| Front page | | Contents | | Previous | | Next |
Geographical, technological and temporal delimitations in LCA
2 Market-based system delimitation
2.1 Building product system models
To build a model of a product system, it is natural to start with the process in which the reference flow occurs (see the guideline “The product, functional unit and reference flows in LCA” for more
information on how to determine the reference flow). Each item in the reference flow is then linked to the next process both backwards and forwards in the life cycle. Backwards, the flow typically consists of
intermediate products, components, ancillary inputs, and raw materials. Forwards, the flow may also consist of final products, products for reuse or recycling, and waste to treatment. To make it simple, we
call all these flows “intermediate product flows”. Flows to the environment (environmental exchanges) are typically not included in the first description of a product system.
The purpose of the procedure presented in section 2.2 is to determine the process(es) that a specific intermediate product flow should be linked to, and which therefore should be included in the studied
product system. It is for these processes that data on environmental exchanges are later to be collected. The overall uncertainty of a life cycle assessment will often be determined by what processes are
included and excluded from the analysed product systems.
The procedure applies to each intermediate product flow between processes in the life cycle, but it may not be necessary to apply the entire procedure in detail for all intermediate products. The procedure is
primarily intended as a guideline for those instances where it is not immediately obvious which processes are to be linked. This may be the case when there are many possible suppliers with very different
production conditions or when one or more of the possible suppliers cannot immediately change production volume in response to a change in demand. In a first iteration, the procedure should only be
applied for such cases of constraints in production volumes (see section 2.2.4), or where there is an order-of-magnitude difference in expected environmental exchanges between different possible processes
(see also section 2.4 for a discussion of uncertainty of the procedure).
It should be noted that the suppliers that are identified by the procedure, and for which data on environmental exchanges are later to be collected, are not necessarily a part of the current supply chain.
The market information required for the procedure is typically available from marketing personnel dealing with each specific market. The collection of the necessary information has been found to be much
less demanding than the collection of data on the environmental exchanges of each process. When the necessary market information cannot be made available, the default assumptions and default data from
section 2.3 can be applied.
2.2 Procedure
Since the purpose of a life cycle assessment is to assess the possible environmental impacts of a potential product substitution, it is the processes affected by this product substitution that should be included in
the studied product systems. A product substitution (e.g. the choice of one chair design instead of another) will result in a change in demand for the intermediate products that enter into the process in which
the substitution occurs (e.g. the steel and plastic components that are used by the chair manufacturer), and likewise in the demand for the further intermediate products backwards in the life cycle (e.g. the
plastic raw materials). The procedure presented here identifies the processes that are expected to be affected by such a change in demand for a specific intermediate product.
A product substitution will also result in a change in supply of the intermediate products leaving the process in which the substitution occurs, and in supply of the further intermediate products forwards in the
life cycle (e.g. the distribution, retail sale, use and disposal of the chair). To make the description less abstract, the explanatory text in this section only covers the situation where an intermediate product is
followed backwards in the life cycle (identifying the effects of changes in demand). However, the 5 steps of the procedure, the decision tree in figure 2.1, as well as the general concepts in the explanatory
text, are also applicable when following an intermediate product flow forwards in the life cycle (identifying the effects of changes in supply).
By the procedure presented here, one or more suppliers will be identified as being affected by a change in demand. The identified suppliers will typically use a specific technology and/or be located within a
specific geographical region (since differences in market conditions and competitiveness typically depend on geographical and technological differences). The number of suppliers and the degree of detail of
describing their technologies, depends on:
- The difference between the suppliers in terms of environmental impacts. It may not always be necessary to distinguish between individual suppliers, when these use similar equipment and procedures.
- The scale and time horizon of the change. Large scale changes and changes over longer time spans may affect several separately identified suppliers or technologies, while for smaller and more temporary
changes one specific supplier or technology may be identified as the one affected. The implicit assumption of the presented procedure is that all other suppliers than the ones identified as most sensitive, will
not be affected by the changes in demand. If this assumption is regarded as too simple, all suppliers that are expected to change should be included in the product system. This can be done either as separate
scenarios or in the form of an average, weighted in proportion to the relative degree to which they are expected to be affected.
