging and deliver it for recycling, for
example to a recycling site, as this is the cheapest recycling option.
If the amount of plastic collected for recycling does not increase at a satisfactory rate in the future, consideration will be afforded as to whether to introduce compulsory
municipal collection schemes for plastic transport packaging, or producer responsibility for plastic transport packaging.
E 22.3 Regulation
According to the Statutory Order on Waste, the municipalities [54] are obliged to ensure recycling of plastic transport packaging from business enterprises. This duty is
further to the 1994 agreement on transport packaging between the Ministry of the Environment, the Confederation of Danish Industries, the Danish Plastics Federation, and
the Packaging Industry.
Easier access for sector organisations to establish nationwide collection schemes and a forthcoming recycling scheme for plastic bottles and containers from households and
business will require a change in the legislation.
E 22.4 Capacity
Assessments indicate that the capacity necessary to reprocess plastic transport packaging is available in Denmark. Since 1999 there has been an increasing export of
plastic packaging waste to the Far East.
At present there is no capacity to reprocess plastic bottles and containers in Denmark, but there is capacity in other European countries and in the Far East.
E 22.5 Environmental assessment
Plastic is normally manufactured on the basis of oil, which is a non-renewable resource. The conversion of oil into plastic is very energy intensive. The consumption of oil is
close to 2 kg per 1 kg plastic manufactured. Recycling of plastic, replacing virgin plastic with recycled plastic, will therefore give a significant environmental benefit.
It is difficult to recycle plastic as there are many different types of plastic. Recycling of plastic at a high environmental level therefore requires that plastic is separated into
pure fractions. Much waste plastic is generated by many small waste producers, especially households, which makes separation and collection difficult and resource
consuming.
When plastic is incinerated, the energy that was used for the conversion of oil into plastic is lost. Energy utilisation of plastic in conventional waste incineration plants is poor,
as electricity generated only corresponds to 20 to 25 per cent of energy fed in through the calorific value of the plastic.
Waste indicators
The new waste indicators for saving resources, for energy and for landfill requirements [55] which are presented in chapter 2 have been calculated on the basis of the
amount of the relevant waste fraction and the factors shown below. The factors show savings per tonne for the relevant treatment option compared with one tonne of waste
being landfilled.
Polyethylene (PE)
The figure below shows the savings for the five indicators through incineration and recycling respectively of one tonne polyethylene compared with landfilling the same
amount.
Figure: Savings from incineration and recycling of one tonne of polyethylene (PE - should not be confused with the units in the figure, mPE or person equivalents),
compared to landfilling the same amount (in mPR, mPE, and 10 mPE).
Click here to see the Figure.
There is a resource and energy saving from recycling compared with incineration. In contrast, there is a slightly smaller saving in the landfill factor through recycling. This is
because of a certain amount of waste from the recycling process, which the calculations assume is landfilled.
Recycling polyethylene (PE) provides energy savings. A more detailed lifecycle study [56] shows that, with regard to energy, it is only worth collecting pure plastic waste
from households. Not surprisingly, a sensitivity analysis shows that the advantages of recycling become relatively greater as energy benefits from waste incineration fall.
Energy benefits from incineration therefore determine the type of plastic fractions it is worth recycling.
E 22.6 Economic aspects
Increased collection of transport packaging from enterprises is not expected to lead to higher net costs for enterprises. Enterprises will incur extra costs for separation, but
there will be a small income from plastic waste and a saving in costs of treatment at incineration plants and waste taxes.
If it is necessary to collect from enterprises with only small amounts of waste, there will be extra costs for enterprises.
A compulsory collection scheme for plastic bottles and containers at recycling sites will cost the public an extra DKK 1.9 million.
E 22.7 Implications for national authorities
Legislation will be changed.
Collection of plastic packaging will be closely monitored so that further initiatives can be implemented if necessary.
E 22.8 Implications for local authorities
In their future planning, local authorities will have to take into consideration that from 2005 there will be a requirement to give citizens the opportunity to deliver certain
plastic bottles and containers for recycling, for example at recycling sites.
Assignment of transport packaging and other plastic packaging from business will have high priority.
E.23. PVC
Environmental problem |
PVC contains a number of environmental contaminants causing environmental
problems in waste management.
On incineration, the chlorine content in waste can contribute to the formation of dioxins. It is therefore important to keep the content of chlorine in waste as low as
possible. As PVC waste is a source of chlorine, as far as possible this fraction must be kept away from incineration plants.
|
Initiatives |
Determine amounts of PVC being marketed and the potential amounts of waste.
Prepare draft requirements for managing PVC waste.
Prepare criteria for exemptions from the PVC tax.
Exempt chemical treatment plants from the waste tax in order to promote new recycling technologies.
Substitute PVC products which end in waste incineration plants.
Ensure that PVC products containing lead and cadmium are separated for either chemical treatment or landfilling.
Complete an environmental and economic analysis of treatment methods for PVC waste.
|
Aims for 2008:
- ensure environmentally sound treatment of PVC waste so that resources are exploited, and problems with additives are eliminated
- keep PVC waste away from waste incineration plants
- ensure that the environmental problems from mechanical recycling are minimised
E 23.1 Status
A focused effort will be made for environmental problems related to PVC. Additives harmful to health and the environment will be phased out, and waste containing
chlorine will be kept away from waste incineration plants, including waste with PVC. Appropriate treatment methods will be established for PVC waste.
Estimates show that about 34,000 tonnes of PVC waste were generated in 2002 [57]. PVC waste is generated in the building and construction sector, the business sector
(trade and office as well as industry), and households, each accounting for around one third.
Amounts of PVC waste from the building and construction sector are expected to increase. From the other sectors, amounts will decrease.
The WUPPI A/S company collects recyclable PVC waste. In 2002, 1,100 tonnes were collected, corresponding to 3 per cent of the total amount of waste, and 16 per
cent of the potential waste amount that could be recycled.
Raw PVC is not manufactured in Denmark. PVC contains various additives such as colorants, stabilisers, anti-static agents, fire inhibiting substances, fillers and plasticisers.
Different environmental aspects are connected to the different additives.
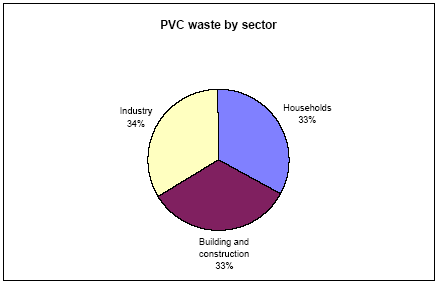
In April 2001, new regulations were introduced for managing PVC waste. These mean that recyclable PVC waste must be separated for recycling, while the rest must be
landfilled. However, it is not possible to separate all PVC, and therefore between 50 and 60 per cent of PVC waste ends in Danish incineration plants. Incineration of PVC
in plants with dry and semi-dry cleaning systems forms acid, and this is subsequently neutralised by adding lime. This increases the amount of flue-gas cleaning waste for
landfilling. In general it is assumed that 1 kg PVC leads to the formation of 0.4-1.7 kg flue-gas cleaning product. Heavy metals (lead and cadmium) become concentrated in
the product after incineration.
Today, mechanical recycling is a possibility for a number of products made of hard PVC. The occurrence of additives previously used such as lead and cadmium inhibit
mechanical recycling. Today it has been decided that the use of lead and cadmium must be phased out in the manufacture of new products. There may be a short-term
exemption on sales of products containing lead.
Alternative treatment methods have been developed that exploit resources and eliminate problems from additives.
Measures:
- determine amounts of PVC being marketed and estimate the potential amounts of waste
- prepare requirements for managing PVC waste
- exempt products being managed in an environmentally sound manner from the PVC tax
- prepare guidelines for mechanical recycling of PVC products containing lead and cadmium
- exempt chemical treatment plants from the waste tax
- assess the possibilities to promote use of alternative products to the products that end in waste incineration plants
- carry out an environmental and economic analysis of waste PVC treatment
E 23.2 Future initiatives
A working group will be set up to determine the amounts of PVC being marketed and design a model for calculating the expected waste amounts. Waste amounts will be
estimated up to 2020.
Efforts must ensure that PVC waste is managed in an environmentally appropriate manner. This could be by preparing requirements for collecting and treating PVC waste,
and by exempting products managed in an environmentally sound manner from taxes. The Ministry of the Environment will contact the Ministry of Taxation with a view to
exempting the relevant treatment plants from the registration duty.
