| Front page | | Contents | | Previous | | Next |
Geographical, technological and temporal delimitations in LCA
3 Handling multi-functional systems
3.1 Solving the co-product allocation problem: From multiple to single functions
Few (if any) products are produced, consumed and disposed of in isolation. Thus, most (if not all) product systems will provide more than one product (material goods or services), either as a part of the
functional unit (see “LCA Guideline no. 2: Determining the object of study, the functional unit, and the reference flow”) or as co-products from one or more of the processes in the life cycle.
To study the environmental impacts of an isolated product substitution, it is therefore necessary to isolate the processes that are affected by the specific substitution, from those processes that are physically
linked to the product systems, but which are nevertheless not affected by the substitution. For those processes that are affected, it is furthermore necessary to determine the extent to which they are affected:
Will it imply a change in the volume of the affected process or only in some specific exchanges? Will a change in volume depend solely on the studied substitution or should the change in volume be shared
with other product systems?
The last question is what is usually referred to as “the (co-product) allocation problem”. Co-product allocation is the partitioning and distribution of the exchanges of a process with multiple co-products over
these co-products. It has been one of the most controversial issues in the development of the methodology for life cycle assessment, as it may significantly influence or even determine the result of the
assessments. In general, the co-product allocation problem can be avoided through the procedure presented in section 3.2. This procedure is in line with the recommendations of ISO 14041 and includes the
traditional allocation procedure (which simply distributes the exchanges of a co-producing process over the co-products according to some allocation factor) as a special case (see section 3.6).
3.2 Procedure
An initial distinction can be made between joint production, where the relative output volume of the co-products is fixed (e.g. chemical processes where outputs are determined by stochiometry), and
combined production with independently variable output volumes (e.g. when different products share the same service). For combined production, allocation can be avoided simply by modelling directly the
consequences of a change in the output of the co-product of interest (that which is used in the product system under study) without change in the output of the other co-products. This situation is dealt with in
step 1 of the procedure (section 3.2.1). The remaining part of the procedure (steps 2 to 4) deals with the situation of joint production where allocation can only be avoided through system expansion.
System expansion is illustrated in figure 3.1, showing a co-producing process with one determining co-product (product A), i.e. a co-product that determines the production volume of that process. In figure
3.1, also just one dependent co-product is shown, but in practice there may be any number of co-products.
Figure 3.1 Model for describing system expansion and delimitation for joint production, valid both when product A and product B is the product used in the life cycle study

Performing a system expansion in relation to joint production is to answer the question: How will the production volume and exchanges of the processes in figure 1 be affected by a change in demand
for the co-product that is used in the life cycle study?
This question is equally relevant when the co-product used in the life cycle study is the determining product for the co-producing process (A) and when it is the product in which the dependent co-product is
utilised (B).
A complete identification of changes in production volume as a function of change in demand would require an economic model for all the involved processes and product flows. The procedure presented
here involves the simplifying assumption that a change in demand for a dependent co-product does not affect the production volume of the co-producing process[6].
The three rules in Box 3 provides the answer of the simplified procedure to the above question.
Box 3: Rules for system expansion and delimitation for joint production
-
The co-producing process shall be ascribed fully (100%) to the determining co-product for this process (product A).
-
Under the condition that the dependent co-products are fully utilised, i.e. that they do not partly go to waste treatment, product A shall be credited for the processes that are displaced by the dependent co-products. The intermediate treatment shall be ascribed to product A. If there are differences between a dependent co-product and the product it displaces, and if these differences cause any changes in the further life cycles in which the dependent co-product is used, these changes shall likewise be ascribed to product A.
- When a dependent co-product is not utilised fully (i.e. when part of it must be regarded as a waste), the intermediate treatment shall be ascribed to the product in which the dependent co-product is used (product) B, while product B is credited for the avoided waste treatment of the dependent co-product.
It should be noted that system expansion implies that data are to be collected for processes that are not necessarily part of the current supply chain.
The amounts to be ascribed from the different processes depend on the amount of co-product used in the specific product system under study. For example, a unit output of product A shall be ascribed the
exchanges from process A relating to the production of this unit, and for the situation when the dependent co-product is not utilized fully, product A shall furthermore be ascribed the waste treatment of that
amount of the dependent co-product, which is co-produced with that one unit of product A. In the same situation, a unit output of product B shall be ascribed the intermediate treatment of this unit, while
being credited for the displaced waste treatment of this unit.
The rationales behind the three rules in Box 3 are:
Rule no. 1 follows logically from product A per definition being the co-product, which causes the changes in production volume of the co-producing process.
Rule no. 2 follows – under the stated condition – from the fact that both the volume of intermediate treatment and the amount of product which can be replaced, is determined by the amount of dependent
co-product available, which again is determined by the change in production volume in the co-producing process, which is finally determined by the change in demand for product A. It follows from this rule
that product B is ascribed neither any part of the co-producing system, nor any part of the intermediate treatment. When studying a change in demand for product B, this product shall be ascribed the change
at the supplier most sensitive to a change in demand (identified by the procedure described in chapter 2), i.e. the same process, which is displaced by a change in demand for product A (but see also rule no. 3). If the condition stated in rule no. 2 (that the co-product is fully utilised in other processes) is not fulfilled, rule no. 3 applies.
Rule no. 3 applies to the situation where a dependent co-product is not utilised fully. In this situation, the volume of the intermediate treatment (and the displacement of waste treatment) is determined by how
much is utilised in the receiving system, and not by how much is produced in the co-producing process. Another way of saying this is that in this situation, process I (the intermediate treatment) is that supplier
to process B, which is most sensitive to a change in demand for product B.
3.2.1 Step 1: Treating combined production: co-products with independently variable outputs
If the output volume of the co-products can be independently varied (combined production), it is possible to describe directly the consequences of a change in the output of the co-product of interest without
change in the output of the other co-products.