Figure 2.1 Decision tree outlining the 5-step procedure for identifying the processes affected by a change in demand for a specific intermediate product. Please se the text for detailed explanations
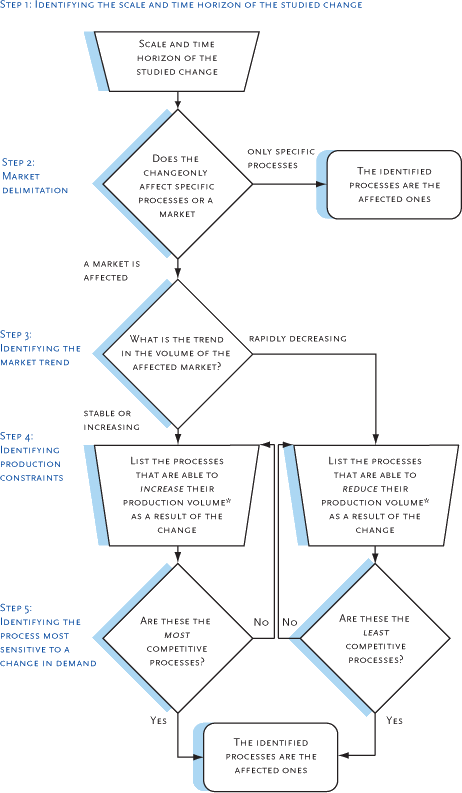
*) For long term changes, the volume relates to production capacity, while for short term changes it relates to output within the existing capacity, see also the text in section 2.2.1 and
2.2.3
2.2.1 Step 1: Identifying the scale and time horizon of the studied change
Before it can be determined what suppliers/technologies that may be affected by a change in demand for an intermediate product, it is necessary to know the scale and time horizon of the change.
Scale of change
If the object of study is a larger change (see Annex 1 for a definition), new suppliers, new markets, or even new products and technologies, may come into play, compared to a small change that only affects
the current suppliers. A small change does not affect the overall market trend, so that an increase in demand will affect the same suppliers as a decrease in demand, as determined by the overall market trend
(see also section 2.2.3). But for a large change that affects the overall market trend, it is necessary to take into account also the direction of the change (increase or decrease in volume), since it is typically
different suppliers that are affected by an increase or a decrease of the overall market.
Large changes are typically seen when introducing new technology or new regulation on a significant market, e.g. if all cars were to be made from polymers and carbon fibres in stead of steel, which among
other consequences would have the market for steel turning from increasing to decreasing. However, many small changes may accumulate to bring about a large change. Therefore, even in studies of small
changes it may sometimes be relevant to apply an additional scenario with the possible larger changes that could be the result of accumulated small changes. For example, even in a life cycle assessment
considering such a shift to polymers and carbon fibres for a single producer of cars, it may be relevant to investigate the possible consequences of other car producers following suit.
Time horizon
Most life cycle assessments study changes with a relatively long time horizon, but the life cycle methodology may also be used to study changes of a more intermediate character. The time horizon is important
for what suppliers may be affected, since:
- a change in the short term is restricted to the existing production capacity and thus does not affect capital investment (installation of new machinery or phasing out of old machinery), while a long-term
change is expected to affect capital investment.
- a change in the short term will typically affect the least competitive suppliers, while for long-term changes the affected suppliers depend on the overall market trend (see section 2.2.3).
In general, changes cannot be isolated to the short-term, since capital investment (i.e. long term changes) is typically a continuous process affected by the current and expected trends in the market volume,
resulting from the accumulation of a large amount of individual short-term purchase decisions.
This is obvious in markets with a short capital cycle (fast turnover of capital equipment, as e.g. in the electronics and polymer industries) and in free market situations (where market signals play a major role
when planning capacity adjustments), but it is also true for markets with a long capital cycle (as e.g. in the building and paper industries).
Thus, the isolated effects of short-term changes (i.e. effects within the existing production capacity) are only of interest in markets where no capital investment is planned (e.g. industries in decline), or where
the market situation has little influence on capacity adjustments (i.e. monopolised or highly regulated markets, which may also be characterised by surplus capacity).
