| Front page | | Contents | | Previous | | Next |
Substitution of cobalt driers in wood coatings
5 Evaluation of drying properties in wood coating prototypes
With focus on the most promising drier and binder systems from the initial screening in pure binders the next step was to evaluate these raw materials in the different types of wood coatings and how the presence of pigments and additives influence on the drying properties.
5.1 Test methods
As a large number of systems where screened also in this part of the project simple reproducible tests has been used for evaluation of the drying properties.
Table 5.1 Test methods
|
Apparatus |
Conditions |
Method |
Demands* |
Drying time |
Applicator,
lenetacards, pen |
50 % HR, 23 °C,
120 µm wet film |
A pen is moved across a
draw-down every hour. When
its possible to draw a line
on the film it is dry. |
<8 hours |
Loss of dry |
Applicator,
lenetacards, pen,
oven |
2 weeks at 40 oC
or >6 weeks at RT |
As drying time but after
storage |
<8 hours |
Tackiness |
Applicator,
lenetacards |
50 % HR, 23 °C,
120 µm wet film |
Tackiness is measured by
pressing a finger against the
film after 6 and 24 hours |
Tack free
after one
day |
Hardness |
König Albert,
applicator, glass
plates |
50 % HR, 23 °C,
120 µm wet film |
The Kùnig hardness is
measured after 1, 7, 14 and
28(-55) days |
At the level
of cobalt
after 28
days |
Yellowing |
GretagMacbeth –
Color i5,
applicator
glas plates |
50 % HR, 23 °C,
120 µm wet film |
b-value is measured after 1
and 28 days. When
measuring on pure binders a
white cardboard is placed
behind the glass plate. |
At the level
of cobalt |
*The demands are indicating when an alternative drier is regarded as interesting in the project more than they are general product demands.
5.2 Choice of systems
Besides the selected driers and binders from the initial screening a few newcomers have been included.
Types of wood coatings as well as test systems have been chosen to target that the conclusions from this project can be related to a full product range.
Below is an overview as regards combinations of systems, binders, primary and secondary driers tested. Beside these combinations many primary and secondary driers are also tested in at least two concentrations.
Table 5.2 Complete overview as regards combinations of systems, binders, primary driers, and secondary driers tested.
System |
Binder |
P01(C0) |
P02(V) |
P06(Mn) |
P07(Mn) |
P10(Mn)/AC |
P13(Mn) |
P14(Mn) |
P15(Fe) |
Pure |
A1 |
Zr |
None |
None |
None |
A3 |
Zr |
None |
None |
None |
None |
A7 |
Zr |
None |
None |
A8 |
Zr |
Table 5.5, None, Zr/Ca, Zn/Ca, Zr/ Zn |
Table 5.5,
None,
Zr/Ca, Zn/Ca, Zr/ Zn |
None |
None, Zr/Ca |
None, Zr/Ca |
None,
Zr/Ca |
Trans-
parent |
A1 |
Zr |
None |
None |
A3 |
Zr |
None |
None |
None |
None |
None |
A7 |
Zr |
None |
None, Zr/Zn |
A8 |
Zr |
Table 5.5, None, Zr/Ca, Zn/Ca, Zr/ Zn |
Table 5.5, None, Zr/Ca, Zn/Ca, Zr/ Zn |
None |
None, Zr/Ca |
None, Zr/Ca |
None,
Zr/Ca |
A7/A8 |
Zr |
None |
None |
Opaque white |
A1/thix |
Zr |
None |
None |
A3/thix |
Zr |
None |
None |
A7/thix |
Zr |
None |
None, Zr/Zn |
A8/thix |
Zr |
None, Zr/Zn |
None, Zr/Ca, |