Some co-products may be separated completely, so that each co-product can be produced alone, allowing separate description of this pure production. However, the combined production of these
co-products is typically done to take advantage of some benefit of co-production, e.g. joint use of capital equipment, reduction in energy or raw material consumption, or reduction in waste generation. Since
a description of the separate pure production does not encompass these advantages, it will not provide a correct reflection of the actual conditions.
Rather, what should be included in the product system is a description of the consequences of the studied change in relative outputs, i.e. the changes in process exchanges as a result of a change in the output
of the co-product of interest while the output of the other co-products is kept constant. In this way, the benefits of the combined production are inherent to the description and will be reflected in the
outcome.
In general, a physical parameter can be identified, which - in a given situation – is the limiting parameter for the co-production. It is the contribution of the co-product of interest to this parameter, which
determines the consequences of the studied change.
Example 1: Combined surface treatment
Surface treatment is often performed on different objects in combination (e.g. legs for chairs in combination with legs for tables), to limit the loss of surface agent (e.g. paint) and to save machine time. Although the different legs might be treated individually to obtain a measure of the environmental exchanges for each treated product, it would be more correct to model the changes in process exchanges when changing the amount of chair-legs while keeping the output of table-legs constant and vice versa. In this case, a physical parameter can be identified, which determines the change in exchanges: additional surface area treated (treated surface area of the leg plus border area). The size of the border area will depend on the extent to which the additional chair-legs will utilize an area that is already border area, or whether the existing border area is already utilized fully so that the additional chair-legs anyway need to be treated separately.
Example 2: Combined transport I
When the same vehicle transports several items, e.g. both plastic chairs and wooden chairs, the effect of adding another item to be transported depends on what physical parameter is limiting the transport capacity. When there are more of the heavy wooden chairs, the transport capacity is limited by weight, which means that the truck volume is not utilised fully. In this situation, adding an extra chair will increase the exchanges from the transport process in proportion to the weight of the extra chair. Heavy ooden chairs demand more trucks than light plastic chairs, even when the chairs have the same volume. However, when there are more of the plastic chairs, it may be the space limit that is reached first, so that the vehicles cannot be loaded at full weight capacity. In this situation, the exchanges from the transport will change in proportion to the volume of the two kinds of chairs. For trucks, the weight capacity is typically utilised fully at a density of 250-300 kg/m3. If the density is lower than this limit, the transport capacity is limited by volume.
3.2.2 Step 2: Identifying a product as determining for the volume of the co-producing process
Identifying a joint product (a product from joint production) as a determining co-product is the same as
showing that the co-producing process will be affected by a specific change in demand for this product. When the co-producing process is identified as the affected process by using the procedure in chapter
2, we have in fact at the same time identified the co-product under study as being a determining co-product.
For a co-product, the crucial point in the procedure in chapter 2 is the identification of the other co-products as production constraints (third bullet of step 4 in section 2.2.4.). The production volume of the
co-producing process is constrained by the demand for the determining joint product(s). Independently variable (combined) co-products cannot provide a constraint and may be simultaneously determining
(as described in the previous step).
To be a determining co-product, a joint product (or a combination of joint products in which the co-product takes part) shall:
-
provide an economic revenue that is in itself adequate reason for changing the production volume
and
- have a larger market trend (change in overall demand) than any other joint product or combination of joint products that fulfil the first condition (taking into account the relative outputs of the co-products).
The reason for this is that the joint product (or combination) with the largest market trend provides a constraint on the ability of the other joint products to influence the production volume of the co-producing
process. Note that within a combination of joint products, the co-product with the smallest market trend is determining the ability of the combination to influence the production volume.
See also Box 4 for an illustration of this.
It follows from the above condition that if more than one joint product or combination of joint products fulfil the condition to provide an adequate economic revenue to change the production volume, only
that co-product or combination which has the relatively largest change in overall demand (market trend) is actually determining. Thus, at any one given moment, typically only one of the joint products
determines the production volume. A notable exception is when no relevant alternative production routes exist for the joint products and their prices therefore must be adjusted to ensure that all the joint
products have the same market trend, since only then the market will be cleared (see example 6). In this situation, a change in demand for one of the joint products will influence the production volume of the
joint production in proportion to its share in the gross margin of the joint production. This is equivalent to the result of an economic co-product allocation. However, the resulting change in output of the other
joint products influences their further downstream lifecycles, including their consumption and disposal phases, and thus requires the inclusion of the processes affected. This latter aspect of system expansion
is ignored in a pure economic allocation of the joint production.
Box 4: Illustration of the constraints between joint products
Assume a process with the 4 joint products A, B, C and D, with the following relative market trends and economic revenues:
Co-product |
Marginal economic revenue |
Relative market trend |
A |
10 |
small |
B |
6 |
medium |
C |
5 |
large |
D |
1 |
large |
Note that the stated market trends and economic revenues are relative to the normalised output volumes of the co-producing process, i.e. differences in the actual physical quantities have already been eliminated.
At a marginal production cost for the co-producing process of 9, only one co-product (A) can provide an adequate economic revenue to change the production volume alone. Product C cannot alone influence the production volume, in spite of the large market trend for this product. However, the combination B and C also fulfil the condition (of providing an adequate economic revenue). The possible influence on the production volume from this combination is determined by the smallest of the trends in the combination, which is the medium trend of product B. Since this is still larger than the trend of product A, product B becomes the co-product that determines the production volume.
Example 3: Joint production of food products and animal fodder I
Many of the less valuable co-products of the food industry are used as animal fodder, and typically there is no alternative way to produce the food product in question. For example, wheat bread can only be produced from wheat, which is milled to flour, while the other fractions (germ, bran, and husk) are used for animal fodder (with the exception of a very small part that is used in speciality products for human consumption). In this case, there is little doubt that the flour is the only co-product that can provide adequate economic revenue to change the production volume of the milling process (and the wheat production), and that the flour is therefore the determining co-product.