Office chair example

Office chair example: This and the following steps in the procedure will be illustrated with examples taken from an LCA of an office chair. The LCA concerns the design for improved reuse of a
specific brand of office chairs.Thus, it is a case of a small change (since it concerns only one specific producer, not the entire market) with a long time horizon (since the new design can be
expected to affect future capital investment in the different processes in the life cycle).
An example of a change with a short time horizon could be an isolated decision to remove heavy metals from the polymers and surface coatings of the chair, which – all other things equal –
would not involve capital investment in the metal industry, since heavy metals are already being phased out.
2.2.2 Step 2: Market delimitation
Given the scale and time horizon of the studied change, the next step in the procedure is to determine the possible suppliers of the intermediate product.
Market ties
If only one specific supplier is possible, or a group of specified suppliers can be identified as the ones affected, the whole procedure may be cut short here. This is the case if:
- the decision-maker for the study is expecting to control or influence the production volume of a specified supplier or group of suppliers, or
- two or more companies are tied so closely together in a supply chain that the production volumes of the specific suppliers fluctuate with the demand of the specific customers.
Many examples can be found of the latter situation, especially:
- When products have a low price compared to their weight, so that transport costs prohibit all other than the local producers, as e.g. for the supply of straw for heat and power production, where only the
farmers closest to the power plant will supply the straw. Other examples of this can be found in the forestry sector and the building- and glass-industries.
- When two or more companies are tied together by tradition, or when a supplier has developed its product to meet specific demands of the customer.
- When the choice of supplier is not subject to normal market conditions.
If a specific supplier (or group of suppliers) is identified as the one affected, it may be useful to justify that the production volume of this process is actually able to change. For this purpose, step 4 in the
procedure (section 2.2.4) may be applied.
The procedure can only be terminated here if the production volume of the specific suppliers is actually expected to change as a result of the studied product substitution, i.e. as a result of a change
in demand for the intermediate product. If the change in demand is transferred on to other suppliers of the intermediate product, the production volume of the specific supplier will not change. This may be
the case in spite of close relations between supplier and customer, even in spite of ownership relations or sole-supplier-status, i.e. it is not the closeness of the relation, which is important, but whether the
overall production volume of the supplier is actually expected to be affected.
An example of this is in-house electricity production. If the in-house production fluctuates with in-house demand and thereby does not affect the production volume of the general electricity market, then the
in-house production can be regarded as the affected electricity source for the in-house demand. However, if the in-house production takes place on normal market conditions, and the in-house production
does not fluctuate with in-house demand (even when the company is closed), then the electricity supply for the in-house demand must be regarded as coming from the general electricity market, and not from
the specific in-house production.
This also means that a life cycle assessment will only give credit for - and incentive to - a shift to specific products or suppliers with more environmentally friendly technologies, e.g. “green electricity”, when
this shift is actually expected to lead to an increase in the capacity of the “green” technology. If the shift only pretends to be an improvement, and no change is expected in the composition of the overall
output, no credit is given.
However, the effects of a shift may be delayed, so that the expected increase in the “green” technology will only appear after some time. An example of this may be the initial immature market for ecological
foods, where an increase in demand may not lead to an increase in production, because of the transaction costs of the initial small quantities or because of the time it takes to implement the new technology on
the farms. In such instances, a demand for “green” products should still be credited for its long-term influence on the production capacity of the “green” technology.
Also, the effects of a shift may be indirect, via the political signal that it sends. For example, a constraint on a specific “green” product may be overcome, e.g. by political intervention or because a private
company takes up the challenge, as a result of a consistent unsatisfied demand for this product. Likewise, a consumer boycott of a particular product may be followed up by political action or “voluntary”
changes in company behaviour that limits the production beyond the effects of the boycott itself.
Since such indirect effects may be controversial and difficult to predict, it may be preferable to include them in separate scenarios.
Market identification
In most situations, the intermediate product is demanded on a market with several potential suppliers. Therefore, the potential suppliers must be identified in terms of those who deliver:
- a product with the required obligatory product properties, described on the basis of the needs fulfilled by the product (very different products may serve the same need, thus being in competition on the
same market),
- within the geographical and temporal boundaries of the market affected by the specific demand.
The identification of the obligatory product properties and the geographical and temporal market boundaries is parallel to the first two steps described in the guideline “The product, functional unit, and
reference flows in LCA”. While the description in that guideline may be useful also for intermediate products, it should be noted that the procedure does not need to be elaborated in detail for every
intermediate product.