Zr,Ca |
Zr,Ca |
Opaque dark |
A1/thix |
Zr |
None |
None |
A3/thix |
Zr |
None |
None |
A7/thix |
Zr |
None |
None, Zr/Zn |
A8/thix |
Zr |
None, Zr/Zn |
None, Zr/Ca, |
Zr,Ca |
Zr,Ca |
Base red (T) |
A3 |
Zr |
None |
None |
None |
A8 |
Zr |
None |
None |
Base yellow (T) |
A3 |
Zr |
None |
None |
None |
A8 |
Zr |
None |
None |
Base red |
A3 |
Zr |
None |
None |
None |
A8 |
Zr |
None |
None |
Base blue |
A3 |
Zr |
None |
None |
None |
A8 |
Zr |
None |
None |
VOC2010 pure binder |
A8/
linseed |
Zr |
None, Zr/Ca |
None, Zr/Ca |
None, Zr/Ca |
A9 |
Zr |
None, Zr/Ca |
None, Zr/Ca |
None, Zr/Ca |
VOC2010 trans-
parent |
A7/
linseed |
Zr |
None |
None, Zr/Zn |
A8/
linseed |
Zr |
None, Zr/Ca |
None, Zr/Ca |
None, Zr/Ca |
A9 |
Zr |
None, Zr/Ca |
None, Zr/Ca |
None, Zr/Ca |
5.2.1 Driers
5.2.1.1 Primary driers
The main focus has been on the best candidates P02(V) and P07(Mn) from the initial screening in pure binders, and when going through the different drying properties (5.4) only these driers will be discussed.
P06(Mn) was tested in a few systems as it in pure binders showed good results with the modified binder A3, but no benefits compared to P07(Mn) has been observed. Also the expected advantages of A3 didn’t take place.
Table 5.3 Comparison of key drying properties of P06(Mn) and P07(Mn) in binder A3
Systems (5.2.4) |
Hardness 28 days* |
Drying time – hours |
Loss of dry - hours |
P06(Mn) |
P07(Mn) |
P06(Mn) |
P07(Mn) |
P06(Mn) |
P07(Mn) |
Pure binder |
15 |
15 |
5 |
4 |
- |
- |
Transparent |
11 |
12 |
6 |
6 |
- |
- |
Opaque dark |
18 |
20 |
10 |
18 |
25 |
30 |
Opaque white |
22 |
23 |
7 |
7 |
24 |
25 |
Base/Yellow(T) |
15 |
15 |
6 |
5 |
- |
- |
Base/Red(T) |
14 |
14 |
5 |
6 |
- |
- |
Base/Blue |
13 |
13 |
6 |
7 |
- |
- |
Base/Red |
12 |
11 |
8 |
7 |
- |
- |
* exceeds 28 days in some systems
P10(Mn) optimized with the organic accelerator AC2 showed some potential in the initial screening too, but again the behaviour in the later studies was very similar to P07(Mn).
Table 5.4 Comparison of key drying properties of P10(Mn)/AC2 and P07(Mn)
Binder |
Systems (5.2.4) |
Hardness 40 days |
Drying time - hours |
P10(Mn)/AC2 |
P07(Mn) |
P10(Mn)/AC2 |
P07(Mn) |
A8 |
Pure binder |
23 |
23 |
5 |
5 |
A8 |
Transparent |
16 |
18 |
19* |
19* |
A1 |
Pure binder |
15 |
16 |
5 |
5 |
A1 |
Transparent |
12 |
12 |
23* |
25* |
*the drying time is unusually high in transparent systems compared to identically test with P07(Mn)
Two new manganese driers P13(Mn) and P14(Mn) have been included in the project and tested in a few relevant systems with and without recommended secondary driers but again the same limitations are observed as with P07(Mn)
Finally a drier based on Iron P15(Fe) was tested which, although interesting considering the type of metal, still cannot compete with vanadium and manganese. Main problems are drying times above 10 hours and after storage above 20 hours.
5.2.1.2 Secondary driers
To improve the drying properties the following secondary driers have been tested in minimum and maximum concentration recommended by supplier or literature. Relevant combinations of secondary driers are tested as well.