Example 4: Joint production of zinc and heavy metals I
Approximately 90% of all primary cadmium are a co-product of zinc extraction. In addition, lead and sulphur are produced as co-products of zinc extraction. The demand for zinc is increasing moderately, while the demand for the heavy metals cadmium and lead is stagnating mainly due to environmental regulations. The supply of cadmium from compulsory take-back and recycling of cadmium-containing products means that some primary cadmium is currently deposited. The same situation can be expected in the future for the other heavy metals. Sulphur is increasingly produced from desulphurisation of flue gases from refineries, power plants etc. In Europe, there is no longer demand for primary production of sulphur. Thus, it should be clear that only changes in demand for zinc can be determining the size of the primary extraction.
Example 5: Joint production of chlorine and sodium hydroxide I
The joint production of chlorine and sodium hydroxide is one of the classical examples of allocation problems. The chlor-alkali process yields three co-products:
2 NaCl + 2 H2O ⇔ 2 NaOH + Cl2 + H2
Hydrogen is produced in relatively small quantities (27 g for every kg of chlorine) providing approximately 3% of the world market for hydrogen. The main production route is steam reforming of natural gas and this will probably also be the most competitive process to cover a change in demand for hydrogen. Thus, hydrogen cannot be the determining co-product.
In practice, the chloralkali process is the exclusive production route for chlorine, which cannot be easily stored and is typically sold locally. Sodium hydroxide is a more flexible product that can be stored and transported over long distances. Sodium hydroxide can be substituted by soda ash directly or by sodium hydroxide produced by caustification of soda ash, thus providing both a floor and a ceiling on the price of this co-product. Chlorine and sodium hydroxide are produced in approximately equal quantities by the chloralkali process and their share in the total income for the process is approximately the same. However, during the last 10 years there has only been one short period in 1990/1991 where the price of sodium hydroxide was so high that it could by itself provide adequate revenue to change the production volume.
Based on this analysis of the market situation, it is concluded that long-term decisions on capacity adjustments are based on the existence of local, stable demands for chlorine, making chlorine the determining co-product for the chloralkali process when applied in LCAs with a long time horizon.
Example 6: Pork production
In the abattoir, the slaughtered pig is separated into a large number of co-products. Independent variation among co-products is limited, although some flexibility exists, notably in the share of minced meat. All co-products must therefore be regarded as joint, and with some minor exceptions no alternative production routes exist. Thus, the pork market is governed solely by the output from the abattoirs and all prices are continuously adjusted so that all products are sold. Market trends are therefore aligned so that all joint products are simultaneously determining for the production volume. A change in demand for one specific part of the pig, e.g. tenderloin, will therefore influence the volume of production in proportion to the gross margin obtained for this part, relative to the average gross margin, equivalent to the result of an economic allocation. Since there are no alternative production routes, this change in production volume in turn affects the output, pricing and consequent consumption of all other parts of the pig.
The illustration in Box 4 also shows that:
- the determining co-product is not necessarily the co-product, which yields the largest economic value to the process (although this will often be the case),
- the determining co-product is not necessarily the co-product, which is having the largest increase (or decrease) in demand.
If adequate data are not available to allow one of the joint products to be identified as determining, several scenarios should be used to reflect the limited knowledge. A scenario may be made for each
product that may possibly be determining. The scenarios may be presented separately or as a combination of the relevant scenarios weighted in proportion to their expected probability or in proportion to the
relative expected influence of the joint products on the production volume of the co-producing process[7].
3.2.3 Step 3: Identifying the co-product that determines the volume of intermediate processes
The intermediate processes are those processes that take place between the split-off point where a dependent co-product leaves the processing route of the determining co-product and the point of
displacement where the dependent co-product can displace another product. While it is always relevant to determine the split-off point, it is only relevant to determine a point of displacement when the
dependent co-product is utilised fully in other processes and actually displaces other products there (i.e. when rule no. 2 of Box 3 applies).
The determining co-product for the intermediate processes is identified by investigating whether the condition of rule no. 2 is fulfilled or not, i.e. whether the dependent co-product is utilised fully in other
processes.
If the condition is fulfilled, the volume of intermediate treatment (and the amount of product being displaced) depends on the product volume of dependent co-product. Since the co-products cannot be
independently varied, this volume is fixed by the determining product of the co-producing process (product A in figure 3.1). A change in demand for the dependent co-product will not lead to any change in
the intermediate treatment (exactly because it is not determining, i.e. it cannot affect the volume of the co-producing process). Thus, the intermediate treatment and the co-producing process have the same
determining product, and (as stated by rule no. 2 of Box 3) the intermediate process shall be fully ascribed to this product (A).
Example 7: Joint production of chlorine and sodium hydroxide II
When chlorine is the determining co-product, chlorine is ascribed the full chlor-alkali process, the intermediate processes (concentration, transport, and storage of the sodium hydroxide), but is credited for the avoided production, transport and storage of sodium hydroxide from caustification of soda ash (see example 14 in section 3.5.3 for further treatment of this avoided process).
Example 8: Co-generation of electricity and heat I
Electricity is often co-generated with heat, since the overall efficiency of combustion is much higher when the heat can also be utilised. When the heat is fully utilised, a change in the production of electricity will affect the distributed amount of co-generated heat and will affect the alternative heat source. Thus, in this situation the electricity shall be ascribed the additional energy requirement for distribution and credited for the alternative heat supply which is displaced. A change in demand for heat cannot be covered by co-generated heat (since this is already utilized fully) and will therefore affect the alternative heat source.