Office chair example

Office chair example: For most of the materials in the office chair (mainly steel and plastic materials), several suppliers are possible. These materials are traded on a competitive market
without specific ties between suppliers and customers. Therefore, a change in demand from the office chair manufacturer cannot be expected to only affect the current suppliers, but will rather
affect the entire market for these materials. This market can be identified as being European, since for steel and plastic materials, Europe constitutes a fairly closed market, as can be seen e.g.
from Eurostat production and trade statistics databases and publications (EUROPROMS; Panorama of European business; Intra- and extra-EU trade, and Iron and steel yearly statistics).
2.2.3 Step 3: Identifying the market trend
Within the identified market, not all suppliers will be equally affected by a change in demand. For short-term changes (see also section 2.2.1), the affected suppliers will typically be the least competitive
(often using older technology), since it is mostly these suppliers that have capacity available. For long-term changes, the affected suppliers depend on the overall market trend. In a market that decreases (at a
higher pace than what can be covered by the decrease from regular, planned phasing out of capital equipment) the affected suppliers will typically be the least competitive. If the market is generally increasing (or decreasing at a rate less than the
average replacement rate for the capital equipment), new capacity must be installed, typically involving a modern, competitive technology.
Therefore, it is important to identify the market trend (“Is the market increasing or decreasing?”) especially for long-term changes involving capacity adjustments.
It follows from the above distinction, that if the general market volume is decreasing at about the average replacement rate for the production equipment, the effect of a change may shift back and forth
between suppliers with very different technologies, which makes it necessary to make two separate scenarios. This may be relevant for a fairly large interval of trends in market volume, since the replacement
rate for production equipment is a relatively flexible parameter (planned decommissioning may be postponed for some time, e.g. by increasing maintenance).
Note that it is the overall market trend, which is of interest, and not the direction of the specific demand studied. This is because - as long as the overall trend in the market is not affected – it is the same
suppliers that will be affected by an increase in demand and a decrease in demand.
The trends in market volumes should preferably be determined using the same kind of information as that available to those deciding on capacity adjustments in the affected industry. This information is
typically a combination of statistical data showing the past and current development of the market and different forecasts and scenarios. If no information is available, it is safest to assume that the market is
increasing, since this is the most typical situation.
Office chair example

Office chair example: For most of the materials in the office chair the market trend is increasing.Trade statistics and forecasts are available from industry associations and consultants, for
steel e.g. the International Iron and Steel Institute (http://www.worldsteel.org/) and World Steel Dynamics (http://www.worldsteeldynamics.com/). Despite an increasing global trend, the
European production of steel is stagnating, however not below the replacement rate of the production equipment.This implies that the affected suppliers are to be found among the most
competitive steel makers in Europe, since it is here that new capacity is being installed.
The result of this step is that we can concentrate our search for the affected suppliers to one end of the market, either among the most competitive (for long-term changes in an increasing market) or among
the least competitive suppliers (for long term changes in a rapidly decreasing market and for short-term changes).
2.2.4 Step 4: Identifying production constraints
The possible suppliers (among the most or least competitive, depending on the conclusion of the previous step) may be subject to constraints that render them unable to react to a change in demand with a
change in production volume. Since their production volume (and environmental impacts) cannot be affected by the studied change in demand, such constrained suppliers should not be included in the
product system.
A supplier or an entire technology can be constrained in its ability to change its production volume in response to a change in demand, for one or more of the following reasons:
-
Political constraints, typically in the form of minimum or maximum quotas on the process (like the Danish minimum quotas on the use of biofuels for heat and electricity generation) or any of its exchanges,
e.g. product quotas (like the EU milk quotas) or emission quotas (like the Danish SO2 and NOX quotas for electricity generation, which limits the use of coal based technology).
- Constraints in the availability of raw materials, waste treatment capacity, or other production factors.
- If the change in demand is for a co-product, and the production volume of the co-producing process is determined by one or more of the other co-products. In general, this will be the case if the studied
product has a low value compared to the other co-products, so that the studied co-product cannot in itself provide an economic revenue that is adequate reason for changing the production volume (like
animal manure versus milk and meat, or rape seed cakes versus rape seed oil), or if the market trend for the studied co-product is low compared to the market trend for the other co-products. See section
3.2.2 for a precise procedure for identifying which co-products determine the production volume of a co-producing process.