Table 5.5 Secondary driers tested in the project
Calcium |
Barium |
Potassium |
Zirconium |
Bismuth |
Cerium |
Aluminium |
Lithium |
Vanadium |
Strontium |
Zinc |
|
Cerium and Vanadium is in fact primary driers but are in this connection screened in combination with either P02(V) or P07(Mn).
5.2.2 Binders
5.2.2.1 VOC2007 compliant binders
The two long oil alkyds A1 and A8 are evaluated with most focus on A8 as it has a better hardness development.
In the initial screenings it was concluded that the binder A3 modified with conjugated acid reduces the drying times compared to the traditional binders.
However when the drying properties are examined in general no improvements of the drawbacks of the alternative driers are observed.
In pure binder, bases, opaque and transparent systems A3 behave very similar to A1 and do not reduce the problems with e.g. tackiness, hardness and loss of dry.
Table 5.6 examples of test results for A3 compared to A8 in the transparent prototype (6.1.4.1)
Drier |
Tackiness 1 day |
Hardness 55 days |
Loss of dry - hours |
A3 |
A8 |
A3 |
A8 |
A3 |
A8 |
P01(Co) |
1 |
1 |
17 |
24 |
|
7 |
P02(V) |
3 |
2,5 |
19 |
26 |
3 |
5 |
P07(Mn) |
1,5 |
1 |
12 |
12 |
24 |
24 |
Tackiness: 5 – bad, 1 – good/ tack-free
The urethane modified alkyd A7 is tested alone and in combination with other binders. It gives a harder film and has less need for driers in general (5.4).
5.2.2.2 VOC2010 compliant binders
The driers are tested in a high solid binder A9, which is new for the project as well as A8 and A7 combined with linseed oil.
5.2.3 Solvent
A few tests have been carried out using solvents with different boiling points to see the influence on mainly initial drying properties like tackiness.
As expected a lower boiling point reduces the drying time slightly but no effect is observed on e.g. the tackiness after one day which is a problem with P02(V)
5.2.4 Types of coatings
5.2.4.1 Pure binders
As in the initial screening the pure binder is evaluated with no other additives present.
5.2.4.2 Transparent high build coating
Beside binder and drier it contains UV-absorber, anti-skinning agent, fungicide and pigment mix (medium shaded wood colour). All screenings in transparent systems are based on this raw material mix with parallel tests in the pure binder.
Influence of the different raw materials is evaluated in chapter 5.3
5.2.4.3 Opaque high build coatings
A white coating highly loaded with titanium dioxide and a dark coating with a high level of carbon black are tested.
Both are Dyrup formulations.
The white coating is sensitive to yellowing, and high levels of pigments, especially carbon black, are suspected to affect the long-term stability of the driers (loss of dry).
5.2.4.4 Bases
A base for transparent colours and one for opaque colours each tinted with two different universal tinting pastes.
Bases together with universal tinting pastes have a higher level of especially surfactants to ensure compatibility and in some coincidences this causes a negative influence on drying properties even with cobalt
5.2.4.5 VOC2010 compliant coatings
VOC2010 compliant binders are tested alone and with the raw material mix mentioned above in the transparent prototype. These recipes are not optimised as coatings and are included to see how the alternative driers behave with these potentially more challenging binder systems.
5.3 Influence of additives and pigments
In order to evaluate the influence of typical raw materials used in the coating industry a 26-3 fractional factorial design is used where the parameters are the presence or non-presence of MEKO, pigment mix, thix-alkyd, UV-absorber, HALS and fungicide (appendix A).
For the pigments a combination corresponding to a medium pigmented transparent wood color is chosen.
In the 26-3 fractional factorial designs the primary driers Co, P02(V) and P07(Mn) are tested together with the two traditional long oil alkyds A1 and A8. The driers and binders are regarded as constants in the tests giving six combinations and thus six 26-3 fractional factorial designs.