Since in this situation, where the dependent co-product is fully utilised, it is product A that determines the amount of product being displaced, product A shall also be ascribed other possible changes resulting
from this displacement. This applies to the changes in the alternative raw material supply, as in the examples above, where product A is ascribed (credited for) the changes in the displaced process D (still
referring to figure 3.1), but also to such changes in the further life cycle of the dependent co-product (process B in figure 3.1) that are a consequence of differences between the dependent co-products and
the products they displace.
Example 9: Consequences of quality differences when using co-products
Compared to the displaced product, the co-product may be of a different (typically lower) quality than the displaced product. This is often of no importance to the user (else the substitution would not have been accepted) but sometimes it may lead to an additional need for maintenance or other supplementary activities. These additional activities shall be ascribed to product A.
Example 10: Contaminated co-product
Compared to the displaced raw material, the co-product may contain a contamination, e.g. of heavy metals, which gives it a different performance during the final waste treatment of product B. The difference in waste treatment and/or in environmental exchanges form the waste treatment shall be ascribed to product A.
If the condition of full utilisation is not fulfilled, it means that part of the dependent co-product is treated as a waste. In this situation, the volume of the intermediate treatment (and the displacement of waste
treatment) is determined by how much is utilised in the receiving system, and not by how much is produced in the co-producing process. Thus, product B is the determining product for the intermediate process and shall
be ascribed these (while being credited for the avoided waste treatment), as stated by rule no. 3 of Box 3.
Example 11: Co-generation of electricity and heat II
When the market for co-generated heat is saturated and the heat is still not fully utilized, a change in the production of electricity will just produce more surplus heat, but not affect the distributed amount of co-generated heat. A change in demand for heat in this situation will not affect the amount of heat generated, but will influence the amount distributed.
Thus, the energy requirement for heat distribution shall be ascribed to the heat, while the electricity is ascribed the co-generation, but is given no credit for displacement (since there is none).
As illustrated by the examples 8 and 11, whether a co-product is utilised fully and whether it displaces other products, depend on market conditions that may change:
- over time,
- depending on location, and
- depending on the scale of change.
Thus, it is important always to note the conditions under which the determinant for the intermediate processes has been identified.
If the investigated change is of such a size that it in itself changes the conditions for the system expansion, i.e. changes which product is determining or whether the dependent co-product is utilised fully, the
system expansion shall be calculated on the basis of the resulting conditions after the change.
The information needed to determine whether a dependent co-product is fully utilised are obtained from market and waste statistics and market studies, often available in-house in the involved industries. If it
is uncertain whether this condition is fulfilled, it may be necessary to apply different scenarios to reflect the limited knowledge.
3.2.4 Step 4: Identifying displaced processes
System expansion typically involves displaced or avoided processes, either avoided raw material supply (process D in figure 3.1) or avoided waste treatment (process W in figure 3.1). Thus, the final step of
the system expansion is to identify the displaced processes more precisely. This is done by applying the procedure in chapter 2 to the market situation of the displaced processes.
3.2.5 The procedure as a flow-chart
Figure 3.2 presents an overview of the procedure in the form of a flow-chart.
3.3 Waste or co-product?
In the procedure presented here, the distinction between wastes and co-products is not important. If in doubt whether an output is a waste or a co-product, the output can be regarded as a dependent
co-product and passed through the procedure. It will then either fall under rule no. 2 (if the output is utilised fully, but does not displace any other products, it is a waste, and product A is ascribed all
processes in the waste treatment) or rule no. 3 (for “near-to-wastes” that are not fully utilised). Even when an output is without economic value to the process that produces it, the “waste treatment” for the
utilised part is in fact a recycling (process I in figure 3.1), and rule no. 2 or 3 should therefore be applied in order to model correctly the consequences of this “waste treatment.”
Figure 3.2. Decision tree showing the 4-step procedure for handling multifunctional processes. For definition of determining co-products, see the text (especially section 3.2.2). For explanation of the rules and process
lettering, see the text, Box 3 and Figure 3.1 in this section
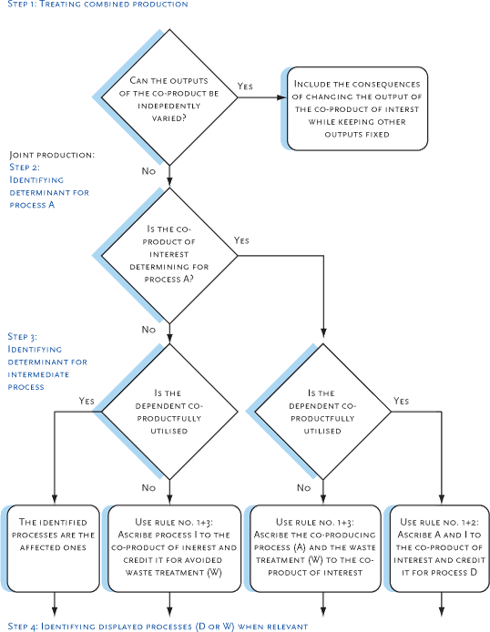
3.4 Recycling
Recycling is often mentioned as presenting distinct allocation problems needing a separate treatment. However, the procedure in section 3.2 is equally applicable to recycling as to any other situation where
the same processes are shared by several products. In figure 3.3 the recycling situation is presented, re-using the layout and lettering of figure 3.1.
In this situation, it is no problem to identify the determining product for the primary life cycle. This is obviously the product of this life cycle (product A), not the scrap.
The central issue is what determines the recycling rate and thus the degree to which the scrap is utilised in the secondary life cycle.