In some cases, an entire market may be constrained, so that none of the suppliers will change their production volume in response to a change in demand. The change in demand will instead mean a change
in the supply of the intermediate product to that application area (or customer) of the product, which is most sensitive to a change in supply. Here, the change in supply will imply an equivalent change in
consumption.
Production constraints may change:
- over time,
- depending on location, and
- depending on the scale of change.
Thus, it is important to note the conditions for which the constraints are valid. Especially, when studying long-term changes (the typical situation for life cycle assessments, see section 2.2.1), it should be
avoided that a process is excluded from further considerations because of constraints that only apply in the short term (in day-to-day operations, many constraints apply, e.g. in raw material availability and production capacity, that are irrelevant when considering long-term changes).
In case of missing information on production constraints, it must be tentatively assumed that there are none. Unjustified exclusion of processes is thereby avoided. If a constrained process is thereby included,
this will normally be discovered in the next step in the procedure.
Office chair example

Office chair example: A change in demand for steel in the office chair cannot affect plants that use the electric arc furnace (EAF) technology, since this technology is constrained by the
availability of its main raw material (steel scrap).This leaves only the basic oxygen furnace (BOF) technology to be affected by a change in demand from the office chair manufacturer. Note
that we assume a small change with a long time horizon (see step 1), so that we expect the same reaction to an increase in demand as to a decrease in demand, and we look at changes in
production capacity.
2.2.5 Step 5: Identifying the suppliers/technologies most sensitive to a change in demand
Among the unconstrained suppliers/technologies, some will be more sensitive to a change in demand than others. For long-term changes in an increasing market, the most sensitive supplier/technology is
identical to the most competitive, while in a rapidly decreasing market and for short-term changes, the most sensitive supplier/technology is the least competitive (see section 2.2.3).
Competitiveness is typically determined by the production costs per unit. For capacity adjustments it is the expected production costs over long-term that matters. The distinction between constraints (section
2.2.4) and costs is not completely sharp, since some constraints may be translated into additional costs and some costs may be regarded as prohibitive and therefore in practice function as constraints.
However, if not taken too strictly, the distinction is useful for practical decision making. Also the definition of costs itself is not sharp, since concerns for flexibility (as a concern for future costs), environmental
costs and other externalities – whether monetarised or not - may enter the decision-making process. When predicting the actual decisions with regard to changes in capacity or capacity utilisation, it is
therefore necessary to include all those constraints and nonmonetarised costs which are relevant to the decision makers, but on the other hand not such which are not going to influence the actual decisions.
The kind of costs included may also vary depending on the interests of the decision makers, e.g. private investors may place less emphasis on environmental externalities than a public investor.
Thus, the most sensitive suppliers/technologies are determined from the production costs, while taking into account constraints and non-monetarised costs as perceived by those who decide about the change
in capacity (longterm) or capacity utilisation (short-term). The important point is to model as closely as possible the actual decision making context.
Data on production costs for individual plants, countries, or technologies are obtained from the industry in question, from industry consultants, or from research organisations, for steel e.g. World Steel
Dynamics. If data cannot be obtained, it may be assumed that modern technology is the most competitive and the oldest applied technology is the least competitive. With respect to geographical location, it
can be assumed that competitiveness is determined by the cost structure of the most important production factor (labour costs for labour intensive products, else energy and raw material costs). When
comparing labour costs, local differences in productivity and labour skills should be taken into account.
Office chair example

Office chair example:The source of the crude oil used for producing the plastic parts in the office chair will come from the most competitive oil sources (since the oil market is increasing).
According to the International Energy Agency (http://www.iea.org/),World Energy Outlook 1994, the most competitive sources (those with the lowest extraction costs) are the sources in the
Middle East and Venezuela, which are expected to increase their share in the global supply from 30% in 1991 to 45-57% in year 2010.