Preparation of future regulations for managing waste PVC will ensure that PVC waste containing lead and cadmium is separated for either chemical treatment or landfilling.
Any dispensation to sell products containing lead will be prepared with guidelines on how recycling of regenerated PVC containing lead can take place.
In order to promote use of new technology to treat waste PVC, there will be work to amend the legislation regarding taxes on waste and raw materials [58] so that the new
plants are exempt from waste taxes.
It is not possible to keep PVC completely away from incineration plants. In 2002, the Danish Environmental Protection Agency completed an analysis of alternatives to
building products made of softened PVC. The Danish EPA will assess other areas regularly in order to examine possibilities to promote the use of alternatives to the
products that end at waste incineration plants.
An environmental and economic study has been initiated on managing PVC waste. The analysis will assess the extra costs involved in mechanical recycling and chemical
treatment compared to landfilling. Completion of the study is expected in 2003.
E 23.3 Regulation
The Minister for Environment and the Danish Plastics Federation made an agreement in 1991 on the management of PVC waste.
The overall goal of the agreement has been to keep PVC away from waste incineration plants. The agreement lays down specific targets for building materials, packaging,
and other products, as well as heavy metals and fire inhibitors [59].
Non-recyclable PVC waste has so far been regulated in the general provisions in the Statutory Order on waste.
In April 2001, new regulations were issued for managing PVC waste. The regulations ensure that recyclable PVC waste is separated for recycling, while the rest is
landfilled.
At the same time as the regulations were issued, a list was sent to all municipalities of the products the Danish EPA considers are suitable for recycling, and those which are
suitable for landfilling.
In order to make identification of PVC products easier, the Danish EPA has issued a handbook on PVC.
E 23.4 Environmental assessment
Separation of PVC with a view to avoiding delivery to waste incineration plants of this waste fraction will lead to a reduction in amounts of flue-gas cleaning waste.
Furthermore, reduced delivery of PVC waste to incineration plants will also lead to improved quality of slag for recycling.
However, it is assessed that it is impossible to identify some PVC waste. This waste will still be delivered to incineration plants.
New plants for chemical treatment of PVC waste will help improve exploitation of resources, and they will eliminate the problems of environmentally harmful additives.
Waste indicators
The new waste indicators for saving resources, for energy and for landfill requirements [60] which are presented in chapter 2 have been calculated on the basis of the
amount of the relevant waste fraction and the factors shown below. The factors show savings per tonne for the relevant treatment option compared with one tonne of waste
being landfilled.
The figure below shows the savings from incinerating and recycling one tonne of PVC.
Figure: Savings from incineration and recycling of one tonne of PVC, compared to landfilling the same amount (in mPR, mPE, 10 mPE).
Click here to see the Figure.
The figure shows that the savings in total resources (energy resources and other resources in total) and savings in gross energy consumption are greatest from recycling. As
with other types of plastic, it has not been possible to obtain specific data for recycling PVC, and PE data has been applied for recycling. Therefore, as with PE a significant
amount of waste regarding recycling has been included, and the correctness of this should be investigated more closely for the specific plastic material for recycling. Some
landfill space is saved through recycling PVC, as incineration leads to the formation of large amounts of flue-gas cleaning products for landfilling.
The result of the indicator calculation is therefore that there is a significant saving in energy and landfill space from recycling PVC, calculated per tonne.
E 23.5 Economic aspects
An environmental and economic study has been initiated on managing PVC waste. The analysis will assess the extra costs involved in mechanical recycling and chemical
treatment compared to landfilling. Completion of the study is expected in 2003.
E 23.6 Implications for national authorities
When suitable treatment methods have been developed, new requirements for management of PVC waste will be issued.
E 23.7 Implications for local authorities
Local authorities are to ensure that non-recyclable PVC waste is assigned to landfilling.
When suitable treatment methods have been developed, new requirements for management of PVC waste will be issued.
E.24. Residues from biofuels
Environmental problem |
Bioash contains nutrients that should be recycled for agricultural purposes,
taking account of the content of the ash, particularly cadmium. |
Initiatives |
Reassessment of the current regulations for recycling bioash for agricultural
purposes. |
Aims for 2008:
- at least 75 per cent of bioash to be recycled for agricultural purposes
E 24.1 Status
In 2000 a statutory order on recycling bioash was issued. This makes it possible to recycle the contents of nutrients, primarily potassium and phosphorus, in fertilizers
for agricultural land and forests. A specification in an environmental project on separation and recycling ash from biofuel plants (2003) shows that in 2000 about
32,300 tonnes of bioash were produced, of which about 64 per cent was recycled on agricultural soil and in forests.
Most of content of heavy metals in bioash is found in fly ash, and therefore initiatives have been established at power stations where the content of potassium in fly
ash is washed out and recycled for agricultural purposes, while the remaining residues containing heavy metals are landfilled.
Up to 2030 it is expected that the amount of bioash will increase to up to 70,000 tonnes per year as a result of the Action Plan for Biomass.
E 24.2 Future initiatives
Measures:
- reassessment of the current regulations
The Statutory Order on Bioash will be revised to include the most recent knowledge about the availability of nutrients in hardened bioash.
E 24.3 Regulation
Recycling of bioash is regulated by Statutory Order no. 39 of 20 January 2000 on use of ash from gasification and incineration of biomass and biomass waste for
agricultural purposes – called the Bioash Statutory Order.
E 24.4 Capacity
Provided bioash is of adequate quality, it can be recycled without capacity problems in agricultural purposes. Alternatively the ash can be landfilled.
E 24.5 Environmental assessment
No significant changes in environmental aspects are expected.
E 24.6 Implications for national authorities
The Statutory Order on bioash will be revised.
E 24.7 Implications for local authorities
No significant initiatives are expected by municipalities.
E.25. Residues from waste incineration plants
Environmental problem |
Residues contain heavy metals which, by leaching, threaten groundwater. |
Initiatives |
Optimise separation of waste fractions containing heavy metals from the waste
stream.
Optimise the incineration process so that leaching of xenobiotic substances in slag is minimised.
Separate slag with particularly high content of heavy metals immediately after the incineration process.
Prepare an action plan for future management of flue-gas cleaning products manufactured in Denmark on the basis of an environmental and economic calculation.
|
E 25.1 Status
Aims for 2008:
- 85 per cent recycling of slag taking the groundwater into account
- ensure a Danish solution for management of flue-gas cleaning products
Residues from waste incineration contain heavy metals.
Residues cover slag and flue-gas waste, including fly ash.
In 2001, 87 per cent of slag was recycled while the rest was landfilled. The flue-gas waste will be exported and landfilled in Norway and Germany until a permanent
Danish solution is established.
Requirements for recycling of other residues from waste incineration must be adjusted to take account of groundwater. The objective of recycling residues from
waste incineration plants has been achieved [61], as 75 per cent of residues from waste incineration plants was recycled in 2001.
In 2001, 465,600 tonnes of slag and 73,825 tonnes of flue-gas cleaning waste were generated. Flue-gas cleaning waste contains large amounts of environmental
contaminants, and it results in very high leaching of salts and heavy metals when water flows through it. Flue-gas cleaning waste is classified as hazardous waste.
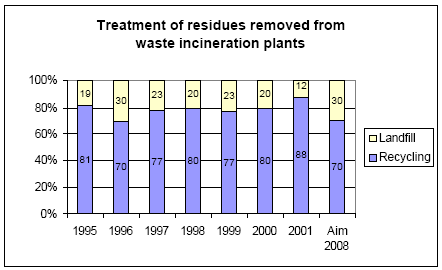
Slag and flue-gas cleaning waste are generated at 31 waste incineration plants and Kommunekemi A/S, as well as the special incineration plant SWS.
Slag from waste incineration is primarily recycled in building and construction works. Present criteria for recycling must be adjusted so that groundwater resources
are protected, since the criteria do not cover organic compounds.
In 2001, 139,000 tonnes flue-gas cleaning waste from waste incineration plants and temporary landfills were exported for landfilling in Norway or Germany. The
flue-gas cleaning waste is exported because there are no existing satisfactory methods for stabilising or reprocessing flue-gas cleaning waste, and landfilling in
Norway or Germany is deemed to be much more environmentally appropriate than temporary landfilling in Denmark.