Figure 3.3 Model for describing system expansion and delimitation in relation to recycling
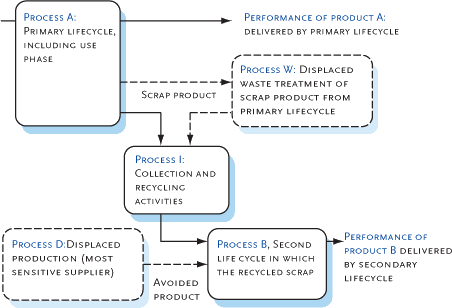
In an increasing market for the scrap product, as is currently the case e.g. for most metals, all scrap collected will be used. In this situation, a change in the volume of the primary life cycle will lead to a
change in the amount of scrap available for collection, and a consequent change in the amount collected (provided the collection percentage is constant), which finally will result in a change in the amount of
scrap utilised in secondary life cycles, and thus in the displacement of “virgin” production (i.e following rule no. 2 of Box 3). A change in the volume of the secondary life cycle will have no direct influence on
the amount of scrap utilised, since all the scrap collected is already utilised fully. Thus, the change in the volume of the secondary life cycle must be covered by a change in “virgin” production (i.e. still
following rule no. 2). Thus, in an increasing market, all changes in all life cycles affect the amount of “virgin” material extraction, and only the production that ensures an increase in the collection (by providing more material for recycling, or by specifically increasing recycling capacity, either technically, by economic support, or by stimulating political intervention) will be credited for the resulting increase in recycling (displacement of “virgin” extraction and decrease in waste handling).
It should be noted that an increase in recycling can be an indirect or delayed consequence of the signal that is sent by a change in demand for scrap, e.g. via political intervention or private investment in
capacity increases, as also described in section 2.2.2. Of course, such indirect effects are only possible when significant quantities of scrap are available for collection, in addition to the amount already
collected. Since such indirect effects can be controversial and difficult to predict, it may be preferable to include them in separate scenarios.
In a decreasing market, some of the available material is being deposited, since there is not an adequate demand. A change in volume of the primary life cycle will only lead to a change in the amount of
material to be deposited, while a change in the volume of the secondary life cycle will lead to a change in the amount being recycled, and thus indirectly also to a change in the amount being deposited (i.e.
following rule no. 3 of Box 3). This is the situation for cadmium and some other materials that are being phased out because of their severe environmental impacts (this example does not imply a
recommendation to increase the use or reuse of these substances). Thus, in a decreasing market without “virgin” inflow, all life cycles that utilize scrap products will be credited for the resulting increase in
recycling (decrease in waste handling), and no life cycle will be credited for supplying additional material to recycling (since this would just mean that an equivalent amount would require waste treatment
elsewhere).
In this way, the procedure provides incentive for using scrap when the market for the material in question is decreasing, and for supplying scrap when the market is increasing, which is exactly what is
needed to increase recycling in these two respective situations. When the recycling rate is below its environmental optimum, the procedure furthermore gives credit for specific actions that increase recycling
capacity.
It may be argued that the studied changes in either the primary or secondary life cycle may also have a secondary effect on the market prices, and that this would equally affect the price of the primary
product and of the collected scrap. However, the “virgin” production and the collection do not react to a price change with the same change in volume. At the high collection rates that exist in a free market
situation, the resulting volume change in collection is likely to be much less (probably often negligible) compared to the change in “virgin” production. This would support the above conclusion of applying rule
no. 2 in the situation of increasing markets. Also in the case of a moderately decreasing market, where the supply from “virgin” production still plays a role, the difference in reaction to a price change would imply that the “virgin” production is affected most. However, in a
rapidly decreasing market, the scrap can cover the entire demand and virgin supply would not be relevant. In this situation, a small change in volume of the secondary life cycle would only be able to affect
the scrap collection, which is in line with our above conclusion of applying rule no. 3 in case of decreasing markets.
3.4.1 Downcycling
In some situations, the recycled material cannot displace “virgin” material, either
- because its technical properties have been reduced (e.g. paper fibres that become shorter for each recycling, so that after approximately 6 cycles they are so short that they must be discarded), or
- because it has been contaminated (e.g. silicon alloys of aluminium cannot be recycled with the ordinary aluminium scrap).
In these cases, several distinct markets may exist for different qualities of recycled material, and the displacements that will occur will be determined by the supply and demand on these markets, see figure
3.4, which shows three markets for recycled material (scrap qualities 1, 2 and 3) besides the market for “virgin” material. If a demand for a specific scrap quality is not satisfied completely, scrap of higher
quality or virgin material may be used (dotted lines connecting processes I and D in figure 3.4), while scrap of lower quality cannot be used. When upstream processes deliver more scrap than the capacity of
its downstream markets, some of the scrap will not be used.
Thus:
- A change in demand for a specific scrap quality will affect the next upstream, unused supply and will displace waste there. If all upstream supplies are used fully, it will affect “virgin” production.
- A change in supply of a specific scrap quality will affect the next downstream, unsatisfied demand. If no downstream markets have unsatisfied demands, the scrap produced will not be used, thus affecting
the immediate waste treatment.
A change in demand for a specific product, produced with scrap material, will cause both of the above. For example, a change in demand for product B in figure 3.4 will lead both to a change in demand for
scrap quality 1 and a change in the supply of scrap quality 2.
Figure 3.4 System expansion and delimitation in relation to downcycling
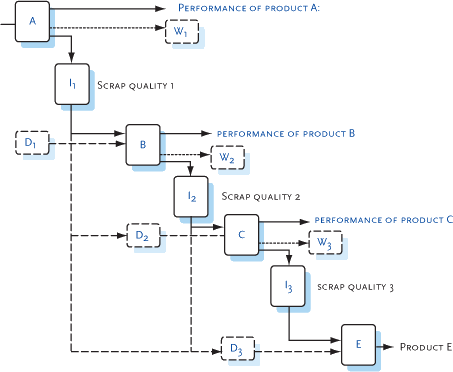
Example 12: Paper recycling I
In recycling of newsprint, we have at least three pools of recycled material with distinct qualities:
- the recycled newsprint pool, which can be used in production of tissue paper, cardboard, moulded paper and a lot of other paper products (and typically 20% in newsprint itself),
- the cardboard pool, which can be used e.g. for corrugated board production (product C),
- the corrugated board pool, which is a nearly closed loop with a recycling of approx. 75% (i.e. in this case product E and product C is identical).
