| Front page | | Contents | | Previous | | Next |
Substitution of cobalt driers in wood coatings
4 Evaluation of drying properties as a function of alkyd and primary drier
The scope of this initial screening was to make a rough evaluation of the primary driers. Simple drying tests with selected binders combined with different driers were performed to reveal potential driers for further test in stains and to evaluate the consequence of different types of alkyds
4.1 Alkyds
As mentioned earlier the key parameters for an alkyd with respect to drying are oil length, oil type, molecular weight and whether the acid is iso- or orthophthalic. These parameters are not independent and it is hardly possible to evaluate each isolated.
Initially seven different alkyds with different variations produced by Cray Valley and a standard alkyd produced by Dyrup were included in the project.
Table 4.1 Types of alkyds included in the project
Product code |
Description |
A1 |
Standard long oil alkyd |
A2 |
High molecular version of A1 |
A3, A4 |
A1 modified with two levels of conjugated acids |
A5 |
High solids version of A1 for VOC < 300 g/l. |
A6 |
High solids for VOC < 250 g/l base on different oil type than A5 |
A7 |
Urethane modified alkyd. Standard long oil alkyd |
A8 |
Standard long oil alkyd produced by Dyrup. Different oil type than A1. |
Even though a systematic evaluation of the influence of every parameter not is achieved, the different types of alkyds were expected to give an indication of possibilities in combination with the primary drier.
4.2 Driers
In the initial screening it was investigated how the type and level of primary driers influence the drying of alkyd coatings.
4.2.1 Primary driers
The newest developed alternatives from the suppliers where tested. Most of these are mixtures of a primary drier and an organic accelerator. In some cases the drier products also contain some secondary driers.
Beside the drier products containing drying accelerator, common primary drier products, where the metal has been combined with different acids have also been tested, both alone and in combination with a variation of accelerators. In this way the influence of acids and accelerators was evaluated. Table 4.2 lists the driers tested in the project.
In earlier studies only vanadium and manganese has shown some potential as alternatives in wood coatings and as the drier manufactures are focusing on these metals they are also dominating in this project.
Table 4.2 Driers to be tested in the project.
Product code |
Metal |
Accelerator |
P1 |
Cobalt |
No |
P2 |
Vanadium |
Yes |
P3-P8 |
Manganese |
Yes |
P9 |
Vanadium |
No |
P10-P12 |
Manganese |
No |
4.2.2 Secondary driers
In a pre-evaluation of the test design it was concluded that secondary driers only have a limited influence on the drying time. This conclusion was confirmed by the participating drier producer and the secondary driers was therefore excluded in the initial screening. Later in the process, where the most promising systems are optimised, it is relevant to include these driers as they can enhance film hardness, gloss, stability of the drier system etc.
4.2.3 Organic accelerators
These are expected to have a pronounced influence on drying time and are already included in many of the commercial products.
However, to reduce the amount of tests they were postponed and tested later together with the best primary drier without accelerators from the first screening.
Two accelerators from two different suppliers were selected.
Product codes: AC1and AC2.
The active content in both is 2,2’-Bipyridyl only differing in solid content and solvent.
4.3 Screening tests
4.3.1 Test systems
Eight binders and fourteen primary driers were selected for the tests in the first screening. Besides a traditional alkyd from Dyrup, Cray Valley delivered seven alkyds of which most were made specifically for this project (4.1). The primary driers were delivered from Sasol Servo and other suppliers.
As other raw materials in the coating, such as pigments and additives, will affect the drying time their presence reduce the possibility to examine the influence of the variations in alkyd against different driers. Thus the driers were tested in the pure binder.
It is important how pigmentation, anti-skinning agents, co-solvents etc. affect the drying properties but it is aimed to reduce the selection of test system as much as possible before studying these aspects.
The alkyds were diluted to the same solid content with two exceptions due to viscosity issues with respect to application.
After the initial screening, selected driers were tested with accelerators in different combinations.