Methods have been developed for stabilising flue-gas cleaning waste but the methods are not deemed to be environmentally or economically competitive in the long
term with the reprocessing technologies expected to be developed within the next few years.
At foreign plants, good results have been achieved with regard to stabilising flue-gas cleaning waste. The tests have shown that it is possible to recycle zinc and lead.
The minerals in flue-gas cleaning products have also been recovered as slag that can be recycled for building and construction works.
Measures:
- Statutory Order no. 655 of 27 June 2000 to be extended to cover limit values for organic substances
- reduce leaching of xenobiotic substances from slag
- filter out fractions with particularly high contents of heavy metals from the remaining slag
- prepare an action plan for a permanent solution to management of flue-gas cleaning products produced in Denmark
E 25.2 Future initiatives
On 1 January 2001, Statutory Order no. 655 of 27 June 2000 on recycling of residual products and soil in building and construction work entered into force, and this
Statutory Order regulates recycling of slag from waste incineration plants.
The purpose of the Statutory Order is to ensure recycling of residues with due respect for groundwater resources. To ensure this, the Statutory Order will be extended to
cover limit values for organic substances.
Recycling slag from waste incineration plants is dependent upon the risk of leaching of heavy metals and salts from the slag. Increased recycling of slag is thus dependent
upon the content of these substances in the slag and on how the substances are bound in the slag. In addition to this, the slag is not a homogeneous waste stream, which is
why separation of the slag immediately after it comes out of the ovens may increase the recycling potential.
It is expected that recycling slag from waste incineration plants can be increased when it becomes possible to register the effect of the regulations on separation of the waste
fractions containing heavy metals, namely PVC, impregnated wood and electrical and electronic products. Recycling other fractions containing heavy metals may become
relevant, but not until they have been analysed environmentally and economically.
In 2002, studies were initiated with the purpose of determining the incineration conditions under which xenobiotic substances are best bound in the slag and whether the
slag can be separated according to heavy metal content immediately after coming out of the ovens.
On the basis of the stabilisation tests made, it is assessed that stabilising flue-gas cleaning products and subsequently landfilling them in Denmark is not the optimal solution
with regard to the environment and economy in the long term.
At global level, reprocessing technologies have been developed that, on the basis of results so far, look very promising with regard to the environment as well as
economically. Also within the field of "development of Danish reprocessing technologies" positive results are anticipated within the next few years (1 to 2 years).
On the basis of this, the Danish EPA will, in 2003, prepare an action plan for future management of flue-gas cleaning products in cooperation with waste incineration plants.
The action plan will contain time limits for the solution of the problems with flue-gas cleaning products. If possible, Denmark will solve its own problems with flue-gas
cleaning products, and one element of the action plan will be to establish environmentally appropriate reprocessing methods so that flue-gas cleaning products may be
recycled.
When environmentally appropriate reprocessing methods have been established, specific regulations regarding management of flue-gas cleaning products from waste
incineration plants will be prepared.
E 25.3 Regulation
According to general rules on waste [62] local authorities must assign slag to disposal, and they are responsible for collecting flue-gas cleaning waste.
Recycling of slag is regulated by Statutory Order no. 655 of 27 June 2000 on Recycling of Residual Products and Soil in Building and Construction Work.
Exports of flue-gas cleaning products for landfilling in Norway and Germany are covered by bekendtgørelse nr. 971 af 19. november 1996 om import- og eksport af affald
(Statutory Order no. 971 of 19 November 1996 on imports and exports of waste).
E 25.4 Capacity
It may become necessary to landfill increasing amounts of slag, due to revised regulations regarding recycling.
E 25.5 Implications for national waste authorities
The counties are permitted to omit to plan for establishment of national coastal landfills when environmentally appropriate reprocessing methods are being developed.
E 25.6 Implications for local waste authorities
The municipalities must, in their future planning, take into account the changed conditions for management of residues from waste incineration plants, including the future
management of flue-gas cleaning products.
If Statutory Order no. 655 of 27 June 2000 on Recycling of Residual Products and Soil in Building and Construction Work results in landfilling of a larger volume of slag,
the municipalities must include increased landfilling capacity in their planning.
E.26. Residues from power plants fired by coal, oil or natural gas
Environmental problem |
The residues contain trace elements that are harmful to health and the environment.
The residues constitute a large amount of resources that should be recycled instead of taking up capacity at landfills.
|
Initiatives |
Prepare requirements for recycling of residues in order to secure groundwater
resources. |
Aims for 2008:
- 99 per cent recycling of the bottom ash and fly ash produced in coal-fired power plants
E 26.1 Status
Today, energy generation at power plants is based on either coal, oil, natural gas or biofuels. During the process, a number of residues are generated which can be
recycled for various purposes.
According to Energy 21, the use of coal for energy generation will be more or less phased out within the next 30 years. Phasing-out will be done as energy
generation based on biofuels becomes more widespread. As a consequence, the generation of residues from coal-fired power plants will drop in this period,
whereas amounts of residues from bio-based power plants will increase.
Hardly any residues are generated at oil and natural gas-fired power plants.
Residues from coal-fired power plants
Residues from coal-fired power plants are slag, fly ash, gypsum, TASP and sulphuric acid. Residues from coal-fired power plants contain a number of heavy metals
that may limit recycling.
In 2001, 1.21 million tonnes residues were produced and this corresponds to the figure for the year before.
The goal for recycling of residues from coal-fired power plants has been achieved. In 2001, 99 per cent were recycled, and the previous objective was 90 per
cent recycling in 2004.
The following figure shows the development of treatment of residues from coal-fired power plants.
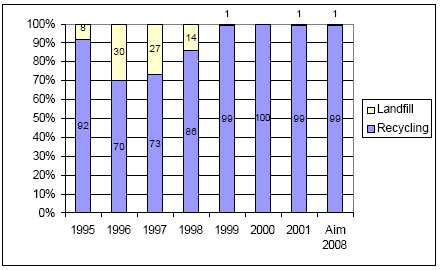
A good 70 per cent of recycled residues in 1997 was used in industrial production as recyclable materials (see table below).
The remaining residues are recovered in connection with building and construction work in the form of fills under buildings, roads and squares, filling-up piping
trenches etc. The residues may also be recovered as fill for harbour filling or building of coalyard barriers.
Recycling in 2001 of residues from coal-fired power plants |
Fly ash |
Slag/ bottom ash |
Gypsum |
TASP |
Sulphuric acid |
Total |
Cement |
303 |
|
64.7 |
|
|
367.7 |
Concrete |
237.4 |
|
|
|
|
237.4 |
Porous concrete |
5.8 |
|
|
|
|
5.8 |
Asphalt |
26.1 |
|
|
|
|
26.1 |
Roofing felt/concrete blocks |
|
7.3 |
|
|
|
7.3 |
Fill (S. O. 655) |
|
8.3 |
|
|
|
8.3 |
Fill (Environmental Protection Act, Part V approval) |
115.5 |
20.6 |
|
|
|
136.1 |
Granulates |
|
|
|
2.2 |
|
2.2 |
Fertiliser |
|
6.3 |
|
|
|
6.3 |
Fill |
|
|
|
12.4 |
|
12.4 |
Gypsum boards |
|
|
278.1 |
|
|
278.1 |
Miscellaneous |
|
|
2.5 |
|
|
2.5 |
Exports, recycling |
0.26 |
21.5 |
|
|
|
21.76 |
Desulphurisation |
|
|
|
48 |
|
48 |
Refining |
3 |
|
|
|
|
3 |
Landfilled |
6.2 |
1.8 |
4.7 |
2.5 |
|
15.2 |
For storage |
39 |
5.5 |
6.7 |
|
|
51.2 |
Total |
736.2 |
71.3 |
356.7 |
65.1 |
8 |
1229.5 |
Only 1 per cent of residues were landfilled.
When landfilling, coastal landfilling is preferred out of consideration for the groundwater.
Measures:
- requirements for recycling of residues
E 26.2 Future initiatives
Statutory Order no. 655 of 27 June 2000 on Recycling of Residual Products and Soil in Building and Construction Work will be extended to cover limit values for organic
substances. The purpose of the Statutory Order is to protect groundwater resources through recycling.