The volume of the “recycled newsprint pool” is determined by the supply to this pool, since the demand for recycled newsprint is currently larger than the supply in most markets, due to the many possible applications. Due to the high recycling rate in the corrugated board loop, the demand for recycled cardboard is easily saturated, which means that the demand for corrugated board may typically determine the volume of recycling in this pool.
In this market situation, “virgin” paper will be affected both by a change in supply of recycled newsprint (by displacement) and by a change in demand for recycled newsprint (because “virgin” is the next upstream unused supply). The recycling process itself (I1) shall be ascribed to the newsprint (product A). An increased supply of or demand for recycled cardboard will affect the alternative waste treatment of this cardboard (W2) and the recycling process (I2) shall be ascribed to the user of the recycled cardboard (typically the corrugated board production).
In the case of contamination of virgin material, it should be noted that it is not only the current market situation that must be considered, but rather a very long-term market situation. As long as the current
demand for scrap qualities is larger than the supply, all the contaminated scrap will be used and will displace “virgin” material. The contamination will be diluted due to the constant inflow of virgin material.
However, at some stage in the future the scrap markets may become saturated, so that the contamination becomes a limitation for the recycling. The current contamination may thus lead to a future need for
waste treatment of the contaminated material, or at least to a different displacement than on the current market. It is this future market situation that should be used to determine what processes to include in
the system expansion, since the immediate displacement of “virgin” material is only a temporary postponement of the necessary supply of “virgin” material in the future situation, when the contaminated
material can no longer be used. The need to take into account these future effects is included in the third sentence of rule no. 2 of Box 3: “If there are differences between a dependent co-product and the
product it displaces, and if these differences cause any changes in the further life cycles in which the co-product is used, these changes shall likewise be ascribed to product A.”
Example 13: Copper-contamination of steel
The current demand for steel allows copper-contaminated fractions to be incorporated in hot-rolled steel (contamination limit approximately 0.28%). However, in the (not-so-far-away) future, a further supply of copper-contaminated fractions may no longer find a market. These fractions will then be deposited instead of being recycled. Thus, a current copper-contamination of steel can be predicted to incur a future deposition of the contaminated steel. This implies that although the contaminated steel is currently recycled and not deposited, the life cycle causing the contamination should not be credited for the recycling of this steel, but instead be burdened with its (future) deposition.
For materials where the technical properties are reduced on recycling, each additional life cycle will imply a change in the quality of the material in the recycling pools, influencing the requirements for supplies
of “virgin” material to the pools. The need for new material may be caused e.g. by degradation of fibres or polymers, as can be seen with paper or plastics. Thereby, the change in material quality may also
be expressed as a change in the ability of the material to displace “virgin” material. A life cycle that delivers as much material to recycling as it receives will cause a change in material quality equivalent to the
amount of “virgin” material supply that is needed to compensate for the reduction in technical properties (see also example 14). When less material is sent to recycling than what is received (i.e. when material
is sent to waste treatment), the change in requirements for supplies of “virgin” material to the recycling pool (the change in displacement ability) will depend on the actual quality of the material that is thereby
leaving the recycling systems. The quality (the ability to displace “virgin” material) can be estimated specifically by the physical properties or be calculated theoretically from the average recycling rate in the specific
recycling pool, since the material quality will be reverse proportional to the recycling rate (with a low recycling rate the supplies of “virgin” material will be relatively large, which gives a relatively high material
quality in the recycling pool – and opposite with a high recycling rate, see also example 14).
3.4.2 Relation to the EDIP'97-procedure
The EDIP'97-method[8] applies a factor, called the grade loss, to express the loss of grade or material quality on recycling. This grade loss is used as an allocation factor, in that every life cycle using the material is burdened with this fraction of the primary material production. The grade loss is calculated as the percentage of virgin material that must be introduced on recycling. Therefore, in terms of system expansion, the grade loss is equivalent to the difference between the amount used in a lifecycle and the amount displaced by the recycling from this life cycle, expressed in percentage of the amount used, i.e. the change in displacement ability as explained in the previous section. Thus, given the same information on displacement, the EDIP’97-procedure will lead to the same result as the procedure presented here. Note, however, that he EDIP'97-method does not take into account the situation where the recycling pools are not utilised fully, which implies e.g. that in EDIP'97 the recycling process is always ascribed to the preceding life cycle.
Example 14: Paper recycling II
If it is assumed that paper fibres can only be used on average 6 times since the fibres become shorter and eventually must be discarded, each life cycle will imply an average loss of 17% of the “virgin” material. In EDIP'97-terminology this is expressed by a grade loss for paper of 0.17 per use, which means that a life cycle that receives 1 ton of recycled paper and after use sends 1 ton to recycling should be ascribed 17% of the exchanges from the primary production of 1 ton of paper and 17% of the exchanges from disposal of 1 ton of discarded fibres. In the terminology of system expansion, the life cycle that receives 1 ton of recycled paper (under the condition of full utilisation of the specific recycling pool and that “virgin” paper is displaced in the proportion 1 to 1) shall be ascribed a consumption of 1 ton of “virgin” paper, and – when 1 ton is sent to recycling after use – be ascribed the waste treatment from this (the scrapping of 170 kg discarded fibres) and be credited for the displacement ability of this after one life cycle (830 kg primary production; again under the condition of full utilisation of the recycling pool). The result is that this life cycle is ascribed 170 kg primary production and 170 kg waste treatment, exactly equivalent to the 17% of the used amount of 1 ton prescribed by the EDIP'97-method. When less material is sent to recycling than what is received, or when the receiving market is saturated, less “virgin” material is displaced, depending on the material quality in the lost material, for example the displacement ability of recycled newsprint in 1995 could be estimated to be 50% (based on a realised recycling rate of 65%) and for corrugated board with a recycling rate of 75% the displacement ability will be approximately 32% (meaning that for each time 1 ton of corrugated board is sent to waste treatment, the requirement for “virgin” material in the recycling pool is increased with 320 kg). The displacement ability is directly corresponding to the concept of “residual material grade of scrap” in the EDIP'97-method.