Table 5.7 One out of six test designs - P01(Co) and A8.
Drier |
Binder |
Solid content |
Thix binder |
Color |
Meko |
UV abs. |
HALS |
Fungicide |
P01 |
A8 |
50 |
yes |
Trans |
yes |
no |
no |
no |
P01 |
A8 |
50 |
no |
Trans |
yes |
yes |
yes |
no |
P01 |
A8 |
50 |
yes |
no |
yes |
yes |
no |
yes |
P01 |
A8 |
50 |
no |
no |
yes |
no |
yes |
yes |
P01 |
A8 |
50 |
yes |
Trans |
no |
no |
yes |
yes |
P01 |
A8 |
50 |
no |
Trans |
no |
yes |
no |
yes |
P01 |
A8 |
50 |
yes |
no |
no |
yes |
yes |
no |
P01 |
A8 |
50 |
no |
no |
no |
no |
no |
no |
Table 5.8 Overview as regards which raw materials affects the drying properties significantly. A general linear model is used to estimate the factors with a significant influence at a 90 % confidence level.
|
Drying time |
Loss of dry |
Tackiness after 6 h |
Tackiness after 1 day |
Hardness after 1 day |
Hardness after 7 days |
Colour |
Yellowing 28 days |
MEKO |
X |
X |
X |
|
|
|
|
|
Pigment mix |
|
|
|
|
|
|
(X) |
X |
Thix-alkyd |
|
|
|
|
|
X |
X |
|
UV-abs |
|
|
|
|
|
X |
|
|
HALS |
|
|
|
|
|
X |
|
|
Fungicide |
X |
|
|
|
|
X |
|
|
Binder |
|
|
|
|
X |
X |
|
|
Drier |
X |
X |
X |
X |
X |
X |
X |
X |
With the exception of the thix-alkyd giving a harder film after seven days, the influence of other raw materials is always negative when significant.
The anti-skinning agent, before it evaporates, affects the initial properties after application like drying time and tackiness after six hours.
The pigments of course introduce colour to the film and therefore also prevent darkening of the wood and thus the yellowing. UV-absorber and HALS are also expected to prevent yellowing but after 28 days it is not significant.
UV-absorber, HALS and fungicide do all reduce the hardness and the fungicide has a negative influence on the drying time as well. As mentioned earlier the thix-alkyd gives a harder film and comparing the two traditional binders the one produced by Dyrup is the hardest.
The driers have influence on all properties. The drawbacks using P02(V) are reduced hardness, long term tackiness and colouring of the film. For P07(Mn) the drawbacks are reduced hardness, longer drying time and loss of dry.
5.4 Evaluation of drying properties
The alternative driers have some limitations compared to cobalt especially when moving from pure binder systems to wood coatings. Several initiatives have been carried out to optimise the performance of these driers in different types of wood coatings.
First the addition levels of P02(V) and P07(Mn) have been further investigated in pure binder and transparent prototype. Initially they were screened in just minimum and maximum recommended level and then a level in the middle of the interval was included.
P02(V) was earlier concluded to be most efficient at the high level but cutting the amount to the half does not affect drying time, tackiness or hardness and the colouring of the film is reduced. In the further tests this level was used where nothing else is mentioned.
The conclusion for P07(V) remains, it performs better at the lowest recommended addition.
5.4.1 Drying Time
In general the drying time using P02(V) is at the same level as with cobalt. Typically the drying time will be below five hours.
Only in the red tinted opaque base and the VOC2010 transparent system with high solid binder A9 it is not as efficient. In VOC2010 compliant system, using the highest recommended level reduces the difference bringing the drying time down to seven hours. This has not been tested in the base.
It should be noticed though that the VOC2010 systems in this project are very experimental and not satisfying even with cobalt looking at the drying properties in general.