E 26.3 Regulation
Recycling of slag and fly ash from coal-fired power plants is regulated by Statutory Order no. 655 of 27 June 2000 on Recycling of Residual Products and Soil in Building
and Construction Work.
A waste tax was introduced on residues on 1 January 1998. The purpose was to ensure constant motivation to reduce the amount of residues and alternatively to recycle
them.
E 26.4 Environmental assessment
In the long term, energy generation based on coal will be phased out. This will reduce amounts of residues from coal-fired power plants.
E 26.5 Implications for national waste authorities
The revision of Statutory Order no. 655 of 27 June 2000 regulating recycling of residual products and soil will safeguard the groundwater in recycling of residual products.
E 26.6 Implications for local authorities
In their future planning, local authorities are to take into consideration changed conditions for management of residues from coal-fired power plants.
If the revision of Statutory Order no. 655 of 27 June 2000 on recycling of residual products and soil results in landfilling of a larger volume of residues it will affect municipal
planning.
E.27. Beet soil
Environmental problem |
Disposal of large volumes of beet soil |
Initiatives |
No new initiatives have been planned. |
E 27.1 Status
Beet soil is the residual fraction that remains when beets are washed and cleaned before sugar production.
The figure below shows the trend in the volume of beet soil from 1995 to 2001. In 2001, 264,000 tonnes beet soil were produced. This constitutes approx. 10 per cent of
the total waste generated by Danish industry.
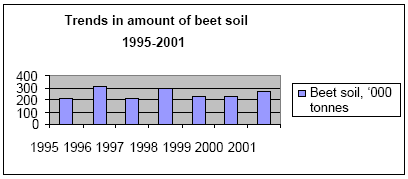
In the mid-1990s, the Danish EPA subsidised two projects to reduce the volume of beet soil through the Technology Programme for Soil and Groundwater Pollution.
E 27.2 Future initiatives
No new initiatives have been planned.
E 27.3 Regulation
Disposal of beet soil in beet soil deposits is covered, in most cases, by the Statutory Order on Landfills. This means that counties will have to assess whether or not the
existing beet soil deposits at sugar factories meet (or may be brought to meet) the requirements of the Statutory Order on Landfills. If this is not possible, the existing beet
soil deposits must be closed down no later than on 16 July 2009. For more on the Statutory Order on Landfills, please see appendix A 2.3.1 and appendix D 3.
Beet soil landfilled in beet soil deposits is exempt from waste taxes. This exemption was specified in the most recent amendment to the Waste Tax Act and entered into
force on 1 January 2003.
E 27.4 Capacity
Provided that beet soil can still be landfilled in beet soil deposits at sugar factories, the landfill capacity at sugar factories is sufficient for the next many years. However, if
the current beet soil deposits cannot be approved for continued operation after 16 July 2009, new landfill capacity will be required. This may be obtained by establishing
new landfills at sugar factories or by landfilling the beet soil at local landfills (eg. on Funen and Lolland-Falster).
E 27.5 Environmental assessment
As can be seen from the above figure, 200,000-300,000 tonnes beet soil are landfilled annually in beet soil deposits at sugar factories. The reason the beet soil is landfilled
instead of being returned to agriculture is the desire to avoid risks of infecting agricultural soil with plant-disease pathogens from the previous years' harvest. The beet soil
remains in the soil deposits. The problem with this approach is the very large volumes of beet soil to be landfilled each year, including the more rigorous requirements
expected for landfilling of beet soil under the requirements for design and operation in the Statutory Order on Landfills.
E 27.6 Economic aspects
If it is decided that the beet soil in future must be landfilled at landfills that comply with the requirements of the Statutory Order on Landfills, this could have major financial
consequences for sugar factories.
E 27.7 Implications for national authorities
None.
E 27.8 Implications for local authorities
The regional authorities (the counties) administrate the regulations in the Landfill Directive and must therefore assess requirements for landfilling of beet soil in the future.
The supervisory authority and the sugar factories should continue to work for a reduction in the volume of beet soil.
E.28. Shredder waste
Environmental problem |
Shredder waste has a high content of environmental contaminants. It is classified
as hazardous waste and constitutes a large part of the industrial waste landfilled
today. |
Initiatives |
Development of new treatment methods for extraction of heavy metals. |
E 28.1 Status
Aims for 2008:
- 30 per cent recycling and better utilisation of the shredder waste resources
- reduction in the volume of shredder waste for landfilling
Shredder waste arises in the form of production waste at enterprises shredding various metal-containing products, such as cars and white goods. The majority of
shredder waste is landfilled today.
Shredder waste has a high content of environmental contaminants (heavy metals, PCBs). The treatment of waste from shredder plants must be improved, and the
possibility of developing new treatment techniques must be investigated.
In 2001, the production of shredder waste constituted 92,000 tonnes which were landfilled.
It is aimed to recover 30 per cent of shredder waste in 2008 in a way that ensures that heavy metals are recovered and the energy is utilised.
In 2002, a Danish project to optimise the shredding process was completed. This project resulted in a considerable reduction in the content of heavy metals in
shredder waste, particularly copper and iron.
Trials of reprocessing shredder waste at special plants, primarily gasification plants, have caused large problems in the past. In recent years, however, many
resources have been invested in the development of new technology to treat shredder waste and other heavy metal-containing waste fractions, in an environmentally
appropriate manner. In order to participate in this development, the Council for Recycling and Cleaner Technology subsidised a study of industrial-scale plants at
global level and if they can be adapted to Danish waste conditions. The project was completed in January 2003. The study showed that there are two plants
operating in Japan and that several interesting plants are being established.
In addition, several pilot tests have been carried out with regard to development of a Danish reprocessing method.
In 2001, all shredder waste was landfilled.
Measures:
- development of methods for reprocessing fractions containing heavy metals
- collection and dissemination of knowledge
- requirements for management of shredder waste
- requirements for enterprises that handle shredder waste
- full-scale tests with new treatment technology
E 28.2 Future initiatives
The results of the projects are so promising that, in the course of 2003-2004, they are expected to form the basis of a realistic decision on which technique for treatment of
shredder waste is most adaptable to the Danish waste structure.
The technologies are structured as a series of thermal processes ending with a process at such a high temperature that zinc and lead evaporate and can be separated from
the exit air while the other metals are separated as an alloy that has to be landfilled. In a subsequent process, zinc and lead can be recycled. The slag from these
high-temperature processes contains so few heavy metals that it can be recycled in connection with building and construction work.
Some of the processes where the energy of the shredder waste is recovered in connection with reprocessing of flue-gas cleaning products look particularly promising.
Initiatives that follow and support the development of better treatment methods that can utilise the resources of the shredder waste will be promoted as much as possible.
When the treatment technique is ready, regulations will be prepared, on the basis of a socio-economic report, for the future management of shredder waste
E 28.3 Regulation
Management of shredder waste has so far been regulated by the general rules in the Statutory Order on Waste and in environmental approvals of enterprises using shredder
plants in reprocessing composite products. The enterprises reprocessing the products are iron and metal recycling enterprises. These enterprises are on the list of
particularly polluting enterprises issued pursuant to the Danish Environmental Protection Act as item K2. Car breaking enterprises are on the same list under item K5.
In addition, the implementation of the EU directives on waste in the form of motor vehicles and waste electrical and electronic equipment is expected have important
influence of the operation of shredder plants and the content of environmental contaminants in waste.
E 28.4 Capacity
It is estimated that sufficient capacity is available for landfilling shredder waste, but in the light of developments in the area, it is expected that it will take between 6 and 7
years before there is sufficient reprocessing capacity.
E 28.5 Environmental assessment
Environmental impacts from reprocessing shredder waste will be a reduction of waste for landfilling and thereby reduced risk of leaching to groundwater, increased
recycling of the contents of metals in shredder waste, and utilisation of the energy in the organic waste fraction.
E 28.6 Implications for national authorities
When an applicable treatment method is ready and it is socio-economically profitable, regulations about management of shredder waste will be issued.
In the coming planning period, efforts will be made to prepare guidelines for green product design and to exploit the possibilities offered by the Danish Electronics Panel,
which has been established under the Product-Oriented Environmental Strategy.
E 28.7 Implications for local waste authorities
When the Statutory Order on management of shredder waste has been issued, municipalities will assign waste to plants complying with requirements for management of
shredder waste.