3.5 Complex situations
The situation described by figure 3.1 (and 3.3) is a simplification, in that there is only one determining and one dependent co-product shown (i.e. only two products coming out of process A) and none of the
other processes have co-products. Therefore, this section deals with the more complex situations:
- where process A has more than two co-products,
- where the intermediate process has multiple products or the dependent co-products have other applications than in process B, and
- where the displaced process has multiple products.
3.5.1 More than two co-products
Most of the examples in the previous sections actually involve more than two co-products. It seems to be rather the rule than the exception that processes with more than one product also have more than
two co-products. This, however, poses no problem for the procedure in section 3.2. Each co-product can be treated separately:
- when studying a change in output of a determining co-product, and there are more than one dependent co-product, the consequences for each of the dependent co-products can be analysed in isolation,
one at a time,
- when studying a change in output of a determining co-product, and there are more than one determining co-product, the changes in the co-producing process can be analysed in isolation, separately from
the analysis of any dependent co-products,
- when studying a change in output of a dependent co-product, the only thing to be investigated is whether the dependent co-product is utilised fully or not, which can be done without concern for any of the
other co-products.
3.5.2 Intermediate processes that have multiple products
After the split-off point (see section 3.2.3) and before displacing other products, a dependent co-product may be split up in two or more fractions, each following its own route. Each fraction may be fully
utilised in other processes (rule no. 2, see Box 3) or only partly (rule no. 3). Each fraction can be treated separately, although fractions that follow the same rule may be treated together for convenience
(listing the affected products and processes together).
Example 15: Recycling of demolition waste
Mixed demolition waste may be processed separating a large number of fractions. The concrete alone may be separated into fractions that substitute sand, gravel and crushed stone, respectively. Depending on the local demand (these materials are not valuable enough to justify transport over longer distances) the fractions may be fully or partially utilised. When larger quantities are available, crushing of demolition waste will be economically preferable to “virgin” extraction, and full utilisation will therefore often be possible. For those fractions that are expected to be fully utilised, the primary building may be credited for the displaced primary production, while the fractions that are not expected to be fully utilised, are calculated with full waste handling and no displacement. A building that utilises recycled materials is ascribed the additional efforts in demolition, crushing and separation, and the displaced waste treatment for the fractions that are not fully utilised, while the fractions that are fully utilised is calculated as primary materials.
Even when the co-product is not composed of separable fractions, it may have many different applications. The process which is affected (i.e. process B in figure 3.1) is the application most sensitive to a
change in supply (as identified by the procedure in chapter 2).
3.5.3 Displaced processes that have multiple products
When a displaced process does not only yield the displaced product, but also other co-products, see figure 3.5, these co-products are also displaced and the demand that they fulfilled must now be met in
another way. Thus, the procedure must be repeated for these co-products, but with a negative sign.
If this leads again to another process with multiple products, as illustrated by process E in figure 3.5, one might fear that this system expansion would continue without end. However, the number of possible
processes involved in the system expansion is limited by the very procedure, since:
- the number of markets affected by each displaced process is limited, and the displaced process is only that specific supplier to each market, which is most sensitive to a change,
- the three rules for system expansion (Box 3) provides clear cut-offs between the different product systems involved (either a process is included or excluded from the studied system),
- for each time the system expansion is iterated, both the economic value and the volume of the displaced processes tend to decrease, because in each iteration the avoided product is the determining
co-product of the displaced process and therefore typically of higher value (and often also larger in quantity) than the dependent co-products which go on to the next iteration. The system expansion can
therefore be terminated when the amount of product that goes on to the next iteration is below the uncertainty on the initial amount of co-product.
Example 16: Joint production of chlorine and sodium hydroxide III
In Europe, the displaced production route for sodium hydroxide (see also examples 5 and 7) is assumed to be the combination of the Solvay process: 2 NaCl + CaCO3 ⇔ Na2CO3 + CaCl2 and the lime-soda process (caustification): Na2CO3 + Ca(OH)2 ⇔ 2 NaOH + CaCO3 with recycling of the calcium carbonate, giving net process: 2 NaCl + Ca(OH)2 ⇔ 2 NaOH + CaCl2. Thus, this displaced production route has a co-product, calcium chloride, which can be used for de-icing and dust control because of its hygroscopic properties. However, it is not a very valuable product and part of it is deposited. Thus, following rule no. 3 (see Box 3), the displacement of the alternative production route for sodium hydroxide will lead to a reduction in calcium chloride deposition. In summary, chlorine will be ascribed the displacement of the alternative production route for sodium hydroxide and credited for the reduced calcium chloride deposition. Using the nomenclature of figure 3.5, the cut-off is after process D and W2, since there is no displacement of alternative supplies to process C (de-icing and dust control with calcium chloride) as long as there are adequate unused supplies in W2. Therefore, proces G is not affected by the changes in the chlor-alkali system and can be excluded from the analysis.