4.3.2 Tests
The criterion in the first screening was the drying time. Other properties like yellowing, hardness and loss of dry are of course also important, but they are more relevant in the testing of wood coating prototypes and thus evaluated at a later stage.
In real life there is a distinction between minimal, low and high build coatings and therefore it is relevant to test how the driers perform at different film thicknesses. To compare the alkyds directly it is also rational to test different systems at the same film thickness.
It was decided to measure the drying time of wet coating film applied with a hand-held applicator blade with a gap of 120 µm and 210 µm respectively, where the dry film thickness in advance has been estimated for each type of binder. It is assumed that different types of driers will not affect the film thickness.
In this way the measurements can be corrected theoretically to an equal film thickness, as variations can occur due to different solid contents and viscosities.
The application of the coating was made as a draw-down on a Letena card. A Letena card is a varnished card normally used for testing of the hiding power of a paint. The drying time was measured by drawing a line with a pen across the applied coating film every hour. When it is possible to write on the coating film it is dry. It is a fast method, which gives clear results and it is relative independent of the performer.
To evaluate the variation in film thickness achieved, when applying different alkyds (50 wt-% solid content) with a hand-held applicator at different gap sizes, the dry film thickness was measured for the draw-downs after drying, see table 4.3. The results showed acceptable variations.
Table 4.3 Dry film thickness measured on alkyds with 50 % solid content applied at different wet film thicknesses
Binder. |
Filmthickness [µm] |
|
120 |
150 |
180 |
210 |
A1 |
41 |
53 |
63 |
67 |
A2 |
42 |
54 |
64 |
72 |
A3 |
49 |
59 |
72 |
80 |
A4 |
50 |
62 |
72 |
80 |
A5 |
44 |
53 |
64 |
64 |
A6 |
43 |
52 |
68 |
80 |
A7 |
45 |
56 |
66 |
82 |
A8 |
44 |
52 |
58 |
68 |
Mean value |
46 |
|
|
73 |
4.4 Screening results
4.4.1 Handling of data
The method of measuring the drying time requires a manual evaluation every hour. Some systems will dry in a period of time (~10-15 hours) where such an hourly evaluation is not possible. In these cases the drying result is taken as an interval where the middle value is used as the drying time in the further handling of data.
Using intervals and middle values will affect the accuracy in the statistical treatment. The situation arises especially with slow drying systems but still the promising and thus most interesting systems will stand out, which is the purpose of this screening.
As mentioned above the tested binders differ in viscosity and thus the film thickness will differ too. Presuming that the correlation between drying time and film thickness is linear all results are adjusted to a middle dry film thickness at respectively 120 µm and 210 µm (wet film applied).
All driers were tested in two levels in each binder. Only the drier level with the best drying result is included in the evaluation.
An exception is cobalt, where the standard dosage used in Dyrup, calculated on solid binder is used.
4.4.2 Drying time - results
The experimental results have been treated by general linear statistic analyses (an example of a statistic analysis is given in the appendix A with reference to the results in chapter 5.3).
All conclusions refer only to the drying time and only as defined in this screening.
All parameters - binder, drier and film thickness - have a significant influence, and as expected the drying time is shorter at lower film thickness.
Diagram 4.1 Influence of film thickness on drying time
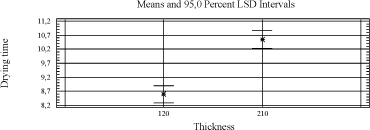
P02(V) is the best of the alternatives performing at the same level as cobalt. Among the manganese driers are P06(Mn) and P07(Mn) the most promising and the only ones that stand out from the driers without accelerator.
Diagram 4.2 Influence of drier on drying time
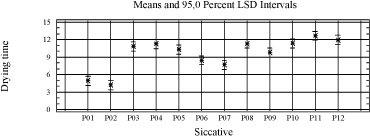
For the binders an improvement in drying is seen with higher content of conjugated acid. The high solid binder A5 is in general the most difficult to dry. The rest of the binders are at the same level.