E.29. Sludge from municipal wastewater treatment plants
Environmental problem |
Sewage sludge is a resource that is not utilised sufficiently today. |
Initiatives |
General phase-out of xenobiotic substances. |
E 29.1 Status
Aims for 2008:
- 50 per cent recycling for agricultural purposes
- 25 per cent incineration of sludge and recycling of ashes in industrial processes
- 20 per cent incineration
- 5 per cent landfilling
In 1999, about 157,000 tonnes of sludge (dry matter) was generated at municipal wastewater treatment plants. Of this, 61 per cent was recycled, fulfilling the
previous objective of 50 per cent recycling in 2004. In addition, 9 per cent was incinerated and the ashes recycled in industry, 21 per cent was incinerated, and 9
per cent landfilled.
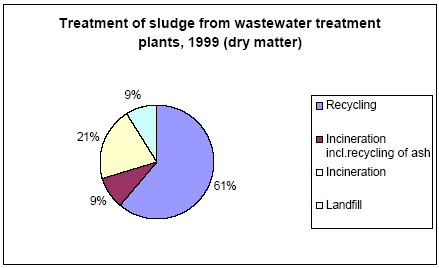
There are certain requirements regarding contents of xenobiotic substances in sludge applied to farmland. These requirements entered into force in 1997 and were
tightened in 2000 and 2002 [65]. The new requirements have led to a decrease in recycling of sludge for agricultural purposes over the years.
The present high rate of application of sludge to farmland is not expected to be upheld due to increased pressure on soil from livestock manure, so that municipalities
are having difficulties finding acreages for recycling. The trend is geographically dependent. It is expected that in the forthcoming years, more sludge will be used in
thermic processes in industry, such as manufacturing of sandblasting agents and cement. In these processes the sludge is incinerated and the inorganic part, typically
30-40 percent of the sludge's dry matter content, is integrated in the products and thus recycled.
The aim for 2008 is therefore to recycle 50 per cent of the sludge and incinerate 25 per cent in industrial processes whereby inorganic elements of the sludge are
utilised. In 2008, it is expected that no more than 20 per cent of the sludge will be incinerated and that no more than 5 per cent will be landfilled.
The quality of sludge and possibilities of increased recycling are expected to improve by reducing the use of xenobiotic substances. The content of certain chemical
substances in the sludge, for which limit and cut-off values have been laid down, is expected to be reduced further.
The Ministry of the Environment does not consider incineration processes which recycle ashes, e.g. sandblasting and cement manufacturing, as recycling; rather such
use constitutes disposal and intelligent exploitation/recycling of inorganic leftovers. It is the Ministry's opinion that a full recycling of the sludge includes exploiting the
content of nutrients in the sludge.
E 29.2 Future initiatives
Measures:
- a general phase-out of xenobiotic substances
No initiatives are planned in the area of sludge from municipal wastewater treatment plants.
E 29.3 Regulation
Recycling of sludge on farmland is subject to regulation under the Statutory Order on sludge, [66] and the Statutory Order from the Ministry of Food, Agriculture and
Fisheries on supervision of the quality of municipal sewage sludge and composted household waste etc. applied to farmland [67]. The Statutory Order on sludge lays down
limit values for a number of heavy metals and cut-off values for organic xenobiotic substances NPE, DEHP, LAS, and certain PAHs.
E 29.4 Capacity
According to estimates, there will be enough capacity for incinerating at least 30 per cent of the sludge amounts via industrial processes, and at least 50 per cent of the
sludge will have a quality suitable for application on farmland.
E 29.5 Environmental assessment
In the long term, contents of xenobiotic substances in sludge are expected to fall allowing for the continued use of the sludge for agricultural purposes. In addition, the
sludge's content of nutrients, especially phosphorous, which is a limited resource, can be recycled.
As to sludge which is not recycled via application to farmland, it is important that the inorganic contents (ashes) can be recycled in industrial processes such as the
manufacturing of sandblasting agents.
Waste indicators
The new waste indicators for saving resources, for energy and for landfill requirements [68] which are presented in chapter 2 have been calculated on the basis of the
amount of the relevant waste fraction and the factors shown below. The factors show savings per tonne for the relevant treatment option compared with 1 tonne of waste
being landfilled.
Data for the crediting of the fertilizer value of the sludge is missing. Upon incineration of sludge, the incineration process is considered energy neutral. This is because sludge
has a high content of water and therefore, contrary to organic household waste, has to dry before it can be incinerated.
The figure below shows what can be saved in landfill requirements for waste by choosing the treatment options of incineration and recycling respectively.
Figure: Savings from incineration and recycling of one tonne of sludge, compared to landfilling the same amount (in mPR, mPE, 10 mPE).
Click here to see the Figure.
The figure shows that great savings in landfill requirement are achieved on recycling. This is because the total sludge amount contains about 50 per cent slag/ashes, which
upon incineration of the sludge would require landfilling. Upon recycling, the same slag amount is recycled - which is also the case with slag from waste incineration plants,
unless the slag is contaminated. In this case, the landfill factor is not detailed enough to provide a comprehensive picture of the different consequences of the two treatment
options.
Apart from the landfill factor, there is the loss of fertilizer value, which, however, has not been included in the calculations due to lack of data. It is not possible from the
calculations to assess whether incineration or recycling are the most advantageous option, since this rests, in particular, on the content of toxic residual substances in the
sludge.
E 29.6 Implications for national authorities
None.
E 29.7 Implications for local authorities
None.
E.30. Used oil
Environmental problem |
Used oil is hazardous waste, and the fractions originate primarily from
around 10,000 mechanics workshops and 200-300 dismantling plants |
Initiatives |
None |
E 30.1 Status
Aims for 2008:
- regeneration of at least 90 per cent of total collected amounts of used oil
Used oil is collected, and at least 75 per cent is reprocessed via regeneration. The remainder is recovered via incineration. The mineral industry has established a
scheme, ensuring highly efficient collection of used oil.
Used oil is collected from, for example, mechanics, transport companies, industry, the military, and private car owners. The collection of used oil is carried out by
private enterprises. From collection, the used oil is delivered to regeneration plants, which manufacture base oil and a fuel product similar to heavy fuel oil.
Upon regeneration of used oil, 2,000-3,000 tonnes of water and distillation residues are produced. Distillation residues are sold to Aalborg Portland A/S for
recovery in cement production.
In addition, waste oil is collected from shipping (slop oil). Such waste is primarily delivered to municipal transfer stations and transferred on to Kommunekemi A/S
for destruction. In 1997, Kommunekemi A/S received a total of 13,217 tonnes of waste oil.
The mineral industry's scheme creates economic incentives to collect and recover used oil with great efficiency
E 30.2 Future initiatives
None.
E 30.3 Regulation
The Statutory Order on waste includes regulations on used oil management. Used oil is hazardous waste, and local authorities are obliged to establish collection
schemes for such waste under the Statutory Order on waste.
Local authorities must notify any exemption from the duty of enterprises to deliver used oil to municipal collection schemes for hazardous waste.
E 30.4 Capacity
Used oil is reprocessed at a Danish regeneration plant and at additional regeneration plants abroad. The Danish regeneration plant has substantially more capacity
than Danish requirements. The plant therefore also reprocesses used oil from other Scandinavian countries.
E 30.5 Environmental assessment
Waste indicators
The new waste indicators for saving resources, for energy and for landfill requirements [69]which are presented in chapter 2 have been calculated on the basis of the
amount of the relevant waste fraction and the factors shown below. The factors show savings per tonne for the relevant treatment option compared with 1 tonne of
waste being landfilled.
The advantage of re-refining used oil is not having to spend resources on extraction of crude oil, desulphurisation, and refinement. However, recycling costs around
25 per cent extra energy compared to refining crude oil. LCA data is available for these specific processes, and has been included in calculations.
Thus, the figure below shows a minor savings potential for recycling. However, this difference is not decisive taken into account the uncertainty of the data.
Figure: Savings from incineration and recycling of one tonne of oil.
Click here to see the Figure.
The figure shows a minor energy advantage from recycling the oil when the energy from incinerating the oil is credited. If energy recovery from waste incineration is
not optimal, recycling the oil proves clearly the best option, both from an energy and a resource perspective.
E 30.6 Implications for national authorities
None.