2.3 Default assumptions
For the initial phases of a life cycle study, and for parts of the life cycle that are less important, the procedure described in section 2.2 may be too elaborate and too demanding. Also, there may be situations
where it is not possible to obtain the necessary market information. In these situations, the defaults in table 2.1 may be applied. The detailed arguments for these defaults are given in LCA Report No. 1:
Market information in LCA.
Table 2.2 lists some typical processes, which may be assumed to be the ones affected by a change in demand for the listed products under the stated conditions. When used in a specific study, please check
whether the stated conditions apply. The conditions stated in table 2.2 are the expected conditions on the European market in the years 2000-2010, provided that the studied changes are small. Unless
otherwise stated, the defaults in table 2.1 apply. The main differences in assumptions between the products relate to differences in market trend (increasing to stable versus rapidly decreasing) and geographical market boundaries (local,
continental or global). For documentation and sources of these assumptions, please see the background report “Market information in LCA”.
It can be seen from table 2.2 that the specific affected suppliers/technologies are often very different from the corresponding average supplying the market. Thus, only in exceptional cases can average data
be used as proxy data, when market-based data are not available. This may e.g. be the case when the market in question is supplied exclusively by one main, slowly developing technology. In most other
situations, it is preferable to make one or more estimates of the affected process, based on the available data.
Table 2.1. Default assumptions on market conditions
Item: |
Default assumption: |
Scale of change |
Small |
Time horizon |
Long-term |
Market ties |
None |
Market segment |
Narrow, i.e. not assuming substitution between very different products |
Geographical market |
Products with a low value to weight ratio: Local market* Products with medium value to weight ratio: Continental market* Products with a high value to weight
ratio: Global market* |
Market trend |
Overall increasing production volume |
|
Production constraints Only for co-products with a low value relative to the remaining co-products from the same process |
Affected (most competitive) supplier/
technology |
Technology: Modern Geographical location (within the above defined geographical market): Depending on relative importance of labour costs and skills. |
* In that transport costs have been attributed large importance here. However, also other factors may be of significance, such as possible toll barriers, trade patterns, and geographical differences in overall
production volume.
If you have data for a market average, the market range may be estimated by coefficients of variance of:
- 10-30% for energy consumption,
- 10-20% for raw materials and regulated emissions that occur as a result of substances in fuels and raw materials,
- 60-150% for unregulated emissions that occur as a result of substances in fuels and raw materials. Substances that naturally vary significantly, e.g. cadmium, lead, mercury and other metals in coal and
crude oil, may in extreme cases give emissions that vary with a factor of 1000 or more.
- Larger variation (factor 5-10) should be applied for emissions that are created during the production process, and which vary significantly depending on the physical conditions during production, and
emissions that occur from the use of specific chemicals during the production process.
When the range is known or has been estimated, the affected process can then be assumed to be at one of the ends of this range, depending on realistic assumptions with respect to the items listed in table 2.1. It is thereby assumed that all the above exchanges co-vary, so that large energy consumption is linked to large raw material consumptions and large
exchanges to the environment.
When relevant, several alternative scenarios should be included to reflect the limits of knowledge.