Diagram 4.3 Influence of binder on drying time
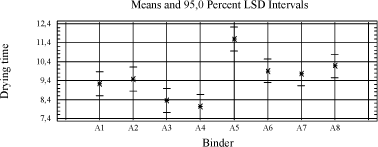
Splitting the data up in 120 µm and 210 µm respectively does not alter the conclusions, except for the standard from Dyrup (A8) that joins A5 as a slow drying binder at 210 µm.
In the statistical analyses the driers are evaluated with regard to their universality against different types of binders and visa versa, and particularly for the driers this is of course relevant to product development in general.
However as the conclusion from earlier studies has been that no alternatives have matched cobalt in this respect, one of the scopes in this project is to evaluate the influence of the properties of the alkyd to find a scenario for a cobalt free product range. Therefore it is also relevant to look at specific combinations of driers and alkyds.
Beside the driers P02, P06 and P07, which have already been estimated as promising cobalt alternatives in the statistical treatment, P09 is doing quite well within a few binders even without the presence of an accelerator.
A rough overview of the performance of the best driers with different binders is given in the table below.
Table 4.4 Overview of performance of best driers with binders
|
P01(Co) |
P02(V) |
P06(Mn) |
P07(Mn) |
P09(V) |
A1 |
|
|
|
|
|
A2 |
|
A3 |
|
A4 |
|
A5 |
|
|
|
|
A6 |
|
|
A7 |
|
|
A8 |
|
|
|
|
|
Dark grey: Drying time less or equal to 6 h at both 120 µm and 210 µm
Light grey: Drying time less or equal to 8 h at both 120 µm and 210 µm
4.4.3 Test with accelerators
Using the standard binder A8, the driers P09(V) and P10(Mn) have been tested together with the accelerators AC1 and AC2 in different combinations
Diagram 4.4 Test with organic accelerator
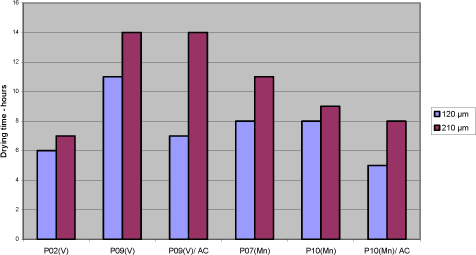
In both cases the drying is improved compared to when the driers are used with no accelerator, but only P10(Mn) reaches the level of P01(Co) and P02(V).
P10(Mn) is similar to P07(Mn) only without the accelerator. The results reflect a better combination of drier and accelerator than represented by P07(Mn) when used in A8.
4.4.4 Conclusions
The assumption for this screening was that no alternatives to Cobalt exhibit the same universality as cobalt driers. However looking at results obtained with the pure binders, P02(V) comes out as a clear candidate moving the focus against the influence of other raw materials. In the simple test of drying time it performs at the same level as cobalt but still there is a challenge with tackiness in specific binders and yellowing.
Among the Manganese driers P10(Mn) optimised with an accelerator might be a possible candidate. P07(Mn) and P06(Mn) are also of interest, but in these cases modification of the alkyd has to be considered to avoid compromising the drying time, compared to the performance of cobalt in standard binders.
With regard to the binders modified with conjugated acids, the modification improves the drying in general. Of the high solid binders A6 is performing best and is generally at the level or better than the traditional binders A1 and A8.
It is very different how the driers perform with the different types of alkyds. But besides the general observations it is not possible from the pool of data to relate drying times to connections between properties of respectively alkyd and drier.
The variety in the drying time, even among pure primary driers, indicates that not only the type of metal or combination with accelerator but also the type of salts plays a role.
| Front page | | Contents | | Previous | | Next | | Top |
Version 1.0 August 2006, © Danish Environmental Protection Agency
|