Diagram 5.1 Drying times in tested systems with vanadium drier P02(V)
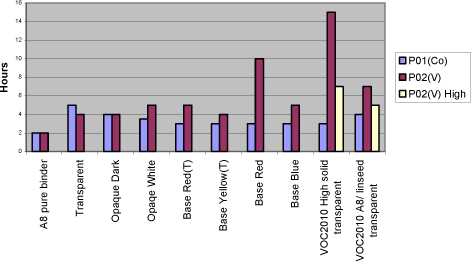
With P07(Mn) the drying times are typically between 5 and 7 hours although in the VOC2010 high solid system secondary driers are needed to keep this level. Except for this coincidence practically no reduction in drying time is observed from the use of secondary driers.
In the opaque dark system the drying time is quite long and the use of secondary driers or even faster drying binders like A7 does not reduce it to a satisfactory level.
Diagram 5.2 Drying times in tested systems with Manganese drier P07(Mn)
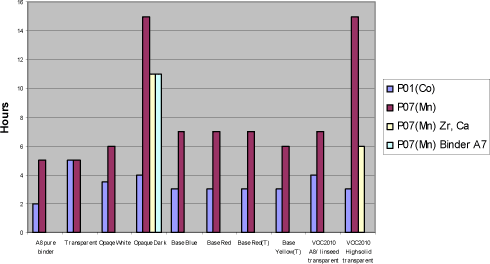
5.4.2 Loss of dry
In transparent systems P02(V) is stable and perform at the same level as cobalt but in the red bases, opaque systems and the VOC2010 compliant systems the drying time is increased to 14 to 24 hours. Using the highest recommendable dosage brings the drying time down to an acceptable level in some systems but introduces other problem like colouring of the film in the opaque white. Another option is to partly introduce the modified alkyd A7. Combination of A7 and high dosage of P02(V) should reduce the drying time further.
Diagram 5.3 Drying times after storage with vanadium drier P02(V).
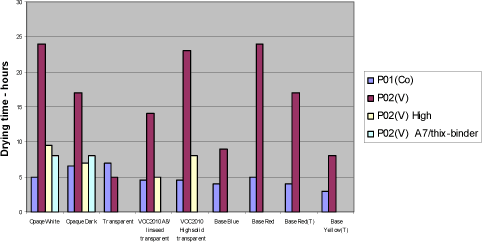
The bases have not been optimised due to lack of time and material. Beside the dosage and use of special alkyds it would be natural to look at the tinting pastes as different technologies for ensuring compatibility is available.
Any use of secondary siccatives has a negative influence together with P02(V) on loss of dry as well as other drying properties.
Loss of dry is a problem in general when using P07(Mn). The drying times exceed 20 hours no matter dosage level or use of secondary driers alone or in combinations.
Using the alkyd A7 alone in transparent systems has solved the problem reducing the drying time to 6 hours after storage. Substituting the binder partly is not efficient when tested in the transparent and opaque systems.
Diagram 5.4 Examples of drying times after storage with manganese drier P07(Mn).
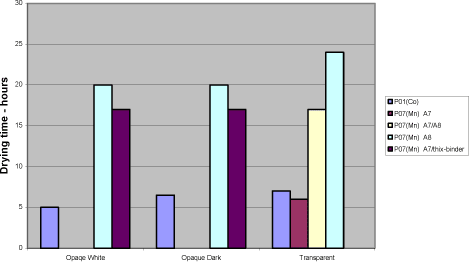
5.4.3 Tackiness
The main issue with P02(V) is tackiness. Except for the opaque dark all other systems stays tacky even one day after the film was applied. Again secondary siccatives make no difference and the only way for improvement is the binder.
Using pure urethane modified binder A7 eliminates the tackiness at least after one day and a one to one combination with A8 reduces it to a level that could be acceptable.
Also a few tests have been carried out with anti-blocking agents and although it does not solve the problem the tackiness is reduced.
Still these improvements are only seen after one day where cobalt normally is almost tack-free after 6 hours.