Table 2.2 Default list of processes affected by a change in demand for selected products, under the expected conditions for the European market in the years 2000-2010 and when the studied changes are small
NACE-code |
Product |
Geography |
Market trend |
Other differences in assumptions compared to table 2.1 |
Affected supplier/technology |
01.1 |
Crops in general |
EU I |
Increase |
Limits on fertiliser per ha in some areas |
Current suppliers, increasing yield per ha by additional fertiliser. When not possible, or for larger changes, barley will be displaced. |
01.1 |
Fodder protein |
Global |
Increase |
None |
Soy bean (Brazil) |
02.01 |
Wood for pulp |
Local |
Increase |
None |
Local |
11.1 |
Crude oil |
Global |
Increase |
None |
Heavy crude from Venezuela or Middle East |
13.2 |
Aluminium |
Global |
Increase |
None |
Hall-Heroult. Point feeders. Separate electricity market. |
13.2 |
Copper |
Global |
Increase |
None |
Modern, raw material flexible: Solvent-
extraction-electrowinning |
13.2 |
Cadmium, Mercury, Lead |
Global |
Decrease |
None |
Recycled material (reducing the material going to waste deposits) |
15.4 |
Vegetable fat |
Global |
Increase |
No |
Specific fatty acid composition requested EU rape oil |
20 |
Wood and products of wood |
Depending on product requirement |
Increase |
None |
Modern, often local: Drying plants with heat pumps and variable speed |
21.2 |
Pulp, paper, board |
Local to regional |
Increase |
None |
Local to regional, modern |
23.2 |
Propylene |
EU |
Increase |
None |
Fluid catalytic cracking off-gas cleaning |
23.2 |
Ethylene |
EU |
Stable to increase |
None |
Steam cracking of LPG or gas oil |
24.13 |
Chlorine |
Europe |
Decrease |
None |
Old technology (mercury process) |
24.15 |
Ammonia |
Europe |
Decrease |
Surplus capacity in Eastern Europe |
Older natural-gas based technology (Eastern Europe or Greece) |
25.1 |
Rubber |
Global |
Increase |
None |
Synthetic rubber from modern plants |
26.4 |
Bricks |
Local |
Decrease |
None |
Oldest local tunnel kiln |
26.5 |
Cement clinker |
Local |
Decrease |
Technology is raw material dependent |
Wet process in Denmark. Dry process in general. |
26.5 |
Cement |
Local |
Decrease |
Fly ash cements etc. constrained by raw material availability |
Portland. Older, local plants. |
27.1 |
Steel |
Europe |
Increase |
Electric Arc Furnace technology constrained by scrap availability |
Modern Basic Oxygen Furnace technology |
40.1 |
Grid electricity |
Central Europe |
Increase |
Nuclear, hydro and lignite based power politically constrained |
Coal-based technology |
40.1 |
Grid electricity |
North Europe |
Increase |
As above + emission limits for SO2, NOx (and CO2). Surplus coal based capacity. |
Coal-based technology within existing capacity likely to cover demand for next 10 years. Else: natural gas-based technology. |
40.1 |
Grid electricity |
Greece |
Increase |
Nuclear and hydro power politically constrained |
Lignite-based technology |
2.4 Uncertainties in identifying the correct processes to include
The procedures for identifying the correct processes to include in the studied product systems, as described in section 2.2, rely on market data,
in which the following uncertainties are of importance:
- Uncertainty re. the scale of change that may influence the boundary conditions of the market.
- Uncertainty re. what intermediate products will substitute each other in different market segments and geographical markets.
- Uncertainty re. the temporal and geographical boundaries of the actual market of an intermediate product.
- Uncertainty re. what technologies and processes are constrained in their ability to change their volume in response to a change in demand.
- Uncertainty re. market trends.
- Uncertainty re. the parameters that influence decisions on capacity adjustment, e.g. prices of different technologies and the effect of information on buying behaviour and investment decisions.
These uncertainties will often be dominating the overall uncertainty of a life cycle assessment, since they may affect which processes are included and excluded from the analysed product systems. The
importance increases in proportion to the possible variation in the technologies and processes that may be substituted, i.e.:
- Variation in the relevant technologies and processes between different possible markets.
- Variation in the relevant technologies and processes within the same market, especially the variation between the least and the most competitive technology/process.
This means that the higher the variation in possible outcomes, the higher is the demand on the quality of the market data.
A reduction of the uncertainty can only be obtained through a better understanding of the different intermediate products in the life cycle and the markets on which they are traded. Thereby, the individual
processes to be included in the product system can be determined with more precision. Use of quality assurance and critical review as part of the life cycle assessment can contribute to the reduction of
uncertainties.
The above considerations are also valid for the standard assumptions in traditional system delimitation (see section 1.3), but since this does not include market information it will be difficult to estimate the real
uncertainties as a result of the system delimitation. The uncertainty on a traditionally delimited system will therefore typically be calculated from the uncertainties on the average data for the included processes.
Since this uncertainty is an expression of a real variation, it cannot be reduced through additional data collection.
When relevant, several alternative scenarios should be included to reflect the limits of knowledge.
The mentioned major sources of uncertainty also apply to the handling of multi-functional systems, following the procedure described in chapter 3.
The issue of uncertainty is dealt with in more detail in the technical report “Reducing uncertainty in LCI.”
| Front page | | Contents | | Previous | | Next | | Top |
Version 1.0 December 2005, © Danish Environmental Protection Agency
|