E 30.7 Implications for local authorities
None.
E 31 Foundry waste
Environmental problem |
Foundry waste contains chemicals, and this is a barrier to recycling.
Today, this waste type comprises a large part of waste from industry that goes
to landfills. |
Initiatives |
Development of recycling methods. |
E 31.1 Status
Aims for 2008:
- 80 per cent recycling of foundry waste
- 10 per cent waste reduction
Foundry waste comprises a large part of waste from industry led to landfill. Adequate recycling solutions have now been developed for this waste type and are
becoming more and more common in the sector. However, solutions for around 25,000 tonnes/year are still required.
The foundry industry covers almost 40 foundries (10 iron foundries, the rest metal foundries) with between one and 300 employees. In 2001, 85,000 tonnes of
foundry waste were generated.
Environmental problems related to foundry waste primarily derive from discarded foundry sand, amounting to 75,000 tonnes per year. Such sand contains chemicals
which are used in the production of moulds. Around 5,000 tonnes of slag are generated each year. Furthermore, around 400 tonnes of furnace filter dust are
generated annually. This residue product constitutes hazardous waste.
The larger foundries have introduced environmental management, and are working on waste mapping and waste minimisation. The outcome of this work has led to a
reduction in waste amounts of around 10 per cent by the help of an environmental review of the enterprise. This reduction could probably be reduced by a minimum
of a further 10 per cent.
Good treatment methods have been developed, so that, for example, black sand can be recycled, and zinc and lead can be extracted from filter dust. The sector is
currently looking into possible ways of recycling the slag from melding furnaces and foundry ladles. Thus, from a technical perspective, large parts of waste generated
at foundries can be recycled today.
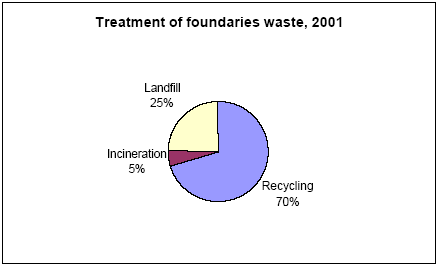
Measures:
- improved treatment methods for chemically-bound foundry sand
- environmental management
E 31.2 Future initiatives
Initiatives supporting the development of recycling methods for chemically-bound foundry sand will be promoted. Results and developments will be evaluated regularly.
Technically, large parts of waste generated by the sector can be recycled today. All foundries in Denmark must therefore make efforts to recycle waste. This will be
ensured in co-operation between the Danish Environmental Protection Agency and the foundry industry.
E 31.3 Capacity
Spent black sand is suitable for application as foundations in construction works and is expected to replace virgin sand in products.
Moreover, a lot of spent foundry sand is used in connection with manufacturing cement and other building materials.
Recycling capacity is available for the large fractions, and furnace filter dust is reprocessed at enterprises in Germany and Sweden.
The need for landfill capacity will decrease over time, as the rate of recycling increases.
E 31.4 Environmental assessment
Environmental impacts from recycling of foundry sand and filter dust from furnaces are expected to be almost similar to the use of virgin raw materials, whereas recycling of
slag will have a minimal impact.
E 31.5 Economic aspects
The introduction of environmental management at foundries will allow for recycling of larger parts of waste. Increased recycling will entail savings for enterprises, as
- no tax is due on waste that is recycled. Such savings would amount to DKK 335 x 60,000 tonnes = approx. DKK 22.5 mill. and
- minor expenses in connection with raw materials procurement.
E 31.6 Implications for national authorities
Foundry sand is used for cover at landfills, and in their planning local authorities will therefore have to take into consideration that, in the long term, less waste of this type
will be available.
E 31.7 Implications for local authorities
A decreasing landfill requirement for waste from foundries can be of importance to municipal planning.
E 32 Tiles
Environmental problem |
Tiles constitute a significant proportion of the total waste from building
and construction, and will take up landfill capacity if it is not recycled. |
Initiatives |
Efforts must ensure that tiles are recycled in an environmentally appropriate
manner. |
E 32.1 Status
Aims for 2008:
- ensure high recycling of tiles
- ensure that recycling of tiles takes place appropriately in relation to the environment
Concrete and tiles comprise the most significant part of building waste and could replace about 5 per cent of the total Danish gravel and stone consumption.
In 2001, tiles comprised 8 per cent of the total amount of waste from building and construction.
Tiles can be recycled e.g. as gravel for paving stones, whereas their use as a bearing course in roads with heavy traffic is less appropriate, as the water-absorbing
ability of the tiles can give cause to broken road surfaces due to freeze-thaw cycles. As in the case of concrete, distances to landfills and gravel quarries will
determine how attractive it is to recycle tiles.
The number of tiles led to treatment plants as a pure waste fraction is shown in the table below.
Tonnes |
1995 |
1996 |
1997 |
1998 |
1999 |
2000 |
2001 |
Recycling |
|
|
|
123,000 |
126,000 |
227,000 |
271,280 |
Source: Waste Statistics
E 32.2 Future initiatives
Measures:
- alter rules on management of tiles
In the long term, management of tiles will be included in a statutory order on recycling residual products and soil.
E 32.3 Regulation
Tiles in building and construction waste are managed primarily through the circular "Circular on municipal regulations on separation of building and construction waste with a
view to recycling", 1995, as well as the circular "Utilisation of pure, separated building waste for building and construction purposes", 1990.
The circular states that municipalities are to prepare a regulation for managing building and construction waste. Municipalities have two options in developing the scheme:
- In the first option waste can either be assigned to recycling on-site or to a reprocessing plant.
- In the second option waste can either be assigned to recycling on-site or the local council may decide that waste that is not recycled on-site is covered by a
collection scheme for recyclable building and construction waste.
In accordance with the circular from 1990, there is a free choice for recycling of pure fractions of tiles. This means that recycling of pure fractions of tiles does not require
authorisation under section 19 of the Danish Environmental Protection Act.
E 32.4 Capacity
There is considered to be adequate treatment capacity in Denmark.
E 32.5 Environmental assessment
By amending the Statutory Order on recycling of residual products and soil in building and construction work to include tiles, there will be a more uniform set of regulations
ensuring the recycling, on equal terms, of a number of larger waste fractions.
Waste indicators
The new waste indicators for saving resources, energy and landfill requirements [70] which are presented in chapter 2 have been calculated on the basis of the amount of
the relevant waste fraction and the factors shown below. The factors show savings per tonne for the relevant treatment option compared with 1 tonne of waste being
landfilled.
Savings in waste amounts requiring landfilling upon recycling of waste tiles are shown in the Figure below.
Figure: Reduction from recycling 1 tonne of tiles compared to landfilling the same amount (in mPE).
Click here to see the Figure.
The energy needed for crushing tiles before recycling them as filling has not been included in the calculations. Conversely, the energy needed for extracting sand and stone
has also not been included, which must therefore be offset in the calculation. The result will probably be close to zero.
The figure simply shows that for each tonne of tiles recycled as filling material, 2.5 PE (=1 tonne) of waste for landfilling is saved.
E 32.6 Economic aspects
An environmental economic assessment will be carried out of the consequences of allowing recycling of tiles to be subject to the Statutory Order on recycling of residual
products and soil.
E 32.7 Implications for national authorities
The basis for preparing new guidelines for recycling tiles must be laid down.
The national authorities will be responsible for preparing the new guidelines and for carrying out the environmental-economic assessments of impacts.
E 32.8 Implications for local authorities
In their supervision, the municipalities must ensure compliance with the regulations and guidelines for recycling tiles.
E 33 Wood
Environmental problem |
Impregnated wood contains a number of environmental contaminants which
cause problems in disposal. The amount of impregnated waste wood will be increasing. |
Initiatives |
Ensure that only wood impregnated with chromium, copper and arsenic-containing
agents is handled as waste not suitable for incineration. The capacity for incineration
of hazardous waste in the form of creosote-treated wood must be increased.
When appropriate treatment methods for impregnated wood have been developed, the wood must be collected and treated separately.
Ensure recycling of 15 per cent wood packaging waste under the Packaging Directive in 2008.
|
E 33.1 Status
Aims for 2008:
- utilise energy and raw material resources in impregnated waste wood
Impregnated wood
Impregnated wood has been treated with impregnators containing, for example, chromium, copper, arsenic (CCA), tin, and creosote.