Figure 3.5 System expansion and delimitation when the displaced process has multiple outputs
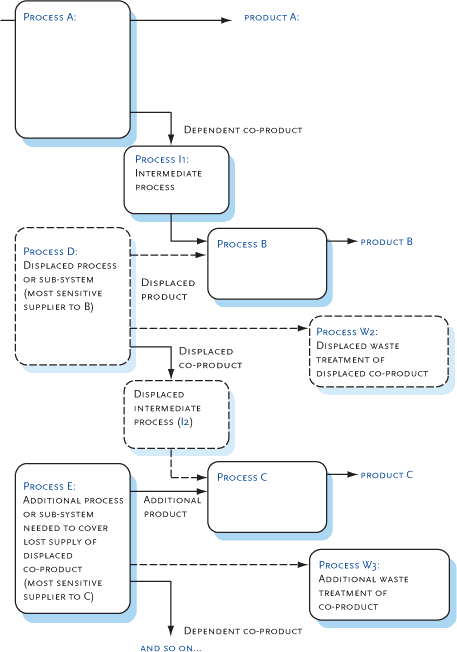
Example 17: Ethylene and propylene
The main production route for ethylene is steam-cracking, which yields ethylene in a relatively high proportion. For each raw material (ethane, LPG, naphta, or gasoil), the relative outputs of ethylene and the by-product propylene is fixed. The raw material that will be affected by a change in demand for ethylene depends on the current the raw material market. In Europe, we may consider a current situation in which LPG is the affected raw material (see table 2). In this case, the additional output of 1 kg ethylene will yield 0.42 kg propylene, which will displace an alternative production route yielding a larger proportion of propylene. This secondary route uses the off-gases from fluid catalytic cracking (FCC) yielding 0.3 kg ethylene per 0.42 kg propylene.
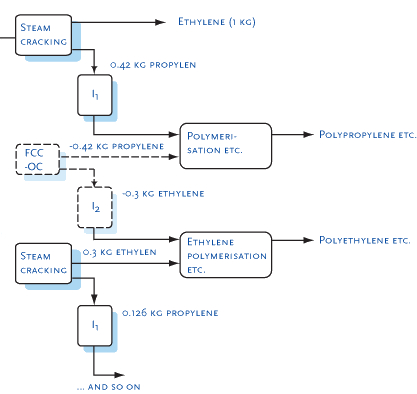
By iteration, it can be calculated that 1 kg of additional ethylene output requires the following system expansion: a reduction in volume of fluid catalytic cracking off-gas cleaning (FCC-OC) corresponding to an output of 0.3 + 0.32 +0.33 + …. = 0.43 kg ethylene, and an increase in steam cracking corresponding to an output of 1 + 0.3 + 0.32 +0.33 + …. = 1.43 kg ethylene.
The same calculations can be made for changes in the demand for propylene, in which case process A would be the FCC-OC route. In practice, the two process routes have a number of other by-products, which would also have to be accounted for. The use of linear regression models of the refinery industry facilitates such calculations.
3.6 Traditional co-product allocation as a special case of the presented procedure
In traditional co-product allocation, the exchanges of the co-producing process is partitioned and distributed over several of the co-products, and there is no inclusion of intermediate and displaced
processes. Thus, traditional co-product allocation may be regarded as a special case of the procedure in section 3.2, occurring when:
- several co-products are determining the volume of the co-producing process in different periods within the time horizon of the study, so that the exchanges of the co-producing process can be allocated
over the co-products in relation to the relative lengths of these periods[9], and
- the co-products can be stored (without additional environmental impact) during the periods that they are not determining, so that no additional intermediate treatment and no displacement occurs.
3.7 Relation to the procedure of ISO 14041
Applying the procedure in section 3.2 will lead to the same results as if applying the stepwise procedure of ISO 14041:
- Step 1 in the ISO procedure requires that system expansion shall be performed wherever possible. As shown above, system expansion is always possible for cases of joint production, by following steps 2
to 4 of the procedure in section 3.2.
- Step 2 in the ISO procedure requires that when ISO step 1 cannot be applied, allocation should be done according to physical relationships (causalities). This is equivalent to step 1 of the procedure in
section 3.2, and is relevant for cases of combined production.
- Step 3 in the ISO procedure (allocation according to other relationships) does not come into play, since all possible cases can be covered by either step 1 or 2.
In the procedure in section 3.2, step 1 deals with combined production (ISO step 2), while steps 2 to 4 deals with system expansion (ISO step 1), since it appears more logical to deal first with the simple
case, where the outputs of the other co-products can be kept constant without system expansion, before dealing with the more complicated cases, where the outputs of the other co-products can only be
kept constant by applying system expansion. However, in practice the order does not matter: If applying system expansion to a case of combined production, the same result will be obtained as when
applying the more simple procedure of step 1 (in section 3.2).
Besides the three-step procedure, the ISO 14041 (section 6.5.2) states an allocation principle, which has popularly become known as “the 100% rule”:
“The sum of the allocated inputs and outputs of a unit process shall equal the unallocated inputs and outputs of the unit process”, i.e. there should not be any exchanges that are allocated twice or not
allocated at all. Although, according to the ISO text, this principle applies only to allocation and not to avoiding allocation, it is worth noting that the procedure in section 3.2 adheres to this principle: The
three rules in Box 3 ensures that all processes are fully ascribed to (allocated to) either one or the other co-product.
Foot notes
6 When this assumption is regarded as too simplified (especially as it may change over time, depending on location, and depending on the scale of change), i.e. when more than one joint product is found to be determining within the studied scale or geographical or temporal horizon, a scenario may be calculated for each joint product that may be determining. See also footnote 7.
7 Aggregating scenarios with different determining co-products is parallel to an allocation of the co-producing process, where the allocation factor is the expected probability that a co-product is determining (or the relative expected influence of the co-product). Some economic allocation factors can be justified as representing such relative expected influence. See also section 3.6.
8 Wenzel H, Hauschild M, Alting L.: Environmental assessment of products. Vol. I: Methodology, tools, techniques and case studies in product development. London: Chapman & Hall, 1997.
9 This may also be expressed in terms of relative influence of the co-products on the production volume of the co-producing process, which may be represented by certain economic allocation factors.
| Front page | | Contents | | Previous | | Next | | Top |
Version 1.0 December 2005, © Danish Environmental Protection Agency
|