With P07(Mn) tackiness is not a problem. When the film is dry it gets tack-free within a few hours. In other words – if the film stays tacky for a long time it is due to a long drying time!
5.4.4 Hardness
In general the same hardness is gained with P02(V) as with cobalt no matter the type of coating but it takes longer time to get there. Cobalt reaches its final hardness faster but after 3 and more often 4 weeks the hardness is the same.
As seen before white opaque causes some problems and here the above is only true if P02(V) is dosed in the highest recommended amount resulting in some colouring of the film.
Again secondary driers should be avoided.
Diagram 5.5 Examples of hardness development with vanadium drier P02(V)
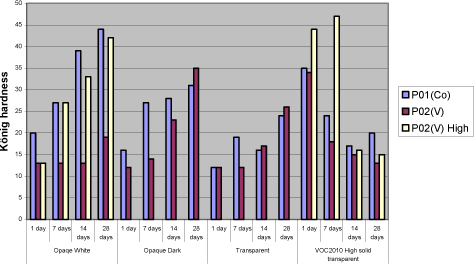
In systems with P07(V) the development of hardness almost stops after 1 to 7 days and never reaches the level of cobalt. High dosage of secondary driers like Zirconium, Zinc and Calcium improve the hardness in transparent system and pure binder, but only in the latter it is to the same level as P02(V) and Cobalt. Combinations of either zinc or zirconium in combination with calcium have been tried in opaque systems with no success.
Aluminium is very efficient but causes a serious viscosity rise or even jellification of the liquid.
In VOC2010 compliant systems the situation is somehow turned around. As regards binder A8 combined with linseed oil the hardness development is very poor with all driers. But when it comes to the high solid binder after 28 days the systems with P07(Mn) are superior to the ones with Cobalt and P02(V). For the two latter the hardness develops very fast but soon it drops again and the result is a rather soft film. With P07(Mn) however the hardness stays at a level which is rather high compared to other systems with this drier.
This is hardly a result of P07(Mn) being more efficient with this type of binder, as the drop in hardness seen with the other driers, most like is due to catalytic activity.
Diagram 5.6 Examples of hardness development with manganese drier P07(Mn)
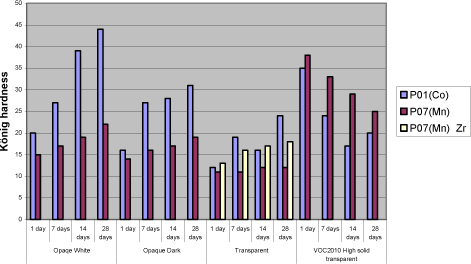
Using harder binders like A7 improves the hardness overall no matter the drier.
Diagram 5.7 Hardness development using binder A7 in transparent prototype
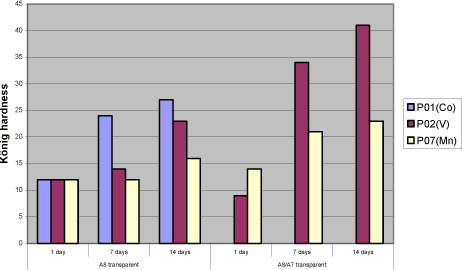
5.4.5 Yellowing – colouring of the film
P02(V) contribute to colouring of the film and the only way to reduce this is to keep the dosage level as low as possible. It will only be a problem in light coloured opaque systems when the need of P02(V) is high as seen with the opaque white system. Here the only option revealed in this project is to introduce a faster drying alkyd, which in this system is also necessary for other drying properties.
Some secondary driers reduces the colouring but as mentioned above together with P02(V) they have a negative influence on properties like drying time, hardness and loss of dry.
Compared to cobalt yellowing, this is not an issue when using P07(Mn)
| Front page | | Contents | | Previous | | Next | | Top |
Version 1.0 August 2006, © Danish Environmental Protection Agency
|