Impregnated wood containing heavy metals causes problems in incineration, as substances are not decomposed but remain in slag and flue-gas waste. Wood impregnated
with arsenic is classified as hazardous waste.
Creosote-treated wood (for example railway sleepers, wood from wharfs) can be decomposed in incineration, as creosote is destroyed. This requires, however, that such
wood is pretreated (shredded), ensuring complete incineration, and that the incineration temperature is sufficiently high.
Sources of impregnated waste wood are primarily bulky waste and the building and construction sector. Since April 2001, it has been mandatory to dispose of all
impregnated wood via landfilling, except wood impregnated with creosote. Wood impregnated with creosote is classified as hazardous waste and can be incinerated in
approved plants.
Better treatment methods are being developed that utilise the resources (energy, chromium and copper) in the impregnated wood.
In the coming years, an increasing volume of impregnated wood that needs to be disposed of as waste is expected. It is estimated that since the 1960s approx. 4 million
tonnes impregnated wood have been used (accumulated) and that, in 2010, it will be necessary to dispose of approx. 100,000 tonnes impregnated wood [71].
Wood packaging
When the Packaging Directive was revised, a goal of 15 per cent recycling of wood packaging in 2008 was adopted in the common position. Most EU countries today
have systems for recycling wood packaging for eg. chipboard.
The supply amount of wood packaging in 2000 was estimated at approx. 150,000 tonnes. Most of this consists of return pallets and disposable pallets. The waste volume
is probably smaller, but it is difficult to gather data for the volumes. The volume of wood packaging waste treated in the traditional waste treatment system is very small.
Part of the wood packaging waste is energy-recovered in private wood-burning stoves. However, this volume is not known. Arisings of wood packaging waste will be
extremely important for possible further initiatives required to achieve the goal of 55 per cent recycling of all packaging waste in 2008.
Denmark has no experience with collection of wood packaging for recycling as eg. chipboard. So far, only one Danish chipboard manufacturer has been identified that will
be technically capable of recycling wood packaging. Some countries include repairs of reused pallets as recycling. In Denmark, approx. 23,000 tonnes of pallets are
repaired each year.
Measures:
Impregnated wood
- requirements for treatment
- further development of new methods for treatment of impregnated waste wood
- information
- statements of volumes and economic assessment
E 33.2 Future initiatives
Efforts must ensure that:
- separation is optimised in relation to treatment options (creosote/arsenic/metals/other/non-impregnated) so that energy and resources can be utilised as efficiently as
possible;
- the capacity for incineration of creosote-impregnated wood (hazardous waste) is increased;
- attempts are made to optimise estimates of waste volumes;
- a socio-economic assessment is prepared in support of treatment requirements;
- requirements for treatment of wood impregnated with chromium, copper and arsenic are included in the Statutory Order;
Wood packaging
- volumes and economic aspects
- agreement on recycling of transport packaging
- amendment of the Statutory Order on Waste
- guidelines are prepared to ensure recovery of the energy from wood that is not impregnated with chromium, copper and arsenic.
Initiatives for the development of methods to recycle heavy metals from impregnators must be promoted.
An assessment must be made of how Denmark can reach the goals of 15 per cent recycling of wood packaging and 55 per cent recycling of all packaging waste in 2008 in
pursuance of new EU regulations in the easiest and most cost-effective manner.
- Analysis of the volume of wood packaging waste and potential consignees
- Wood packaging to be included in the agreement on recycling of transport packaging
- Requirements for separation of wooden transport packaging from industry to be included in the Statutory Order on Waste
E 33.3 Regulation
Since April 2001, all impregnated wood must be separated as waste not suitable for incineration, ie. disposed of at landfills. However, wood impregnated with creosote
can be incinerated.
Wood impregnated with arsenic and creosote is classified as hazardous waste and must be handled as such.
E 33.4 Environmental assessment
Today, impregnated wood is primarily disposed of by landfilling.
Incineration plants must continue to be held free of impregnated wood containing chromium, copper and arsenic in order to ensure a continued reduction in the content of
heavy metals in slag and flue-gas cleaning waste.
When this waste is landfilled, the potential energy and resources are lost. A new treatment method that can ensure energy recovery and make it possible to recycle
impregnators must be promoted.
Neither the European Commission nor the Member States have made environmental assessments of advantages and disadvantages of recycling versus incineration of wood
packaging.
Waste indicators
The new waste indicators for saving resources, energy and landfill requirements, [72] which are presented in chapter 2, have been calculated on the basis of the amount of
the relevant waste fraction and the factors shown below. The factors show savings per tonne for the relevant treatment option compared with one tonne of waste being
landfilled.
Impregnated wood
The figure below shows the savings through incineration and recycling respectively of one tonne impregnated wood compared with landfilling the same amount. There are
no LCA data to illustrate the process of removing an impregnator, so the figure does not show future possibilities, but only status quo.
Figure: Savings from treatment of 1 tonne impregnated wood by incineration and recycling respectively. Figure: Savings should be seen in relation to landfilling one tonne
impregnated wood (in mPR, mPE and 10 mPE).
Click here to see the Figure.
The figure shows that savings for the total resource consumption (energy resources and other resources) are larger when incinerating than when recycling one tonne
impregnated wood. If the two indicators "renewable energy" and "non-renewable energy" are added together, there is a small advantage in recycling. The savings with
regard to the volume of waste to be landfilled are almost the same for the two treatment options. However, incineration of impregnated wood will not become relevant until
it is possible to remove the environmental contaminants before or during the incineration process.
In the long run, it will probably be possible to incinerate impregnated wood if processes can be developed to effectively remove environmental contaminants before or
during the incineration process.
E 33.5 Economic aspects
A socio-economic assessment of the treatment of impregnated wood will be carried out. In the next few years, no considerable extra costs of disposal of impregnated
wood are expected. At present, it is not possible to evaluate costs of treatment in future technologies.
Neither the European Commission nor the Member States have made an environmental-economic analysis of recycling versus incineration of wood packaging.
When the volume of wood packaging waste has been mapped, an economic analysis will be made with regard to how Denmark can reach the goals of 15 per cent
recycling of wood packaging and 55 per cent recycling of all packaging waste in the most cost-effective manner.
E 33.6 Implications for national authorities
The Statutory Order on Waste will be revised. The requirement for separation of all impregnated wood is to be relaxed so that wood that is not impregnated with
chromium, copper and arsenic can be sent to incineration. Treatment requirements for wood impregnated with chromium, copper and arsenic will be introduced on the
basis of technical possibilities and a socio-economic assessment.
Arisings of wood waste must be analysed in 2004. The Statutory Order on Waste must be revised so that it requires that wood packaging (particularly pallets) is recycled.
E 33.7 Implications for local authorities
In their planning, municipalities must take into consideration that impregnated wood is to be separated according to treatment options.
Moreover, wood packaging waste must be recycled.
Footnotes
[1]Defined as kitchens producing more than 100kg food waste per week.
[2] Council Regulation (EC) No 1774/2002 of 3 October 2002 on health rules concerning animal by-products not intended for human consumption.
[3] Statutory Order no. 624 of 30 June 2003 on repealing the Statutory Order on municipal collection of food waste from industrial kitchens.
[4] Consolidated Act no. 698 of 22 September 1998.
[5] Consolidated Act no. 698 of 22 September 1998.
[6] Ole Dall: Ressourcebesparelser ved affaldsbehandlingen i Danmark (Resource savings from waste treatment in Denmark), Danish EPA 2003.
[7] Environmental Project no. 557, 2000, Mass-flow analysis of Cadmium.
[8]Statutory Order no. 619 of 27 June 2000 on waste.
[9]Statutory Order no. 1060 of 4 December 2000 on subsidies for collecting and recycling lead accumulators.
[10]Statutory Order no. 1061 of 4 December 2000 on fees on lead accumulators.
[11]In 1995 Denmark introduced an environmental tax for nickel-cadmium batteries pursuant to Act no. 414.
[12] Statutory Order no. 1062 of 4 December 2000.
[13] Ole Dall: Ressourcebesparelser ved affaldsbehandlingen i Danmark (Resource savings from waste treatment in Denmark), Danish EPA 2003.
[14]The agreement was implemented by Statutory Order no. 144 of 3 March 1995, which is now replaced by Statutory Order no. 111 of 5 February 2000 on fees and
subsidies for recovery of tyres. The Statutory Order is issued among others in pursuance of section 53 of the Environmental Protection Act, empowering the Minister to
decide that importers or manufacturers of specified products shall pay a fee for the disposal of waste, in full or partial coverage of costs incurred in connection with
disposing of the products, and to lay down detailed rules on the collection and application of fees.
[15]Since January 1996 the support scheme has been administered by the Danish Tyre Trade Environmental Foundation.
[16] Ole Dall: Ressourcebesparelser ved affaldsbehandlingen i Danmark (Resource savings from waste treatment in Denmark), Danish EPA 2003.
[17]Of the total waste volumes, approx 43,000 tones are electronic equipment, and approx. 60,000 tonnes are electrical equipment.
[18] Environmental Project No. 696, 2002,
[19] Council Directive 91/689/EEC of 12 December 1991 on hazardous waste.
[20] Commission Decision 2000/532/EC of 3 May 2000 establishing a list of wastes and hazardous waste, Commission Decision 2001/118/EC of 16 January 2001,
Commission Decision 2001/119/EC of 22 January 2001, and Council Decision 2001/573/EC of 23 July 2001.
[21] Statutory Order no. 299 of 30 April 1997 on waste from the Ministry of the Environment and Energy.
[22] The goal for 2008 is not readily comparable to the goal for recycling of glass from households stated in the section on glass fraction in Waste 21, since the goal for
2008 includes more material flows and applies a different calculation method.
[23] Environmental Project no. 697, 2002.
[24] Statistics on glass packaging 2001.
[25] Statutory Order no. 619 of 27 June 2000 from the Ministry of the Environment and Energy.
[26] Ole Dall: Ressourcebesparelser ved affaldsbehandlingen i Danmark (Resource savings from waste treatment in Denmark), Danish EPA 2003.
[27] Statutory Order no. 650 of 29 June 2001 on landfills.
[28] Act no. 476 of 30 June 1993 on the protection of the marine environment.
[29] Bekendtgørelse nr. 975 af 19. december 1986 om dumpning af optaget havbundssediment (Statutory Order no. 975 of 19 December 1986 on dumping dredged
material).
[30] Statutory Order no. 650 of 29 June 2001 on landfills.
[31] Council Directive 99/31/EC of 26 April 1999 on the landfill of waste.
[32] Ole Dall: Ressourcebesparelser ved affaldsbehandlingen i Danmark (Resource savings from waste treatment in Denmark), Danish EPA 2003.
[33]Guideline no. 4 1998, Management of health-care risk waste. This guideline replaces the previous Danish EPA Guideline no. 1/1984 on disposal of health-care risk
waste.
[34]Circular no. 132 of 13 June 1996 on municipal regulation on disposal of refrigeration equipment containing CFCs.
[35]Statutory Order from the Ministry of the Environment no. 619 of 27 June 2000.
[36] In 2001, the amount of organic domestic waste was estimated at just less than 700,000 tonnes.
[37] Approx. 24,000 tonnes for home composting (evaluations of home composting schemes and mapping of the composition of domestic waste) and 37,000 tonnes for
treatment at central plants (statistics on treatment of organic waste from households 2001). The amounts treated at central plants were approx. 27,000 tonnes at
composting plants and 10,000 tonnes for biogasification.
[38] Ole Dall: Ressourcebesparelser ved affaldsbehandlingen i Danmark (Resource savings from waste treatment in Denmark), Danish EPA 2003.
[39] Miljøprojekt nr. 397 og 398, 1998: Organisk restprodukter i industrien, del 1 og 2 (Environmental Project Nos. 397 and 398, 1998 on organic residues in industry,
parts 1 and 2 - only available in Danish).
[40] It appears from the study (data from 1992-1994) that an annual approx. 8.4 million tonnes organic residues are produced in industry. Of this, 99 per cent are recycled
(47 per cent for substitution of raw materials, 8 per cent for biogas production and 44 per cent is used directly as fertiliser on agricultural soil). Less than 1 per cent (52,000
tonnes) is incinerated or landfilled. The study mapped all residues from industry - even the ones that are not normally registered as waste.
[41] Bekendtgørelse nr. 49 af 20. januar 2000 om anvendelse af affaldsprodukter til jordbrugsformål (Statutory Order no. 49 of 20 January 2000 on use of waste
products for agricultural purposes).
[42] Statistics on collected waste paper and cardboard 2001.
[43]It should be noted that according to the ISAG less cardboard and paper has been collected (a total of 70,935,000 tonnes) than appears from the Statistics on
collected waste paper and cardboard 2001.
[44] Statutory Order no. 619 of 27 June 2000 from the Ministry of Environment and Energy on waste.
[45] Ole Dall: Ressourcebesparelser ved affaldsbehandlingen i Danmark (Resource savings from waste treatment in Denmark), Danish EPA 2003
[46] Statutory Order no. 925 of 13 December 1998 on PCBs, PCTs and substitutes for these
[47] Statutory Order no. 1067 of 22 December 1998 on management of waste from electrical and electronic products
[48] Packaging supply in Denmark 2001.
[49] Statistics for plastic packaging 2001
[50] Working report no. 20, 2002.
[51] Environmental Project no. 637, 2001 www.mst.dk/udgiv/Publikationer/637/2001-2001-87-7944/html/default.htm (only in Danish).
[52] Environmental Project no. 657, 2002 http://mst.dk/udgiv/publikationer/657/2002-2002-87-7944/html/ (only available in Danish).
[53] Environmental Project no. 695, 2002 http://mst.dk/udgiv/publikationer/695/2002-2002-87-7972/html/. (only available in Danish).
[54] In section 36 with effect from 1 July 1998.
[55] Ole Dall: Ressourcebesparelser ved affaldsbehandlingen I Danmark (Resource savings from waste treatment in Denmark), Danish EPA 2003.
[56] Environmental Project no. 657, 2002 http://mst.dk/udgiv/publikationer/657/2002-2002-87-7944/html/(only available in Danish).
[57] The primary sources are the building and construction sector (about 10,000 tonnes per year), business, including end-of-life vehicles (about 14,000 tonnes per year),
and households (about 10,000 tonnes per year).
[58] Act on a tax on waste and raw materials, Consolidated Act no. 570 of 3 August 1998.
[59] See the PVC report.
[60] Ole Dall: Ressourcebesparelser ved affaldsbehandlingen i Danmark (Resource savings from waste treatment in Denmark), Danish EPA 2003.
[61] The objective for 2000 was to recycle 53 per cent of the total volume of residues from waste incineration plants. A specific objective has been set to recycle 65 per
cent of slag.
[62] Statutory Order no. 619 of 27 June 2000 from the Ministry of Environment and Energy on waste.
[65] Miljø- og Energiministeriets bekendtgørelse nr. 49 af 20. januar 2000 om anvendelse af affaldsprodukter til jordbrugsformål (Statutory Order no. 49 of 20 January
2000 on the use of waste products for agricultural and related purposes).
[66] Bekendtgørelse nr. 49 af 20. januar 2000 om anvendelse af affaldsprodukter til jordbrugsformål (Statutory Order no. 49 of 20 January 2000 on use of waste
products for agricultural purposes).
[67] Bekendtgørelse nr. 56 af 24. januar 2000 om tilsyn med spildevandsslam m.m. til jordbrugsformål (Statutory Order no. 56 of 24 January 2000 on supervision of
sewage sludge etc. for agricultural purposes).
[68] Ole Dall: Ressourcebesparelser ved affaldsbehandlingen I Danmark (Resource savings from waste treatment in Denmark), Danish EPA 2003.
[69] Ole Dall: Ressourcebesparelser ved affaldsbehandlingen i Danmark (Resource savings from waste treatment in Denmark), Danish EPA 2003.
[70] Ole Dall: Ressourcebesparelser ved affaldsbehandlingen i Danmark (Resource savings from waste treatment in Denmark), Danish EPA 2003.
[71] This estimate assumes an average lifetime of 40 years for the wood.
[72] Ole Dall: Ressourcebesparelser ved affaldsbehandlingen i Danmark (Resource savings from waste treatment in Denmark), Danish EPA 2003.
| Front page | | Contents | | Previous | | Top |
Version 1.0 June 2004, © Danish Environmental Protection Agency
|